Pharma manufacturing process vessels
Ensure contamination-free production of sterile liquid formulations with process vessels designed for seamless integration, precise heating and cooling, and stringent sterilization, meeting all regulatory guidelines for injectable drug manufacturing.
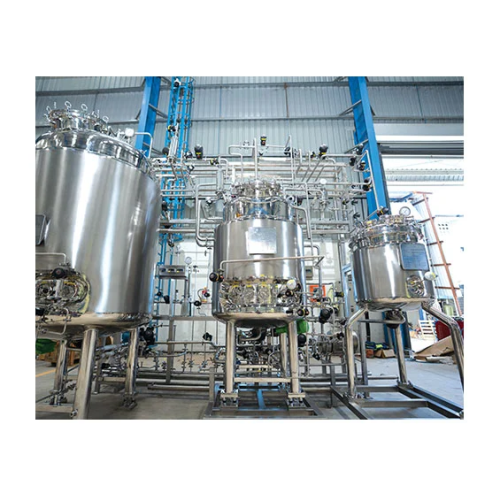
Ensures Sterile Liquid Formulation Production
Fabtech’s skid mounted Process Vessels offer a customizable solution for sterile manufacturing in the pharmaceutical, biotech, and healthcare industries. These vessels excel in producing biopharmaceuticals, injectables, and sterile formulations by integrating seamlessly with existing process equipment and utilities. With features such as auto heating and cooling, they maintain stringent control over sterilization processes, ensuring compliance with USFDA, WHO, and cGMP guidelines. The vessels support applications like vaccine and insulin production, facilitated by electropolished contact surfaces and high-quality orbital welding for contamination-free results. Ergonomically designed with safety features, these vessels include integrated documentation like DQ and IQ/OQ, ensuring thorough validation. Available in automatic and semi-automatic configurations, they support flexible operations within clean and unclean environments.
Benefits
- Ensures contamination-free production, enhancing product safety and quality.
- Streamlines regulatory compliance with USFDA and cGMP-approved design.
- Reduces operational footprint with space-saving skid mounted design.
- Simplifies validation processes with comprehensive documentation and integrated safety features.
- Enhances operational flexibility with customizable configurations and seamless integration.
- Applications
- Liquid formulations, Sterile formulations, Biopharmaceuticals, Healthcare, Injectable drugs, Pharmaceuticals
- End products
- Liquid analgesics, Vaccines, Nutritional supplements, Insulin, Monoclonal antibodies, Iv fluids, Eye drops, Antibiotic injections, Oral vaccines, Sterile injectable solutions
- Steps before
- Purification, Water Treatment, Solution Preparation
- Steps after
- Sterilization, Filling, Packing
- Input ingredients
- sterile drugs, raw materials, injectable ingredients
- Output ingredients
- sterile injectable drugs, contamination-free products
- Market info
- Capacity
- Wide range of volume capacities
- Automation
- Automatic / Semi-automatic
- Heating and Cooling Arrangements
- Auto based on process requirements
- Surface Finish
- Electropolished to less than 0.4 RA microns
- Welding Quality
- High quality orbital welding with boroscopy and videoscopy
- Piping Standard
- ASME BPE grade field piping
- Insulation
- For sterilisation temperatures
- Integration
- Integrated with zero dead leg valves
- Compliance
- 21 CFR Part 11 compliance with SCADA
- Automation level
- Automatic/Semi-automatic with 21 CFR Part 11 compliance, SCADA
- Batch vs. continuous operation
- Batch
- CIP/SIP
- CIP, SIP capability
- Cleaning method
- CIP/SIP
- Integrated steps
- Seamless integration with process equipment
- Compliance,Certifications
- USFDA, WHO, MHRA, ASME BPE, cGMP
- Flexibility
- Customisable configuration
- Safety Features
- Insulated for sterilisation temperatures
- Density/particle size
- 0.5–2.5 g/cm³ / 50–1000 µm
- Machine footprint
- Skid based, space-saving
- Shape
- Vessels - cylindrical
- Size
- Varies based on volume capacity
- Support equipment design
- Ergonomically designed structural platforms and ladders
- Discharge method
- Integrated with transfer piping
- Configuration
- Customizable
- Auto Heating and Cooling
- Based on process requirements
- Skid Based Solutions
- Simple and space-saving
- Access Support
- Ergonomically designed platforms and ladders
- Sterilization Insulation
- Temperature resistant with safety features
- Polished Contact Parts
- Electropolished < 0.4 RA microns
- Automation Level
- Automatic/semi-automatic
- CFR Compliance
- 21 CFR Part 11
- Piping Integration
- ASME BPE Grade
- Drainability
- Fully drainable with zero dead leg
- Documentation Dossiers
- Includes DQ, FAT, IQ, OQ Protocols