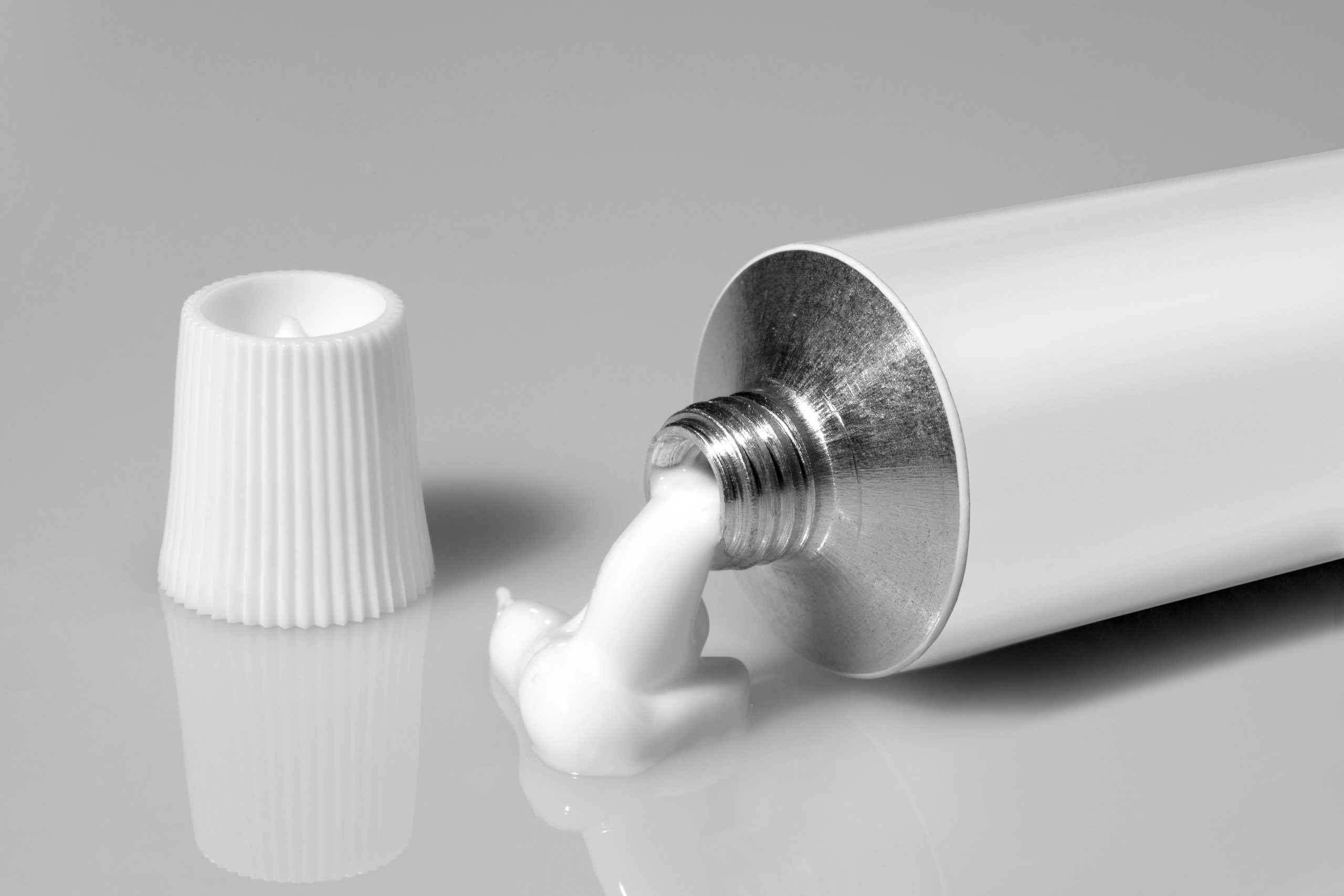
Making Ointments
Find innovative production technology for making ointment and connect directly with world-leading specialists
The most significant decision when making ointments is likely to be the choice between automatic or semi-automatic processes for it. This impacts on individual phases of the ointment cream manufacturing process - the water phase and oil phase.
Select your ointment process
Tell us about your production challenge
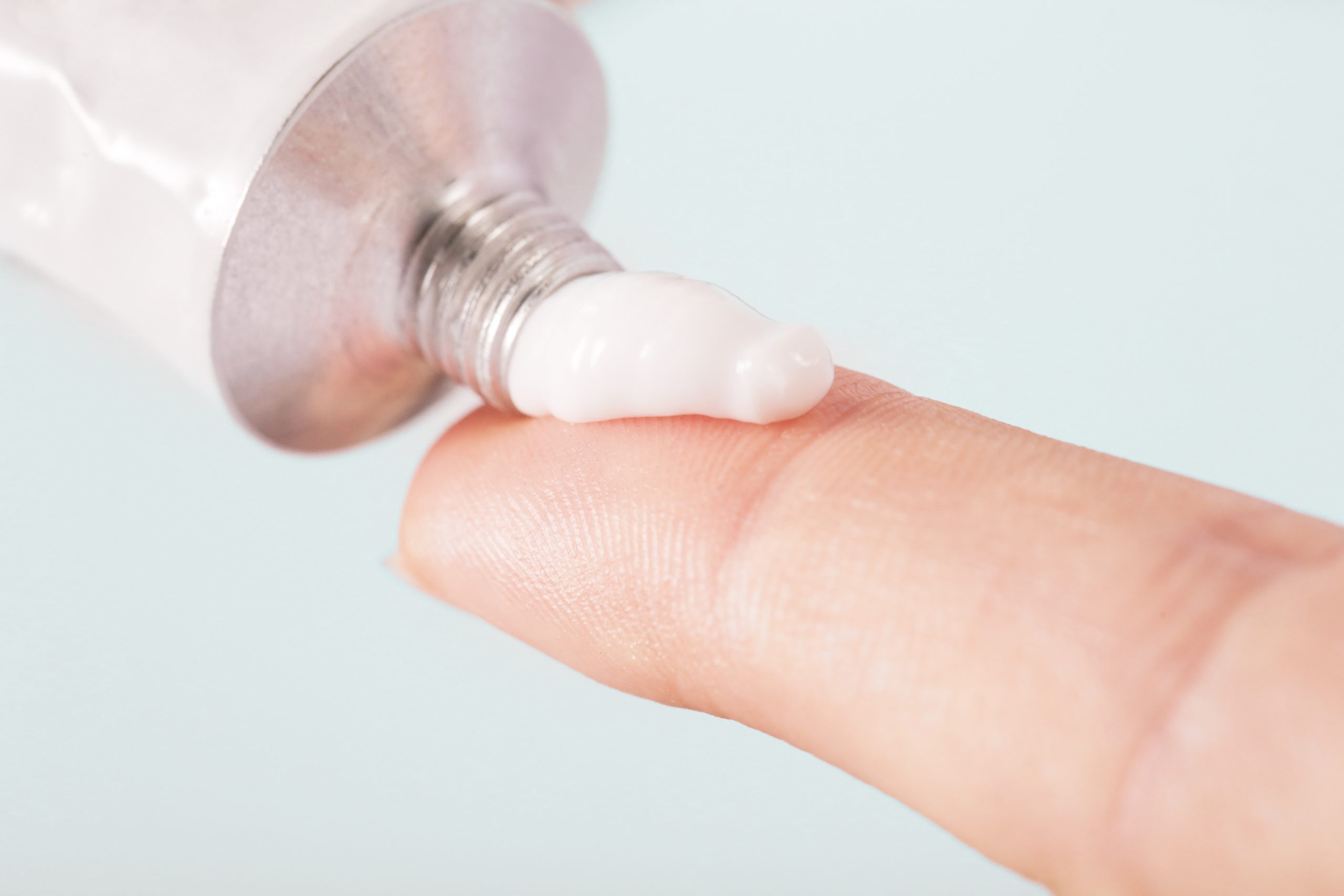
How to manufacture ointments
Before homogenizing ointments, you need to treat each of the product’s main components separately, in specialized vessels. The process begins at the water phase. In it, you dissolve the water-soluble components in demineralized water in a vessel that is proper for it. Next up is the oil phase, involving the mixing of the wax and oil components in a wax phase vessel. Motor-driven agitators heat and mix the containers, then a vacuum system filters and moves them through pipes to the ointment manufacturing vessel. At this stage, you introduce homogenizers and emulsifiers, to ensure that the mixing of the components (including the drug ones) is as uniformly as possible.
When the product is ready, it is time to transfer it to the storage tank, then move it to the filling machine. Finally, before filling the product into tubes, you can use a triple roller mill to remove extra water from the product. In the end, Clean-in-place (CIP) systems take care of all the containers used in the ointment cream manufacturing process.
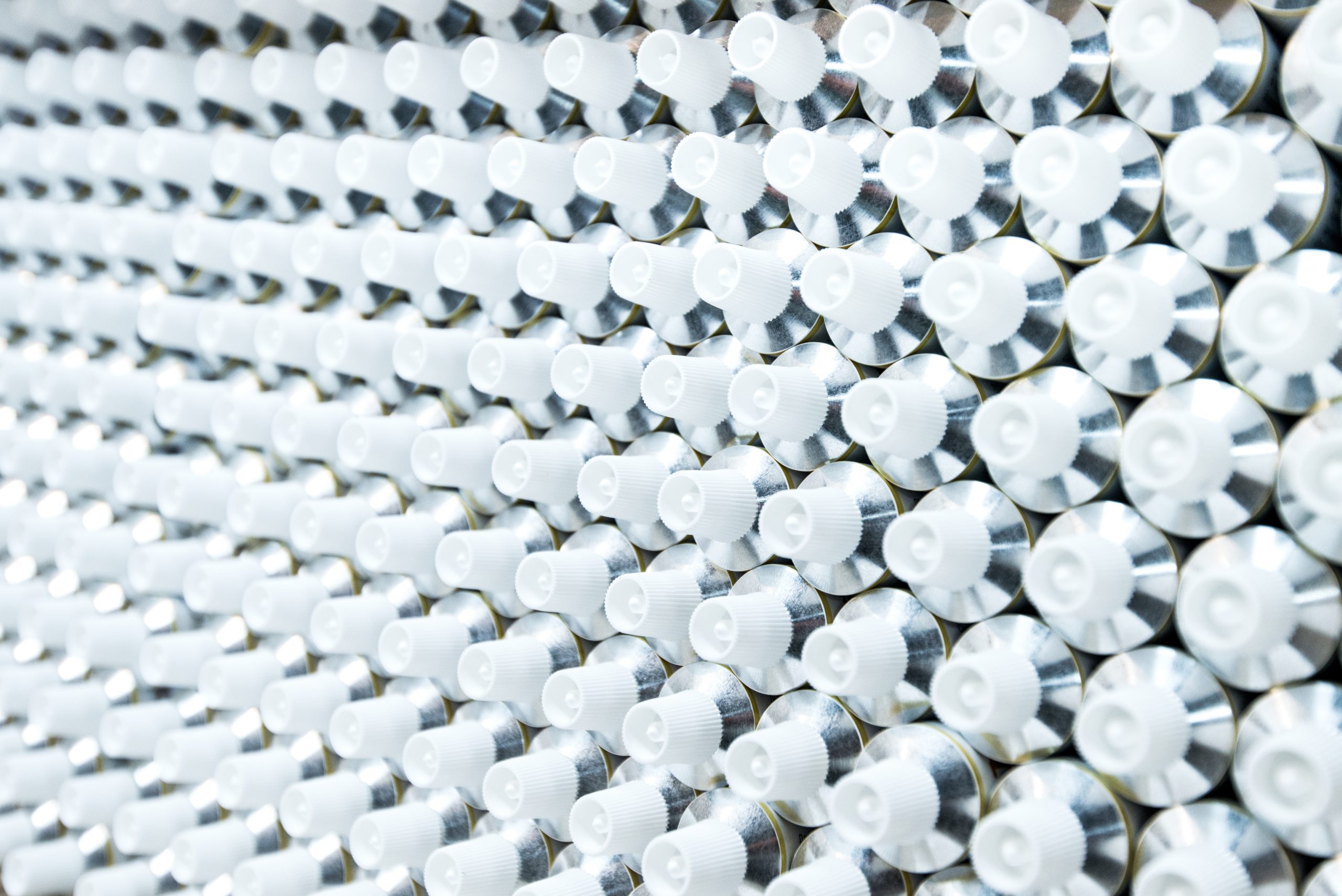
Should you use the automatic or semi-automatic process?
The semi-automatic process is shorter and easier than the automatic process, and it also involves the use of fewer vessels. However, the automatic process ensures a more thorough processing of materials. Essentially, the automatic process is more cost-effective if you’re considering the large-scale production of ointments. The main difference between both processes occurs at the initial stage. In the automatic process, you heat the water-soluble and wax components in different vessels. On the other hand, you can use the same vessel to mix and stir all the different components. Also, a planetary mixer replaces agitators, while colloid mills act in place of homogenizers in this process.
What you should know about making and selling ointments
Under the FD&C Act, in the US, ointments can be both cosmetics and pharmaceuticals. Its categorization depends on the vehicle or base of your finished product. Vehicles include lotions, ointments, pastes, syrups, and suspensions. Vehicles in liquid dosage forms may be aqueous (water, hydro-alcoholic solutions, polyhydric alcohol), or oily (emulsified bases, vegetable or mineral oils, etc.).
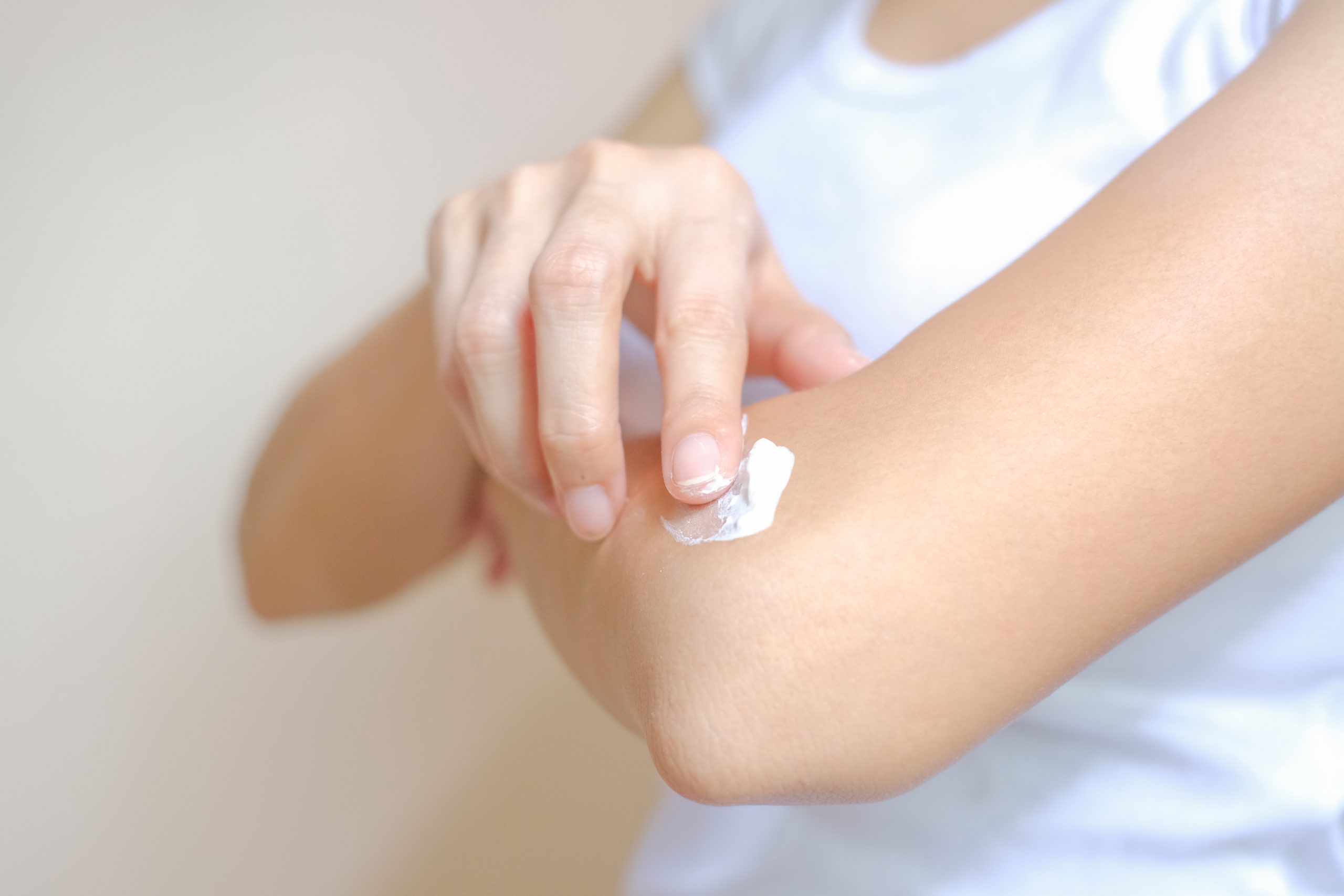
Protective ointments are required to neither penetrate the skin nor facilitate the absorption of substances through the skin. These are regarded as cosmetics. Antiseptic ointments, on the other hand, need to be able to penetrate the skin and are regarded as pharmaceuticals. In general, while the FDA provides regulations for the manufacturing and sale of cosmetic products, you do not require a license before you set up a cosmetic production business. Also, the FDA typically does not need to approve cosmetic products before they go on sale. On the flip side, if your product is a pharmaceutical one, you need to get approval to both start-up and sell the product.
Processing steps involved in ointment making
Which ointment technology do you need?
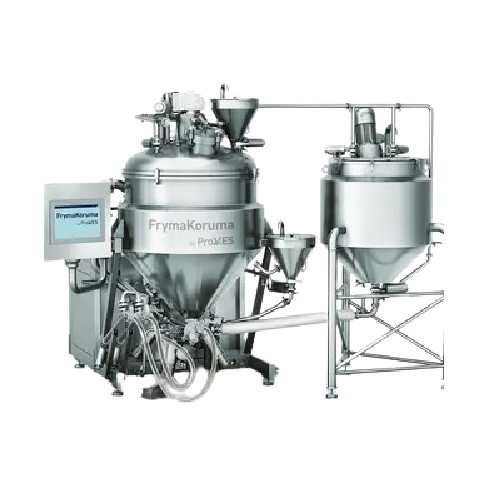
High shear emulsifier for mayonnaise production
Streamline your production of high-quality emulsions with this high-capaci...
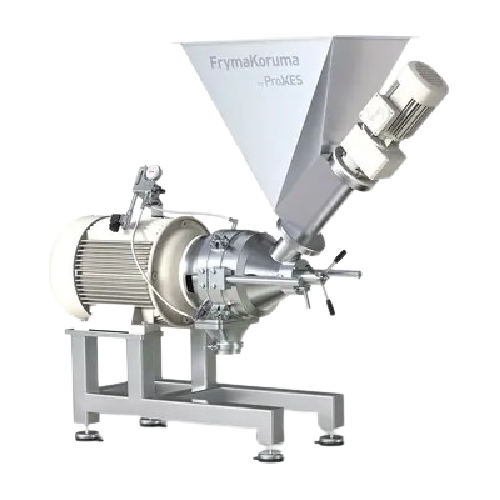
High shear emulsifier for food and pharmaceutical products
Optimize your production line with precise emulsification, ho...

Heat exchangers for efficient heat transfer in industry
Achieve precise temperature control across diverse viscosities wi...
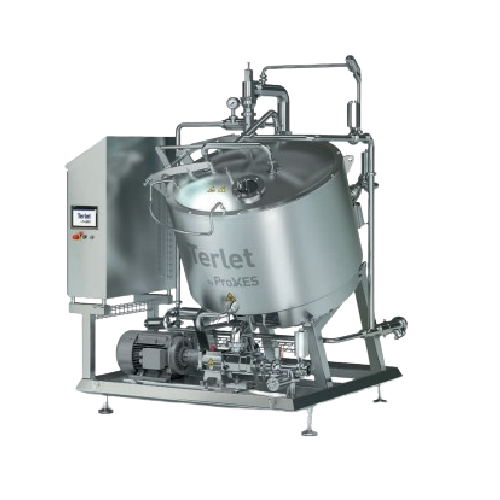
Precise liquid cooling solution for food processing
Ensure high-quality preservation of flavors and textures in liquid fo...
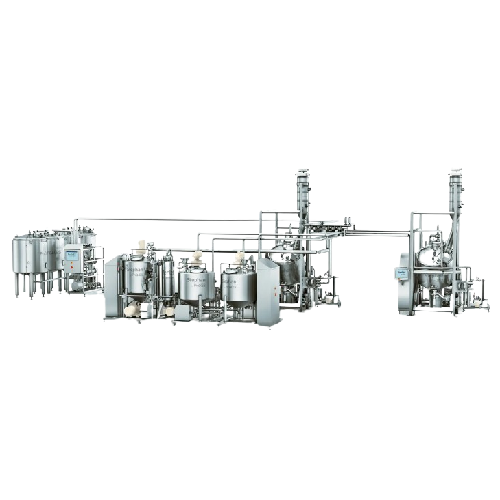
Continuous nut paste production line
Elevate your production efficiency with a versatile preparation line designed to seaml...
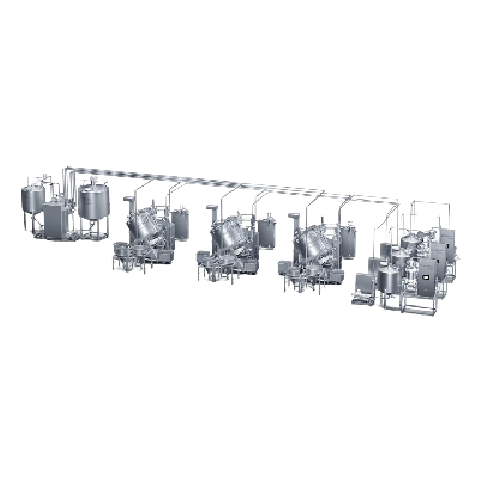
Continuous mustard production line
Optimize your condiment production with precision-engineered systems capable of transfor...
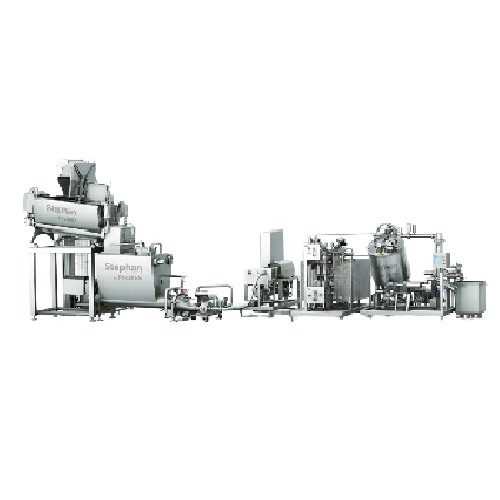
Cheese blending and heating line for processed cheese
Optimize your processed cheese production with a solution that seam...
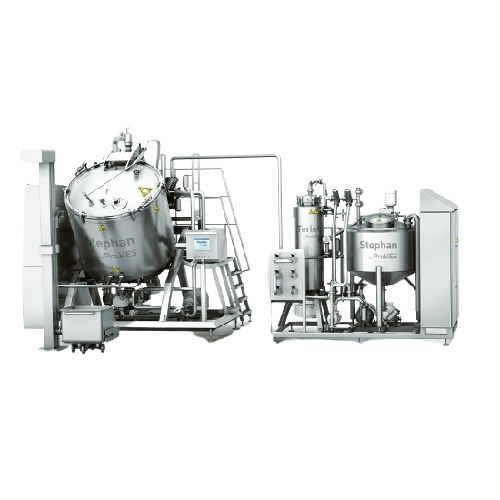
Continuous caramel production line
Optimize your caramel production with seamless integration, achieving precise fat meltin...
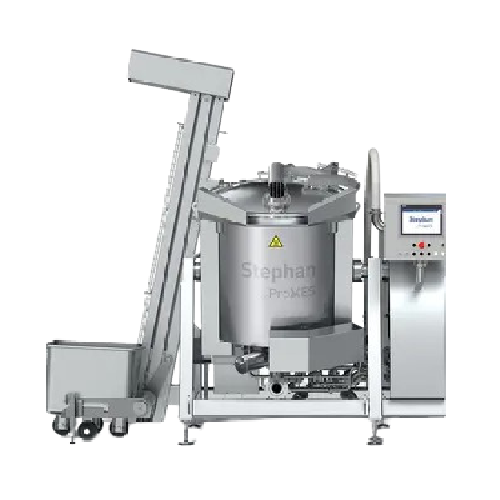
Industrial cooker for sauces and stews
When producing diverse culinary delights such as sauces and stews, achieving even he...
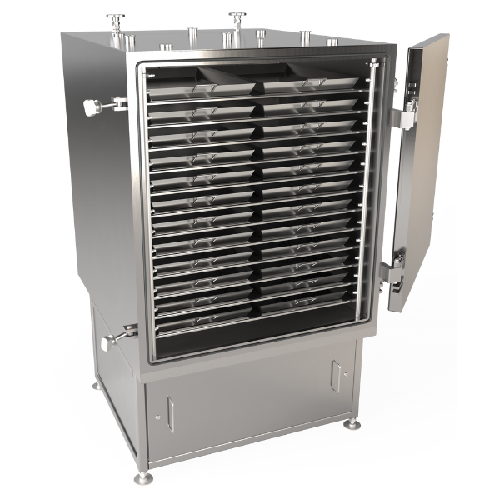
Continuous heat exchanger for soups and sauces
Optimize your soup and sauce production with a continuous heat exchanger th...
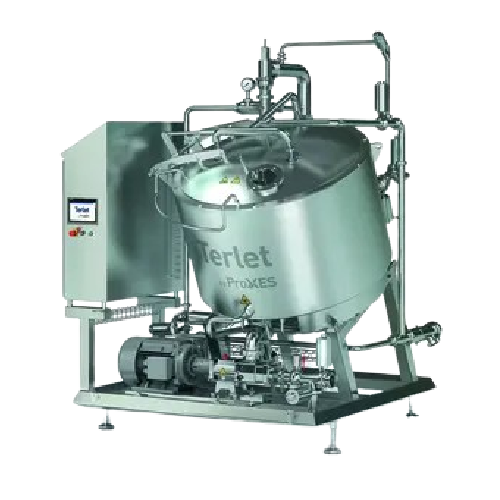
Efficient cooling and cooking systems for food processing
Streamline your production with integrated cooling and cooking...
