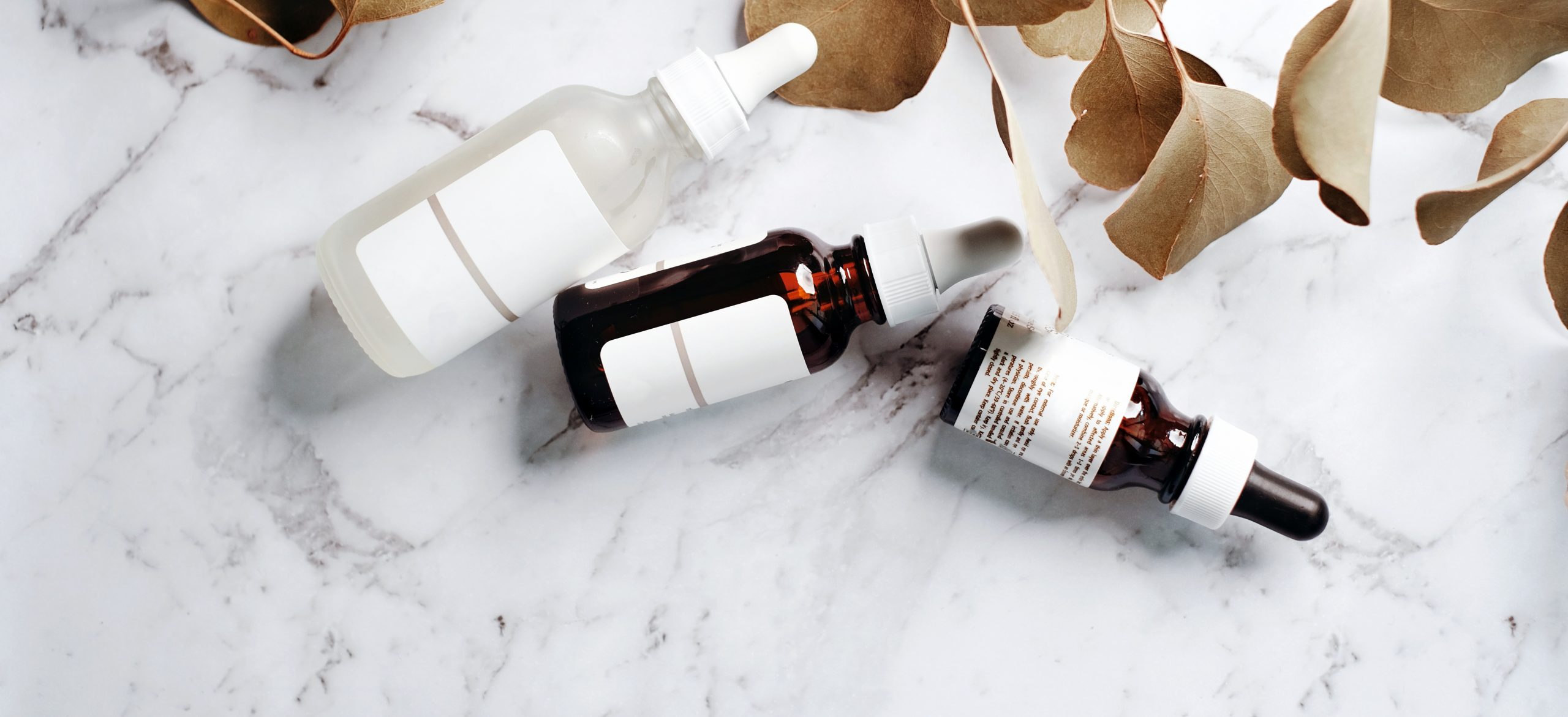
Making Serums
Find innovative production technology for making serums and connect directly with world-leading specialists
Cosmetic serums are a very light formulation with a high density of active ingredients dispersed in oil, water, or gel. This makes serums well suited to the delivery of vitamins, antioxidants, and anti-aging ingredients, but provide less moisturization and protection. Serum production is mainly divided into stages related to optimal mixing and preventing degradation of the active ingredients.
Select your serums process
Tell us about your production challenge
Most important considerations of equipment for making serums
When making cosmetic serums, you start by preparing the oil-soluble and water-soluble constituents separately. Add active ingredients after any thermal treatments as heat may damage or destroy them. Water-based serums will typically comprise oil solubles in very low concentrations of a few percent, active ingredients in a relatively high concentration, and water-solubles forming the majority of the solution. An emulsifier facilitates the distribution of oil solubles, and a preservative protects against microbial growth.
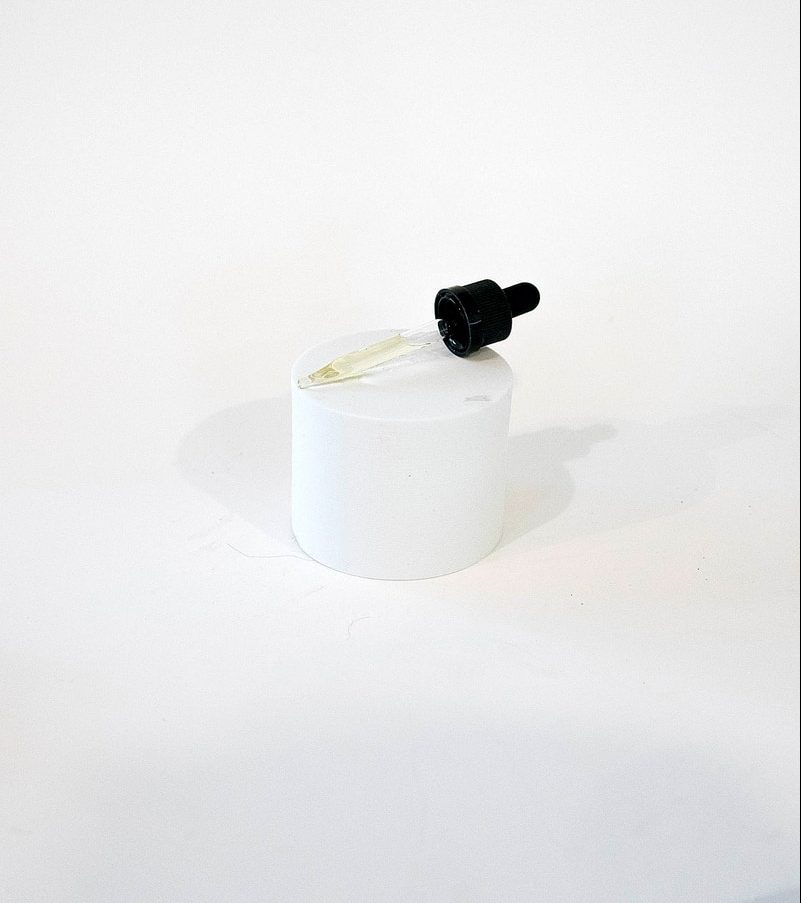
Equipment for making serums requires mixers to prepare the initial stages and to reach a uniform consistency. These may also include thermal functions to assist the incorporation of heat-stable ingredients. You then join the two phases with the help of an emulsifier, and may now introduce your active ingredients safely. Production nuances present with the variety of serum applications, such as acne management, anti-aging, skin-shining, and the reduction of wrinkles. As a result, the selection of your formulation and the necessary accommodations to produce it successfully are important. With oil-based serums, you don’t need to process a water phase entirely for example. Gel-based serums require mixing equipment able to develop the gelling phase.
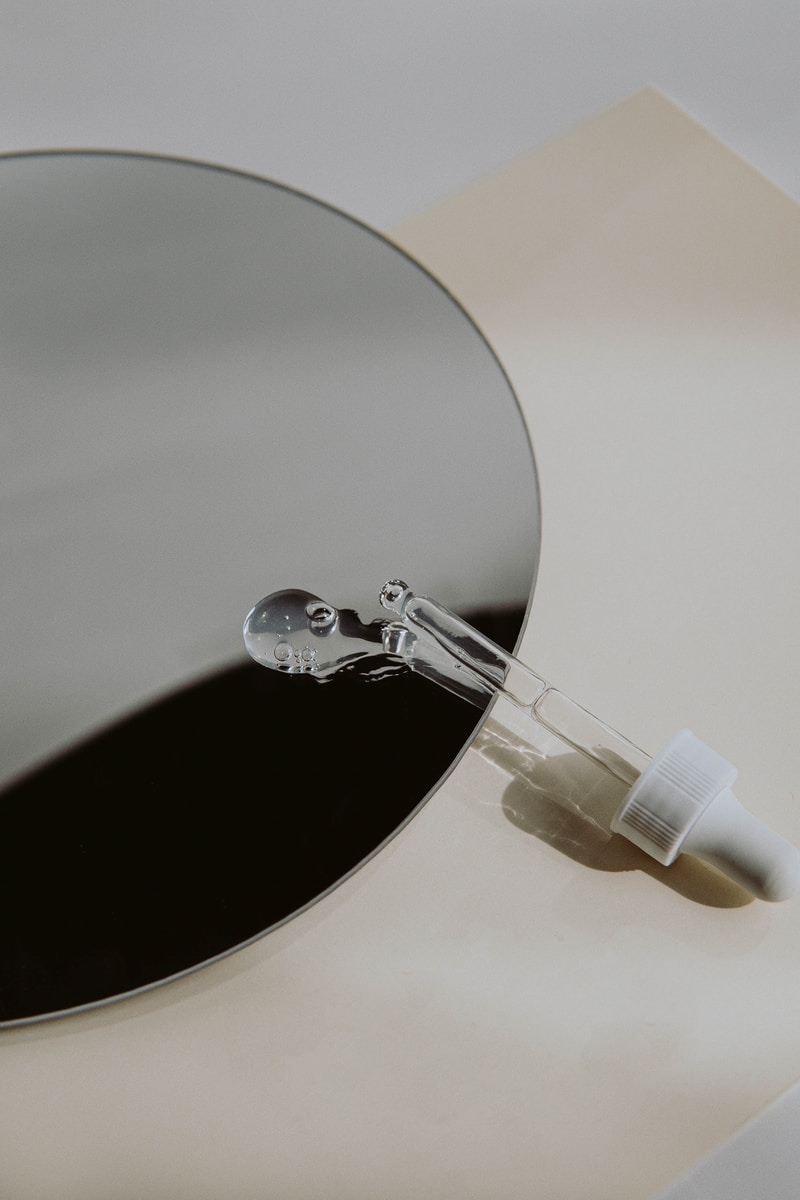
Alternative options for serum bases
Gel-based serums provide better moisturization and need a gelling agent to reach the desired consistency and texture. You still need an emulsifier to incorporate lipid components, and preservatives to prevent microbial growth. Contrary to water-based serums, their oil-based counterparts contain no water, so they don’t need emulsifiers, and to some degree preservatives. Emulsifiers can strip away the natural oils of the skin and may not be desirable in some circumstances. Consumers may also prefer preservative-free cosmetics, though these are very safe ingredients essential to maintaining shelf life in hydrated formulations. Common bases for such serums include Argan oil and Jojoba oil.
Regulatory compliance for crafting cosmetics
Regulations for production and sale of cosmetic serums vary from country to country, but prioritize safety and transparency of ingredients. The EU has defined its expectations in EU Regulation 1223/2009, for example, and includes an extensive list of banned substances. It also highlights good manufacturing practices, and requires accessibility of relevant data to track economic and medical aspects of the serum. You need to appoint a responsible party, and develop an ongoing conversation with your regulatory agency regarding the safety of your serum.
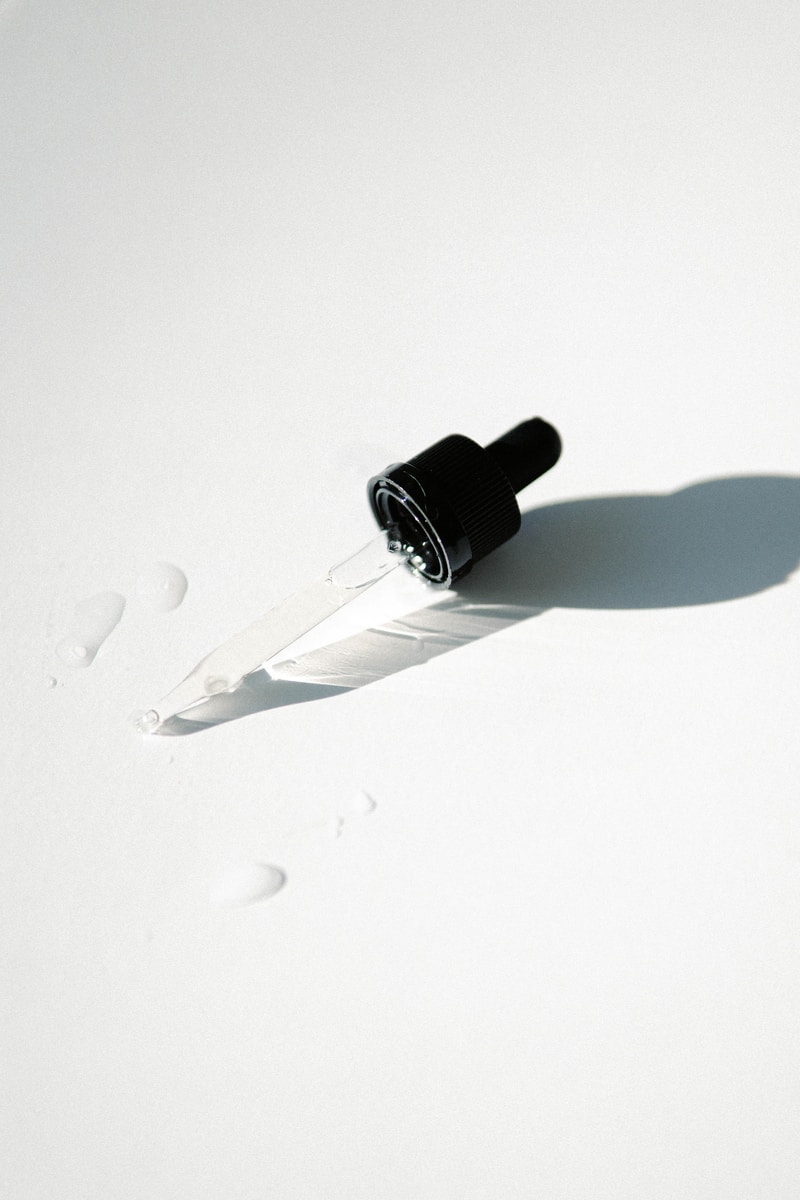
How homogenization gives you consistency
One of the most important aspects of serum production is the homogenization of its composition. A reliable serum should maintain the same look and feel in every batch. Different ingredients behave differently in solution, and clumping can produce irregularities in the texture as well as discrepancies in relative potency. When selecting equipment for making serums, consider the needs of your formula to find the optimal fit. If clumping can be an issue, use agitators to help ingredients disperse into the mixture. Prior to adding active ingredients, you may also want to heat elements to facilitate even incorporation for a smooth, uniform outcome.
Which serums technology do you need?
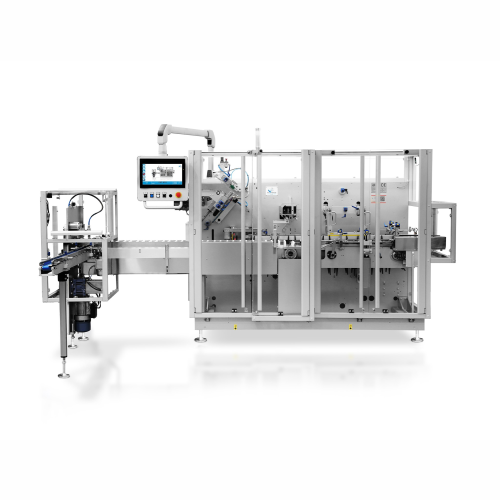
Automatic horizontal cartoning solution for various products
Optimize your packaging line with this advanced cartoning s...
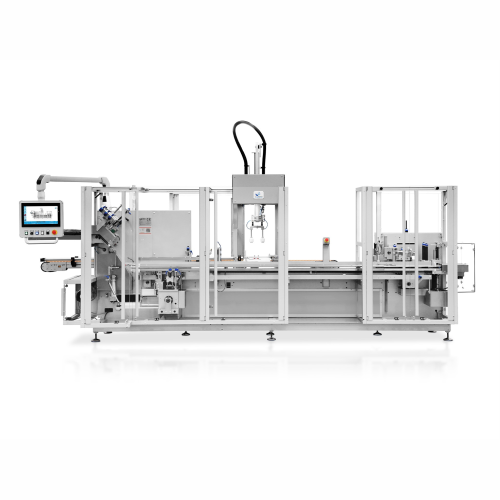
Automatic vertical cartoning solution for jars and bottles
Streamline your production line with a versatile packaging so...
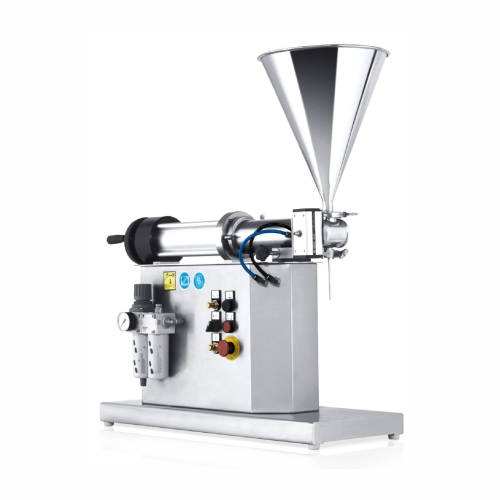
Laboratory filling system for liquid and creamy products
Optimize your laboratory processes by precisely handling liquid,...
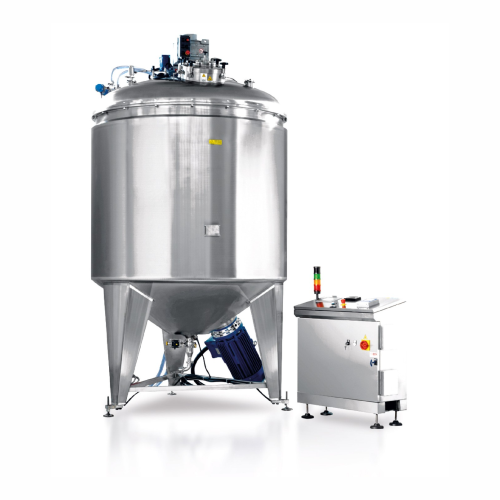
Vacuum turboemulsifier for liquid and creamy products
Achieve precise emulsification and mixing of liquid and creamy form...
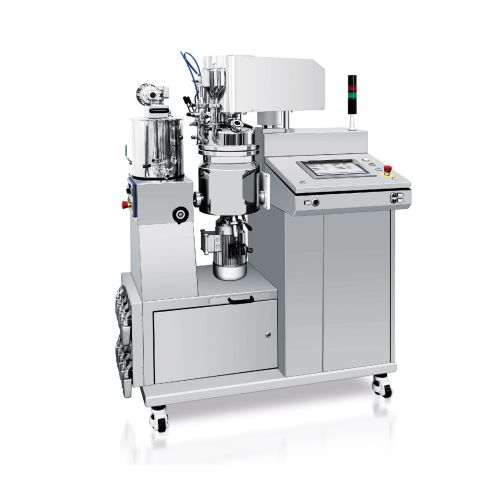
Vacuum turboemulsifier for small-scale production
Optimize your product development with versatile vacuum turboemulsifier...

Pre-glued case cartoning solution
Elevate your cosmetics packaging line with high-speed cartoning, ensuring seamless integr...
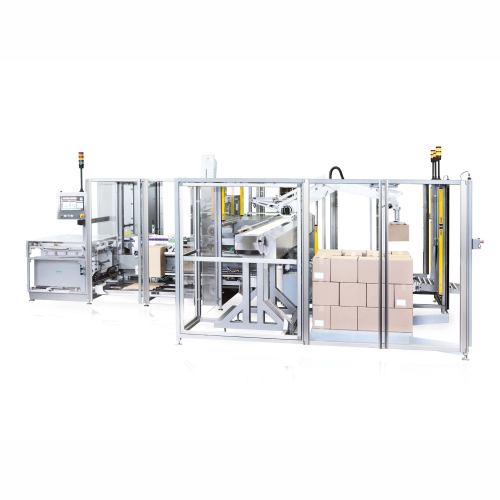
Automatic vertical case packer and palletizer for cosmetic sector
Optimize your packaging process with a compact soluti...
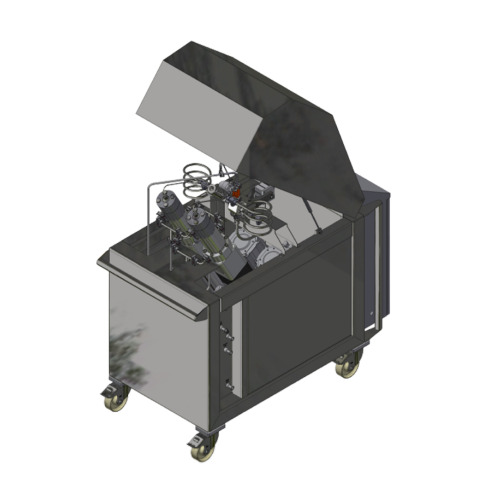
High pressure homogenizer for pharma applications
Achieve precise particle size reduction and stability in liquid formula...
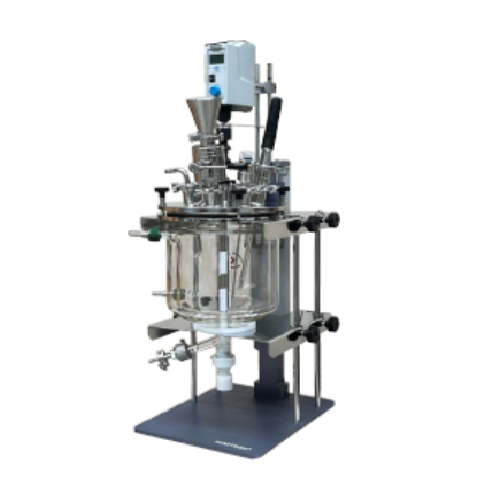
Laboratory dispersion reactor for 10l batch processes
Enhance precision and efficiency in lab-scale liquid formulations w...
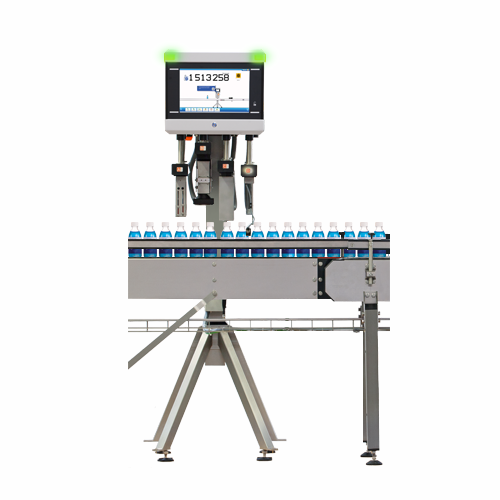
Full container inspection for pharma and food industries
Ensure precise fill levels and secure closures in your productio...
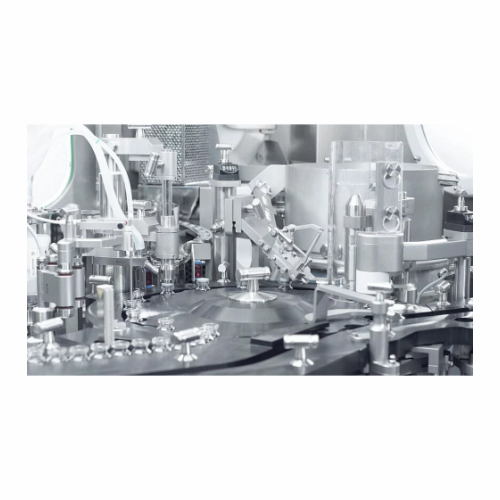
Vial filling for pharmaceuticals
Streamline your aseptic processing with vial filling machines that ensure sterile, precise,...
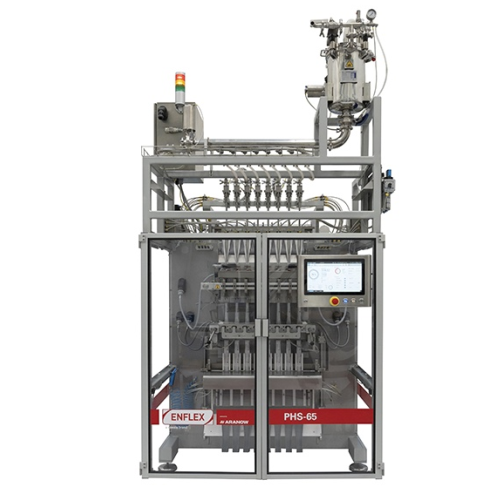
Intermittent stick pack system for pharmaceuticals
Effortlessly streamline your packaging process with a high-speed, mult...
