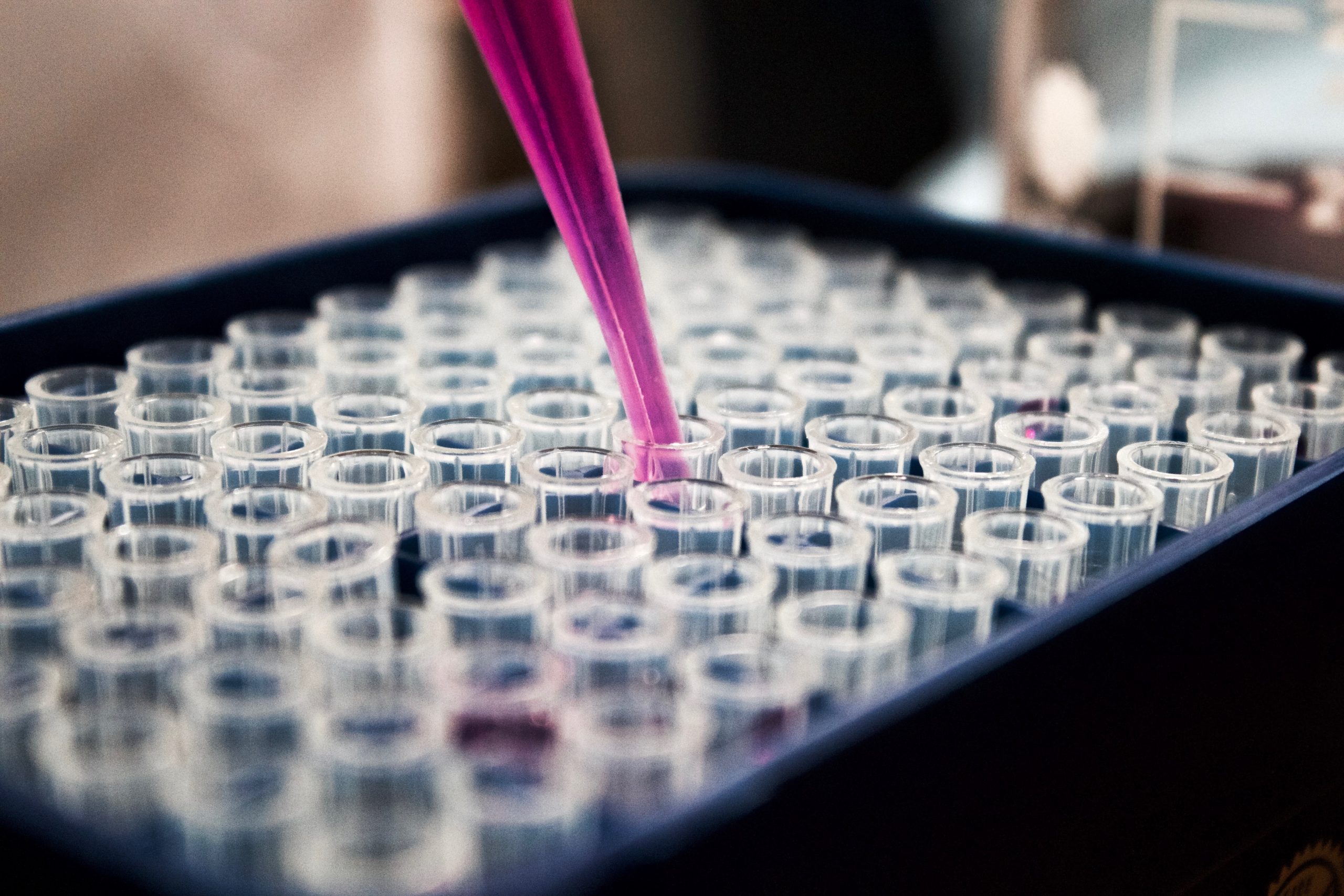
Making Vials
Find innovative production technology for making vials and connect directly with world-leading specialists
During crime scene investigations in any movie, you've probably seen forensic scientists collecting evidence and biological samples in small containers. Here, these are the vials, used to store medicines, especially in liquid form, or laboratory samples. Often made of glass or plastic, vials can be labeled as single-dose vials or sterilized and reused more than once. They are also available with various closure systems depending on the material and storage requirements.
Select your vials process
Tell us about your production challenge
A vial for every application
Vials really do have millions of uses based on the material and application. Glass vials have been used for hundreds of years to store liquid pharmaceutical products. But glass is not always the same. For instance, The United States Pharmacopeia (USP) classifies glass into borosilicate glass as Type I and soda-lime-silica glass as Type II and III, with the difference being that Type II has a special treatment to increase hydrolytic resistance.
Borosilicate glass contains at least 5% of boric oxide and is used for injectables with acid, neutral and alkaline pH. Amber-colored vials, created by adding iron to the glass, protect the substance from UV light and are suitable for light-sensitive samples.
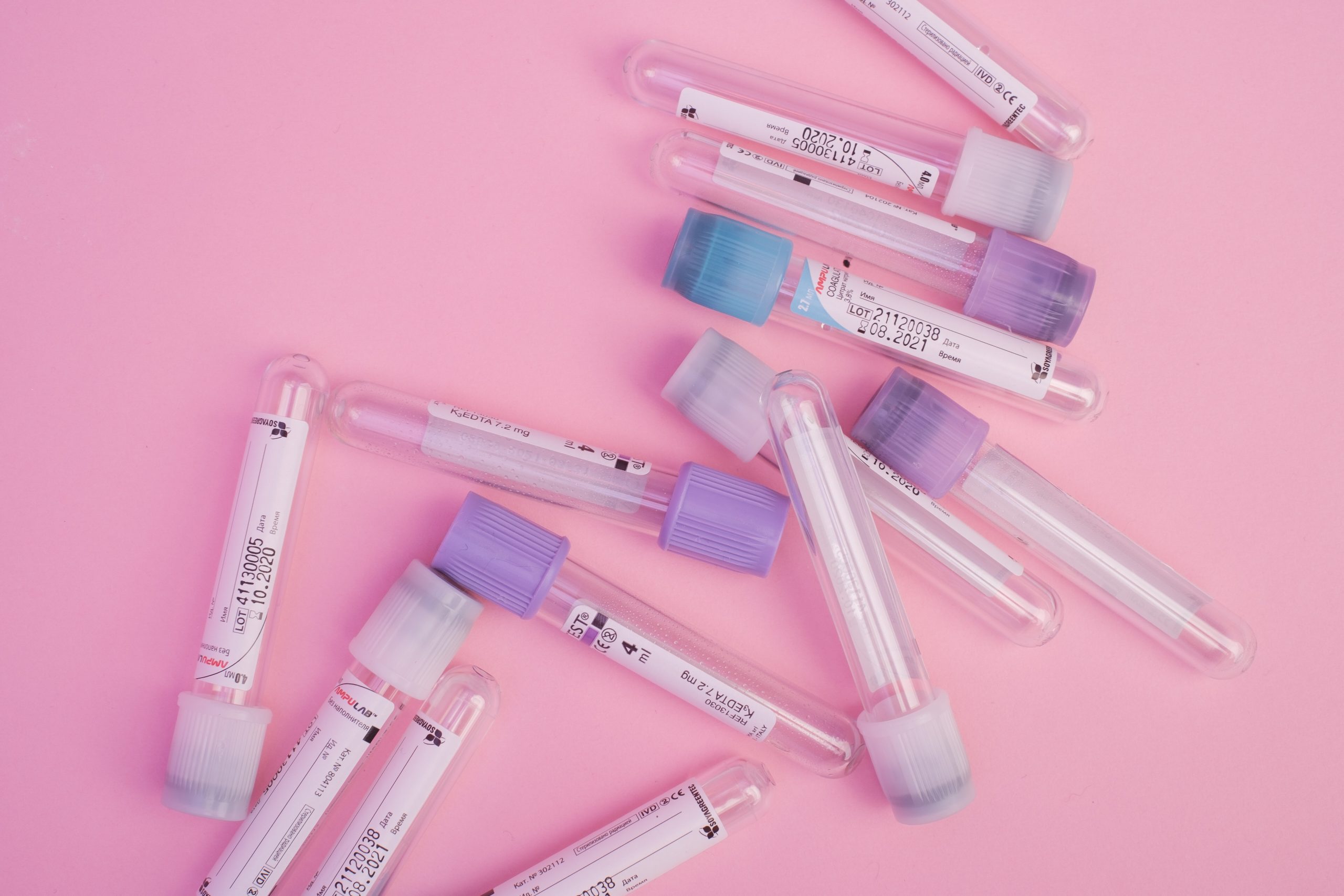
Plastic vials, made of polypropylene or polyethylene, are widely used in cosmetics and law enforcement agencies. Compared to glass vials, they have lower chances of leaching and are much easier to handle. Plastic vials have excellent resistance to bases, alcohol, and acids. Special vials are also made for specific applications like cryogenic or liquid scintillation. Cryogenic vials are made of special polypropylene material to withstand extremely low temperatures. Scintillation vials are mostly glass vials used in liquid scintillation counting; this process is used to measure the substance’s radioactive activity.
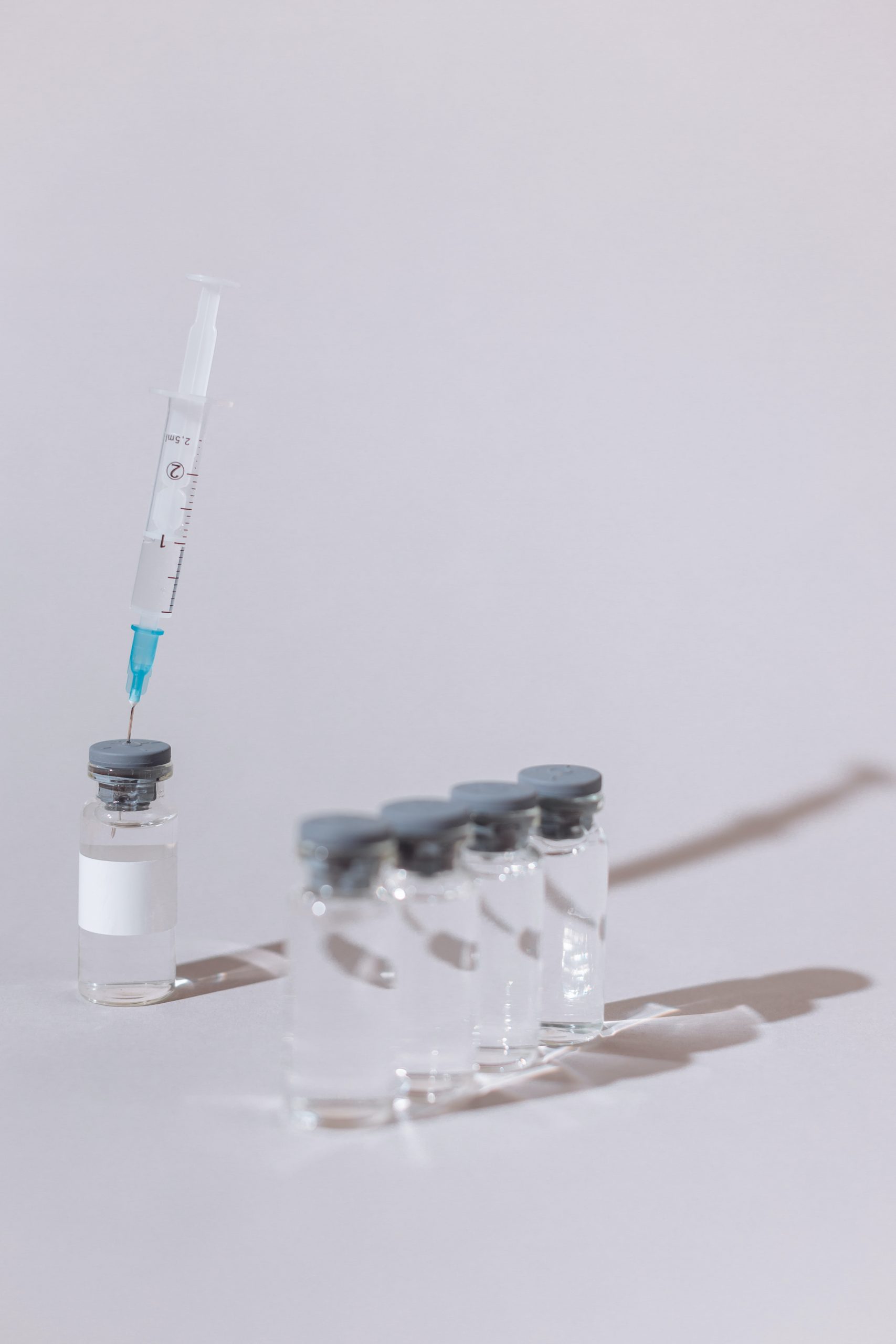
Single-dose vials or multi-dose vials?
In medical applications, single-dose and multiple-dose vials are available. Single-dose vials are intended for one-time use and do not contain anti-microbial preservatives. The contents must be used within an hour after opening and any remaining contents must be discarded. These vials must be appropriately disposed of afterward. Multi-dose vials contain more than one dose of medication and contain anti-microbial preservatives to prevent the growth of bacteria after opening. It must be used for a single patient as much as possible to avoid cross-contamination and must not be used after the beyond-use date indicated on the label.
Coat your vials to improve chemical resistance
Glass delamination occurs in the inner surface of the container when exposed to chemicals due to chemical reactions and leaching of elements from the glass. As a result, glass flakes appear mixed with the chemical solution. If you think about it, this is a serious quality issue. Leaching of elements from the glass, such as sodium affects the pH level of the solution over time and may even lose the product’s efficacy.
As a solution, glass vials are treated by the vapor phase deposition silanization (or siliconization) method. This process involves applying a silicon solution to the surface as a protective layer to minimize the interaction between the vial and the substance. This method provides a uniform glass coating that improves the chemical resistance and gives a low adsorption characteristic preventing chemicals from sticking to the surface.
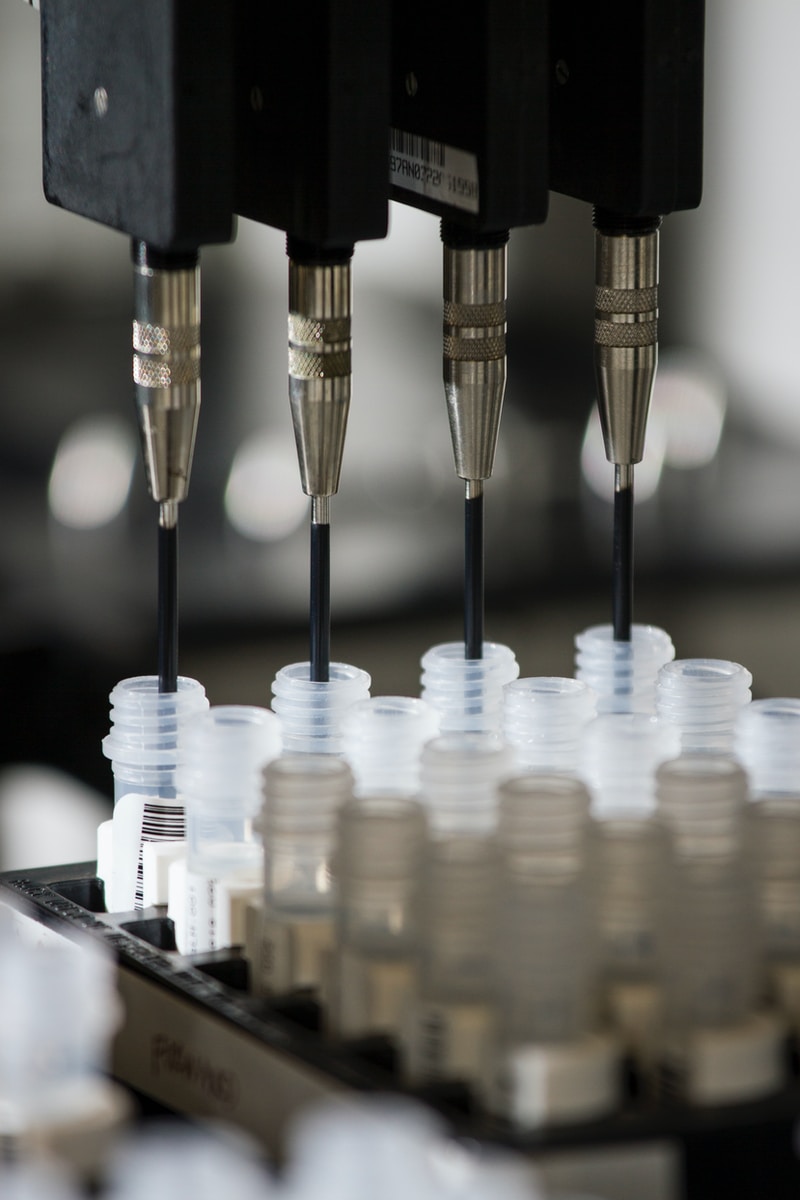
Aseptic vial filling equipment to ensure the safety of pharmaceutical products
Aseptic filling is fundamental in pharmaceutical industries to guarantee the quality and safety of its products from contaminants that may cause a reaction to the product leading to health risks when used. Exposure to contaminants also deteriorates the product quickly. The filling process starts with a vial washer before it goes to depyrogenation tunnels to remove pyrogens such as endotoxins and exotoxins. After sterilizing, vials are filled and stoppered by vial filling equipment. Then, they go to the capping and crimping machine for sealing.
Vial labeling and serialization equipment for product traceability
Serialization is a process used for product traceability operations. Information such as production-expiration date, lot number, and serial numbers are stored in a data center. By assigning a unique code to a drug packaging, counterfeiting of drug products can be prevented. Serialization is usually integrated with the labeling process of the vials. A high-resolution printer writes the labels with all the information required and then a code-reading camera is used during the verification process for readability.
Processing steps involved in vials making
Which vials technology do you need?

Laboratory nutsche filter dryer for solid-liquid separation
Optimize your lab processes with a versatile benchtop filter...
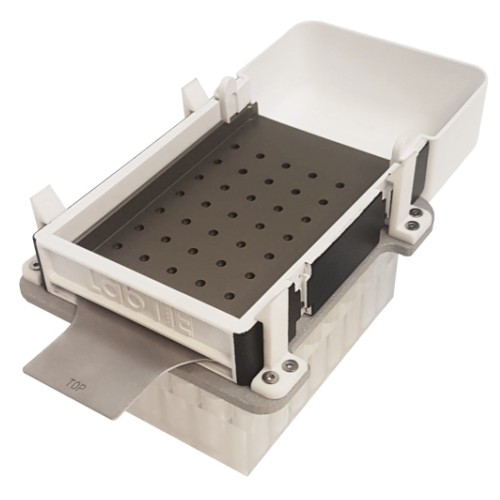
Modular bead dispenser for laboratory applications
Eliminate tedious manual bead loading with a versatile bench-top solut...
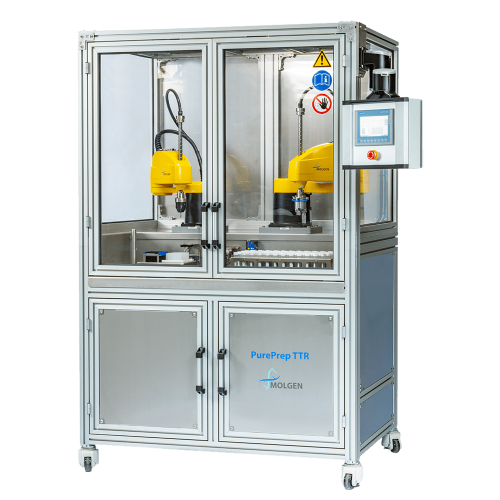
High-throughput tube transfer system for lab automation
Streamline laboratory workflows by automating high-throughput tub...
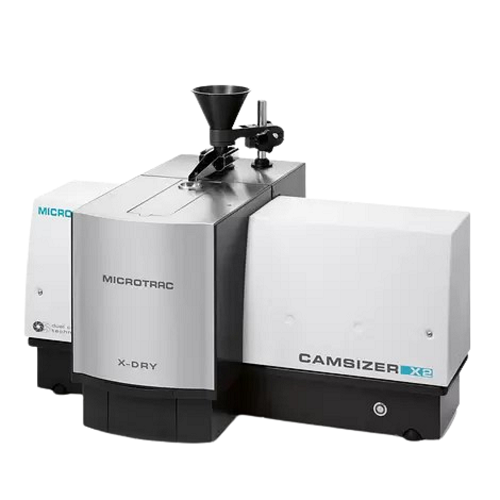
Particle size and shape analyzer
Achieve precise particle size and shape analysis from 0.8 μm to 8 mm with exceptional speed...
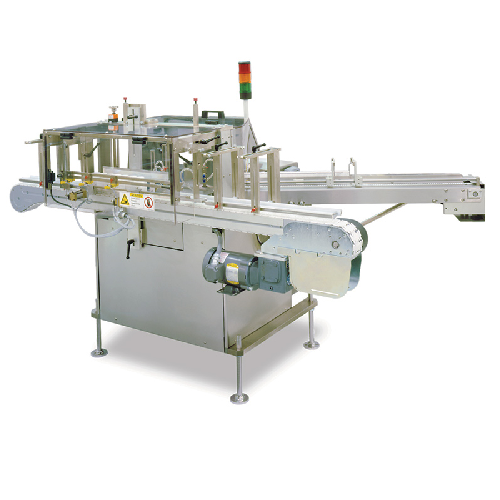
Outsert application system for pharma bottles
Effortlessly enhance packaging efficiency in pharmaceutical lines with this ...
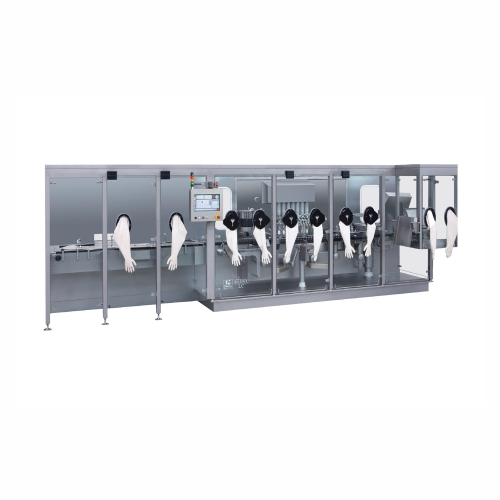
Vial filling and stoppering for aseptic liquid or lyo products
Ensure optimal aseptic conditions in your production line...

Rotary vial filling and stoppering
Ensure precise liquid formulations and lyophilized product consistency with a high-speed...
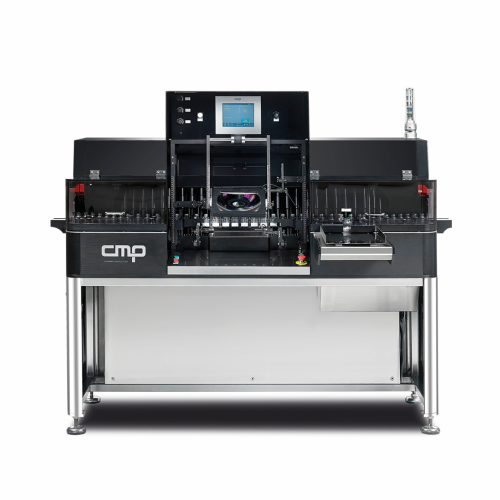
Inspection system for glass containers
Ensure precise inspection of liquid, freeze-dried, and powdered products in glass co...
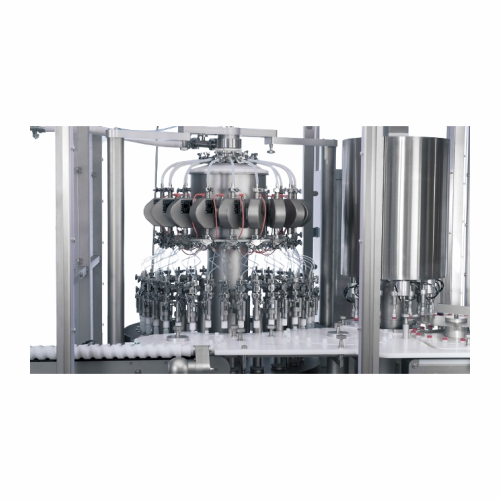
Automatic bottle and vial blower
Ensure purity and compliance in your liquid bottling line with this integrated blowing syst...

External washing and drying system for ampoules and vials
Optimize your aseptic processing by seamlessly integrating a c...
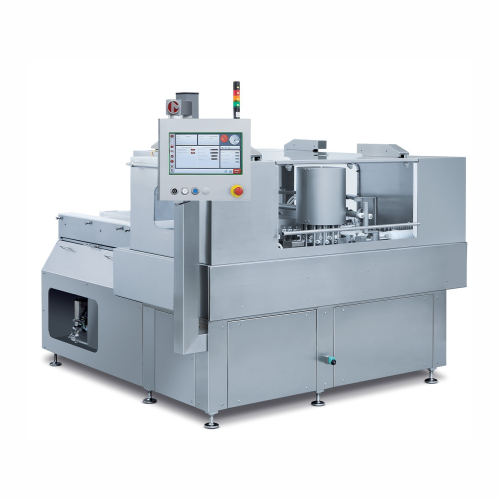
Industrial washing and sterilizing system for ampoules and vials
Ensure the highest hygiene standards in your liquid for...

Glass container Inspection line
Ensure precise quality control with a high-speed inspection line designed for glass containe...
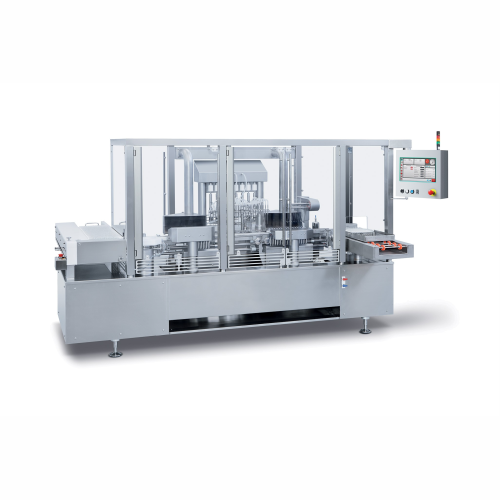
Aseptic ampoule filling and sealing solution
Ensure precise dosing and secure sealing of sterile liquid pharmaceuticals in...
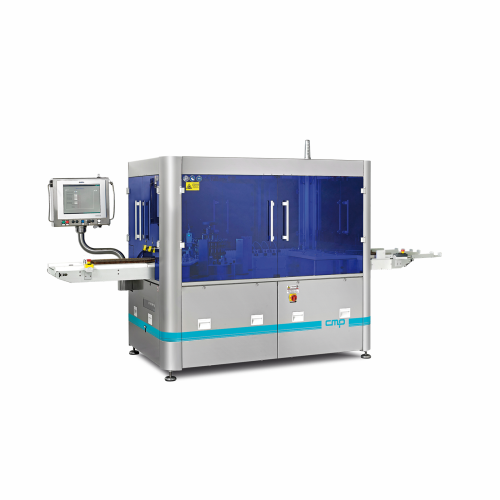
360 and leak Inspection system for glass containers
Ensure the integrity of every glass container with a comprehensive in...
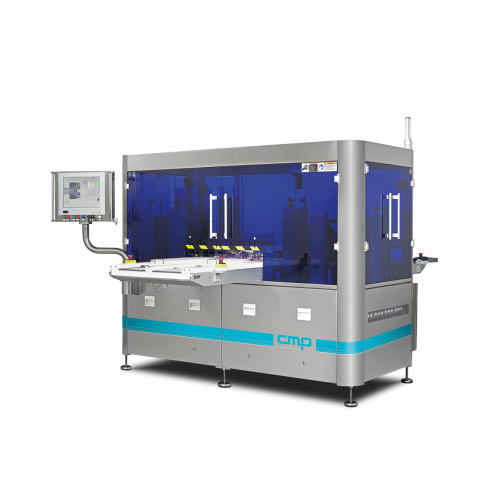
Glass container inspection system
Ensure product integrity with precision inspection for glass containers, detecting partic...
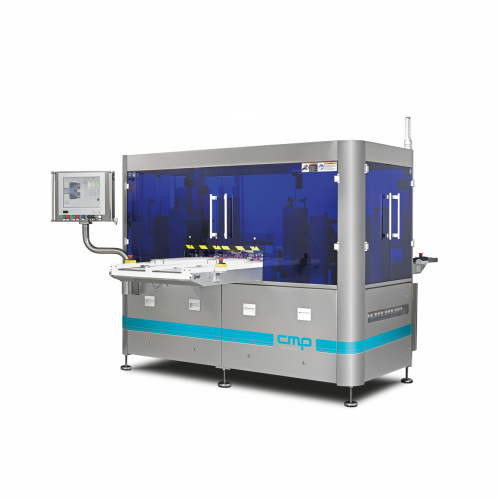
Inspection for glass containers in pharmaceutical production
Ensure the integrity of freeze-dried products with state-of...
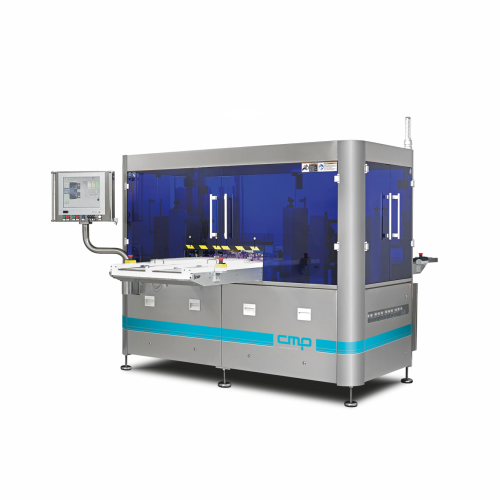
Inspection for glass containers
Ensure the integrity and quality of your liquid formulations with high-speed inspection and ...
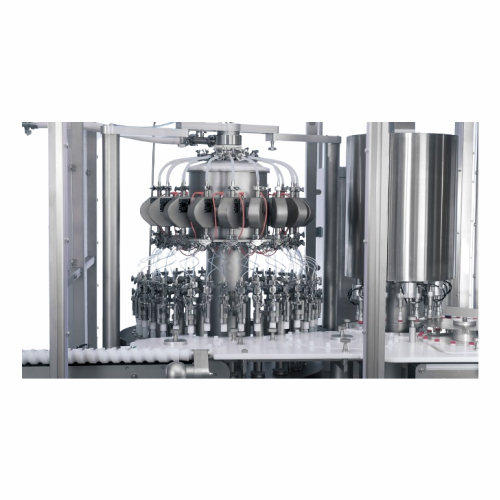
High-speed vial filling and capping system
Ensure precise vial filling and secure capping with this high-speed rotary solu...
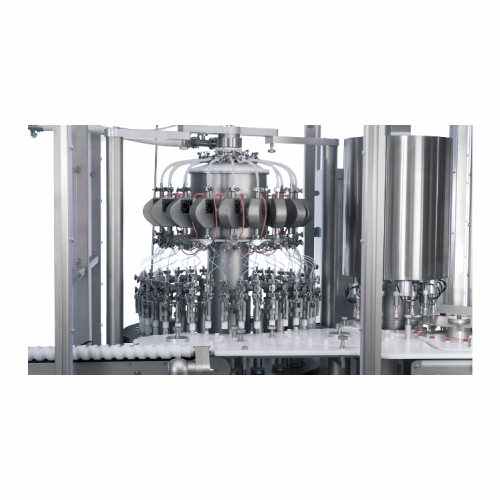
Aseptic vials filling and capping
Ensure precise vial capping and sealing for liquid pharmaceuticals with advanced aseptic ...
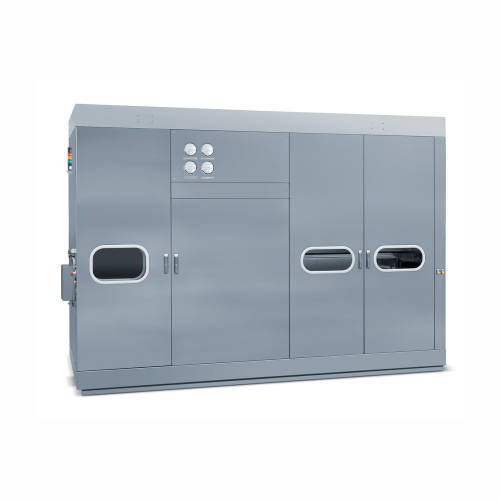
Depyrogenation tunnels for pharmaceutical containers
Ensure precise sterility and safety in pharmaceutical production wit...
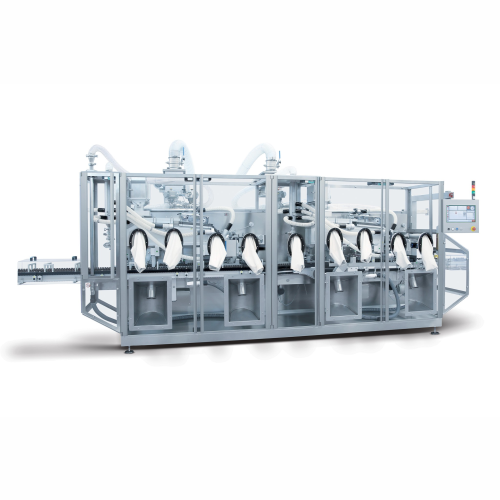
Electronic counting and filling system for vials
Efficiently streamline the packaging of solid dosage forms with a cutting...
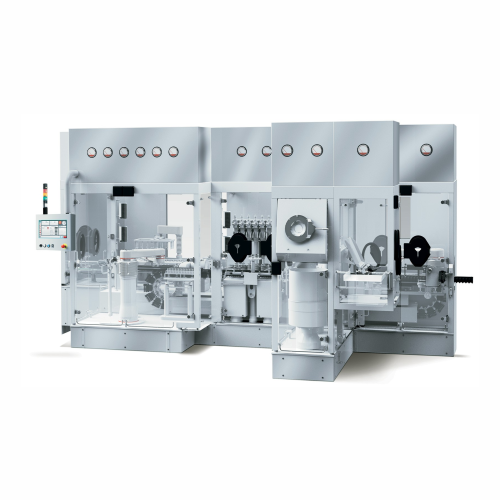
Filling and stoppering system for nested syringes
Ensure aseptic precision in syringe and vial preparation with a high-sp...
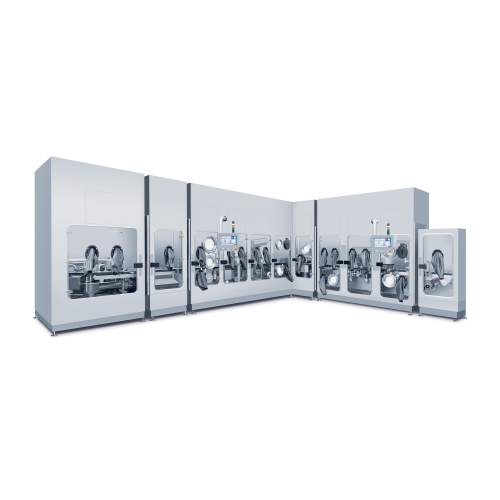
Aseptic filling and capping for vials and syringes
Ensure sterility and precision in vial and syringe filling with advanc...
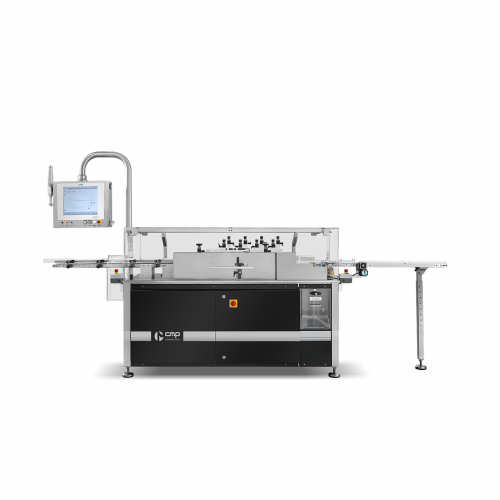
Leak testing for ampoules and vials
Ensure the integrity of sterile liquid containers with high-speed leak testing, detecti...
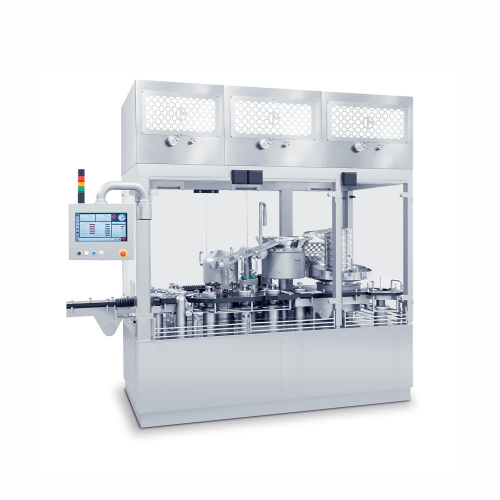
Vial capping for small volume parenteral
Ensure precise sealing and contamination-free environments for small volume parent...
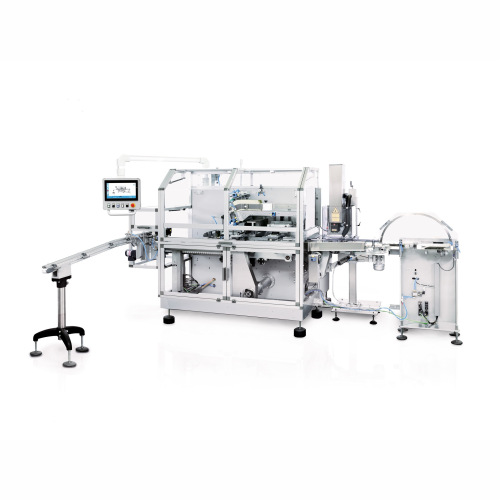
Automatic cartoning solution for cosmetic and fragrance samples
Streamline your cosmetic and fragrance sample packaging ...

