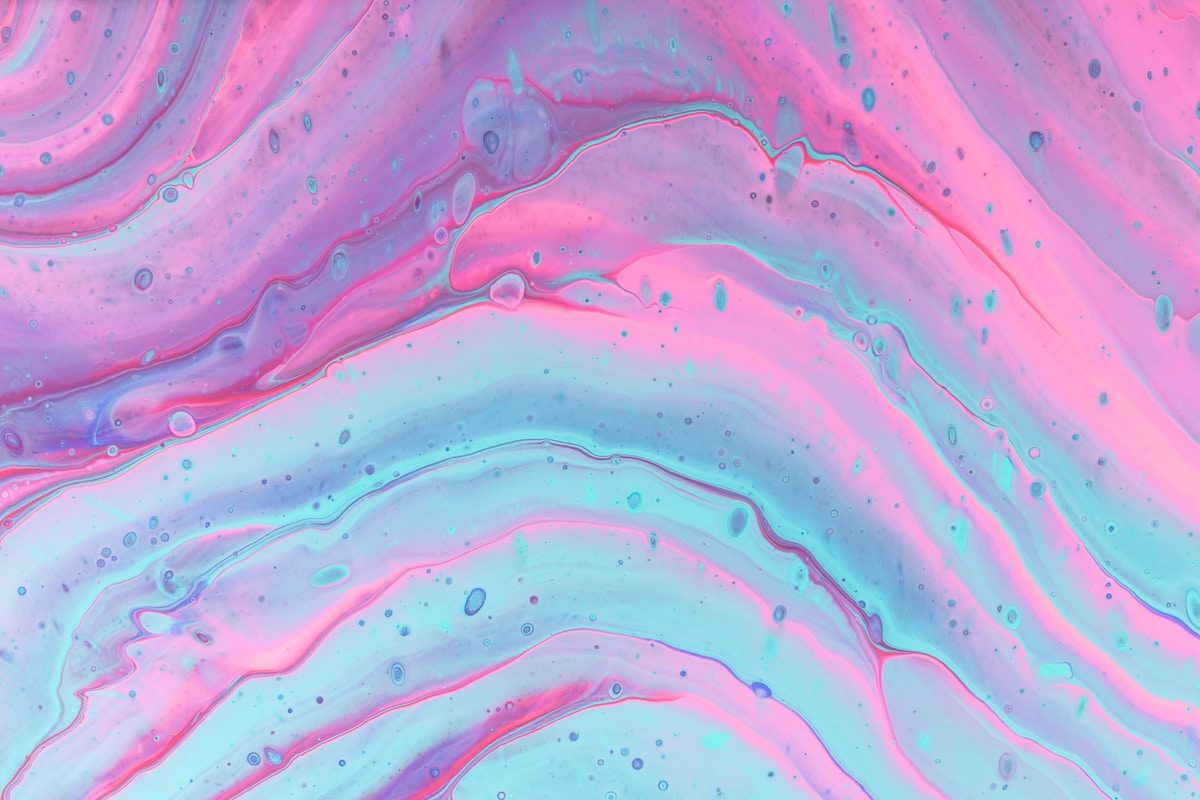
Making Paints
Find innovative production technology for making paint and connect directly with world-leading specialists
Painting as an integral aspect of the human tradition dates to thousand years ago. Of the many properties of the product, the drying time is important to consumers. The thickness of the paint and environmental factors like humidity affect this parameter. Paint manufacturing equipment must include a humidity test chamber to assess the behavior of paint under different weather conditions.
Stories about paint
Tell us about your production challenge
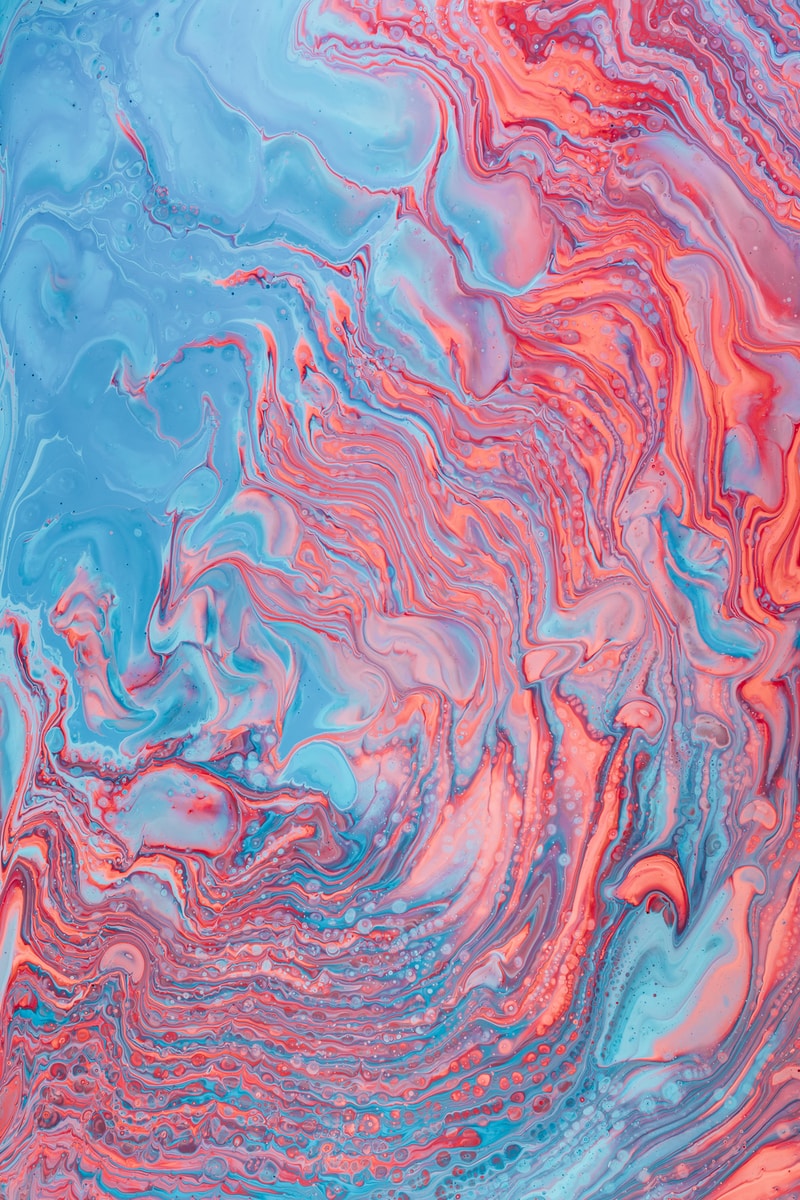
Water-based paints versus oil-based paints
Years ago, nearly all available paints were oil-based, but today consumers have the option of a water-based coating. In the process of paint manufacturing, the solvent determines the paint type. Oil-based paints contain oil as their solvent, while water-based paints use mainly water. Oil- or solvent-based paints have a much higher level of organic compounds than their counterpart. These compounds enhance their application, drying time, and durability. However, they release strong odor and toxic volatile organic compounds that negatively impact the environment.
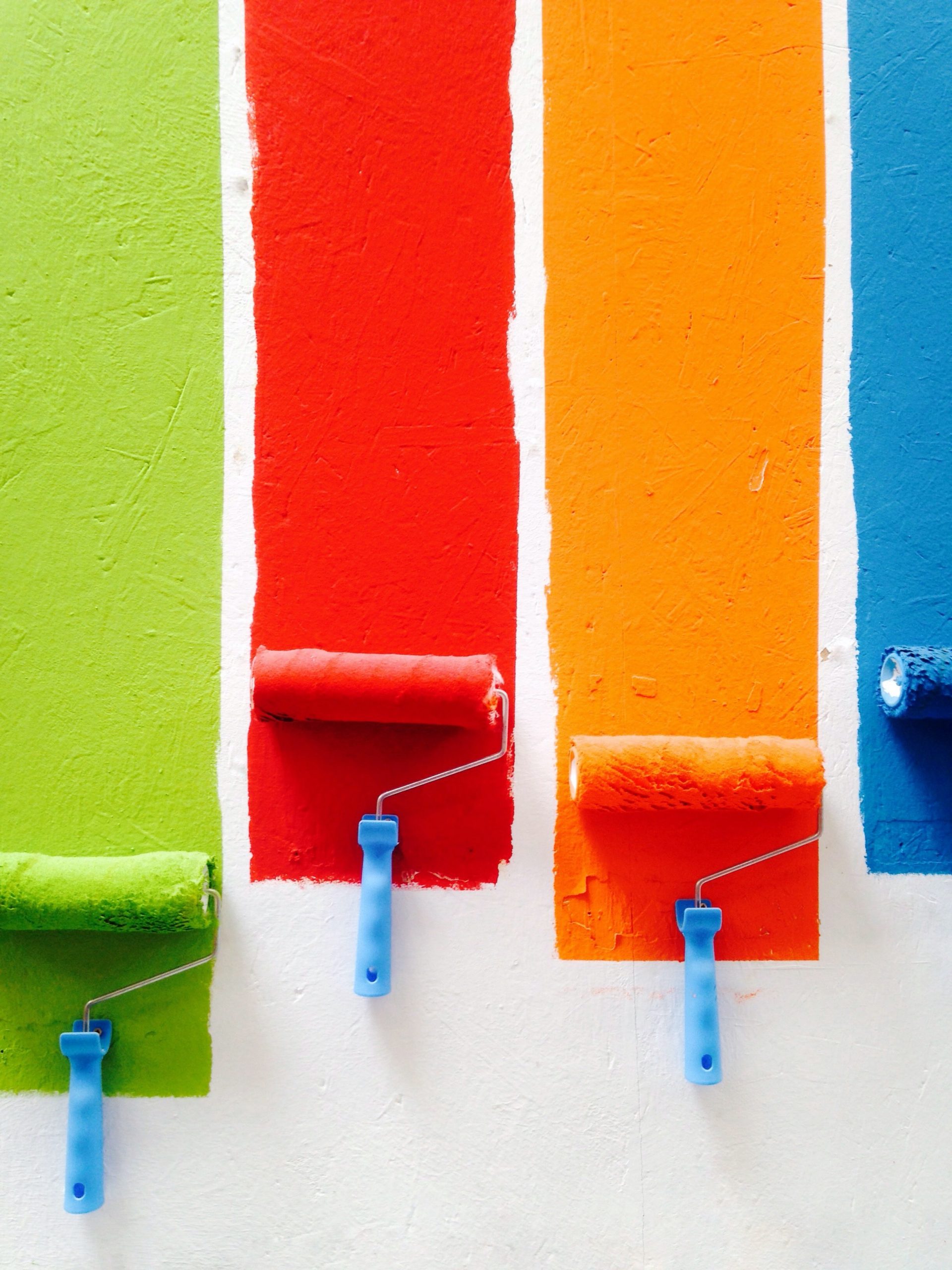
Recently, technological advancements have led to the manufacture of water-based paints that have excellent drying time with far less odor. The common paint manufacturing equipment used for both include mixers, mills, and filters.
Mixers are important for solid-liquid mixing. Mills are used to damage any coagulated particles while filters purify the paint. The choice between both depends on what you want to achieve. Generally, water-based paints retain their colors for a long time and are better for outdoor painting, while rust-resistant oil-based paints go better with moldings and trims.
The impact of Volatile Organic Compounds on the environment
As paints dry, they release Volatile Organic Compounds (VOC), chemical compounds that evaporate at room temperature. When they do it, they negatively impact human health and the environment. Once they are in the air, they play significant roles in forming ozone. These compounds also trigger conditions like allergies, asthmatic reactions, and skin and eyes inflammation.
Water-based paints solve these concerns because they don’t contain organic compounds. As a regulatory measure, the European Union has published a test standard that uniformly controls the emission rate from products. This authorizes manufacturers to test and indicate emission measurements from their products.
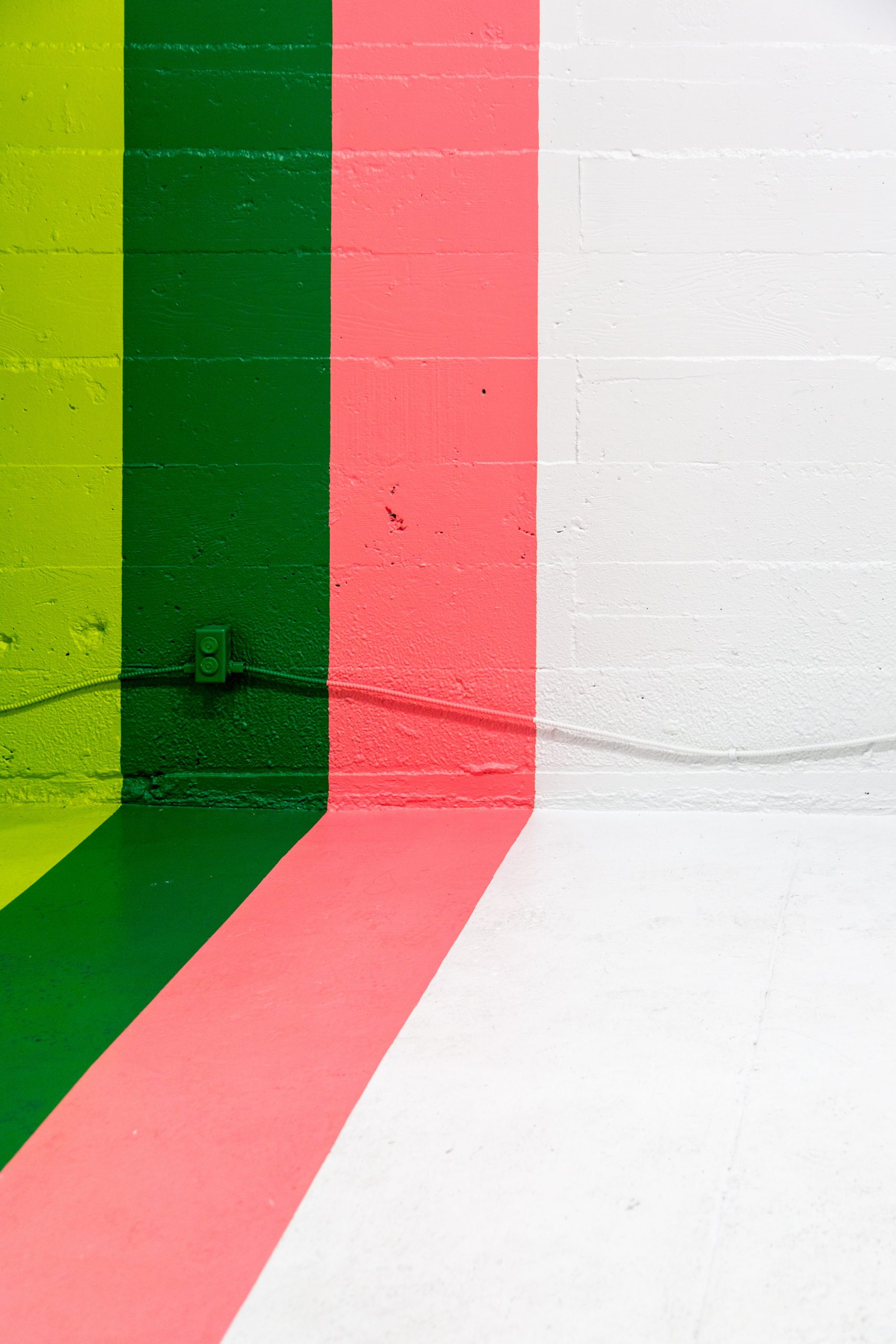
Standard tests made from paint manufacturing equipment
Paint manufacturers must ensure the solvent they use aligns with quality control standards. They do this by testing various parameters. Some of these tests include a density test which checks if the solvent is mixed with other components or not. A pigment test helps to know the amount of binder and resin required to absorb a specific amount of pigment. A fineness test checks how smooth painted surfaces will be, while the gloss test determines the degree of shine for the paint. Other tests are washability and impact resistance. They ascertain the paint’s resistance to washing and measure the film’s resistance against hard shocks, respectively.
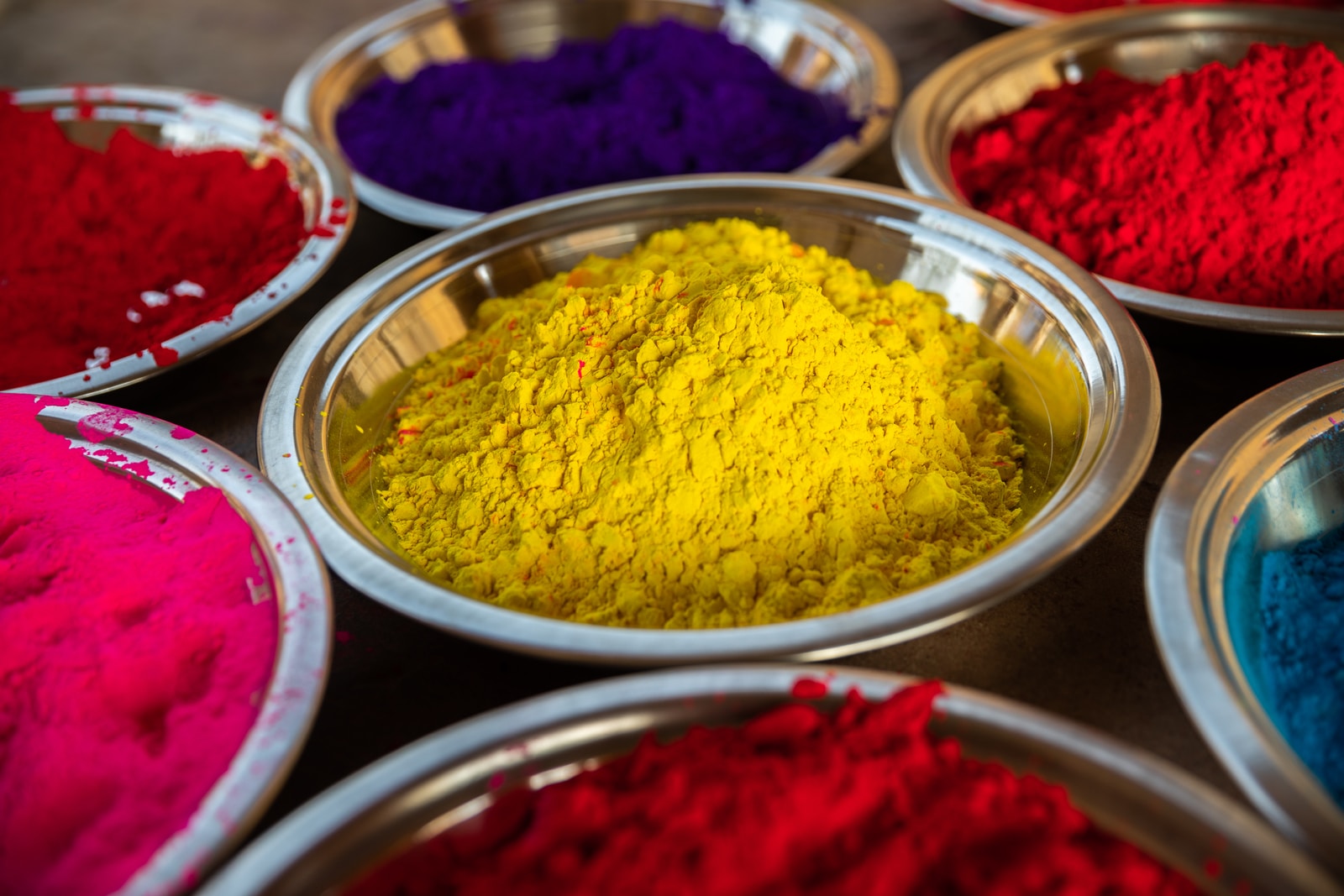
Application of paints, defined by their constituents
End-products from a paint manufacturing machine differ in their application depending on their constituents. Oil-based coatings are tougher than water-based paints and are used for residential furniture, metal railings, and industrial steel equipment.
Enamel additive makes the dried surface harder and less porous. Most water-based flooring paints contain enamel additives.
Urethane additives offer superior water and abrasion resistance and are common in industrial coatings, where durability is of utmost importance. Epoxy coatings are easy to apply, dry quickly, and form protective coatings. You can apply them to concrete and steel to offer resistance to water, alkali, and acids.
Processing steps involved in paint making
Which paint technology do you need?
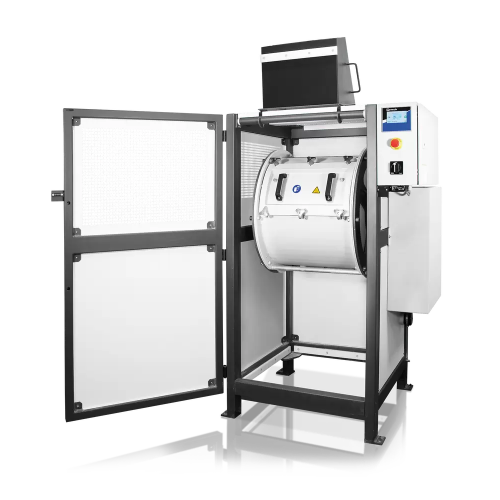
Laboratory drum mill for large sample volumes
Efficiently process large volumes of diverse materials into precise particle...
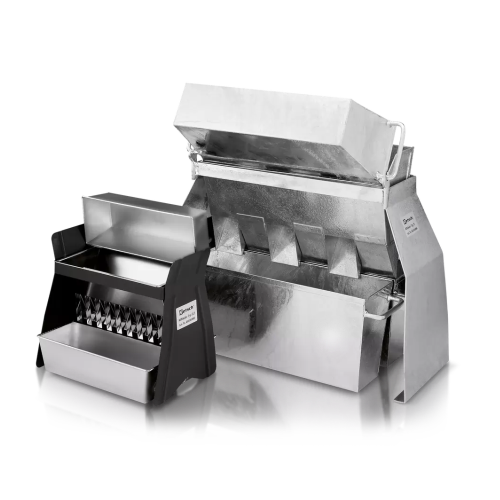
Sample divider for on-site reduction of bulk materials
Ensure consistent sample analysis with precise on-site material di...
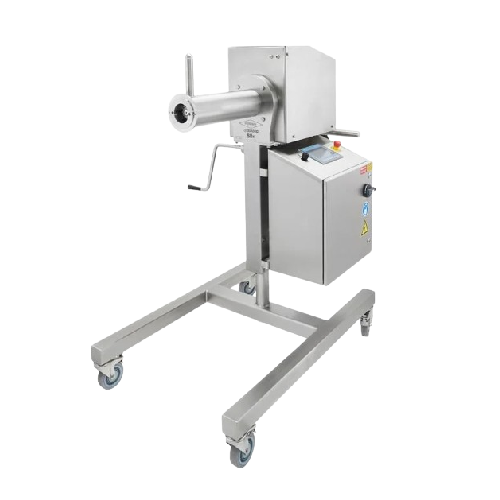
Mid-size milling platform for pilot-scale production
Achieve precise particle size control with this integrated milling s...
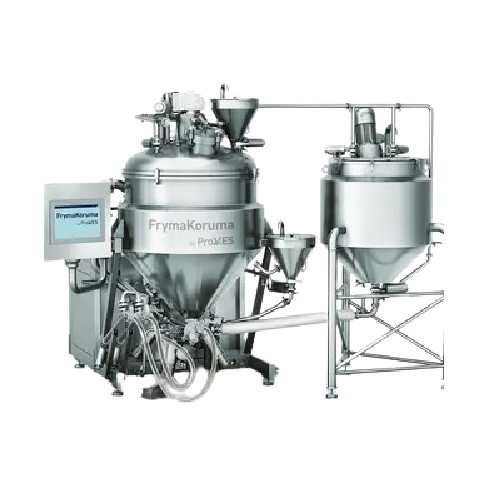
High shear emulsifier for mayonnaise production
Streamline your production of high-quality emulsions with this high-capaci...
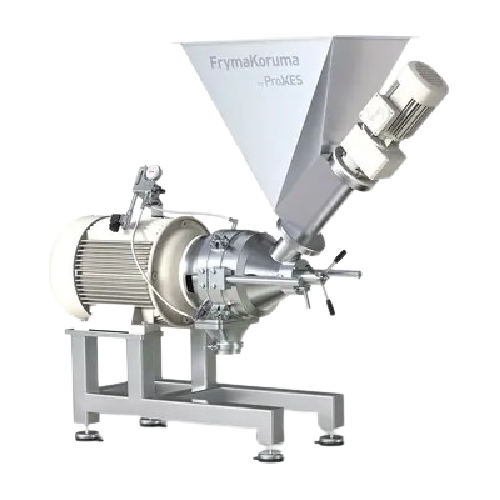
High shear emulsifier for food and pharmaceutical products
Optimize your production line with precise emulsification, ho...

Heat exchangers for efficient heat transfer in industry
Achieve precise temperature control across diverse viscosities wi...
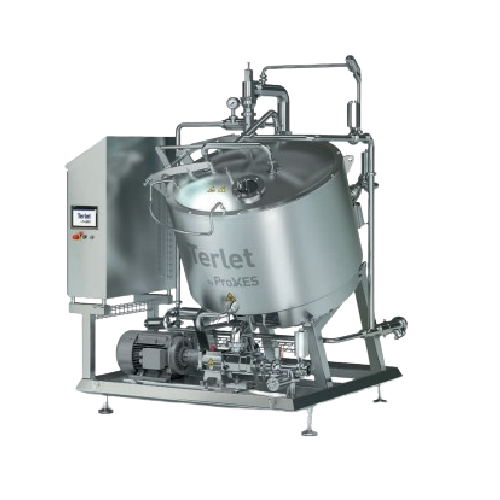
Precise liquid cooling solution for food processing
Ensure high-quality preservation of flavors and textures in liquid fo...
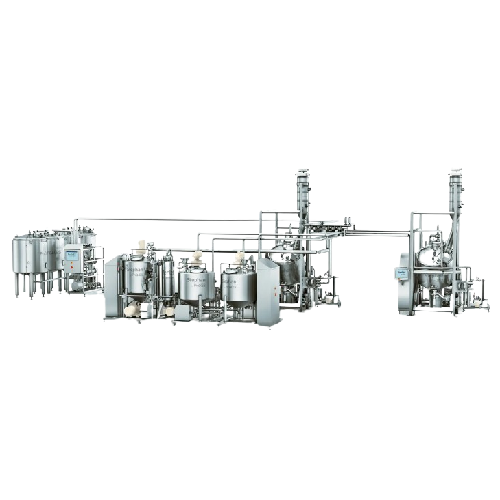
Continuous nut paste production line
Elevate your production efficiency with a versatile preparation line designed to seaml...
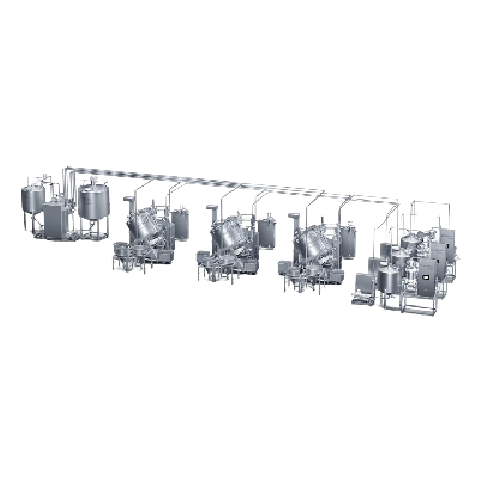
Continuous mustard production line
Optimize your condiment production with precision-engineered systems capable of transfor...
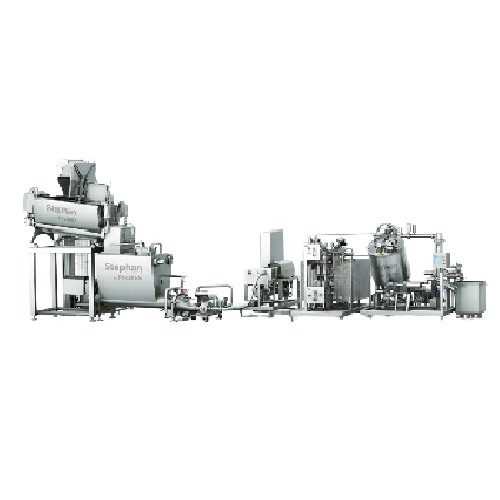
Cheese blending and heating line for processed cheese
Optimize your processed cheese production with a solution that seam...
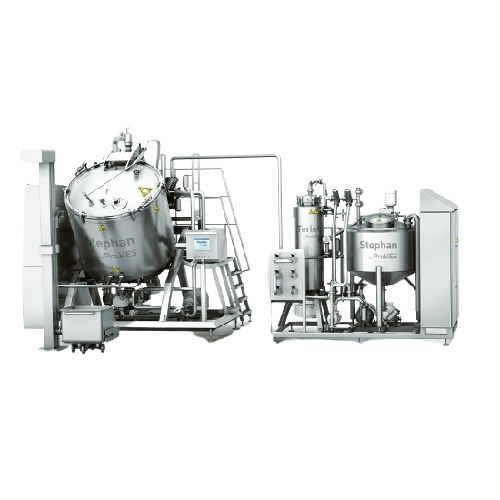
Continuous caramel production line
Optimize your caramel production with seamless integration, achieving precise fat meltin...
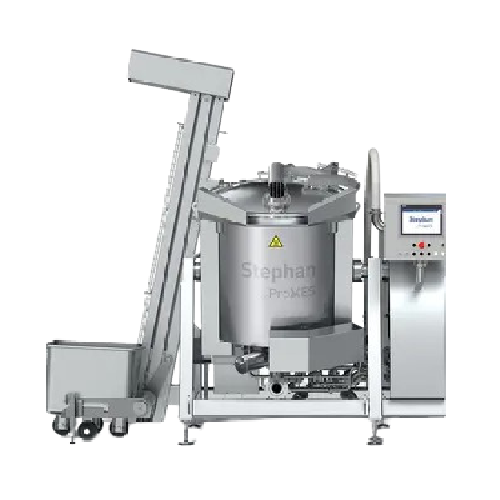
Industrial cooker for sauces and stews
When producing diverse culinary delights such as sauces and stews, achieving even he...
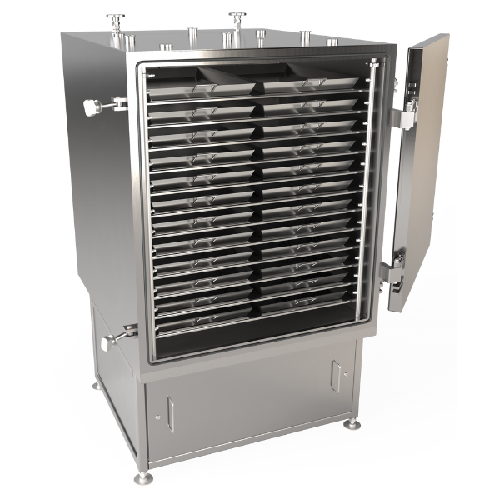
Continuous heat exchanger for soups and sauces
Optimize your soup and sauce production with a continuous heat exchanger th...
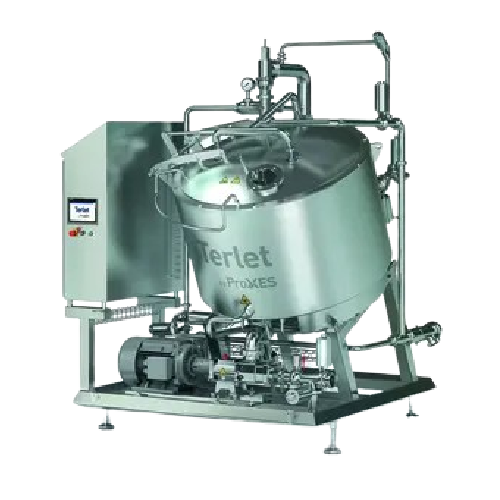
Efficient cooling and cooking systems for food processing
Streamline your production with integrated cooling and cooking...
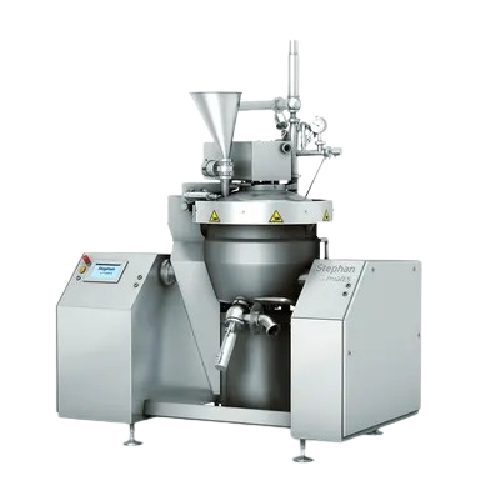
Industrial cutting system for fine emulsions
Optimize your production line with precision cutting and emulsifying, ensurin...
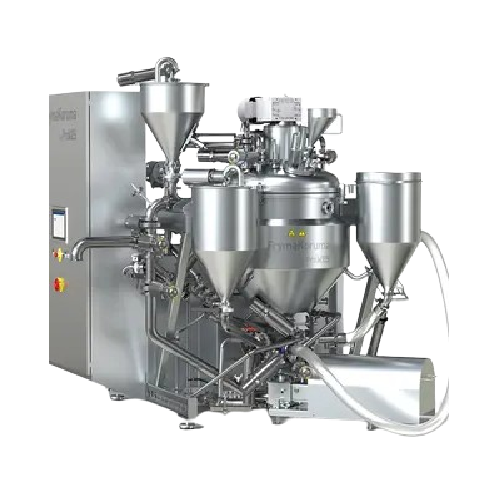
Vacuum deaeration system for mustard and liquid detergents
Ensure optimal product quality by effectively removing air fr...
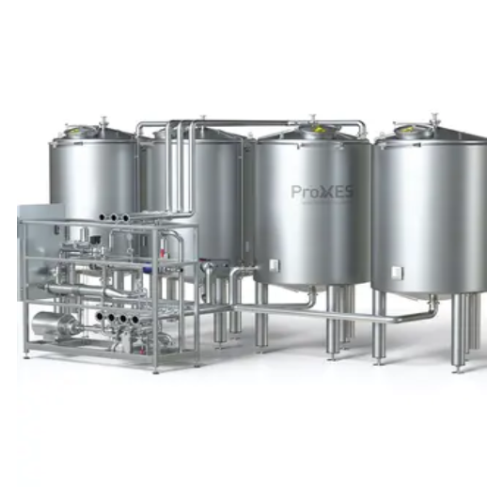
Cleaning systems for food, pharmaceuticals, and cosmetics
Ensure optimal hygiene and safety with advanced cleaning syste...
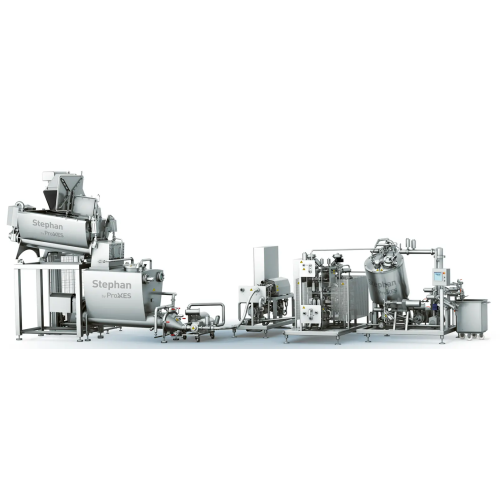
Continuous caramel process line
Optimize your continuous food processing with an engineered-to-order line tailored for preci...
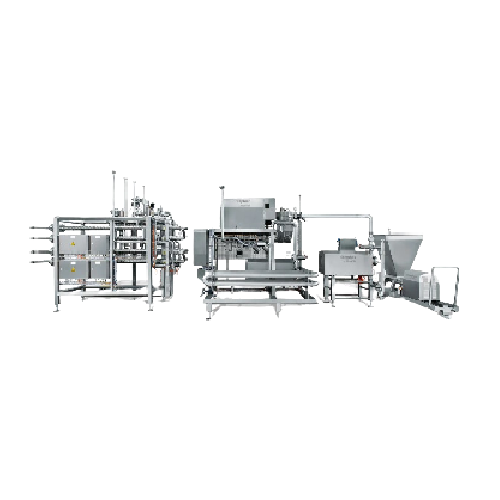
Continuous cheese line
Achieve precise temperature control and seamless product transitions with this equipment, ideal for en...
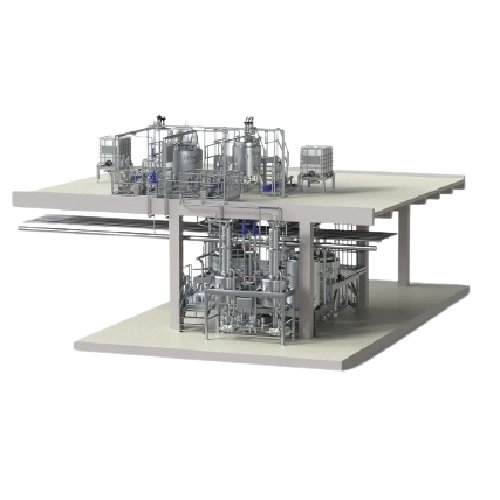
Continuous mustard line
Streamline mustard production with high-capacity continuous processing that reduces air pockets and e...

