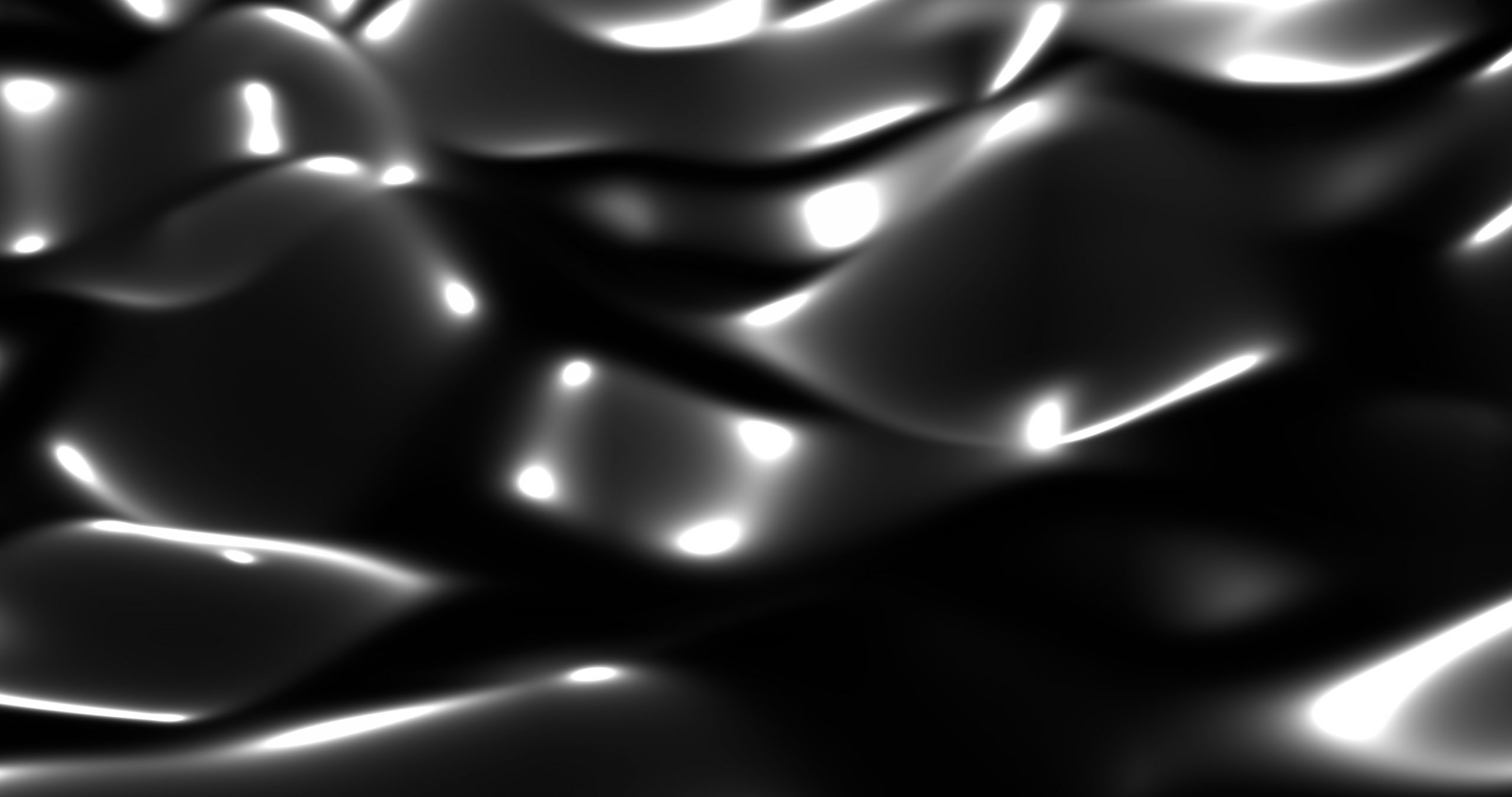
Making Latex
Find innovative production technology for making latex and connect directly with world-leading specialists
When he was in Haiti in 1493, Christopher Columbus noticed that the natives were bouncing on rubber balls made from the milky sap of Hevea brasiliensis, also known as a rubber tree native to South America. The milky sap was nothing but latex, the source material for natural rubber. Latex processing technology includes equipment for coagulation techniques and rollers for natural latex and a sequence of mixers, pumps, and sieves for synthetic latex.
Select your latex process
Tell us about your production challenge

The three faces of the milky liquid
Latex is a milky liquid with a composition of 45% water and 55% rubber concentrated just beneath the mature rubber tree bark, found in South America and Southeast Asia. It is a resistant, flexible, nonabrasive natural material with versatile use ranging from tennis shoes over mattresses to chewing gums.
In order to be manufactured, natural latex has to be made into sheets which is achieved by adding acid to clump the material so it can be rolled. When natural latex is farmed under the supervision and without the use of pesticides it is certified as organic. Synthetic latex, which is produced using petroleum-based chemicals, is used for paints, glues and cement as it tends to solidify once the water evaporates.
Natural latex or synthetic rubber?
