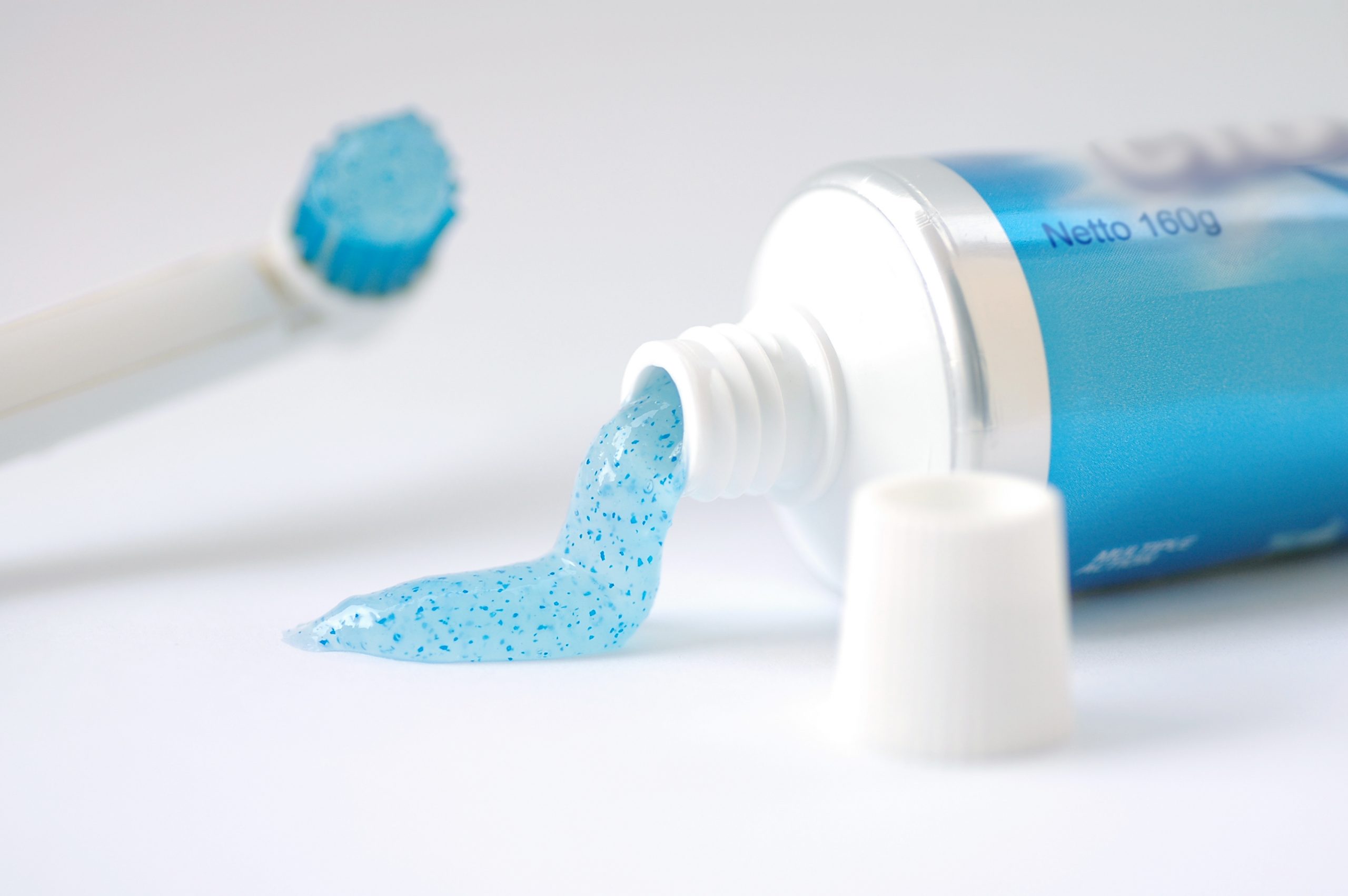
Toothpaste Manufacturing Equipment
Find innovative production technology for making toothpaste and connect directly with world-leading specialists
It's been estimated that we spend an average of 3,000 hours brushing our teeth. In fact, in our daily routine, toothpaste is something we use at least twice a day. Making toothpaste is a very straightforward process; just mix together water, abrasives, humectants, thickening and foaming agents, sweeteners, and flavors in the right amounts until you get a paste. Once you have added the colors, you can fill a tube with your colorful toothpaste and seal it before being shipped to stores.
Stories about toothpaste
Select your toothpaste process
Tell us about your production challenge

So what goes into a tube of toothpaste?
Try reading the label on your toothpaste. What you’ll get is a very long list of ingredients and complicated names like trisodium citrate dihydrate or xantham gum. Some toothpaste even include preservatives such as methylparaben and Sodium benzoate. To keep it simple, let’s break these ingredients down into different categories; first, abrasives.
They are the building block of your toothpaste (30-60% of your final product). Abrasives are essential if you want to scrape food or plaque off your teeth, to prevent cavities or dental disease.
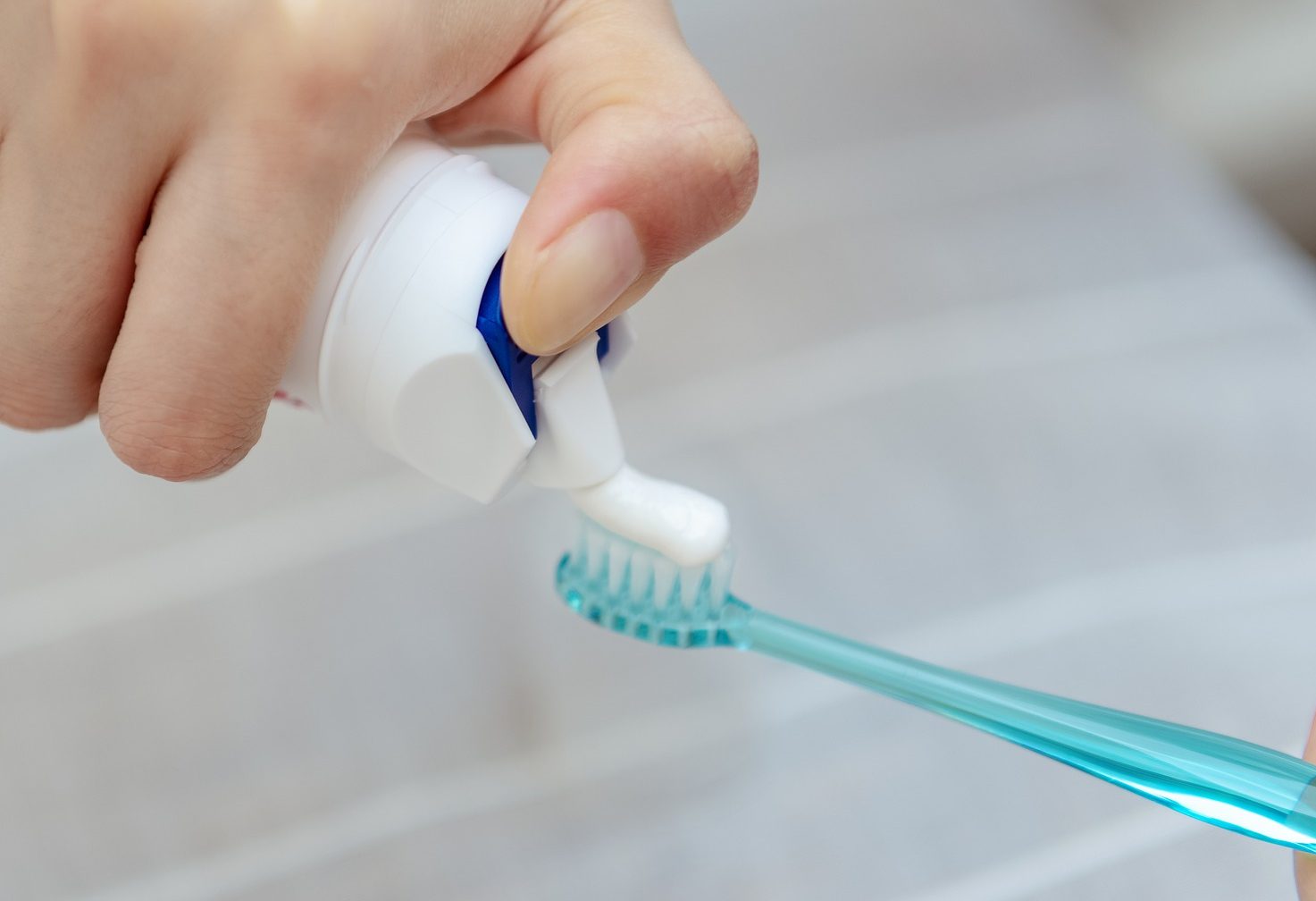
Abrasives, binding agents and humectants in toothpaste production
Thickening and binding agents give the product the right viscosity and keep the shape of the toothpaste when you push it out of the tube. Without them, you’ll have a watery, runny mixture. The third category is humectants, which help retain water and prevent the product from drying out. In addition, humectants are sweet, but not as sweet as sugar. For this reason, some manufacturers may decide to add sweeteners such as saccharine. Other ingredients include flavors, foaming agents, fluoride, and water.
Toothpaste making equipment – what do you need in your production line?
Once the chemical ingredients arrive at the plant, they are ready to be measured and weighed by a check weigher or any weighing equipment. Once you get the correct amounts, you can move on to the mixing step. You first mix the water, humectant (usually glycerin or sorbitol), and hydrophilic colloids (binders). The hydrophilic colloids swell in the presence of the water and are critical in preventing the separation of the solid and liquid phases. That is why a mixer is a crucial step in toothpaste production but also in emulsions, ointments, lotions as well as shampoo.
Now it’s time to add all the rest of the ingredients and mix everything together using a vacuum homogenizer mixer. Homogenization reduces the particles of ingredients by distributing them evenly in the liquid medium. Now it’s up to the imagination of the producers. Different coloring and flavoring agents can be added to the white paste – blue or green, mint or peach, you name it. If you want to stick to the white variety, it is the titanium dioxide that gives toothpaste its white color.
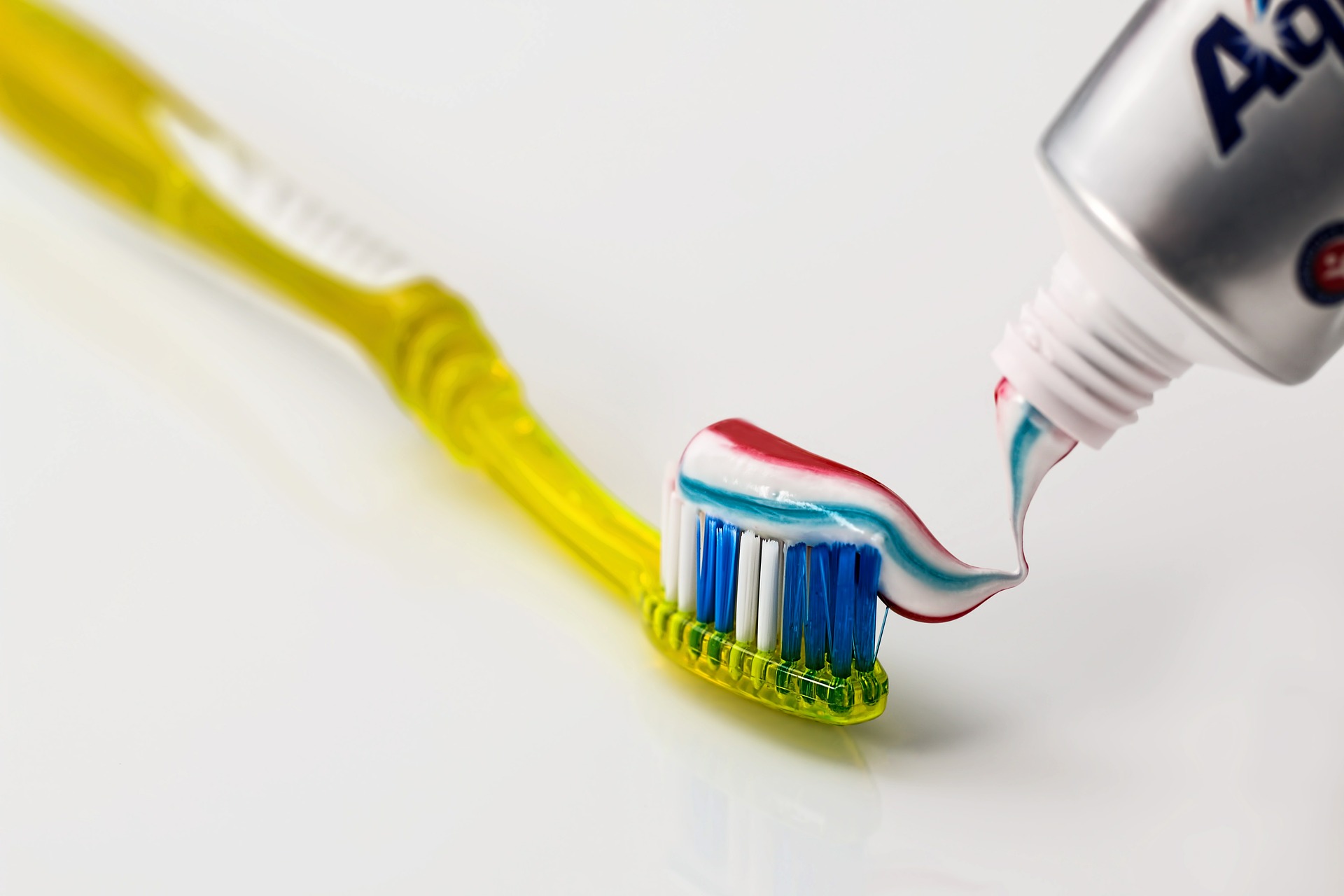
Everyone loves stripes – How to fill them in your toothpaste tube?
It’s been a while since Leonard Maraffino invented the first striped toothpaste; but since then, its popularity has only grown. Getting the stripes, as complicated as it may seem at first glance, is a very simple thing. After mixing, the toothpaste is sent to the filling station. One end is capped while the opposite end is left open for filling. The filling pump consists of three or four nozzles that inject a different color into the tube at the same time. Once the tube is filled, the machine crimps the end; so now you can pack the tubes in boxes and ship them.
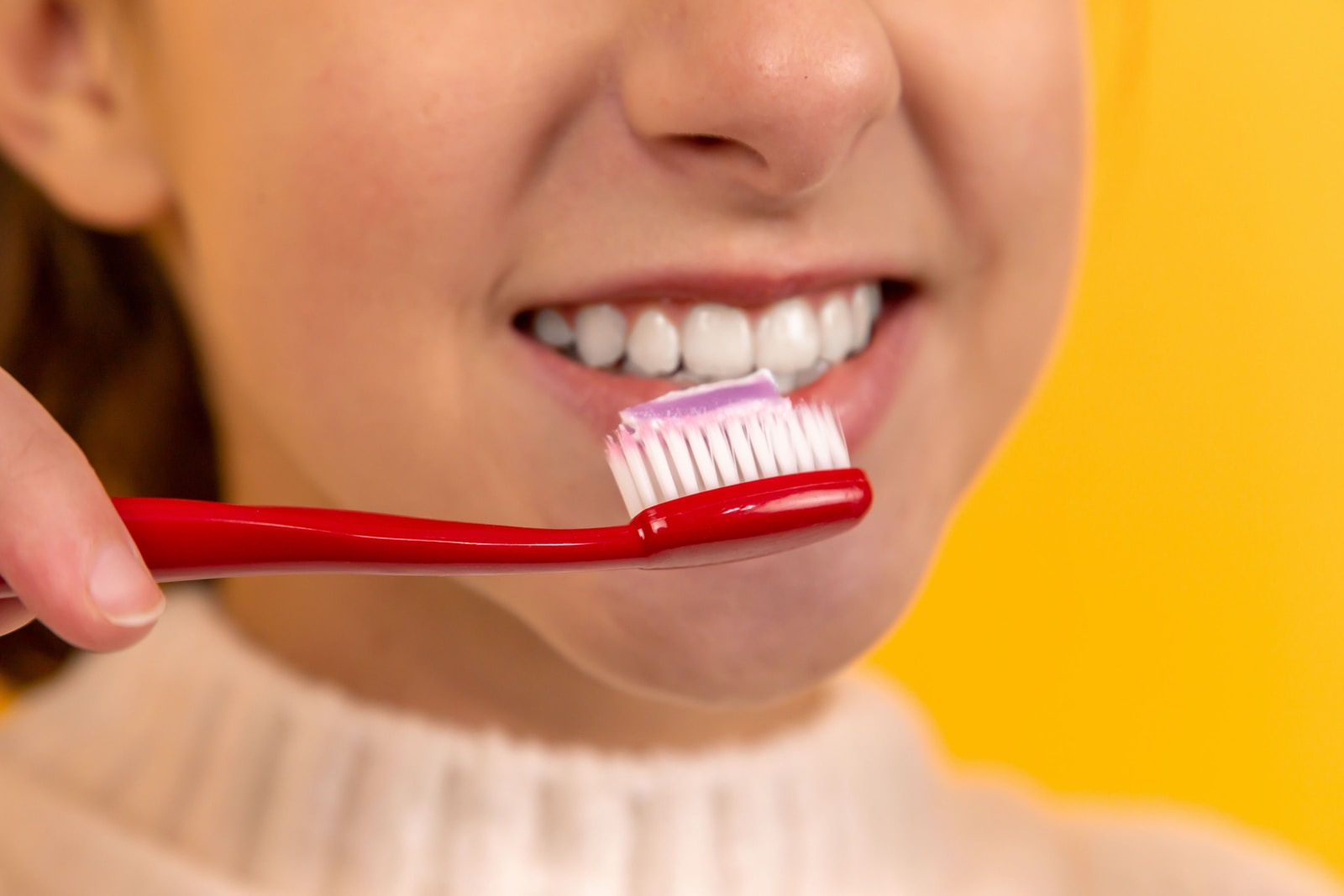
Is there any difference between adult toothpaste and children’s toothpaste?
The answer is yes. Besides the thousands of colors, fruit flavors – kids aren’t super fans of mint – and fun packaging, the key difference between the two kinds of toothpaste is the amount of fluoride. Fluoride is a naturally occurring mineral that prevents tooth decay and helps tooth enamel to be stronger. However, if it is swallowed in large amounts, fluoride can become harmful. During teeth-forming age (8 or younger) children are also more likely to develop dental fluorosis. This is the appearance of white spots on the surface of the teeth, caused by fluoride exposure.
Toothpaste making process
Toothpaste filling process
Toothpaste making process
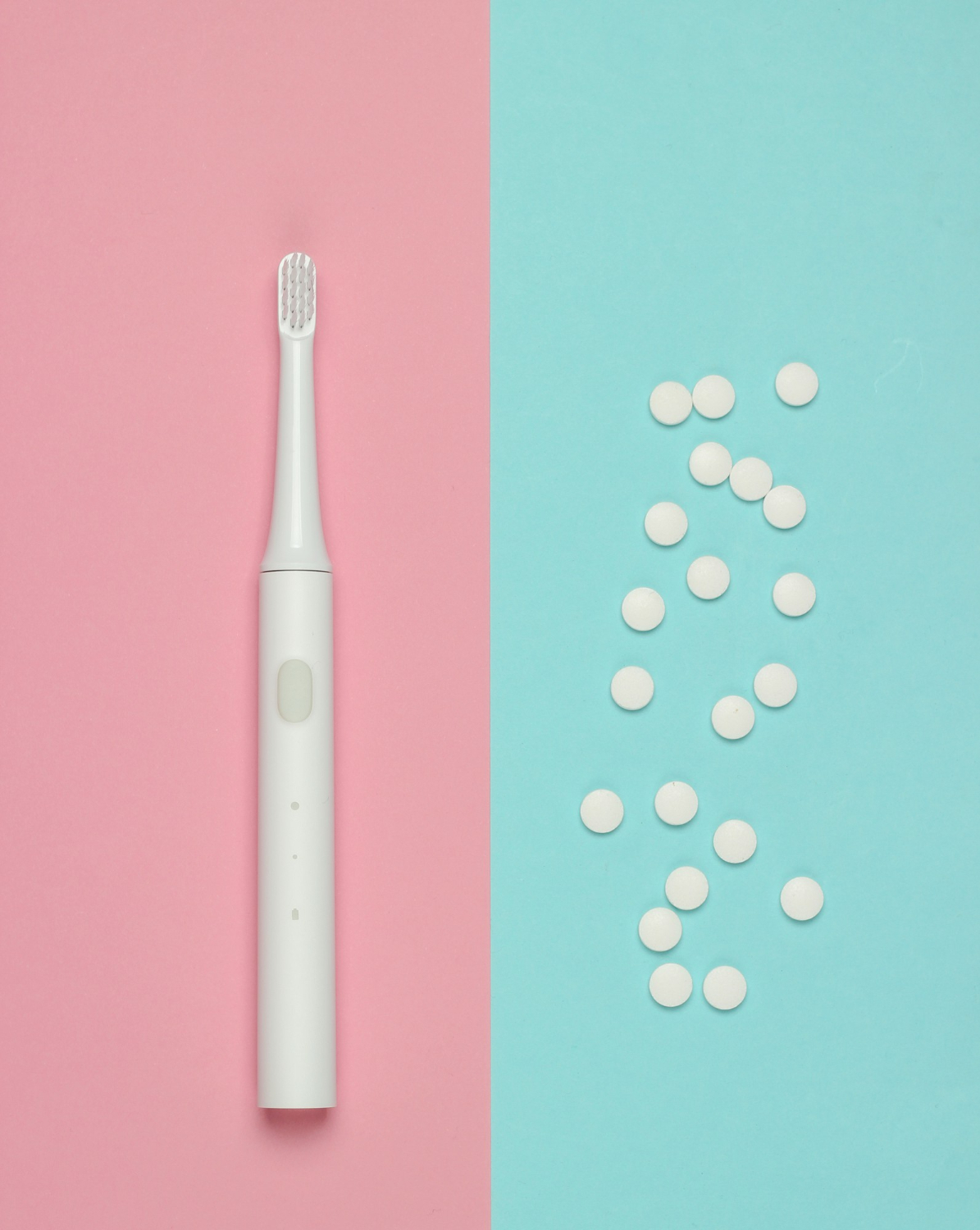
Processing toothpaste into tablet form
Around a tenth of a toothpaste tube is water in the liquid phase. Concerns about water use and transportation costs are spurring innovative products in the form of tablets. The formula typically includes anti-bacterial sweeteners like xylitol and an abrasive like precipitated calcium carbonate. Mix the base ingredients ratios of the formula. Bind the powder particles with a wet or dry agglomeration system to facilitate the processing of the toothpaste tablet. Agglomerates prevent sticking when the formula is sent for compaction and punched through the dyes.