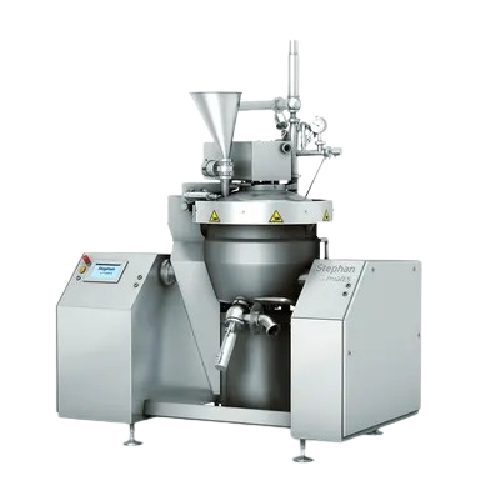
Industrial cutting system for fine emulsions
Optimize your production line with precision cutting and emulsifying, ensurin...
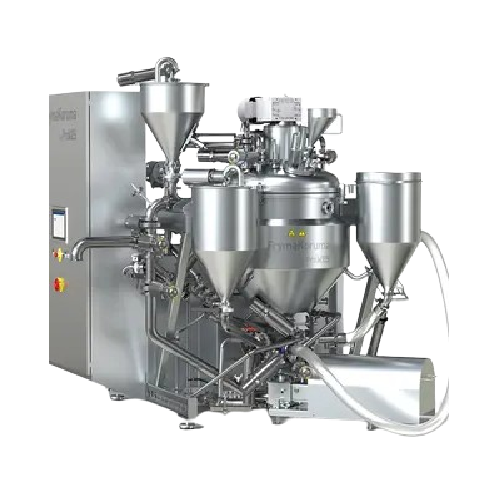
Vacuum deaeration system for mustard and liquid detergents
Ensure optimal product quality by effectively removing air fr...
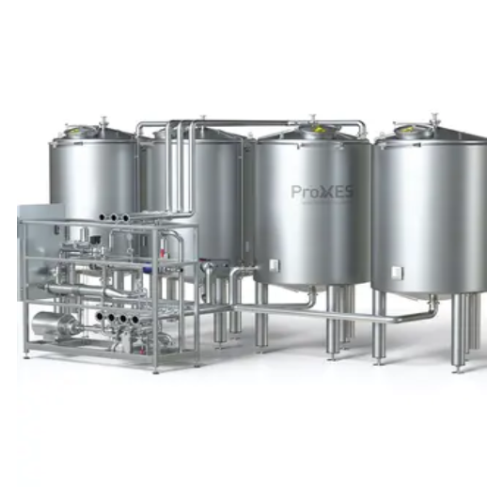
Cleaning systems for food, pharmaceuticals, and cosmetics
Ensure optimal hygiene and safety with advanced cleaning syste...
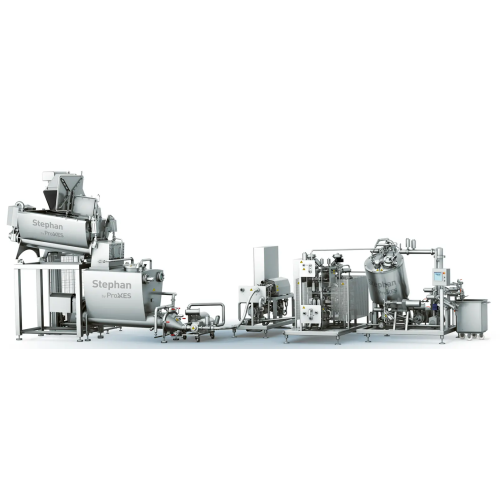
Continuous caramel process line
Optimize your continuous food processing with an engineered-to-order line tailored for preci...
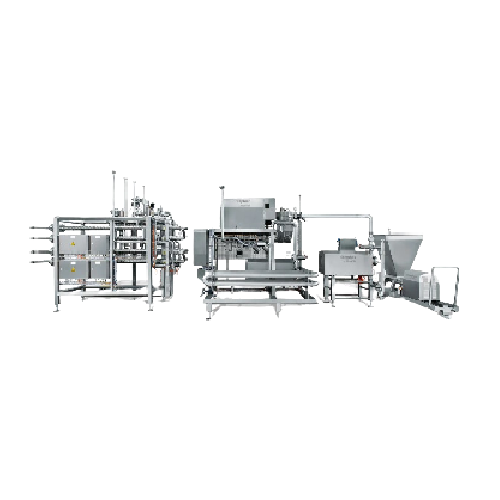
Continuous cheese line
Achieve precise temperature control and seamless product transitions with this equipment, ideal for en...
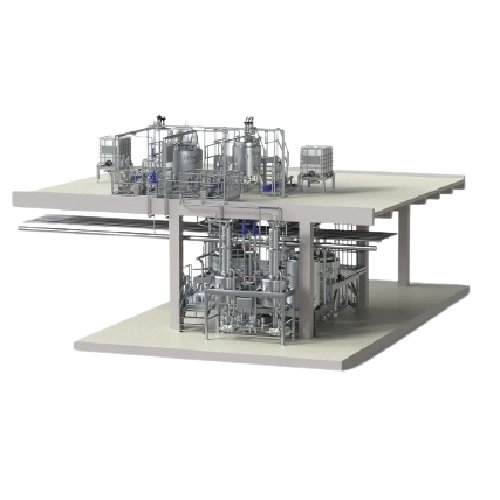
Continuous mustard line
Streamline mustard production with high-capacity continuous processing that reduces air pockets and e...

Continuous tahina production line
Streamline your tahina production with precise grinding and controlled cooling, ensuring ...
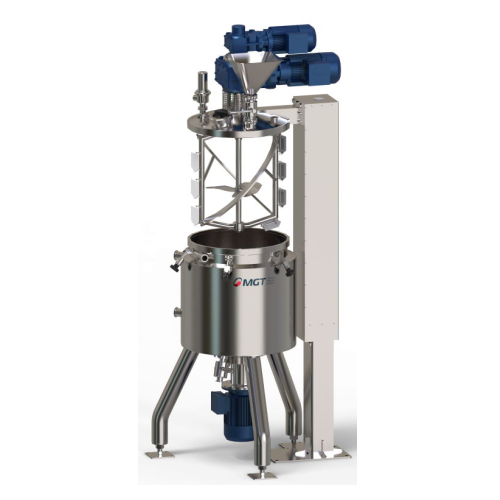
Vacuum mixing system for emulsion and homogenization
Achieve seamless emulsion and homogenization with precision: this sy...
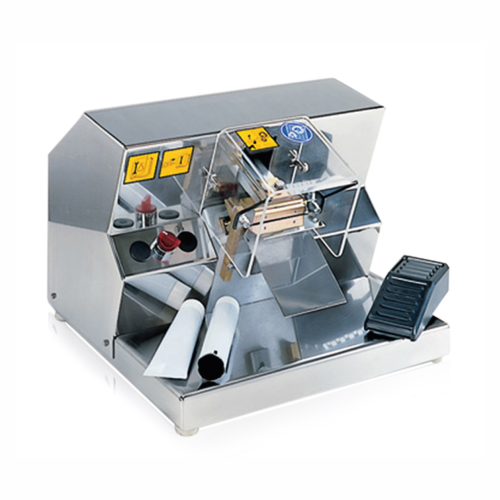
Metal tube crimping system
Optimize your packaging line with this semi-automatic system designed to efficiently crimp metal ...
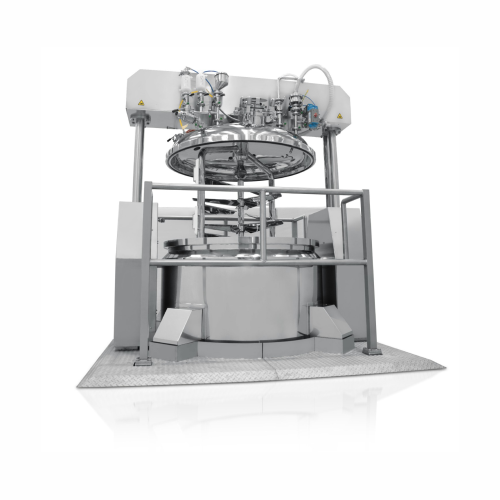
Vacuum turboemulsifiers for liquid and creamy products
Simplify your production workflow with high-capacity vacuum turboe...
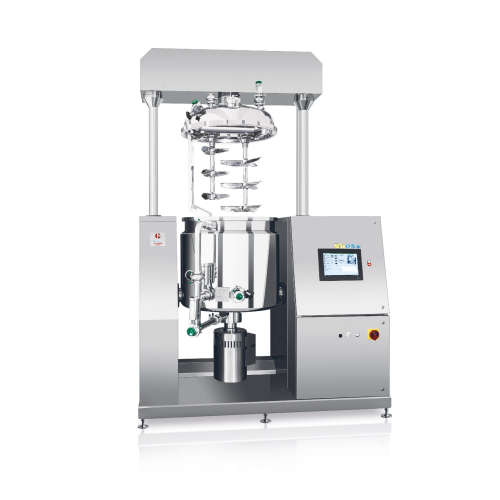
Vacuum turboemulsifier for medium-scale production
Achieve precise emulsification and consistent quality in liquid and cr...
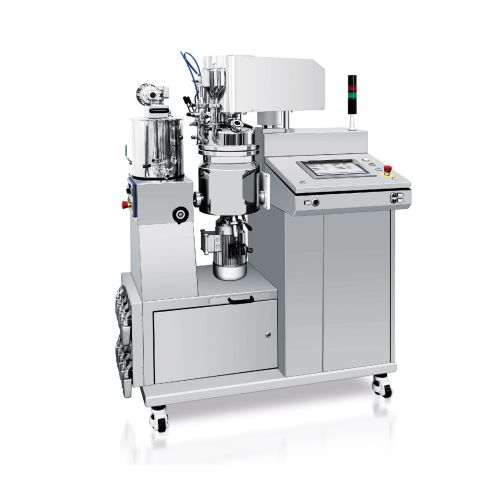
Vacuum turboemulsifier for small-scale production
Optimize your product development with versatile vacuum turboemulsifier...

Automatic tube filling and closing for metal, plastic, and laminate tubes
Enhance your production efficiency with a hi...
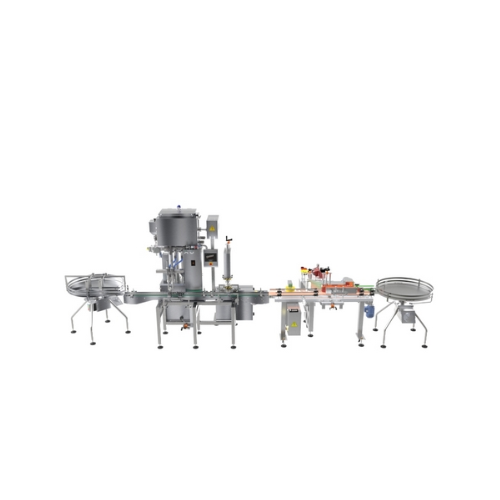
Medium capacity filling line for food and cosmetics
Streamline your production with a versatile filling line that seamles...
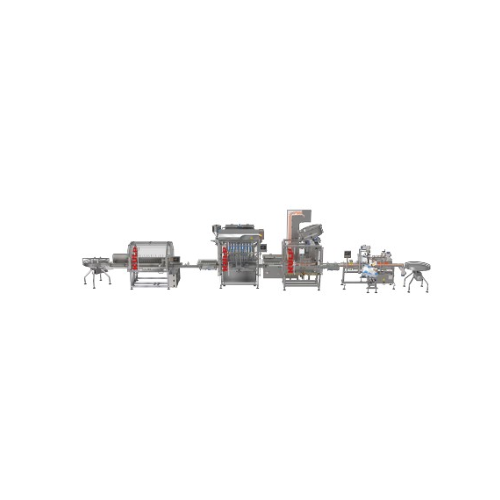
High capacity filling line for jars and bottles
Need to streamline your packaging line? This high-capacity solution proces...
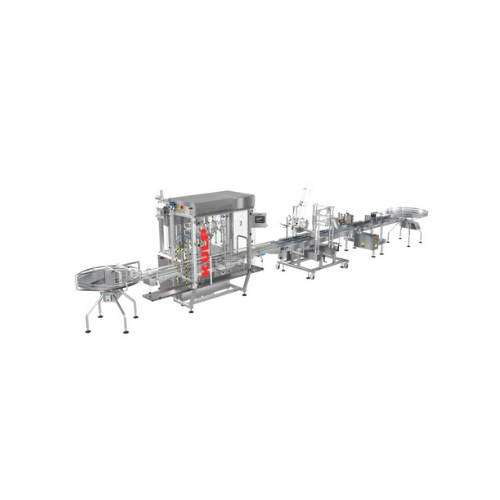
Large container filling line
Optimize your production line with a seamless solution for efficiently filling large containers...
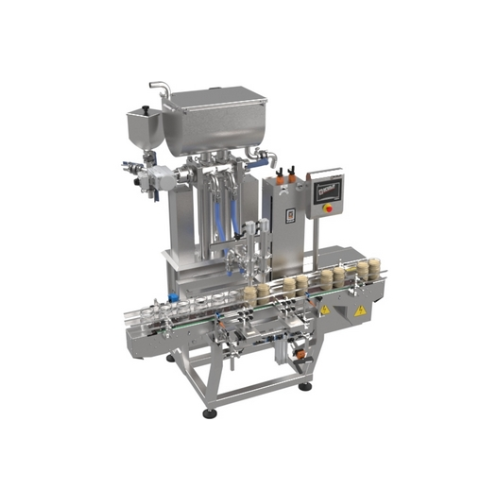
2-head liquid and viscous product filling system
Streamline your filling operations with precision and versatility designe...
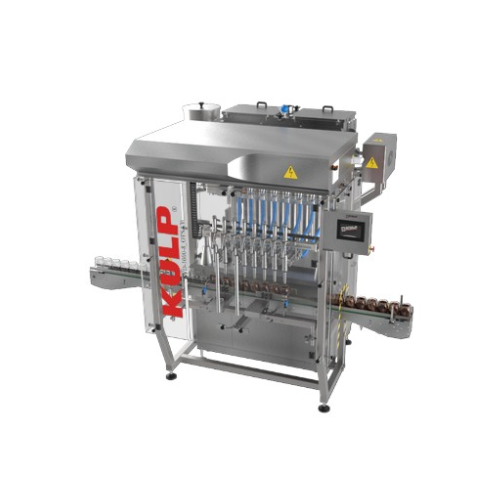
8 head liquid and viscous product filling system
When precision and speed are crucial, this 8 head filling machine ensures...
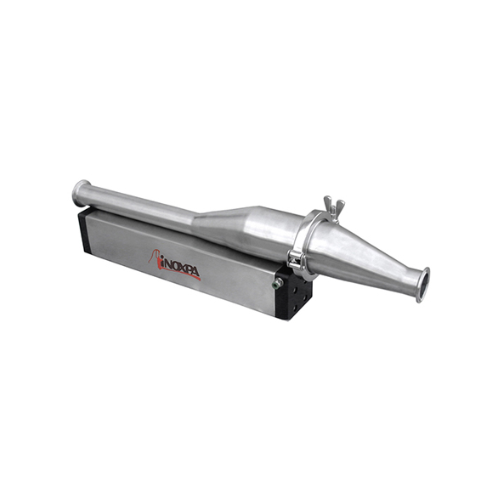
Hygienic pipeline product recovery system
Efficiently recover valuable residuals from pipelines while streamlining your cl...
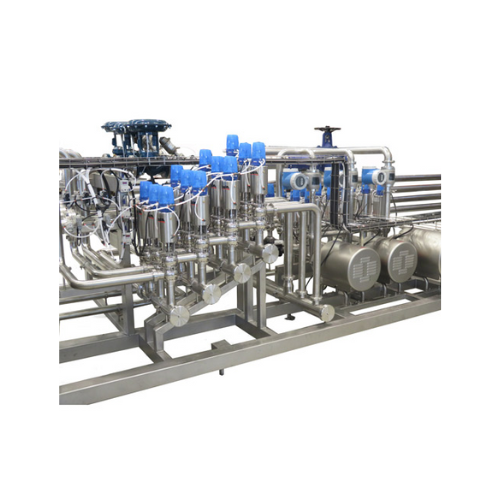
Cip cleaning system for dairy industries
Ensure hygienic operation with this system, designed to maintain optimal cleanline...
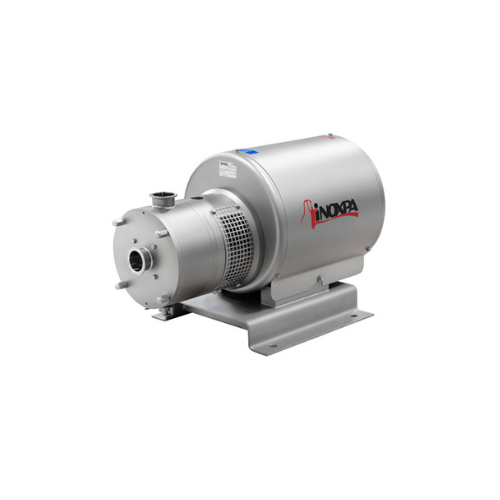
In-line high shear mixing solution
Achieve precise emulsification and particle size reduction with high shear capabilities,...
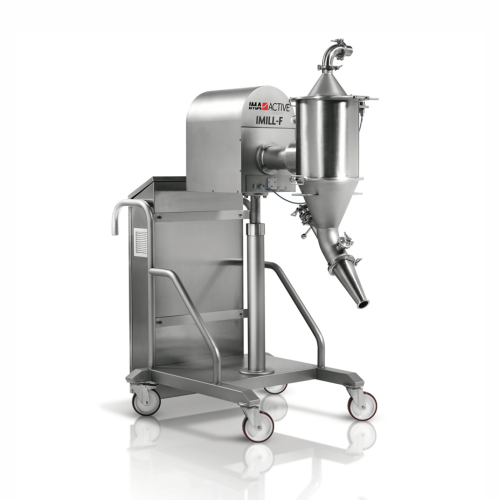
Cone mill for particle size reduction in pharmaceuticals
Achieve precise particle size control with this cone mill, desig...
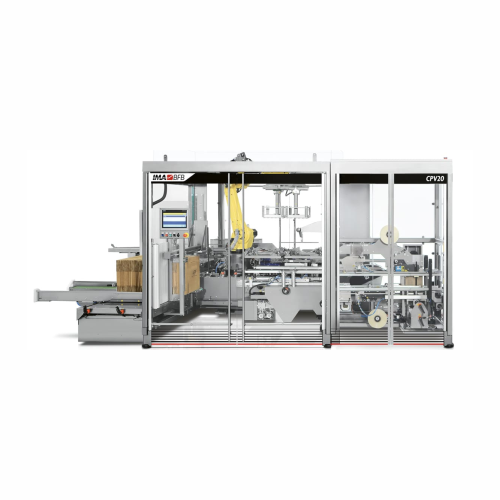
Top-loading case packer for pharmaceutical and cosmetic products
Ensure precision and flexibility in packaging with this...
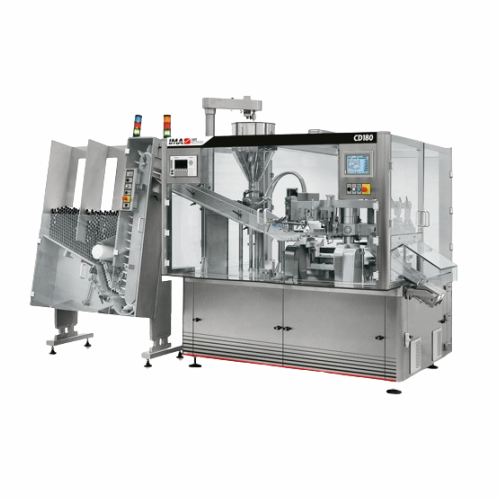
Automatic tubefiller for food and dairy products
Achieve precise dosing and seamless tube filling with high-speed efficien...
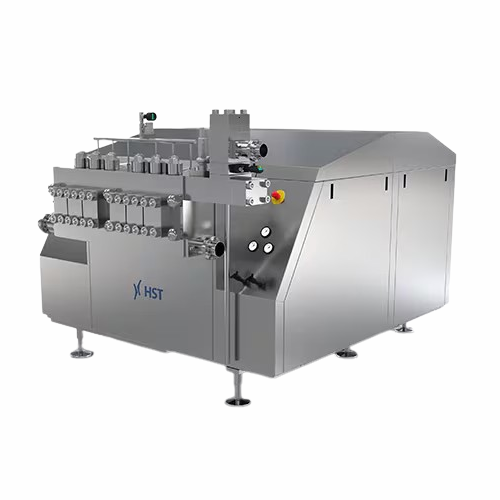
High-pressure homogenizers for liquid products
Achieve consistent emulsions and stable dispersions with high-pressure homo...
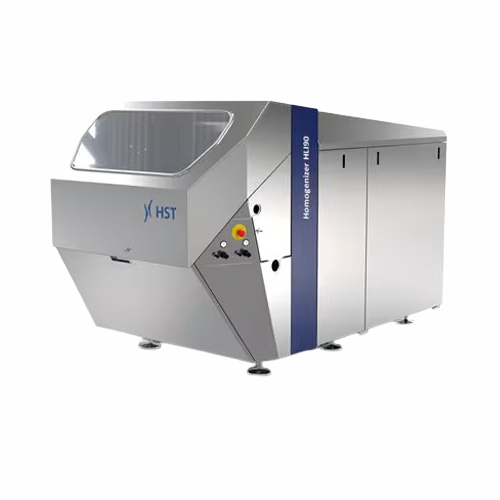
High-pressure homogenizer for food and pharmaceuticals
Achieve unparalleled consistency and stability in emulsions and di...
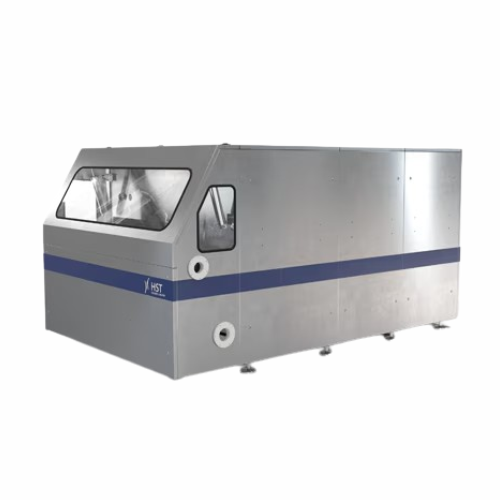
Homogenizers for high-pressure applications
Achieve unparalleled product consistency and stability with precision-engineer...
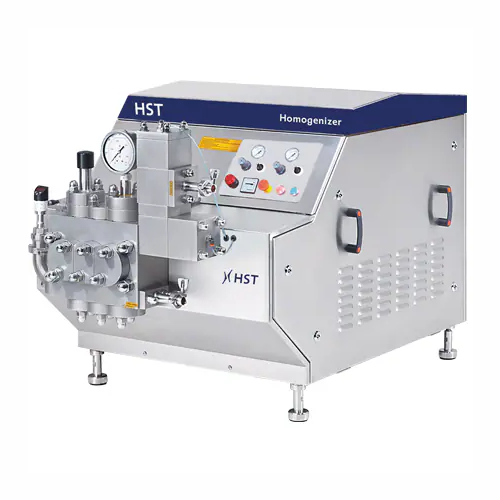
Industrial homogenizer for food and pharmaceutical applications
Ensure product consistency and stability with high-press...
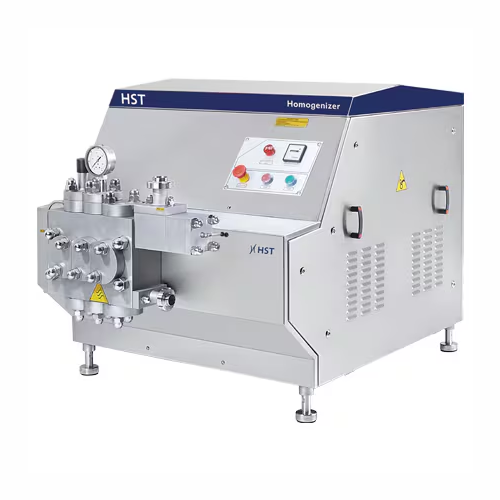
High-pressure homogenizers for dairy and food products
Achieve consistent texture and stability in your liquid products w...
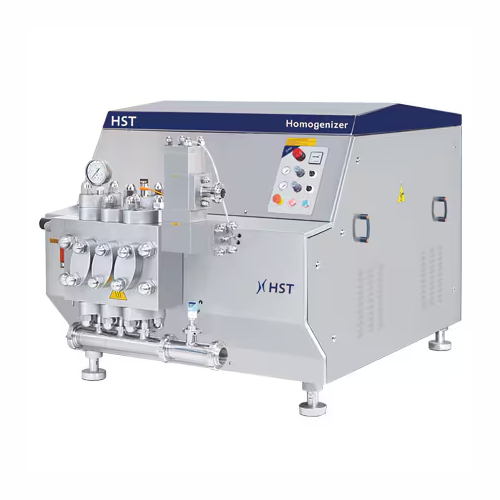
High-pressure homogenizers for dairy and beverage industries
Achieve precise emulsion stability and consistent particle ...
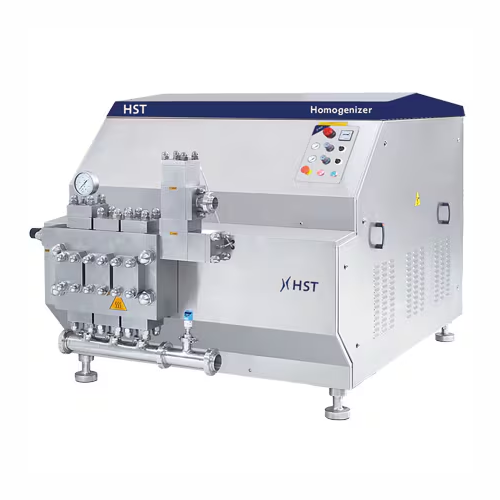
High-pressure homogenizers for dairy and juice processing
Ensure superior texture and stability in your liquid formulati...
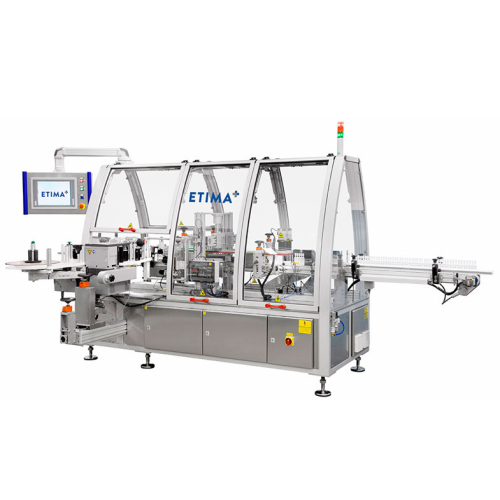
Linear labeller for self-adhesive labels in pharma
Ensure precise labelling with integrated inspections and traceability ...
