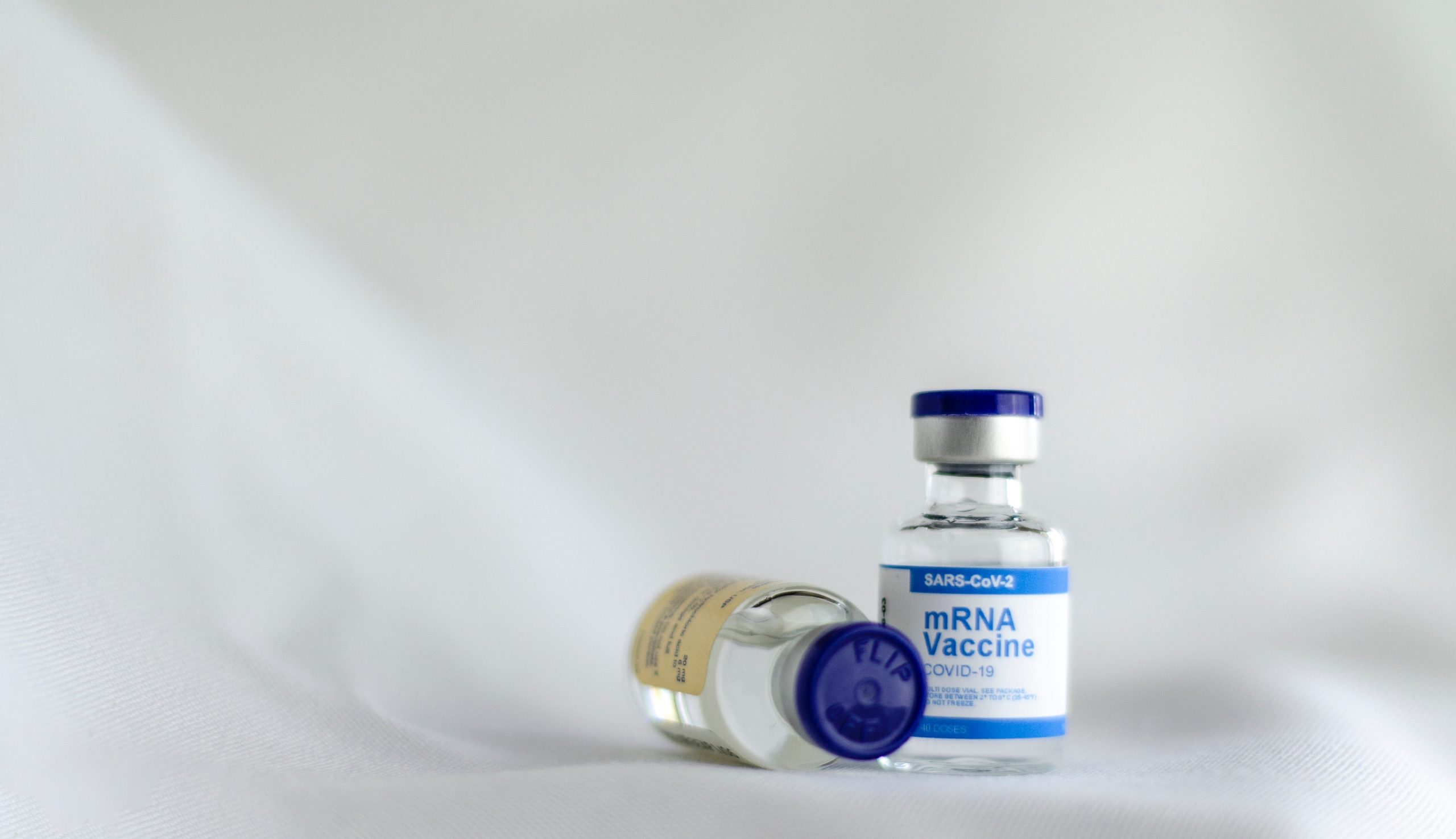
Vaccine Manufacturing Equipment
Find innovative production technology for making vaccines and connect directly with world-leading specialists
Some of the vaccines in use today were originally developed decades ago. But advances in research, expertise and vaccine development equipment provide immunizations from bacterial and viral diseases (antibodies and cell therapy) to more people every year. The Covid 19 pandemic highlights the urgent need to scale up the production of vaccines and ensure an automated as well as reproducible manufacturing environment.
Stories about vaccines
Select your vaccines process
Tell us about your production challenge
Vaccines are over-formulated to protect against potency loss
Vaccines start with the isolation of chemically defined media, but they come into being during formulation. The delicate development process stabilizes the separate components into a uniform mixture and prepares it for batch dosing. Cell cultures are often used in the development as well as formulation of Vaccines and has been that way for decades.
When it comes to producing vaccines, mixtures are typically over-formulated above the required potency. This method lowers yield but compensates for any possible degradation throughout the vaccine’s shelf-life.

Reduce vaccine moisture to max 3% with freeze-drying equipment
The process of lyophilization ensures that your biological formula remains stable along the cold chain. For this reason, freeze-dryers have become critical equipment in modern vaccine production.
Vaccine freeze-drying is a complex procedure involving three major steps. At the freezing stage, the solution solidifies with the formation of crystals. During the dehydration phase in a drying chamber, you subject the material to temperatures not exceeding -50 °C and forces water to sublimate. Finally, another round of drying releases any remaining moisture to between 1% and 3%.
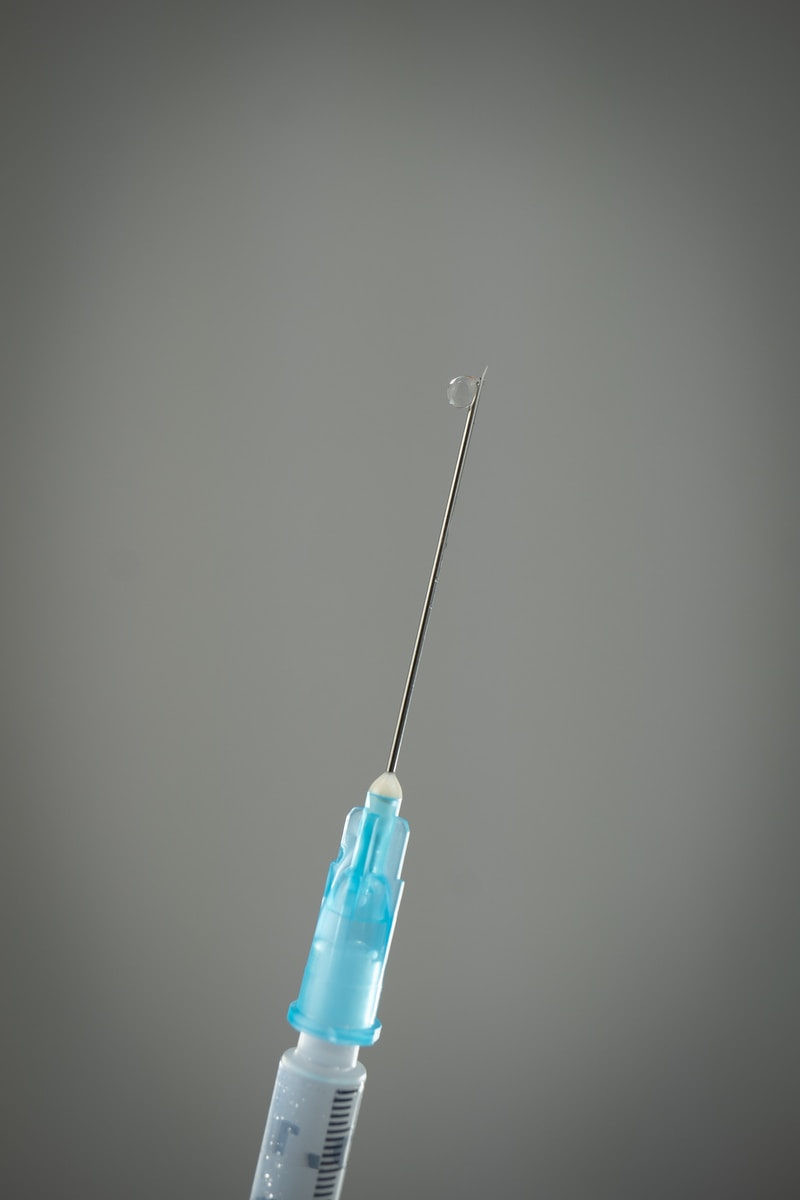
Protect diluent from freezing or heating with cold chain storage
Before clinical trials and before the vaccine enters into the arms of patients, your lyophilized vaccines are reconstituted into liquid solutions using a diluent. World Health Organization guidelines warn that vaccine manufacturing is incomplete without the accompanying diluent.
Sterile water is often used as a diluent, but ingredients may contain a range of other substances such as sodium chloride, xanthan, or calcium carbonate. Whatever the composition, diluents must always be kept at temperatures between +2°C to +8°C.
Chromatography technology and mRNA techniques promise more accessible vaccines
Purification of the reaction mixture remains a challenge for large-scale vaccine development and production. But chromatography is emerging as an ideal purification technique for several biopharmaceuticals. Ligands in the chromatography columns form ‘hooks’ that filter out specific contaminants.
Vaccine manufacturers are taking advantage of this purification technique to reduce vaccine production’s financial and environmental costs. This method is attracting particular interest with the development of mRNA vaccines to combine a relatively simple manufacturing process with the high-yield capabilities of chromatography.
Packaging is a crucial step in vaccine production. This step is often forgotten about but is important in ensuring that the vaccines reach their final destination without getting damaged. But more importantly, safe packing means that the vaccines will reach patients without getting contaminated.
Processing steps involved in vaccines making
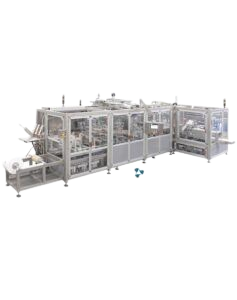
Aseptic filling equipment

Bioreactor systems
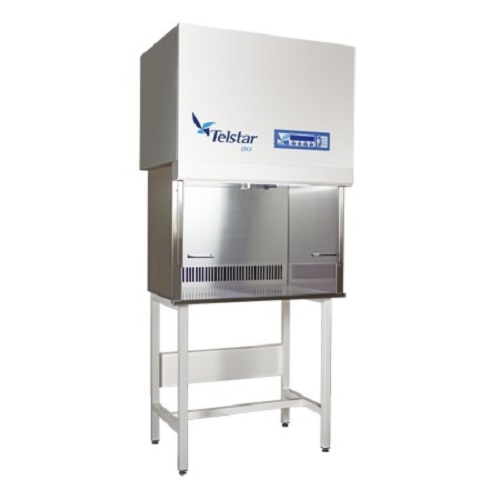
Biosafety cabinets
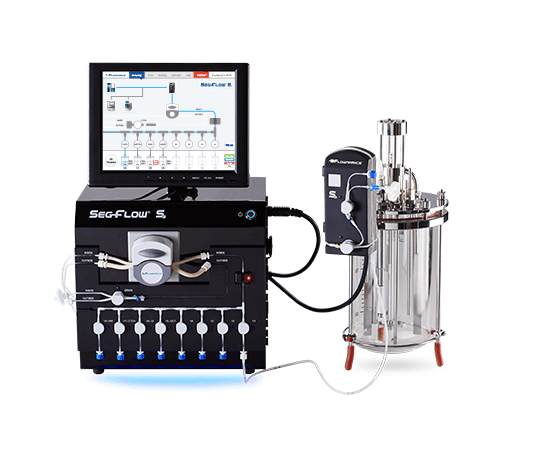
Biotech
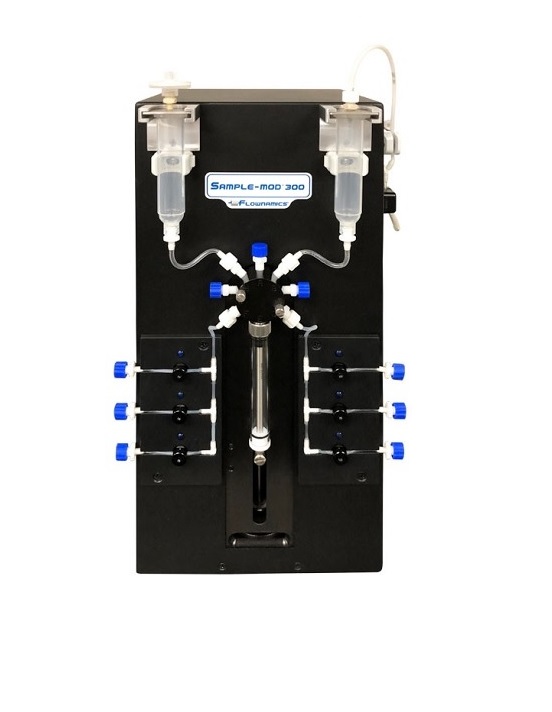
Biotech sampling and control
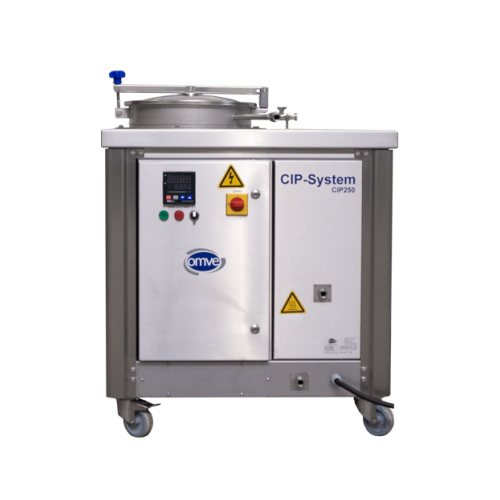
Cleaning
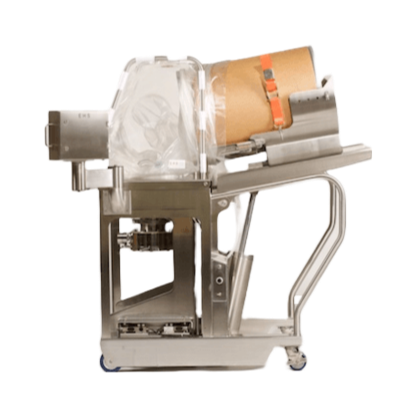
Contained transfer systems
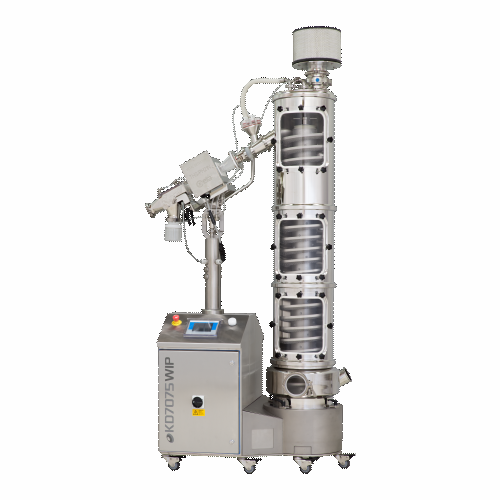
Containment
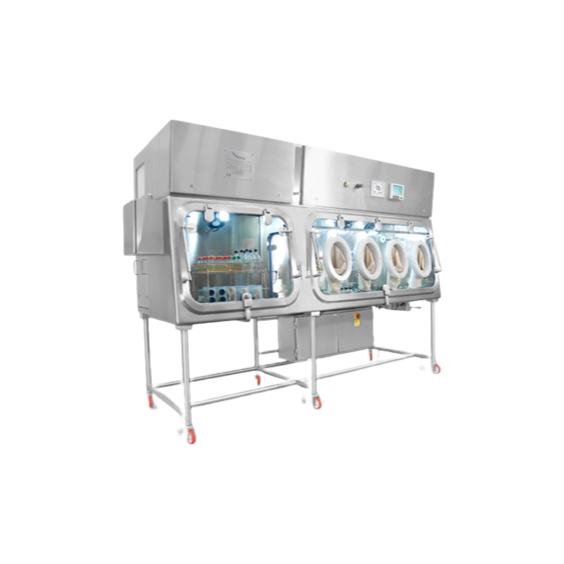
Containment isolators
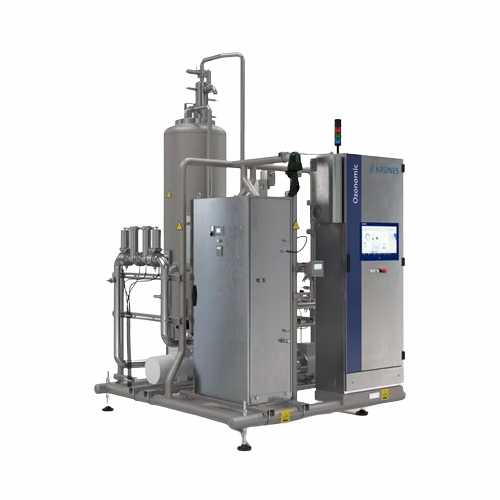
Disinfection
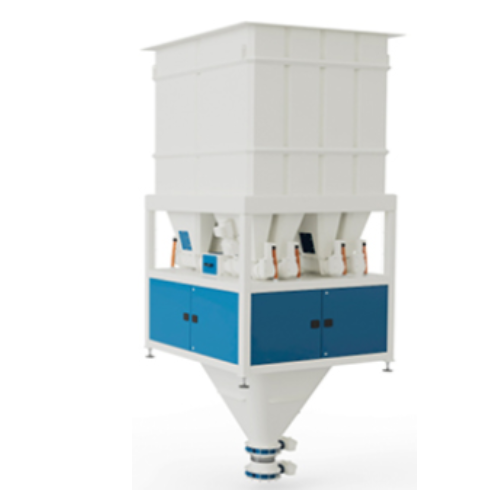
Dosing
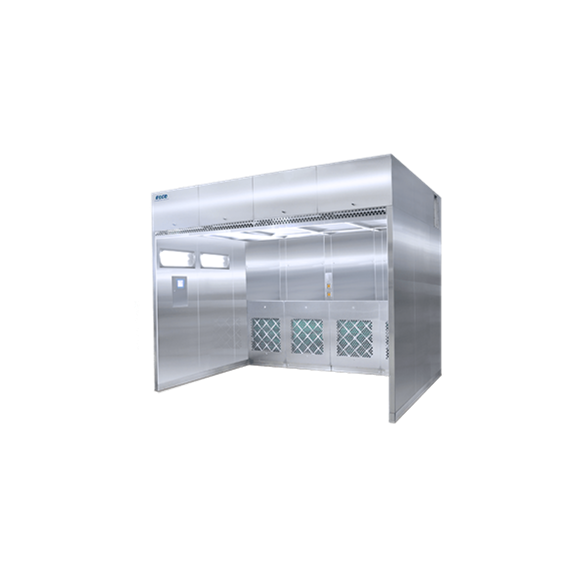
Downflow booths
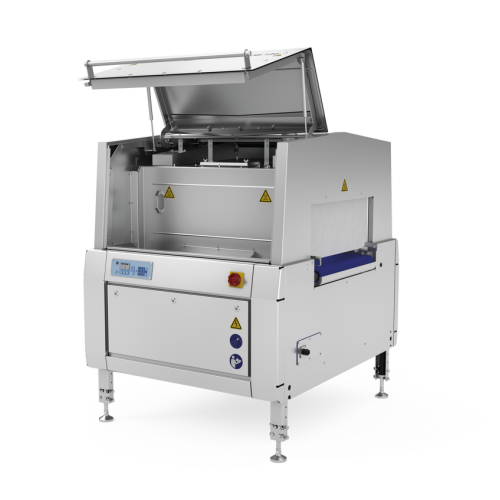
Drying
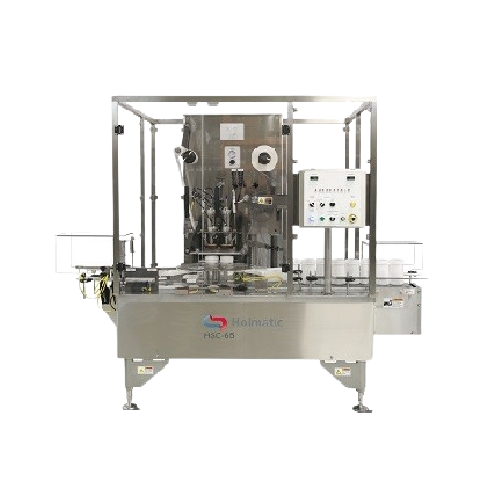
Filling
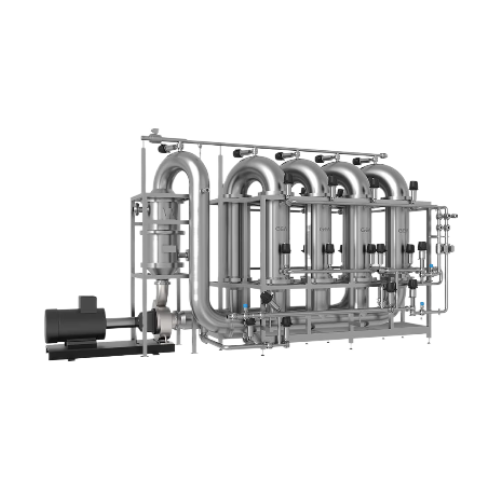
Filtration
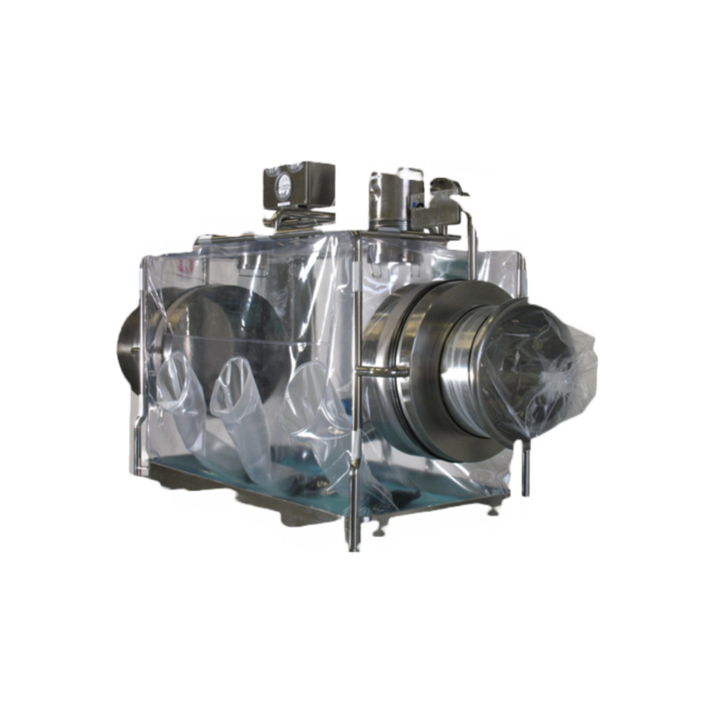
Flexible containment solutions
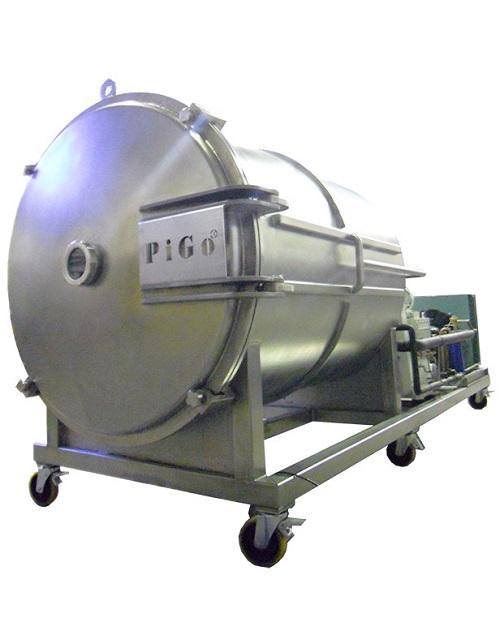
Freeze dryers
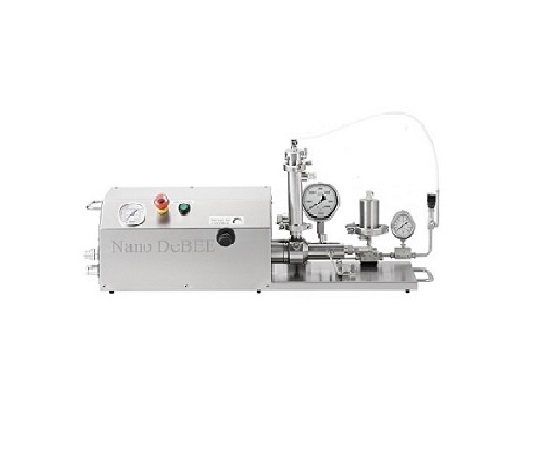
High pressure homogenizers
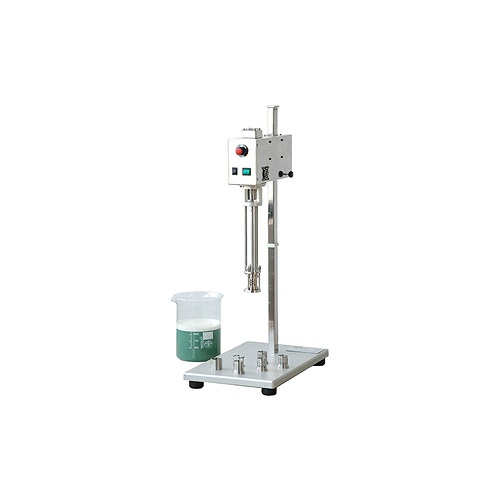
High-shear mixers
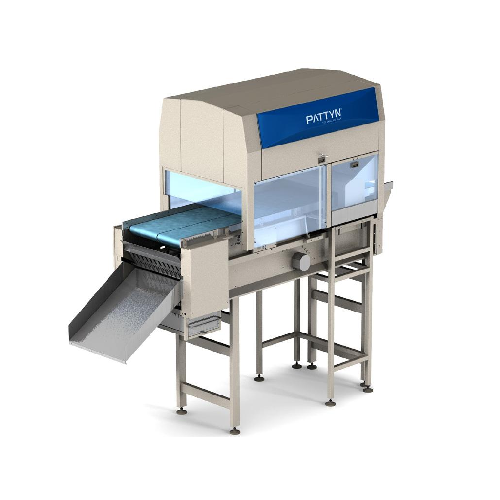
Inspection
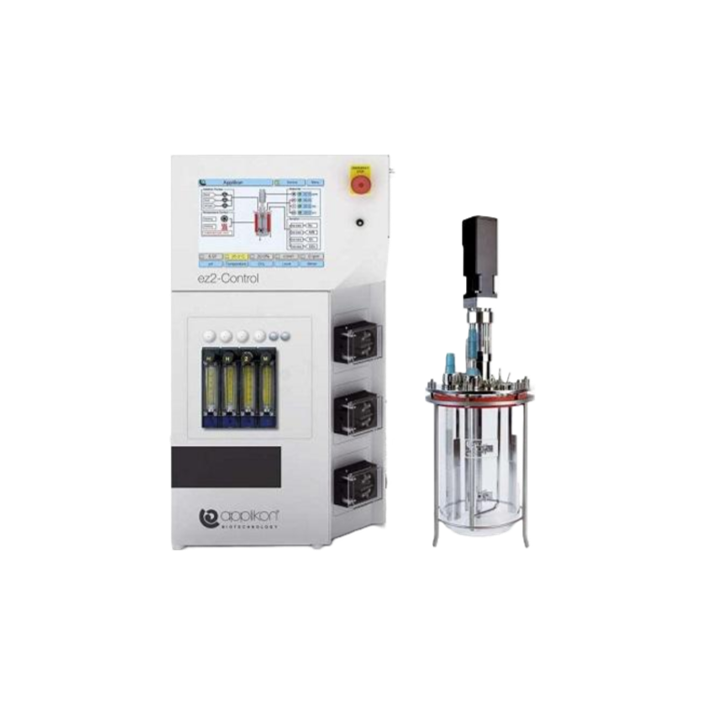
Measurement & Control
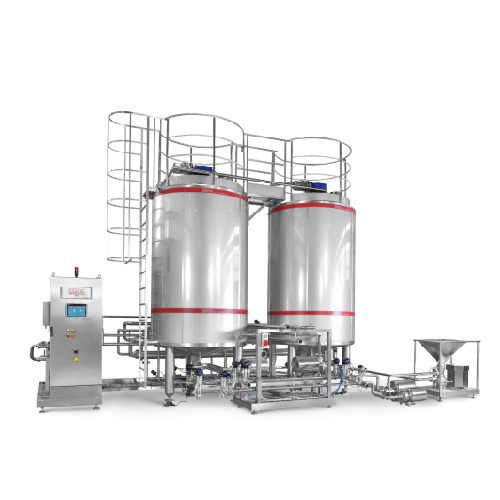
Mixing
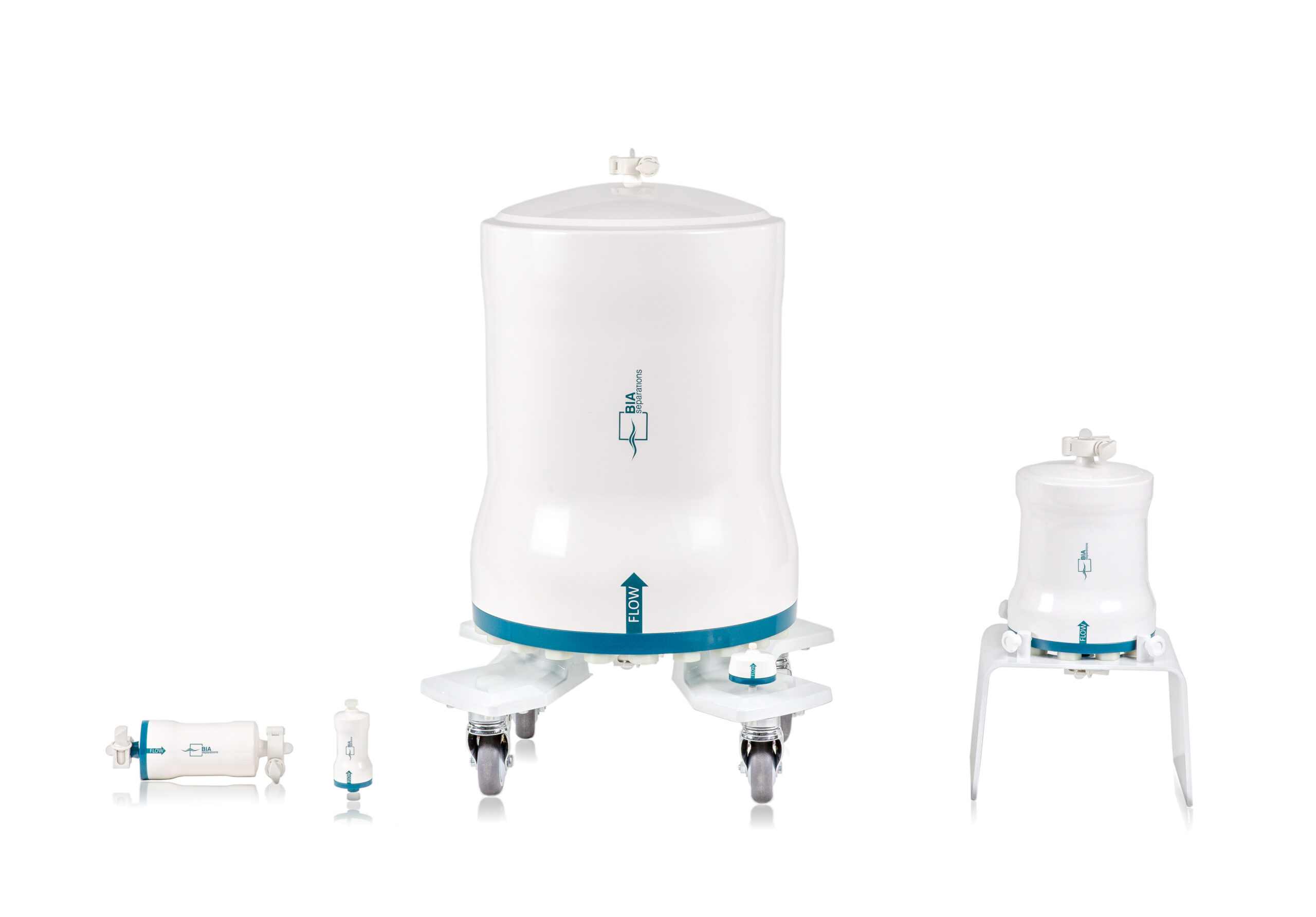
Monolithic columns
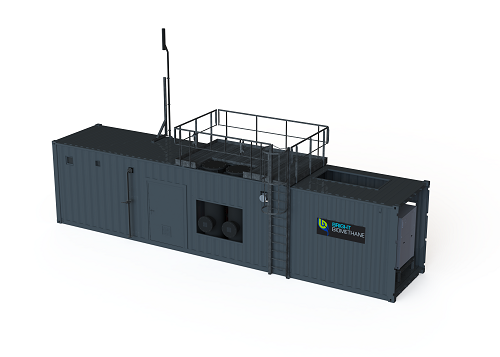
Purification
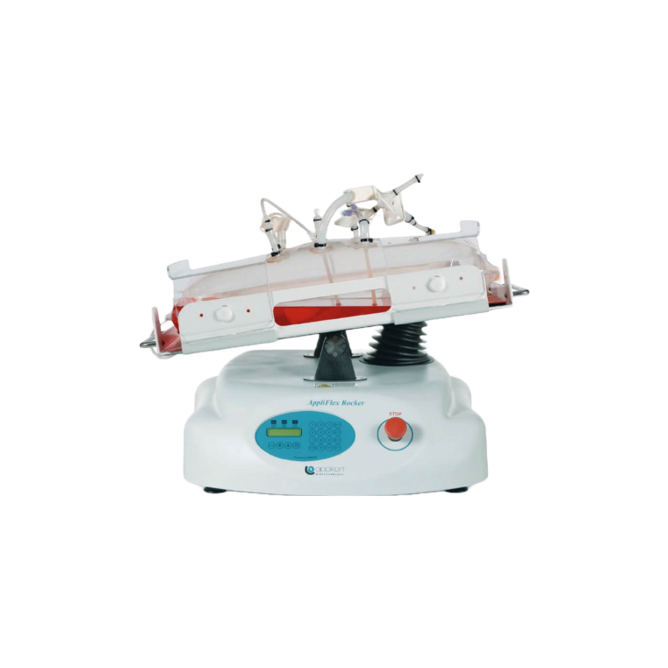
Single use systems
Which vaccines technology do you need?
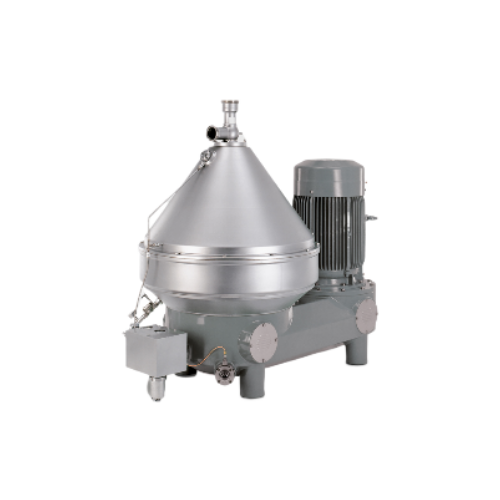
Separators for pharma extraction
Optimize your pharmaceutical extraction process with innovative centrifugal separation tech...
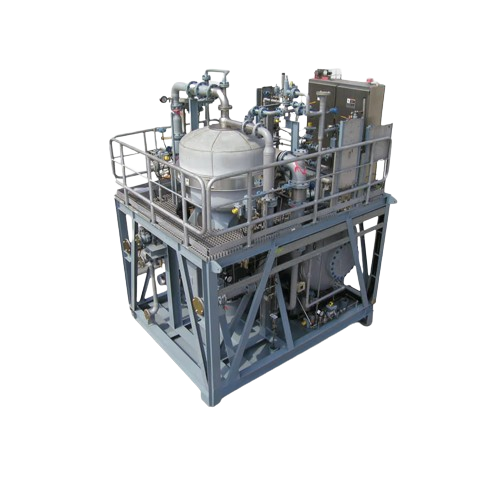
Single-use separator for cell harvesting
Achieve maximum cell harvesting efficiency with single-use technology, streamlinin...
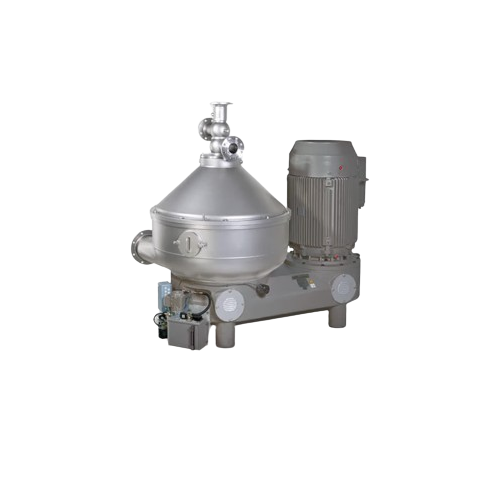
Biopharma separator for low to medium solid content
Ensure precise separation and high yield in biopharmaceutical product...
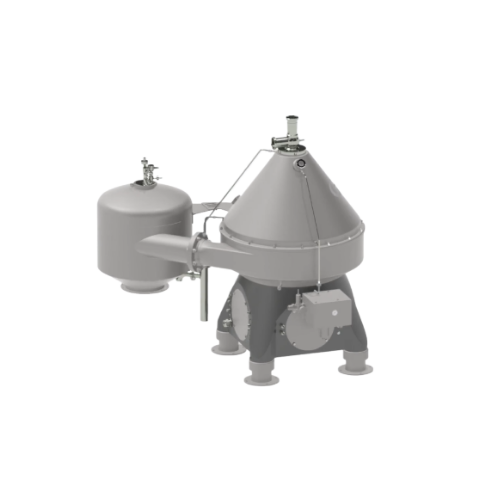
Pharmaceutical centrifuge for particle separation
Effortlessly upscale your biopharmaceutical processes with a compact ce...
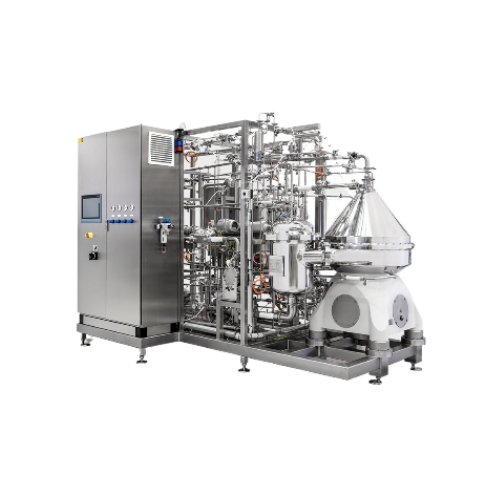
Aseptic separator for high solid content in biopharma
Ensure high yield and optimal purity in biopharmaceuticals with thi...
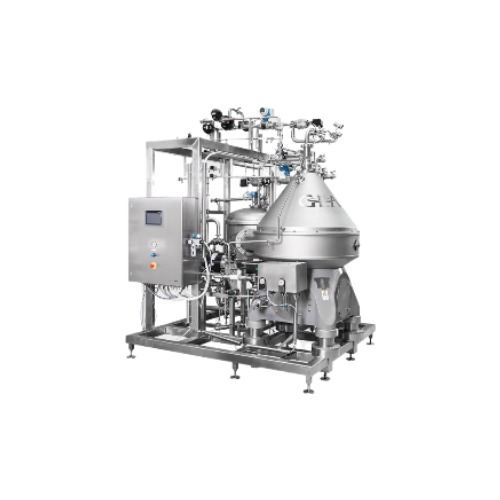
Pharmaceutical separator for high solid contents
Ensure optimal purity in biopharmaceutical processing with a separator de...
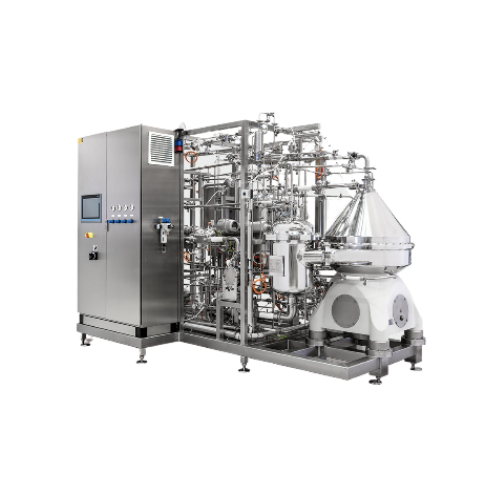
Pharma separator for aseptic biopharma processing
Achieve precise separation and concentration of sensitive biopharmaceut...
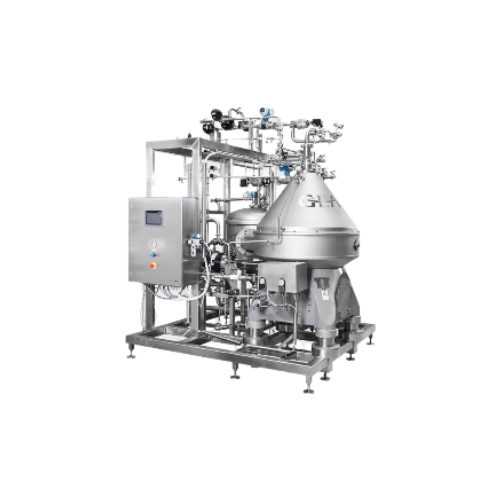
Pharma separator for biopharma processing
Streamline your production with this advanced separator, designed to efficiently...
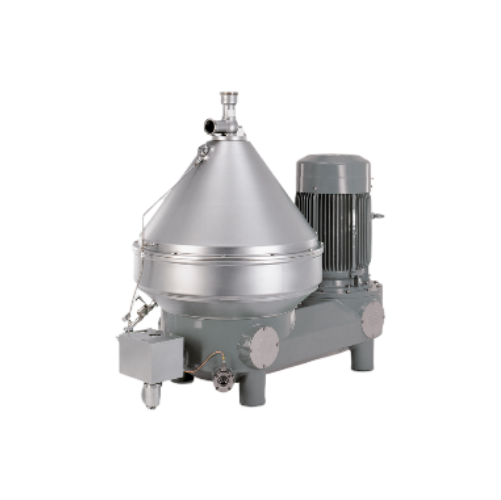
Separators for biochemicals
Achieve precise separation and purification of complex biochemical mixtures with self-cleaning c...
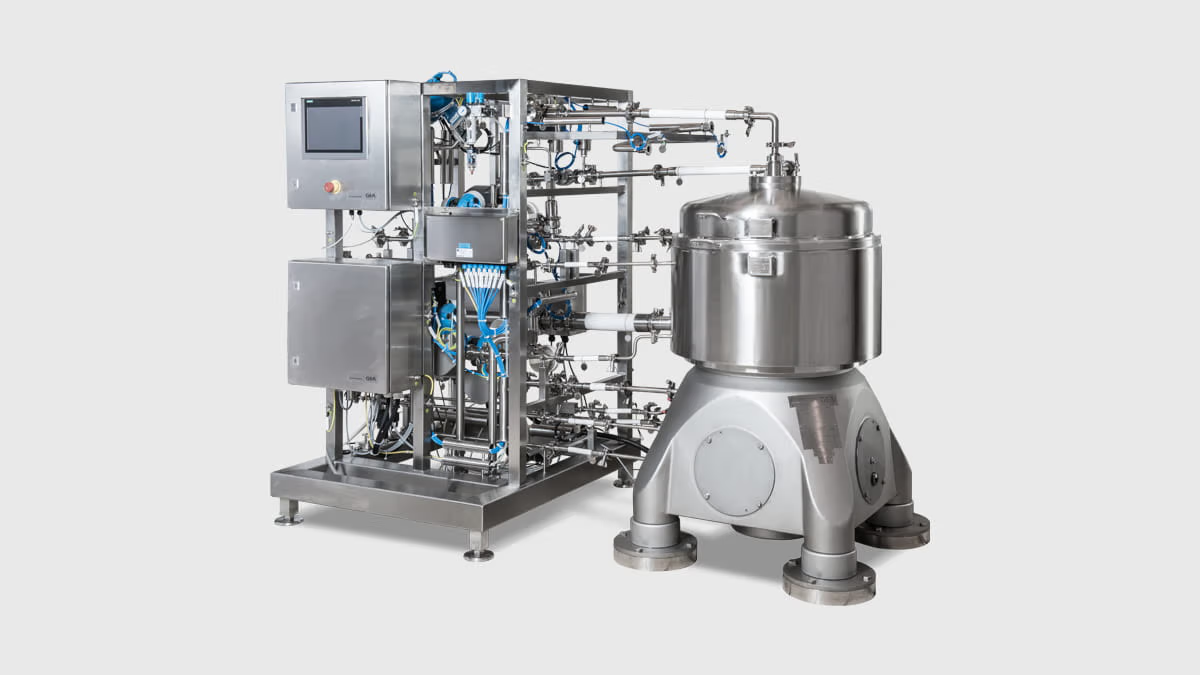
Chamber bowl separator for protein recovery
Efficiently recover high-value proteins with precise separation, optimizing yo...
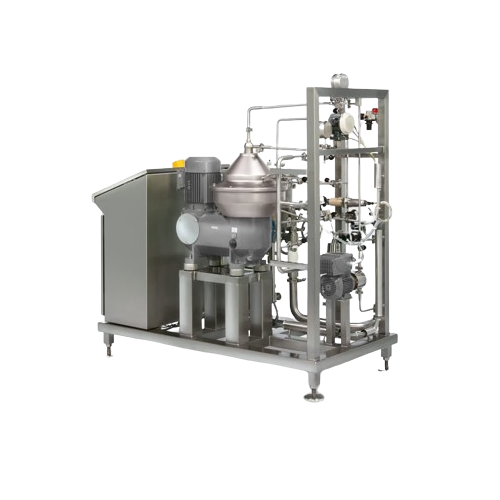
Clarifier for beverages
Enhance beverage clarity and purity with high-performance centrifugal separation, expertly designed t...
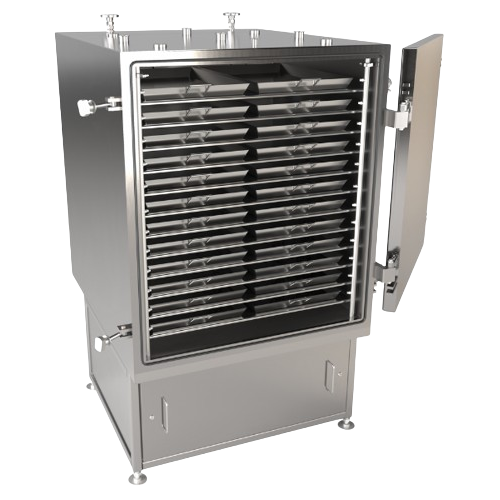
Vacuum tray dryer for pharmaceutical applications
Optimize drying of heat-sensitive compounds while maintaining product i...
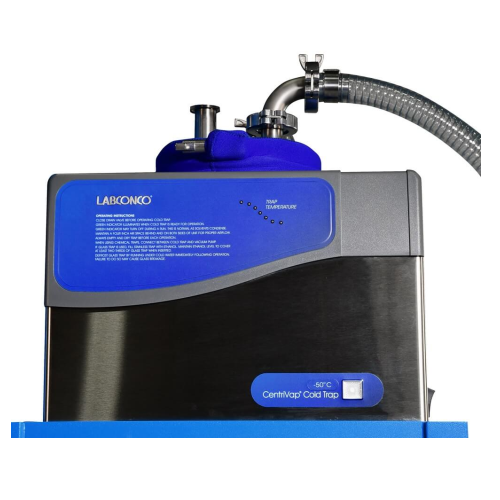
Vacuum cold trap for efficient purging and drying
Optimize your laboratory’s efficiency by integrating high-perform...
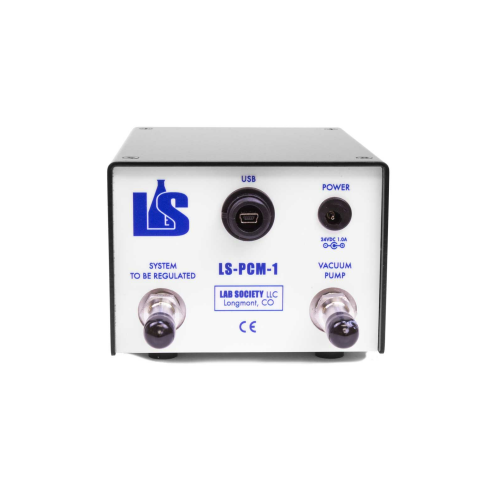
Pressure control monitor for laboratory vacuum systems
Effortlessly maintain precise vacuum pressure in your lab operatio...
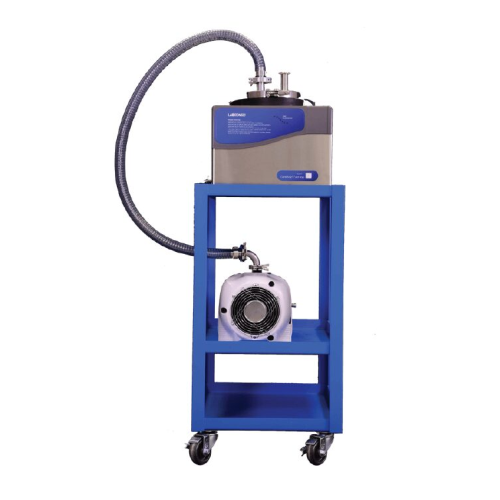
Laboratory vacuum cold trap for extract purification
Optimize your vacuum purging and drying applications with this advan...
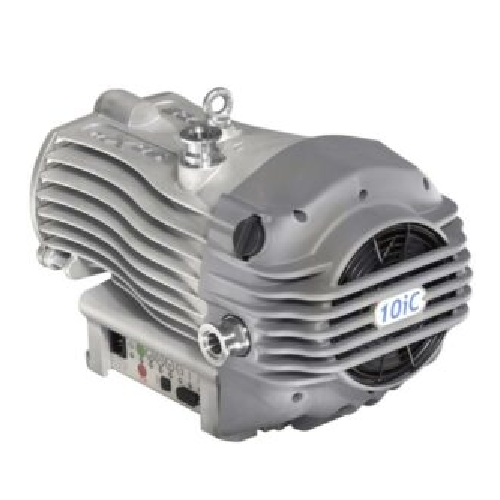
Chemically resistant dry scroll vacuum pump
Effortlessly manage aggressive substances and achieve reliable vacuum conditio...
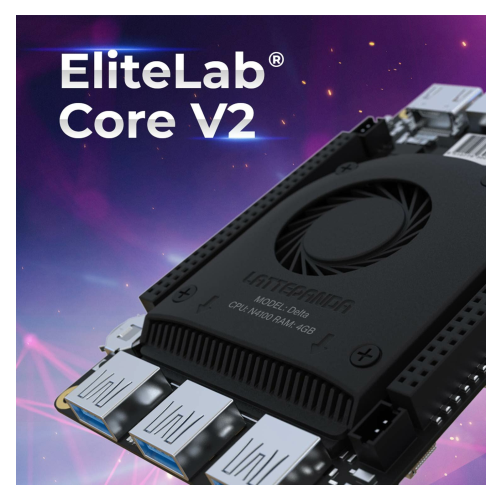
Laboratory automation software for distillation and extraction
Optimize your distillation and extraction processes with ...
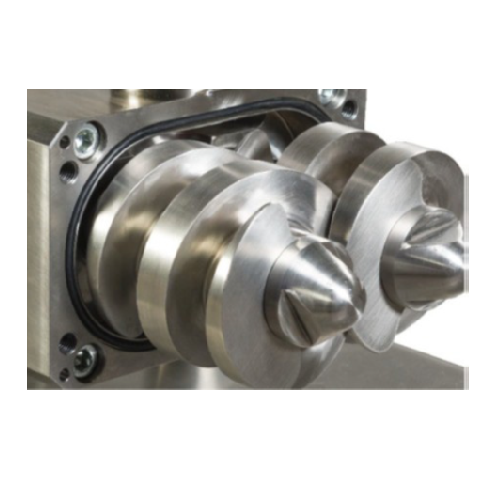
Aseptic sampling devices for biopharmaceutical applications
Secure aseptic sampling ensures your high-value biopharmaceu...
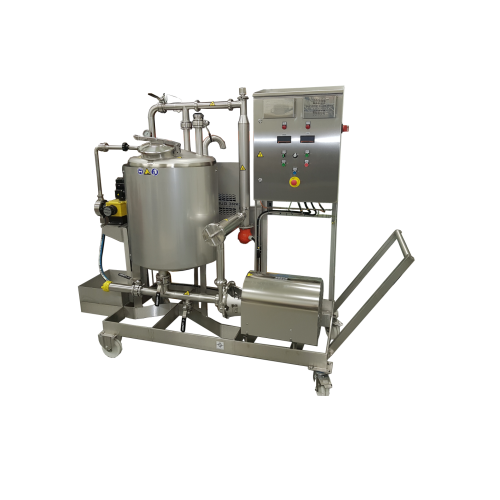
Mobile cleaning-in-place unit for process equipment
Ensure seamless cleaning of diverse process equipment with a mobile, ...
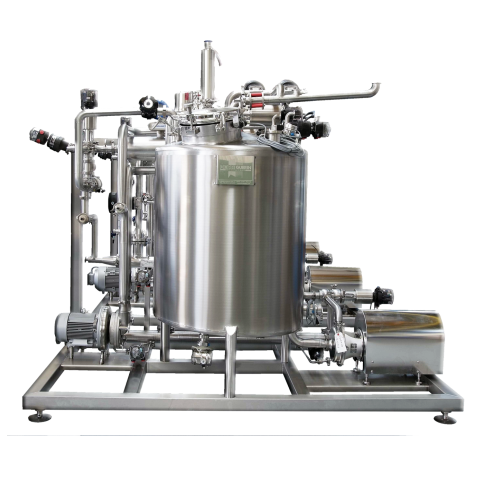
Single use cleaning in place units for biopharma
Eliminate cross-contamination risks in biopharmaceuticals with precision ...
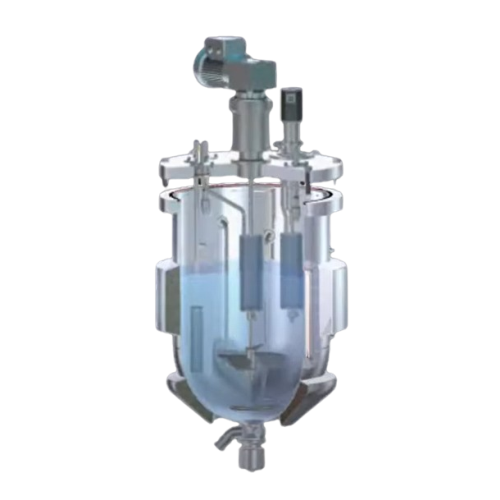
Industrial agitation and mixing solutions
Enhance your production line efficiency with engineered agitation and mixing sys...
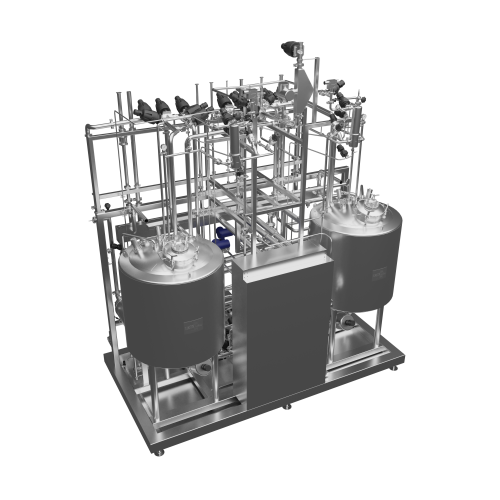
Cleaning and sterilization in place for hygienic control
Ensure maximum hygiene and sterility in your production line wit...
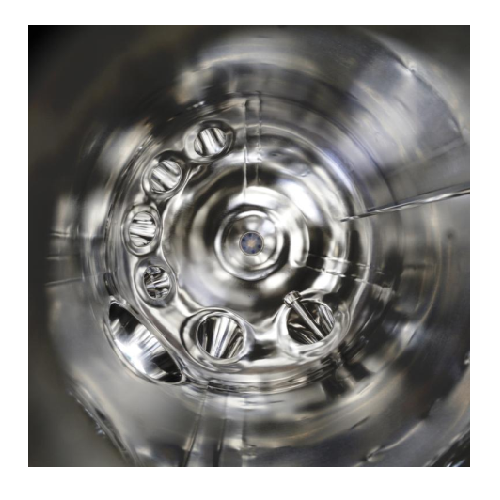
Stainless steel process vessels for biopharmaceutical applications
Ensure seamless mixing and sterilization with engine...
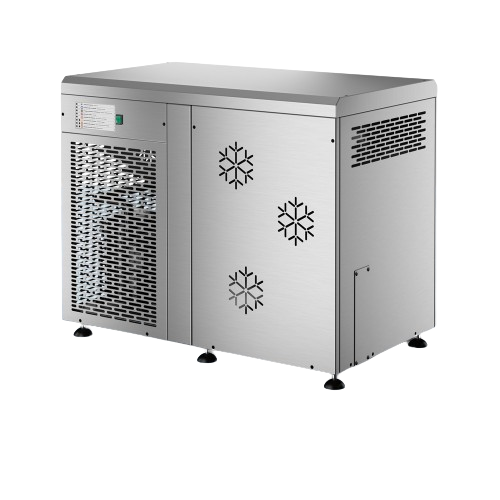
Flake ice maker for food processing applications
Ensure optimal product preservation and temperature control with precisio...
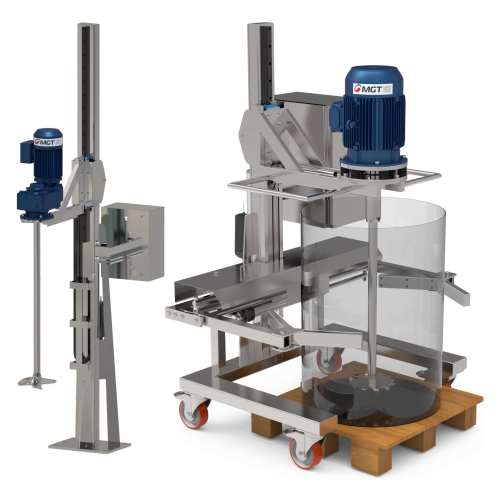
Pneumatic and electric lift for industrial mixing tanks
Enhance operational efficiency and safety with versatile lifts fo...
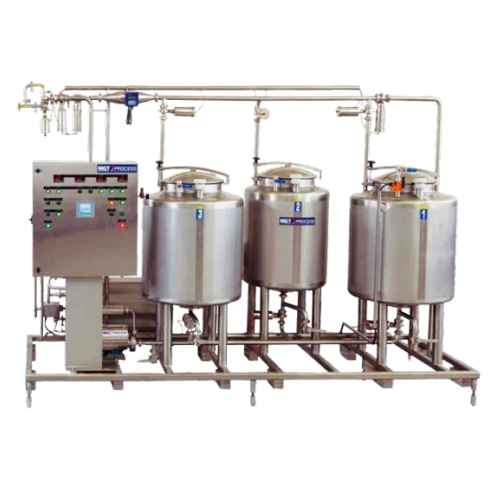
Cleaning-in-place (cip) systems for hygienic processing
Elevate hygiene standards in your liquid processing line with an ...
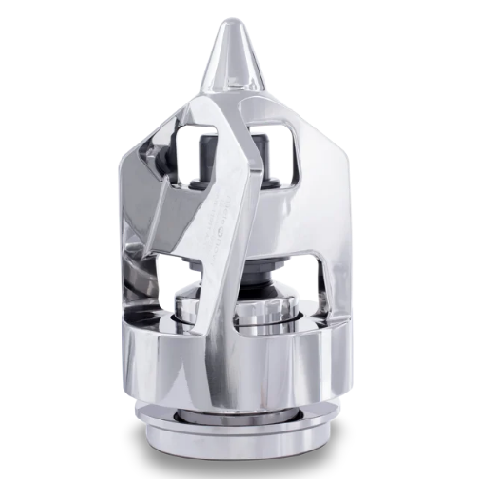
High power mixing solution for powder applications
Achieve rapid, uniform mixing of challenging powders and non-shear sen...
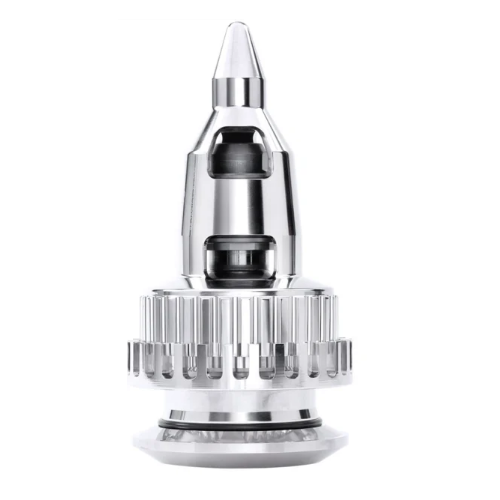
High shear mixer for emulsification
Achieve precise emulsification and dispersions with magnetic high shear technology, ens...
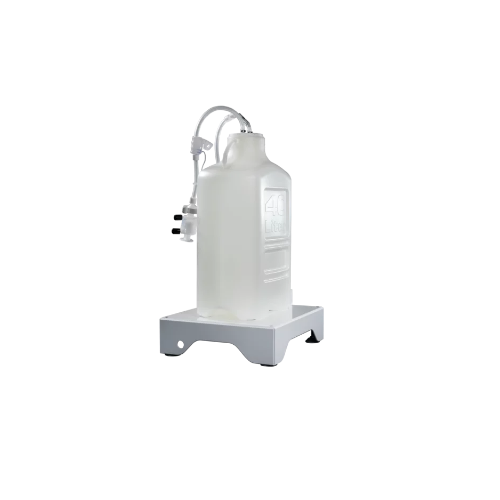
Single-use mixing solutions for downstream processes
Designed for safe and efficient one-time use, this mixing solution e...
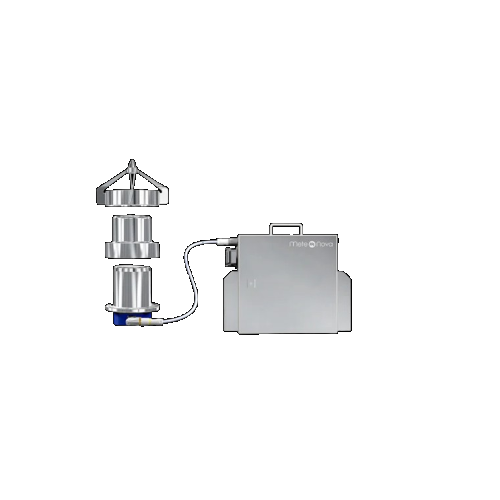
Low shear mixer for shear-sensitive applications
Optimize shear-sensitive mixing with precision control, enhancing product...
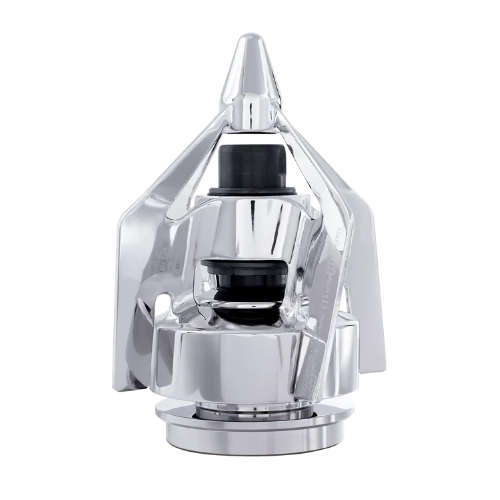
Versatile magnetic mixer for pharmaceutical and biotechnology applications
Optimize your biopharmaceutical mixing proc...
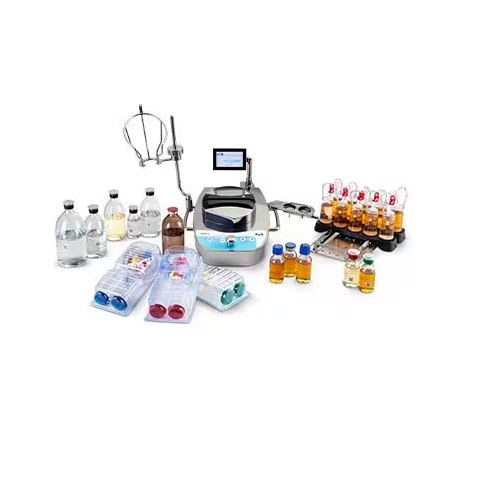
Sterility testing consumables, media & instruments
Ensure your products meet sterility standards with advanced testing to...
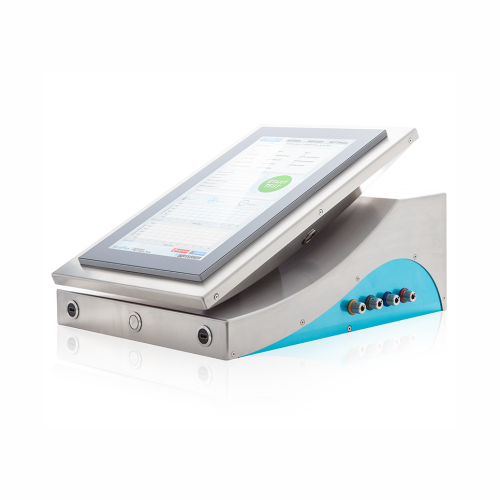
Integrity tester for filtration system validation
Ensure precise validation of your filtration systems with highly accura...
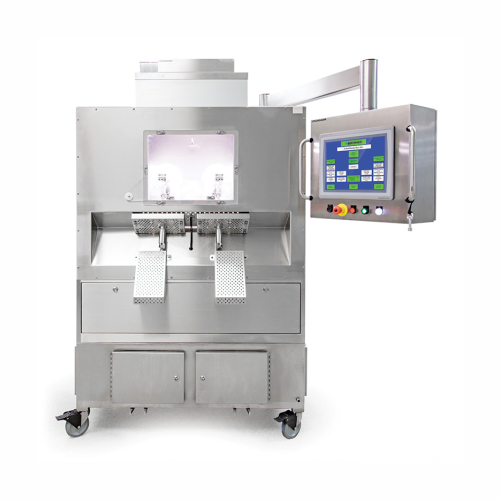
Aseptic filling system for biopharmaceutical products
This system ensures sterility in high-volume aseptic filling operat...
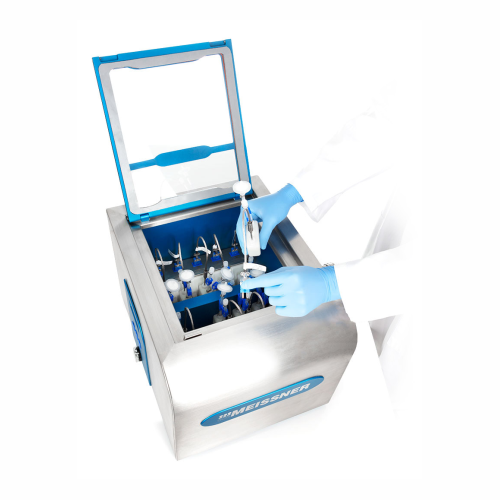
Bench top freezer for bulk drug substance freeze and thaw
Achieve precise temperature control for small-scale freeze and...
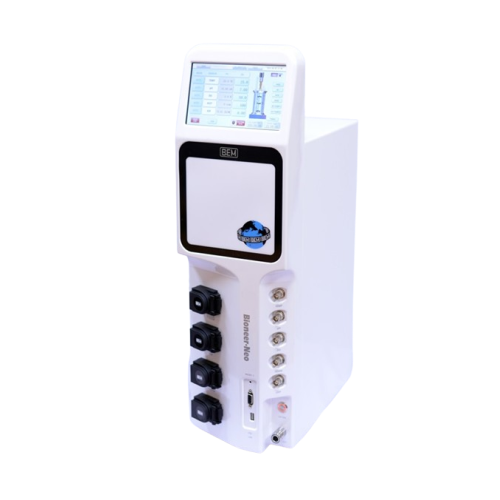
Compact fermentor for research and scale-up studies
Optimize your bioprocess development with a desktop fermentor that of...
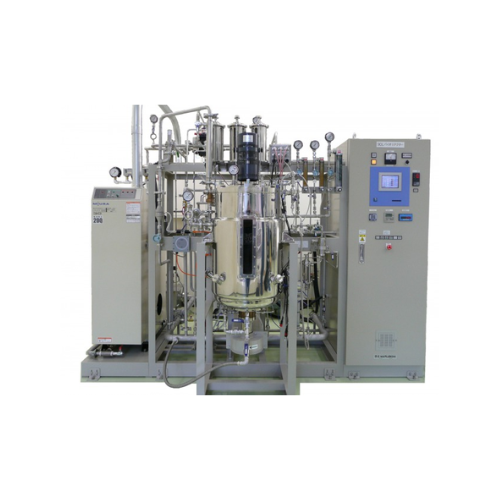
Sterilization in place fermentor for bioprocess applications
Optimize your fermentation processes with seamless integrat...
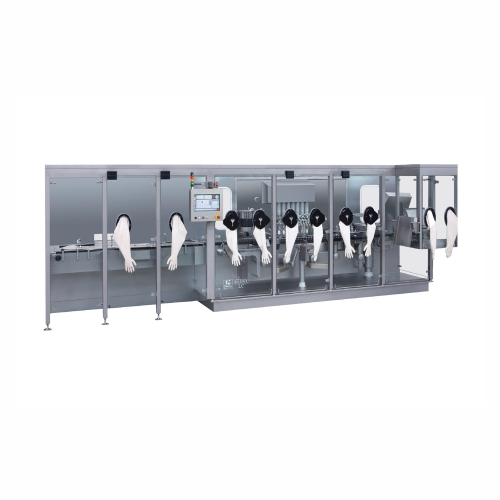
Vial filling and stoppering for aseptic liquid or lyo products
Ensure optimal aseptic conditions in your production line...

