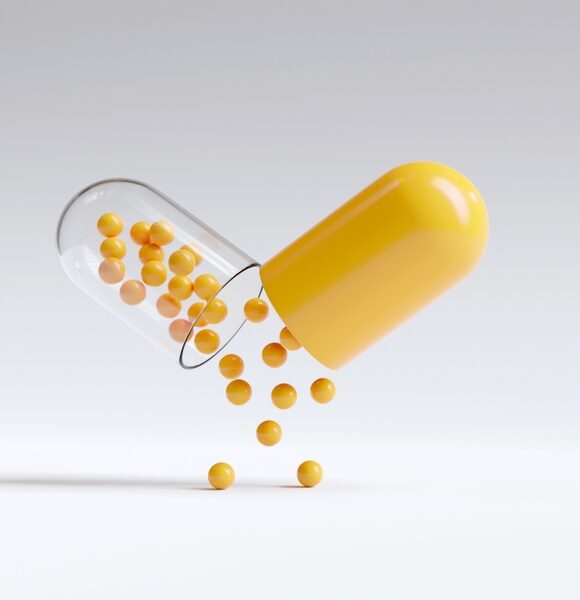
Let's make pharmaceutical granules
Find innovative production technology for making pharmaceutical granules and connect directly with world-leading specialists
Used in the pharmaceutical industry to produce tablets and capsules, among others, pharmaceutical granules are made to enhance the uniformity and flow of powder, increase the density of the blend and reduce dust and, therefore, toxic exposure. The choice of the granulation process, whether it is wet, dry, or direct compression, as well as the selection of appropriate pharmaceutical granulation equipment, depends on the specific drug being formulated.
Stories about pharmaceutical granules
Tell us about your production challenge
Pre-granulation and formulation of granules
Granulation is a commonly used technique for particle enlargement in pharmaceutical manufacturing – mixtures are agglomerated into semi-permanent aggregates by mixing active pharmaceutical ingredients, known as APIs and excipients. The latter has numerous functions, for instance, those that promote binding and improve tablet hardness, such as binders and disintegrants, or enhancing patient acceptance with flavors. Other excipients, such as hydrophilic polymers and wetting agents, optimize or modify drug release, while antioxidants enhance stability.
The granulation process can be divided into two main types: wet and dry granulation. Dry granulation is used when ingredients are moisture or heat-reactive. It is an efficient process due to simple equipment and minimum processing required. On the other hand, wet granulation is a complex process with various pharmaceutical granulation equipment and steps. Although more costly, it is also a more widely used process, especially useful in processing soluble low-dose drugs.
Pharmaceutical granulation equipment for wet, dry, and direct compression processes
As the names imply, the process of wet granulation utilizes a liquid, while dry granulation requires no liquid. The first step in the dry granulation process is weighing all the ingredients which are then mixed until they form a uniform powder. In a process called slugging, the mixture is compressed into pallets and broken into smaller pieces using a hammer mill. To achieve a uniform blend, excipients such as lubricants and disintegrants are added.
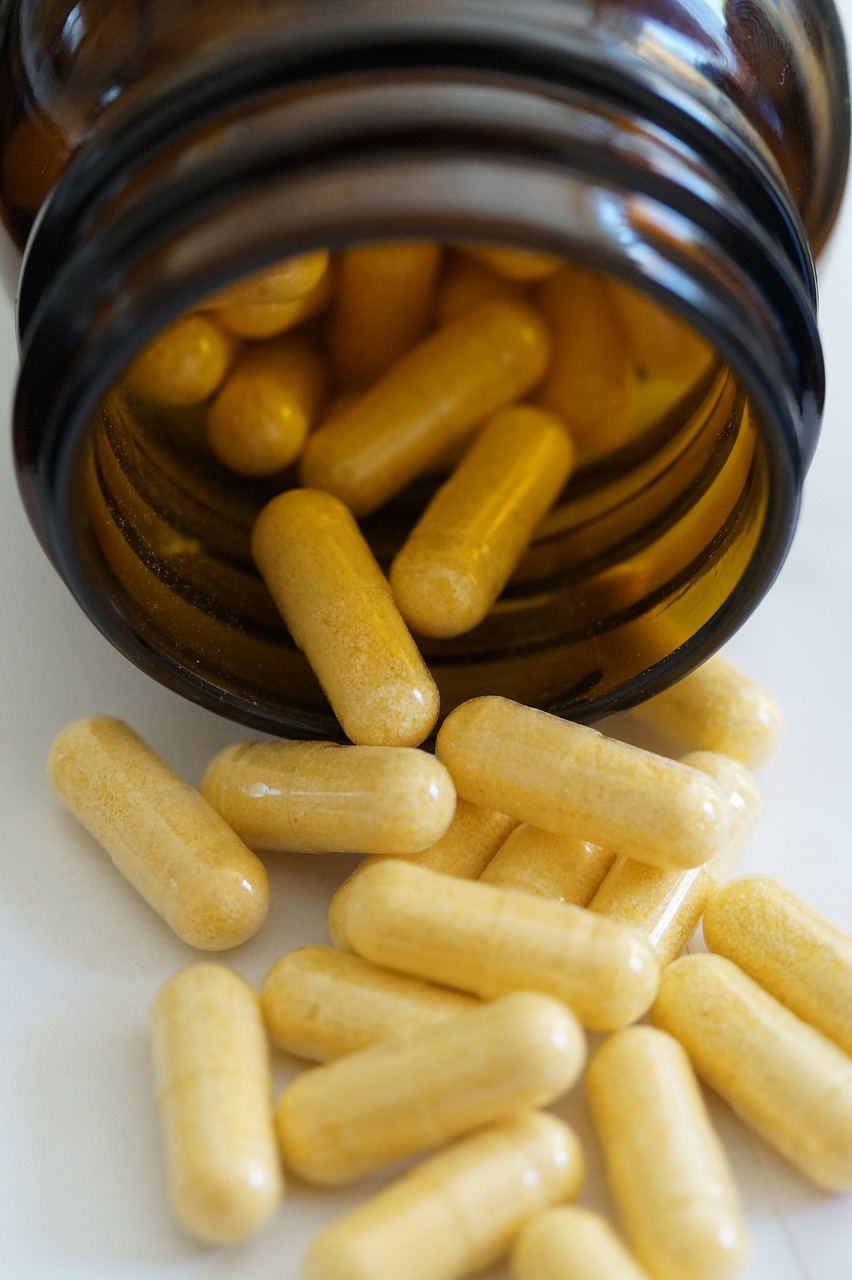
The wet granulation technique uses the same preparatory and finishing steps with the addition of wet massing, wet screening, and drying. Mass wetting is a process during which a granulation agent is added to the mixture until it disperses uniformly. The slurry is then sieved into granules and dried. This method offers a higher level of uniformity and speeds up the dissolution process. In the direct compression process, the blend is added directly into a tablet compression machine that produces tablets.
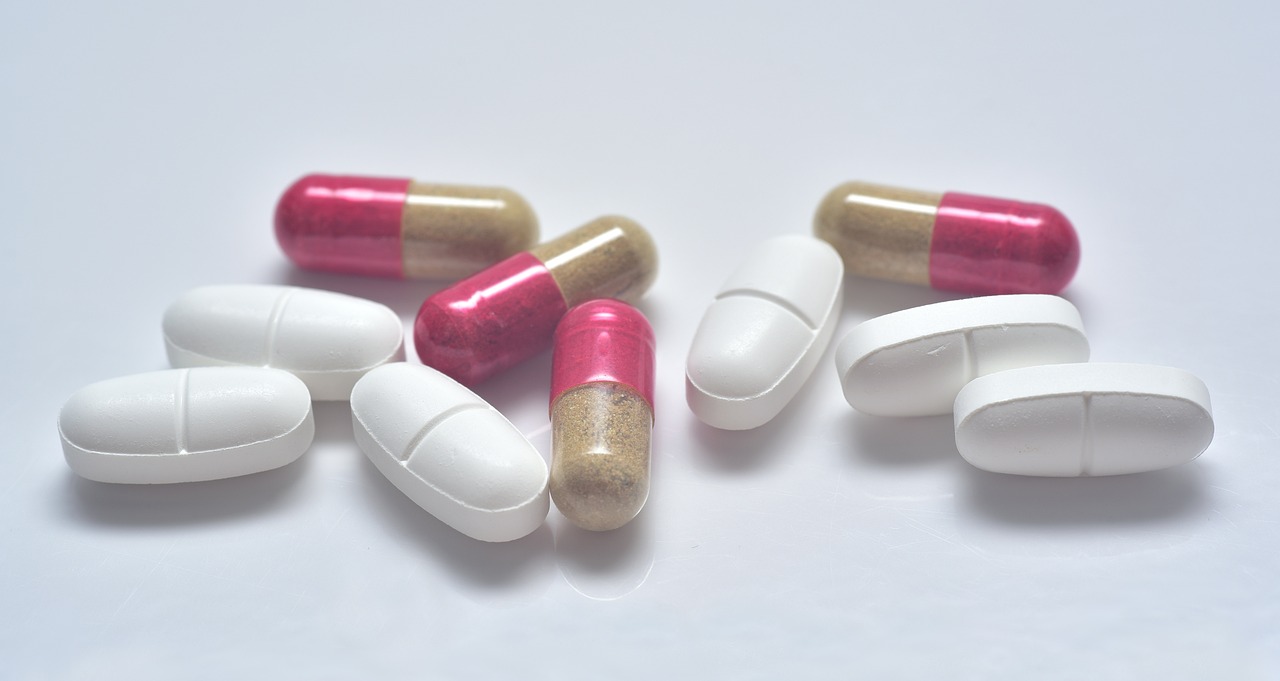
Granulation process for tablets and capsules
Once the granulation process is finished, granules are either pressed into tablets or filled into capsules, depending on their properties. A tablet is a solid form of an active ingredient in which it is possible to pack more material than with capsules. As the tablet presses can manufacture hundreds of thousands of tablets per minute, the formulation must be designed to flow consistently and fill volumetrically to achieve consistency among tablets. Some key excipients in tablet production are lubricants to prevent the granules from sticking, fillers to bulk up tablets, and disintegrants to help the tablet break up upon consumption.
On the other hand, capsules are filled with granulated powder with uniform particle sizes that flow freely; therefore good flow properties are essential. For efficiency and accuracy, granules are filled into hard gelatine capsules with the help of an automated capsule-filler machine.
Innovating high-shear mixers in the granulation industry
Although high-shear mixers have stood the test of time, being used in granulation processes for over six decades, there have been some recent innovations in the pharmaceutical industry. Namely, high-shear mixers can work under a vacuum and dry the wet mass within itself or are provided with fluid bed processors so that all the stages are carried out within the same mainframe equipment. These mixers have the capability to handle very fine particle coating of 75 to 100 microns. The popularity of such mixers lies in their simplicity and the fact that they are used as one-stage one-step equipment from the start till the loading of the granules atop the compression table.
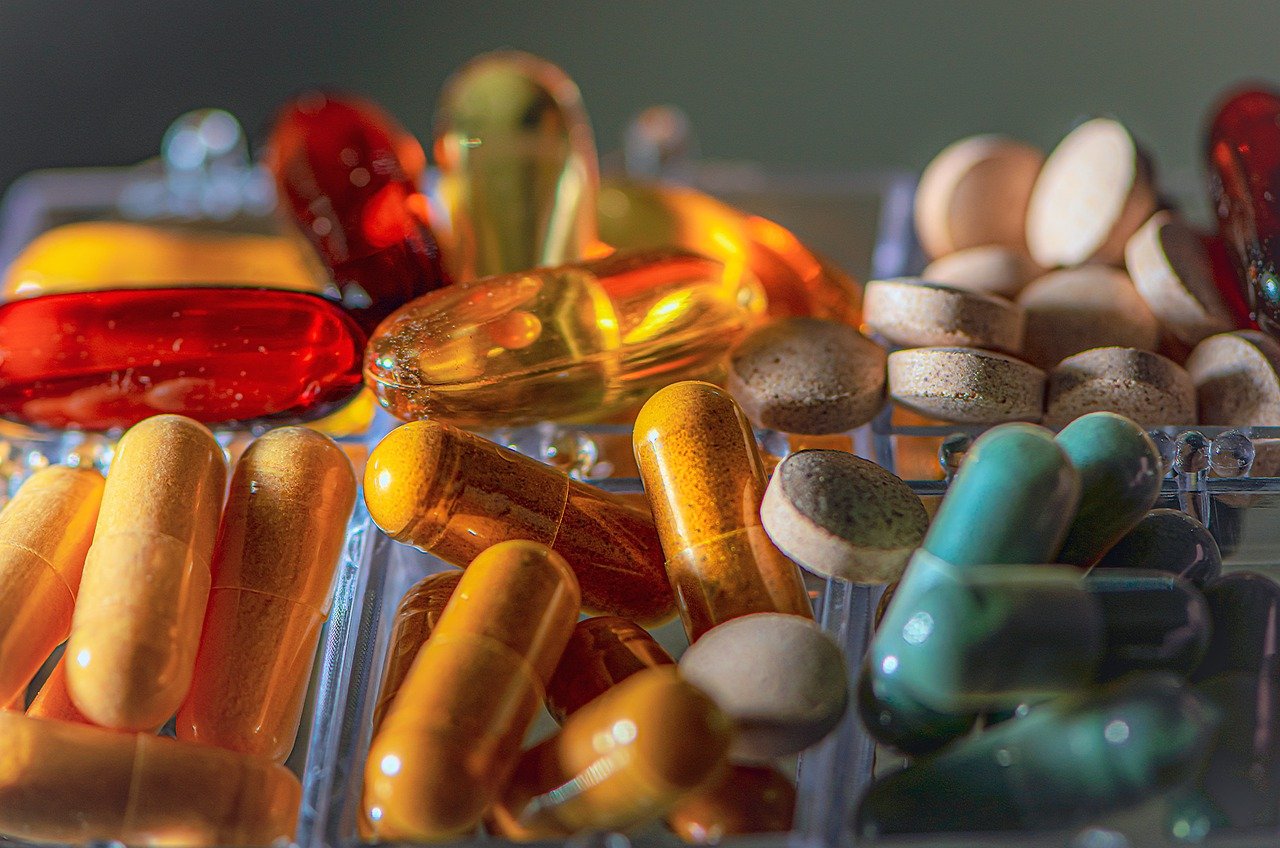
What is the most environmentally sustainable granulation process?