Continuous tahina production line
Streamline your tahina production with precise grinding and controlled cooling, ensuring ...
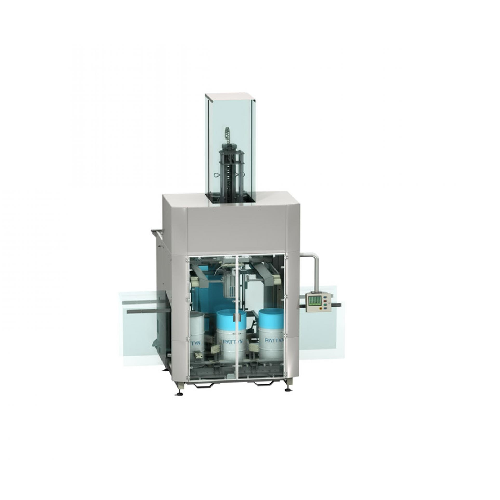
Bag inserter for drums
Effortlessly streamline your packaging process by automatically inserting custom-made bags into drums,...
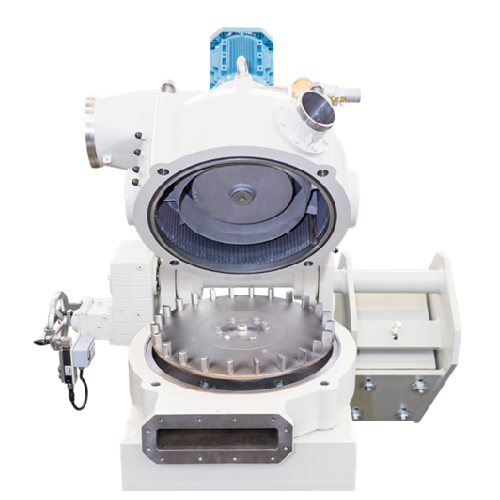
Impact classifier mill for fine grinding of brittle materials
Achieve precise particle size distribution with advanced g...
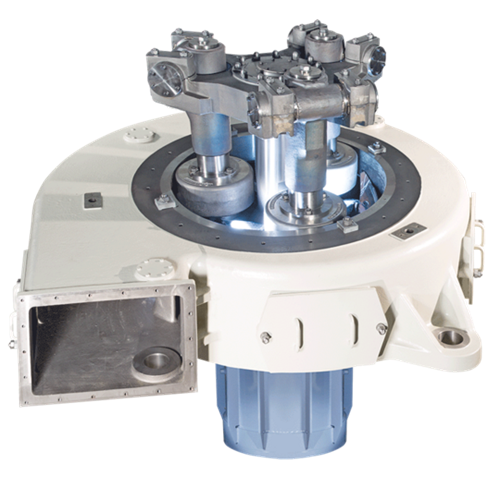
Pendulum mill for fine grinding and drying
Achieve efficient and precise grinding for soft to medium-hard materials while ...
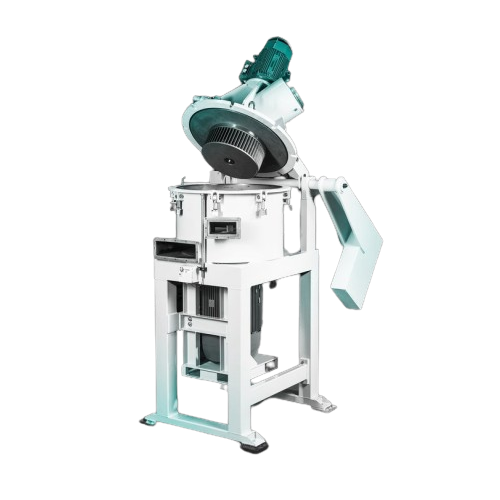
Energy-efficient impact classifier for superfine grinding
Achieve precise superfine grinding with energy efficiency, per...
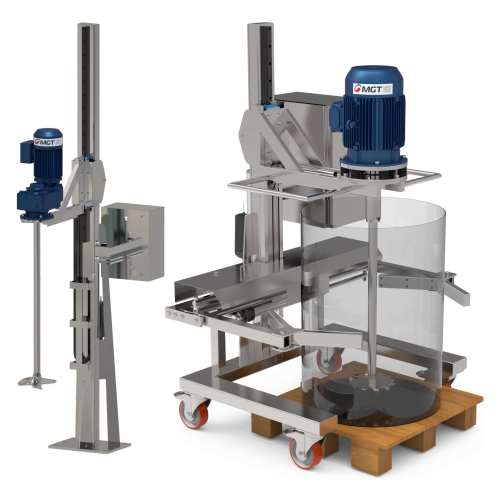
Pneumatic and electric lift for industrial mixing tanks
Enhance operational efficiency and safety with versatile lifts fo...
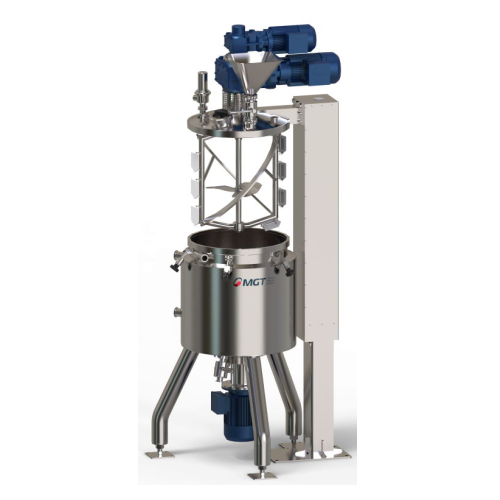
Vacuum mixing system for emulsion and homogenization
Achieve seamless emulsion and homogenization with precision: this sy...
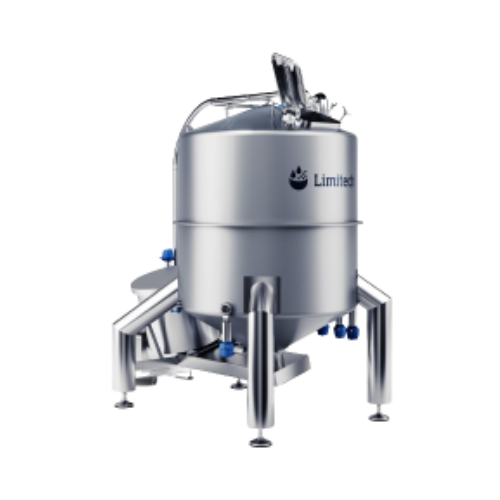
High shear mixer for viscous powder dissolution
Need consistent, homogeneous blending of high-viscosity liquids and powder...
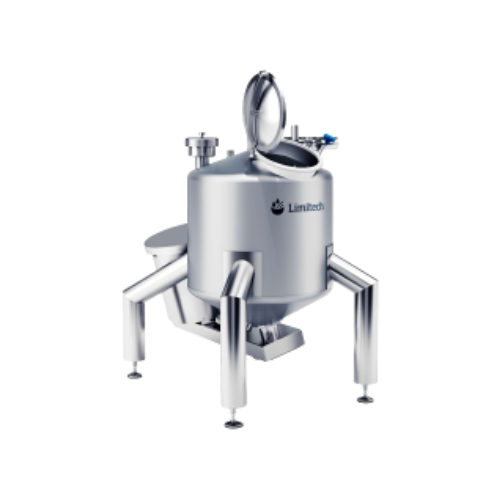
Industrial mixer for high shear mixing and emulsifying
Enhance your production line efficiency with versatile high shear ...
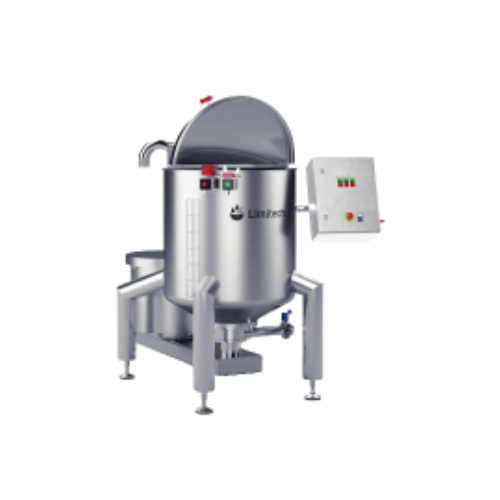
Inline mixer for uniform powder blends
Achieve uniform powder blends in minutes with this high shear inline mixer, designed...
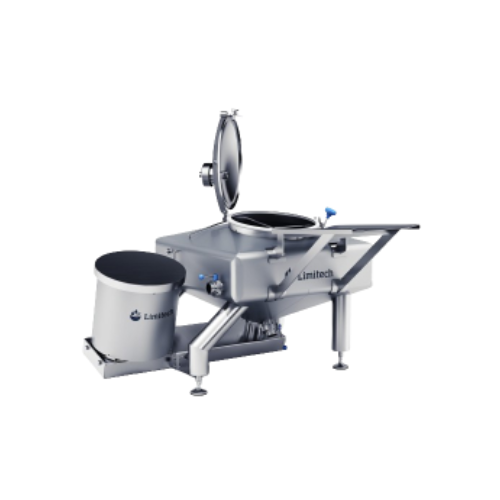
Batch mixer for dry and liquid ingredients
Achieve efficient blending of diverse ingredients with high shear mixing to str...
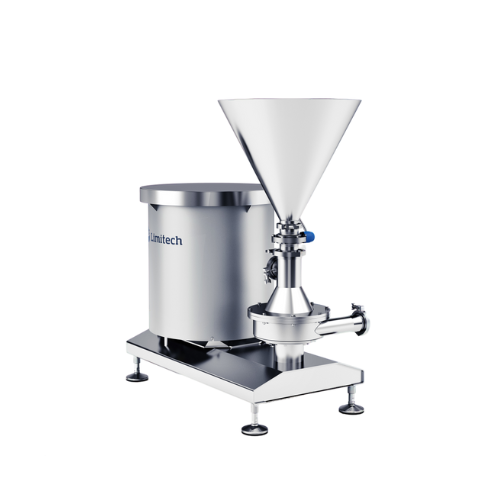
High-shear inline mixer for lump-free products
Achieve consistent texture and prevent clumping in liquid and powder blends...
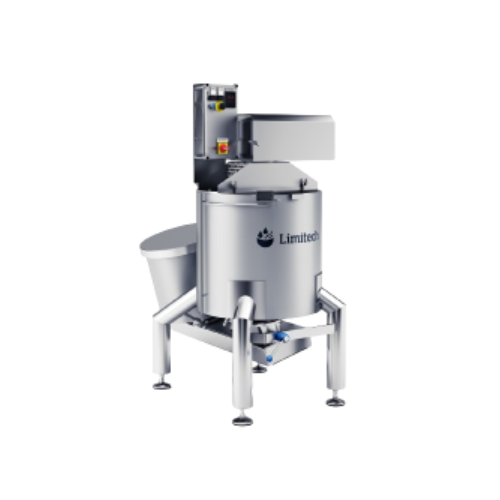
Industrial mixer for baby food and dairy production
Optimize your production line efficiency with a versatile mixing solu...
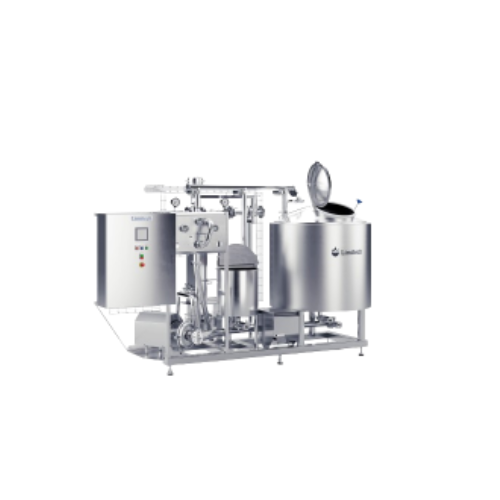
Cip dosing and water unit for industrial cleaning
Elevate your plant’s hygiene with this system, designed for seaml...
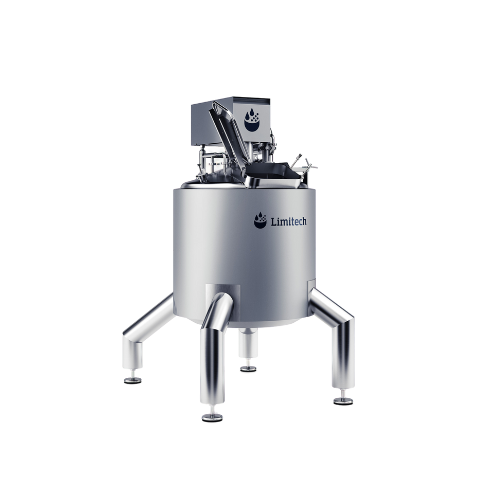
Powder dissolver for large liquid quantities
Achieve uniform powder blending swiftly with a vacuum-assisted system that pr...
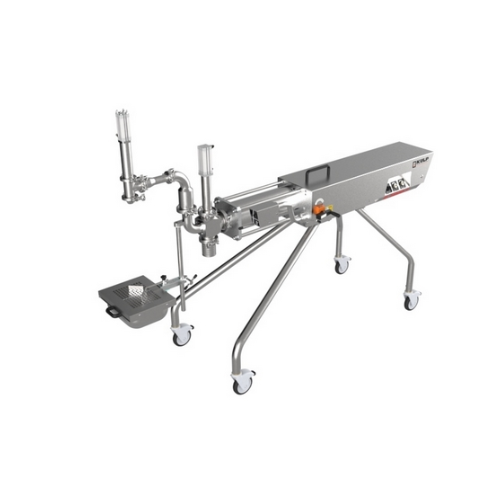
Volumetric filler for liquid and viscous products
Achieve precise and adaptable filling for a wide variety of liquid and ...
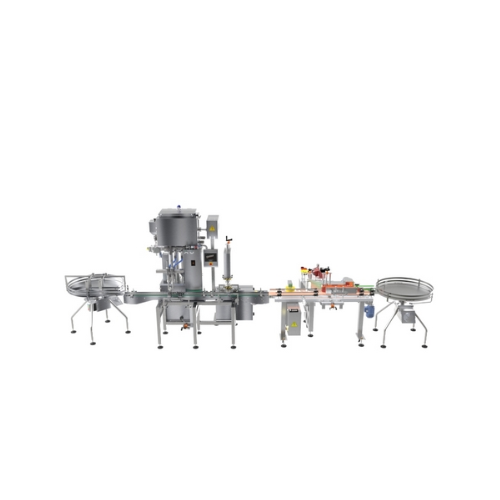
Medium capacity filling line for food and cosmetics
Streamline your production with a versatile filling line that seamles...
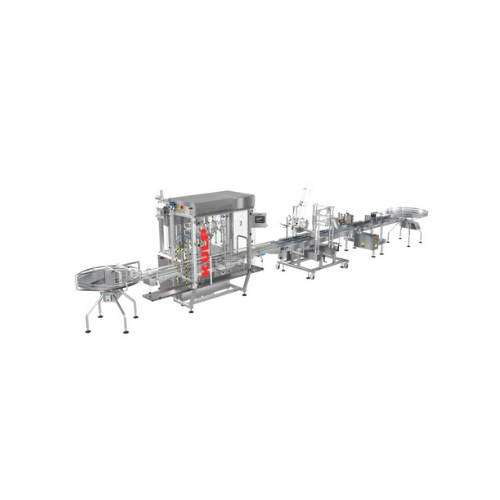
Large container filling line
Optimize your production line with a seamless solution for efficiently filling large containers...
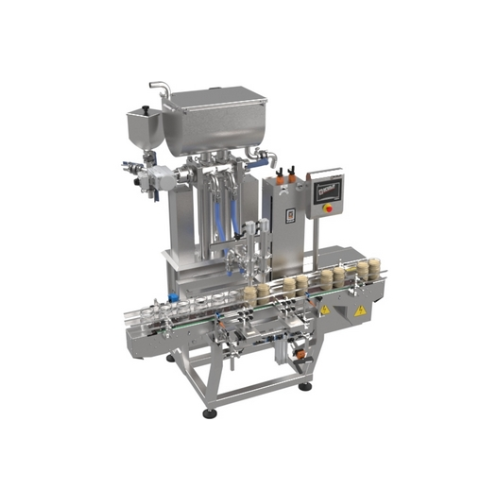
2-head liquid and viscous product filling system
Streamline your filling operations with precision and versatility designe...
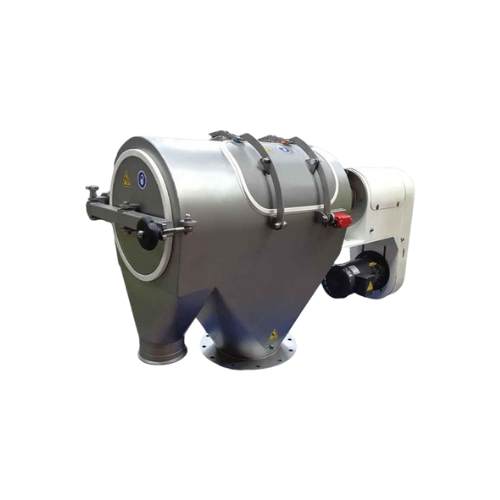
High-speed centrifugal sifter for food and pharma applications
Optimize your powder processing with a high-speed centrif...
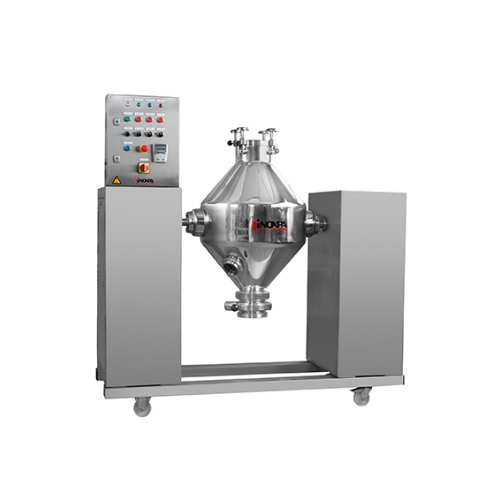
Double cone blender for homogeneous solid-solid mixtures
Need uniform blending for complex solid mixtures with diverse de...
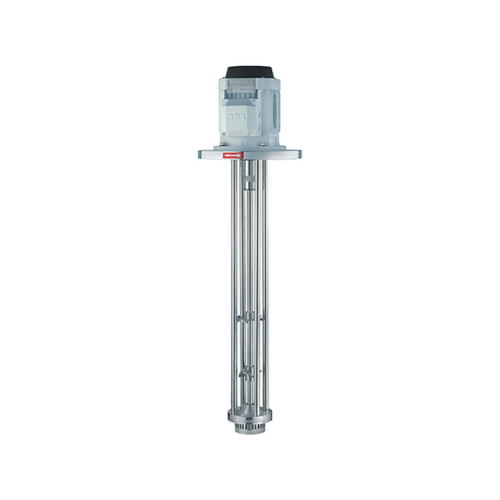
High shear vertical mixer for dispersion and emulsification
Achieve seamless emulsification and homogenization in divers...
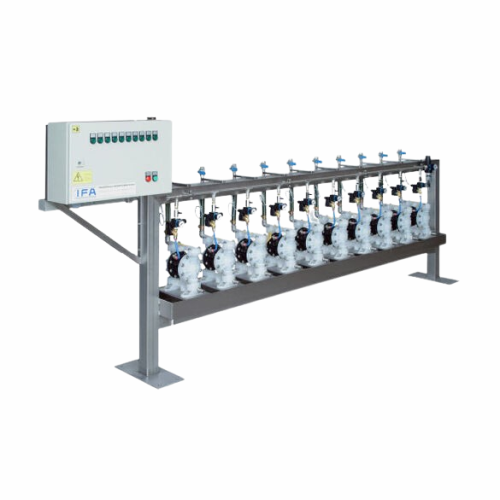
Pneumatic conveying systems for industrial applications
Efficiently transport bulk materials or liquids across your produ...
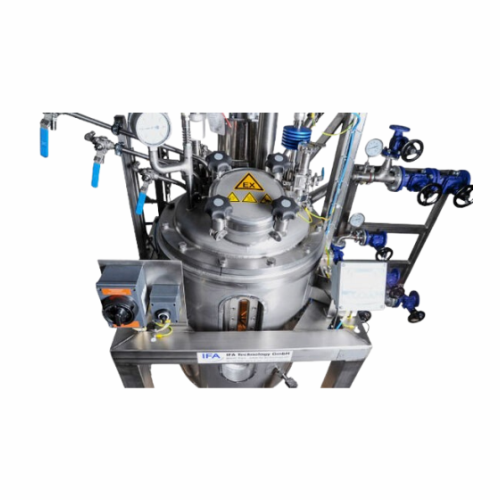
Wastewater treatment system for industrial applications
Optimize resource management and environmental impact by integrat...
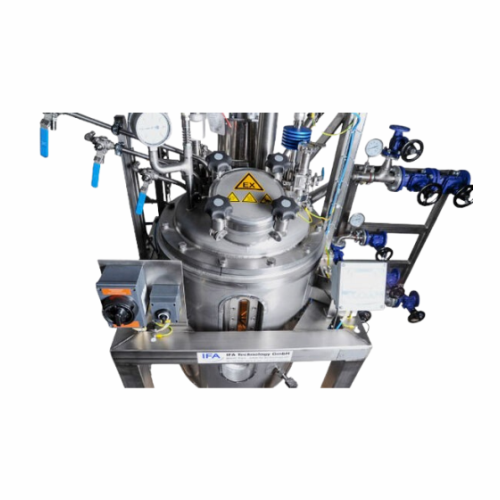
Turnkey resin synthesis plant system
Streamline resin production with a comprehensive turnkey system designed to efficientl...
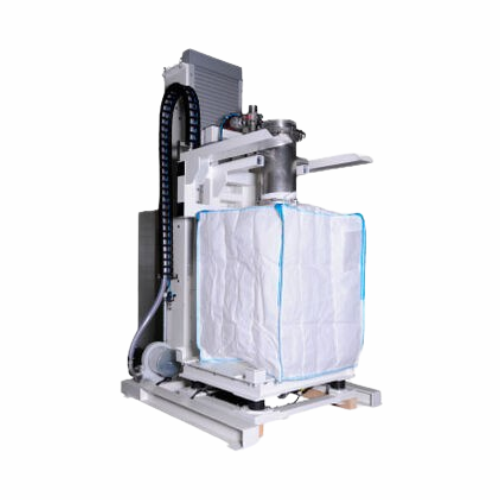
Customised tank systems for liquid and bulk material storage
Ensure safe and compliant storage of liquids and bulk mater...
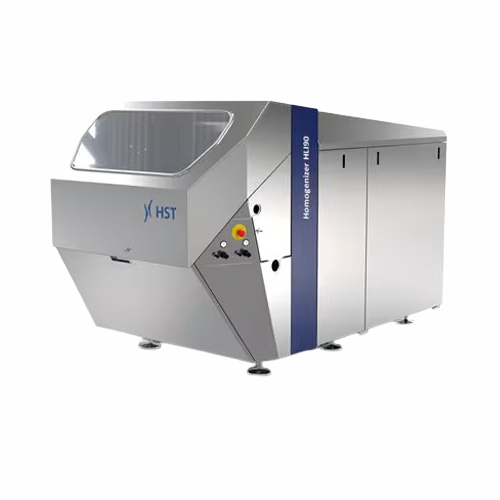
High-pressure homogenizer for food and pharmaceuticals
Achieve unparalleled consistency and stability in emulsions and di...
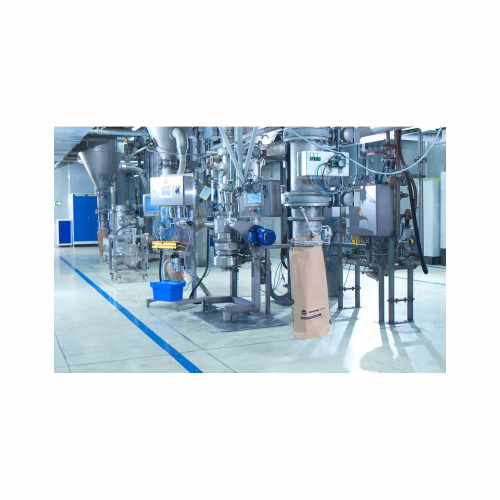
Air classifier for classifying industrial minerals
Achieve precise particle separation with advanced air classifiers, par...
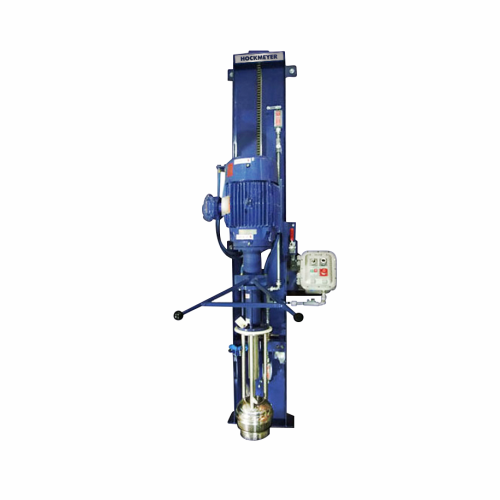
Immersion mill for pail and drum-sized batches
Streamline your production with a versatile solution that efficiently handl...
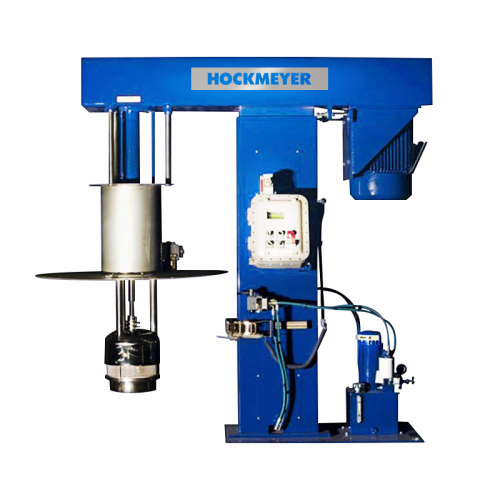
Immersion mill for particle reduction
Achieve streamlined particle size reduction and enhanced mixture homogeneity with imm...
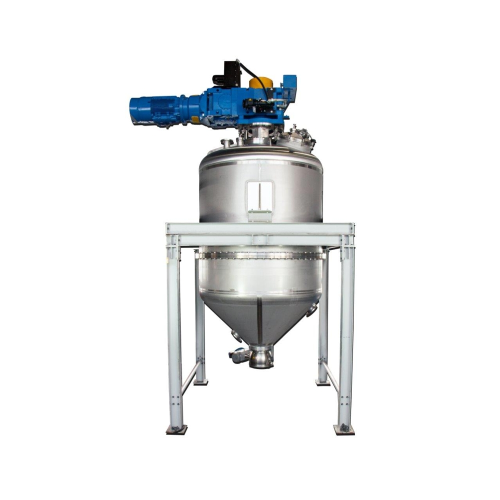
Cylindro conical mixer for batch mixing
Maximize mixing efficiency in compact spaces with this versatile solution, ideal fo...
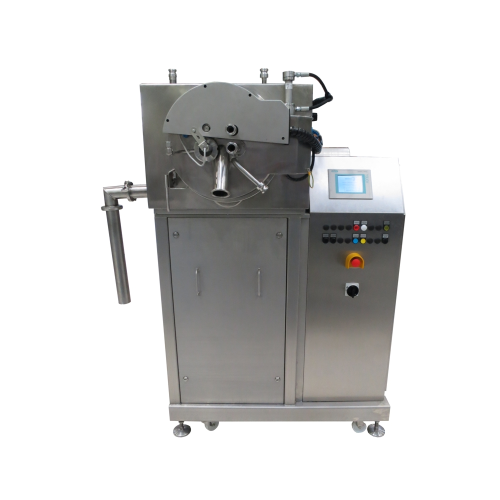
Horizontal pilot centrifuge for pharmaceutical applications
Achieve precise separation of solid and liquid phases with c...
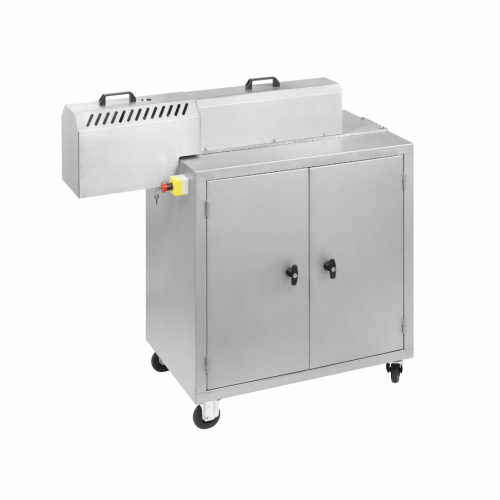
High-viscosity continuous industrial kneader for small volumes
Achieve consistent high-viscosity material processing wit...
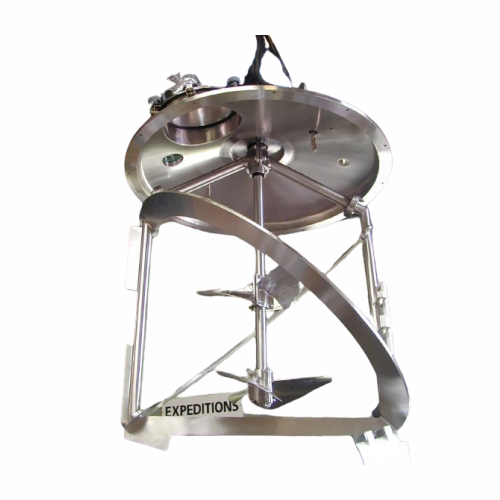
Coaxial mixer for high viscosity liquids
Achieve seamless blending of high-viscosity materials with a coaxial mixer designe...
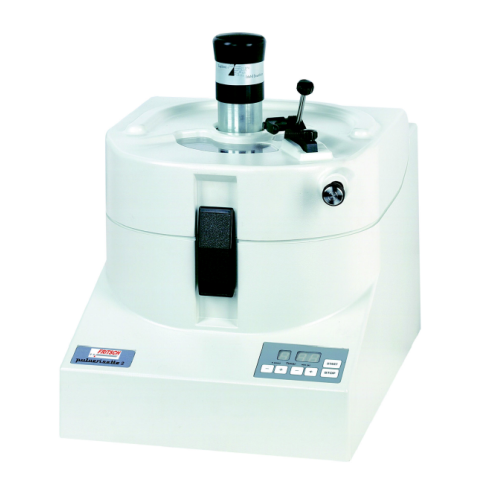
Laboratory mortar grinder for wet and dry grinding
Ensure precise blending of fine powders, pastes, and creams with contr...
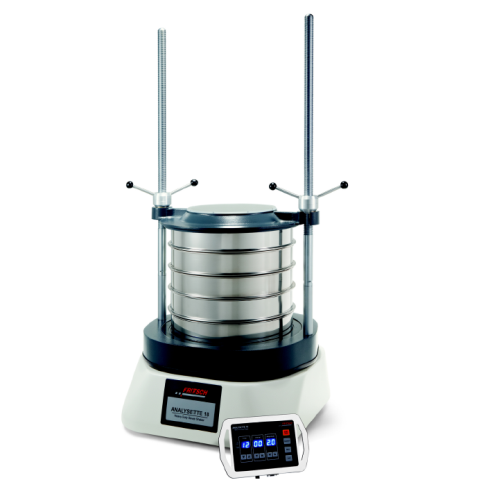
Heavy duty analytical sieve shaker for coarse-grained materials
Need precise particle size distribution for large minera...
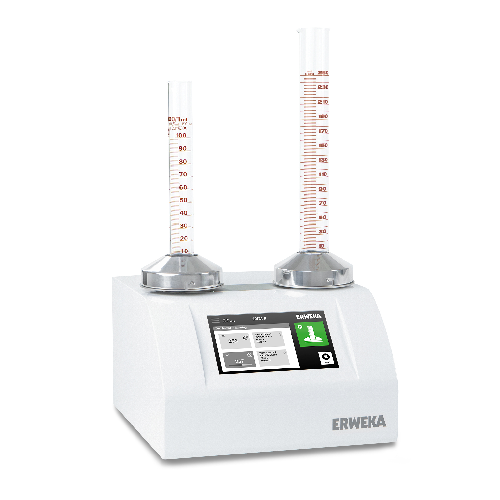
Tapped density tester for pharmaceutical and chemical powders
Ensure precise density measurements for pharmaceuticals an...
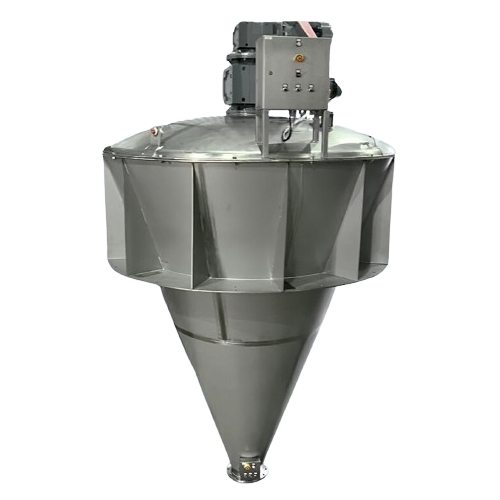
Conical powder mixer for uniform powder blending
Achieve consistent powder blending while preserving the integrity of deli...
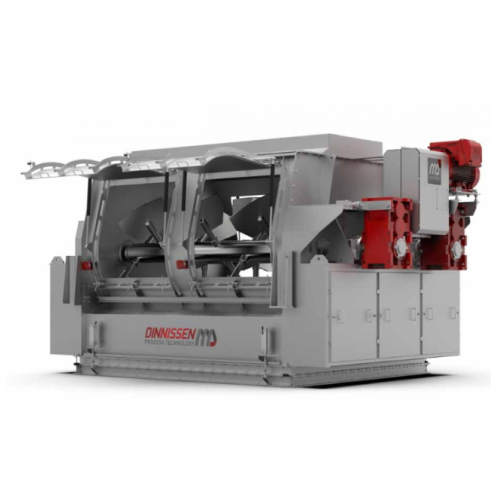
Batch mixer for powder and grain processing
Achieve ultra-fast, homogenous mixing in just 20 to 50 seconds with this versa...
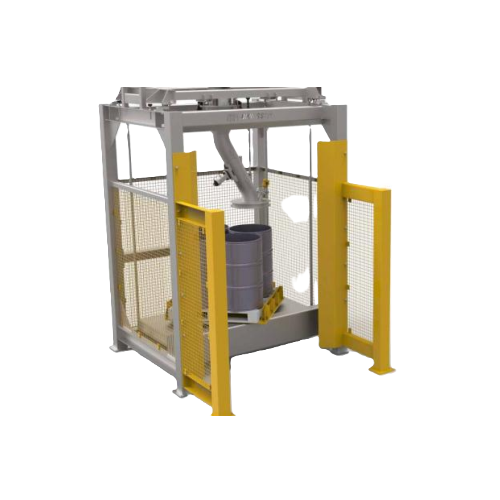
Ibc and drum filling system for chemical substances
Ensure safe and efficient handling of sensitive materials with a modu...
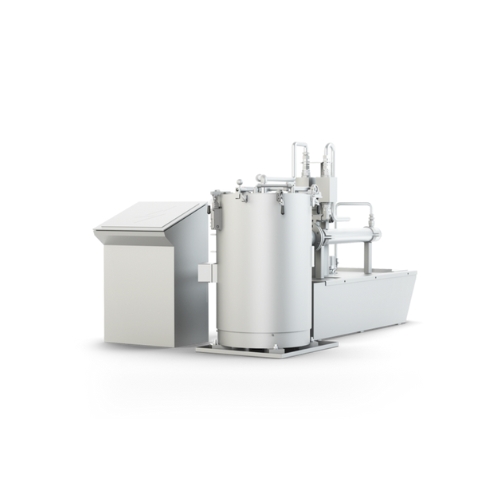
Dipping centrifuge for precision coating processes
Achieve precise coating and oiling with customizable dipping and centr...
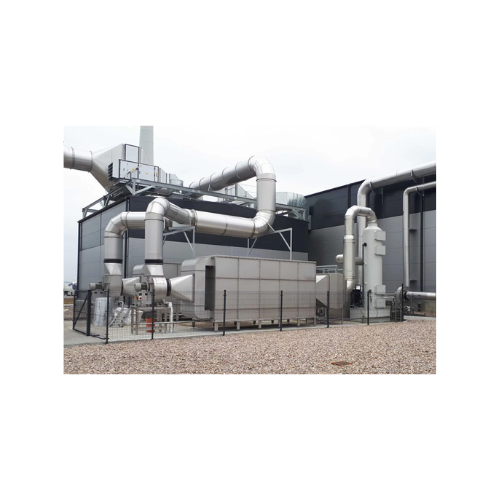
Industrial exhaust air treatment for food processing
Effectively eliminate volatile organic compounds and odors while max...
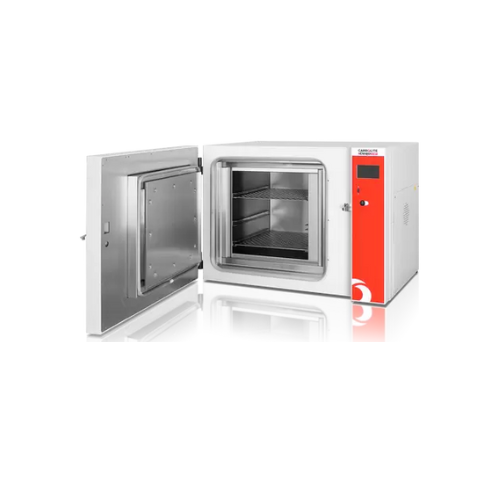
High temperature laboratory oven for precise heating
Achieve precise temperature control and uniformity essential for hea...
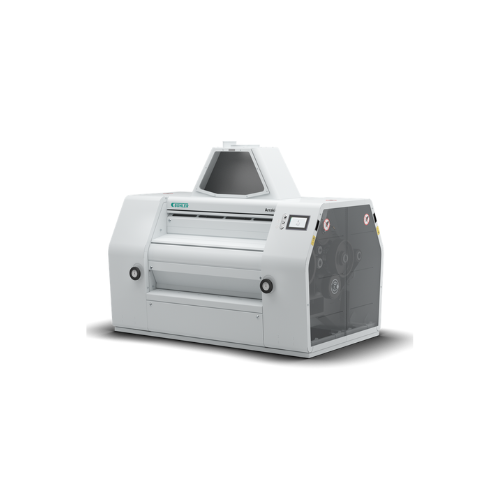
Four-roller and eight-roller mill for wheat and grain grinding
Optimize your grinding operations with this versatile rol...
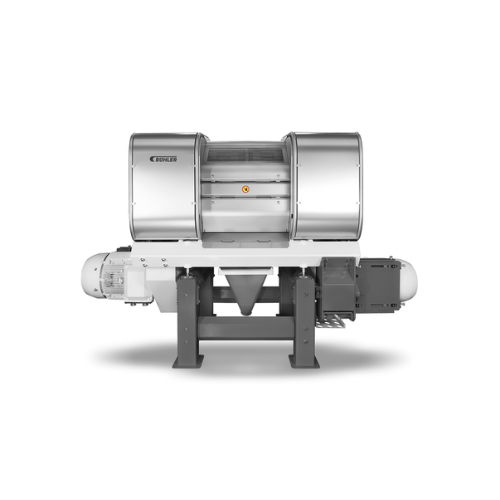
Flaking mill for grain and cereal production
Achieve consistent flake thickness and high throughput with advanced roller t...
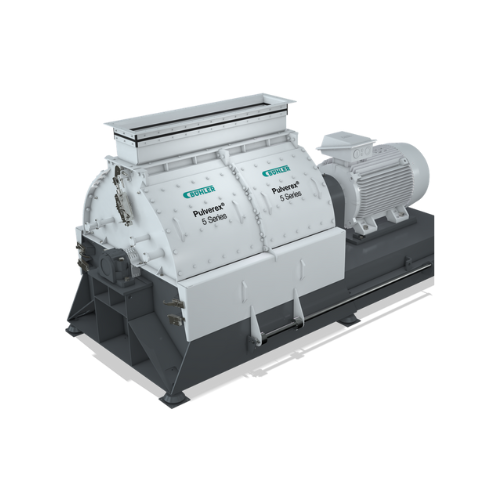
Pulverizer for fine grinding applications
Achieve optimal particle size distribution and enhance throughput with this adva...
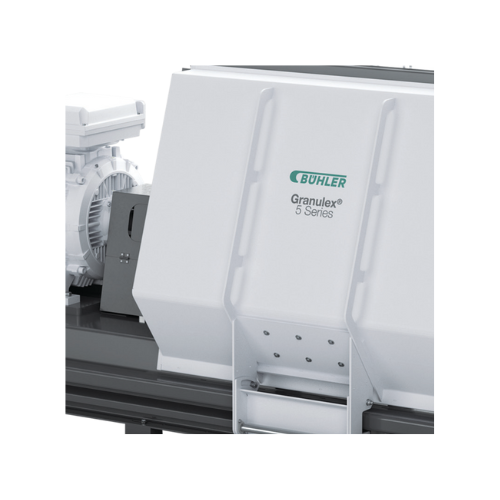
High-throughput hammer mill for animal feed production
Ideal for high-throughput operations, this hammer mill ensures pre...
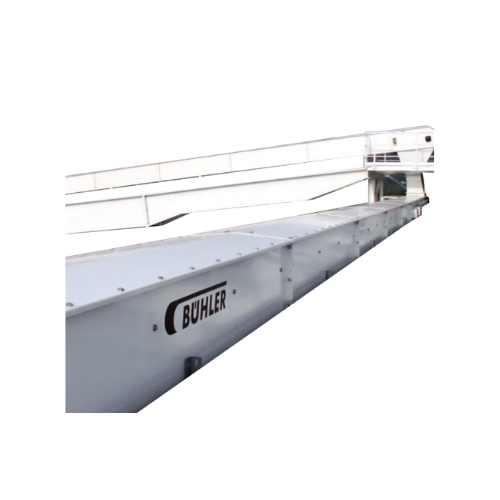
Heavy-duty trough chain conveyor for high throughput applications
Optimized for high-capacity operations, this robust c...