Automated headspace inspection for parenteral containers
Ensure the integrity and quality of pharmaceuticals by inspectin...
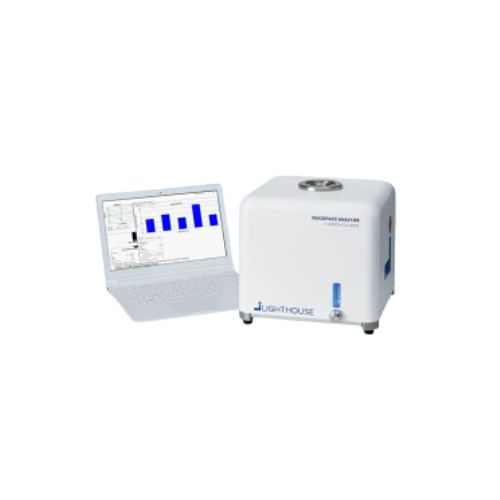
Carbon dioxide headspace analyzer for parenteral containers
Ensure accurate headspace gas analysis to maintain container...
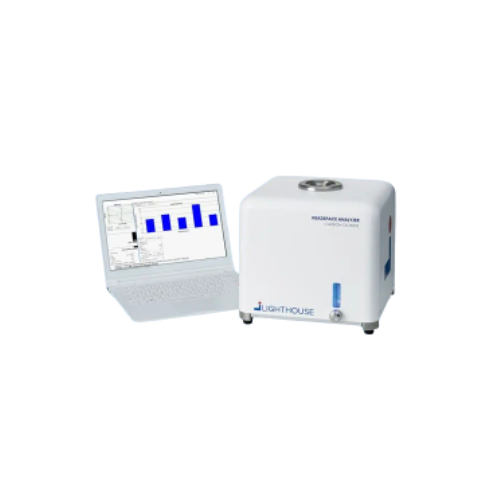
Oxygen headspace analyzer for container closure integrity testing
Ensure the integrity of oxygen-sensitive products wit...
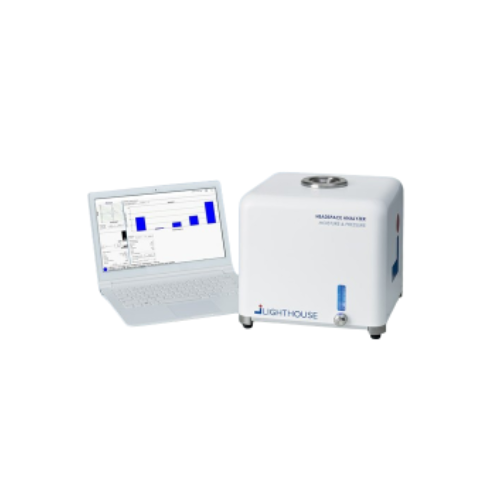
Moisture and pressure headspace analysis for sealed parenteral containers
Ensure accurate moisture and pressure assess...
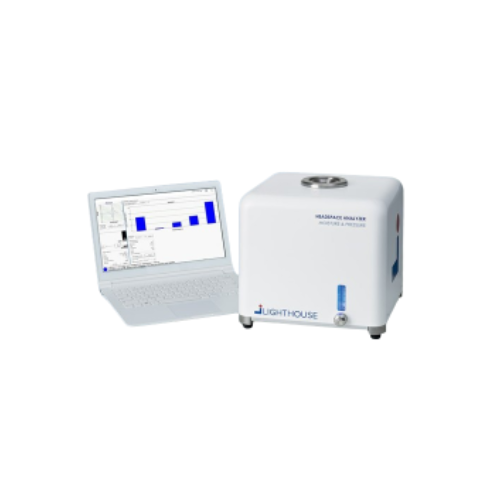
Water activity headspace analyzer for drug product samples
Ensure precise control of moisture levels across the entire p...
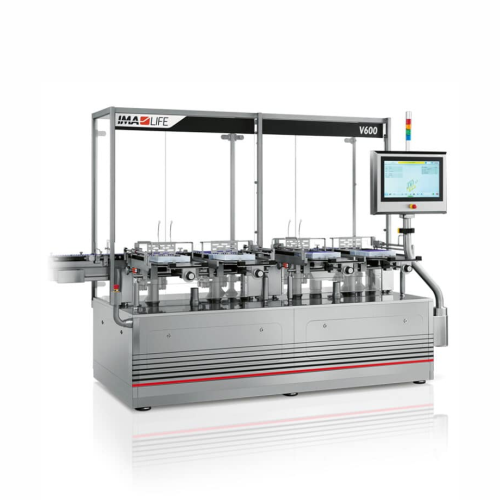
Tray loader for pharmaceutical vial packaging
Seamlessly integrate high-speed vial loading into your aseptic production li...
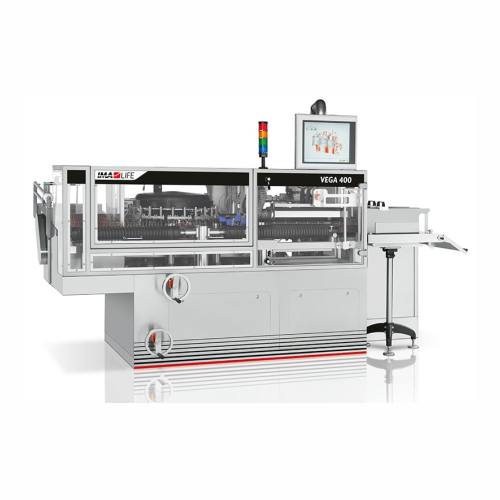
Ampoule external washer for decontamination
Ensure contamination-free glass containers with a high-speed solution designed...
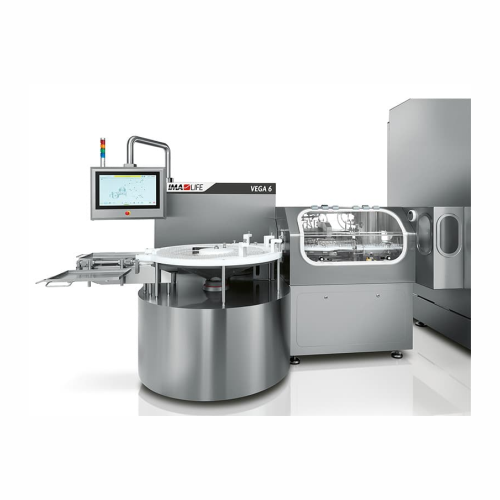
Rotary vial washers for parenteral containers
Ensure sterile and pyrogen-free parenteral preparations with a seamless wash...
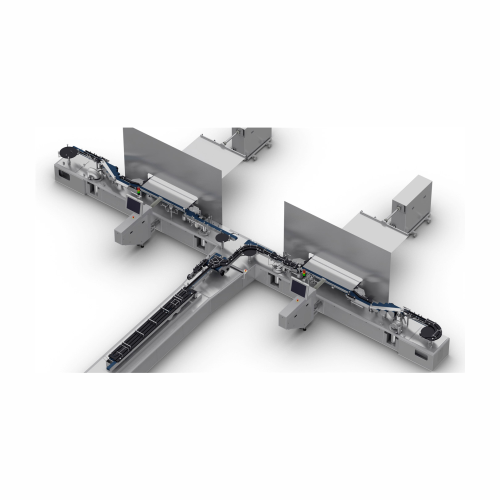
Automatic vial loading and unloading systems for freeze dryers
Optimize your vial handling with automated loading and un...
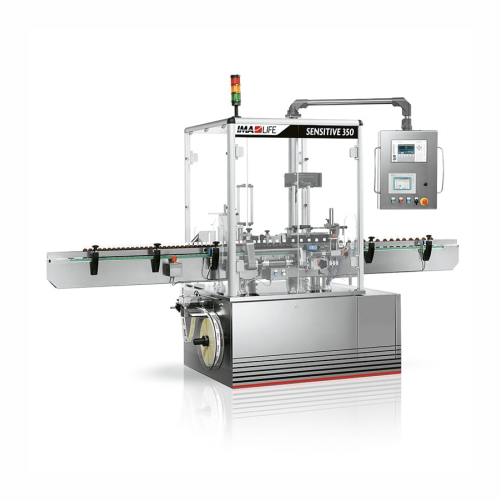
Labelling solution for cylindrical containers
Achieve precise and efficient labelling for cylindrical containers with a sy...
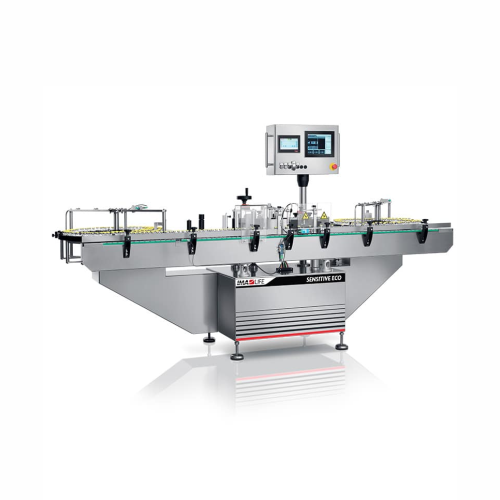
Linear labelling system for vials and bottles
Streamline your labelling process with a compact solution designed for preci...
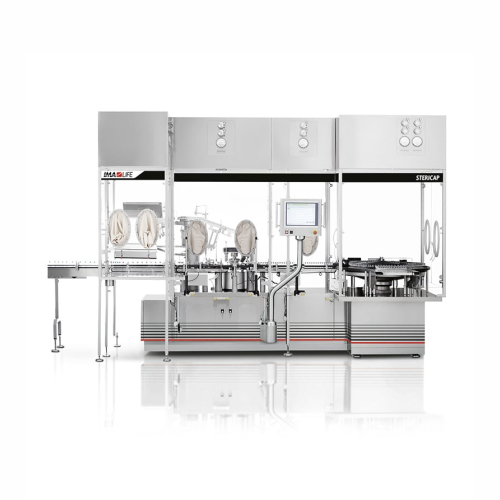
Rotary capping machine for aseptic products
Ensure precision sealing for aseptic liquid formulations with a solution engin...
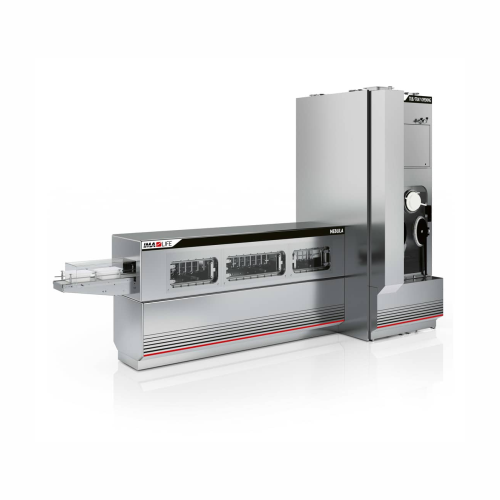
High-speed decontamination tunnel for pharmaceutical Rtu material
Ensure 100% sterility of ready-to-use materials with ...
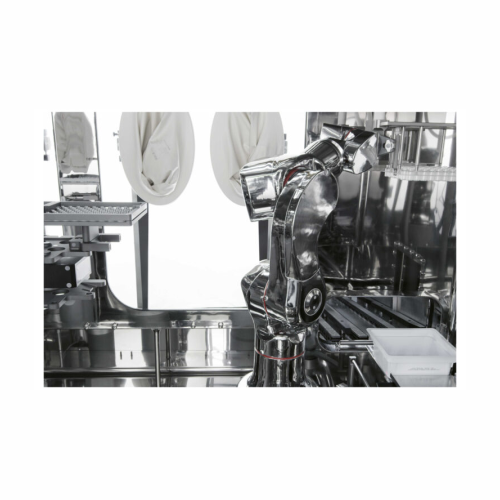
Robotic denesting system for Rtu vials
Streamline vial handling in aseptic environments with a fully robotised system that ...
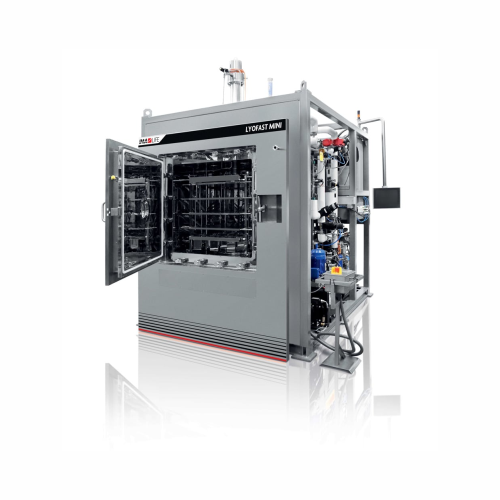
Pilot freeze dryer for pharmaceutical applications
Optimally bridge laboratory development and full-scale production with...
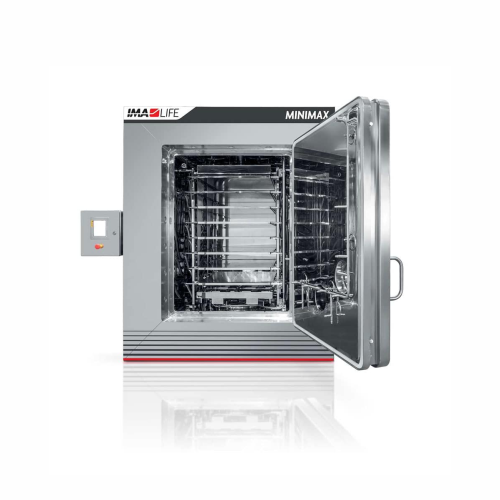
Small-scale freeze dryer for pharmaceutical applications
Optimize small-batch and pilot-scale lyophilization with advance...
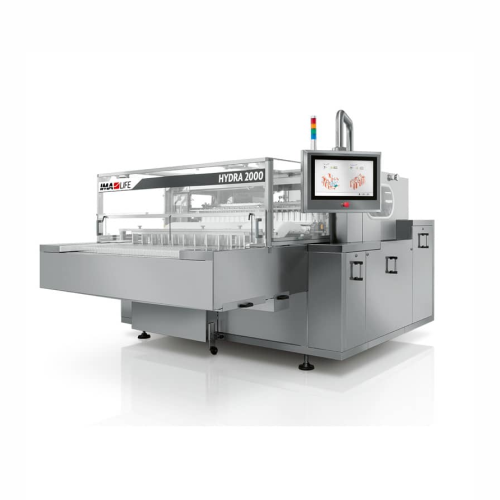
Linear vial washer for injectable drug containers
Achieve sterile conditions by efficiently removing contaminants from va...
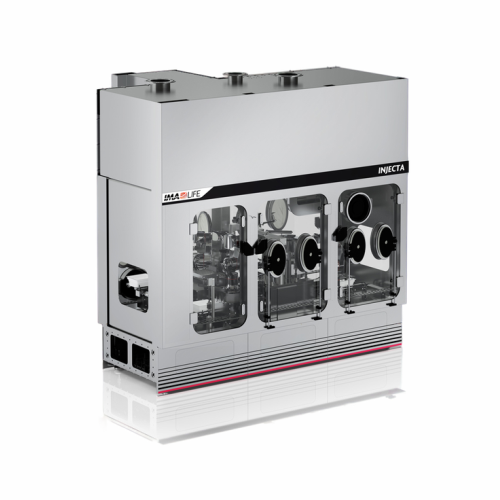
High-speed fill-finish system for ready-to-use components
Enhance aseptic fill-finish operations with a high-speed solut...
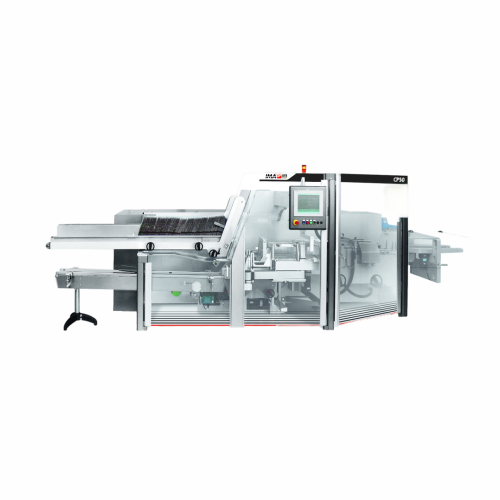
High-speed side loading case packer for small dimensions
Optimize your packaging line with a high-speed solution designed...
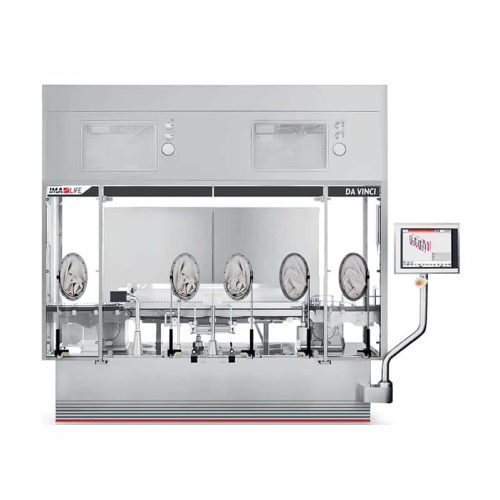
Wireless vial loading and unloading system for freeze-dryers
Enhance aseptic processing with this stand-alone, wireless ...
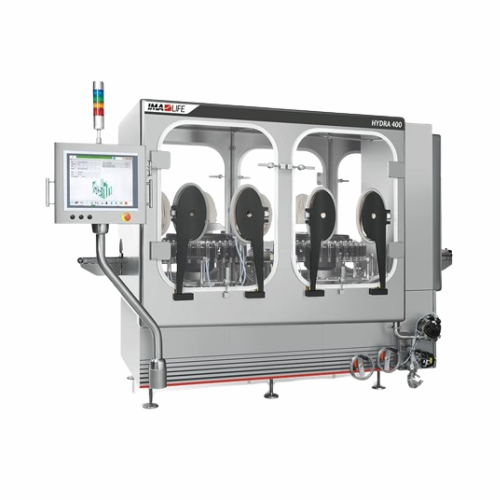
Vial external washer for cytotoxic product decontamination
Optimize the decontamination of pharmaceutical vials and cont...
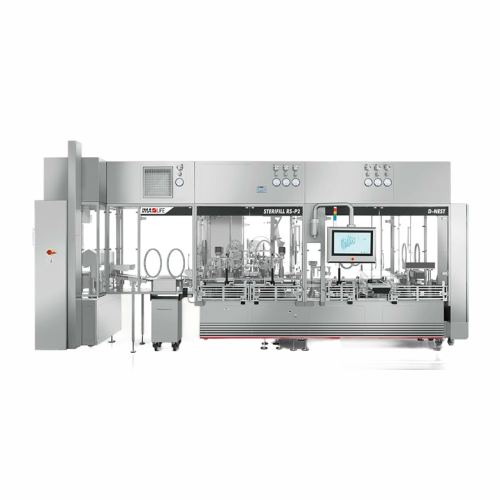
Denesting system for Rtu syringes and vials
Need efficient denesting of sensitive pharmaceutical containers? Streamline yo...
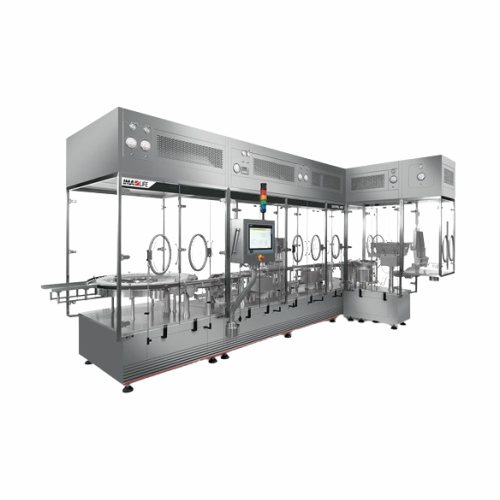
Aseptic filling and stoppering solution for vials
Ensure precise aseptic filling and stoppering of vials with enhanced fl...
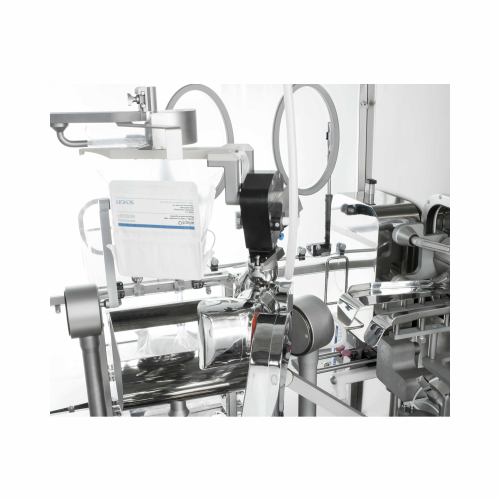
Robotic sterile package opening system
Achieve sterile precision with a fully robotic system that streamlines primary packa...
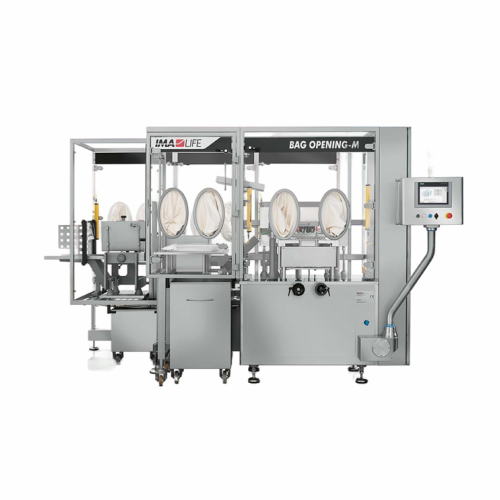
Semi-automatic sterile primary packaging opener
Ensure sterile integrity in pharmaceutical packaging with this solution, w...
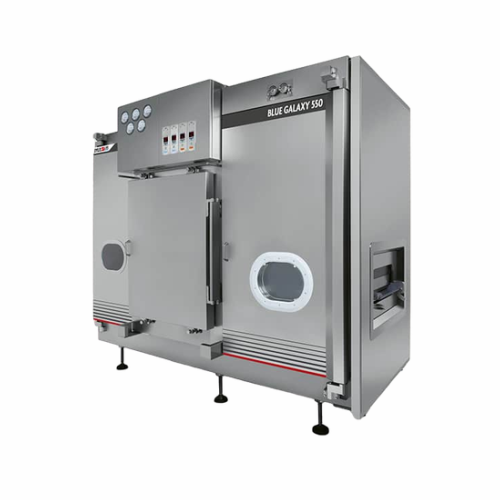
Depyrogenating tunnel for glass containers
Ensure the sterility of injectable medications by achieving reliable endotoxin ...
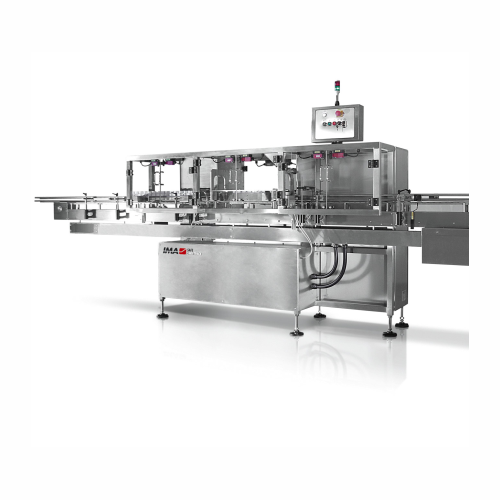
Inline bottle cleaner for pharmaceuticals
Ensure your pill bottles and capsule containers are free from contaminants with ...
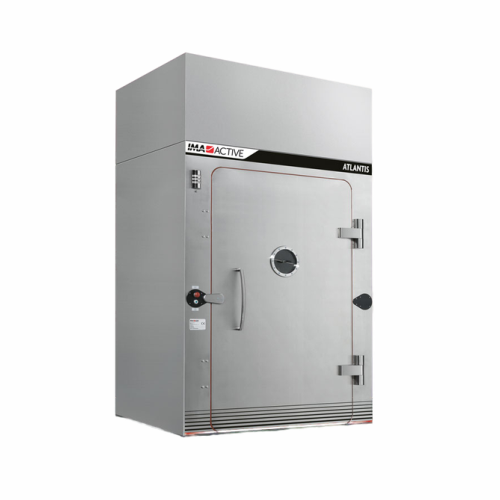
Pharmaceutical components washing station
Ensure optimal cleanliness with high-efficiency washing and drying of pharmaceut...
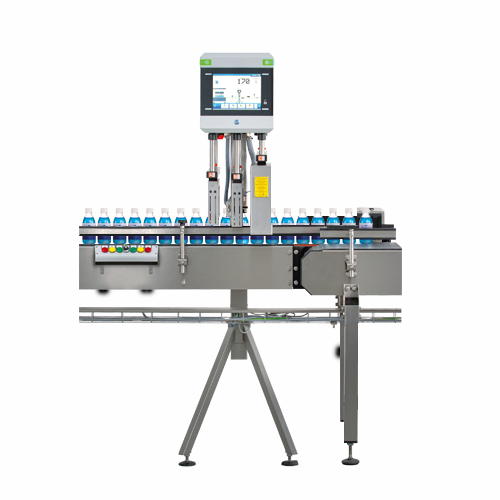
Compact full product inspection system for pharmaceuticals
Easily detect fill level inaccuracies, closure misalignments,...
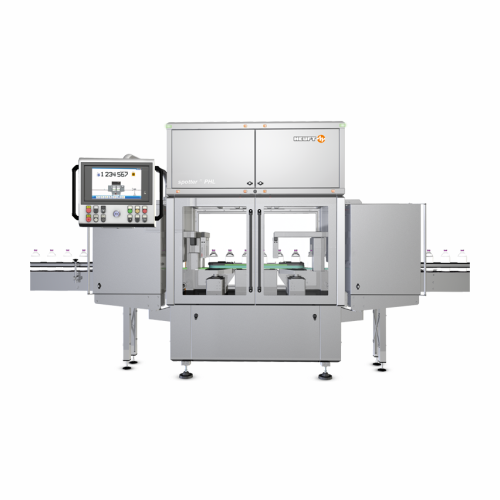
Vial inspection system for pharmaceutical industry
Ensure vial integrity by detecting and rejecting contaminants, glass d...
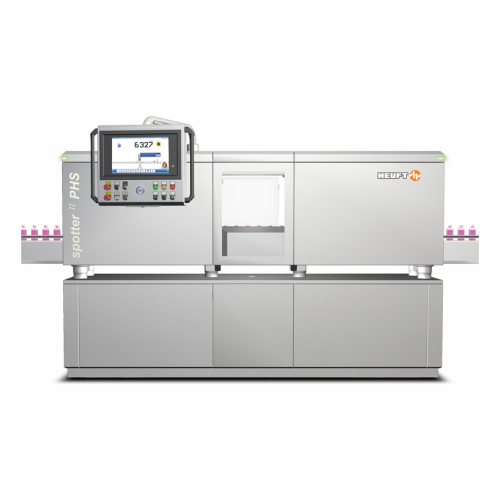
Vial inspection system for pharmaceutical products
Ensure the integrity and safety of parenteral drugs with advanced imag...
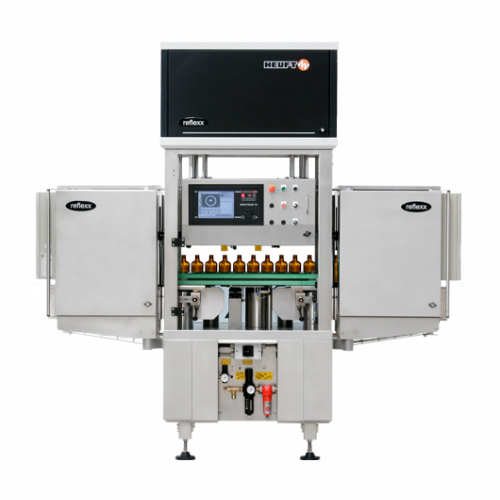
Empty container inspection for pharma packaging
Ensure ultra-clean packaging by detecting glass faults and contaminants be...
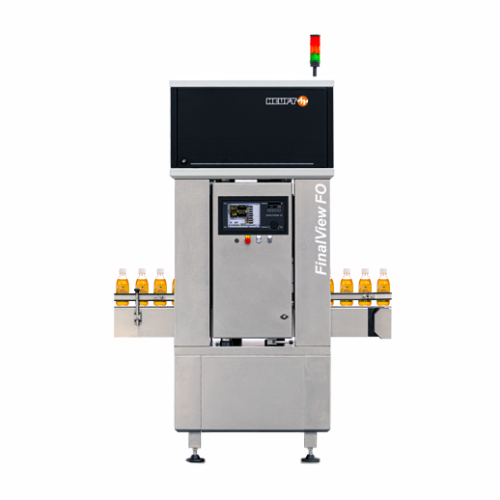
Final product inspection system for pharmaceutical containers
Ensure the integrity and precision of packaged pharmaceuti...
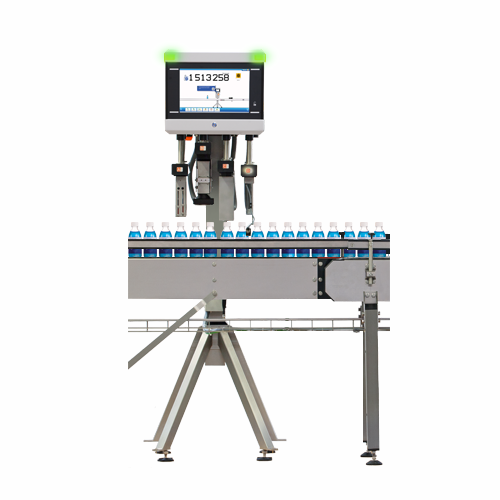
Full container inspection for pharma and food industries
Ensure precise fill levels and secure closures in your productio...
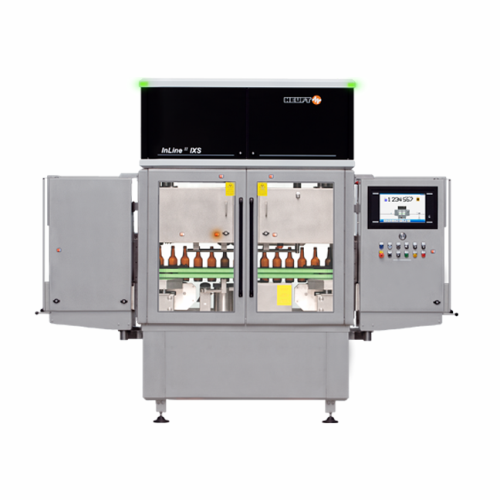
X-ray assisted empty bottle inspection
Enhance your production line with advanced X-ray and optical technology to ensure pr...
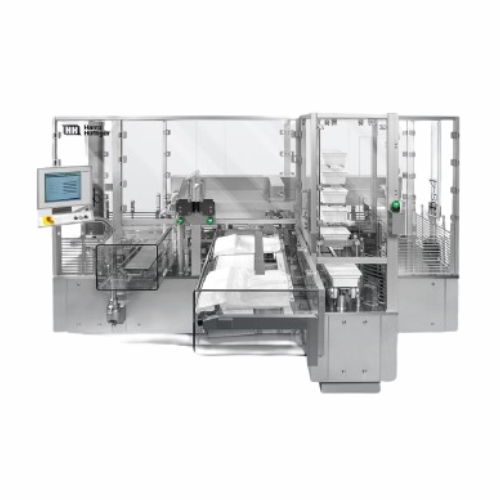
Double bagging solution for sealed tubs
Achieve sterile packaging for medical and pharmaceutical products with a compact, e...
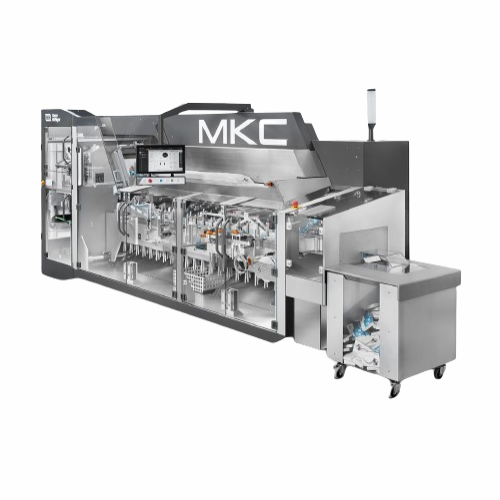
Flexible horizontal cartoning solution for various products
Streamline your packaging process with this versatile carton...
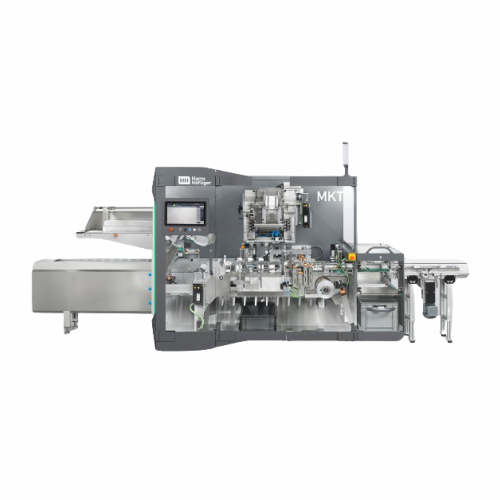
High-performance cartoning system for pharmaceutical products
Optimize your packaging line with a flexible cartoning sol...
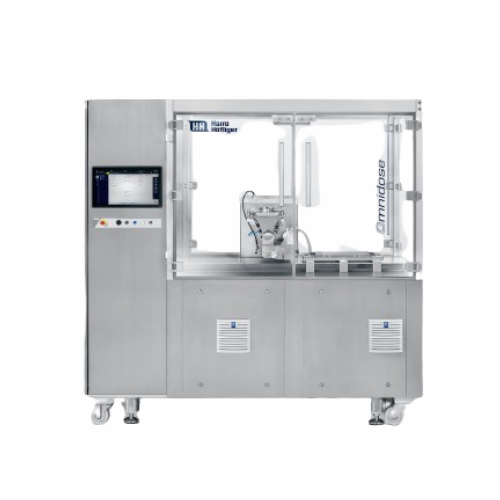
Powder dosing system for development and small batches
Streamline lab-scale pharmaceutical production with a versatile po...

Powder dosing machine for laboratory applications
Achieve precise powder dosing and streamline your R&D processes wi...
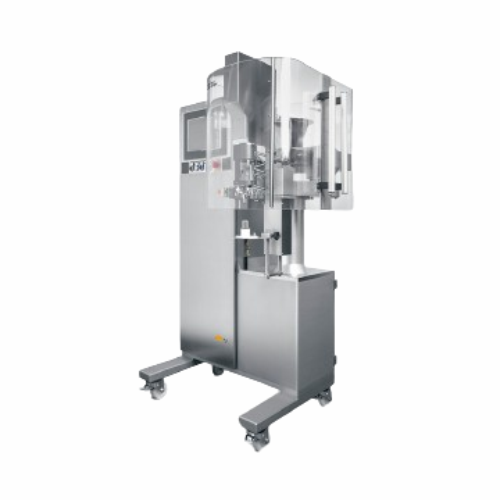
Auger dosing unit for powder dosing in pharmaceuticals
Ensure precise and flexible dosing of pharmaceutical powders with ...
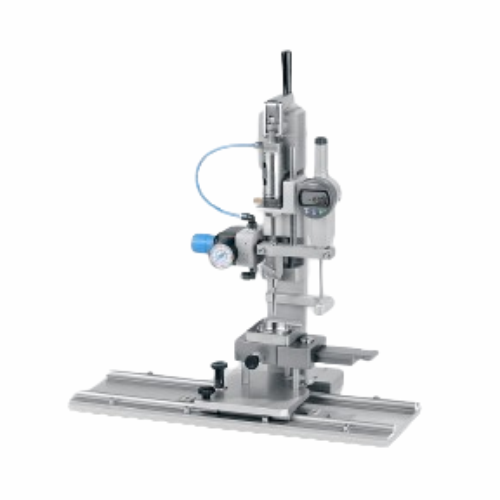
Powder dosing for lab and galenics
Ideal for precise dosing needs, this compact lab device streamlines powder filling proce...
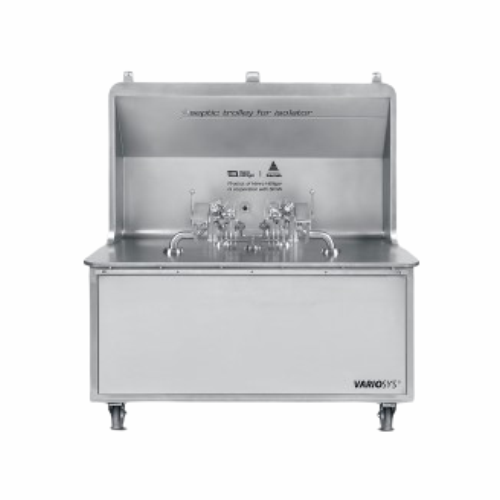
Sterile filling system for Iv bags
Ensure precise and sterile filling of IV and infusion bags with flexible, semiautomatic ...
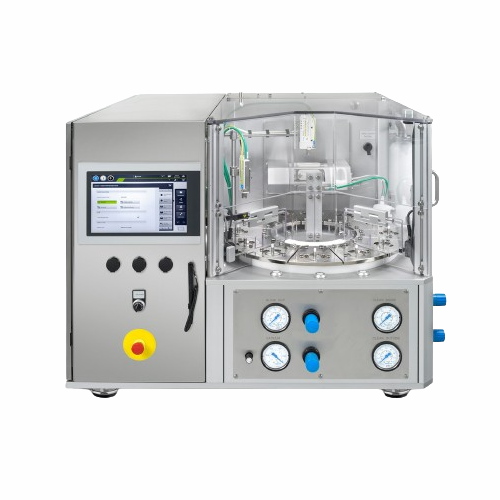
Semi-automatic powder dosing system
Achieve precise micro-dosing for pharmaceutical powders with a flexible system ideal fo...

Lyophilized pellet dosing technology
Eliminate mechanical strain and static charge in your lyophilized pellet dosing proces...
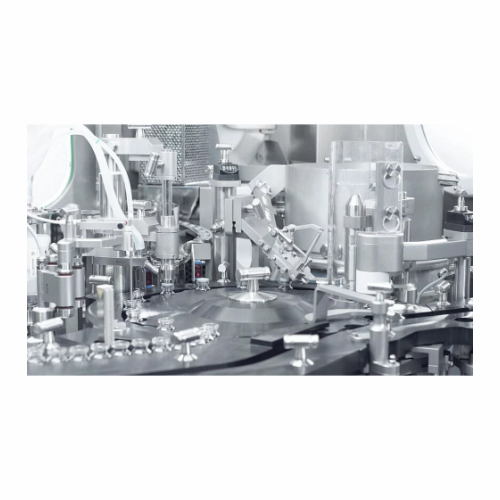
Integrated vial filling system for aseptic and toxic pharmaceuticals
Minimize product loss and ensure high sterility in...
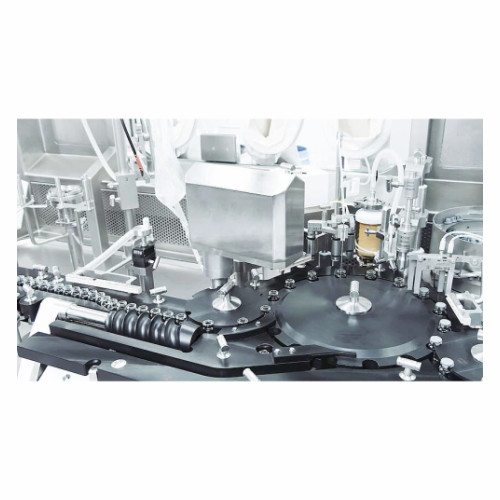
Aseptic filling solutions for Rtu vials, cartridges, and syringes
Optimize your aseptic filling processes with a system...
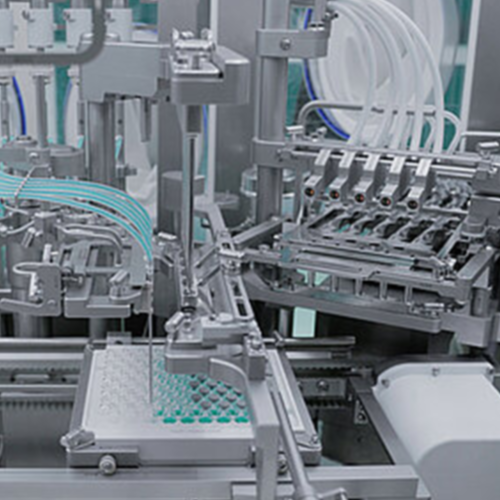
Vial and syringe filling system for pharmaceuticals
Ensure aseptic precision in liquid formulation filling with a modular...
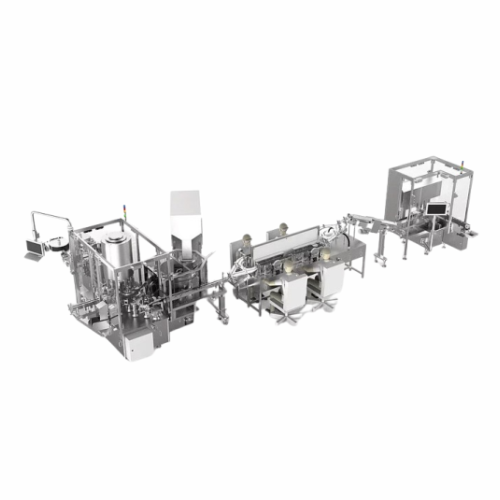
Syringe assembly system for plunger rod, label, and safety device
Ensure precise handling and assembly of pharmaceutica...
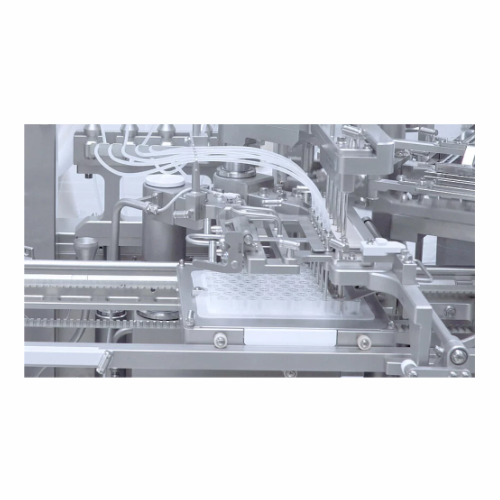
Aseptic syringe filling solution for Rtu containers
Streamline your pharmaceutical liquid filling operations with precise...
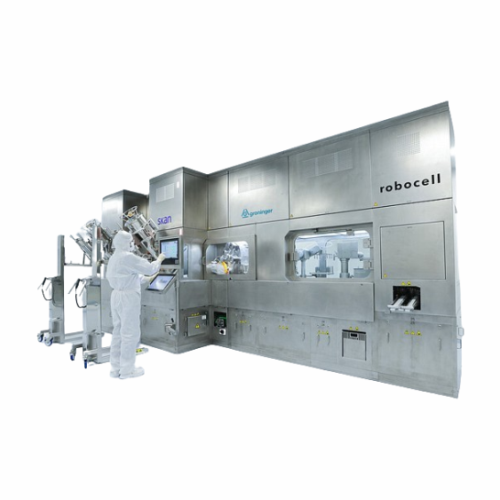
Gloveless robotic filling cell for aseptic pharmaceutical processing
Eliminate human intervention in aseptic filling wi...
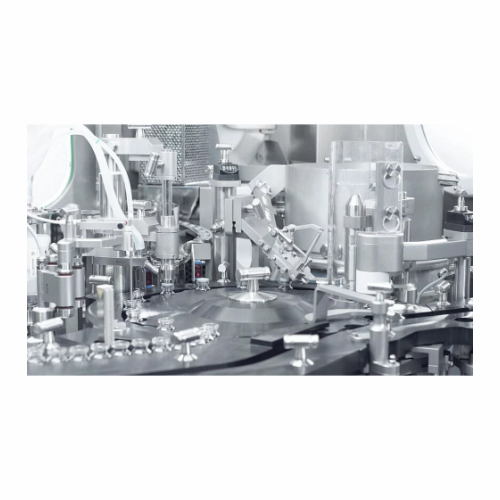
Vial filling for pharmaceuticals
Streamline your aseptic processing with vial filling machines that ensure sterile, precise,...
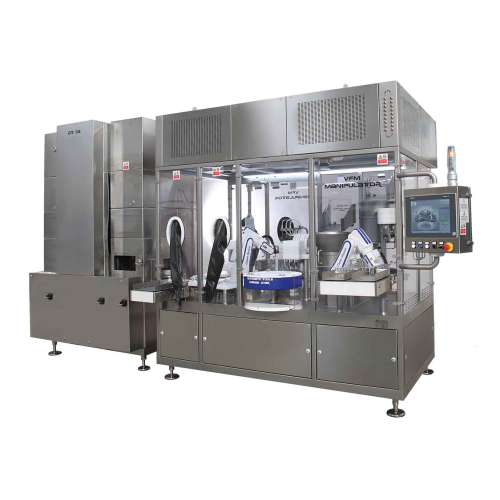
Industrial manipulator for sterile and nonsterile filling
Maintain the integrity of high-value pharmaceuticals with a hi...
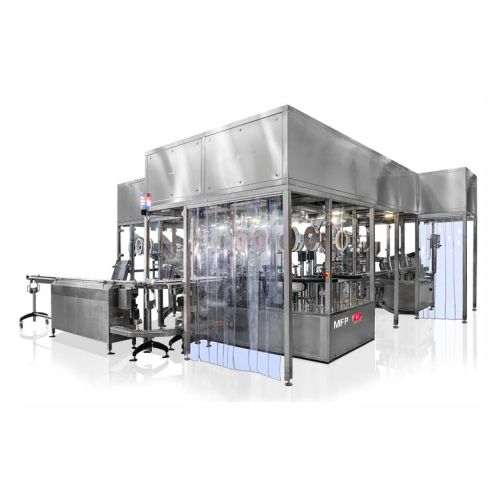
Sterile and nonsterile vial filling system for injectables
Achieve precision and safety in filling and stoppering with a...
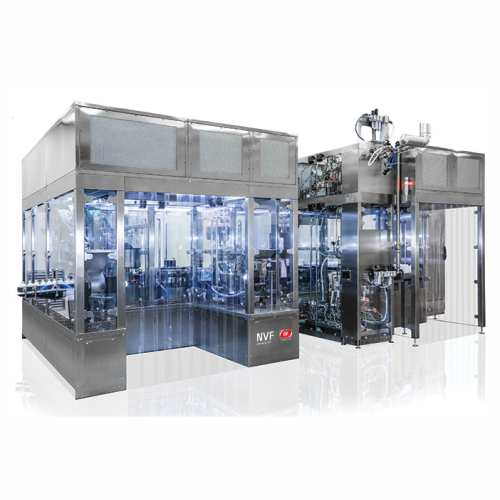
Sterile and nonsterile filling for injectable solutions
Efficiently fill and stopper injectable solutions in both sterile...
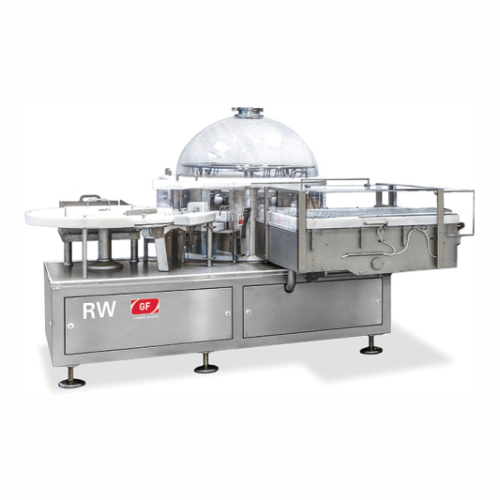
Rotary washer for pharmaceutical containers
Ensure optimal preparation of pharmaceutical containers with advanced rotary w...
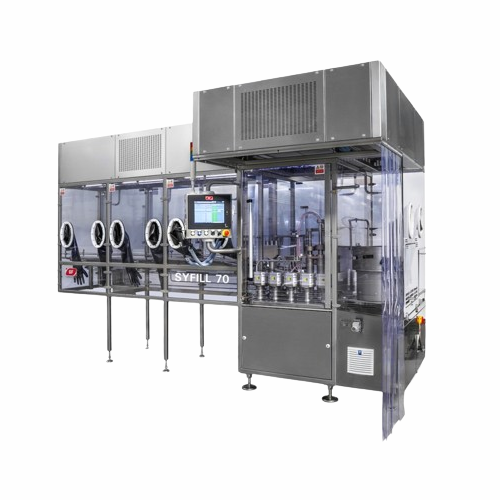
Vial filling system for sterile and nonsterile pharmaceuticals
Enhance precision in injectable drug preparation with a s...
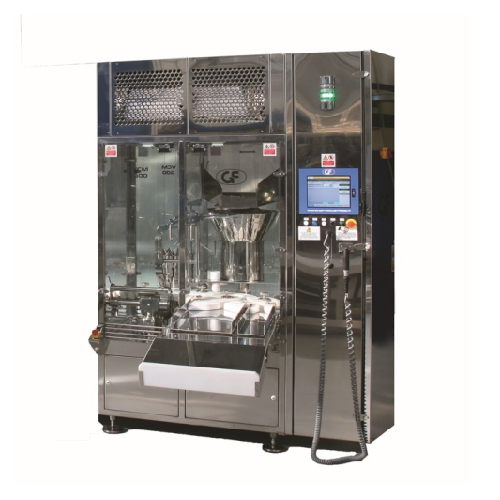
Vial capping solution for pharma applications
Efficiently secure the integrity of sensitive liquid medications with a flex...
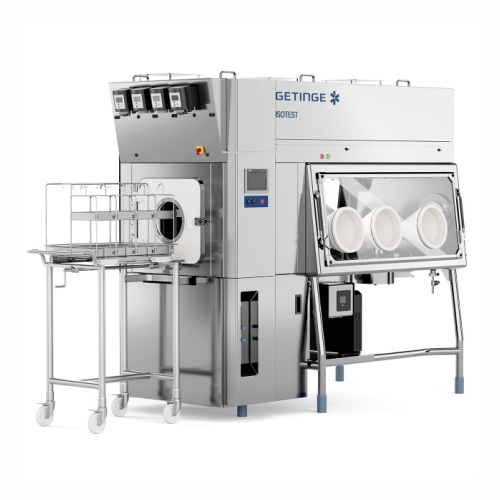
Sterility testing isolator for pharmaceutical labs
Ensure reliable sterility testing in a controlled sterile environment ...
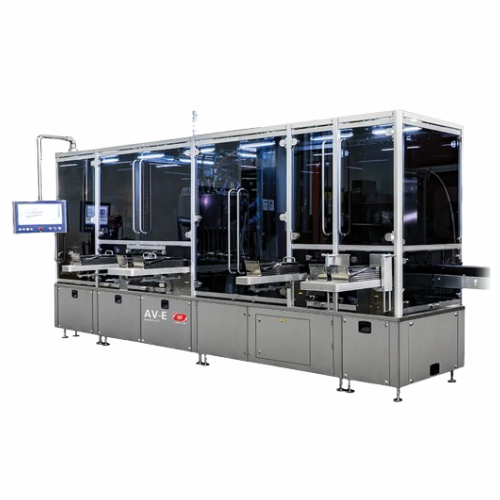
Optical inspection for ampoules, vials, cartridges, and syringes
Ensure product integrity and safety with this advanced ...
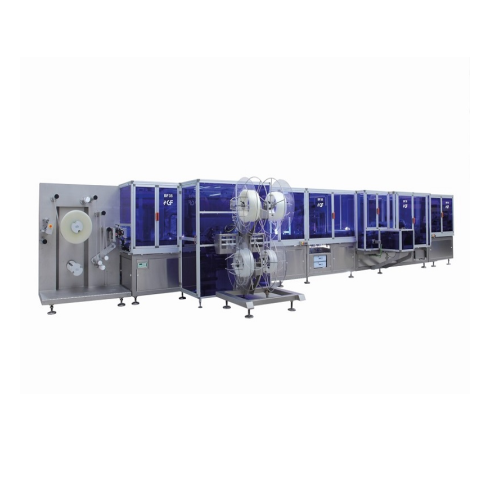
Bag forming system for pharmaceutical industry
For fluid pharmaceutical production, ensure precise formation and sealing o...
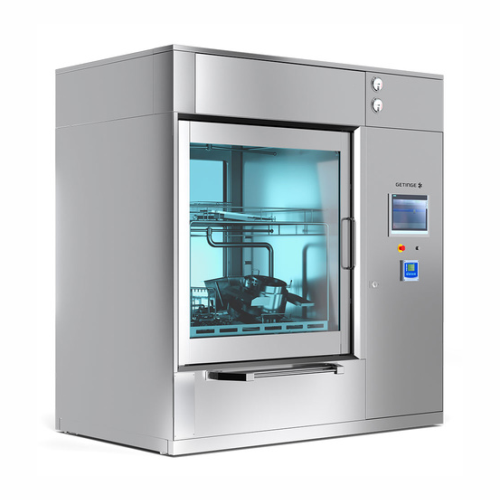
Cgmp washer/dryer for biopharmaceutical cleaning
Achieve optimal cleanliness with precise washing and drying for biopharma...
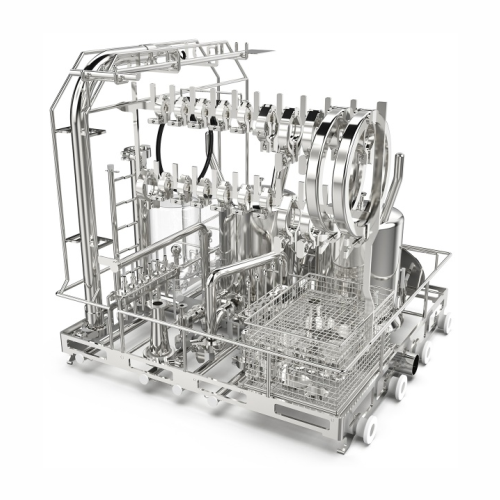
Loading solutions for Gmp washers
Ensure thorough cleaning and drying of biopharmaceutical components with modular loading ...
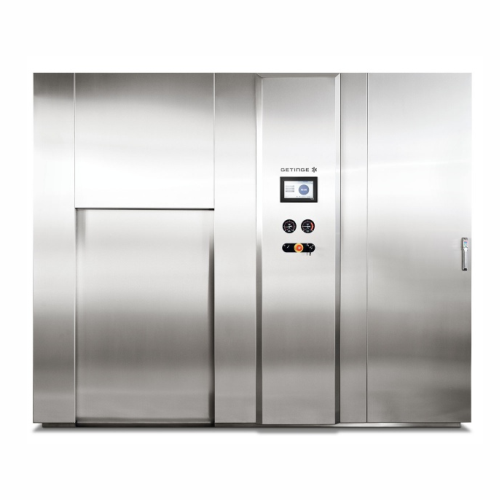
Steam sterilizer for biomedical lab research
Ensure the highest level of biosafety and scientific integrity with this stea...
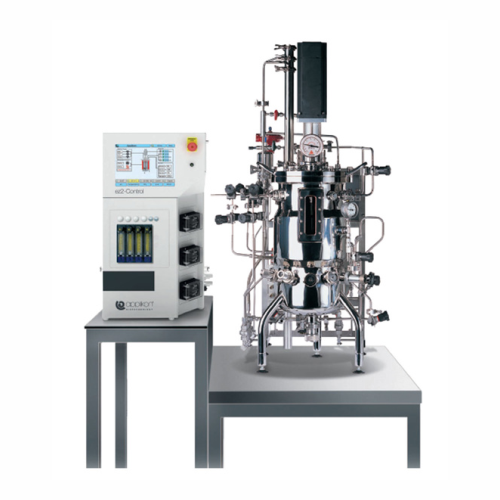
Bench top bioreactor for microbial and cell cultures
Optimize your bioprocessing workflow with this versatile bench top s...
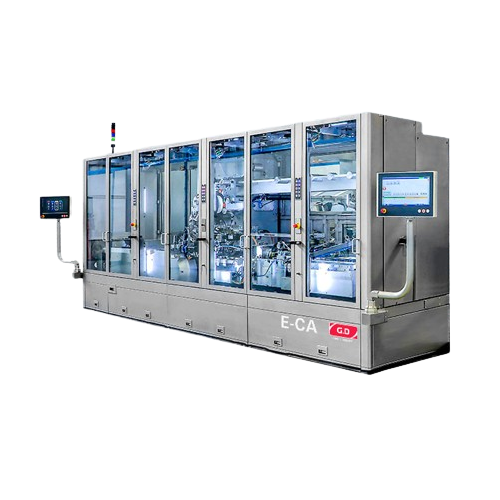
Cartridge assembler for next generation vapour products
Optimize your production of vape cartridges and e-cigarette pods ...
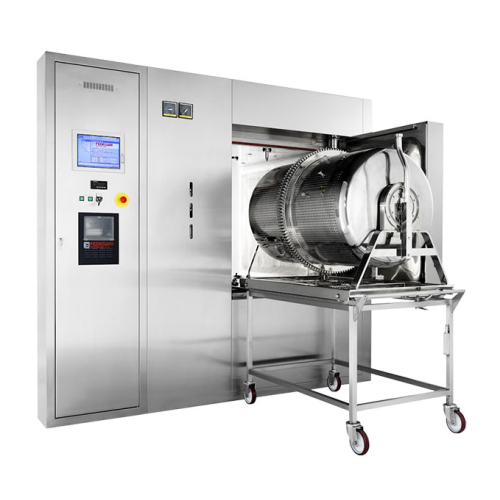
Elastomeric stopper sterilization system
Ensure sterilization and cleanliness of elastomeric vial stoppers with a system de...
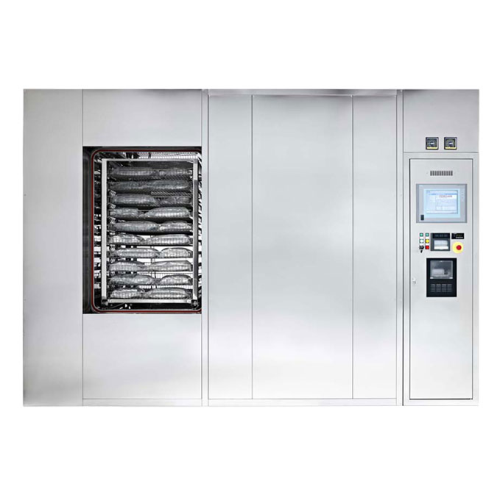
Steam air sterilizer for aqueous solutions
Overcome the pressure challenge in sterilizing aqueous solutions, effectively p...
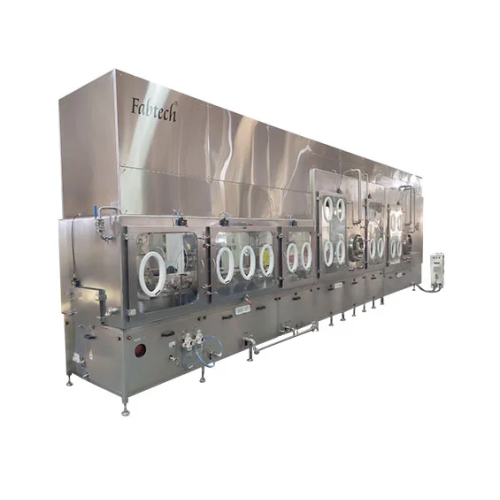
Aseptic filling isolator for vial / Pfs / cartridge
Ensure sterile and contamination-free filling of vials, pre-filled sy...

