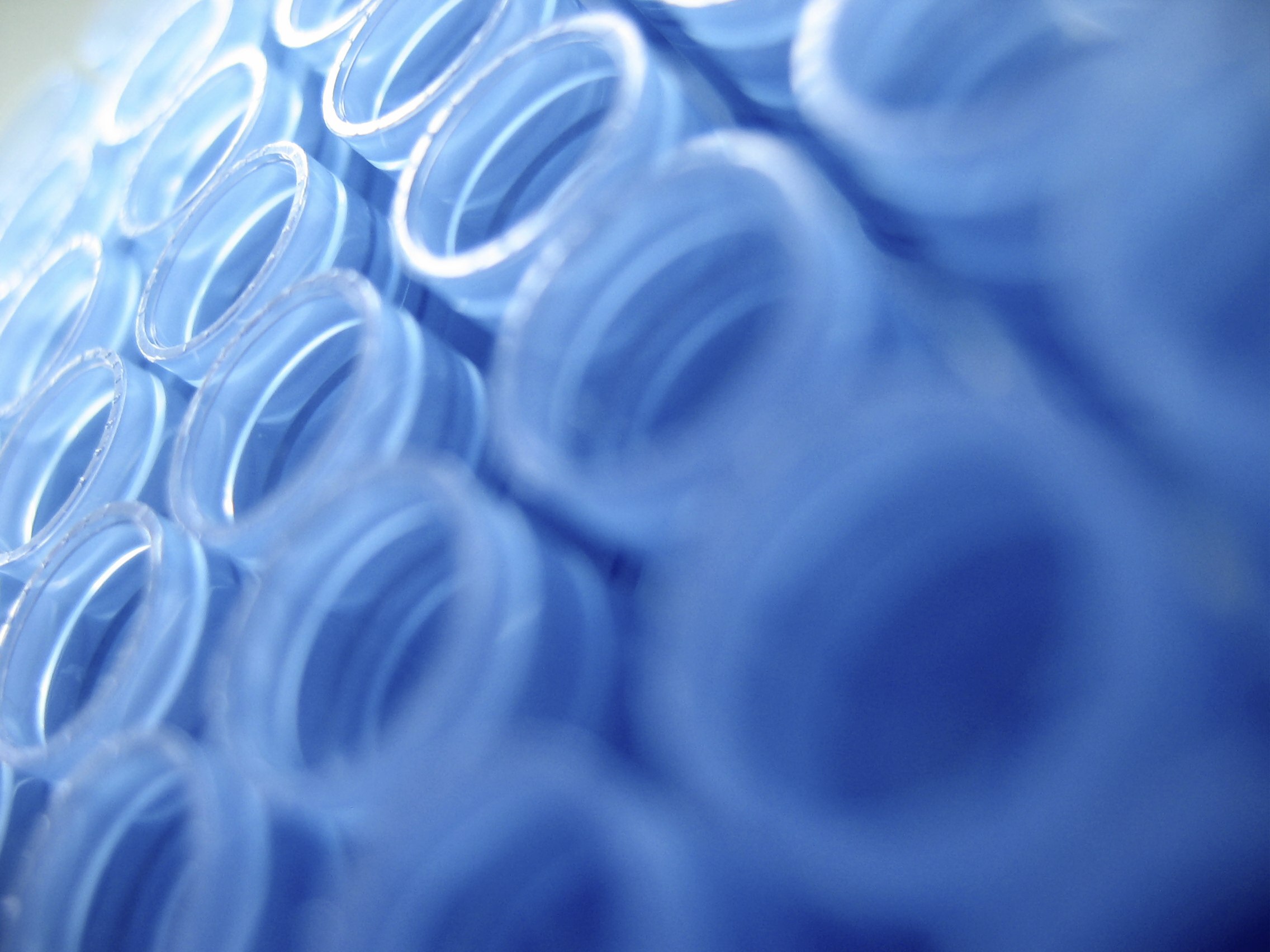
Pharmaceutical Containment Equipment
Explore the best pharmaceutical containment solutions for drug safety. And, learn about high containment systems, regulations, and more.
Pharmaceutical containment solutions are necessary to protect your operator. It’s important to keep your staff separated completely from any hazardous substance. This means you have to enclose the hazardous product at the location where it is produced. You have to keep it closed off from the operator from the point where it enters your site, all through the process, until the final packaging. The pharmaceutical industry demands high levels of safety and quality. In order to ensure the well-being of the workers and patients, it is important to implement the proper containment of pharmaceuticals during the manufacturing process.
What Is Pharmaceutical Containment?
Pharmaceutical containment is the process of preventing cross-contamination. But it also includes protecting the product, the workers, and the environment from exposure to hazardous substances. Containment solutions in pharmaceutical manufacturing range from simple packaging to sophisticated containment systems. Including technology such as isolators and high-containment equipment.
During The Manufacturing Process
Pharmaceutical ingredients used in the manufacturing process may include highly potent active pharmaceutical ingredients (HPAPIs). Which as a result, require a higher level of containment due to their hazardous nature. The Occupational Exposure Limit (OEL) and the Occupational Exposure Band (OEB) are used to determine the level of containment required for HPAPIs.
When your product moves through different production steps it is often handled in different drums, sacks, or bulk bags. Handling these contained transfers can be challenging. For some hazardous chemicals / bio-hazards, legal occupational exposure limits (OEL) have been determined. OEL regulation sets an upper limit on the acceptable concentration of a hazardous substance in workplace air.
Total Containment: When no legal guidance is available, you go through the process of control banding to ensure proper risk assessment. Control banding ranks hazards in different occupational exposure bands (OEB). This ranges anywhere from “light skin and eye irritants” up to “very toxic on single exposure”. Total containment not only protects humans but also needs to protect the environment while preventing cross-contamination.
Rules and Regulations
The pharmaceutical industry has many rules when it comes to the production and distribution of products. For example, GMP regulations ensure that manufacturers follow the correct protocols and procedures for containing pharmaceutical ingredients. This includes labeling, handling, and storage. Containment in this industry aims to minimize the risks of exposing humans and the environment to hazardous substances. But also, to prevent the pharma products from getting contaminated. Which could have disastrous effects on the end-user. Manufacturers must ensure that they can produce certification for their products. And also to undergo rigorous testing before they can enter the market as treatments.
Which pharmaceutical containment technology do you need?
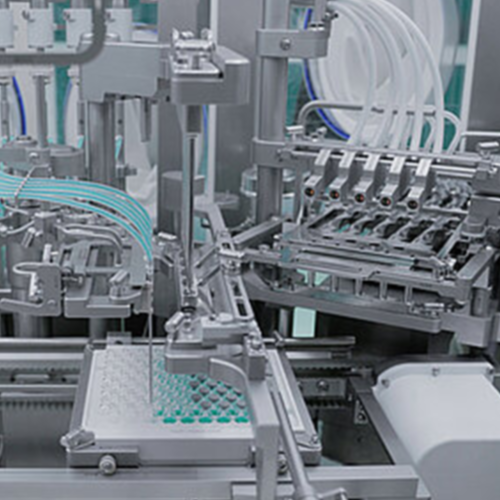
Vial and syringe filling system for pharmaceuticals
Ensure aseptic precision in liquid formulation filling with a modular...
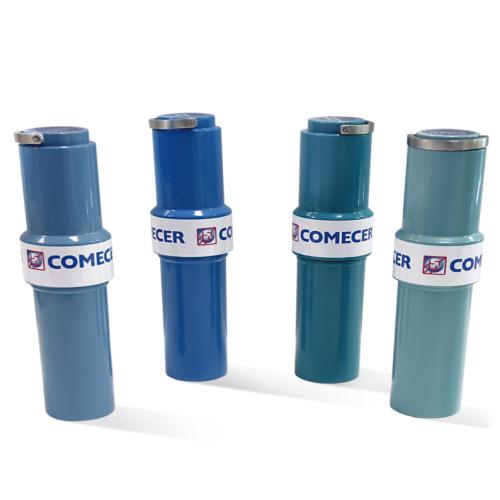
Syringe shielded container for radiopharmaceuticals
Ensure safe and efficient transport of sensitive radiopharmaceuticals...
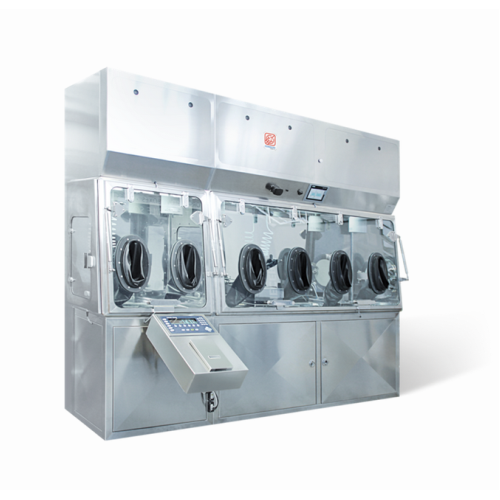
Modular dispensing and weighing isolator for pharmaceuticals
Achieve precise dispensing and weighing of high-potency pha...
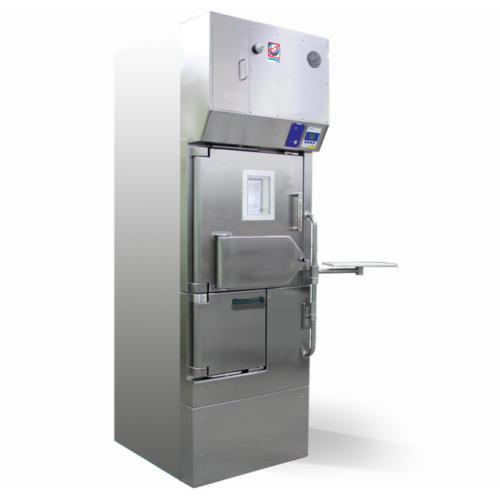
Manual hot cell for r&d in radiopharmaceuticals
Ensure precise dose dispensing and safe handling of radioisotopes with thi...
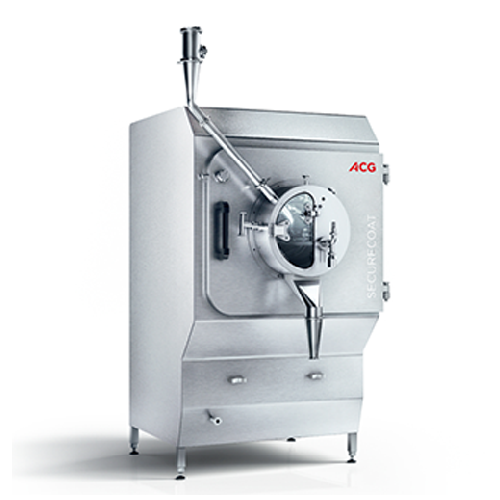
Containment tablet coater for high-potency pharmaceuticals
Ensure operator safety and maintain stringent OEB 4 complianc...
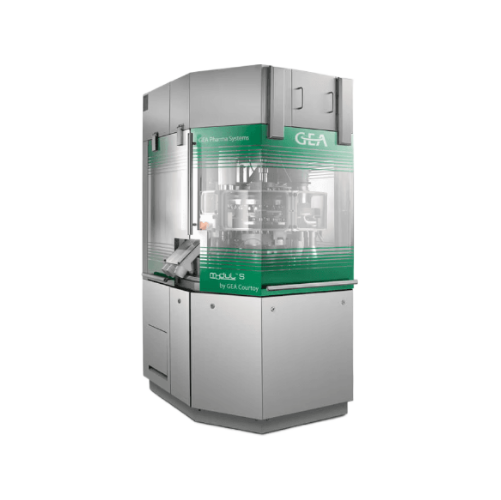
Medium-volume rotary tablet press for pharmaceuticals
Optimize tablet production with high-throughput and rapid changeove...
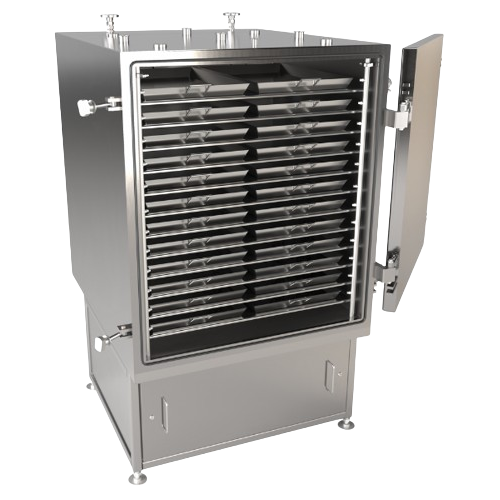
Vacuum tray dryer for pharmaceutical applications
Optimize drying of heat-sensitive compounds while maintaining product i...
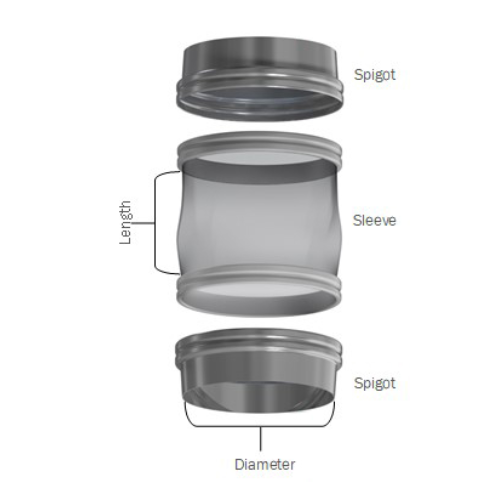
Flexible connector for bulk powder manufacturing
Eliminate leakage and enhance hygiene in your powder processing with a sn...
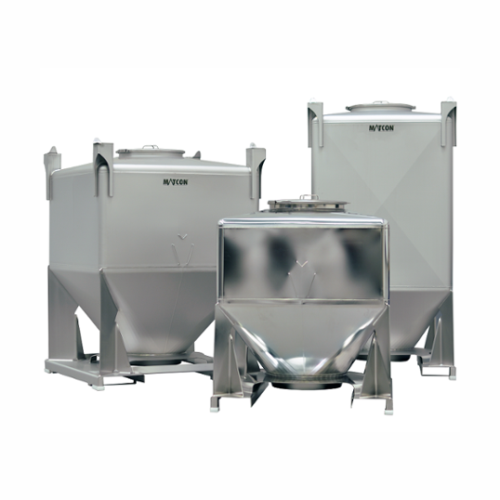
Intermediate bulk containers for powder and materials handling
Optimize your material handling processes with containers...
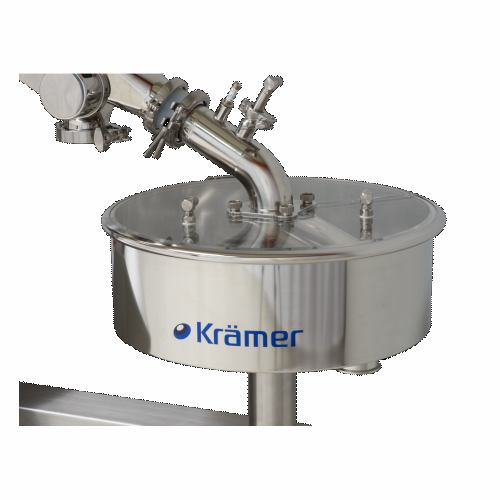
High-containment diverter for continuous tablet and capsule filling
Enhance your production line with a versatile solut...
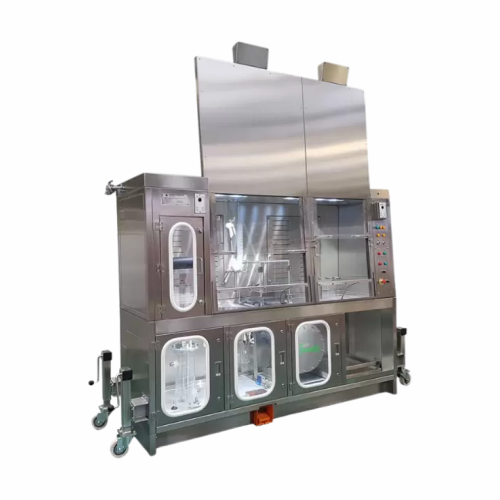
Containment solutions for hazardous material processing
Ensure safe and efficient processing of hazardous materials with ...
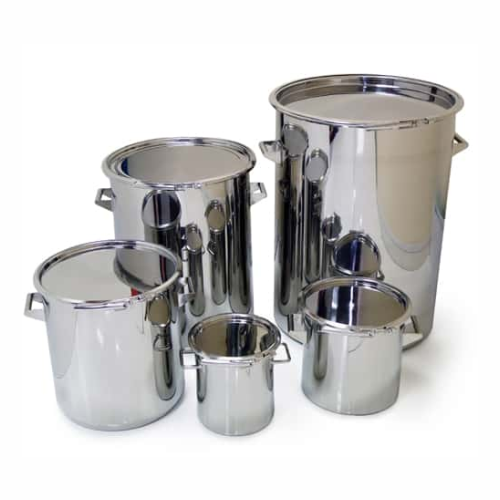
Stainless steel drums for powder storage
For high-value powder storage, these stainless steel drums offer reliable containm...
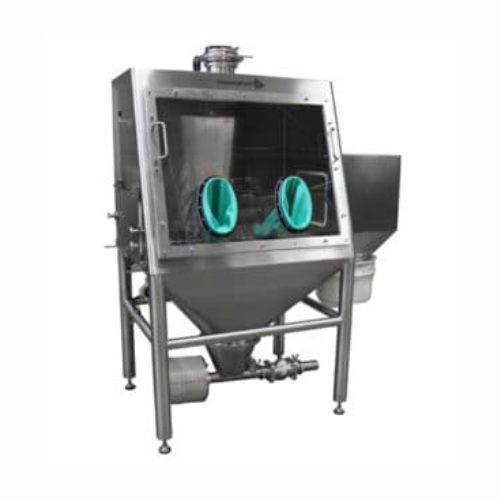
Dust-control sack tip station for industrial loading
Ensure seamless and safe unloading of powders with an integrated dus...
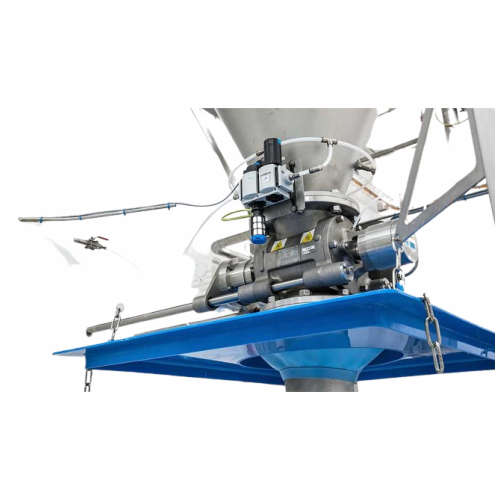
Heavy duty rotary valves for powder handling
Ensure precise material flow and safety in harsh processing environments with...
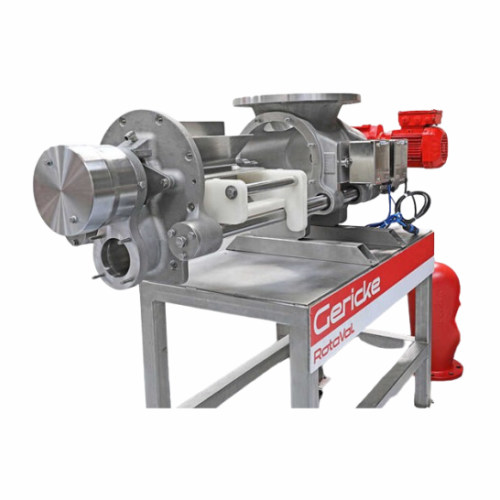
Quick-clean hygienic rotary valves
Ensure seamless cleaning and minimal downtime in your production line with rotary valves...

Big bag unloader for industrial bulk materials
Efficiently handle bulk materials with this modular unloading system, desig...
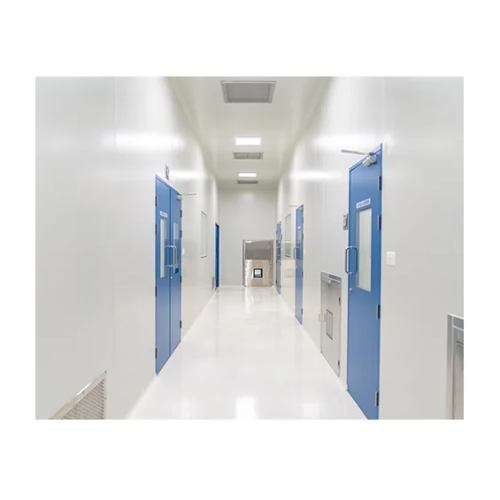
Modular cleanroom panel systems
Transform your cleanroom projects with modular panel systems that streamline installation an...
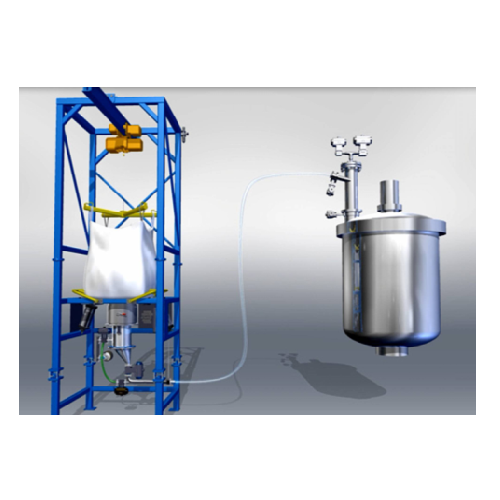
Big bag emptying station for powder handling
Ensure safe and efficient powder discharge with precision containment, adapta...
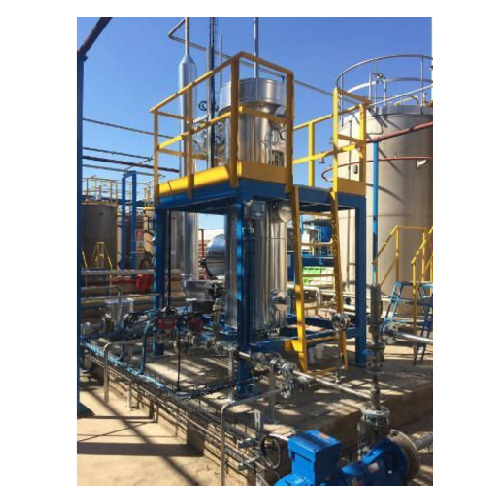
Supercritical Co2 extraction system
Optimize your extraction processes with environmentally friendly and efficient supercri...
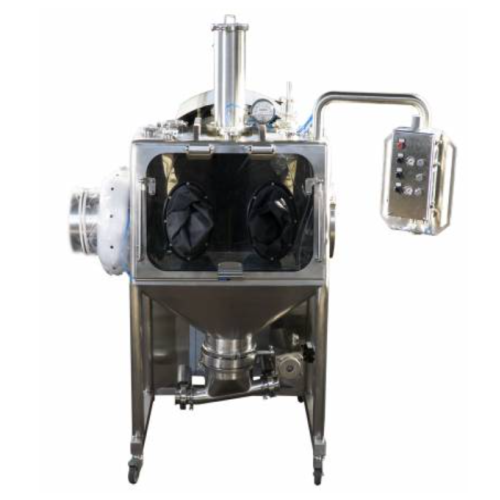
Powder handling drum dock station
Ensure safe and efficient powder transfers with high containment levels, minimizing opera...

Isolator for Vphp decontamination testing
Ensure precise decontamination analysis and stringent monitoring of hydrogen per...
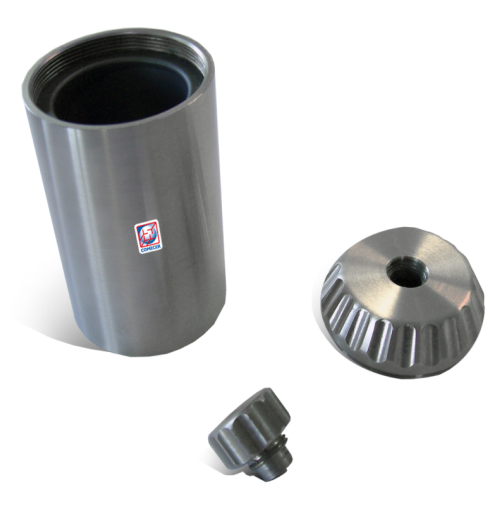
Stainless steel vial container for personal protection
Ensure the safety and integrity of sensitive materials with robust...
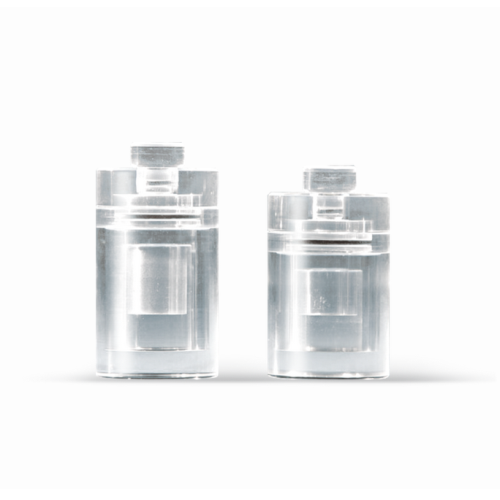
Beta radiation shielding for vials
Ensure the safe handling and storage of radiopharmaceuticals with effective beta radiati...

Shielded isolator for radiopharmaceutical synthesis and dispensing
Ensure radiopharmaceutical purity and operator safet...
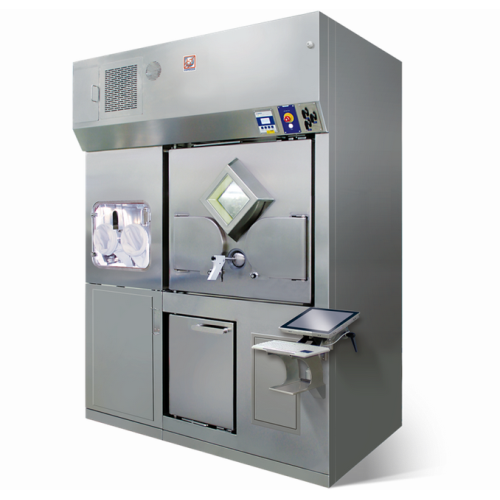
Radiopharmaceutical dispensing isolator for vials and syringes
For precise radiopharmaceutical preparation, this isolato...
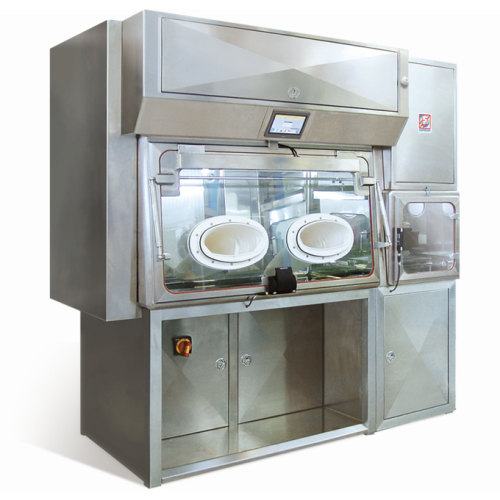
Sterile isolator for cellular labeling
Ensure sterility and protection in cellular labeling processes with an isolator that...
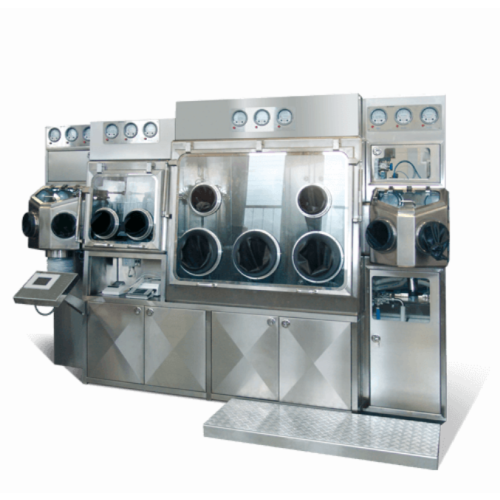
Mini plant isolator for laboratory protection
Ensure maximum operator safety and product integrity with a versatile isolat...
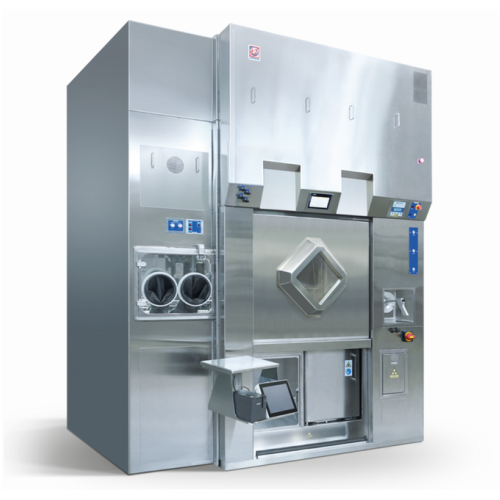
Laminar flow shielded cell for radiopharmaceutical research
Ensure aseptic conditions and precise dose calibration for i...