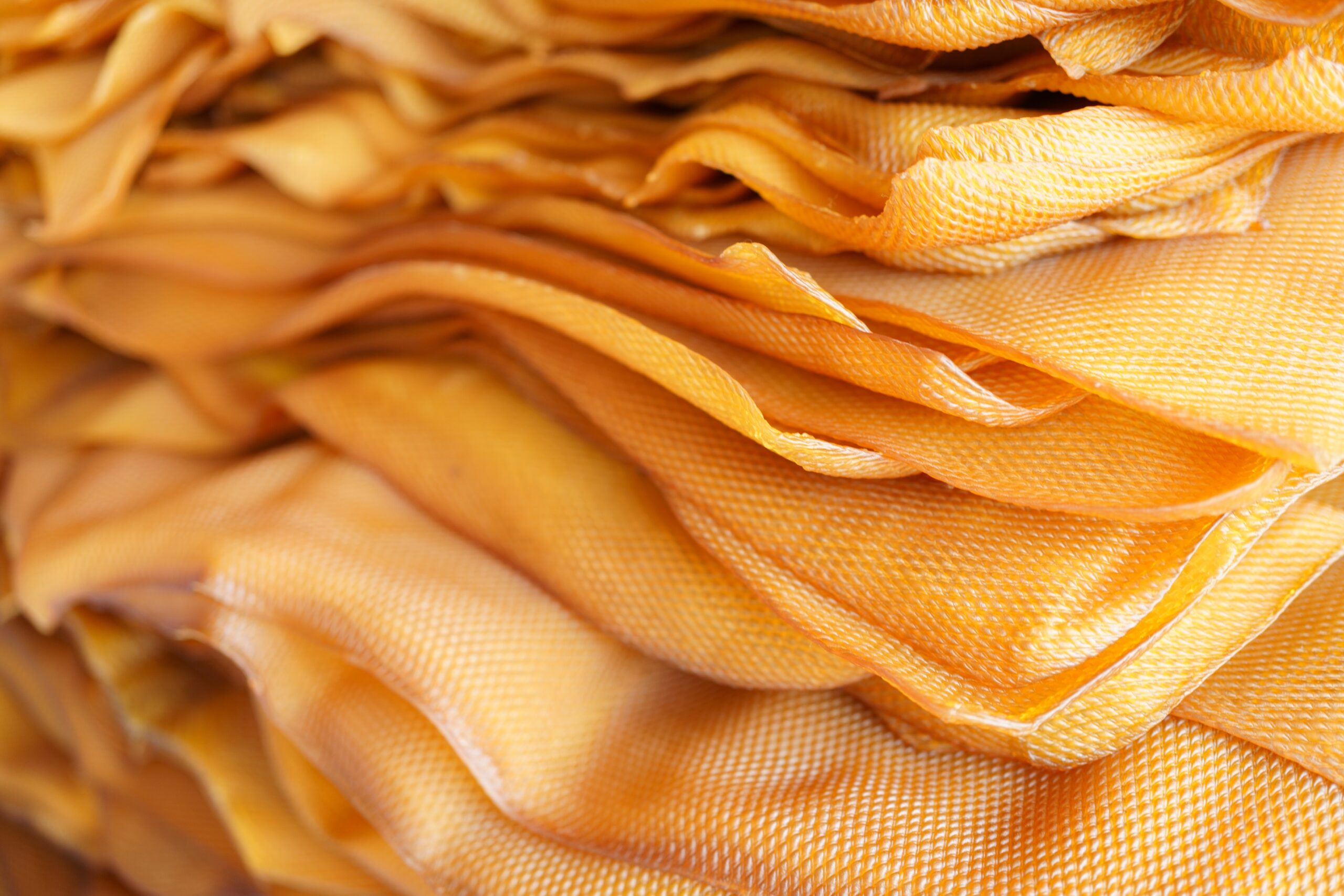
A focus on natural latex processing technology
Each rubber tree produces about half a cup of latex per day. It is harvested by cutting the bark of the rubber tree and accumulating it into cups. However, when mass-harvested, latex is stored in tanks. In order to extract solid rubber from the liquid latex, formic acid is added to the sap to initiate the coagulation process which can take up to 12 hours. The natural latex processing technology is fairly simple: the coagulated product is processed through a set of rollers in order to remove the excess water.
The dehydrated material is further rolled in a textured roller to create thin sheets. The latex sheets are dried by either smoking or air drying. Chemicals such as ammonia are used as a preservative for natural latex and the treatment is called prevulcanization.
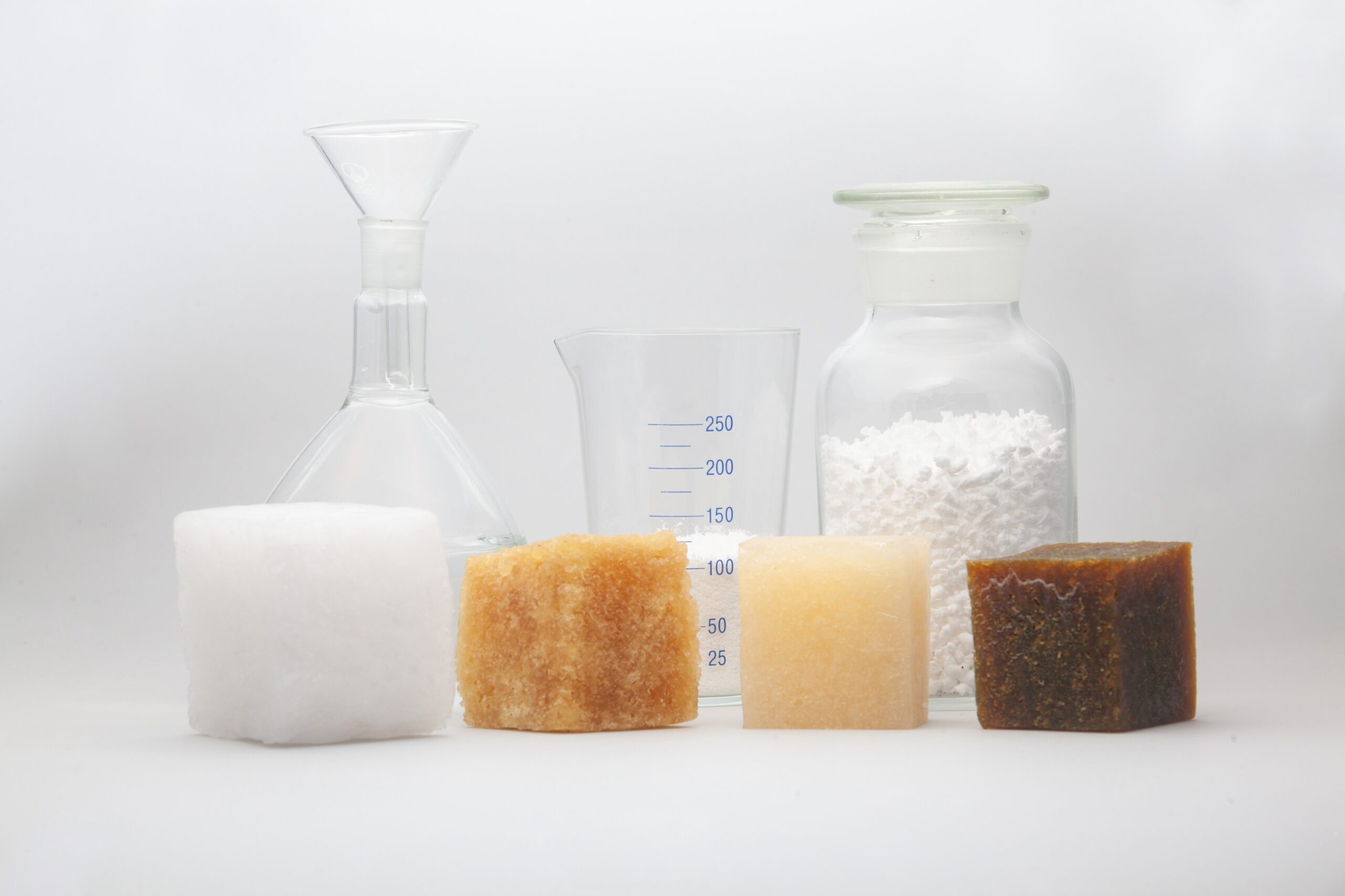
Polymerization process for synthetic rubber
Synthetic latex is composed of petroleum-based chemicals linked into molecules’ strings in a process called polymerization. The reaction is triggered by combining a flammable liquid hydrocarbon called naphtha with natural gasses to produce monomers. The role of the monomers is to form polymers by binding molecules together. But that’s not the end of the story; to get the rubber substance, chemicals must be added to create polymer chains.
