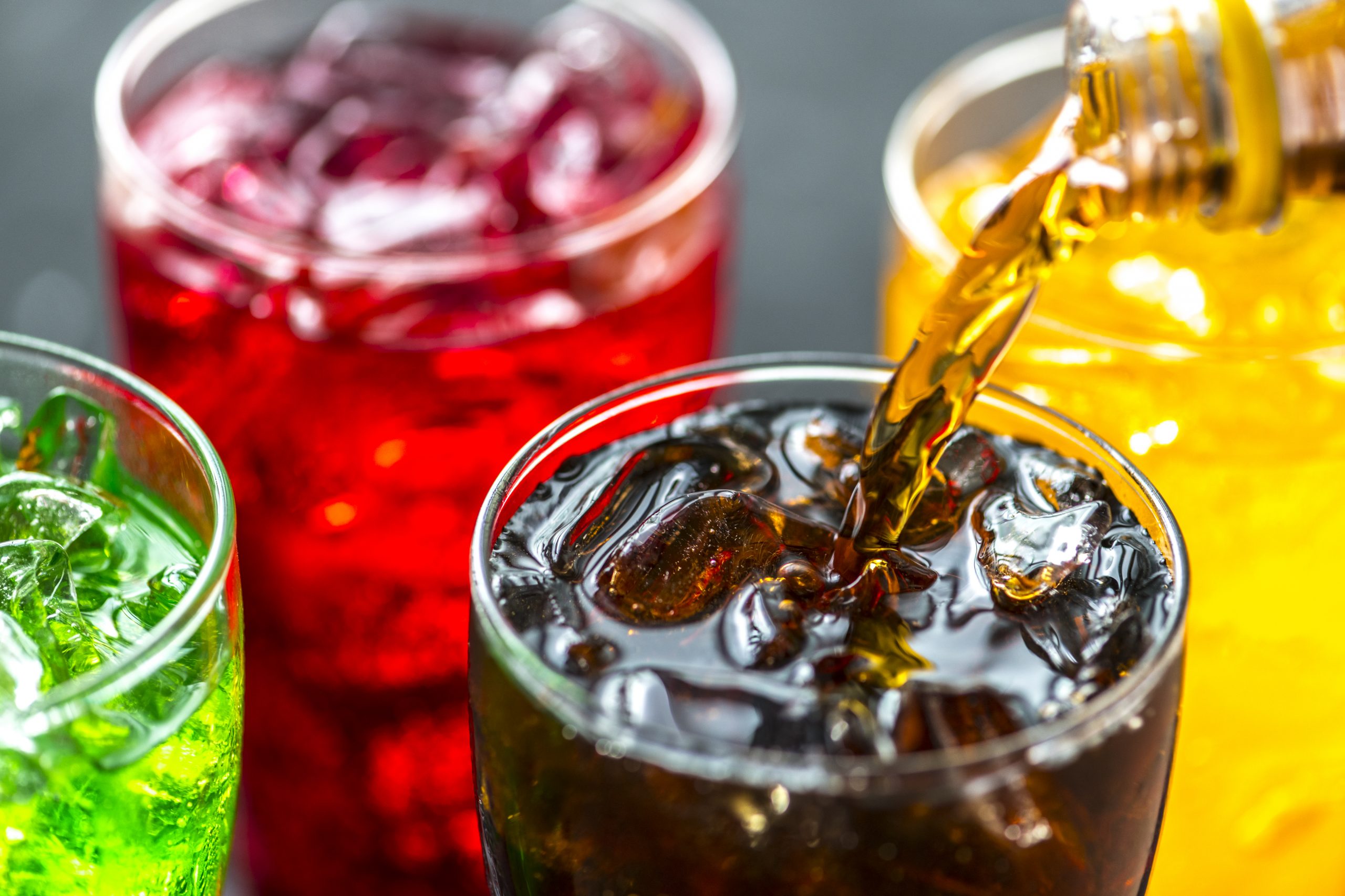
Making Soft Drinks
Find innovative production technology for making soft drinks and connect directly with world-leading specialists
Originally developed as medicinal remedies, soft drinks quickly burst into a whole new category of non-alcoholic beverages. To make a soft drink, simply dissolve one part syrup into five parts water. For extra punch, add carbon dioxide to turn the mixture into a fizzy drink.
Stories about soft drinks
Select your soft drinks process
Tell us about your production challenge
CO2 is what makes soft drinks cool
If you are making a carbonated soft drink (CSD), the CO2 level needs to be uniform across the entire production. A typical CSD formula contains 6-8 grams of carbon dioxide per liter.
But carbon dioxide does more than add tingle to your soft drink. It lowers the level of acidity and chokes out oxygen, eliminating undesired microorganisms. Carbon evaporates quickly from the tongue, leaving drinkers with a sensation of cooling refreshment.
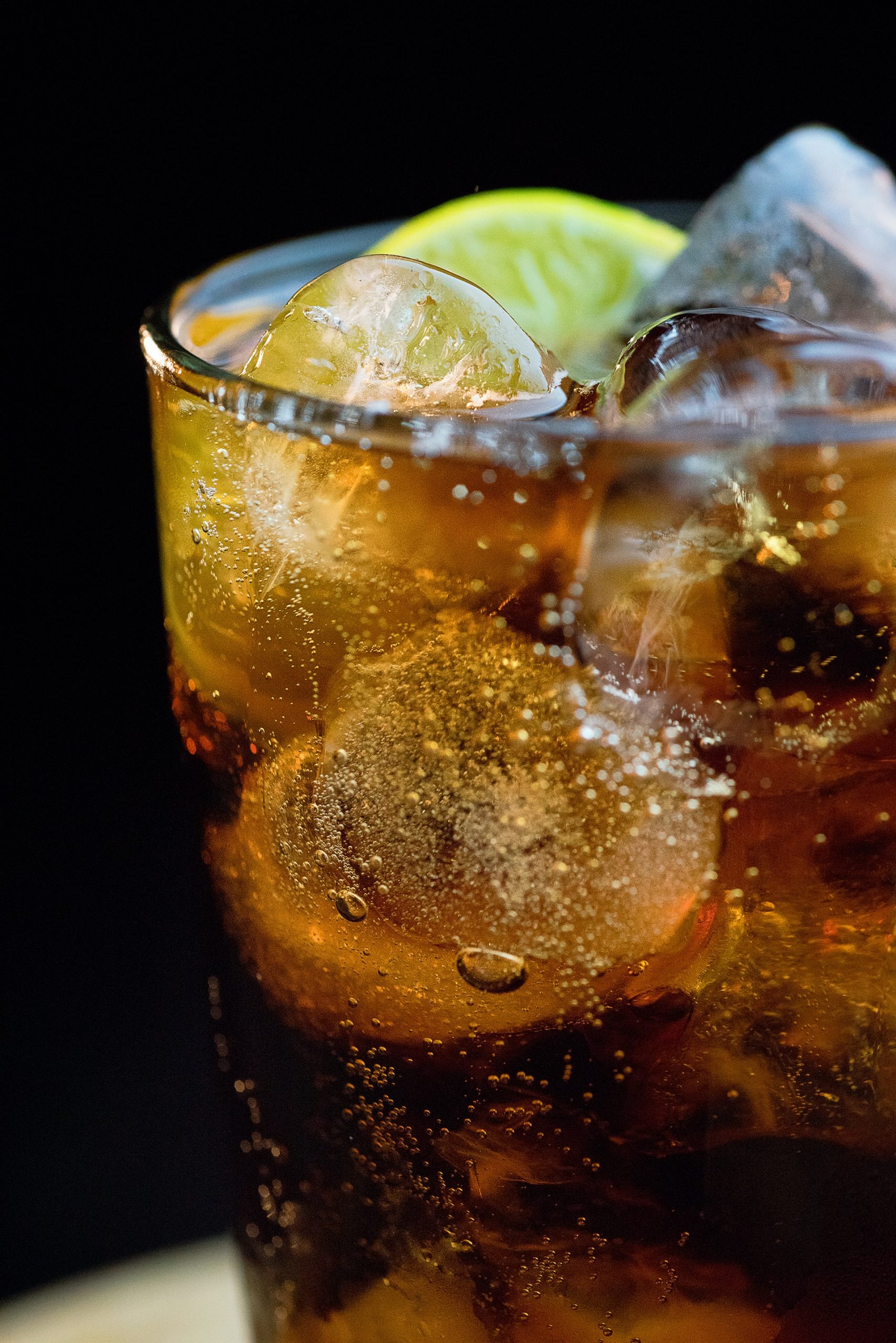
Why carbonated soft drinks make that hissing sound
No matter the brand, all carbonated soft drink bottles crack open with a hiss. That unmistakable sibilance is the sound of dissolved carbon dioxide escaping through the opening.
But not all carbon flees the bottle, otherwise your drink would lose its fizz. The CO2 stampede that produces the hissing is a chemical reaction that takes place because there is an imbalance of gases within the liquid and outside of it. The exchange of CO2 stops as soon as the concentrations reach a state of equilibrium.
The basic equipment you need to make soft drinks
Before your secret syrup recipe can be enjoyed as a soft drink, it needs to be finished by specialized technologies that ensure a homogeneous and high-quality product.
A line of soft drinks equipment typically start with the mixing and blending units while dissolving machines melt sugars. Depending on the ingredients, and particularly in the case of fruit bases, the system requires pasteurization and clarification before the bottles are ready for filling and labelling.
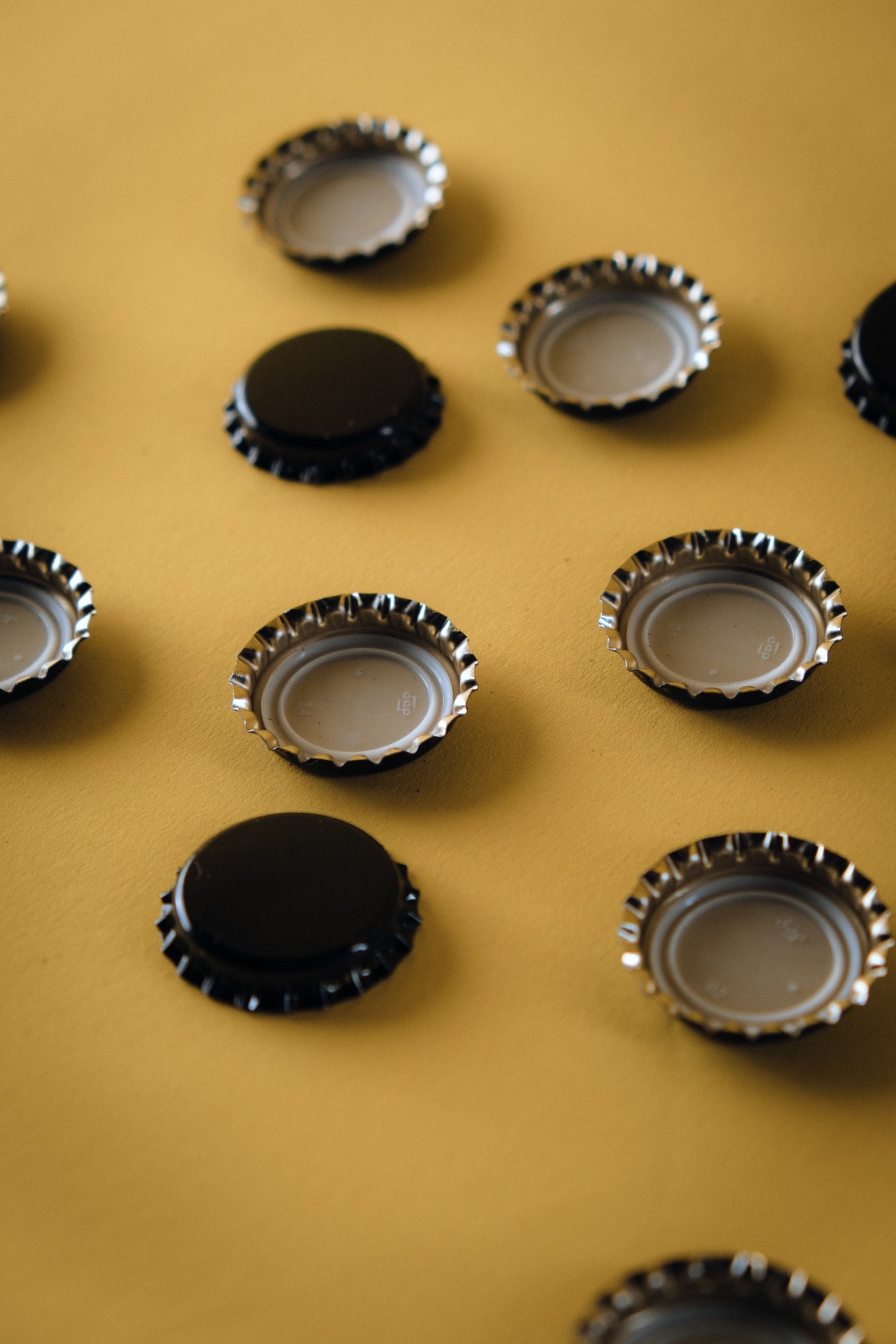
Sealing it with a crown cap or a twist-off stopper
The slender neck of soft drink glass bottles is made for a crown cap. Developed specifically to seal carbonated beverages over 130 years ago, the closure technique still stands the test of time. Over the decades, however, caps have become flatter than the original design and standardized into a 21-tooth rim.
The emergence of PET bottles led to plastic twist-off caps that do the same job, without the need of a bottle opener. This alternative allows consumers to re-close the drinks securely, making it a perfect choice for your larger-sized bottles.
Soft drinks return to the wellness route
A pushback against high sugar content is opening new avenues for soft drinks manufacturers. Classic recipes are experimenting with low-sugar and zero-calorie products. Reducing sugars is already a radical change, but some producers are going further and enriching their recipes with nutrients such as prebiotics and minerals.
Meanwhile, a wave of flavor experimentation is bringing bold new drinks. Particularly in the commercial juice market with, tastes ranging from pear elderflower to salty watermelon.
Processing steps involved in soft drinks making
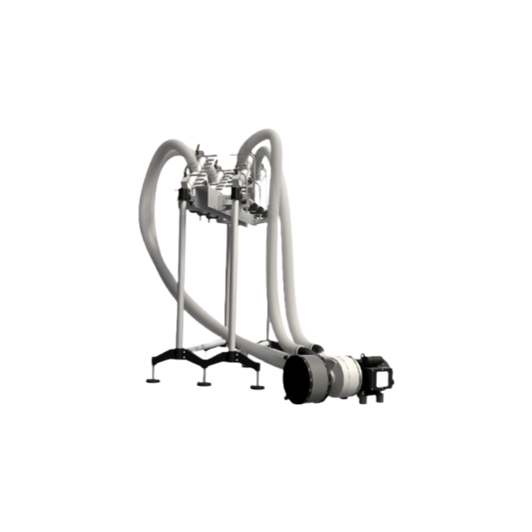
Air knife dryers
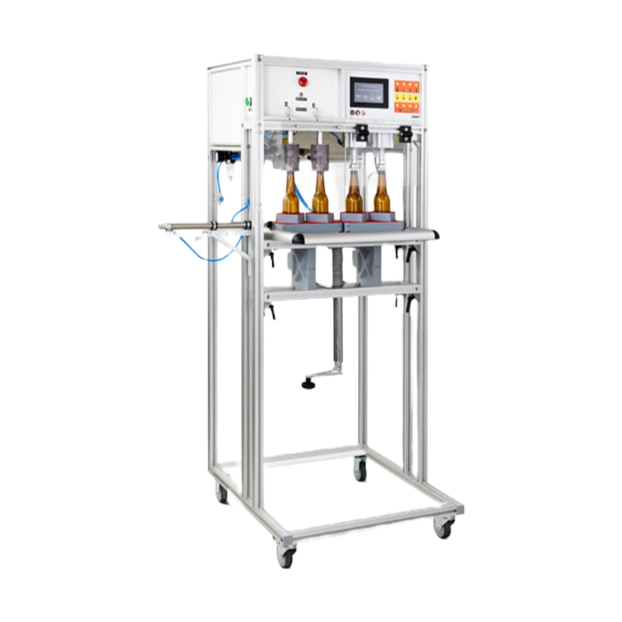
Bottle filling equipment
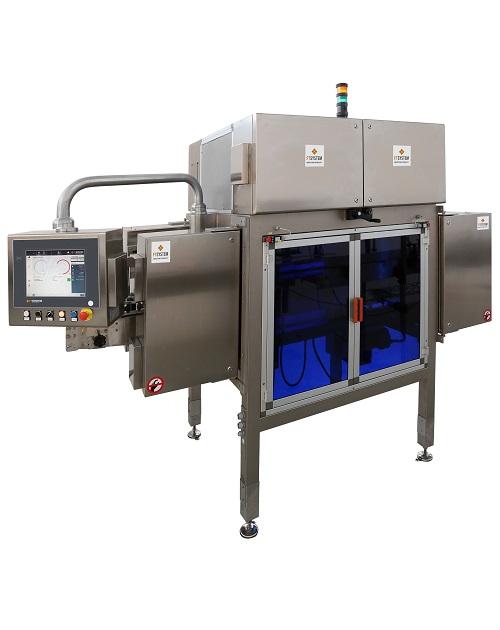
Bottle inspection systems
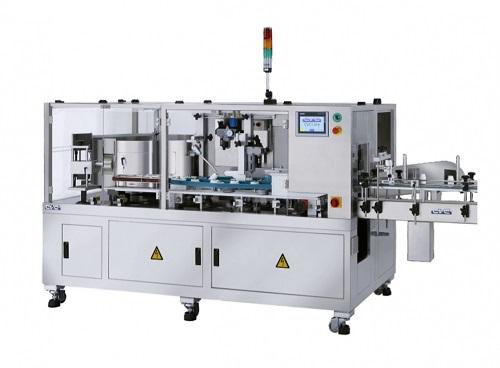
Bottle sorters and unscramblers
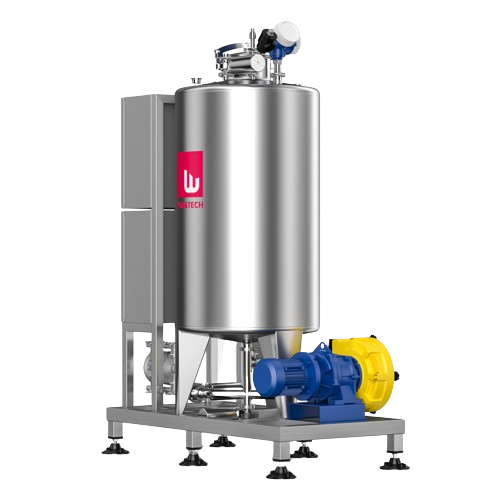
Bottling
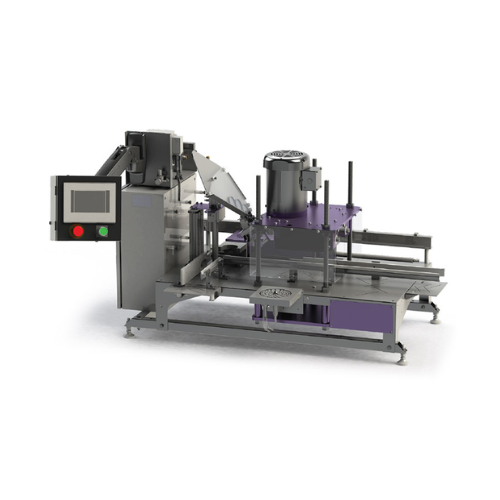
Canning
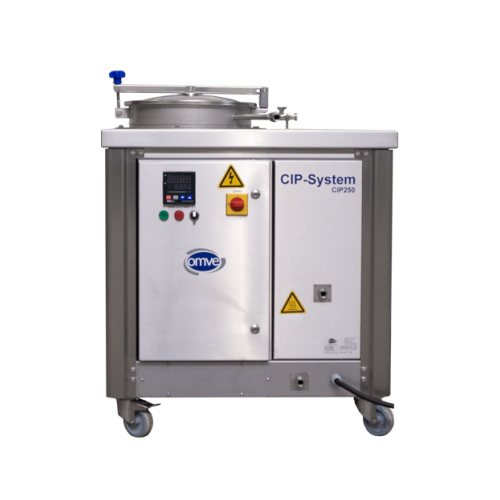
Cleaning
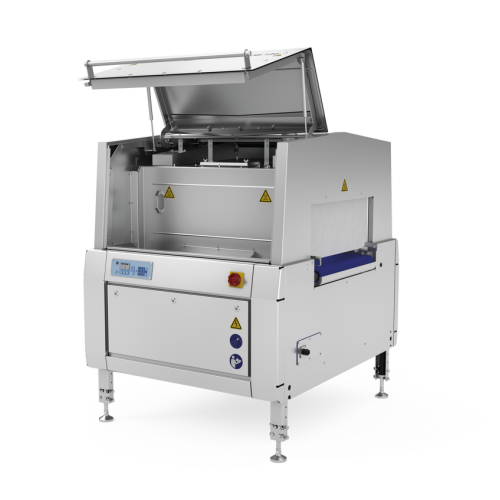
Drying
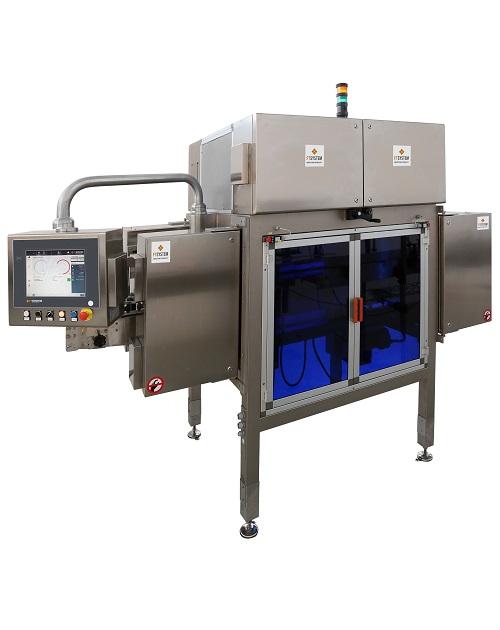
Empty bottle inspection
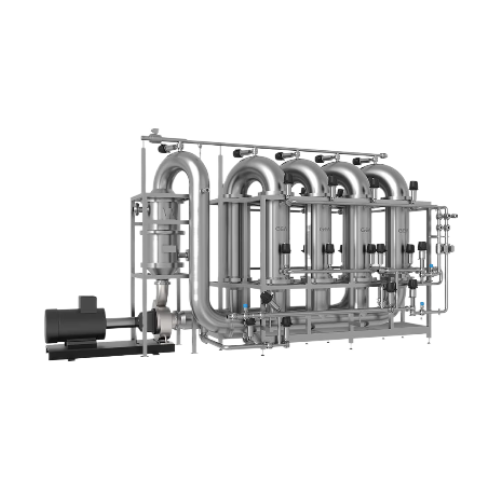
Filtration
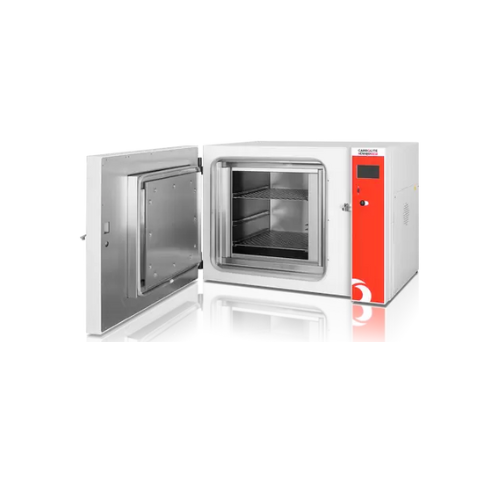
Heating
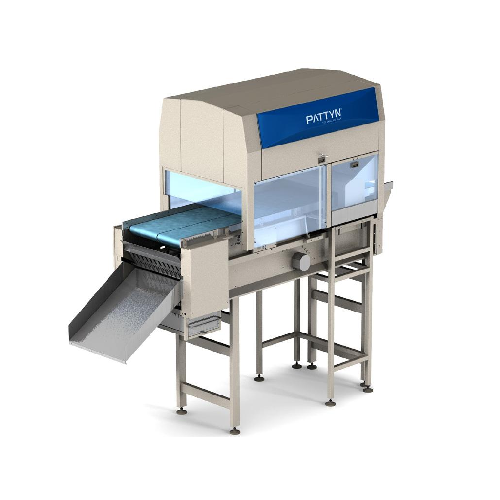
Inspection
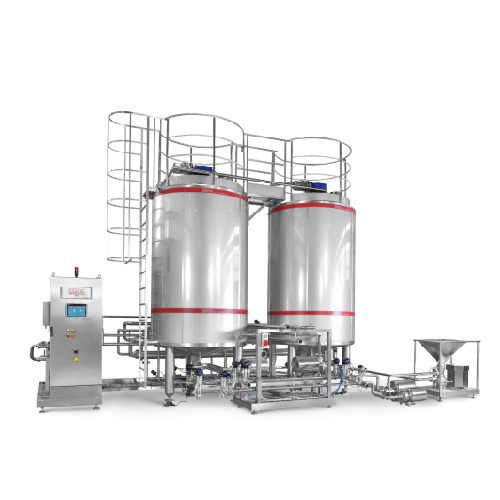
Mixing
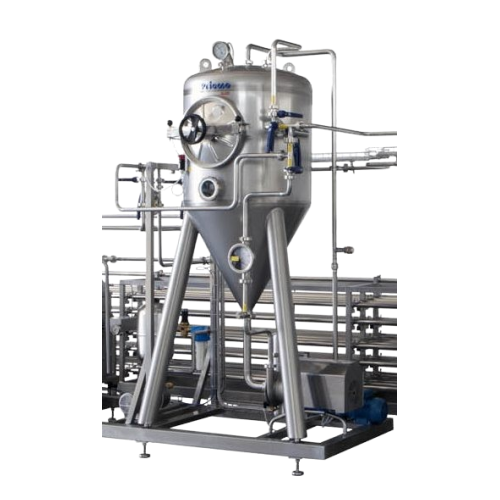
Pasteurization
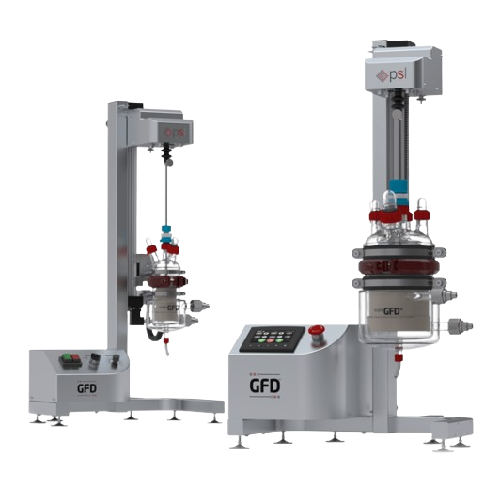
Separation
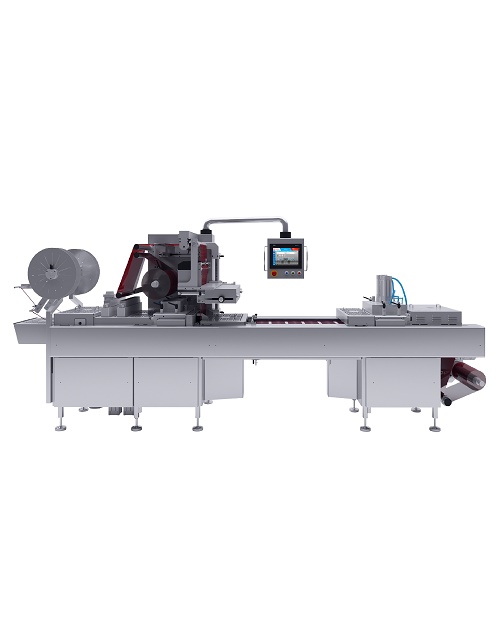
Shrink wrappers
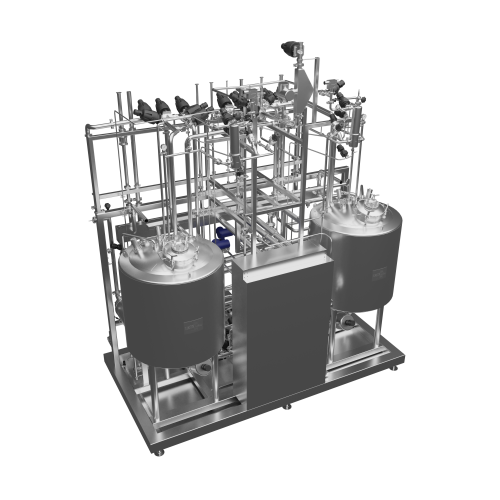
Sterilization
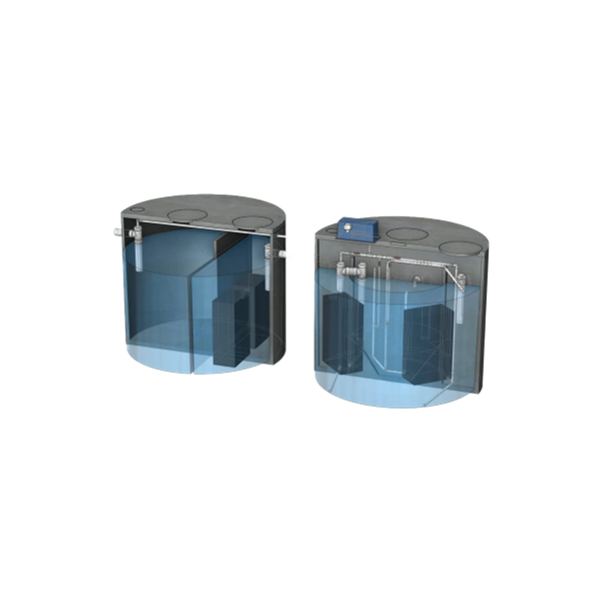
Wastewater treatment systems
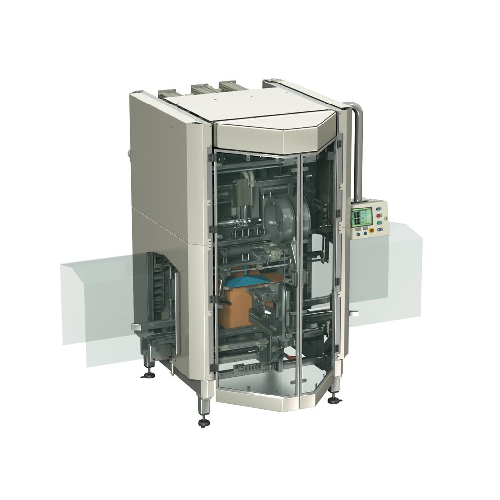
Wrapping

X-ray inspection equipment
Which soft drinks technology do you need?
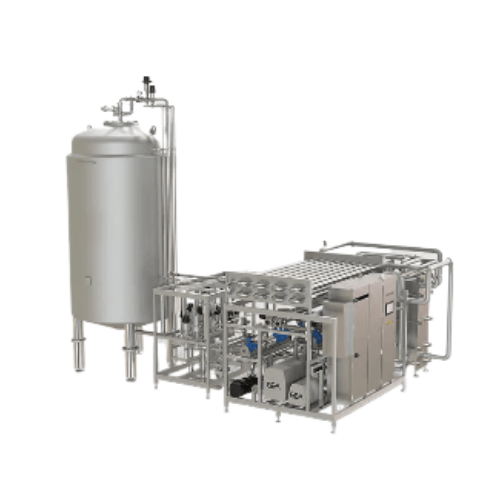
Flash pasteurizer for beer and carbonated beverages
Ensure optimal flavor and safety in your beverages by integrating a c...
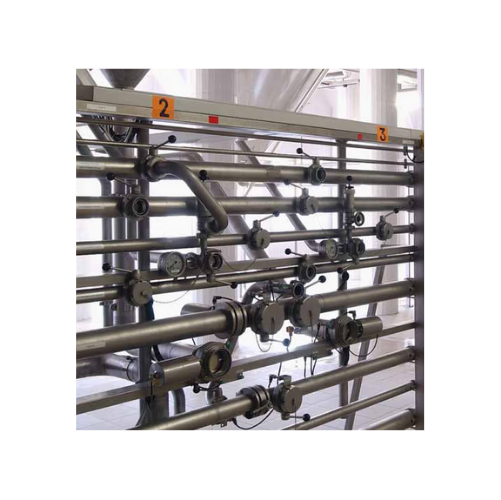
Piping solutions for breweries cold block area
Efficiently distribute and regulate media within your brewing process, ensu...
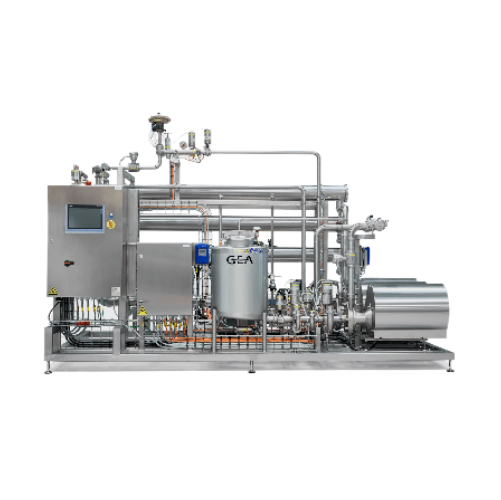
Membrane dealcoholization unit for beer
Enhance your brewery’s capabilities by efficiently removing alcohol while pre...

Beverage multi-pack cartoner for cans and bottles
Optimize your beverage production line with high-speed, continuous mult...
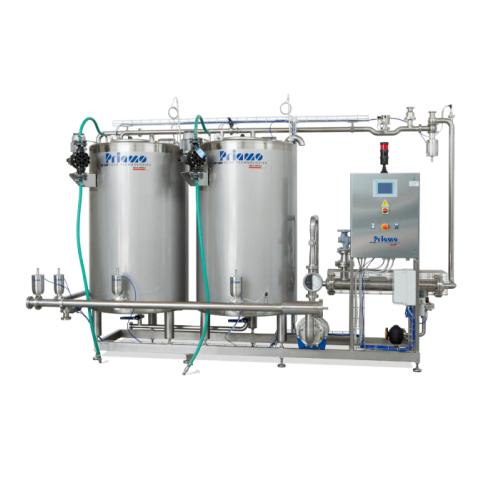
Cip systems for dairy production
Ensure consistent hygiene and sanitation levels in your production line with efficient, aut...
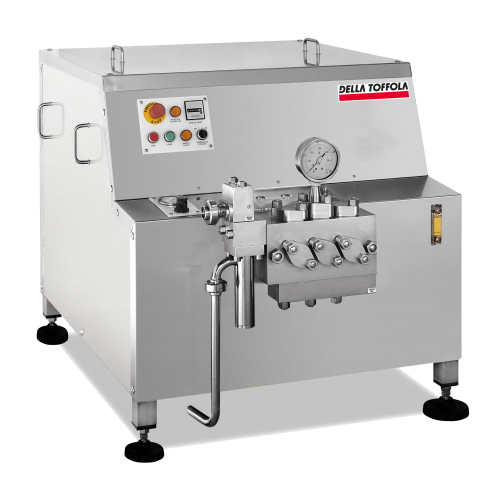
Industrial homogenizers for dairy products
Maximize consistency and quality in your production of milk products and bevera...
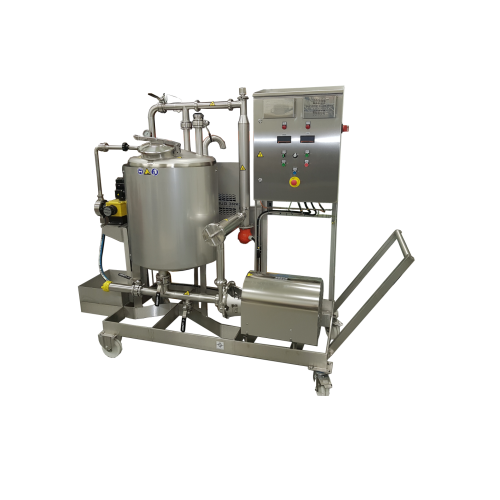
Mobile cleaning-in-place unit for process equipment
Ensure seamless cleaning of diverse process equipment with a mobile, ...
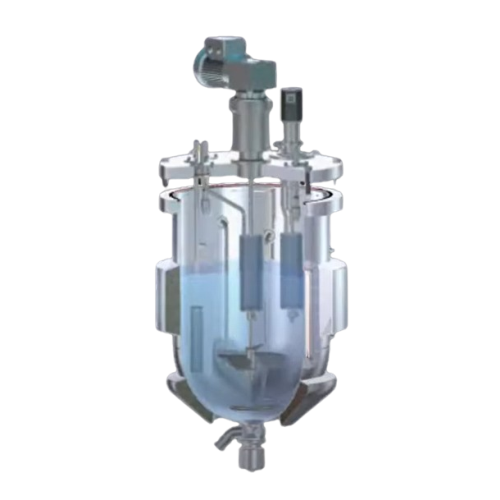
Industrial agitation and mixing solutions
Enhance your production line efficiency with engineered agitation and mixing sys...
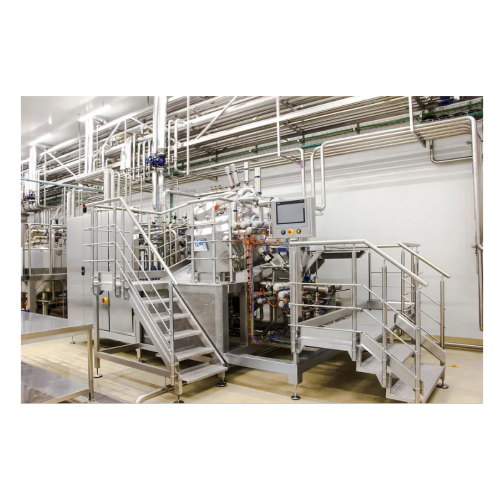
Hygienic fluid storage tanks for food industry
Ensure impeccable hygiene in fluid storage with our customizable tanks, des...
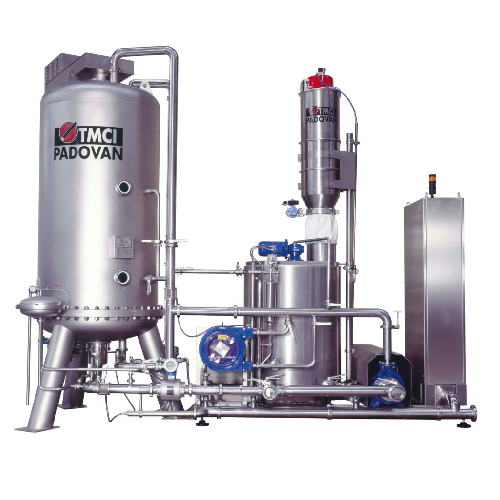
Ped tested filtration system for sparkling wines
Ensure consistent carbonation and clarity in your sparkling beverages wit...
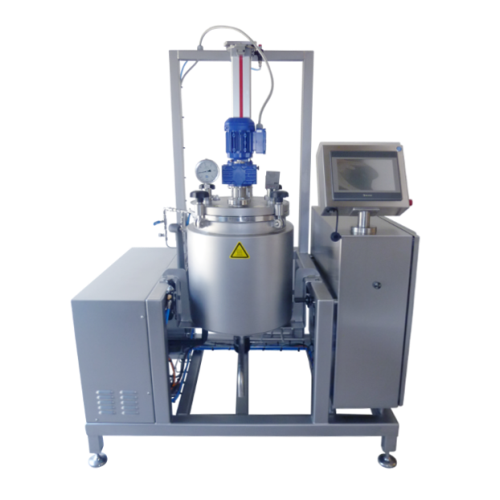
Batch food processing cookers
Achieve precise temperature and pressure control for small-scale food production with modular ...
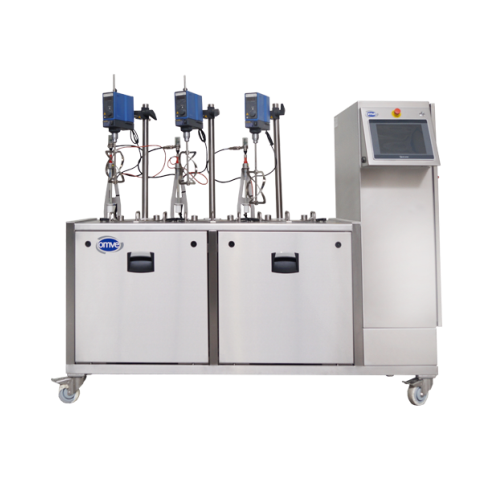
Lab-scale fermenter for simultaneous batch processing
Optimize your lab-scale fermentation process with a versatile solut...
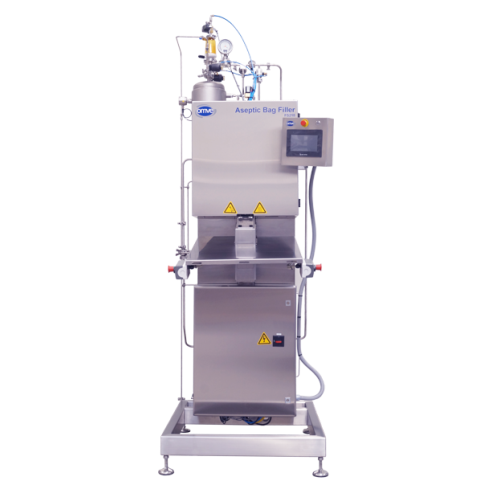
Aseptic bag-in-box filler for laboratory use
Achieve aseptic filling precision on a lab-scale with a compact solution that...
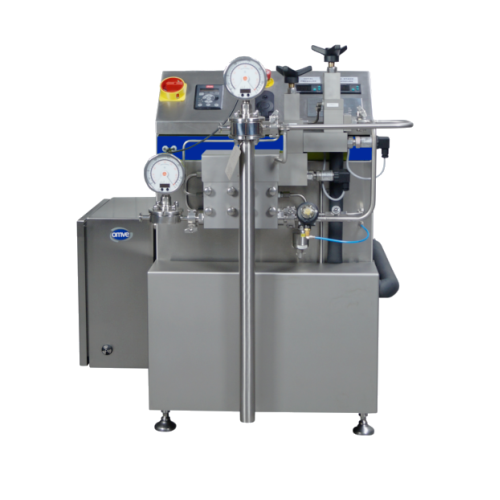
Pilot homogenizer for high-pressure inline homogenization
Achieve precise homogenization and emulsification across vario...
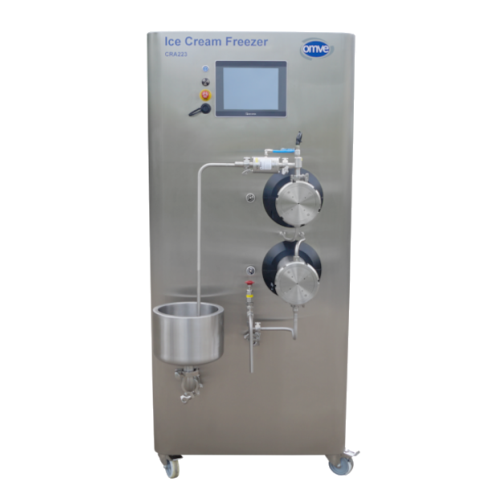
Continuous ice cream freezer for r&d
Achieve precise control of ice cream texture and consistency with a system that seamle...
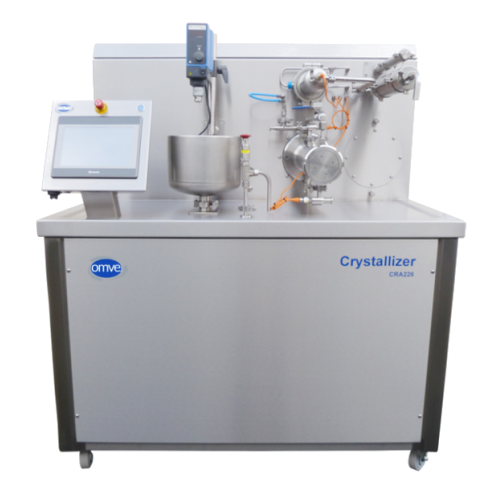
Crystallizer for small-scale aeration and crystallization processes
Streamline your production with a versatile crystal...
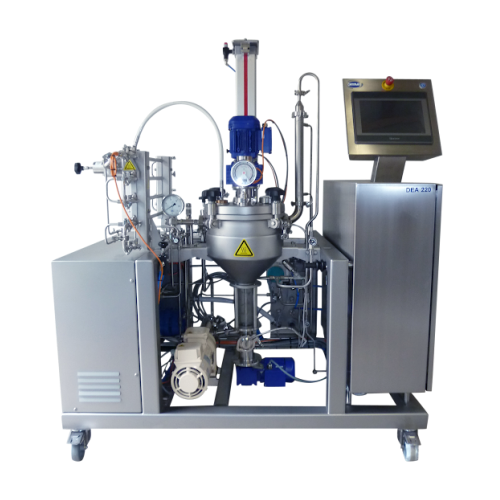
Continuous deaeration solution for laboratory and pilot systems
Achieve superior product stability and minimize foaming ...
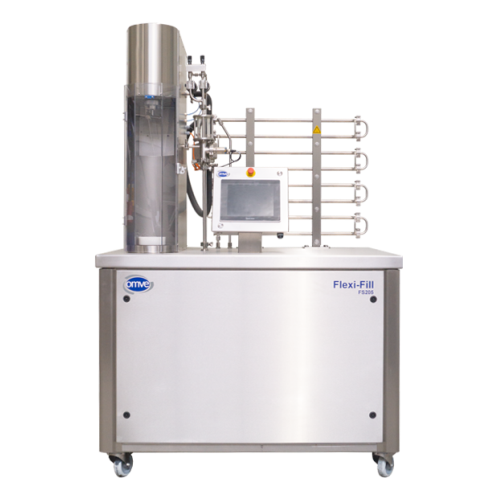
Counter-pressure filler for carbonated drinks
Enhance your carbonated beverage production with advanced counter-pressure f...
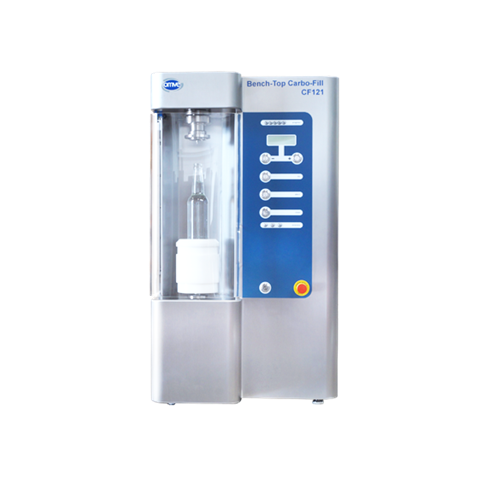
Bench-top carbonation system for postmix drink production
Achieve precise carbonation in small batches with a reliable b...

Lab-scale carbonation system for beverage filling
Streamline your beverage development with precision carbonation and ver...
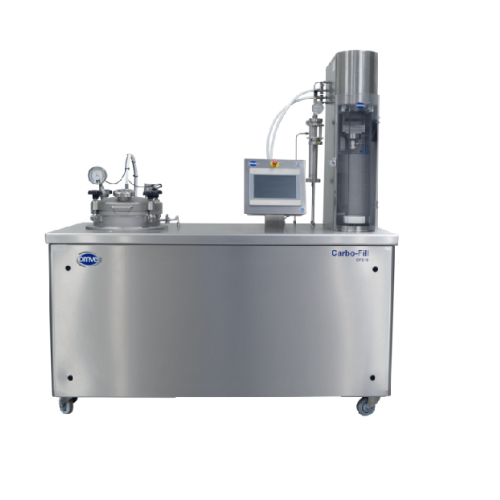
Carbonation and filling system for Pet and glass bottles
Optimize your beverage production with precise carbonation, fill...
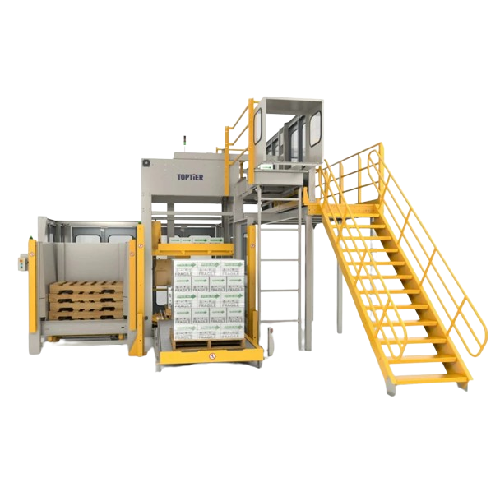
High infeed palletizer for varied product types
Optimize your production line with high infeed palletizers, ensuring seaml...
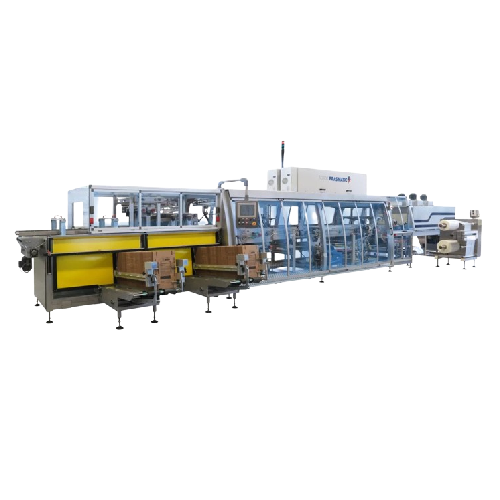
High-speed shrink wrapping for beverage packaging
Optimize end-line packaging with a high-speed solution designed to hand...

