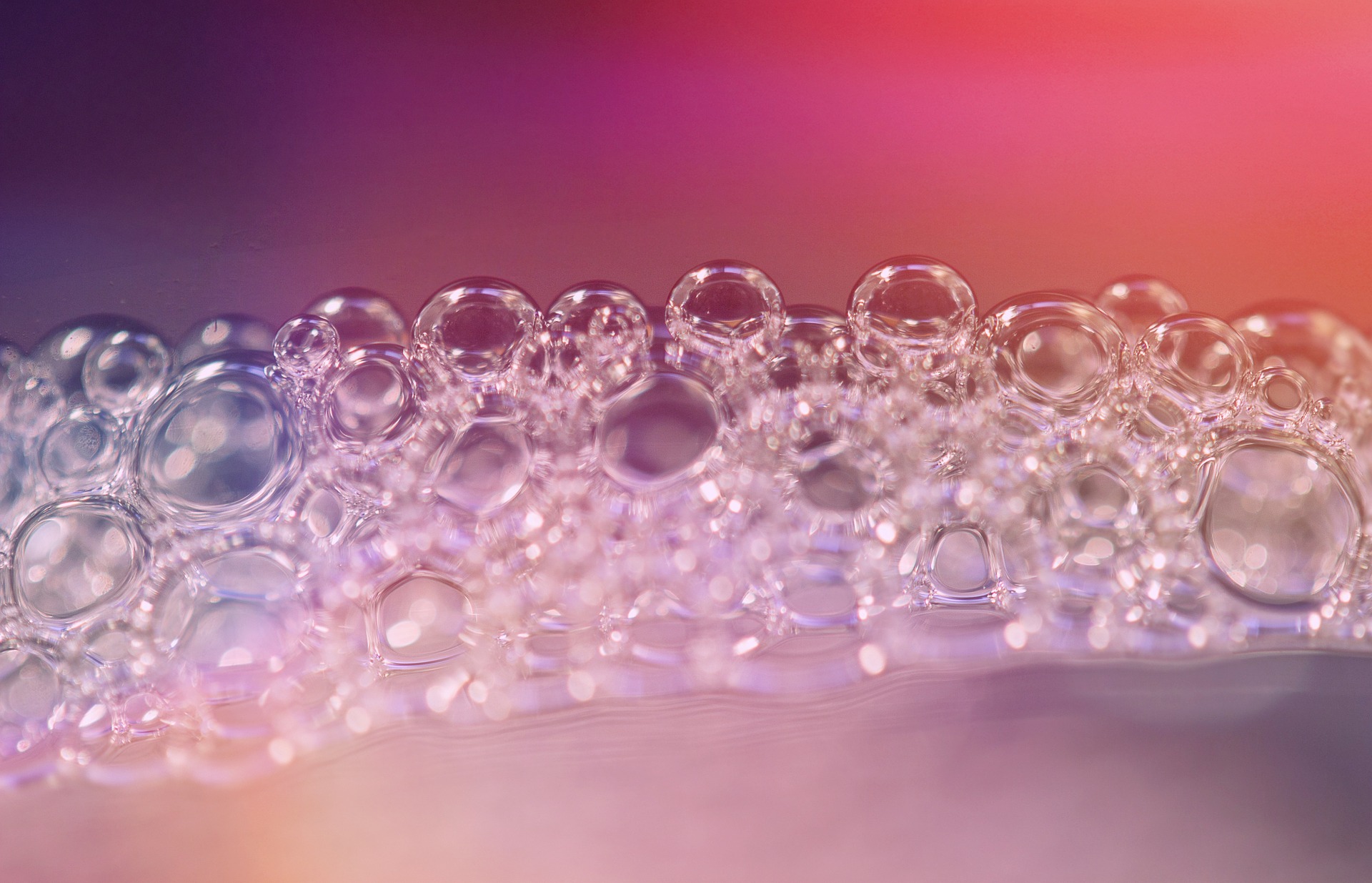
Shampoo Making Equipment And Production
Find innovative production technology for making shampoo and connect directly with world-leading specialists
Shampoo is a unique form of cleaning agent composed primarily of water and some form of surfactant. This surfactant provides the ability to bind oily substances for removal without leaving a residue, as traditional soaps might. The production process involves the batch mixing of its laboratory-defined formula, quality control, and filling stages.
Stories about shampoo
Select your shampoo process
Tell us about your production challenge
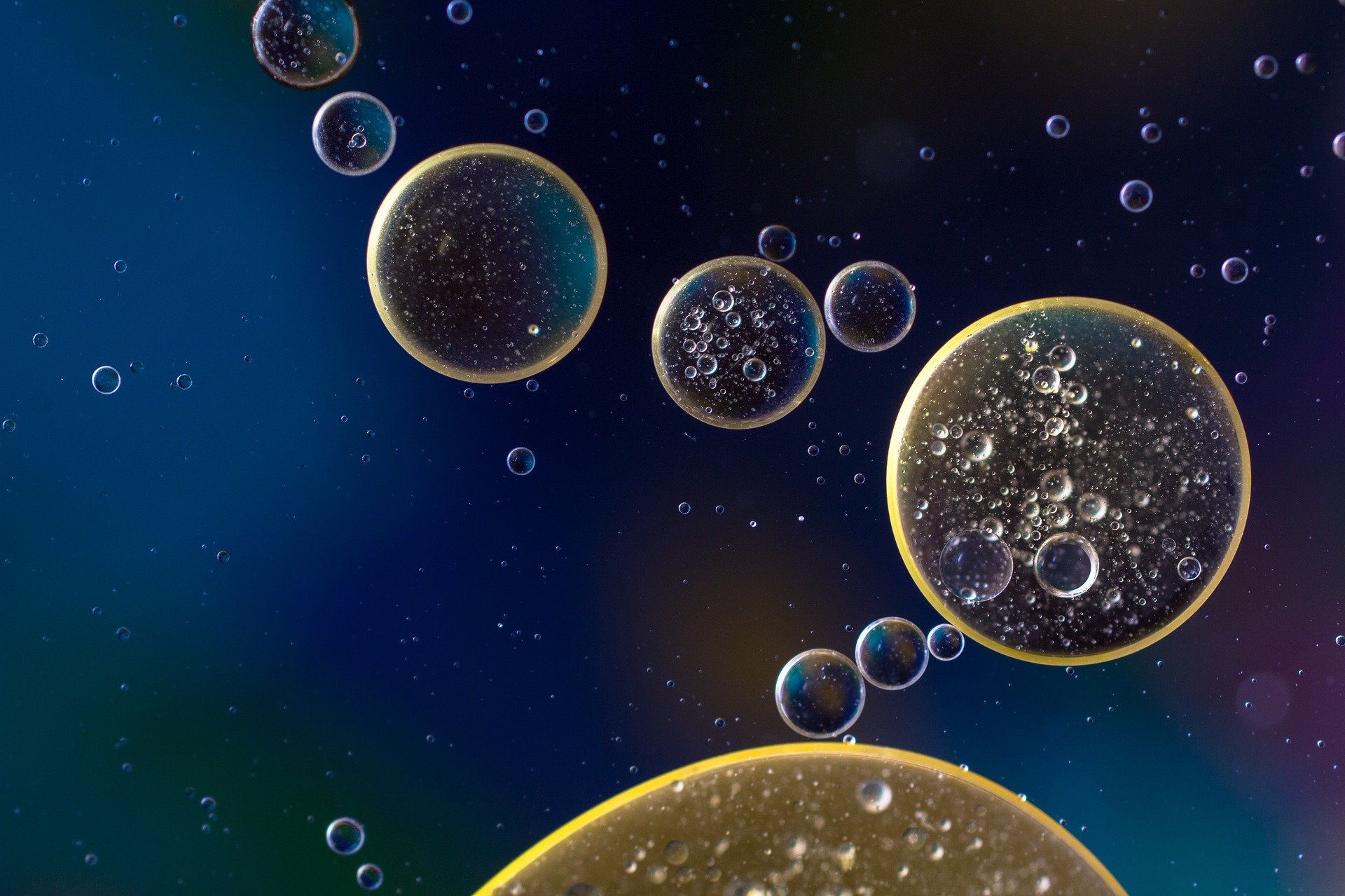
Finding your perfect shampoo making formula
Apart from water and a primary surfactant, typically forms of lauryl sulfate, many other ingredients may be added to the shampoo making formula to provide additional desirable properties for scalp and hair care. Secondary surfactants, typically alkanolamides, may serve as foaming agents. Thickeners improve viscosity, conditioners offset the harshness of detergent surfactants, and preservatives ensure the longevity of the product. Finally, modifiers may adjust pH and opacity, and special additives as well as essential oils may be added for color, fragrance, or other distinguishing qualities.
Considerations of shampoo production equipment
Once you have isolated your desired shampoo recipes, stability testing should be performed to ensure the final product undergoes minimal changes after bottling. You will typically look for physical changes in the color, odor, and texture of your shampoo. This is followed by batch production of the shampoo recipe in large tanks for thorough mixing. To do this, you may simply add ingredients to the tank where temperature and mixing speed may be modulated through computerized shampoo production and processing equipment to facilitate their combination. Following a quality control check, the process concludes with the bottling and packaging of your final product.
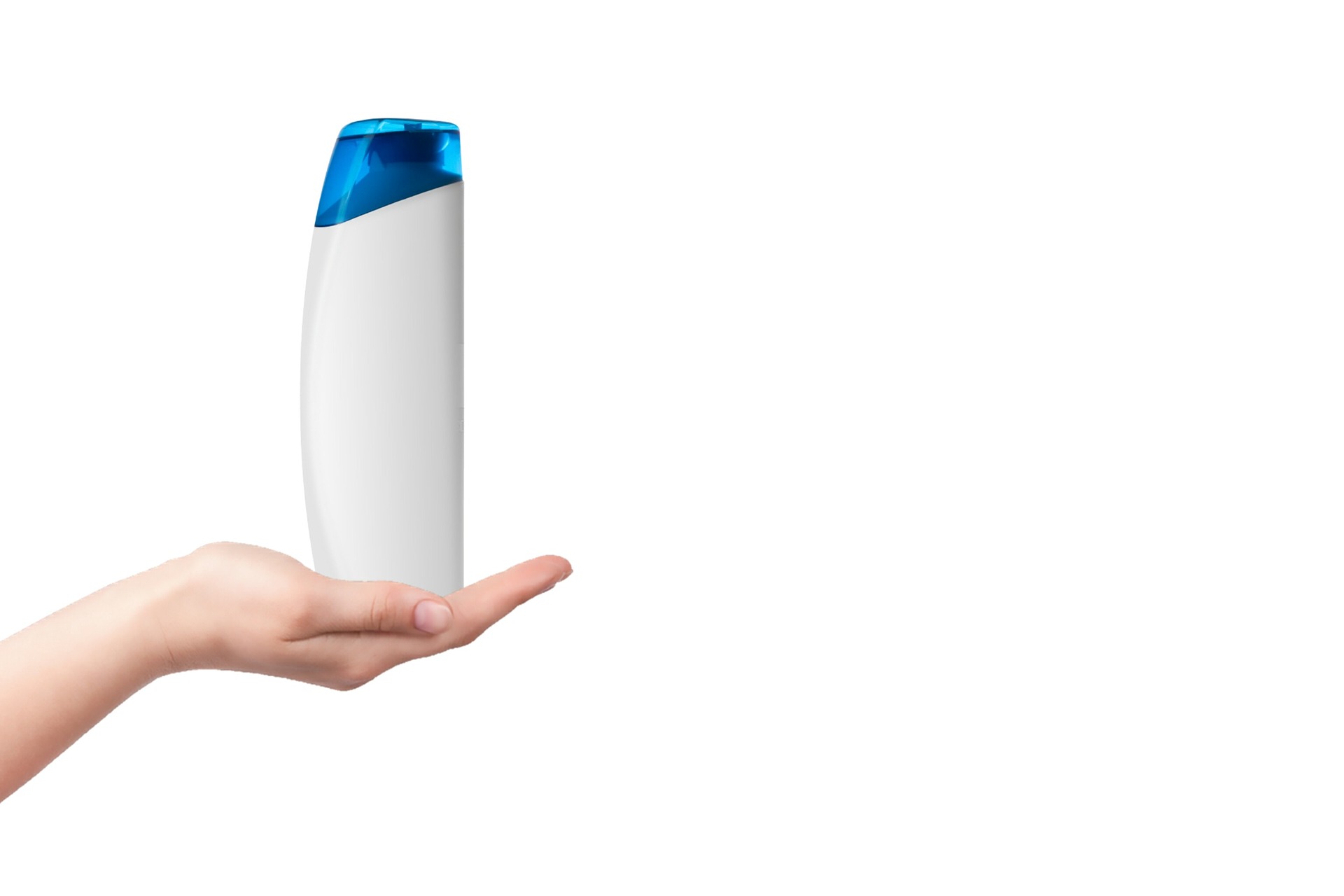
Bottling your liquid shampoo efficiently
This final step is the most involved part of the production process. Following acceptable quality control, you then pump your shampoo mixture from the batch tank into a holding tank for bottling. You first feed bottles upright into a hopper where they then move along a conveyor belt to the filling carousel. Here, calibrated pistons distribute precise quantities of shampoo to each bottle. You will also need to place caps into a hopper and, once correctly aligned, they are twisted tight by a capping machine. The bottles then proceed to labeling, which may be heat pressed or use adhesive labels. Finally, the labeled bottles exit the conveyor system and are ready to be boxed up for distribution.
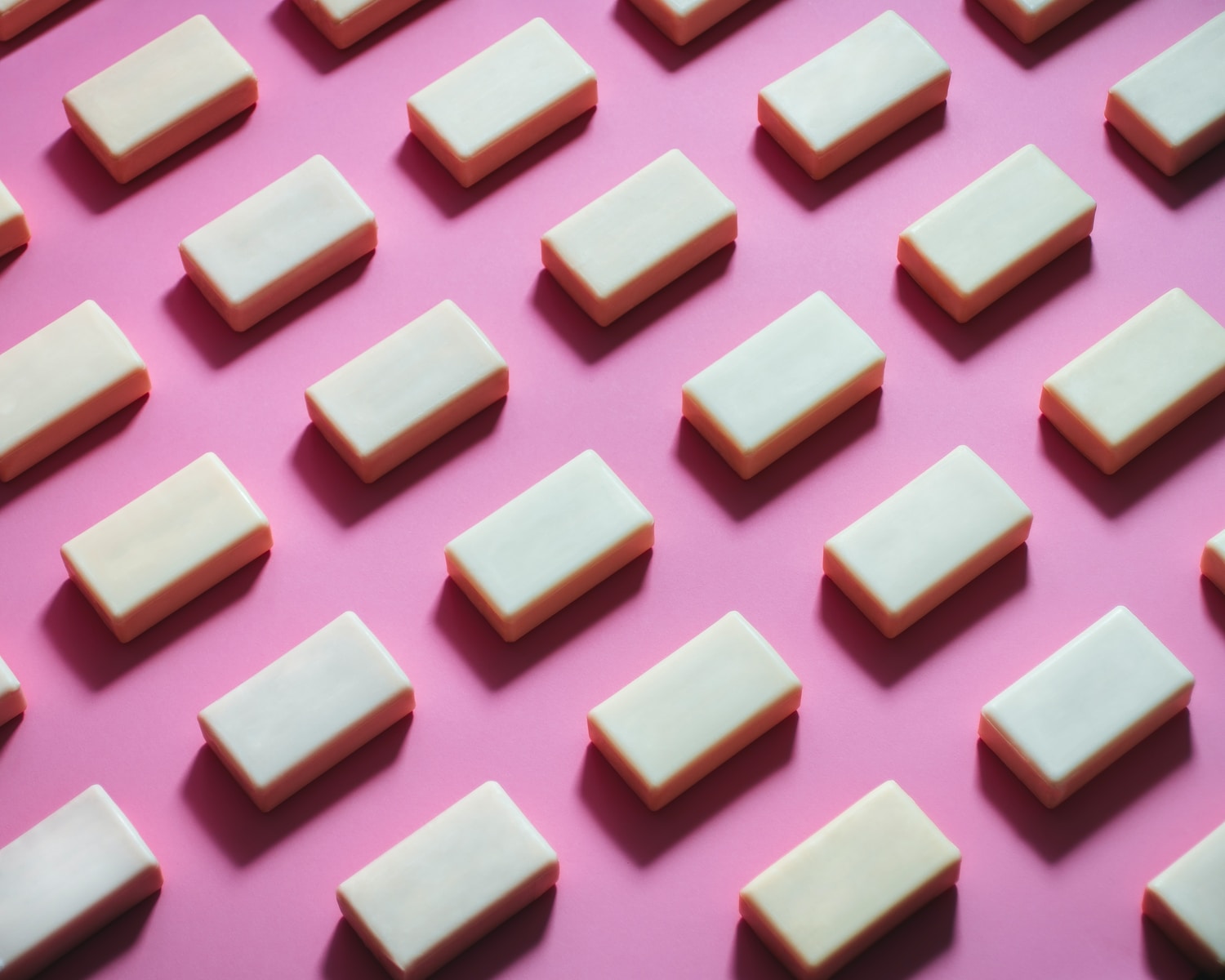
Approaching the process of shampoo bar production
With the growth of the zero-waste movement and consumer conscientiousness, shampoo bars have become an increasingly popular alternative to traditional liquid shampoos. This process differs from the production of liquid solutions in that dry ingredients are combined by mechanical mixing in a hot or cold process, and a long continuous bar is extruded from the mixture. This bar is then cut to individual sizes and may be further customized by stamping and shaping. The final packaging process uses fewer materials for a more environmentally friendly production.
Packing your shampoo bars in boxes
Significantly simpler than packaging liquid shampoo, at its core, packaging your shampoo bars involves meeting your conveyor of individual bars with your conveyor of the desired packaging. After cutting and stamping, your shampoo bars move along a conveyor where they are picked up by a rotary packing machine. A separate machine prepares the boxes from their flattened pre-cut state into the form that will house your shampoo bars. Finally, the rotary packing machine distributes a bar into each box, and the occupied boxes may be further packaged for bulk distribution.
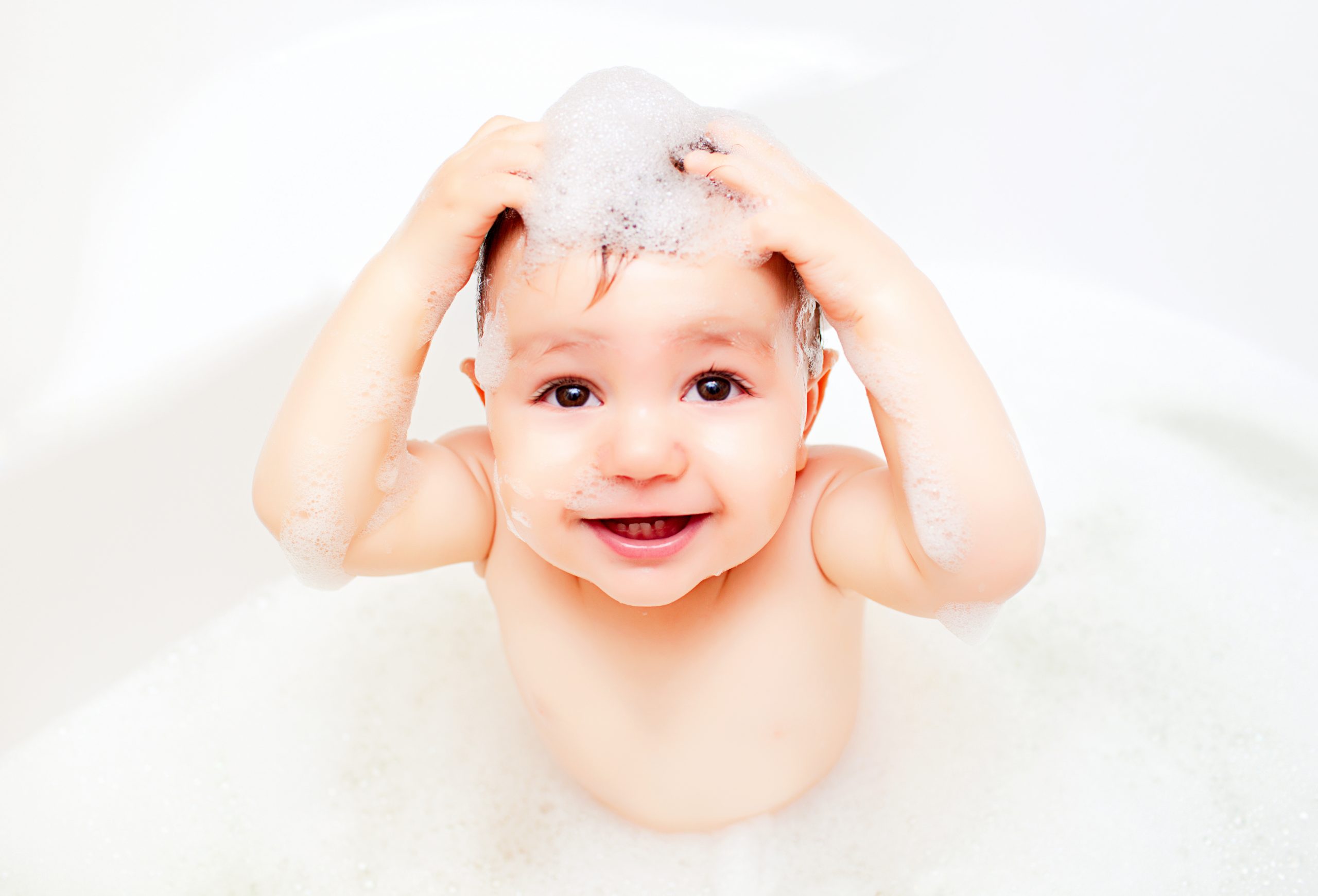
Variables in shampoo formulation
With the great variety of intended purposes, your shampoo formula may be tailored to suit different use cases. Pet shampoo, for example, commonly includes chlorhexidine and castile soap to provide antibacterial properties. Baby shampoo on the other hand requires gentler ingredients and may forgo colorants and scents entirely. Identifying the defining features of your use case is essential to producing an effective formula. Furthermore, some shampoo products contain natural ingredients such as coconut, essential oils and ginger just to name a few. These essential oils and natural ingredients are not only used for their pleasant smell. But, they are added for personal care as each provides unique benefits. For example, ginger in shampoo reduces itchy scalp and decreases dandruff when lathering and massaging your hair. Coconut oil is also used to leave your hair feeling fresh not matter your hair type.
Processing steps involved in shampoo making
Which shampoo technology do you need?
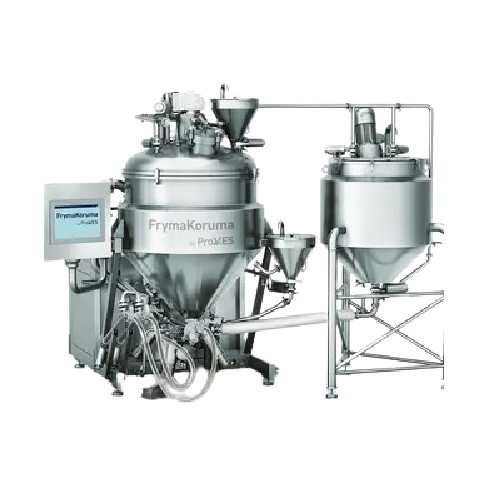
High shear emulsifier for mayonnaise production
Streamline your production of high-quality emulsions with this high-capaci...
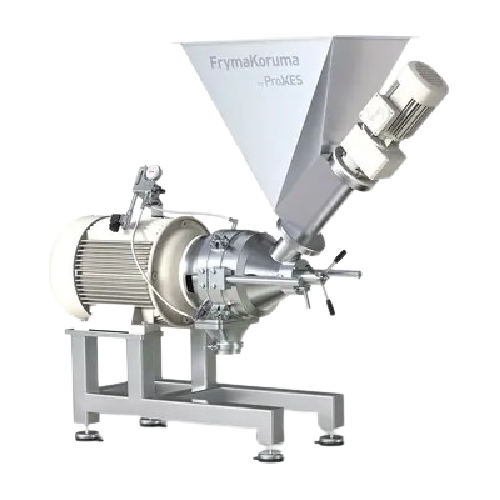
High shear emulsifier for food and pharmaceutical products
Optimize your production line with precise emulsification, ho...

Heat exchangers for efficient heat transfer in industry
Achieve precise temperature control across diverse viscosities wi...
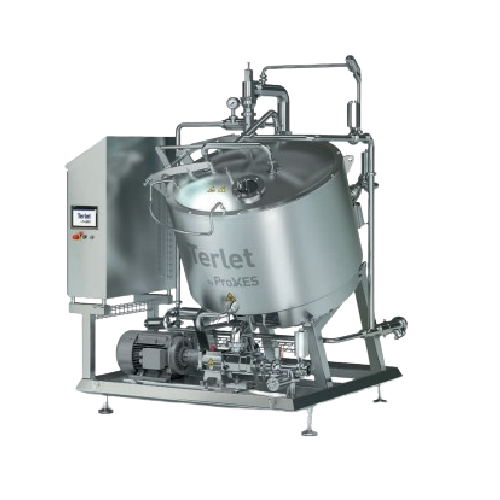
Precise liquid cooling solution for food processing
Ensure high-quality preservation of flavors and textures in liquid fo...
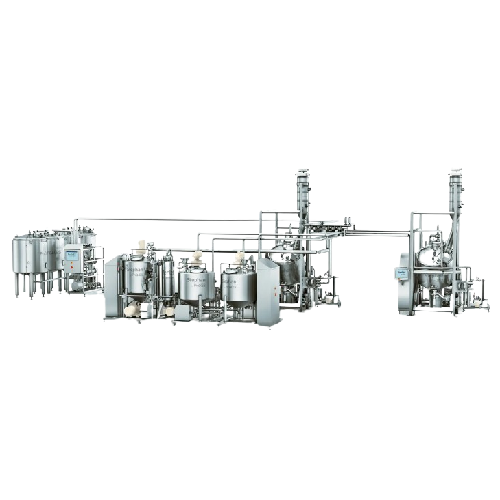
Continuous nut paste production line
Elevate your production efficiency with a versatile preparation line designed to seaml...
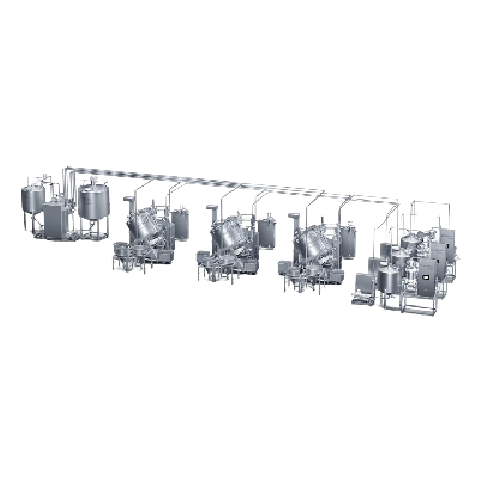
Continuous mustard production line
Optimize your condiment production with precision-engineered systems capable of transfor...
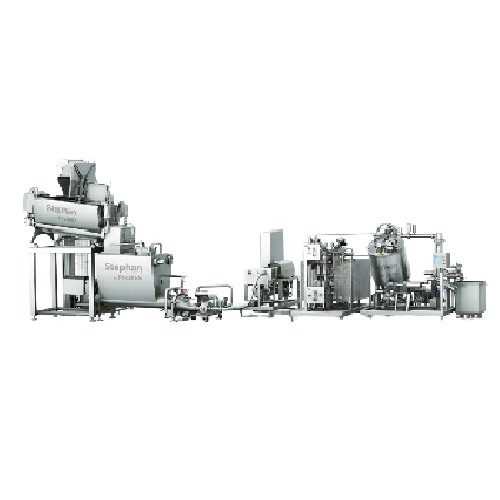
Cheese blending and heating line for processed cheese
Optimize your processed cheese production with a solution that seam...
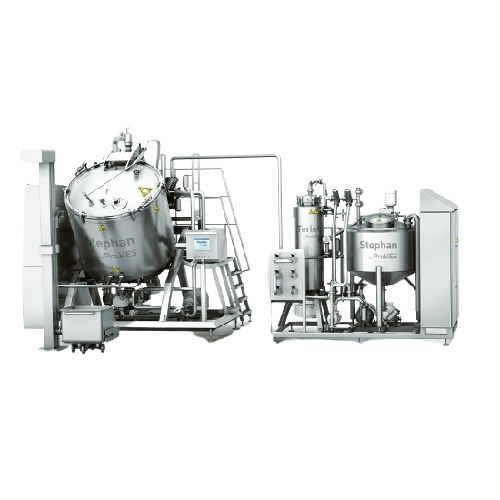
Continuous caramel production line
Optimize your caramel production with seamless integration, achieving precise fat meltin...
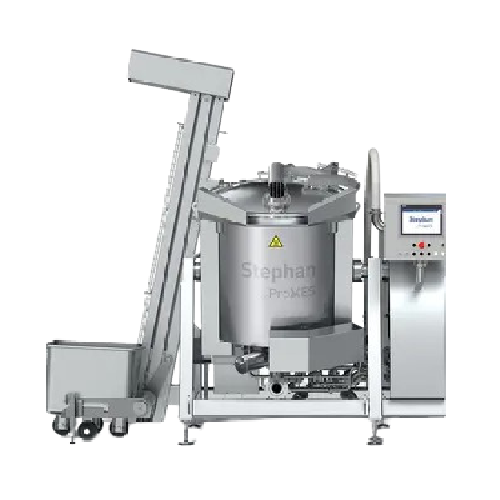
Industrial cooker for sauces and stews
When producing diverse culinary delights such as sauces and stews, achieving even he...
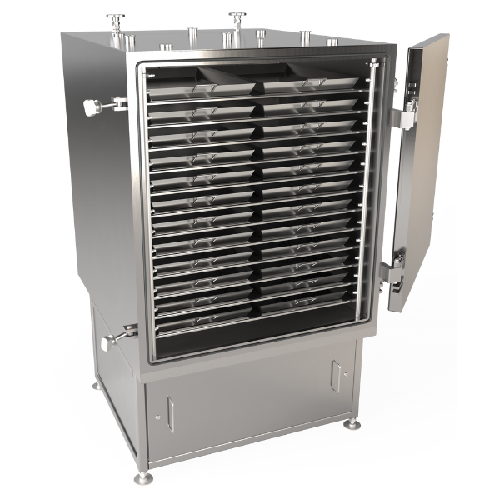
Continuous heat exchanger for soups and sauces
Optimize your soup and sauce production with a continuous heat exchanger th...
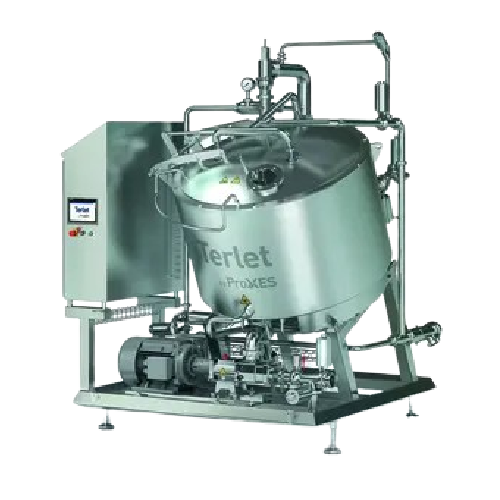
Efficient cooling and cooking systems for food processing
Streamline your production with integrated cooling and cooking...
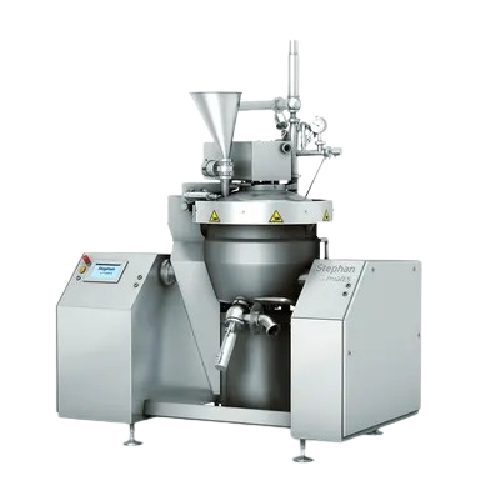
Industrial cutting system for fine emulsions
Optimize your production line with precision cutting and emulsifying, ensurin...
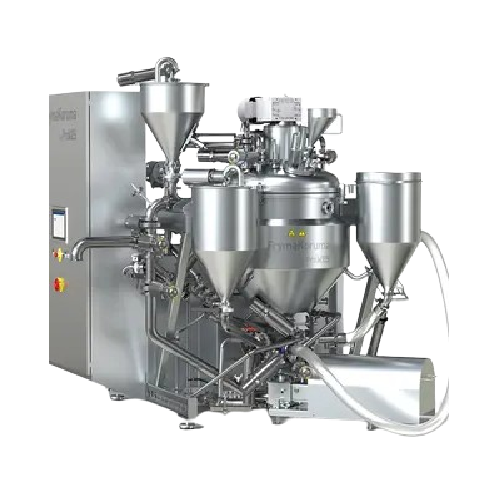
Vacuum deaeration system for mustard and liquid detergents
Ensure optimal product quality by effectively removing air fr...
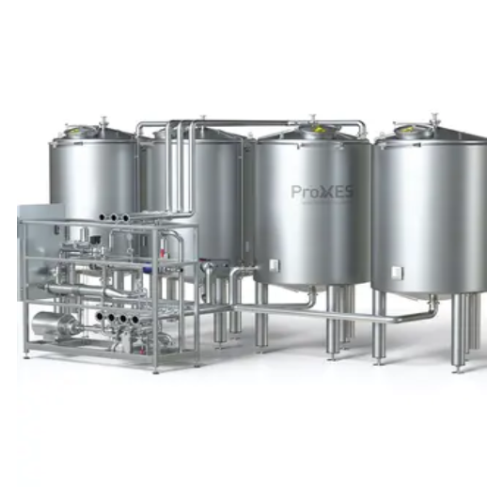
Cleaning systems for food, pharmaceuticals, and cosmetics
Ensure optimal hygiene and safety with advanced cleaning syste...
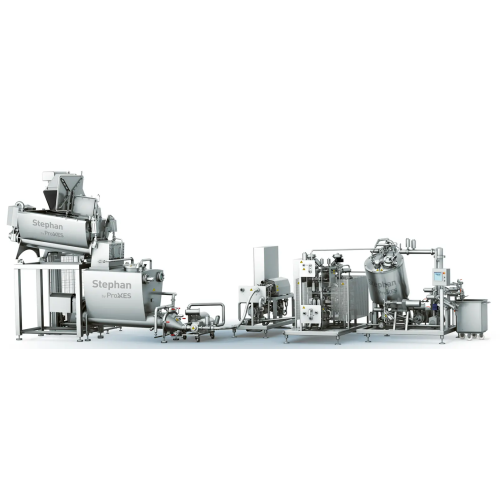
Continuous caramel process line
Optimize your continuous food processing with an engineered-to-order line tailored for preci...
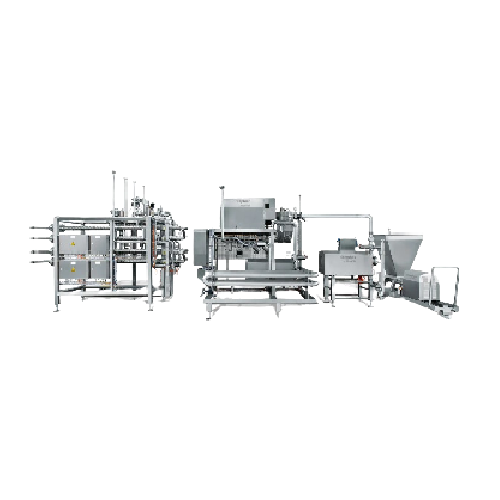
Continuous cheese line
Achieve precise temperature control and seamless product transitions with this equipment, ideal for en...
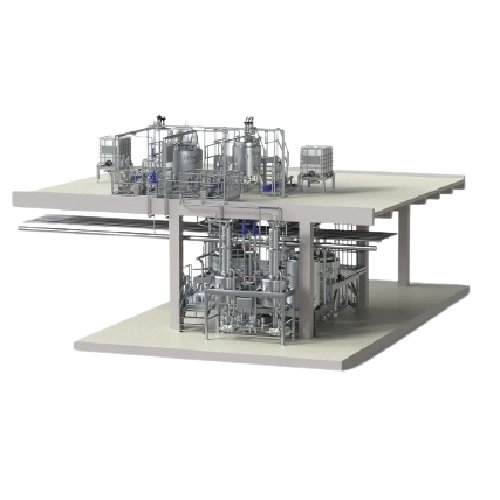
Continuous mustard line
Streamline mustard production with high-capacity continuous processing that reduces air pockets and e...