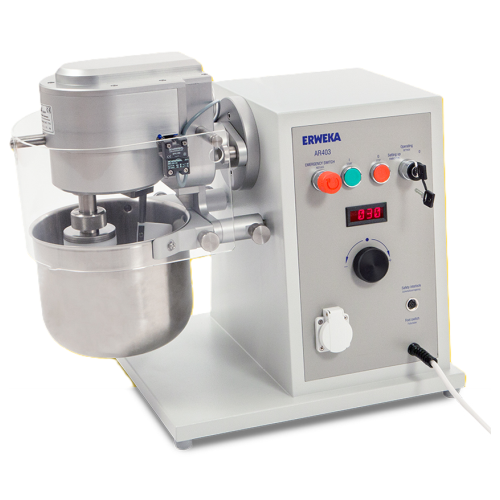
Planetary stirrer for creams and ointments mixing
Achieve homogeneous mixing of creams, ointments, and pastes efficiently...
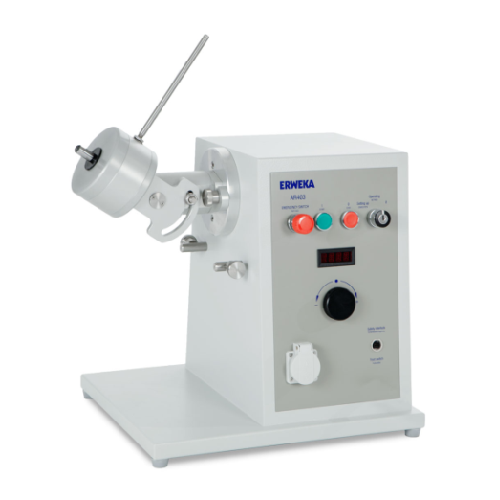
All-purpose mixer and processor for laboratory and small scale production
Optimize your small-scale production with a ...
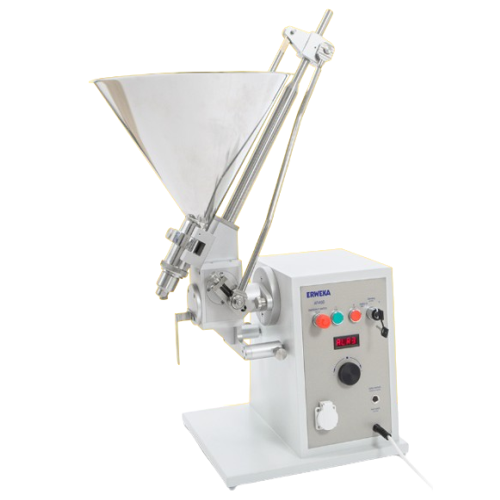
Precision ointment filling and dosing system
Achieve precise filling of liquid formulations with a versatile system capabl...
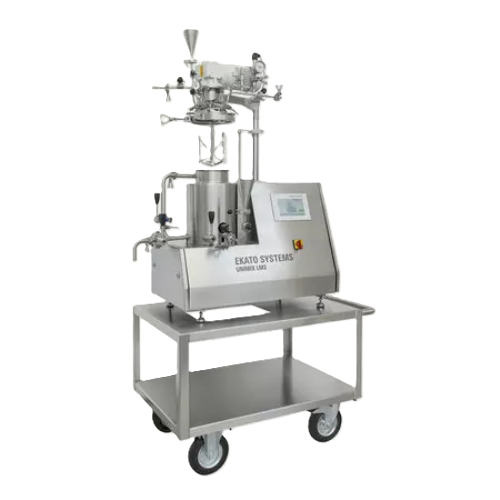
Vacuum processing units for lab scale applications
Optimize the development and scaling of cosmetic and pharmaceutical pr...
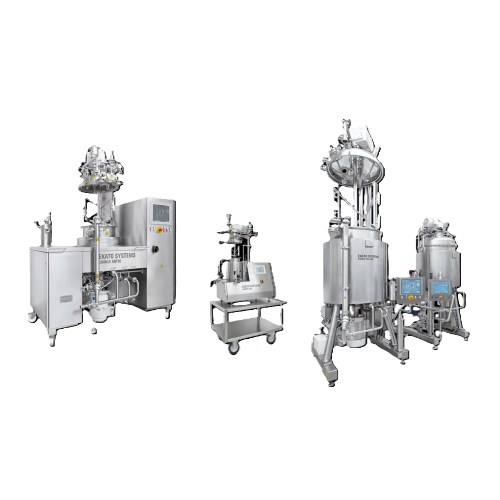
Vacuum processing units for high-viscosity products
For manufacturers seeking to streamline production of high-viscosity ...
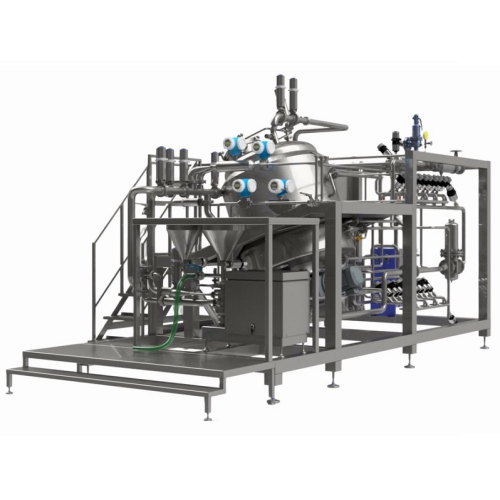
Inline system for personal care product production
Optimize your personal care production with precise mixing, heating, a...
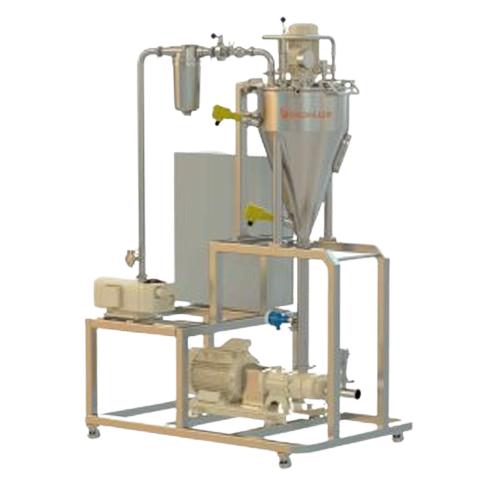
Vacuum deaerator for elimination of gases
Optimize your product quality by eliminating occlusive gases with this advanced ...
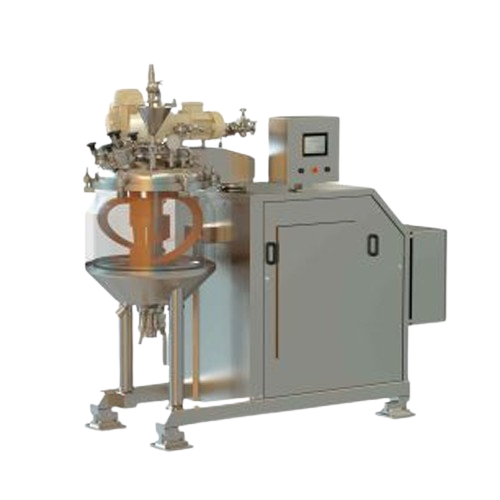
Vacuum mixer for liquids and semi-solids
Achieve precise mixing and homogenization of liquid and semi-solid formulations wi...
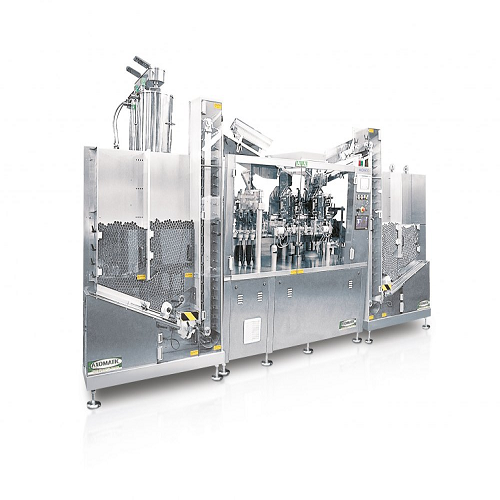
Automatic tube filling and closing system
Enhance production efficiency with a high-speed tube filling and closing system ...
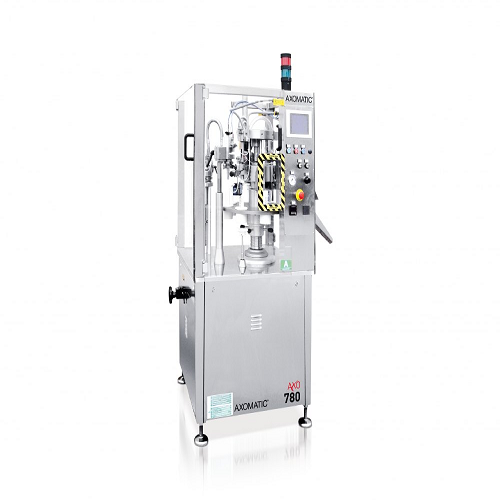
Semi-automatic tube filling and closing system
Achieve precise filling and secure closing for diverse tube types, optimizi...
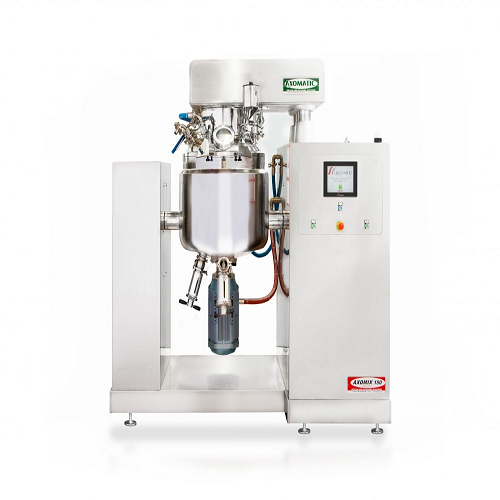
Vacuum homogenizer for high-quality mixing and emulsification
Achieve optimal consistency and enhanced product stability...
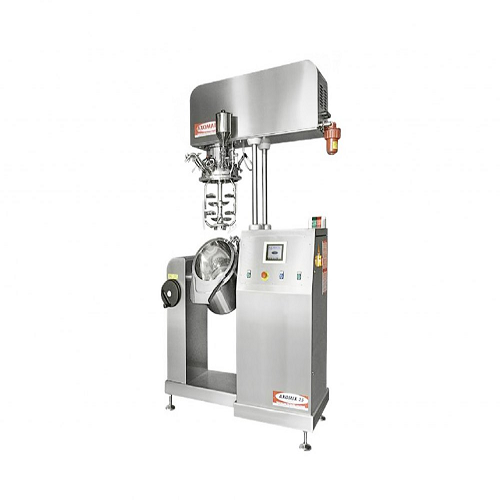
Industrial under vacuum homogenizer
Optimize the consistency and texture of creams and lotions with precision-controlled mi...
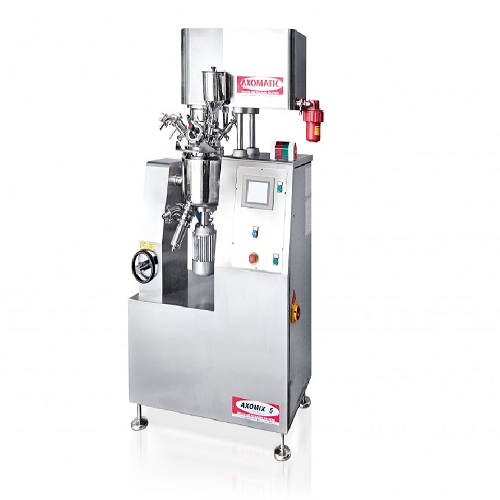
Vacuum homogenizer for creams and ointments
Streamline your production with cutting-edge vacuum homogenization, perfect fo...
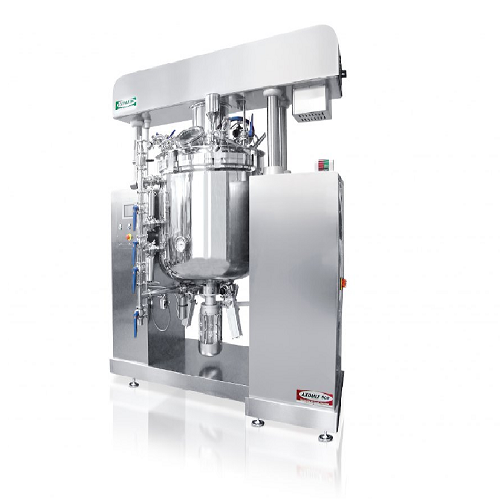
Undervacuum homogenizer for cosmetic and pharmaceutical creams
Optimizing the production of creams and lotions, this und...

Automatic bottle filling and capping line
Streamline your liquid product packaging with this high-speed solution, integrat...

Manual sealing machine for aluminum tubes
Ideal for laboratories and small-scale production, this compact manual sealing m...
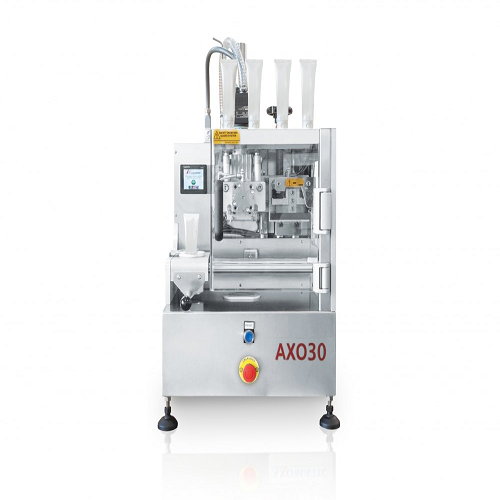
Manual tube sealer for plastic and laminated tubes
Secure precise and reliable seals on plastic and laminated tubes with ...
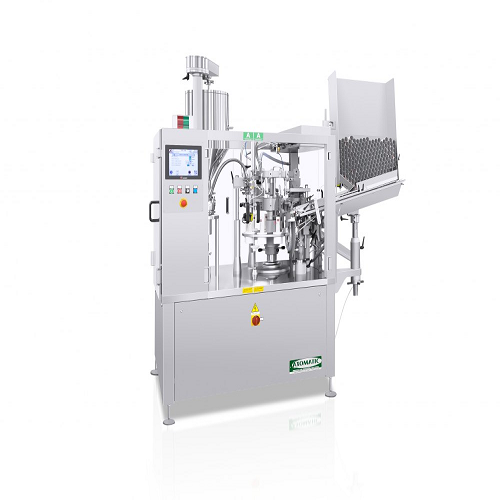
Automatic tube filling and closing solution
Optimize your production line with a high-speed machine for precise tube filli...
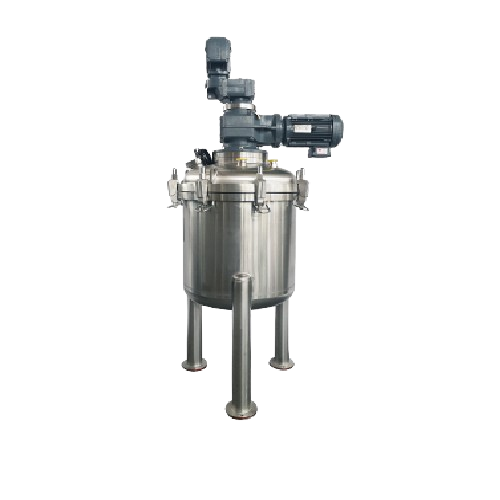
High viscosity product mixer
Struggling with mixing high viscosity products like creams and gels? This co-axial mixer enhanc...
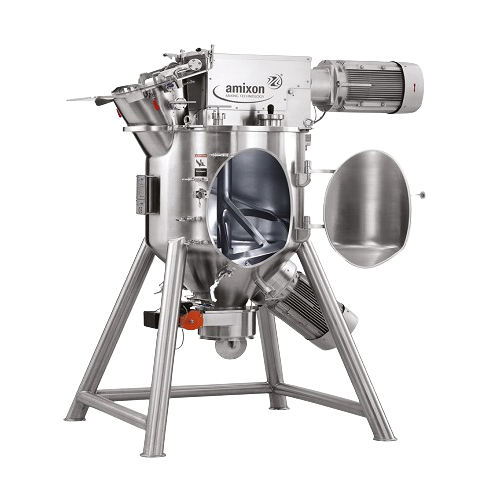
Conical mixer for dry, moist, and viscous materials
Achieve optimal mixing consistency and precision for diverse material...

Narrow belt spiral conveyor for small packages
Optimize your production flow with this compact spiral conveyor system, des...
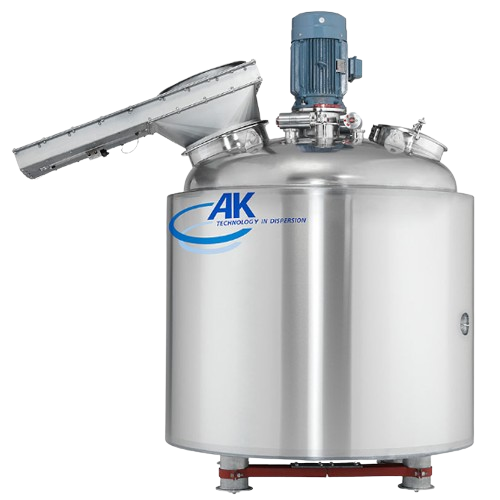
Emulsion processing system for homogenizing solids into liquids
Achieve precision in emulsifying and homogenizing proces...
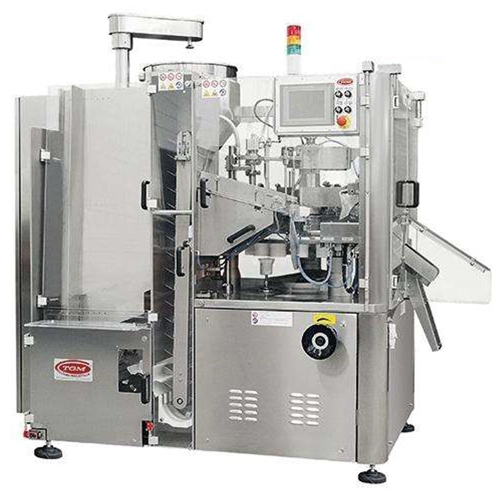
Tube filler & sealer for metal and plastic tubes
Streamline your production line by efficiently filling and sealing metal ...
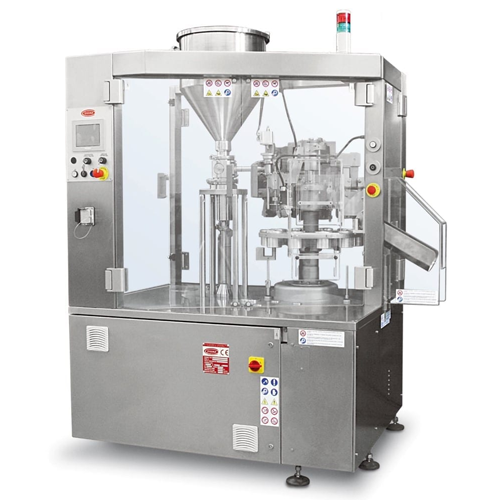
Efficient tube filler and sealer
Optimize your production line with a semi-automatic tube filling and sealing solution, desi...
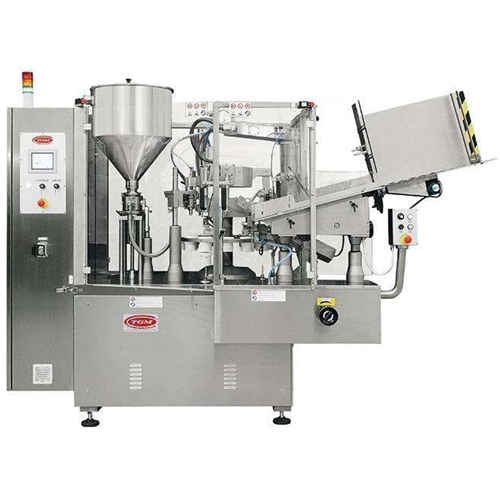
Tube filling and sealing for metal and plastic tubes
Achieve precise tube filling and sealing with high speed and efficie...
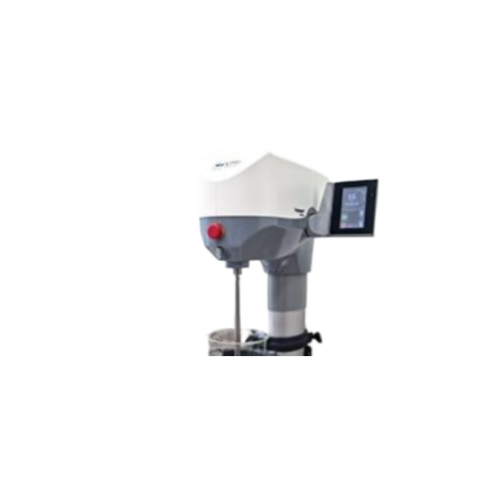
Vacuum homogenizers for cosmeto-pharma and fine chemistry
Bring precision and efficiency to your formulation processes w...
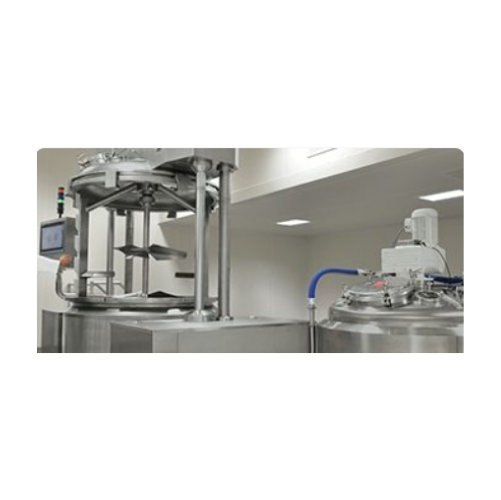
Vacuum homogenizer for cosmeto-pharma applications
Optimize your formulations with our vacuum homogenizers, ensuring prec...

Vacuum homogenizer for cosmetics and pharmaceuticals
Optimize your production with precision mixing and homogenizing, ess...
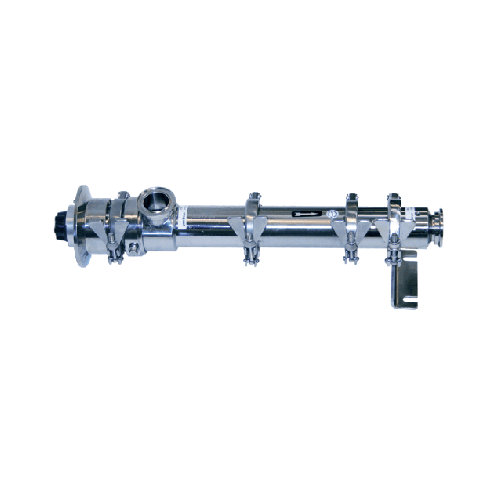
Dosing and filling pump for hygienic applications
Optimize your production line with this dosing and filling pump, design...
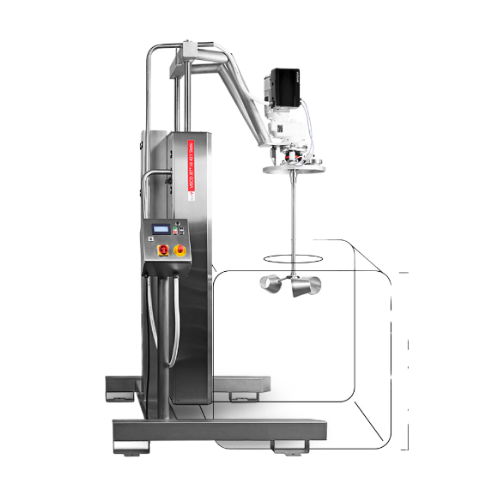
Industrial mixer for product-critical processes
When dealing with high-hygiene requirements and complex mixing tasks acros...
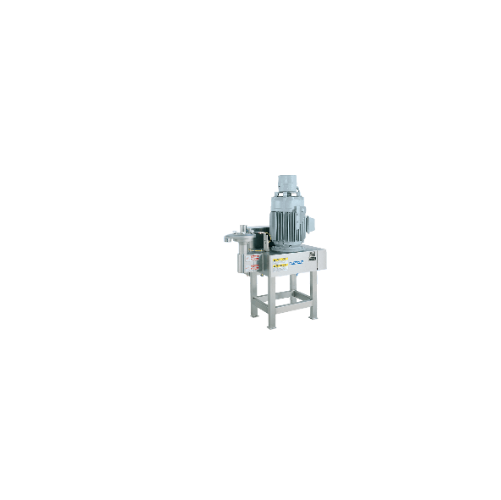
Viscous and liquid product processor
Optimize your production of viscous slurries and liquid formulations with a versatile ...
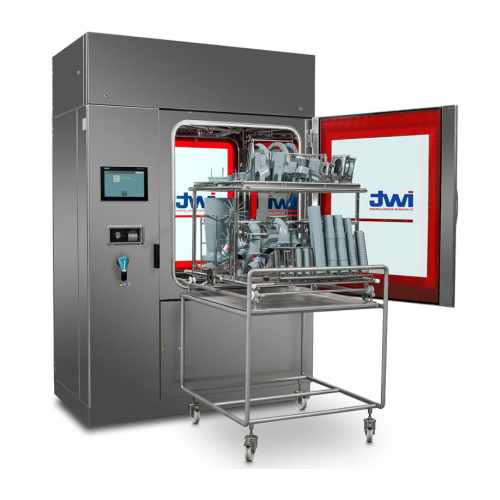
Gmp contact part washers for pharmaceutical industry
Ensure product integrity and hygiene with specialized washing system...
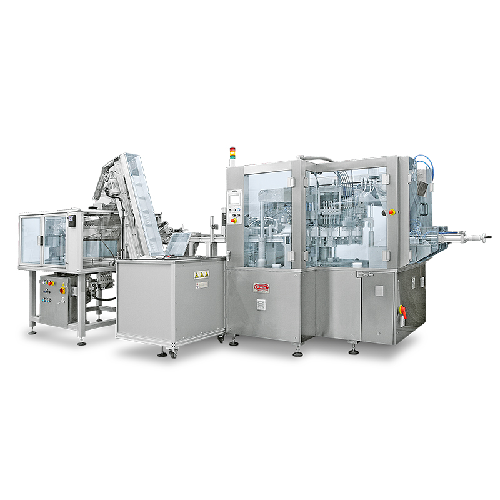
Automatic mono-dose strip filling system
Optimize your liquid product packaging with a multi-functional system designed for...
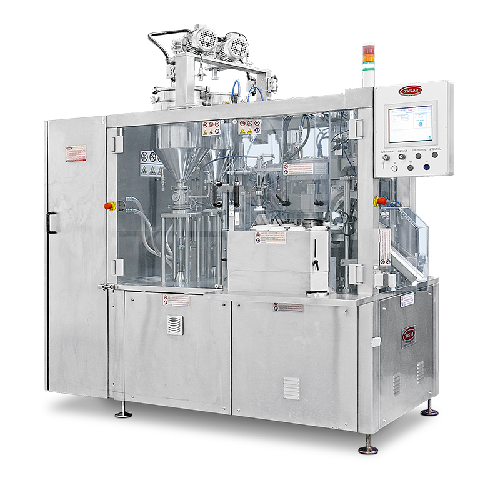
Automatic tube filling for multi-color products
Achieve precision in multi-color product packaging with seamless co-extrus...