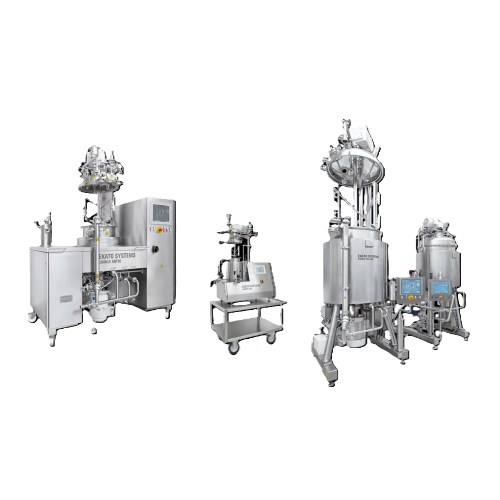
Vacuum processing units for high-viscosity products
For manufacturers seeking to streamline production of high-viscosity ...
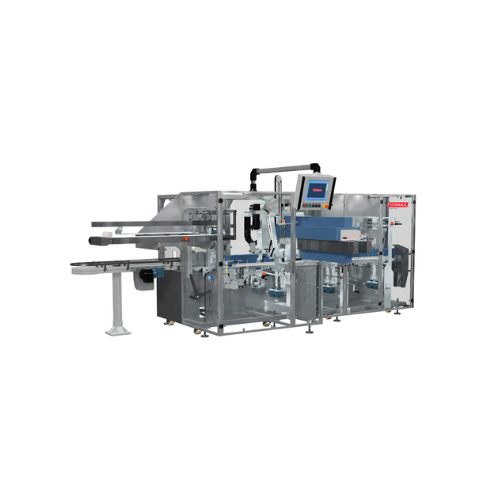
Vertical cartoning solution for fragrance and skincare products
Effortlessly carton even the most delicate cosmetics wit...
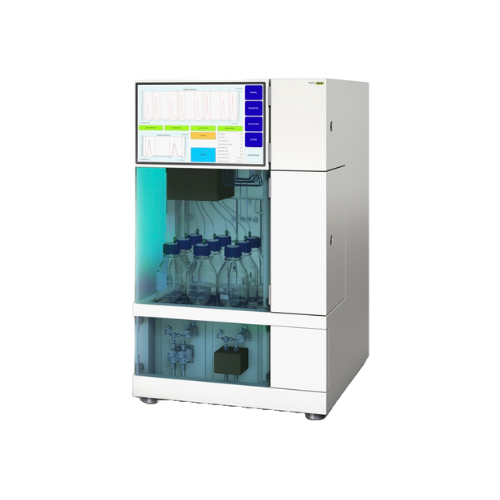
Supercritical fluid chromatography system for preparative separations
For complex substance formulations requiring rapi...
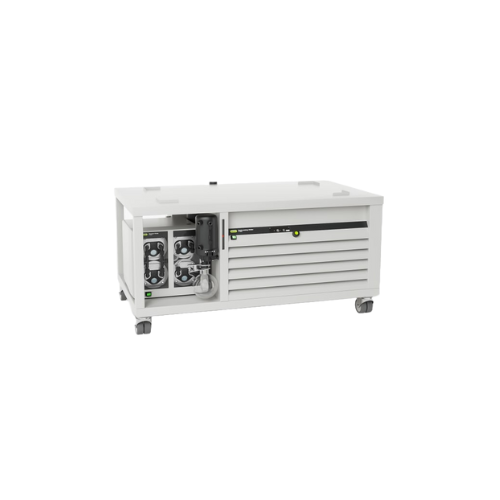
Industrial recirculating chiller for laboratory applications
For consistent distillation results, maintain accurate temp...
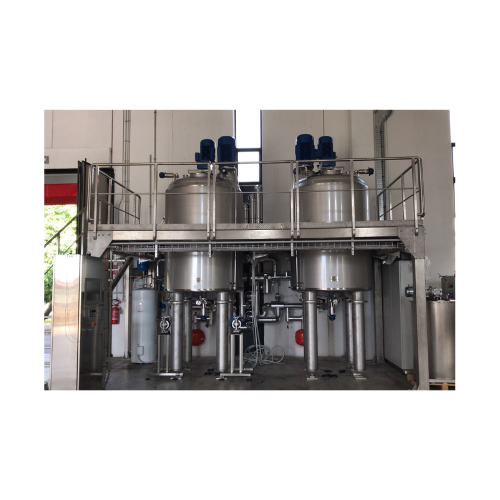
High-pressure reactor for cosmetic and pharmaceutical production
Ensure precise formulation and enhanced product stabili...
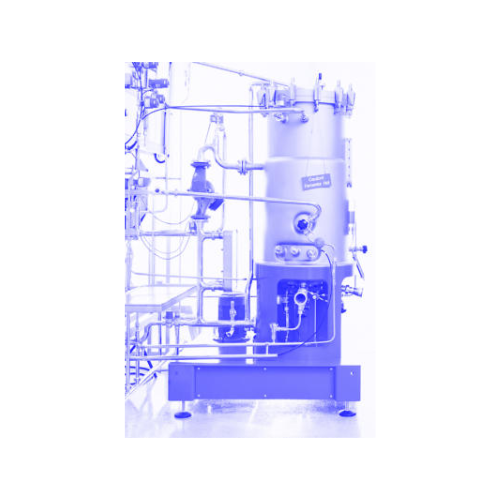
Autoclavable and in-situ sterilizable lab-scale fermentors
For researchers seeking precise control in bioprocessing, the...
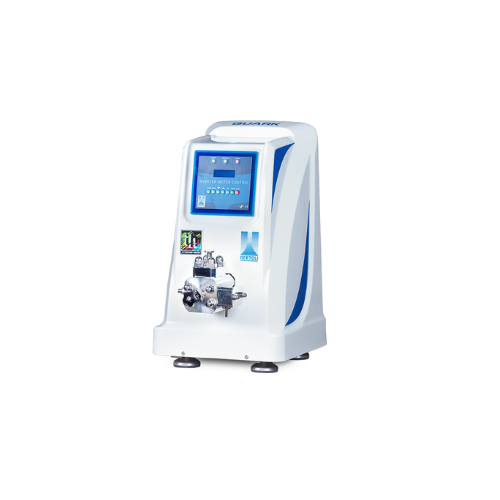
Laboratory homogenizer for pharmaceutical and biotech applications
Achieve precise homogenization for your laboratory n...
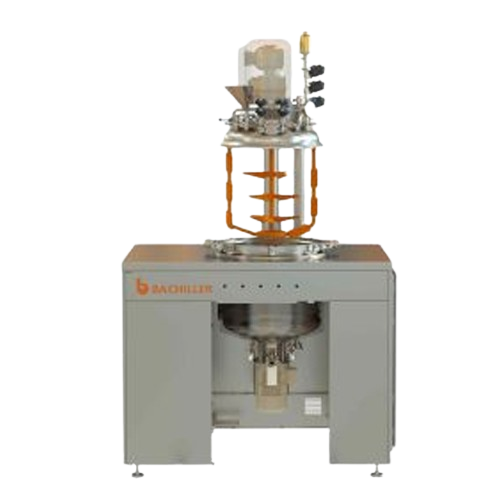
Laboratory vacuum mixer reactor for liquids and semi-solids
Achieve precise emulsification and mixing for high-viscosity...
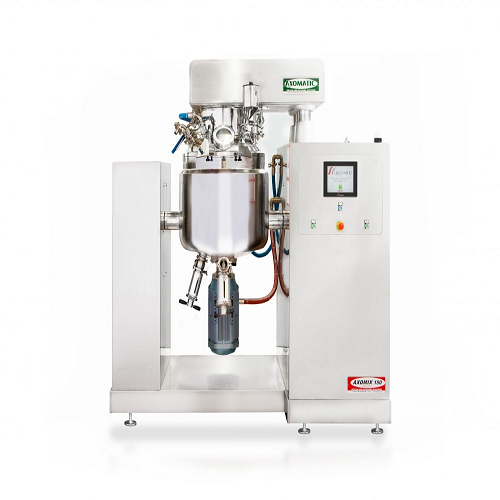
Vacuum homogenizer for high-quality mixing and emulsification
Achieve optimal consistency and enhanced product stability...
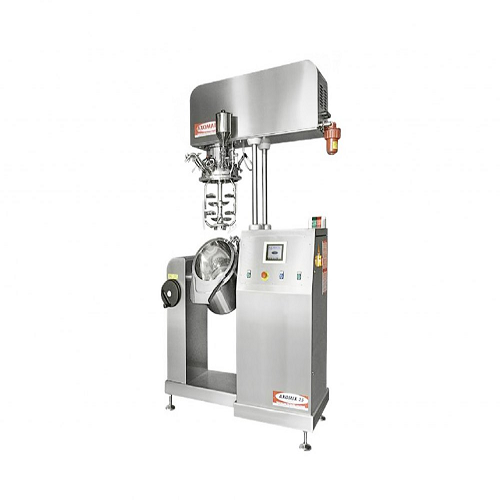
Industrial under vacuum homogenizer
Optimize the consistency and texture of creams and lotions with precision-controlled mi...
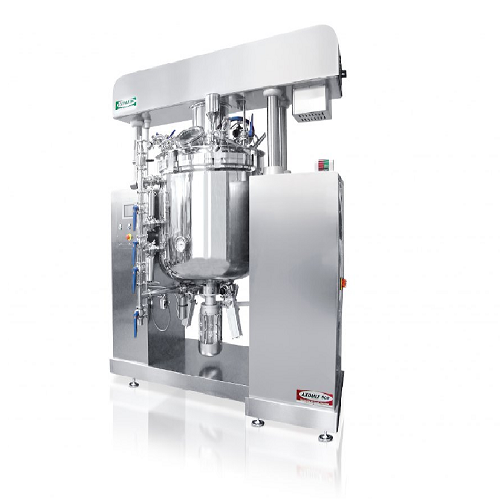
Undervacuum homogenizer for cosmetic and pharmaceutical creams
Optimizing the production of creams and lotions, this und...

Automatic bottle filling and capping line
Streamline your liquid product packaging with this high-speed solution, integrat...
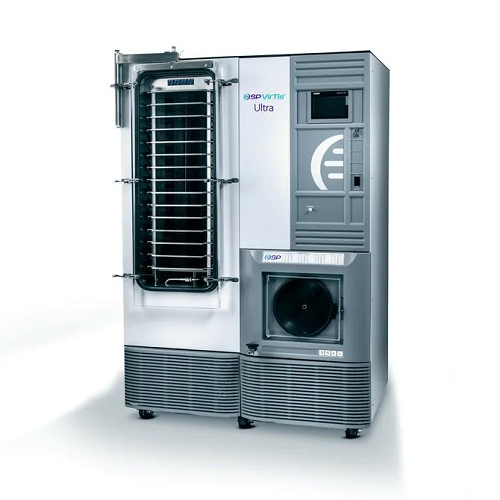
Pilot-production freeze dryers for diagnostic kits and tissue banking
Optimize your freeze-drying process with compact,...
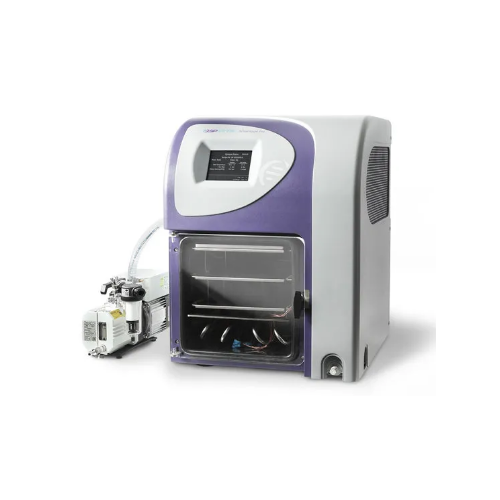
Benchtop freeze dryer for laboratory and small production use
Optimize your lab’s efficiency by adding precise, space-sa...
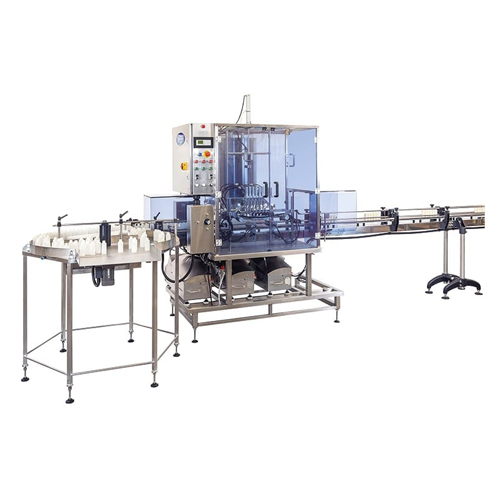
Automated bottle and jar filling solution
Streamline your production and minimize waste with a versatile filling solution,...
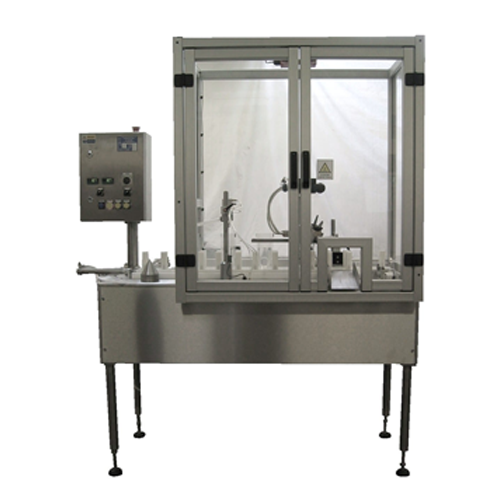
Bag and pouch filling solution for liquid products
Efficiently package diverse liquid products with precision and speed, ...
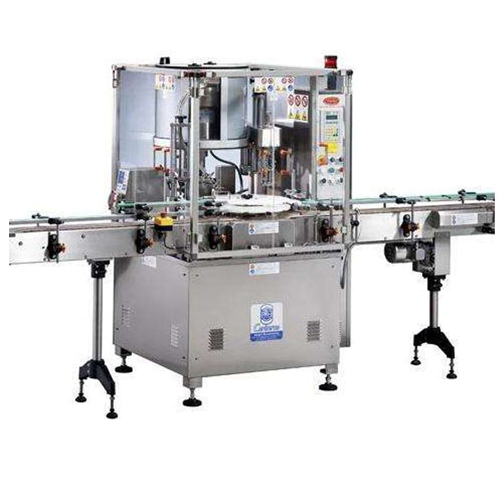
Compact filler and closer for vial processing
Efficiently streamline your vial filling and closing processes with a compac...
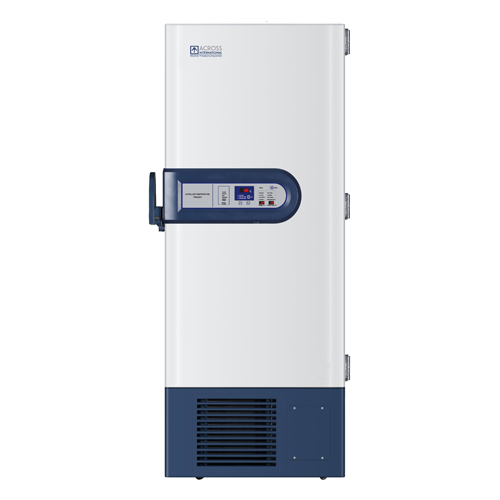
Ultra-low freezer for medical and biological storage
For critical preservation of sensitive samples, this ultra-low tempe...
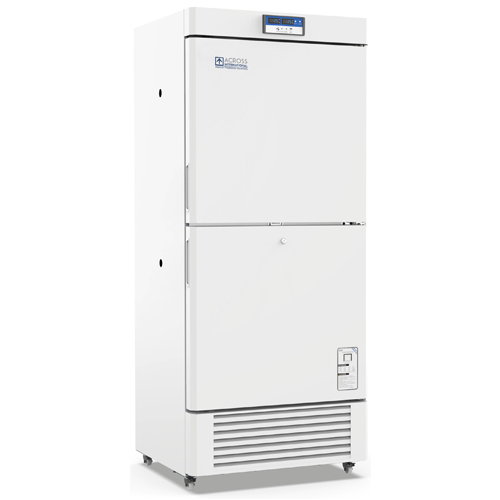
Laboratory -40°c upright freezer
Ensure optimal preservation of sensitive biological samples with a freezer engineered for u...
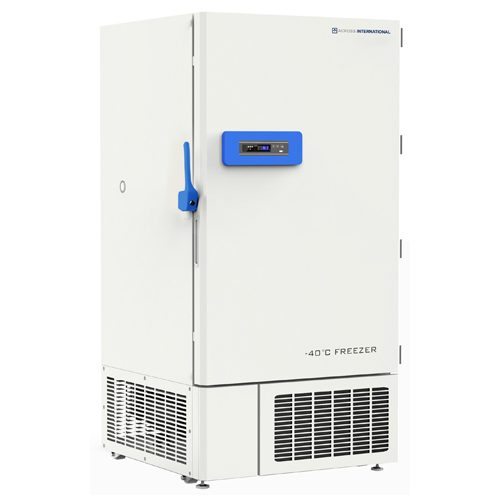
Medical freezer for -40°c storage
Ensure optimal preservation of critical samples with an ultra-low temperature solution de...
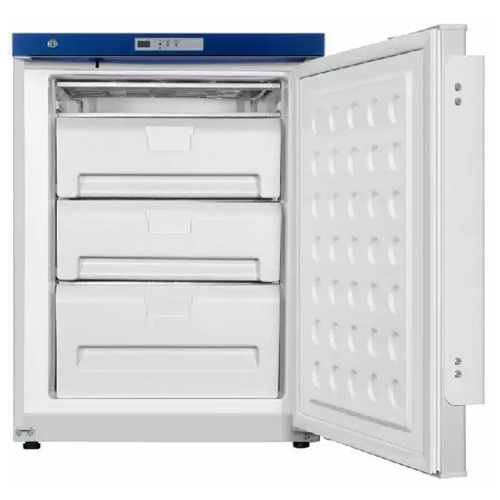
Laboratory freezer for sample storage at -25°c
Ensure precise preservation of sensitive samples with an efficient upright ...
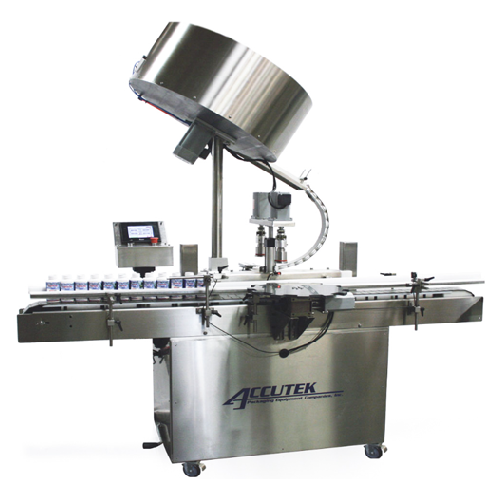
Automatic capper for dual head o-ring chuck
Ensure precise cap application with dual-head precision, handling various bott...

Aseptic sampling system for industrial applications
Achieve reliable, aseptic sampling with precision and safety during c...
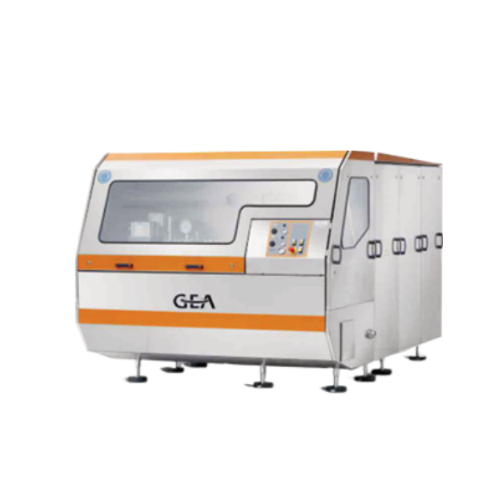
Industrial homogenizer for dairy, beverage, and pharmaceutical applications
Enhance your production efficiency with a ...
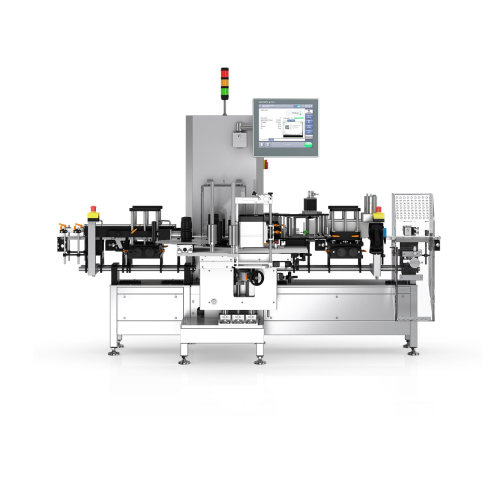
Serialisation system for medicine bottles
Optimize your packaging line with high-speed serialisation and labeling designed...
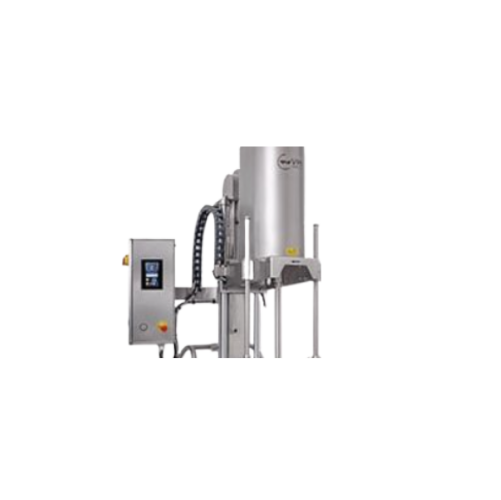
Adjustable industrial mixers for thick product blending
Experience precise blending and control for thick and high-viscos...
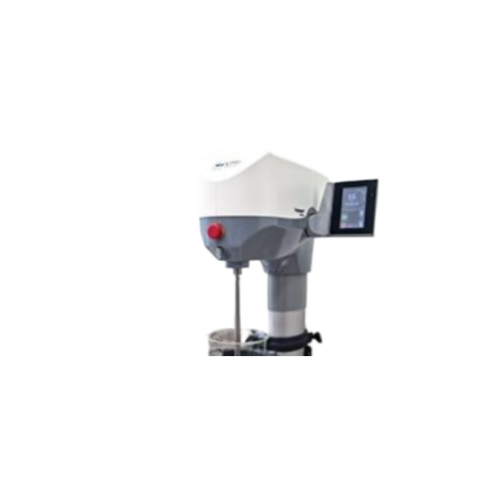
Vacuum homogenizers for cosmeto-pharma and fine chemistry
Bring precision and efficiency to your formulation processes w...

Vacuum homogenizer for cosmetics and pharmaceuticals
Optimize your production with precision mixing and homogenizing, ess...
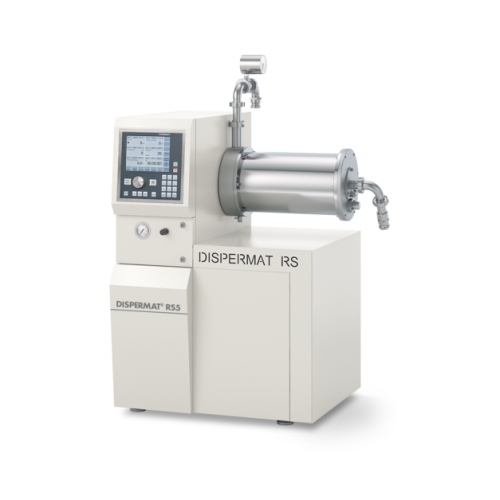
Horizontal bead mill for ultrafine particle grinding
Achieve precision in ultrafine grinding with a system that allows fo...

Explosion-proof dissolver for high-viscosity products
Optimized for safely processing high-viscosity products, this explo...
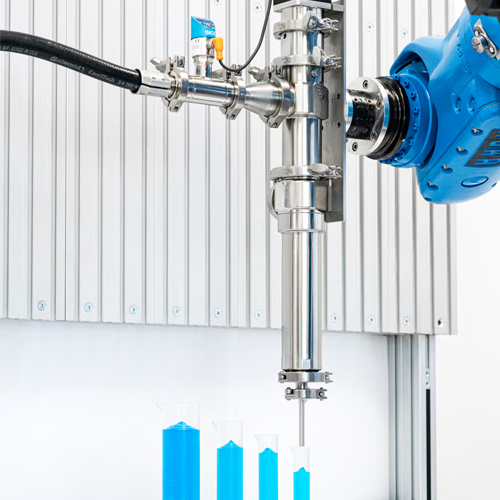
Dosing pump for liquids and pastes
Achieve precise dosing and filling of liquids and pastes with flexibility in dosing volu...