Continuous tahina production line
Streamline your tahina production with precise grinding and controlled cooling, ensuring ...
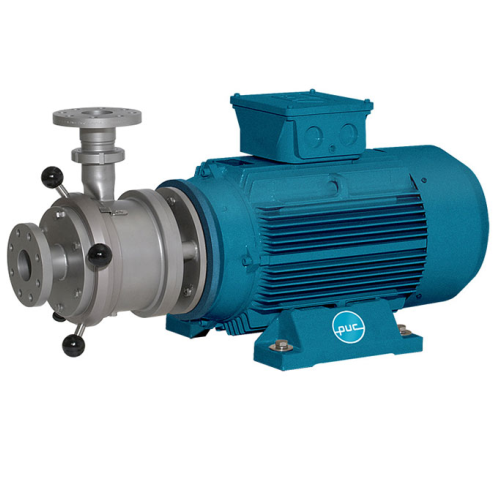
Colloid mill for emulsifying and wet milling applications
Achieve precise mixing and grinding with our colloid mill, des...
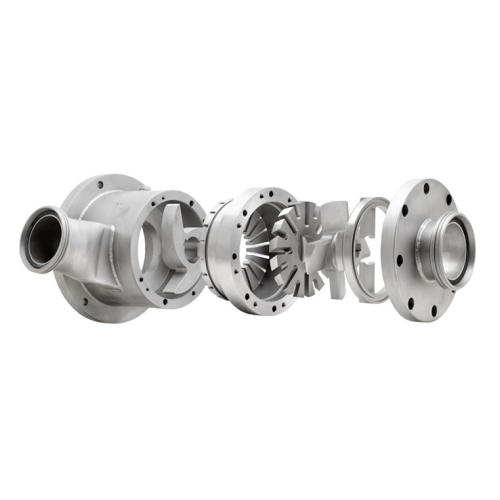
Multistage mixer for emulsions and dispersions
Enhance your production with a versatile multistage mixer that ensures opti...
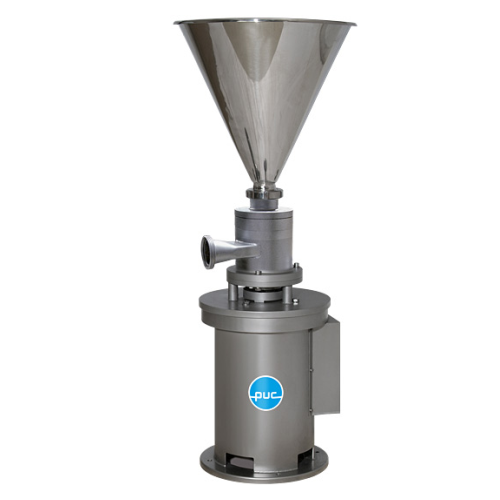
Multistage mixers for emulsions and dispersions
Experience efficient emulsification and dispersion processes with this ver...
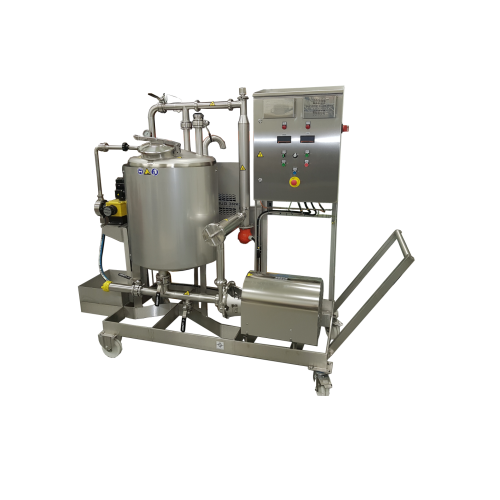
Mobile cleaning-in-place unit for process equipment
Ensure seamless cleaning of diverse process equipment with a mobile, ...

Compact cleaning in place units for food industry
Optimize your production line with a compact system designed for effici...
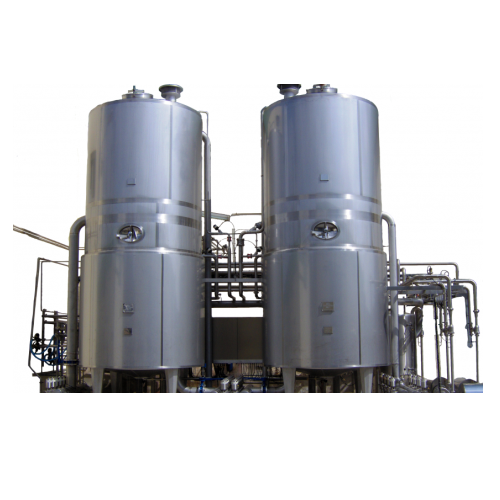
Cleaning-in-place for multiple equipment in food industry
Ensure precise hygiene and traceability with a system designed...
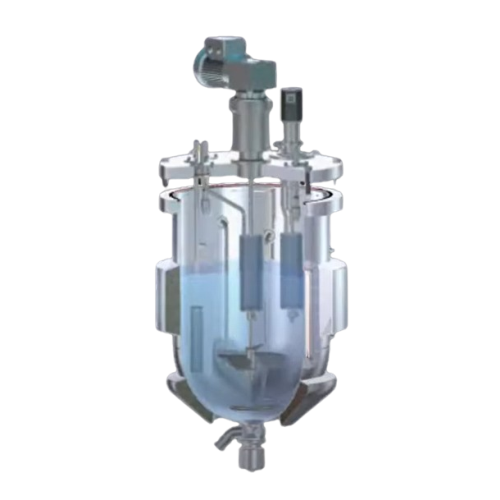
Industrial agitation and mixing solutions
Enhance your production line efficiency with engineered agitation and mixing sys...
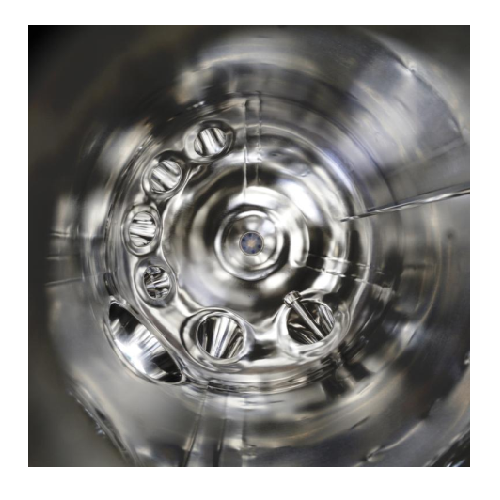
Stainless steel process vessels for biopharmaceutical applications
Ensure seamless mixing and sterilization with engine...
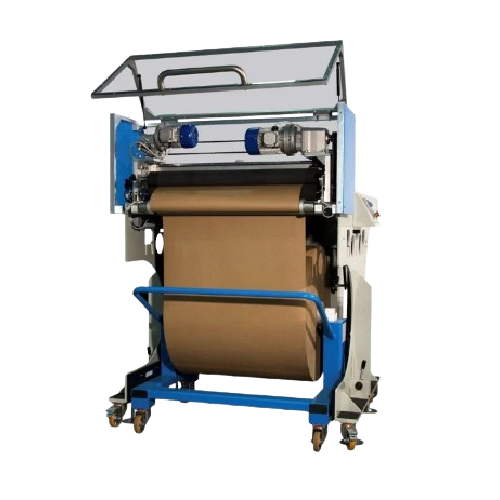
Interlayer sheet dispenser for palletizing
Enhance your palletizing efficiency by integrating a compact interlayer sheet d...

In-line weight filler for drums and kegs
Achieve precise and efficient weight-based filling for large liquid containers, en...
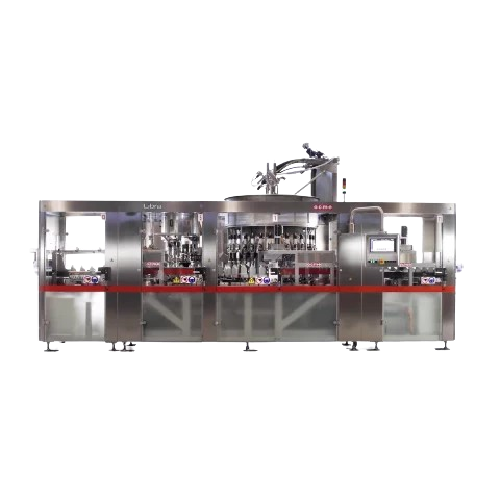
Rotary weight filler for Pet and Hdpe bottles
Enhance your production line with precise weight-based filling, ensuring rap...
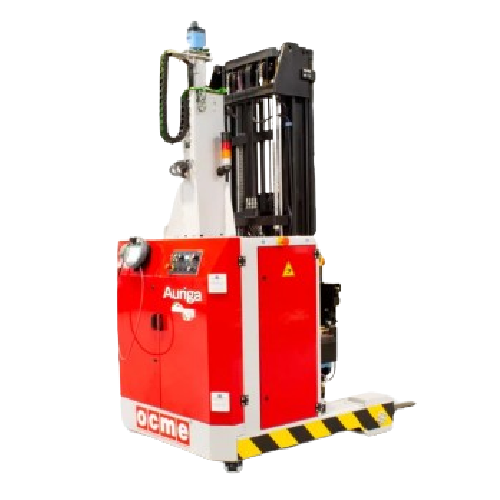
Laser guided reach truck for high-density warehousing
Optimize your warehouse operations with an advanced reach truck des...
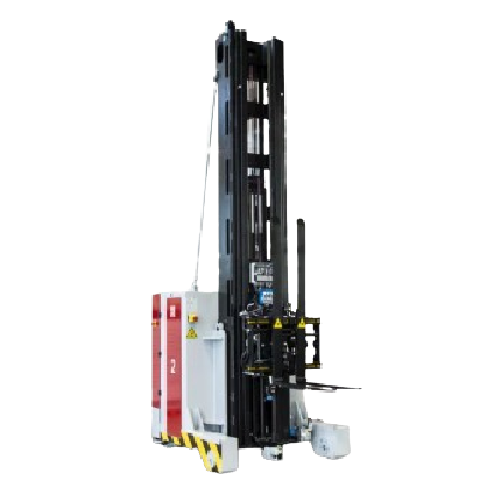
Laser guided vehicle for shuttle management in warehouses
Optimize your warehouse operations with a precision-guided veh...
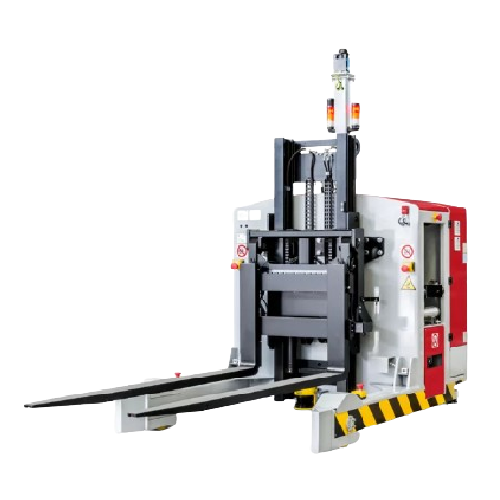
Laser guided vehicles with load stabilizers for pallet handling
Streamline your logistics with state-of-the-art laser gu...
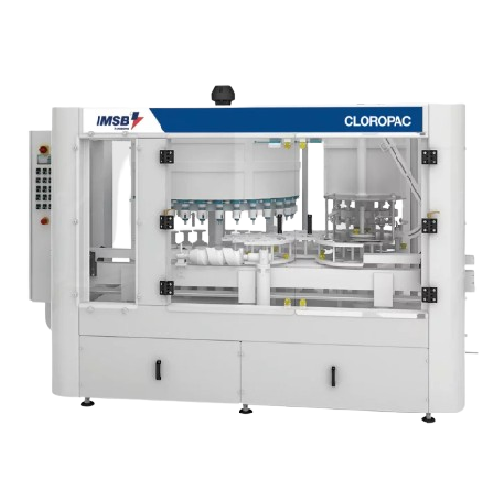
Gravimetric filling and capping system for chlorine solutions
Optimize your filling and capping processes for chlorinate...
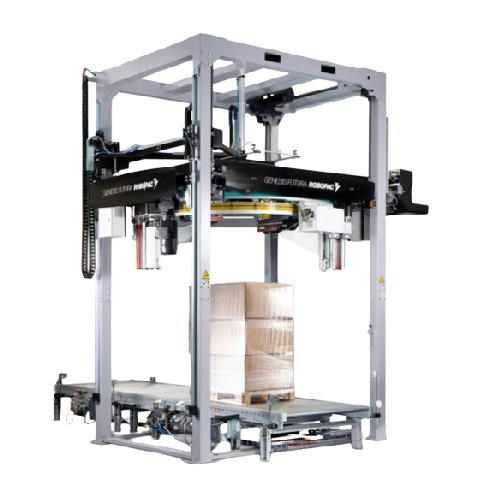
High-speed automatic rotary ring wrapper for stretch wrapping
Optimize your packaging line with a fully automated high-s...
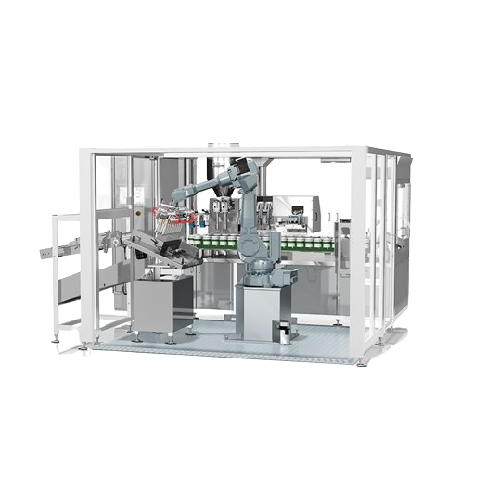
Tube filling machine for cosmetics and food products
Achieve precise and efficient packaging with this advanced twin-head...
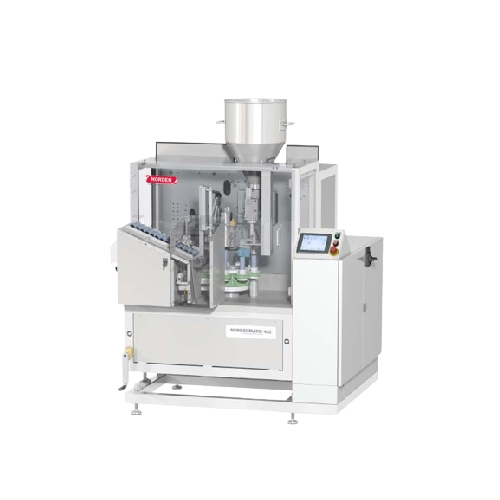
Tube filling solution for plastic and laminate tubes
Ensure precise tube filling and sealing with quick changeovers, enha...
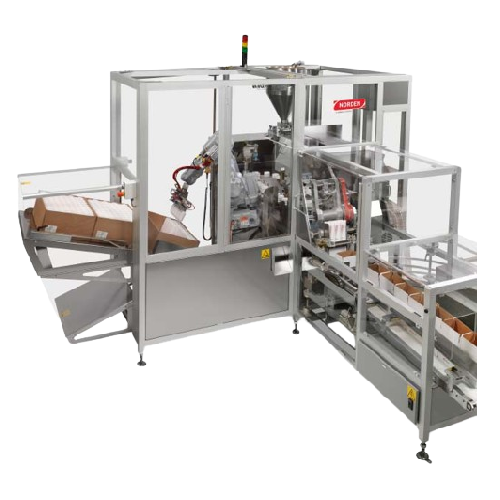
Pick & place robot for packing tubes in boxes
Efficiently streamline your packaging line with this compact case packer, de...
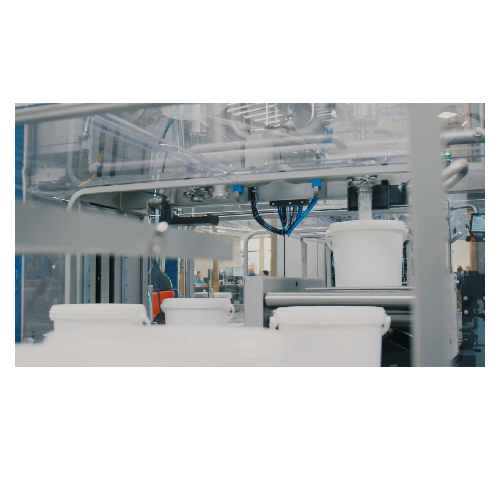
Oil and fat filling system for industrial use
Optimize your production line with this precise filling solution, designed t...
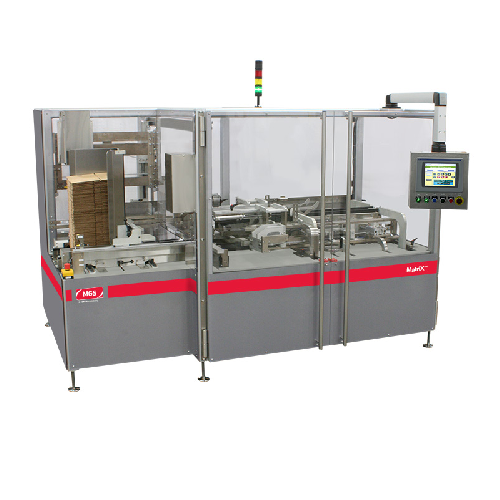
Case packer for pharmaceutical and healthcare products
Streamline your packaging line with a versatile case packer design...
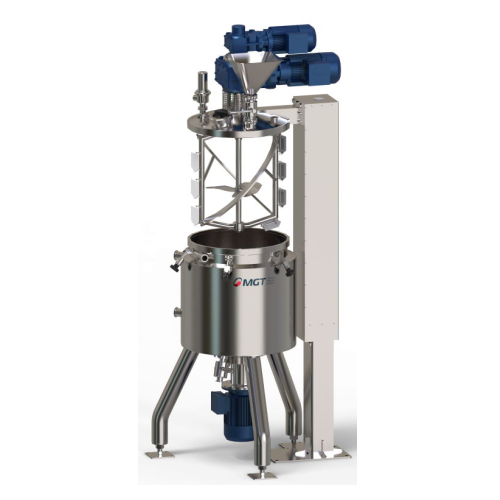
Vacuum mixing system for emulsion and homogenization
Achieve seamless emulsion and homogenization with precision: this sy...
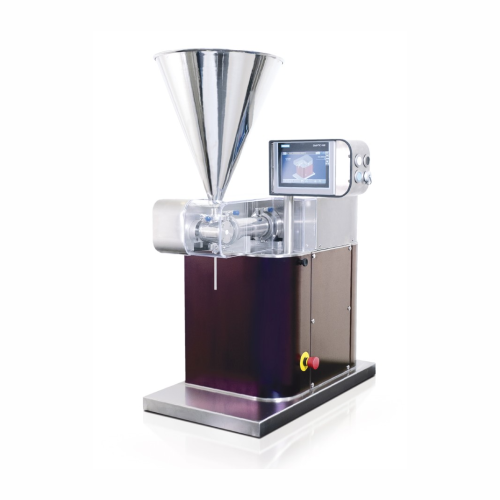
Lab-scale liquid and cream filling system
Streamline your lab production with precise filling of liquids, creams, and past...
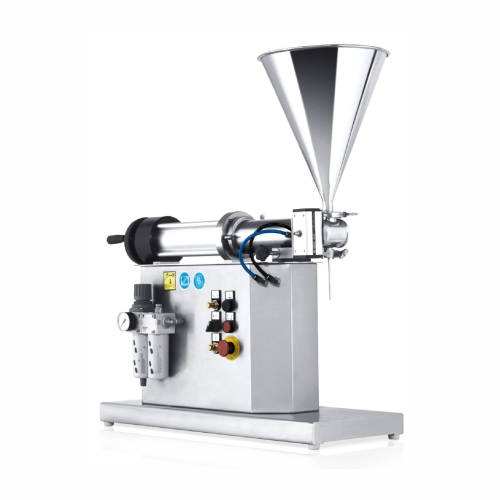
Laboratory filling system for liquid and creamy products
Optimize your laboratory processes by precisely handling liquid,...
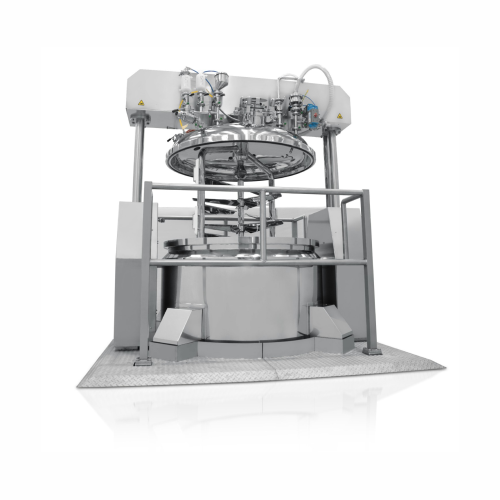
Vacuum turboemulsifiers for liquid and creamy products
Simplify your production workflow with high-capacity vacuum turboe...
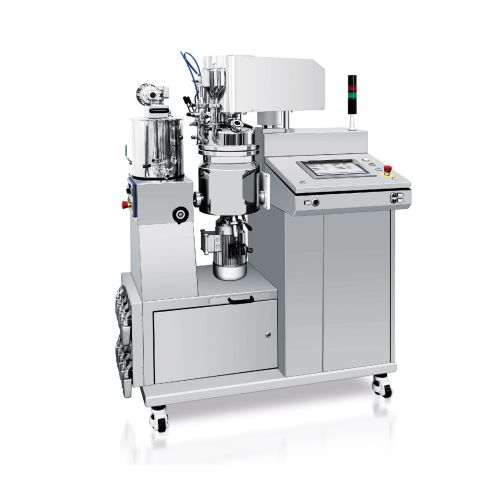
Vacuum turboemulsifier for small-scale production
Optimize your product development with versatile vacuum turboemulsifier...
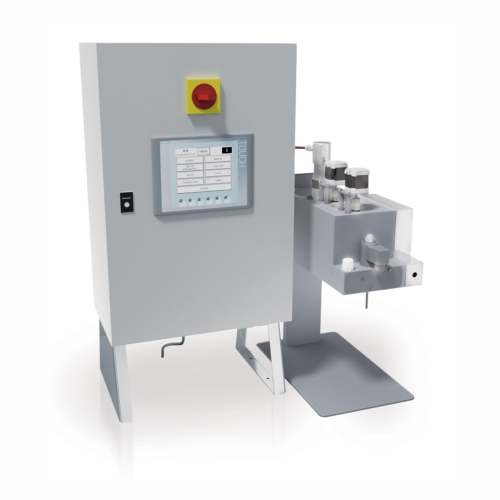
Melting tank for cosmetic production
Achieve precise and consistent melting and dosing of cosmetic liquids, from face cream...

Automatic tube filling and closing for metal, plastic, and laminate tubes
Enhance your production efficiency with a hi...
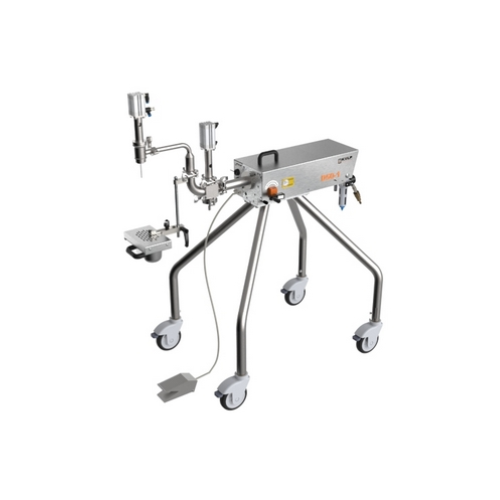
Volumetric filling system for cosmetic products
Streamline your production line with precise volumetric control, ensuring ...
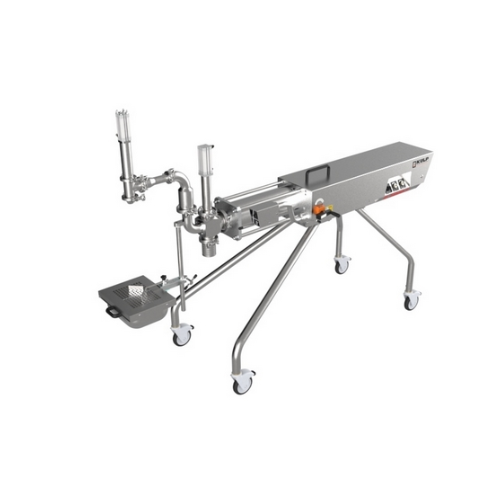
Volumetric filler for liquid and viscous products
Achieve precise and adaptable filling for a wide variety of liquid and ...
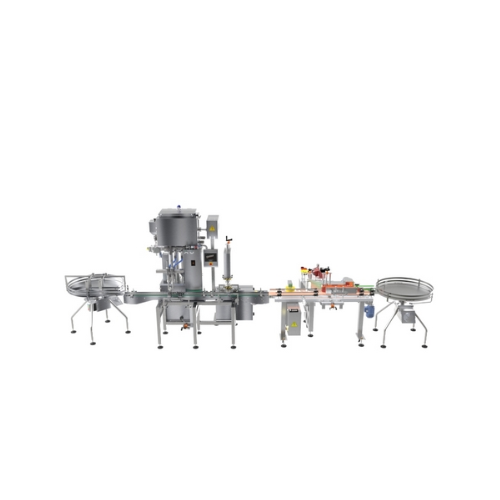
Medium capacity filling line for food and cosmetics
Streamline your production with a versatile filling line that seamles...
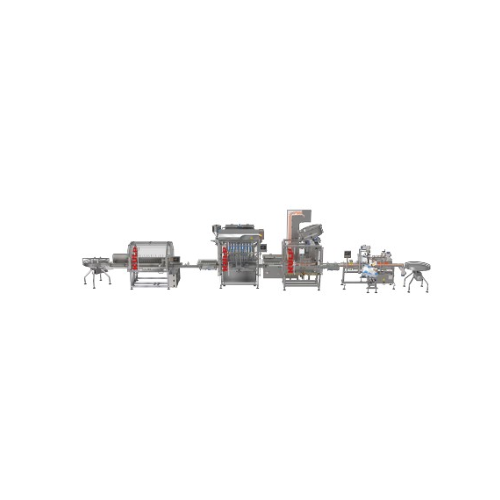
High capacity filling line for jars and bottles
Need to streamline your packaging line? This high-capacity solution proces...
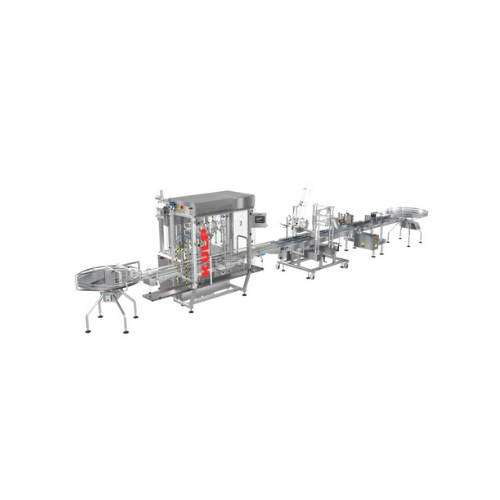
Large container filling line
Optimize your production line with a seamless solution for efficiently filling large containers...
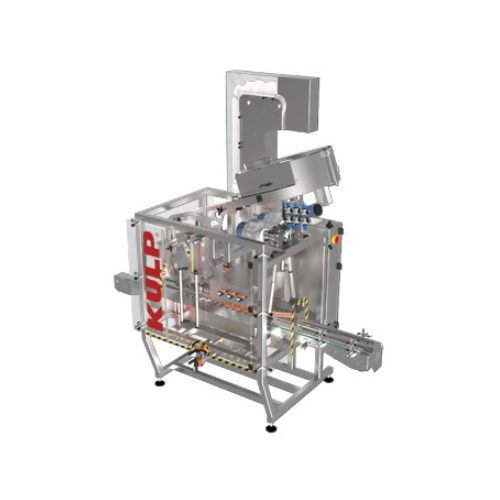
Continuous inline capping system
Perfect for high-speed operations, this system ensures precise capping of diverse container...
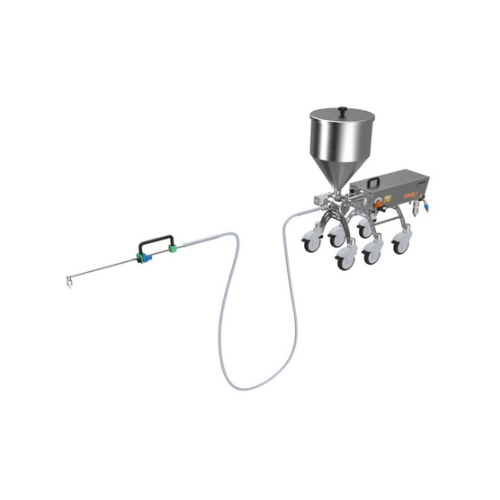
Volumetric filling technology for cosmetic and food products
Achieve precise and contamination-free filling of liquid an...
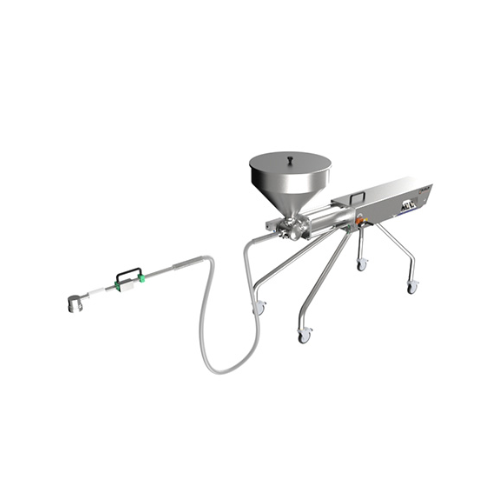
Volumetric filler for packaging liquids and semi-solids
Optimize your filling process with precision control and adaptabl...
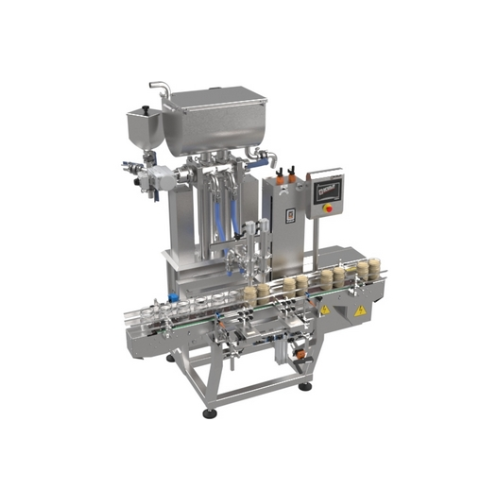
2-head liquid and viscous product filling system
Streamline your filling operations with precision and versatility designe...
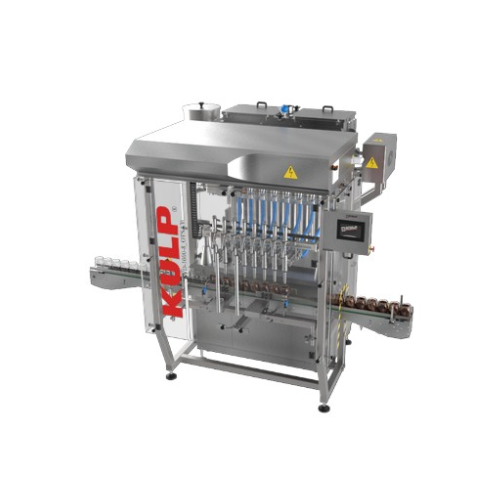
8 head liquid and viscous product filling system
When precision and speed are crucial, this 8 head filling machine ensures...
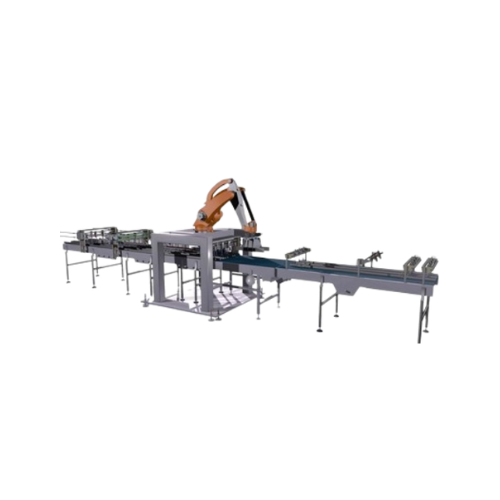
High-performance distribution and combining system
Streamline your packaging operations with a versatile system designed ...
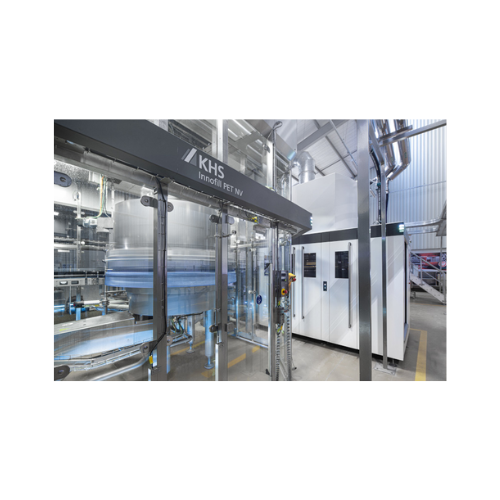
Pet bottle filler for hot and cold still beverages
Achieve high-speed precision in filling and capping for various bevera...
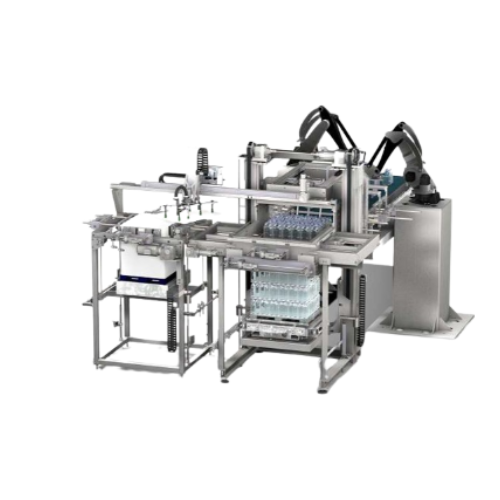
High-speed beverage industry palletizer
Optimize your palletizing process with a flexible, high-speed solution that adapts ...