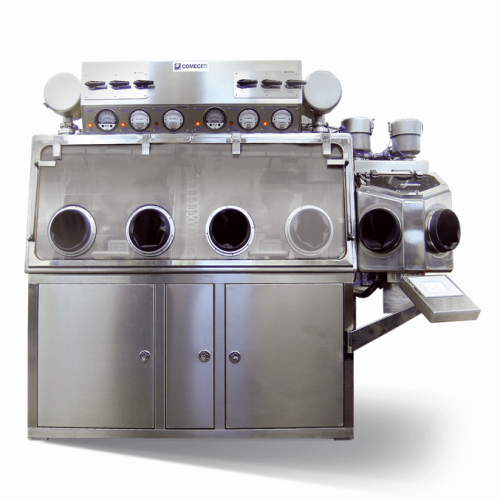
Isolator for cytotoxic drug handling
Ensure safety and compliance in handling cytotoxic drugs and radiopharmaceuticals with...
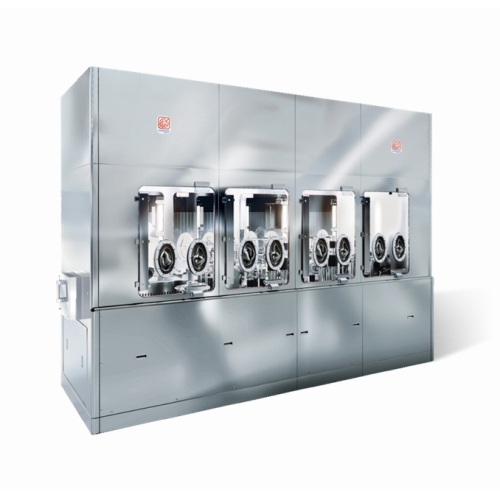
High quality sterile filling system
Experience unparalleled precision in aseptic filling with this advanced system, designe...
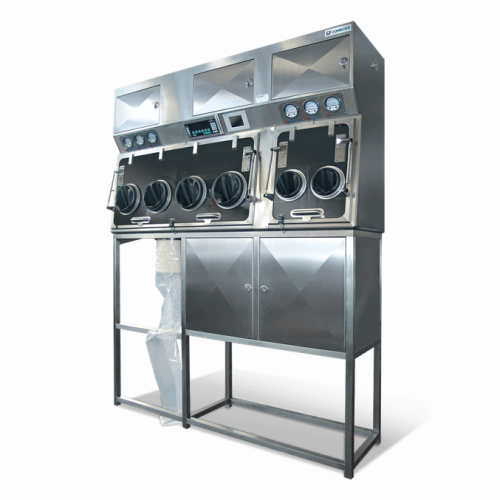
Dispensing isolator for hazardous substance handling
Ensure maximum operator safety and contamination control when handli...
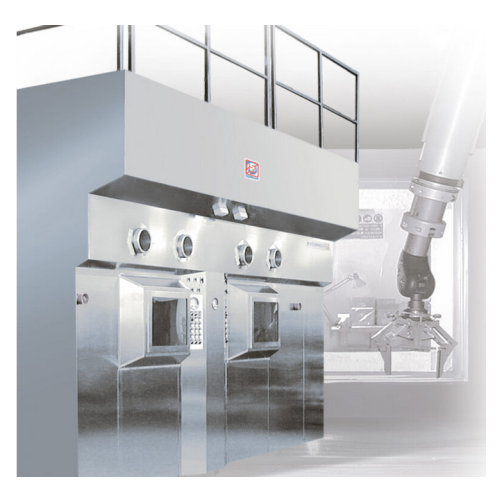
Double hot cell for radiopharmaceutical chemistry
Ensure optimal safety and compliance in handling radiopharmaceuticals w...
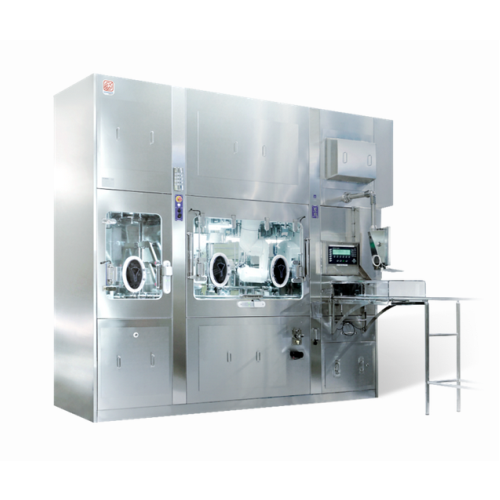
Dry powder filling isolator for cgmp production
Achieve precise powder dosage and secure containment for hazardous materia...
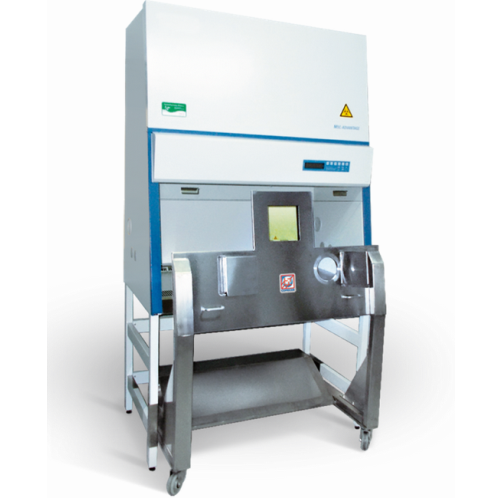
Laminar flow hood with lead glass for laboratory use
Ensure sterility and precision in high-stakes environments with adva...
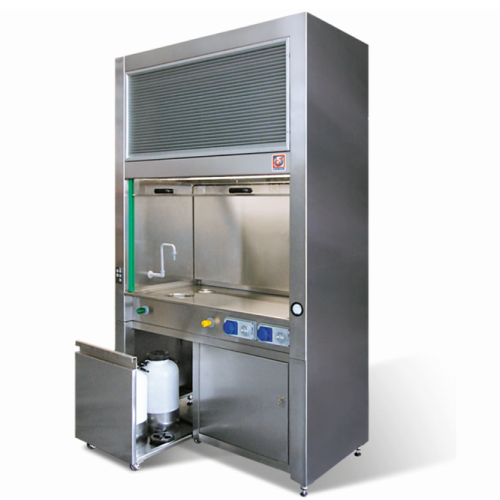
Radiochemistry fume hood
Ensure precise containment and filtration during radiochemical processes, safeguarding both operator...
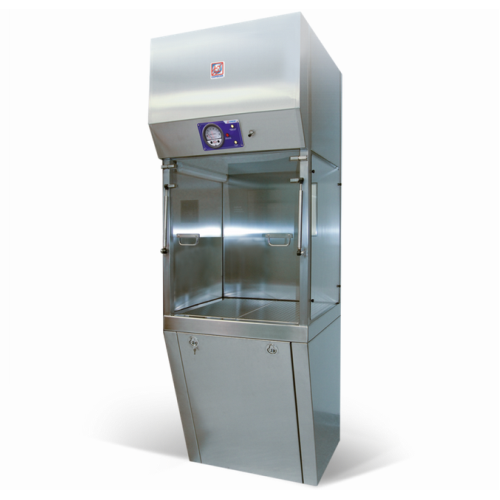
Laminar flow hood for aseptic preparation
Ensure aseptic conditions for sterile injectable drug preparation with this adva...
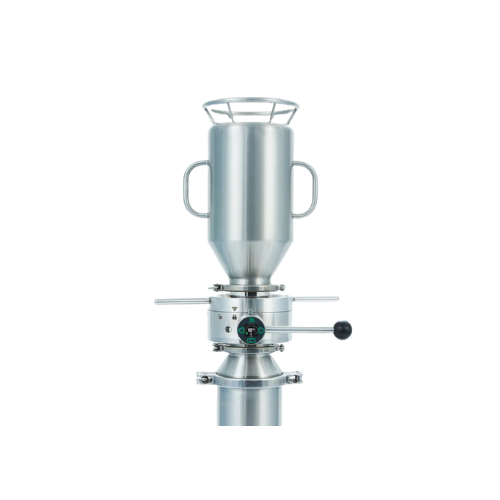
High containment powder transfer valve
Ensure high containment for potent powders in your production line, reducing contami...

High containment powder transfer valve for bulk material
Ensure operator safety and prevent cross-contamination with robu...
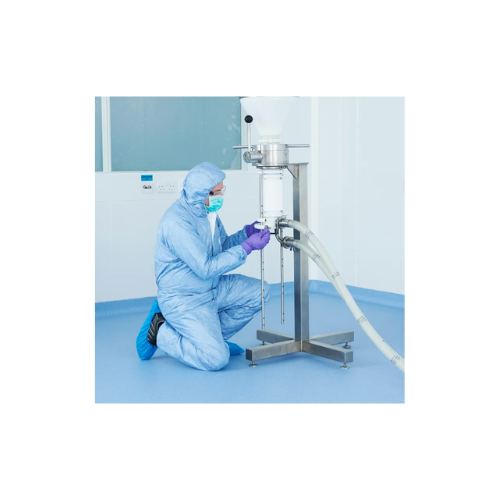
Bottle cleaning station for controlled environments
Ensure high-level decontamination of passive units and containers wit...
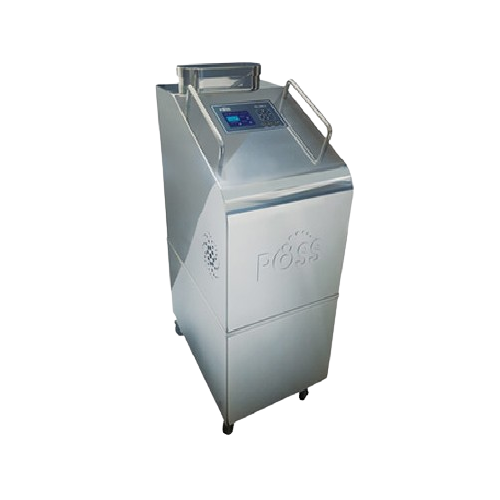
Hydrogen peroxide ultrafine particle sterilizer for contamination control
Ensure thorough sterilization in small space...
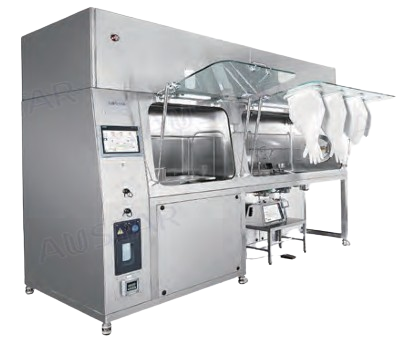
Sterilisable isolator workstation for aseptic containment
Ensure precise contamination control and sterile conditions du...
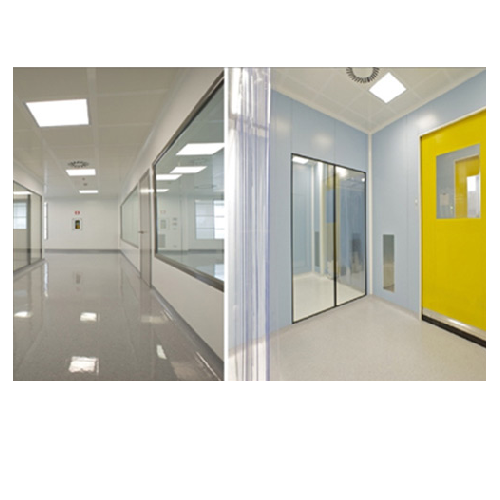
Cleanroom enclosure system for pharmaceutical and chemical industries
Ensure sterile environments with this customizabl...
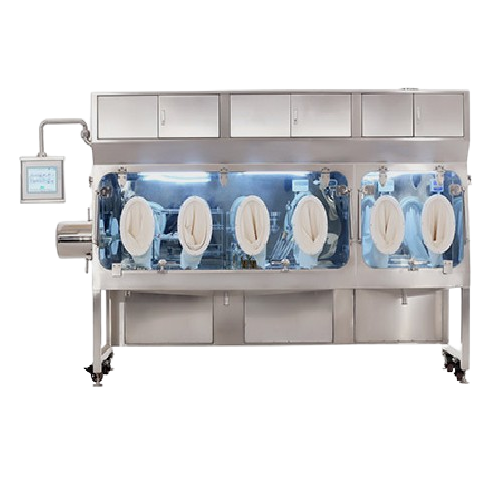
High containment isolator for toxic and active drug handling
Ensure safe handling and environmental protection while pro...
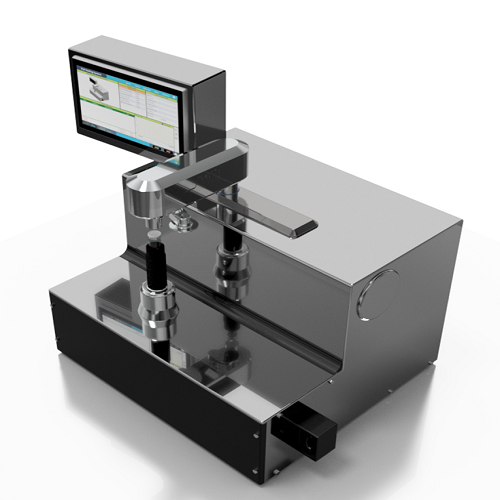
Bench-top vial sealing system for pharmaceutical use
Ensure precise sealing of pharmaceutical vials with a system designe...
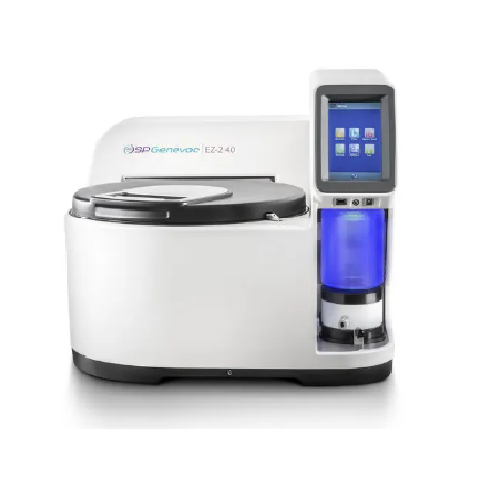
Centrifugal evaporator for medicinal chemistry
Achieve precise evaporation and crystallization with innovative anti-bumpin...
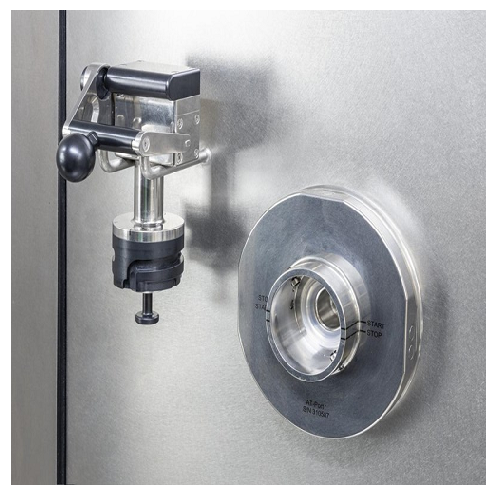
Aseptic liquid transfer connection system
Ensure sterile liquid transfer between containment areas with minimal product lo...
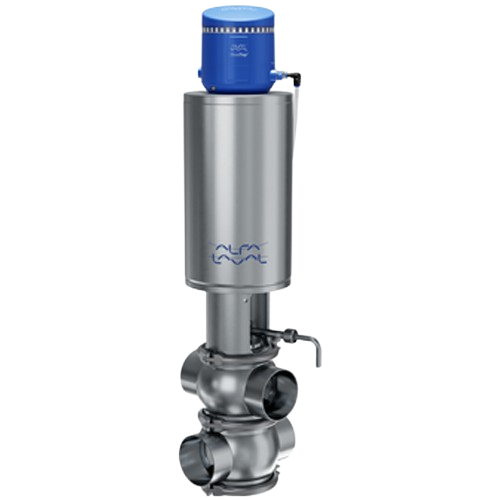
Mixproof valve for cleaning-in-place control
Streamline your cleaning processes and ensure product safety with a versatile...
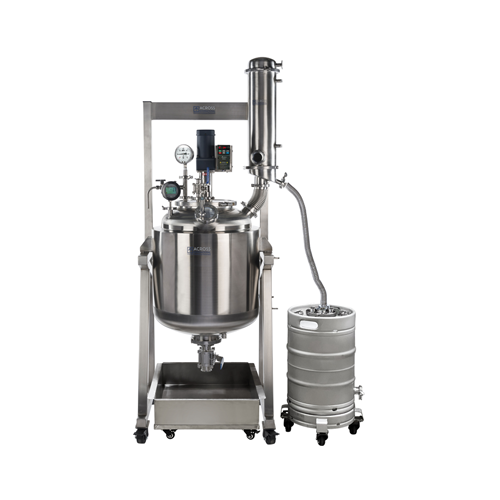
50l stainless steel dual-jacketed reactor for chemical processes
Optimize your laboratory’s efficiency with a dual...
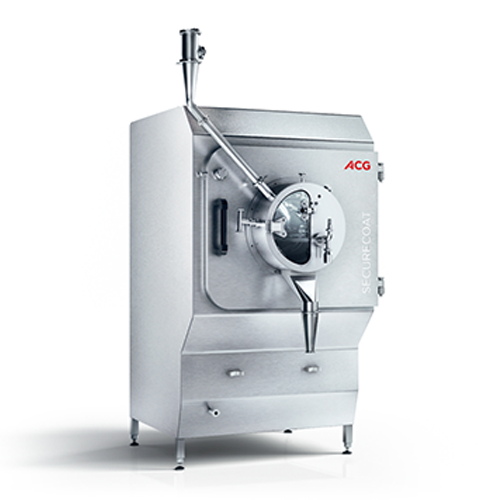
Containment tablet coater for high-potency drugs
Ensure operator safety while achieving precise tablet coating on high-pot...
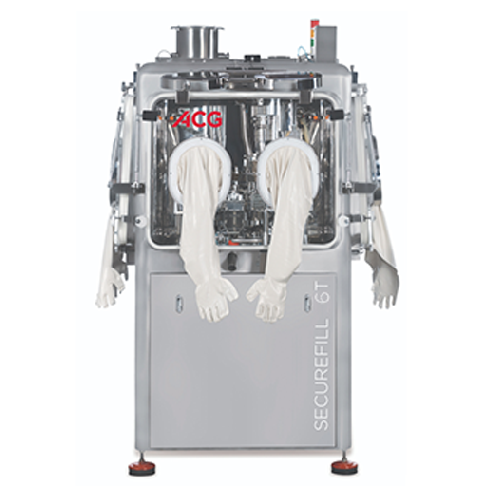
Containment capsule filling system for highly potent drugs
Ensure operator safety while filling capsules with high-poten...
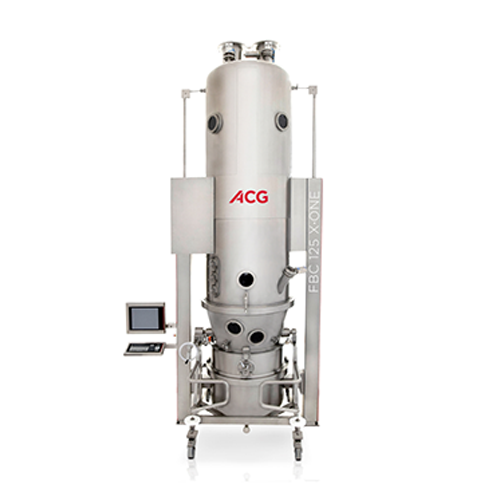
Fluid bed dryer with granulation and coating
Enhance your processing efficiency with a versatile system capable of combini...
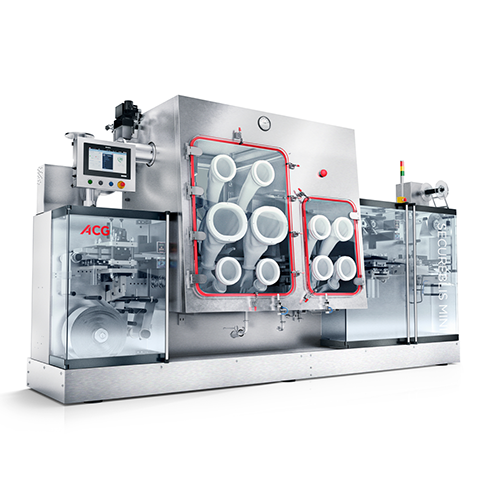
Containment blister packaging for highly potent Apis
Ensure operator safety during the blister packaging of highly potent...
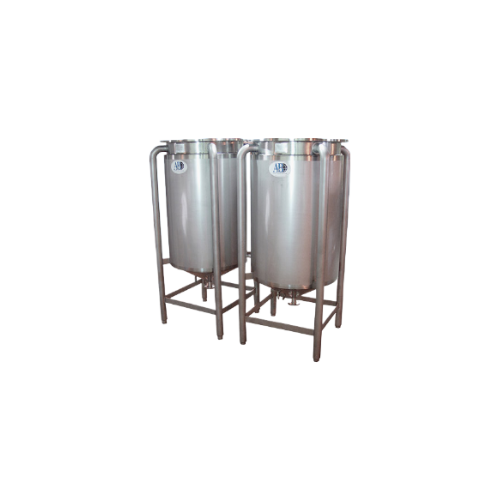
Customizable storage tanks for industrial use
Optimize your production with versatile storage tanks designed for precise c...
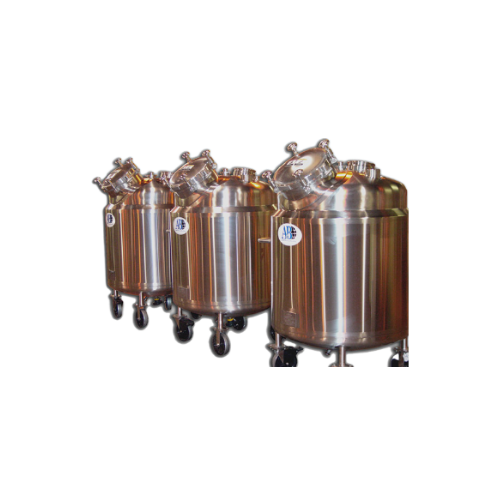
Industrial pressure vessels
Ensure product integrity and regulatory compliance with engineered-to-order pressure vessels, de...
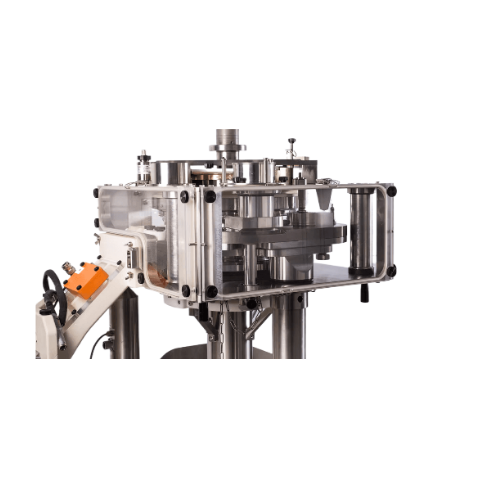
Tablet compression module for high containment applications
Quickly switch between tablet batches without compromising s...
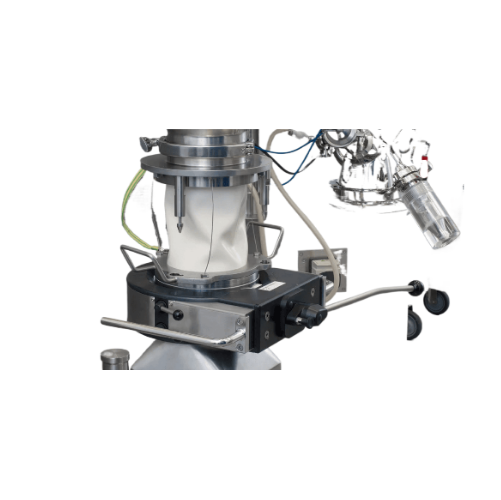
Containment valves for pharmaceutical powder transfer
Ensure safe transfer of highly potent pharmaceuticals with this mod...
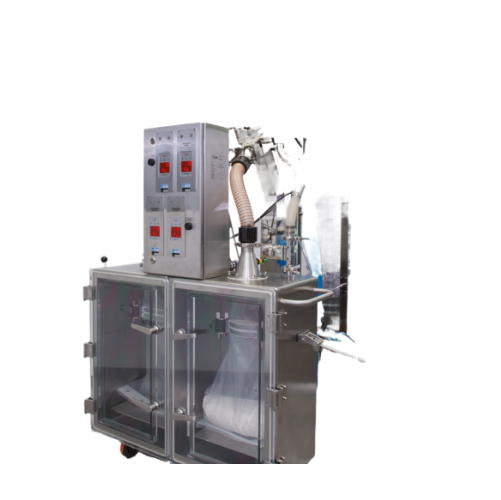
Disposable containment system for solid dosage material
Ensure safe and dust-free transfer of hazardous materials with ou...
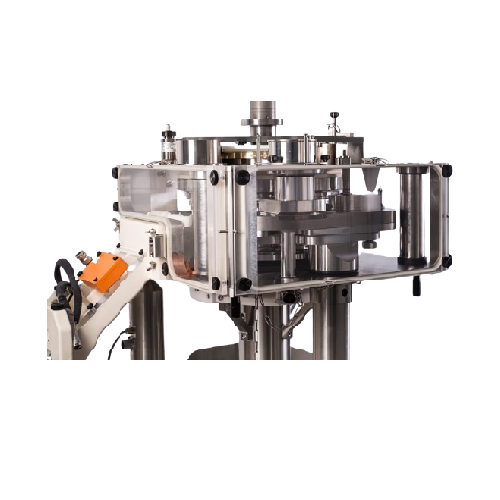
Wash-off-line system for pharmaceutical plants
Optimize your production with a versatile wash-off-line system, ensuring pr...
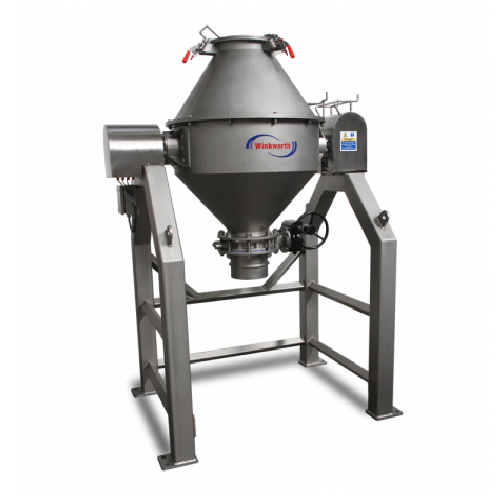
Double cone mixer for free-flowing material blending
Optimize your production with precision blending and gentle drying o...
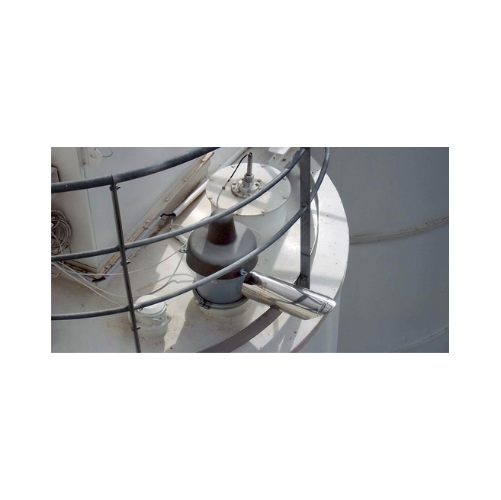
Membrane pressure relief valve for silo protection
Ensure immediate pressure stabilization in your bulk storage silos wit...
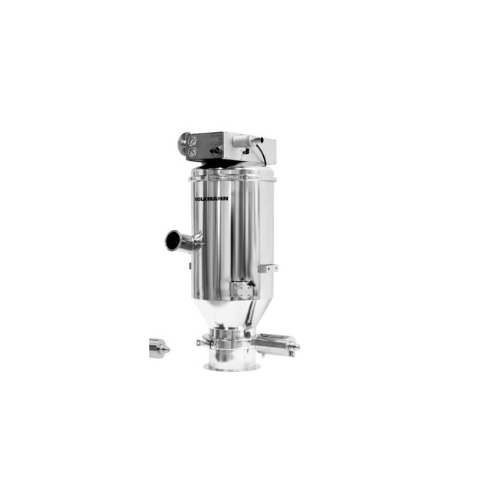
Pharmaceutical vacuum conveyors for hygienic transport
Ensure contamination-free transport of sensitive pharmaceuticals a...
