Blow-moulder and labeller integration for Pet bottles
Streamline and enhance your PET bottle production with seamless blow-moulding and labelling integration, achieving high-speed operations with precise label application and reduced energy consumption.
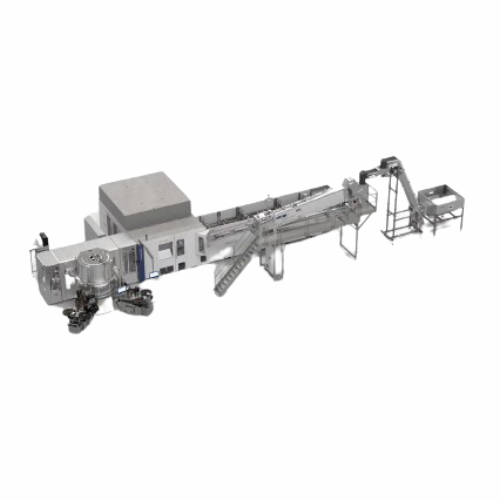
Combines and Labels PET Bottles Efficiently
The Contiform Bloc BL from Krones is an integrated solution that streamlines PET bottle production by combining stretch blow moulding and labelling into one efficient block. This equipment is distinctive for its seamless drive concept and actively controlled transfer grippers, which ensure precise label application on high-speed production lines. Designed for versatility, it accommodates various bottle shapes (cylindrical and square) and volumes (up to 3.5 liters), supporting both standard and lightweight containers as well as up to 100% rPET content.
Capable of processing up to 99,000 containers per hour, the Contiform Bloc BL integrates smoothly into existing production lines, reducing the need for multiple operators due to its unified control system. The infrared heating technology and Air Wizard Triple compressed air recycling ensure energy efficiency while minimizing operational costs. Its modular design allows easy customization and adaptation for specific production needs, while the Servo Joint Control provides flexibility between block and single machine operations, enhancing maintenance efficiency and reducing downtime.
This system is particularly suited for beverage manufacturers and PET bottle producers aiming to optimize high-speed operations in the food and beverage industry, ensuring impeccable label application and energy savings throughout the manufacturing process.
Benefits
- Maximizes throughput with processing capacity reaching up to 99,000 containers per hour.
- Reduces energy consumption significantly through advanced air recycling and infrared heating technologies.
- Optimizes label application by labelling bottles pre-filling, ensuring high-quality results.
- Minimizes operational costs with a unified control system that enables single-operator management.
- Enhances production flexibility with modular design and Servo Joint Control for efficient maintenance and changeovers.
- Applications
- Water, Alternative proteins, Milk and milk-based drinks, Spirits, Plant-based milk alternatives, Juice, Soft drinks, Beer
- End products
- Cola pet bottles, Bottled almond milk, Bottled plant-based milk, Mineral water pet bottles, Whiskey pet bottles, Uht milk bottles, Sparkling water pet bottles, Orange juice pet bottles, Pet beer bottles
- Steps before
- Preform manufacturing, Preform heating
- Steps after
- Filling, Capping, Packaging, Palletising
- Input ingredients
- PET preforms, compressed air, self-adhesive labels, reel-fed plastic labels
- Output ingredients
- cylindrical PET bottles, square PET bottles, lightweight PET containers, up to 100% rPET containers, labelled PET bottles
- Market info
- Krones is renowned for its expertise in manufacturing beverage and liquid food processing and packaging equipment, offering comprehensive solutions that include filling, packaging technology, and processing systems, and is reputed for innovation and quality in the industry.
- Functions
- Stretch blow moulding and labelling
- Output
- Up to 99, 000 containers per hour
- Processing range
- Cylindrical and square PET containers
- Container volume
- Up to 3.5 litres
- Container composition
- Standard and lightweight containers, up to 100% rPET
- Label types
- Self-adhesive labels and reel-fed plastic labels
- Heating technology
- Infrared heating technology
- Containers per hour per blowing station
- Up to 2, 750
- Labelling station capacity
- Up to 50, 000 containers per hour
- Compressed air recycling system
- Air Wizard Triple
- Servo motor technology
- Five high-precision Monotec servo motors
- Energy efficiency features
- Energy-efficient separated vacuum, height-adjustable base thermal shield
- Energy savings
- Significantly reduced switching time dispersion
- Transfer technology
- Actively controlled transfer grippers
- Drive technology
- Servo drives use throughout all applications
- Automation
- Servo Joint Control for decoupling and synchronisation
- Glue Application
- "Gravure Glue Application" for reduced hotmelt consumption
- Label fit
- Consistently excellent label fit
- Labelling sequence
- Pre-filling labelling
- Operation mode
- Automatic
- Automation level
- PLC / SCADA
- Changeover time
- Quick changeover via Servo Joint Control
- CIP/SIP
- Automatic self-optimisation
- Blocking
- Integrated blow-moulder and labeller
- Energy efficiency
- Highly energy efficient
- Container size and shape
- Cylindrical, square, up to 3.5 litres
- Container material
- PET, 100% rPET
- Label type
- Self-adhesive, reel-fed plastic
- Machine Footprint
- Compact with significantly smaller space requirement compared to individual systems
- Container Processing Range
- Up to 3.5 litres
- Container Shape
- Cylindrical and square PET containers
- Container Material
- Standard and lightweight PET, up to 100 percent rPET
- Base Reflector Adjustability
- Adjustable to the respective preform length
- Transfer Points
- Only four internal horizontal preform and container transfer points
- Drive and Transfer Technology
- Torsion-resistant platform with skip-and-run technology
- Reflector Type
- Maintenance-free system of ceramic reflectors
- Heating Technology
- Highly-efficient infrared heating technology with parabolic reflector
- Transfer Grippers
- Actively controlled transfer grippers
- Servo Motors
- Five high-precision Monotec servo motors with real-time synchronization
- Integration possibilities
- Block mode or single machine
- Footprint
- Compact design
- Drive technology
- Servo motor technology
- Label application
- Self-adhesive or reel-fed plastic labels
- Container processing range
- Cylindrical and square PET containers