Industrial code verification system for product packaging
Ensure flawless packaging integrity with high-speed code verif...
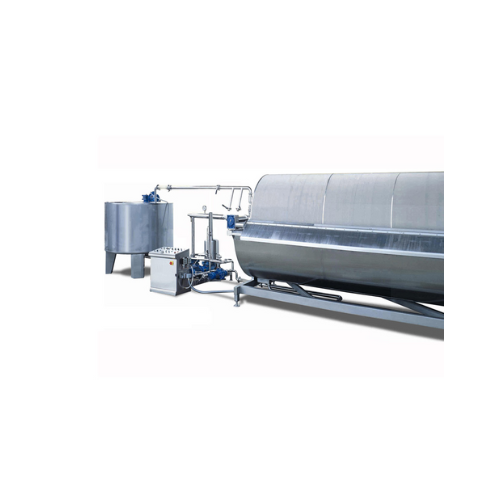
Vacuum rotary filter for liquid filtration
Enhance your production line’s efficiency with precise filtration, ensuri...
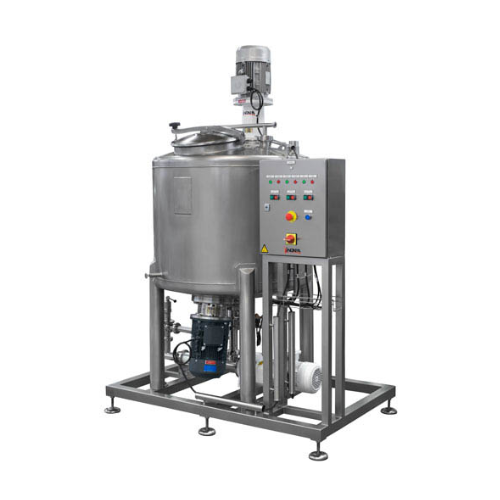
Hydrocolloid powder dispersion unit
Achieve seamless dispersion of hydrocolloid powders in liquids, eliminating common issu...
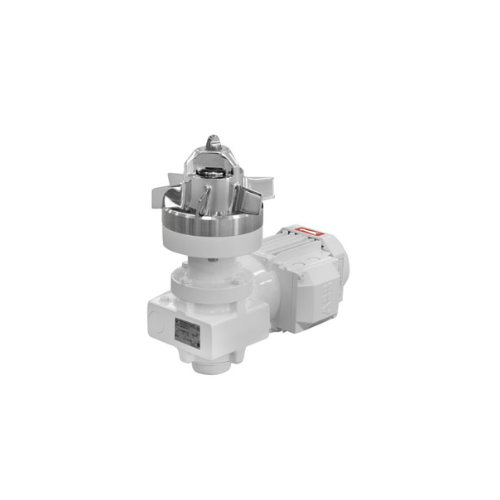
Industrial magnetic agitator for homogenizing pharmaceutical products
Achieve precise dispersion and homogenization in ...
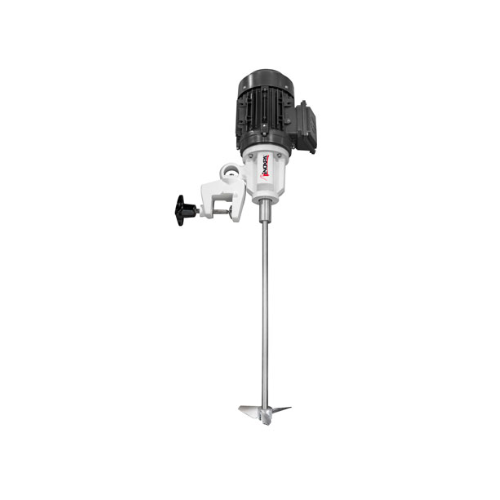
Portable agitator for high-speed mixing
Enhance your liquid formulation processes with an efficient solution for rapid mixi...
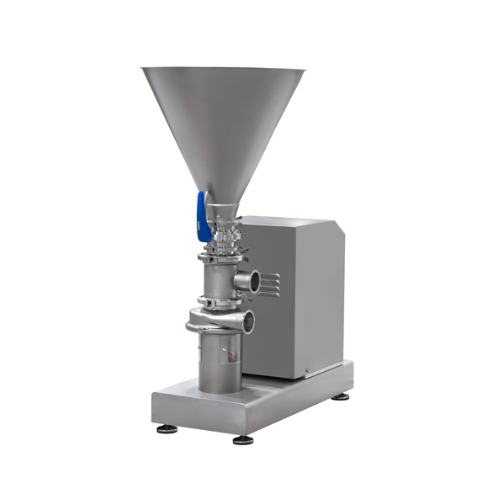
Powder liquid blender for food processing
Achieve seamless integration of solids into liquids with precision-engineered bl...
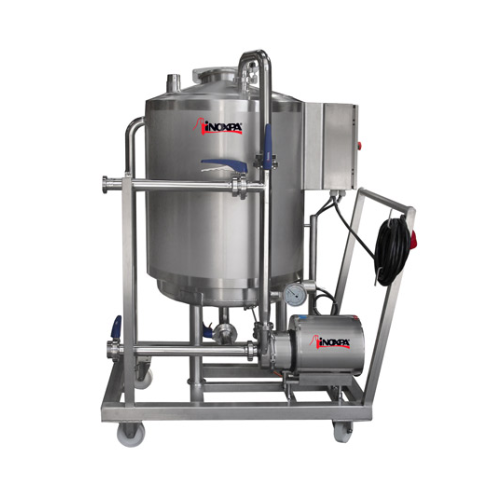
Manual Cip system for food processing hygiene
Designed for small-scale hygiene needs, this mobile clean-in-place system en...
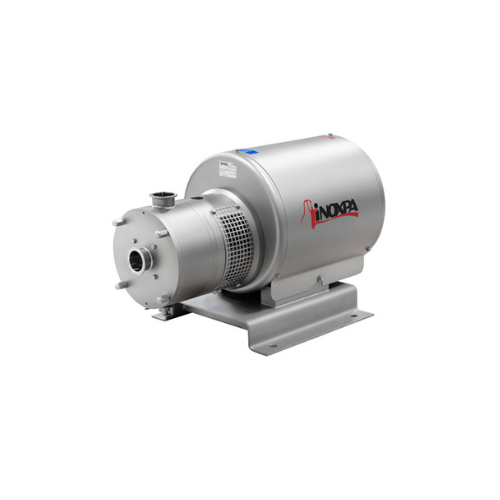
In-line high shear mixing solution
Achieve precise emulsification and particle size reduction with high shear capabilities,...
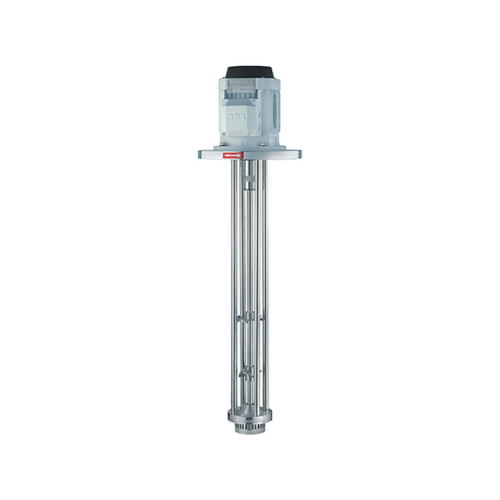
High shear vertical mixer for dispersion and emulsification
Achieve seamless emulsification and homogenization in divers...
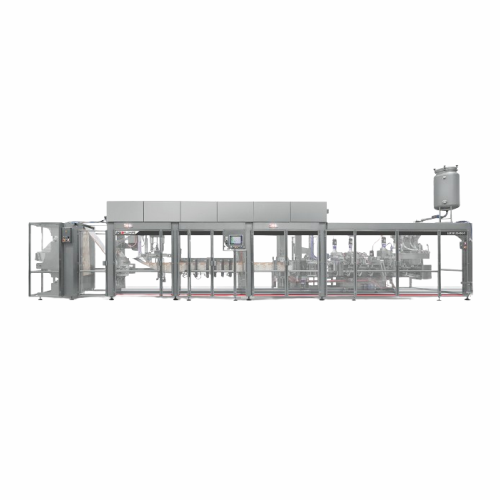
High-speed drift-dwell motion doypack forming system
Optimize your liquid packaging efficiency with a dual-motion system ...
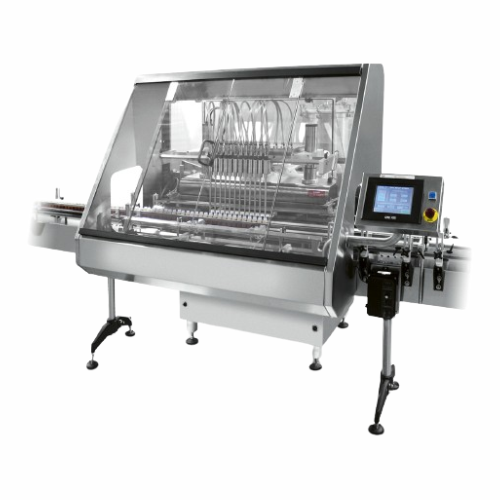
Positive displacement gear pump liquid filler
Optimize your liquid filling operations with precision gear pump technology,...
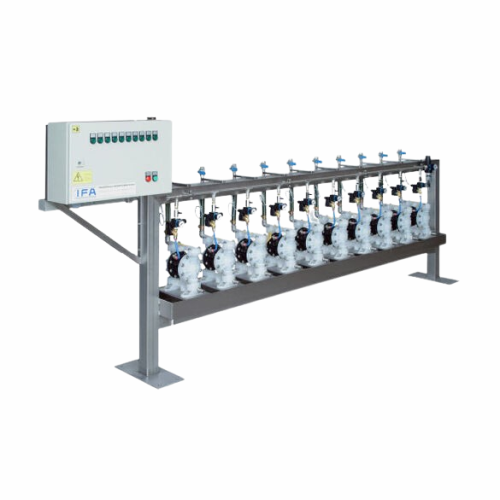
Pneumatic conveying systems for industrial applications
Efficiently transport bulk materials or liquids across your produ...

Industrial grinder for ultra-fine grinding and homogenizing
Enhance your production line with versatile grinding technol...
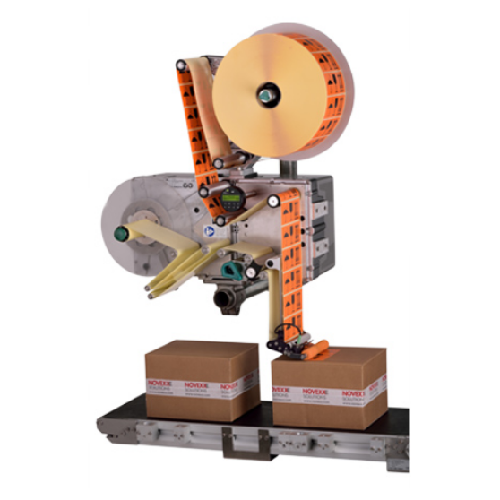
Fast labelling head for high-speed production lines
Achieve precise labeling at high speeds with robust equipment tailore...

Ultraclean aseptic storage tanks for hygienic liquid food
Ensure your liquid products remain uncontaminated and maintain...
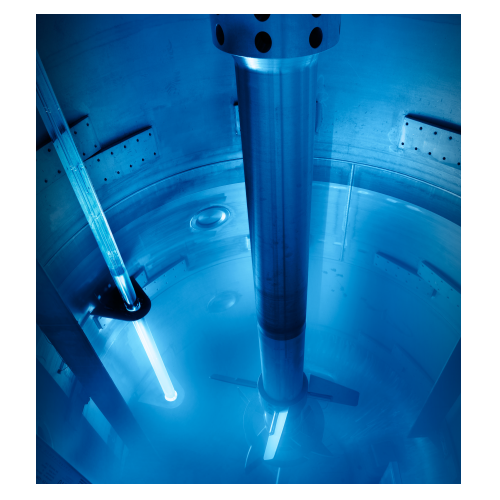
Industrial photochemical reactors for multiphase reactions
Optimize multiphase chemical reactions with light-activated p...
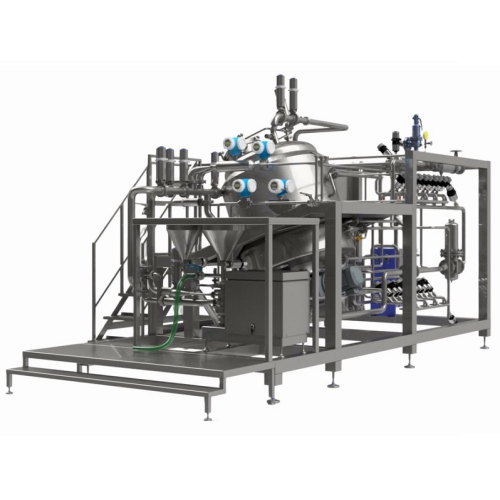
Inline system for personal care product production
Optimize your personal care production with precise mixing, heating, a...
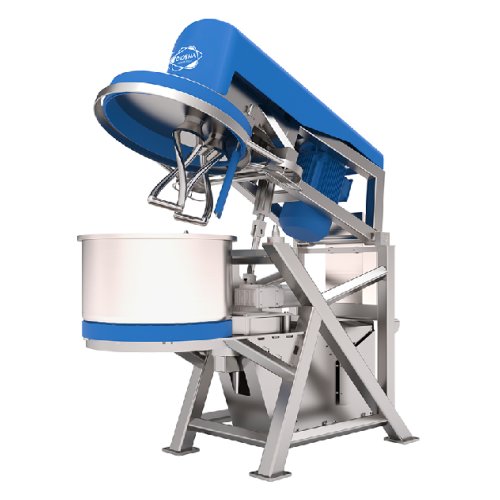
Hygienic design dough mixer
Achieve superior dough consistency and safety with our hygienic design mixer, ideal for reducing...
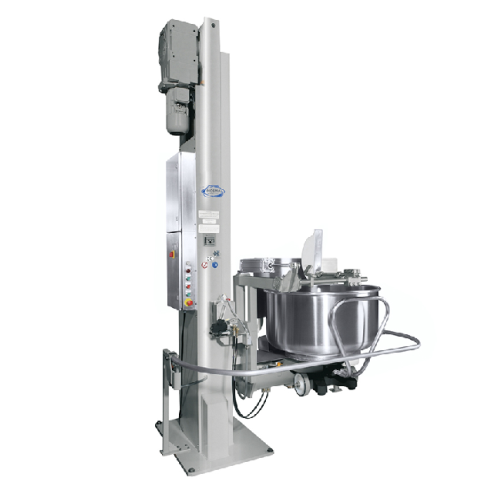
Elevator tipper for flexible dough handling
Achieve maximum flexibility in your production line with a versatile lifting s...
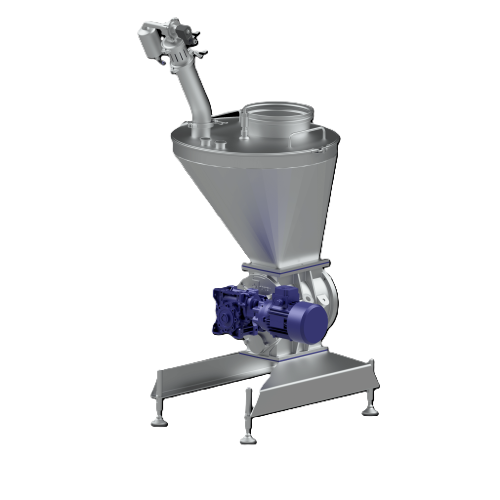
Dilute-phase conveying solution for powder handling
Efficiently transfer powders and granules with robust leak containmen...
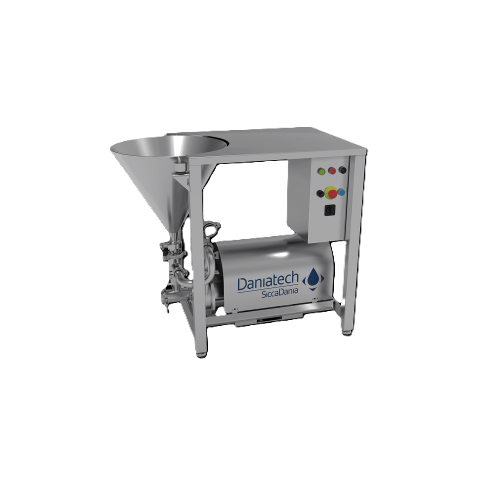
Inline high-shear mixer for powders and liquids
Achieve efficient mixing and homogenization in your production line with a...
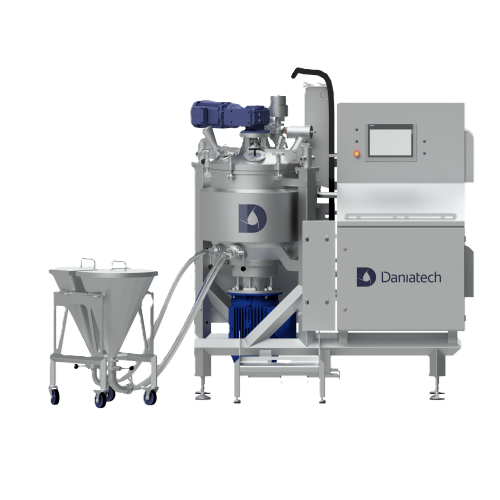
Lab-scale high-shear mixer for recipe development
Optimize your recipe development process with precise mixing, homogeniz...
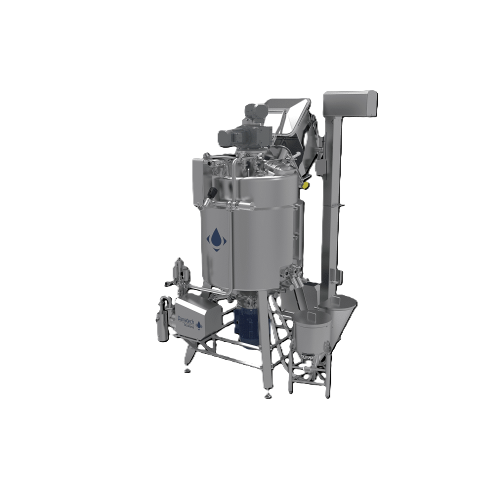
High-shear mixer for high viscosity products
Achieve consistent, homogeneous mixtures of high-viscosity products with a ve...
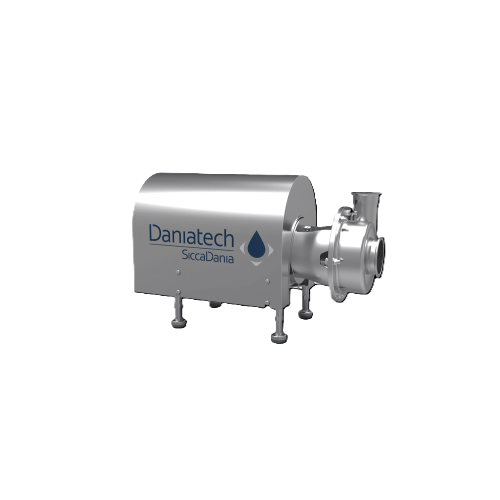
Ultra-high shear mixer for emulsification and homogenization
Optimize your production with ultra-high shear mixing, acce...

Vacuum high shear mixer for medium to high viscosity products
Achieve flawless blending and air-free consistency in visc...
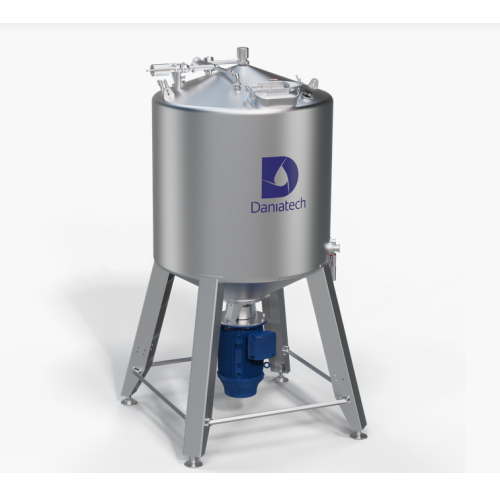
High-capacity manual mixer for industrial applications
Optimize your mixing process with a highly efficient, manually ope...
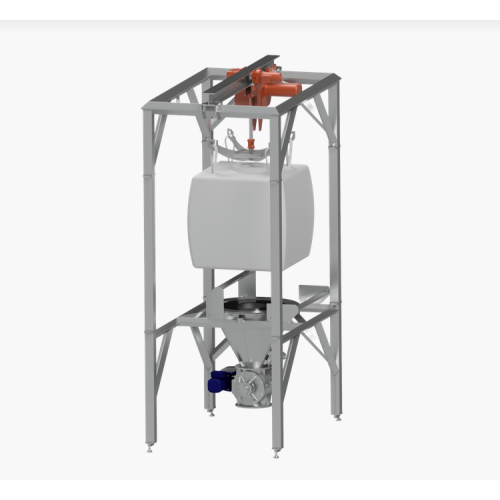
Bigbag discharge system for food, chemical, and pharmaceutical industries
Ensure precise and dust-free handling of bul...
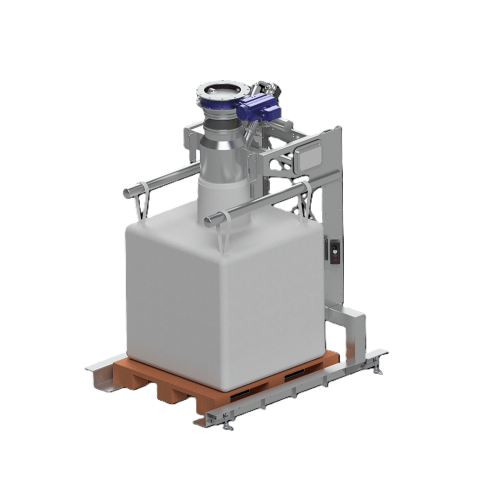
Bigbag filling system for powder and bulk materials
Ensure precise and dust-free bigbag filling with this versatile syste...
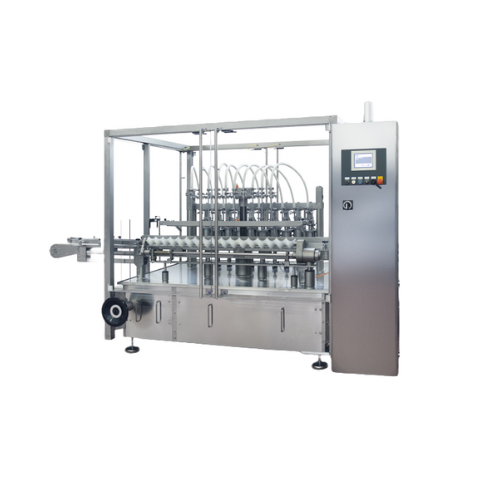
Linear intermittent motion filling system for high-density liquids
Ensure precise dosing of high-density liquids like c...
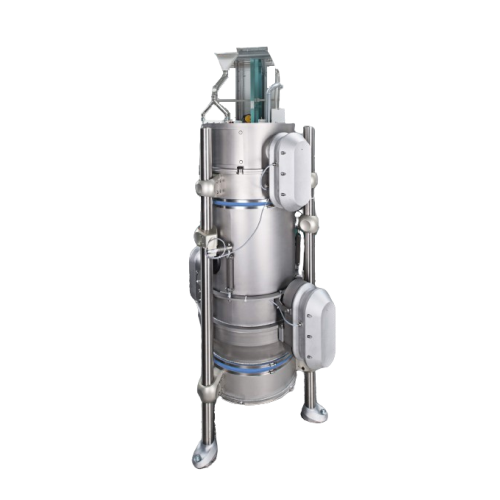
Advanced superheated steam drying solution
Harness the power of consistent drying technology to achieve optimal moisture c...
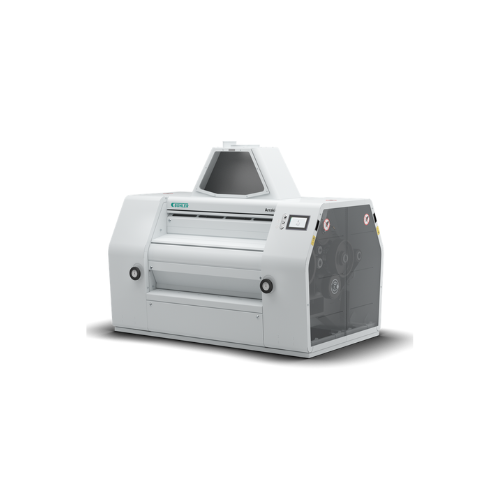
Four-roller and eight-roller mill for wheat and grain grinding
Optimize your grinding operations with this versatile rol...
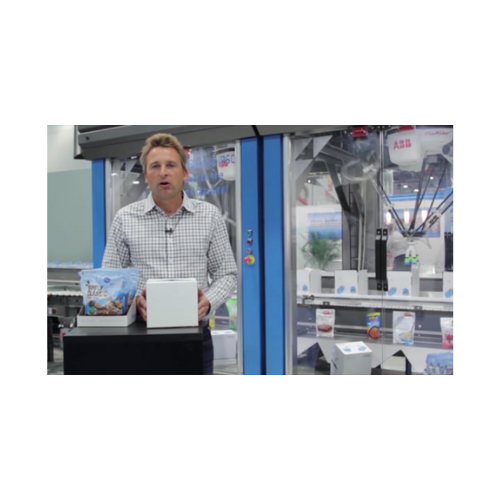
Automated retail ready case closer
Optimize your retail packaging process with a solution that seamlessly seals and closes ...
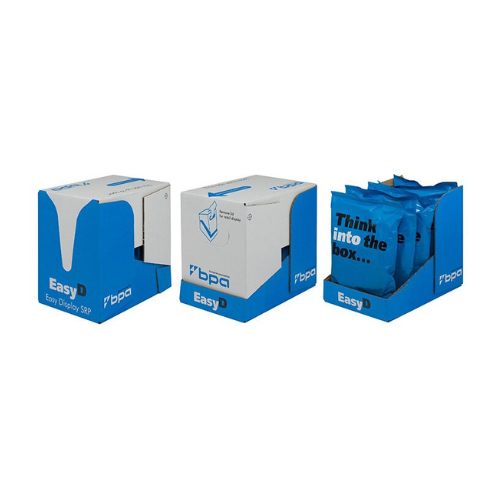
Retail ready packaging system for easy store stocking
Simplify shelf stocking with a sturdily designed packaging system t...
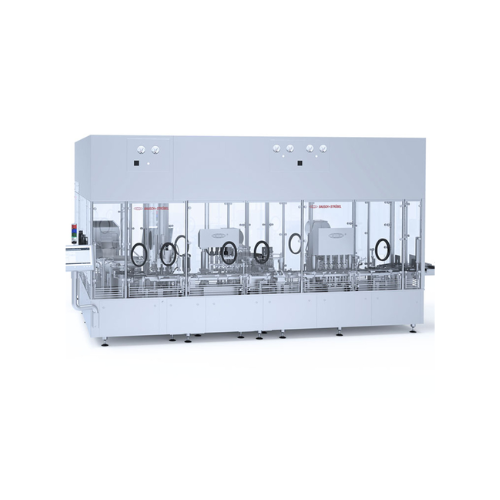
Filling and closing solution for plastic bottles
Efficiently sort, fill, and close a variety of plastic bottles with preci...
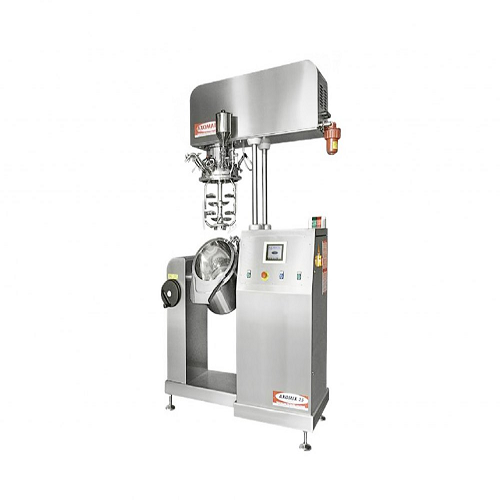
Industrial under vacuum homogenizer
Optimize the consistency and texture of creams and lotions with precision-controlled mi...
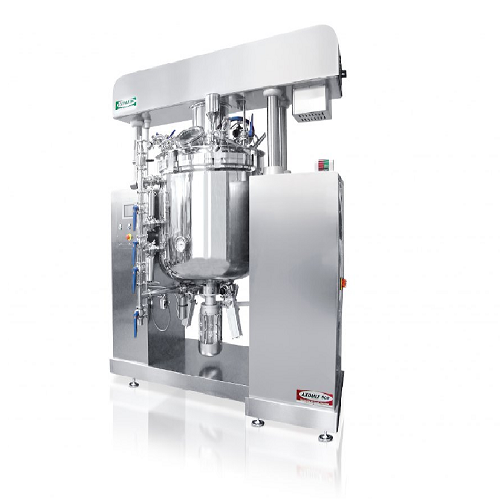
Undervacuum homogenizer for cosmetic and pharmaceutical creams
Optimizing the production of creams and lotions, this und...

Automatic bottle filling and capping line
Streamline your liquid product packaging with this high-speed solution, integrat...
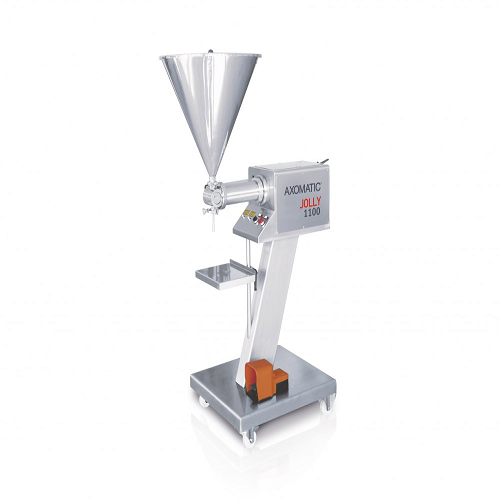
Pneumatic dosing system for dense and semi-dense products
For precise dosing of dense and semi-dense liquids, this pneum...
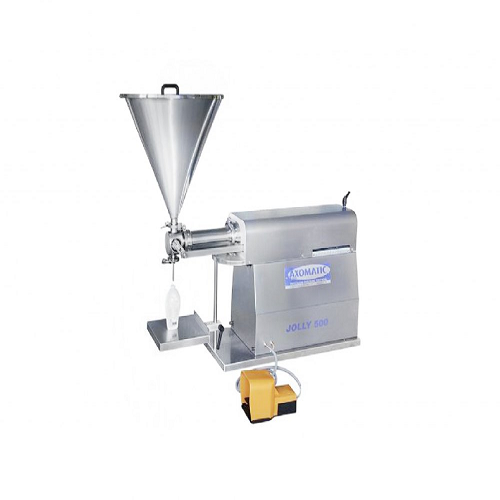
Pneumatic dosing system for dense and semi-dense products
Easily handle dense and semi-dense products with precision dos...

Full-membrane water for injection (wfi) generation system
Ensure consistent high-quality injections by integrating real-...
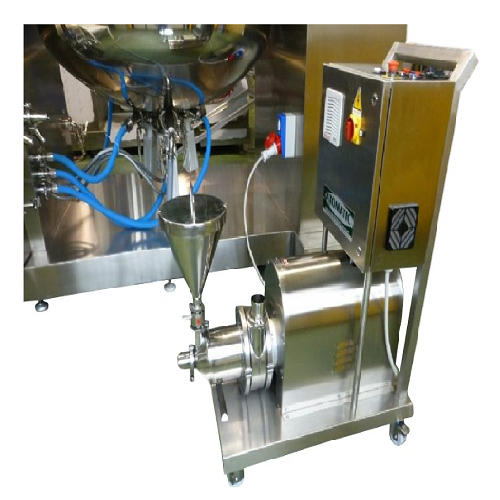
In-line external homogenizer for industrial fluid processing
Maximize fluid consistency and ensure efficient material di...
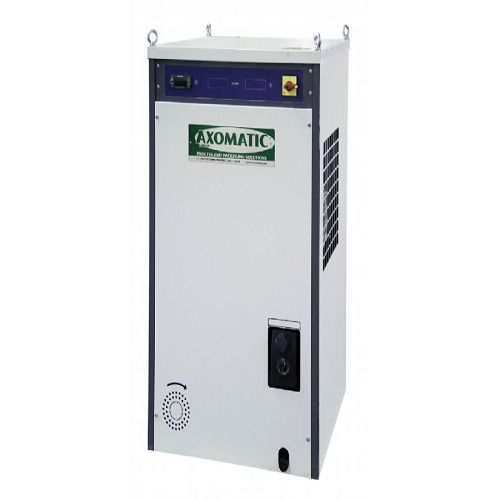
Industrial water chiller for homogenizers and filling machines
Optimize your production line with customizable water chi...
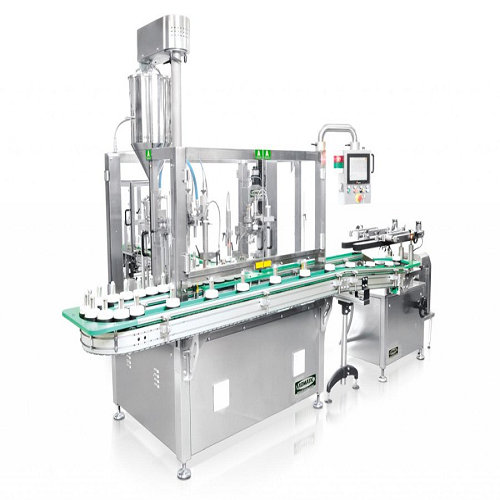
Alternate movement bottle filling and capping system
Enhance your production line with a versatile filling and capping so...
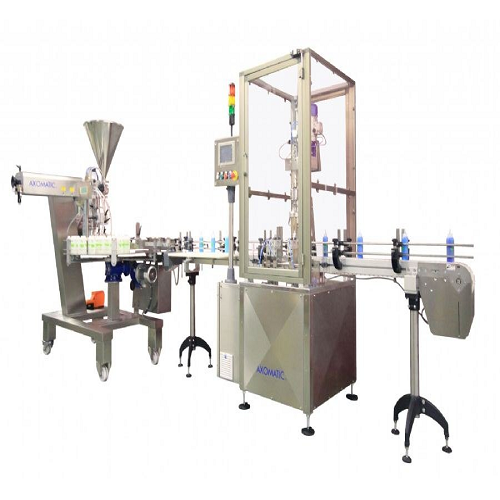
Automatic bottles and jars filling and capping line
Streamline your liquid product packaging with this high-speed solutio...
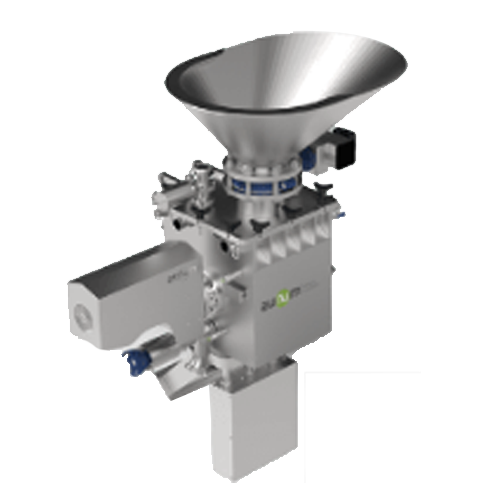
High-efficiency high-capacity reactor for industrial processing
Enhance production efficiency with a reactor system desi...
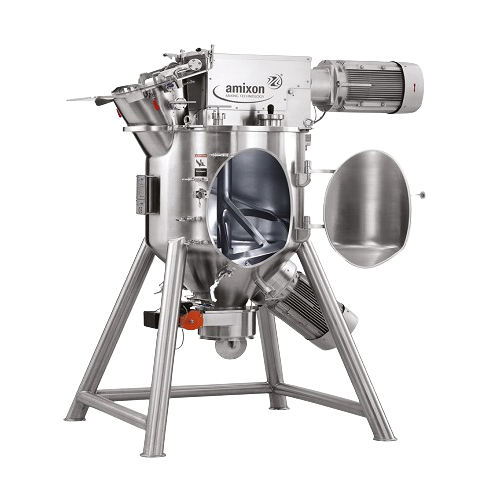
Conical mixer for dry, moist, and viscous materials
Achieve optimal mixing consistency and precision for diverse material...
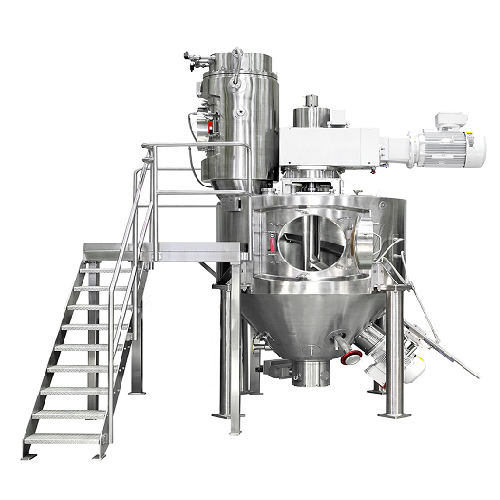
Conical vacuum dryer for viscous materials
Achieve precise drying and mixing of moist and viscous materials, ensuring cons...
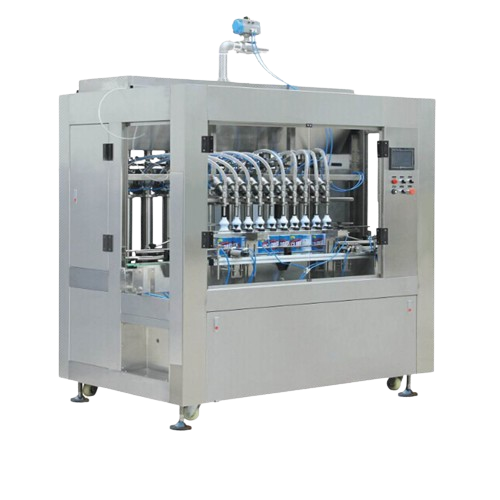
Automatic detergent shampoo filling solution
Streamline your filling process with precise volume control, achieving consis...
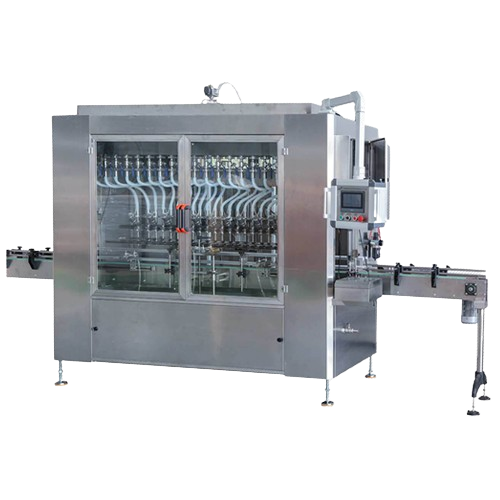
Automatic edible oil filling & capping solution
Streamline your liquid packaging operations with precise, high-speed filli...
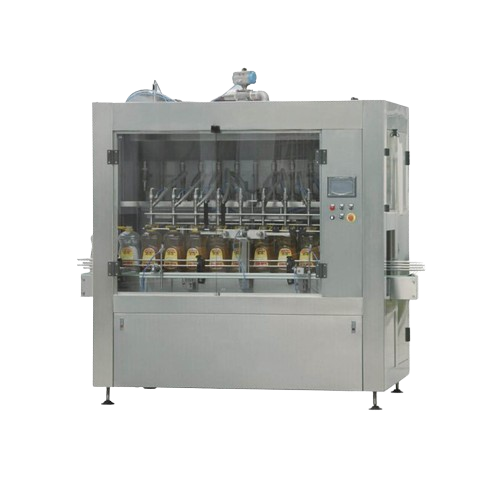
Automatic food cooking oil bottling solution
Ensure precise volumetric filling for a range of liquid products, enhancing y...