Synthetic latex processing technology – beyond the chemistry
Combining the purified raw materials, butadiene and the solvent hexane, and a catalyst triggers a chemical reaction which results in a white milky liquid – synthetic rubber. Depending on the desired use, it can be treated with chemicals that are added in with the help of mechanized whisks and pumps. The mixture is piped into insulated storage tanks and mixed constantly. It is coagulated in big coagulation units by boiling out the solvent mixture.
Subsequently, the water is drained by using a series of rotary and vibrating sieves, and the mixture is dried on a quivering spiral conveyor. The dried crumbs are pressed into bales using a baler machine which are processed into the final product and desired shape by using techniques such as extrusion, molding and vulcanization. The extrusion process uses the extruder to heat and compress the material, molding techniques shape the rubber by using molds, while vulcanization adds accelerators such as sulphur to make polymers more enduring.
Dandelions: the evolution in latex industry?
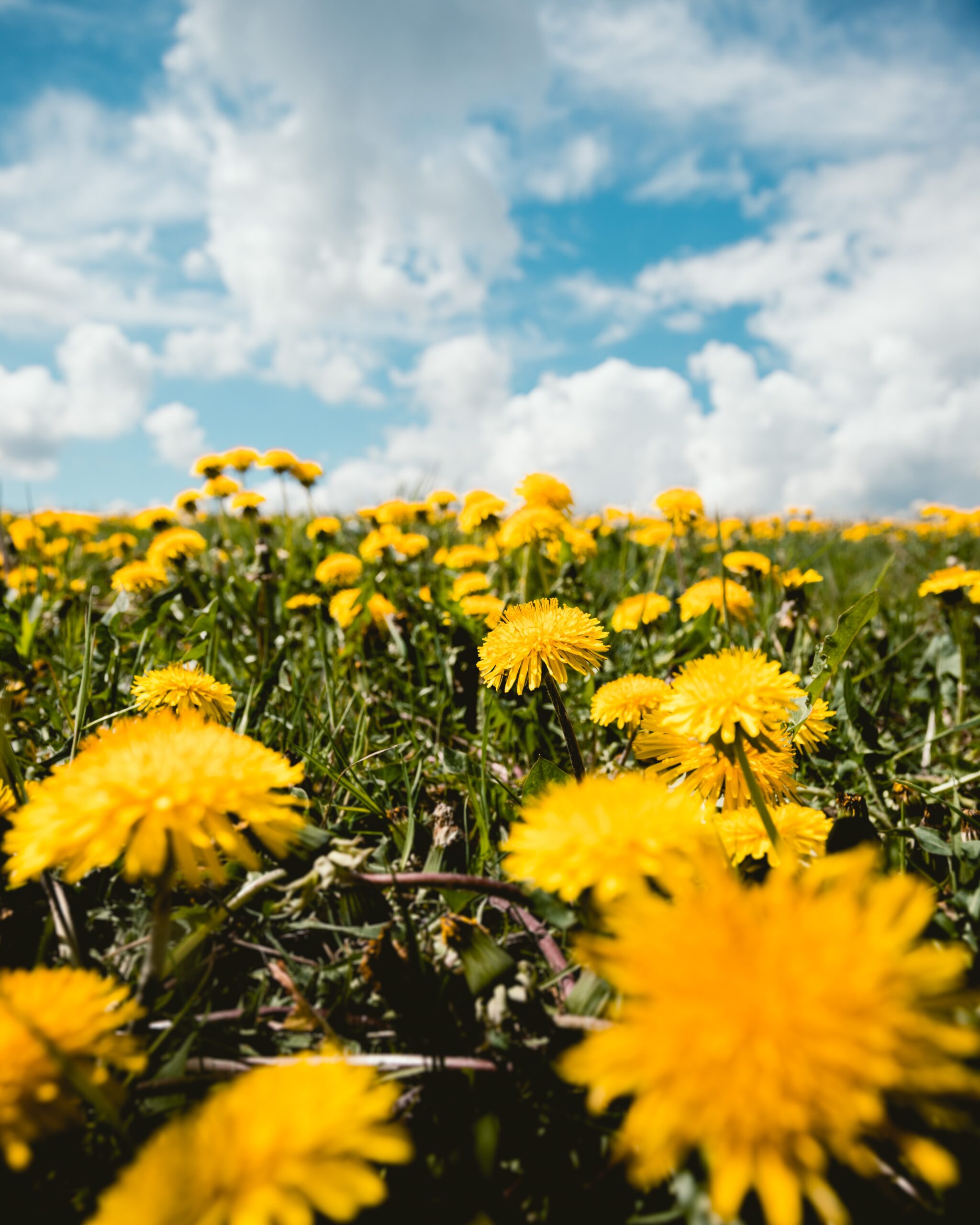
As a natural latex harvest annihilates forests and pollutes soil, air and water, as well as the trees being exposed to diseases and a shortage of workforce, scientists ought to find new, innovative yet more environment-friendly methods to produce latex.
As found in a study conducted by Wageningen University and Research and the Keygene company, one alternative method is extracting latex from flowers, namely dandelions, which contain a small amount of the latex needed to make rubber. In order to harvest latex from dandelion, Dutch scientists crossed the Russian dandelion, which has latex roots, with the Dutch dandelion for its size. Although the goal is to harvest 750 kilos of rubber per hectare, it is still a complex process that needs to be simplified to become profitable.
Processing steps involved in latex making
Which latex technology do you need?
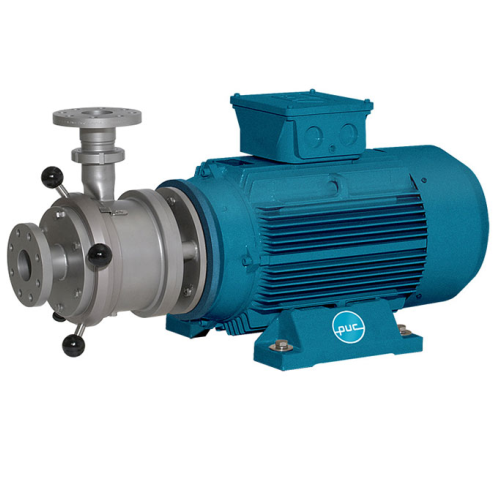
Colloid mill for emulsifying and wet milling applications
Achieve precise mixing and grinding with our colloid mill, des...
