High-speed FFS machine for water cups
Packing water in cup containers, asks for good hygiene in order to avoid contamination risk. The filling and packaging process must take place in a no dust environment, minimizing human intervention. With an automated FFS machine that has a cleaning system for liquid containers, contamination risk is avoided.
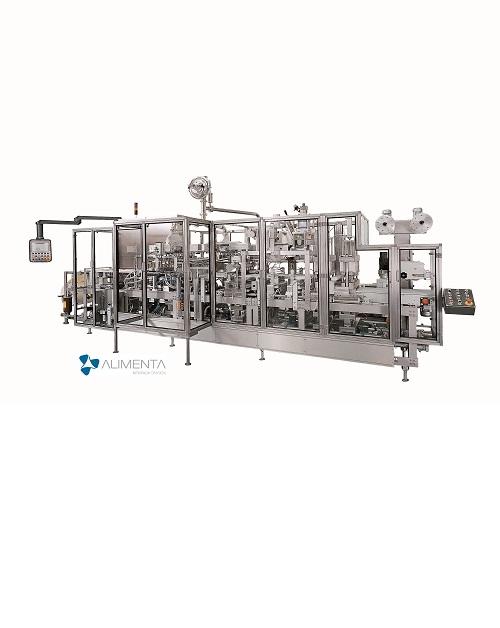
Packing liquids under clean room conditions
The Thermoforming machine designed by Newpack (Alimenta Group) is a horizontal Form-Fill-Seal machine that forms a container, fills it with a product and then seals it in one single process. The machine handles a wide range of food liquid products with water being one of them.
Newpack Thermoforming machine for liquid products can be manufactured in accordance with the required capacity and product shelf life. Newpack customises the shape and size of the cup in compliance with manufacturers end product. As water is sensitive to contamination, the whole process needs to be carried out under a controlled hygiene environment, so a High-Clean or Ultra-Clean version is suggested.
Starting from a reel of thermoformable plastic film, Newpack Thermoforming machine forms the container according to a pre-established shape, by heating the plastic film and shaping it through a mould. At this point, cups are automatically filled by a cup filling station. Based on the product to be packed and the shape of the cup, the filling system type changes. Afterwards the machine applies a lid on each cup by heat sealing it. When cups arrive to the cutting station, they’re cut and separated. The High clean version is provided with a tunnel with an overpressure of ultra-filtrated air. Moreover, UV rays are used to sanitize the lid film.
All machine components are in compliance with CE regulations and other hygiene standards. The machine capacity depends on the product and the volume of the cup; generally speaking, 9,000 c/h is the minimum production capacity.
Benefits
- A customized solution
- A CIP and SIP system to meet hygiene standards
- Able to form a wide range of cup sizes and shapes
- A 3 in 1 machine for forming, filling and sealing
- Work cycles completely managed from operator panel