Rotary vial filling and stoppering
Ensure precise liquid formulations and lyophilized product consistency with a high-speed...
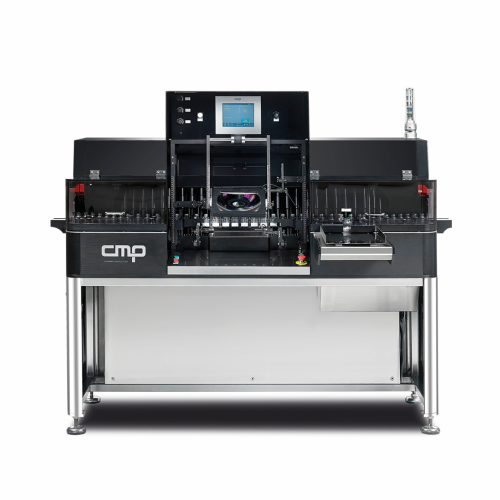
Inspection system for glass containers
Ensure precise inspection of liquid, freeze-dried, and powdered products in glass co...

Glass container Inspection line
Ensure precise quality control with a high-speed inspection line designed for glass containe...
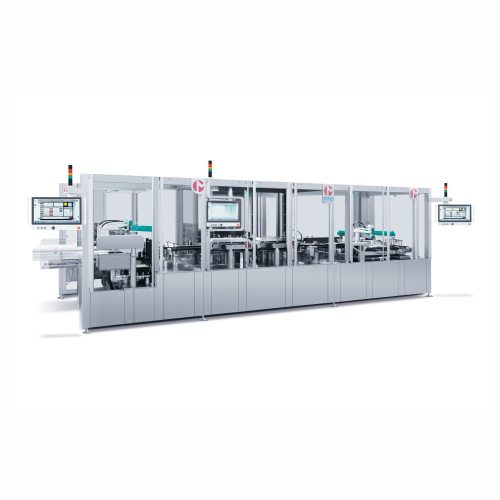
Inspection for glass syringes
Ensure comprehensive quality control for syringe-based medical products with high-speed, no-co...
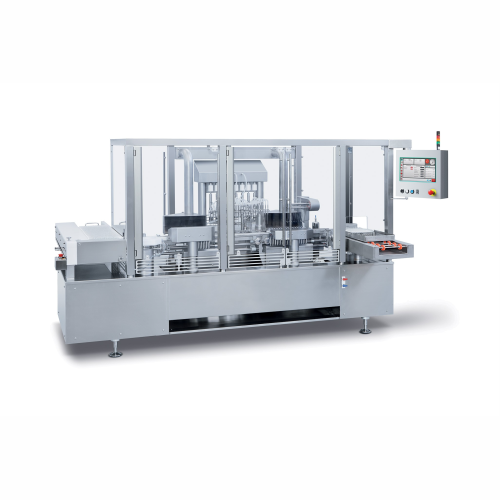
Aseptic ampoule filling and sealing solution
Ensure precise dosing and secure sealing of sterile liquid pharmaceuticals in...
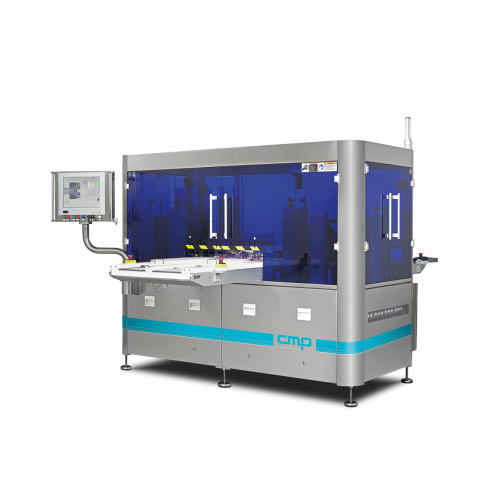
Glass container inspection system
Ensure product integrity with precision inspection for glass containers, detecting partic...
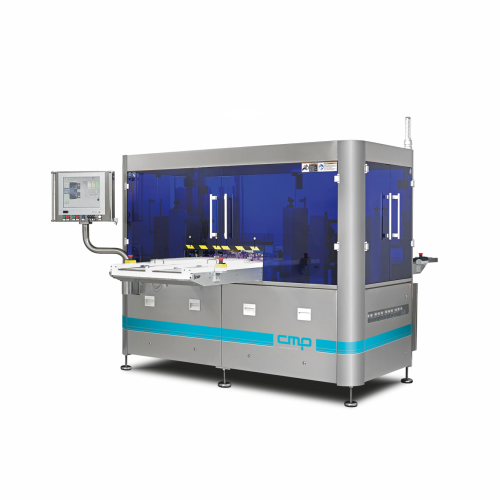
Inspection for glass containers
Ensure the integrity and quality of your liquid formulations with high-speed inspection and ...
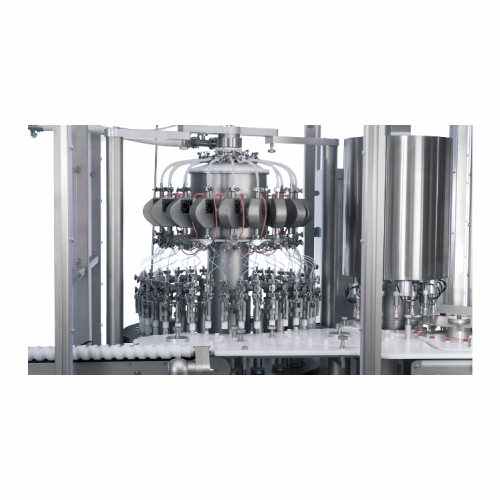
Aseptic vials filling and capping
Ensure precise vial capping and sealing for liquid pharmaceuticals with advanced aseptic ...
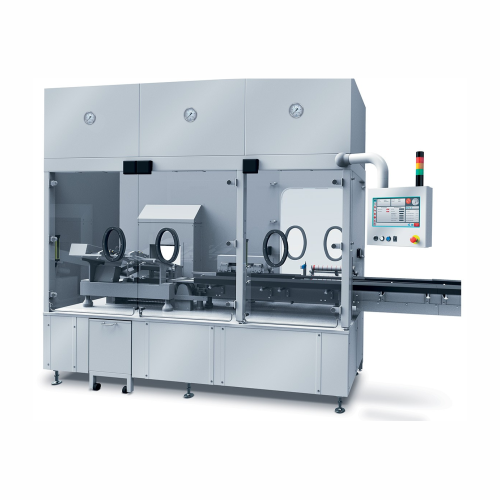
Nested syringe filling and stoppering line
Streamline your aseptic filling process with advanced machinery that handles ne...
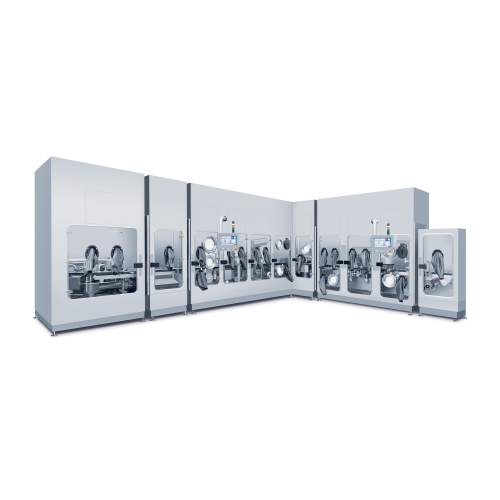
Aseptic filling and capping for vials and syringes
Ensure sterility and precision in vial and syringe filling with advanc...
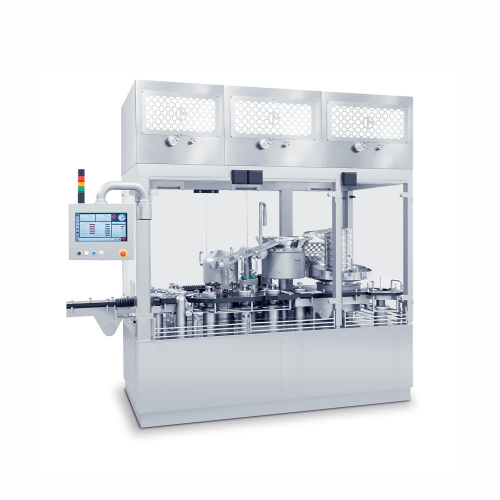
Vial capping for small volume parenteral
Ensure precise sealing and contamination-free environments for small volume parent...
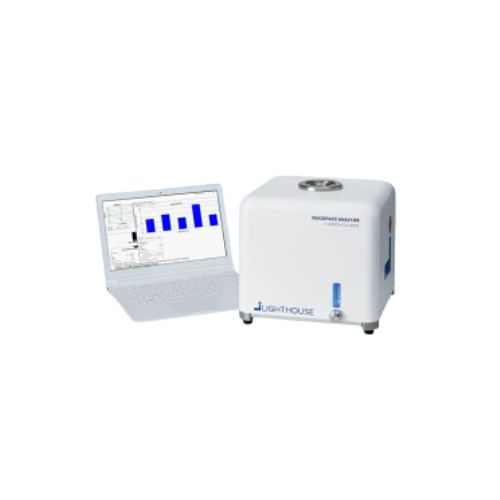
Carbon dioxide headspace analyzer for parenteral containers
Ensure accurate headspace gas analysis to maintain container...
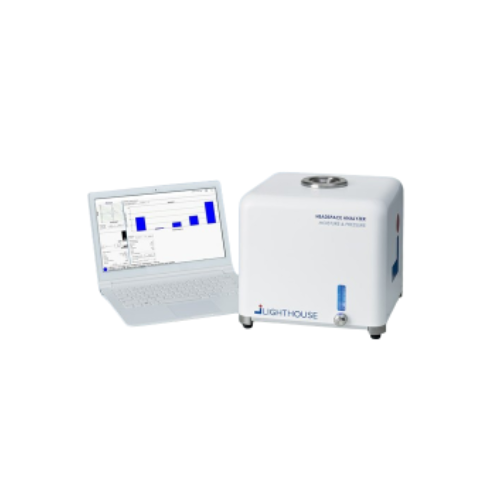
Moisture and pressure headspace analysis for sealed parenteral containers
Ensure accurate moisture and pressure assess...
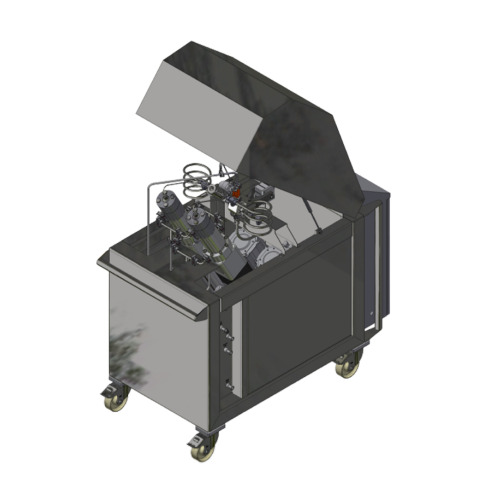
High pressure homogenizer for pharma applications
Achieve precise particle size reduction and stability in liquid formula...
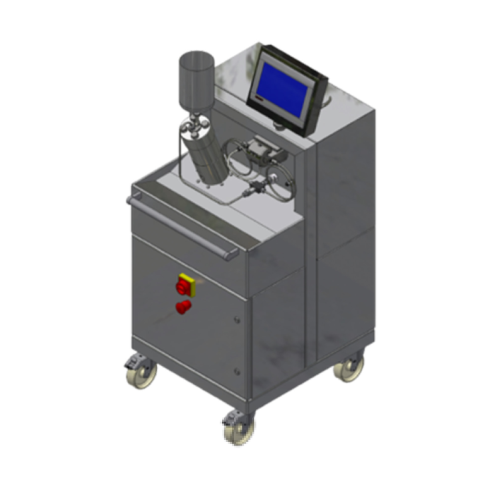
High pressure homogenizer for lab applications
Achieve precise control over droplet size and consistency in high-viscosity...
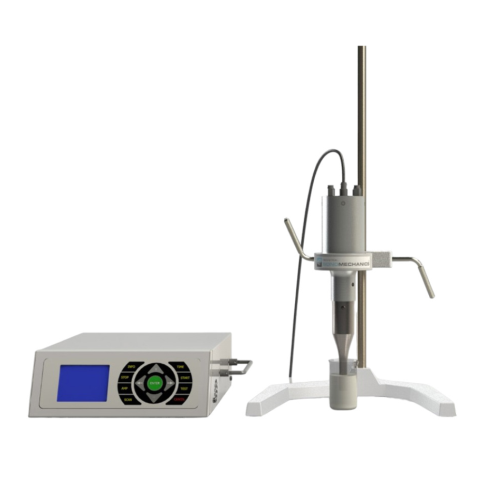
Ultrasonic liquid processor for feasibility testing and procedure optimization
Optimize your liquid formulations by en...
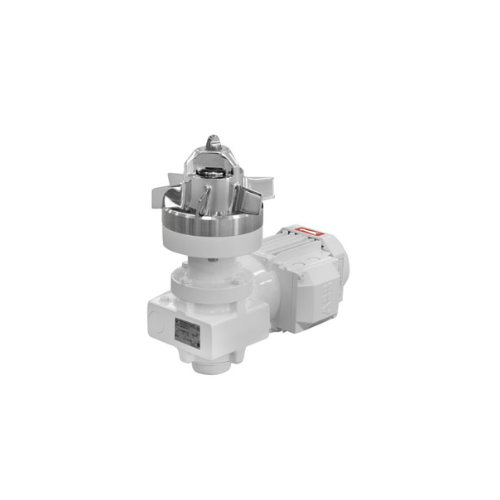
Industrial magnetic agitator for homogenizing pharmaceutical products
Achieve precise dispersion and homogenization in ...
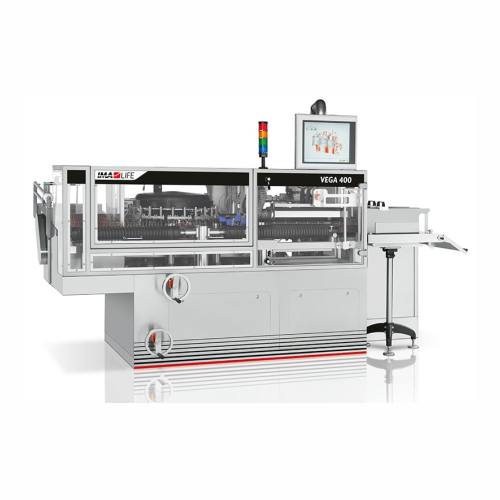
Ampoule external washer for decontamination
Ensure contamination-free glass containers with a high-speed solution designed...
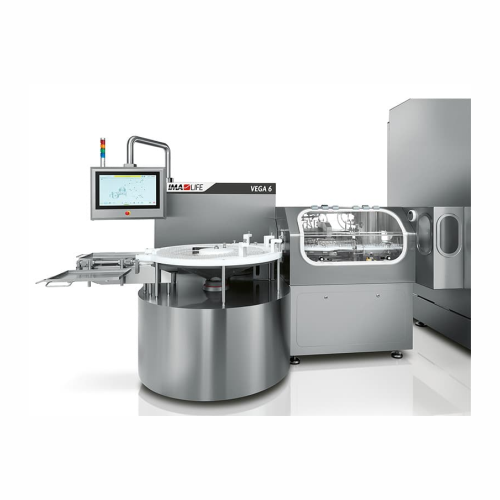
Rotary vial washers for parenteral containers
Ensure sterile and pyrogen-free parenteral preparations with a seamless wash...
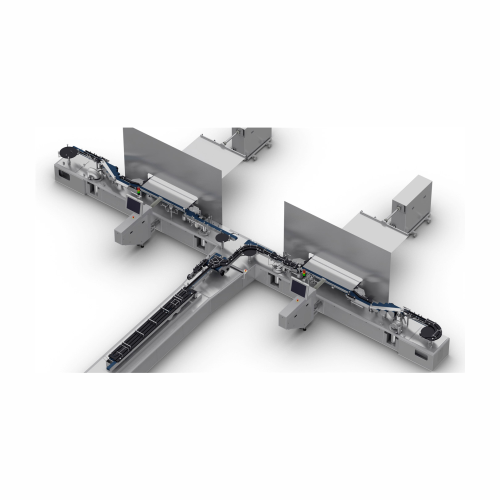
Automatic vial loading and unloading systems for freeze dryers
Optimize your vial handling with automated loading and un...
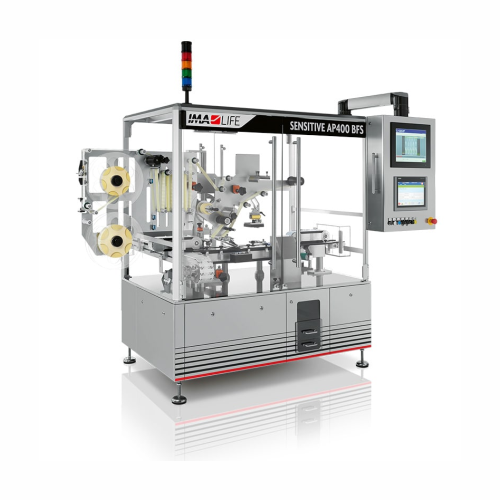
Labelling system for blow fill seal (bfs) strips
Ensure precise labeling and traceability for your blow fill seal containe...
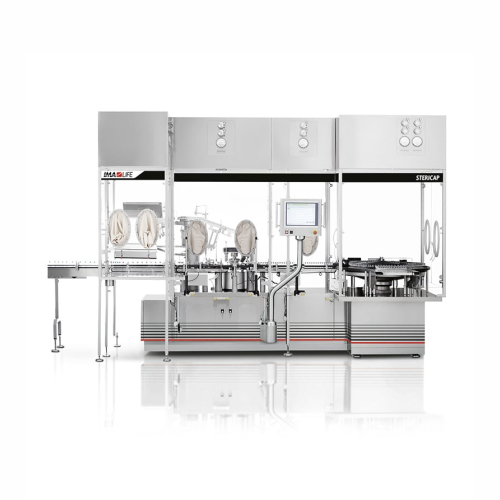
Rotary capping machine for aseptic products
Ensure precision sealing for aseptic liquid formulations with a solution engin...
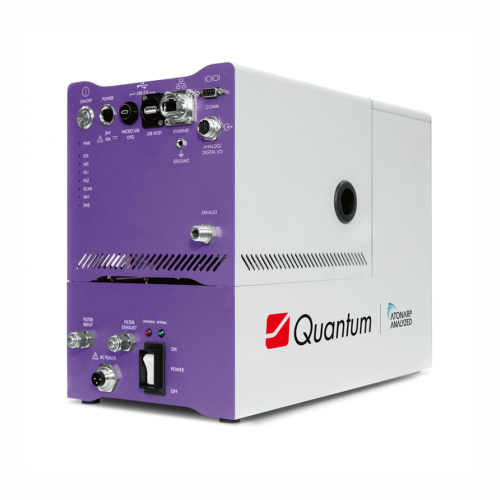
Smart miniature mass spectrometer for pharma freeze dryers
Optimize your freeze-drying process with a non-invasive tool ...
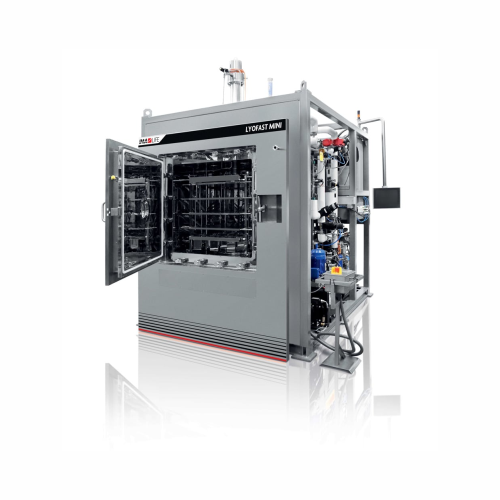
Pilot freeze dryer for pharmaceutical applications
Optimally bridge laboratory development and full-scale production with...
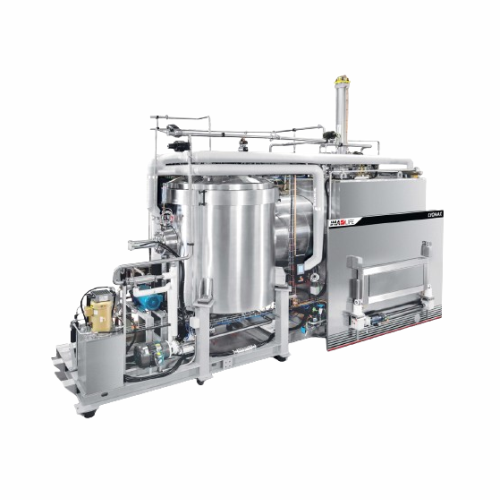
Industrial GMP freeze dryer
Optimize the lyophilization of sensitive pharmaceutical compounds with a machine designed for pr...
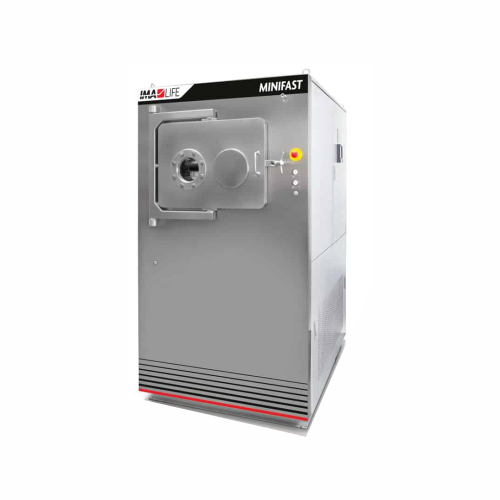
Pilot freeze dryer for r&d and small batch production
Optimize your freeze-drying process for pilot and laboratory applic...
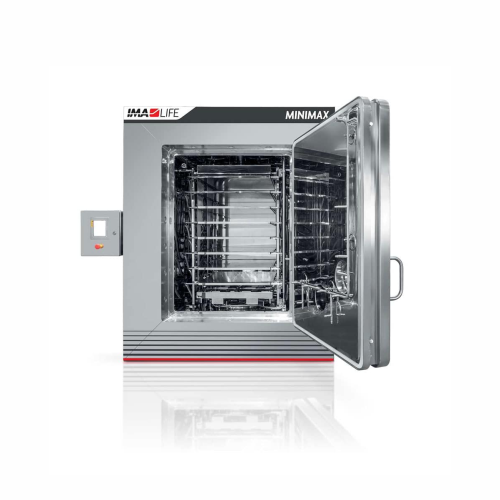
Small-scale freeze dryer for pharmaceutical applications
Optimize small-batch and pilot-scale lyophilization with advance...
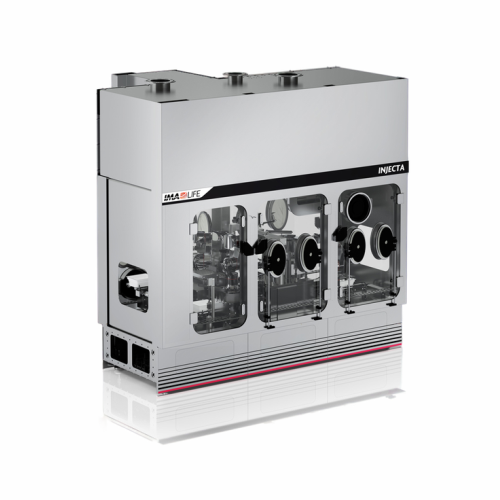
High-speed fill-finish system for ready-to-use components
Enhance aseptic fill-finish operations with a high-speed solut...
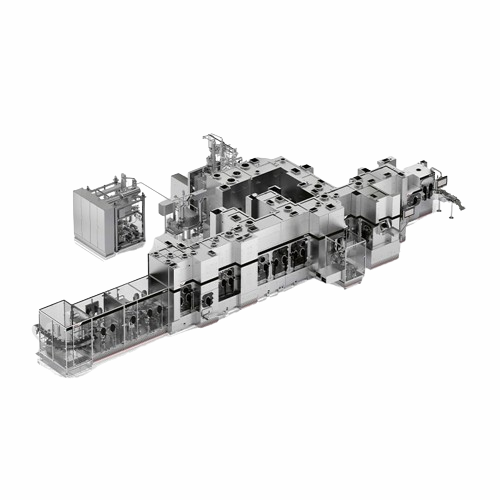
Isolation solutions for aseptic fill-finish lines
Achieve maximum product sterility with advanced isolation solutions, mi...
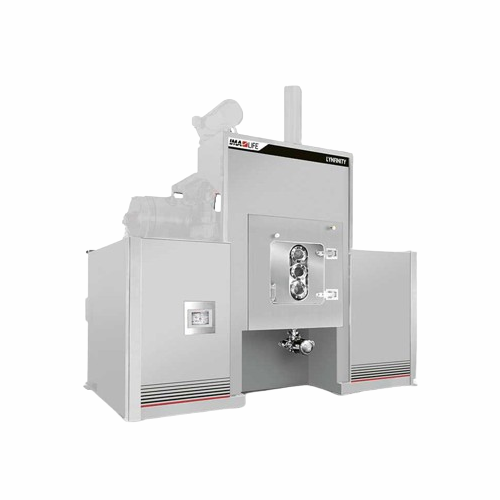
Continuous aseptic spray-freeze-drying system
Achieve higher sterility and improved product uniformity with a continuous a...
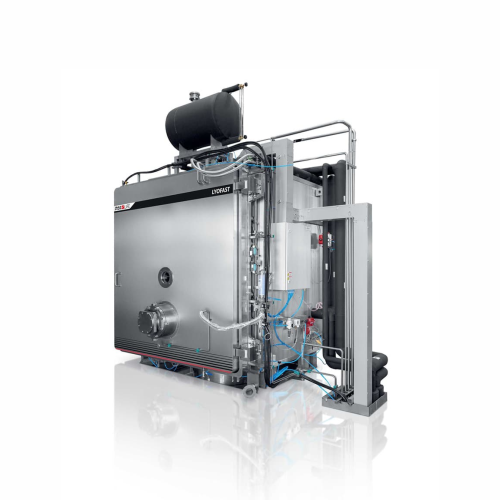
Industrial freeze dryer for biopharmaceuticals
Ensure the stability and longevity of your sensitive biopharmaceuticals thr...
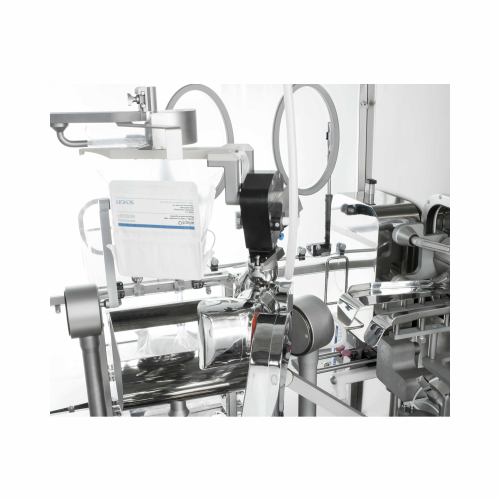
Robotic sterile package opening system
Achieve sterile precision with a fully robotic system that streamlines primary packa...

Purified water generation system for pharma applications
Ensure consistent purity in your therapeutics production with a ...

Purified water storage and distribution for pharmaceuticals
Ensure seamless water quality for critical pharmaceutical pr...
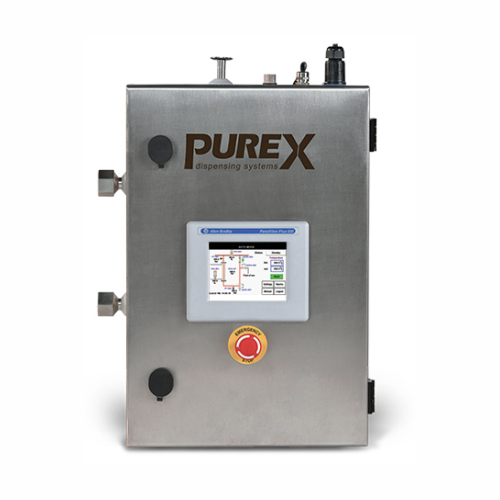
Wfi cooler
Ensure precise temperature control and contamination-free dispensing for high-value liquid formulations with this a...
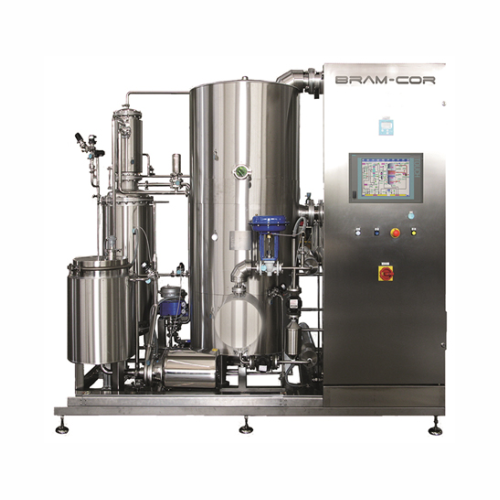
Water for injection (wfi) generation technology
Optimize your purification process with precise distillation and efficient...
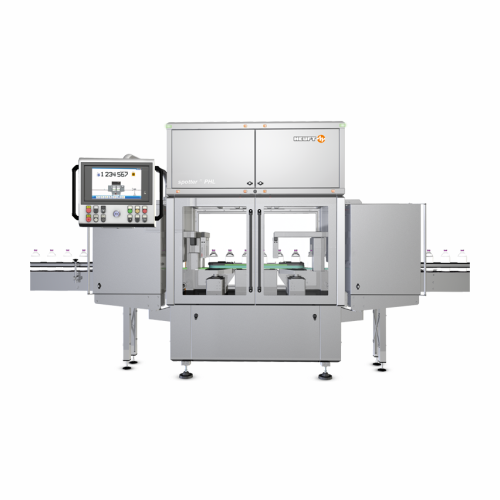
Vial inspection system for pharmaceutical industry
Ensure vial integrity by detecting and rejecting contaminants, glass d...
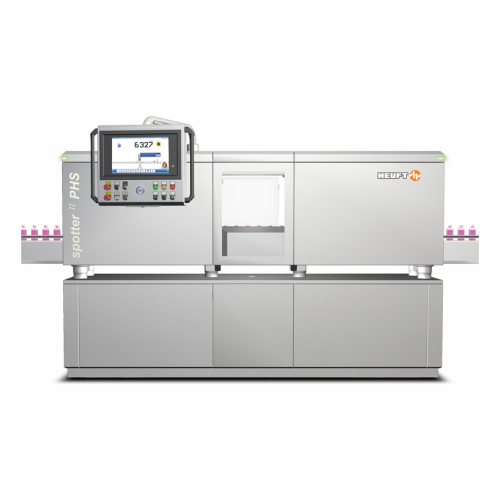
Vial inspection system for pharmaceutical products
Ensure the integrity and safety of parenteral drugs with advanced imag...
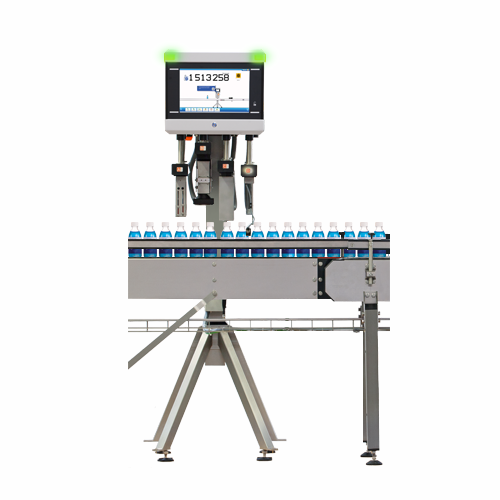
Full container inspection for pharma and food industries
Ensure precise fill levels and secure closures in your productio...
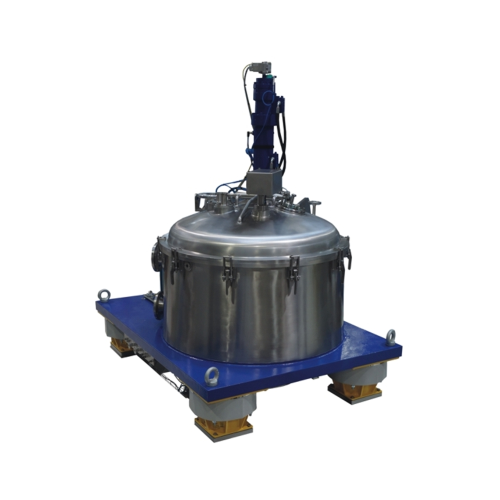
Vertical peeler centrifuge for pharmaceutical industry
Ensure thorough separation and purification of products with this ...

Liquid dosing and assembly platform for pharmaceutical products
Optimize your production line with a seamless solution f...

Lyophilized pellet dosing technology
Eliminate mechanical strain and static charge in your lyophilized pellet dosing proces...
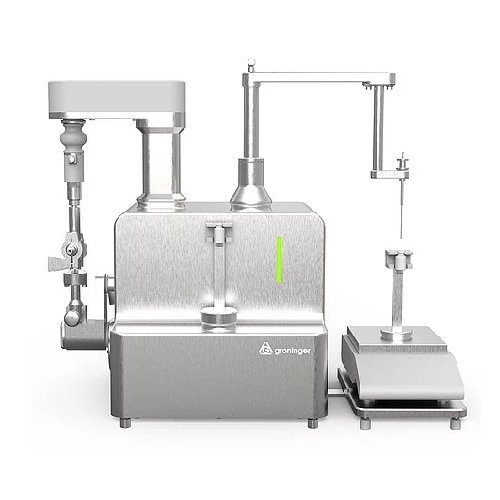
Benchtop filling solutions for small batch liquid medicine
Streamline your small batch liquid medicine production with p...
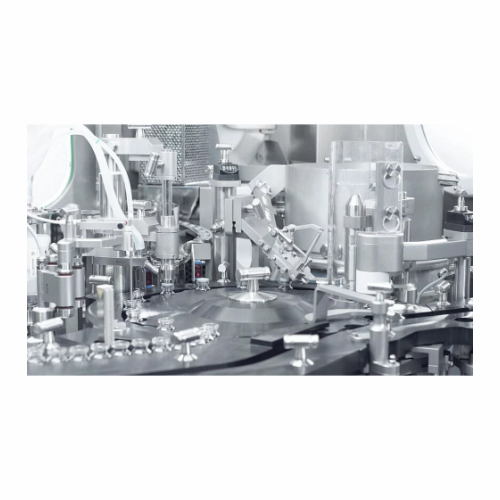
Vial filling for pharmaceuticals
Streamline your aseptic processing with vial filling machines that ensure sterile, precise,...
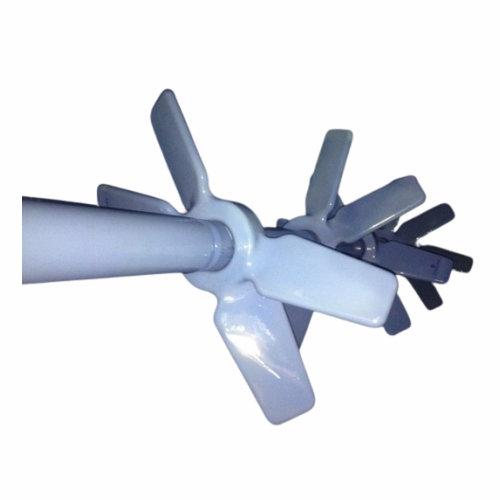
Glass-lined mixing systems for pharmaceutical industry
Achieve consistent mixing and thorough agitation for complex formu...
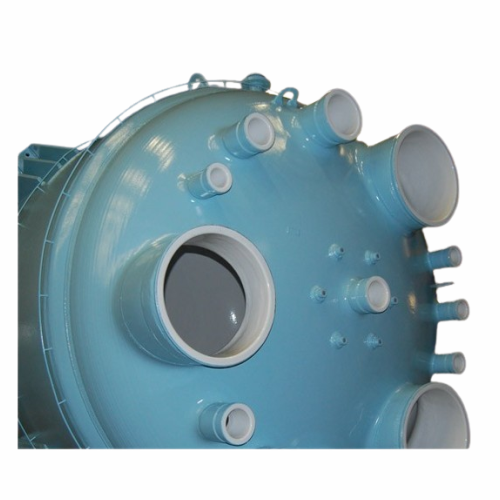
Asme glass-lined reactors for chemical processing
Optimize your chemical processes with high-pressure, corrosion-resistan...
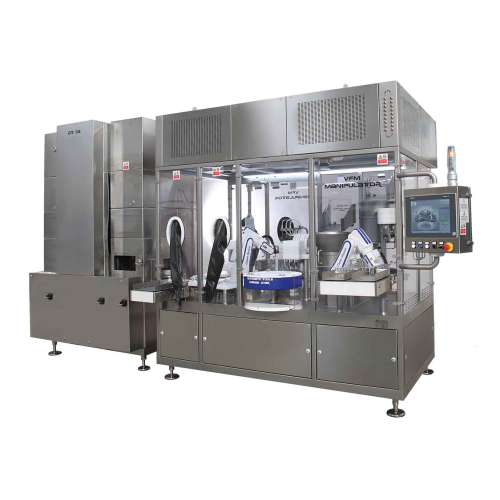
Industrial manipulator for sterile and nonsterile filling
Maintain the integrity of high-value pharmaceuticals with a hi...
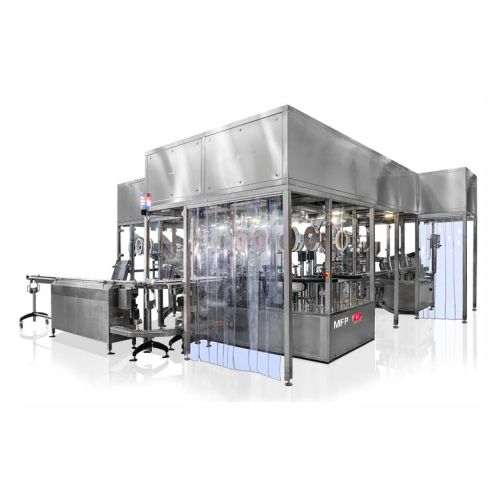
Sterile and nonsterile vial filling system for injectables
Achieve precision and safety in filling and stoppering with a...
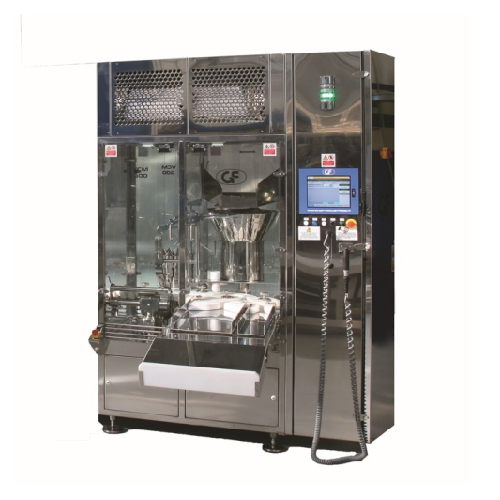
Vial capping solution for pharma applications
Efficiently secure the integrity of sensitive liquid medications with a flex...
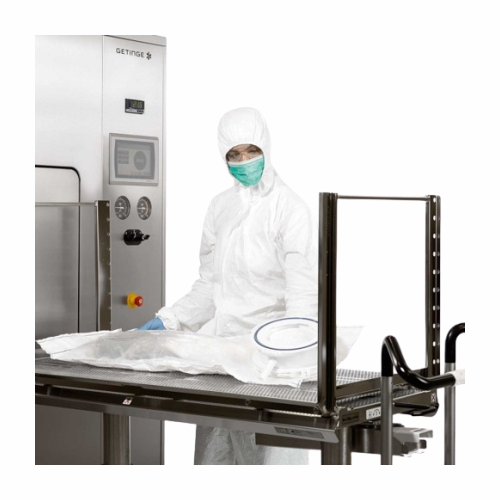
Sterilizer loading solutions for biopharma and research laboratories
Streamline your sterilization process with ergonom...
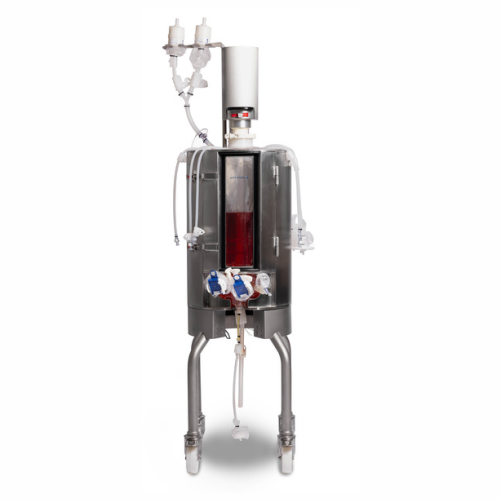
Single-use bioreactor for pilot and production scale
Streamline your bioprocessing with a scalable single-use solution th...
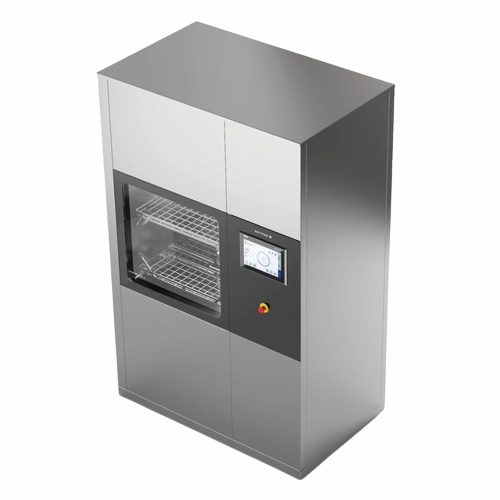
High-capacity cgmp washer/dryer for cleanrooms
Optimize your cleanroom operations with this compact washer/dryer, designed...
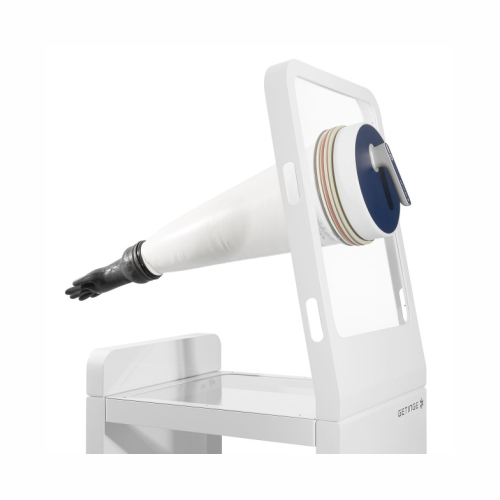
Wireless glove leak tester for isolation environments
Achieve effortless contamination control in sterile environments wi...
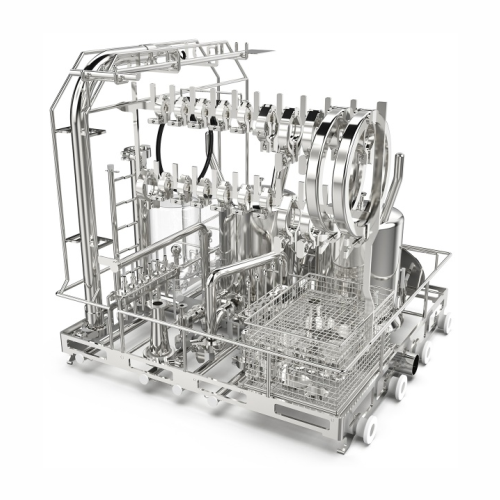
Loading solutions for Gmp washers
Ensure thorough cleaning and drying of biopharmaceutical components with modular loading ...
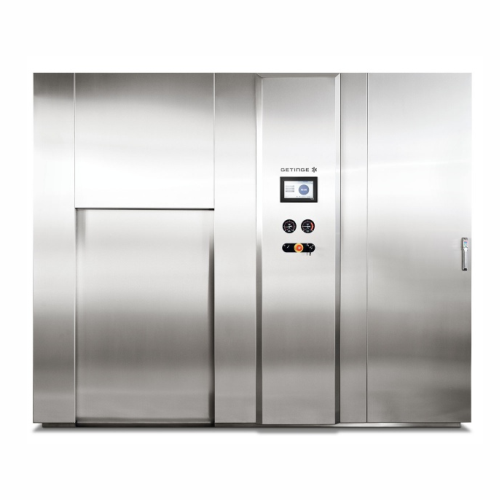
Steam sterilizer for biomedical lab research
Ensure the highest level of biosafety and scientific integrity with this stea...
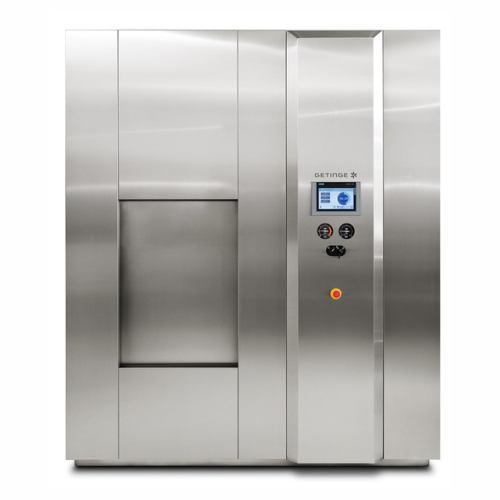
Steam sterilizer for pharmaceutical production
Ensure consistent, contamination-free sterilization of pharmaceutical compo...
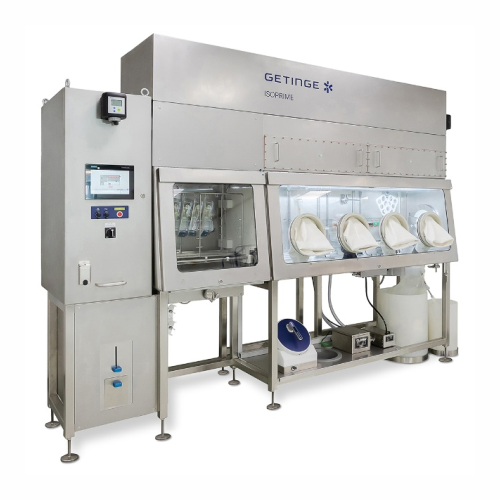
Cost-effective rigid-wall isolator for aseptic applications
Ensure sterility and safety with a versatile isolation and d...
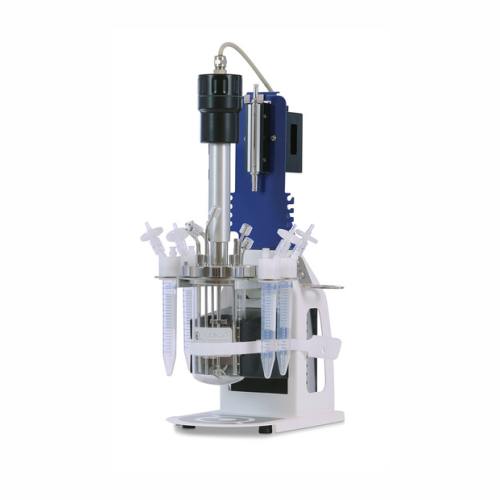
Small size multi-use glass autoclavable bioreactor
Optimize your laboratory space with this compact bioreactor that reduc...

Aseptic transfer port for secure bi-directional transfer
Ensure seamless and contamination-free transfer of sterile mater...
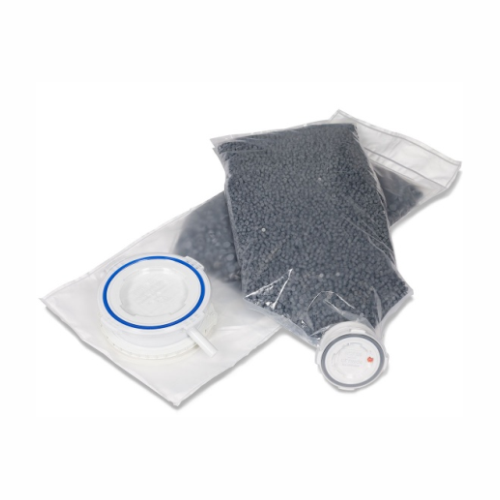
Sterile transfer bags for aseptic production
Ensure contamination-free and efficient component transfer in high-speed asep...
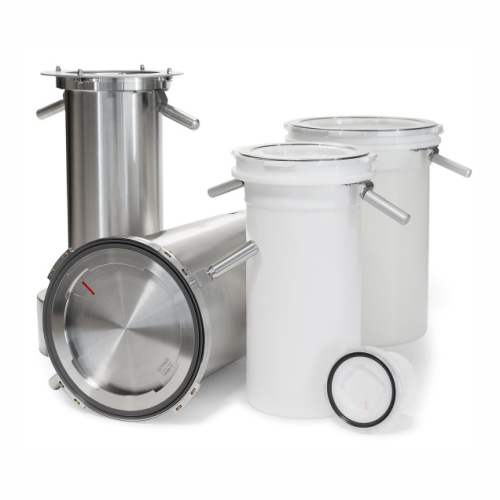
Reusable containers for sterile and toxic material transfer
Ensure safe and contamination-free transfer of sterile and t...
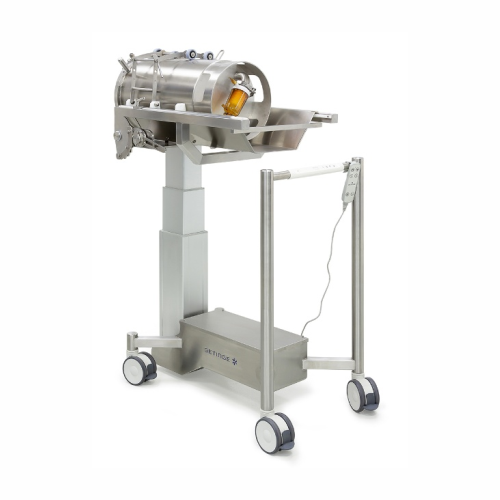
Ergonomic transfer trolley for beta bags and containers
Ensure aseptic integrity and streamline your handling of sensitiv...
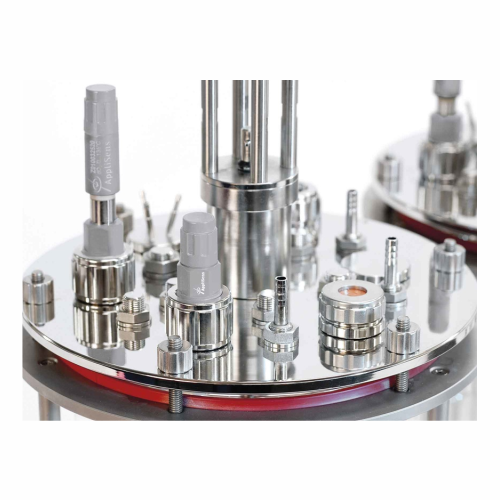
Bioprocess sensor for accurate measurement
Optimize your bioprocessing with advanced sensors designed to deliver precise m...
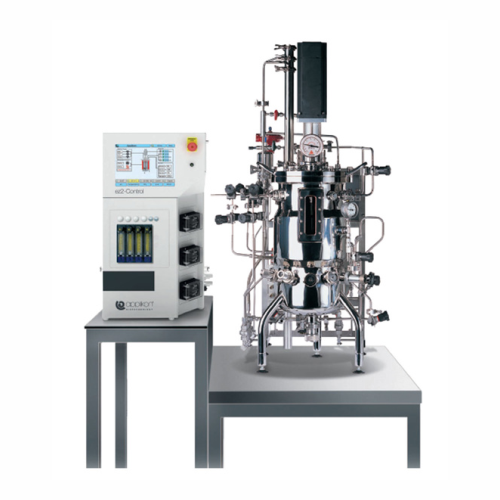
Bench top bioreactor for microbial and cell cultures
Optimize your bioprocessing workflow with this versatile bench top s...
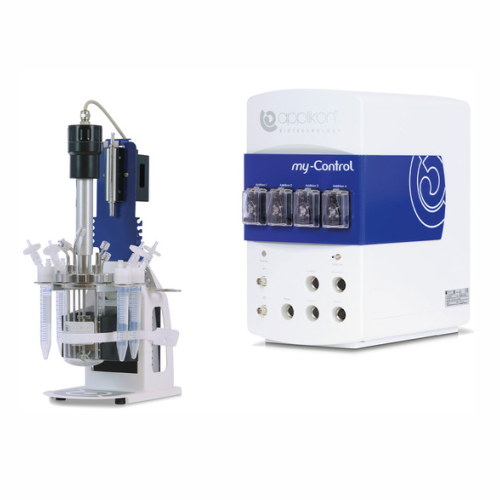
Turnkey bioreactor system for cell culture
Streamline your bioprocessing with a complete cultivation system; ideal for pro...
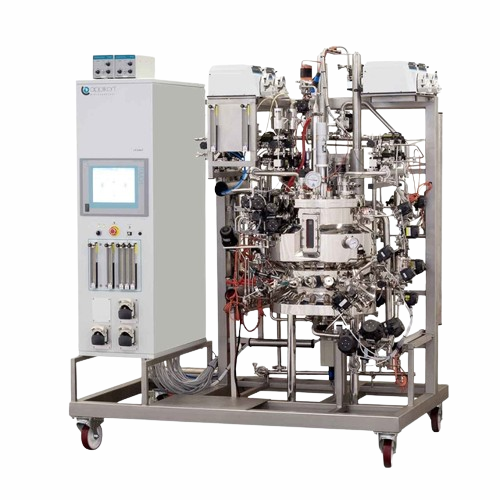
Stainless steel bioreactor for small-scale bioprocess production
Optimize your bioprocess development with a modular sta...
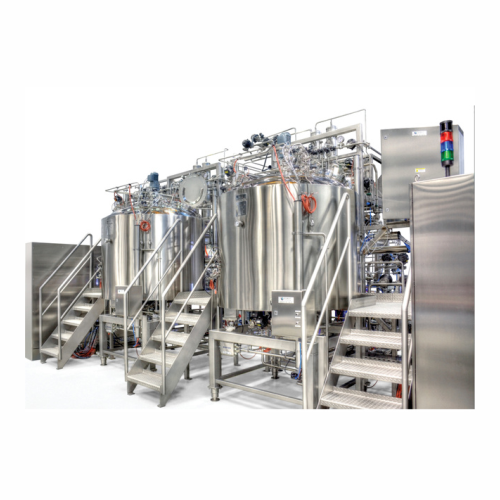
Stainless steel bioreactor for cgmp production
Achieve reliable and scalable production of life-saving medicines with a cu...
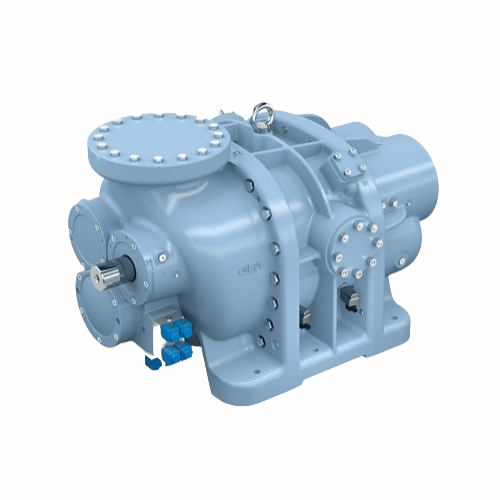
Industrial screw compressor for various refrigerants
Optimize your refrigeration systems with high-performance screw comp...
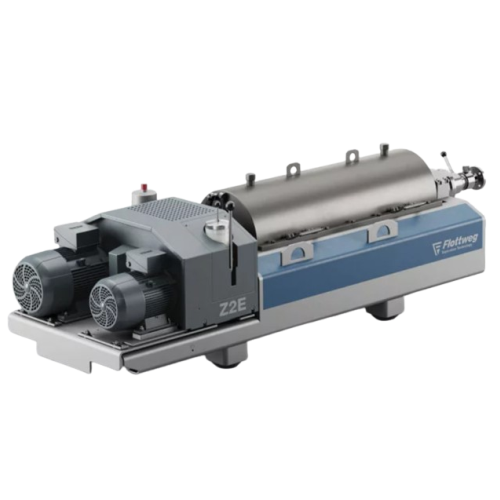
3 phase decanter centrifuge for industrial separation
Optimize your production line with efficient three-phase separation...
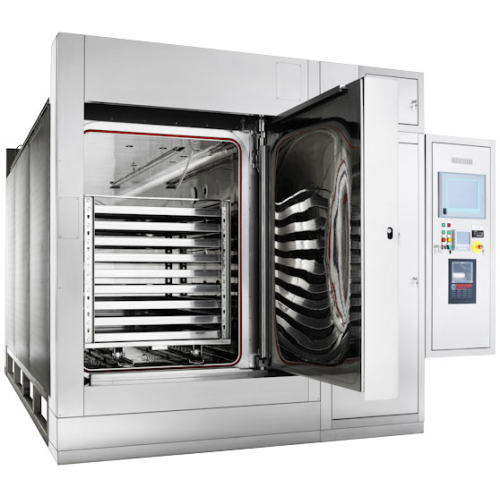
Saturated steam sterilizer for bio-pharma applications
Ensure sterility and compliance in your production line with versa...
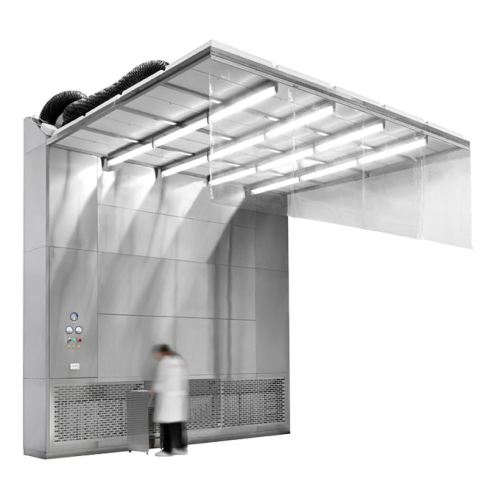
Cleanroom air filtration unit for pharmaceutical production
Ensure sterile integrity in your manufacturing process with ...

Bio-decontamination unit for heat-sensitive loads
Ensure the integrity of heat-sensitive biopharmaceutical products by em...