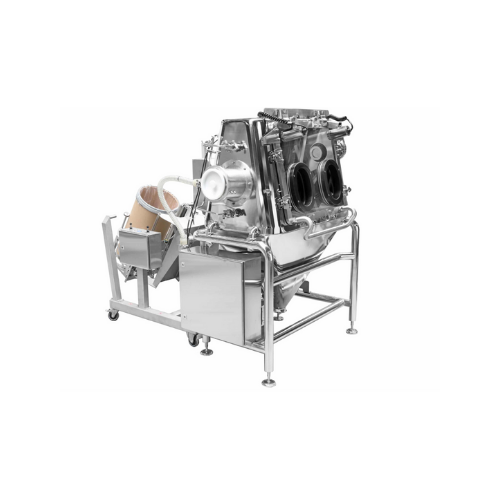
Containment system for product loading
Ensure safe handling of hazardous materials with this containment system, designed t...
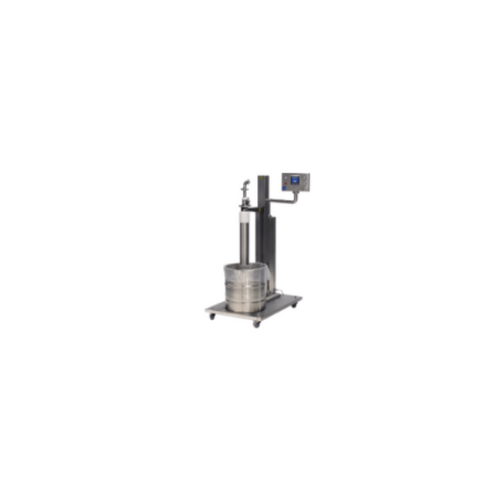
Drum discharge system for bulk material handling
Achieve precise, gentle transfer of sensitive pharmaceuticals and granula...
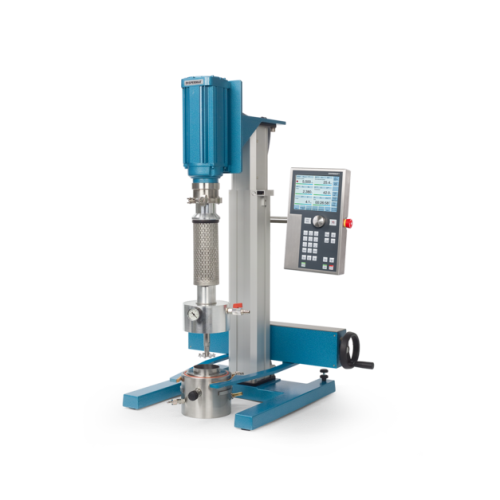
Vacuum dispersion system for laboratory applications
Achieve precise mixing and homogenization under vacuum conditions, e...
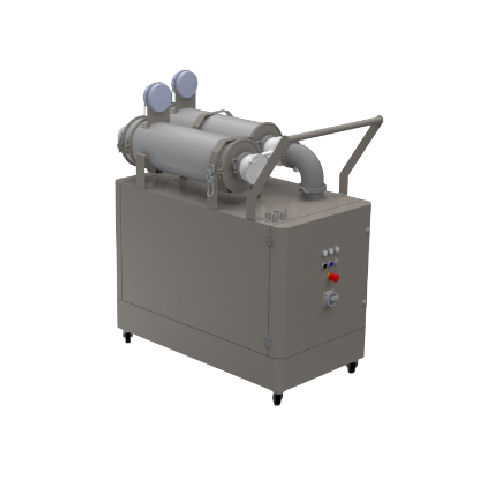
Containment single-use filter module
Ensure safe handling of high-potency substances and streamline filtration processes wi...
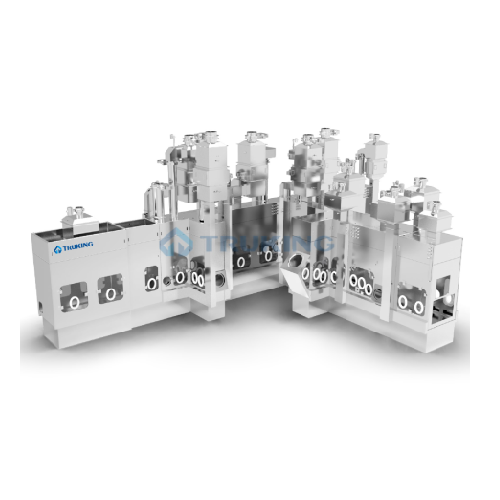
Pharmaceutical isolator system for aseptic production
Ensure aseptic conditions and operator safety with a robust isolati...
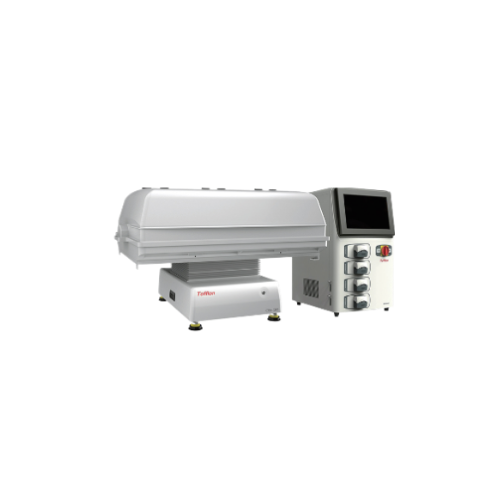
Cell expansion system for antibody drug production
Enhance your biopharmaceutical production with efficient cell expansio...
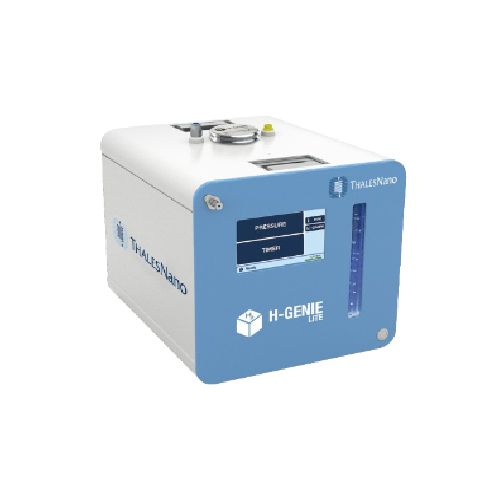
High-pressure hydrogen generator for laboratory use
Replace cumbersome hydrogen cylinders with an on-demand generation so...
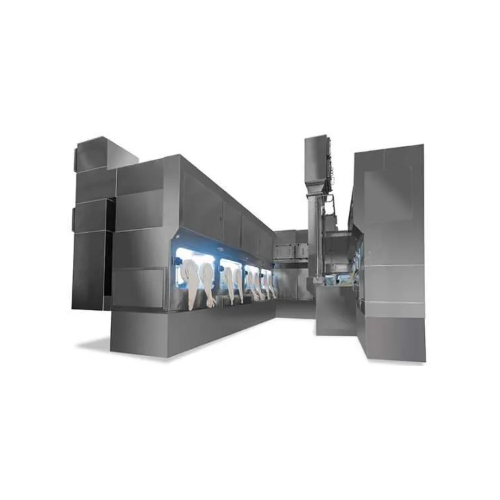
Freeze dryer & filling line aseptic isolator for cytotoxic products
Handle cytotoxic and high-potent drugs with precisi...
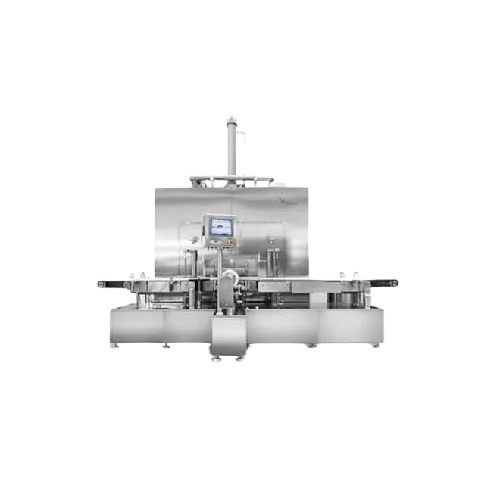
Sterile lyophilisation and filling line
Ensure aseptic conditions while freeze-drying biopharmaceuticals and high-potent dr...

Downflow booths for hazardous material processing
Ensure product integrity and operator safety during hazardous material ...
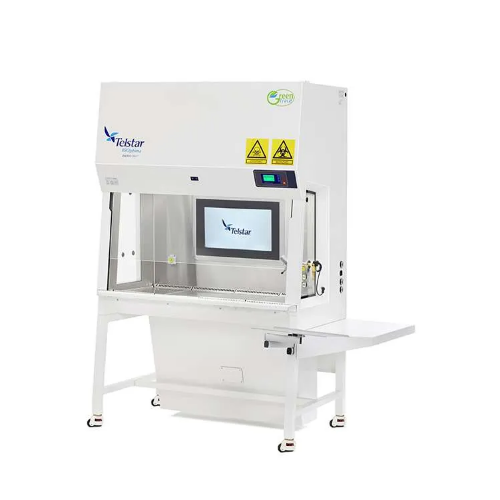
Biological safety cabinet for medication preparation
Enhance medication preparation safety and reduce error rates with a ...
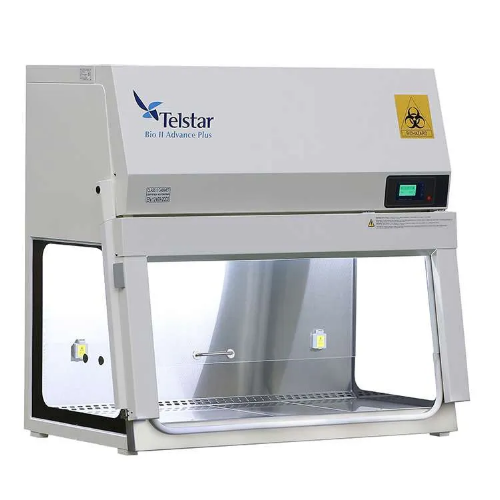
Class Ii biological safety cabinet
Ensure optimal safety levels while handling biological agents with a compact, ergonomic ...
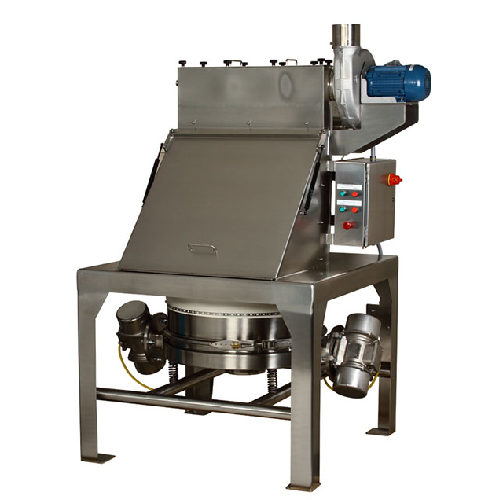
Round vibratory separation equipment - bag dump screener system
Enhance your material handling and safety by efficiently...
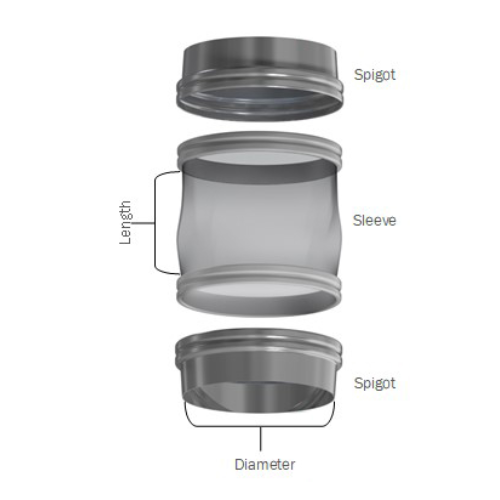
Flexible connector system for bulk powder processing
Eliminate leaks and enhance hygiene in your powder processing line w...
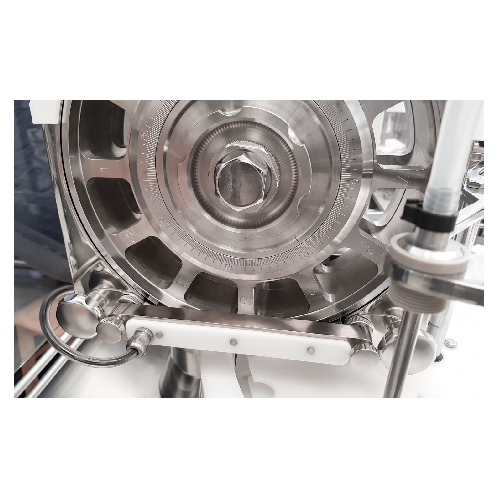
Micro-dosing system for pharmaceutical powders in vials
Ensure accurate aseptic dosing of sensitive pharmaceutical powder...
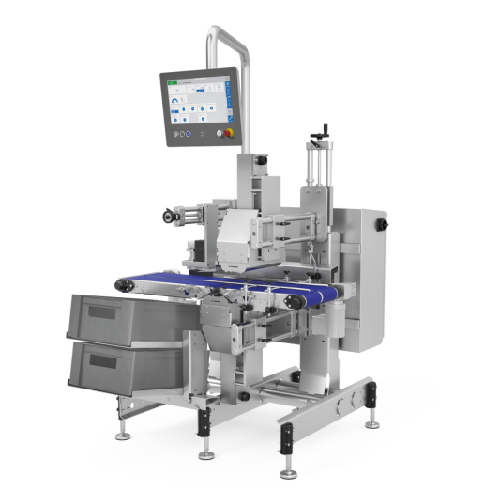
Visual inspection systems for packaging quality control
Detect and eliminate packaging and labeling faults early in your ...
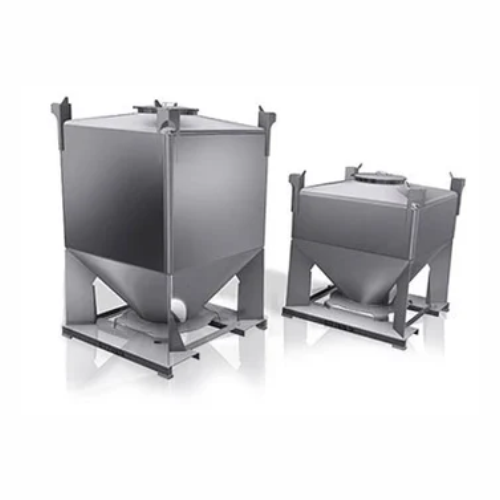
Powder handling system for industrial applications
Overcome powder flow issues and enhance production efficiency with adv...
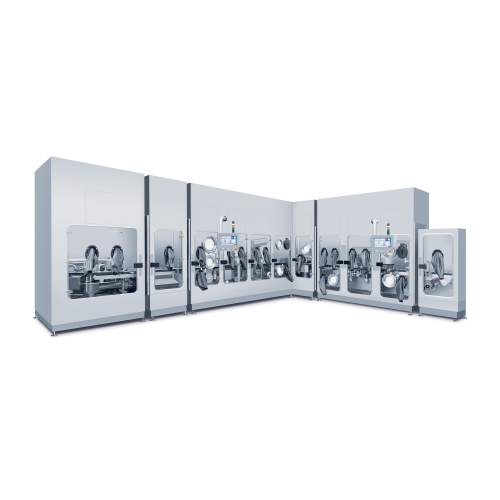
Aseptic filling and capping for vials and syringes
Ensure sterility and precision in vial and syringe filling with advanc...
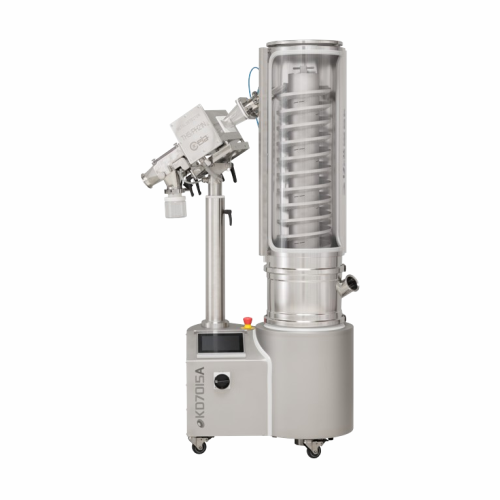
High performance tablet deduster with metal detection
Achieve precision dedusting and metal detection in tablet processin...
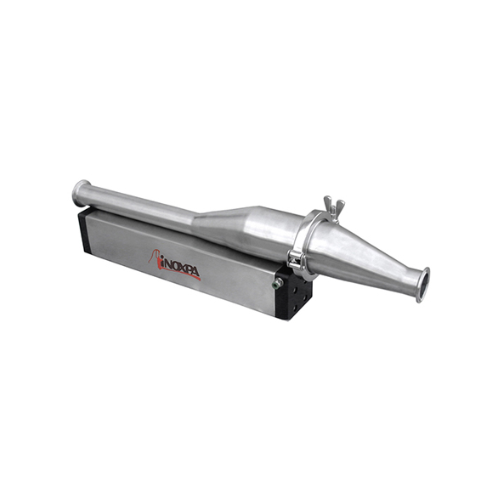
Hygienic pipeline product recovery system
Efficiently recover valuable residuals from pipelines while streamlining your cl...
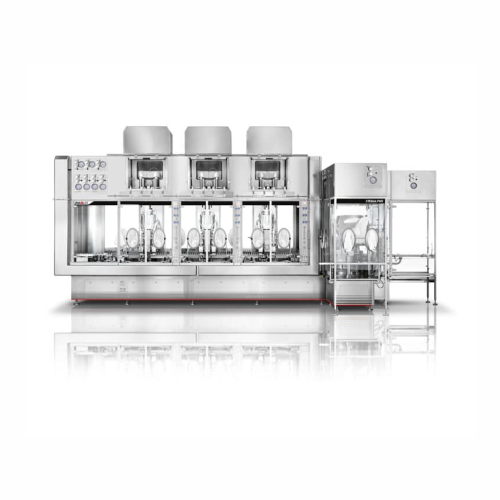
High speed powder dosing and stoppering for antibiotics
Address the threat of antibiotic-resistant bacteria with precisio...
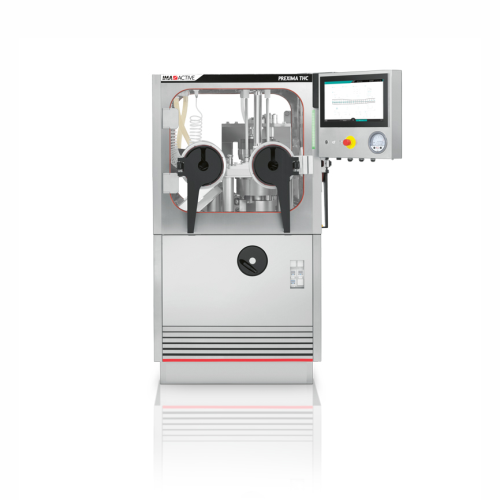
Tablet press for high containment environments
For handling potent compounds without compromising safety, a high-containme...
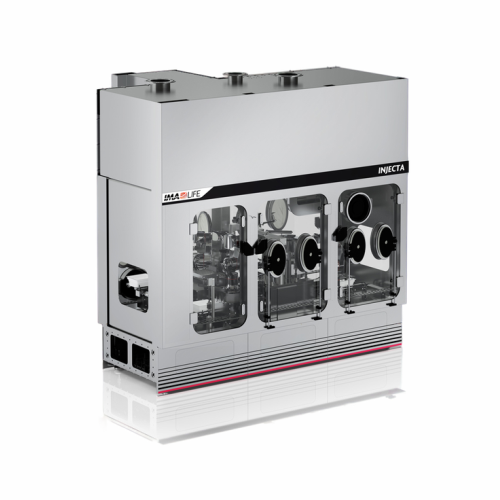
High-speed fill-finish system for ready-to-use components
Enhance aseptic fill-finish operations with a high-speed solut...
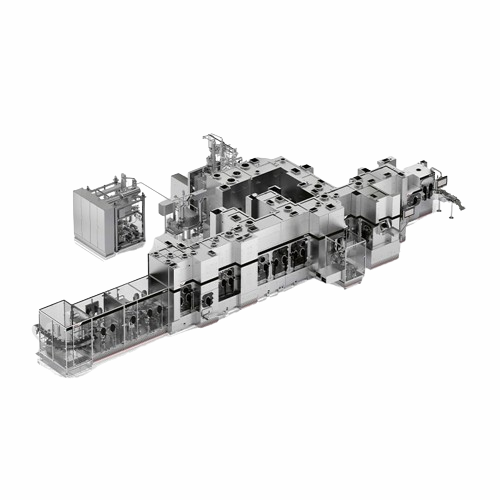
Isolation solutions for aseptic fill-finish lines
Achieve maximum product sterility with advanced isolation solutions, mi...
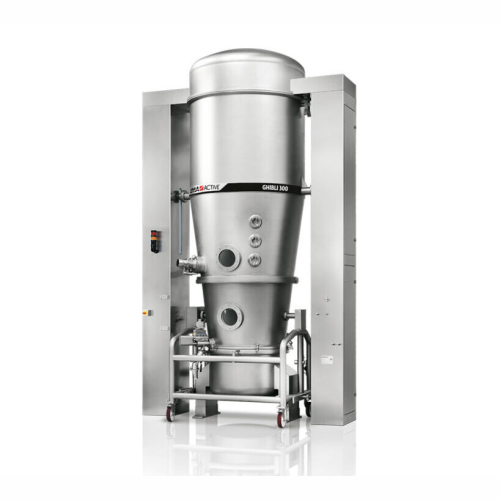
Fluid bed processor for pharmaceutical granulation and drying
Achieve precise drying, granulation, and coating of pharma...
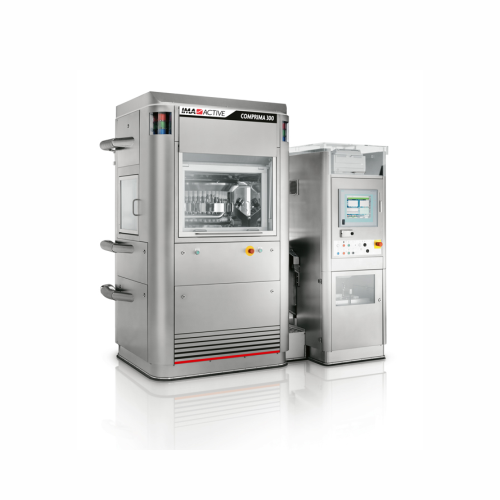
Tablet press for high-quality pharmaceutical tablets
Ensure optimal tablet quality and yield with an advanced compression...
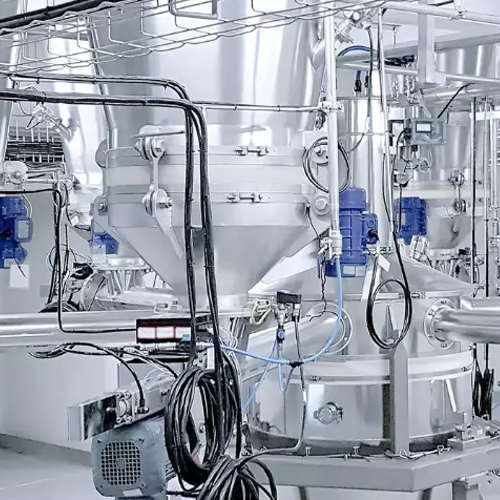
Conical screw mixer for powder blending
Achieve precise and homogeneous blending with the conical screw mixer, ensuring uni...
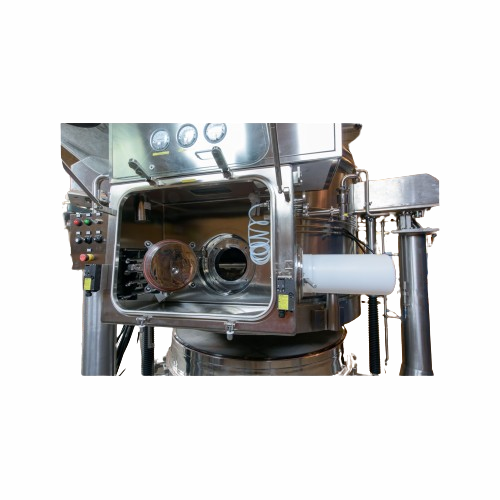
Filter dryer with containment system for hazardous materials
Ensure operator safety and product integrity during hazardo...
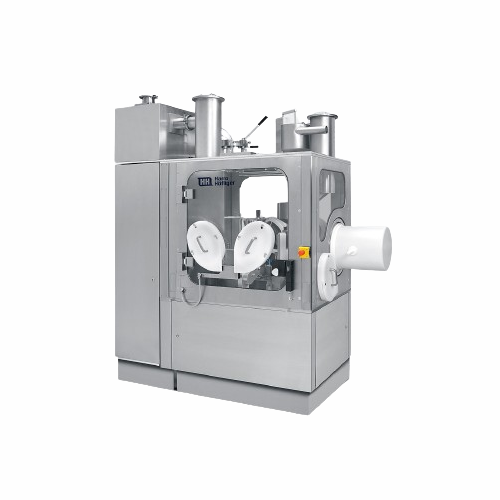
Containment capsule filling system for lab and small batch production
Designed to ensure maximum safety in pharmaceutic...
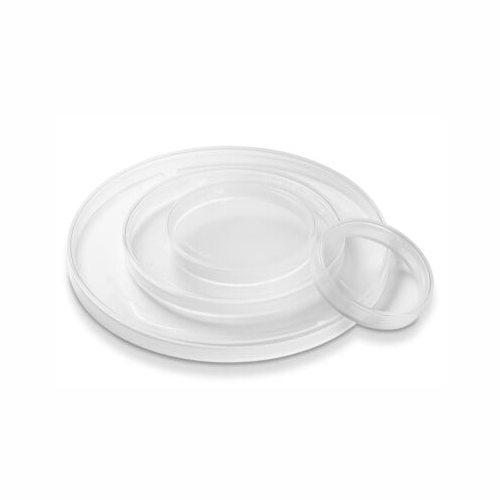
Silicone dust caps for dust-tight powder transfer
Achieve dust-tight containment and efficient powder transfer with flexi...
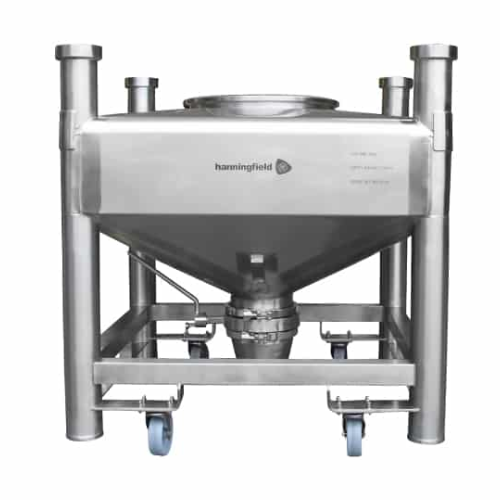
Tablet storage and transport containers
Ensure the safe and gentle handling of tablets during storage and transport, minimi...
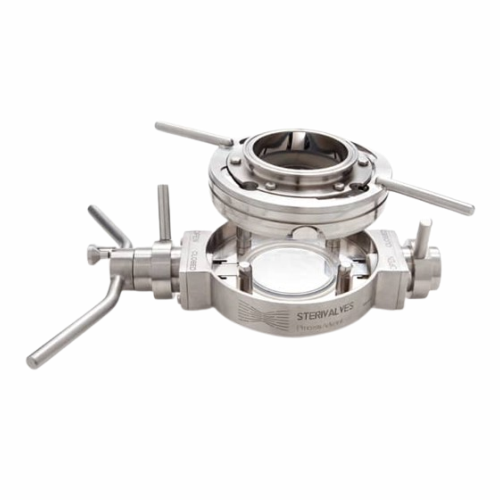
Split butterfly valve for sterile powder transfer
Ensure safe and sterile transfer of powders with unparalleled containme...
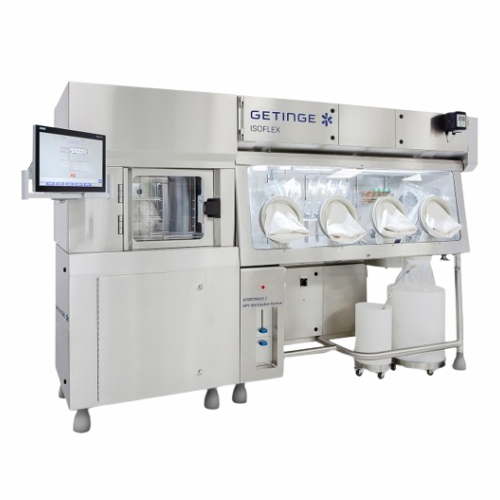
Modular Gmp isolator for aseptic processing
Ensure contamination-free production with this modular aseptic isolator, desig...
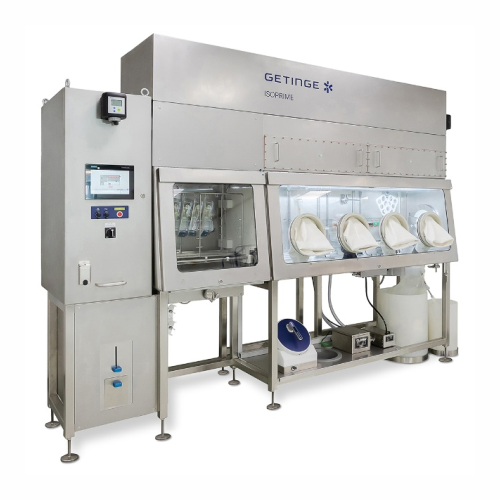
Cost-effective rigid-wall isolator for aseptic applications
Ensure sterility and safety with a versatile isolation and d...