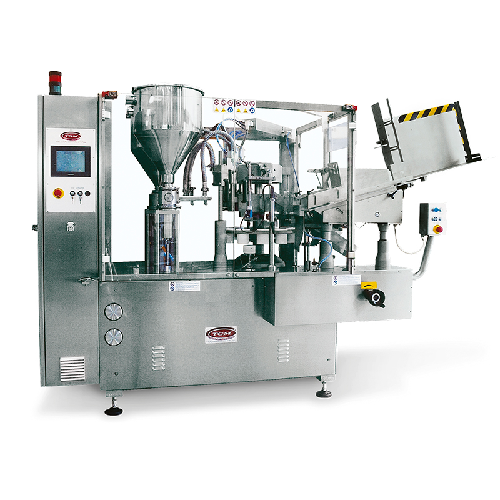
Automatic tube filler for multi-color coextruded products
Achieve precise dual- or tri-color product designs with except...
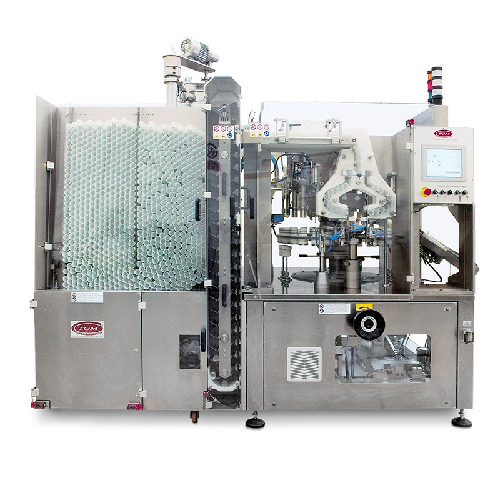
Automatic tube filling for coextruded products
Maximize efficiency in high-volume production with precision co-extruding c...
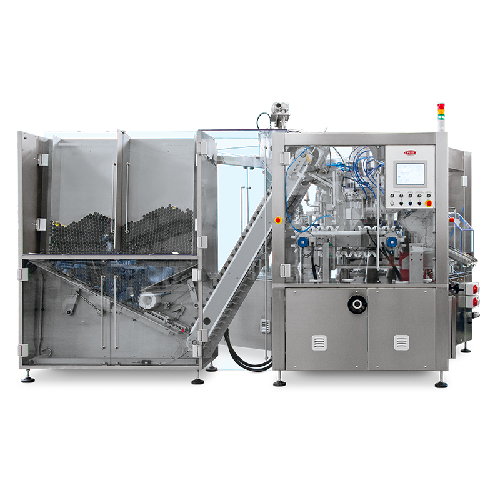
Automatic tube filling solution for high-volume production
Effortlessly streamline your production with this high-speed ...
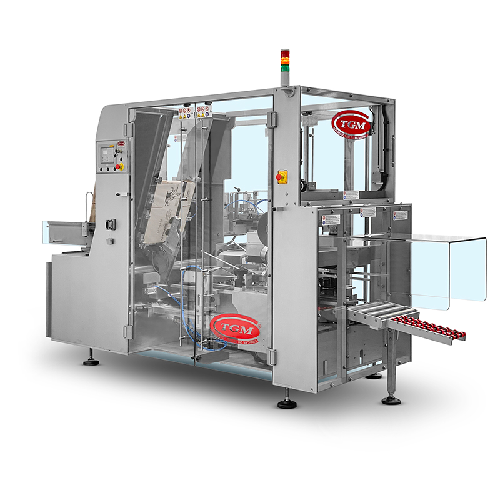
Automatic case packer for cartons and bundles
Optimize your packaging process by efficiently inserting single cartons and ...
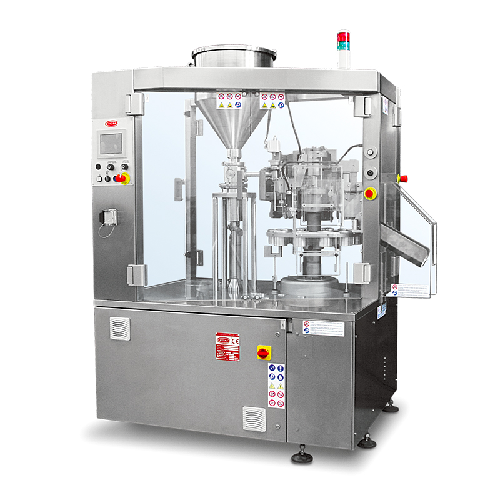
Small batch tube filling system for metal and plastic tubes
Optimize your small-batch production with precise tube filli...
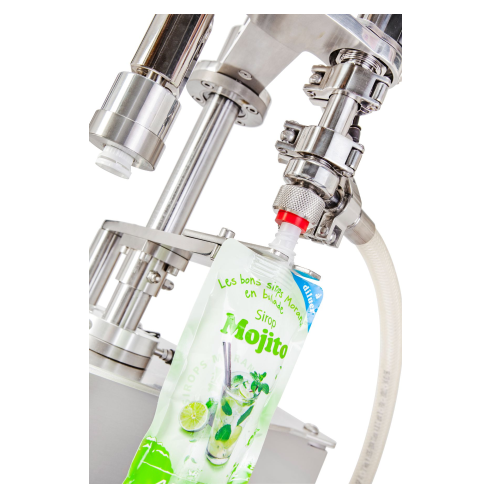
Manual monoblock for filling and capping spouted pouches
For those handling liquid or semi-dense products, this manual mo...
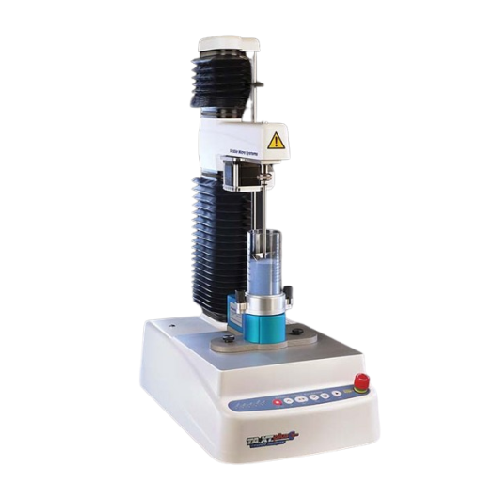
Powder flow measurement system
Achieve precise control over powder consistency and prevent process disruptions by assessing ...
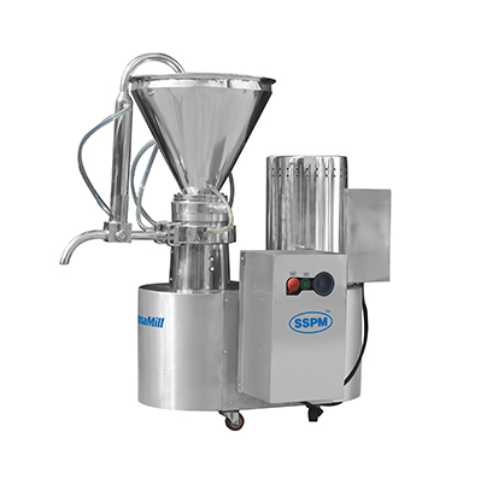
Colloid mill for particle size reduction and emulsification
Achieve precise particle size reduction and stable emulsions...
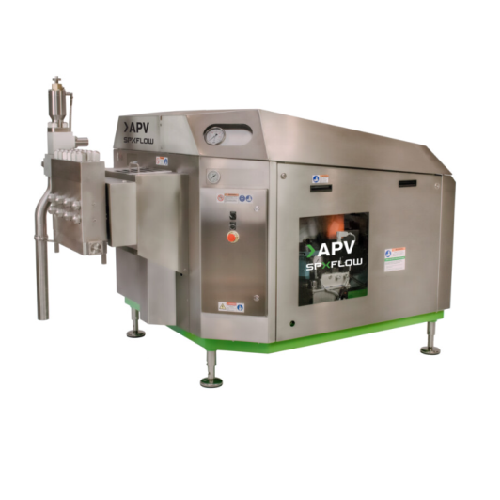
High pressure homogenizer for dairy and pharmaceutical industries
When uniform texture and stable emulsions are critica...
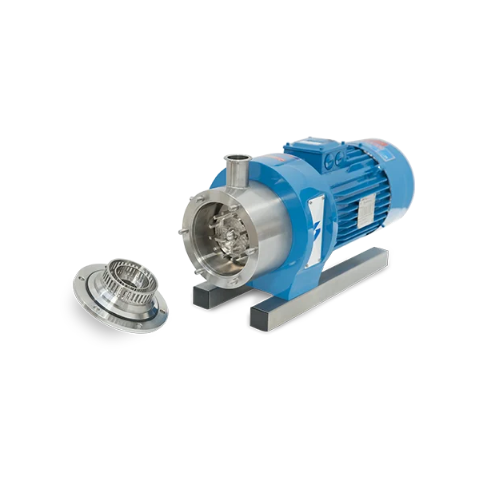
Homogenizers for creams and ointments
Achieve superior consistency and particle size reduction in skincare creams, sauces, ...
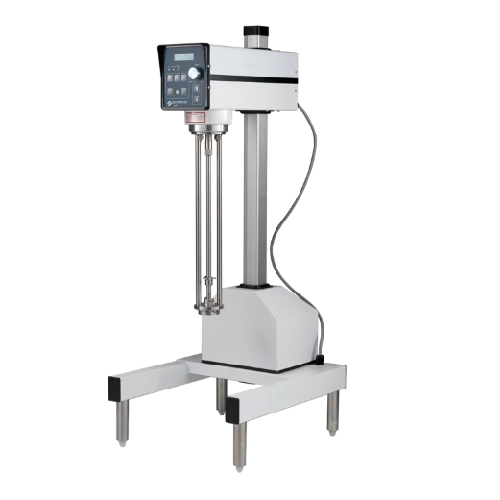
Pilot scale batch mixer for small scale production
Achieve precise control and consistency in small-scale production with...
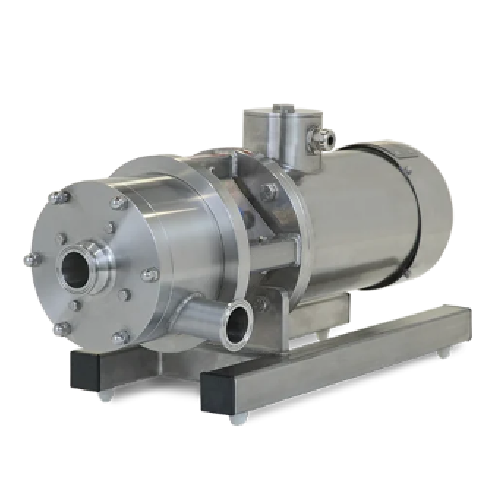
Sanitary high shear mixers for pharmaceutical production
Achieve unparalleled hygiene and efficiency in your mixing proce...
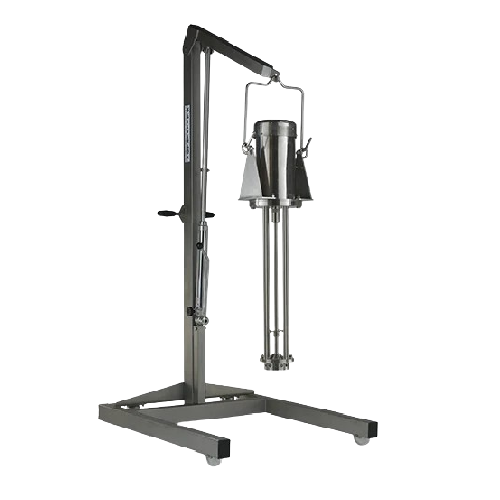
High shear batch mixer for industrial mixing
Optimize your production cycle with this high shear batch mixer, designed to ...
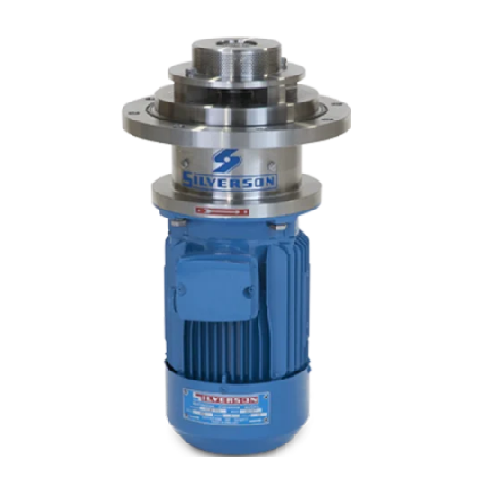
Bottom entry mixers for high viscosity products
Optimize your production line with mixers designed to handle both high and...
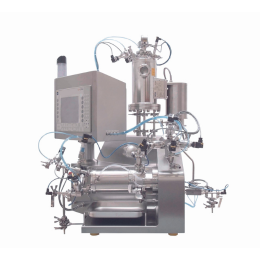
Agitator bead mill for API
To achieve precisely defined API properties and safe and reproducible production, rigorous implem...
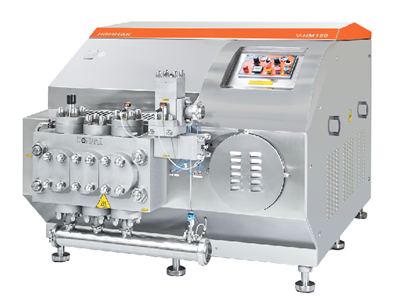
Pilot plant homogeniser
From food to pharma, homogenization is an essential step in the production process that provides unif...
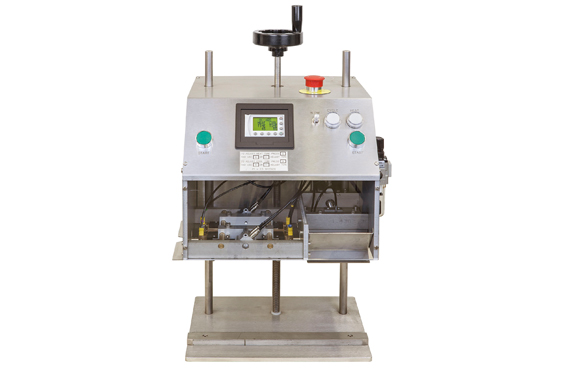
Manual plastic tube sealing equipment
Working in labs or with small batch production lines where you have to seal plastic o...
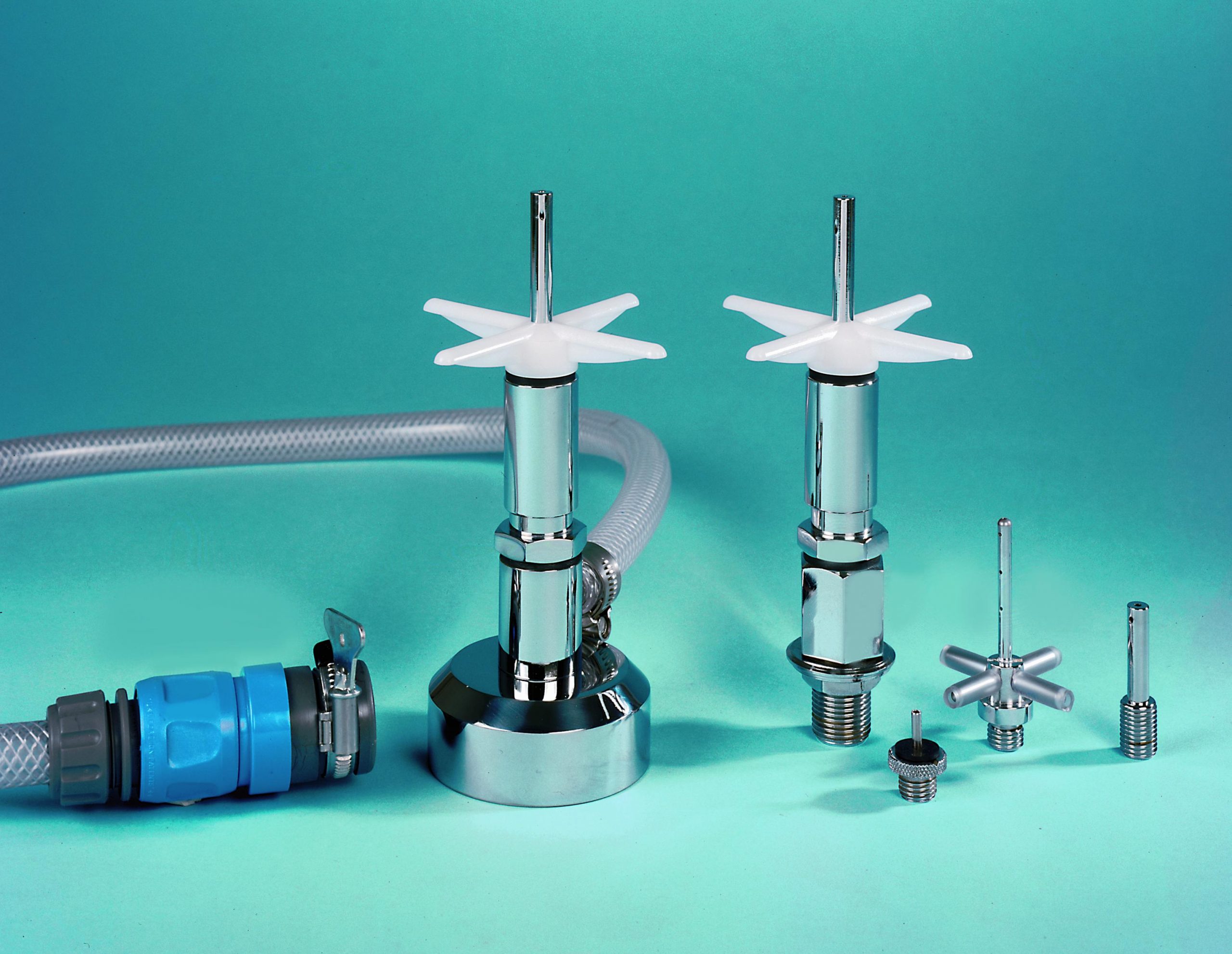
R&D bottle washer
When you pack your products in bottles, vials, syringes, and test tubes you need to wash them before fillin...
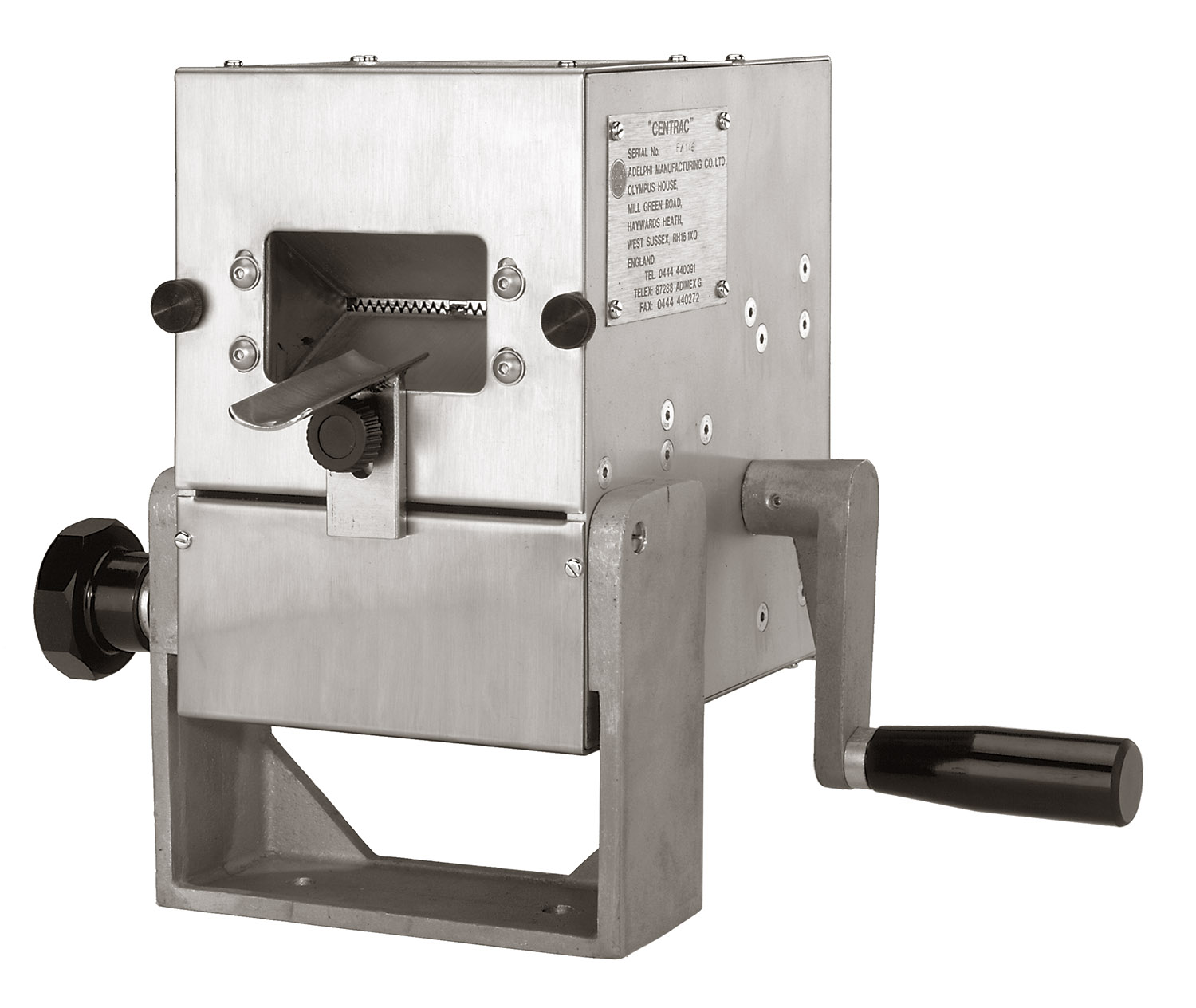
Manual metal tube sealing equipment
For small-batch productions where you utilize metal tubes as containers for your produc...
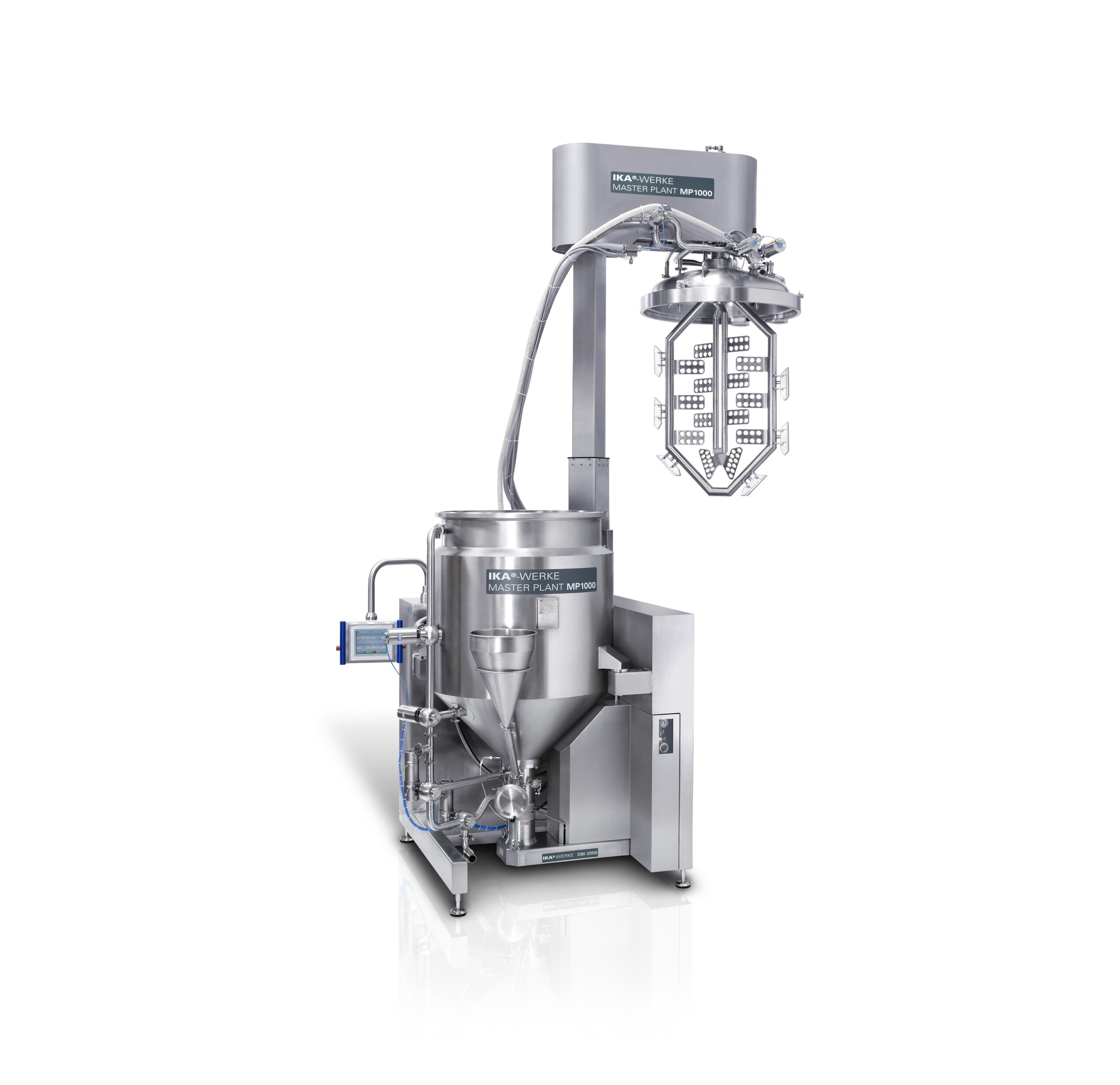
GMP homogenizing system
Manufacturers need production mixing equipment that is capable, flexible, and easy to maintain. Accur...
