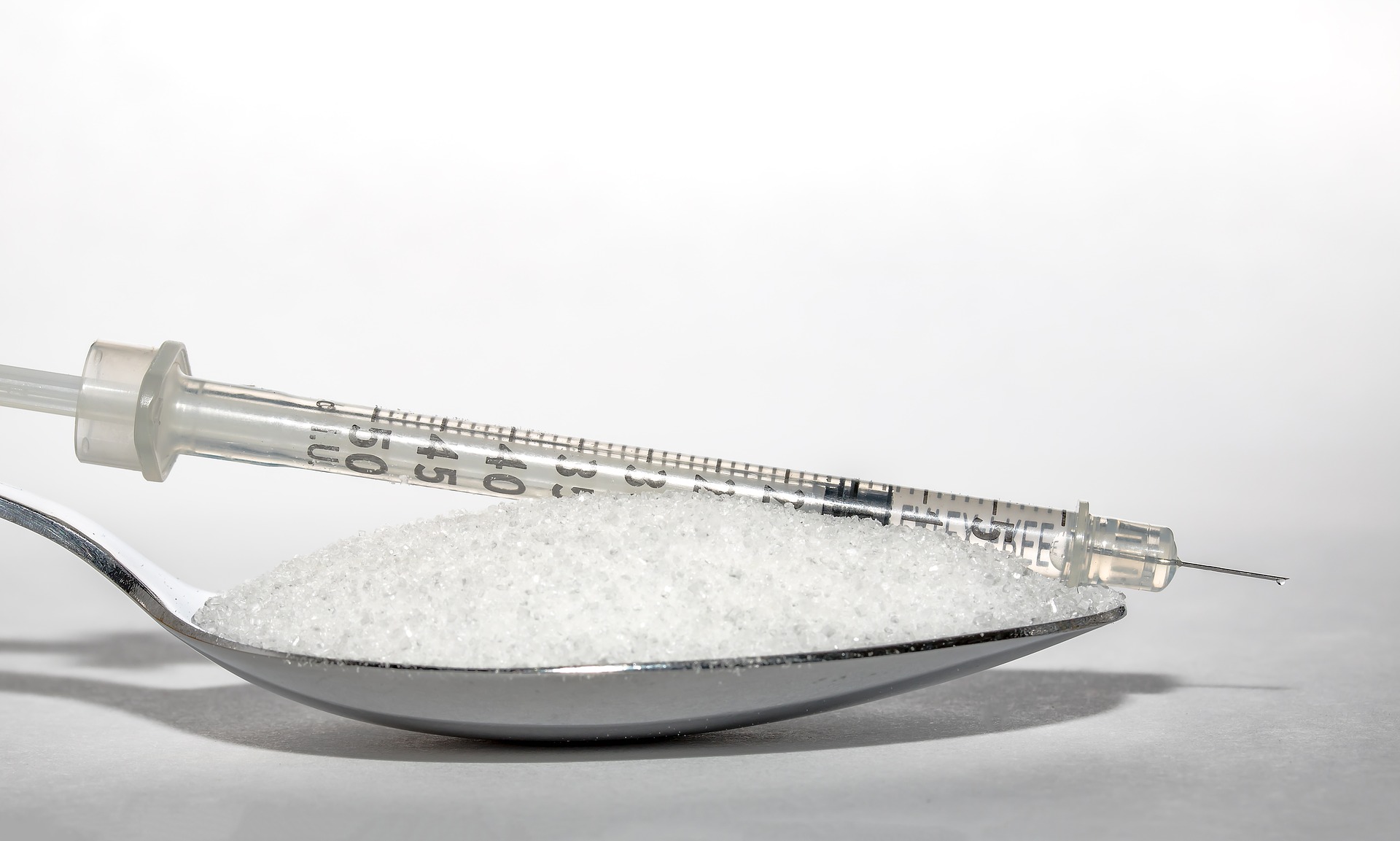
Insulin Production Technology
Find innovative production technology for making insulin and connect directly with world-leading specialists
Insulin is a hormone that controls blood glucose levels produced by the beta cells in the pancreas. As a medication, insulin was discovered by Frederick Banting and Charles Best in 1921, for which Banting was awarded a Nobel Prize in 1923. The insulin production process involves manipulating the biological precursor to insulin and cultivating it inside bacteria using specialized technology.
Select your insulin process
Tell us about your production challenge
The differences between animal-derived insulin and human insulin
Insulin injections are used for managing blood sugar levels in individuals who can’t naturally produce insulin. For many years, using insulin derived from animals, mainly porcine or bovine pancreases was the norm, but the production of human insulin became a more popular alternative since its discovery in the 1980s. Manufacturing biosynthetic human insulin via gene technologies is a preferred method for not having to depend on animals as well as the possibility to produce unlimited amounts by multiplying the insulin gene inside bacteria.
Aside from production efficiency, as extracting large amounts from animal tissue is challenging, some issues with animal-derived insulin production are related to the raw animal tissues and diseases such as Bovine Spongiform Encephalopathy (BSE) and Transmissible Spongiform Encephalopathy (TSE) and possible cross-contamination through injections. Furthermore, the chemical differences between human and animal insulin can lead to antibody attacks, inactivation and inflammation.
However, a shortage of animal-sourced insulin in developed countries is a concern for a small number of individuals who experience severe hypoglycemic episodes when using biosynthetic insulin, and generally feel healthier when undergoing an animal-derived insulin treatment.
The steps and technology in recombinant insulin production processes
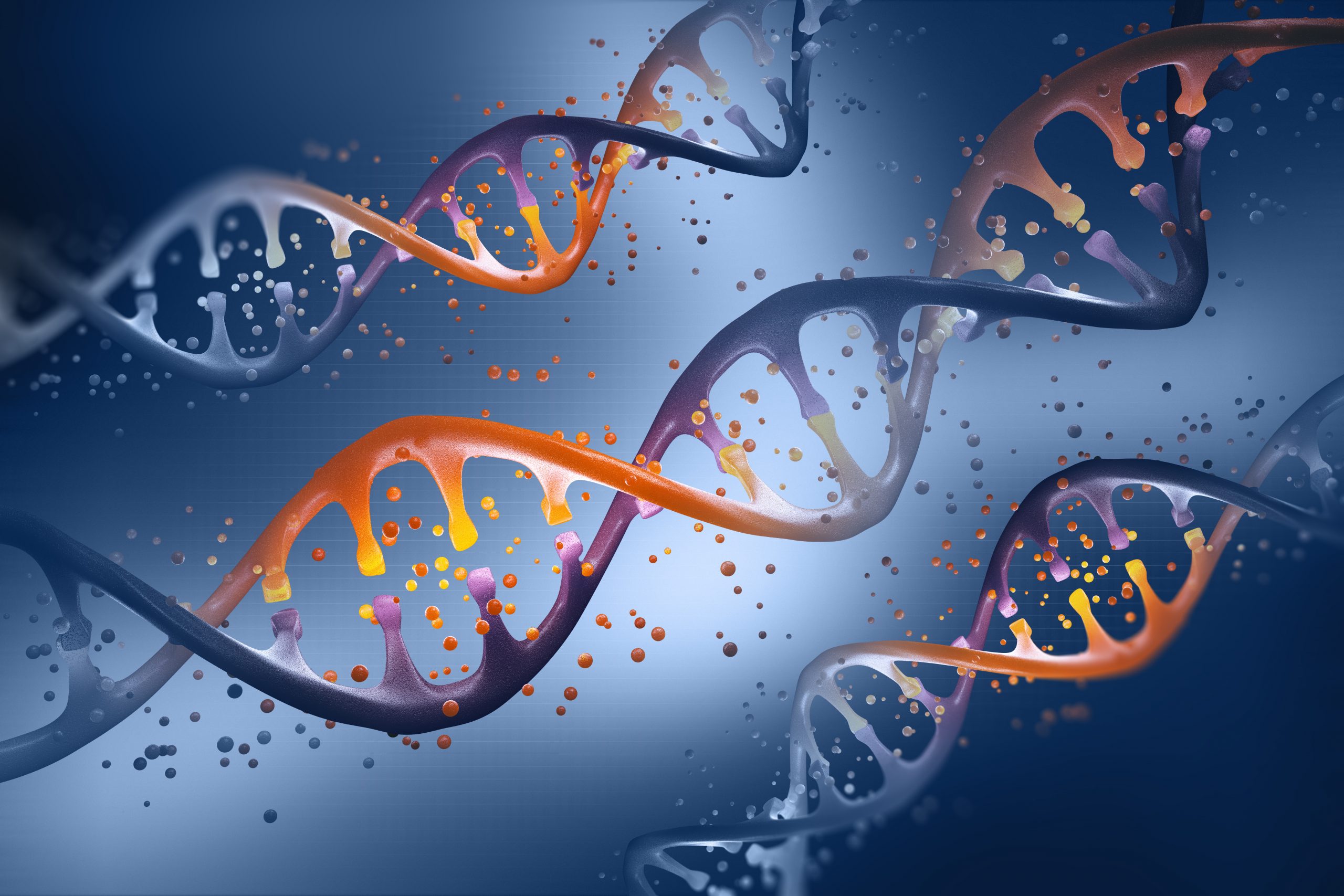
Recombinant DNA is a technology for the large-scale production of insulin by inserting the human gene which carries codes for the protein insulin into a plasmid of a simple bacteria, most commonly Escherichia coli. Producers then add ligase, an enzyme that acts like glue to help the plasmid stick to the bacterium’s DNA. The bacteria undergo a fermentation process inside a large fermentation tank, where millions of bacteria replicate every 20 minutes. The insulin harvest starts by adding a mixture of lysozyme which digests the outer layer of the cell wall and a detergent mixture which separates the fatty cell wall membrane.

The insulin is separated from the bacterium’s DNA with the help of a cyanogen bromide treatment which splits protein chains at the methionine residues. An oxidizing agent is added and the mixture is placed in a centrifuge to separate cell components. The DNA mixture is purified by using one of the following techniques: ion-exchange column, reverse-phase high-performance liquid chromatography or a gel filtration chromatography column. Finally, the purified substance is ready for medical use.
The future of insulin patents and treatment delivery
Although the use of insulin pens is a practical therapy due to their reusable nature, ability to increase patient compliance and accuracy, and there are innovative solutions to enhance the delivery of insulin in the future. An alternative for diabetes care would be oral application, however, scientists are looking for ways to avoid enzymatic degradation upon consumption. Solutions can be found in nanoparticle-based approaches which protect insulin from gastrointestinal conditions and enhance the permeability of the enzyme.
A further option is the bioresponsive insulin delivery system, which accelerates insulin release with increasing glucose levels. Furthermore, manufacturers are working on the production of inhaled insulin devices, with insulin particles small enough to reach the deep lung and pass into the bloodstream. Another aerosol option is buccal insulin, a spray absorbed through the inner cheek wall. Finally, absorbing insulin through the skin with the help of insulin patches is another idea in development.
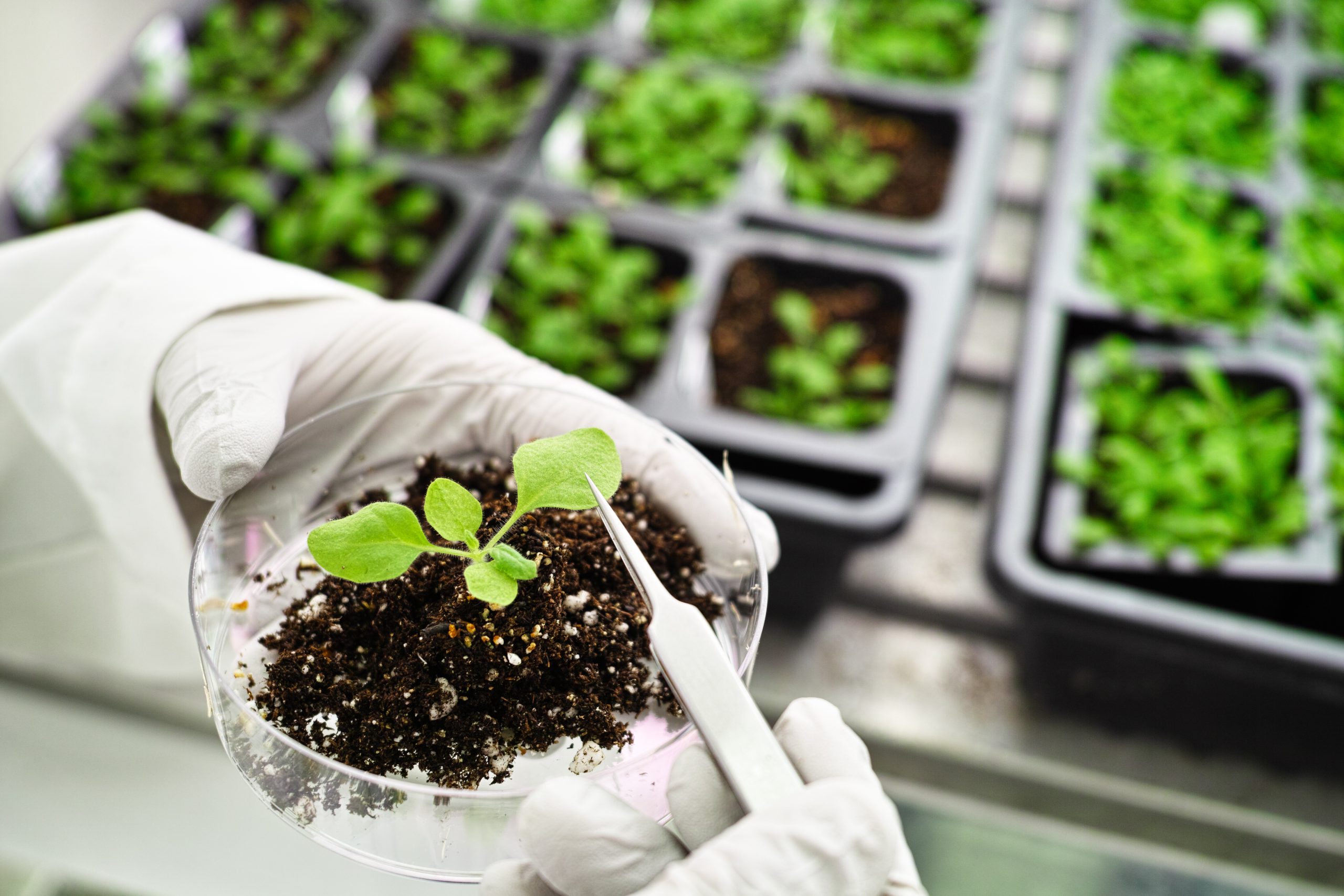
Transgenic plants as a solution for high demand
The insulin production process and its current manufacturing technologies struggle to keep up with the steadily increasing demand for affordable insulin due to a rising number of patients with diabetes. This is especially the case in the United States. One of the most effective alternatives is the manufacture of recombinant human insulin from the plant Arabidopsis Thaliana and its oilseeds. Plant-based insulin is easy to produce, cost-effective, free from human pathogens and involves high-quality protein processing.
The oilseeds are genetically engineered with the recombinant protein targeting oil bodies and then processed by separating oil bodies via liquid-liquid phase to reduce chromatography steps in the purification of insulin. Transgenic plants can produce a high level of biologically active proinsulin and it can further be enzymatically treated in vitro which is an economic method for mass production.
Processing steps involved in insulin making
Which insulin technology do you need?
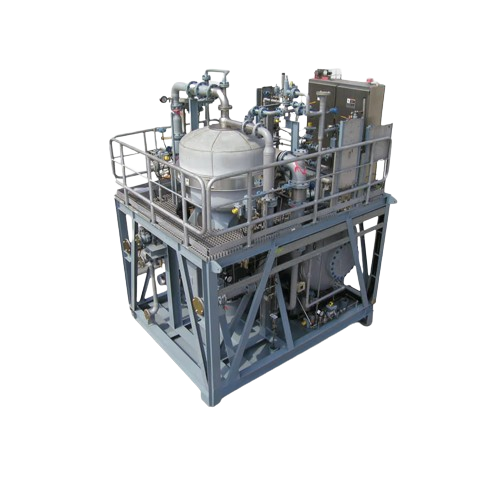
Single-use separator for cell harvesting
Achieve maximum cell harvesting efficiency with single-use technology, streamlinin...
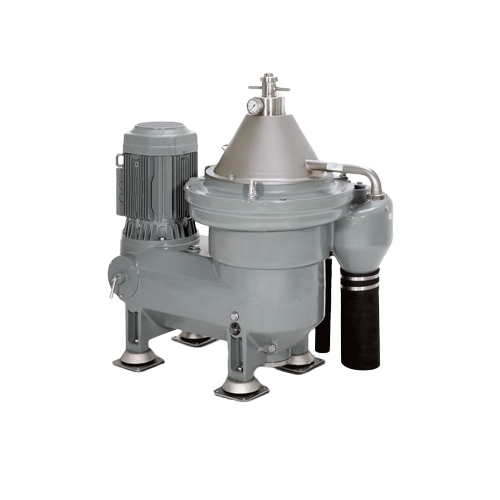
Aseptic separator for biopharma applications
Achieve high purity for your pharmaceutical liquids with a centrifuge that en...
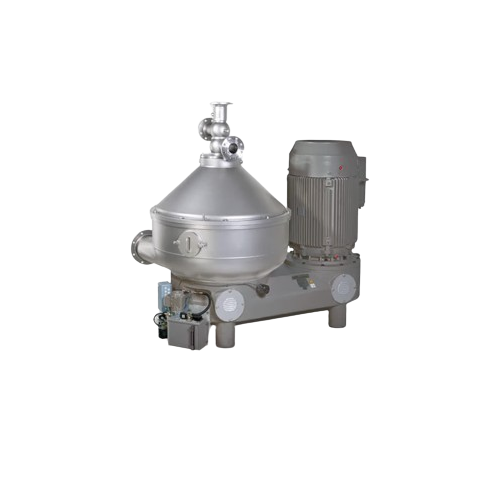
Biopharma separator for low to medium solid content
Ensure precise separation and high yield in biopharmaceutical product...
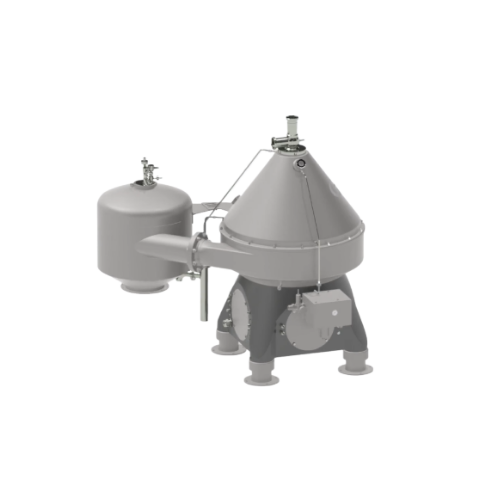
Pharmaceutical centrifuge for particle separation
Effortlessly upscale your biopharmaceutical processes with a compact ce...
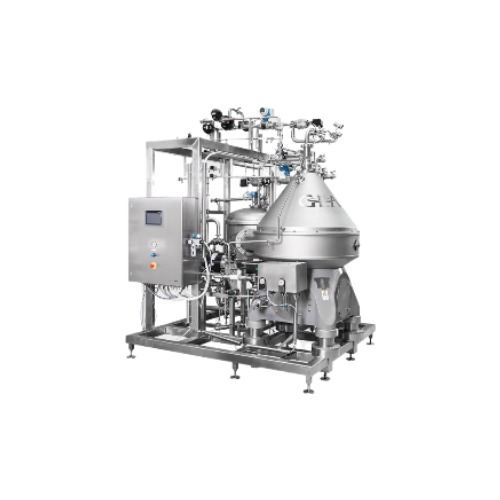
Pharmaceutical separator for high solid contents
Ensure optimal purity in biopharmaceutical processing with a separator de...
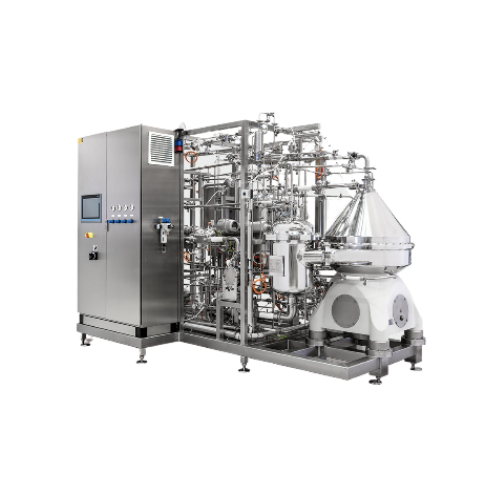
Pharma separator for aseptic biopharma processing
Achieve precise separation and concentration of sensitive biopharmaceut...
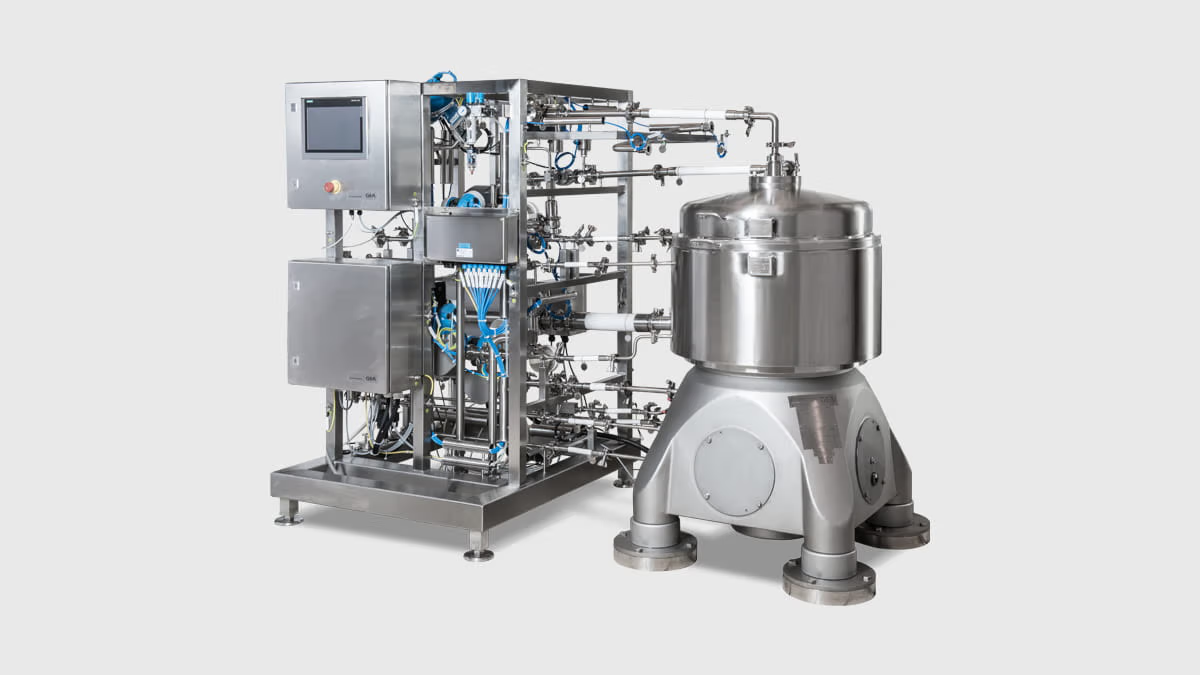
Chamber bowl separator for protein recovery
Efficiently recover high-value proteins with precise separation, optimizing yo...
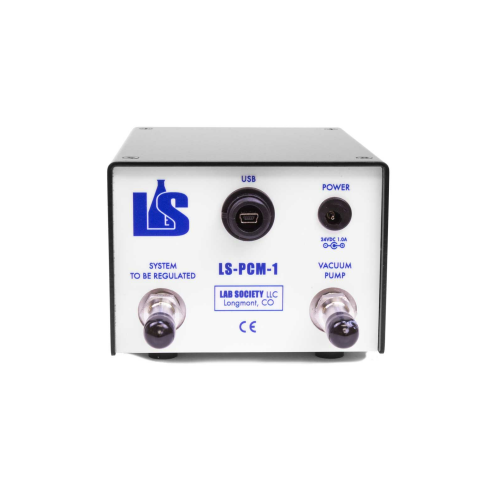
Pressure control monitor for laboratory vacuum systems
Effortlessly maintain precise vacuum pressure in your lab operatio...
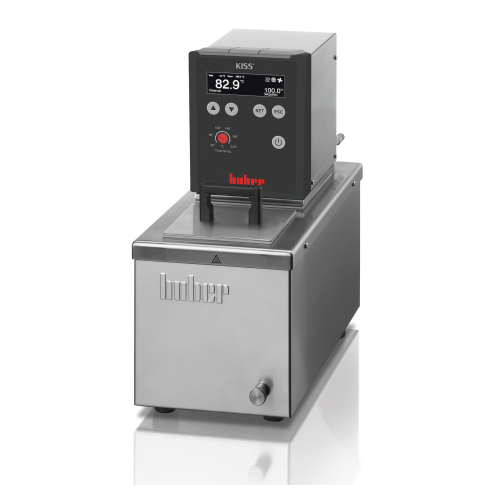
Heated circulator for laboratory temperature control
Achieve precise temperature control for demanding applications like ...
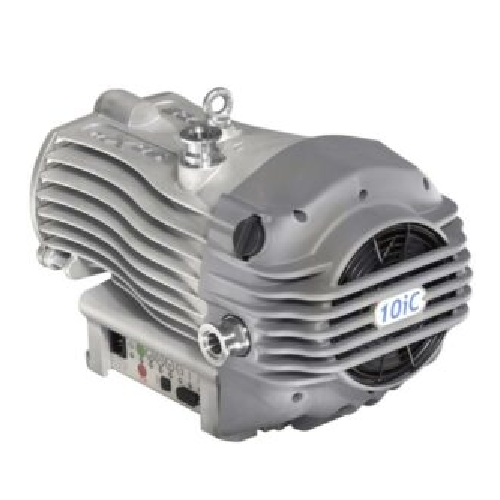
Chemically resistant dry scroll vacuum pump
Effortlessly manage aggressive substances and achieve reliable vacuum conditio...
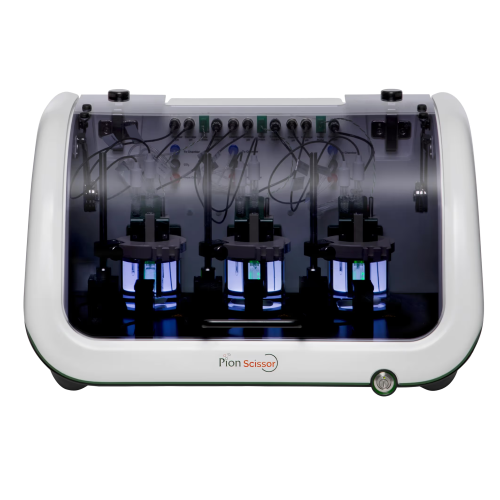
In vitro subcutaneous injection simulator
Optimize drug formulation screening and selection with an innovative solution th...
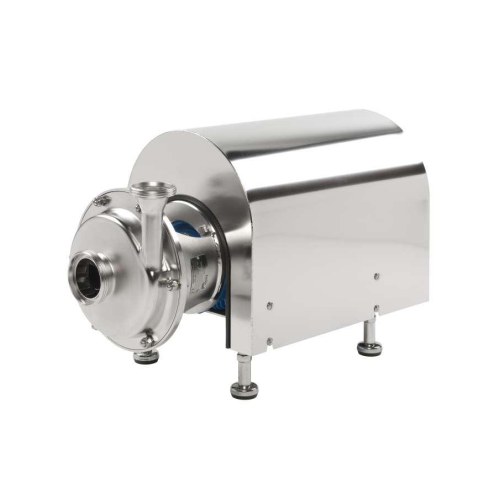
Centrifugal pumps for food & beverage and biopharmaceutical applications
Optimize your liquid transfer processes with p...
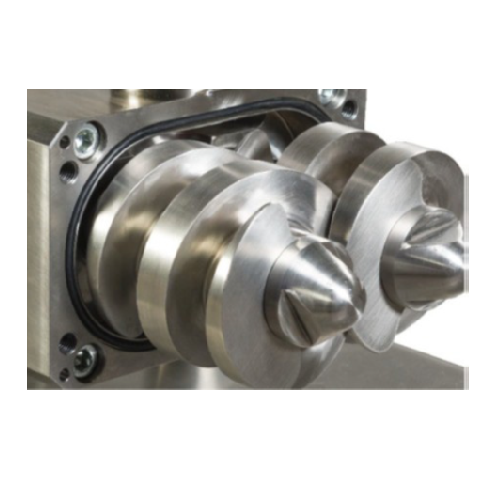
Aseptic sampling devices for biopharmaceutical applications
Secure aseptic sampling ensures your high-value biopharmaceu...
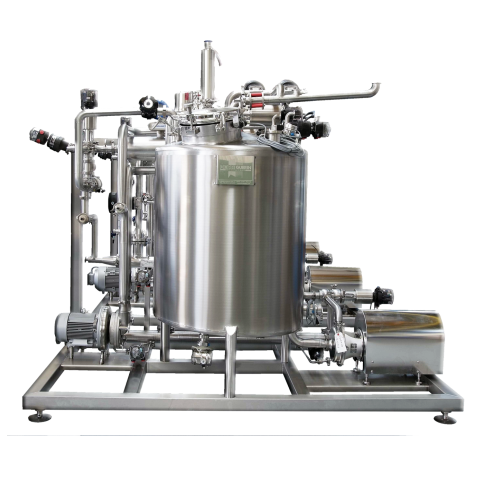
Single use cleaning in place units for biopharma
Eliminate cross-contamination risks in biopharmaceuticals with precision ...
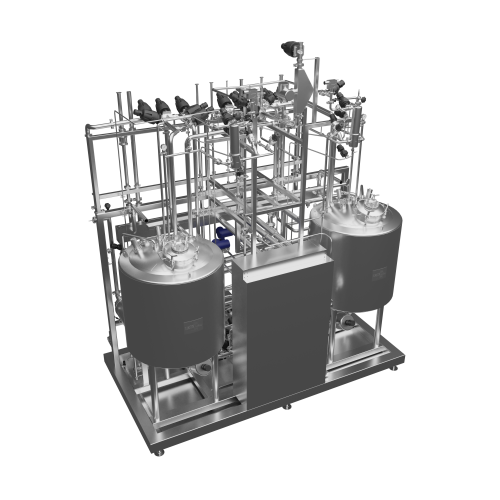
Cleaning and sterilization in place for hygienic control
Ensure maximum hygiene and sterility in your production line wit...
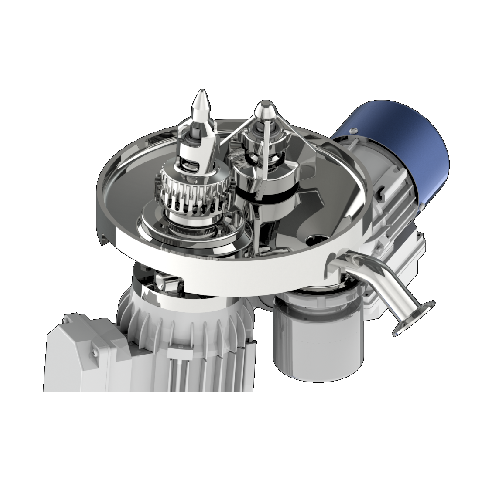
Dished end for optimized mixing in small-volume vessels
When space constraints challenge vessel design, this solution eli...
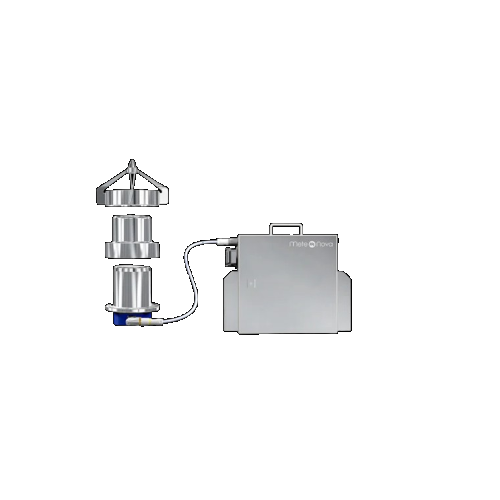
Low shear mixer for shear-sensitive applications
Optimize shear-sensitive mixing with precision control, enhancing product...
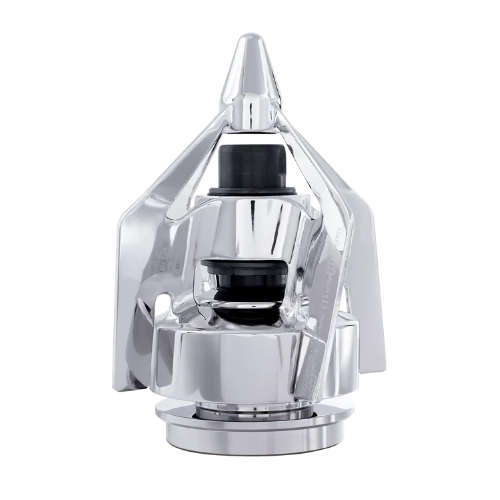
Versatile magnetic mixer for pharmaceutical and biotechnology applications
Optimize your biopharmaceutical mixing proc...
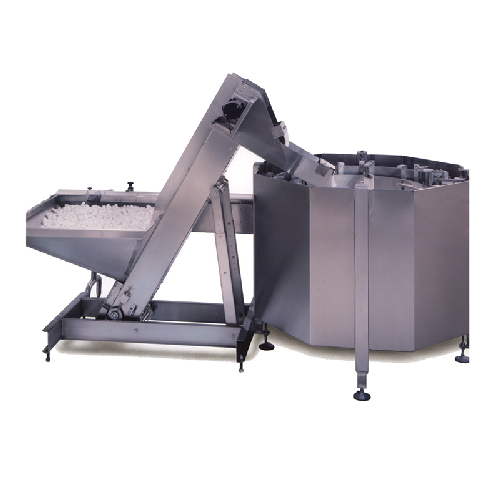
Centrifugal bowl feeder for high-speed bulk item feeding
Optimize your production line with high-speed feeding of diverse...
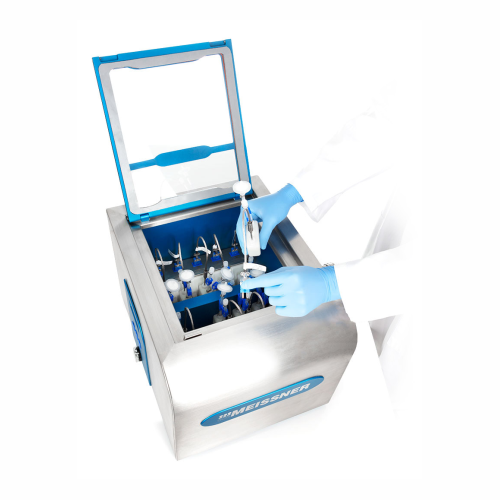
Bench top freezer for bulk drug substance freeze and thaw
Achieve precise temperature control for small-scale freeze and...
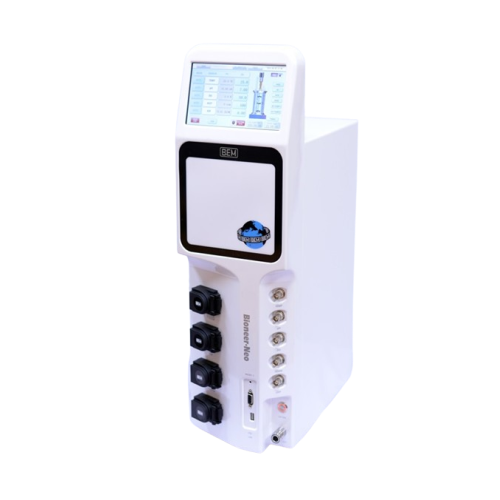
Compact fermentor for research and scale-up studies
Optimize your bioprocess development with a desktop fermentor that of...
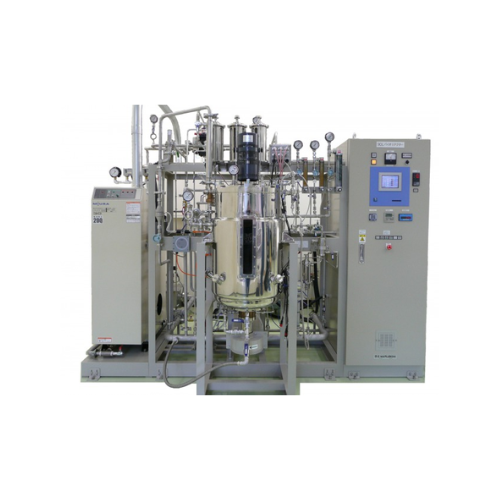
Sterilization in place fermentor for bioprocess applications
Optimize your fermentation processes with seamless integrat...
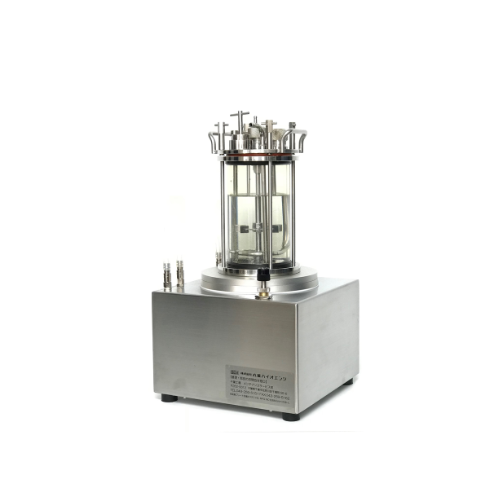
Small scale fermentor/bioreactor for multi-condition bioprocessing
Explore diverse fermentation conditions with precisi...
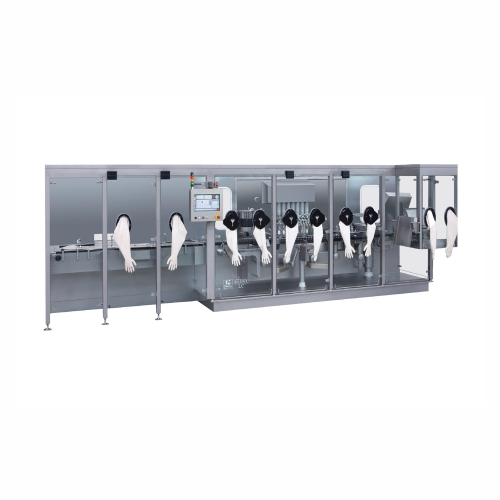
Vial filling and stoppering for aseptic liquid or lyo products
Ensure optimal aseptic conditions in your production line...
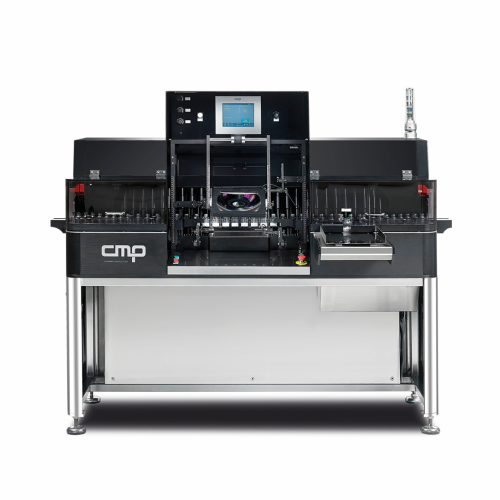
Inspection system for glass containers
Ensure precise inspection of liquid, freeze-dried, and powdered products in glass co...