Aseptic transfer port for secure bi-directional transfer
Ensure seamless and contamination-free transfer of sterile mater...
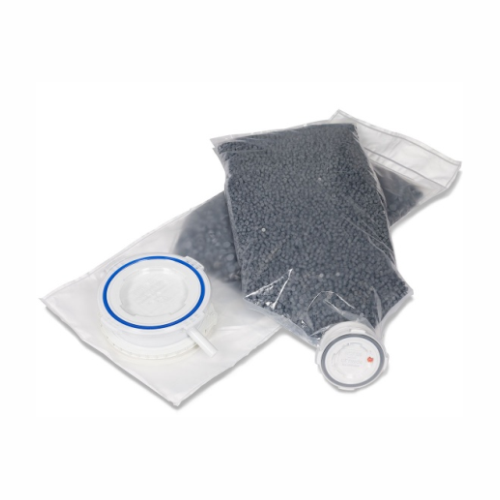
Sterile transfer bags for aseptic production
Ensure contamination-free and efficient component transfer in high-speed asep...
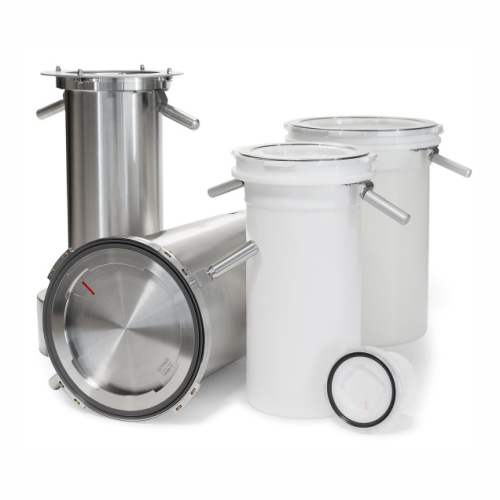
Reusable containers for sterile and toxic material transfer
Ensure safe and contamination-free transfer of sterile and t...
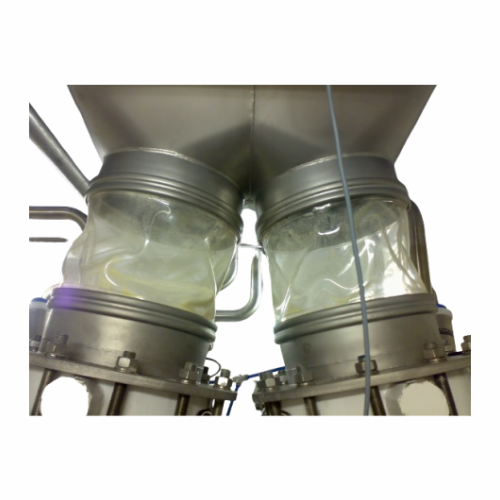
Hygienic flexible sleeves for food and pharmaceutical use
Say goodbye to contamination risks with this tool-free, quick-...
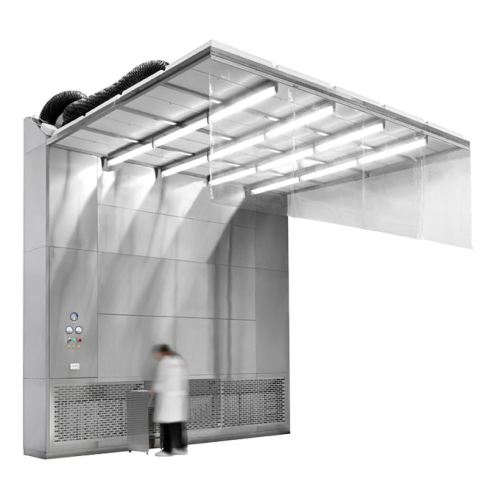
Cleanroom air filtration unit for pharmaceutical production
Ensure sterile integrity in your manufacturing process with ...
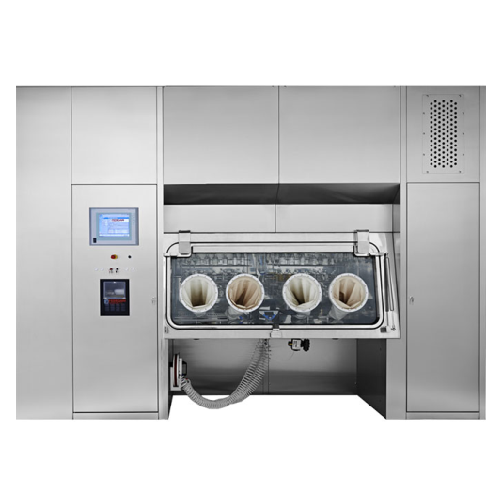
Pharmaceutical isolator for contamination control
Ensure sterility and safety in pharmaceutical manufacturing with advanc...
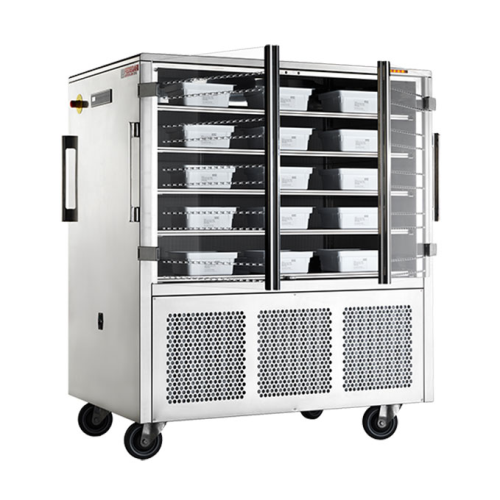
Iso 5 Hepa cart for aseptic material transfer
Ensure aseptic conditions during storage and transfer with this compact HEPA...
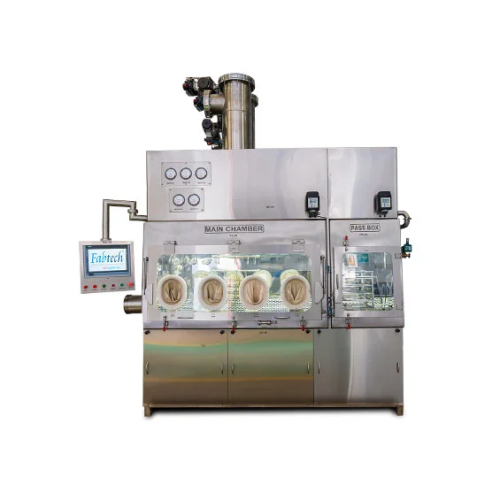
Sterility testing isolator for aseptic environments
Ensure aseptic conditions and process integrity during sterility test...
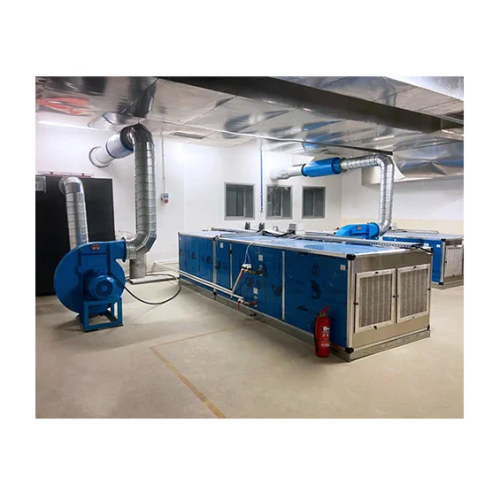
Cleanroom infrastructure for contaminant control
Ensure optimal contaminant control and regulatory compliance in cleanroom...
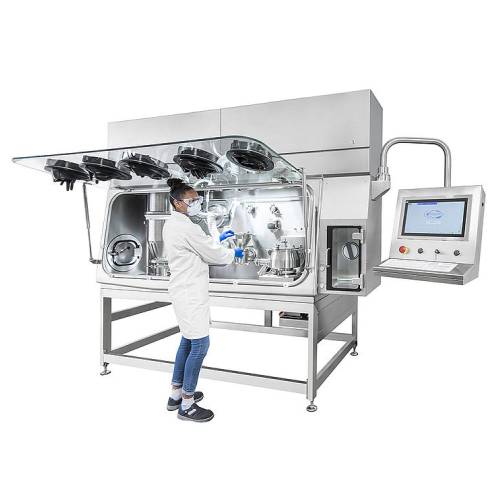
Containment solutions for pharmaceutical production
Enhance operator safety and product integrity with advanced containme...
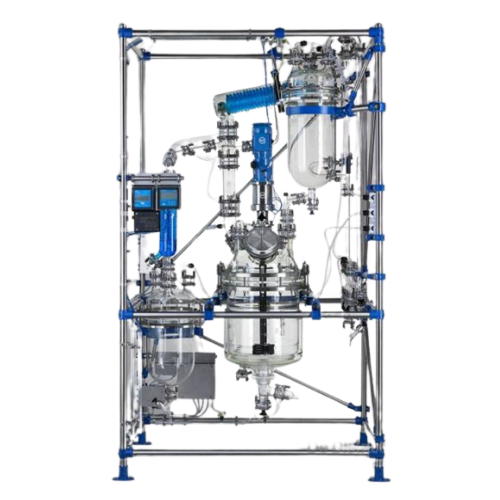
Industrial universal reactor for large-scale chemical synthesis
For chemical producers scaling past laboratory setups, t...
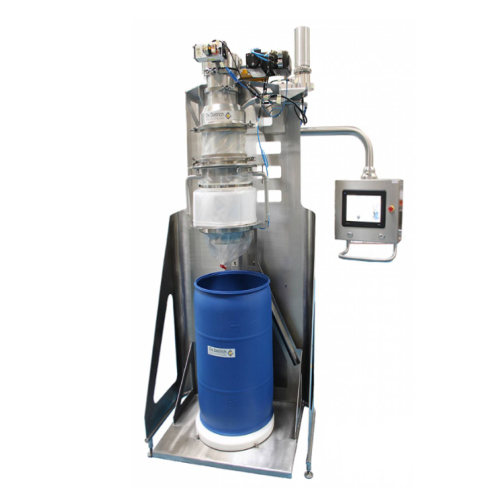
Powder conditioning station for high containment applications
Ensure safe and precise handling of hazardous powders with...
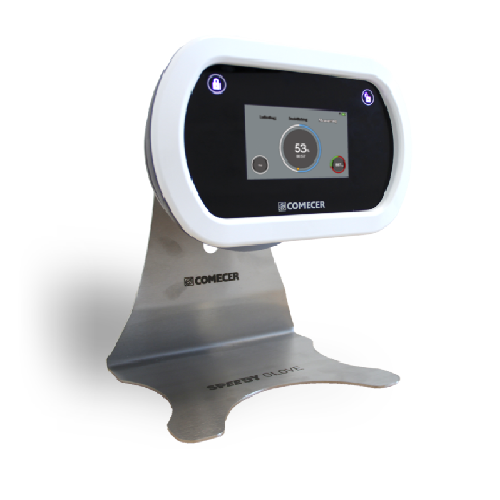
Automatic portable glove tester
Ensure glove integrity in critical environments with rapid, precise leak testing, safeguardi...
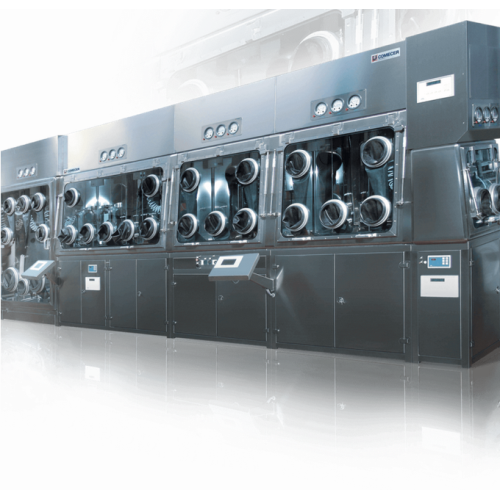
Six stage r&d isolator for safe material handling
Ensure optimal operator safety and material containment during complex ...
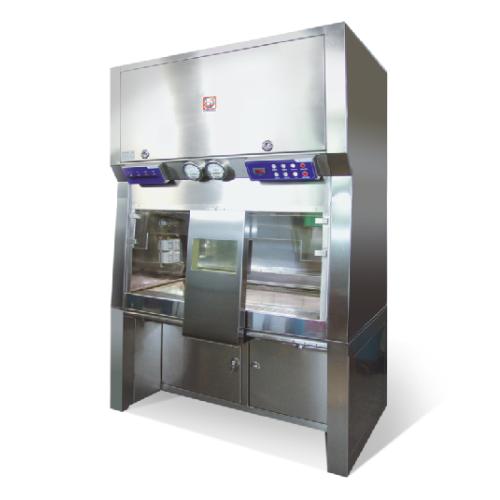
Shielded radiochemistry fume hood
Enhance your lab’s safety and efficiency with a fume hood designed for precise hand...
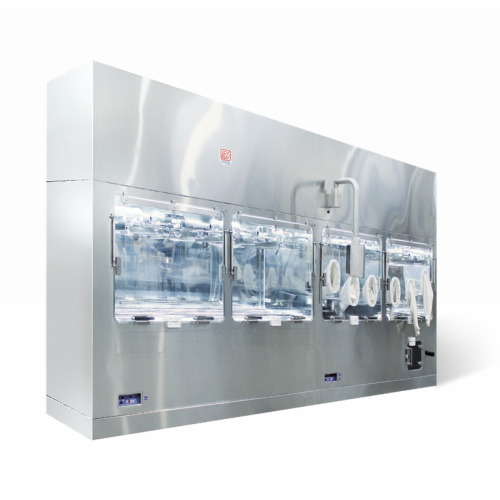
Custom automation for drug-device filling and assembly
Efficiently integrate precise filling and assembly for biopharmace...
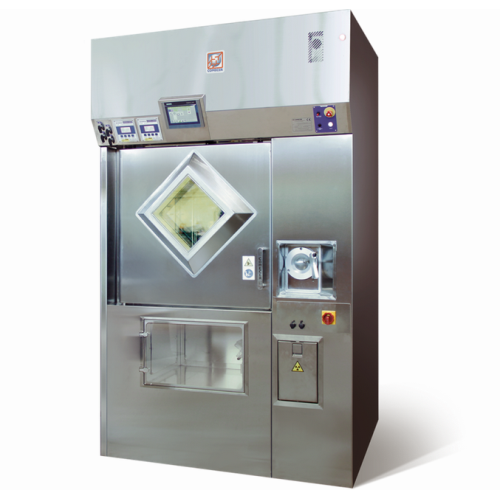
Shielded cell for radiopharmaceutical synthesis
Ensure operator safety and seamless radiopharmaceutical synthesis with adv...
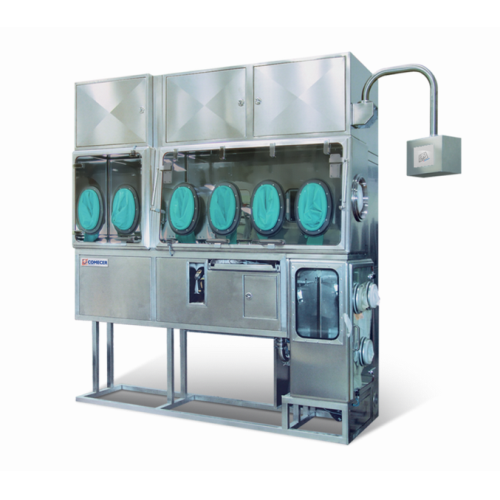
Isolators for safe Hapi transfer and dispensing
Ensure the safe, precise transfer and dispensing of highly active pharmace...
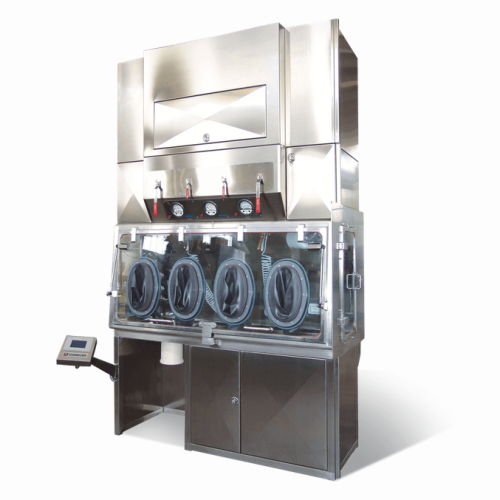
Isolator for washing procedures in pharma industry
Ensure complete isolation and safety during manual cleaning of pharmac...
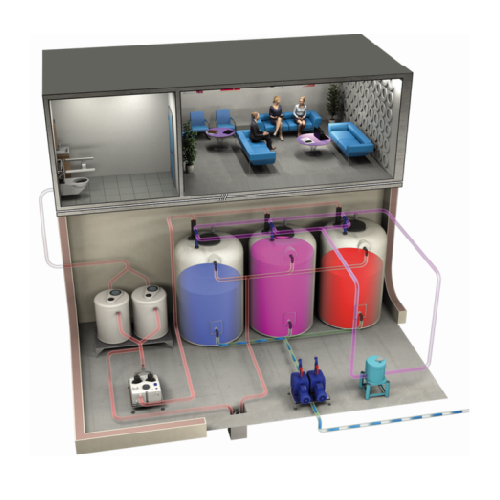
Radioactive waste disposal system for medical facilities
Handle radioactive waste safely by utilizing an automated system...
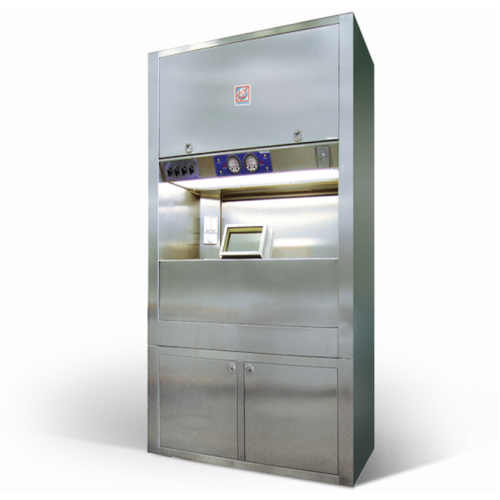
Fume hood for handling medium activity radioisotopes
Ensure safety and precision in your laboratory processes with a fume...
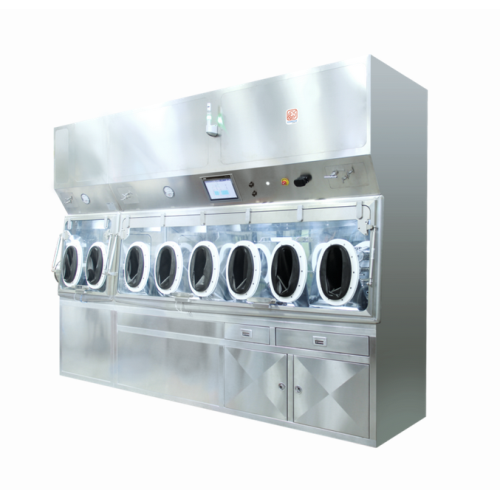
High containment isolator for wet analysis in pharma
Achieve high containment and precise wet analysis with this isolator...
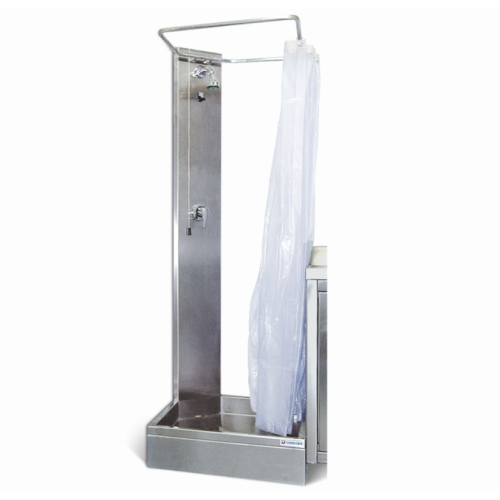
Decontamination shower system for industrial use
Ensure optimal purification and safety with a specialized shower system d...
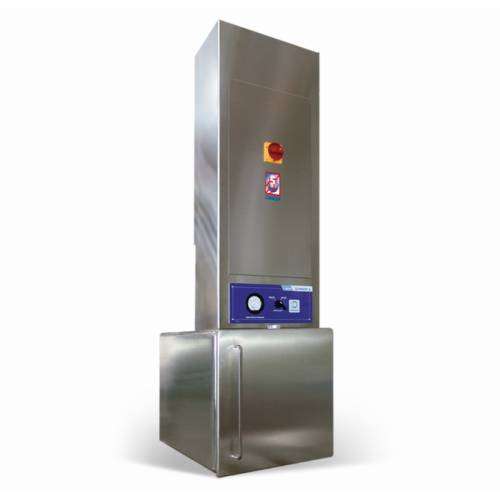
Ventilated pass-through for classified environment transition
Ensure sterile and secure transfer between environments wi...
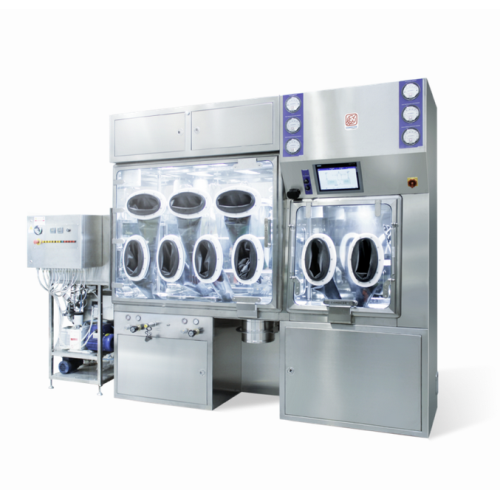
Custom r&d isolator for precise dispensing operations
When handling sensitive compounds, precision and operator safety ar...
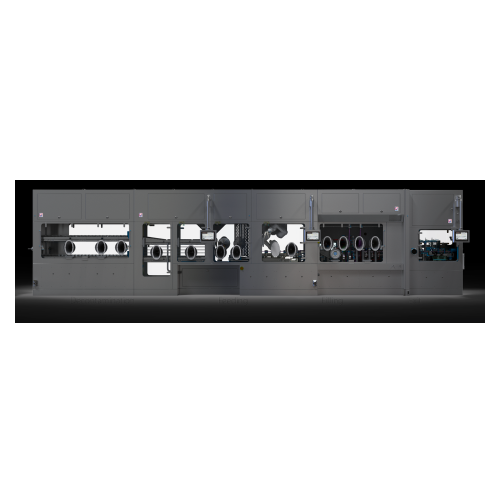
Automatic aseptic filling line for Iv bags
Ensure aseptic integrity and high-speed processing of IV bags with a filling li...

Air compressing station for radiopharmaceutical labs
Efficiently manage and monitor potentially contaminated air in radio...
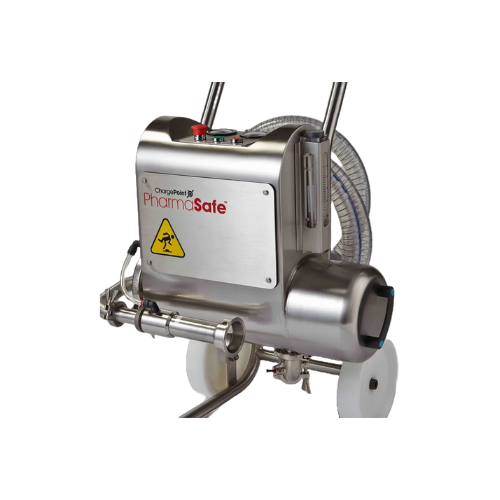
Dust particulate extraction system
Ensure safe containment and minimize airborne particulates in your production line with ...
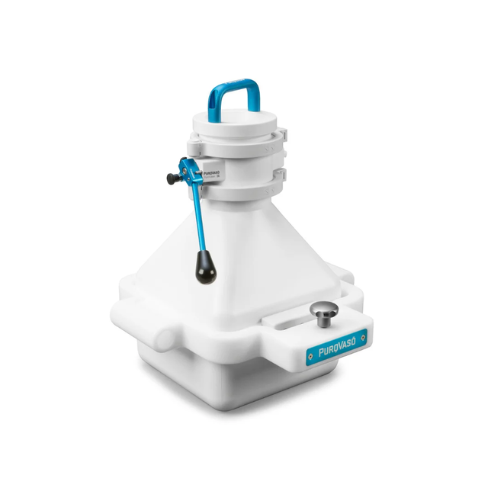
Lightweight plastic butterfly valve for industrial use
Achieve precise flow control and quick disassembly during pharmace...
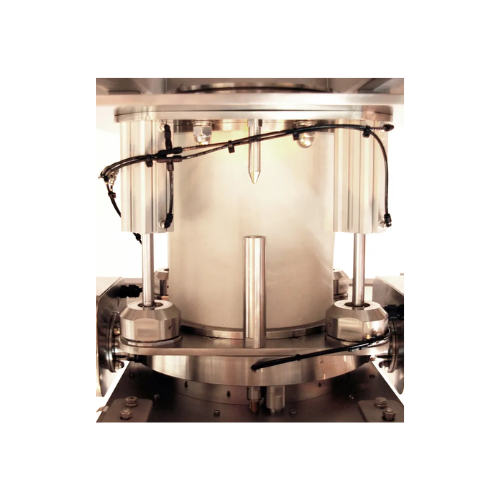
Automatic docking system for bulk powder handling
Optimize docking precision and ensure seamless alignment in bulk powder...
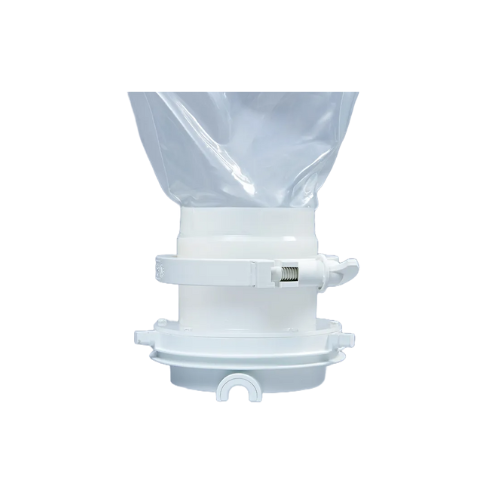
Single use valves for powder transfer
Efficiently transfer powder ingredients with a single-use containment solution, ensur...
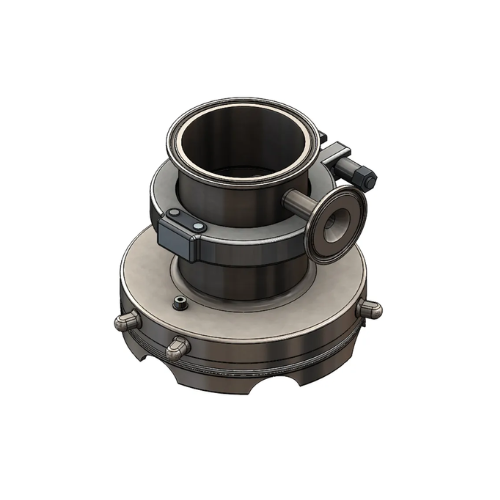
Transfer valve cleaning for sterility assurance
Ensure seamless cleaning and sterility while maintaining containment integ...
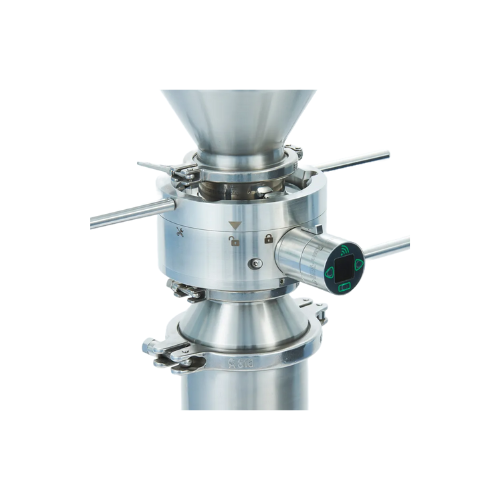
Aseptic transfer valve for sterility assurance
Ensure sterility and safety in your critical production processes with adva...
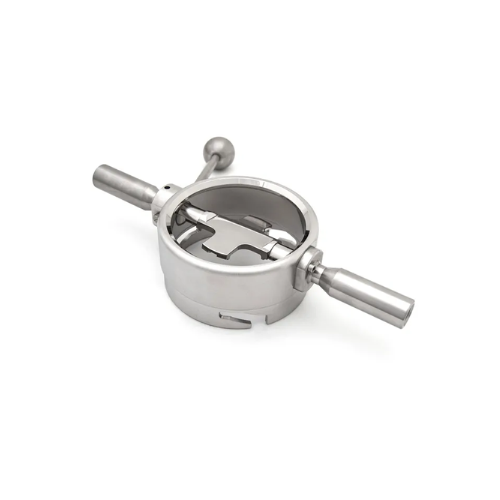
Autoclave passive opener for sterilisation of passive valves
When sterilising passive valves, ensuring maximum exposure ...