In-line weight filler for drums and kegs
Achieve precise and efficient weight-based filling for large liquid containers, en...
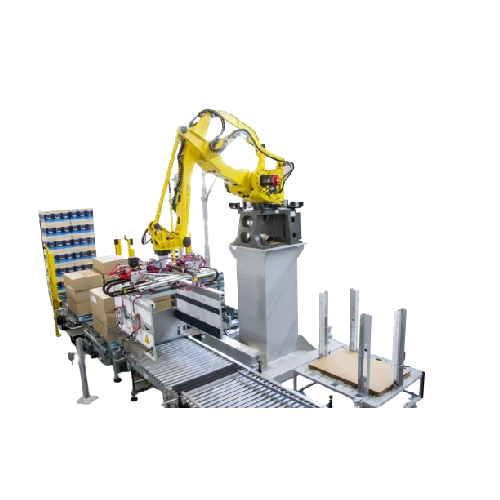
Robotic palletizer for row gripping
Optimize your palletizing efficiency with a robotic system designed for fast, continuou...
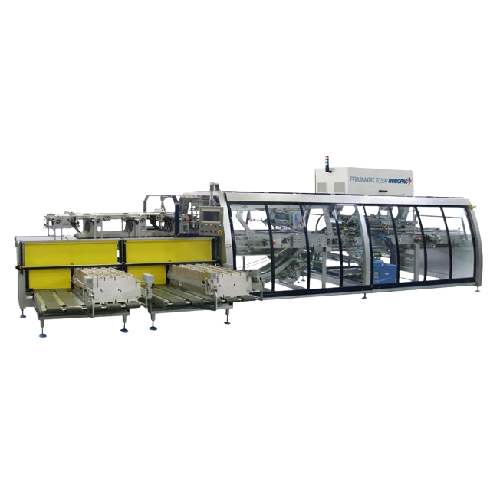
Medium to high-speed carton packing solution
Optimize your packaging operations with a versatile solution capable of handl...
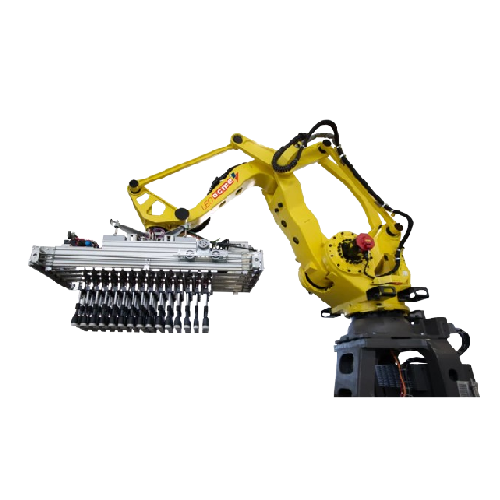
Robotic crating and decrating solution for returnable glass bottles
Streamline your bottling line by efficiently handli...
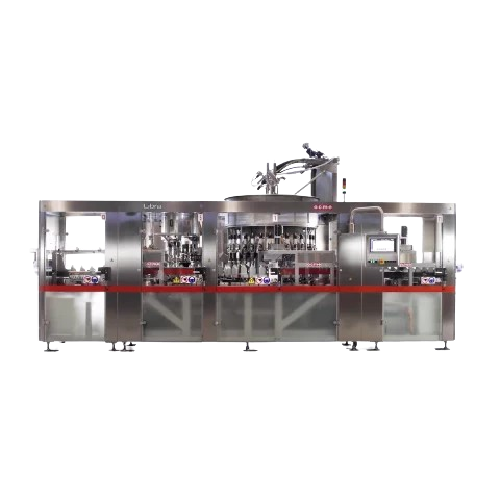
Rotary weight filler for Pet and Hdpe bottles
Enhance your production line with precise weight-based filling, ensuring rap...
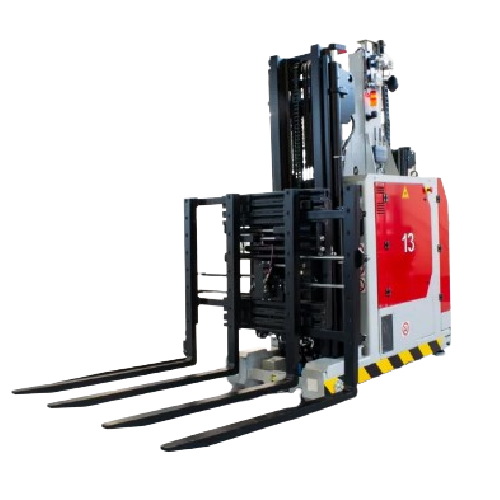
Laser guided vehicle for pallet handling
Efficiently streamline your internal logistics with cutting-edge laser guidance, e...
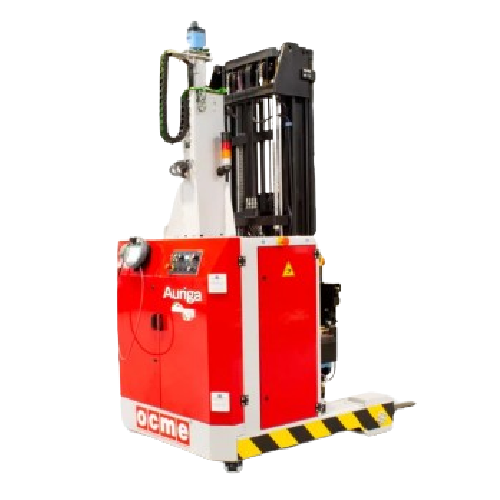
Laser guided reach truck for high-density warehousing
Optimize your warehouse operations with an advanced reach truck des...
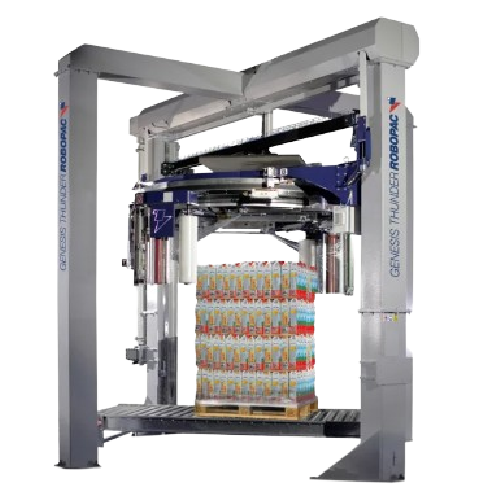
Automatic rotary ring wrapper for high-speed pallet wrapping
Achieve optimal load stability and reduce material usage wi...
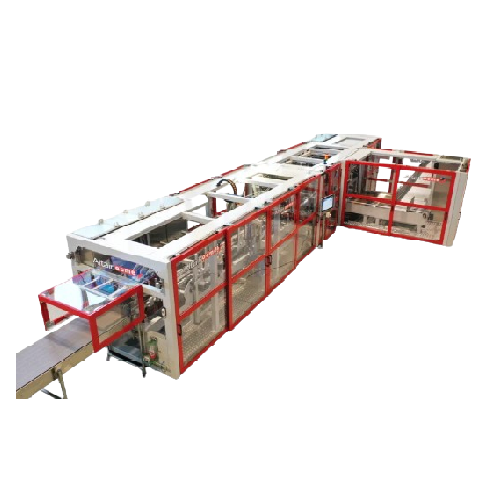
High-speed wrap-around case packer for beverage industry
Optimize your packaging line with a high-speed case packer that ...
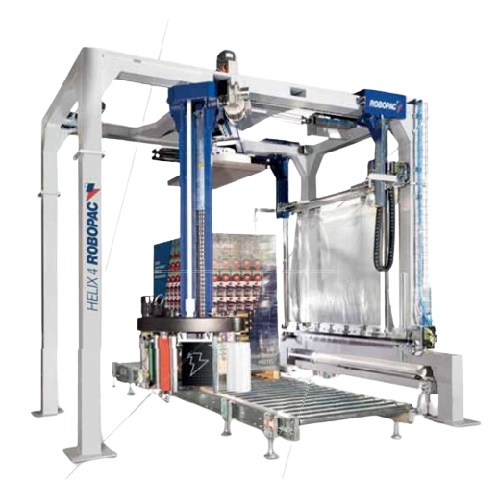
Fully automatic rotary arm wrapper for palletized loads
Enhance load stability in your packaging processes with a low-spe...
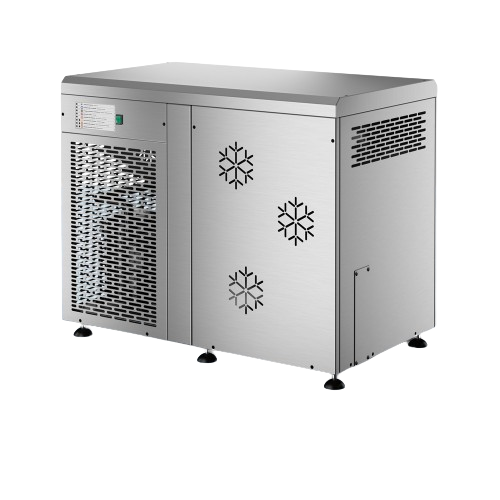
Flake ice maker for food processing applications
Ensure optimal product preservation and temperature control with precisio...
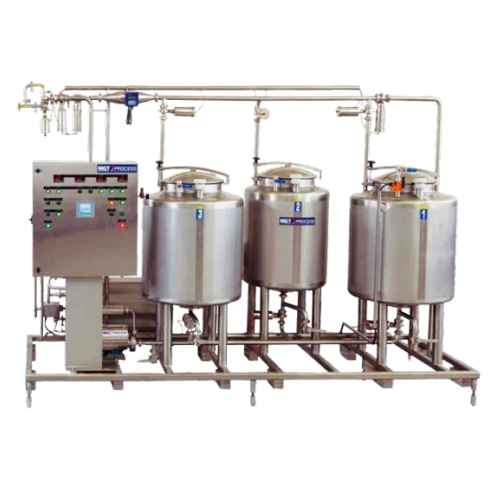
Cleaning-in-place (cip) systems for hygienic processing
Elevate hygiene standards in your liquid processing line with an ...
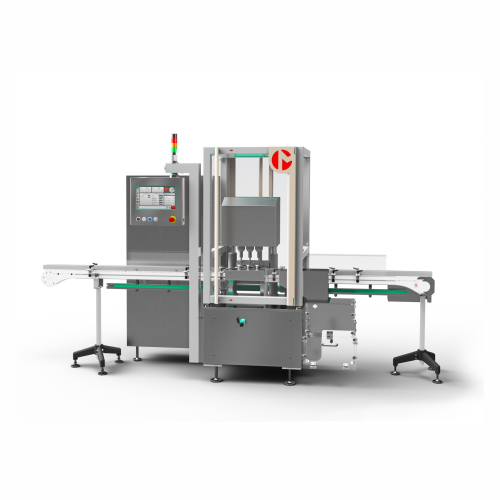
Filling and capping solution for bottles
Optimize your bottling efficiency with a robust solution designed to streamline fi...
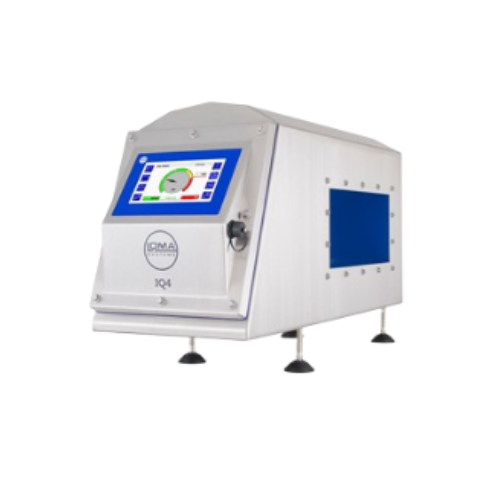
Industrial metal detector for food production lines
Ensure product safety and compliance by seamlessly detecting metal co...
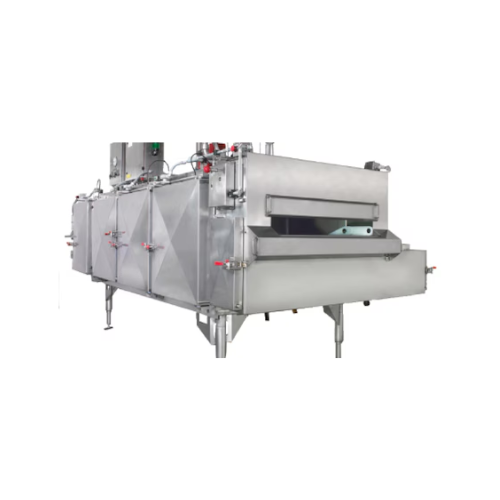
Cryogenic tunnel freezer for optimized food freezing
Enhance your production line with advanced cryogenic freezing techno...
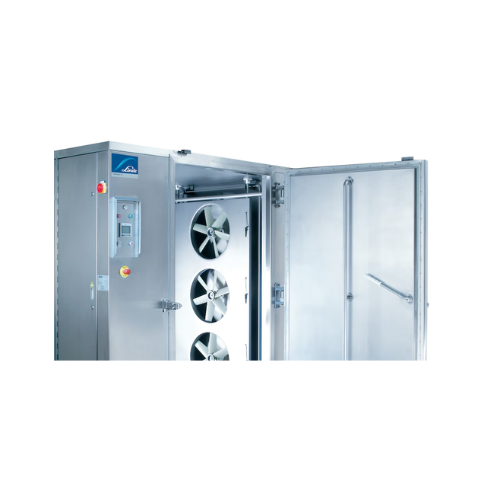
Cryogenic freezer for food industry applications
Efficiently tackle high-speed freezing and chilling challenges with a ver...
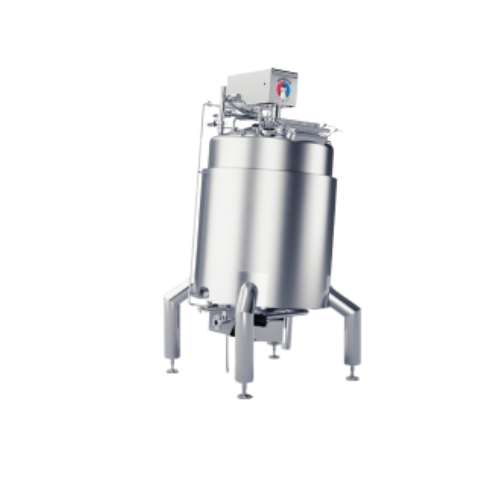
Heating and cooling system for food and dairy products
Achieve precise temperature control and efficient processing with ...
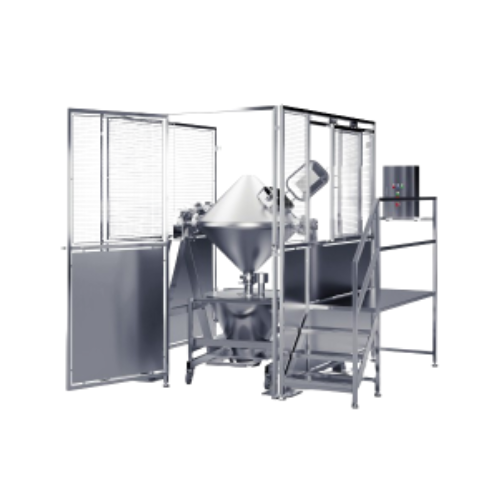
Industrial powder blender
Optimize your production with precise dry blending, ensuring efficient mixing processes and seamle...
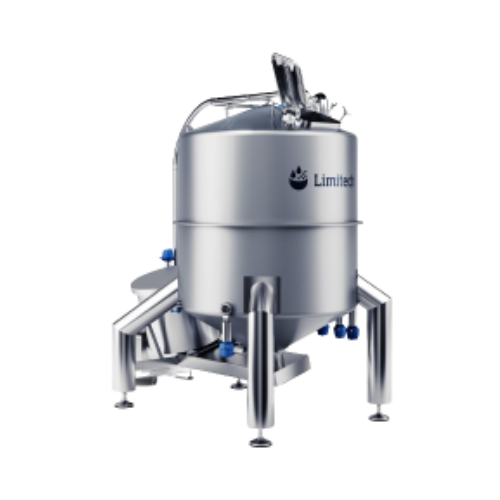
High shear mixer for viscous powder dissolution
Need consistent, homogeneous blending of high-viscosity liquids and powder...
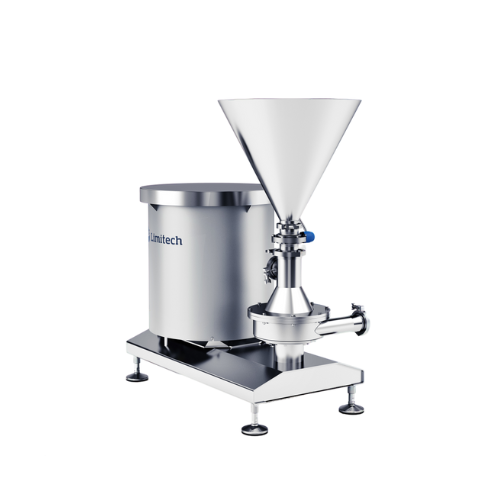
High-shear inline mixer for lump-free products
Achieve consistent texture and prevent clumping in liquid and powder blends...

Pre-mixer for dissolving powders fast
Quickly dissolve powders without lumps or “fisheyes,” ensuring a smooth a...

Customized oil storage tank for industrial use
Enhance production efficiency and ensure seamless integration with customiz...
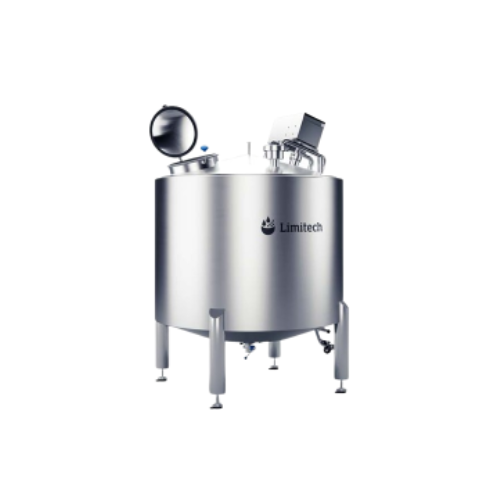
Cylindrical buffer tank for processing lightly liquid products
Optimize production continuity with this cylindrical buff...
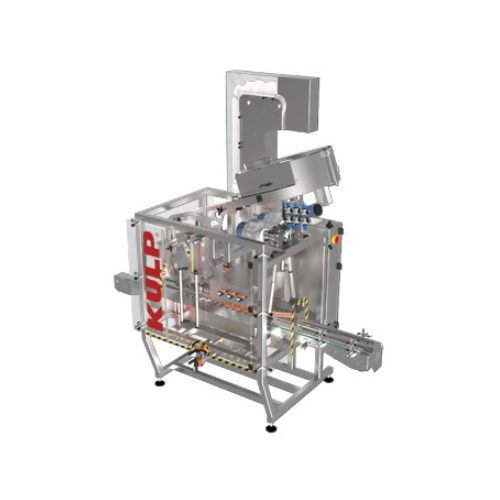
Continuous inline capping system
Perfect for high-speed operations, this system ensures precise capping of diverse container...
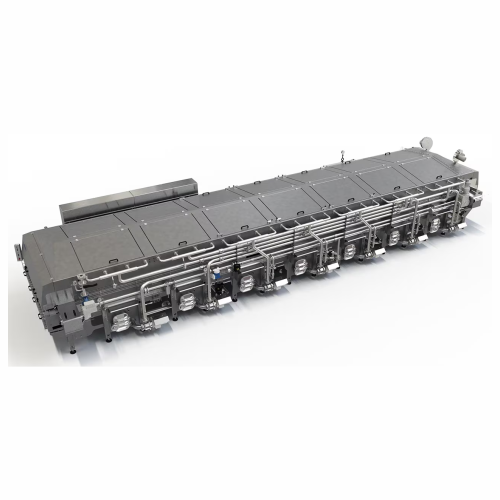
Compact tunnel pasteuriser for beverages
Ensure beverage safety with precise pasteurisation in a compact design that integr...
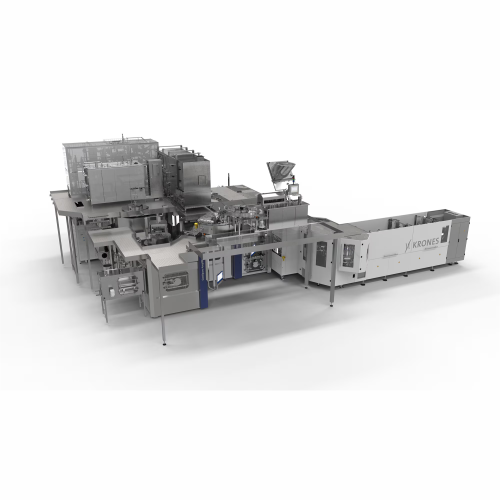
Ultrahygienic block for aseptic filling
When handling sensitive beverages, ensuring microbiological safety and quick produc...

High-performance stretch blow moulding and labelling system
Maximize space and efficiency with this compact system that ...
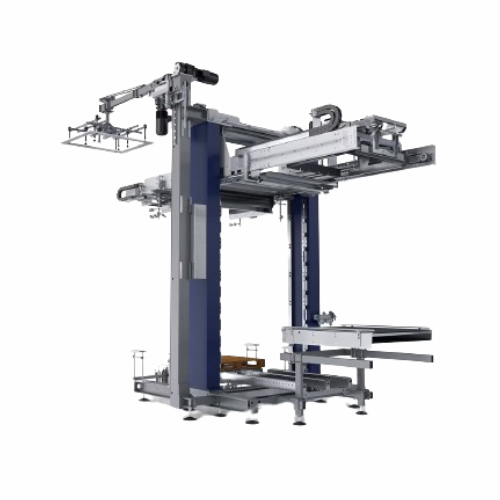
Container sweep-off depalletiser
Enhance your beverage production line efficiency with a high-performance depalletising solu...
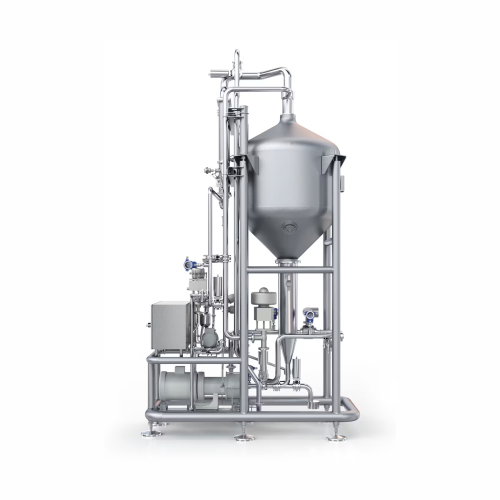
Juice product deaerator
Ensure high-quality filling without foam formation through efficient deaeration, perfect for manufact...
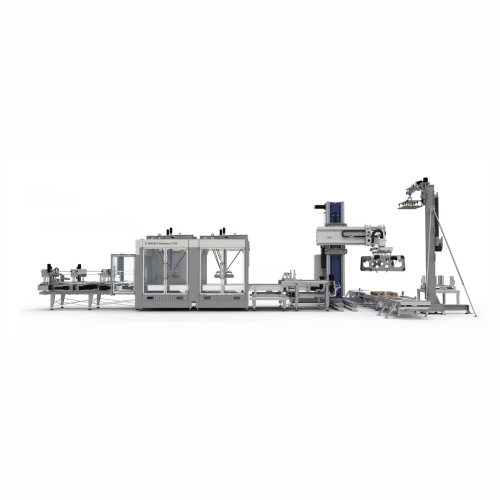
Palletizing grouping system for non-returnable packs
For beverage and packaging lines, precise and rapid palletizing of n...
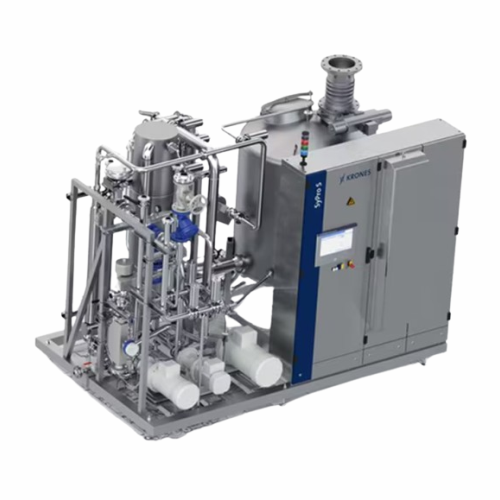
Syrup room for customized beverage ingredient preparation
Achieve unparalleled flexibility in beverage production with a...
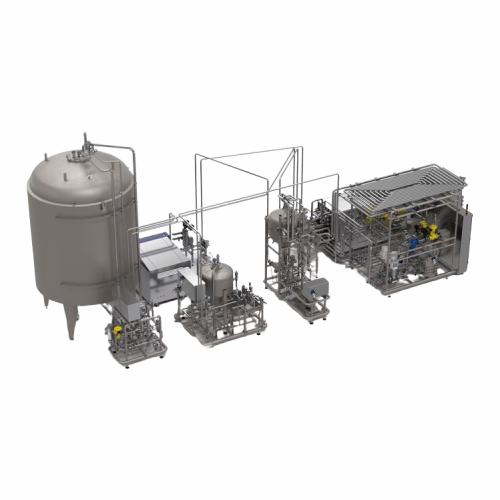
Uht system for aseptic filling of beverages
Ensure microbiological safety and retain natural flavors in your liquid produc...
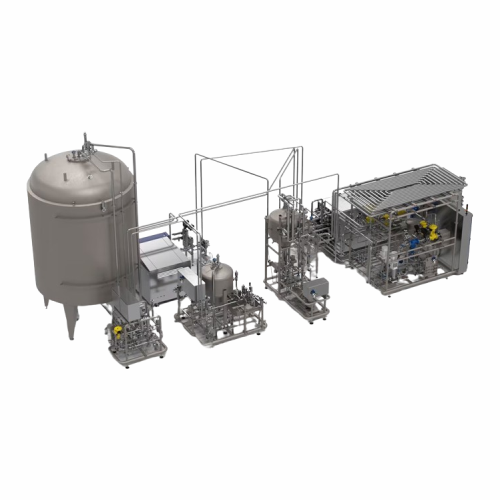
Uht system for milk products
Achieve optimal product safety and quality for dairy and plant-based beverages with precise UHT...
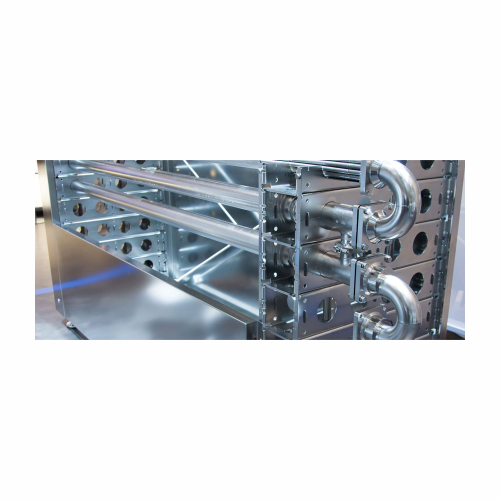
Heat exchanger for beverage production
Ensure your beverages maintain their quality and safety with a versatile heat exchan...
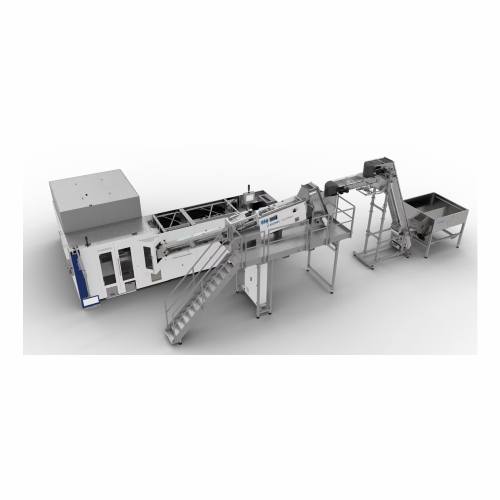
Stretch blow moulder for Pet containers
Optimize energy efficiency and production versatility with this stretch blow moulde...
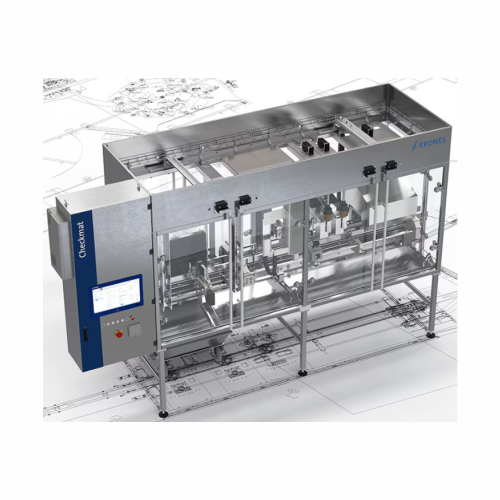
Compact fill level and cap inspection system
Ensure flawless beverage quality by integrating a compact system for precise ...
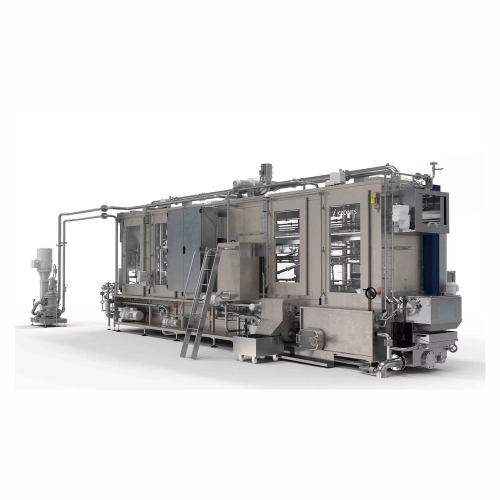
Crate washer for beverage manufacturers
Ensure thorough cleaning of beverage crates with an advanced washing system featuri...
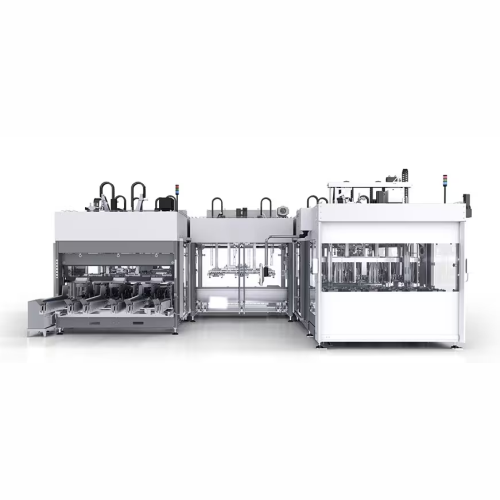
Flexible packaging line for beverage production
Streamline your beverage production with a flexible system capable of hand...
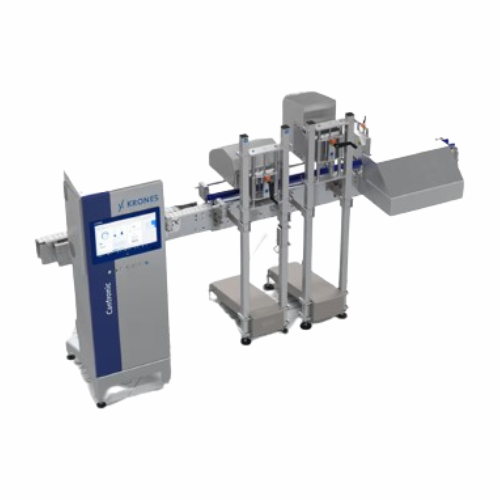
Can inspection unit for quality control
Ensure the integrity of your beverage cans with precise defect detection and qualit...
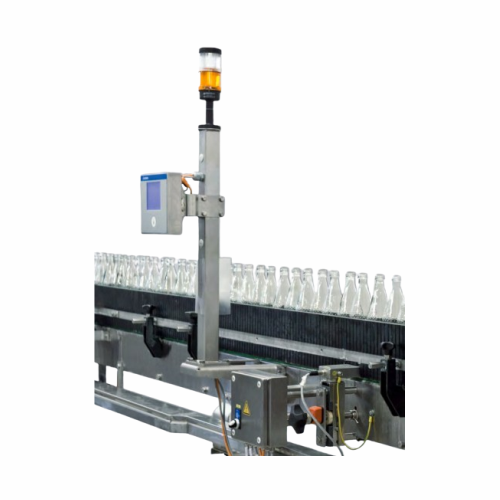
Caustic residue detection for bottle washing
Ensure product purity by detecting and eliminating residual caustic in return...
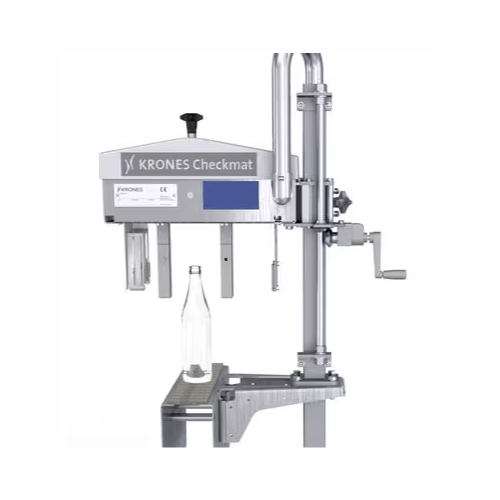
Inspection systems for fillers and cappers
Ensure precise fill levels and secure cap placements with advanced inspection s...
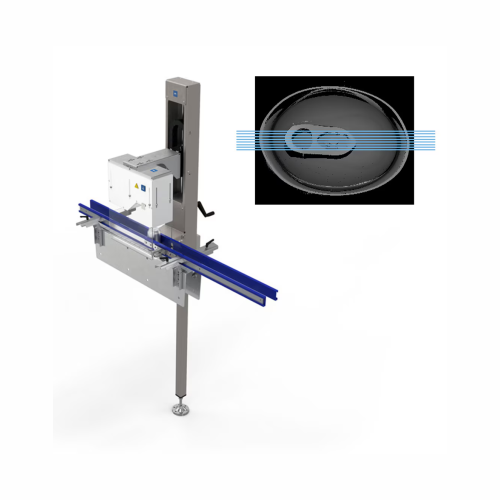
Leakage detection for beverage cans
Ensure each canned beverage leaves your facility ready to impress, with precise leak de...
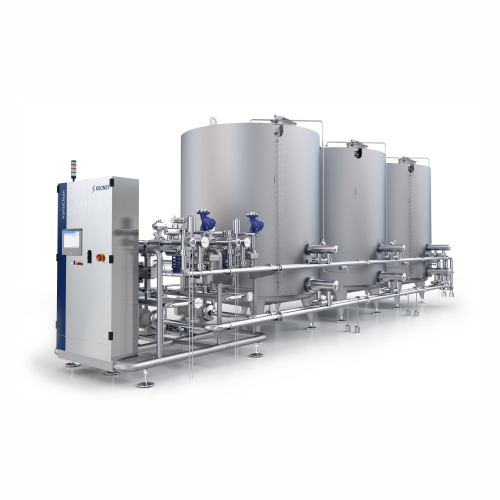
Cip system for cleaning bottling lines and processing sections
Ensure a sterile production environment by integrating a ...
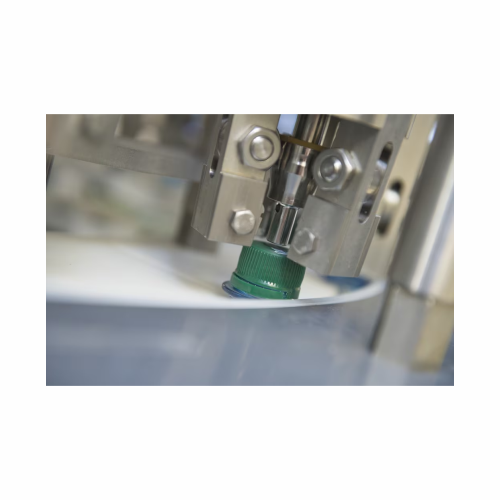
Decapper for removing screw caps
Efficiently unscrew caps from various bottle types without damaging the threads, even under...
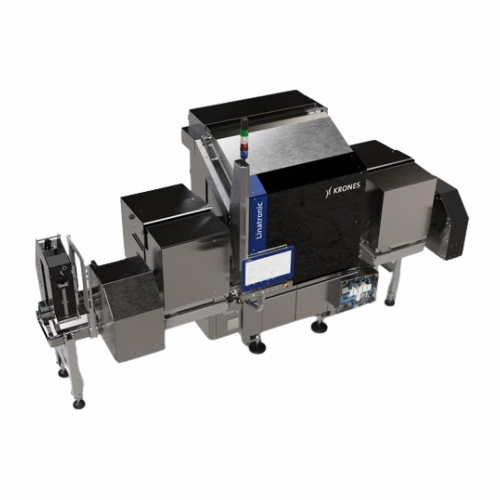
Bottle inspection system for foreign particles detection
Ensure your beverage products remain uncontaminated with high-pr...
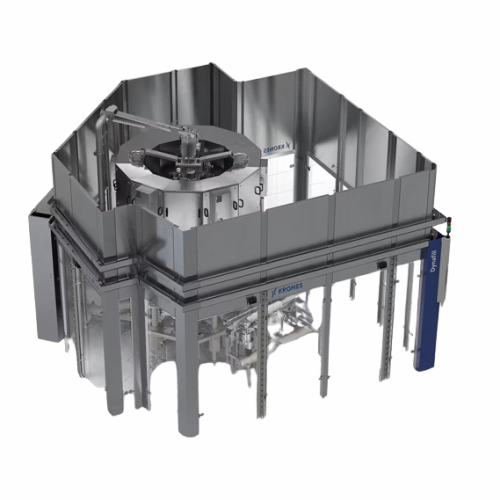
Innovative beer filling and capping technology
Revolutionize your filling process with an integrated system that combines ...
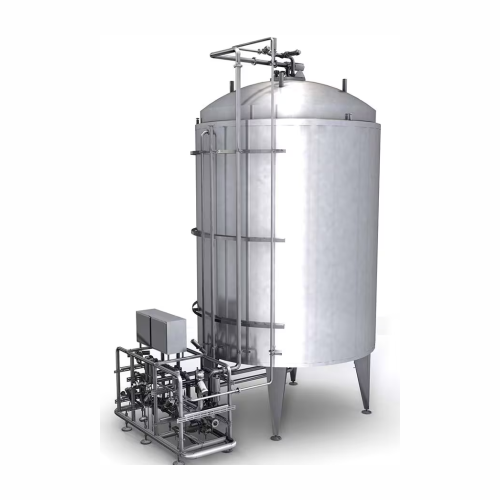
Sterile tank system for aseptic processing
Optimize your production with aseptic tank systems that ensure sterile storage ...
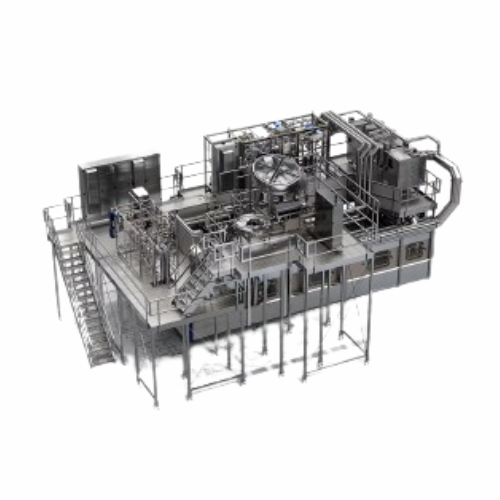
Aseptic bottle sterilisation system for Pet containers
Ensure aseptic integrity and high-speed efficiency in beverage pro...
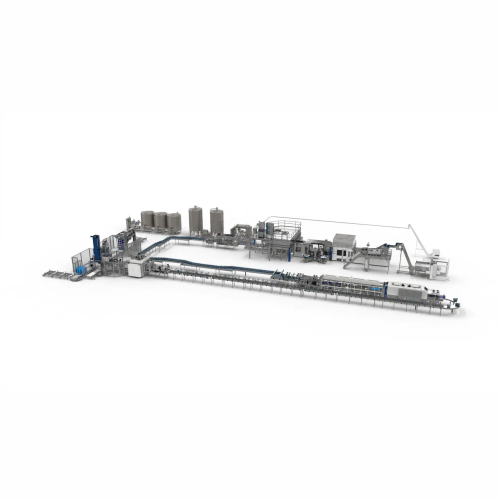
Automated product change-over system
Maximize your production line efficiency by reducing downtime during product changeove...
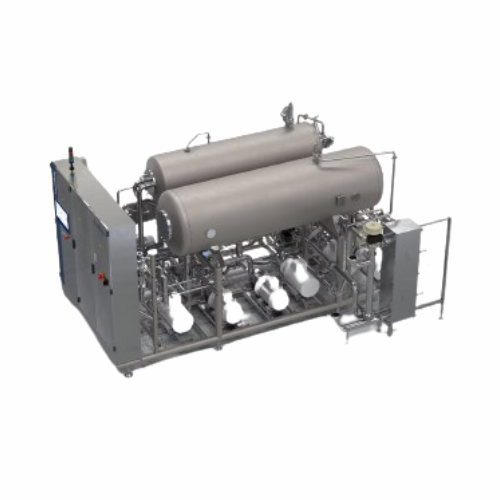
Mixer for carbonated and non-alcoholic drink production
Efficiently mix and carbonate a variety of beverages while optimi...
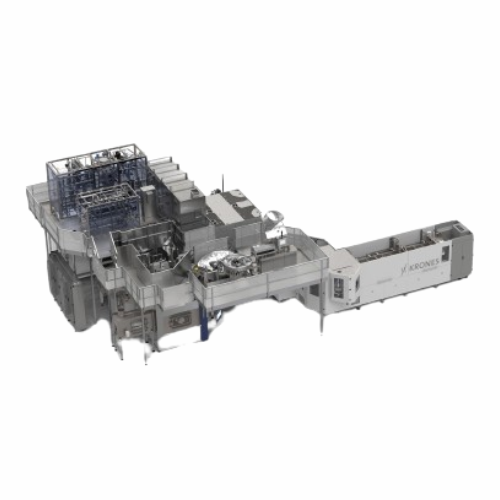
Aseptic filling system for Pet containers
Ensure your beverage products maintain sterility and longevity with a high-speed...
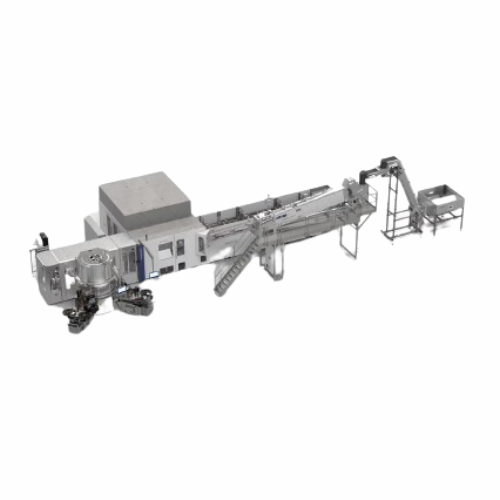
Blow-moulder and labeller integration for Pet bottles
Streamline and enhance your PET bottle production with seamless blo...
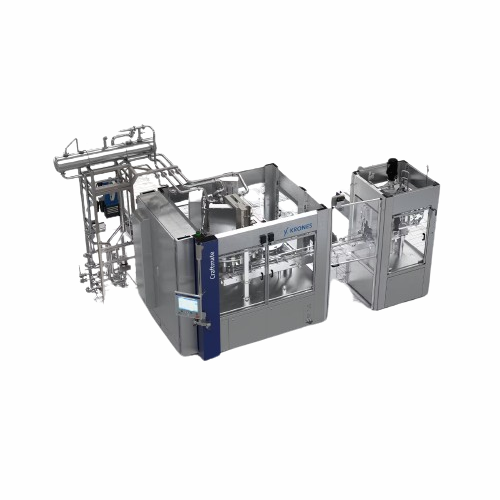
Low output can filler for craft beer
For beverage producers looking to efficiently fill cans with precision, this versatile...
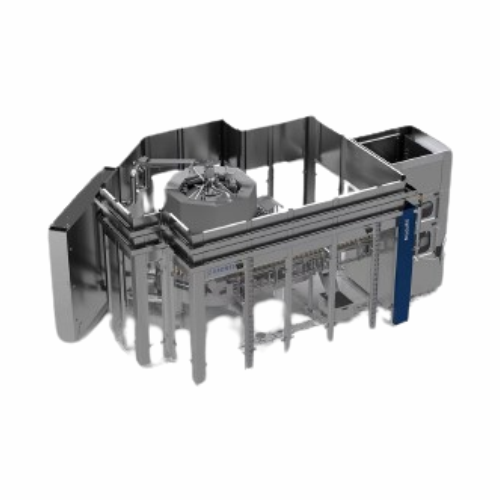
Filler-seamer block for cans
For high-speed beverage production, this solution integrates filling, seaming, and cleaning in ...
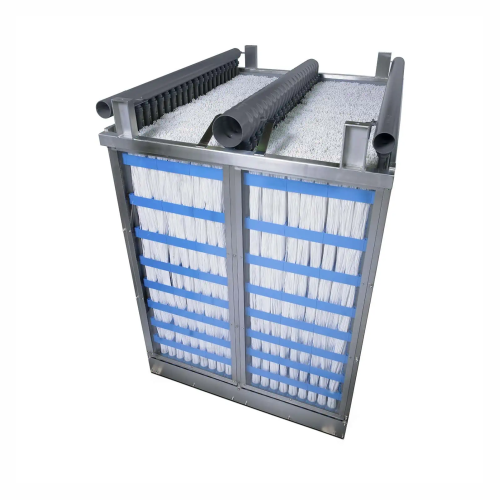
Mbr module for wastewater treatment
Optimize your wastewater management with efficient membrane bioreactors, designed to en...
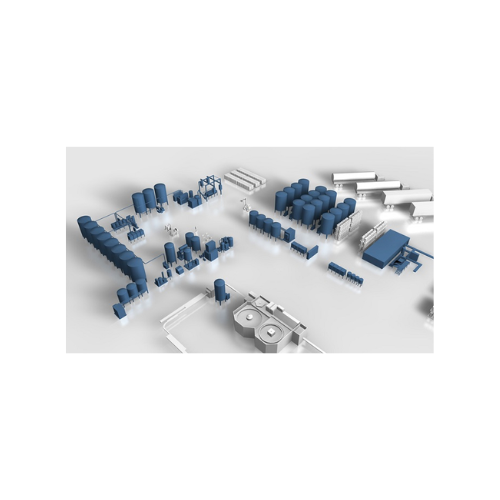
Versatile syrup room systems
Streamline beverage production with a system that expertly handles dissolving, mixing, and past...
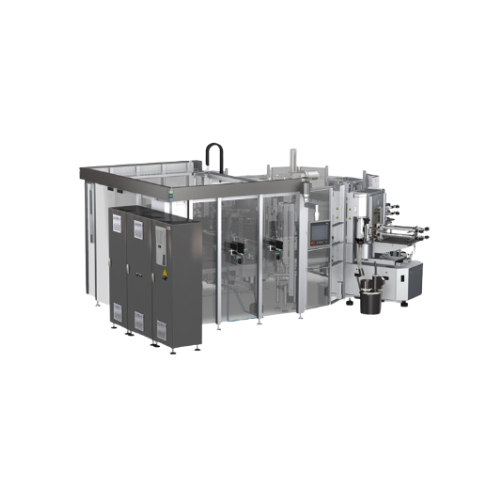
Flexible labeling system for returnable and non-returnable containers
Achieve precise labeling and enhanced alignment w...
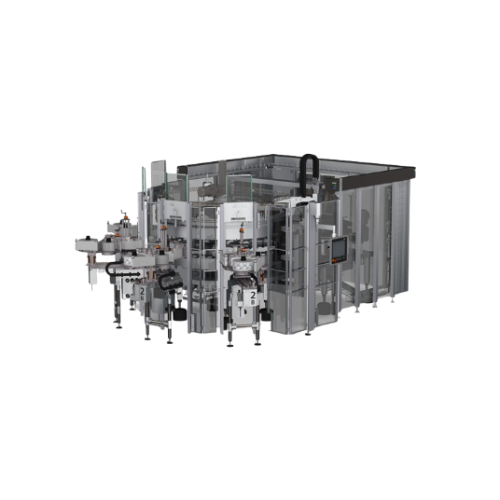
Self-adhesive labeling for glass and Pet bottles and beverage cans
Maximize your production efficiency with a labeling ...
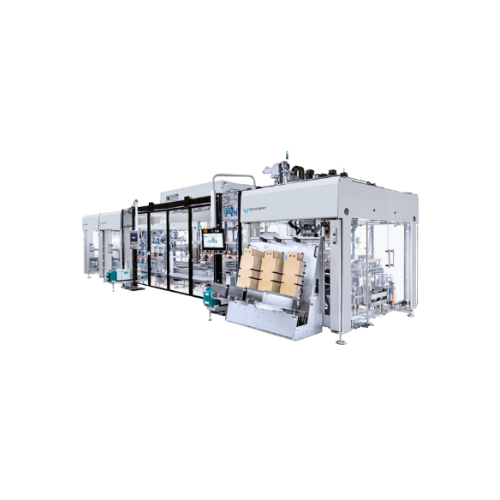
Flexible packaging system for beverage containers
Streamline your packaging process with a modular system that adapts sea...
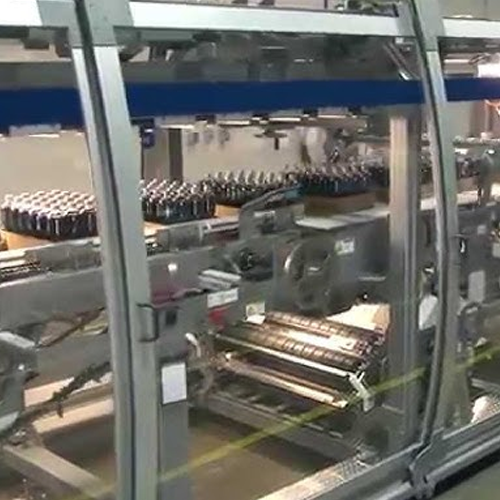
Enclosed film packaging solution
Eliminate the need for corrugated trays and minimize packaging waste with a robust solution...
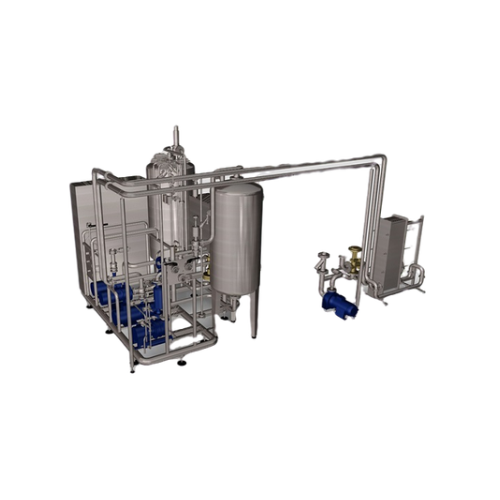
Demineralization and carbonation for bottled table water
Ensure consistent carbonation and precise blending for beverage ...
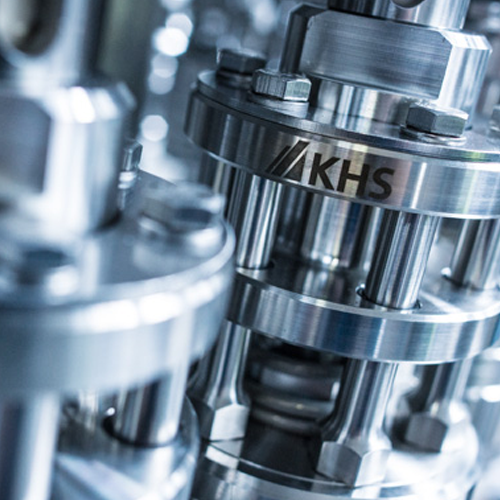
Batch sugar dissolver for syrup production
Streamline your syrup production with precise control over sugar dissolution, w...
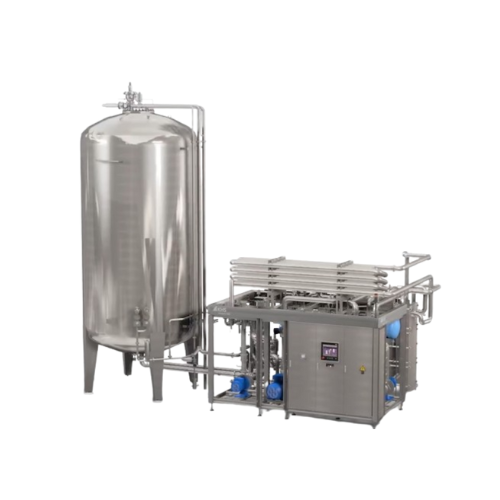
Bright beer tank cellar for beer storage
Enhance your beverage production efficiency with a fully automated solution that m...

Water deaerator for beverage production
Enhance the quality and extend the shelf life of your beverages with our cutting-ed...
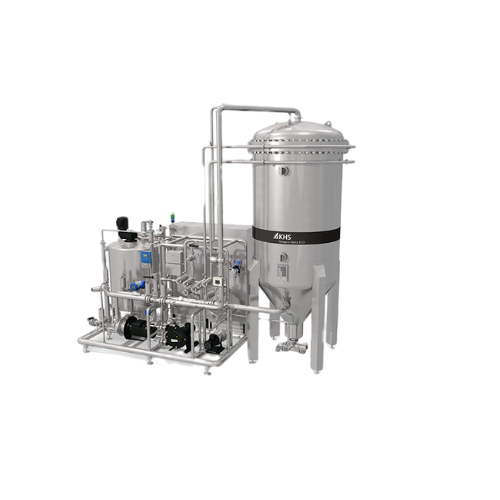
Filter system for beverage stabilization and clarification
Ensure your beverages are crystal clear and stable with a ver...
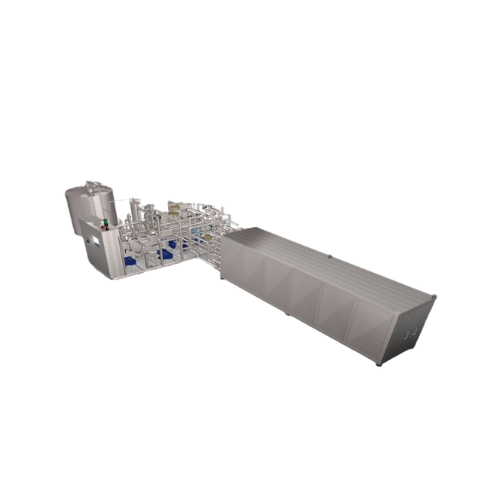
Energy-efficient hot filling system for beverages
Optimize your beverage filling processes with a system that ensures pre...
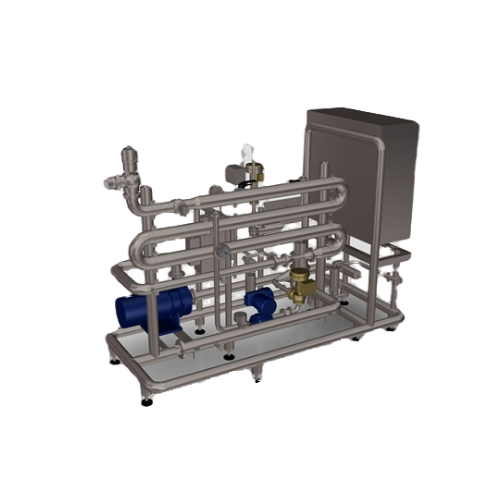
Blending system for fine adjustment of original gravity in beer
Ensure precise control over your beer’s original gravity...
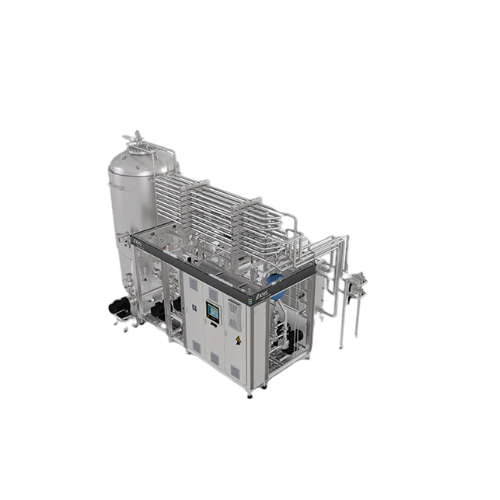
Continuous flash pasteurizer for beverage shelf life extension
Maximize beverage shelf life with precise microbial and e...
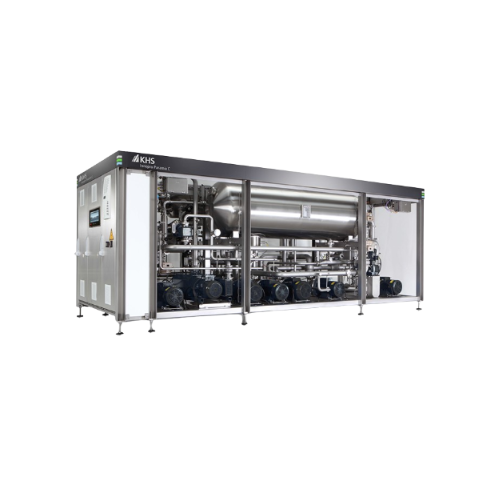
Blending system for deaeration and carbonation of beverages
Achieve precise blending, efficient deaeration, and accurate...
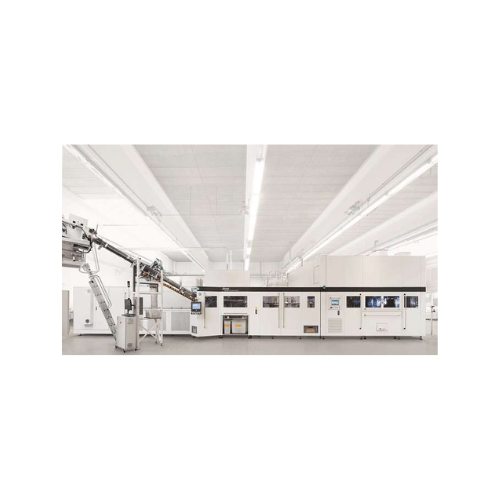
Stretch blow molding with integrated coating for Pet bottles
Enhance product longevity and quality by integrating stretc...

Pet bottle stretch blow molding with coating and filling
Extend the shelf life of your beverages and liquid products with...
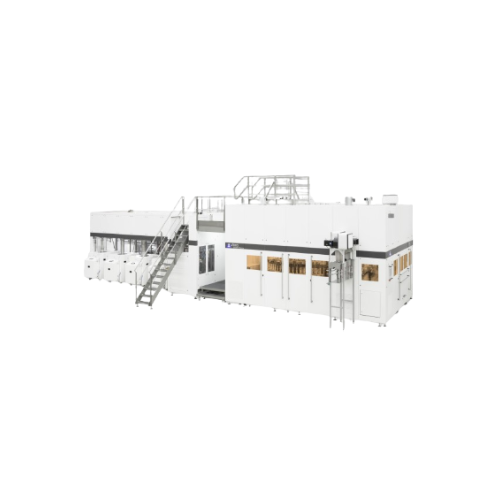
Transparent glass barrier coating for Pet bottles
Ensure the longevity of sensitive beverages and liquid foods with glass...
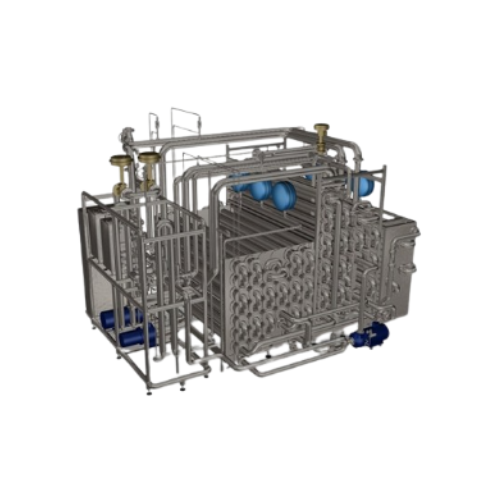
Cold aseptic filling system for beverages
Ensure microbiological safety and high product quality with a versatile cold ase...
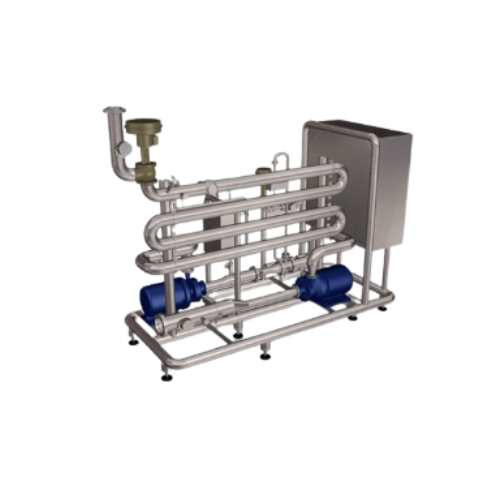
Carbonating solution for precise Co2 content in beverages
Enhance your beverage production with seamless CO2 integration...