Scraped surface heat exchanger for viscous products
Efficiently handle challenging viscosities and heat-sensitive product...
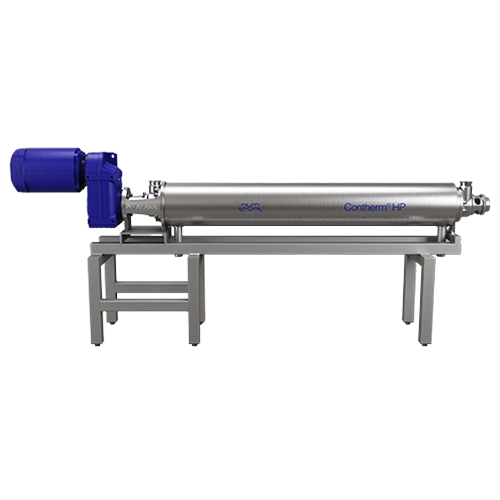
Scraped surface heat exchanger for high-pressure applications
Handle high-viscosity and particulate-rich products with p...
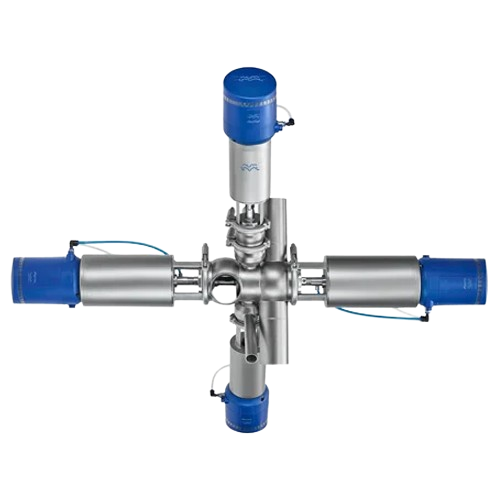
Aseptic mixproof valve for sterile processing
Ensure absolute product safety and optimize cleaning efficiency in sterile p...
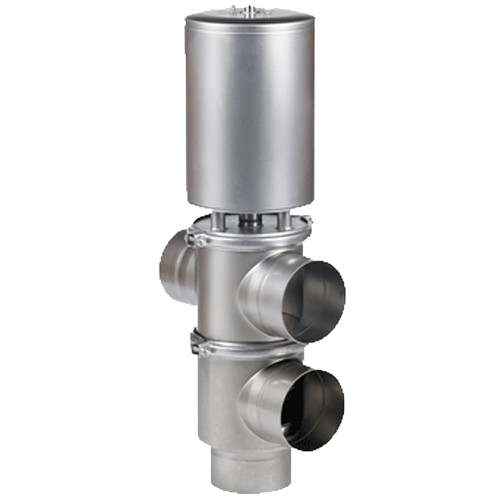
Single seat valve for hygienic applications
Ensure optimal hygiene and safety with a versatile pneumatic valve designed to...
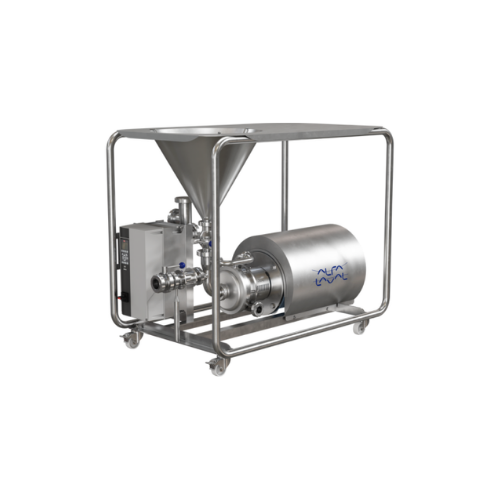
Hybrid powder mixer for powder-liquid blending
Achieve consistent powder-liquid blends with reduced processing times and e...
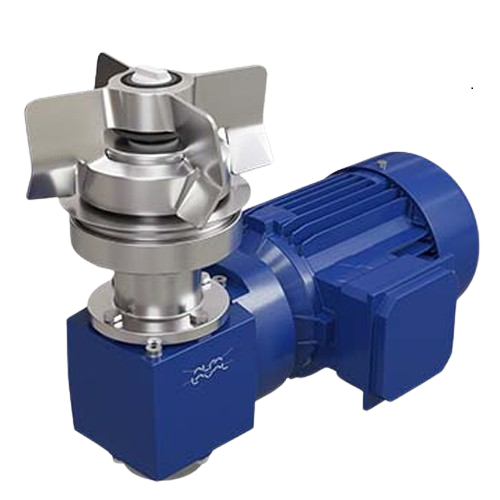
Aseptic magnetic mixer for hygienic production
Experience seamless mixing to the last drop with advanced levitating impell...

Rotary jet head tank cleaning system for food and beverage industry
Reduce your tank cleaning costs by up to 70% with a...
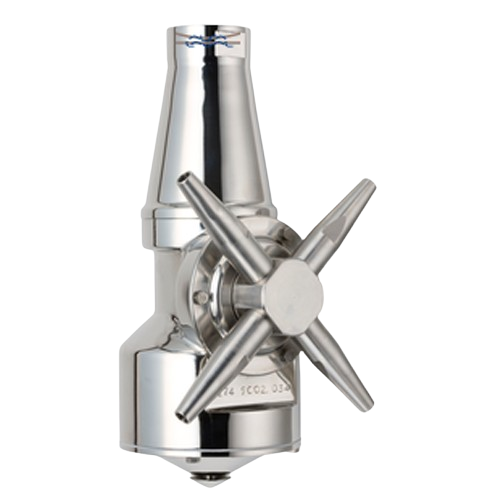
Rotary jet head for hygienic tank cleaning
Ensure efficient, hygienic cleaning with a rotary jet head designed to optimize...
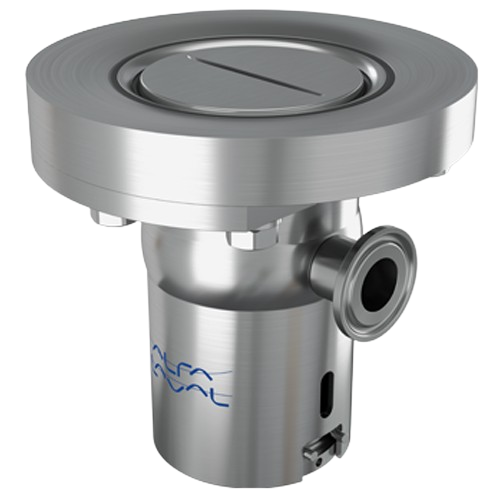
Cleaning nozzle for pharmaceutical tank cleaning
Ensure complete tank hygiene with innovative cleaning technology that tar...
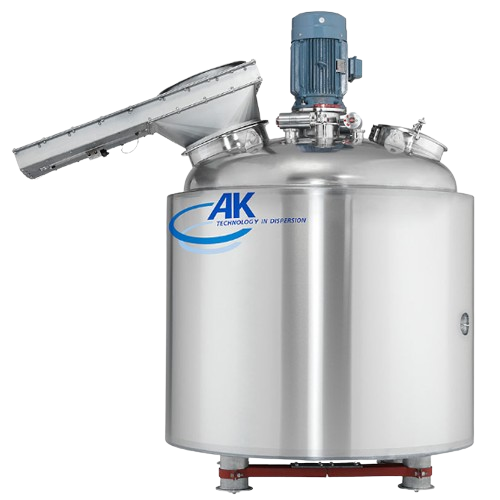
Emulsion processing system for homogenizing solids into liquids
Achieve precision in emulsifying and homogenizing proces...
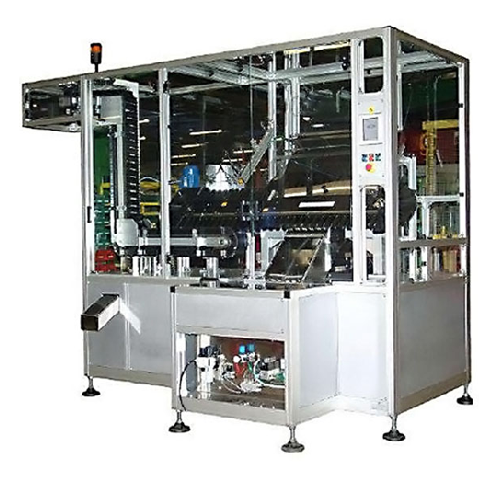
Tube feeder for pharmaceutical and personal care industries
Optimize your production line with this high-speed tube feed...
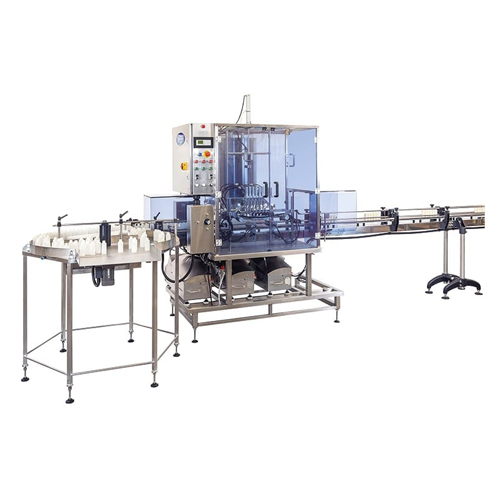
Automated bottle and jar filling solution
Streamline your production and minimize waste with a versatile filling solution,...
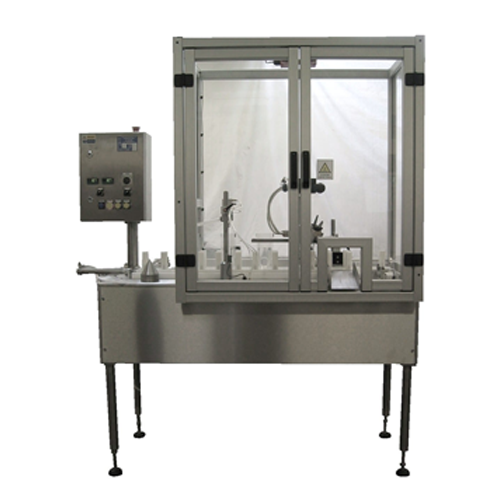
Bag and pouch filling solution for liquid products
Efficiently package diverse liquid products with precision and speed, ...
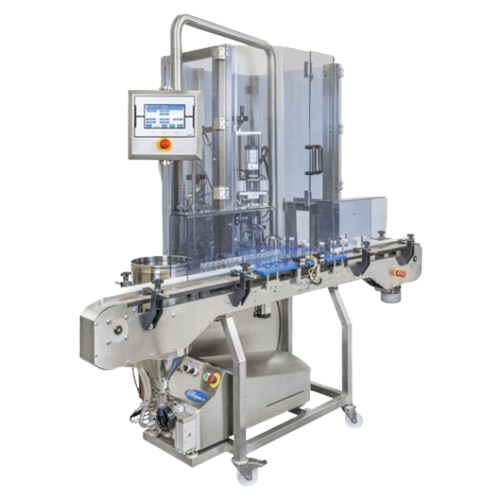
Filler and capper for bottles and jars
Optimize your production with a compact filling and capping solution that delivers f...
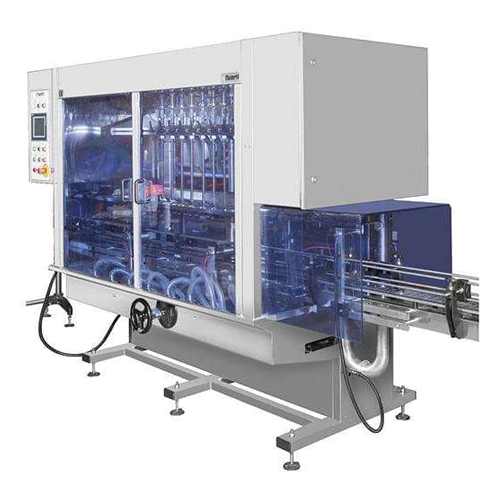
Automatic flowmeter filler for liquid packaging
Streamline your liquid production with precise filling capabilities, reduc...
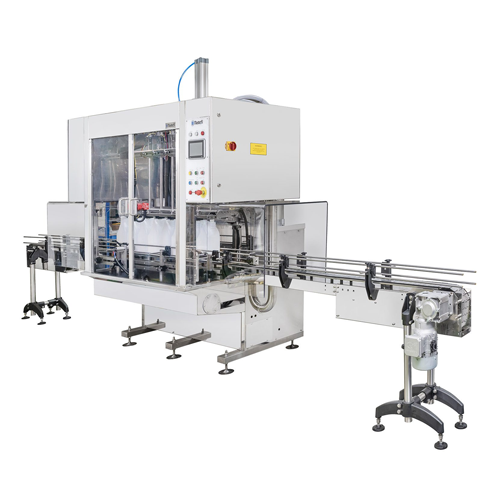
Automatic volumetric filler for liquid products
Optimize your production with this high-precision volumetric filler, desig...
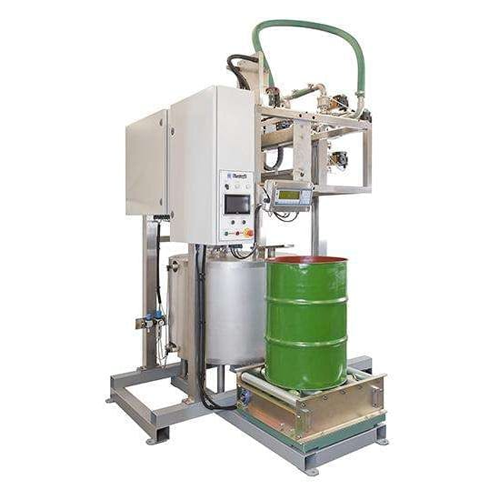
Drum decanting unit for high viscosity liquids
Efficiently decant high viscosity liquids like solvent-based paints and ess...

Semi-automatic flowmeter boom filler for large volume containers
Effortlessly handle large volume liquid filling with pr...
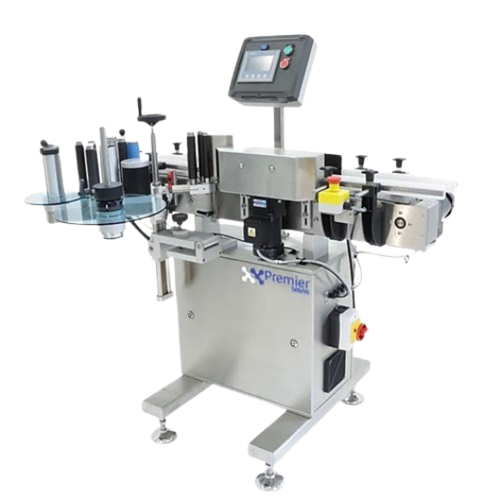
Compact wraparound labelling system for bottles
Streamline your packaging process with a fast and reliable wraparound labe...
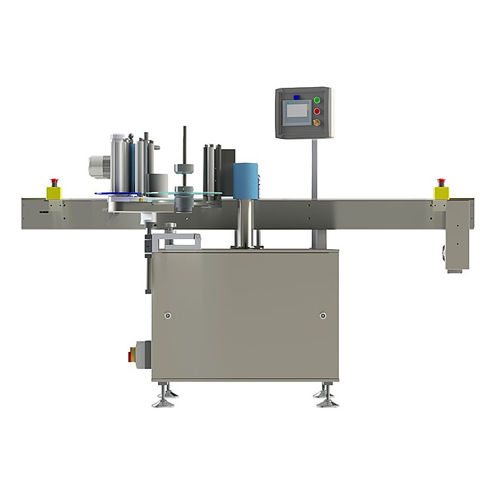
High precision three-roller wraparound labeller
Achieve precise label placement on round containers effortlessly with a th...
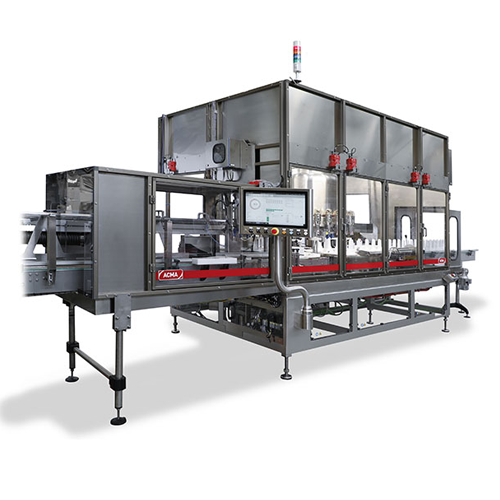
Rotary filler capper for personal care products
Ensure consistent filling and capping of liquid products with high-speed p...
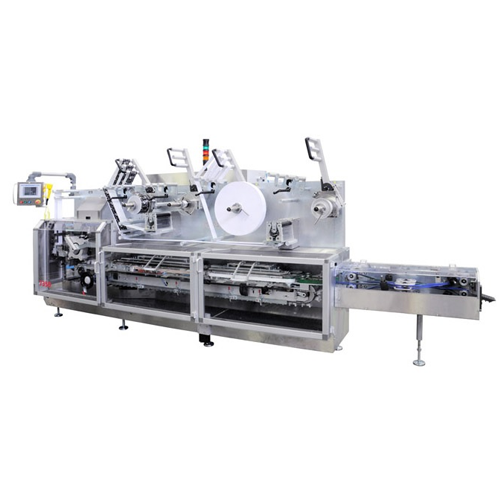
Soap bar fold wrapping solution
Ensure precise wrapping and sealing of soap bars with continuous motion, enhancing efficienc...
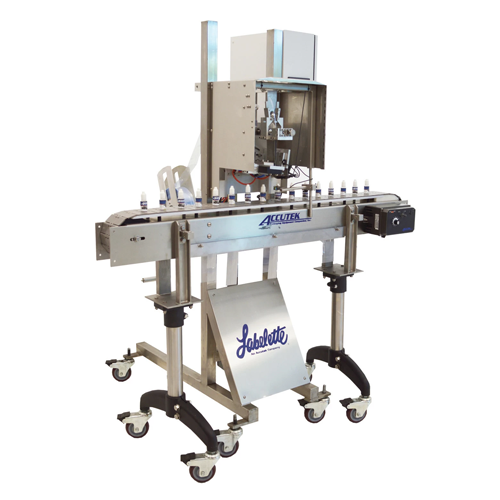
Tamper evident banding system
Ensure product integrity with a high-speed system designed to apply tamper-evident bands effic...
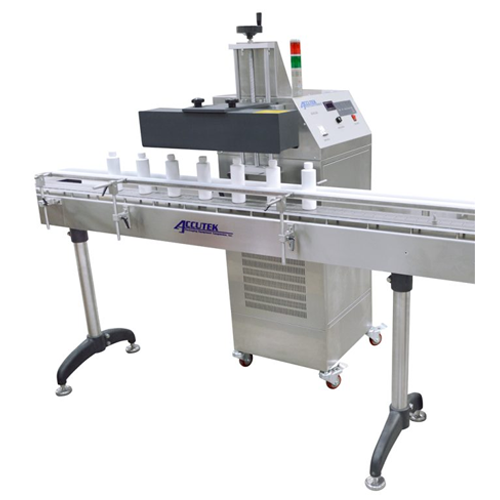
Automatic induction sealer for cap sealing
Achieve precise and reliable cap sealing with our advanced induction technology...
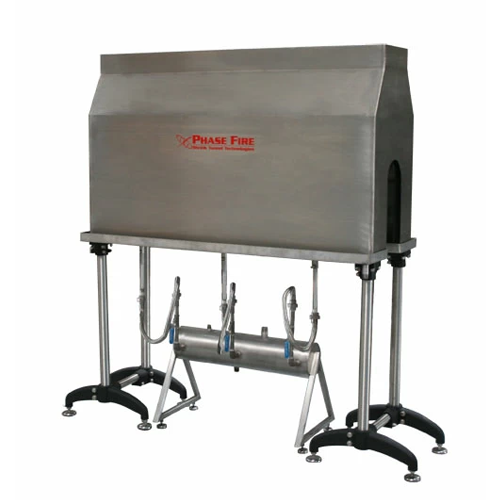
Steam shrink tunnels for versatile packaging
Enhance your packaging efficiency with this adaptable steam shrink tunnel, de...

Auto-indexing filler for aqueous solutions and light oils
Streamline your bottling process with this six-head filler, pe...
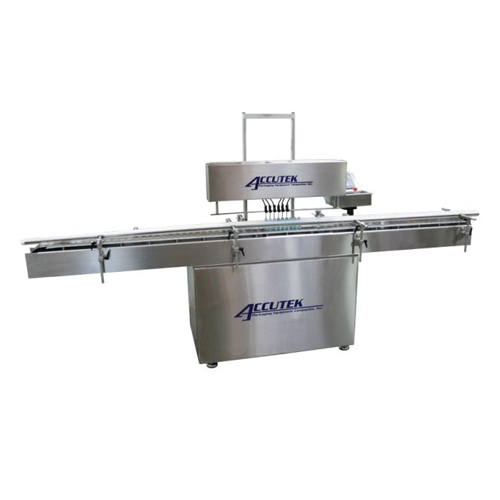
Automatic timed flow volumetric filling machine
Streamline your liquid packaging process with precise volumetric filling o...
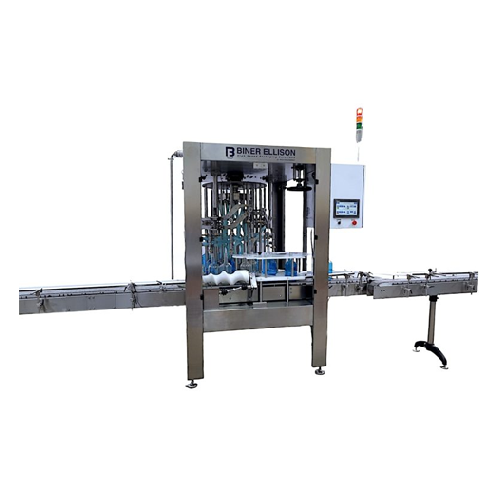
Rotary overflow filler for non-carbonated liquids
Achieve precise fill levels effortlessly with a high-speed rotary overf...
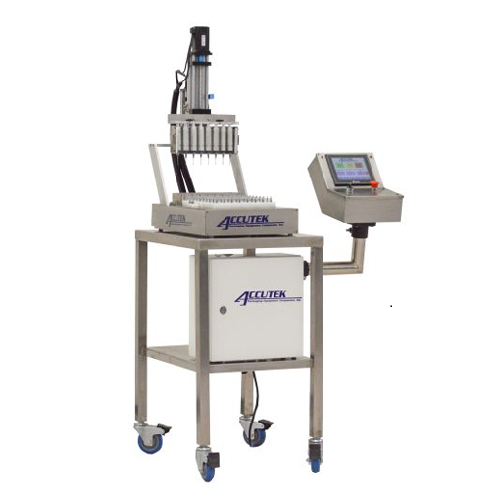
High precision automatic mini dose filler
Achieve unparalleled precision when filling small volumes, from 0.1 ML to 200 ML...

Rotary volumetric filling solution for viscous products
Achieve precision in volumetric filling with a machine designed f...
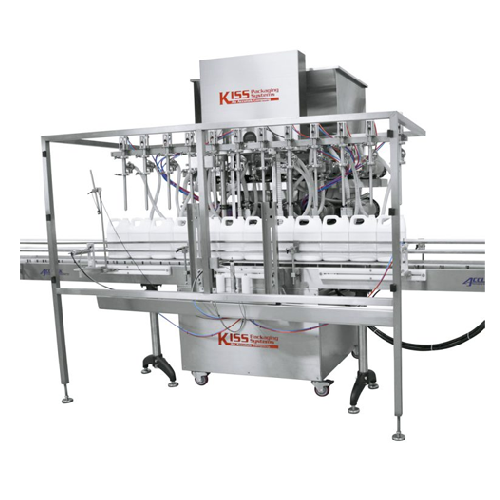
Automatic positive displacement filler for various liquids
Achieve precision and versatility in liquid filling operation...
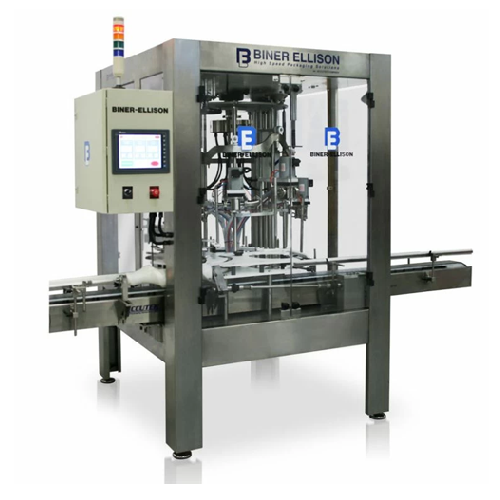
Automatic positive displacement bottle filler
Streamline your liquid filling operations with precision and flexibility, id...
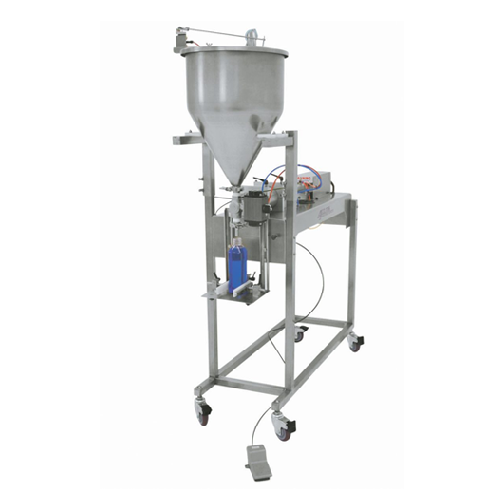
Semi-automatic volumetric piston filler
Achieve precise filling of diverse liquids and viscous products while minimizing wa...
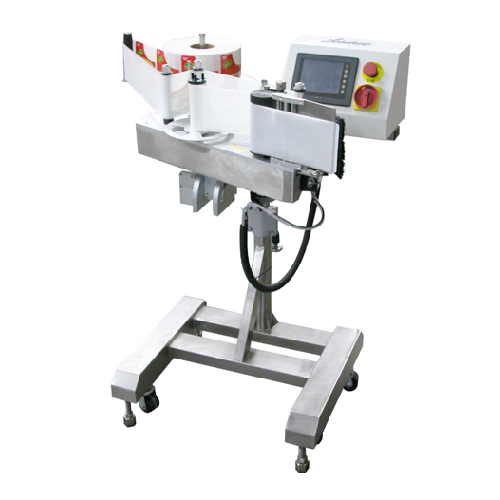
Semi-automatic pressure sensitive labeling system
Optimize your labeling efficiency with this versatile system designed t...
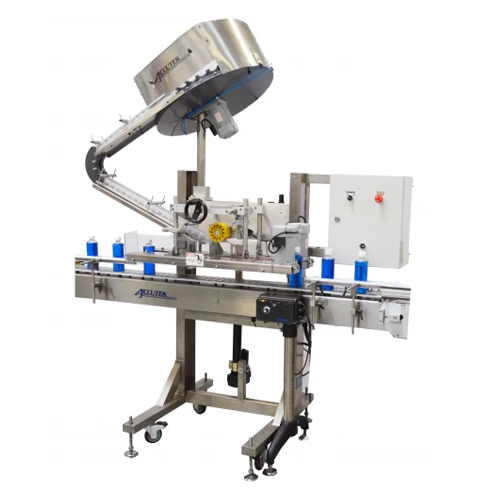
Automated snap capper for various container types
Eliminate manual errors and repetitive strain with this high-speed snap...
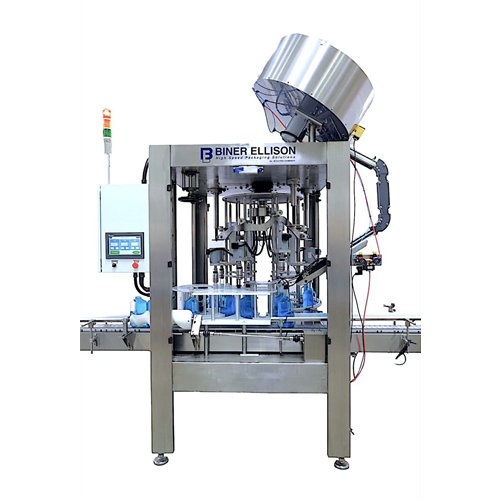
Rotary capper for high-speed bottling
Streamline your bottling process with a rotary capper designed to ensure accurate and...
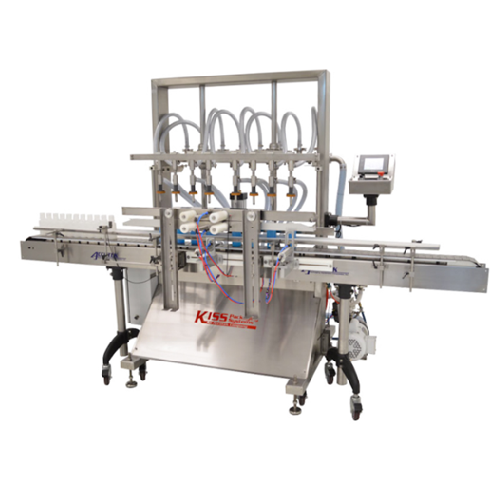
Automatic pressure overflow filler for low to medium viscosity liquids
Ensure consistent fill levels for low to medium ...
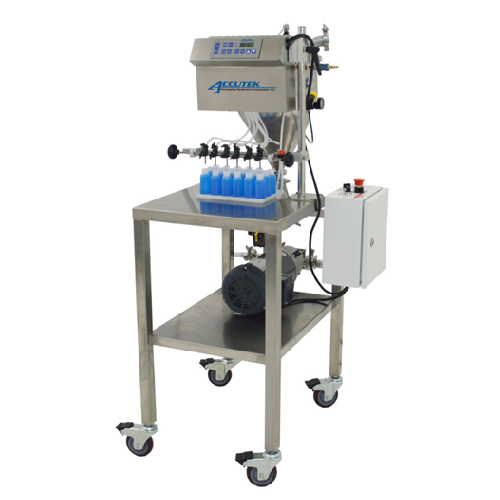
Semi-automatic timed flow filler for aqueous solutions
Handle diverse liquid filling needs with precision, from thin oils...