Processing steps involved in toothpaste making
Which toothpaste technology do you need?
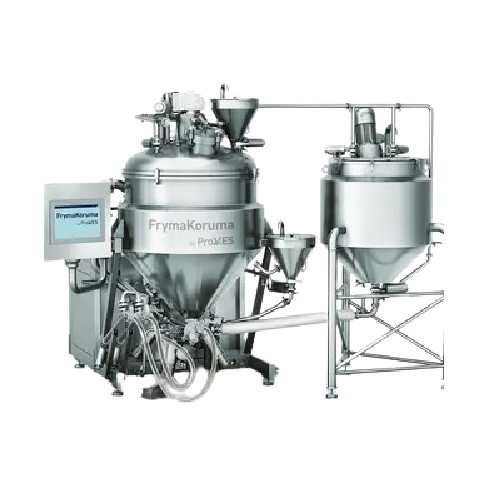
High shear emulsifier for mayonnaise production
Streamline your production of high-quality emulsions with this high-capaci...
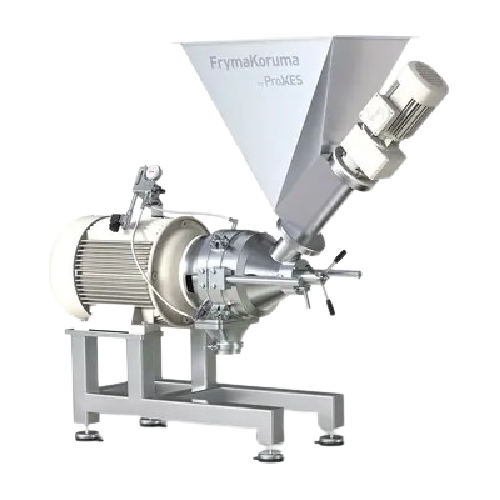
High shear emulsifier for food and pharmaceutical products
Optimize your production line with precise emulsification, ho...

Heat exchangers for efficient heat transfer in industry
Achieve precise temperature control across diverse viscosities wi...
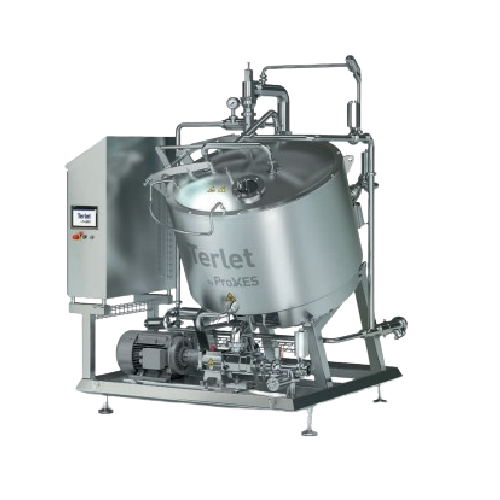
Precise liquid cooling solution for food processing
Ensure high-quality preservation of flavors and textures in liquid fo...
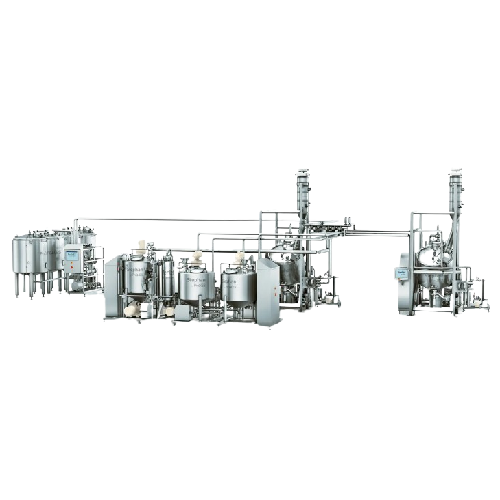
Continuous nut paste production line
Elevate your production efficiency with a versatile preparation line designed to seaml...
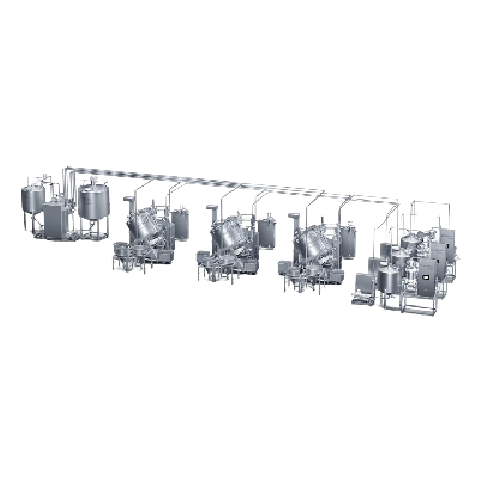
Continuous mustard production line
Optimize your condiment production with precision-engineered systems capable of transfor...
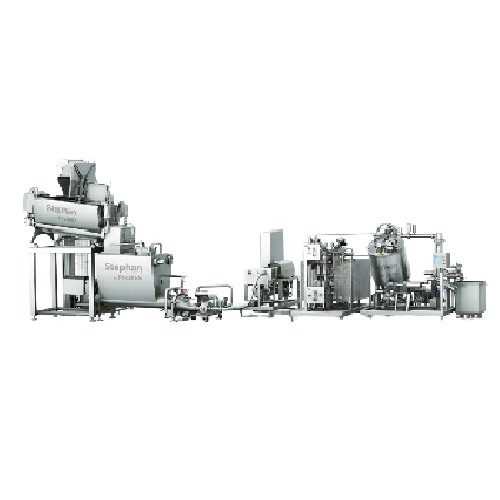
Cheese blending and heating line for processed cheese
Optimize your processed cheese production with a solution that seam...
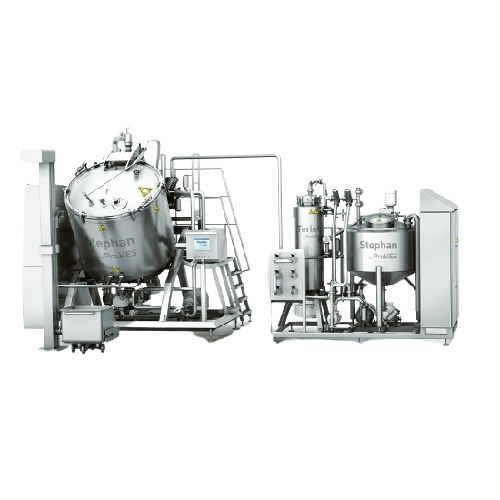
Continuous caramel production line
Optimize your caramel production with seamless integration, achieving precise fat meltin...
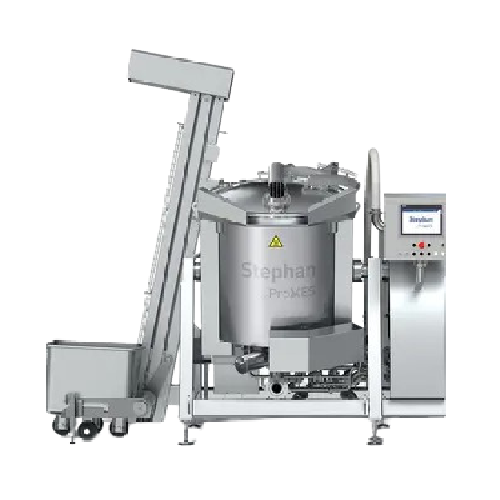
Industrial cooker for sauces and stews
When producing diverse culinary delights such as sauces and stews, achieving even he...
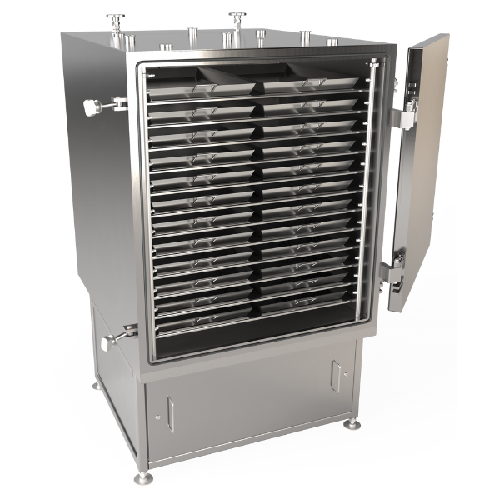
Continuous heat exchanger for soups and sauces
Optimize your soup and sauce production with a continuous heat exchanger th...
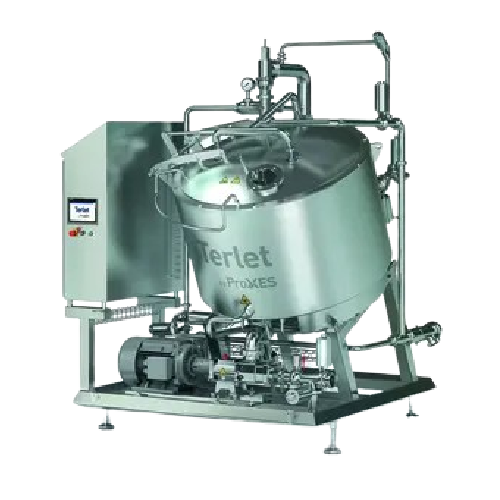
Efficient cooling and cooking systems for food processing
Streamline your production with integrated cooling and cooking...
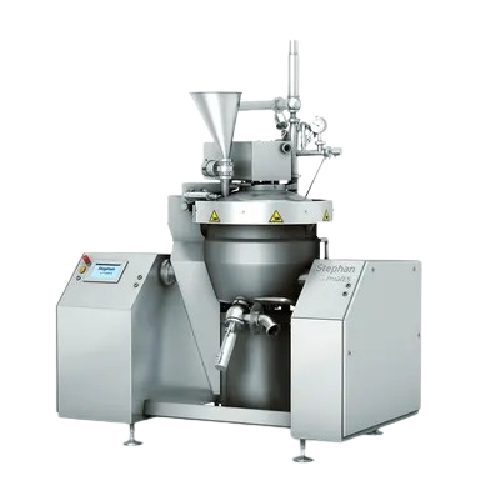
Industrial cutting system for fine emulsions
Optimize your production line with precision cutting and emulsifying, ensurin...
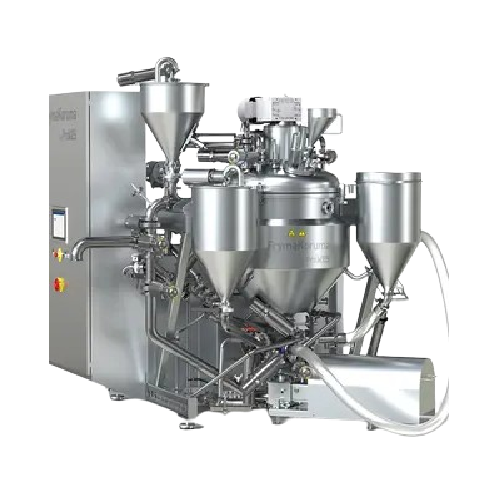
Vacuum deaeration system for mustard and liquid detergents
Ensure optimal product quality by effectively removing air fr...
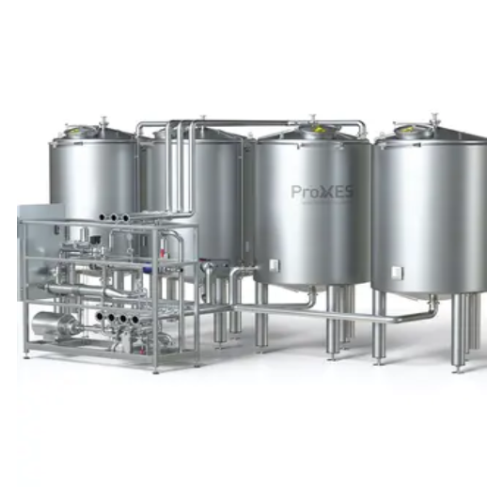
Cleaning systems for food, pharmaceuticals, and cosmetics
Ensure optimal hygiene and safety with advanced cleaning syste...
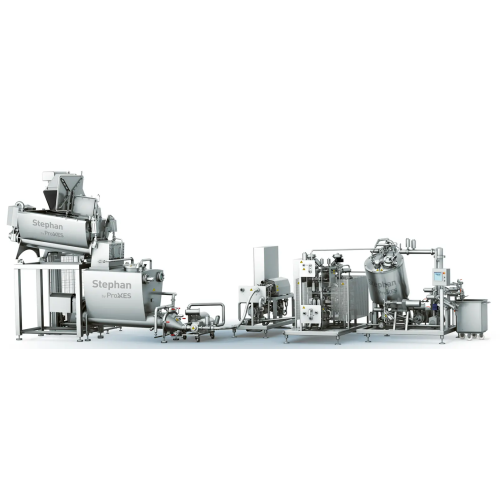
Continuous caramel process line
Optimize your continuous food processing with an engineered-to-order line tailored for preci...
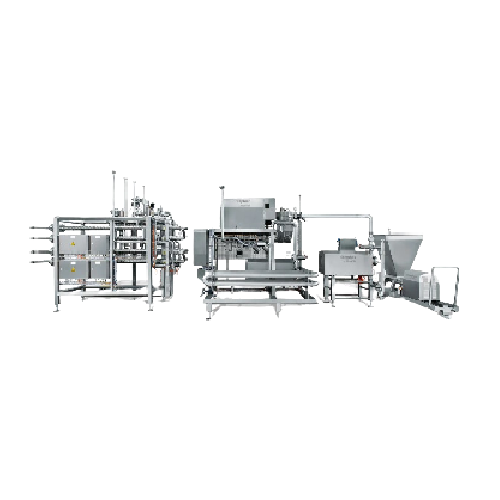
Continuous cheese line
Achieve precise temperature control and seamless product transitions with this equipment, ideal for en...
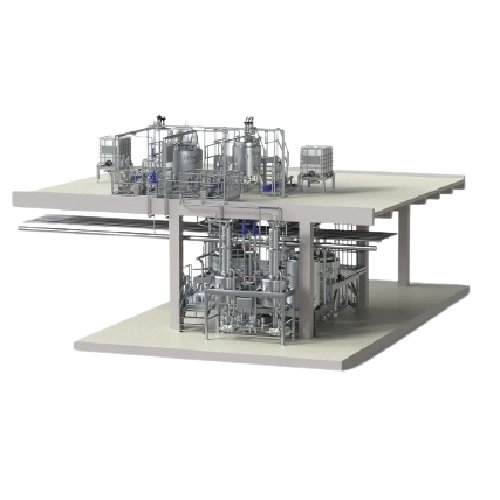
Continuous mustard line
Streamline mustard production with high-capacity continuous processing that reduces air pockets and e...

Continuous tahina production line
Streamline your tahina production with precise grinding and controlled cooling, ensuring ...
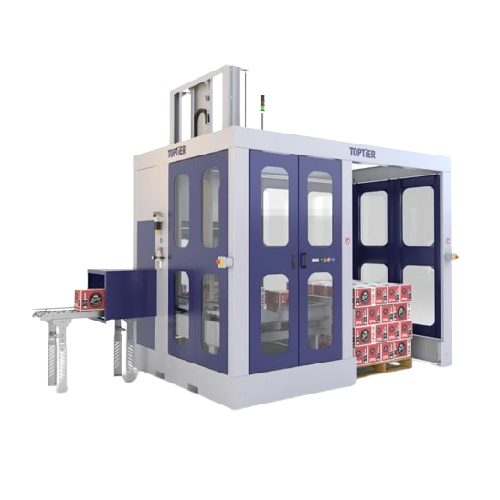
Robotic palletizing solution with smallest footprint
Optimize your production line with a space-efficient robotic palleti...
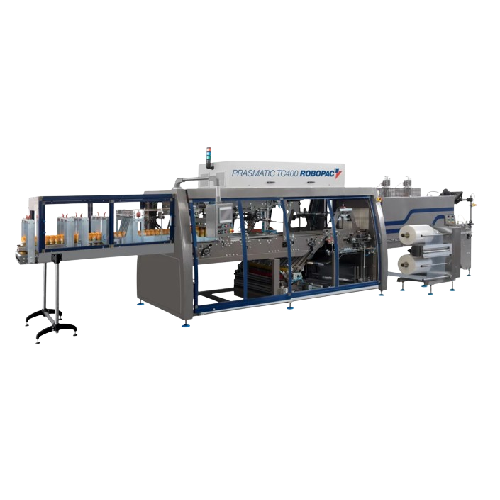
Medium-speed shrink-wrapping solution for various packaging types
Streamline your end-line packaging with a modular shr...
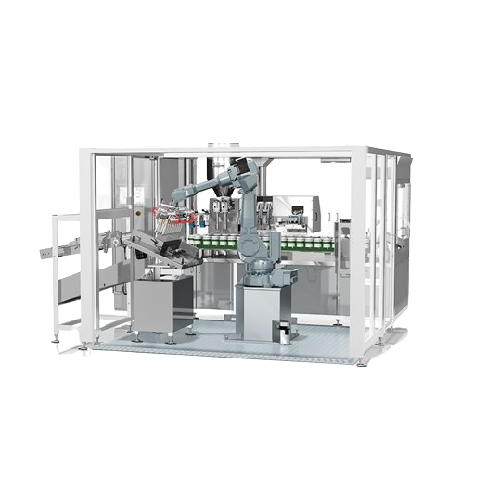
Tube filling machine for cosmetics and food products
Achieve precise and efficient packaging with this advanced twin-head...
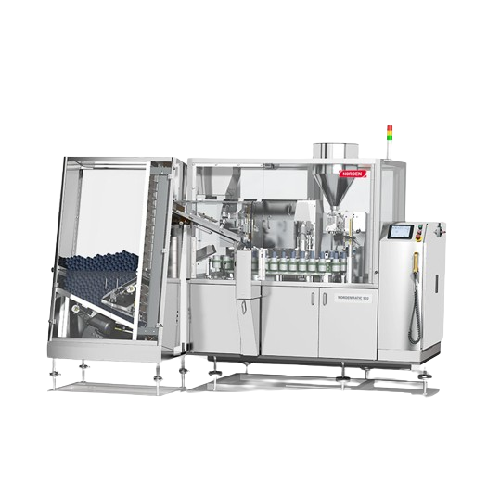
Tube filling solution for plastic, laminate, and aluminum tubes
Optimize your production line with a versatile tube fill...
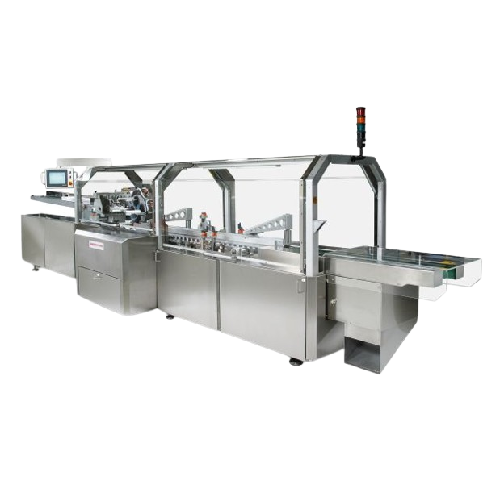
Hig Speed Tube Cartoner
Achieve seamless integration into your high-speed packaging line with a cartoning solution that ensur...
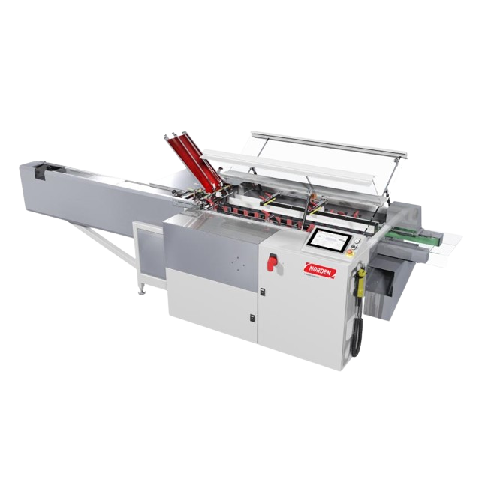
Cartoning solution for tube applications
Streamline your cartoning operations with a machine designed for flexible size cha...
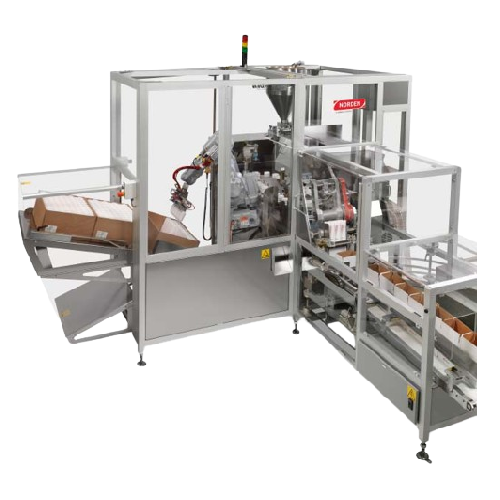
Pick & place robot for packing tubes in boxes
Efficiently streamline your packaging line with this compact case packer, de...
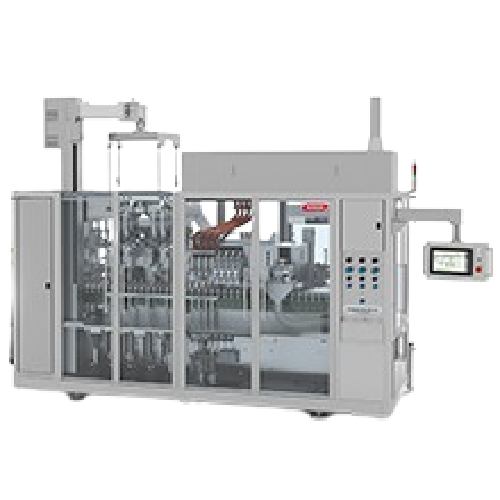
Tube filling station for plastic, laminate, and aluminum tubes
Efficiently seal and fill various tube materials, ensurin...
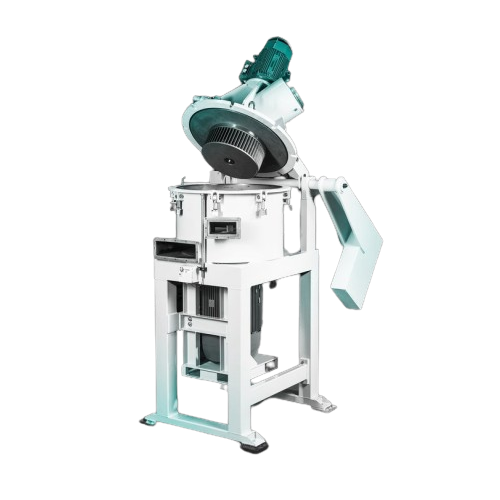
Energy-efficient impact classifier for superfine grinding
Achieve precise superfine grinding with energy efficiency, per...