Representing one of the most carbon-intensive industries due to the complex chemistry of APIs, the pharmaceutical industry has put efforts into improving the environmental sustainability of its manufacturing process. In granulation processes, the environmental impact of production is ruled by process-level energy usage – a more complex process means more impact on the environment. Therefore, a shorter process, such as direct compression, which uses more energy, is a more environmentally friendly choice. However, this applies to drugs with good flowability, as those with poor flowability require either pre-compaction treatment, increased excipients’ proportion in the tablets, or using excipients with unfavorable sustainability profiles. Furthermore, organic solvent-free processes, such as using lipid excipients, are an excellent alternative for making the granulation process greener.
Processing steps involved in pharmaceutical granules making
Which pharmaceutical granules technology do you need?
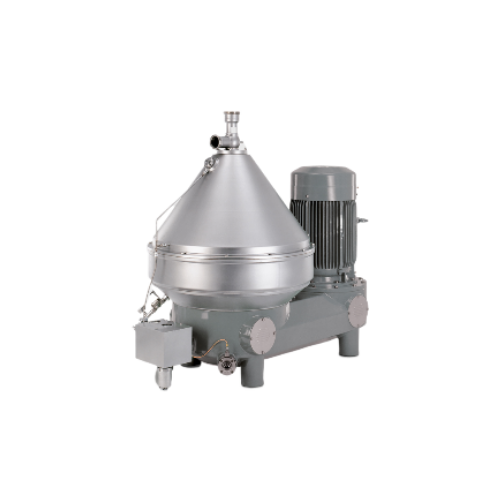
Pharma extraction clarifier
Achieve superior purity in pharma extraction with efficient separation of solids and liquids, se...
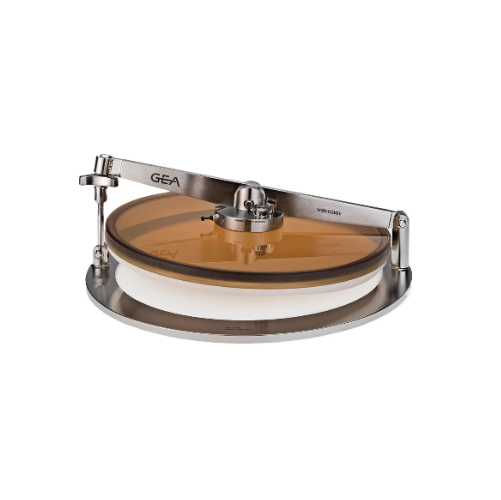
Sanitary cover for visual inspection
Ensure optimal hygiene and easy access in your production line with a transparent cove...
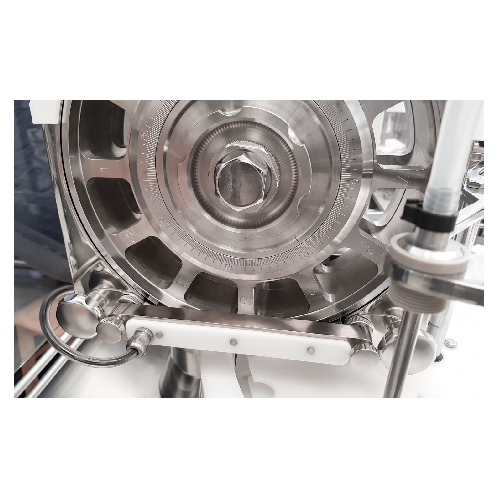
Micro-dosing system for pharmaceutical powders in vials
Ensure accurate aseptic dosing of sensitive pharmaceutical powder...
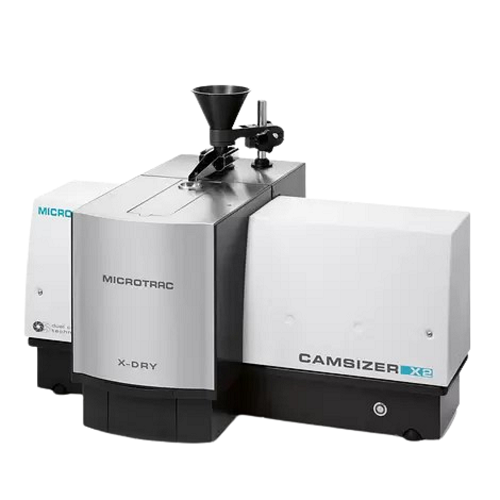
Particle size and shape analyzer
Achieve precise particle size and shape analysis from 0.8 μm to 8 mm with exceptional speed...
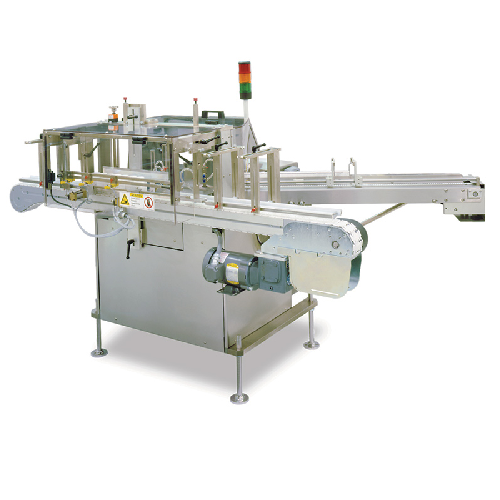
Outsert application system for pharma bottles
Effortlessly enhance packaging efficiency in pharmaceutical lines with this ...
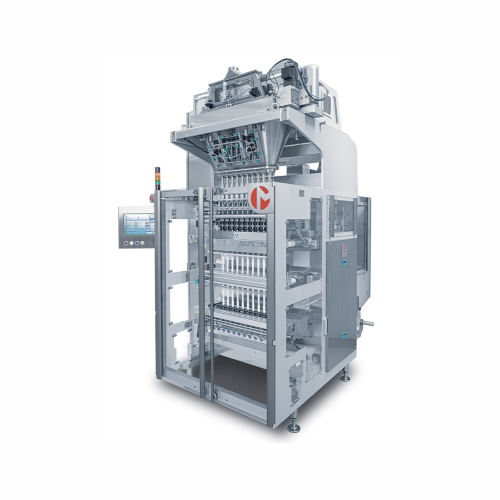
Stickpack filling and closing system for pharmaceutical powders
Achieve precise dosing and secure packaging for pharmace...
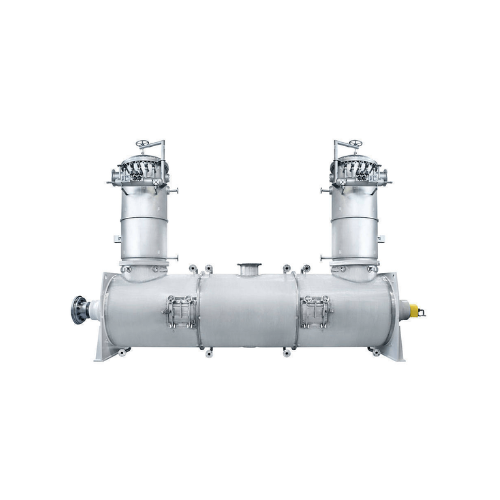
Vacuum paddle dryer for chemical and pharmaceutical applications
Achieve precise moisture control and efficient drying i...

Super high shear inline disperser for nanoparticle production
Achieve unmatched particle size reduction with cutting-edg...
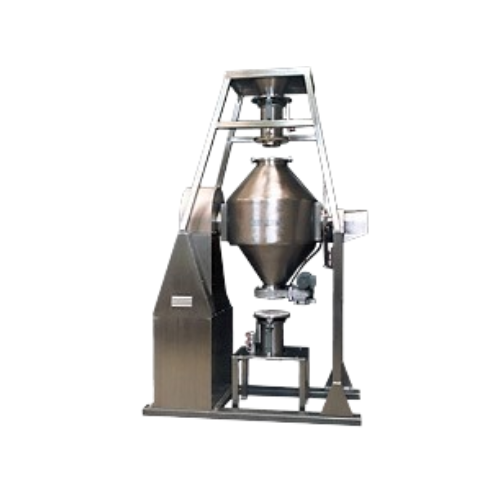
Double cone blender for fragile and abrasive material
Achieve homogeneous blends of fragile materials while minimizing da...
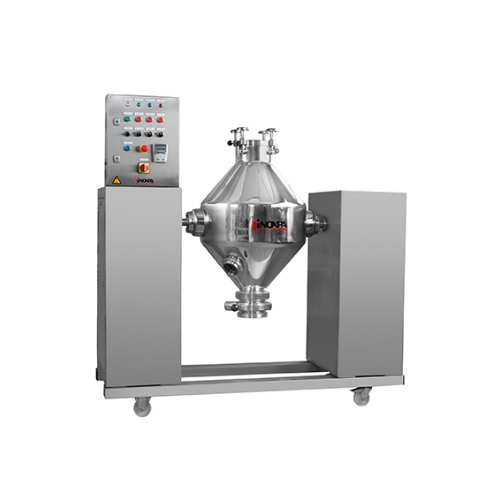
Double cone blender for homogeneous solid-solid mixtures
Need uniform blending for complex solid mixtures with diverse de...
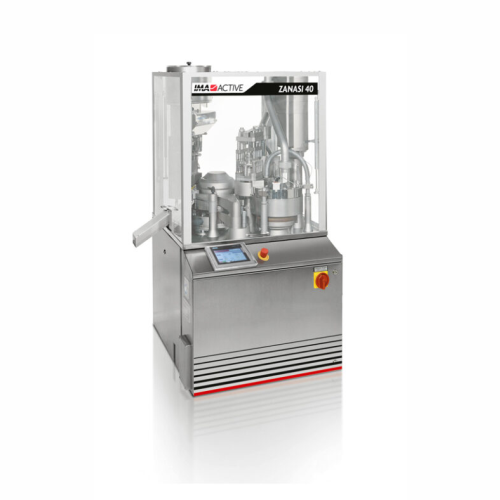
Automatic capsule filling machines
Efficiently fill capsules with precise doses of powders, liquids, and tablets to enhance...
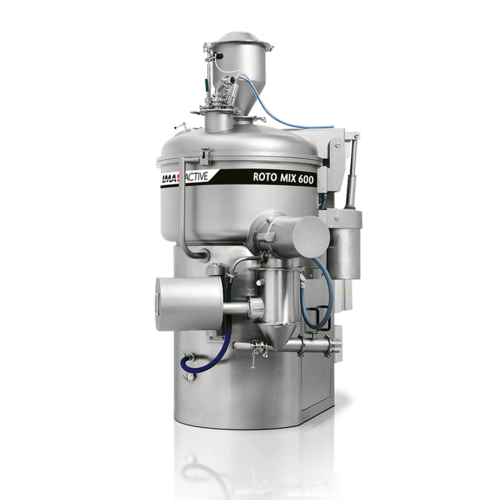
High shear mixer granulator for pharmaceutical applications
Achieve optimal granulation with precise shear control, enha...
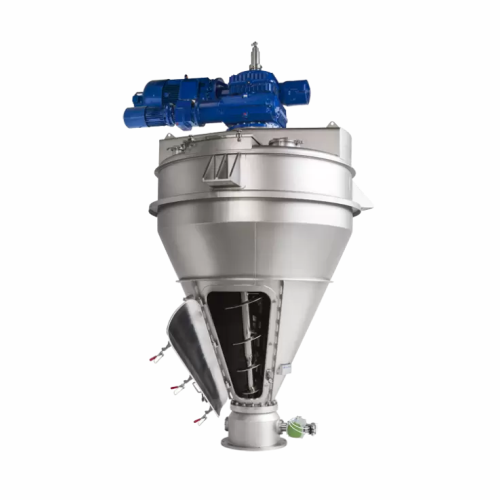
Mid-shear mixer for powders and bulk solids
Achieve ultra-short mixing cycles and superior homogeneity without the need fo...
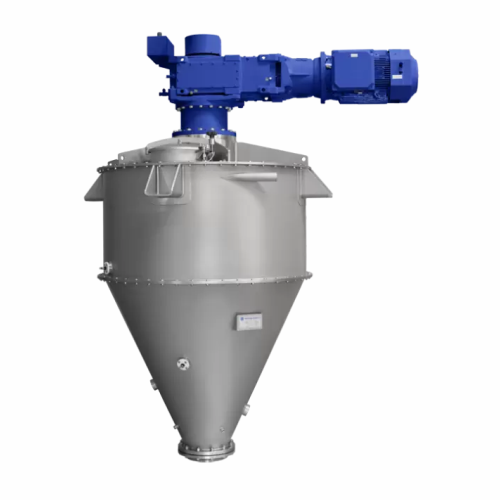
Conical paddle mixer for accurate powder blending
Achieve precise blending of fragile powders and liquids with a versatil...
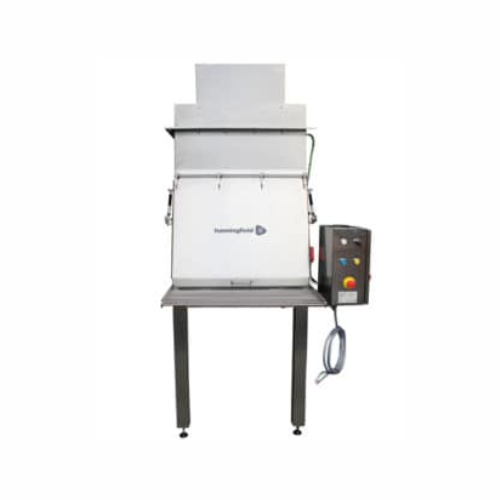
Dust control sack tip station for bag unloading
Ensure efficient powder unloading and minimize dust emissions in your prod...