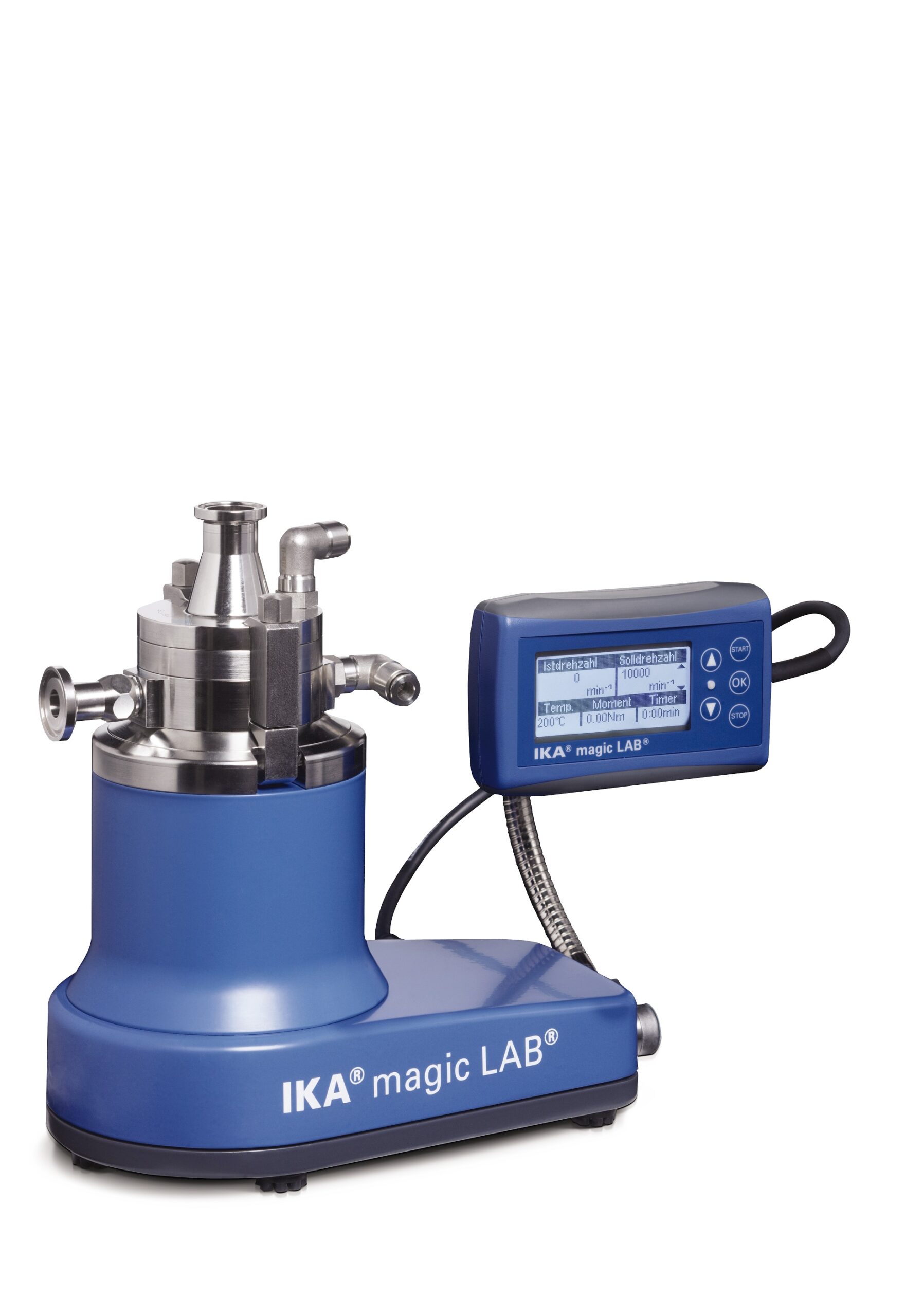
Small-scale laboratory dispersing machine
Developing and validating new processes requires reliable and highly versatile e...
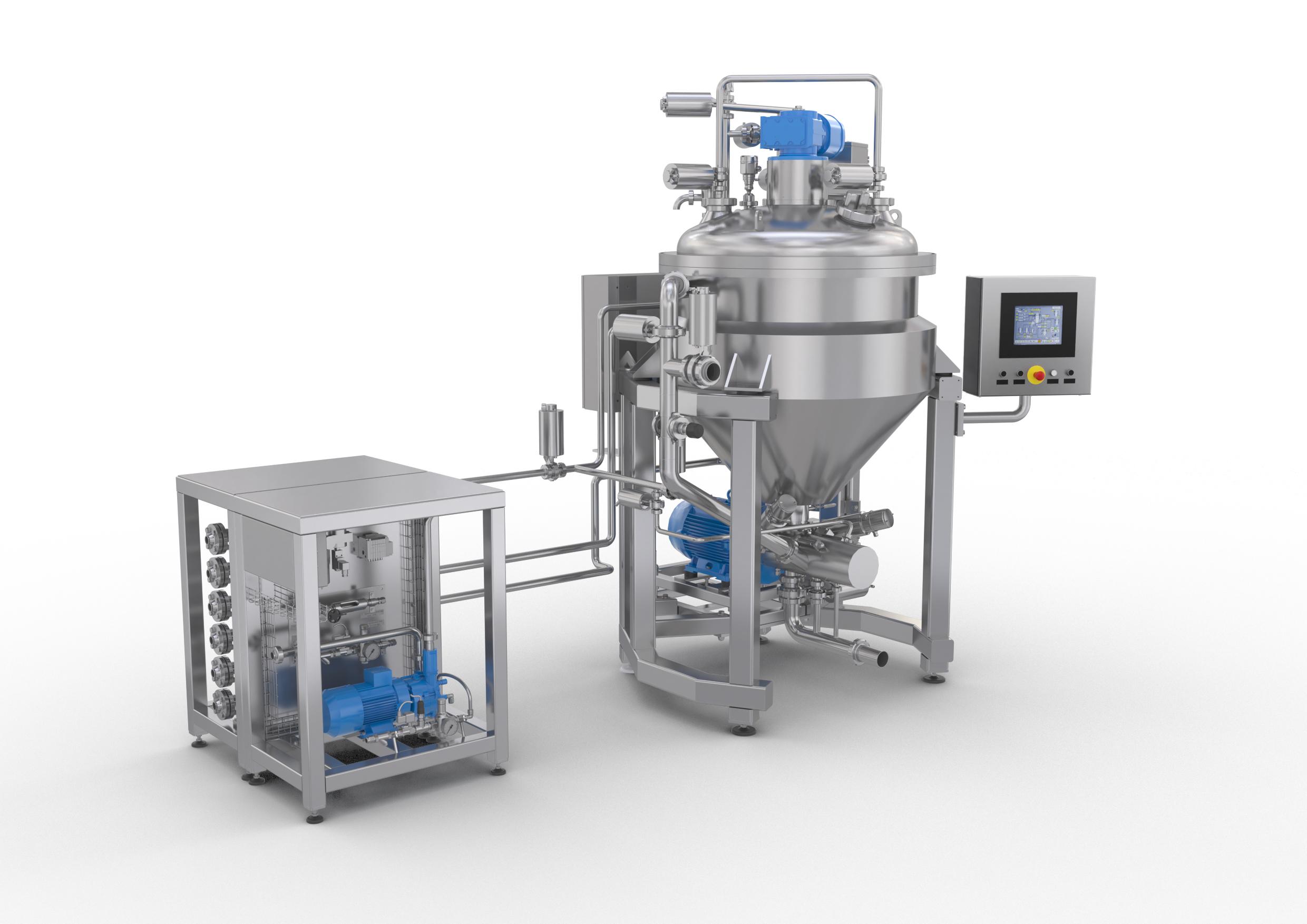
Batch vacuum mixer for emulsion-based products
The production of creams or ointments can be either be a water in oil (w/o)...
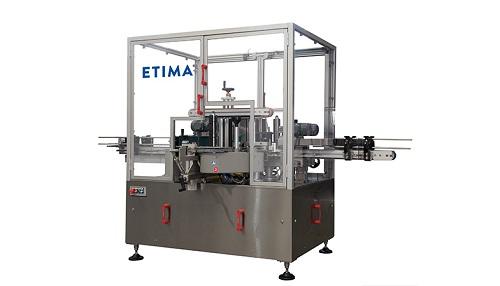
Self-adhesive linear labeling machine for bottles
It is vital to have precise and long-lasting labels on bottles to avoid...
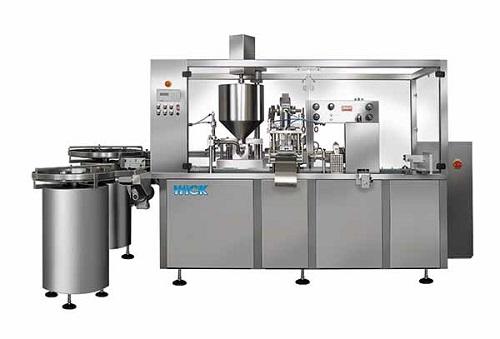
Cosmetic cream filler
From thin liquid baby oils and perfumes to thicker lotions and creams for hair and skincare, cosmetic p...
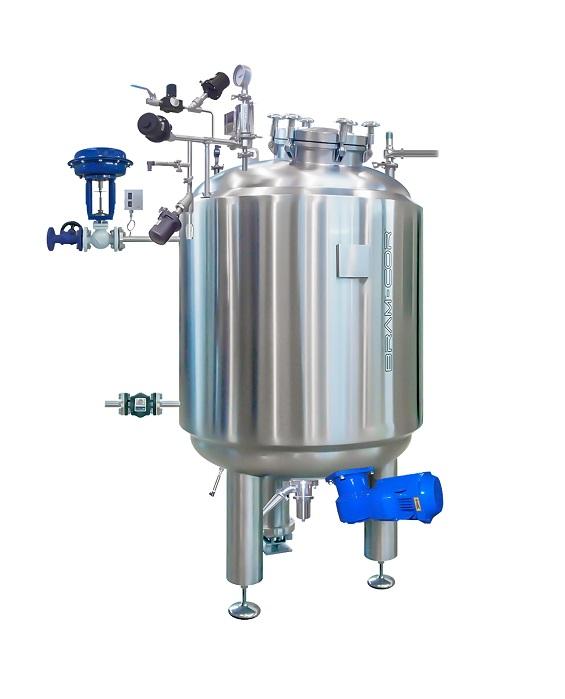
Pharmaceutical formulation and mixing tanks
Preparation lines for formulating pharmaceuticals include fixed and mobile tan...
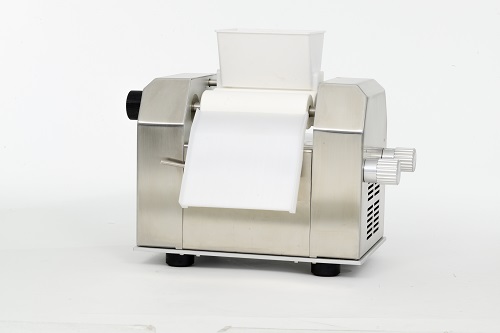
Benchtop mill for ointments
Pharmaceutical and cosmetic creams, ointments, gels and pastes can deliver a wide range of activ...
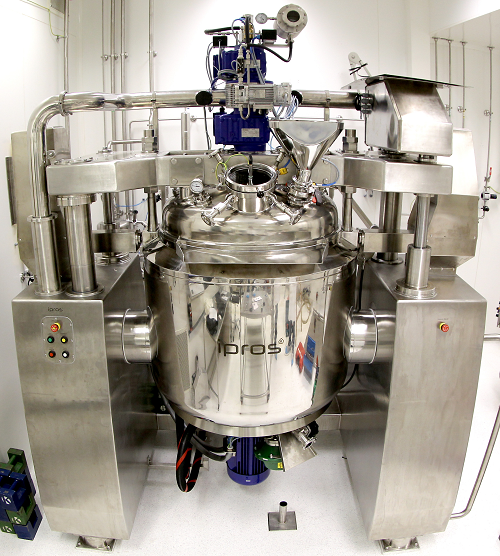
Homogenizer for creams
Homogenization (or pharmaceutical micronization) is the process of reducing particle sizes, and is a v...
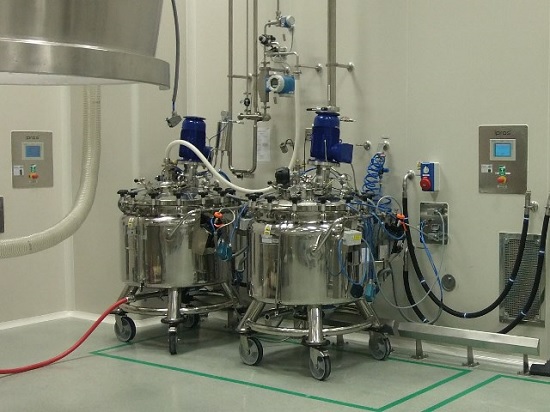
Vacuum mixer for suspensions
The production of high quality pharmaceuticals often requires mixing of suspensions and similar...
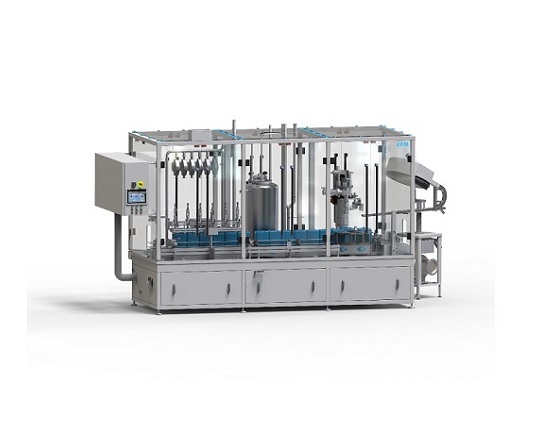
In-line monoblock linear filler & capper
In many food, chemicals and cosmetic industry processes it is vital to have a...

Flowmeter filler
For larger production runs of food, non-food and cosmetics industries, where accuracy and volume of filling i...
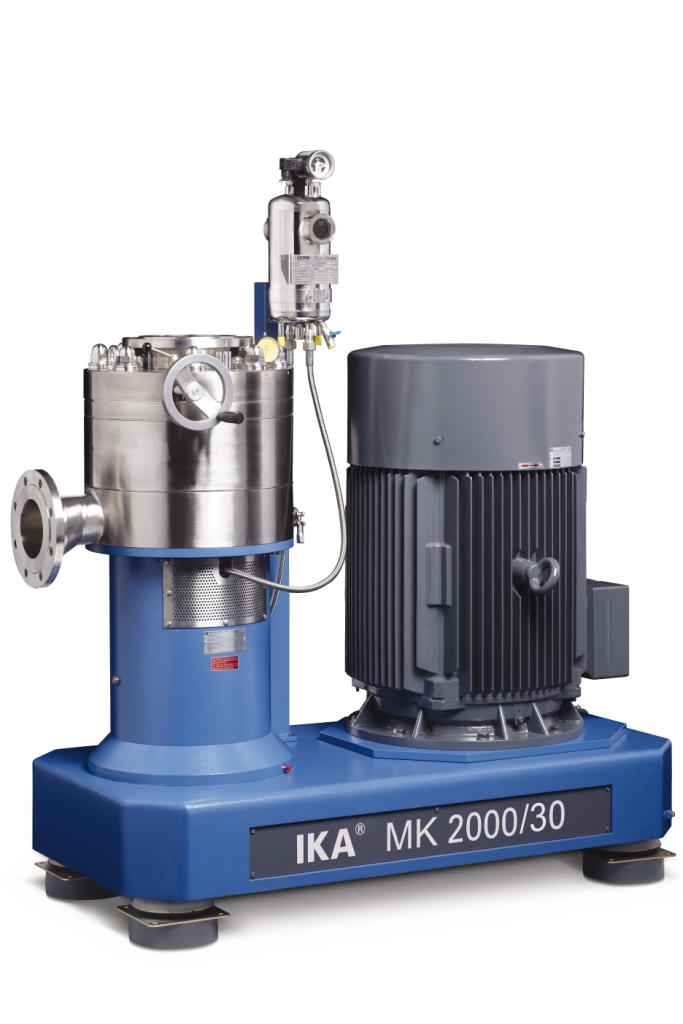
Colloid mill
For creating extremely fine emulsions and high quality dispersions a high pressure homogenizer is often chosen. ...
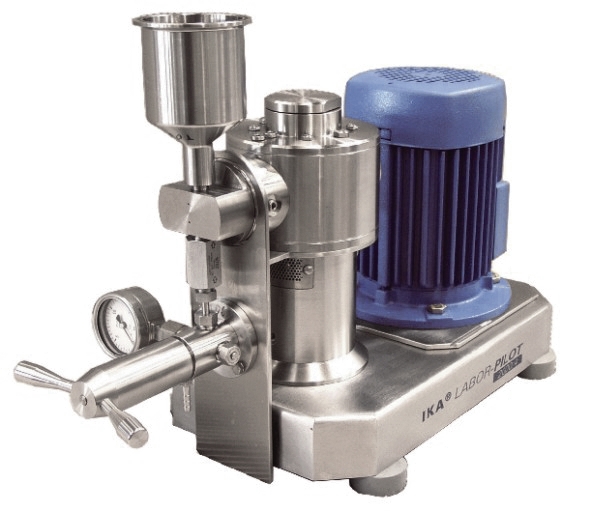
High-pressure homogenizer
When processes call for homogenized emulsions with extremely fine particle sizes the traditional t...
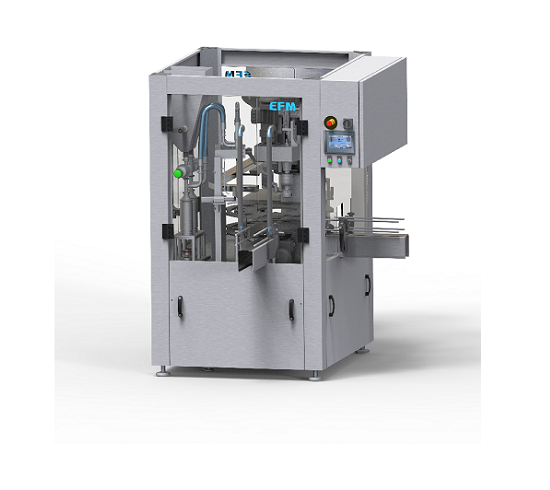
Compact monoblock filler
Filling and capping bottles and pots for food, chemical and cosmetics industries using separate mach...
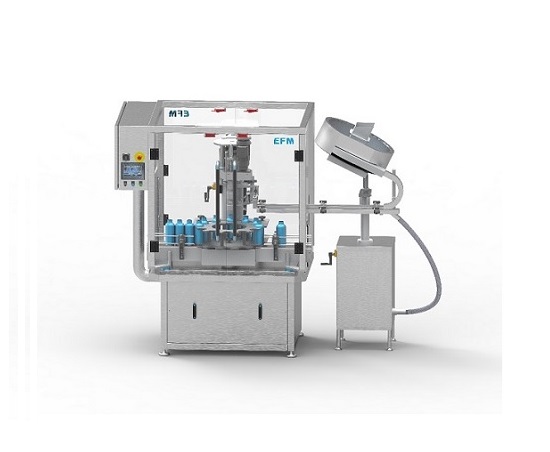
Single head capper
For the stand-alone capping of bottles of up to 30 litre capacity for smaller-scale production you need a ...
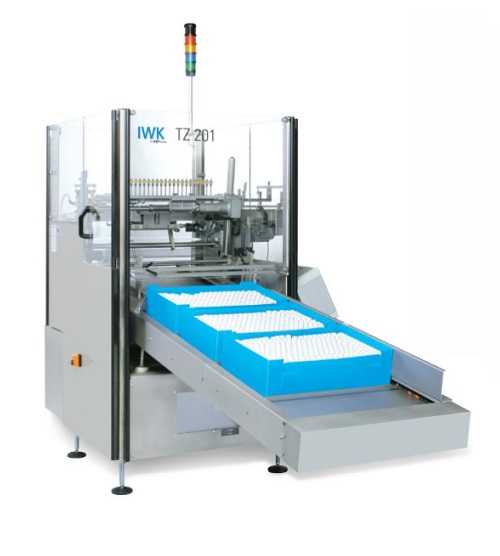
Tube unloader and feeder
The pharmaceutical and cosmetic industries utilise high speed tube fillers on large-scale production...
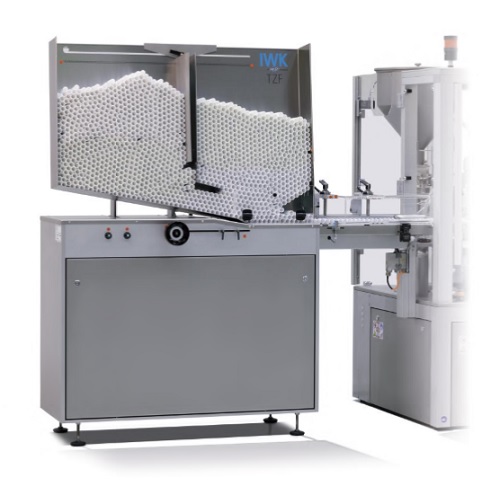
Tube feeding unit for high volume and high speed tube filler
High performance tube-filling machines are used for large s...
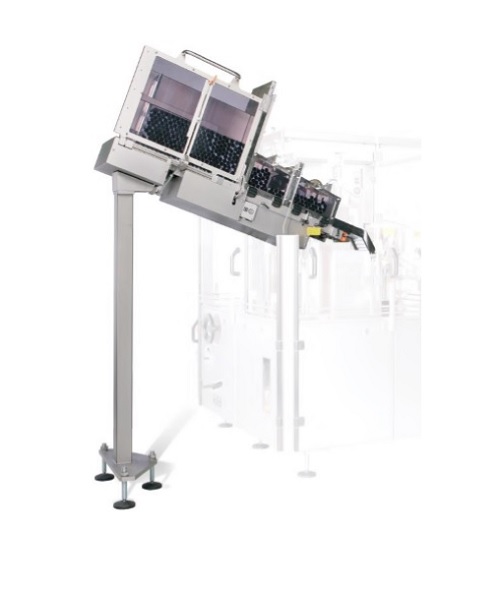
Loading cassette for a tube filler
High performance tube-filling machines are used in the pharmaceutical and cosmetic indus...
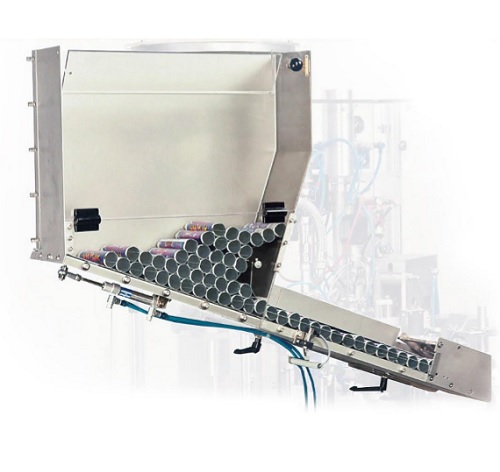
Tube feeder for a small scale production tube filler
Low speed tube-filling machines are used for small scale production ...
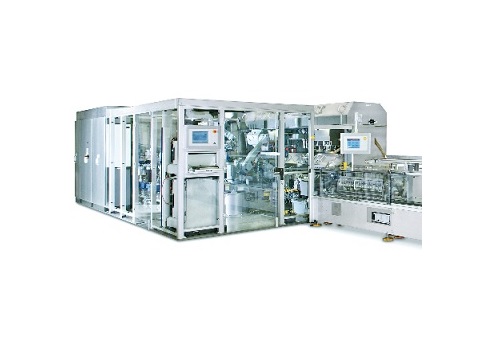
High speed automatic tube filler
For high-volume lines filling pharmaceutical, cosmetic or food products into tube container...
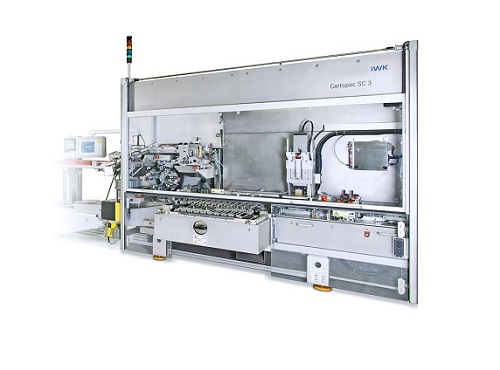
High-capacity horizontal cartoner for pharma and cosmetics appliances
Cartoners take carton blanks which are formed and...
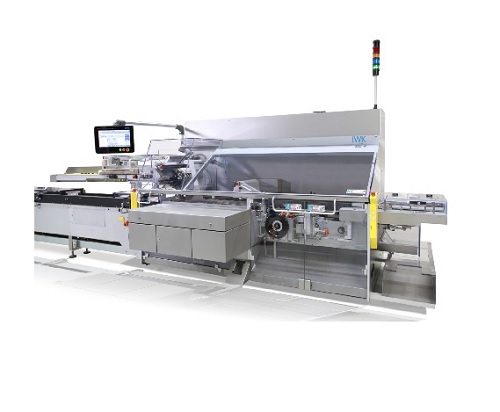
Automatic cartoner for applications in pharma and cosmetics
For high capacity production of cosmetics and pharmaceutical...
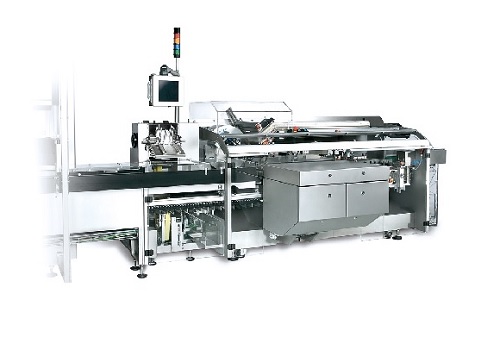
Pharmaceutical and cosmetic industry products cartoner
A large number of cosmetic and pharmaceutical products are packed ...

Horizontal cartoner for pharma and cosmetics
Most pharmaceutical and cosmetics products are packed in cardboard cartons fo...
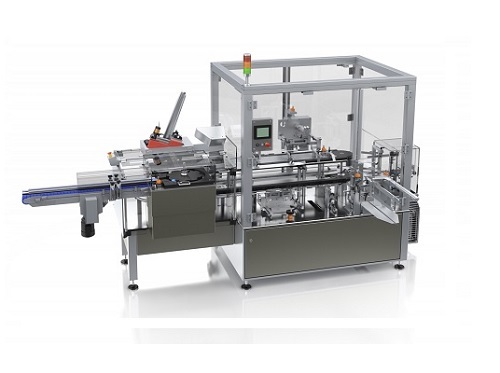
High capacity cartoner for pharmaceutical applications
Many pharmaceutical products are packed in protective and decorati...
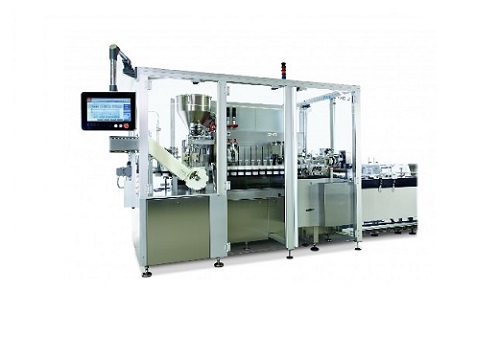
Medium speed tube filler and sealer
For scale-up filling of tube packaging for pharmaceuticals, cosmetics and food products...