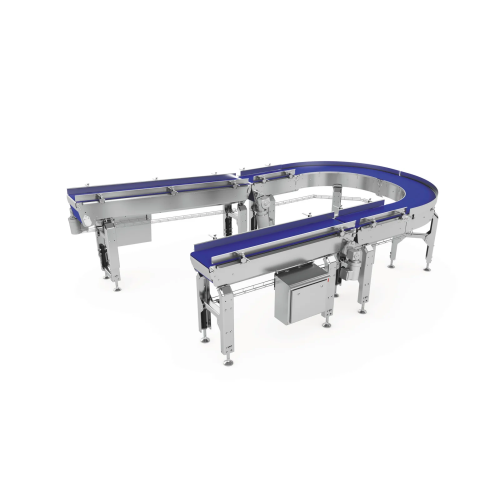
Automated conveyor systems for food packaging lines
Seamlessly integrate high-speed product transport and handling into y...
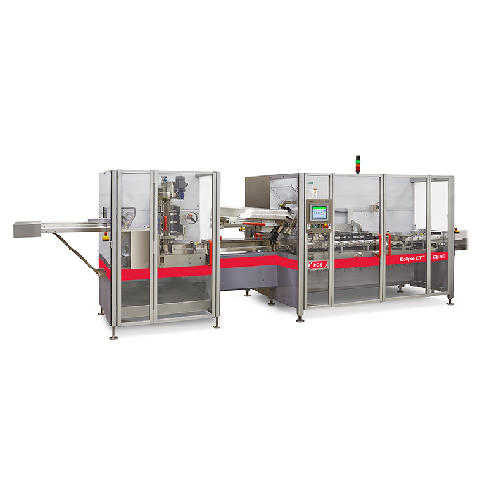
Horizontal cartoner for diverse industries
Streamline your packaging process with precise cartoning capabilities, effectiv...
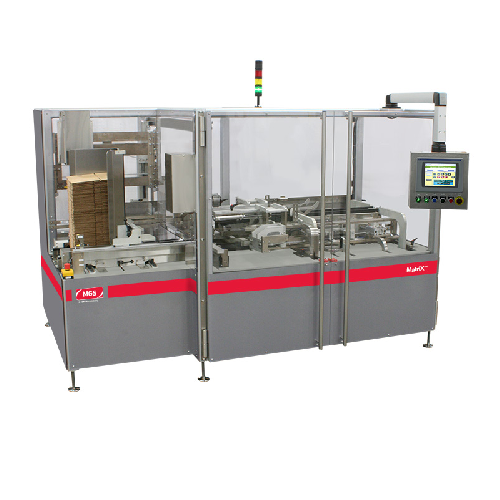
Case packer for pharmaceutical and healthcare products
Streamline your packaging line with a versatile case packer design...
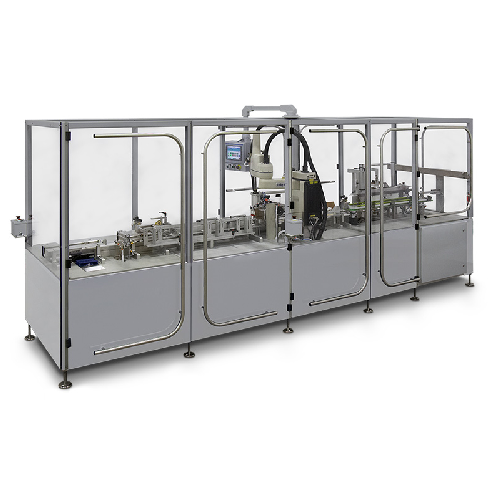
Top load cartoning system for pharmaceuticals
Optimize your packaging line with precision top-load cartoning, designed for...
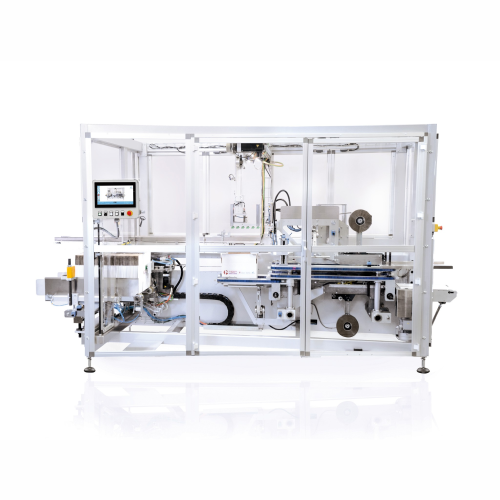
Automatic top load case packer for bottles and jars
Streamline your packaging process with reliable case packing for prod...
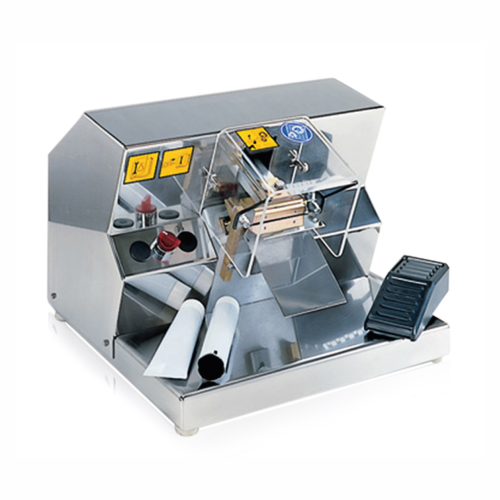
Metal tube crimping system
Optimize your packaging line with this semi-automatic system designed to efficiently crimp metal ...
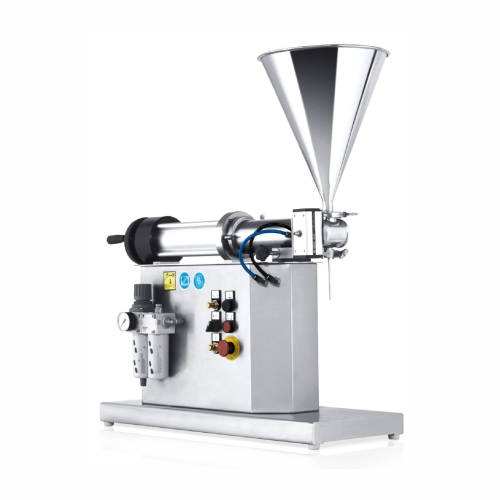
Laboratory filling system for liquid and creamy products
Optimize your laboratory processes by precisely handling liquid,...
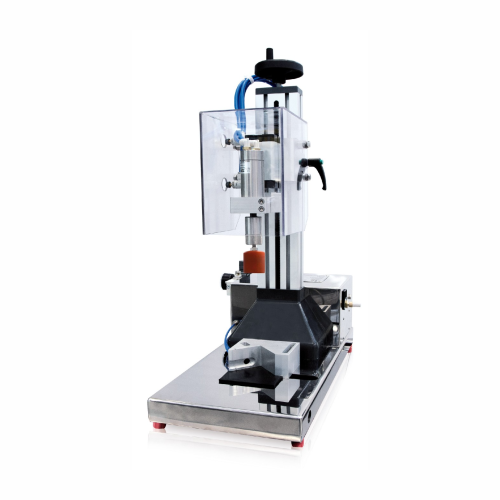
Semi-automatic screw capper for bottles and jars
Ensure your packaging line operates smoothly by seamlessly capping a wide...
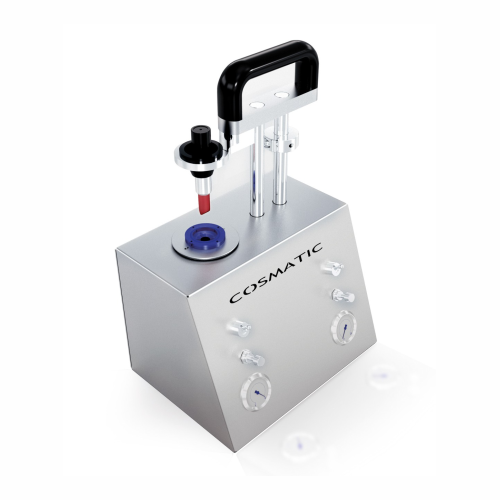
Laboratory demoulding unit for lipstick samples
Streamline your laboratory’s lipstick sampling process with a versat...

Automatic tube filling and closing for metal, plastic, and laminate tubes
Enhance your production efficiency with a hi...
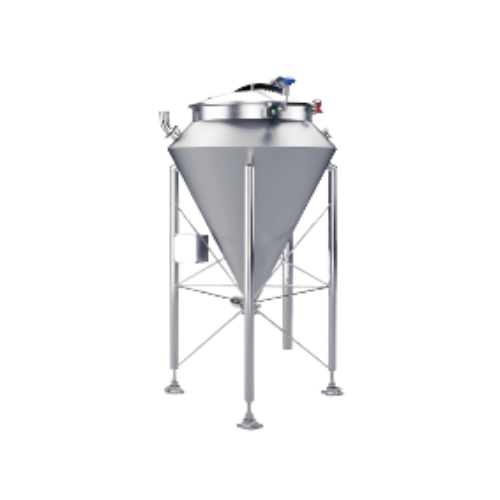
Precision weighing tank for liquid and dry ingredient blending
Enhance your production line with precision control over ...
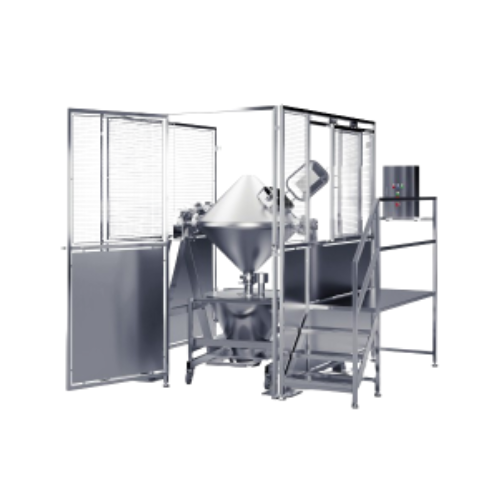
Industrial powder blender
Optimize your production with precise dry blending, ensuring efficient mixing processes and seamle...
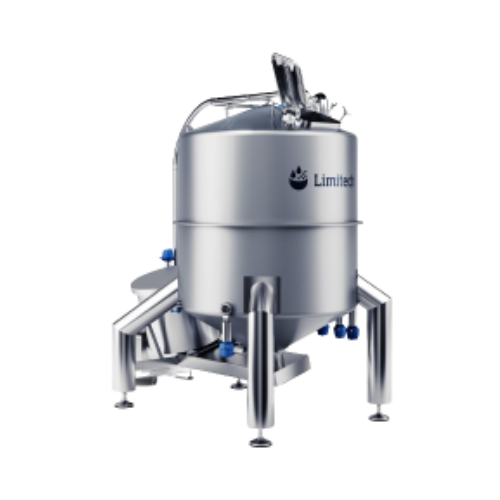
High shear mixer for viscous powder dissolution
Need consistent, homogeneous blending of high-viscosity liquids and powder...
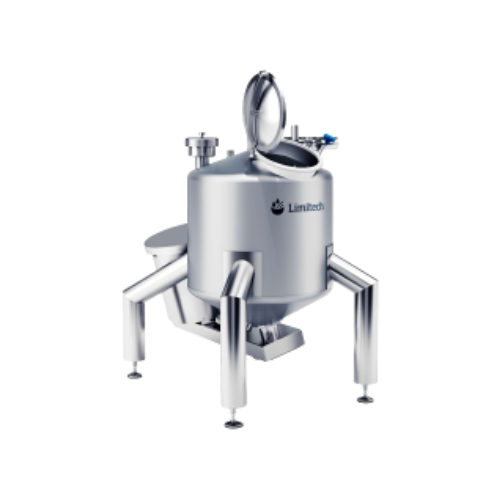
Industrial mixer for high shear mixing and emulsifying
Enhance your production line efficiency with versatile high shear ...
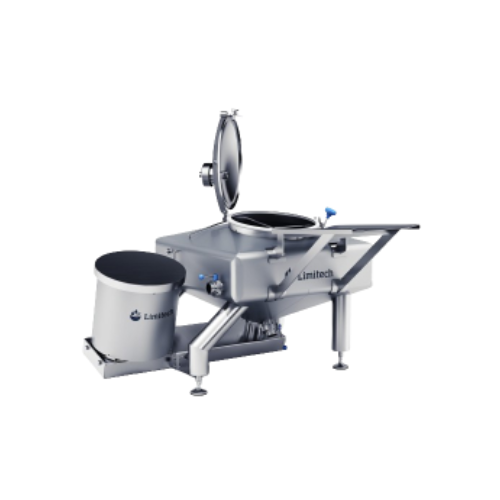
Batch mixer for dry and liquid ingredients
Achieve efficient blending of diverse ingredients with high shear mixing to str...
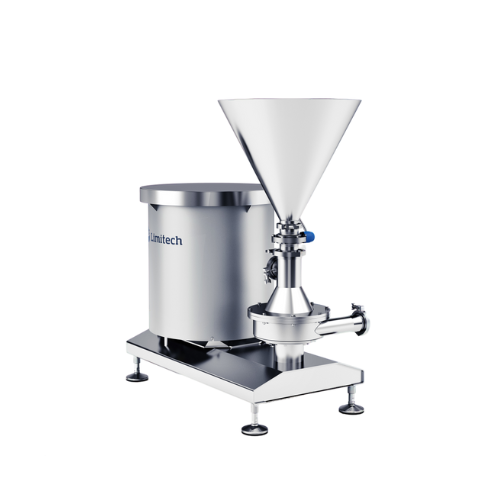
High-shear inline mixer for lump-free products
Achieve consistent texture and prevent clumping in liquid and powder blends...

Pre-mixer for dissolving powders fast
Quickly dissolve powders without lumps or “fisheyes,” ensuring a smooth a...
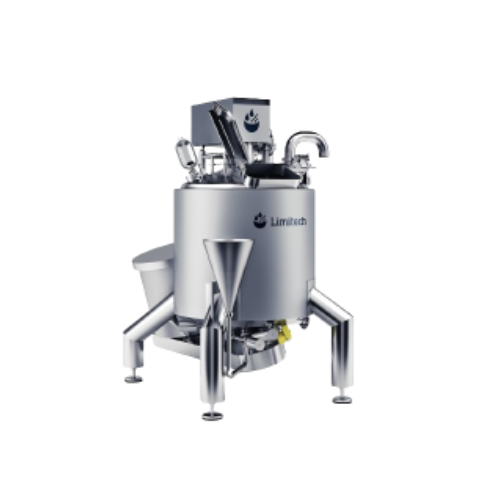
Process mixer for food production
Optimize your production line with a versatile and adaptable process mixer that offers se...
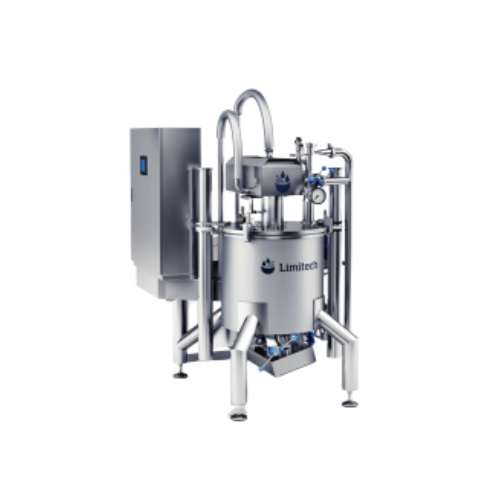
Multifunctional mixer for high volume batches
Efficiently handle complex mixing, emulsifying, and homogenizing tasks with ...
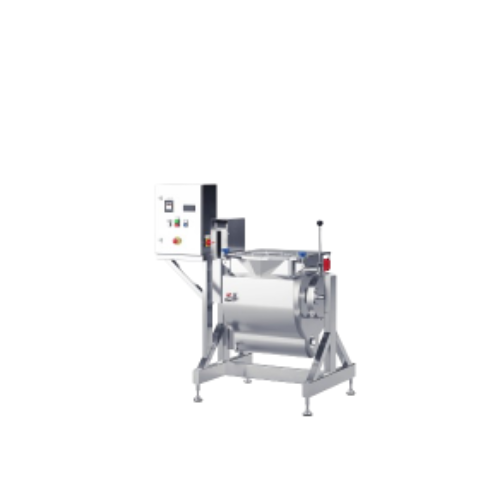
Industrial melting tank for diverse manufacturing applications
Optimize your production with this versatile melting tank...
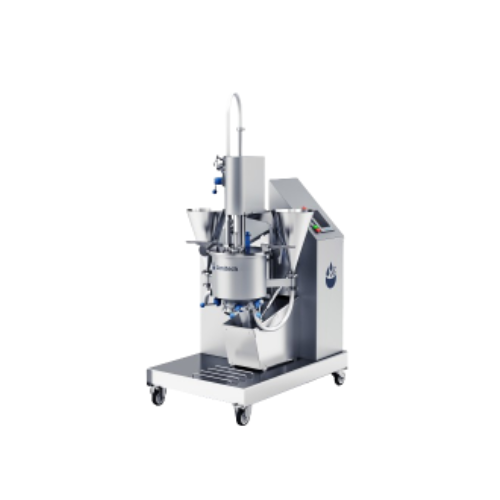
Blender for high viscous products
Tackle high-viscosity challenges with an advanced blending solution designed for efficien...

Customized oil storage tank for industrial use
Enhance production efficiency and ensure seamless integration with customiz...
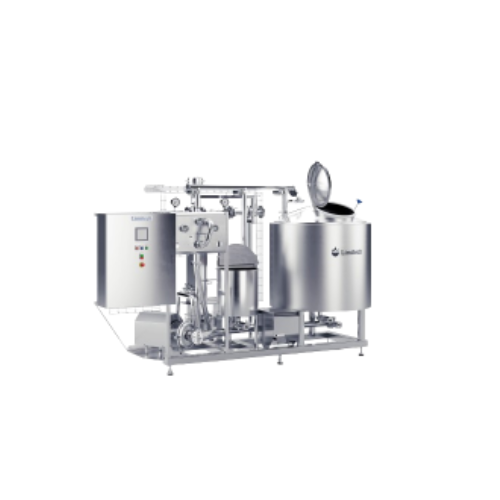
Cip dosing and water unit for industrial cleaning
Elevate your plant’s hygiene with this system, designed for seaml...
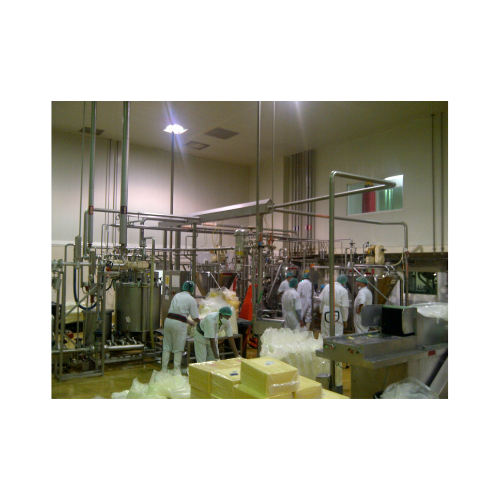
Ultra high temperature treatment system
Achieve extended shelf life and product stability with ultra high temperature treat...
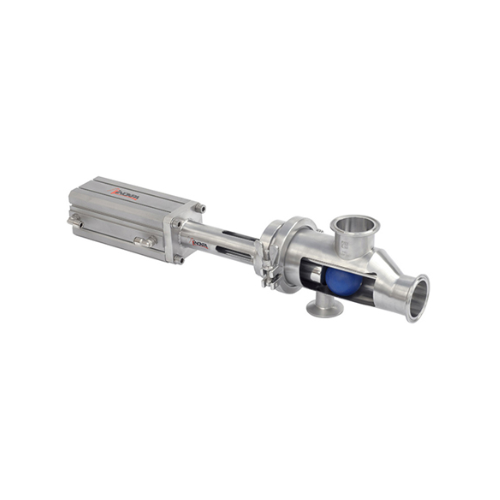
Sanitary pigging system for viscous food products
Efficiently recover high-value viscous products like chocolates and cre...
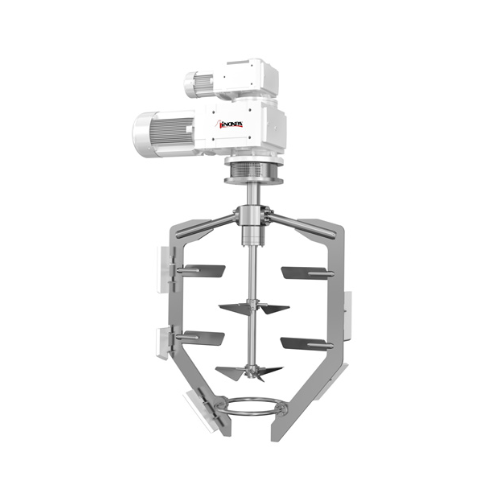
Counter-rotating agitator for high viscosity products
Achieve seamless heat transfer and precise mixing with a counter-ro...
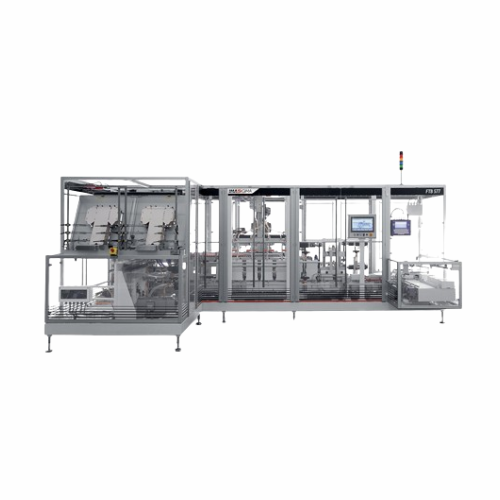
Top loading cartoner for variable box sizes
Achieve precision packaging with a versatile top-loading cartoner that adapts ...
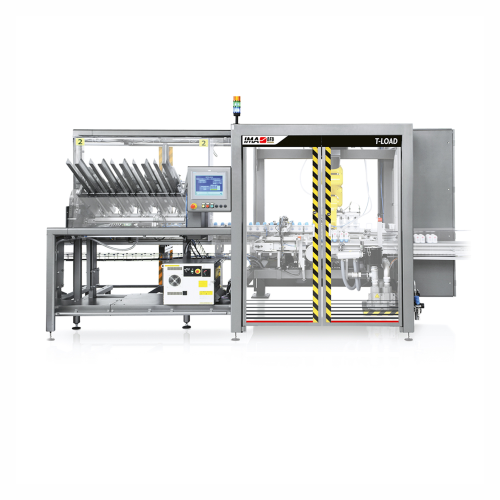
Robotic system for loading personal care products
Enhance efficiency and precision in your packaging line with a robotic ...