Sterility test isolator for injectables and sterile powders
Ensure sterility and compliance for injectables and biopharm...
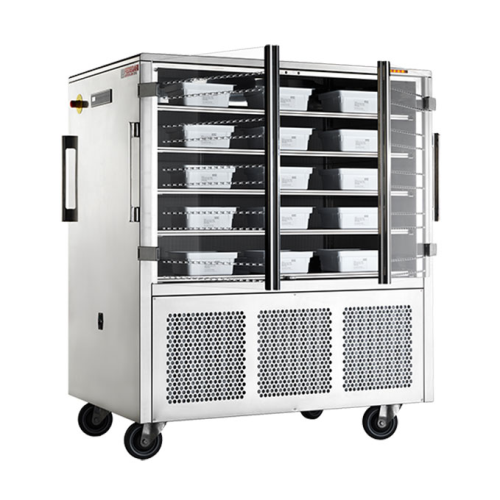
Iso 5 Hepa cart for aseptic material transfer
Ensure aseptic conditions during storage and transfer with this compact HEPA...
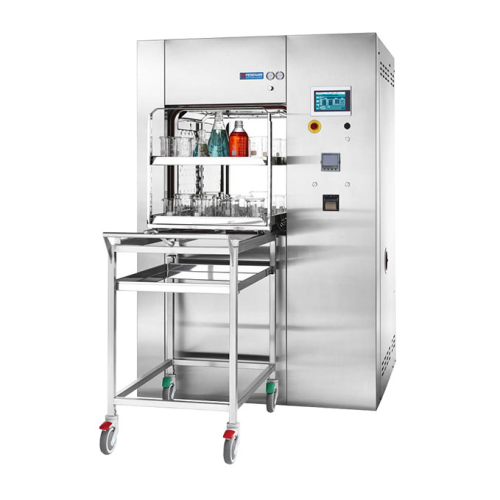
Laboratory sterilizer for microbiology and analytical labs
Designed for laboratories requiring versatile sterilization s...
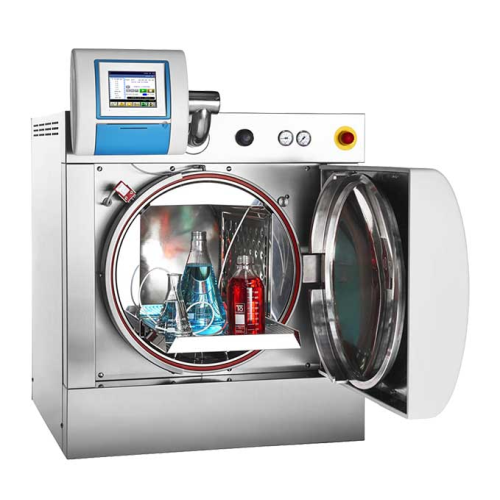
Benchtop lab sterilizer for laboratory use
Ensure precise sterilization of various lab materials with a compact solution d...
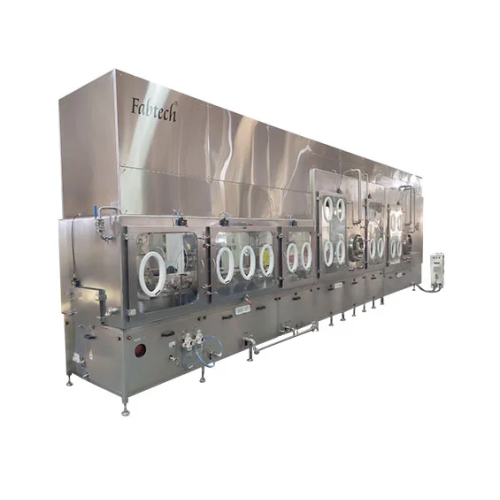
Aseptic filling isolator for vial / Pfs / cartridge
Ensure sterile and contamination-free filling of vials, pre-filled sy...
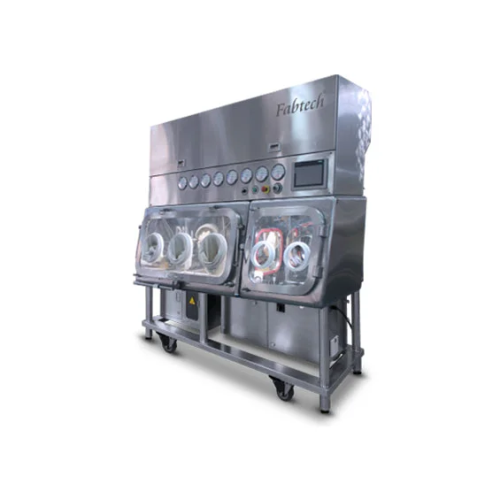
Mobile isolator for aseptic environment transfer
Ensure aseptic conditions and seamless material transfer with this mobile...
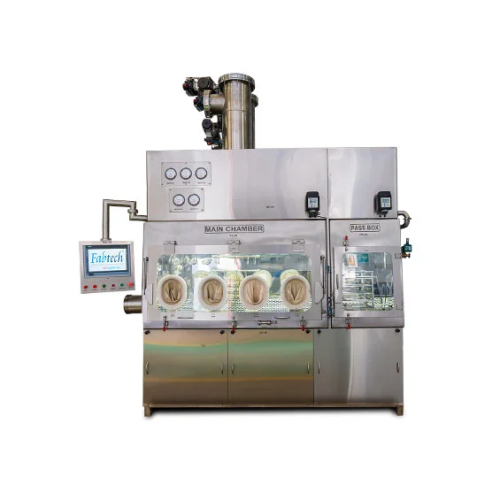
Sterility testing isolator for aseptic environments
Ensure aseptic conditions and process integrity during sterility test...
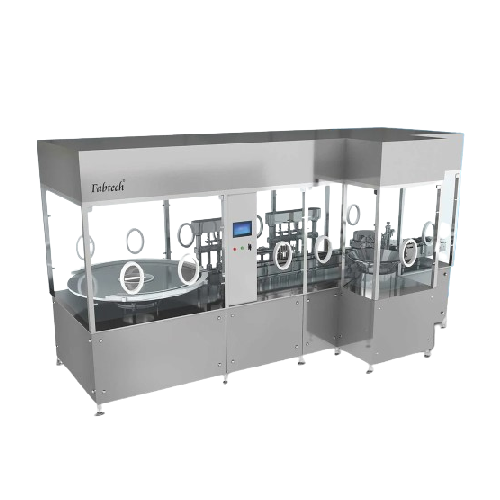
Pharmaceutical turnkey project consultants
Streamline your biopharma production with turnkey solutions that cover everythi...
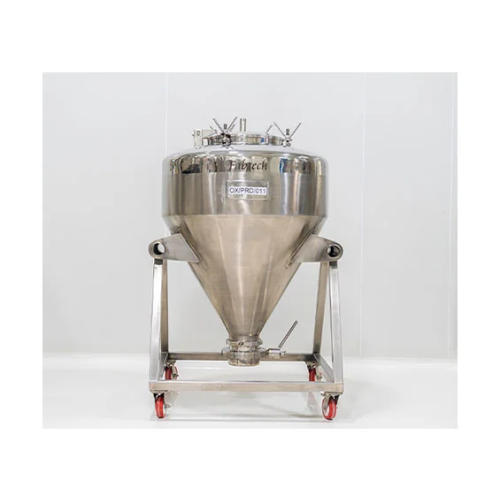
Vacuum transfer system for powders and granules
Effortlessly transfer and manage powders and granules with seamless integr...
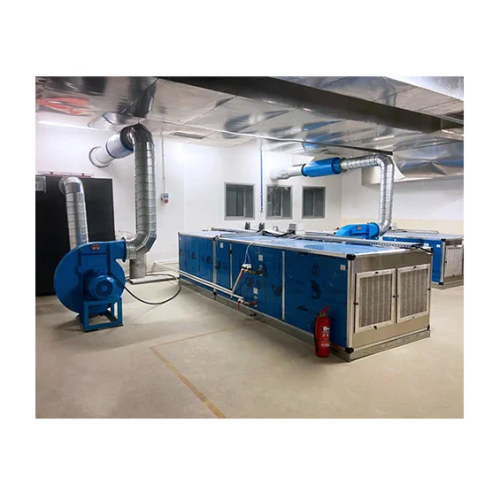
Cleanroom infrastructure for contaminant control
Ensure optimal contaminant control and regulatory compliance in cleanroom...
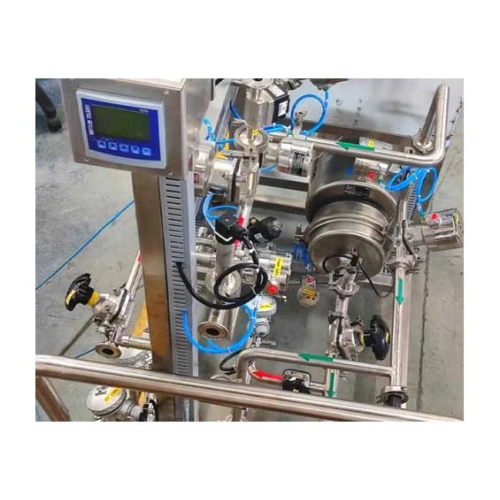
Cip & Sip systems for pharmaceutical cleaning
Ensure effective cleaning and sterilization in production lines with customi...
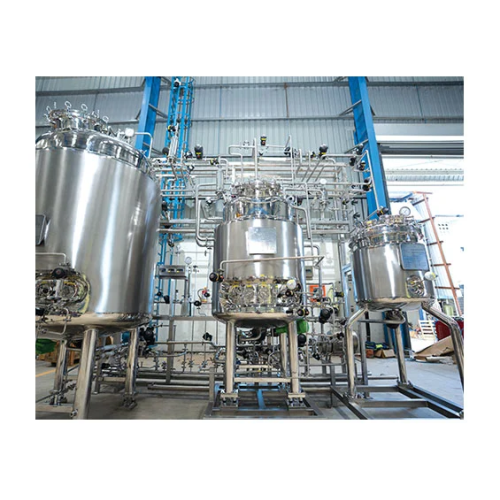
Pharma manufacturing process vessels
Ensure contamination-free production of sterile liquid formulations with process vesse...
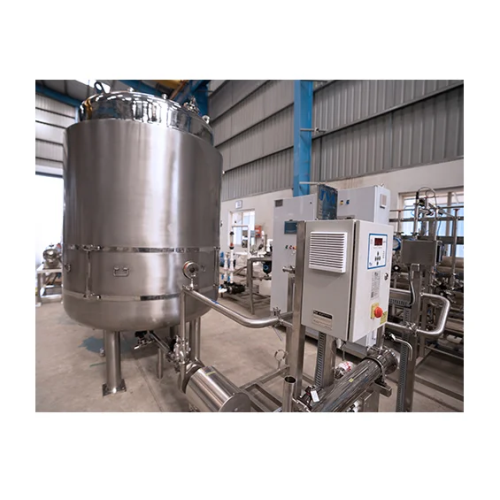
Pure steam generation system for sterilization purposes
Ensure sterile production with pure steam capable of eradicating ...
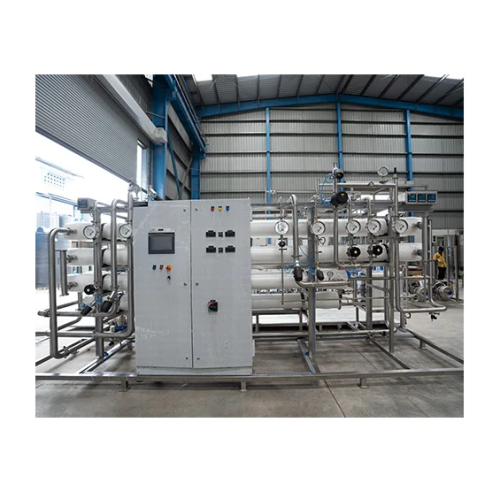
Purified water generation system for pharmaceutical applications
Ensure consistent water purity for critical drug formul...
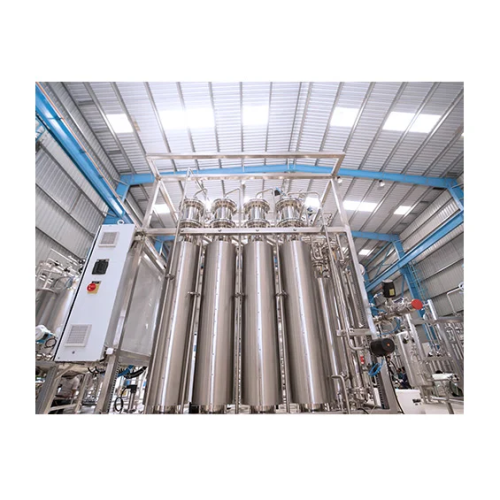
Water for injections generation system
Ensure compliance with strict regulatory standards while providing pyrogen-free wate...
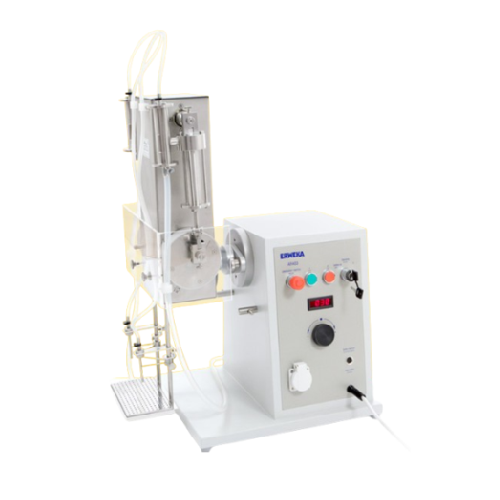
Industrial liquid filler for small to medium volume operations
Ensure accuracy and efficiency in liquid formulation with...
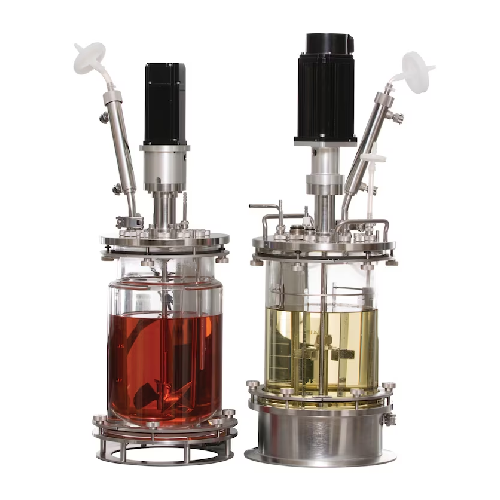
Bioreactor for mammalian and microbial cell cultivation
Optimize your bioprocesses with advanced temperature and heat tra...
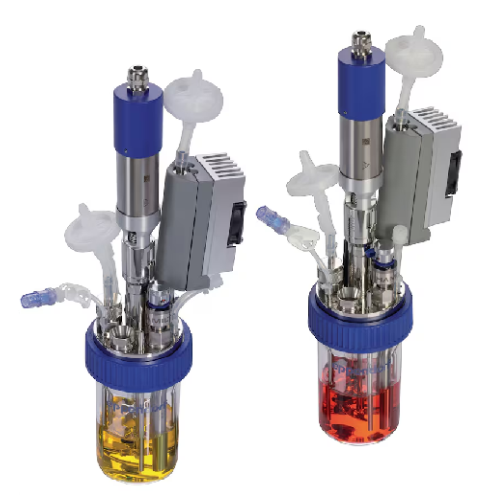
Mini bioreactor for cell culture and microbial process development
Achieve precise control and reproducibility in small...
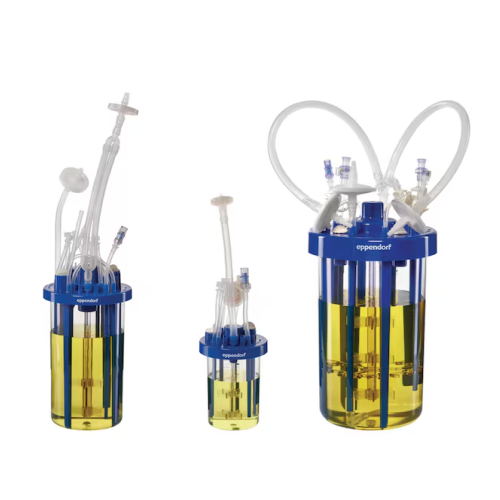
Single-use bioreactors for microbial fermentation
Optimize high-density fermentation with advanced single-use bioreactor ...
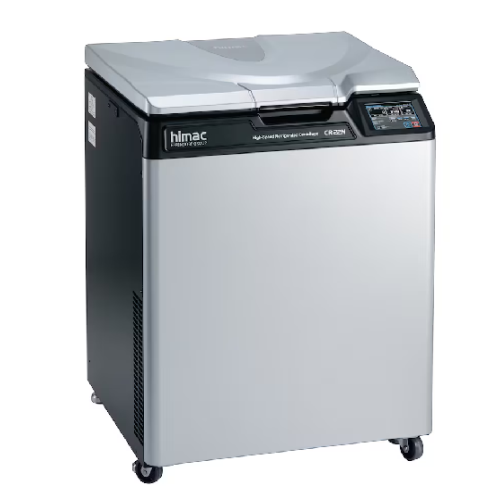
High-speed centrifuge for laboratory applications
Maximize efficiency in high-volume centrifugation tasks with this versa...
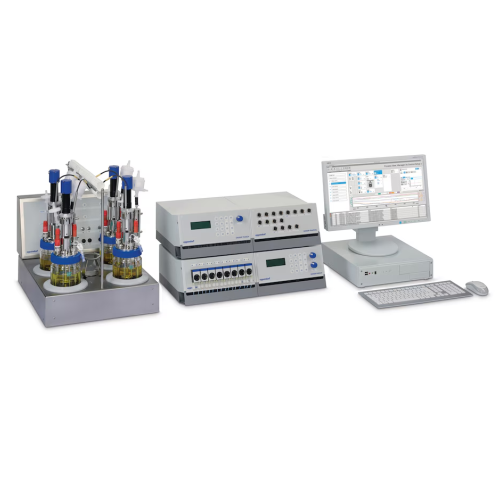
Parallel bioreactor system for cell culture and microbiology
Optimize bioprocess development with a scalable system desi...
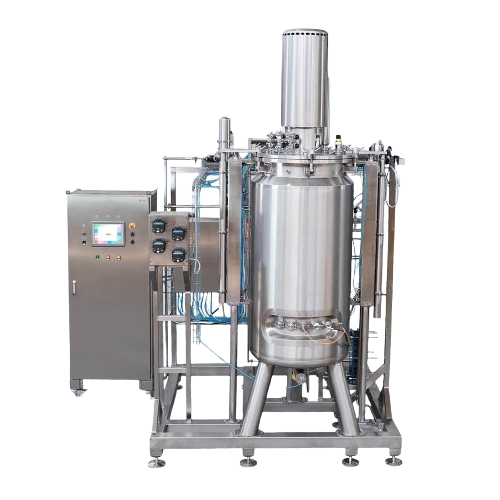
Fermenter for microbial fermentation processes
Optimize your fermentation and biopharmaceutical production with stainless ...
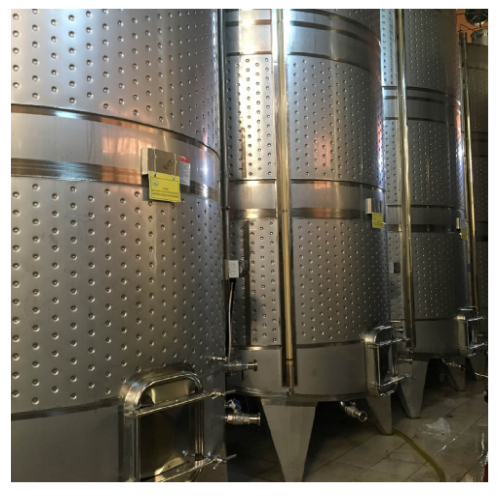
Stainless steel fermentation tanks
Optimize your fermentation efficiency with stainless steel tanks that provide precise te...
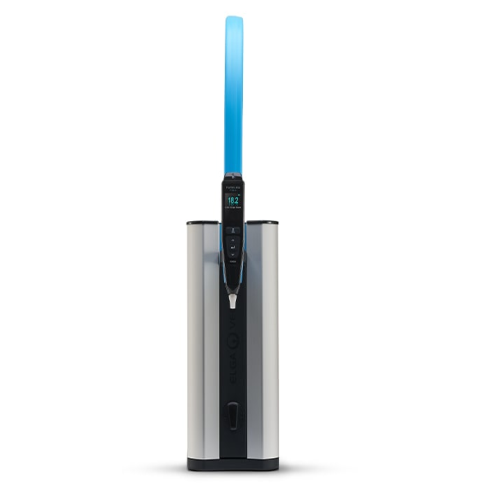
Ultrapure water system for analytical applications
Ensure critical purity for your molecular and analytical processes wit...
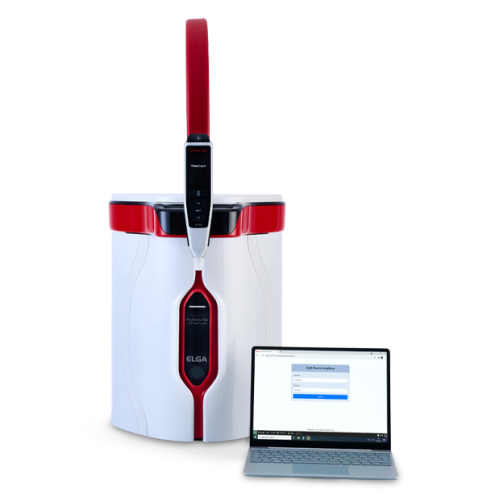
Pharmaceutical water purification system
Ensure compliance with stringent pharmaceutical standards by integrating a reliabl...
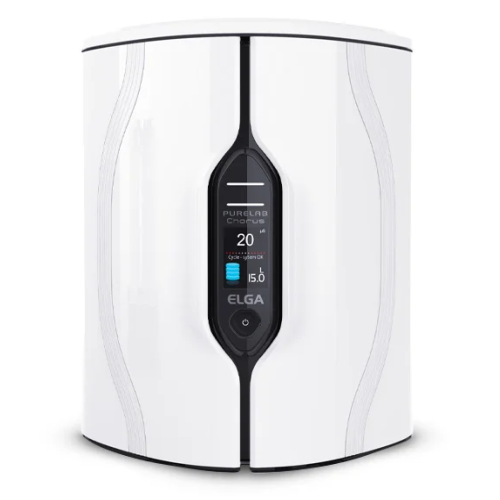
Type Iii water purification system for general lab use
Achieve consistent and reliable Type III water quality for laborat...
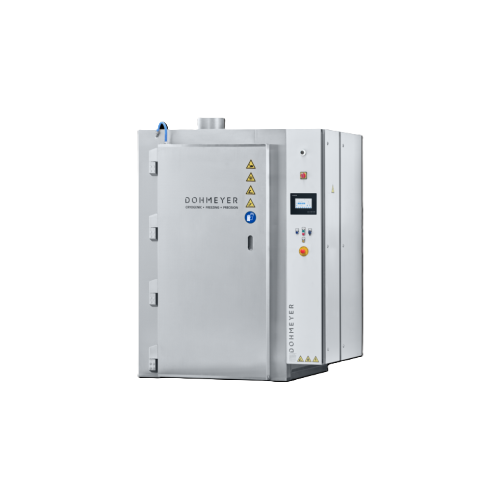
Cryogenic batch freezer for industrial processing
Achieve precise temperature control for sensitive materials with a cryo...
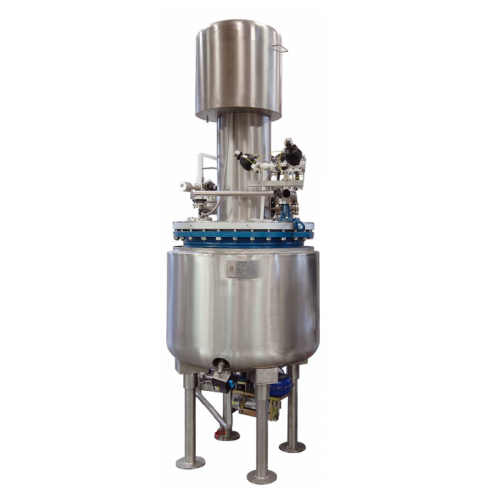
Pharmaceutical reactor for efficient cleanability
Optimize your production with this reactor, designed for efficient mixi...
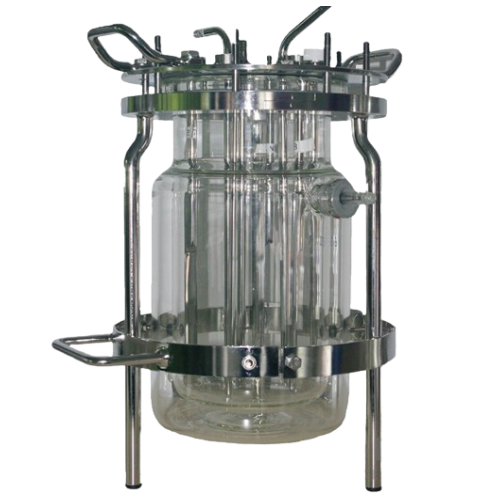
Bioreactor for cell culture yield optimization
Streamline complex cell culture processes with a bioreactor designed to enh...
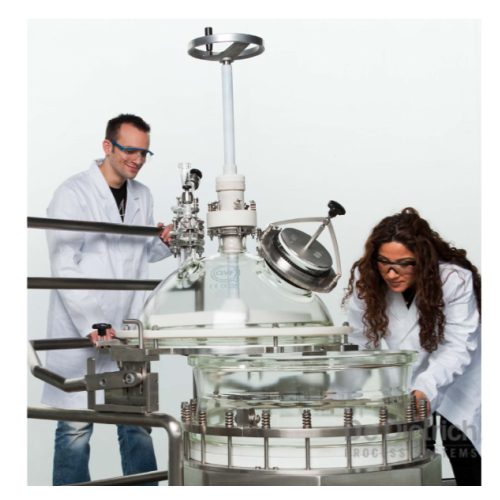
Glass nutsche filter for fine chemical and pharmaceutical filtration
For precise separation and filtration in R&D ...
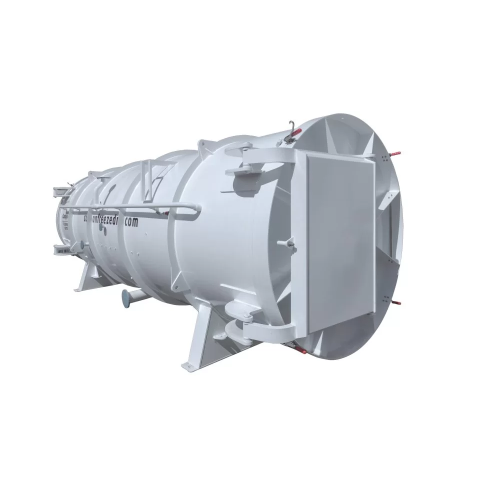
Large-scale industrial freeze dryer
Achieve precise moisture control and preserve product integrity with a large-scale free...
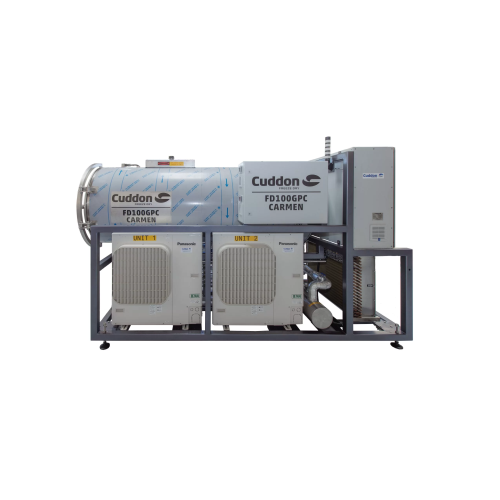
General purpose freeze dryer for small commercial batches
Maximize your production line’s flexibility with this ve...
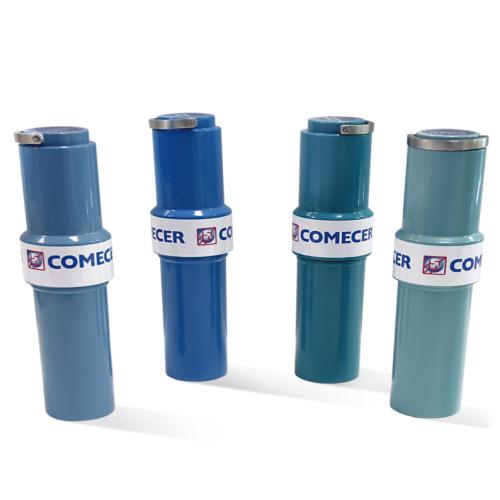
Syringe shielded container for radiopharmaceuticals
Ensure safe and efficient transport of sensitive radiopharmaceuticals...
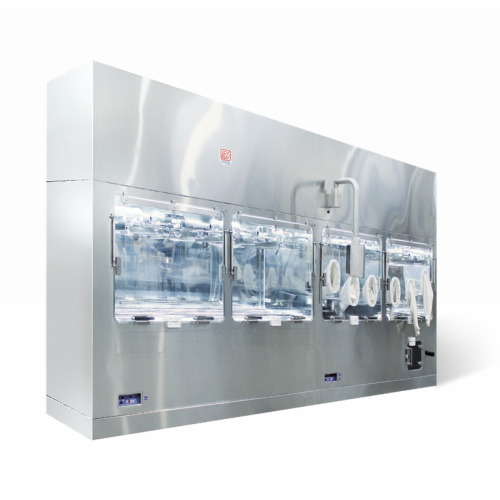
Custom automation for drug-device filling and assembly
Efficiently integrate precise filling and assembly for biopharmace...
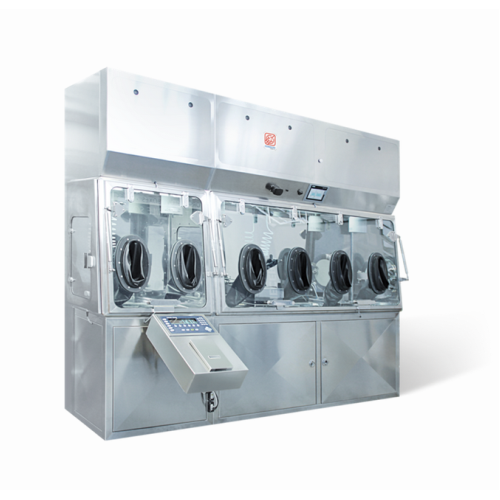
Modular dispensing and weighing isolator for pharmaceuticals
Achieve precise dispensing and weighing of high-potency pha...
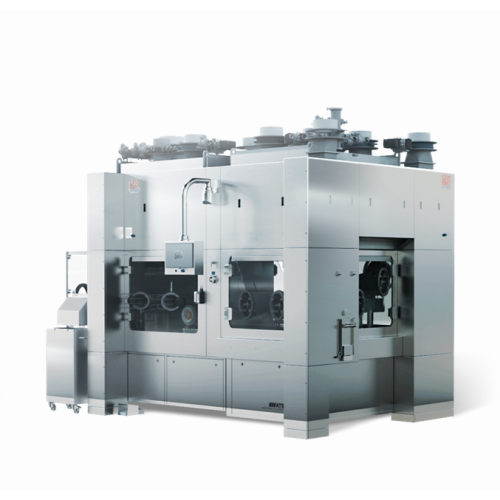
Sterile robotic filling for ready-to-use vials and syringes
Achieve precise and contamination-free filling for biopharma...
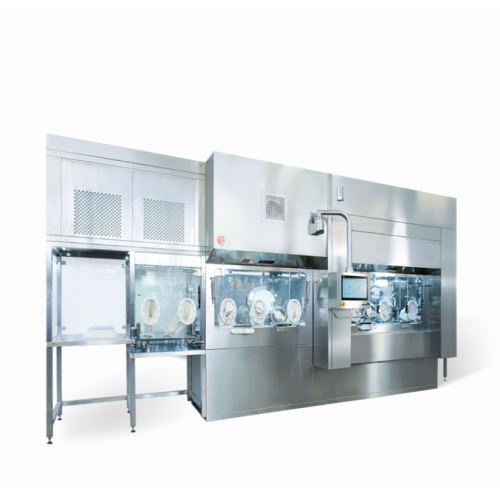
Compact aseptic vial filling system
Optimize your aseptic liquid filling with a compact system designed for seamless integr...
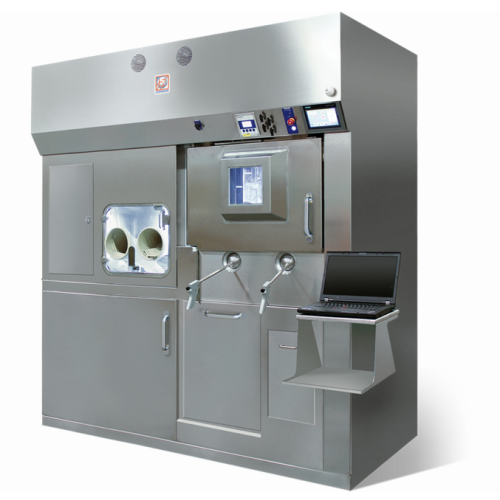
Synthesis and dispensing hot cell for radiopharmaceuticals
Ensure precise synthesis and dispensing of radiopharmaceutica...

Rotary filling system for Rtu vials in pharma production
Optimize your sterile liquid and powder handling with a versatil...
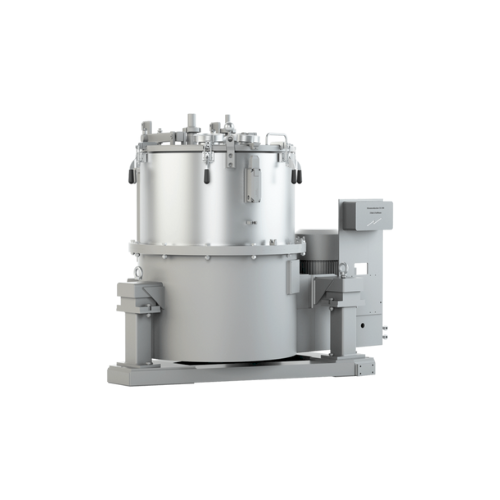
Industrial filter centrifuges for high solids content processing
Optimize processing of high-solid slurries with efficie...
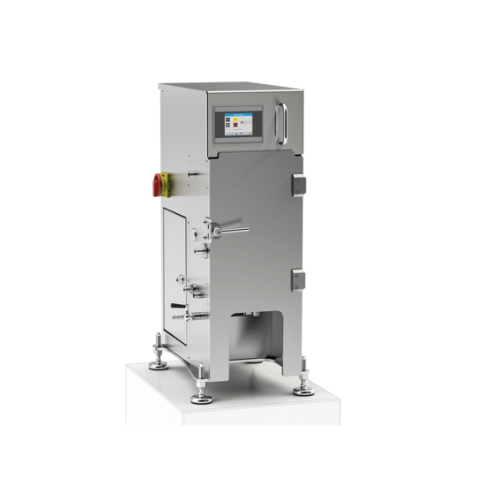
High-speed tubular centrifuges for solid-liquid separation
Efficiently separate microscopic solids from liquids in high-...
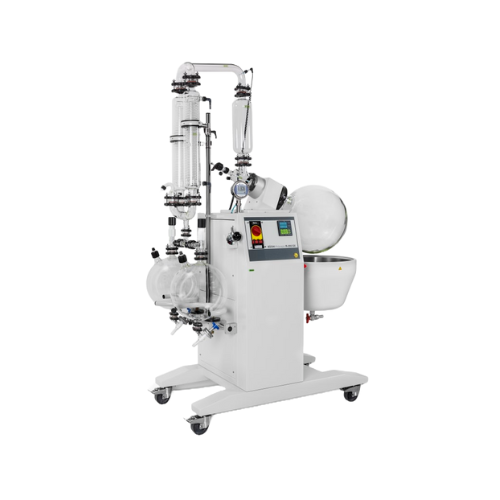
Rotary evaporator for large-scale industrial distillation
Achieve precise separation and concentration with a rotary eva...
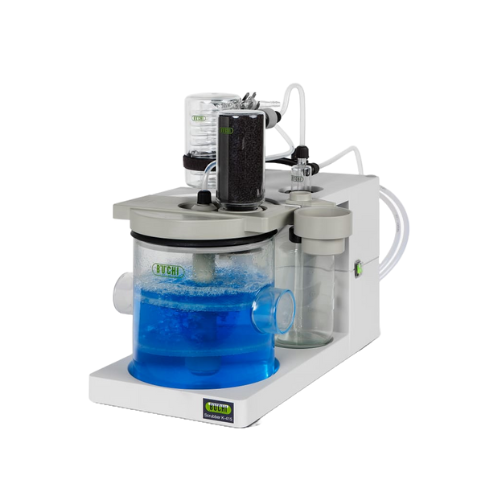
Industrial fume scrubber for safety compliance
Enhance workplace safety by efficiently neutralizing hazardous fumes and va...
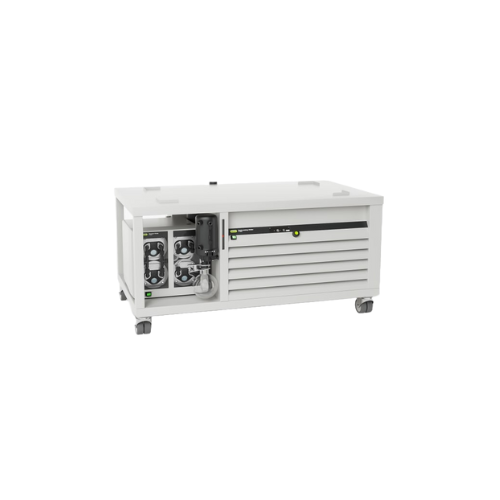
Industrial recirculating chiller for laboratory applications
For consistent distillation results, maintain accurate temp...
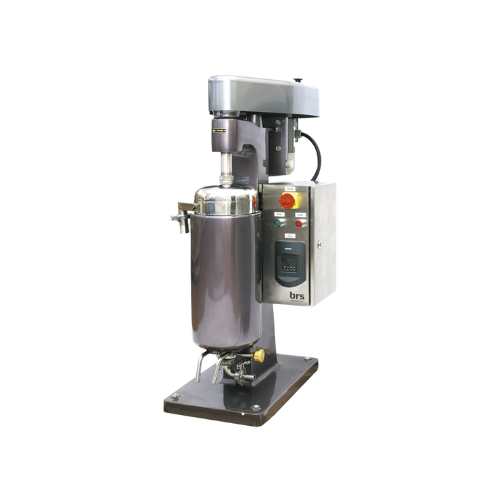
High-speed tubular centrifuges for liquid-solid separation
For efficient component separation in high-viscosity fluids, ...
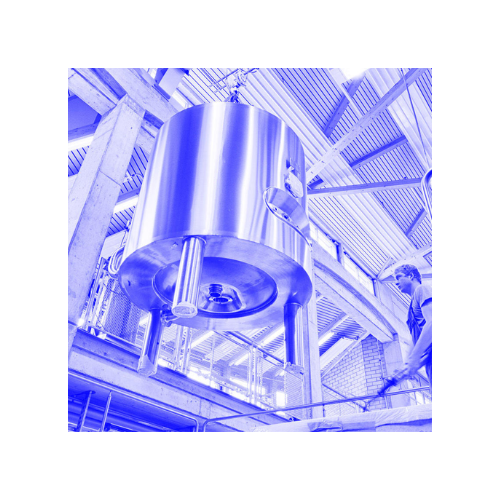
Sterile media and buffer storage tanks
Ensure uninterrupted bioproduction with our tanks designed for secure storage and pr...
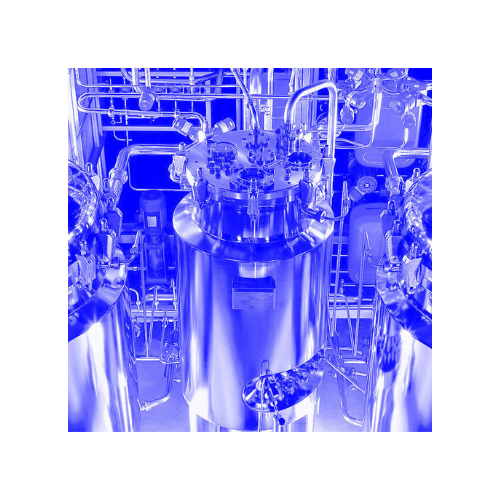
Media and buffer preparation solution for bioprocessing
Achieve seamless media and buffer preparation with precise dosing...
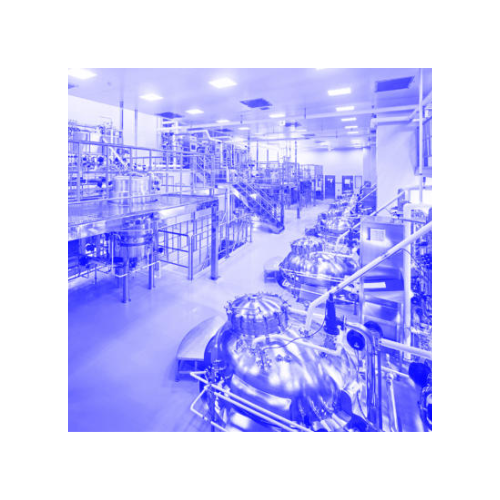
Bioreactors for cell culture processes
Efficiently cultivate sensitive cell lines with customizable bioreactors designed to...
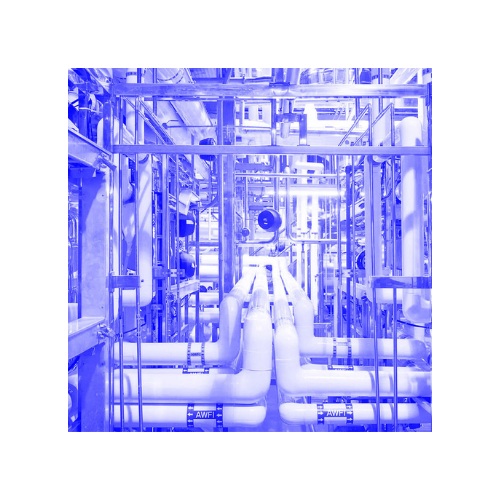
Cleaning in place systems for bioreactors
Ensure seamless sanitization with a mobile cleaning system designed to maintain ...
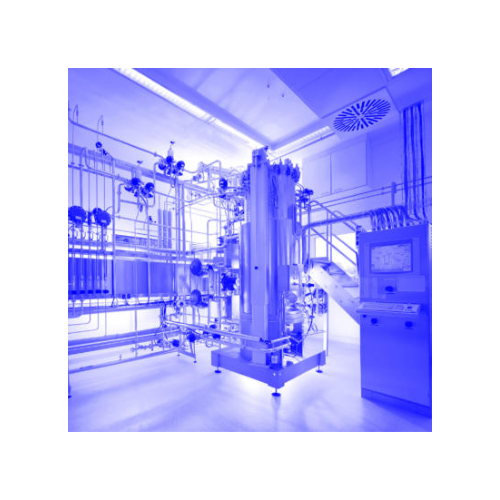
Lab-scale fermentors for microbial cultivation
Optimize microbial cultivation with lab-scale fermentors designed for preci...
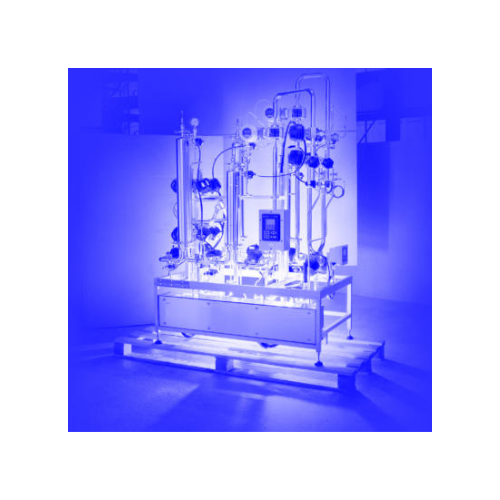
Filter stations for sterile filtration in biopharmaceuticals
Ensure sterility and precision in your biopharmaceutical pr...
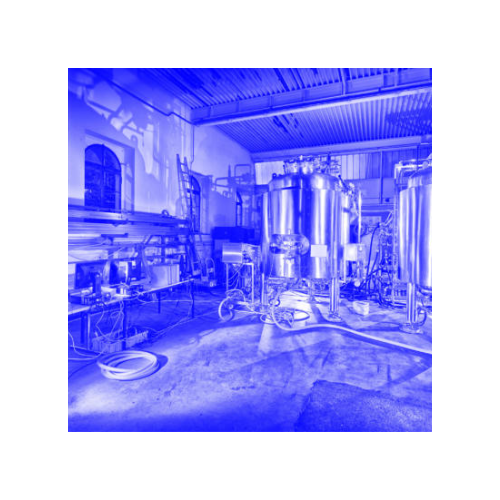
Formulation vessel for biopharmaceutical homogeneity
Achieve precise homogeneity in liquid formulations with vessels opti...
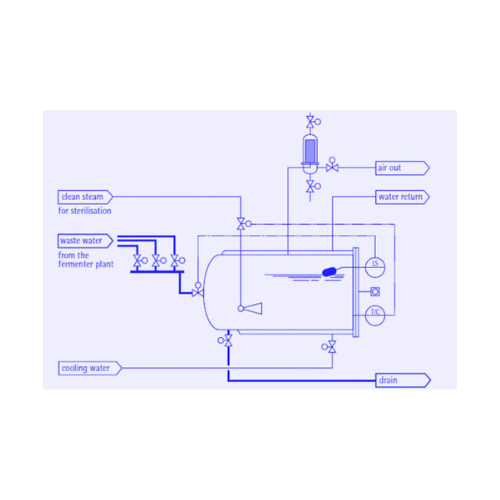
Biowaste decontamination system
Ensure safe handling of pathogenic and genetically modified organisms in wastewater with pre...

High-pressure homogenizer for dairy and food production
Optimize your product consistency and stability with a high-press...
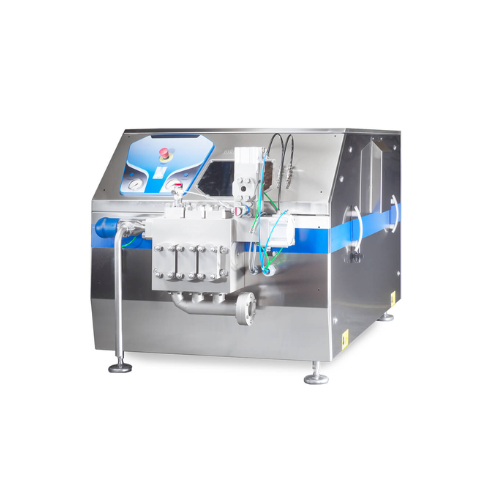
Industrial homogenizers for high-pressure applications
Optimize homogenization with high-pressure solutions designed for ...
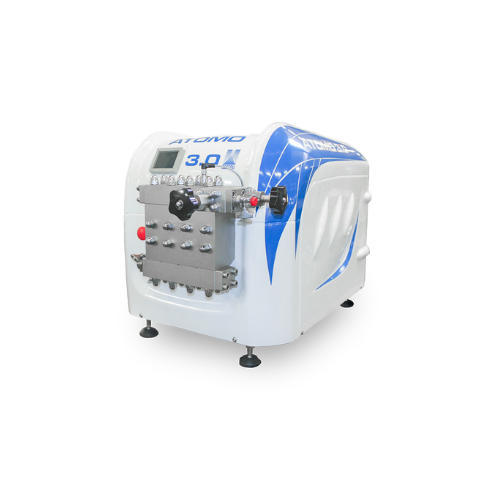
Laboratory homogenizer for dairy and biotech applications
Ensure precise particle size reduction and consistent texture ...
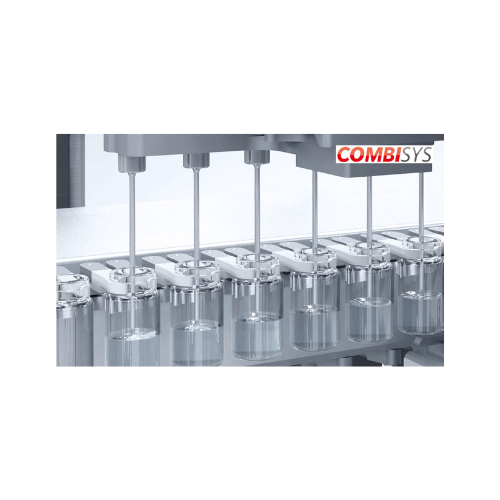
Combisys filling and closing system for pharmaceutical containers
Ensure precise filling and closing of pharmaceutical ...
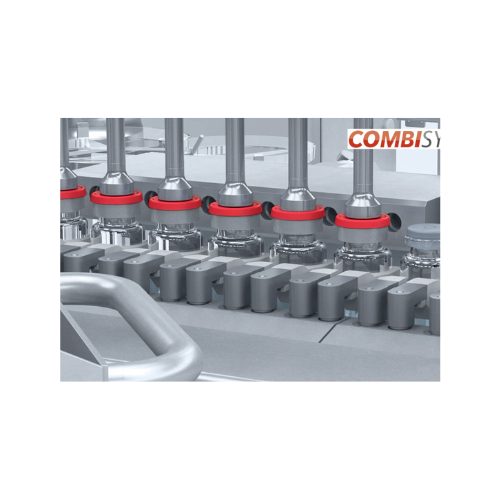
Automated vial closing system
Ensure reliable vial sealing with unparalleled flexibility and precision, optimizing your liqu...
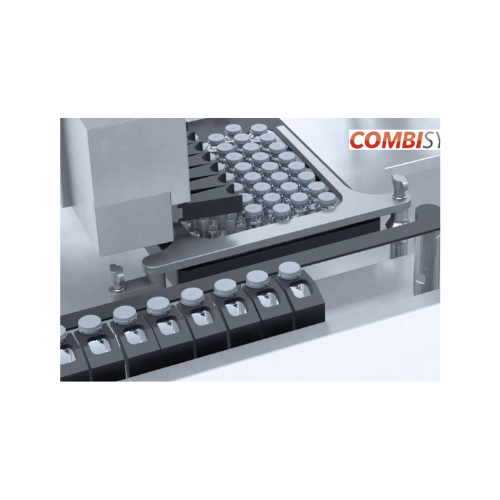
Automated container loading system for ampoules and syringes
Ensure precise loading and nesting of sterile containers in...
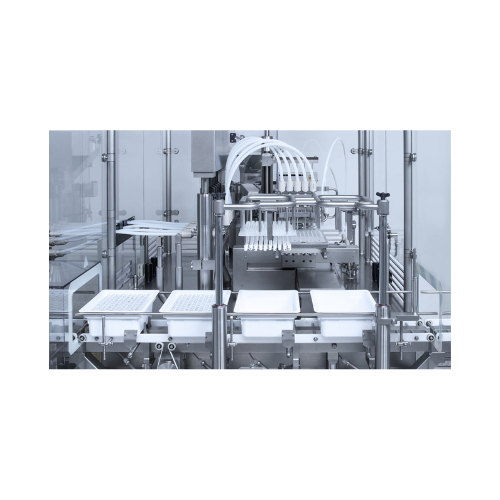
Filling and closing solution for nested containers
Streamline your vial, cartridge, and syringe production with precise d...
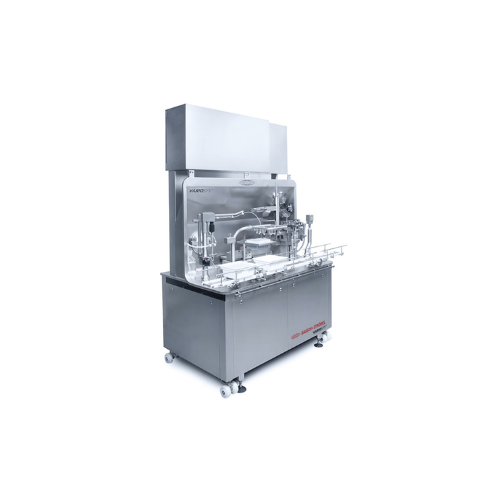
Filling and closing system for nested containers
Optimize liquid formulation packaging with a high-speed system designed f...
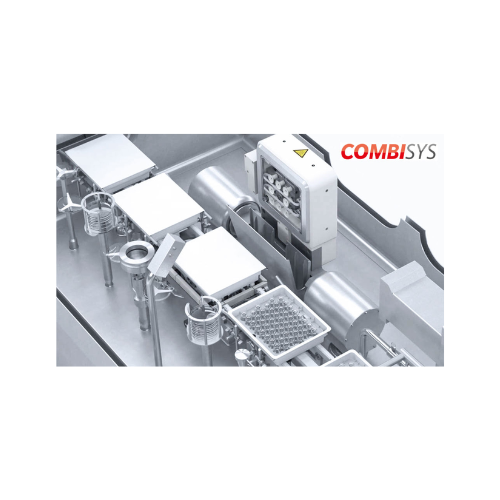
Automatic tub de-bagging and de-nesting solution
Efficiently prepare your RTU containers by seamlessly integrating de-bagg...

Tray loader for pharmaceutical containers
Maximize efficiency in aseptic fill-finish lines with precise and rapid tray loa...
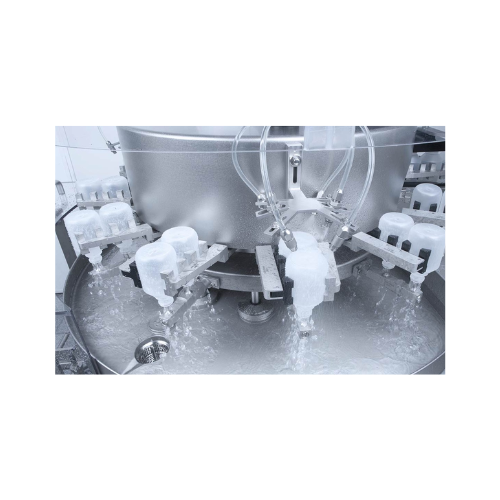
Vial and bottle cleaning system for pharmaceutical use
Ensure pharmaceutical-grade cleanliness for your vials, ampoules, ...
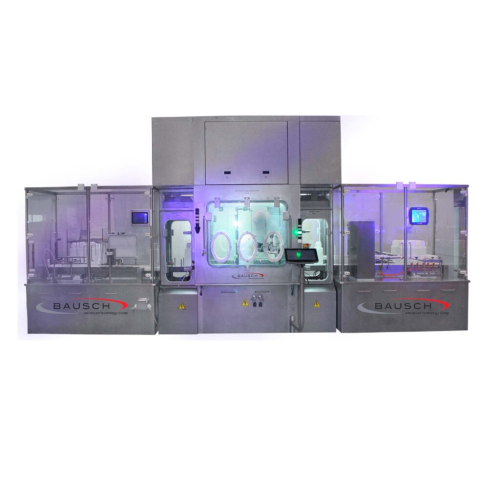
Automated filling and closing system for vials and bottles
Optimize your vial and bottle filling line with precise liqui...
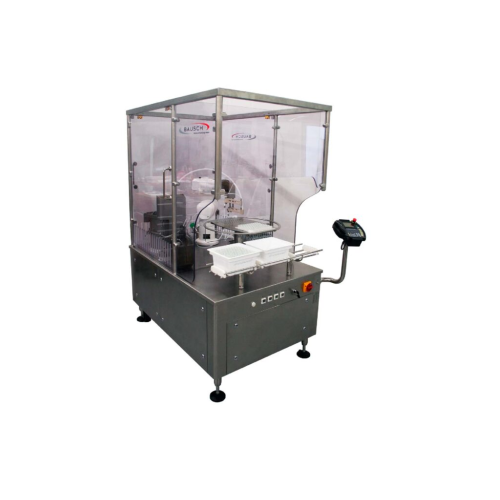
Nested vial and syringe filling and closing system
Achieve precise aseptic filling and closing for clinical products with...
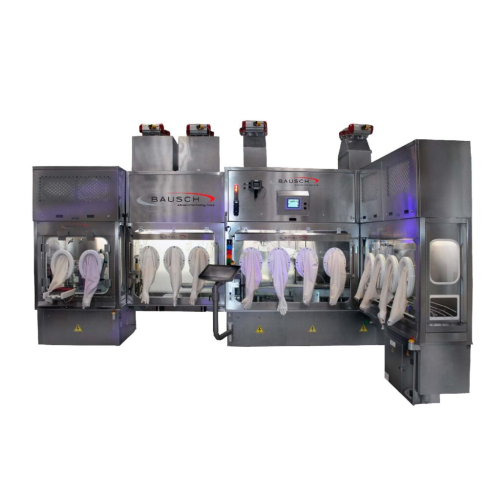
Cell and gene therapy packaging system
Streamline cell and gene therapy packaging with a versatile system that accelerates ...
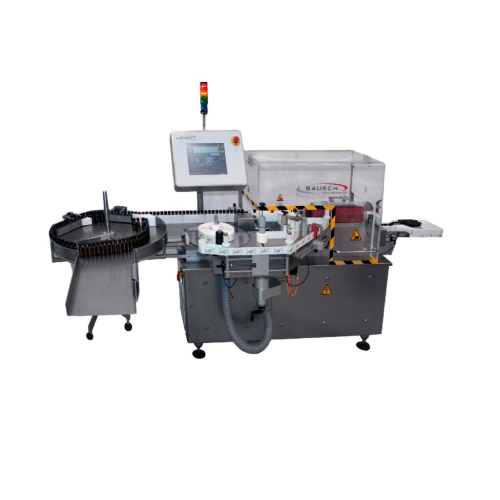
Fully automatic linear labeling system for bottles
Optimize your bottle labeling process with precision and speed, ensuri...
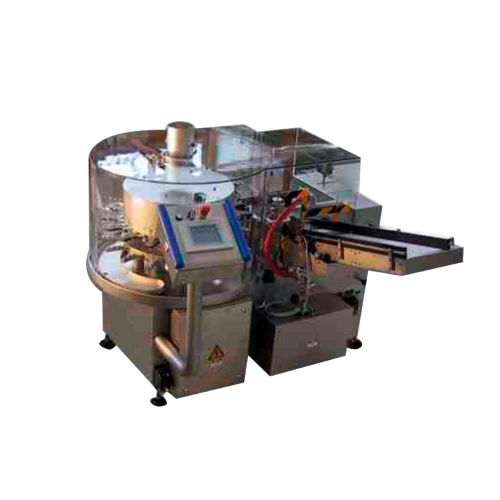
Automated washing system for vials, syringes, cartridges, and ampoules
Achieve sterile conditions with this high-speed ...
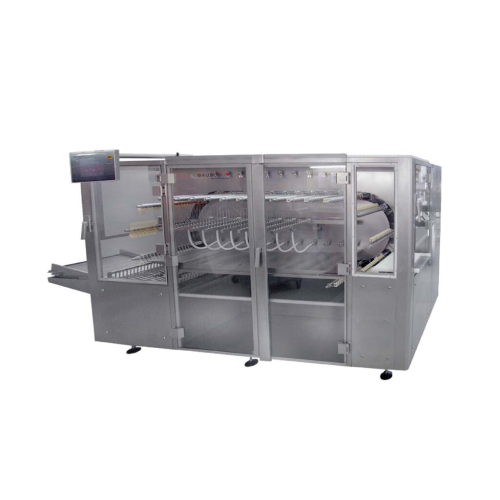
High-speed washing system for ampoules and vials
Ensure contamination-free ampoules and syringes with this advanced washin...
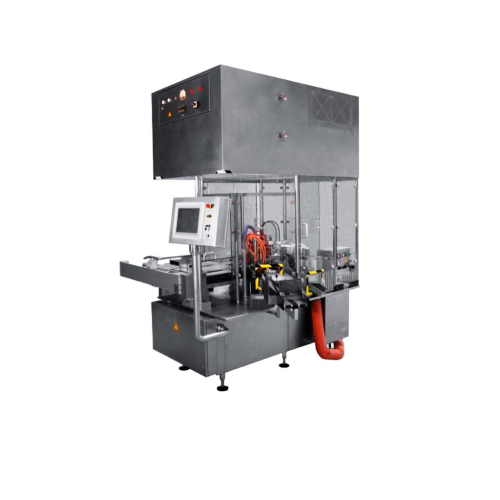
Ampoule filling and closing system
Optimize your production line with a high-speed system designed for seamless filling and...
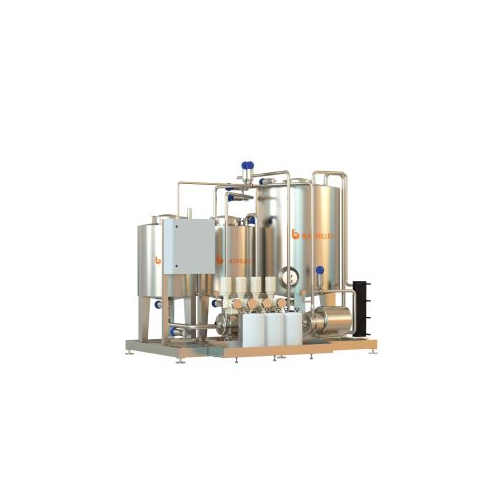
Cip system for process tanks
Ensure high-level cleanliness and compliance in your production line with an efficient in-place...
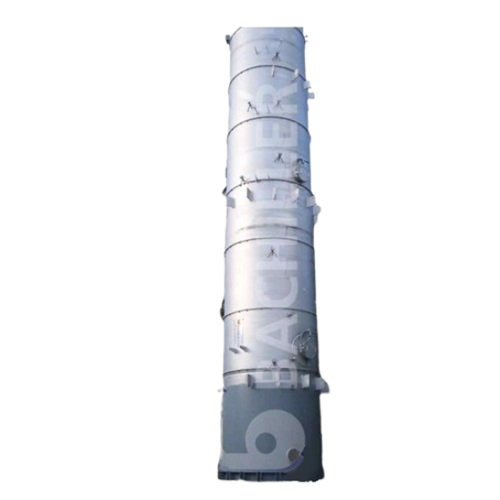
Industrial columns and towers for chemical processing
Optimize your chemical production with robust columns and towers, d...

Full-membrane water for injection (wfi) generation system
Ensure consistent high-quality injections by integrating real-...
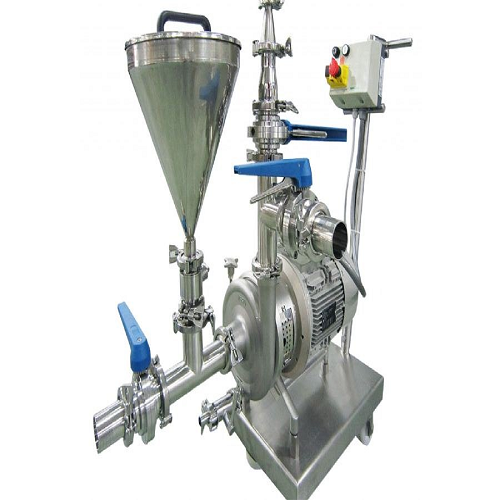
Cleaning system Cip for internal equipment maintenance
Ensure optimal hygiene and production efficiency with this portabl...
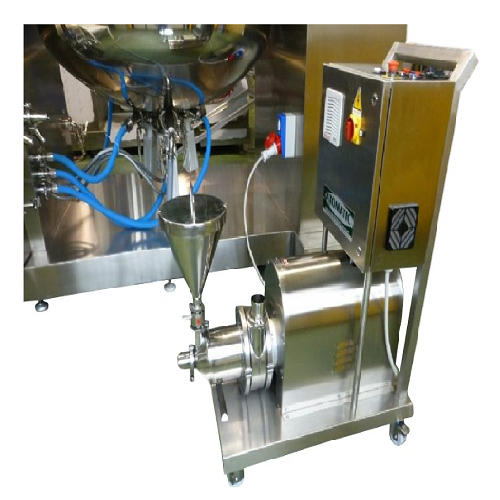
In-line external homogenizer for industrial fluid processing
Maximize fluid consistency and ensure efficient material di...
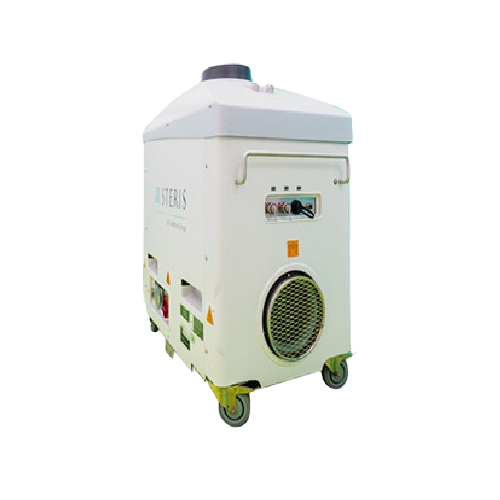
Hydrogen peroxide sterilizer for biosafety applications
Ensure optimal biosafety and contamination control with swift hyd...
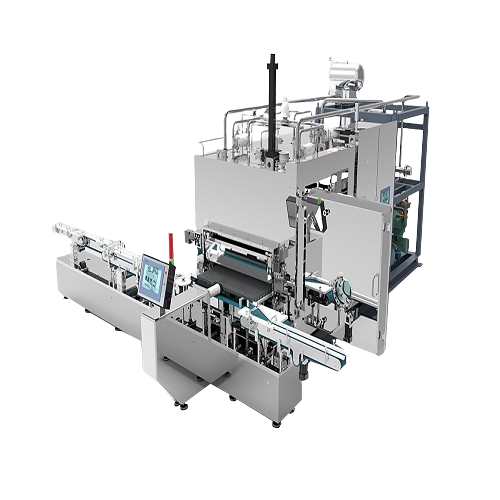
Commercial freeze dryer for pharmaceutical Api production
Ensure the stability and potency of your biopharmaceutical pro...

