Standard FFS machine for spreads and sauces in mini portions
In the food industry, from a microbiological point of view, different types of foods are subject to the growth of food poisoning microorganisms. For this reason, clean room conditions are required when they are processed. However, there are some products such as ketchup, mayonnaise, dip sauces, or jam/honey, that don’t require a special controlled environment, as they are considered low-risk foods. Adhering always to the hygiene standards, these products can be processed in a FFS machine with a standard environment which could be the right cost/benefit solution for mini portions production.
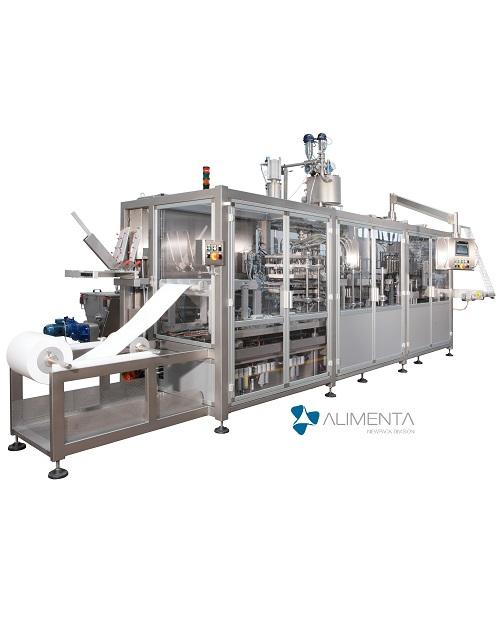
A thermoforming solution customizing cup shape and size
The Thermoforming machine designed by Newpack (Alimenta Group), is a horizontal Form-Fill-Seal machine that forms a container, fills it with a product and then seals it in a single process. The machine handles food products from liquids to semi liquids, even high viscosity ones like jam, honey, spreadable chocolate, dip sauces, and more.
The Thermoforming machine is adjusted to the demands of the product to be processed and its demands in regard to shelf life. Newpack customises the shape and size of the cup in accordance with manufacturer’s end product requirements. Depending on hygiene levels, Newpack has different versions: Standard, High-Clean, Ultra-Clean and Aseptic. For products such as jam, spreadable chocolate, ketchup, mayonnaise and dip sauces, that are not sensitive to the growth of food poisoning microorganisms, a Standard version is suggested.
Starting from a reel of thermoformable plastic film, the Newpack Thermoforming machine forms the bottom of the container according to a pre-established shape, by heating the plastic film and shaping it through a mould. At this point, cups are automatically filled by a cup filling station. Based on the product to be packed and the shape of the cup, the filling system type changes. Afterwards, the machine applies a lid on each cup by heat sealing it. When cups arrive to the cutting station, they’re cut and separated.
Machine capacity depends on the product and volume of the cup; generally speaking, 9,000 – 15.000 c/h is the minimum production capacity.
Benefits
- A customized solution
- Work cycles completely managed from operator panel
- Wide range of cup sizes and shapes
- A 3 in 1 machine for forming, filling and sealing
- Available in a range for different cleaning levels