Liquid dispensing isolator for sterile environments
Maintain product sterility by utilizing a liquid dispensing isolator ...
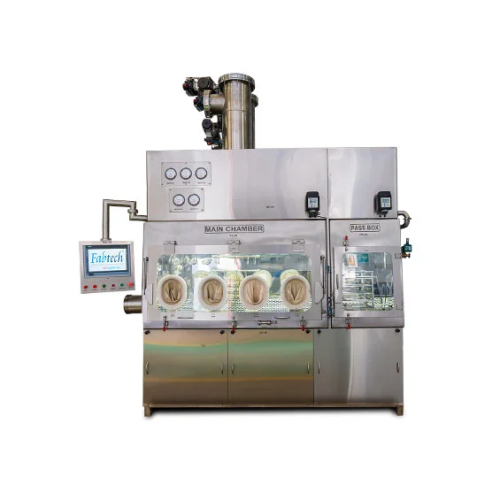
Sterility testing isolator for aseptic environments
Ensure aseptic conditions and process integrity during sterility test...
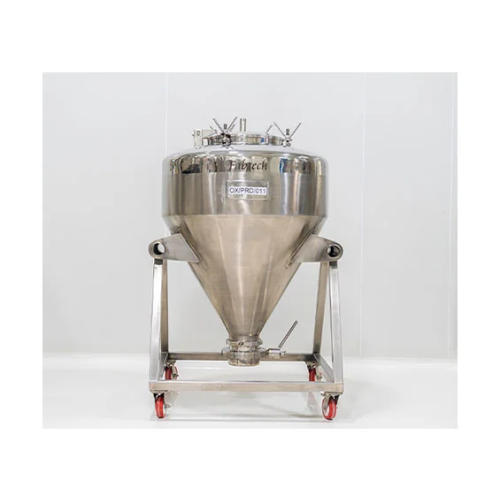
Vacuum transfer system for powders and granules
Effortlessly transfer and manage powders and granules with seamless integr...
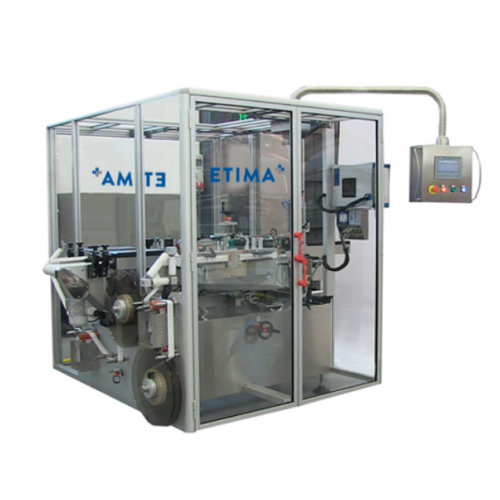
Linear tamper evident labeler
Secure product integrity with high-speed labeling that ensures tamper evidence, while seamless...
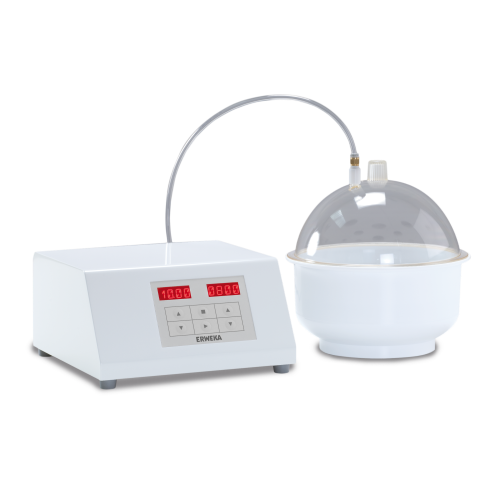
Blister packaging leak tester
Ensure airtight integrity in your blister packaging with precise vacuum and dye penetration te...
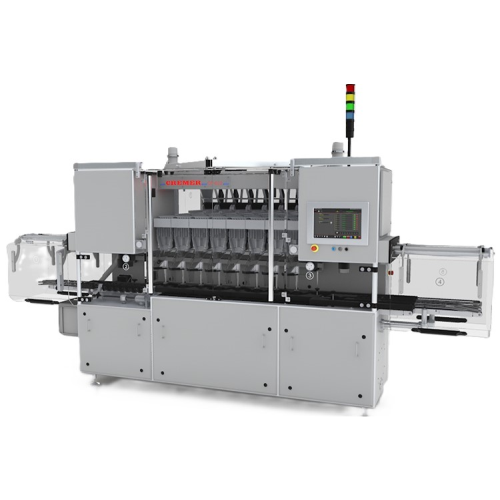
In-motion pharmaceutical bottle filler
Achieve up to 400 bottles per minute with this modular bottle filling solution, desi...
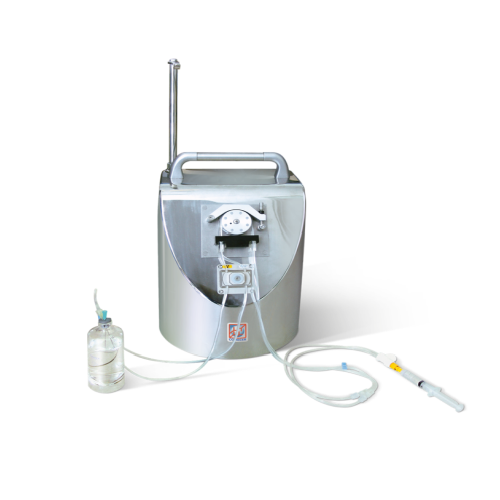
Syringe dispensing system for nuclear medicine
Optimize your radiopharmaceutical workflows with a system designed to preci...
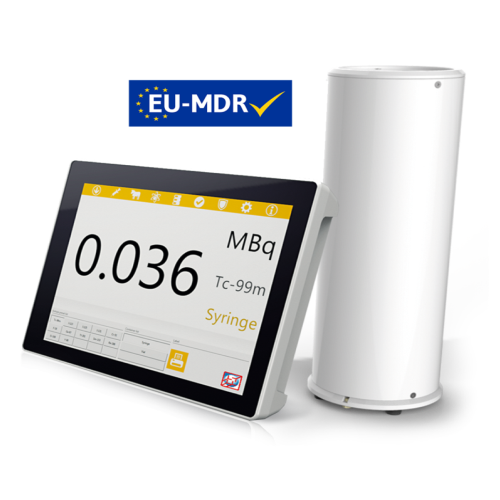
Touch screen dose calibrator for nuclear medicine
Achieve precise radiopharmaceutical dosing with seamless touchscreen op...
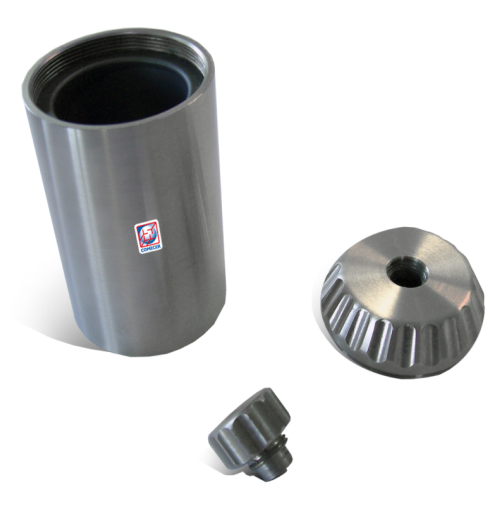
Stainless steel vial container for personal protection
Ensure the safety and integrity of sensitive materials with robust...
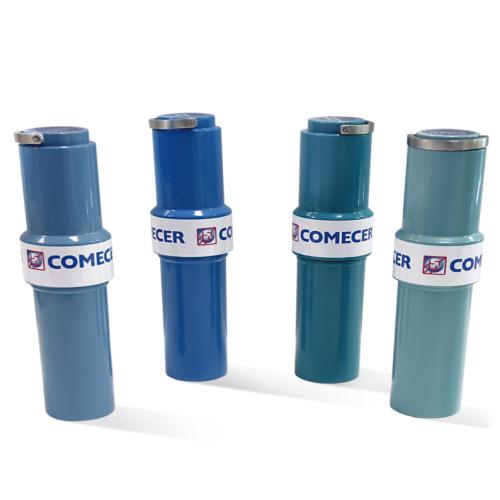
Syringe shielded container for radiopharmaceuticals
Ensure safe and efficient transport of sensitive radiopharmaceuticals...
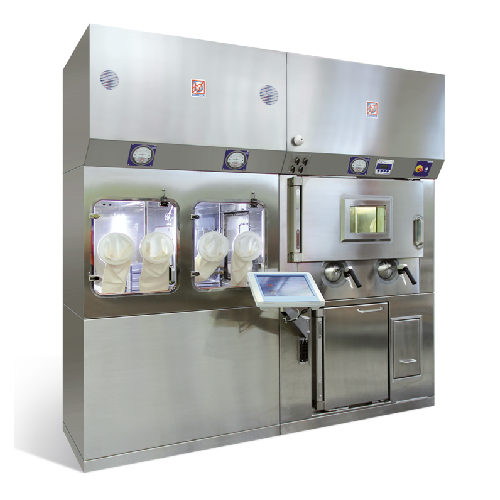
Radiopharmaceuticals dispensing isolator
Ensure precise and sterile dispensing of radiopharmaceuticals and other liquid for...
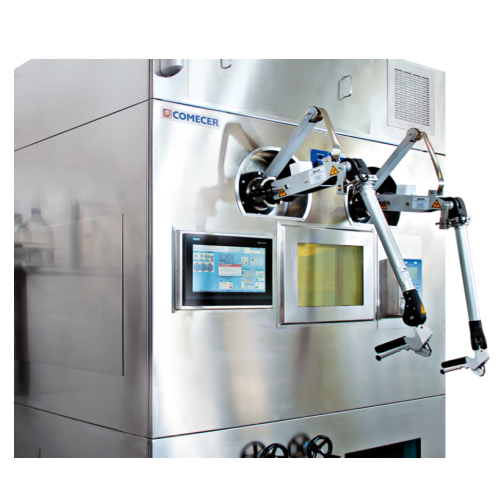
Technetium-99m generator production line
Streamline your radiopharmaceutical production with our solution, ensuring precise...
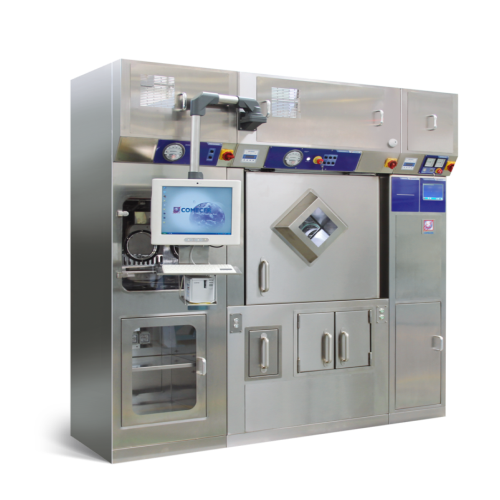
Robotic dispenser for radiopharmaceuticals
Ensure precise and safe handling of radiopharmaceuticals with a fully automated...
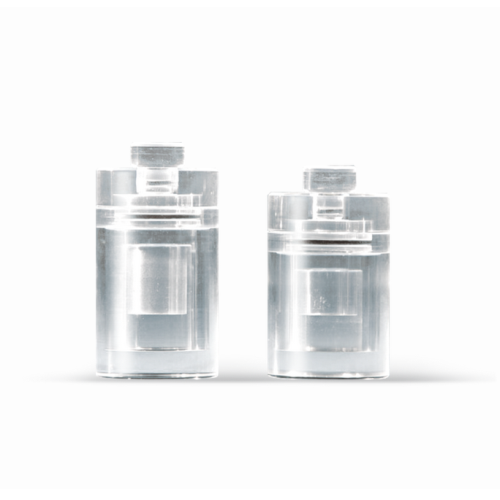
Beta radiation shielding for vials
Ensure the safe handling and storage of radiopharmaceuticals with effective beta radiati...
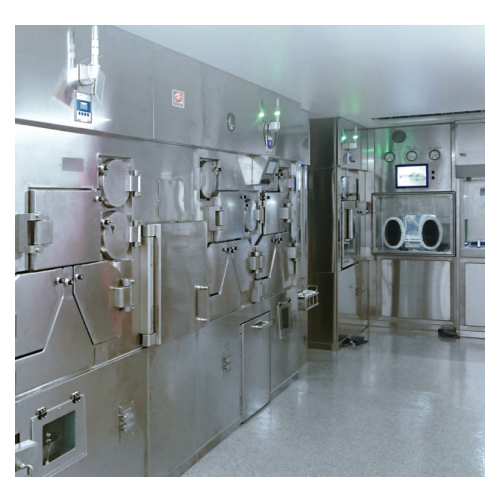
Ra-223 dichloride production and dispensing suite
Ensure precise production of Ra-223 dichloride and related radiopharmac...
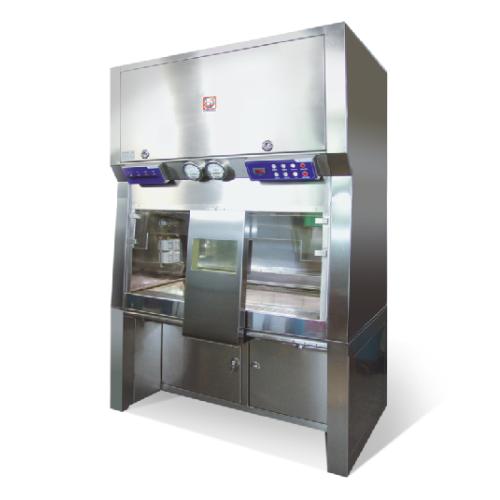
Shielded radiochemistry fume hood
Enhance your lab’s safety and efficiency with a fume hood designed for precise hand...
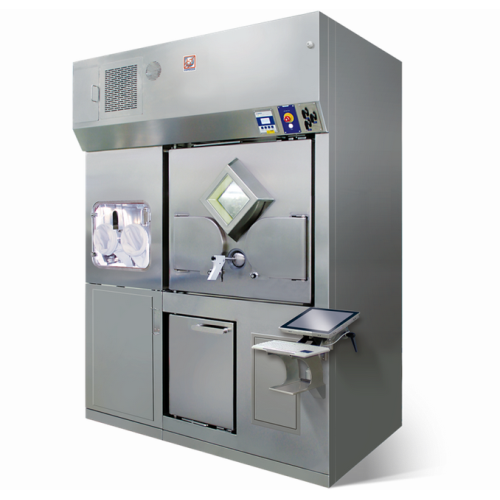
Radiopharmaceutical dispensing isolator for vials and syringes
For precise radiopharmaceutical preparation, this isolato...
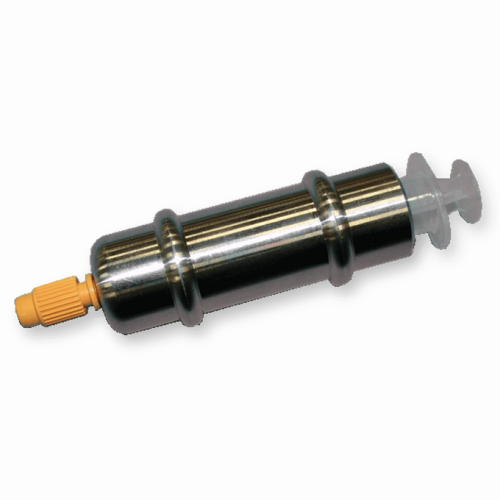
Tungsten syringe shield for radiopharma applications
Enhance radiation safety during syringe handling with specialized sh...
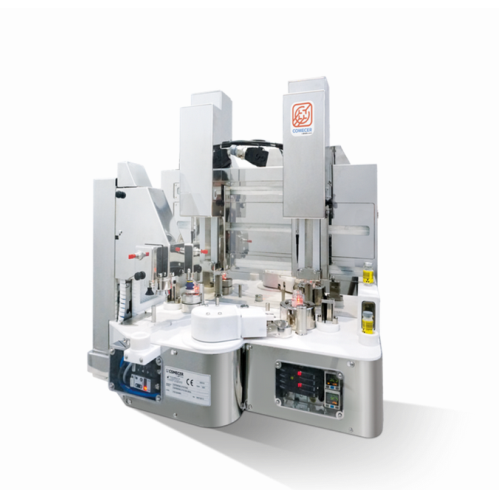
Micro-dispenser for lu-177 and ac-225
Efficiently dispense precise volumes of radioisotopes for diagnostic and therapeutic ...
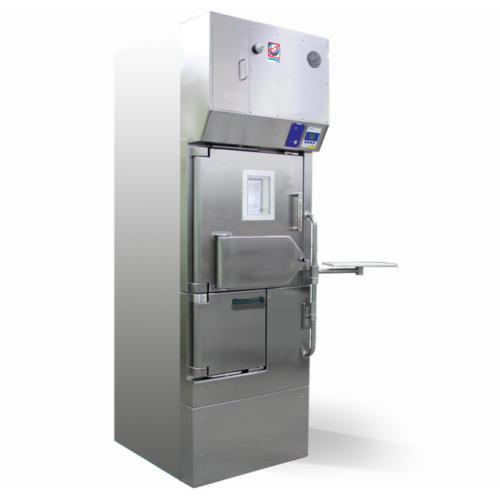
Manual hot cell for r&d in radiopharmaceuticals
Ensure precise dose dispensing and safe handling of radioisotopes with thi...
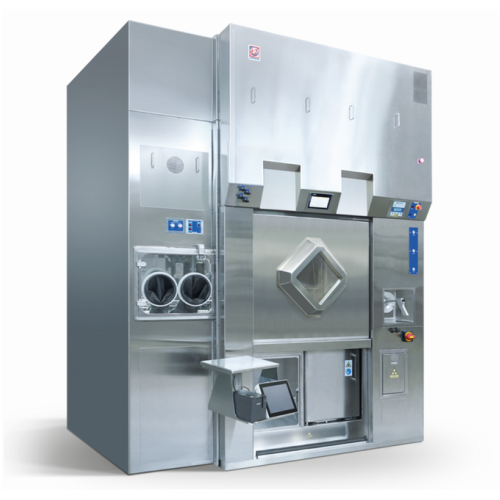
Laminar flow shielded cell for radiopharmaceutical research
Ensure aseptic conditions and precise dose calibration for i...
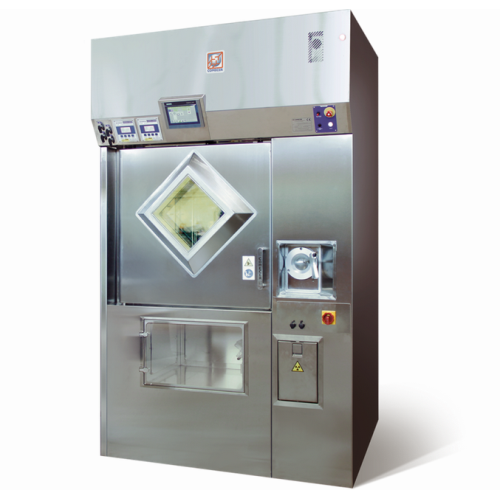
Shielded cell for radiopharmaceutical synthesis
Ensure operator safety and seamless radiopharmaceutical synthesis with adv...
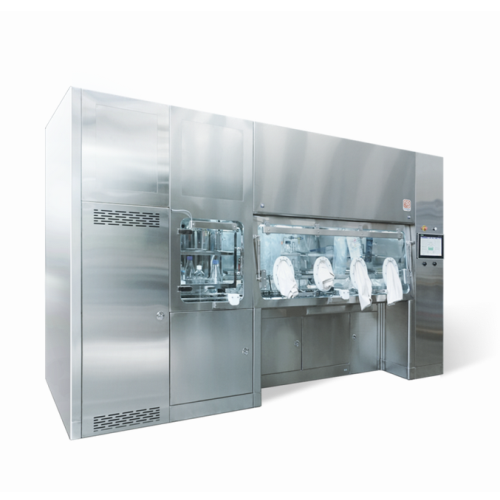
Modular sterility testing isolator for pharmaceuticals
Achieve uncompromised sterility with modular isolators designed fo...
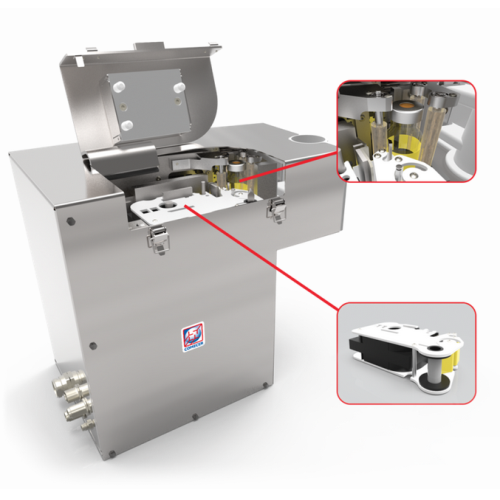
Automatic vial labeling for shielded isolators
Eliminate manual labeling errors and ensure precise data with this solution...

Semiautomatic lu-177 production and dispensing plant
Optimize your radiopharmaceutical production with an advanced system...
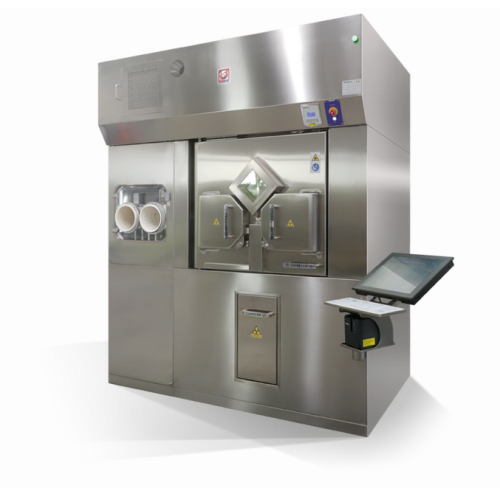
High-throughput aseptic isolator for syringes and vials filling
Streamline your aseptic filling process with a high-spee...
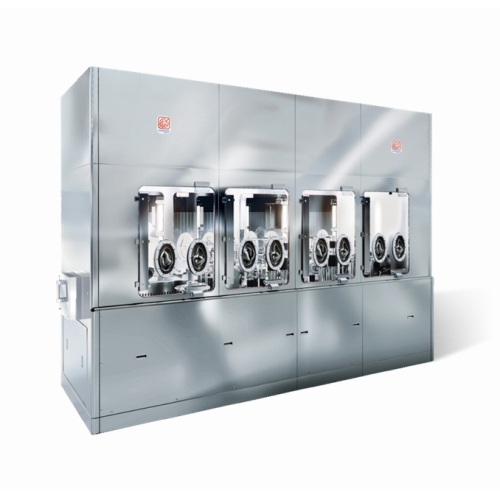
High quality sterile filling system
Experience unparalleled precision in aseptic filling with this advanced system, designe...
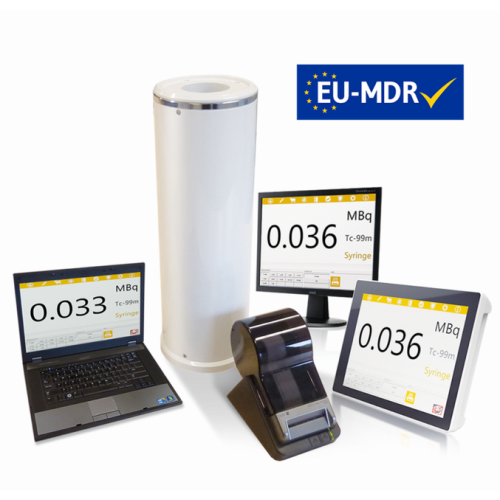
Digital dose calibrator for radiopharmacy
Ensure precision in your nuclear medicine or radiopharmacy operations with this ...

Radiopharmaceutical multidose injector for Fdg injection
Enhance patient care and streamline radiopharmaceutical handling...
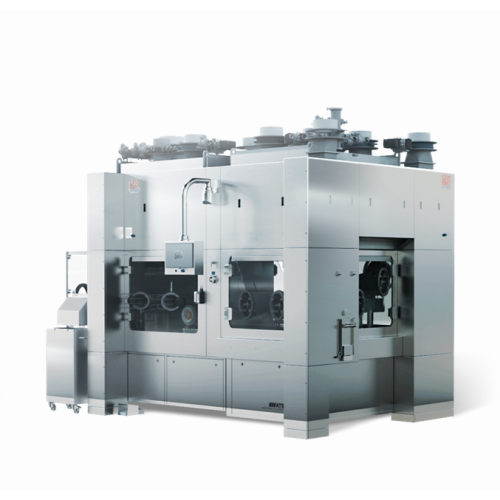
Sterile robotic filling for ready-to-use vials and syringes
Achieve precise and contamination-free filling for biopharma...

Volumetric dispensing system for radiopharmaceuticals
Ensure precise dosing of radiopharmaceuticals like FDG and tracer i...
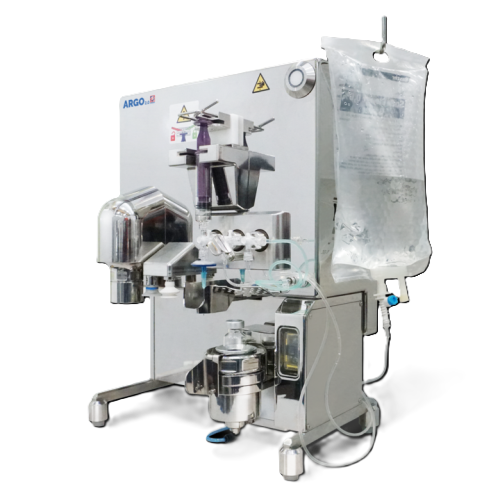
Automatic vial dispensing system for nuclear medicine
Ensure precise, compliant dispensing of radiopharmaceuticals with a...
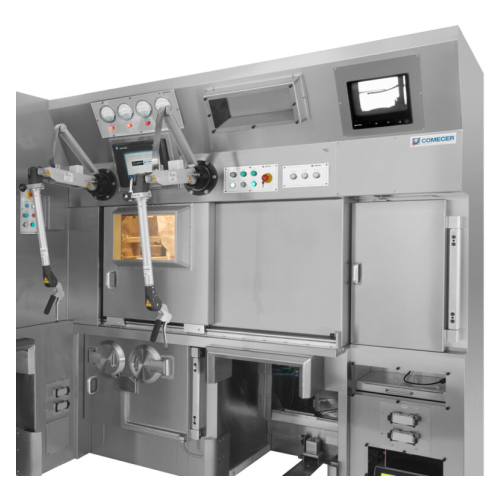
Aseptic filling line for 131i sodium Iodide
Ensure compliant production of iodine-131 radiopharmaceutical vials with preci...
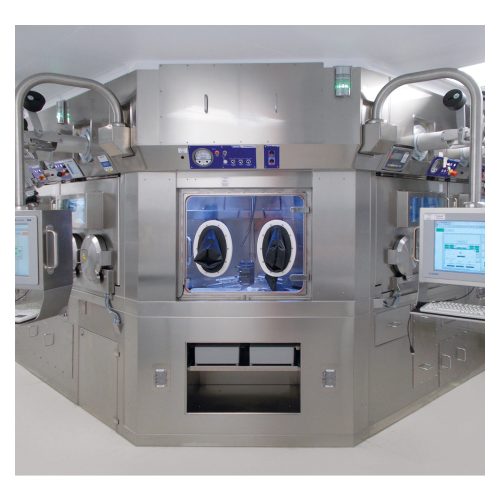
Automated ioflupane i-123 injection dispensing solution
Ensure precision and efficiency in radiopharmaceutical production...
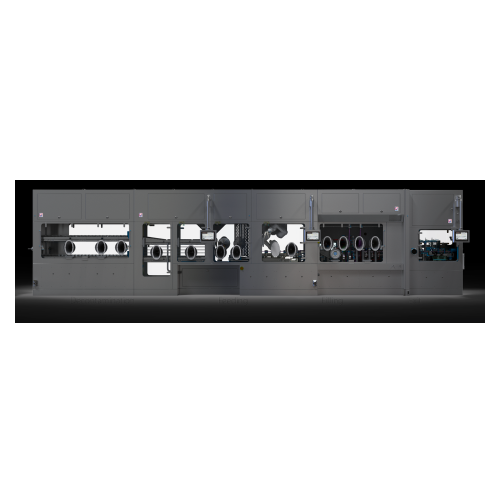
Automatic aseptic filling line for Iv bags
Ensure aseptic integrity and high-speed processing of IV bags with a filling li...
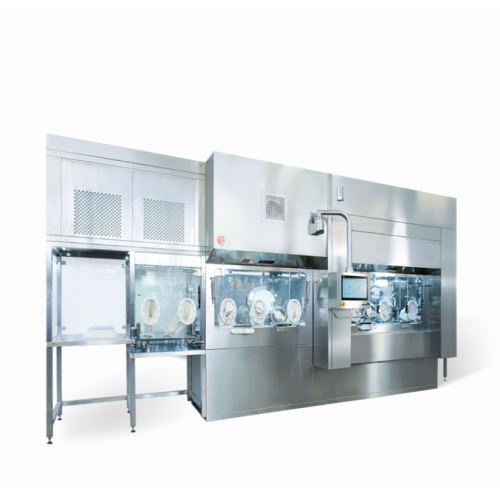
Compact aseptic vial filling system
Optimize your aseptic liquid filling with a compact system designed for seamless integr...
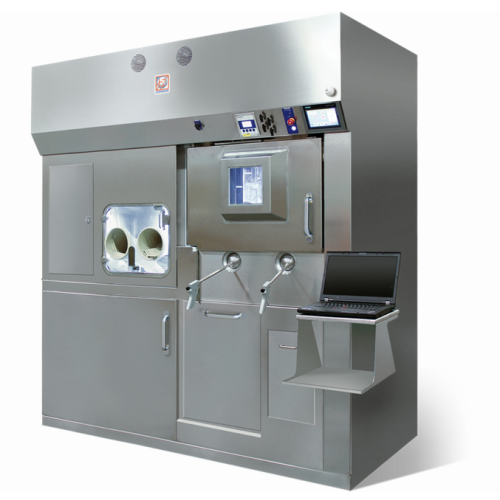
Synthesis and dispensing hot cell for radiopharmaceuticals
Ensure precise synthesis and dispensing of radiopharmaceutica...
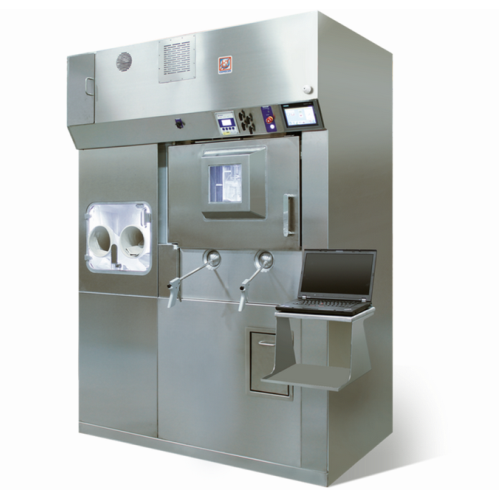
Shielded isolators for radiopharmaceutical dispensing
Ensure precise radiopharmaceutical dose preparation with complete o...

Rotary filling system for Rtu vials in pharma production
Optimize your sterile liquid and powder handling with a versatil...

Closed vial dispensing system for radiopharmaceutical production
Ensure precise radiotracer dosages and maintain sterili...
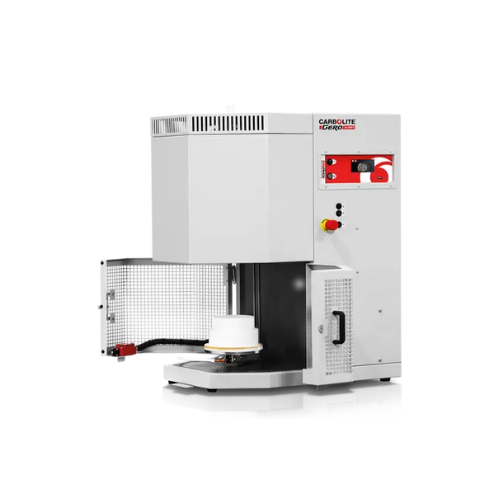
High temperature bottom loading furnace for sintering zirconia
Achieve precise sintering of zirconia dental crowns with ...
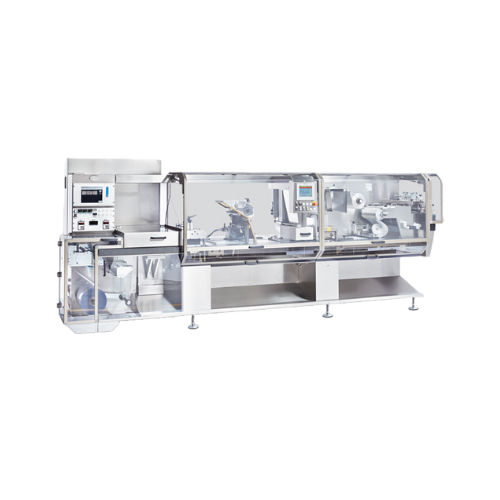
High speed blister packaging for pharmaceuticals
Need efficient packaging with quick format changeovers for various capsul...
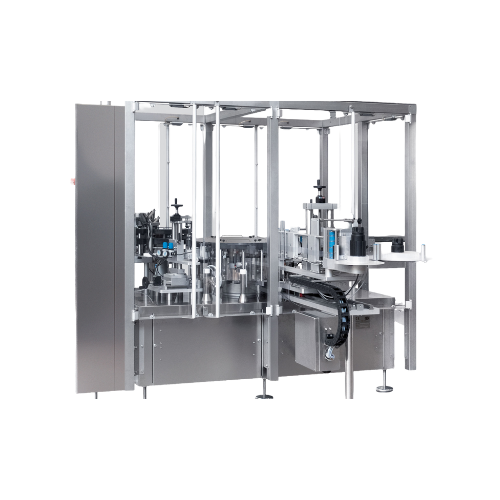
High-speed labelling solution for syringes and vials
Optimize your pharmaceutical packaging process with a cutting-edge l...
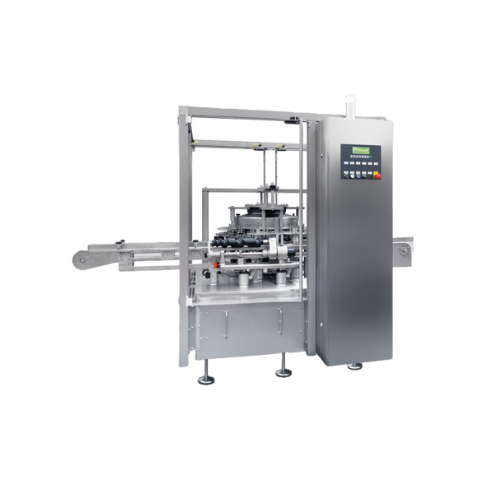
Rotary continuous motion bottle cleaning solution
Ensure pristine product integrity by effectively eliminating particles ...
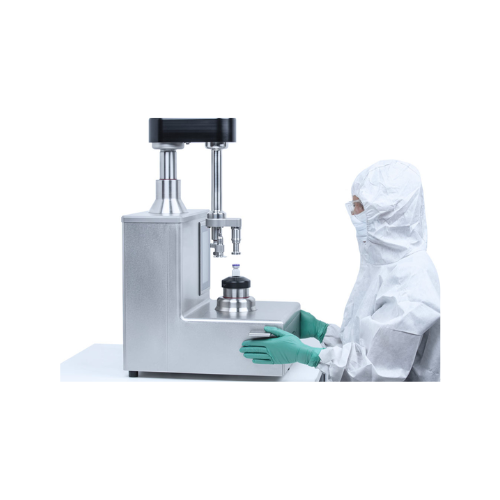
Vial and cartridge crimping solution
Streamline your packaging process with a compact solution for precise crimping and cap...
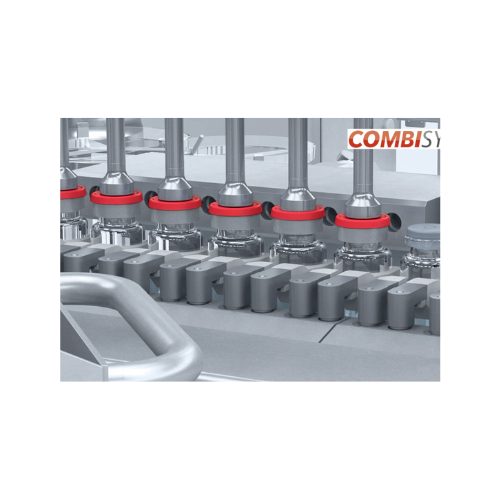
Automated vial closing system
Ensure reliable vial sealing with unparalleled flexibility and precision, optimizing your liqu...
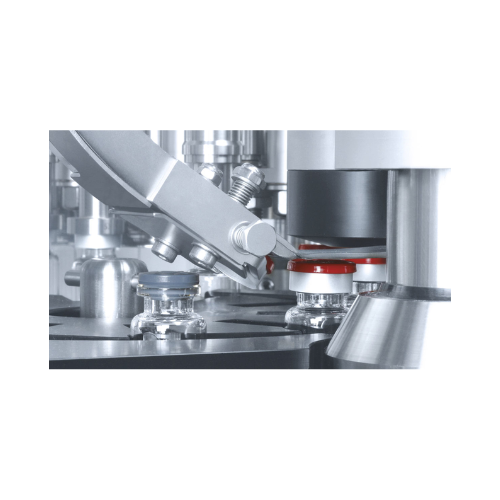
Pharmaceutical container closing solution
Ensure precise capping and inspection of pharmaceutical containers, reducing con...
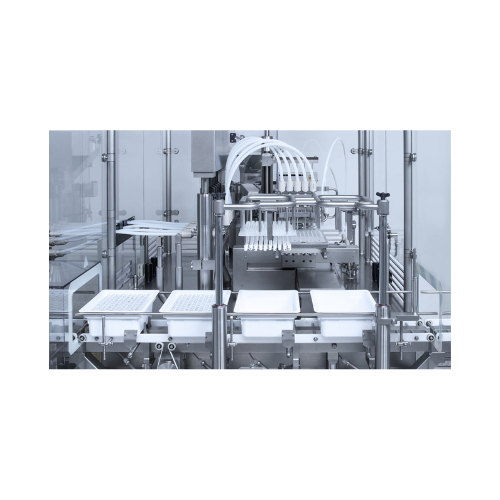
Filling and closing solution for nested containers
Streamline your vial, cartridge, and syringe production with precise d...
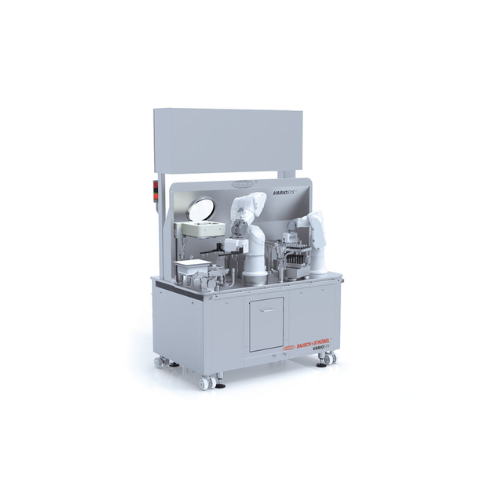
Automatic tub opening and denesting module
Optimize sterile vial processing by efficiently opening and denesting tubs for ...
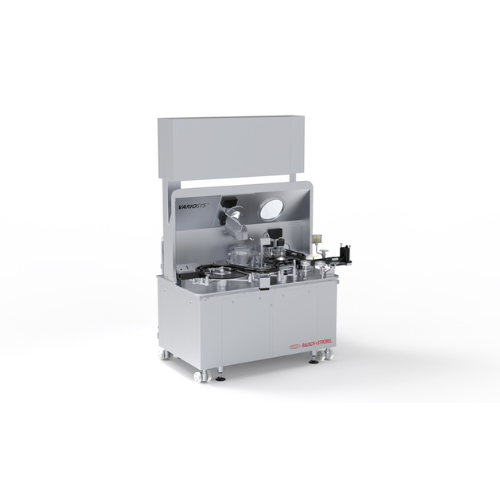
Sealing system for bottles and vials
Ensure precise sealing and capping of liquid pharmaceuticals with minimal particle emi...
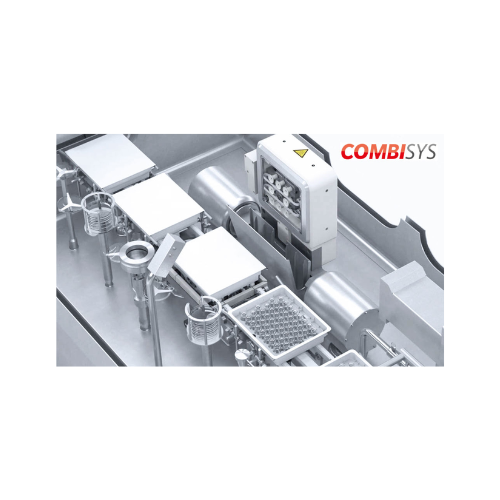
Automatic tub de-bagging and de-nesting solution
Efficiently prepare your RTU containers by seamlessly integrating de-bagg...
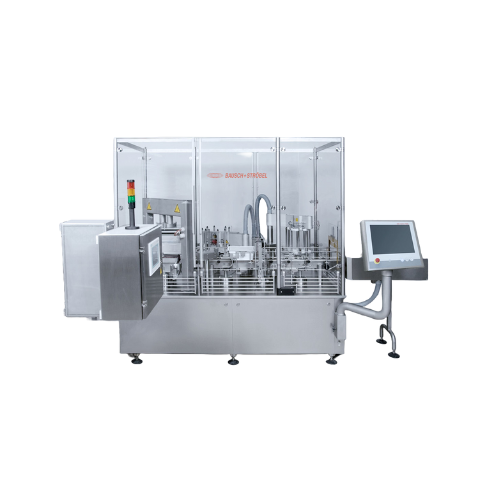
Tub sealing solution for pharmaceutical packaging
Achieve precision sealing for nested pharmaceutical containers with an ...