Twin-screw extruder for breakfast cereals production
Enhance your product range with flexible twin-screw extrusion techno...

Four-roller and eight-roller mill for grains
Optimize your grain processing with precise roller configurations, ensuring c...

Discharge station for bags and big bags
Ensure consistent material flow and hygiene in your production line with a versatil...

Control systems for wet grinding industry
Enhance precision and efficiency in your production line with advanced control s...
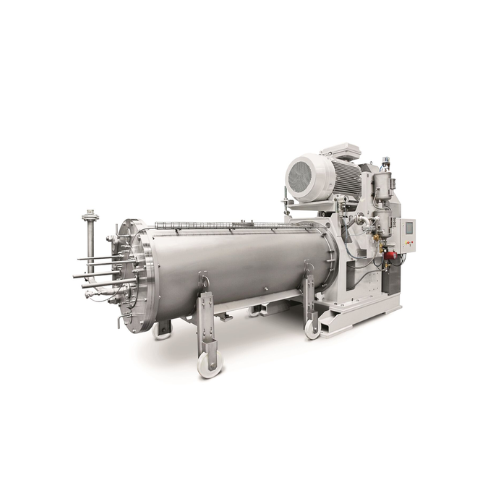
Full-volume bead mill for wet grinding applications
Achieve superior dispersion and particle size consistency with advanc...
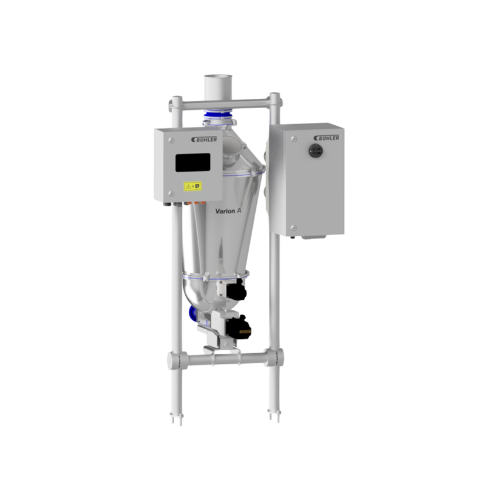
Batch scale for high accuracy weighing of powdery products
Achieve unparalleled precision in powder dosing with our batc...
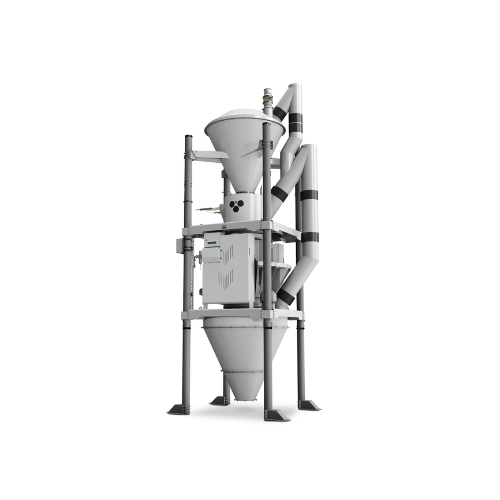
Fully automatic batch scale for powdery and granular products
Achieve precise and repeatable dosing for powdery and gran...

Twin-screw extruder for breakfast cereal
Optimize your production with a robust twin-screw extruder that accommodates high ...

Ultra-fine pulverizer for aqua feed and pet food
Achieve precise granulation with high efficiency for your feed and food p...
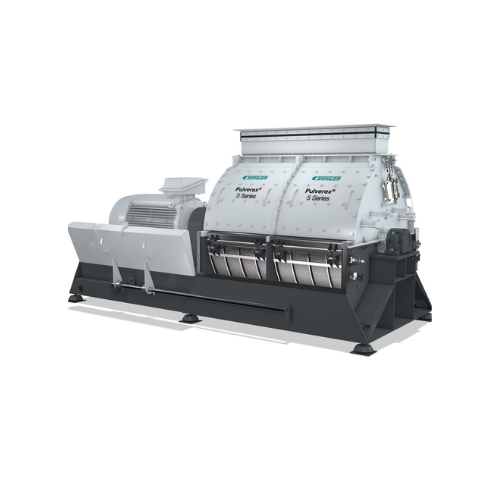
Industrial fine grinding pulverizer
Achieve consistent fine granulation at high capacity with reduced energy consumption, u...
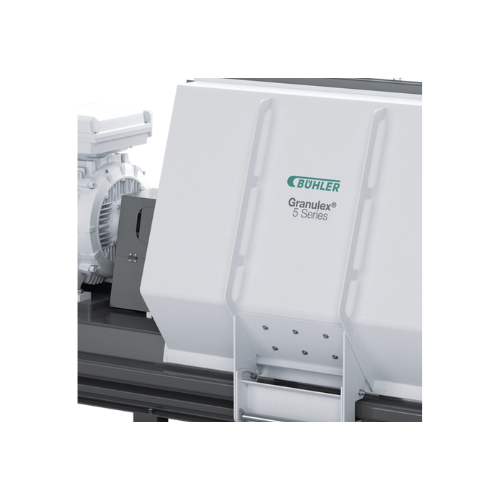
Hammer mill for animal feed grinding
Achieve precise granulation with high throughput and energy efficiency, while reducing...
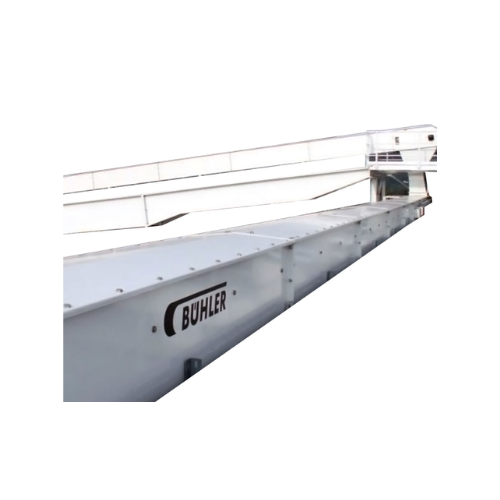
High-capacity horizontal conveyor for bulk storage
Optimize your high-speed bulk material handling with a durable and eff...
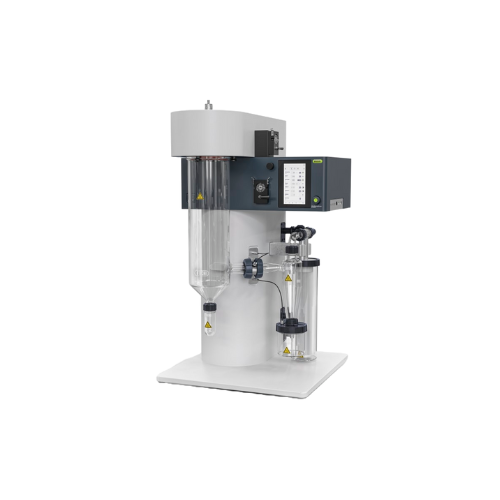
Laboratory spray dryer for organic solvent samples
Experience precise particle control and enhanced safety when convertin...
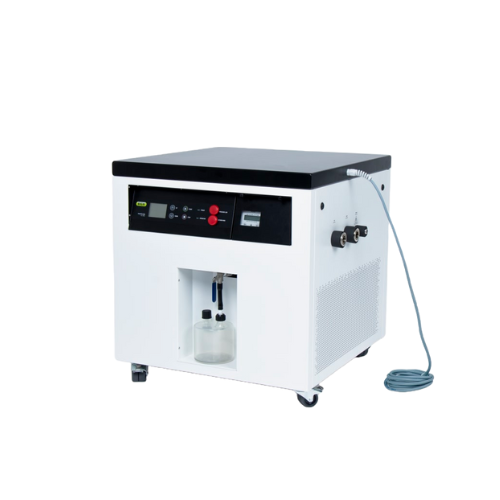
Inert loop for safe organic solvent spray drying
Ensure safe handling and efficient recovery of organic solvents in spray ...
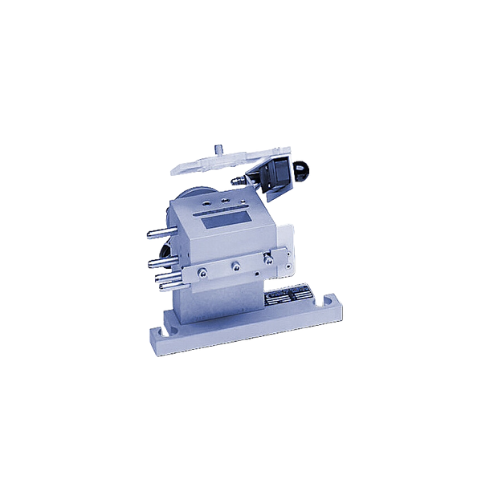
Measuring mixer for small grain samples
Optimize the precision of your formulation processes with a solution designed for p...
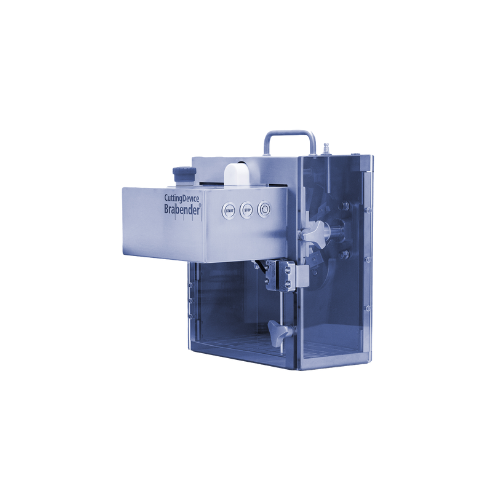
Laboratory cutting device for extrudates
For precise shaping of snack or feed extrudates, this compact cutting solution ens...
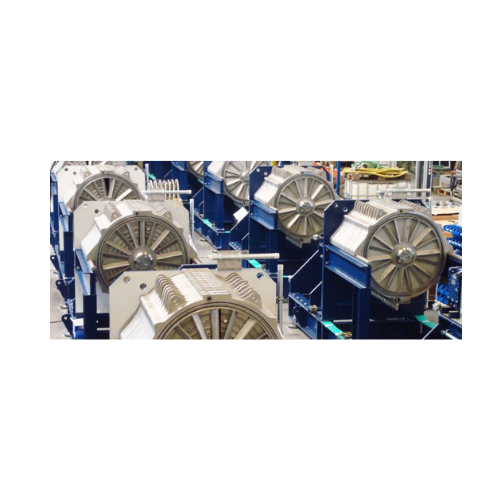
Crossflow filtration with sieve filter for difficult suspensions
Achieve precise separation and recovery in challenging ...
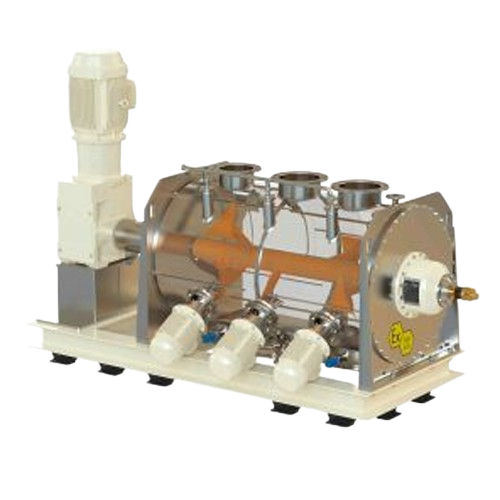
Horizontal ploughshare mixer for solids and powders
Achieve uniform blends of diverse solids and powders with precision a...
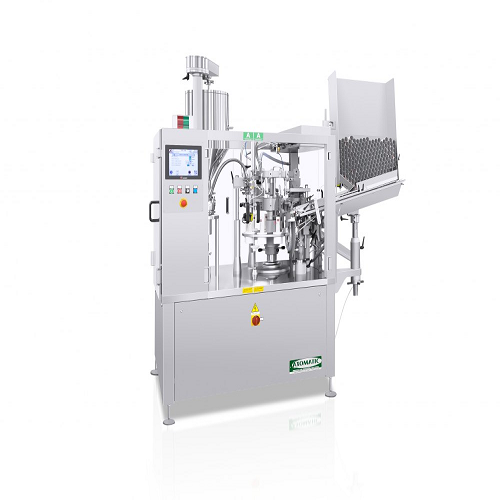
Automatic tube filling and closing solution
Optimize your production line with a high-speed machine for precise tube filli...
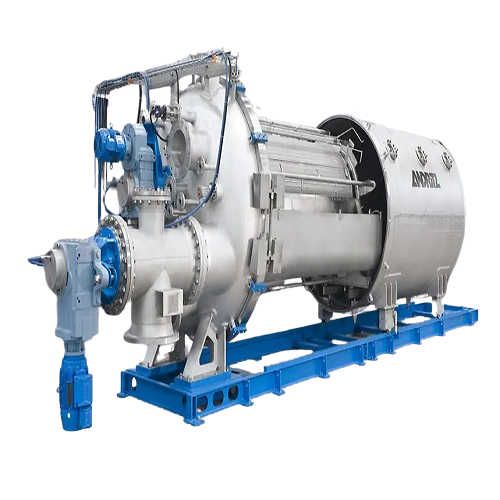
Pressure drum filter for ultra fine-grained products
When traditional filtration methods fall short, ensure ultra-fine pr...
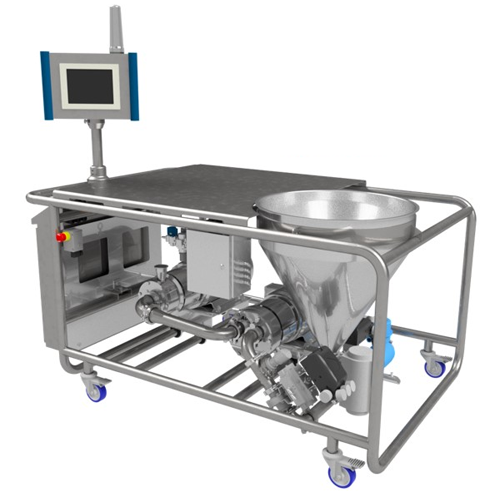
Automated powder induction and dispersion system for industrial mixing
Achieve rapid and efficient incorporation of pow...
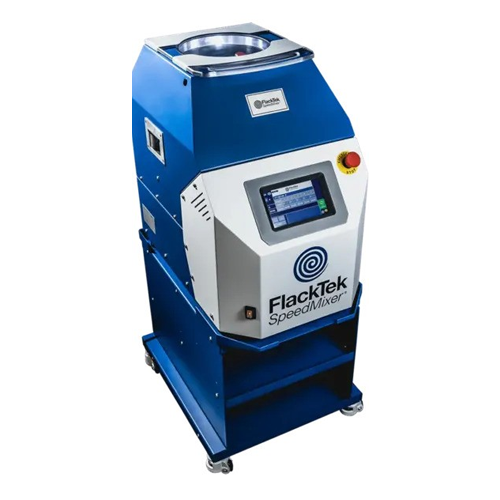
Dual asymmetric centrifugal mixer for epoxy and slurry mixing
Achieve precise mixing and consistency in your formulation...
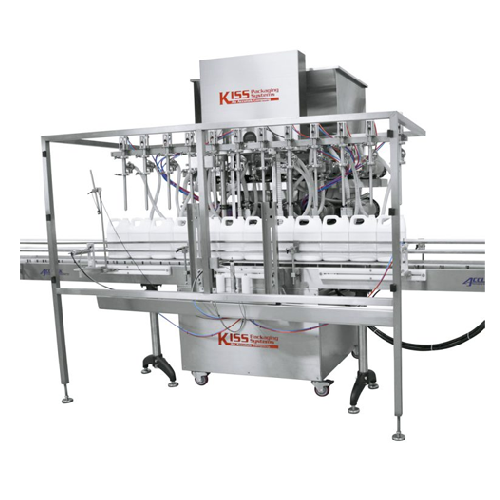
Automatic positive displacement filler for various liquids
Achieve precision and versatility in liquid filling operation...
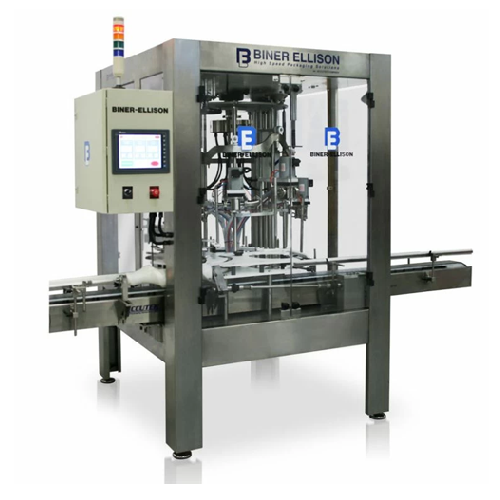
Automatic positive displacement bottle filler
Streamline your liquid filling operations with precision and flexibility, id...
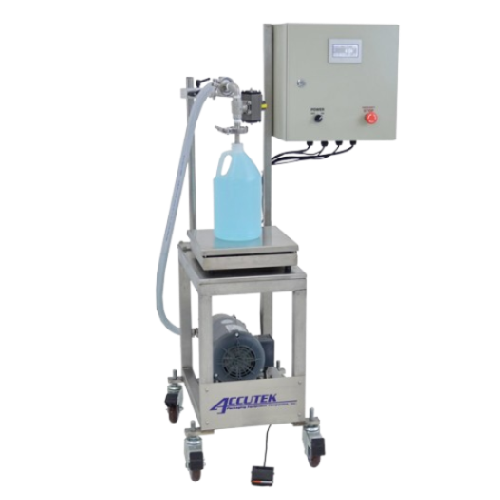
Accurate net weight filling for liquid and semi-liquid products
Ensure precise filling of diverse viscosities, from thin...
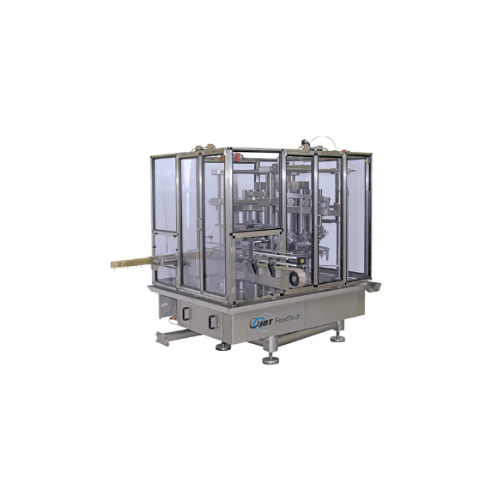
Volumetric piston filler for liquid and viscous products
Achieve precise volume control and enhance product integrity wit...
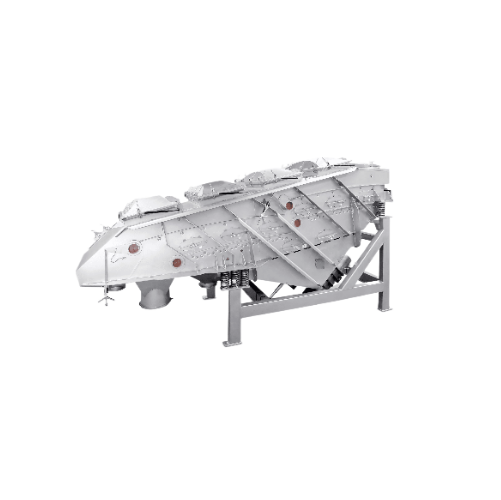
Vibrating sifter for chemical applications
Achieve precise particle separation with this vibrating sifter, ensuring optima...
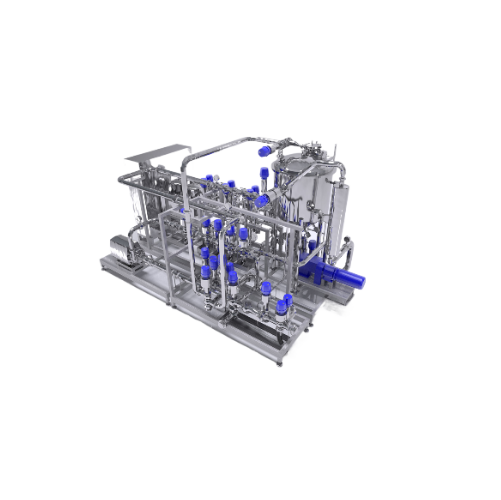
Tailor made mixing systems for personal and home care products
Achieve precise mixing for liquid formulations with conti...
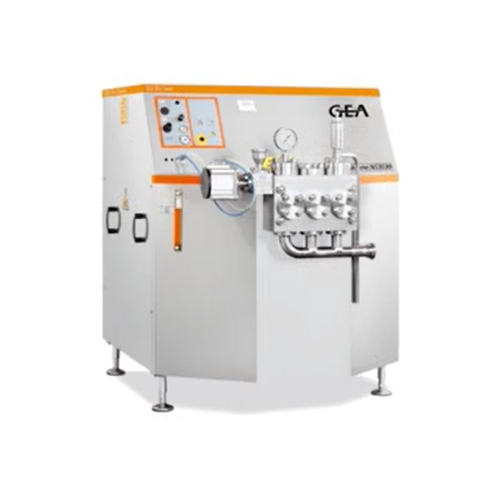
High pressure industrial homogenizer
Enhance liquid formulations with precision and efficiency—our high-pressure homogenize...
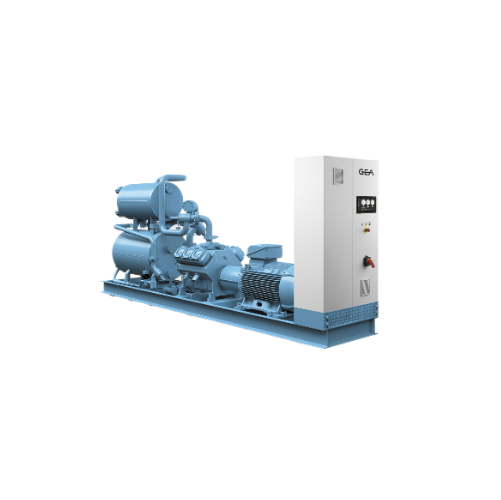
Ammonia chiller for industrial refrigeration
Achieve optimal energy efficiency and reduced operational costs in your cooli...
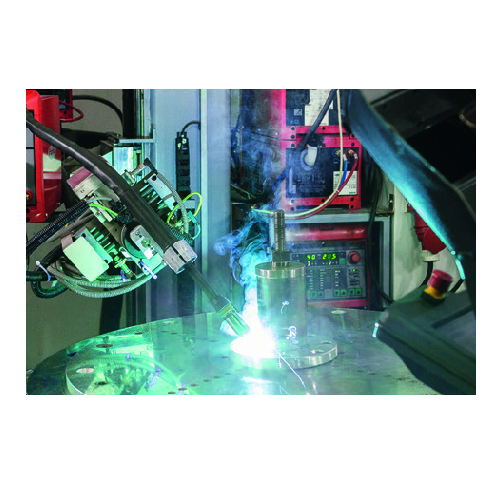
Traditionally welded silos for constrained installation sites
Ideal for facilities with limited space, these traditional...
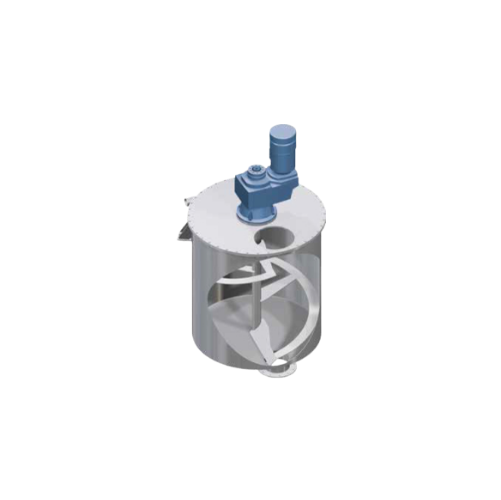
Screw belt mixer for dry materials
Achieve uniform mixing of bulk dry materials with variable speed control, ensuring preci...
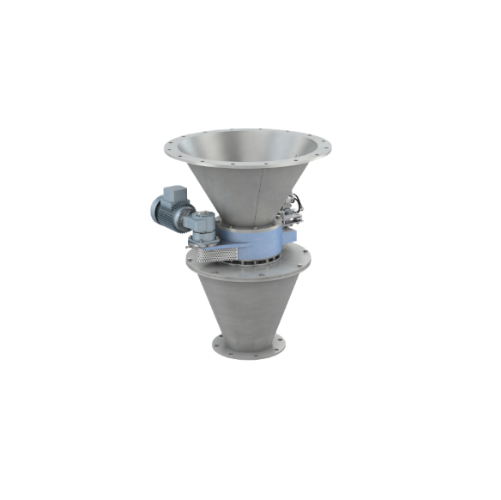
Precise discharge and dosing module for silos and containers
Ensure seamless material flow and accurate dosing with adva...
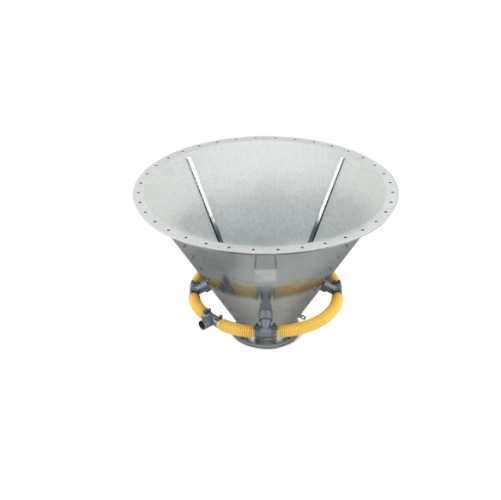
Bulk materials discharge solution for silos and containers
Ensure reliable material flow with a robust discharge solutio...
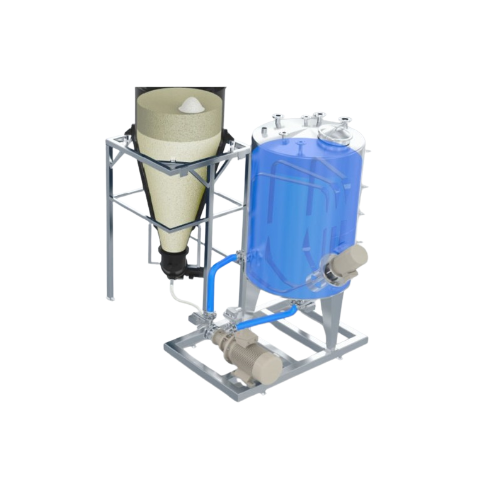
Powder wetting and dispersion system
Revolutionize your production with a system that seamlessly inducts, wets, and dispers...
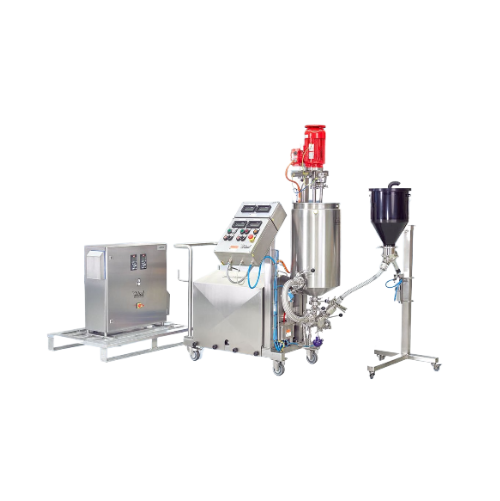
Laboratory disperser for powder induction and wetting
Optimize your pilot and laboratory processes with a high-speed disp...
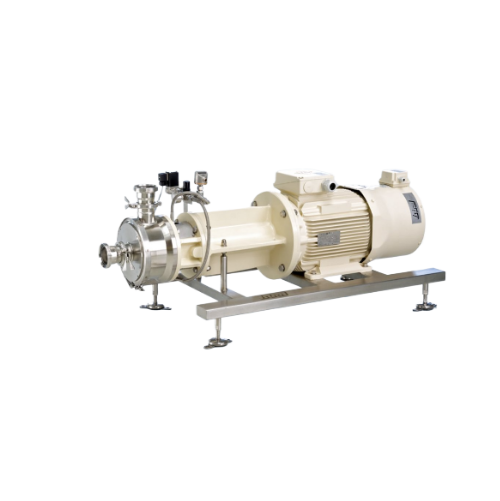
Inline disperser for homogeneous emulsions and suspensions
Achieve precise control over particle size and distribution w...
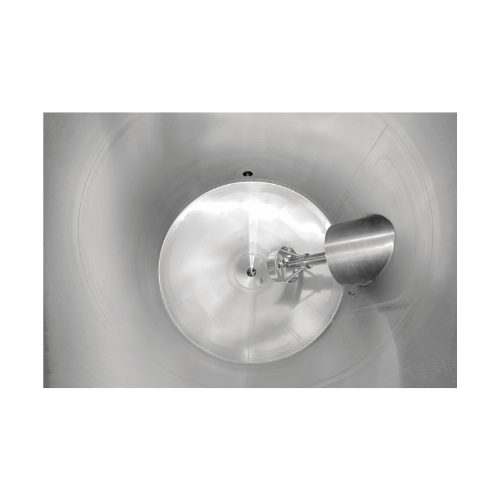
Industrial jetstream mixer for homogeneous mixing
Achieve consistent product quality with precise micro and macro mixing ...
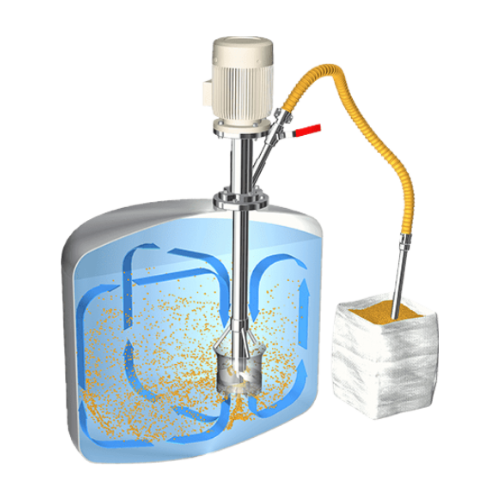
Low-dust powder induction mixer for liquids
Achieve dust-free induction and homogenization of powders in liquids with prec...
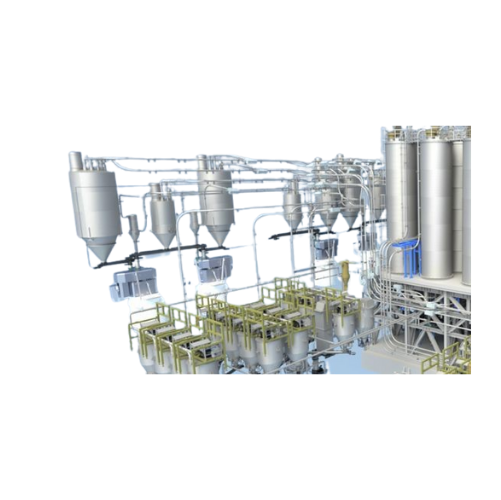
Dispersion paint production systems
Achieve 100% color accuracy and flexible production with our advanced system, ensuring ...
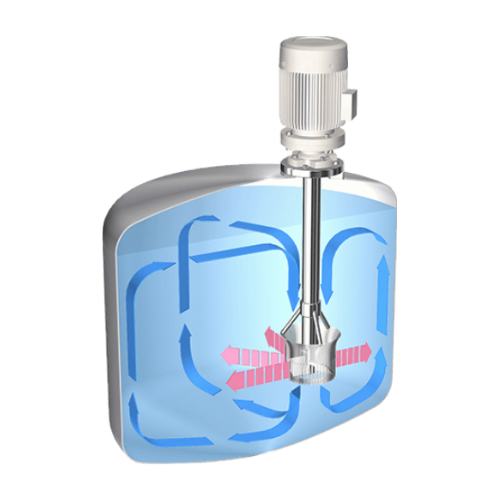
High-performance dispersing and mixing solutions
Enhance your mixing and dispersing processes with advanced fluid stream t...
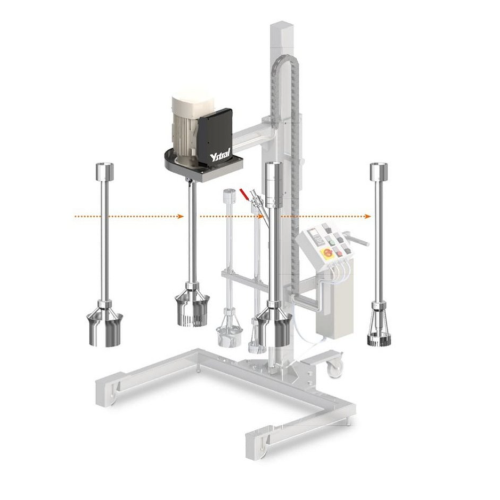
Multipurpose mixing equipment for chemical and pharmaceutical production
Achieve unparalleled flexibility with modular,...
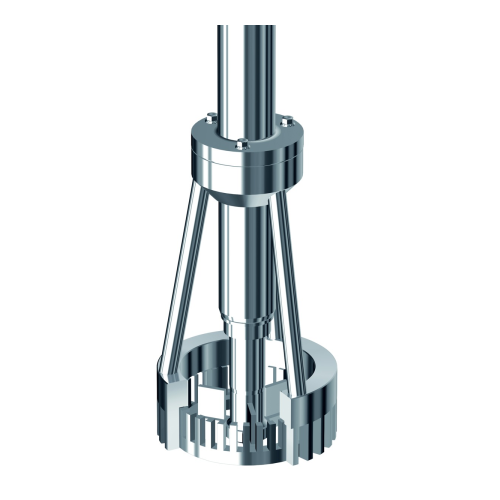
High-shear batch disperser for chemical and food industries
Achieve unmatched dispersion and emulsification precision wi...
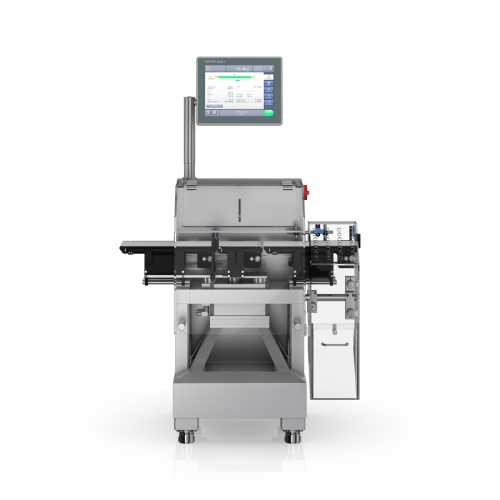
High-speed checkweigher for dynamic weighing
Achieve precision and consistency in high-speed production environments with ...
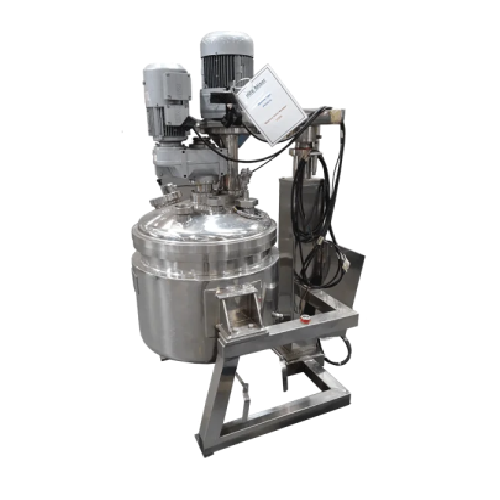
Mixing vessel for liquid, sauce, and cream products
Maximize efficiency in your production line with a versatile solution...
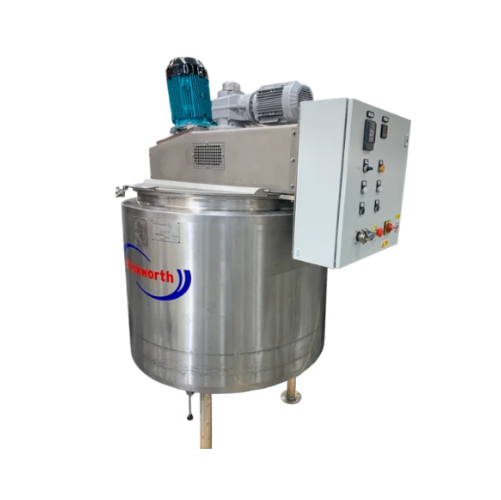
Pv processing vessels for liquid and cream mixing
Optimize your mixing operations with versatile processing vessels desig...
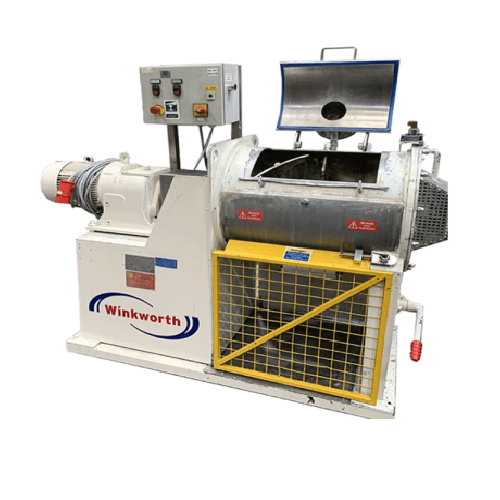
Industrial rapid turbulent mixer for homogeneous mixing
Achieve unparalleled homogeneity with rapid turbulent mixing, ess...
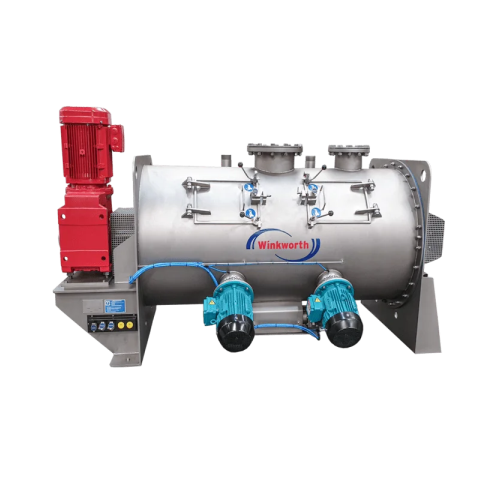
High-speed mixer for industrial mixing applications
Achieve rapid, consistent mixing and dispersion across diverse materi...
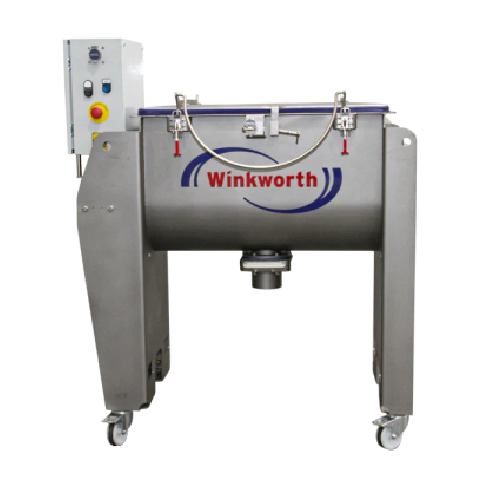
Horizontal shaft mixer for free-flowing materials
Achieve consistent mixing of diverse free-flowing materials with a reli...
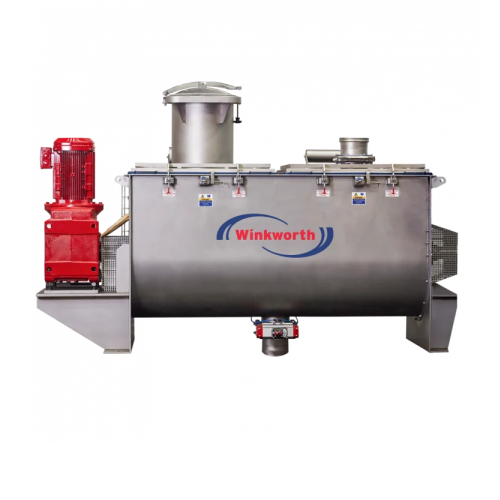
Efficient ribbon mixers for precise powder blending
Achieve consistent and uniform blending with this advanced U-Trough m...
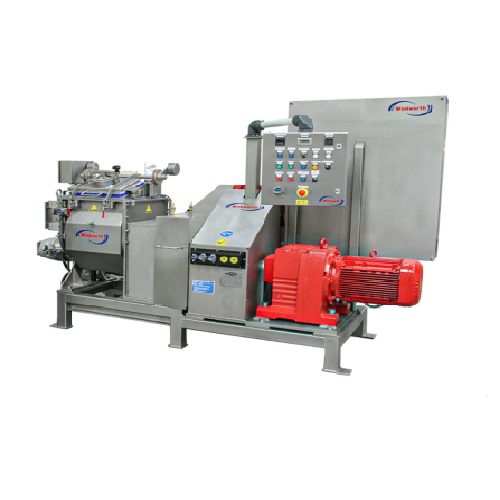
Industrial sigma mixer extruder for homogeneous mixing and extrusion
Achieve precise mixing and seamless extrusion of d...
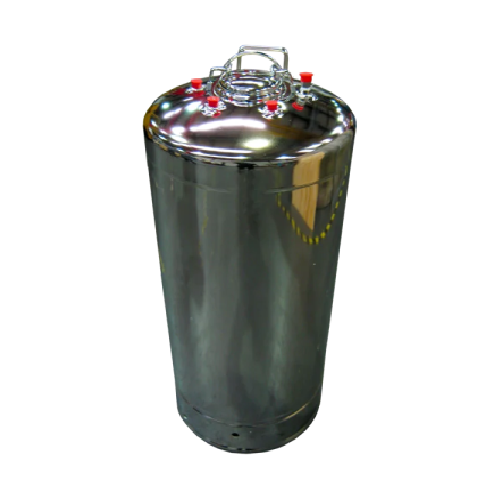
Pressure vessel for hazardous and non-hazardous liquids and gases
Ensure safety and compliance when handling hazardous ...
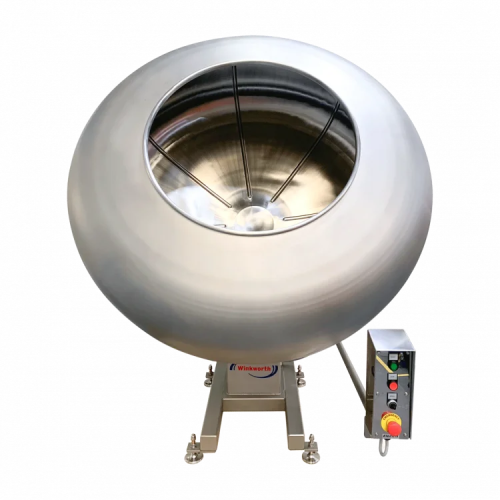
Coating pans for precision culinary coatings
Achieve consistent, high-quality coatings on a diverse range of products, fro...
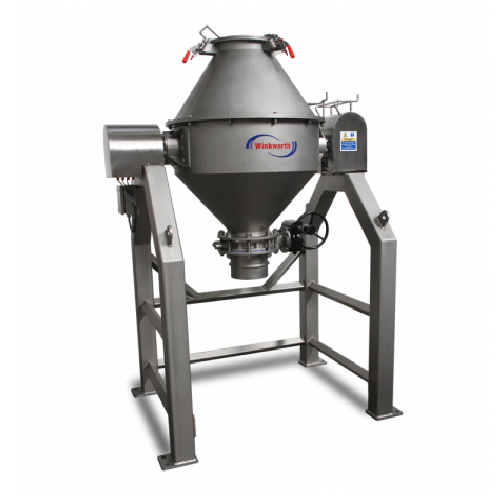
Double cone mixer for free-flowing material blending
Optimize your production with precision blending and gentle drying o...
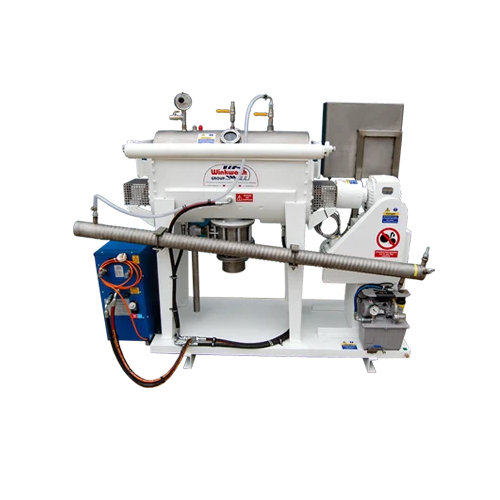
Industrial blenders for powder and granule mixing
Optimize your production line with advanced mixing solutions designed f...
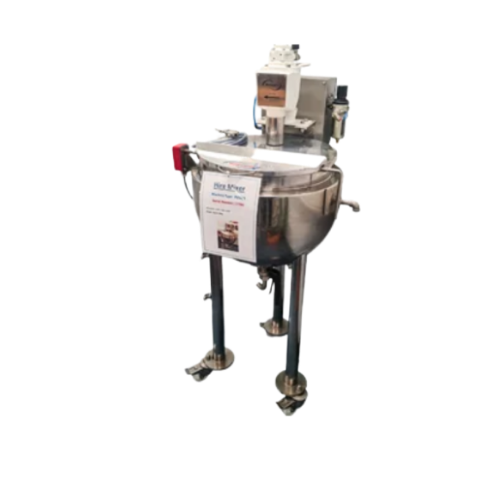
Pv mixing vessels for industrial hire
Optimize your production mix with vessels that ensure precise blending, heating, and ...
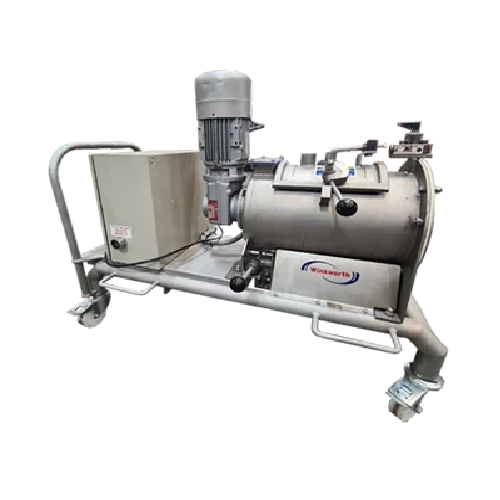
Industrial mixers for hire
Optimize your production line with versatile mixers designed for precision blending, heating, and...
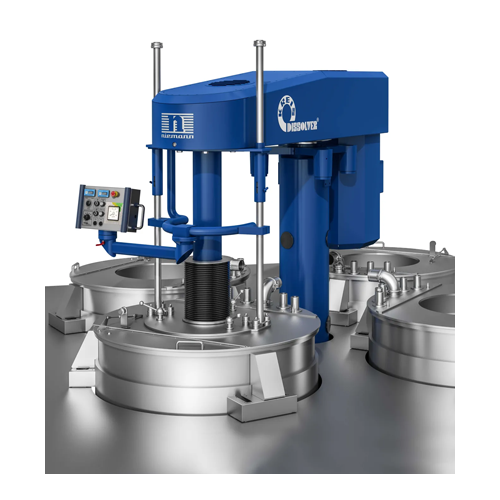
Dissolver for high-viscosity products through floor installation
Optimize production of ultra-high viscosity products wi...