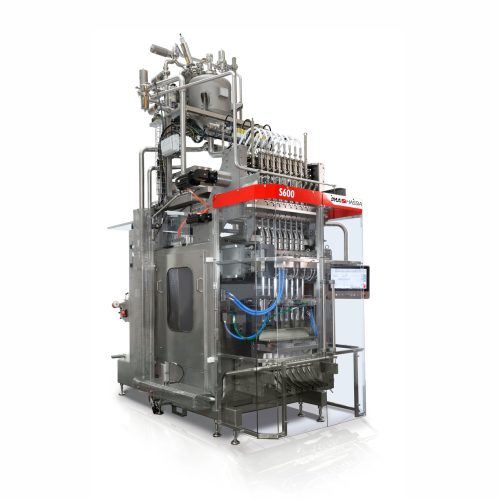
Stick pack forming, filling, and sealing solution
Enhance packaging efficiency with a high-speed solution designed for pr...
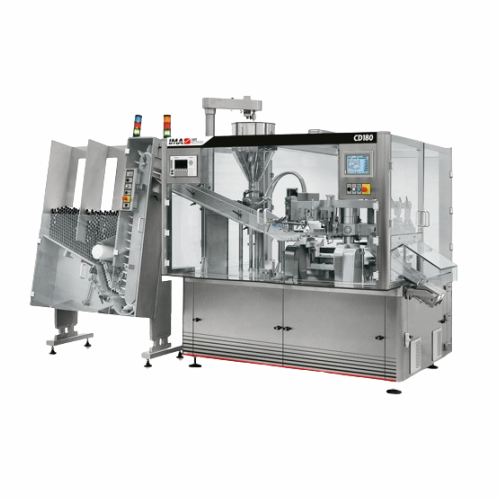
Automatic tubefiller for food and dairy products
Achieve precise dosing and seamless tube filling with high-speed efficien...
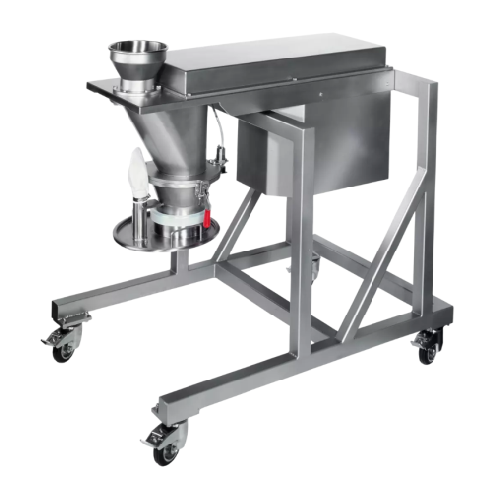
Flake crushers for gentle crushing of brittle materials
For processes needing precise granule control, our equipment ensu...
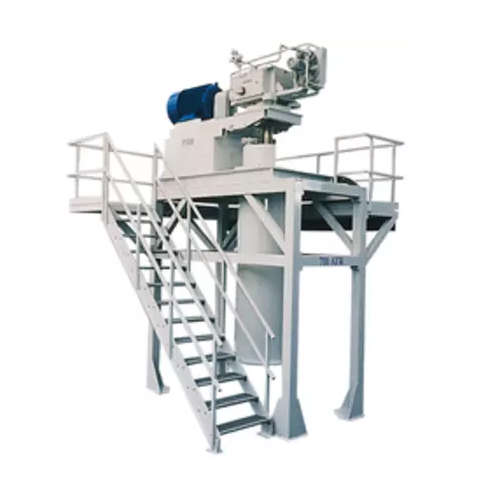
Ultra-fine grinding with ball mills and agitated media mills
Achieve precision in ultra-fine grinding for demanding mate...
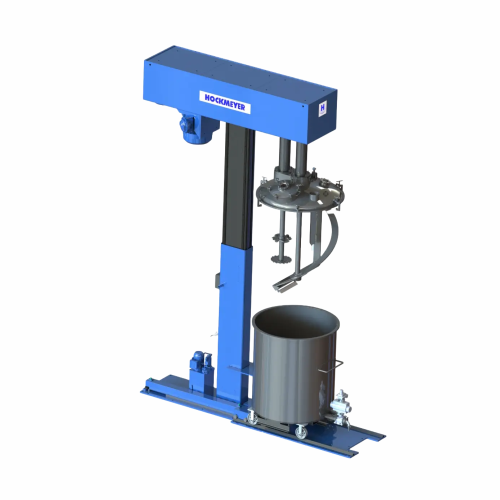
Dual shaft mixer for high viscosity products
Achieve uniform dispersions in high-viscosity processes with a dual-shaft mix...
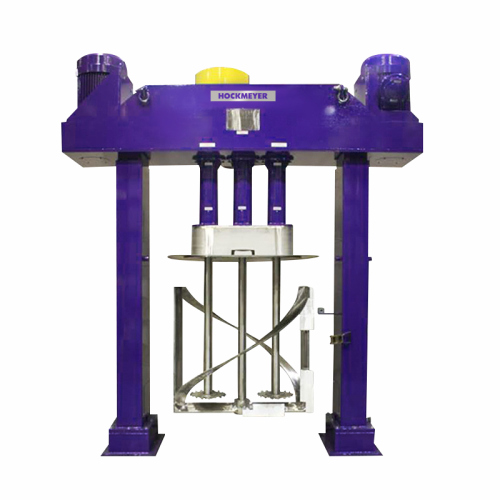
Triple shaft mixer for high viscosity products
Achieve uniform mixing and dispersion for high-viscosity materials with tri...
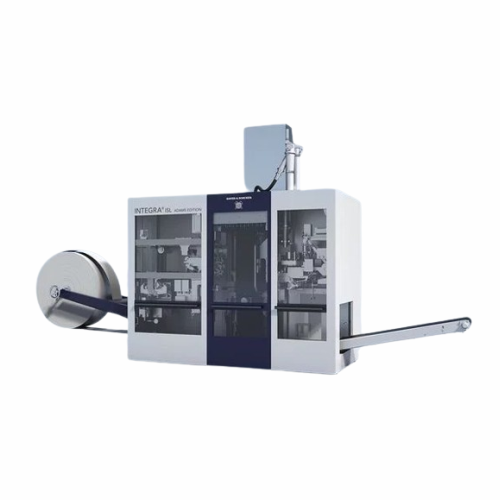
Integrated packaging system for cement and building materials
Streamline your packing operations with a fully enclosed s...
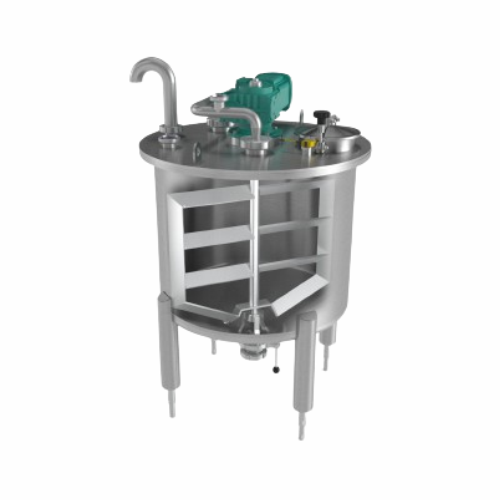
Stainless steel buffer tanks for food, pharma, and cosmetics
Ideal for maintaining process fluidity, these stainless ste...
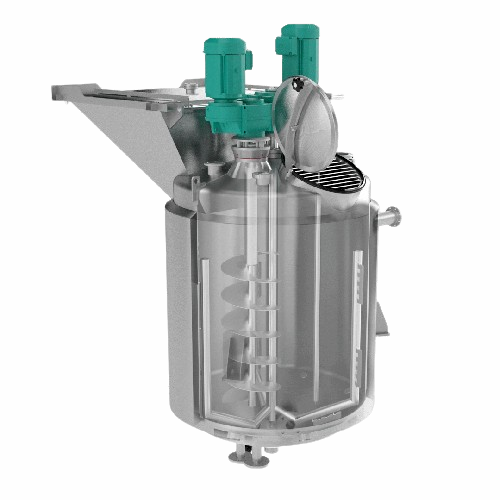
Stainless steel cooking kettle for food, pharma, and cosmetics
Efficiently streamline your production with versatile sta...

Stainless steel agitators for pharmaceutical and food applications
Optimize your production line with tailored agitator...
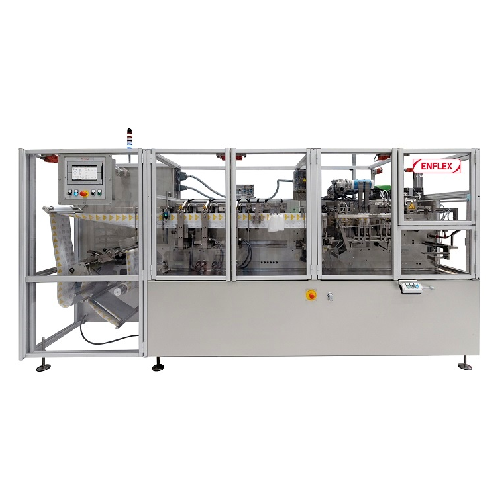
Horizontal flat pouching system for liquid soaps
Optimize your liquid packaging with high-speed, continuous operations tha...
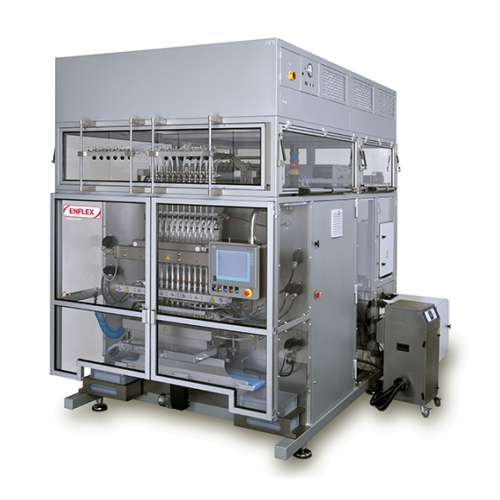
Intermittent stick pack machine for pharma and healthcare
Looking to streamline your packaging operations with high-spee...
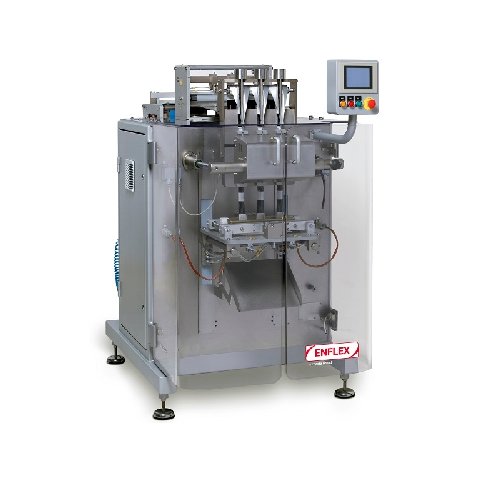
Intermittent stick pack packaging system for pharma products
Achieve precise dosage and packaging of pharmaceutical and ...
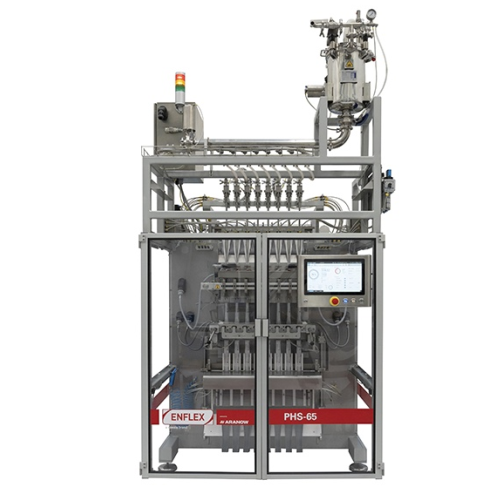
Intermittent stick pack system for pharmaceuticals
Effortlessly streamline your packaging process with a high-speed, mult...

High-speed multi-lane flat pouch packaging system
Boost your packaging efficiency with a high-speed solution designed for...
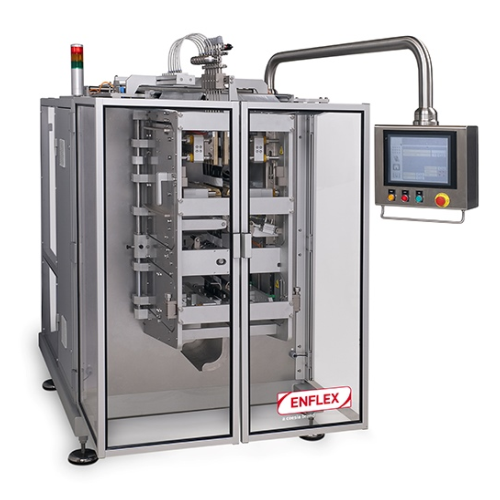
Multi-lane vertical pouching solution for pharma industry
Achieve precision and high-speed efficiency in single-dose liq...
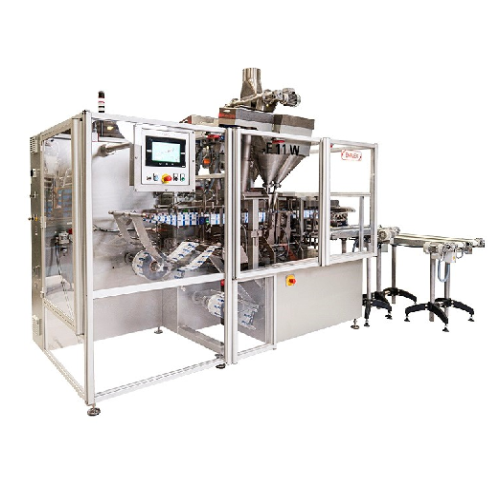
Horizontal flat pouching line for liquid soaps
Streamline your liquid product packaging with a dual-lane flat pouching lin...
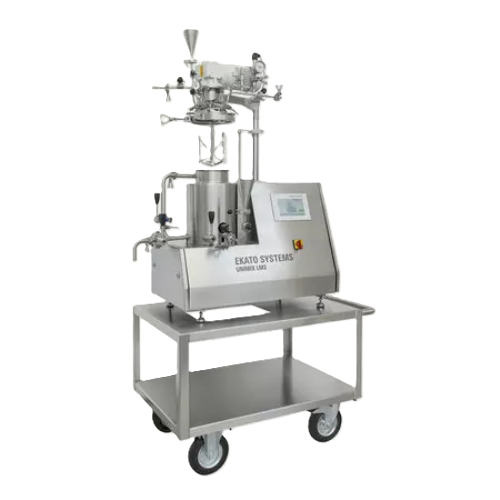
Vacuum processing units for lab scale applications
Optimize the development and scaling of cosmetic and pharmaceutical pr...
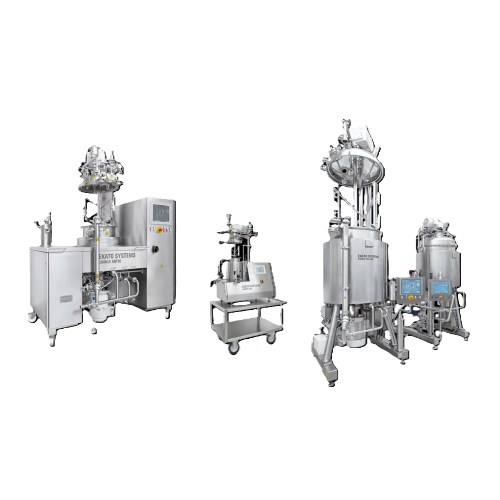
Vacuum processing units for high-viscosity products
For manufacturers seeking to streamline production of high-viscosity ...
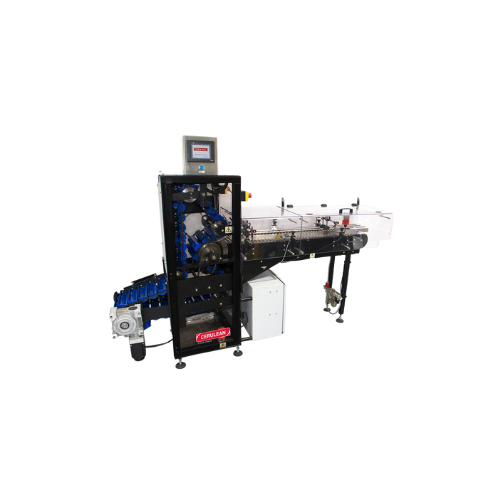
Tube in-feed conveyor for cosmetic packaging lines
Streamline your packaging process with precision by efficiently transf...
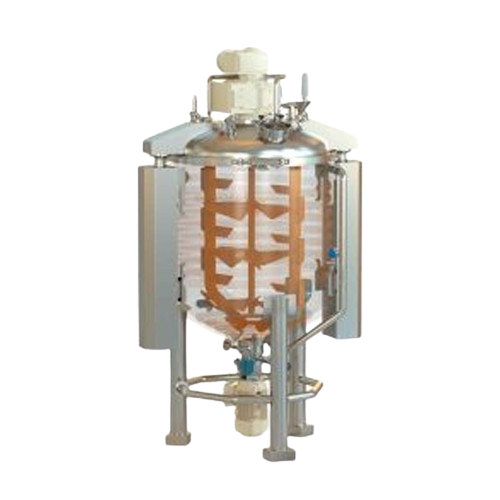
Industrial mixer for liquid and viscous products
Achieve precise mixing and homogenization of high-viscosity liquids and s...
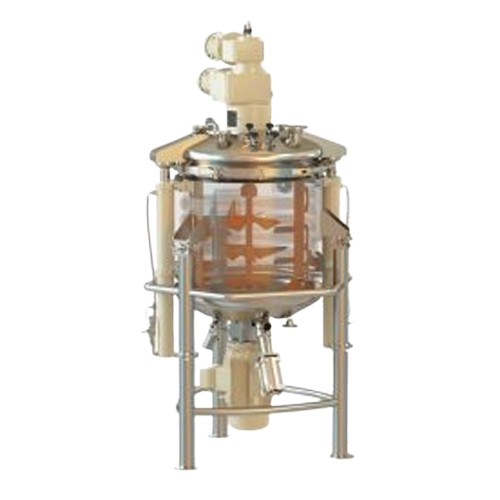
Industrial vacuum mixer and reactor for liquids
For manufacturers needing precise blending and stability, this advanced va...
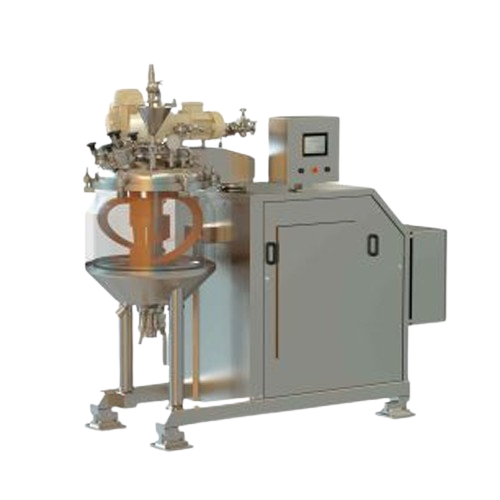
Vacuum mixer for liquids and semi-solids
Achieve precise mixing and homogenization of liquid and semi-solid formulations wi...
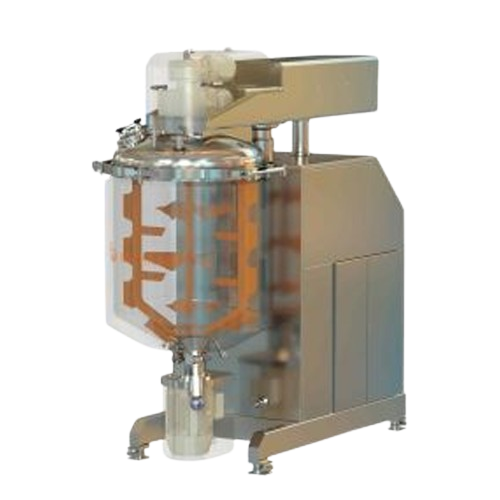
Vacuum mixer reactor for liquids and semi-solids
Achieve precise mixing and emulsification of complex liquid formulations ...
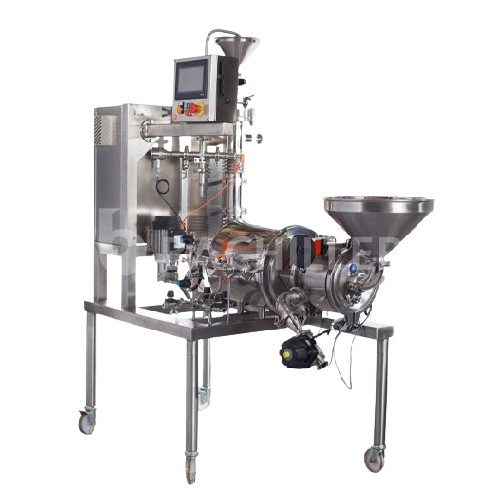
Colloidal mill for fine grinding and homogenisation
Optimize your liquid and semi-solid processing by achieving precise p...
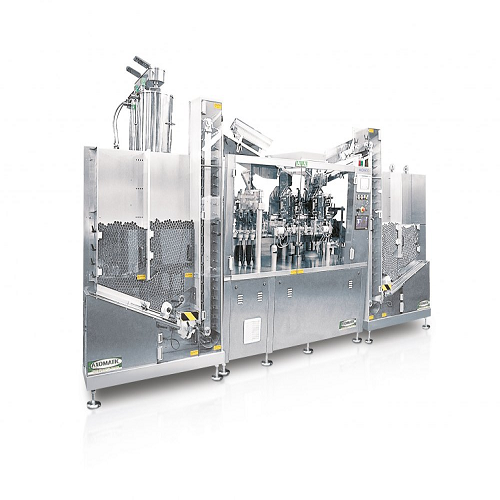
Automatic tube filling and closing system
Enhance production efficiency with a high-speed tube filling and closing system ...
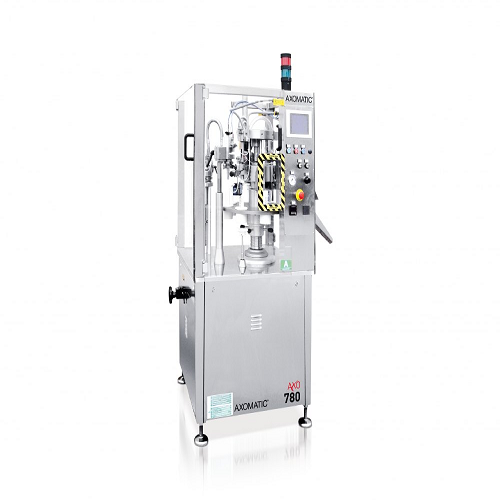
Semi-automatic tube filling and closing system
Achieve precise filling and secure closing for diverse tube types, optimizi...