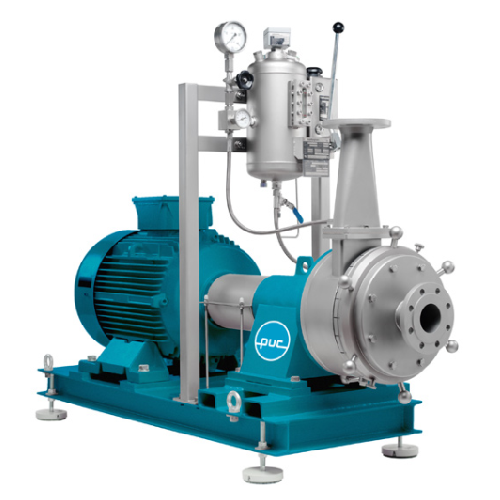
Horizontal colloid mill for precise grinding
Achieve precise particle size reduction and reproducible results with our adv...

Pre-mixer for dissolving powders fast
Quickly dissolve powders without lumps or “fisheyes,” ensuring a smooth a...
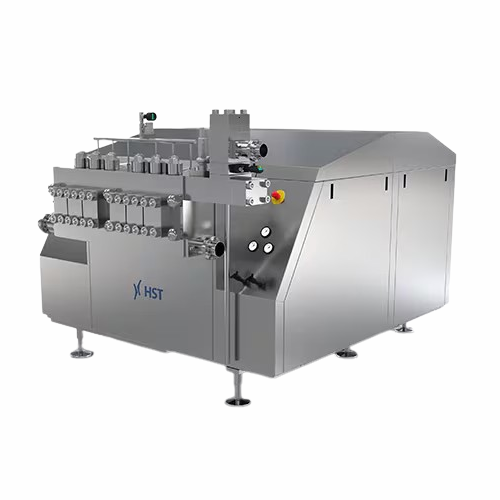
High-pressure homogenizers for liquid products
Achieve consistent emulsions and stable dispersions with high-pressure homo...
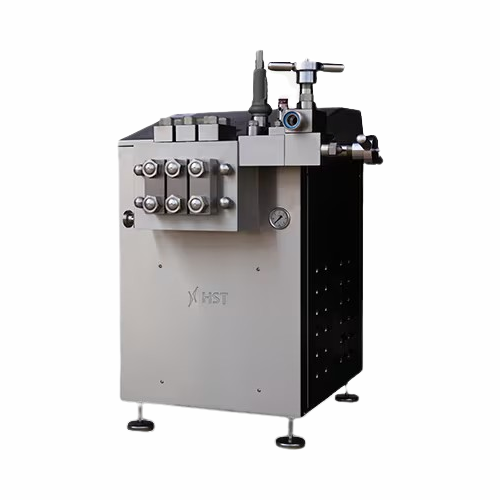
Homogenizer for high-pressure homogenization
Optimize your production with high-pressure homogenization, essential for ach...
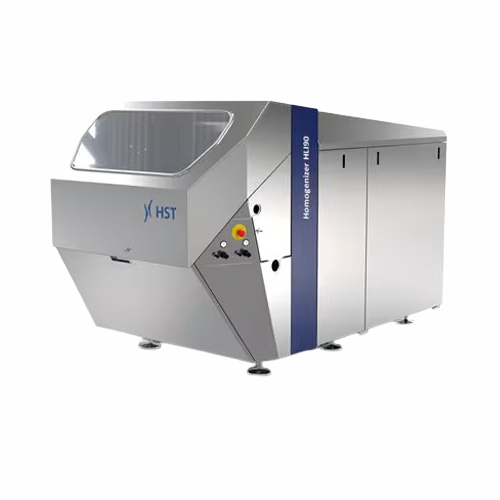
High-pressure homogenizer for food and pharmaceuticals
Achieve unparalleled consistency and stability in emulsions and di...
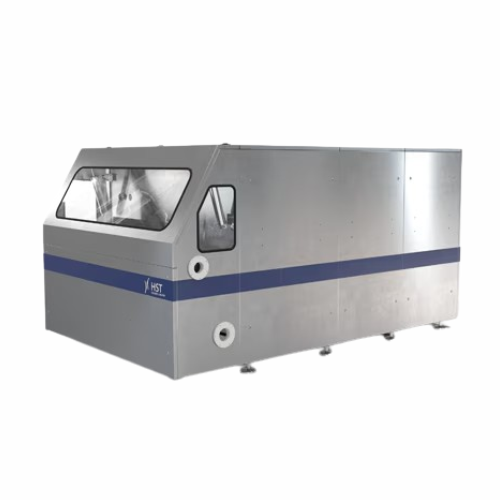
Homogenizers for high-pressure applications
Achieve unparalleled product consistency and stability with precision-engineer...
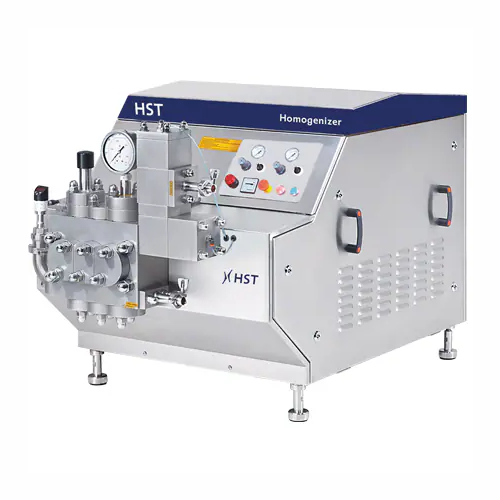
Industrial homogenizer for food and pharmaceutical applications
Ensure product consistency and stability with high-press...
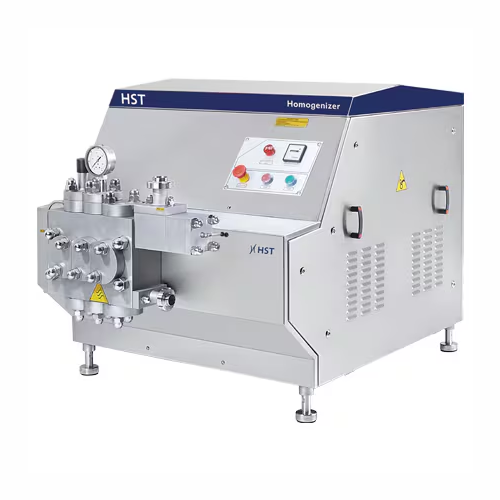
High-pressure homogenizers for dairy and food products
Achieve consistent texture and stability in your liquid products w...