Laboratory disperser for high-viscosity products
Optimize your laboratory processes with precise mixing and dispersing of ...
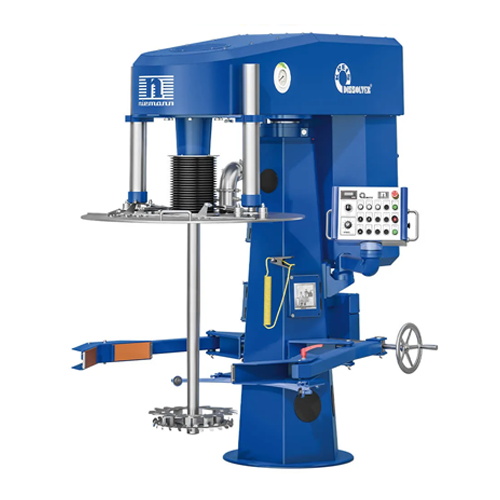
Dispersing system for high-viscous products
Achieve precise mixing and dispersing of high-viscous products with advanced f...
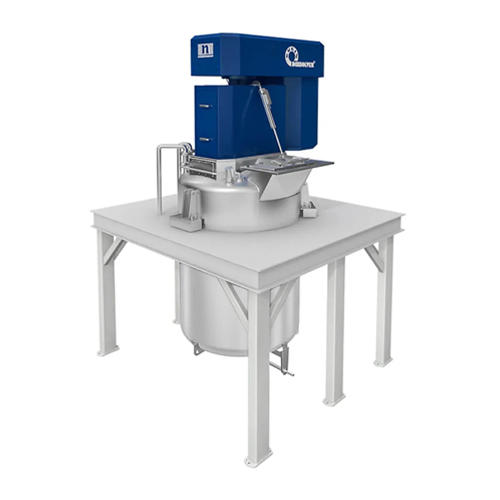
Top-mounted disperser for high-viscosity products
Achieve rapid, uniform dispersion of ultra-high viscosity materials wit...
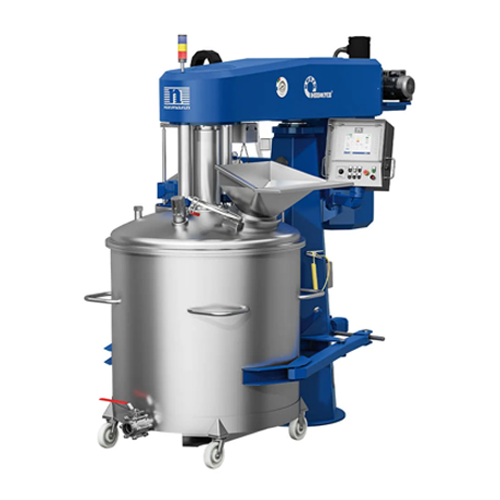
Vacuum dissolver for high-viscosity products
Elevate your production with precision mixing and deaeration, ideal for tackl...
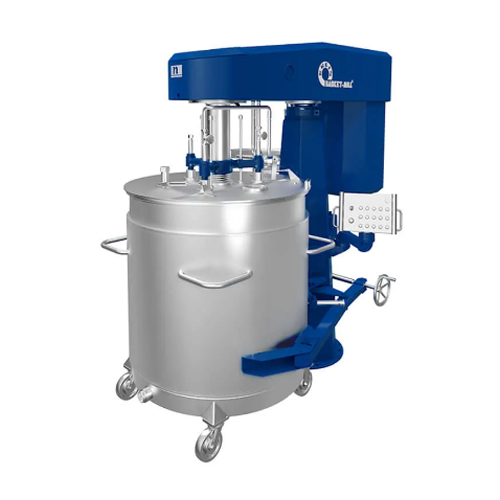
High-performance mill for paint and varnish industry
Achieve superior fine dispersing and grinding efficiency for liquid ...
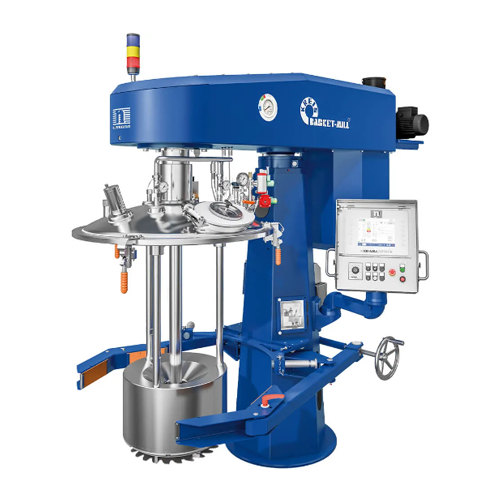
Basket mill for paint and varnish production
Achieve optimal particle size and product consistency with this advanced bask...
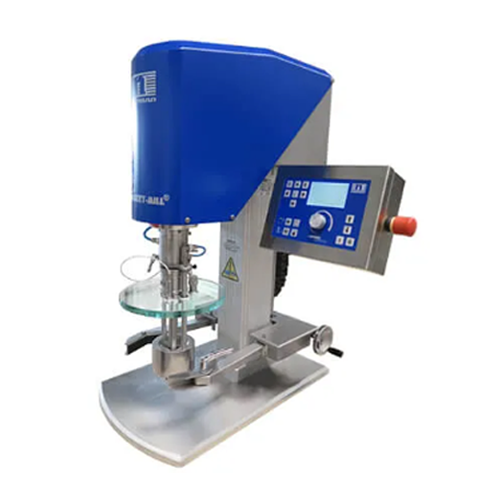
Laboratory basket mill for fine grinding in industrial applications
Optimize your laboratory’s efficiency with hi...
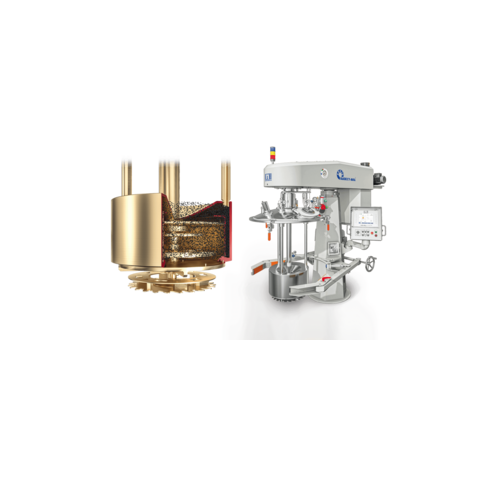
Milling beads for wet grinding in paint industry
Enhance product uniformity and grinding efficiency with specialized milli...
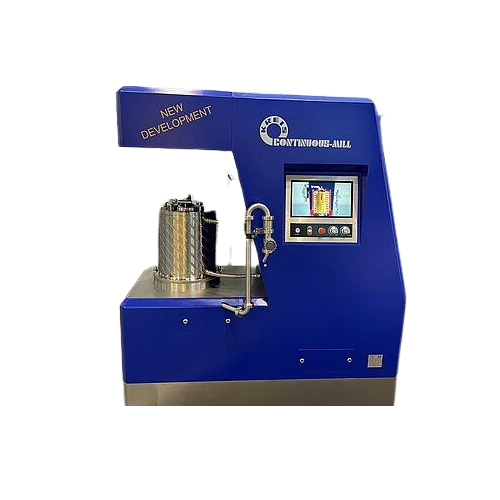
Continuous mill for nano range fine grinding
Achieve ultra-fine particle size in continuous processes, ensuring consistent...
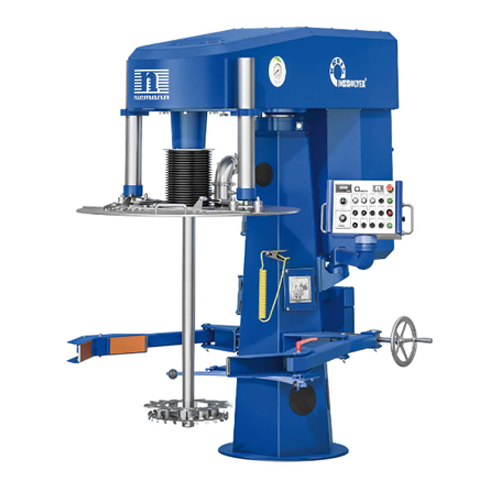
High-efficiency disperser for viscous products
Achieve precise control over the mixing and dispersing of high-viscosity ma...
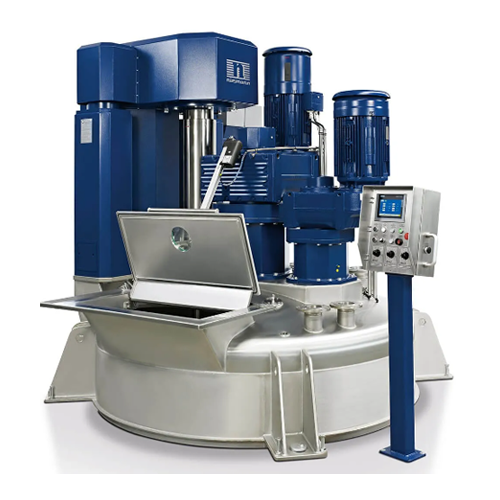
Triple shaft mixer for high-viscosity products
Achieve precision mixing and dispersing of high-viscosity products with a p...
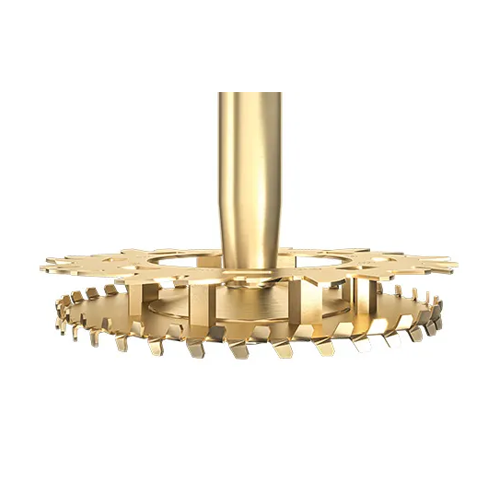
Mixer for high viscosity products
Enhance your production line with a versatile solution designed for precise mixing and di...
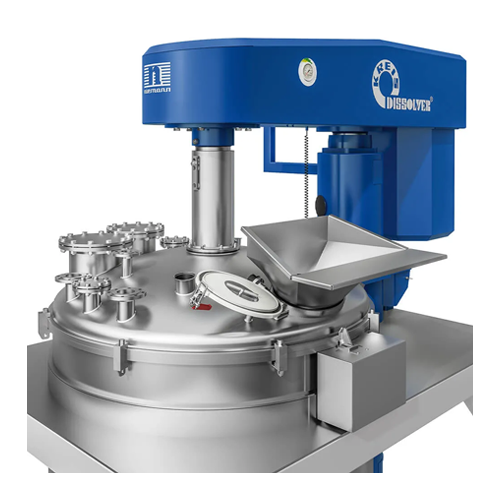
Advanced dissolver for high-viscosity products
Handle ultra-high viscosity mixing challenges effortlessly with this advanc...
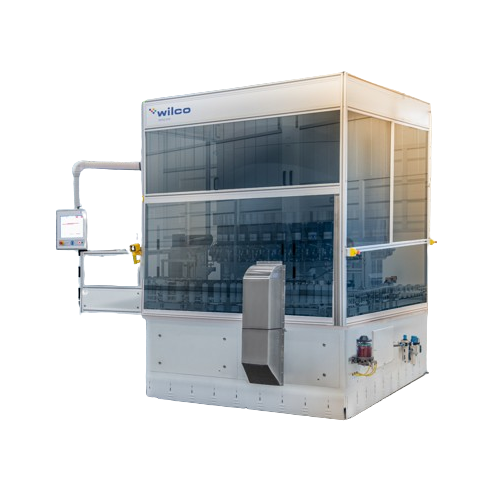
Leak testing system for aerosol cans
Ensure the integrity of your aerosol and metal packaging with a high-speed leak testin...
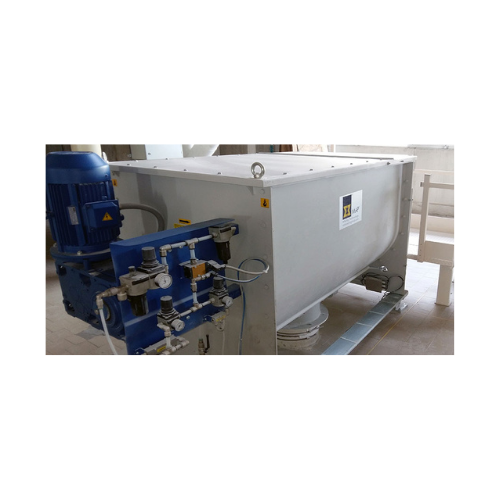
Single-shaft ribbon blender for homogeneous mixing
Achieve high-quality, precise blending of delicate and temperature-sen...
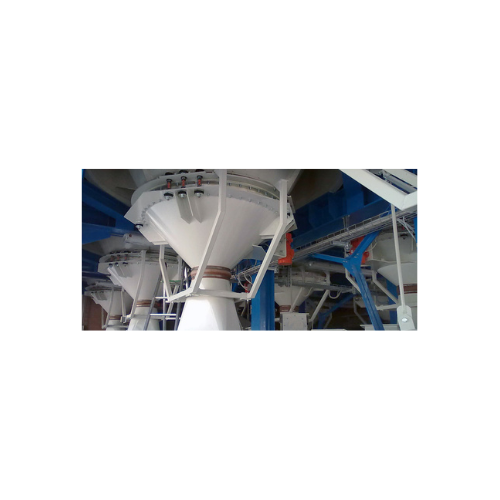
Bulk solids discharging and loading solution
Optimize your bulk material handling with equipment that ensures efficient an...
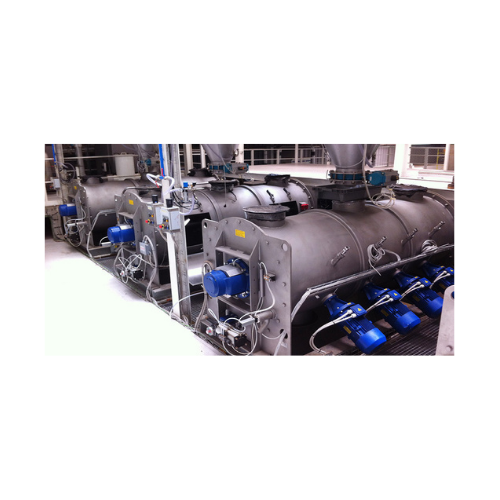
Batch-type single shaft mixer for industrial mixing
Achieve precise and uniform mixing with high-speed, single-shaft mixe...
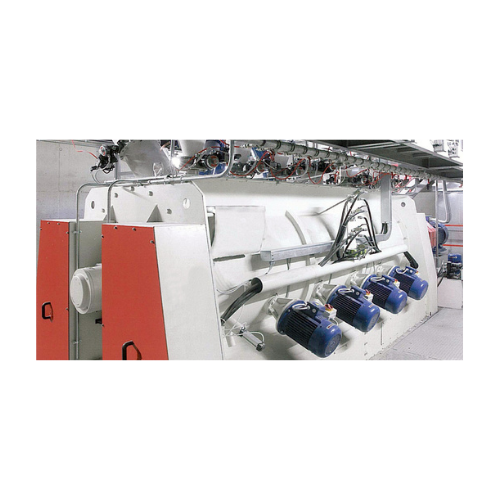
Batch-type single shaft mixers with bomb-bay discharge
When you need rapid, residue-free discharge in your batch mixing p...
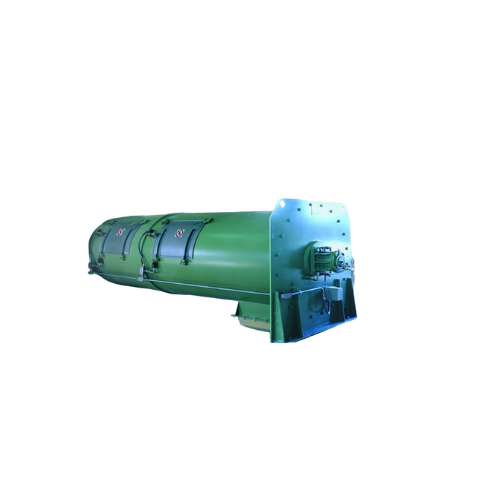
Continuous single shaft mixer for waste treatment
Achieve consistent mixing homogeneity and prevent dead spots in your pr...
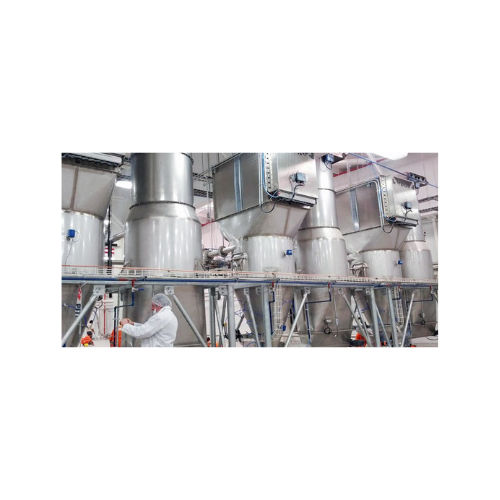
Atex-certified flanged polygonal dust collectors
Ensure dust control and compliance in explosive environments with our com...
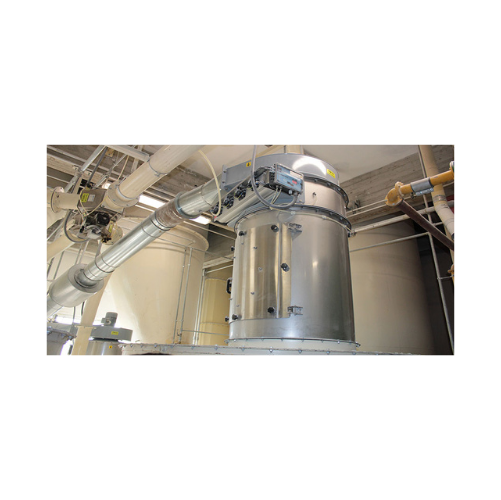
Food-grade round dust collectors
Maintain a clean production environment with this food-grade dust collector, designed to ma...
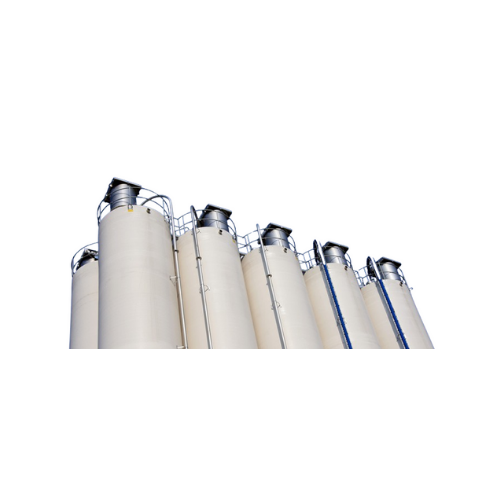
Flanged round dust collectors for industrial air filtration
Optimize your industrial processes with a dust collection sy...
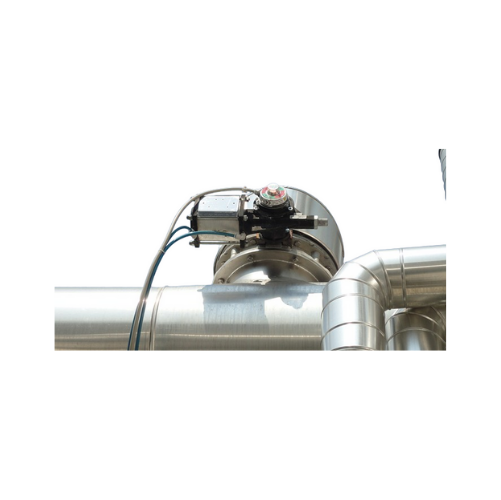
Fit-frame butterfly valves for dry bulk solids
Achieve precise control and minimize contamination in your dry bulk materia...
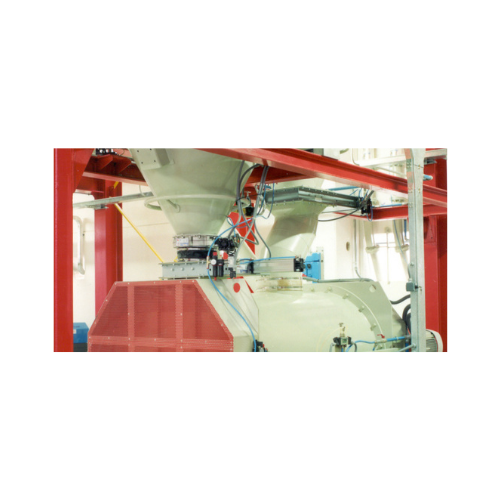
Butterfly valves for powders and granules
Ensure precise flow control and reliable sealing for gravity-fed or pneumatic sy...
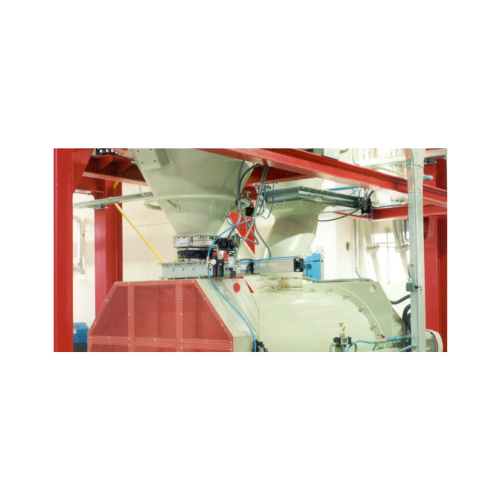
Butterfly valves for powder and granular material handling
Experience seamless material control with advanced butterfly ...
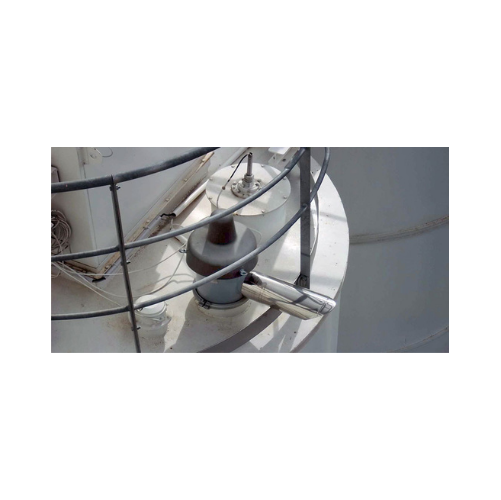
Membrane pressure relief valve for silos and bins
Ensure silo safety with our valve that instantly balances internal pres...
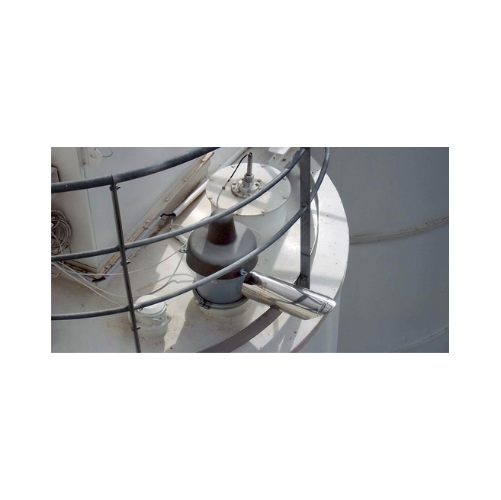
Membrane pressure relief valve for silo protection
Ensure immediate pressure stabilization in your bulk storage silos wit...
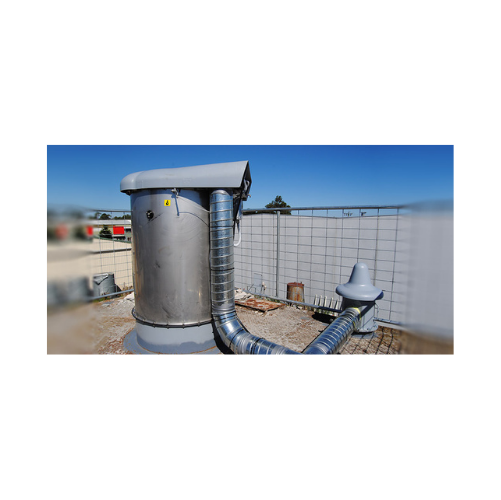
Low profile slide valve for controlling powder flow
Optimize your powder and granule flow management with precision-engin...
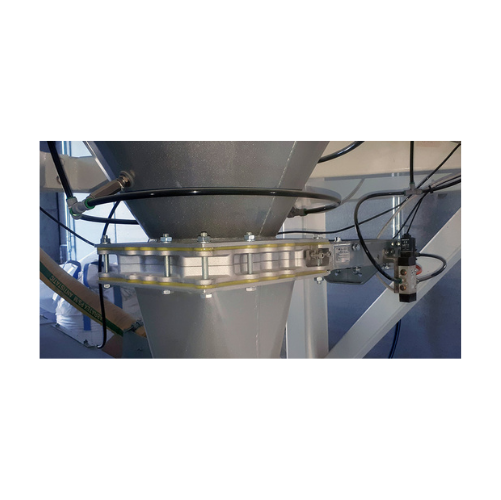
Slide valves for flow interception in powder and granular materials
Effectively manage the flow of powdery and granular...
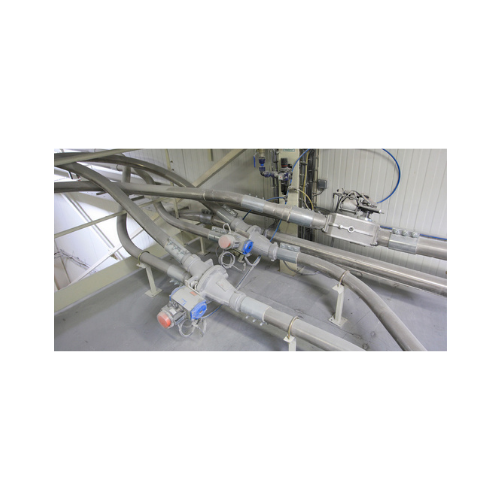
Flap diverter valves for pneumatic conveying
Streamline material flow in your pneumatic conveying system by effortlessly r...
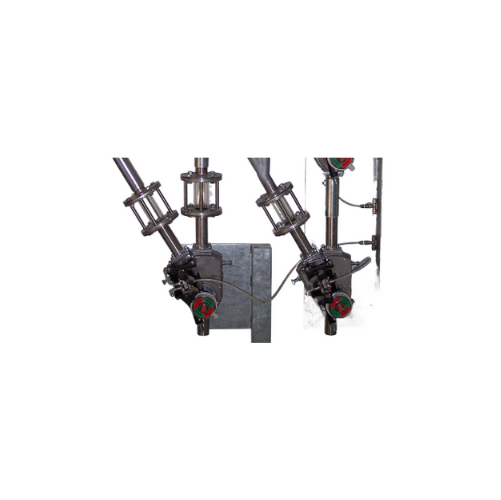
Diverter valves for pneumatic conveying lines
Experience precise flow control in pneumatic conveying with diverter valves ...
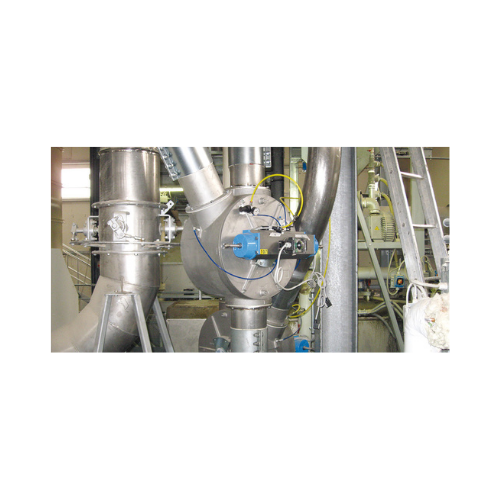
Drum-type diverter valves for pneumatic conveying
Optimize your pneumatic conveying system by effortlessly controlling th...
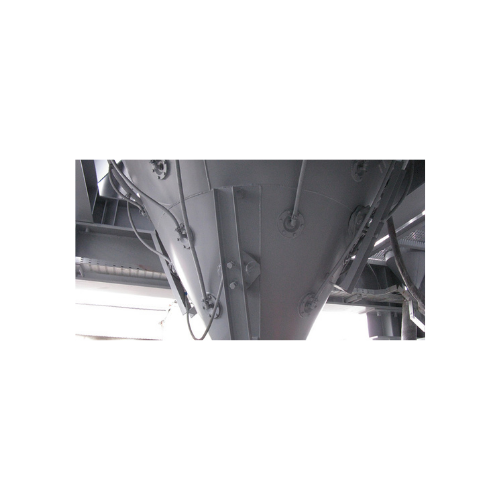
Vibro-aerators for bulk solids discharging
Optimize your powder flow and ensure consistent discharge with this advanced ae...
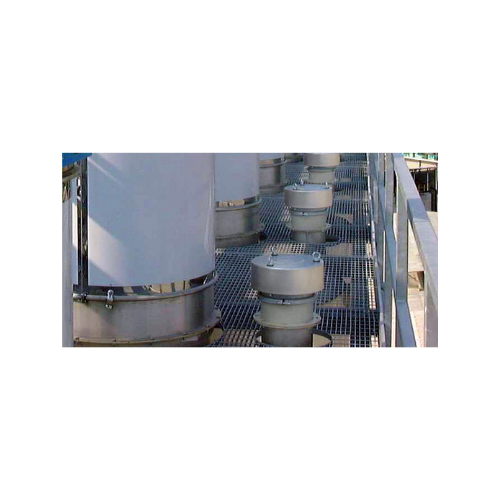
Spring-loaded pressure relief valves for silo overfill protection
Ensure safety and prevent costly overfills with press...