Compact cleaning system in container format
Optimize your production lines with a space-saving cleaning system capable of ...
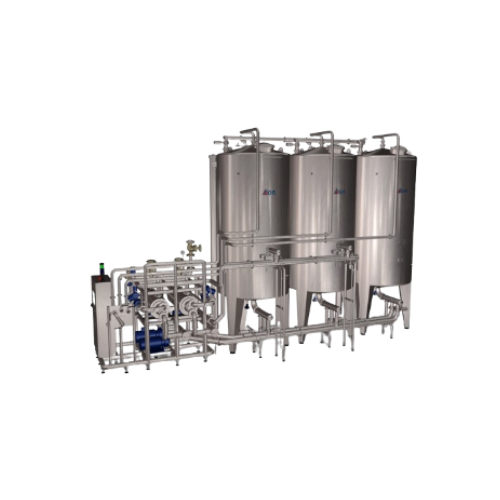
Cip cleaning system for food and beverage production lines
Ensure microbiological safety and maintain quality standards ...
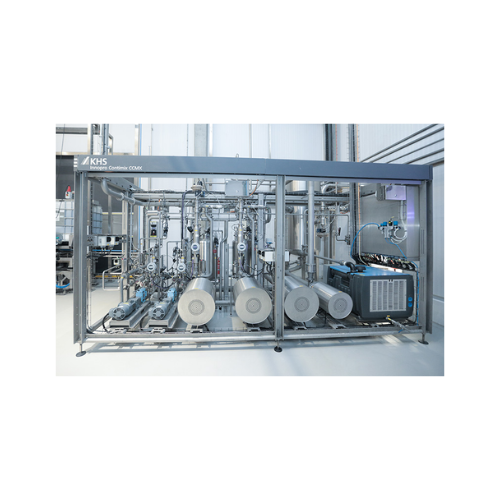
Dosing and blending system for beverage production
Enhance your beverage production with a flexible system capable of pre...
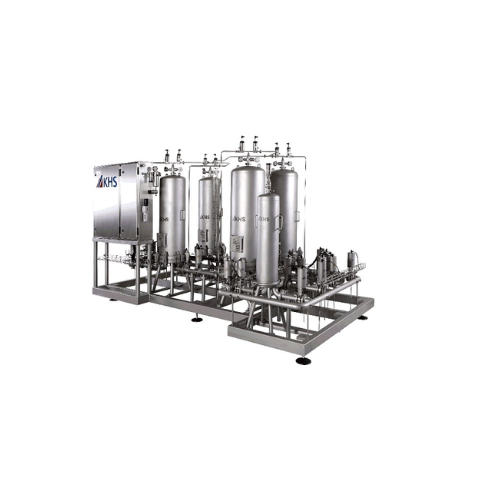
Multifunctional filter system for beverages and gases
Achieve precise filtration across multiple beverage and gas mediums...
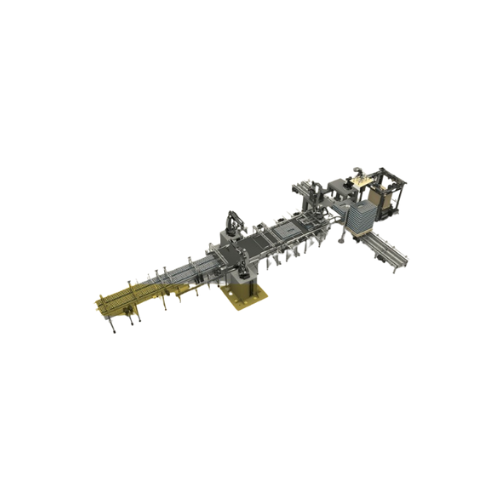
High-performance palletizer for cans, Pet, and glass containers
Elevate your palletizing efficiency with cutting-edge ro...
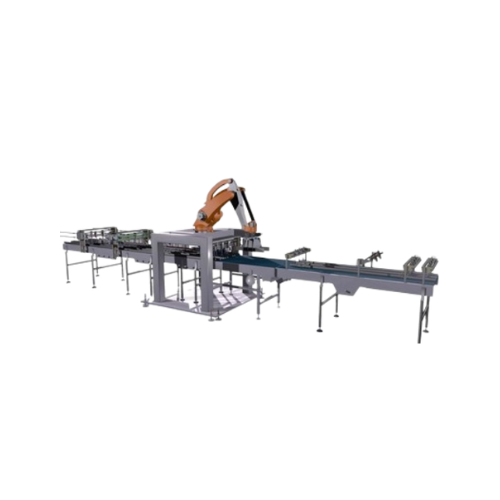
High-performance distribution and combining system
Streamline your packaging operations with a versatile system designed ...
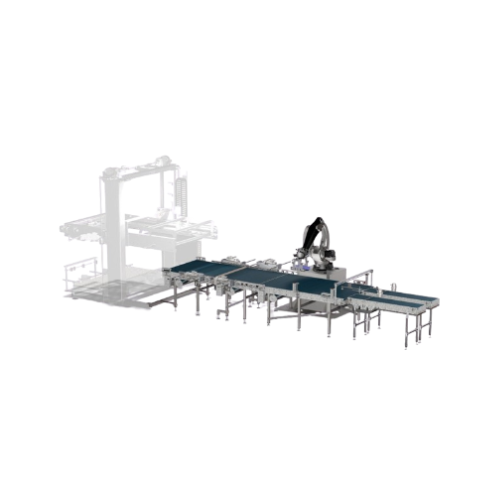
Robotic layer grouping system for container distribution
Streamline your packaging line with precise, high-speed containe...
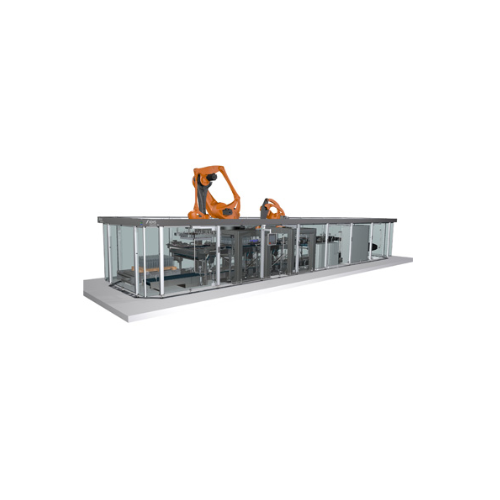
360° palletizing and depalletizing robot
Optimize your packaging flow with a robot offering seamless 360° operation for pre...
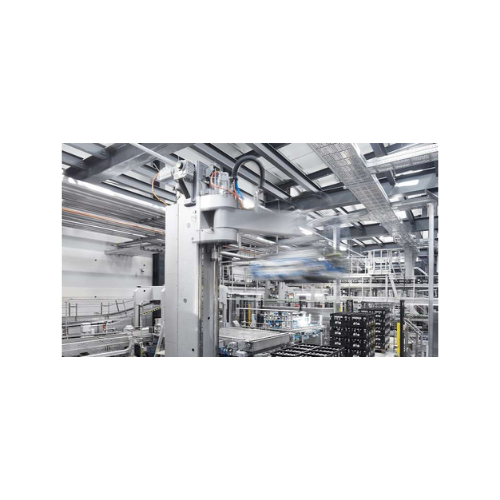
180° palletizing robot for automated palletizing and depalletizing
Optimize your production line with a versatile solut...
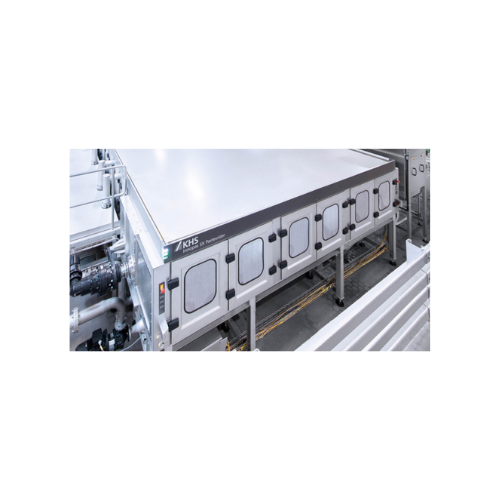
Flexible tunnel pasteurizer for beverage sterilization
Maximize product safety and flexibility in your production line wi...
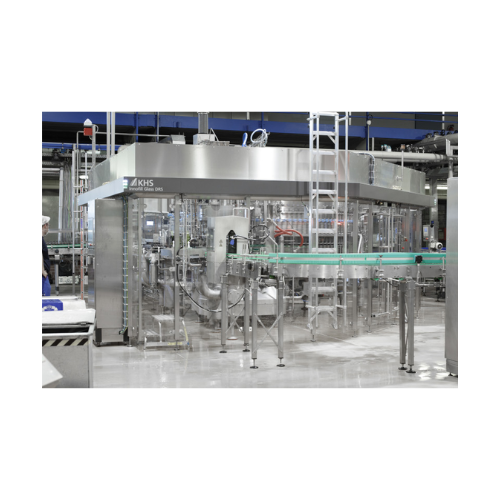
Glass bottle filler for beer and soft drinks
Optimize your beverage production with a high-speed filling solution that red...
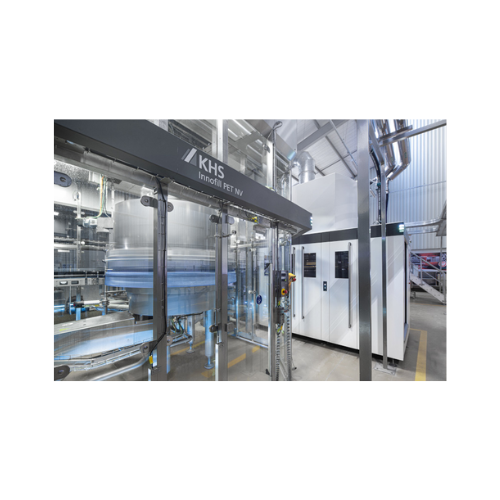
Pet bottle filler for hot and cold still beverages
Achieve high-speed precision in filling and capping for various bevera...
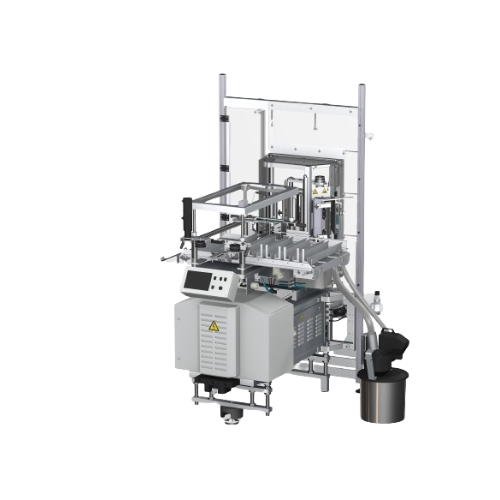
Modular labeling system for beverage containers
Easily adapt to evolving labeling needs with this flexible system, designe...
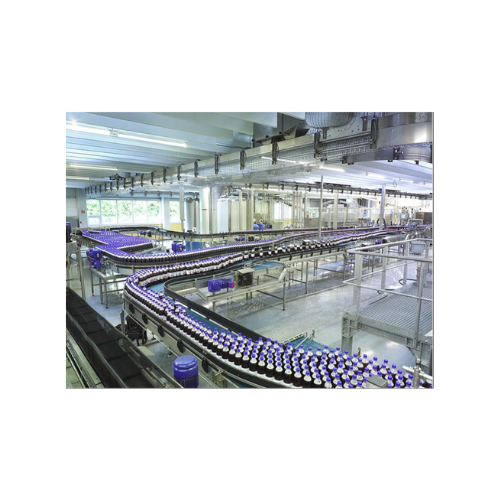
Gentle container conveyor for bottles and cans
Achieve seamless container flow with minimal noise and enhanced precision, ...
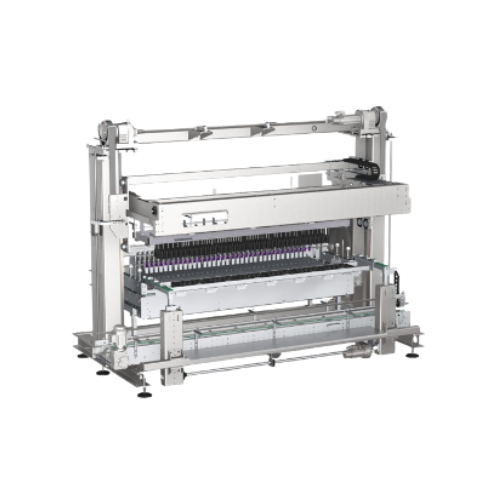
Multifunctional packing system for beverage containers
Maximize your facility’s packing efficiency with a versatile...
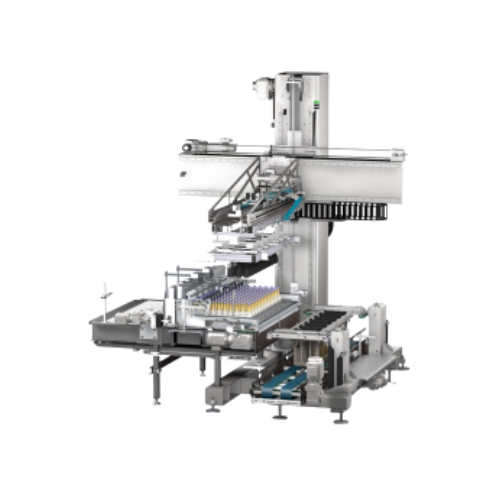
Packer and unpacker for returnable and non-returnable containers
Streamline your packaging line with a versatile machine...
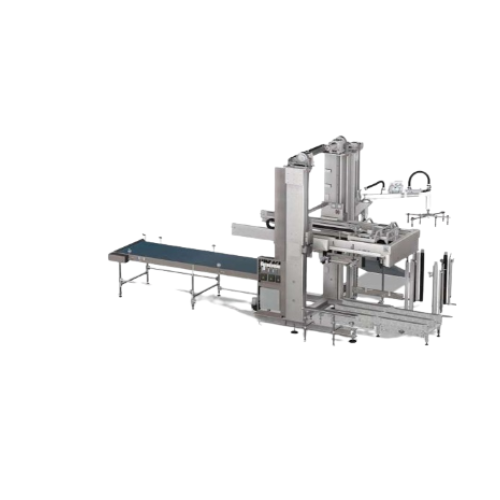
Depalletizer with accurate level compensation
Optimize your high-speed assembly line with a depalletizer designed for prec...
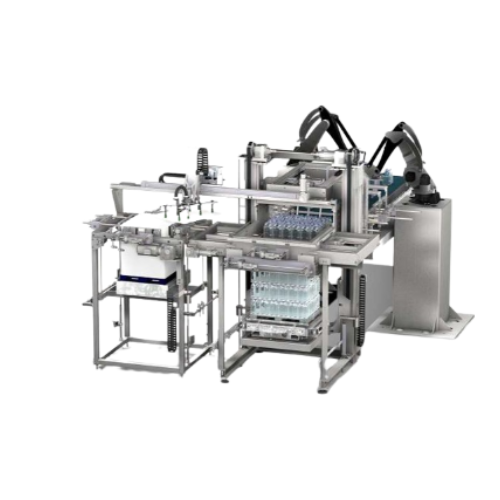
High-speed beverage industry palletizer
Optimize your palletizing process with a flexible, high-speed solution that adapts ...
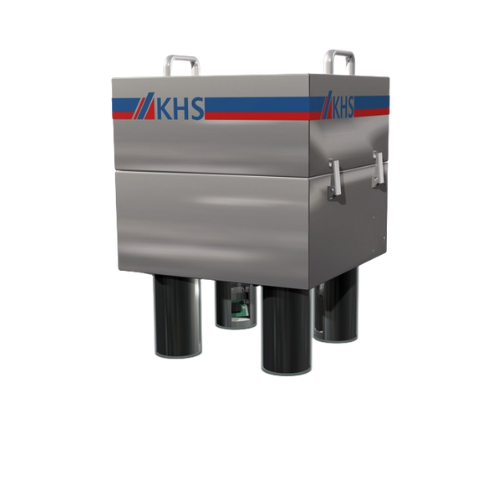
Closure inspection system for crown corks and metal caps
Ensure product integrity with high-speed 360° closure inspection...

Industrial code verification system for product packaging
Ensure flawless packaging integrity with high-speed code verif...
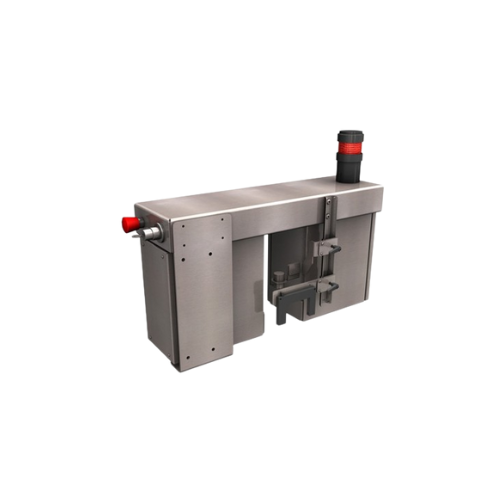
High-precision fill level checker for beverages and containers
Ensure precise fill levels and prevent product wastage by...
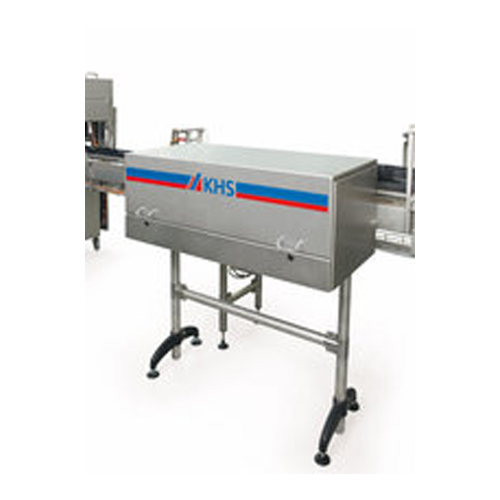
Rejection system for standing bottles and cans
Ensure seamless quality control by precisely rejecting defective bottles an...
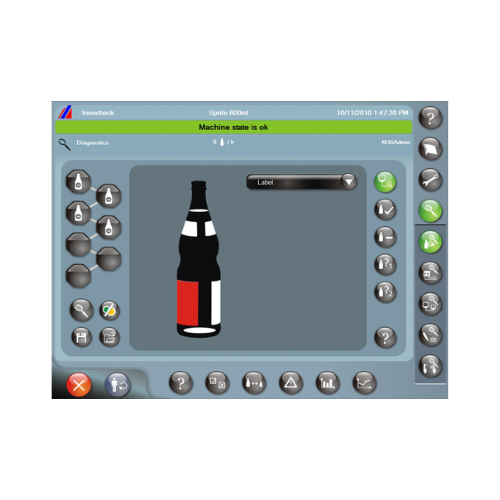
Label inspector for beverage and food containers
Ensure precise label application with high-speed inspection, crucial for ...
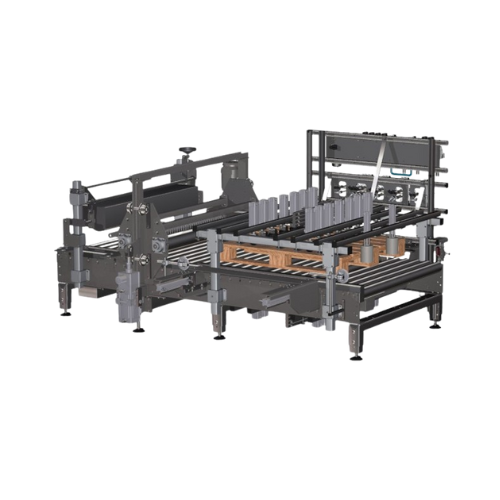
Pallet inspection system
Ensure the stability and integrity of diverse pallets with a high-speed inspection system that minim...
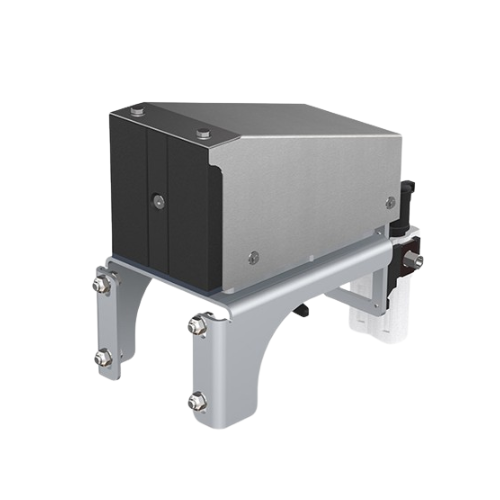
Container ejection system for Pet bottles and beverage cans
Ensure product quality by seamlessly ejecting defective cont...
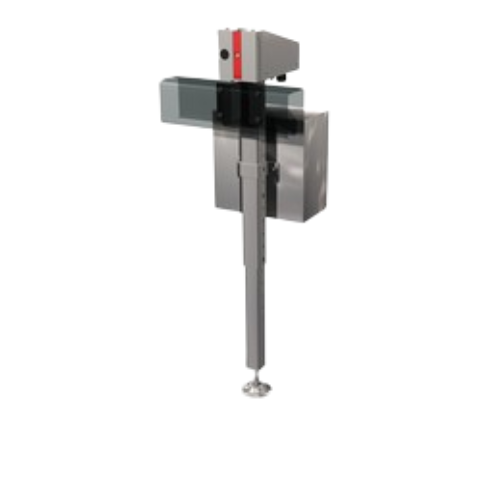
Container rejection system for high-speed operations
Ensure product safety by swiftly removing defective containers at hi...
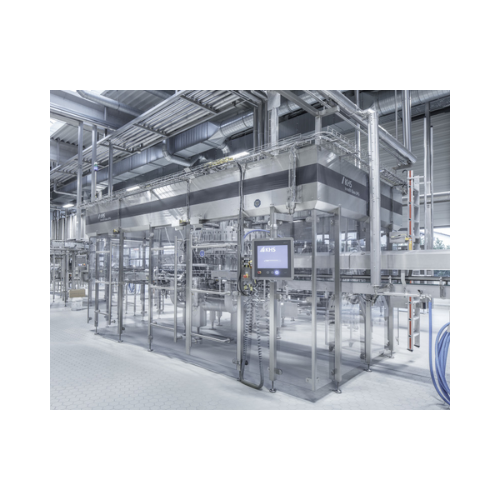
Bottle filler for beer and soft drinks in glass bottles
Achieve precision in bottling with reduced CO2 emissions and low ...
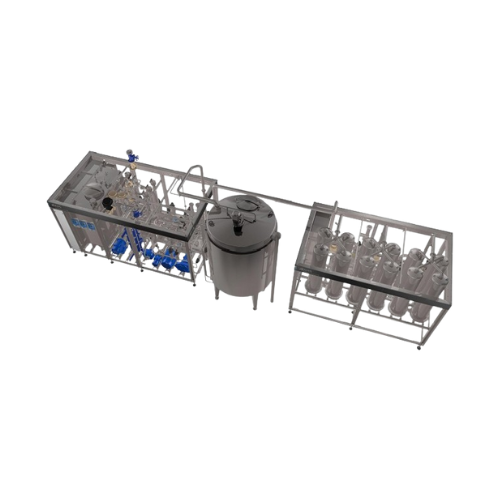
Pvpp beer stabilization system for breweries
Reduce beer hazing and extend shelf life with this advanced stabilization sys...
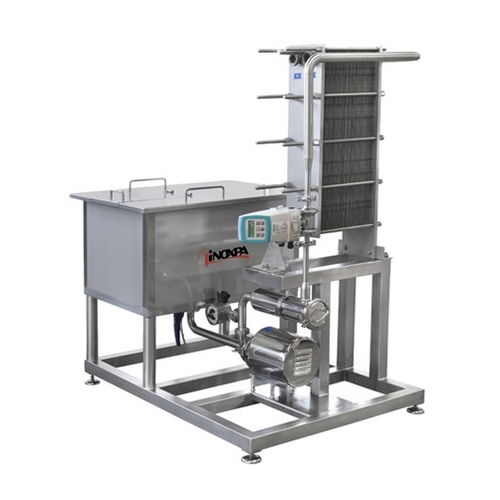
Industrial skids for liquid processing
Efficiently manage large-scale liquid and solid processing in your production line w...
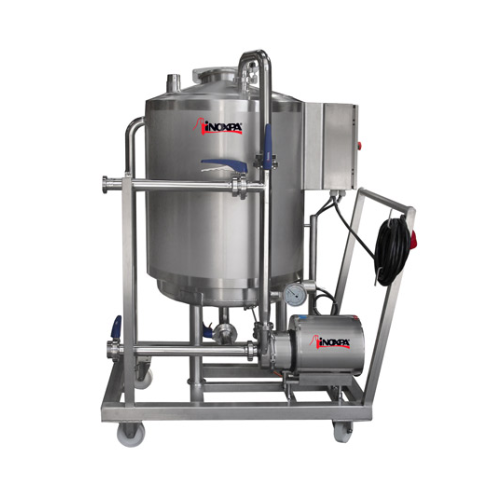
Manual Cip system for food processing hygiene
Designed for small-scale hygiene needs, this mobile clean-in-place system en...
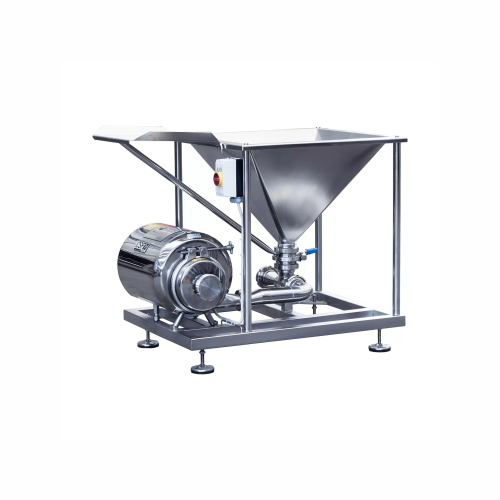
Sugar dissolving system for industrial applications
Efficiently dissolve sugar and low-viscosity blends to achieve perfec...

Oxygen and carbon dioxide monitoring and elimination system
Achieve precise control over dissolved gases with a system t...
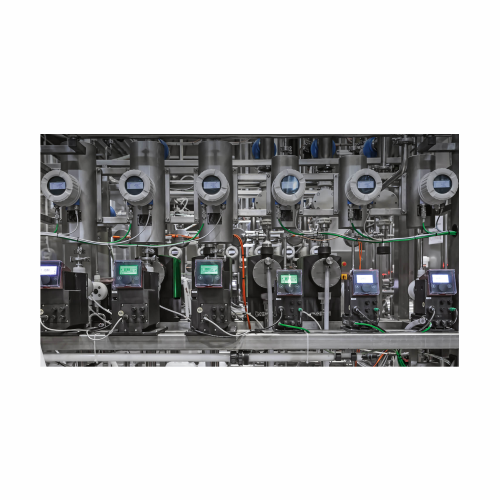
In-line additive dosing systems for beverages
Ensure precision and safety in beverage production by integrating in-line do...
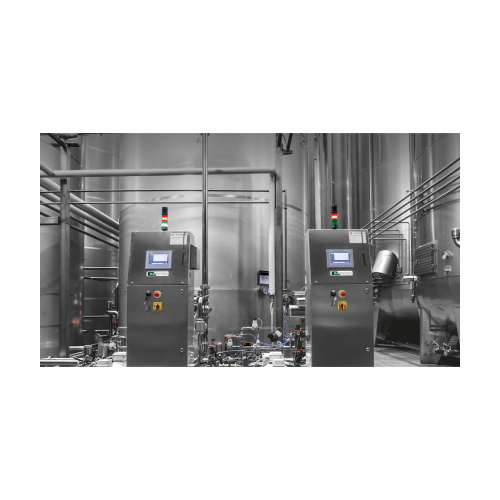
Piping discharge system for product separation in transfer lines
Optimize your beverage production by preventing product...

Micro-filtration system for beverage industry
Achieve microbiological stability at cold temperatures with our micro-filtra...
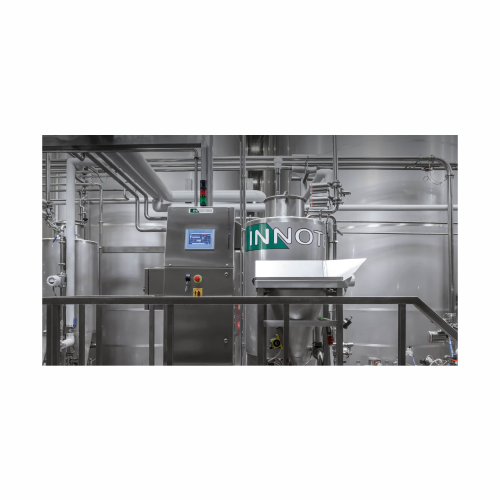
Powder mixing system for beverage industry
Enhance your beverage production with an advanced powder mixing system that ens...
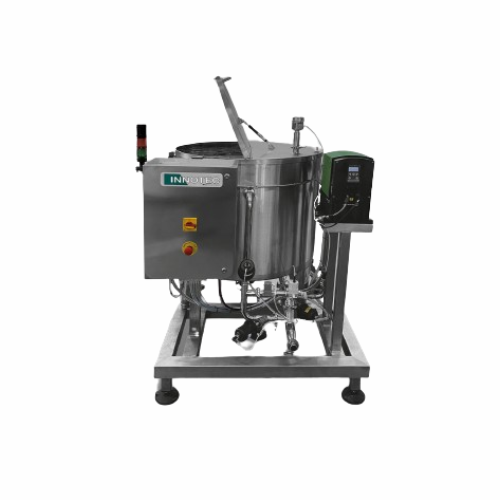
Wine recovery system for bottling processes
Streamline bottling operations by recovering and re-dosing valuable wine, redu...
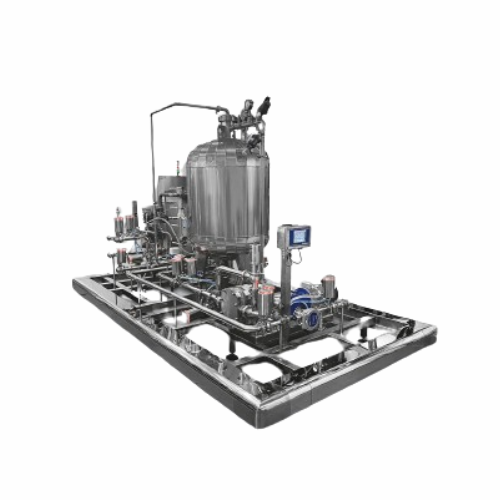
Co2 dosing system for effervescent beverage bottling
For beverage manufacturers requiring precise carbonation, this solut...
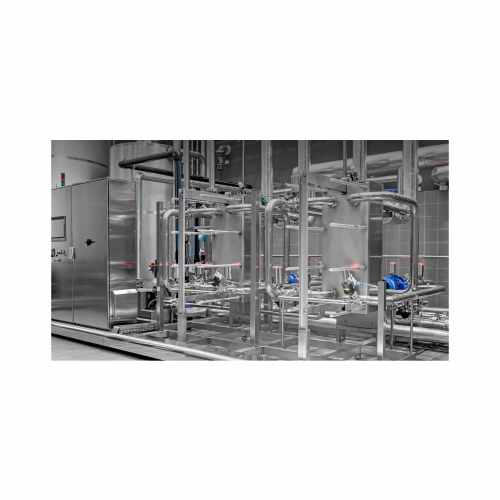
Automated system for cleaning in place (cip)
Ensure thorough, efficient cleaning of your production equipment with a syste...
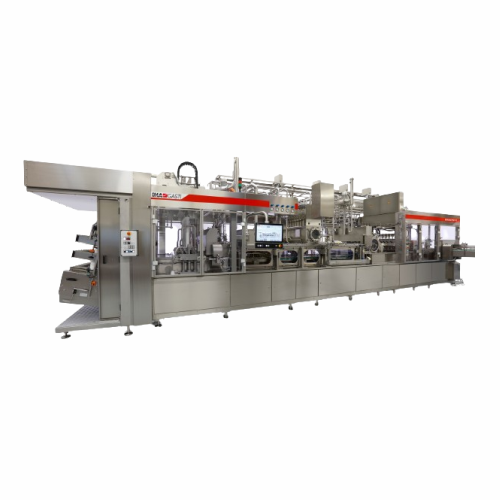
Filling and sealing pre-formed cups solution
Ensure ultra-clean and aseptic processing for pre-formed cups with a fully en...
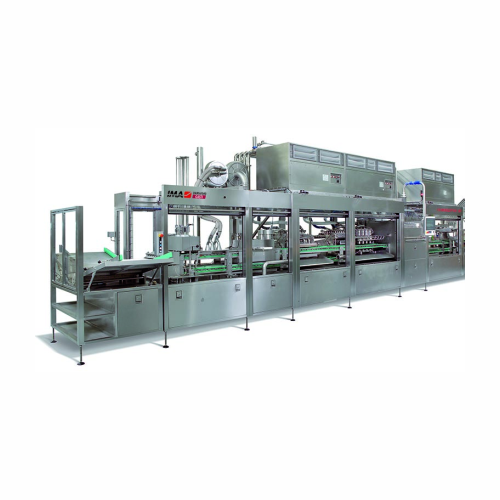
Filling and sealing solution for pre-formed cups
Optimize your liquid and solid product filling with a continuous-motion s...
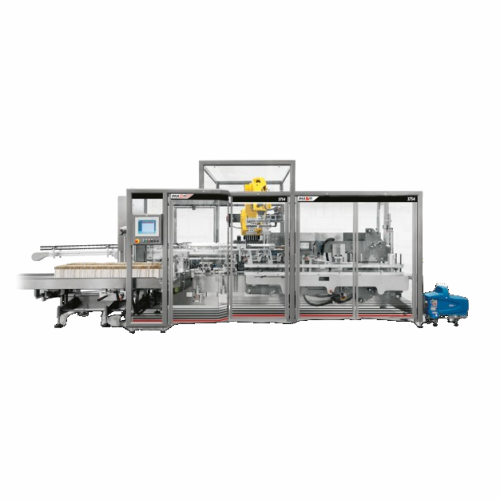
Top loading case packer for loose or bundled bottles
Effortlessly handle and pack both standard and uniquely shaped bottl...
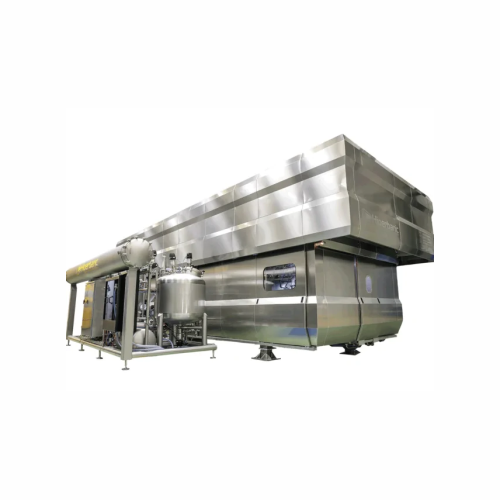
High pressure processing for bulk liquid beverages
Streamline your liquid processing with high-pressure in-bulk technolog...
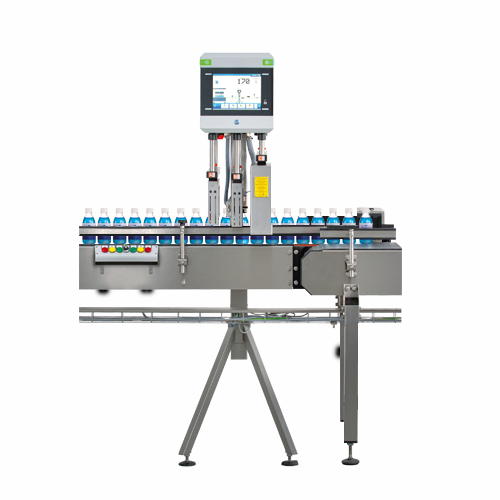
Compact full product inspection system for pharmaceuticals
Easily detect fill level inaccuracies, closure misalignments,...
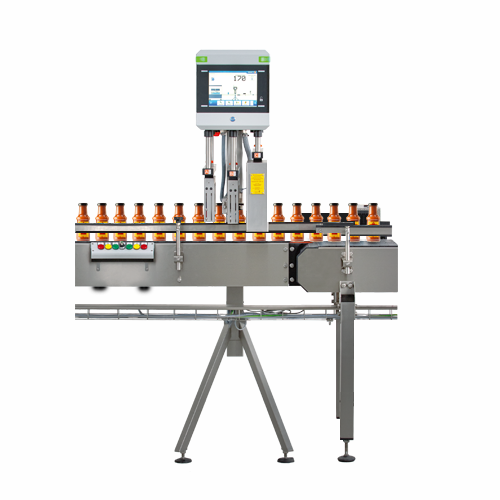
Full container check for fill level and closure inspection
Ensure the integrity of your liquid products with this advanc...
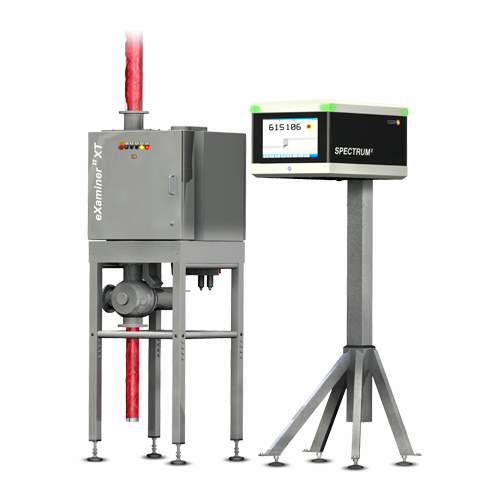
Pipeline inspection for liquid and paste-like products
Ensure your liquid and paste-like products are free from foreign o...
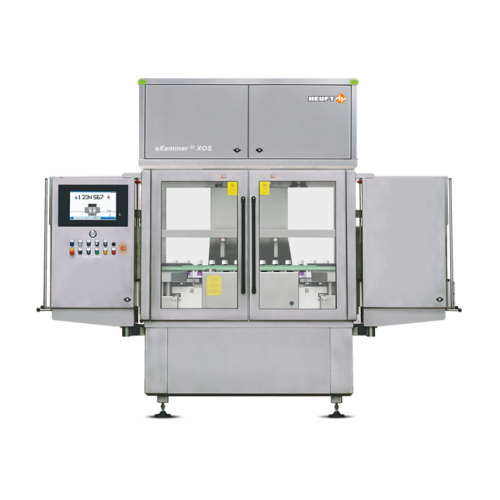
Foreign matter detection for syrup and medicine bottles
Ensure the quality and safety of your liquid products with precis...
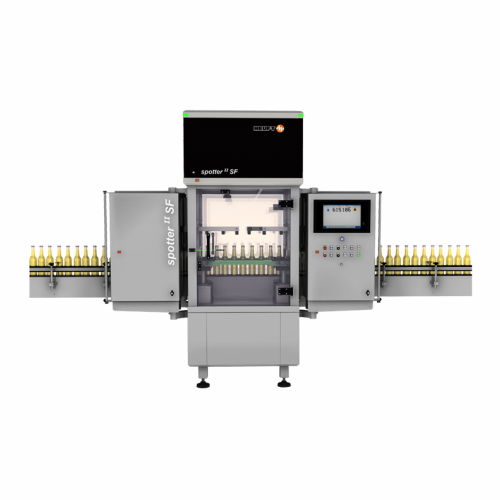
Full container inspection for glass and Pet bottles
Ensure the highest product quality by detecting foreign objects and m...
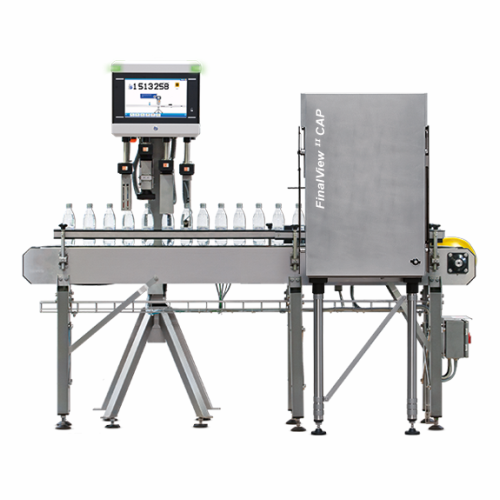
Closure inspection for beverage containers
Ensure the integrity of your bottled products with precision closure inspection...

Ultrasonic leak detection system for carbonated beverages
Ensure the integrity of your carbonated beverages by precisely...
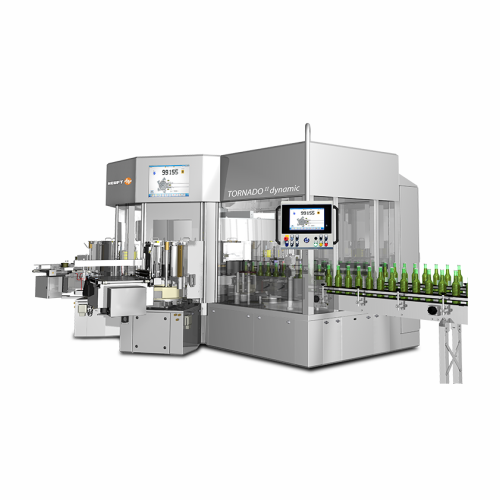
Semi-modular labeller for precise beverage bottle labelling
Achieve millimeter-precision bottle labelling with seamless ...
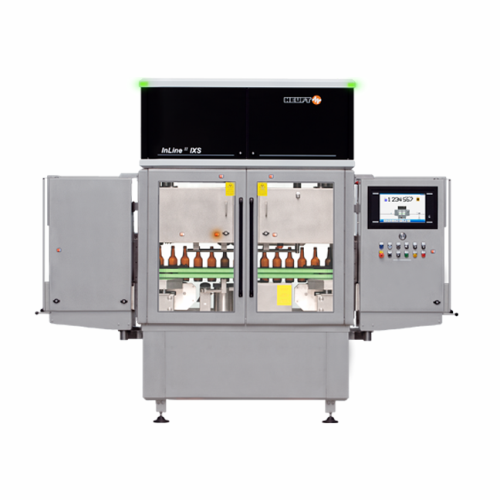
X-ray assisted empty bottle inspection
Enhance your production line with advanced X-ray and optical technology to ensure pr...
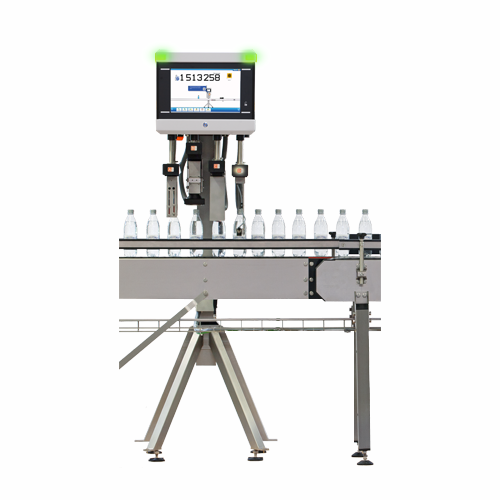
Fill level and closure inspection system
Ensure precise fill levels and secure closures in high-speed liquid packaging envi...
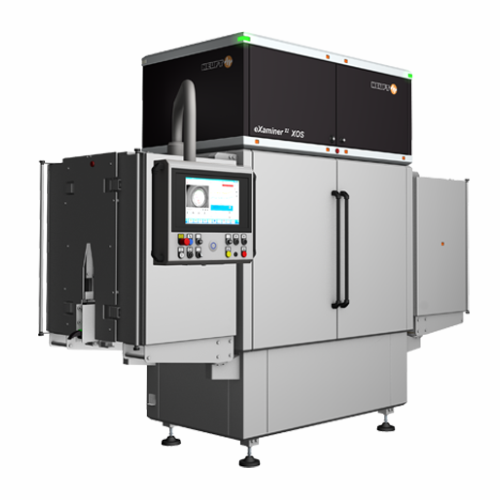
Advanced foreign object inspection for full beverage containers
Ensure consumer safety and brand protection with advance...
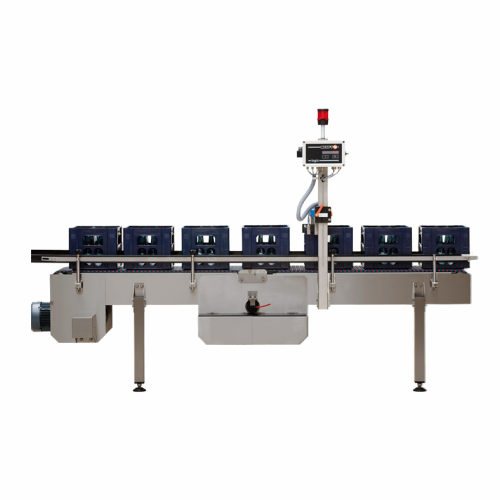
Full case check for beverage production lines
Ensure complete packaging integrity by detecting and removing cases with mis...
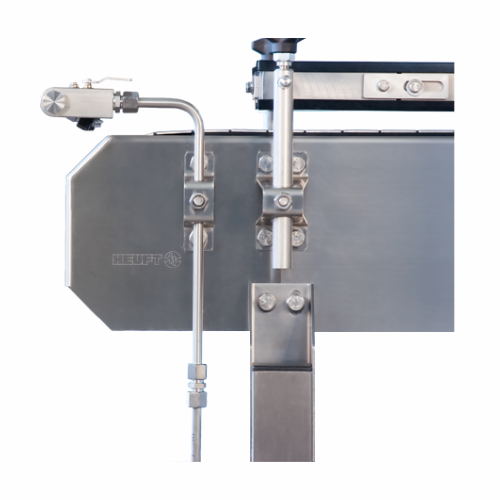
Conveyor system for efficient container transport
Optimize your filling line with a versatile container transport system ...
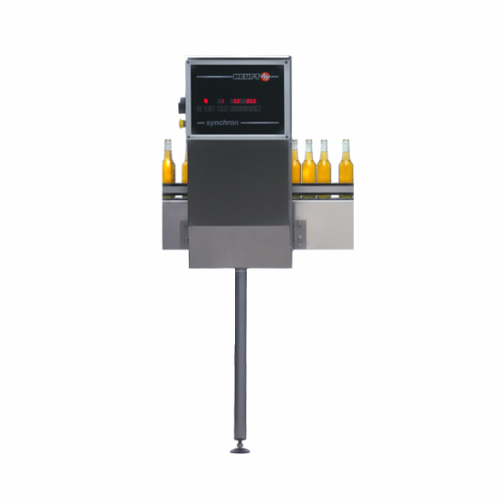
Conveyor control system for beverage filling lines
Optimize your production line’s efficiency by seamlessly managin...
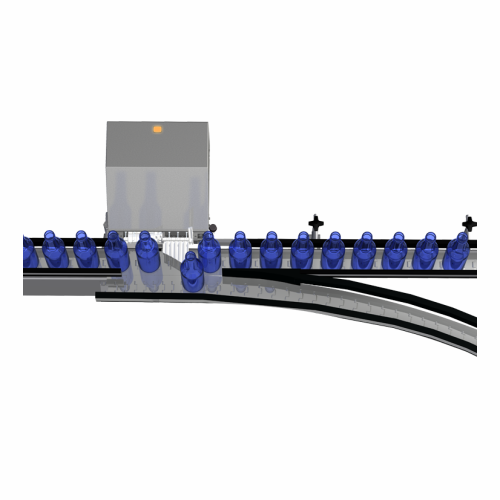
Curve rejector for beverage containers
Ensure seamless and upright rejection of faulty containers in tight spaces, maintain...
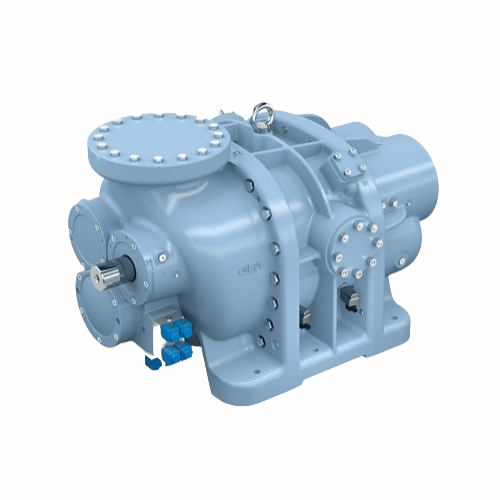
Industrial screw compressor for various refrigerants
Optimize your refrigeration systems with high-performance screw comp...
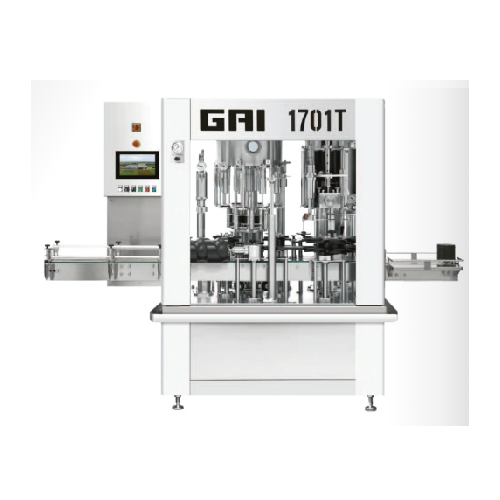
Complete bottling lines for beverage industries
Optimize your bottling process with high-speed, precision-engineered lines...
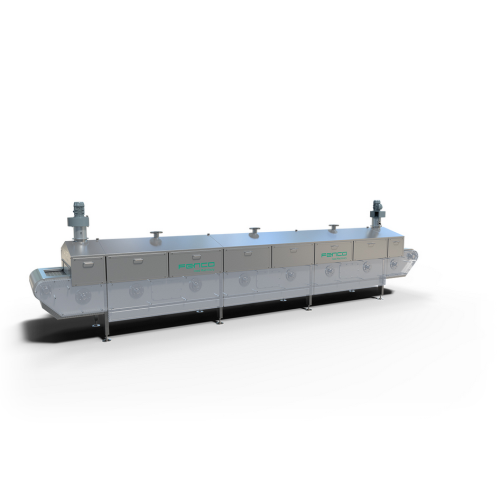
Industrial tunnel pasteurizer for rigid containers
Ensure consistent product quality and safety with a tunnel pasteurizer...
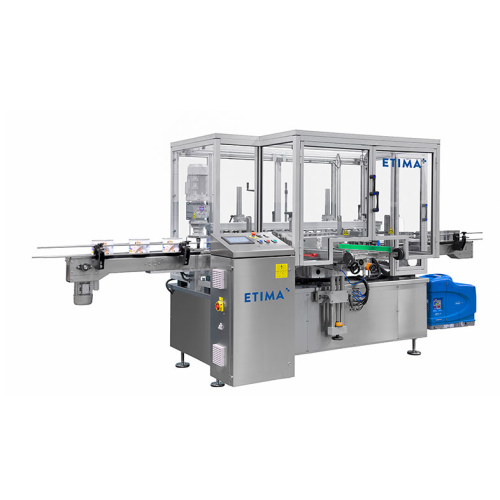
High speed wraparound label applicator for cylindrical containers
Experience efficient high-speed labelling for cylindr...
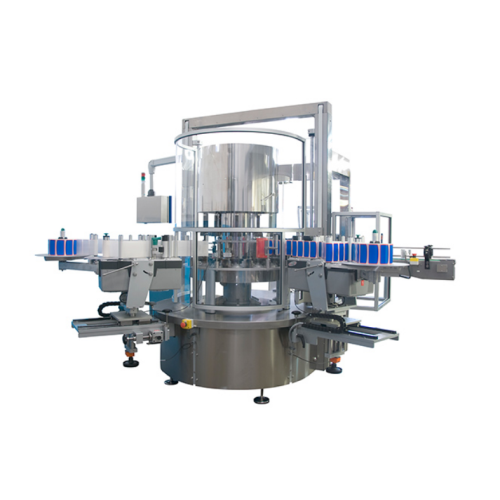
Rotary label applicator for self-adhesive labels
Streamline your packaging line with this high-speed rotary applicator, de...
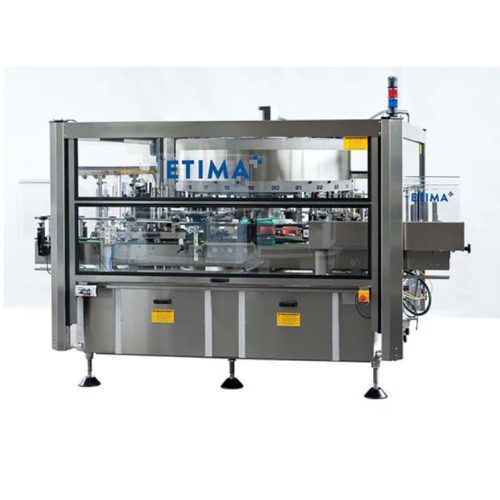
Cold glue label applicator for pre-cut labels
Optimize your packaging line with high-speed labeling for a variety of conta...