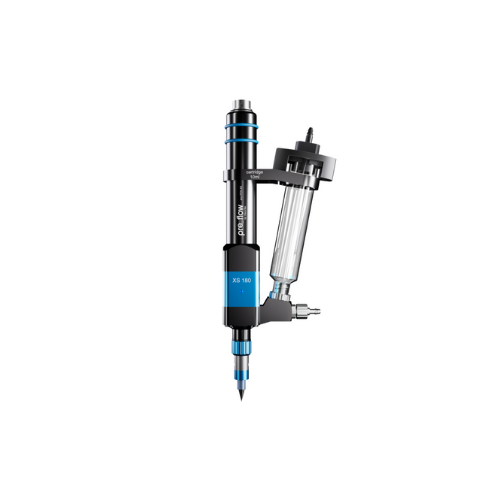
1-component industrial dispenser for precision dosing
Achieve unparalleled precision in microdispensing across diverse ap...
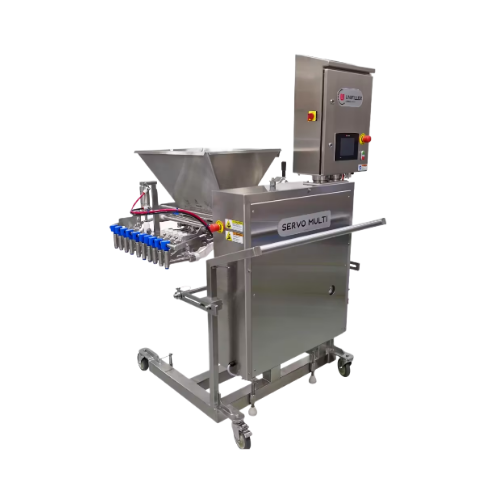
Servo multi food portioner
Achieve precise portion control and high-speed depositing for diverse applications with this adva...
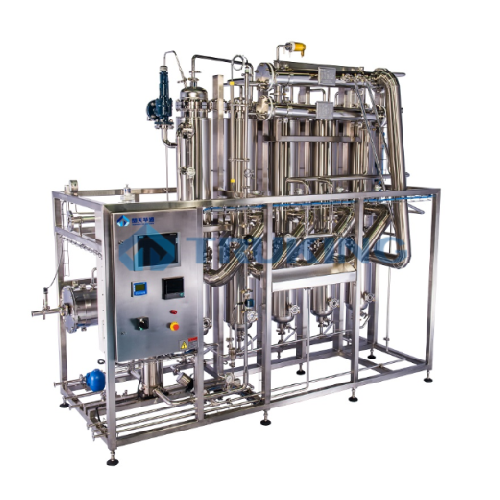
Multi-effect water distillator for pharmaceutical applications
Ensure your production line meets stringent regulatory st...
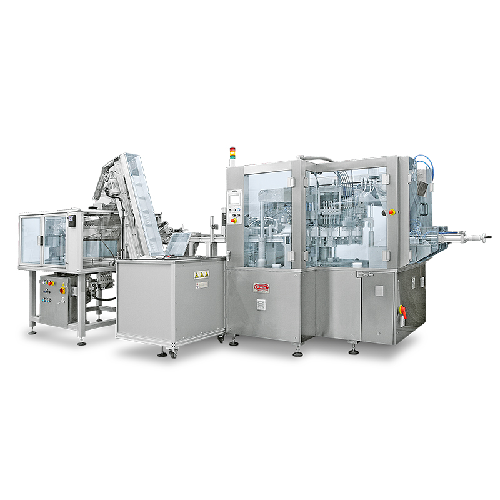
Automatic mono-dose strip filling system
Optimize your liquid product packaging with a multi-functional system designed for...
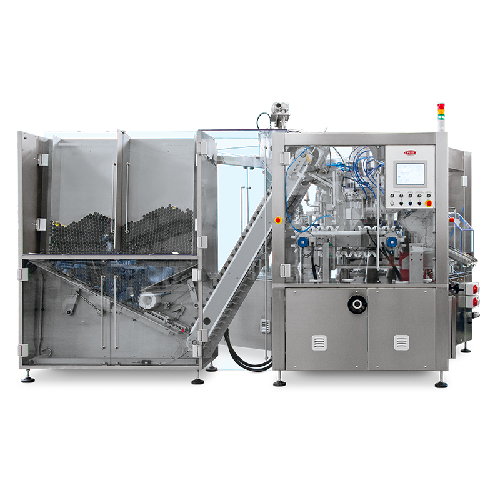
Automatic tube filling solution for high-volume production
Effortlessly streamline your production with this high-speed ...
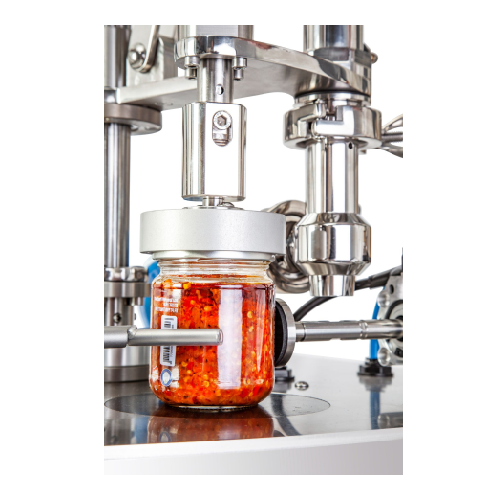
Manual dosing and capping for semi-dense products
Enhance your production line efficiency by seamlessly integrating manua...
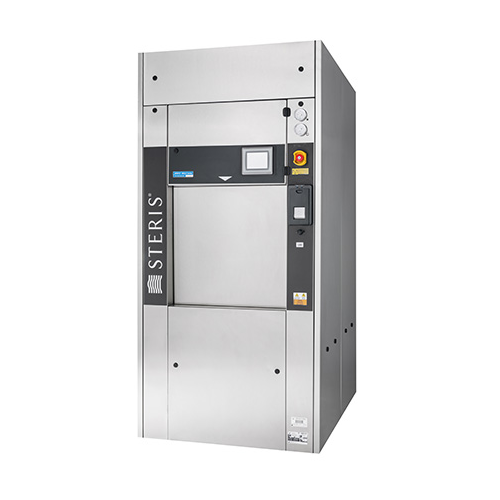
Medium steam sterilizer for laboratory applications
Ensure consistent and reliable sterilization of heat- and moisture-st...
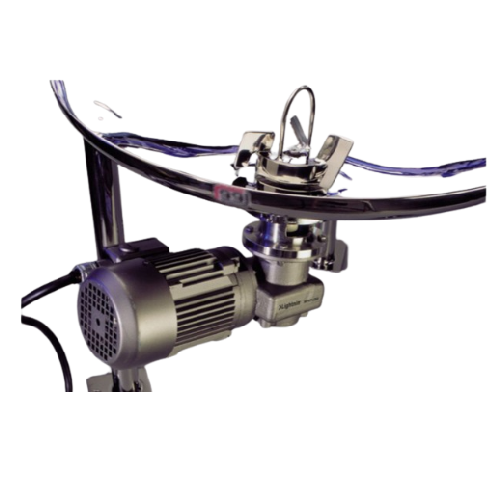
Sanitary mixer for food and pharmaceutical processing
Eliminate contamination risks while achieving high-speed, efficient...
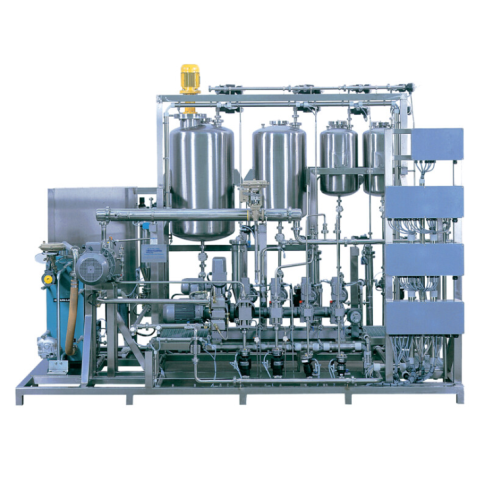
Automated body lotion blending system
Streamline your personal care product manufacturing with a seamless blending and emul...
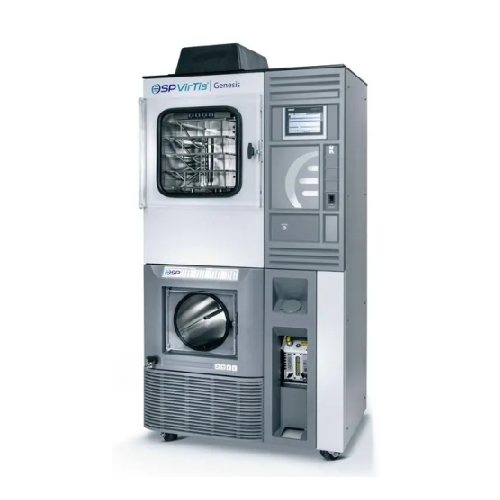
Pilot freeze dryer for laboratory and small-scale production
Achieve precise temperature and vacuum control for consiste...
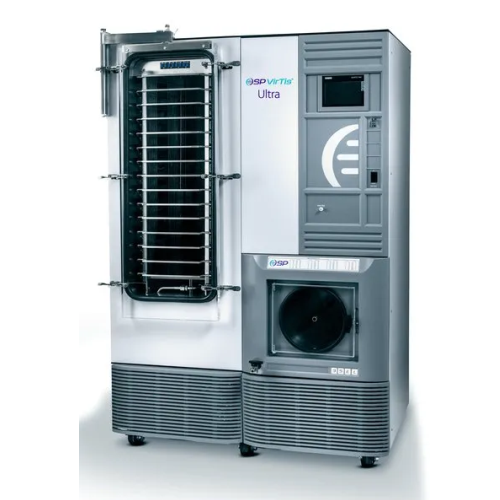
Pilot-production freeze dryer for diagnostic kits and Api
Optimize your lyophilization process with this versatile freez...
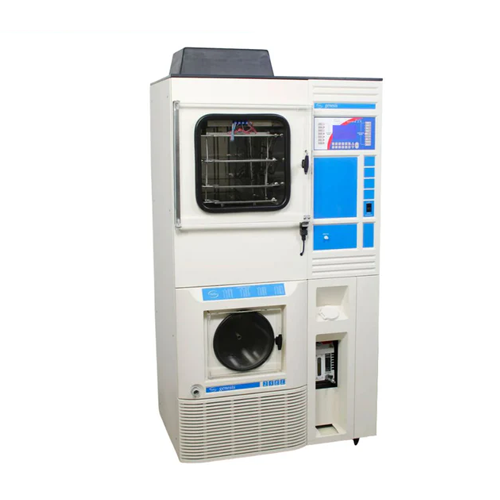
Optimized lyophilization with Smart freeze dryer technology
Streamline lyophilization cycle development with cutting-edg...
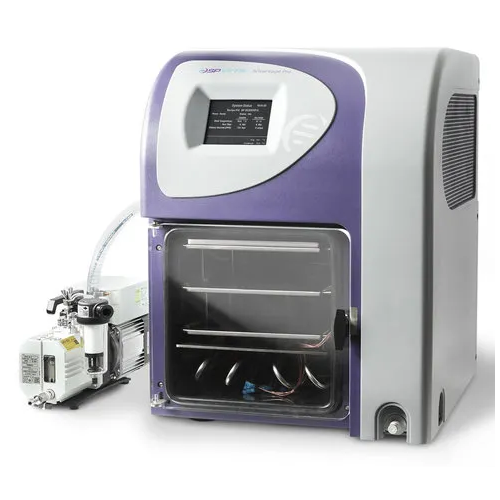
Benchtop freeze dryer for laboratory research
Streamline your lab’s freeze-drying processes with precision temperatu...
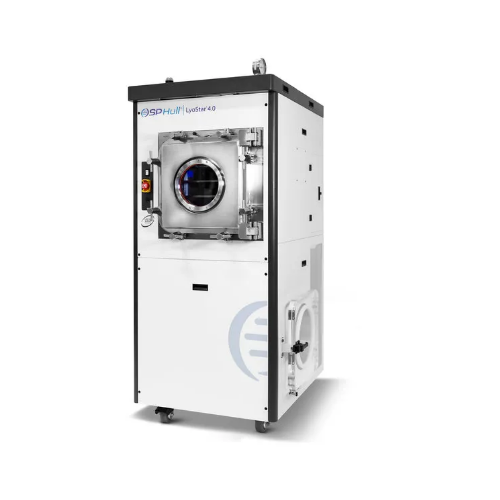
R&d and process development freeze dryer
Speed up your biologic development with precise lyophilization control, ensuring r...
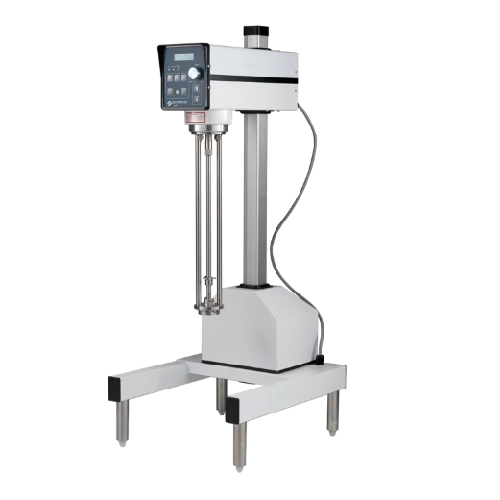
Pilot scale batch mixer for small scale production
Achieve precise control and consistency in small-scale production with...
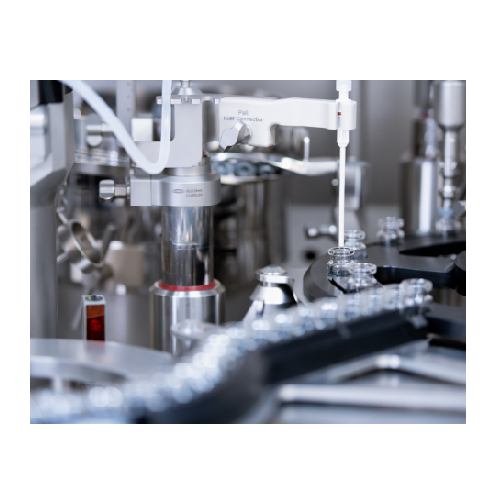
Rotary stoppering and capping for vials
Achieve precise and efficient stoppering, capping, and crimping for high-speed vial...
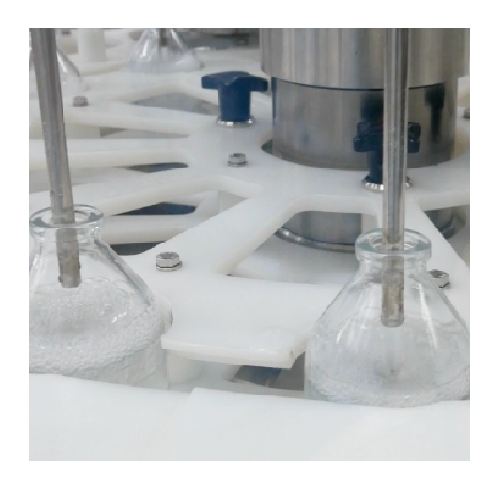
Rotary vial filling and stoppering system
For high-speed production of sterile injectable vials, this continuous motion ro...
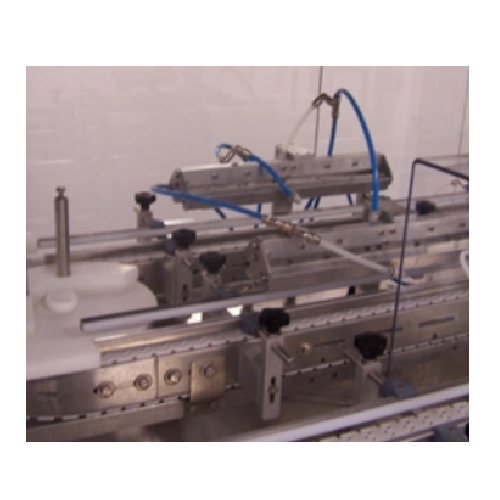
External washing and drying system for sealed vials
Ensure contamination-free packaging of liquid vials with this precise...
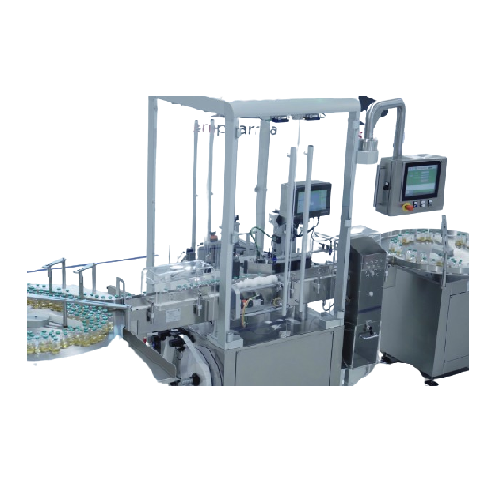
Automatic labelling system for pharmaceutical vials
Ensure precise and efficient packaging for cylindrical containers wit...
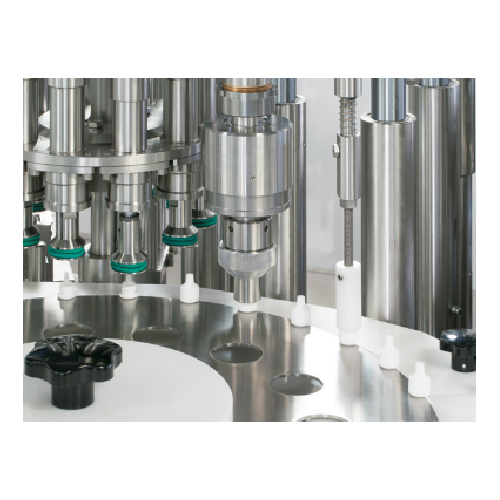
Automatic capping solution for pharmaceutical vials
Cap your liquid formulations with precision and efficiency using this...
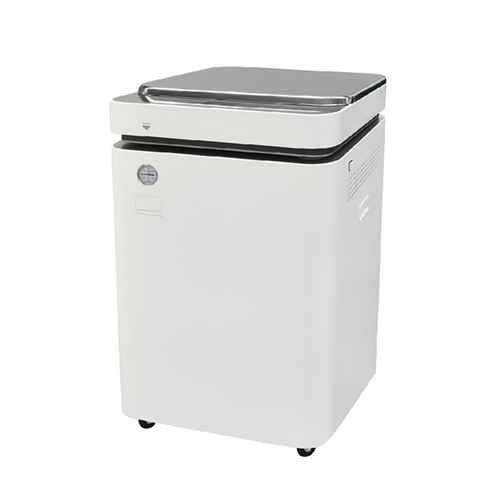
Laboratory series steam sterilizers
Ensure the sterility of your labware and culture media with reliable steam-based steril...
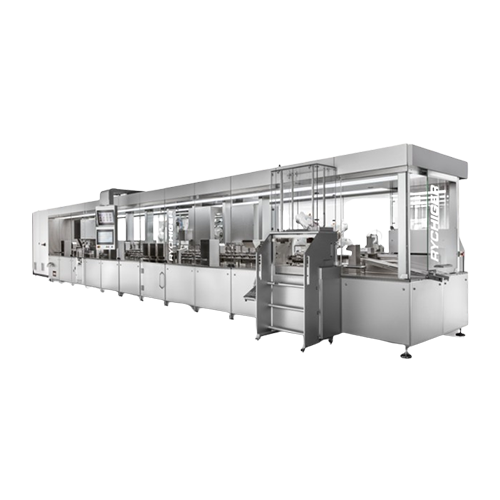
Production system for molecular diagnostics
Eliminate bottlenecks in molecular diagnostics production with a versatile sys...
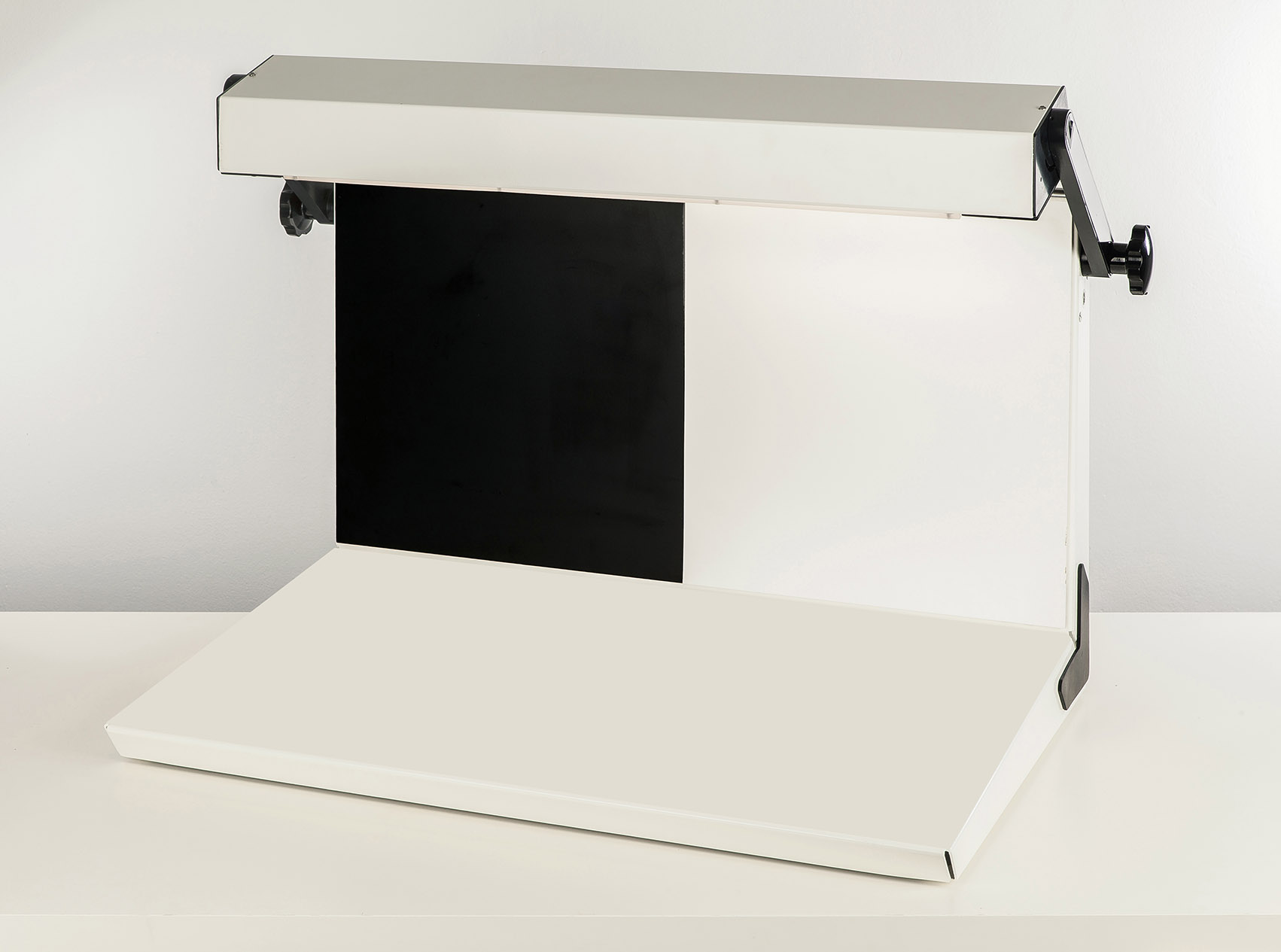
Laboratory liquid viewer for colored glass bottles
In the pharmaceutical industry, an inspection to detect any particulat...