External washing and drying system for ampoules and vials
Optimize your aseptic processing by seamlessly integrating a c...
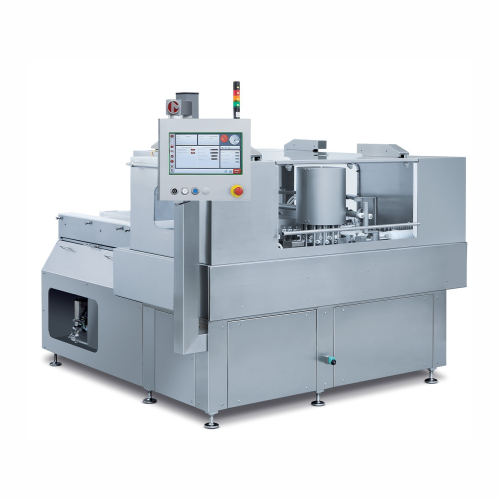
Industrial washing and sterilizing system for ampoules and vials
Ensure the highest hygiene standards in your liquid for...
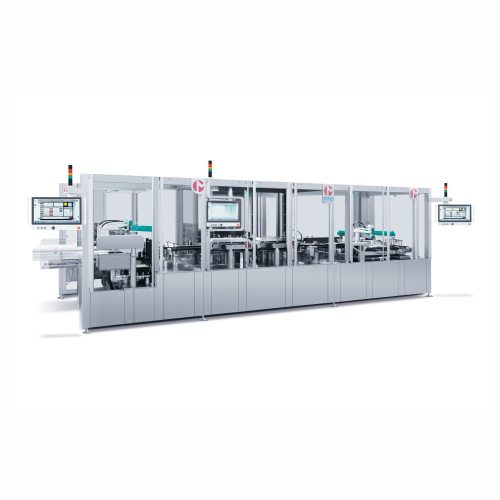
Inspection for glass syringes
Ensure comprehensive quality control for syringe-based medical products with high-speed, no-co...
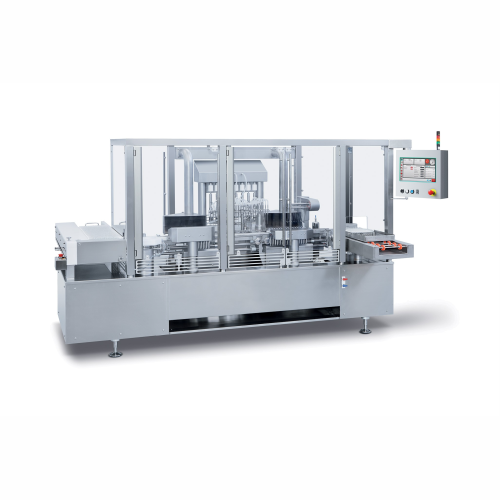
Aseptic ampoule filling and sealing solution
Ensure precise dosing and secure sealing of sterile liquid pharmaceuticals in...
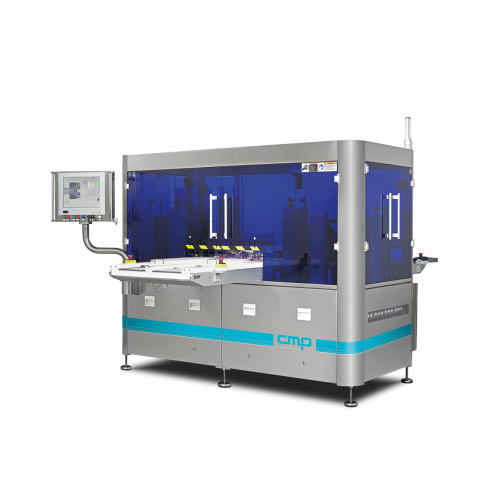
Glass container inspection system
Ensure product integrity with precision inspection for glass containers, detecting partic...
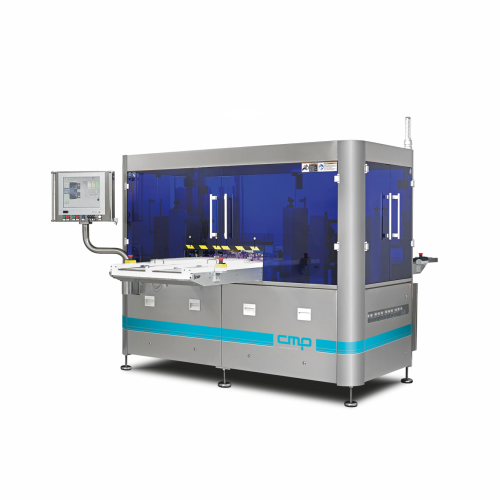
Inspection for glass containers
Ensure the integrity and quality of your liquid formulations with high-speed inspection and ...
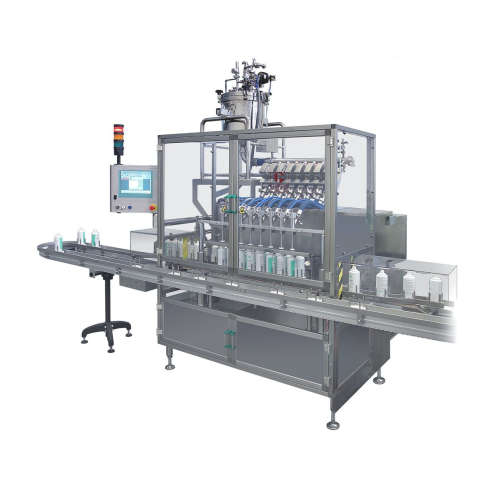
Bottle filler and capper
Achieve precise liquid filling and secure capping with high-speed, intermittent motion, ensuring con...
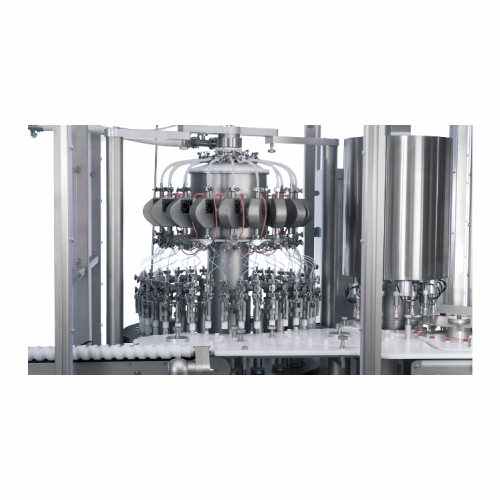
Aseptic vials filling and capping
Ensure precise vial capping and sealing for liquid pharmaceuticals with advanced aseptic ...
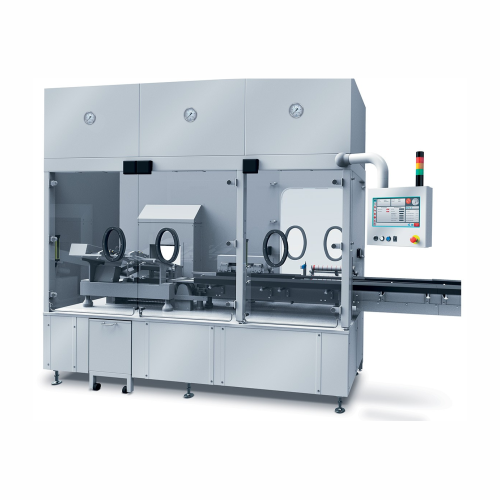
Nested syringe filling and stoppering line
Streamline your aseptic filling process with advanced machinery that handles ne...
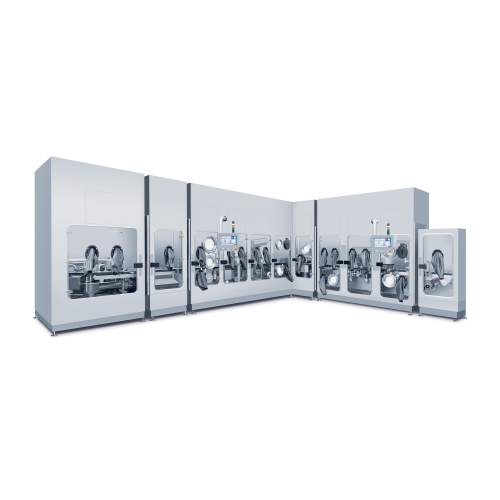
Aseptic filling and capping for vials and syringes
Ensure sterility and precision in vial and syringe filling with advanc...
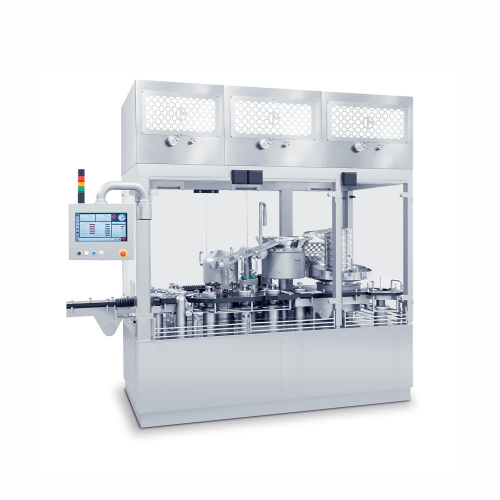
Vial capping for small volume parenteral
Ensure precise sealing and contamination-free environments for small volume parent...
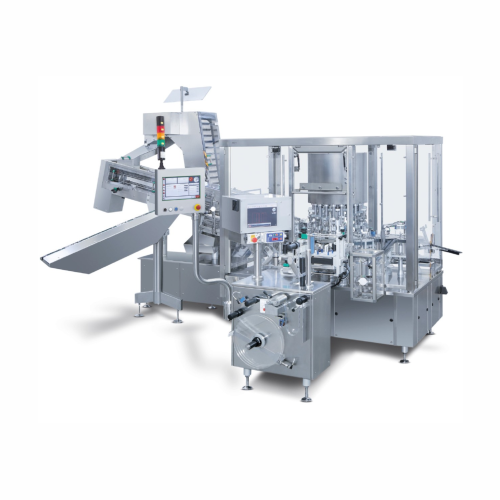
Automatic syringe plungering and labeling system
Optimize your production line with precision syringe handling and labelin...

Syringe assembly system
Achieve precise and efficient assembly of medical syringes with a system designed for continuous, hig...
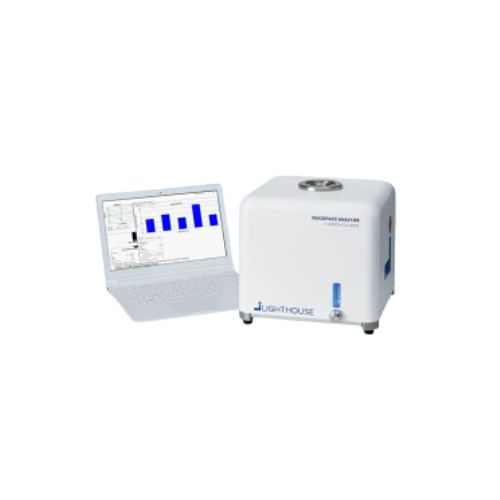
Carbon dioxide headspace analyzer for parenteral containers
Ensure accurate headspace gas analysis to maintain container...
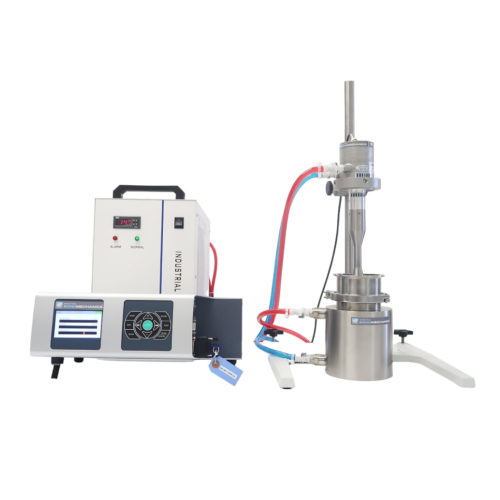
Ultrasonic liquid processor for medium-scale production
Streamline your production with a robust ultrasonic solution capa...
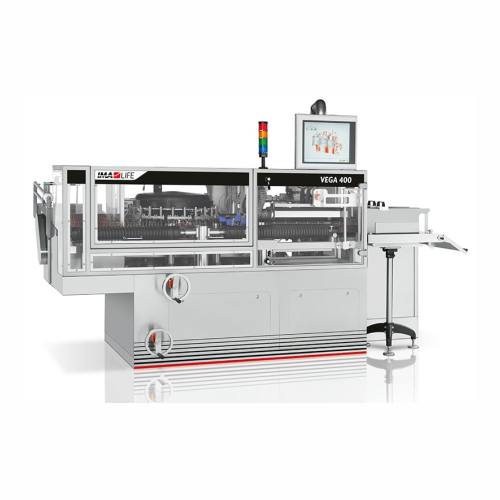
Ampoule external washer for decontamination
Ensure contamination-free glass containers with a high-speed solution designed...
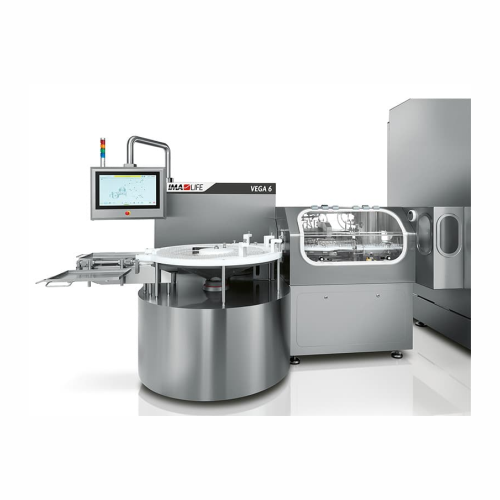
Rotary vial washers for parenteral containers
Ensure sterile and pyrogen-free parenteral preparations with a seamless wash...
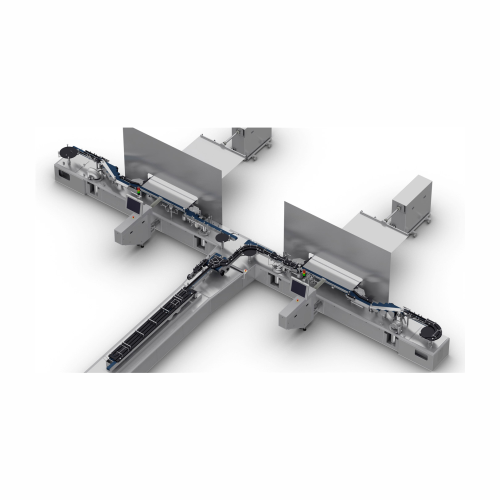
Automatic vial loading and unloading systems for freeze dryers
Optimize your vial handling with automated loading and un...
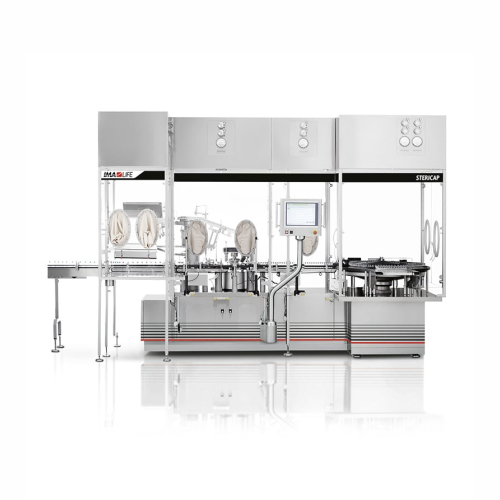
Rotary capping machine for aseptic products
Ensure precision sealing for aseptic liquid formulations with a solution engin...
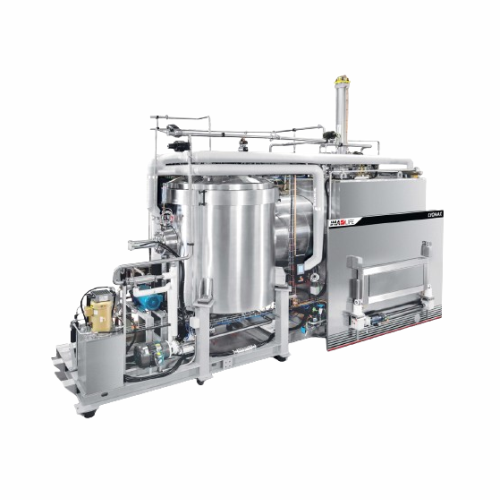
Industrial GMP freeze dryer
Optimize the lyophilization of sensitive pharmaceutical compounds with a machine designed for pr...
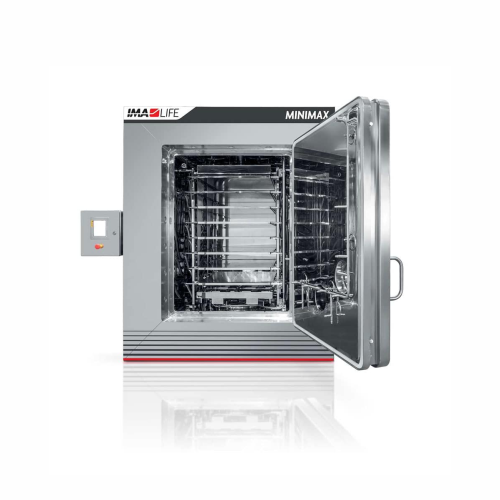
Small-scale freeze dryer for pharmaceutical applications
Optimize small-batch and pilot-scale lyophilization with advance...
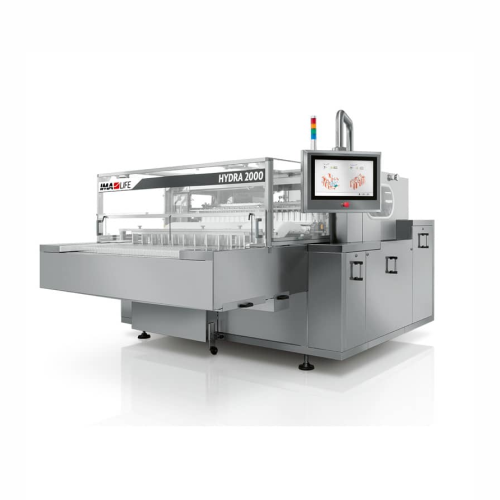
Linear vial washer for injectable drug containers
Achieve sterile conditions by efficiently removing contaminants from va...
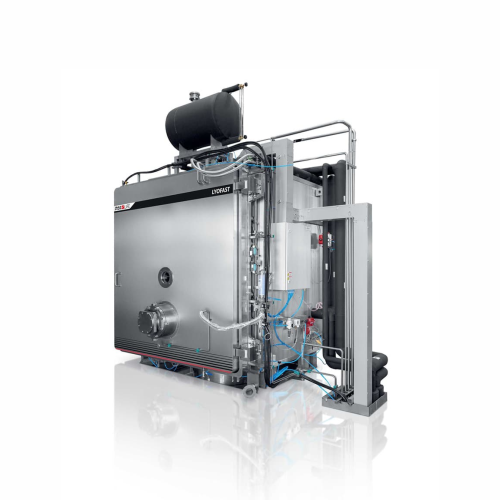
Industrial freeze dryer for biopharmaceuticals
Ensure the stability and longevity of your sensitive biopharmaceuticals thr...
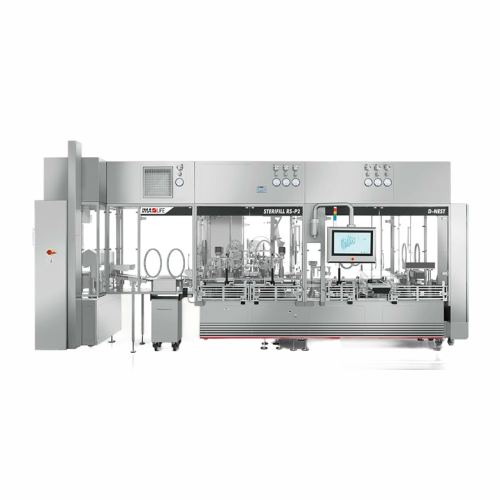
Denesting system for Rtu syringes and vials
Need efficient denesting of sensitive pharmaceutical containers? Streamline yo...
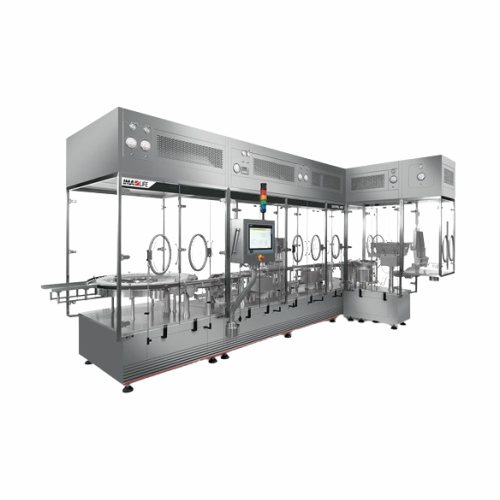
Aseptic filling and stoppering solution for vials
Ensure precise aseptic filling and stoppering of vials with enhanced fl...
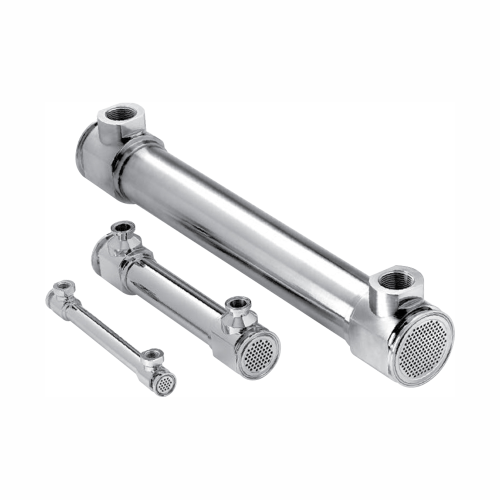
Sanitary shell & tube heat exchangers for pharmaceutical applications
Ensure sterility and precision in thermal managem...
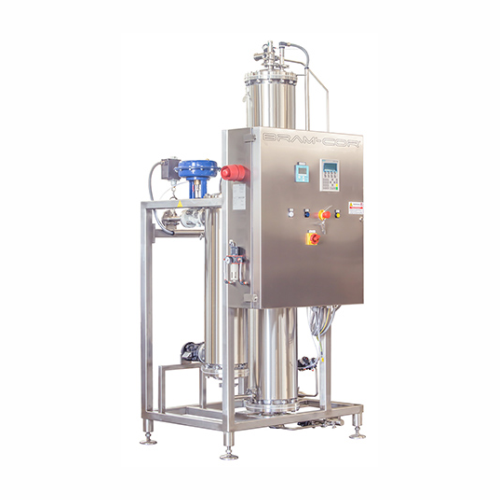
Pure steam generation and distribution system
Ensure reliable sterilization with pure steam that’s free from contami...
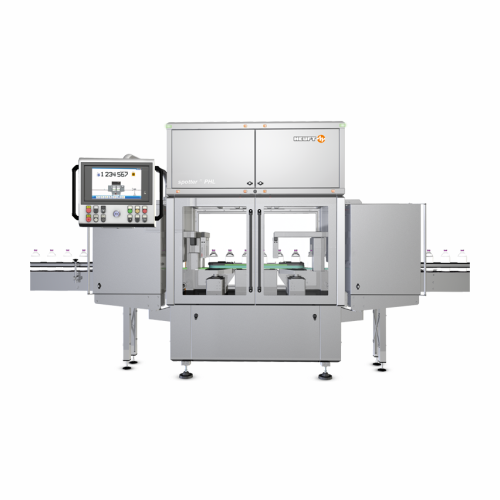
Vial inspection system for pharmaceutical industry
Ensure vial integrity by detecting and rejecting contaminants, glass d...
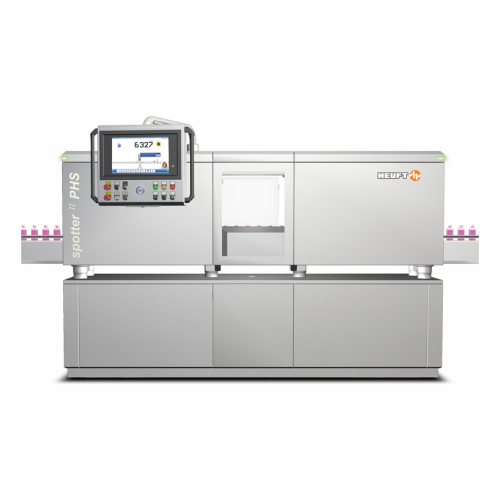
Vial inspection system for pharmaceutical products
Ensure the integrity and safety of parenteral drugs with advanced imag...
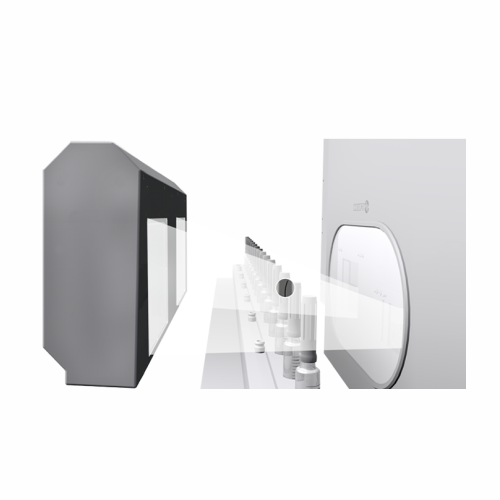
Syringe and cannula inspection system
Ensure flawless quality in injectable products with advanced inspection technology th...
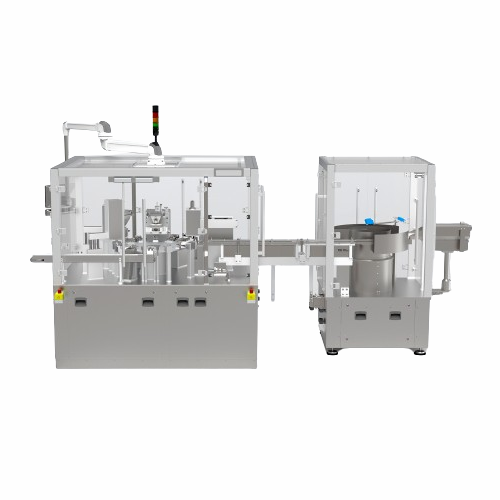
Rotary indexing table for dosing and assembly
Optimize production efficiency with a compact rotary indexing table that str...
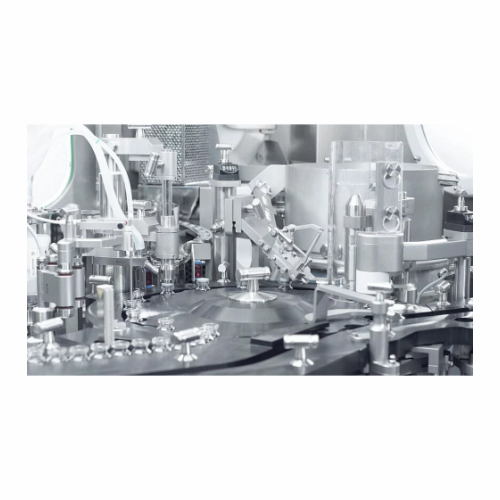
Integrated vial filling system for aseptic and toxic pharmaceuticals
Minimize product loss and ensure high sterility in...
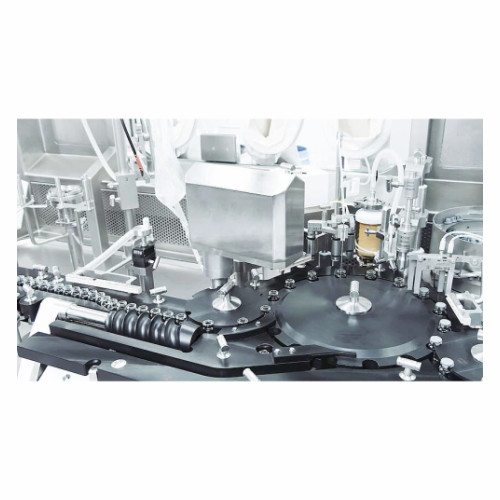
Aseptic filling solutions for Rtu vials, cartridges, and syringes
Optimize your aseptic filling processes with a system...
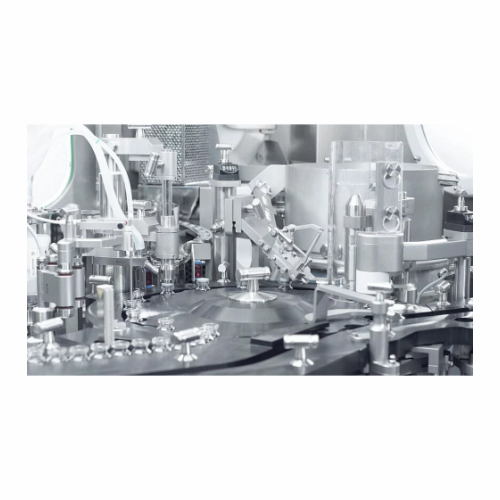
Vial filling for pharmaceuticals
Streamline your aseptic processing with vial filling machines that ensure sterile, precise,...
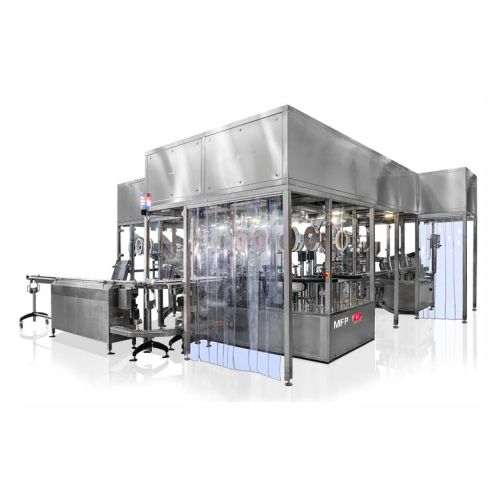
Sterile and nonsterile vial filling system for injectables
Achieve precision and safety in filling and stoppering with a...
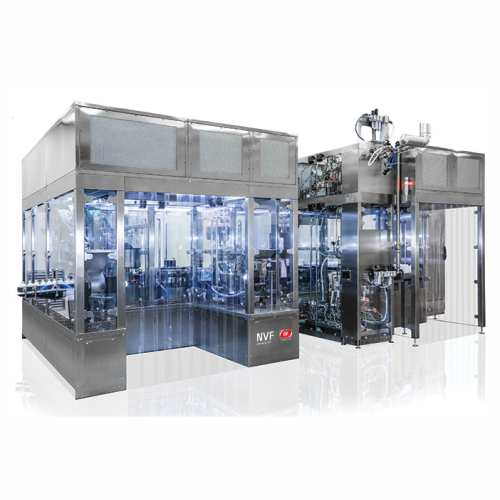
Sterile and nonsterile filling for injectable solutions
Efficiently fill and stopper injectable solutions in both sterile...
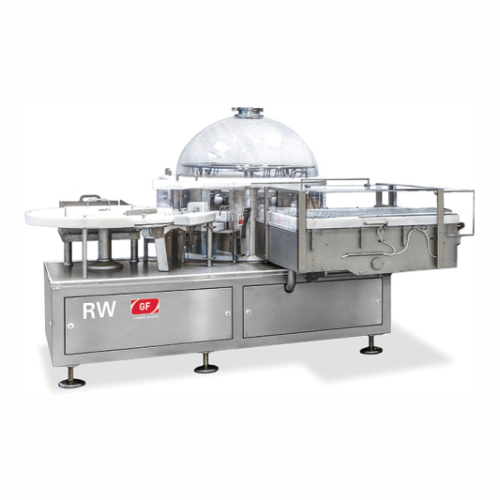
Rotary washer for pharmaceutical containers
Ensure optimal preparation of pharmaceutical containers with advanced rotary w...
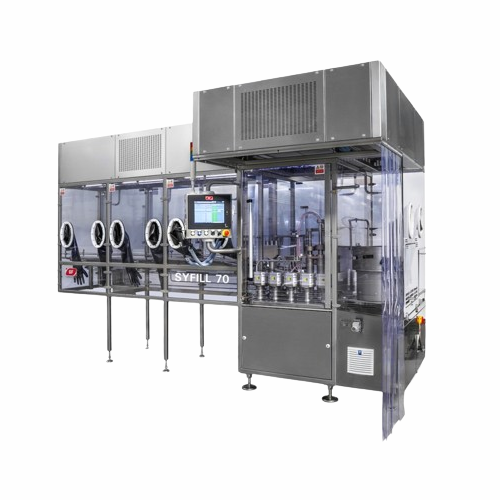
Vial filling system for sterile and nonsterile pharmaceuticals
Enhance precision in injectable drug preparation with a s...
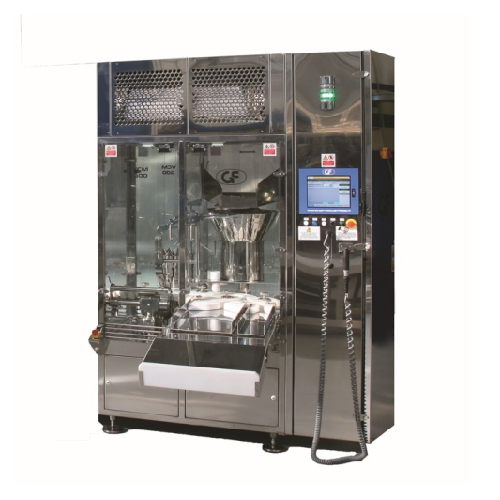
Vial capping solution for pharma applications
Efficiently secure the integrity of sensitive liquid medications with a flex...
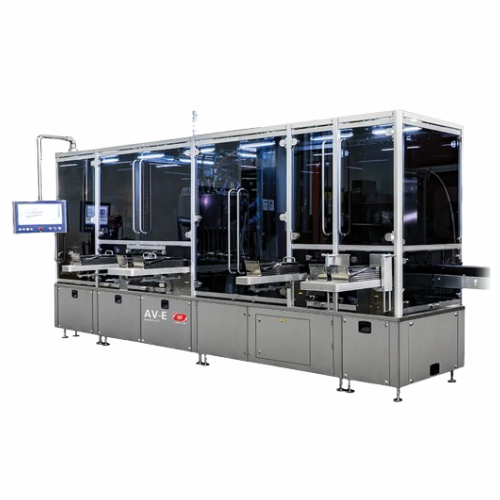
Optical inspection for ampoules, vials, cartridges, and syringes
Ensure product integrity and safety with this advanced ...
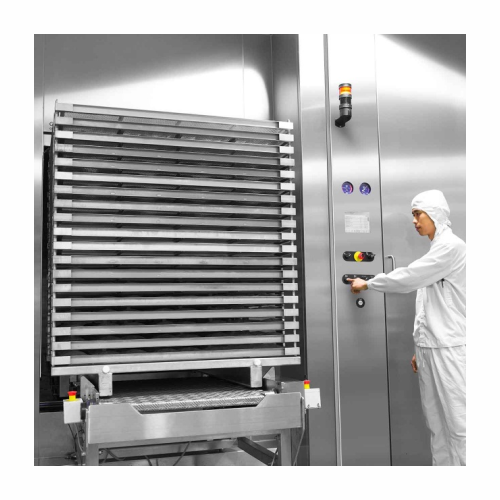
Pharmaceutical sterilization with steam/air mixture
Achieve sterile, dry, and ready-to-use pharmaceutical products with p...
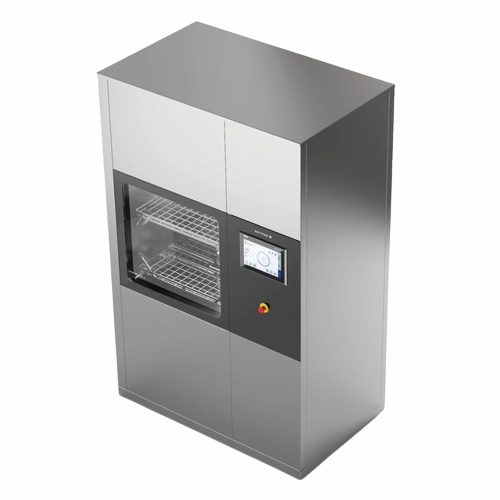
High-capacity cgmp washer/dryer for cleanrooms
Optimize your cleanroom operations with this compact washer/dryer, designed...
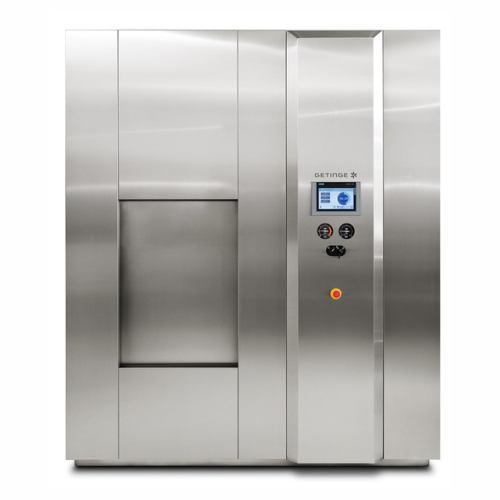
Steam sterilizer for pharmaceutical production
Ensure consistent, contamination-free sterilization of pharmaceutical compo...
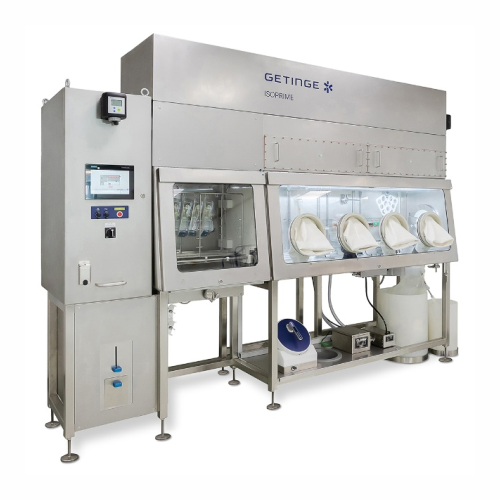
Cost-effective rigid-wall isolator for aseptic applications
Ensure sterility and safety with a versatile isolation and d...
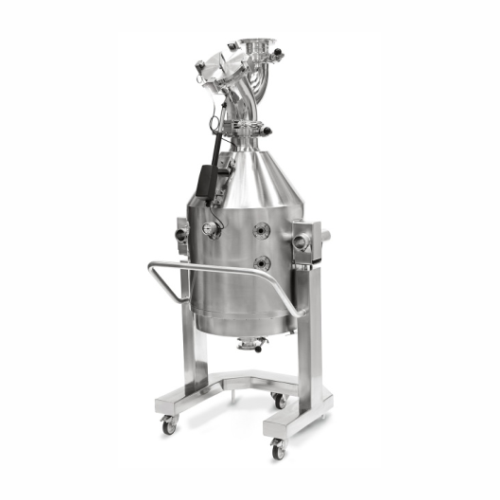
Sterile closure processing system for pharmaceutical production
Ensure your pharmaceutical closures remain sterile and i...
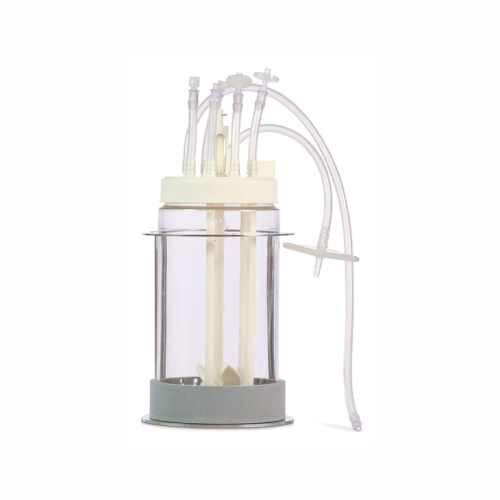
Single-use lab-scale bioreactor for upstream bioprocessing
Streamline your bioprocess development with a customizable, s...
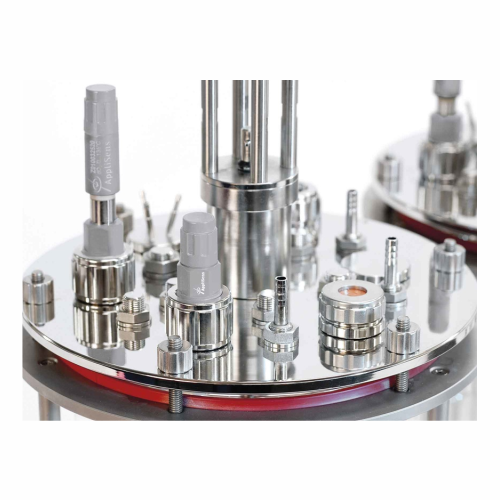
Bioprocess sensor for accurate measurement
Optimize your bioprocessing with advanced sensors designed to deliver precise m...
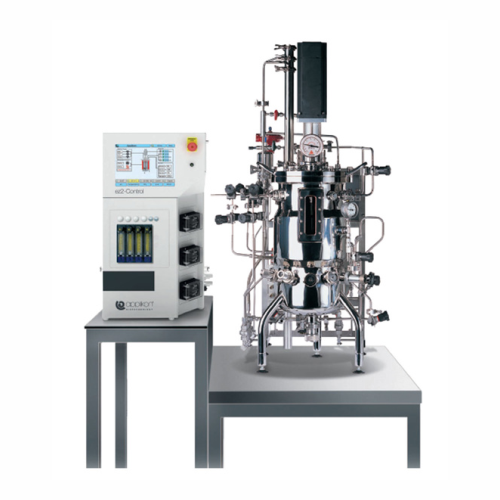
Bench top bioreactor for microbial and cell cultures
Optimize your bioprocessing workflow with this versatile bench top s...
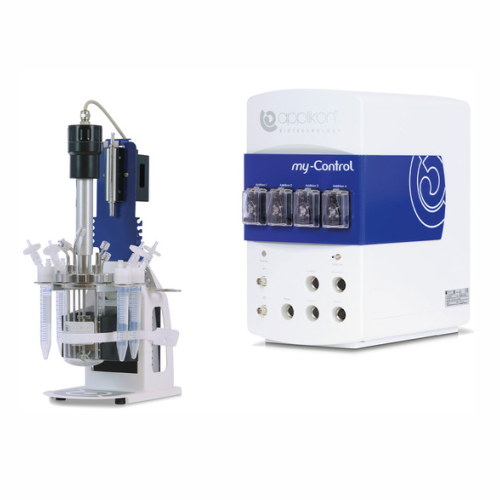
Turnkey bioreactor system for cell culture
Streamline your bioprocessing with a complete cultivation system; ideal for pro...
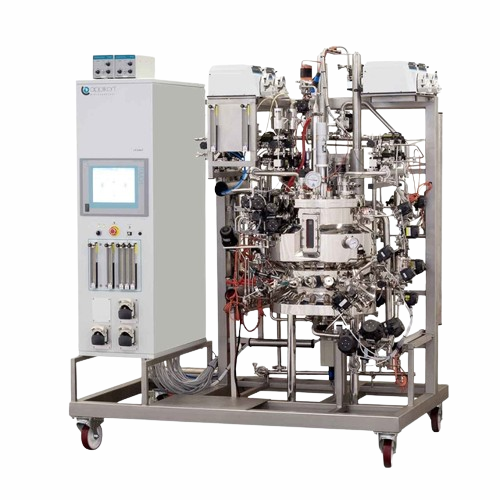
Stainless steel bioreactor for small-scale bioprocess production
Optimize your bioprocess development with a modular sta...
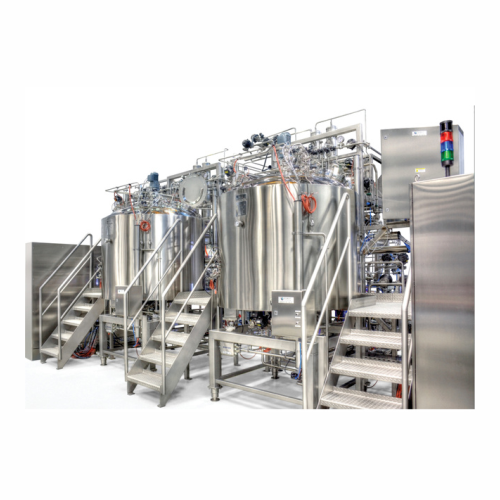
Stainless steel bioreactor for cgmp production
Achieve reliable and scalable production of life-saving medicines with a cu...
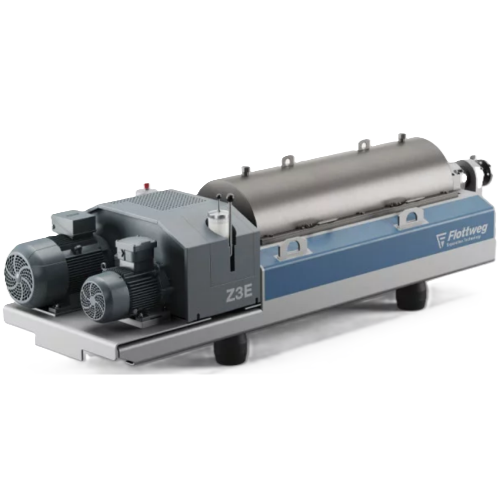
High-performance decanter centrifuge for industrial separation
Optimize your production with a centrifuge solution that ...