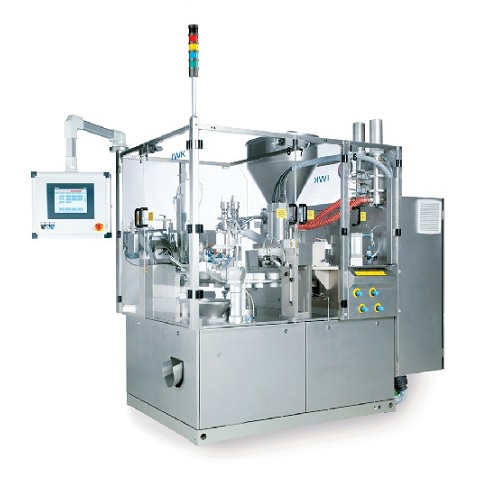
Medium and high speed range automatic tube filler
When scaling up production of pharmaceutical, food or cosmetic products...
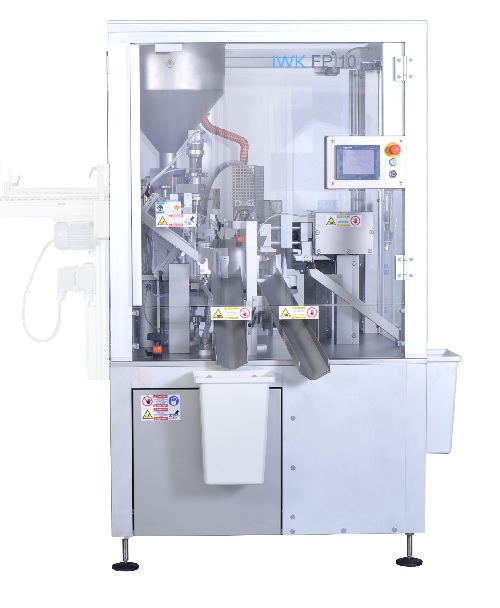
Low speed tube filler
Increasing numbers of products in the pharmaceutical, cosmetic and food industries are delivered in fle...
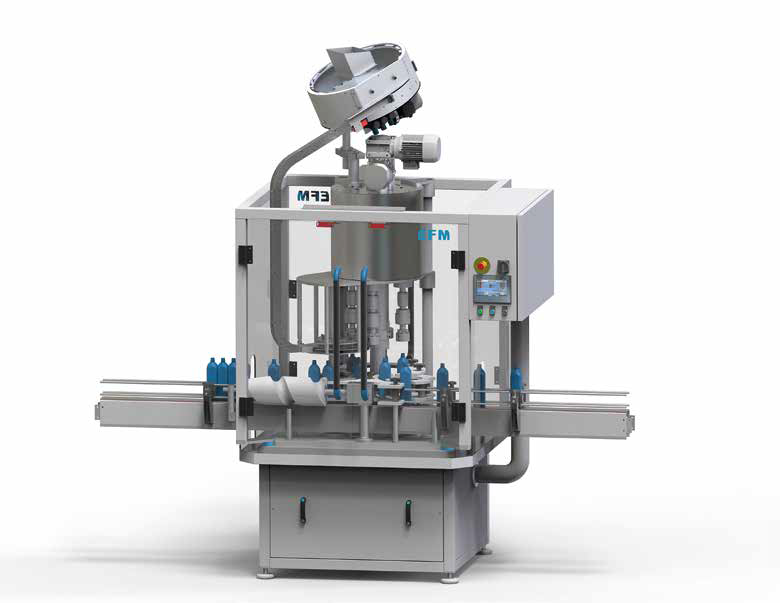
Multi-head capper
For the stand-alone capping of bottles of up to 2.5litre capacity you need a robust and flexible machine wi...
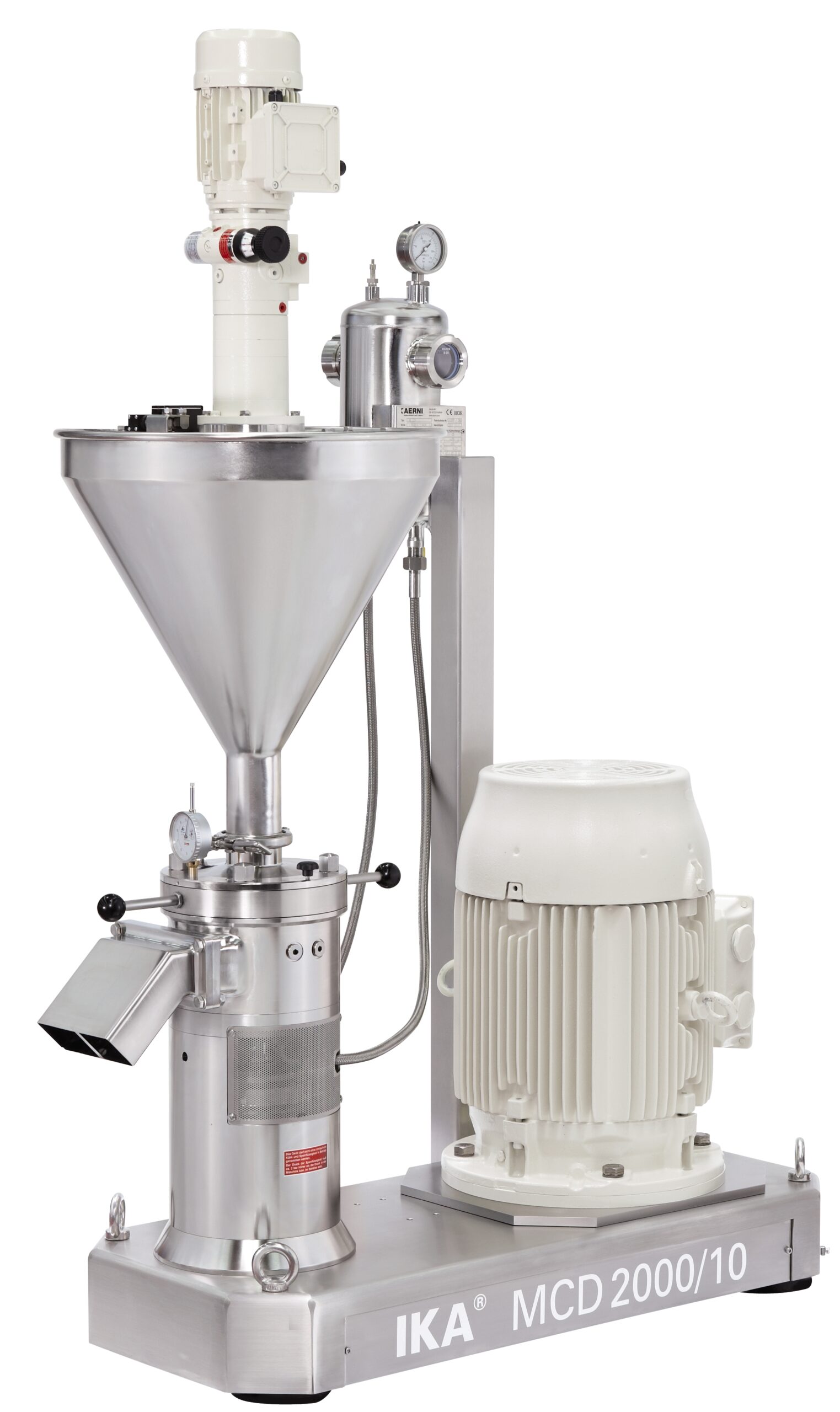
Corundum disk mill
Wet milling and grinding of viscous liquids or pastes containing solid particles such as peanut butter,mus...
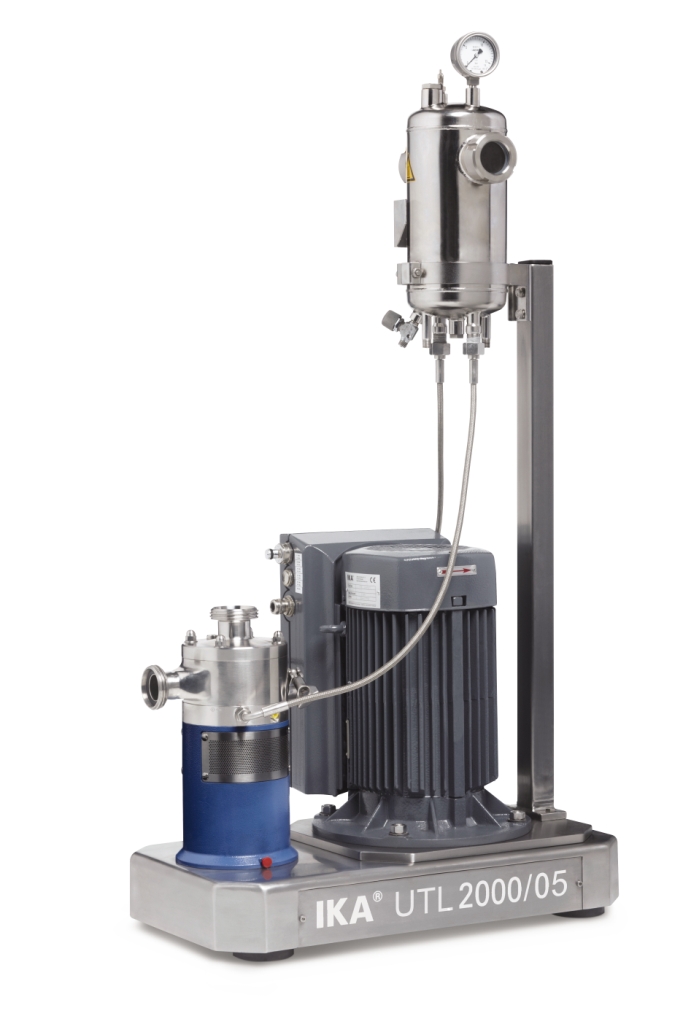
Dispersing machine for emulsions and suspensions
Equipment operating under the rotor/stator principal is often employed wh...
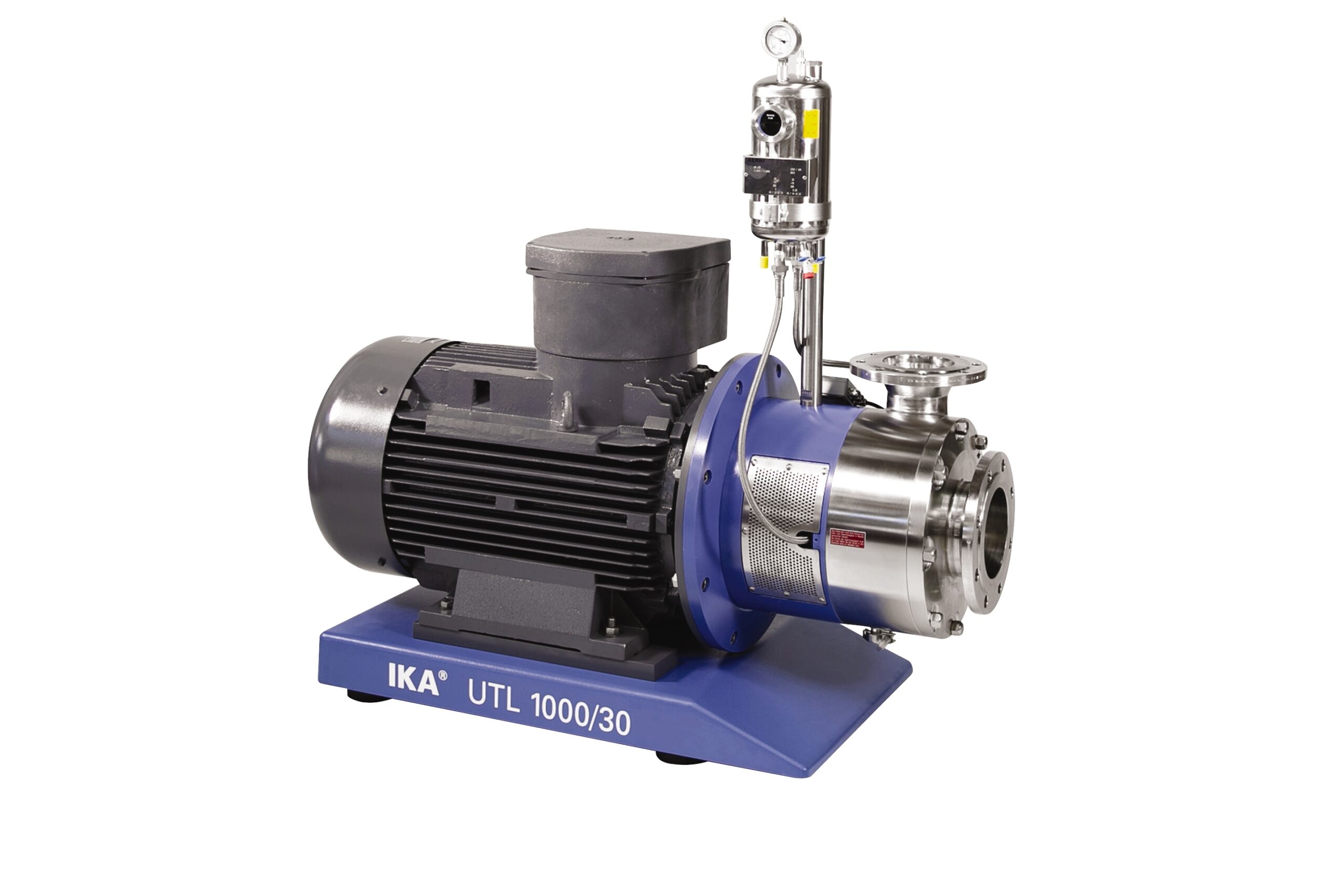
Economic dispersing machine for emulsions and suspensions
For products of medium viscosity and relatively consistent par...
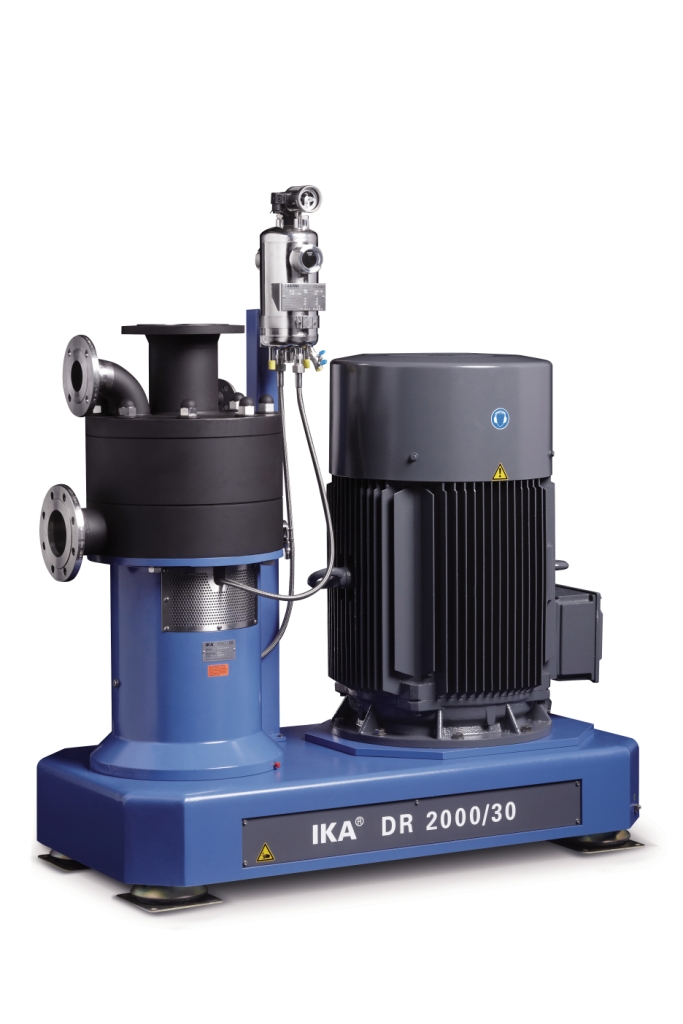
Dispersing machine for very fine emulsions and suspensions
For continuous high performance mixing of solid and liquid ra...
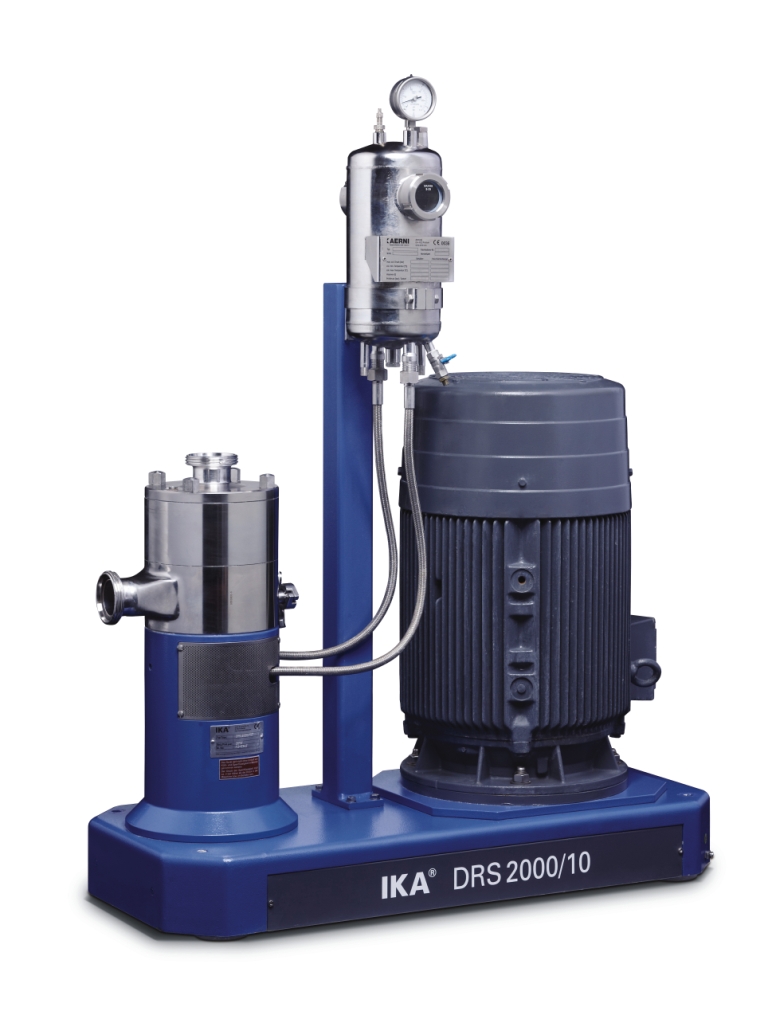
Ultra-fine dispersing machine for emulsions and suspensions
Producing the finest micro-emulsions and suspensions require...
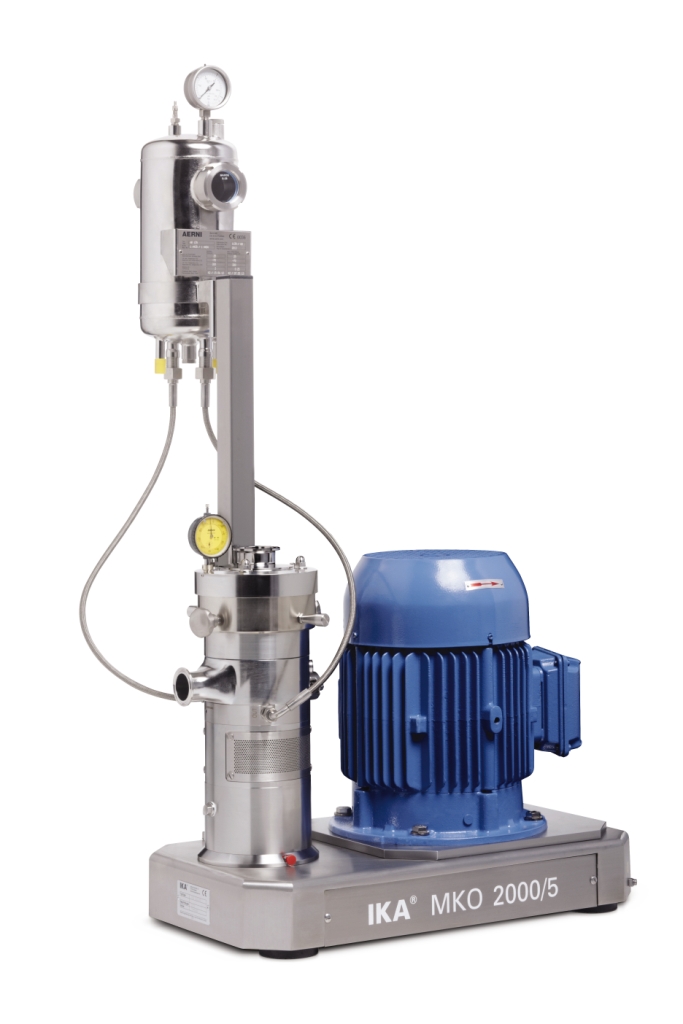
Cone mill machine
When your raw materials include agglomorated suspensions of grainy or crystalline solids and your process n...
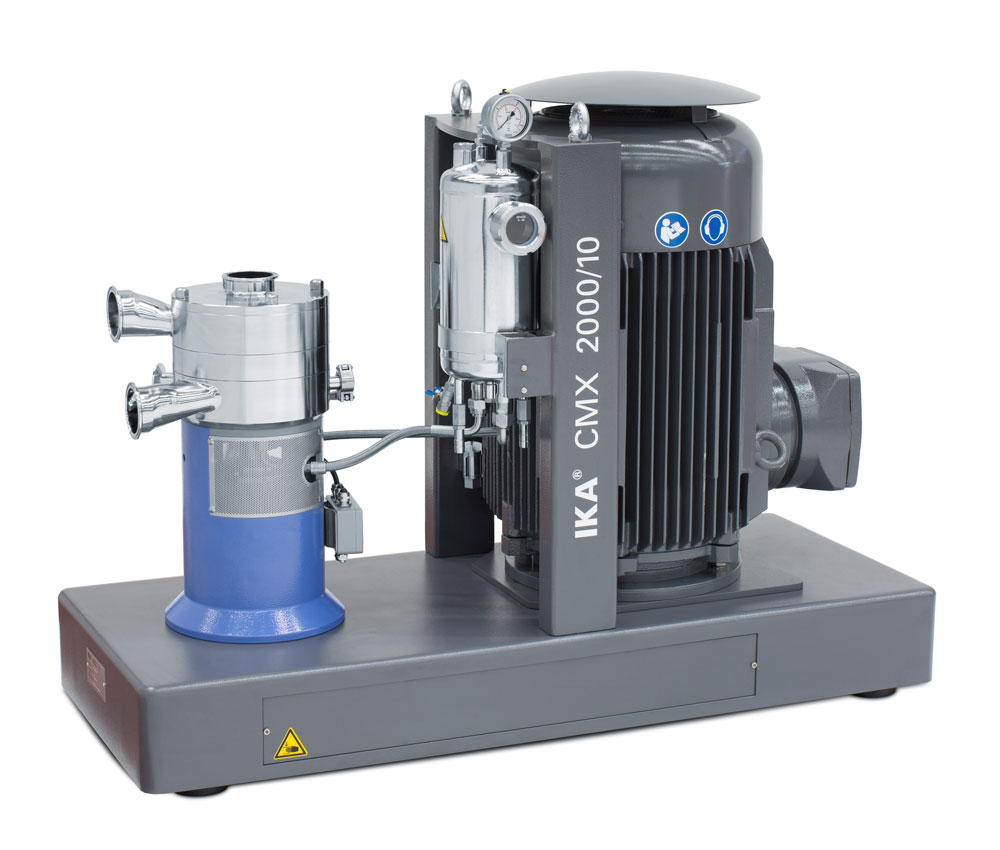
Inline batch mixer for solids and liquids
Several issues often arise when your process requires batch-wise mixing of powde...
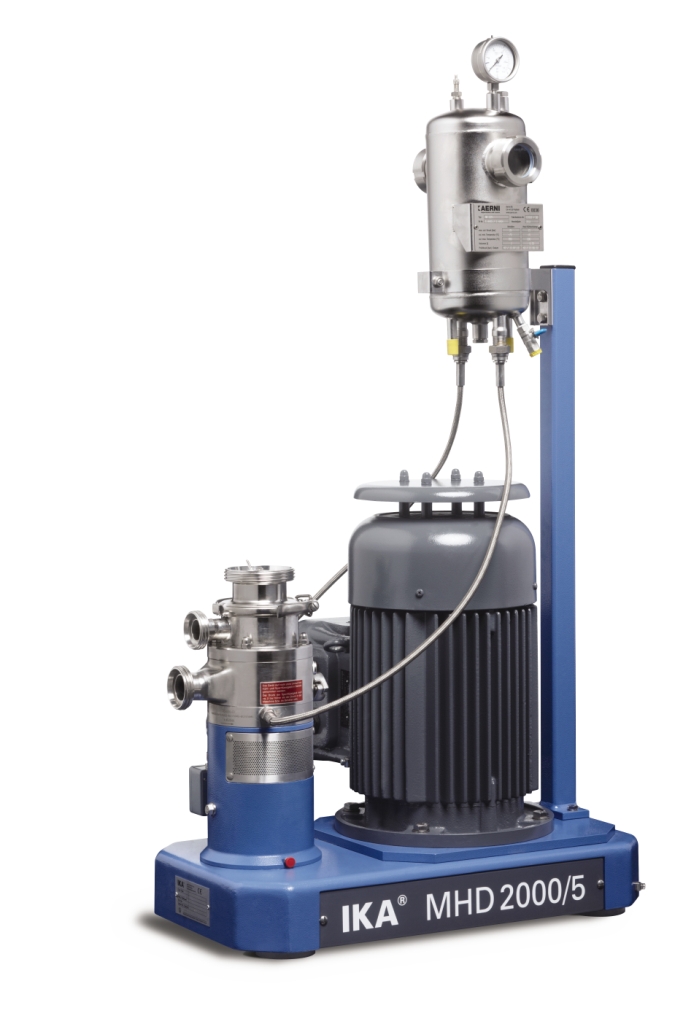
Continuous homogenizing system
Certain mixing tasks present unique challenges and manufacturers need equipment that is speci...