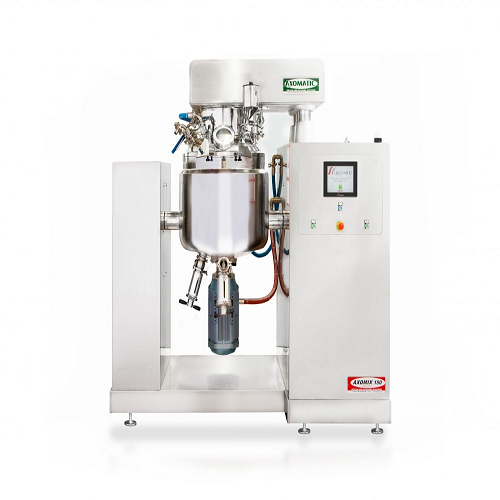
Vacuum homogenizer for high-quality mixing and emulsification
Achieve optimal consistency and enhanced product stability...
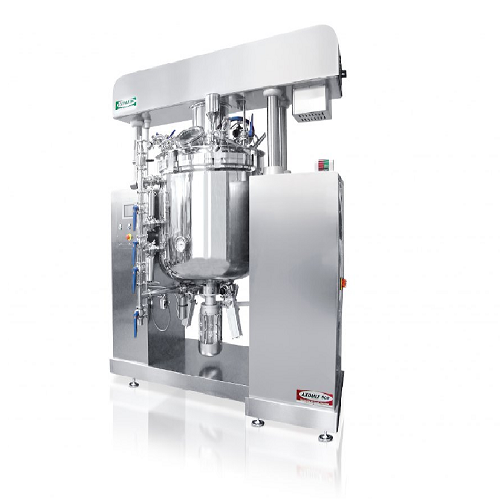
Undervacuum homogenizer for cosmetic and pharmaceutical creams
Optimizing the production of creams and lotions, this und...

Manual sealing machine for aluminum tubes
Ideal for laboratories and small-scale production, this compact manual sealing m...
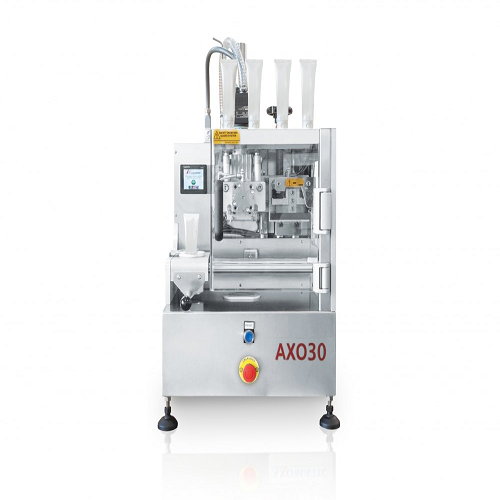
Manual tube sealer for plastic and laminated tubes
Secure precise and reliable seals on plastic and laminated tubes with ...
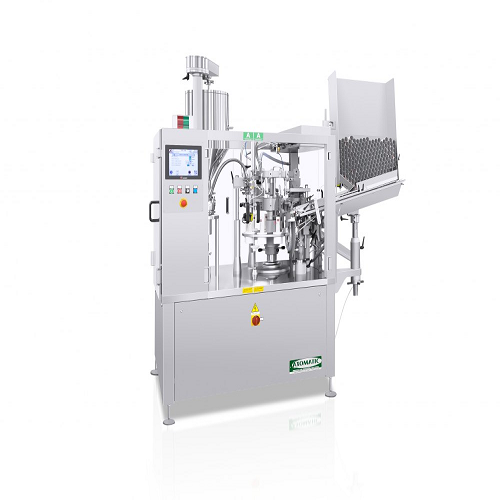
Automatic tube filling and closing solution
Optimize your production line with a high-speed machine for precise tube filli...
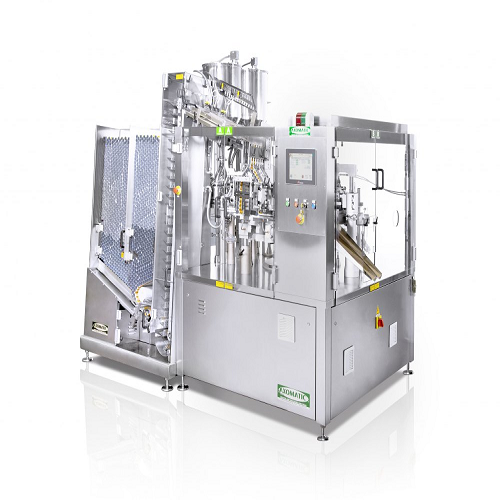
Automatic tube filling and closing system
Enhance your packaging efficiency with a high-speed tube filling and closing sol...
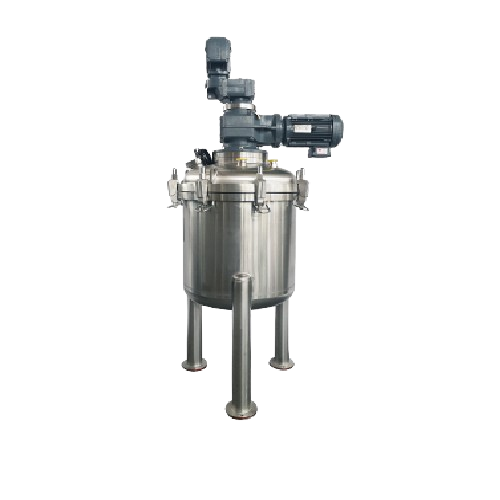
High viscosity product mixer
Struggling with mixing high viscosity products like creams and gels? This co-axial mixer enhanc...
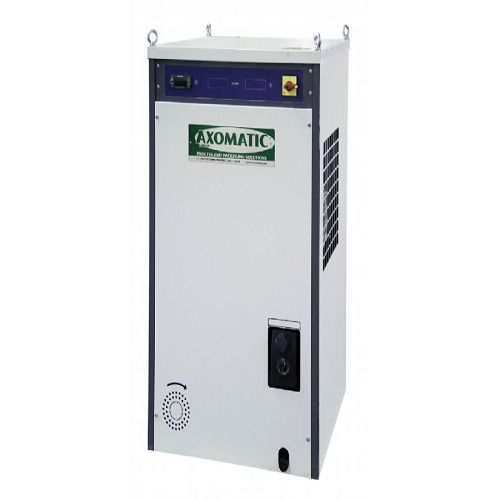
Industrial water chiller for homogenizers and filling machines
Optimize your production line with customizable water chi...
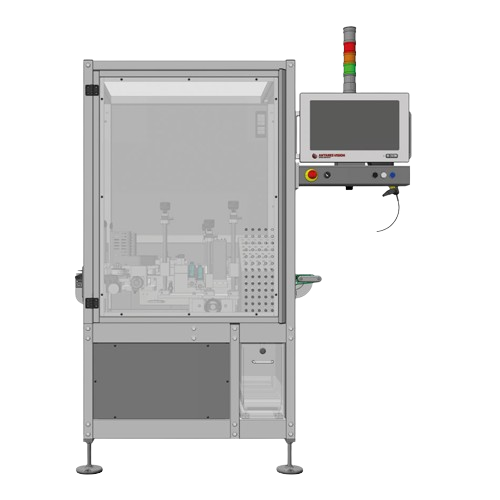
Serialization system for printing and verifying carton codes
Ensure accurate serialization with high-speed printing and ...
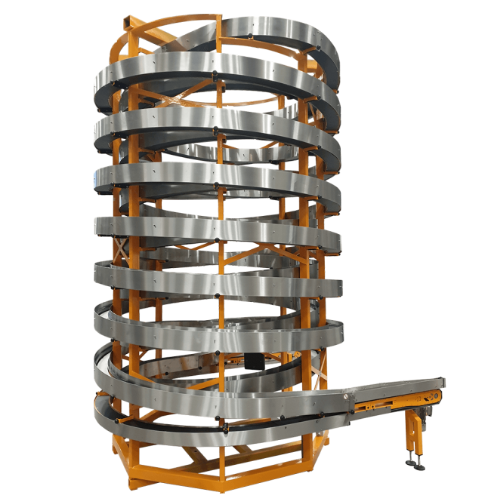
Compact accumulation conveyor for liquid containers
Optimize your space with an ultra-compact conveyor that ensures seaml...
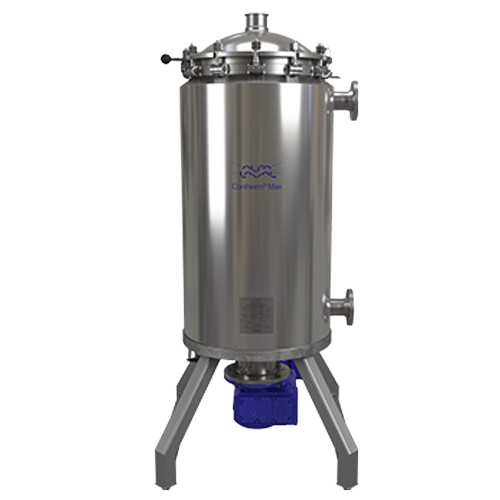
Double-wall scraped surface heat exchanger
Achieve high-capacity processing with gentle handling for shear-sensitive produ...

Scraped surface heat exchanger for viscous products
Efficiently handle challenging viscosities and heat-sensitive product...
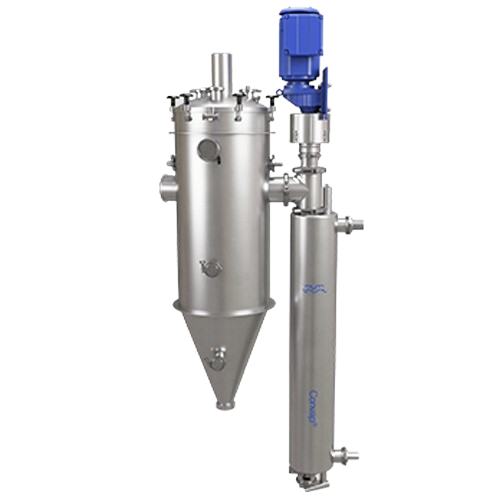
Scraped surface evaporator for high-viscosity materials
Efficiently concentrate high-viscosity and hard-to-handle materia...
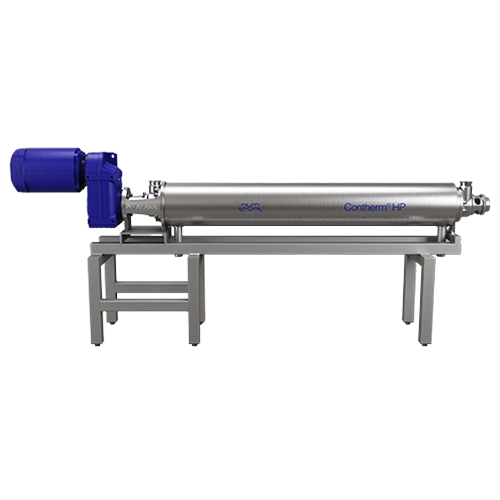
Scraped surface heat exchanger for high-pressure applications
Handle high-viscosity and particulate-rich products with p...
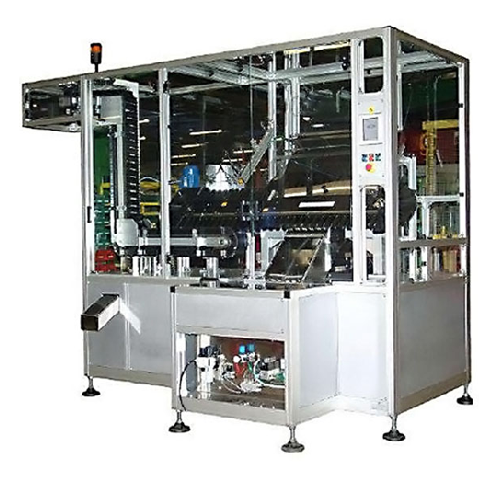
Tube feeder for pharmaceutical and personal care industries
Optimize your production line with this high-speed tube feed...
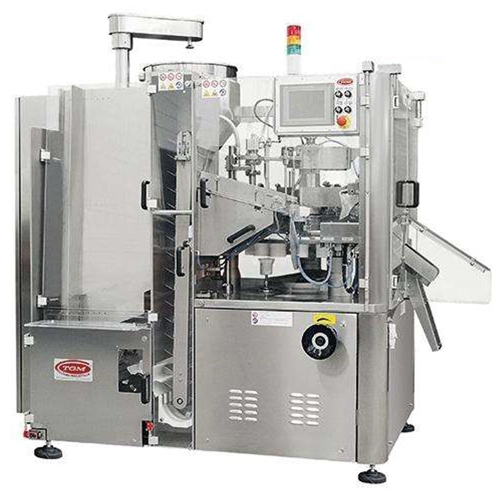
Tube filler & sealer for metal and plastic tubes
Streamline your production line by efficiently filling and sealing metal ...
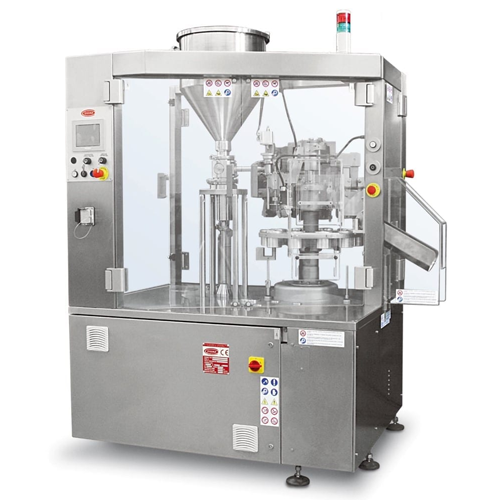
Efficient tube filler and sealer
Optimize your production line with a semi-automatic tube filling and sealing solution, desi...
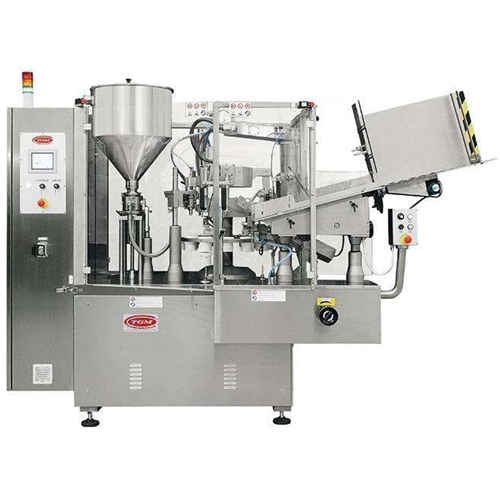
Tube filling and sealing for metal and plastic tubes
Achieve precise tube filling and sealing with high speed and efficie...
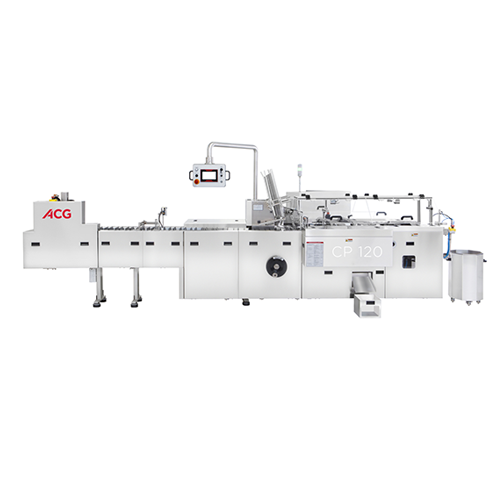
Continuous motion horizontal cartoner for blister packs
Effortlessly streamline your cartoning process with a continuous ...
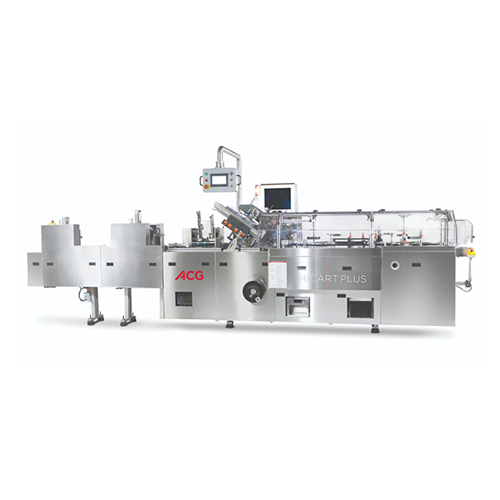
Continuous cartoning solution
Enhance your production line with efficient high-speed cartoning, designed to streamline packa...
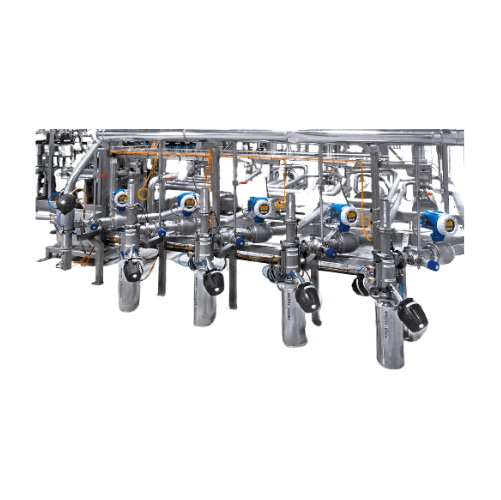
3a certified product recovery system for food and pharmaceuticals
Optimize your production line with a system designed ...
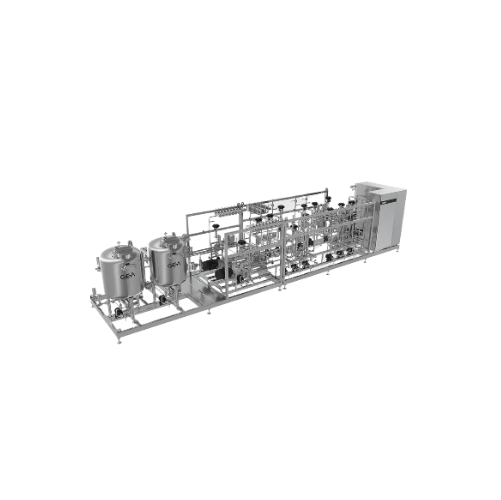
Continuous in-line blender for home and personal care products
Achieve precision and flexibility in blending liquid mult...

Modular and combined labeling machines for bottling
Achieve high-speed labeling with unmatched flexibility, combining mul...
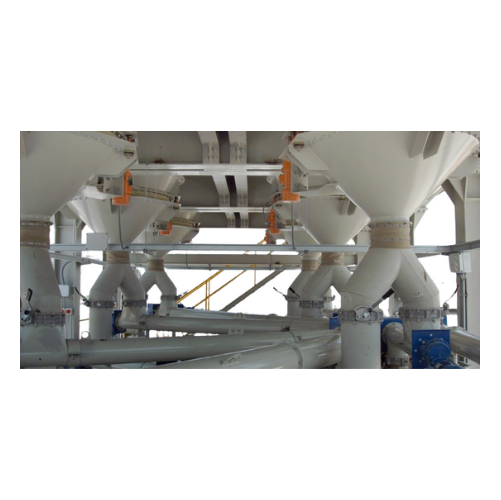
Vibratory outlet hopper for bulk material discharge
Struggling with material bridging and inconsistent discharge? Enhance...
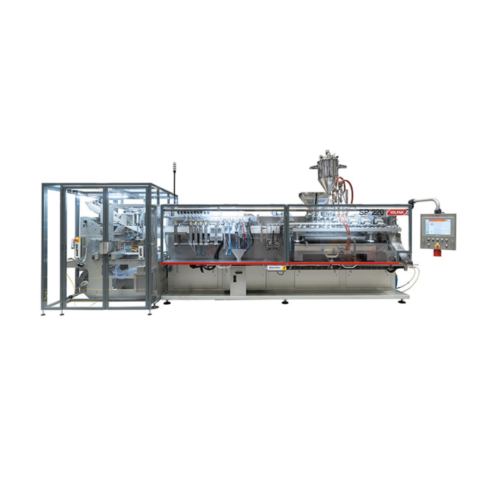
Stand-up pouch packaging for various industries
Elevate your packaging capabilities with a high-speed horizontal pouching ...
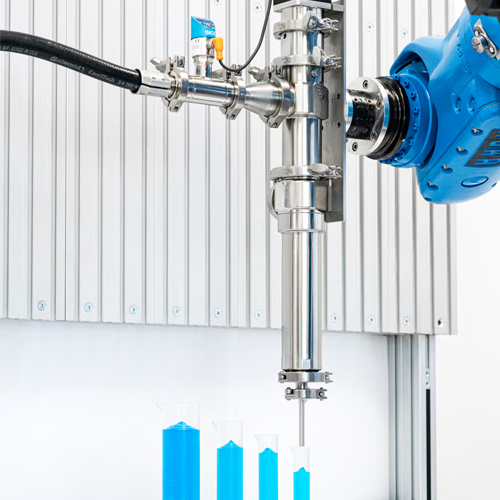
Dosing pump for liquids and pastes
Achieve precise dosing and filling of liquids and pastes with flexibility in dosing volu...
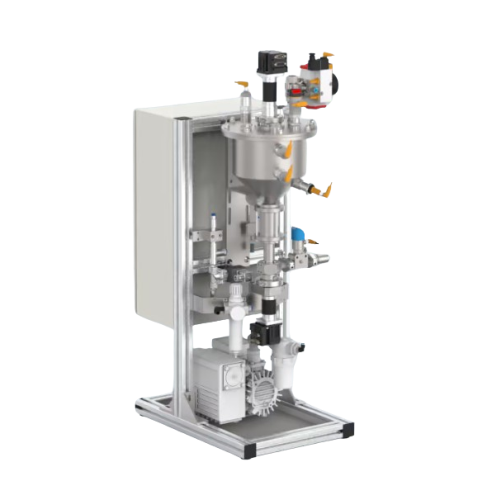
Industrial fluid and paste preparation system
Eliminate air bubbles and achieve uniform viscosity in fluids and pastes to ...

Dosing and filling pump for liquids and pastes
Achieve precise dosing and filling of liquids and pastes with compact, hygi...