Sterile filling line for liquid and powder
Achieve seamless integration of filling, sterilization, and packaging with this...
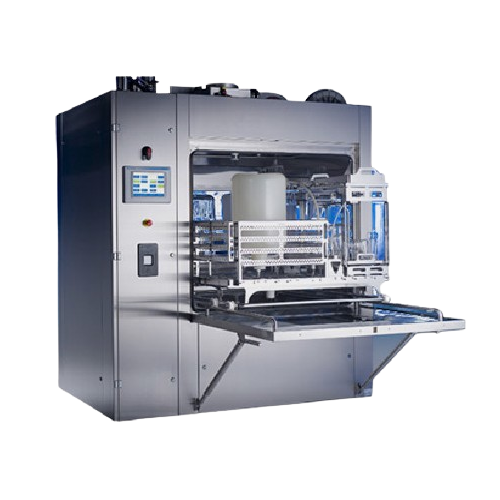
Gmp washer for pharmaceutical contamination control
Ensure verifiable cleaning and drying of critical components in bioph...
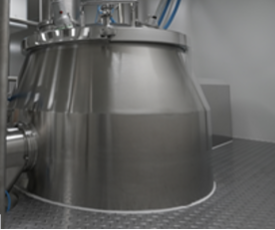
Continuous wet granulation equipment
Achieve optimal particle size and uniformity in pharmaceutical production with our con...
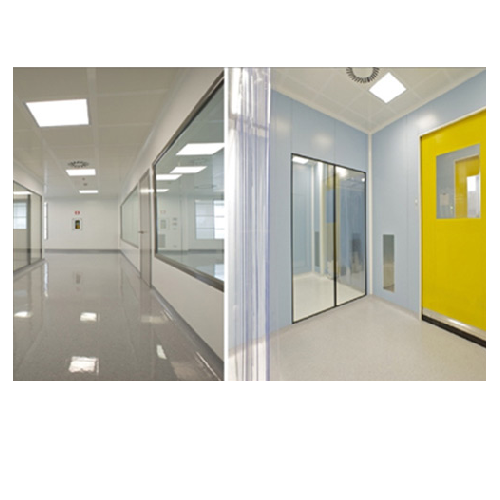
Cleanroom enclosure system for pharmaceutical and chemical industries
Ensure sterile environments with this customizabl...
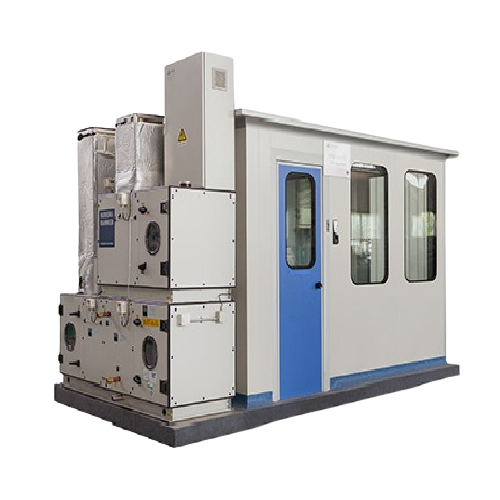
Customized Hvac system for pharmaceutical clean rooms
Achieve seamless sterilization and contamination control in clean r...
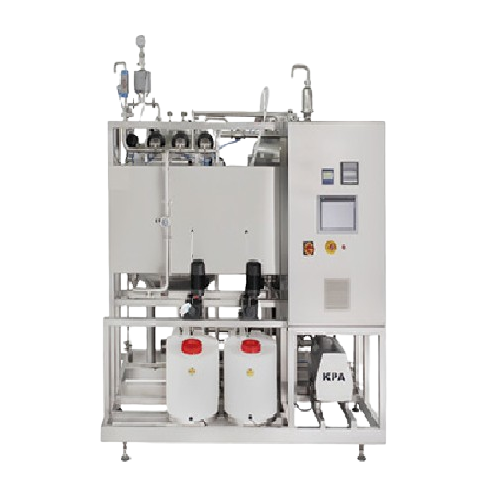
Cip workstation for pharmaceutical liquid preparation systems
Optimize your liquid formulation process with precise clea...
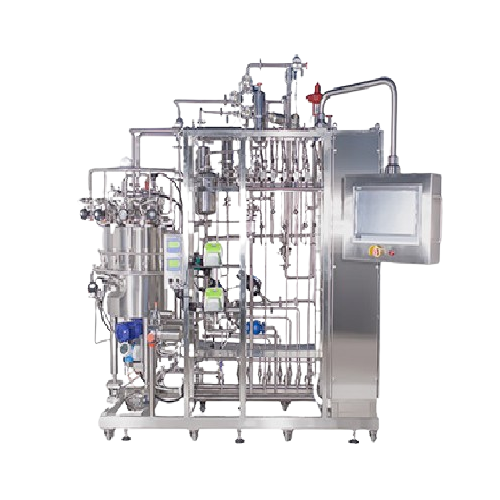
Bioreactor for mammalian cell culture
Optimize your biopharmaceutical production with precise control over cell culture con...
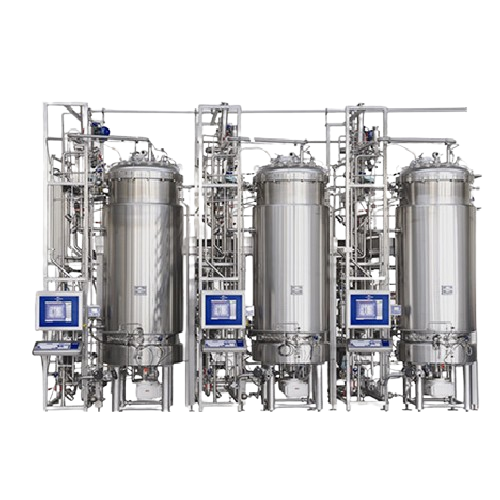
Biological fermentation tank for pharmaceutical production
Ensure consistent high-yield biological culture results with ...
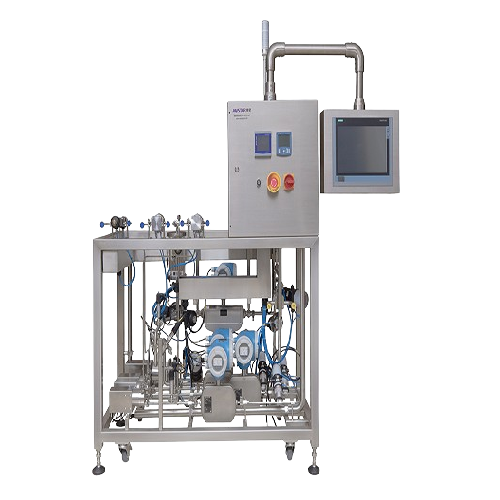
In-line conditioning system for buffer preparation
Optimize your buffer management with precise in-line conditioning, ens...
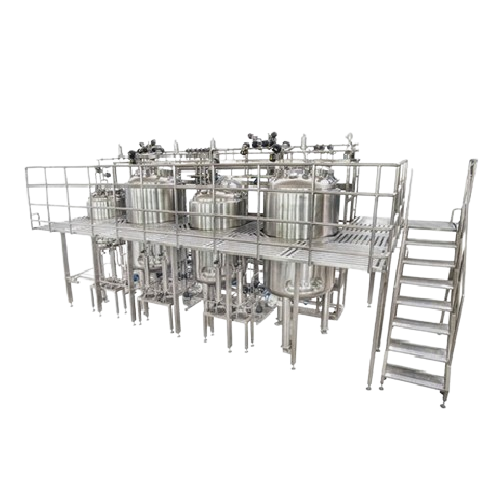
Bioprocess preparation system for vaccines and monoclonal antibodies
Streamline your biopharmaceutical production with ...
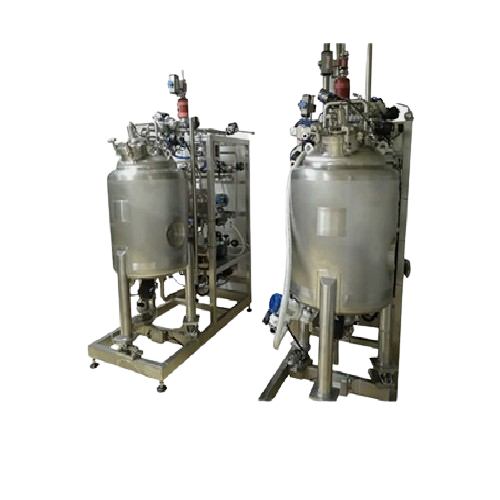
Ultrafiltration and depth filtration system for biopharmaceuticals
Achieve precise separation and purification of bioph...
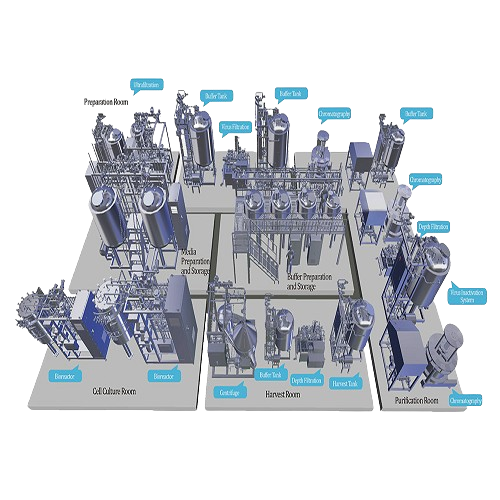
Bioprocess system for protein and antibody drugs
Streamline biopharmaceutical production with a system engineered to optim...
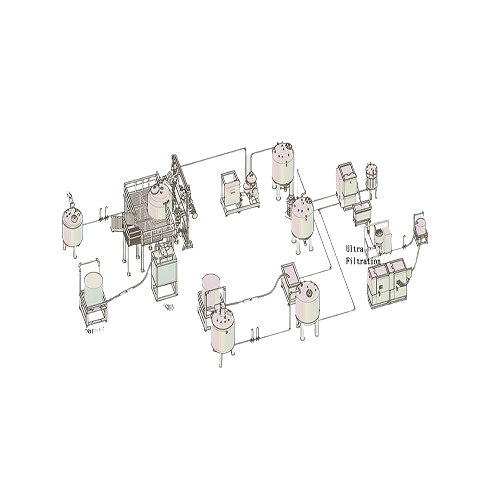
Hybrid bioprocess system for cell culture and purification
Streamline your bioprocessing operations with a versatile sol...
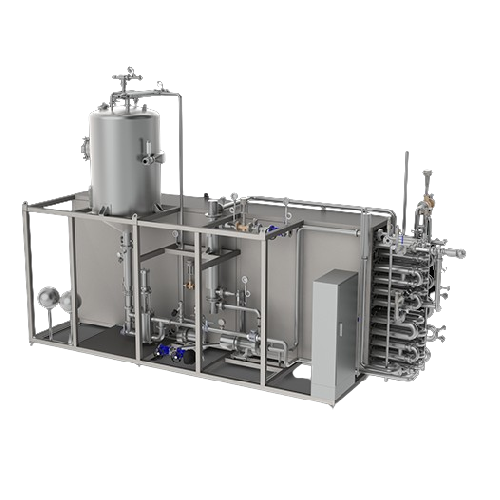
Sterilization for food and pharmaceutical processing lines
Ensure your liquid product’s sterility before productio...
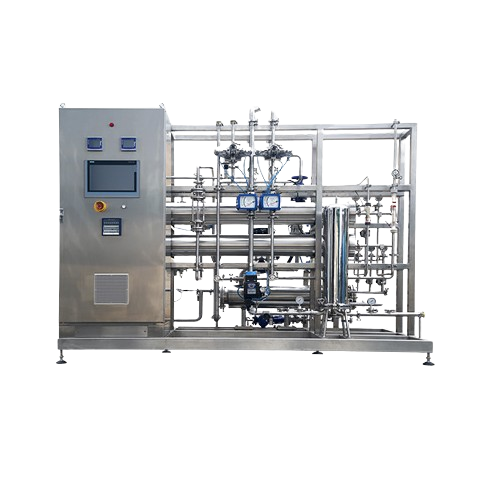
Purified water system for pharmaceutical industry
Ensure consistent purity and compliance in your production line with a ...
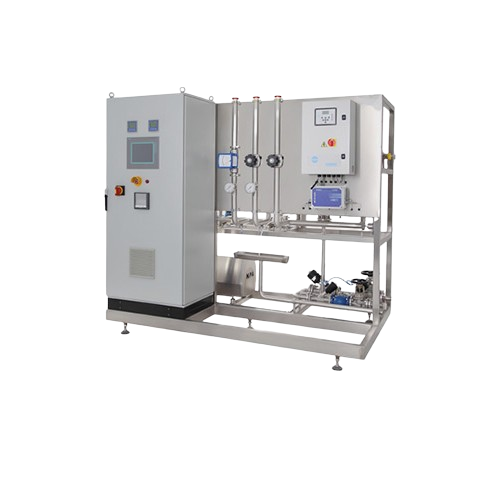
Pharmaceutical-grade Pw storage and distribution system
Ensure consistent purity and compliance in your pharmaceutical wa...
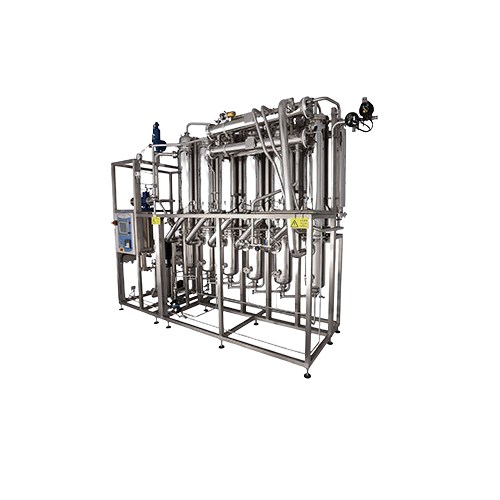
Multi-effect water distiller for pharmaceutical and biological applications
Achieve unmatched water purity for sterile...
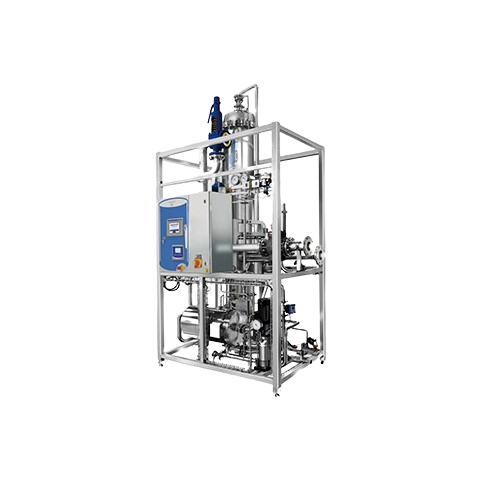
Pure steam generator for pharmaceutical sterilization
Achieve ultra-pure steam for critical sterilization tasks, ensuring...
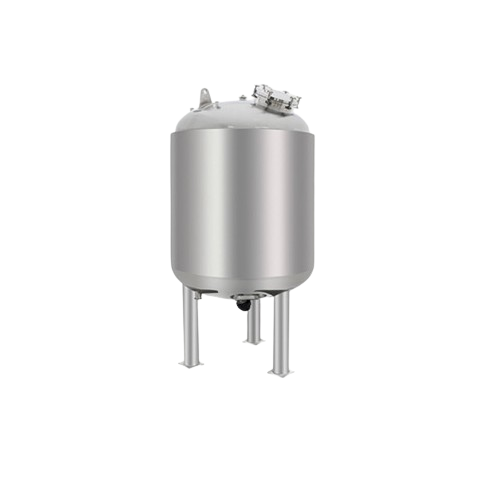
Purified water storage tank for pharmaceutical use
Ensure the integrity of your pharmaceutical formulations with precisio...
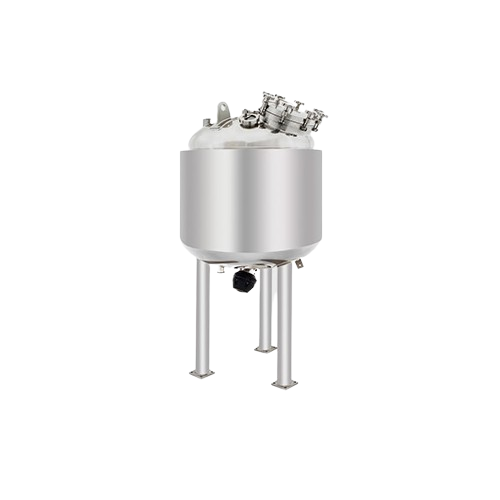
Wfi storage tank for pharmaceutical use
Ensure the integrity and sterility of Water for Injection in your pharmaceutical pr...
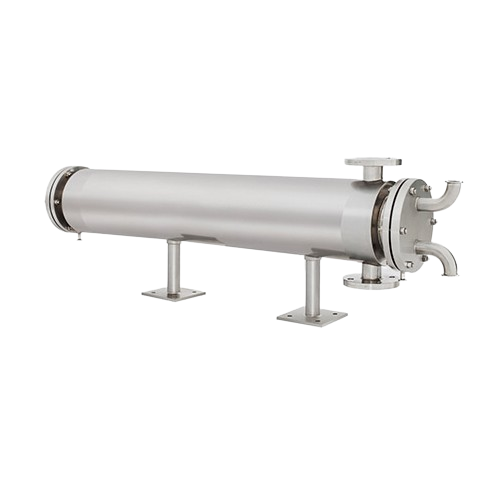
Industrial heat exchanger for pharmaceutical applications
Optimize your pharmaceutical formulations with precise thermal...
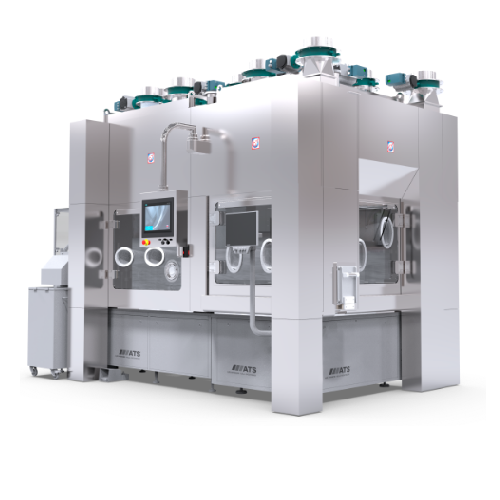
Robotic filler for aseptic pharmaceutical packaging
Effortlessly manage complex aseptic filling tasks with a system desig...
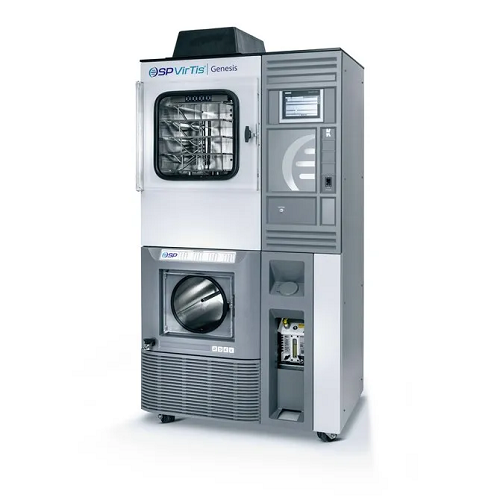
Pilot freeze dryer for research and small-scale production
Optimize moisture removal and sample preservation with this v...
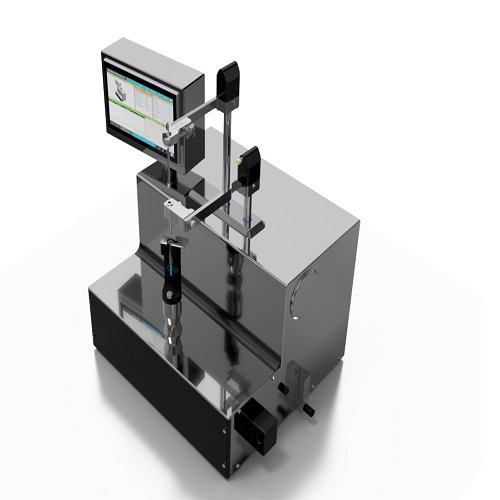
Bench-top syringe & cartridge closing system
Ensure precise and repeatable syringe and cartridge closure with this versati...
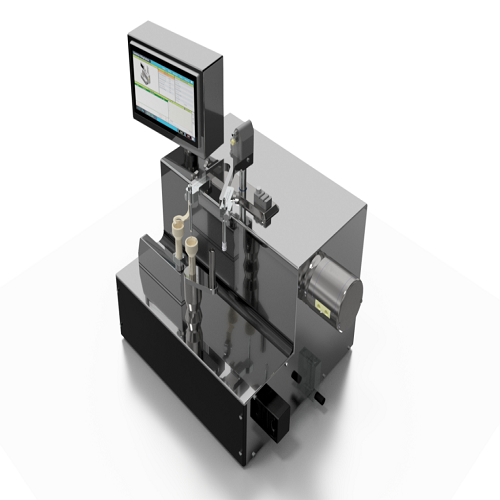
Tabletop vial and syringe filling system
Ensure precise dosing and maintain sterility in small batch production with a comp...
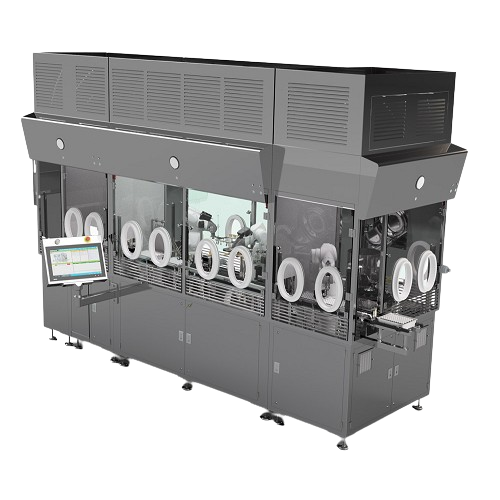
Aseptic small batch filling and closing system
Optimize your small-batch aseptic processing with this versatile system, de...
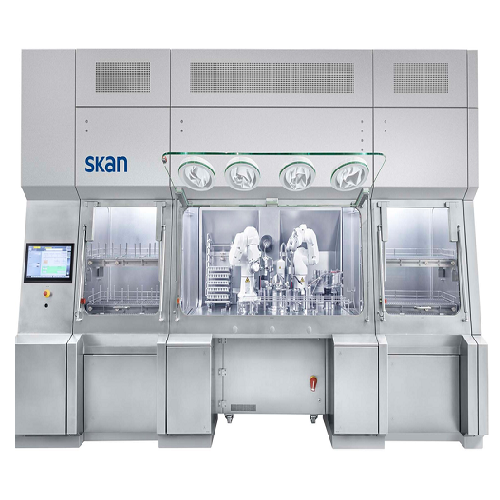
Aseptic vial filling system for gene therapy products
Elevate the sterility of your fill-and-finish process with a high-s...
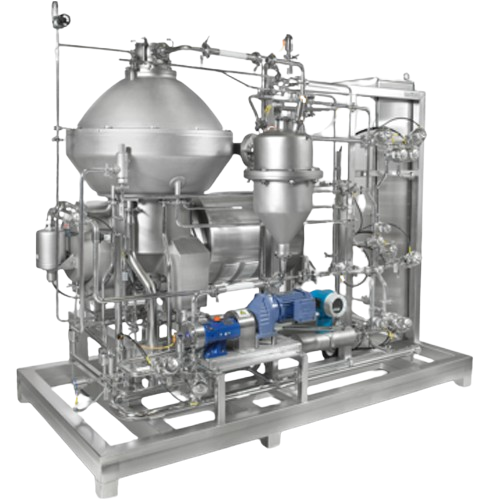
Microbial cell clarification solution
Achieve high-yield, foam-free microbial cell clarification with minimal shear stress ...
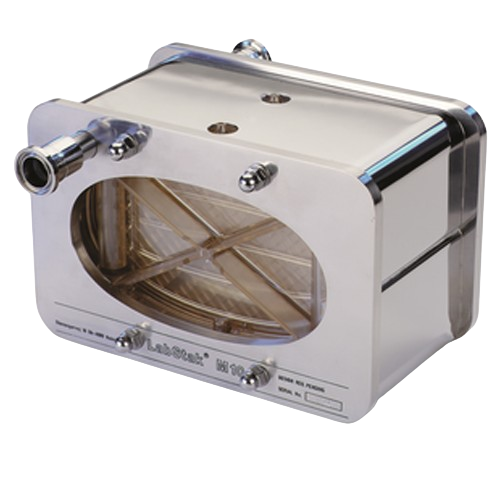
Cross-flow membrane filtration for lab use
Optimize laboratory filtration processes with compact, dual-membrane testing to...
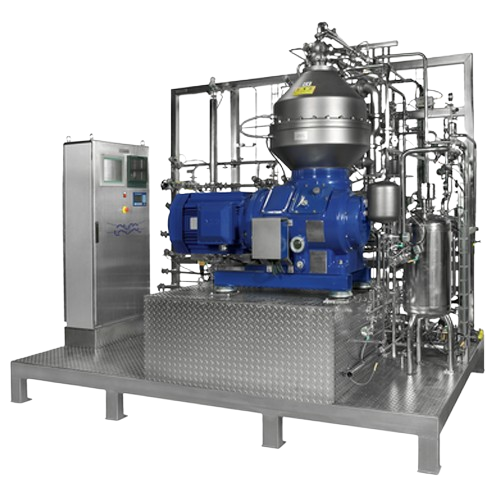
Biotech fermentation centrifuge for continuous solids discharge
Ensure high-density fermentation processes achieve optim...
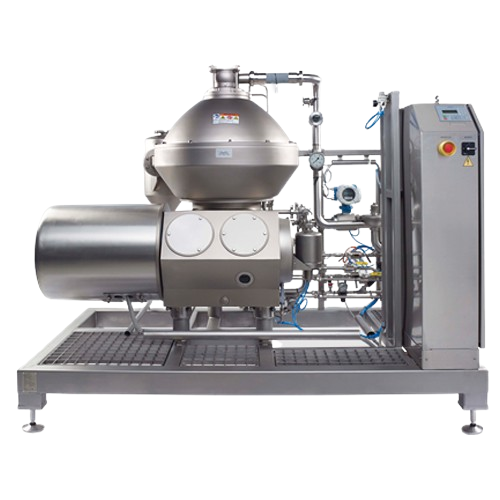
Centrifuge separator for food and beverage clarification
Ensure high efficiency and minimal product loss in your producti...
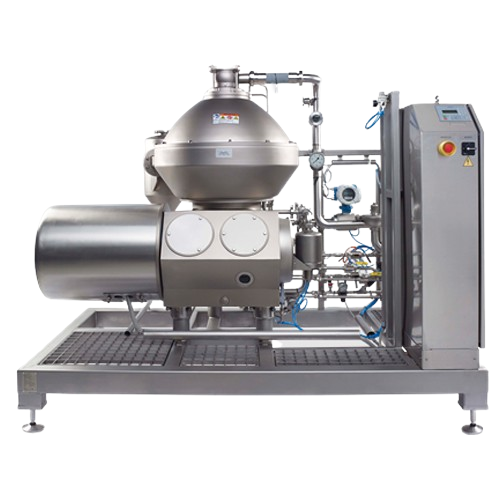
Biopharma cell centrifuge for gentle protein recovery
Ensure gentle cell harvesting and enhanced yield in bioprocessing w...
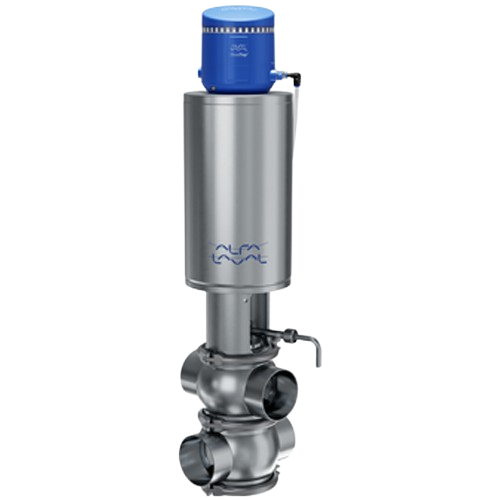
Mixproof valve for cleaning-in-place control
Streamline your cleaning processes and ensure product safety with a versatile...
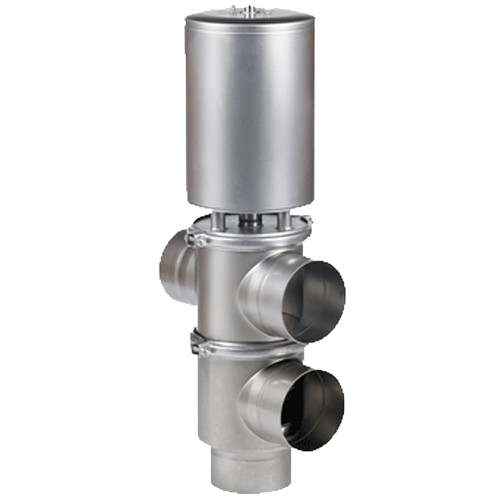
Single seat valve for hygienic applications
Ensure optimal hygiene and safety with a versatile pneumatic valve designed to...
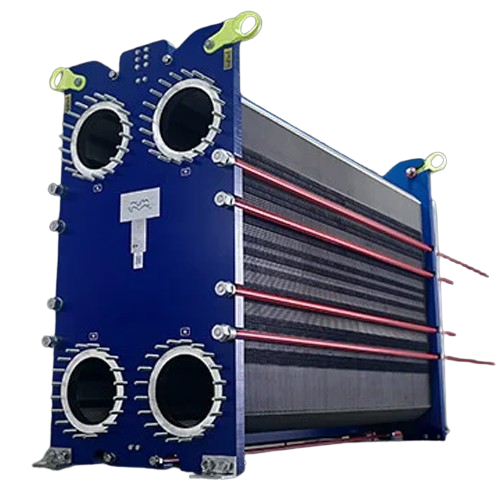
Gasketed plate-and-frame heat exchangers for industrial applications
Optimize your production with precise thermal mana...
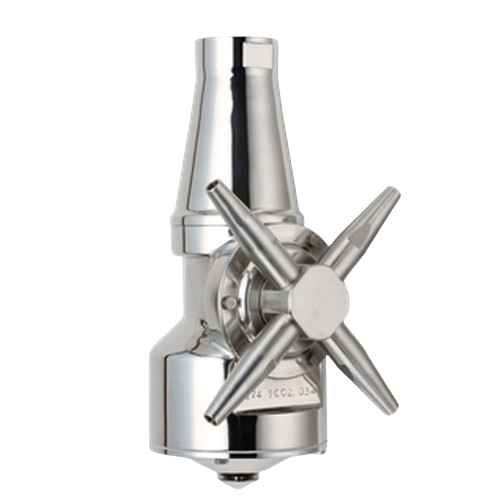
Rotary jet mixer for efficient liquid, gas, and powder mixing
Achieve seamless integration and efficiency in liquid, gas...
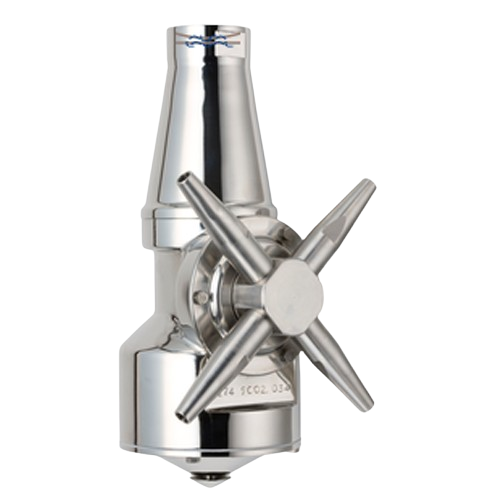
Rotary jet head for hygienic tank cleaning
Ensure efficient, hygienic cleaning with a rotary jet head designed to optimize...
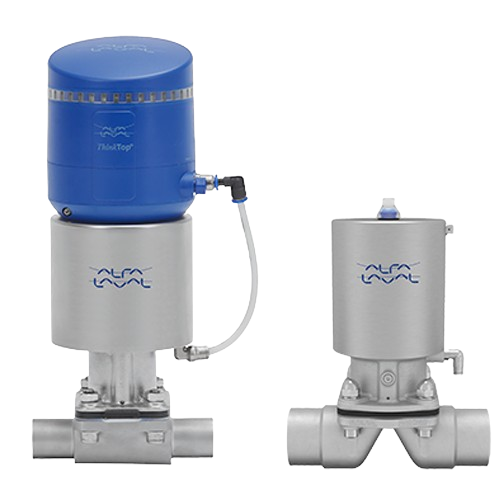
Diaphragm valve for hygiene-focused processes
Ensure aseptic conditions and precise flow control in sensitive liquid proce...
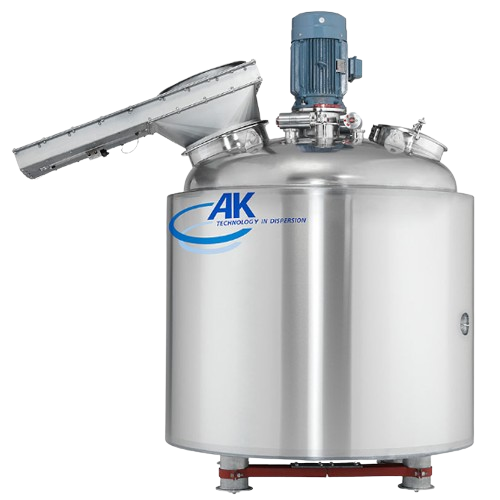
Emulsion processing system for homogenizing solids into liquids
Achieve precision in emulsifying and homogenizing proces...
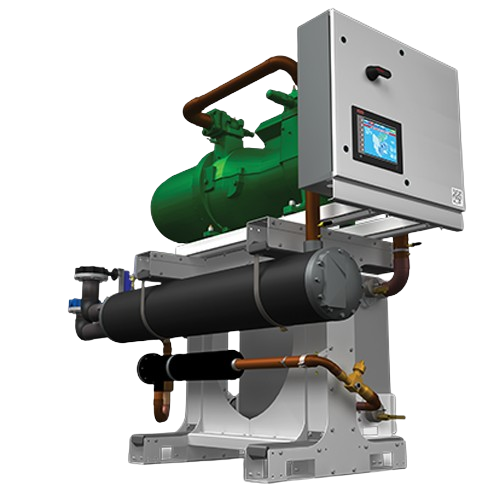
Central chiller for consistent process cooling
Optimize your production with modular central chillers offering scalable co...
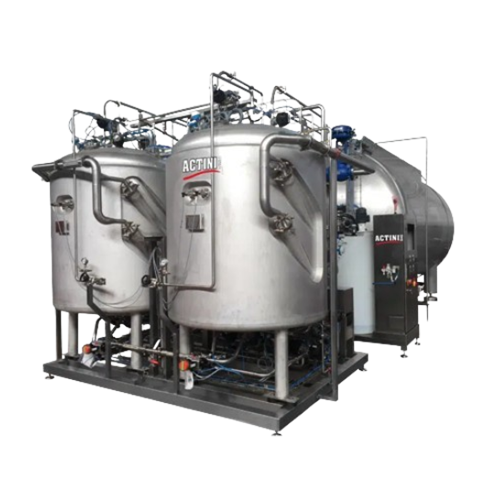
Batch decontamination system for effluents with particles and variable viscosity
Effectively manage complex effluent s...
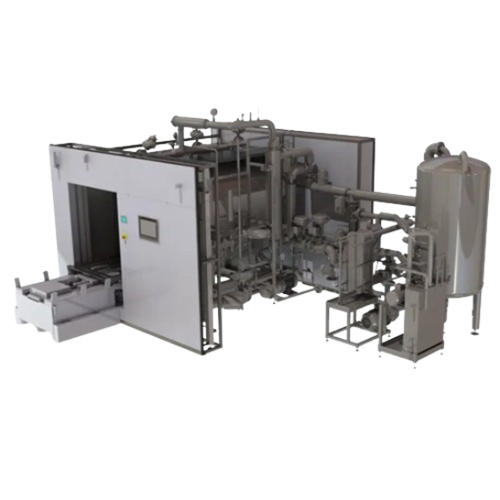
Superheated water sterilization autoclave for pharmaceutical applications
Ensure precise sterilization of sensitive li...
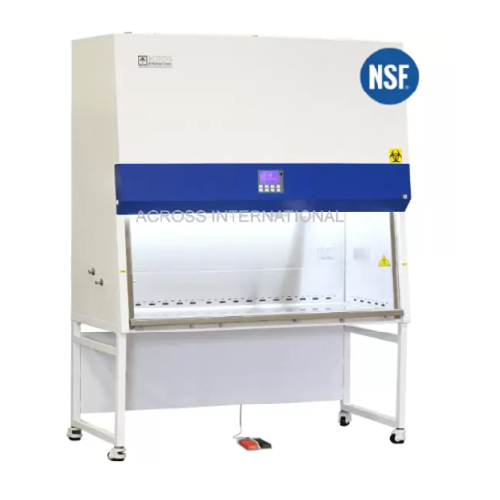
Nsf certified class Ii a2 biosafety cabinet
Ensure laboratory safety and specimen integrity with a biosafety cabinet desig...
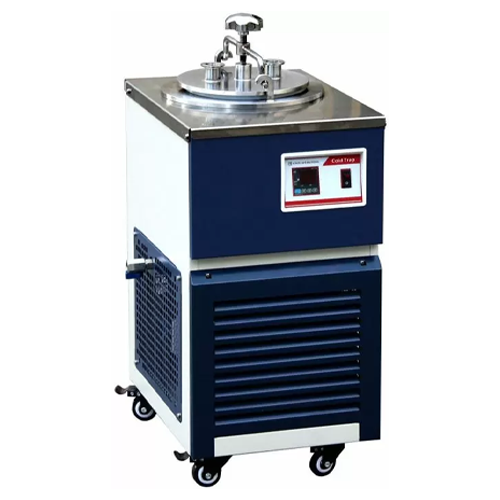
Cold trap for laboratory applications
Achieve efficient condensation and separation in laboratory processes with this versa...
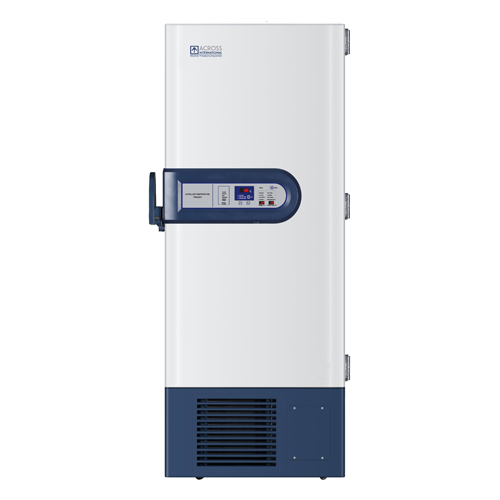
Ultra-low freezer for medical and biological storage
For critical preservation of sensitive samples, this ultra-low tempe...
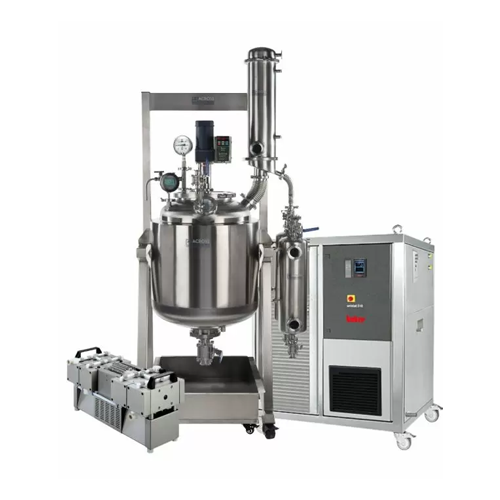
Stainless steel crystallization reactor 100l
Optimize your crystallization and formulation processes with precision-contro...
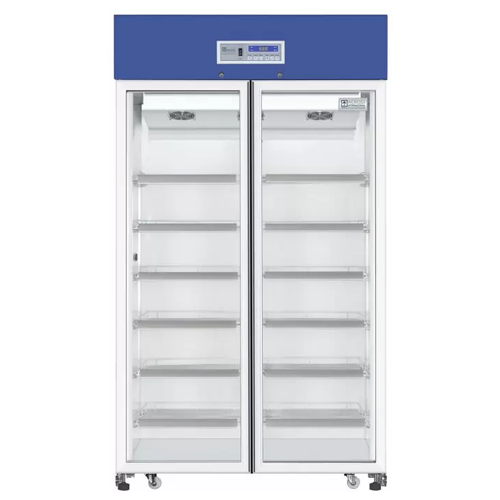
Laboratory upright refrigerator for vaccine storage
Ensure the optimal preservation of critical vaccines and specimens wi...
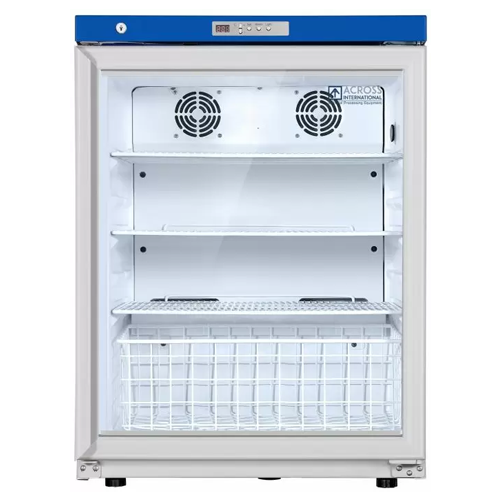
Compact refrigerator for vaccine storage
Ensure critical temperature stability for sensitive pharmaceuticals and vaccines, ...
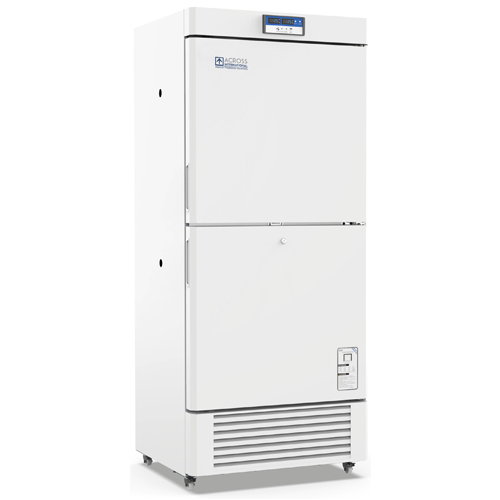
Laboratory -40°c upright freezer
Ensure optimal preservation of sensitive biological samples with a freezer engineered for u...
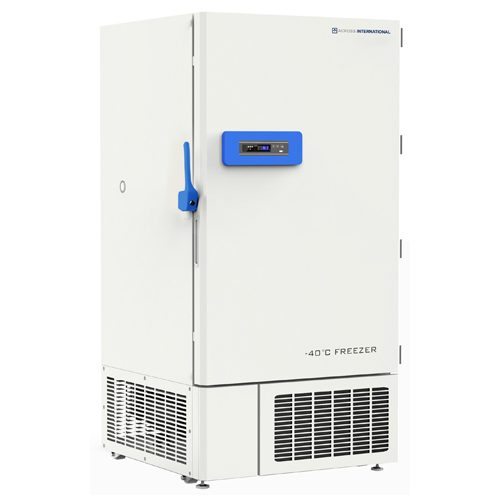
Medical freezer for -40°c storage
Ensure optimal preservation of critical samples with an ultra-low temperature solution de...
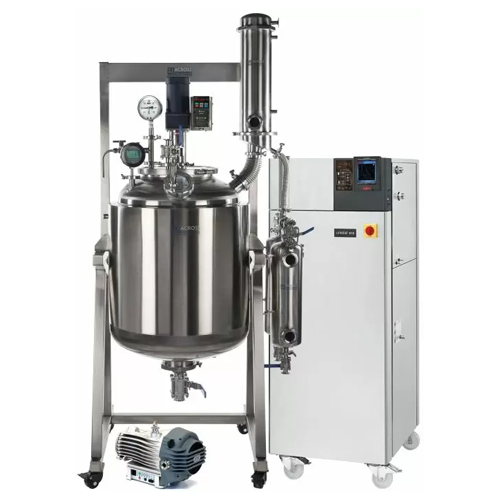
Dual-jacketed reactor for botanical extraction winterization
Optimize your production with precise temperature control a...
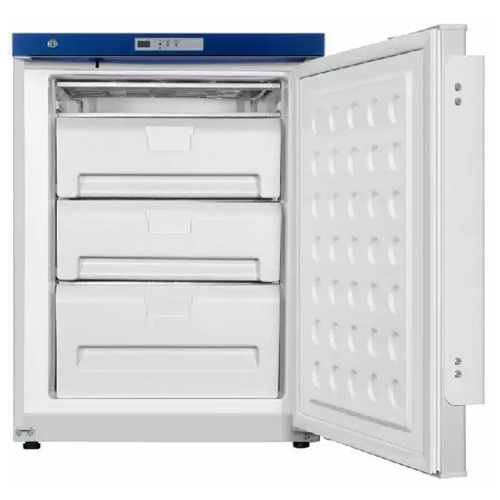
Laboratory freezer for sample storage at -25°c
Ensure precise preservation of sensitive samples with an efficient upright ...

Aseptic sampling system for industrial applications
Achieve reliable, aseptic sampling with precision and safety during c...
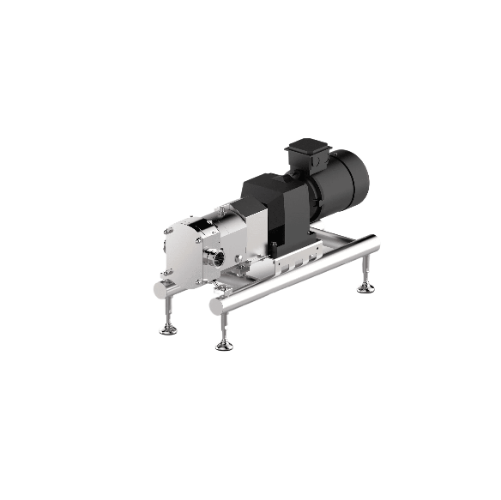
Rotary lobe pump for viscous media
Ensure precise handling and gentle transfer of viscous liquids with advanced rotary lobe...
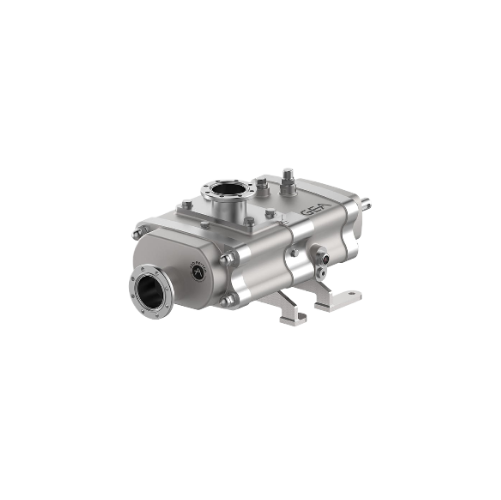
Twin screw pump for viscous media
Streamline your production with a twin screw pump that effortlessly handles viscous media...
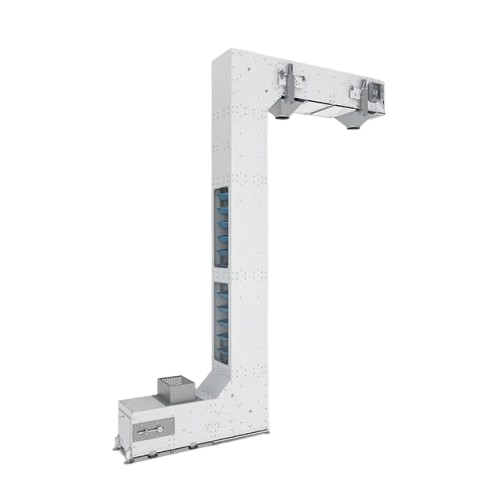
Industrial bucket elevator for efficient product conveyance
Enhance production efficiency by elevating and transferring ...
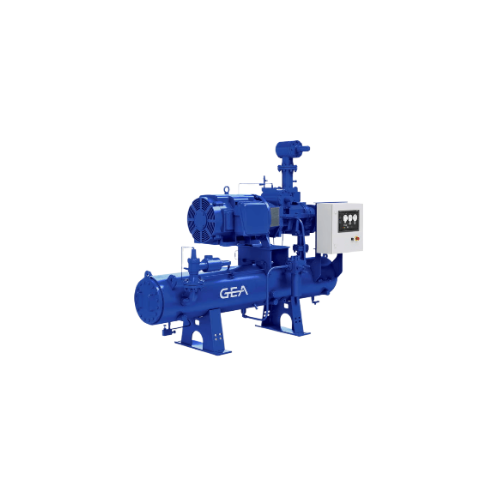
Compact refrigeration compressor package
Optimize your industrial refrigeration with a compact compressor package designed ...
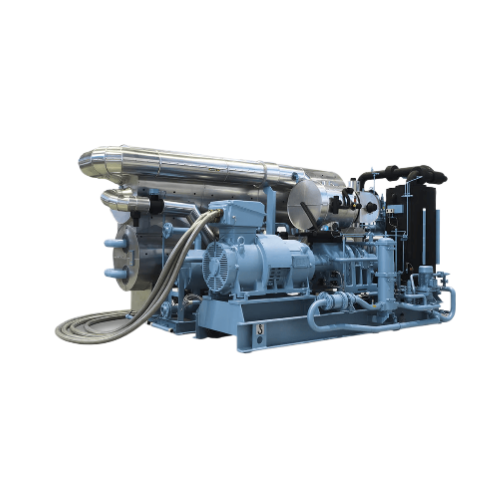
Customized industrial heat pumps
Optimize your industrial processes with versatile heat pumps that recover and utilize waste...
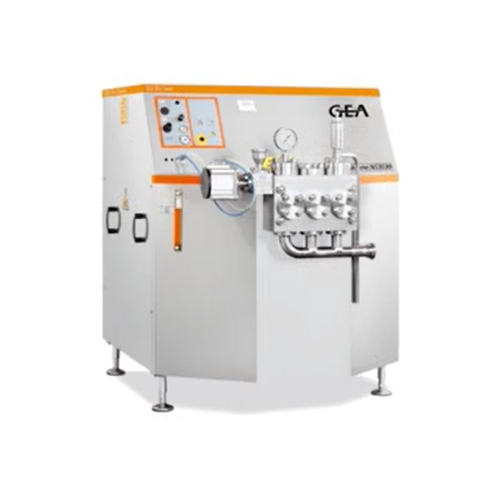
High pressure industrial homogenizer
Enhance liquid formulations with precision and efficiency—our high-pressure homogenize...
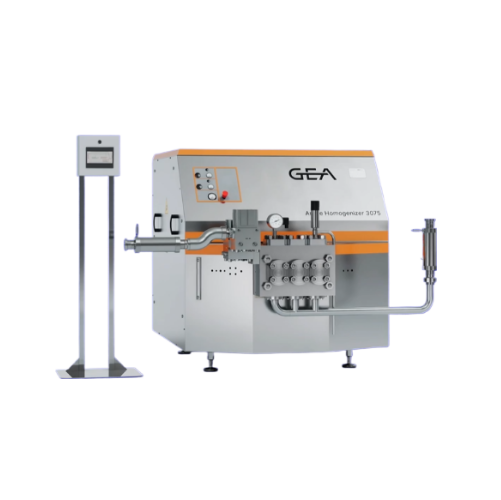
Inline real-time fluid quality monitoring system
Optimize fluid quality control with continuous, inline measurements that ...
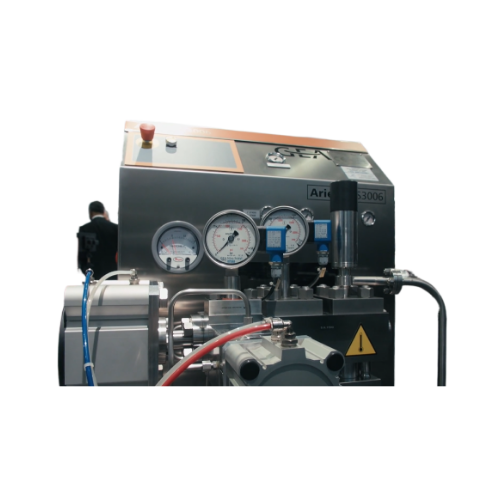
Pharmaceutical homogenization skid system
Achieve precise particle size reduction and efficient cell rupture with an auton...

Process analytical technology for lyophilization
Ensure product integrity by detecting trace contaminants and optimizing l...
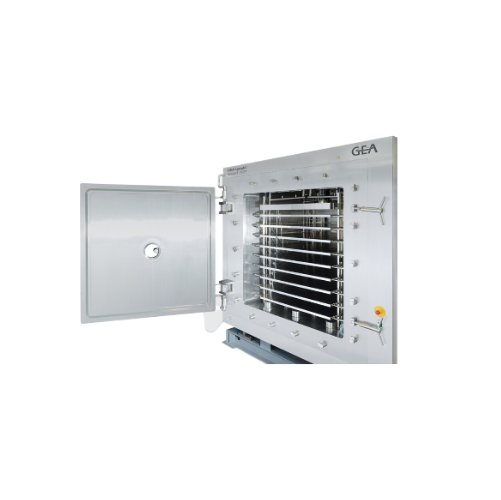
Pharmaceutical freeze dryer for large-scale production
Streamline your freeze-drying process with precision-engineered ly...
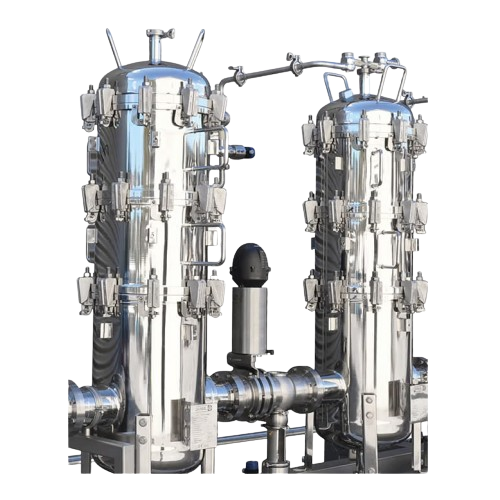
Aseptic spray dryer for pharmaceutical products
Optimize your sterile powder production with precise control over particle...
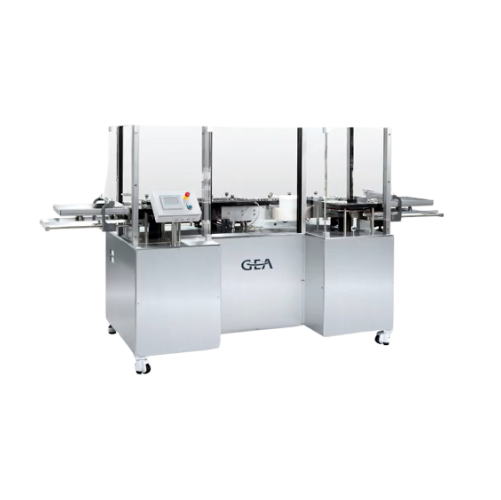
Automatic loading and unloading system for pharma freeze dryers
Enhance the efficiency and safety of your freeze-drying ...
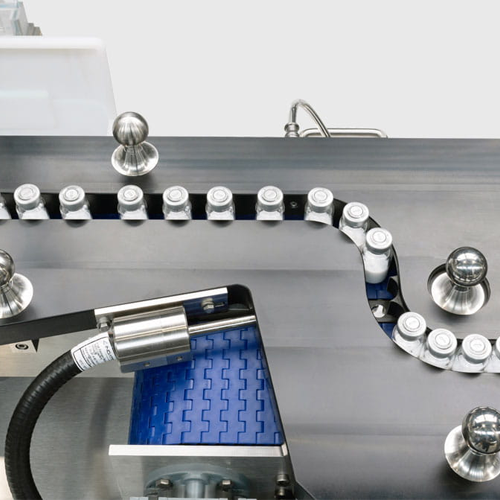
Online moisture control for lyophilized pharmaceutical products
Ensure precise moisture control in lyophilized products ...
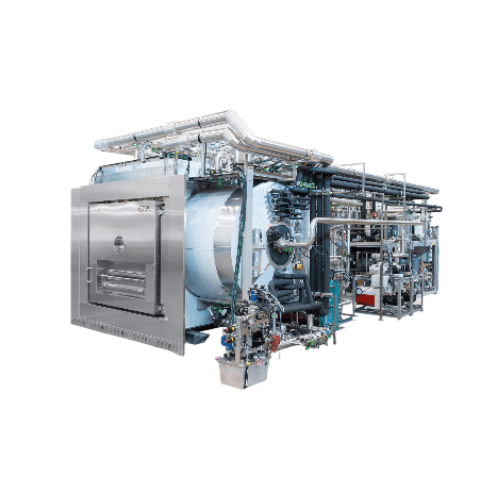
Pharmaceutical lyophilization for large-scale production
Ensure precision in pharmaceutical freeze drying with controlled...
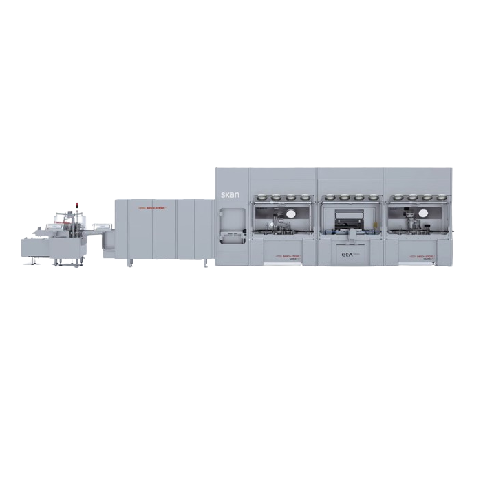
Freeze dryer for small-scale production
Optimize your production line with reliable lyophilization that ensures precise moi...
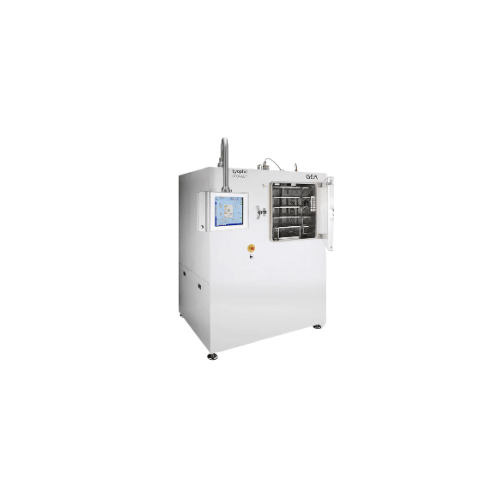
Small-scale pharmaceutical freeze dryer
Enhance precision in biopharmaceutical preparation with this versatile freeze dryer...
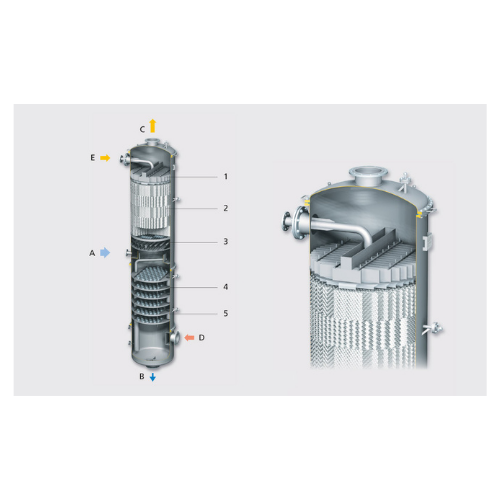
Industrial tray and packing column solutions
For efficient separation and product purification, tray and packing columns o...
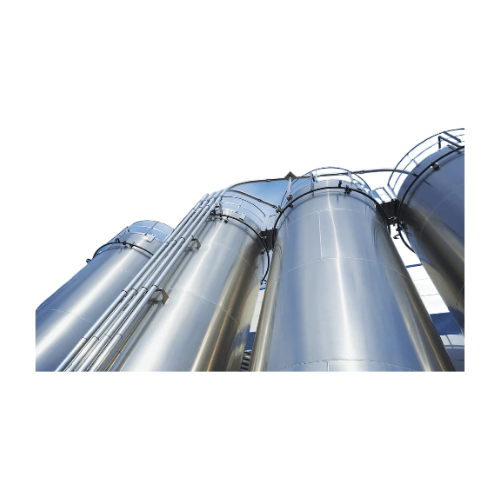
High-yield fermentation system for raw material processing
Achieve precise control in fermentation with advanced systems...
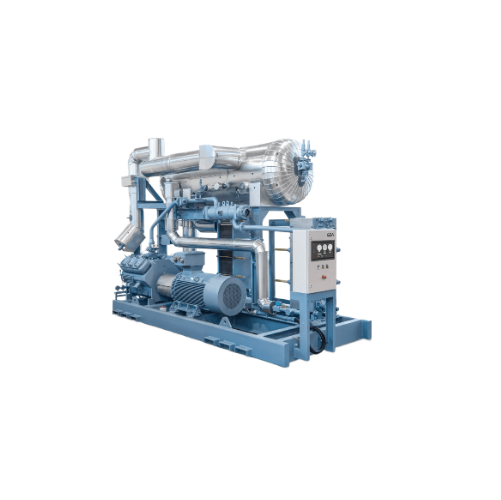
Industrial chiller with high part-load efficiency
Optimize your cooling processes with a versatile chiller designed for p...