Ultraclean aseptic storage tanks for hygienic liquid food
Ensure your liquid products remain uncontaminated and maintain...
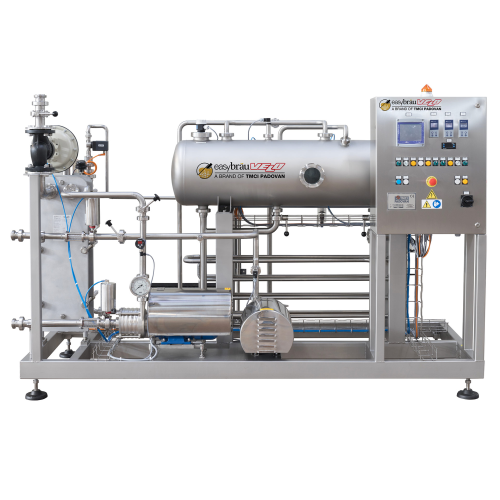
Carbonation system for Co2 dosing in beer production
Achieve precise carbonation in every beverage batch with seamless CO...
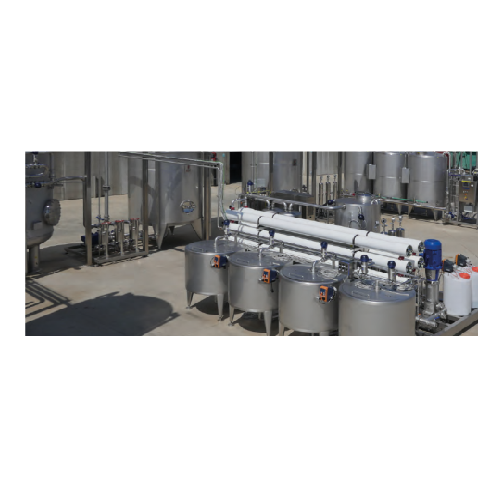
Reverse osmosis with remineralization for drinking water production
Enhance your beverage production with precise water...
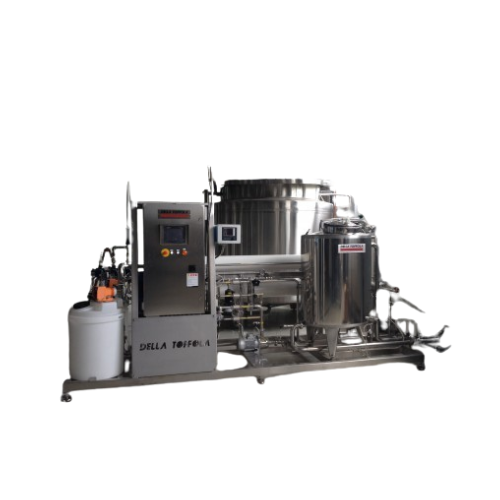
Nanofiltration systems for water pretreatment
Achieve precise water quality with advanced nanofiltration systems designed ...
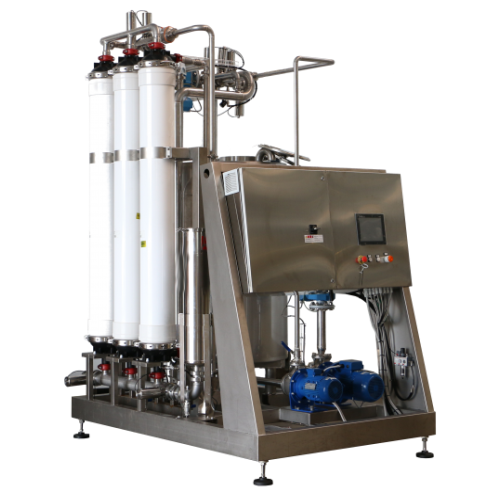
Organic ultrafiltration for water bottling lines
Optimize your beverage production with efficient pre-treatment, ensuring ...
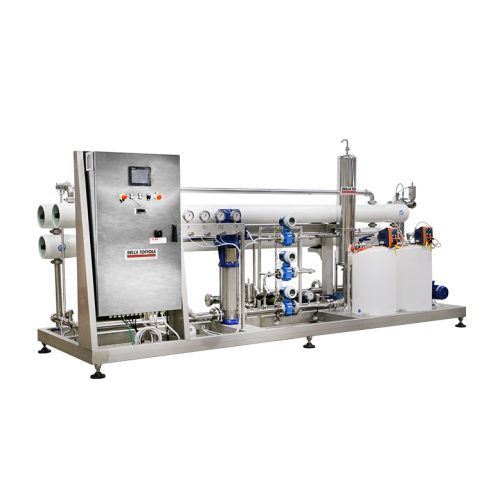
Reverse osmosis systems for industrial water treatment
Achieve optimal water purification in beverage production lines wi...
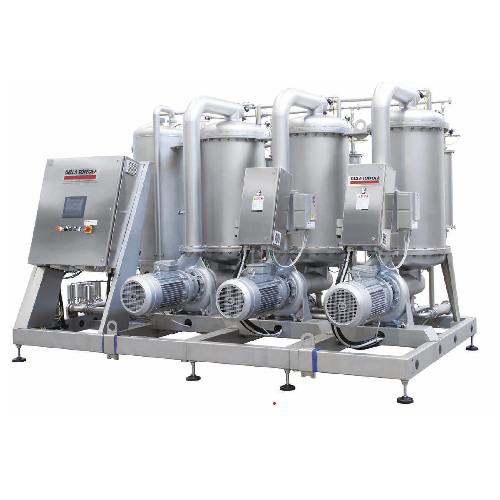
Industrial crossflow filters with ceramic membranes
Achieve precise filtration with robust ceramic membranes, ideal for h...
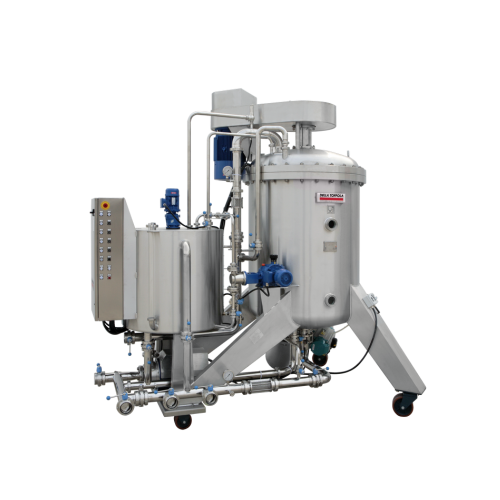
Kieselgur filter for wine and lees
Enhance clarity and purity in your beverage filtration process with a system designed to...
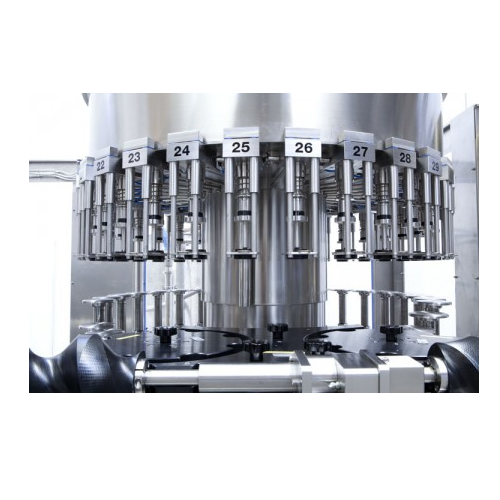
Gravity filling systems for still beverages
Ensure precise and clean filling for still beverages with gravity systems that...
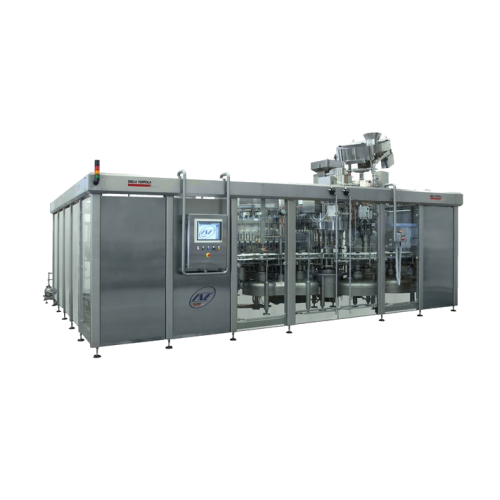
Isobaric filling solution for carbonated drinks
Achieve precision filling for carbonated and still beverages with advanced...
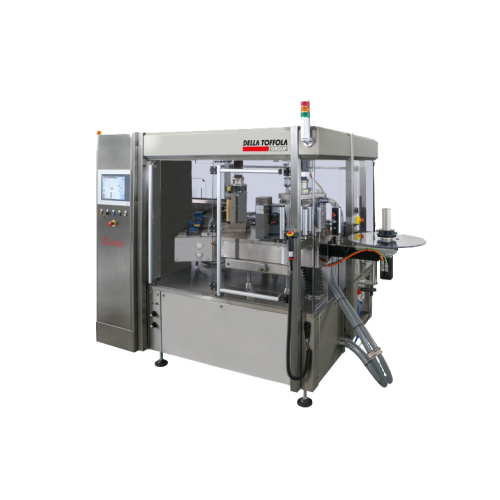
Roll linear labelling machines for bottling and packaging
Achieve precise and efficient labeling with roll linear labell...
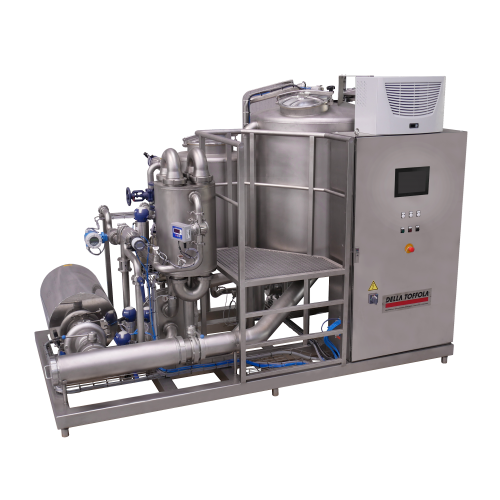
Continuous sugar dissolving system for beverage production
Effortlessly transform granulated sugar into a consistent, hi...
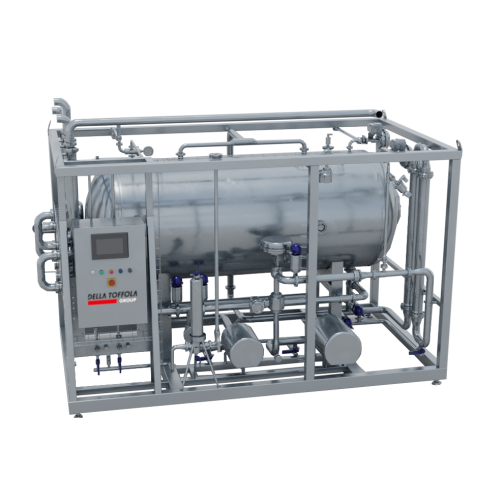
Inline carbonation solution for beverages
Achieve precise carbonation control and consistency in your beverage production ...
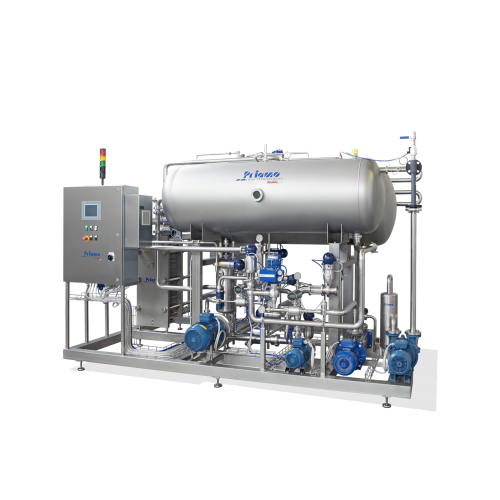
In-line batching and blending system for carbonated drinks
Optimize your carbonated beverage production with seamless in...

Kieselgur filter for beer filtration
Achieve crystal-clear beer without compromising flavor through efficient kieselgur fil...
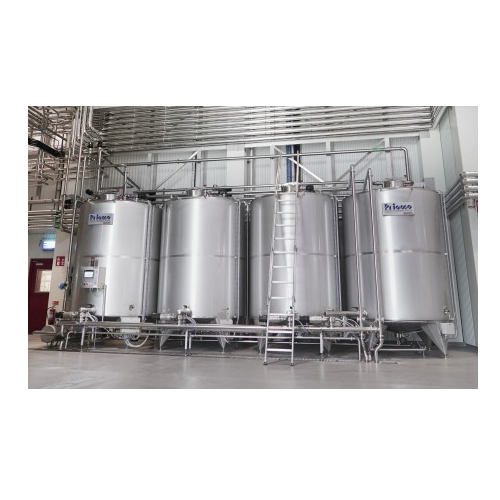
Automated Cip systems for beverage and food industry
Ensure high hygiene standards in your production line with advanced ...
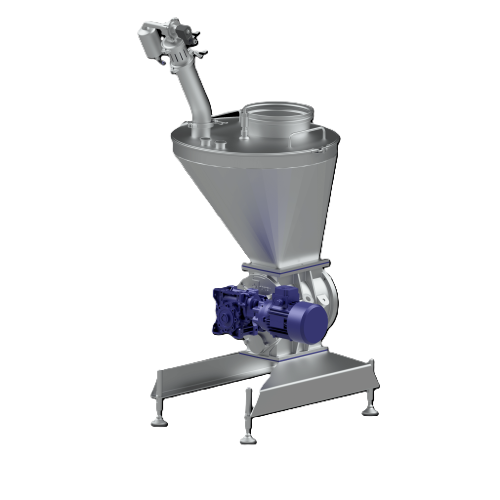
Dilute-phase conveying solution for powder handling
Efficiently transfer powders and granules with robust leak containmen...
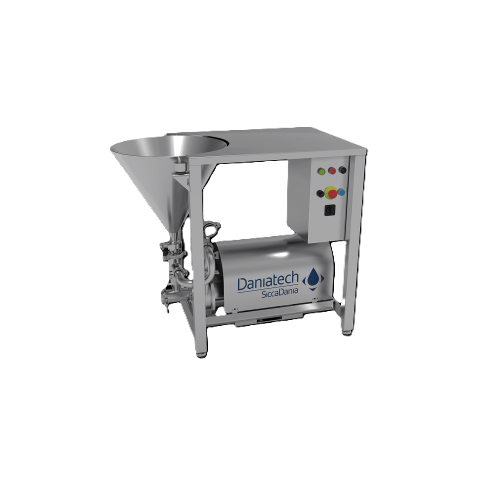
Inline high-shear mixer for powders and liquids
Achieve efficient mixing and homogenization in your production line with a...
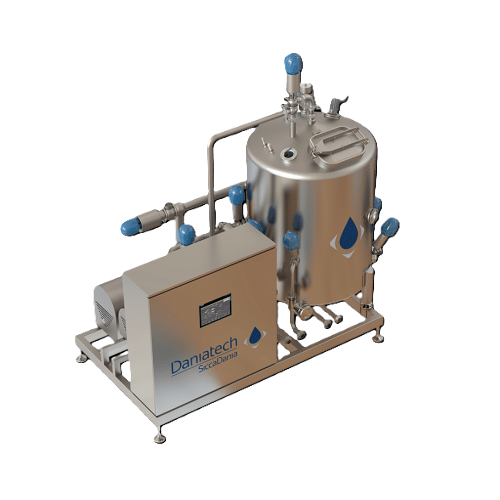
High-capacity inline mixer for dairy and beverages production
Achieve a rapid and homogeneous mix in high-capacity produ...
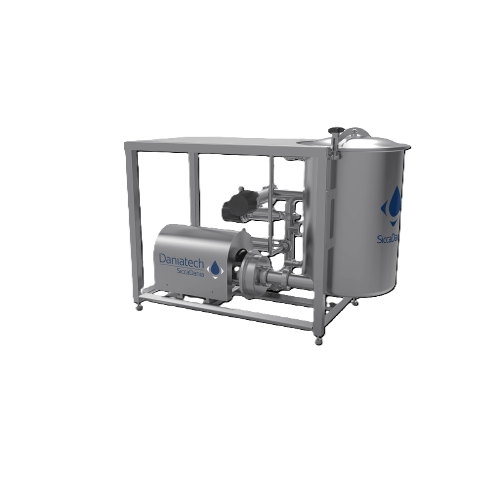
Mixer for low to medium viscosity products
Optimize your mixing, dosing, and homogenization processes with a versatile mix...
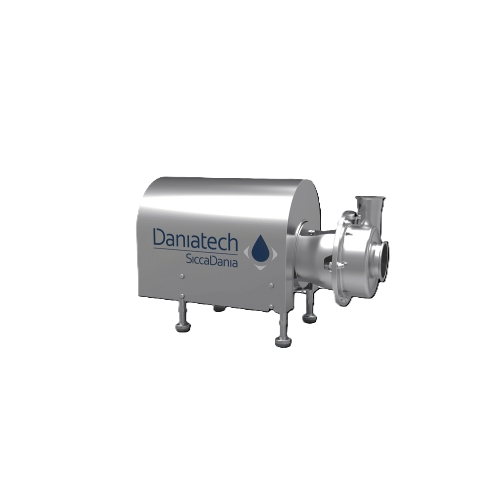
Inline high shear mixing unit for low to medium viscosity products
Achieve precise emulsification and size-reduction wi...
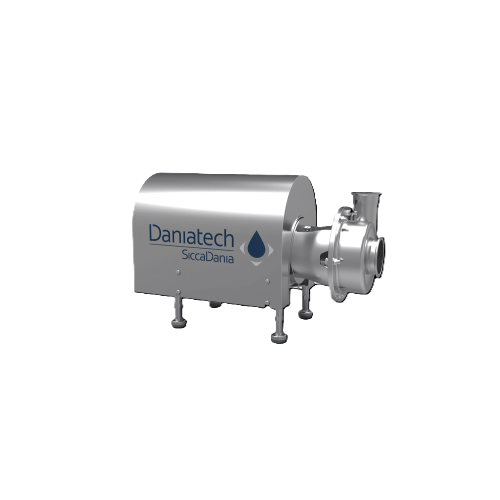
Ultra-high shear mixer for emulsification and homogenization
Optimize your production with ultra-high shear mixing, acce...

Vacuum high shear mixer for medium to high viscosity products
Achieve flawless blending and air-free consistency in visc...
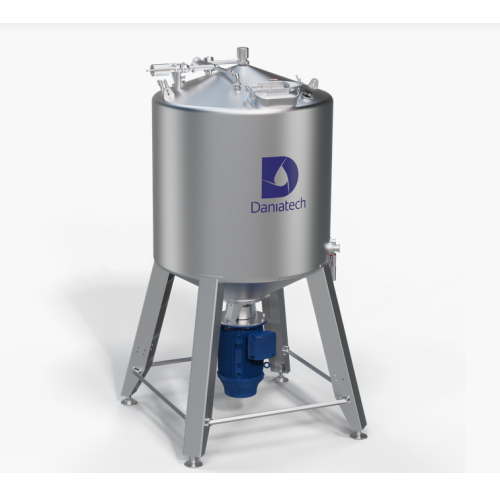
High-capacity manual mixer for industrial applications
Optimize your mixing process with a highly efficient, manually ope...
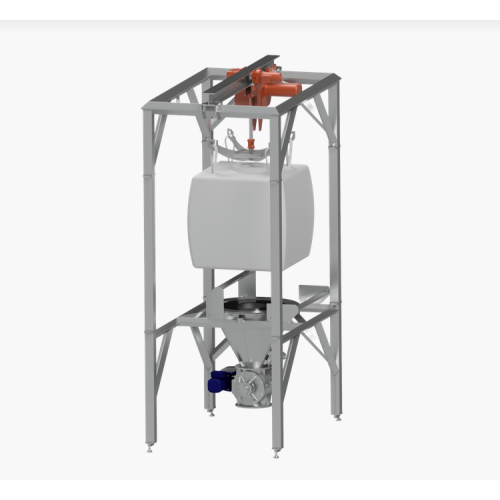
Bigbag discharge system for food, chemical, and pharmaceutical industries
Ensure precise and dust-free handling of bul...
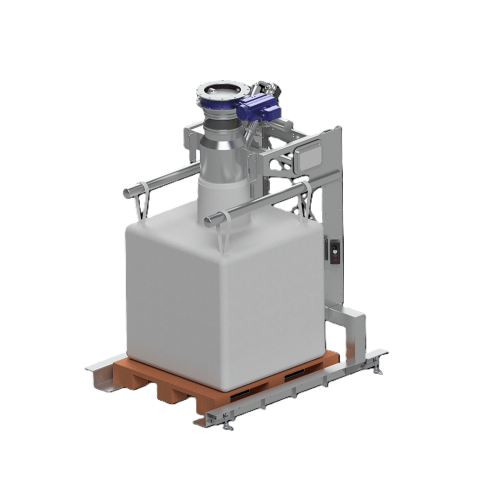
Bigbag filling system for powder and bulk materials
Ensure precise and dust-free bigbag filling with this versatile syste...
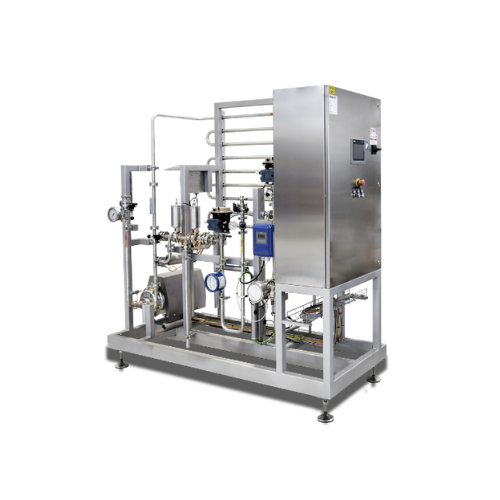
Saturation unit for carbonating beverages
Elevate your beverage production with continuous carbonation, ensuring precise g...
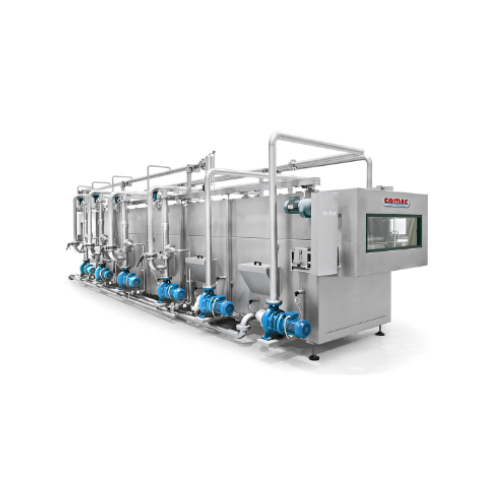
Tunnel pasteurizer for beverages
Optimize your beverage production with precise pasteurization control, ensuring product qua...
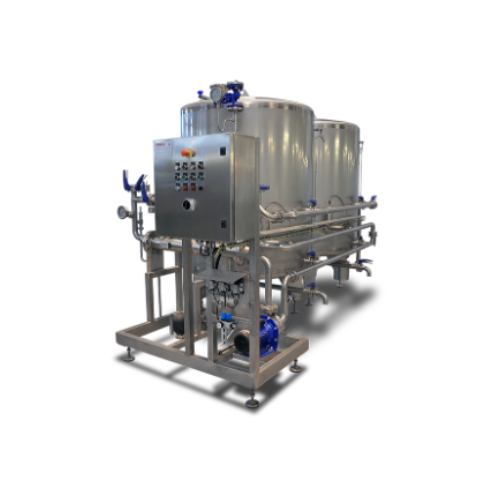
Cip systems for beverage filling plants
Ensure optimal cleanliness and hygiene in your beverage production line with advanc...
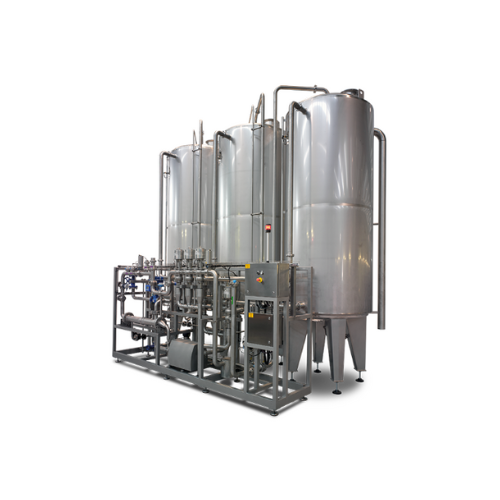
Cleaning solution tanks for beverage production
Achieve superior internal cleaning of beverage containers with our advance...
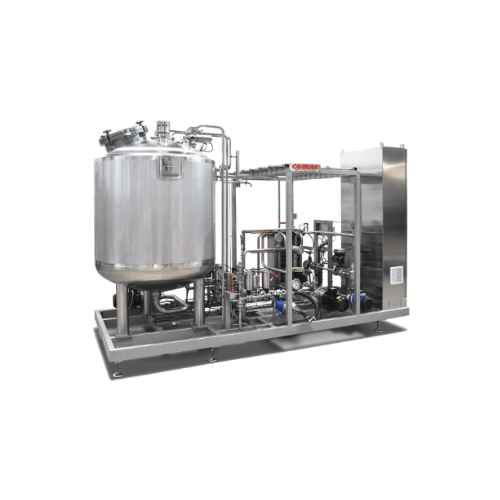
Flash pasteurizer for beverage production
Ensure beverages maintain quality and safety with precise temperature control an...

Heating and cooling tunnel for beverages
Achieve consistent temperature regulation for beverages, ensuring optimal product ...
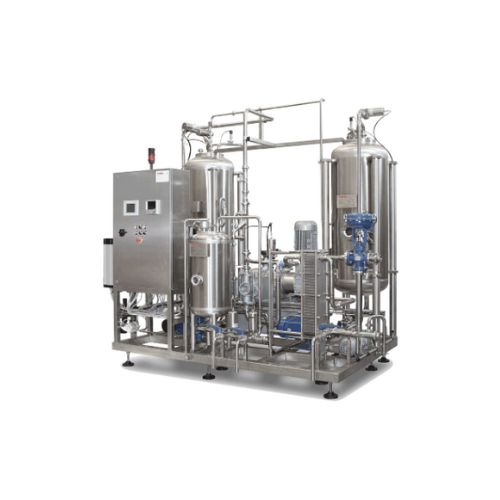
Premix system for carbonated beverages
Ensure precise carbonation and blending for your beverage lineup with this advanced ...
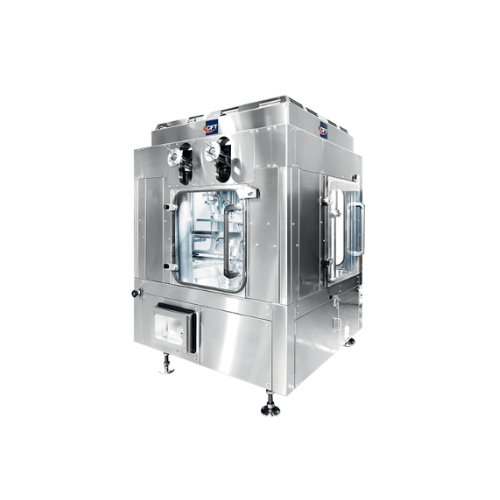
Industrial can seamers for food and beverage packaging
Streamline your canning process with precision seaming solutions d...
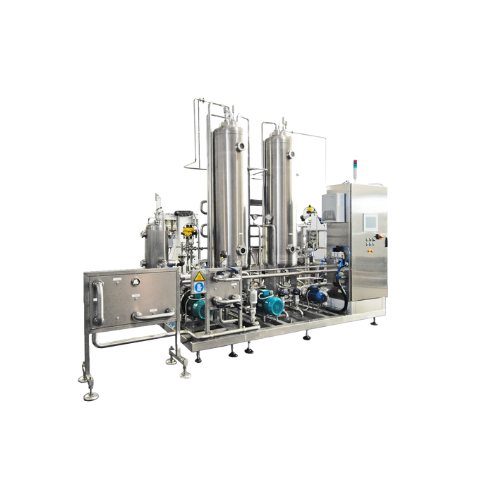
Powder dissolution unit for beverage production
Achieve precise and rapid dissolution of powders like sugar and acids, opt...
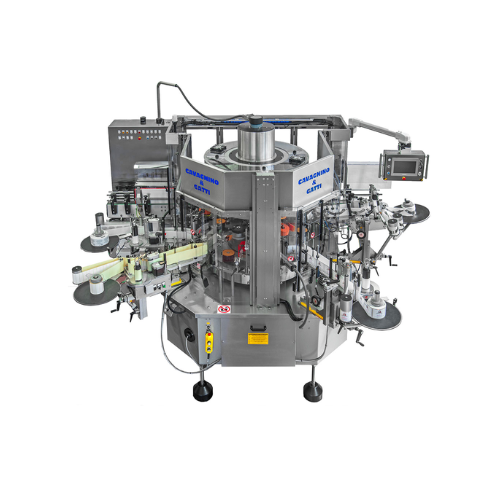
Self-adhesive labelling system for bottles
Enhance your bottling line with a versatile labelling system that supports medi...
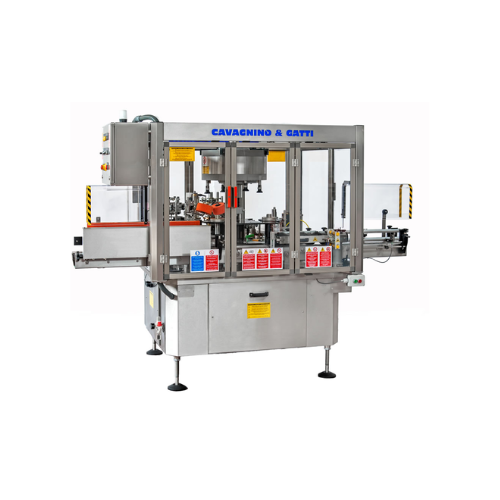
Compact wet glue labeling system for low volume production
Achieve precise, high-quality labeling with compact machinery...
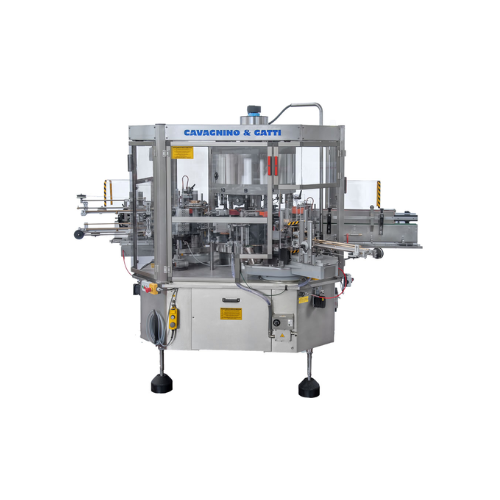
High-speed wet glue labelling system
Ensure precise labelling on diverse bottle types with our versatile rotary labelling s...
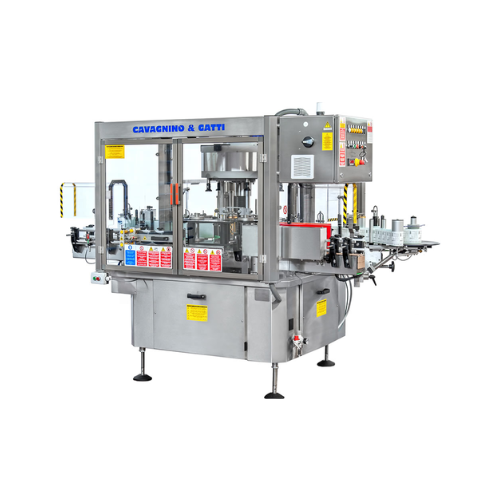
Compact combined labelling solution for bottling lines
Optimize your bottling line with a versatile, compact labelling so...
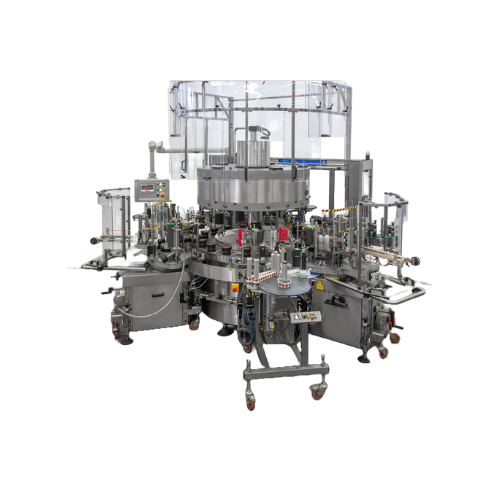
Combined wet glue and self-adhesive labeling system
Achieve seamless labeling with combined wet glue and self-adhesive te...
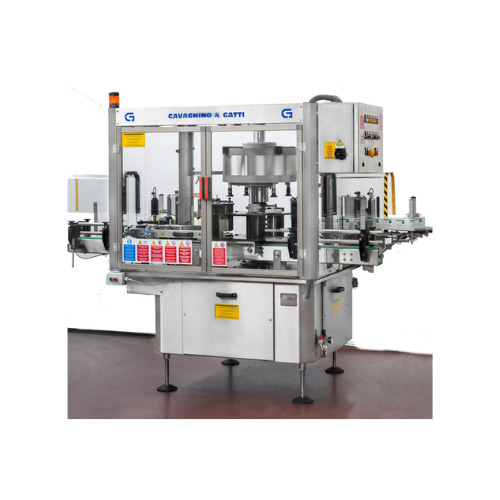
Self-adhesive labeling system for bottles
Streamline your bottling operations with high-precision labeling that enhances p...
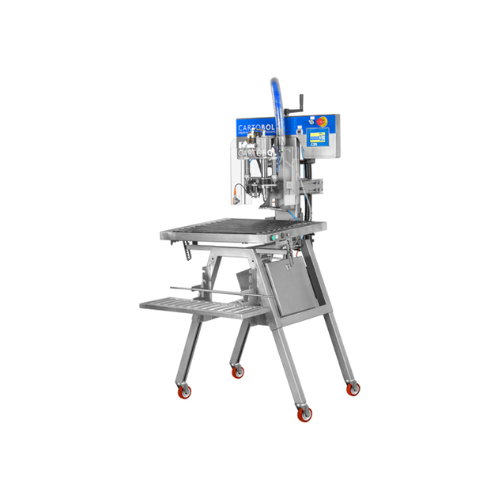
Semi-automatic filler for bag-in-box packaging
Streamline your liquid packaging process with a versatile filler that integ...
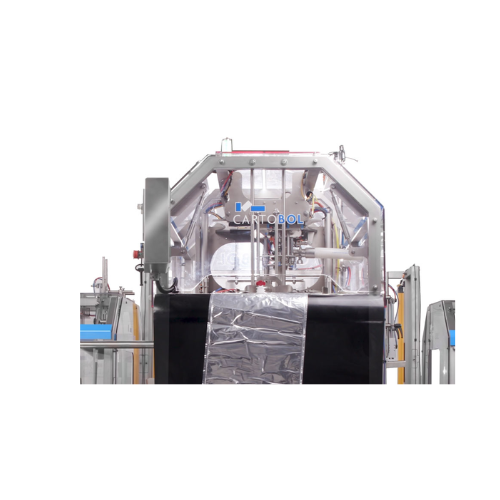
Bag-in-box fully automatic filling line
Streamline your liquid packaging operations with a modular system designed to enhan...
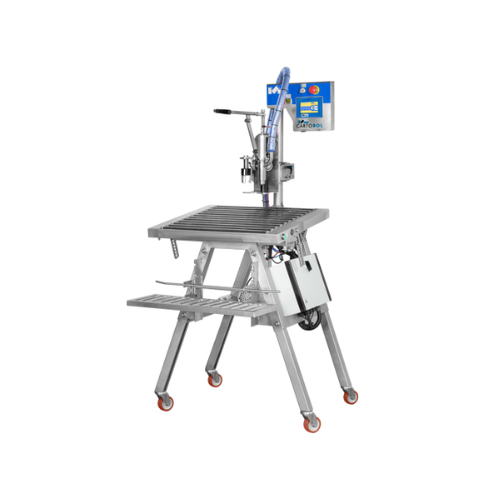
Manual bag-in-box filling solution
Streamline your liquid packaging with a compact, easy-to-operate filling system that sim...
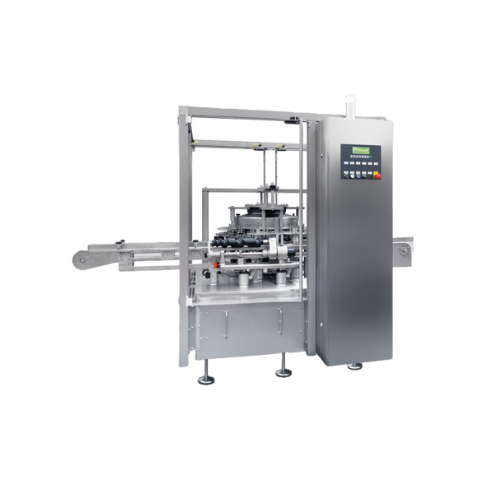
Rotary continuous motion bottle cleaning solution
Ensure pristine product integrity by effectively eliminating particles ...
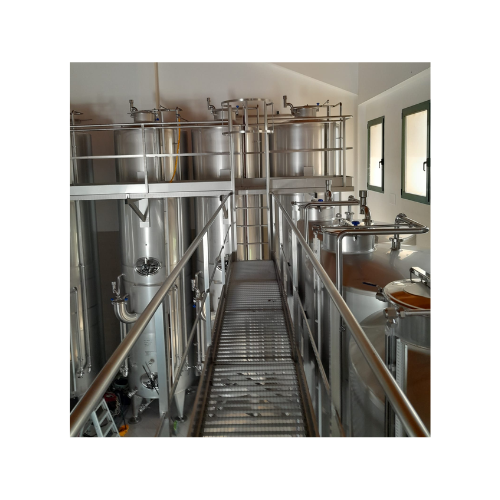
Storage tanks for wine preservation
Ensure optimal preservation of beverages with robust storage solutions featuring precis...
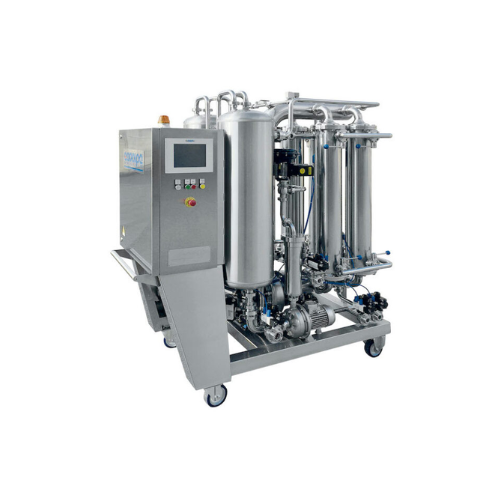
Automatic cross-flow filter for wine
Experience enhanced filtration efficiency with reduced waste, as this cross-flow filte...
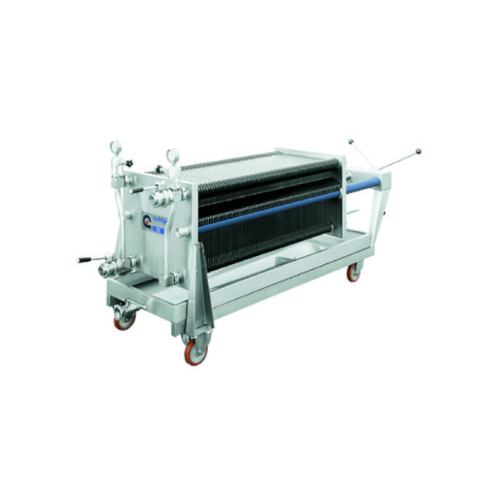
Plate filter for beverage sterilization
Achieve absolute clarity and sterilization of your beverages with a versatile plate...
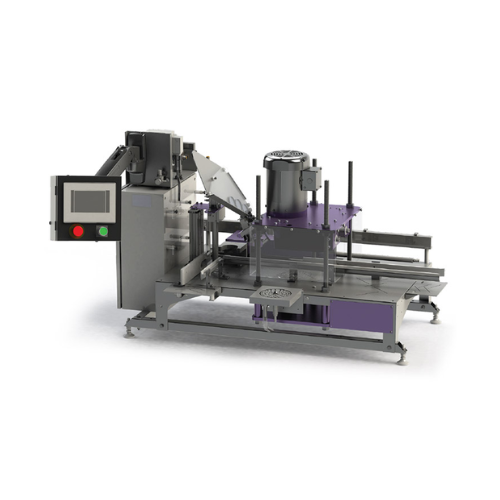
Automated beverage canning line
Optimize your beverage packaging with a high-speed canning line that seamlessly integrates f...
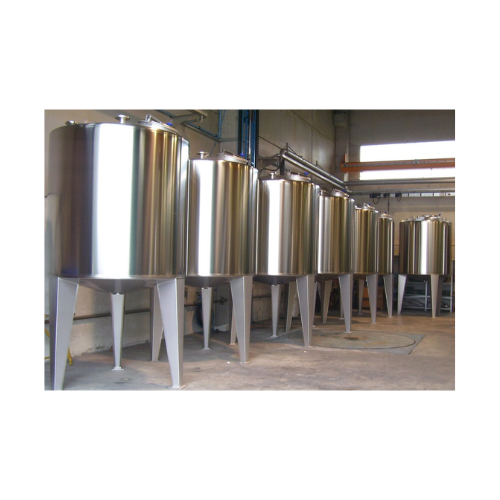
Storage tank for dairy products and juices
Designed for optimal preservation and hygiene, these storage tanks prevent sedi...
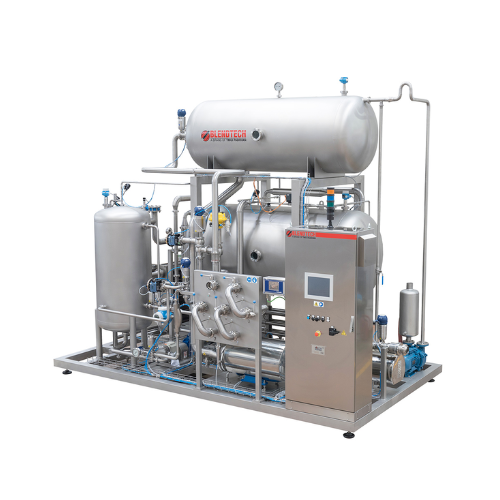
Premix system for soft drinks production
Efficiently produce both carbonated and non-carbonated beverages by integrating th...
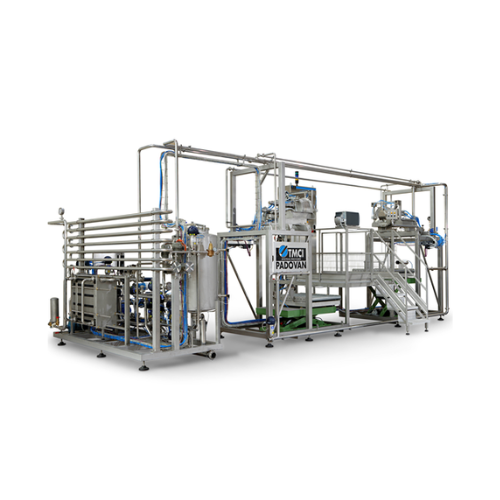
Aseptic filling system for fruit juices and nectars
Effortlessly integrate aseptic filling into your beverage production ...
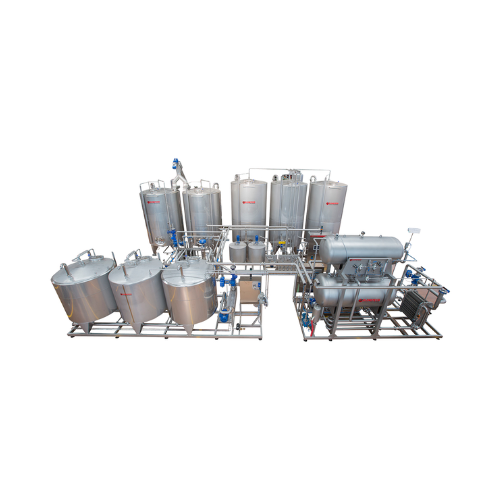
Syrup room for beverage production
Optimize your beverage production with advanced syrup room solutions, offering precise c...
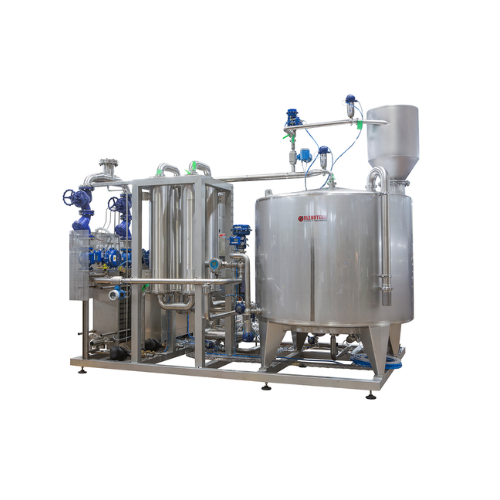
Industrial sugar dissolver for soft drink and juice production
Effortlessly produce high-quality sugar syrup essential f...
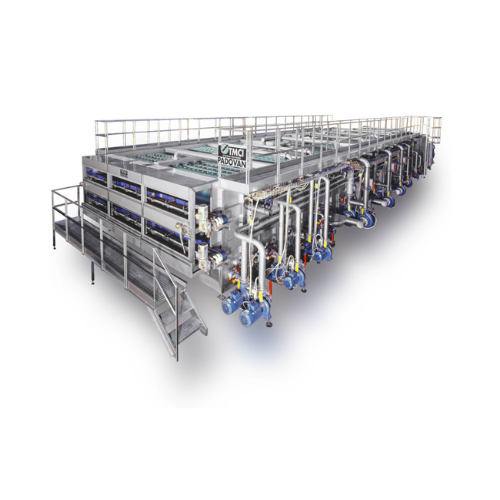
Tunnel pasteurizer, heater, recooler for fruit juices and soft drinks
Optimize your beverage production with a versatil...
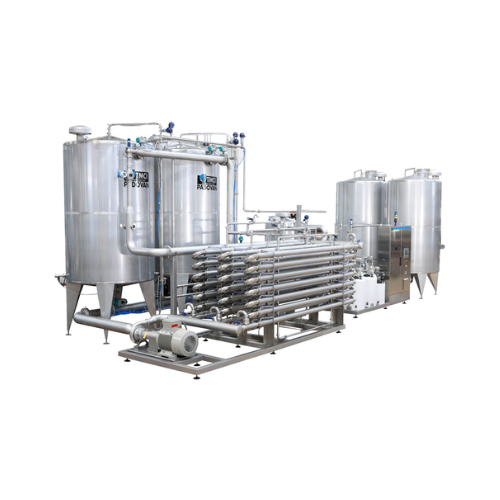
Ultrafiltration for fruit juices and nectars
Optimize your juice and nectars production with precise ultrafiltration, ensu...
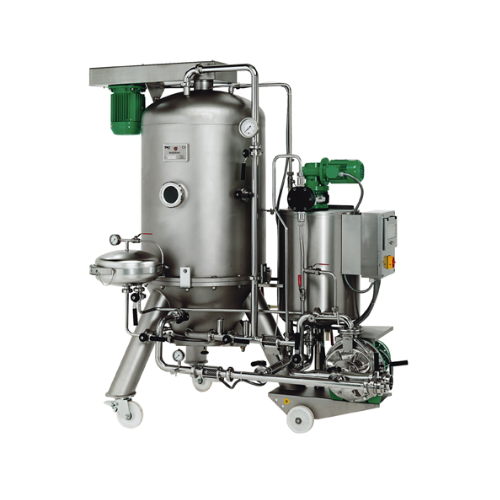
Horizontal plate filtration for fruit juices
Ensure optimal clarity in beverage production with a filtration unit that exp...
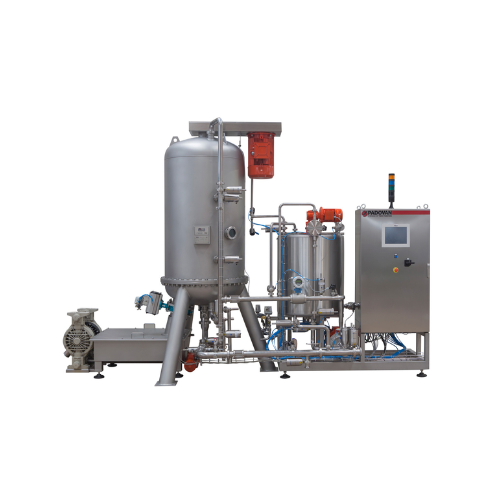
Diatomaceous earth pressure filter for fruit juices and soft drinks
Achieve exceptional clarity and taste in your bever...
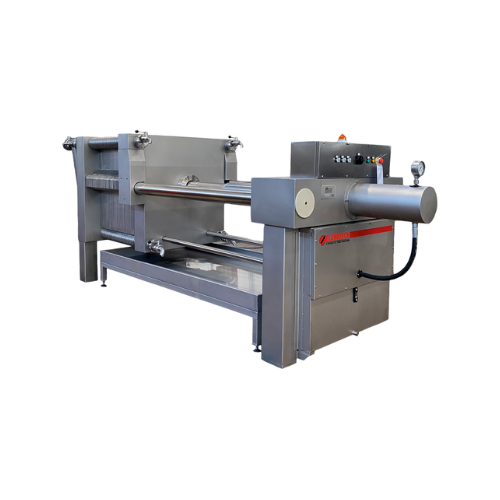
Plate and sheet filter for fruit juices
Ensure precision and clarity in your beverage production by utilizing this advanced...
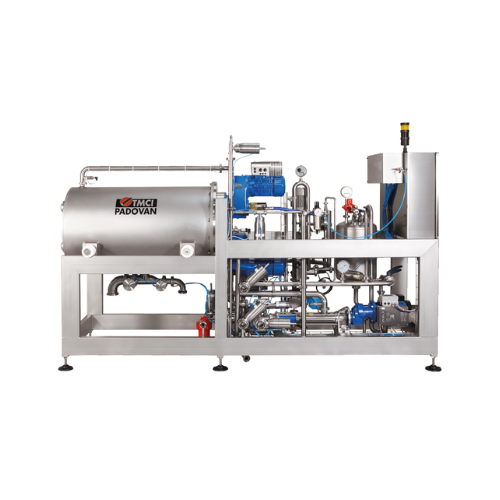
High solids crossflow filter for fruit juices and nectars
Eliminate the challenges of suspended solids in beverage produ...
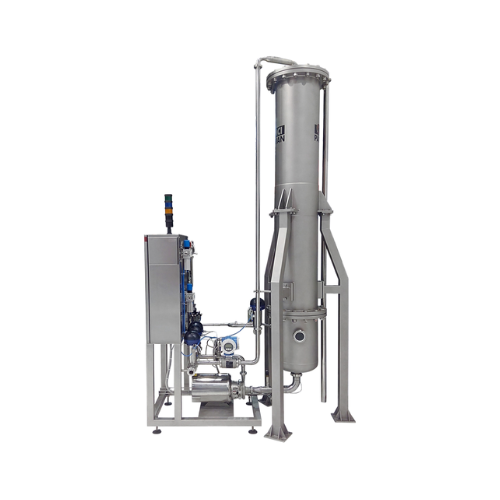
Deaeration system for fruit juices and soft drinks
Enhance your beverage quality by efficiently deaerating and carbonatin...

Enzyme inactivation for fruit juices and nectars
For fruit juice and nectar production, ensuring product quality starts wi...

Microfiltration system for fruit juice and soft drinks
Ensure optimal purity and flavor retention in your beverages with ...
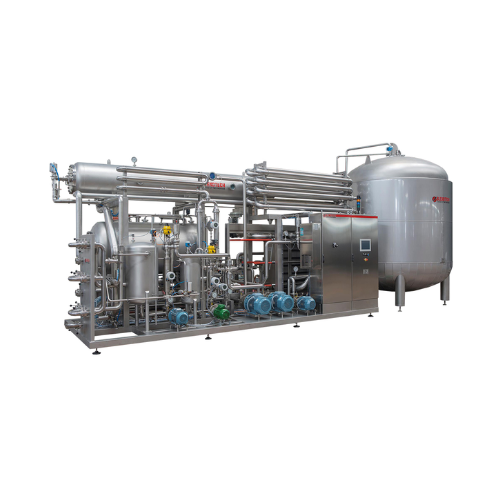
Mixer-pasteurizer-carbonator for soft drinks and juices
Optimize your beverage production with a versatile system that se...
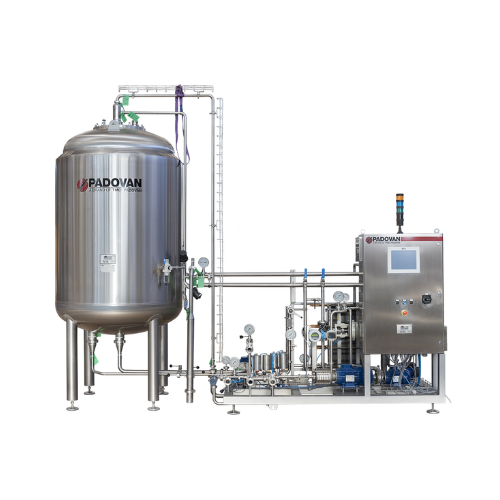
Plate flash pasteurizer for fruit juices and soft drinks
Ensure the purity and safety of your beverages with precision th...
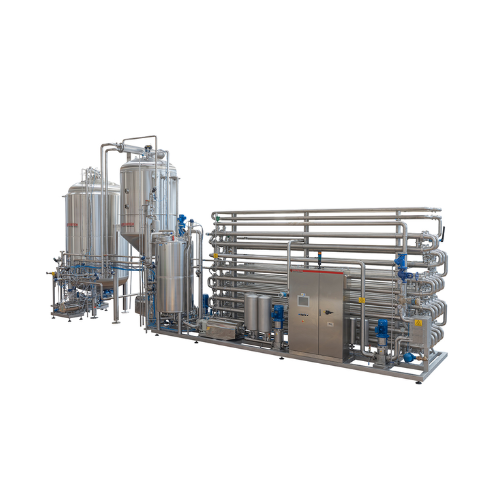
Tubular pasteurizer for fruit juices and nectars
Preserve flavor and ensure safety in your beverage production with high-e...