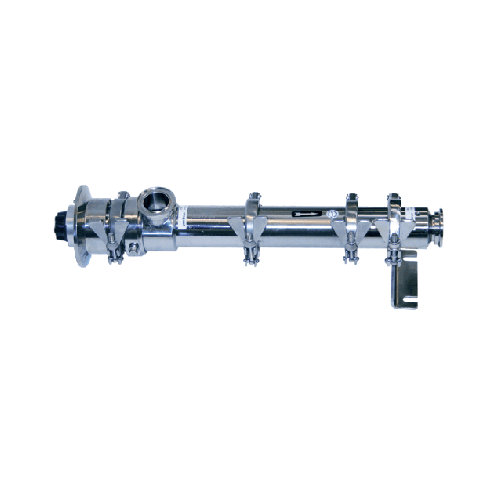
Dosing and filling pump for hygienic applications
Optimize your production line with this dosing and filling pump, design...
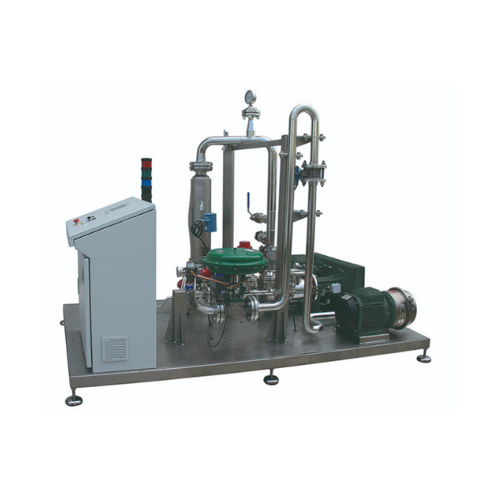
Complete mixing solution for food, cosmetics, and chemical industries
Optimize your production line with a system that ...
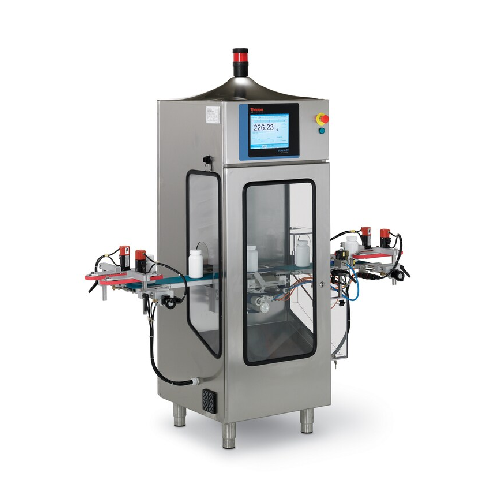
Checkweigher for pharmaceutical and food industries
Ensure precise weight measurement and reliable product rejection in h...
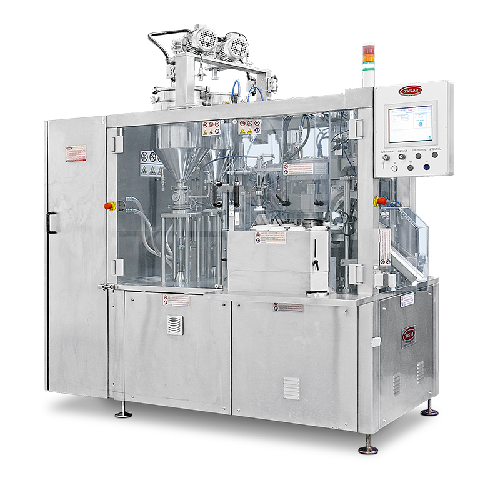
Automatic tube filling for multi-color products
Achieve precision in multi-color product packaging with seamless co-extrus...
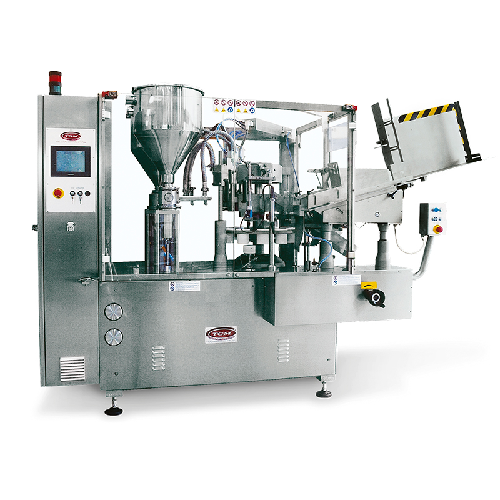
Automatic tube filler for multi-color coextruded products
Achieve precise dual- or tri-color product designs with except...
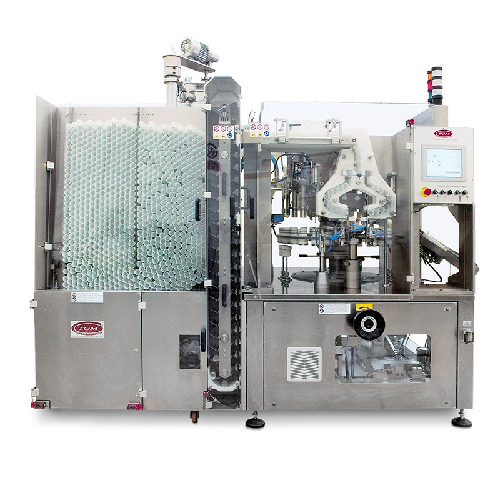
Automatic tube filling for coextruded products
Maximize efficiency in high-volume production with precision co-extruding c...
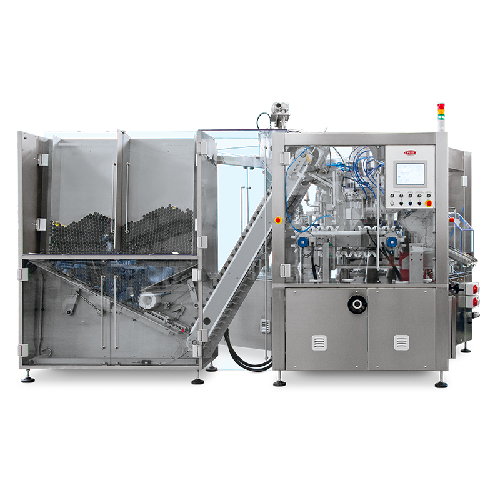
Automatic tube filling solution for high-volume production
Effortlessly streamline your production with this high-speed ...
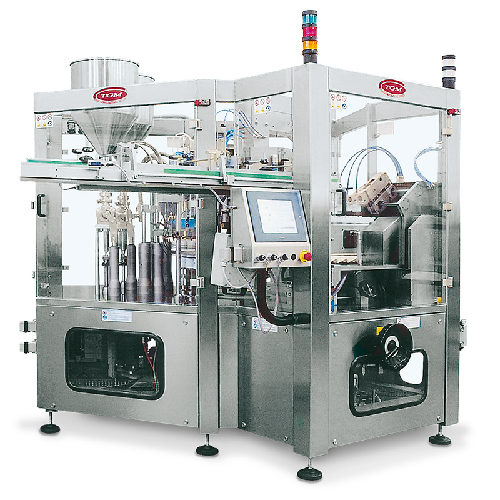
Automatic tube filler for co-extruded products
Achieve precise multicolor co-extrusion filling with high-speed accuracy, o...
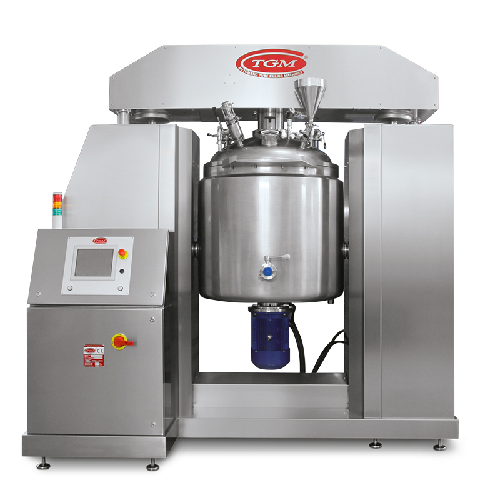
Turbo emulsifier for creams, gels, toothpastes
Achieve perfect emulsification and homogenization for your creams, gels, an...
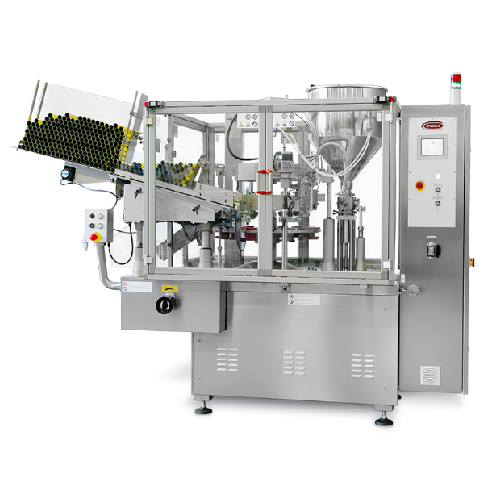
Automatic tube filling solution for medium to high volume production
Boost your production line efficiency with a robus...
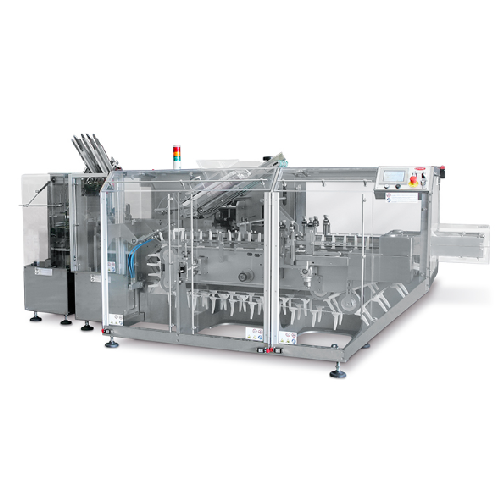
Horizontal cartoning machine for medium to high-speed production
Optimize your cartoning process with precise loading an...
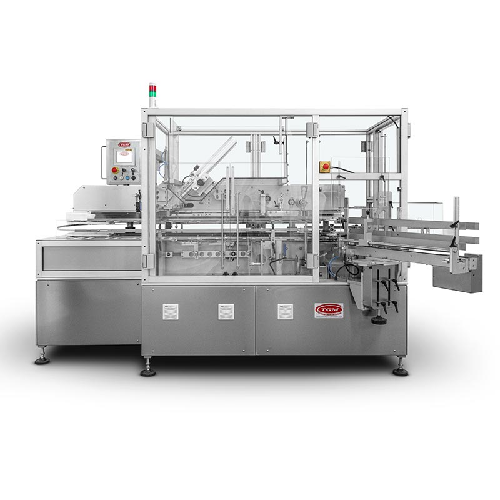
Vertical cartoning solution for manual product loading
Streamline your cartoning process with a versatile solution design...
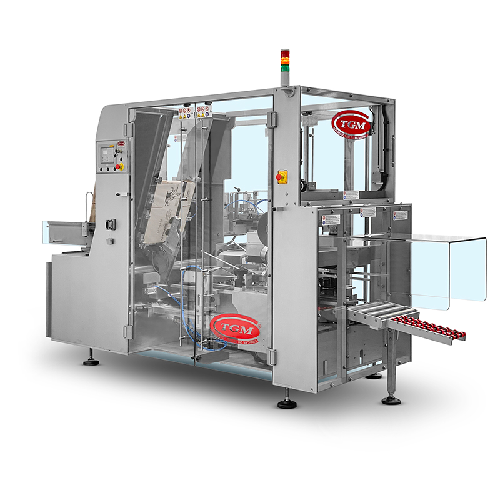
Automatic case packer for cartons and bundles
Optimize your packaging process by efficiently inserting single cartons and ...
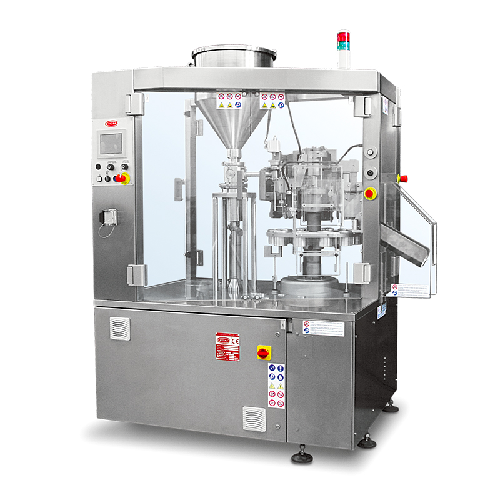
Small batch tube filling system for metal and plastic tubes
Optimize your small-batch production with precise tube filli...
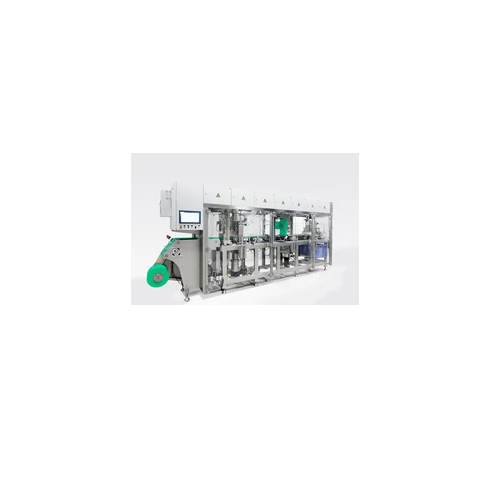
Paper forming technology for sustainable packaging
Elevate your product’s sustainability with advanced paper formin...
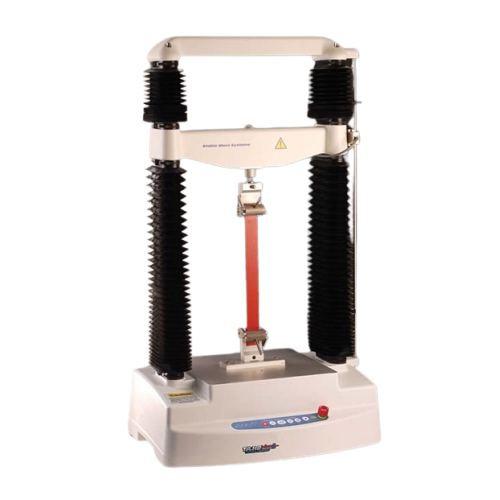
Texture analyzer for high force applications
Achieve precise texture measurement across a vast array of products with a so...
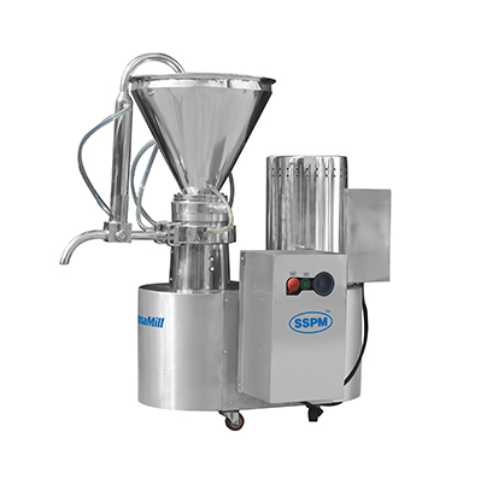
Colloid mill for particle size reduction and emulsification
Achieve precise particle size reduction and stable emulsions...
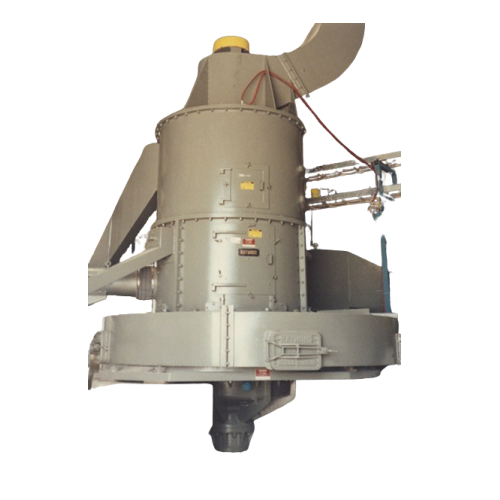
Vertical ring-roll mill for pulverizing minerals
Achieve precise particle size control and efficient material processing w...
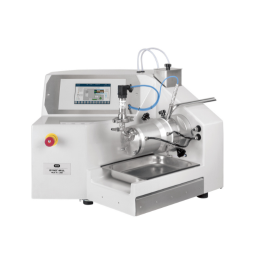
Flexible R&D wet agitator mill for cosmetics
Using nanoparticles in cosmetics requires precise control over material break...
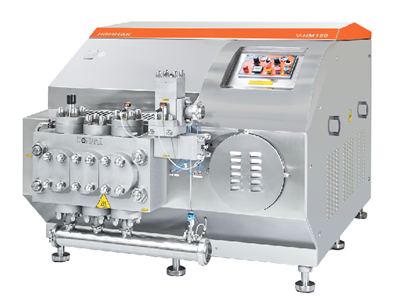
Pilot plant homogeniser
From food to pharma, homogenization is an essential step in the production process that provides unif...
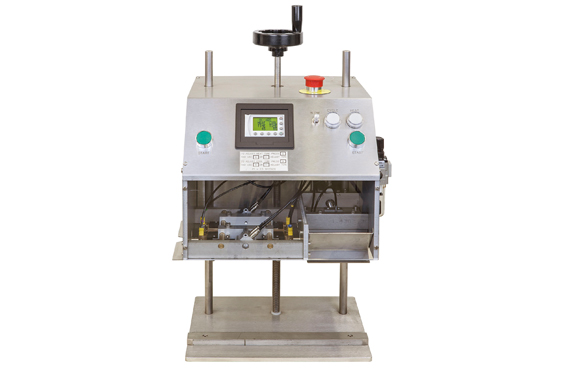
Manual plastic tube sealing equipment
Working in labs or with small batch production lines where you have to seal plastic o...
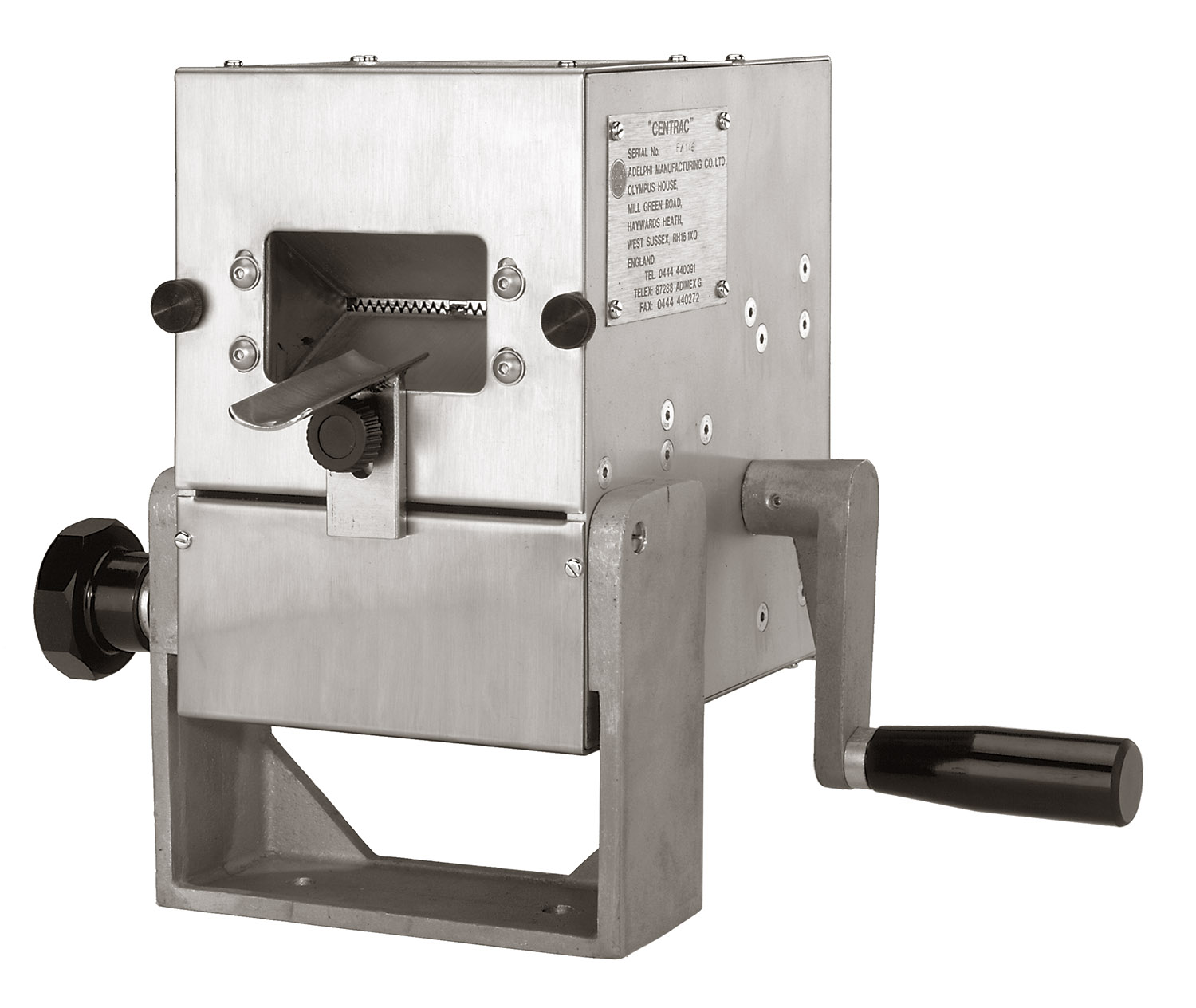
Manual metal tube sealing equipment
For small-batch productions where you utilize metal tubes as containers for your produc...