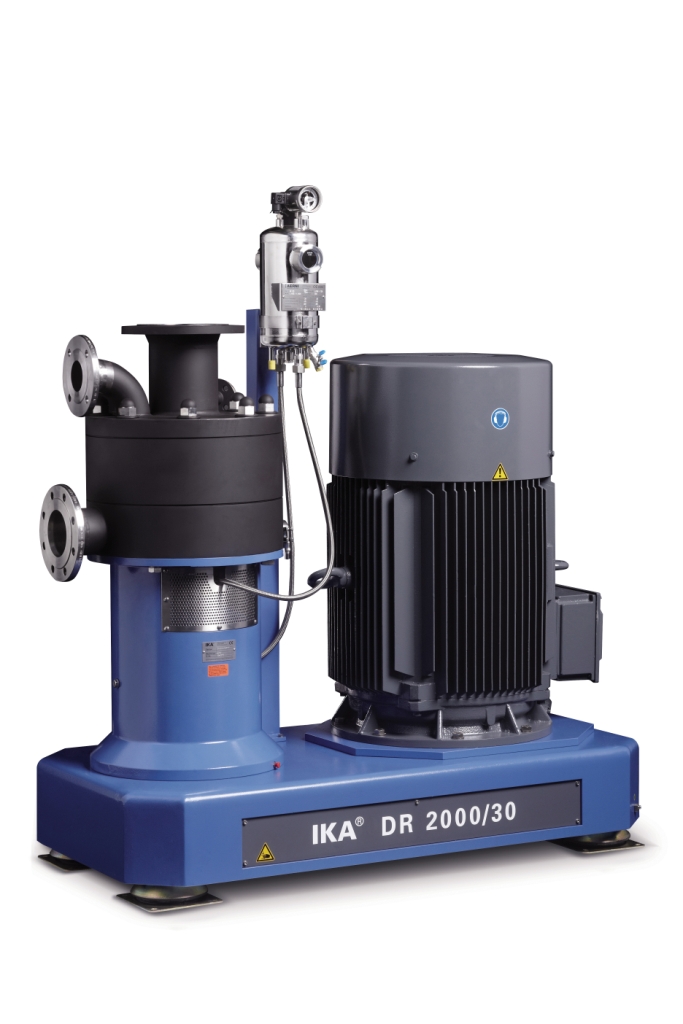
High accuracy homogenizing system
When extremely high accuracy is required in your recipe or formulation traditional mixing...
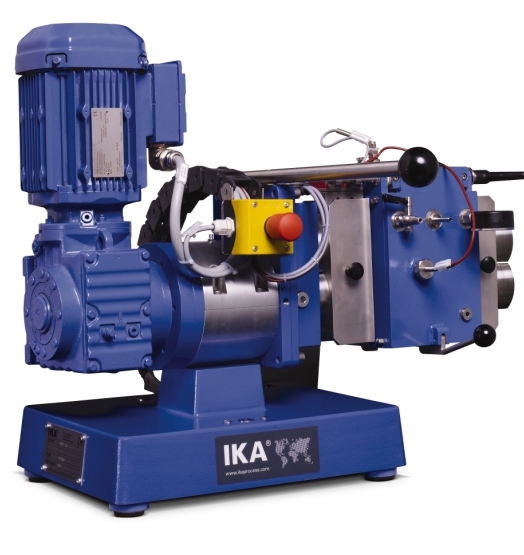
Horizontal kneader
For high viscosity products, better results and reduced process times can be achieved with kneading type r...
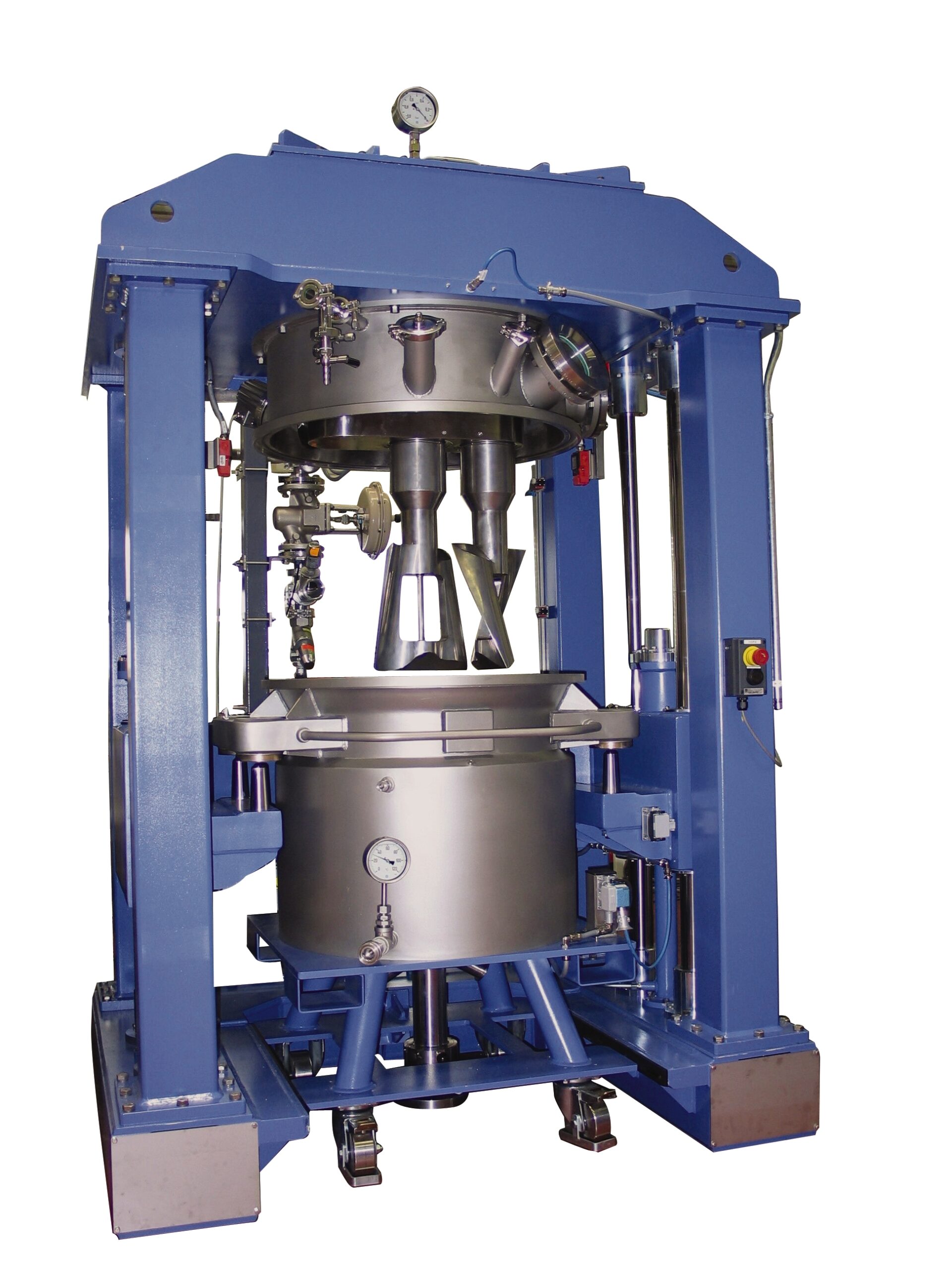
Vertical kneader
Production of highly viscous products with high solid content often benefits from kneading processes rather t...
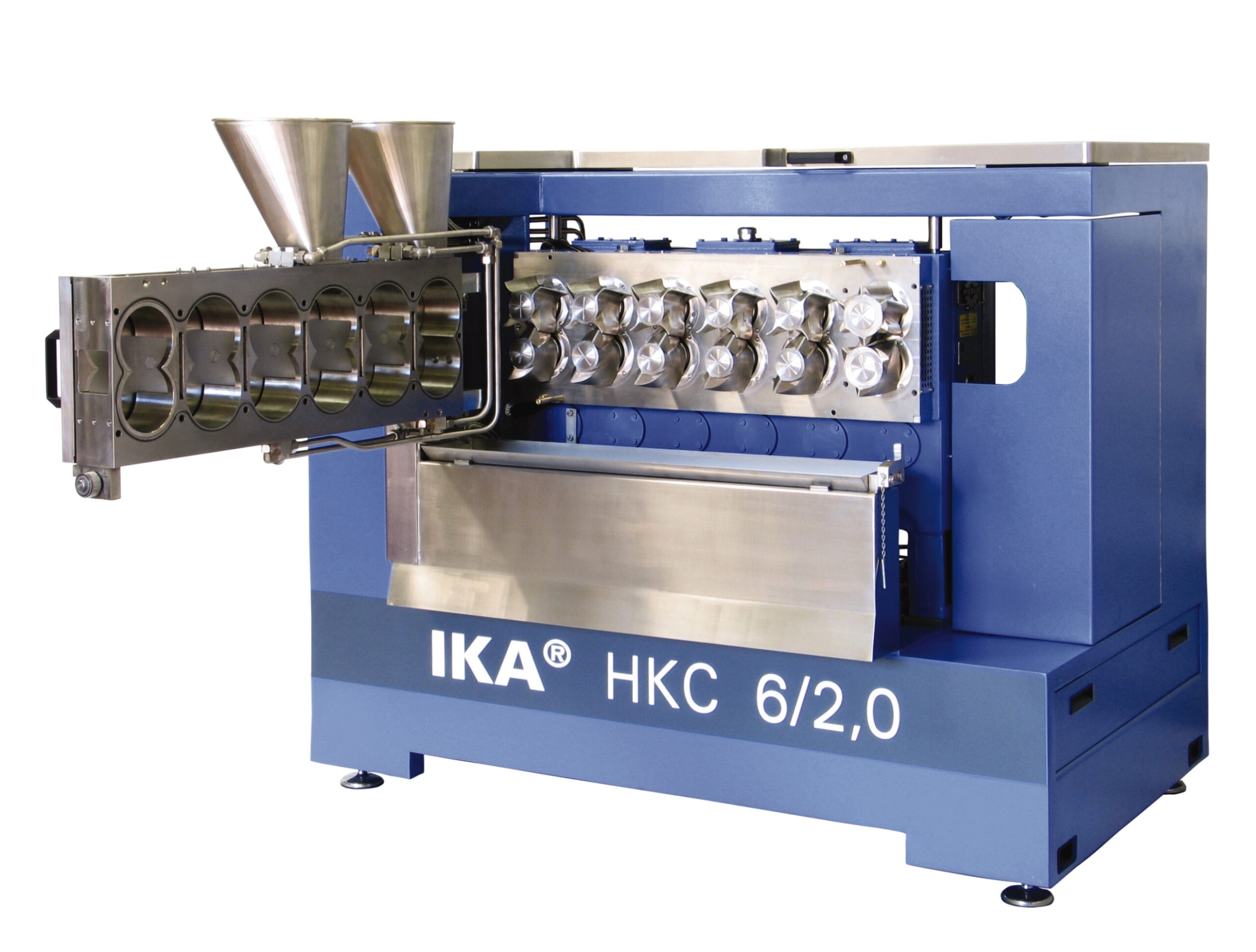
Continuous kneader
Effective mixing of highly viscous products with extremely high solids content can be difficult and the re...
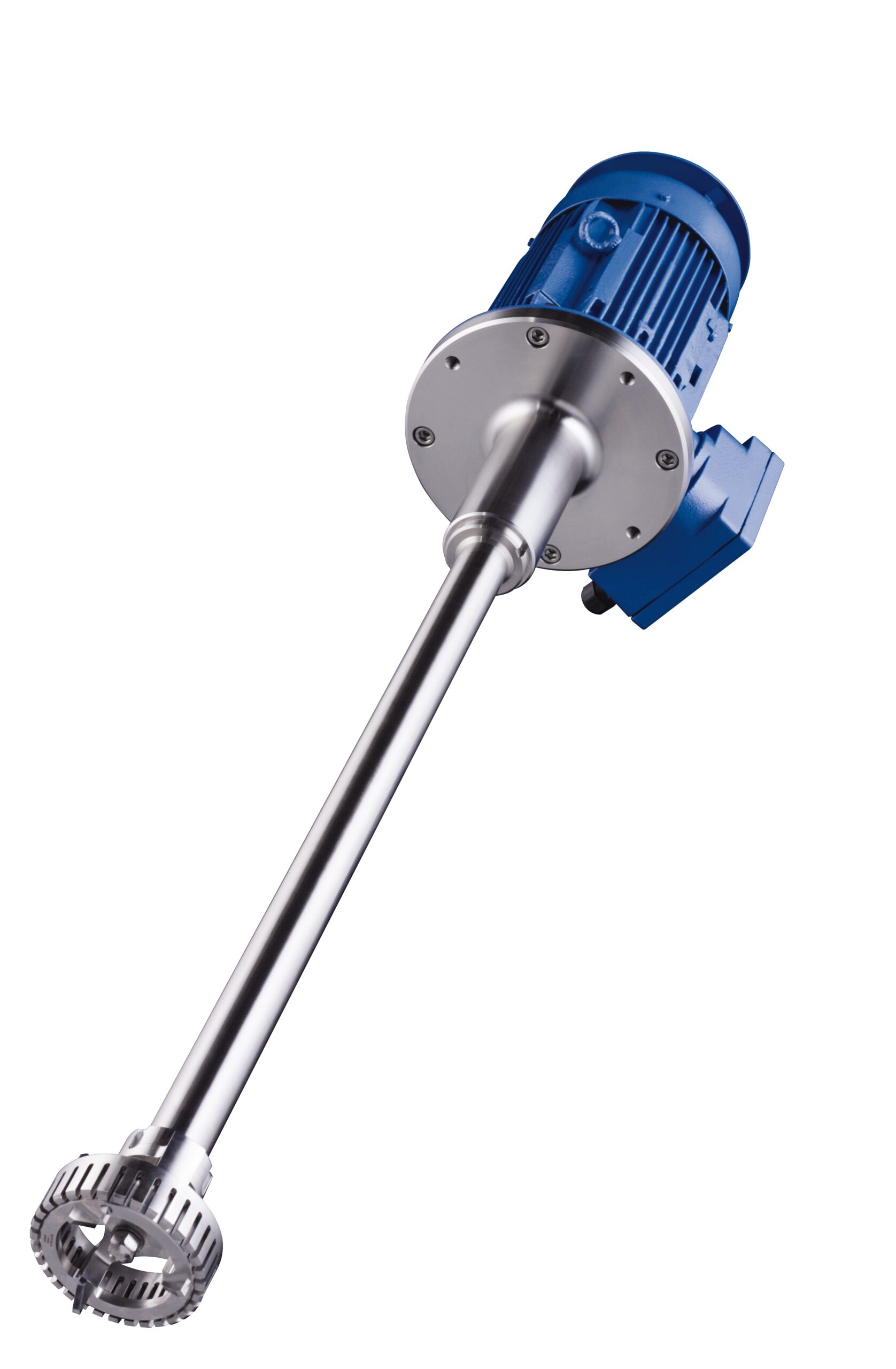
Batch dispersing machine
Equipment operating under the rotor/stator principal is often employed when more traditional methods...
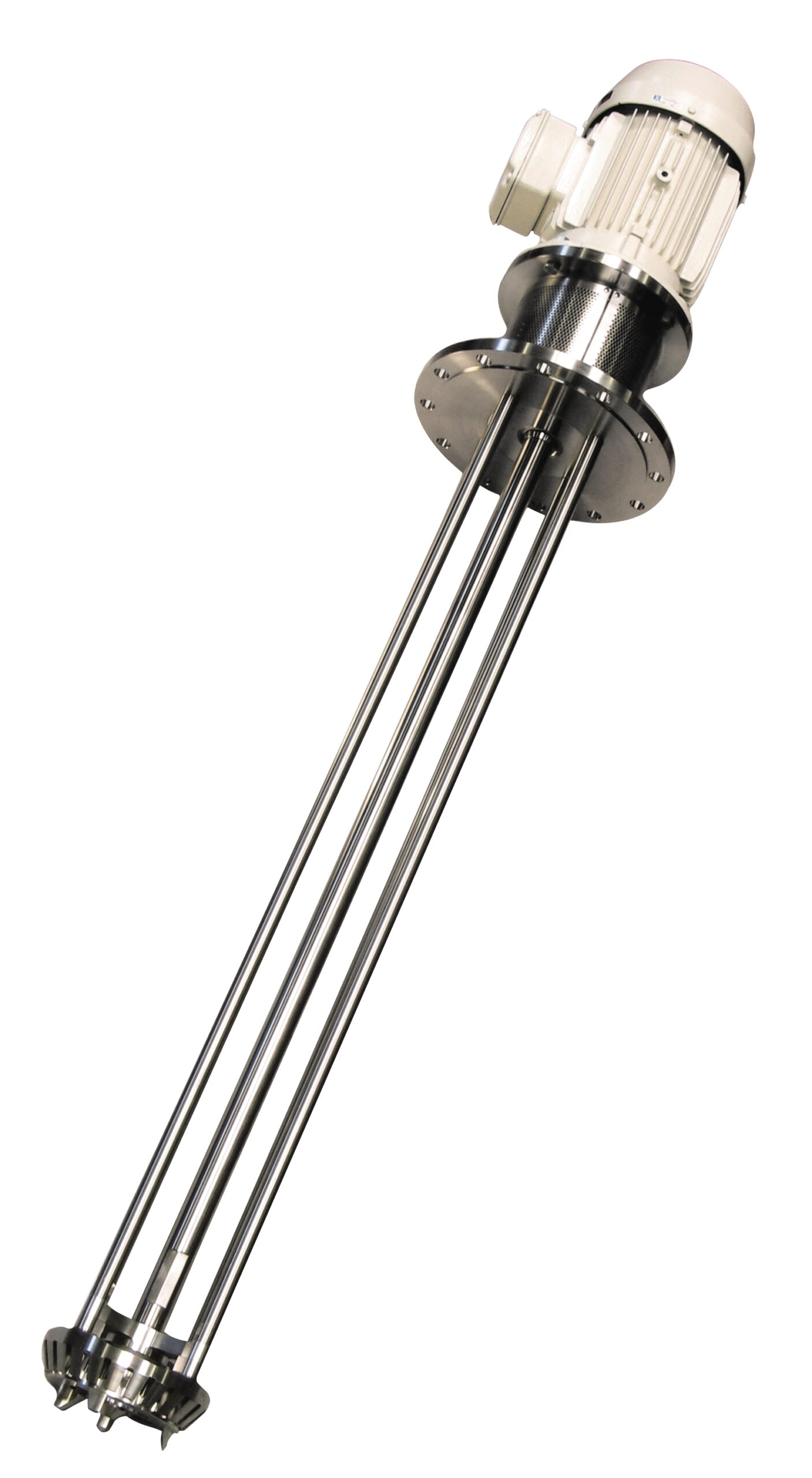
Batch dispersing machine for abrasive products
For mixing and dispersing tasks that cannot be completed by conventional st...
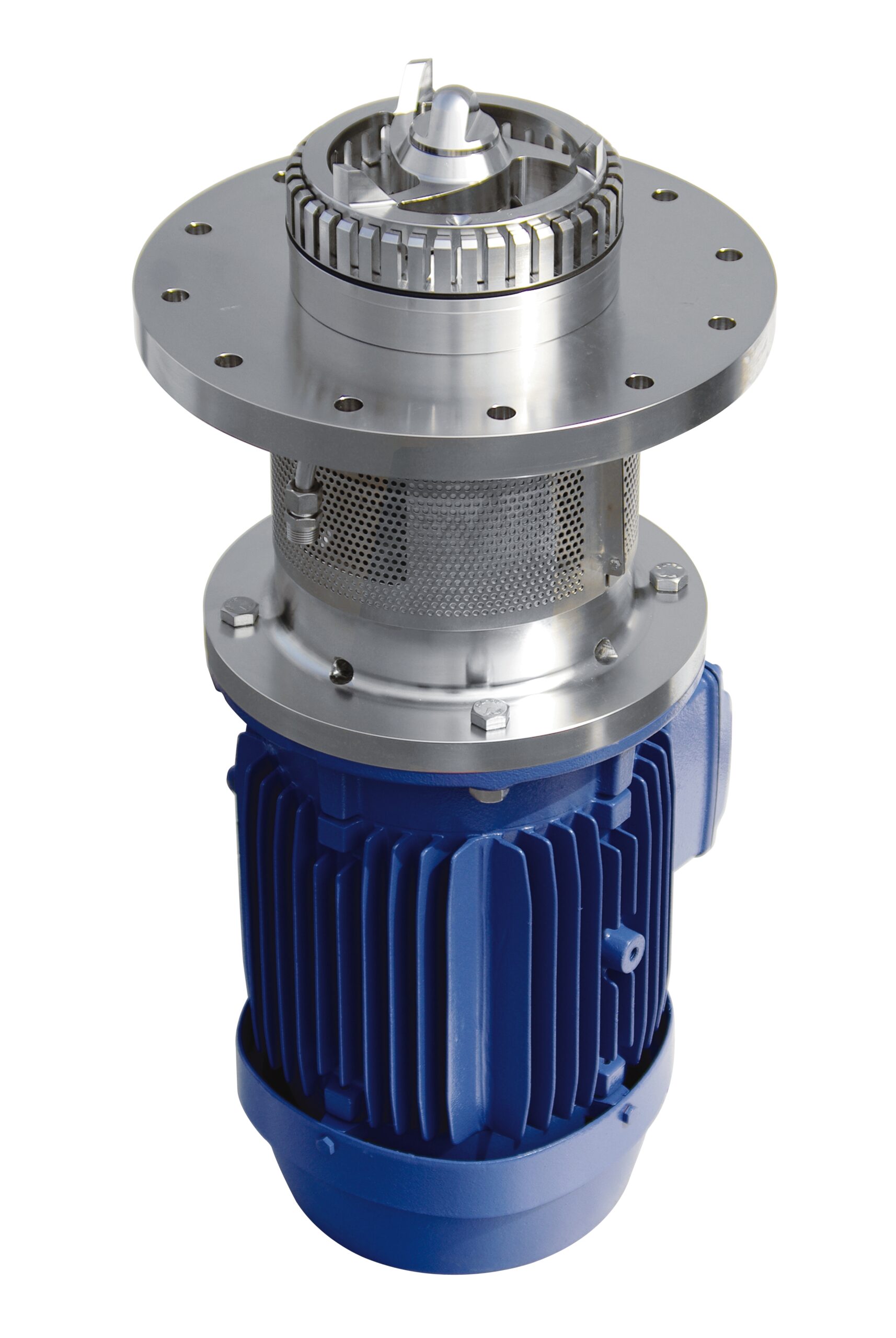
Batch dispersing machine for bottom entry into vessels
When your process requires high performance mixing or dispersion b...
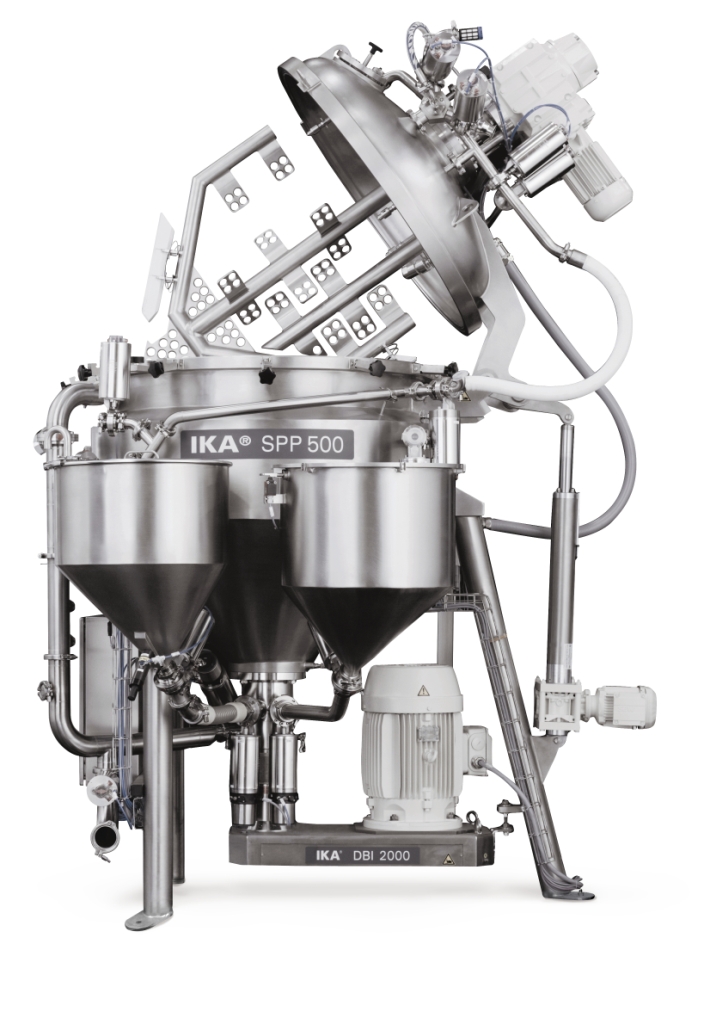
Cost-effective homogenizing and emulsifying system
Manufacturers of cosmetic products need mixing equipment that is capab...
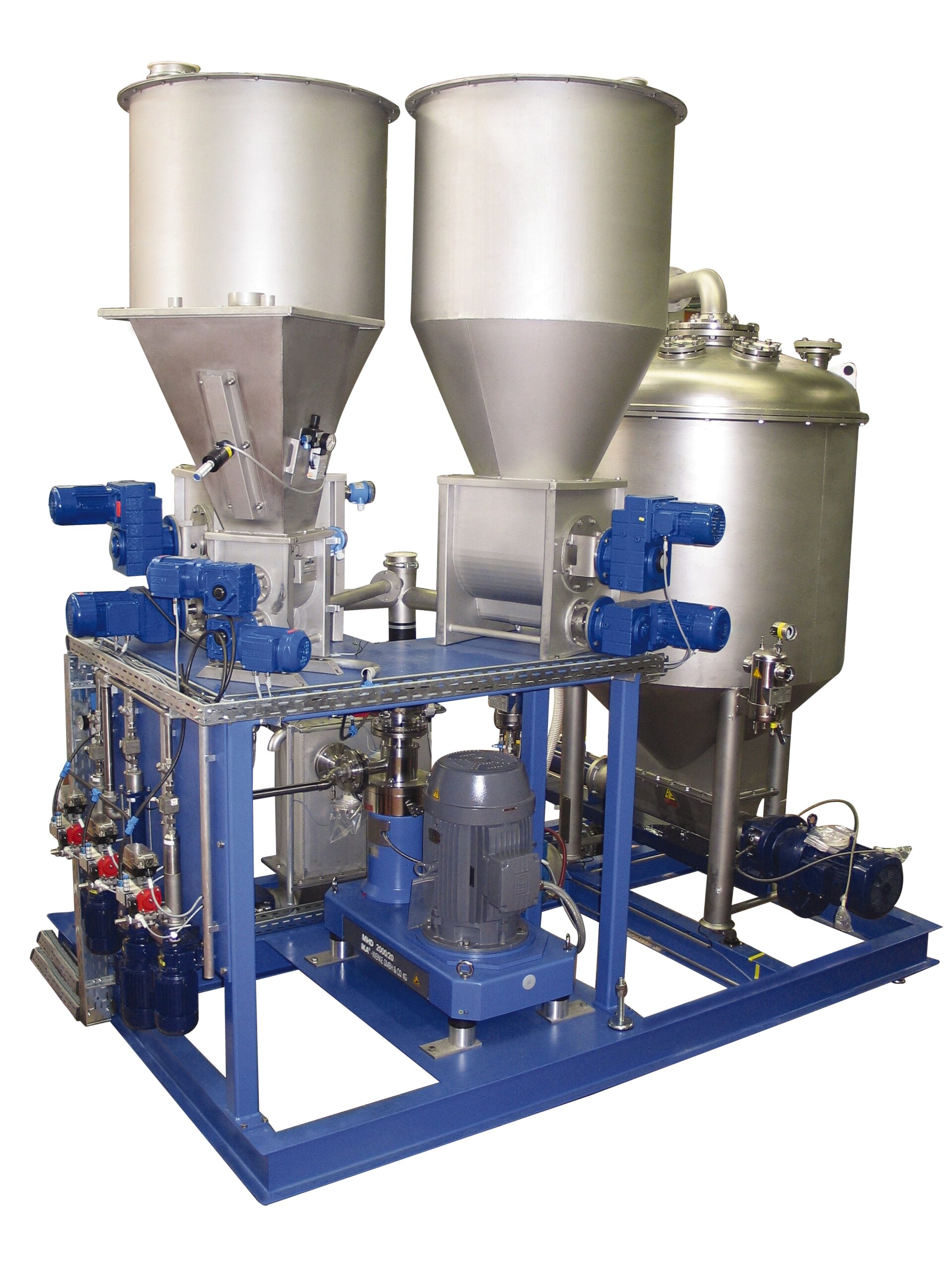
Dust-free continuous homogenizing system
Producers in a wide variety of industries benefit from equipment that can continuo...
