Space-saving packaging solution for high-velocity production
Optimize your manufacturing floor space with a versatile integrated solution, enhancing productivity by synchronizing packaging operations without conveyor dependency.
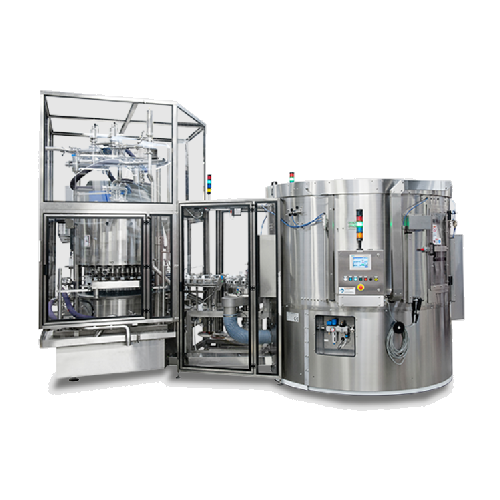
Integrates Multifunctional Packaging and Filling Operations
The SUPERBLOCK from Serac revolutionizes packaging lines by combining multiple high-speed operations—such as filling, capping, sealing, blowing, unscrambling, cleaning, and labeling—into a single, compact unit. This synchronization reduces floor space by up to 25%, directly coupling machines to eliminate conveyors, thus offering seamless integration in continuous operations. Ideal for a wide range of industries, including dairy, beverages, household products, and agrochemicals, it can handle diverse liquid products like milk, soft drinks, shampoos, and industrial coatings. With a production throughput of up to 40,000 bottles per hour, it ensures consistent packaging quality. The machine is equipped with servo-motor synchronization for precise operation and easy format changeovers, thereby enhancing efficiency. Available material options include PET, PP, PS, aluminum, and glass, suitable for various end-product container shapes and materials. Maintenance is simplified with uncoupling options and a central control system that improves safety and supervision. Optional features such as ATEX protections and corrosive-resistant materials are available for specialty applications, ensuring durability and compliance with industry standards.
Benefits
- Minimizes floor space requirements by up to 25%, optimizing plant layout.
- Enhances operational efficiency with synchronized, high-speed multifunction processes.
- Reduces energy consumption through integrated servo-motor synchronization.
- Simplifies maintenance and changeovers, reducing downtime and operational disruptions.
- Customizable for diverse industry applications, ensuring flexibility in production.
- Applications
- Personal care, Sauces, Automotive products, Agrochemicals, Household products, Oils, Lube oils, Drinks, Thinners, Syrups, Paints, Dairy products
- End products
- Fruit syrup bottles, Engine oil bottles, Cooking oil bottles, Soft drink pet bottles, Salad dressing bottles, Paint thinner bottles, Brake fluid bottles, Paint cans, Pesticide bottles, Yogurt containers, Shampoo bottles, Milk bottles, Detergent bottles
- Steps before
- Bottle Unscrambling, Material Orientation, Blow Molding
- Steps after
- Labeling, Capping, Packaging
- Input ingredients
- unstable bottles, sticking bottles, topdown shapes bottles, PET, PP, PS, Aluminum, Glass
- Output ingredients
- packaged products, tracked packages, up to 40, 000 bottles per hour for 1 L bottles
- Market info
- Serac Group is known for its expertise in designing and manufacturing cutting-edge filling and capping machines for various industries, including food, beverage, and cosmetics, renowned for innovative technology and reliable, high-quality equipment.
- Speed
- up to 40, 000 bph (1 L)
- Container Material
- PET, PP, PS, Aluminum, Glass
- Container Type
- Unstable, sticking and topdown shapes bottles
- Compact footprint
- Saves up to 25% floor space
- Automation
- Servo motor synchronization
- Changeover Time
- Easy format changeovers without adjusting conveyors
- Energy Efficiency
- Lower operating costs with less energy consumption
- Synchronization Method
- Mechanical (shaft), Electronical (motion), screws or starwheels
- Servicing
- Machines can be uncoupled during maintenance, changeovers, or cleaning
- Customizability
- Multiple Rotary Blow Molder, Linear Blow Molder, Unscrambler, Orientator, Rotary Bottle Cleaner, Trigger capper, Labeler
- Corrosive Resistant Material
- PP or PE parts
- Optional Equipment
- ATEX protections
- Working mechanism
- Synchronized multi-machine operation
- Integrated steps
- Filling, Capping, Sealing
- Batch vs. continuous operation
- Continuous
- Changeover time
- Minimal with colored change parts
- Cleaning method
- Uncouple machines for maintenance/cleaning
- Automation level
- Centralized control system
- Corrosive resistant
- PP or PE parts
- Material type
- PET, PP, PS, Aluminum, Glass
- Machine footprint
- Save up to 25% floor space
- Footprint reduction
- Compact line
- Material type
- PET, PP, PS, Aluminum, Glass
- Discharge Method
- Direct coupling, eliminates conveyors
- Container compatibility
- Unstable, sticking, top-down shapes
- Outputs
- up to 40, 000 bph (1 L)
- Synchronization method
- Mechanically, electronically, screws, starwheels
- Machine uncoupling
- Possible during maintenance
- Compact footprint
- Save up to 25% floor space
- Discharge method
- Tracked (held or moved without touching)