Single shaft screw feeders for consistent material feeding
Tackle challenging materials with poor flow characteristics b...
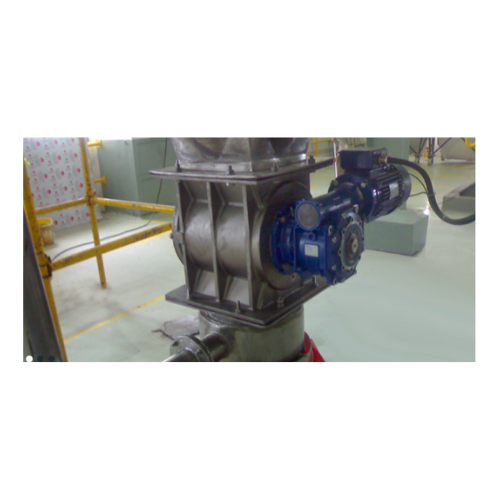
Drop-through rotary valve for powder and granular material feeding
Achieve precise control in discharging and feeding p...
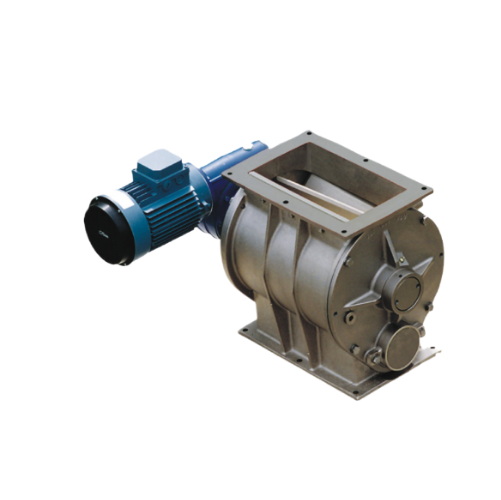
Drop-through rotary valve for precise powder and granule feeding
Ensure precise material handling with this drop-through...
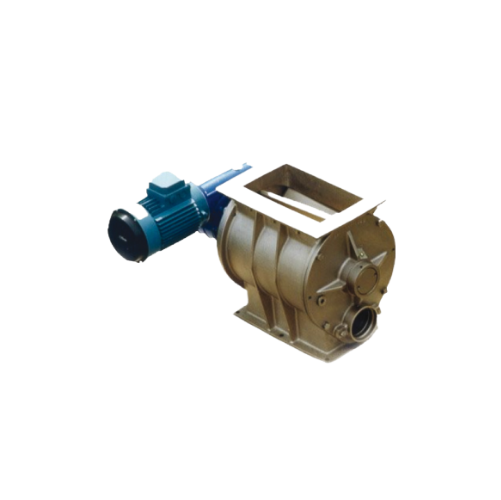
Blow-through rotary valves for pneumatic conveying
Optimize your pneumatic conveying systems with high-efficiency blow-th...
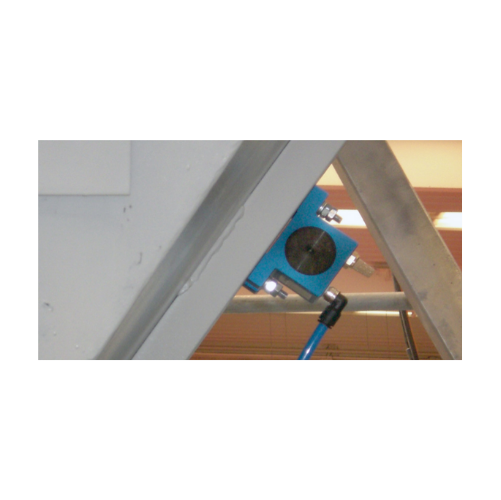
Rotary ball vibrators for fine powders and granular materials
Ideal for preventing material build-up and blockages, thes...
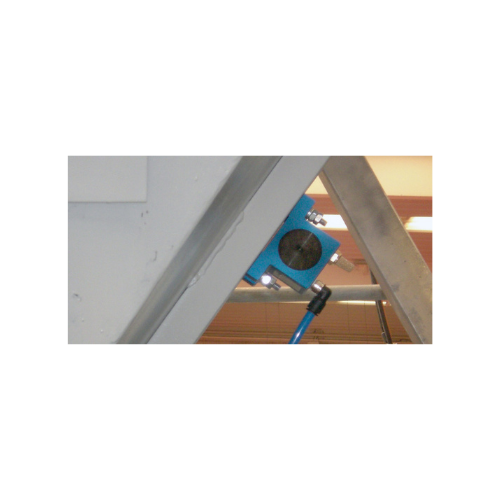
Rotary ball vibrators for aggregate reclaiming
Enhance efficiency in your production line with a solution that optimizes t...
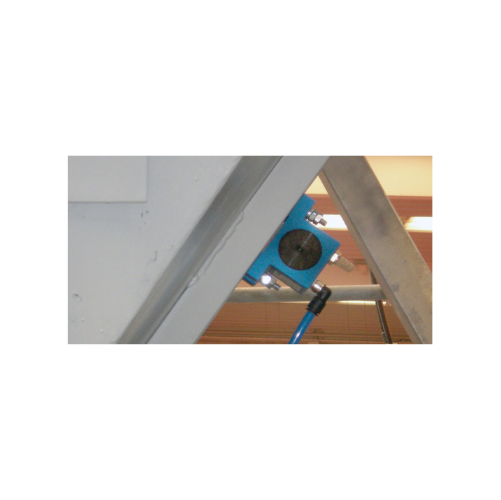
Rotary ball vibrators for bulk solids discharging
Ideal for enhancing material flow, this equipment efficiently handles f...
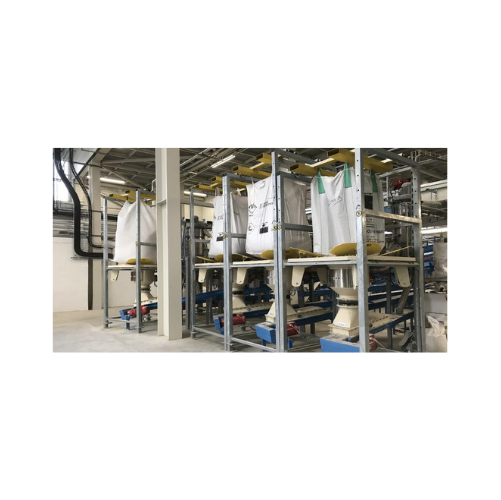
High flow rate Fibc discharger
Optimize your bulk material handling with a system designed for efficient and dust-free FIBC ...
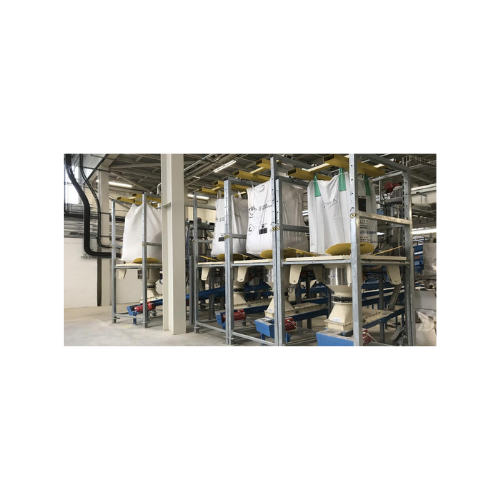
High flow rate Fibc dischargers for wastewater treatment
Optimize your material handling with efficient, dust-proof disch...
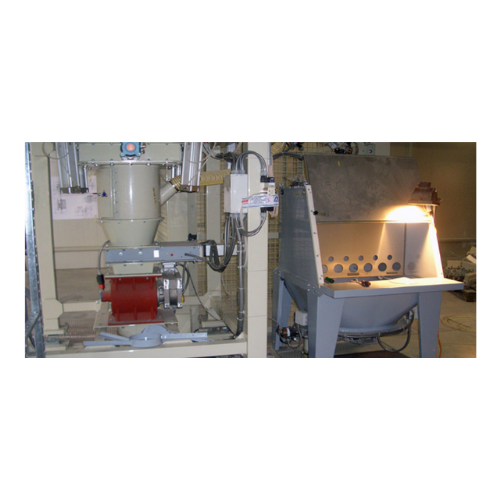
Manual bag opener for bulk solids discharging
Effortlessly open and empty bags while containing dust emissions, ensuring a...
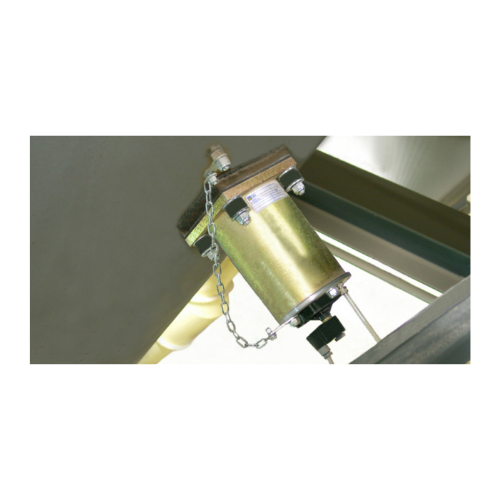
Single impact pneumatic hammers for flow aids
Combat material clogs and ensure smooth flow in your production line with pn...
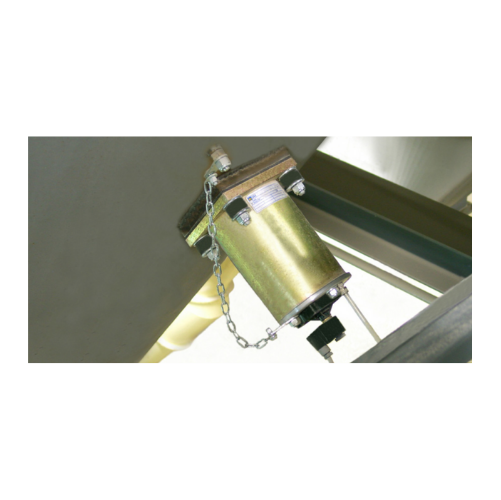
Pneumatic hammers for bulk solids discharging
Optimize your production efficiency and solve material flow challenges with ...

Pneumatic hammers for aiding material flow
Optimize material flow and eliminate blockages in your processing line with pne...
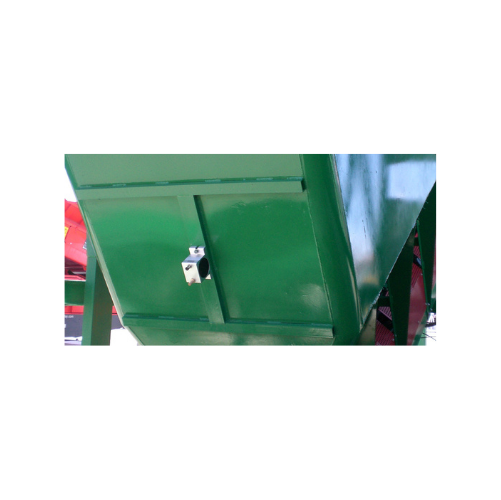
Industrial vibrator for high-frequency vibration
Achieve efficient material flow and compaction across various production ...
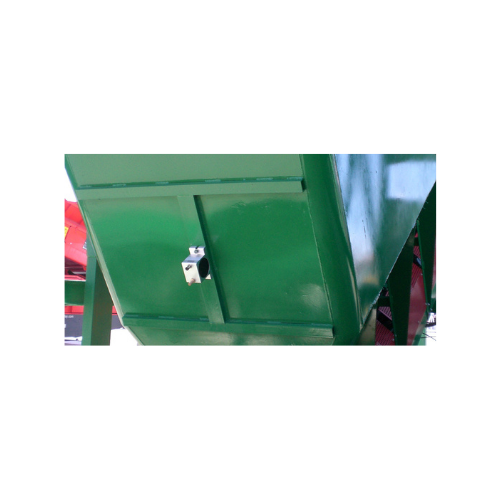
Rotary turbine vibrators for bulk solids discharging
Enhance the efficiency of material handling with high-speed, low-noi...
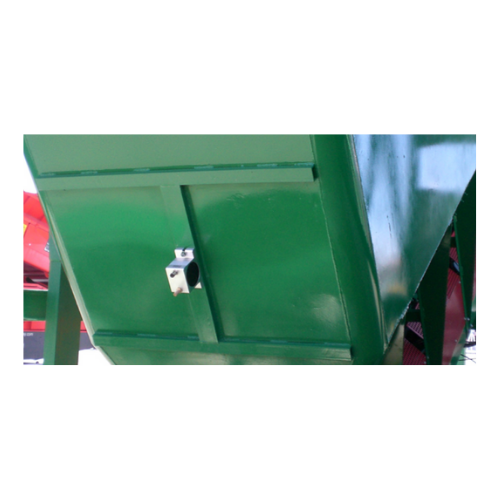
Rotary turbine vibrators for material flow aid
Optimize your production efficiency with high-speed, silent operation vibra...
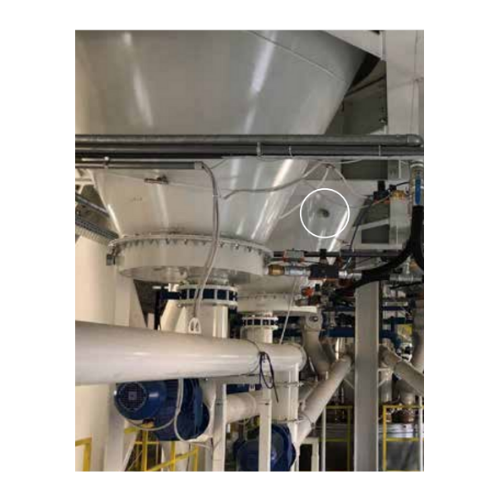
Continuous impact vibrators for bulk material removal
Combat material flow issues like bridging and rat-holing with our i...
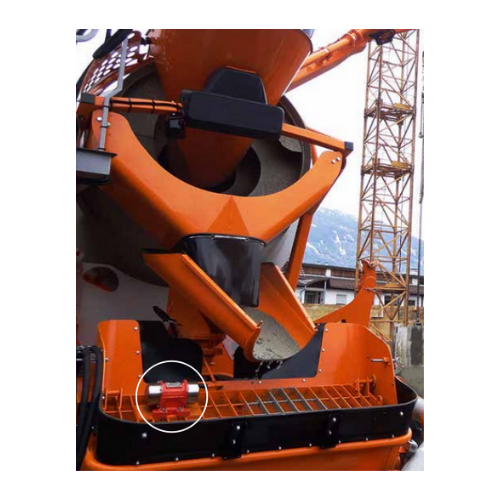
Continuous impact vibrator for aggregate reclaiming
Tackle material flow challenges head-on by preventing common issues l...

Continuous impact vibrators for bulk solids discharging
Optimize your discharging process with vibrators that effectively...
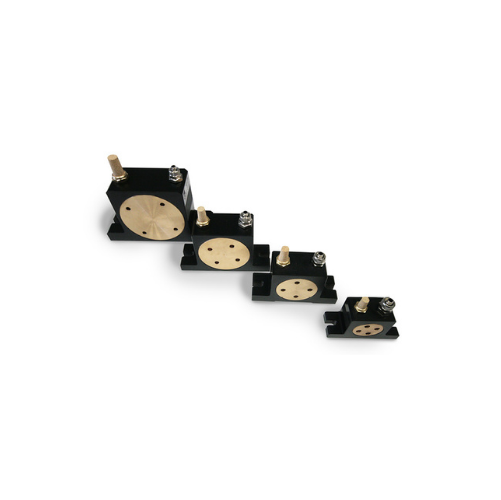
Rotary roller vibrators for concrete compacting and hopper emptying
Achieve higher compaction and efficient emptying wi...
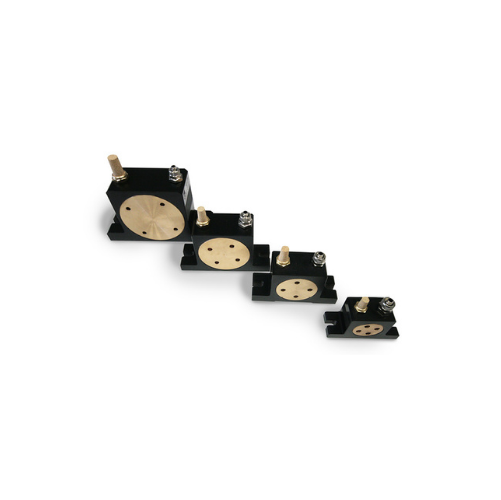
Rotary roller vibrators for material flow assistance
Enhance material flow efficiency in your production line with high-f...
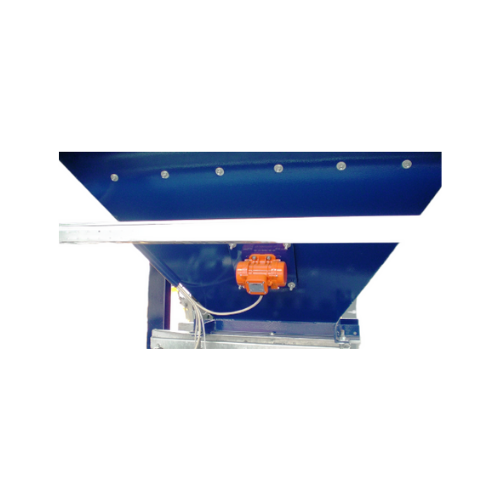
External electric motovibrators for industrial applications
Optimize material movement and improve discharge efficiency ...
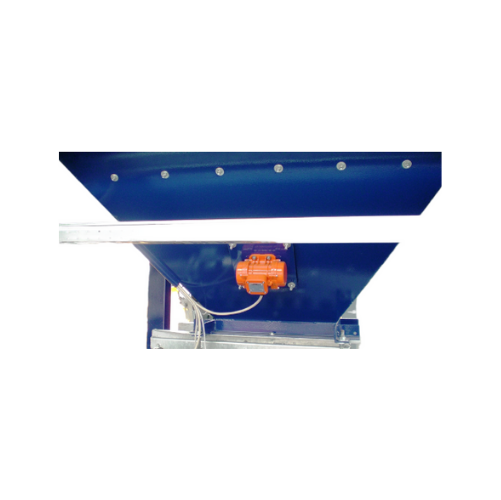
External electric motovibrators for bulk solids conveying
Enhance material flow efficiency and solve challenging dischar...
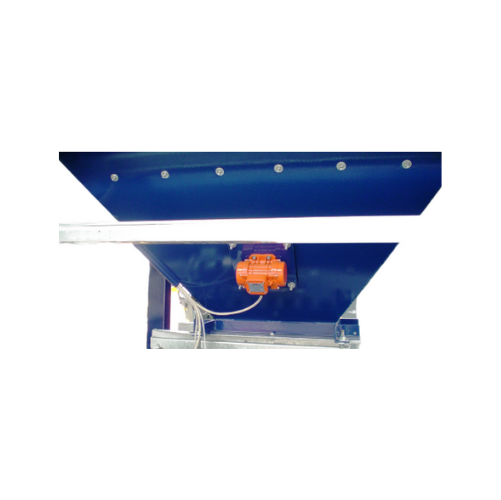
Industrial electric vibrator for bulk solids discharging
Enhance material flow efficiency and ensure consistent output ac...
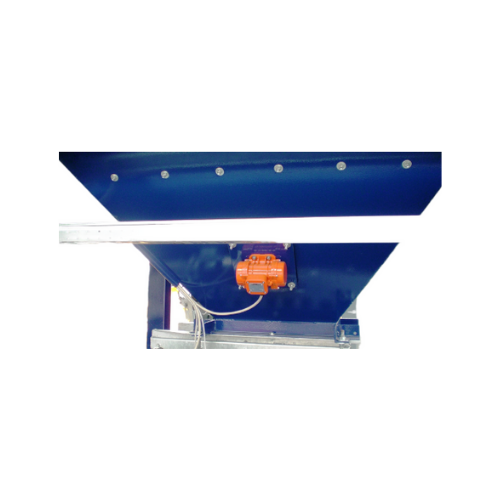
External electric motovibrators for industrial material flow
Experience enhanced material flow and precise material disc...
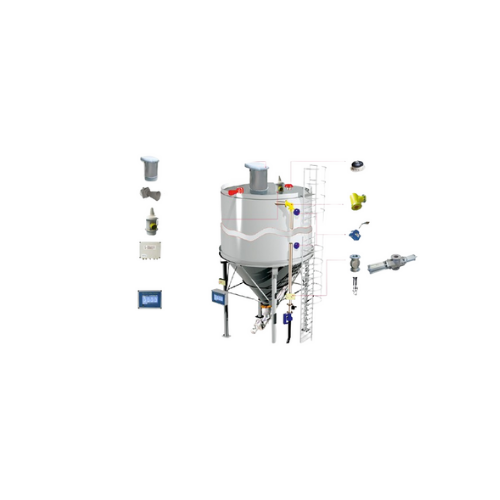
Silo overfill protection system
Prevent silo overfilling and excess pressurization with a system designed to safeguard silos...
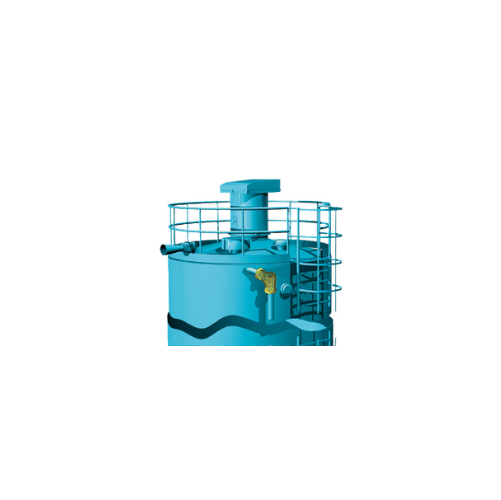
Silo overfilling safety system
Ensure safe silo filling with our system that prevents overfilling and excess pressurization,...
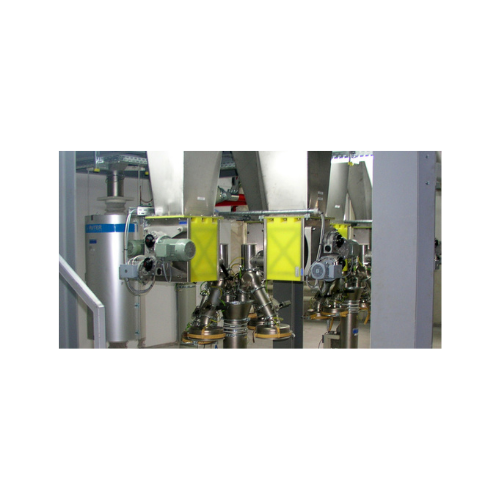
Micro-batch feeders for powder and granular material
Struggling with clog-prone powders? Gain precise control and consist...
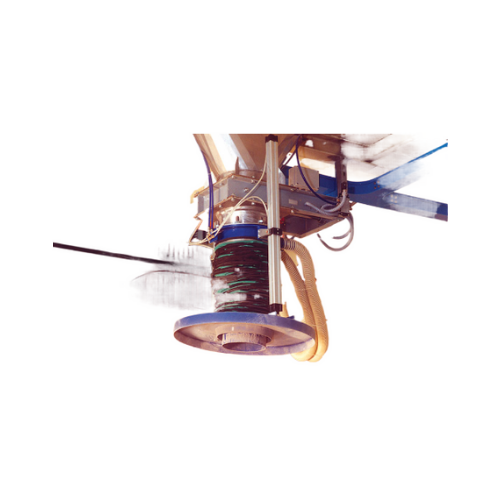
Loading bellows for drums and Ibcs
Ensure dust-free loading of bulk solids into confined spaces with compact, pneumatically...
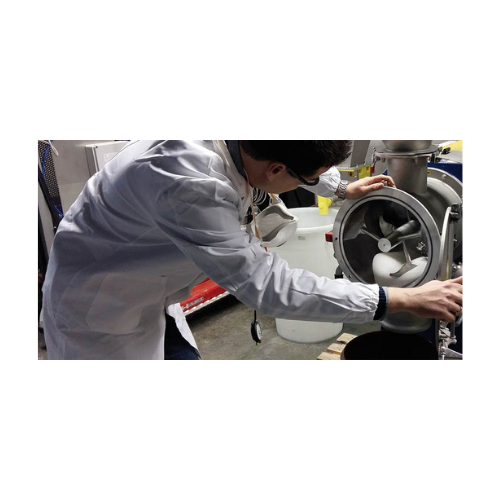
Laboratory batch mixer for small scale production
Achieve rapid and reproducible mixing results with this laboratory batc...
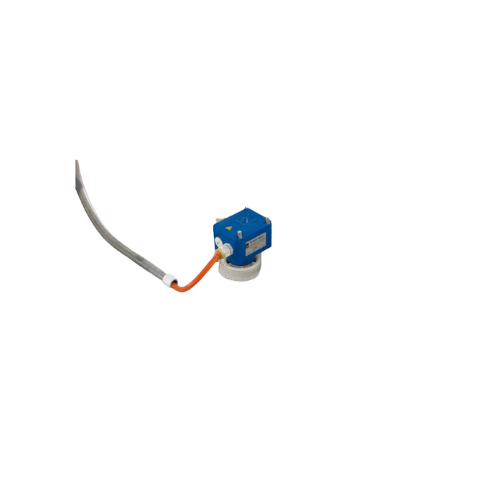
Bin level indicator for bulk solids
Ensure precise material level detection across your production processes, minimizing th...
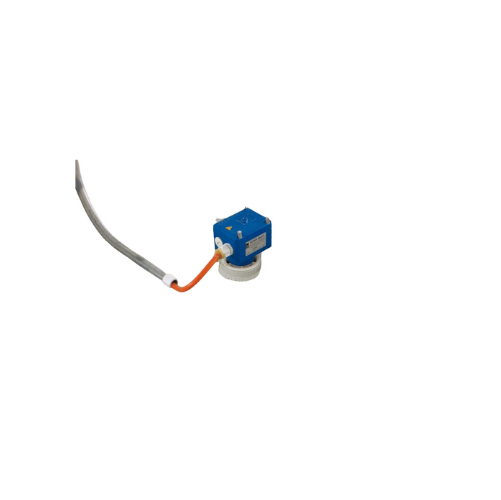
Bin level indicators for wastewater treatment
Ensure reliable material level monitoring in your silos and hoppers with ILT...
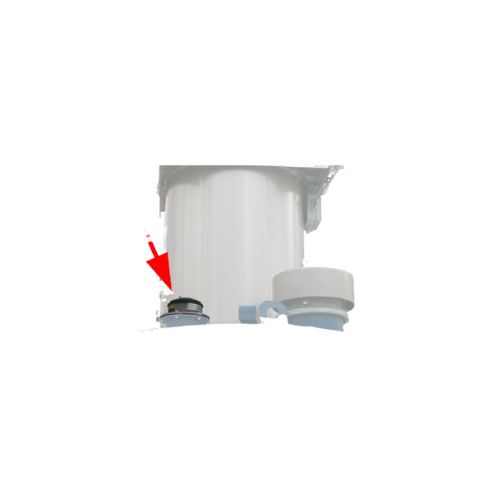
Electronic pressure meter for silo safety
Ensure the safety of your silos by efficiently monitoring internal pressure chan...
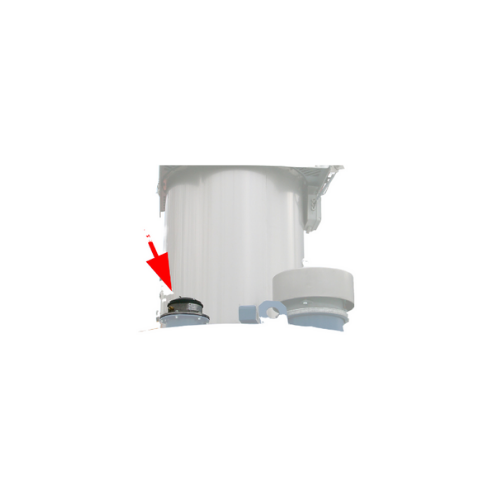
Electronic pressure meters for silo safety monitoring
Ensure precise pressure management in your systems with this advanc...
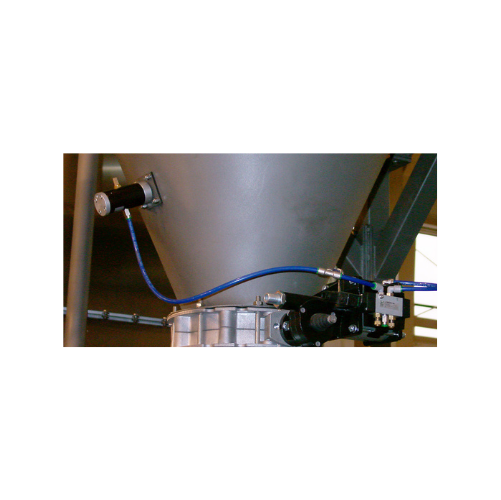
Pneumatic linear vibrators for bulk material flow
Prevent bridging and rat-holing in your production process with silent,...
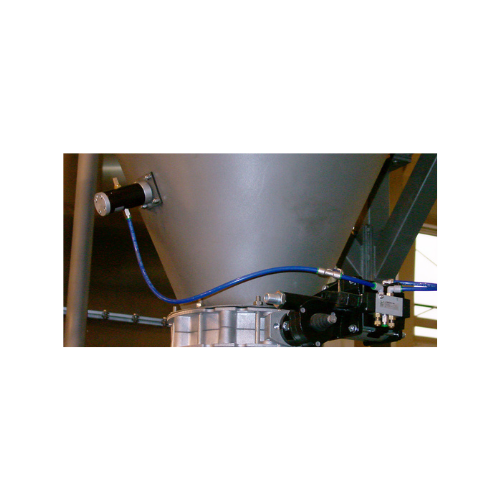
Cushioned pneumatic linear vibrators for bulk solids
Combat material bridging and rat-holing with silent vibratory techno...
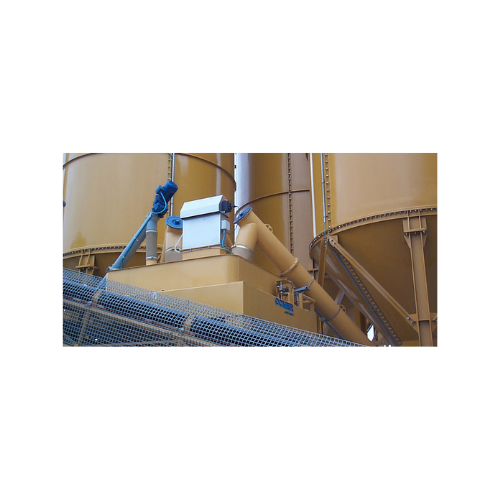
Hopper venting filter for efficient dust filtration
Achieve superior dust control and efficient material handling with a ...
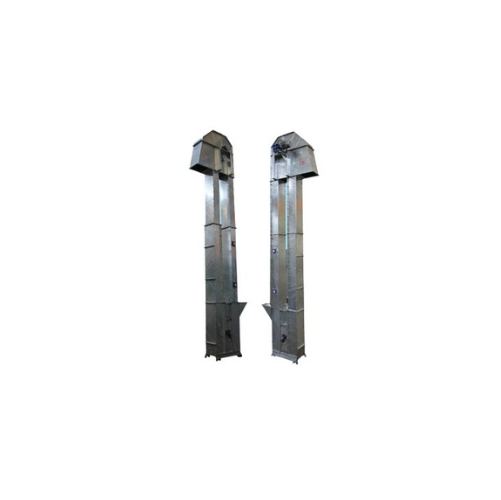
Vertical conveyor for fine aggregates and minerals
Optimize the handling of abrasive materials with a vertical conveying ...
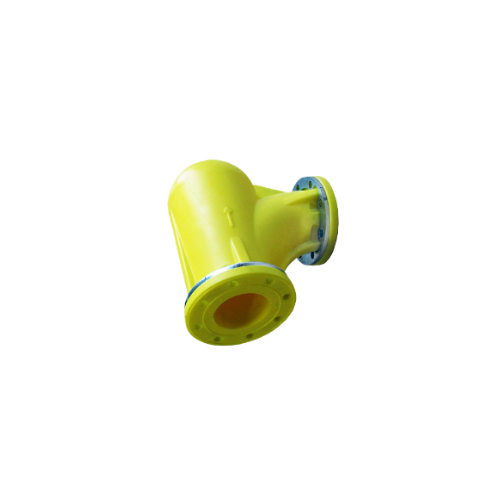
Anti-wear elbows for pneumatic conveying systems
Reduce wear and extend the lifespan of your pneumatic conveying systems w...
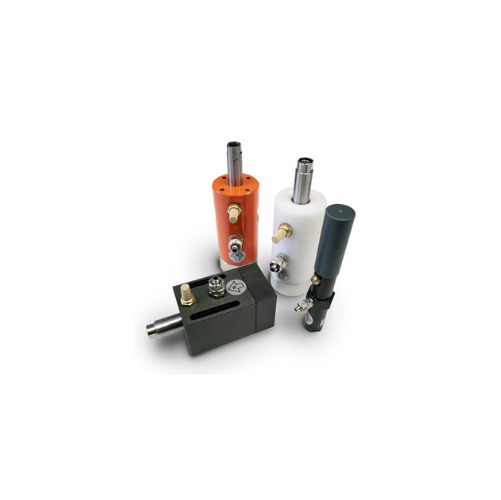
Cushioned pneumatic vibrators for coarse particle materials compaction
Enhance your material flow and compaction proces...
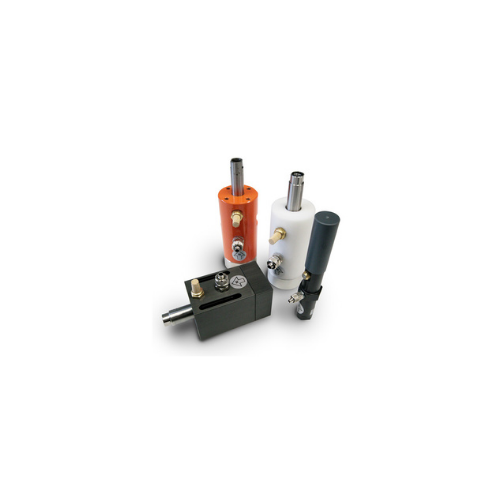
Cushioned pneumatic vibrators for bulk solids conveying
Streamline your material handling with precision vibration contro...
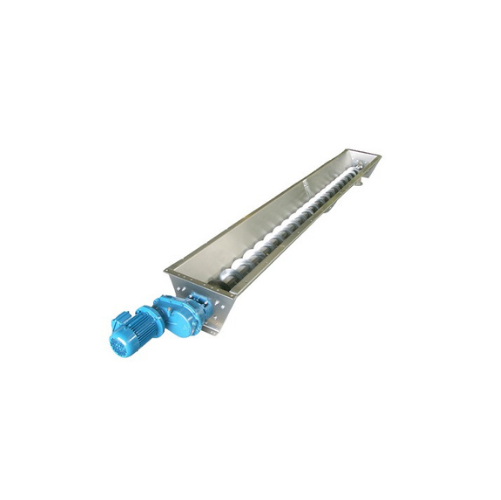
Stainless steel trough screw conveyor
Ideal for precise handling of powdery and granular materials, this solution ensures m...
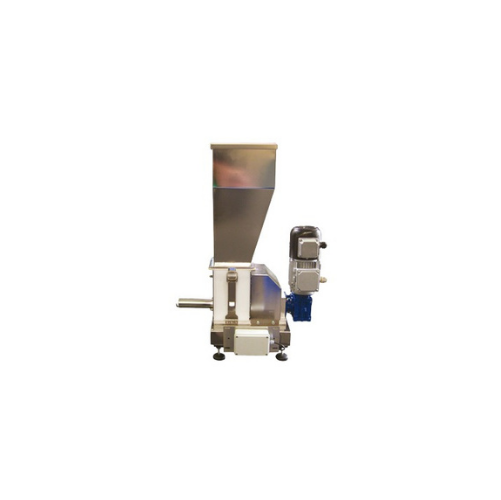
Loss-in-weight screw feeder for precise powder dosing
Achieve high precision in continuous dosing with this advanced scre...
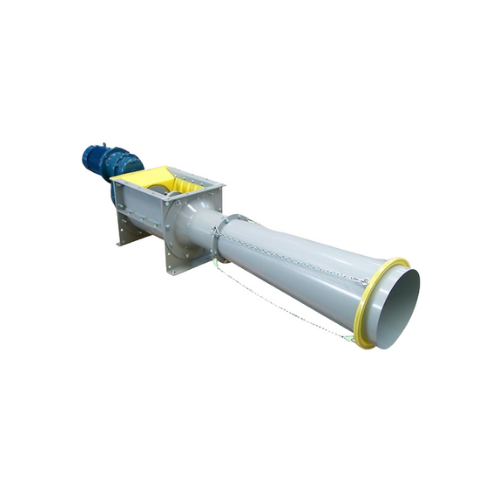
Waste bag compactor for bulk solids
Efficiently compact waste bags to a fraction of their volume, streamlining disposal whi...
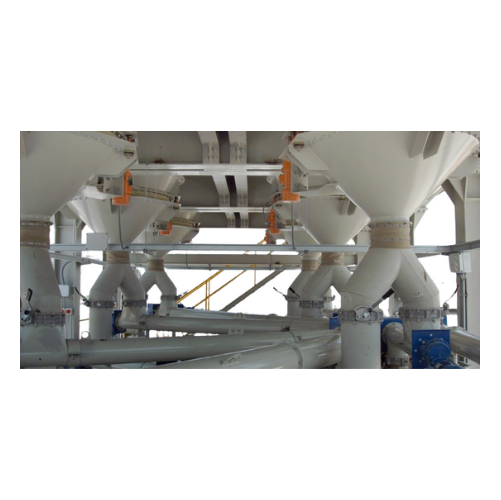
Vibratory outlet hopper for bulk material discharge
Struggling with material bridging and inconsistent discharge? Enhance...
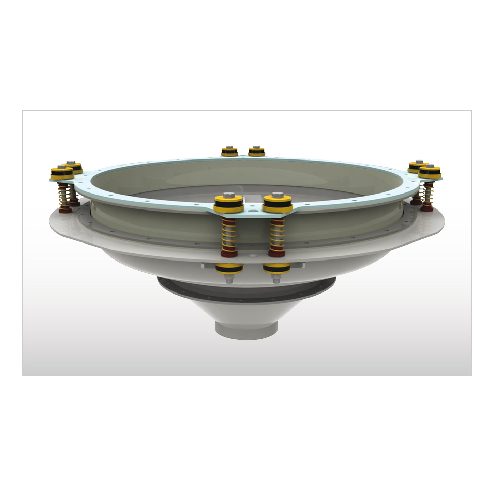
Industrial bin activator for smooth material flow
Enhance your material handling process with a solution that ensures con...
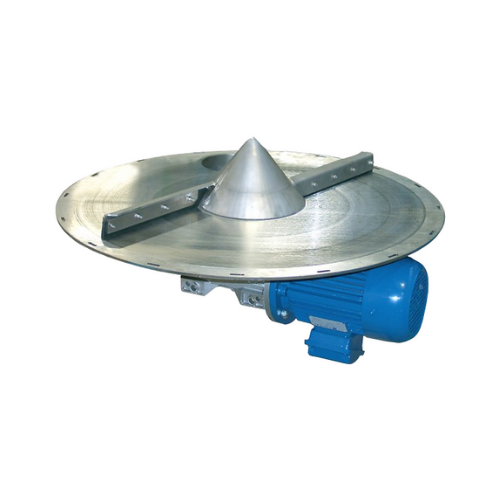
Rotary bin discharger for bulk solids
Efficiently manage bulk solids with a rotary bin discharger that minimizes residue an...
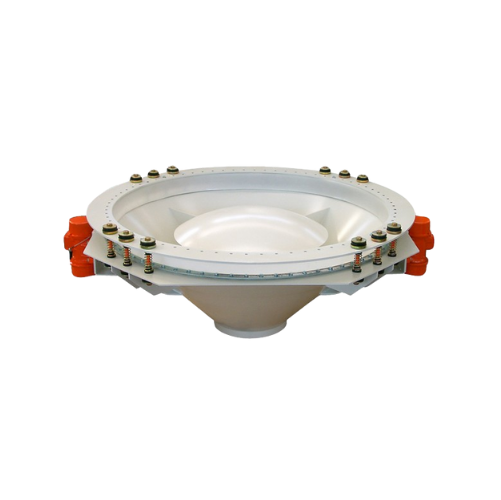
Vibratory hopper for bulk solids discharge
Ensure consistent material flow and prevent bridging in storage silos with this...
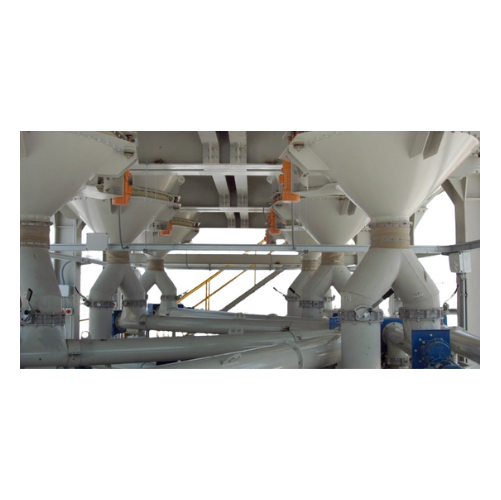
Bin activator for silo and hopper discharge
Ensure optimal material flow and prevent blockages in your storage systems wit...
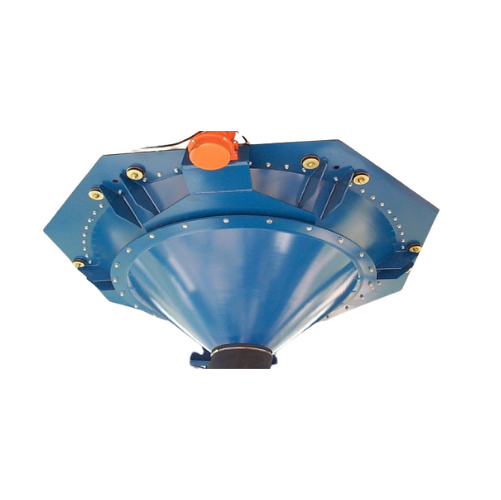
Vibratory outlet hopper for bulk solids discharge
Reduce material handling challenges with highly efficient vibration tec...