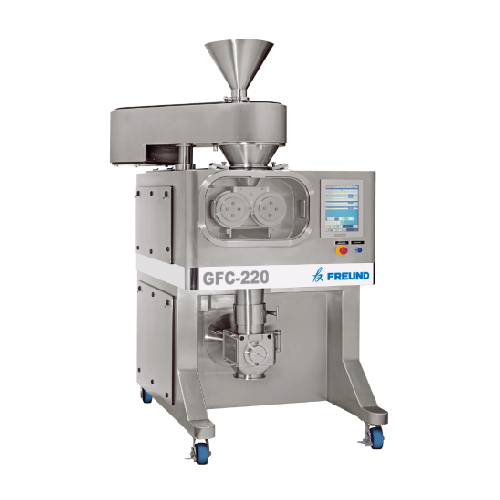
Roll compactor system for dry granulation
Achieve consistent tablet hardness and increased powder density with a versatile...

High shear wet granulation system
Experience efficient wet granulation with precise control over granule density and moistu...
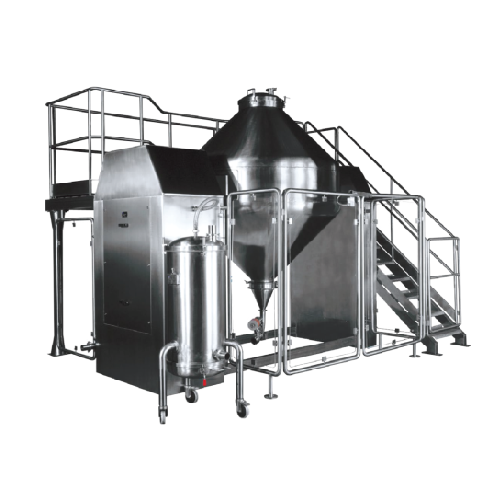
Pharmaceutical powders and granules dry blending
Achieve uniform blending of diverse powder and granule formulations with ...
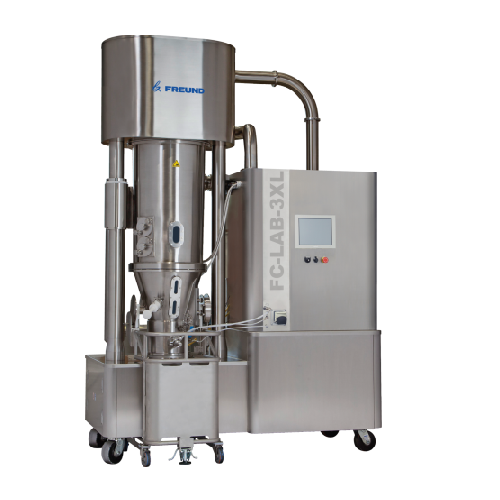
Laboratory fluid bed granulator and coater
For researchers and manufacturers requiring precise control in drying, granulat...

Closed loop granulator for pharmaceutical production
Streamline your production with a fully automated closed-loop system...
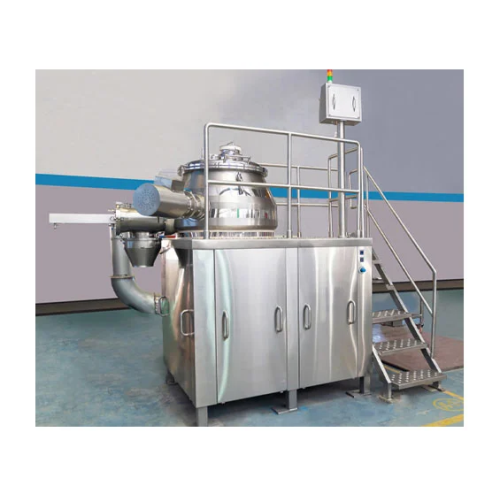
High shear mixer granulator for efficient wet granulation
Achieve consistent and precise granule formation with high she...
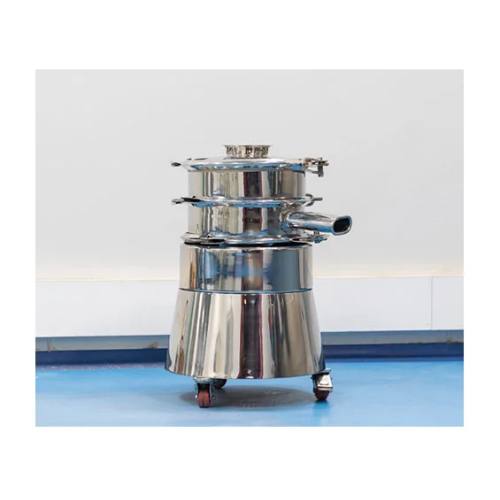
Particle sizer for precise sifting
Optimize your production line with high-speed particle sizing, ensuring precise control ...
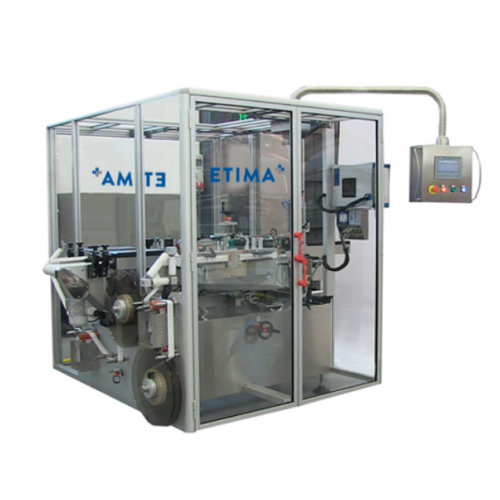
Linear tamper evident labeler
Secure product integrity with high-speed labeling that ensures tamper evidence, while seamless...
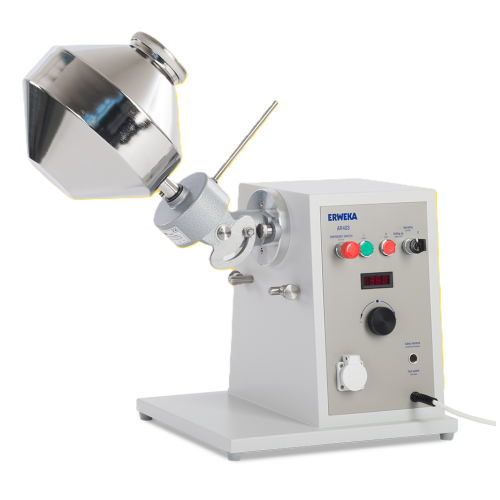
Double cone mixer for free flowing powders and granules
Achieve uniform blending of powders and granules with precision, ...
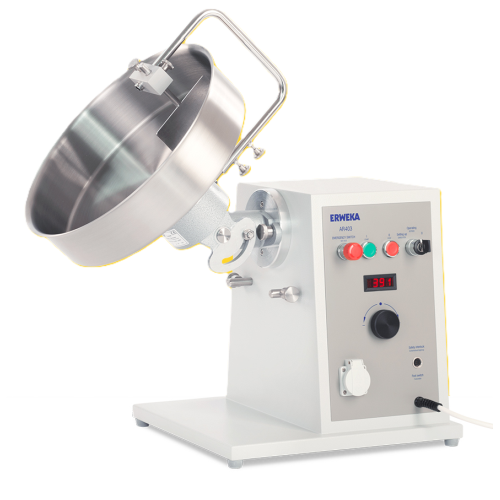
Pelletizer for pharmaceutical and biotech applications
Achieve precise pellet formation with adjustable pan angles and li...
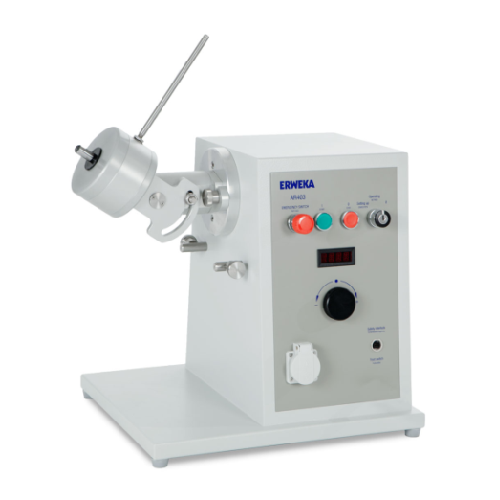
All-purpose mixer and processor for laboratory and small scale production
Optimize your small-scale production with a ...
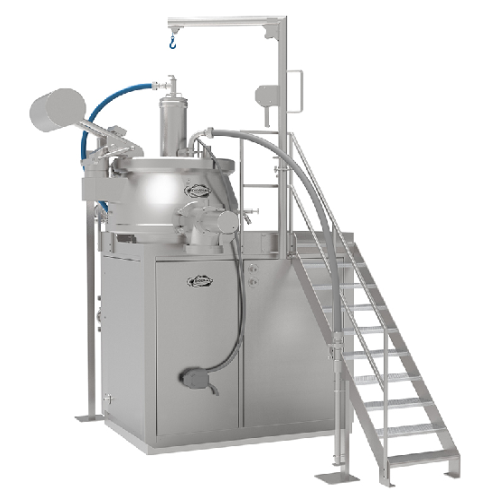
Pharmaceutical high-shear mixer granulator
Enhance your production efficiency with a high-shear mixer granulator, designed...
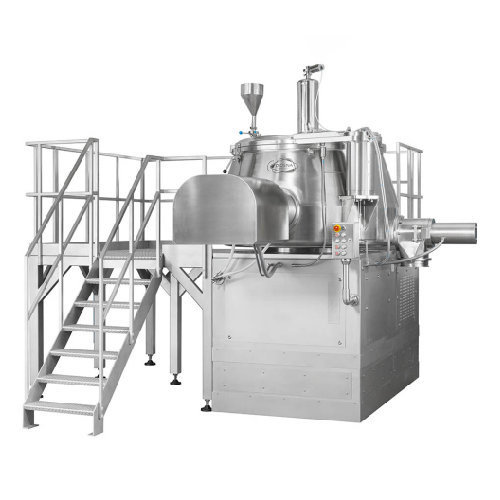
High-capacity universal mixer for industrial applications
Optimize your batch processing with a versatile high-speed mix...
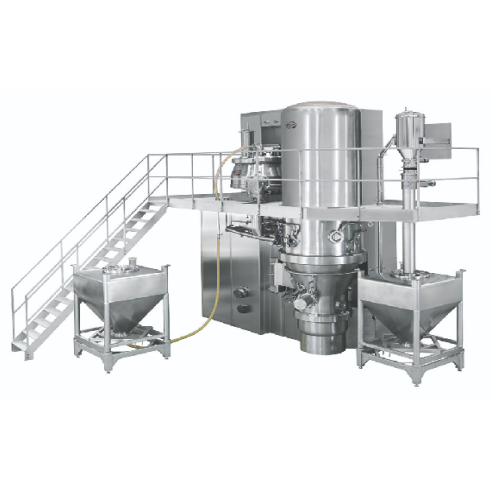
Pharmaceutical granulation line
Streamline your production with an integrated system that combines mixing, granulation, and ...
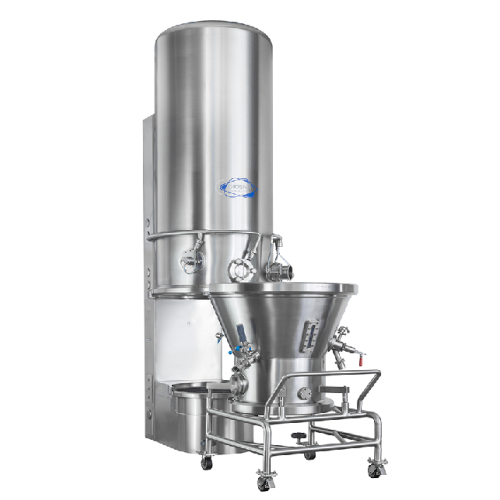
Fluid bed processor for large batch spray granulation
Optimize your production with precision granulation, drying, and co...
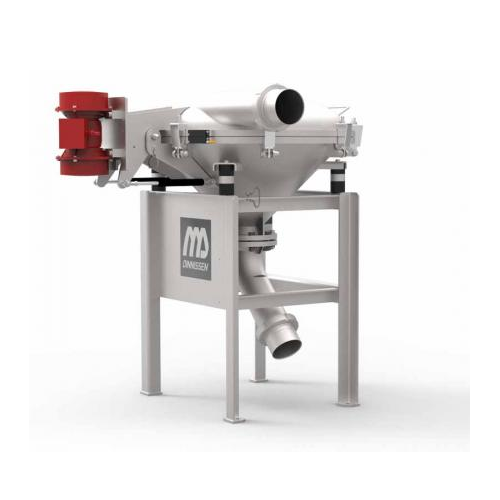
Industrial vibrating sifters for granular material separation
Achieve precise particle separation and ensure product pur...
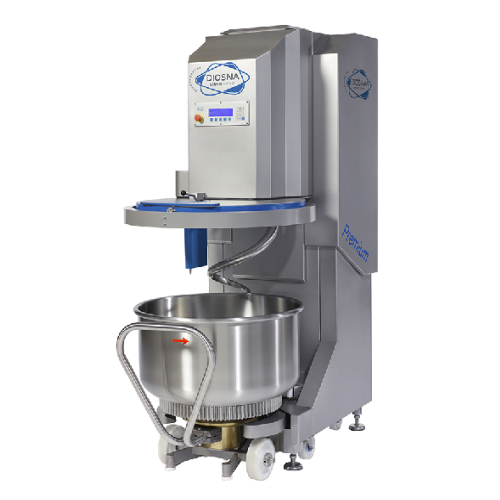
Interchangeable tool stainless steel kneader
Streamline your batch processing with this flexible mixing technology that of...