Bio-decontamination unit for heat-sensitive loads
Ensure the integrity of heat-sensitive biopharmaceutical products by em...

Sterility test isolator for injectables and sterile powders
Ensure sterility and compliance for injectables and biopharm...
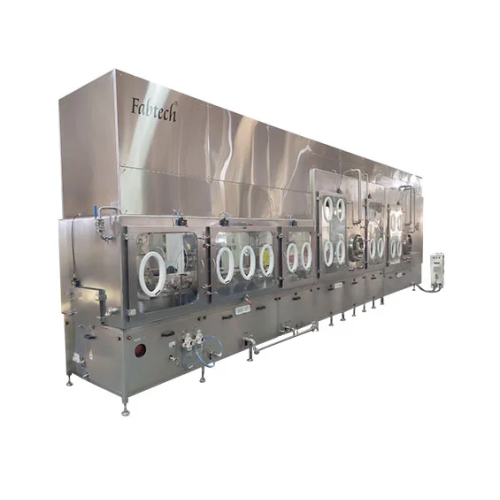
Aseptic filling isolator for vial / Pfs / cartridge
Ensure sterile and contamination-free filling of vials, pre-filled sy...
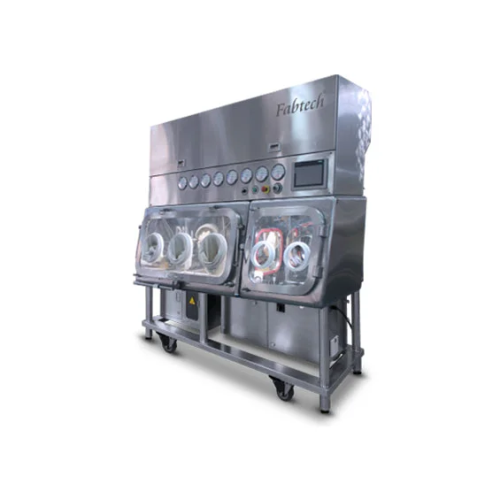
Mobile isolator for aseptic environment transfer
Ensure aseptic conditions and seamless material transfer with this mobile...
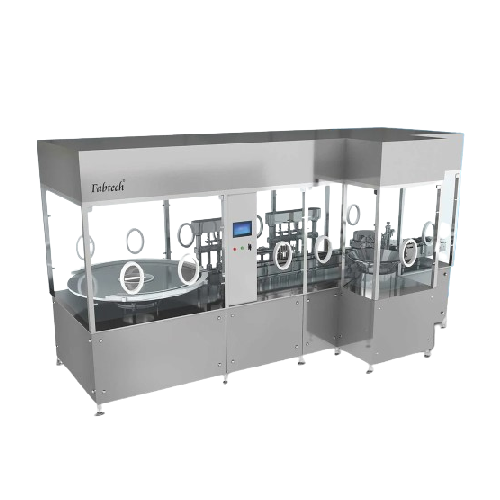
Pharmaceutical turnkey project consultants
Streamline your biopharma production with turnkey solutions that cover everythi...
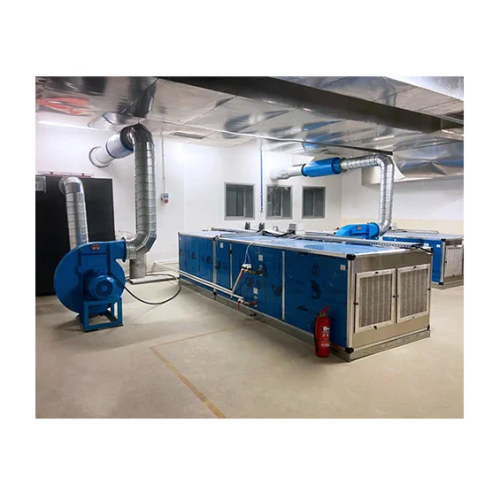
Cleanroom infrastructure for contaminant control
Ensure optimal contaminant control and regulatory compliance in cleanroom...
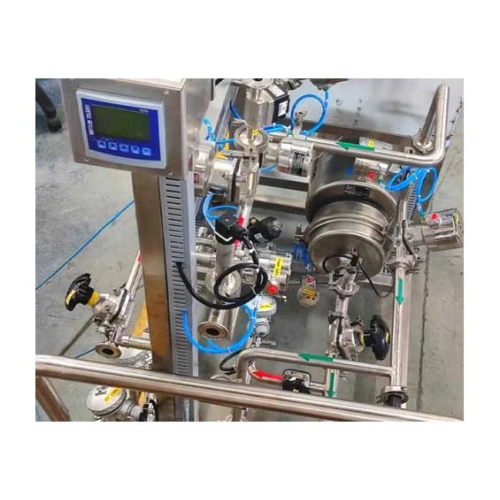
Cip & Sip systems for pharmaceutical cleaning
Ensure effective cleaning and sterilization in production lines with customi...
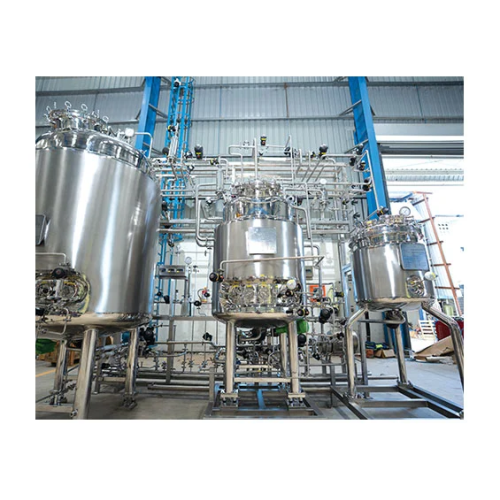
Pharma manufacturing process vessels
Ensure contamination-free production of sterile liquid formulations with process vesse...
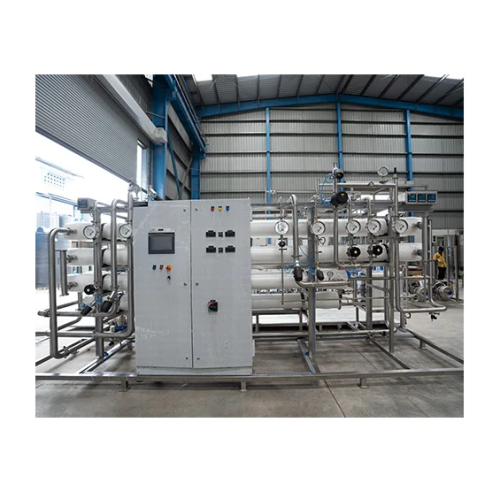
Purified water generation system for pharmaceutical applications
Ensure consistent water purity for critical drug formul...
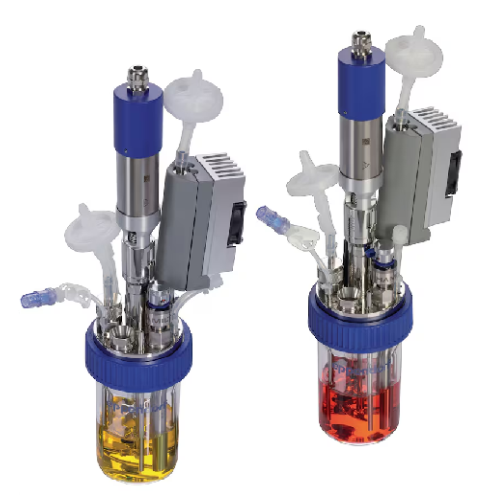
Mini bioreactor for cell culture and microbial process development
Achieve precise control and reproducibility in small...
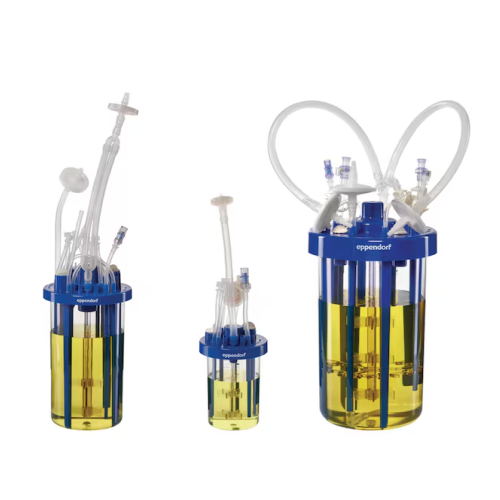
Single-use bioreactors for microbial fermentation
Optimize high-density fermentation with advanced single-use bioreactor ...
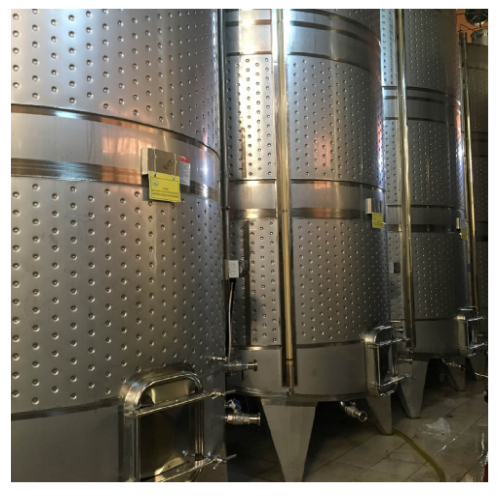
Stainless steel fermentation tanks
Optimize your fermentation efficiency with stainless steel tanks that provide precise te...
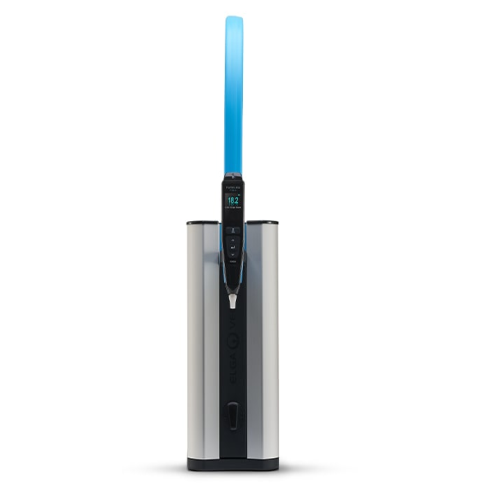
Ultrapure water system for analytical applications
Ensure critical purity for your molecular and analytical processes wit...
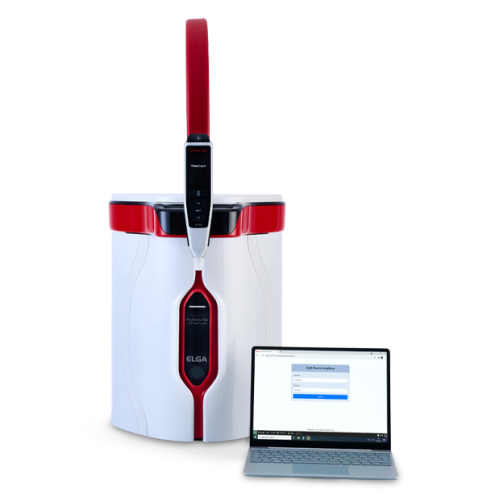
Pharmaceutical water purification system
Ensure compliance with stringent pharmaceutical standards by integrating a reliabl...
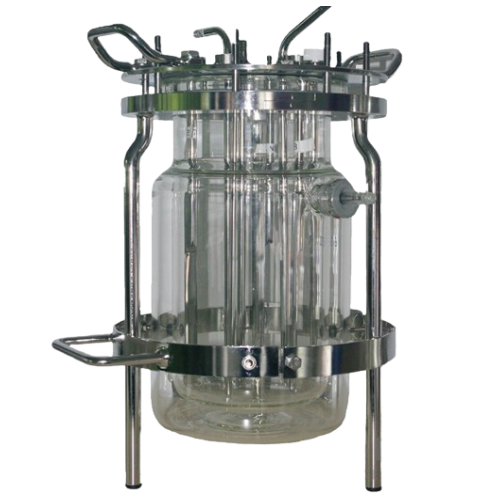
Bioreactor for cell culture yield optimization
Streamline complex cell culture processes with a bioreactor designed to enh...
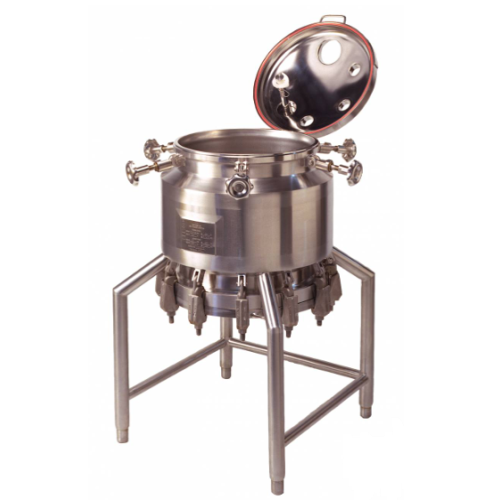
Static nutsche filters for liquid-solid separation
Achieve efficient separation of solids from liquids with precise contr...
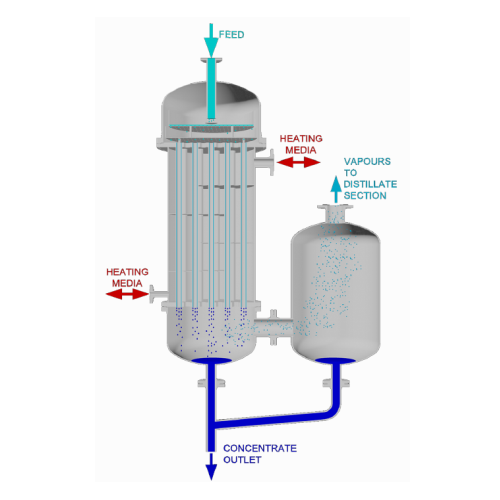
Falling film evaporator for thermal separation
Optimize energy efficiency in separation processes by utilizing gravity-dri...
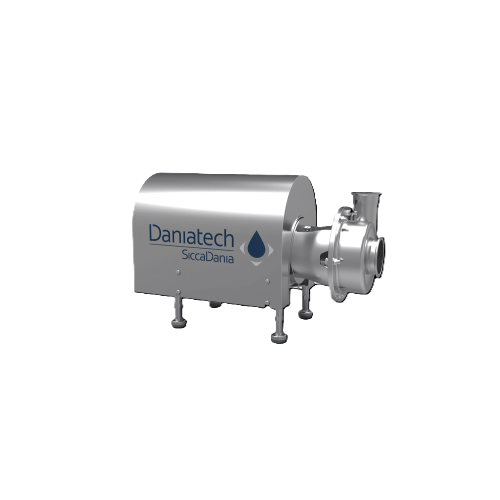
Ultra-high shear mixer for emulsification and homogenization
Optimize your production with ultra-high shear mixing, acce...
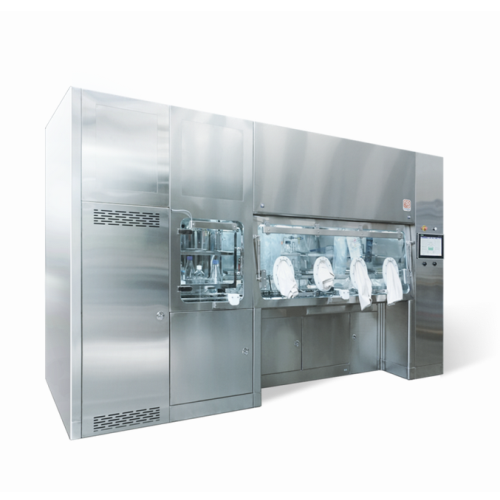
Modular sterility testing isolator for pharmaceuticals
Achieve uncompromised sterility with modular isolators designed fo...

Rotary filling system for Rtu vials in pharma production
Optimize your sterile liquid and powder handling with a versatil...
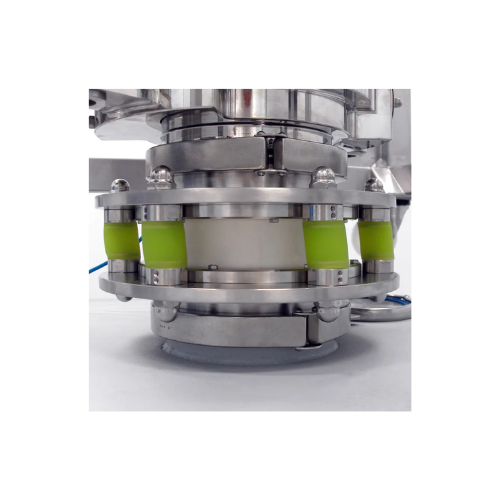
Bulk powder transfer safety device
Ensure stable and secure docking by minimizing equipment damage during powder transfer p...
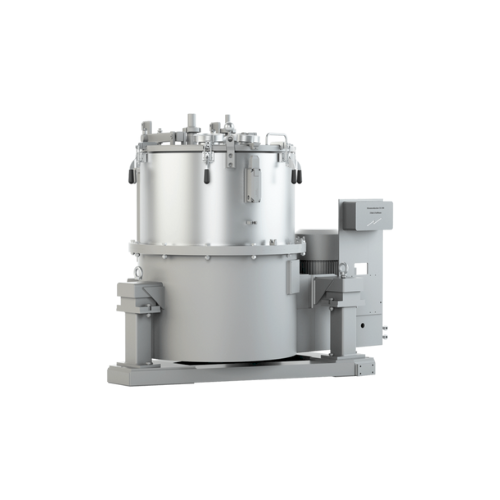
Industrial filter centrifuges for high solids content processing
Optimize processing of high-solid slurries with efficie...
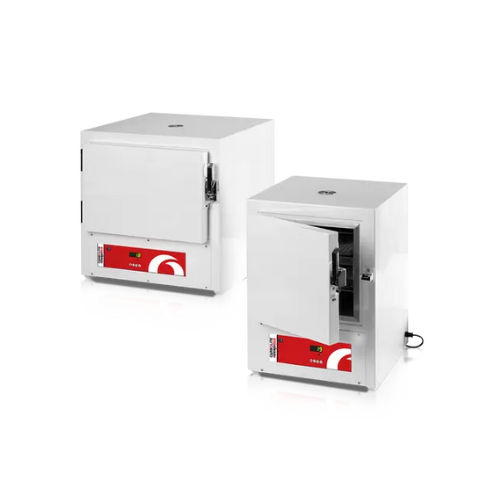
Clean room oven for class 100 environments
Achieve precise temperature control and maintain particle integrity in critical...
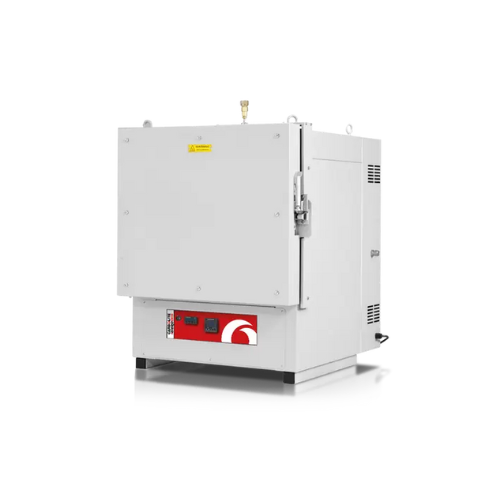
High temperature clean room ovens
Achieve precise environmental control for heating, drying, and sterilizing sensitive mate...
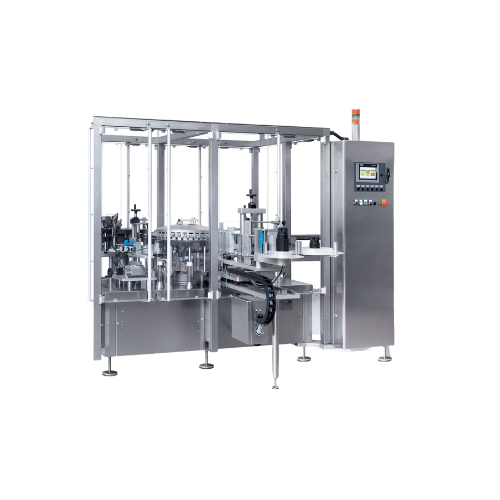
High-speed syringe assembler and labeller
Streamline your syringe production with a high-speed solution that assembles and...
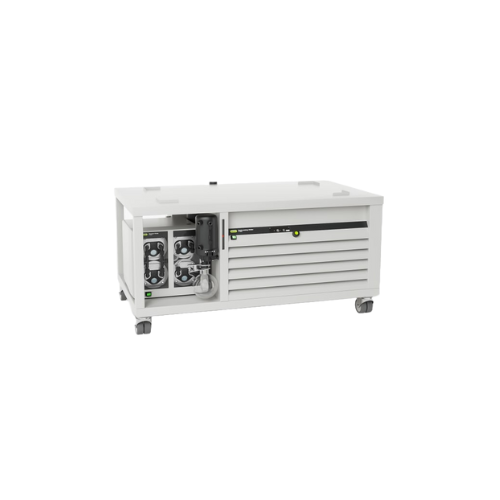
Industrial recirculating chiller for laboratory applications
For consistent distillation results, maintain accurate temp...
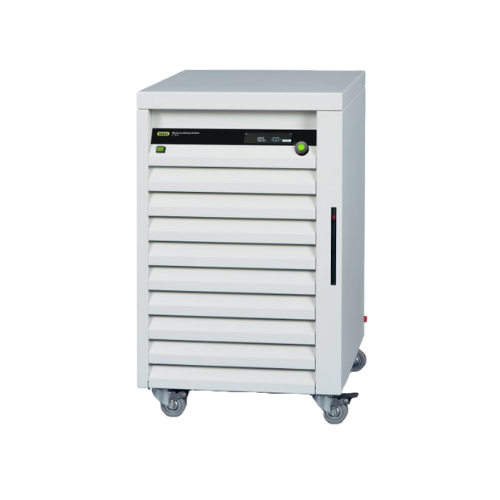
Recirculating chiller for evaporation and extraction
Streamline your laboratory processes with a chiller that efficiently...
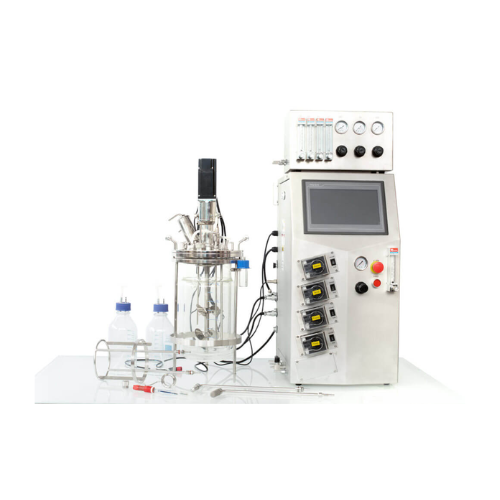
Autoclavable glass fermentor for biotech research
Optimize your fermentation processes with a versatile benchtop solution...
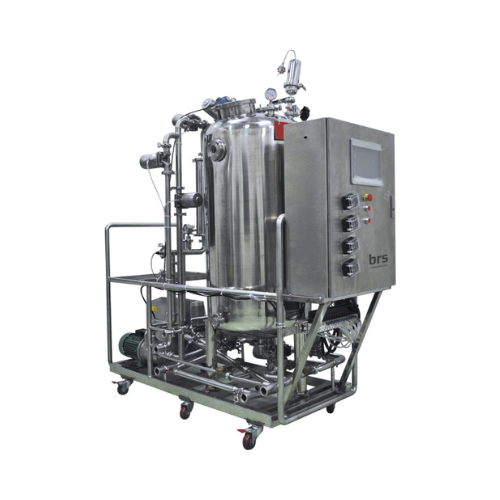
Clean-in-place systems for biotechnology and pharma
Ensure seamless transitions between production batches with efficient...
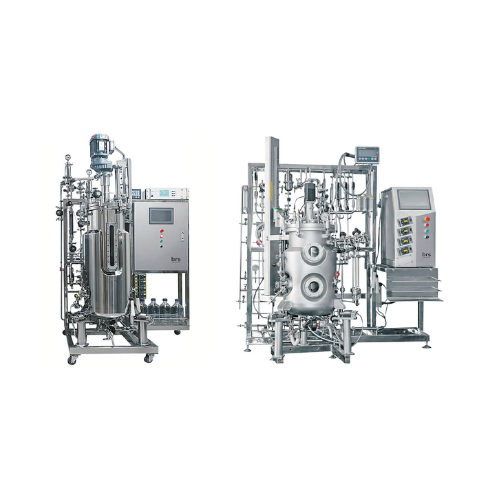
Industrial fermentors for large-scale bioprocessing
Enhance yield and consistency in fermentation processes with precise ...
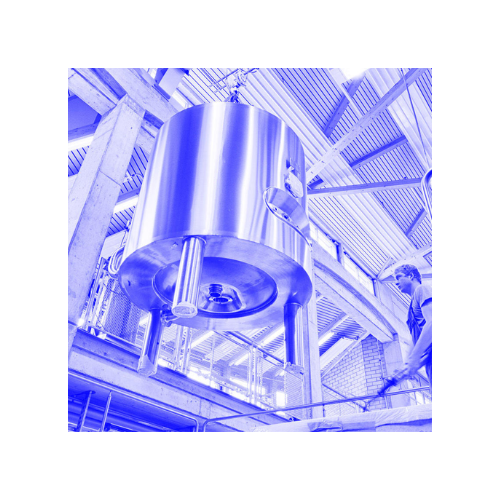
Sterile media and buffer storage tanks
Ensure uninterrupted bioproduction with our tanks designed for secure storage and pr...
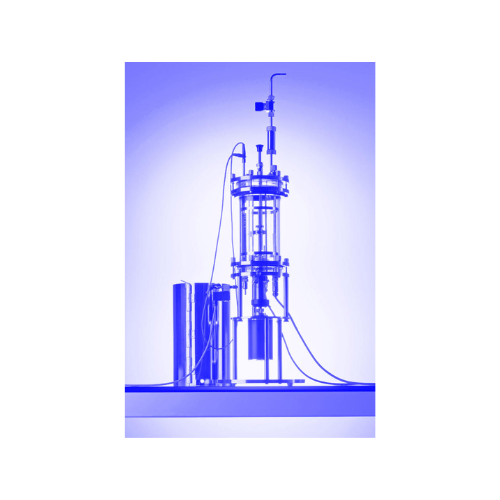
Lab-scale in-situ sterilizable bioreactor
Ensure precision in your laboratory and pilot projects with this bioreactor, des...
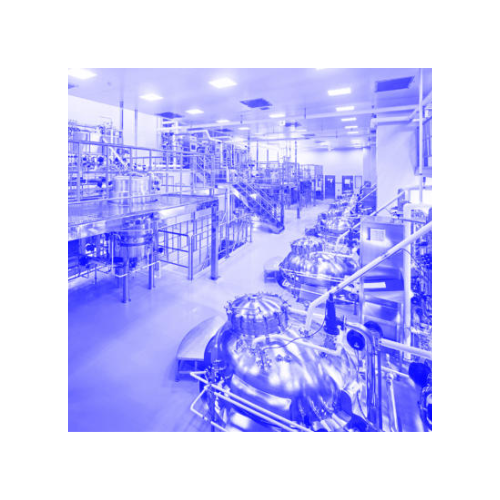
Bioreactors for cell culture processes
Efficiently cultivate sensitive cell lines with customizable bioreactors designed to...
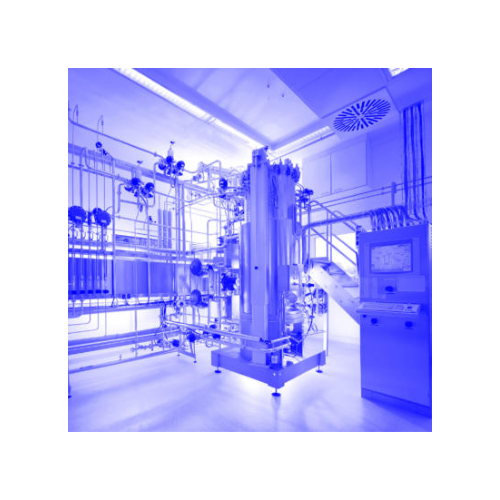
Lab-scale fermentors for microbial cultivation
Optimize microbial cultivation with lab-scale fermentors designed for preci...
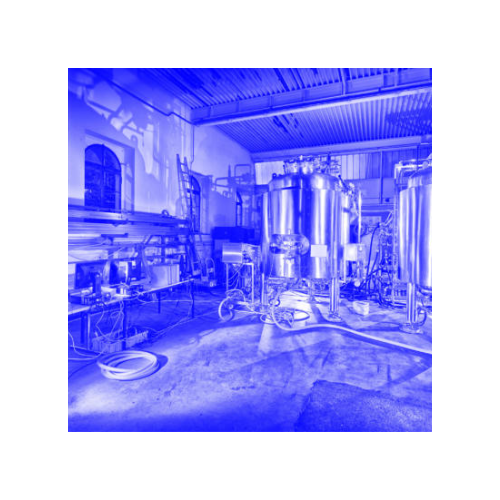
Formulation vessel for biopharmaceutical homogeneity
Achieve precise homogeneity in liquid formulations with vessels opti...
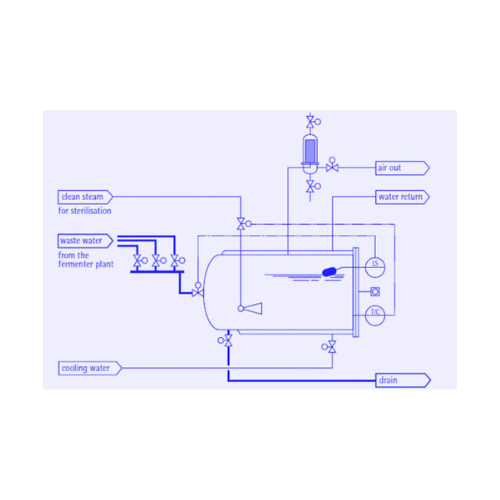
Biowaste decontamination system
Ensure safe handling of pathogenic and genetically modified organisms in wastewater with pre...
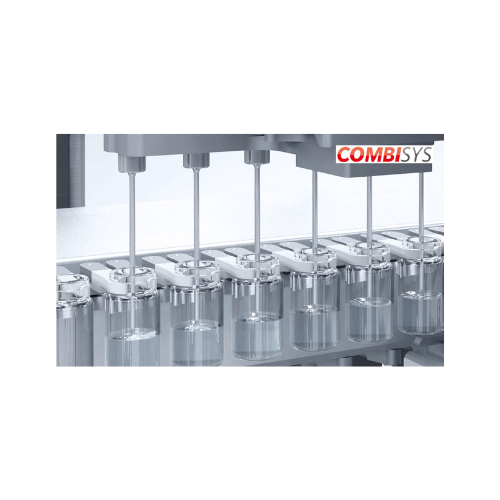
Combisys filling and closing system for pharmaceutical containers
Ensure precise filling and closing of pharmaceutical ...
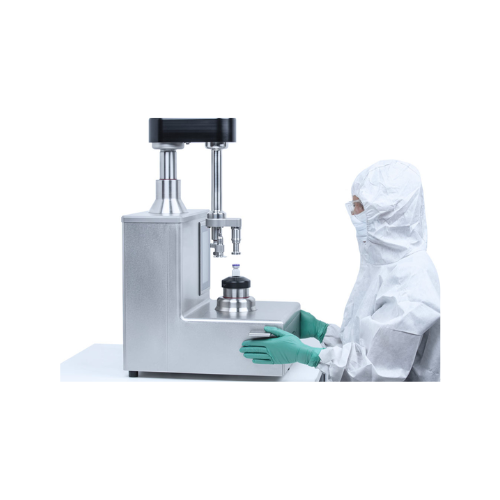
Vial and cartridge crimping solution
Streamline your packaging process with a compact solution for precise crimping and cap...
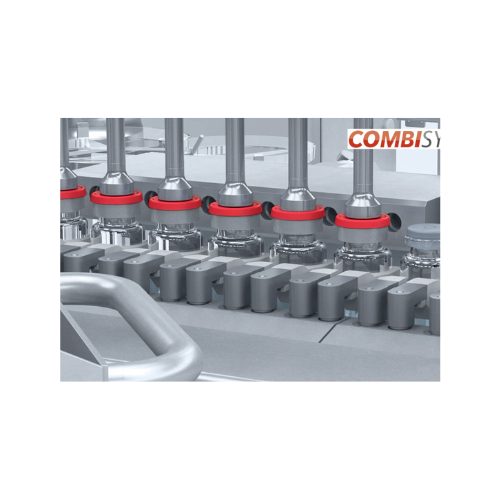
Automated vial closing system
Ensure reliable vial sealing with unparalleled flexibility and precision, optimizing your liqu...
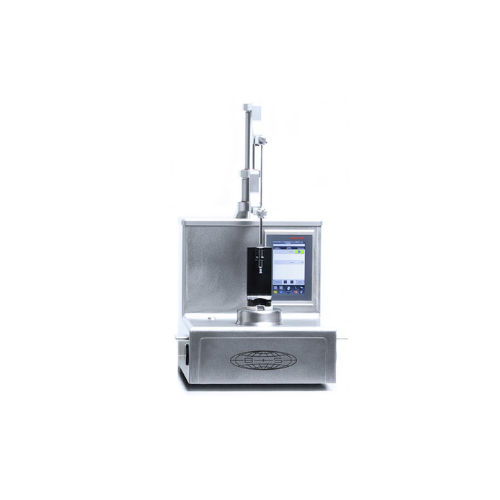
Cartridge and disposable syringe closing solution
Ensure precise closing of pre-filled syringes and cartridges with custo...
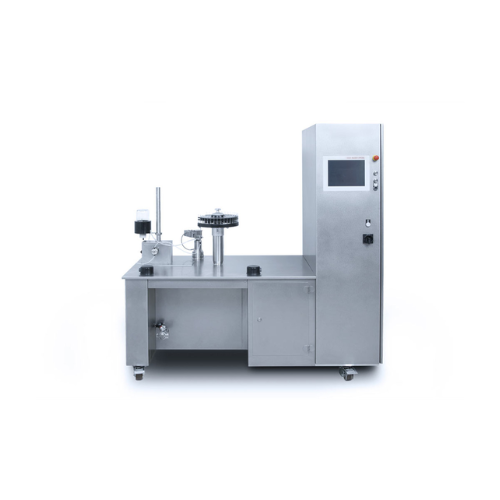
Silicone spraying unit for laboratory and small-scale production
Ensure precise silicone application for cartridges, syr...
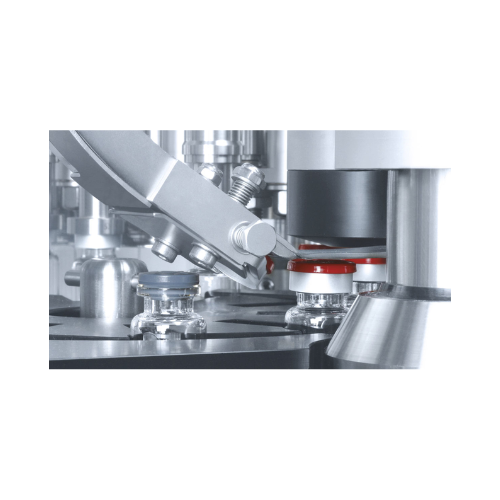
Pharmaceutical container closing solution
Ensure precise capping and inspection of pharmaceutical containers, reducing con...
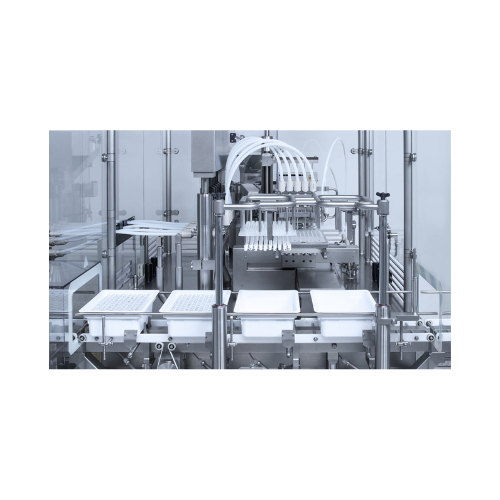
Filling and closing solution for nested containers
Streamline your vial, cartridge, and syringe production with precise d...
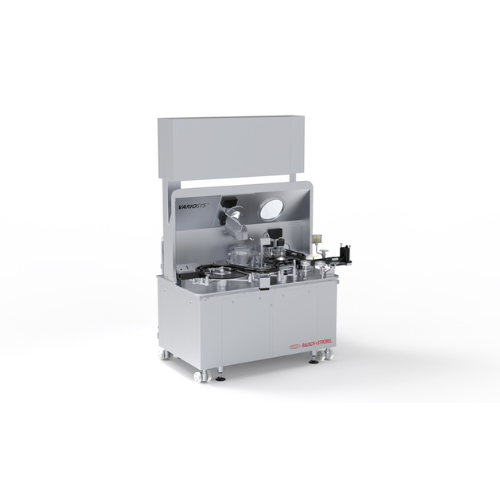
Sealing system for bottles and vials
Ensure precise sealing and capping of liquid pharmaceuticals with minimal particle emi...
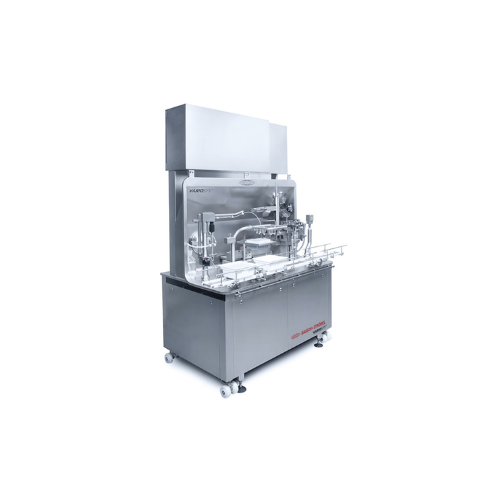
Filling and closing system for nested containers
Optimize liquid formulation packaging with a high-speed system designed f...
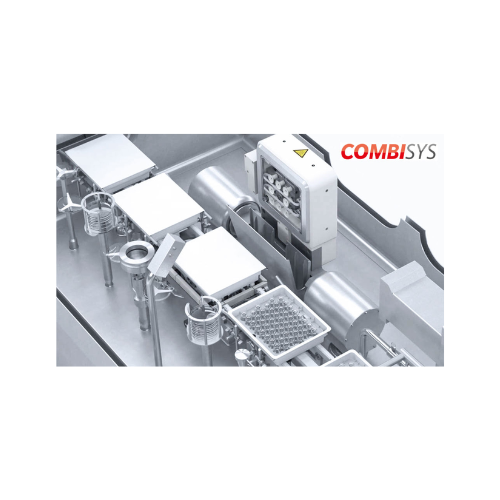
Automatic tub de-bagging and de-nesting solution
Efficiently prepare your RTU containers by seamlessly integrating de-bagg...
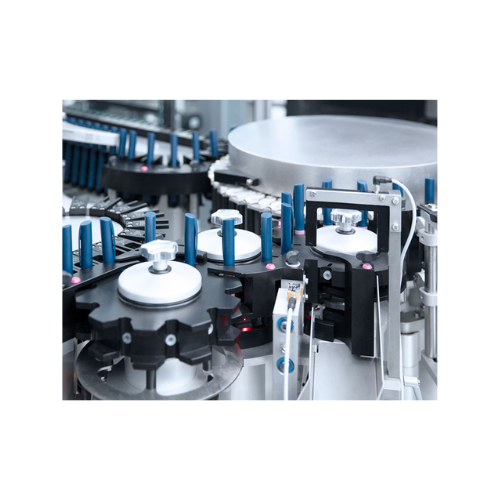
Labeling system for insulin pens
Achieve precise labeling of self-medication pens with guaranteed accuracy and gentle handli...