Industrial vacuum pumps for efficient powder conveyance
Harness the power of efficient vacuum generation to streamline th...
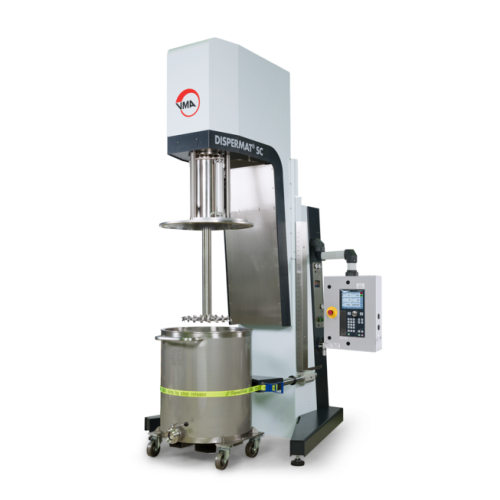
Explosion-proof production disperser for paint manufacturing
Ensure safe and efficient dispersion in volatile environmen...
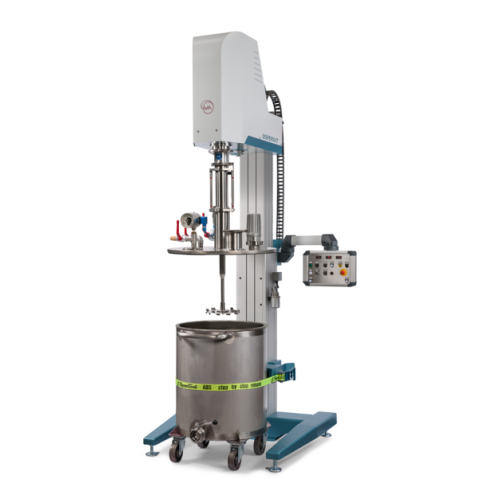
Vacuum dispersion system for high-viscosity products
Eliminate air inclusions during production with a modular vacuum sys...
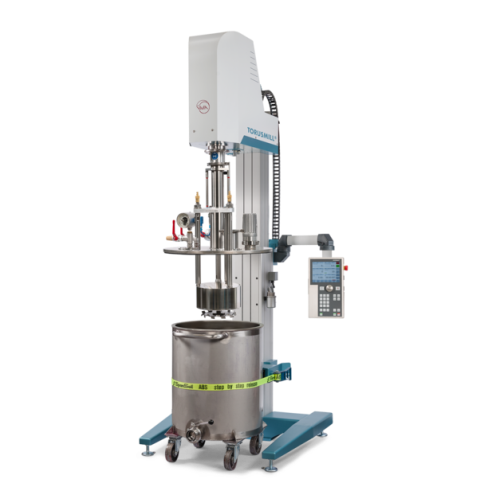
Vacuum basket mill for high-viscosity product processing
Achieve exceptional fine milling results while preventing air in...
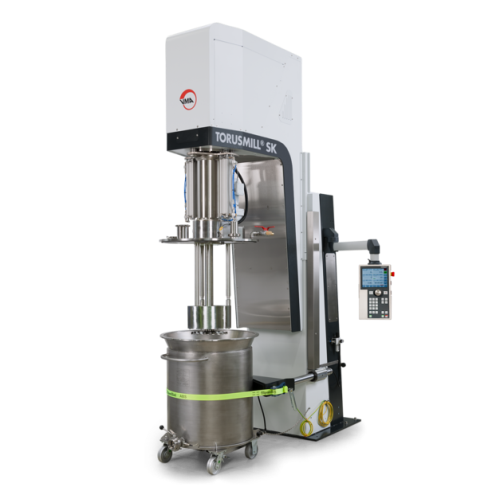
Vacuum basket mill for high viscosity products
Achieve efficient fine grinding of high-viscosity products while minimizing...
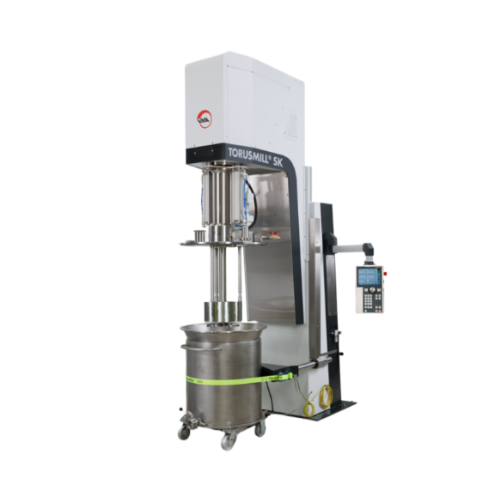
Vacuum dissolver for high viscosity products
Optimize your production with a vacuum dissolver designed to efficiently prev...
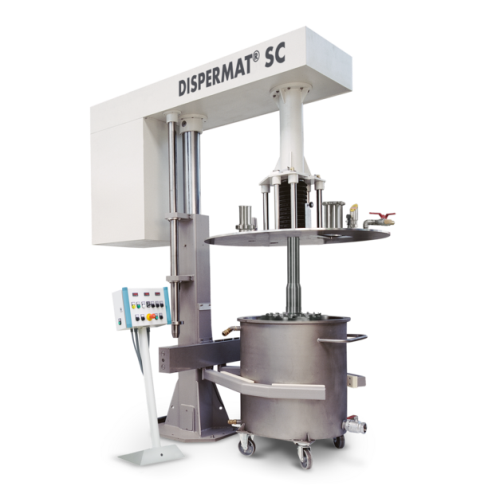
Vacuum disperser for high-viscosity products
Optimize high-viscosity product dispersion and prevent air inclusions with a ...

Vacuum dissolving system for high-viscosity products
Achieve flawless dispersion of high-viscosity substances under vacuu...
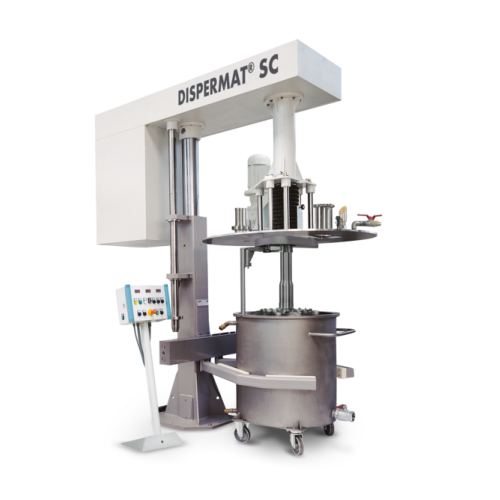
Production dissolver for high-viscosity products
Achieve optimal dispersion and grinding of high-viscosity substances with...
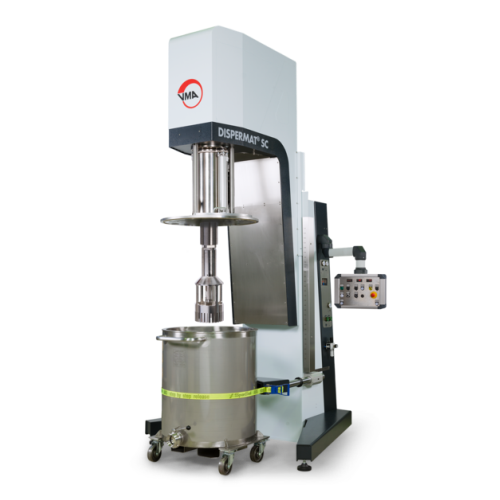
Rotary homogenizer for high shear mixing
Achieve precise homogenization of various viscosities with advanced rotor-stator t...
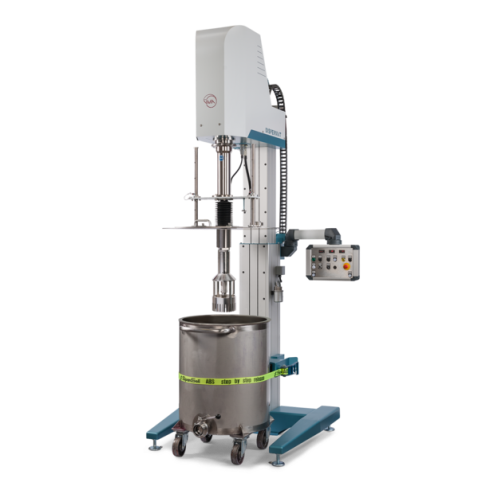
Rotor-stator homogenizer for high shear batch processing
Achieve ultra-fine particle distribution and stable emulsions wi...
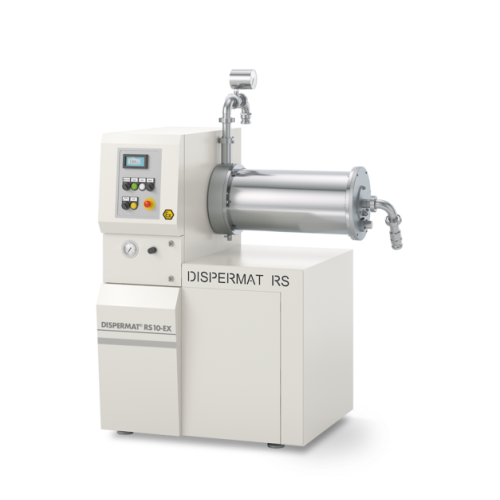
Explosion-proof bead mill for industrial grinding applications
For manufacturers seeking precise particle size control, ...
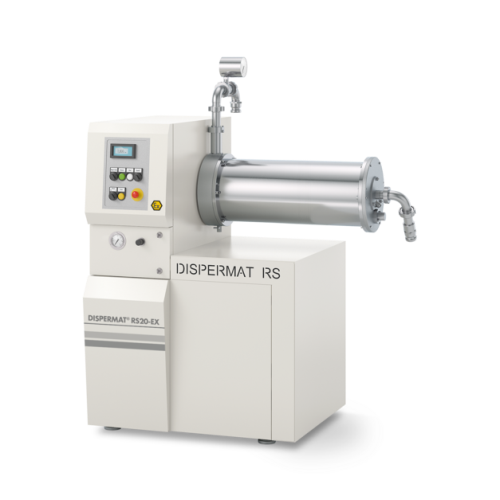
Explosion-proof horizontal bead mill for paint production
Ensure ultra-fine particle size and consistent quality with an...
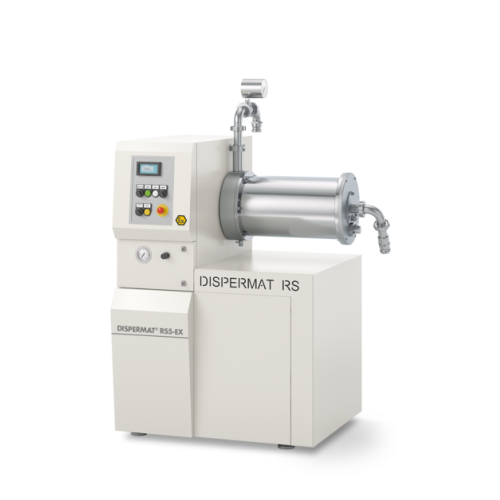
Explosion-proof horizontal bead mill
For manufacturers seeking precise particle sizing, this explosion-proof bead mill ensu...
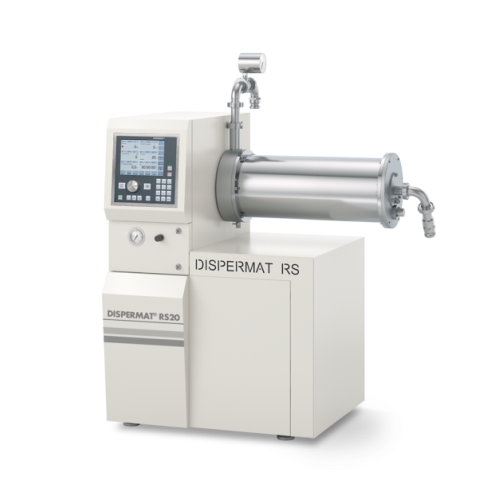
Horizontal bead mill for fine grinding in continuous process
Achieve ultrafine particle dispersion and consistent mixing...
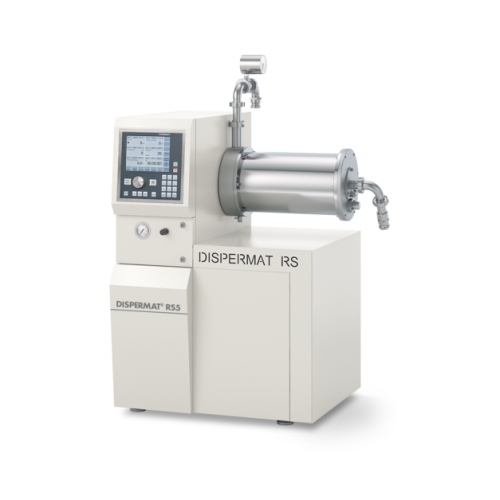
Horizontal bead mill for ultrafine particle grinding
Achieve precision in ultrafine grinding with a system that allows fo...
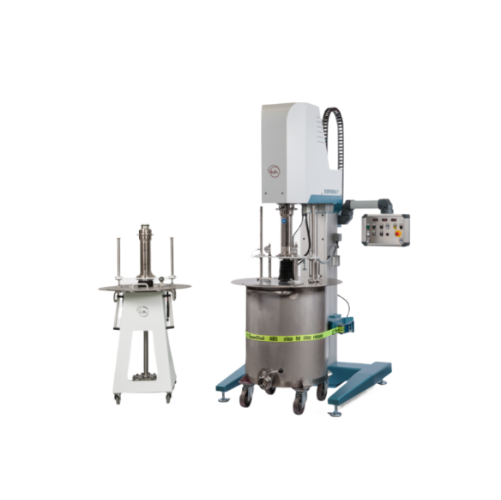
High-capacity dissolvers for industrial mixing
Enhance your production line with precision mixing, achieving consistent di...
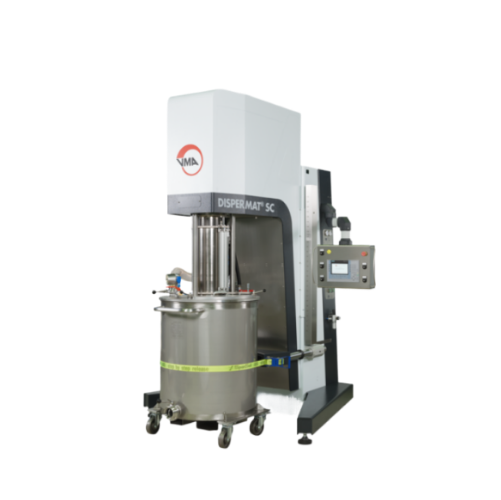
Modular basket mill for industrial dispersion
Effortlessly enhance your production efficiency with this versatile solution...
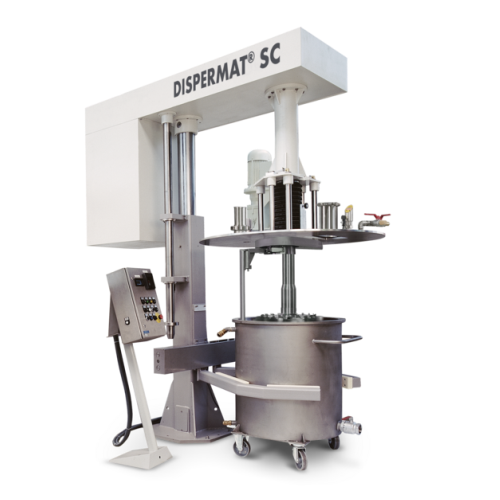
Explosion-proof production vacuum disperser for viscous products
Achieve precise and reliable dispersion of high-viscosi...

Industrial basket mill for medium viscosity products
Achieve precise particle size reduction and rapid pigment dispersion...
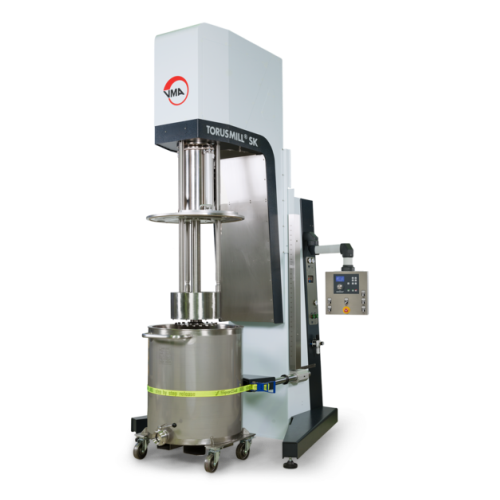
High-efficiency immersion mill for medium viscosity products
Achieve precise particle size reduction and superior disper...

High-efficient industrial immersion mill
Achieve rapid, efficient dispersion and fine grinding in demanding production envi...
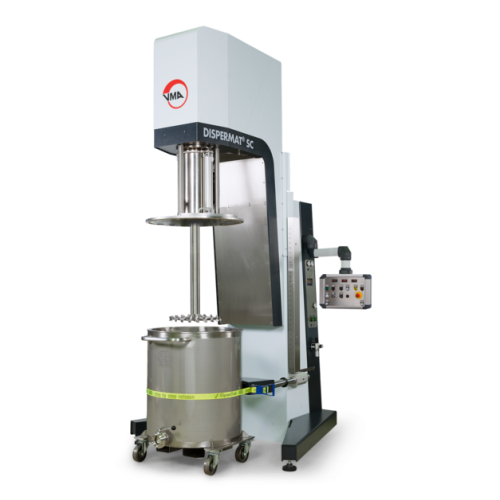
High-performance dissolver for industrial dispersion processes
Optimize your dispersion processes with this advanced dis...
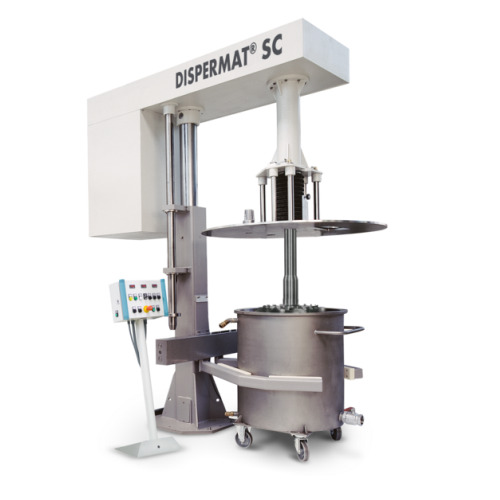
High-performance production dissolver for large batches
Achieve precise and repeatable dispersion for complex formulation...
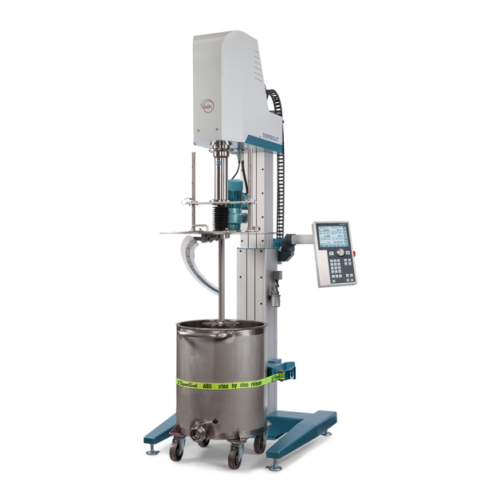
Dissolving system for high-viscosity products
Optimize the dispersion of high-viscosity liquids and pastes with this versa...
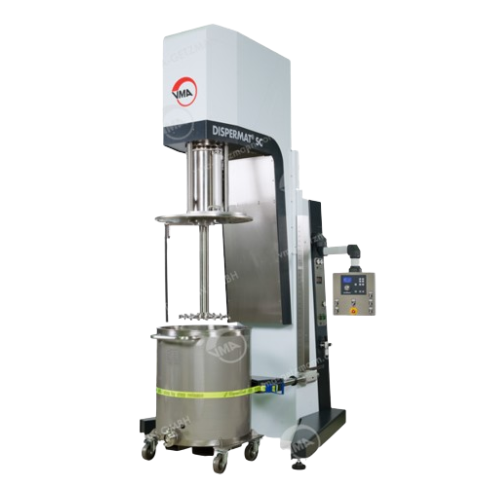
Production dissolver with scraper for high-viscosity products
Efficiently tackle high-viscosity material processing with...
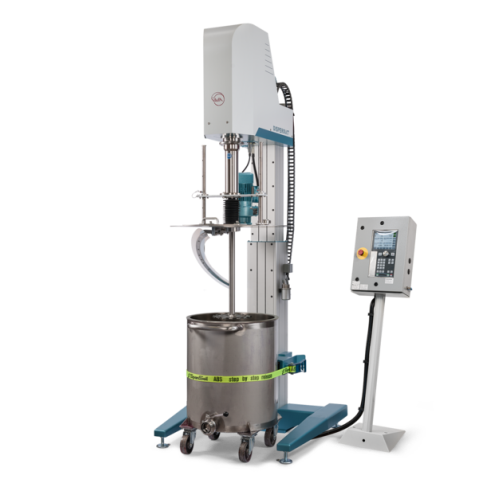
Explosion-proof dissolver with scraper for high viscosity substances
Ensure flawless dispersion with enhanced safety, d...
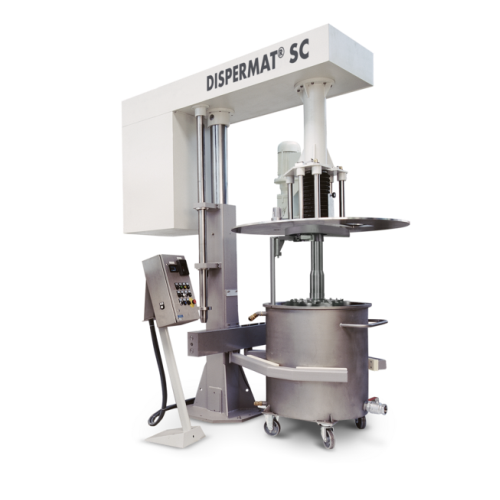
Explosion-proof dissolver for high viscosity products
Optimize your high-viscosity material processing with an explosion-...
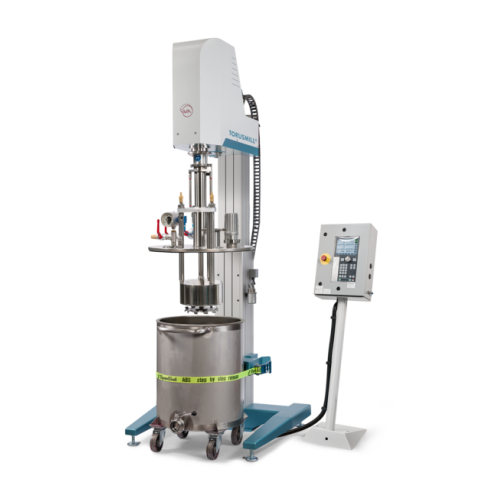
Vacuum basket mill for highly viscous products
Achieve precision in fine milling under vacuum to prevent air inclusions in...
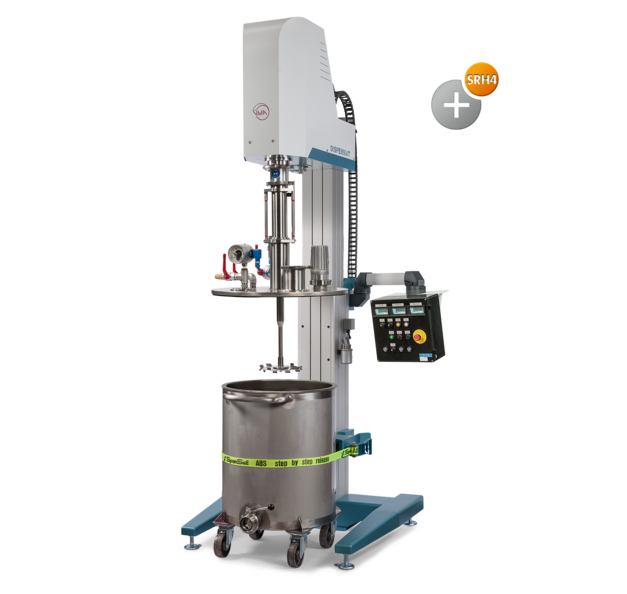
ATEX vacuum dissolver for high viscosity products
Ensure safe and efficient dispersion of high-viscosity materials under...
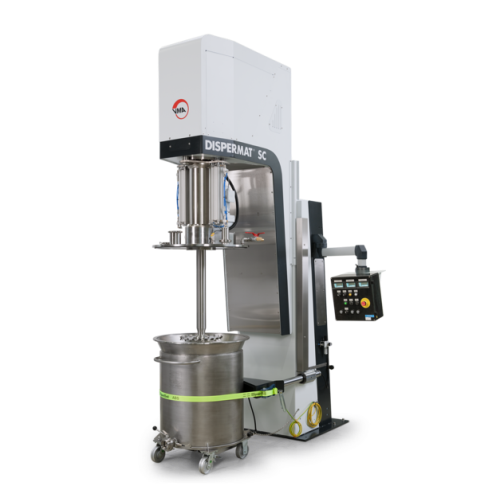
Explosion-proof vacuum dissolver for high-viscosity products
Optimize your production by eliminating air inclusions and ...
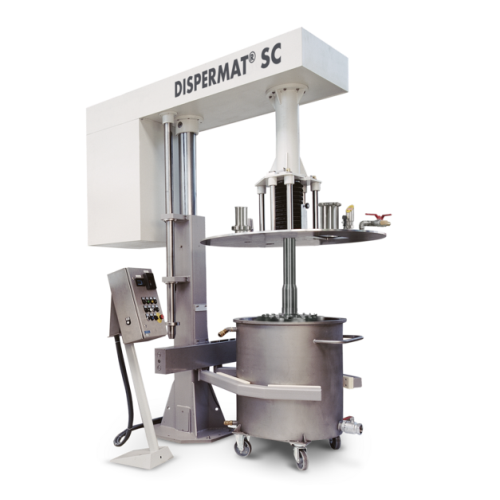
Explosion-proof vacuum dissolver for high viscosity products
Achieve precise dispersion of high-viscosity products under...
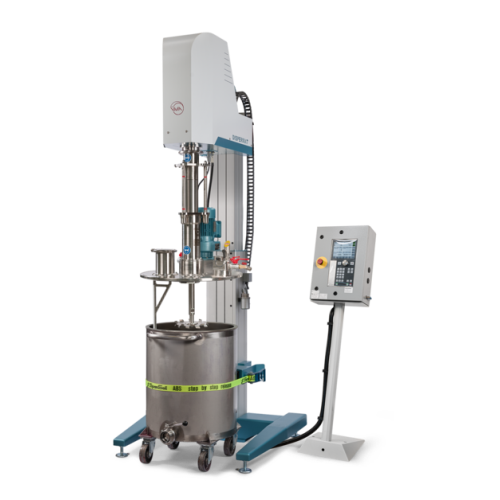
Explosion-proof vacuum dissolver for high viscosity applications
For operations requiring precise control in high-viscos...
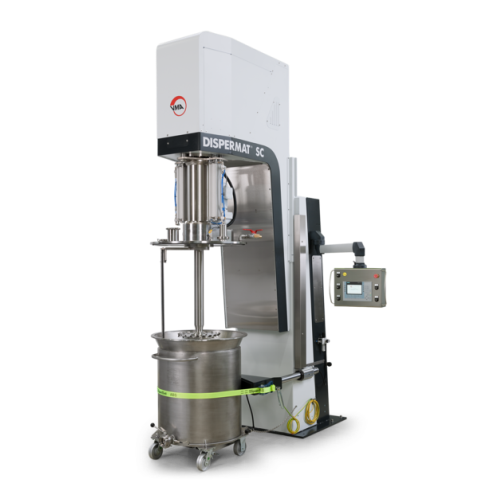
Explosion-proof vacuum disperser for high-viscosity substances
Achieve precise dispersion and eliminate air inclusions w...
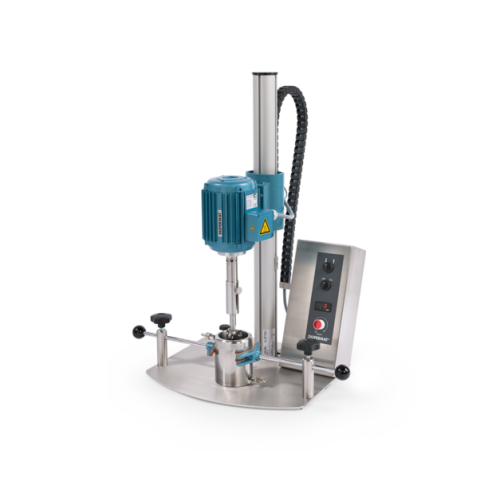
Laboratory stirrers for high viscosity materials
Efficiently mix and stir high-viscosity materials with ease, enabling pre...
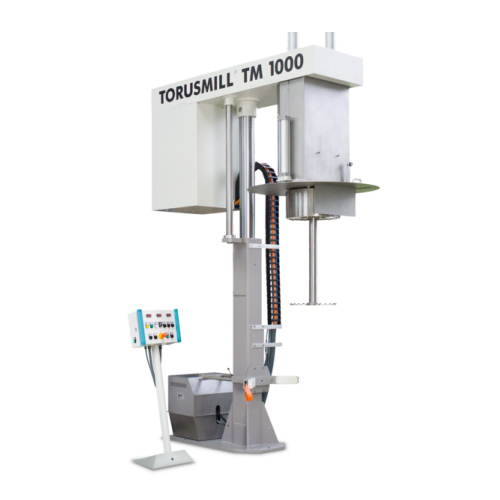
Basket mill with integrated dissolver for high viscosity products
Optimize your production efficiency by combining disp...
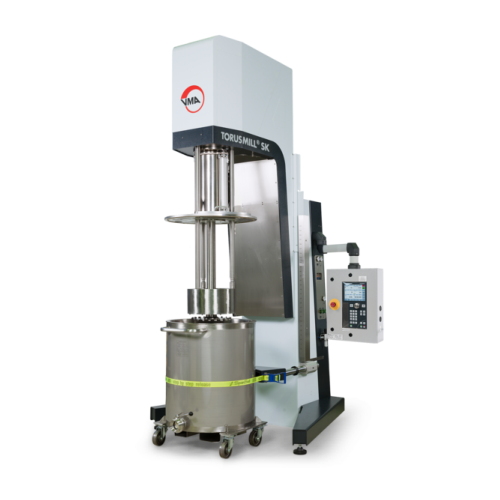
Explosion-proof immersion mill for paints and varnishes
Optimize high-performance coatings production with an explosion-p...
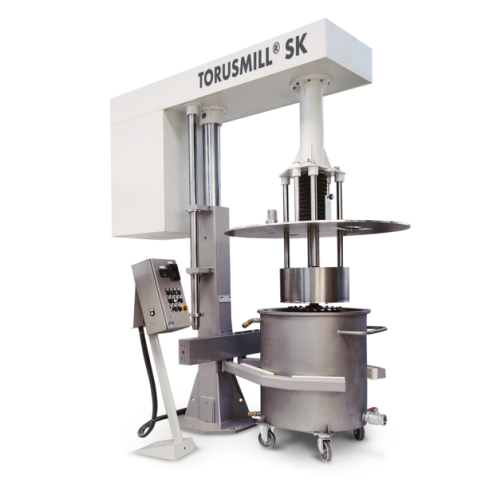
Explosion-proof basket mill for large scale production
Enhance your production line with an explosion-proof basket mill t...
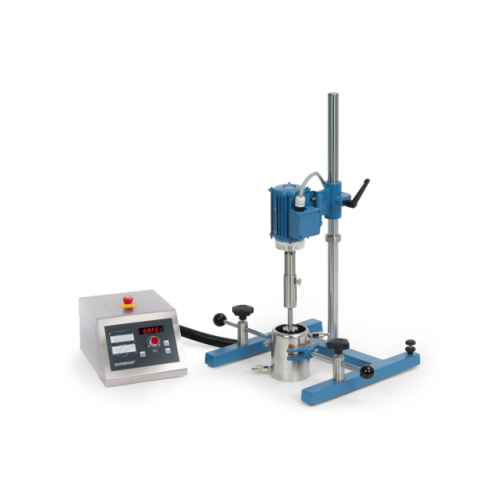
Lab and pilot plant dissolver for dispersion and fine grinding
Achieve efficient dispersion and fine grinding in laborat...
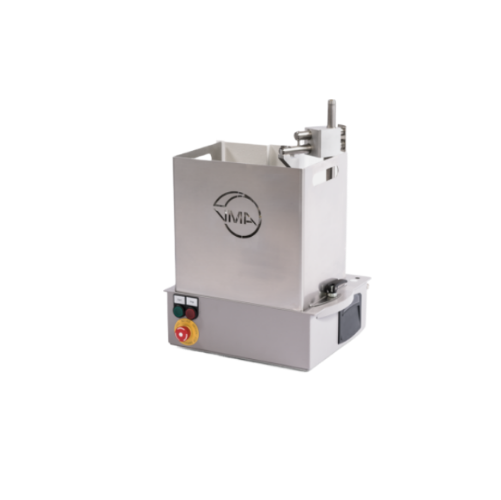
Industrial dissolver for high-viscosity materials
Efficiently disperse and mix high-viscosity materials with precision, e...
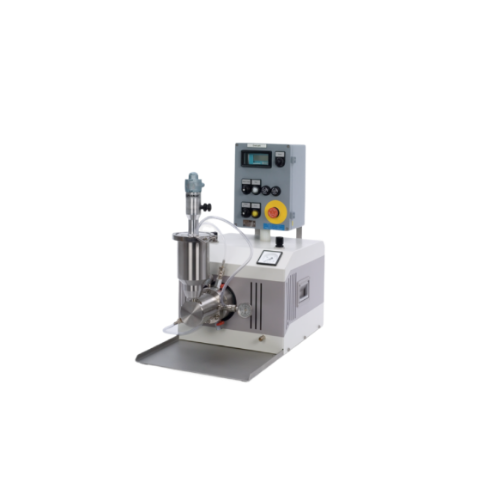
Atex horizontal bead mill
Ensure precision and safety in explosive environments with a robust solution that finely grinds an...
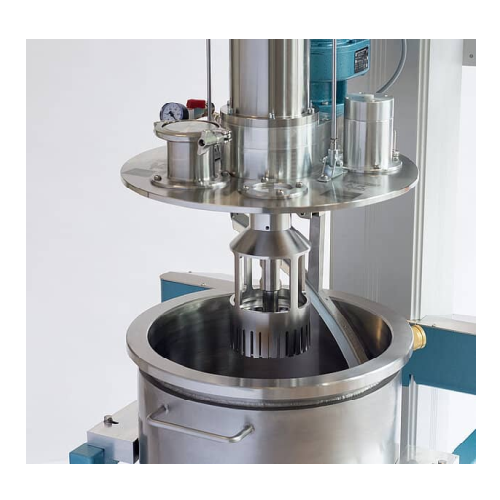
Efficient high-volume dissolver with scraper
For high-viscosity formulations, this advanced dissolver with integrated scra...
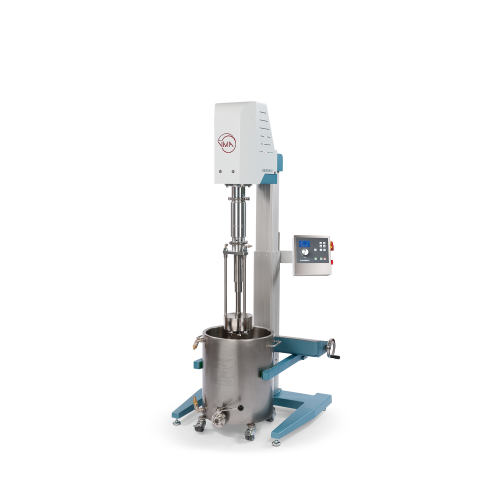
Entry-level vacuum dispersion system for laboratory applications
Achieve precise dispersion and milling with this versat...
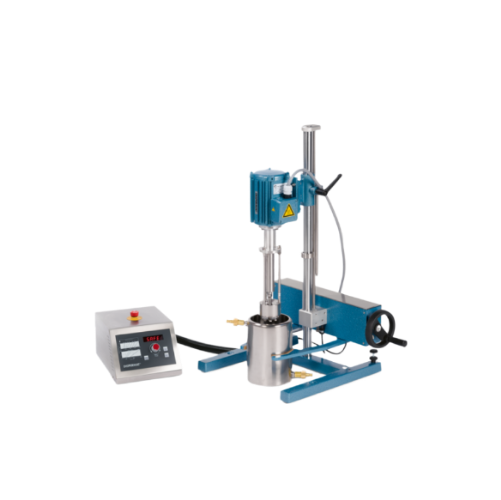
Laboratory bead mill for sample dispersion
Ensure precise particle size reduction with versatility and ease, enabling effi...
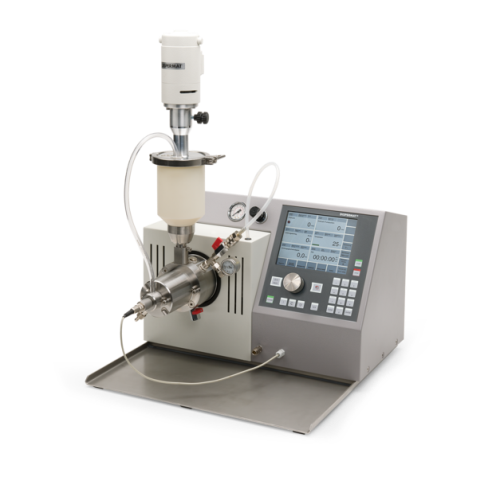
Nano bead mill for laboratory wet grinding
Achieve ultra-fine particle dispersion and consistent milling results with this...
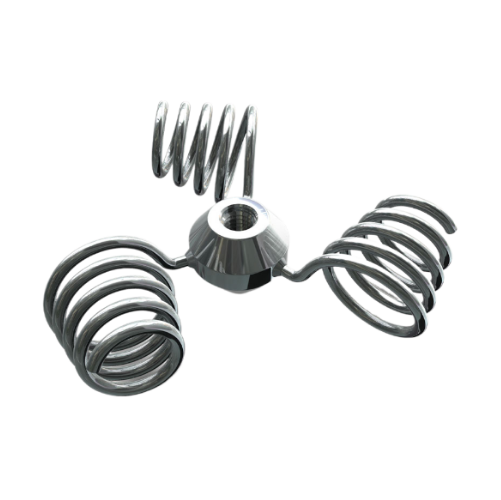
Homogenizer for high viscosity liquids and solid suspensions
Struggling with homogenizing high-viscosity ingredients and...
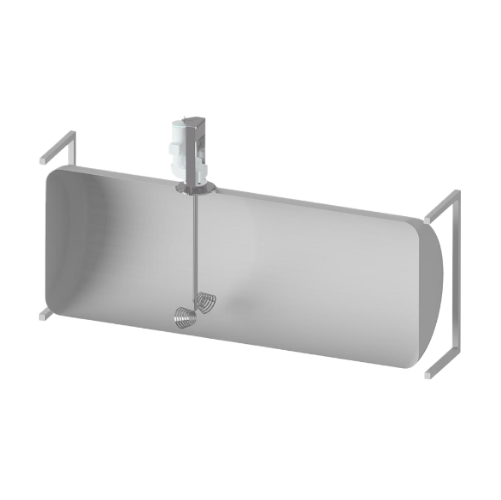
Agitator for horizontal storage tanks
Efficiently blend various viscosities in horizontal tanks, ensuring optimized flow pa...
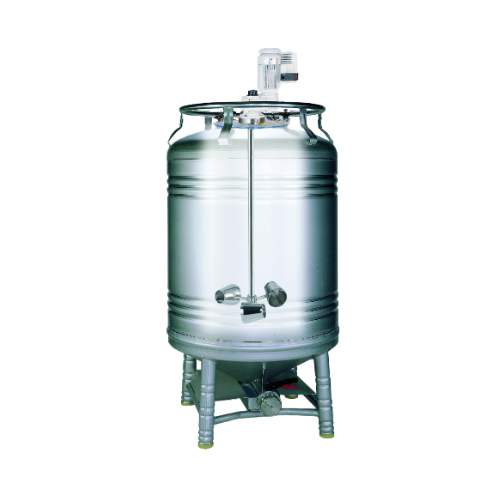
Mobile stainless steel tank agitator for various industries
Optimize liquid blending processes with this mobile tank agi...
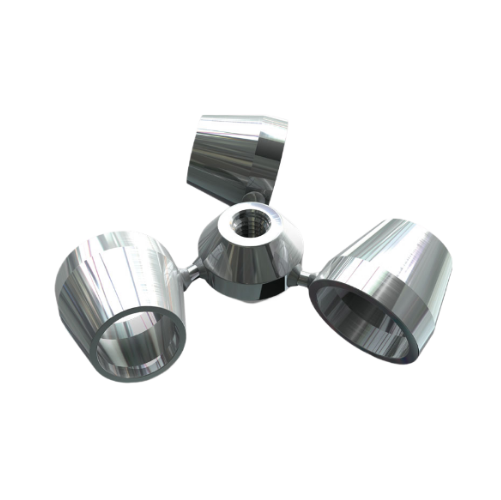
Homogenizer for low to medium viscosity media
Achieve uniform mixing and prevent air entrapment in low to medium viscosity...
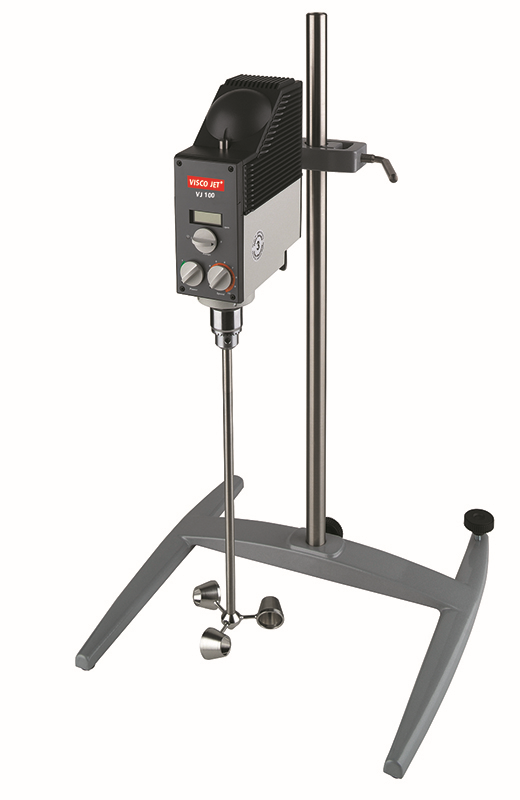
Laboratory stirrer for high-viscosity materials
Streamline your laboratory mixing processes with a powerful stirrer design...
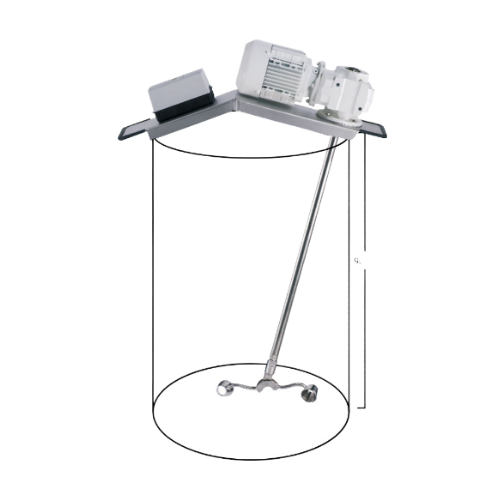
Drum blender for closed barrels
Efficiently mix liquids and slurries inside closed drums with a specialized agitator designe...
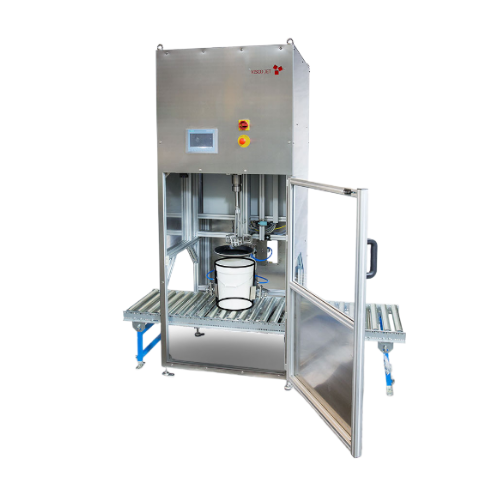
Industrial mixer for facade paint and plaster
Optimize your facade paint and plaster production with this mixer designed f...
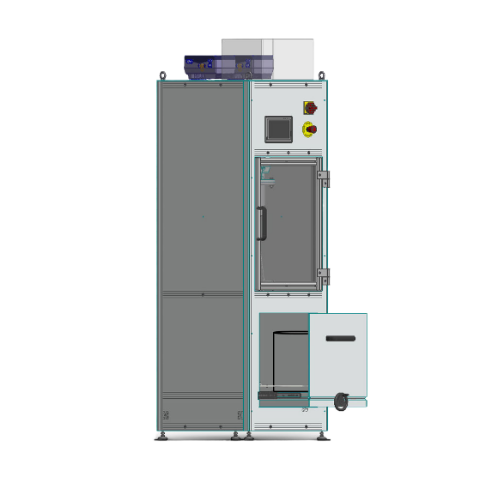
Semi-automatic stands blender for facade paints
Optimize your paint production with a versatile stirring system designed f...
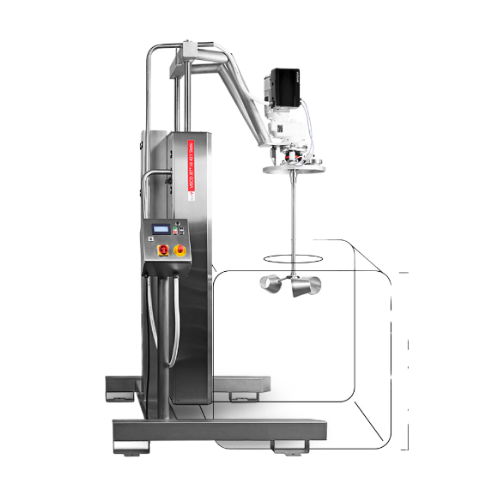
Industrial mixer for product-critical processes
When dealing with high-hygiene requirements and complex mixing tasks acros...
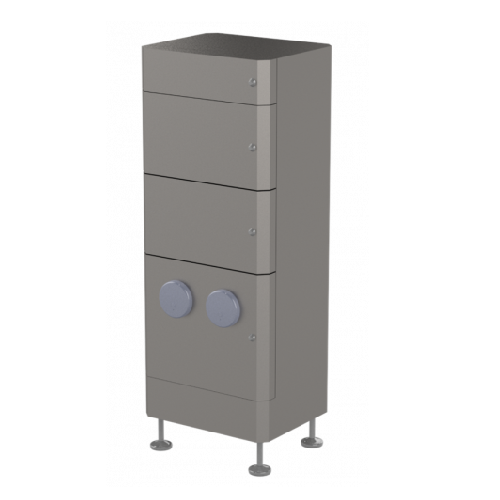
Supply air filter systems for industrial cleanrooms
Ensure critical air purity and operational safety in sensitive enviro...
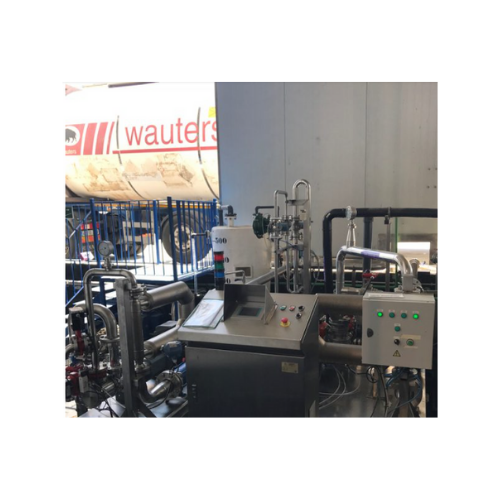
Complete mixing solutions for food, chemical, and cosmetic industries
Enhance your production line with precision mixin...
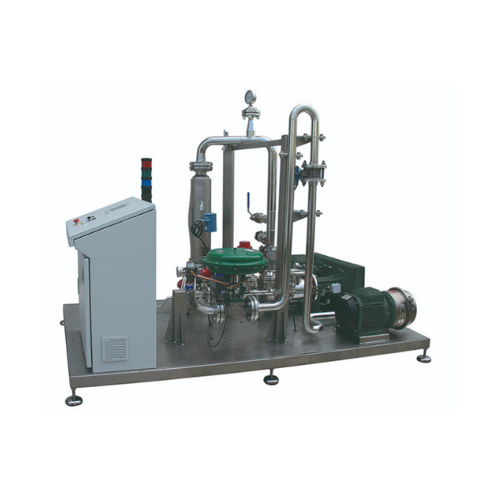
Complete mixing solution for food, cosmetics, and chemical industries
Optimize your production line with a system that ...
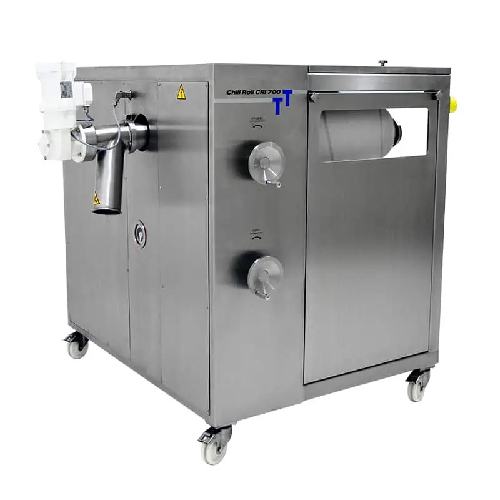
Continuous cooling roller for extrudates
Ensure rapid and efficient cooling of high-heat capacity extrudates with a compact...