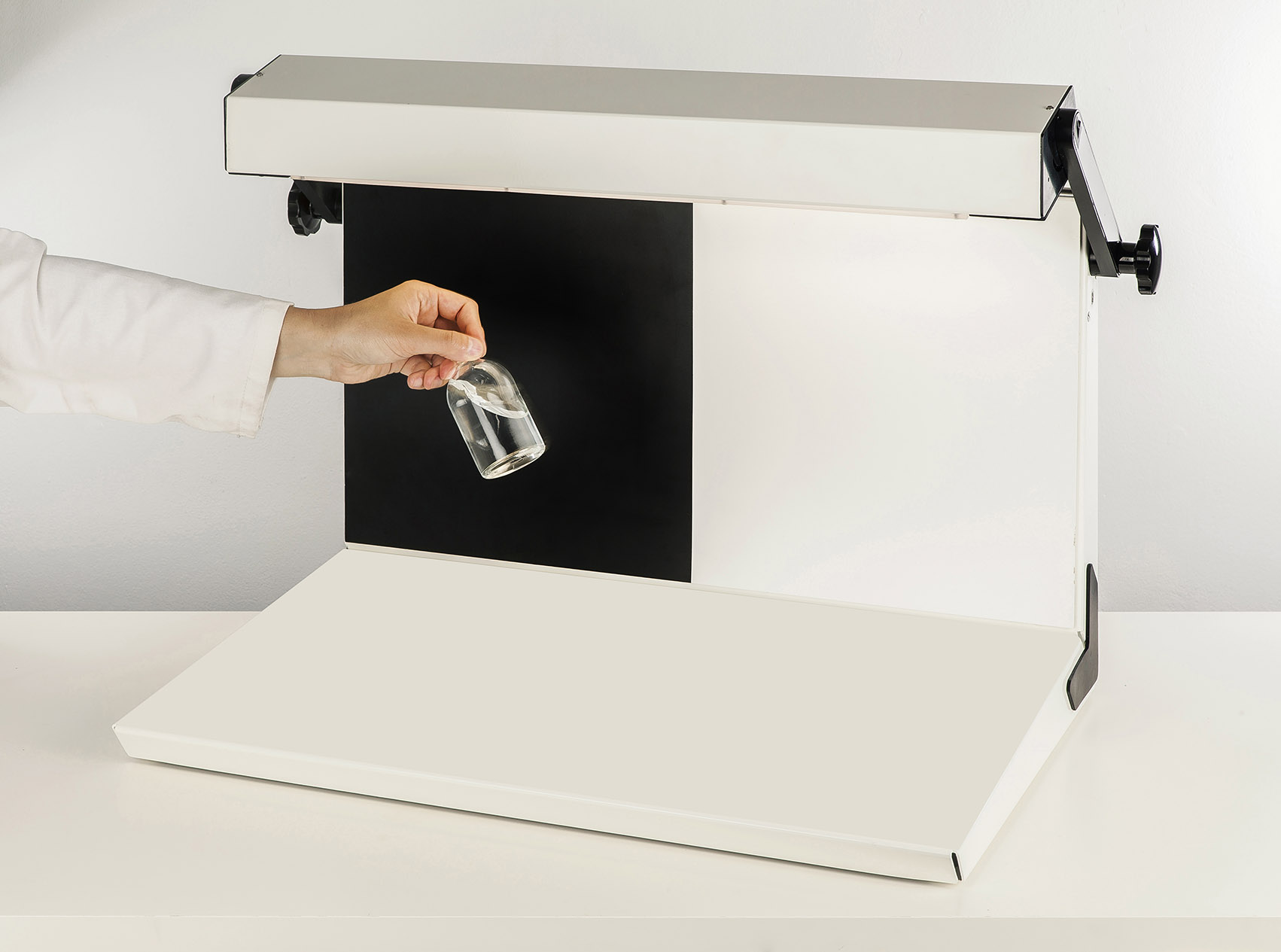
Laboratory liquid viewer for varying light conditions
In the pharmaceutical industry, you must inspect liquids in vials o...
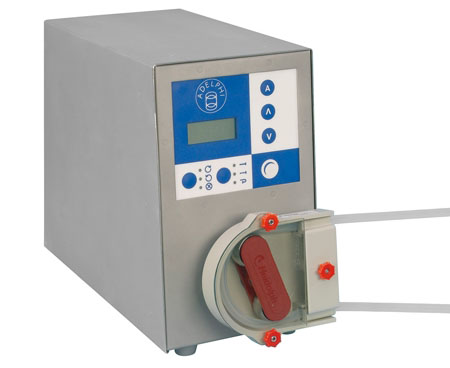
Benchtop peristaltic dispenser
When you fill vials and ampoules, high standards of hygiene are required to avoid the risk of...
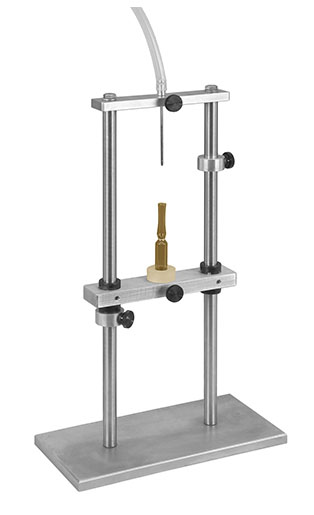
Manual ampoule filler
When you fill ampoules it is essential to avoid wetting the inside walls of the container, as it may af...
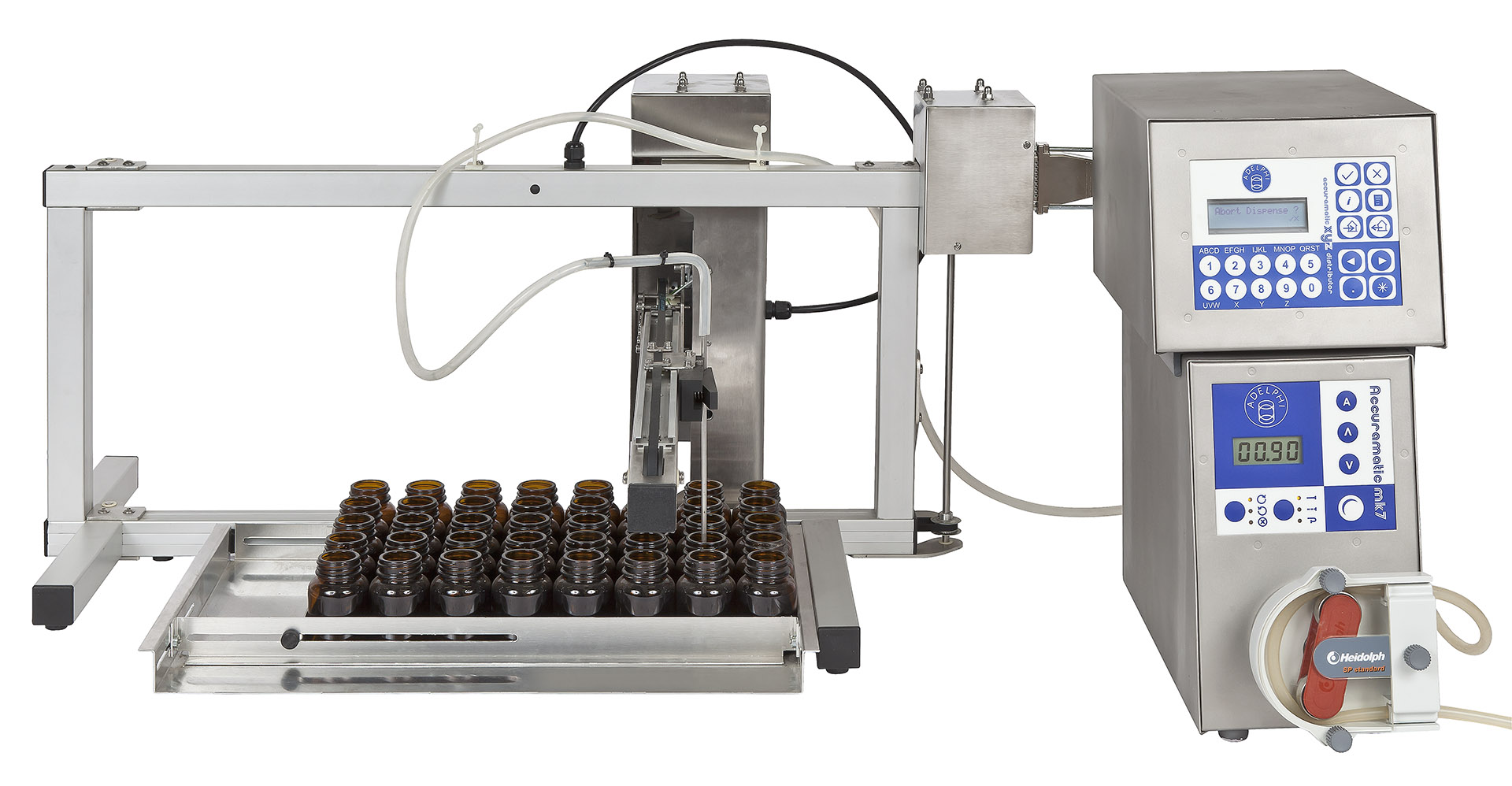
Benchtop piston filling equipment for vials in trays
Vials are difficult to fill individually through manual methods due ...
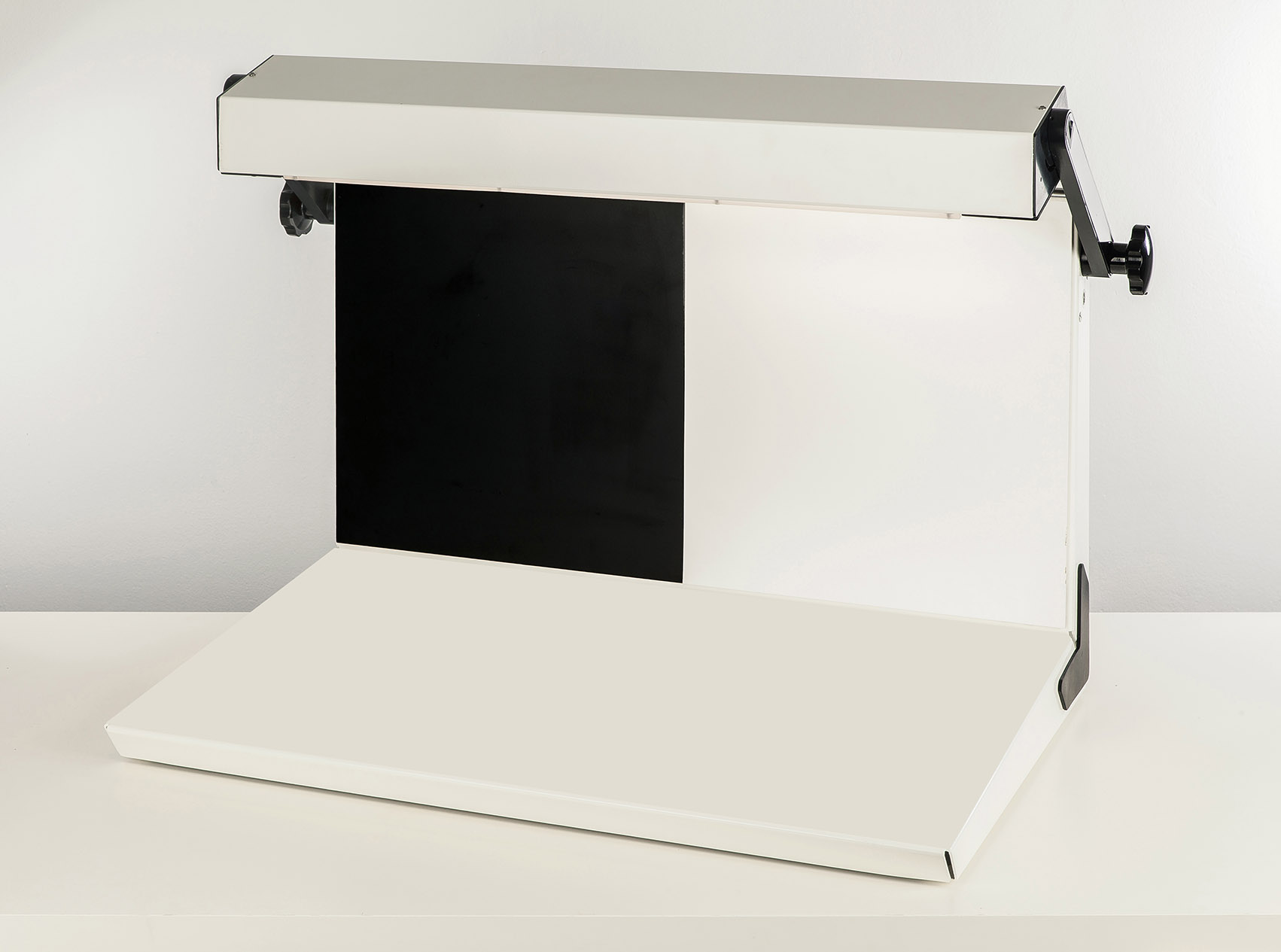
Laboratory liquid viewer for transparent glass bottles
Impurities like hair, fibers, or glass, sourced from the environme...
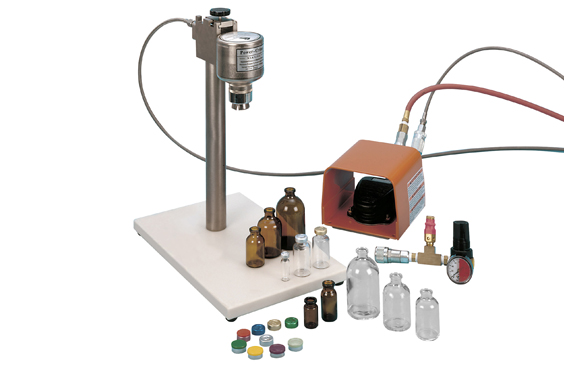
Semi-automatic vial crimper
In a small production line, crimping vials manually can cause fatigue to your operator due to mu...
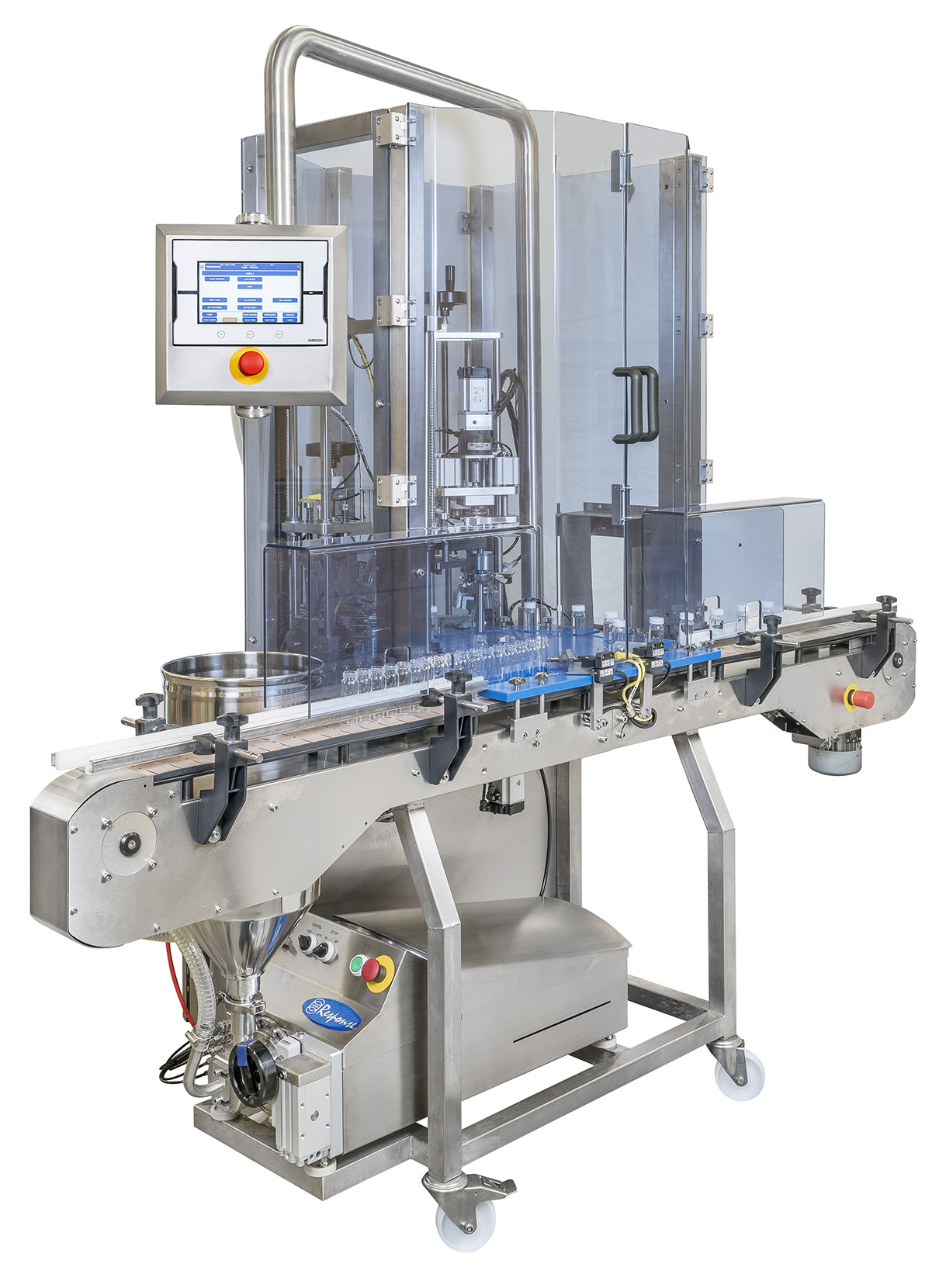
Monobloc filler and capper
If you have separate filling and capping stations you may experience lower throughput rates due t...
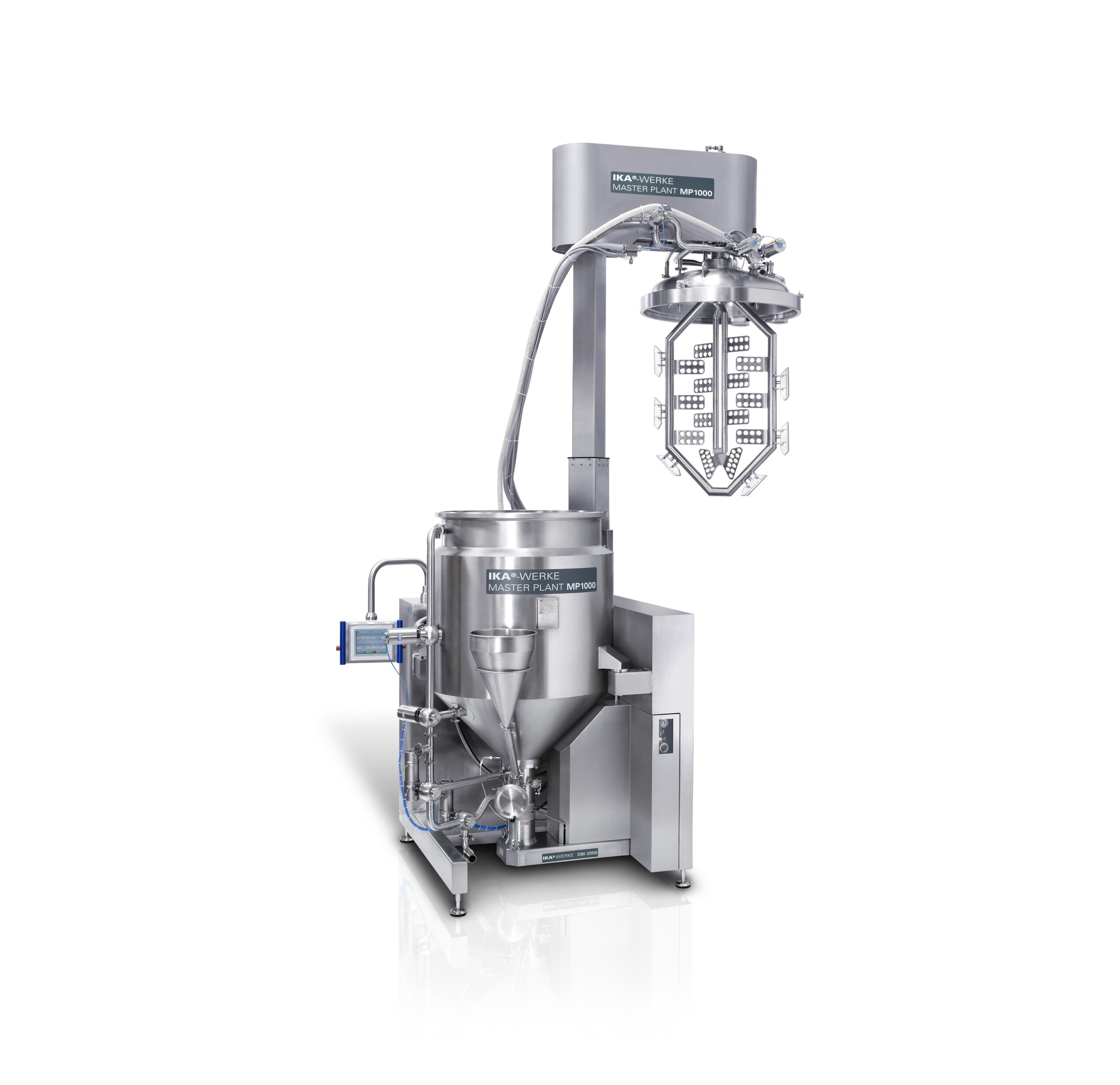
GMP homogenizing system
Manufacturers need production mixing equipment that is capable, flexible, and easy to maintain. Accur...
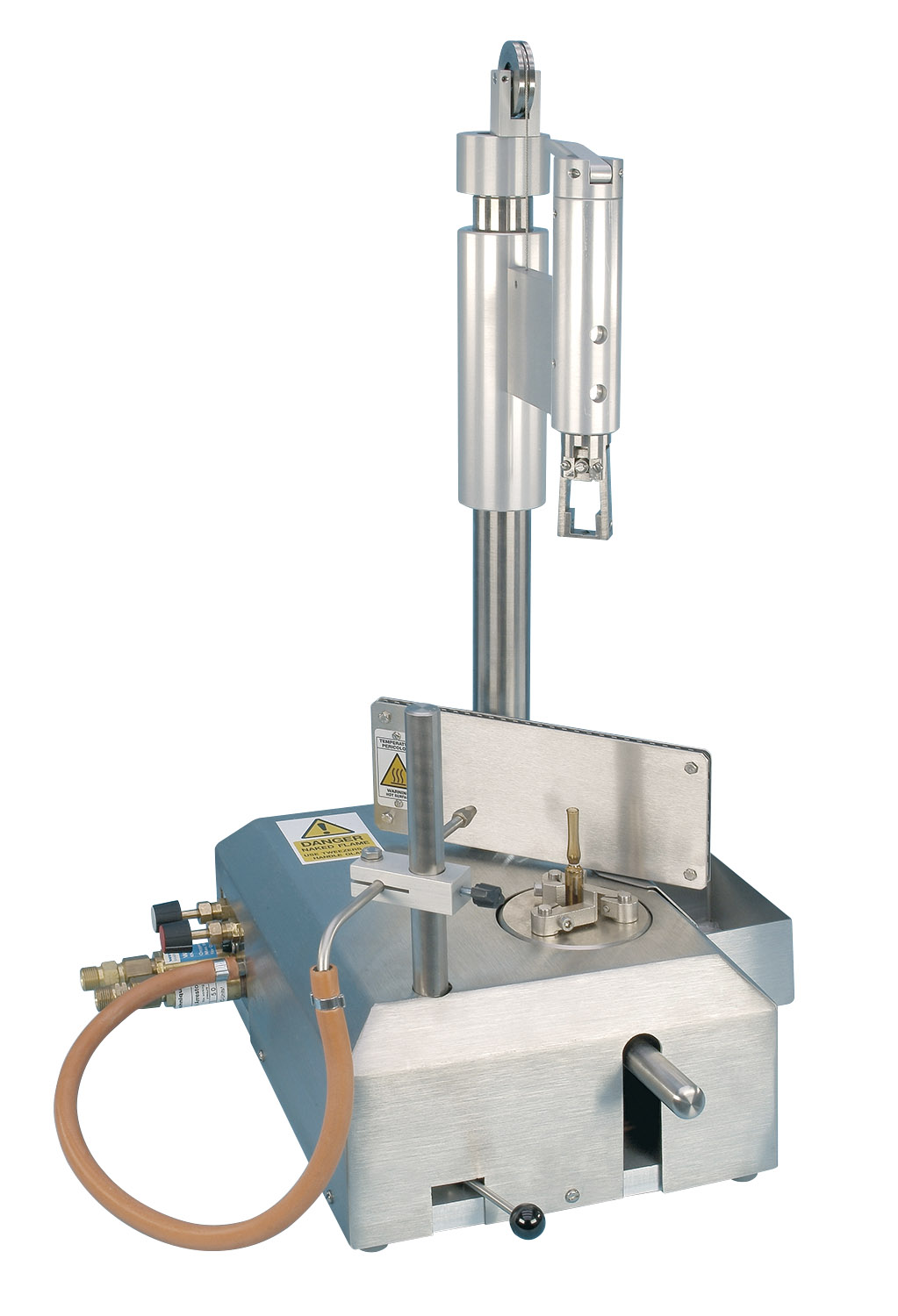
Benchtop ampoule opening and closing equipment
The procedure for opening or closing ampoules requires you to handle gas an...