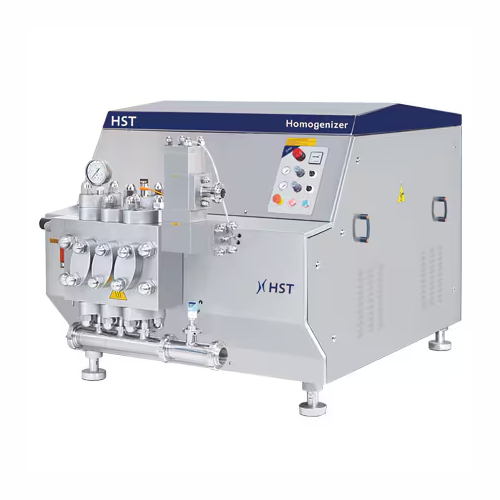
High-pressure homogenizers for dairy and beverage industries
Achieve precise emulsion stability and consistent particle ...
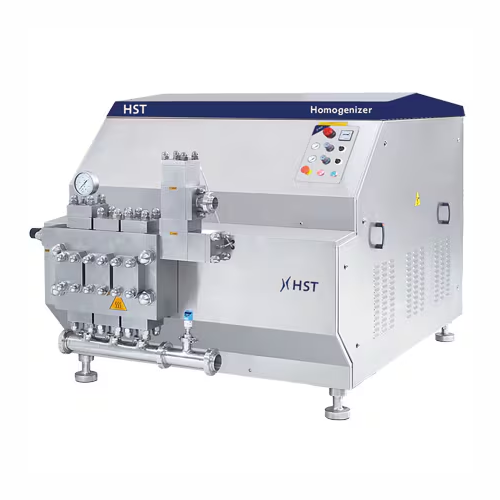
High-pressure homogenizers for dairy and juice processing
Ensure superior texture and stability in your liquid formulati...
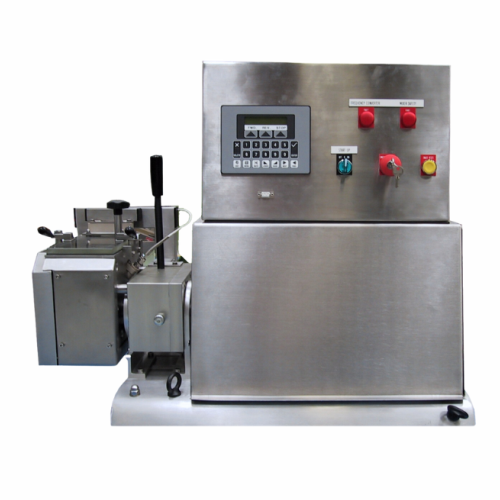
Laboratory z-arm kneader for high-viscosity materials
Ideal for R&D, this advanced Z-arm kneader efficiently handles...
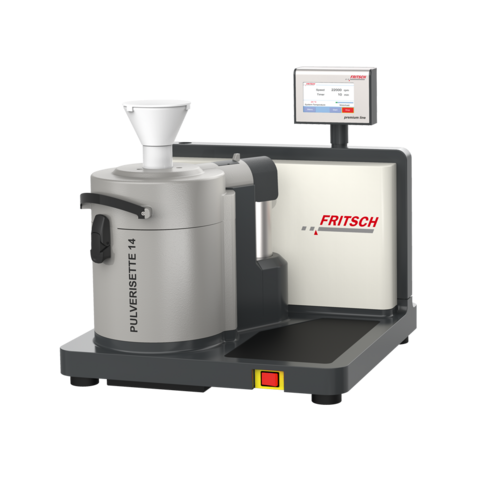
Variable speed rotor mill for sample preparation
Achieve rapid and precise grinding of various materials with a versatile ...
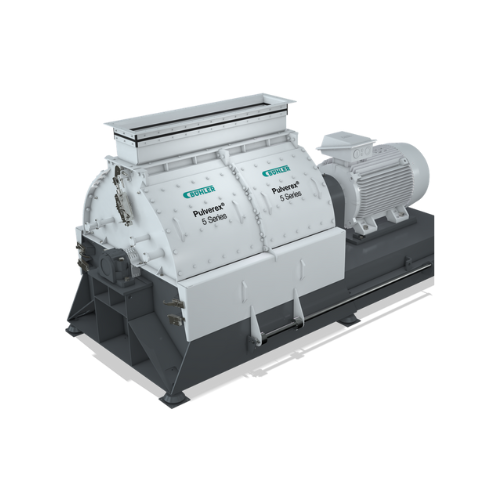
Pulverizer for fine grinding applications
Achieve optimal particle size distribution and enhance throughput with this adva...
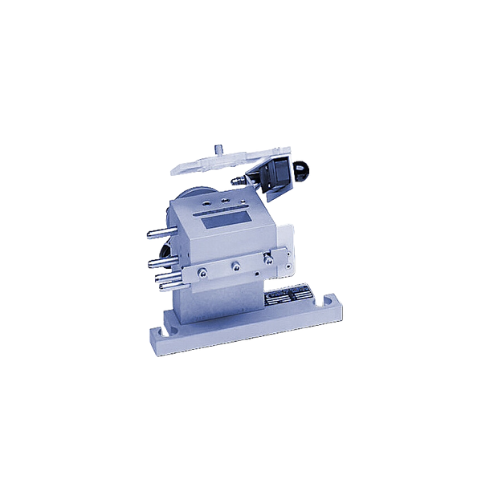
Measuring mixer for small grain samples
Optimize the precision of your formulation processes with a solution designed for p...
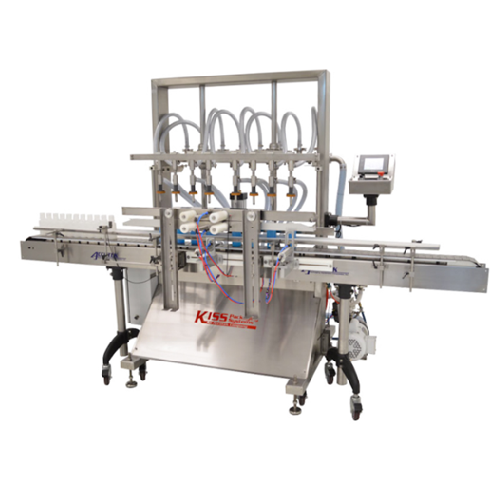
Automatic pressure overflow filler for low to medium viscosity liquids
Ensure consistent fill levels for low to medium ...