Tray loader for pharmaceutical containers
Maximize efficiency in aseptic fill-finish lines with precise and rapid tray loa...
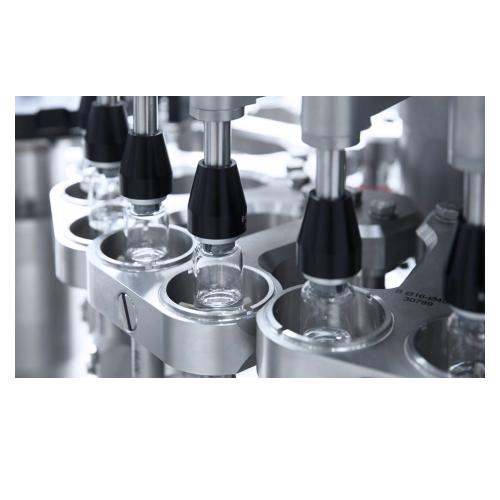
Container exterior cleaning for pharmaceutical applications
Achieve consistent cleanliness and dryness for your containe...
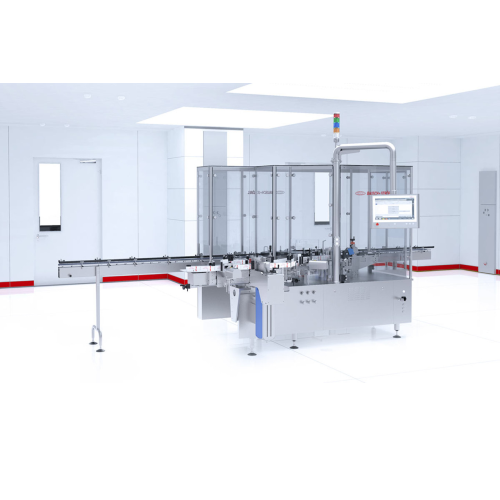
Labeling solution for bottles and vials
Optimize your packaging line with this advanced labeling solution, designed to ensu...
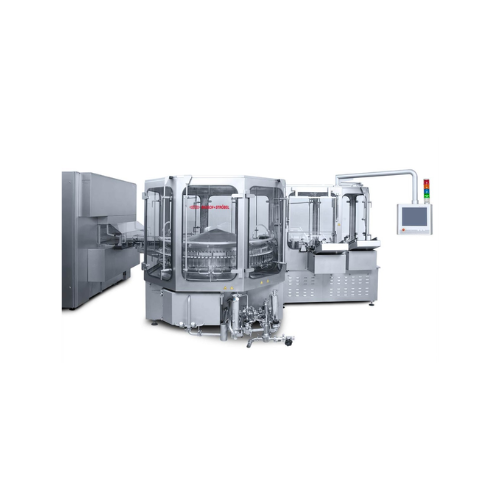
Compact cleaning system for glass and plastic containers
Ensure exceptionally thorough cleaning and gentle handling of di...
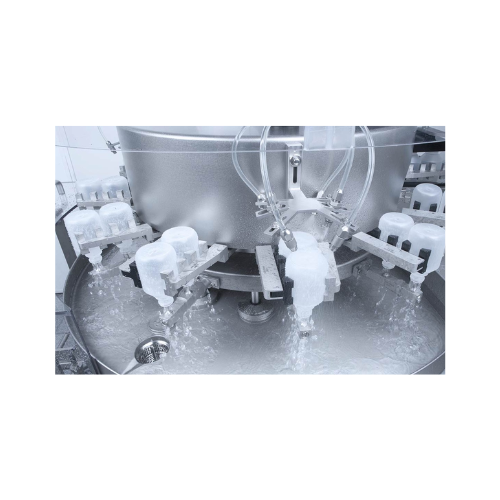
Vial and bottle cleaning system for pharmaceutical use
Ensure pharmaceutical-grade cleanliness for your vials, ampoules, ...
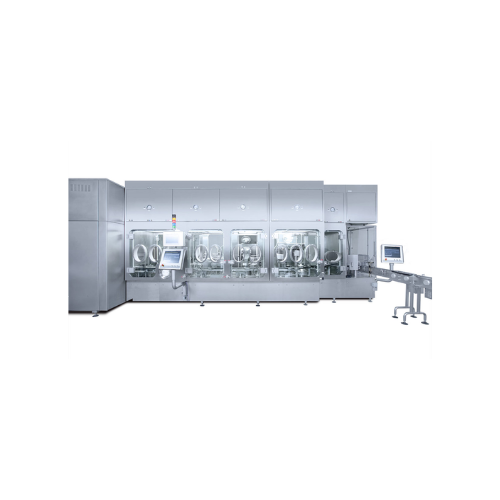
Filling and closing solution for vials and stable bottles
Optimize vial and bottle processing with a seamless solution d...
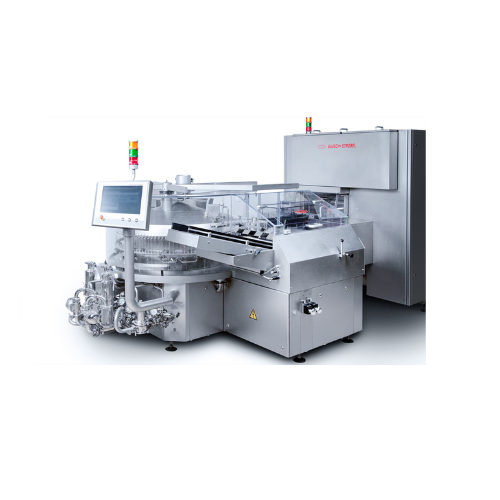
Wet cleaning system for pharmaceutical cartridges
For optimal sterile product outcomes, this system ensures precise and e...
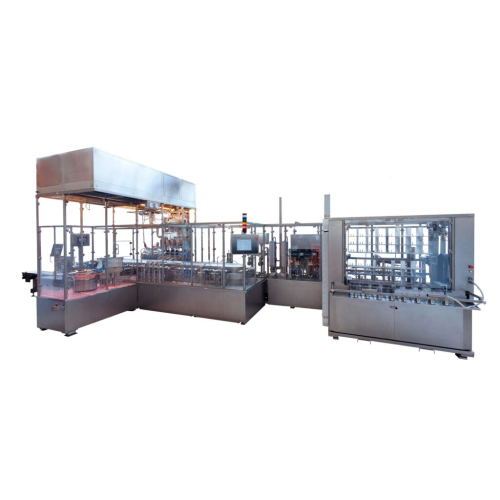
Aseptic filling and closing for flexible Iv bags
Streamline your production line with high-speed aseptic filling and seali...
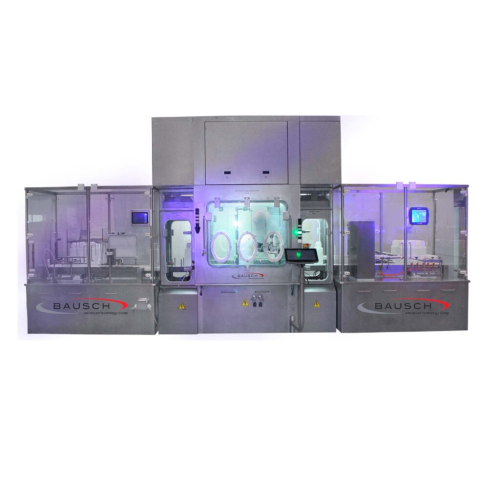
Automated filling and closing system for vials and bottles
Optimize your vial and bottle filling line with precise liqui...
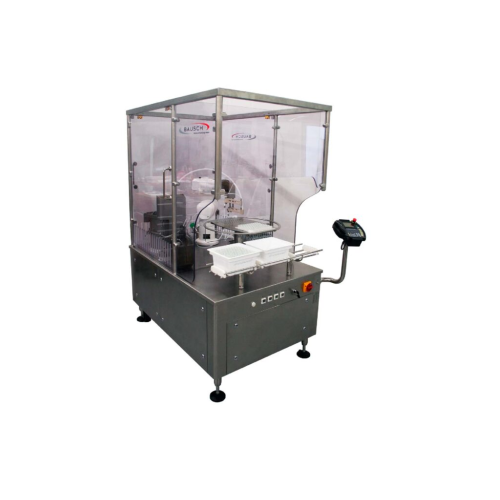
Nested vial and syringe filling and closing system
Achieve precise aseptic filling and closing for clinical products with...
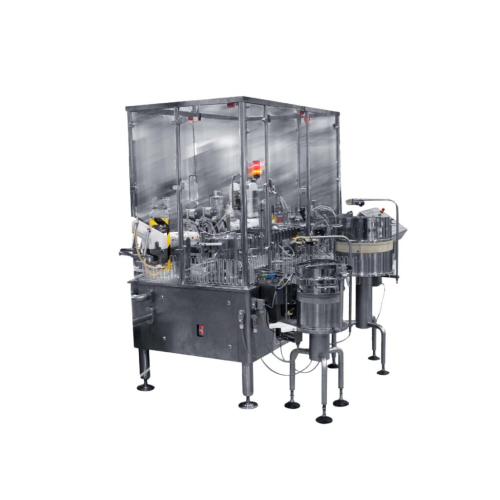
Filling and closing system for vials, syringes, and cartridges
Optimize your aseptic fill-finish operations with a versa...
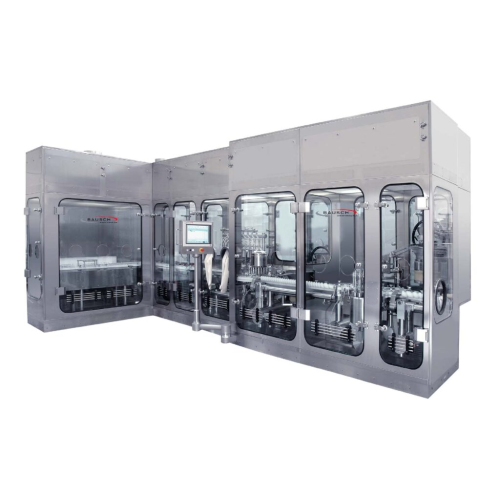
Vial and cartridge filling and closing system
Optimize your aseptic fill-finish process with high-speed, continuous operat...
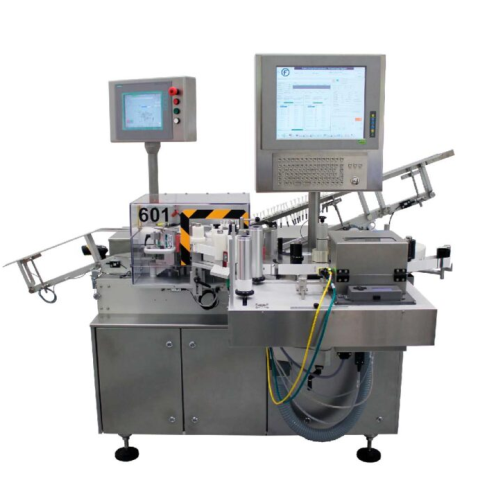
Automatic labeling system for pharmaceutical containers
Streamline your pharmaceutical packaging with precision labeling,...

Automatic vial labeling system
Achieve precise labeling at high speeds with a system designed for seamless integration into ...
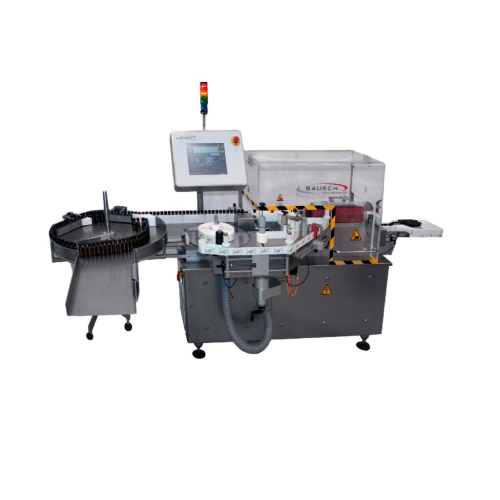
Fully automatic linear labeling system for bottles
Optimize your bottle labeling process with precision and speed, ensuri...
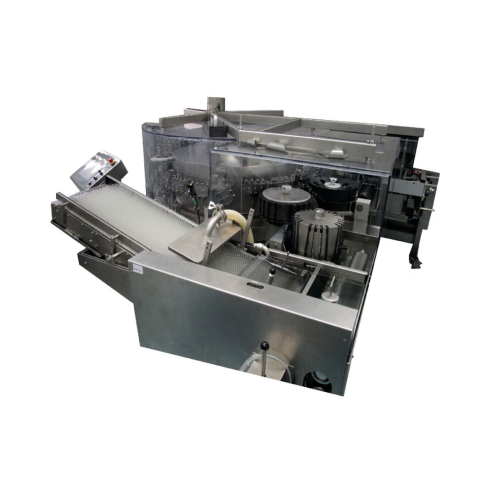
Rotary washing system for pharmaceutical containers
Achieve superior cleanliness and efficiency with a high-speed rotary ...
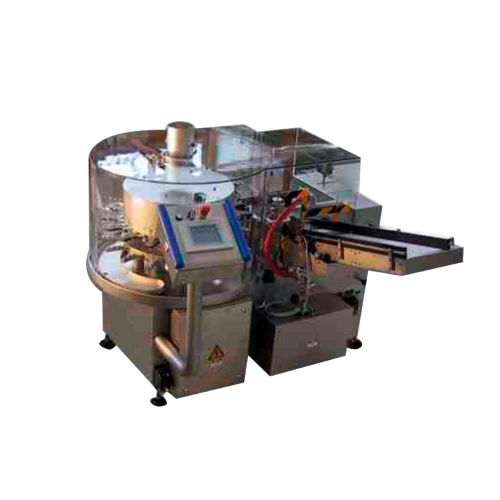
Automated washing system for vials, syringes, cartridges, and ampoules
Achieve sterile conditions with this high-speed ...

Semi-automatic washer for pharmaceutical containers
Achieve precise cleaning for pharmaceutical containers with a semi-au...
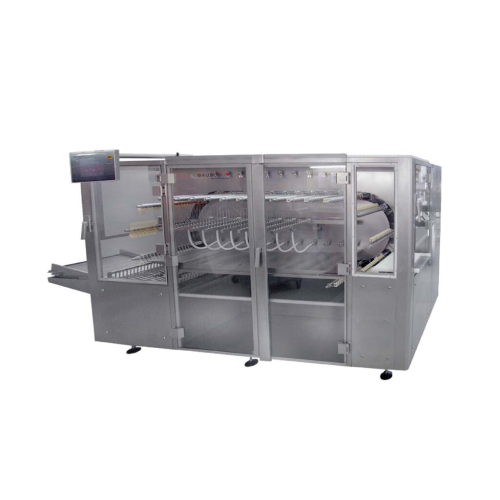
High-speed washing system for ampoules and vials
Ensure contamination-free ampoules and syringes with this advanced washin...
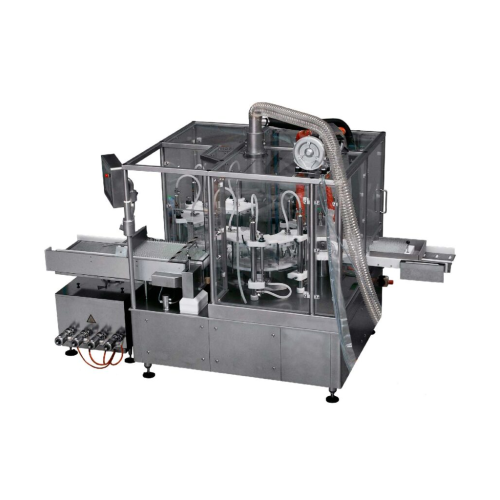
Automatic external washing system for ampoules and vials
Ensure optimal cleanliness of liquid medication containers with ...
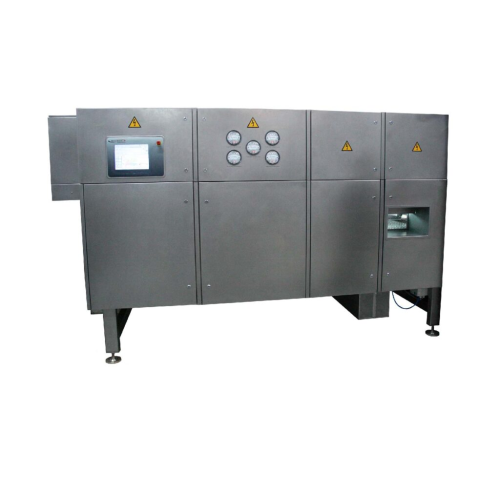
Hot air sterilization for glass containers
Ensure precise and uniform sterilization of glass ampoules, vials, and syringes...
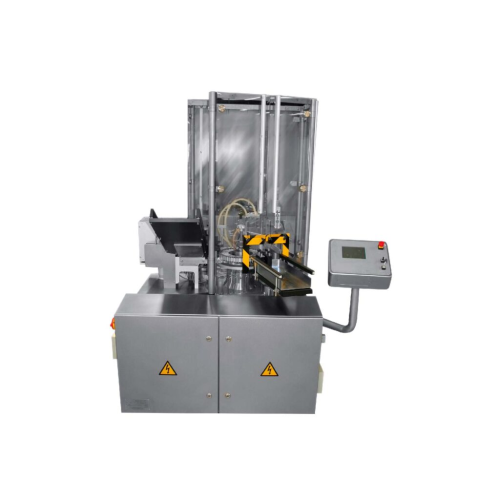
Filling and closing system for ampoules
Ensure precision and efficiency in your aseptic fill-finish operations with a compa...
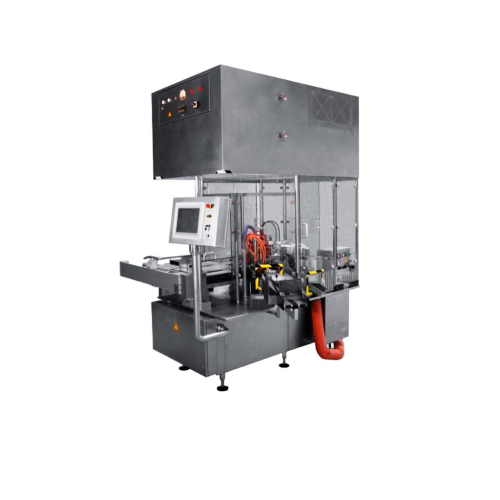
Ampoule filling and closing system
Optimize your production line with a high-speed system designed for seamless filling and...
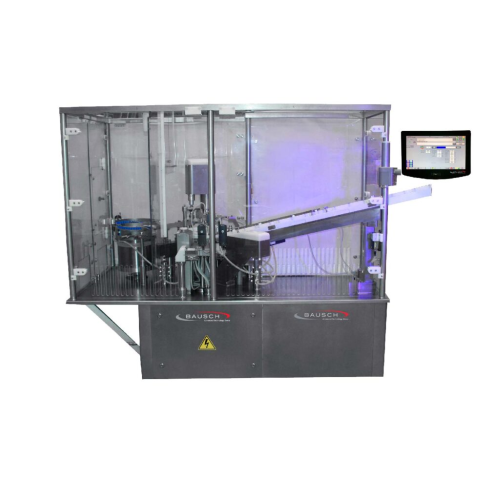
Filling and closing solution for vials and syringes
Achieve precise aseptic fill-finish of liquid formulations in vials a...
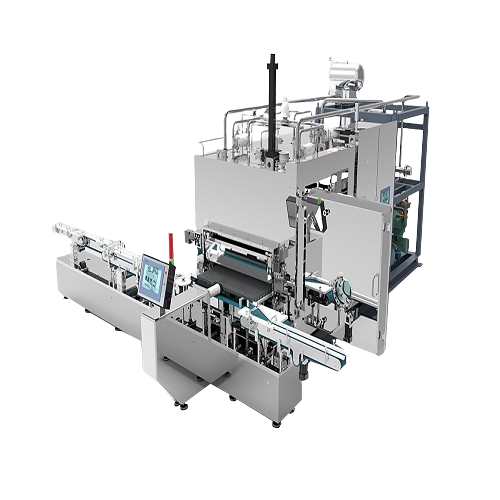
Commercial freeze dryer for pharmaceutical Api production
Ensure the stability and potency of your biopharmaceutical pro...

Sterile filling line for liquid and powder
Achieve seamless integration of filling, sterilization, and packaging with this...
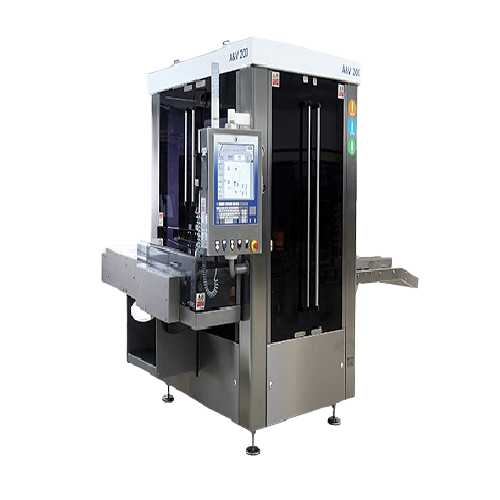
Automatic visual inspection for sterile preparations
Ensure the integrity of sterile products with precise visual inspect...
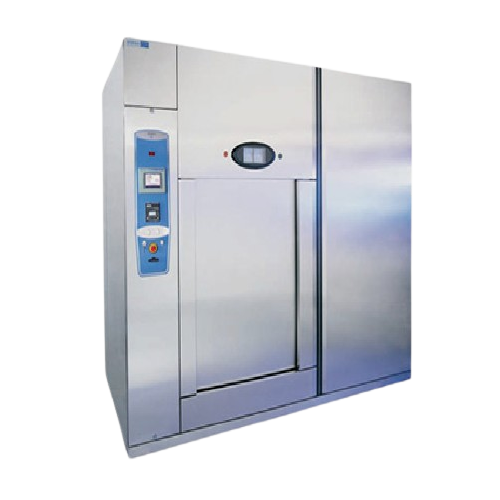
Gmp steam sterilizer for pharmaceutical applications
Ensure consistent sterilization and contamination control across you...
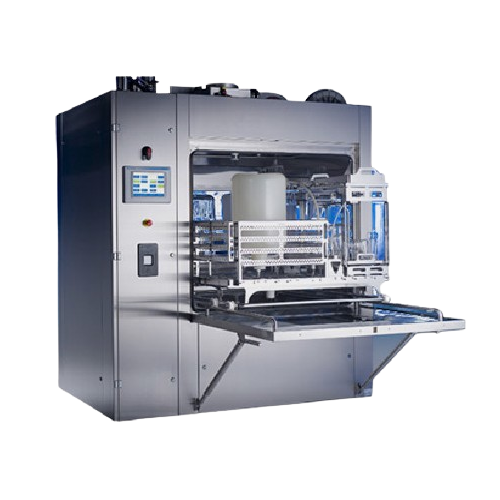
Gmp washer for pharmaceutical contamination control
Ensure verifiable cleaning and drying of critical components in bioph...
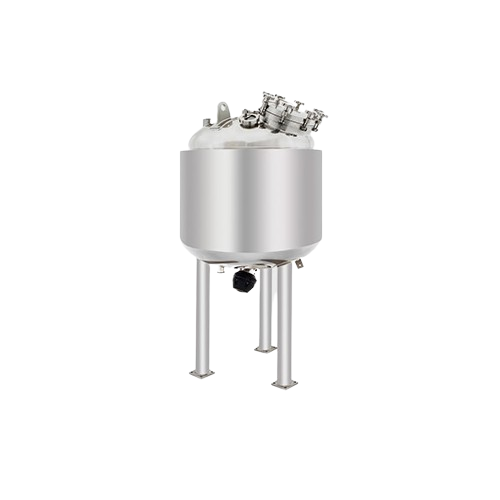
Wfi storage tank for pharmaceutical use
Ensure the integrity and sterility of Water for Injection in your pharmaceutical pr...
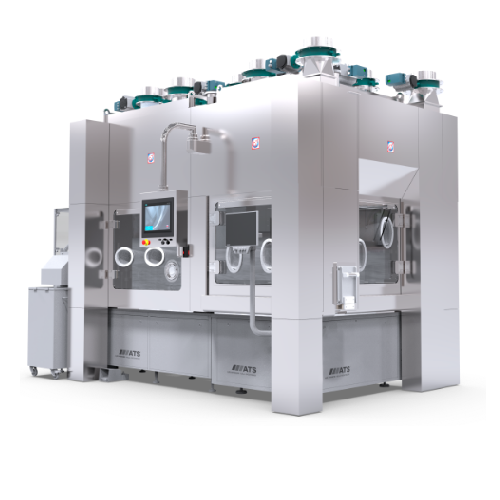
Robotic filler for aseptic pharmaceutical packaging
Effortlessly manage complex aseptic filling tasks with a system desig...
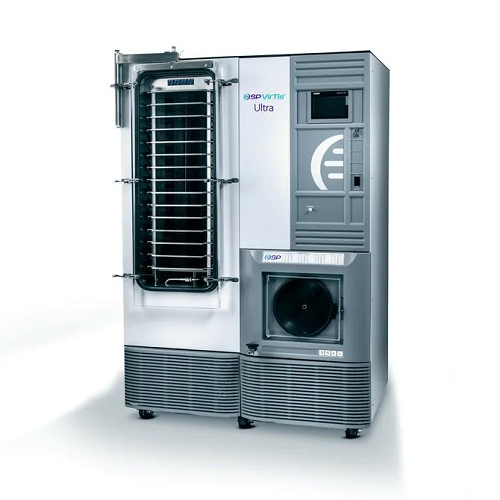
Pilot-production freeze dryers for diagnostic kits and tissue banking
Optimize your freeze-drying process with compact,...
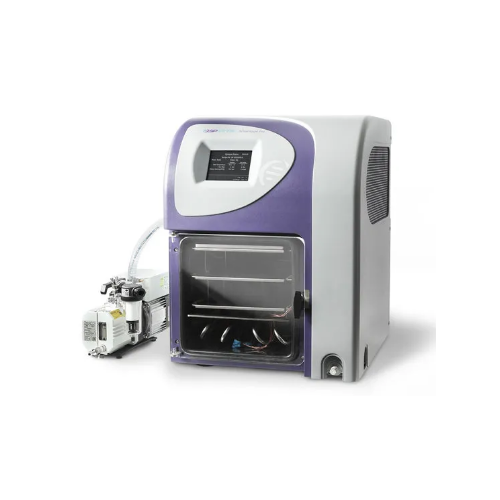
Benchtop freeze dryer for laboratory and small production use
Optimize your lab’s efficiency by adding precise, space-sa...
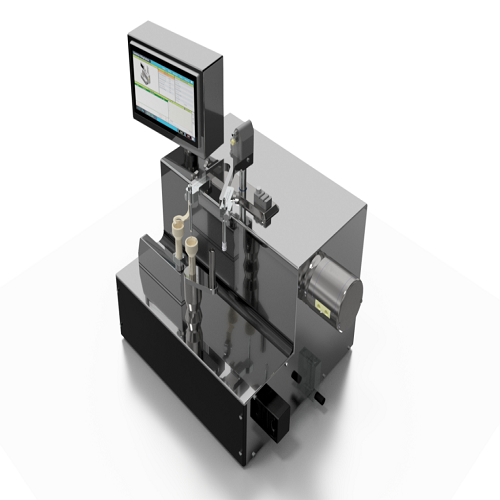
Tabletop vial and syringe filling system
Ensure precise dosing and maintain sterility in small batch production with a comp...
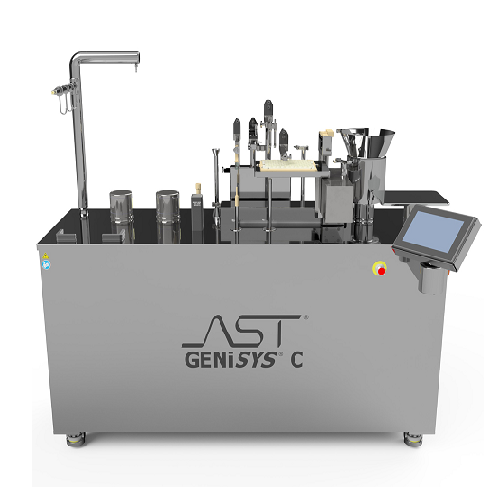
Automated aseptic filling and closing system for vials and syringes
Optimize small-batch production with precision fill...
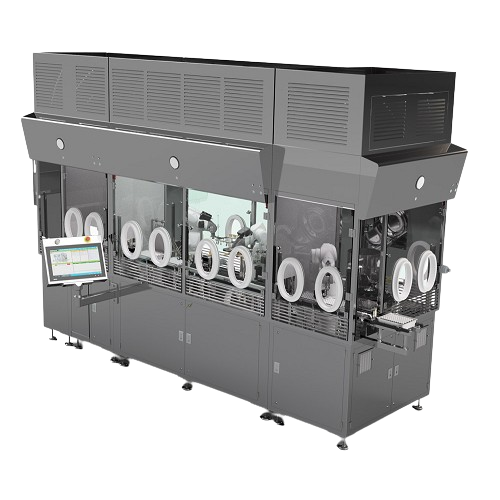
Aseptic small batch filling and closing system
Optimize your small-batch aseptic processing with this versatile system, de...
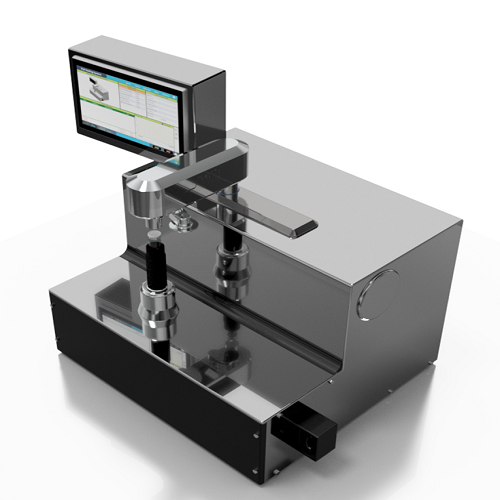
Bench-top vial sealing system for pharmaceutical use
Ensure precise sealing of pharmaceutical vials with a system designe...

Pilot lyophilizers for pharmaceutical development
For precision freeze-drying in clinical trial production, these pilot l...
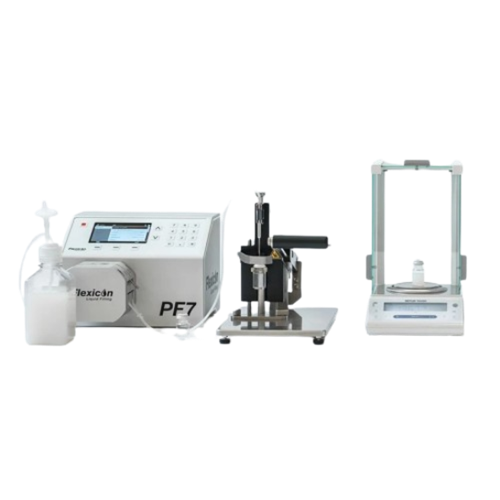
Aseptic filling station for small batch processes
Streamline small batch manufacturing with a tabletop filling station th...
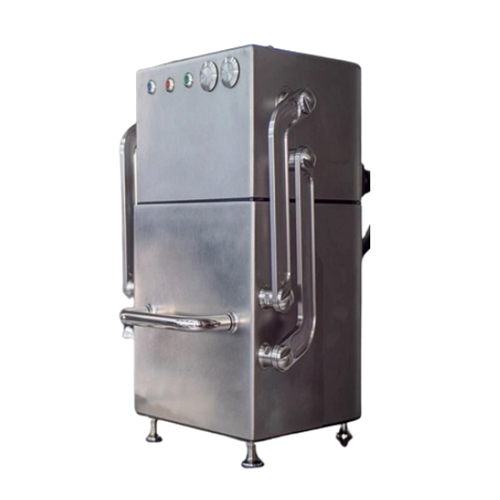
Aseptic filling isolator for small cgmp batches
Guarantee aseptic integrity for small-scale batches with this isolator, of...
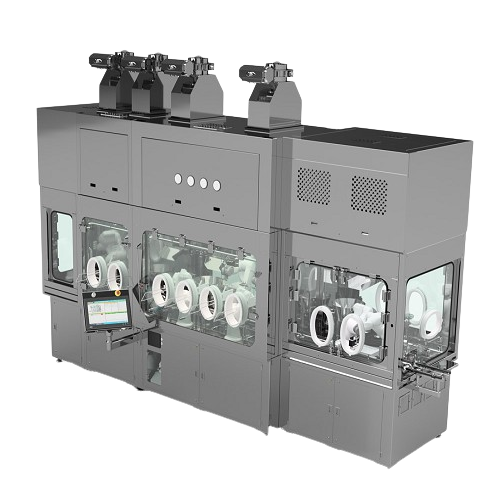
Aseptic small / medium batch filling and closing system
Ensure sterility in drug production by seamlessly integrating a v...
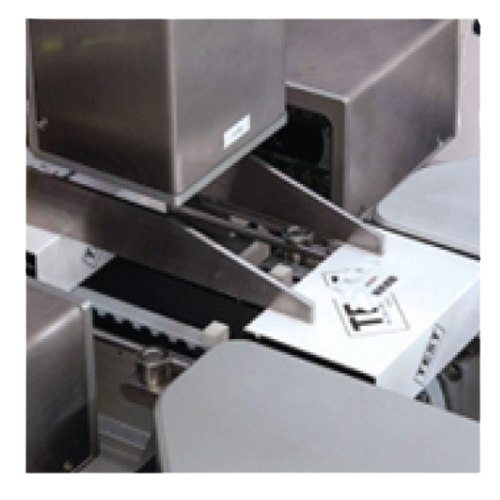
Serialization and inspection kit for packaging machines
Effortlessly enhance packaging integrity and compliance with high...
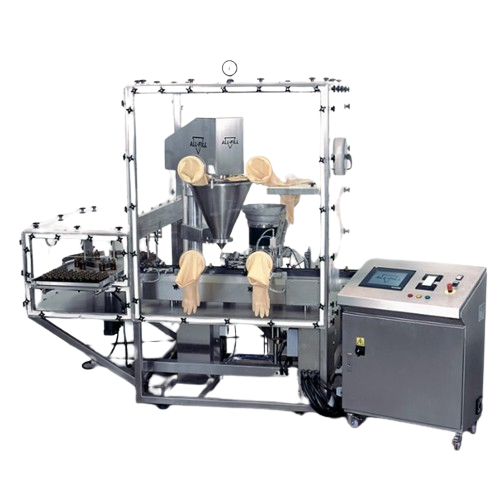
Special purpose auger filling systems for diverse industries
For manufacturers handling precise dosing, our advanced aug...
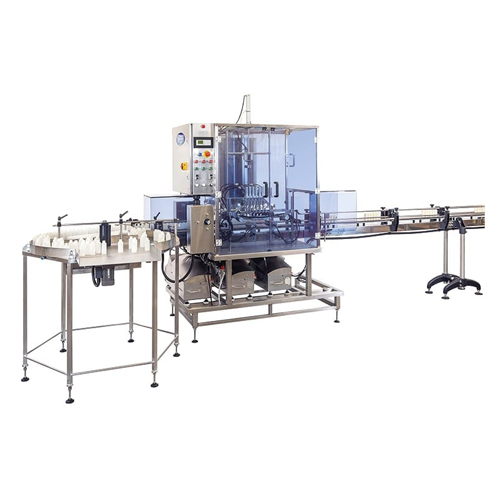
Automated bottle and jar filling solution
Streamline your production and minimize waste with a versatile filling solution,...
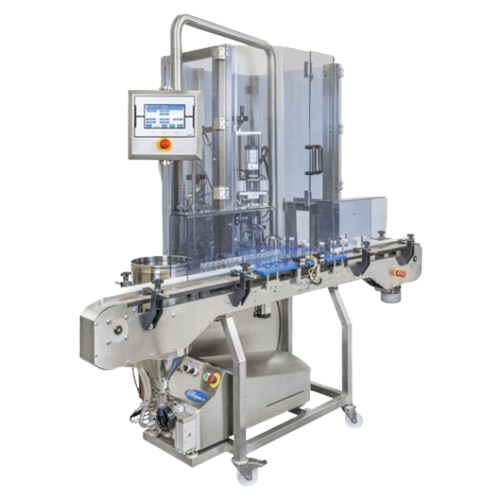
Filler and capper for bottles and jars
Optimize your production with a compact filling and capping solution that delivers f...
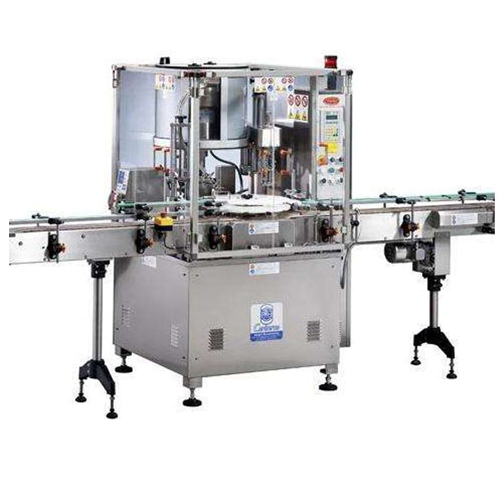
Compact filler and closer for vial processing
Efficiently streamline your vial filling and closing processes with a compac...
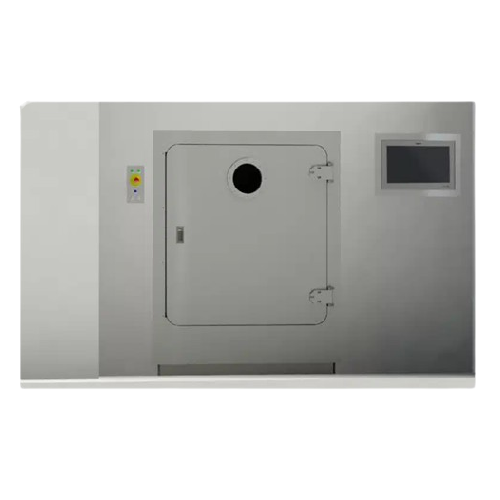
Vhp biodecontamination passbox for laboratory equipment
Ensure effective decontamination for heat-sensitive and non-autoc...
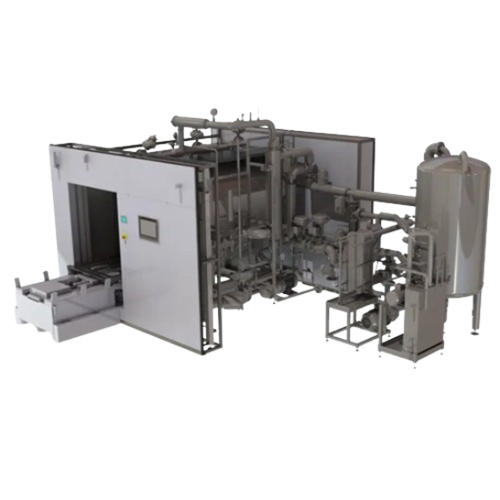
Superheated water sterilization autoclave for pharmaceutical applications
Ensure precise sterilization of sensitive li...
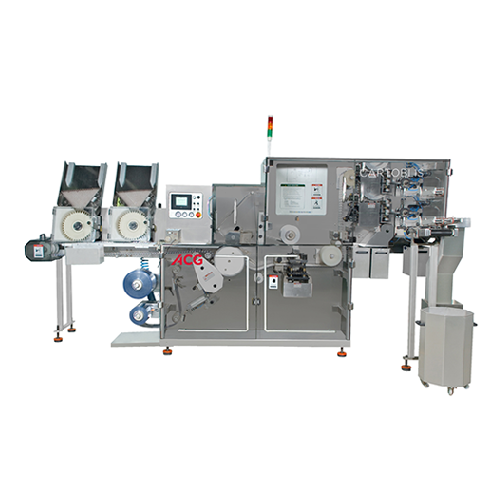
Blister packaging for solid dosage forms
Optimize your packaging line with high-speed, continuous blister packaging that en...
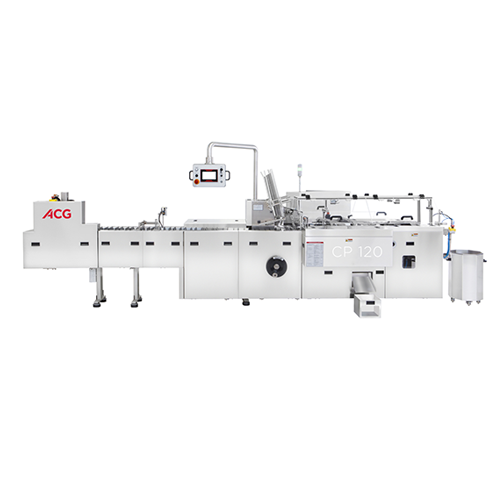
Continuous motion horizontal cartoner for blister packs
Effortlessly streamline your cartoning process with a continuous ...
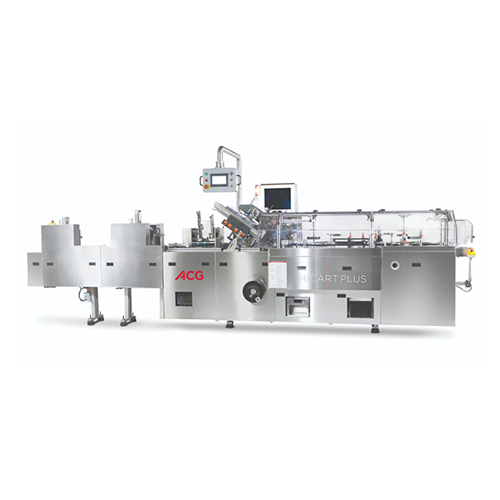
Continuous cartoning solution
Enhance your production line with efficient high-speed cartoning, designed to streamline packa...
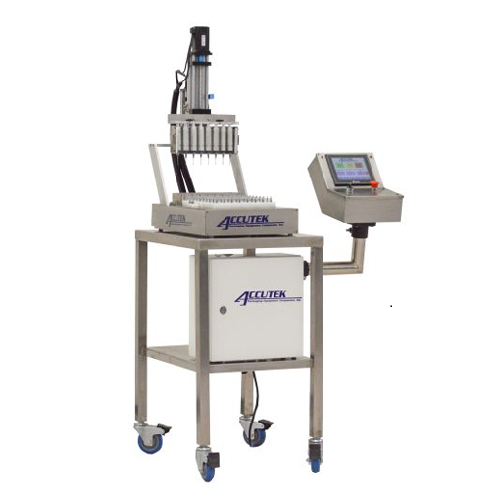
High precision automatic mini dose filler
Achieve unparalleled precision when filling small volumes, from 0.1 ML to 200 ML...
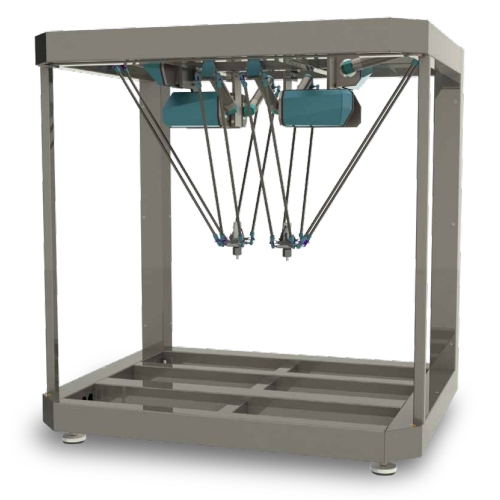
Direct drive delta robots for precision handling
Enhance operational speed and precision with innovative direct drive delt...
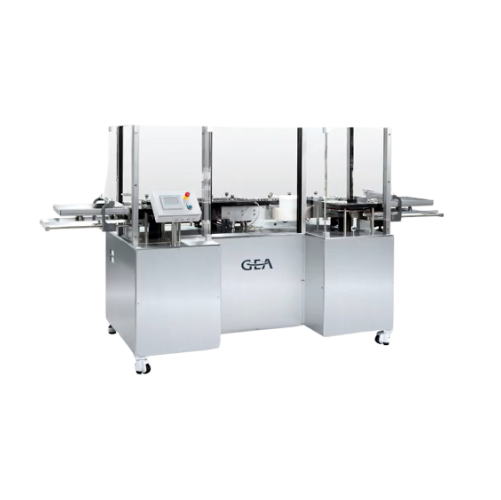
Automatic loading and unloading system for pharma freeze dryers
Enhance the efficiency and safety of your freeze-drying ...
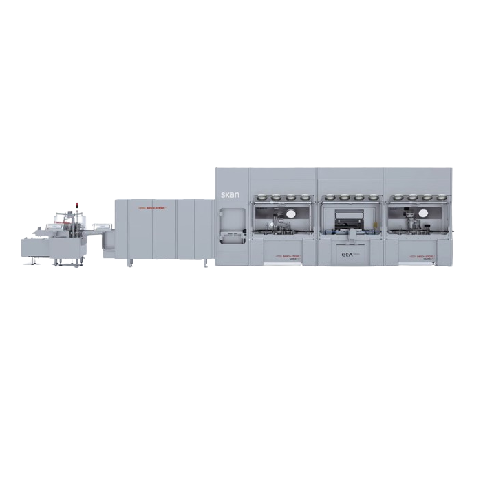
Freeze dryer for small-scale production
Optimize your production line with reliable lyophilization that ensures precise moi...
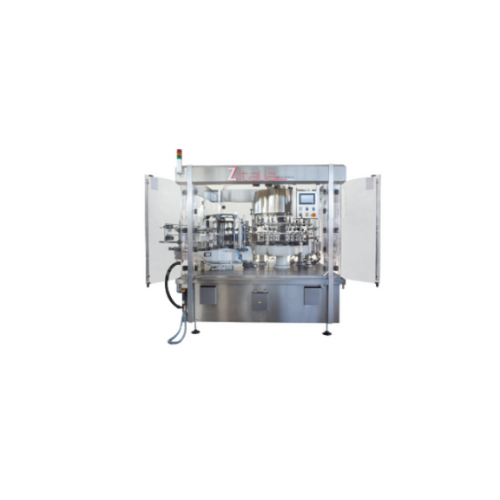
Stand-alone autoclaves with round chamber for laboratory and pharmaceutical use
Achieve seamless sterilization and pre...
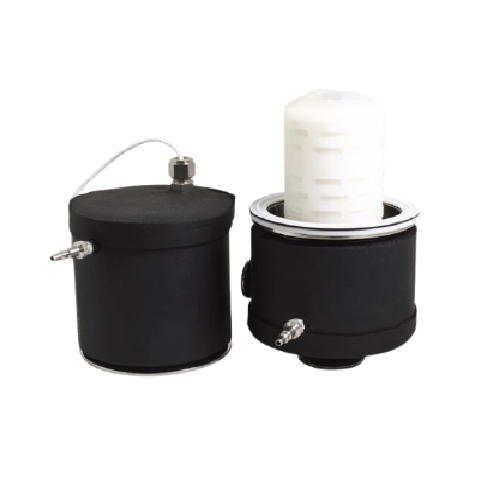
Large production autoclaves for laboratory and pharmaceutical use
Enhance your production line with our large autoclave...
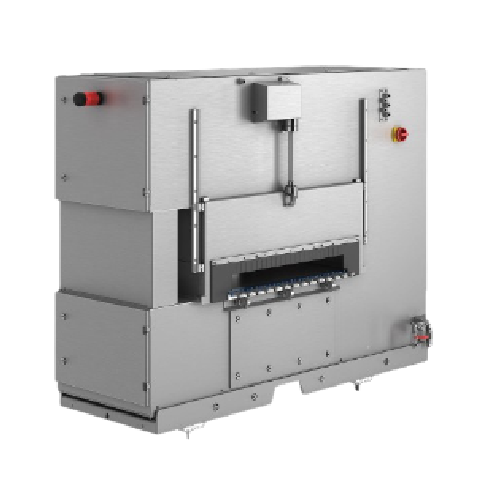
X-ray scanner for sealed container inspection
Ensure the integrity and quality of sealed containers while seamlessly integ...
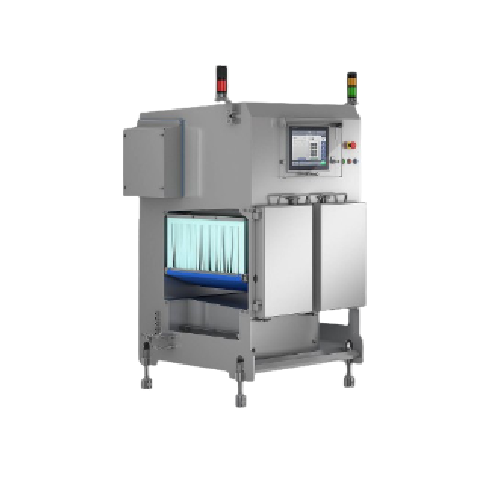
X-ray inspection system for wet environments
Ensure unparalleled product inspection under extreme cleaning conditions with...
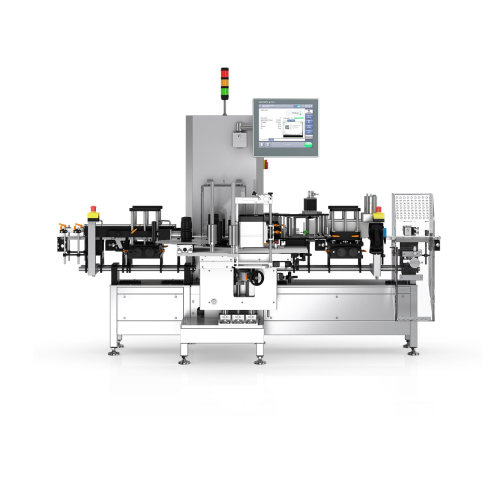
Serialisation system for medicine bottles
Optimize your packaging line with high-speed serialisation and labeling designed...
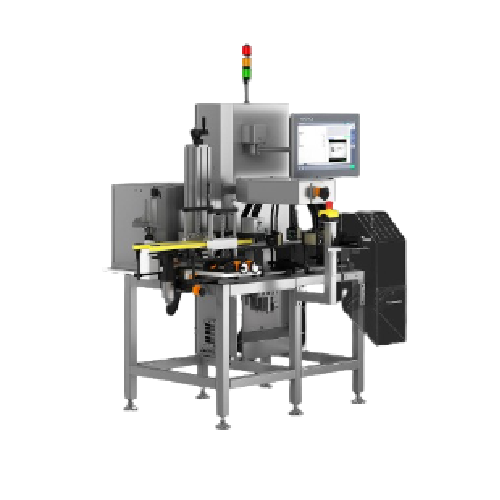
Bottle and vial inspection and coding system
Ensure seamless coding and inspection of vials and bottles with rapid 360° ev...
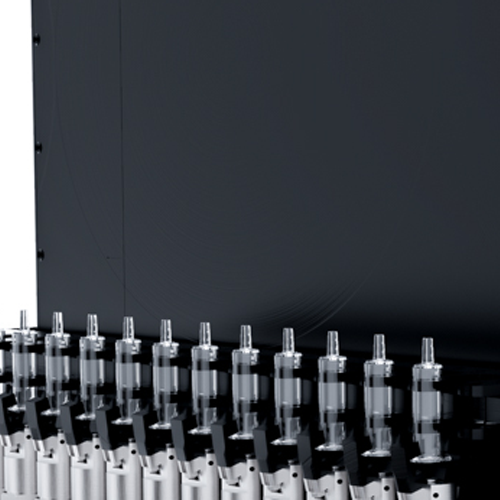
X-ray inspection module for pre-filled syringe needles
Ensure sterility and product integrity in high-speed syringe produ...
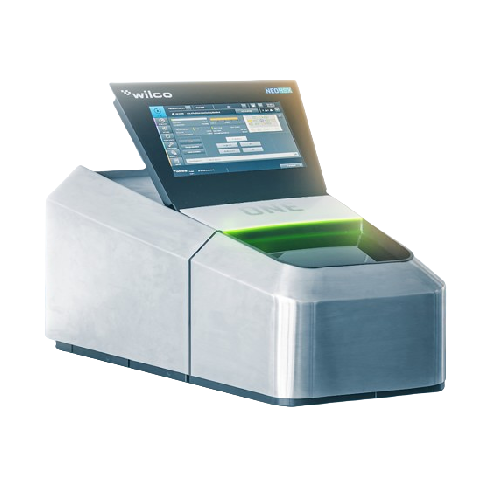
Lab headspace analyzer for small volume parenterals
Enhance your quality control with precise gas concentration measureme...
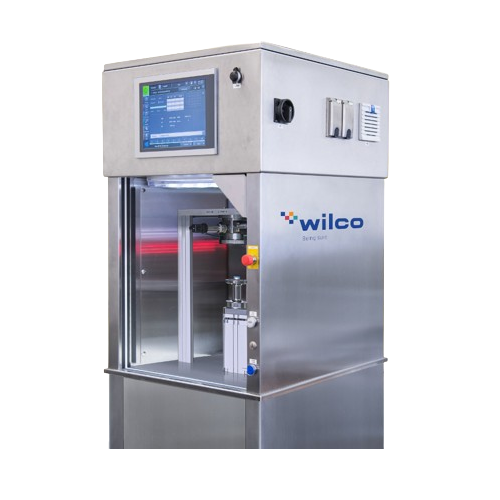
Headspace gas analyzer for large volume parenterals
Ensure the sterility and quality of injectable pharmaceuticals with p...
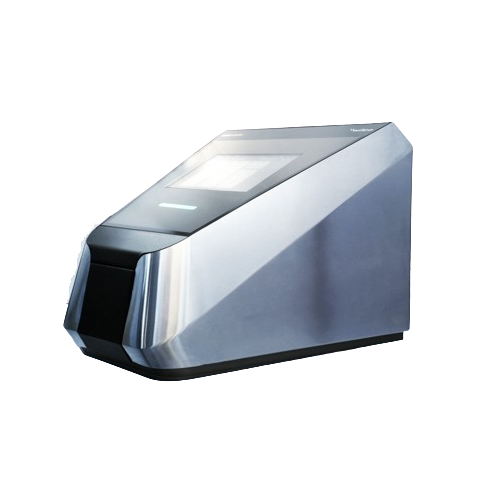
Headspace analyzer for small volume parenterals
Ensure precise gas concentration measurements in sterile pharmaceutical pa...
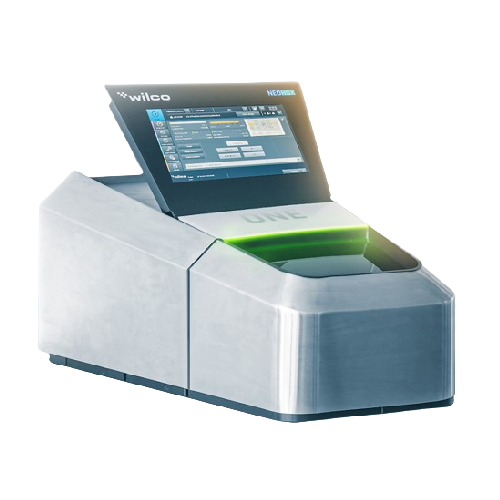
Headspace analyzing system for small volume parenterals
Ensure the integrity of sterile pharmaceuticals with precise head...
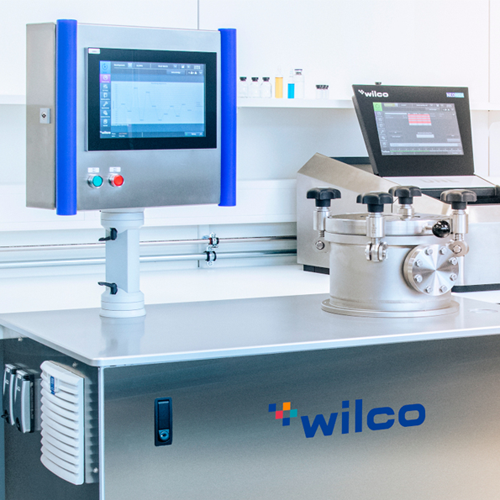
Headspace analyzation for small volume parenterals
Achieve unparalleled precision in gas concentration measurement for sm...
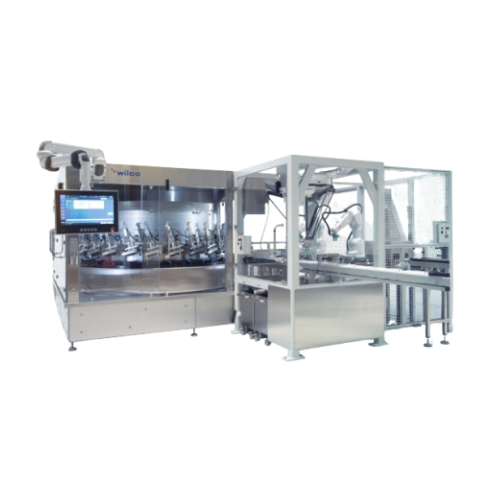
Automated container closure integrity tester
Ensure the integrity of your sterile pharmaceutical containers with high-spee...
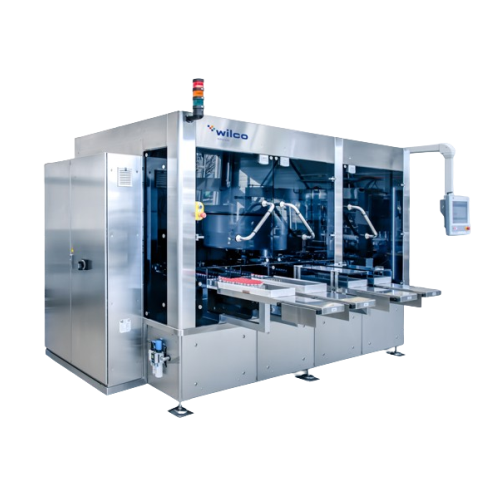
Automated Cci tester for primary packaging containers
Ensure the integrity of pharmaceutical packaging with precise and n...
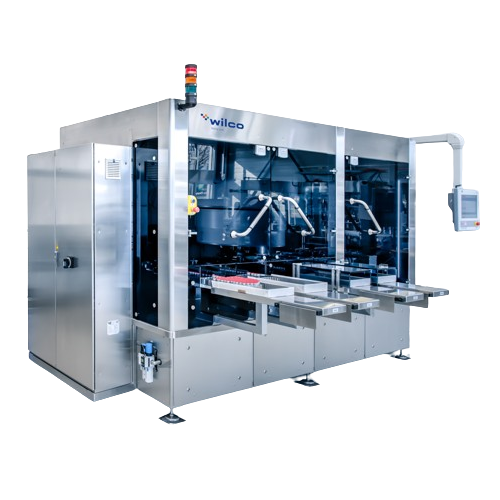
Non-destructive headspace analyzer for pharmaceutical packages
Ensure non-destructive and accurate headspace analysis fo...
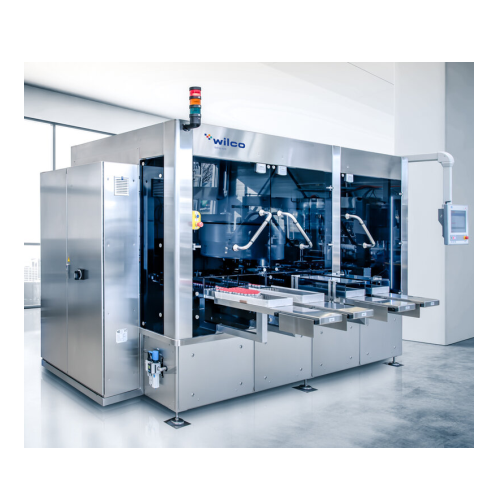
Automated headspace analyzer for small volume parenterals
Optimize container closure integrity with high-speed, non-dest...
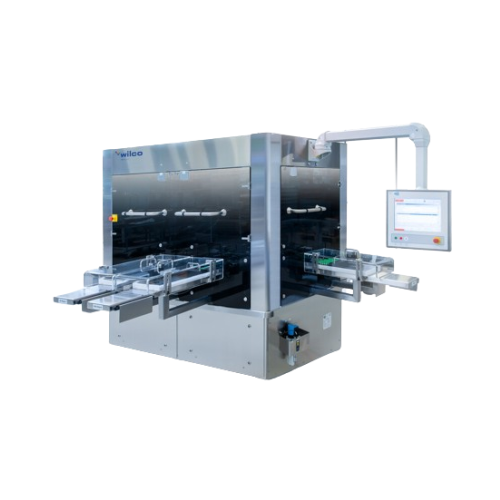
Automated headspace analysis for small volume parenterals
Ensure the integrity and quality of parenteral packaging with ...
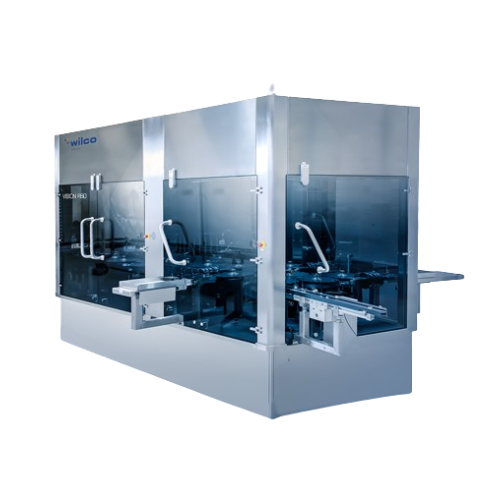
Visual inspection for small volume parenterals
Ensure pristine injectable solutions by detecting cosmetic and particle def...
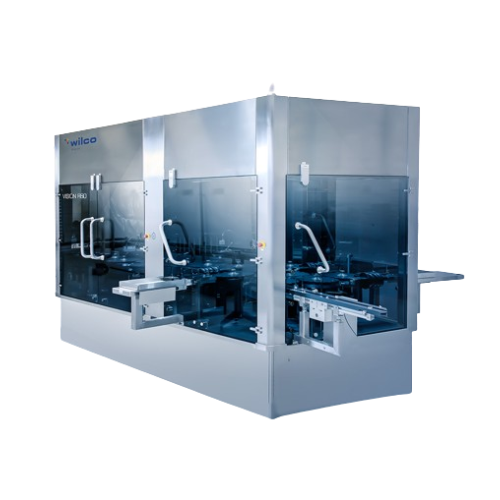
Automated visual inspection for small volume parenterals
Ensure the integrity of high-value parenteral drugs by detecting...
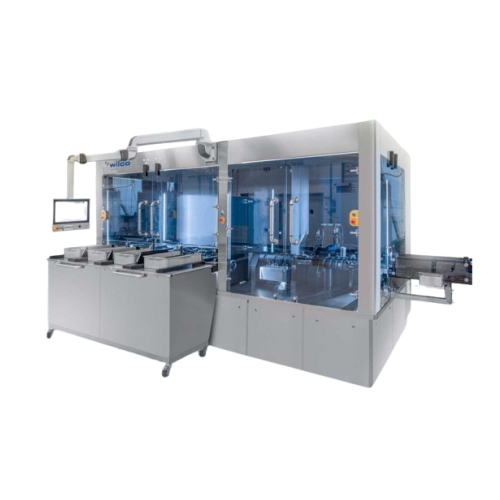
Combined Avi and Cci tester for vials
Ensure comprehensive quality control of parenteral products with an integrated soluti...
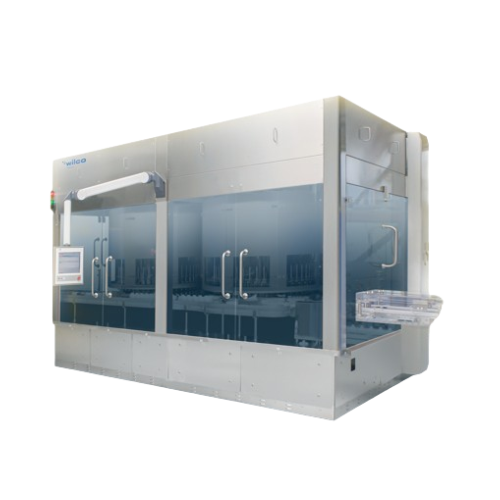
Combined visual and container closure integrity testing for vials
Ensure the integrity and quality of parenteral packag...
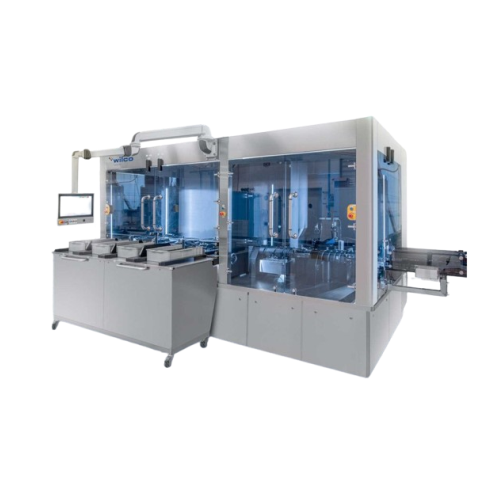
Combined visual and container closure integrity tester for vials
Ensure precise quality control of pharmaceutical packag...
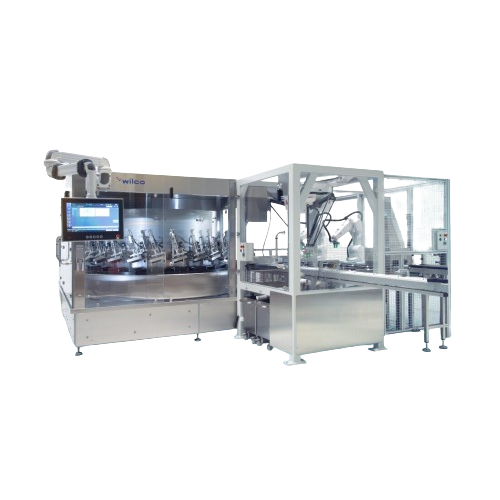
Automated container closure integrity tester for pharmaceutical packaging
Ensure the integrity of your pharmaceutical ...
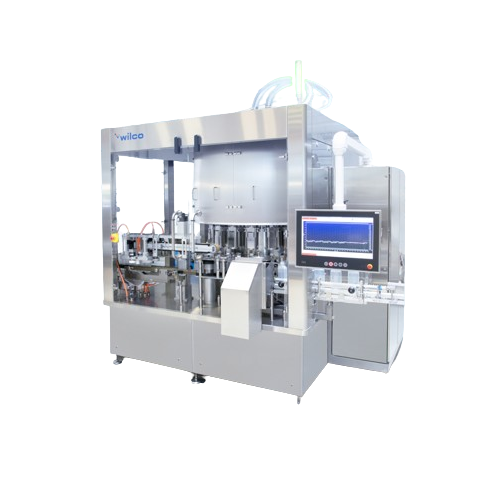
Automated Cci tester for pharmaceutical containers
Ensure the integrity of every pharmaceutical package swiftly with high...
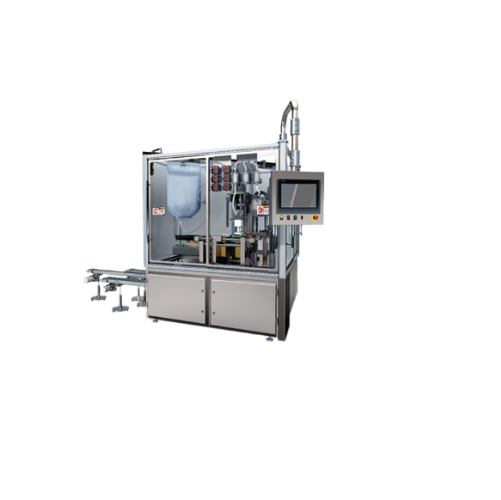
Blow/fill/seal packaging for laboratory and clinical trials
Streamline your small-scale pharmaceutical production with p...
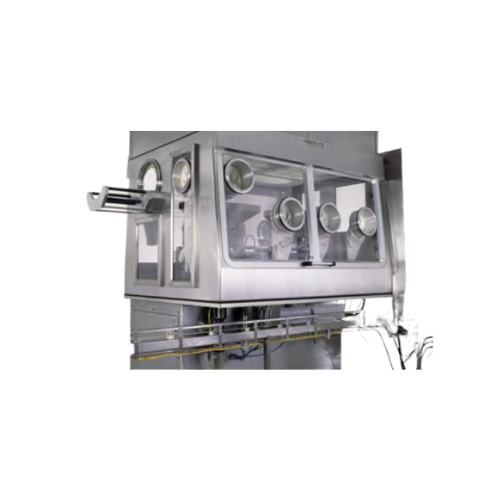
Insertion technology for sterile blow/fill/seal systems
Ensure sterility and precision in liquid pharmaceutical packaging...
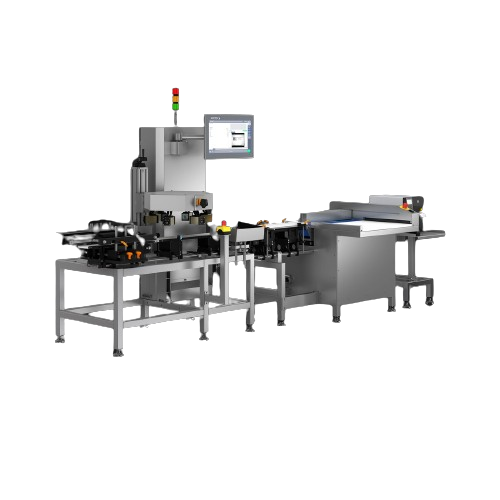
Omnidirectional inspection system for bottles and vials
Ensure precise serialization and aggregation with a 360° inspecti...
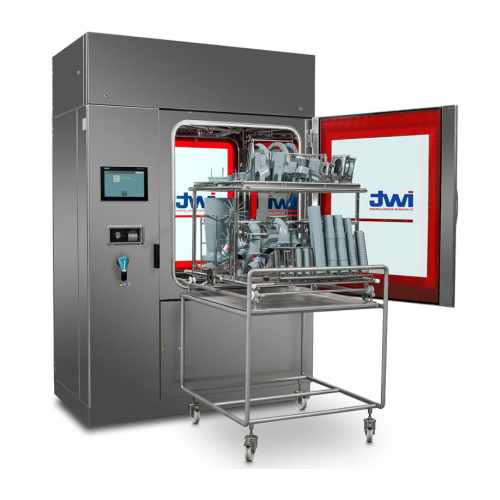
Gmp contact part washers for pharmaceutical industry
Ensure product integrity and hygiene with specialized washing system...
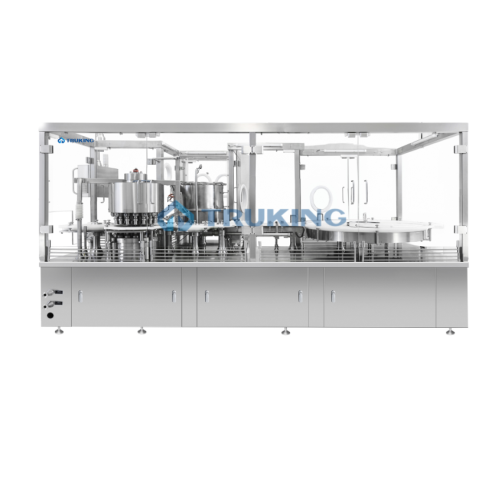
Vial capping machine for pharmaceutical production
Ensure precise and reliable vial sealing in high-throughput pharmaceut...
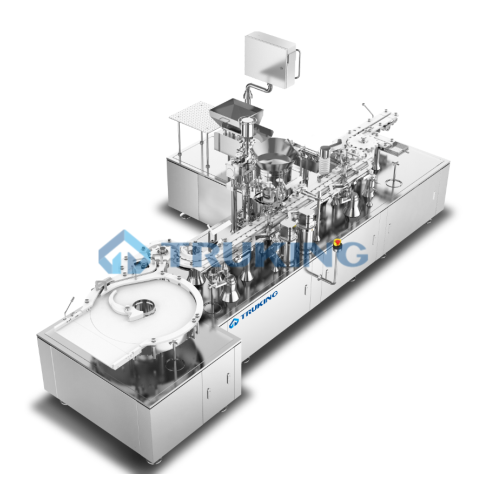
Vial powder dispensing system
Optimize your aseptic fill process with high-precision powder dispensing that minimizes contam...
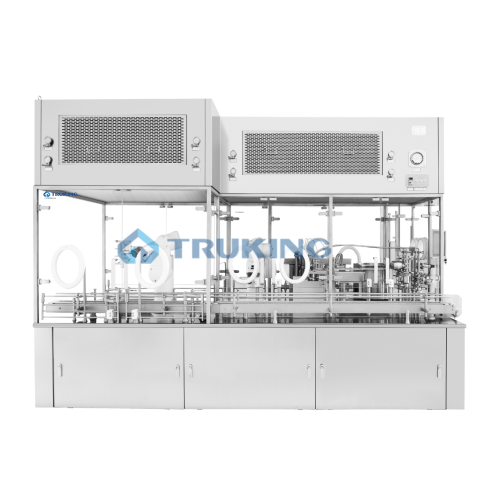
Nested fillers for vials, pre-filled syringes, and cartridges
Optimize your aseptic filling processes with precision dos...