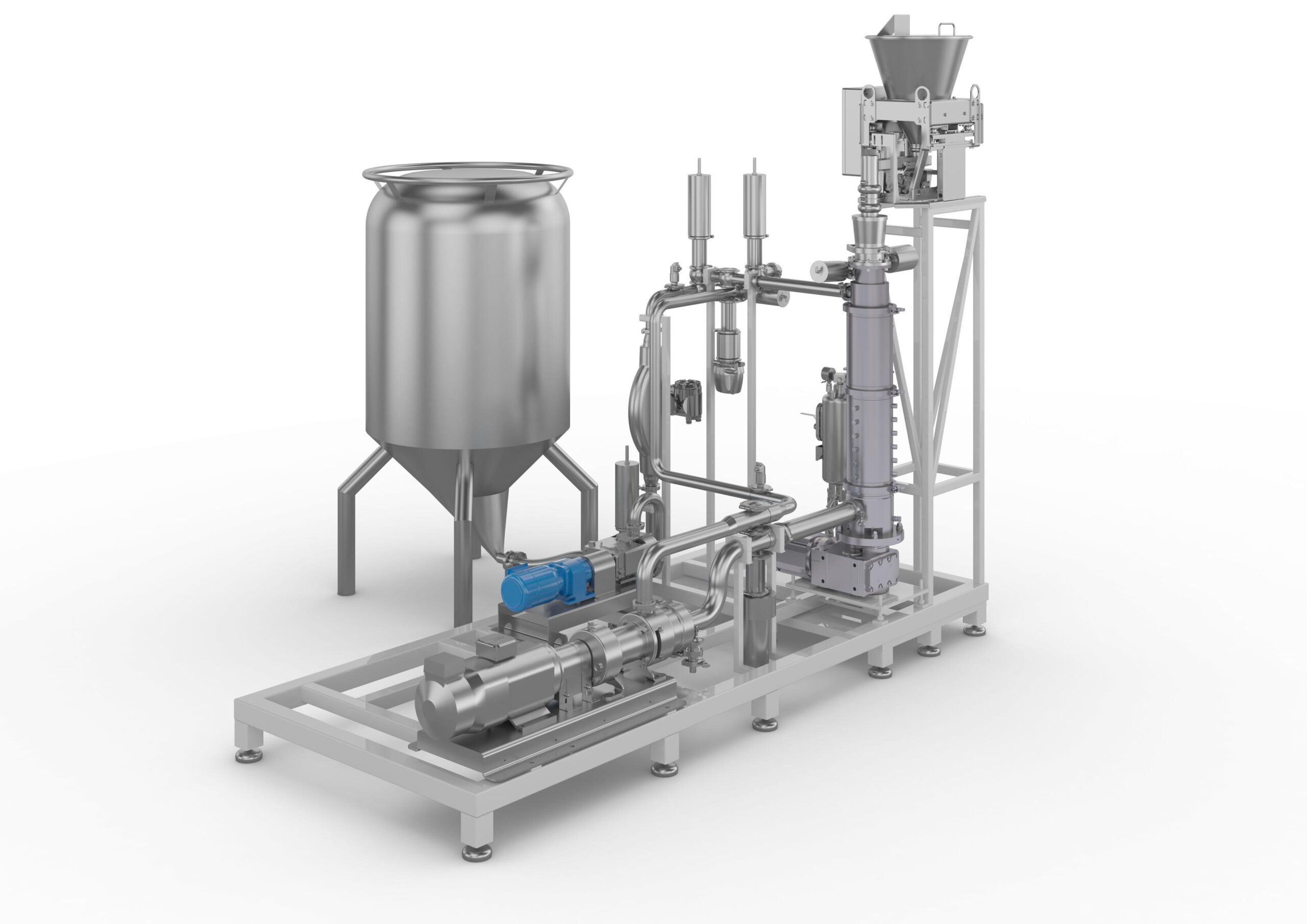
Continuous mixer for toothpaste production
When manufacturing toothpaste, dispersing and mixing powders into liquids to cr...

Flowmeter filler
For larger production runs of food, non-food and cosmetics industries, where accuracy and volume of filling i...
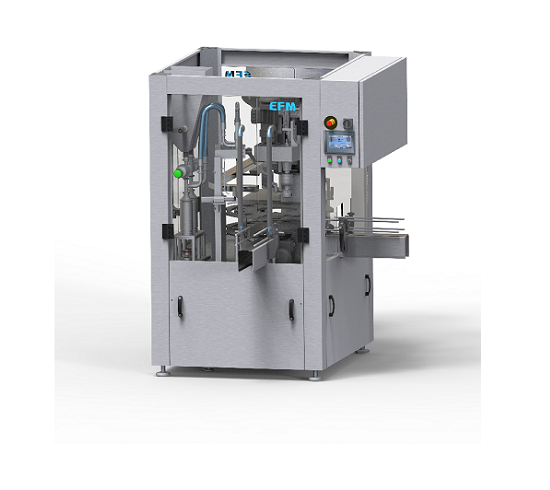
Compact monoblock filler
Filling and capping bottles and pots for food, chemical and cosmetics industries using separate mach...
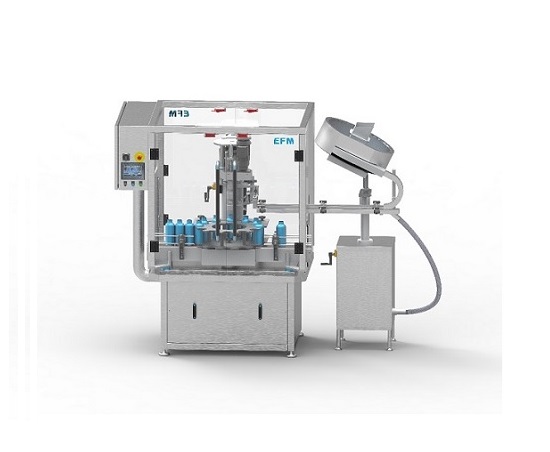
Single head capper
For the stand-alone capping of bottles of up to 30 litre capacity for smaller-scale production you need a ...
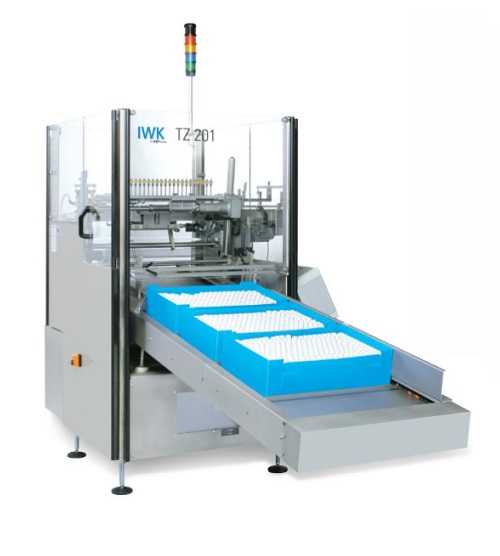
Tube unloader and feeder
The pharmaceutical and cosmetic industries utilise high speed tube fillers on large-scale production...
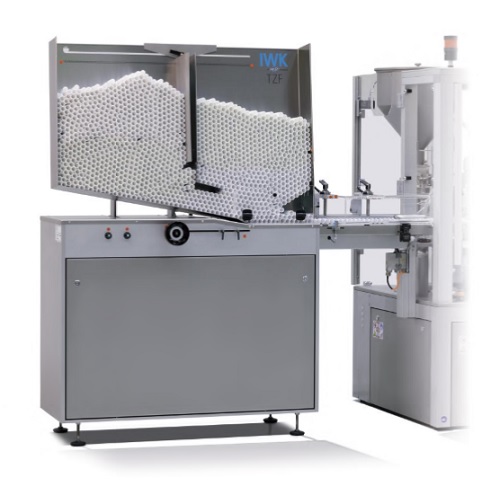
Tube feeding unit for high volume and high speed tube filler
High performance tube-filling machines are used for large s...
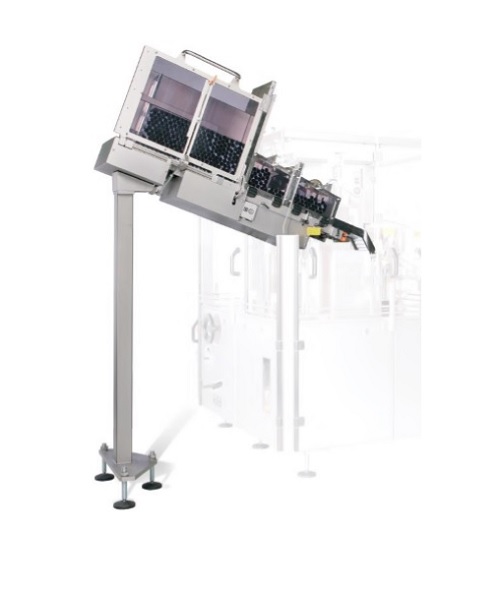
Loading cassette for a tube filler
High performance tube-filling machines are used in the pharmaceutical and cosmetic indus...
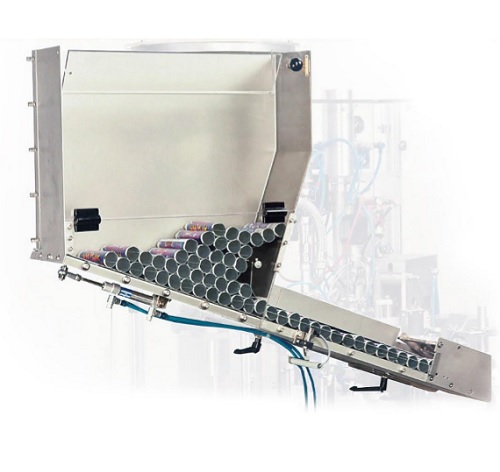
Tube feeder for a small scale production tube filler
Low speed tube-filling machines are used for small scale production ...
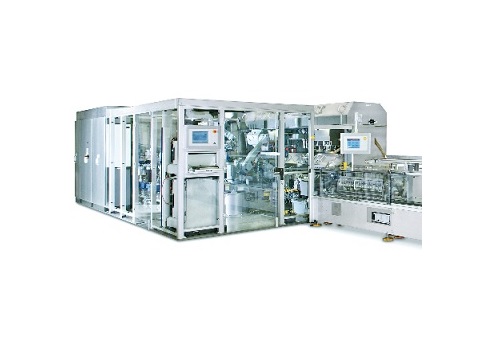
High speed automatic tube filler
For high-volume lines filling pharmaceutical, cosmetic or food products into tube container...
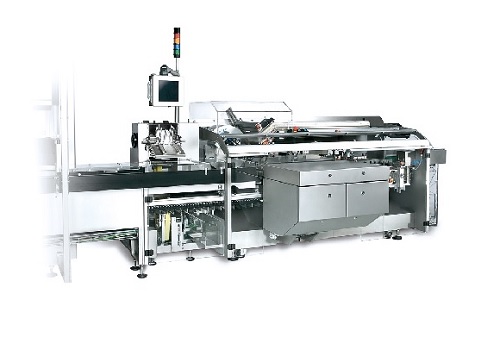
Pharmaceutical and cosmetic industry products cartoner
A large number of cosmetic and pharmaceutical products are packed ...
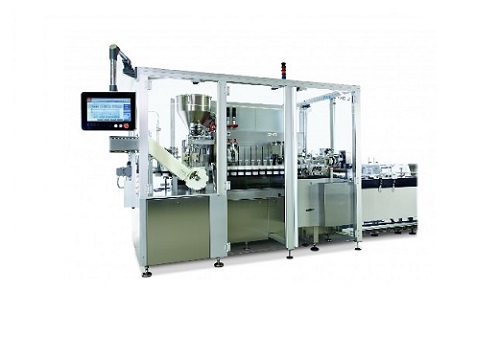
Medium speed tube filler and sealer
For scale-up filling of tube packaging for pharmaceuticals, cosmetics and food products...
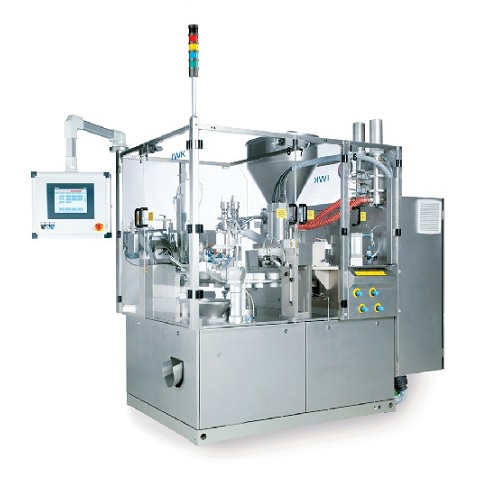
Medium and high speed range automatic tube filler
When scaling up production of pharmaceutical, food or cosmetic products...
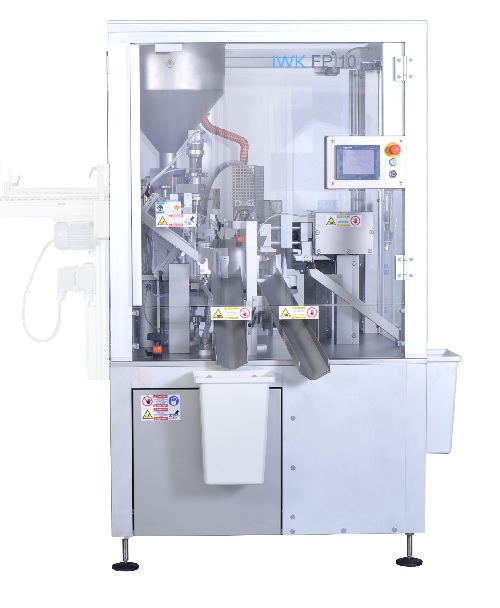
Low speed tube filler
Increasing numbers of products in the pharmaceutical, cosmetic and food industries are delivered in fle...
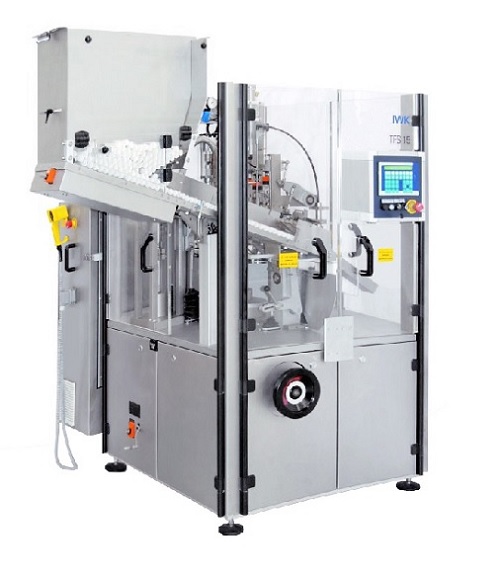
A two-component filling application tube filler
A wide variety of pharmaceutical, cosmetic and food products require tube-...
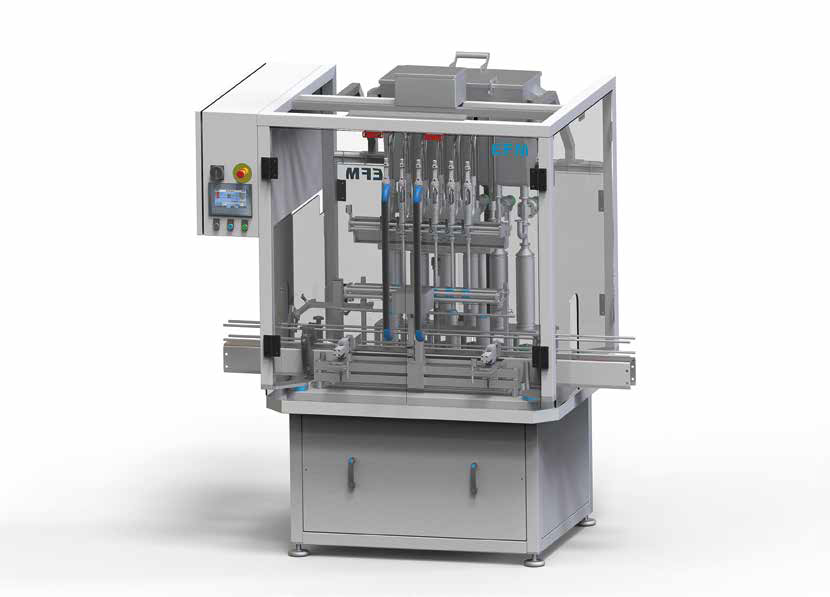
Servo controlled filler
For food and non-food liquid products that are high foam or have a high viscosity a specialist fillin...
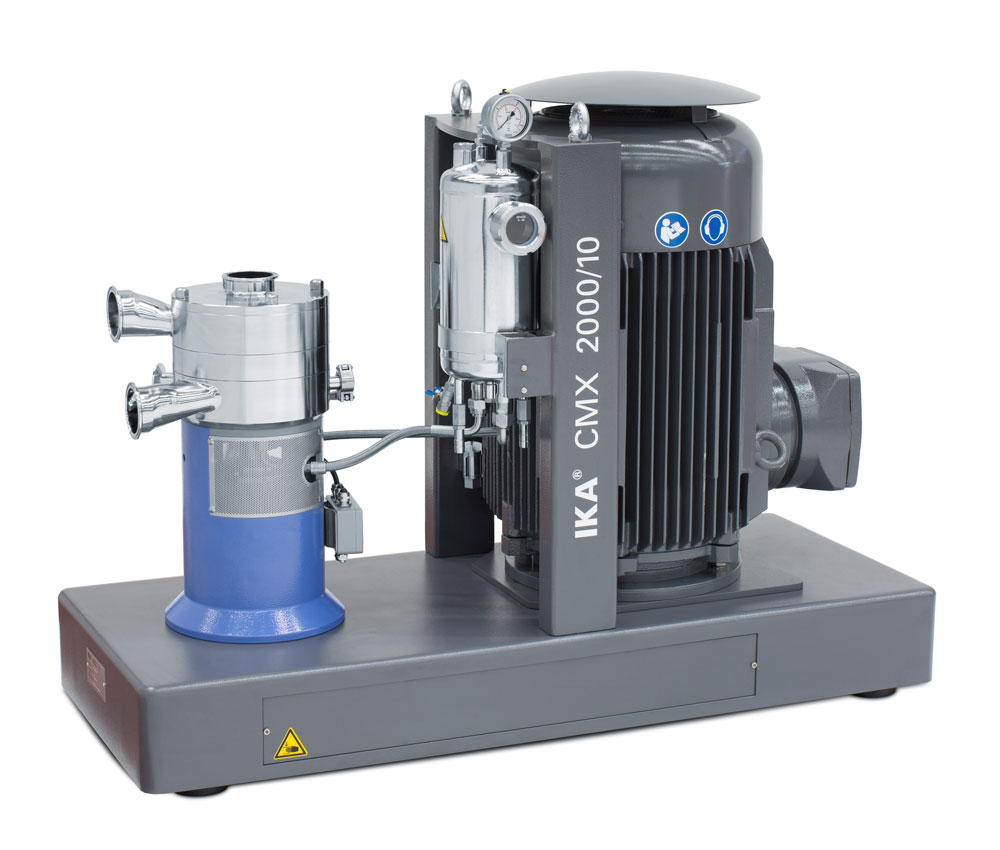
Inline batch mixer for solids and liquids
Several issues often arise when your process requires batch-wise mixing of powde...
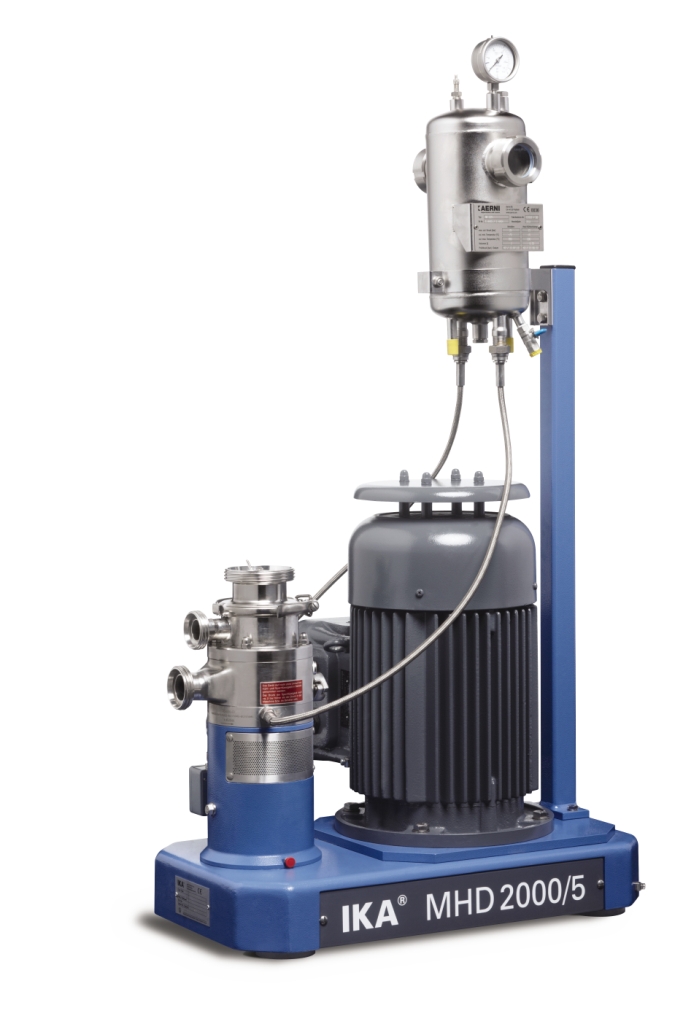
Continuous homogenizing system
Certain mixing tasks present unique challenges and manufacturers need equipment that is speci...
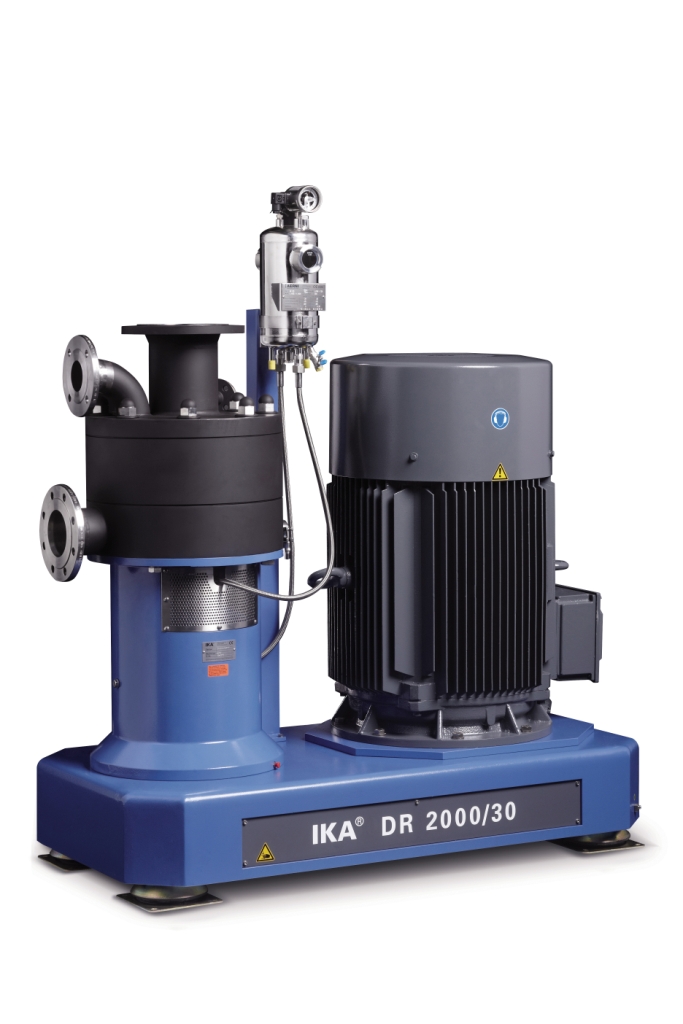
High accuracy homogenizing system
When extremely high accuracy is required in your recipe or formulation traditional mixing...