Semi-automatic overflow liquid filler
Optimize your production line with a reliable filling solution for low to medium visc...
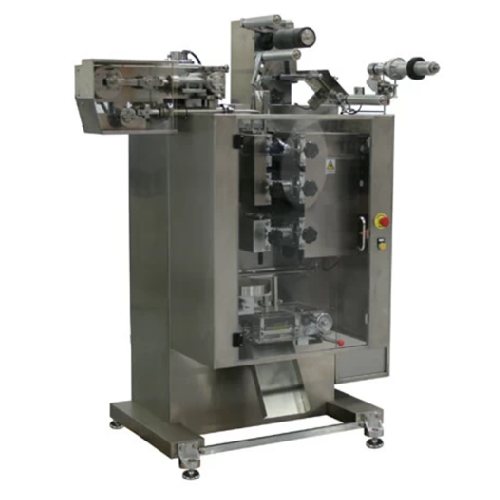
Form, fill, and seal system for single-use pouches
Achieve precise portion control and secure sealing with an integrated ...
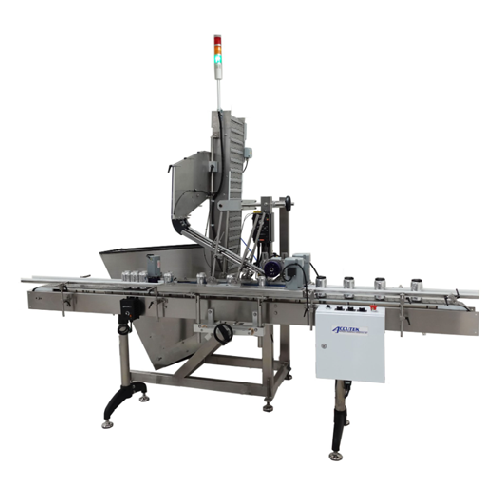
Indexed stomp capper for continuous bottle capping
Solve the challenge of manual snap cap placement with a seamless, cont...
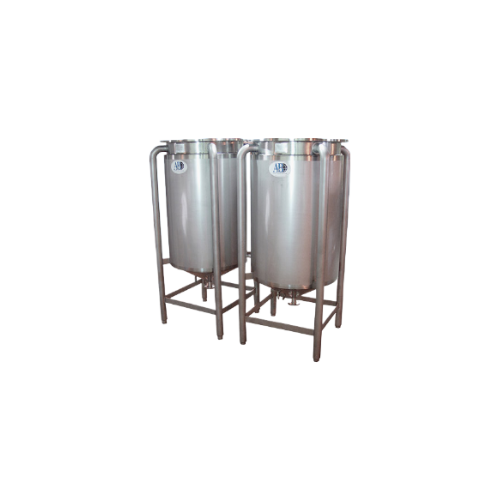
Customizable storage tanks for industrial use
Optimize your production with versatile storage tanks designed for precise c...
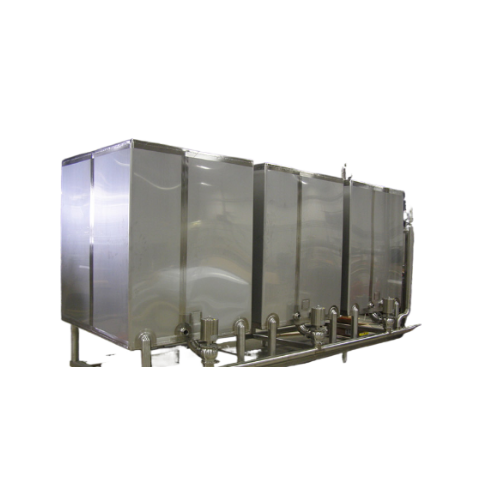
Clean-in-place tanks for industrial sanitation
Optimize your sanitation processes with clean-in-place tanks, designed to r...
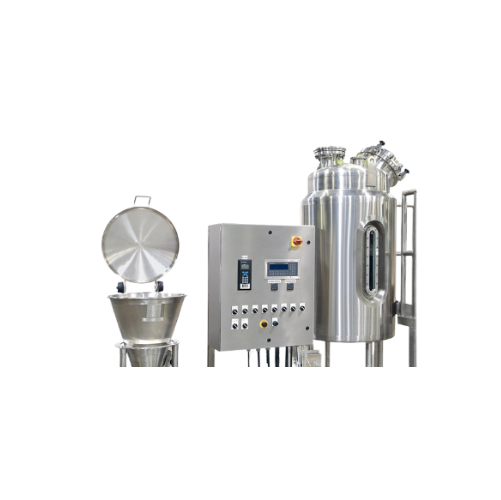
Powder induction system for efficient liquid powder mixing
Achieve precise and dust-free powder incorporation into liqui...
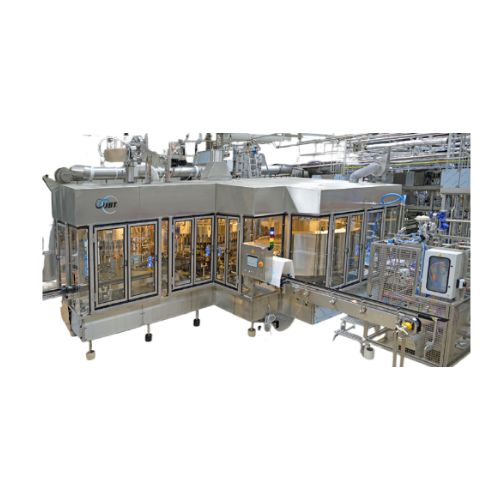
Rotary level filler for low to high viscosity liquid products
Ensure precise fill levels and enhance production efficien...
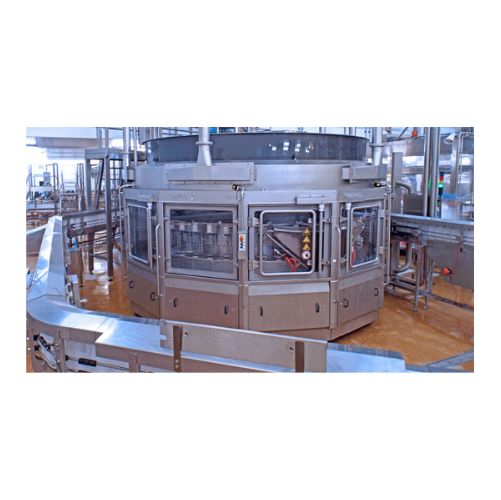
Industrial weight filler for bottles and jars
Achieve precise product filling with our weight filler system, expertly desi...
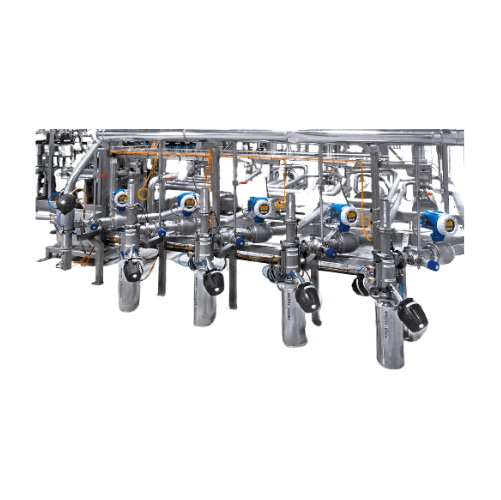
3a certified product recovery system for food and pharmaceuticals
Optimize your production line with a system designed ...
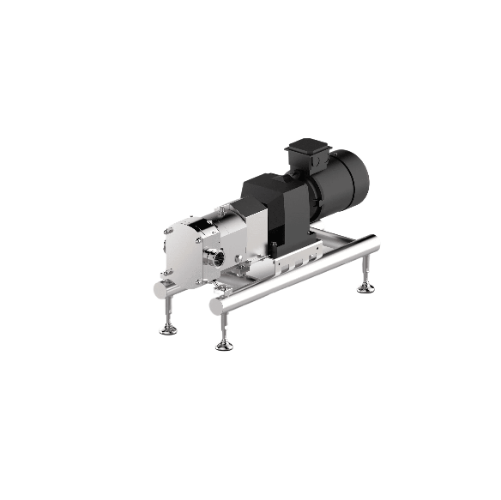
Rotary lobe pump for viscous media
Ensure precise handling and gentle transfer of viscous liquids with advanced rotary lobe...
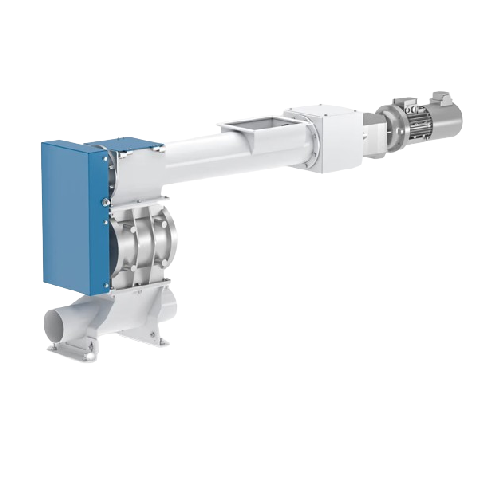
Continuous raw material distribution screw doser
Optimize your material flow with a screw doser designed for precise and c...
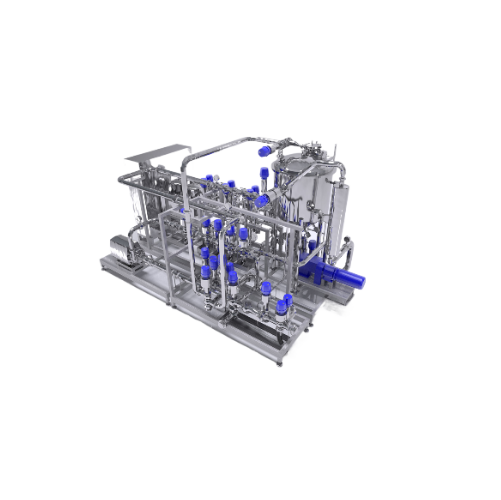
Tailor made mixing systems for personal and home care products
Achieve precise mixing for liquid formulations with conti...
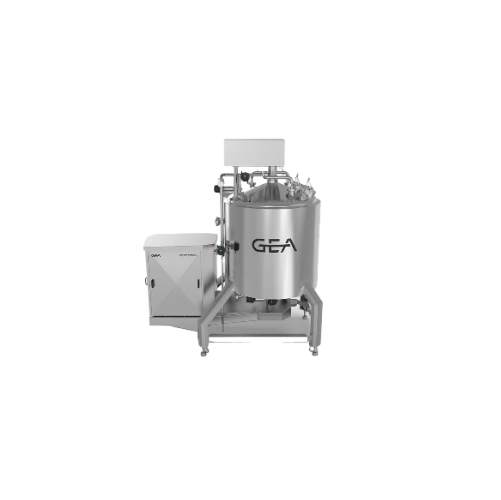
High shear mixer for dairy and personal care products
Achieve consistent emulsification and stable homogeneity with high ...
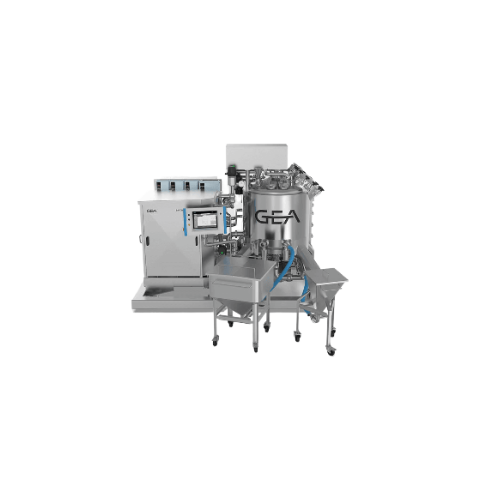
High shear test mixers for developing new products
Streamline product development with high shear test mixers, allowing y...
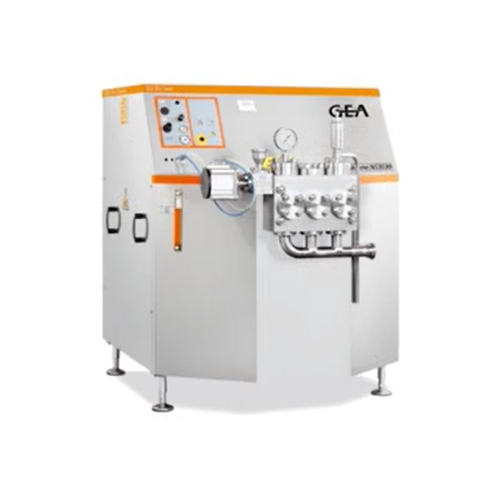
High pressure industrial homogenizer
Enhance liquid formulations with precision and efficiency—our high-pressure homogenize...
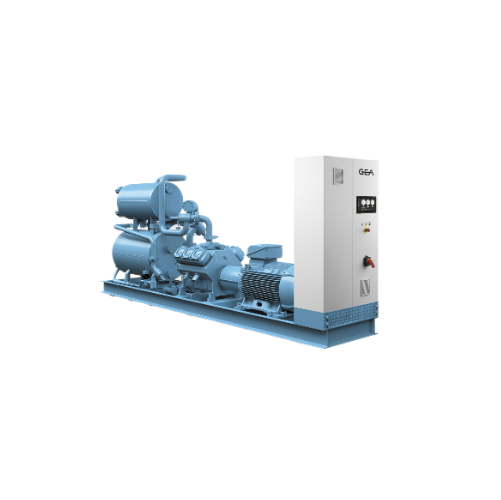
Ammonia chiller for industrial refrigeration
Achieve optimal energy efficiency and reduced operational costs in your cooli...
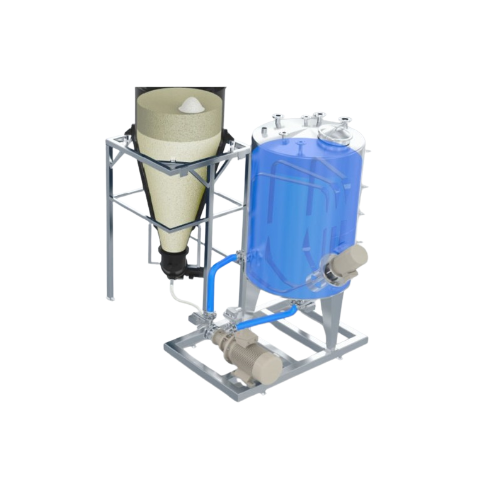
Powder wetting and dispersion system
Revolutionize your production with a system that seamlessly inducts, wets, and dispers...
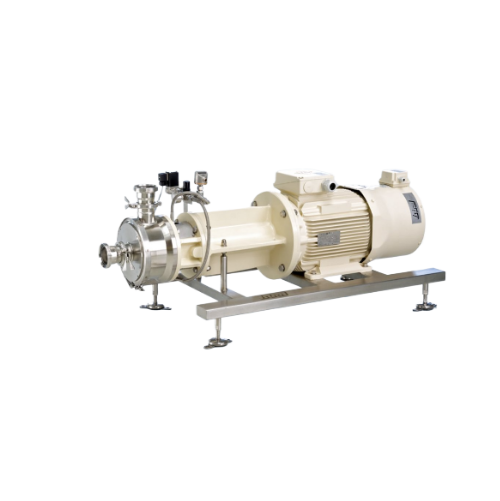
Inline disperser for homogeneous emulsions and suspensions
Achieve precise control over particle size and distribution w...
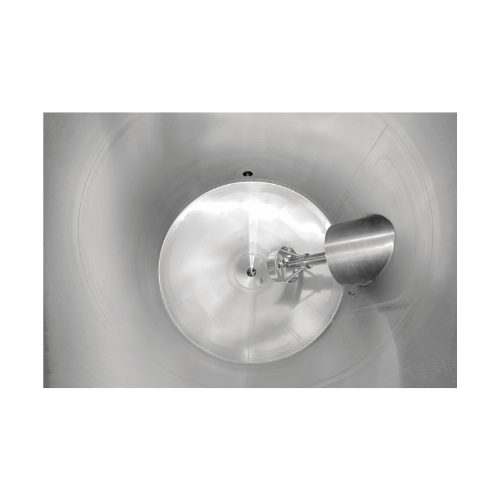
Industrial jetstream mixer for homogeneous mixing
Achieve consistent product quality with precise micro and macro mixing ...
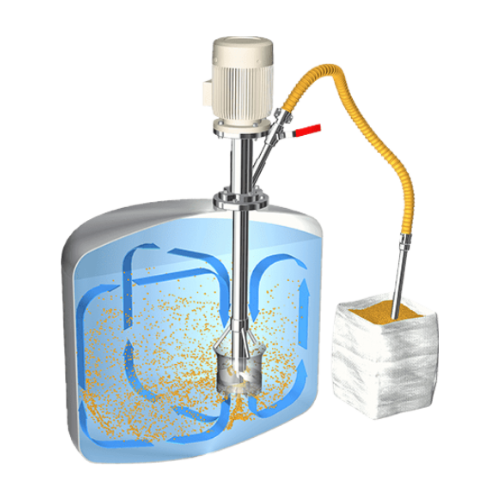
Low-dust powder induction mixer for liquids
Achieve dust-free induction and homogenization of powders in liquids with prec...

Hot fill bottling unit for juices and isotonic beverages
Ideal for producers handling delicate or specialty liquids, this...
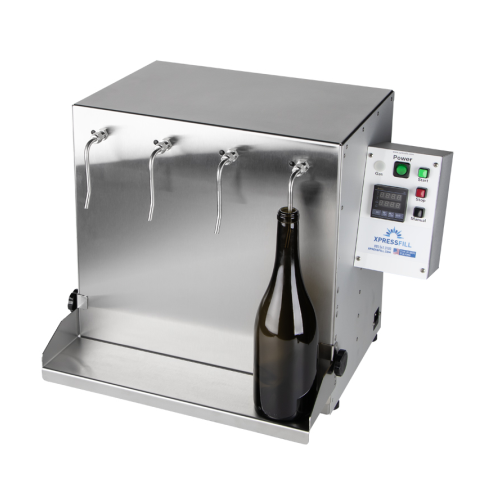
Volumetric bottle filler for distilled spirits
Ensure precise volume control and compliance with regulatory standards in y...
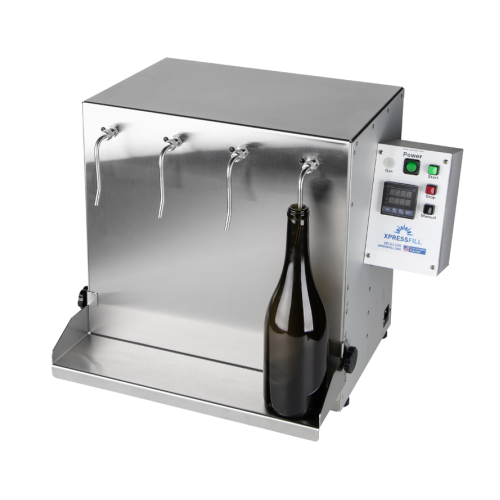
Volumetric bottle filler for high proof spirits
Ensure precise and consistent bottle filling for high-proof spirits with t...
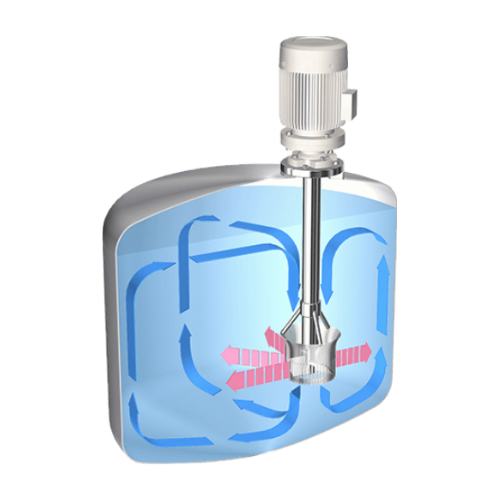
High-performance dispersing and mixing solutions
Enhance your mixing and dispersing processes with advanced fluid stream t...
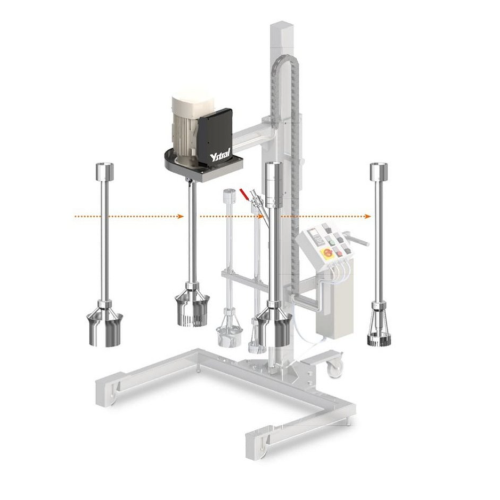
Multipurpose mixing equipment for chemical and pharmaceutical production
Achieve unparalleled flexibility with modular,...
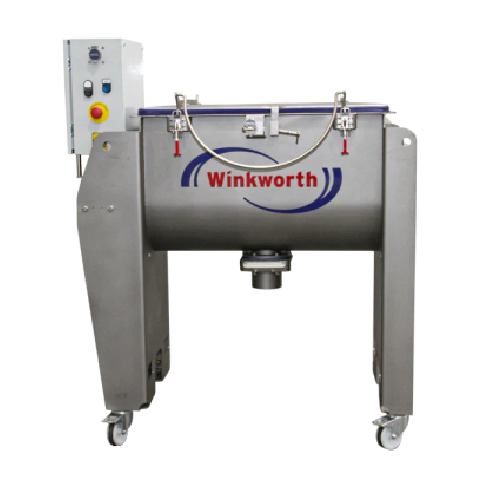
Horizontal shaft mixer for free-flowing materials
Achieve consistent mixing of diverse free-flowing materials with a reli...
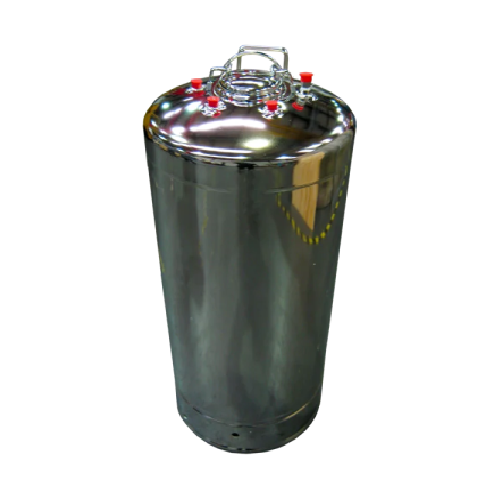
Pressure vessel for hazardous and non-hazardous liquids and gases
Ensure safety and compliance when handling hazardous ...
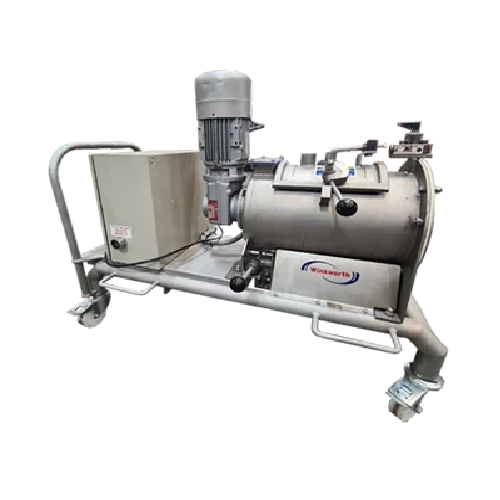
Industrial mixers for hire
Optimize your production line with versatile mixers designed for precision blending, heating, and...
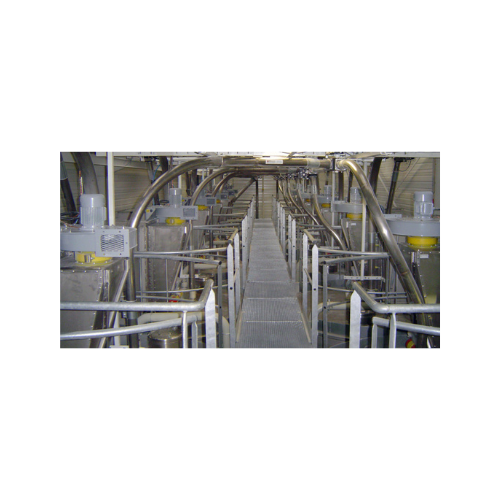
Atex certified flanged round dust collectors
Designed for potentially explosive environments, these flanged round dust col...
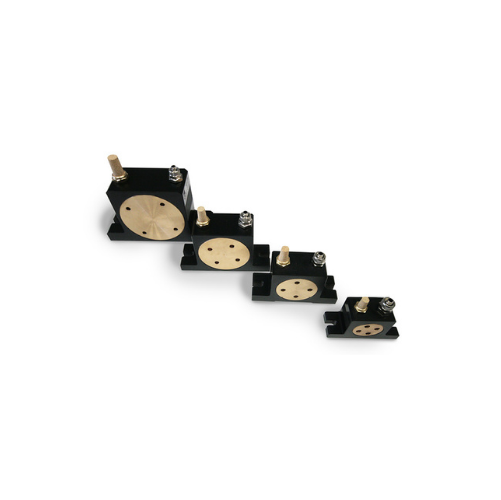
Rotary roller vibrators for material flow assistance
Enhance material flow efficiency in your production line with high-f...
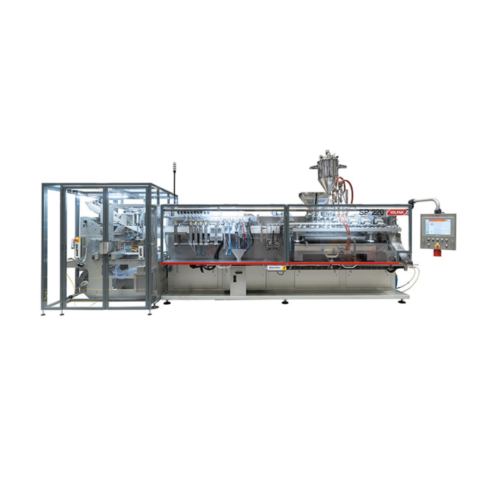
Stand-up pouch packaging for various industries
Elevate your packaging capabilities with a high-speed horizontal pouching ...
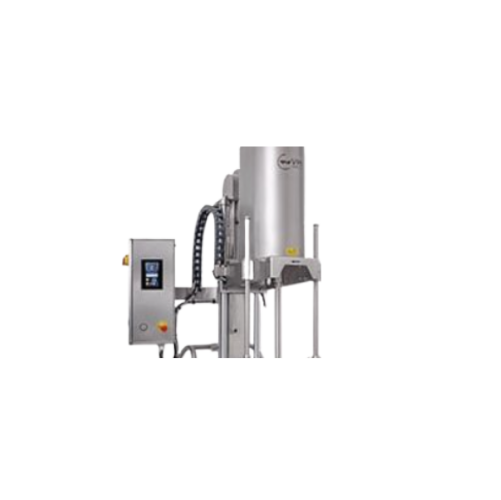
Adjustable industrial mixers for thick product blending
Experience precise blending and control for thick and high-viscos...
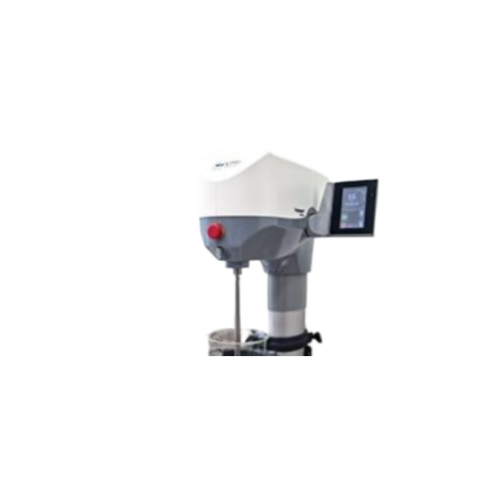
Vacuum homogenizers for cosmeto-pharma and fine chemistry
Bring precision and efficiency to your formulation processes w...
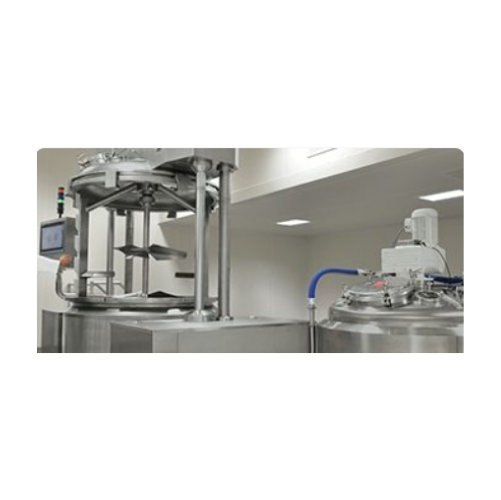
Vacuum homogenizer for cosmeto-pharma applications
Optimize your formulations with our vacuum homogenizers, ensuring prec...

Vacuum homogenizer for cosmetics and pharmaceuticals
Optimize your production with precision mixing and homogenizing, ess...
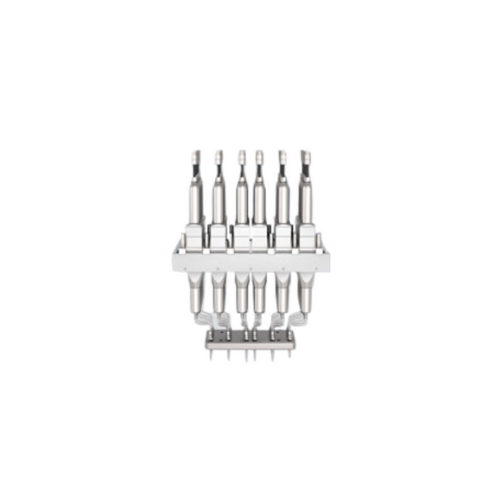
Fully automatic filling lines for liquids
Achieve precise dosing and filling of liquids with minimal cycle times using com...
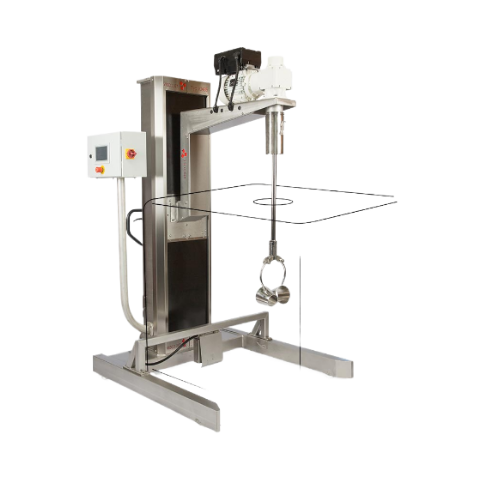
Industrial stativ mixer with adjustable height
Achieve precise mixing and stirring across diverse batches with a mobile, a...
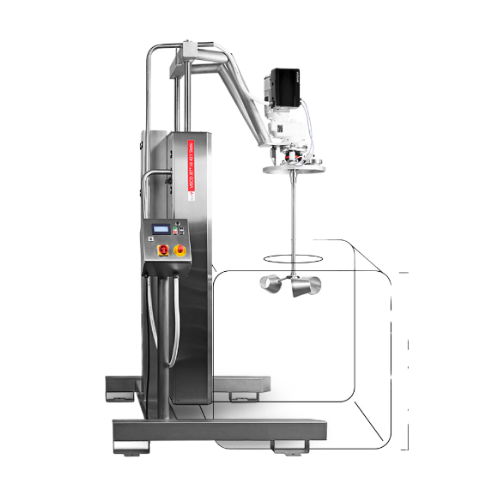
Industrial mixer for product-critical processes
When dealing with high-hygiene requirements and complex mixing tasks acros...
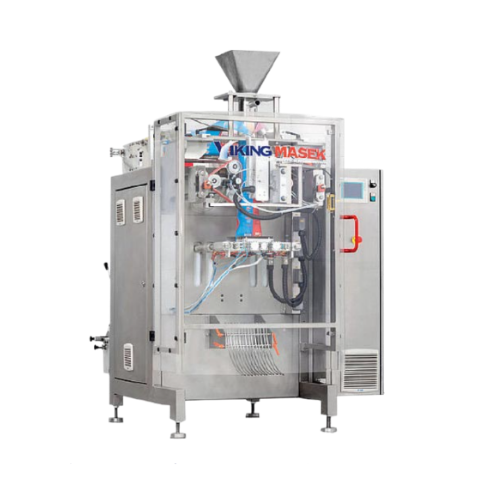
Continuous motion liquid packaging system
Achieve precise and clean liquid packaging with advanced servo-driven squeegee s...
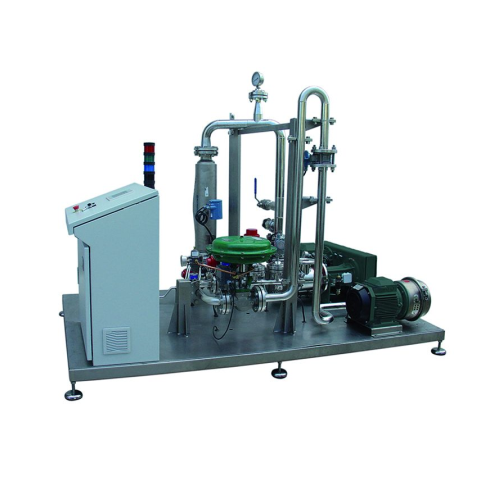
Complete mixing systems for industrial applications
Optimize your production efficiency and product consistency with adva...
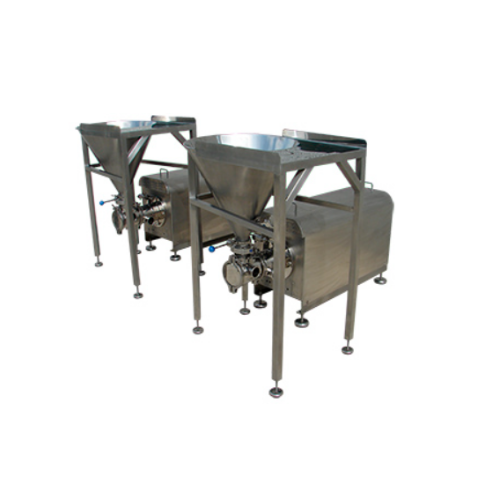
In-line mixer for solid-liquid blending
Efficiently combine powdered and liquid ingredients in real-time with high-shear pr...
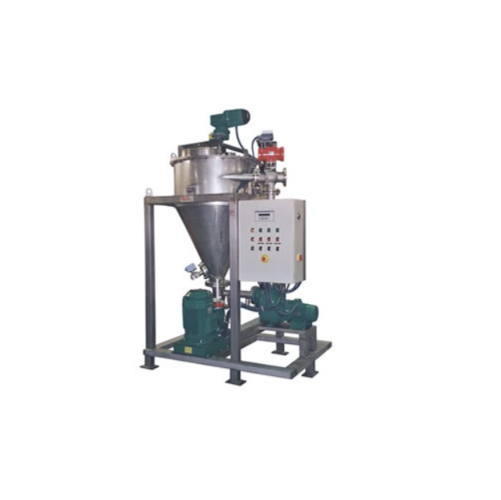
Solid-liquid in-line mixer for chemical product manufacturing
Effortlessly integrate and disperse high-solids content in...
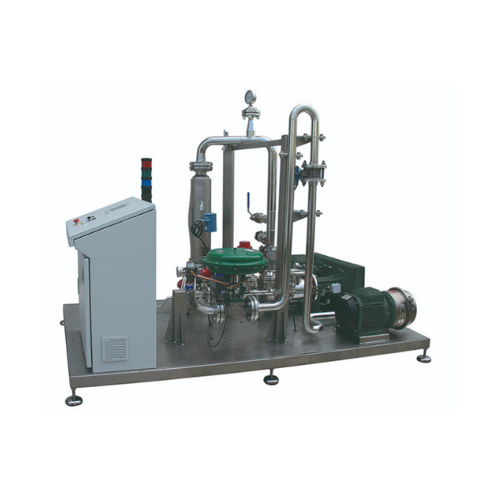
Complete mixing solution for food, cosmetics, and chemical industries
Optimize your production line with a system that ...
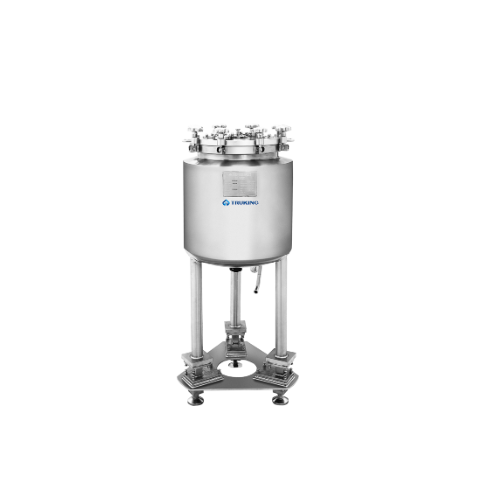
Sanitary vessels for pharmaceutical applications
Ensuring the highest standards of aseptic processing, these sanitary vess...
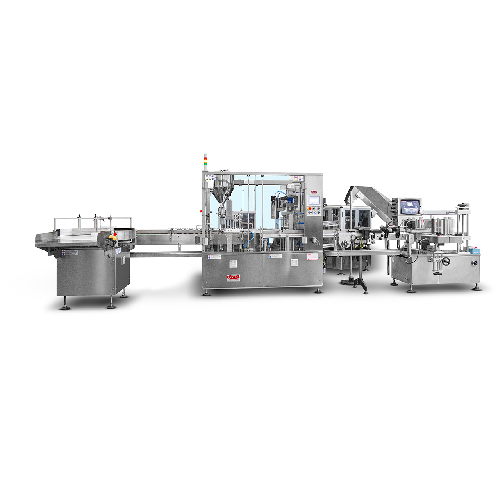
Medium volume bottle and jar filling system
Efficiently manage filling operations for diverse liquid and semi-dense produc...
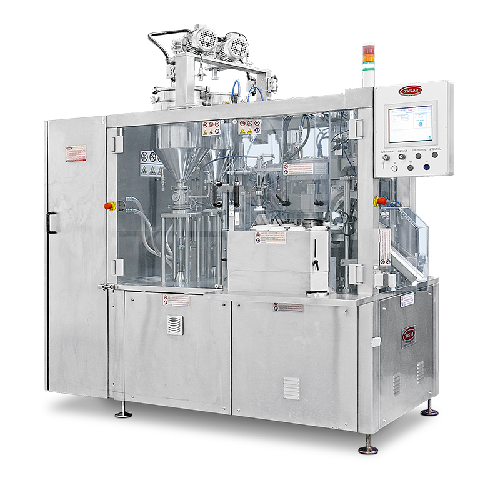
Automatic tube filling for multi-color products
Achieve precision in multi-color product packaging with seamless co-extrus...
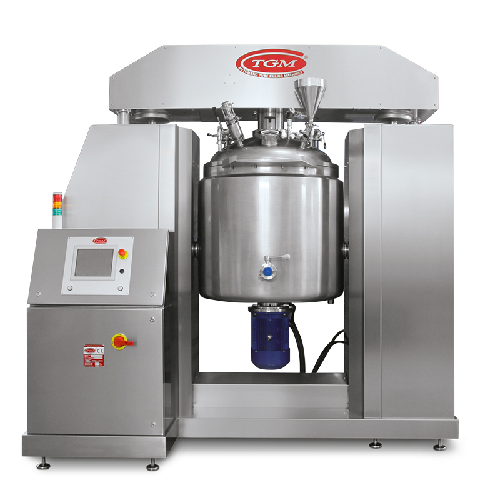
Turbo emulsifier for creams, gels, toothpastes
Achieve perfect emulsification and homogenization for your creams, gels, an...
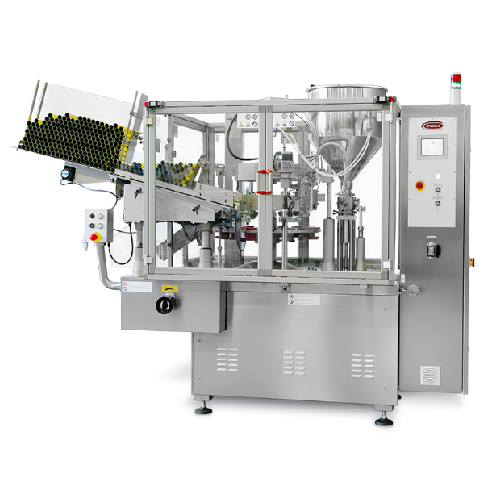
Automatic tube filling solution for medium to high volume production
Boost your production line efficiency with a robus...
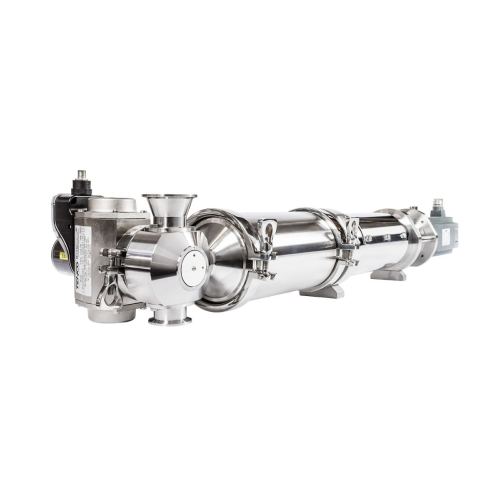
Volumetric piston fillers for liquid and dense products
Perfect for diverse packaging needs, these volumetric piston fill...
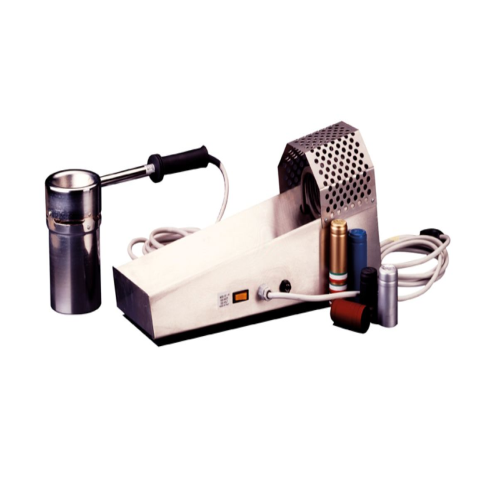
Manual heat shrink capsule applicator
Quickly and precisely apply shrink capsules to bottlenecks, ensuring perfect adherenc...
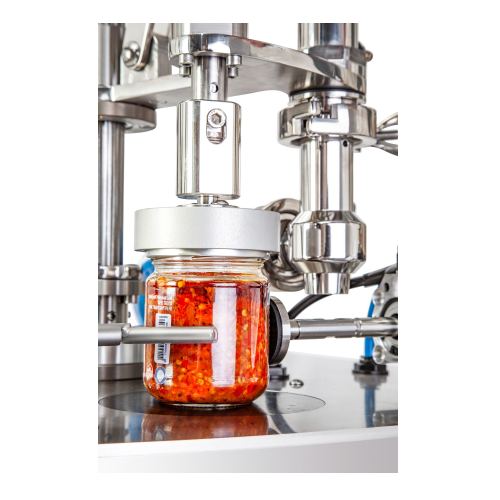
Manual system for filling and capping jars
Ideal for efficiently handling liquid and semi-dense products, this manual syst...
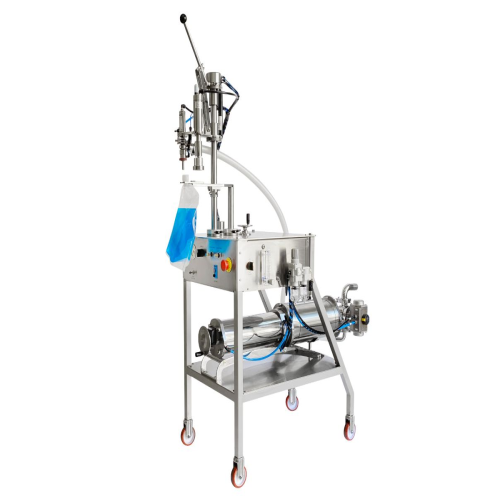
Manual filling and capping for spouted pouches
Optimize your production line with a versatile solution for filling and cap...