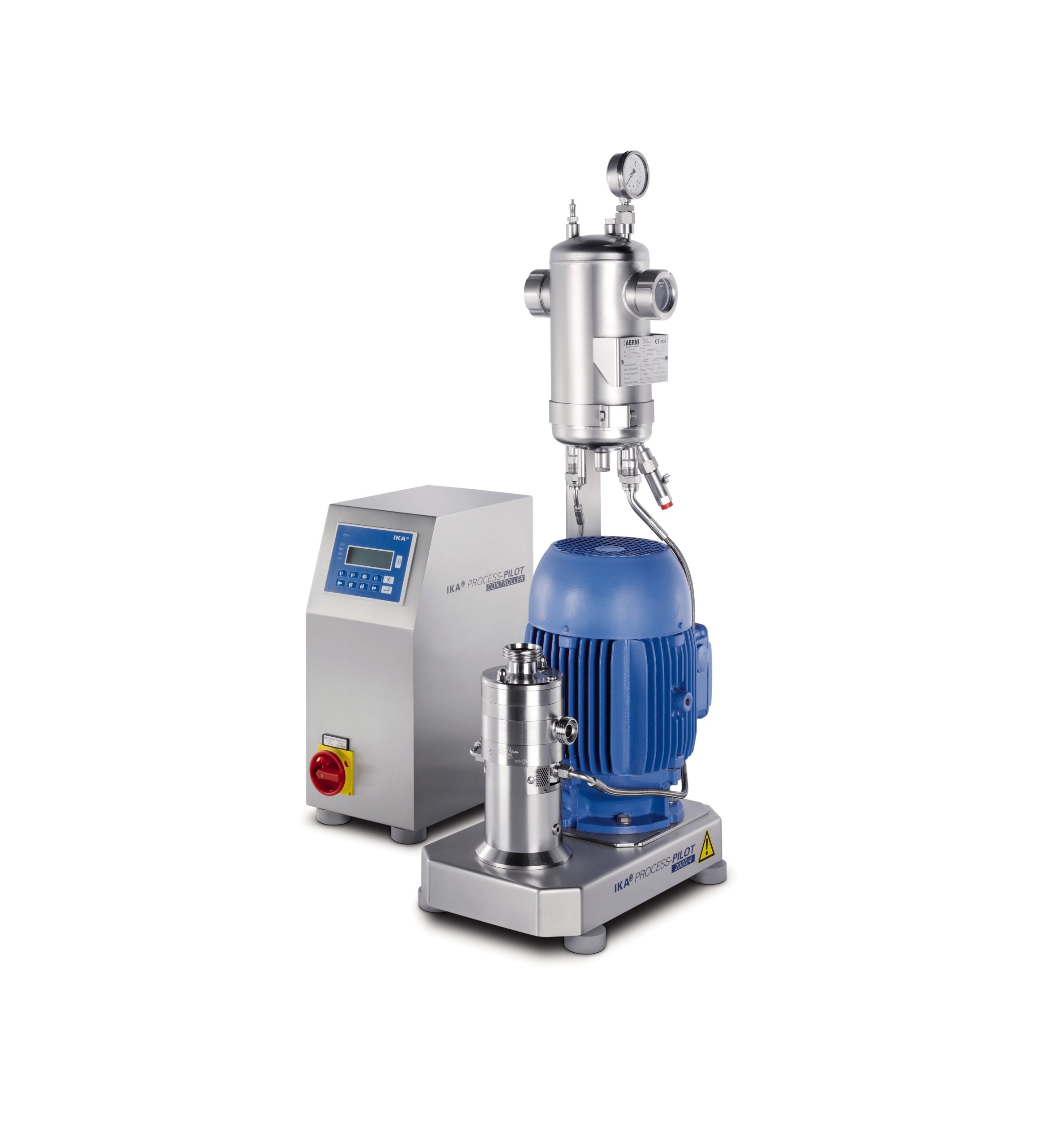
Dilution system for two or more liquids in one pass
Onsite dilution of liquid process ingredients has historically been a...
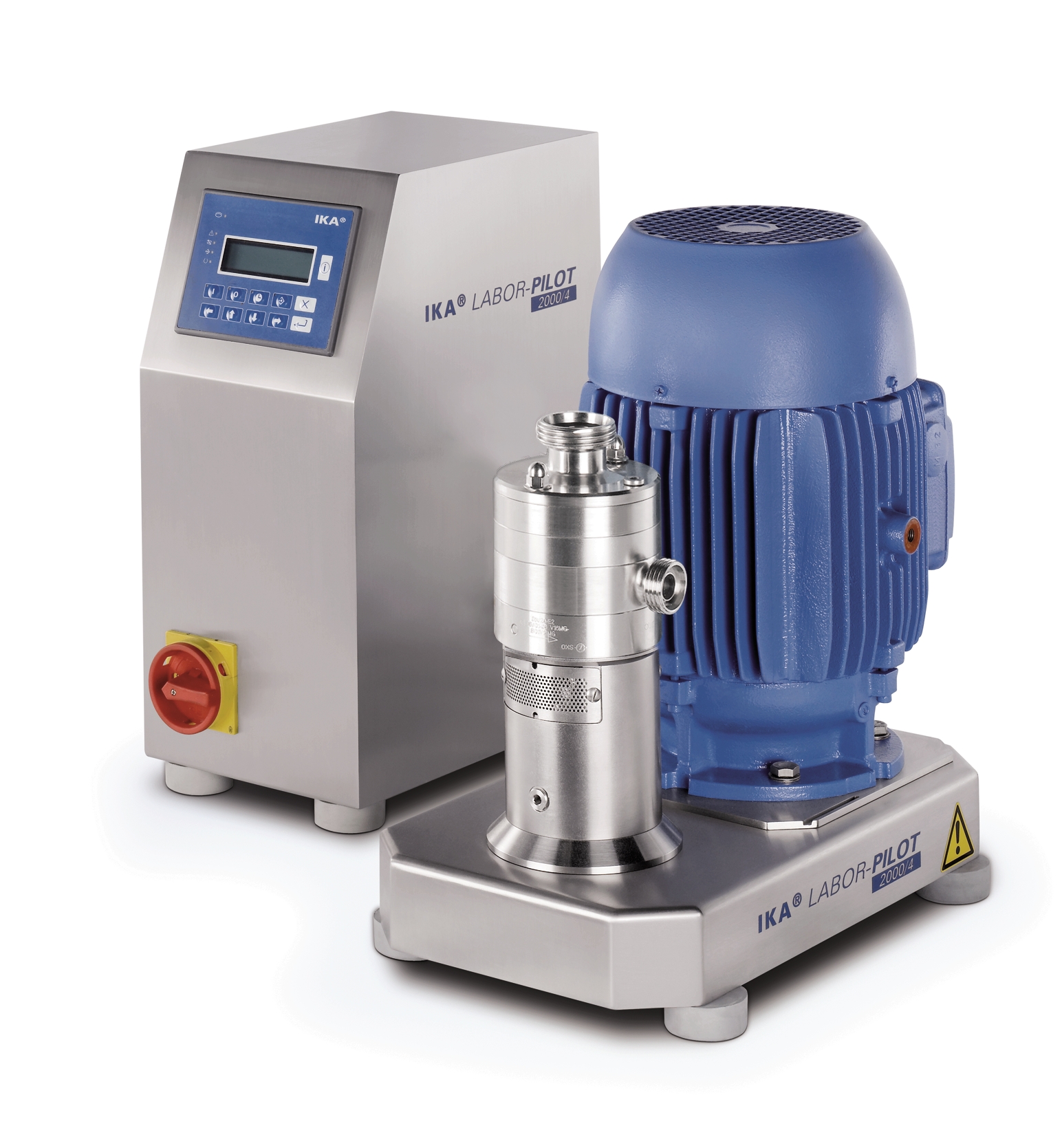
Pilot dispersing machine for testing and scale-up
Innovators in process development need laboratory equipment that helps ...
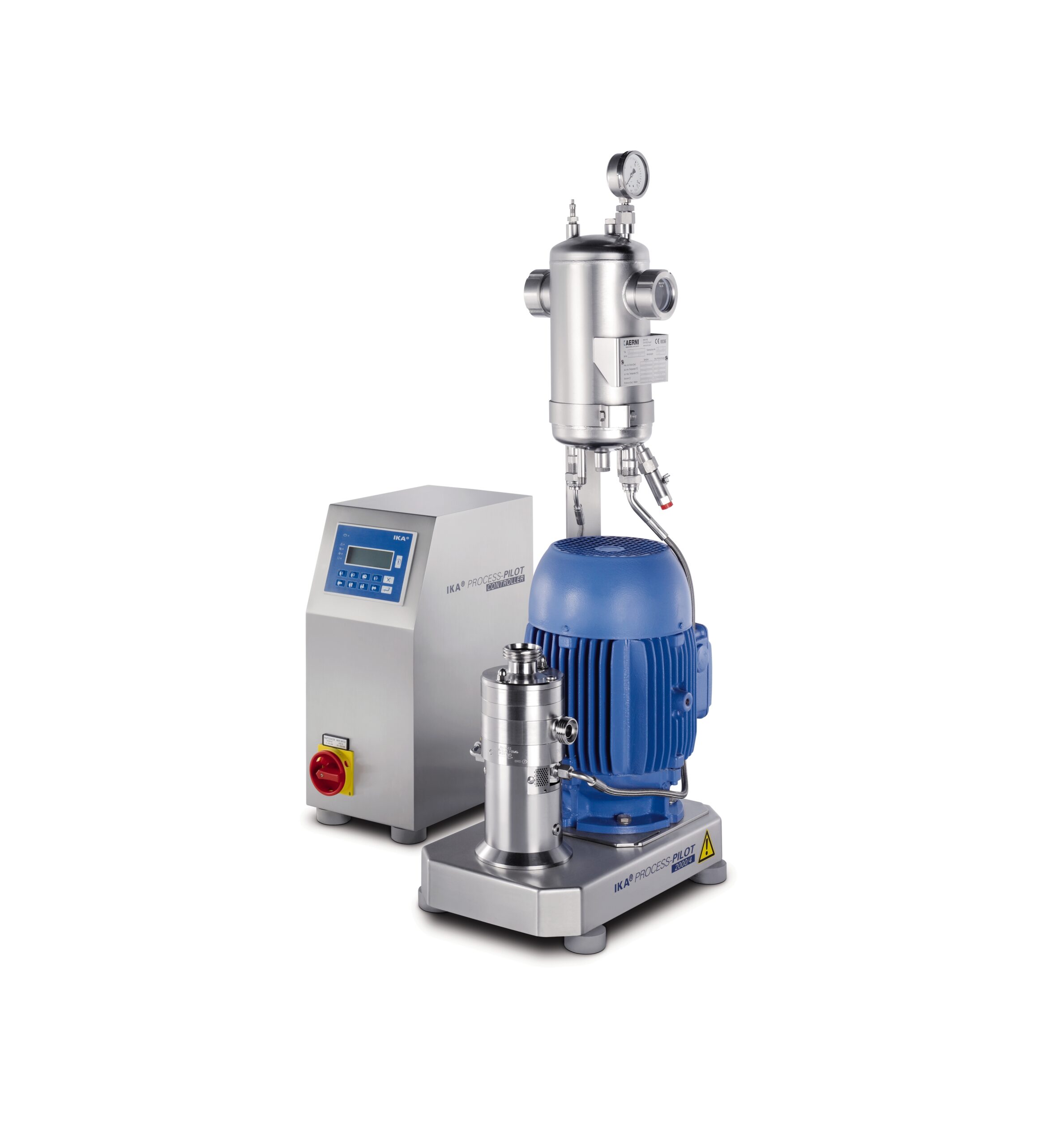
In-line laboratory dispersing machine
Innovators in a wide variety of industries need laboratory equipment on which process...
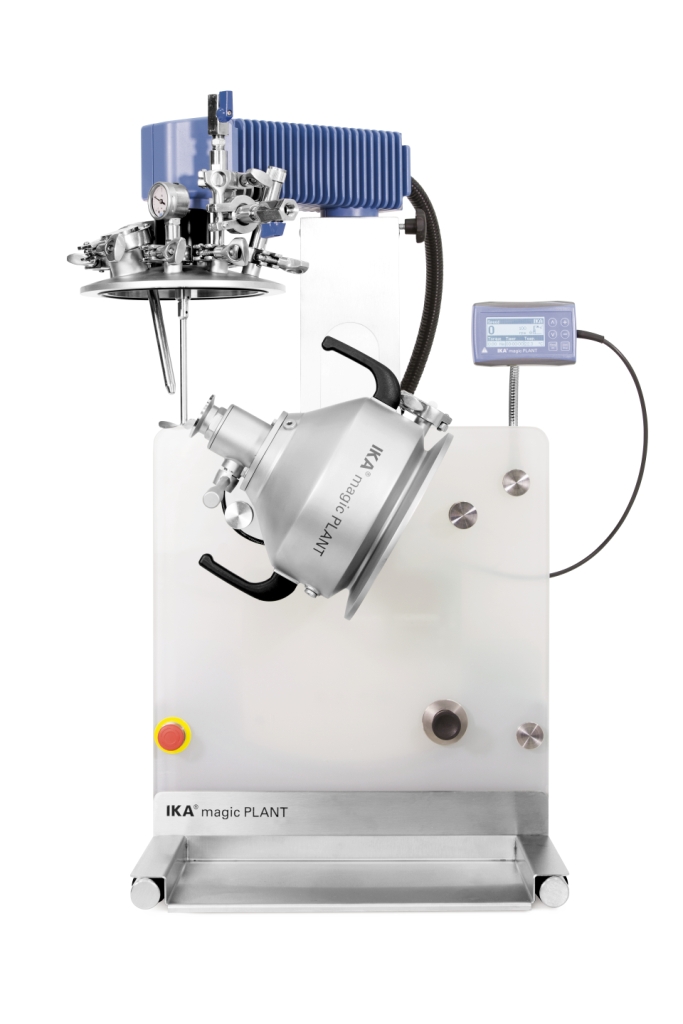
Laboratory dispersing machine for low-viscous masses
Laboratory mixers have not always been easy to work with. Getting a...
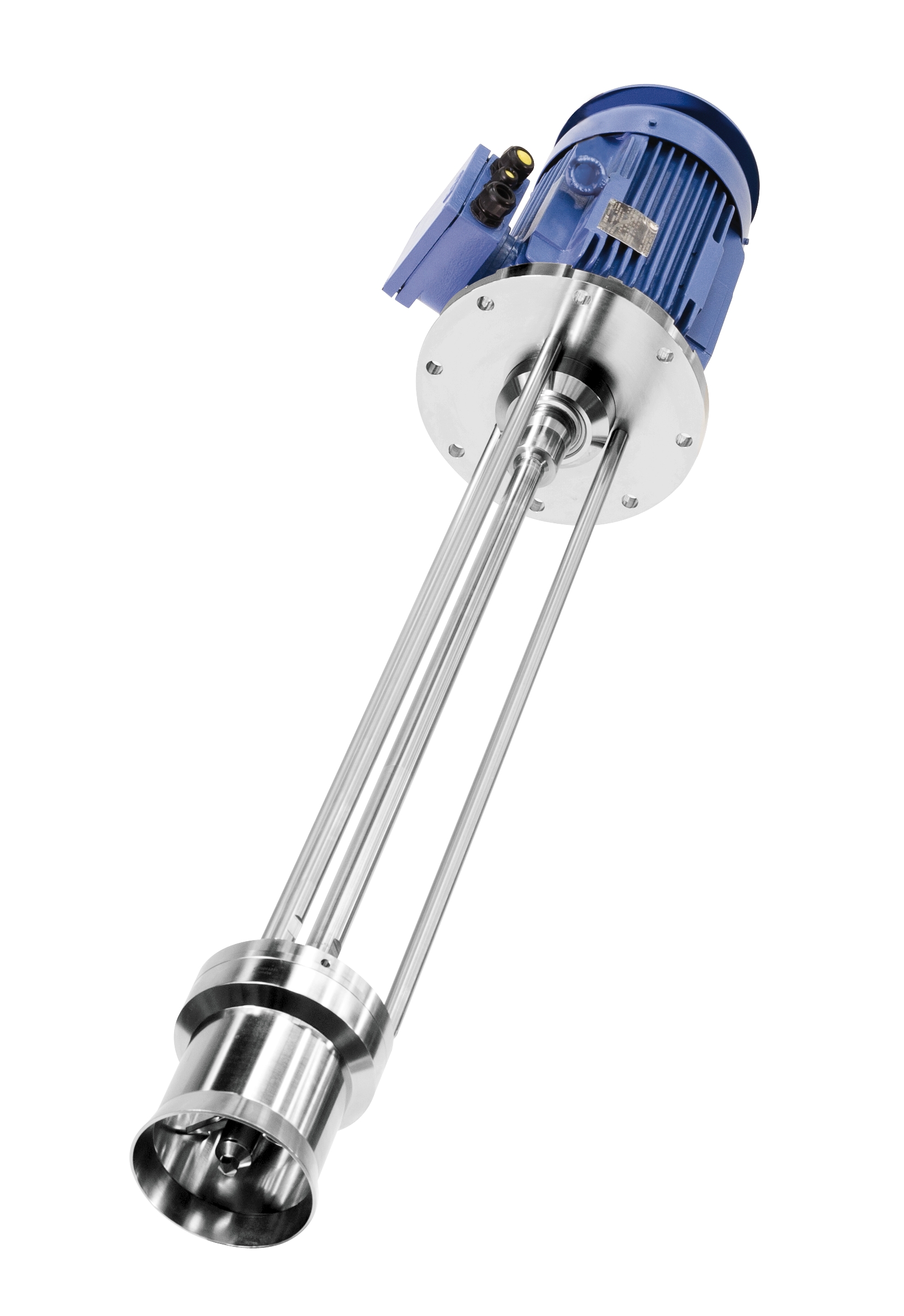
Jet flow agitator for high-viscosity media
Processes including homogenization, dispersing, suspension, emulsification and ...
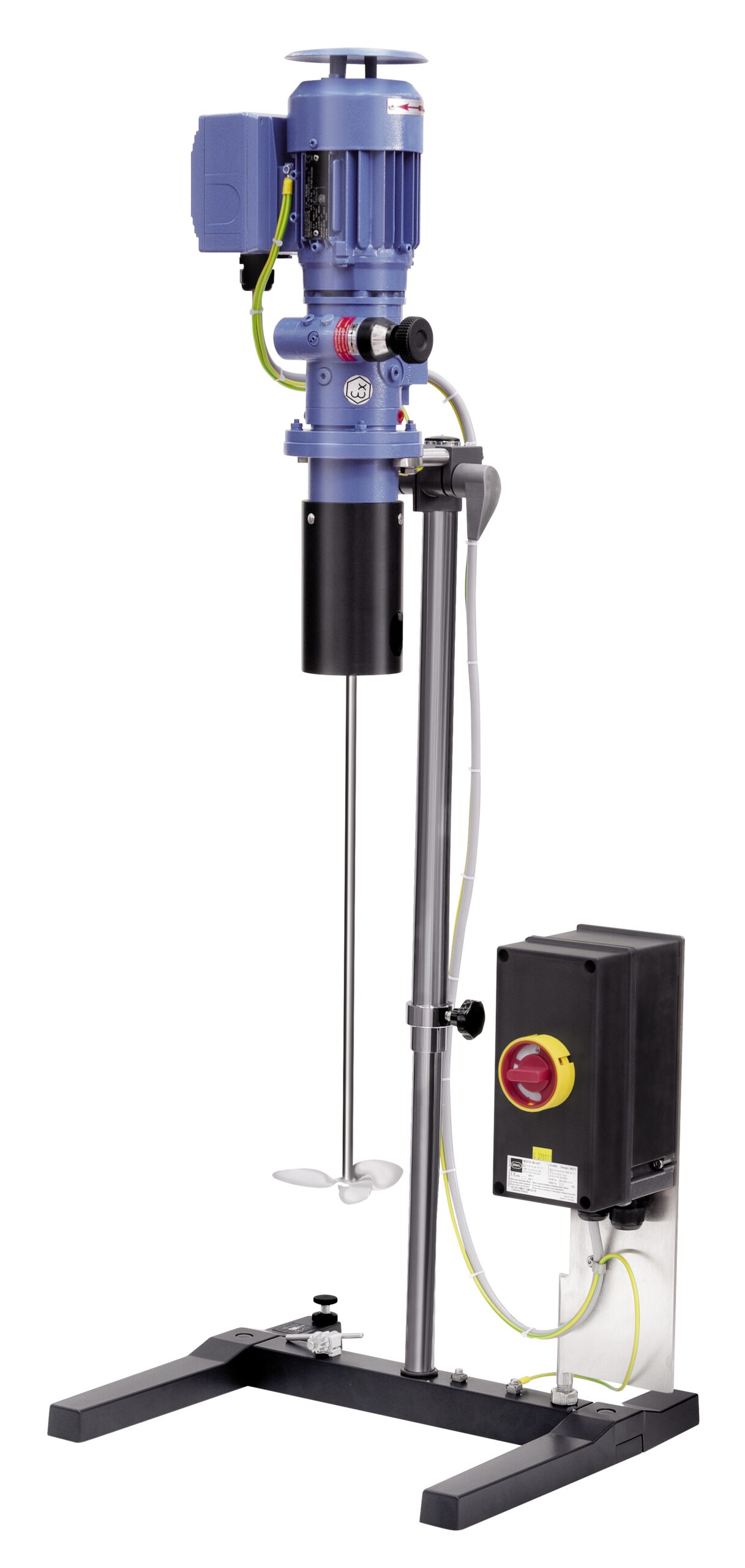
Agitator for medium viscosity media
Mixing fluids of medium viscosity for many production processes requires an agitator wi...
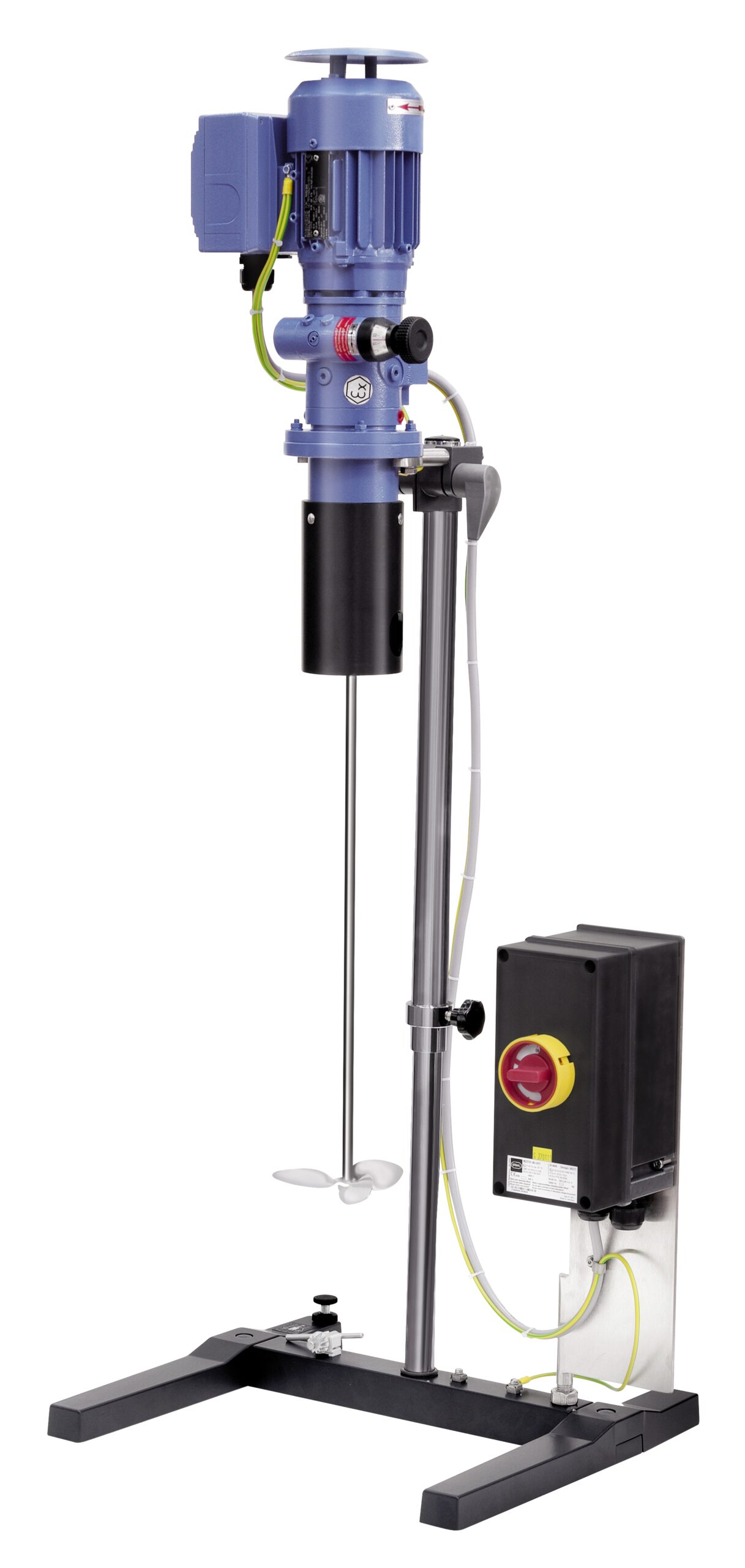
Agitator for low viscosity media
Reliably agitating fluids in open or pressure-less vessels in a laboratory or small scale p...