Laboratory freeze dryer for small batch processing
Ensure precise moisture control and stability in sensitive samples wit...
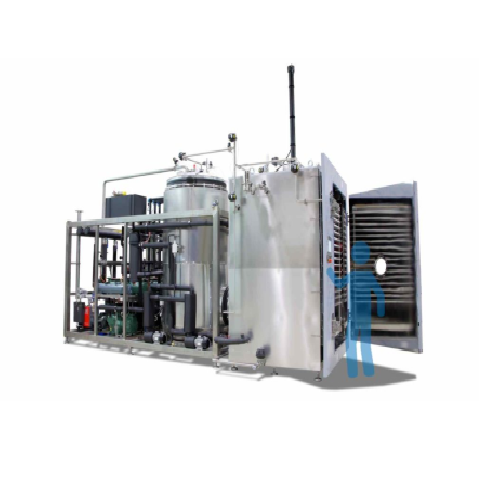
Freeze drying systems for pharmaceutical production
Optimize your production line with advanced freeze drying systems des...
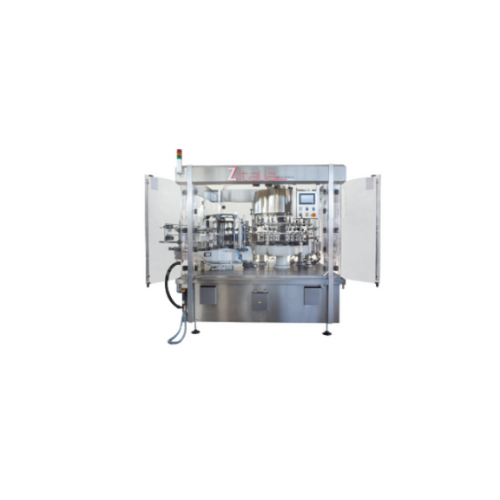
Stand-alone autoclaves with round chamber for laboratory and pharmaceutical use
Achieve seamless sterilization and pre...
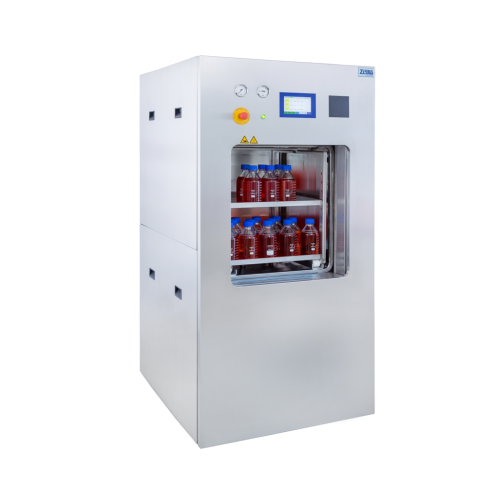
Autoclaves for laboratory and production with square chamber
Optimize your laboratory space with compact autoclaves that...
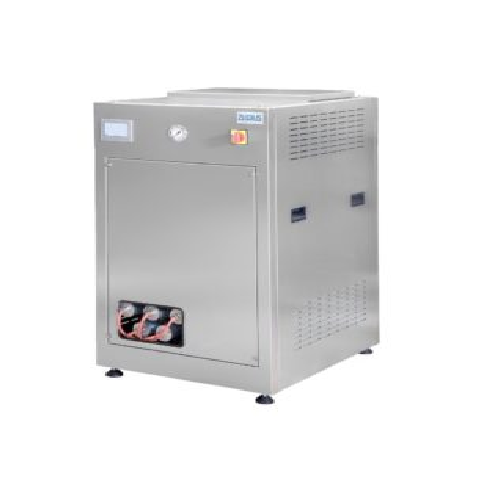
Pure steam generator for industrial applications
Ensure the highest levels of steam purity and precise pressure control fo...
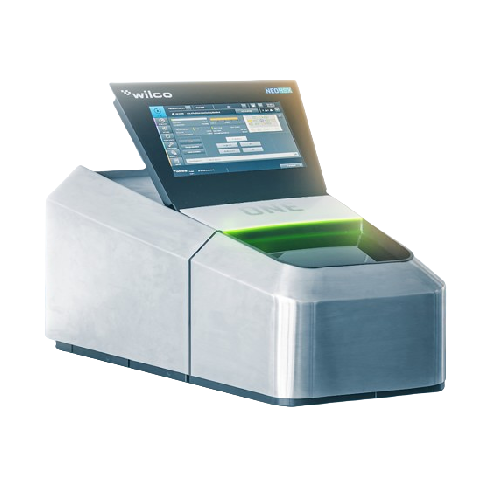
Lab headspace analyzer for small volume parenterals
Enhance your quality control with precise gas concentration measureme...
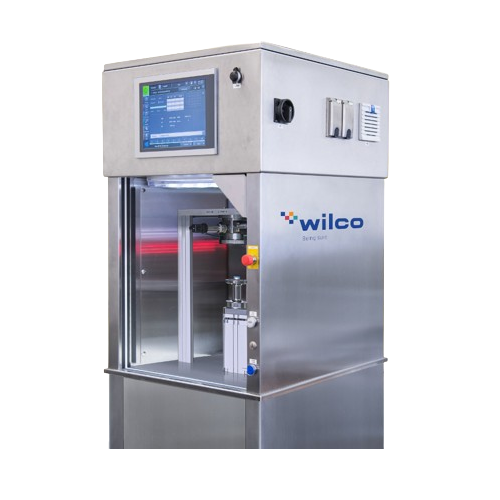
Headspace gas analyzer for large volume parenterals
Ensure the sterility and quality of injectable pharmaceuticals with p...
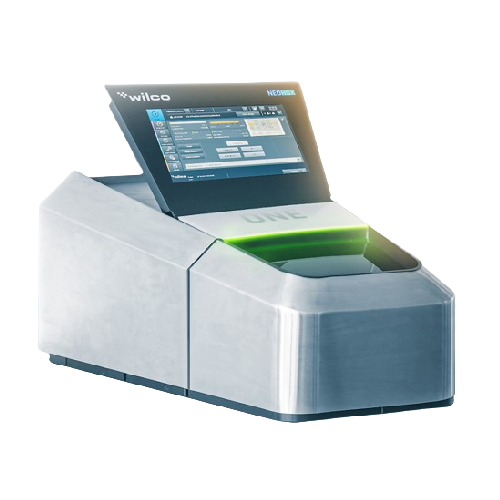
Headspace analyzing system for small volume parenterals
Ensure the integrity of sterile pharmaceuticals with precise head...
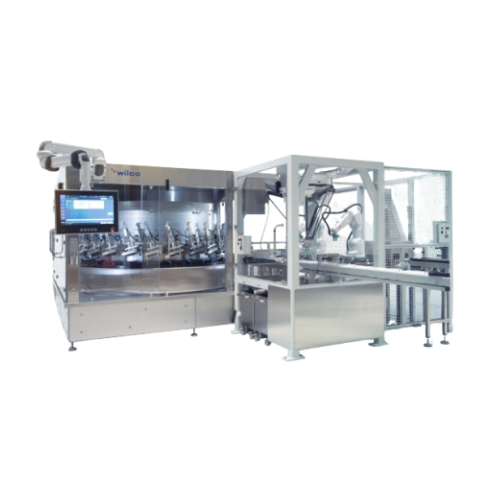
Automated container closure integrity tester
Ensure the integrity of your sterile pharmaceutical containers with high-spee...
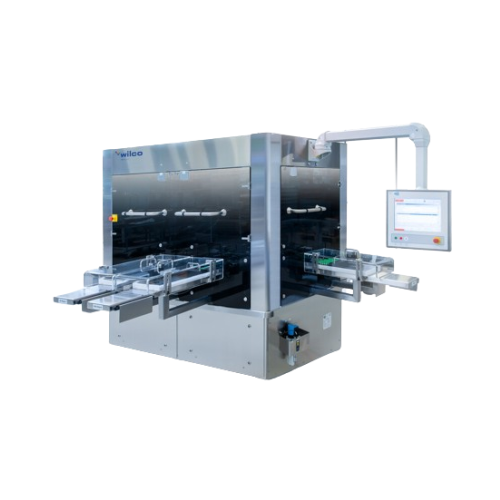
Automated headspace analysis for small volume parenterals
Ensure the integrity and quality of parenteral packaging with ...
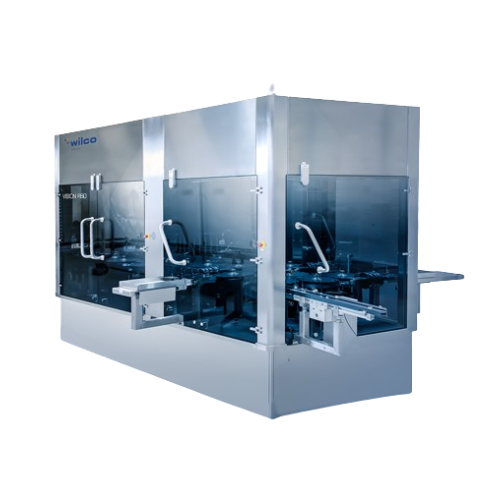
Visual inspection for small volume parenterals
Ensure pristine injectable solutions by detecting cosmetic and particle def...
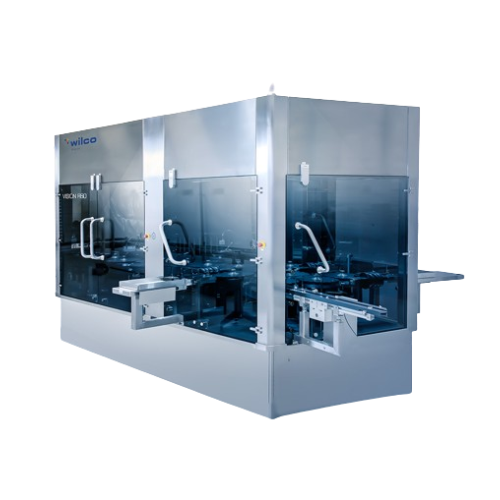
Automated visual inspection for small volume parenterals
Ensure the integrity of high-value parenteral drugs by detecting...
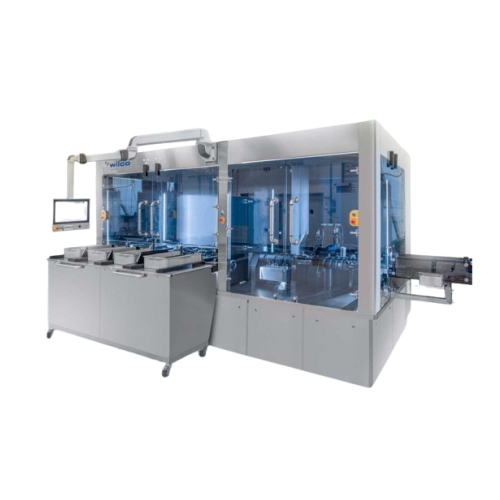
Combined Avi and Cci tester for vials
Ensure comprehensive quality control of parenteral products with an integrated soluti...
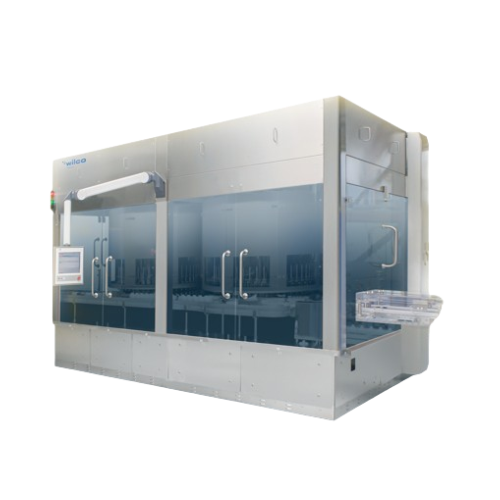
Combined visual and container closure integrity testing for vials
Ensure the integrity and quality of parenteral packag...
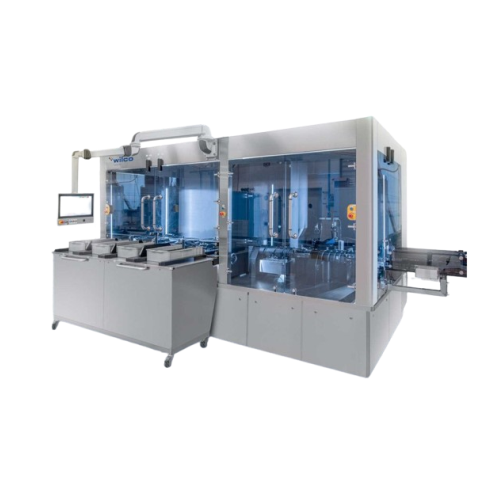
Combined visual and container closure integrity tester for vials
Ensure precise quality control of pharmaceutical packag...
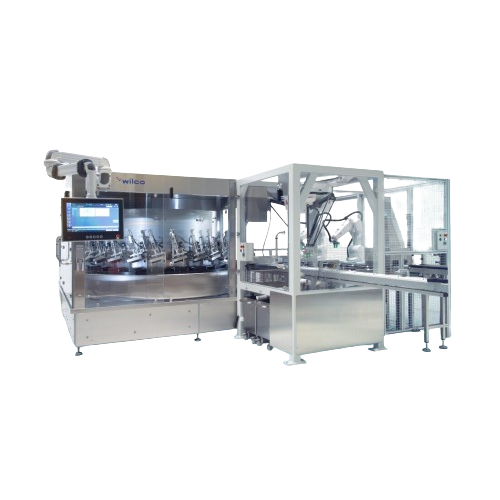
Automated container closure integrity tester for pharmaceutical packaging
Ensure the integrity of your pharmaceutical ...
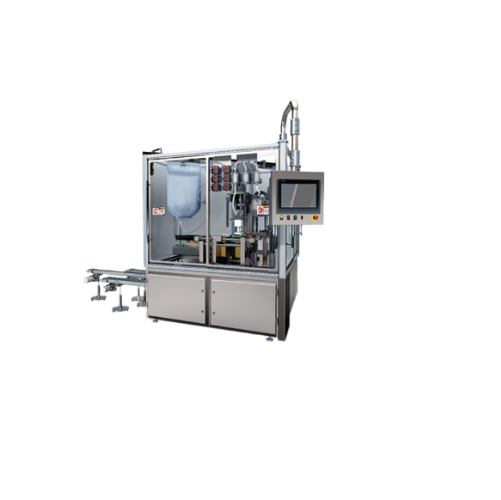
Blow/fill/seal packaging for laboratory and clinical trials
Streamline your small-scale pharmaceutical production with p...
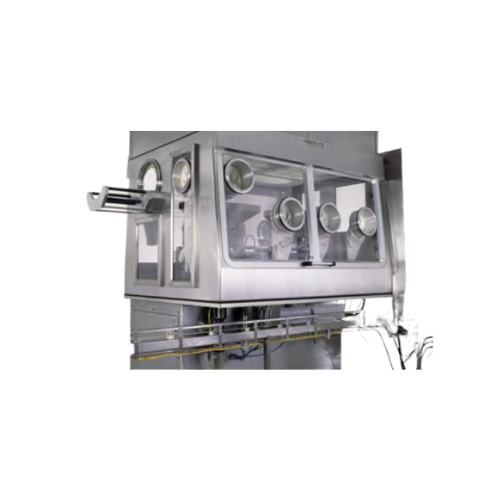
Insertion technology for sterile blow/fill/seal systems
Ensure sterility and precision in liquid pharmaceutical packaging...
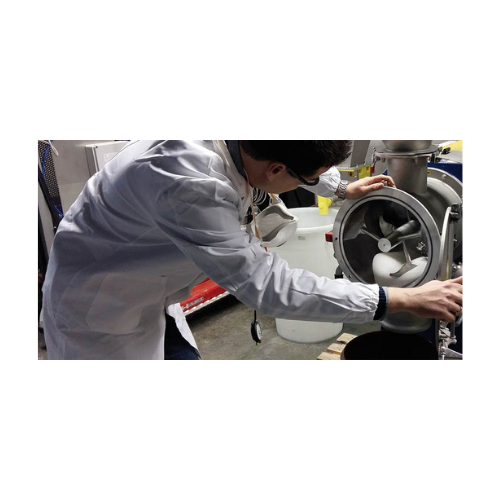
Laboratory batch mixer for small scale production
Achieve rapid and reproducible mixing results with this laboratory batc...
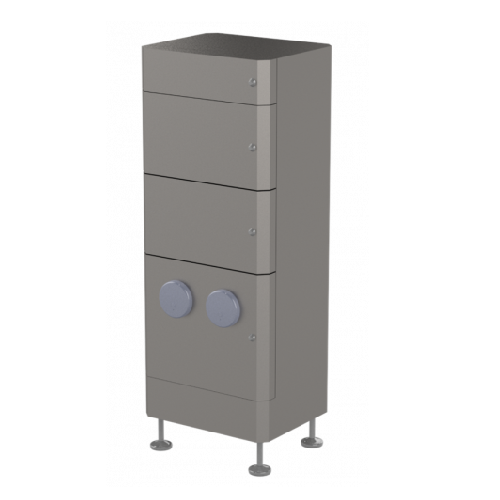
Supply air filter systems for industrial cleanrooms
Ensure critical air purity and operational safety in sensitive enviro...
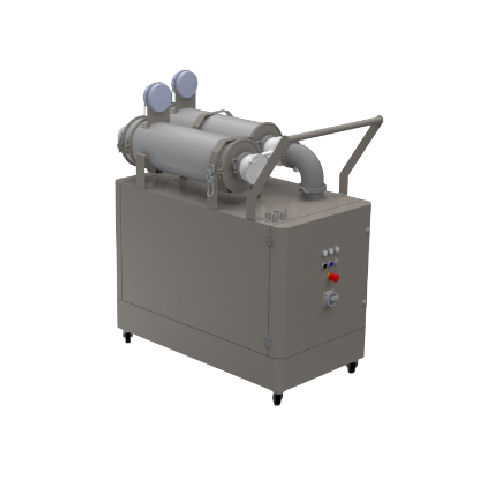
Containment single-use filter module
Ensure safe handling of high-potency substances and streamline filtration processes wi...
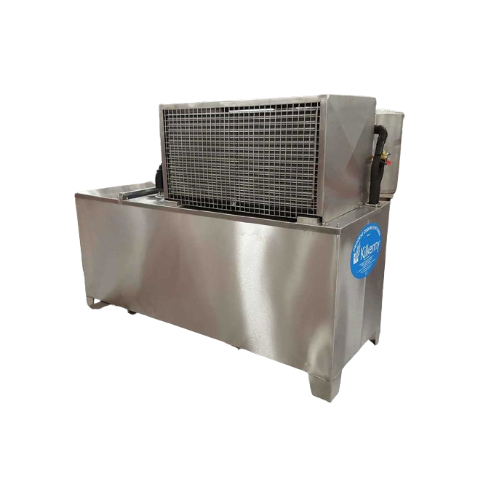
Industrial chiller systems for processing cooling
Optimize your production line with advanced chiller systems designed to...
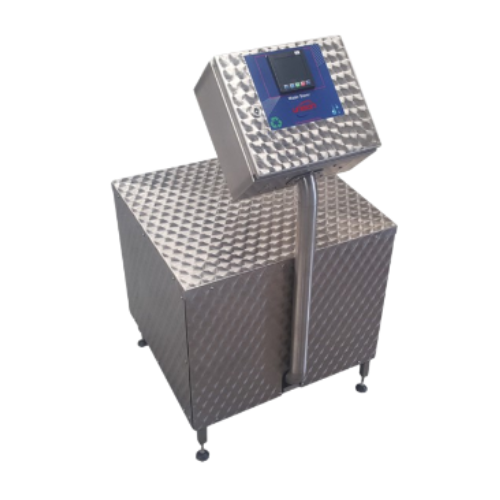
Industrial water recycling system
Reduce excess water consumption in your process line by recycling and reusing up to 96% o...
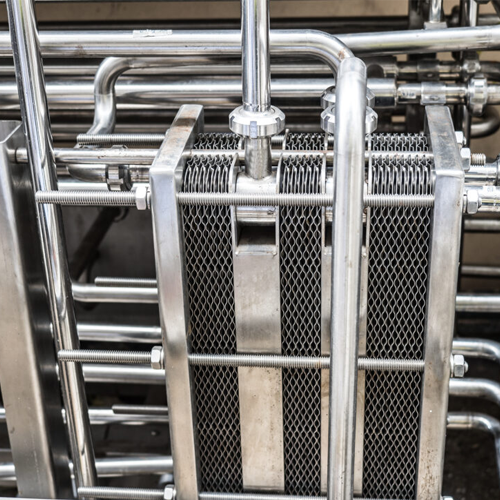
Hygienic plate heat exchanger
Optimize temperature control for liquid processing with precision-engineered heat exchangers, ...
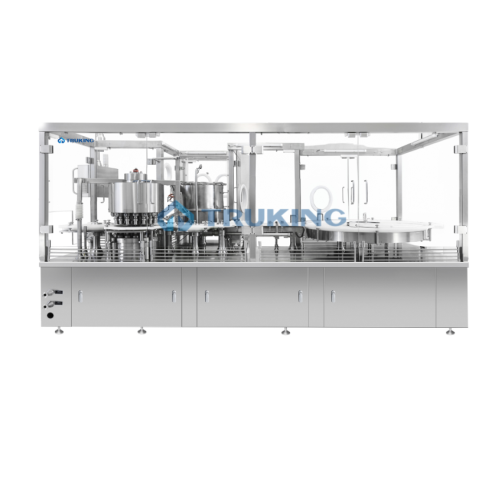
Vial capping machine for pharmaceutical production
Ensure precise and reliable vial sealing in high-throughput pharmaceut...
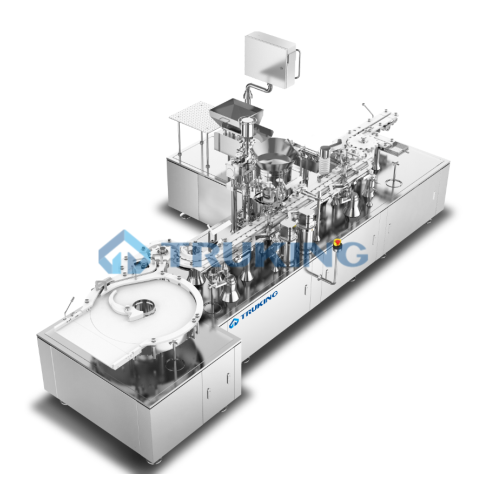
Vial powder dispensing system
Optimize your aseptic fill process with high-precision powder dispensing that minimizes contam...
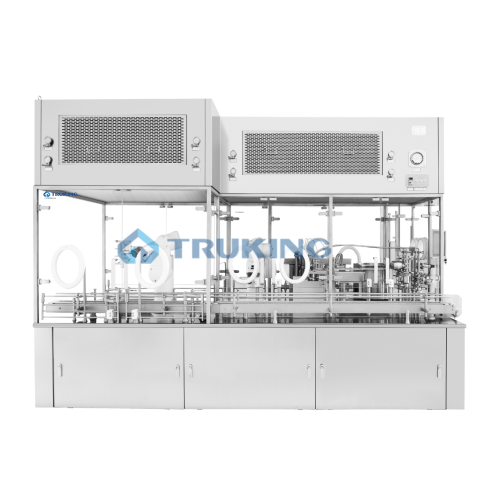
Nested fillers for vials, pre-filled syringes, and cartridges
Optimize your aseptic filling processes with precision dos...
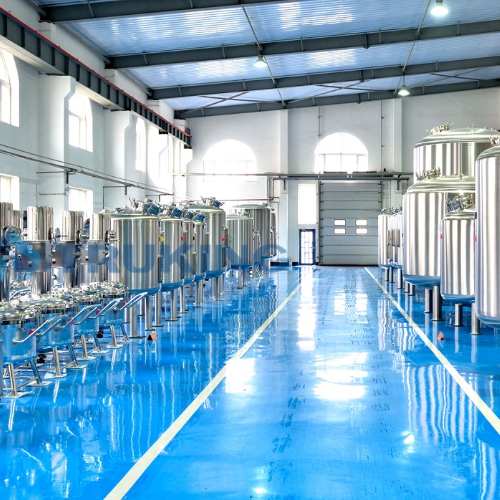
Stainless steel craft tanks for biopharmaceuticals
Ensure precise temperature control and customized capacity for your fo...

Robotic sterilization logistics system
Ensure seamless aseptic transfers across production stages with this robotic logisti...
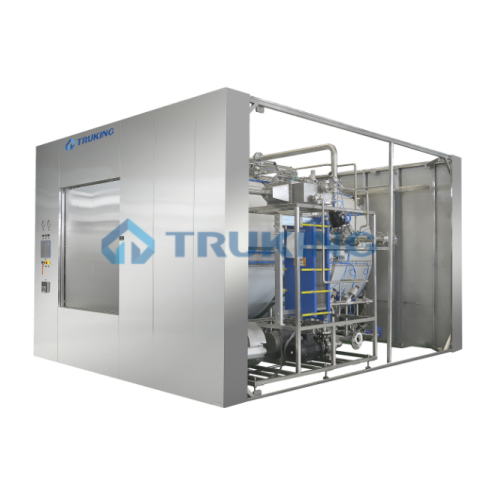
Superheated water sterilizer for pharmaceutical applications
Ensure precise sterilization with real-time monitoring and ...
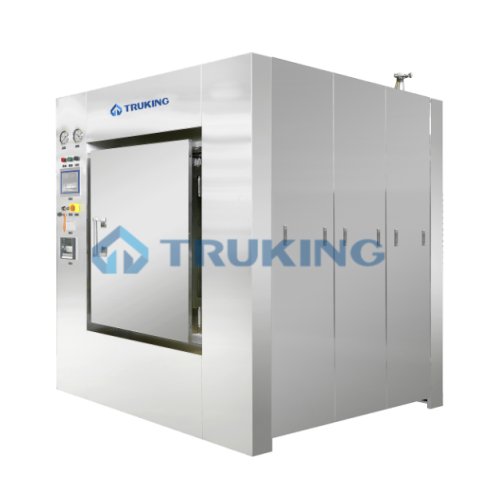
Pharmaceutical autoclave for terminal sterilization
Optimize your sterile production with high-precision terminal sterili...
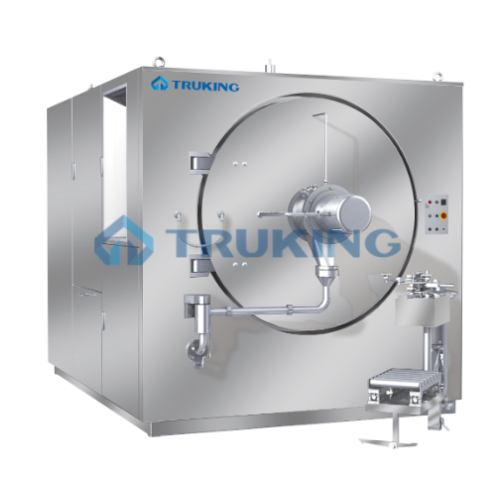
Washing machine for pharmaceutical rubber stoppers
Ensure sterile sealing and siliconization in rubber stopper processing...
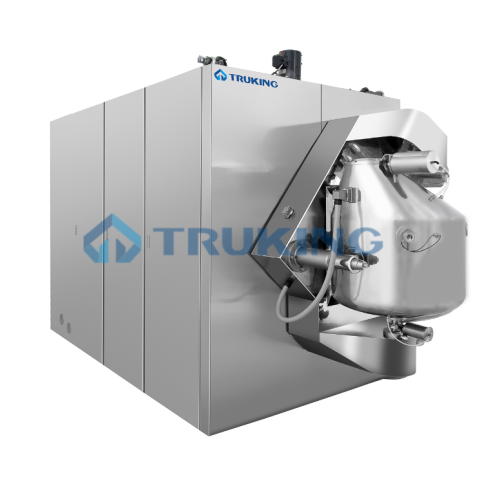
Washing machine for pharmaceutical stoppers and caps
Streamline your aseptic processing with precise washing, sterilizati...
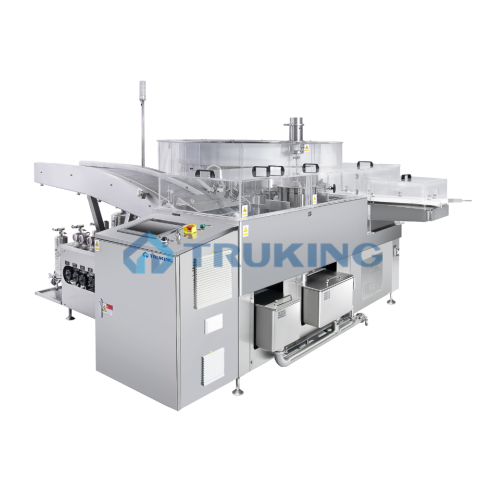
Vertical ultrasonic washing for pharmaceutical containers
Ensure immaculate cleanliness and sterilization of pharmaceuti...
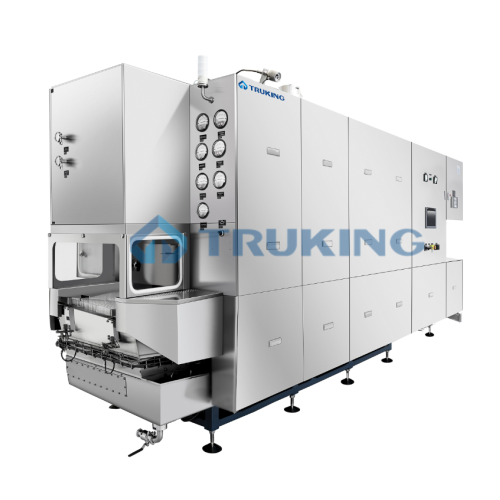
Sterilizing and depyrogenization tunnel for ampoules
Ensure sterile and pyrogen-free ampoules with precision control in d...
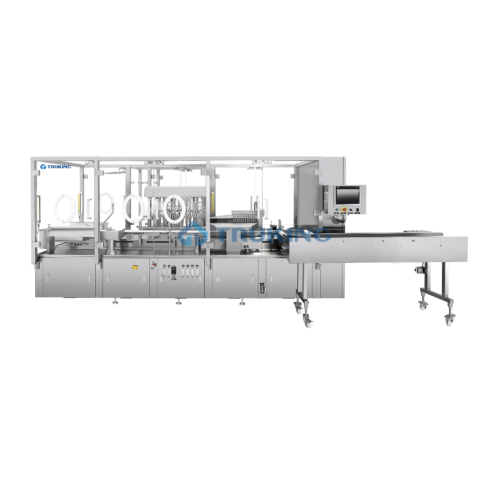
High-speed ampoule filling unit
Ensure precision and speed with this cutting-edge solution designed for efficient filling an...
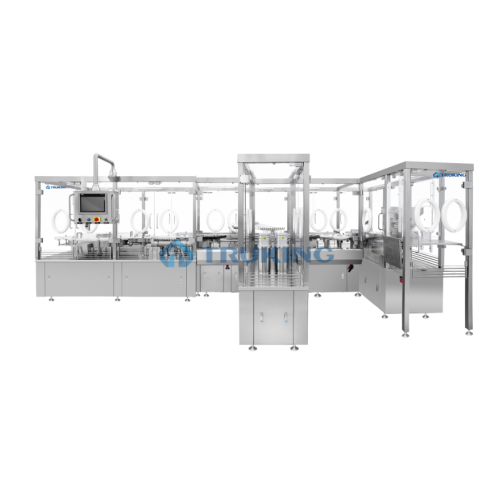
Vial filling and stoppering system for aseptic production
Streamline aseptic production by integrating high-speed vial f...
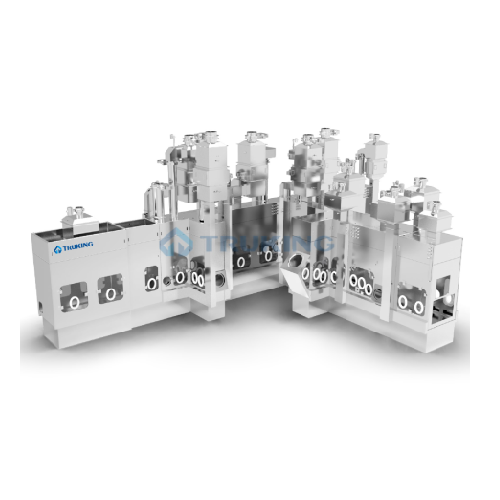
Pharmaceutical isolator system for aseptic production
Ensure aseptic conditions and operator safety with a robust isolati...
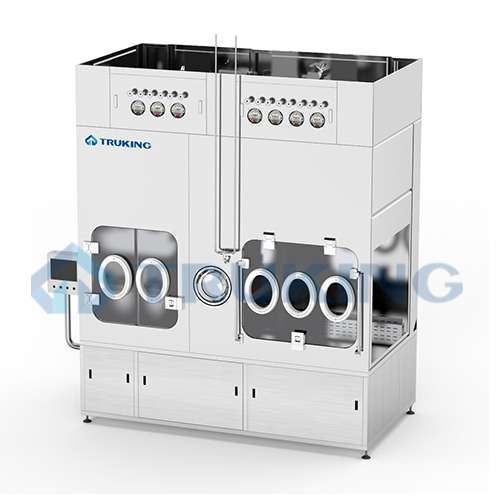
Autoclave unloading isolator for sterile assembly
Ensure aseptic conditions and prevent microbial contamination during th...
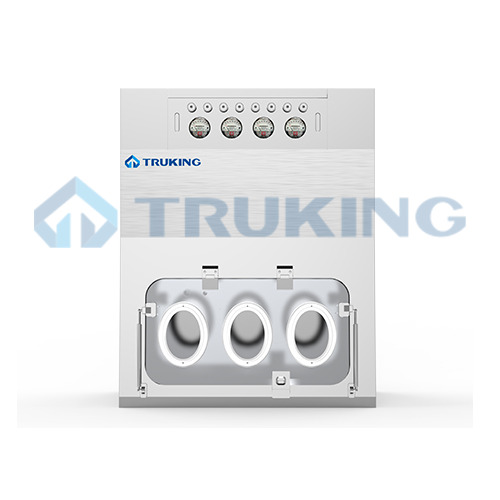
Feeding isolator for liquid preparation in pharmaceuticals
Ensure precise and contamination-free preparation of liquid p...
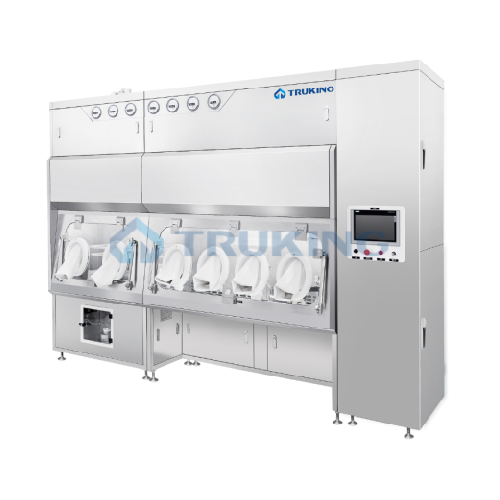
Sterility testing isolator for aseptic environment
Ensure precise sterility testing and prevent contamination with an iso...
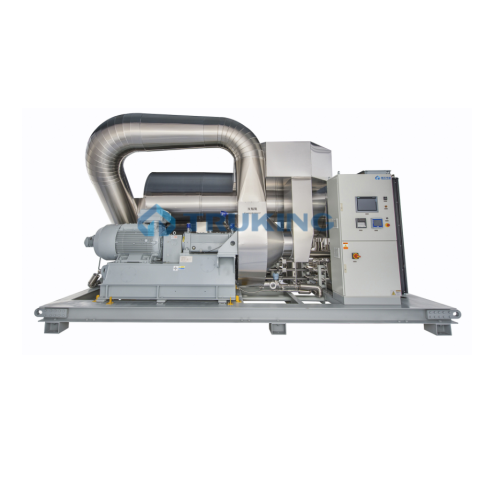
Hot press distilled water unit for pharmaceutical applications
Ensure superior water purity in pharmaceutical production...
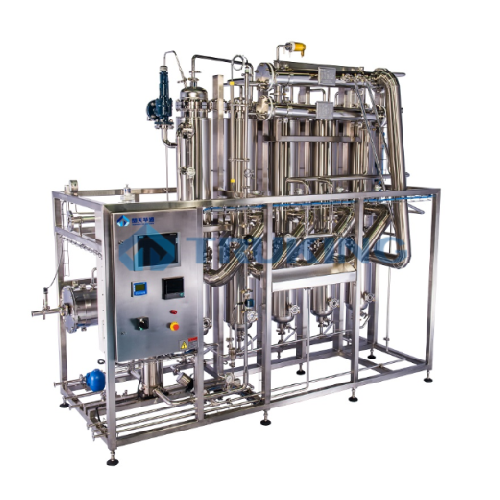
Multi-effect water distillator for pharmaceutical applications
Ensure your production line meets stringent regulatory st...
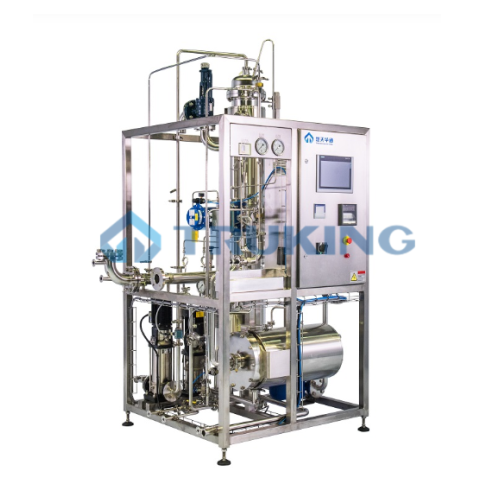
Pure steam generator for pharmaceutical and biotech industries
Ensure optimal steam quality and compliance with stringen...
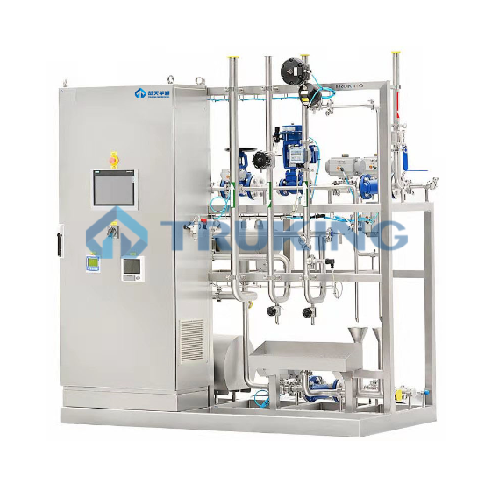
Pharmaceutical ultra pure water distribution system
Ensure stringent purity standards with a modular water distribution s...
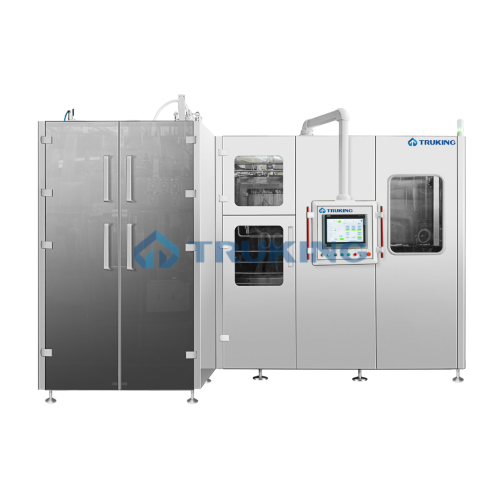
Aseptic blow fill seal system
Ensure sterile, high-speed production of liquid pharmaceuticals by integrating a cutting-edge ...
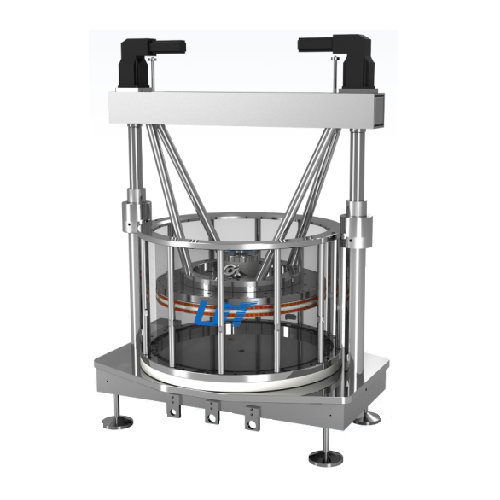
Automatic chromatography column for biopharmaceutical separation
Ensure high-purity monoclonal antibodies and herbal ext...
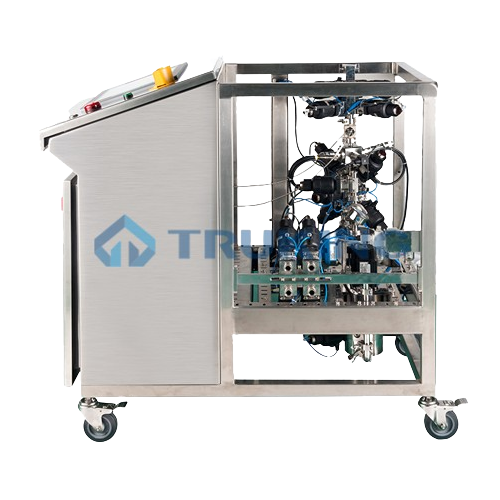
Chromatography systems for large-scale biopharmaceutical purification
Ensure precision purification of biopharmaceutica...
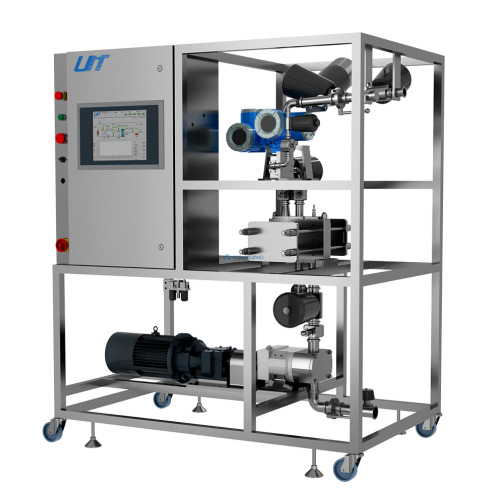
Production-level ultrafiltration system for industrial applications
Achieve precise concentration and separation of val...
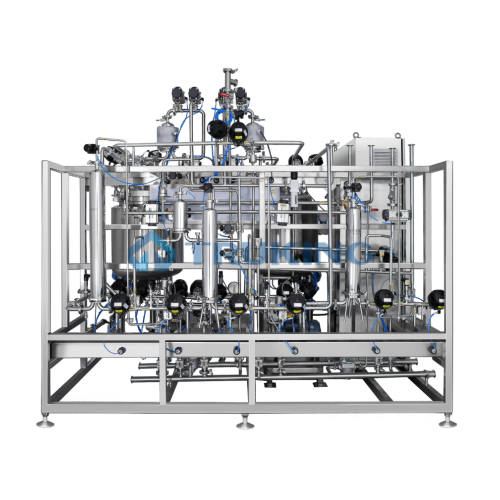
Pharmaceutical preparation system
Achieve seamless integration in pharmaceutical processes with a preparation system that o...
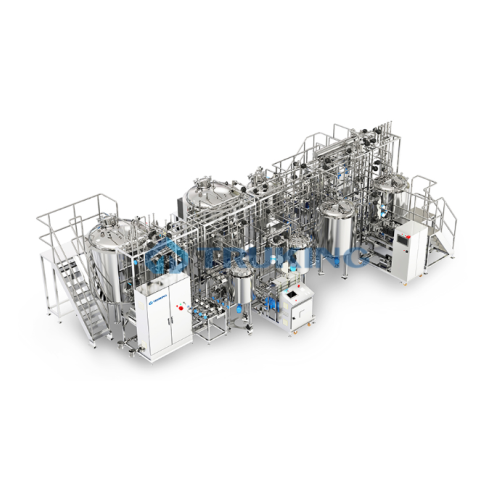
Complex preparation system for industrial microsphere production
Achieve precise particle size and uniform drug encapsul...
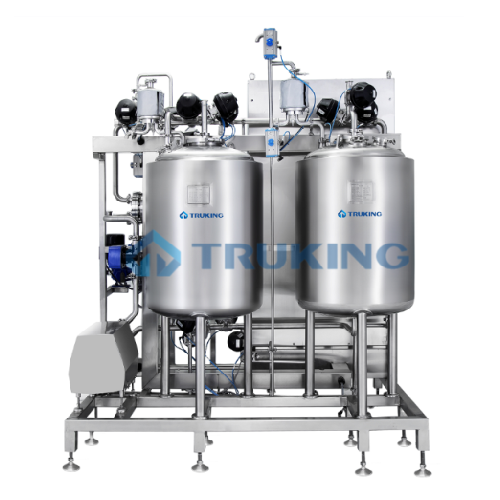
Comprehensive auxiliary system for online cleaning and temperature control
Ensure reliable and precise control in phar...
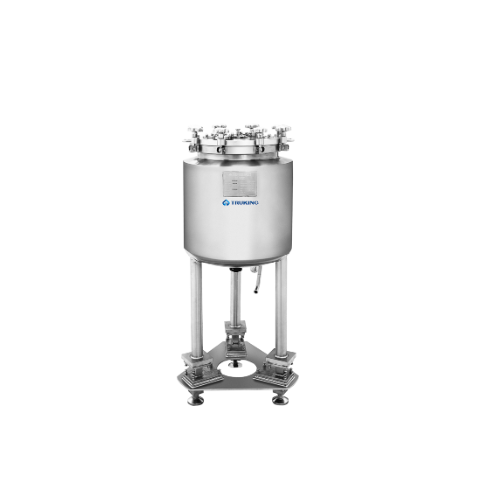
Sanitary vessels for pharmaceutical applications
Ensuring the highest standards of aseptic processing, these sanitary vess...
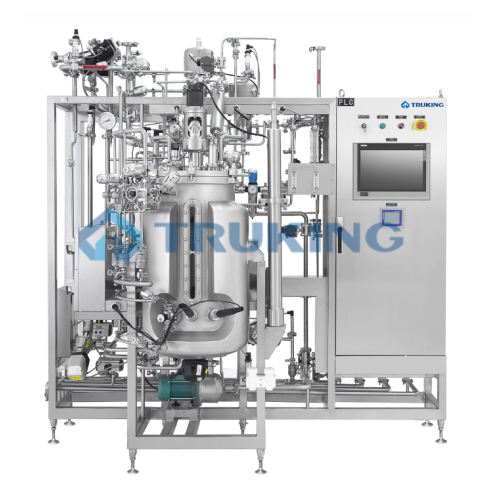
Bioreactor system for protein and enzyme reaction
Ensure precise control in biopharmaceutical production with a bioreacto...
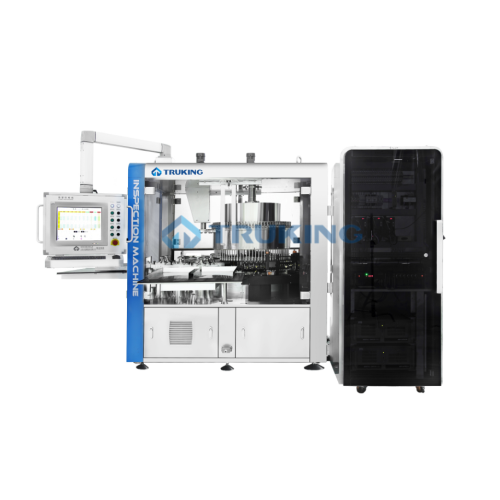
Automatic inspection system for ampoules and vials
Ensure precision in pharmaceutical production with a comprehensive ins...
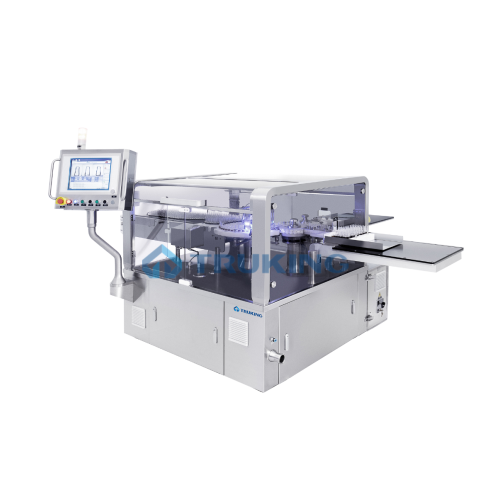
Automatic inspection system for sealing defects in ampoules
Ensure flawless ampoule sealing with a high-precision inspec...
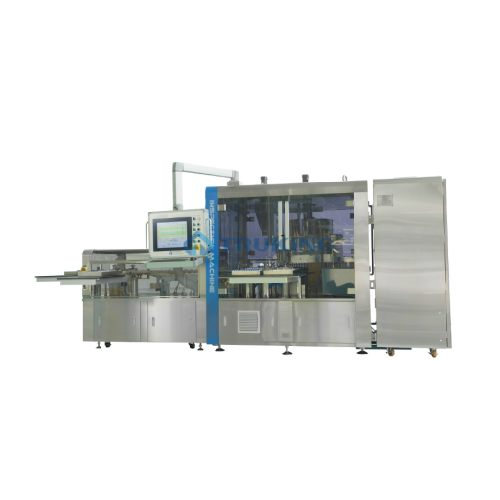
Automatic inspection and leak test for pharma containers
Ensure container integrity for injectables with high-speed inspe...
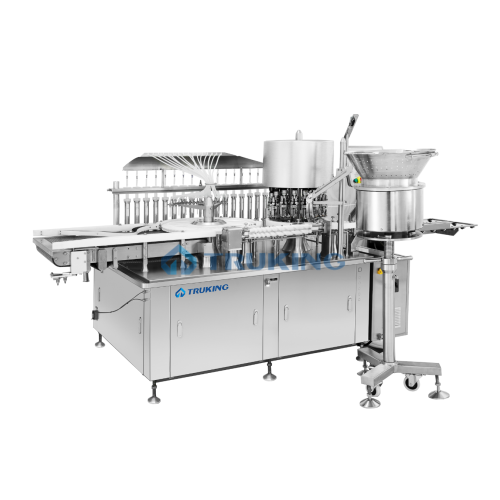
Oral liquid bottle filling & capping system
Streamline your liquid manufacturing processes with precise filling and secure...
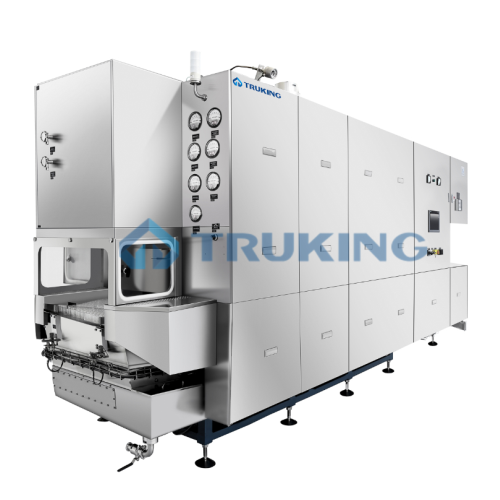
Sterilizing and drying tunnel for pharmaceutical vials
Ensure precise sterilization and depyrogenation of pharmaceutical ...
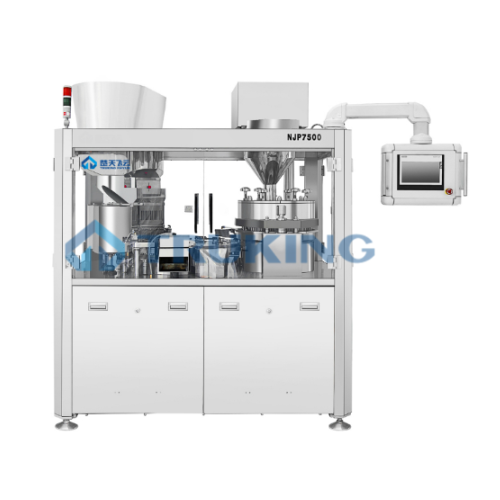
Fully automatic hard capsule filling machine
Enhance pharmaceutical production with precise capsule filling, ensuring opti...
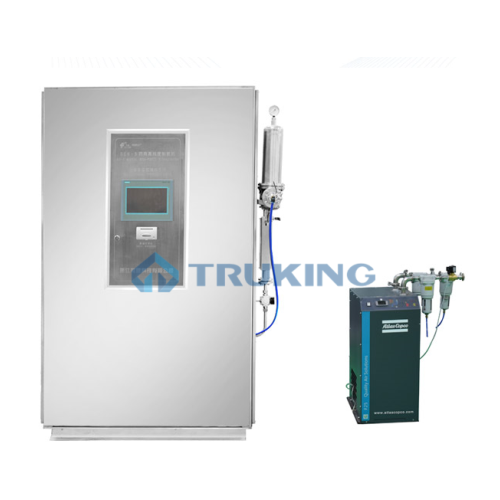
High-purity nitrogen generator for pharmaceutical and food industries
Achieve ultra-high purity levels in your producti...
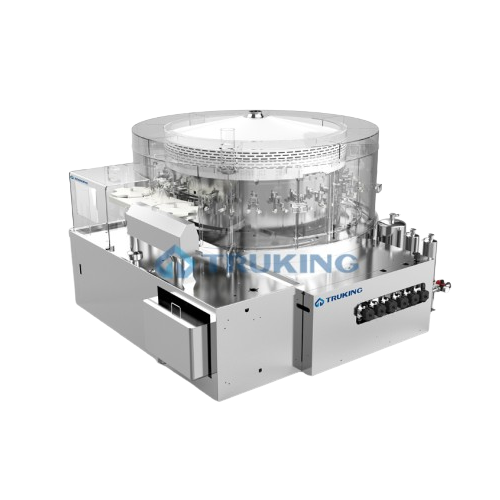
Industrial freeze dryer for pharmaceutical applications
Enhance your production line with precision cleaning solutions fo...
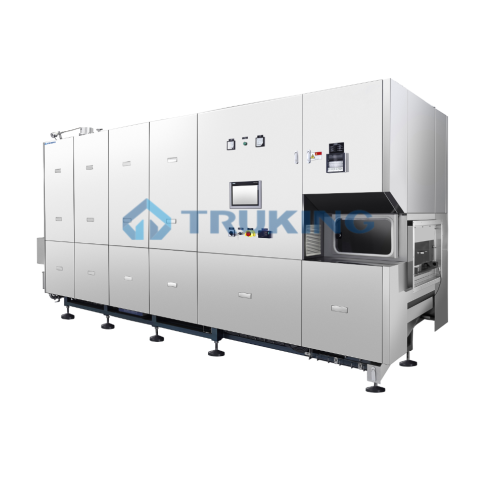
Sterilization and drying tunnel for glass bottles
Ensure aseptic integrity and regulatory compliance in injectable produc...
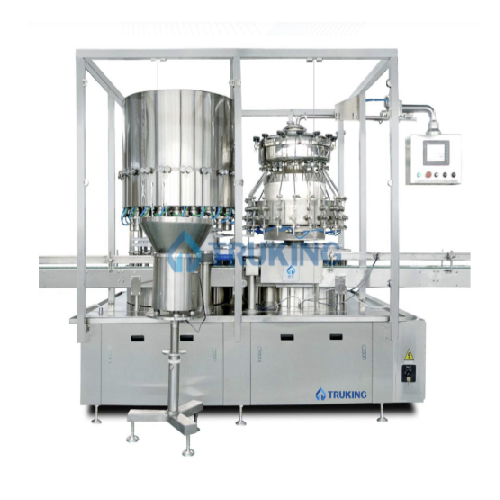
Gravity rotary filling for large infusion bottles
Ensure precise filling and secure stoppering of large infusion bottles ...
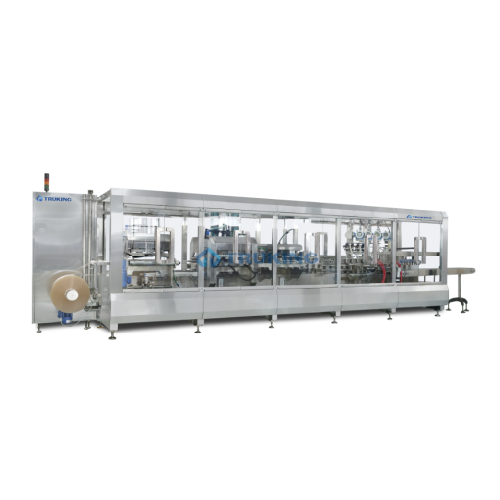
Non-pvc film large infusion compact line
Streamline your infusion production with a compact line designed for high-speed, p...

High capacity automatic blister packaging system
Streamline your production line with a high-speed blister packaging syste...
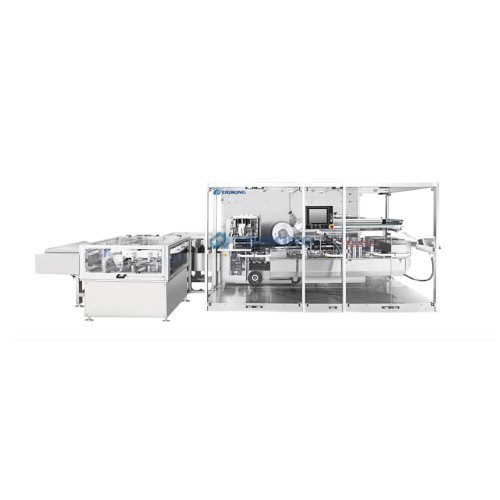
Secondary packaging cartoner for ampoules and vials
Optimize your aseptic production with efficient high-capacity carton ...
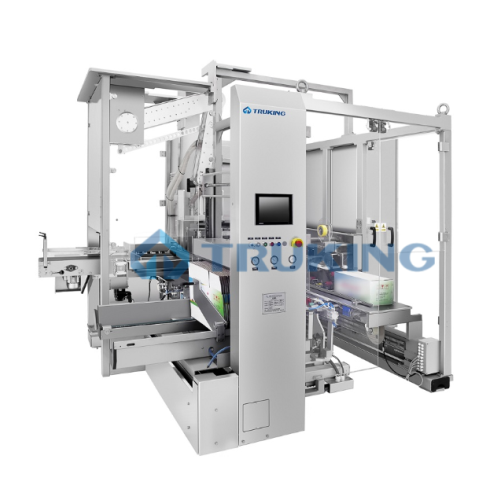
Automatic case packer for pharmaceutical industry
Optimize your packaging process with a versatile case packer designed t...
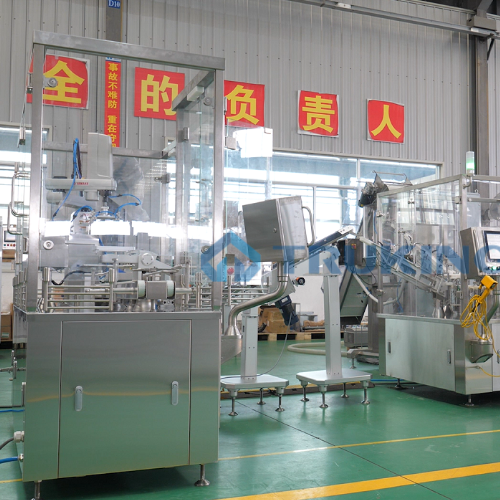
Pre-filled syringe plunger rod insertion and labeling system
Ensure precise labeling and efficient pre-filled syringe ha...

Large volume oral liquid filling system
Ensure precision and efficiency in liquid filling with a system designed to handle ...
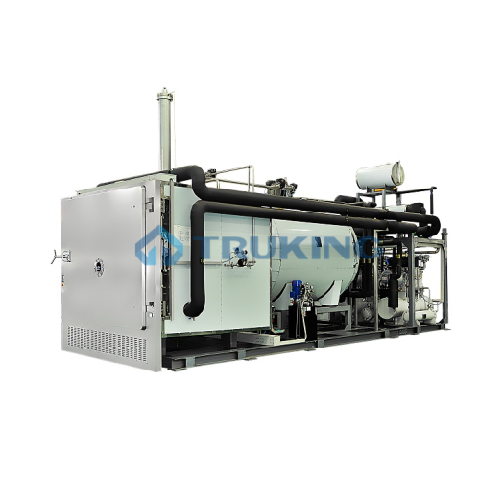
Industrial freeze dryer for pharma
Optimize moisture removal in lyophilized products with precise thermal conduction and ef...
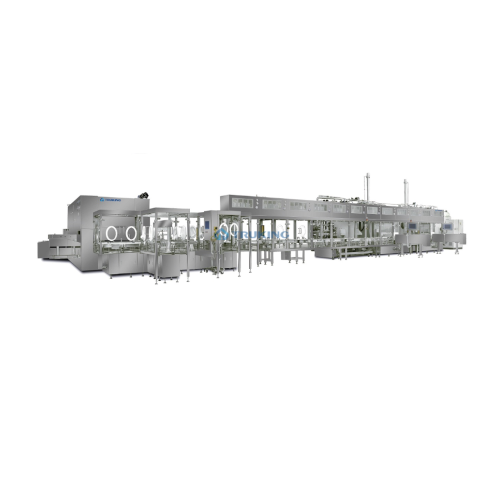
Auto loading & unloading system for freeze dryers
Efficiently manage vial handling in freeze-drying processes with automa...
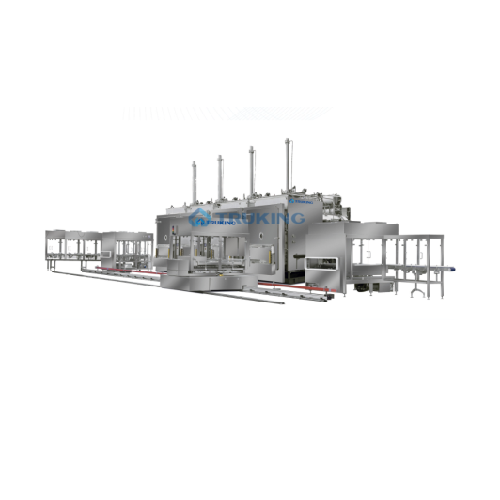
Mobile transfer loading system for freeze dryers
Streamline your lyophilization process with a high-capacity mobile loadin...
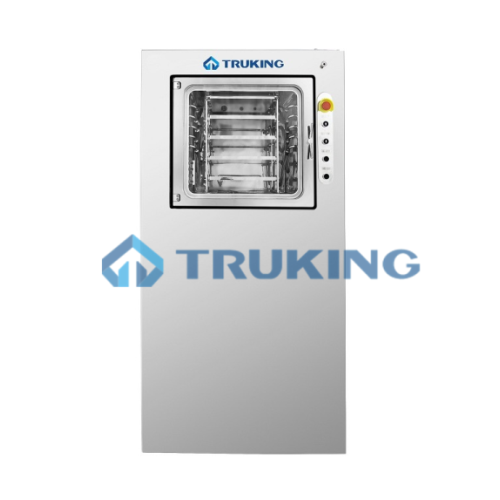
Laboratory freeze dryer for research and development
Optimize moisture removal with precision control during research and...
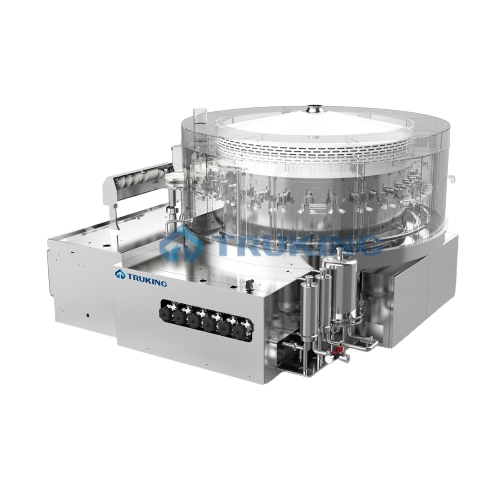
Ultrasonic pre-washing system for large infusion glass bottles
Optimize your cleaning process with an ultrasonic pre-was...
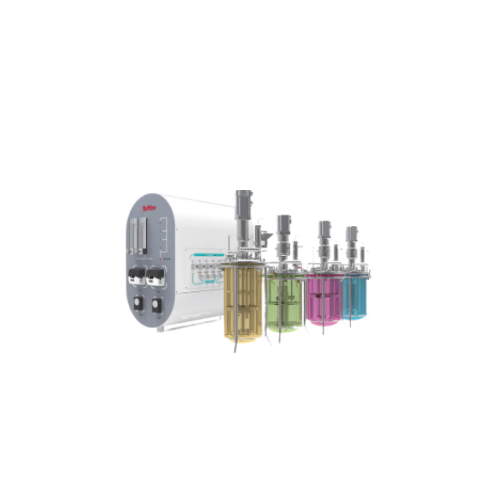
Glass bioreactor for microbial fermentation and cell cultivation
Streamline your bioprocessing with this customizable gl...
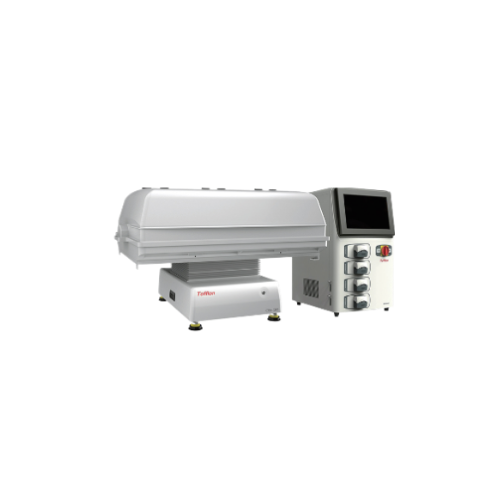
Cell expansion system for antibody drug production
Enhance your biopharmaceutical production with efficient cell expansio...
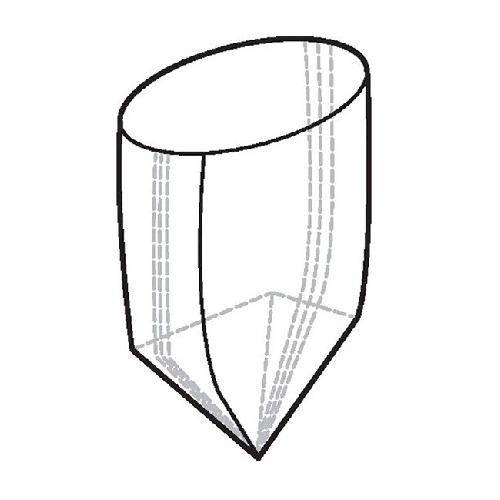
200l sterile tank liners for bioprocessing
Streamline your bioprocessing operations by eliminating tank cleaning steps and...
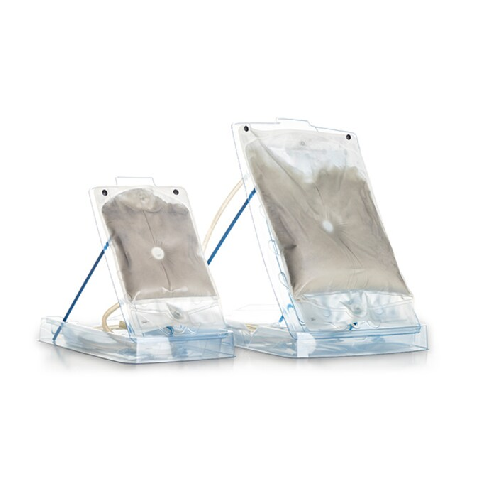
Microcarrier separation system for adherent cell cultures
Enhance your production efficiency with a scalable, single-use...
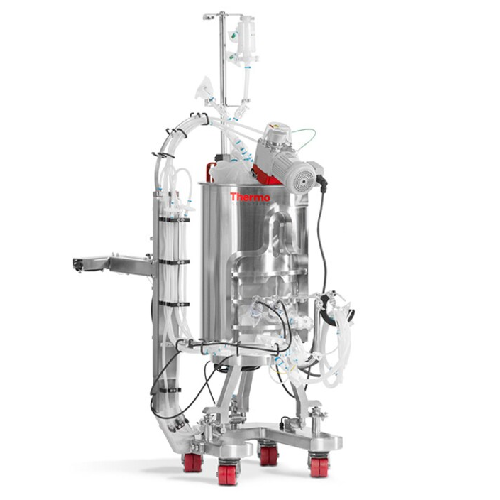
Single-use bioreactor for protein expression
Optimize your biopharmaceutical production with an advanced single-use biorea...
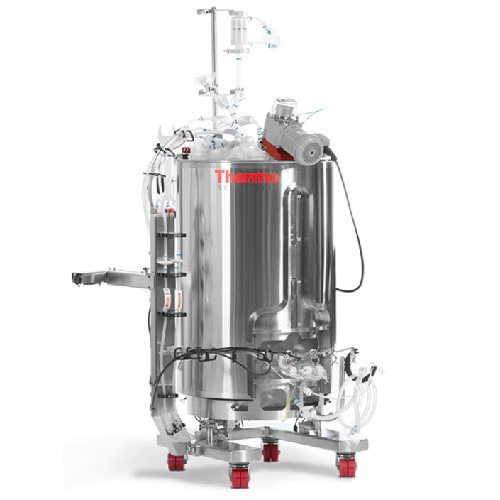
Single-use bioreactor for cell culture applications
Achieve optimal cell growth and product yield with a single-use biore...
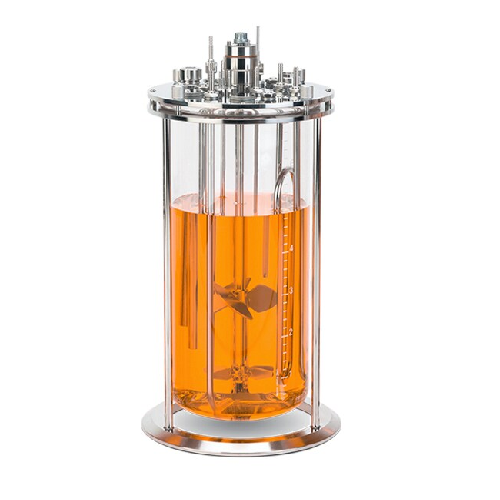
Glass bioreactor for mammalian cell culture
Optimize your bioprocessing with advanced mixing and cooling capabilities, des...
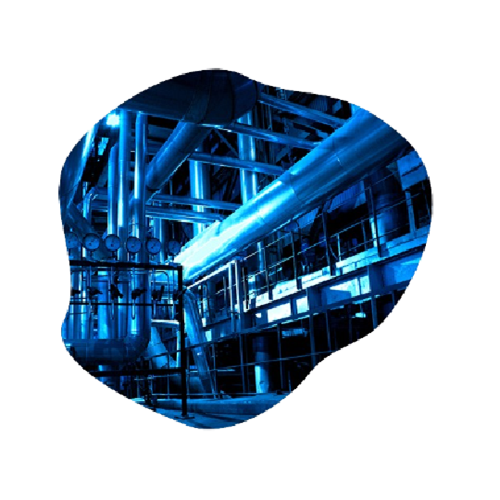
Industrial-scale bioreactors for large-scale biomanufacturing
When producing at large volumes, efficient and reliable bi...
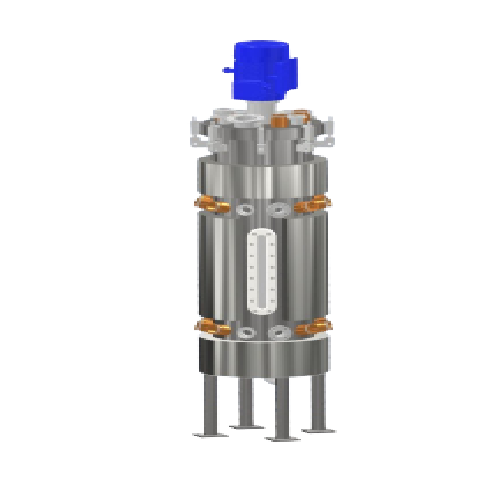
Pilot-scale bioreactors for bioprocess scale-up
Bridge the gap between experimentation and large-scale production with pil...
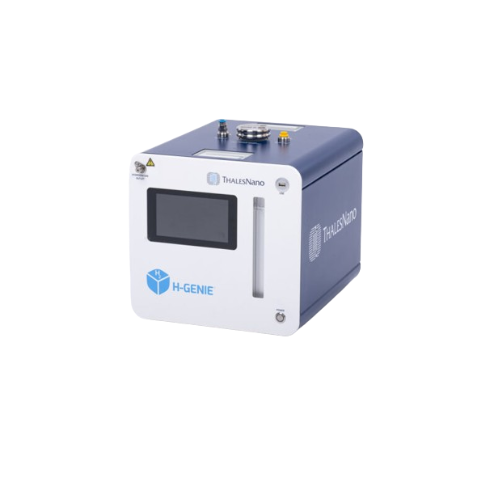
High-pressure hydrogenation reactor for chemical labs
Achieve precise high-temperature hydrogenation with integrated on-d...
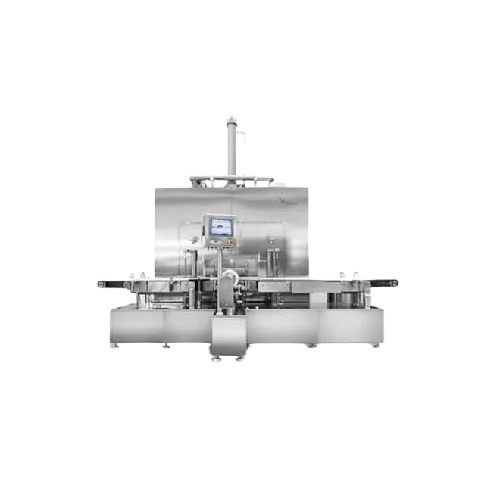
Sterile lyophilisation and filling line
Ensure aseptic conditions while freeze-drying biopharmaceuticals and high-potent dr...
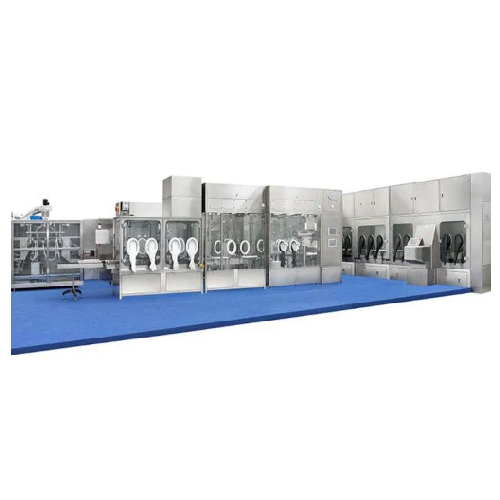
Lyophilization for live bacteria vaccine production
Ensure precise moisture control when freeze-drying live attenuated ba...
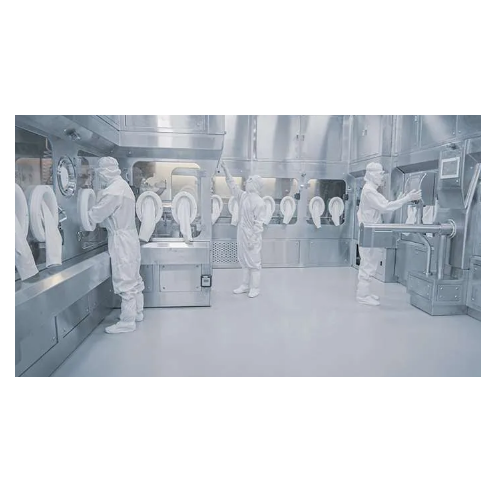
Vial filling line and freeze dryer system
For seamless drug production, integrate reliable vial filling with precision fre...