Volumetric piston fillers for dense liquid products
Ensure precise filling of liquids and dense products with versatile i...
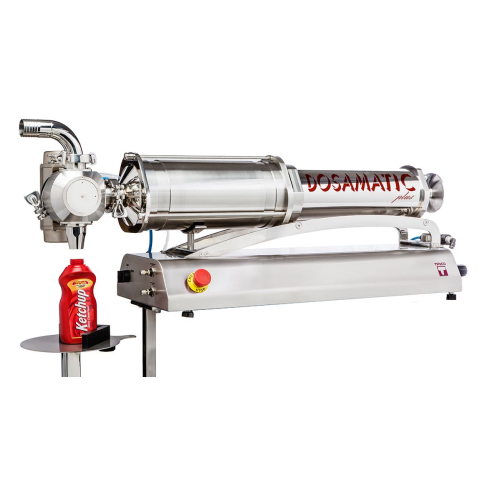
Accurate volumetric filler for liquid and semi-dense products
Achieve precise dosing and filling of various liquid and s...
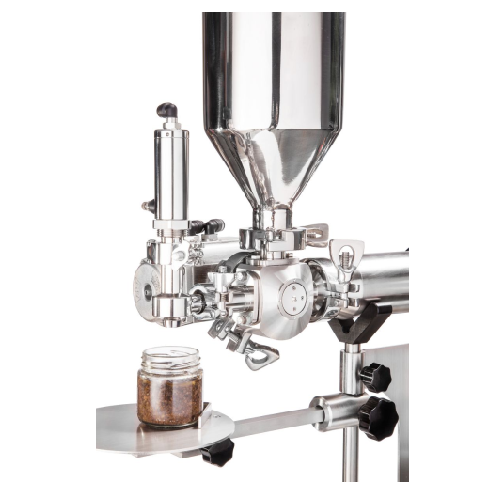
Bench-top piston filler for liquid and semi-dense products
Optimize your filling precision with a versatile piston fille...
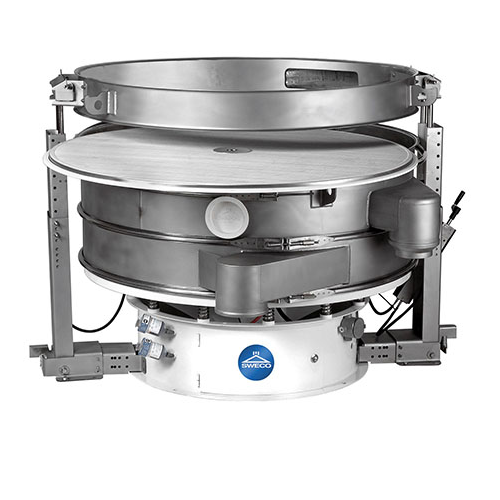
Quickchange systems for vibratory separator screen changes
Streamline your production with a system that enables rapid s...
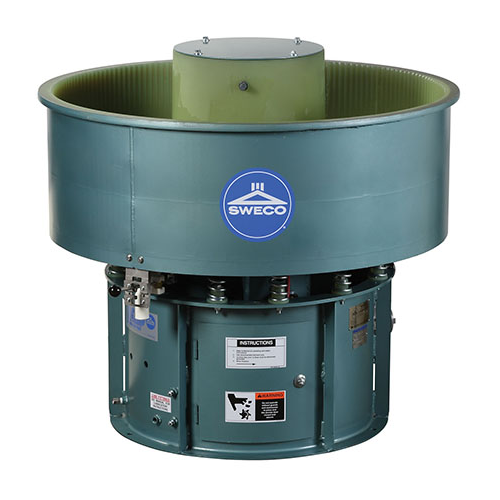
Vibratory finishing and deburring technology
Achieve precise surface finishing and deburring with advanced vibratory motio...
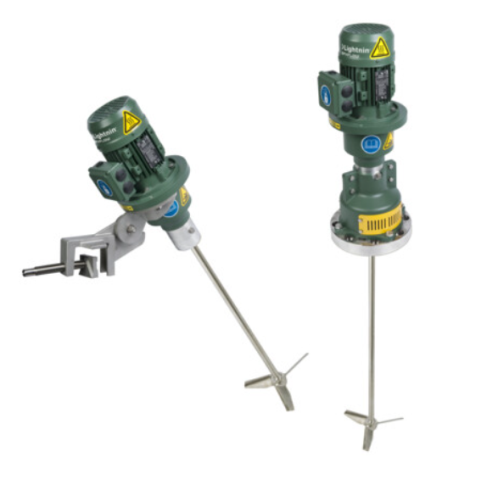
Portable and fixed mount mixing system
Optimize your mixing operations with a versatile system that adapts seamlessly betwe...

Continuous drying for cohesive and non-cohesive pastes
Transform high-viscosity liquids and pastes into fine, flowable po...
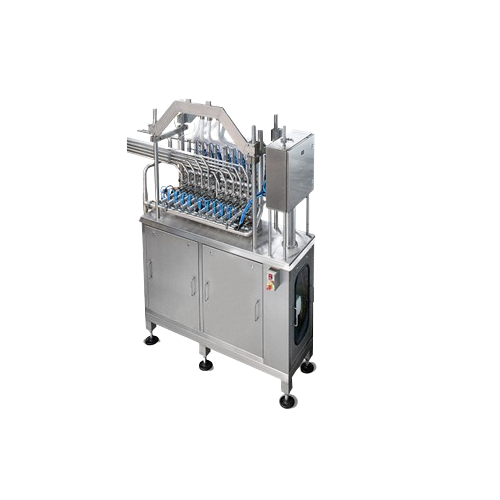
Dosing system for packaging lines
For producers looking to optimize their packaging lines, this dosing system offers precis...
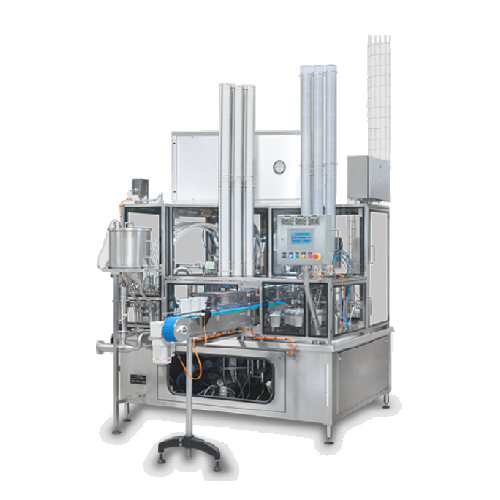
Filler for yoghurt and white cheeses
For manufacturers seeking efficient, versatile filling for products like yoghurt and s...
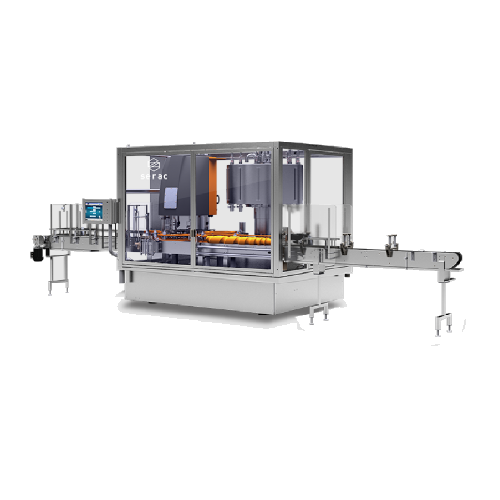
Versatile rotary filler-capper for liquid products
Optimize your liquid product production with a versatile solution that...
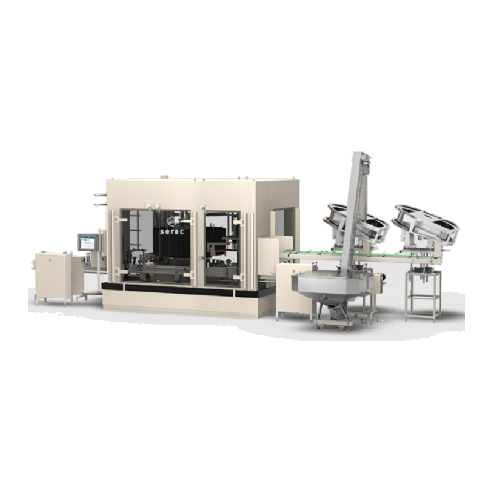
Anti-corrosion filling system for aggressive liquids
When dealing with corrosive liquids, ensure durability and safety wi...
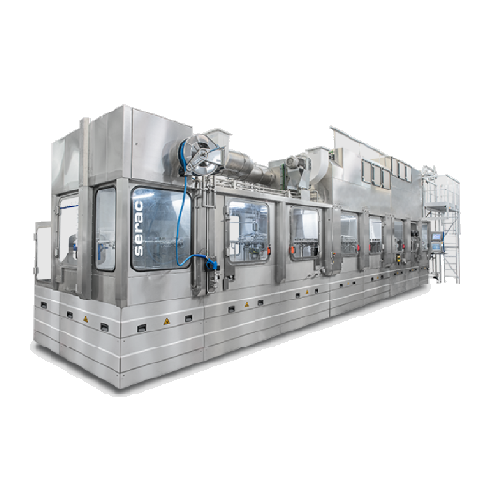
Aseptic filling technology for dairy products
Ensure product integrity and extend shelf life with a high-speed aseptic fil...
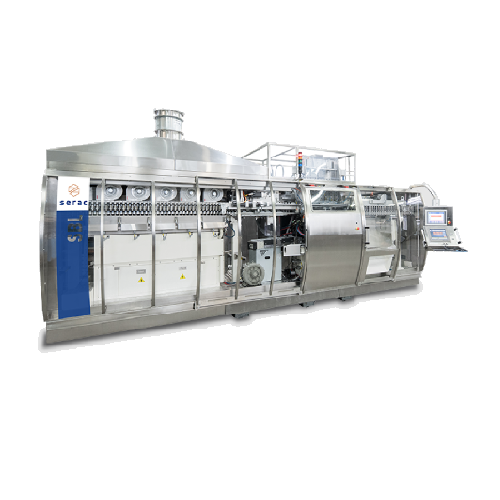
Pet bottle production for small and medium outputs
Optimize your production line by manufacturing PET bottles in-house, r...
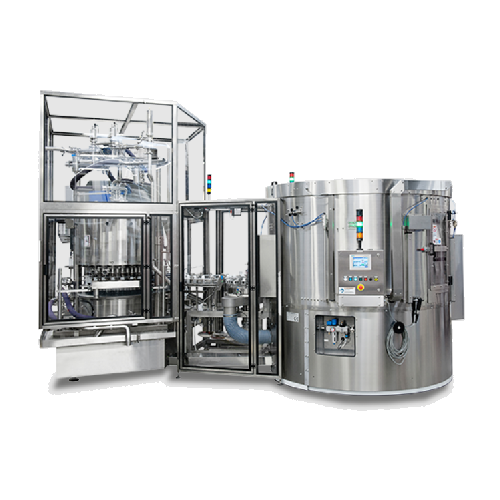
Space-saving packaging solution for high-velocity production
Optimize your manufacturing floor space with a versatile in...
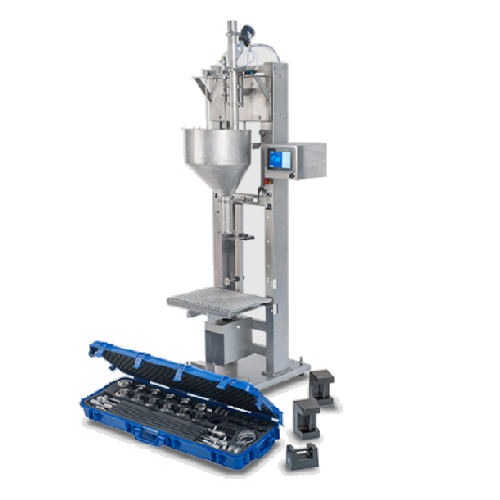
Semi-automatic weight filling system for liquid products
Achieve precise and versatile liquid filling performance with th...
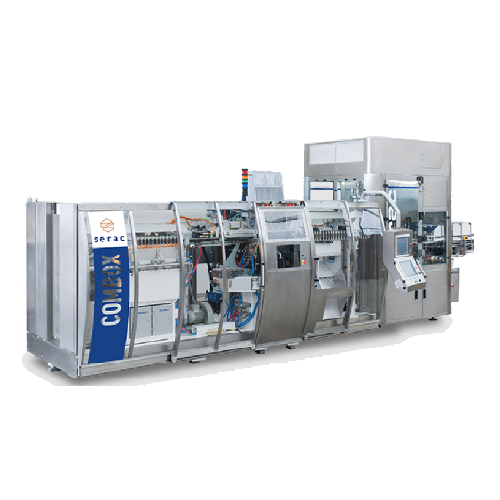
Blow-fill-cap solution for low/medium batch production
Streamline your production line with a compact blow-fill-cap syste...
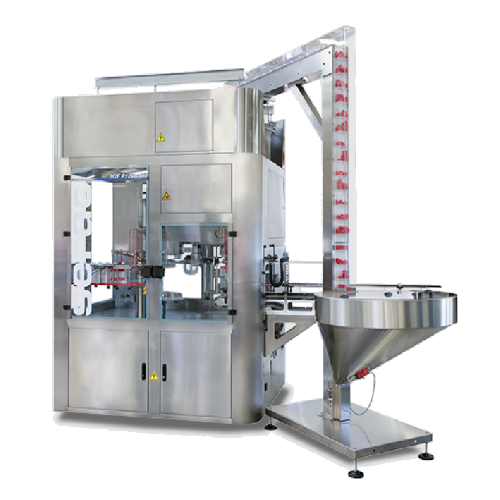
High hygienic filler for chilled beverages
Enhance cold beverage production with a modular, hygienic filler offering chemi...