Tray loader for pharmaceutical containers
Maximize efficiency in aseptic fill-finish lines with precise and rapid tray loa...
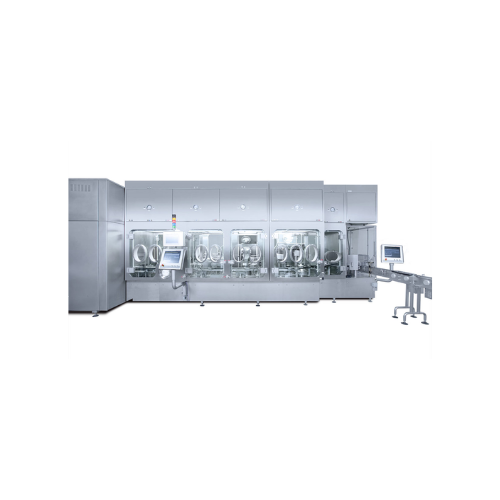
Filling and closing solution for vials and stable bottles
Optimize vial and bottle processing with a seamless solution d...
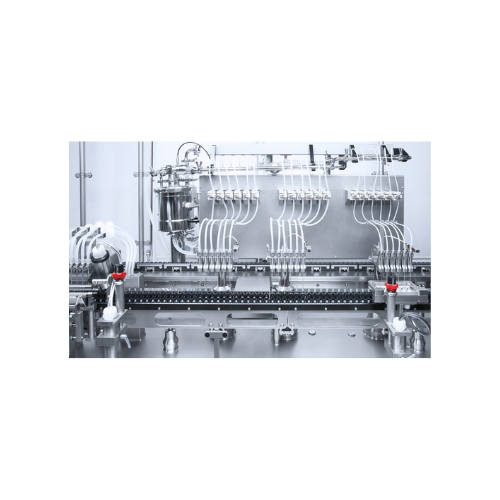
Filling and closing system for cartridges
Enhance your cartridge production with precise filling and closing technology de...
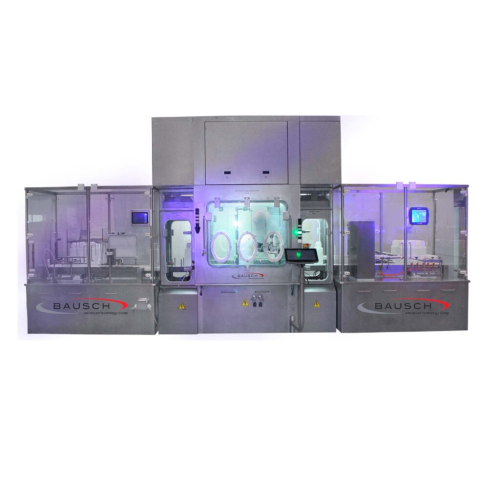
Automated filling and closing system for vials and bottles
Optimize your vial and bottle filling line with precise liqui...
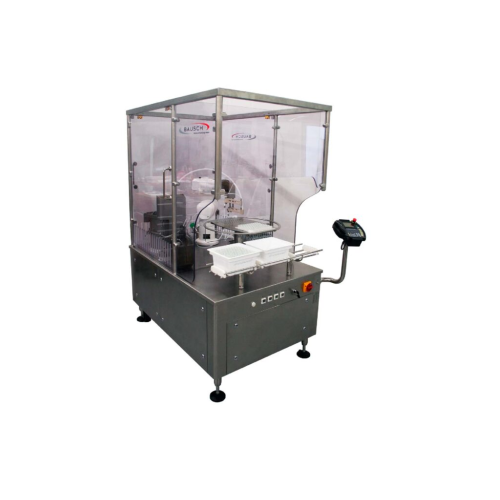
Nested vial and syringe filling and closing system
Achieve precise aseptic filling and closing for clinical products with...
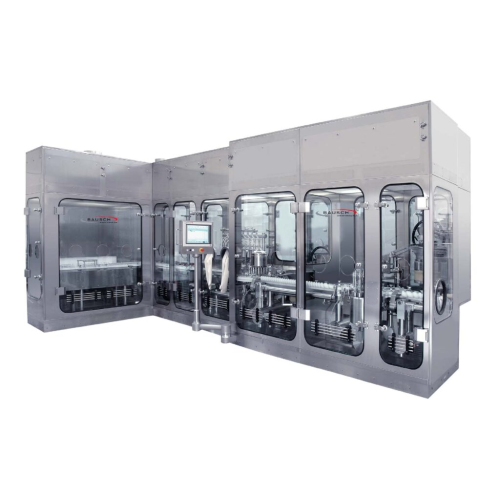
Vial and cartridge filling and closing system
Optimize your aseptic fill-finish process with high-speed, continuous operat...
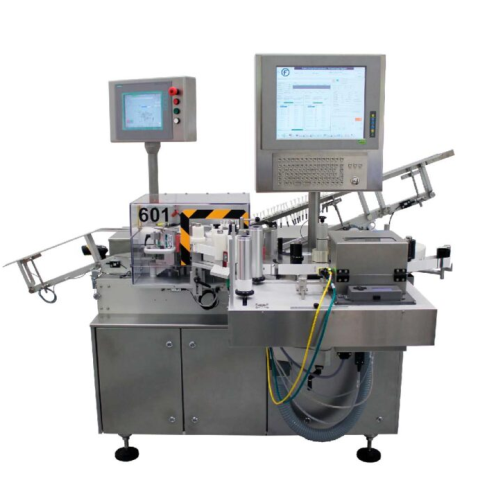
Automatic labeling system for pharmaceutical containers
Streamline your pharmaceutical packaging with precision labeling,...
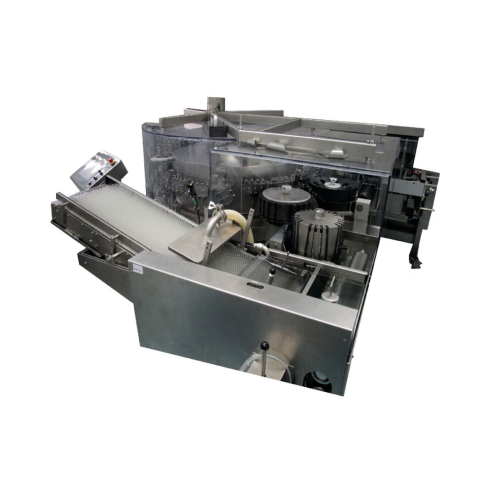
Rotary washing system for pharmaceutical containers
Achieve superior cleanliness and efficiency with a high-speed rotary ...
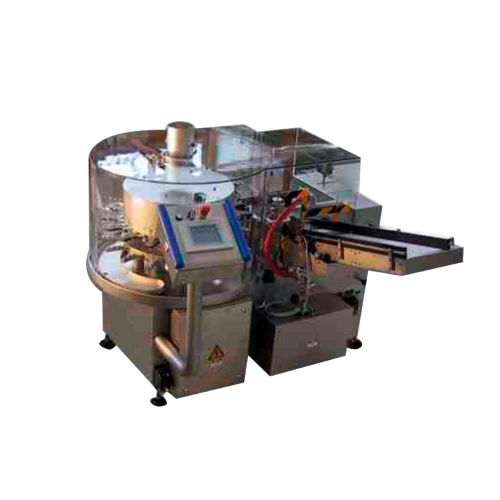
Automated washing system for vials, syringes, cartridges, and ampoules
Achieve sterile conditions with this high-speed ...
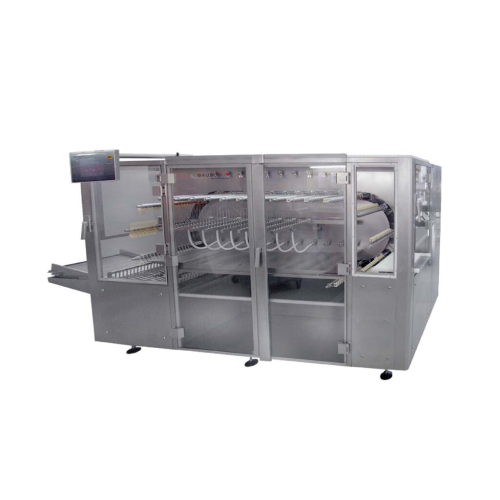
High-speed washing system for ampoules and vials
Ensure contamination-free ampoules and syringes with this advanced washin...
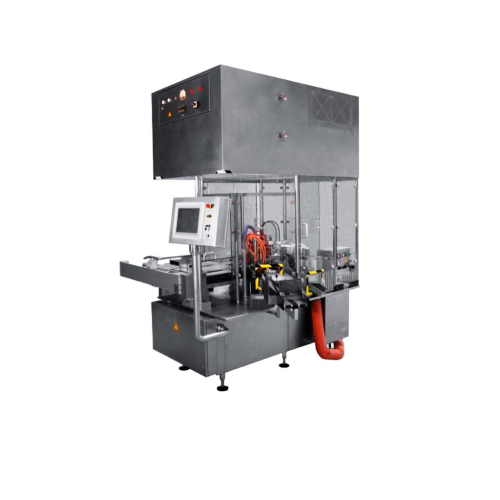
Ampoule filling and closing system
Optimize your production line with a high-speed system designed for seamless filling and...
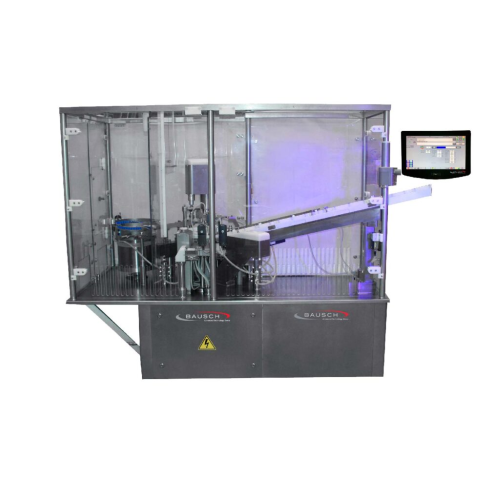
Filling and closing solution for vials and syringes
Achieve precise aseptic fill-finish of liquid formulations in vials a...
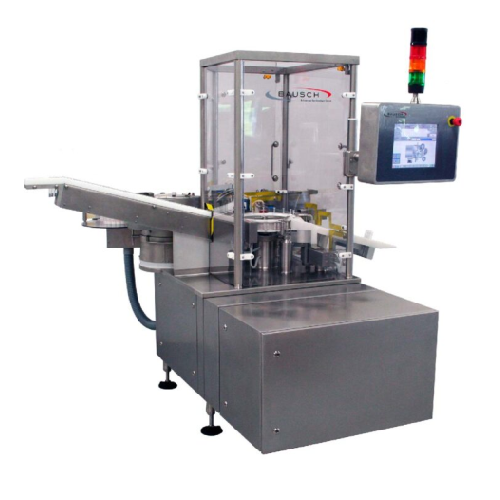
High-speed syringe plunger rod assembly
Achieve seamless syringe preparation with high-speed plunger rod assembly, ensuring...
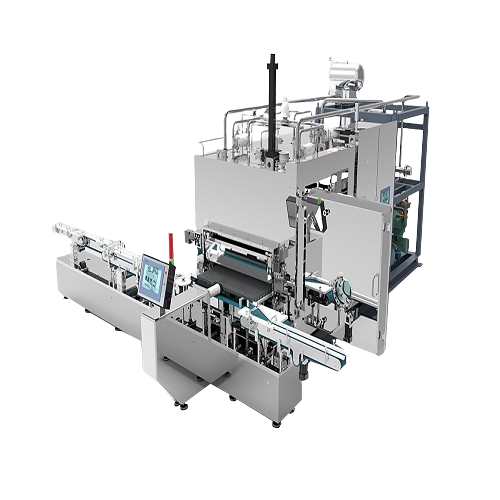
Commercial freeze dryer for pharmaceutical Api production
Ensure the stability and potency of your biopharmaceutical pro...
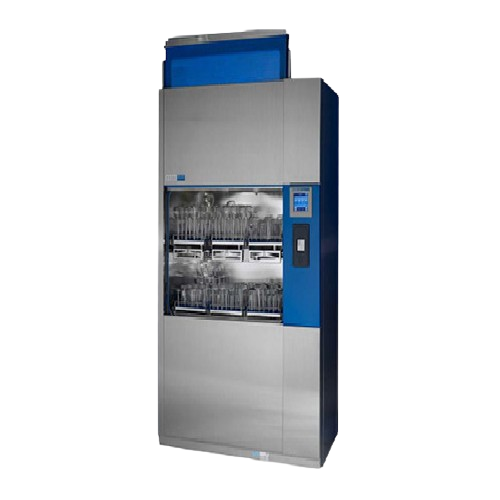
Laboratory instrument washer for scientific research and quality control
Achieve consistent results with thorough clean...
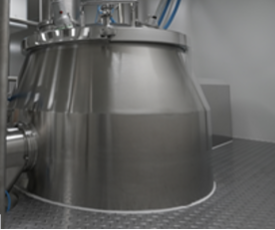
Continuous wet granulation equipment
Achieve optimal particle size and uniformity in pharmaceutical production with our con...
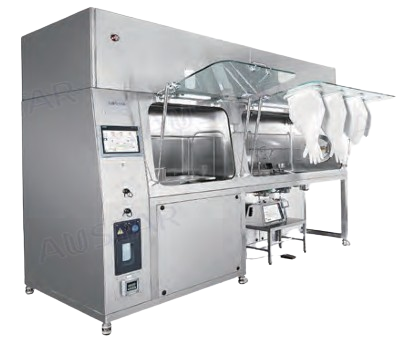
Sterilisable isolator workstation for aseptic containment
Ensure precise contamination control and sterile conditions du...
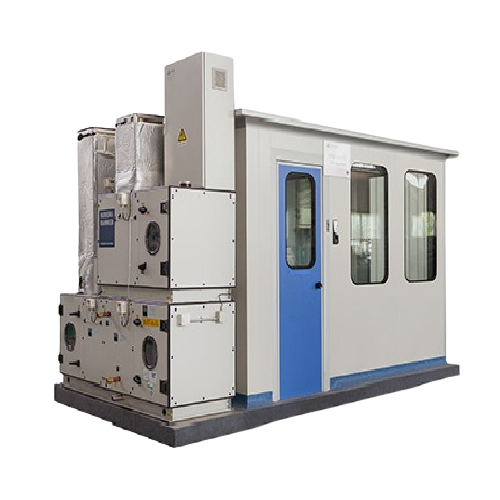
Customized Hvac system for pharmaceutical clean rooms
Achieve seamless sterilization and contamination control in clean r...
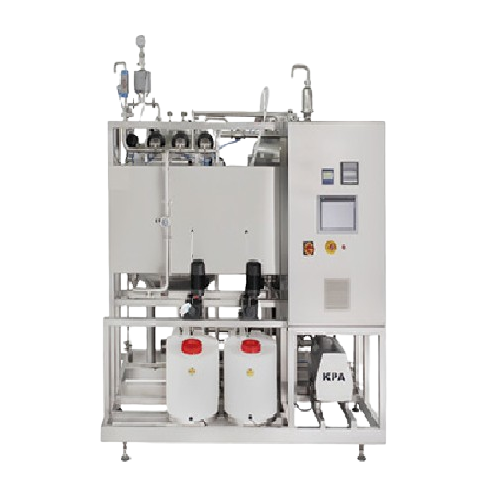
Cip workstation for pharmaceutical liquid preparation systems
Optimize your liquid formulation process with precise clea...
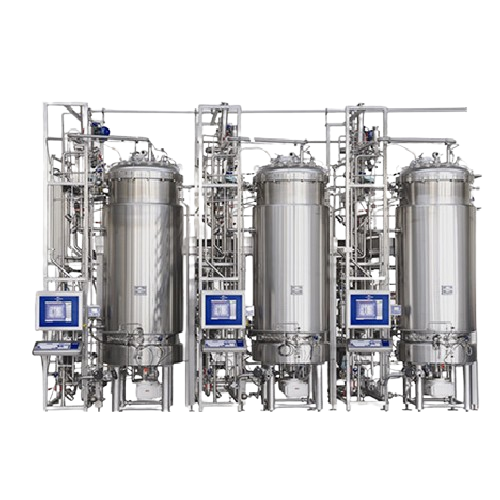
Biological fermentation tank for pharmaceutical production
Ensure consistent high-yield biological culture results with ...
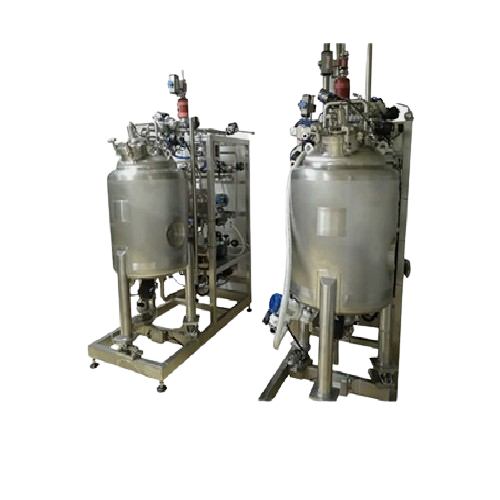
Ultrafiltration and depth filtration system for biopharmaceuticals
Achieve precise separation and purification of bioph...
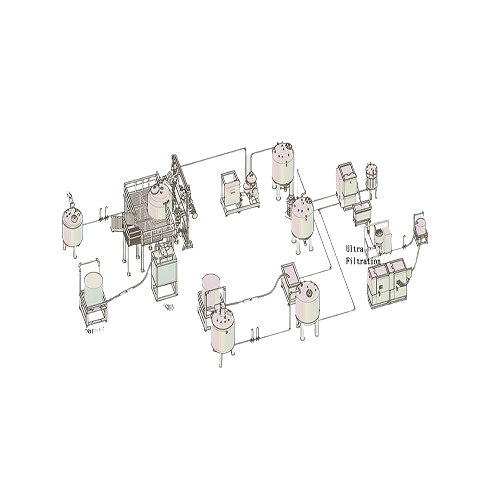
Hybrid bioprocess system for cell culture and purification
Streamline your bioprocessing operations with a versatile sol...
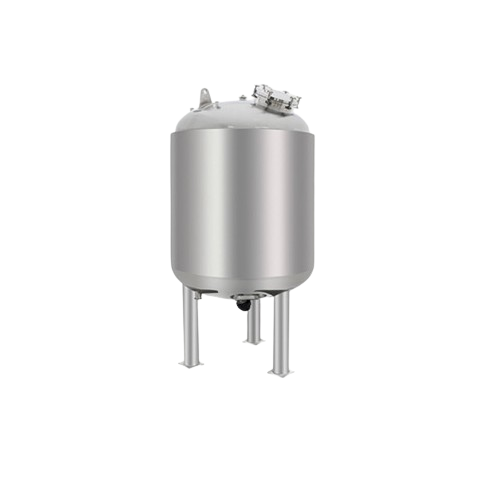
Purified water storage tank for pharmaceutical use
Ensure the integrity of your pharmaceutical formulations with precisio...
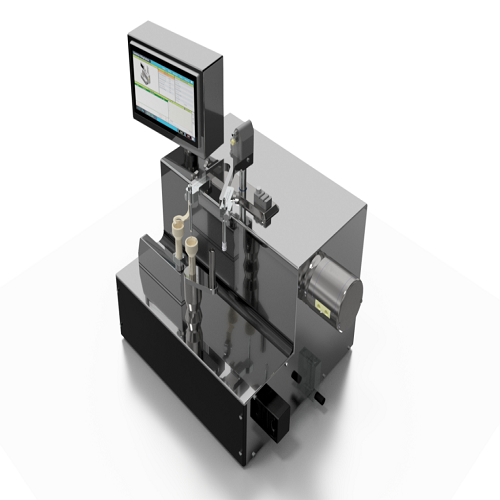
Tabletop vial and syringe filling system
Ensure precise dosing and maintain sterility in small batch production with a comp...
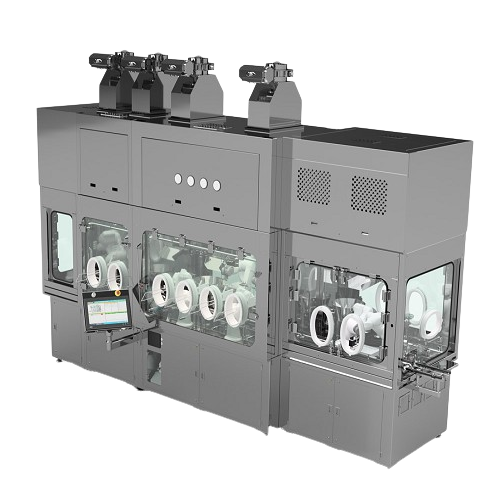
Aseptic small / medium batch filling and closing system
Ensure sterility in drug production by seamlessly integrating a v...
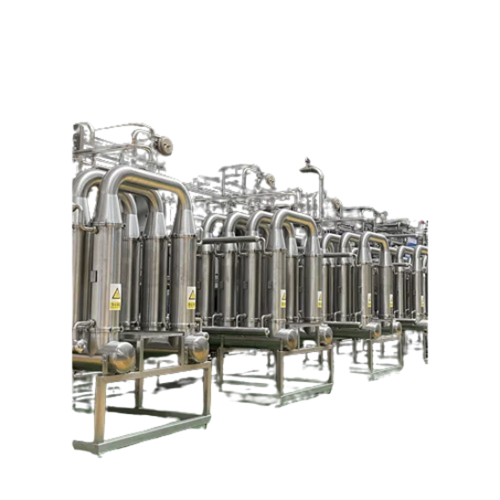
Cross flow filtration for industrial liquid purification
Optimize your production process with advanced cross flow filtra...
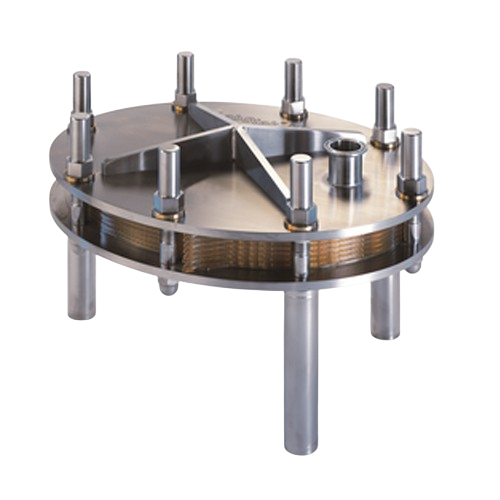
Ultrafiltration and microfiltration test unit
Streamline your filtration and membrane testing with a flexible, scalable un...
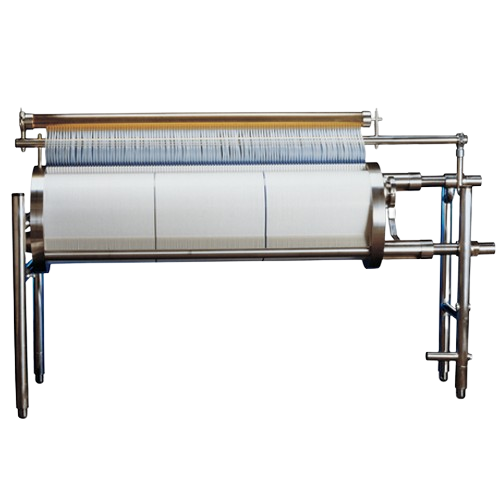
Ultrafiltration and microfiltration module for low to medium viscosity products
Streamline the separation and concentr...
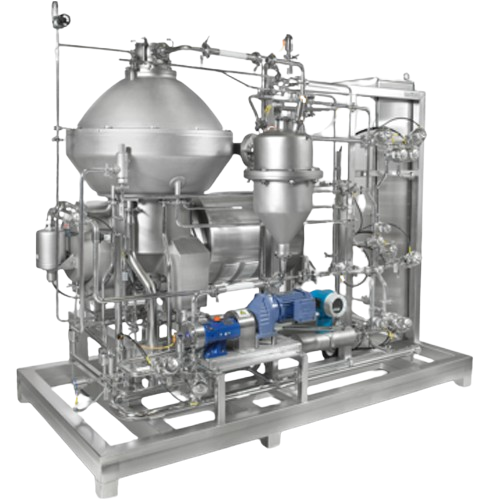
Microbial cell clarification solution
Achieve high-yield, foam-free microbial cell clarification with minimal shear stress ...
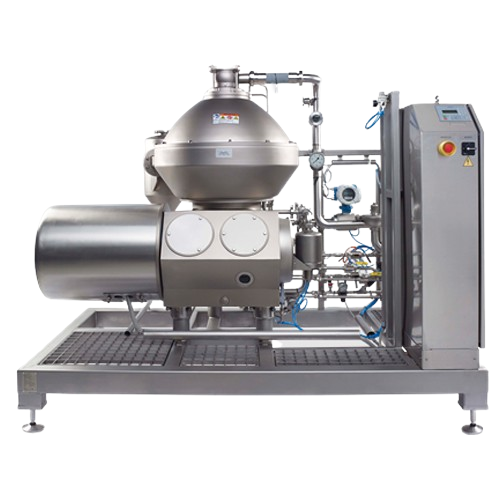
Biopharma cell centrifuge for gentle protein recovery
Ensure gentle cell harvesting and enhanced yield in bioprocessing w...
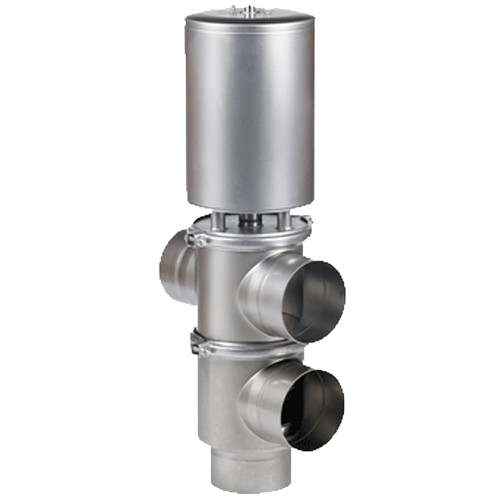
Single seat valve for hygienic applications
Ensure optimal hygiene and safety with a versatile pneumatic valve designed to...
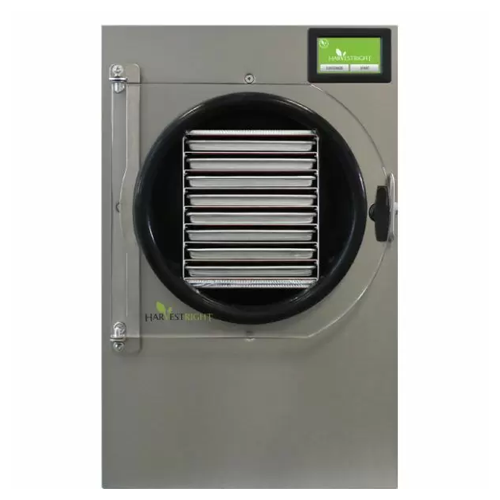
Pharmaceutical freeze dryer for medium scale production
Ensure optimal preservation of active ingredients through precise...
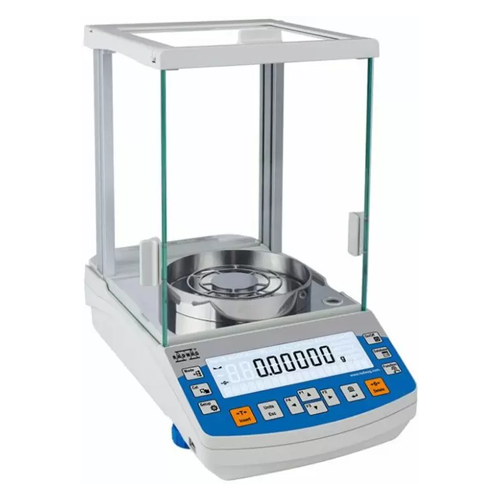
Analytical balance for precise laboratory measurements
Achieve unparalleled precision and reliability in your lab’s...
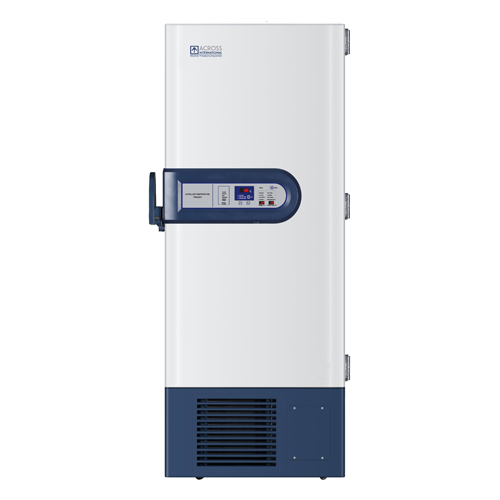
Ultra-low freezer for medical and biological storage
For critical preservation of sensitive samples, this ultra-low tempe...
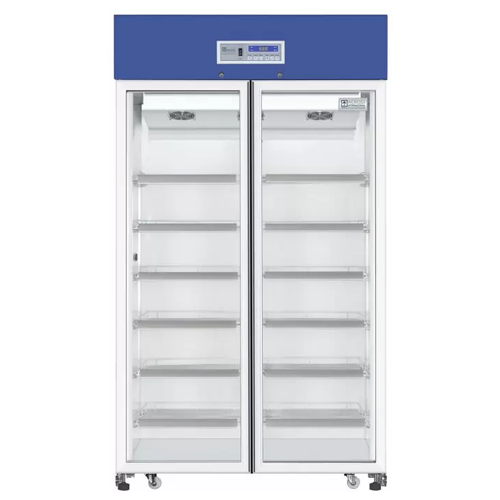
Laboratory upright refrigerator for vaccine storage
Ensure the optimal preservation of critical vaccines and specimens wi...
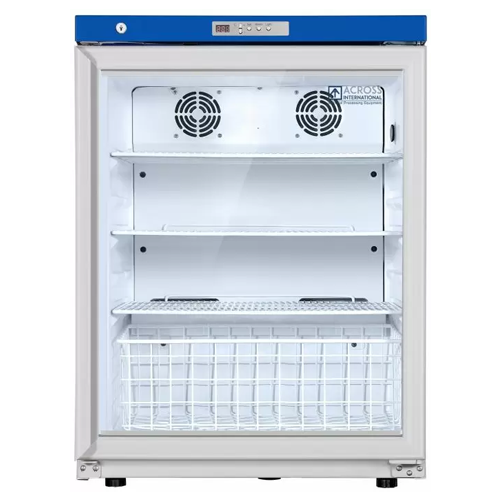
Compact refrigerator for vaccine storage
Ensure critical temperature stability for sensitive pharmaceuticals and vaccines, ...
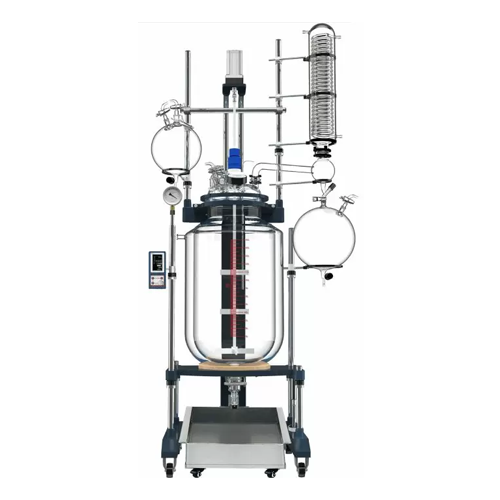
150l jacketed glass reactor for chemical synthesis
Achieve precise control over complex chemical processes with this sing...
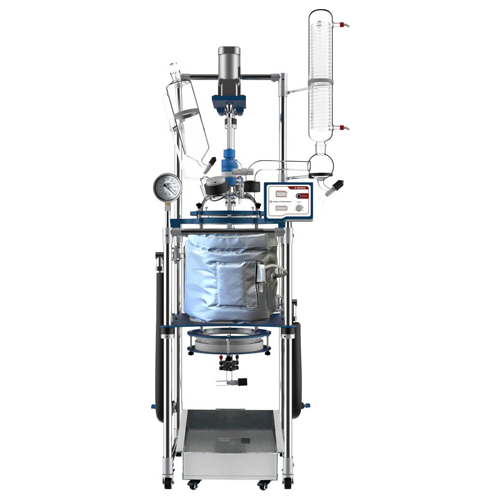
20l jacketed glass reactor for controlled chemical reactions
Optimize your chemical synthesis with precise temperature c...
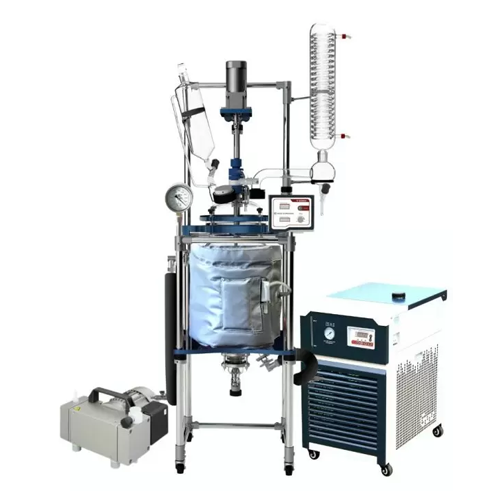
Large capacity jacketed glass reactor
Achieve precise control over temperature and vacuum conditions with this versatile re...
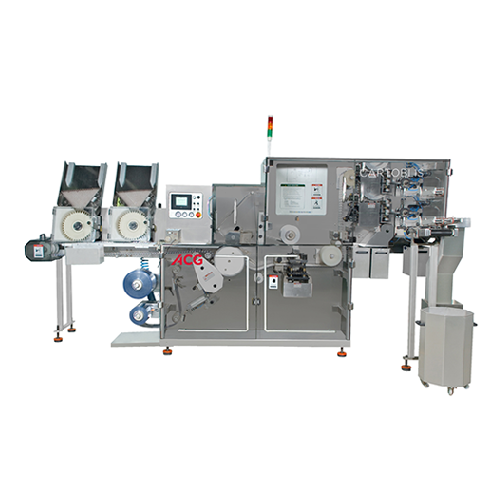
Blister packaging for solid dosage forms
Optimize your packaging line with high-speed, continuous blister packaging that en...
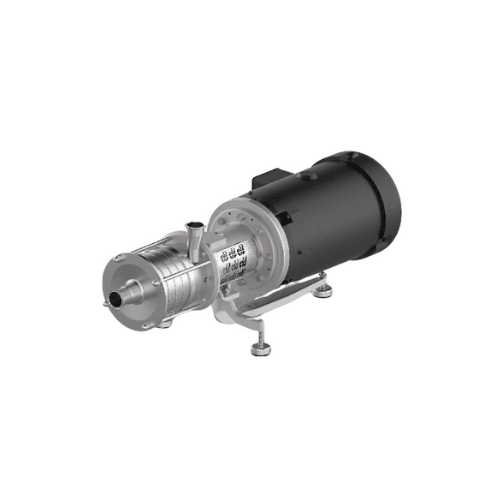
Hygienic pump for beverage and pharmaceutical industries
Engineered to meet stringent hygiene demands, this versatile pum...
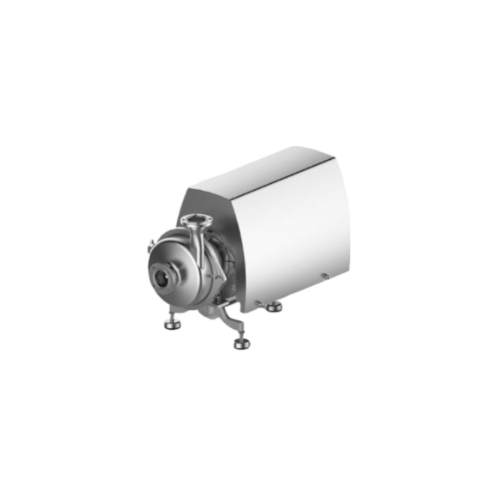
Centrifugal pumps for hygienic applications
Ensure precise liquid handling for high-stakes applications with this hygienic...
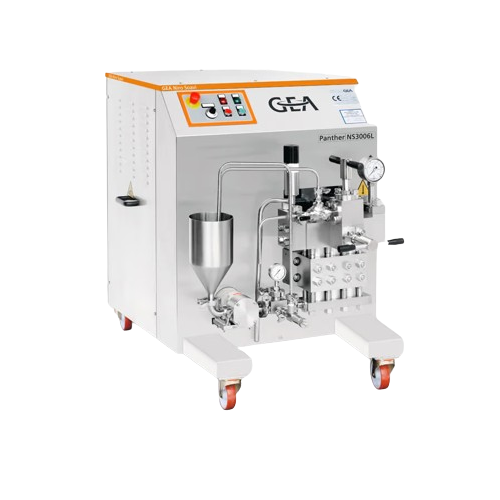
Pilot plant homogenizer for continuous operation
Achieve consistent fluid textures and prolonged shelf life with high-pres...

