High-precision biscuit sandwiching system
Efficiently align, fill, and sandwich high-speed biscuit rows while ensuring precise quality control, enabling seamless production of various confectionery treats.
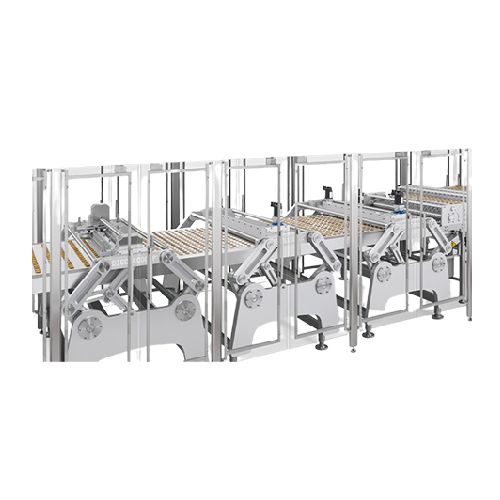
Deposits and Sandwiches Fillings for Confectionery
The Sollcocap® from SOLLICH is a sophisticated depositing and sandwiching system designed for the precise assembly of filled confectionery products. By integrating an alignment and turnover device with a volumetric dosing system, it ensures accurate and consistent deposition of fillings, accommodating a variety of fat and sugar masses. The system’s flexibility allows for multiple-row outputs, catering to high-speed production environments with a capacity of up to 300 biscuit rows per minute. It uses advanced suction nozzles to delicately position sandwich tops, while optical quality control systems manage automated rejection of defective products, ensuring superior product quality. With its accommodating working width of up to 1600 mm, the Sollcocap® seamlessly integrates into existing production lines, providing gentle product handling and adaptability for double-filled variations. Its design supports customizable dosing pistons and nozzles, allowing users to adjust to their specific production needs, making it ideal for diverse industries ranging from bakery to chocolate manufacturing.
Benefits
- Enhances production efficiency with high-speed, continuous operation of up to 300 biscuit rows per minute.
- Ensures consistent product quality with precise volumetric dosing and advanced optical quality control.
- Reduces waste and re-processing with automatic rejection of defective products.
- Offers flexibility in production with individually adjustable dosing pistons and multiple-row design.
- Minimizes handling-related damage through gentle product alignment and turnover processes.
- Applications
- Biscuits, Snacks, Pralines, Dragees, Brittles, Fruit bars, Chocolate products, Cereal bars, Sweets, Candy bars, Ice cream, Protein bars
- End products
- Coated dragees, Granola bars, Nut brittles, Cereal granola bars, Stuffed biscuits, Chocolate enrobed bars, Ice cream sandwiches with cookie or biscuit layers, High-protein energy bars, Fruit-filled bars, Assorted pralines
- Steps before
- Biscuit Alignment, Biscuit Turnover, Mixing, Dosing
- Steps after
- Sandwiching, Quality Control, Cooling, Packing
- Input ingredients
- biscuits, fat masses, sugar masses, ingredients
- Output ingredients
- sandwich biscuits, double-filled products, biscuit rows
- Market info
- Sollich is known for manufacturing engineered-to-order equipment for the confectionery industry, particularly chocolate processing and enrobing machines. They have a strong reputation for innovation, quality, and tailored solutions to meet specific customer requirements.
- Capacity
- Up to 300 biscuit rows/min
- Capacity
- Up to 150 sandwich rows/min
- Working width
- Up to 1600 mm
- Weight-accurate volumetric dosing
- Yes
- Individual nozzle control
- Yes
- Multiple-row design
- Available
- Double-filled products capability
- Yes
- Camera system for quality control
- Possible
- Defective product rejection
- Automatic
- Automation level
- PLC / Manual
- Batch vs. continuous operation
- Batch
- Cleaning method
- Automatic / Manual
- Product alignment and turnover
- Gentle system
- Suction nozzle control
- Individually adjustable
- Quality control
- Camera system possible
- Defective product rejection
- Optical quality control
- Density/particle size
- 0.5–2.5 g/cm³ / 50–1000 µm
- Material Viscosity
- Low, Medium, High
- Product Heat Sensitivity
- High / Low
- Foaming Tendency
- High / Medium / Low
- Container Size and Shape
- Varied
- Applicable Ingredients
- Fat and Sugar Masses
- Temperature Tolerance
- -10°C to 70°C
- Working width
- up to 1600 mm
- Capacity
- up to 300 biscuit rows/min, 150 sandwich rows/min
- Control panel type
- HMI / PLC
- Nozzle adjustability
- Individually switchable