Blending system for fruit juices and soft drinks
Optimize your beverage production with precise blending and carbonation, ...
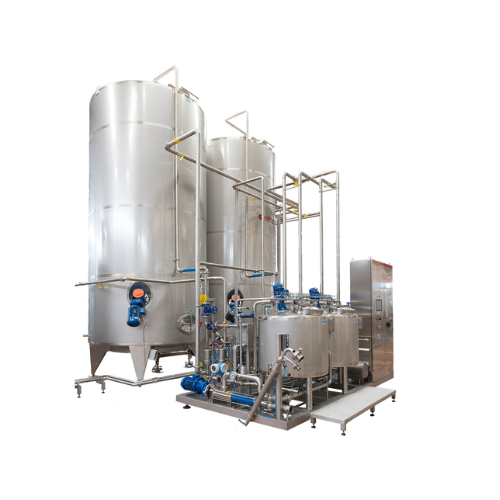
Aroma-batch blender for beverage production
Optimize your beverage formulation process with precise aroma dosing and effic...
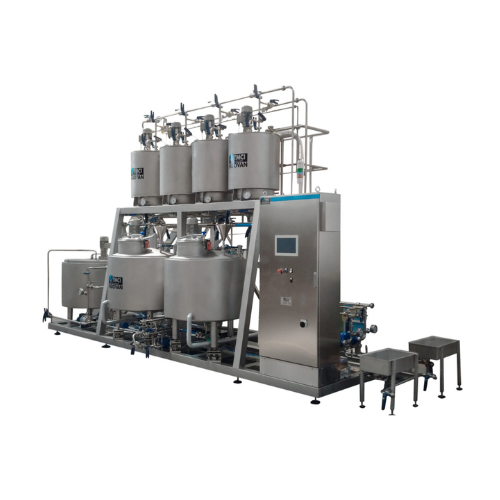
Batch blenders for fruit juices and nectars
Achieve precise ingredient ratios and uniform mixing in beverage production wi...
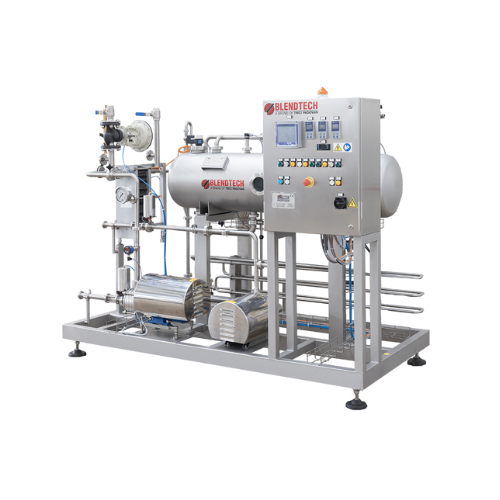
Carbonators for fruit juice and soft drinks
Achieve optimal carbonation in your beverages with precise CO2 dosing equipmen...

Syrup clarification for fruit juices and soft drinks
Enhance the clarity and quality of your beverages by efficiently rem...
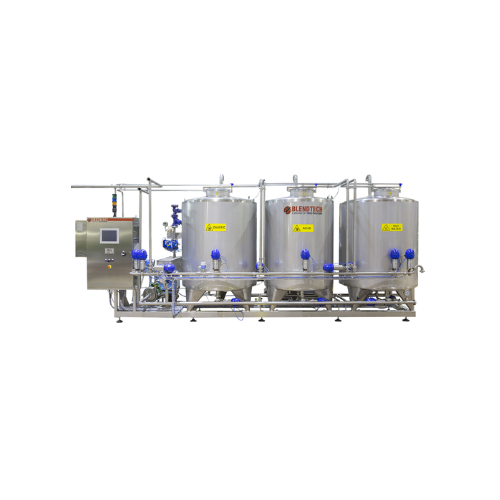
Cleaning in place for fruit juices and soft drinks
Ensure maximum hygiene and reduce downtime in your beverage production...
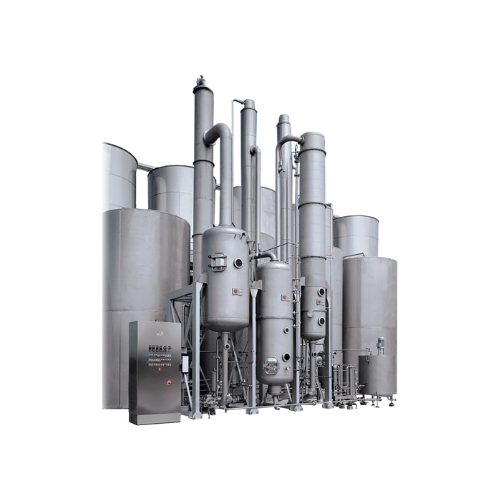
Desulphurizer for fruit juices and nectars
Enhance beverage quality by efficiently removing sulphur dioxide from fruit jui...
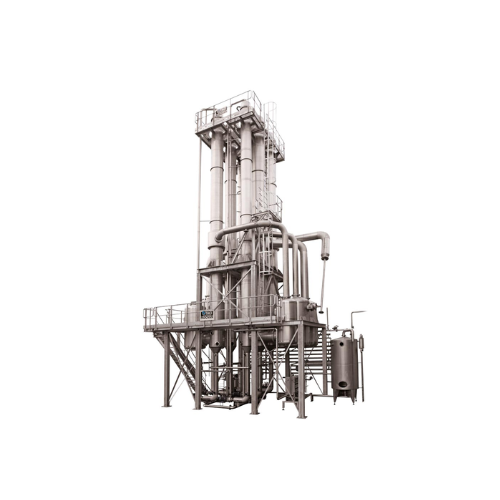
Evaporators for fruit juices and syrups
Optimize your beverage production line with advanced evaporators designed to effici...
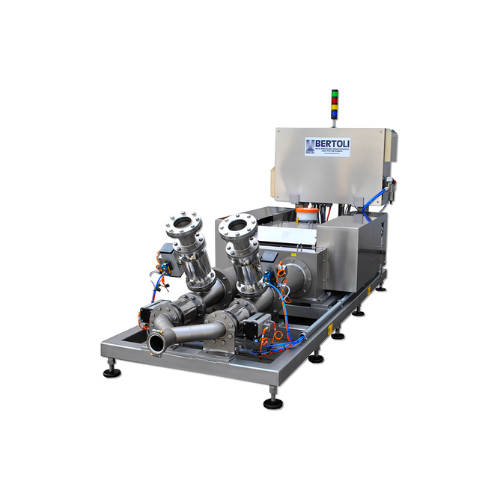
Industrial homogenizer for food and beverage applications
For manufacturers seeking consistent quality, this homogenizer...
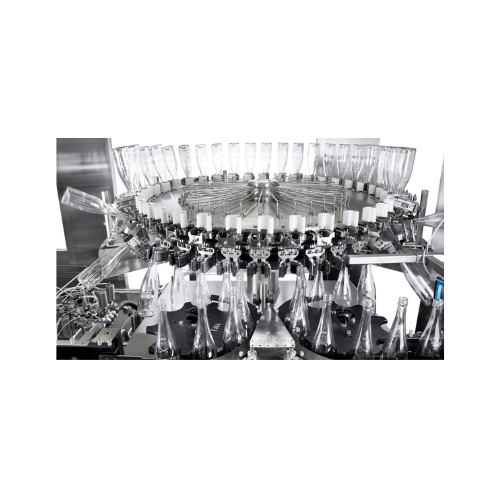
Industrial bottle rinsing systems
Ensure pristine bottle hygiene and maintain high production standards with advanced rinsi...
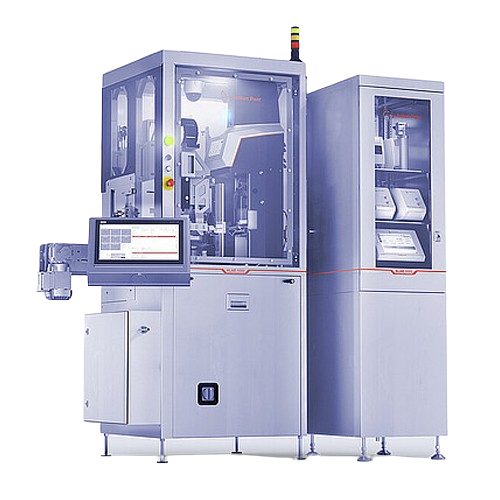
Automated quality control for beverage packaging
Streamline beverage quality control with 24/7 automated analysis, ensurin...
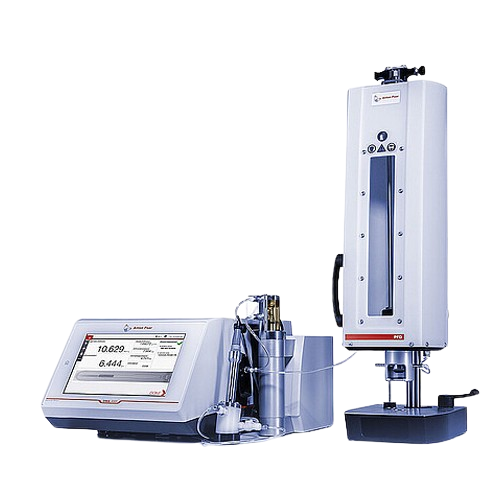
Co2/o2 beverage filling device
Ensure precise beverage analysis by maintaining carbonation integrity with a system that tran...
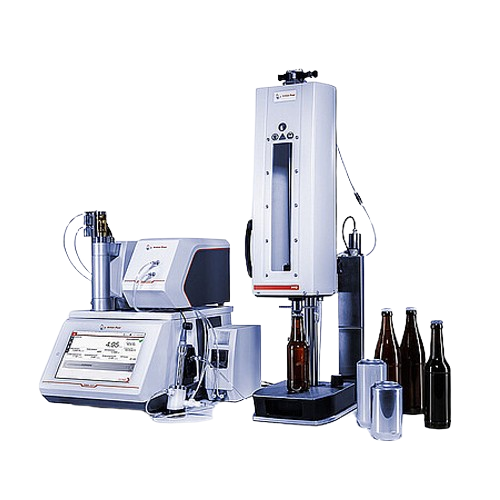
Packaged beverage analyzer for alcohol and Co2
Ensure precise beverage analysis with a streamlined solution that integrate...

Packaged beverage analyzer for beer, wine, and cider
Ensure precision in beverage quality control with rapid, direct samp...
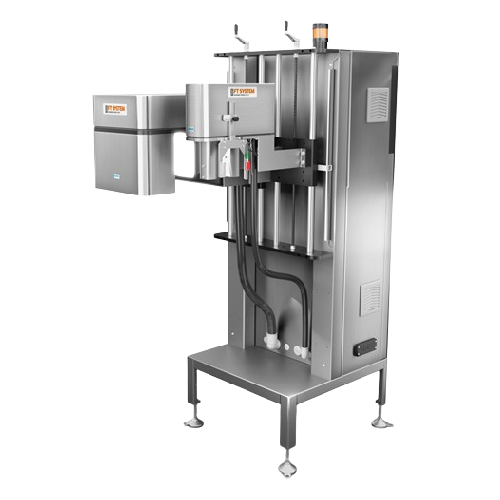
Cap and fill level inspection system for bottles
Ensure precise cap placement and accurate fill levels in your bottling li...
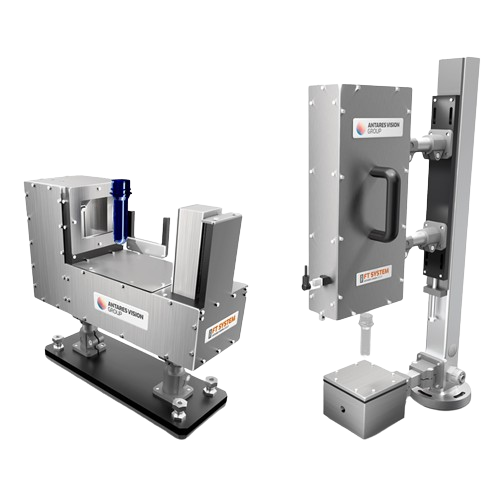
Preform inspection system for blown containers
Ensure defect-free blown containers and minimize line jams with a robust pr...
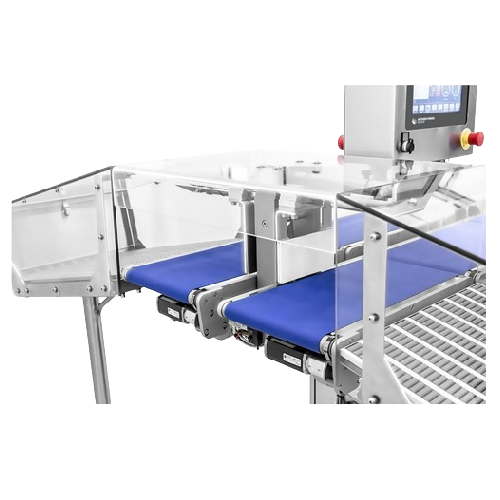
Special checkweighers for industrial applications
Enhance your production line efficiency by precision weighing your prod...
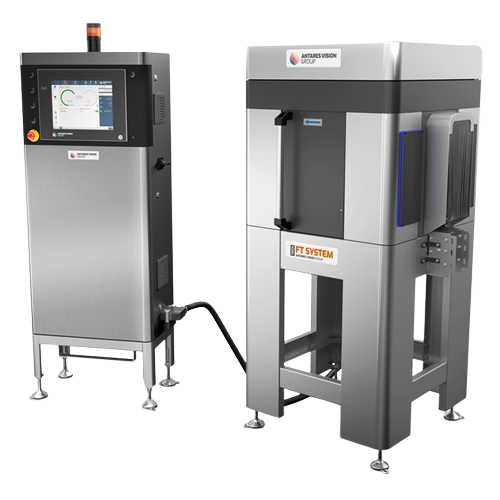
Full label inspection system for not-oriented containers
Ensure precise label application and integrity on any container ...
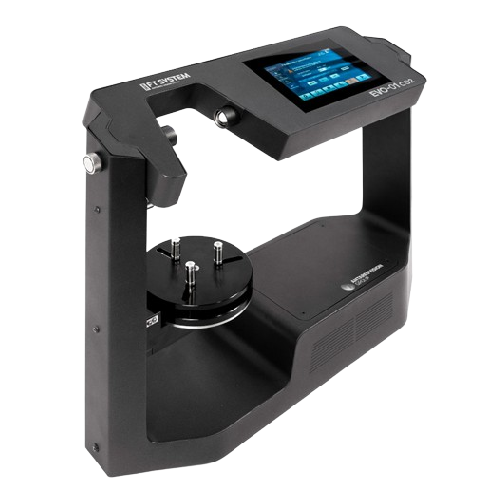
Co2 gas analyzer for beverage bottles
Ensure consistent carbonation levels with precise, non-destructive CO2 measurements i...

Gas analyzer for beverage bottle vacuum level
Ensure precise vacuum level measurement in bottle headspace with non-destruc...
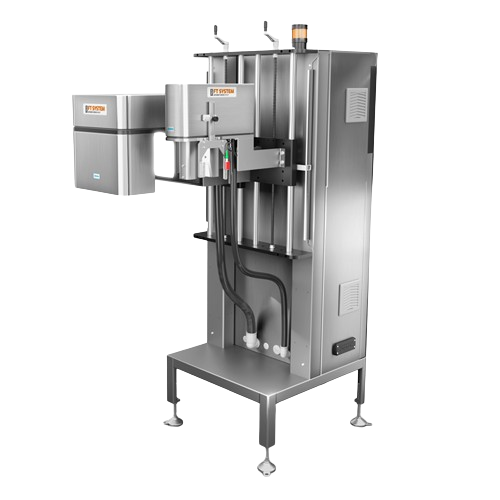
Cap inspection and fill level inspection system for beverage containers
Ensure precise cap application and fill level m...
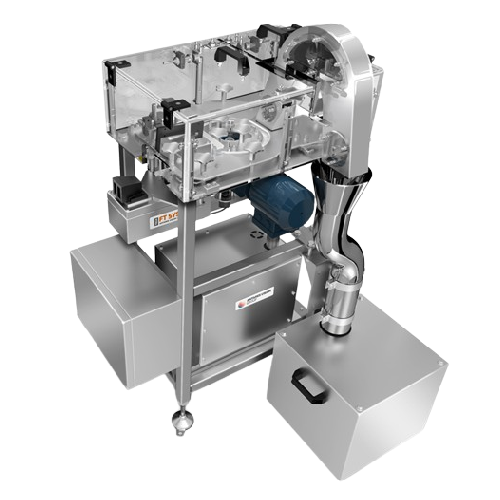
Cap quality inspection system for beverage industry
Ensure flawless cap performance and prevent production disruptions wi...
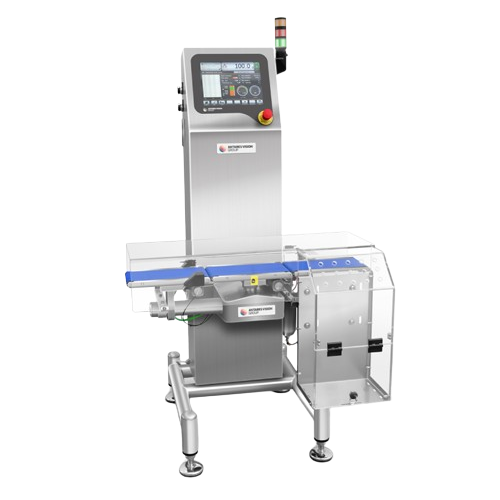
Checkweighers for medium and small products
Ensure precise weight control in high-speed production lines with advanced che...
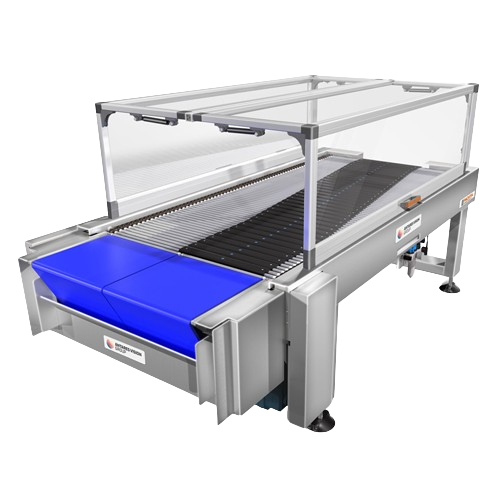
High-speed sliding systems for beverage lines
Streamline your high-speed production lines with advanced sliding systems de...
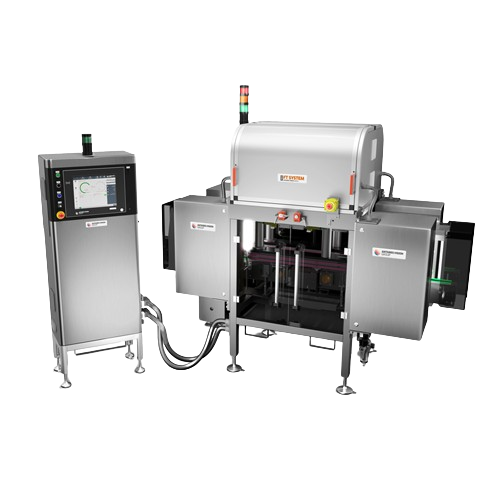
Empty bottle inspection system for beverage industry
Enhance your production line’s efficiency by detecting defects...
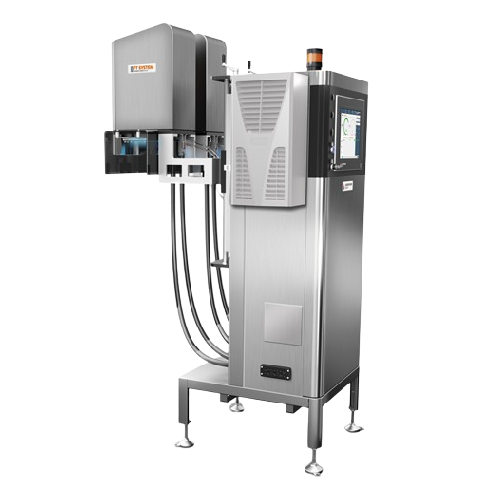
Application angle inspection for Pet bottle caps
Ensure perfect cap alignment on PET bottles to prevent leaks and ensure e...
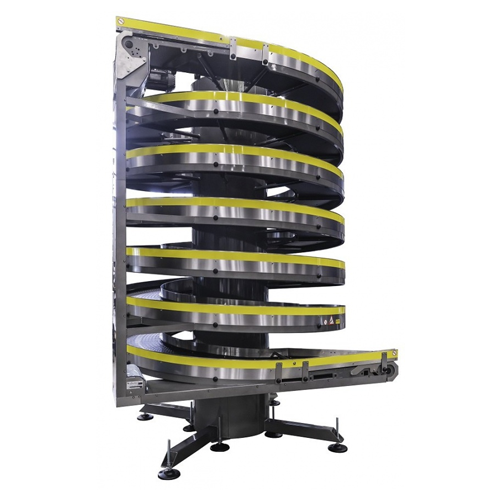
Spiral conveyor for individual bottles and cans
Streamline your production line’s space and layout with a compact co...
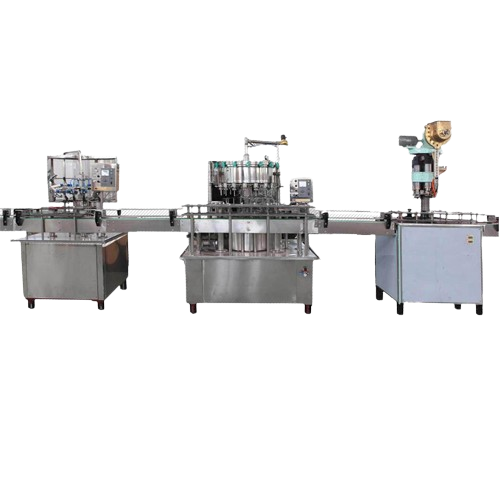
Small bottle linear type beverage filling production line
Optimize your bottling efficiency with a high-speed solution d...
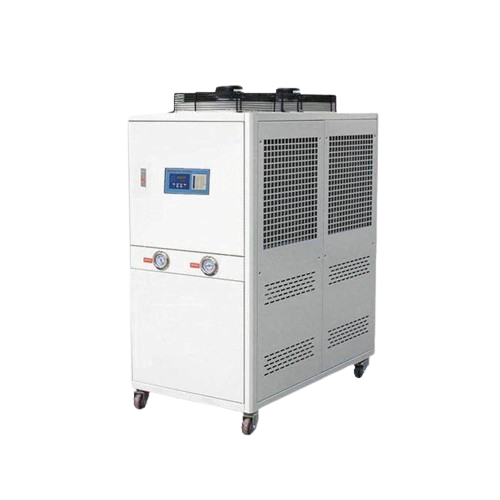
Industrial air cooled chiller for carbonated beverages
Optimize your beverage production with precise temperature control...
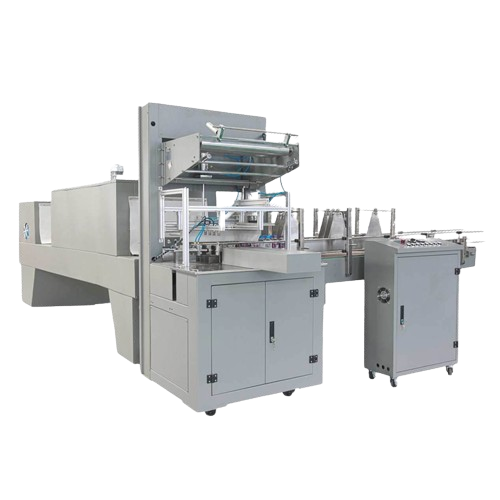
Automatic beverage bottle shrink packaging solution
Optimize your beverage packaging process with advanced shrink wrappin...
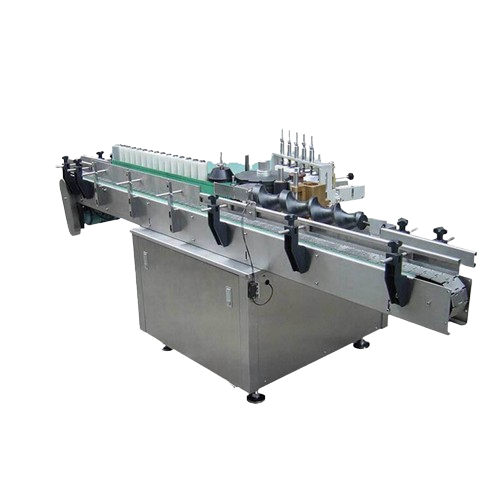
Automatic bottle cold glue labeling solution
Achieve precise labeling for diverse container types, enhancing your producti...
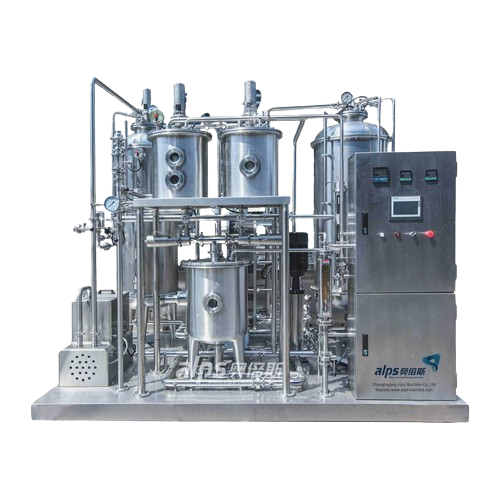
Automatic carbonated beverage mixing system
Optimize your beverage production by ensuring precise carbonation and mixing w...
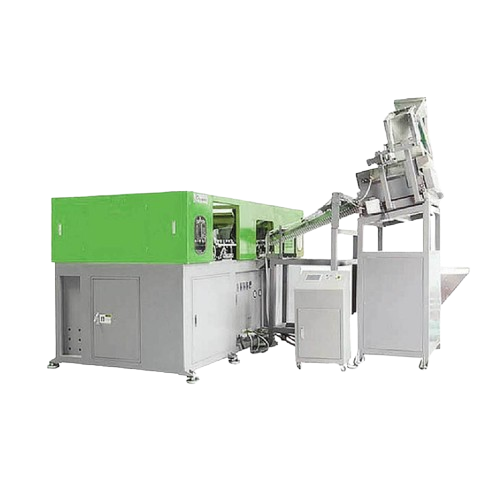
Automatic servo Pet bottle blower
Elevate your production capabilities with a PET bottle blowing machine designed for high-...

High-capacity carbonated drink filling system
Optimizing your carbonated beverage production, this high-speed filling syst...
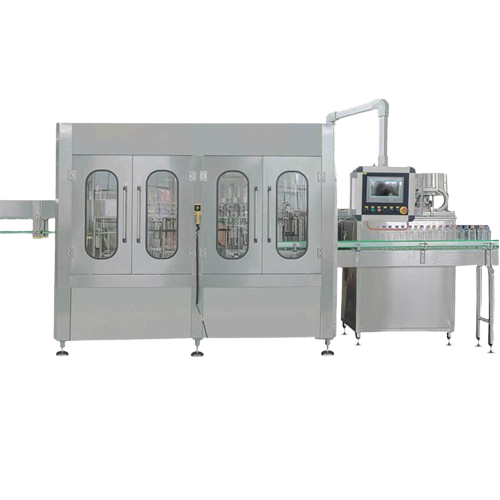
Carbonated drink filling solution for Pet bottles
Optimize your carbonated beverage production with an all-in-one filling...
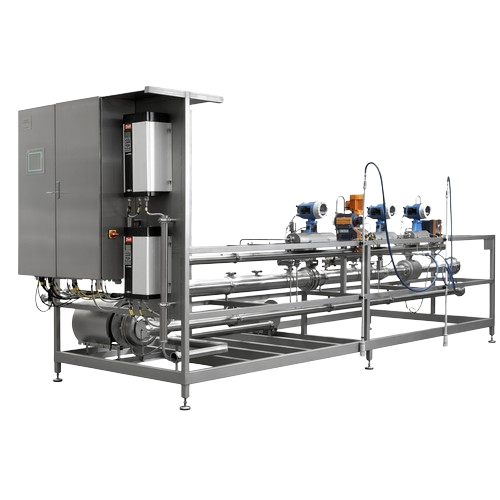
Modular dosing system for brewing and beverage industry
Ensure precise formulation of beverages by seamlessly integrating...
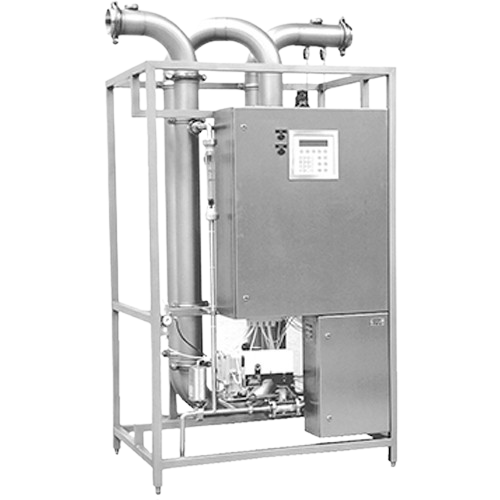
Beer carbonation system
Achieve consistent and precise carbonation in beverages, ensuring optimal gas dissolution for enhance...
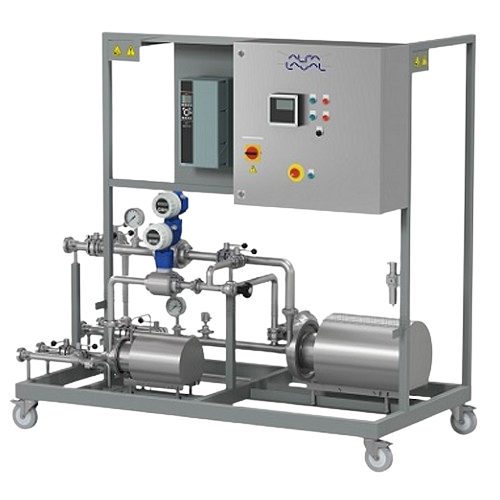
Mobile mixing system for beverages in breweries
Optimize blending and carbonation processes with a mobile solution that st...
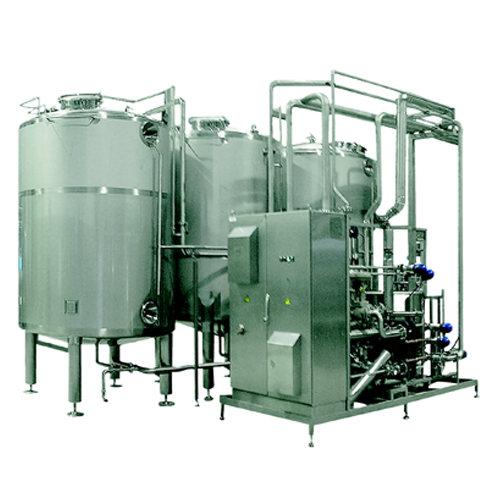
Automated Cip station for brewery cleaning
Ensure thorough hygiene and product integrity in your brewing process with a ve...
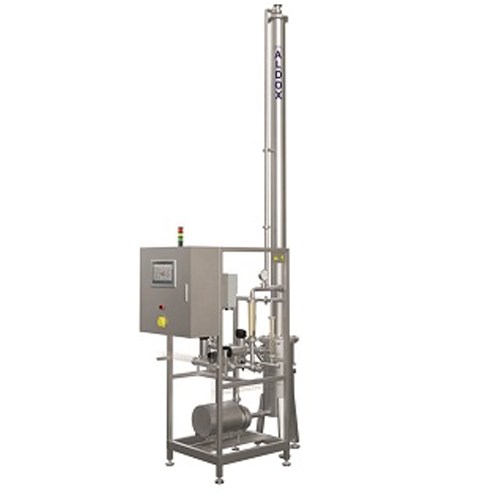
Water deaeration module for breweries and soft drink manufacturers
Ensure high-quality beverage production by efficient...
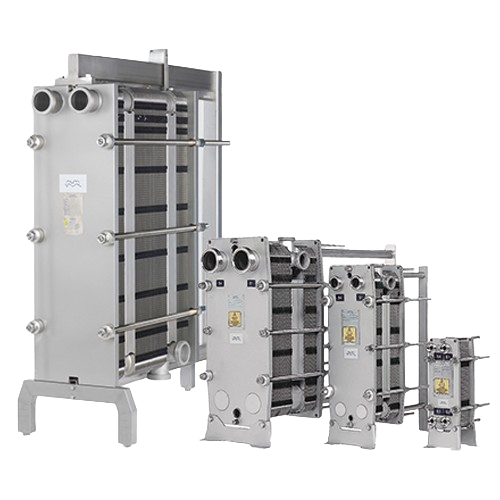
Gasketed plate heat exchangers for hygienic applications
Ensure optimal hygiene and thermal efficiency in your processing...
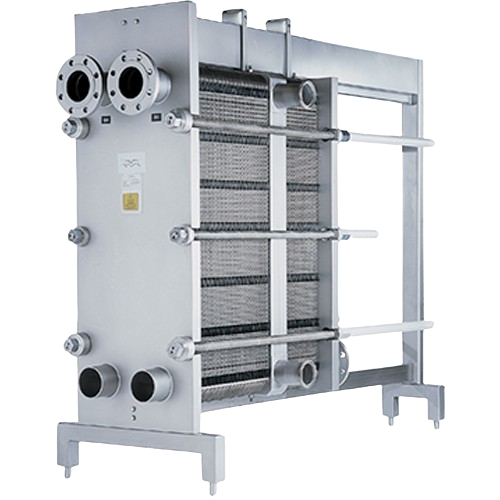
High pressure gasketed plate heat exchangers for carbonated beverages
When ensuring high-pressure handling in your past...
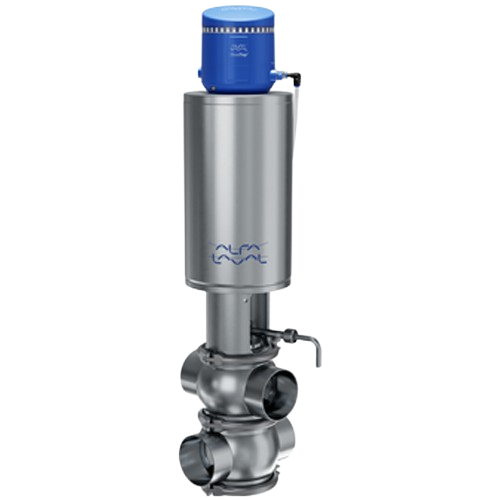
Mixproof valve for cleaning-in-place control
Streamline your cleaning processes and ensure product safety with a versatile...

Double seat valve for hygienic processing
Eliminate cross-contamination risks and enhance efficiency with a modular valve ...
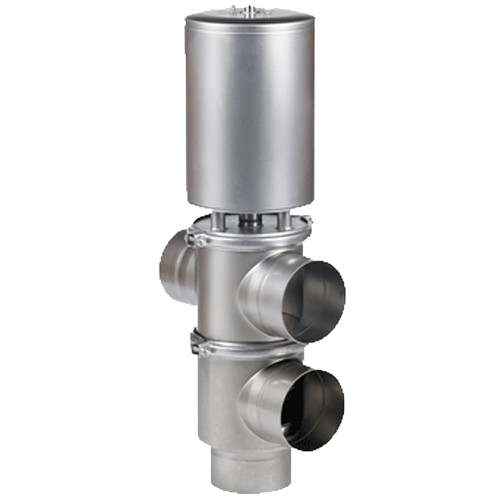
Single seat valve for hygienic applications
Ensure optimal hygiene and safety with a versatile pneumatic valve designed to...
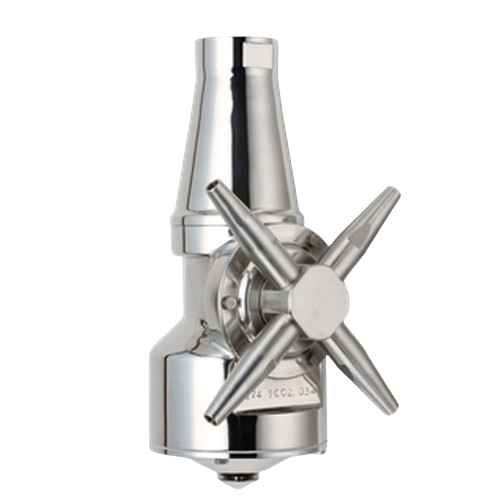
Rotary jet mixer for efficient liquid, gas, and powder mixing
Achieve seamless integration and efficiency in liquid, gas...

Rotary jet head tank cleaning system for food and beverage industry
Reduce your tank cleaning costs by up to 70% with a...
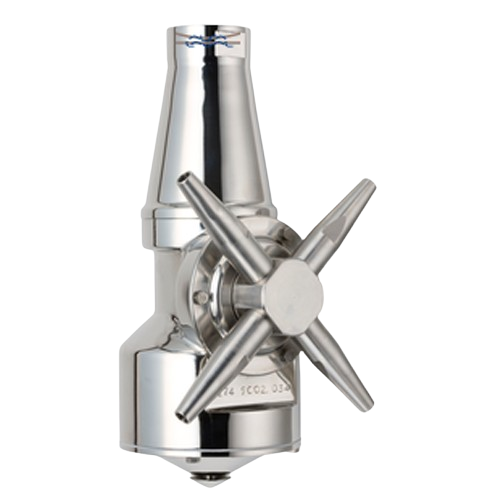
Rotary jet head for hygienic tank cleaning
Ensure efficient, hygienic cleaning with a rotary jet head designed to optimize...
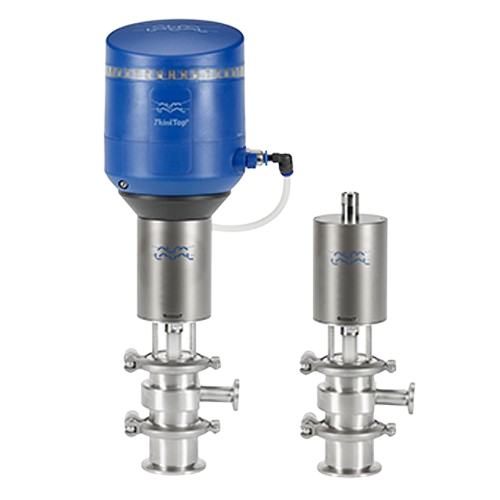
Vacuum breaker valve for Htst pasteurization systems
Prevent vacuum conditions in high-temperature pasteurization systems...
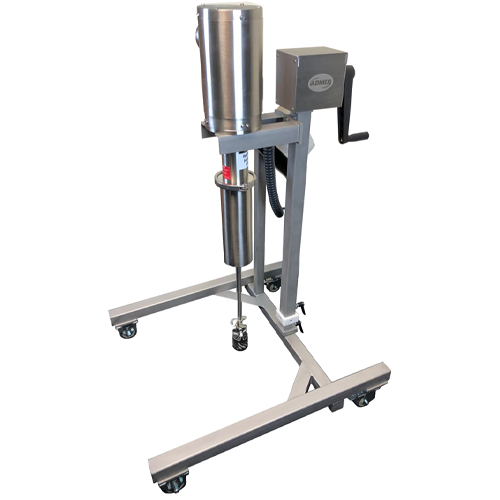
Pilot scale mixers for product development and small production runs
Optimize your mixing processes with precision cont...
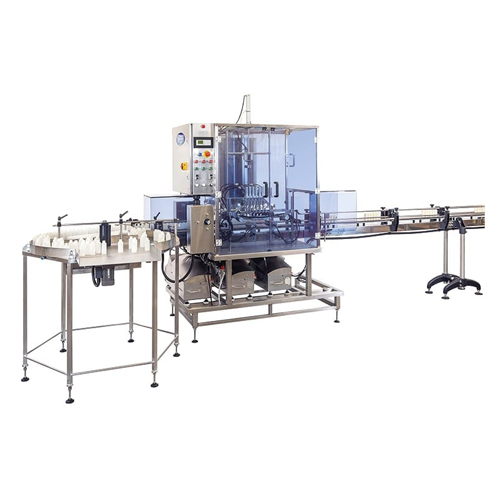
Automated bottle and jar filling solution
Streamline your production and minimize waste with a versatile filling solution,...
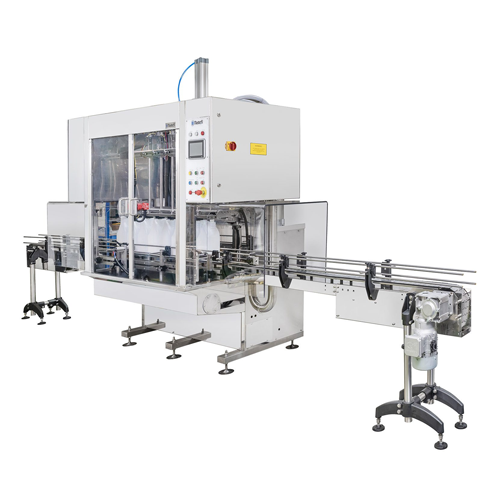
Automatic volumetric filler for liquid products
Optimize your production with this high-precision volumetric filler, desig...
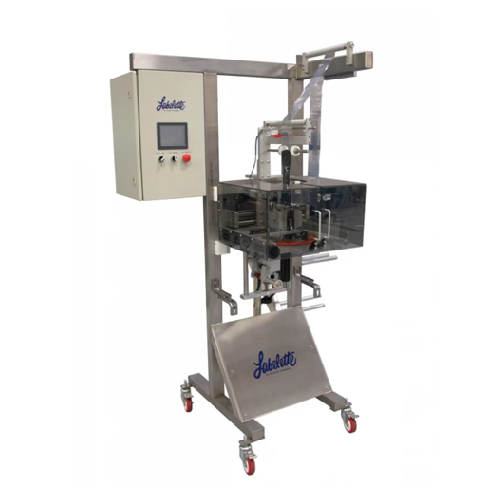
Full body sleeving systems for packaging applications
Achieve seamless, high-speed labeling precision for diverse contain...
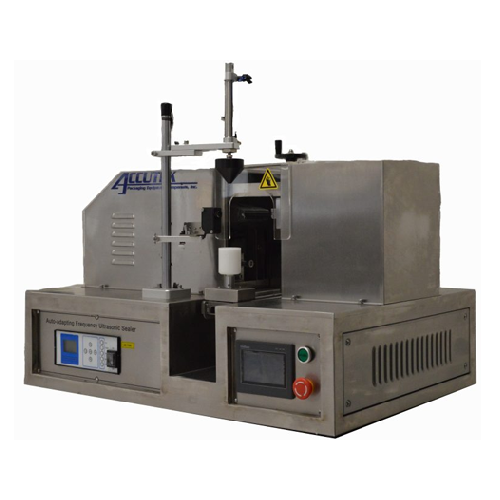
Ultrasonic tube sealer for plastic tubes
Seal plastic tubes with precision and speed using our ultrasonic technology, ensur...
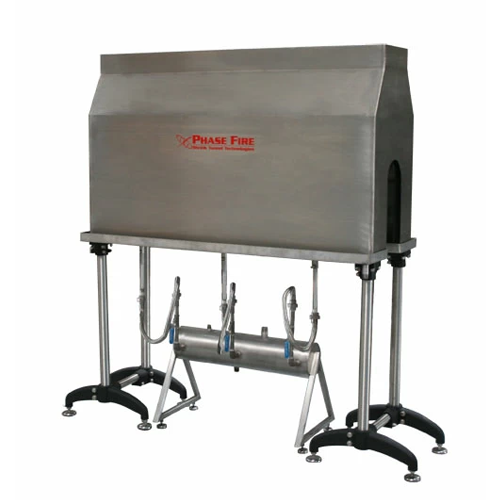
Steam shrink tunnels for versatile packaging
Enhance your packaging efficiency with this adaptable steam shrink tunnel, de...
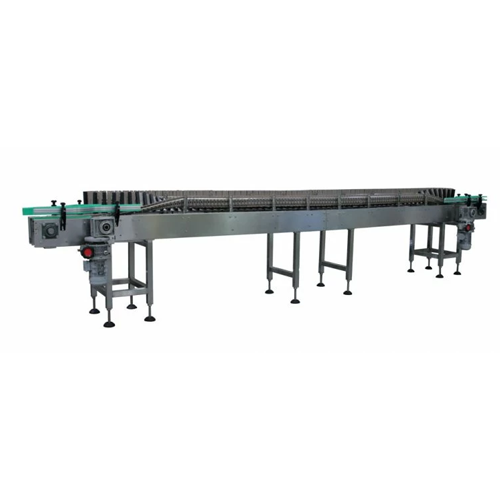
Inversion sterilizing conveyor for hot beverage bottle sanitation
Ensure sanitary filling of hot beverages by utilizing...
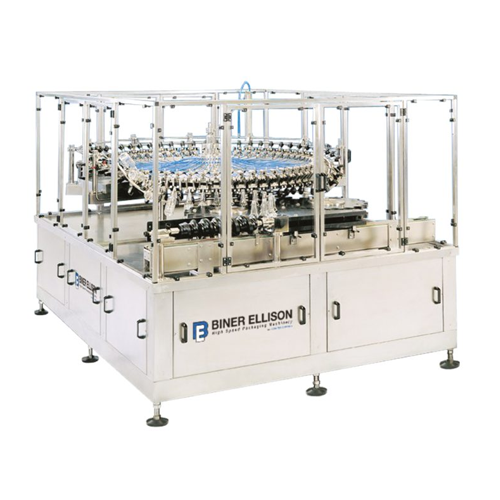
Rotary bottle rinser for high-speed production lines
Ensure thorough cleaning and preparation of containers with a high-s...
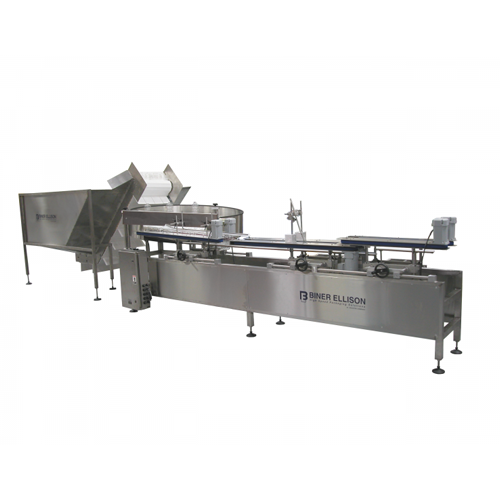
High-speed bottle orientator
Efficiently streamline your bottling process by ensuring containers are swiftly and accurately ...
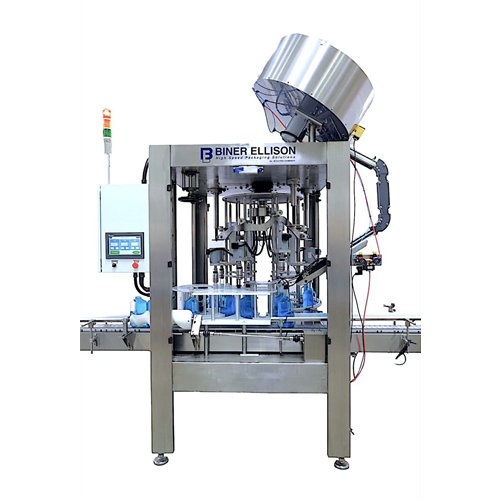
Rotary capper for high-speed bottling
Streamline your bottling process with a rotary capper designed to ensure accurate and...
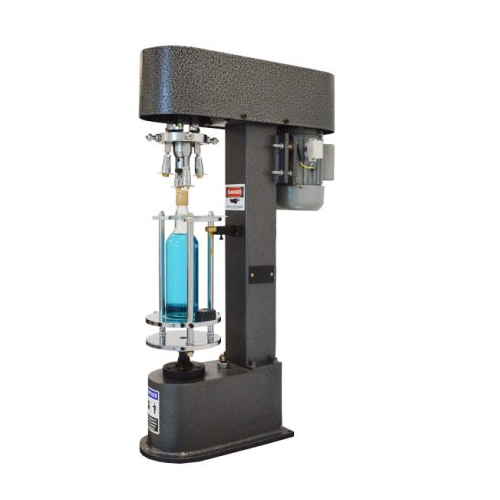
Roll-on bottle capping solution for aluminum caps
Ensure precise threading and sealing of aluminum caps on diverse bottle...

Bottomless conveyor for 90° bottle transfer and coding
Efficiently connect disparate production systems in your bottling ...
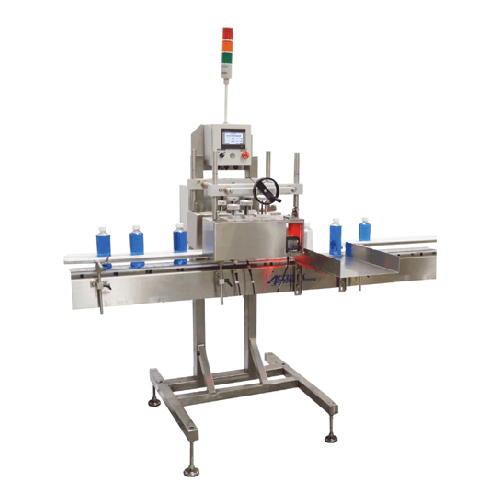
Inspection-rejection station for bottled products
Ensure your bottled and packaged products ship defect-free by automatic...
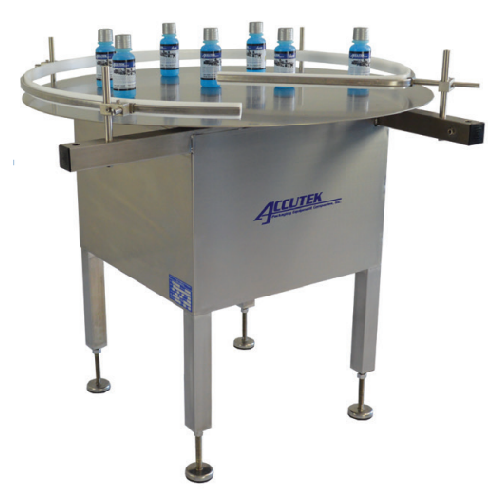
Accumulation turntable for bottling lines
Optimize your production line’s efficiency with a 42-inch diameter accumul...
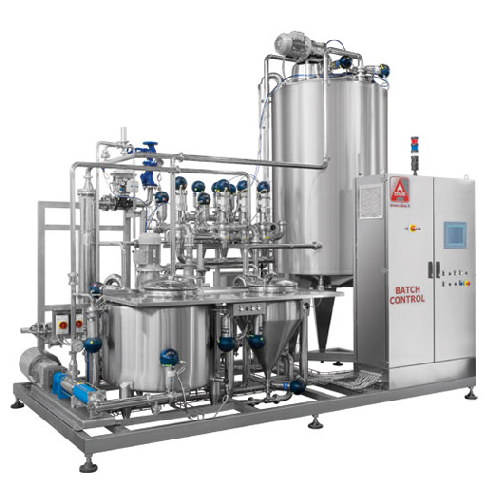
Ingredient management system for beverage production
Efficiently manage a diverse range of solid and liquid ingredients t...
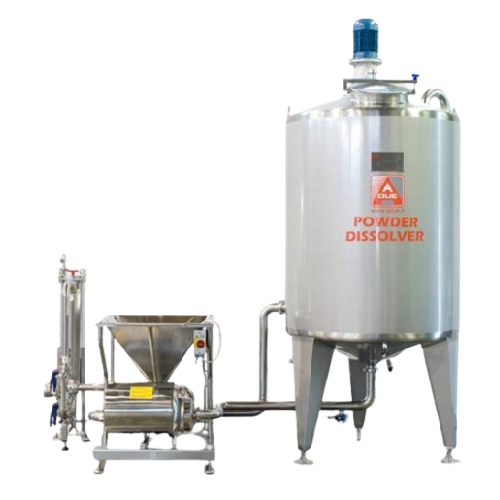
Stabilizer dissolver for beverage production
Achieve optimal dispersion and hydration of stabilizers in beverages to enhan...
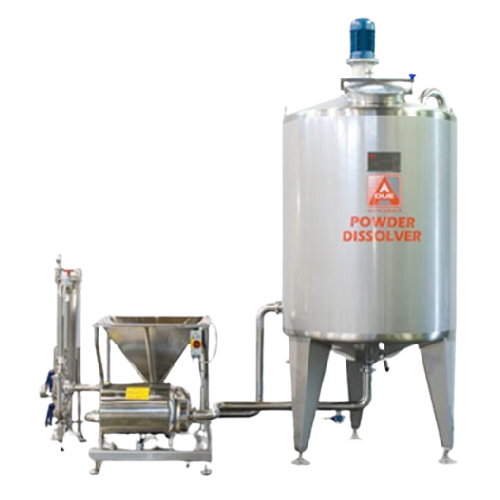
Stabilizer dissolving system for beverage production
Optimize drink consistency and shelf life with advanced stabilizer d...
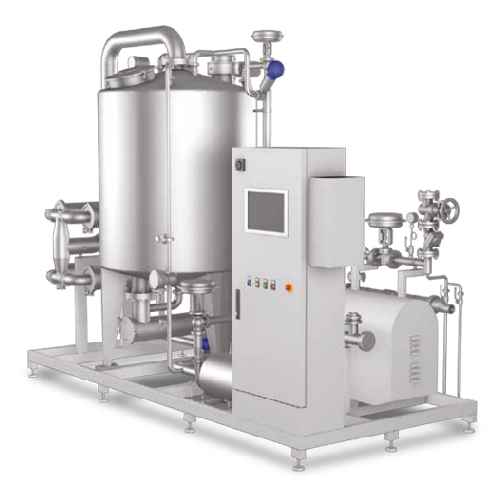
Continuous sugar dissolving system for beverages
Optimize your beverage production with an efficient sugar dissolving solu...
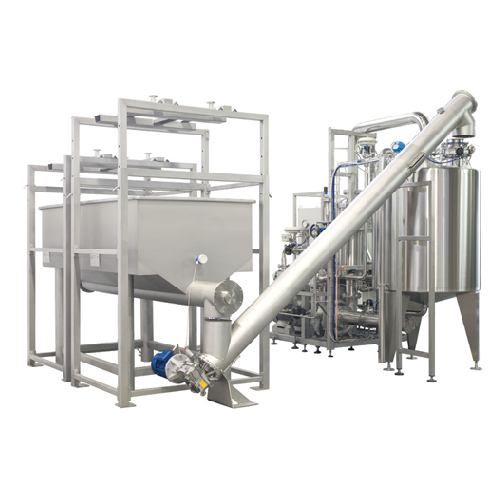
Granulated sugar storage and conveyance solutions
Optimize your sugar processing with versatile solutions for storage, pr...
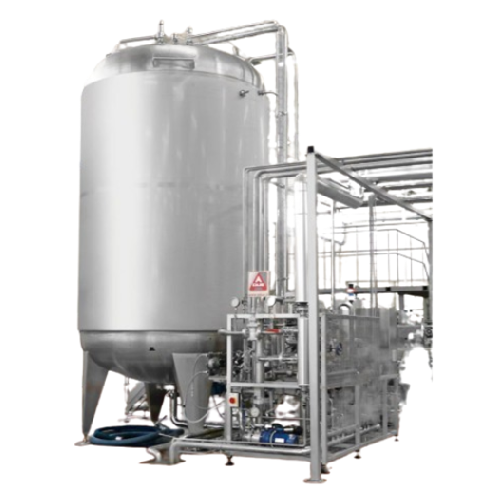
Aseptic storage tank for beverage industry
Ensure product sterility with advanced aseptic storage that compensates for fil...
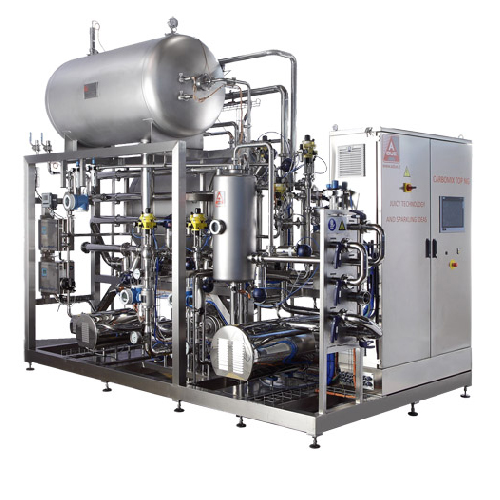
Beverage deaeration, carbonation and mixing system
Streamline your beverage production process with an efficient solution...
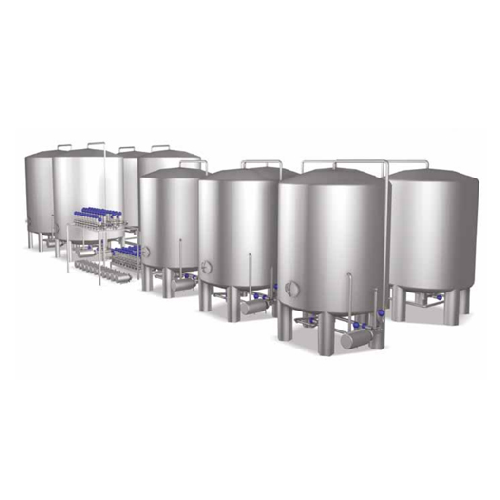
Industrial beverage preparation systems
Optimize beverage production with integrated systems designed for seamless mixing, ...
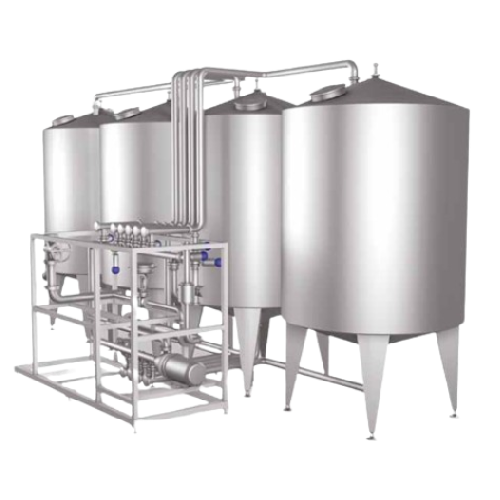
Cleaning in place system for beverage production
Ensure maximum hygiene and efficiency in beverage production with a modul...
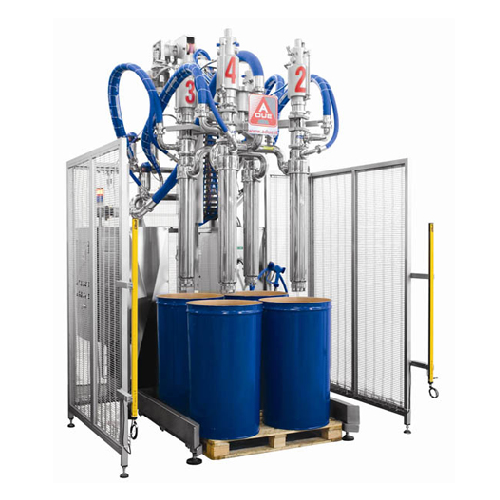
Fruit pieces handling for juice production
Achieve perfect fruit piece integration in juice with a system designed to prev...
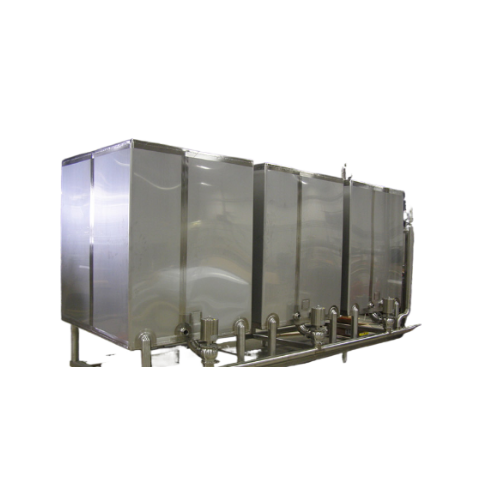
Clean-in-place tanks for industrial sanitation
Optimize your sanitation processes with clean-in-place tanks, designed to r...

