Aseptic blow fill system for beverage bottling
Designed for high-speed aseptic bottling, this system ensures sterility throughout the blow molding to capping process, enhancing product safety and shelf life for sensitive beverages.
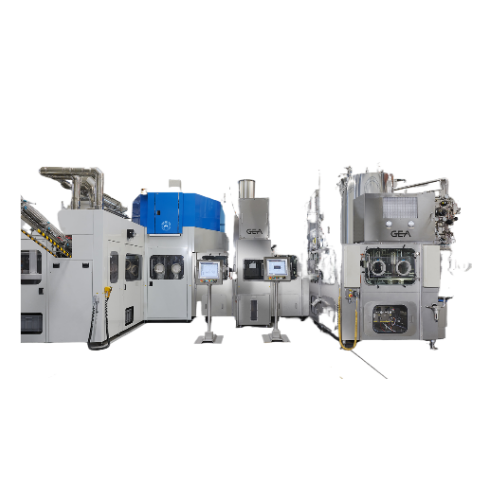
Aseptically Sterilizes, Molds, Fills, and Caps Beverages
The GEA Aseptic Blow Fill System ABF 2.0 is an innovative solution for beverage and dairy producers aiming to boost production efficiency while maintaining aseptic integrity. This advanced system integrates blow molding, sterilization, filling, and capping within a single continuous operation, suited for both high and low acid beverages, including carbonated and still varieties.
With its patented dry hydrogen peroxide-based sterilization, the ABF 2.0 ensures a 6 log reduction in microbial contamination for preforms and caps. The system operates with an air recovery process that reduces energy consumption by up to 31%, maintaining environmental responsibility.
Capable of aseptic runs up to 165 hours, it handles diverse liquid products such as fruit juices, milk-based drinks, and protein shakes, ensuring flexibility and minimizing cleaning downtime to just three hours. Its fully automated PLC-controlled operations allow seamless integration into existing production lines and remote monitoring capabilities enhance operational oversight.
Constructed from chemical-resistant materials, the equipment supports rigorous sterilization protocols and meets stringent microbiological validation standards, including FDA approvals. Tailored customizable features and engineering support are available to fit specific production needs, ensuring optimal performance across various beverage processing applications.
Benefits
- Enables extended aseptic production runs of up to 165 hours, minimizing operational pauses.
- Lowers energy consumption with an air recovery system, cutting costs by up to 31%.
- Ensures product safety with 6 log reduction in microbiological contamination.
- Reduces labor intervention through fully automated sterilization processes.
- Minimizes chemical residue with controlled vaporized hydrogen peroxide sterilization.
- Applications
- Carbonated beverages, Beverages, Milk-based drinks, Sensitive beverages, High acid beverages, Low acid beverages, Still beverages, Dairy products
- End products
- Lemonade, Non-dairy creamers, Milkshakes, Fruit smoothies, Tomato juice, Protein shakes, Almond milk, Iced tea, Soy milk, Sparkling water, Energy drinks, Cold brew coffee, Fermented milk drinks, Yogurt drinks, Probiotic beverages, Carbonated soft drinks, Fruit juices, Flavored water
- Steps before
- Preform heating, Preform sterilization, Vaporized hydrogen peroxide (VHP) treatment
- Steps after
- Aseptic filling, Aseptic capping, Bottle transfer
- Input ingredients
- preforms, caps, sterile air, hydrogen peroxide vapor
- Output ingredients
- high acid beverages, low acid beverages, sterilized bottles, aseptic beverages, carbonated beverages, still beverages
- Market info
- GEA is known for its expertise in engineering innovative and sustainable equipment and solutions, focusing on sectors such as food, beverages, pharmaceuticals, and energy, with a reputation for quality, efficiency, and advanced technological applications in industrial processing.
- Shelf life compatibility
- High and Low Acid Beverages
- Sterilization technology
- Dry Hydrogen Peroxide
- Decontamination performance
- 6 Log Reduction
- Production capacity
- Continuous Runs of 165 Hours
- Cleaning cycle downtime
- 3 Hours
- Cap sterilization
- Sterilcap VHP R
- High reactivity and reliability
- Patented Air Blowing Block
- Automation level
- Full automation
- Sterilization method
- Hydrogen peroxide vapor (VHP)
- Changeover time
- Limited downtime (3 hours)
- Resource efficiency
- Energy consumption reduction up to 31%
- Aseptic processing duration
- 165 hours continuous production
- Microbiological validation
- 6 log decontamination performance
- Cleaning method
- Automated CIP/SIP
- Cap and preform decontamination
- Single sterilization phase
- Flexibility
- High and low acid beverage compatibility
- Preform blowing process
- Sterile air
- Density/particle size
- 0.5–2.5 g/cm³ / 50–1000 µm
- FDA compliance
- Yes
- FDA materials
- Yes
- Machine footprint
- Compact
- Sterile zone size
- Integrated sterile environment
- Control panel type
- Automated Control
- Preform handling
- Sterile neck transfer
- Discharge method
- Sterile transfer between modules
- Control panel type
- Touchscreen HMI
- Integration possibilities
- SCADA integration
- Customization levels
- Modular design
- Automation level
- Fully automated
- Aseptic features
- VHP sterilization
- Resource-efficient technology
- Air recovery system
- Adjustability
- Rapid changeovers
- Cap sterilization options
- Sterilcap VHP R