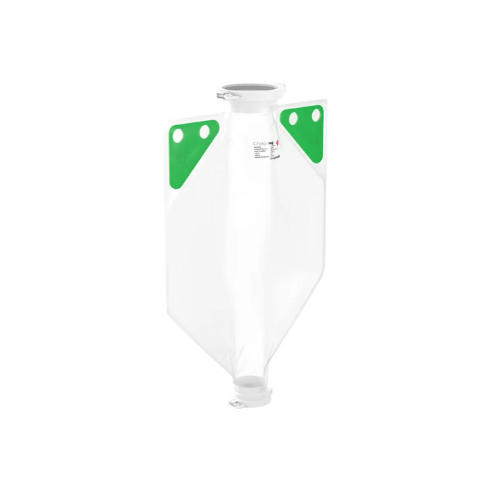
Single use powder handling bags for pharmaceutical ingredients
Achieve contamination-free powder transfers with ease, ma...
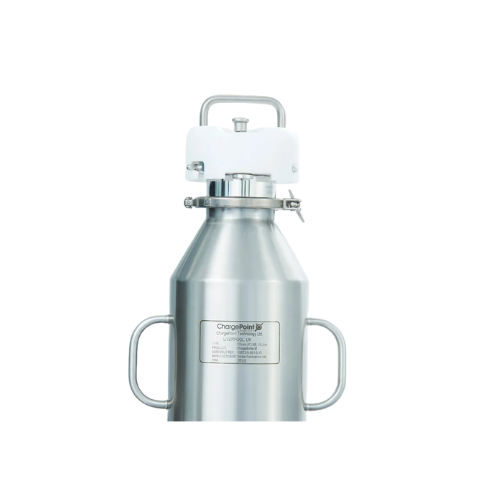
Stainless steel container for powder transfer
Ensure seamless and sterile movement of high-value powders with this contain...
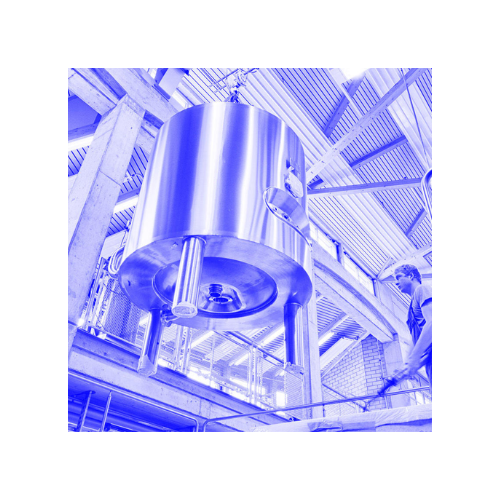
Sterile media and buffer storage tanks
Ensure uninterrupted bioproduction with our tanks designed for secure storage and pr...
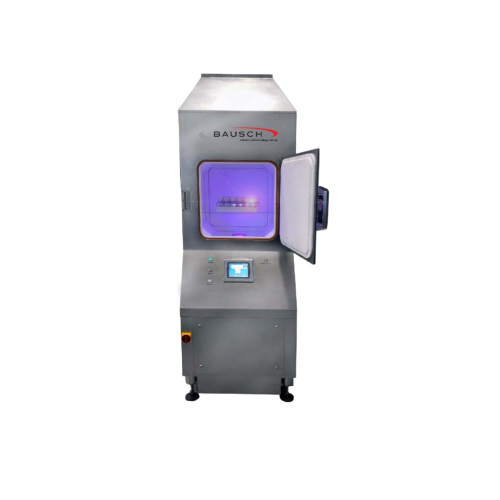
Sterile transfer chamber for pharmaceutical components
Ensure the sterility of your components rapidly with an enclosed c...
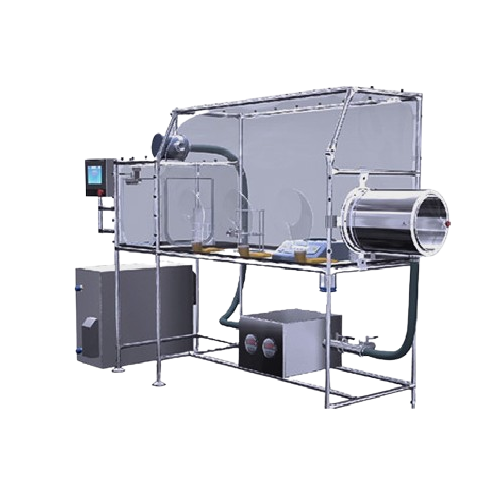
Flexible isolator for aseptic containment
Ensure sterility and safety with a flexible isolator designed for efficient cont...
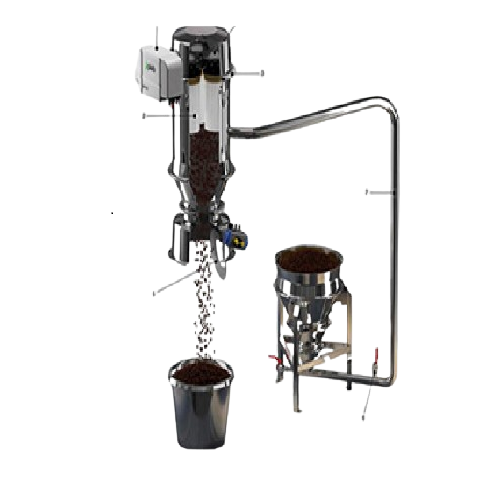
Non-sterile Api production line for powder and solid formulations
Ensure a dust-free, automated process for pharmaceuti...
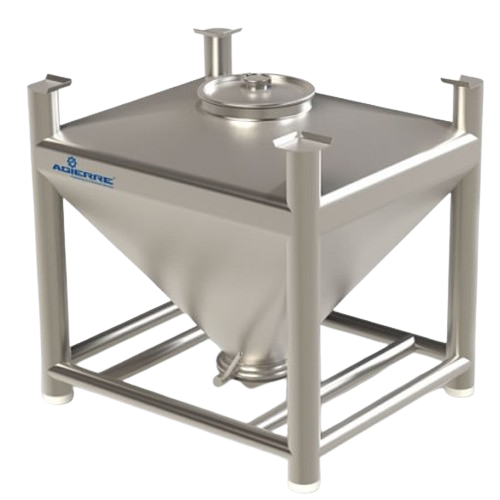
Stainless steel pharma bin for powder containment
Ensure precise powder handling and containment with this stainless stee...
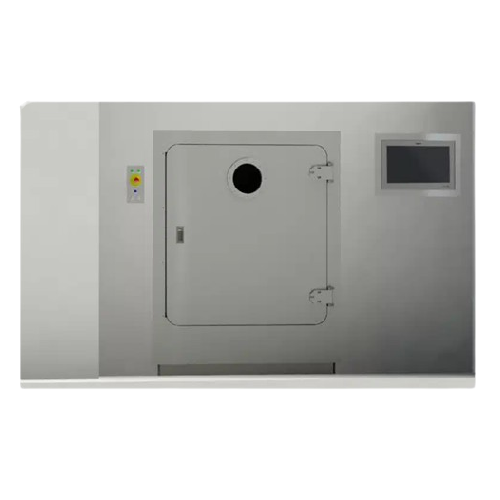
Vhp biodecontamination passbox for laboratory equipment
Ensure effective decontamination for heat-sensitive and non-autoc...
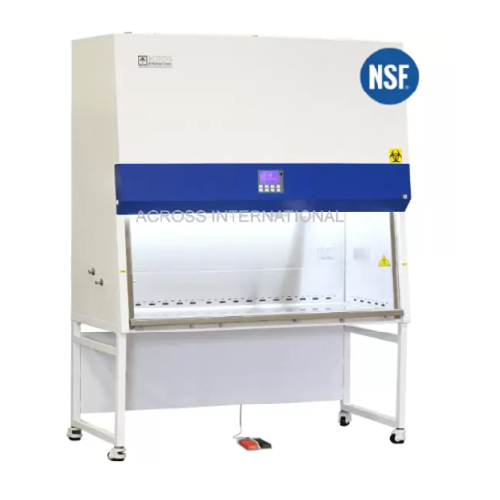
Nsf certified class Ii a2 biosafety cabinet
Ensure laboratory safety and specimen integrity with a biosafety cabinet desig...
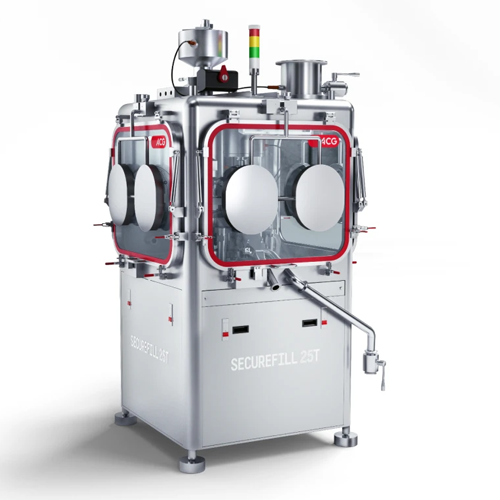
Containment capsule filler for highly potent drugs
Achieve complete operator safety while encapsulating potent pharmaceut...
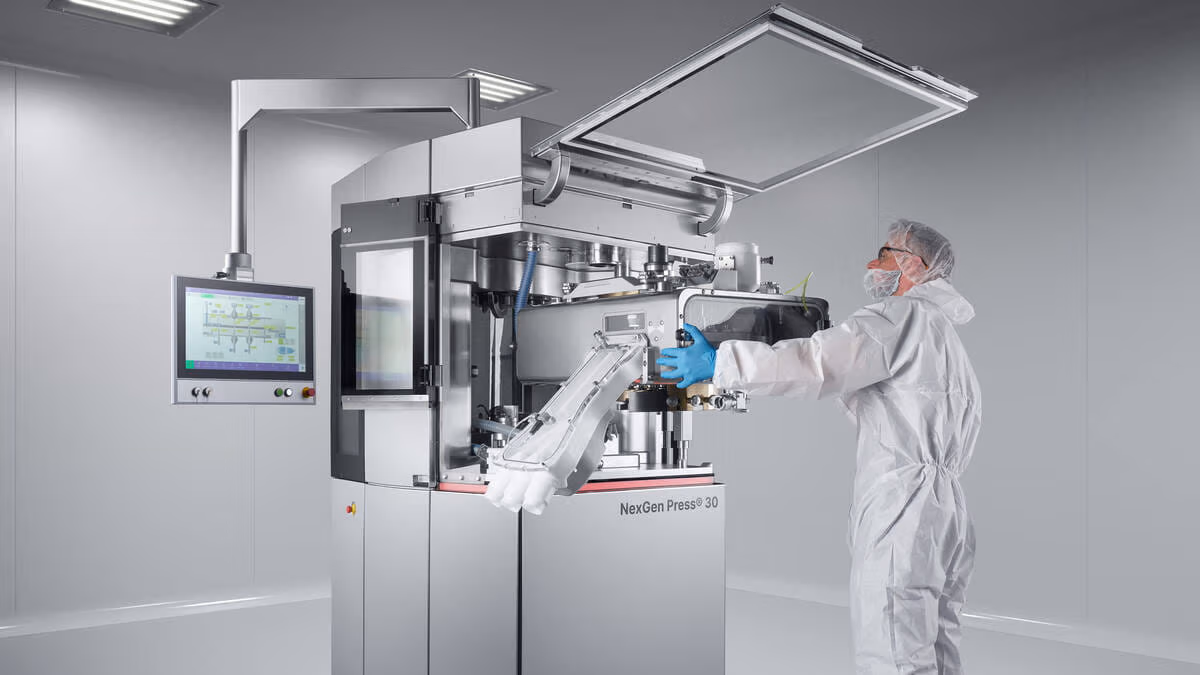
Next generation tablet compression unit
Meet the demands of modern tablet production with advanced modular design, ensuring...
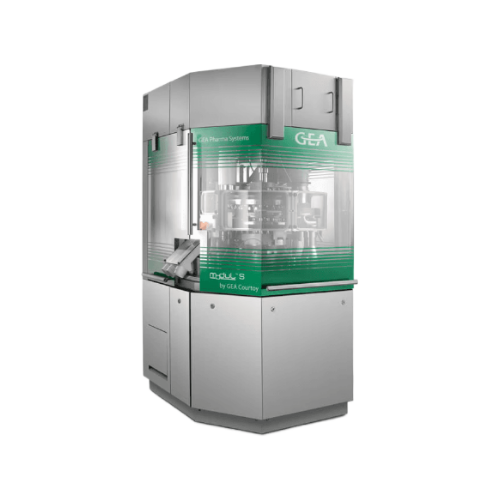
Rotary tablet press for small to medium scale production
Optimize your tablet production with a versatile rotary press, o...
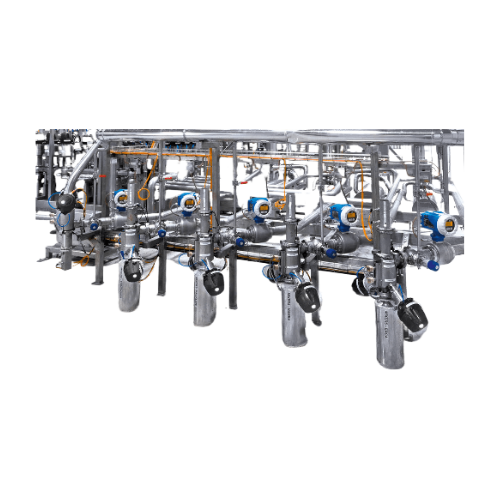
Product recovery system for hygienic applications
Efficiently reclaim valuable products from your production lines while ...
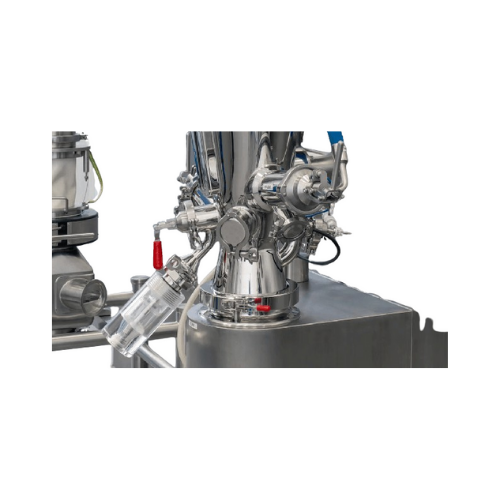
Contained powder sampling system
Ensure contamination-free sampling of active powders with fully contained system integratio...
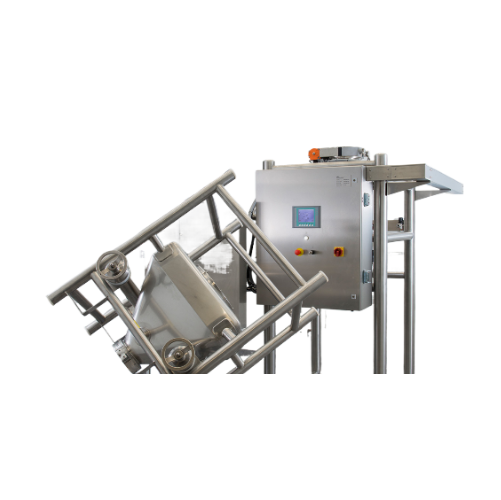
Intermediate bulk container (ibc) blending for pharmaceutical manufacturing
Streamline your pharmaceutical blending pr...
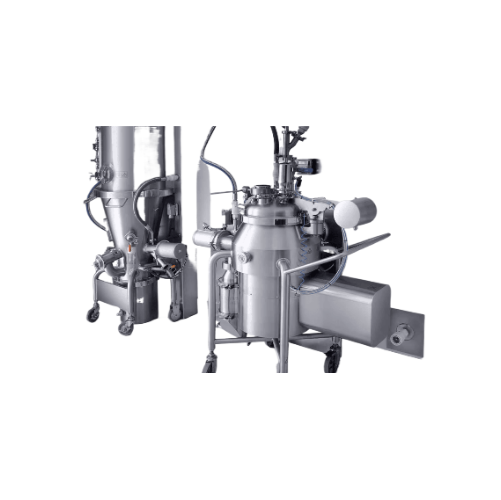
Integrated small-scale granulation and drying system
Ensure precise granule size and moisture control for enhanced tablet...
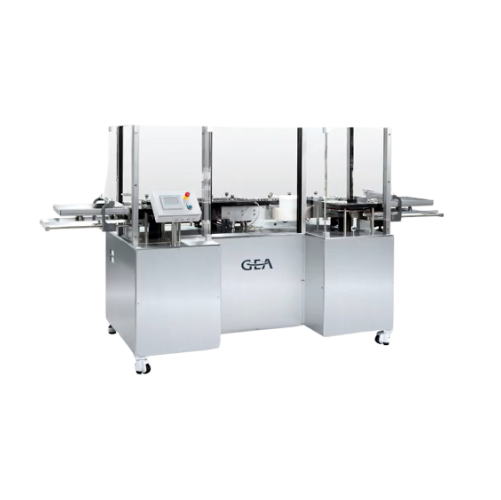
Automatic loading and unloading system for pharma freeze dryers
Enhance the efficiency and safety of your freeze-drying ...
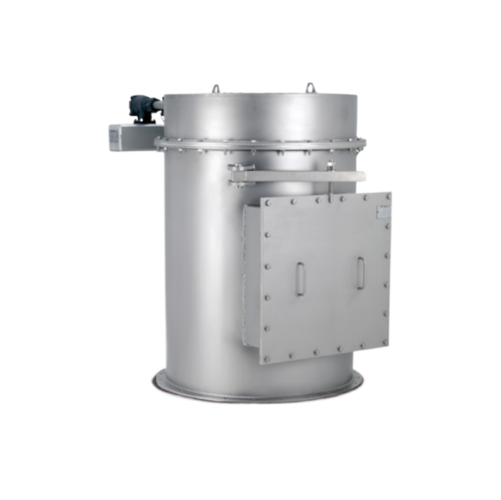
Industrial bin vent filter for fine dust particles
Enhance your production line with efficient fine dust filtration to en...
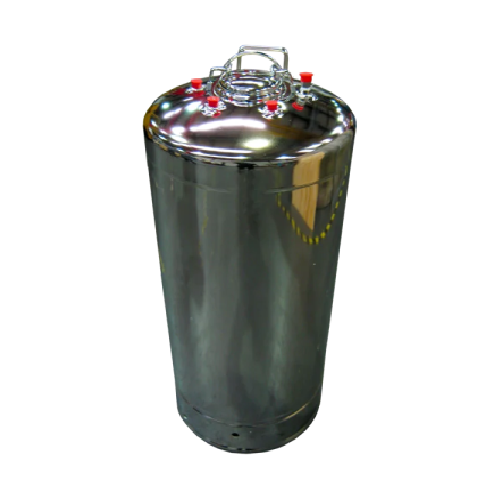
Pressure vessel for hazardous and non-hazardous liquids and gases
Ensure safety and compliance when handling hazardous ...
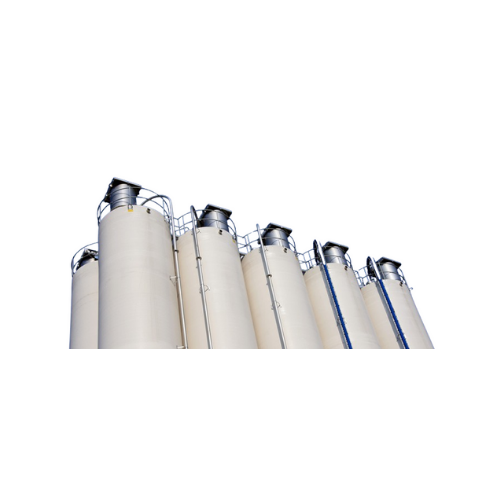
Flanged round dust collectors for industrial air filtration
Optimize your industrial processes with a dust collection sy...
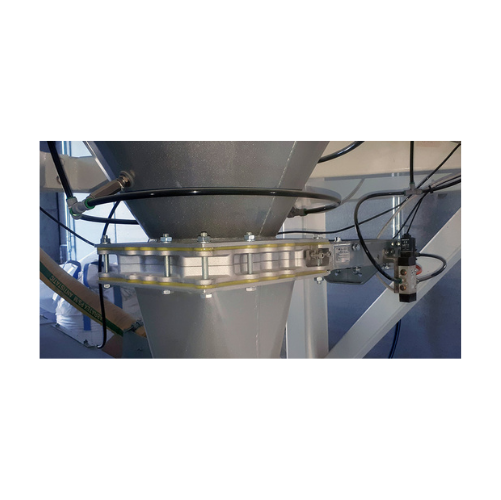
Slide valves for flow interception in powder and granular materials
Effectively manage the flow of powdery and granular...
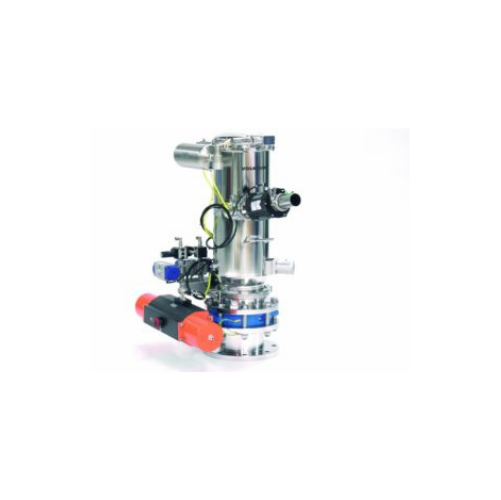
Vacuum conveyors for explosive and inert gas environments
Optimize the safe transfer of hybrid mixtures and fine powders...
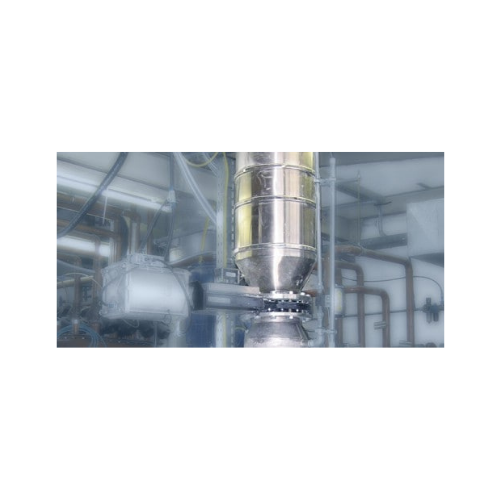
Powder locks for safe bulk material handling
Ensure containment and prevent contamination while processing sensitive bulk ...
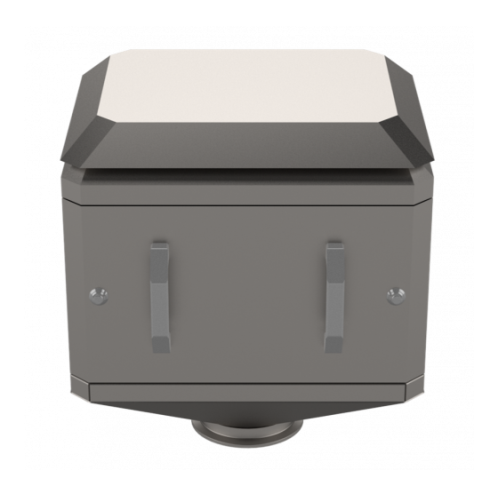
Laboratory dedusting systems
Designed for high-containment lab environments, this solution efficiently captures and manages ...
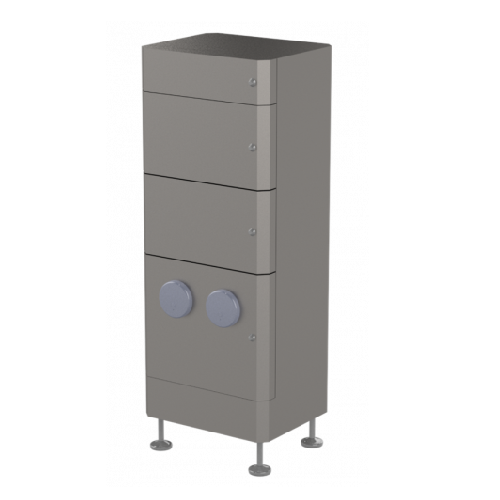
Supply air filter systems for industrial cleanrooms
Ensure critical air purity and operational safety in sensitive enviro...
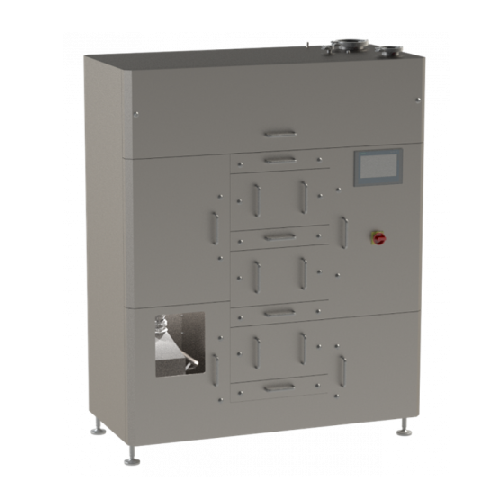
Compact dust extractors for cleanroom applications
Ensure safe and efficient dust extraction in cleanroom environments wi...
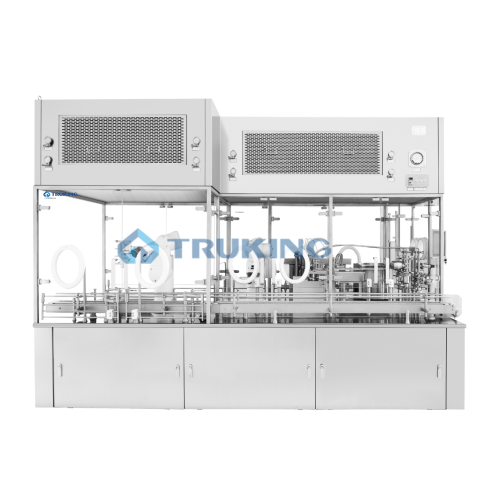
Nested fillers for vials, pre-filled syringes, and cartridges
Optimize your aseptic filling processes with precision dos...

Robotic sterilization logistics system
Ensure seamless aseptic transfers across production stages with this robotic logisti...
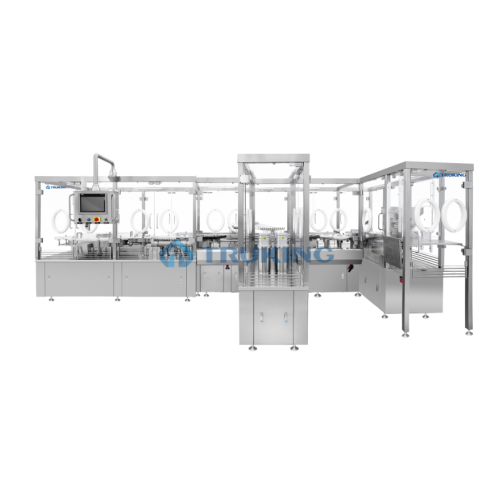
Vial filling and stoppering system for aseptic production
Streamline aseptic production by integrating high-speed vial f...
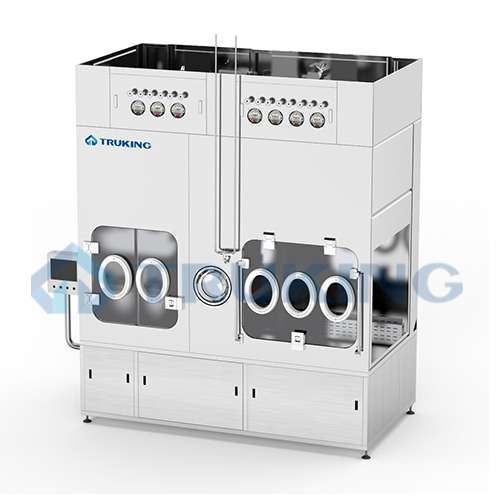
Autoclave unloading isolator for sterile assembly
Ensure aseptic conditions and prevent microbial contamination during th...
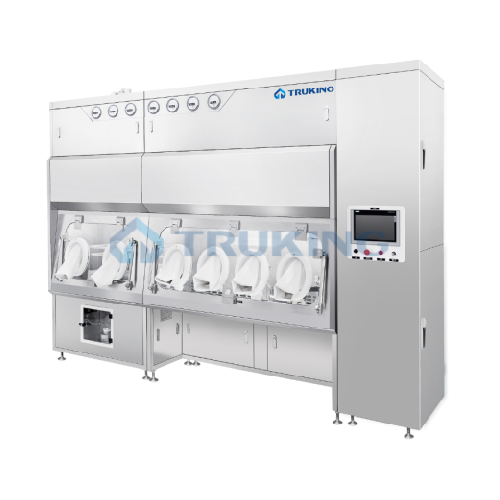
Sterility testing isolator for aseptic environment
Ensure precise sterility testing and prevent contamination with an iso...