Robotic sterilization logistics system
Ensure seamless aseptic transfers across production stages with this robotic logisti...
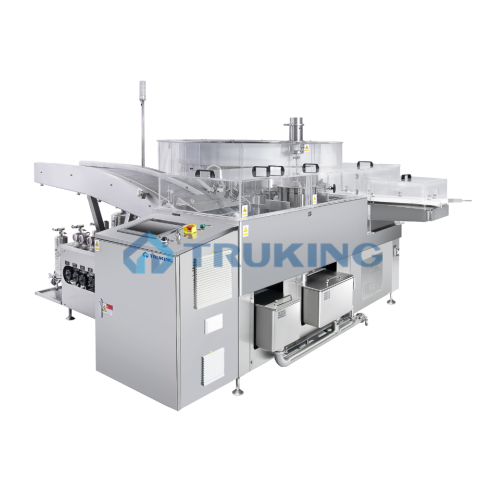
Vertical ultrasonic washing for pharmaceutical containers
Ensure immaculate cleanliness and sterilization of pharmaceuti...
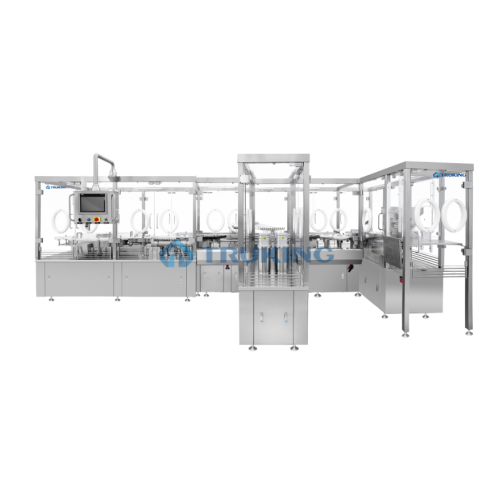
Vial filling and stoppering system for aseptic production
Streamline aseptic production by integrating high-speed vial f...
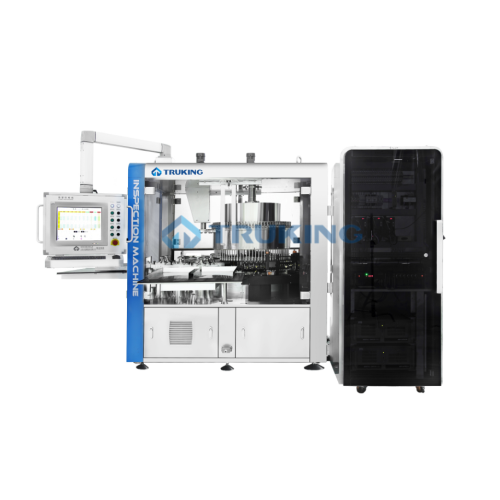
Automatic inspection system for ampoules and vials
Ensure precision in pharmaceutical production with a comprehensive ins...
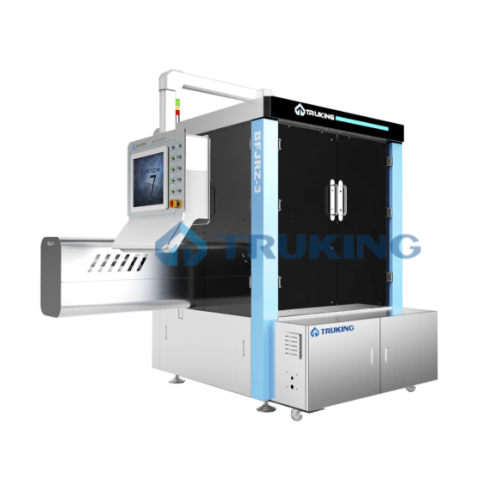
X-ray inspection for pharmaceutical vials
Ensure product purity by detecting contaminants in pharmaceutical vials with adv...
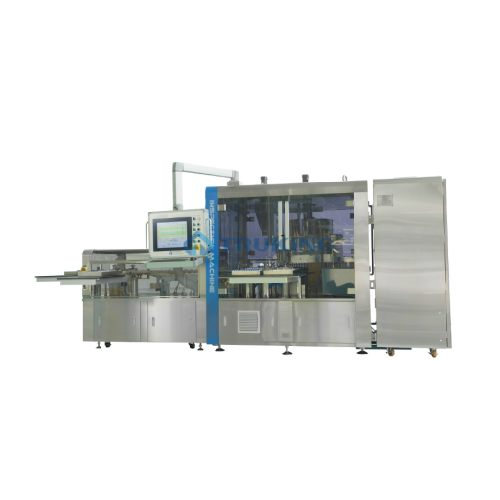
Automatic inspection and leak test for pharma containers
Ensure container integrity for injectables with high-speed inspe...
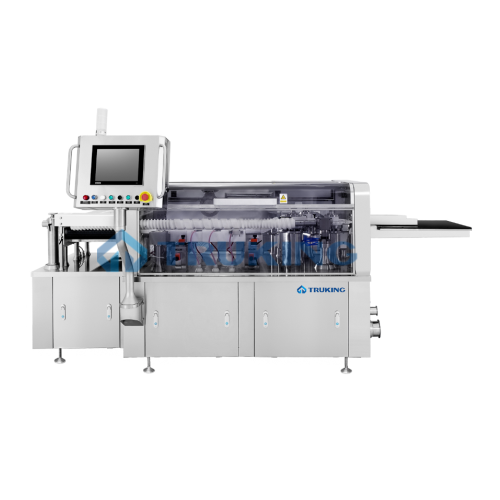
Automatic leak detection system for pharmaceutical containers
Ensure the integrity of pharmaceutical containers with pre...
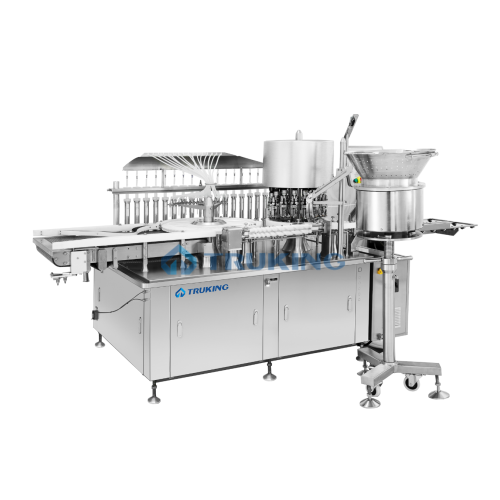
Oral liquid bottle filling & capping system
Streamline your liquid manufacturing processes with precise filling and secure...
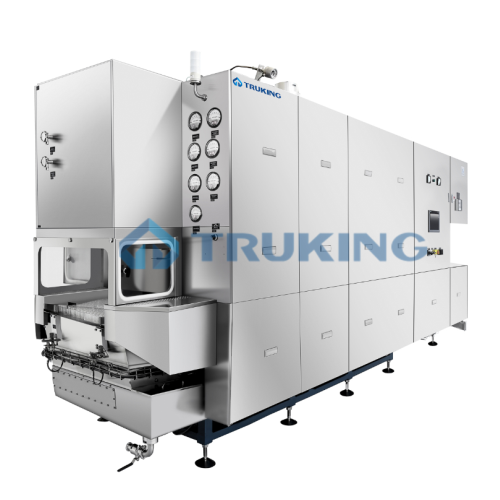
Sterilizing and drying tunnel for pharmaceutical vials
Ensure precise sterilization and depyrogenation of pharmaceutical ...
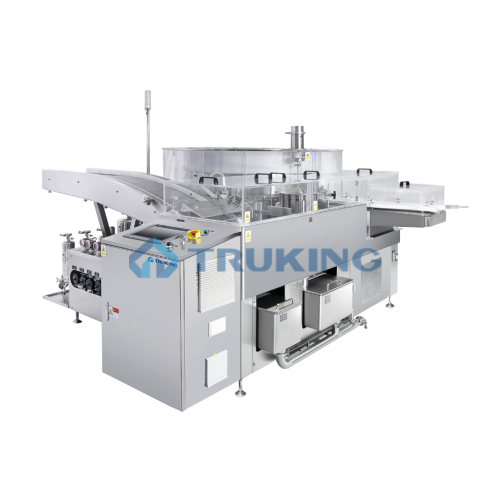
Vertical ultrasonic washing system for oral liquid bottles
Ensure optimal cleaning and sterilization with a compact vert...
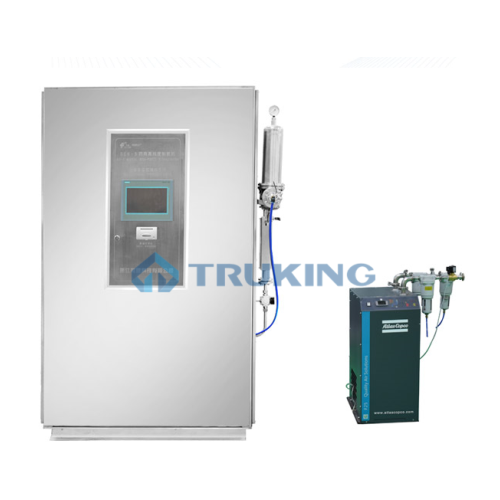
High-purity nitrogen generator for pharmaceutical and food industries
Achieve ultra-high purity levels in your producti...
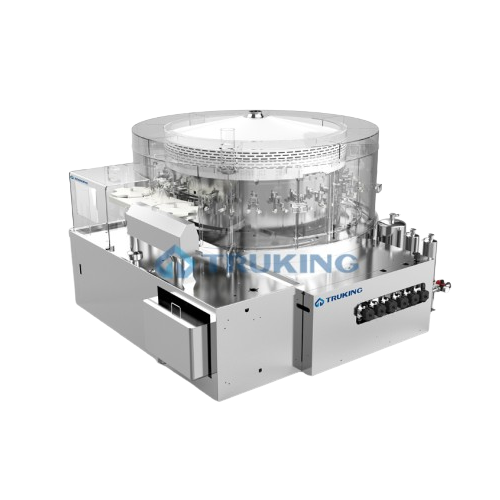
Industrial freeze dryer for pharmaceutical applications
Enhance your production line with precision cleaning solutions fo...
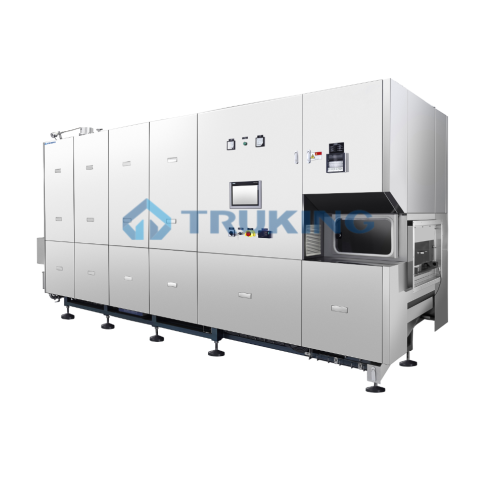
Sterilization and drying tunnel for glass bottles
Ensure aseptic integrity and regulatory compliance in injectable produc...
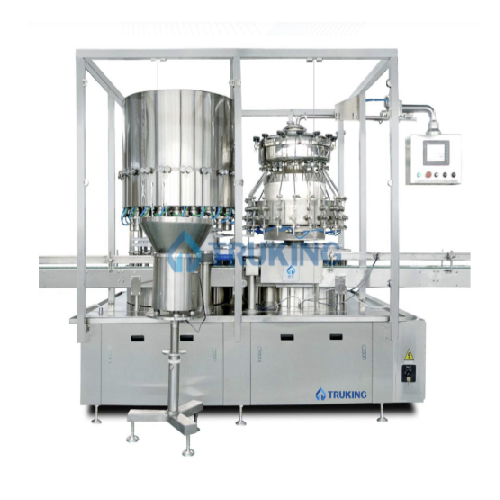
Gravity rotary filling for large infusion bottles
Ensure precise filling and secure stoppering of large infusion bottles ...

High capacity automatic blister packaging system
Streamline your production line with a high-speed blister packaging syste...
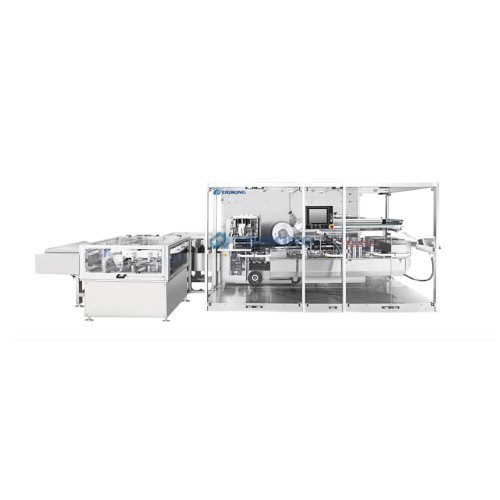
Secondary packaging cartoner for ampoules and vials
Optimize your aseptic production with efficient high-capacity carton ...
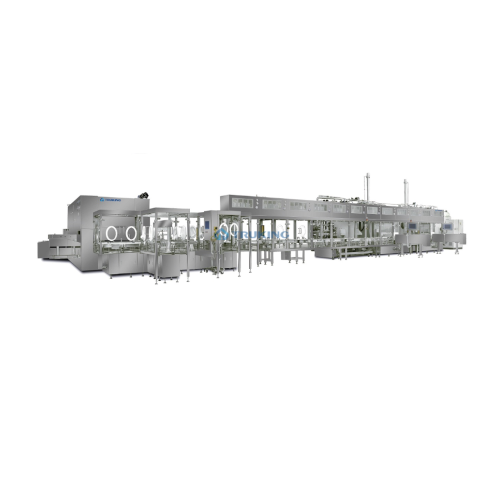
Auto loading & unloading system for freeze dryers
Efficiently manage vial handling in freeze-drying processes with automa...
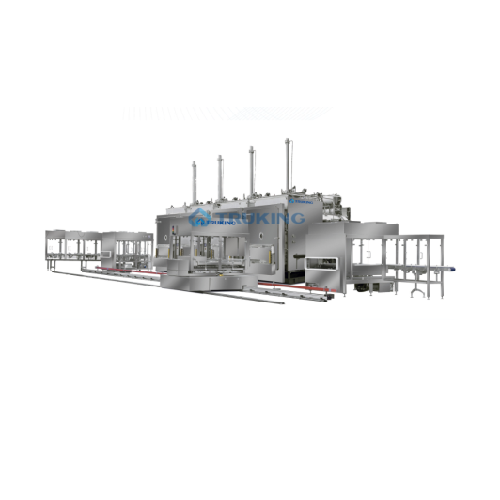
Mobile transfer loading system for freeze dryers
Streamline your lyophilization process with a high-capacity mobile loadin...
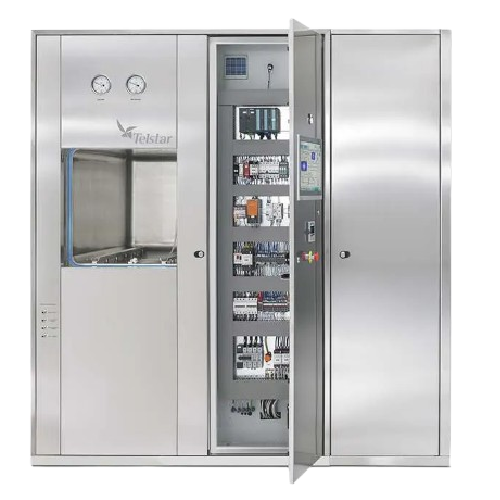
Saturated steam sterilizer for pharmaceutical production
Ensure sterility for a diverse range of pharmaceutical products ...
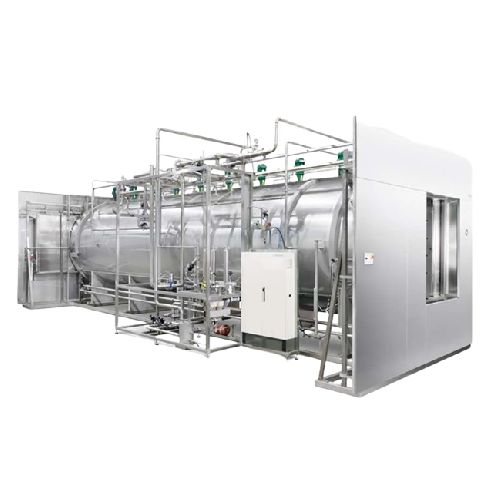
Steam & air mixture sterilizer for parenteral solutions
Achieve robust and effective sterilization for delicate pharmaceu...
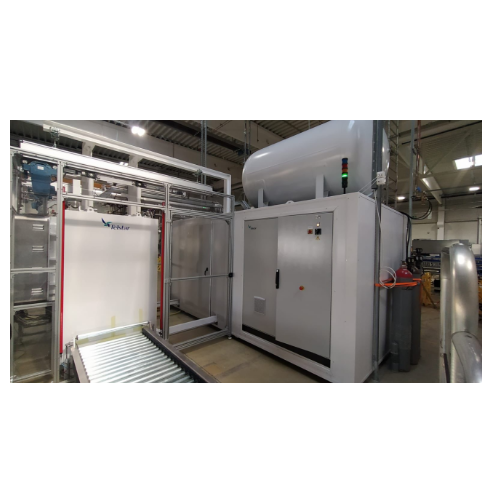
Leak detection and gas filling for electric switchgears
Achieve precise leak detection and efficient gas filling for elec...
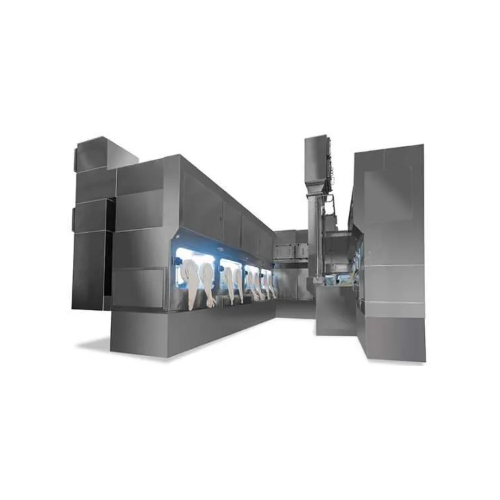
Freeze dryer & filling line aseptic isolator for cytotoxic products
Handle cytotoxic and high-potent drugs with precisi...
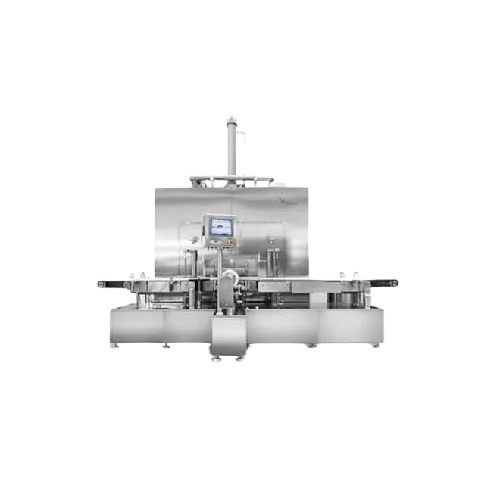
Sterile lyophilisation and filling line
Ensure aseptic conditions while freeze-drying biopharmaceuticals and high-potent dr...
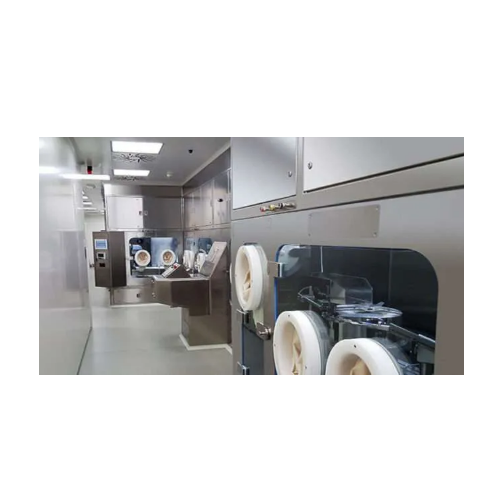
pharmaceutical lyophilised filling line
For high-precision production of moisture-sensitive drugs, this aseptic system ensu...
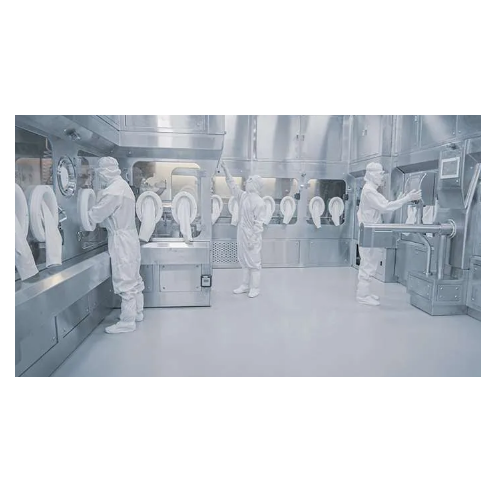
Vial filling line and freeze dryer system
For seamless drug production, integrate reliable vial filling with precision fre...
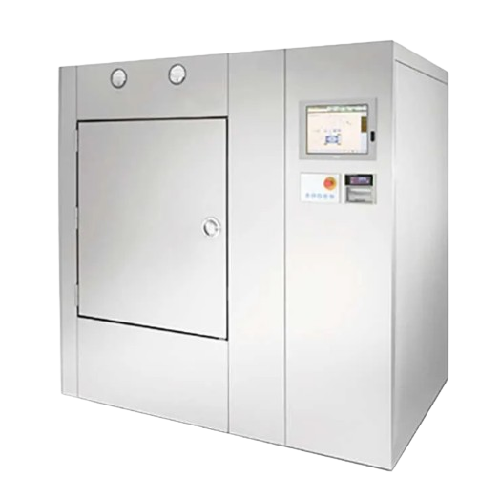
Dry heat sterilization and depyrogenation oven for glassware
Achieve precise sterilization and depyrogenation of glasswa...
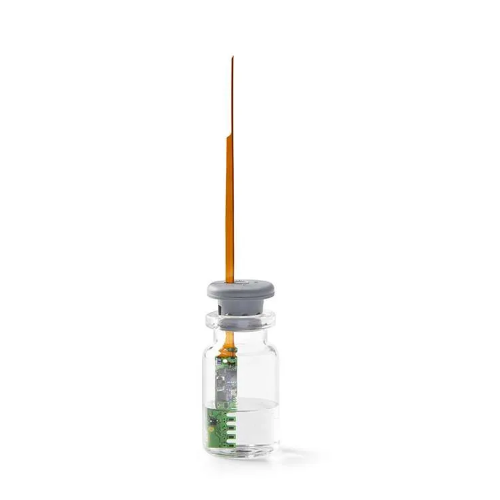
Gmp freeze dryer for small batch production
Optimize small-scale biopharmaceutical production with precise freeze-drying t...
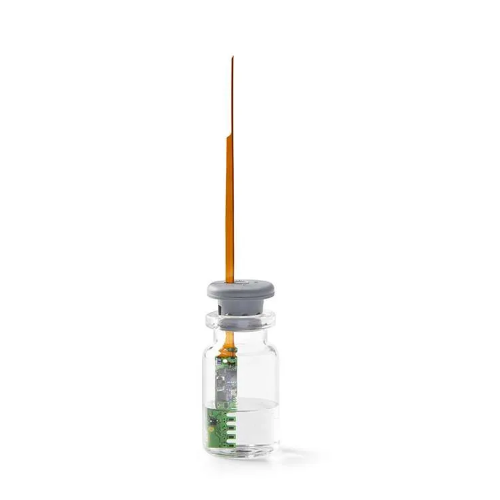
Sublimation front monitoring system for freeze drying
Ensure precise control over your freeze-drying process with real-ti...
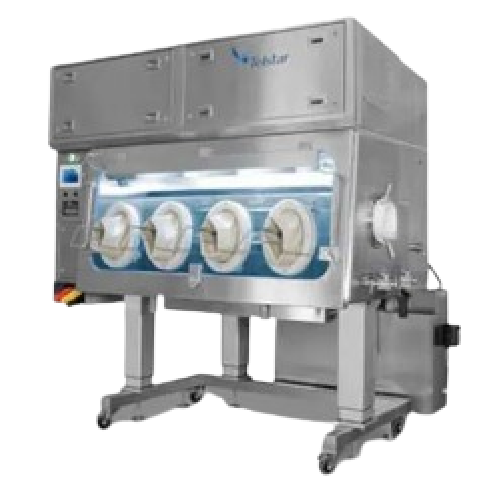
Aseptic ophthalmic filling isolator
Ensure sterility and precision in ophthalmic solutions with a controlled aseptic enviro...
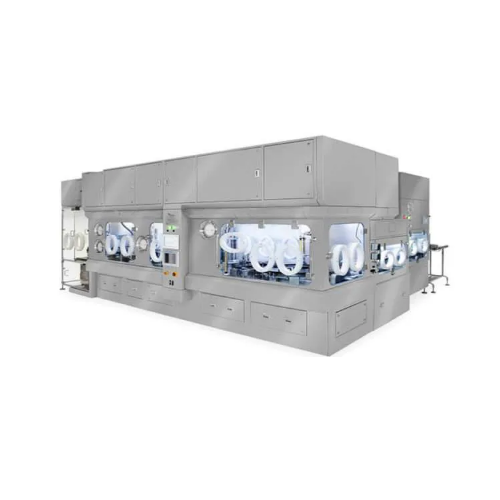
Sterile lyophilized filling line
Ensure sterility and precision in filling pharmaceuticals with advanced isolator lines desi...
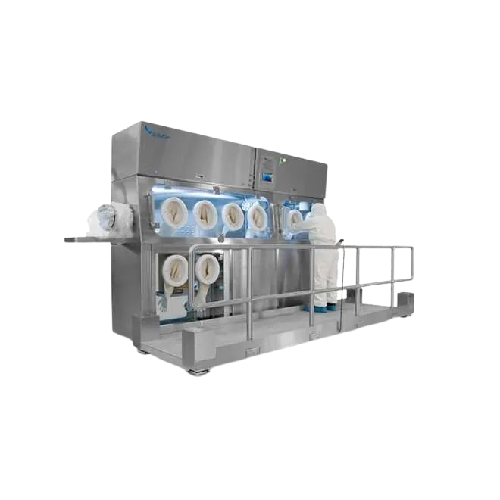
Sterile lyophilised filling solution
Achieve precise filling and control of moisture-sensitive pharmaceuticals while ensuri...
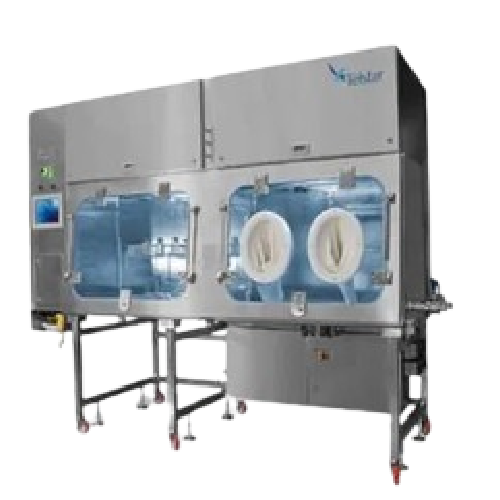
Sterility test isolators for continuous batch testing
Ensure aseptic integrity during high-throughput sterility testing w...
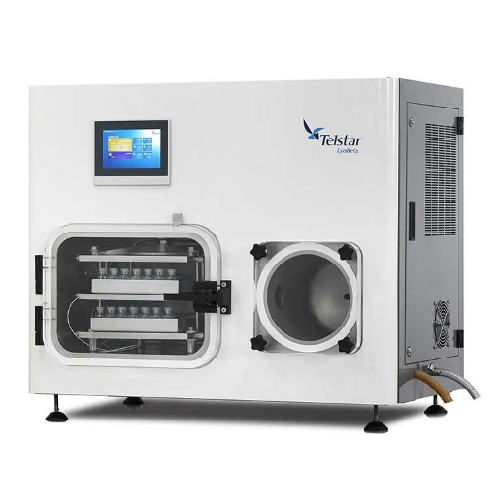
Freeze dryer for small batch scale-up in biotech and pharma
Optimize freeze-drying processes for small batches or high-v...
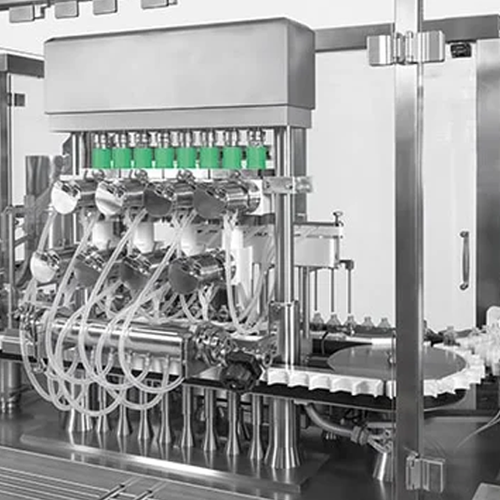
Bulk vial liquid filling system
Ensure reliable and efficient processing of critical biopharmaceutical and pharmaceutical li...
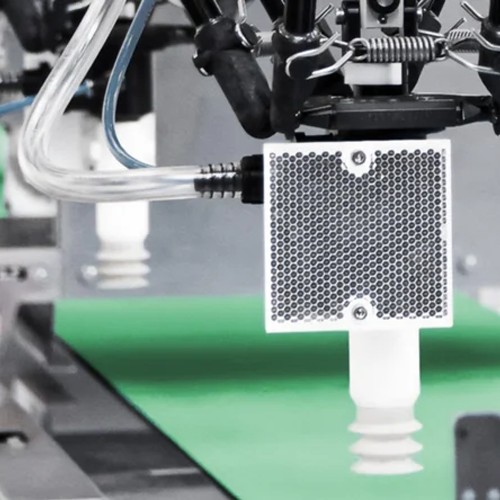
Robotic pick and place platform for food packaging
Enhance your packaging efficiency and product quality with a scalable ...
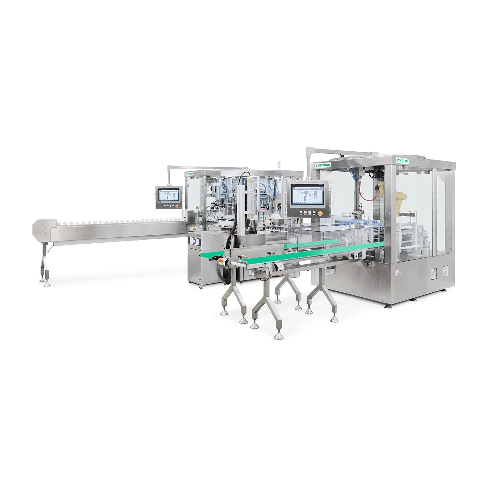
Medical device assembly and labeling solutions
Streamline assembly and labeling processes for medical devices with technol...
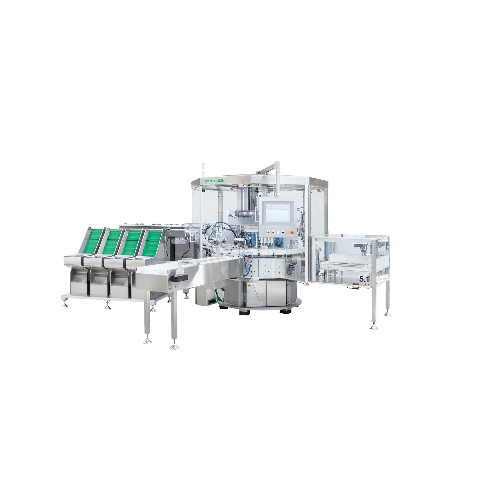
Assembly solutions for medical devices
Optimize your medical device production with specialized assembly solutions that ens...
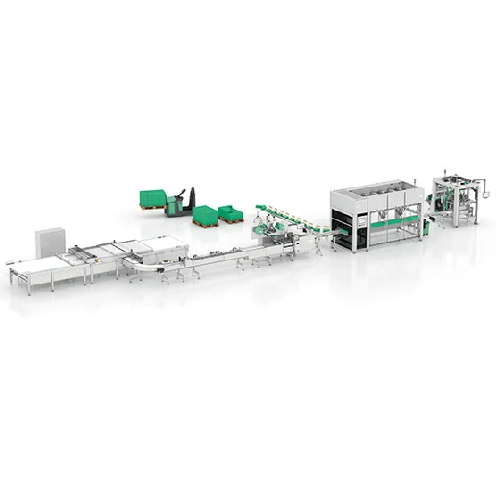
Automated visual inspection for pharmaceutical products
Ensure the integrity and safety of your parenteral products with ...
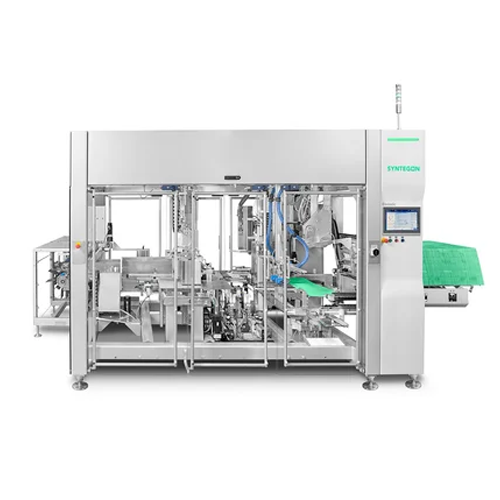
Case packer for diverse food products
Optimize your packaging line with this versatile case packer, capable of handling a w...
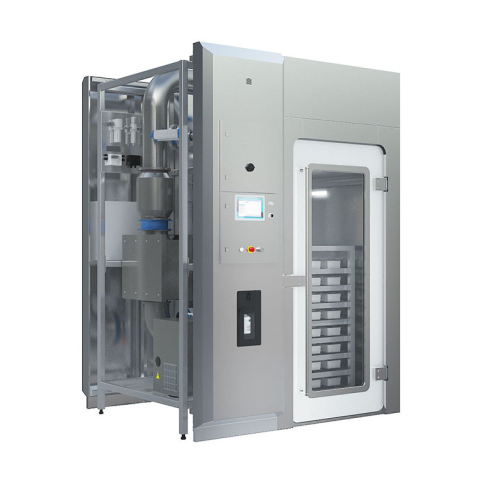
Vaporized hydrogen peroxide decontamination chamber
Ensure aseptic material safety with a decontamination chamber designe...