Sterile lyophilised filling line
Ensure precision in filling and sterilization with an integrated system designed for stream...
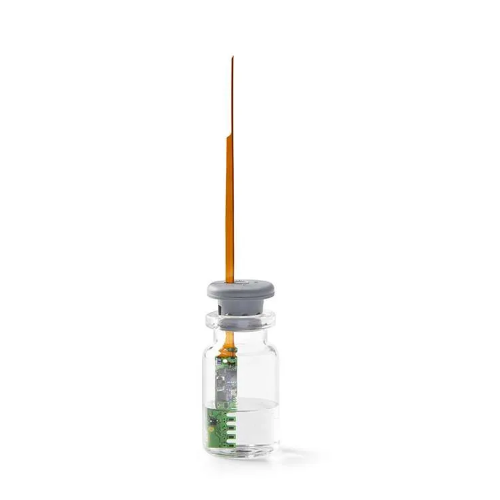
Gmp freeze dryer for small batch production
Optimize small-scale biopharmaceutical production with precise freeze-drying t...
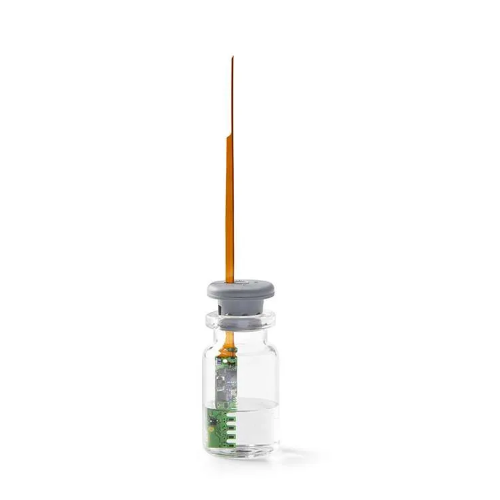
Sublimation front monitoring system for freeze drying
Ensure precise control over your freeze-drying process with real-ti...
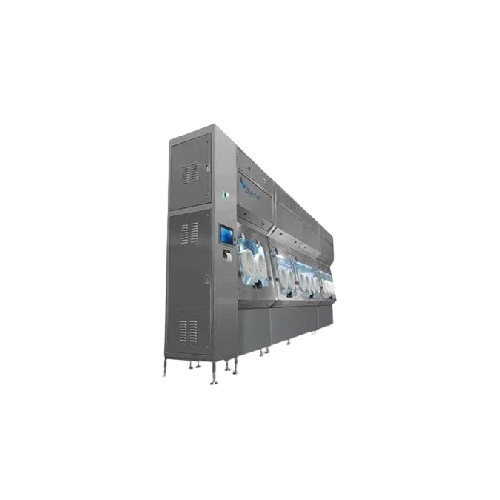
Aseptic syringe filling isolator system
Ensure product sterility and precision with a cutting-edge solution for aseptic syr...
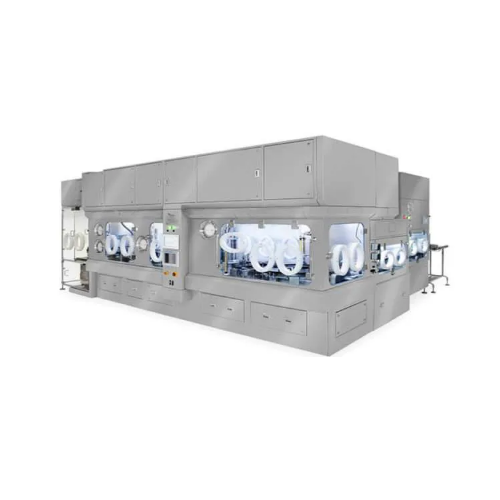
Sterile lyophilized filling line
Ensure sterility and precision in filling pharmaceuticals with advanced isolator lines desi...
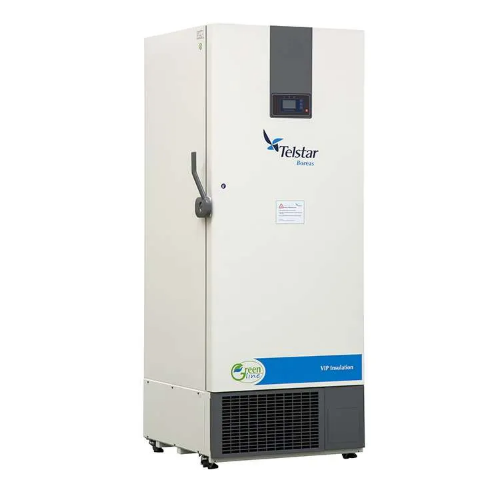
Upright ultra low temperature freezer for laboratory use
Ensure long-term preservation of biological integrity and high-v...
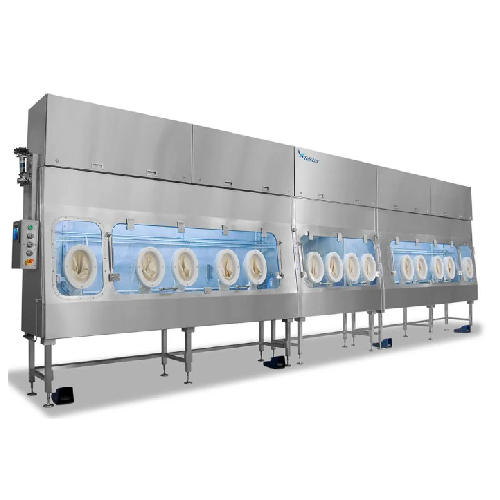
Aseptic barrier isolators for pharmaceutical applications
Enhance sterility and operator safety during aseptic processin...
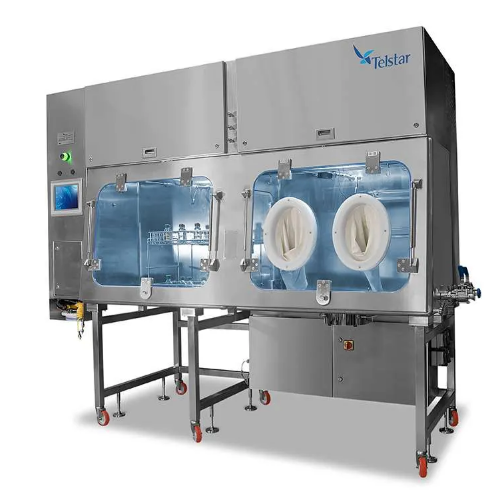
Sterility test isolator for pharmaceutical processes
Ensure precise sterility testing with an isolator that maintains an ...
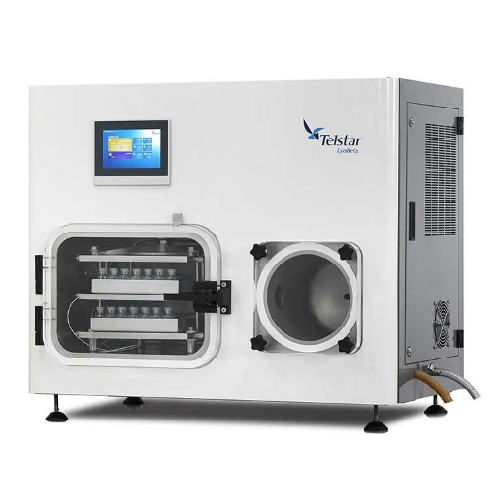
Freeze dryer for small batch scale-up in biotech and pharma
Optimize freeze-drying processes for small batches or high-v...
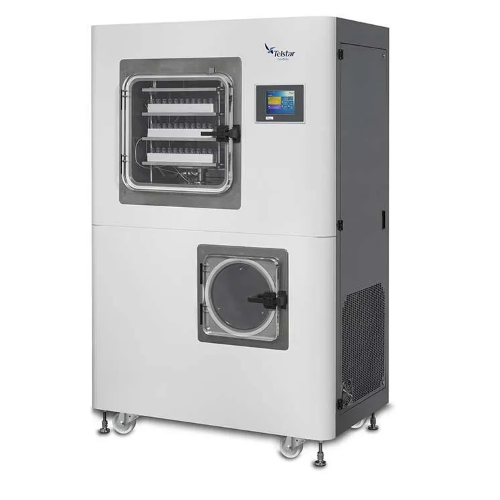
Research and scale-up freeze dryer for biological and pharmaceutical applications
Allows efficient scale-up of lyophi...
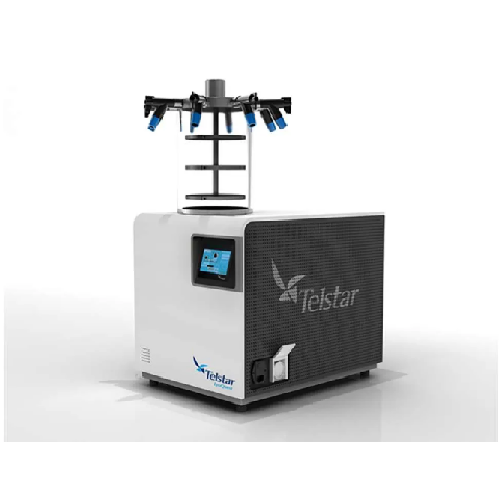
Basic research laboratory freeze dryer
Achieve unparalleled precision in lyophilization with a compact solution tailored fo...
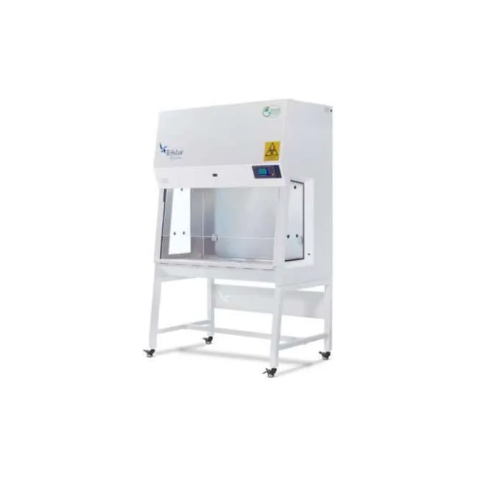
Biological safety cabinet for cytotoxic drug handling
Ensure the safe preparation and handling of cytotoxic drugs in hosp...
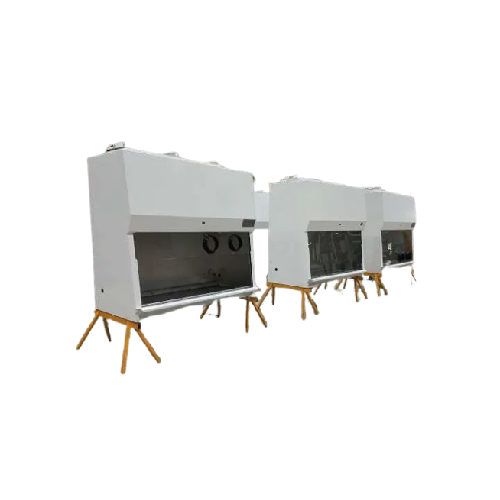
Class Ii biological safety cabinets for vaccine production
Ensure stringent safety and environmental standards with cust...
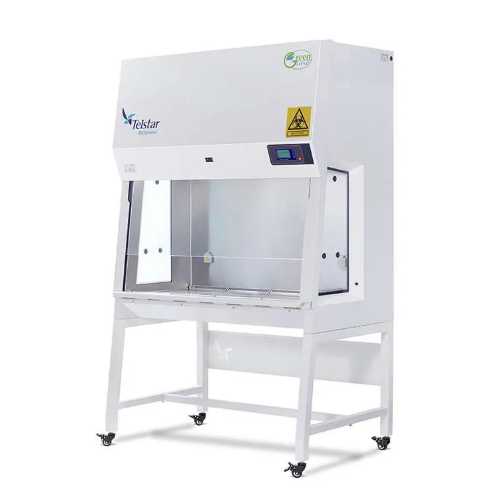
Microbiological safety cabinet for laboratory containment
Ensure seamless microbiological containment and operator prote...
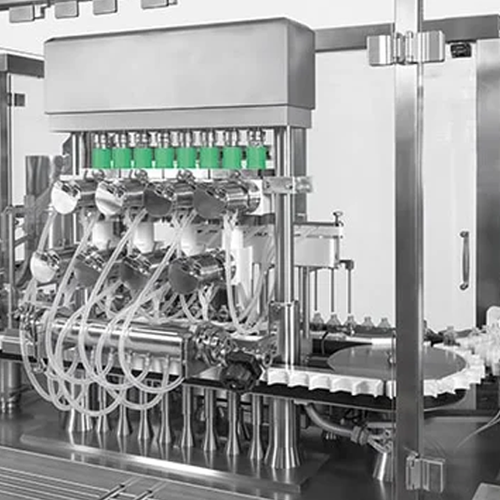
Bulk vial liquid filling system
Ensure reliable and efficient processing of critical biopharmaceutical and pharmaceutical li...
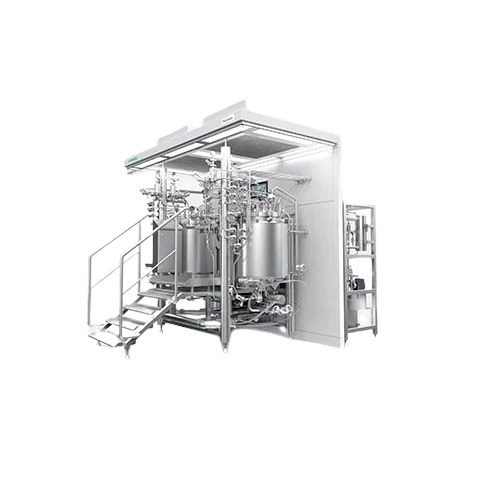
Syringe filling line for parenteral drugs
Ensure precise dosage and sterility with this high-speed syringe filling line, i...
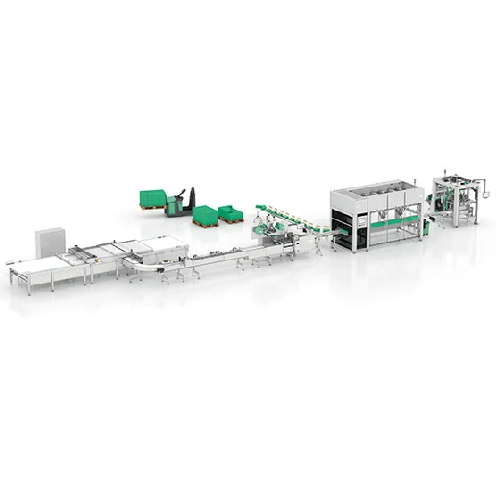
Automated visual inspection for pharmaceutical products
Ensure the integrity and safety of your parenteral products with ...
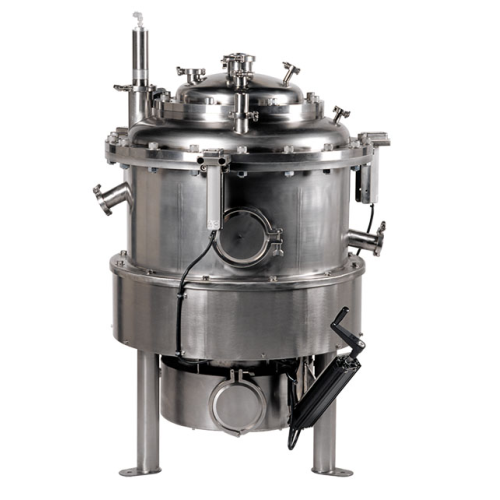
Pharmaceutical aseptic separation system
Achieve precise separation and efficient drying of pharmaceutical powders with an ...
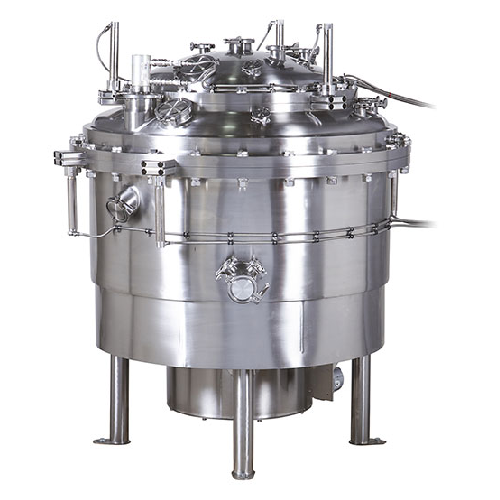
Pharmaceutical aseptic separator tumble dryer
Streamline moisture reduction with precision: this solution accelerates dryi...
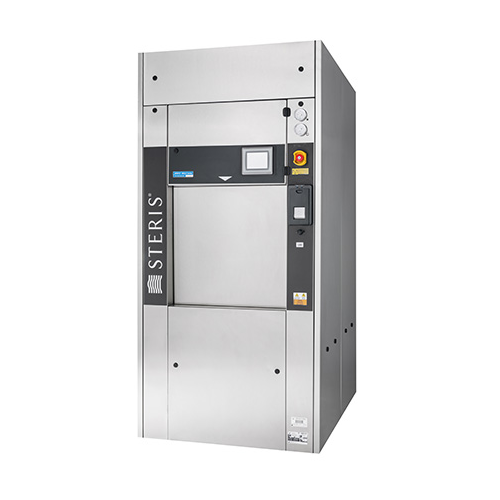
Medium steam sterilizer for laboratory applications
Ensure consistent and reliable sterilization of heat- and moisture-st...
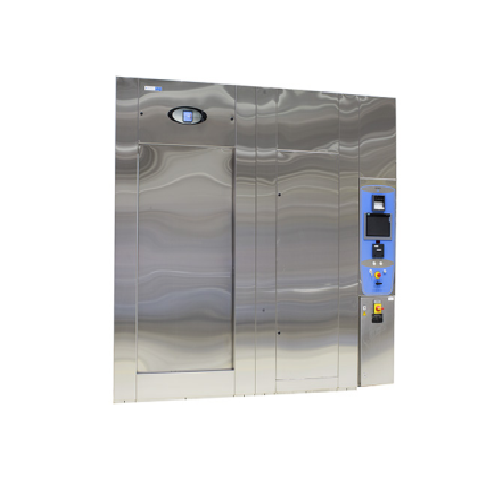
Sterilization system for biosafety applications
Ensure sterility and compliance in critical manufacturing processes with a...
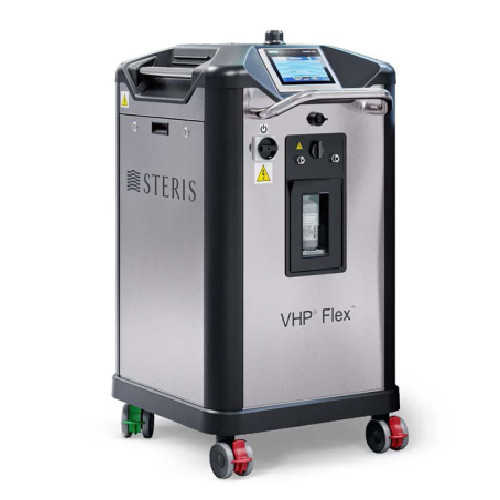
Mobile biodecontamination unit for small to mid-size rooms
Efficiently achieve 6-log bioburden reduction in controlled e...
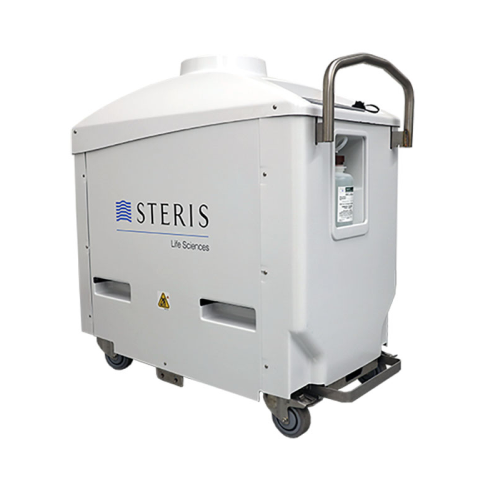
Mobile biodecontamination unit for cleanroom environments
Achieve rapid, high-capacity sterilization in cleanrooms effor...
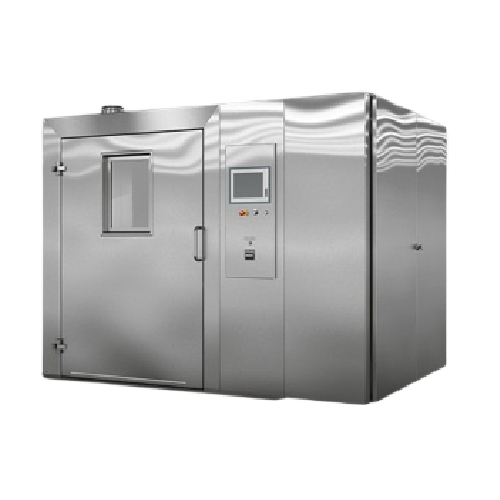
Pharmaceutical grade washer for large components
Ensure compliance and maximize productivity with a high-performance solut...

Saturated steam autoclave for pharmaceutical decontamination
Ensure precise decontamination and sterilization with a sol...
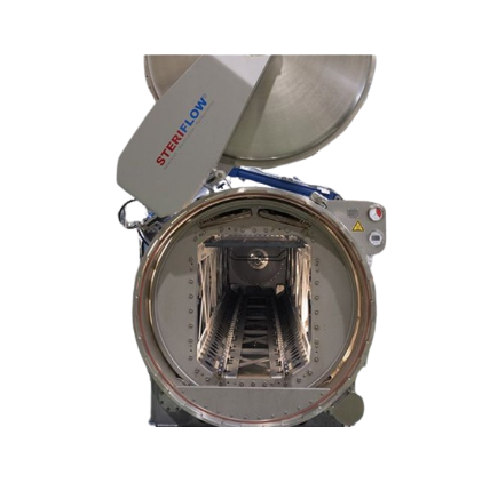
Static autoclave for pharmaceutical sterilization
Ensure reliable sterilization with a static autoclave that maintains cr...

Multiple-effect water still for pharmaceutical applications
Optimize your pharmaceutical water production with a system ...
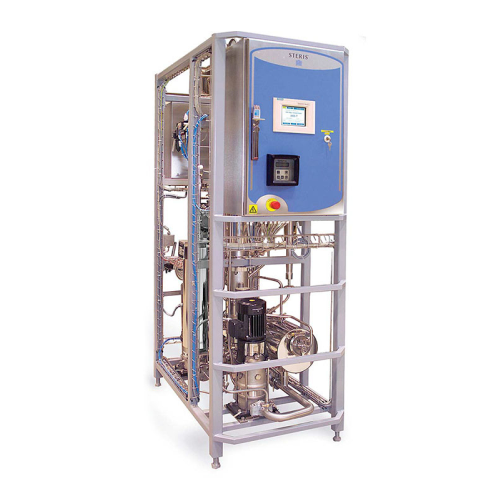
Pure steam generator for pharmaceutical applications
Ensure your sterilization process consistently achieves high purity ...
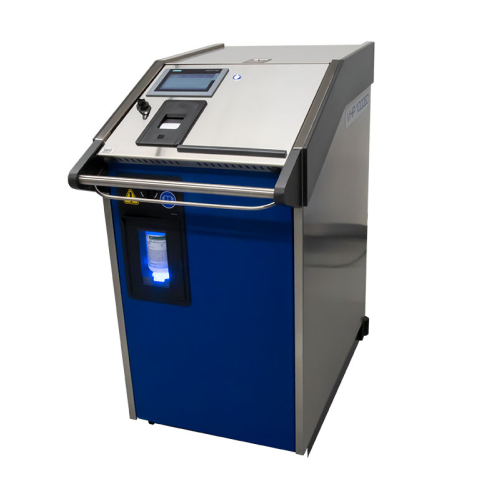
Hydrogen peroxide vapor biodecontamination unit for cleanrooms
Ensure a sterile environment by effectively biodecontamin...

3d printer for high-precision microbioreactors
Achieve unprecedented precision in bioprocessing with a 3D printer capable ...
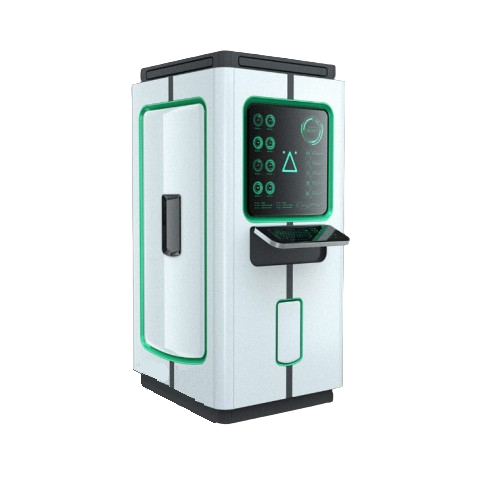
Desktop bioprocessor for continuous biomanufacturing
Shrink your biotech facility to a bench-top unit, achieving seamless...
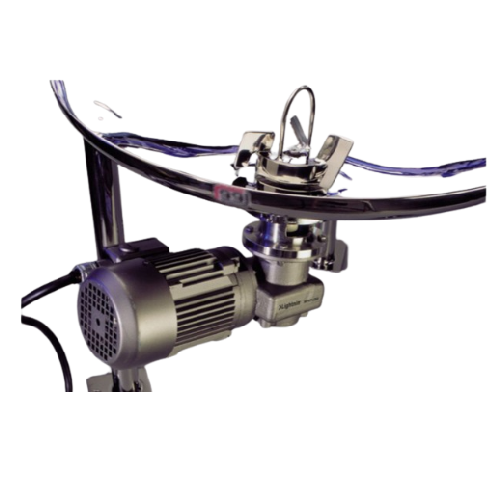
Sanitary mixer for food and pharmaceutical processing
Eliminate contamination risks while achieving high-speed, efficient...
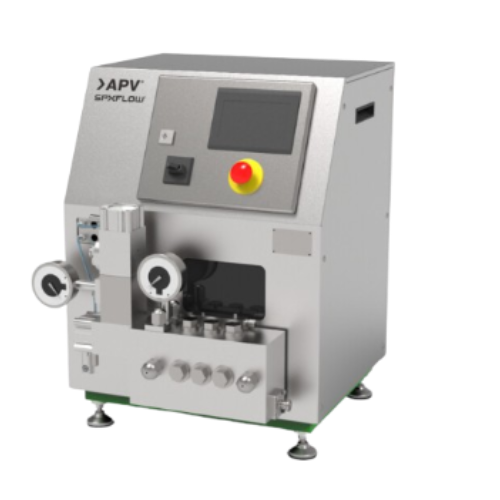
Pilot plant homogenizer for immiscible liquids
Streamline your R&D with precise homogenization, allowing you to test ...
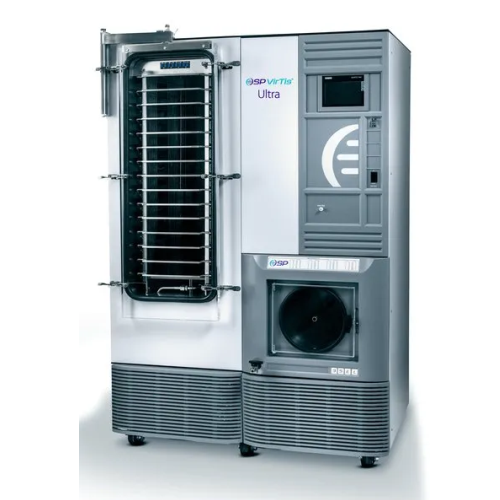
Pilot-production freeze dryer for diagnostic kits and Api
Optimize your lyophilization process with this versatile freez...
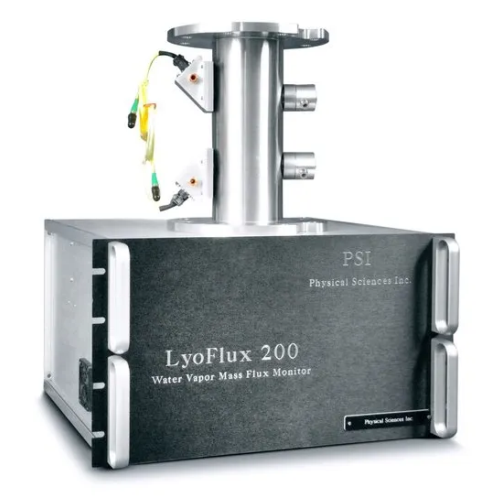
Lyophilization process optimization sensors
Achieve precise real-time monitoring of water vapor during freeze-drying, stre...
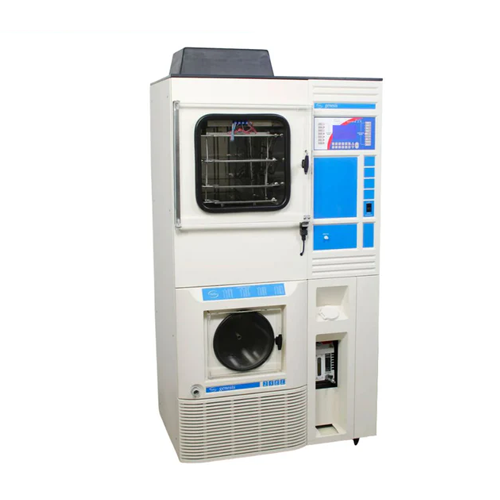
Optimized lyophilization with Smart freeze dryer technology
Streamline lyophilization cycle development with cutting-edg...
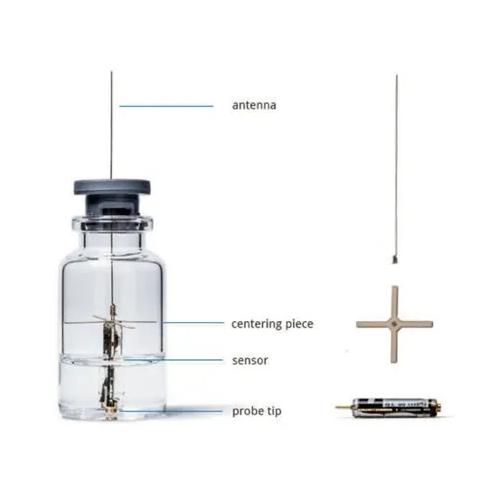
Wireless temperature sensors for lyophilization
Enhance your lyophilization workflow with precise, real-time temperature m...
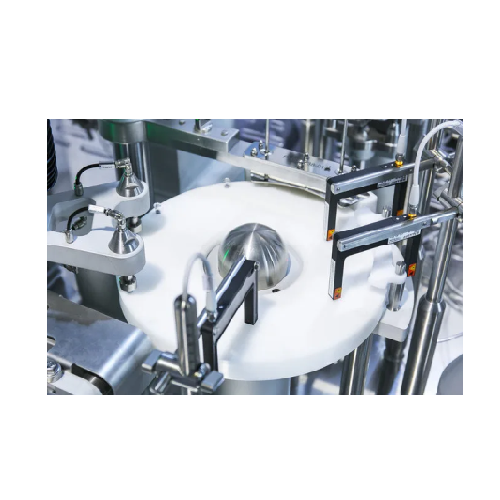
Sterile syringe plunger placement system
Ensure precision in syringe assembly with enhanced plunger placement, maintaining ...
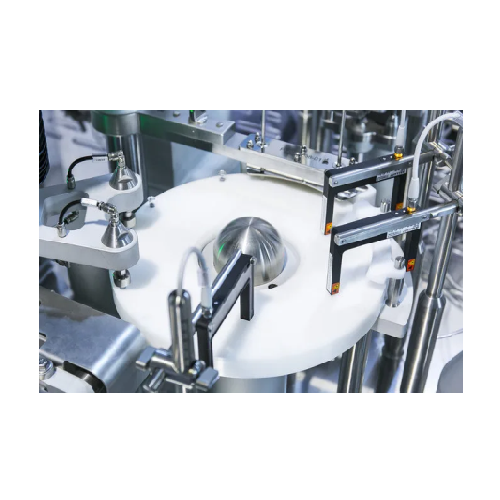
Robotic syringe filling system for sterile pharmaceutical production
For high-precision liquid dosing in sterile enviro...
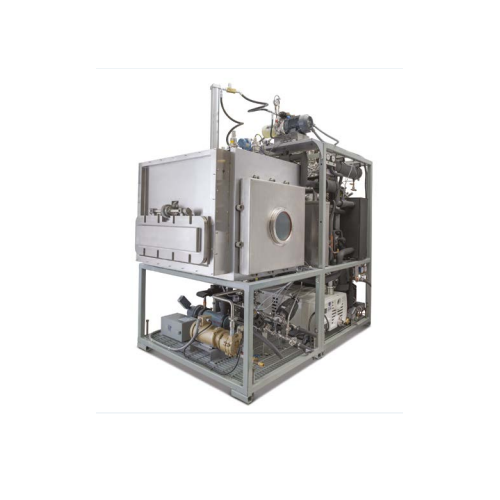
Controlled lyophilization nucleation system for drug development
Achieve consistent freeze-drying outcomes with precise ...
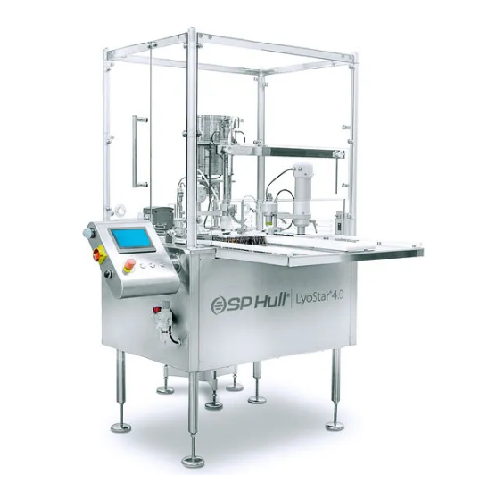
Small scale pharmaceutical filler and stoppering system
Optimize your R&D operations with a versatile filling and st...
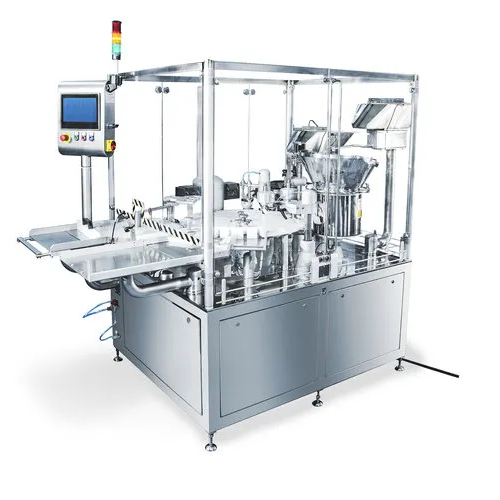
Micro-line vial filling solution for biopharmaceuticals
Ensure batch consistency and sterility in fill-finish operations ...
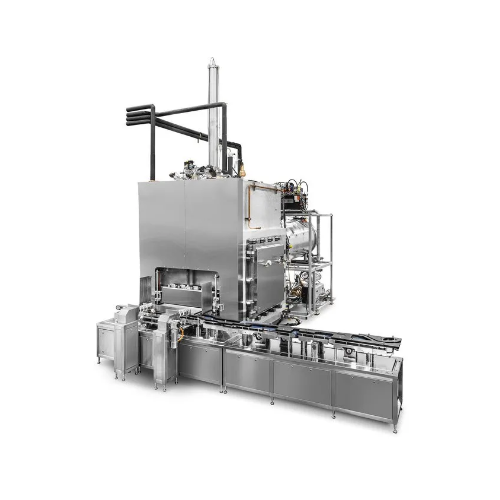
Freeze dryer loading and unloading systems for pharmaceutical processes
Optimize aseptic pharmaceutical processes with ...
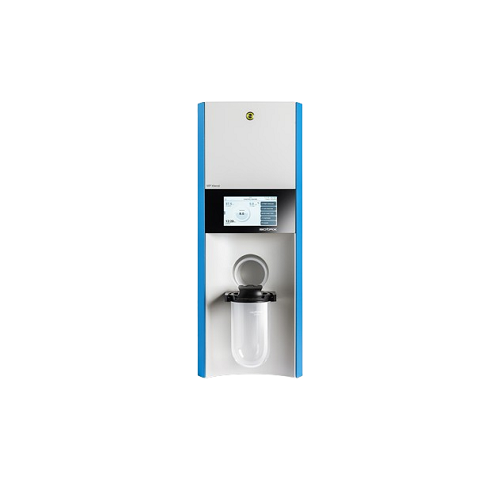
Dissolution medium preparation system
Streamline your laboratory workflows with a system that prepares and manages dissolut...
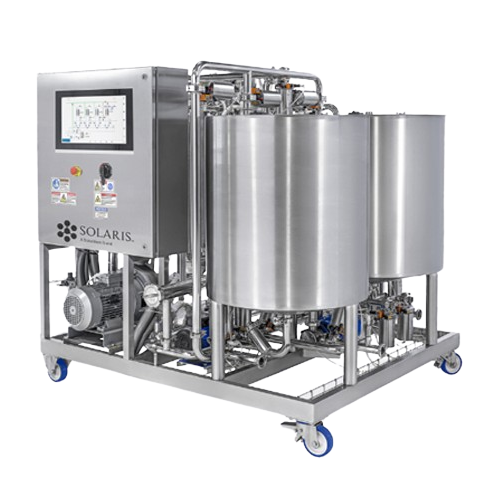
Pilot industrial tangential flow filtration system
Enhance precision in filtration and separation processes with this sys...
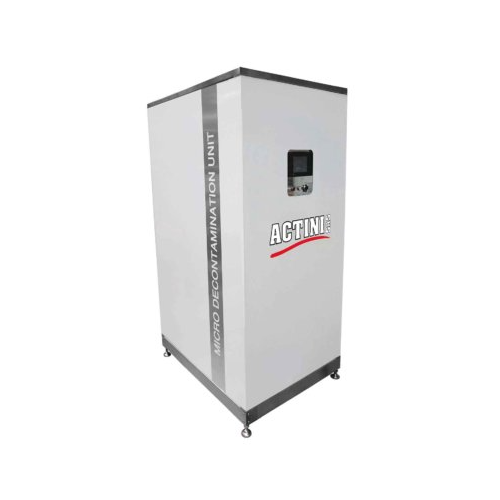
Ventilated autoclave for sterilization processes
Optimize sterile production with advanced ventilated autoclaves, ensuring...
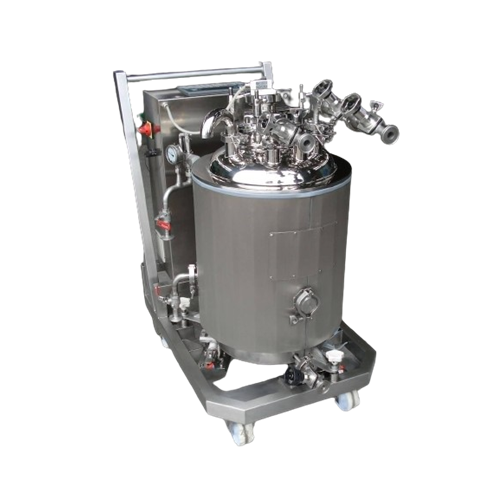
Ventilated autoclave for sterile product preparation
Ensure precise sterilization for injectable drugs and vaccine produc...
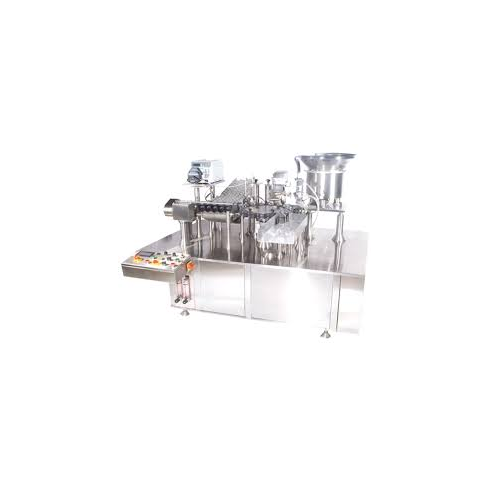
Combi r&d ampoule and vial filling equipment
Optimize your R&D operations with a versatile machine designed for preci...
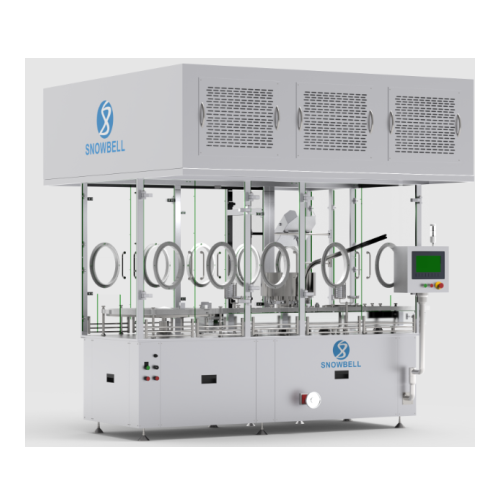
Vial washing system for internal and external cleaning
Streamline vial preparation with comprehensive washing, sterilizin...
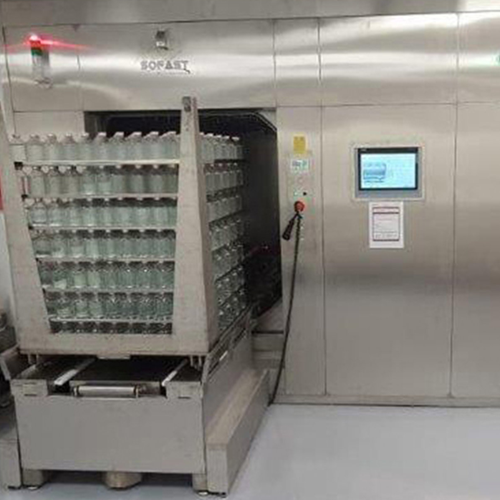
Medical lab sterilization autoclave
Ensure product sterility with high-performance ventilated autoclaves designed to optimi...
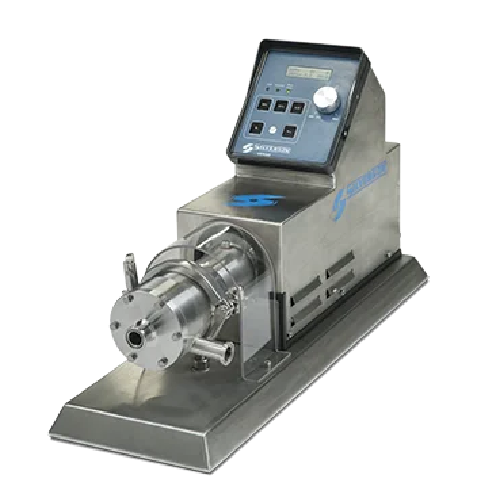
Laboratory in-line mixer for precise mixing and reproducibility
Achieve precise laboratory-scale mixing with rapid proce...
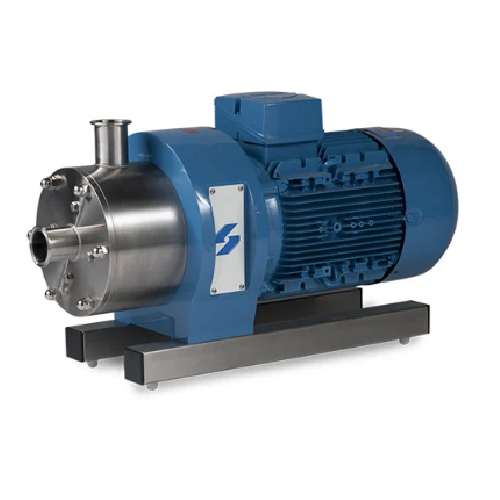
High shear inline mixer for continuous processing
Effortlessly streamline your mixing process with this solution capable ...
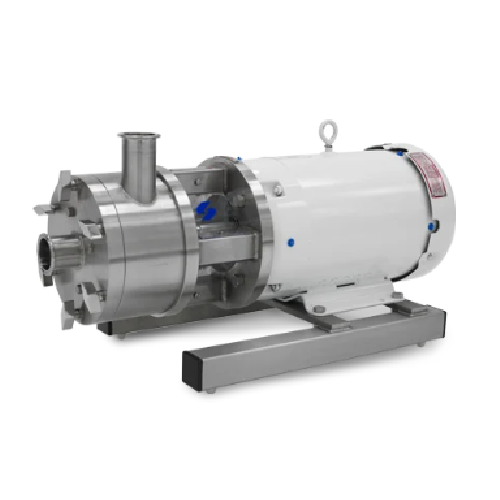
In-line ultra sanitary mixer for pharmaceutical and food applications
Enhance your liquid formulations with precision m...
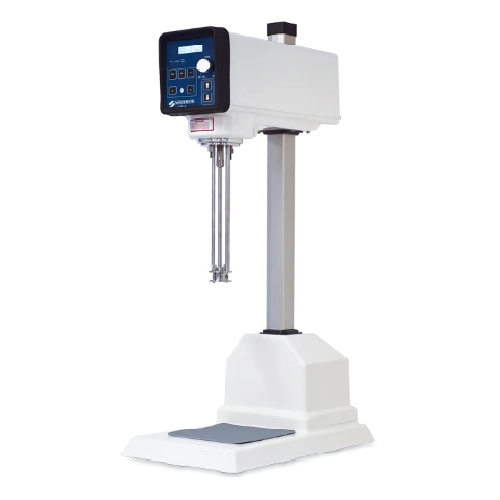
High shear lab mixer for laboratory work and r&d
Achieve unparalleled precision and consistency in laboratory and pilot-sc...
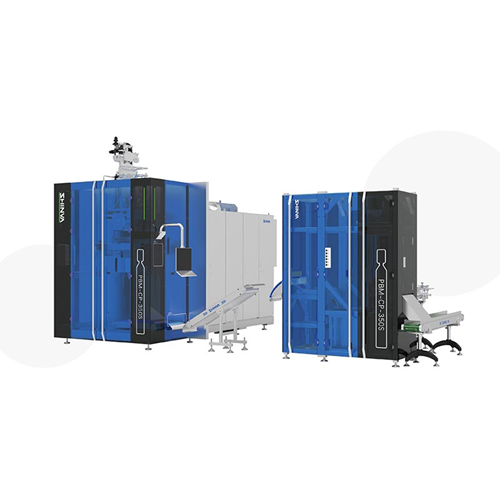
Single-mold continuous bottle Bfs solution
Optimize aseptic production with this advanced solution, offering superior ster...
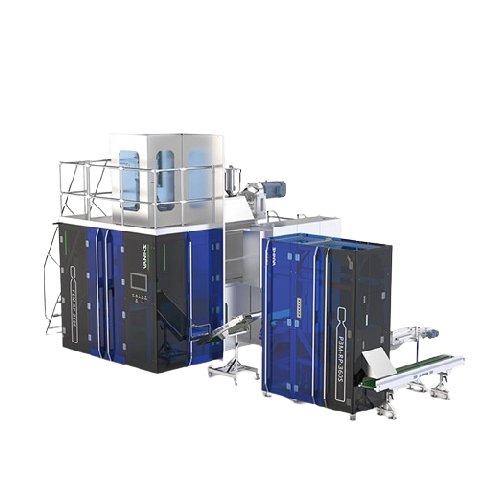
Multi-mold continuous plastic bottle Bfs solution
Optimize your aseptic product operations with a high-efficiency solutio...
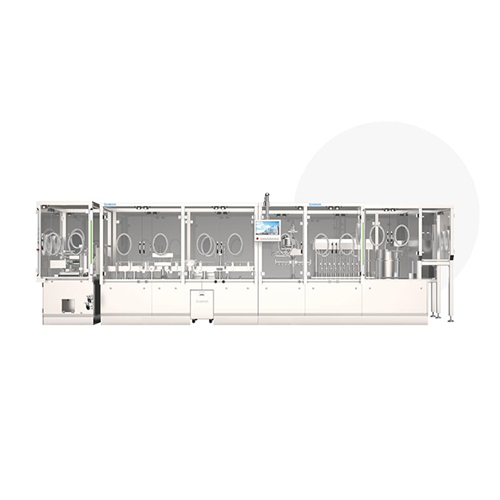
Intelligent pre-filled syringe production line
Optimize your sterile liquid medication production with a streamlined pre-f...
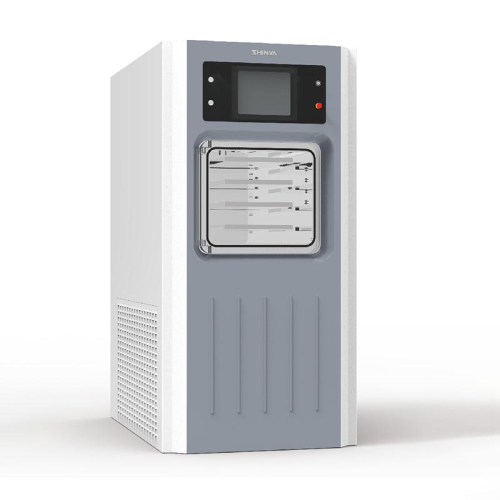
Laboratory freeze dryer for research and process amplification
Optimize freeze-drying processes with precision control, ...
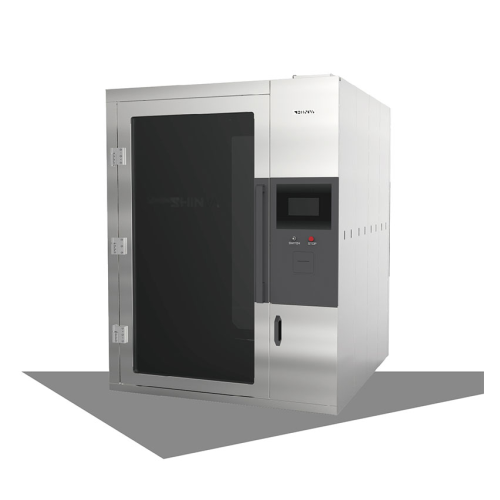
Disinfection transfer chamber for medical and laboratory use
Ensure surface sterilization of large quantities with preci...
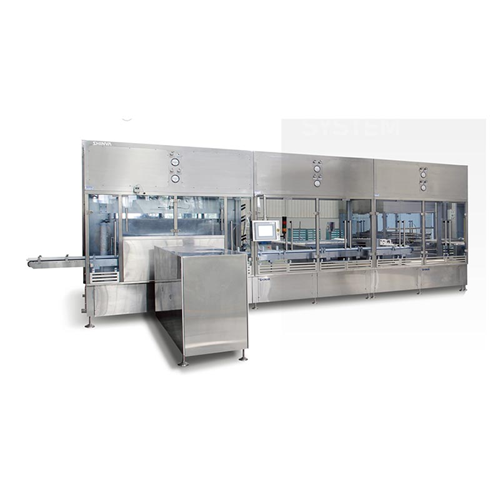
Automatic loading and unloading system for freeze-drying
Eliminate contamination risks and improve operational efficiency...
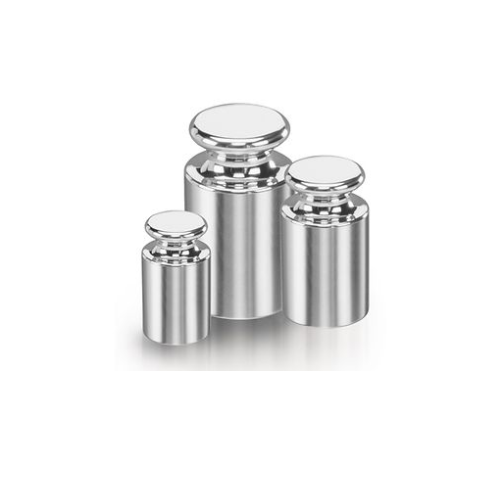
Metrological weights and weight sets for precise measurements
Ensure accuracy in your laboratory weighing processes with...
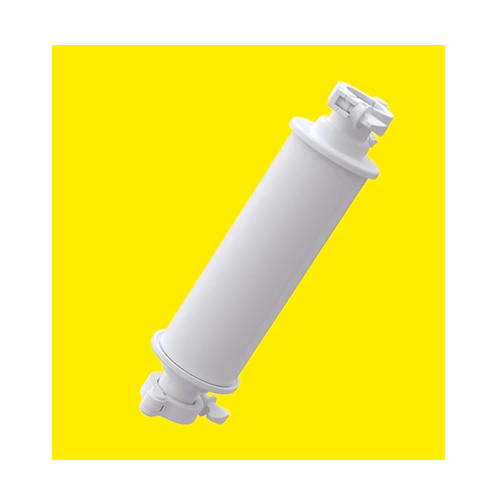
Single-use batch chromatography systems for biopharmaceuticals
Streamline your purification process with high productivi...
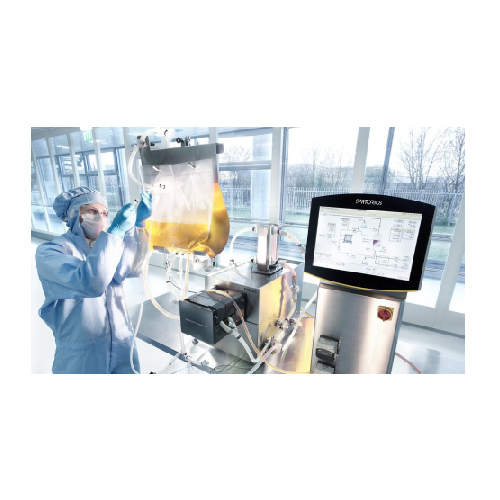
Tangential flow filtration system for cell harvesting
Optimize your biopharmaceutical production by integrating a versati...
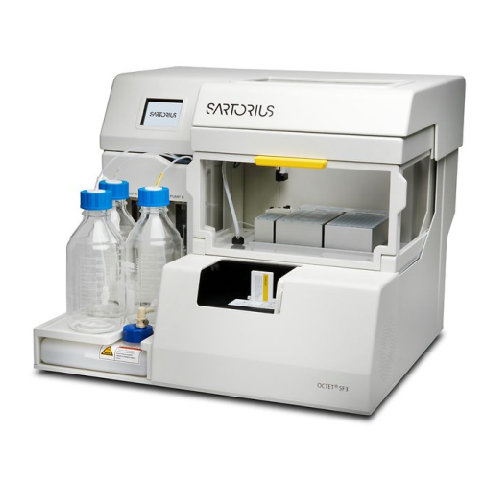
High-throughput surface plasmon resonance (spr) system
Rapidly achieve high-quality binding kinetics for drug discovery w...
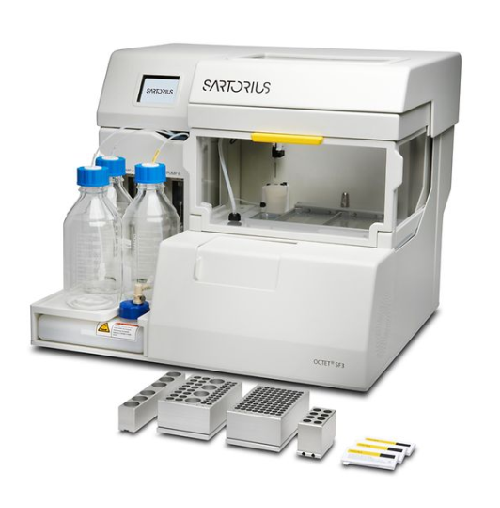
Surface plasmon resonance maintenance services
Maximize the lifecycle and performance of your surface plasmon resonance sy...

Surface plasmon resonance (spr) sensor chips
Enhance your molecule interactions analysis with precise sensor technology th...
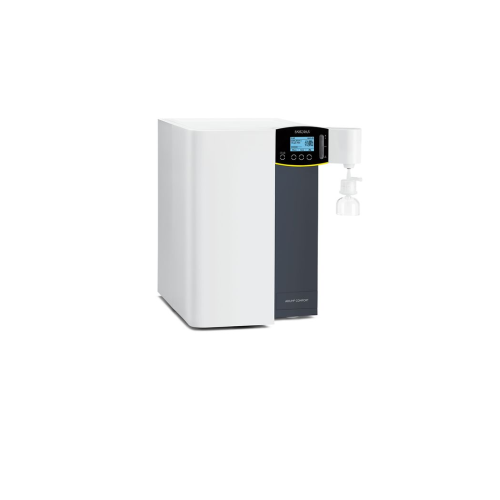
Combined lab water purification system
Optimize lab efficiency with a streamlined system delivering ultrapure and pure wate...
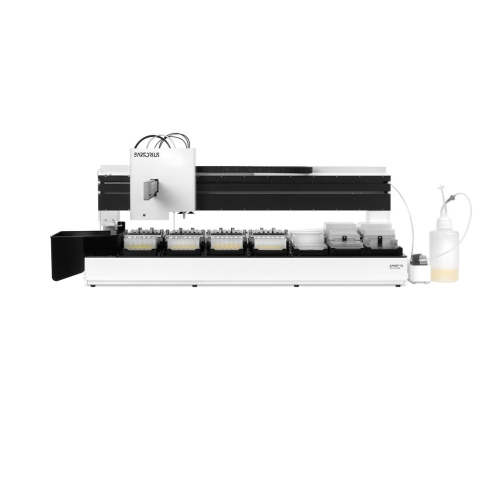
Multi-parallel bioreactors for cell line selection and process development
Enhance your biopharmaceutical production w...
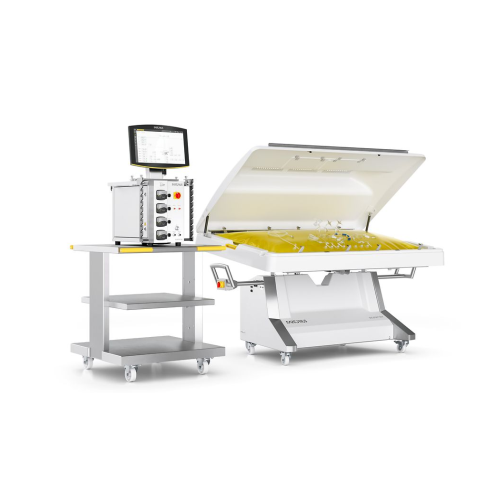
Cell culture bioreactor for mabs and vaccines
Optimize your biopharmaceutical production with advanced cell culture capabi...
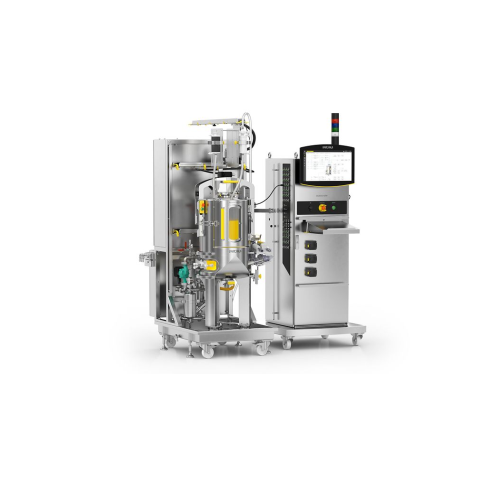
Single-use fermenter for microbial applications
Optimize biopharmaceutical production with a single-use fermenter engineer...
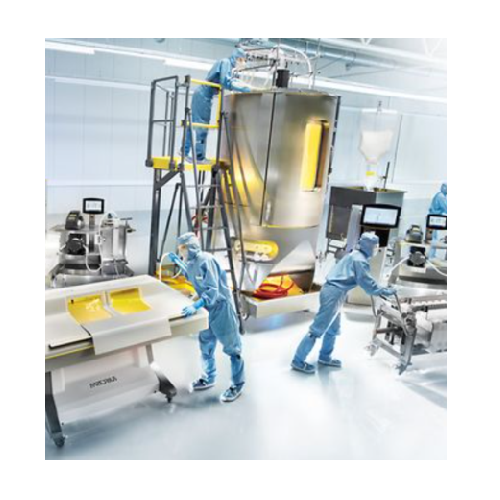
Single-use bioreactors for mammalian cell culture
Enhance agility and cut costs with scalable, single-use bioreactors ide...
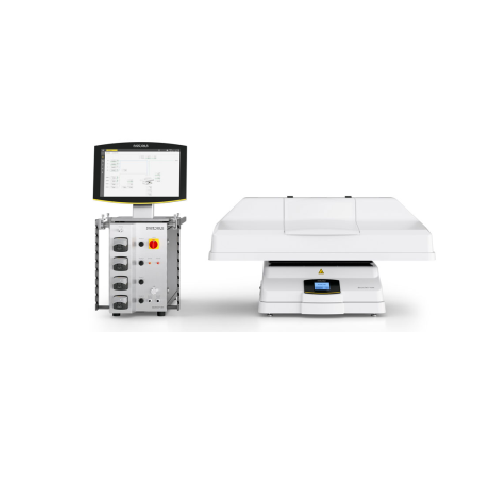
Wave-mixed bioreactor for shear-sensitive cell cultures
Optimize cell cultivation with a modular, wave-induced mixing sys...
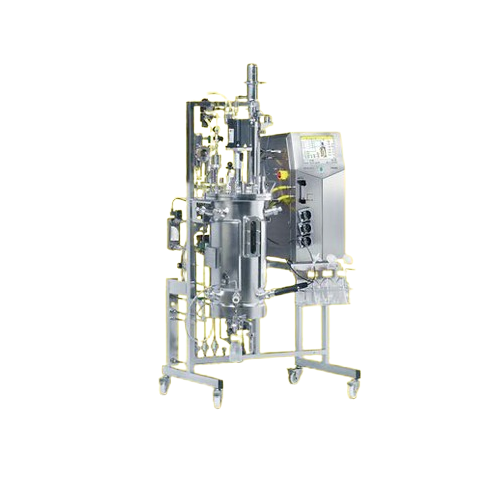
Stainless steel bioreactors
Enhance your bioproduction capabilities with robust solutions designed for efficient fermentatio...
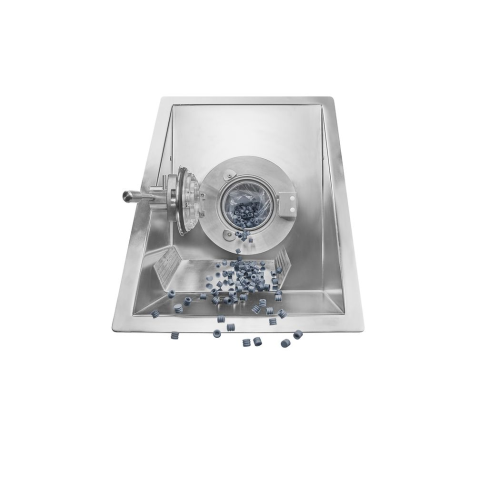
Single-use transfer and filling solutions in barrier isolated filling lines
Ensure sterile, high-volume liquid transfe...
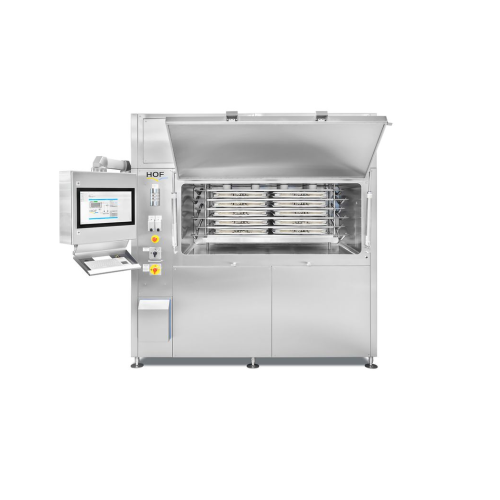
Frozen storage and shipping for biopharmaceuticals
Ensure the integrity of critical biopharmaceuticals with a robust solu...
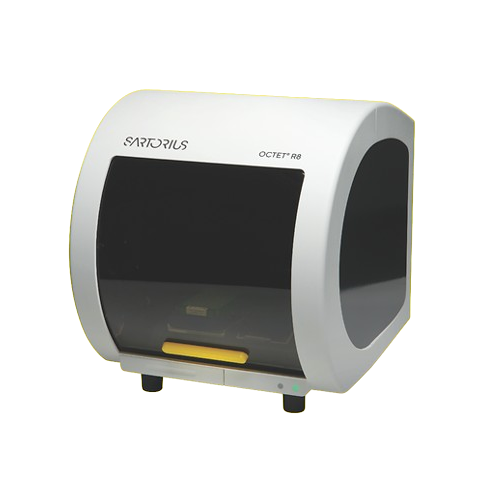
High throughput protein analysis system
Enhance your laboratory’s capability to perform high-throughput kinetic and q...
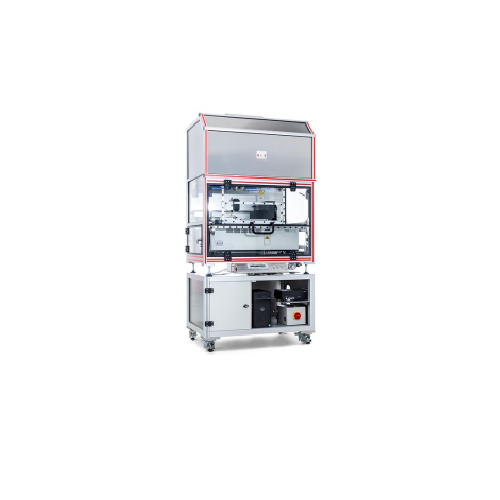
Cell culture hood with Co2 incubator
Achieve precise environmental control for sensitive cell studies with an integrated la...
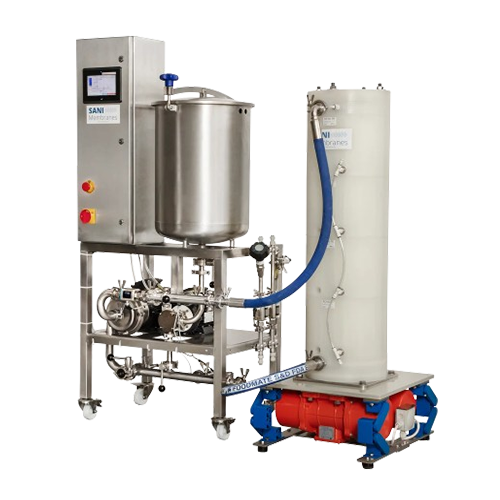
Feed system for pilot-scale microfiltration and ultrafiltration applications
Optimize your small-scale production with...
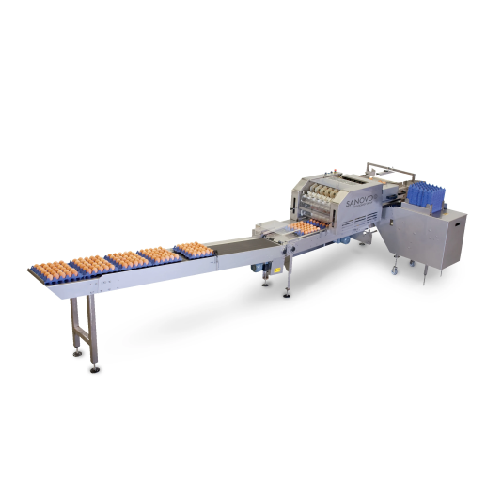
Egg packer for farm operations
Streamline your egg handling process with an efficient solution that ensures gentle, precise ...

