Liquid additive dosing system for industrial mixers
Achieve unparalleled precision in liquid ingredient integration with a system designed to eliminate cross-contamination and ensure seamless dosing accuracy, supporting efficient and reliable production across various formulations.
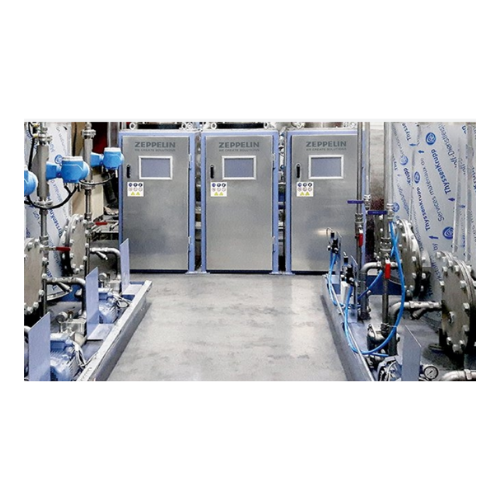
Doses and Injects Liquids with Precision
Zeppelin Systems’ Liquid Dosing System (LDS) revolutionizes precise liquid dosing across diverse industries, including rubber, food, plastics, and chemicals. Engineered for closed-system operations, it effectively eliminates cross-contamination while allowing simultaneous injection of multiple liquids through a modular setup. The LDS integrates seamlessly into existing plants, offering a fully automatic solution with complete traceability of raw materials. With a versatile dosing capability for high- and low-viscosity liquids, it features a unique six-head injection valve, ensuring efficiency and reliability. Constructed for durability, it supports operations up to 80°C and is available in corrosion-resistant materials. The system complies with stringent industrial standards, enhancing your production line’s safety and dependability.
Benefits
- Ensures process safety and product integrity with a closed-system design.
- Enhances flexibility and scalability with a modular, retrofittable setup.
- Increases formulation accuracy and traceability, improving overall production quality.
- Minimizes contamination risk, securing product purity and compliance.
- Optimizes operational efficiency through fully automatic control and precise multi-liquid dosing.
- Applications
- Liquid formulations, Food industry, Chemical industry, Plastics, Rubber and tire industry
- End products
- Pharmaceutical suspensions, Food additives, Yogurt formulations, Emulsion polymers, Tire rubber compounds, Liquid soap formulations, Bread dough, Acrylic paints, Plastic pellets, Polyethylene films
- Steps before
- Mixing, Ingredient Preparation, Batch Loading
- Steps after
- Formulation Verification, Quality Control, Packaging
- Input ingredients
- high-viscosity liquids, low-viscosity liquids, oils, small ingredients
- Output ingredients
- precise formulation, complete traceability, minimal cross-contamination, optimal process safety
- Market info
- Zeppelin Systems excels in designing and manufacturing high-quality bulk material handling and processing equipment. Renowned for its engineering expertise, the company serves industries including plastics, chemicals, and food, ensuring efficient, reliable, and innovative solutions tailored to customer needs.
- Automation
- Fully automatic
- Temperature control
- Up to 80°C
- Liquid dosing capacity
- Up to 24 or 36 liquids
- Injection capability
- Simultaneous injection of up to 4 liquids
- Valve injection capacity
- Up to 6 oils
- System type
- Closed system
- Modularity
- Seamlessly retrofittable
- Dosing accuracy
- Outstanding precision
- Cross-contamination
- Minimal
- Automation level
- Fully automatic
- Batch vs. continuous operation
- Batch
- Simultaneous liquid injection
- Up to four liquids
- Temperature control
- Up to 80°C
- Closed system dosing
- Yes
- Modular system
- Seamlessly retrofittable
- Cross-contamination prevention
- Minimal
- Dosing cylinder
- Single with multiple injections
- Injection valve
- 6-head
- Density/particle size
- 0.5–2.5 g/cm³ / 50–1000 µm
- Suitable for all mixing types
- Yes
- Machine footprint
- Compact
- Control panel type
- Integrated
- Discharge method
- Closed system
- Modular system
- Seamlessly retrofittable
- Number of liquids handled
- Up to 24 or 36
- Temperature control
- Up to 80°C
- Integration possibilities
- Existing plants retrofitting
- Dosing options
- Up to 24 or 36 liquids
- Temperature control
- Up to 80°C
- Injection head configuration
- 6-head injection valve
- Process safety
- Closed system
- Modular system
- Seamlessly retrofittable