Ultra-clean FFS machine for yoghurt in cups
Dairy products like yoghurt are very susceptible to spoilage. Yeasts and moulds are prone to develop due to contamination in a filling operation or packaging process. To prevent contamination, a machine needs to have a decontamination treatment to sterilize the packaging material. A protected environment ensures a good microbiological quality of the air during filling process.
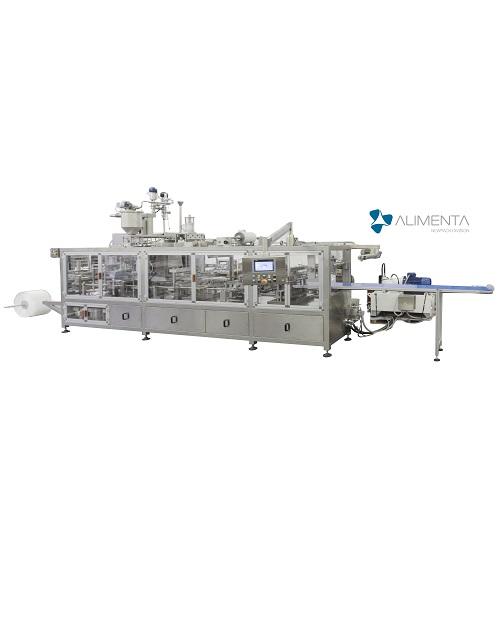
Sterilizing lid film using a peroxide bath before sealing
The Thermoforming machine designed by Newpack, (Alimenta Group), is a horizontal Form-Fill-Seal machine that forms a container, fills it with a product and then seals it, in one single process. The machine can handle different foods, from liquids to semi liquids with yoghurt being one of the most common application.
The Thermoforming machine is adjusted according to the product to be processed and its shelf life. Newpack customises the shape and size of the cup according to manufacturer’s requirements. For products such as desserts and yoghurt which need a longer shelf life, an Ultra-Clean version is recommended.
Starting from a reel of thermoformable plastic film, Newpack Thermoforming machine forms the bottom of the container according to a pre-established shape, by heating the plastic film and shaping it through a mould. At this point, the cups are automatically filled by a cup filling station. Based on the product to be packed and the shape of the cup, the filling system type changes. Afterwards the machine applies a lid on each cup by heat sealing it. When cups arrive to the cutting station, they are cut and separated. The Ultra-clean version is provided with a tunnel with an overpressure of sterile air. Moreover, a tank filled with peroxide solution is used to sanitize the thermoformable lid film. This process happens before the sealing stage.
All machine components are in compliance with CE regulations and other hygiene standards. Machine capacity depends on the product and the volume of the cup; generally speaking, 9,000 is the minimum production capacity.
Benefits
- Typically for primary packaging of yoghurt
- A CIP and SIP system to meet hygiene standards
- Wide range of cup sizes and shapes
- A 3 in 1 machine for forming, filling and sealing
- Work cycles completely managed from operator panel