Multistage mixers for emulsions and dispersions
Experience efficient emulsification and dispersion processes with this versatile mixer, perfect for achieving precise droplet sizes and thorough distribution in various liquid-solid mixtures. Whether you’re optimizing formulations or enhancing product consistency, this solution integrates seamlessly into both in-line and batch operations.
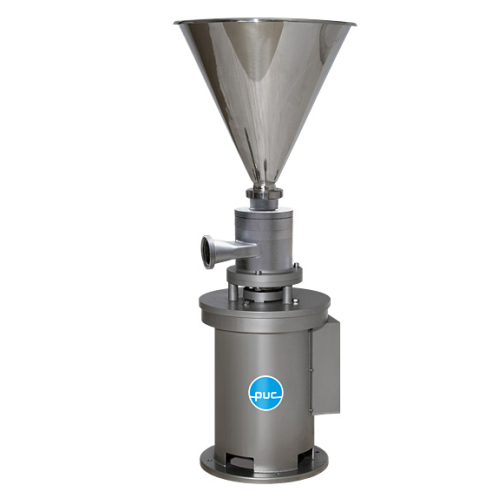
Processes and Homogenizes Liquid-Solid Mixtures Efficiently
The Multistage Mixer Type O from Probst & Class is an innovative solution designed to enhance emulsification and dispersion in various industrial applications, including the pharmaceutical, food and beverage, chemical, petrochemical, and cosmetics sectors. Utilizing a sophisticated three-stage rotor-stator system, this equipment achieves precise homogenization and consistent droplet size reduction, optimizing your production line for liquids, slurries, and solid mixtures.
Equipped with a vertical enclosed motor, it supports both in-line and batch operations with a throughput of up to 50,000 liters per hour, adapting seamlessly to continuous and pilot processes. Its flexibility extends to a range of material viscosities, ensuring efficient mixing and de-agglomeration. The unit’s robust construction features adaptable hoppers and piping connections, including threaded nozzles and tri-clamps, facilitating integration into diverse processing setups and enhancing workflow efficiency.
With options for various mechanical seals and a PTFE FDA-compliant seal system, the Multistage Mixer Type O prioritizes ease of maintenance and long-term durability. Additionally, the machine can be tailored with custom stator-rotor combinations and advanced automation features like a frequency converter and recirculation system. Meeting stringent industry standards, it offers reliable, energy-efficient performance, ideal for producing high-quality end products such as mayonnaise, face creams, and bitumen emulsions.
Benefits
- Enhances product quality with precise droplet size reduction and distribution.
- Increases production efficiency with up to 50,000 liters per hour capacity.
- Streamlines maintenance and reduces operational delays with customizable seal systems.
- Ensures seamless integration and adaptability across diverse processing setups.
- Supports a wide range of viscosities, optimizing processes from homogenizing to de-agglomeration.
- Applications
- Colors and lacquers, Bitumen-emulsions, Shampoos, Concentrated juices, Cosmetics, Shower gels, Pesticides, Resin oils, Emulsions, Fruit and vegetable juices, Herbicides, Juices, Bubble bath, Fungicides
- End products
- Dandruff-control shampoo, Apple juice, Alkyd resin, Mosquito repellent spray, Acrylic paint, Cranberry concentrate, Anti-fungal nail treatment, Mayonnaise, Face cream, Rose bath foam, Orange juice concentrate, Road paving bitumen, Weed killer solution, Fruit puree, Lavender bath gel
- Steps before
- De-agglomeration, Wetting, Size reduction, Pre-comminution
- Steps after
- Homogenizing, Mixing, Filling, Packaging
- Input ingredients
- liquid/solid mixtures, emulsions, dispersions, pumped materials, fruit and vegetable juices, concentrated juice, resin oils, pesticides, herbicides, fungicides
- Output ingredients
- homogenized mixtures, de-agglomerated materials, emulsified products, dispersed substances, cosmetic products, shower gels, bubble bath, shampoos, bitumen-emulsions
- Market info
- Probst und Class is known for manufacturing high-performance industrial homogenizers and wet milling equipment, offering customized solutions for dispersing, emulsifying, and grinding applications, with a strong reputation for quality and innovation in the process industry.
- Flow Rate
- Up to 50, 000 l/h
- Motor Type
- Enclosed Motor
- Operation Type
- In-line and Batch Operation
- Droplet Size
- Below 5 µm
- Configuration
- Three-stage Rotor-Stator System
- Seal Type
- Single and Double-acting Mechanical Seals / Lip Seals (PTFE)
- Seal Compliance
- FDA Requirements
- Mount Position
- Vertical
- Recirculation System
- Yes
- ATEX Version
- Available
- Sterilization Design
- Available
- Drives
- IE3 Standard Motors
- Sizes
- 150 to 50, 000 l/h
- Fittings
- Threaded Nozzle, Flange, Tri-clamp
- Working mechanism
- Rotor-stator system
- Operating position
- Vertical
- Batch vs. continuous operation
- Batch / Inline
- Material feeding method
- Hopper / In-line piping
- Turbulence level
- High
- Automation level
- Option for PLC controls
- Integrated process steps
- Wetting, de-agglomeration, dispersing, emulsifying, homogenizing, mixing
- Seal types
- Single and double-acting mechanical seals
- CIP/SIP
- Available as an option
- Optional explosion protection
- ATEX version available
- Connection types
- Threaded nozzle, flange, tri-clamp
- Density/particle size
- 0.5–2.5 g/cm³ / 50–1000 µm
- Droplet size
- Below 5 µm
- Machine Position
- Vertical
- Motor Enclosure
- Enclosed motor
- Flow Rate
- Up to 50, 000 l/h
- Feed Method
- Flange, threaded nozzle, tri-clamp
- Customization Options
- Standard sizes or bespoke solutions
- Seal Type
- Single and double-acting mechanical seals, lip seals
- Recirculation system
- Hopper through stator-rotor system
- Explosionproof version
- ATEX version available
- Sterilization design
- Designed for sterilization
- Mobility
- Mobile version available
- Motor type
- IE3 standard motors
- Connection types
- Threaded nozzle, flange, tri-clamp