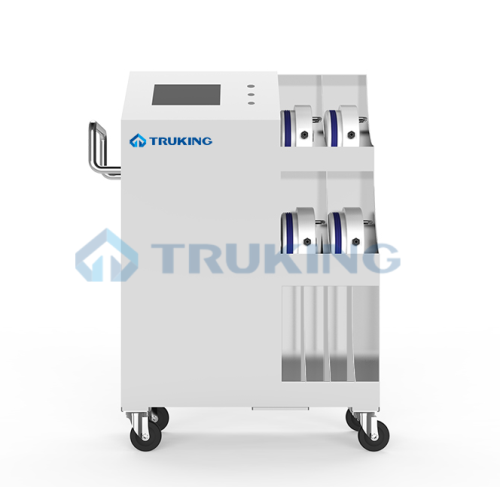
Isolator for sterility testing in pharmaceutical manufacturing
Ensure precise sterility testing with advanced isolators ...
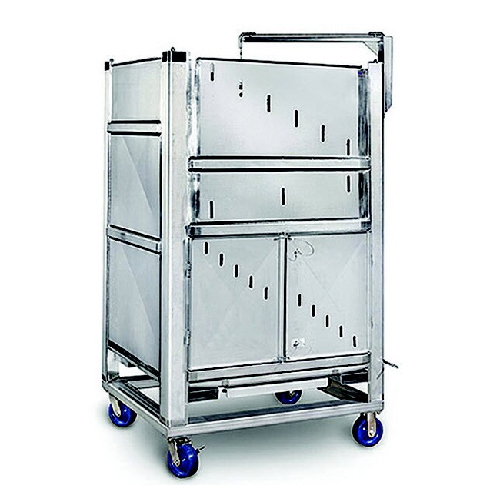
Stainless steel container for bioprocessing
Optimize the containment and handling of large-volume biopharmaceutical liquid...
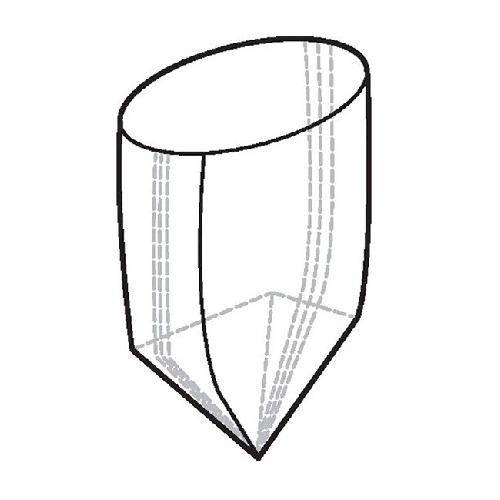
200l sterile tank liners for bioprocessing
Streamline your bioprocessing operations by eliminating tank cleaning steps and...
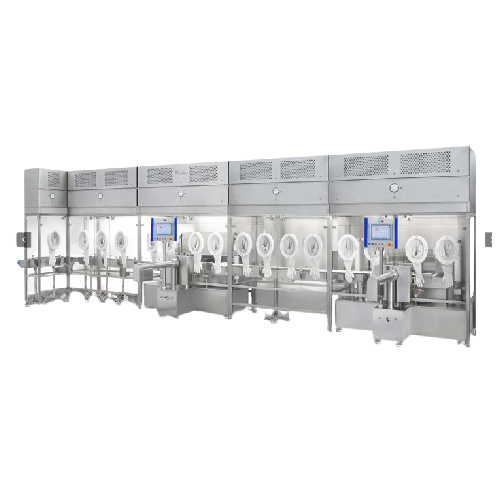
Restricted access barriers systems for aseptic processing
Enhance product safety by separating operators from the critic...

Bio-decontamination pass-through hatch for aseptic facilities
Ensure sterile transfer of materials between classified ar...
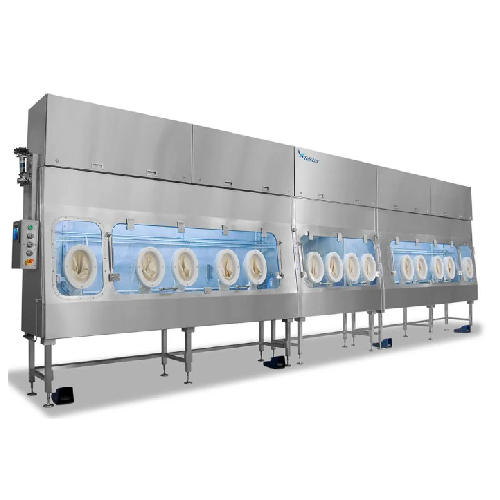
Aseptic barrier isolators for pharmaceutical applications
Enhance sterility and operator safety during aseptic processin...
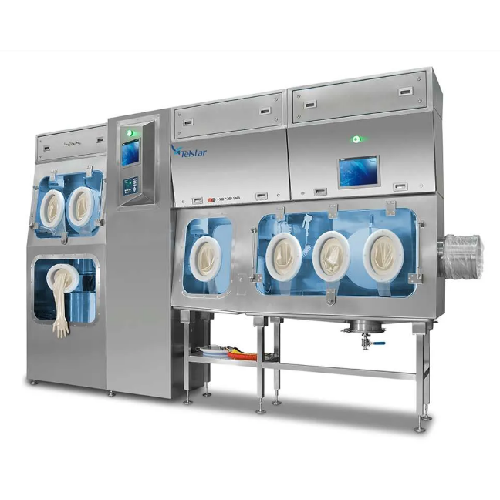
Containment isolators for pharmaceutical and biotech applications
Ensure operator safety and product integrity during t...
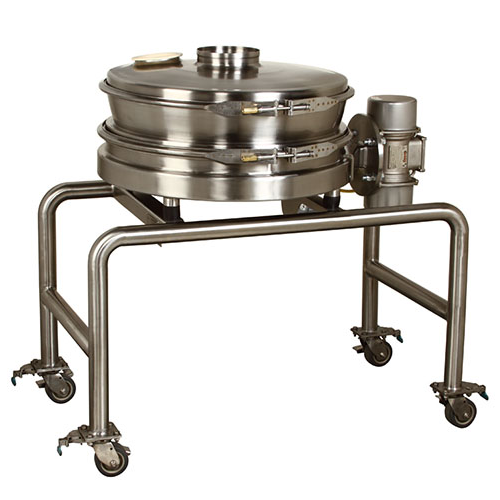
Sanitary separator for food processing applications
Ensure efficient separation and prevent contamination in food product...
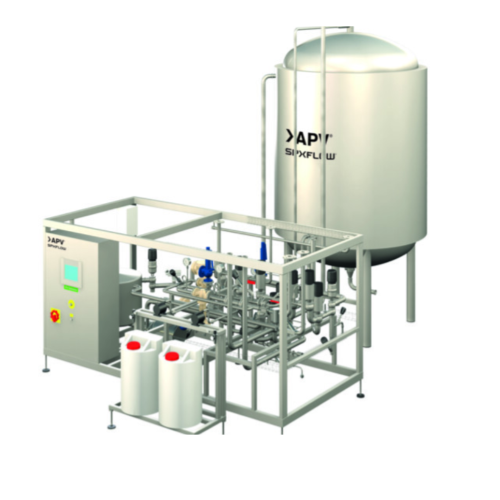
Aseptic storage tank for aseptic products
Ensure uninterrupted aseptic product storage with this advanced tank system, des...
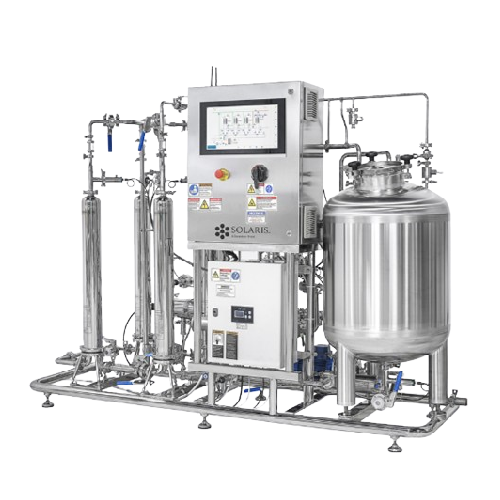
Full flow filtration system for bioprocess applications
Ensure sterile filtration of process liquids and aseptic chemical...
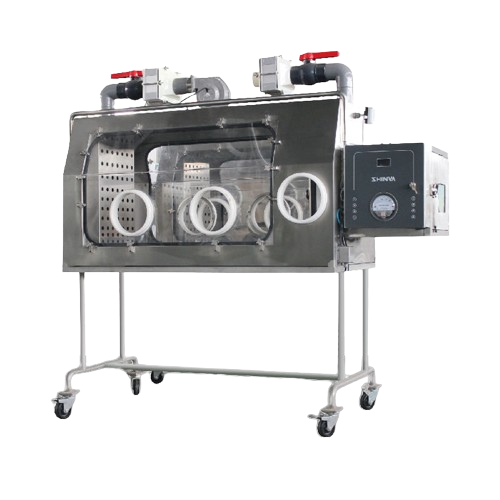
Soft pack isolator for rats and mice
Ensure a sterile and controlled environment for laboratory mice and rats with this sof...

Storage cabinet for endoscopes
Ensure the safe, contamination-free storage and easy monitoring of endoscopes with a hanging ...
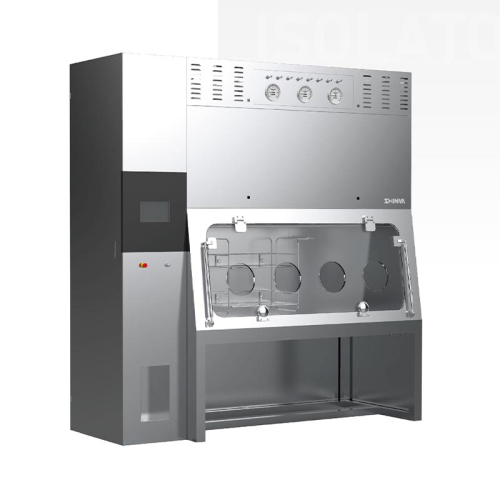
Aseptic test isolator for sterility inspection
Ensure stringent sterility control in your laboratory or production line wi...
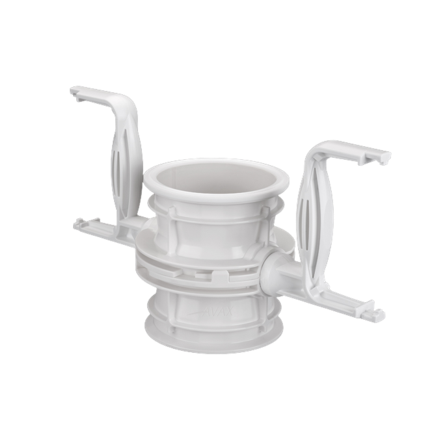
Single-use containment valves
From GMP and HSE perspective material transfer is critical for chemical and pharmaceutical for...
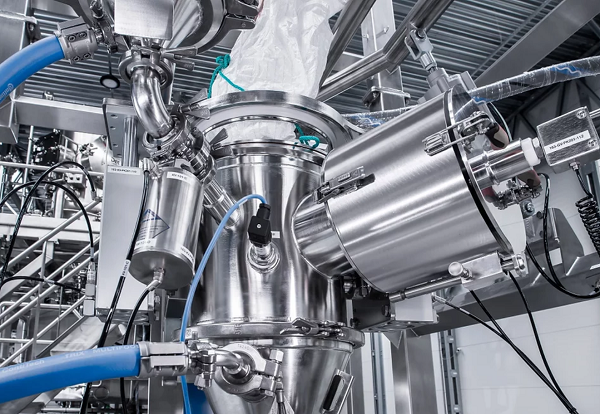
High containment big bag discharge docking system
The discharge of materials demands strict containment, particularly in ...
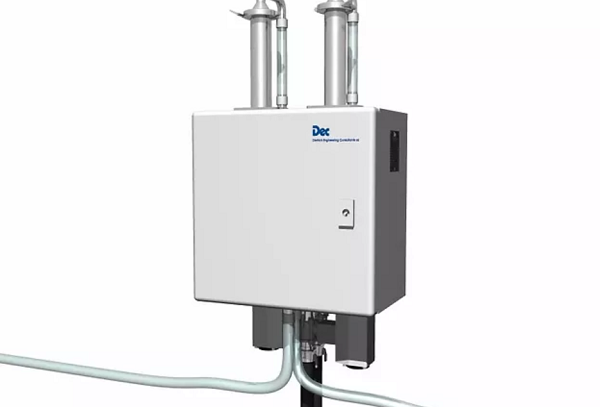
Powder dosing system
Dosing of powder products must be done in a continuously controlled manner to provide a precise amount o...
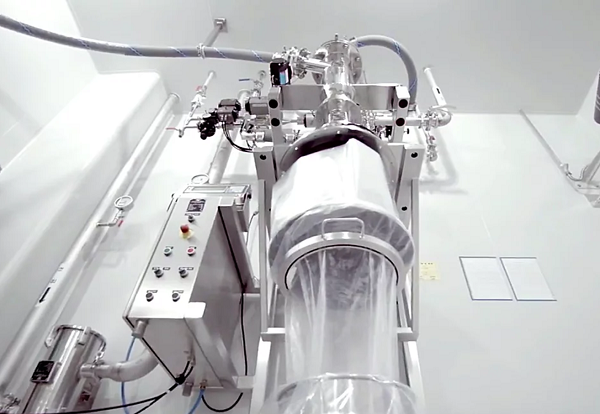
Drum filling system
Pharmaceutical and chemical products may be toxic or prone to contamination from environmental exposure. ...
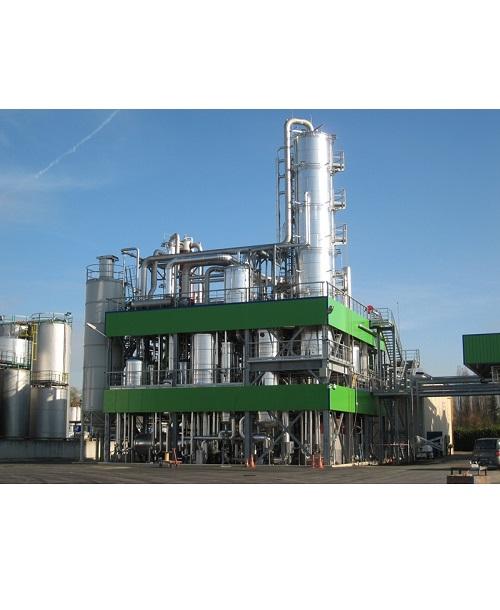
Production plant for biodiesel
As a biofuel producer, making biodiesel from several types of treated vegetable oils or anima...
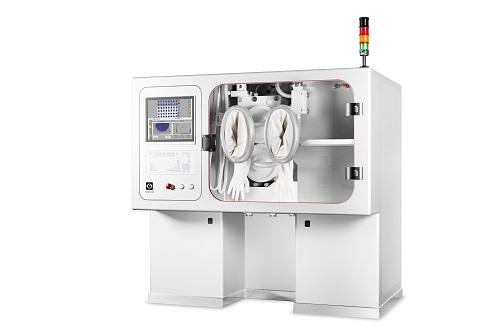
Contained Visual Inspection System
In the medicine industry, it is important to ensure there are no defects in tablets or c...
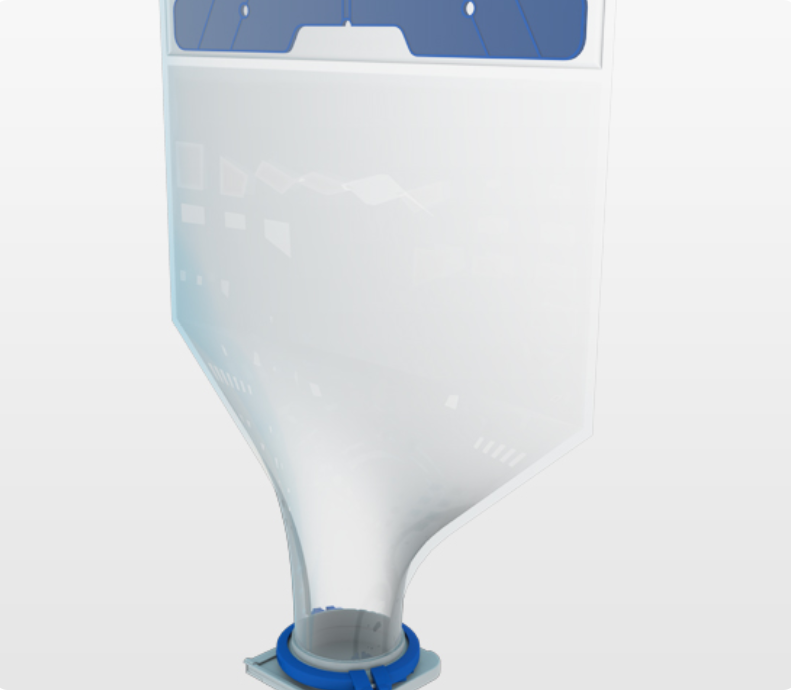
Single-use powder handling bag
Containers for handling pharmaceutical and biopharmaceutical powders may be disposable, to av...
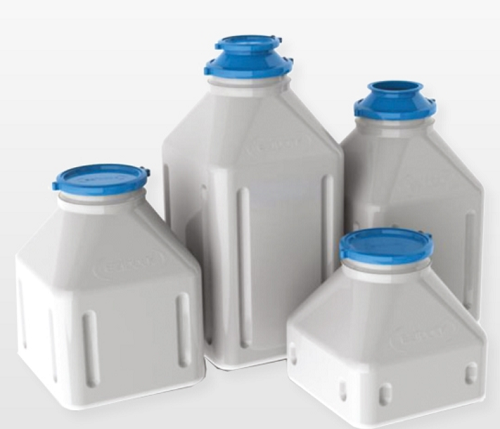
API powders storage bottle
Users who prefer rigid storage over single-use pharma charge bags, require lightweight solutions ...
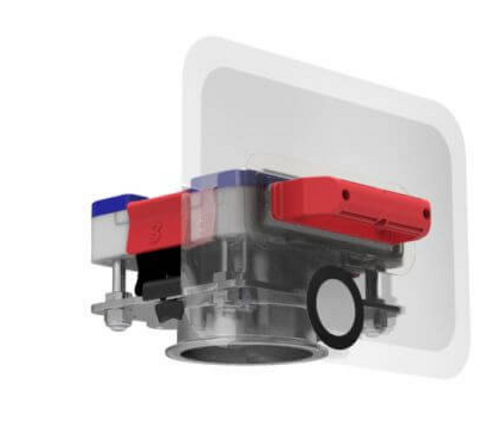
Single-use containment valve
Safe transfer of liquids and hazardous powders into systems can be a challenge in pharma, bioph...
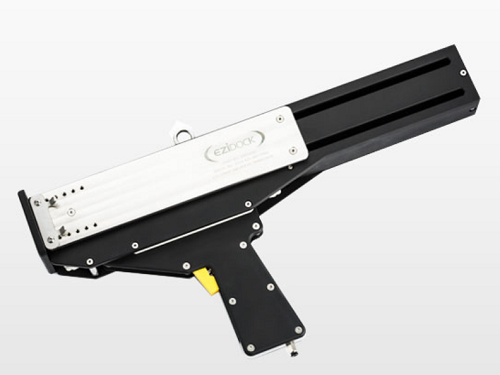
High containment closing system
Pharma and biopharma laboratories need fast effective solutions for tightly sealing bags for...
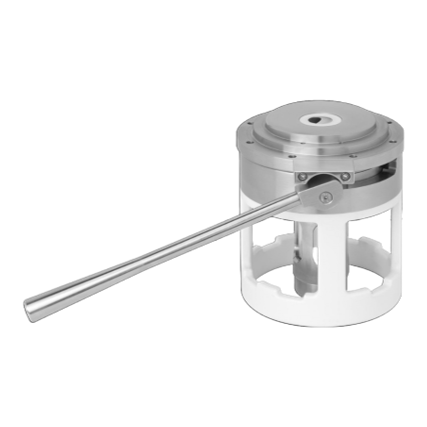
High containment sampler
Drawing a sample for evaluation from a running process is not a simple task, especially when dealing...
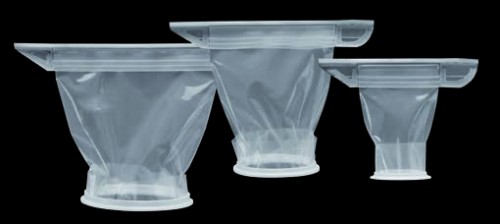
Flexible containment docking solution
When sampling or transferring hazardous substances and sensitive bulk goods, a dust-t...
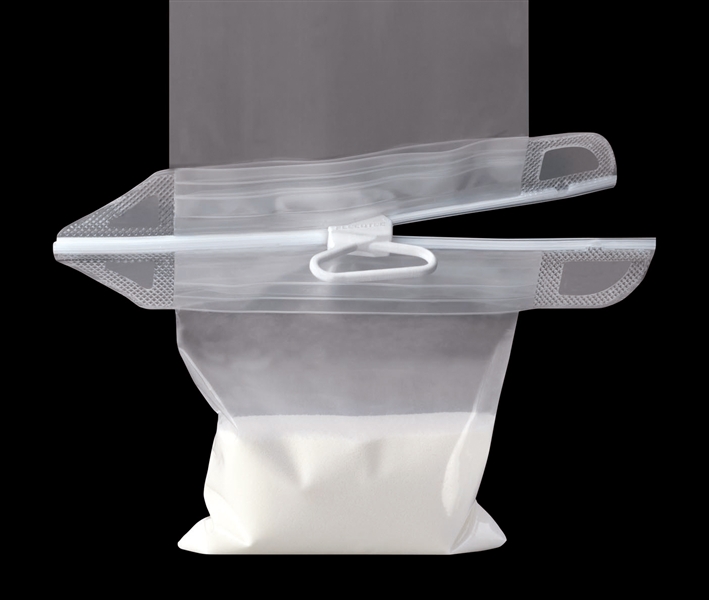
Flexible containment zip
Transfer of sensitive and toxic bulk goods across process units requires specialist handling to prev...
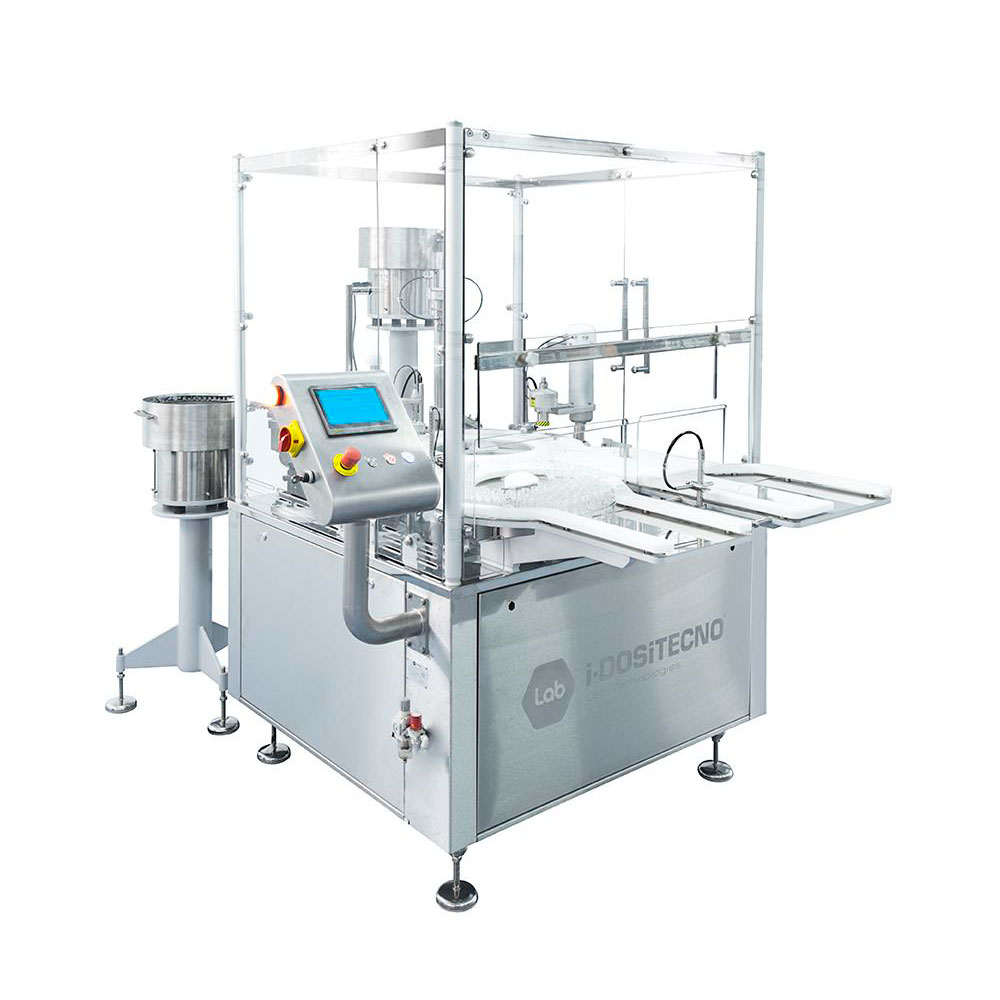
Start-up sterile filling line for injectables
For smaller-scale production of vials and syringes for the injectables marke...
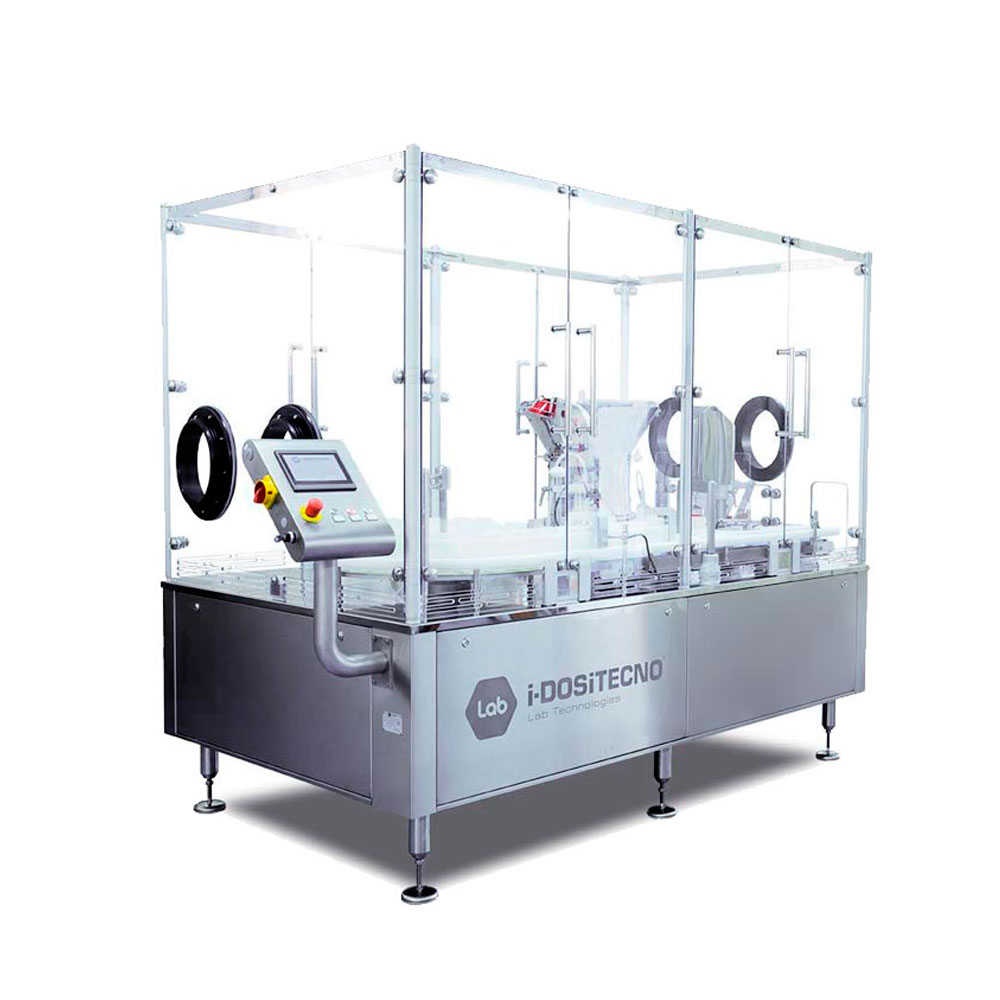
Start-up sterile filling line for ophthalmics
Commencing ophthalmic production requires sterile conditions and accurate me...