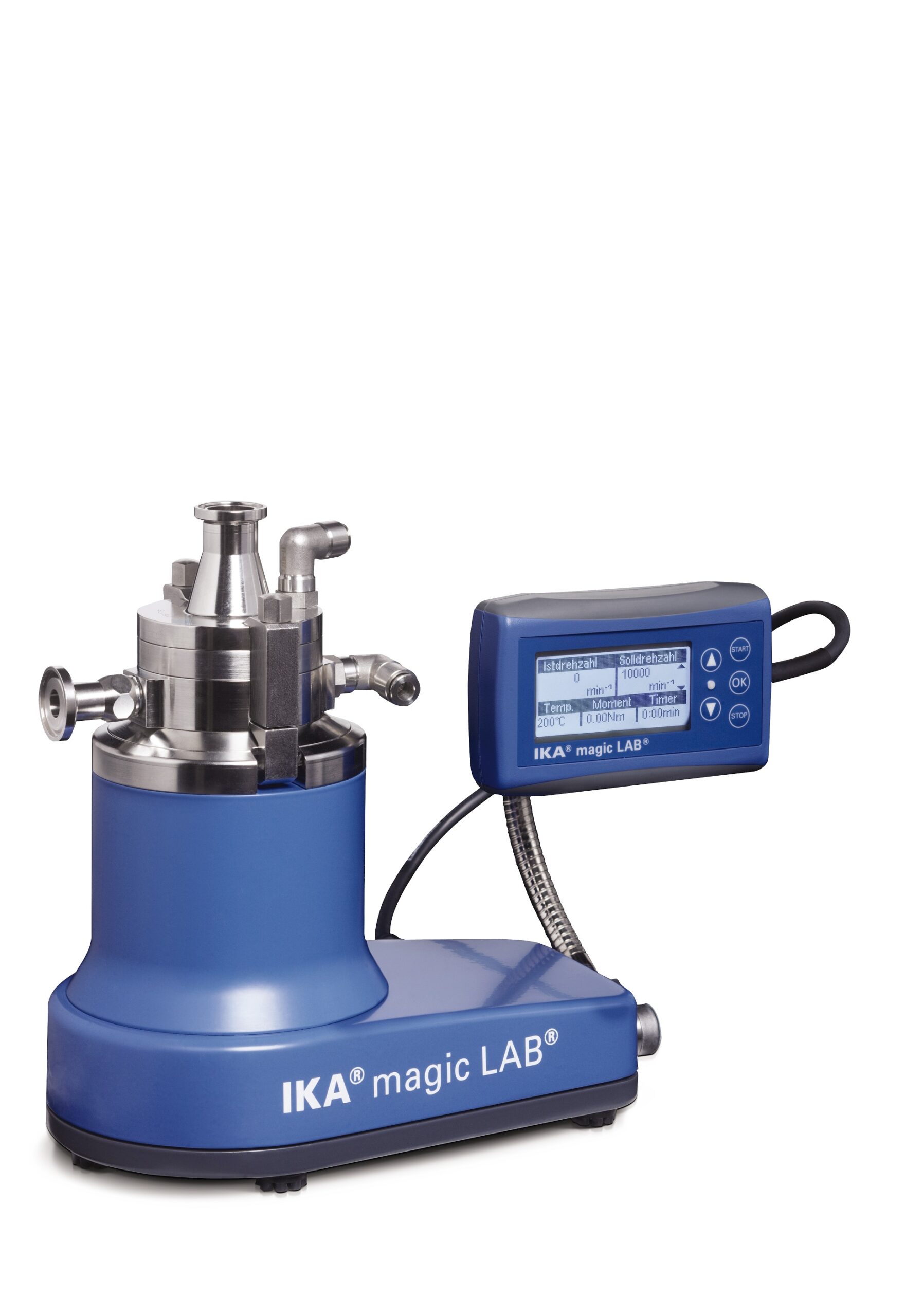
Small-scale laboratory dispersing machine
Developing and validating new processes requires reliable and highly versatile e...
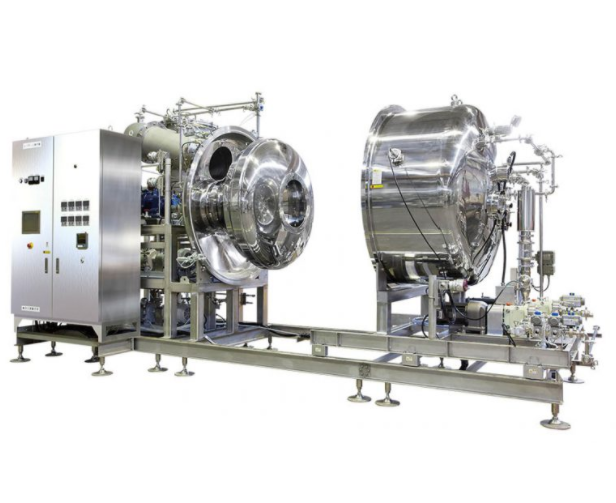
Evaporator for heat sensitive products
The removal of solvents when making products in industries like food, cosmetics, pha...
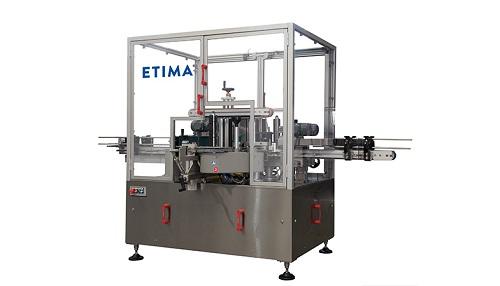
Self-adhesive linear labeling machine for bottles
It is vital to have precise and long-lasting labels on bottles to avoid...
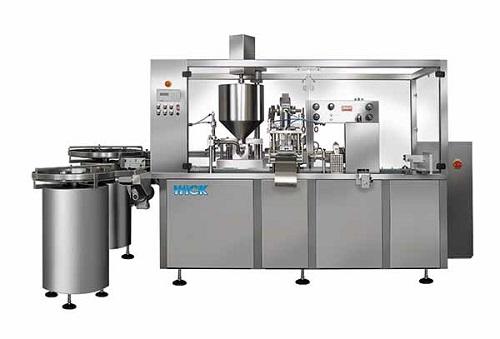
Cosmetic cream filler
From thin liquid baby oils and perfumes to thicker lotions and creams for hair and skincare, cosmetic p...
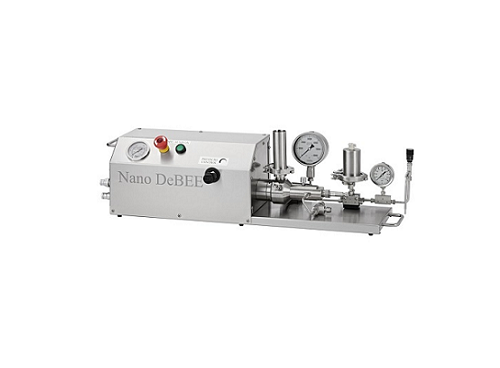
High pressure electric laboratory homogenizer
It’s vital that small units for experimentation can scale up with 100% accur...
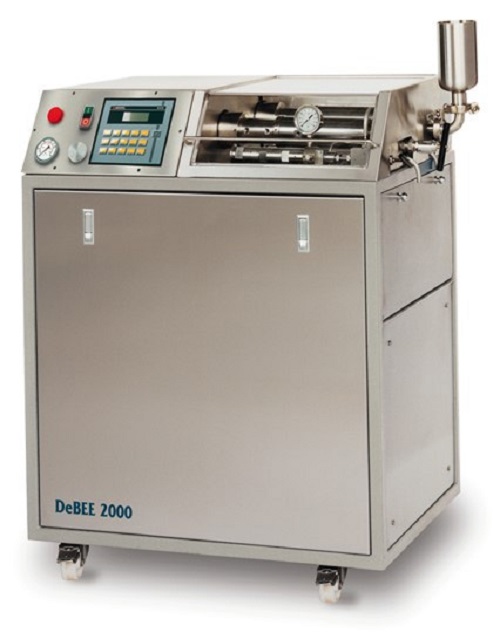
High pressure pilot homogenizer
Biotech and pharmaceutical development programs often require a mixing method that achieves ...
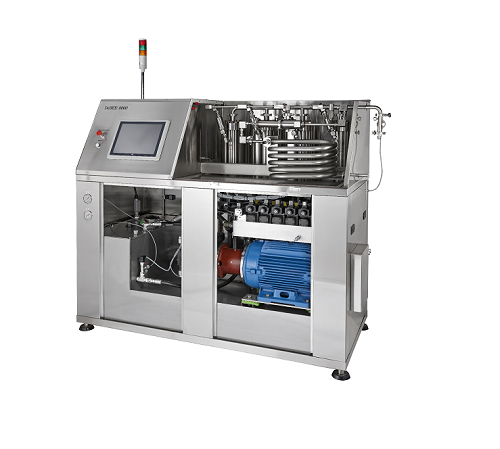
High pressure industrial homogenizer
For any industrial pharmaceutical process that relies on high pressure homogenization ...
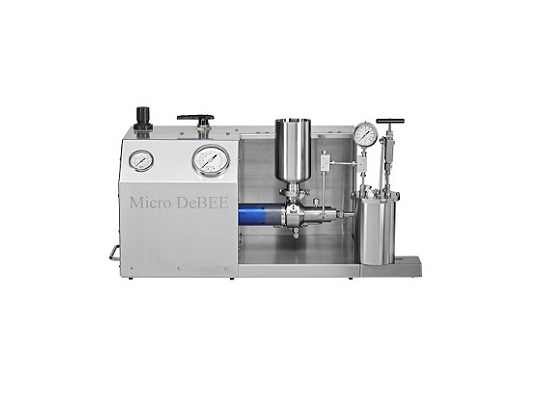
High pressure air powered laboratory homogenizer
Offering lab-scale to small pharmaceutical production scale output for in...
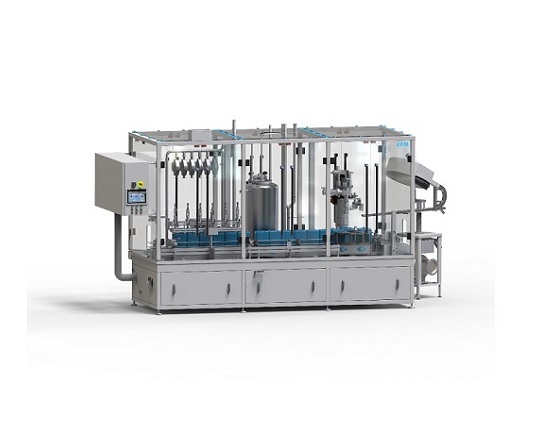
In-line monoblock linear filler & capper
In many food, chemicals and cosmetic industry processes it is vital to have a...
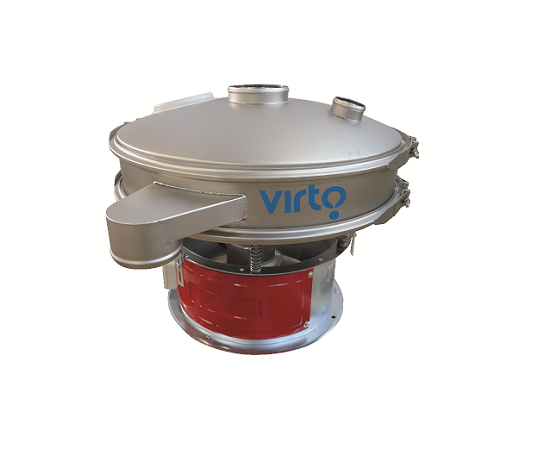
Vibrating sieve for liquid solid separation
Many industrial processes require the efficient separation of solids from a sl...
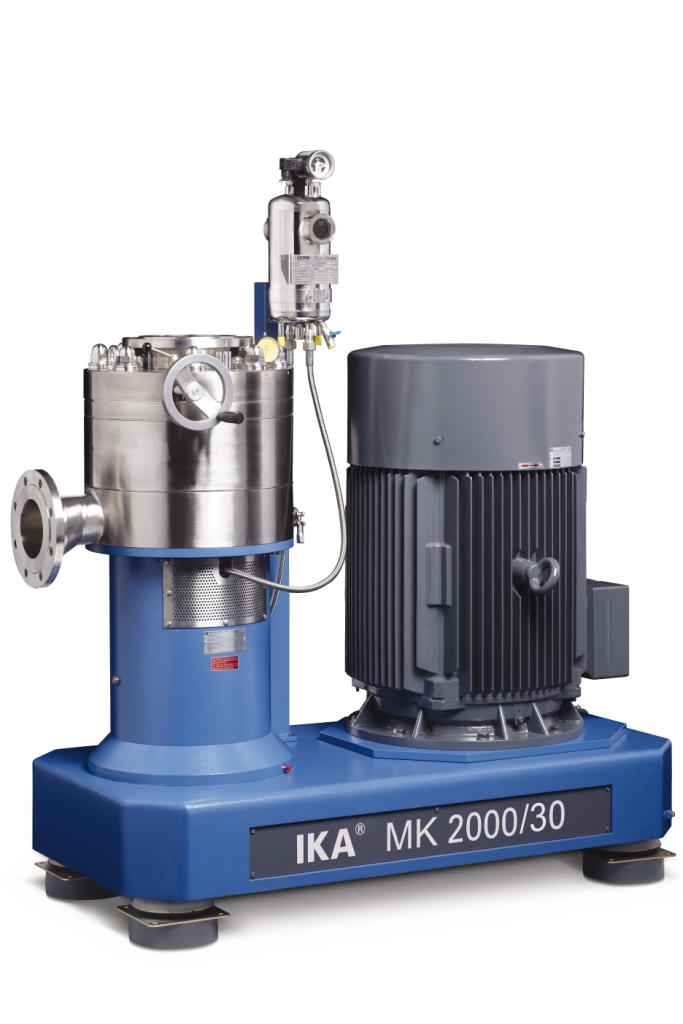
Colloid mill
For creating extremely fine emulsions and high quality dispersions a high pressure homogenizer is often chosen. ...
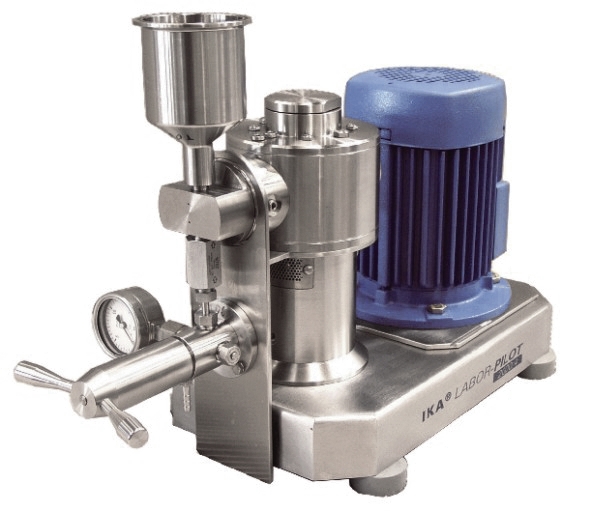
High-pressure homogenizer
When processes call for homogenized emulsions with extremely fine particle sizes the traditional t...
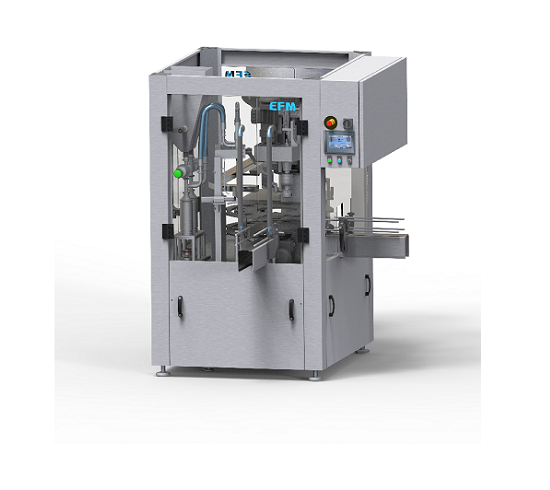
Compact monoblock filler
Filling and capping bottles and pots for food, chemical and cosmetics industries using separate mach...
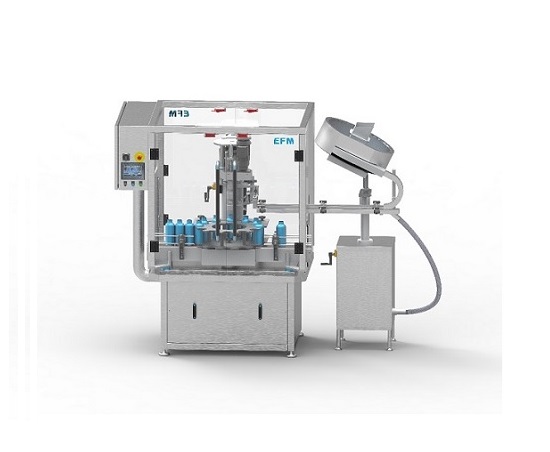
Single head capper
For the stand-alone capping of bottles of up to 30 litre capacity for smaller-scale production you need a ...
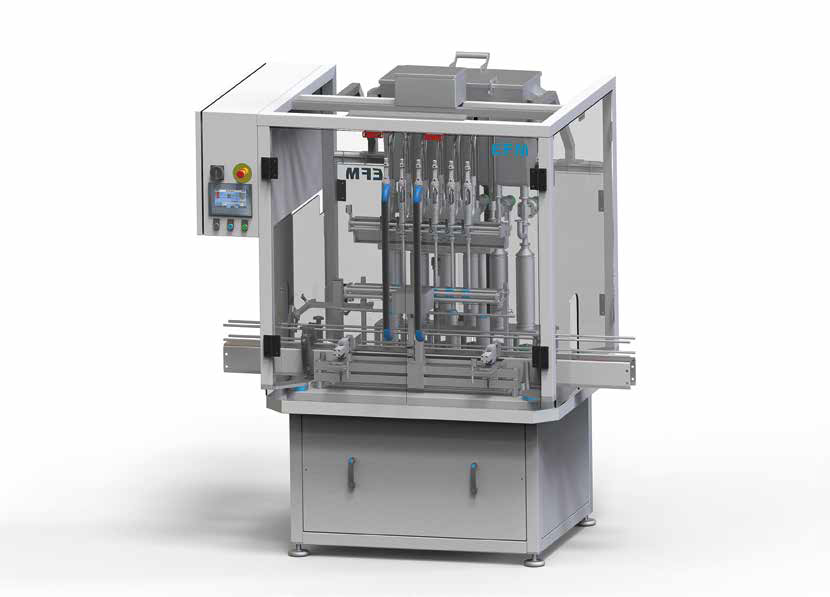
Servo controlled filler
For food and non-food liquid products that are high foam or have a high viscosity a specialist fillin...
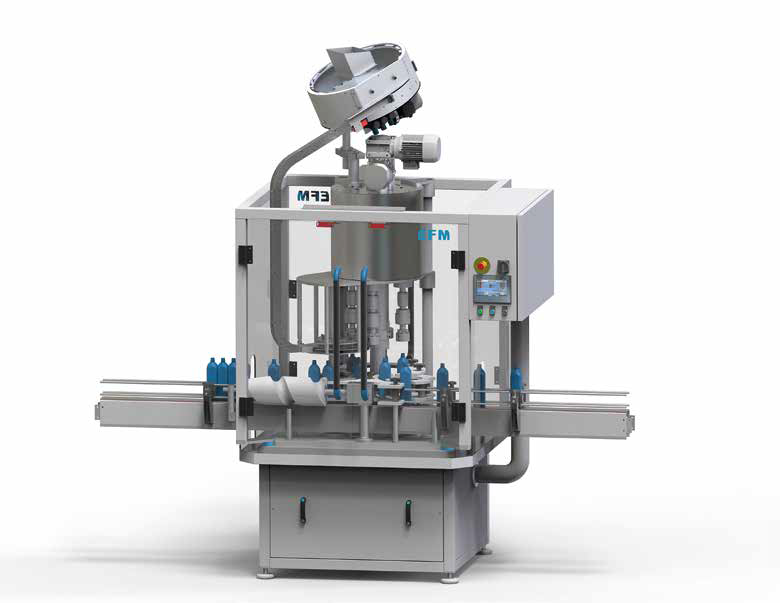
Multi-head capper
For the stand-alone capping of bottles of up to 2.5litre capacity you need a robust and flexible machine wi...
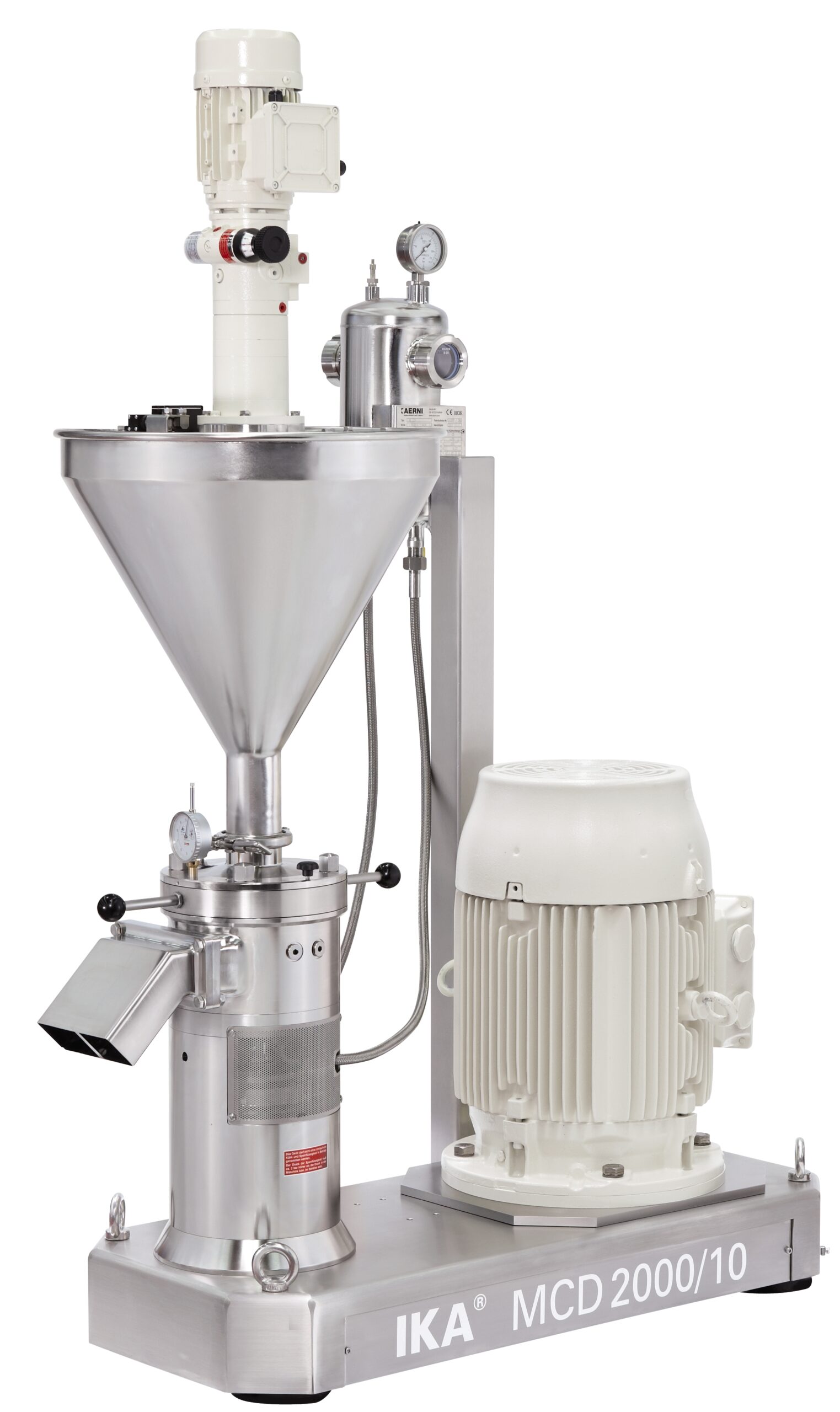
Corundum disk mill
Wet milling and grinding of viscous liquids or pastes containing solid particles such as peanut butter,mus...
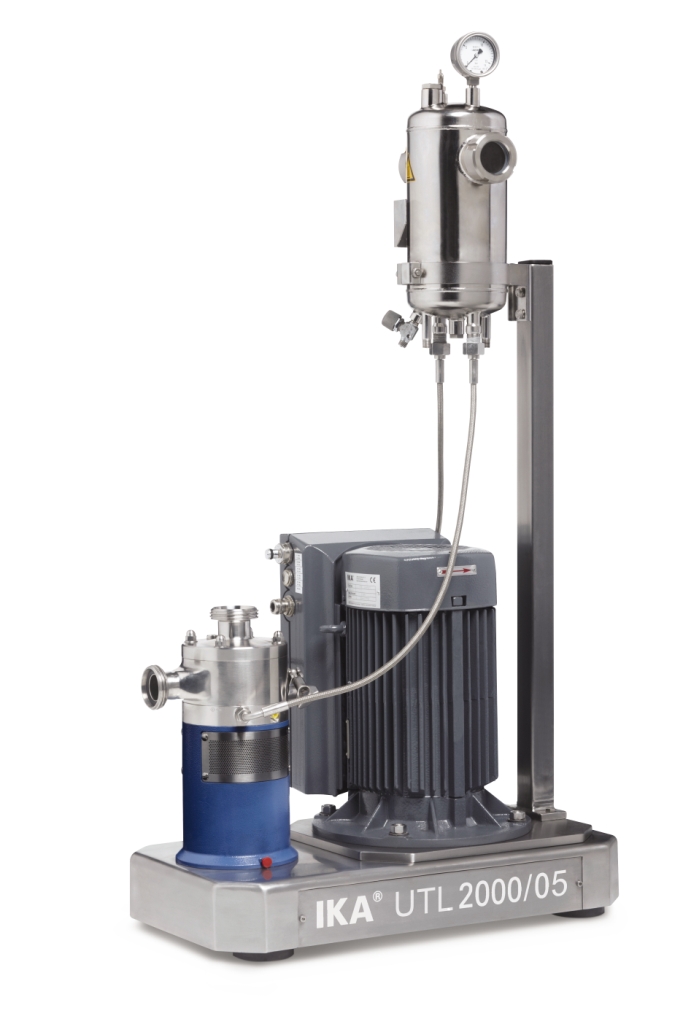
Dispersing machine for emulsions and suspensions
Equipment operating under the rotor/stator principal is often employed wh...