Basket tracking system for automated batch retort systems
Efficiently manage and monitor your batch processing with a sy...
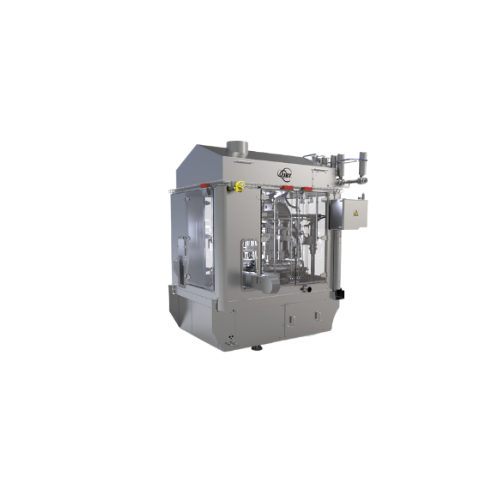
Volumetric filler for various food products
Achieve high precision and flexibility in your filling processes with a volume...
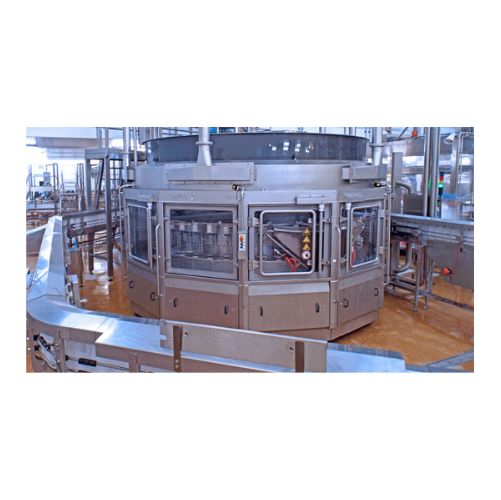
Industrial weight filler for bottles and jars
Achieve precise product filling with our weight filler system, expertly desi...
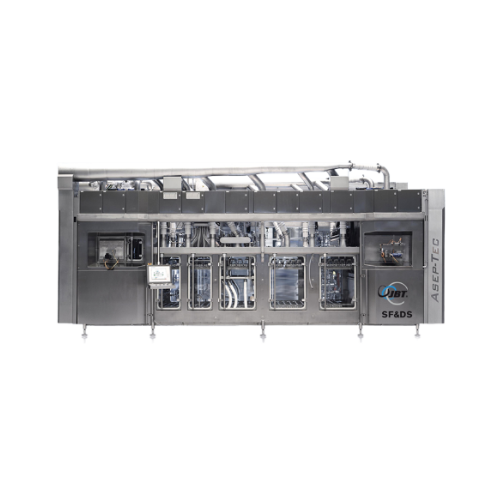
Aseptic filler for packaged dairy and beverages
Ensure product sterility and extend shelf life efficiently with high-speed...
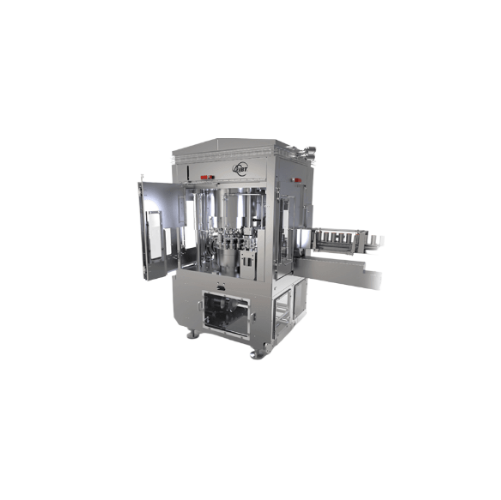
Can seamer for high-speed liquid applications
Ensure consistent seal integrity and maximize throughput with this advanced ...
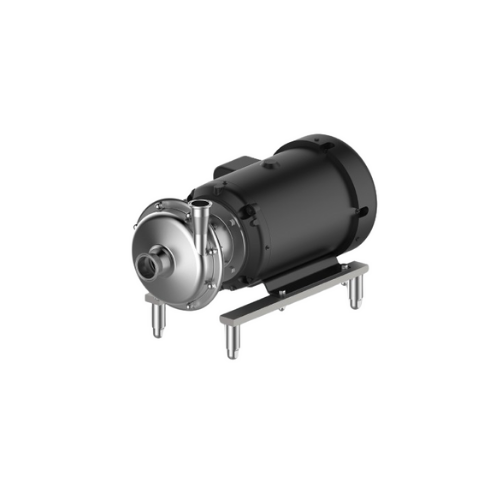
Hygienic centrifugal pump for beverage applications
Ensure gentle handling and efficient transfer of sensitive liquids wi...
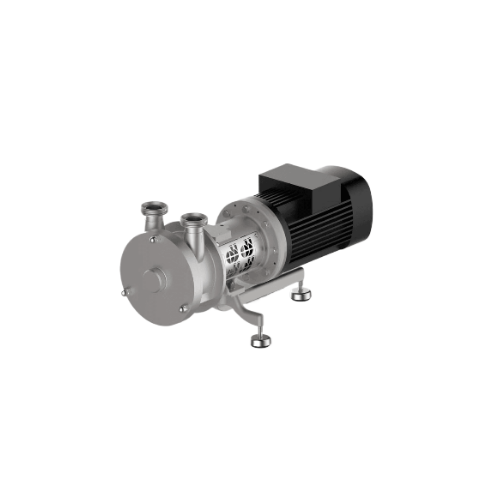
Self-priming side channel pump for high gas content media
When handling media with high gas content, achieving efficient...
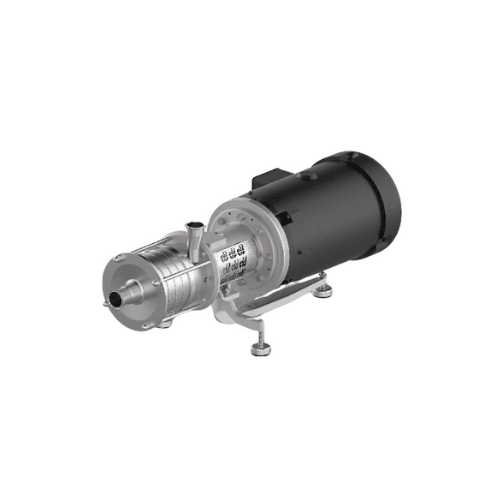
Hygienic pump for beverage and pharmaceutical industries
Engineered to meet stringent hygiene demands, this versatile pum...
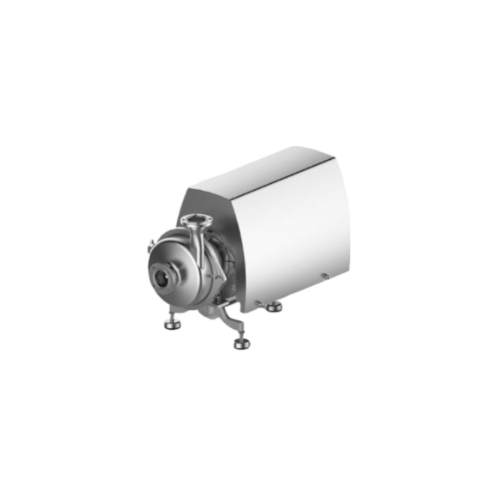
Centrifugal pumps for hygienic applications
Ensure precise liquid handling for high-stakes applications with this hygienic...
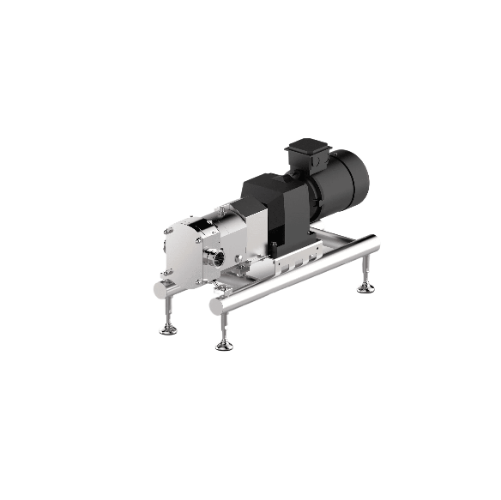
Rotary lobe pump for viscous media
Ensure precise handling and gentle transfer of viscous liquids with advanced rotary lobe...
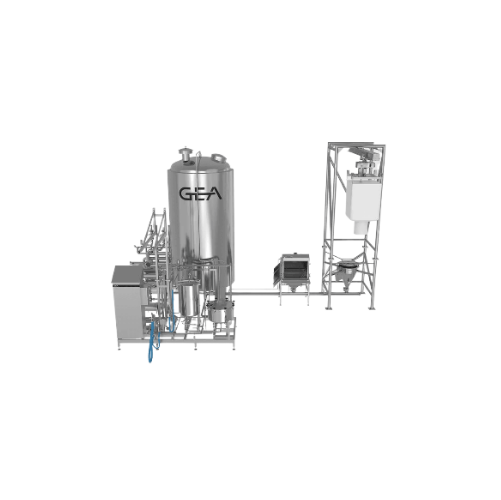
Modular batch mixing system for beverages
Streamline your beverage production with a flexible solution that manages comple...

Screw compressor package for efficient industrial cooling
Optimize your cooling processes with a flexible, space-saving ...

Continuous in-line blender for beverage industry
Enhance your blending precision and process flexibility with a system des...
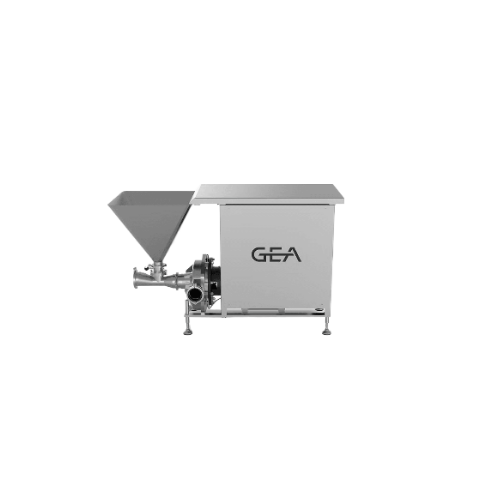
High shear powder dissolver for homogeneous products
Achieve consistent powder-liquid blends effortlessly with a compact ...
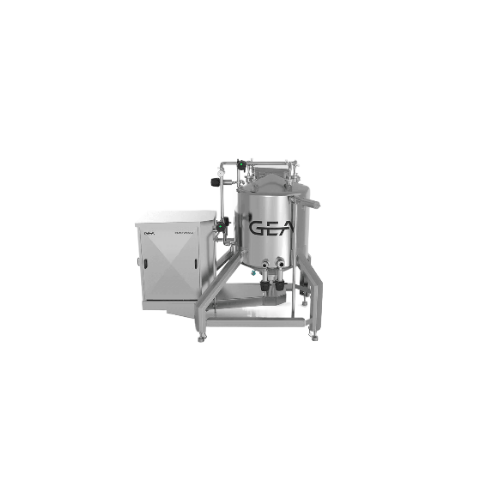
High shear mixer for low viscosity products
Achieve precise mixing and dispersion for diverse liquid applications with a h...
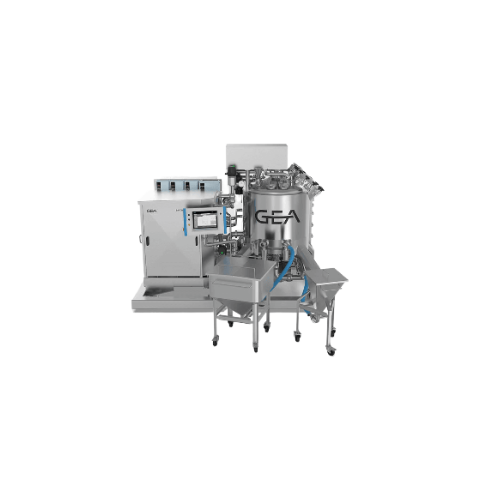
High shear test mixers for developing new products
Streamline product development with high shear test mixers, allowing y...
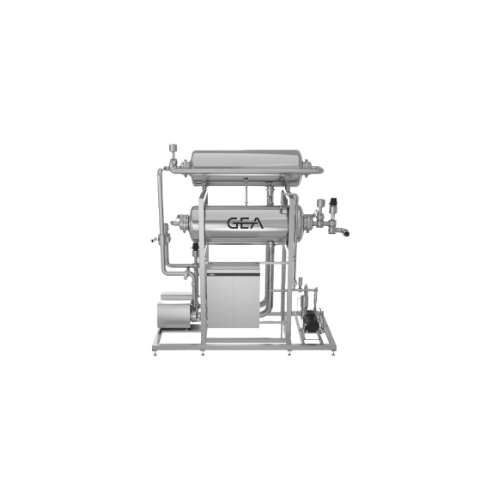
Water deaeration system for beverages
Achieve ultra-low oxygen content in beverage water to enhance taste and prolong shelf...
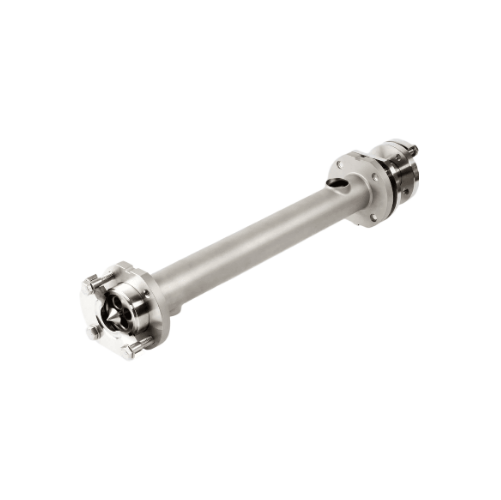
Tubular heat exchanger for thermal treatment of viscous products
Optimize efficiency in heating, cooling, and pasteuriza...
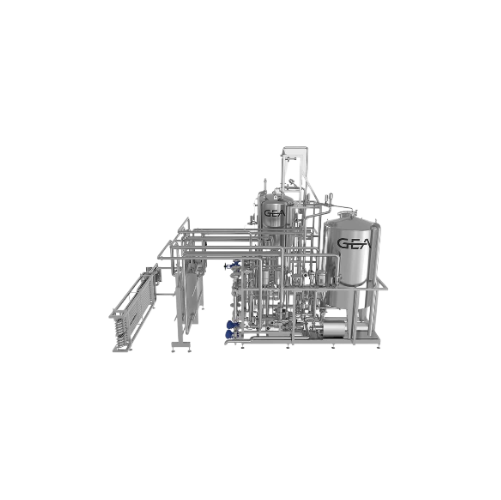
Pasteurizer for non-alcoholic beverages
Ensure microbiological safety and extend shelf life of your non-alcoholic beverages...
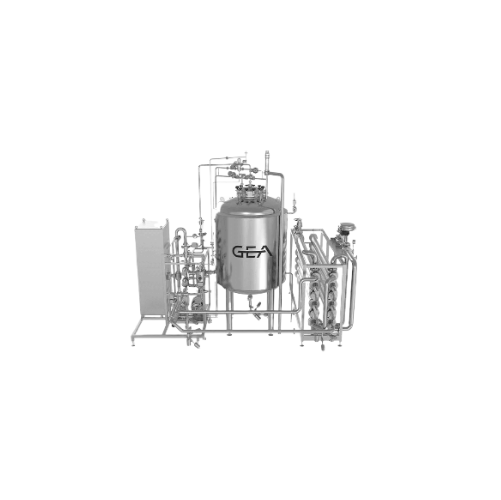
Carbonation system for non-alcoholic beverages
Achieve precise carbonation for diverse beverages with this system, ensurin...
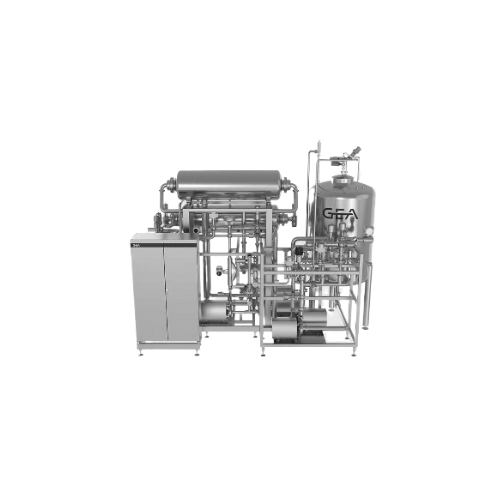
Mixer and carbonator for soft drinks
Achieve precision in continuous mixing and carbonation, ensuring perfect beverage cons...
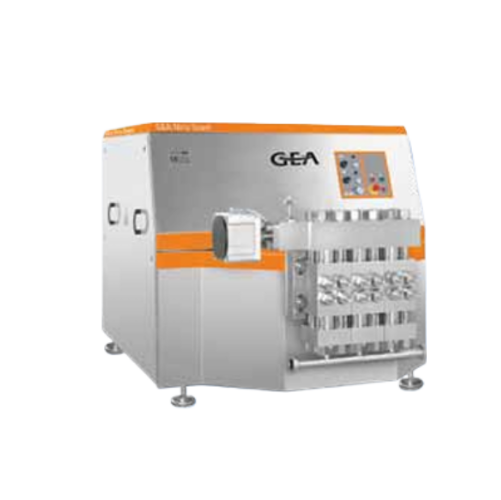
Very high pressure homogenizer compression block
Experience reliable performance at extreme pressures with a compression b...
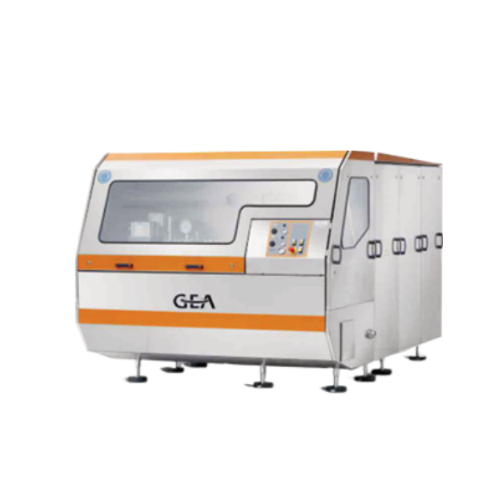
Industrial homogenizer for dairy, beverage, and pharmaceutical applications
Enhance your production efficiency with a ...
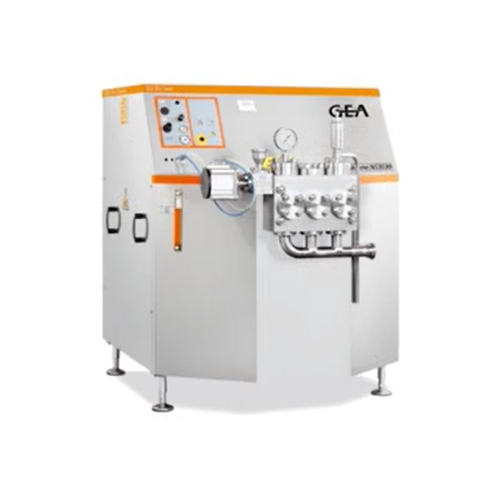
High pressure industrial homogenizer
Enhance liquid formulations with precision and efficiency—our high-pressure homogenize...

Hot fill gravity filler for beverages
Achieve precise hot filling with versatile gravity filling technology that maintains ...
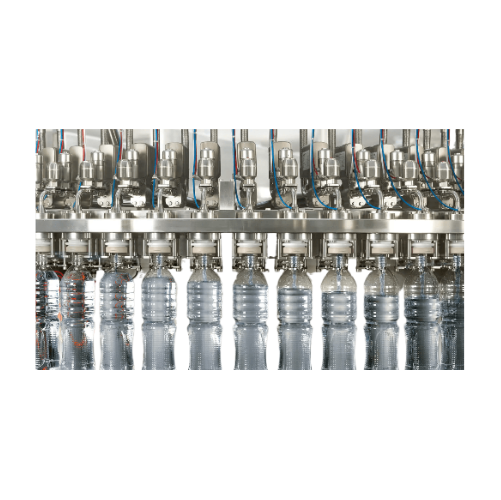
Rotary volumetric filler for still drinks
Optimize your bottling line with a versatile rotary volumetric filler, designed ...
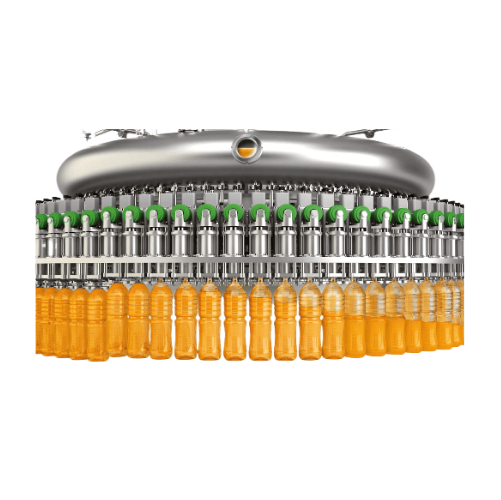
Bottle filler for still and carbonated drinks
Maximize efficiency in your bottling process by seamlessly filling both stil...
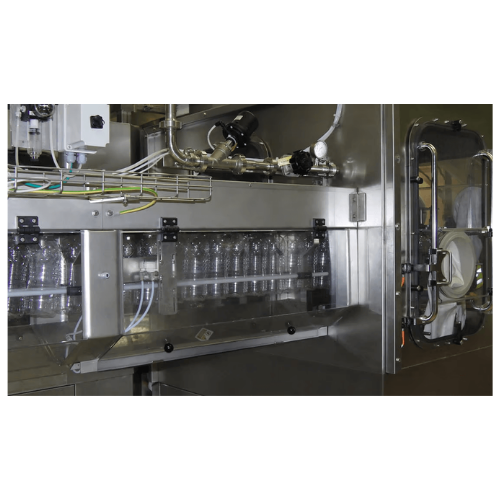
Air conveyor for empty Pet bottles
Optimize your bottling line with an advanced air conveyor that reduces energy consumptio...
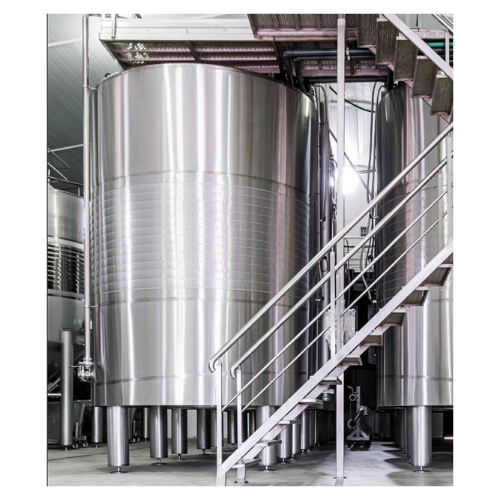
Centrifuge for beverage clarification
Elevate your beverage production with enhanced clarification, ensuring your drinks me...
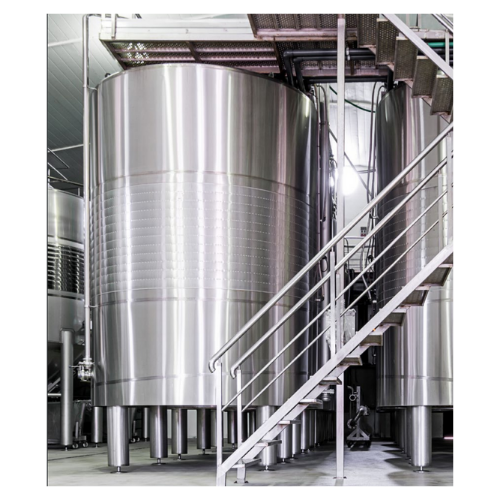
Reverse osmosis dealcoholization technology for beer
Achieve consistent flavor profiles in your non-alcoholic beer produc...
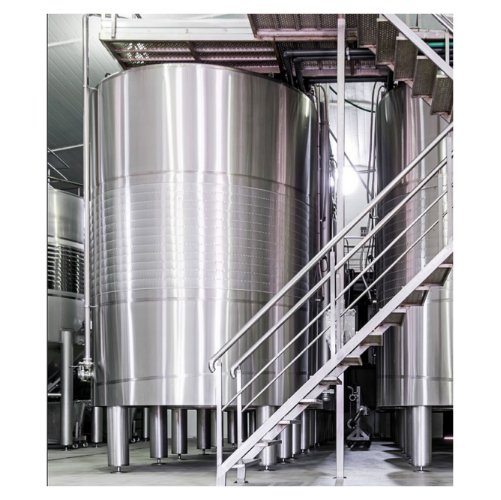
Reverse osmosis beer dealcoholization technology
Achieve precise alcohol removal from beer while preserving flavor integri...
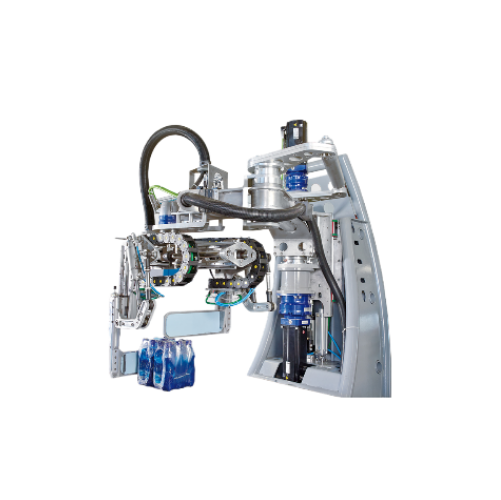
Layer preparation system for high-speed palletizing
Optimize your palletizing process with a system that ensures precise ...
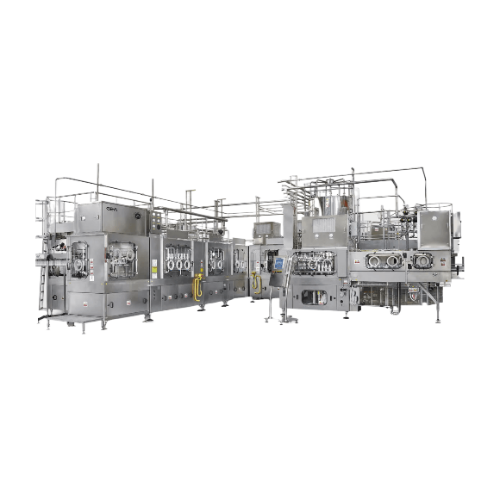
Advanced aseptic filling system for beverage bottles
Seeking a sterilization and filling system that maximizes sterilizat...
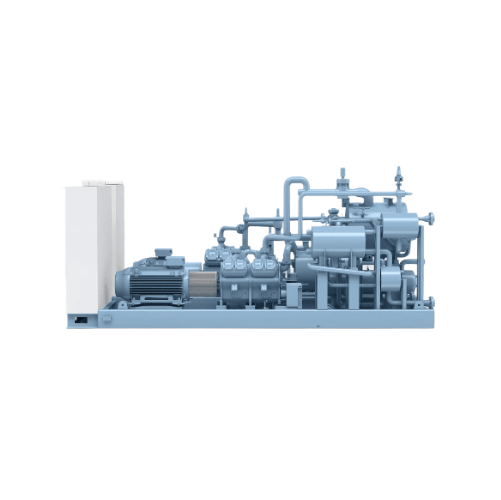
Combined heating and cooling solution
Optimize your production with a dual-purpose system designed to efficiently manage bo...
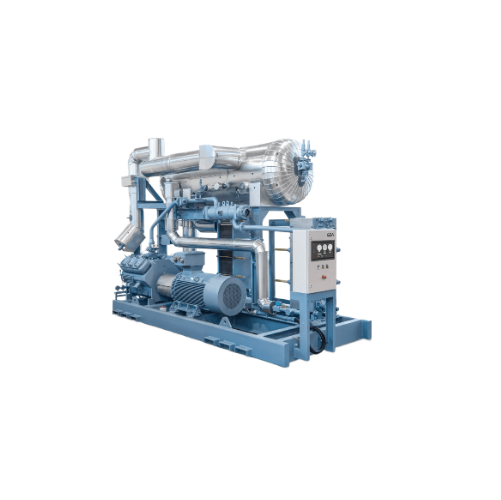
Industrial chiller with high part-load efficiency
Optimize your cooling processes with a versatile chiller designed for p...
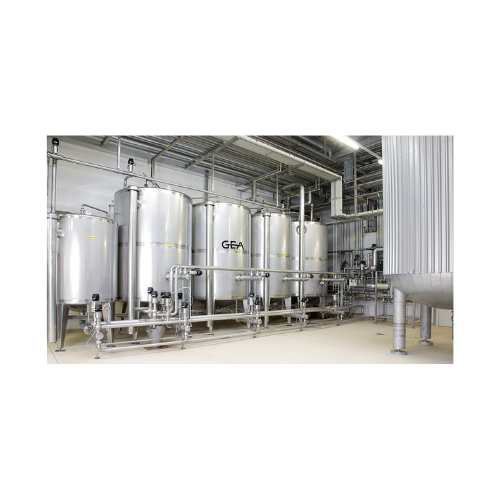
Cip system for breweries
Optimize your brewing efficiency by integrating a comprehensive cleaning and sterilization system th...
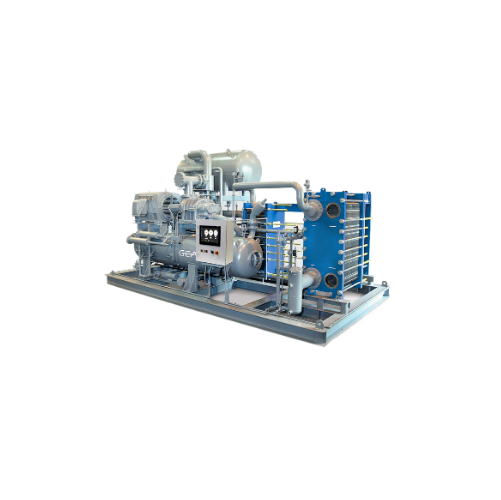
High-efficiency ammonia chiller package for industrial applications
Optimize your cooling and refrigeration processes w...
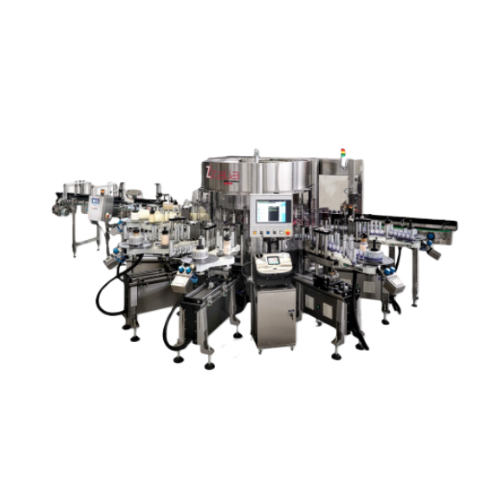
Glass bottle washing and delabelling system
Effortlessly transform used bottles into pristine, reusable containers with th...

Modular and combined labeling machines for bottling
Achieve high-speed labeling with unmatched flexibility, combining mul...
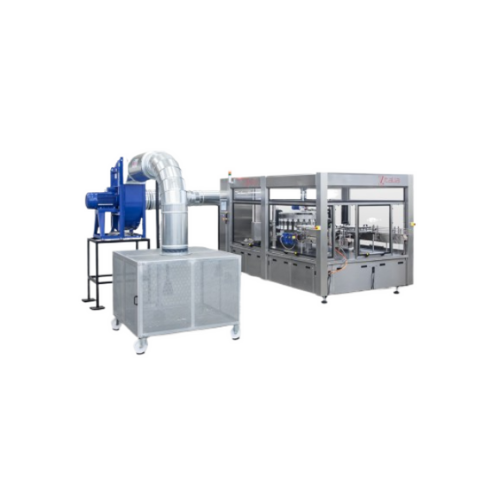
Pre-cut hot-melt label applicator for bottles
Optimize efficiency and precision in your labeling process with this advance...
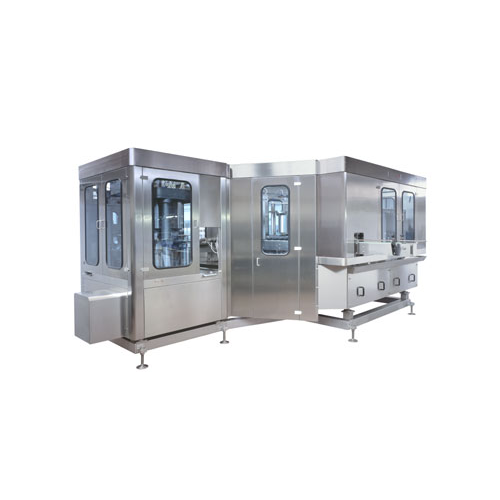
Filling and seaming groups for aluminium and tin plate cans
Smoothly synchronize filling and seaming of liquid and dense...
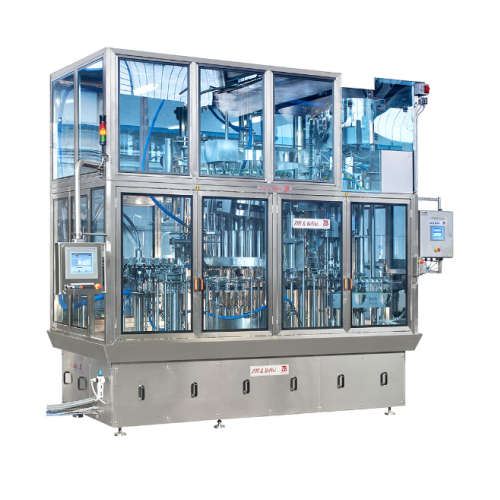
Integrated filling and capping system for food and soft drinks
Streamline your bottling operations with an integrated sy...
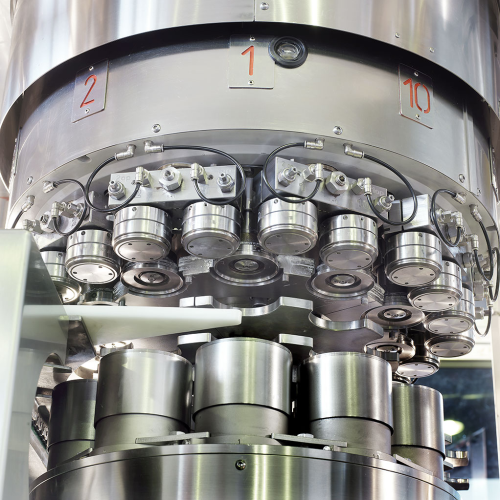
Automatic can seamers for food and beverage industry
Ensure airtight sealing of canned goods with precision seamers desig...
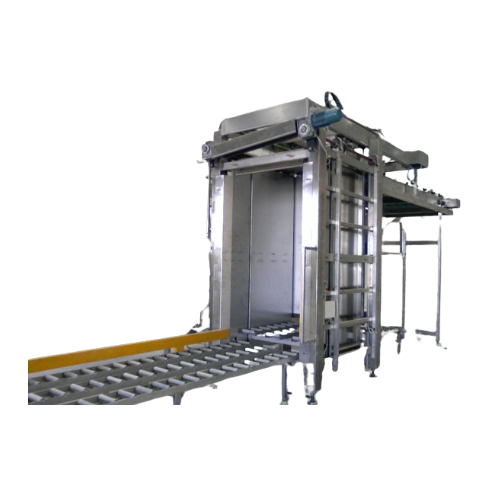
Complete filling and closing line for food containers
Optimize your production line with a versatile solution that ensure...
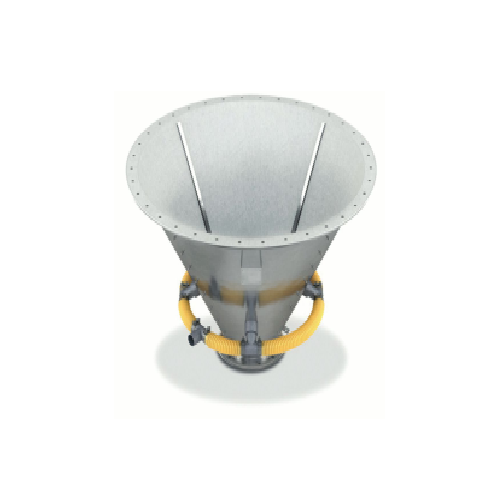
Automated material flow system for starch processing
Streamline the handling of powdered starches with precise dosing, mi...
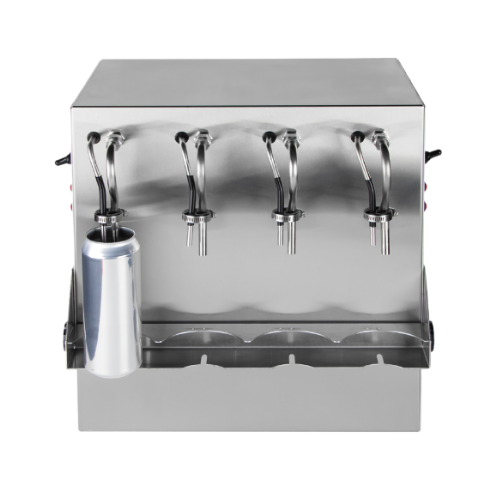
Carbonated beverage can filler - 4 spout open fill
Optimize canning carbonated beverages while minimizing CO2 loss with t...
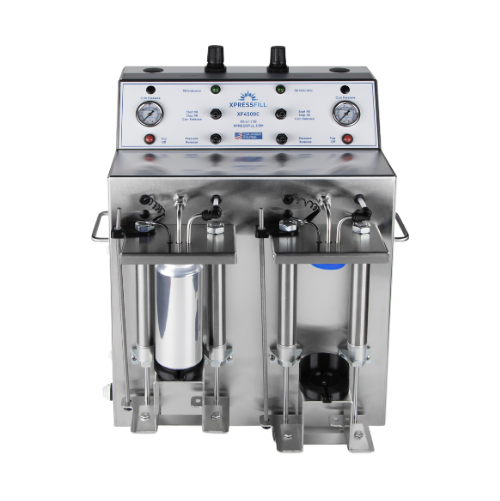
Counter pressure can filler for carbonated beverages
Achieve precise carbonation levels and minimal oxygen exposure in ca...
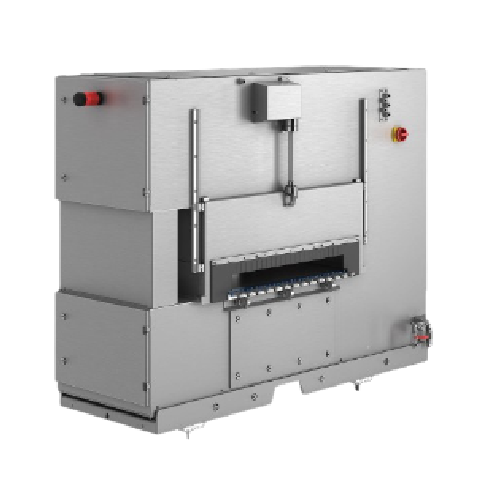
X-ray scanner for sealed container inspection
Ensure the integrity and quality of sealed containers while seamlessly integ...
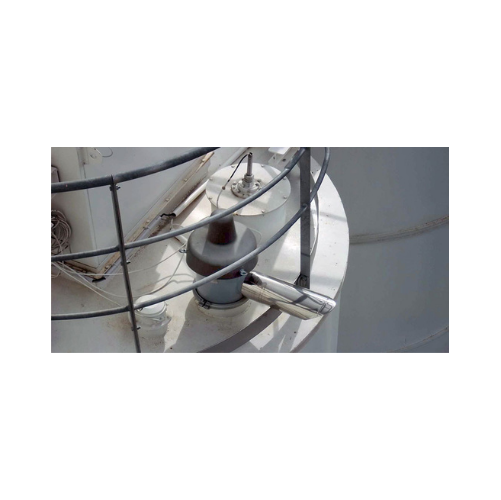
Membrane pressure relief valve for silos and bins
Ensure silo safety with our valve that instantly balances internal pres...
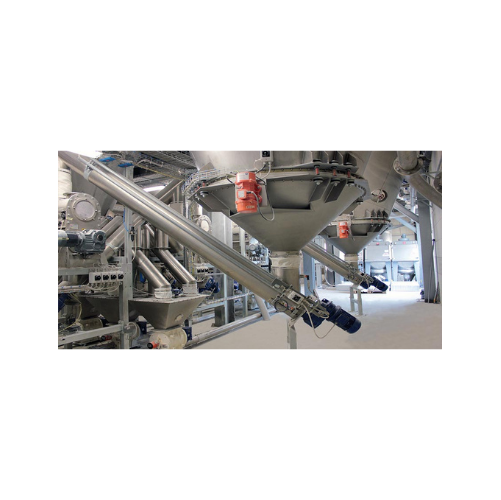
Food-grade stainless steel tubular screw conveyors
Ensure contamination-free material handling with our tubular screw con...
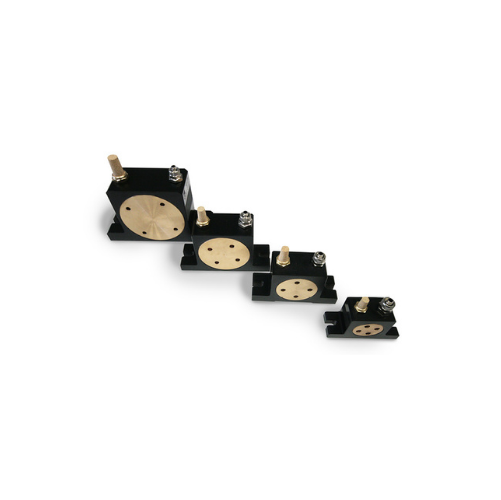
Rotary roller vibrators for concrete compacting and hopper emptying
Achieve higher compaction and efficient emptying wi...
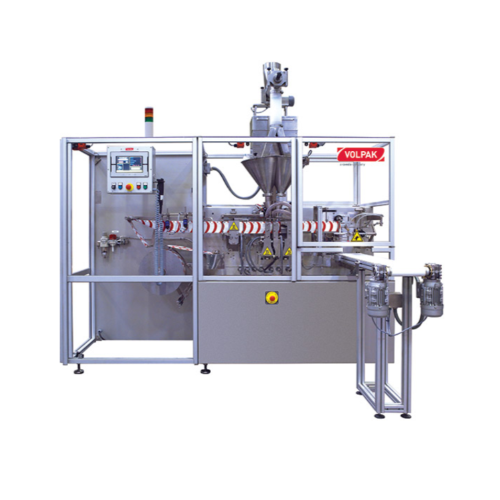
Horizontal flat pouching solution for foods and chemicals
Achieve precision in pouching liquids and powders with high-sp...
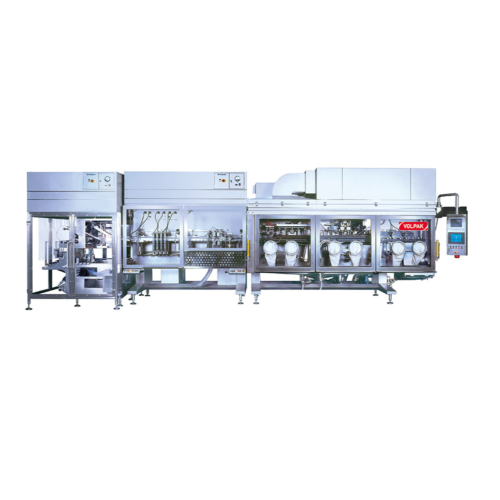
Horizontal stand-up pouching for beverages, dairy, and pet care
Optimize your liquid product packaging with rapid, high-...
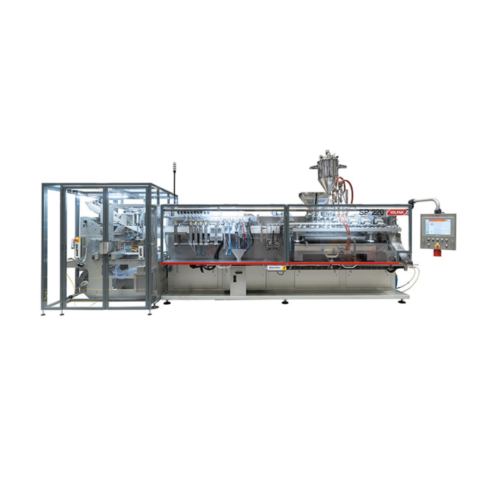
Stand-up pouch packaging for various industries
Elevate your packaging capabilities with a high-speed horizontal pouching ...
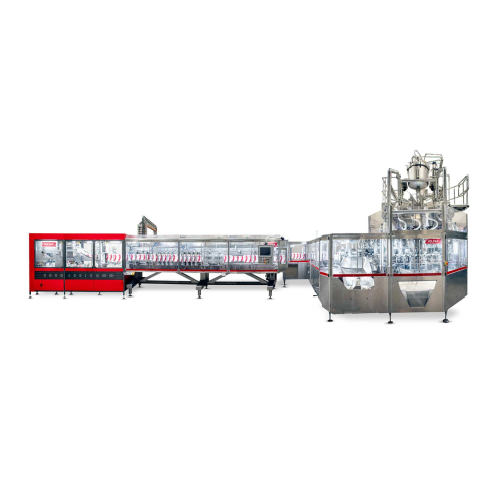
Continuous stand-up pouching solution for up to 1000ml
Maximize efficiency in high-speed production lines with precise st...
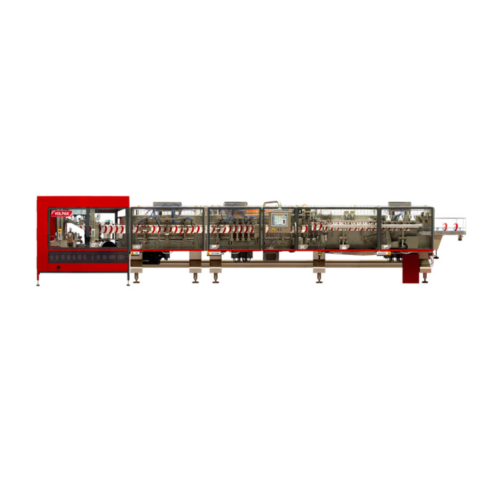
Horizontal stand-up pouching system for liquids and solids
For producers aiming to optimize efficiency and precision, th...
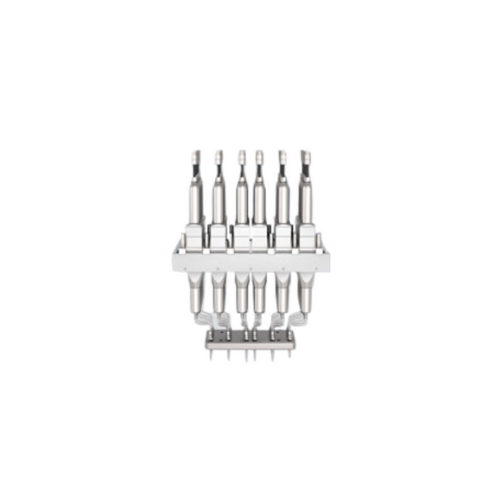
Fully automatic filling lines for liquids
Achieve precise dosing and filling of liquids with minimal cycle times using com...
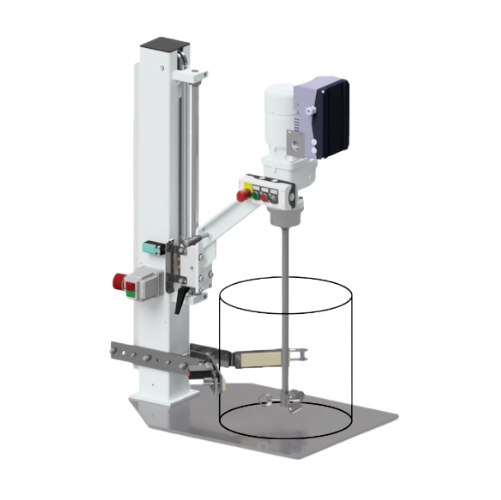
Laboratory stirrer for research and small-scale production
Optimize your research and scale up your production with a ve...
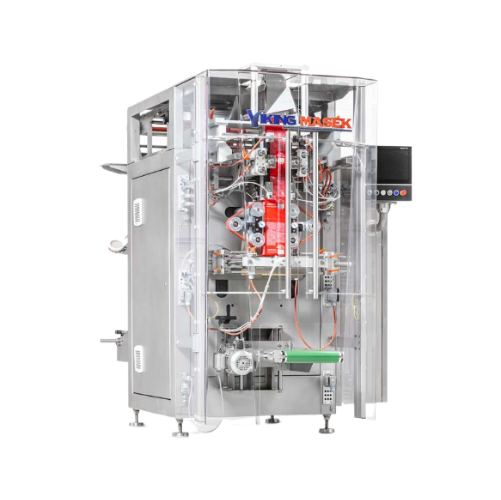
High-speed vertical form fill seal for various packaging needs
Streamline your packaging process with an advanced vertic...
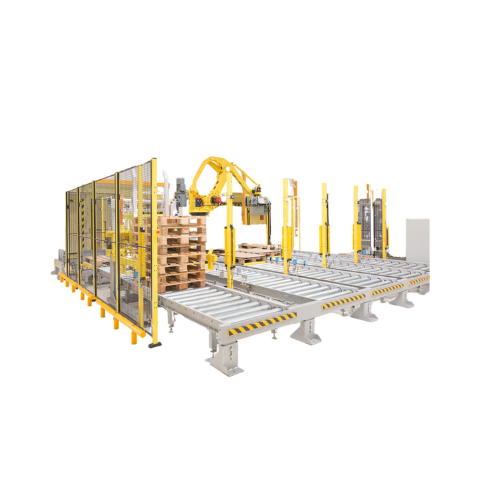
Robotic palletizing and depalletizing systems
Enhance your production efficiency by automating the repetitive and labor-in...
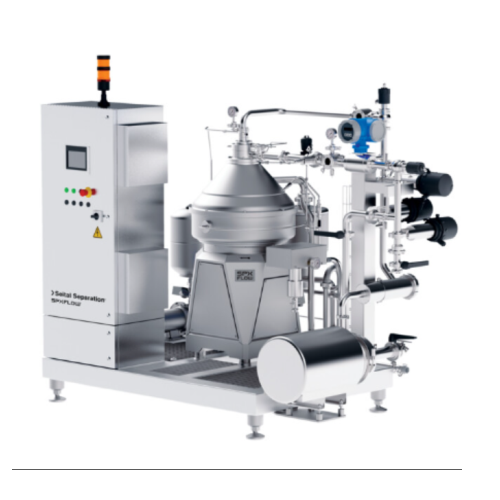
Centrifugal separators for liquid/liquid/solid separation
Achieve efficient separation and clarification for diverse app...