Pneumatic syringe dosing system
Streamline your liquid dosing process with precision and efficiency, ensuring each applicati...
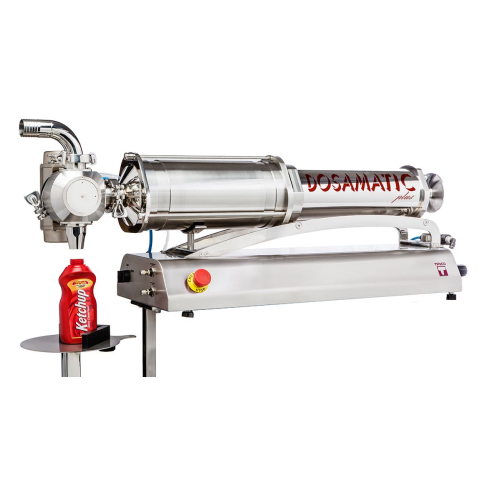
Accurate volumetric filler for liquid and semi-dense products
Achieve precise dosing and filling of various liquid and s...
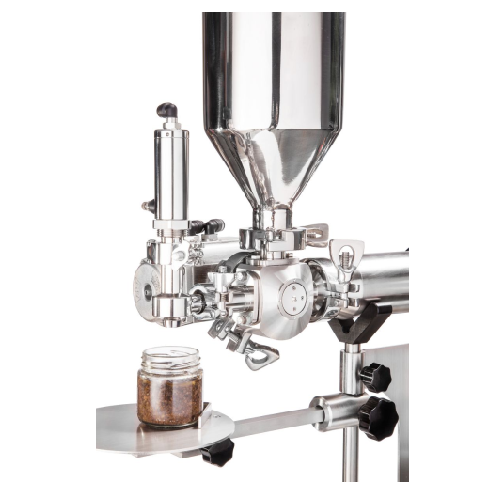
Bench-top piston filler for liquid and semi-dense products
Optimize your filling precision with a versatile piston fille...
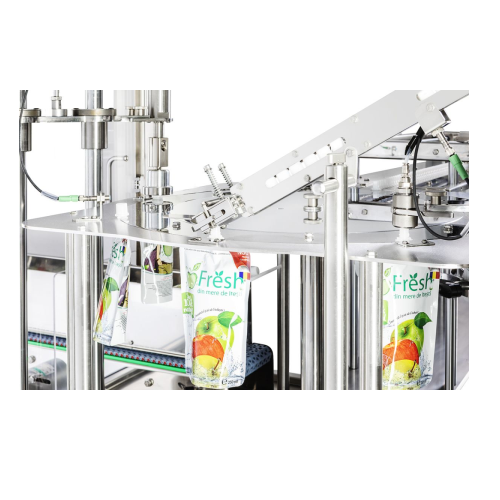
Automatic line for filling and capping spouted pouches
Streamline your production line with high-speed filling and cappin...
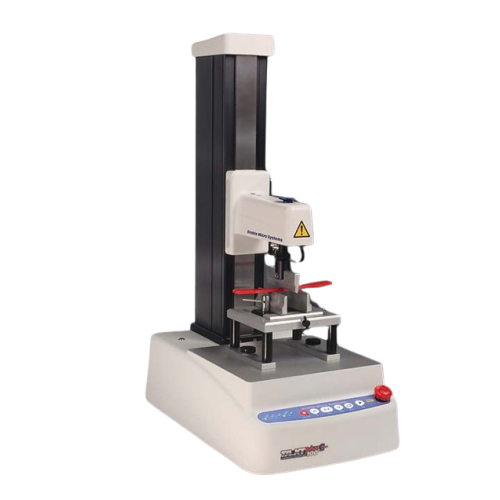
High-force texture analyser for precise measurement
Achieve unparalleled precision in texture analysis for high-force app...
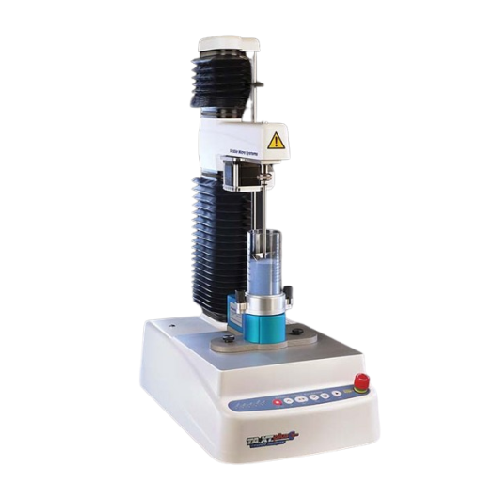
Powder flow measurement system
Achieve precise control over powder consistency and prevent process disruptions by assessing ...
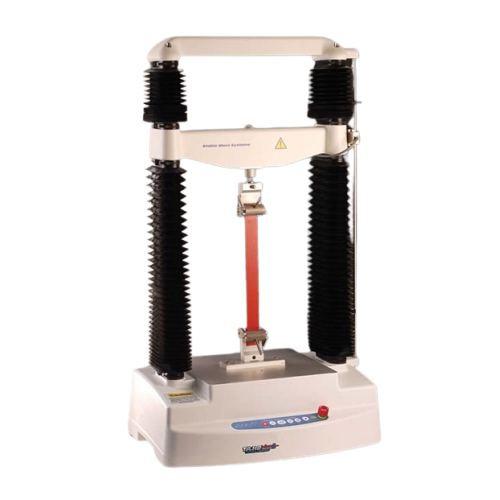
Texture analyzer for high force applications
Achieve precise texture measurement across a vast array of products with a so...
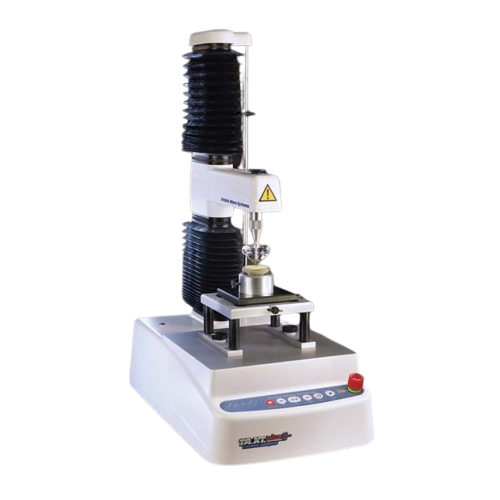
Texture analyser for food and cosmetics testing
Ensuring consistent product quality across diverse food and cosmetic appli...
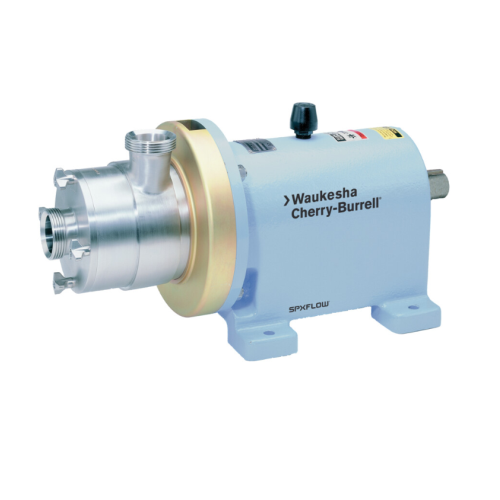
Shear pumps for continuous on-line dispersion
Effortlessly achieve consistent shearing and mixing with versatile shear pum...
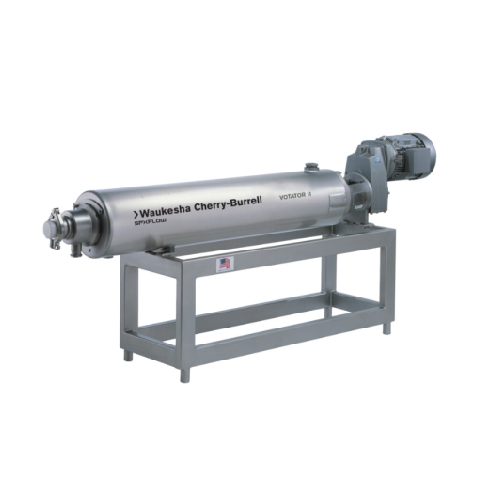
Food processing scraped surface heat exchanger
Enhance your production line with precise temperature control and continuou...
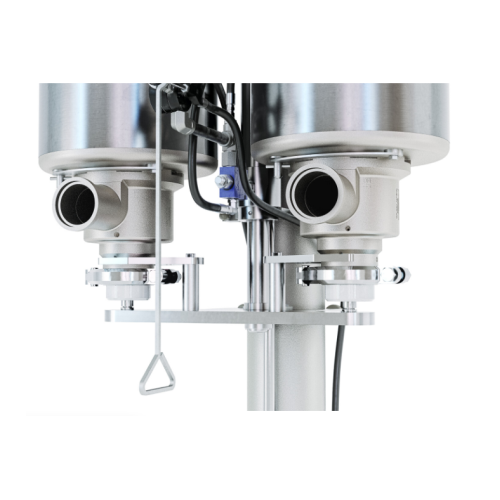
Vertical scraped surface heat exchanger for food processing
For continuous production that demands consistent texture an...

Line blender for continuous flow mixing
Achieve instantaneous mixing with minimal space and maintenance using a continuous ...
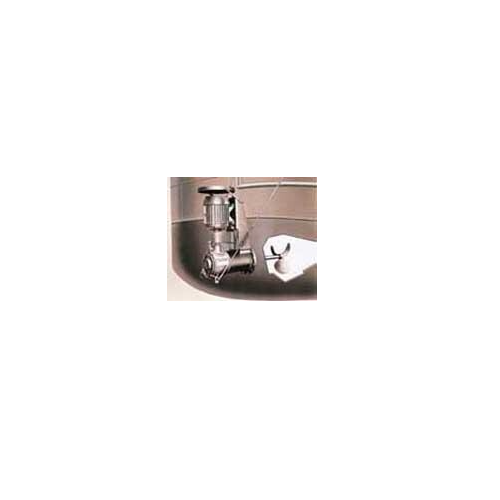
Side entry mixer for industrial tank applications
Ensure optimal mixing and blending of liquids and slurries with high ef...
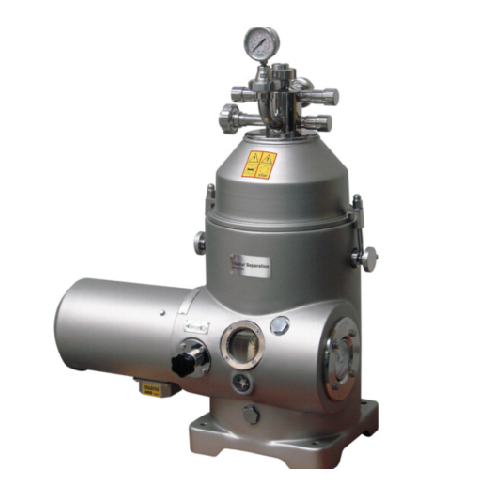
Solids retaining separator for liquid/liquid/solid separation
Achieve precise liquid-liquid-solid separation even with l...
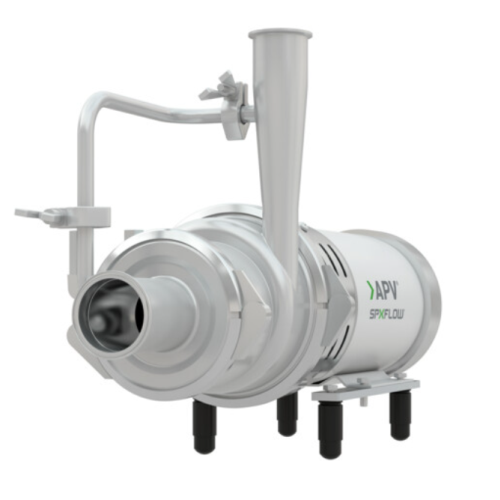
Self-priming centrifugal pump for entrained air handling
Effortlessly manage entrained air and foam in fluid processing w...
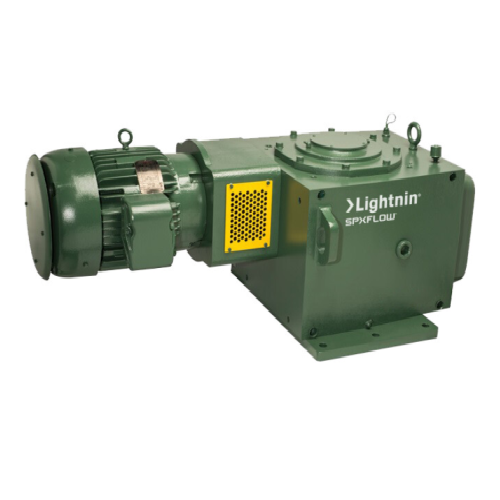
Medium torque top entering mixer for industrial applications
Optimize your mixing and blending operations with precise t...
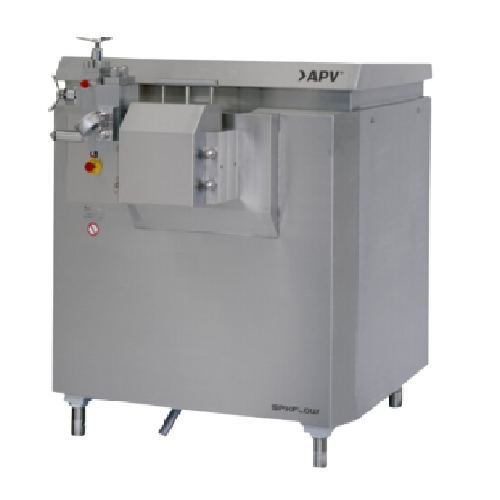
High pressure homogenizers for dairy and pharmaceutical applications
Optimize your production line with high-pressure h...
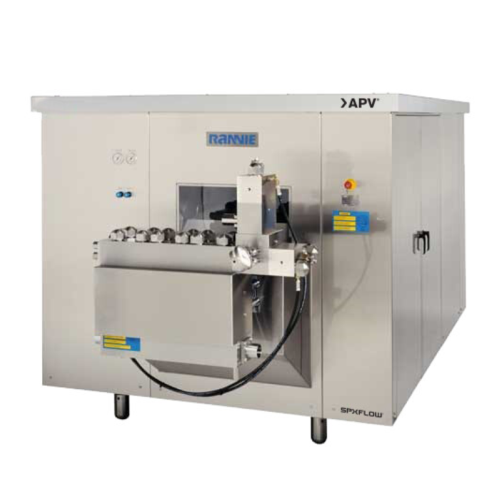
High pressure homogenizer for dairy and food processing
Achieve uniform particle size and enhance product stability with ...
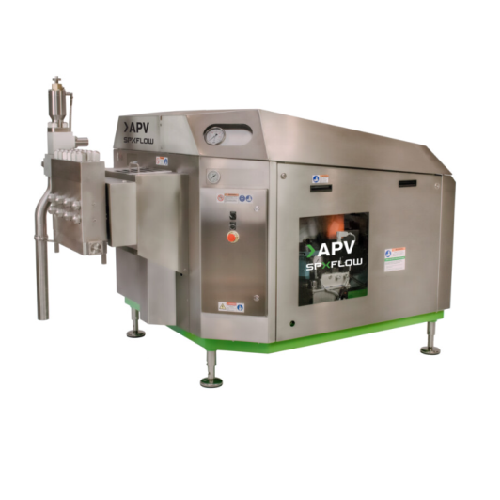
High pressure homogenizer for dairy and pharmaceutical industries
When uniform texture and stable emulsions are critica...
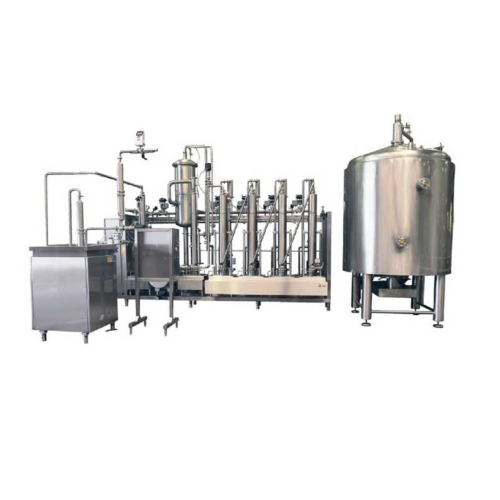
Scraped surface heat exchanger for high-viscosity products
Designed for handling high-viscosity products, this system en...
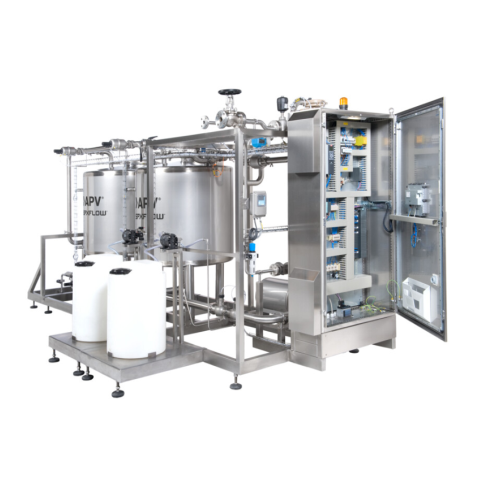
Clean in place (cip) system for industrial cleaning
Ensure optimal hygiene and production efficiency with a system that s...

Integrated preform production and bottling system for Pet bottles
Achieve seamless production of PET bottles, from pref...