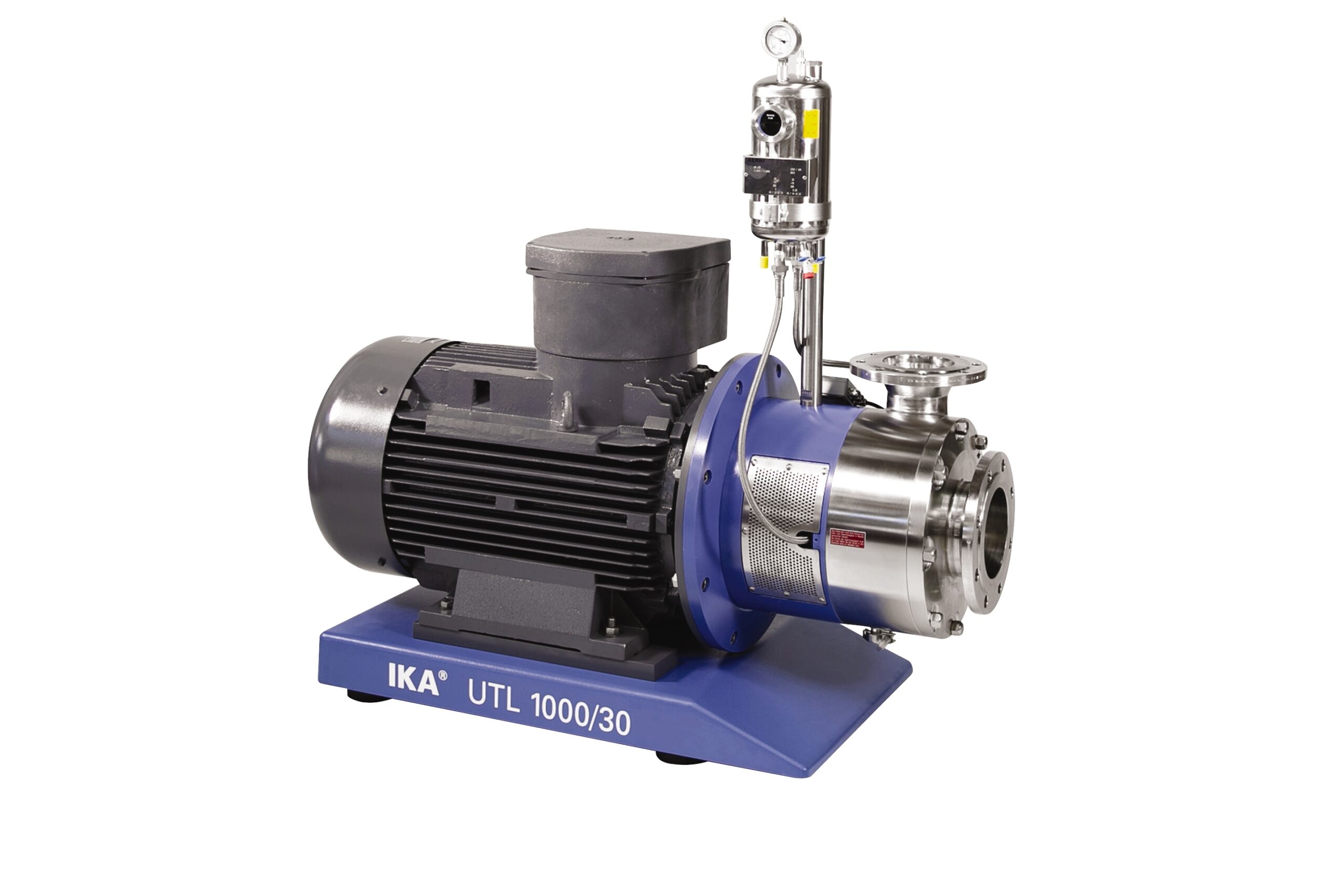
Economic dispersing machine for emulsions and suspensions
For products of medium viscosity and relatively consistent par...
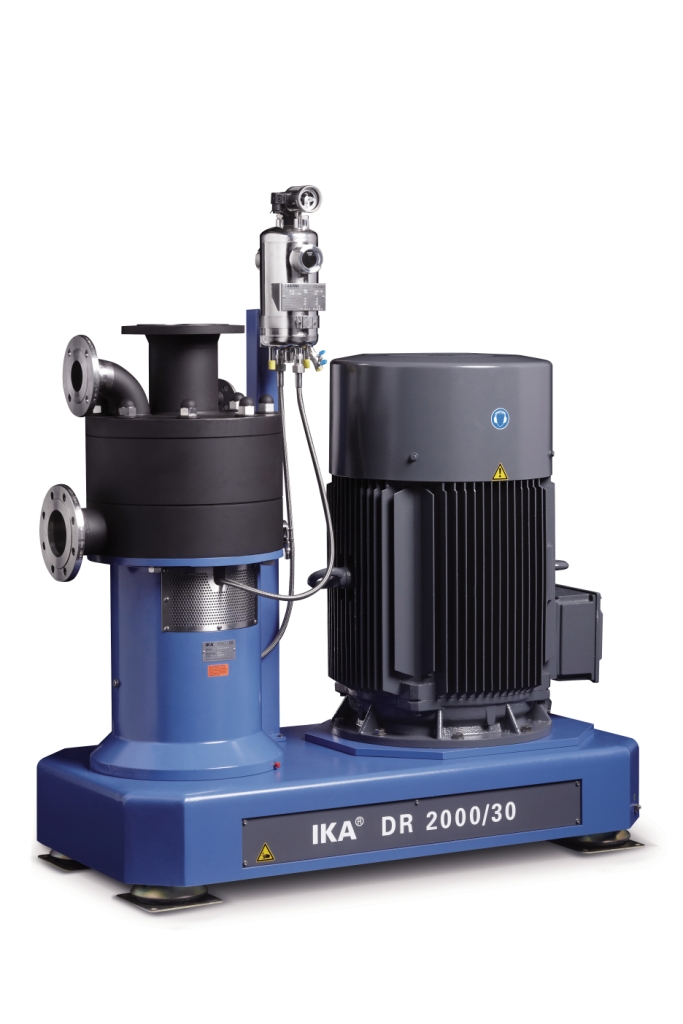
Dispersing machine for very fine emulsions and suspensions
For continuous high performance mixing of solid and liquid ra...
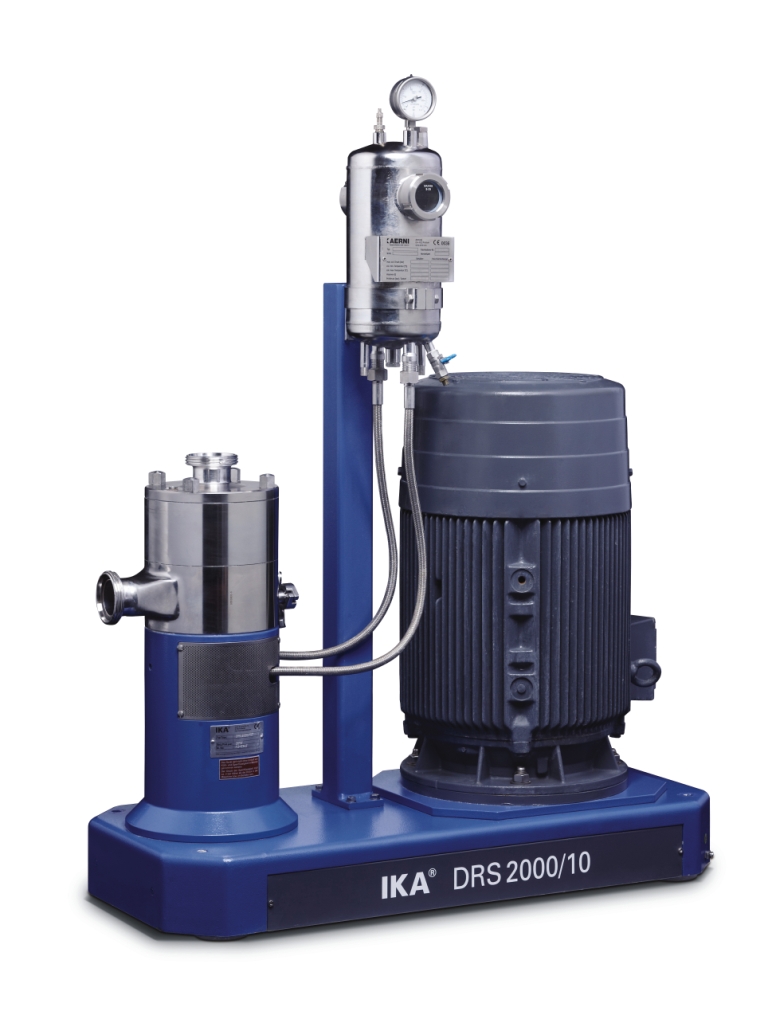
Ultra-fine dispersing machine for emulsions and suspensions
Producing the finest micro-emulsions and suspensions require...
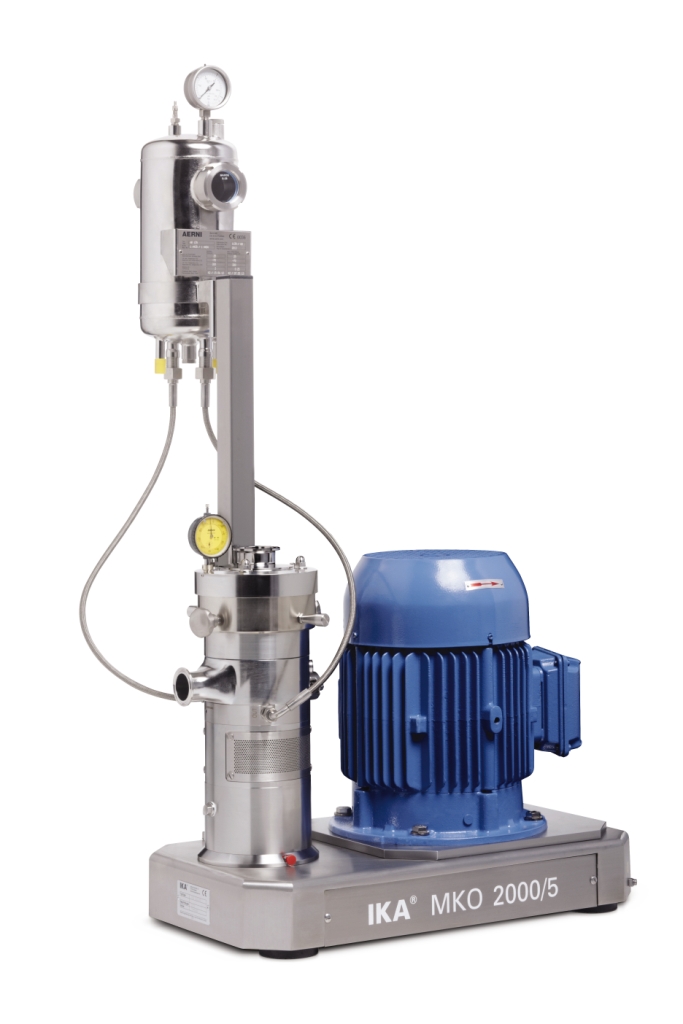
Cone mill machine
When your raw materials include agglomorated suspensions of grainy or crystalline solids and your process n...
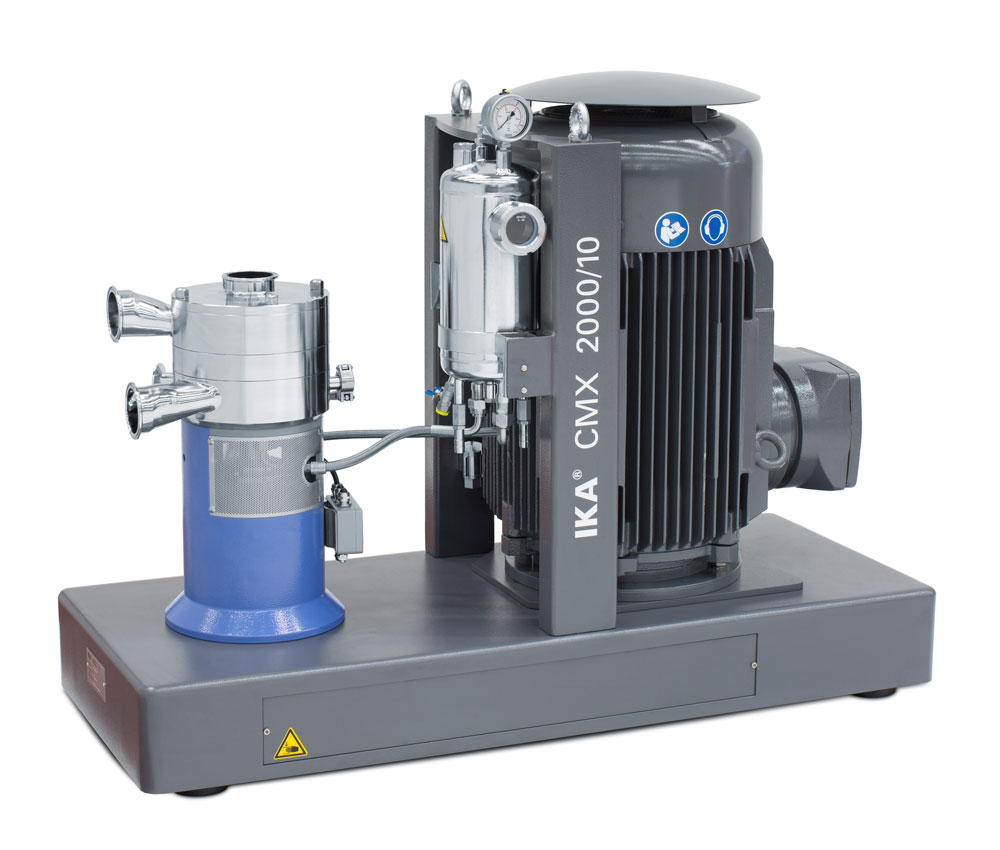
Inline batch mixer for solids and liquids
Several issues often arise when your process requires batch-wise mixing of powde...
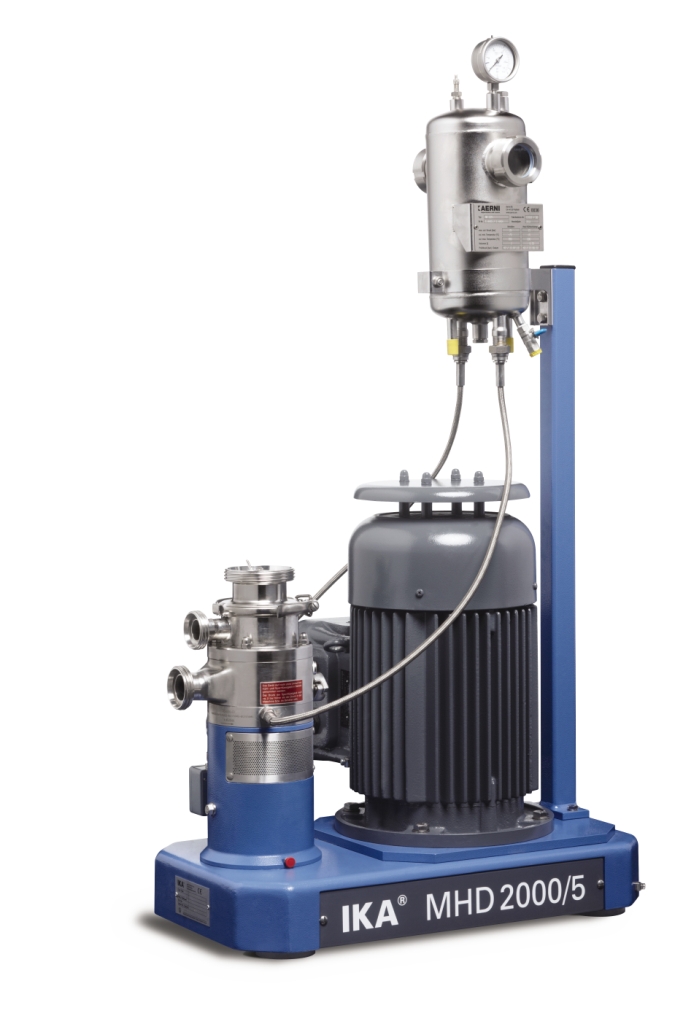
Continuous homogenizing system
Certain mixing tasks present unique challenges and manufacturers need equipment that is speci...
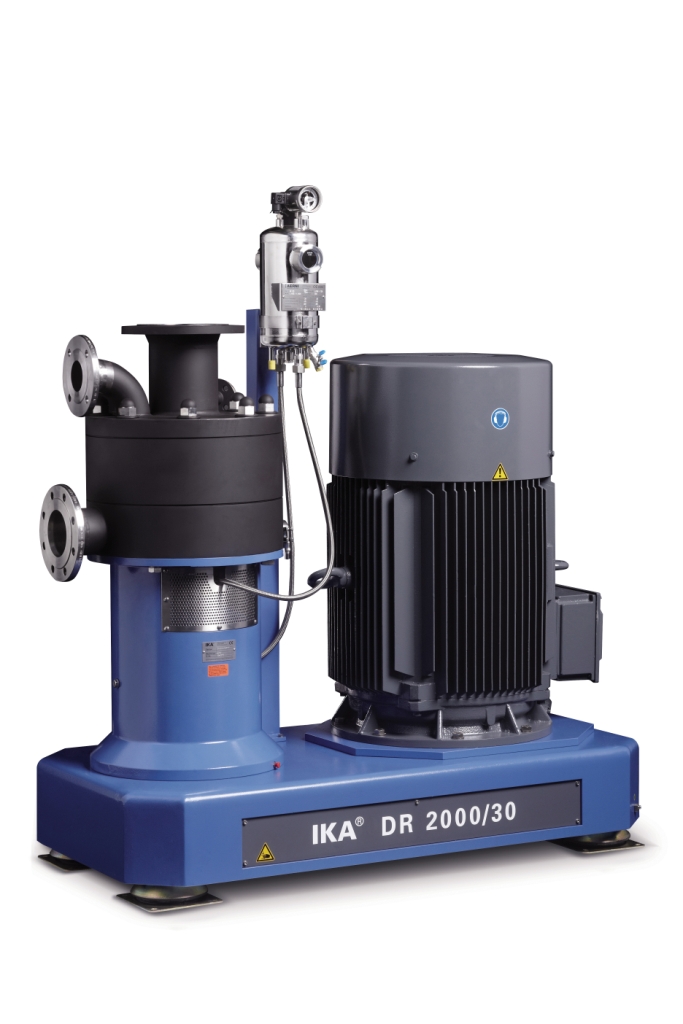
High accuracy homogenizing system
When extremely high accuracy is required in your recipe or formulation traditional mixing...
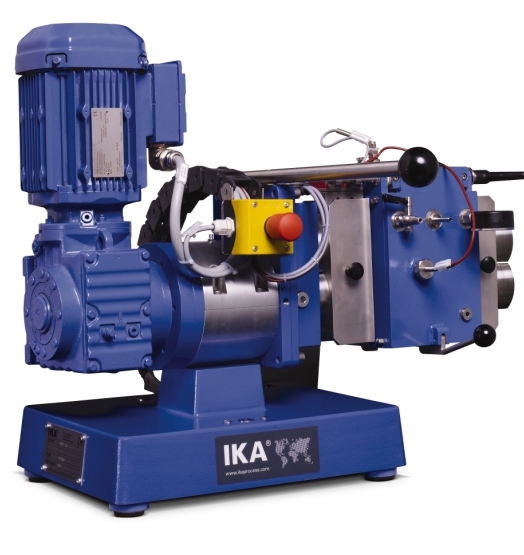
Horizontal kneader
For high viscosity products, better results and reduced process times can be achieved with kneading type r...
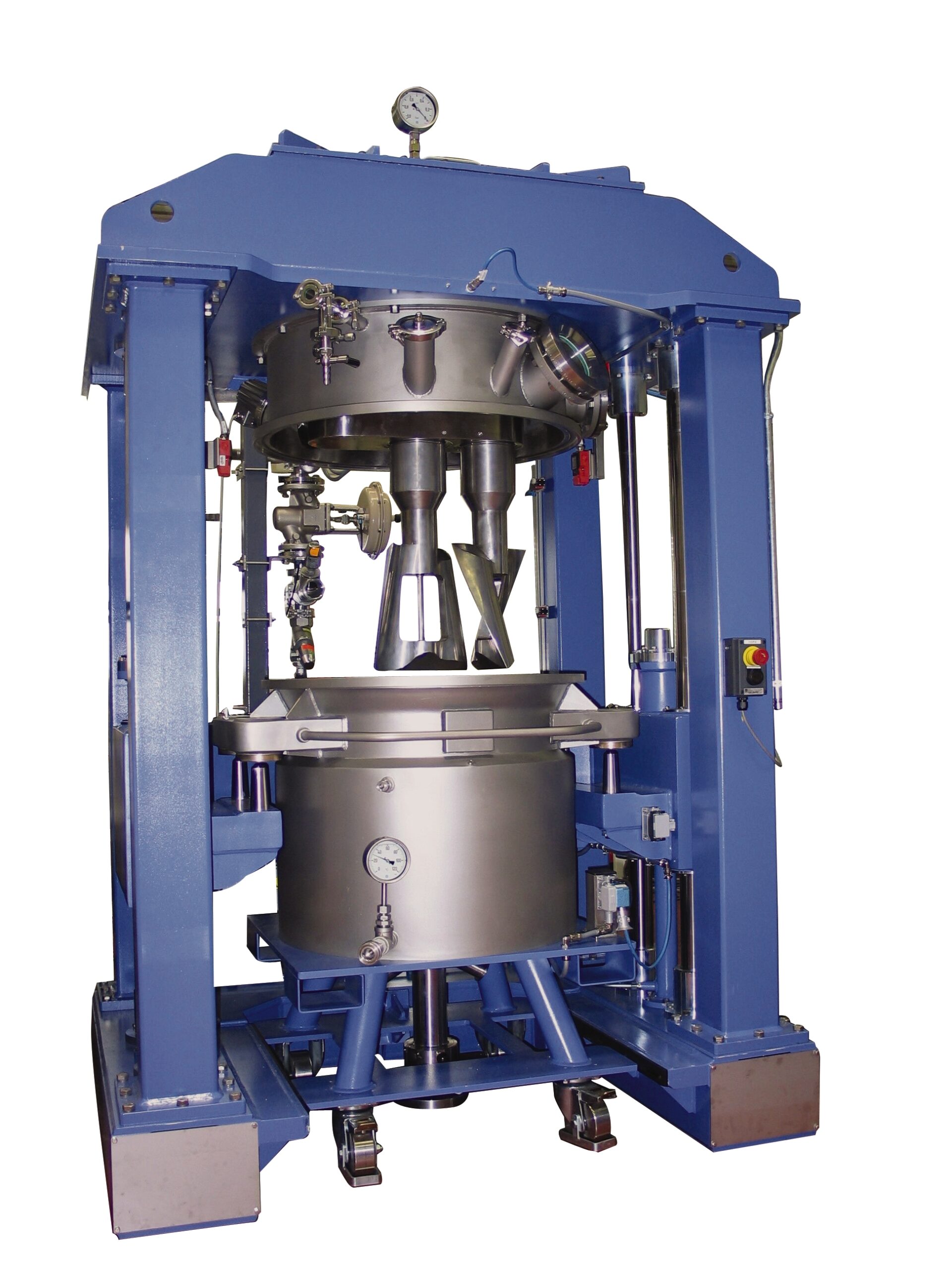
Vertical kneader
Production of highly viscous products with high solid content often benefits from kneading processes rather t...