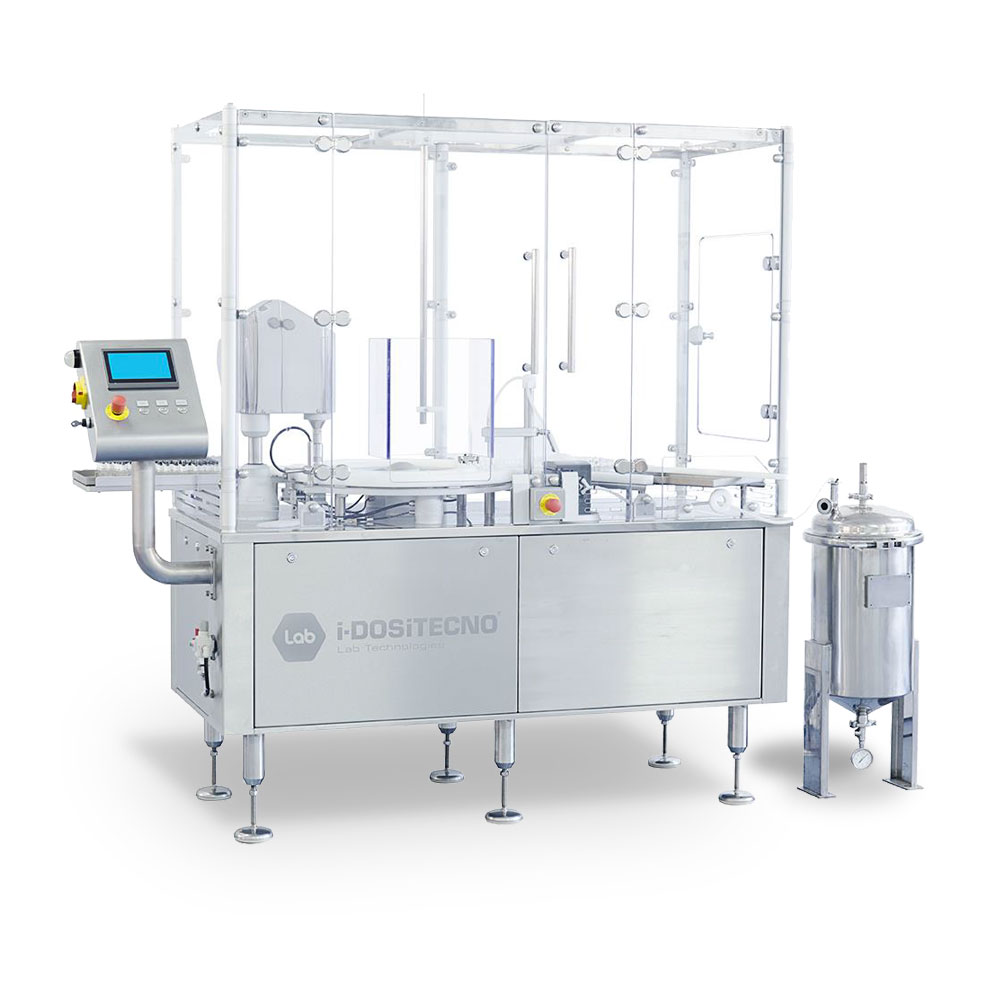
Table top sterile filling line for injectables
Where a compact solution is required for filling vials for the injectables ...
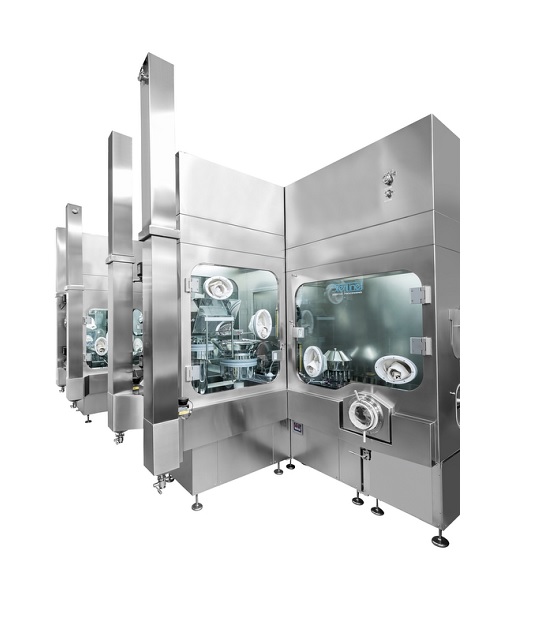
Closed restricted access barrier system
Pharmaceutical production techniques often require isolation of compounds and chemi...
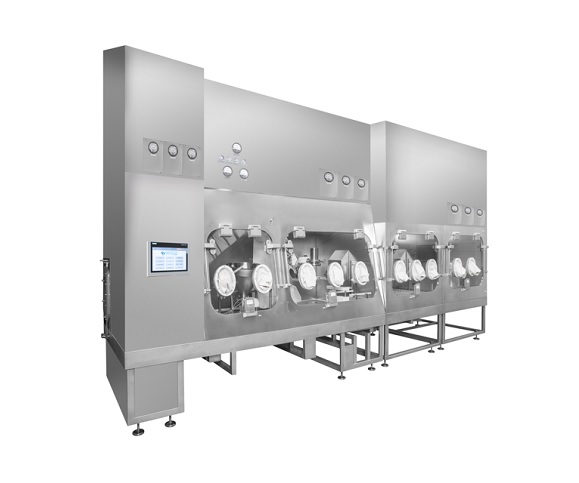
Compounding aseptic isolator
Bespoke aseptic isolators designed for production environments don’t meet the needs of small-sc...
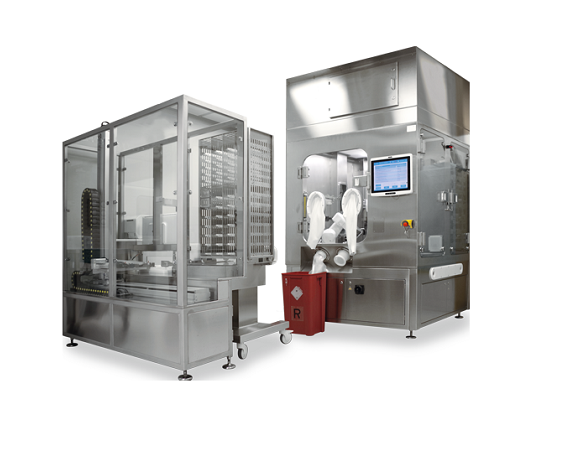
Sterile compounding system
Hospitals and compounding centres have traditionally used manual aseptic compounding processes. A...
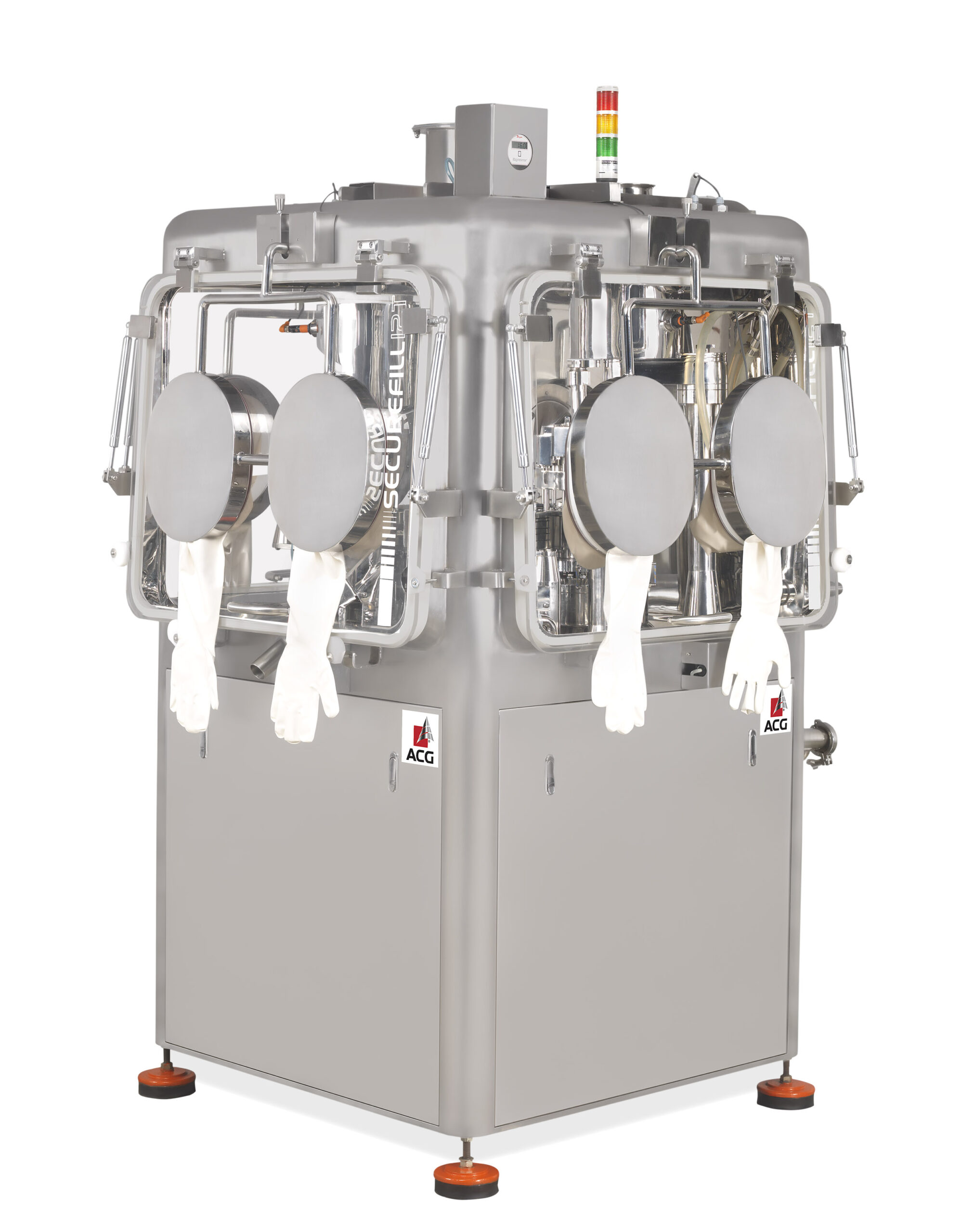
Contained capsule filler
For pharmaceutical formulations that are highly active specialized capsule filling equipment is ofte...
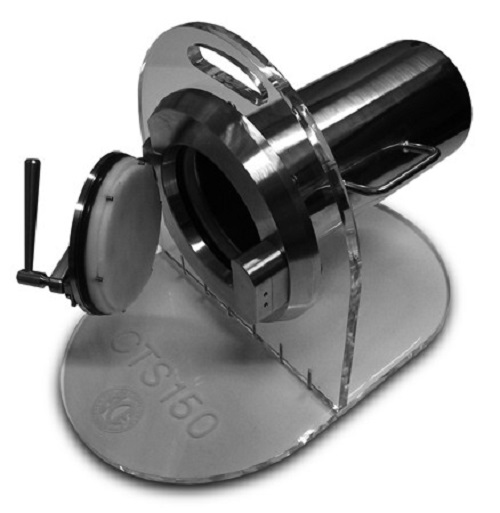
Transfer system for high-containment environments
A high-performance transfer port system that combines ultimate safety, ...

Half-suit tester
Designed to allow operators to perform sterility testing in an aseptic environment providing assurance of mat...
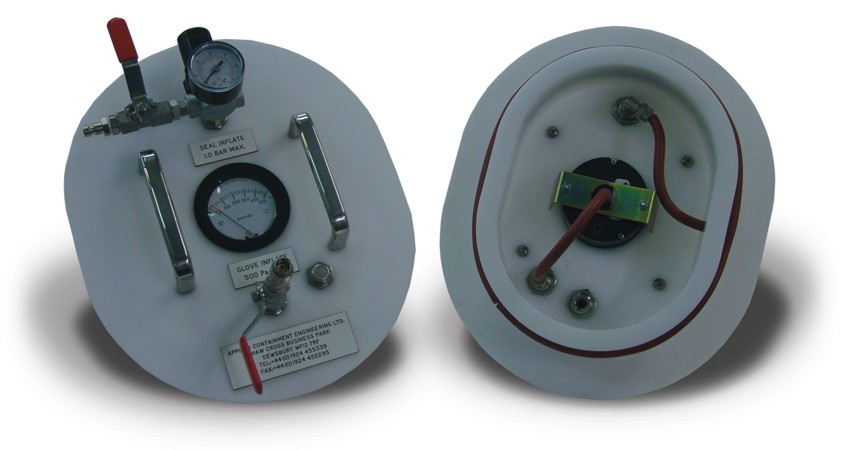
Glove tester
Testing device of the containment capability of gloves, which is as important as the other parts of the integrate...
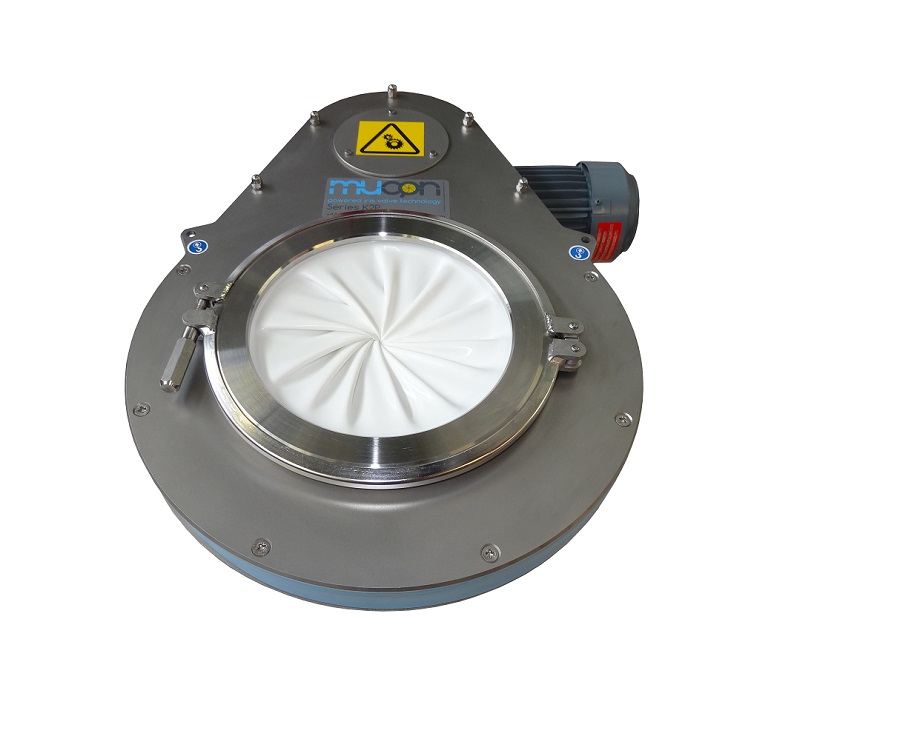
Hygienic automatic iris valve
In automated systems where controlled discharge of powders and bulk solids is required with a ...
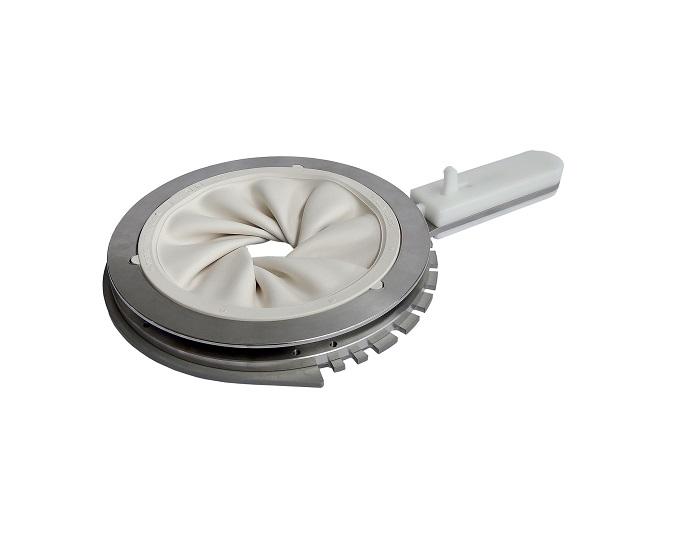
Hygienic hand-operated iris valve
Hand-operated valves are required for the walls of clean rooms for glanding around cables...
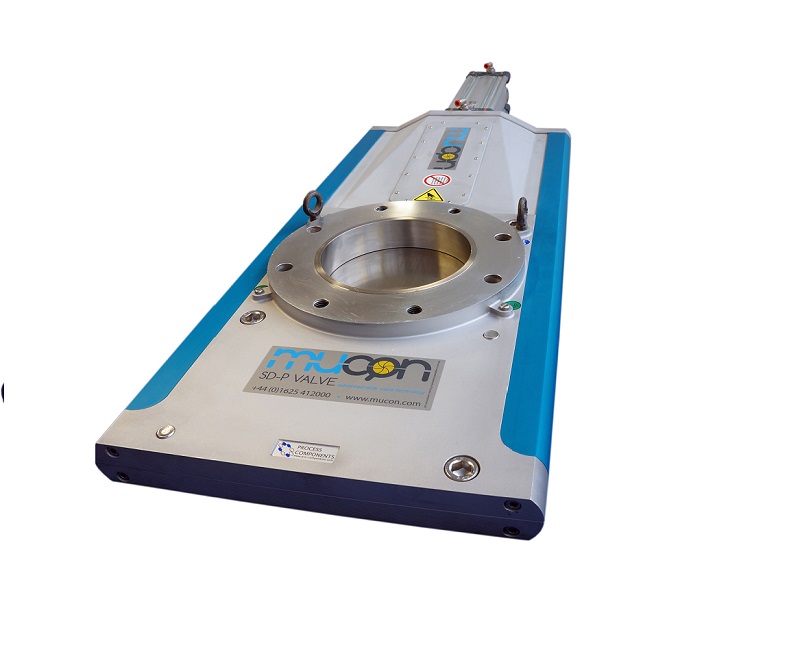
Slide gate valve
In the powder and bulk handling industries, in-line shut off valves are required to provide uninterrupted smo...
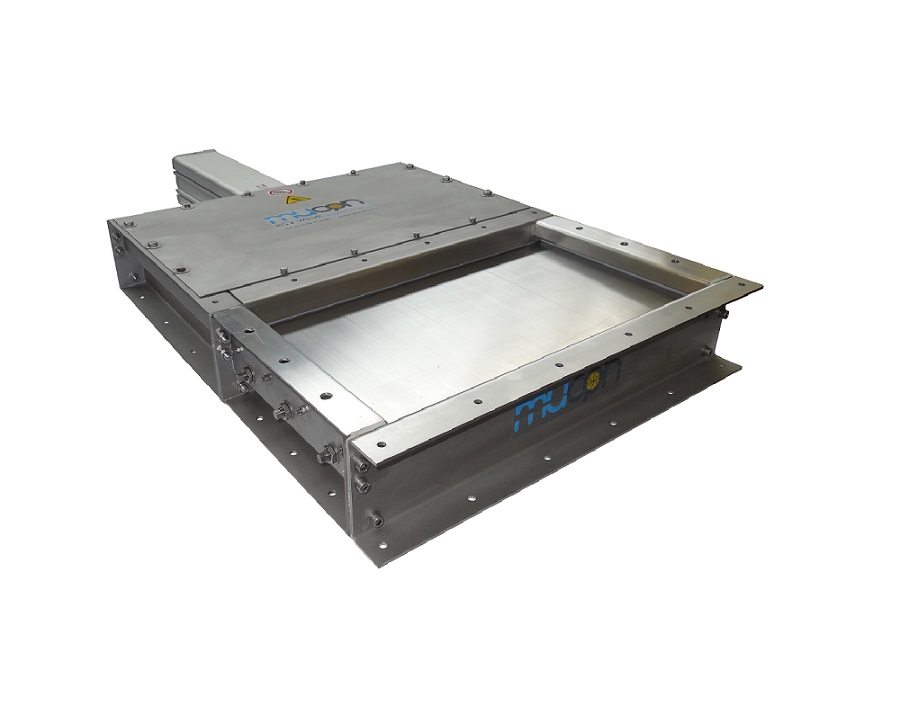
Roller gate valve
In large scale operations, modular and configurable valves are required to isolate and control dry powders,...
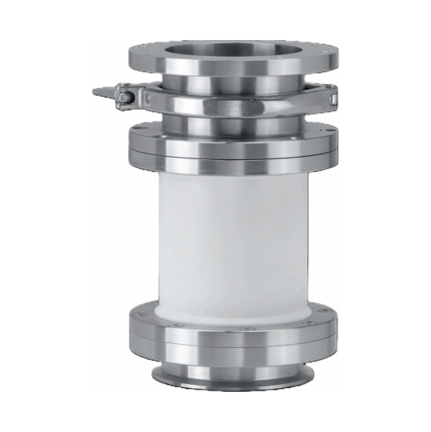
Bellows for pharmaceutical powders
Thermal and mechanical changes can lead to stresses in industrial piping systems. These ...
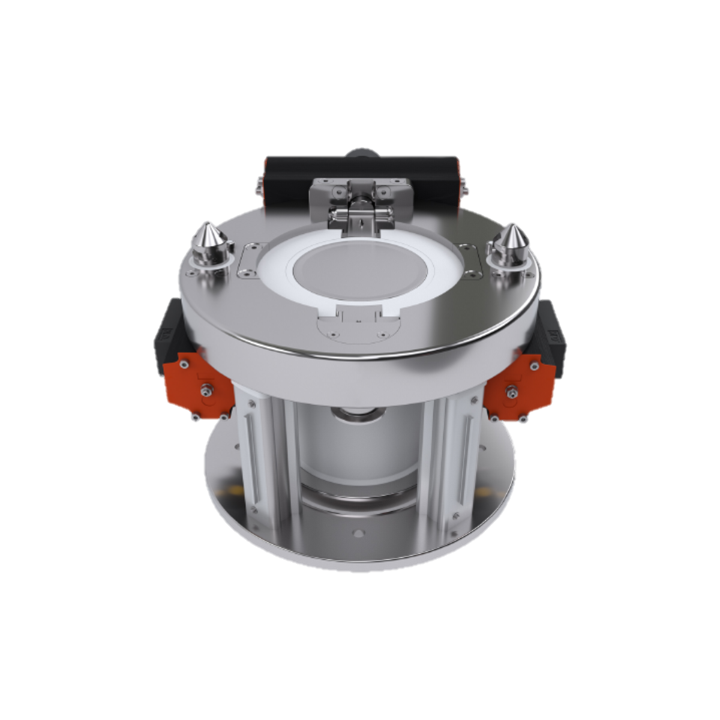
High containment split butterfly valve
Powder containment is the cornerstone of chemical and pharmaceutical manufacturing. ...
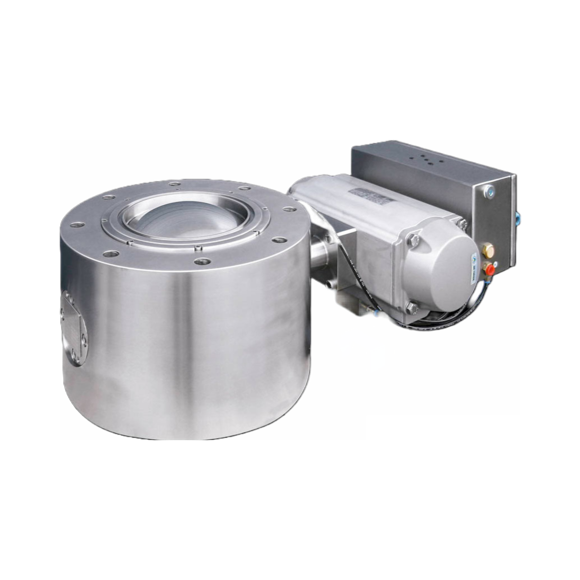
High containment segment ball valve
Valves fitted in blenders and dryers can have dead spaces that prevent complete process...
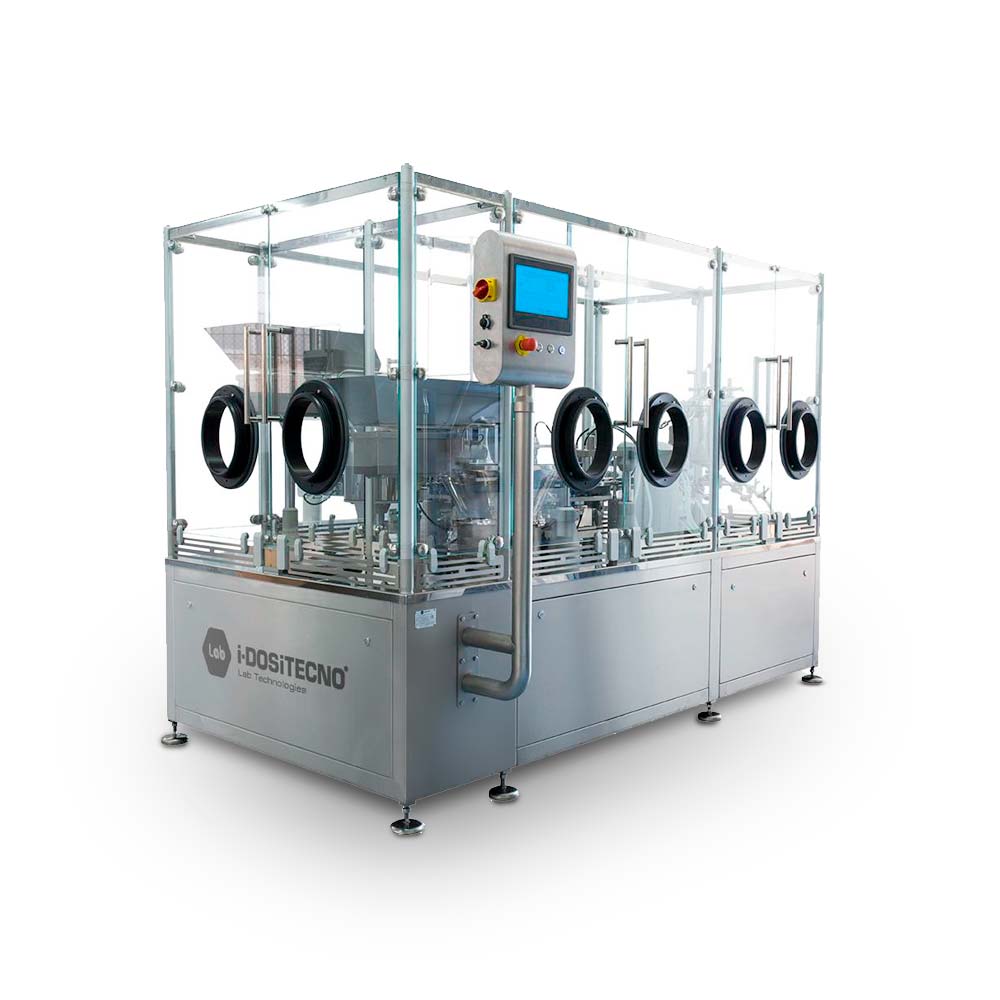
Sterile filling line for injectables
Sterile filling of liquids and powders for the pharmaceutical and cosmetic industries ...
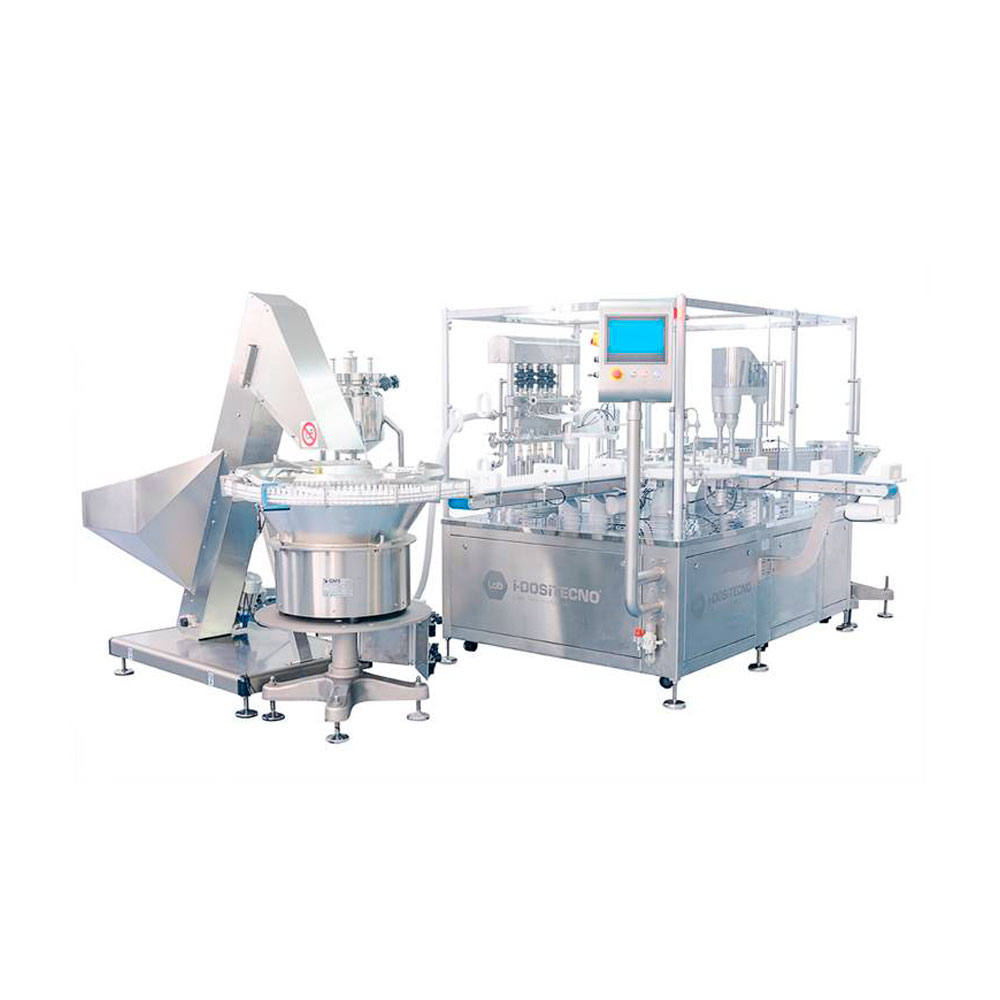
Sterile filling line for ophthalmics
Demanding very high standards, the ophthalmic market requires quality solutions for fi...