Process analytical technology for lyophilization
Ensure product integrity by detecting trace contaminants and optimizing l...
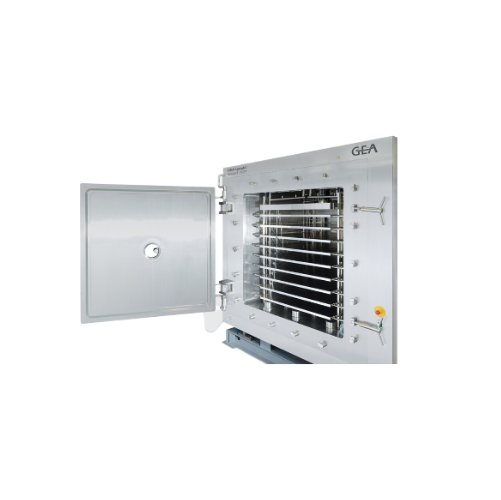
Pharmaceutical freeze dryer for large-scale production
Streamline your freeze-drying process with precision-engineered ly...
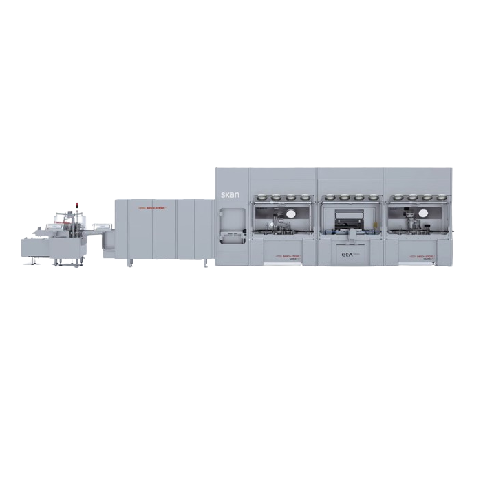
Freeze dryer for small-scale production
Optimize your production line with reliable lyophilization that ensures precise moi...
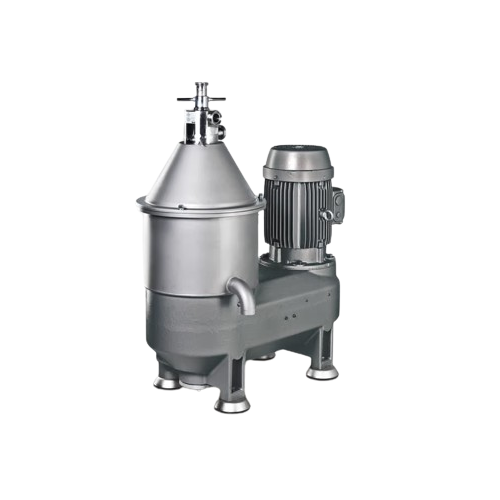
Solid-wall bowl separators for pharma extraction
Optimize your extraction processes with precision solid-wall bowl separat...
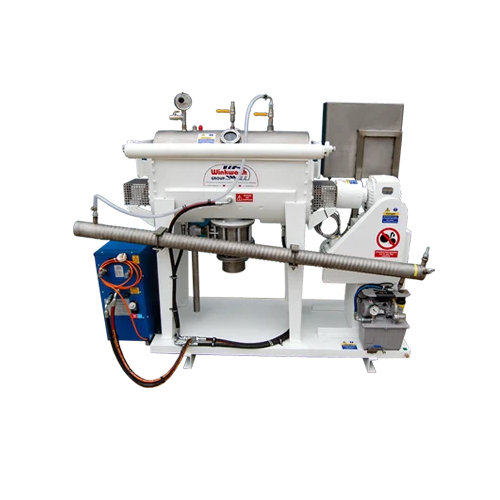
Industrial blenders for powder and granule mixing
Optimize your production line with advanced mixing solutions designed f...
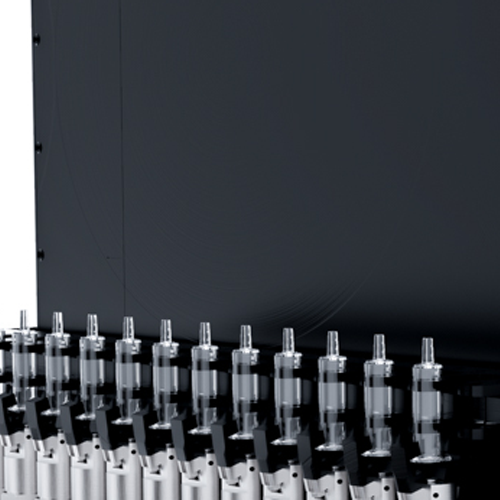
X-ray inspection module for pre-filled syringe needles
Ensure sterility and product integrity in high-speed syringe produ...
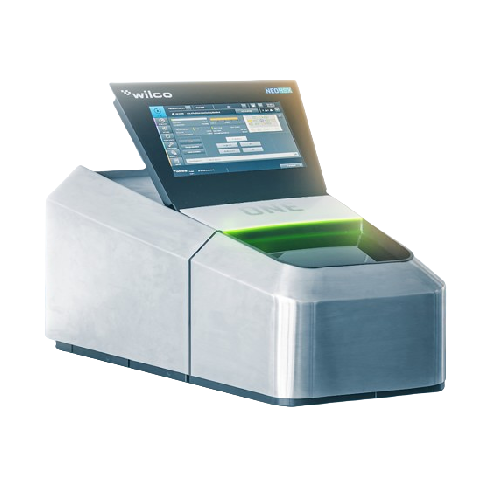
Lab headspace analyzer for small volume parenterals
Enhance your quality control with precise gas concentration measureme...
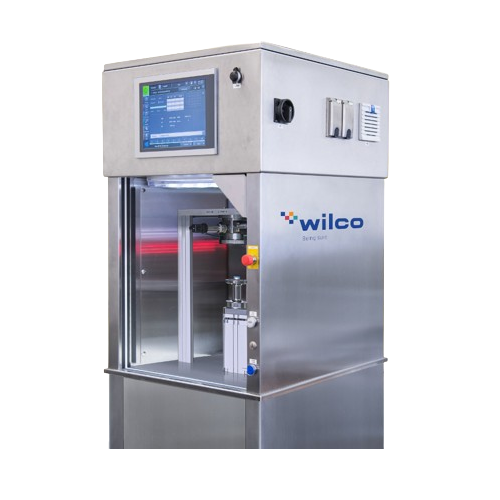
Headspace gas analyzer for large volume parenterals
Ensure the sterility and quality of injectable pharmaceuticals with p...
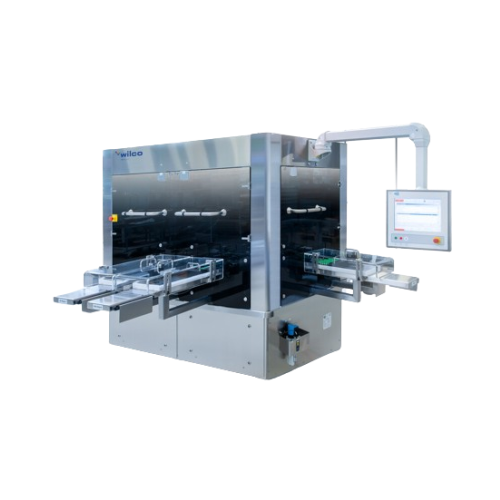
Automated headspace analysis for small volume parenterals
Ensure the integrity and quality of parenteral packaging with ...
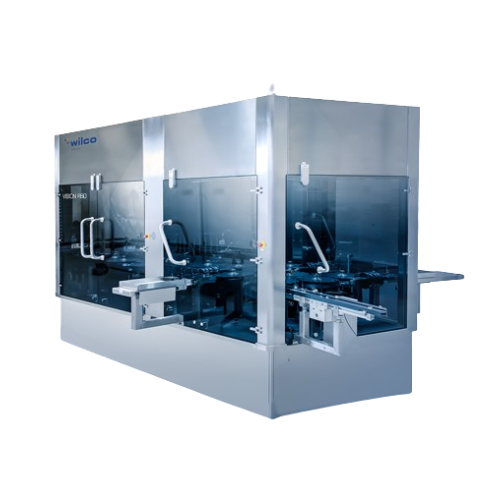
Visual inspection for small volume parenterals
Ensure pristine injectable solutions by detecting cosmetic and particle def...
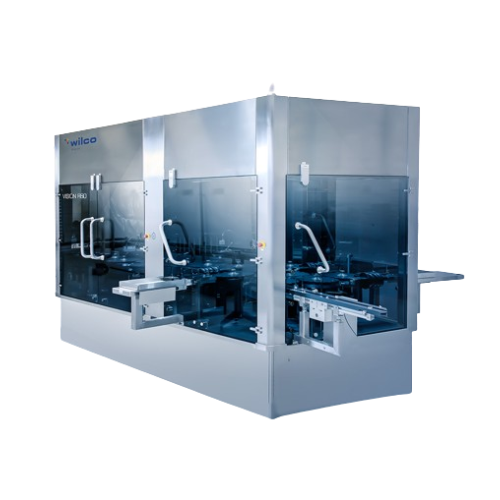
Automated visual inspection for small volume parenterals
Ensure the integrity of high-value parenteral drugs by detecting...
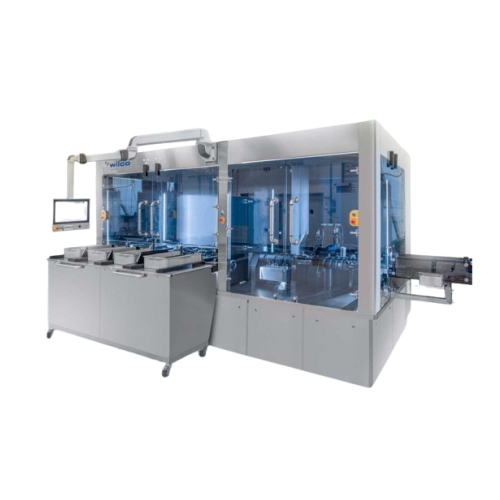
Combined Avi and Cci tester for vials
Ensure comprehensive quality control of parenteral products with an integrated soluti...
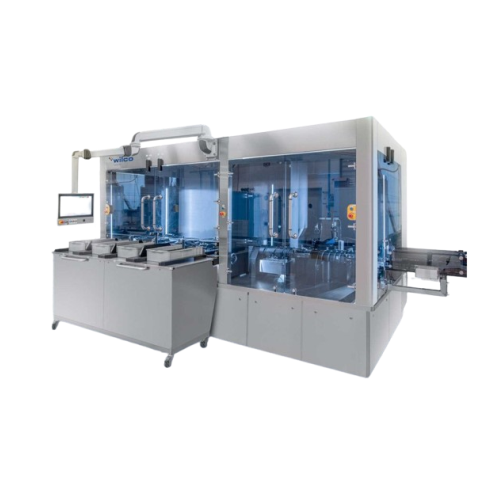
Combined visual and container closure integrity tester for vials
Ensure precise quality control of pharmaceutical packag...
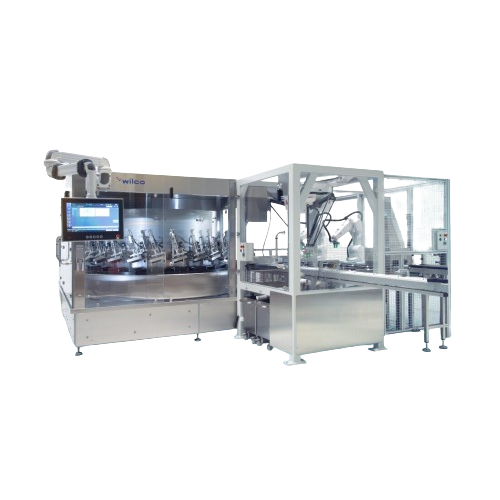
Automated container closure integrity tester for pharmaceutical packaging
Ensure the integrity of your pharmaceutical ...
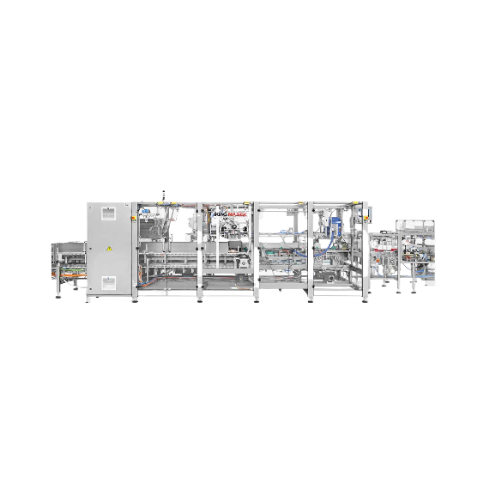
Endload automatic cartoning solution
Streamline your packaging line with this versatile cartoning solution, perfect for eff...
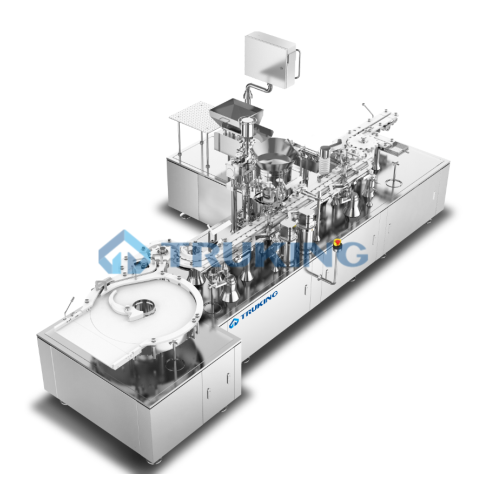
Vial powder dispensing system
Optimize your aseptic fill process with high-precision powder dispensing that minimizes contam...
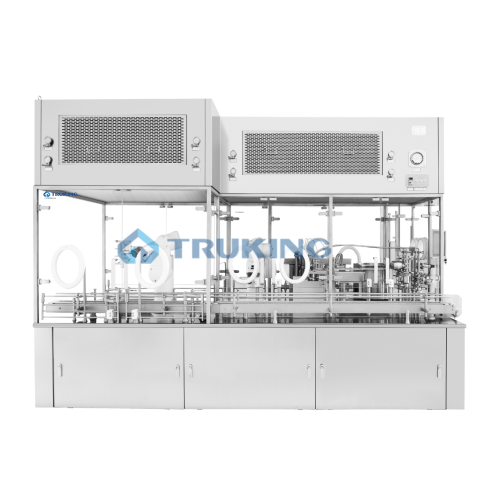
Nested fillers for vials, pre-filled syringes, and cartridges
Optimize your aseptic filling processes with precision dos...
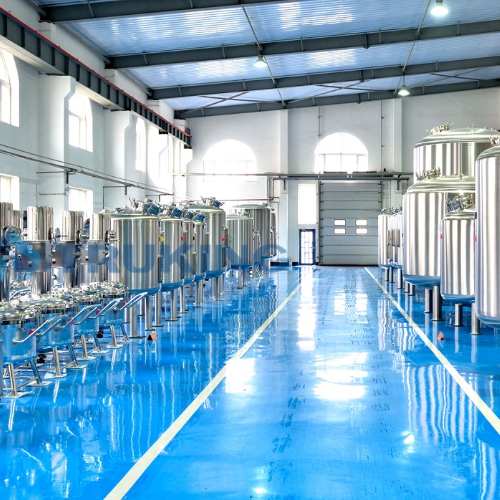
Stainless steel craft tanks for biopharmaceuticals
Ensure precise temperature control and customized capacity for your fo...
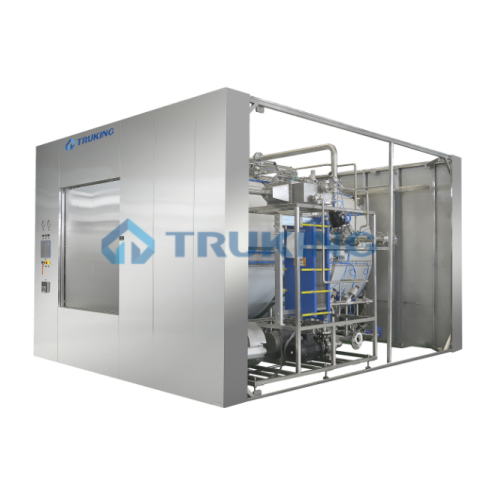
Superheated water sterilizer for pharmaceutical applications
Ensure precise sterilization with real-time monitoring and ...
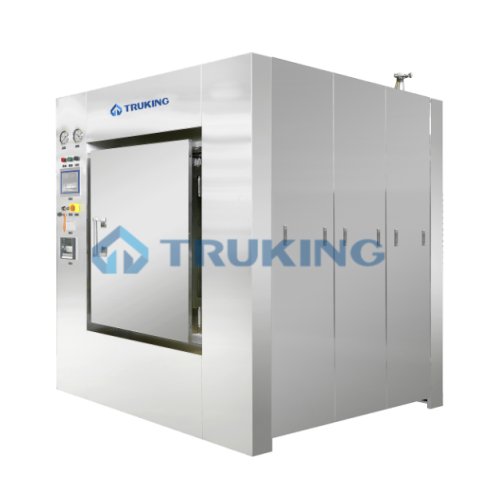
Pharmaceutical autoclave for terminal sterilization
Optimize your sterile production with high-precision terminal sterili...
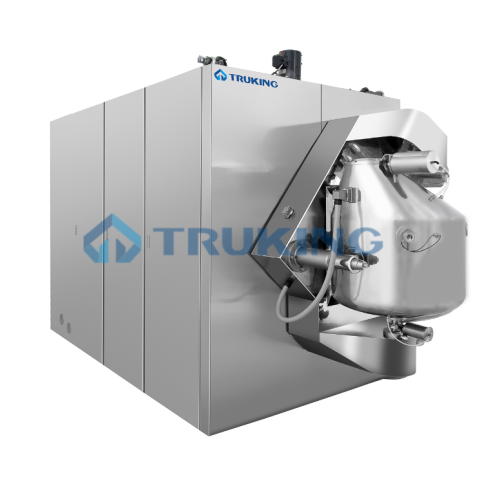
Washing machine for pharmaceutical stoppers and caps
Streamline your aseptic processing with precise washing, sterilizati...
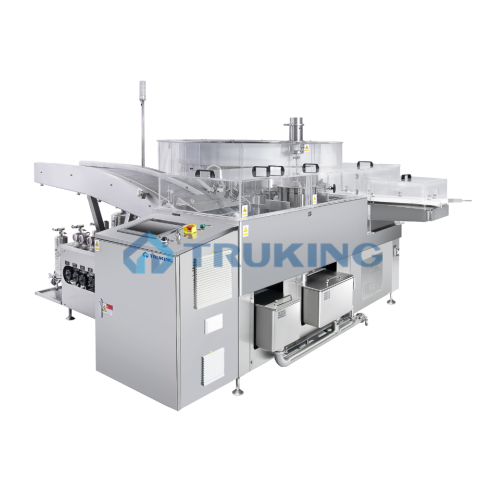
Vertical ultrasonic washing for pharmaceutical containers
Ensure immaculate cleanliness and sterilization of pharmaceuti...
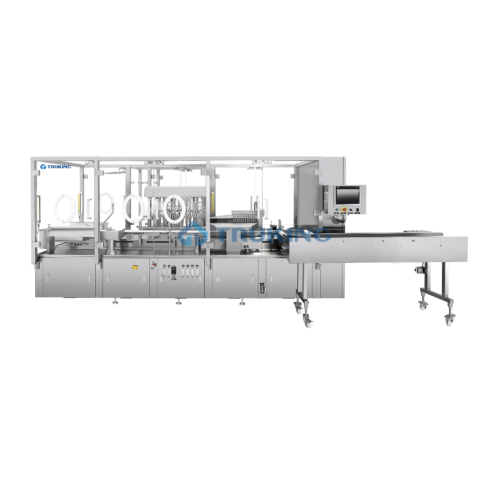
High-speed ampoule filling unit
Ensure precision and speed with this cutting-edge solution designed for efficient filling an...
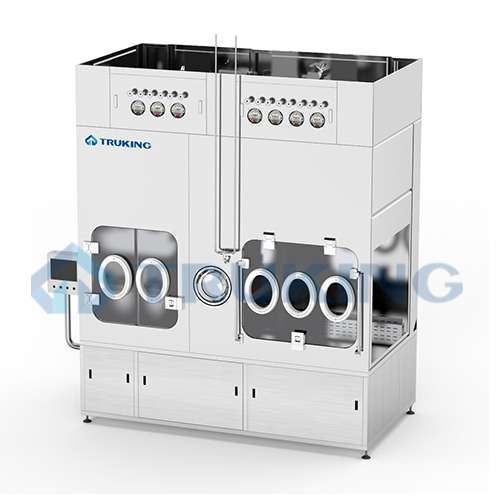
Autoclave unloading isolator for sterile assembly
Ensure aseptic conditions and prevent microbial contamination during th...
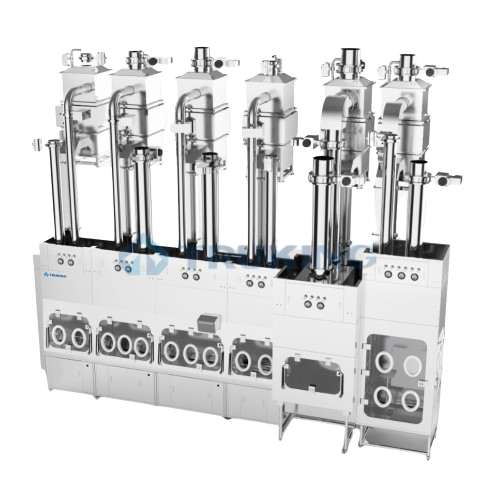
Active pharmaceutical ingredient isolation system
Ensure the aseptic production of pharmaceuticals while protecting perso...
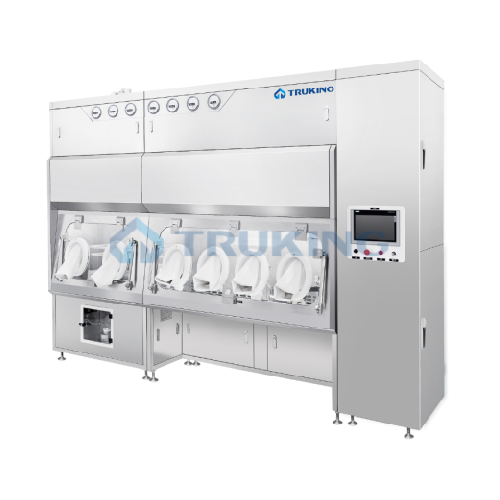
Sterility testing isolator for aseptic environment
Ensure precise sterility testing and prevent contamination with an iso...
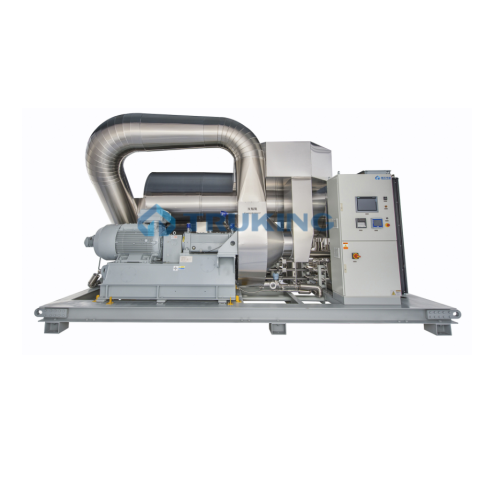
Hot press distilled water unit for pharmaceutical applications
Ensure superior water purity in pharmaceutical production...
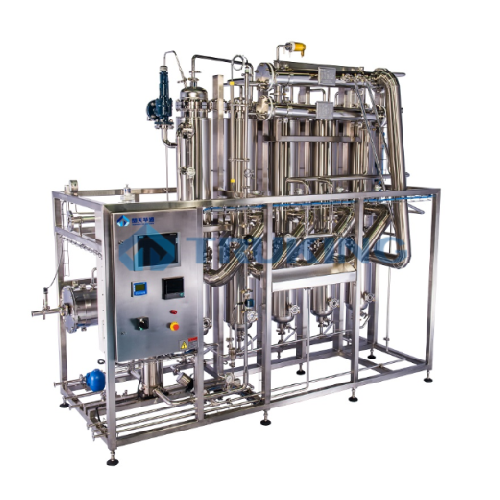
Multi-effect water distillator for pharmaceutical applications
Ensure your production line meets stringent regulatory st...
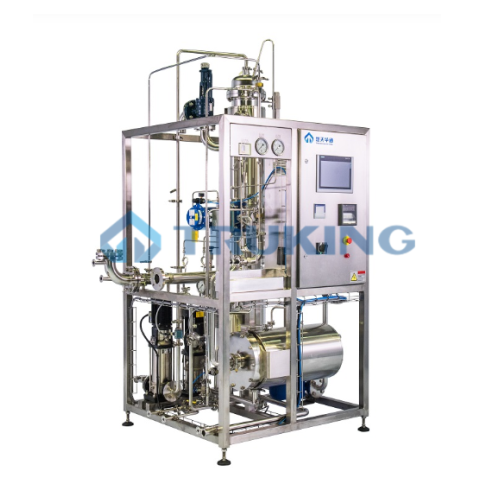
Pure steam generator for pharmaceutical and biotech industries
Ensure optimal steam quality and compliance with stringen...
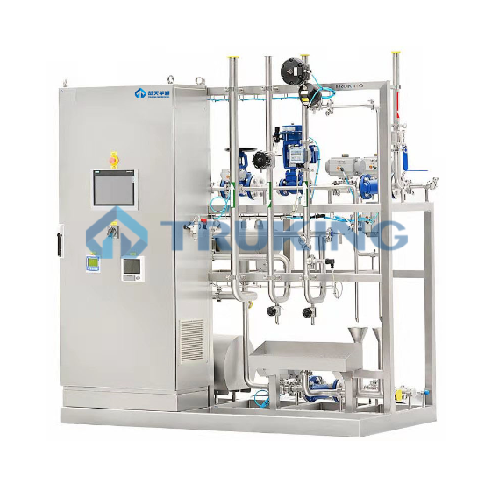
Pharmaceutical ultra pure water distribution system
Ensure stringent purity standards with a modular water distribution s...
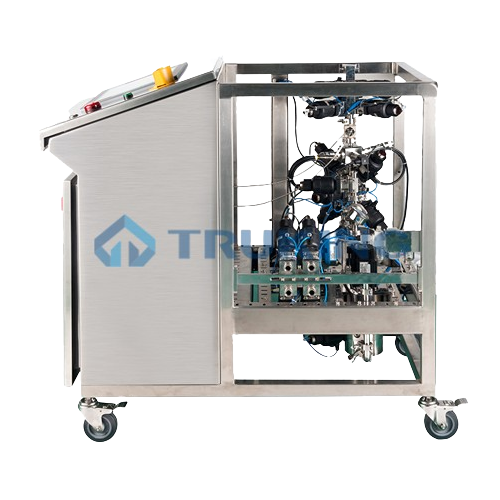
Chromatography systems for large-scale biopharmaceutical purification
Ensure precision purification of biopharmaceutica...
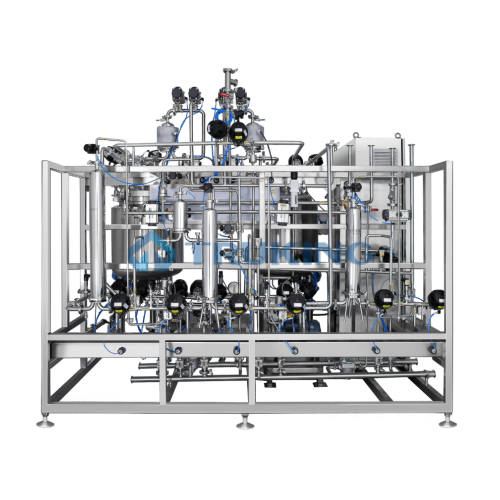
Pharmaceutical preparation system
Achieve seamless integration in pharmaceutical processes with a preparation system that o...
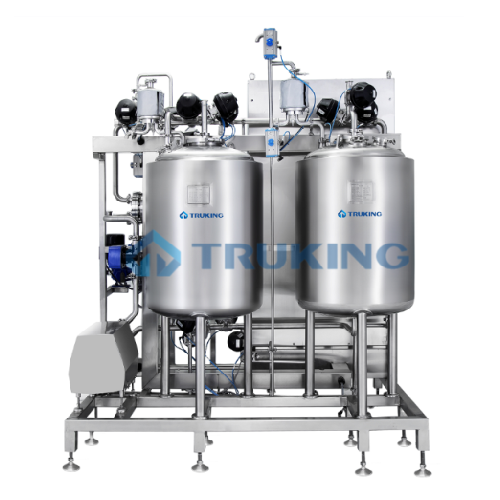
Comprehensive auxiliary system for online cleaning and temperature control
Ensure reliable and precise control in phar...
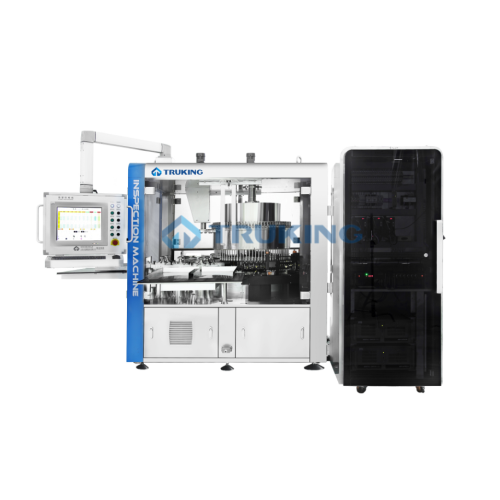
Automatic inspection system for ampoules and vials
Ensure precision in pharmaceutical production with a comprehensive ins...
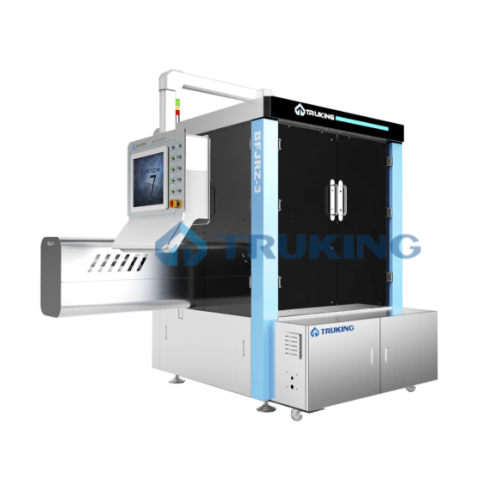
X-ray inspection for pharmaceutical vials
Ensure product purity by detecting contaminants in pharmaceutical vials with adv...
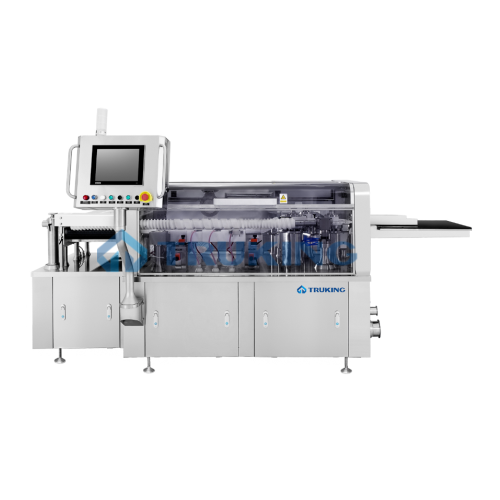
Automatic leak detection system for pharmaceutical containers
Ensure the integrity of pharmaceutical containers with pre...
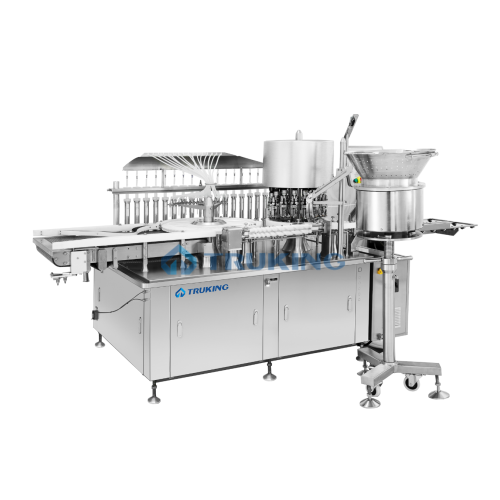
Oral liquid bottle filling & capping system
Streamline your liquid manufacturing processes with precise filling and secure...
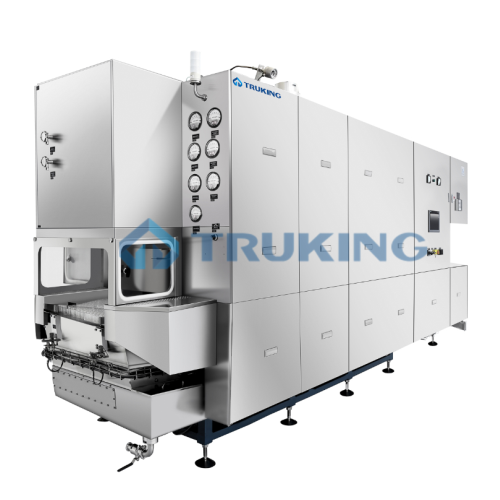
Sterilizing and drying tunnel for pharmaceutical vials
Ensure precise sterilization and depyrogenation of pharmaceutical ...
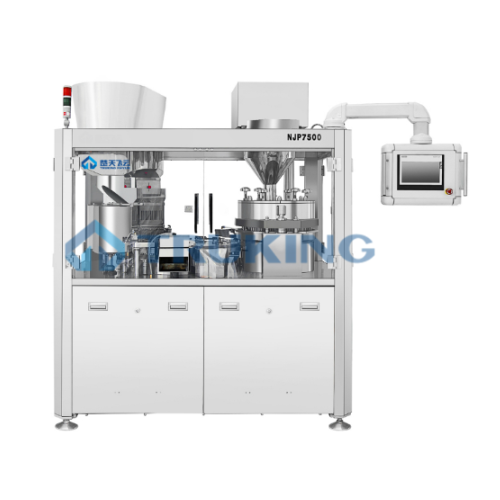
Fully automatic hard capsule filling machine
Enhance pharmaceutical production with precise capsule filling, ensuring opti...
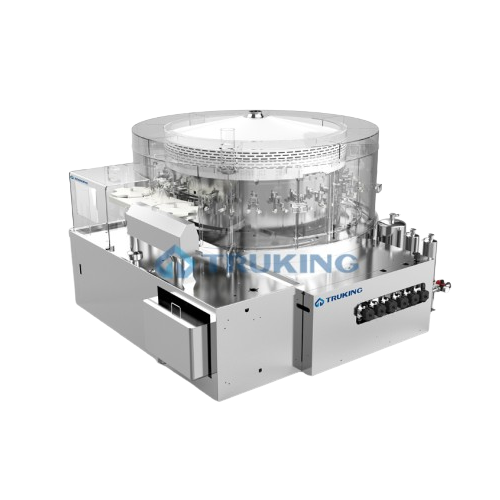
Industrial freeze dryer for pharmaceutical applications
Enhance your production line with precision cleaning solutions fo...
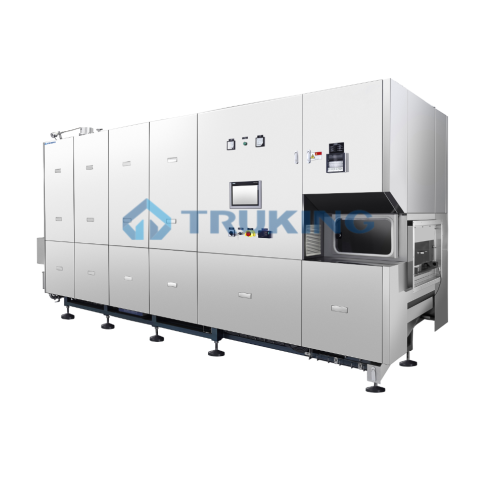
Sterilization and drying tunnel for glass bottles
Ensure aseptic integrity and regulatory compliance in injectable produc...
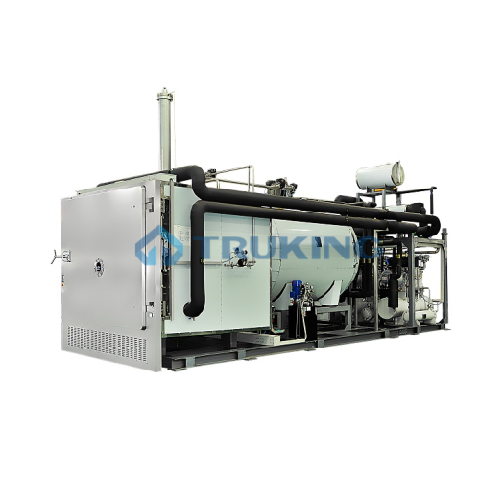
Industrial freeze dryer for pharma
Optimize moisture removal in lyophilized products with precise thermal conduction and ef...
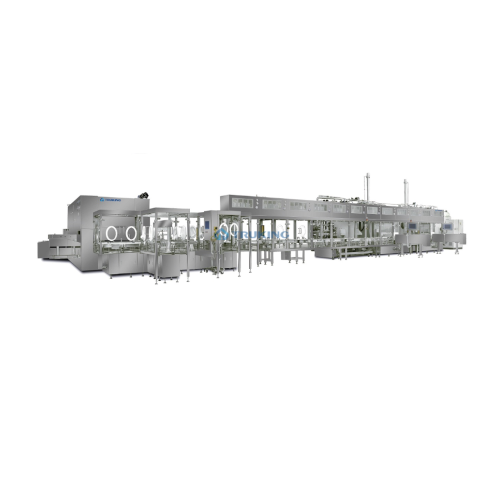
Auto loading & unloading system for freeze dryers
Efficiently manage vial handling in freeze-drying processes with automa...
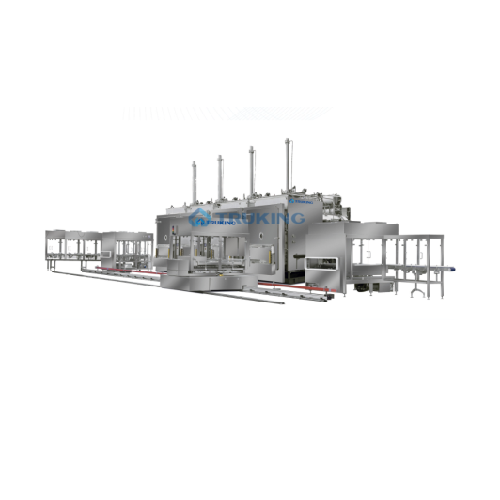
Mobile transfer loading system for freeze dryers
Streamline your lyophilization process with a high-capacity mobile loadin...
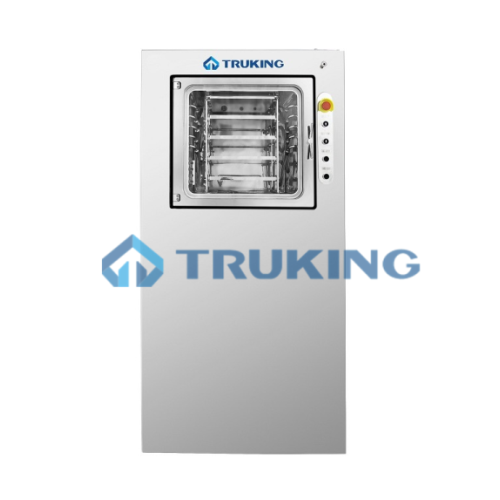
Laboratory freeze dryer for research and development
Optimize moisture removal with precision control during research and...
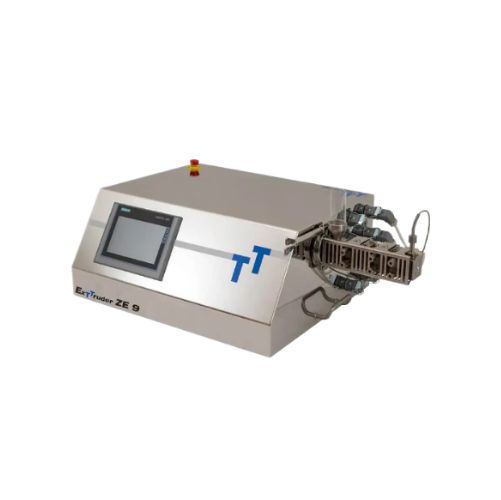
Mini extruder for small batch processing
Ideal for precise control in experimental formulations, this mini extruder streaml...
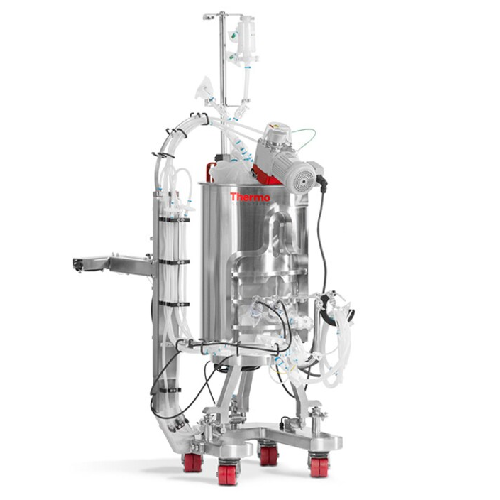
Single-use bioreactor for protein expression
Optimize your biopharmaceutical production with an advanced single-use biorea...
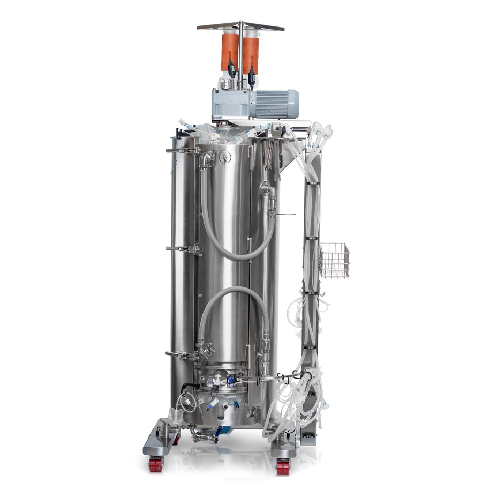
Single-use fermentor for microbial fermentation
Enhance your microbial fermentation processes with a system designed for p...
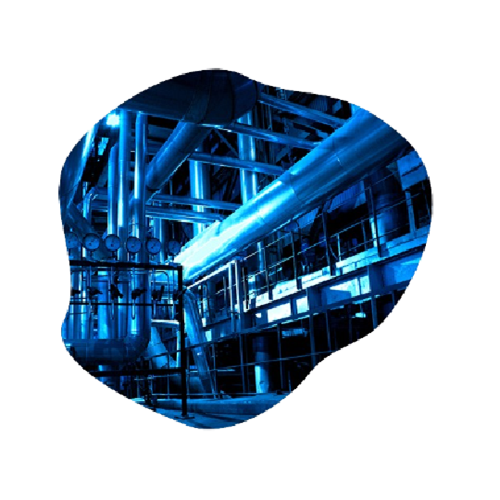
Industrial-scale bioreactors for large-scale biomanufacturing
When producing at large volumes, efficient and reliable bi...
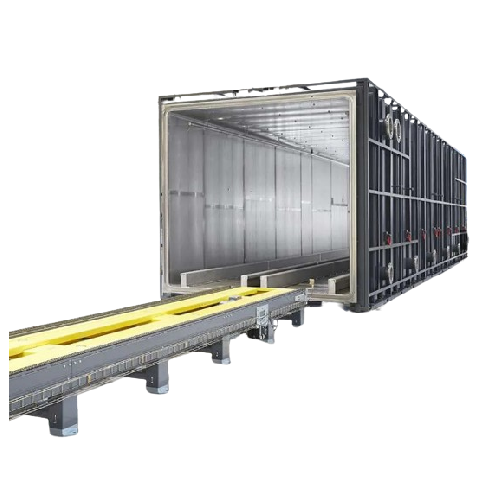
Ethylene oxide sterilizers for medical devices
Ensure the complete sterilization of complex medical devices with advanced ...
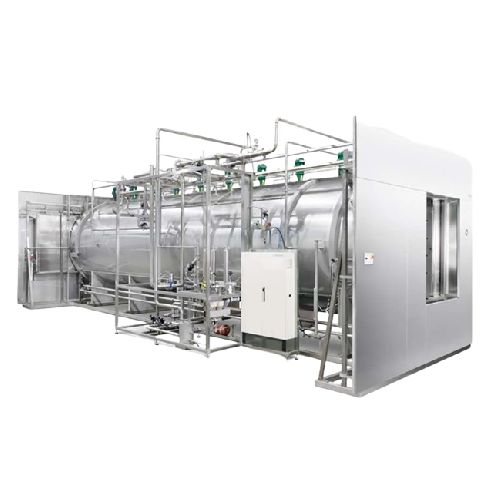
Steam & air mixture sterilizer for parenteral solutions
Achieve robust and effective sterilization for delicate pharmaceu...
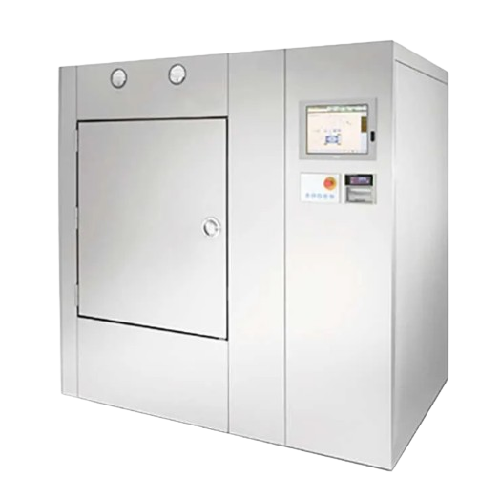
Dry heat sterilization and depyrogenation oven for glassware
Achieve precise sterilization and depyrogenation of glasswa...
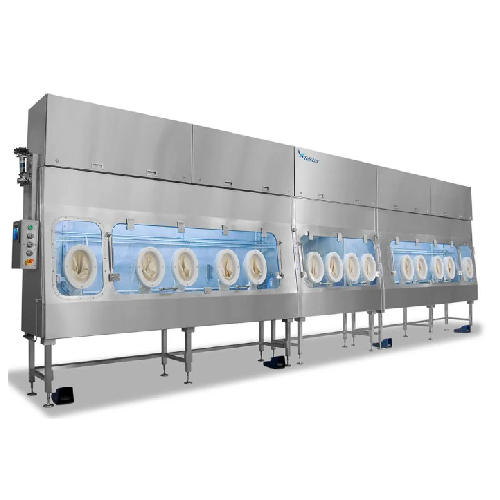
Aseptic barrier isolators for pharmaceutical applications
Enhance sterility and operator safety during aseptic processin...
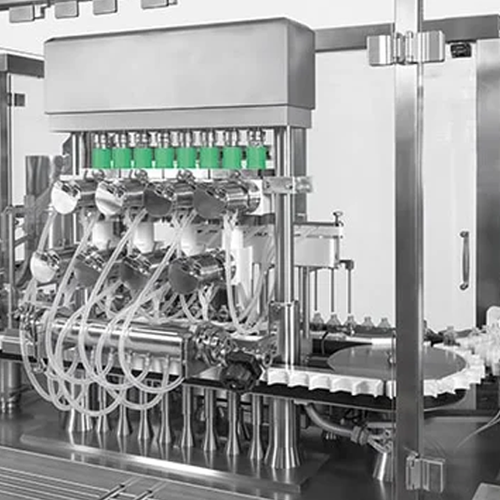
Bulk vial liquid filling system
Ensure reliable and efficient processing of critical biopharmaceutical and pharmaceutical li...
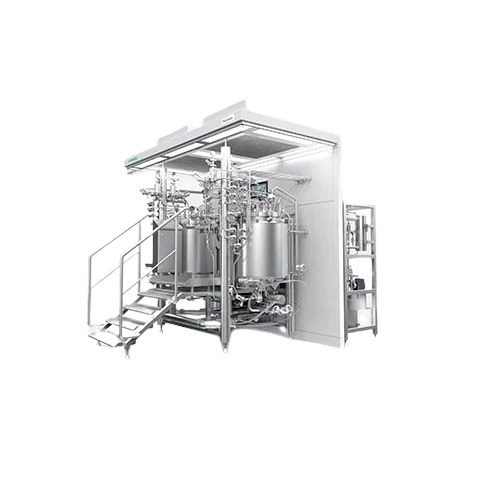
Syringe filling line for parenteral drugs
Ensure precise dosage and sterility with this high-speed syringe filling line, i...
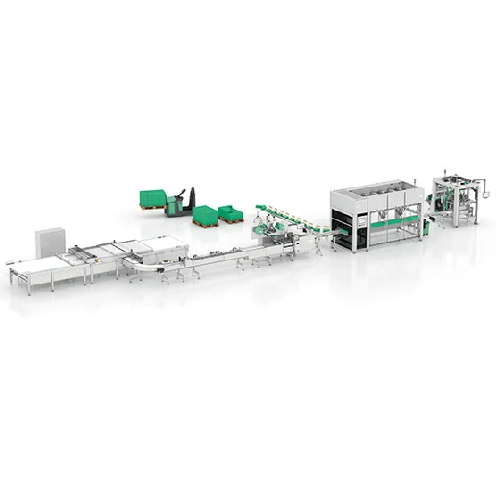
Automated visual inspection for pharmaceutical products
Ensure the integrity and safety of your parenteral products with ...
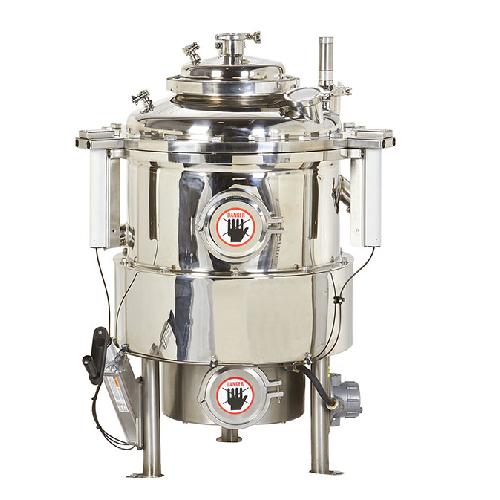
Pilot pharmaceutical aseptic separator and dryer
Achieve high-yield recovery of potent compounds with a separator that com...
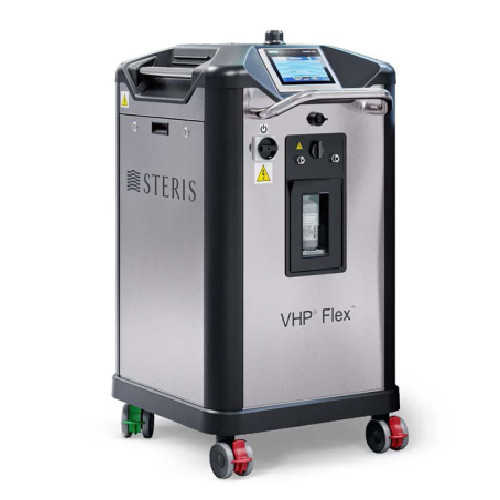
Mobile biodecontamination unit for small to mid-size rooms
Efficiently achieve 6-log bioburden reduction in controlled e...
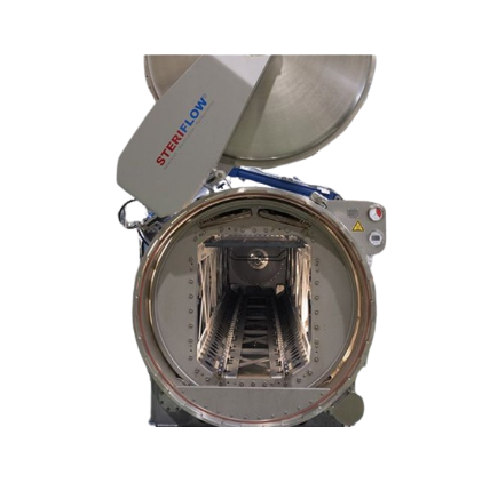
Static autoclave for pharmaceutical sterilization
Ensure reliable sterilization with a static autoclave that maintains cr...
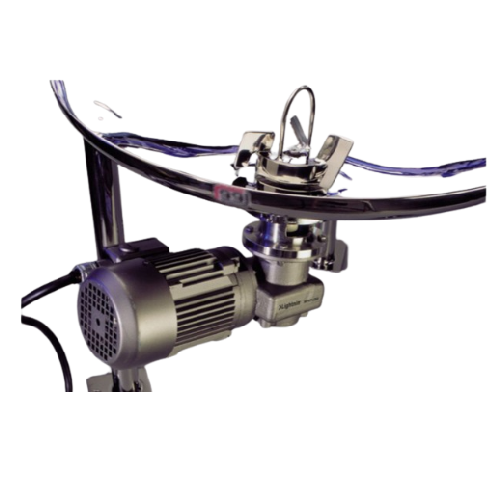
Sanitary mixer for food and pharmaceutical processing
Eliminate contamination risks while achieving high-speed, efficient...
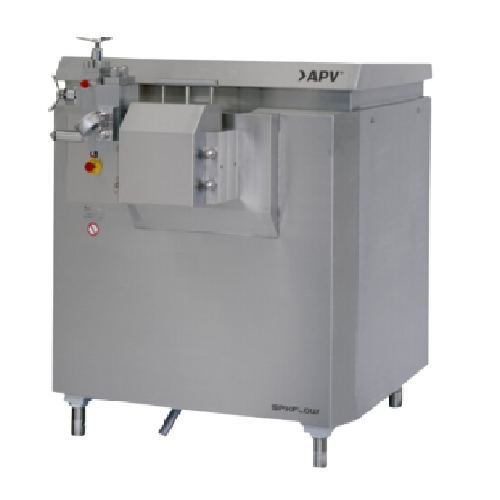
High pressure homogenizers for dairy and pharmaceutical applications
Optimize your production line with high-pressure h...
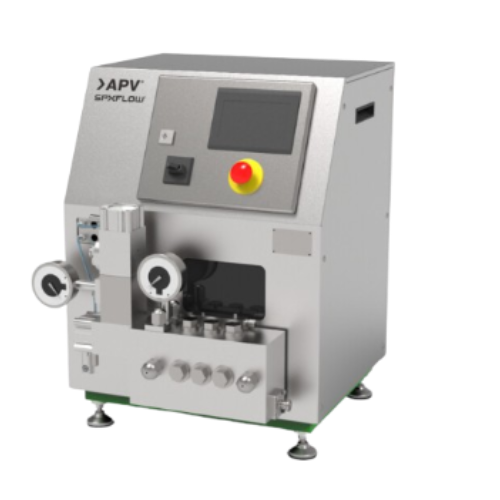
Pilot plant homogenizer for immiscible liquids
Streamline your R&D with precise homogenization, allowing you to test ...
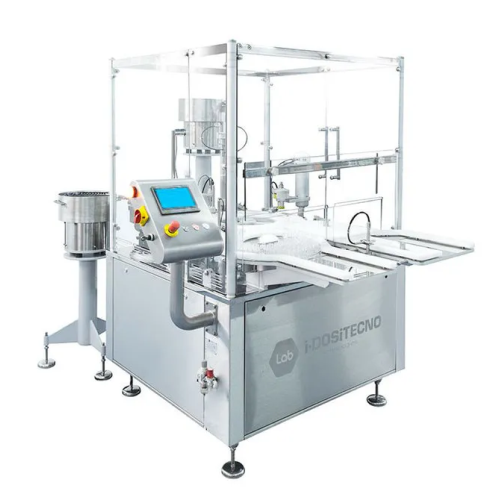
Rotary filler for pharmaceutical vials
Optimize precision and efficiency in fill-finish operations with a rotary system des...
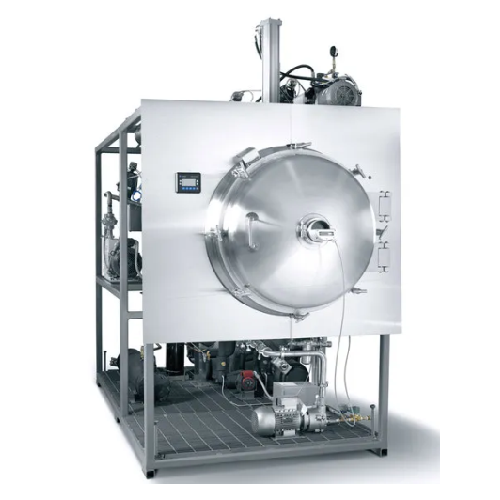
Production freeze dryer for pharmaceutical manufacturing
Achieve precise lyophilization for sensitive products with custo...
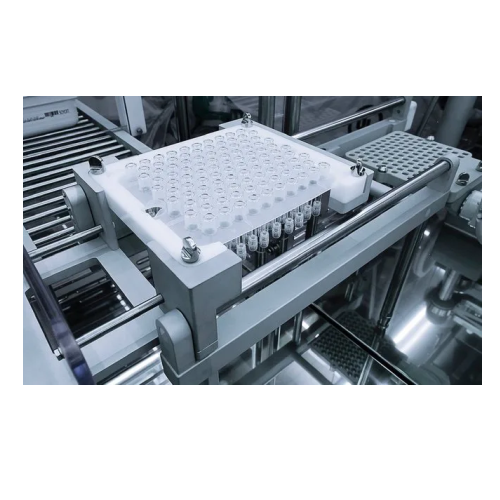
Ready-to-use denesting equipment for pharmaceutical fill-finish
Ensure sterility and precision in your fill-finish workf...
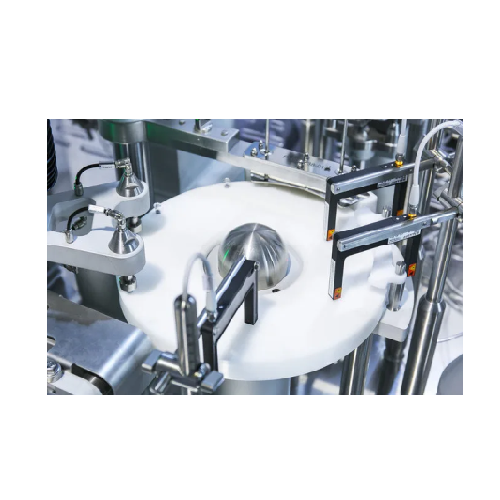
Sterile syringe plunger placement system
Ensure precision in syringe assembly with enhanced plunger placement, maintaining ...
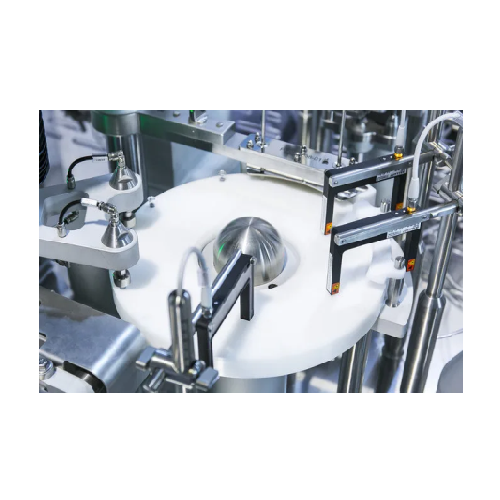
Robotic syringe filling system for sterile pharmaceutical production
For high-precision liquid dosing in sterile enviro...
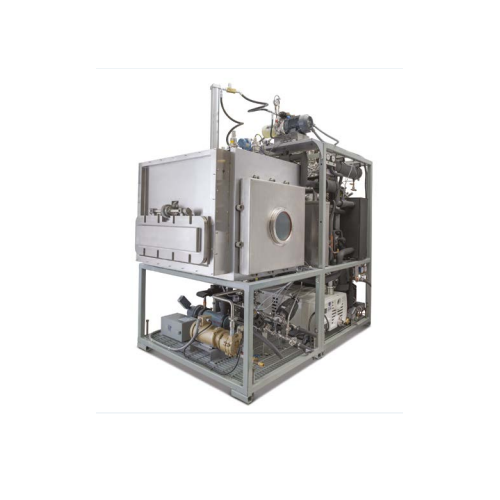
Controlled lyophilization nucleation system for drug development
Achieve consistent freeze-drying outcomes with precise ...
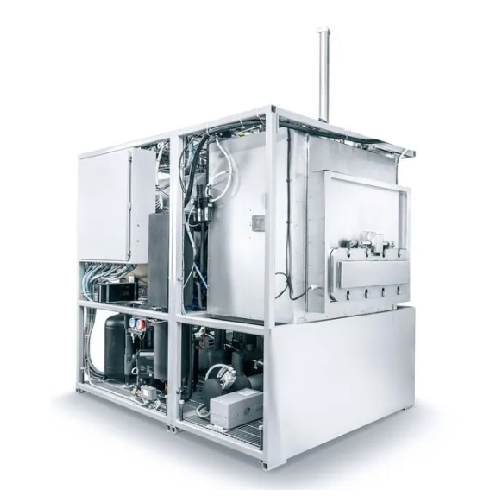
Pilot lyophilizers for therapeutic proteins and clinical trials
Optimize your freeze-drying process with advanced lyophi...
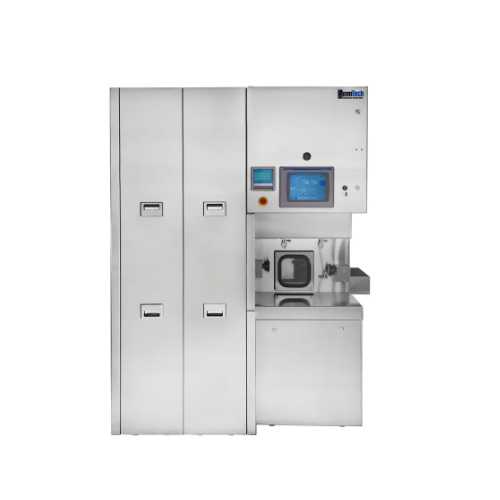
Depyrogenation tunnel for pharmaceutical vials
Achieve reliable sterility with fully automated depyrogenation tunnels, ens...
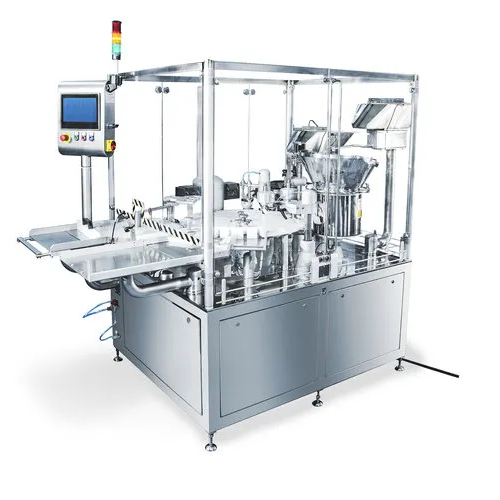
Micro-line vial filling solution for biopharmaceuticals
Ensure batch consistency and sterility in fill-finish operations ...
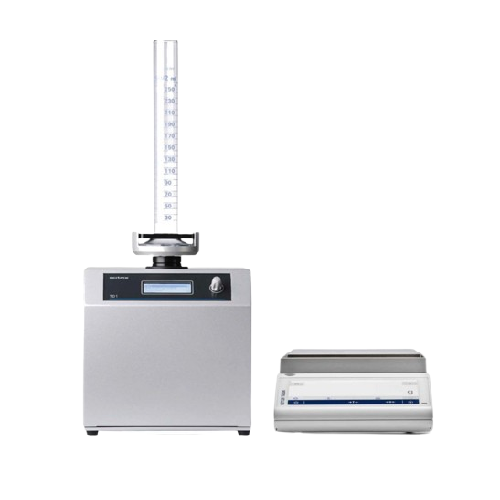
Tapped density tester for pharmaceutical powders
Ensure precise quality control in pharmaceuticals by accurately measuring...
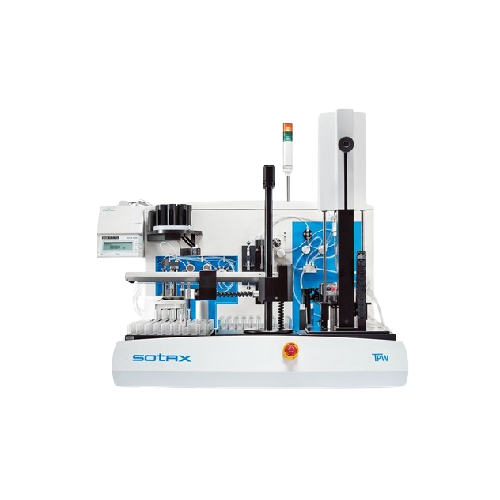
Automated sample preparation workstation for content uniformity testing
Streamline your laboratory workflows with autom...