Biodecontamination system for small pharmaceutical enclosures
Achieve reliable sterilization in compact settings with th...
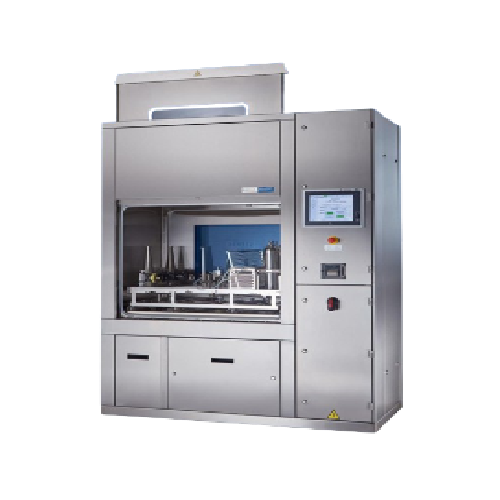
Pharmaceutical grade washer for biotechnology and pharmaceutical manufacturing
Efficiently clean and prepare your labo...
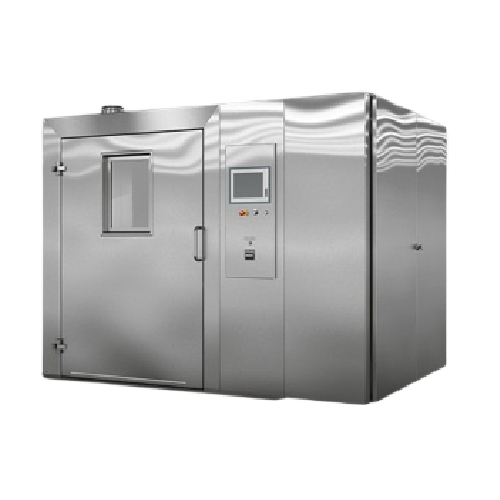
Pharmaceutical grade washer for large components
Ensure compliance and maximize productivity with a high-performance solut...
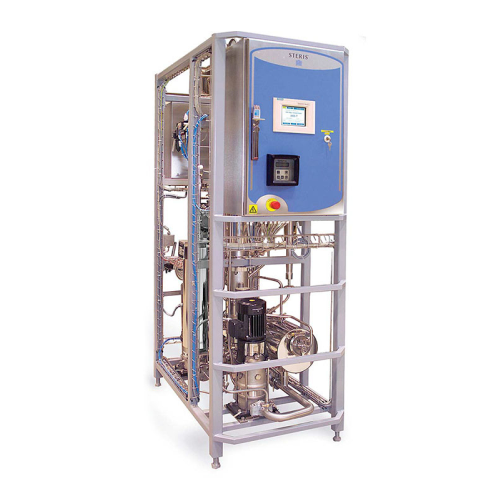
Pure steam generator for pharmaceutical applications
Ensure your sterilization process consistently achieves high purity ...
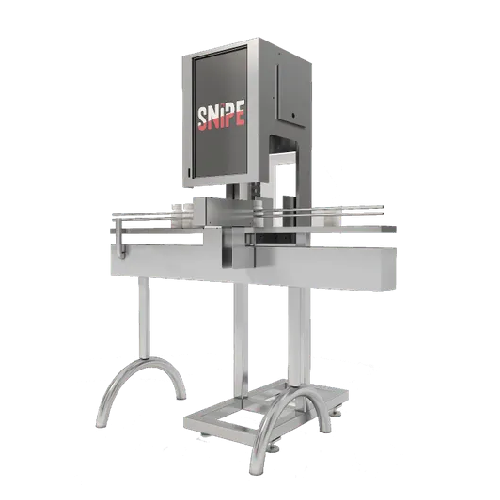
Bottle induction seal integrity inspection
Ensure uncompromised product quality by accurately inspecting and verifying the...
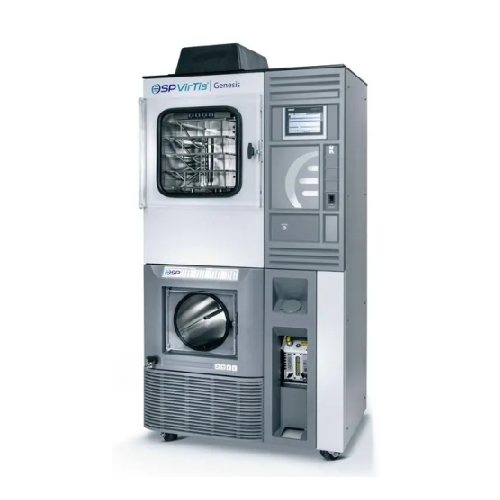
Pilot freeze dryer for laboratory and small-scale production
Achieve precise temperature and vacuum control for consiste...
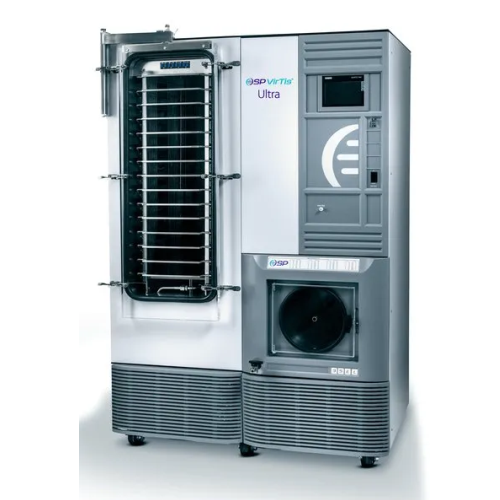
Pilot-production freeze dryer for diagnostic kits and Api
Optimize your lyophilization process with this versatile freez...
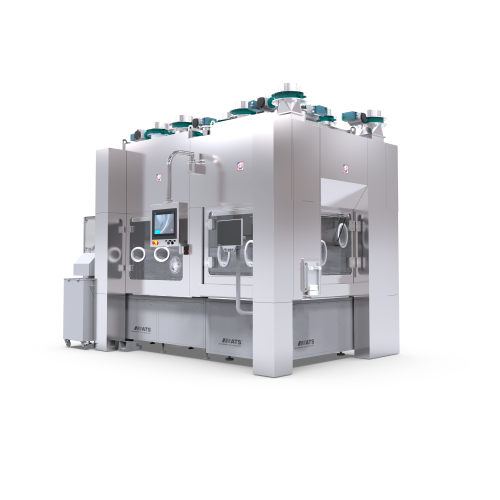
Robotic filler for aseptic pharmaceutical production
Streamline your aseptic filling process with high-speed robotic prec...
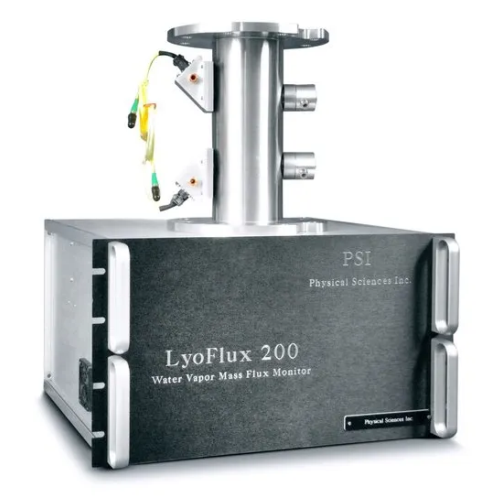
Lyophilization process optimization sensors
Achieve precise real-time monitoring of water vapor during freeze-drying, stre...
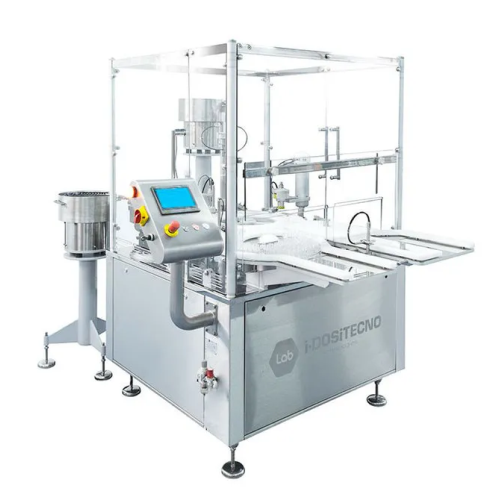
Rotary filler for pharmaceutical vials
Optimize precision and efficiency in fill-finish operations with a rotary system des...
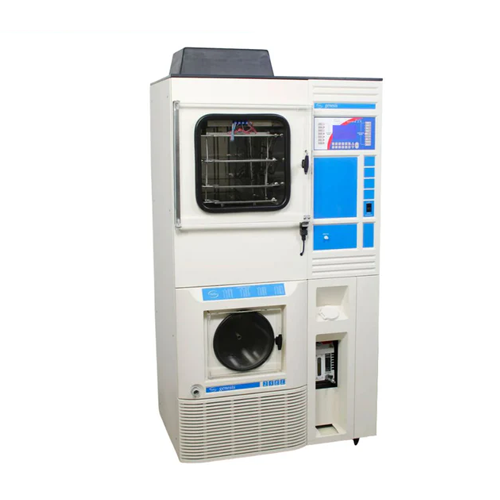
Optimized lyophilization with Smart freeze dryer technology
Streamline lyophilization cycle development with cutting-edg...
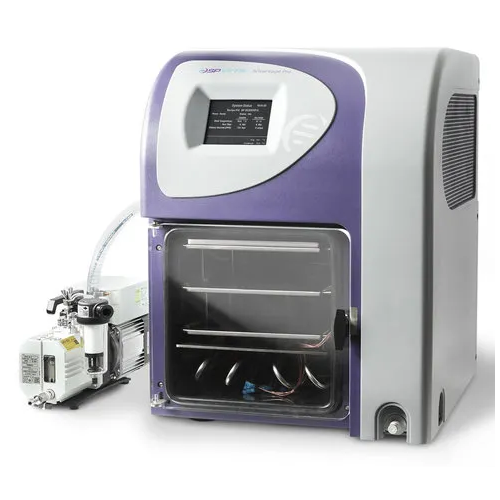
Benchtop freeze dryer for laboratory research
Streamline your lab’s freeze-drying processes with precision temperatu...
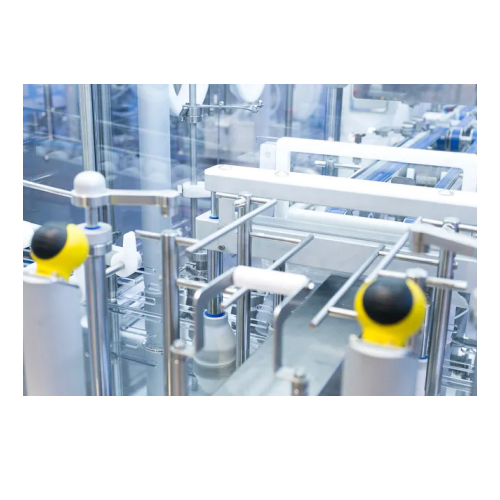
Rtu debagging system for pharmaceutical sterile environments
Designed to streamline your fill-finish process, this syste...
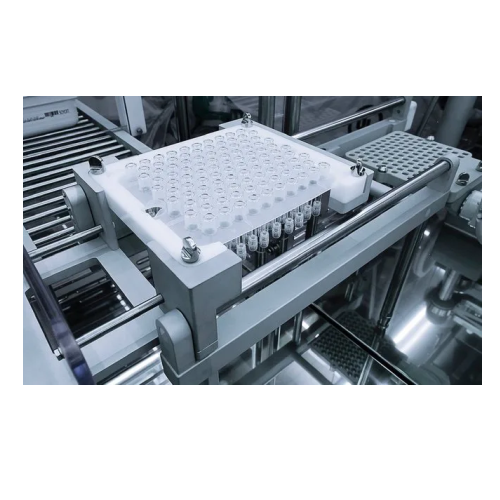
Ready-to-use denesting equipment for pharmaceutical fill-finish
Ensure sterility and precision in your fill-finish workf...
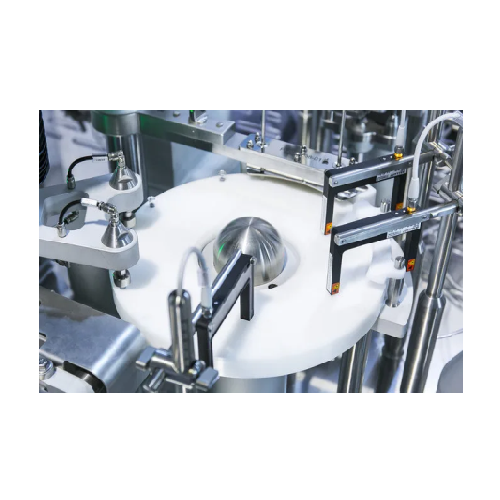
Robotic syringe filling system for sterile pharmaceutical production
For high-precision liquid dosing in sterile enviro...

Pharmaceutical liquid and powder filling solution
Achieve precise filling and capping of diverse formulations with a vers...
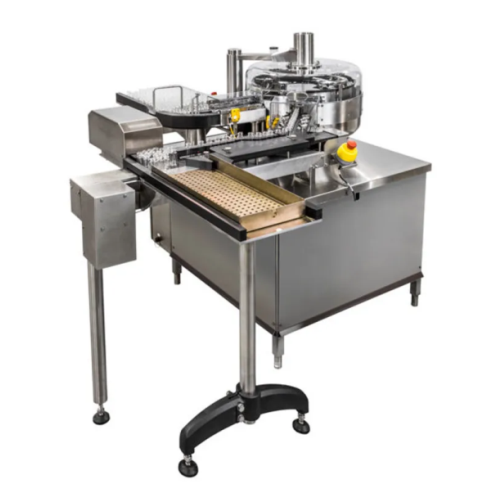
Vial washer for pharmaceutical processing
Ensure efficient vial washing with minimal water usage, reducing particulates an...
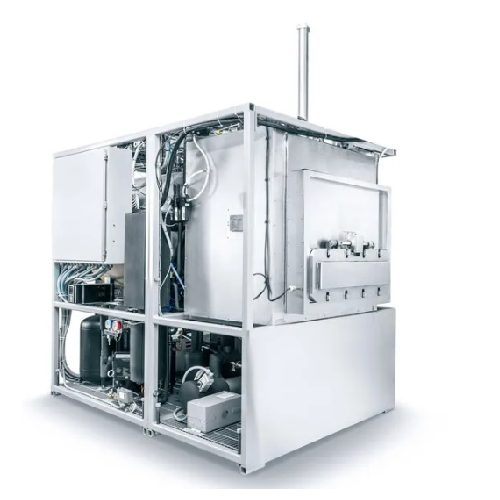
Production lyophilizer for pharmaceuticals
Ensure precise freeze-drying for high-value pharmaceuticals with cutting-edge t...
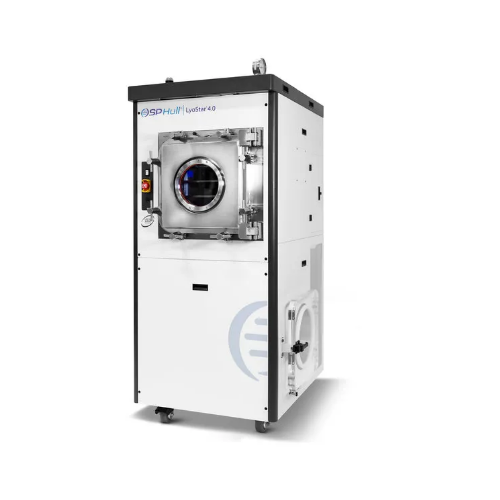
R&d and process development freeze dryer
Speed up your biologic development with precise lyophilization control, ensuring r...
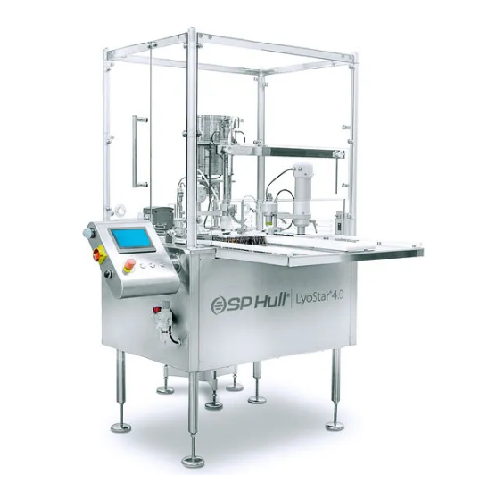
Small scale pharmaceutical filler and stoppering system
Optimize your R&D operations with a versatile filling and st...
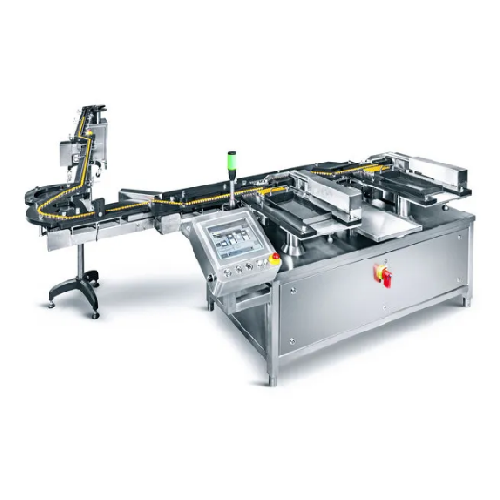
Vial tray loader for pharmaceutical processing
Streamline your vial handling process with a high-speed, flexible tray load...
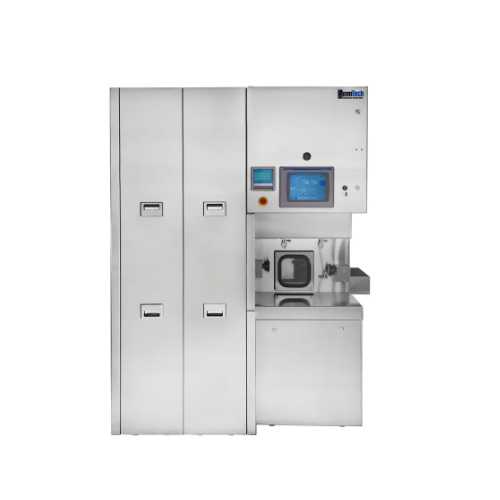
Depyrogenation tunnel for pharmaceutical vials
Achieve reliable sterility with fully automated depyrogenation tunnels, ens...
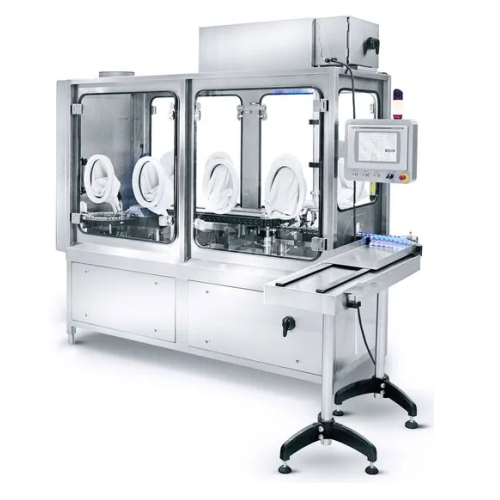
External vial washer for pharmaceutical industry
Ensure complete decontamination of vial exteriors with precision washing ...
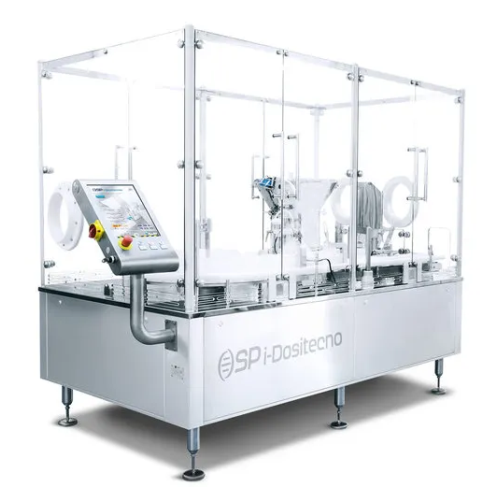
Vial capping system for aseptic processing
Ensure precise vial sealing under aseptic conditions while maintaining high thr...
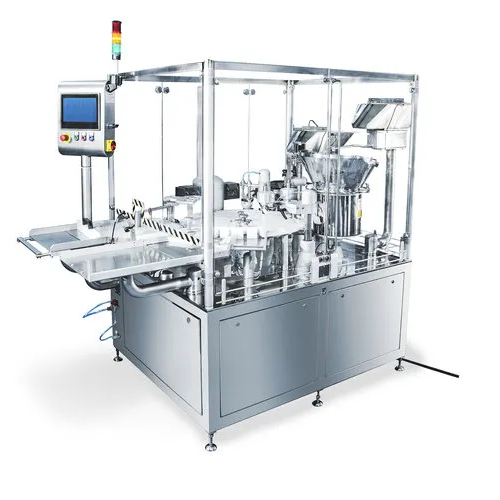
Micro-line vial filling solution for biopharmaceuticals
Ensure batch consistency and sterility in fill-finish operations ...
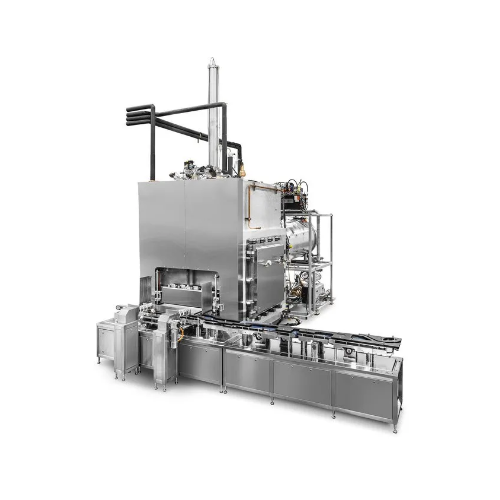
Freeze dryer loading and unloading systems for pharmaceutical processes
Optimize aseptic pharmaceutical processes with ...
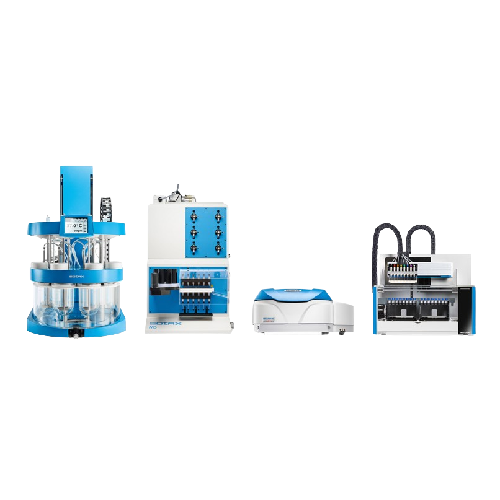
Benchtop dissolution tester for multiple test runs
Streamline your laboratory’s workflow with a fully automated ben...
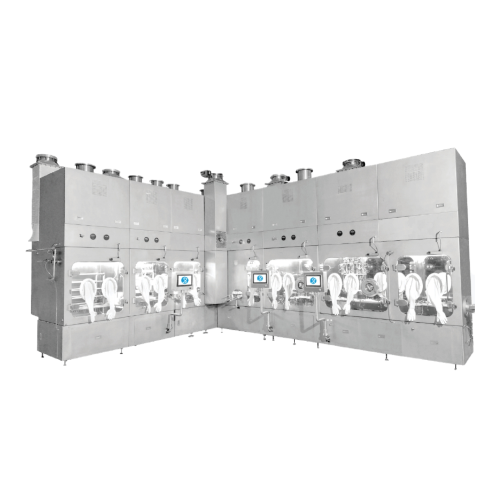
Ampoule filling and sealing line
Streamline your ampoule production with an integrated solution that expertly handles everyt...
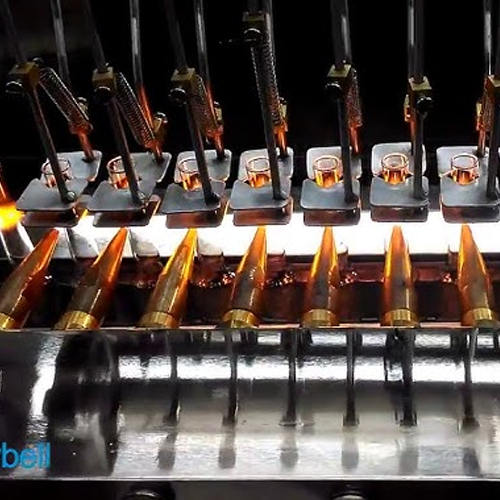
Triple combi filling and stoppering system for vials and ampoules
Optimize your liquid formulation process with a versa...
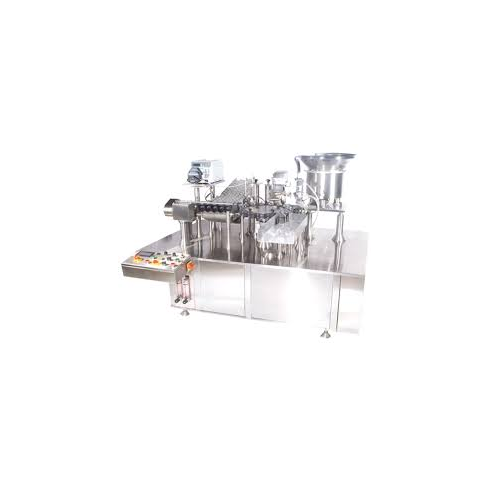
Combi r&d ampoule and vial filling equipment
Optimize your R&D operations with a versatile machine designed for preci...
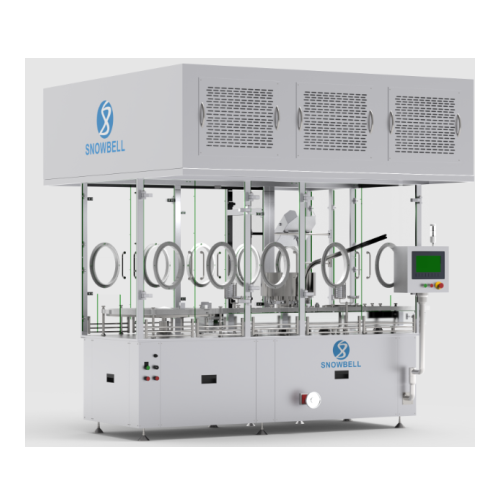
Vial washing system for internal and external cleaning
Streamline vial preparation with comprehensive washing, sterilizin...

Injection stretch-blow molding system for Pet containers
For manufacturers aiming to produce versatile, high-quality PET ...
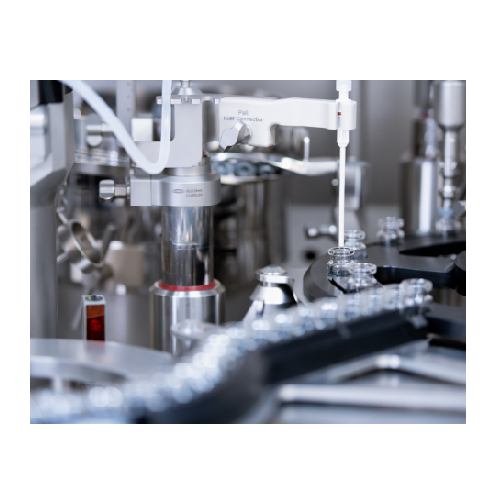
Rotary stoppering and capping for vials
Achieve precise and efficient stoppering, capping, and crimping for high-speed vial...
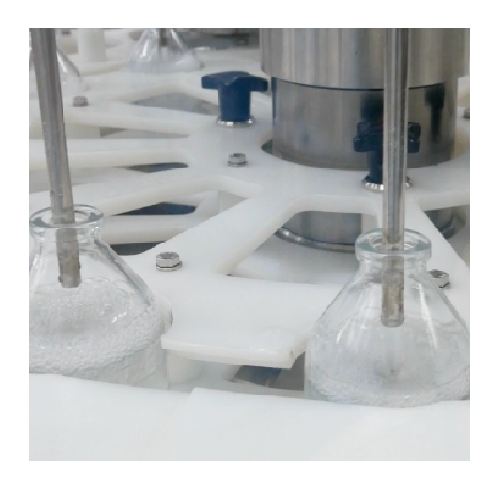
Rotary vial filling and stoppering system
For high-speed production of sterile injectable vials, this continuous motion ro...
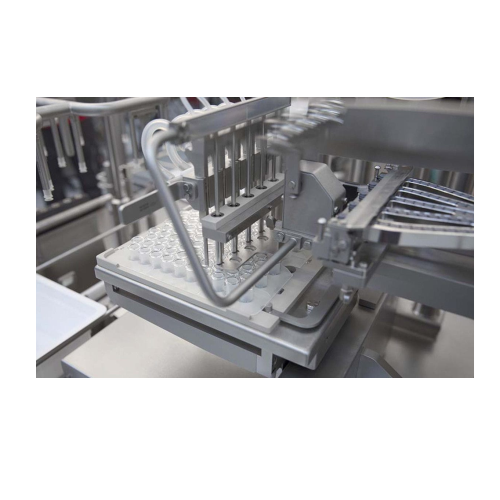
Nested syringe filling and stoppering system
Optimize your syringe production with precise filling and stoppering, ensurin...
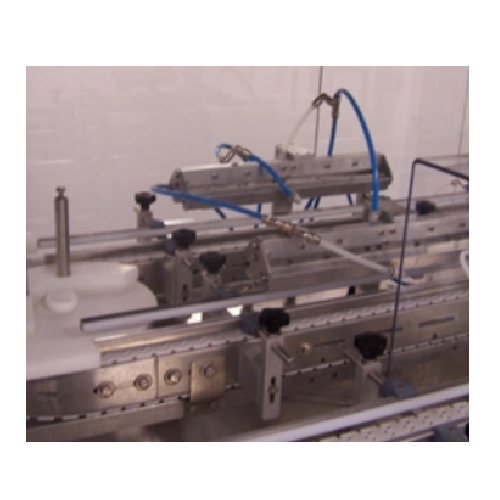
External washing and drying system for sealed vials
Ensure contamination-free packaging of liquid vials with this precise...
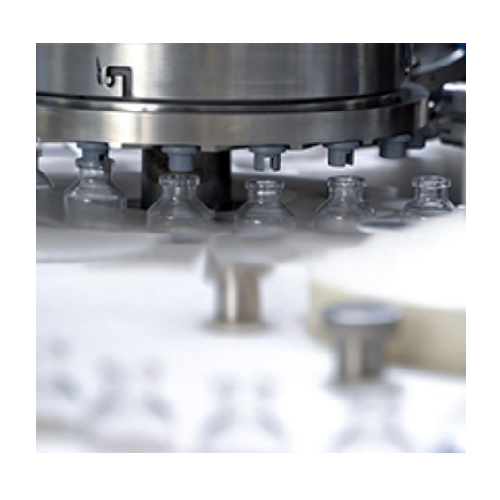
Continuous motion rotary vial filling and stoppering solution
Optimize your vial production with a high-speed, continuou...
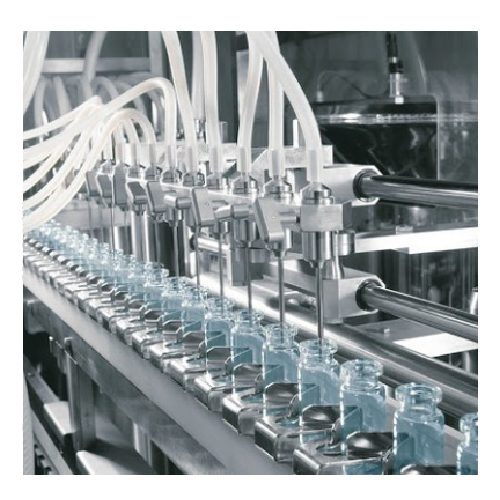
Automatic vial capping system
Ensure precise capping and sealing for sterile vial production with a compact, high-speed solu...
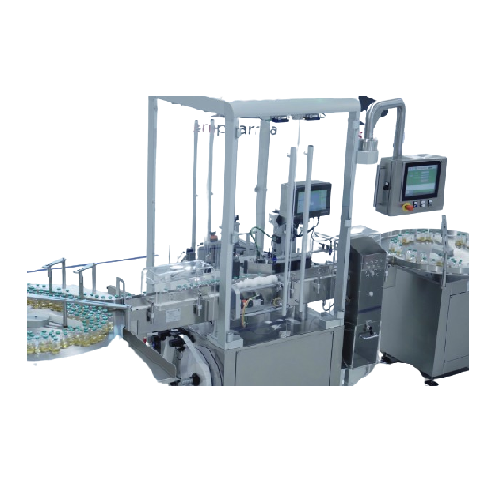
Automatic labelling system for pharmaceutical vials
Ensure precise and efficient packaging for cylindrical containers wit...
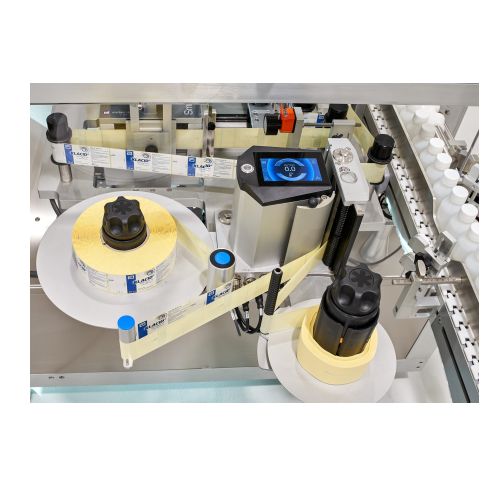
Automatic labelling system for pharmaceutical vials and bottles
Optimize your bottle labelling process with precision al...
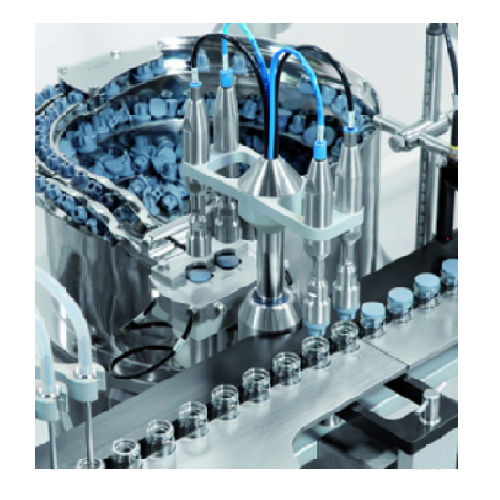
Automatic linear filling stoppering system for large volume vials
Ensure precise vial filling and secure sealing with a...
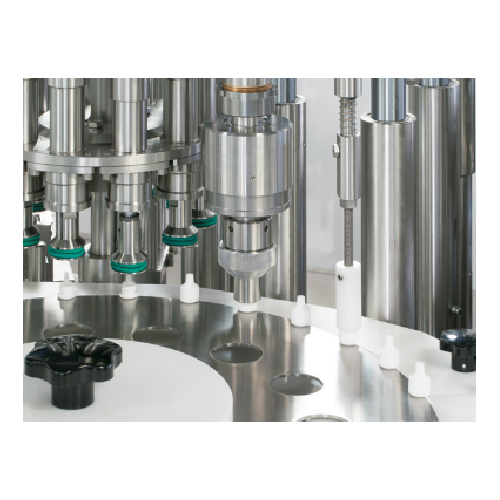
Automatic capping solution for pharmaceutical vials
Cap your liquid formulations with precision and efficiency using this...
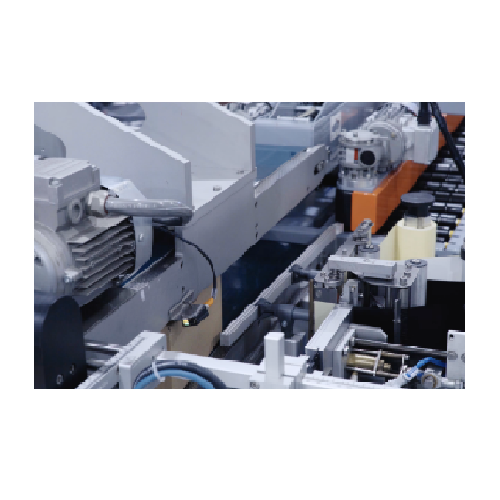
Vertical case packer for bottles and vials
Efficiently pack hard-to-handle items like bottles and vials with precision aut...
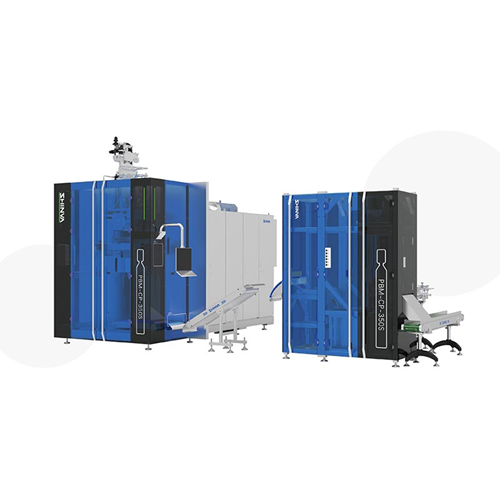
Single-mold continuous bottle Bfs solution
Optimize aseptic production with this advanced solution, offering superior ster...
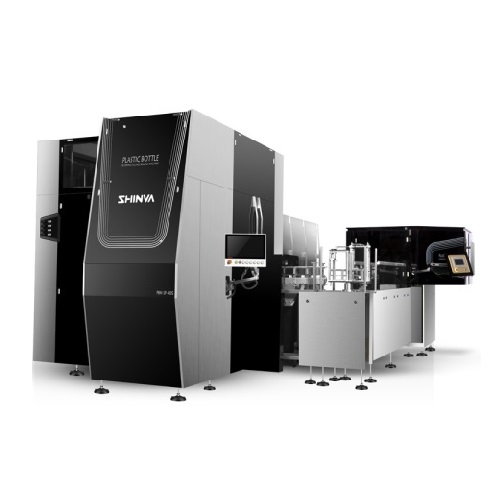
Blow-fill-seal system for small volume injection production
Ensure precise aseptic liquid packaging with integrated blow...
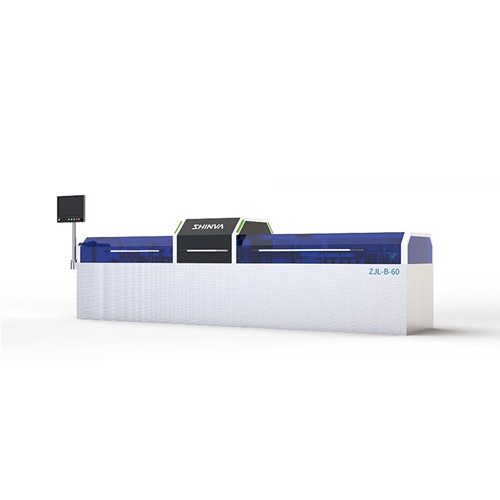
Plastic bottle Bfs leak detection solution for small volume injections
Ensure sealed integrity with precision leak dete...
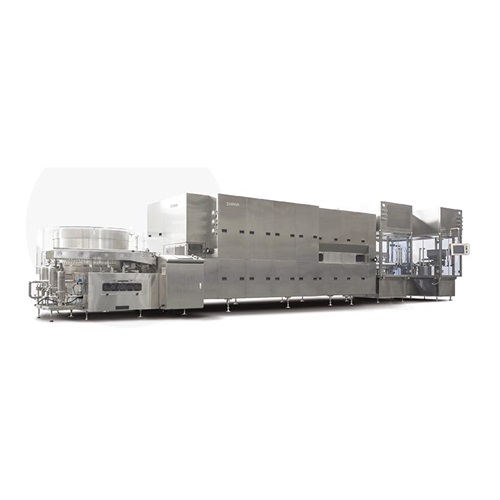
Vial washing drying filling sealing line for pharmaceutical production
Streamline your vial production with this integr...
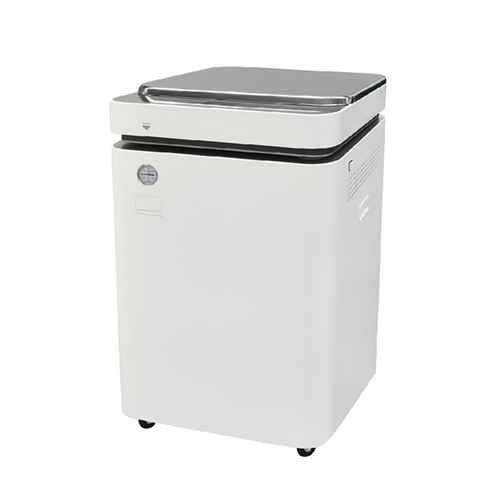
Laboratory series steam sterilizers
Ensure the sterility of your labware and culture media with reliable steam-based steril...
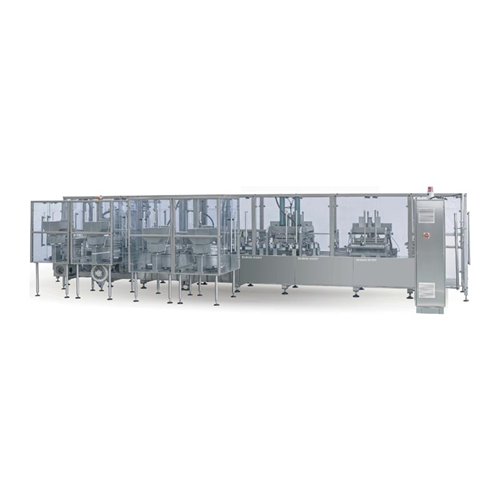
Non Pvc soft bag form fill seal system
Efficiently form, fill, and seal non-PVC infusion bags while ensuring precision and ...
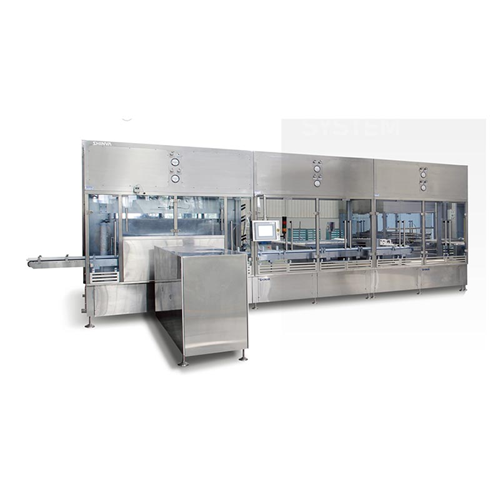
Automatic loading and unloading system for freeze-drying
Eliminate contamination risks and improve operational efficiency...
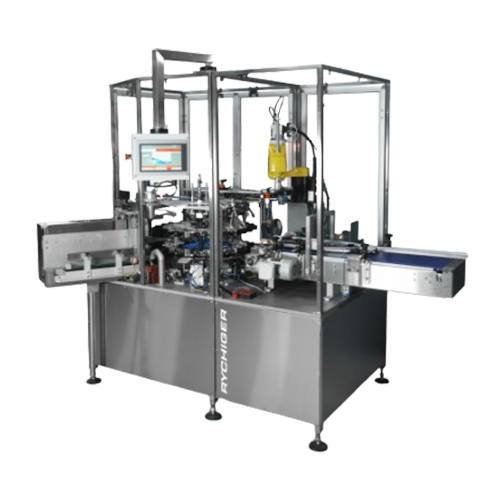
Cartoner for pharmaceutical products
Effortlessly streamline your packaging line with compact cartoning capabilities, ensur...
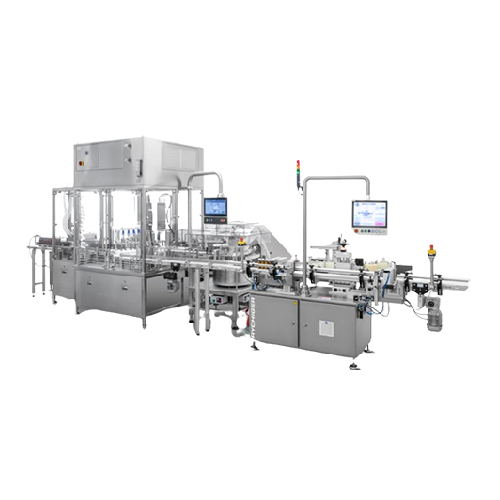
Rotary transfer system for pharmaceutical product filling
Ensure precise and hygienic filling of diverse pharmaceutical ...
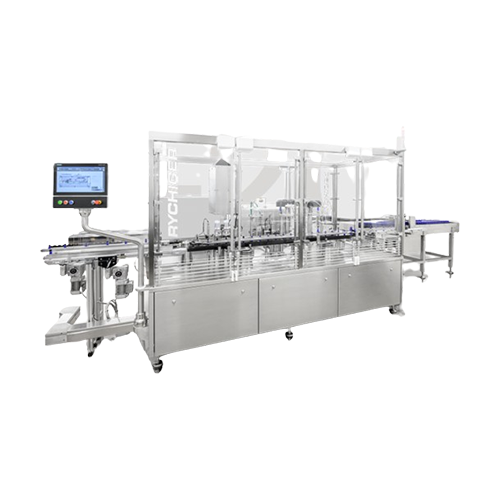
Sterile filling platform for pharmaceuticals
Achieve precise, high-speed aseptic filling and packaging with advanced compl...