Turnkey stainless steel tanks
Optimize your liquid processing with versatile stainless steel tanks designed for efficient st...
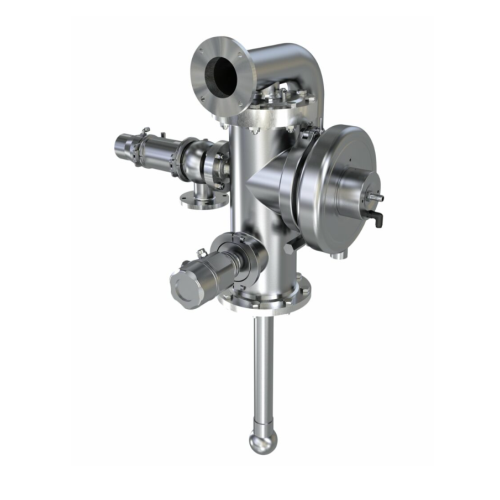
Vessel dome fittings for tank protection
Ensure seamless production by preventing tank damage due to overpressure or vacuum...
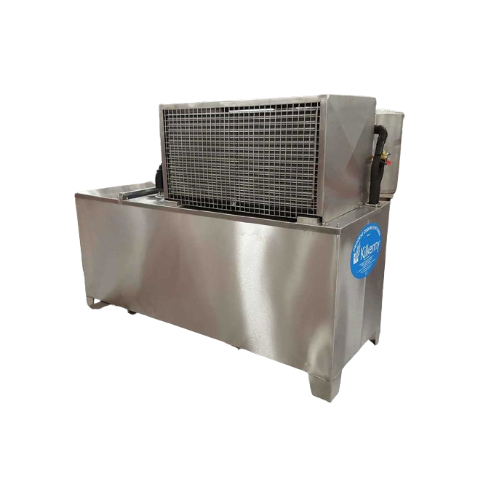
Industrial chiller systems for processing cooling
Optimize your production line with advanced chiller systems designed to...
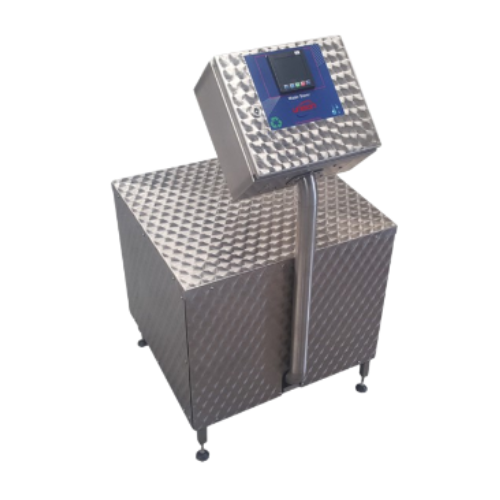
Industrial water recycling system
Reduce excess water consumption in your process line by recycling and reusing up to 96% o...
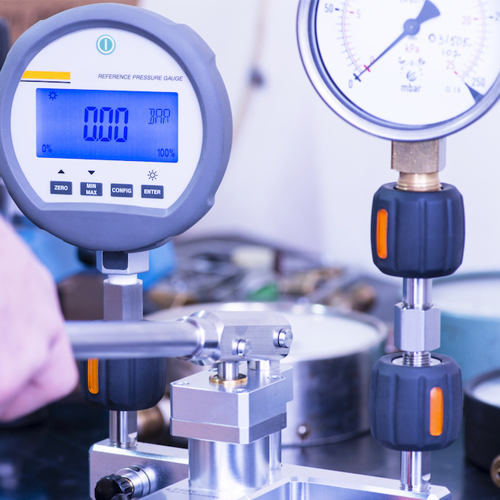
Instrumentation calibration services for accurate measurements
Ensure precise control over your production variables by ...
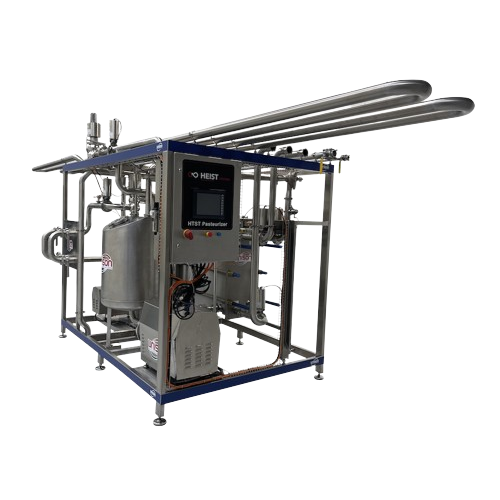
Holding time verification for pasteurizers
Ensure your pasteurized products meet safety standards by verifying they’...
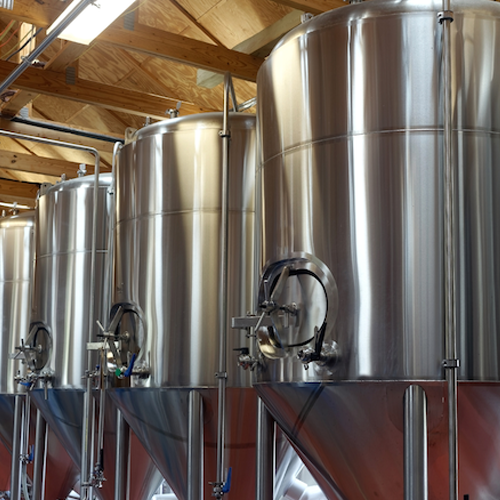
Storage tank integrity testing
Prevent costly contamination and streamline your operations with advanced tank integrity test...
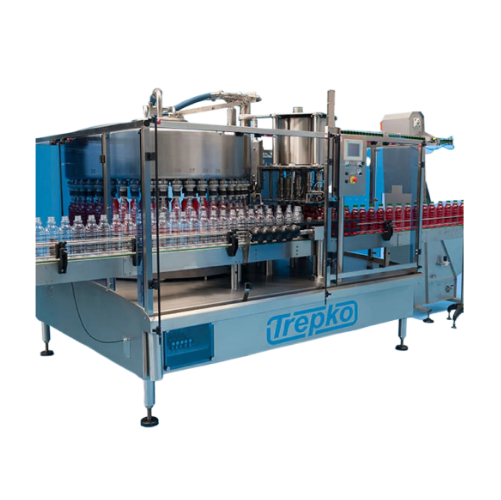
Bottle filling system for diverse specifications
Optimize your bottle-filling operations with a modular system that seamle...
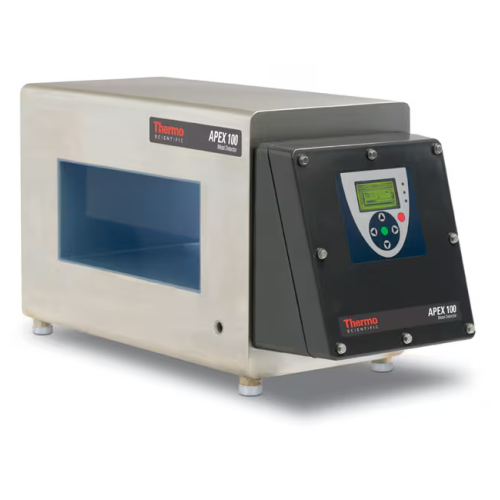
Entry-level metal detector for food production
Ensure your food and beverage products remain contaminant-free with a cost-...
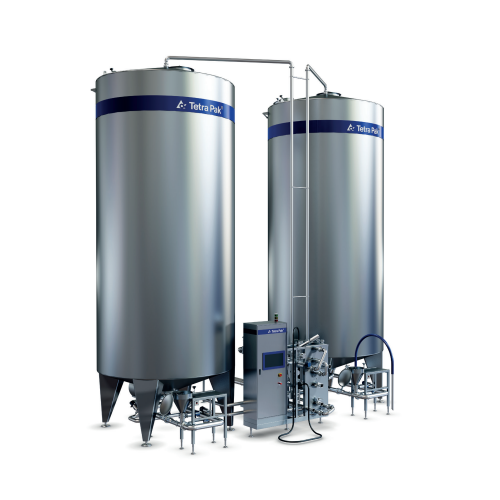
Beverage preparation system for large-scale production
Ideal for producers looking to scale up, this versatile system eff...
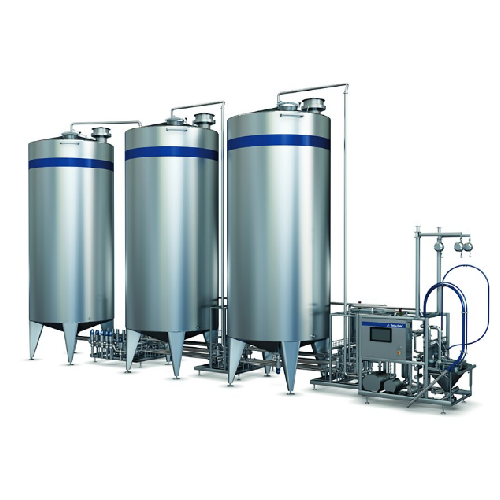
Syrup and beverage preparation system
Enhance your beverage production with a versatile solution that optimizes mixing, hyd...
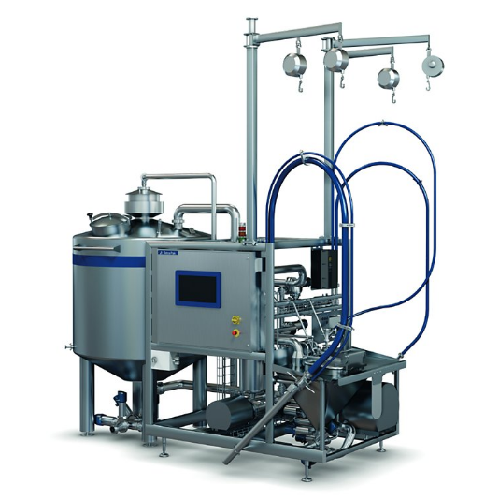
Batch mixer for soft drinks
Efficiently mix and dissolve complex beverage formulations with high-speed batch processing, ens...
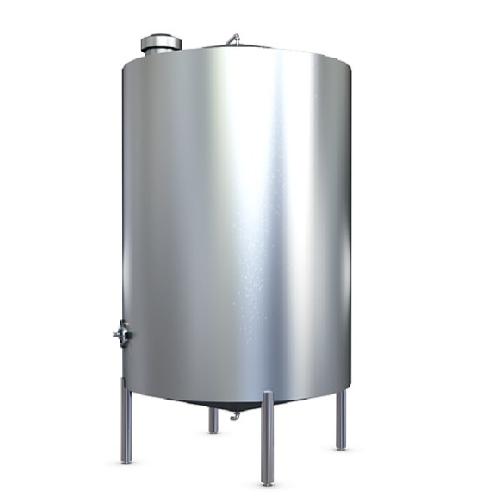
Liquid ingredient reception tank
Optimize your liquid processing with versatile tanks designed for efficient storage and han...
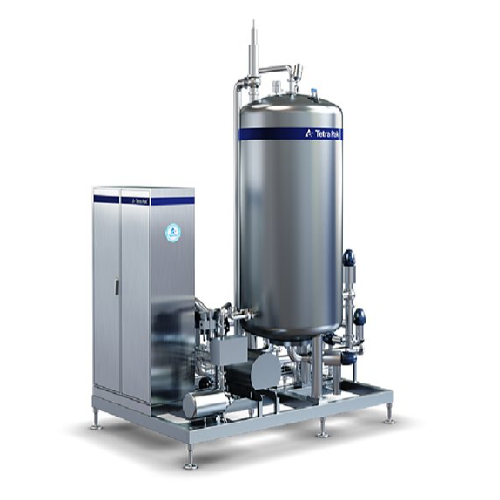
Continuous carbonator for beverage production
Optimize your beverage production with seamless continuous carbonation, ensu...
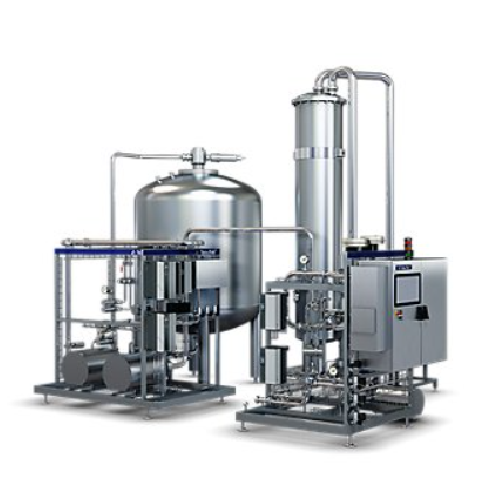
In-line blender for carbonated soft drinks
Enhance your beverage production capabilities with a solution that precisely bl...
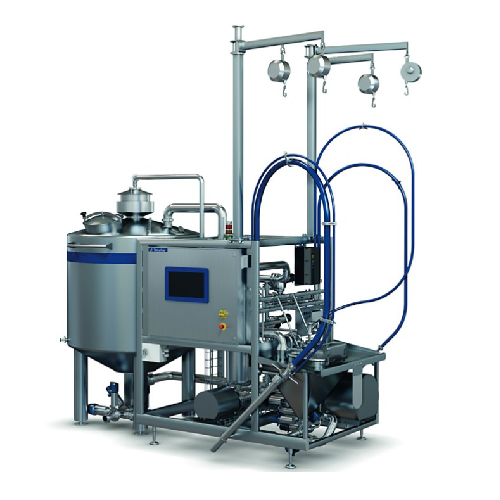
Batch mixer for soft drinks ingredients
Effectively manage diverse ingredient formats with a high-performance mixing system...
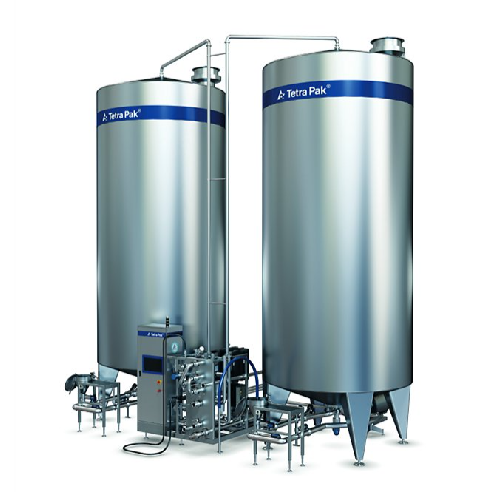
Final syrup and beverage preparation system
Optimize your beverage production with a modular system designed for flexibili...
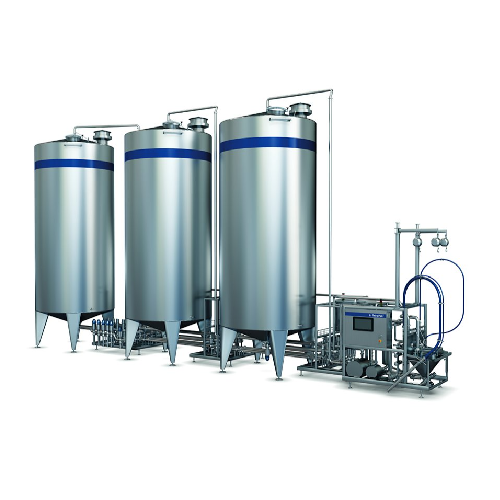
Preparation system for syrup and beverages
Streamline syrup and beverage preparation with a versatile system designed to r...
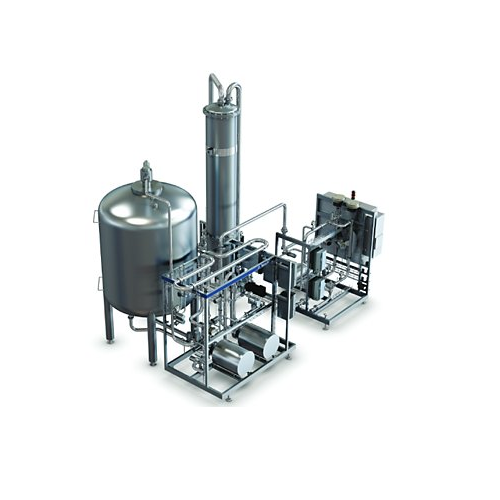
In-line blender for carbonated drinks
Optimize your beverage production with precise in-line blending and carbonation, redu...
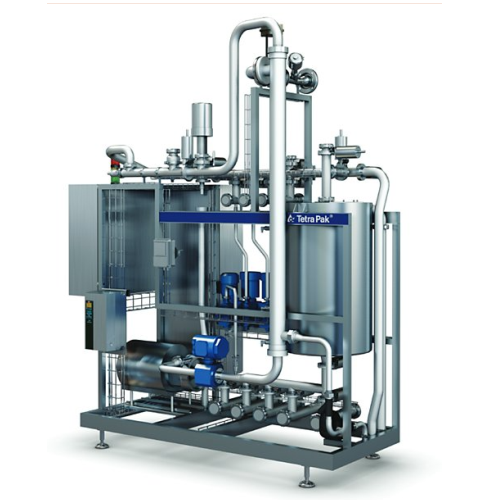
Cleaning-in-place system for food and beverage processing equipment
Effortlessly manage the cleaning of diverse process...

Dual-line filler for tetra top packages
Maximize your production flexibility with a high-speed, dual-line filling solution ...
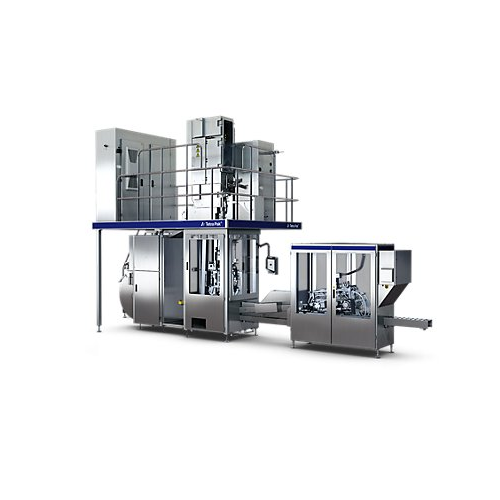
Filling system for tetra wedge aseptic packages
Optimize your production line with a reliable filling system designed to e...
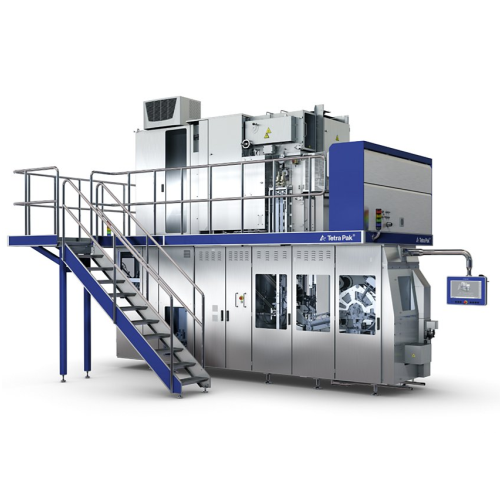
Compact aseptic filling solution for versatile production
Maximize production line efficiency with a compact filling sys...
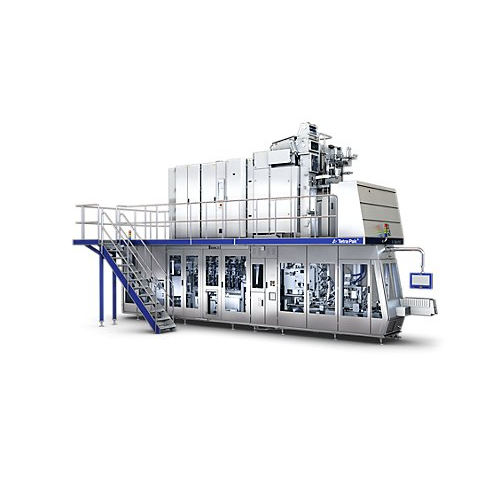
Aseptic filling solution for liquid food packaging
Optimize liquid food production with advanced aseptic filling, ensurin...
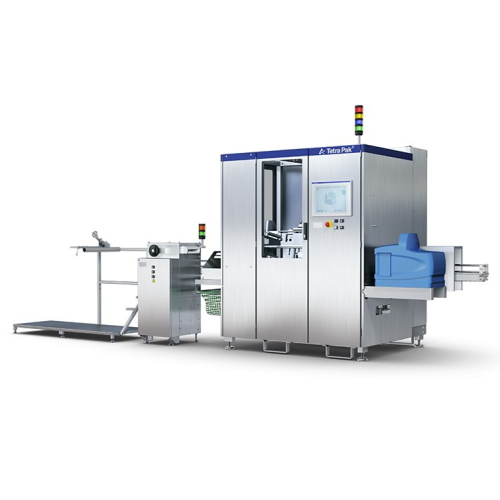
Straw applicator for tetra pak cartons
Ensure precise straw attachment and minimize production interruptions with a high-sp...
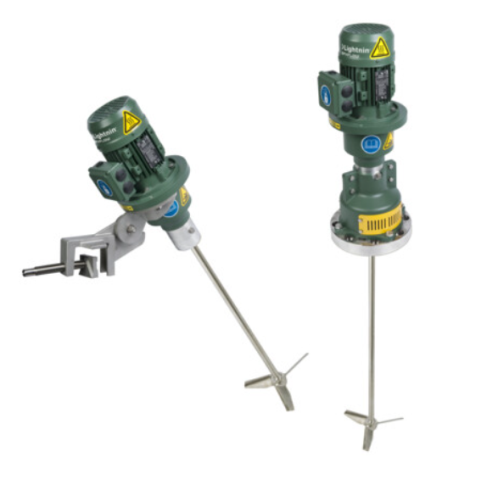
Portable and fixed mount mixing system
Optimize your mixing operations with a versatile system that adapts seamlessly betwe...
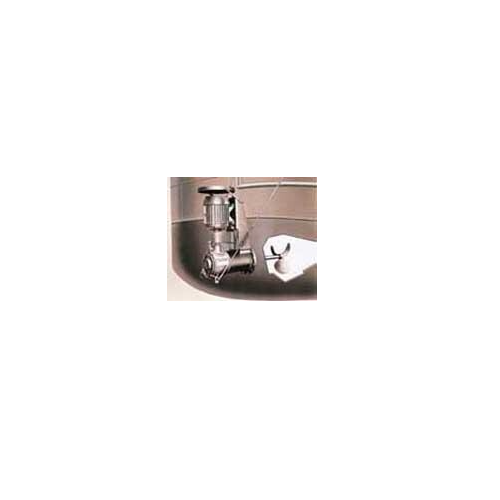
Side entry mixer for industrial tank applications
Ensure optimal mixing and blending of liquids and slurries with high ef...
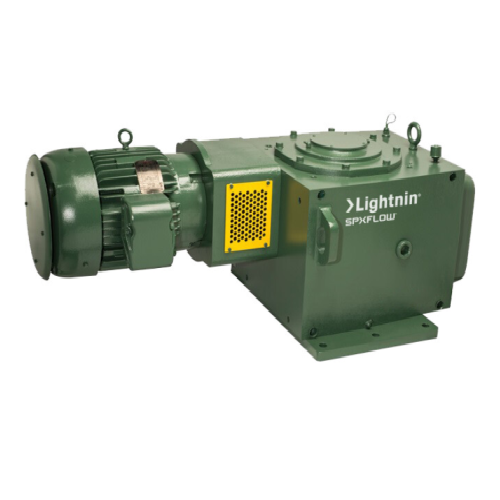
Medium torque top entering mixer for industrial applications
Optimize your mixing and blending operations with precise t...
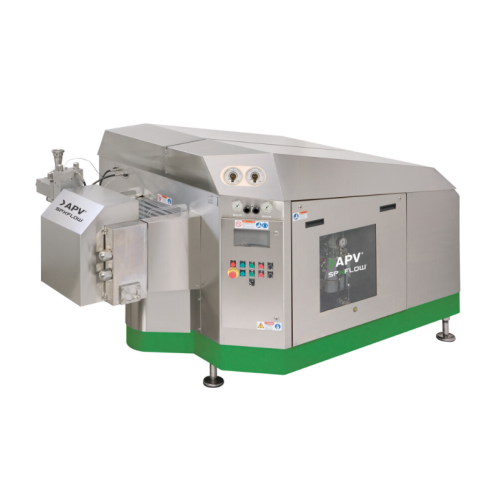
High pressure homogenization system for dairy and creams
Optimize your high-speed homogenization processes with precise c...
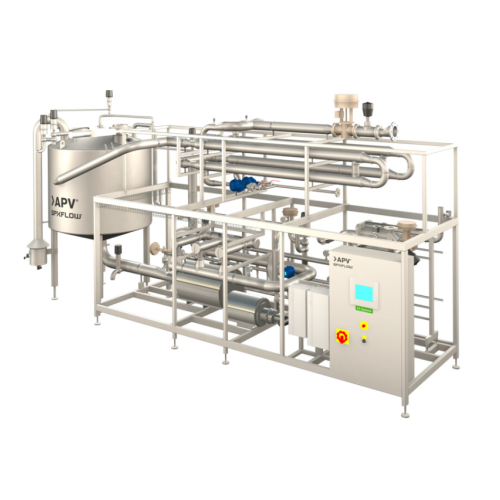
Continuous sugar dissolver for beverage processing
Achieve precise sugar syrup production with minimal raw material waste...
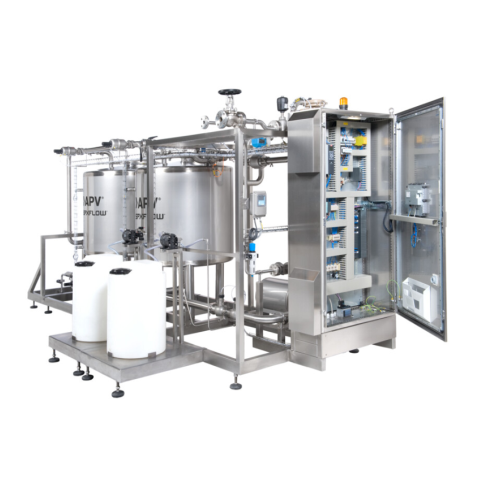
Clean in place (cip) system for industrial cleaning
Ensure optimal hygiene and production efficiency with a system that s...
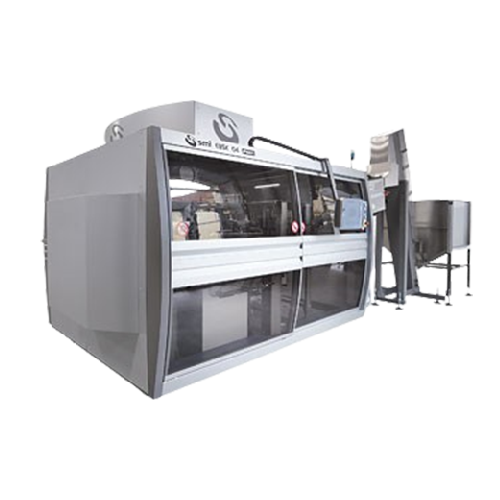
Rotary stretch-blow moulders for Pet bottles
Achieve efficient and high-speed production of diverse plastic containers wit...
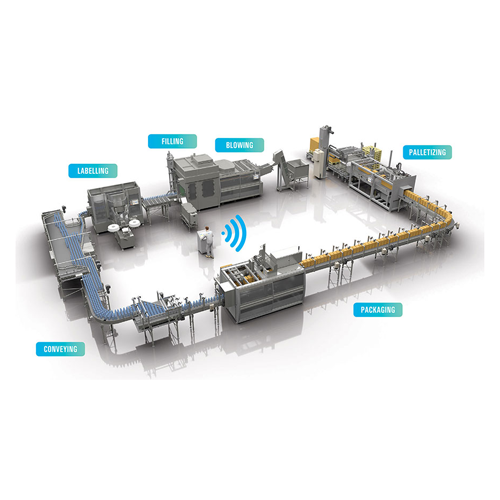
Complete bottling lines for beverages
Achieve seamless integration and high-speed efficiency in your liquid product packagi...
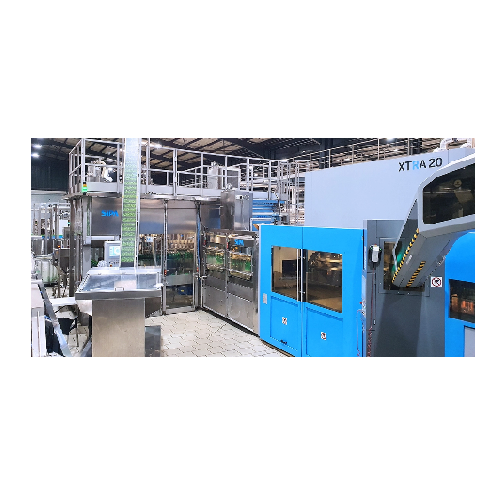
Integrated rotary blowing and filling system for Pet bottles
Optimize your beverage production with an integrated rotary...

Integrated preform production and bottling system for Pet bottles
Achieve seamless production of PET bottles, from pref...
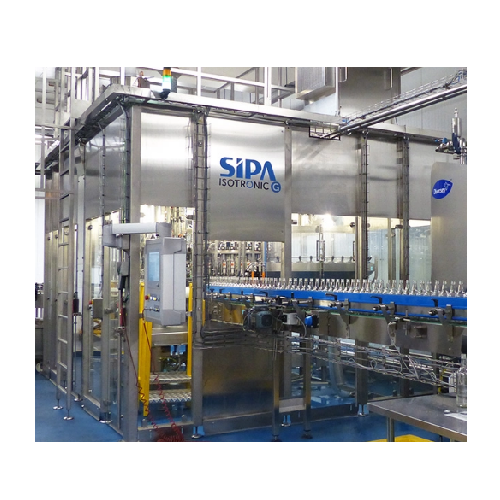
Isobaric filler for glass and Pet bottles
Achieve precise liquid filling with enhanced operational flexibility and hygiene...
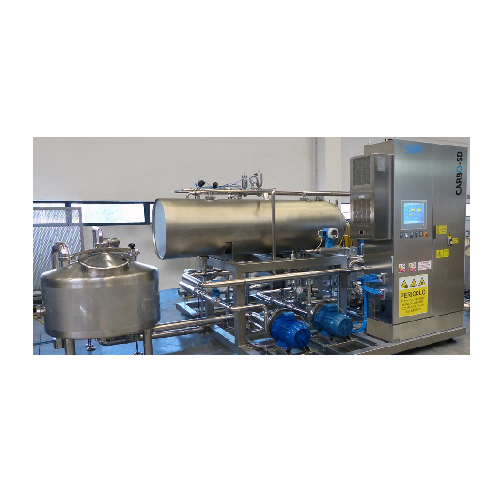
Compact carbonation unit for carbonated beverages
Enhance beverage quality with precise carbonation, ensuring consistent ...
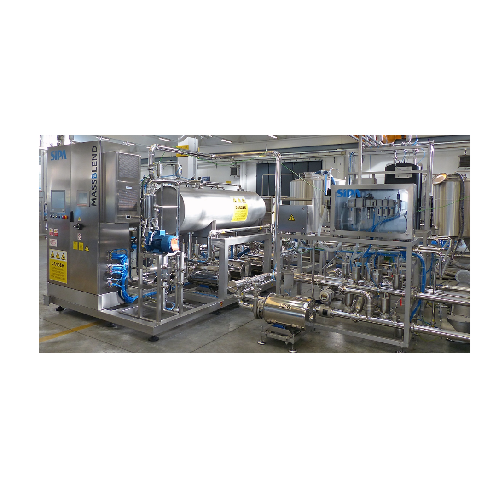
Beverage carbonation and mixing unit
Streamline your beverage production with a unit that ensures precise carbonation and m...
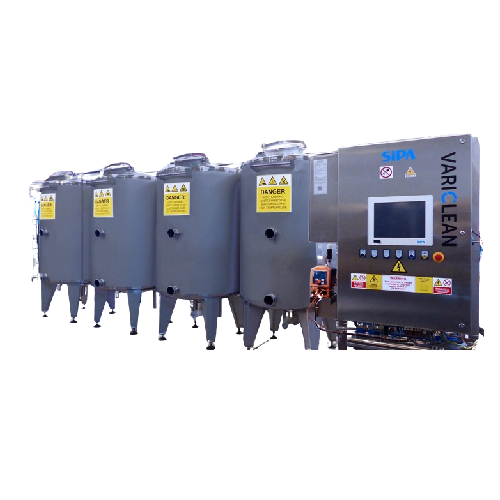
Cip sanitizing unit for food and beverage production
Ensure meticulous hygiene with a compact unit designed for seamless ...
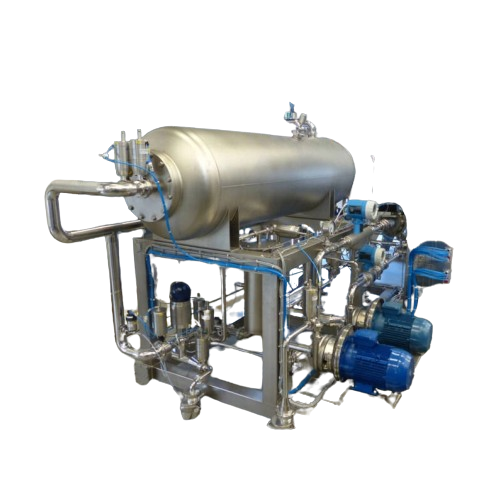
Degassing and mixing unit for beverage production
Ensure precise beverage formulation and maintain high quality standards...
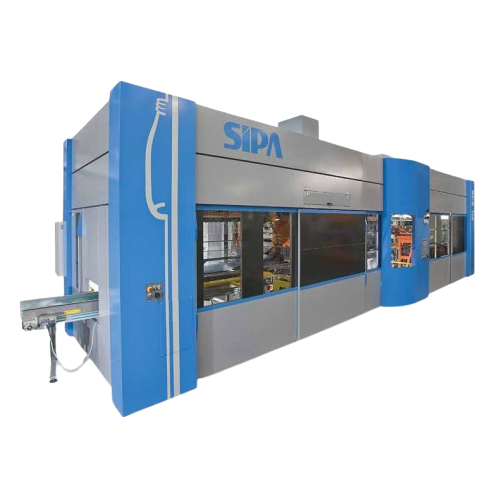
Single-stage plastic container production system
Eliminate multiple steps and minimize production costs with an integrated...
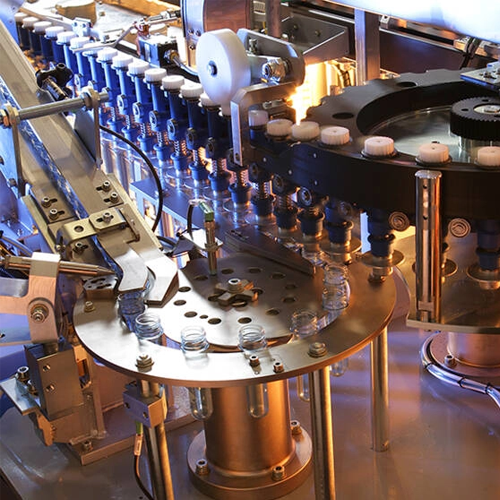
Linear blowing systems for Pet bottle production
Ideal for producers seeking versatile container solutions, this system en...

Rotary blower for Pet bottle production
Optimize PET bottle production with cutting-edge efficiency, reducing energy consum...

Volumetric filler for Pet bottle beverages
Experience seamless integration into your bottling line with this advanced volu...
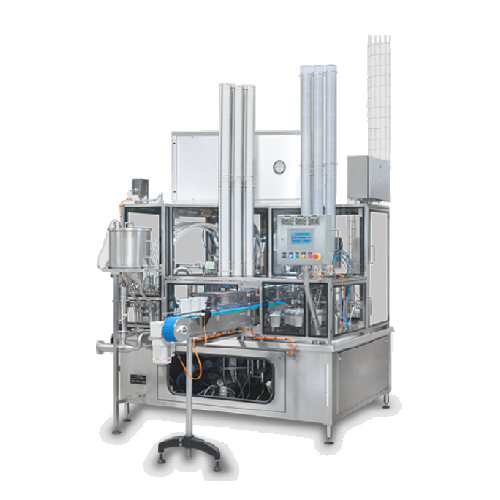
Filler for yoghurt and white cheeses
For manufacturers seeking efficient, versatile filling for products like yoghurt and s...
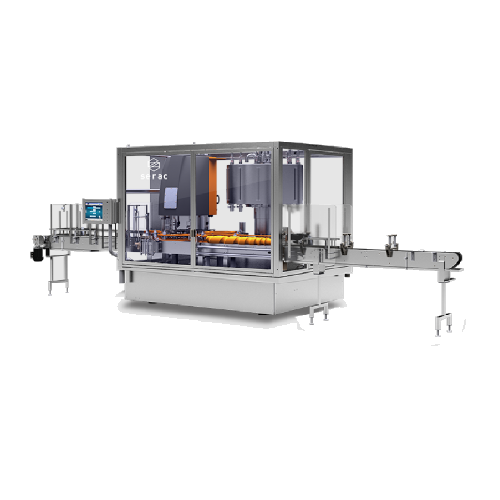
Versatile rotary filler-capper for liquid products
Optimize your liquid product production with a versatile solution that...
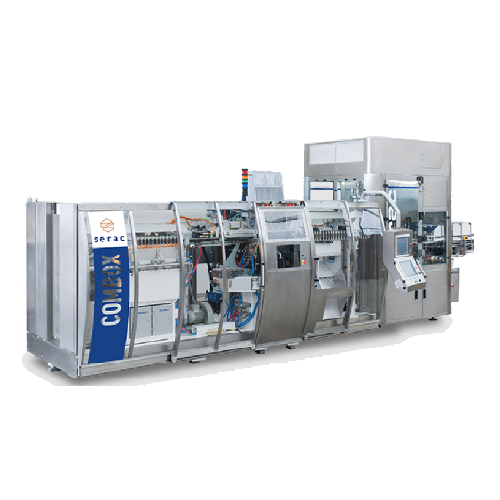
Blow-fill-cap solution for low/medium batch production
Streamline your production line with a compact blow-fill-cap syste...
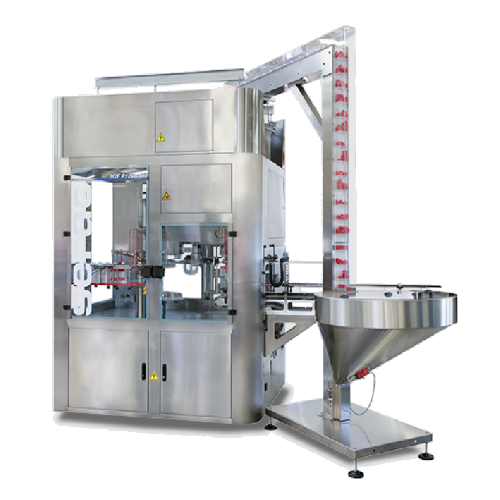
High hygienic filler for chilled beverages
Enhance cold beverage production with a modular, hygienic filler offering chemi...
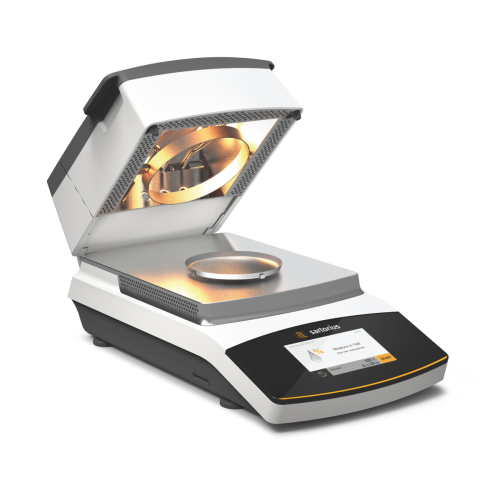
Fast and accurate moisture meter for various samples
Quickly determine moisture content in solids, liquids, and pastes wi...

Aseptic tank for liquid food storage
Store and maintain the sterility of low and high acid liquid foods while ensuring prod...
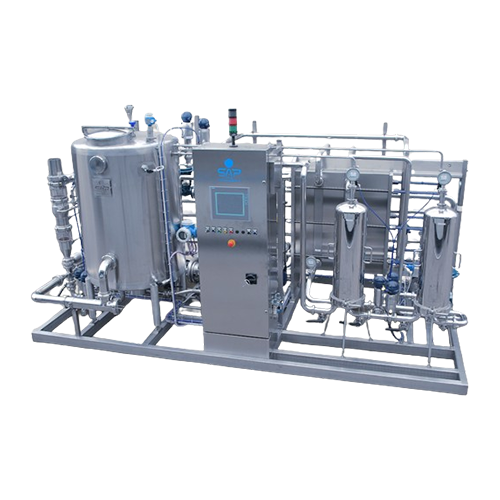
Continuous sugar dissolver for high brix solutions
Optimize your beverage production with a system that dissolves sugar u...
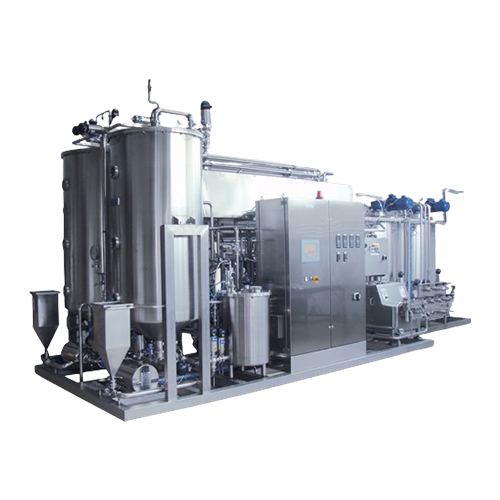
Pasteurization solution for food liquids
Extend the shelf-life of your liquid products while maintaining their quality with...
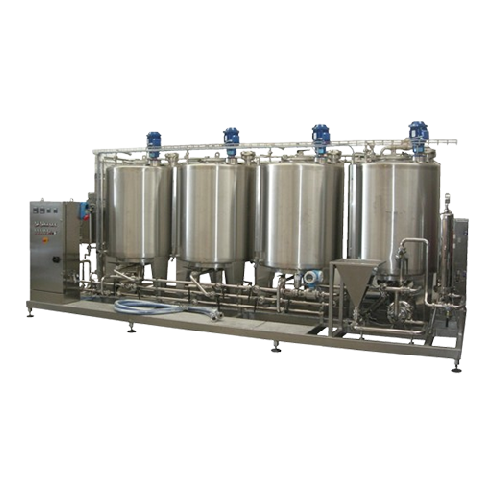
Custom syrup preparation systems
Optimize your beverage production with precision-engineered syrup preparation systems desig...
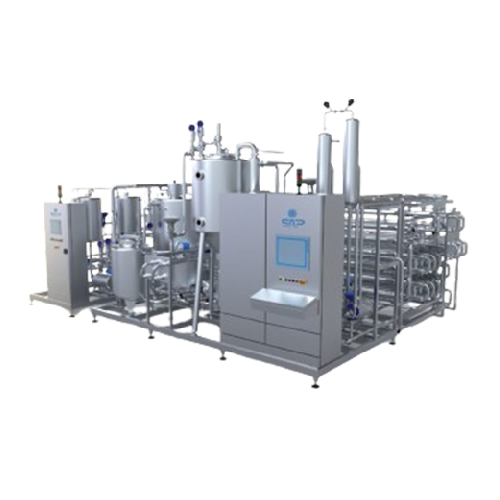
Uht sterilization solution for liquid food products
Enhance your liquid food processing with reliable UHT sterilization, ...
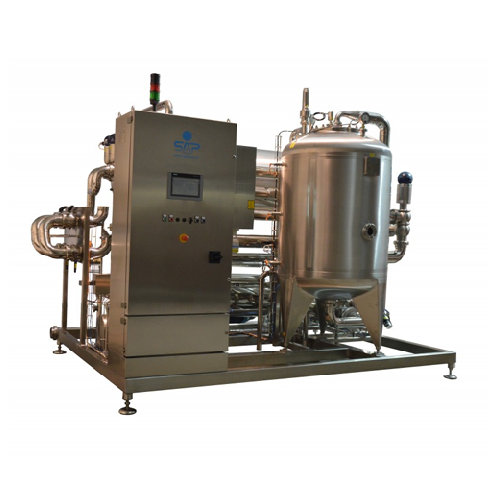
Industrial solutions for beverage mixing and carbonation
Optimize your beverage production with precise mixing and carbon...
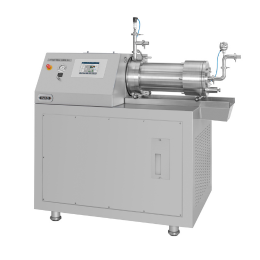
Agitator bead mill for functional foods and flavors
Fine-grinding solid flavors to improve taste properties and integrati...
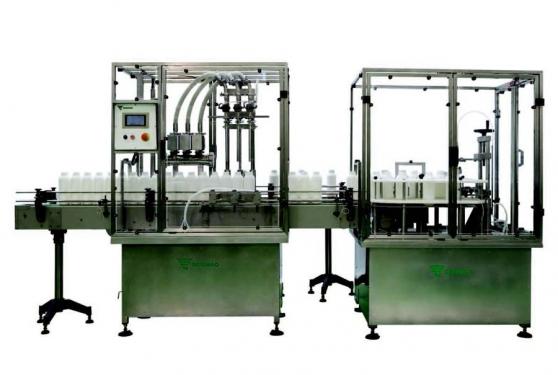
Linear automatic bottling machine for liquids
Autonomous filling systems are a very widely utilized solution for the consi...
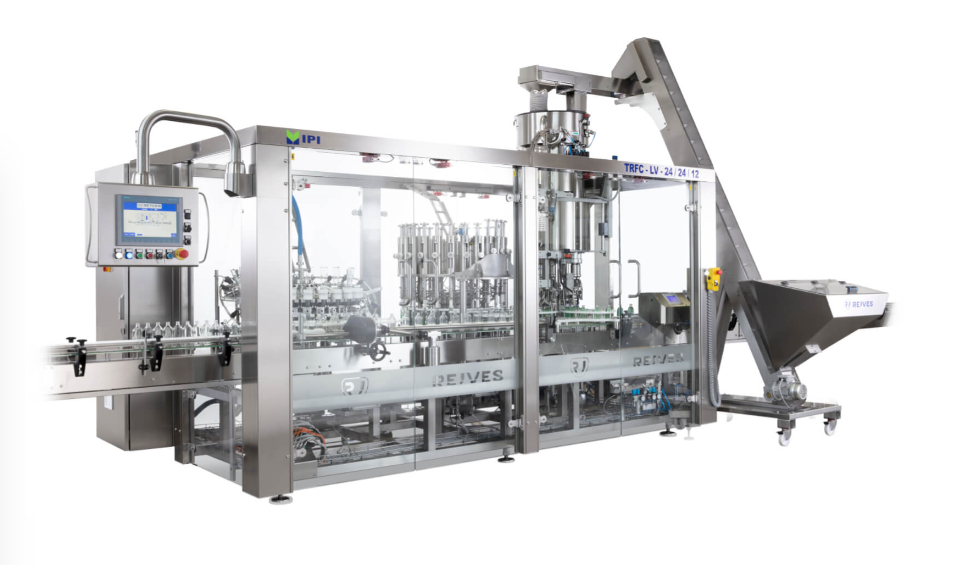
Bottle filling and capping monobloc
Spillage and overfilling are common problems in most production lines for bottled produ...
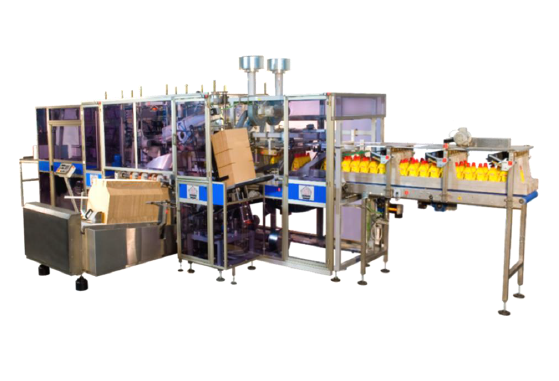
Multifunction case packer for bottles and jars
New ways of packaging products are popping up all the time on the market. T...
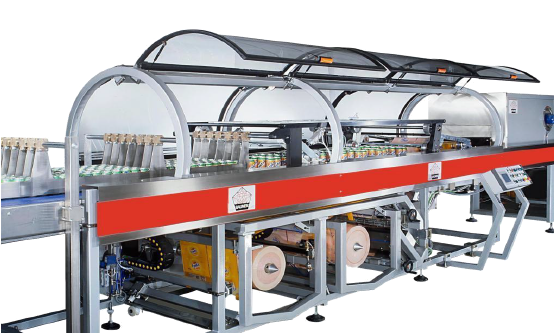
Shrink wrapping machine for PET bottles
During a shrink-wrapping process, a change of reel can slow down the production cyc...
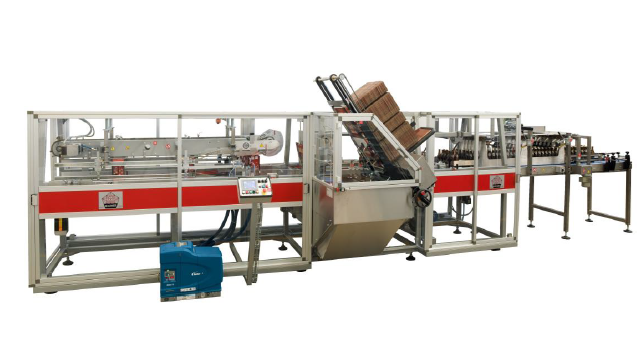
Wrap-around case packer for cans or bottles
When it comes to beer packaging, most of the manufacturers use plain box carto...
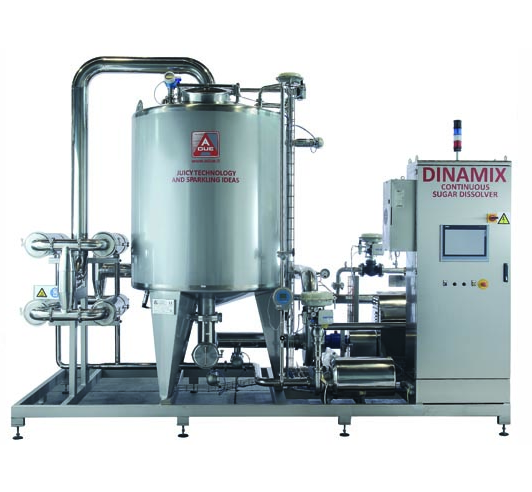
Sugar dissolving system for beverages
In the beverage industry, production of sweet drinks requires the addition of sugar s...
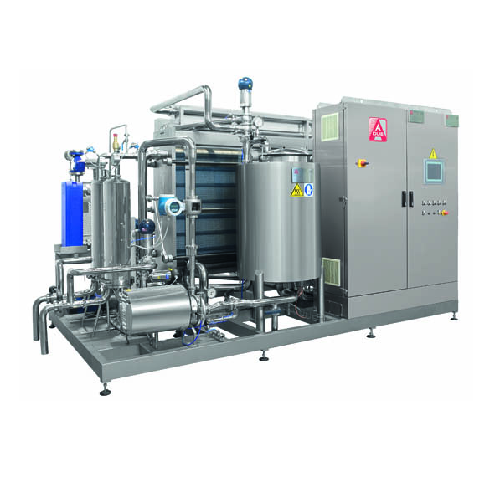
Pasteurizer machine for sensitive beverages
When you want to expand your beverage production line, following a new global ...
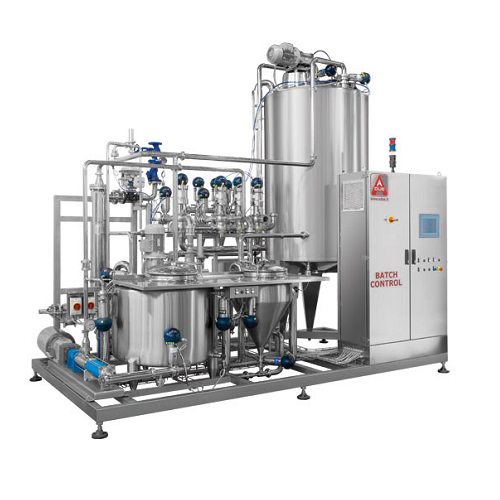
Mixing tanks for beverages
Juice production lines require multiple ingredients to be typically mixed with water. The incorpo...
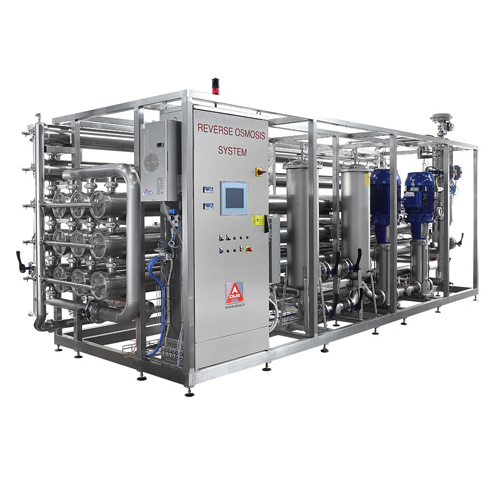
Water treatment for beverage preparation
Water is one of the main ingredients in producing juices and other beverages. If i...
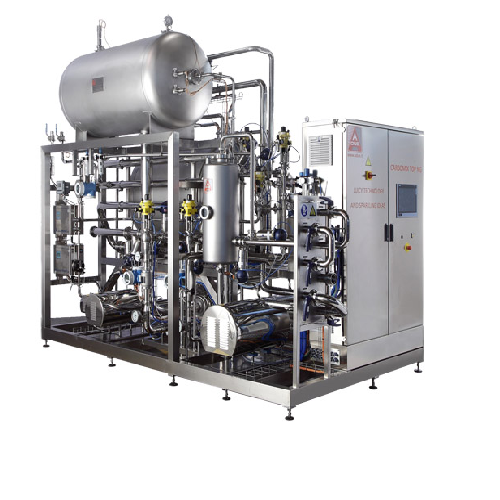
Carbonation machine for beverages
For producers of alcoholic beverages it can be interesting to include hard seltzer in the...
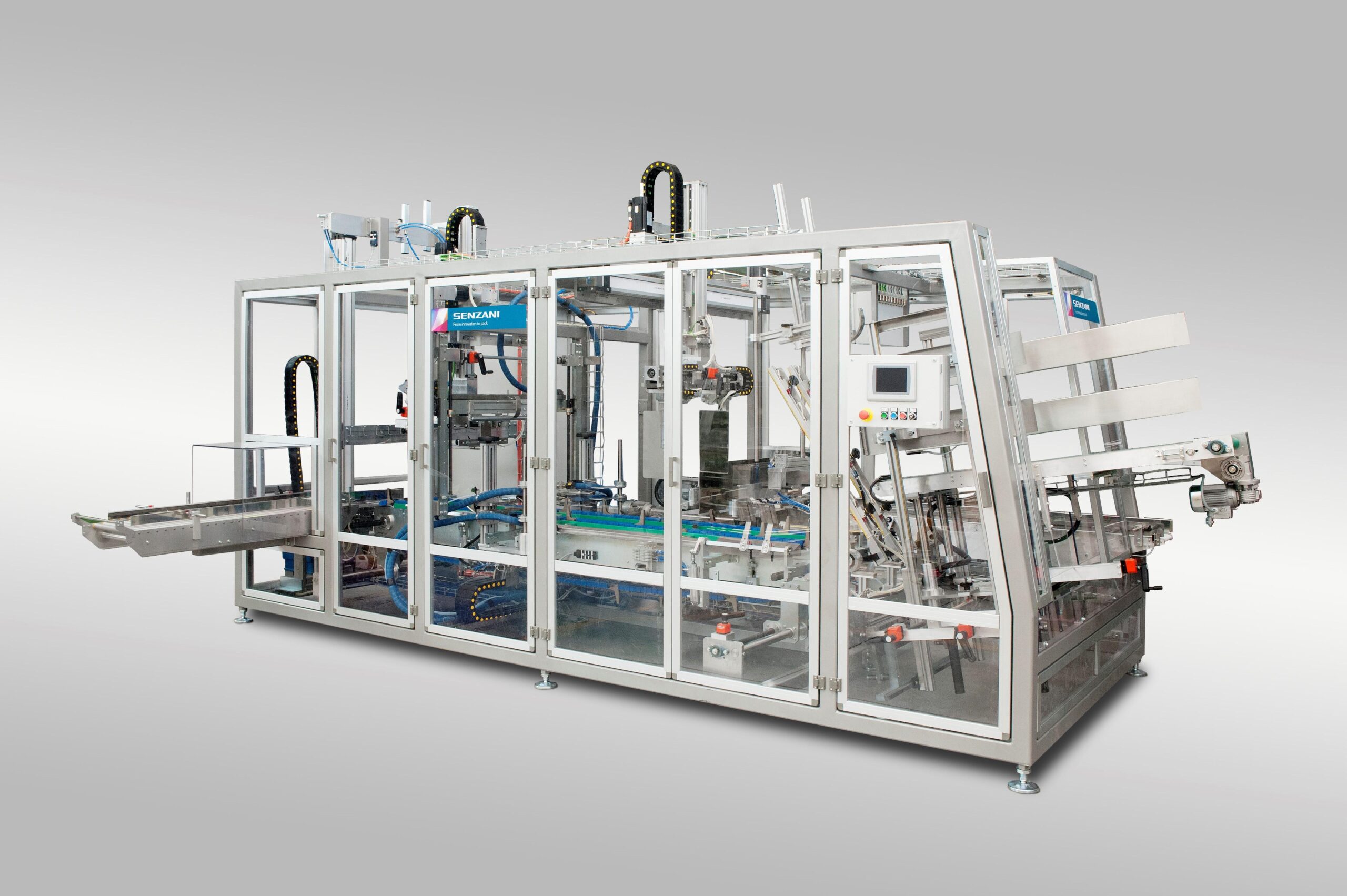
Wraparound case packer
Packaging companies need to pay attention to personalization in shape and design in addition to the at...
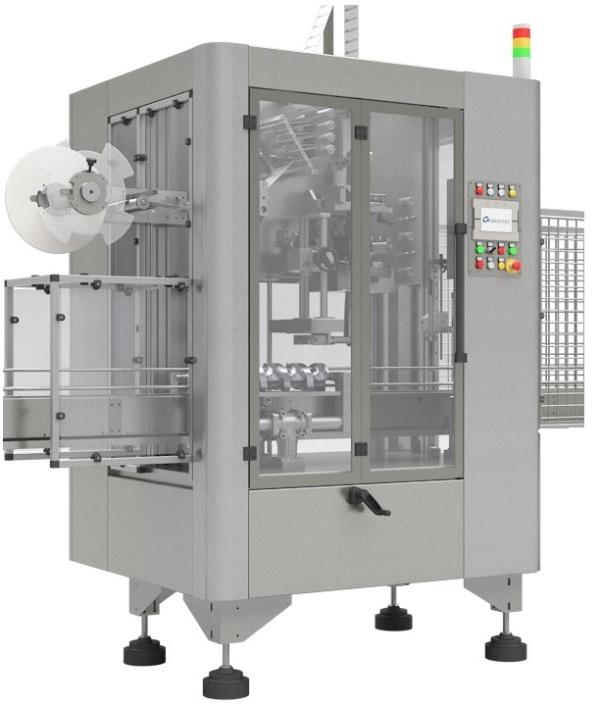
Shrink sleeve labeling machine
Shrink sleeves are new type of full-colour labels that give the opportunity to create a 360-d...
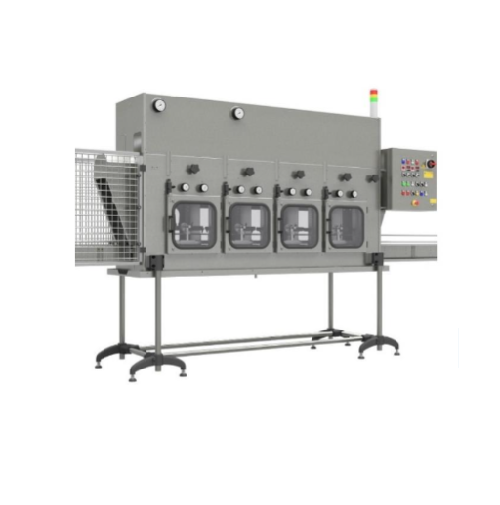
Steam tunnel for shrink sleeve labels
When it comes to the option of applying sleeves or film on a container without wrinkl...