Egg tray stacking for small and medium farms
Effortlessly enhance your egg packing operations with a compact tray stacking...
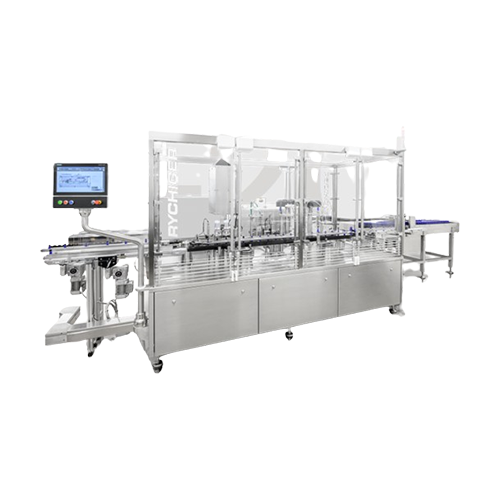
Sterile filling platform for pharmaceuticals
Achieve precise, high-speed aseptic filling and packaging with advanced compl...

Semi-automatic filling solution for syringes and vials in isolators
Achieve precise aseptic fill-finish operations for ...
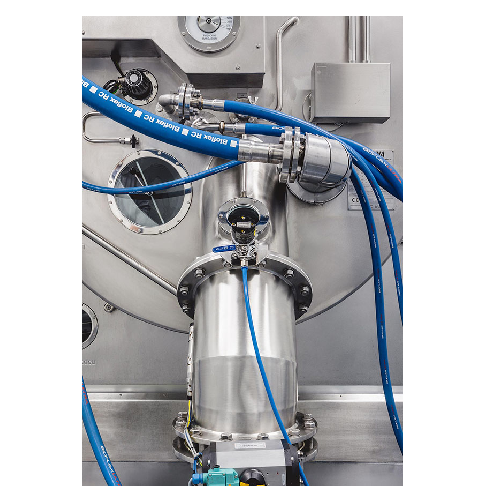
Pharmaceutical horizontal batch centrifuge
Ensure unparalleled product purity and operational efficiency with a centrifuge...
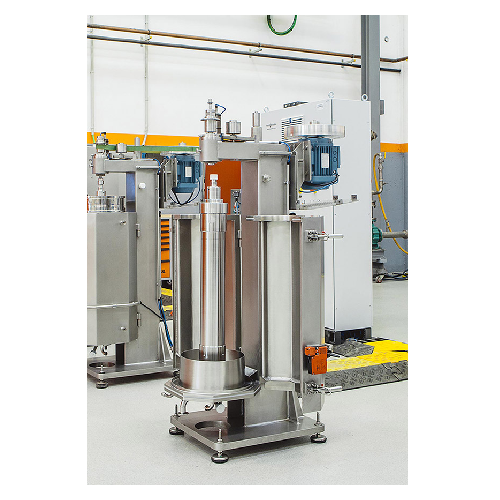
High-speed decanting centrifuges for solid-liquid and liquid-liquid separation
Optimize your separation processes with...
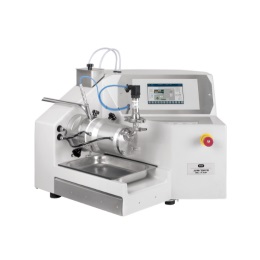
Flexible laboratory bead mill for vaccines
For precise, efficient, and reproducible cell disruption, optimization of proce...
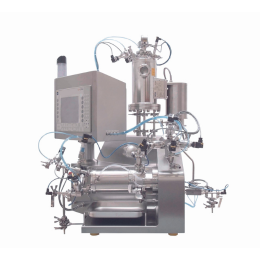
Agitator bead mill for API
To achieve precisely defined API properties and safe and reproducible production, rigorous implem...
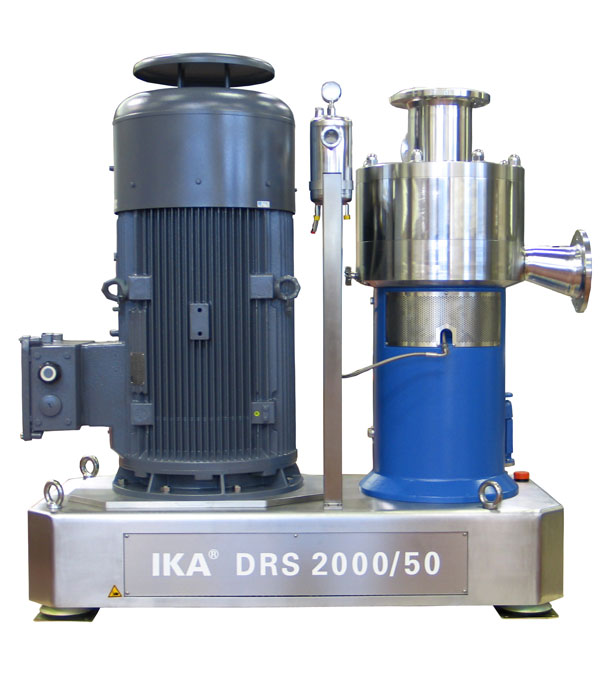
GMP dispersing machine for liquid formulations
Multi-staged rotor/stator mixers generate the high shear forces required to...
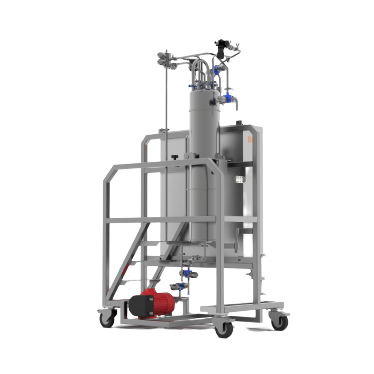
Sterile Filtration System for GMP-grade products
Processing equipment used in industries regulated by GMP must ensure full...
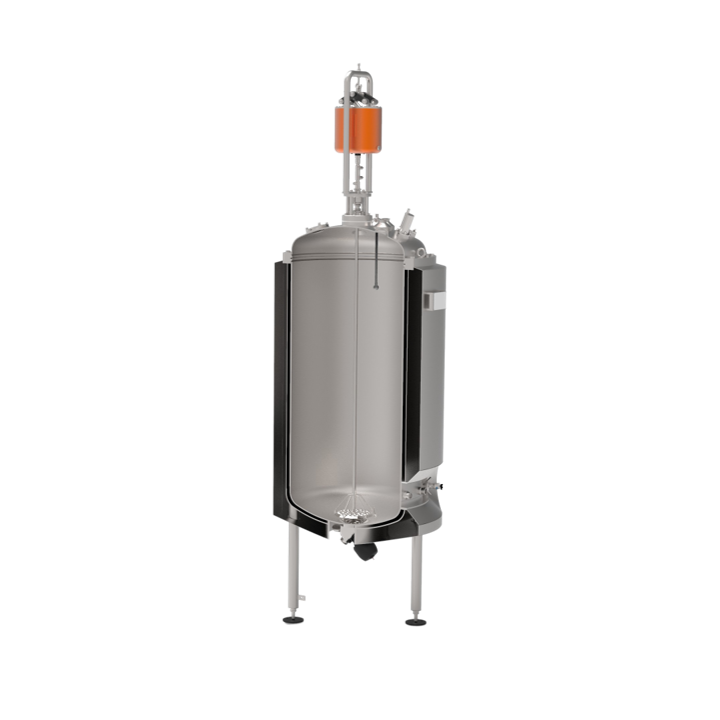
High-frequency vibratory mixer
Mixing liquid products by stirring method generates heat from friction and shear forces. This...
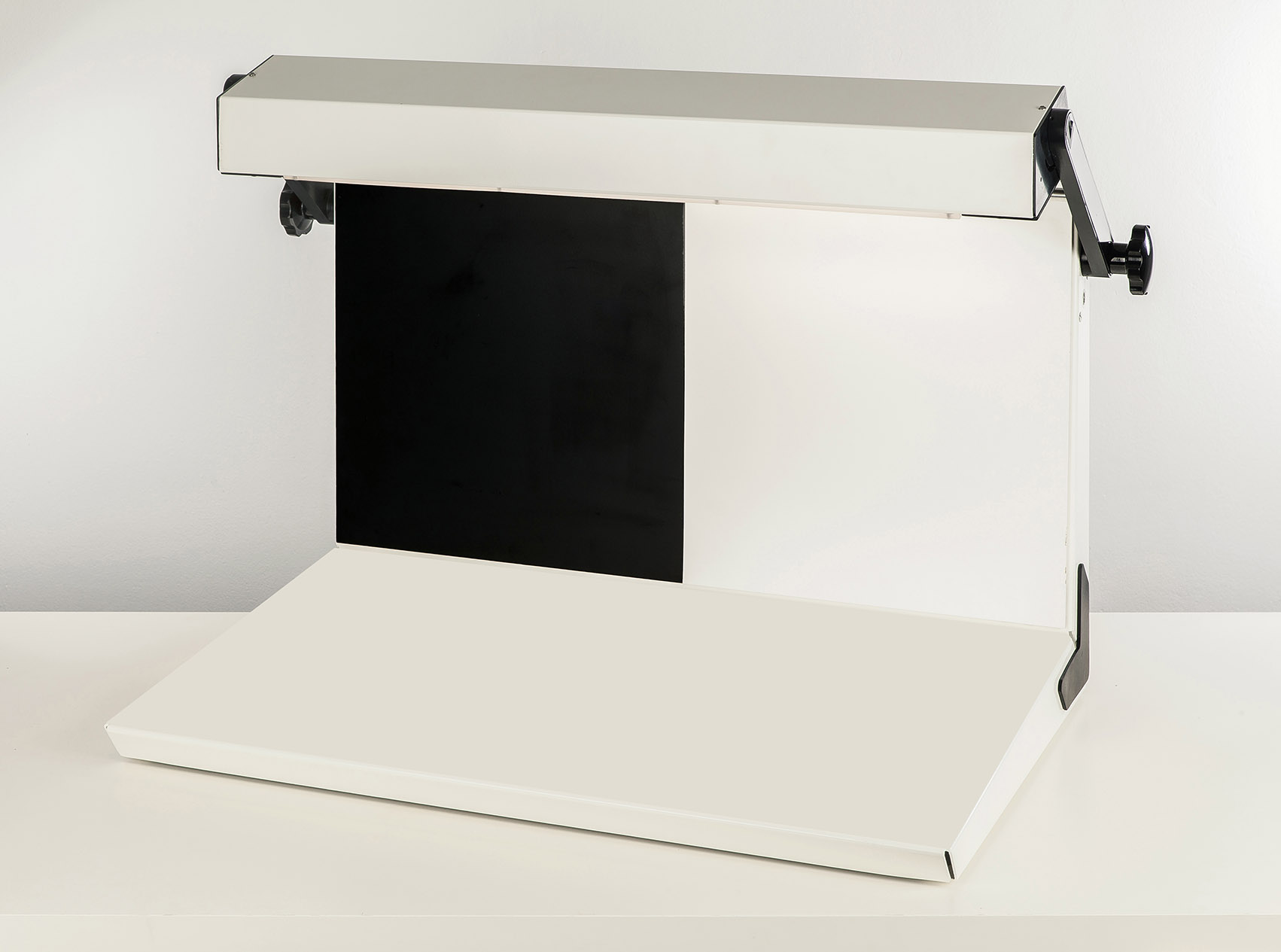
Laboratory liquid viewer for colored glass bottles
In the pharmaceutical industry, an inspection to detect any particulat...
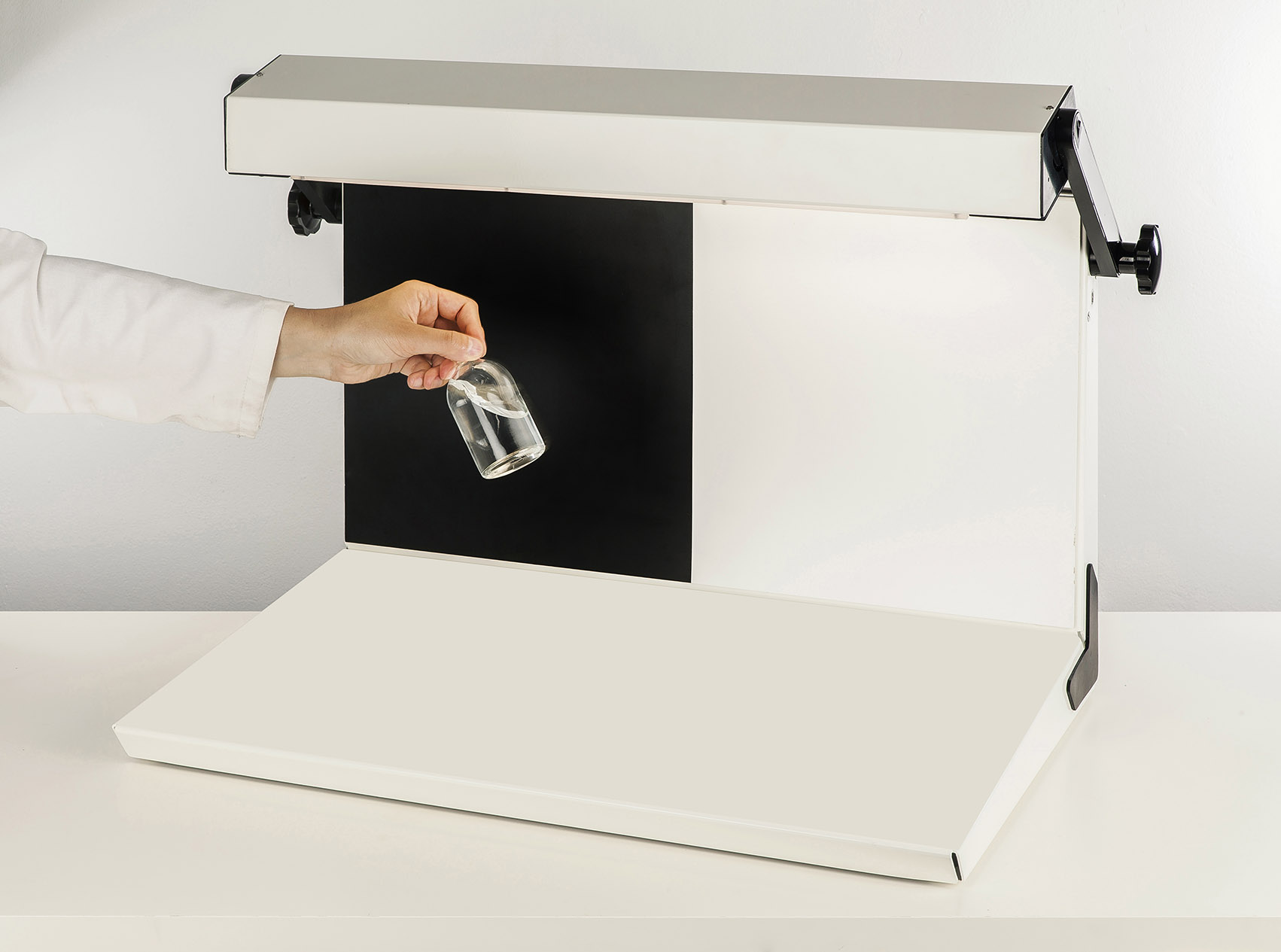
Laboratory liquid viewer for varying light conditions
In the pharmaceutical industry, you must inspect liquids in vials o...
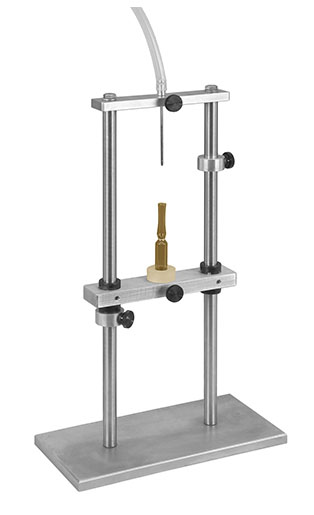
Manual ampoule filler
When you fill ampoules it is essential to avoid wetting the inside walls of the container, as it may af...
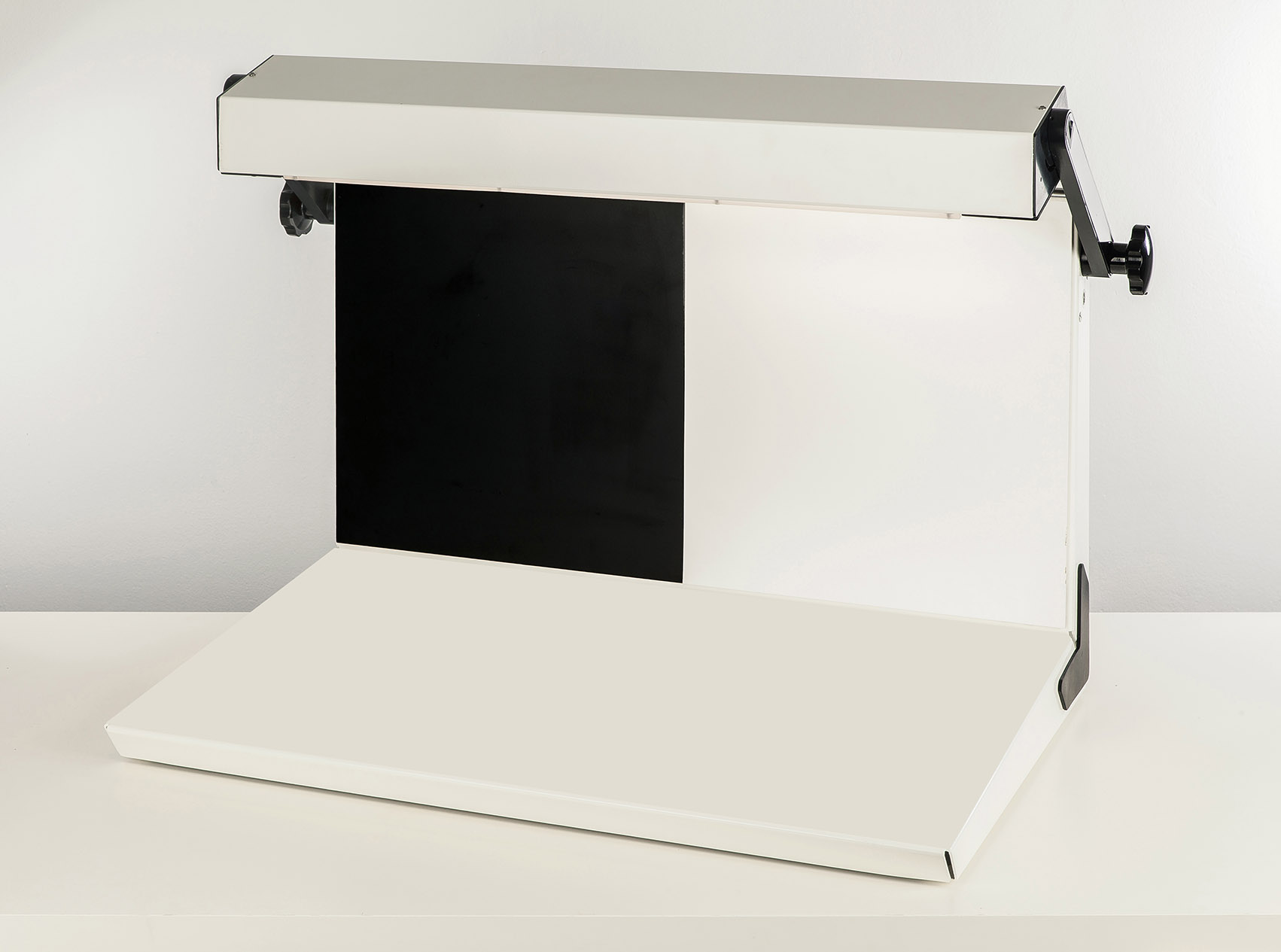
Laboratory liquid viewer for transparent glass bottles
Impurities like hair, fibers, or glass, sourced from the environme...
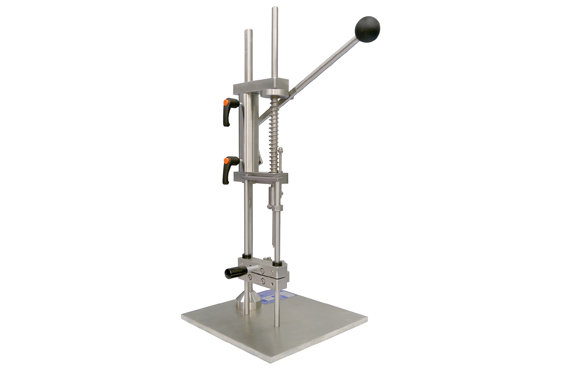
Manual stoppering equipment for pre-filled syringes
Air present in the empty space of pre-filled syringes may prevent you...
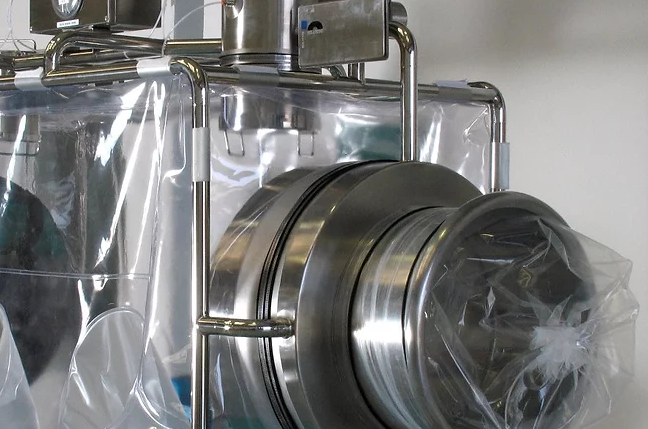
Disposable isolator
Pharmaceutical powders need to be contained in the strictest conditions. But handling powders and cleanin...
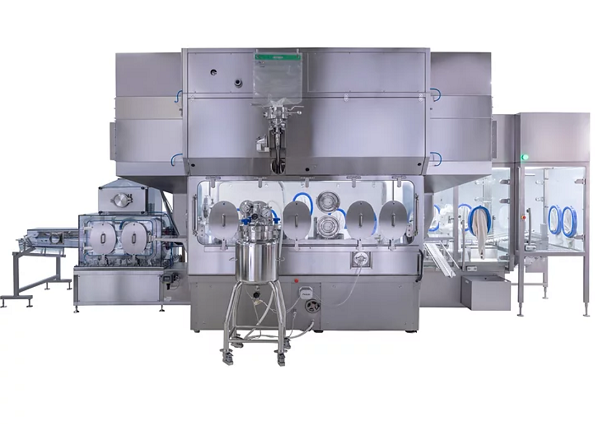
Aseptic filling machine for liquids and powders
Aseptic filling of containers such as vials, syringes, bottles, and cartri...
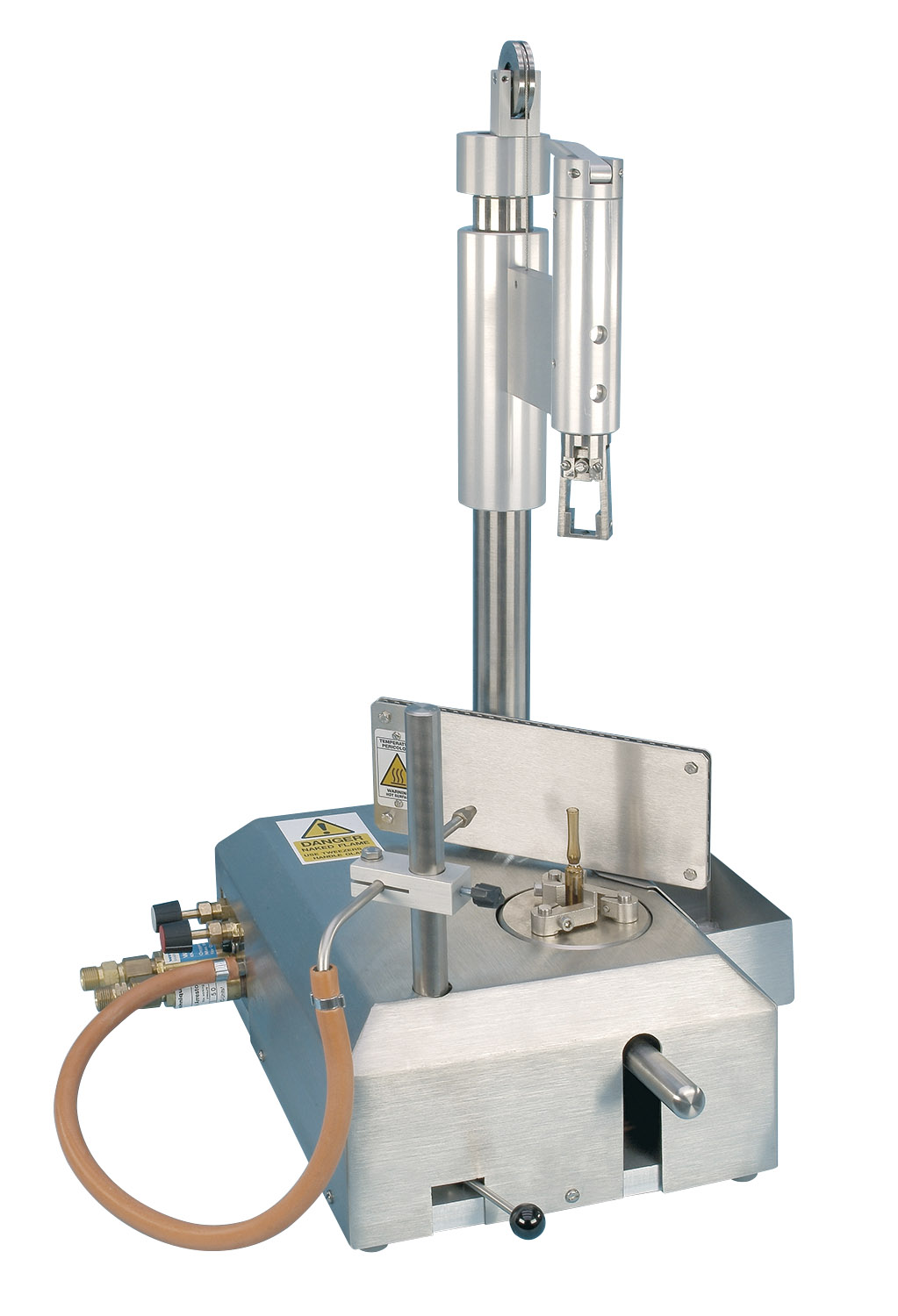
Benchtop ampoule opening and closing equipment
The procedure for opening or closing ampoules requires you to handle gas an...
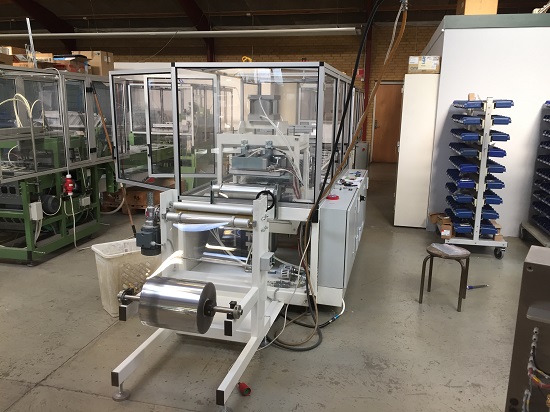
Automatic forming and sealing blister machine for packing syringes
Controlling contamination is on every manufacturer...
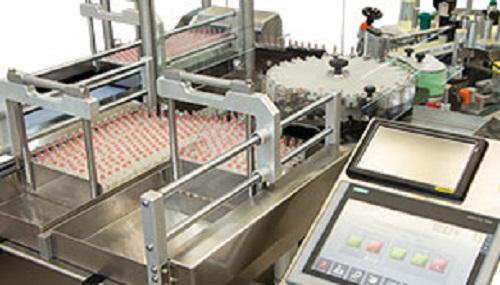
Pharmaceutical rotary labeling machine for vials
Small, cylindrical-shaped glass bottles or vials are mainly used for vacc...
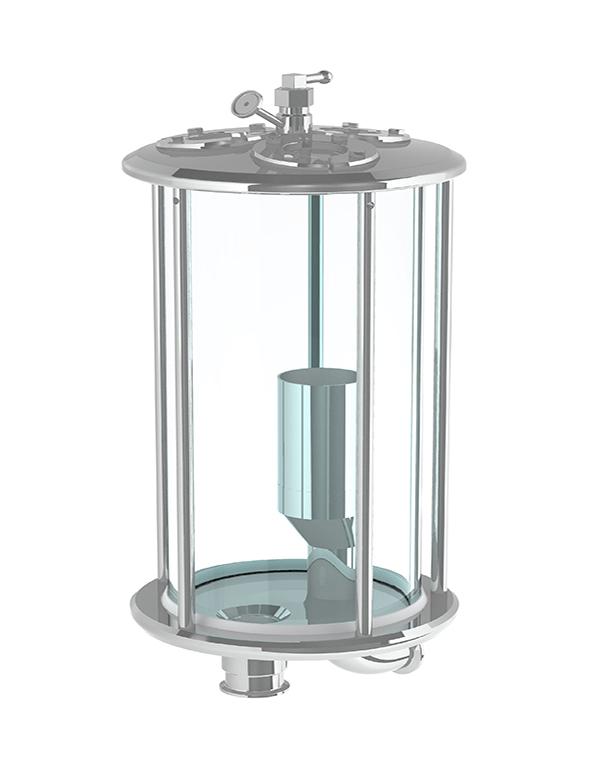
Automated bubble traps for chromatography
Radial flow chromatography processes require special attention and the right use...
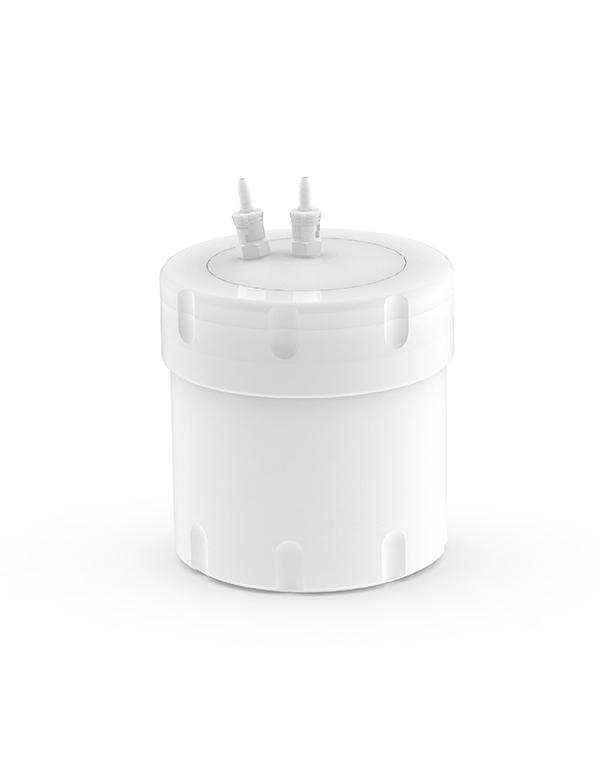
Pre-packed and pre-validated chromatography columns
In chromatography, you must always take into account the apparatus th...
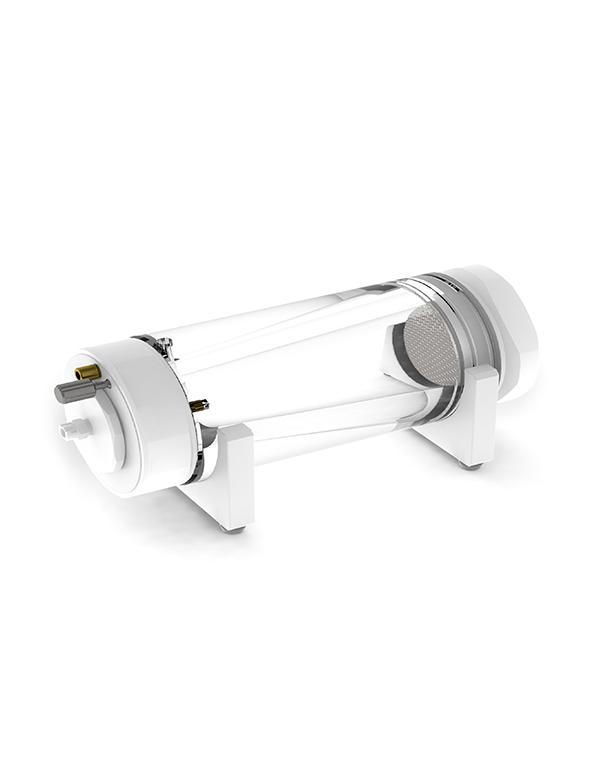
Lab-scale radial chromatography columns for virus validation
In the food industry, as an example, during lab-testing and...

Form fill seal thermoforming machine for medical devices
Form Fill Seal thermoforming machines are those that produce pac...
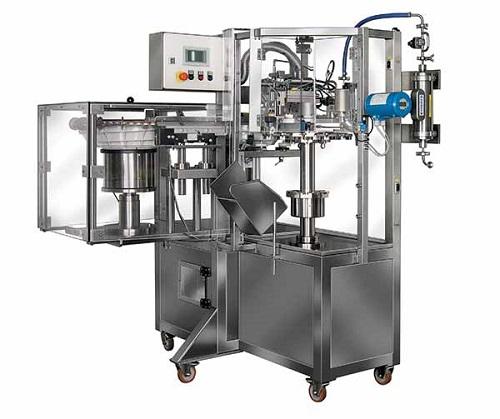
Low speed Filler for large-volume parenterals
Large-volume parenteral bottles are usually manufactured with a resin that c...
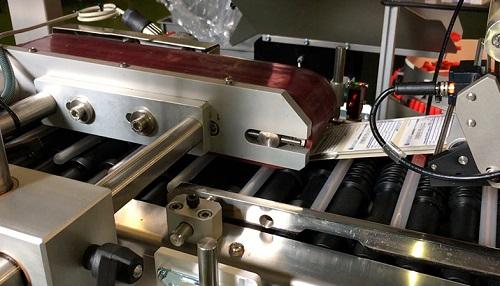
Labeling machine for ampoules
It’s essential for pharmaceutical companies to provide the highest quality ampoules to custome...

Ethylene oxide sterilizer
When medical devices like syringes, catheters, dialysis cartridges, plastic dressings and sutures ...
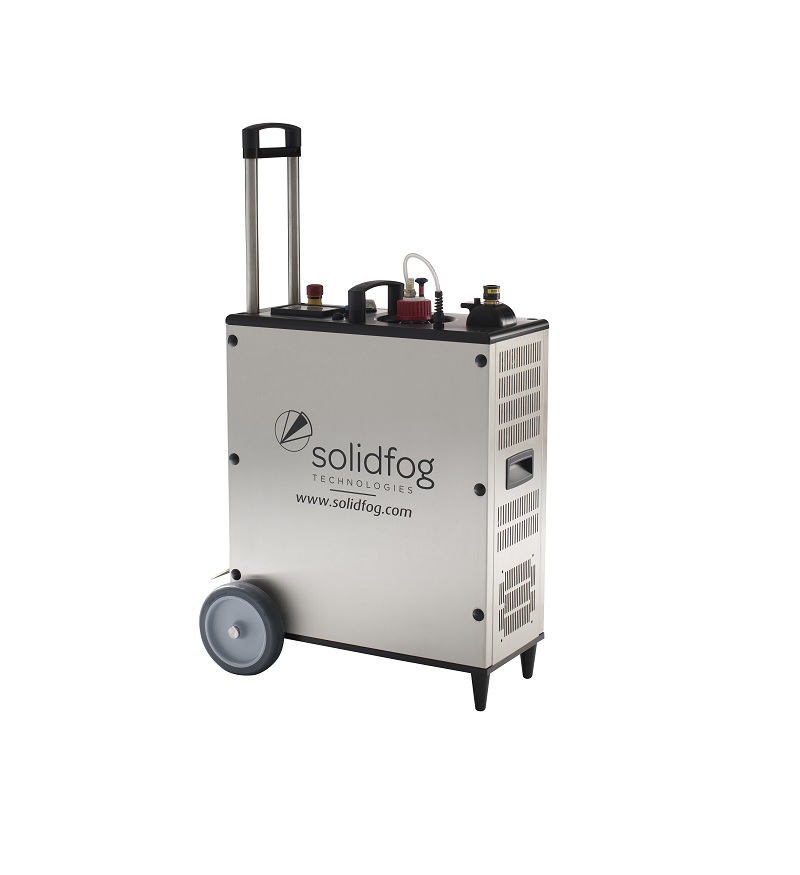
Compact H2O2 disinfection system
Dry fogging provides safe, effective microbiological cleaning of critical areas in biotech,...
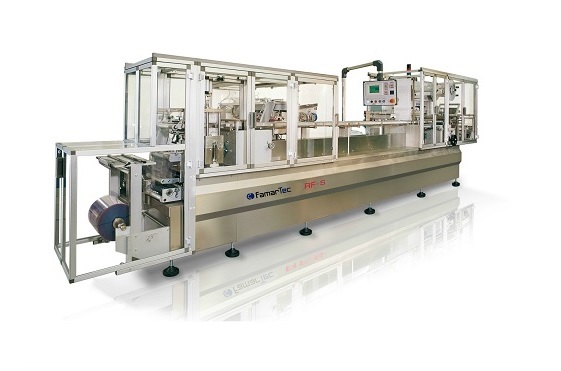
Packaging machine for syringes in trays
Pre-dosed syringes are rapidly becoming the method of choice for the delivery of in...
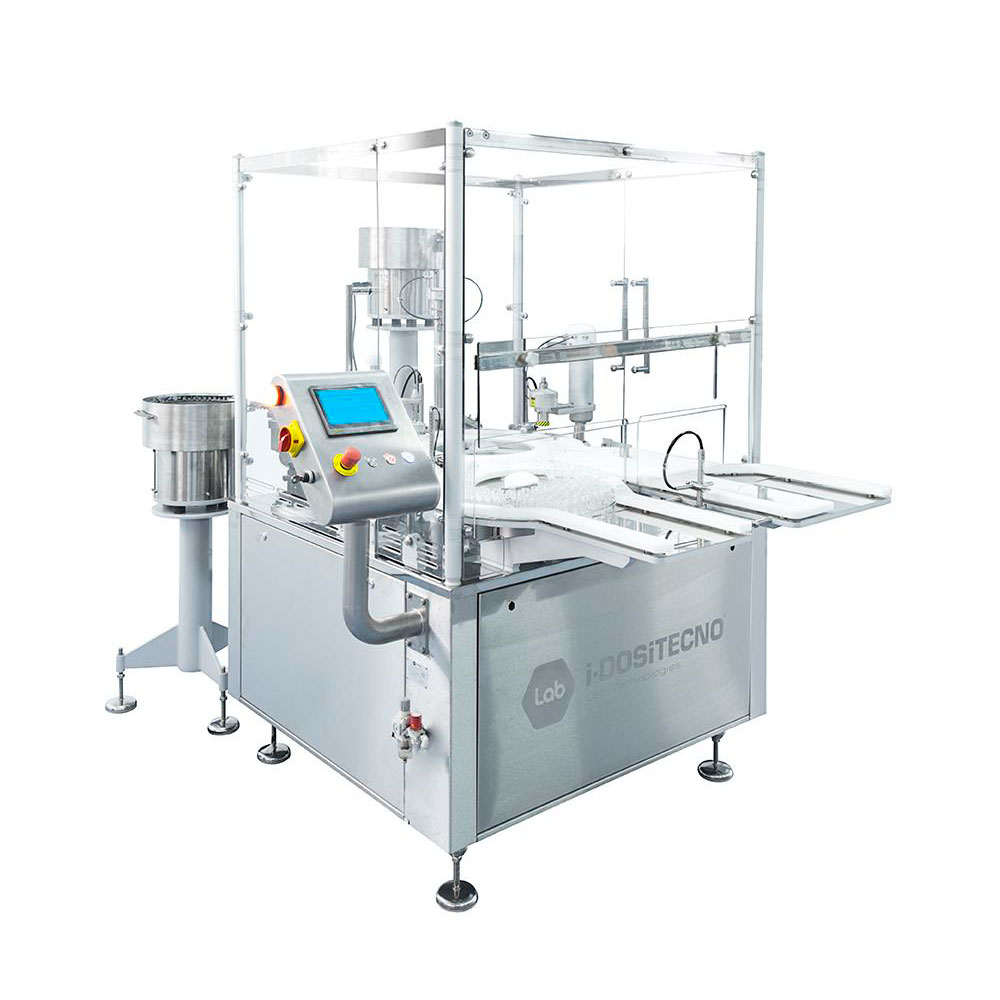
Start-up sterile filling line for injectables
For smaller-scale production of vials and syringes for the injectables marke...
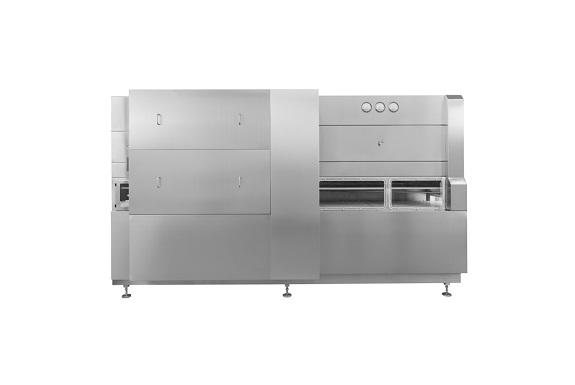
Vial sterilization tunnel
Sterilization of vials, ampoules and syringes before filling is a vital step in the production of ...
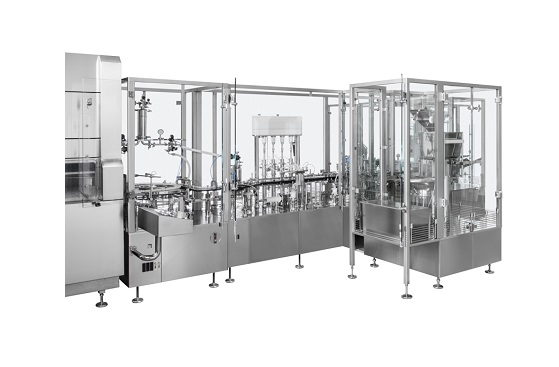
Vial filling machine
The volume filling of vials, cartridges and syringes is a vital part of the production of a wide range o...
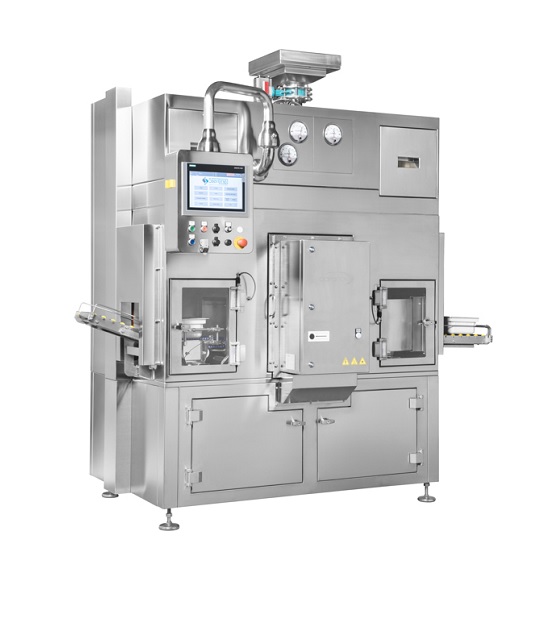
Syringe tub sterilizer
A common challenge is how to transfer nested syringe tubs to the aseptic filling area without compromi...
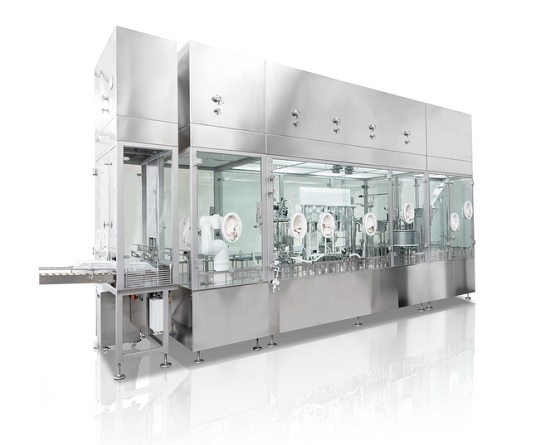
Nested syringe filling machine
Increasingly, pre-sterilized Ready To Use (RTU) nested vials, cartridges and syringes are the...
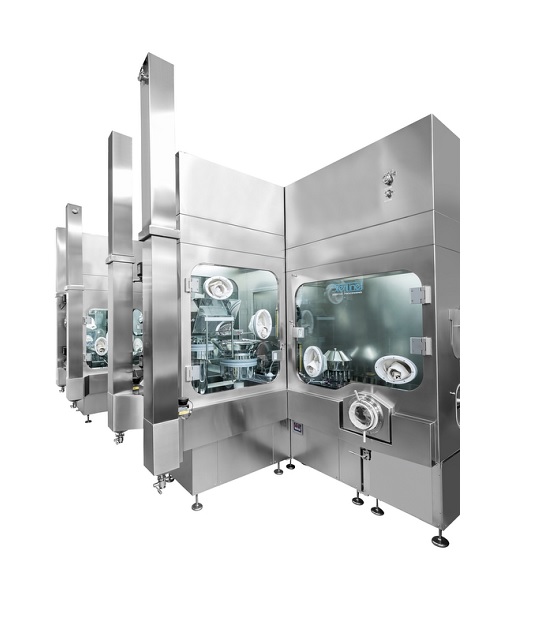
Closed restricted access barrier system
Pharmaceutical production techniques often require isolation of compounds and chemi...
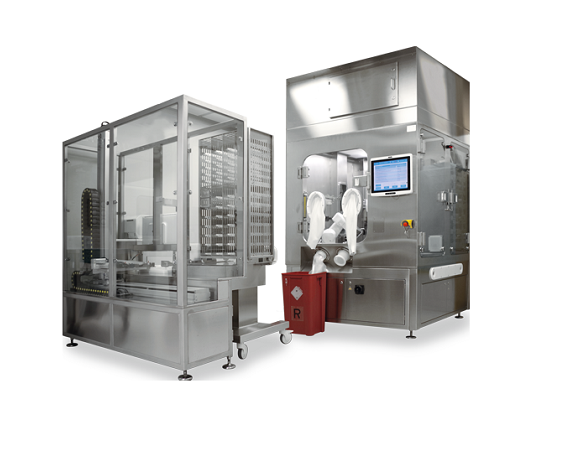
Sterile compounding system
Hospitals and compounding centres have traditionally used manual aseptic compounding processes. A...
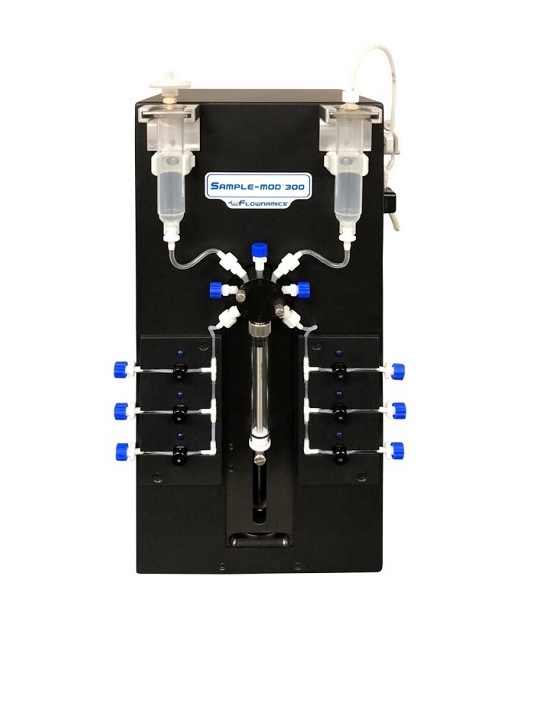
Distributor of samples to different devices
The ability to expand your automatic sampling solution provides increased flex...
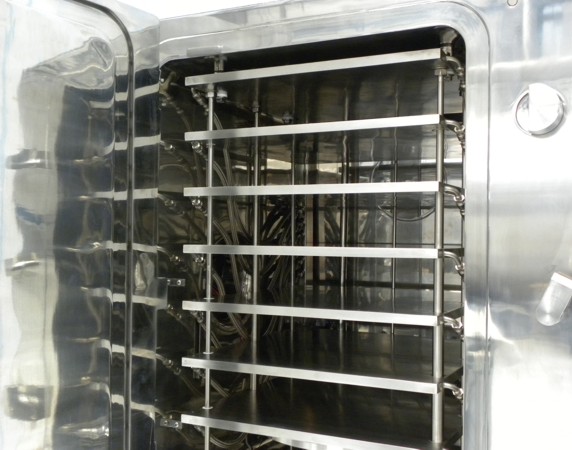
GMP laboratory freeze dryer
Freeze dryer designed for aseptic and small-scale production of high-value products.
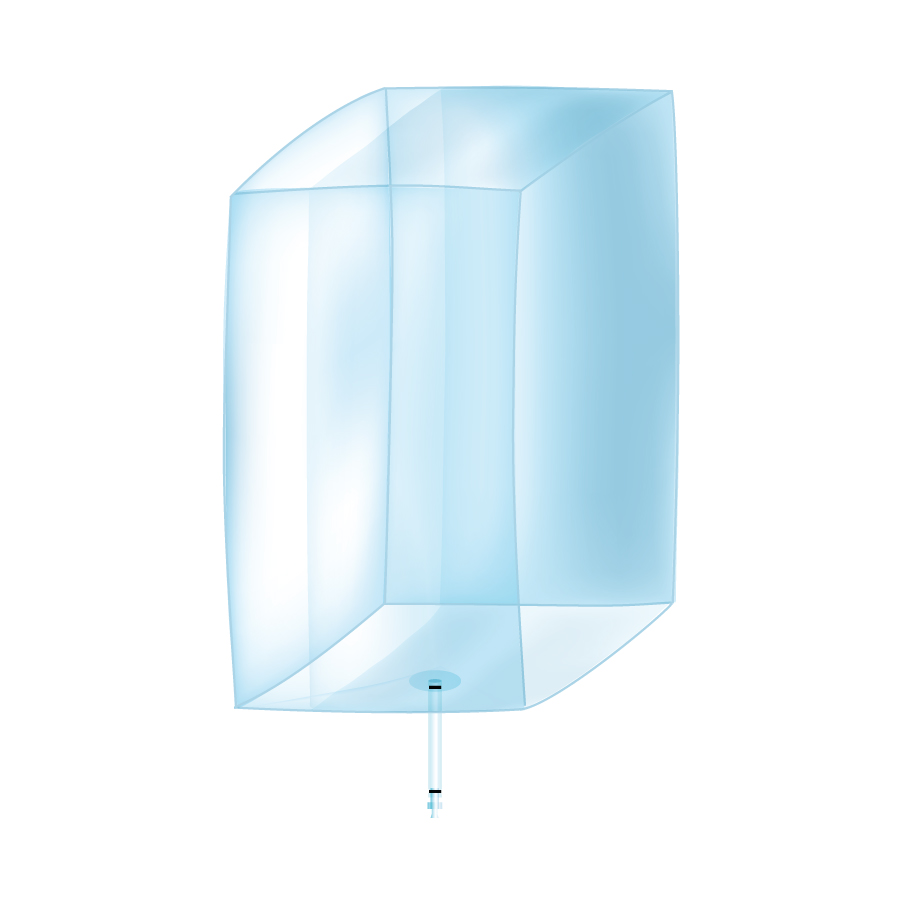
Disposable tank liners
Manufacturers in the bioprocessing industries are increasingly turning to single use solutions for the...
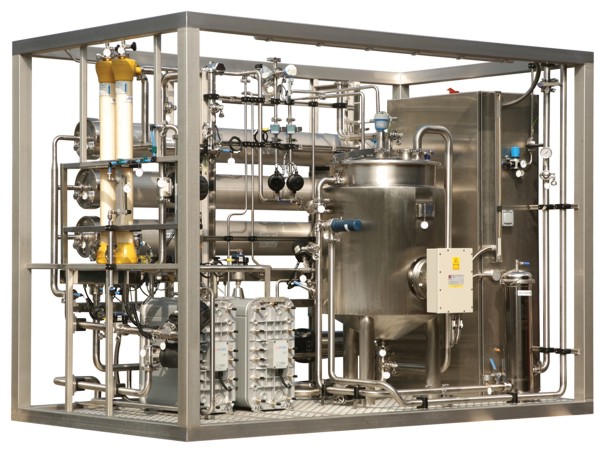
Purified water systems
Highly Purified water is used in the preparation of medicinal products where bacterial endotoxins need...