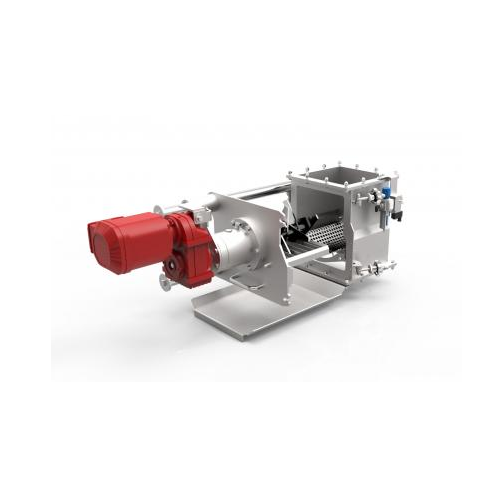
Industrial breaker for reducing large lumps and agglomerates
Efficiently break down challenging materials with a robust ...
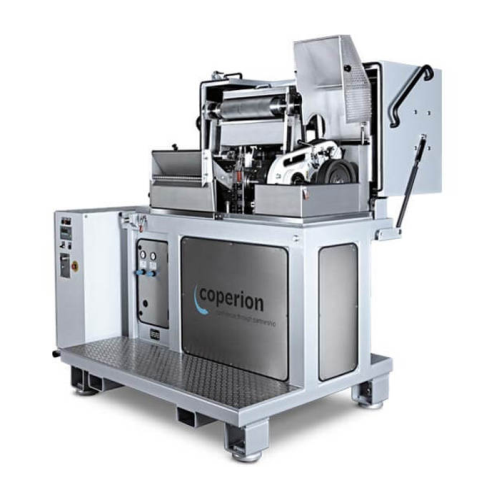
Industrial strand pelletizer for polymer processing
Optimize polymer pellet production with precision engineering, ensuri...

Laboratory twin screw extruder for small batch processing
Efficiently develop formulations and conduct precise research ...
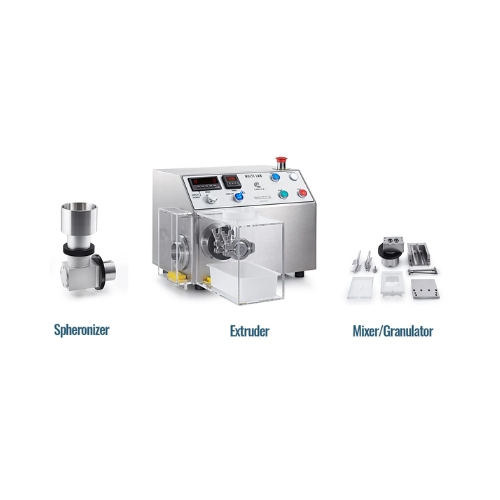
Lab scale mixer, extruder & spheronizer for r&d formulation
Optimize and streamline your research and development proces...
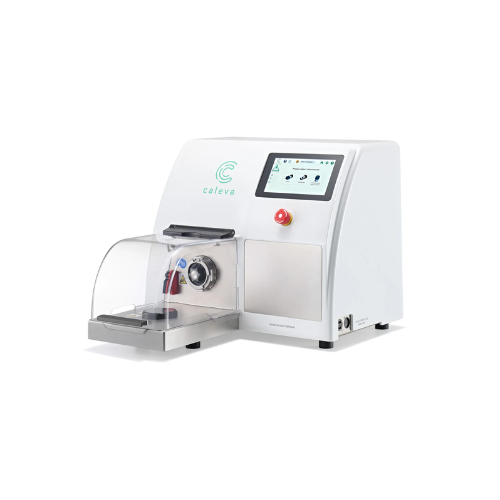
Bench-top mixer and spheronizer for formulation development
Accelerate R&D success by seamlessly integrating mixing...
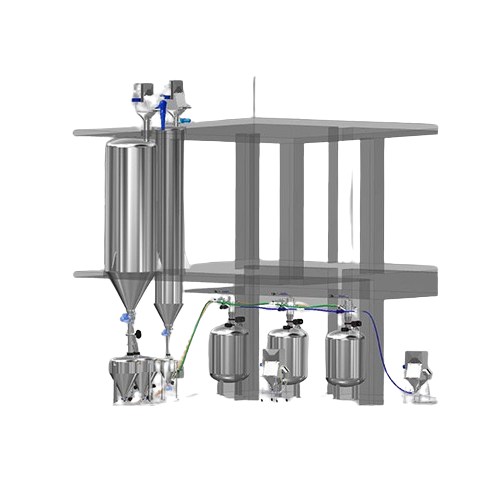
Automatic powder vacuum conveying system for infusion production
Enhance your production line with our vacuum conveying ...
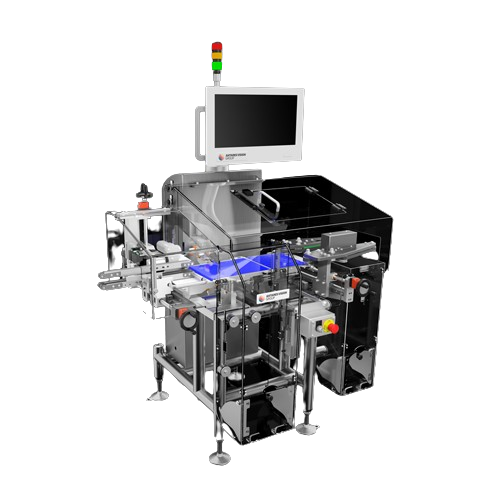
Pharmaceutical checkweigher for milligram-level accuracy
Ensure precision and compliance in your pharmaceutical packaging...
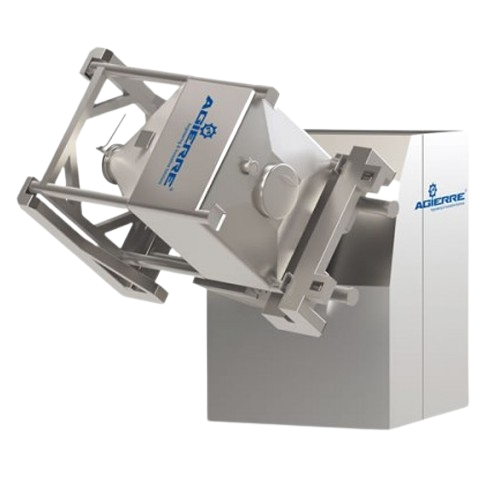
Bin blender for pharmaceutical powder mixing
Achieve uniform mixing and homogenization of dry powders directly in storage ...
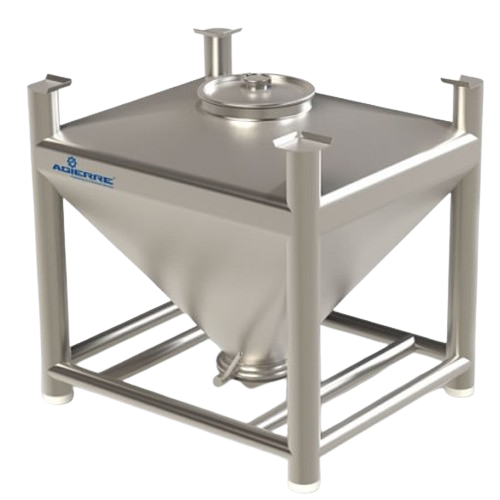
Stainless steel pharma bin for powder containment
Ensure precise powder handling and containment with this stainless stee...
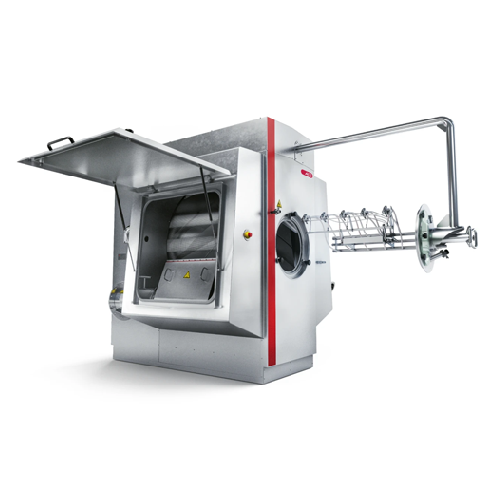
Tablet coater for batch sizes up to 250 liters
Enhance your tablet production process with high-speed coating solutions de...
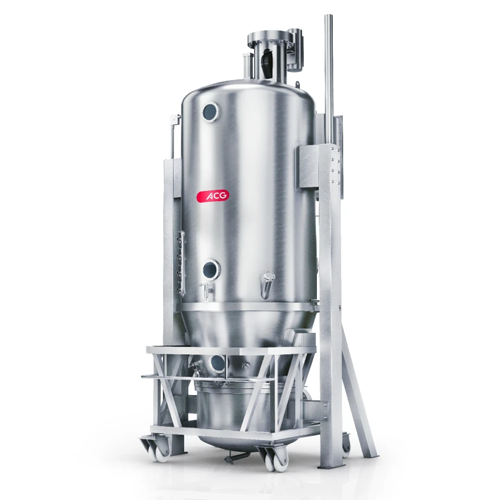
Advanced fluid bed for pharmaceutical granulation
Achieve precise granulation and drying for pharmaceutical powders with ...
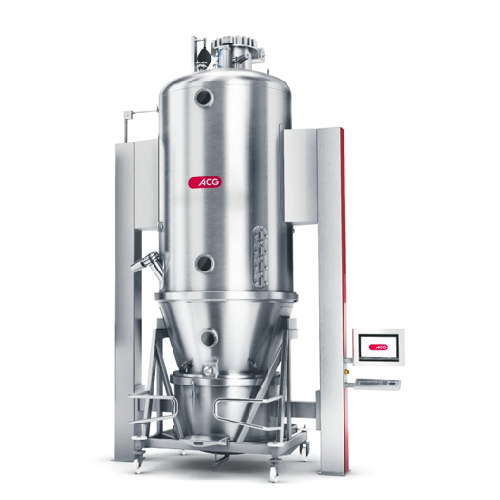
Fluid-bed granulator for top-spray applications
Need precise granulation and drying for sensitive materials? This fluid-be...
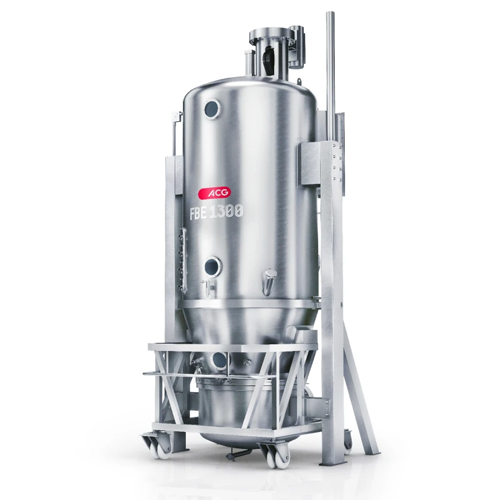
Fluid-bed drying and granulation system
Optimize your production line with high-speed batch processing for efficiently dryi...
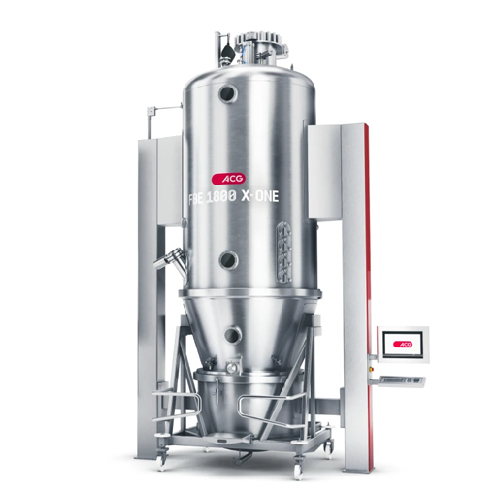
Fluid bed granulator for pharmaceutical applications
Optimize your granulation and drying processes with advanced fluid-b...
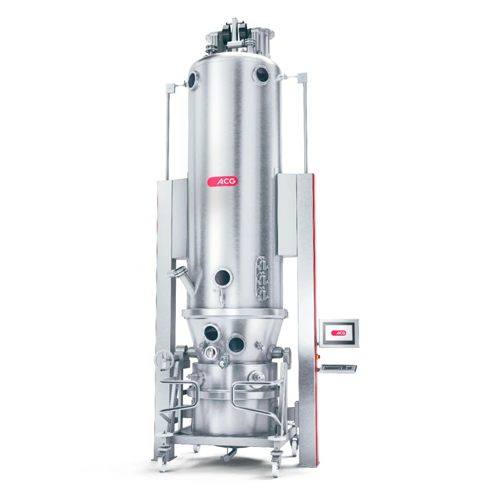
Fluid bed combo for granulation and coating
Achieve seamless granulation and coating with batch and high-speed operations,...
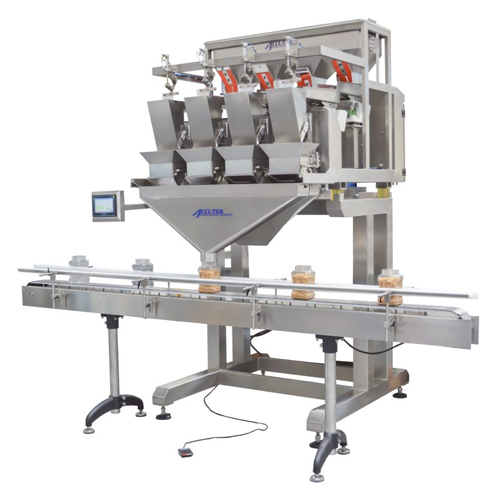
Automatic granular product weighing system
Effortlessly achieve precise fills for dry granular products and powders while ...

Desiccant inserter for pharmaceutical containers
Prevent product degradation by efficiently inserting desiccants into cont...
