High temperature bottom loading furnace for sintering zirconia
Achieve precise sintering of zirconia dental crowns with uniform heating and easy sample loading, all while minimizing the risk of contamination and optimizing temperature control throughout your production process.
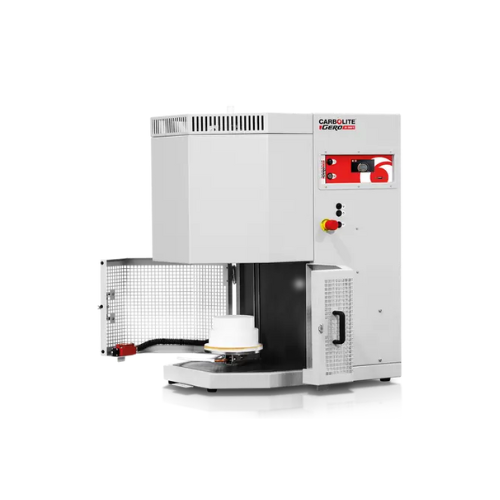
Sintering and Melting Solution for Ceramics and Glass
Carbolite Gero’s BLF 17/3 is an electrically operated high-temperature bottom loading furnace designed for precision in ceramic and glass processing. Unique for its electrically operated elevator hearth, it facilitates easy sample loading and achieves uniform heating with elements embedded in all chamber walls, reaching up to 1800°C. This furnace excels in applications like zirconia sintering and high-performance ceramic manufacturing, producing zirconia dental crowns and specialty glass products with precision due to its excellent temperature uniformity and rapid heat cycling capabilities. The programmable EPC3016P1 controller allows for batch and programmable operations, ensuring integration and full automation within your production line. It leverages energy efficiency through its silicon carbide and molybdenum disilicide heating elements across different models. A safety interlock hearth cage and overtemperature protection enhance operational safety, while customization options such as modified hearths and digital programming interfaces offer tailored solutions. With Ethernet communication support and optional enhancements like radiation shutters, the BLF 17/3 is built for advanced and flexible processing in modern laboratories and manufacturing facilities.
Benefits
- Ensures precise temperature control for high-quality sintering and melting of ceramics and glass.
- Increases operator safety with protective hearth cages and overtemperature safeguards.
- Enhances production efficiency with rapid heating and cooling cycles to minimize process time.
- Supports flexible processing with programmable operations and Ethernet connectivity for streamlined automation.
- Customization options allow integration into specialized production environments, enhancing operational versatility.
- Applications
- Glass materials, Dental crowns and frameworks, High-performance ceramics, Modified atmospheres, Zirconia sintering
- End products
- Specialty glass products, High-performance ceramic components, Heat-resistant ceramic tiles, Glass vials, Zirconia dental crowns, Zirconia dental frameworks
- Steps before
- Molding, Casting, Forming
- Steps after
- Cooling, Inspection, Assembly
- Input ingredients
- zirconia dental crowns, zirconia frameworks, high performance ceramics, glass, inert gases, reactive gases, modified atmospheres
- Output ingredients
- sintered zirconia dental crowns, sintered zirconia frameworks, sintered high performance ceramics, melted glass
- Market info
- Carbolite Gero is renowned for designing and manufacturing high-temperature laboratory and industrial furnaces and ovens, offering expertise in heat treatment solutions, with a reputation for quality, reliability, and precise thermal processing across various industries.
- Maximum Operating Temperature
- 1600°C, 1700°C, 1800°C
- Chamber Capacity
- 3 to 21 litre
- Controller Type
- Programmable EPC3016P1
- Heating Elements
- Silicon carbide / Molybdenum disilicide
- Temperature Uniformity
- Excellent due to hexagonal chamber
- Overtemperature Protection
- Included
- Heating,Cooling Cycle
- Rapid via elevator hearth
- Ethernet Communication
- Available
- Safety Interlock
- Hearth cage with safety interlock
- Working mechanism
- Electrically operated elevator hearth
- Heating mechanism
- Elements in all six side walls
- Automation level
- Programmable EPC3016P1 controller
- Temperature uniformity
- Hexagonal chamber design
- Loading process
- Bottom loading with elevator hearth
- Overtemperature protection
- Yes (to protect load or furnace)
- Rapid heating,cooling cycles
- Achieved by raising, lowering the hearth
- Safety feature
- Hearth cage with safety interlock
- Atmosphere control
- Options for modified atmospheres
- Abrasion resistance
- High, suitable for zirconia
- Corrosive resistance (e.g. acids)
- Suitable with protective coatings
- Temperature compatibility
- Up to 1800°C
- Contamination prevention
- Silicon carbide elements prevent discoloration
- Gas compatibility
- Modified inert and reactive atmospheres
- Density/particle size
- Uniform heating in hexagonal chamber
- Use Case
- Sintering, Melting, Modified Atmospheres
- Sample Heating Zone
- Uniform due to six side wall elements
- Machine Footprint
- Customizable
- Hearth Type
- Elevator Hearth
- Chamber Shape
- Hexagonal
- Load Capacity
- 3 to 21 litres
- Discharge Method
- Elevator-based
- Control Panel Type
- Programmable EPC3016P1 controller
- Heating Element Type
- Silicon carbide or molybdenum disilicide
- Digital Communication Options
- Ethernet communications
- Programmability
- Multisegment programmers
- Data Logging
- Available with digital communication options
- Introduction of Gases
- Modified hearth for inverted crucible
- Radiation Protection
- Radiation shutter
- Cage Type
- Hearth cage with safety interlock
- Temperature Protection
- Overtemperature protection
- Custom Modifications
- Thermocouple or stirrer through chamber roof
- Rotating Hearth
- Available as a customized option
- Element Protection
- Plasma sprayed alumina protection tube