X-ray assisted empty bottle inspection
Enhance your production line with advanced X-ray and optical technology to ensure precise empty bottle inspection, detecting hidden defects and contaminants with unparalleled accuracy, while safeguarding product integrity and reducing operational downtime.
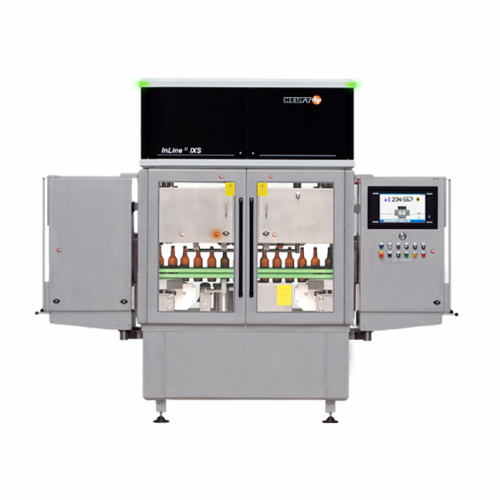
Inspects and Detects Faults in Empty Bottles
The HEUFT InLine II IXS from HEUFT SYSTEMTECHNIK is a versatile X-ray and optical inspection system designed for comprehensive empty bottle examination. Utilizing pulsed X-ray strobes and high-performance optical cameras, it ensures maximum detection accuracy for identifying chips, fractures, and residual liquids, which are typically hard to spot. This system is engineered for industries such as beverage, food, and pharmaceuticals, ensuring that products like bottled water, soft drinks, and pharmaceutical syrups meet stringent quality standards. Capable of inspecting up to 72,000 bottles per hour, it integrates seamlessly into high-speed production lines thanks to its advanced servo technology for container alignment and automated brand changes. The HEUFTreflexx A.I. image processing system enhances detection reliability with real-time image analysis, while its HEUFT SPECTRUM II platform offers an intuitive user interface that minimizes operator intervention. The system’s modular design permits future upgrades and bespoke configurations, supported by HEUFT’s engineering expertise. Emphasizing sustainability, the equipment’s low radiation X-ray technology and robust construction reduce energy consumption and maintenance costs, with features like CIP (Clean-In-Place) compatibility optimizing hygiene and efficiency.
Benefits
- Ensures product quality and safety by detecting virtually invisible faults in bottles.
- Increases production efficiency by inspecting up to 72,000 bottles per hour.
- Minimizes operational costs with automated alignment and brand changes, reducing manual intervention.
- Enhances sustainability with low radiation pulsed X-ray technology, decreasing energy usage.
- Facilitates compliance with hygiene standards through CIP-compatible design and easy maintenance.
- Applications
- Food, Beverages, Package inspection, Labelling, Container transport, Full containers, Empty containers, Fault rejection, Pharmaceuticals
- End products
- Labeled medicine bottles, Bottled water, Spirits, Ketchup bottles, Soft drinks, Beer, Rejected faulty pharmaceuticals, Mayonnaise jars, Wine, Inspected milk bottles, Labeled food jars, Pharmaceutical syrups, Labeled beverage bottles, Transported beverage containers, Juice, Empty beverage bottles, Tablet bottles, Glass containers for cosmetics, Glass vials, Filled food jars, Ampoules
- Steps before
- Empty bottle collection, Empty bottle delivery, Container sorting
- Steps after
- Filling, Bottle capping, Labeling, Packing
- Input ingredients
- empty bottles, containers, foreign objects, residual liquids, dirt, defects
- Output ingredients
- inspected bottles, fault-free containers, rejected faulty bottles
- Market info
- HEUFT is known for its expertise in inline quality inspection systems and automation solutions for the food, beverage, and pharmaceutical industries, with a reputation for innovation and reliability in ensuring product safety and integrity.
- Inspection Type
- X-ray / Optical
- Detection Technologies
- X-ray strobes / High-performance cameras
- Inspection Coverage
- 360° all-around inspection
- Automation Level
- Highly automated / Self-explanatory user guidance
- Capacity
- Up to 72, 000 empty bottles per hour
- False Rejection Rate
- 0.03% for base and sidewall / 0.01% for residual liquid
- Radiation Type
- Pulsed X-ray technology
- Radiation Safety
- Minimal radiation exposure
- Servo Technology
- Automatic alignment during inspection
- Network Interface
- Gigabit Ethernet / TCP/IP
- Brand Changeover
- Automatic servo-controlled adjustment
- Automation level
- Highly automated / AI integrated
- Batch vs. continuous operation
- Inline Continuous
- Changeover time
- Automatic adjustment during brand changes
- CIP/SIP
- Not applicable
- Cleaning method
- Automatic / Manual Intervention minimised
- Energy efficiency
- Low radiation / Environmentally optimised
- Operation type
- Real-time detection and analysis
- Density/particle size
- 0.5–2.5 g/cm³ / 50–1000 µm
- Container type
- Glass bottles
- Fault detection
- Chips, cracks, dirt
- Compact footprint
- Yes
- Control panel type
- Self-explanatory touch screen
- Discharge method
- Servo-controlled rejection system
- Control panel type
- Self-explanatory human machine interface
- Integration possibilities
- Network-based with future-proof network interfaces
- Automatic brand change
- Servo-controlled conveyor belt adjustment
- X-ray technology
- Pulsed X-ray technology for reduced radiation exposure