Manual tablet disintegration tester
Ensure precise and reliable disintegration testing of pharmaceutical tablets, capsules,...
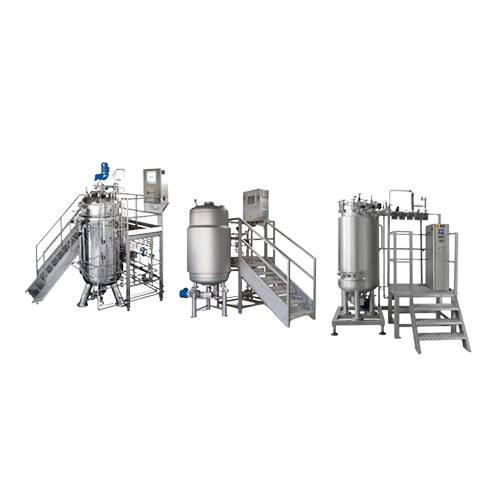
Reactors and tanks for bioreactors and fermenters
Enhance bioprocessing efficiency with robust solutions for mixing, aera...
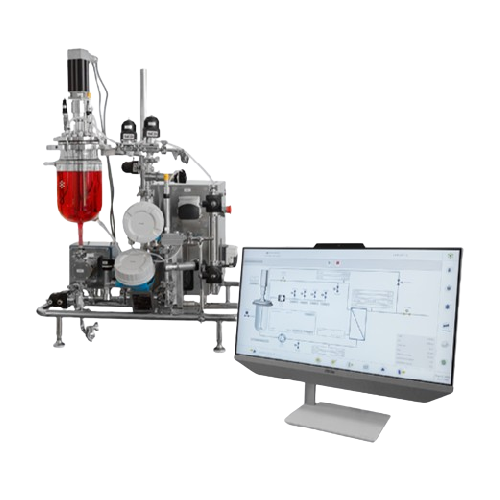
Benchtop tangential flow filtration system
Ensure high-purity yields and streamline your filtration processes with this be...
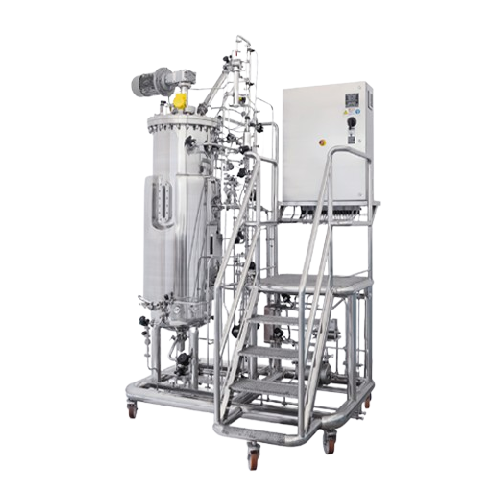
Customizable pilot-industrial fermenters bioreactors
Designed for precision fermentation, these fermenters and bioreactor...
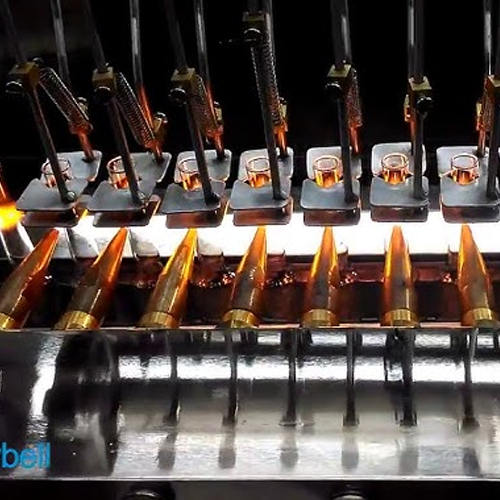
Triple combi filling and stoppering system for vials and ampoules
Optimize your liquid formulation process with a versa...
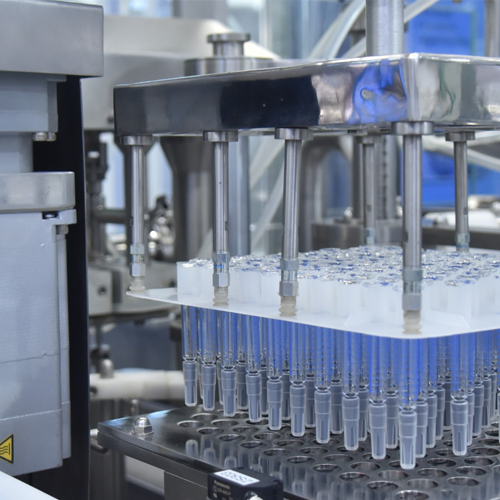
Prefilled syringe filling and stoppering system
Achieve precision in drug administration with this integrated system for f...
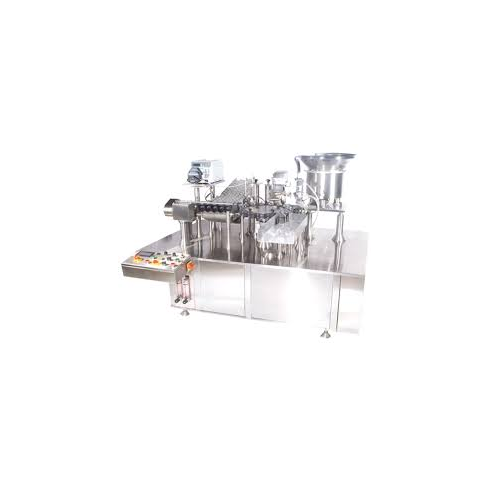
Combi r&d ampoule and vial filling equipment
Optimize your R&D operations with a versatile machine designed for preci...
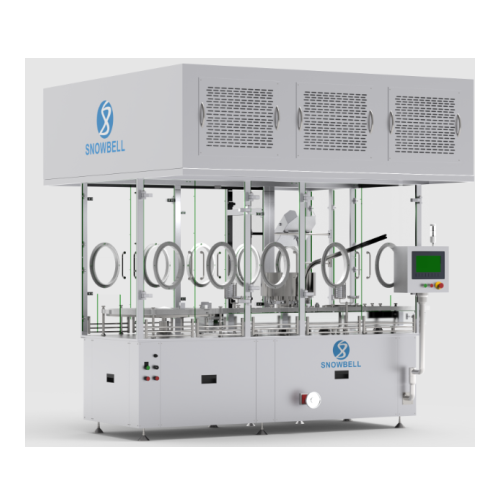
Vial washing system for internal and external cleaning
Streamline vial preparation with comprehensive washing, sterilizin...
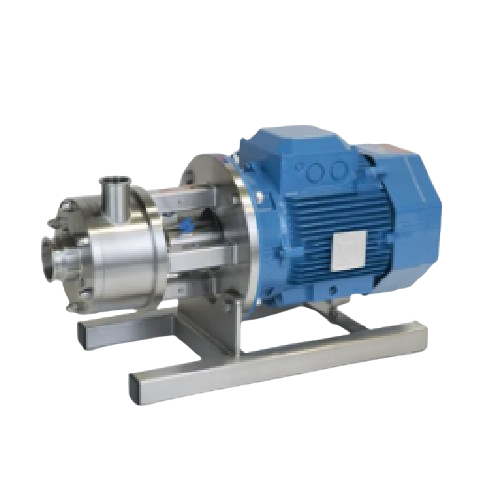
High shear mixer for efficient particle size reduction
Achieve rapid and precise blending and particle reduction in your ...
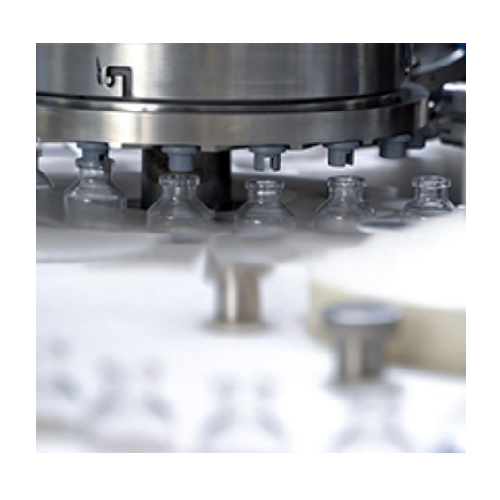
Continuous motion rotary vial filling and stoppering solution
Optimize your vial production with a high-speed, continuou...

Automatic syringe de-nester for pharmaceutical production
Streamline your syringe production line with high-speed de-nes...
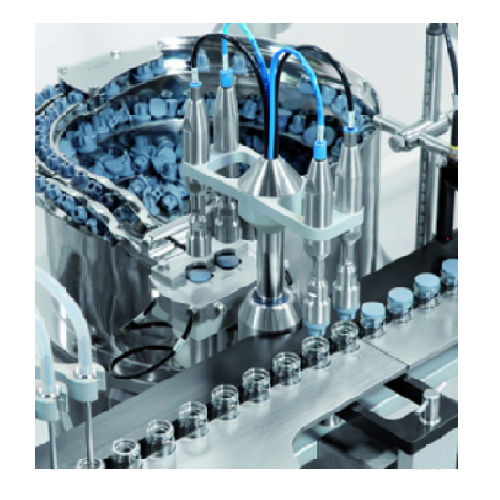
Automatic linear filling stoppering system for large volume vials
Ensure precise vial filling and secure sealing with a...
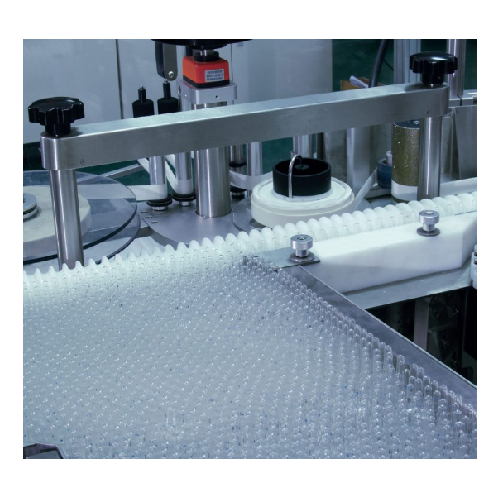
Pharmaceutical ampoule labelling system
Achieve precise and efficient labelling of ampoules with a high-speed system design...
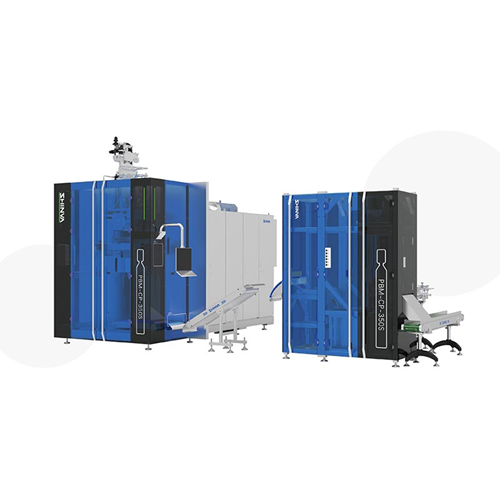
Single-mold continuous bottle Bfs solution
Optimize aseptic production with this advanced solution, offering superior ster...

Surface plasmon resonance (spr) sensor chips
Enhance your molecule interactions analysis with precise sensor technology th...
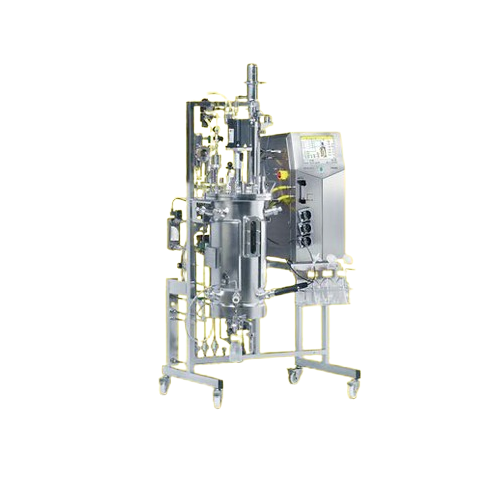
Stainless steel bioreactors
Enhance your bioproduction capabilities with robust solutions designed for efficient fermentatio...

Aseptic handling and fill-finish platform for Rtu syringes, vials, and cartridges
Ensure aseptic precision and high t...
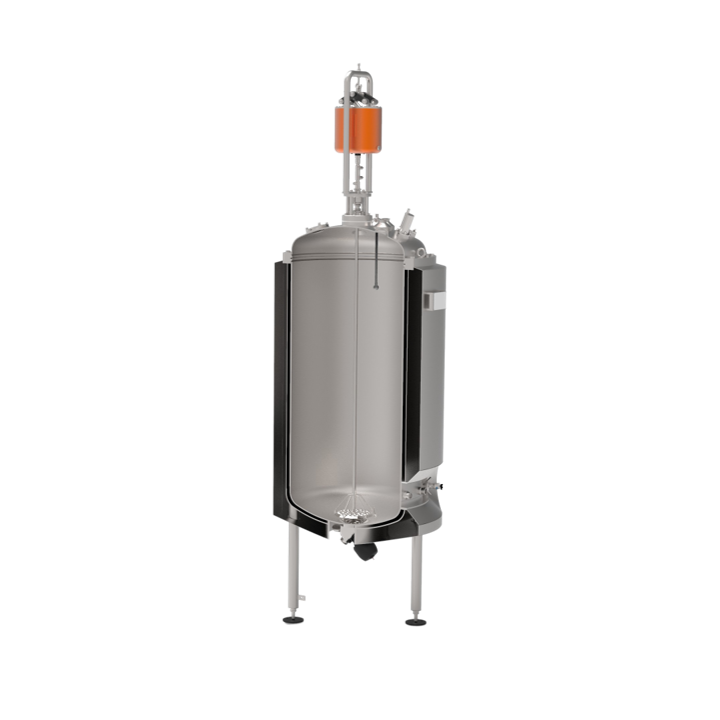
High-frequency vibratory mixer
Mixing liquid products by stirring method generates heat from friction and shear forces. This...
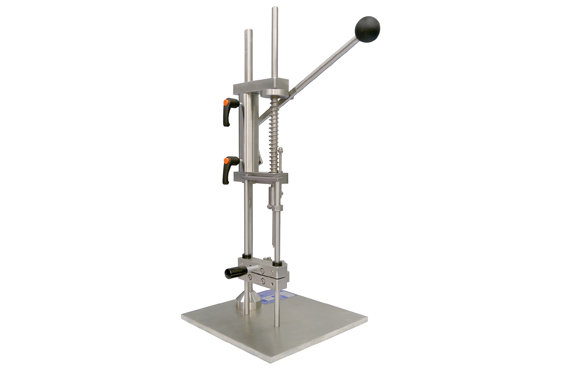
Manual stoppering equipment for pre-filled syringes
Air present in the empty space of pre-filled syringes may prevent you...
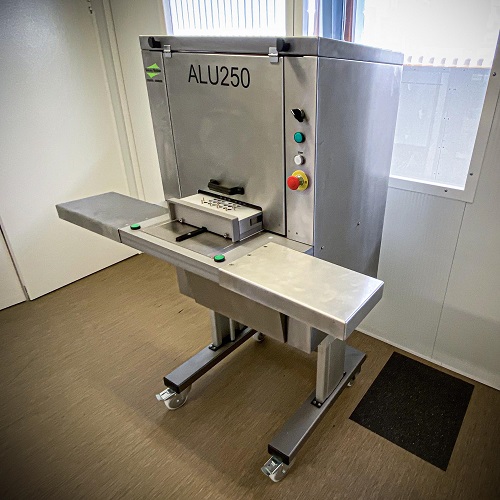
Cold forming aluminum blister machine for capsules
Aluminum blisters are mainly used for packaging products that are sens...
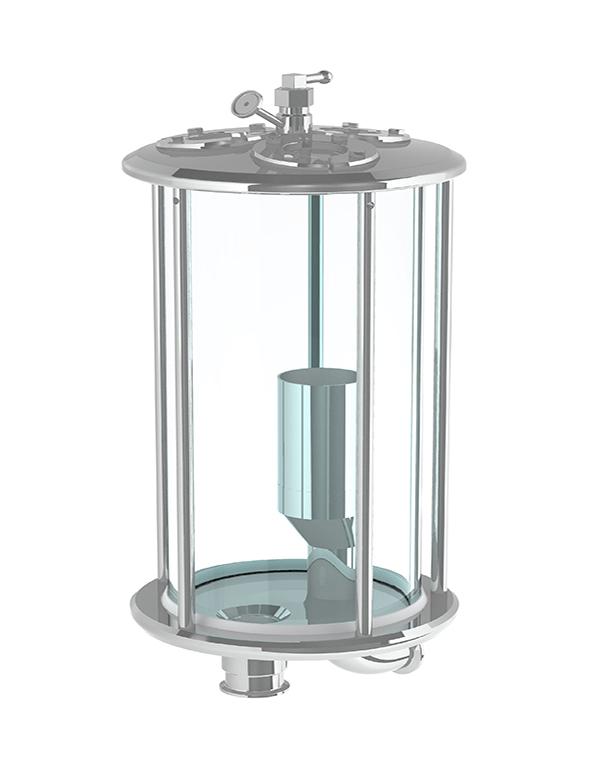
Automated bubble traps for chromatography
Radial flow chromatography processes require special attention and the right use...
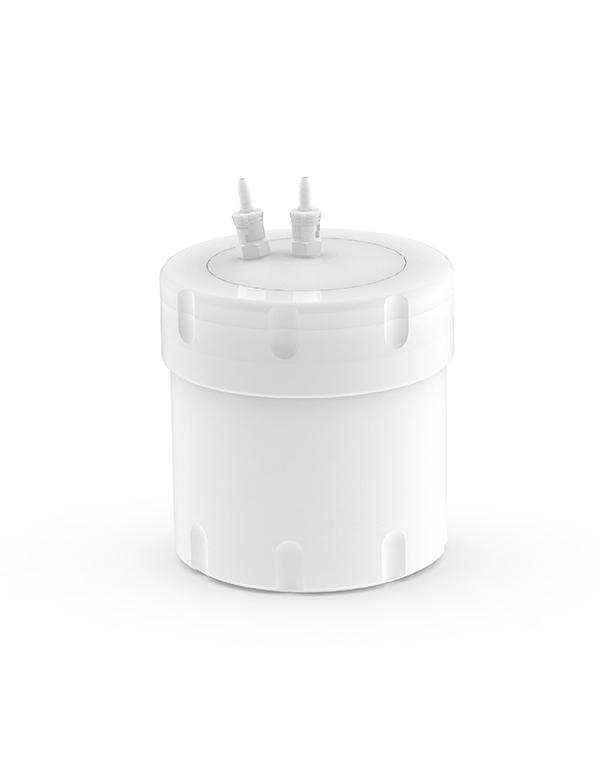
Pre-packed and pre-validated chromatography columns
In chromatography, you must always take into account the apparatus th...
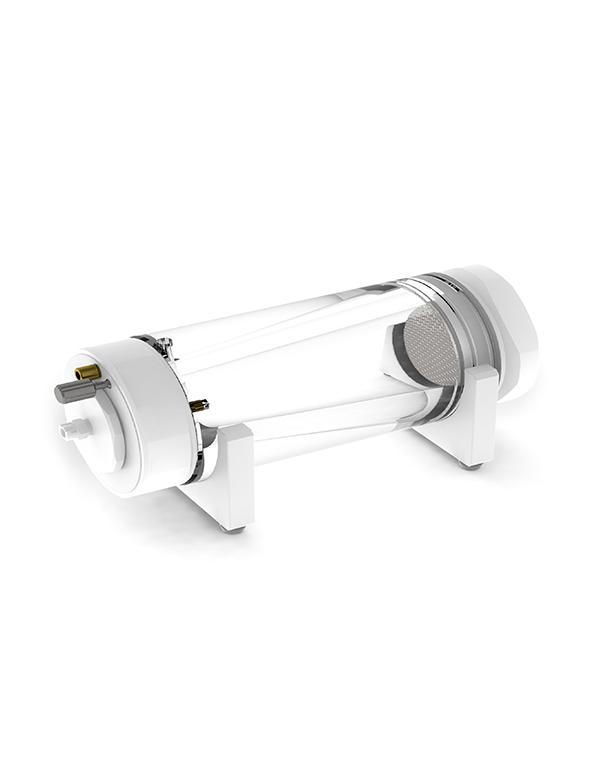
Lab-scale radial chromatography columns for virus validation
In the food industry, as an example, during lab-testing and...
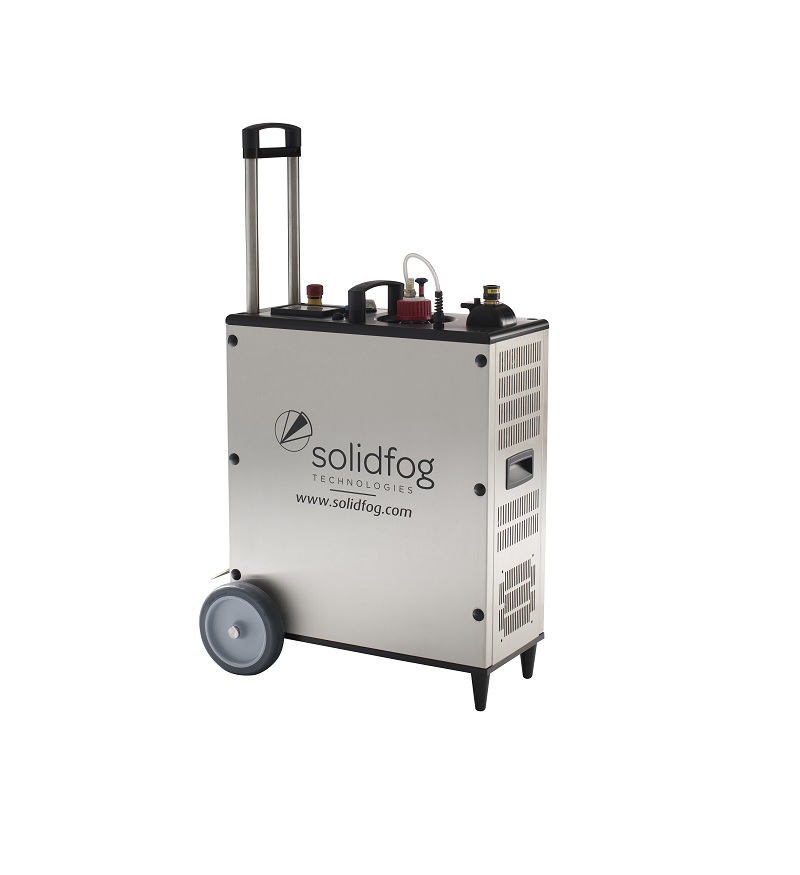
Compact H2O2 disinfection system
Dry fogging provides safe, effective microbiological cleaning of critical areas in biotech,...
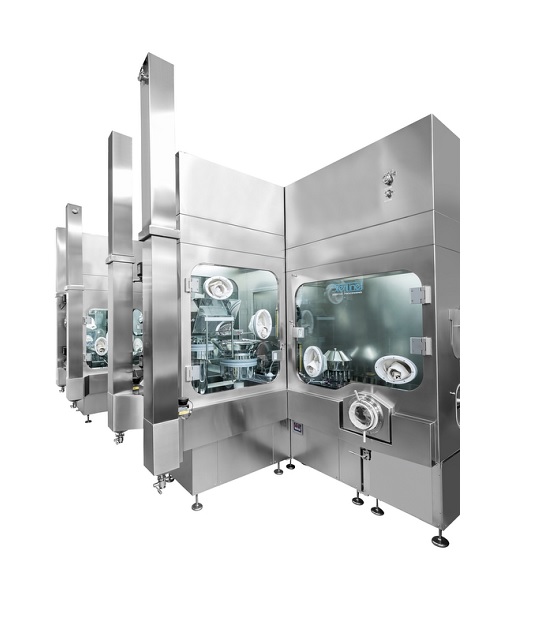
Closed restricted access barrier system
Pharmaceutical production techniques often require isolation of compounds and chemi...
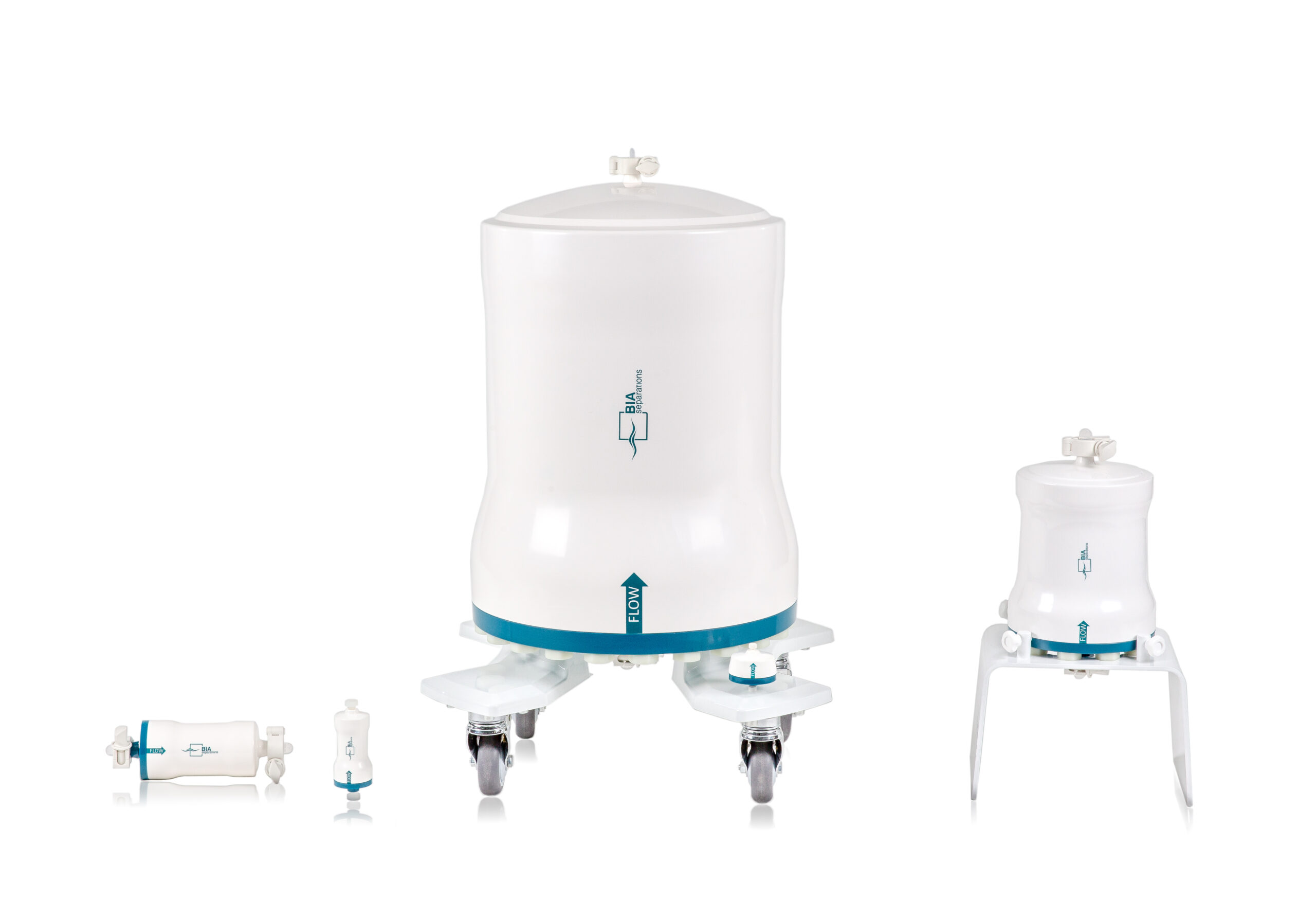
Disposable monolithic columns
Chromatographic monolithic columns for working with large proteins, viruses, VLPs and pDNA req...