Aseptic handling and fill-finish platform for Rtu syringes, vials, and cartridges
Ensure aseptic precision and high t...

Semi-automatic filling solution for syringes and vials in isolators
Achieve precise aseptic fill-finish operations for ...

Filling and assembling solution for Ivd and Poc products
Optimize precision and efficiency in cleanroom environments with...
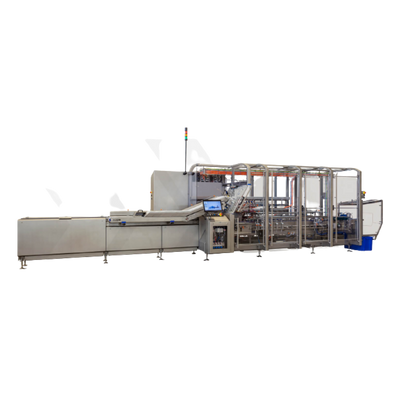
Hygienic Cartoning Machine For Pharma and Health Products
When packing single or multiple vials, ampoules or devices int...
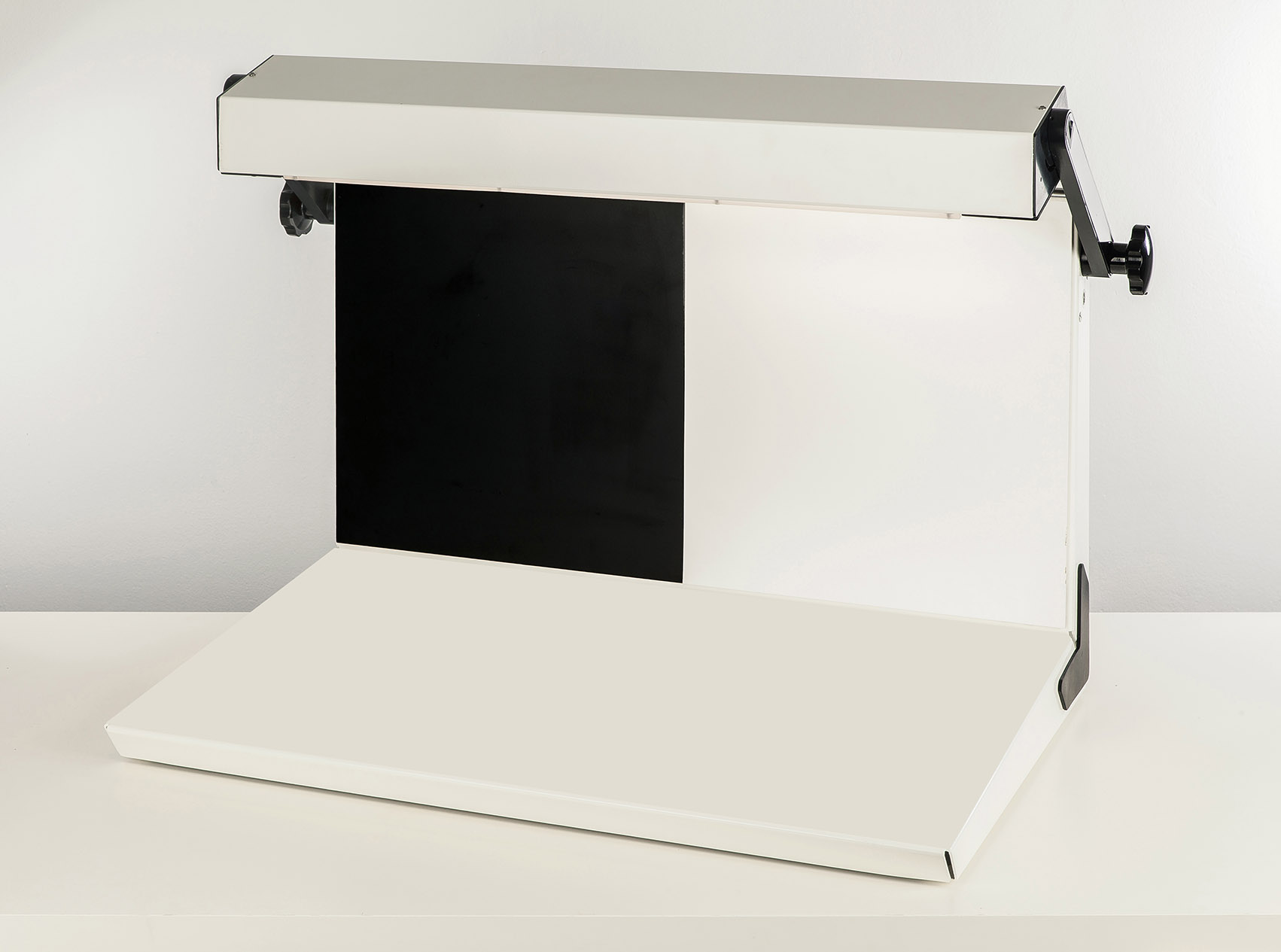
Laboratory liquid viewer for colored glass bottles
In the pharmaceutical industry, an inspection to detect any particulat...
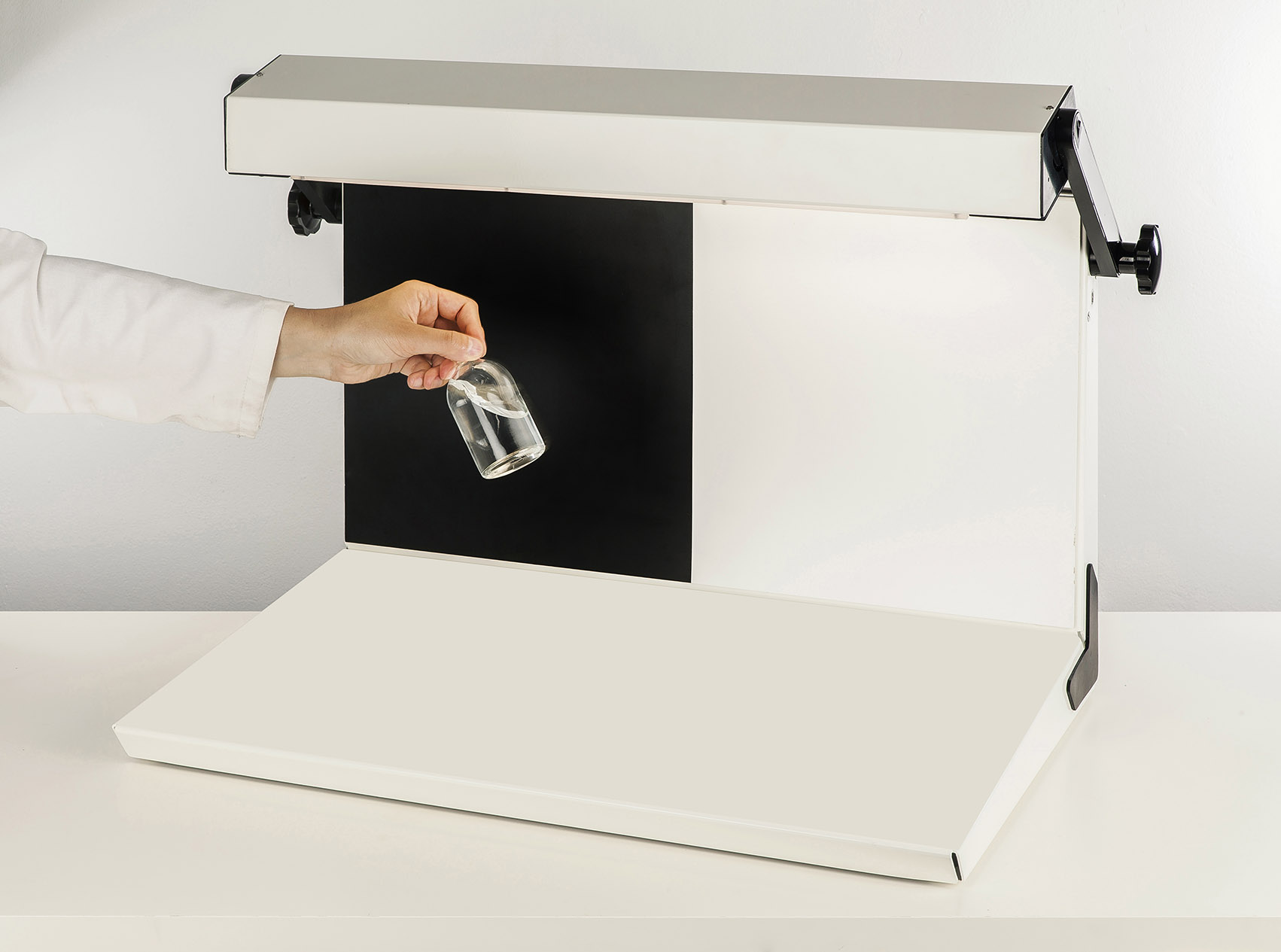
Laboratory liquid viewer for varying light conditions
In the pharmaceutical industry, you must inspect liquids in vials o...
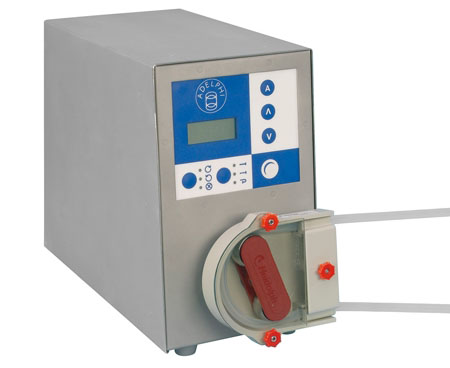
Benchtop peristaltic dispenser
When you fill vials and ampoules, high standards of hygiene are required to avoid the risk of...
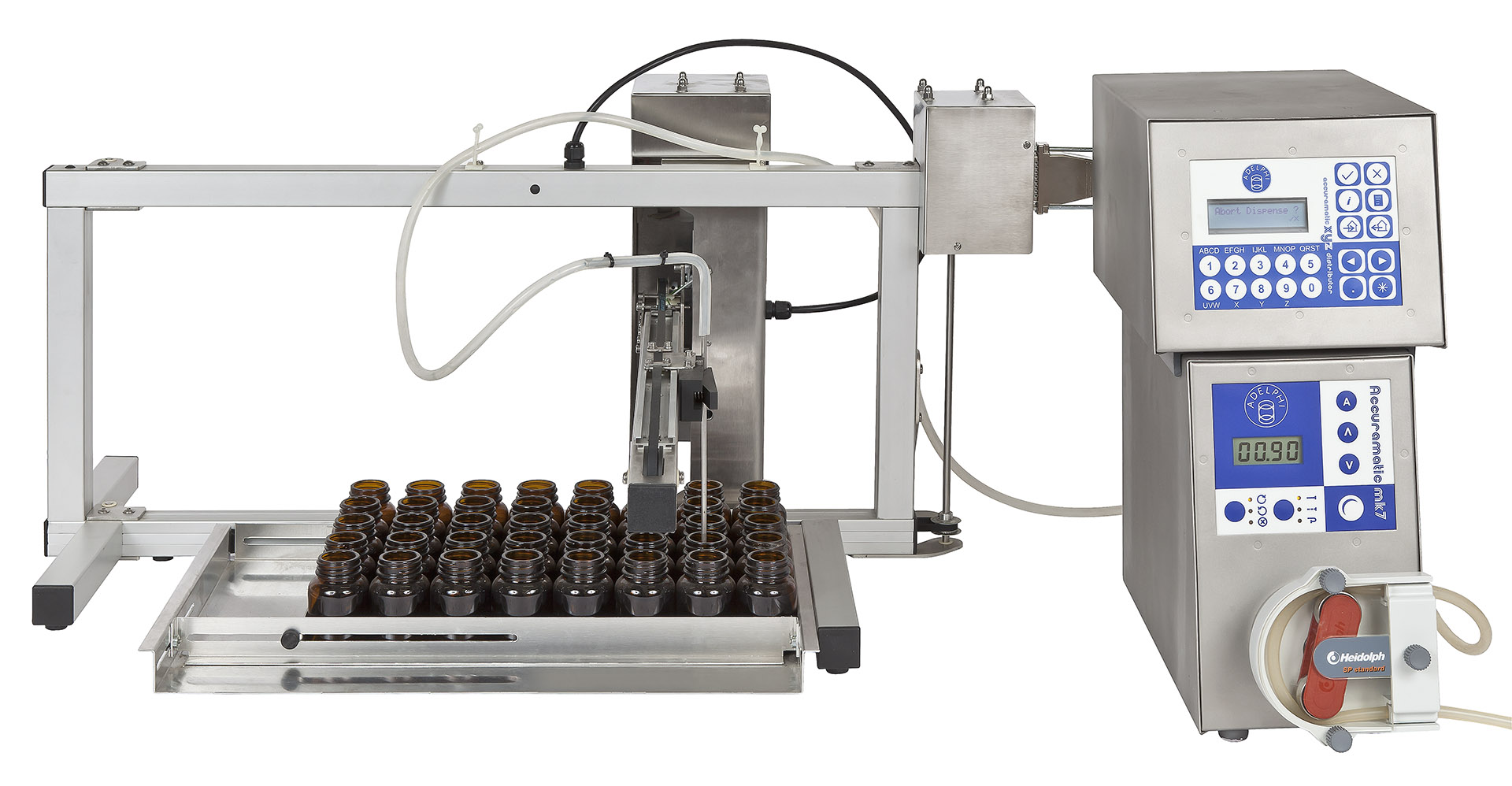
Benchtop piston filling equipment for vials in trays
Vials are difficult to fill individually through manual methods due ...
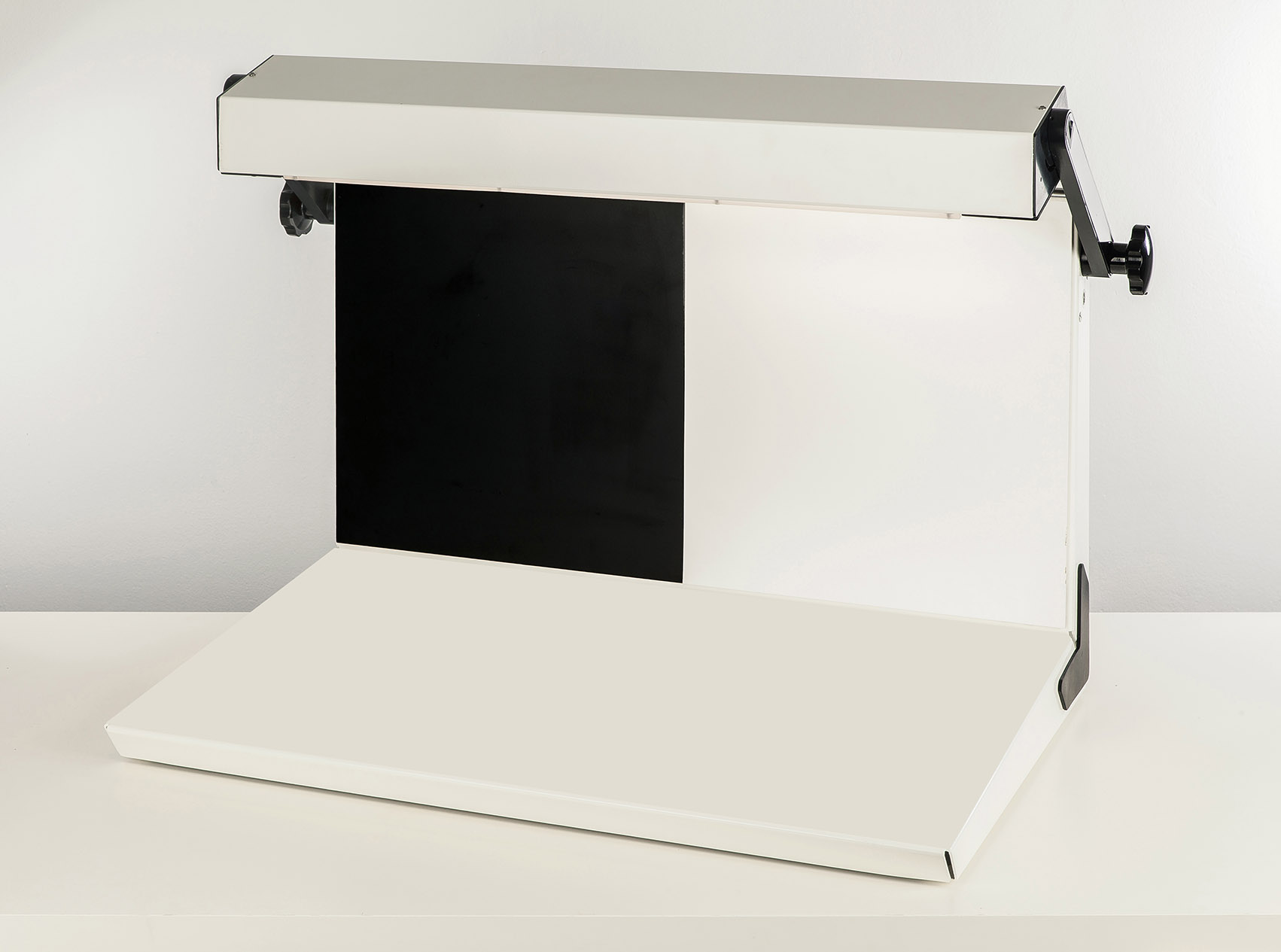
Laboratory liquid viewer for transparent glass bottles
Impurities like hair, fibers, or glass, sourced from the environme...
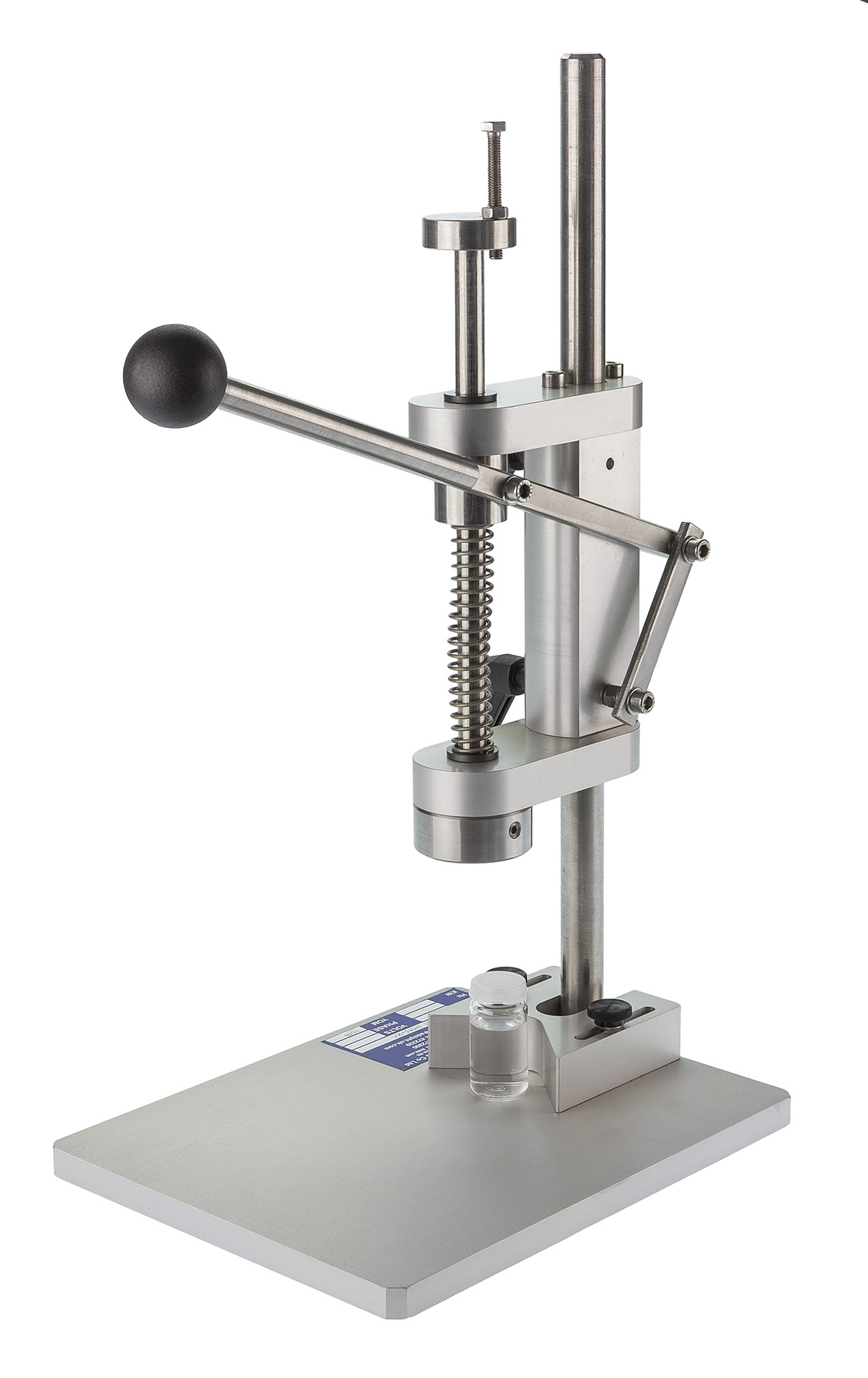
R&D bottle cap press
When you are a small-scale producer of liquids contained in bottles with press-on lids and caps you need...
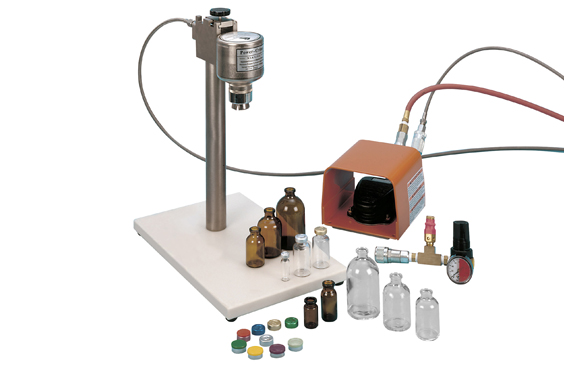
Semi-automatic vial crimper
In a small production line, crimping vials manually can cause fatigue to your operator due to mu...
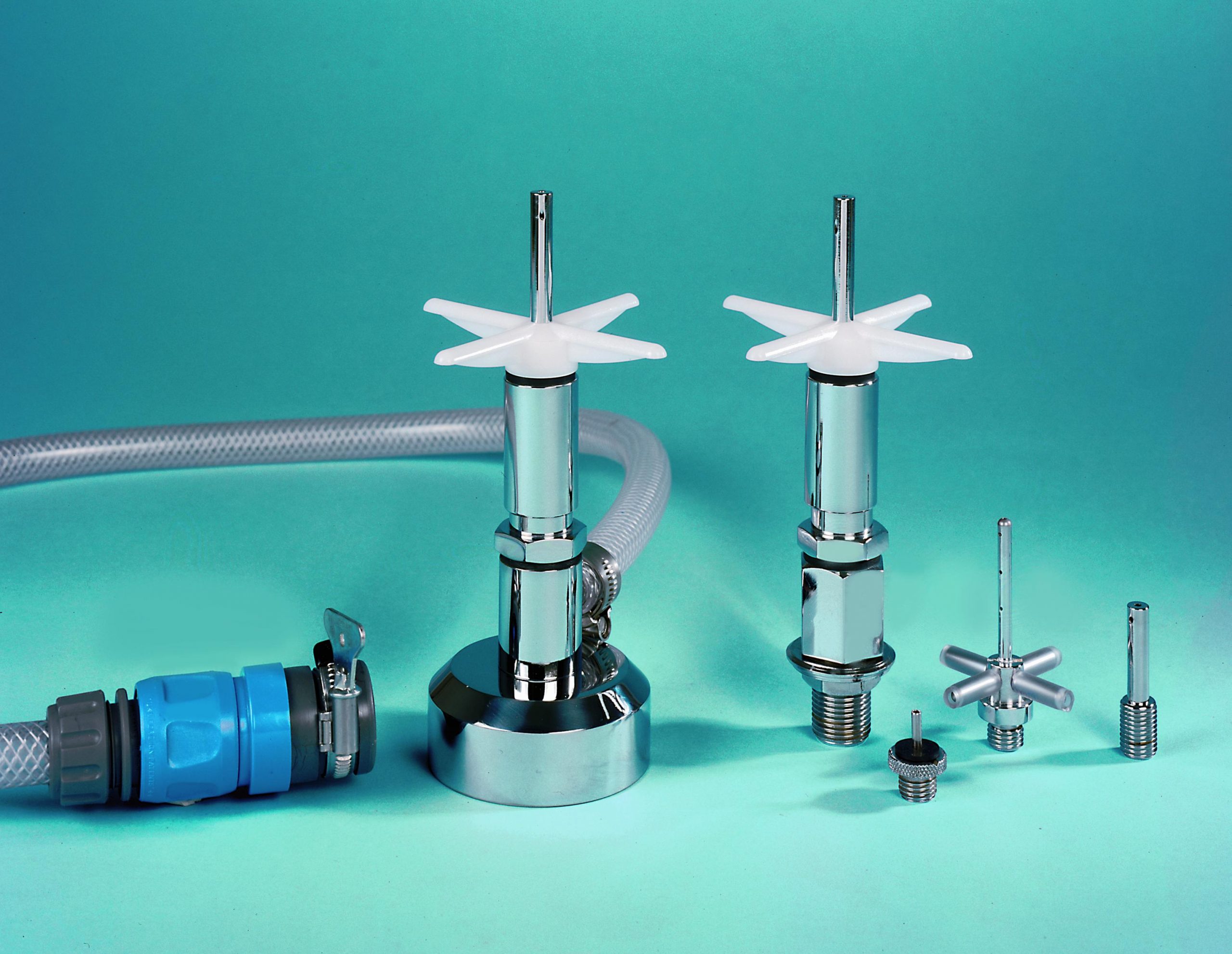
R&D bottle washer
When you pack your products in bottles, vials, syringes, and test tubes you need to wash them before fillin...
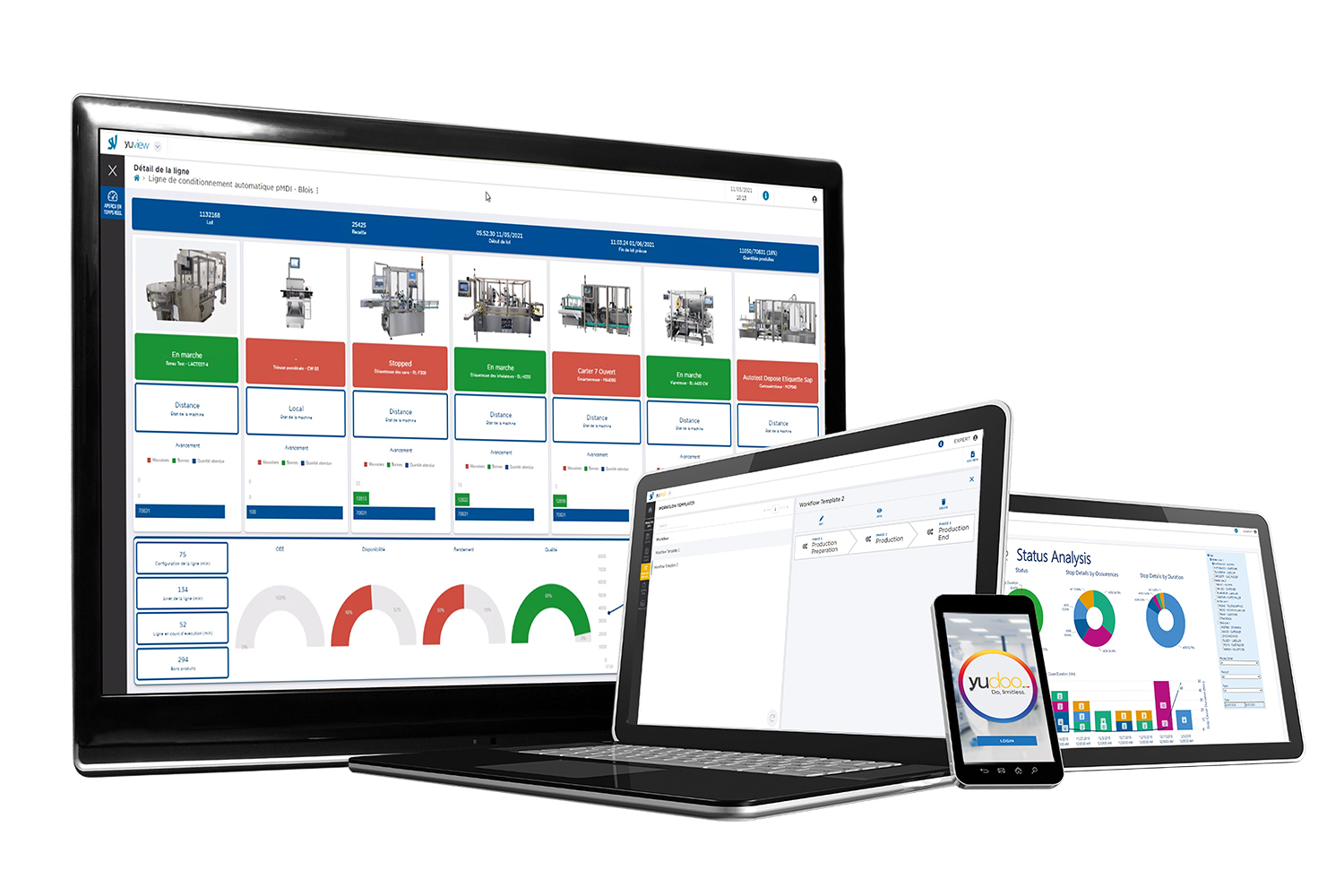
Pharmaceutical data management software
A typical pharmaceutical production handles numerous work flow activities like mana...
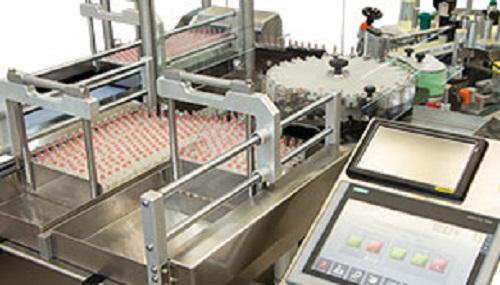
Pharmaceutical rotary labeling machine for vials
Small, cylindrical-shaped glass bottles or vials are mainly used for vacc...
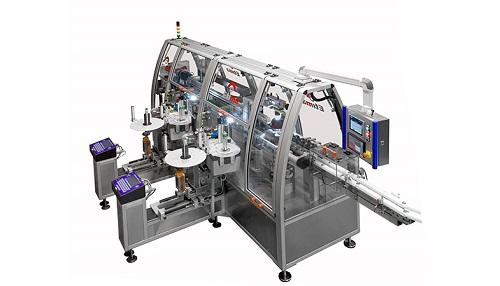
Labeling machine for BFS containers
The pharmaceutical sector is unquestionably one of the major industries that rely on th...
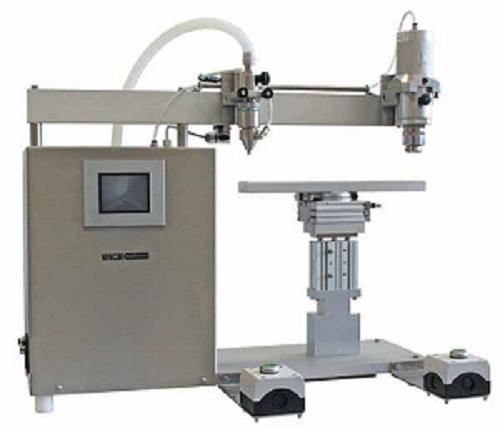
Entry-level filler for large-volume parenterals
Large volume parenterals are unit-dose containers that are larger than 100...
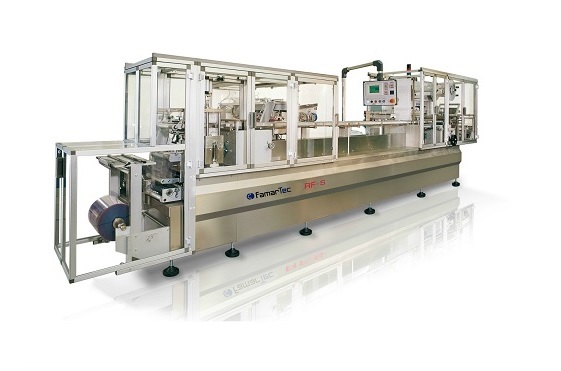
Packaging machine for syringes in trays
Pre-dosed syringes are rapidly becoming the method of choice for the delivery of in...
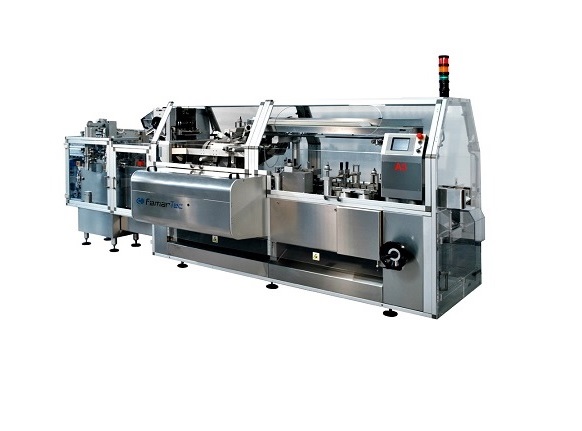
Continuous pack cartoner
High volume automatic cartoning is vital for large scale production of cosmetic or pharmaceutical pr...
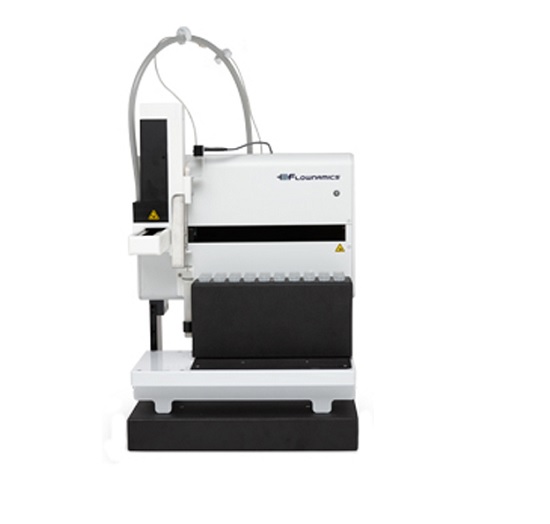
Online fraction collector for offline bioprocess analysis
Many bioprocesses require offline analysis of samples to monit...
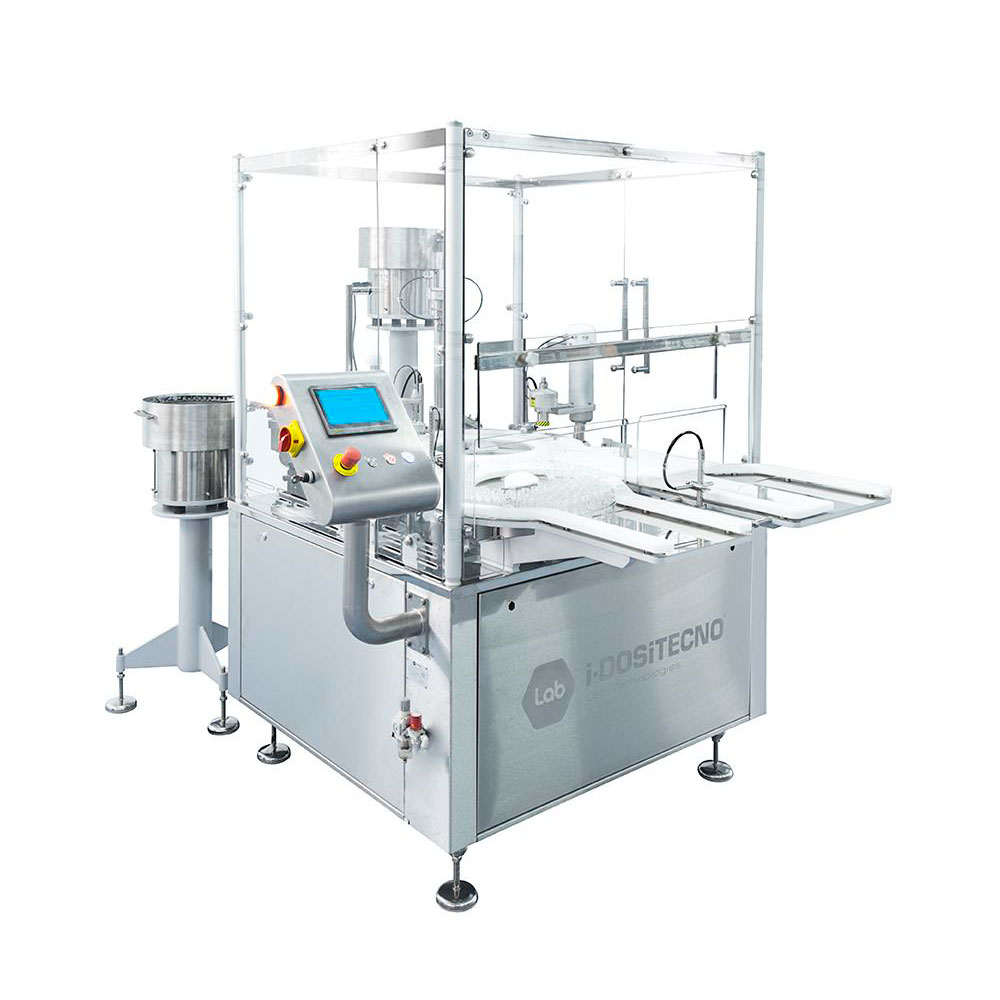
Start-up sterile filling line for injectables
For smaller-scale production of vials and syringes for the injectables marke...
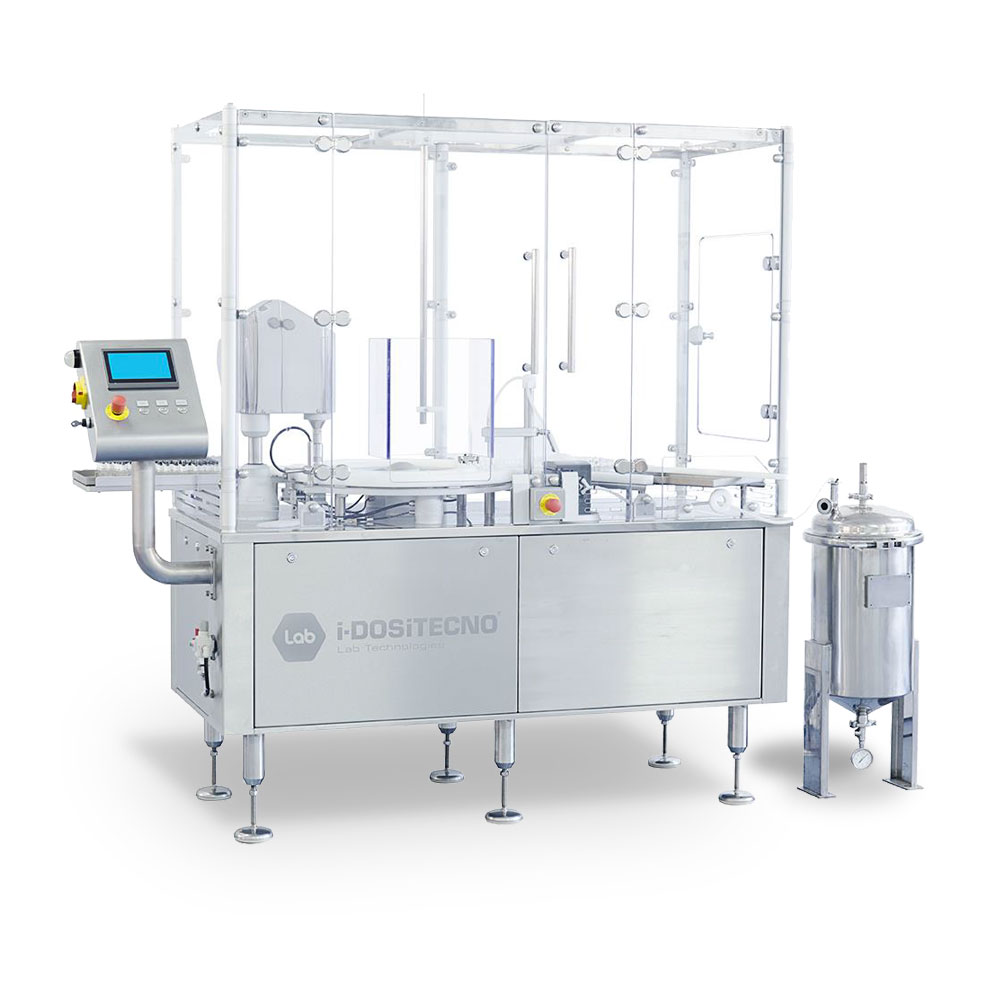
Table top sterile filling line for injectables
Where a compact solution is required for filling vials for the injectables ...
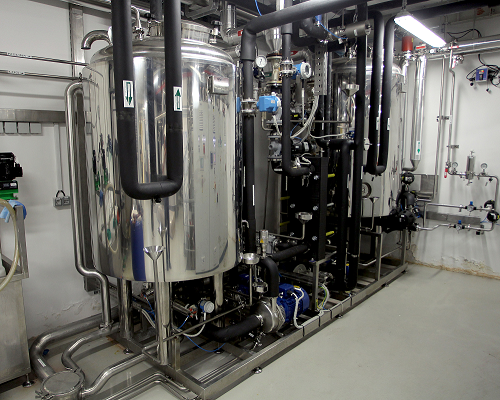
Cleaning and sterilization systems
An increasingly vital part of high quality pharmaceutical production is a dedicated Clea...
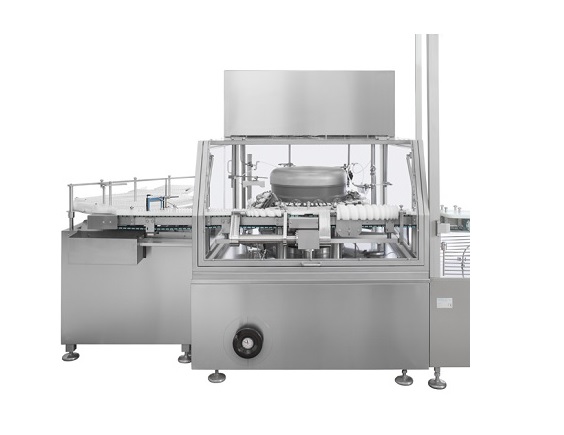
Rotary vial washing machine
When washing vial, ampoules, or cartridges for pharmaceutical production there is often a trade-...
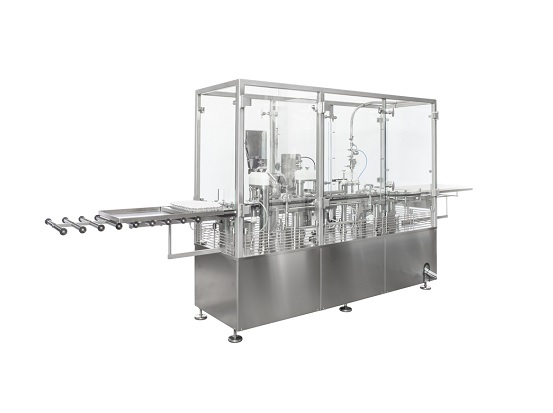
Industrial vial capping machine
The high capacity production of pharmaceuticals delivered in vials and cartridges requires a...
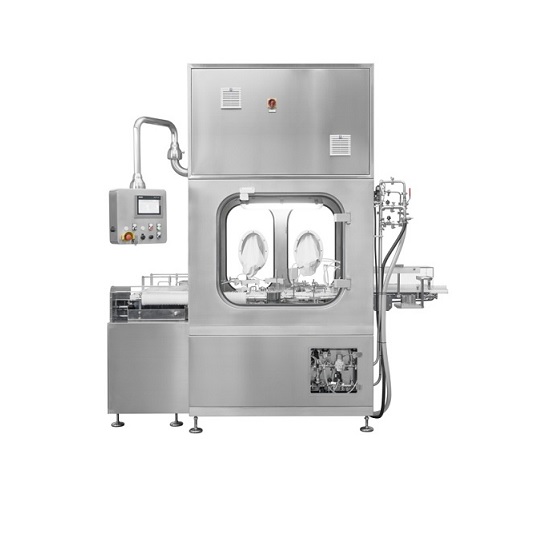
External vial washing machine
Exterior washing solutions for vials often suffer from high water consumption and low throughp...
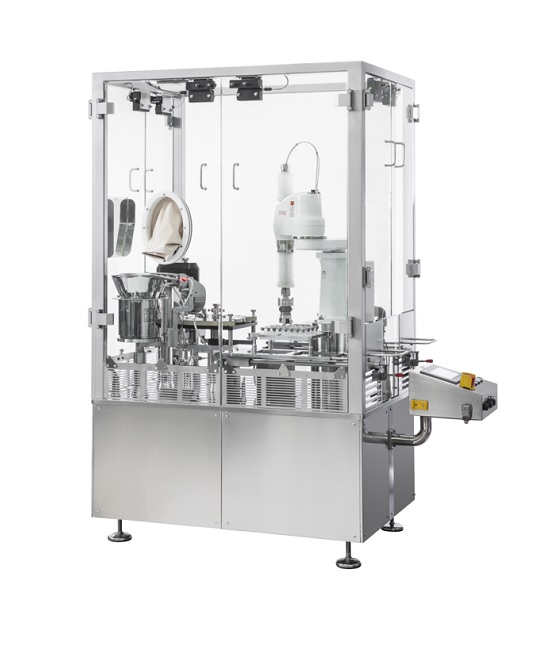
Aseptic vial cap sealing machine
Aseptic production methods are at the heart of the latest development in pharmaceuticals in...
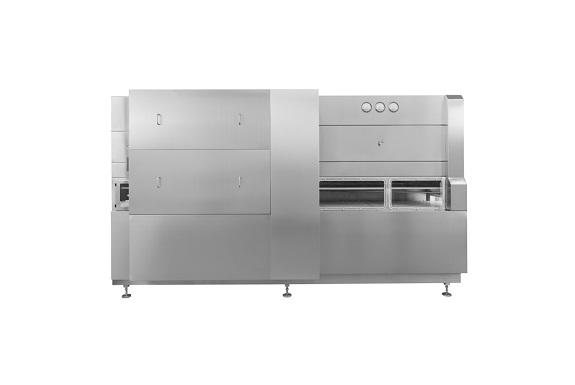
Vial sterilization tunnel
Sterilization of vials, ampoules and syringes before filling is a vital step in the production of ...
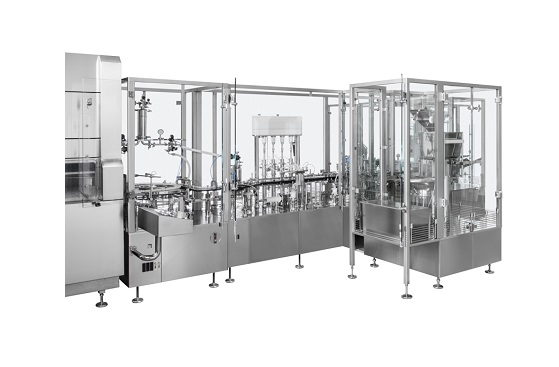
Vial filling machine
The volume filling of vials, cartridges and syringes is a vital part of the production of a wide range o...
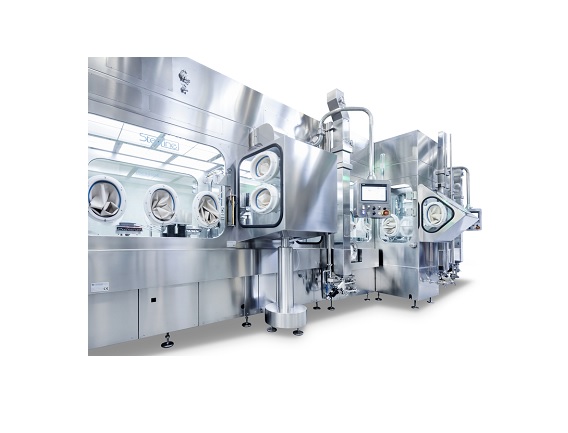
Aseptic automatic vial filling machine
Current and future developments in pharmaceuticals increasingly rely on aseptic prod...
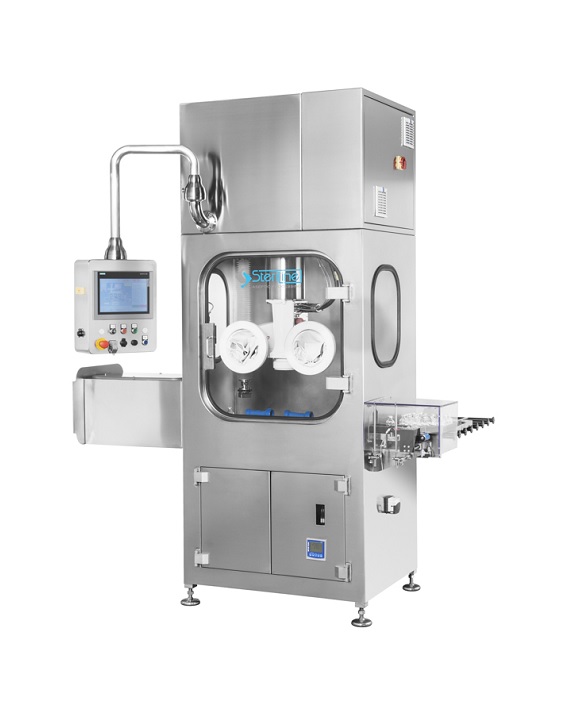
Aseptic automatic vial washing machine
The production of the latest high value pharmaceuticals often requires aseptic handl...
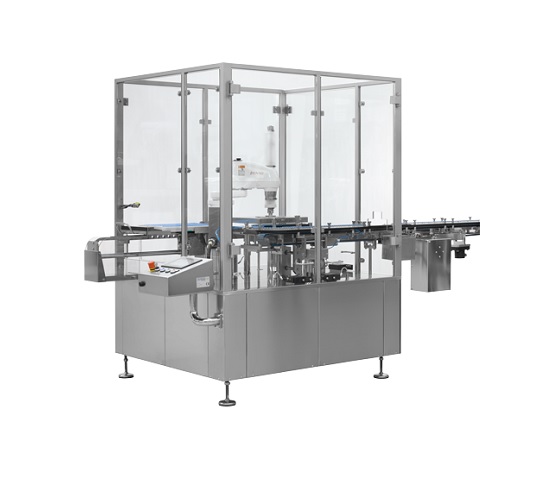
Automatic vial tray loader
In modern pharmaceutical production, end-line processes are often still manual or slow. This can ...
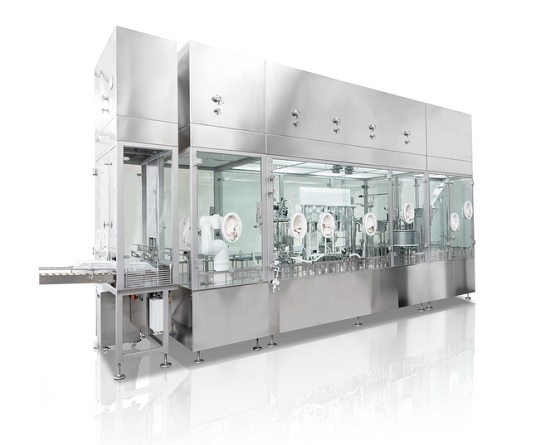
Nested syringe filling machine
Increasingly, pre-sterilized Ready To Use (RTU) nested vials, cartridges and syringes are the...
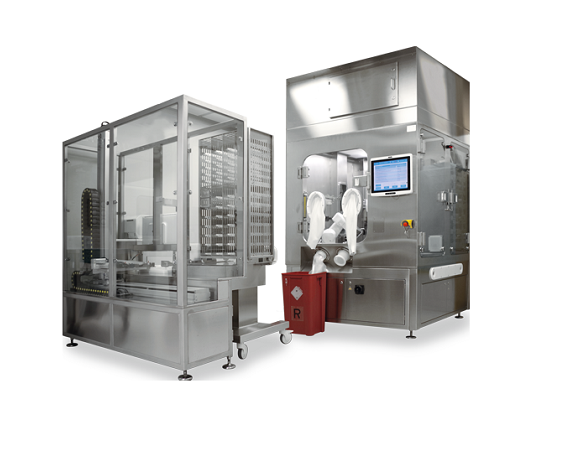
Sterile compounding system
Hospitals and compounding centres have traditionally used manual aseptic compounding processes. A...
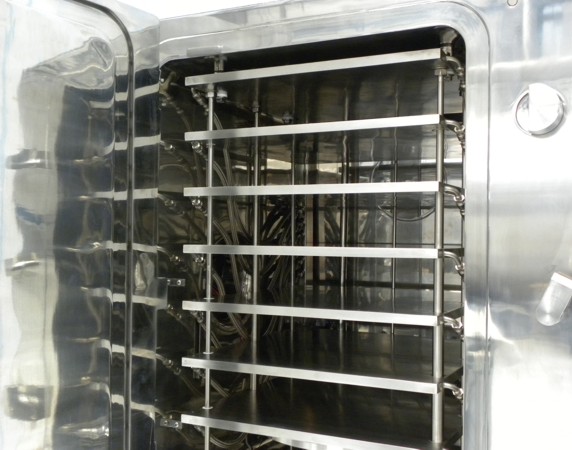
GMP laboratory freeze dryer
Freeze dryer designed for aseptic and small-scale production of high-value products.
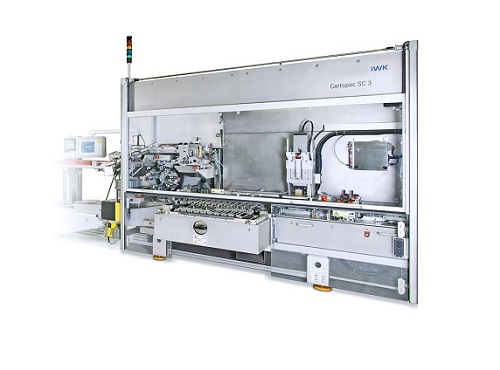
High-capacity horizontal cartoner for pharma and cosmetics appliances
Cartoners take carton blanks which are formed and...
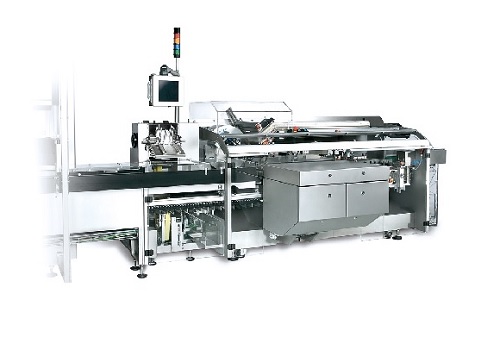
Pharmaceutical and cosmetic industry products cartoner
A large number of cosmetic and pharmaceutical products are packed ...