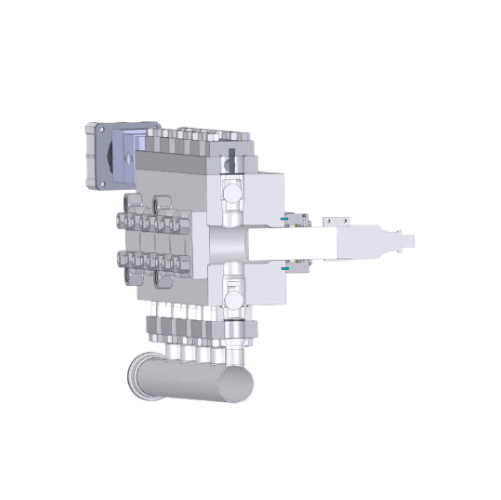
High pressure homogenization for polymer nanodispersions
Effortlessly handle challenging products with fibers or solid pa...
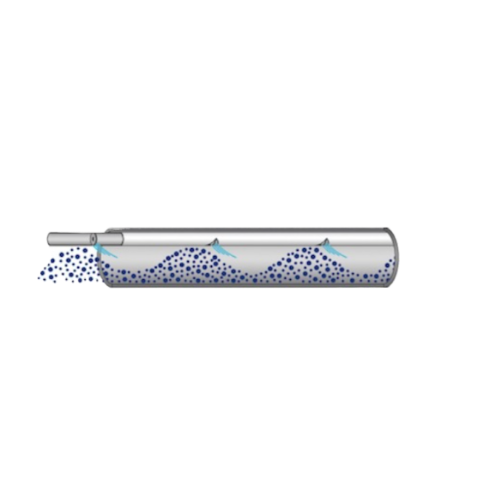
Pta and Pet production systems
Maximize throughput while minimizing dust fines in your production of PTA and PET pellets wit...
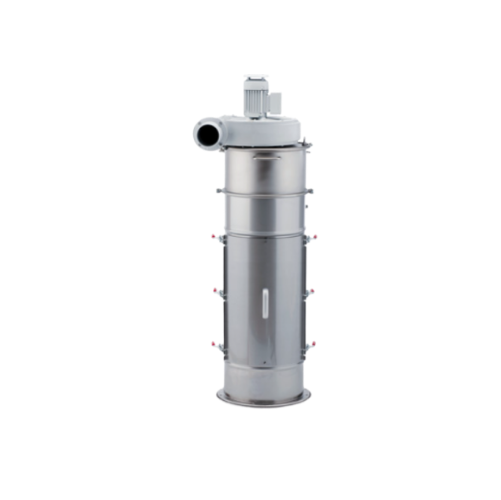
Industrial fine dust particle ventilation filter
Optimize your production line with a modular filtration system designed t...
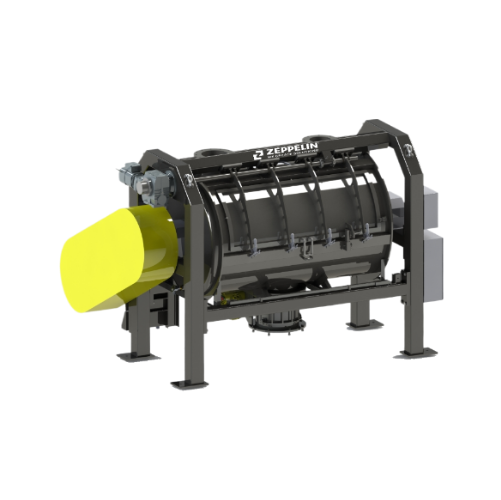
Horizontal homogenizing mixer for all-purpose applications
Achieve uniformity and consistency in your products with a ve...
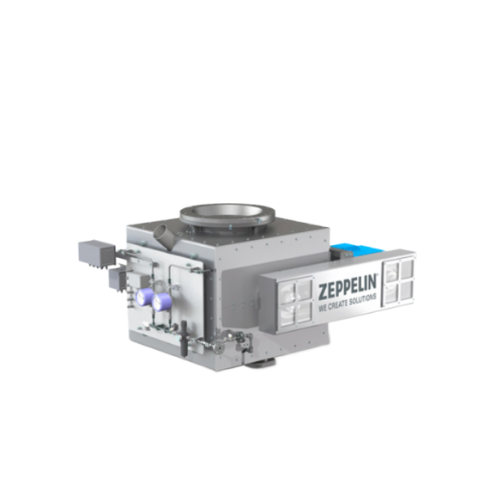
High-pressure rotary feeder for bulk material handling
Manage high-pressure bulk material distribution with precision, en...
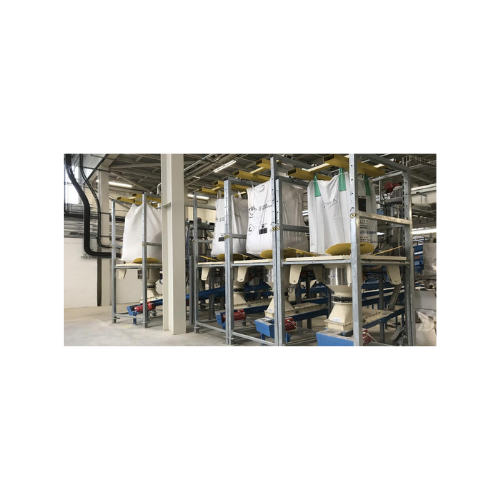
High flow rate Fibc dischargers for wastewater treatment
Optimize your material handling with efficient, dust-proof disch...
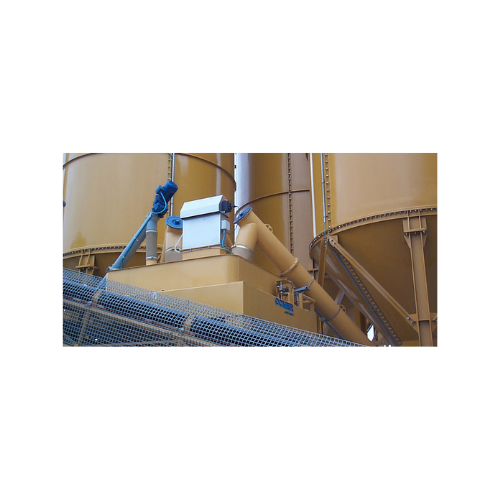
Hopper venting filter for efficient dust filtration
Achieve superior dust control and efficient material handling with a ...
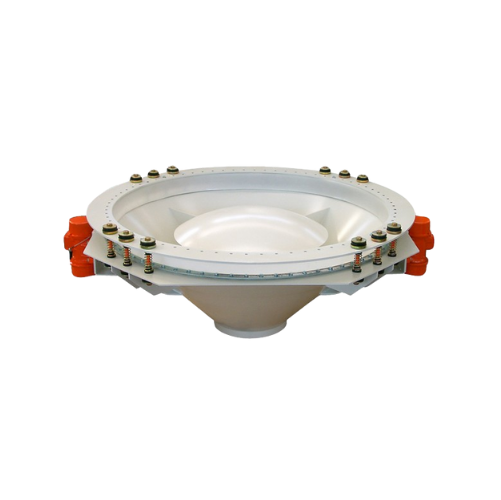
Vibratory hopper for bulk solids discharge
Ensure consistent material flow and prevent bridging in storage silos with this...