Short bed monolithic columns for analytics
Samples taken at various process steps need to be analysed quickly and accurate...
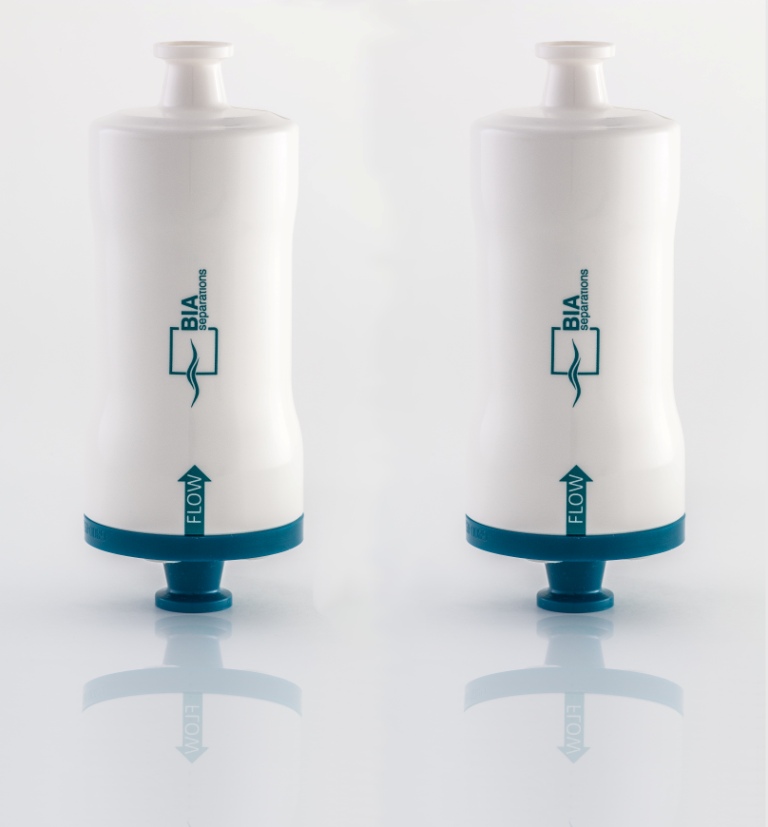
Plasmid process pack for your pDNA purification process
When developing a pDNA purification process for eventual transfer...
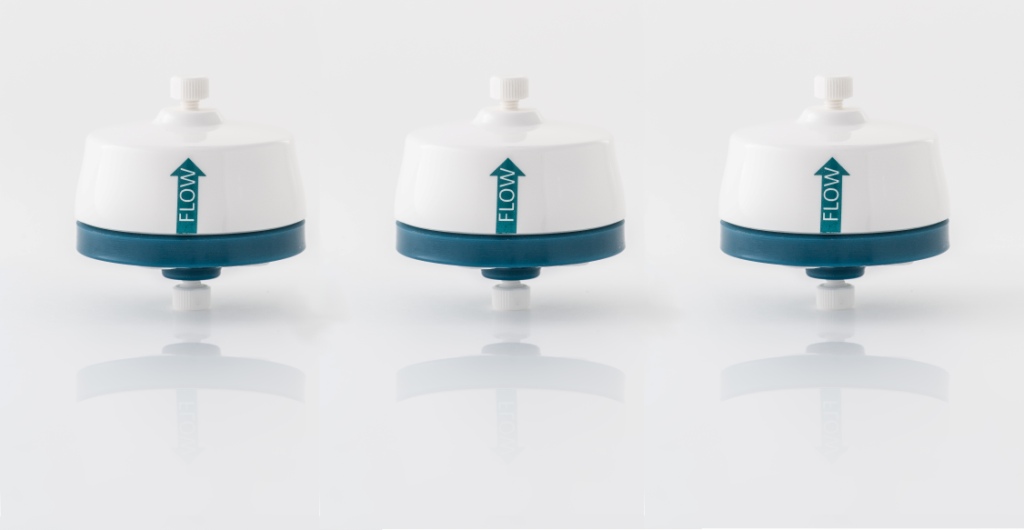
Purification screening kit for large biomolecules
To purify a specific large biomolecule, for example IgM or a virus or v...
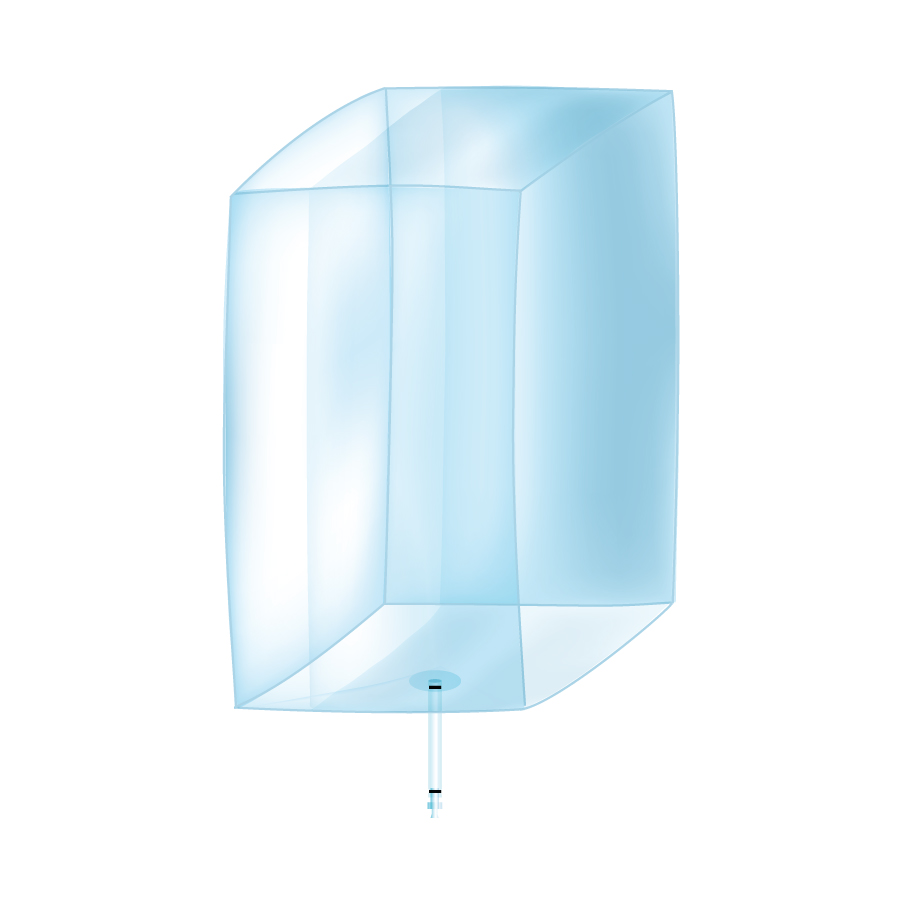
Disposable tank liners
Manufacturers in the bioprocessing industries are increasingly turning to single use solutions for the...
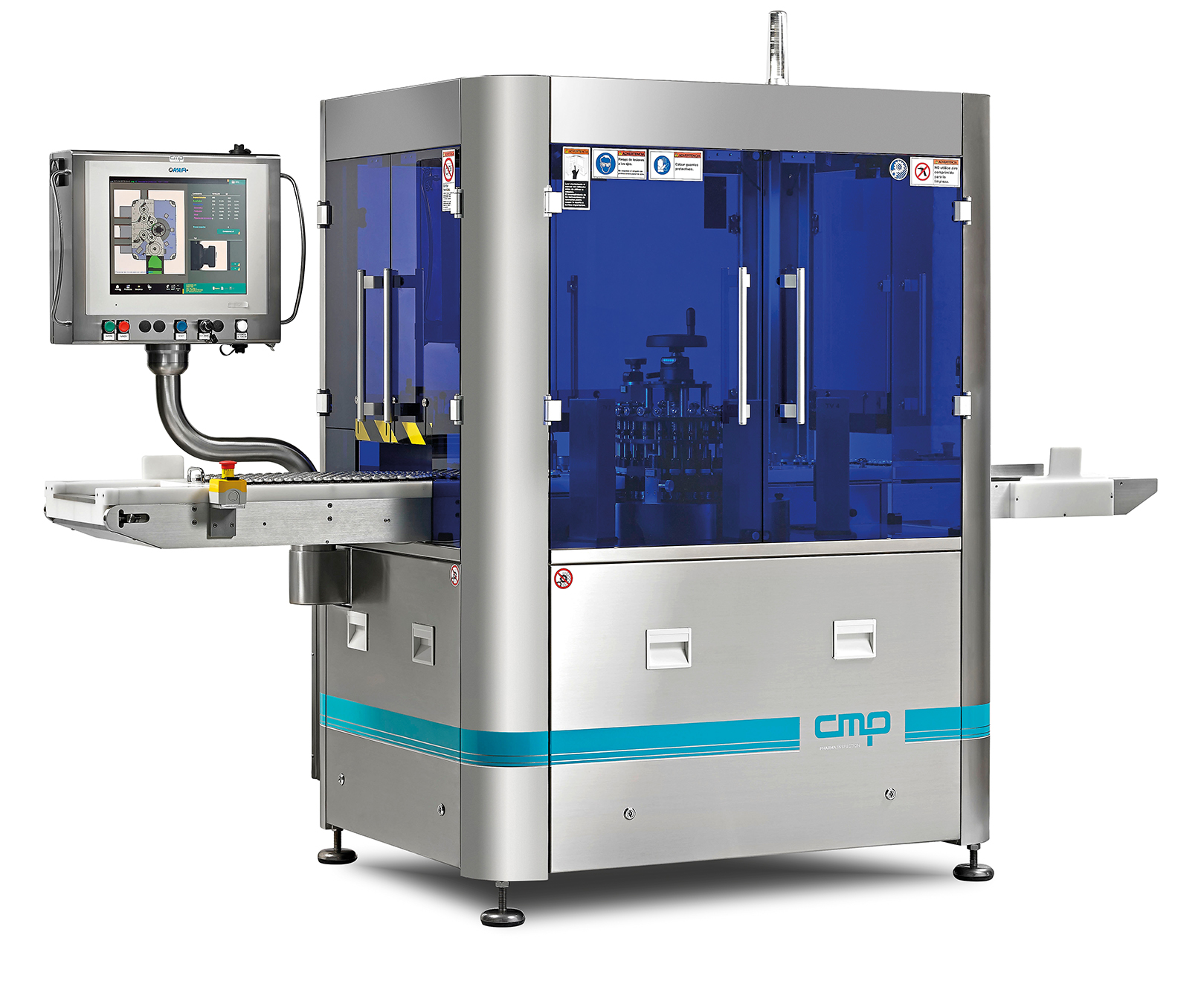
Flexible automatic inspection machine for ampoules, vials, cartridges
If you are looking to improve the efficiency of y...

Flexible automatic inspection machine for syringes
Manufacture of pre-filled syringes requires the highest quality inspec...
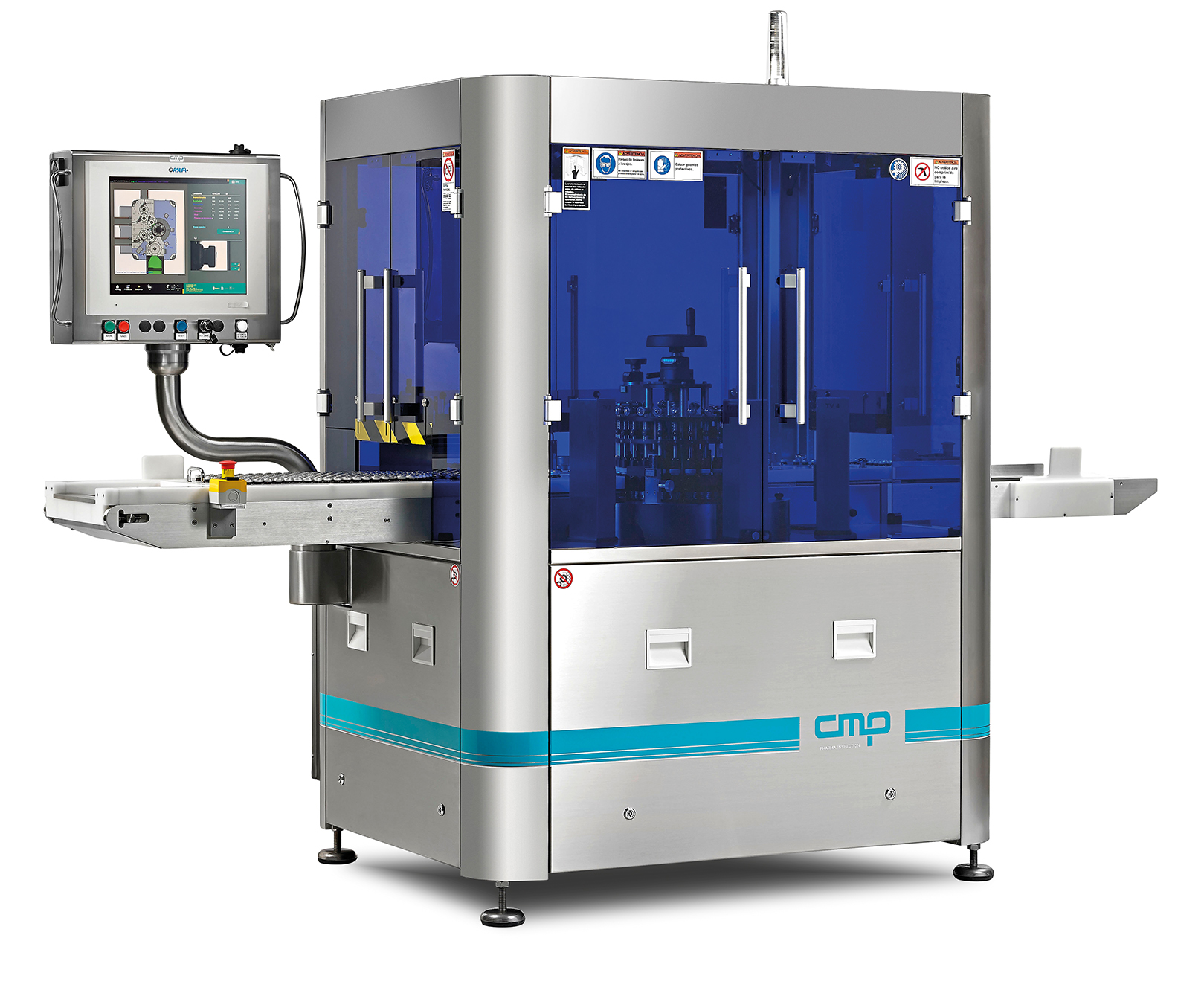
Small automatic inspector for ampoules, vials, or cartridges
Inspect small batch production of ampoules, vials, or cartr...
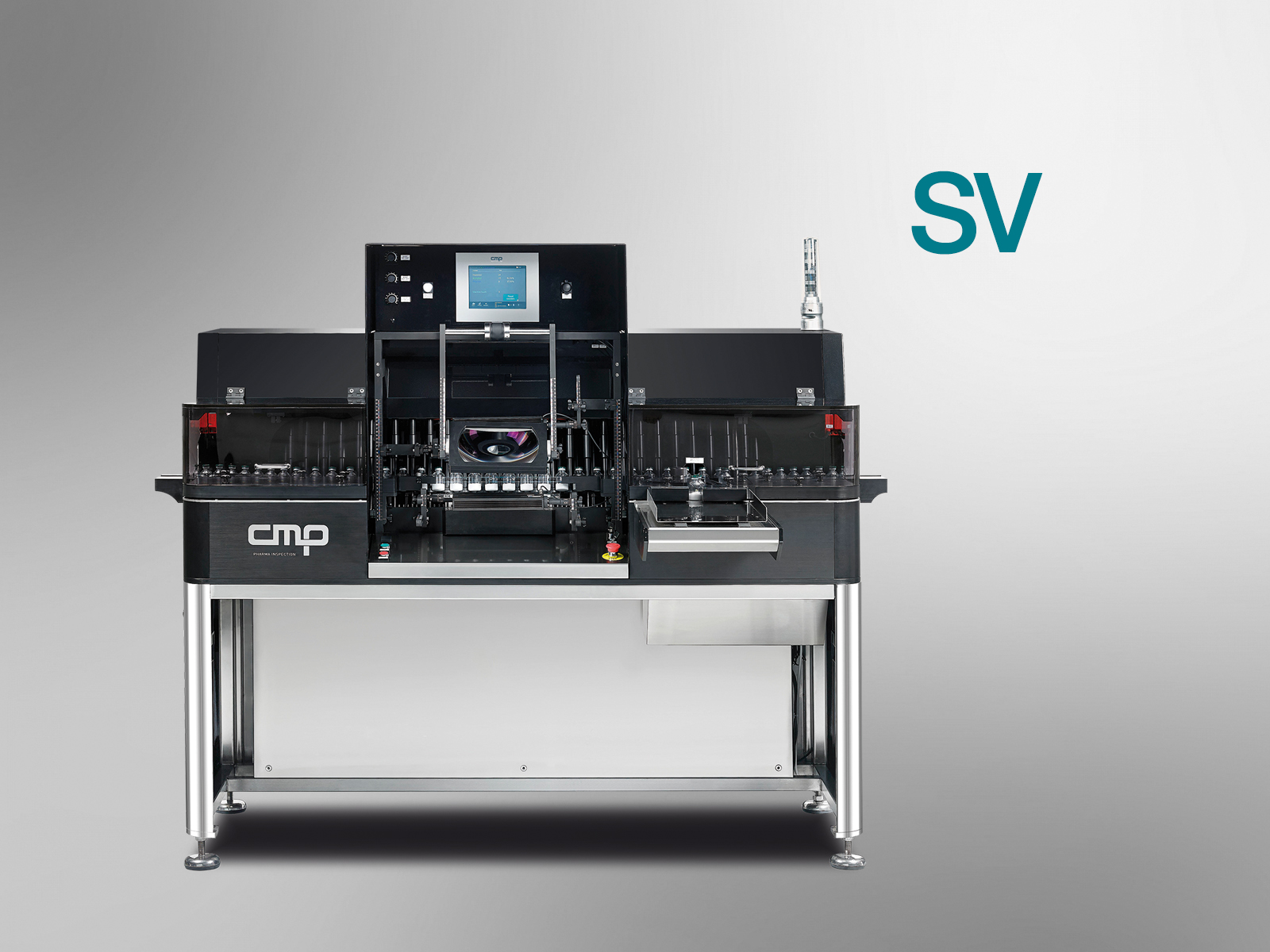
Semi-automatic inspection machine for ampoules, vials or cartridges
If you need to increase the efficiency of your manu...
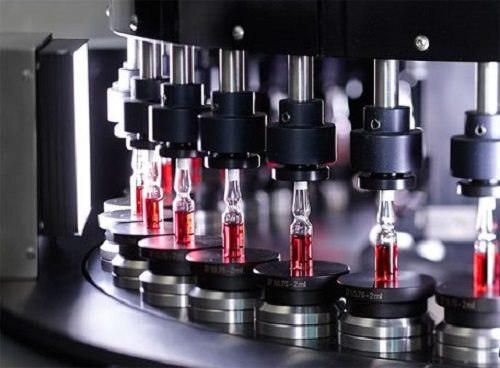
Visual and HVLD inspection for ampoules, vials and cartridges
Do you need to improve the efficiency and capability of yo...
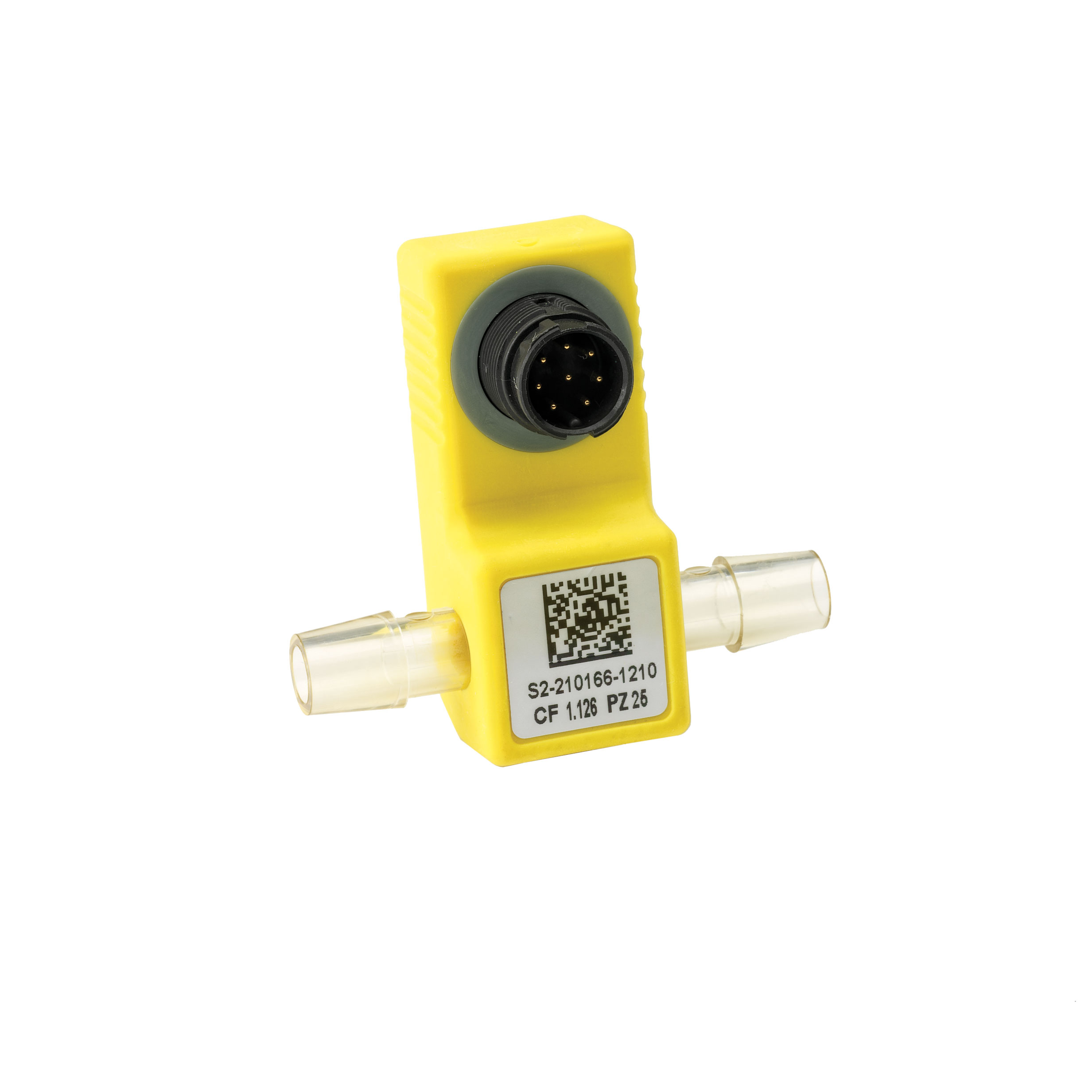
Single-use pressure sensor
Biopharmaceutical manufacturers are increasingly making use of Single-use pressure sensors to enh...
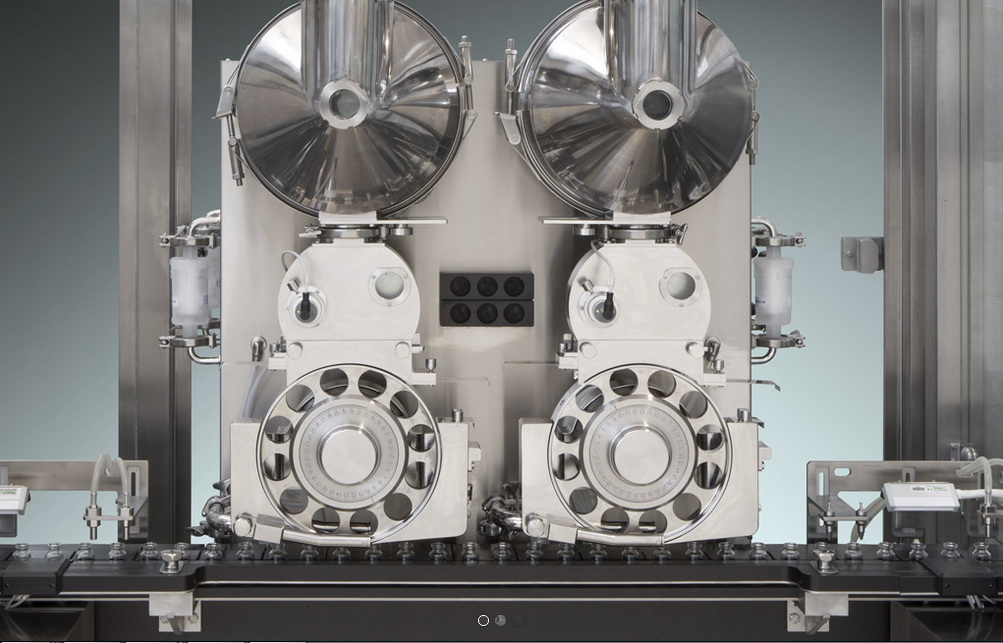
High-speed aseptic injectable vial filling machine
Fill up to 24,000 vials per hour with pharmaceutical powders or liquid...
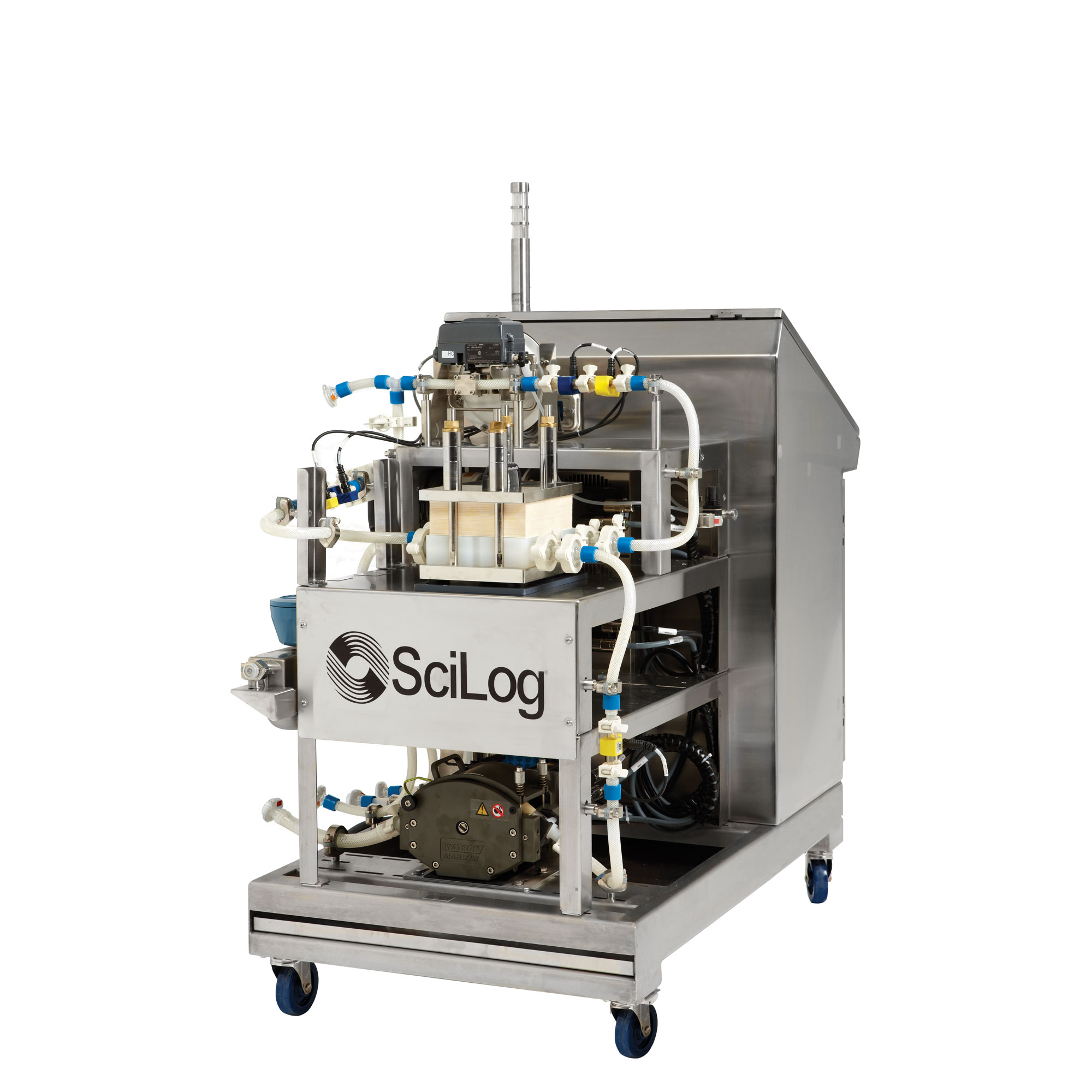
Automated single use tangential flow filtration system
Tangential Flow Filtration is an essential to the biopharmaceutica...
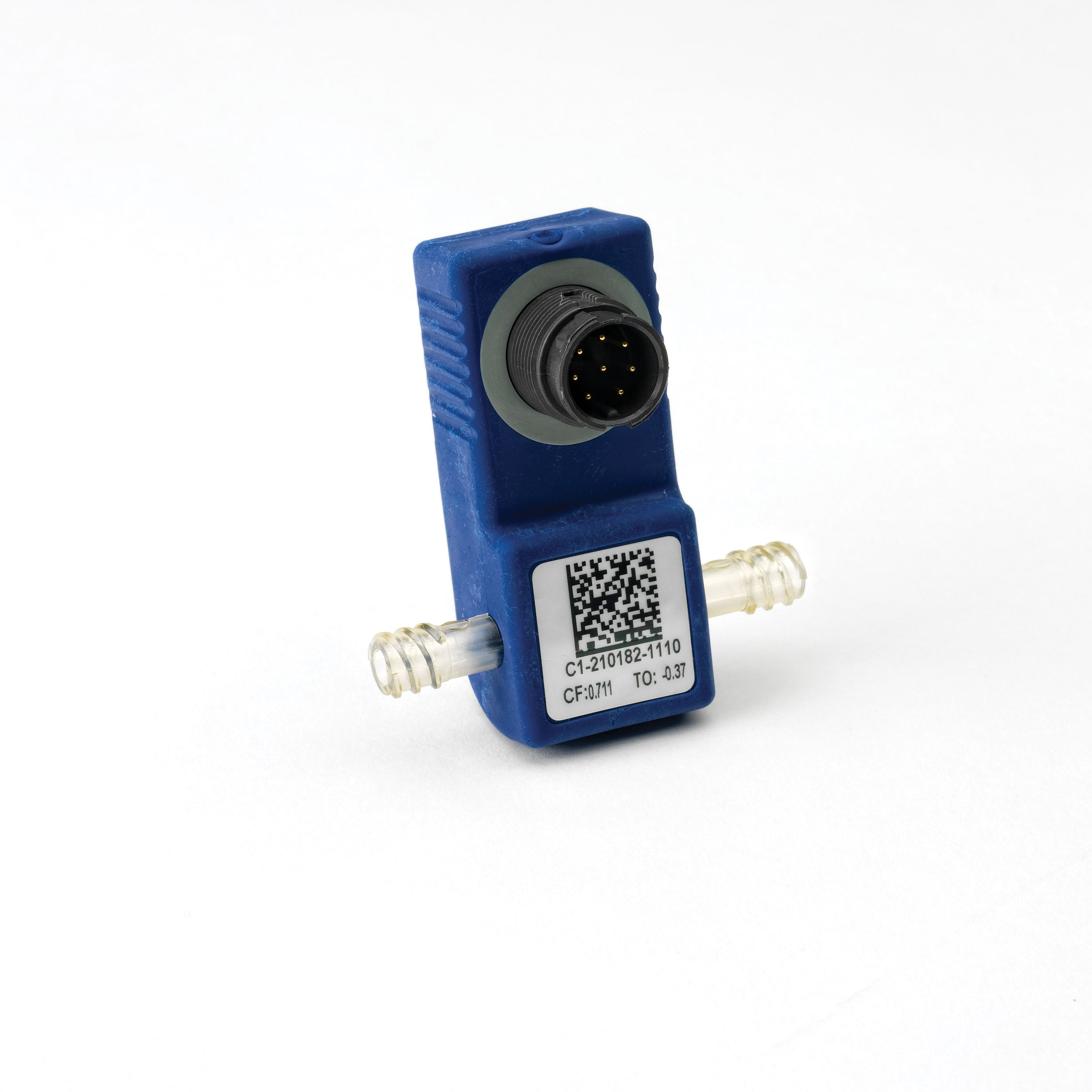
Single-use conductivity sensor
Biopharmaceutical manufacturers are increasingly making use of single-use conductivity sensor...