Injection stretch-blow molding system for Pet containers
For manufacturers aiming to produce versatile, high-quality PET ...
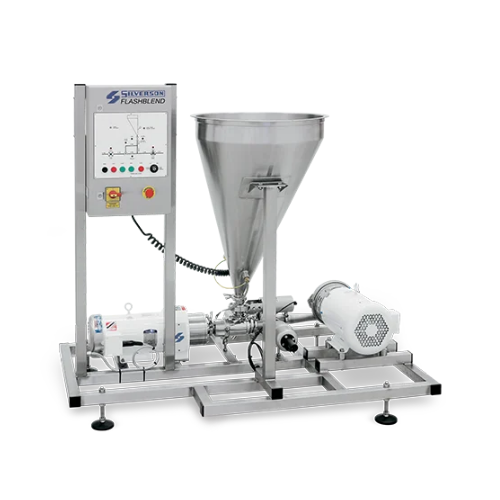
Powder/liquid mixing system for homogeneous dispersions
Struggling to integrate challenging powders into liquid formulati...
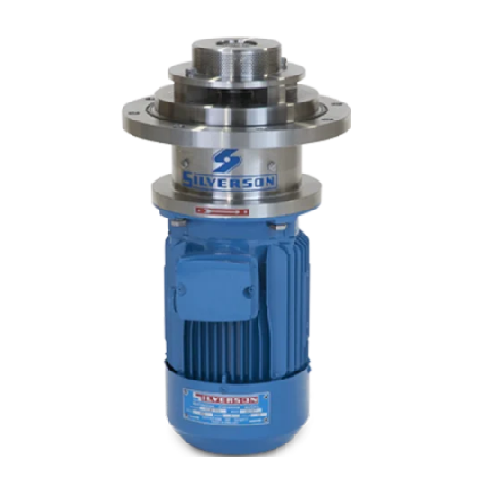
Bottom entry mixers for high viscosity products
Optimize your production line with mixers designed to handle both high and...
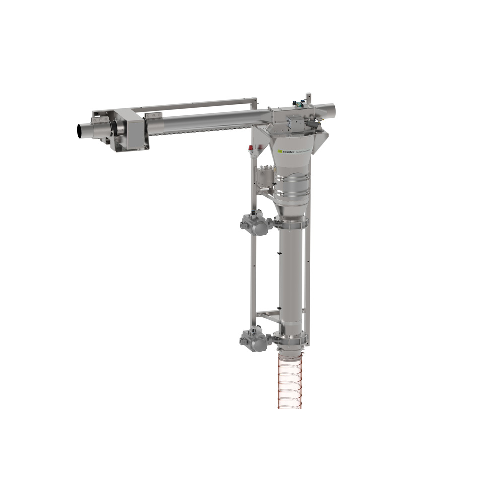
In-line metal detector for pneumatic systems
Ensure product purity and operational efficiency with a solution that effecti...
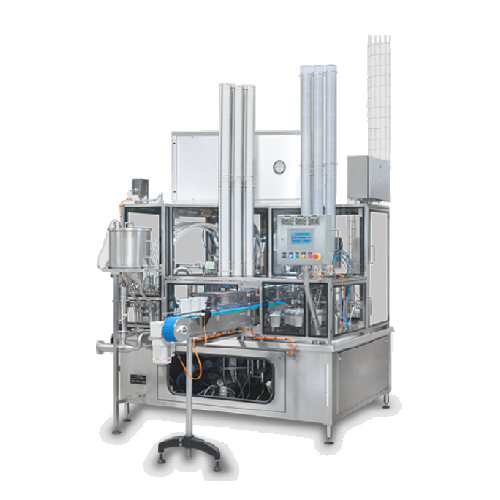
Filler for yoghurt and white cheeses
For manufacturers seeking efficient, versatile filling for products like yoghurt and s...
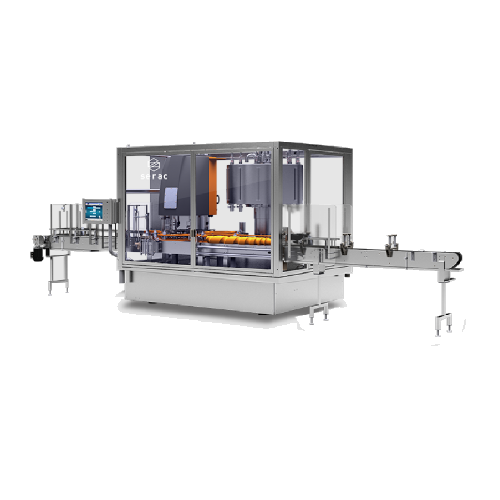
Versatile rotary filler-capper for liquid products
Optimize your liquid product production with a versatile solution that...
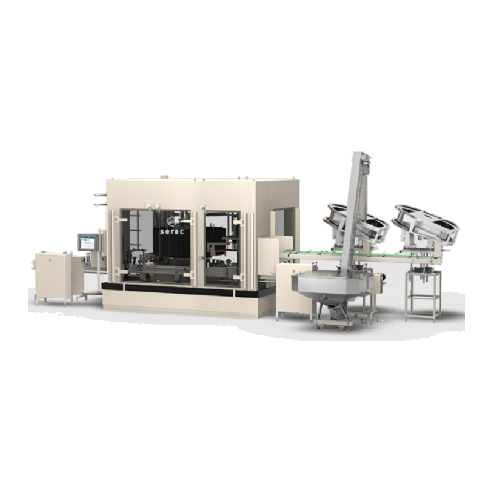
Anti-corrosion filling system for aggressive liquids
When dealing with corrosive liquids, ensure durability and safety wi...
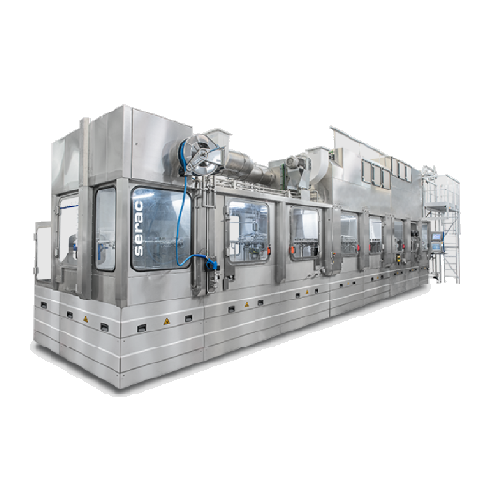
Aseptic filling technology for dairy products
Ensure product integrity and extend shelf life with a high-speed aseptic fil...
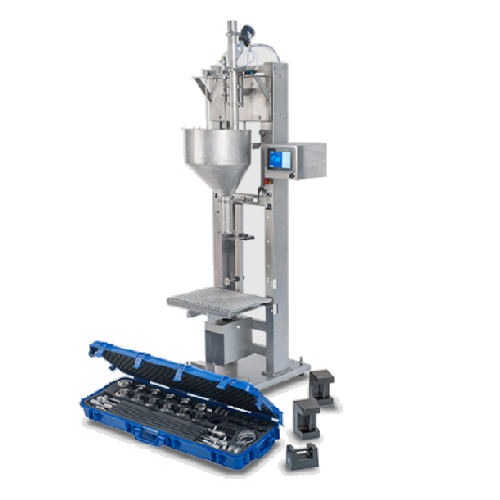
Semi-automatic weight filling system for liquid products
Achieve precise and versatile liquid filling performance with th...
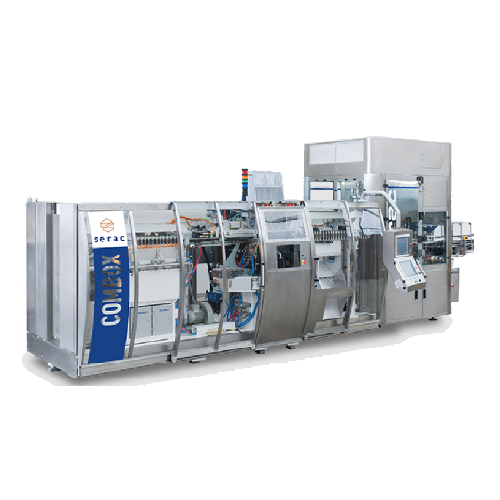
Blow-fill-cap solution for low/medium batch production
Streamline your production line with a compact blow-fill-cap syste...
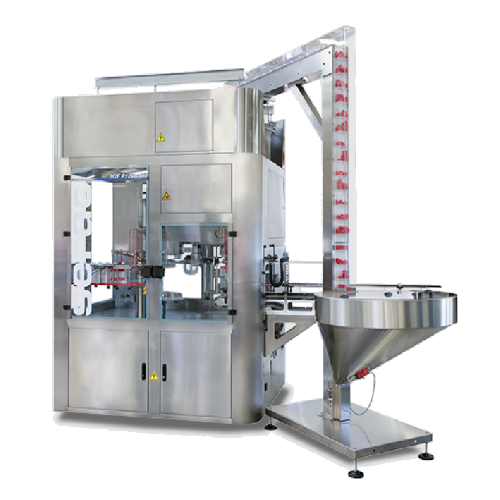
High hygienic filler for chilled beverages
Enhance cold beverage production with a modular, hygienic filler offering chemi...
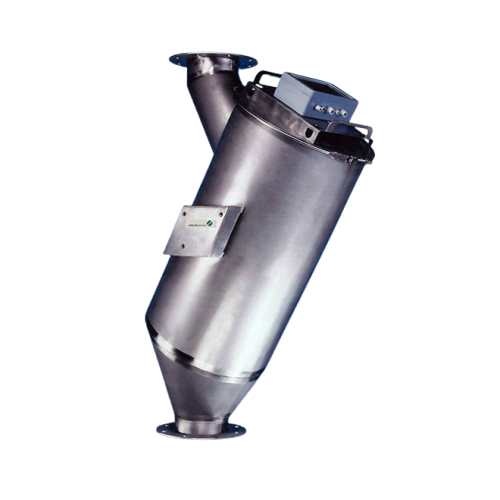
Solid flow meter for granular and powdered bulk materials
Ensure accurate mass flow measurement and seamless integration...
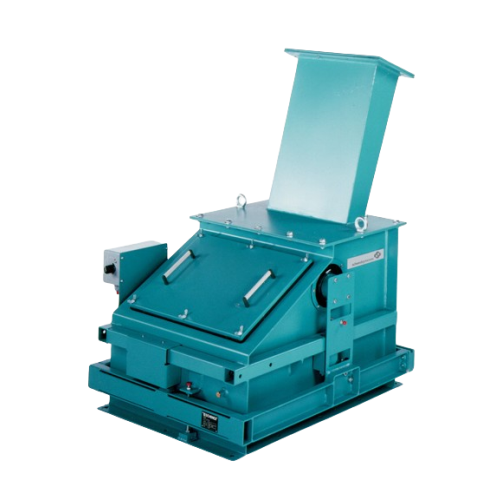
Solids flow meter for bulk solid streams
Ensure precise bulk material measurement with a system designed for accuracy and r...
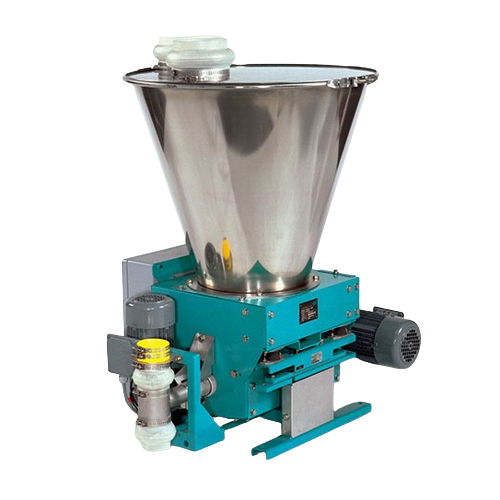
Loss-in-weight feeder for bulk solids
Ensure precise and reliable dosing of bulk solids with a compact feeder that eliminat...
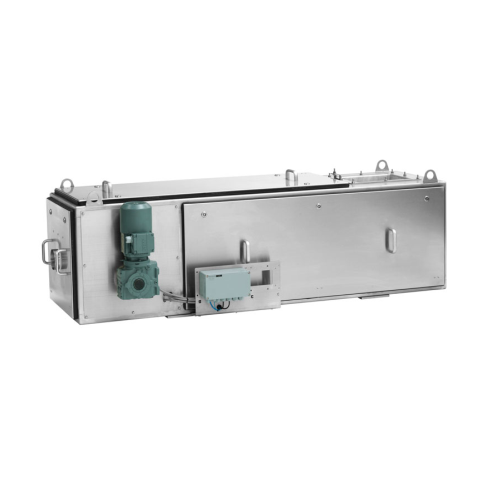
Continuous and batch feeding system for bulk materials
Achieve precise bulk material feeding with seamless integration in...
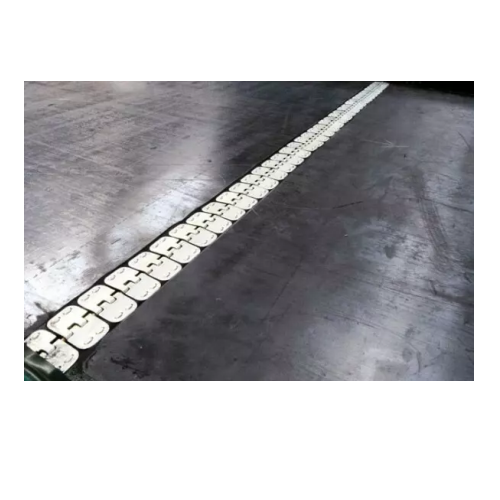
Optimal maintenance solution for industrial weighfeeders
Streamline your processing operations with a solution that minim...
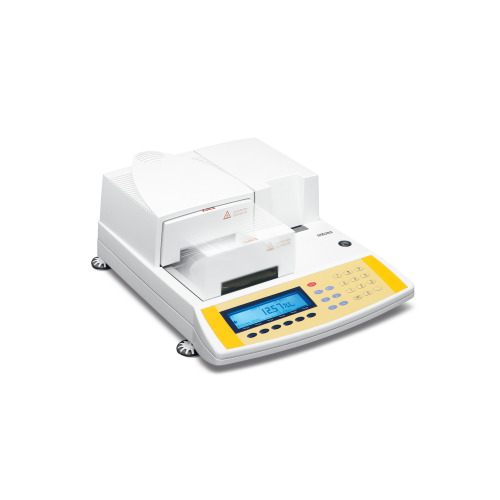
High-accuracy moisture analyzer for lab weighing
Achieve precise and reproducible moisture content determination for diver...
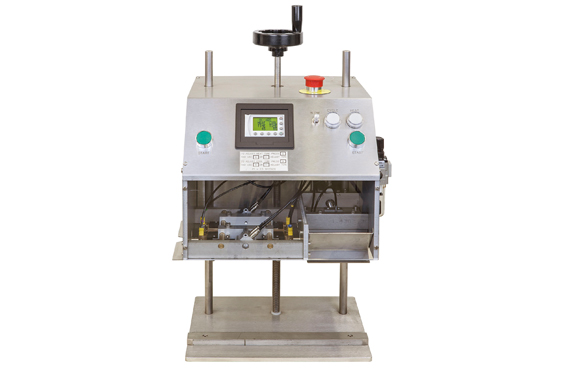
Manual plastic tube sealing equipment
Working in labs or with small batch production lines where you have to seal plastic o...
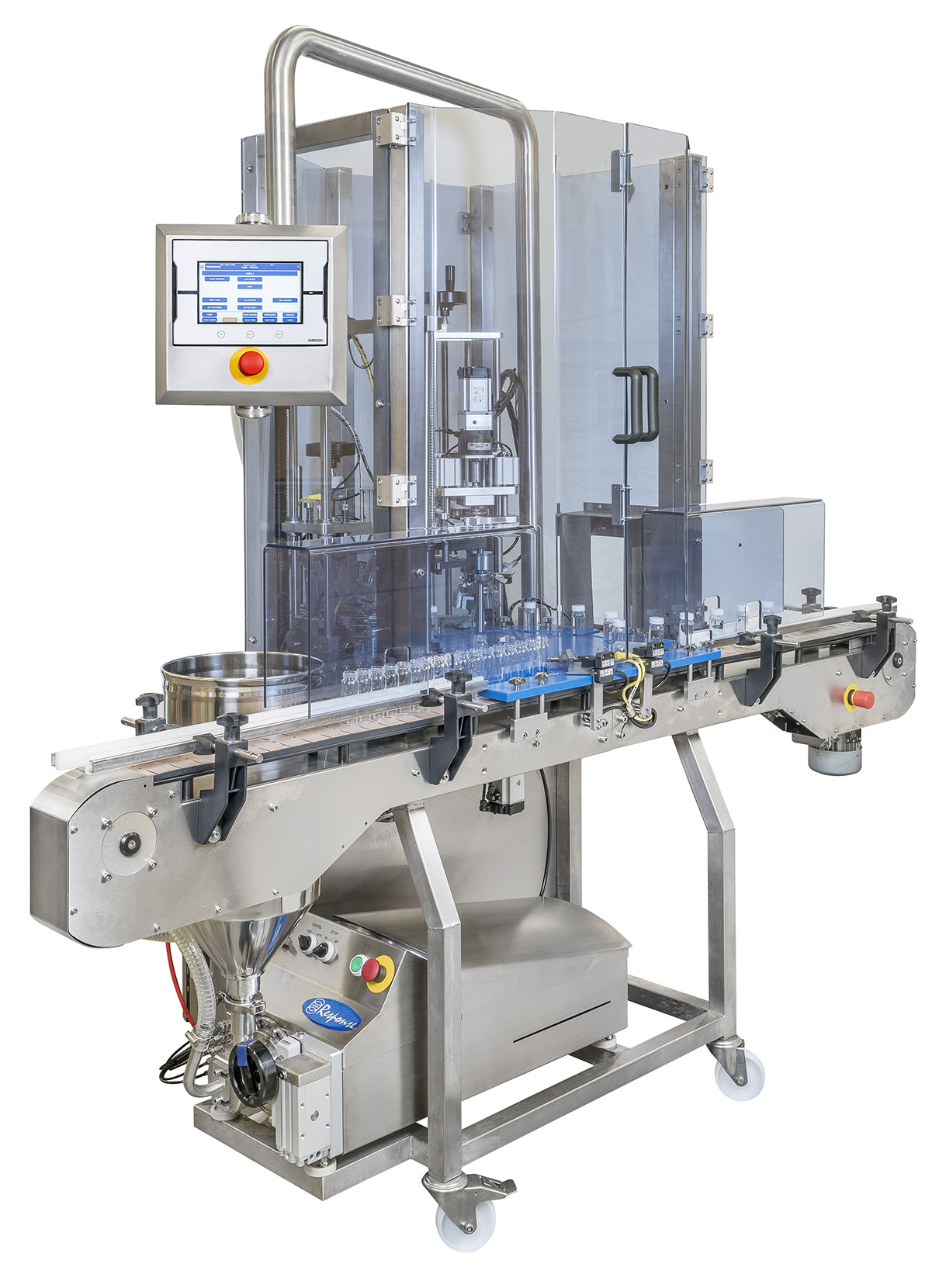
Monobloc filler and capper
If you have separate filling and capping stations you may experience lower throughput rates due t...
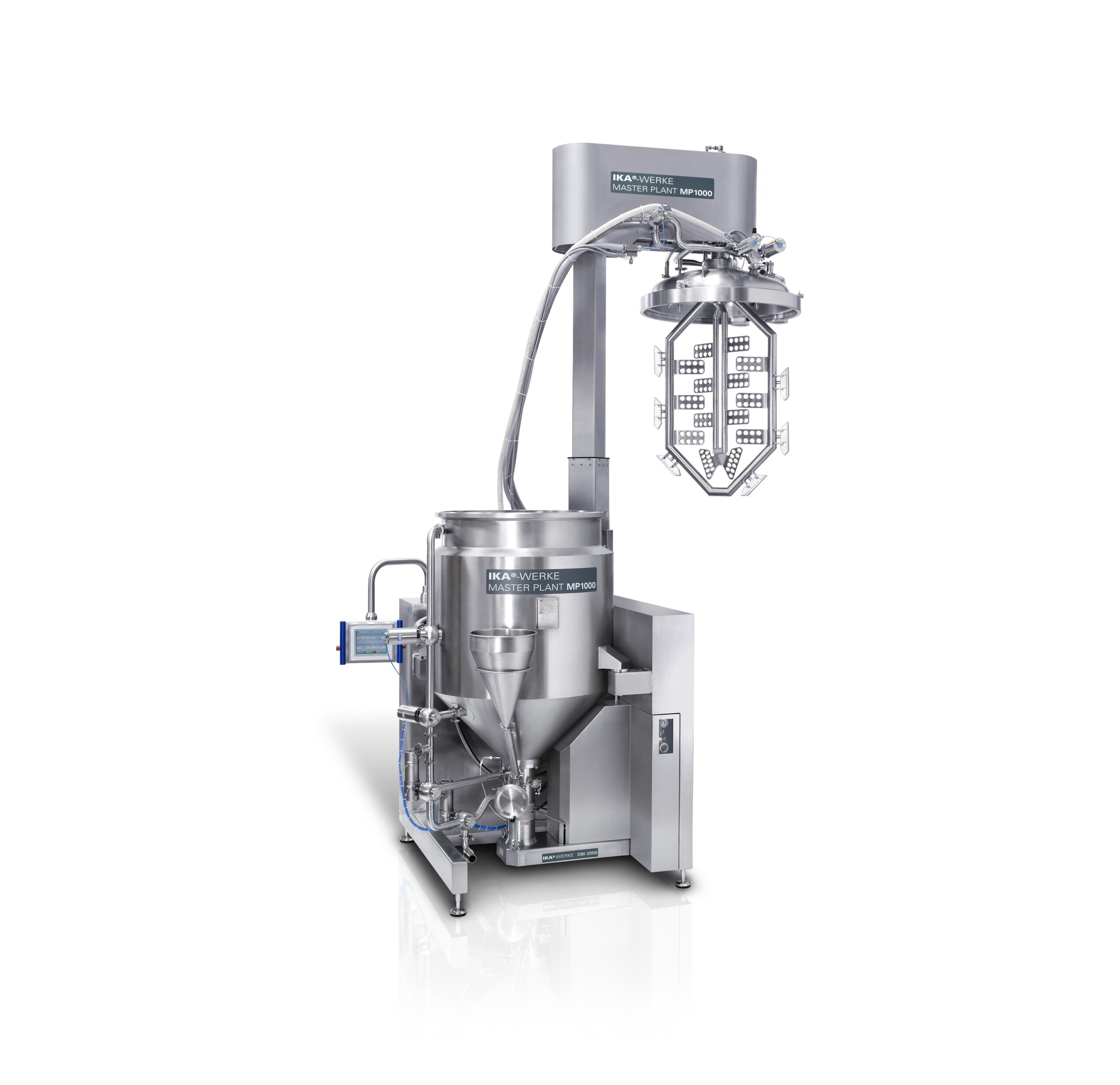
GMP homogenizing system
Manufacturers need production mixing equipment that is capable, flexible, and easy to maintain. Accur...
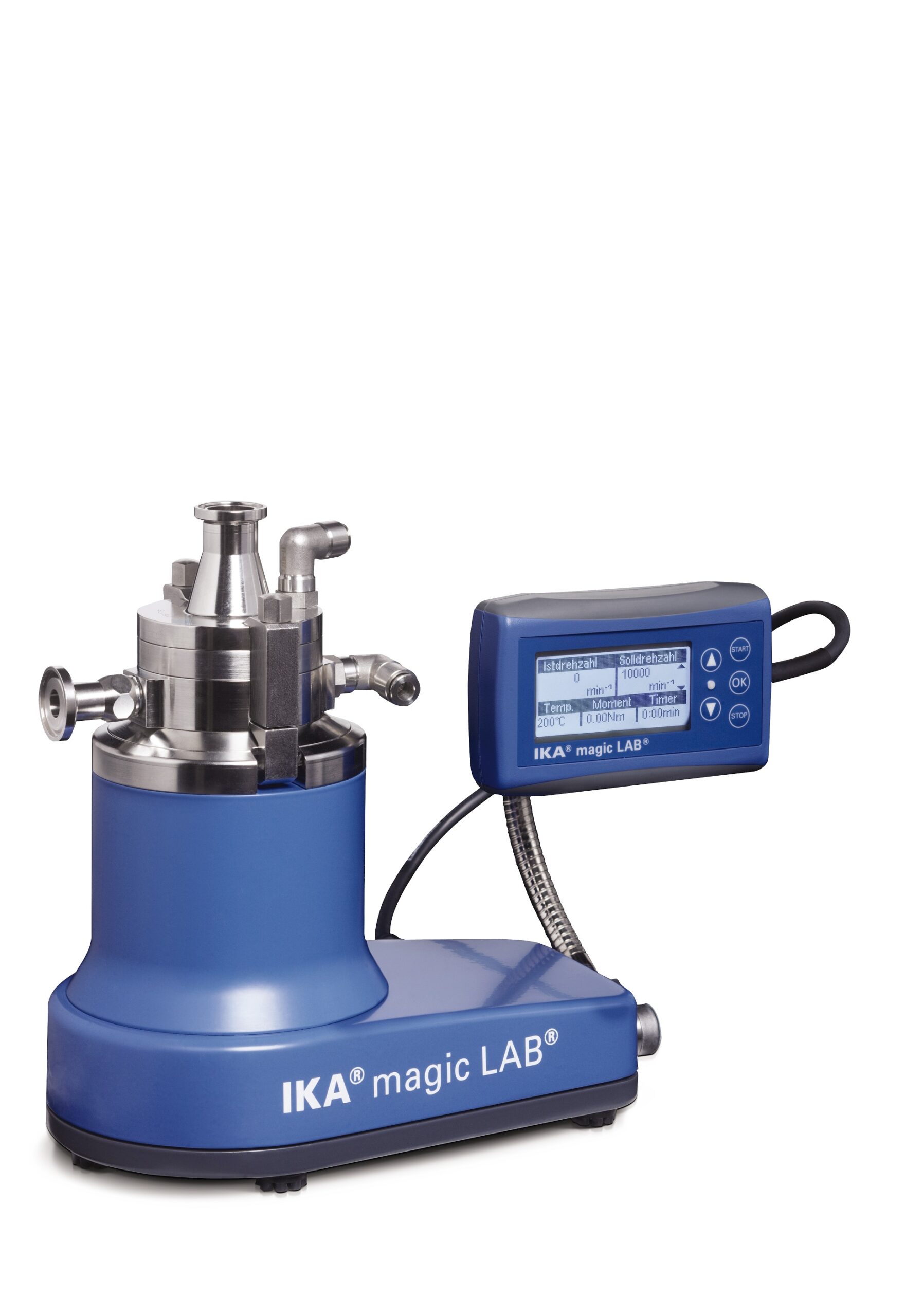
Small-scale laboratory dispersing machine
Developing and validating new processes requires reliable and highly versatile e...
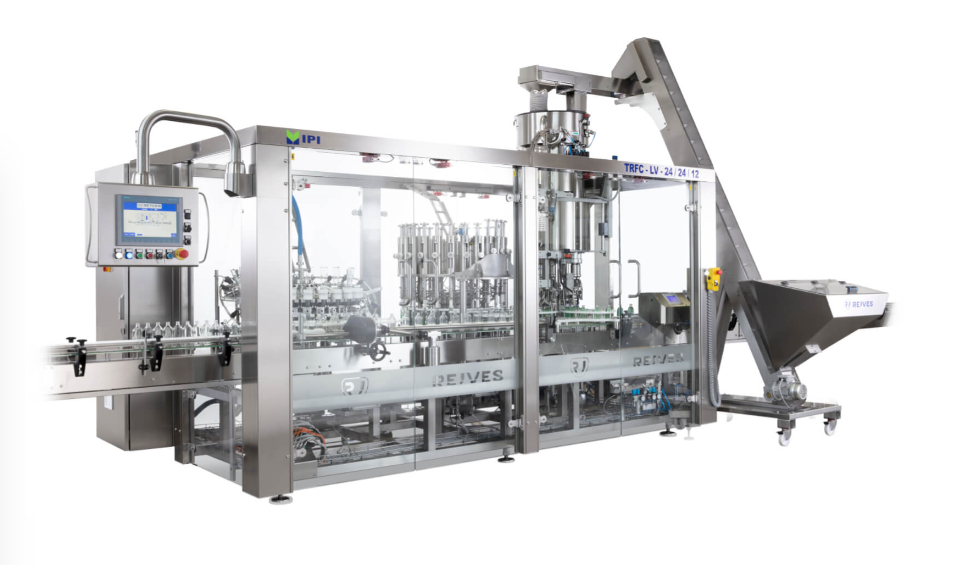
Bottle filling and capping monobloc
Spillage and overfilling are common problems in most production lines for bottled produ...
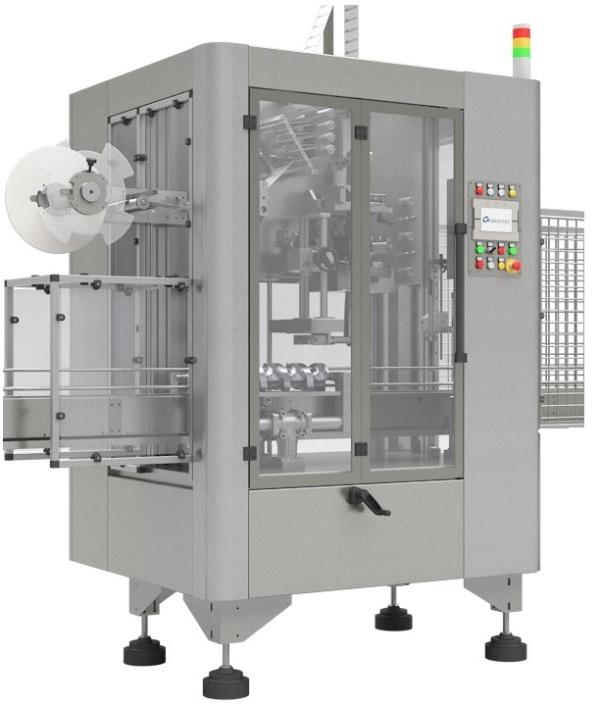
Shrink sleeve labeling machine
Shrink sleeves are new type of full-colour labels that give the opportunity to create a 360-d...
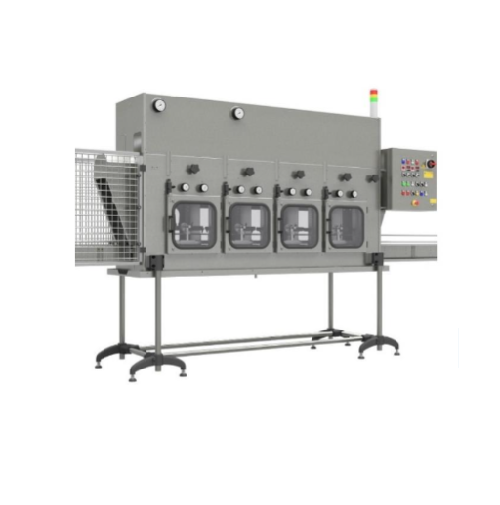
Steam tunnel for shrink sleeve labels
When it comes to the option of applying sleeves or film on a container without wrinkl...

Hot air tunnel for shrink sleeve labels
Sleeves are very popular in food, beverage, Chemical and pharmaceutical industry be...
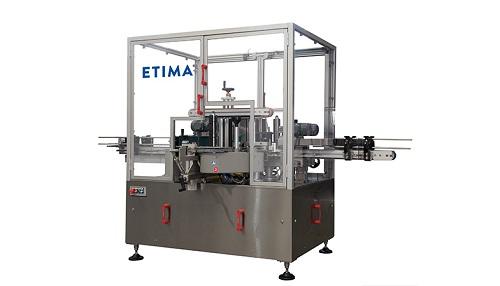
Self-adhesive linear labeling machine for bottles
It is vital to have precise and long-lasting labels on bottles to avoid...
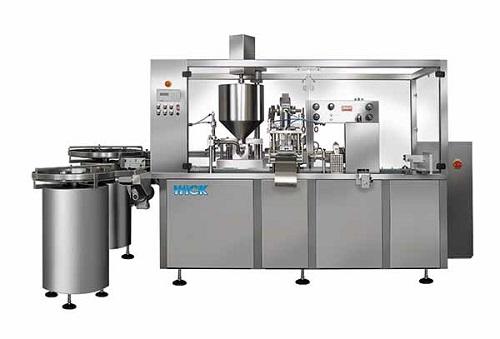
Cosmetic cream filler
From thin liquid baby oils and perfumes to thicker lotions and creams for hair and skincare, cosmetic p...
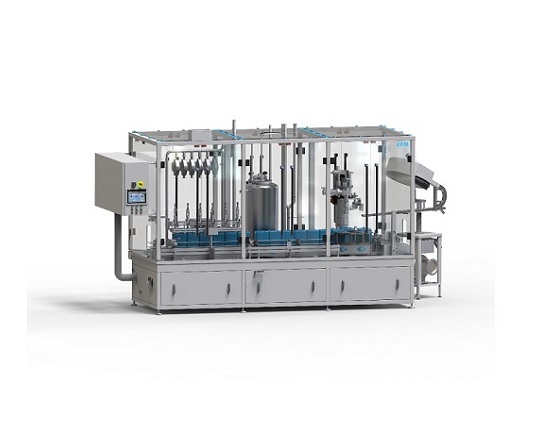
In-line monoblock linear filler & capper
In many food, chemicals and cosmetic industry processes it is vital to have a...

Flowmeter filler
For larger production runs of food, non-food and cosmetics industries, where accuracy and volume of filling i...
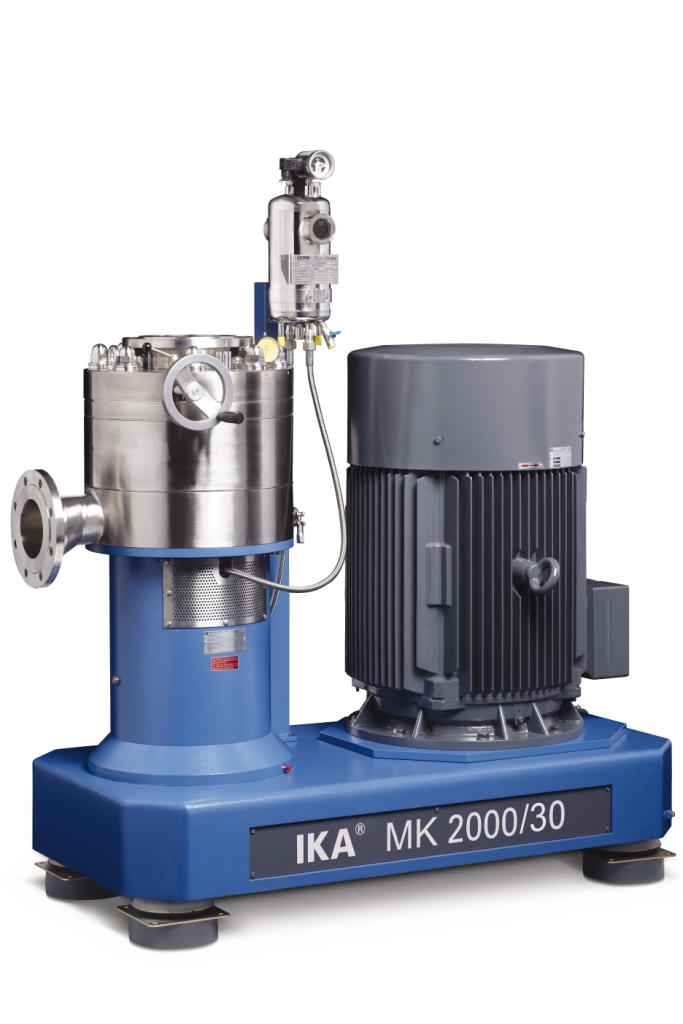
Colloid mill
For creating extremely fine emulsions and high quality dispersions a high pressure homogenizer is often chosen. ...
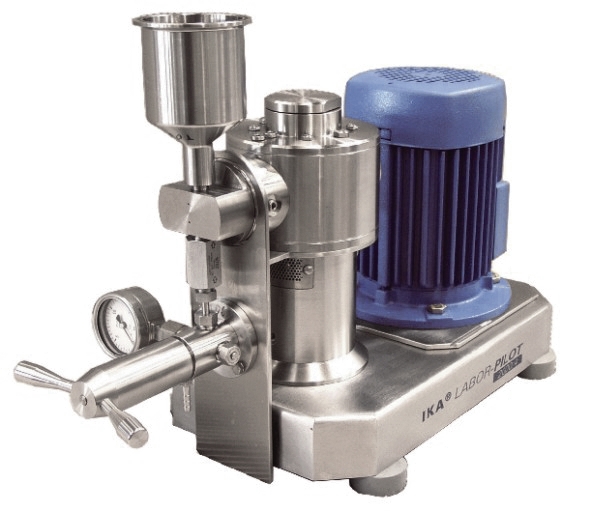
High-pressure homogenizer
When processes call for homogenized emulsions with extremely fine particle sizes the traditional t...
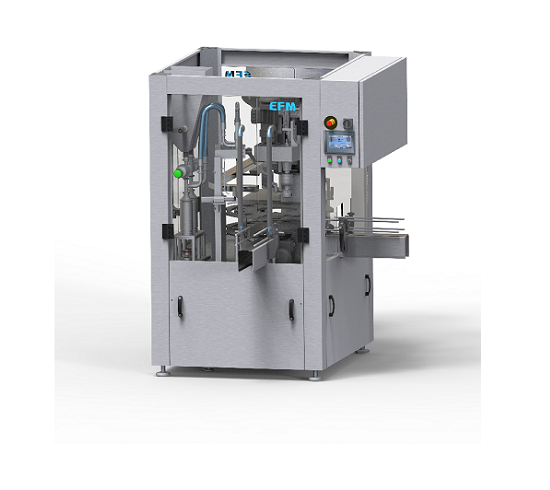
Compact monoblock filler
Filling and capping bottles and pots for food, chemical and cosmetics industries using separate mach...

High-end empty bottle inspection system
If you are looking for a system with empty bottle inspection; base, residual liquid...
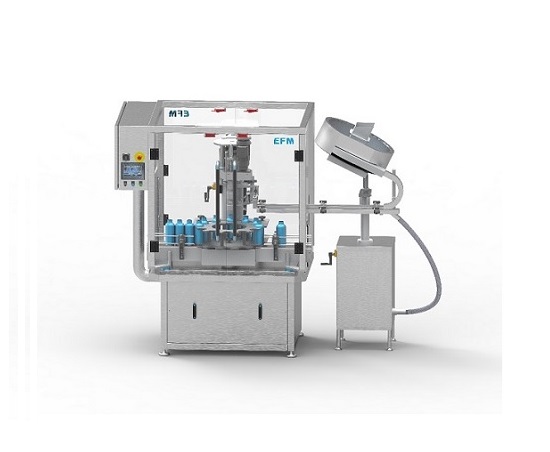
Single head capper
For the stand-alone capping of bottles of up to 30 litre capacity for smaller-scale production you need a ...
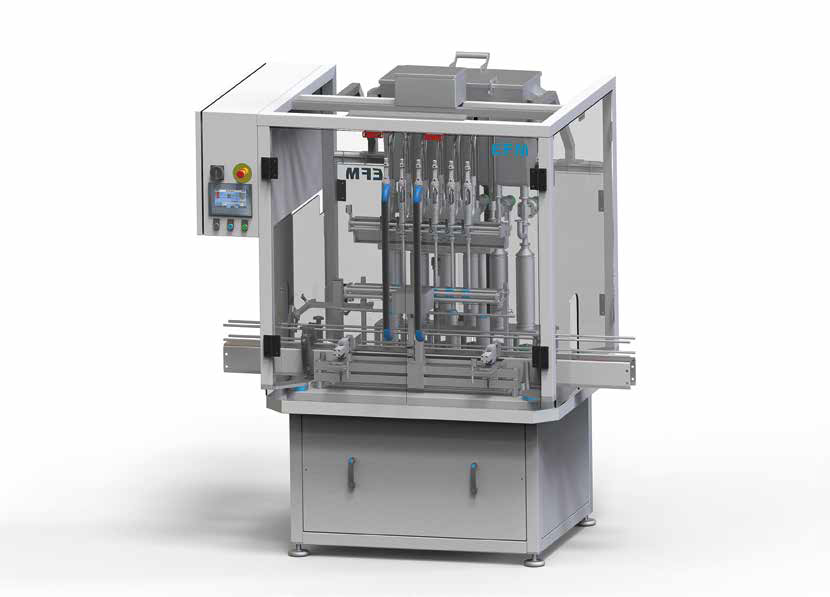
Servo controlled filler
For food and non-food liquid products that are high foam or have a high viscosity a specialist fillin...
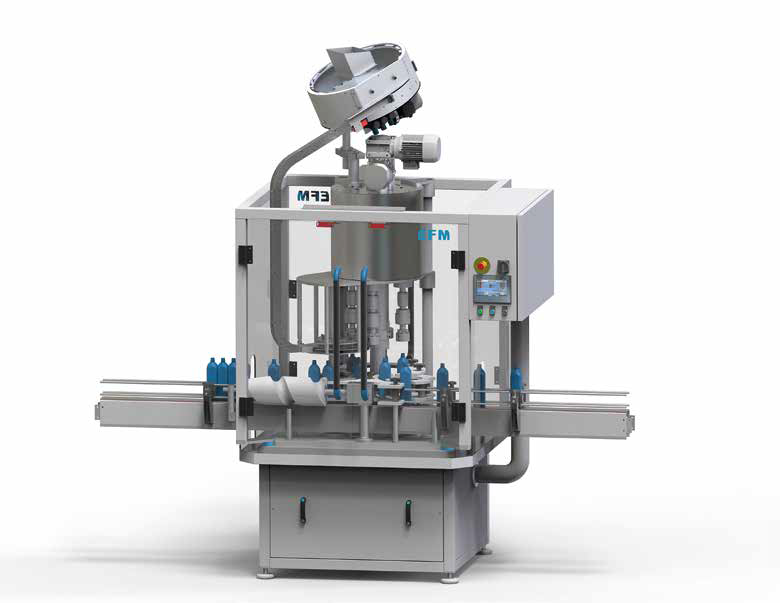
Multi-head capper
For the stand-alone capping of bottles of up to 2.5litre capacity you need a robust and flexible machine wi...

