Linear vial washer for injectable drug containers
Achieve sterile conditions by efficiently removing contaminants from various container types, ensuring your injectable drug production maintains high purity standards with customizable high-pressure washing cycles.
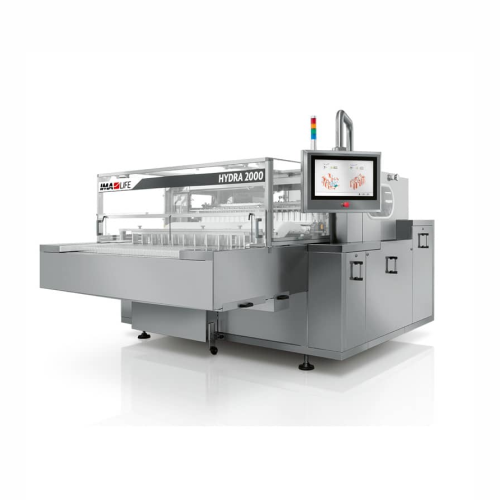
Decontaminates and Sterilizes Pharmaceutical Containers
The HYDRA Linear Vial Washer from IMA Group is engineered for the rigorous demands of the pharmaceutical and biotech industries. This cutting-edge washer excels in decontaminating and sterilizing vials, bottles, plastic containers, and even oval containers, ensuring a 3-log endotoxin reduction for terminal sterilization applications. Using a linear washing system, it performs customized washing cycles tailored to container materials and product needs. Capable of processing thousands of containers per hour, the HYDRA series features vacuum-assisted unloading for high-speed stability and automatic integration with existing production lines. Its special upper guide rail enables high-pressure washing without container vibration or movement, while complete segregation of process, circuit, and mechanical areas eliminates cross-contamination risks. Equipped with an ultrasonic bath unit, the HYDRA ensures thorough internal and external washing, followed by efficient drying. Designed to comply with cGMP guidelines, it incorporates a recycled water loop, significantly reducing Water for Injection (WFI) consumption while maintaining cleaning performance. Available with variable configurations, this machine supports different container sizes through interchangeable basket options, meeting diverse production requirements.
Benefits
- Maximizes sterility and purity in pharmaceutical production with 3-log endotoxin reduction.
- Minimizes cross-contamination through complete process circuit segregation.
- Enhances operational efficiency with automated high-speed and continuous processing.
- Reduces Water for Injection (WFI) consumption through an innovative recycled water loop.
- Complies with cGMP standards, ensuring quality and regulatory adherence.
- Applications
- Pharmaceutical bottles, Plastic containers, Sterile preparations, Pharmaceutical vials, Injectable drugs, Oval containers
- End products
- Antibiotic vials, Dental anesthesia cartridges, Vaccine vials, Chemotherapy drug bottles, Pre-filled syringes, Plastic infusion bags, Sterile saline bottles, Insulin ampoules
- Steps before
- Container decontamination, Container feeding, Container depacking
- Steps after
- Sterilization, Packing, Terminal sterilisation, Endotoxin reduction
- Input ingredients
- vials, bottles, plastic containers, oval containers
- Output ingredients
- washed vials, washed bottles, cleaned containers, decontaminated containers
- Market info
- IMA is known for its expertise in manufacturing automated packaging machines and solutions, particularly for the pharmaceutical, cosmetics, food, tea, and coffee industries, offering innovative, high-quality equipment and comprehensive customer service.
- Compliance
- cGMP
- Container Size Compatibility
- Vials/Bottles of all sizes
- Material Compatibility
- Glass, plastic, oval containers
- Endotoxin Reduction
- 3-log for terminal sterilisation
- Water Usage
- Recycled water loop
- Production Capacity
- 3, 600–39, 600 pcs/hour
- Washing Pressure
- High pressure without vibration
- Automation Compatibility
- Possible direct connection to automatic feeding systems
- Technical Feature
- Vacuum-assisted positive unloading
- Container Handling
- No vial breakages
- Ultrasonic Cleaning
- Ultrasonic bath unit available
- Cycle Customization
- Thousands of customised washing cycles
- Working mechanism
- Linear washing
- Container types processed
- Vials, bottles, plastic, oval containers
- Customised washing cycles
- Available
- Segregation in design
- Complete segregation between process, circuit, and mechanical areas
- Container unloading method
- Vacuum-assisted positive unloading
- Level of automation
- Possible direct connection to automatic container feeding systems or conveyors
- Dripping prevention
- Positive discharge prevents dripping of contaminated water
- Endotoxin reduction capability
- 3-log reduction for terminal sterilisation
- Cleaning performance
- Recycled water loop for high cleaning performance
- Density/particle size
- 0.5–2.5 g/cm³ / 50–1000 µm
- Container type
- Vials / Bottles / Plastic / Oval Containers
- Container size
- All sizes
- CGMP Compliance
- Yes
- FDA Materials
- Yes
- Machine footprint
- Specified according to model
- Basket size
- Varies with model type A, B, C, D, I
- Maximum height
- 66 mm (depending on model type)
- External diameter
- 25 mm to 80 mm (depending on model type)
- Minimum mouth diameter
- 14 mm to 50 mm (depending on model type)
- Control panel type
- Not specified
- Discharge method
- Vacuum-assisted positive unloading
- Container type
- Vials, bottles, plastic, oval containers
- Ultrasonic bath unit availability
- Available
- Special upper guide rail
- Prevents vibration or movement during washing
- Container Size Compatibility
- All sizes
- Plastic and oval upon request
- Washing Cycle Customization
- Thousands of customized cycles
- Production Plant
- IMA Life
- Guide Rail Design
- Special upper guide rail for high-pressure washing without vibration
- Connection Options
- Direct connection to automatic container feeding systems
- Unloading Assistance
- Vacuum-assisted positive unloading
- Ultrasonic Bath Unit
- Available for containers
- Recycled Water Loop
- For WFI consumption saving