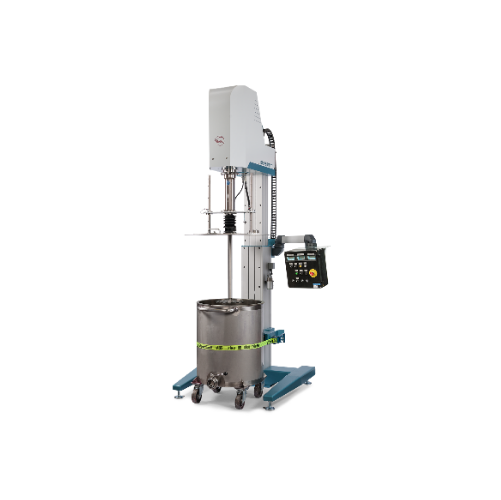
High-performance dissolver for large-scale production
Optimize your production line with precision-controlled dispersion ...
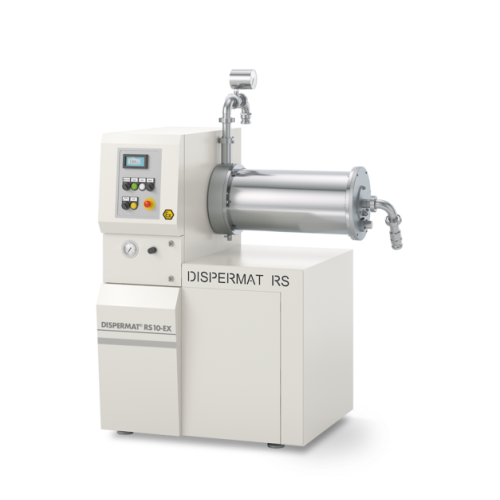
Explosion-proof bead mill for industrial grinding applications
For manufacturers seeking precise particle size control, ...
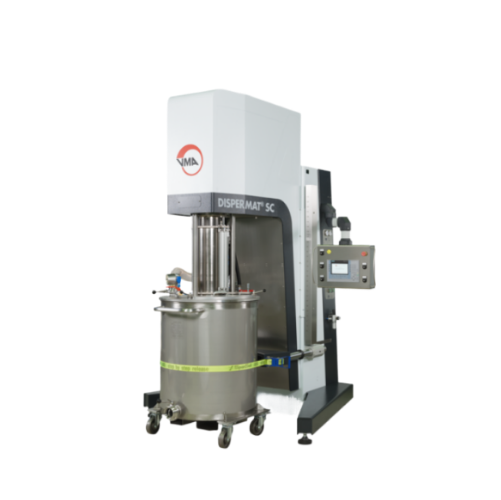
Modular basket mill for industrial dispersion
Effortlessly enhance your production efficiency with this versatile solution...

Industrial basket mill for medium viscosity products
Achieve precise particle size reduction and rapid pigment dispersion...
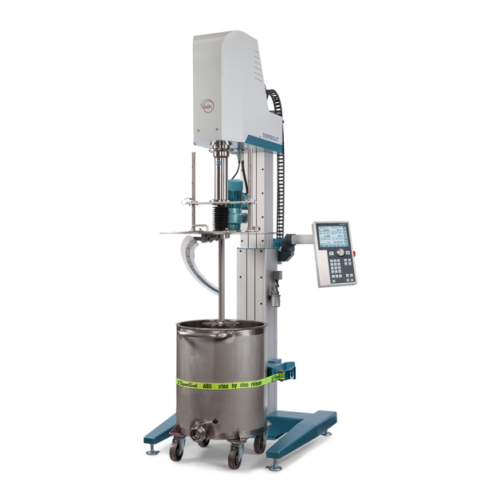
Dissolving system for high-viscosity products
Optimize the dispersion of high-viscosity liquids and pastes with this versa...
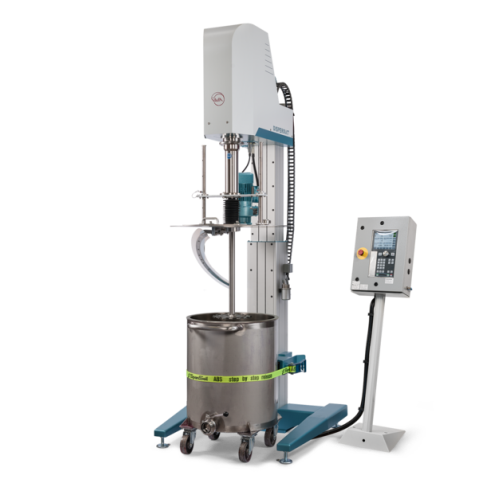
Explosion-proof dissolver with scraper for high viscosity substances
Ensure flawless dispersion with enhanced safety, d...
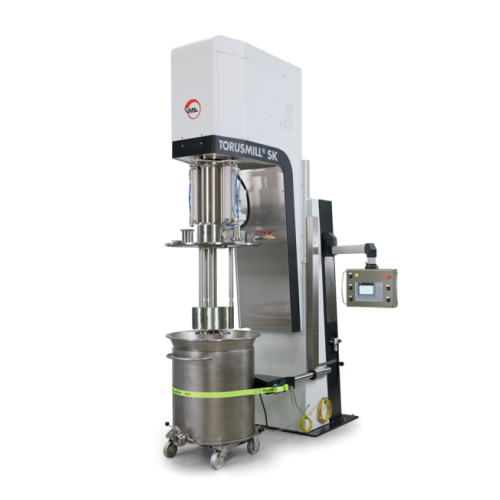
Vacuum basket mill for high-viscosity product milling
Achieve refined particle size and smooth texture in your high-visco...
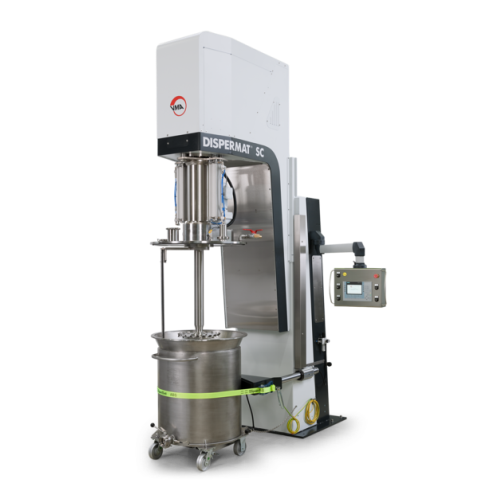
Explosion-proof vacuum disperser for high-viscosity substances
Achieve precise dispersion and eliminate air inclusions w...