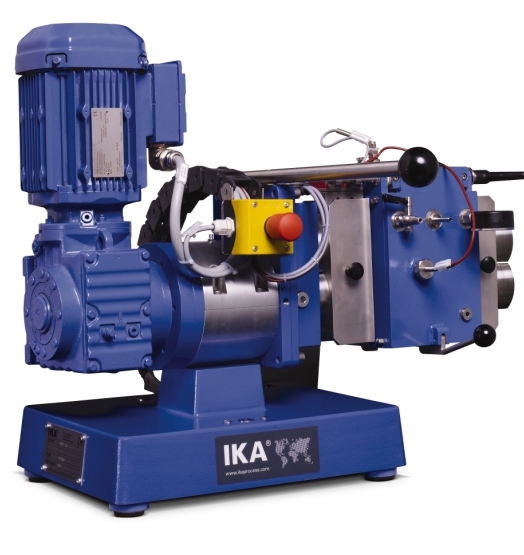
Horizontal kneader
For high viscosity products, better results and reduced process times can be achieved with kneading type r...
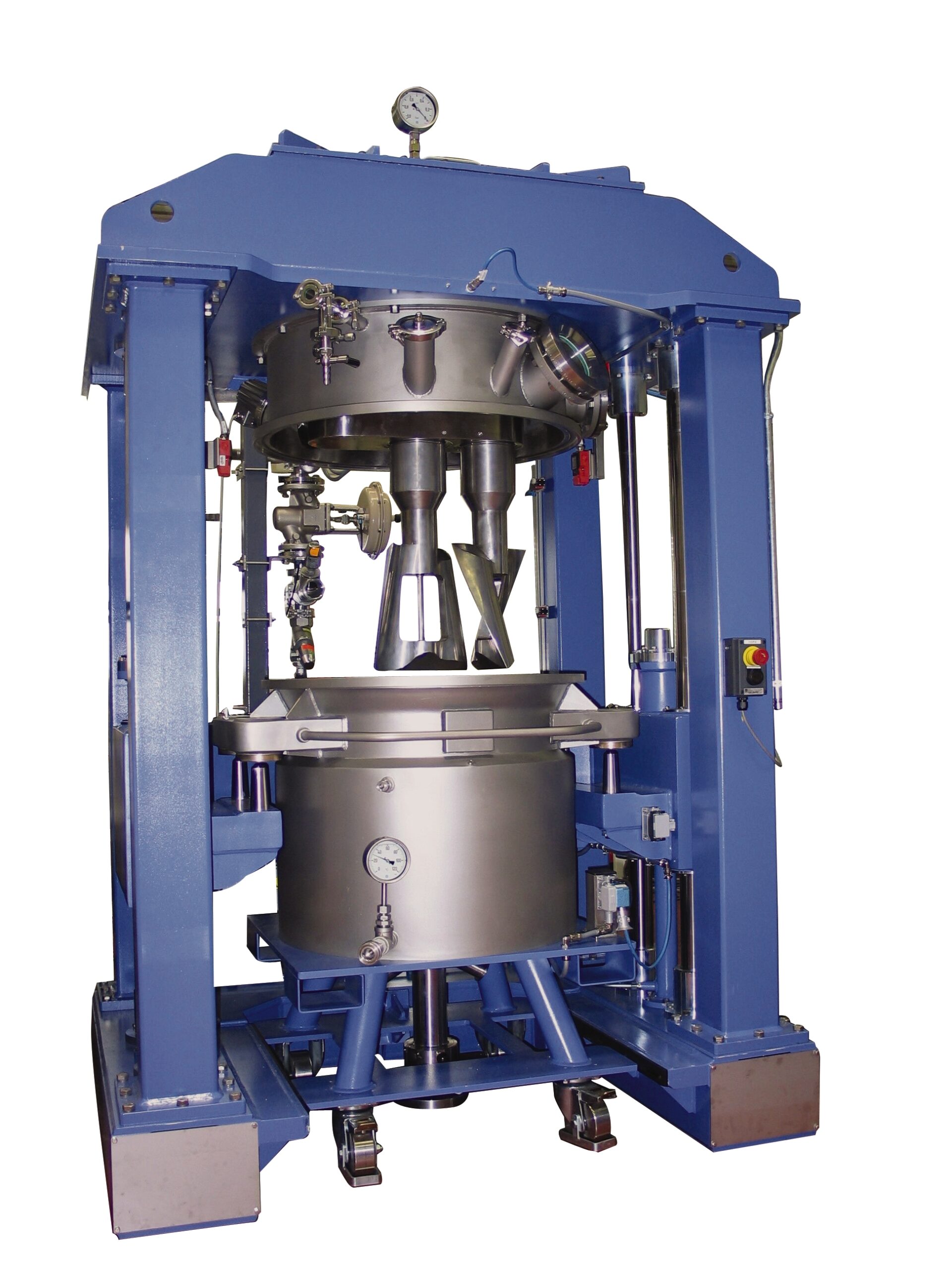
Vertical kneader
Production of highly viscous products with high solid content often benefits from kneading processes rather t...
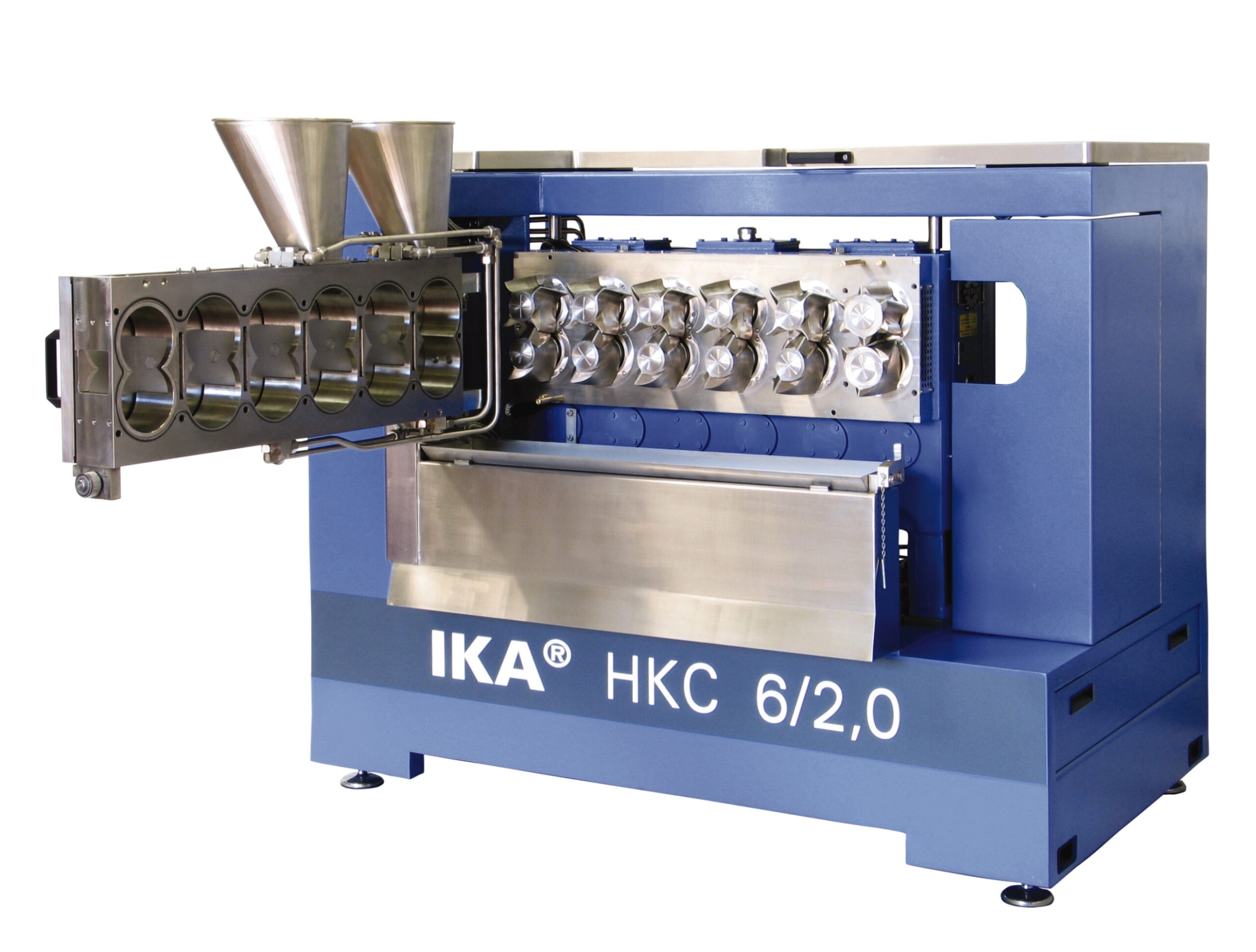
Continuous kneader
Effective mixing of highly viscous products with extremely high solids content can be difficult and the re...
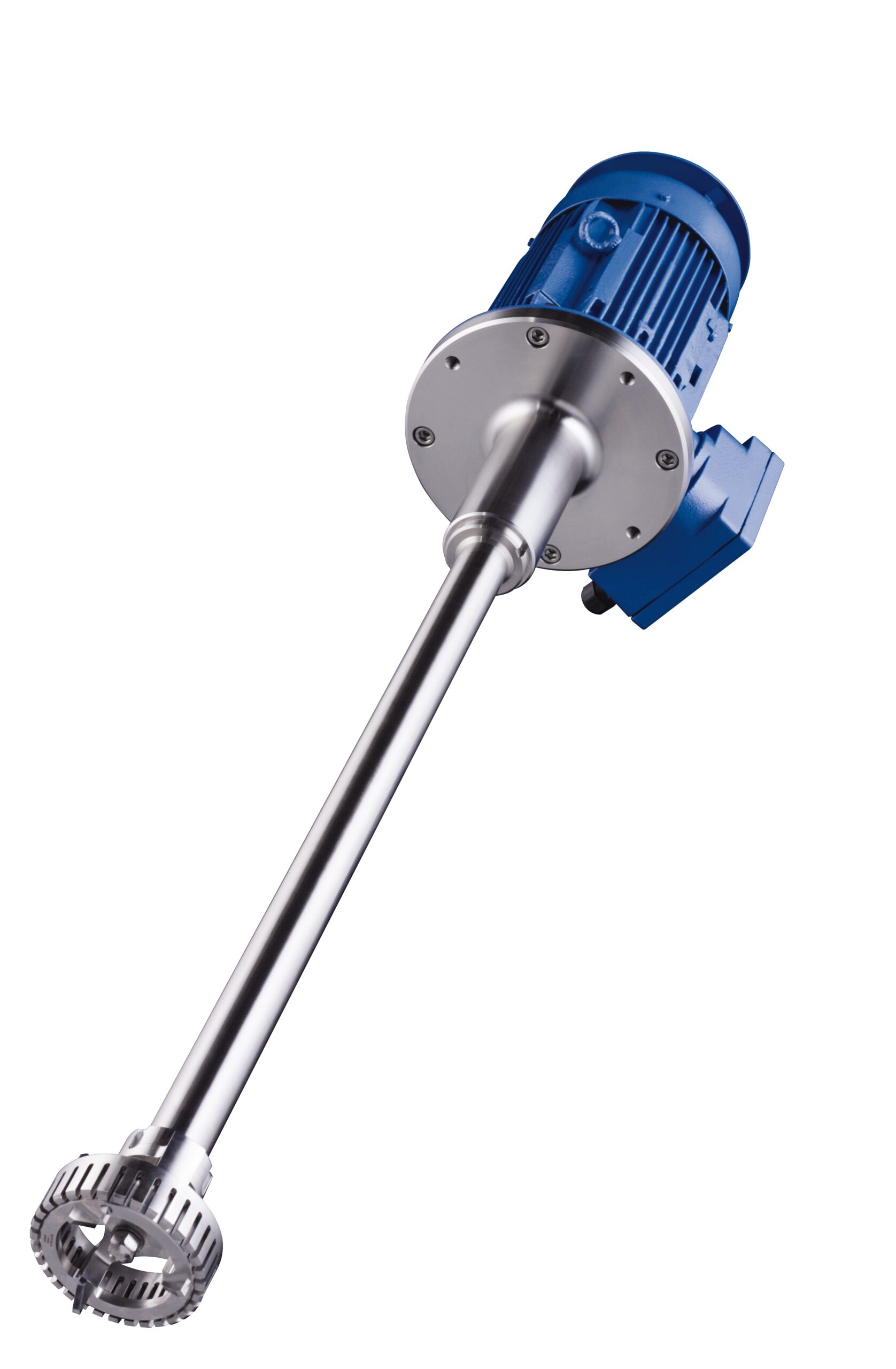
Batch dispersing machine
Equipment operating under the rotor/stator principal is often employed when more traditional methods...
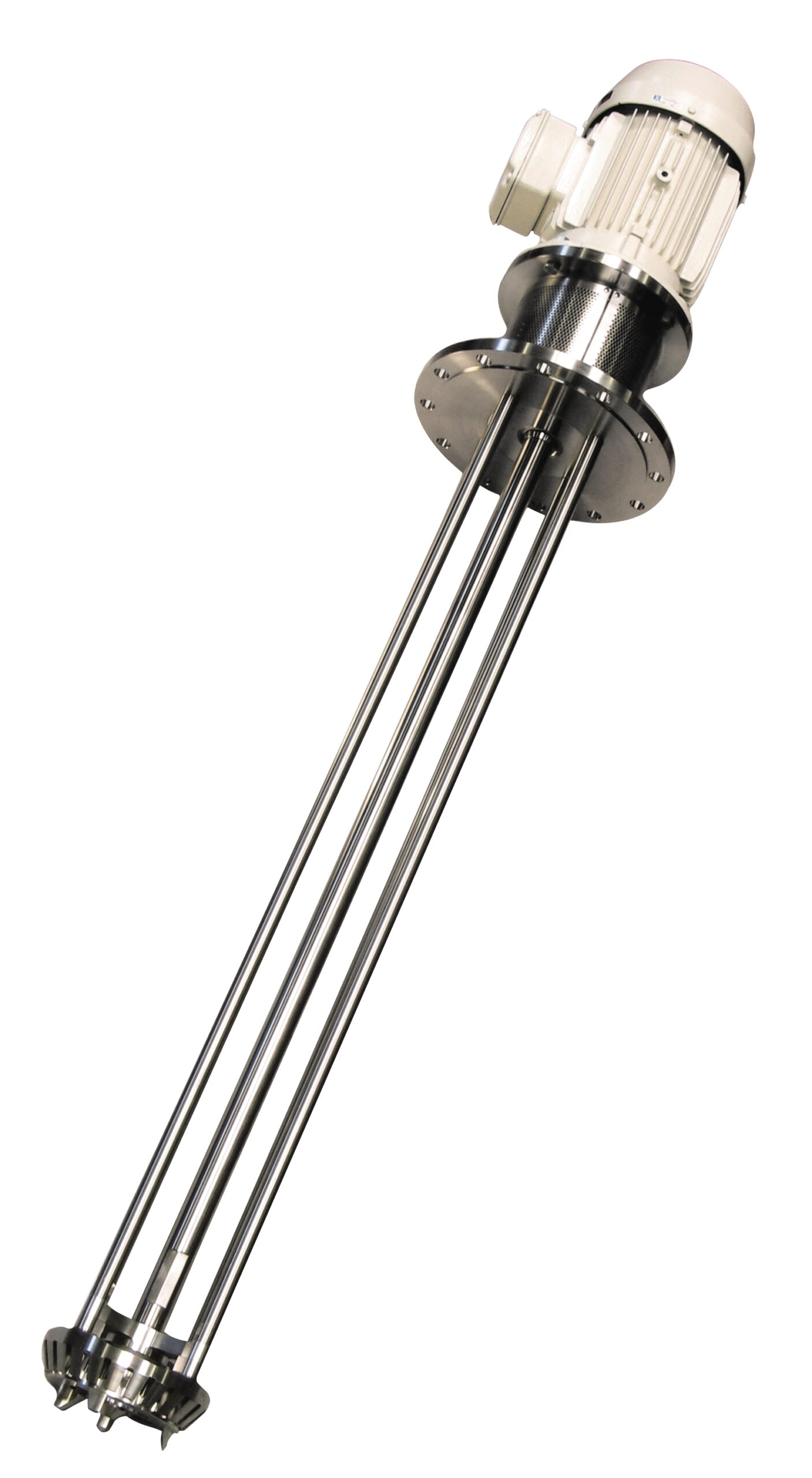
Batch dispersing machine for abrasive products
For mixing and dispersing tasks that cannot be completed by conventional st...
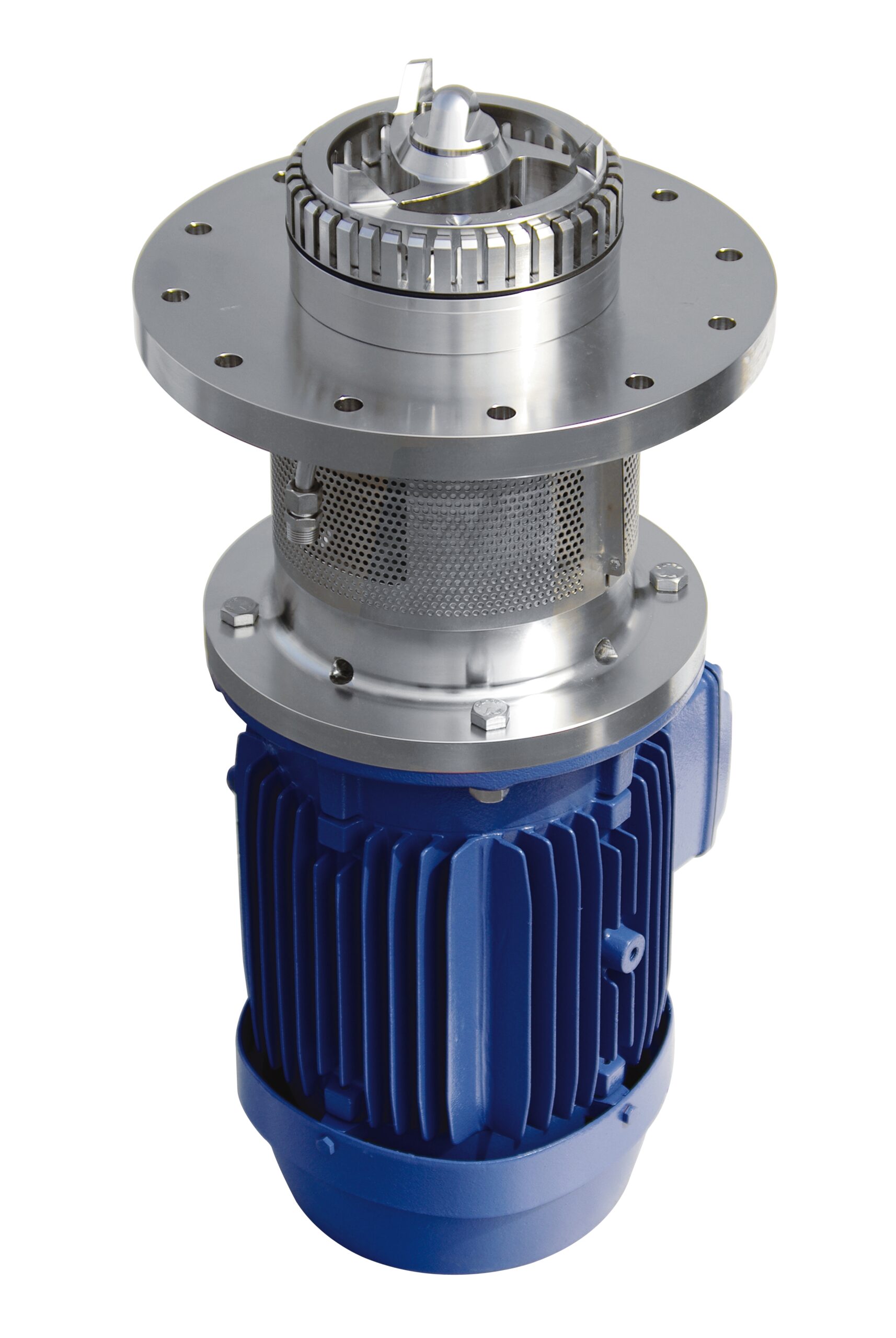
Batch dispersing machine for bottom entry into vessels
When your process requires high performance mixing or dispersion b...
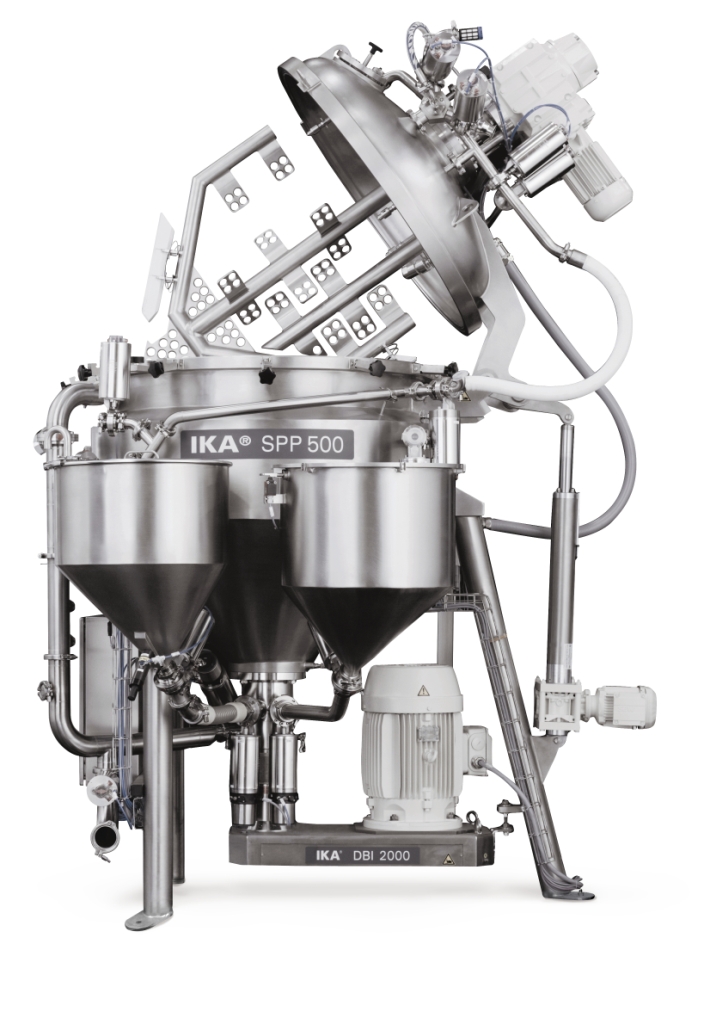
Cost-effective homogenizing and emulsifying system
Manufacturers of cosmetic products need mixing equipment that is capab...