Hot air tunnel for shrink sleeve labels
Sleeves are very popular in food, beverage, Chemical and pharmaceutical industry be...
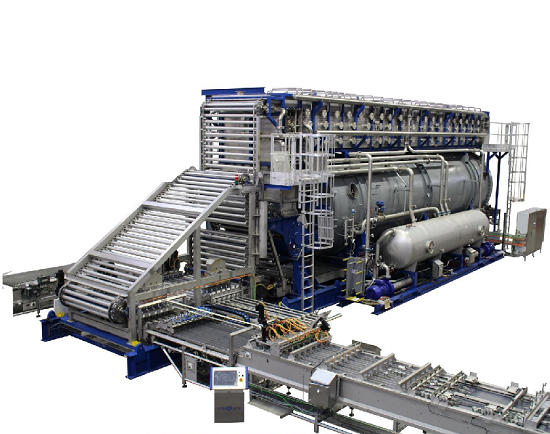
Continuous sterilizer for tin cans and jars
A concern in the coffee industry is maintaining the freshness, taste, and qual...
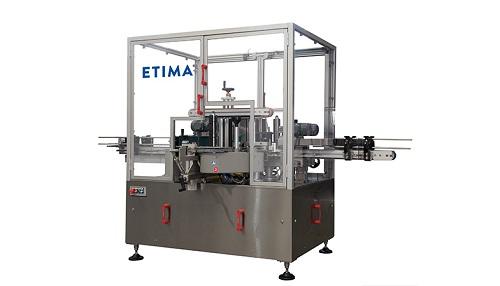
Self-adhesive linear labeling machine for bottles
It is vital to have precise and long-lasting labels on bottles to avoid...
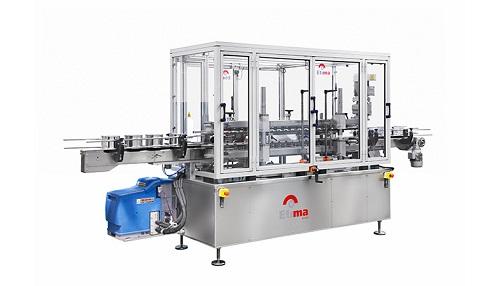
Linear machine for wraparound label
Wraparound labels allow you to offer detailed information using a small space or fit ex...
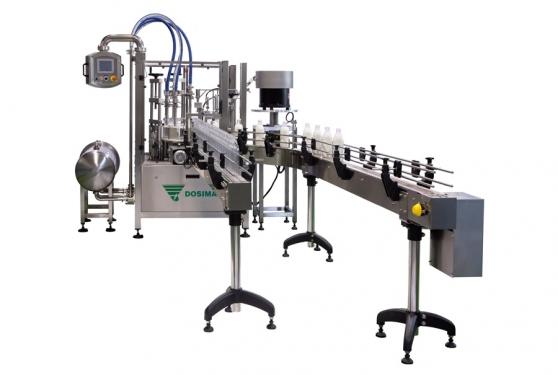
Automatic bottling machine for beverage
One of the biggest challenges when bottling beverage drinks is that many of the bot...

Industrial crate washing machine
In order to meet the increasing demand of the beverage industry, it’s essential to find a c...
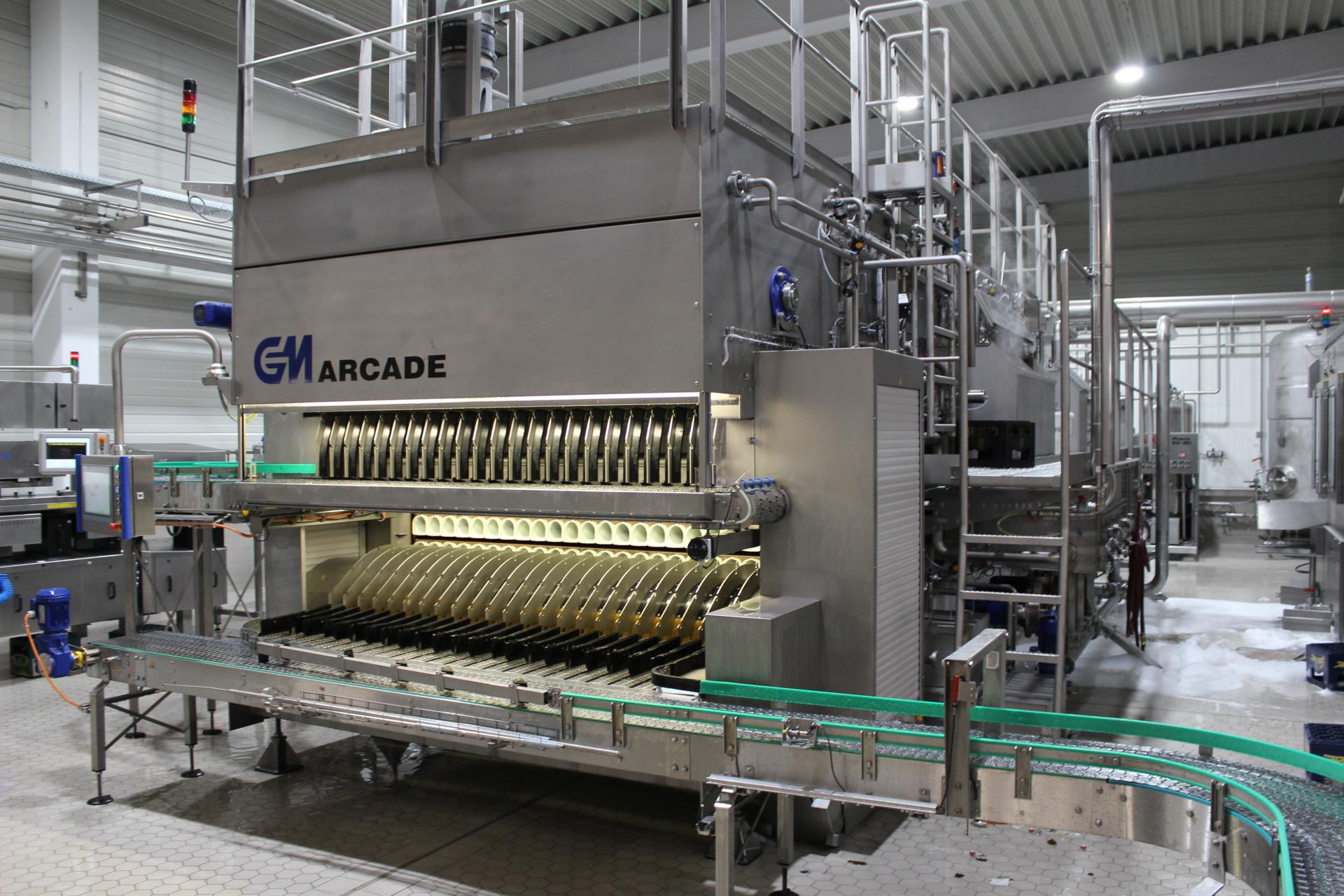
Industrial bottle washing machine
Polyethylene terephthalate (PET) and glass bottles are widely used in the beverage indust...
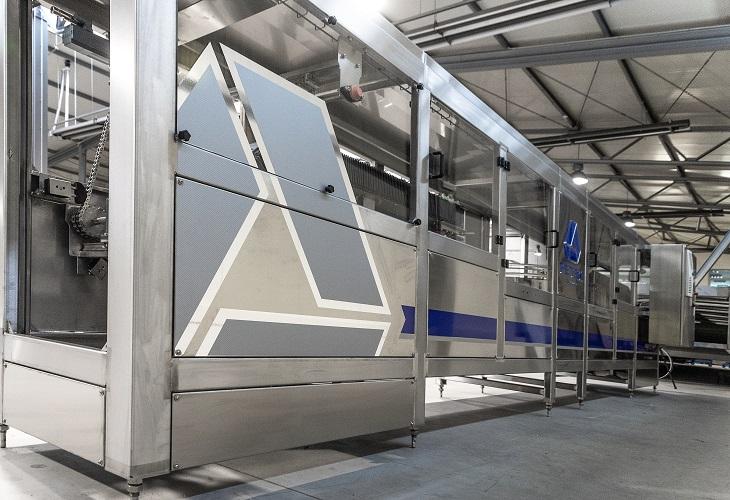
Industrial bottle sterilizer
Sterilization is an important process in the beverage industry to kill microorganisms. It is im...
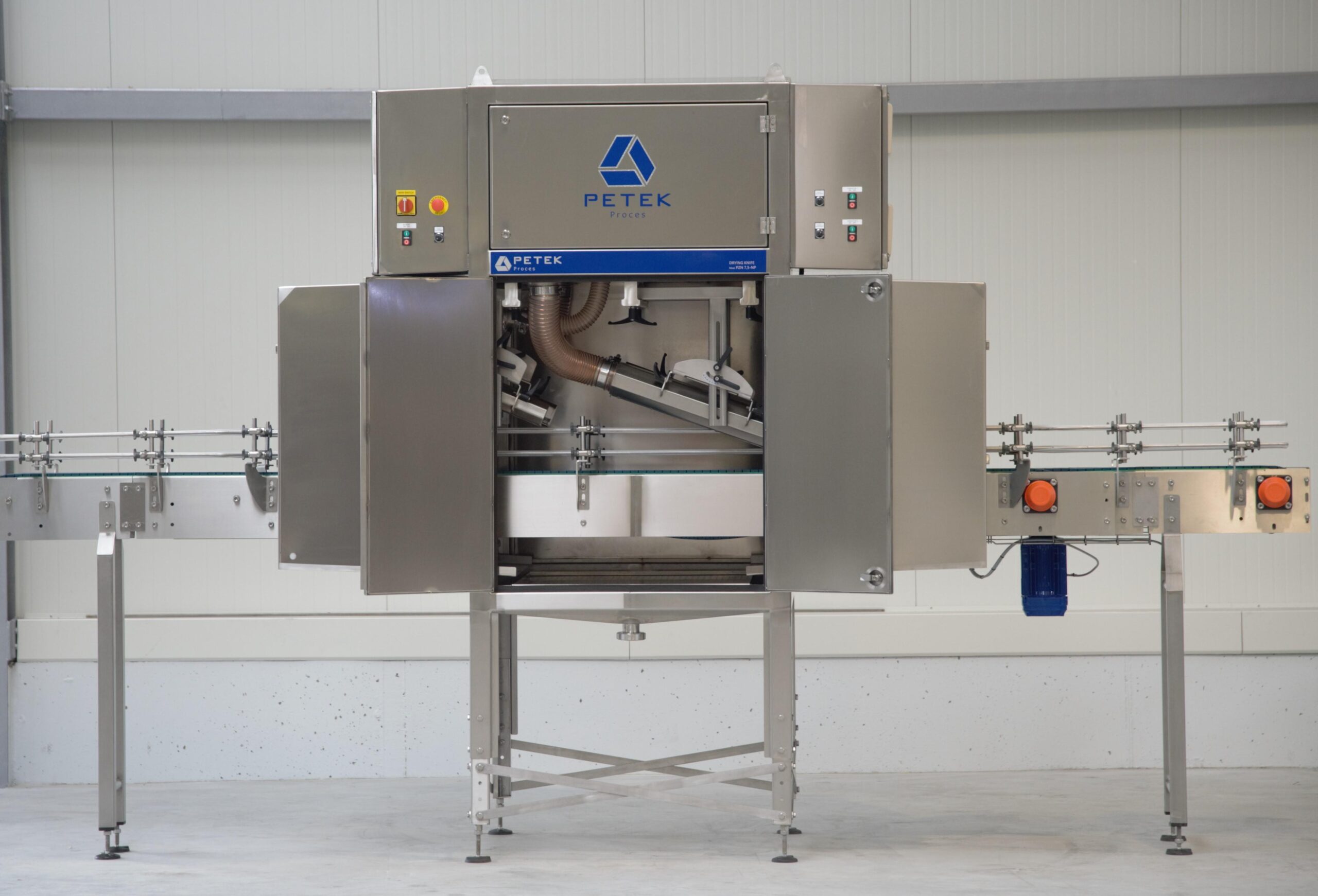
Air knife system for bottling lines
Wet containers are unacceptable and can be problematic in the food and beverage industr...
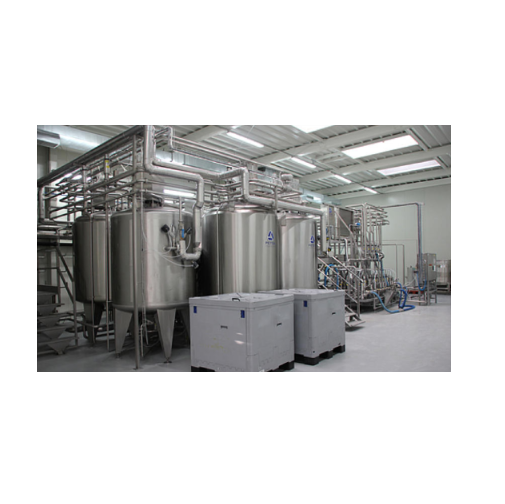
Inline syrup room
The beverage industry requires high-quality syrup. Soft drinks, fruit juices, still drinks, ice tea, flat o...
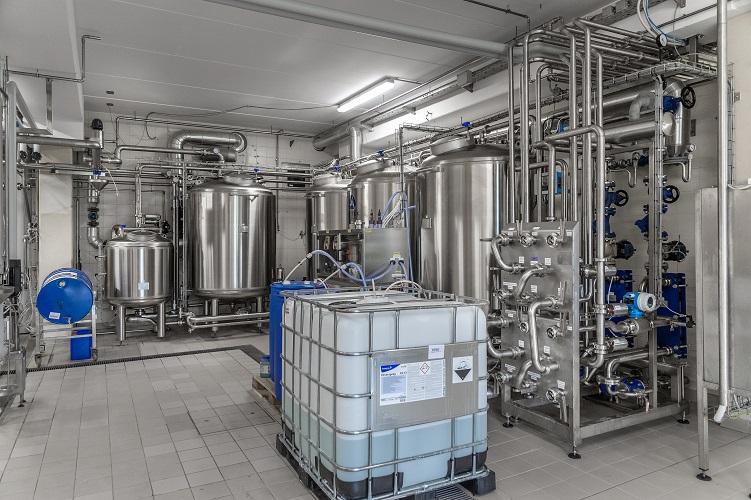
CIP system for beverage
Clean-in-place operations are a mandatory part of food and beverage processing which cannot fail. How...
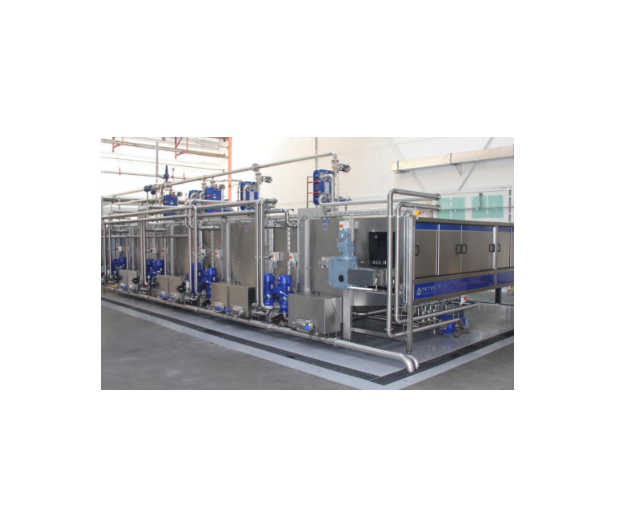
Tunnel pasteurizer for beverage
In the beverage industry, beverages need to be pasteurized in order to destroy pathogens, an...
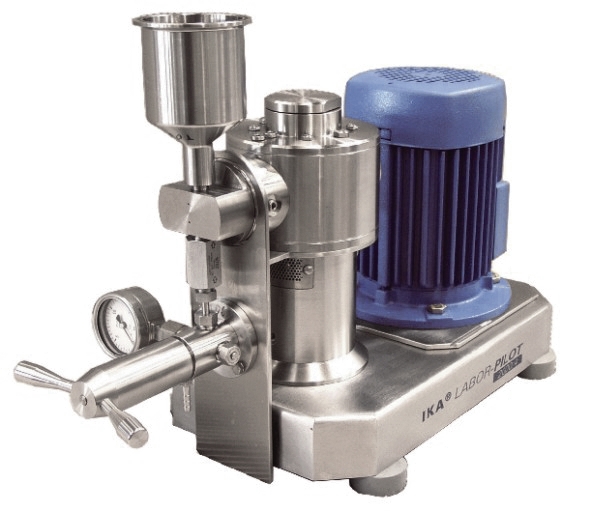
High-pressure homogenizer
When processes call for homogenized emulsions with extremely fine particle sizes the traditional t...
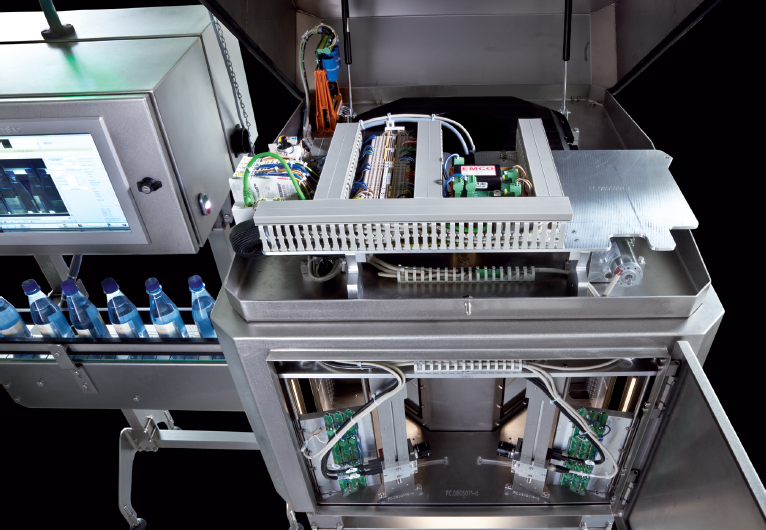
Versatile bottle sorting system
Quality bottle sorting machine and inspection system which can be put to use not only after ...

High-end empty bottle inspection system
If you are looking for a system with empty bottle inspection; base, residual liquid...
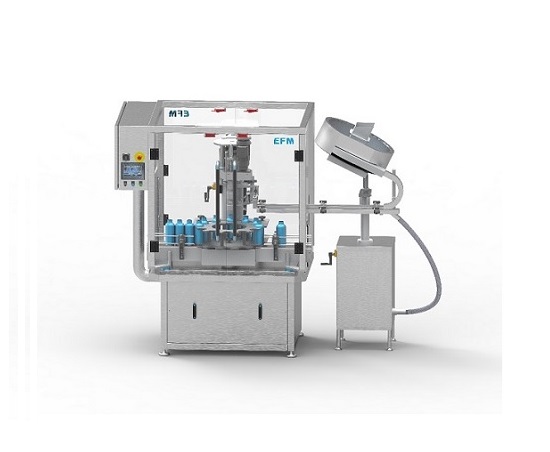
Single head capper
For the stand-alone capping of bottles of up to 30 litre capacity for smaller-scale production you need a ...
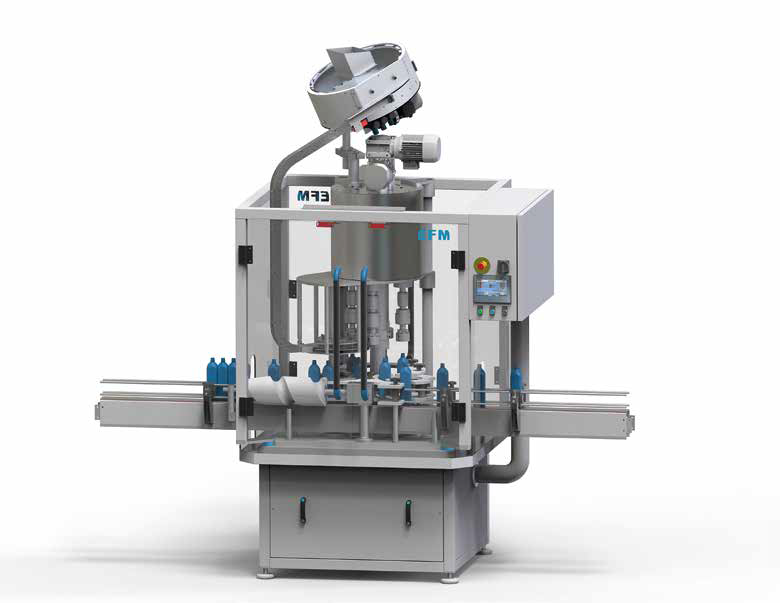
Multi-head capper
For the stand-alone capping of bottles of up to 2.5litre capacity you need a robust and flexible machine wi...

Shrink sleeve applicator - 400 per minute
Flexible medium to high speed application of shrink sleeveing to containers is u...
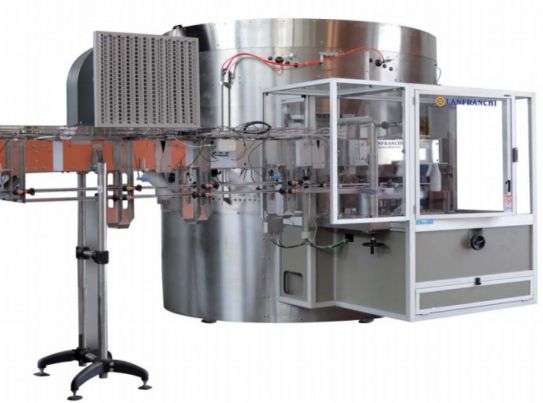
High-speed unscrambler for large bottles
Large volume plastic bottling plants need high-speed unscramblers suitable for lar...
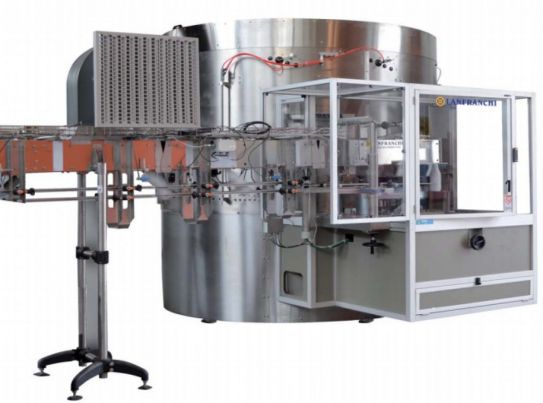
High-speed unscrambler for small bottles
Large-scale production of smaller volume bottled product needs a gentle, accurate ...
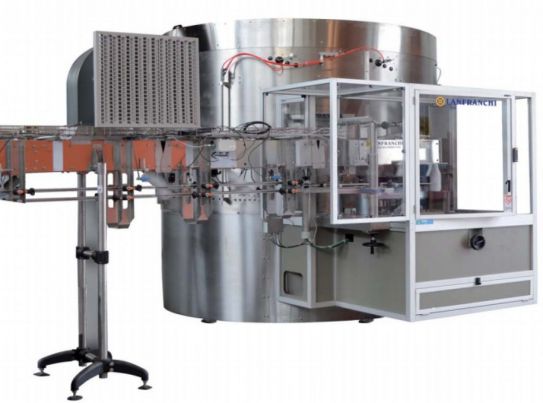
Low-speed unscrambler
Smaller plastic bottling lines need a lower cost, lower volume unscrambling machine that maintains gent...
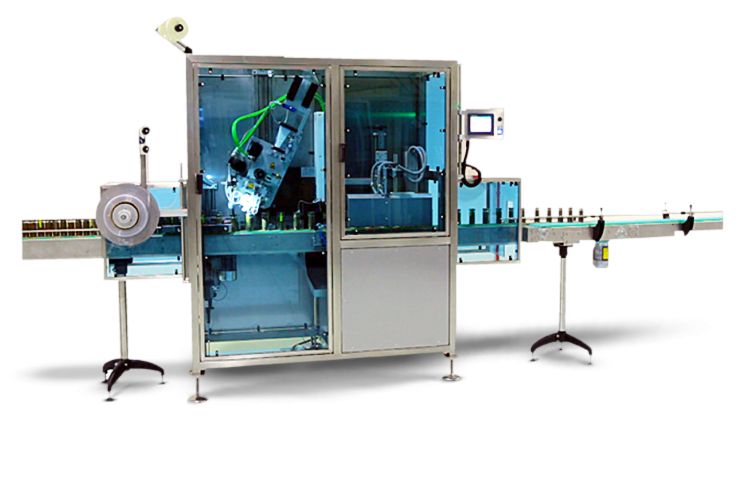
Compact shrink sleeve applicator
Adding tamper prevention to product packaging can be expensive and difficult to set up. Thi...
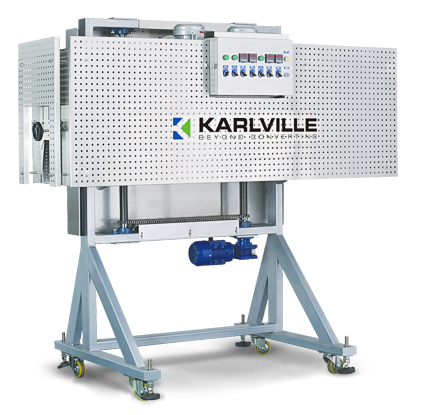
Electric shrink tunnel solution
Adapting shrink sleeve heating tunnels for different applications can be a lengthy and expen...
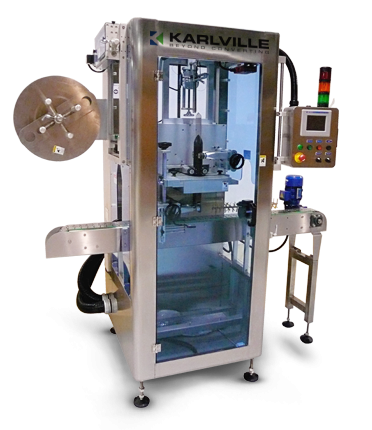
Low speed can sleeve applicator
Flexible automatic low speed application of shrink sleeving to cans is used in various indus...
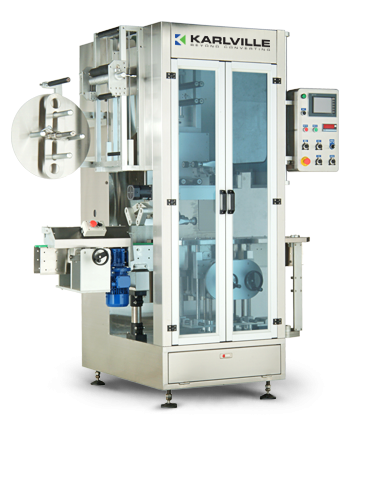
Low speed shrink sleeve applicator
A variety of industries require flexible addition of shrink sleeves to containers on the...

Laboratory size auto-steam shrink system
When managing sleeving projects, fast prototyping and testing can gain massive com...
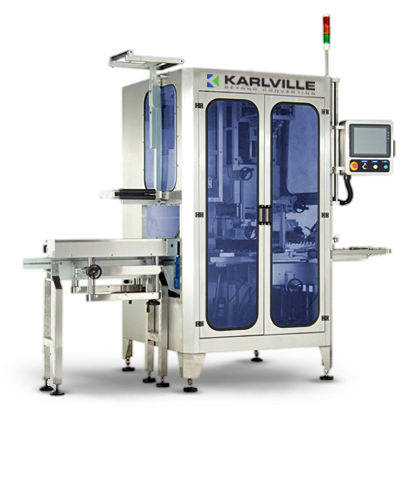
Shrink sleeve applicator - 600 per minute
Several industries require the flexible addition of shrink sleeves to containers...
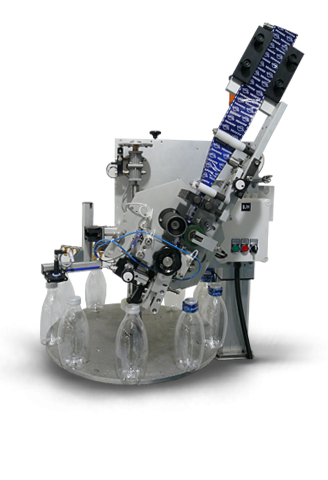
In-line tamper evident applicator head
Integrating tamper protection equipment into an existing production line means addit...
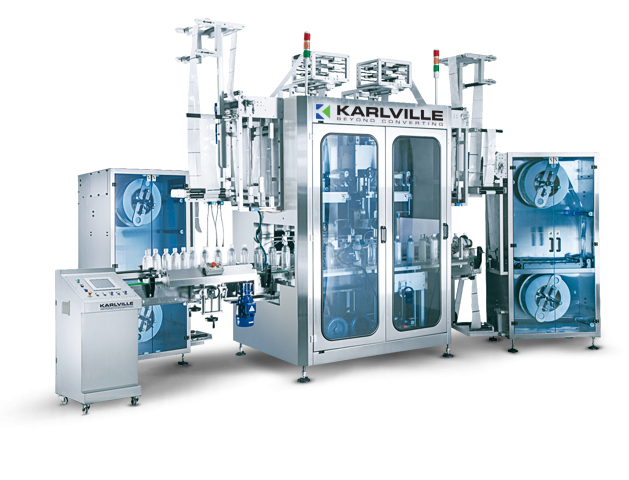
Shrink sleeve applicator - 800 per minute
High speed, in-line shrink sleeving systems require dual head capability with hi...
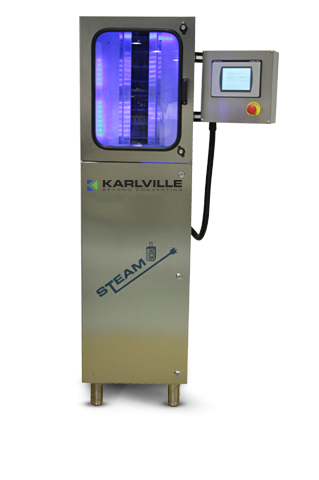
Advanced auto-steam shrink system
Design and development of shrink sleeves could be made much easier if small batches of sa...
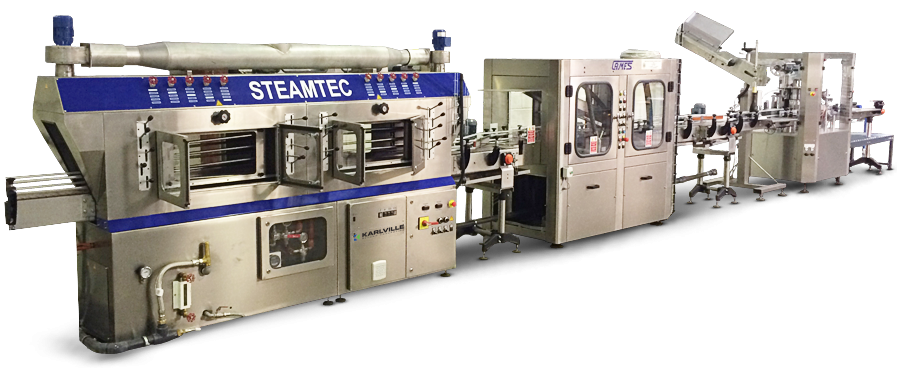
Premium steam tunnel for sleeve application
Maximum flexibility in terms of pressure, temperature and ramp setting and adj...
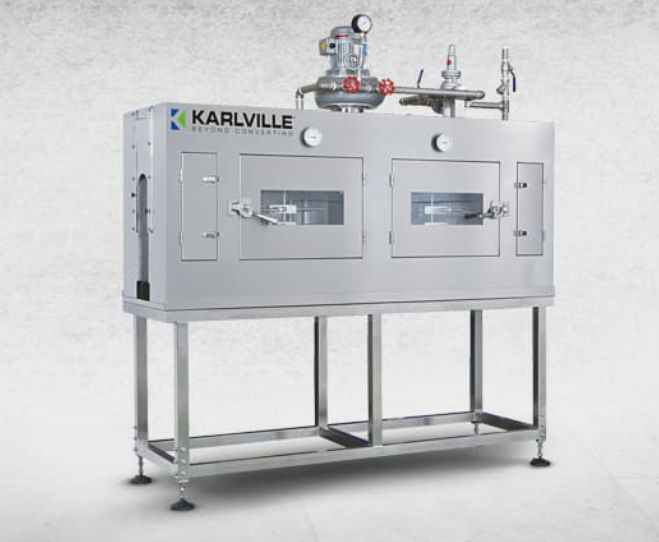
Shrink tunnel for applying sleeves to different containers
Maximum flexibility is required when setting pressure and dir...
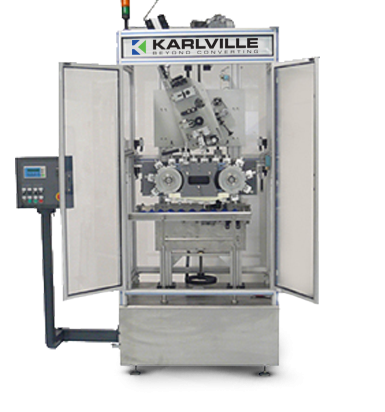
Tamper-evident sleeve applicator for caps
Reliability, continuity and changeover time are key success factors for tamper-e...
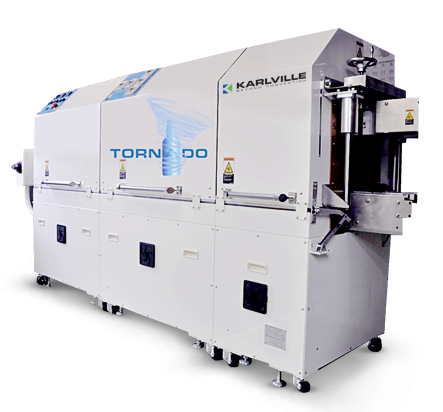
Energy efficient tunnel for sleeve application
Hot air application of shrink sleeves is much more efficient than tradition...
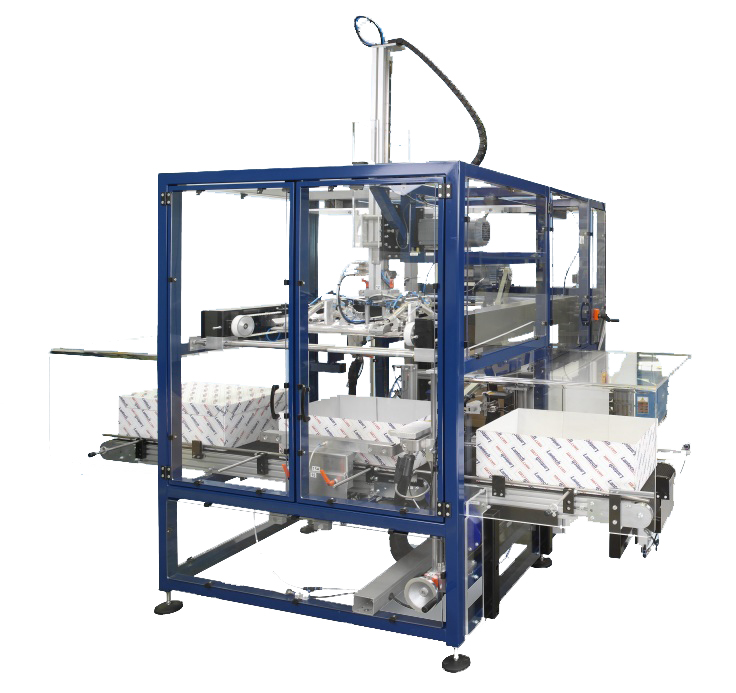
Lid applicator for corrugated cases
For your secondary packaging, you may be considering packing into boxes that require a ...
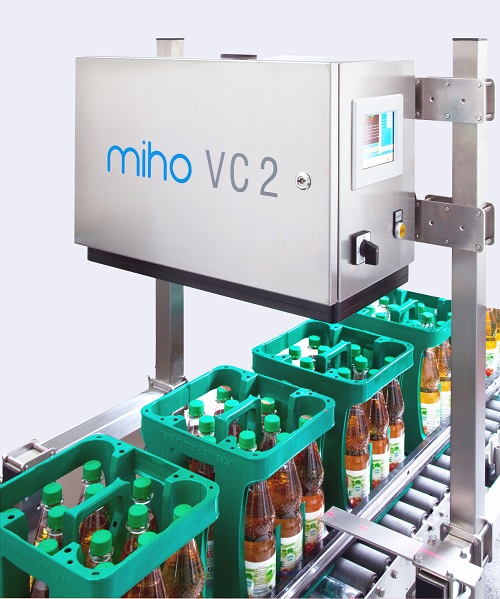
Full crate inspection system
State of the art crate inspection system that uses a laser camera system to see if the bottles ...
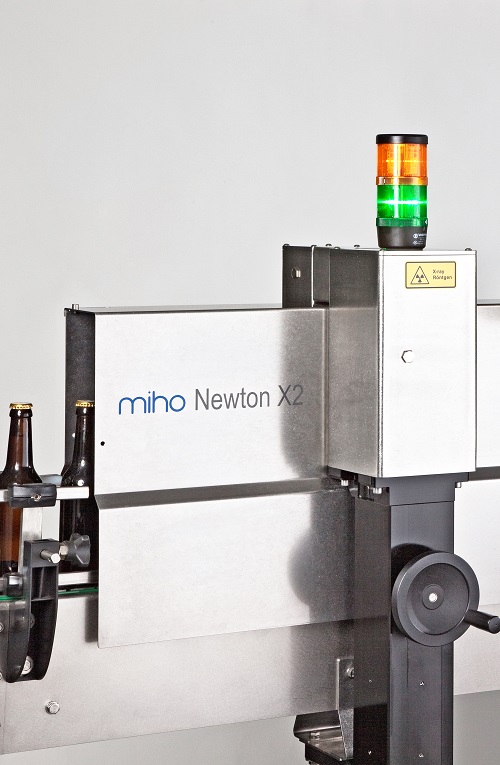
High-precision X-ray fill level controller
High-speed, high precision X-ray system to inspect containers that are difficul...
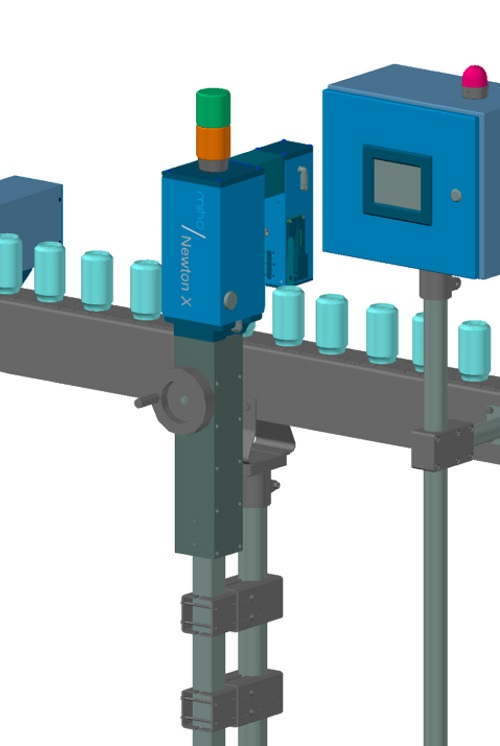
X-ray fill level controller
For containers that are difficult to see through, such as cans or cartons lined with aluminium, ...
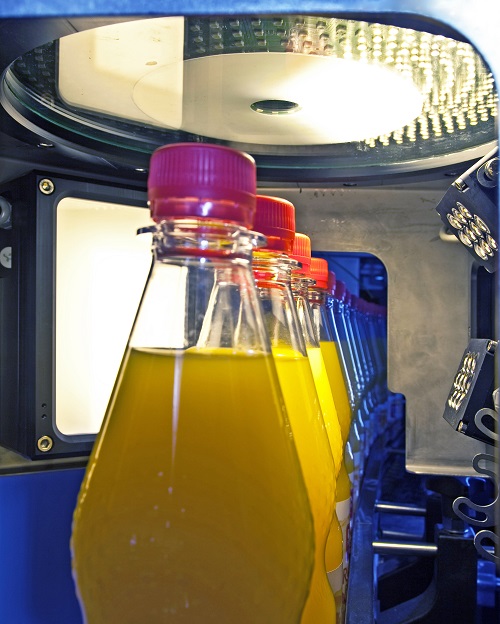
Optical fill level controller
Accurate fill level inspection for transparent, opaque and foaming liquids, that makes sure th...
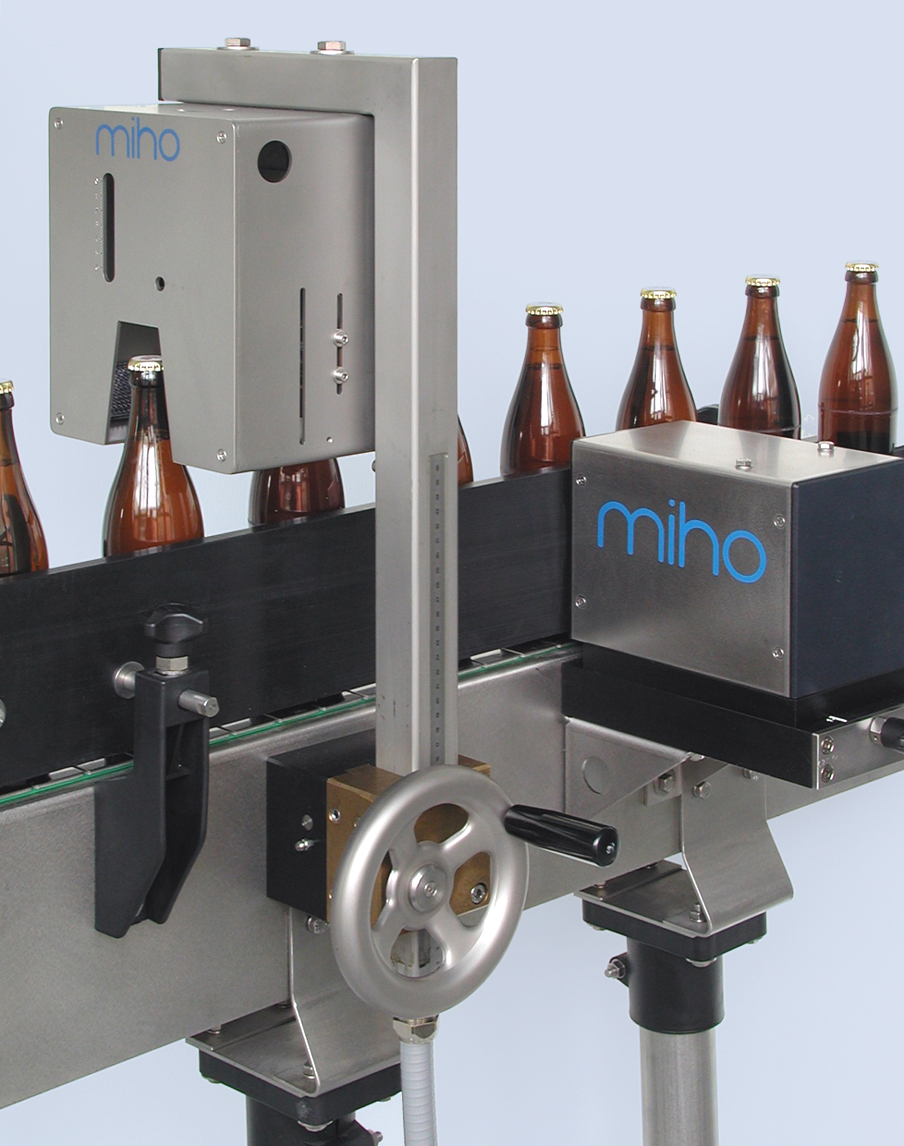
High-frequency fill level controller
In terms of high-frequency technology, the fill level detection is considered a standa...
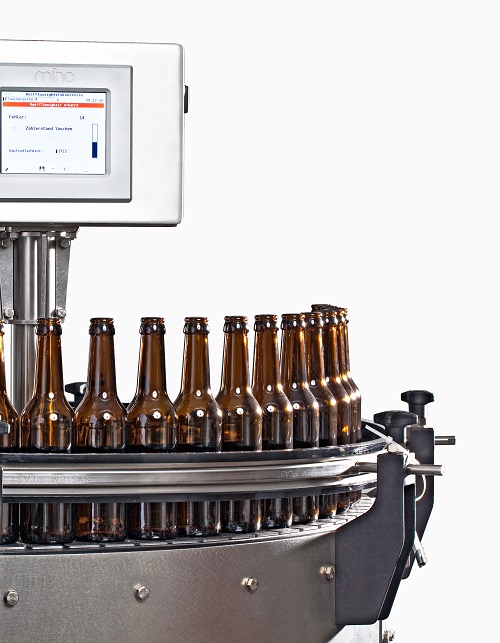
Advanced residual liquid inspection system
Advanced and easy to use inspection system that eliminates the risk of residual...
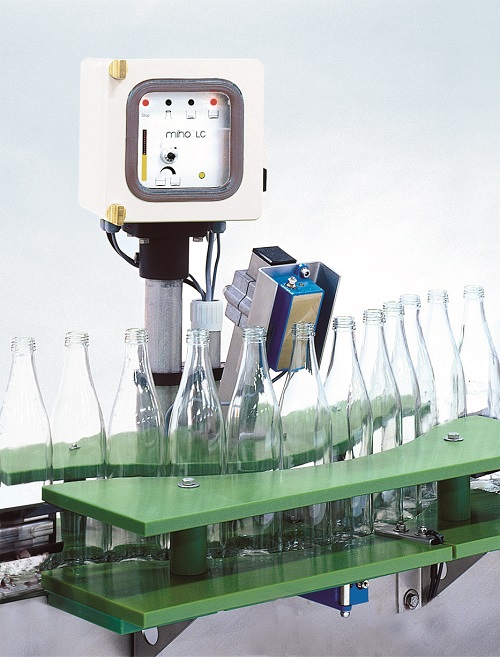
Residual liquid inspection system
Inspection system that eliminates the risk of residual liquid, water or left over drink i...
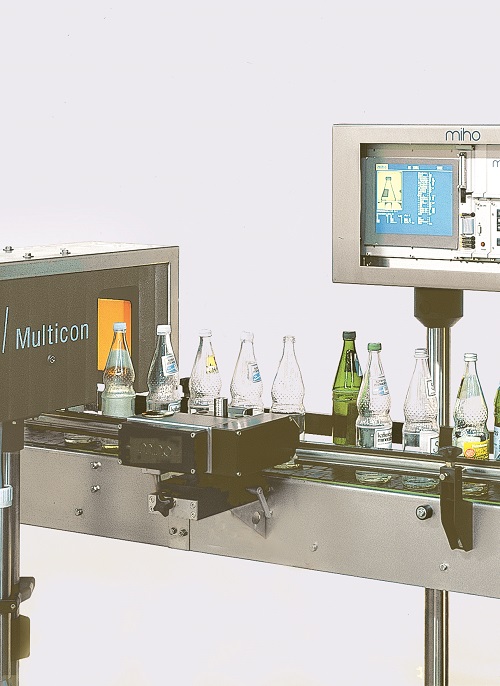
Empty bottle shape, colour and size sorting system
Accurate bottle sorting system that differentiates between the bottles...
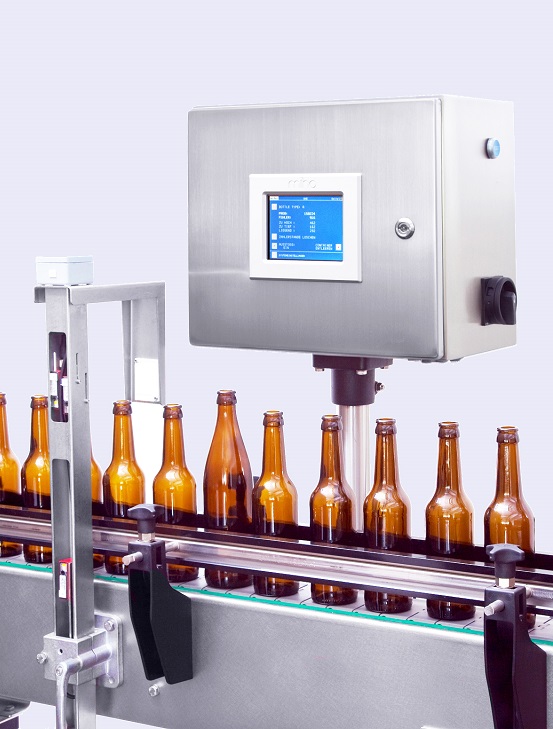
Empty bottle height sorting system
An empty bottle sorting system that uses the light barrier technology. It detects bottle...
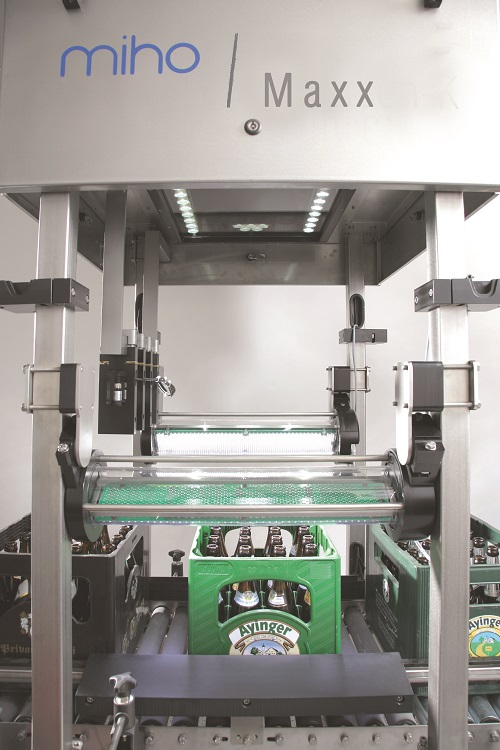
Empty crate inspection system
Extensive and much-differentiated inspection of both the crate and the bottle that allows you ...