Horizontal cartoner for pharma and cosmetics
Most pharmaceutical and cosmetics products are packed in cardboard cartons fo...
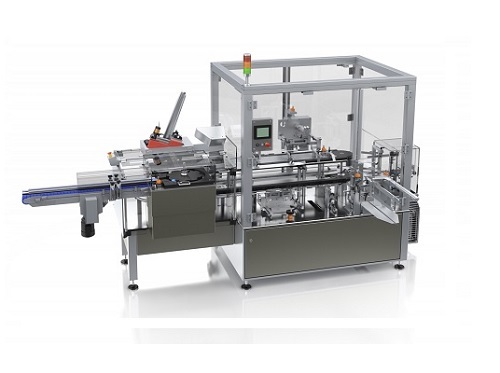
High capacity cartoner for pharmaceutical applications
Many pharmaceutical products are packed in protective and decorati...
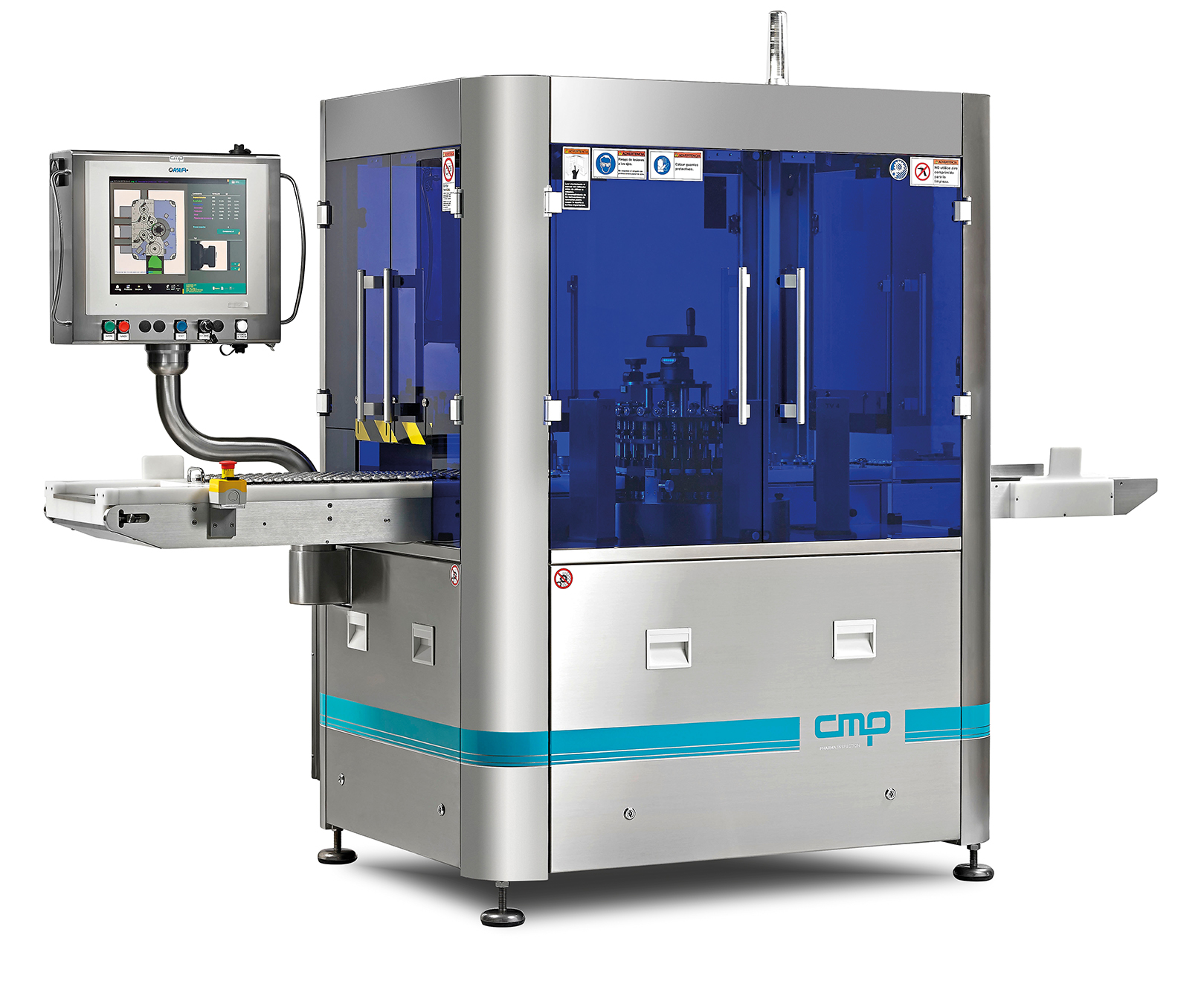
Flexible automatic inspection machine for ampoules, vials, cartridges
If you are looking to improve the efficiency of y...

Flexible automatic inspection machine for syringes
Manufacture of pre-filled syringes requires the highest quality inspec...
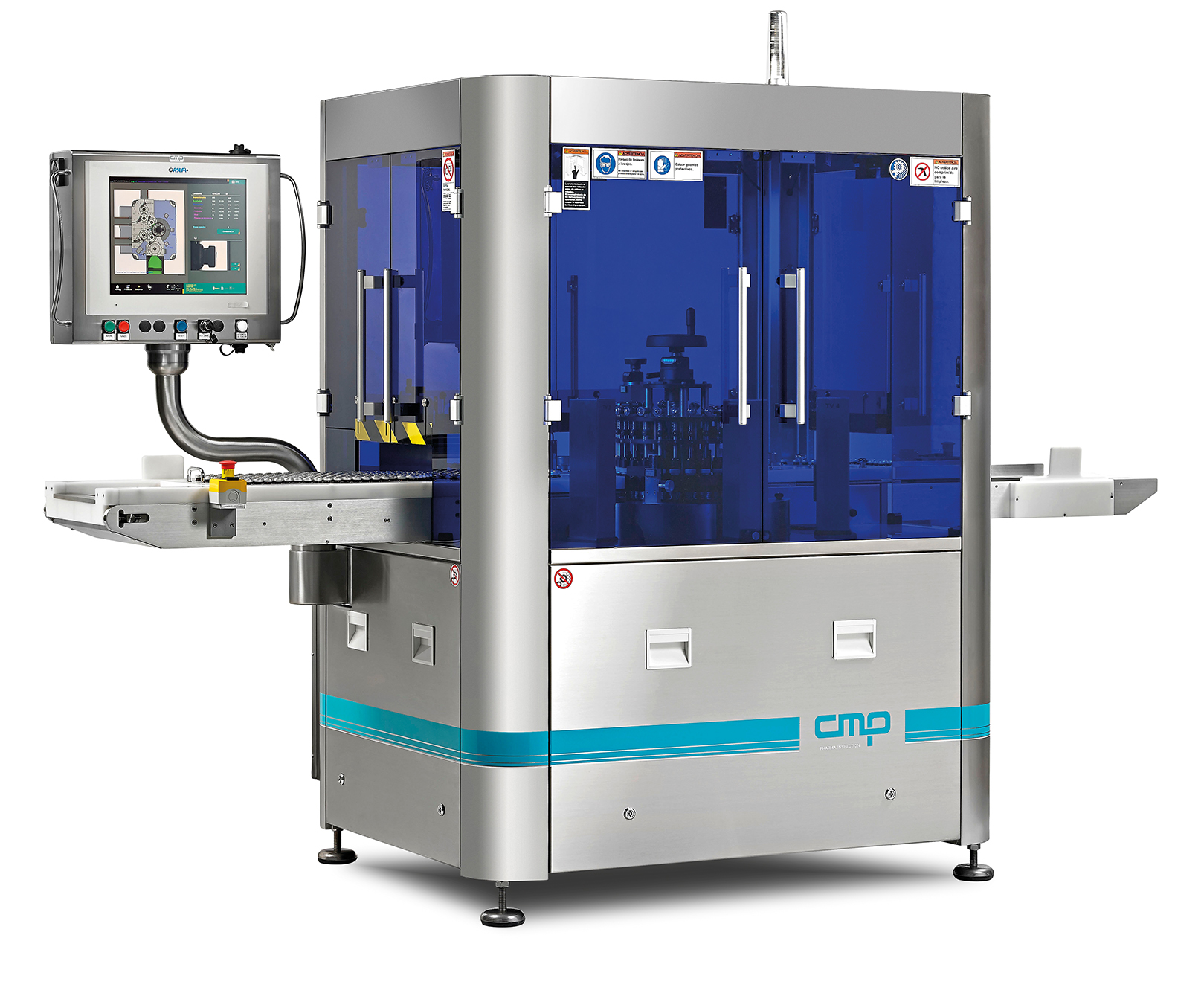
Small automatic inspector for ampoules, vials, or cartridges
Inspect small batch production of ampoules, vials, or cartr...
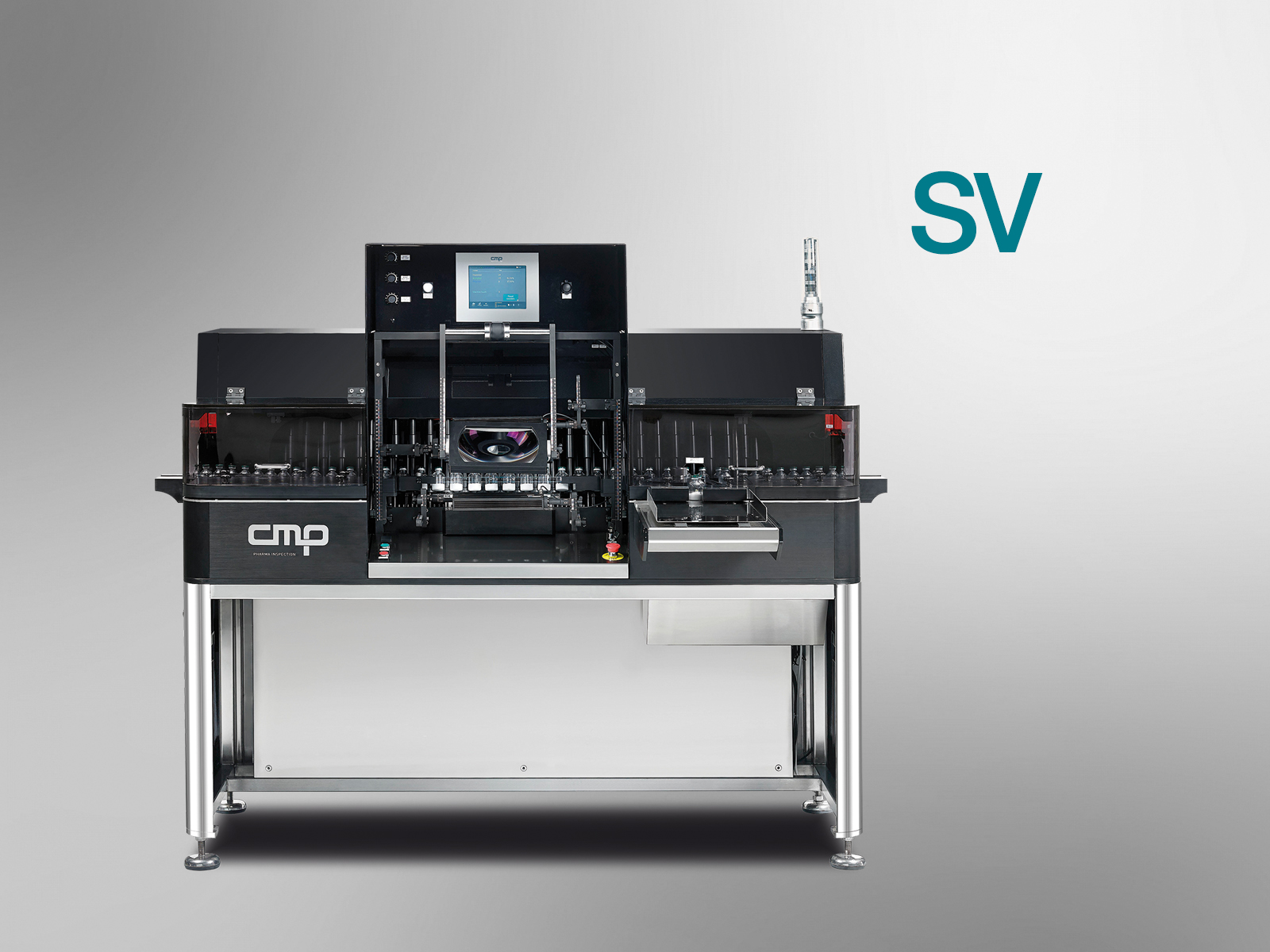
Semi-automatic inspection machine for ampoules, vials or cartridges
If you need to increase the efficiency of your manu...
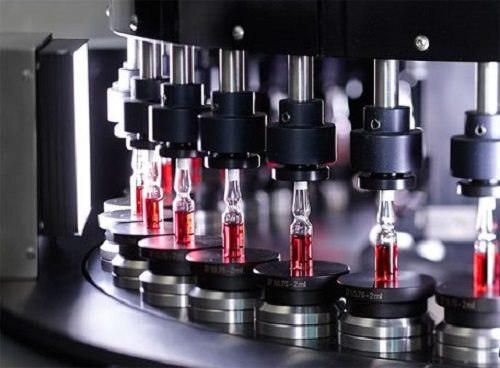
Visual and HVLD inspection for ampoules, vials and cartridges
Do you need to improve the efficiency and capability of yo...
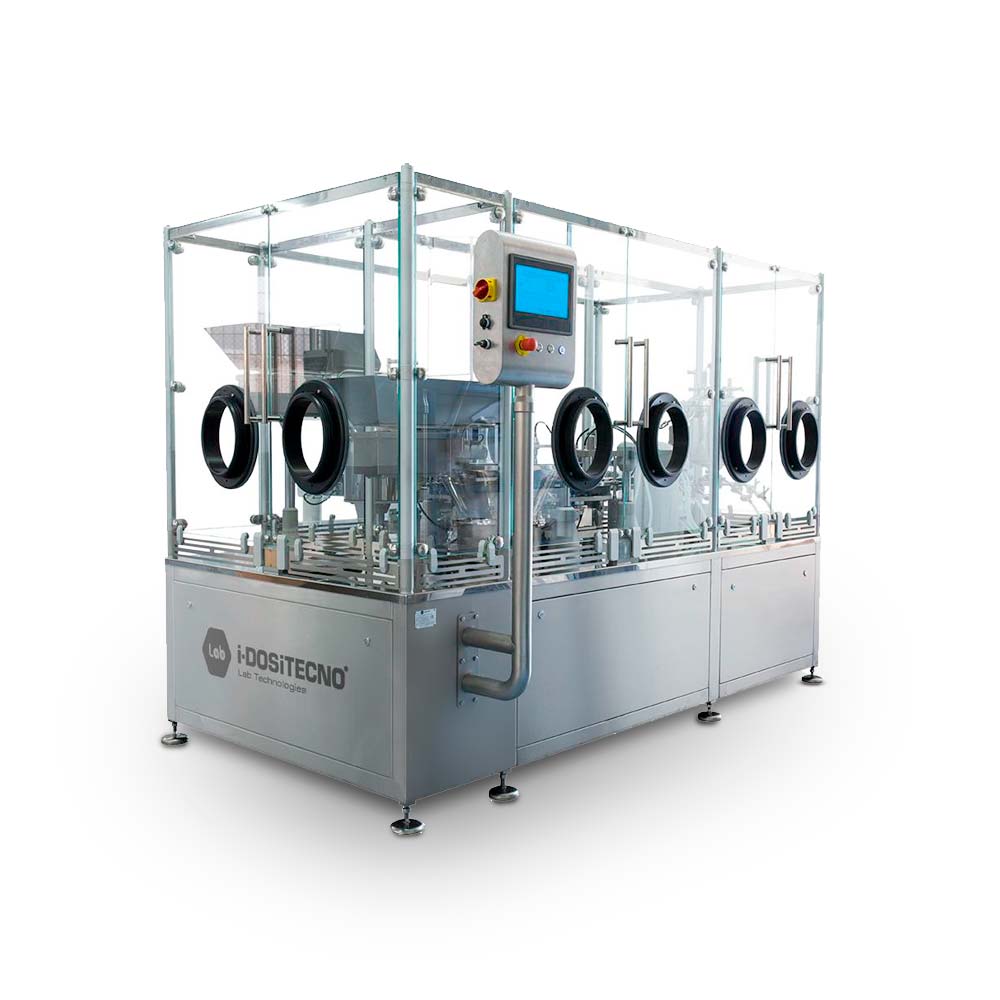
Sterile filling line for injectables
Sterile filling of liquids and powders for the pharmaceutical and cosmetic industries ...
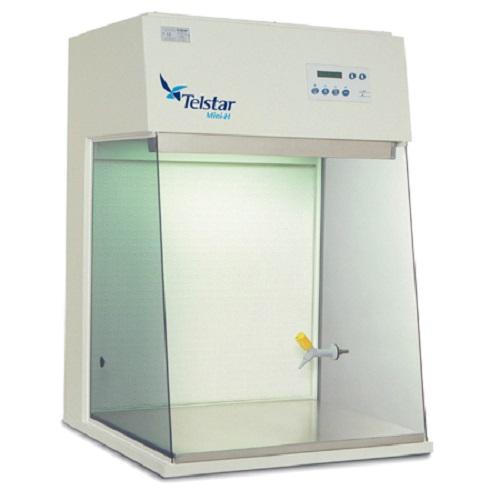
Compact horizontal laminar flow bench
HEPA filtered horizontal laminar airflow (cross-flow) creates an optimized free space...
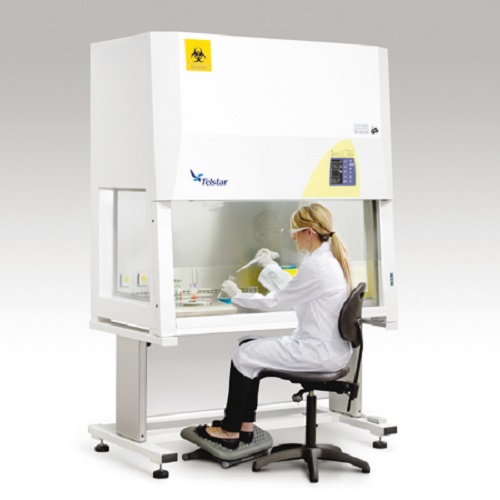
Microbiological safety cabinet class II
This handy device offers the most advanced features in product-operator protection ...
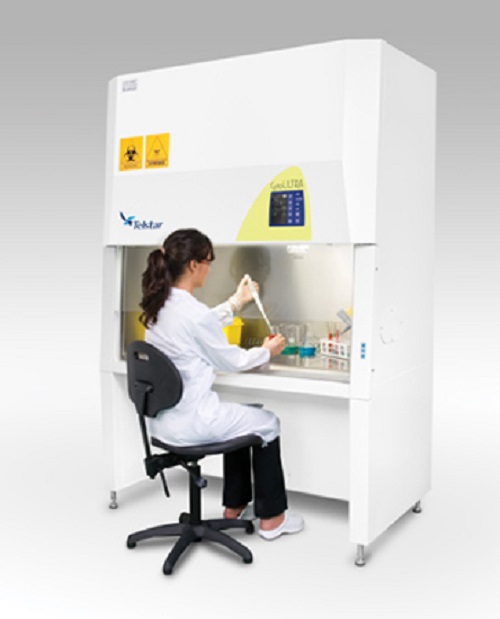
Biosafety cabinet class II for cytotoxic medicines
For the manipulation of hazardous substances utilized during the prepa...
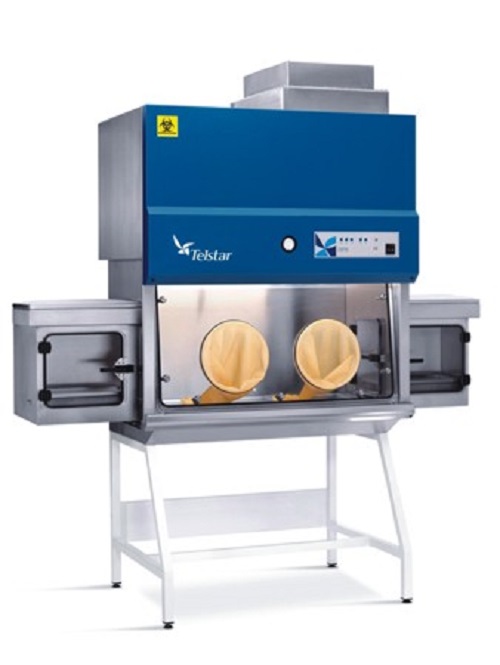
Positive pressure isolator
Ideal for products which have no biological risk but require high sterile conditions.
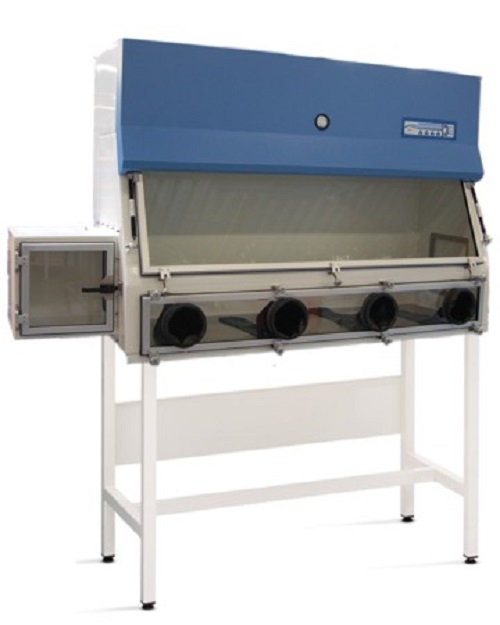
Biological safety cabinet class III
Specially designed for the handling of microbiological agents, when working with indige...
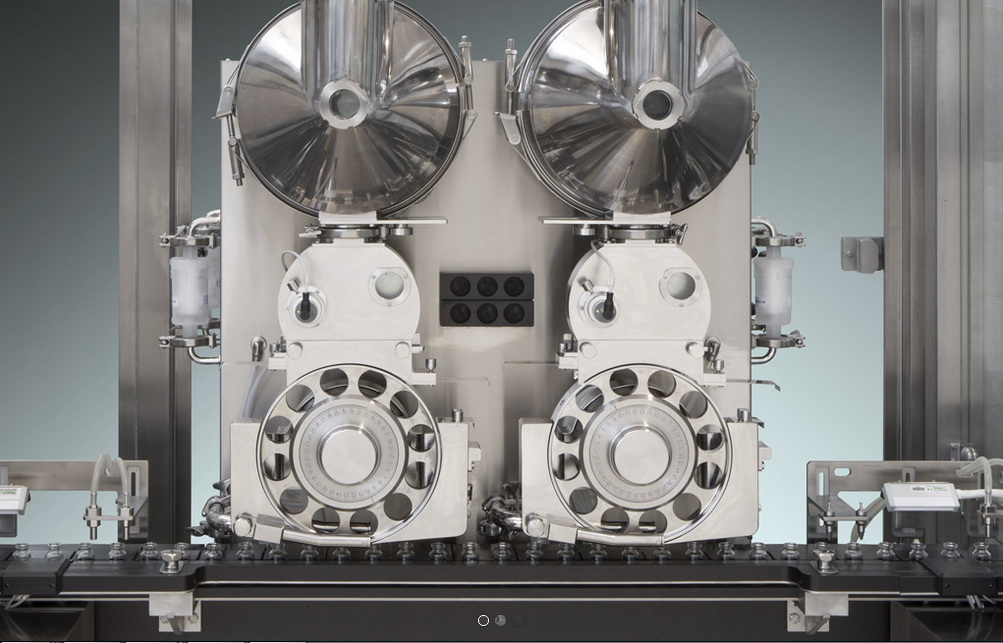
High-speed aseptic injectable vial filling machine
Fill up to 24,000 vials per hour with pharmaceutical powders or liquid...
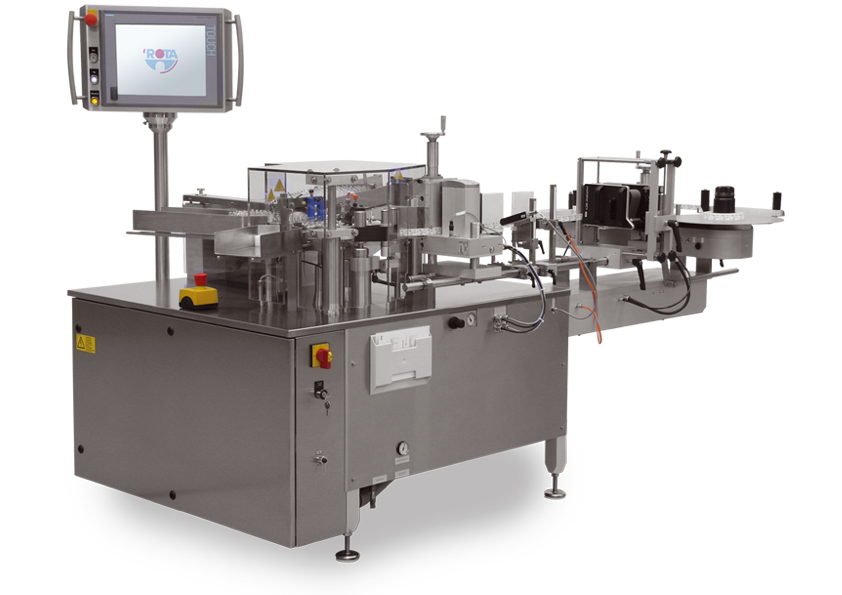
Labeling machines for pharmaceutical bottles
Labels for ampoules, vials and bottles are typically applied at the end of th...
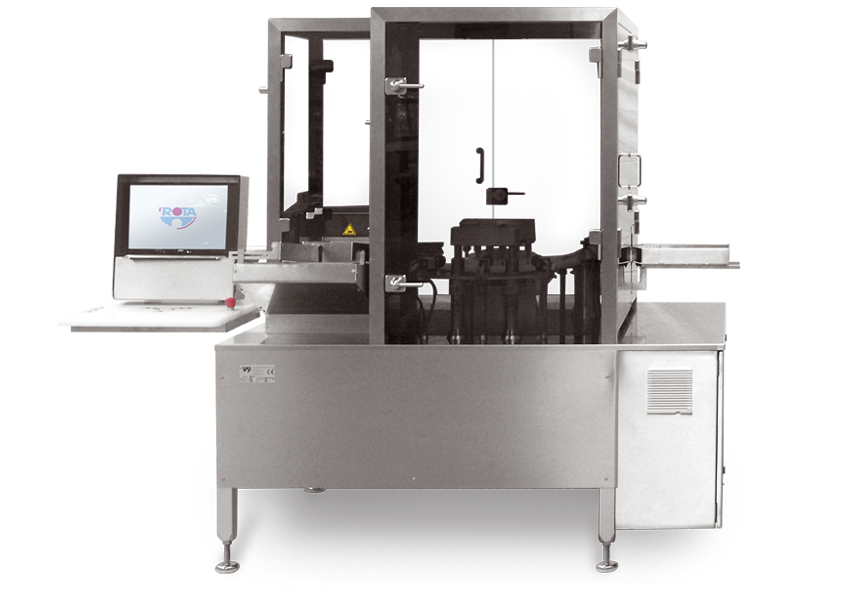
Pharmaceutical bottles inspection machine
For the visual inspection of small to medium batch-sizes of vials, ampoules or b...
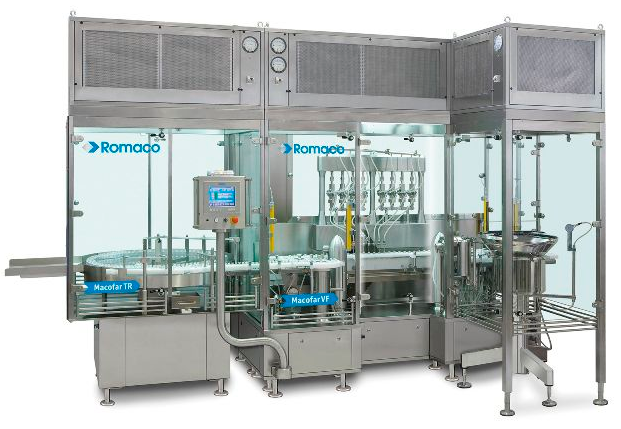
Aseptic liquid filler for vials
Compact modular aseptic filler of vials with parenteral medicines and freeze-dried products.
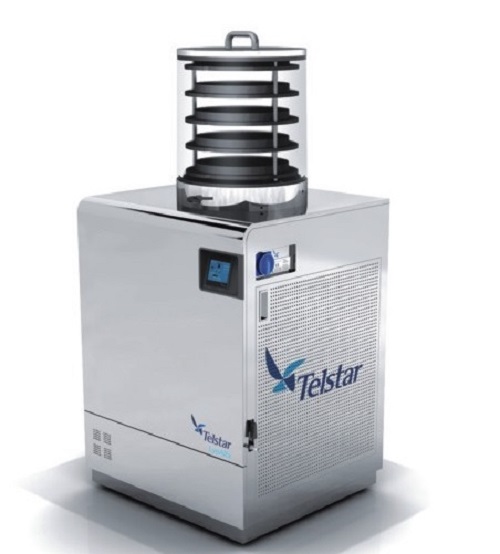
Compact laboratory freeze dryer
Particularly suitable for research centers requiring greater freeze drying capacity. Some of...
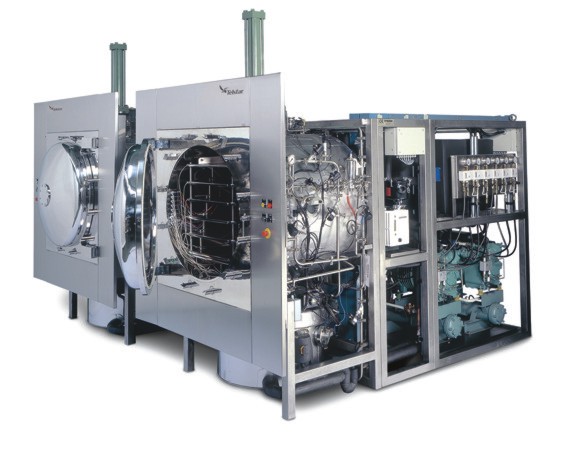
GMP freeze dryer
Designed to perform clinical trials, pilot, and small scale or large scale industrial drying processes, in ac...
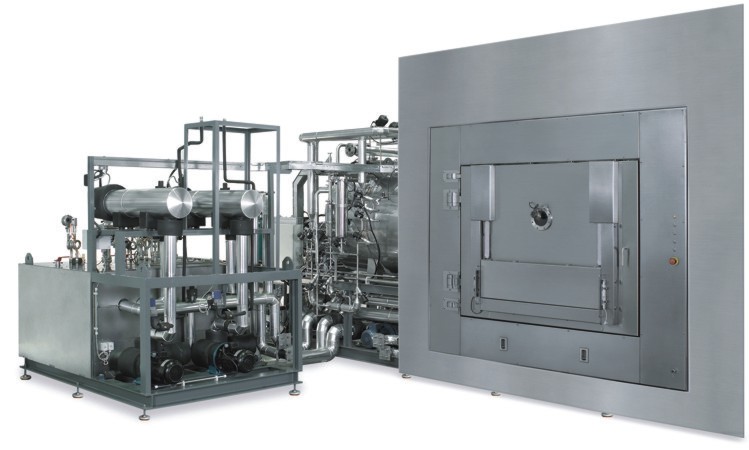
Custom engineered freeze dryer
For either bulk format or liquid in vials, ampoules or syringes, the Lyomega units are design...
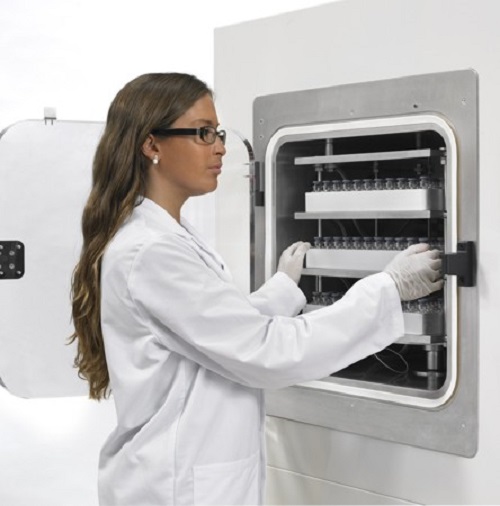
Pilot freeze dryer for scale up
Designed for biological, pharmaceutical and food products formulation and “scale up...
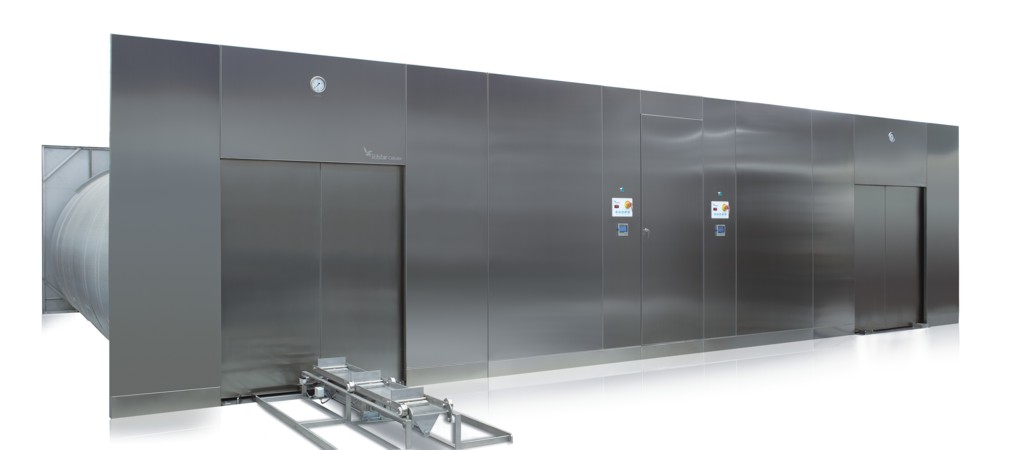
Superheated water shower autoclave
Specially designed for sterilizing large batches of parenteral solutions.
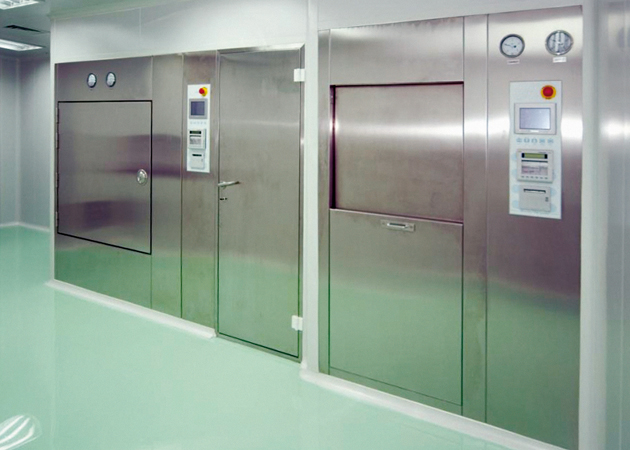
Dry heat depyrogenation oven
Specially designed for the drying and sterilization of glass containers, vials or ampoules, and...
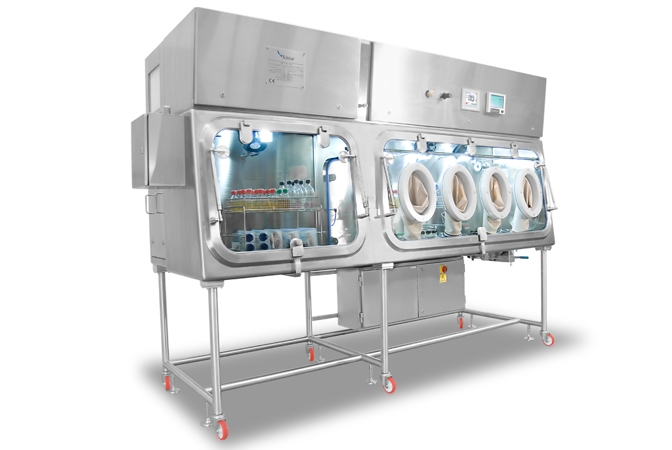
Sterility test isolators
Designed to avoid this risk and protect the product from both the process and externally generated f...
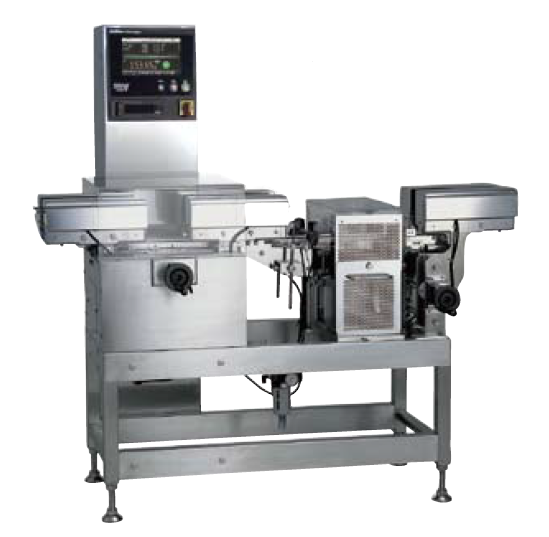
Small bottle checkweigher
Any small-diameter bottle, containing prescription medication or cosmetic applications, can be pro...
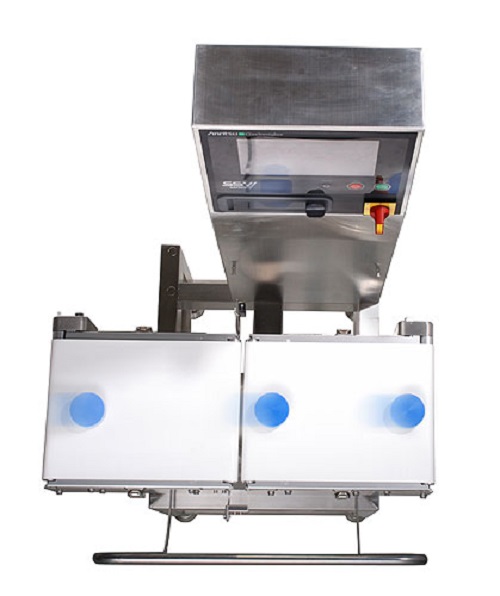
Versatile checkweigher
This Versatile checkweigher is equipped with a highly versatile strain gauge load cell. It is also sui...