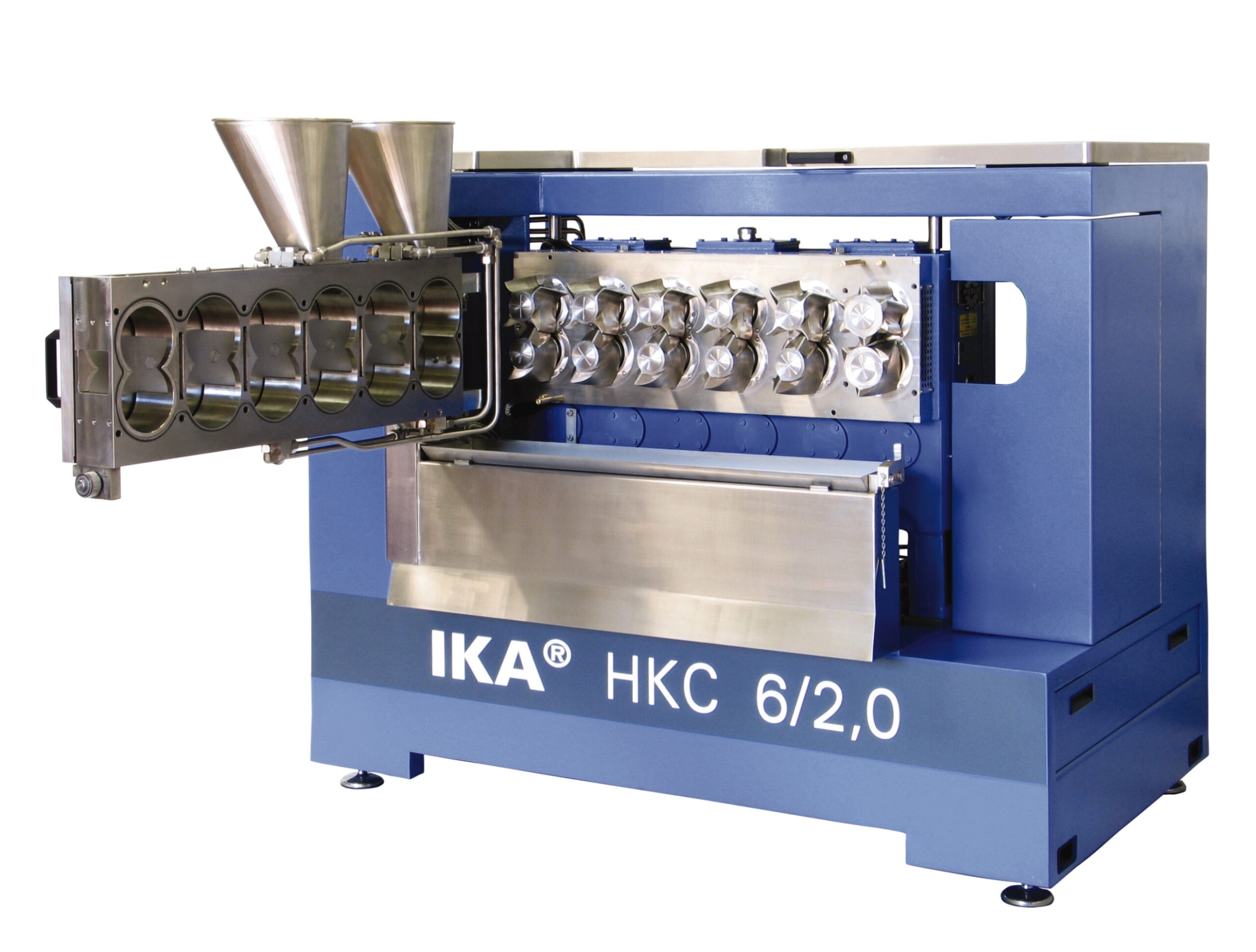
Continuous kneader
Effective mixing of highly viscous products with extremely high solids content can be difficult and the re...
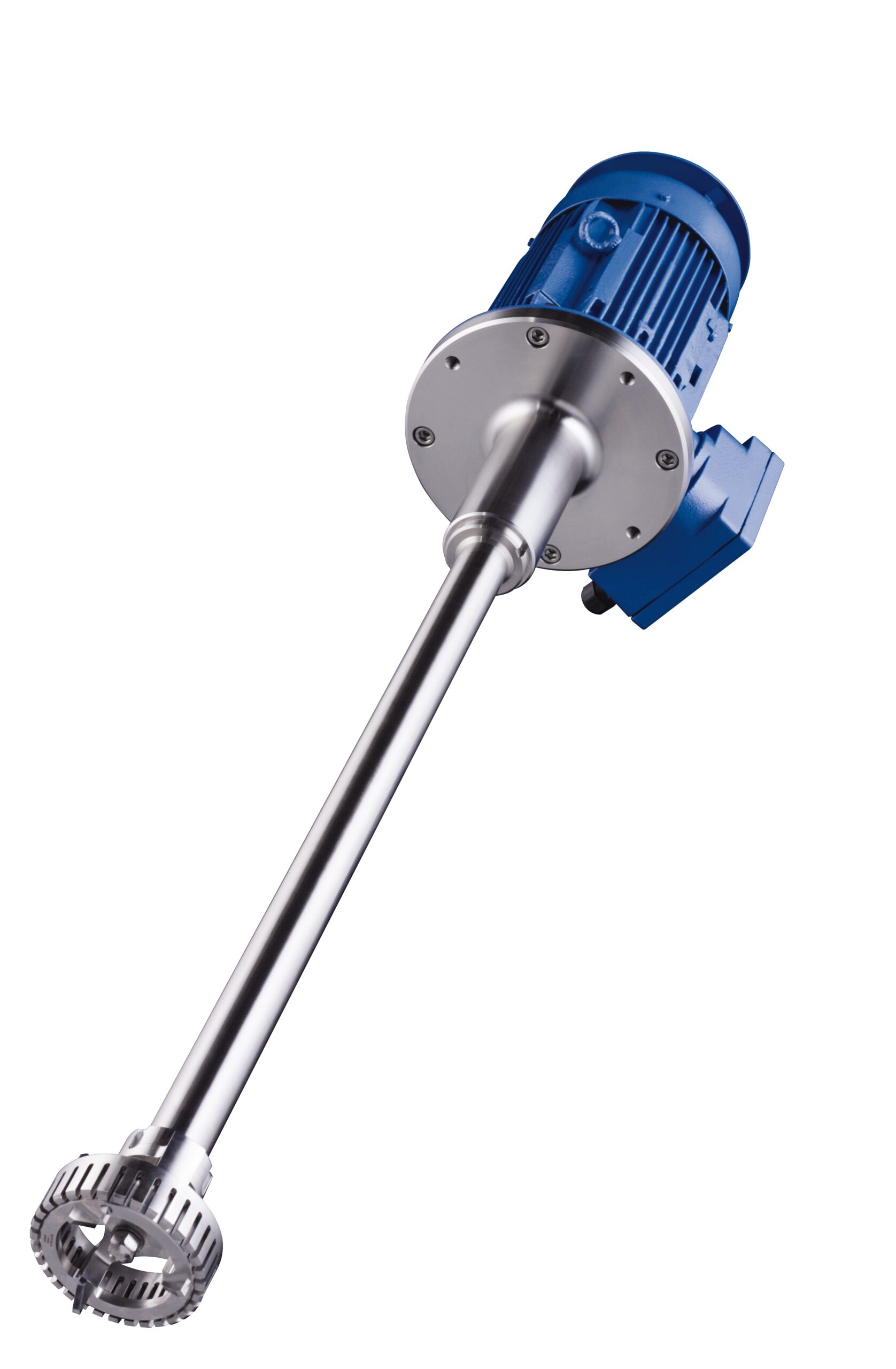
Batch dispersing machine
Equipment operating under the rotor/stator principal is often employed when more traditional methods...
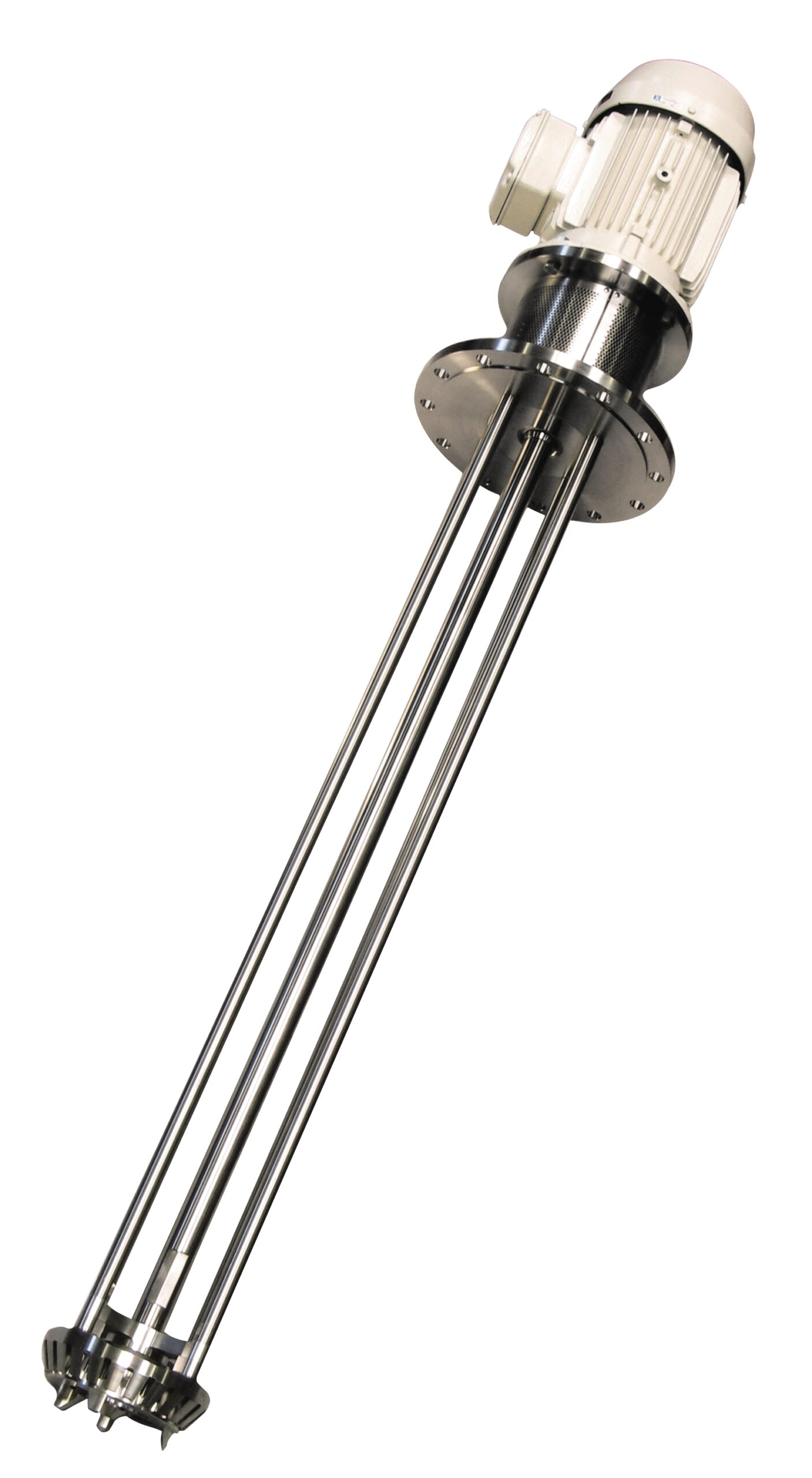
Batch dispersing machine for abrasive products
For mixing and dispersing tasks that cannot be completed by conventional st...
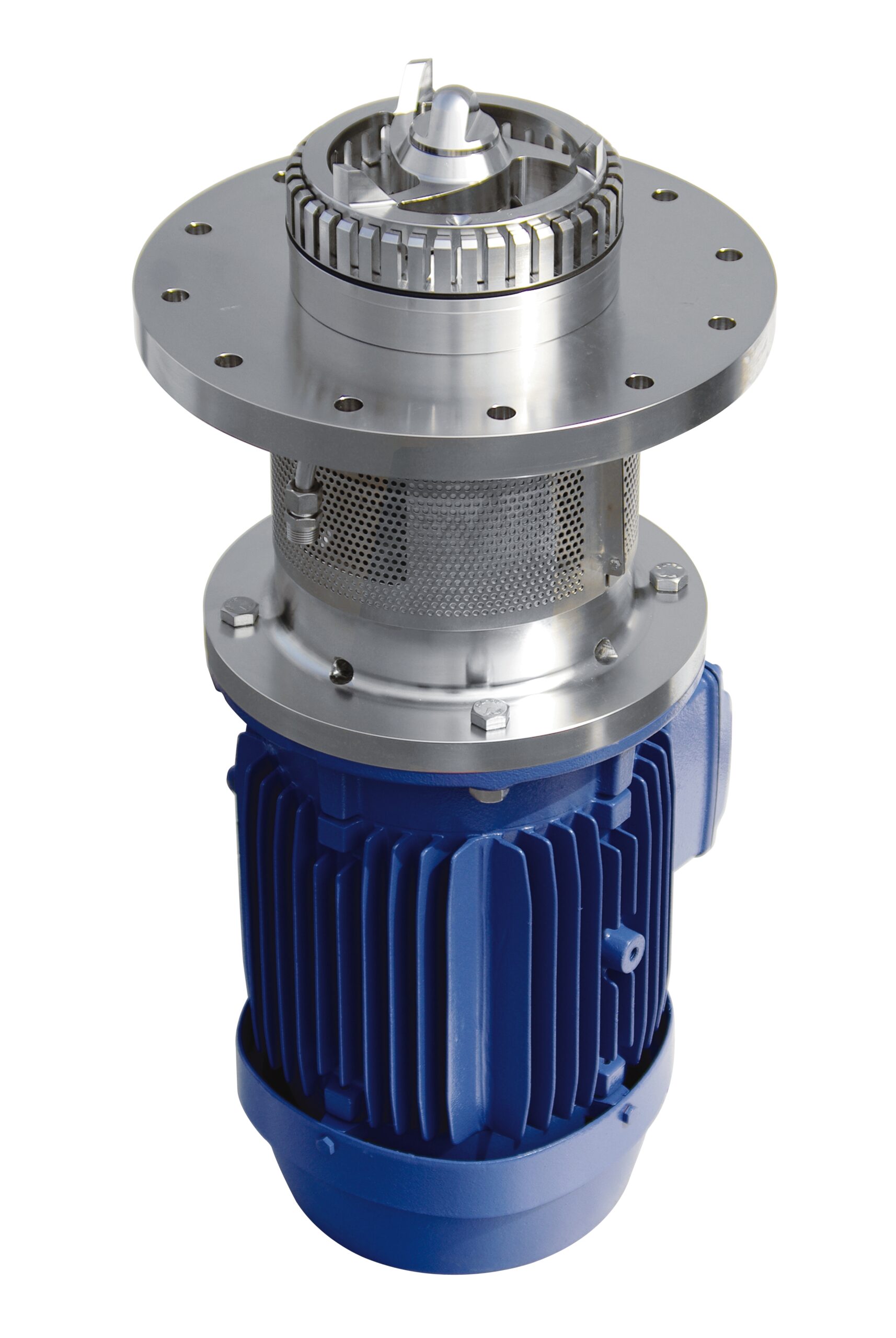
Batch dispersing machine for bottom entry into vessels
When your process requires high performance mixing or dispersion b...
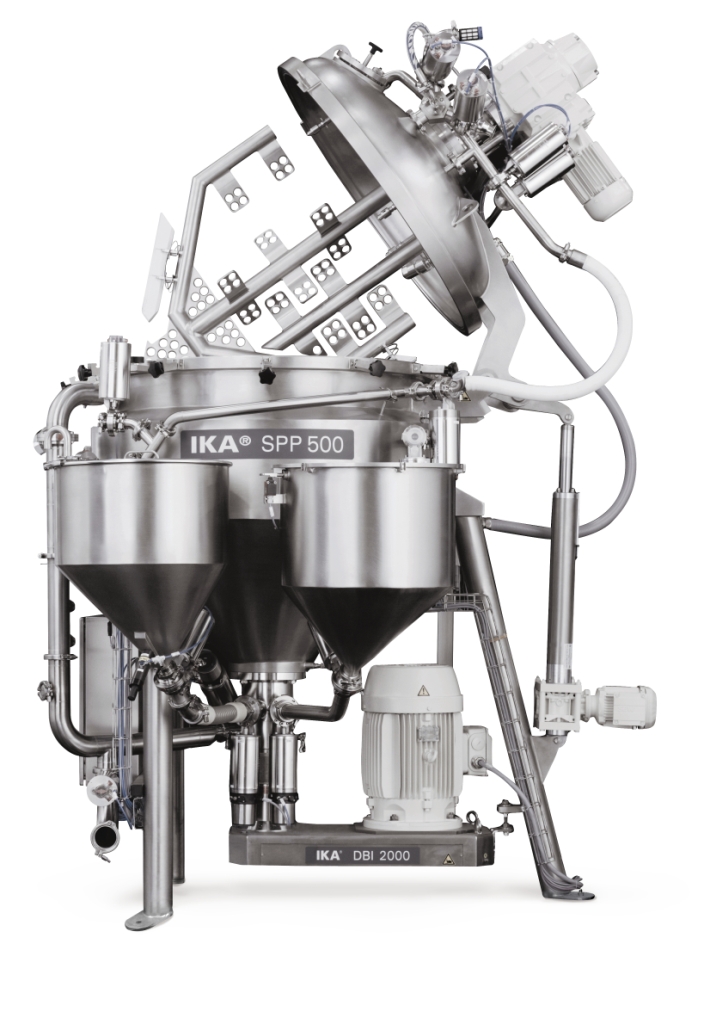
Cost-effective homogenizing and emulsifying system
Manufacturers of cosmetic products need mixing equipment that is capab...
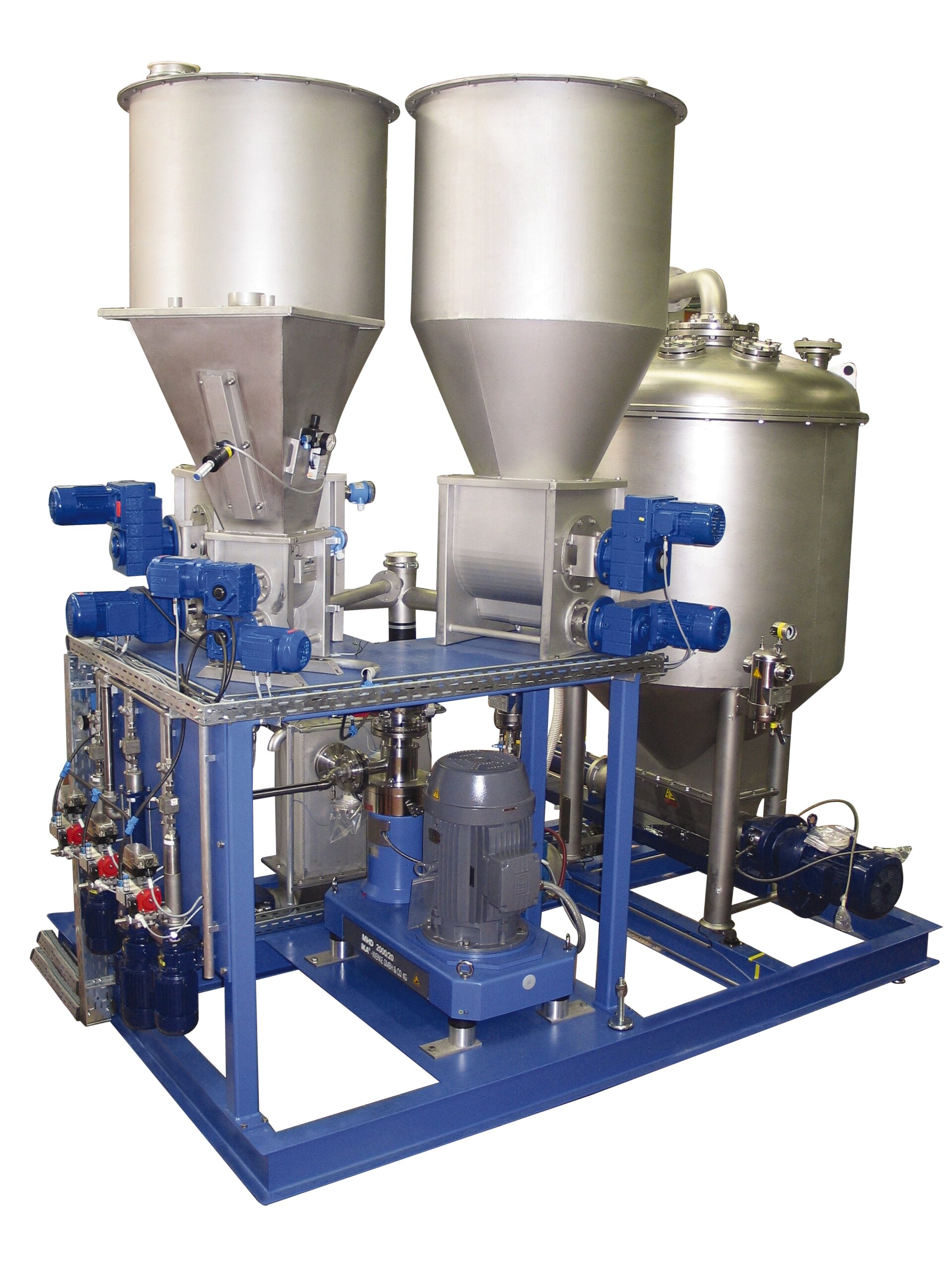
Dust-free continuous homogenizing system
Producers in a wide variety of industries benefit from equipment that can continuo...
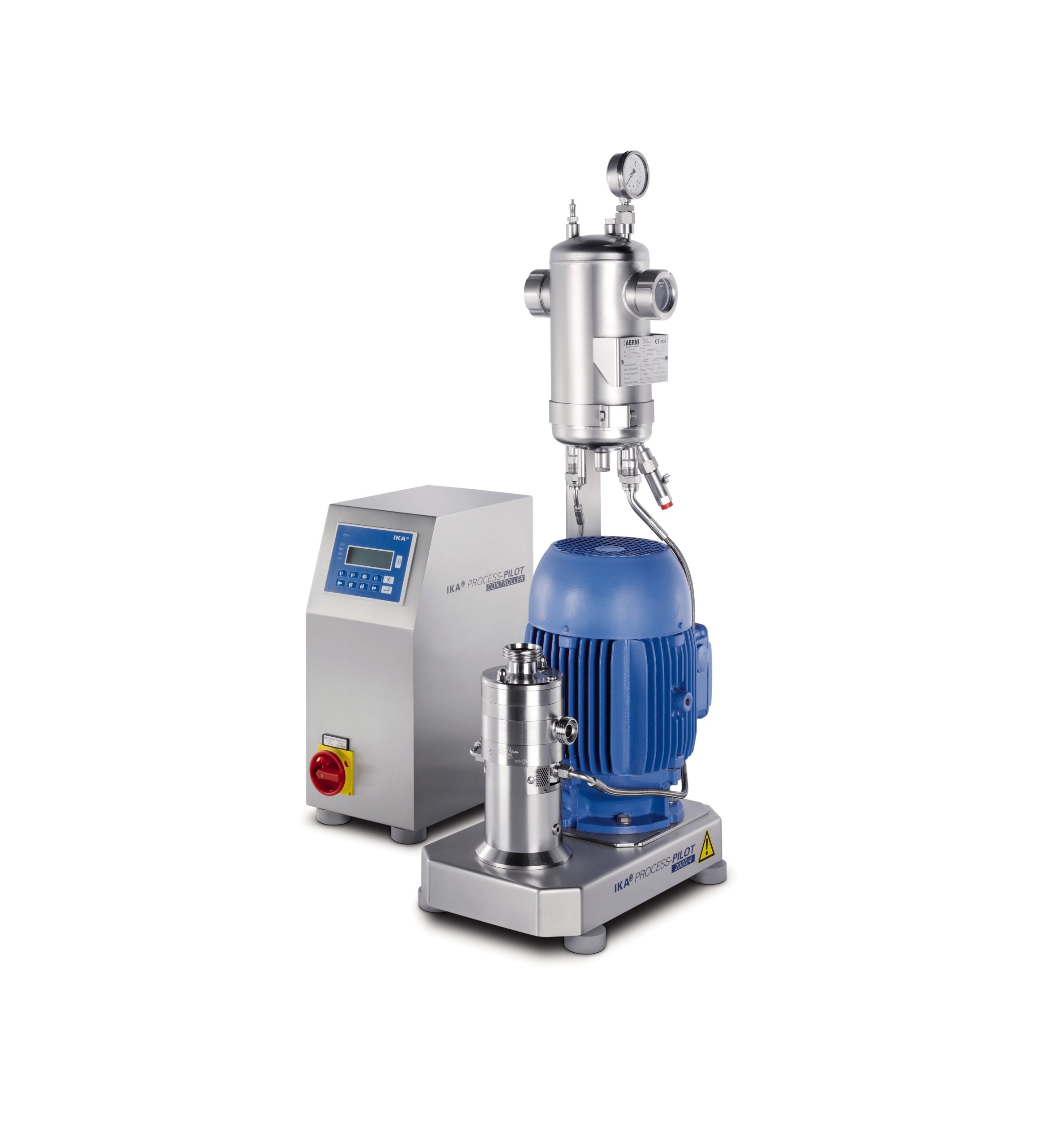
Dilution system for two or more liquids in one pass
Onsite dilution of liquid process ingredients has historically been a...