Shrink sleeve applicator - 400 per minute
Flexible medium to high speed application of shrink sleeveing to containers is u...
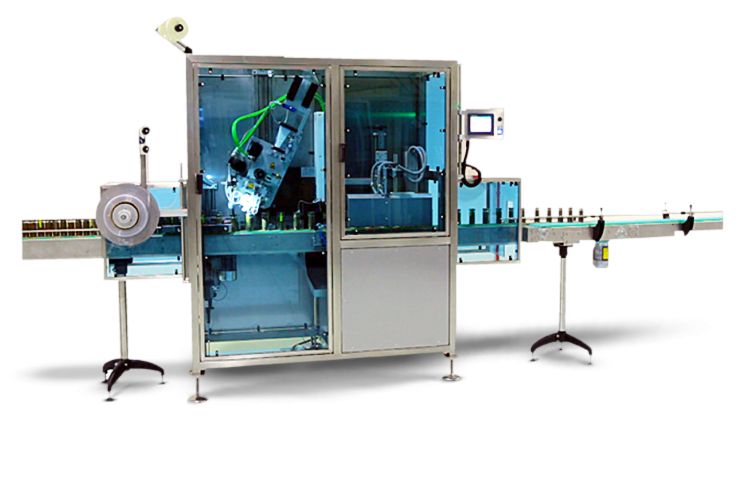
Compact shrink sleeve applicator
Adding tamper prevention to product packaging can be expensive and difficult to set up. Thi...
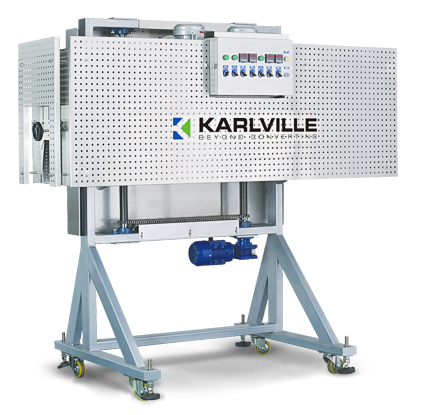
Electric shrink tunnel solution
Adapting shrink sleeve heating tunnels for different applications can be a lengthy and expen...
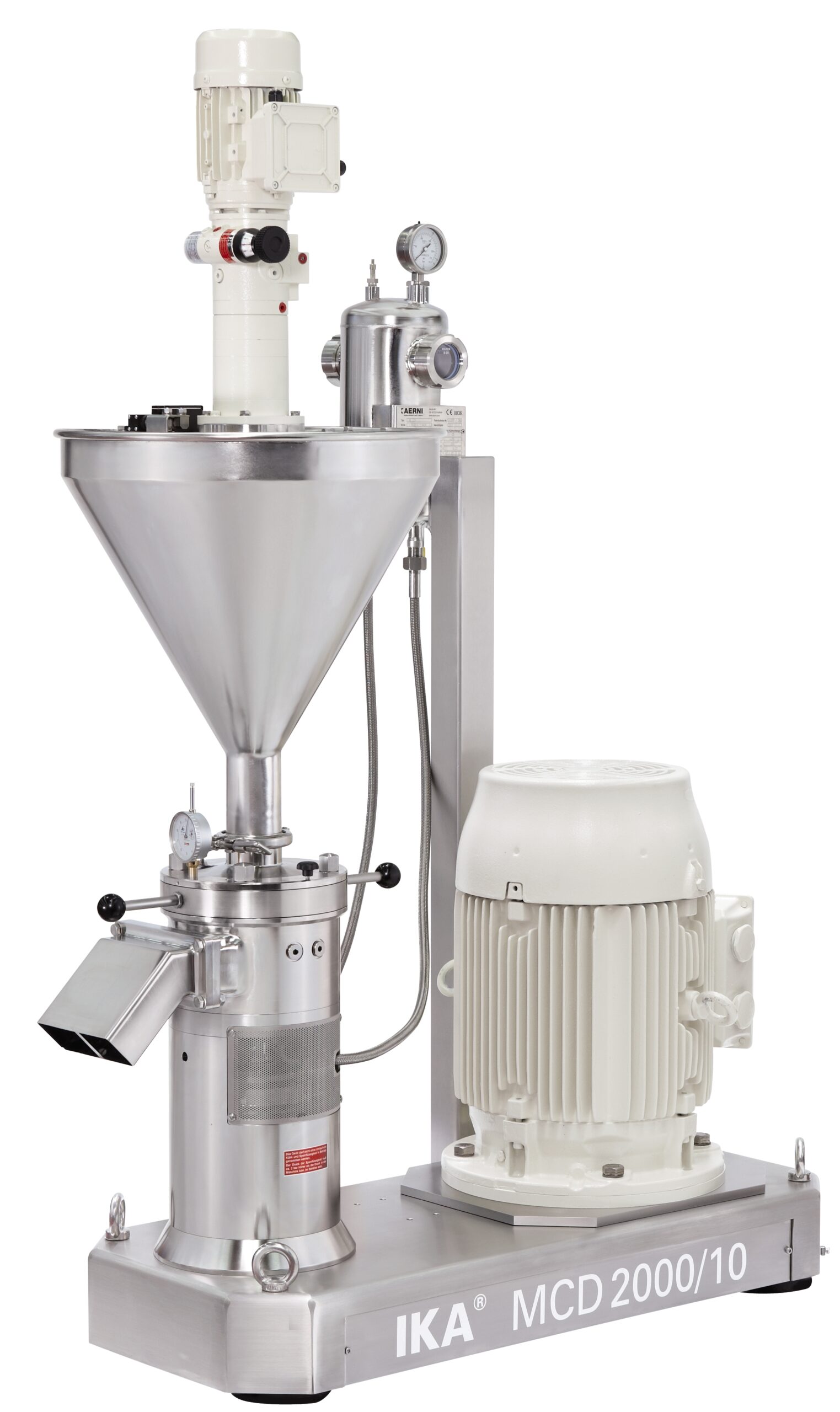
Corundum disk mill
Wet milling and grinding of viscous liquids or pastes containing solid particles such as peanut butter,mus...
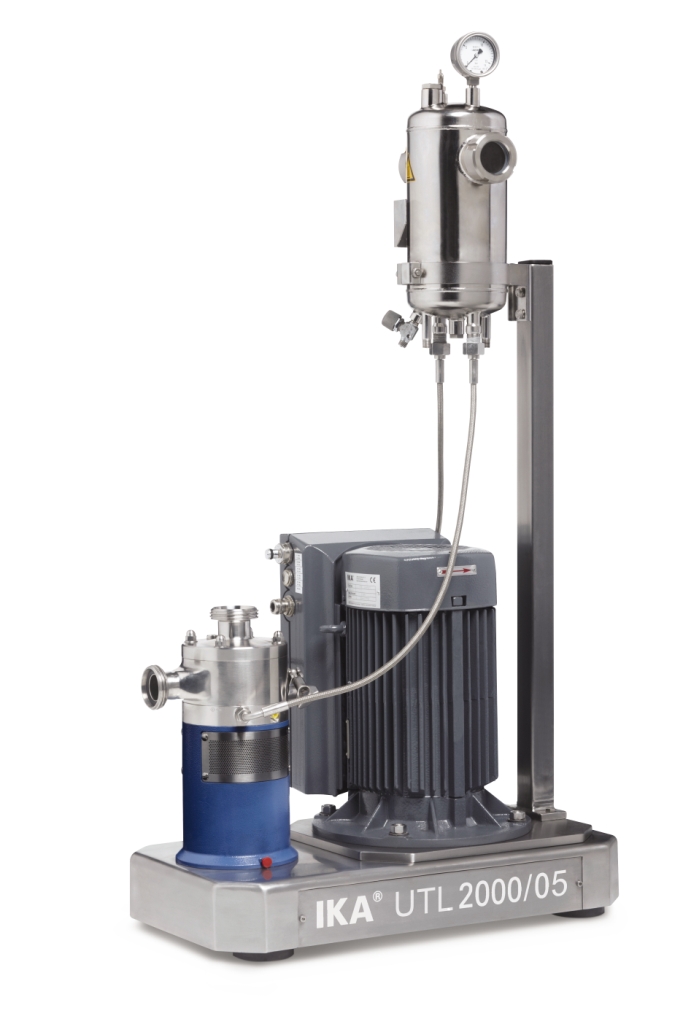
Dispersing machine for emulsions and suspensions
Equipment operating under the rotor/stator principal is often employed wh...
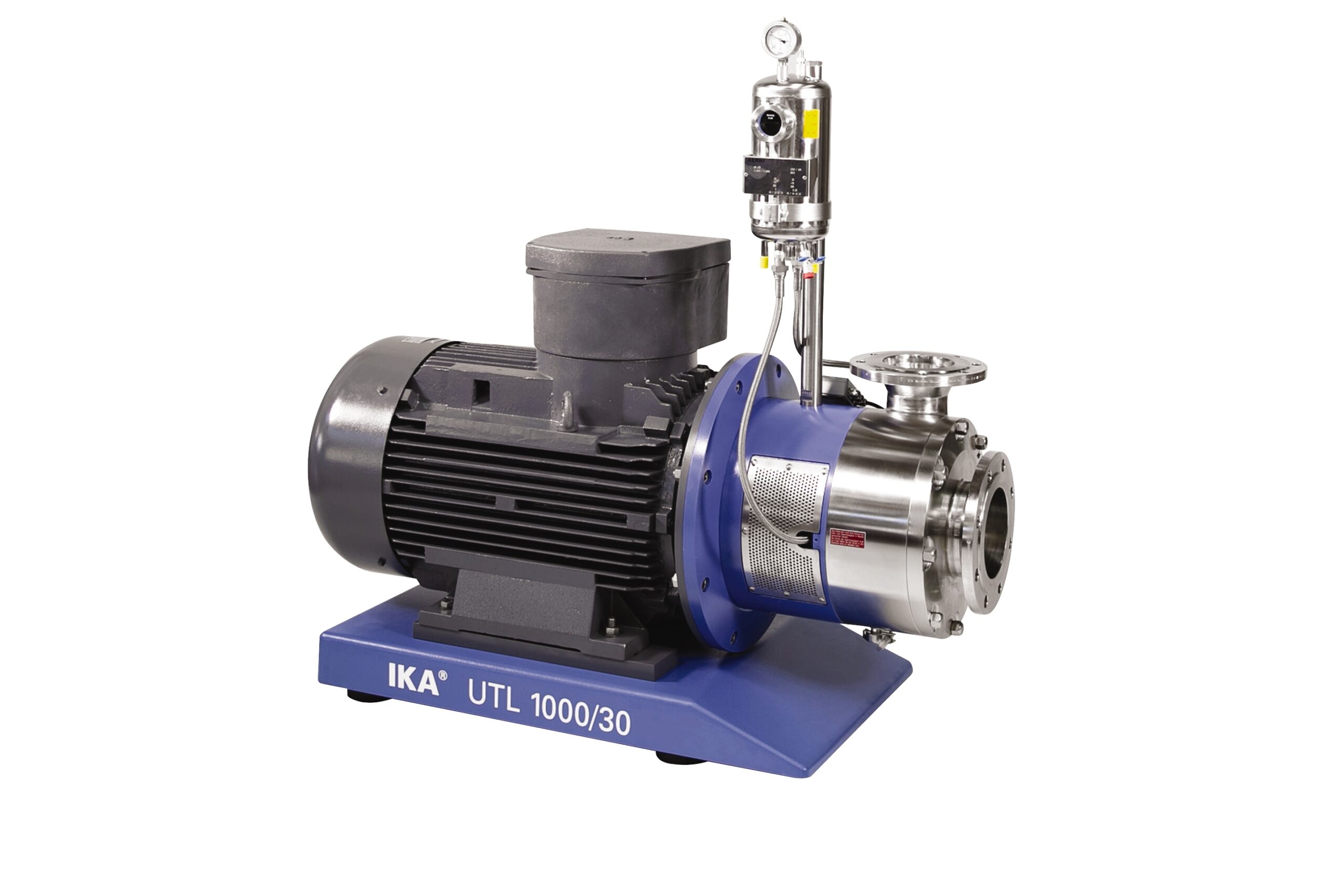
Economic dispersing machine for emulsions and suspensions
For products of medium viscosity and relatively consistent par...
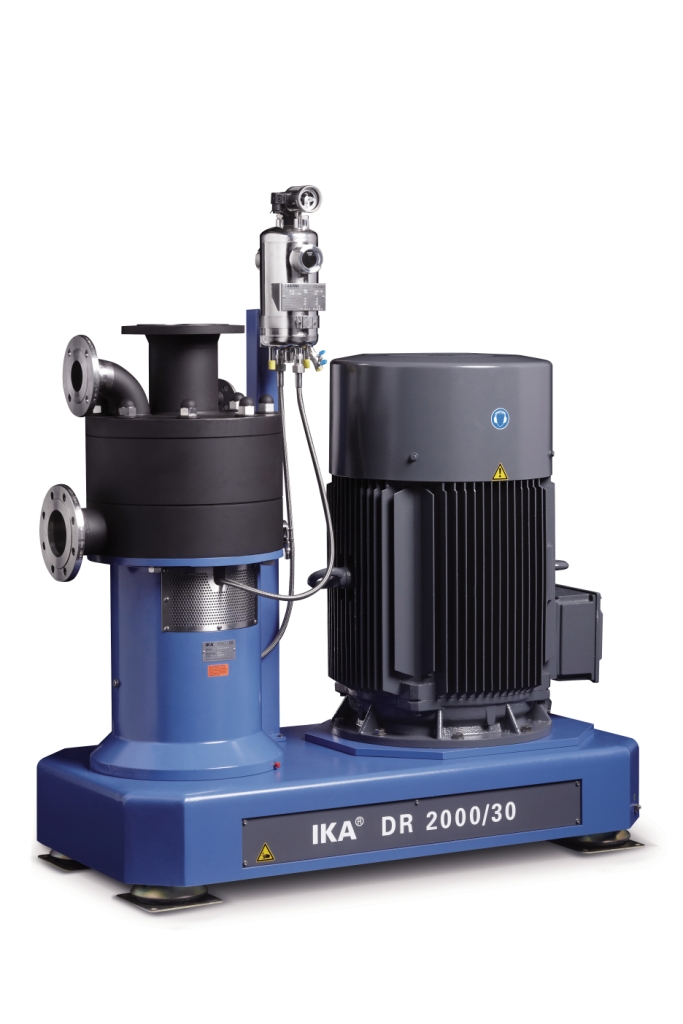
Dispersing machine for very fine emulsions and suspensions
For continuous high performance mixing of solid and liquid ra...
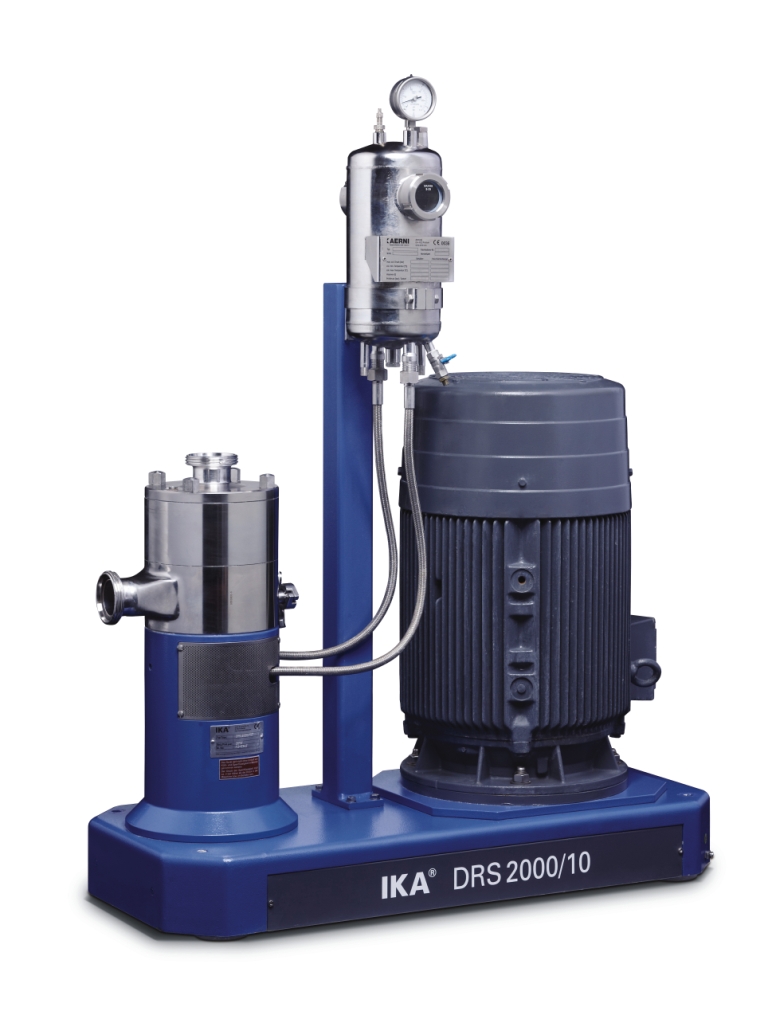
Ultra-fine dispersing machine for emulsions and suspensions
Producing the finest micro-emulsions and suspensions require...
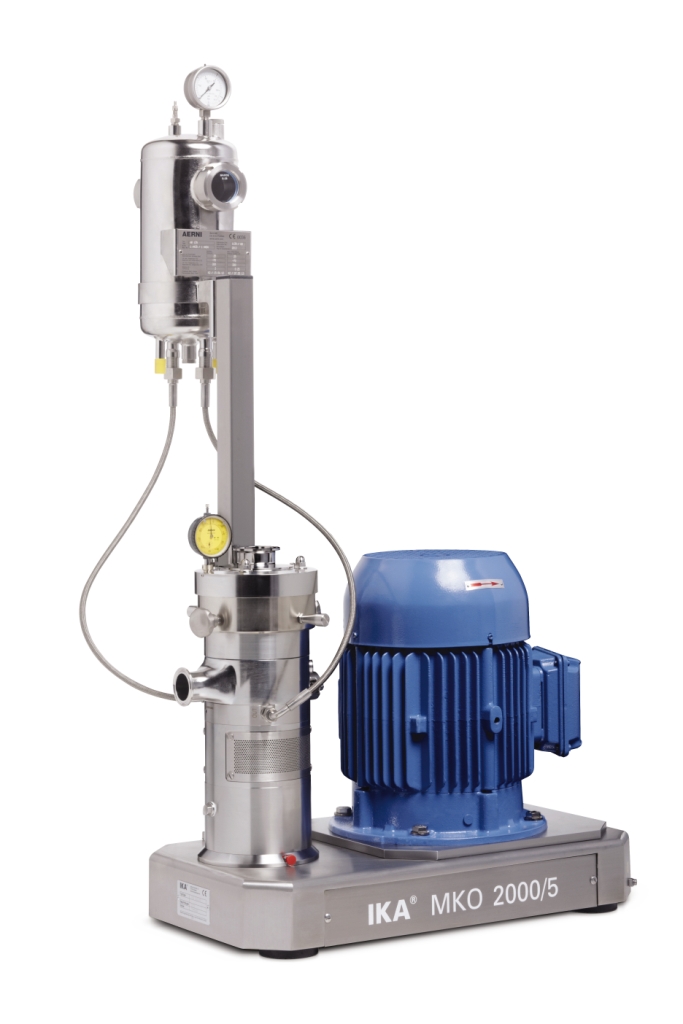
Cone mill machine
When your raw materials include agglomorated suspensions of grainy or crystalline solids and your process n...
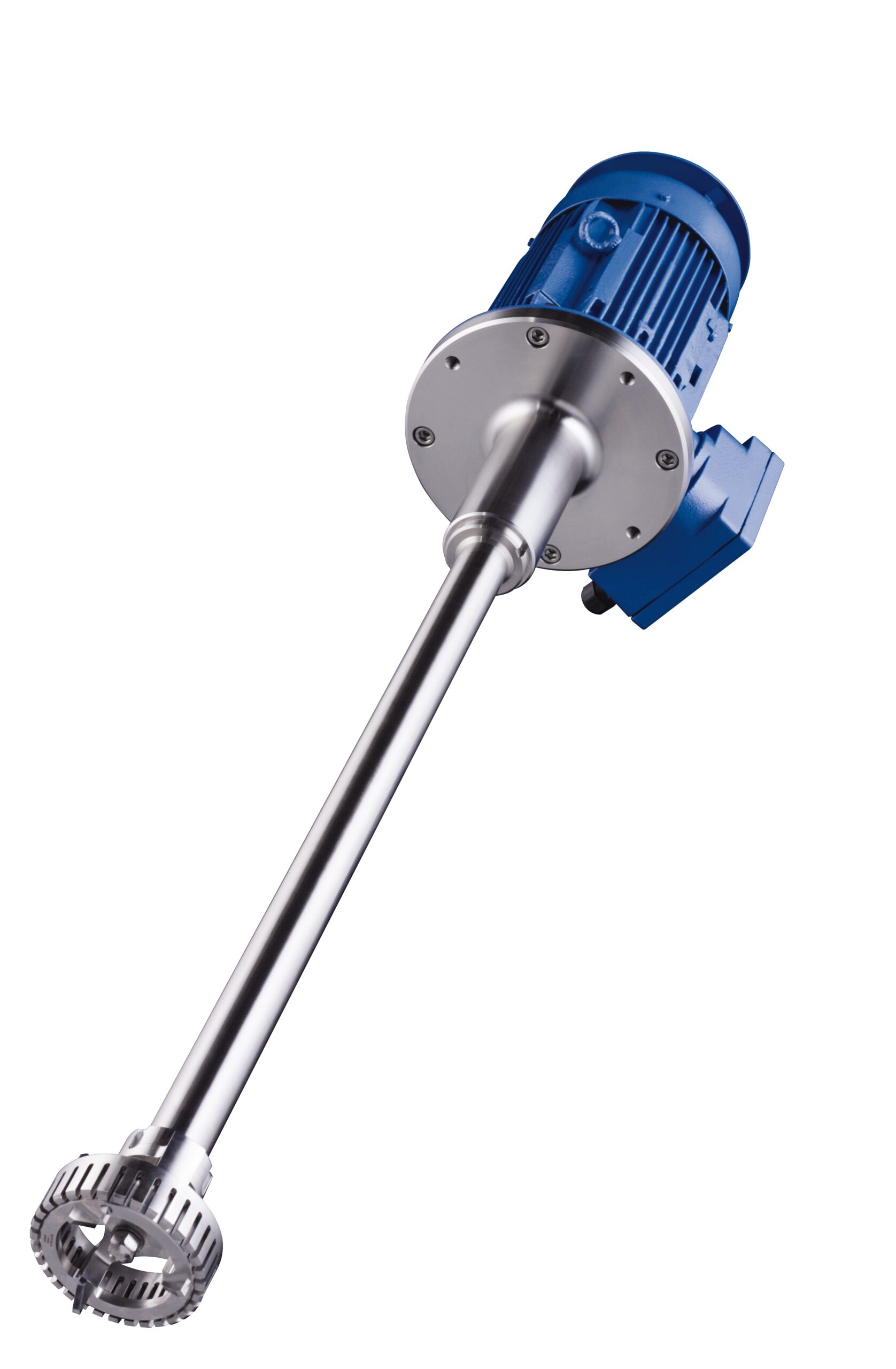
Batch dispersing machine
Equipment operating under the rotor/stator principal is often employed when more traditional methods...
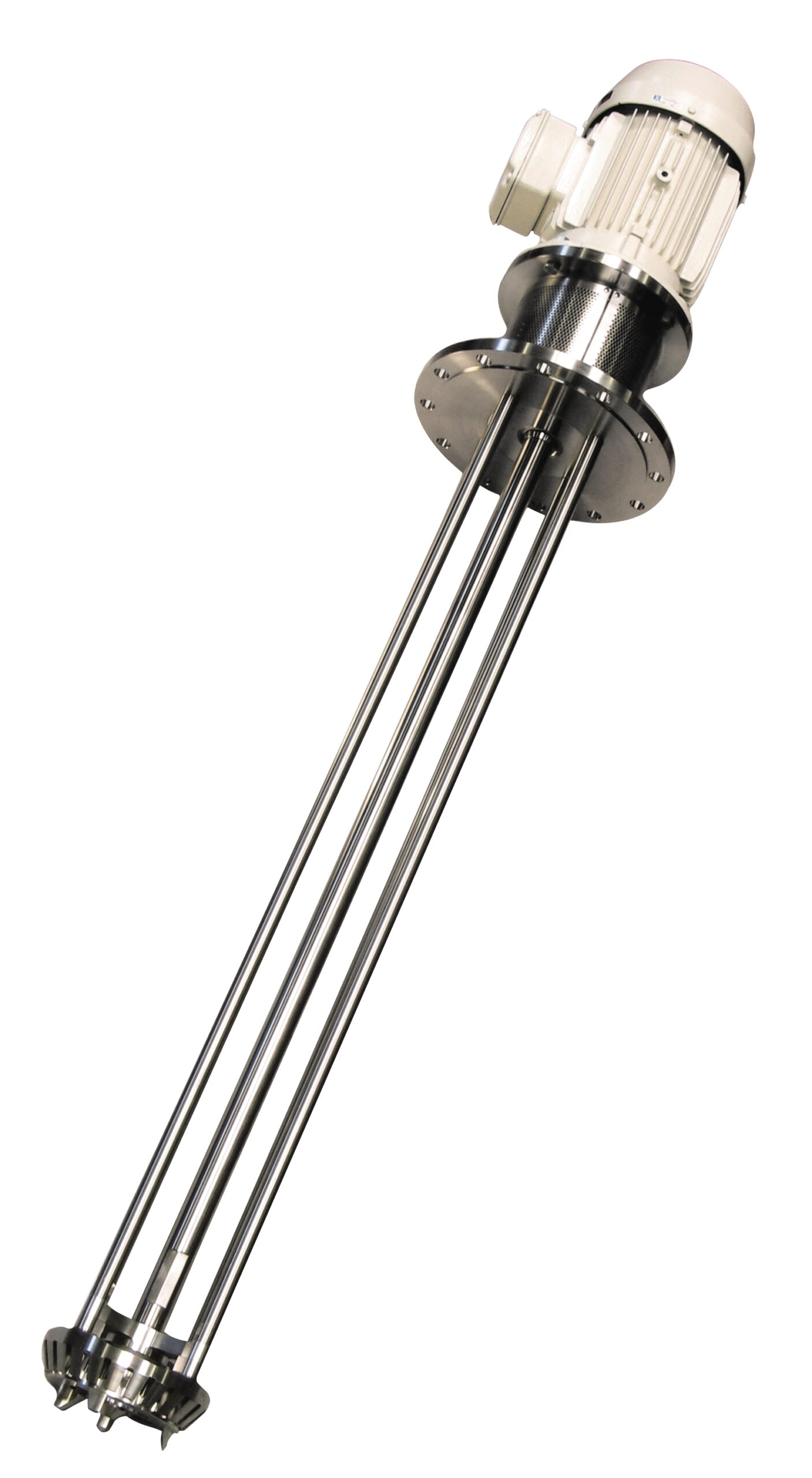
Batch dispersing machine for abrasive products
For mixing and dispersing tasks that cannot be completed by conventional st...
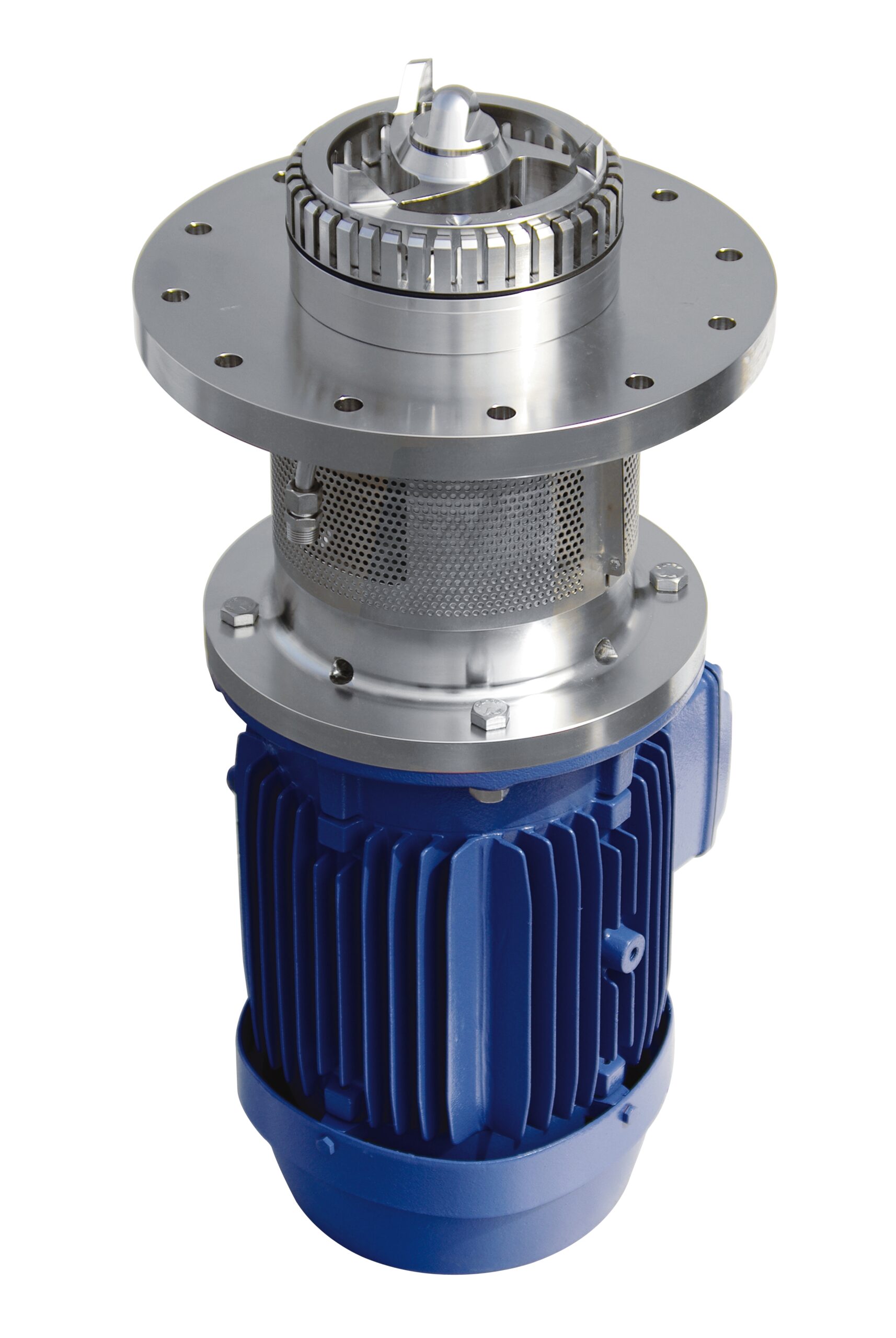
Batch dispersing machine for bottom entry into vessels
When your process requires high performance mixing or dispersion b...
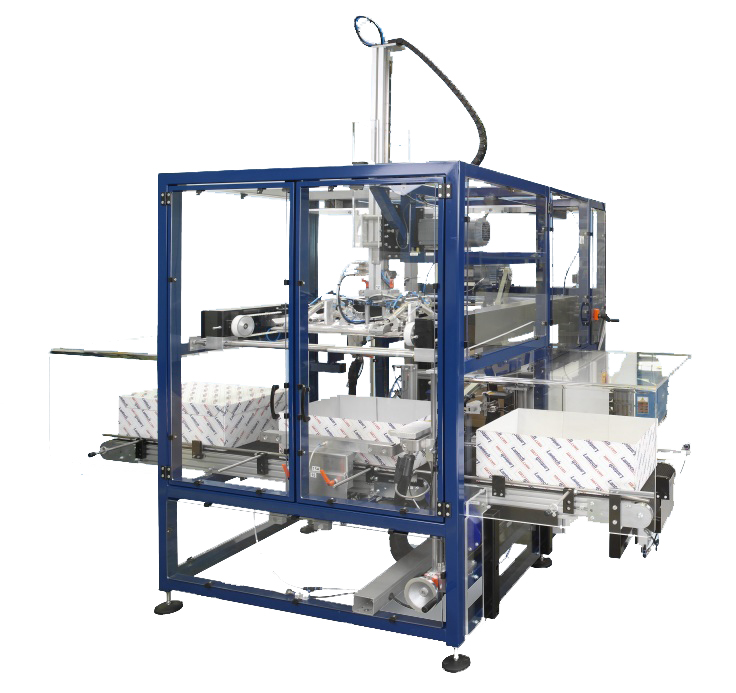
Lid applicator for corrugated cases
For your secondary packaging, you may be considering packing into boxes that require a ...
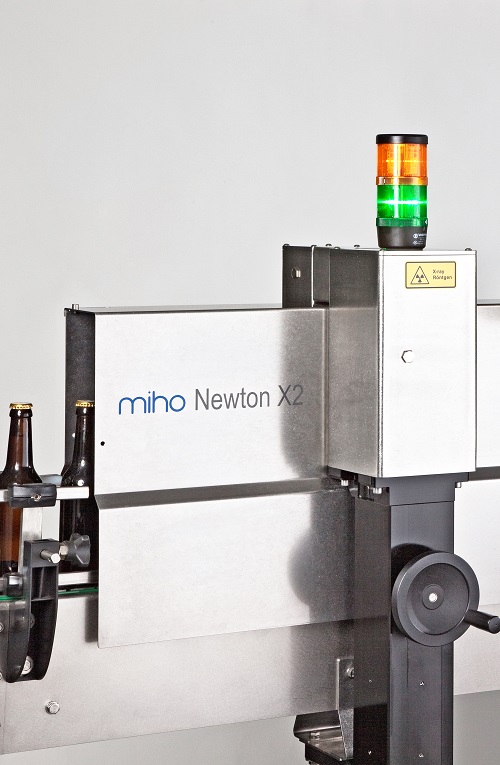
High-precision X-ray fill level controller
High-speed, high precision X-ray system to inspect containers that are difficul...
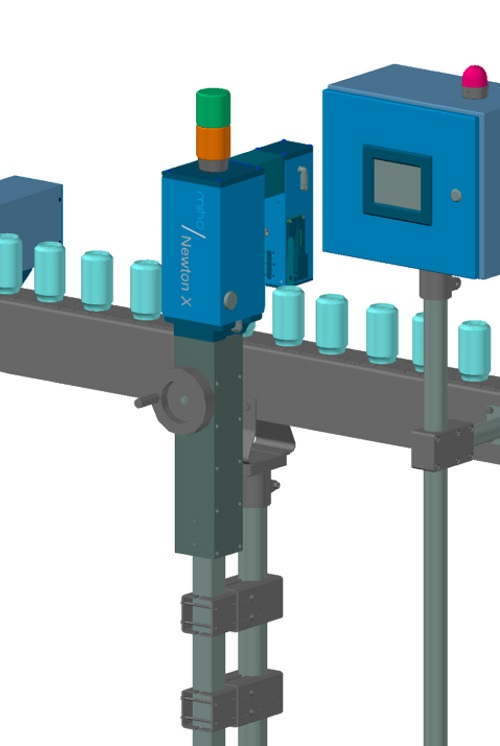
X-ray fill level controller
For containers that are difficult to see through, such as cans or cartons lined with aluminium, ...
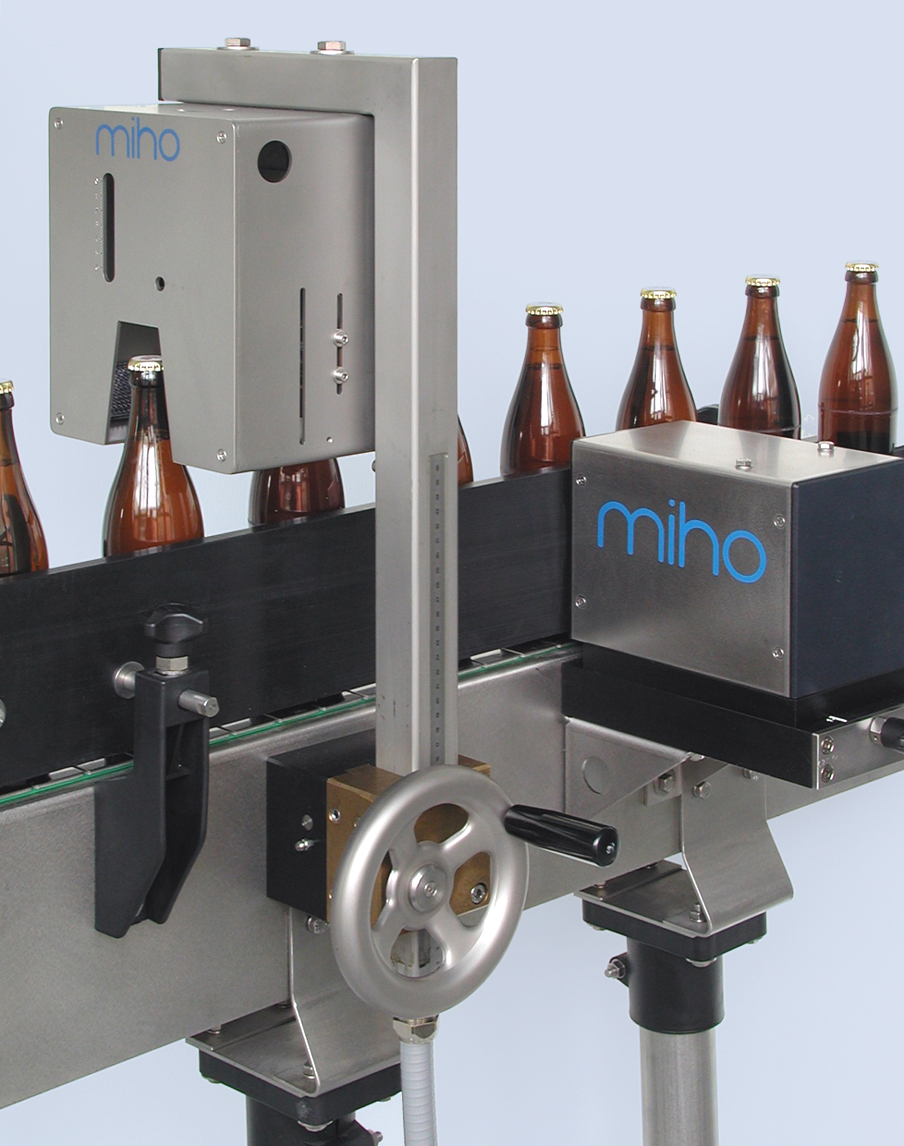
High-frequency fill level controller
In terms of high-frequency technology, the fill level detection is considered a standa...
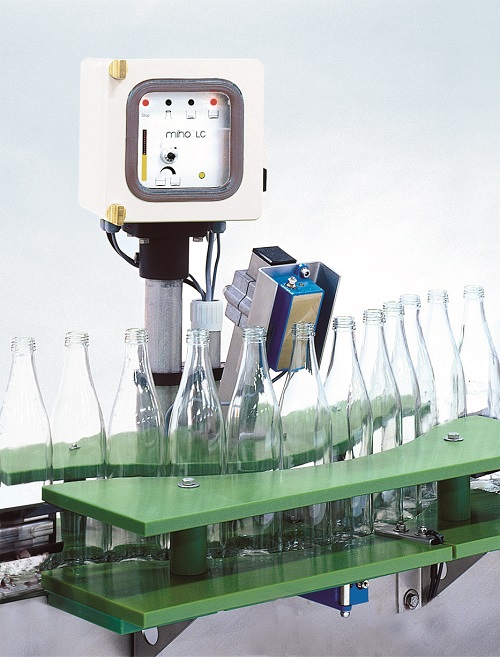
Residual liquid inspection system
Inspection system that eliminates the risk of residual liquid, water or left over drink i...