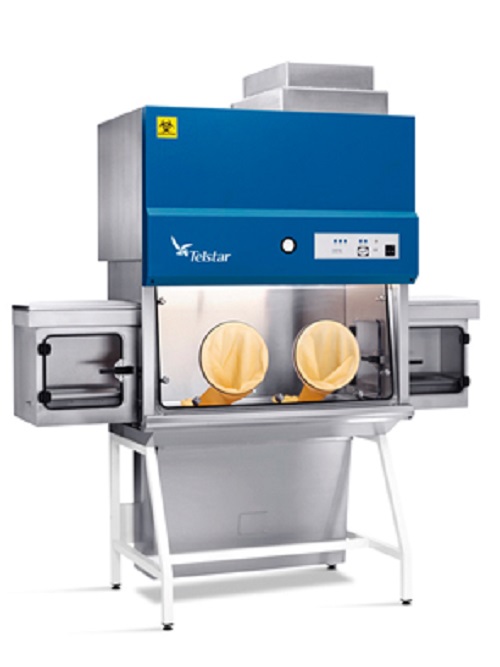
Negative pressure isolator
Used for products biologically hazardous, that also require minimized cross contamination.
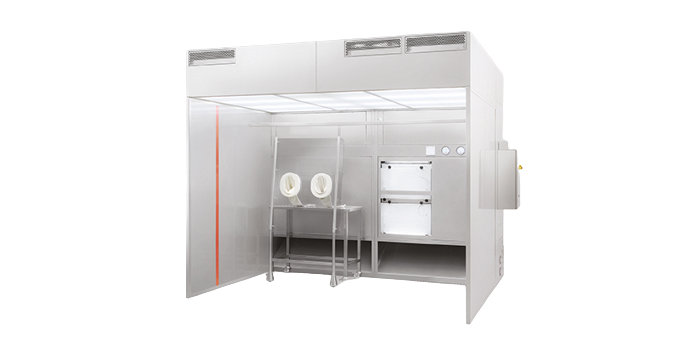
Downflow booth
Provides the highest levels of operator protection from potentially harmful airborne contaminants generated dur...
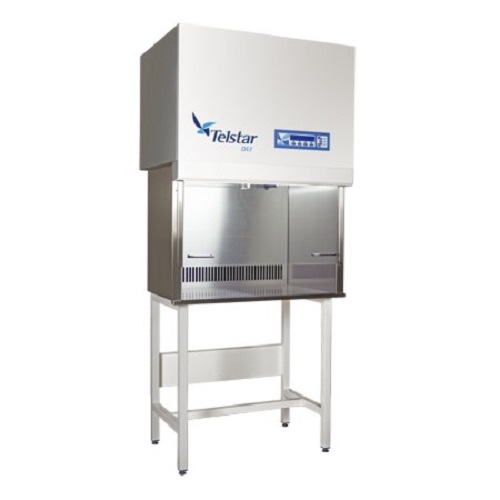
Vertical laminar flow cabinet
HEPA filtered vertical laminar airflow (down flow) creates an ISO 14644-1 (Class 5) work area ...
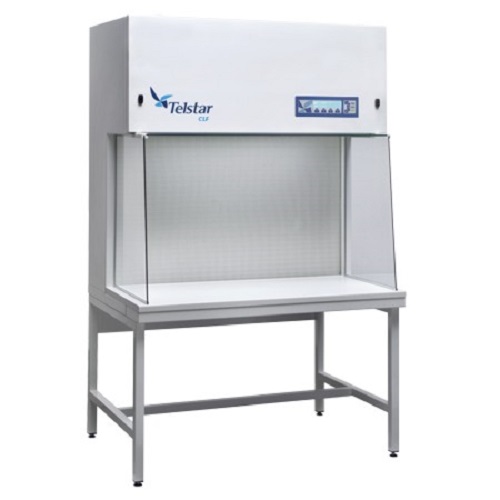
Horizontal laminar flow benches
HEPA filtered horizontal laminar airflow (crossflow) creates an ISO 14644-1 (Class 5) work a...
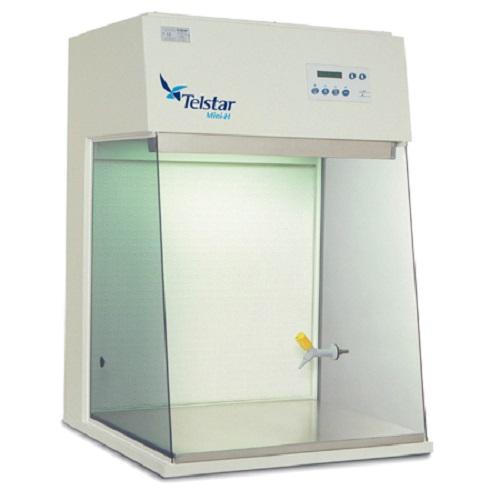
Compact horizontal laminar flow bench
HEPA filtered horizontal laminar airflow (cross-flow) creates an optimized free space...
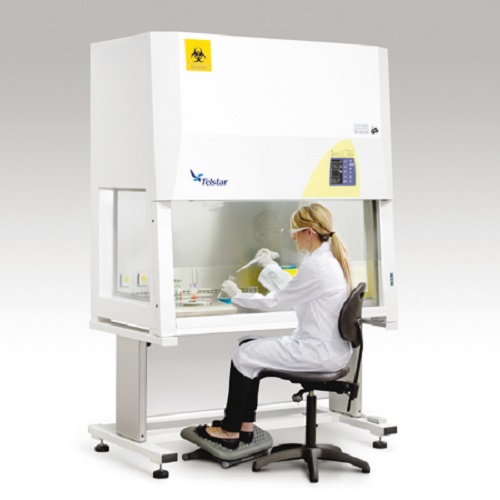
Microbiological safety cabinet class II
This handy device offers the most advanced features in product-operator protection ...
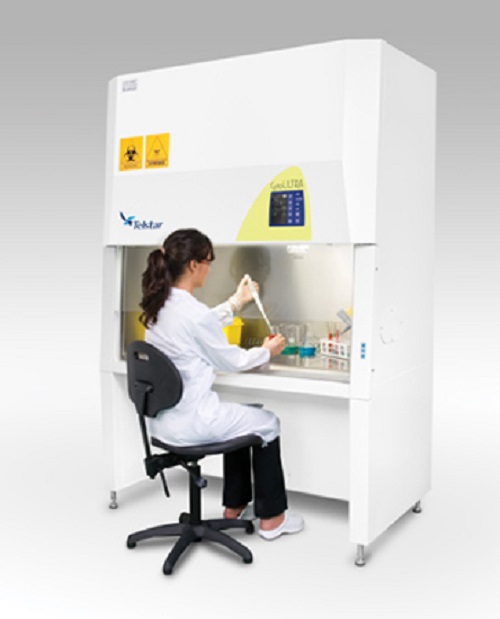
Biosafety cabinet class II for cytotoxic medicines
For the manipulation of hazardous substances utilized during the prepa...
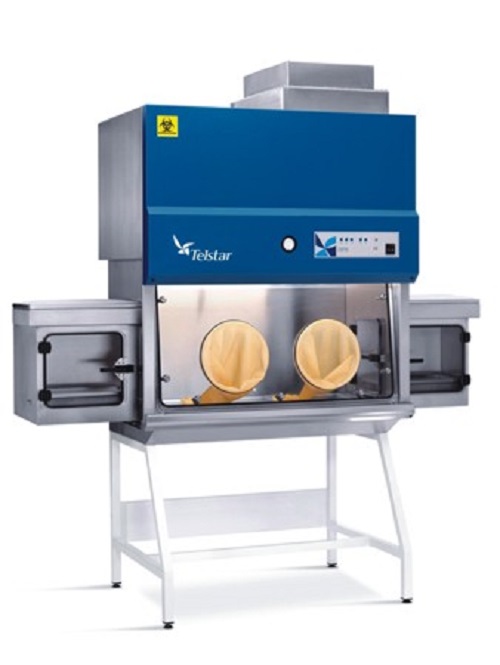
Positive pressure isolator
Ideal for products which have no biological risk but require high sterile conditions.
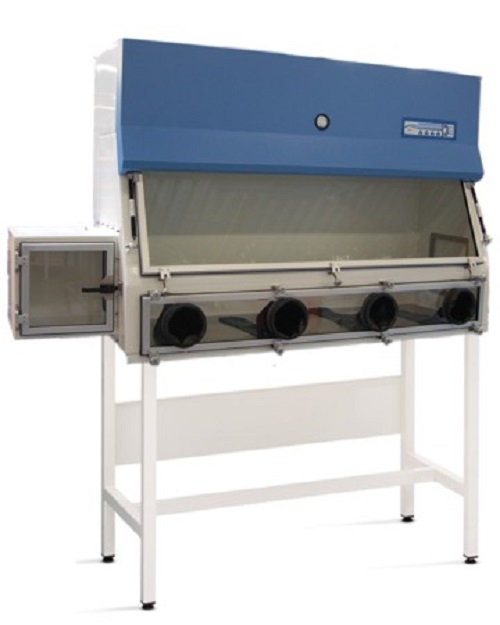
Biological safety cabinet class III
Specially designed for the handling of microbiological agents, when working with indige...
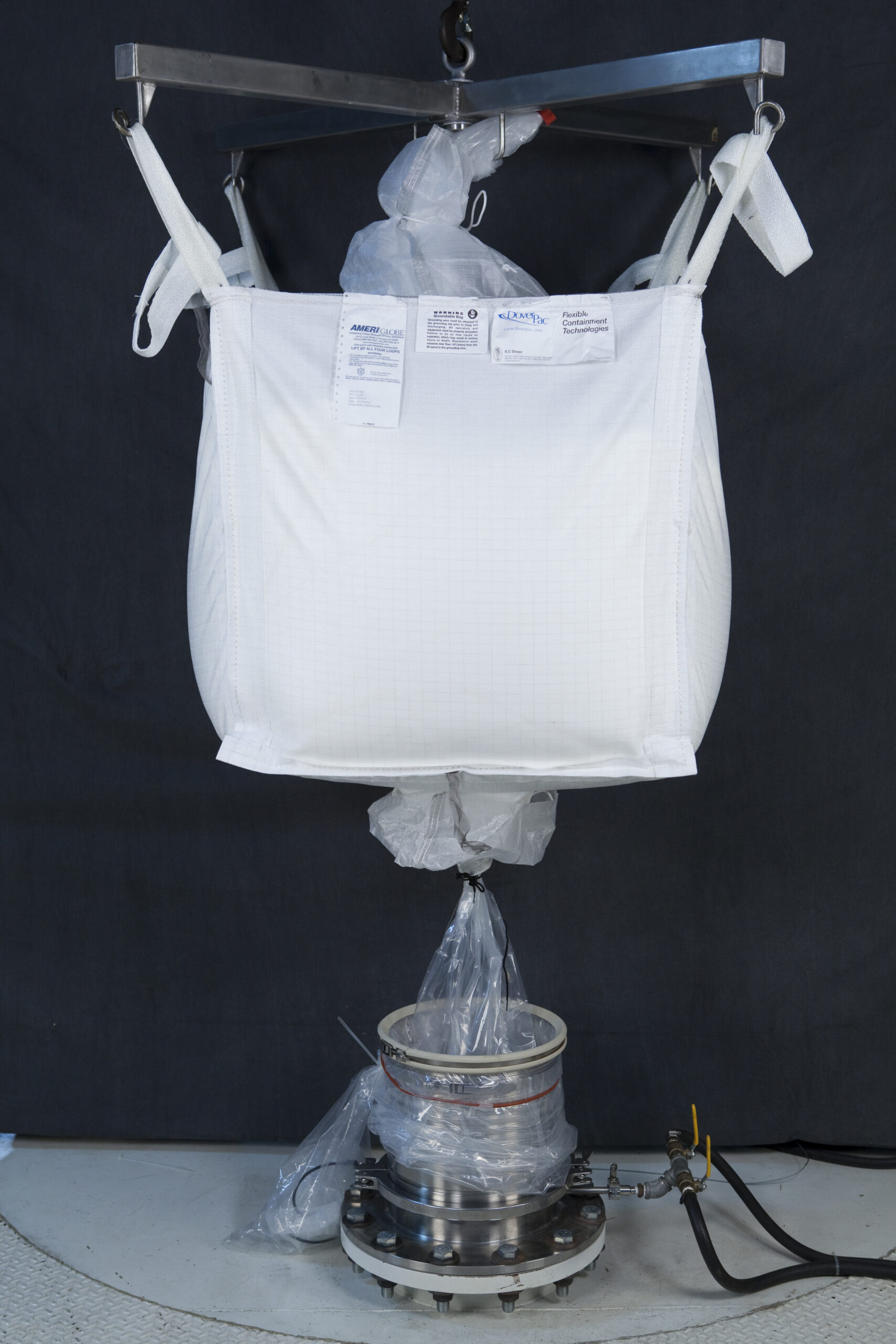
Flexible contained powder charging solution
Filling of transportation bags and discharging them into mix tanks or reactor ...
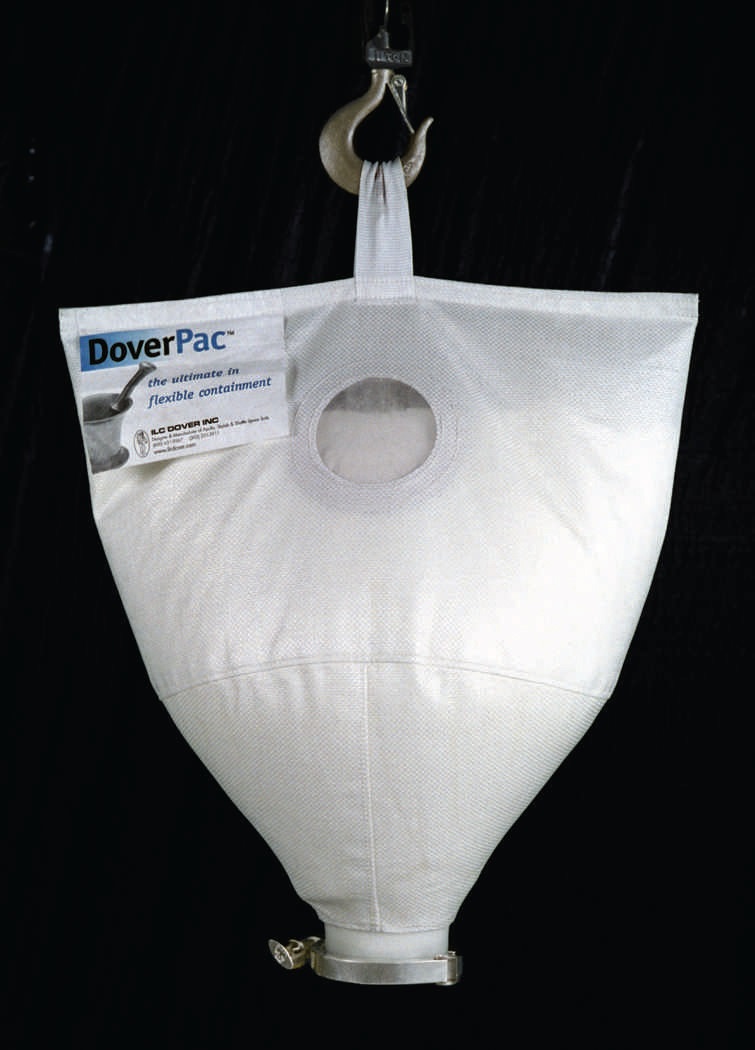
Flexible contained charging for split butterfly valves
Poly bottles with split butterfly valves are often used to transfe...
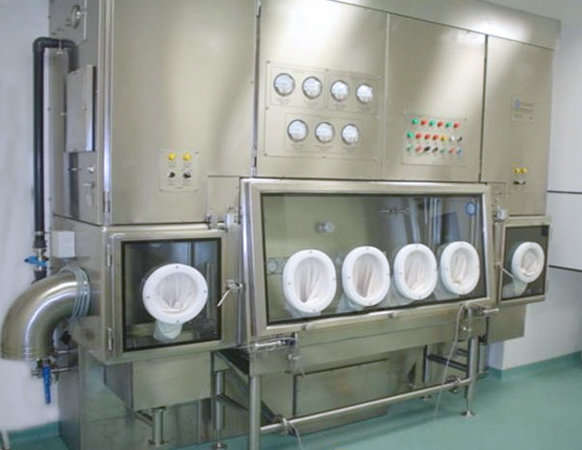
Aseptic barrier systems
Designed for sterile product and Potent API’s either with low or high OEL requirements.
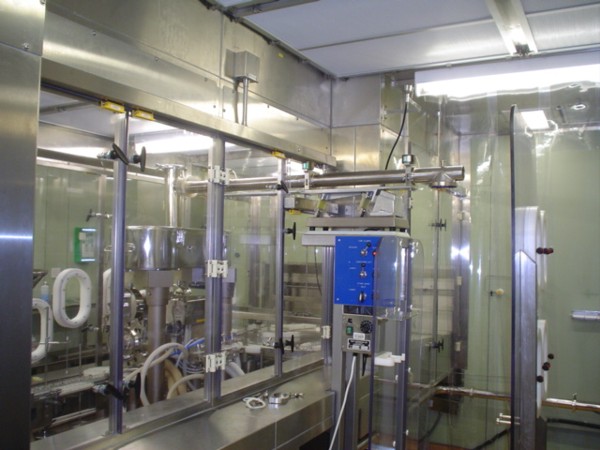
Restricted-access barrier systems
Create a physical barrier between the operator and the product. More flexible than an iso...
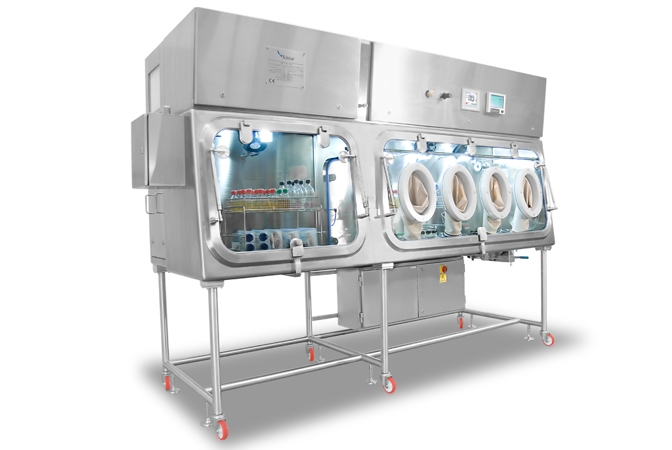
Sterility test isolators
Designed to avoid this risk and protect the product from both the process and externally generated f...
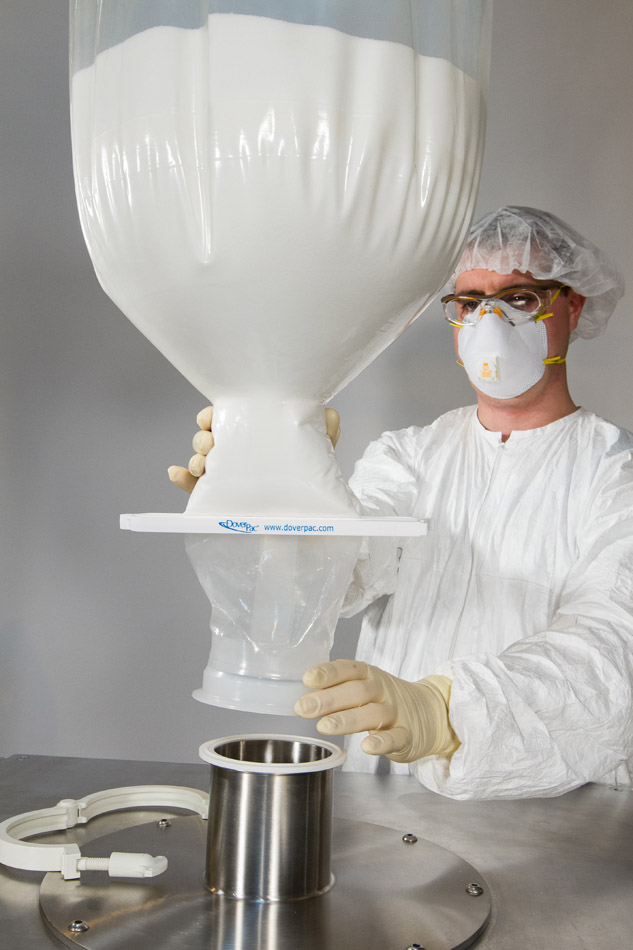
Flexible contained handling of powder transfer bags
Filling of transportation bags and discharging them into mix tanks or...
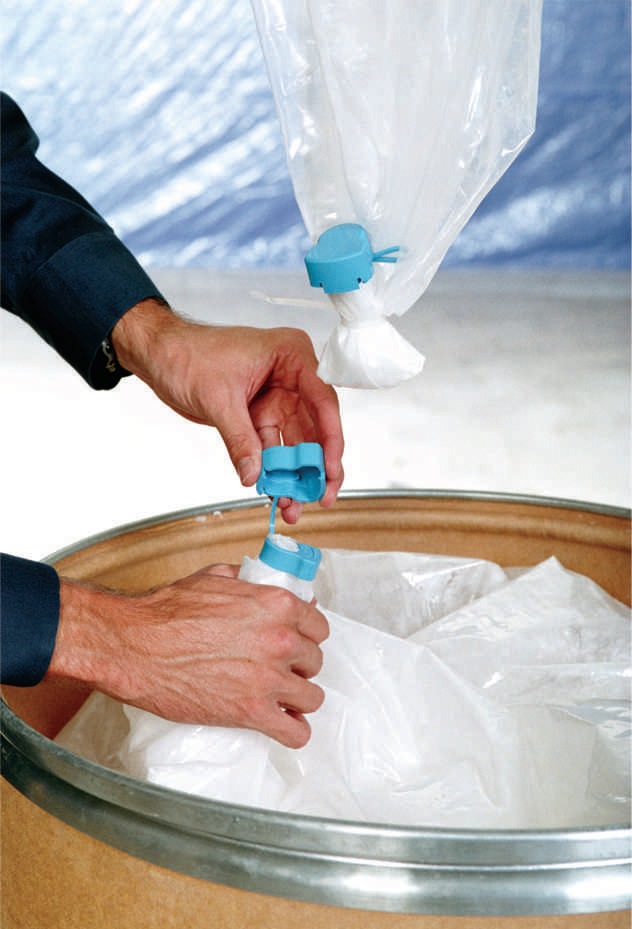
Crimping system
Flexible disposable containment systems in the form of specially designed plastic bags are an excellent choice...
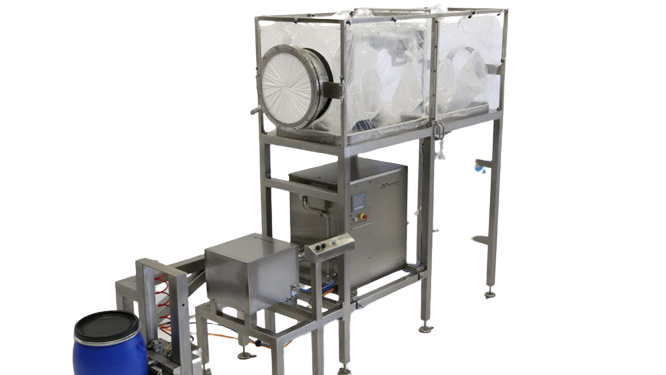
Flexible contained drum transfer system
Transferring powders from drums to process equipment such as reactors or mills can ...
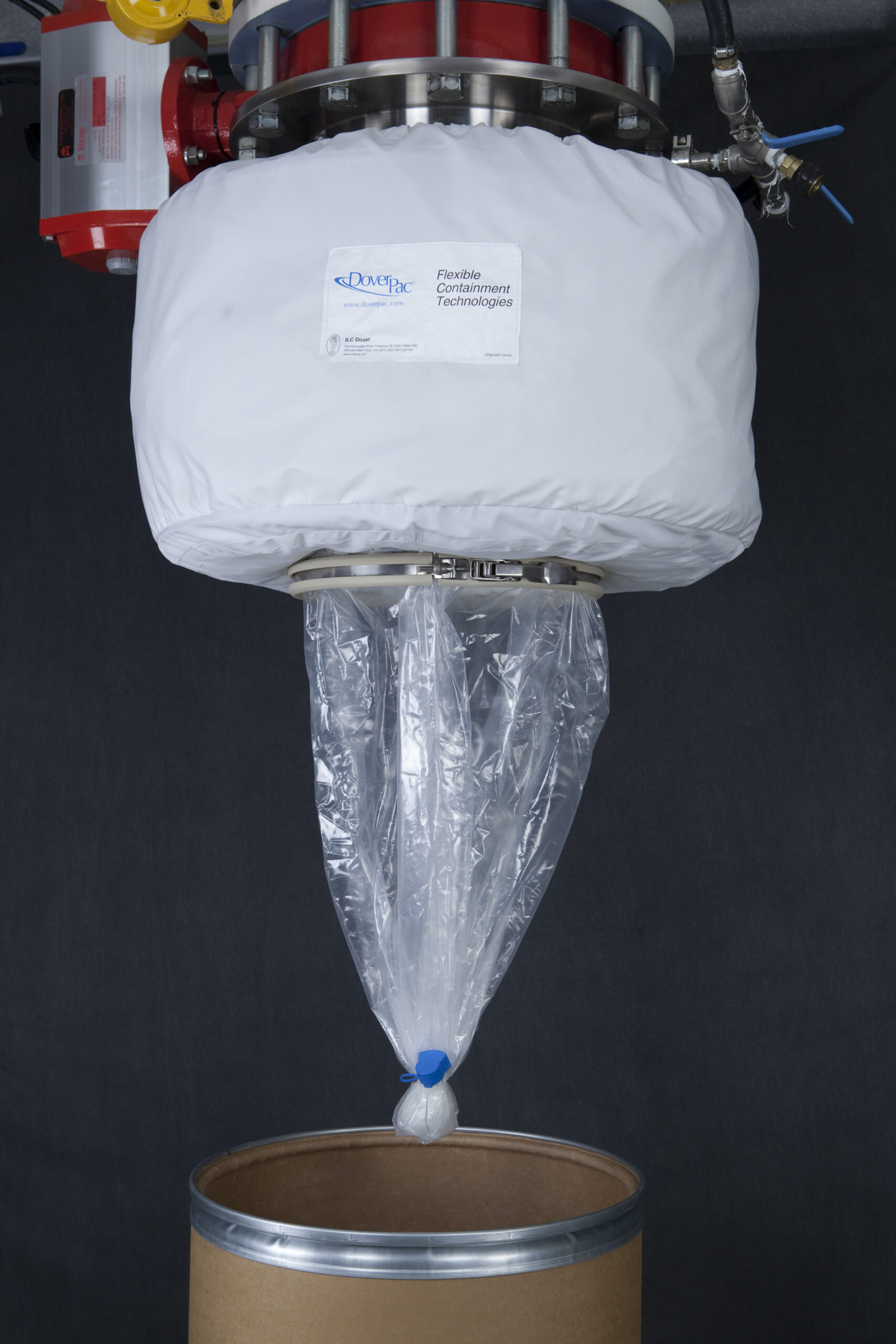
Flexible contained powder discharge into drums
Powdered products are handled every day in the pharmaceutical and bioproces...