Flexible automatic inspection machine for syringes
Manufacture of pre-filled syringes requires the highest quality inspec...
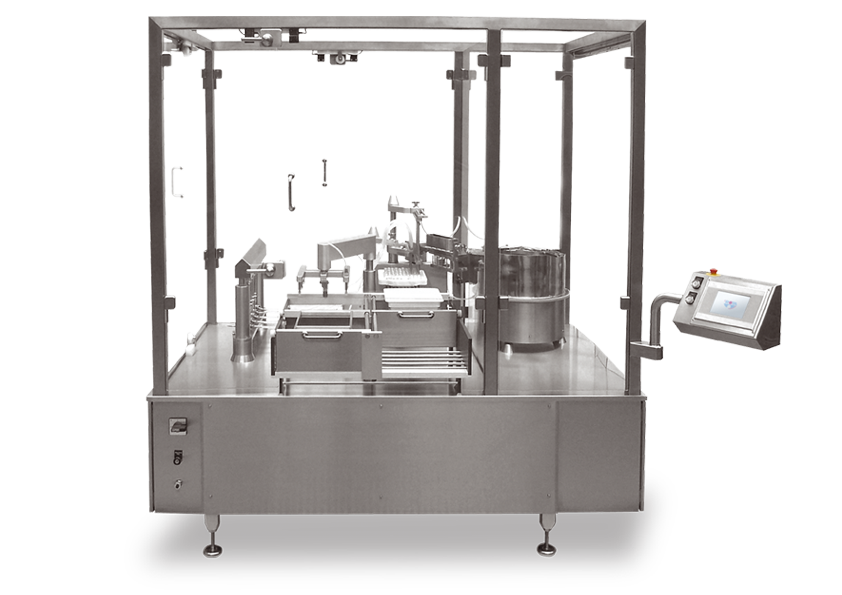
Filling and closing machine for parenterals
Any pre-filled syringe can be filled and closed with this fast and easy machin...
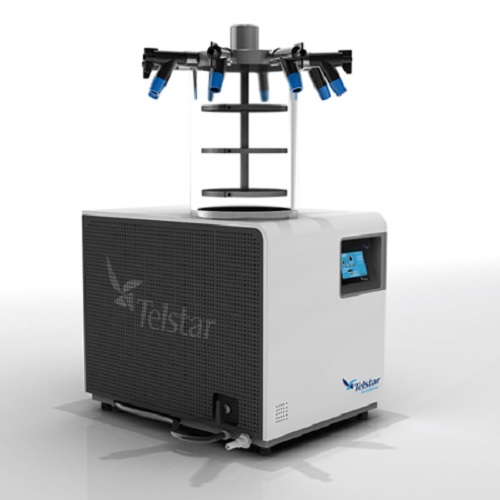
Multipurpose and R&D freeze dryer
A multipurpose unit in the research and development field. Some of the most common applic...
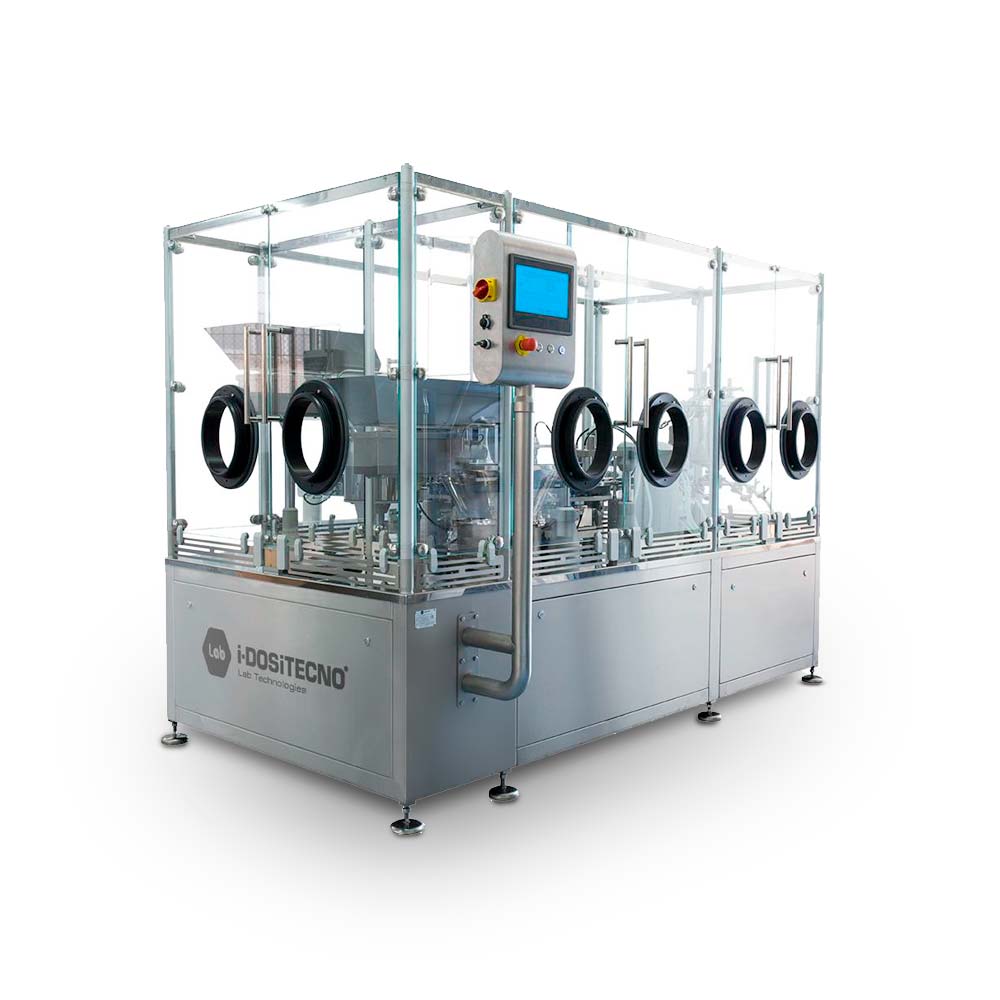
Sterile filling line for injectables
Sterile filling of liquids and powders for the pharmaceutical and cosmetic industries ...
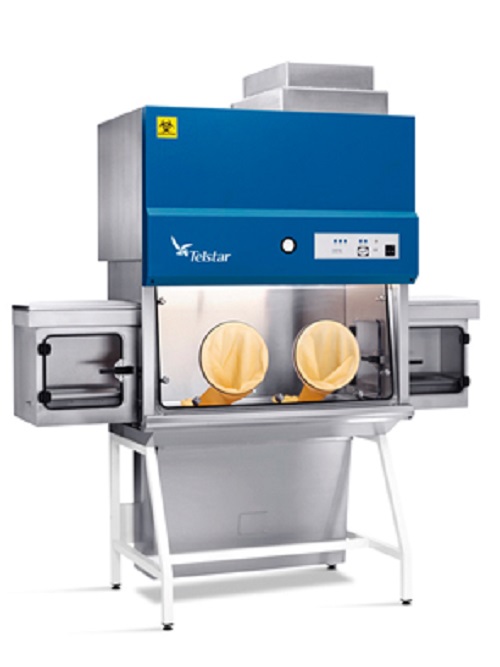
Negative pressure isolator
Used for products biologically hazardous, that also require minimized cross contamination.
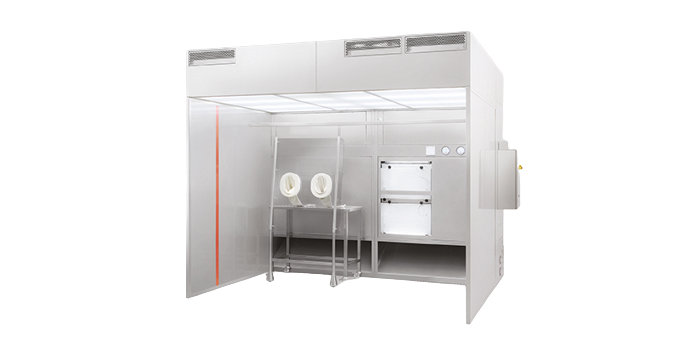
Downflow booth
Provides the highest levels of operator protection from potentially harmful airborne contaminants generated dur...
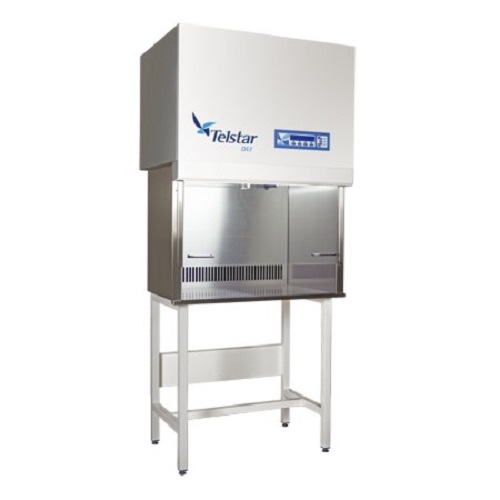
Vertical laminar flow cabinet
HEPA filtered vertical laminar airflow (down flow) creates an ISO 14644-1 (Class 5) work area ...
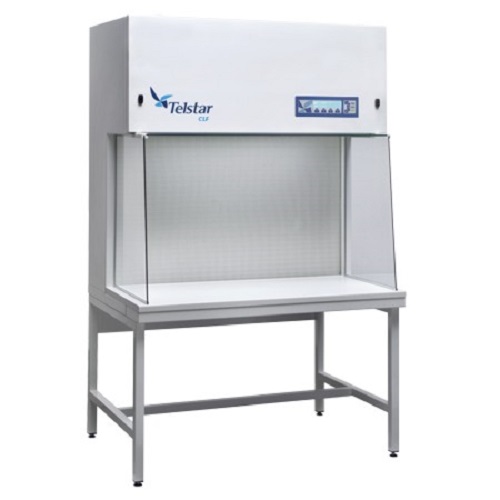
Horizontal laminar flow benches
HEPA filtered horizontal laminar airflow (crossflow) creates an ISO 14644-1 (Class 5) work a...
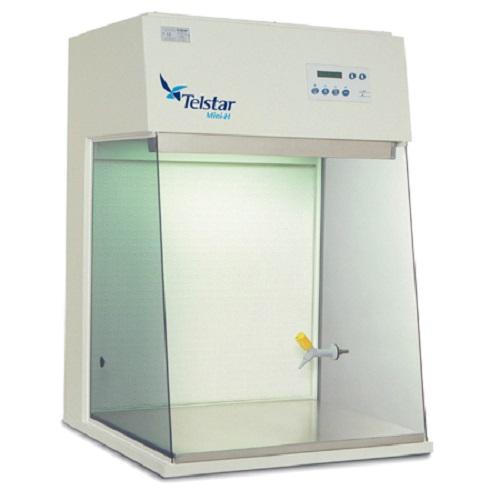
Compact horizontal laminar flow bench
HEPA filtered horizontal laminar airflow (cross-flow) creates an optimized free space...
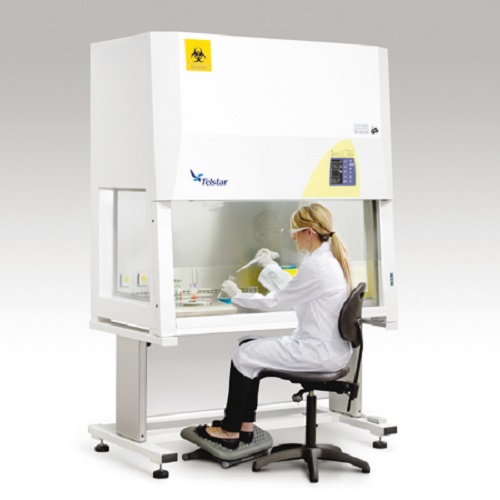
Microbiological safety cabinet class II
This handy device offers the most advanced features in product-operator protection ...
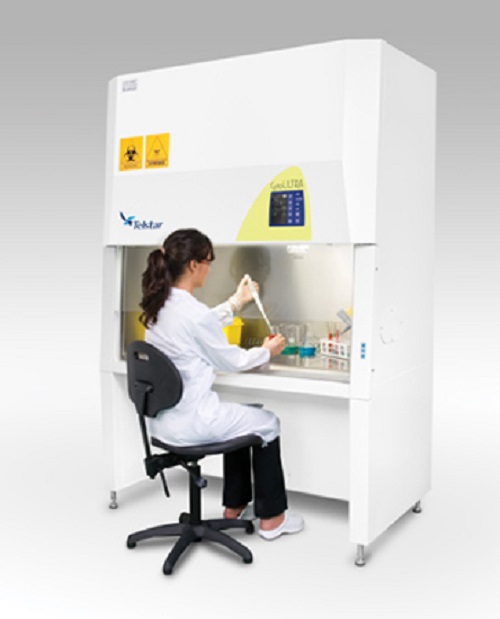
Biosafety cabinet class II for cytotoxic medicines
For the manipulation of hazardous substances utilized during the prepa...
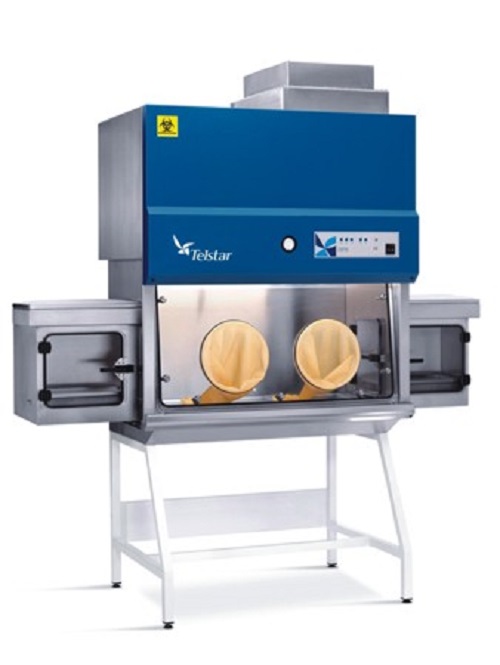
Positive pressure isolator
Ideal for products which have no biological risk but require high sterile conditions.
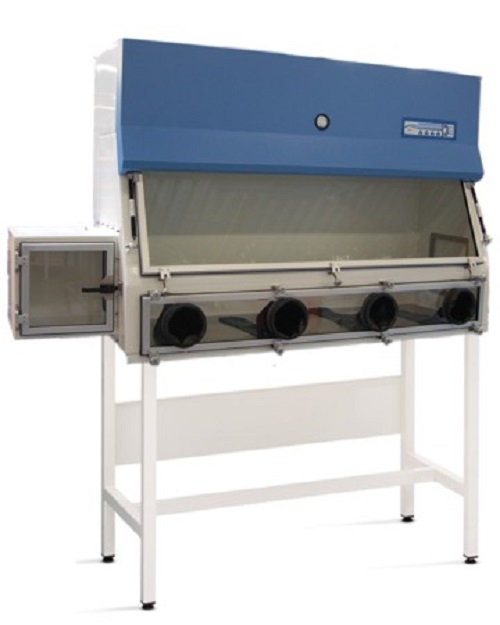
Biological safety cabinet class III
Specially designed for the handling of microbiological agents, when working with indige...
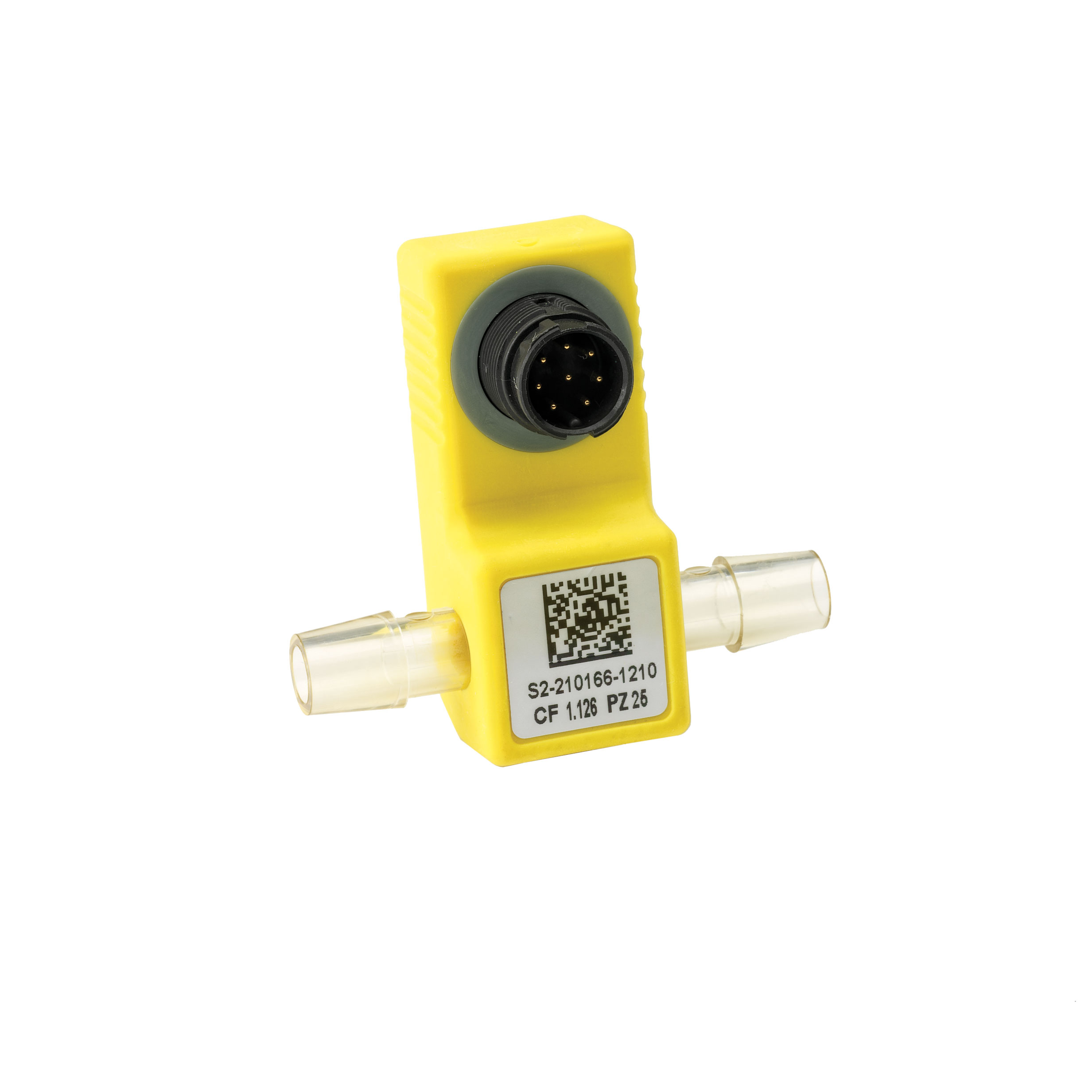
Single-use pressure sensor
Biopharmaceutical manufacturers are increasingly making use of Single-use pressure sensors to enh...
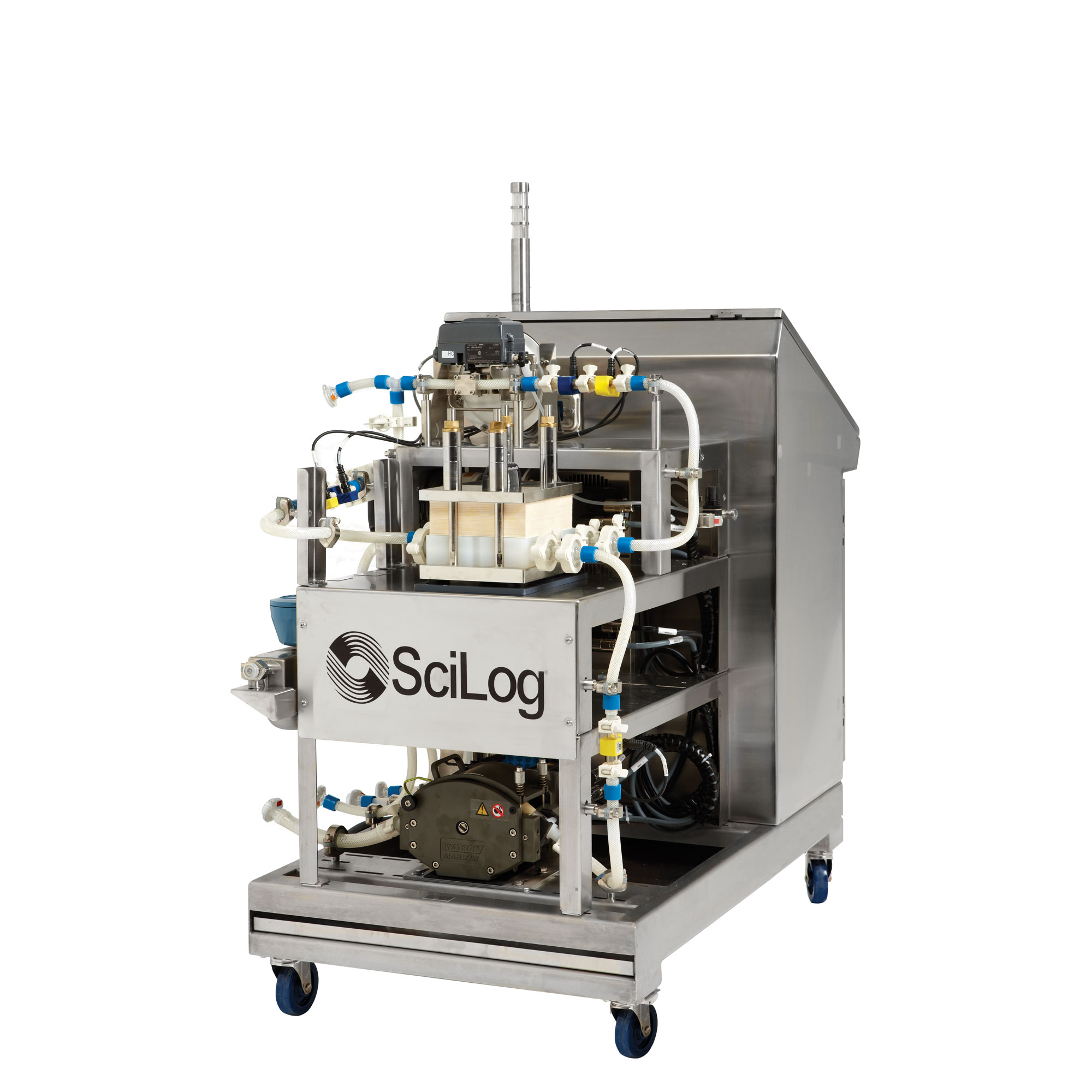
Automated single use tangential flow filtration system
Tangential Flow Filtration is an essential to the biopharmaceutica...
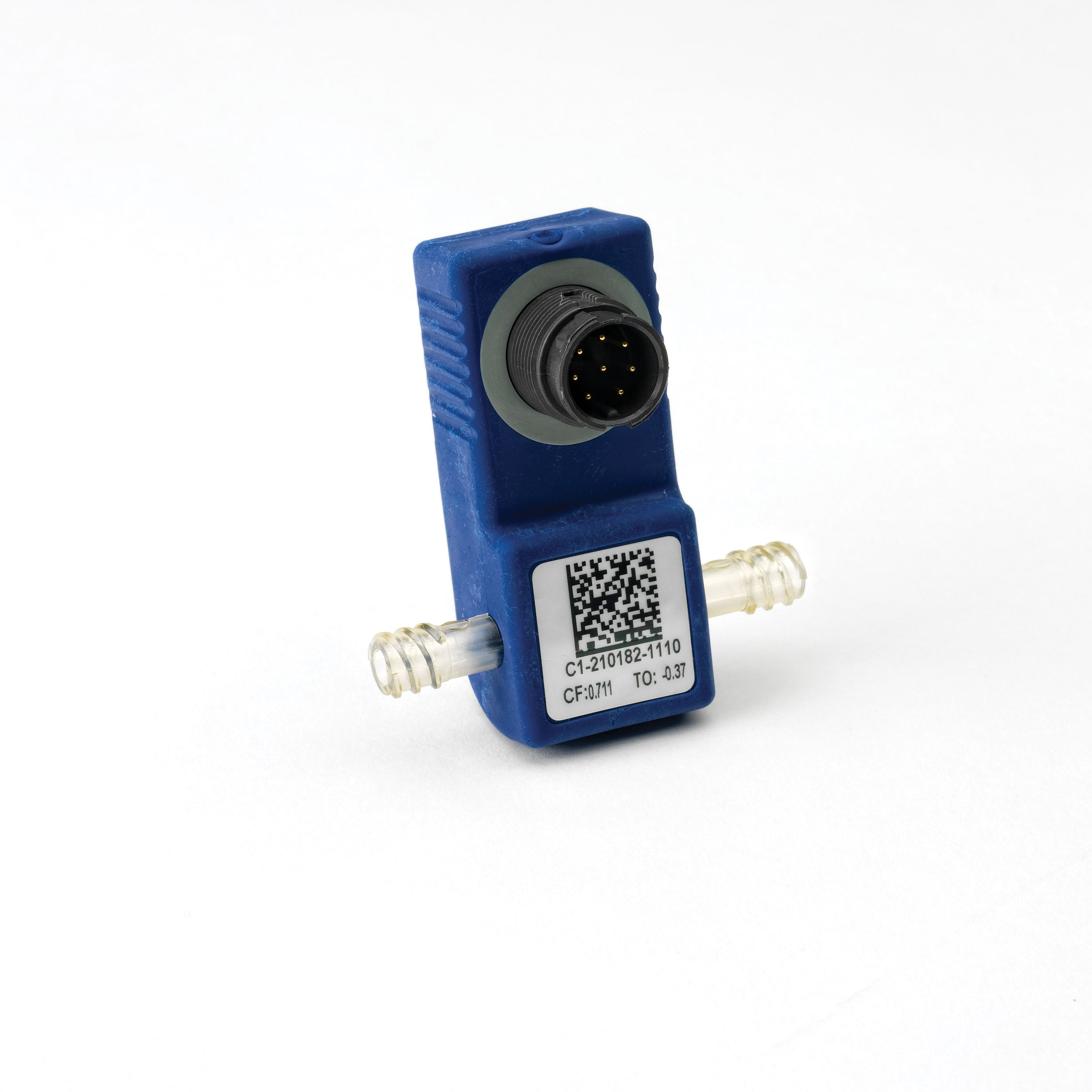
Single-use conductivity sensor
Biopharmaceutical manufacturers are increasingly making use of single-use conductivity sensor...

Single-use temperature sensor
Biopharmaceutical manufacturers are increasingly making use of single-use temperature sensors ...
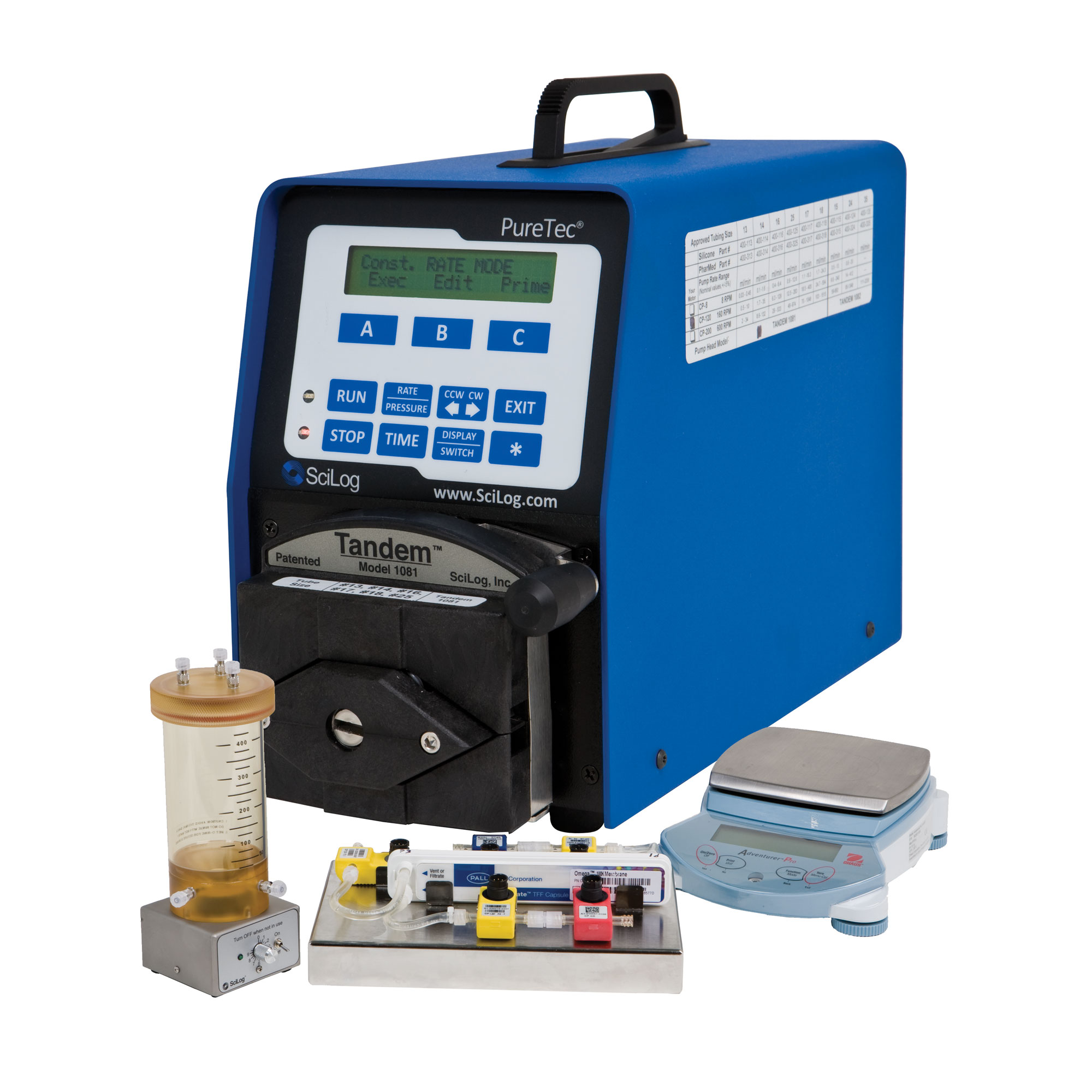
Lab scale tangential flow filtration system
Tangential Flow Filtration is an essential to the biopharmaceutical processing...
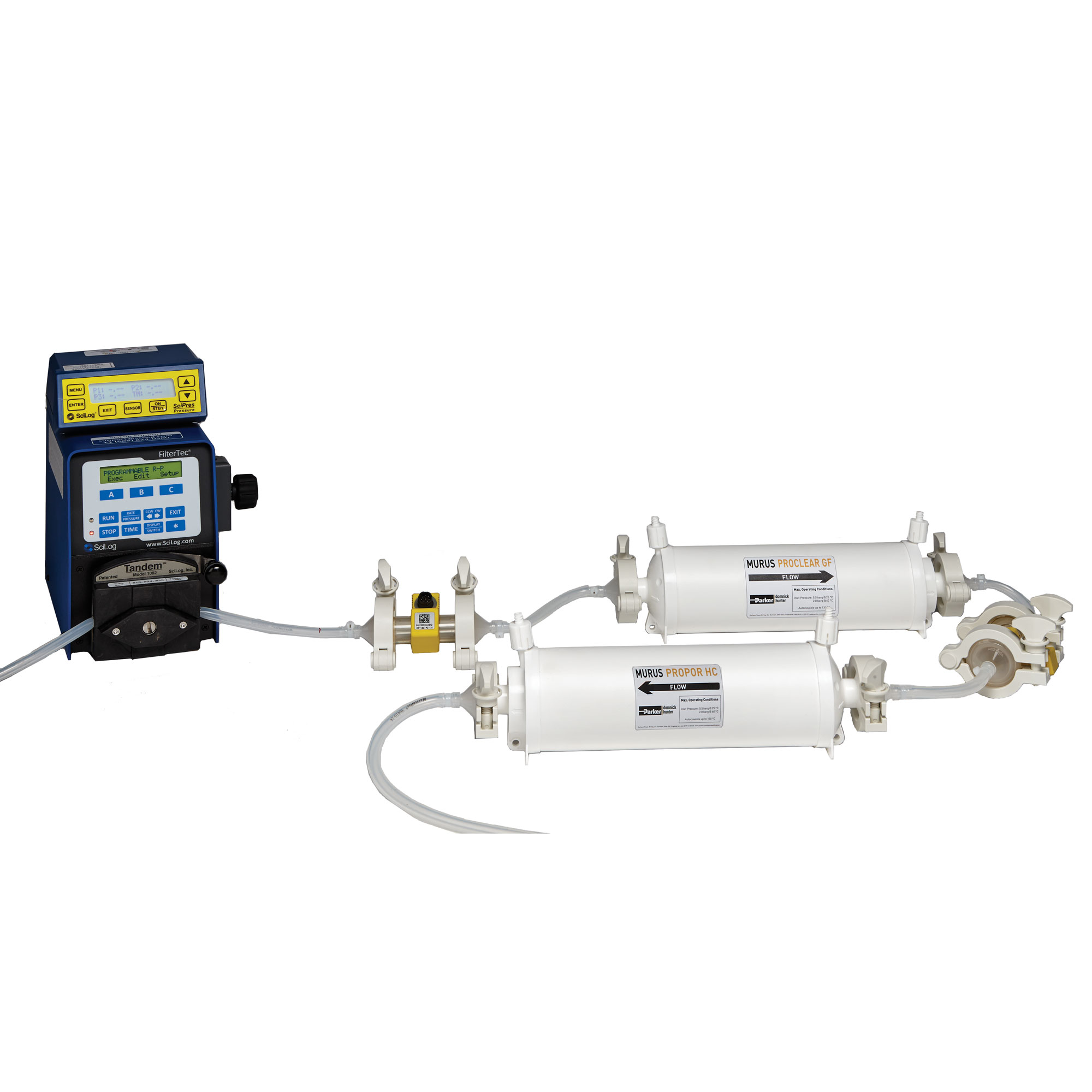
Automated cell culture clarification system
Efficient harvest from the bioreactor is essential to any successful cell cult...
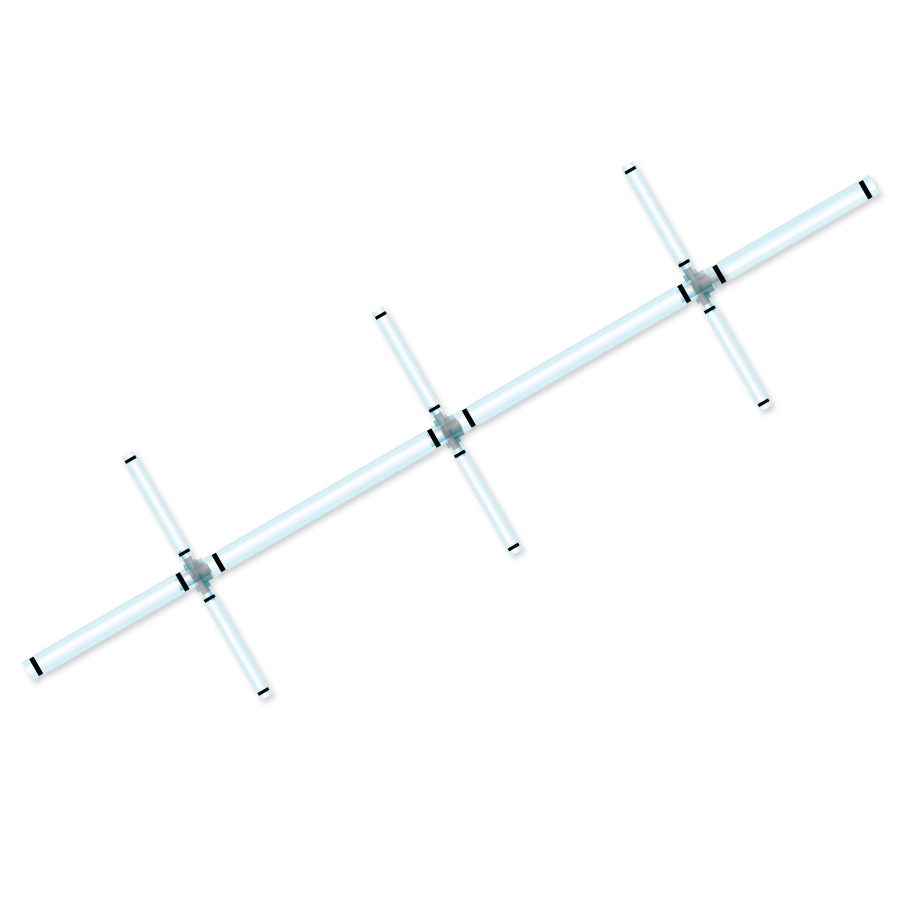
Disposable tubing for manifolds in bioprocesses
Manufacturers in the bioprocessing industries are increasingly turning to ...
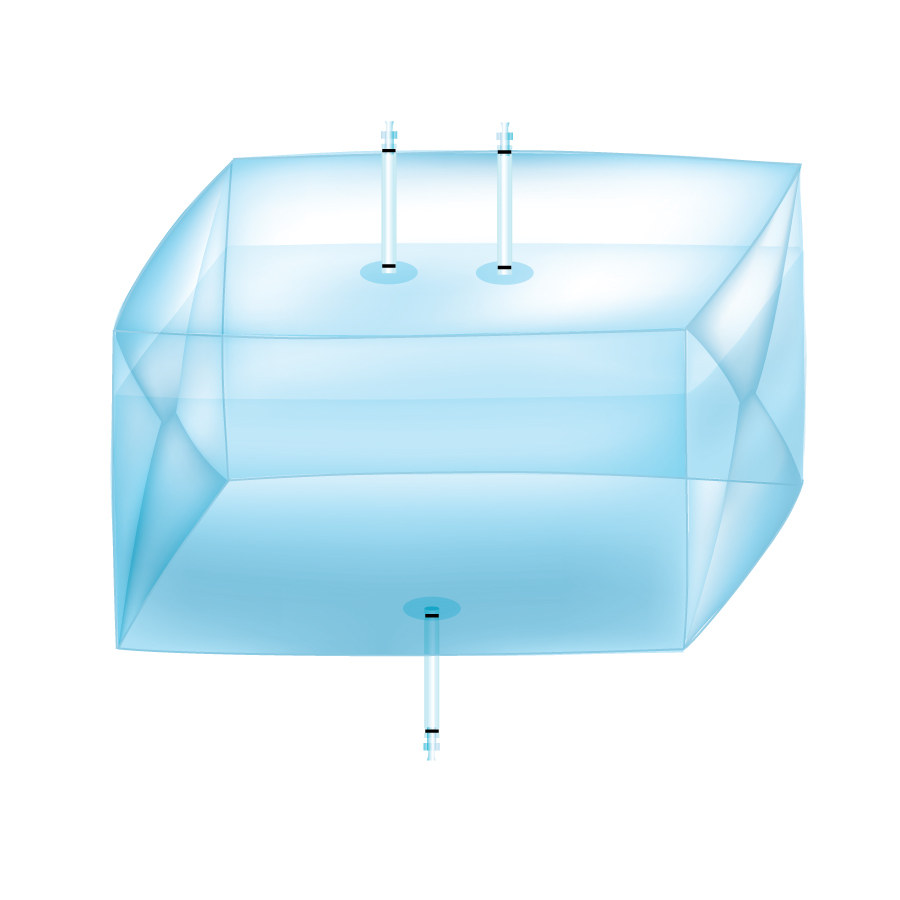
3D disposable bags for bioprocesses
Manufacturers in the bioprocessing industries are increasingly turning to single-use so...
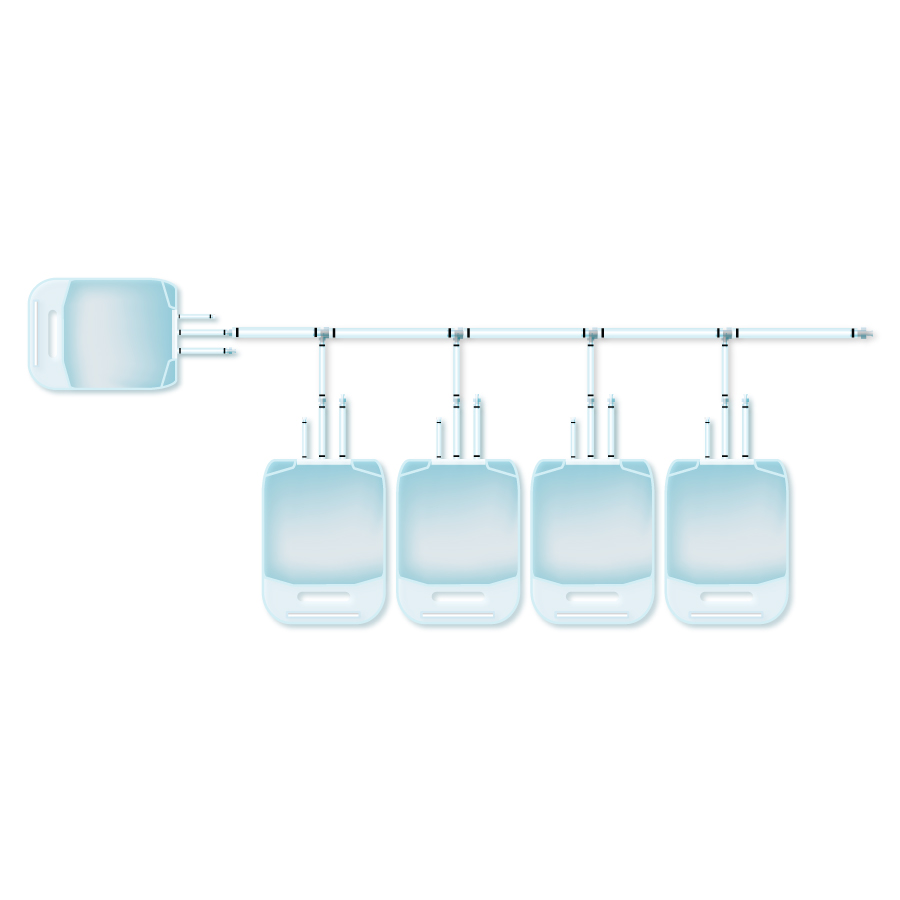
Disposable manifold bags for bioprocesses
Manufacturers in the bioprocessing industries are increasingly turning to dispos...
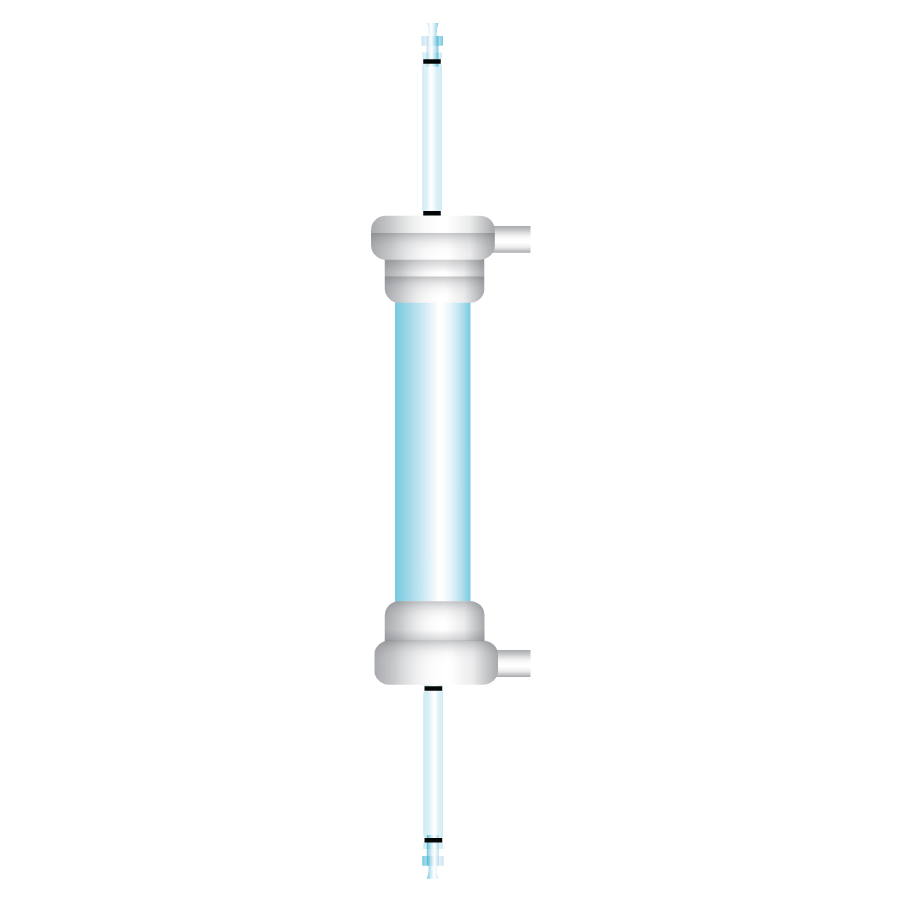
Normal flow filtration sets for bioprocesses
Bio-processors require reliable, high quality, easy to maintain, filtration e...
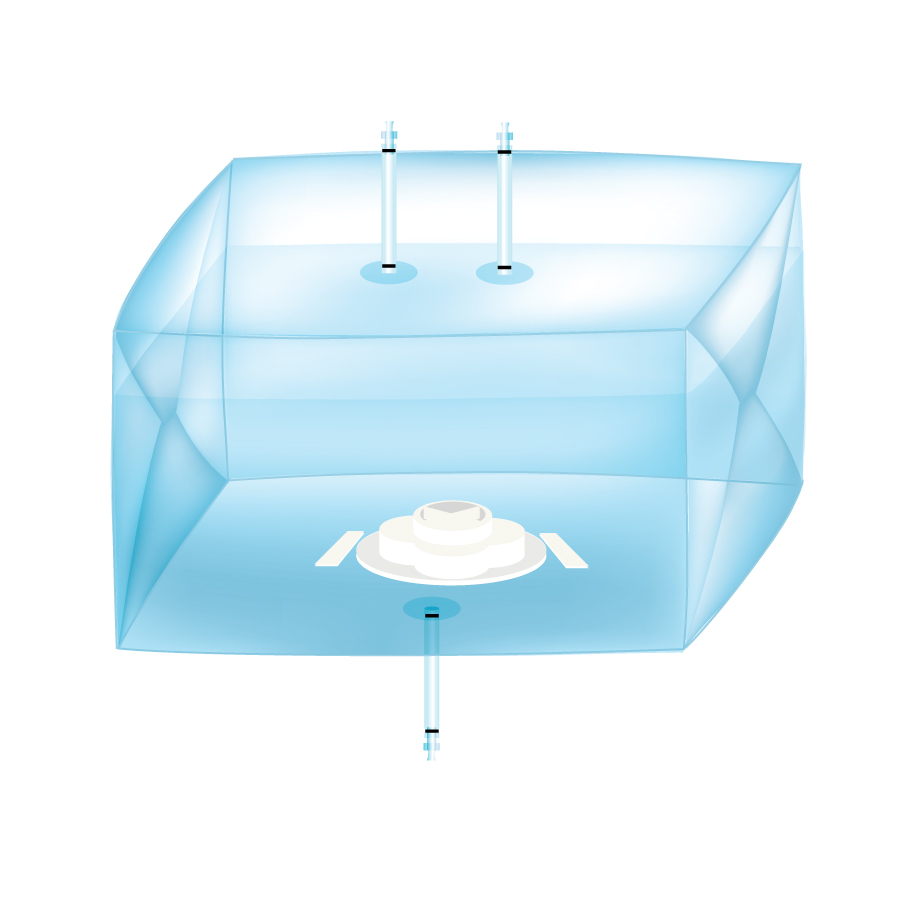
Disposable mixer bags for bioprocesses
Bioprocessors must use ingredients of known high quality and consistency. Inconsist...
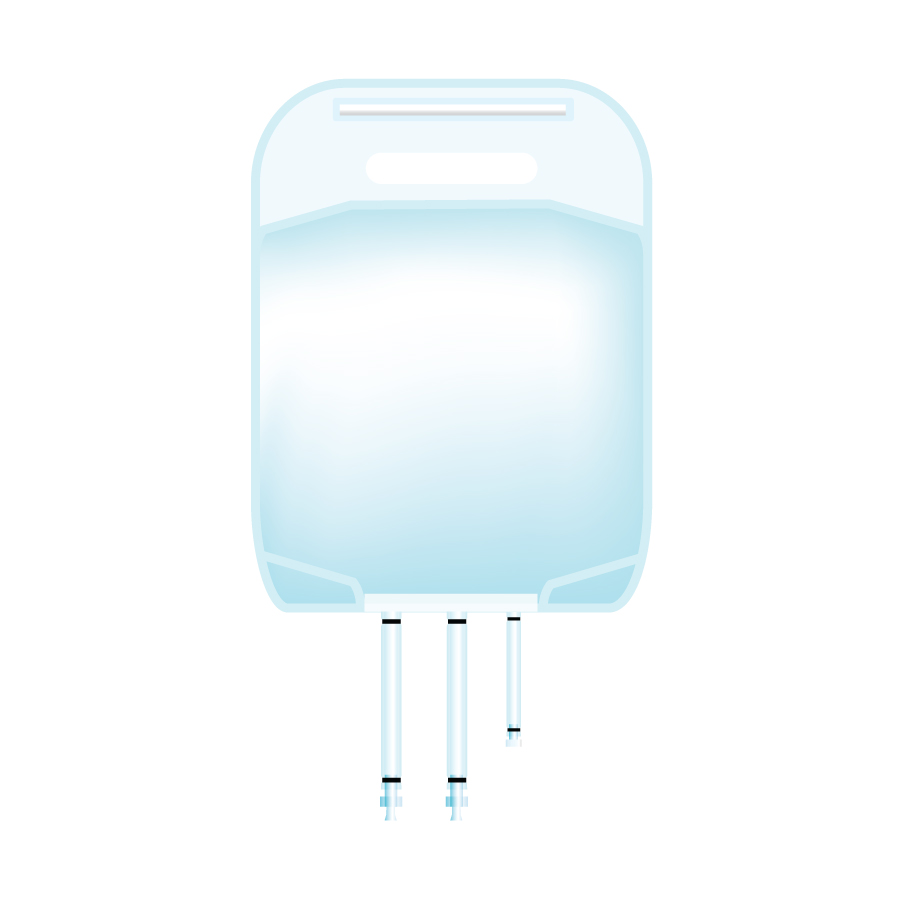
Disposable pillow bags for bioprocesses
Manufacturers in the bioprocessing industries are increasingly turning to single us...
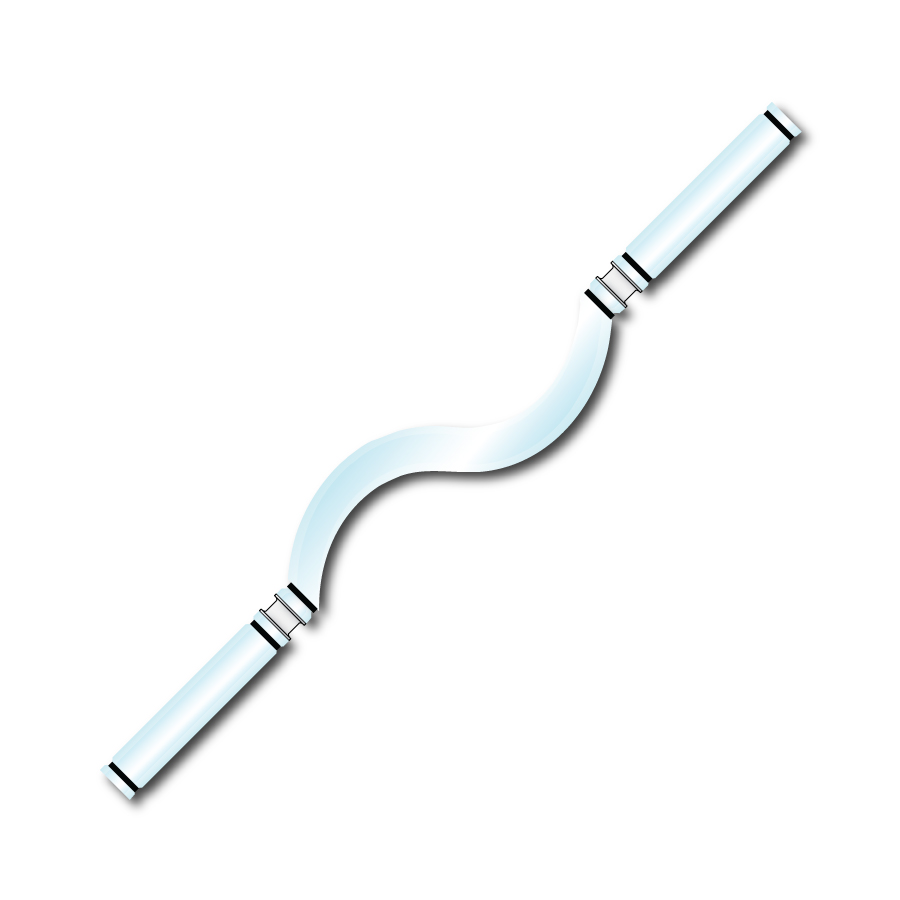
Biocompatible tubing for peristaltic pumps
Sensitive bioprocess applications requires equipment that will not interfere wi...
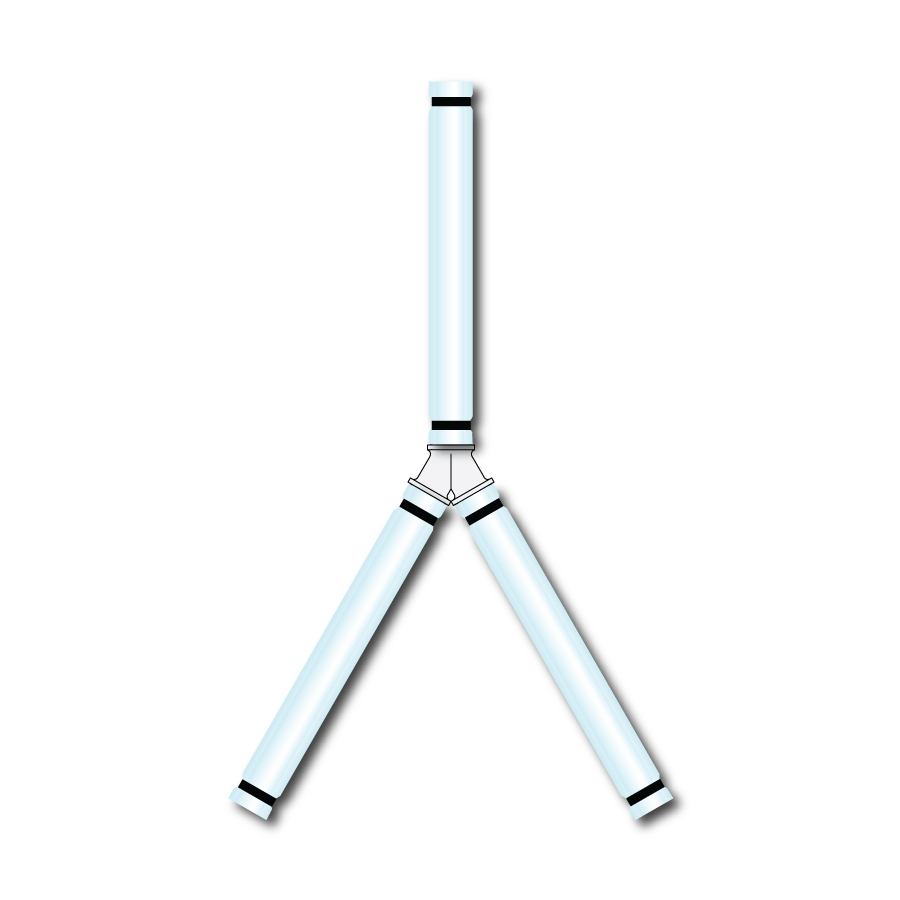
Y sets tubing for bioprocesses
Manufactueres in the bioprocessing industries are increasingly turning to single use solution...
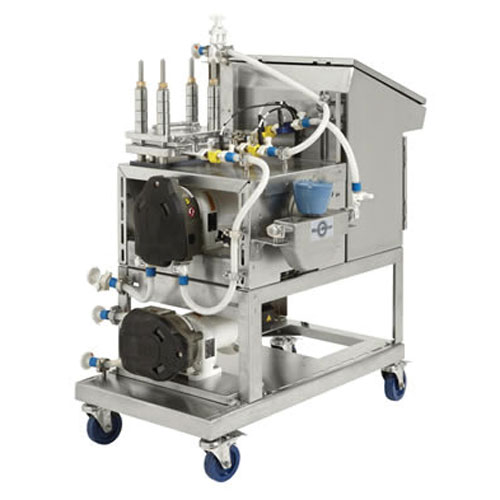
Semi-automated tangential flow filtration system
Tangential Flow Filtration is an essential to the biopharmaceutical proce...
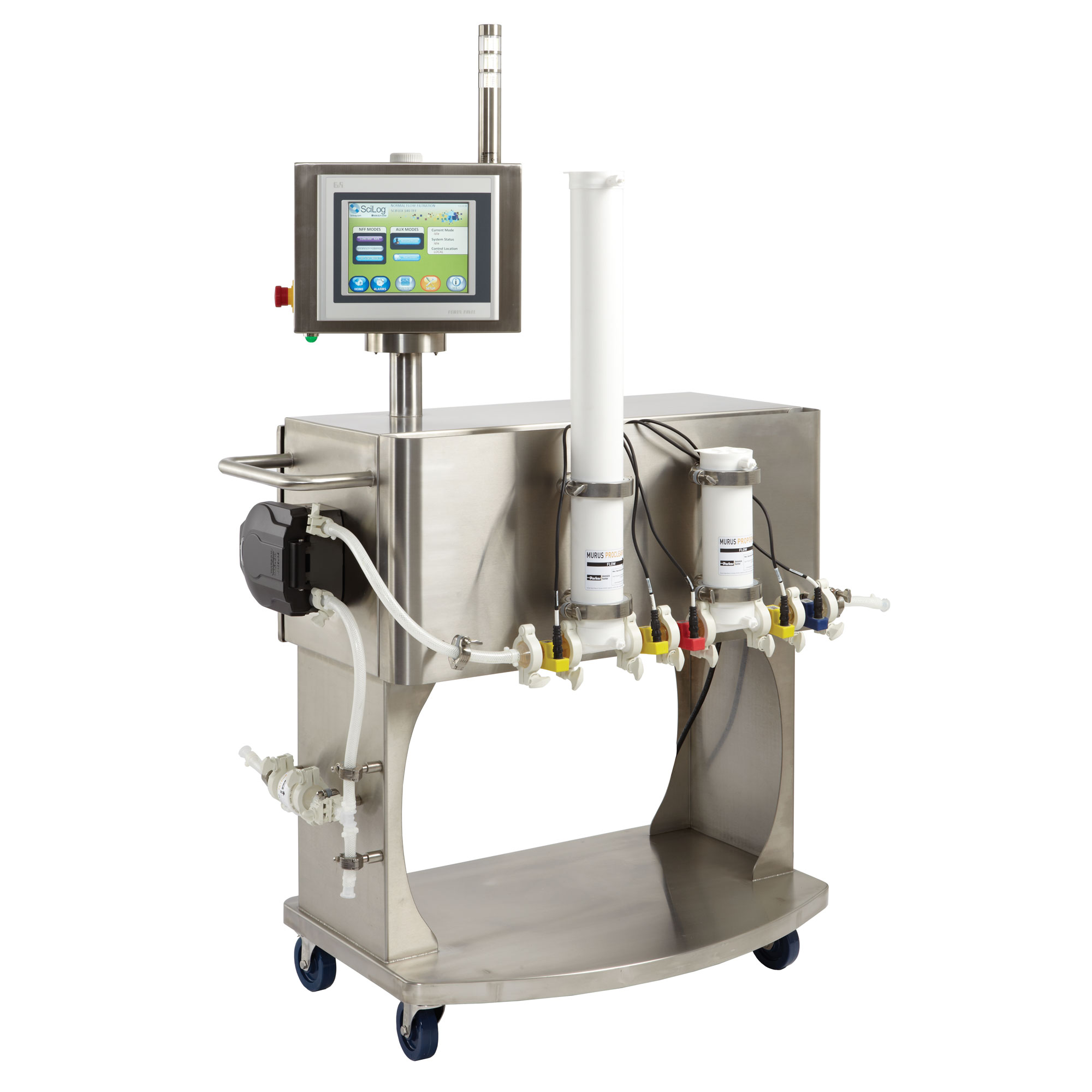
Semi-automated normal flow filtration system
Normal Flow Filtration is frequently used the biopharmaceutical processing in...
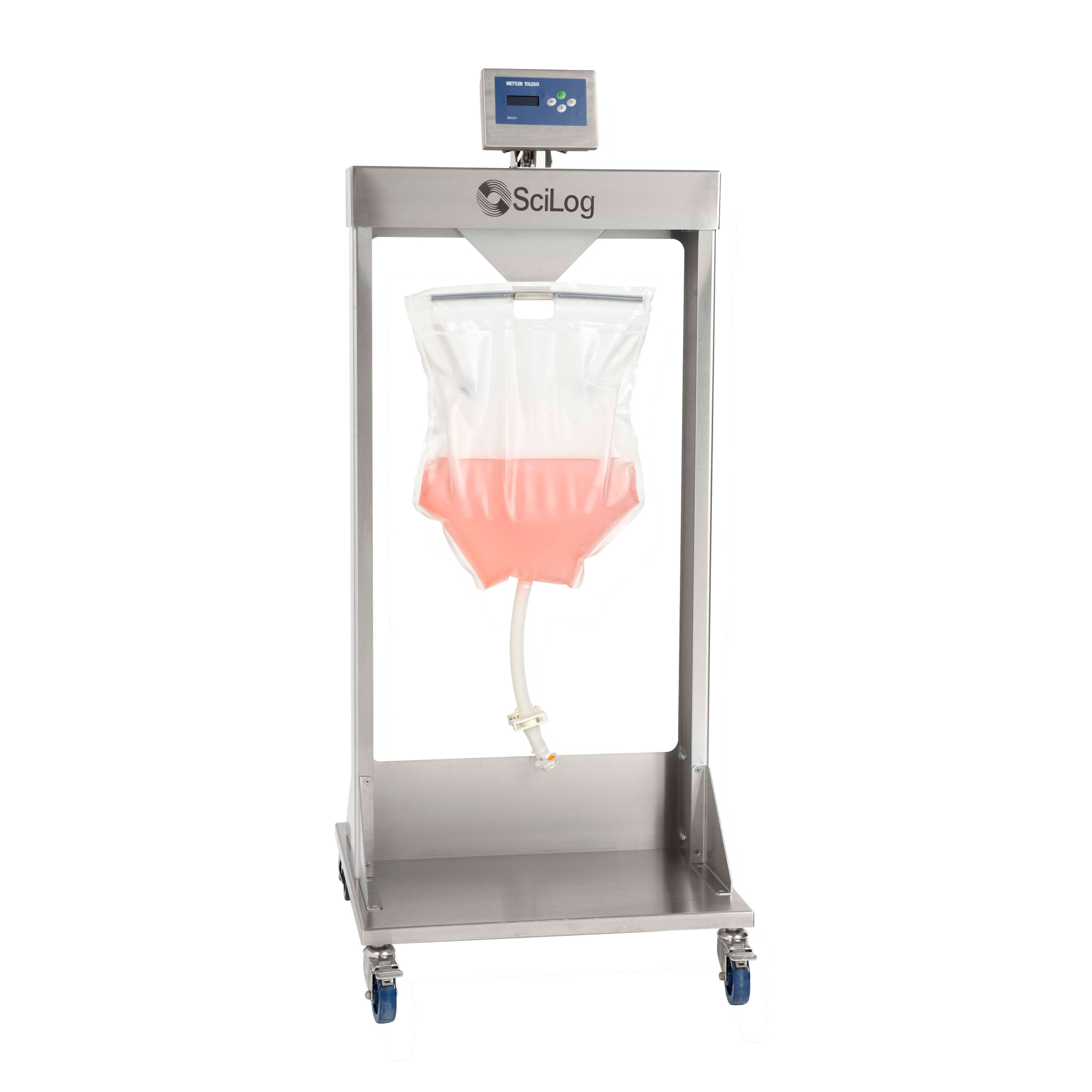
Bag holder and weighing platform for bioprocesses
Single use bags for biopharmaceutical process containment and liquid st...
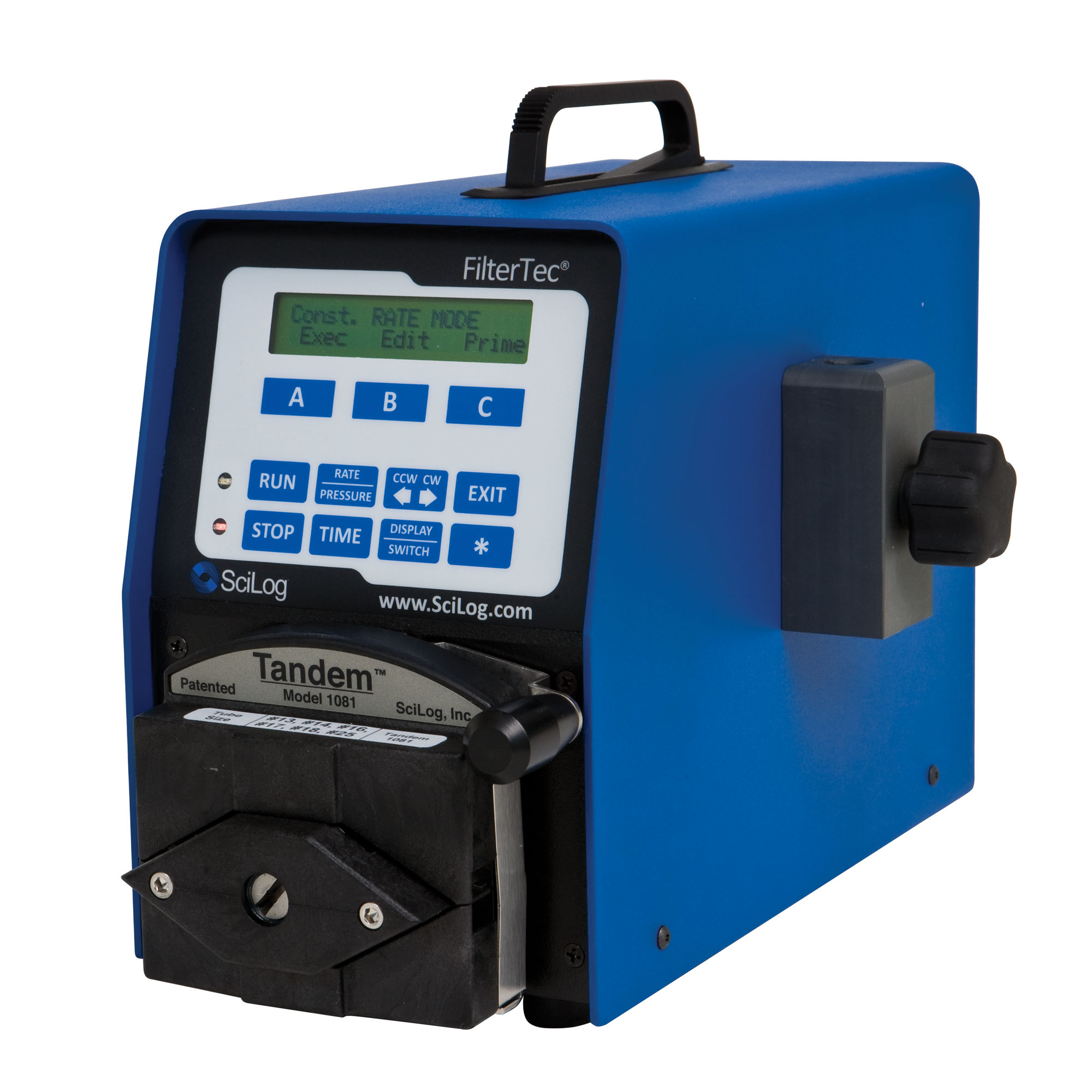
Lab scale normal flow filtration system
Normal Flow Filtration is frequently used the biopharmaceutical processing industry...
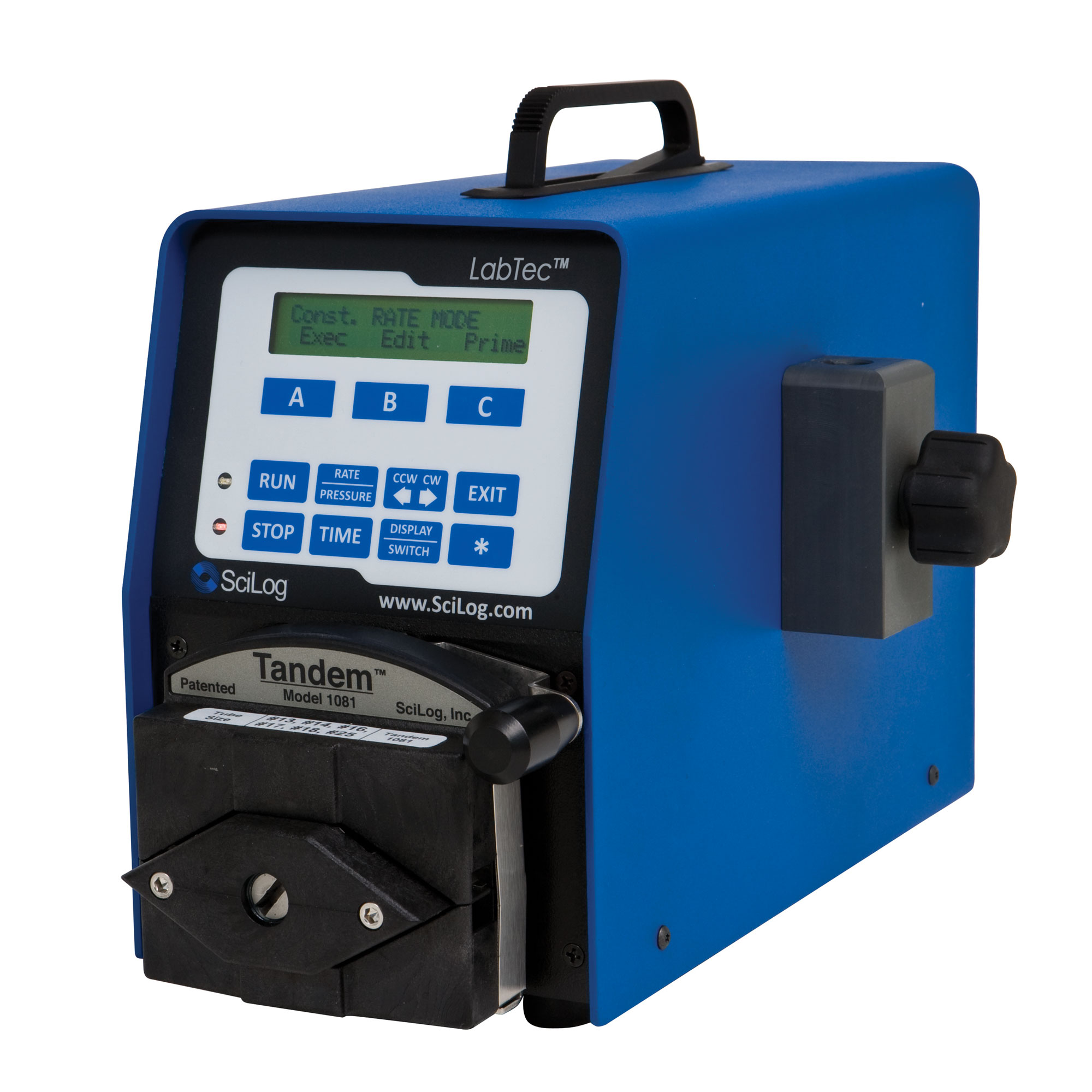
Automated dispensing system for bioprocesses
Biopharmaceutical manufacturers require precisely known liquid quantities for...
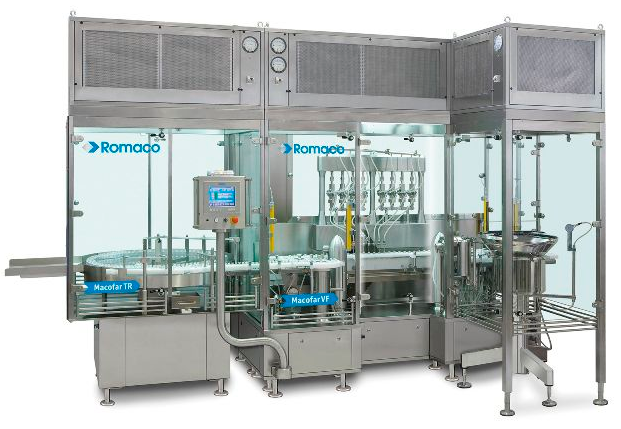
Aseptic liquid filler for vials
Compact modular aseptic filler of vials with parenteral medicines and freeze-dried products.
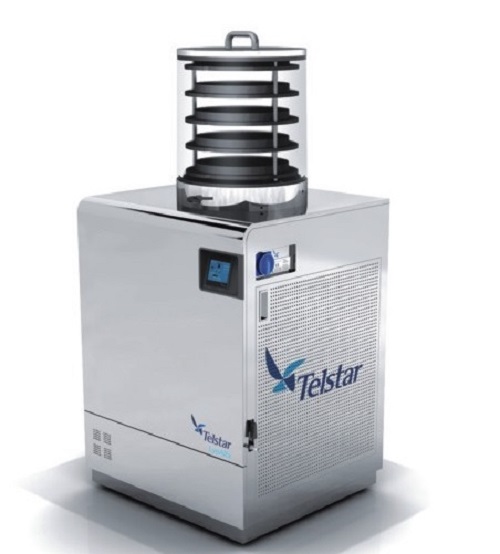
Compact laboratory freeze dryer
Particularly suitable for research centers requiring greater freeze drying capacity. Some of...
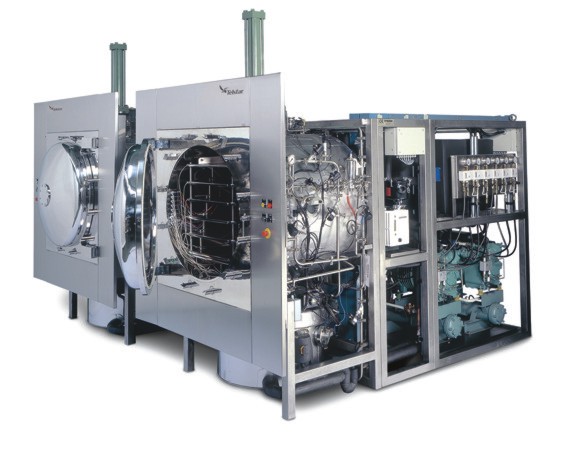
GMP freeze dryer
Designed to perform clinical trials, pilot, and small scale or large scale industrial drying processes, in ac...
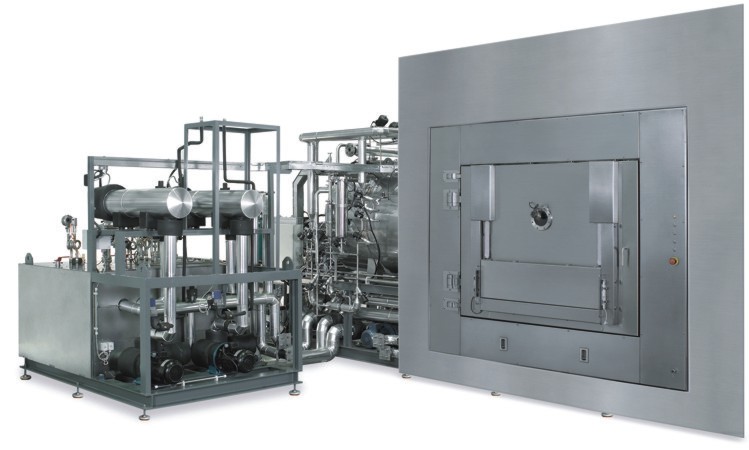
Custom engineered freeze dryer
For either bulk format or liquid in vials, ampoules or syringes, the Lyomega units are design...
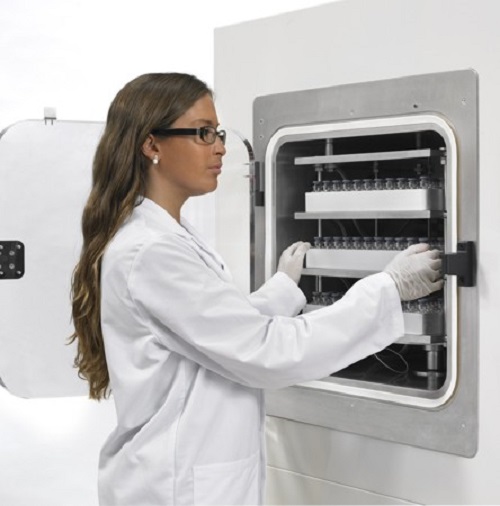
Pilot freeze dryer for scale up
Designed for biological, pharmaceutical and food products formulation and “scale up...
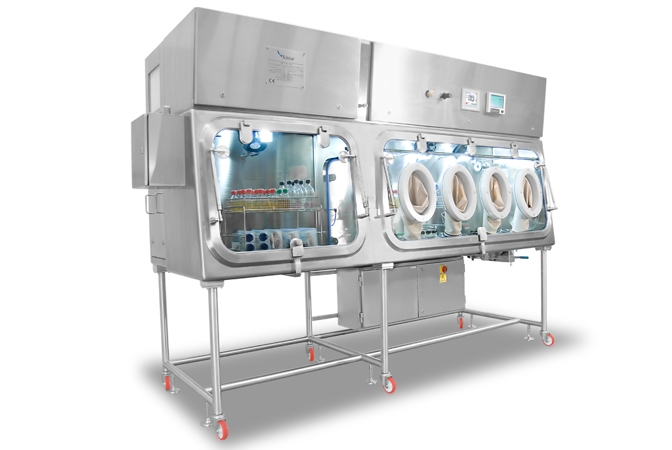
Sterility test isolators
Designed to avoid this risk and protect the product from both the process and externally generated f...