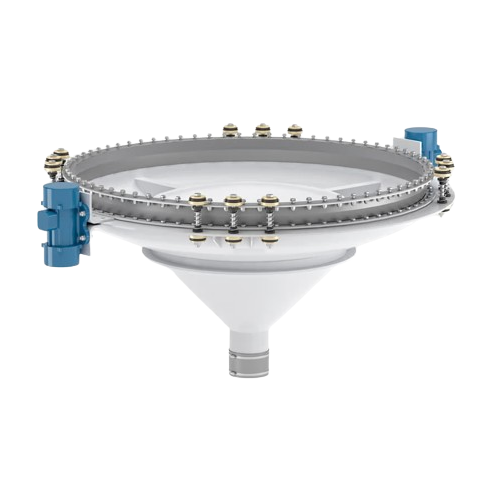
Industrial vibrating extractor for homogeneous product conveyance
Ensure consistent flow of dry bulk materials with a v...
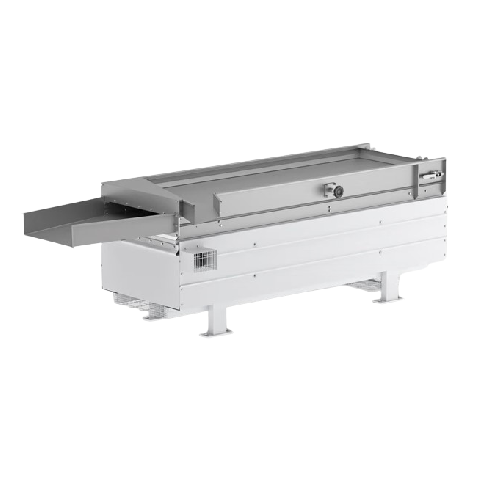
Industrial vibrating sieve for powder and lump separation
Ensure precise separation of powders and lumps with this oscil...
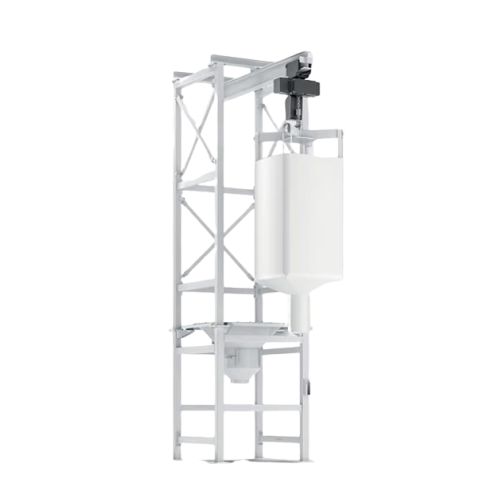
Big bag emptying station for raw materials
Streamline your material handling process by efficiently lifting, emptying, and...
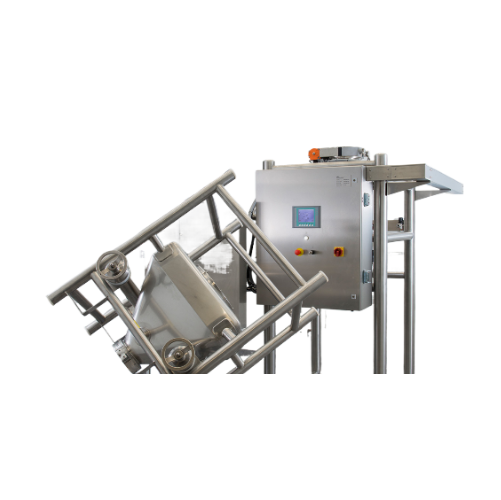
Intermediate bulk container (ibc) blending for pharmaceutical manufacturing
Streamline your pharmaceutical blending pr...
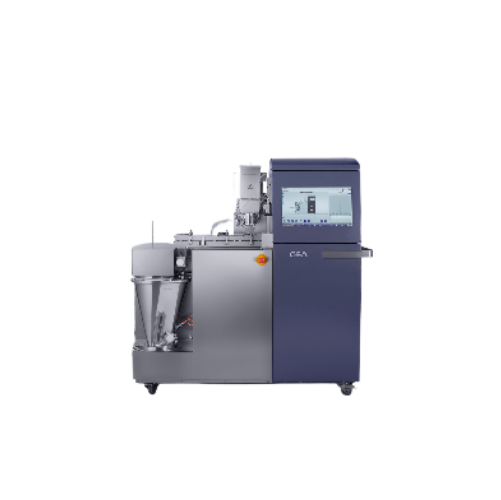
Continuous granulation and drying system for r&d
Develop precise pharmaceutical granules with this compact system, tailore...
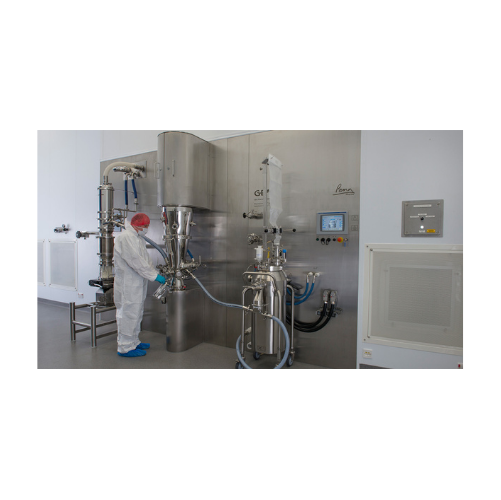
Pharmaceutical r&d granulation system
Optimize your pharmaceutical research with a versatile small-scale granulation system...
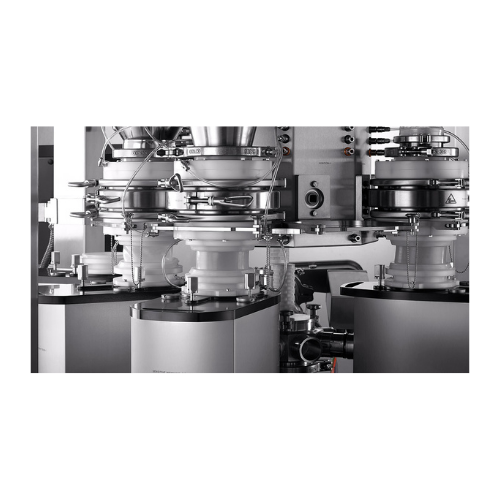
Powder feeding behavior characterization solution
Optimize your R&D with precise powder feeding behavior analysis, c...
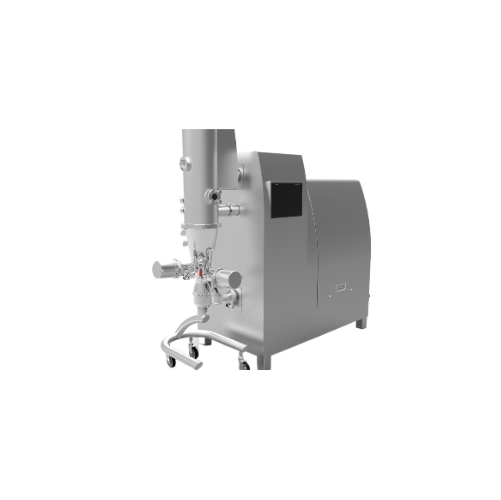
Pharmaceutical fluid bed processor for r&d
Optimize your pharmaceutical R&D with a versatile fluid bed processor desi...
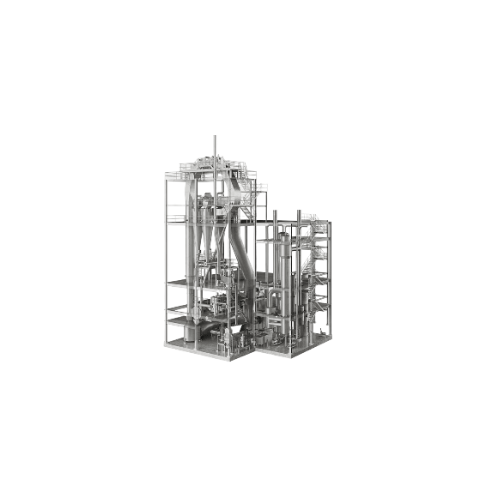
Feed-type ring dryer for industrial drying processes
Optimize your production with a versatile drying solution designed f...
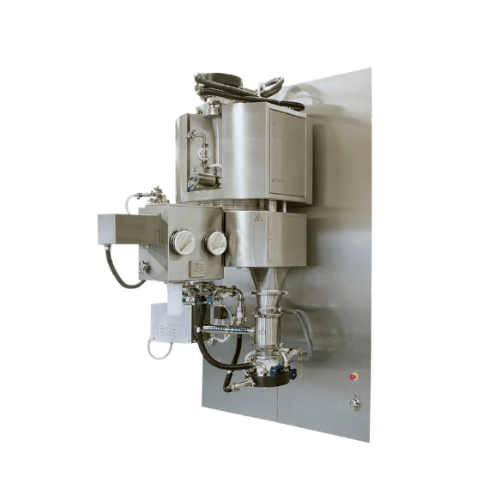
Single pot processor for granulation and drying
Streamline your pharmaceutical production with an integrated solution that...
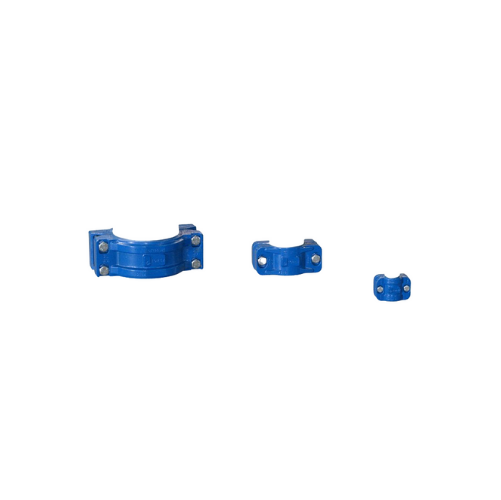
Pipe couplings for pneumatic conveying lines
Ensure a secure and quick connection for your pneumatic lines with these pipe...
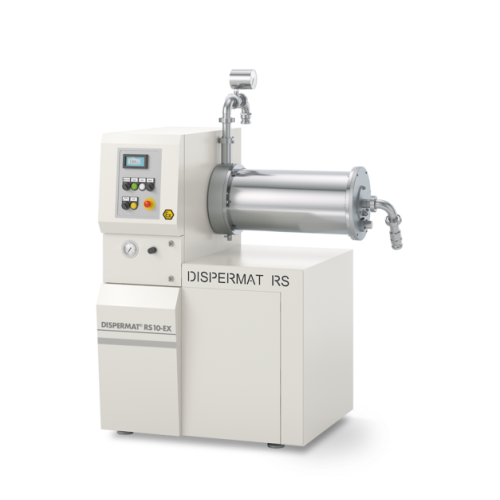
Explosion-proof bead mill for industrial grinding applications
For manufacturers seeking precise particle size control, ...
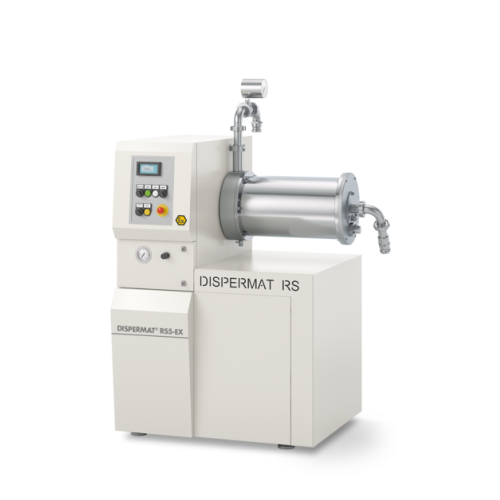
Explosion-proof horizontal bead mill
For manufacturers seeking precise particle sizing, this explosion-proof bead mill ensu...
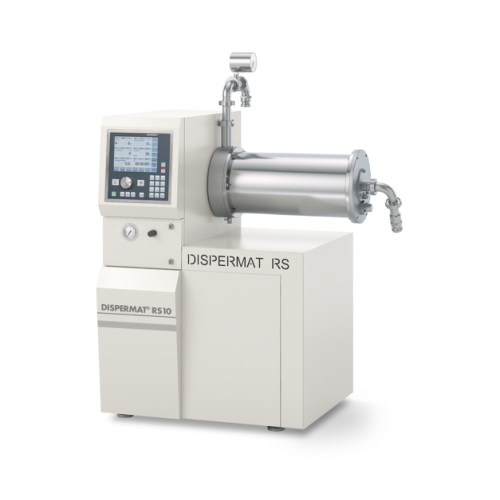
Horizontal bead mill for industrial production
Ensure ultra-fine particle size reduction in high-demand processes with thi...
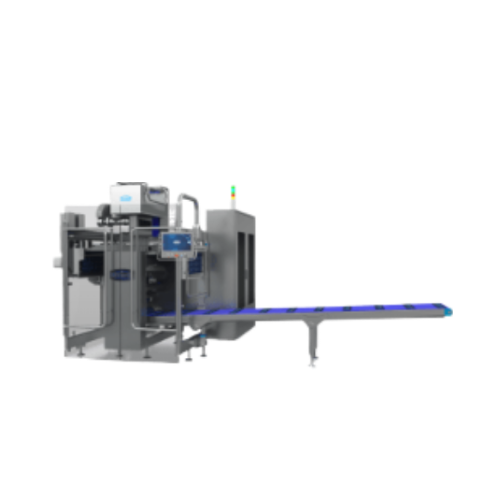
Sachet packaging for pharmaceuticals
Streamline your pharmaceutical packaging with high-precision sachet solutions, ensurin...