Yoghurt and dairy desserts filling solution
Maximize efficiency in filling and sealing multi-product dairy desserts and be...
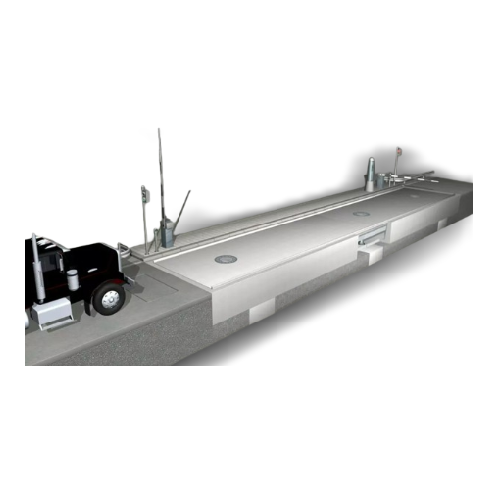
Pit scales for industrial weighing
Optimize material flow and ensure precise load determination with a robust pit scale sol...
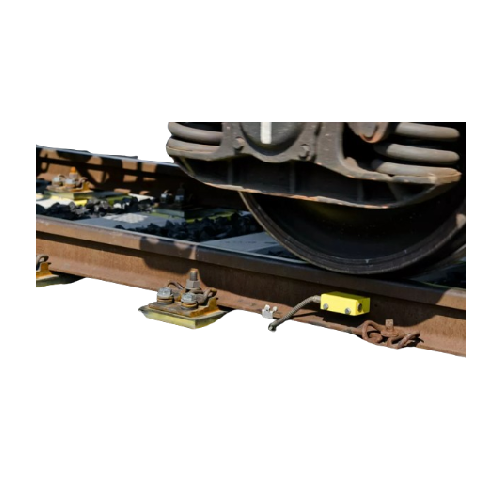
Dynamic weighing for solids and liquids
Ensure precision in rail transport with innovative dynamic scales that provide lega...
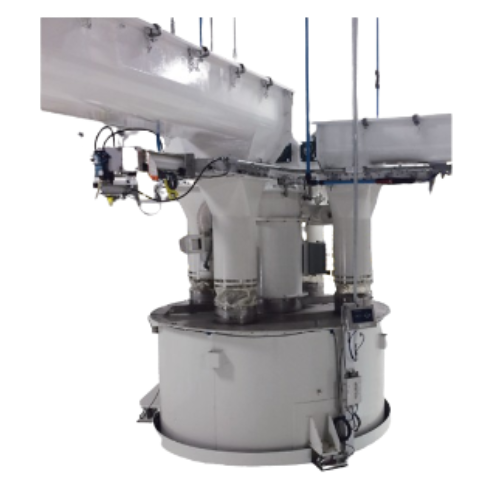
Scale hopper for bulk solid material handling
Ensure precise measurement and efficient transport of bulk solid materials w...
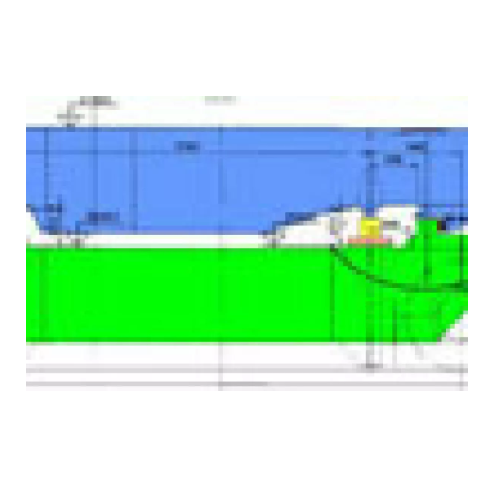
Crane weighing system for precision measurement
Ensure precise and temperature-resistant weighing during high-demand opera...
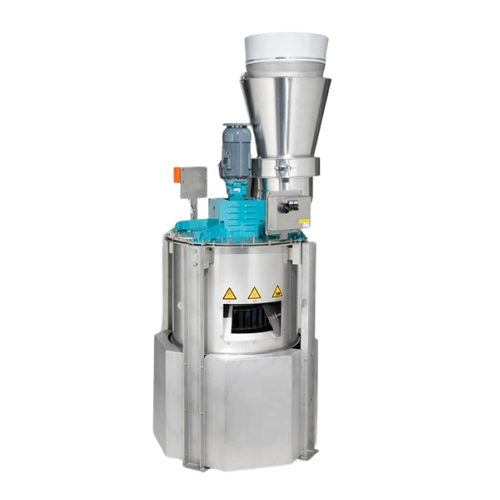
Mass flow rate feeder for bulk powders
Achieve precise control and consistent material flow in high-speed manufacturing env...
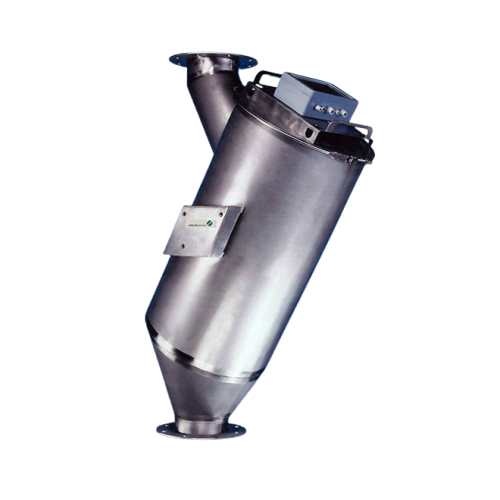
Solid flow meter for granular and powdered bulk materials
Ensure accurate mass flow measurement and seamless integration...
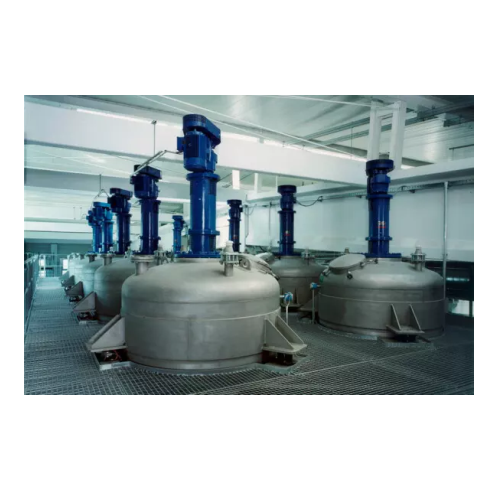
Bin weighing system kits for precise weight control
Ensure accurate material measurement in challenging environments with...
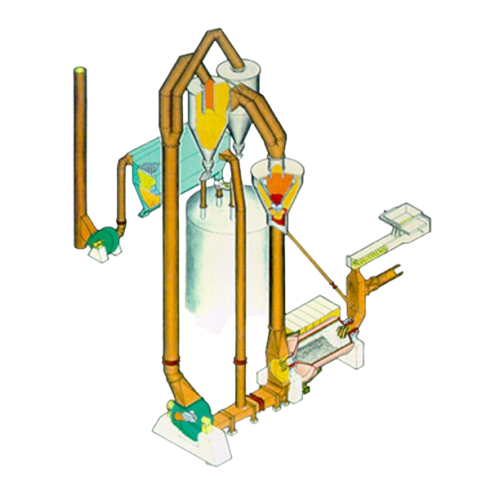
Industrial grinding solution for hard and abrasive materials
Efficiently grind and mill a spectrum of materials from coa...
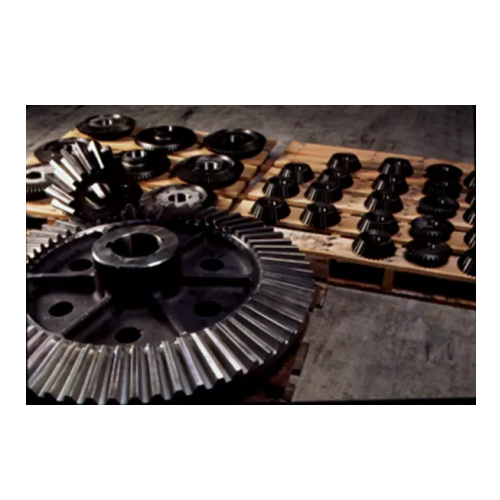
Industrial grinding mill replacement parts service
Optimize production efficiency with high-precision grinding solutions ...
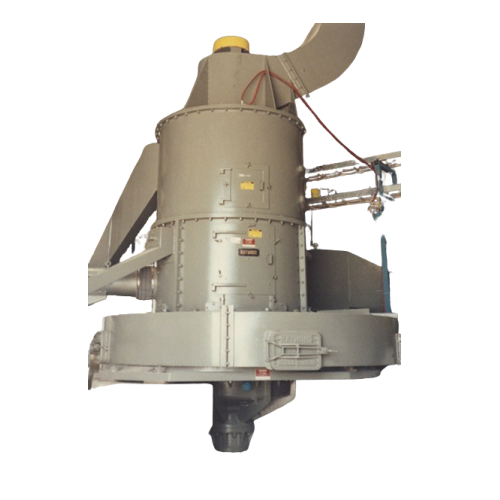
Vertical ring-roll mill for pulverizing minerals
Achieve precise particle size control and efficient material processing w...
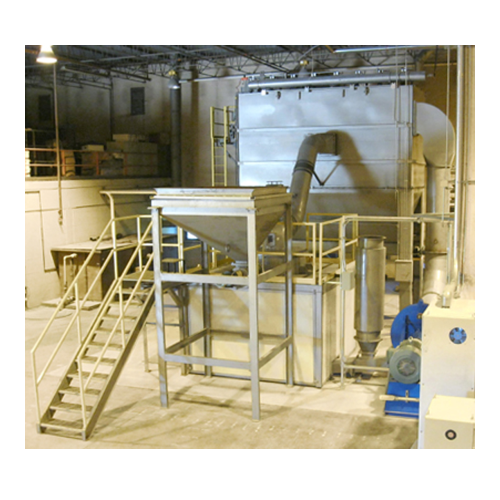
Ultrafine powder mill for coatings and pigments
Optimize your ultra-fine powder production with this precise grinding and ...
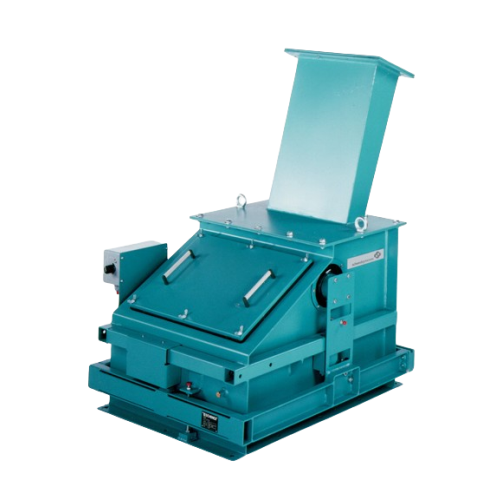
Solids flow meter for bulk solid streams
Ensure precise bulk material measurement with a system designed for accuracy and r...
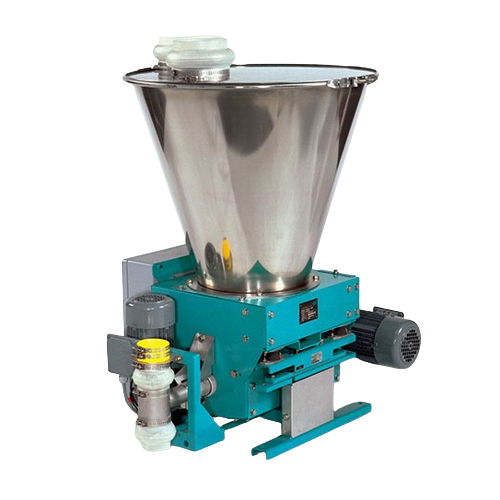
Loss-in-weight feeder for bulk solids
Ensure precise and reliable dosing of bulk solids with a compact feeder that eliminat...
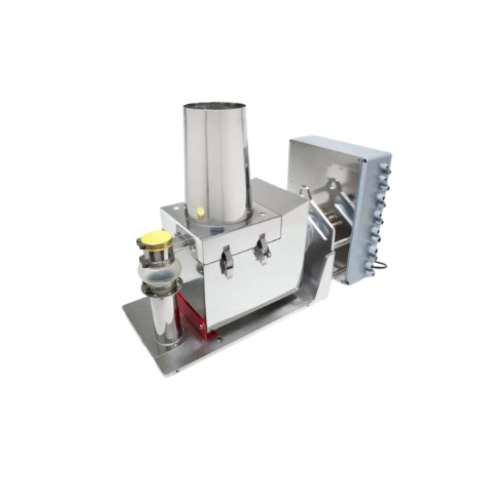
Loss-in-weight feeder for small volume bulk solids
Achieve precision feeding for small volume bulk solids with this advan...
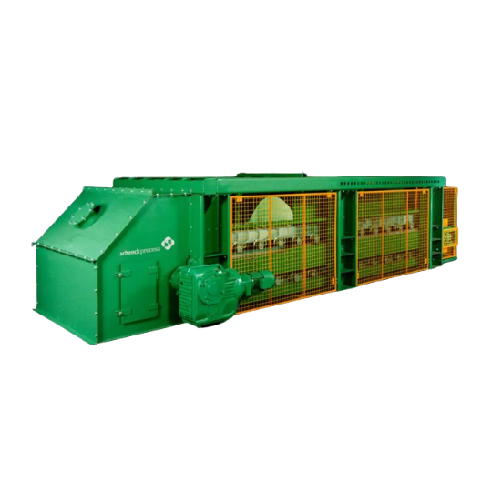
Apron weighfeeder for sticky bulk materials
Optimally handle challenging, sticky materials with precision and consistency ...
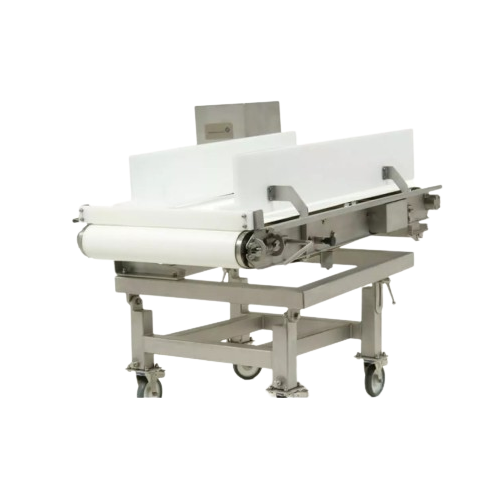
Industrial weighfeeder for hygienic applications
Achieve precise mass flow control with a hygienic design, ideal for appli...
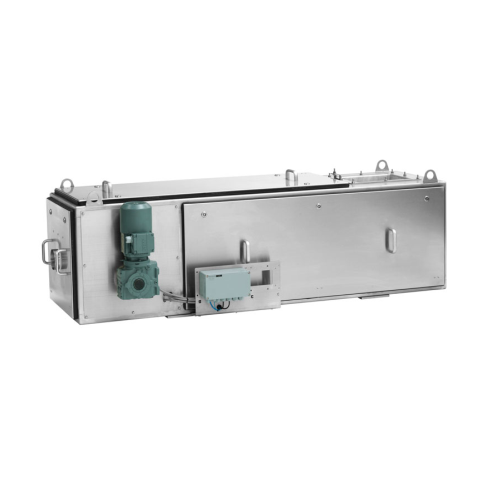
Continuous and batch feeding system for bulk materials
Achieve precise bulk material feeding with seamless integration in...
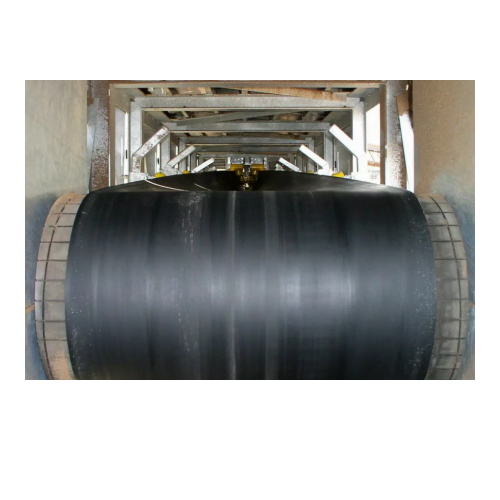
U-belt conveyor for bulk material transport
Optimize your high-speed bulk material transport with this space-saving convey...
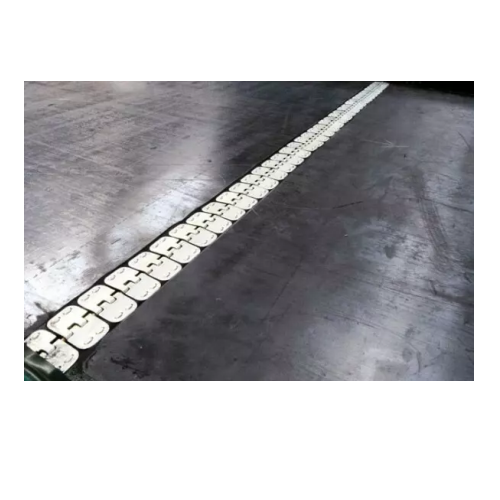
Optimal maintenance solution for industrial weighfeeders
Streamline your processing operations with a solution that minim...
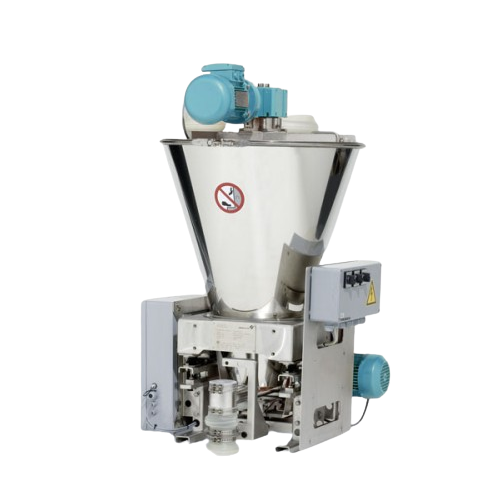
Loss-in-weight feeder for poor flowing bulk solids
Efficiently handle poorly flowing bulk solids with unparalleled precis...
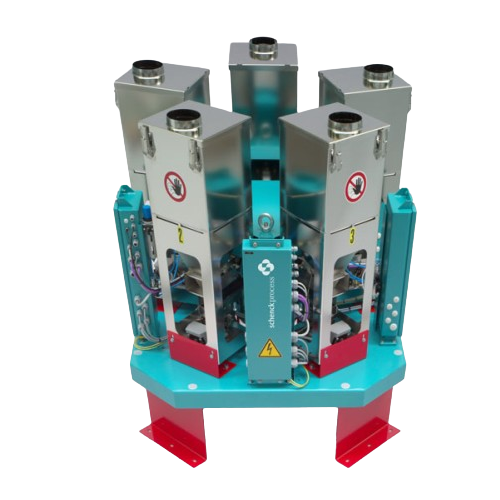
Multipurpose feed station for bulk solids
Optimize your production line with a versatile feeding station designed for simu...
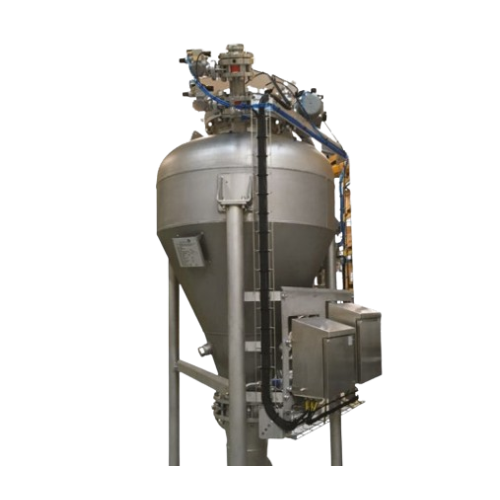
Dense phase pneumatic conveying accessories
Optimize material flow and reduce power consumption with dense phase pneumatic...
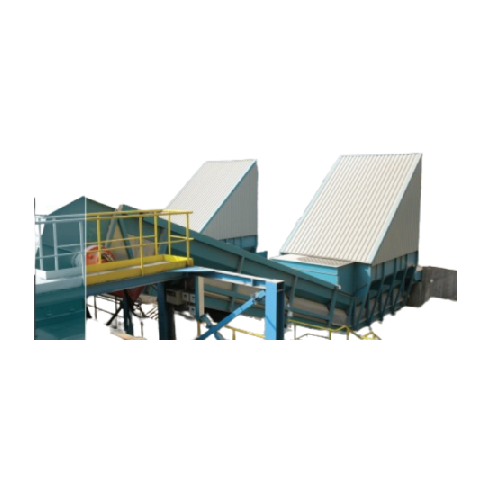
Bulk reception solution for industrial material handling
Optimize your operations with an above-ground bulk reception sys...
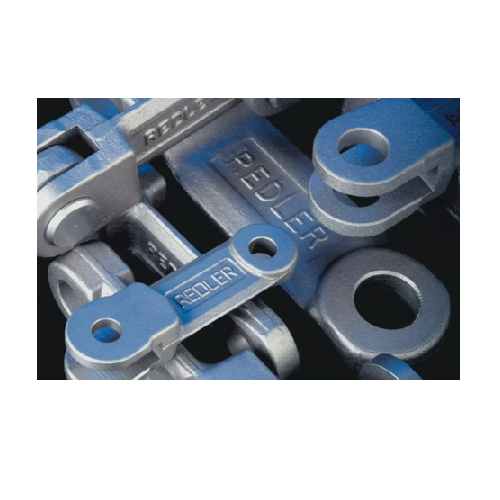
Drop forged chain for drag chain conveyors
Enhance your material flow efficiency with a robust drop forged chain designed ...
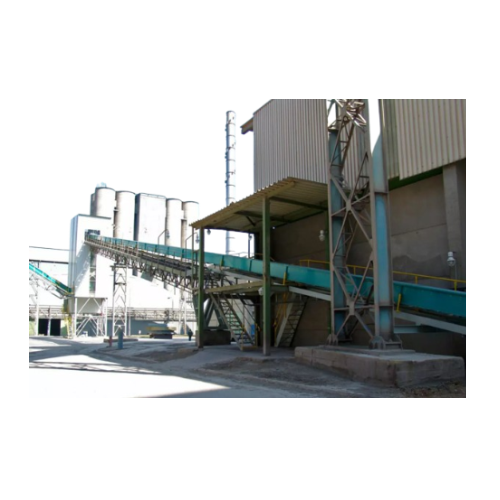
En-masse chain conveyor for bulk material handling
Streamline your bulk material handling with a gentle, efficient system...
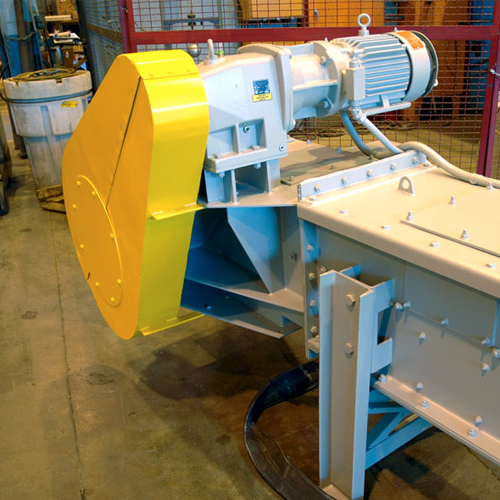
Bulk material handling with chain conveyor
Optimize your material transport with a solution designed for reliability in de...
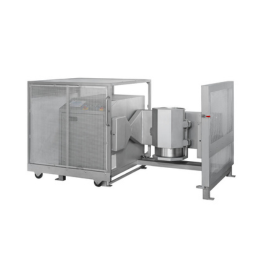
High volume 3D shaker mixer for ceramics
Achieving consistent homogeneity and the logistics of handling and introducing lar...
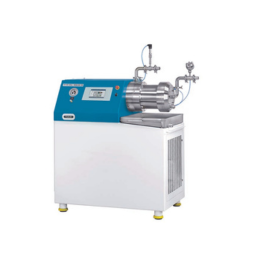
Self-cleaning bead mill for highly viscous materials
To prevent blockages, clogging, and cross-contamination coming from ...

Horizontal disc bead mill for liquid chemicals
Processing toxic chemicals requires high compliance with safety standards a...
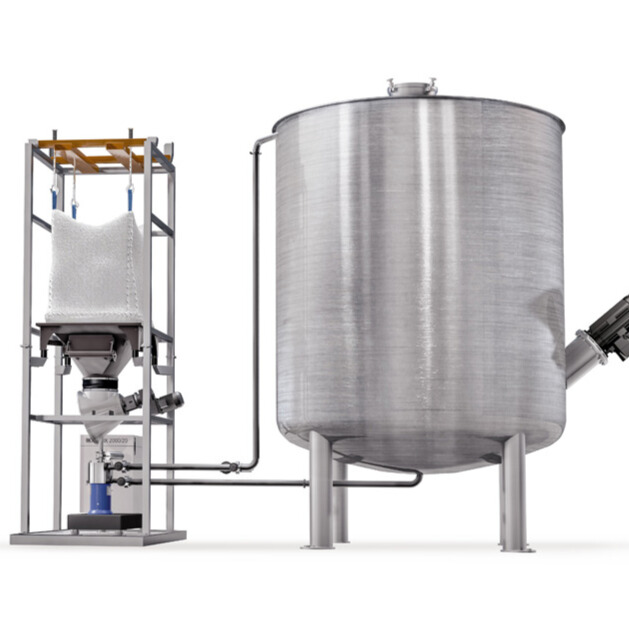
Inline solid-liquid mixer for chemicals and paints
Incorporating solids into liquids is a critical process in producing p...
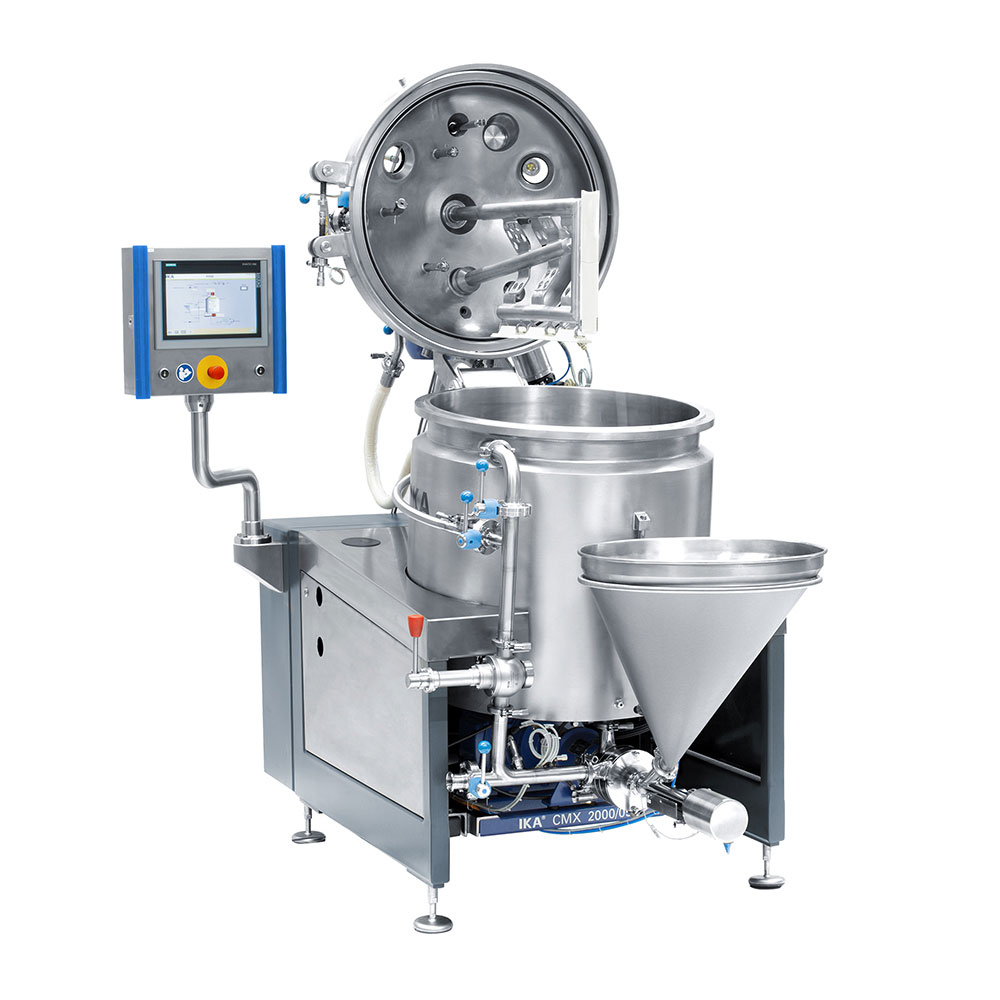
Compact Mixing Plant for Paints and Coatings
A smooth finish in paints and coatings depends on the grade of dispersal duri...
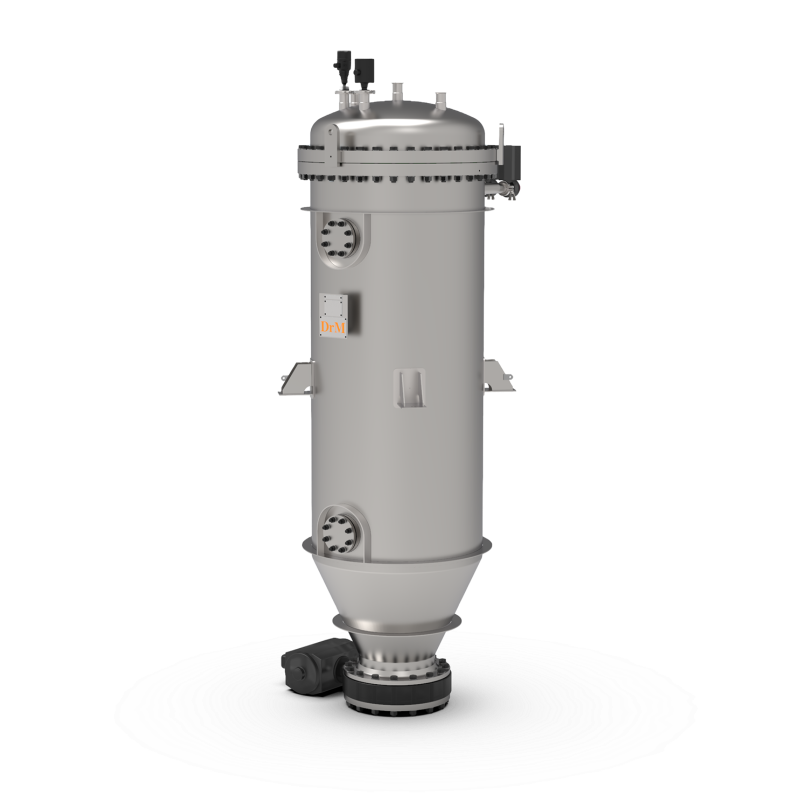
Self-cleaning candle filtration system
Separating solids from liquids by filtration requires frequent cleaning or replaceme...
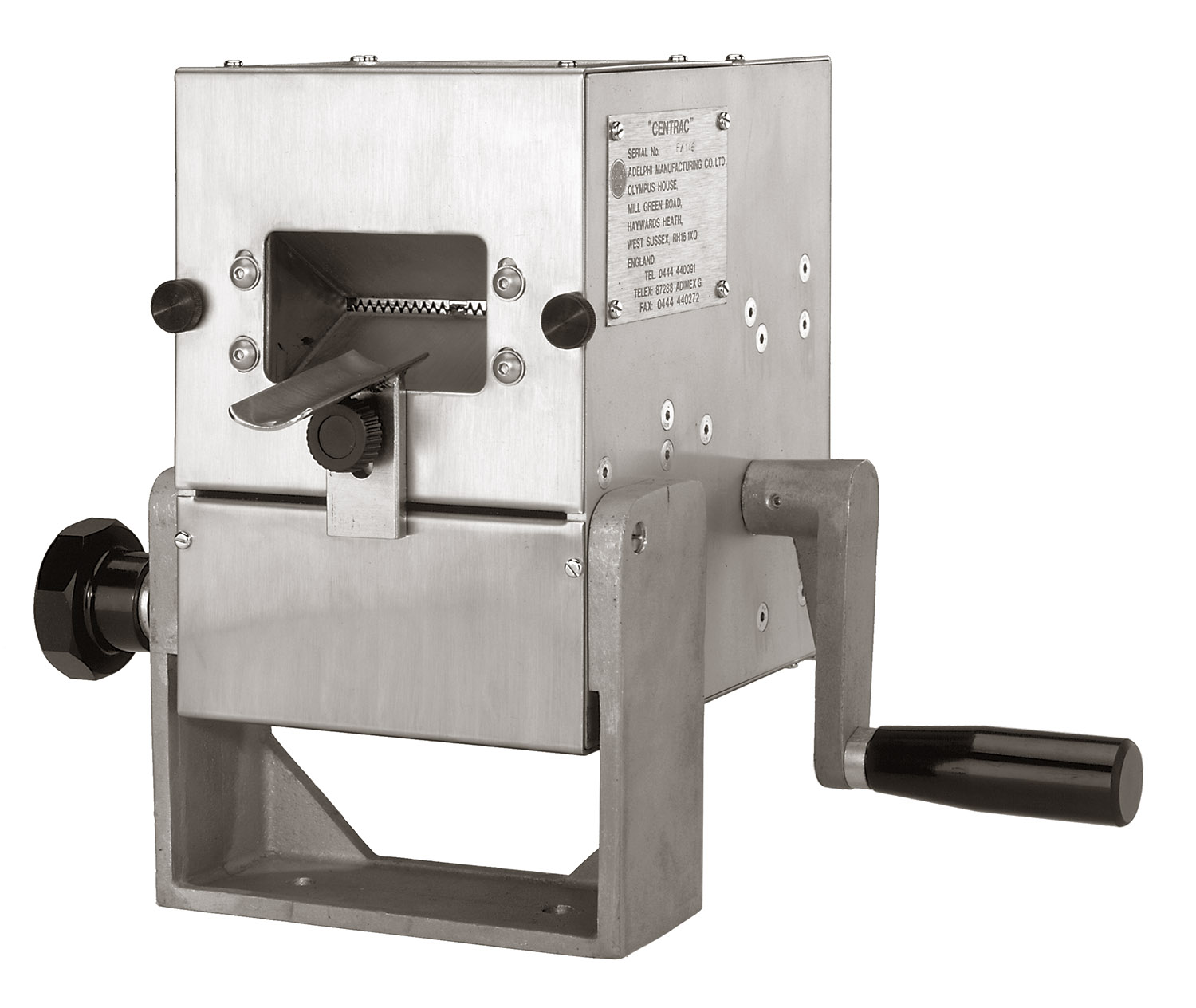
Manual metal tube sealing equipment
For small-batch productions where you utilize metal tubes as containers for your produc...
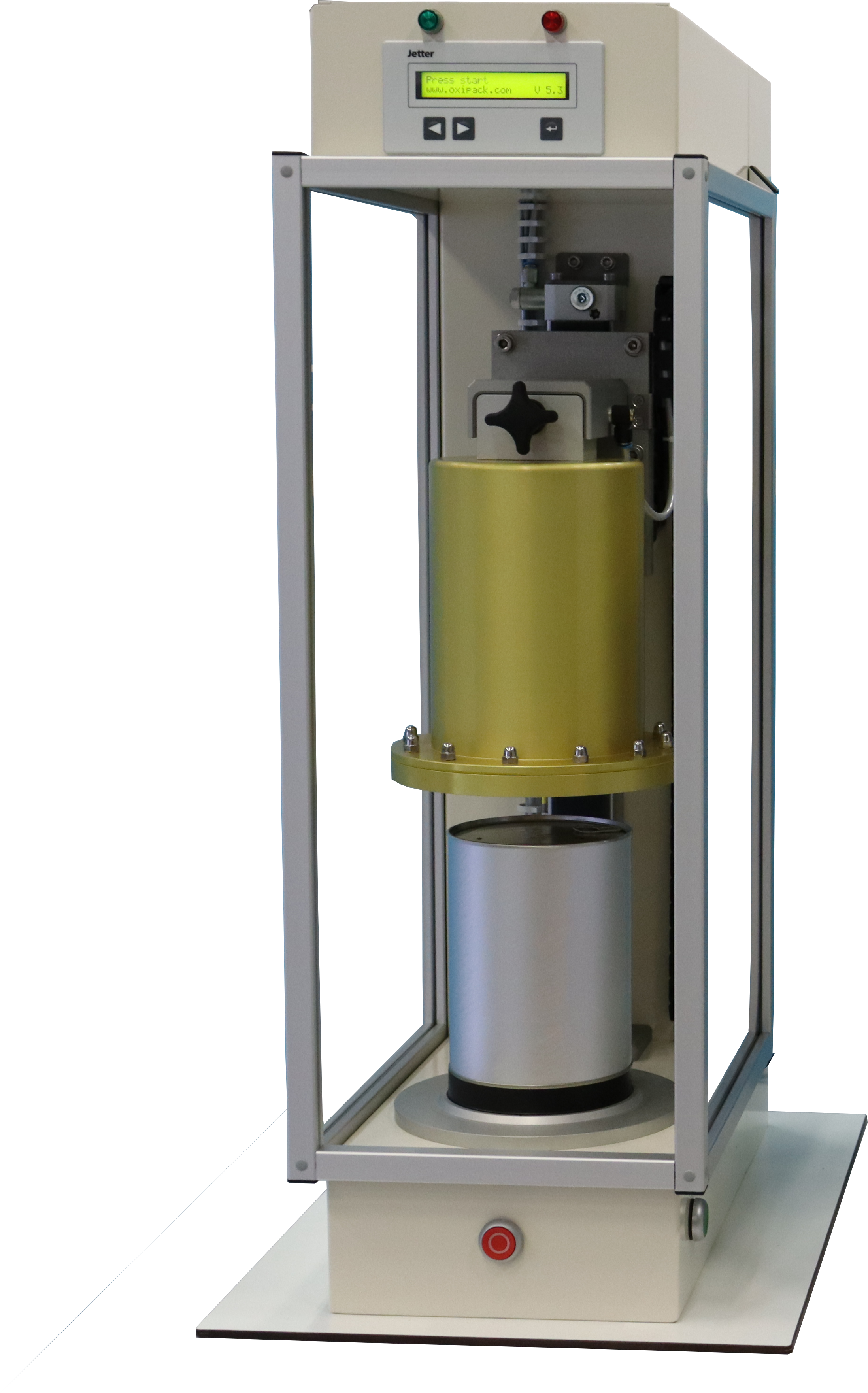
Can leak tester
Every canned pet food producer knows that their product should avoid the growth of microorganisms that could s...
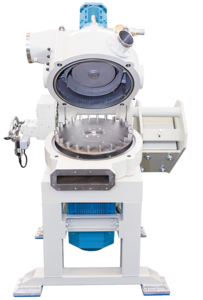
Classifier mill for powder coating
High-quality powder coatings are often required to manufacture equipment, appliances, an...
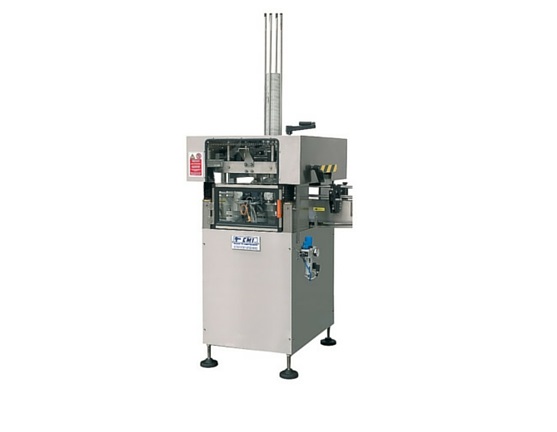
Automatic can sealer
If you need to cap paint, glues, and solvents containers and are currently manually placing the lids, yo...
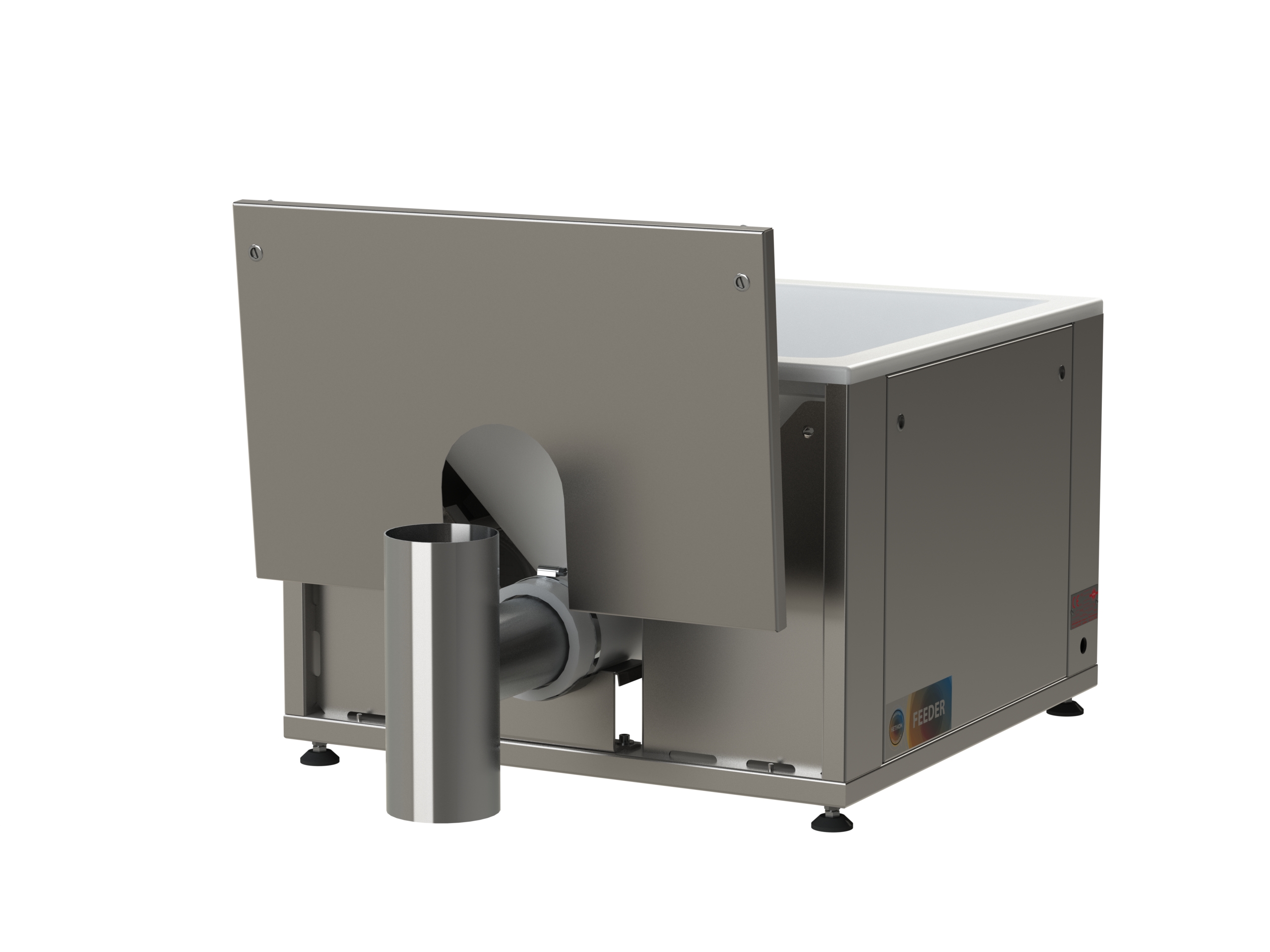
Feeder with flexible wall hopper
The varying properties of dry powder products mean that specialized feeders are required fo...
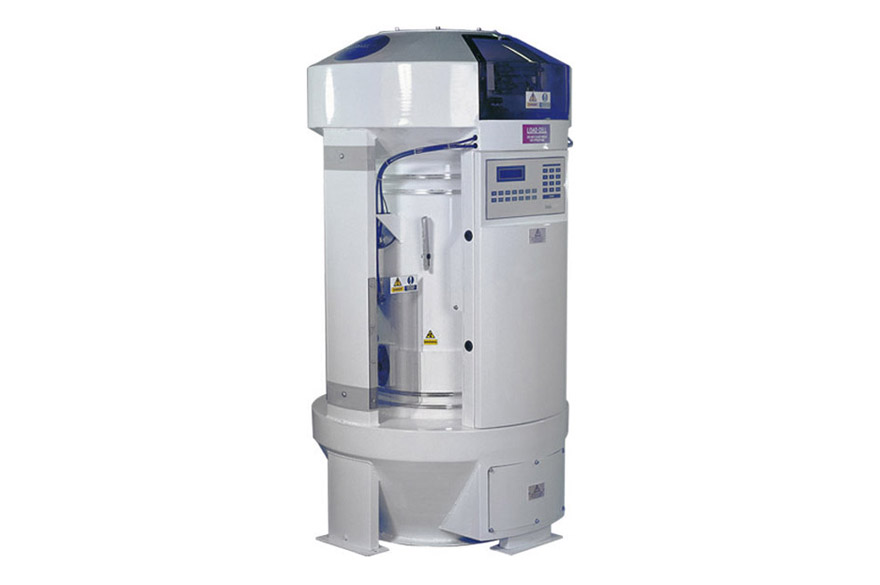
In-process weighing system for mills
When you need a throughput weigher for modern flour/grain milling applications, the we...
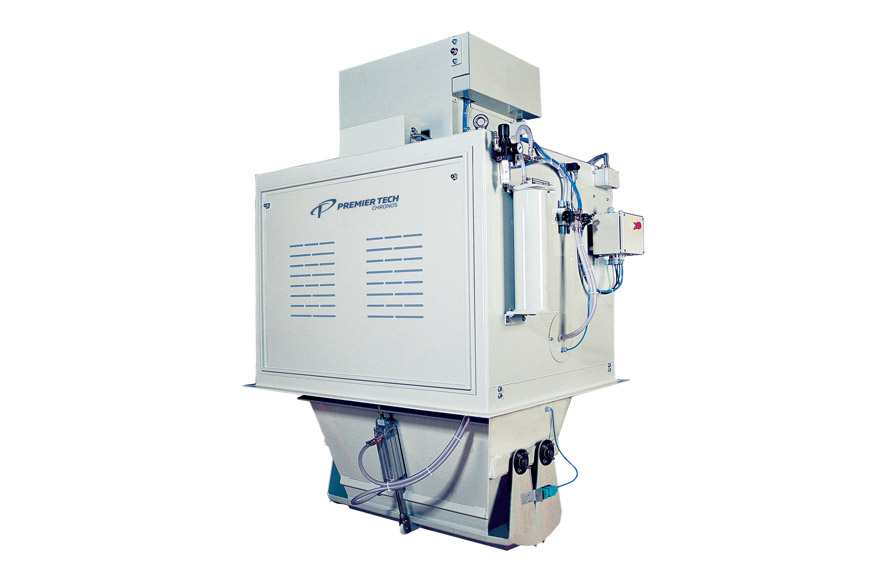
High-capacity bulk weighers
A checking weigher recognized for receiving and shipping bulk materials, typically in mills and ...
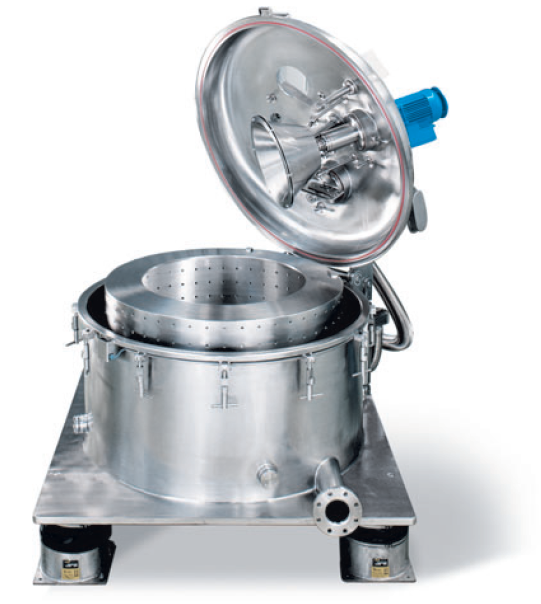
Vertical scraper centrifuges
Vertical Bottom discharge Centrifuges work discontinuously, discharging the solids to the botto...