Automatic filling and sealing machine for yogurt
One of the biggest challenges when filling yogurt in containers is that the product itself is quite viscous in nature when dosing. Due to the rapid movement of the cups in a high-speed production environment, there is a higher risk of spilling the product during the filling process. Thus, you need a fast, hygienic and fully regulated solution to fill liquids and seal rigid containers.
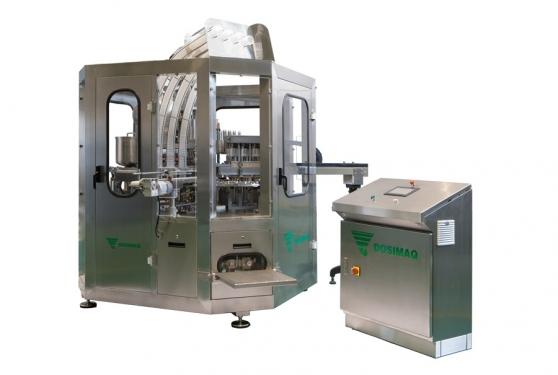
Fully automated filling and heat sealing packaging system
Dosimaq’s FS-34 is a fully automatic and multi-functional equipment configured for the filling of yogurt and the heat sealing of rigid containers. It can produce up to 10,000 containers per hour. It has an intermittent rotary system with 16 stations for container movement. Each station has 4 nozzles, which are anti drip and synchronised with the Clean-in-Place system, which is a method of cleaning the interior surfaces of pipes, vessels, process equipment, filters and associated fittings, without disassembly.
To carry out the filling process, the automatic filling and sealing machine for yogurt first de-stacks the container in a mechanical destacking system with 4 channels for firm stacking of the containers. It is also designed with a filling head with 4 pistons to fill up to 350 cc, equipped with a servo motor. It has electric automation with a touch screen, making it very user-friendly.
The unit also has a filling capacity for containers of between 30 mm and 120 mm in diameter. In order to carry out the sealing process, it is equipped with a destacking unit for pre-cut aluminium lids for the containers. The sealing unit itself allows you to regulate temperature, pressure, and time with the ease of a touch screen.
The equipment has a combination of servo motors for pulling the container from the inside of the machine. The system is also equipped with a mechanical lift system for containers which ensures filling from the bottom of the container to minimise spillage. It is a hygienic and compact unit with an extraction system allowing easy cleaning and maintenance.
Benefits
- Capacity of up to 10,000 containers per hour
- 4 anti-drop nozzles with pre-installed synchronization to the Clean-in-place system facilitation for minimal waste
- Mechanical and servo-motorised performance