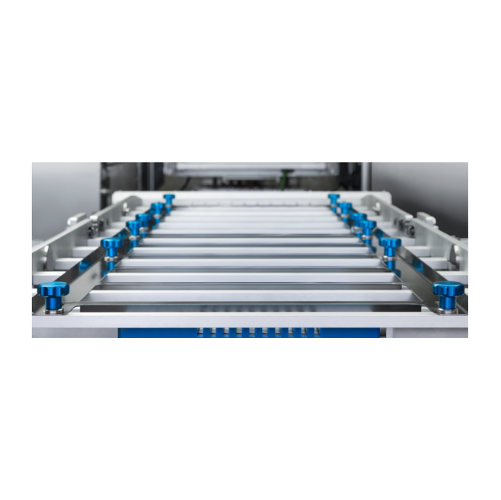
Stick pack packaging line for pharmaceuticals
Optimize your pharmaceutical production with stick pack packaging lines that...
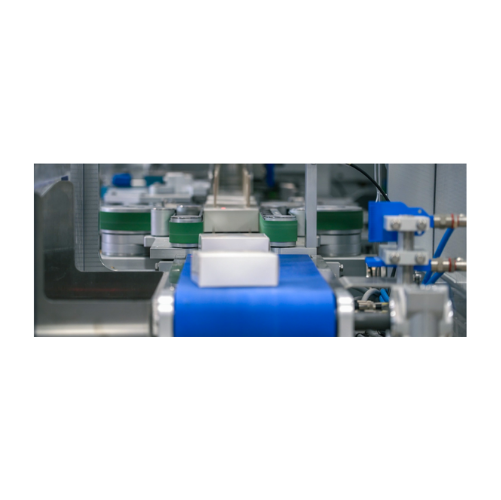
Cartoning solution for pharmaceutical products
Ensure accurate and efficient packaging of pharmaceutical products with pre...

Hybrid laboratory extruders for reproducible scale-up applications
Easily switch between screw diameters to enhance fle...
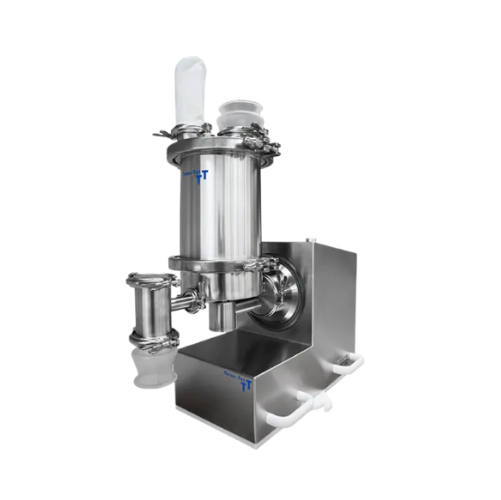
Gravimetric twin screw feeders for pharma powders
Optimize feeding for challenging materials with dust and water-resistan...

Side feeding device for extruders
Enhance your extrusion process with a side feeding device that gently introduces powders,...
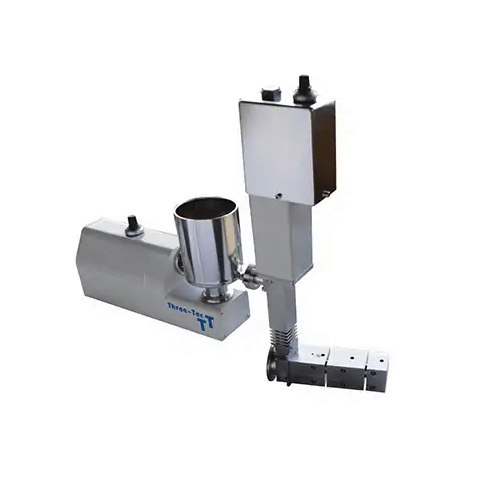
Stuffing feeding device for extruders
Efficiently feed cohesive or lightweight powders into extruders to enhance product qu...
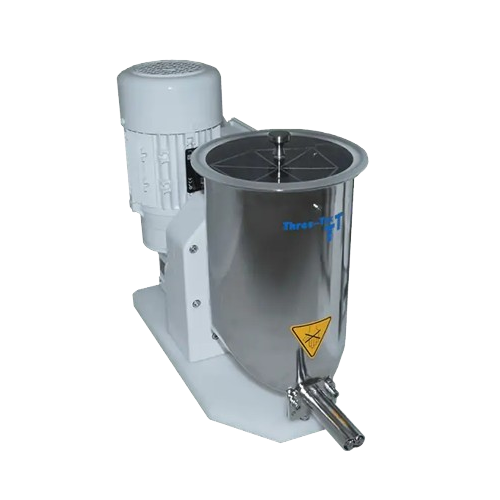
Twin screw feeder for dosing bulk solids
Ideal for precise bulk solids dosing, this twin screw feeder ensures consistent fl...
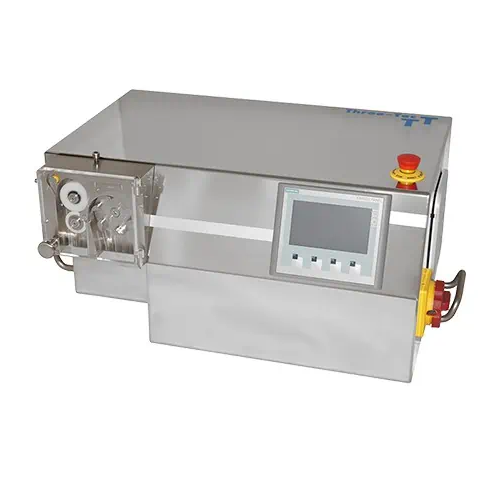
Granulator for processing strands into granulate
Optimize granule production with precise control over pellet size and ext...
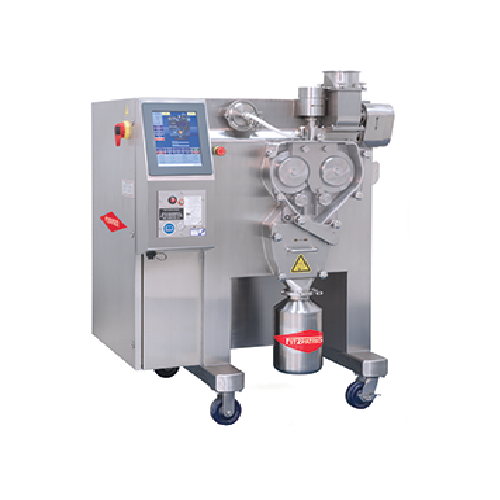
Roller compaction for dry granulation in pharmaceuticals
Ensure consistent granule size and density in your product line ...
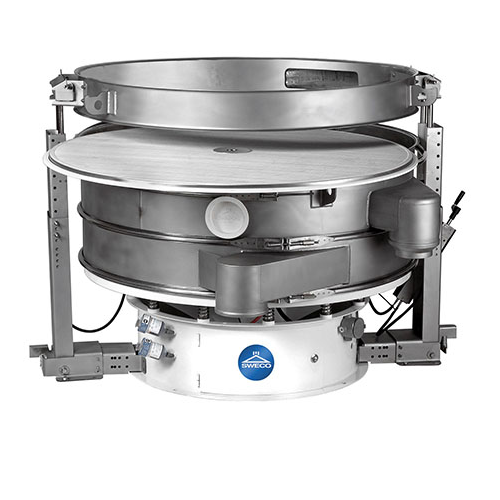
Quickchange systems for vibratory separator screen changes
Streamline your production with a system that enables rapid s...
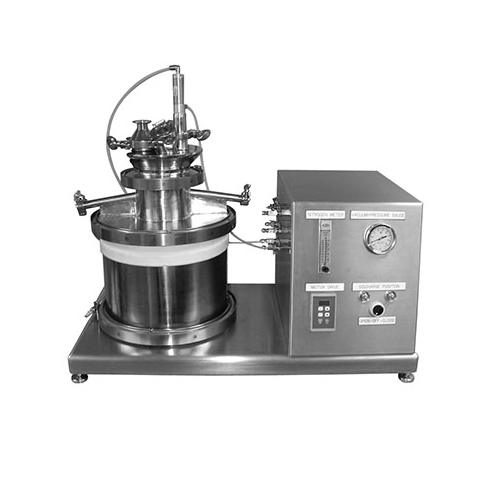
Pharmaceutical aseptic separator filter dryer
Achieve seamless filtration, washing, and vacuum drying in a single aseptic ...
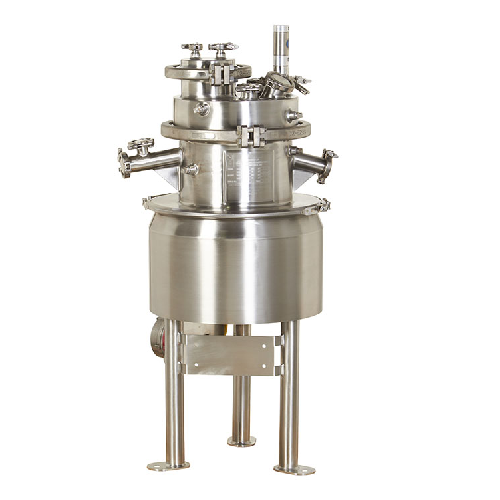
Lab Pharmaceutical aseptic separator
Achieve high-yield recovery and safe handling of potent pharmaceuticals with this asep...

Biodecontamination system for small pharmaceutical enclosures
Achieve reliable sterilization in compact settings with th...
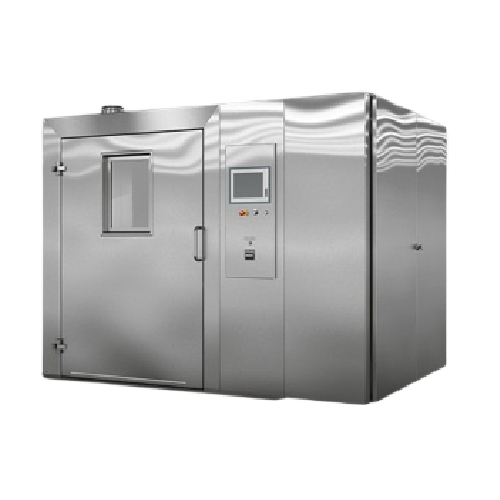
Pharmaceutical grade washer for large components
Ensure compliance and maximize productivity with a high-performance solut...
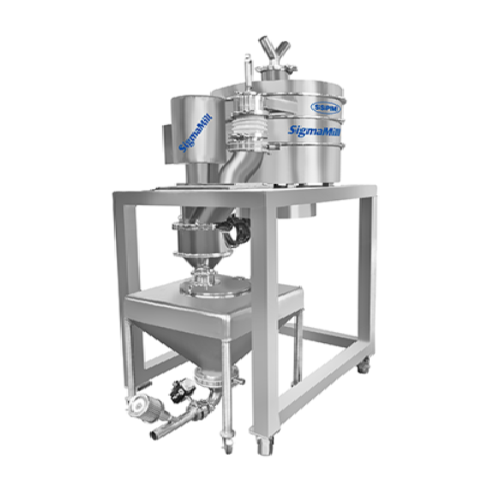
Wet granulation for pharmaceutical products
Achieve seamless integration of sifting and milling with precise powder handli...
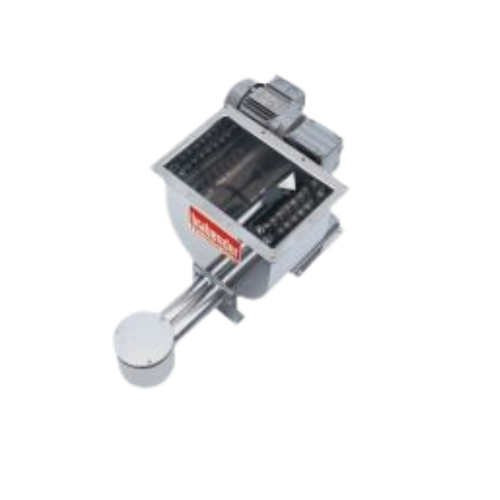
Twin screw volumetric feeder for poor flowing powders
Struggling with poor flowing or floodable powders? This twin screw ...
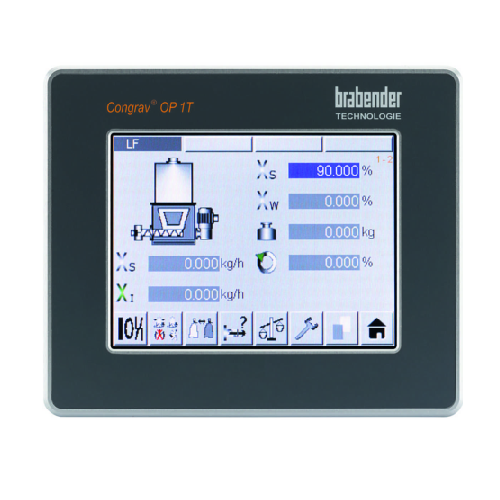
Single feeder operator interface for gravimetric feeders
Enhance precision in your dosing operations with an intuitive to...

Automated sample preparation software
Enhance your laboratory’s efficiency with a software solution that automates sa...

Industrial batch mixer agitators
Achieve precise and efficient mixing of diverse materials with industrial batch mixer agita...
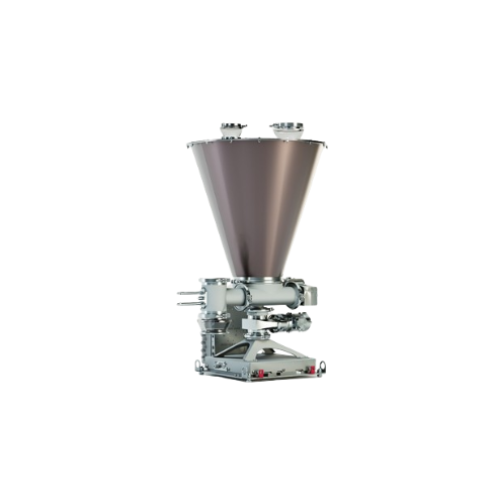
Loss-in-weight feeder for battery cell production
In battery cell production, achieving precise dosing and safe handling ...