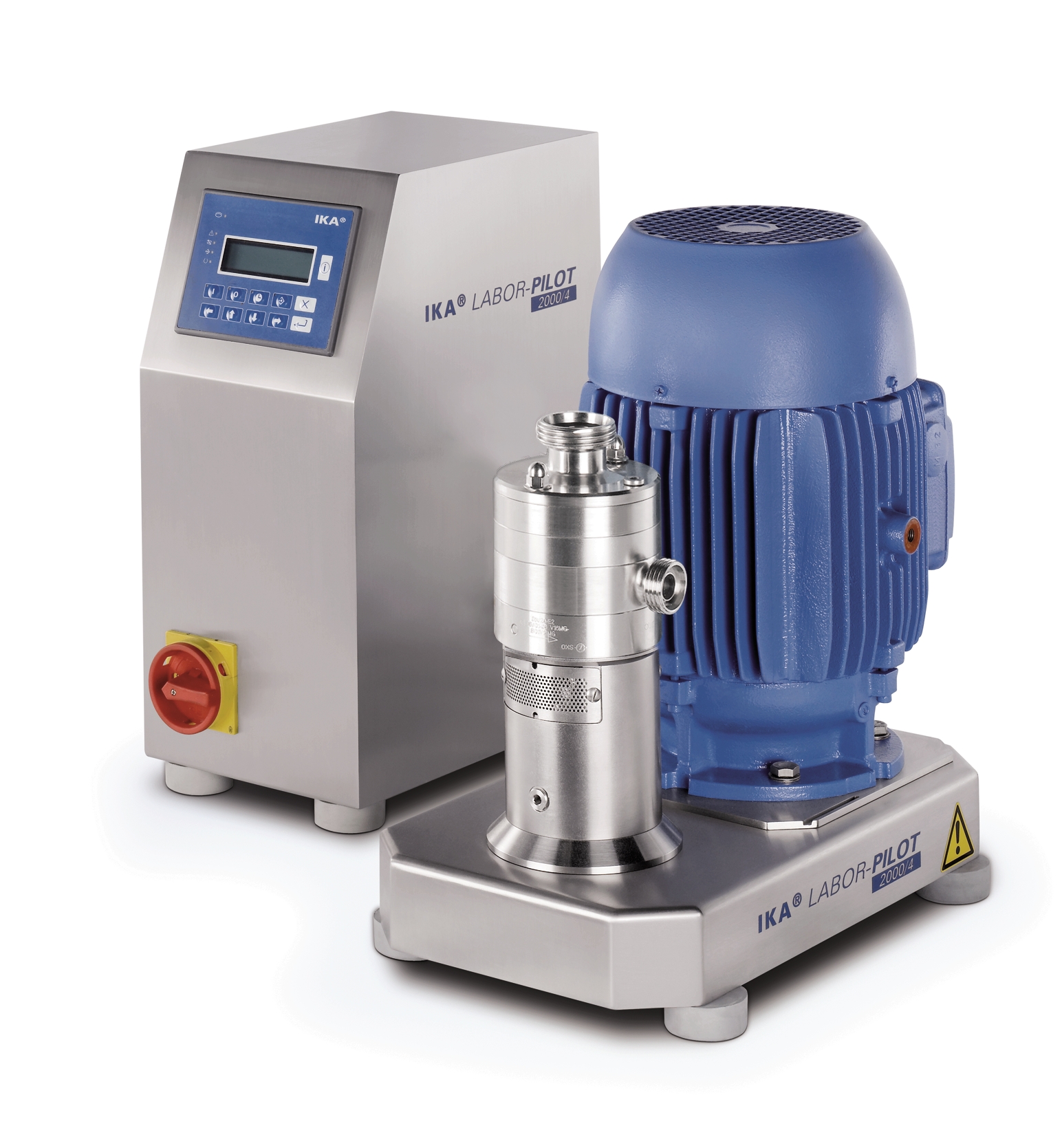
Pilot dispersing machine for testing and scale-up
Innovators in process development need laboratory equipment that helps ...
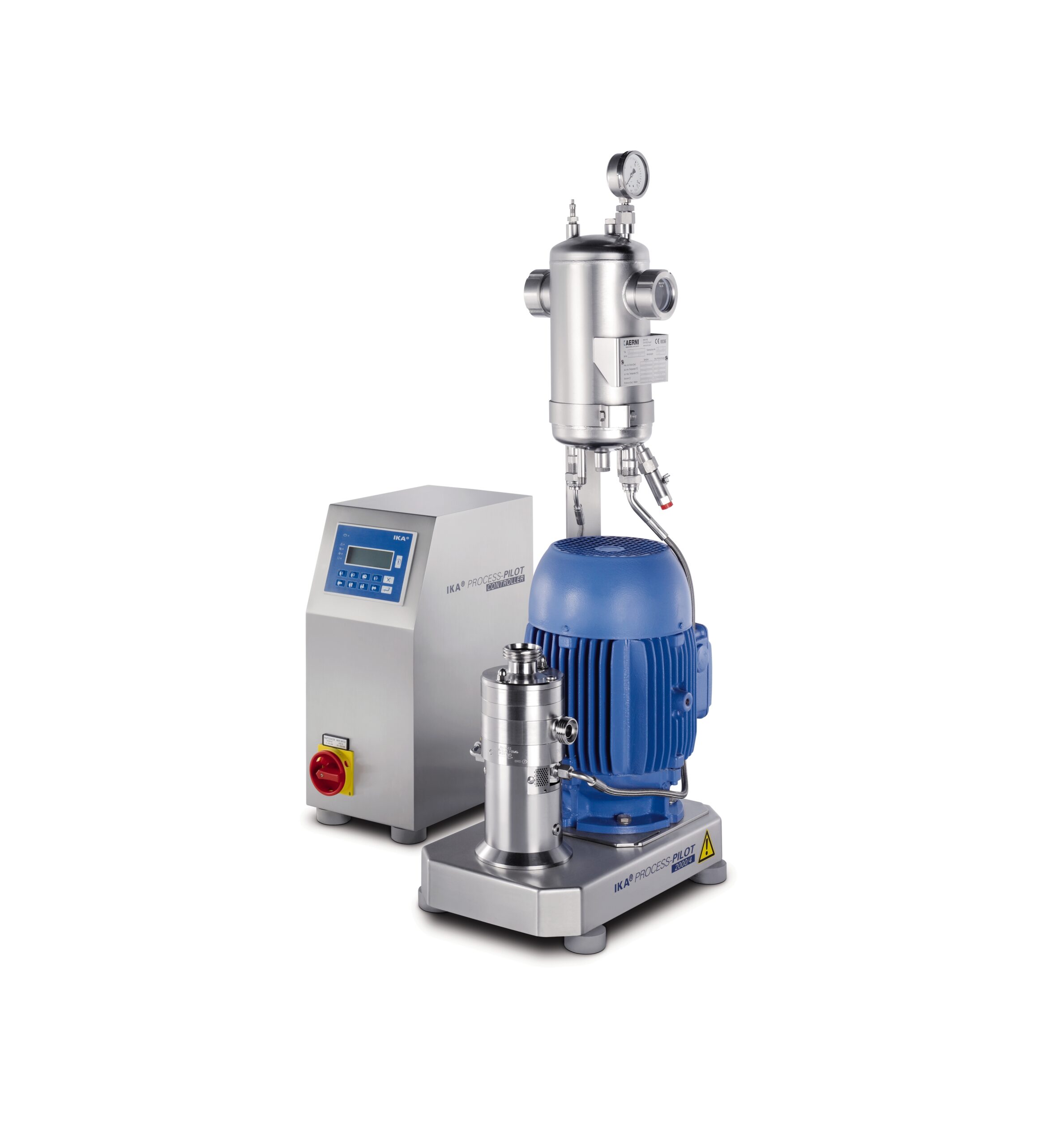
In-line laboratory dispersing machine
Innovators in a wide variety of industries need laboratory equipment on which process...
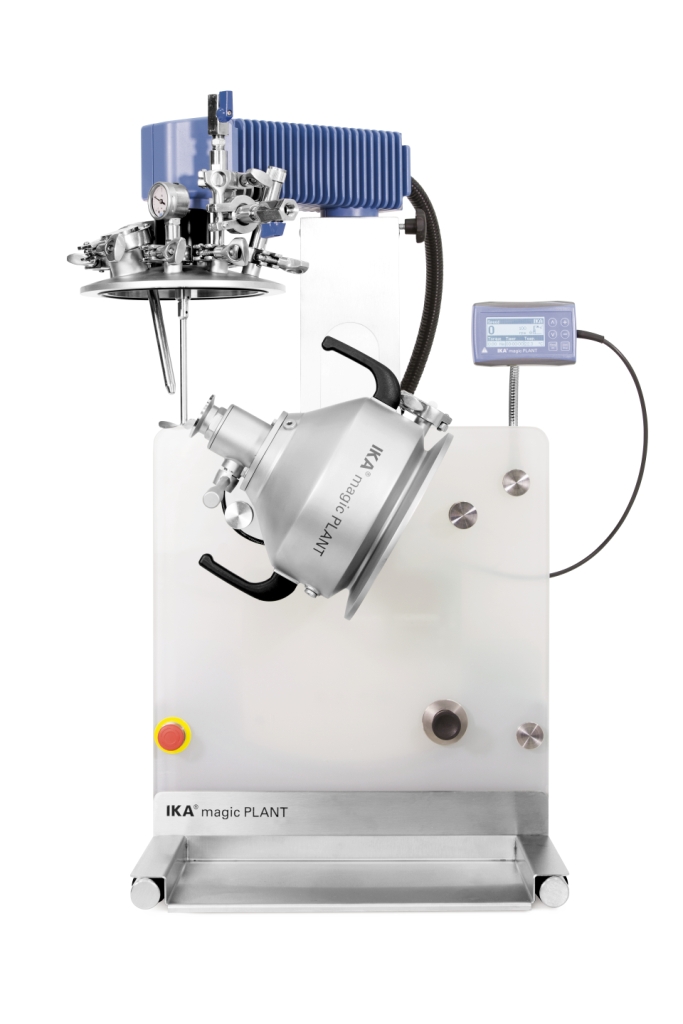
Laboratory dispersing machine for low-viscous masses
Laboratory mixers have not always been easy to work with. Getting a...
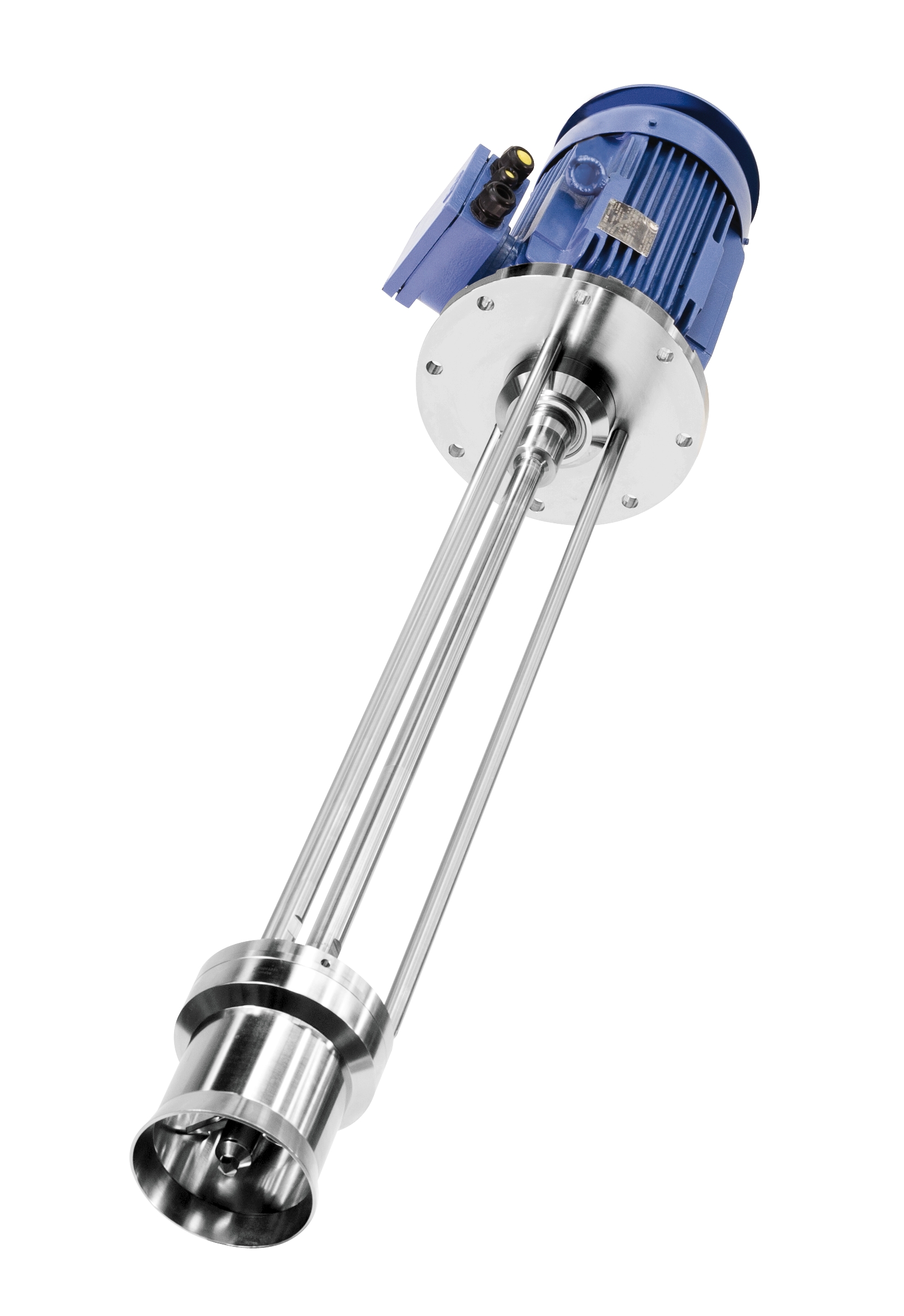
Jet flow agitator for high-viscosity media
Processes including homogenization, dispersing, suspension, emulsification and ...
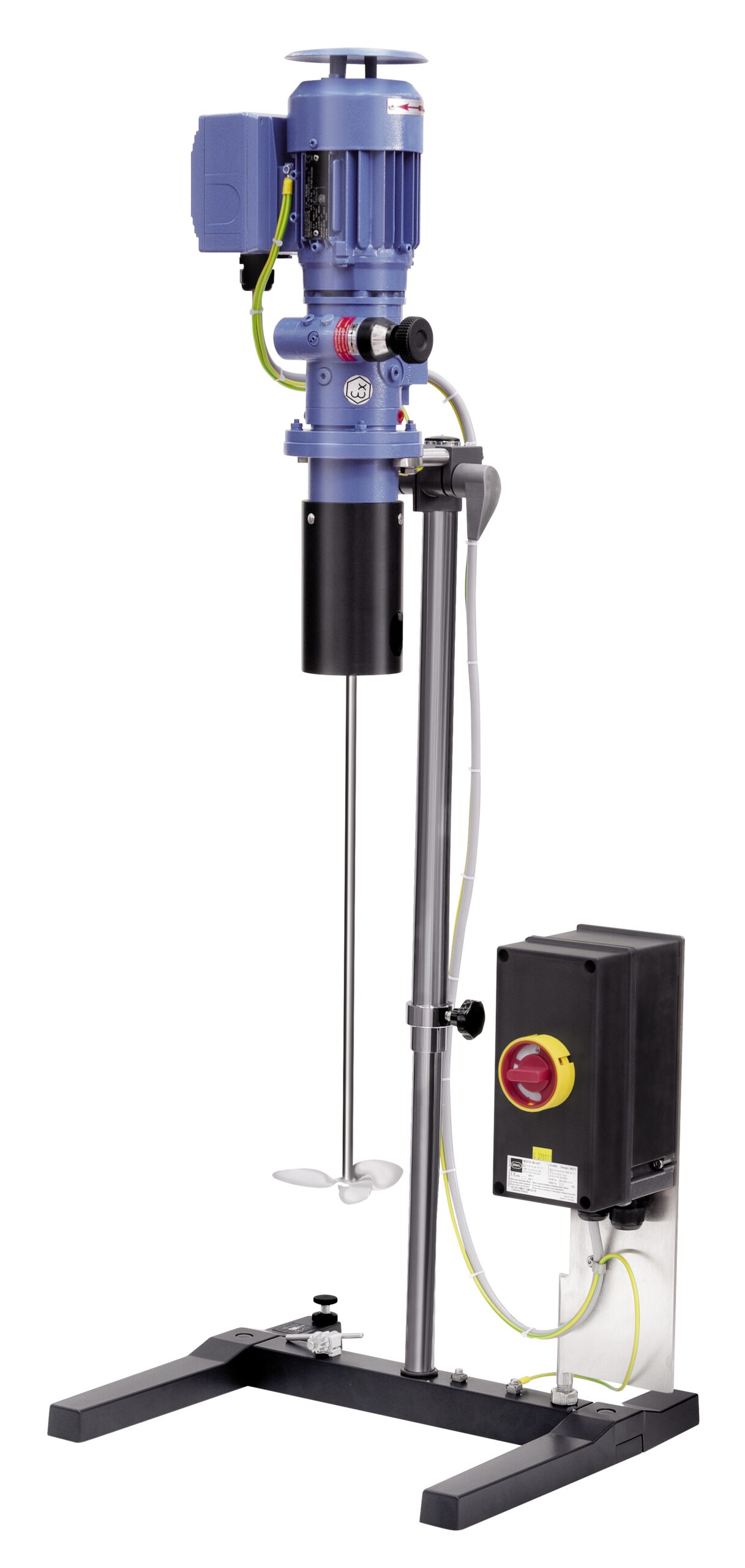
Agitator for medium viscosity media
Mixing fluids of medium viscosity for many production processes requires an agitator wi...
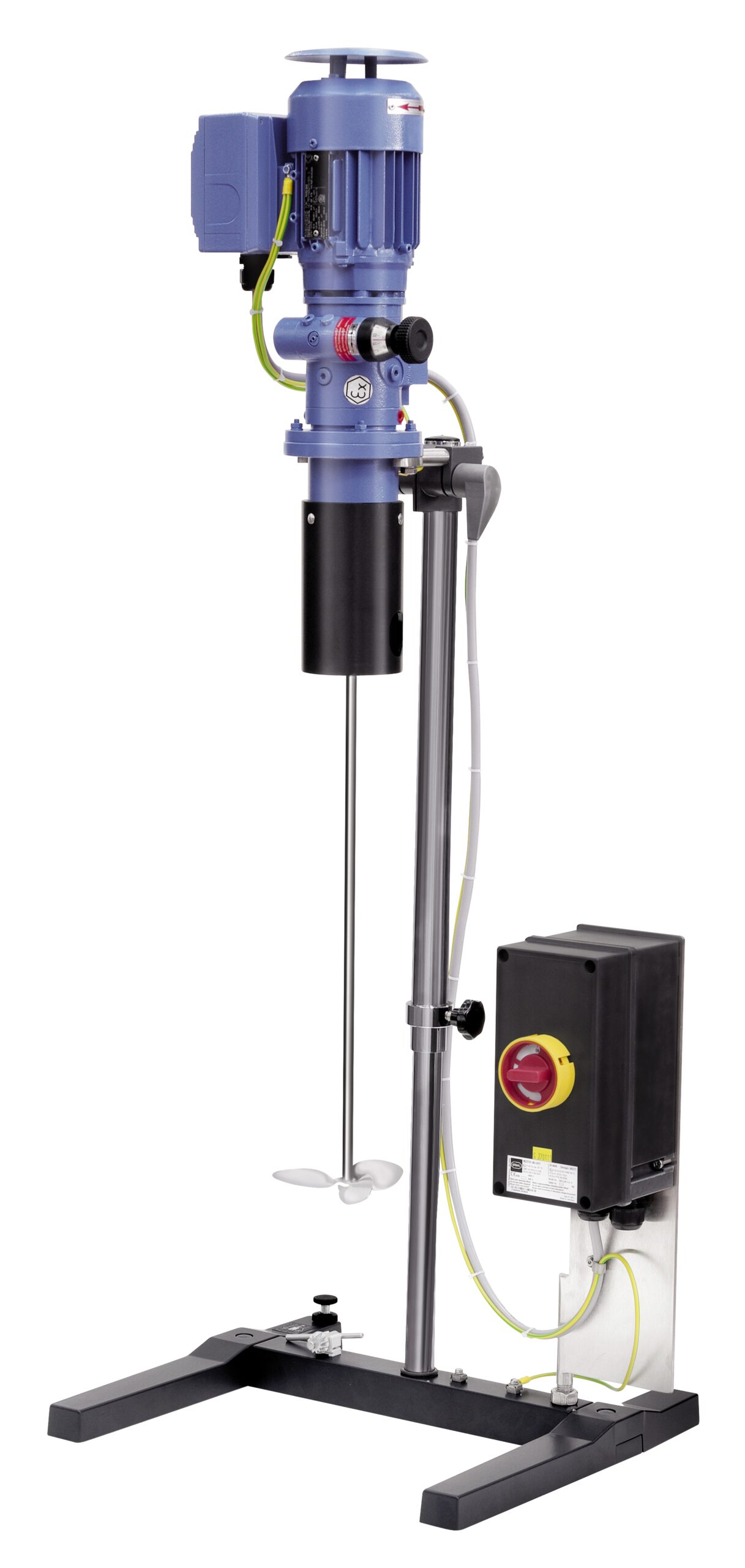
Agitator for low viscosity media
Reliably agitating fluids in open or pressure-less vessels in a laboratory or small scale p...
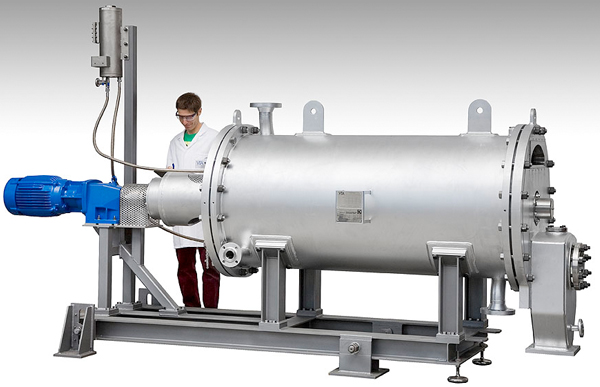
Horizontal thin film evaporators
Horizontal thin film evaporators can increase the residence time of the product and achieve...
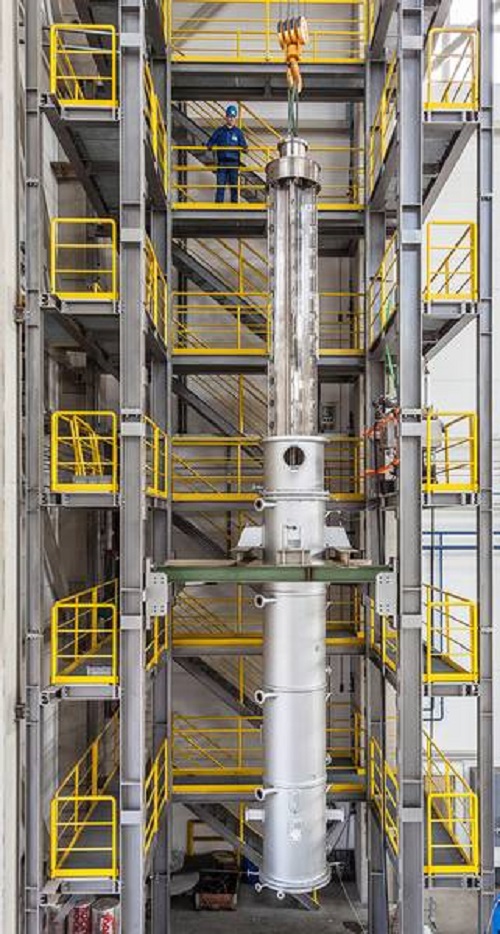
Thin film dryers
Dry dissolved or slurried crystallizing or amorphous products to a pourable powder.