Single-use temperature sensor
Biopharmaceutical manufacturers are increasingly making use of single-use temperature sensors ...
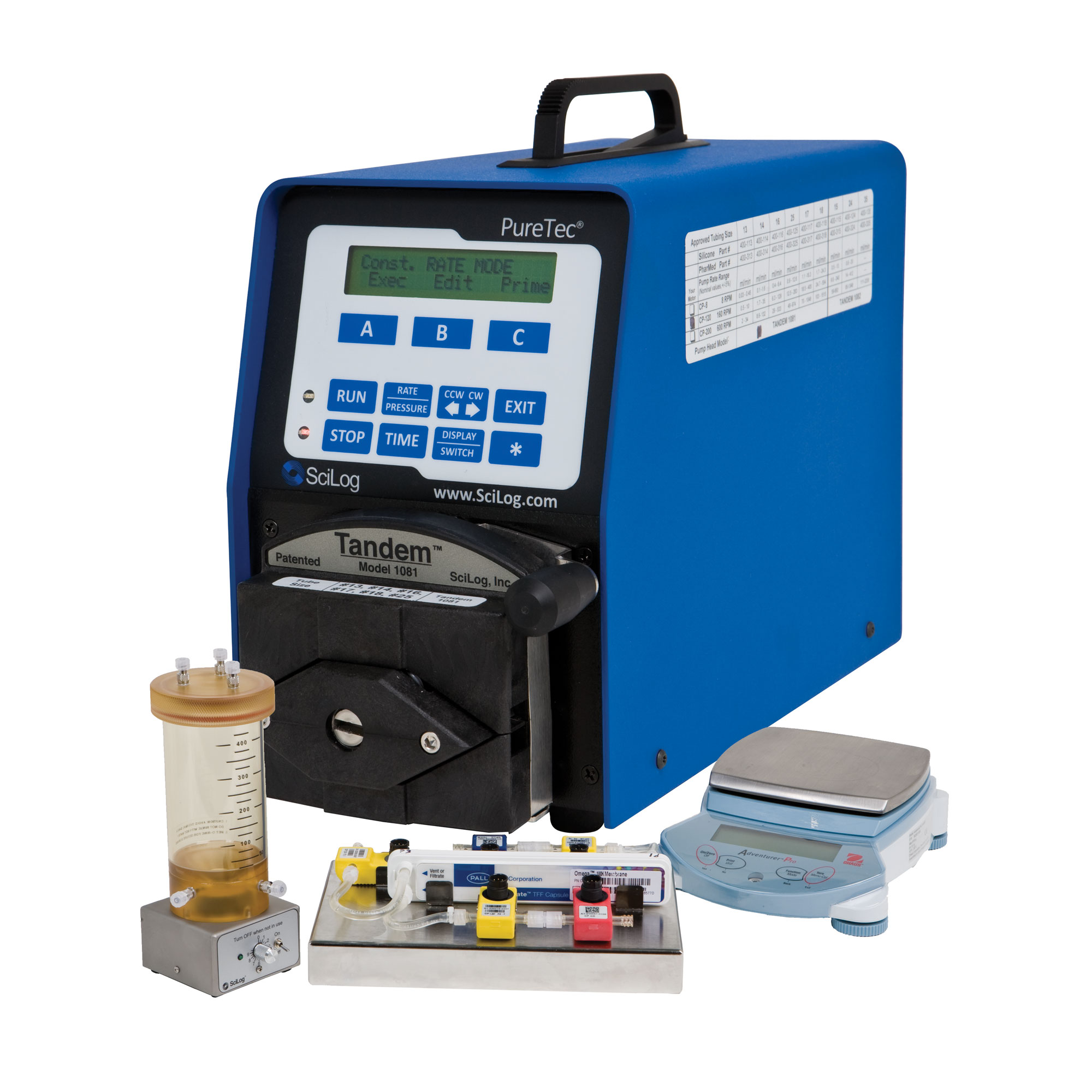
Lab scale tangential flow filtration system
Tangential Flow Filtration is an essential to the biopharmaceutical processing...
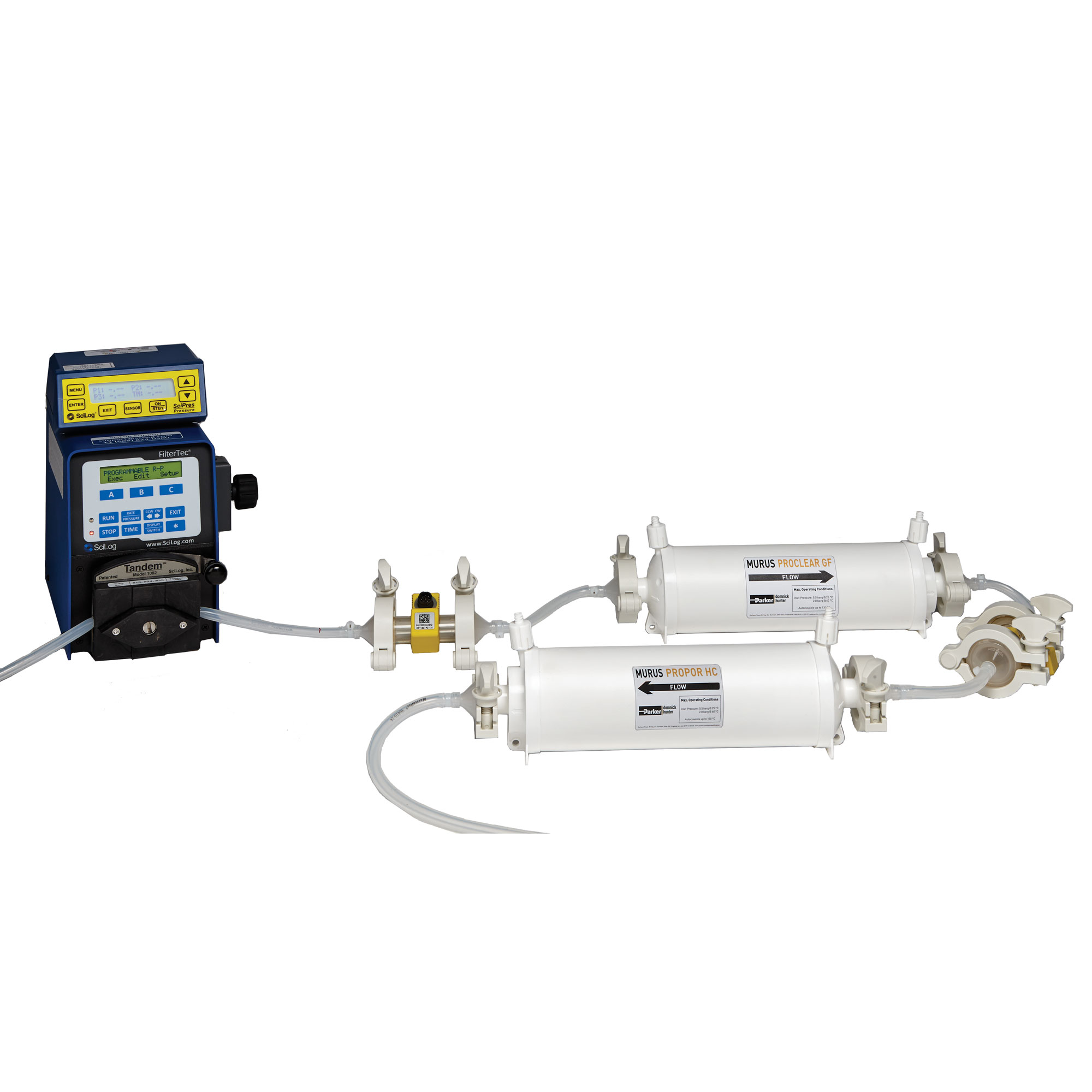
Automated cell culture clarification system
Efficient harvest from the bioreactor is essential to any successful cell cult...
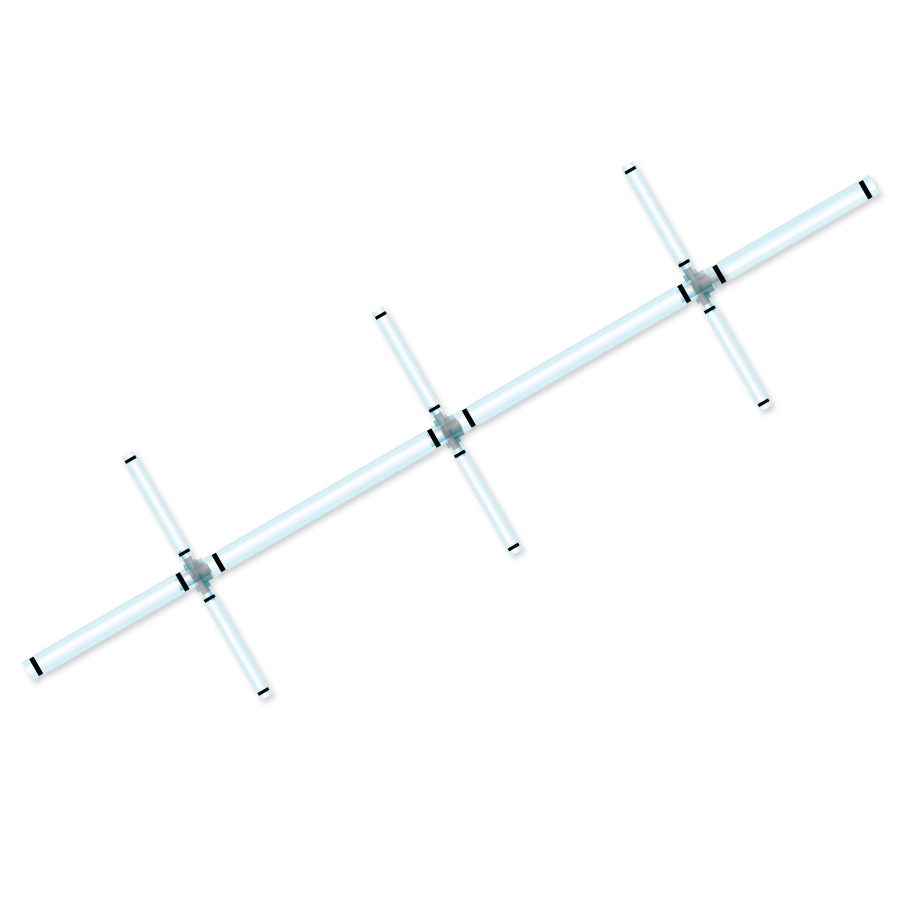
Disposable tubing for manifolds in bioprocesses
Manufacturers in the bioprocessing industries are increasingly turning to ...
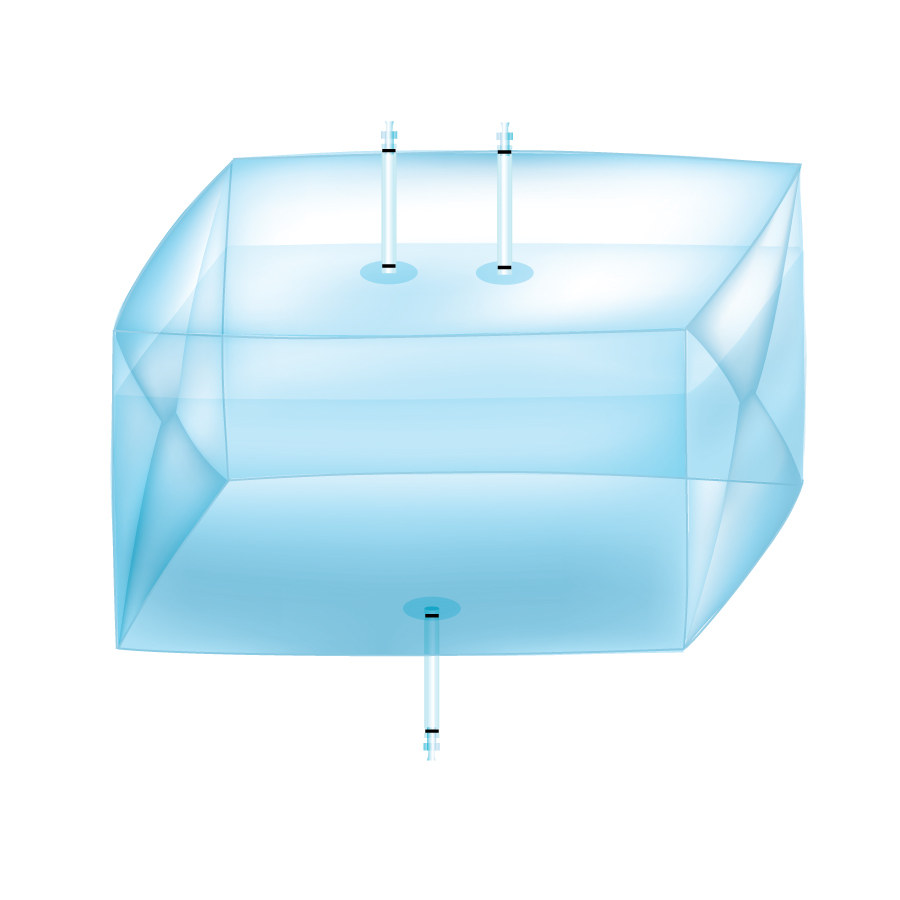
3D disposable bags for bioprocesses
Manufacturers in the bioprocessing industries are increasingly turning to single-use so...
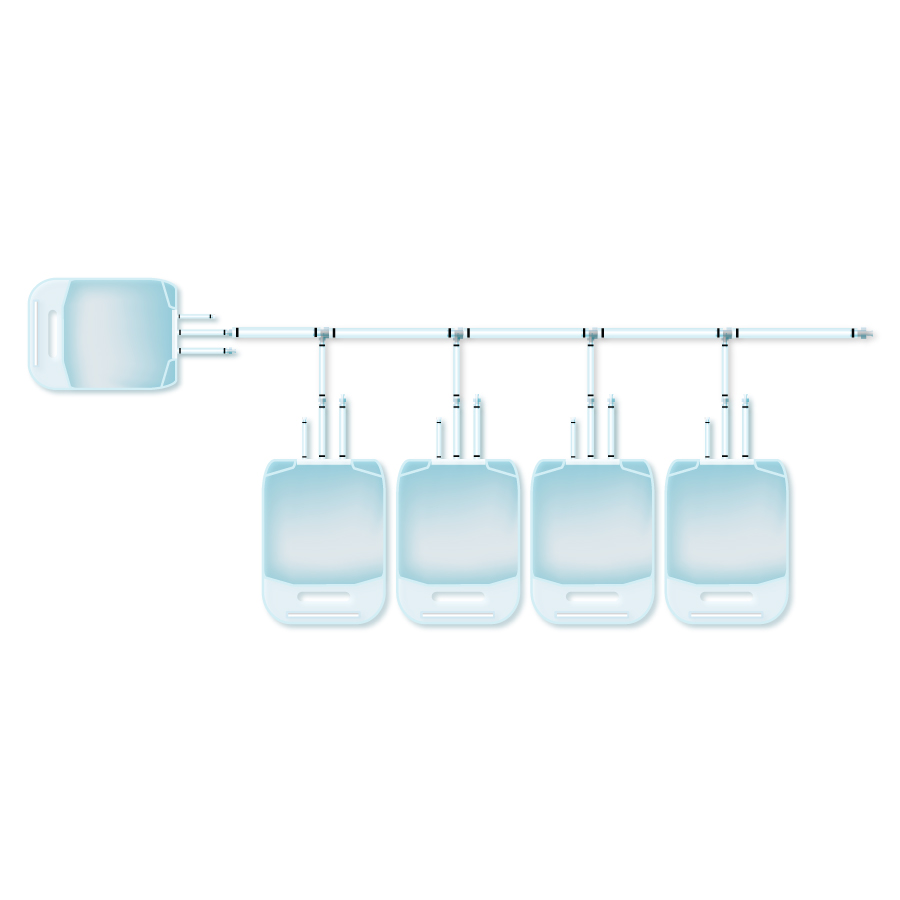
Disposable manifold bags for bioprocesses
Manufacturers in the bioprocessing industries are increasingly turning to dispos...
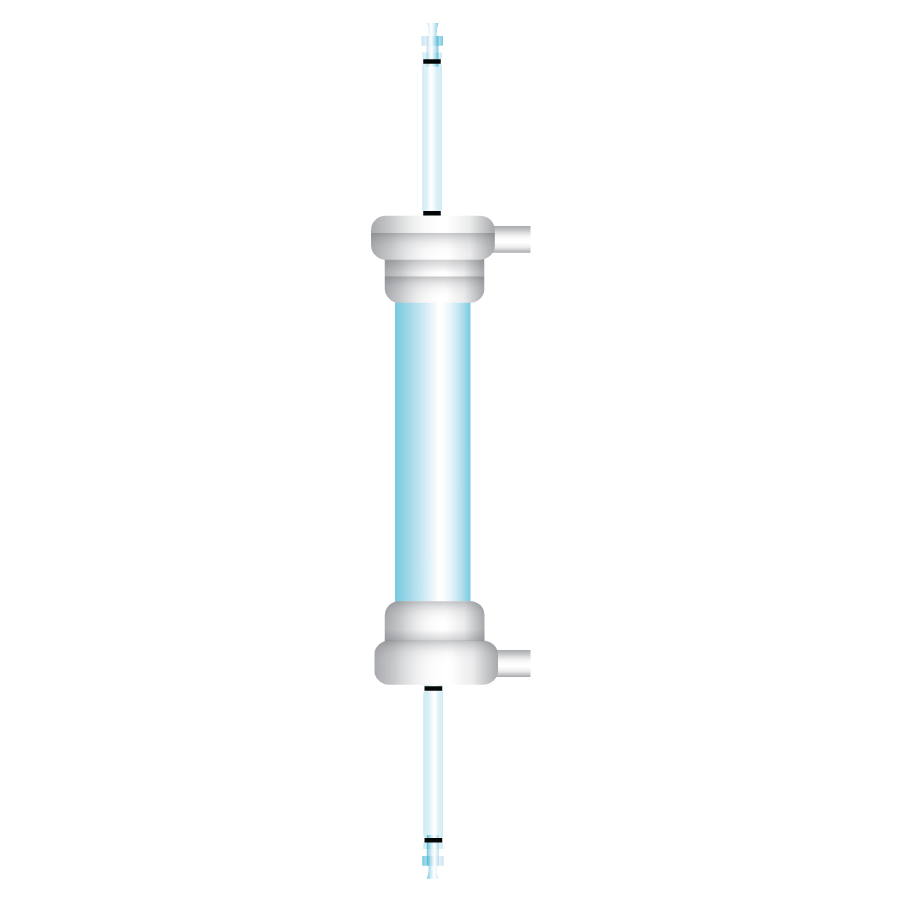
Normal flow filtration sets for bioprocesses
Bio-processors require reliable, high quality, easy to maintain, filtration e...
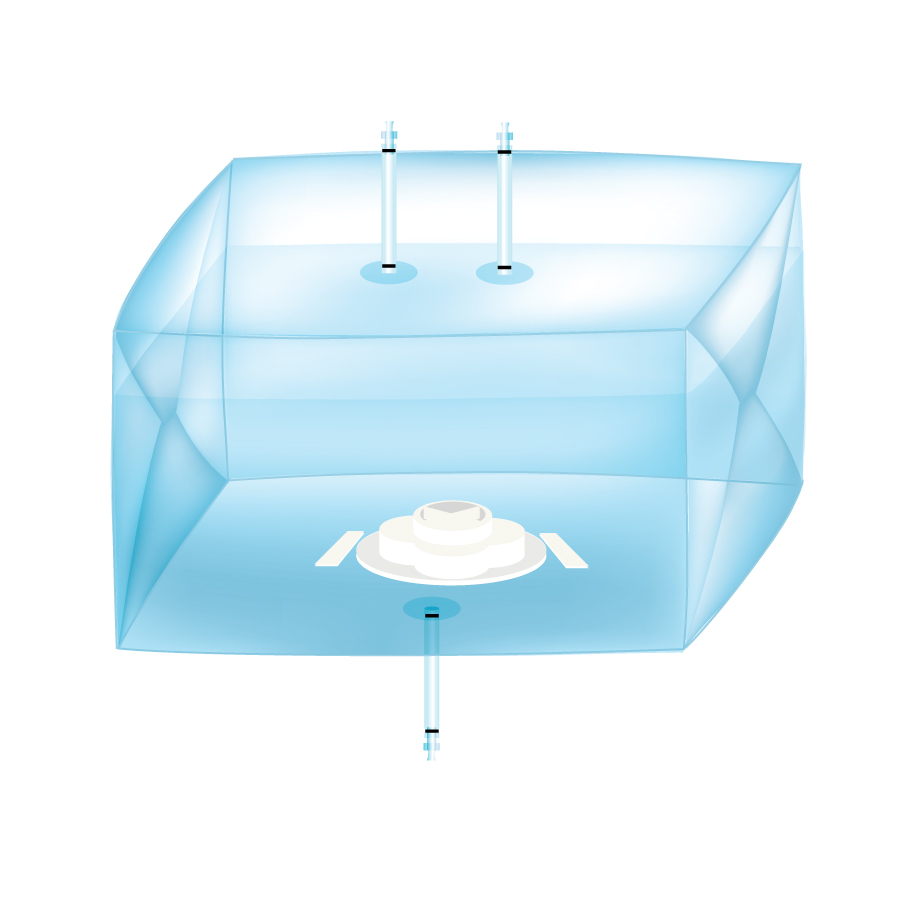
Disposable mixer bags for bioprocesses
Bioprocessors must use ingredients of known high quality and consistency. Inconsist...
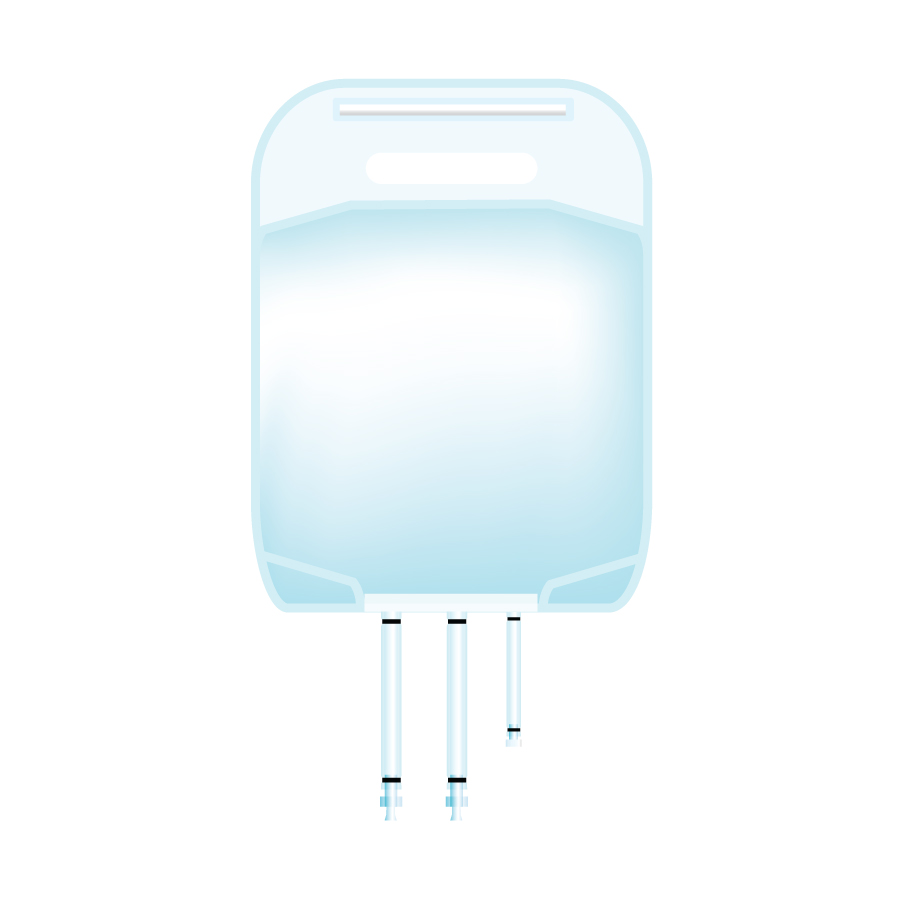
Disposable pillow bags for bioprocesses
Manufacturers in the bioprocessing industries are increasingly turning to single us...
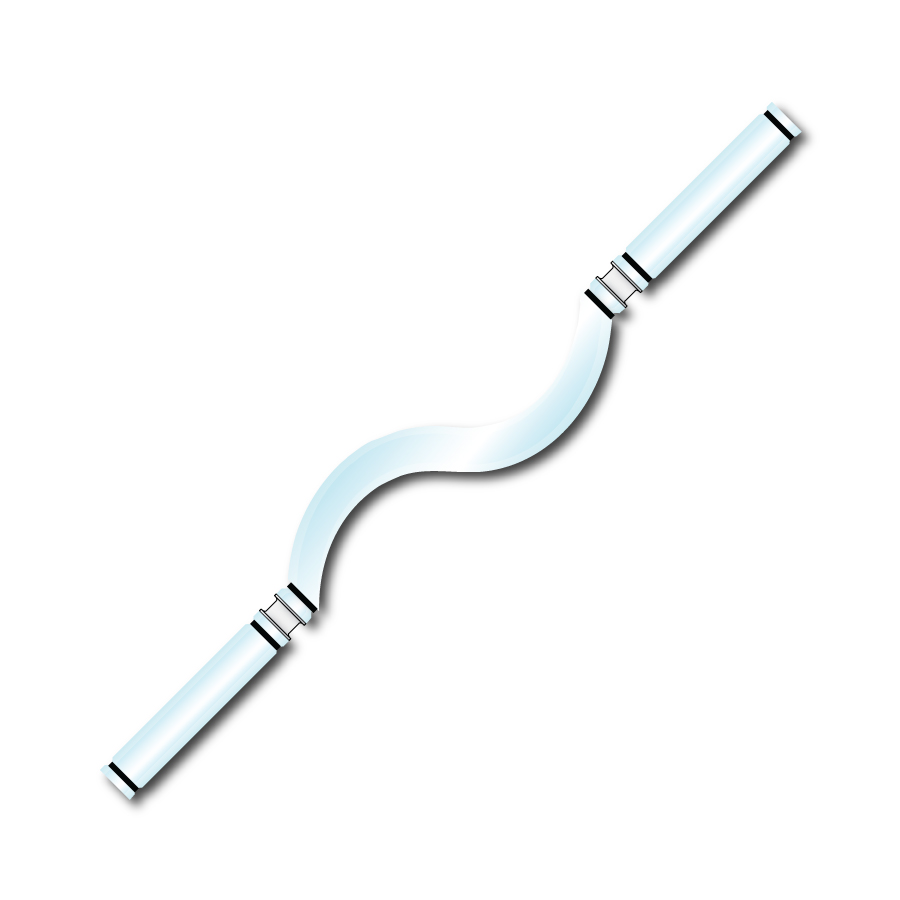
Biocompatible tubing for peristaltic pumps
Sensitive bioprocess applications requires equipment that will not interfere wi...
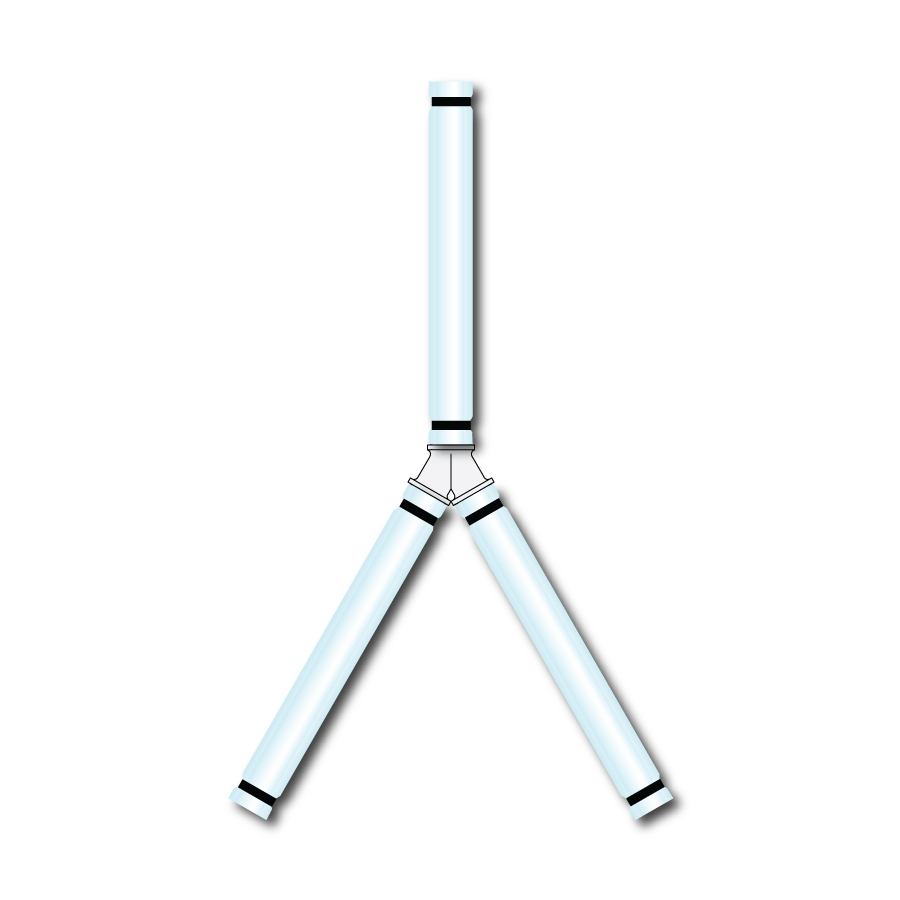
Y sets tubing for bioprocesses
Manufactueres in the bioprocessing industries are increasingly turning to single use solution...
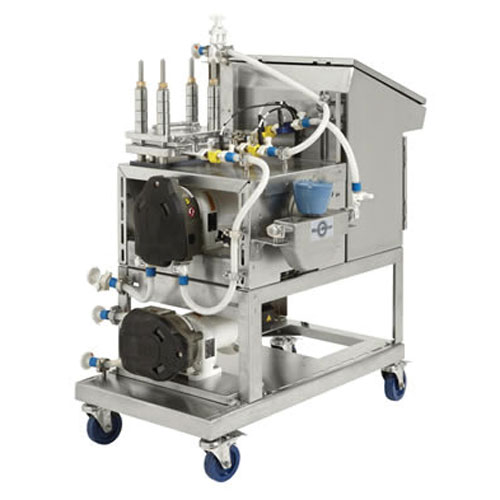
Semi-automated tangential flow filtration system
Tangential Flow Filtration is an essential to the biopharmaceutical proce...
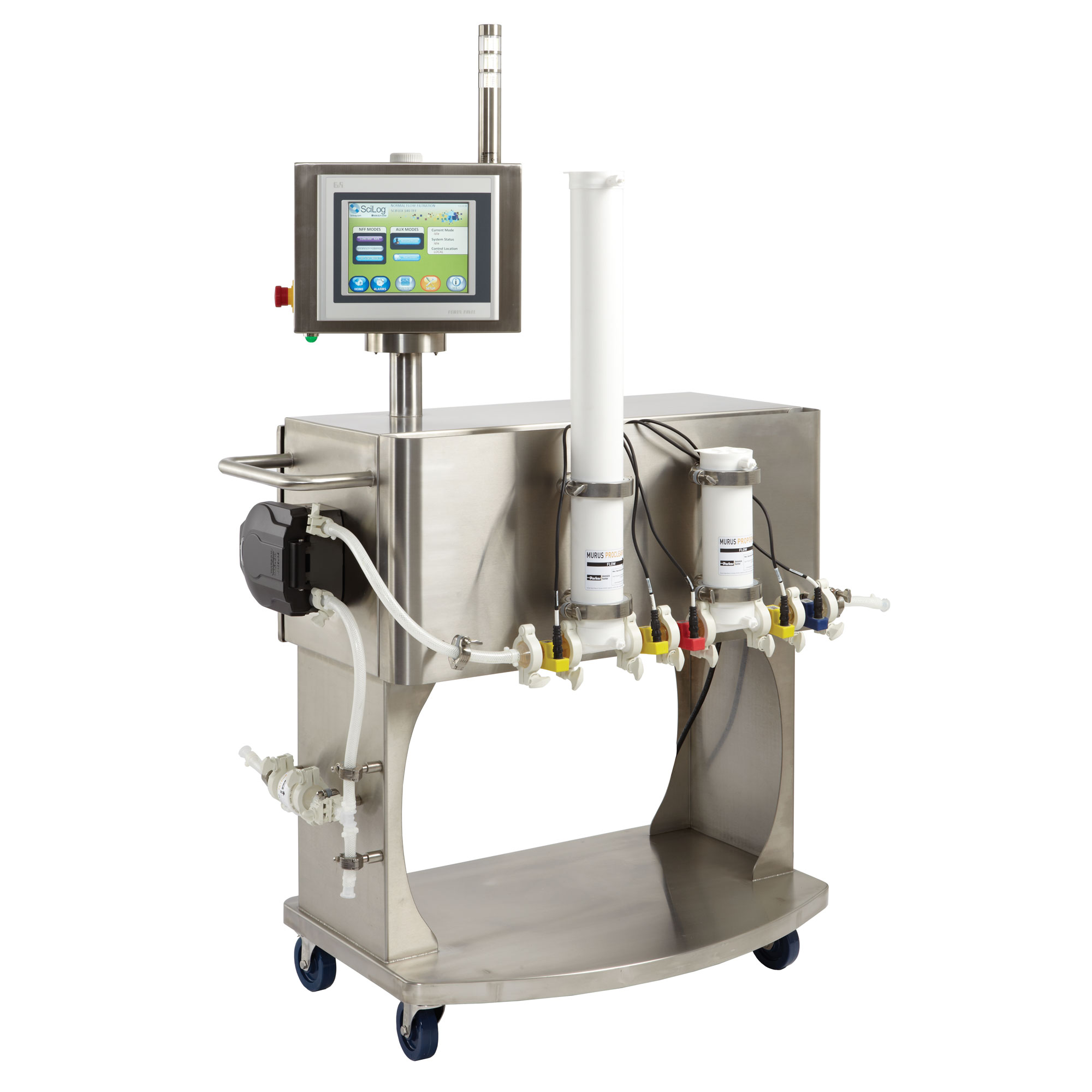
Semi-automated normal flow filtration system
Normal Flow Filtration is frequently used the biopharmaceutical processing in...
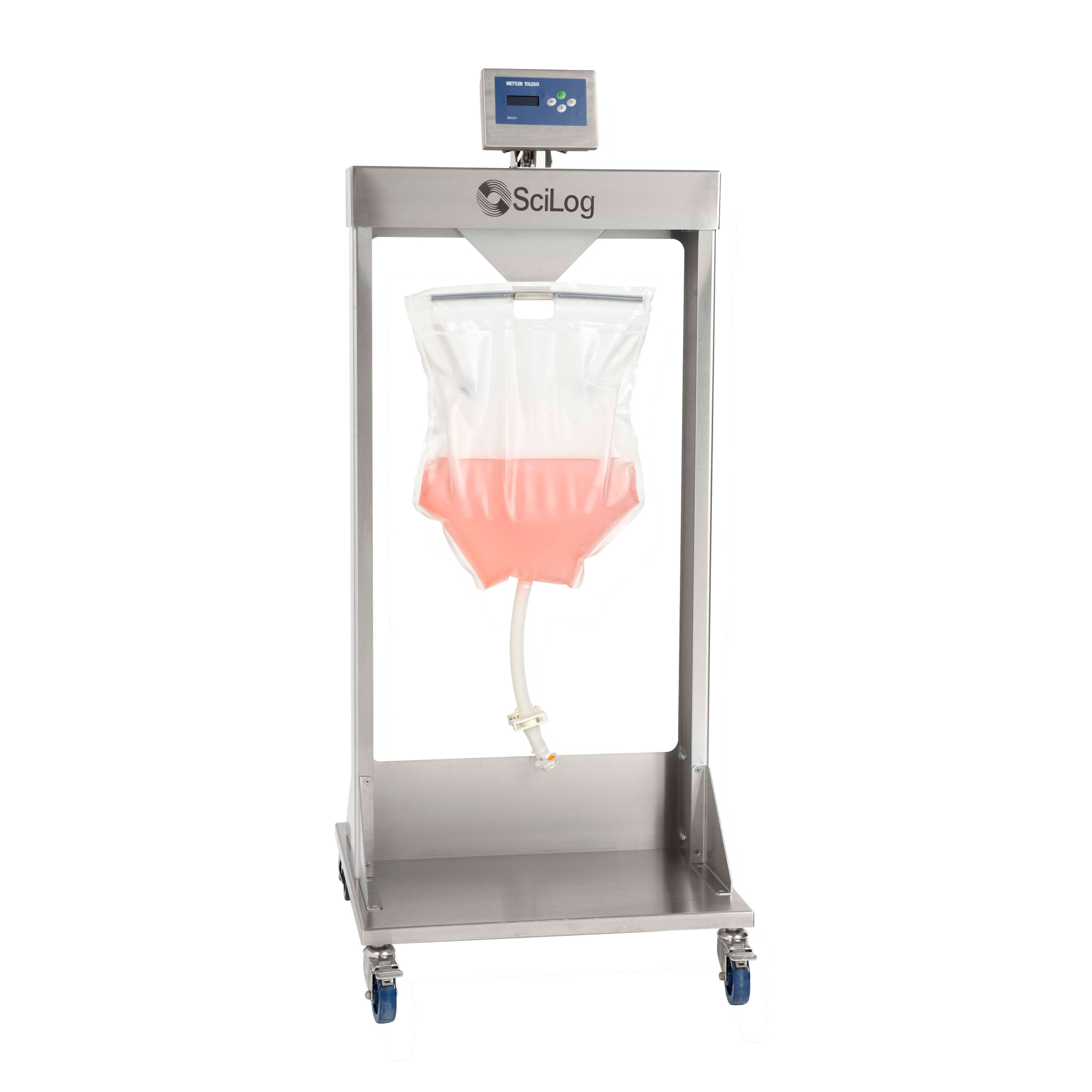
Bag holder and weighing platform for bioprocesses
Single use bags for biopharmaceutical process containment and liquid st...
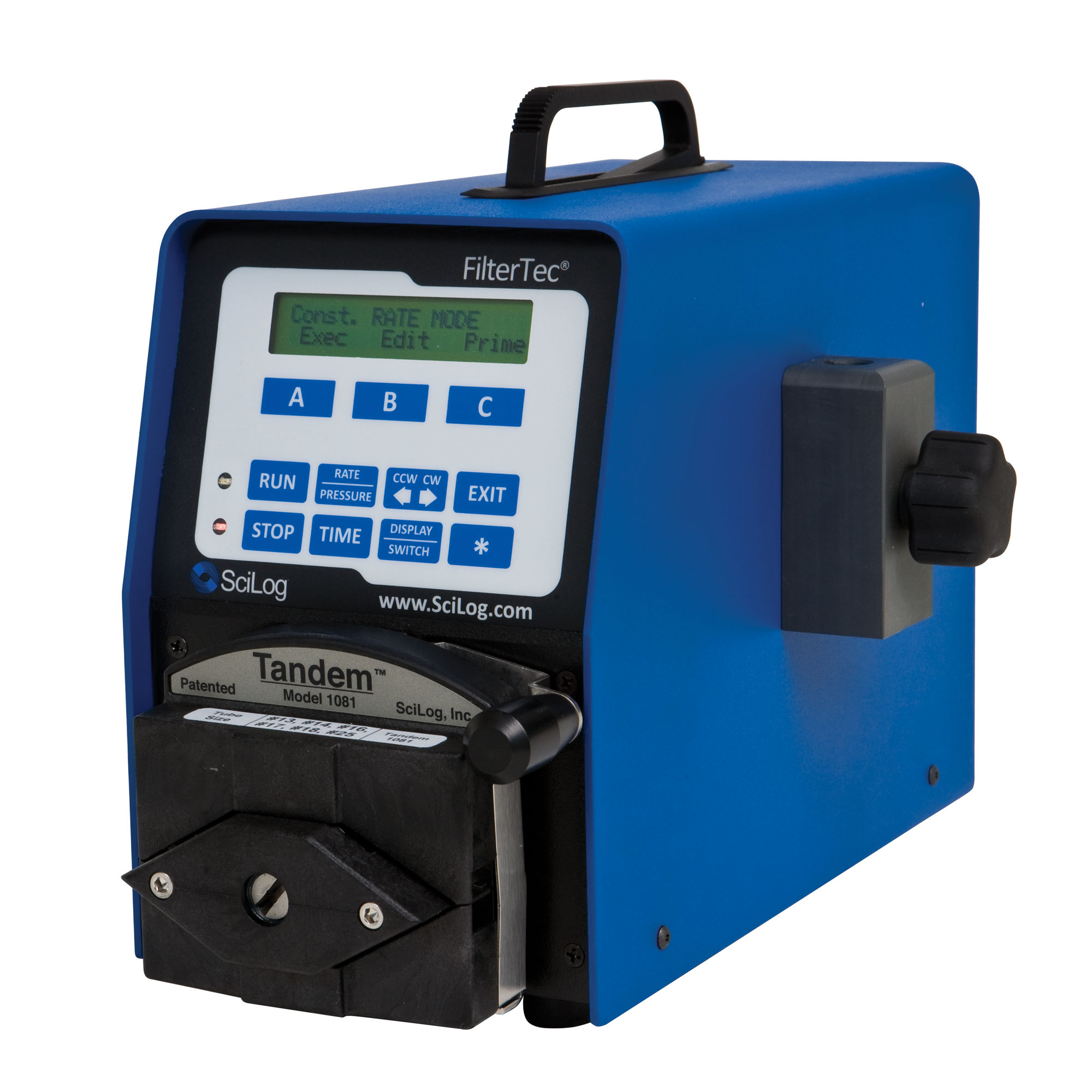
Lab scale normal flow filtration system
Normal Flow Filtration is frequently used the biopharmaceutical processing industry...
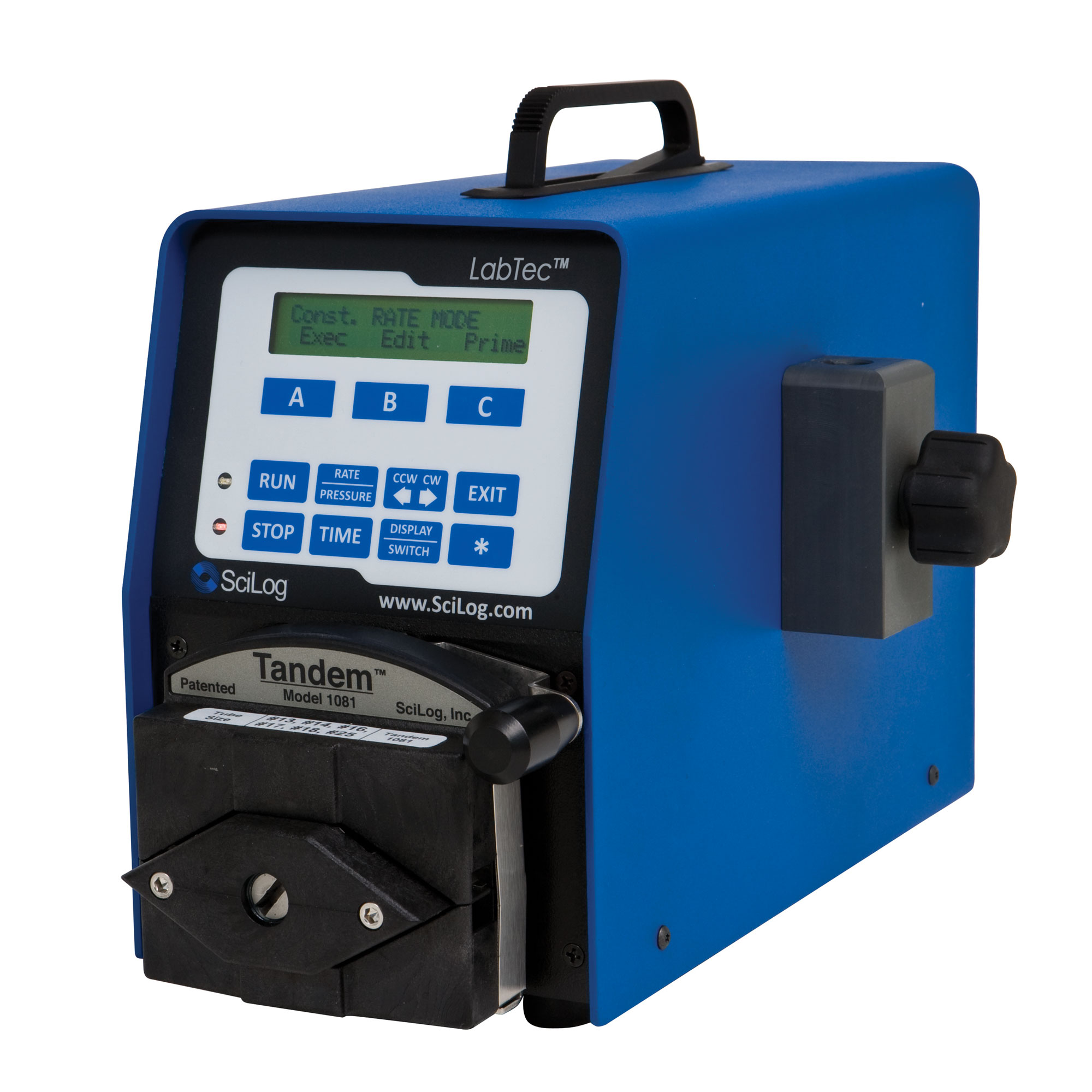
Automated dispensing system for bioprocesses
Biopharmaceutical manufacturers require precisely known liquid quantities for...
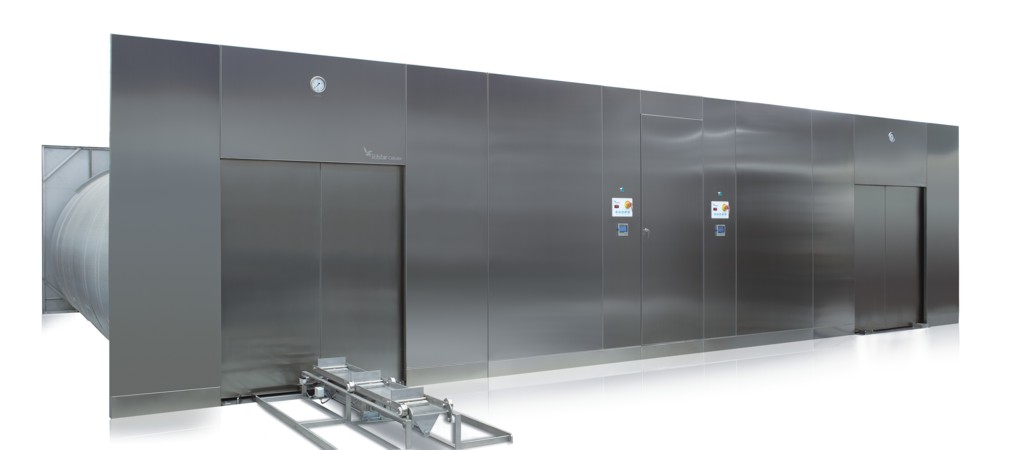
Superheated water shower autoclave
Specially designed for sterilizing large batches of parenteral solutions.
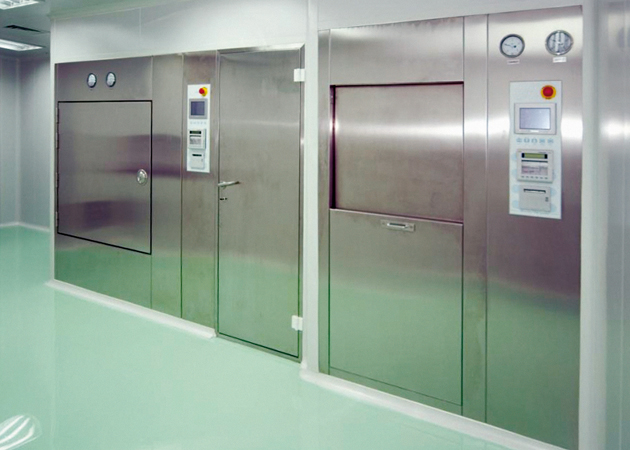
Dry heat depyrogenation oven
Specially designed for the drying and sterilization of glass containers, vials or ampoules, and...
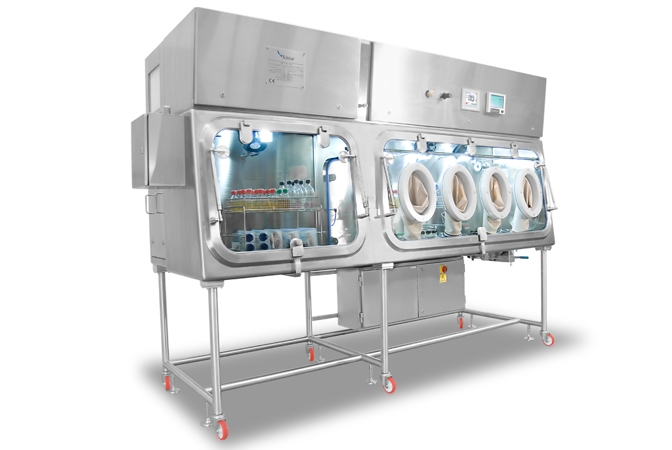
Sterility test isolators
Designed to avoid this risk and protect the product from both the process and externally generated f...