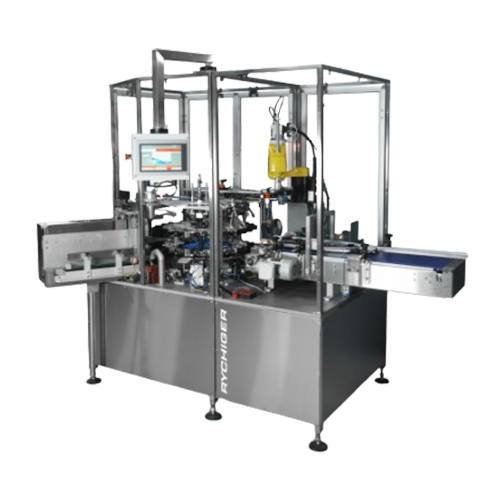
Cartoner for pharmaceutical products
Effortlessly streamline your packaging line with compact cartoning capabilities, ensur...
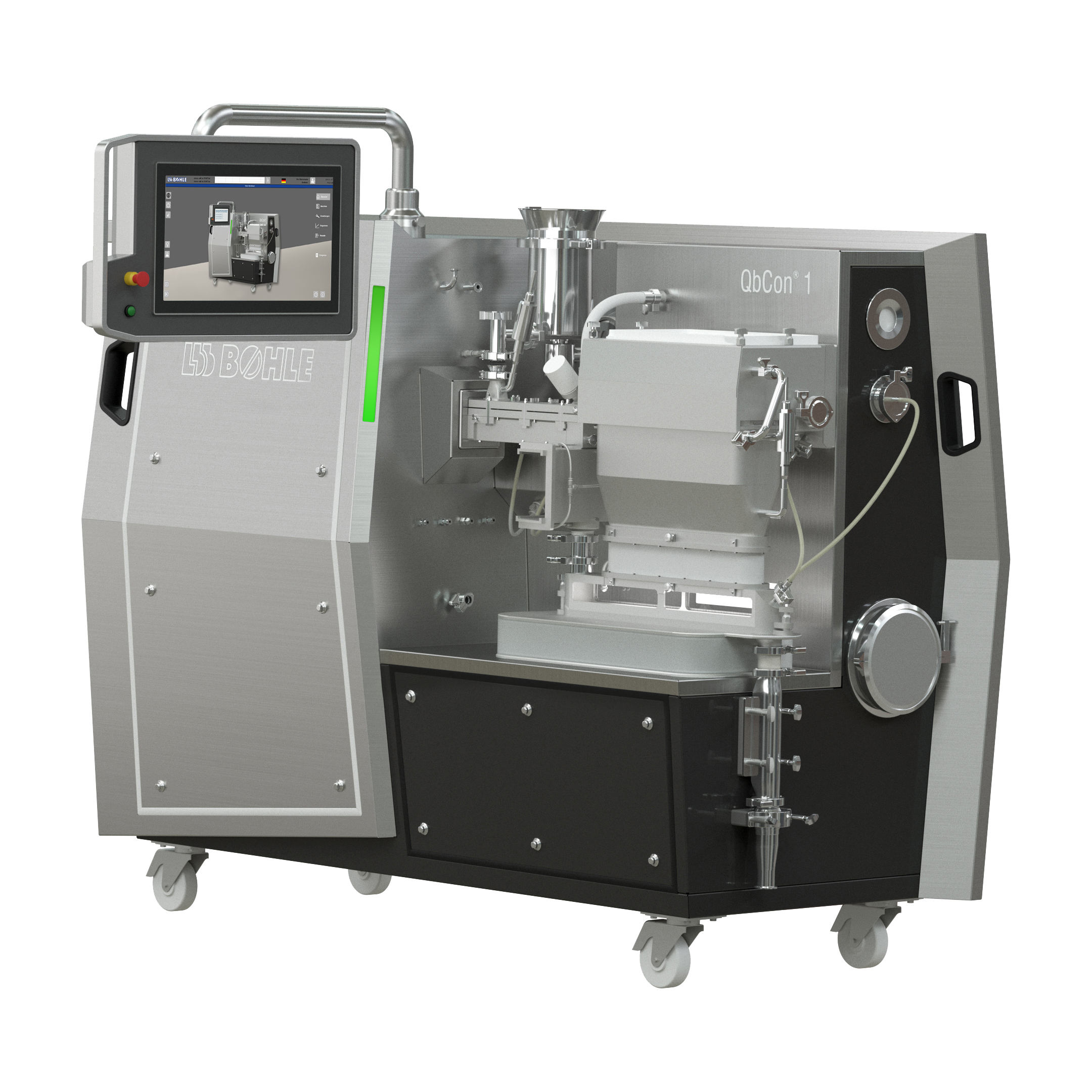
Continuous wet granulator and dryer for R&D
Pharmaceutical laboratories need compact equipment to handle and produce small...
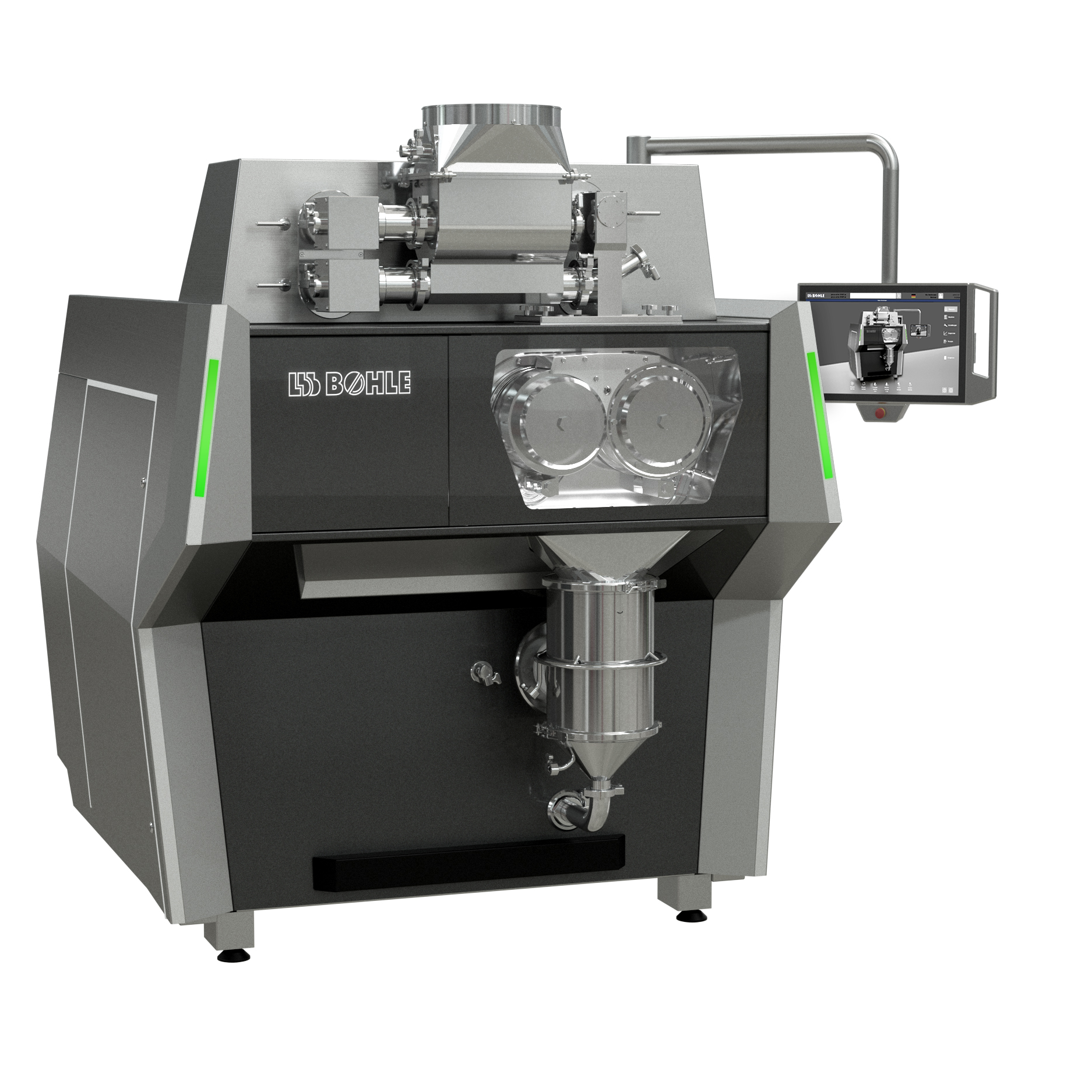
Dry granulator for pharmaceutical powders
In pharmaceutical industries, where large-volume production is the norm, compact...
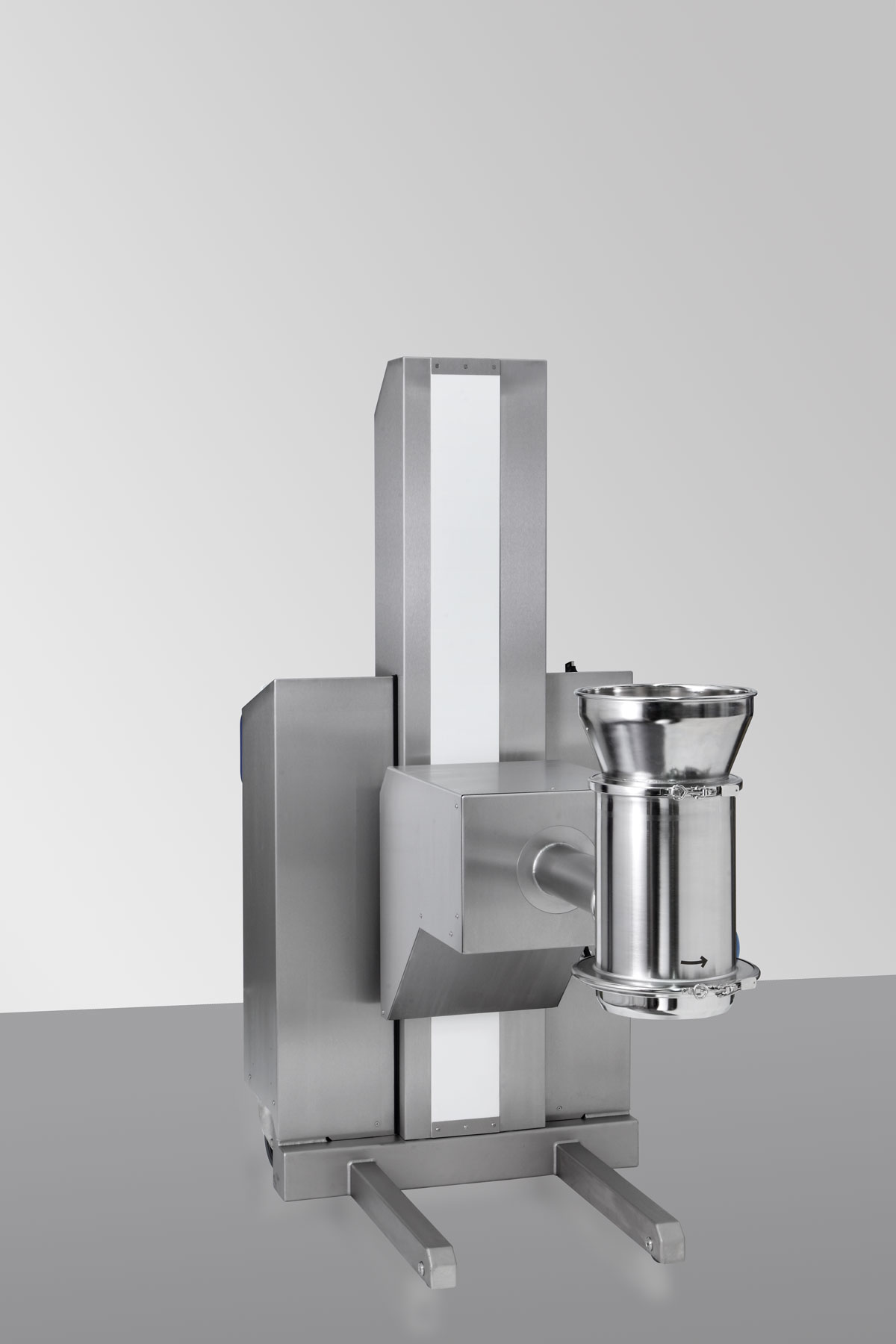
Industrial sieving machine for pharmaceuticals
One of the physical attributes that granular pharmaceutical products must h...
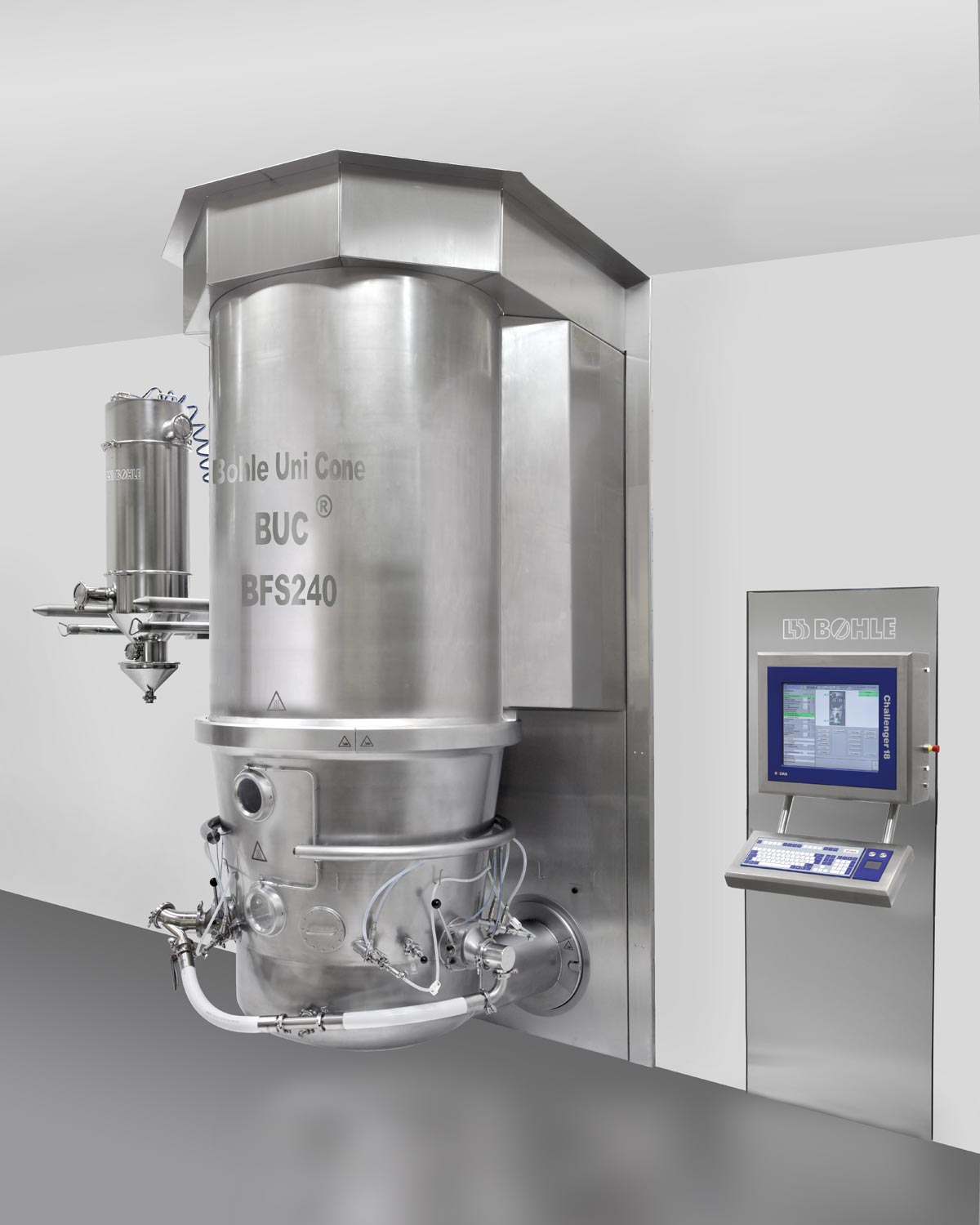
Fluidized bed system for the granulation and drying of pharmaceuticals
Pharmaceutical industries employ several process...

Continuous roller compactor for dry granulation of pharmaceuticals
When making tablets, pharmaceutical manufacturers ne...
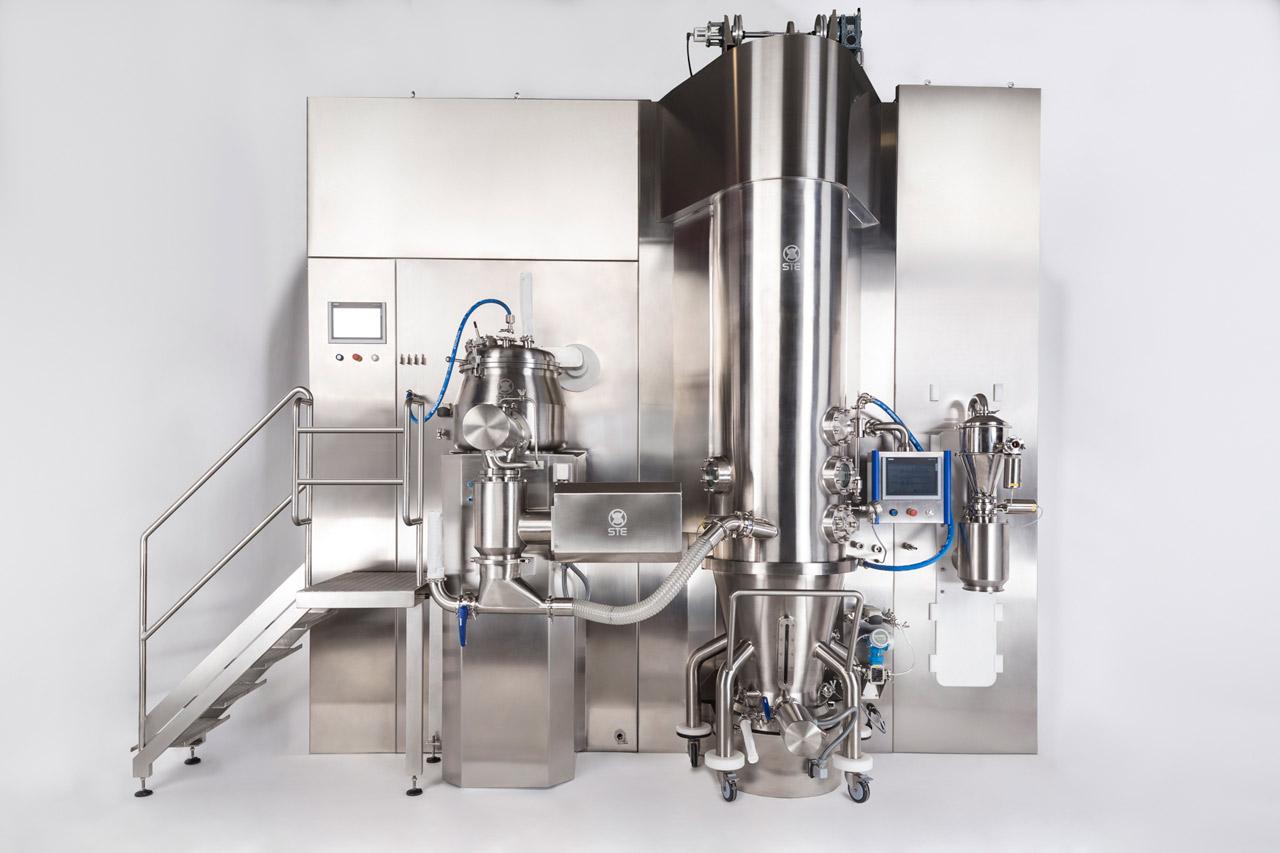
Granulation line for pharmaceutical solid dosage forms
Granulation is a common technique in production of pharmaceutical ...
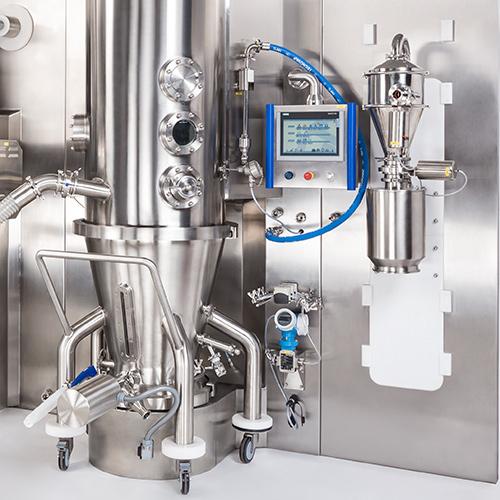
Fluid bed dryer for pharmaceutical solid dosage form
Fluid bed drying is a pharmaceutical process carried out to reduce t...

Industrial high shear mixer granulator for drug formation
It is rather difficult to successfully produce a pharmaceutica...
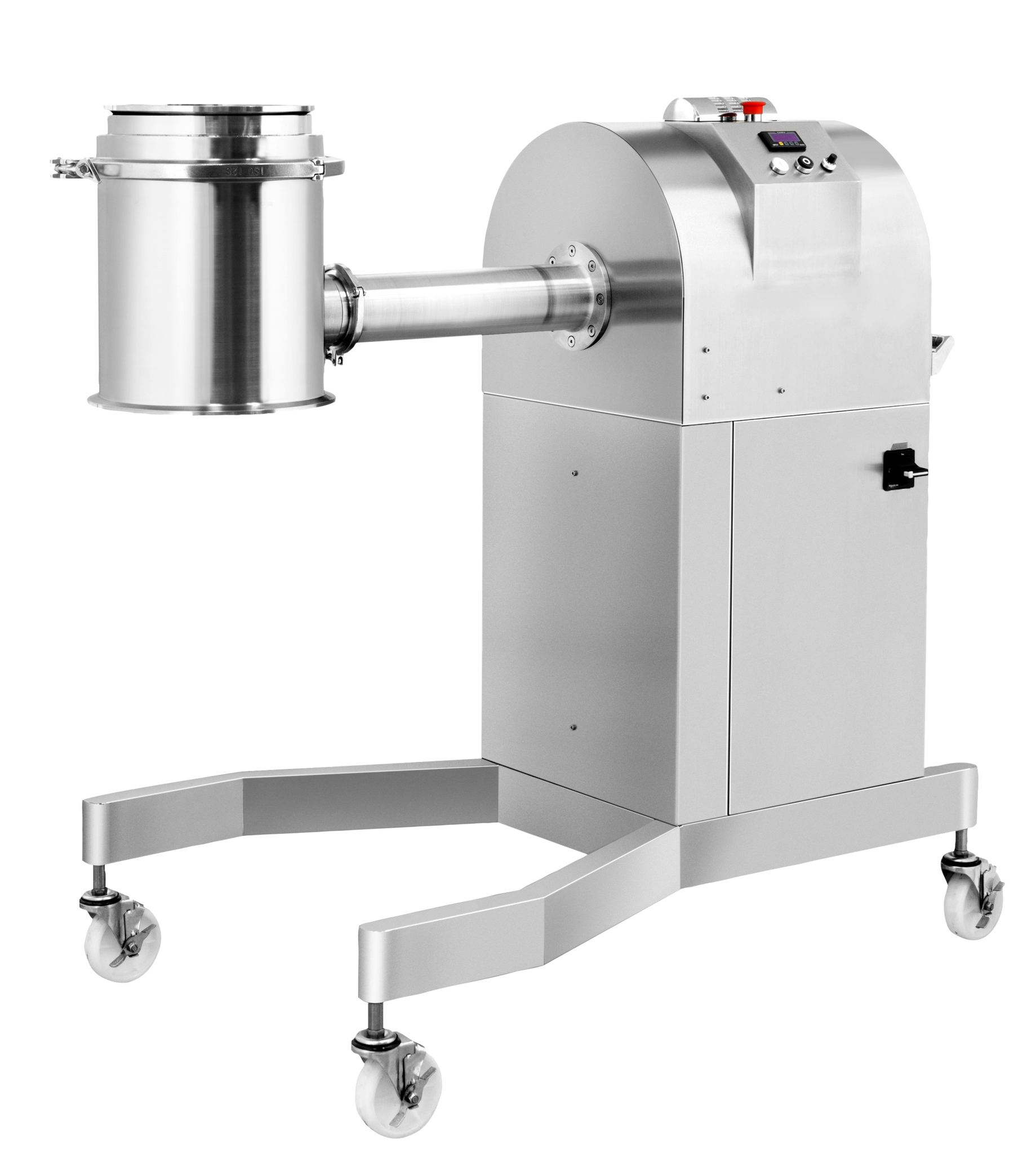
Conical mill for drug formulation
The efficient size reduction of granular powders is a key step in many pharmaceutical pro...
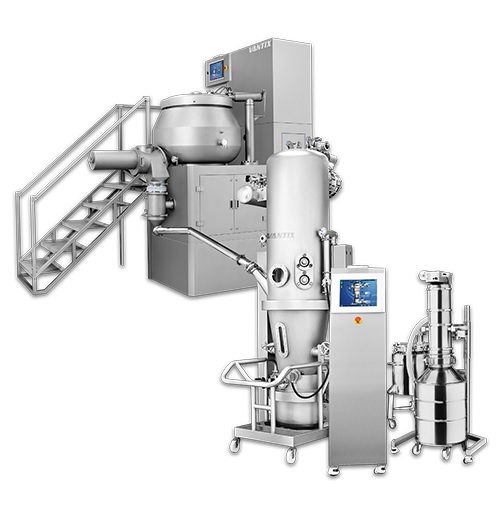
Granulation line of mixer and fluid bed dryer
A complete granulation line allows for the mixing and granulation of pharmac...
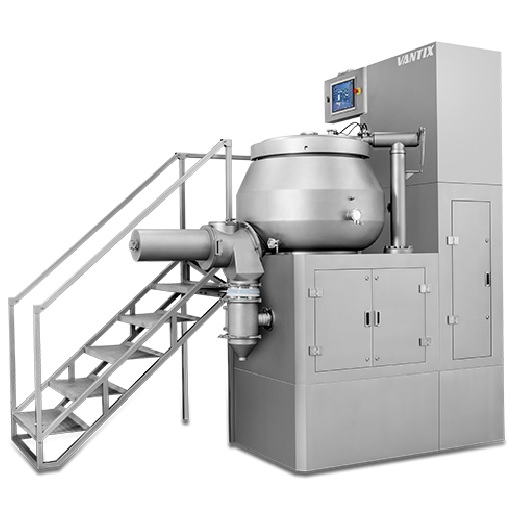
High-shear mixer
For the efficient mixing of larger batches of pharmaceutical compounds and high-shear mixer provides the opti...
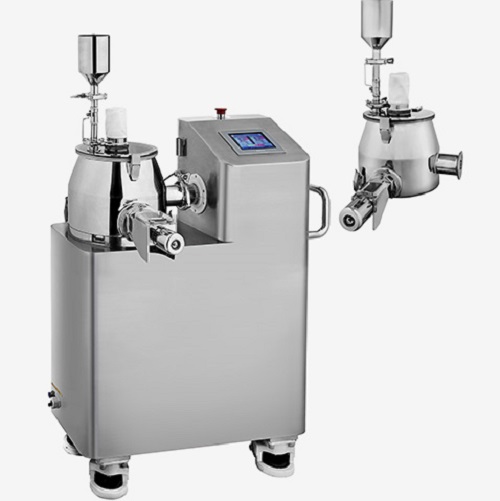
Entry-level high-shear mixer for drug formulation
For pilot and lab-scale pharmaceutical formulations, a high-shear granu...