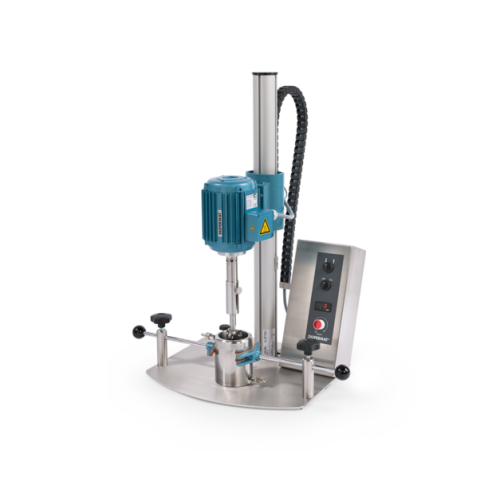
Laboratory stirrers for high viscosity materials
Efficiently mix and stir high-viscosity materials with ease, enabling pre...
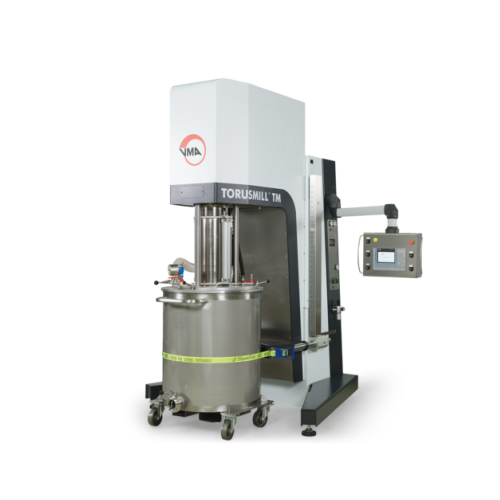
Dissolver for high-volume industrial dispersion
Achieve precise and efficient mixing with this dissolver, designed for sea...
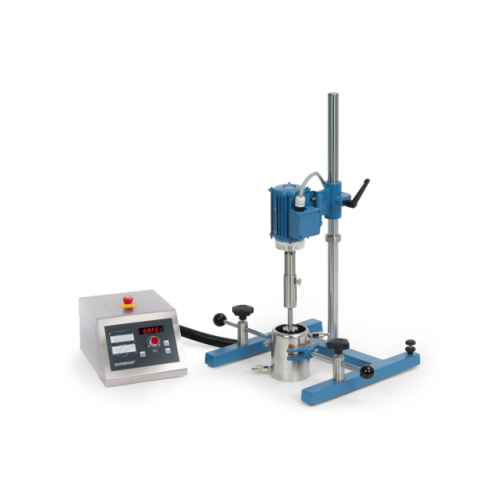
Lab and pilot plant dissolver for dispersion and fine grinding
Achieve efficient dispersion and fine grinding in laborat...
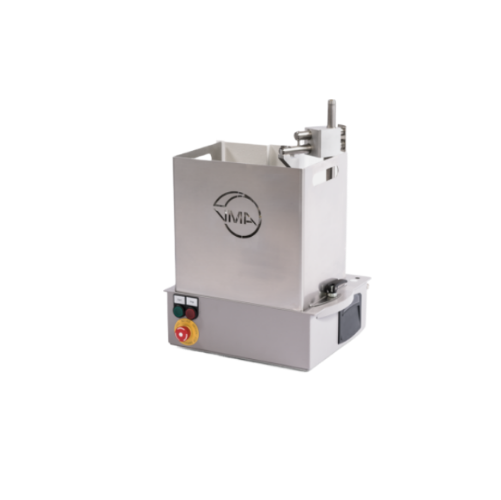
Industrial dissolver for high-viscosity materials
Efficiently disperse and mix high-viscosity materials with precision, e...
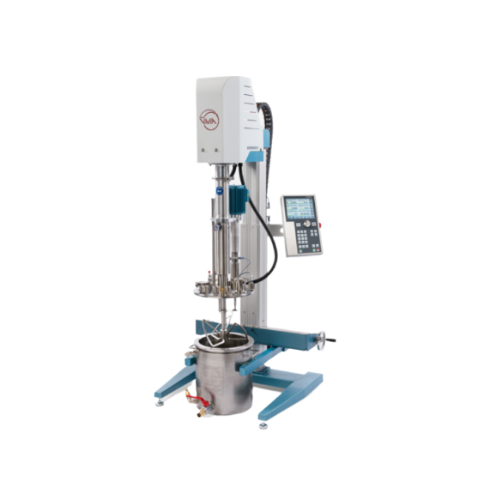
Vacuum dissolver for highly viscous products
Efficiently mix and disperse high-viscosity substances under vacuum to ensure...
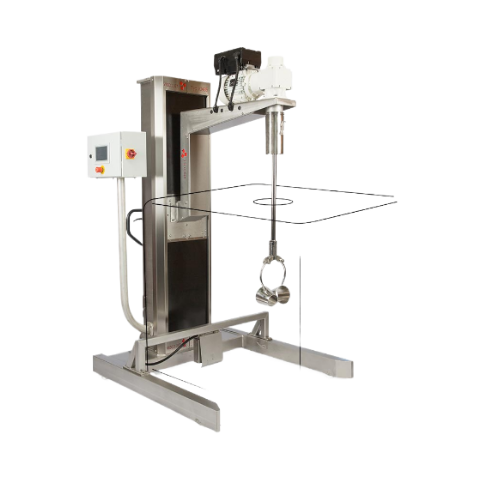
Industrial stativ mixer with adjustable height
Achieve precise mixing and stirring across diverse batches with a mobile, a...
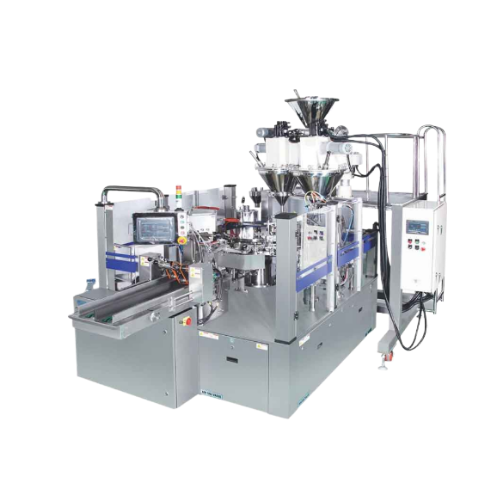
Automatic rotary filler and sealer for premade pouches
Enhance your production line efficiency with a dual-lane system th...

Robotic packaging integration for automated systems
Enhance your production line efficiency with seamless robotics integr...
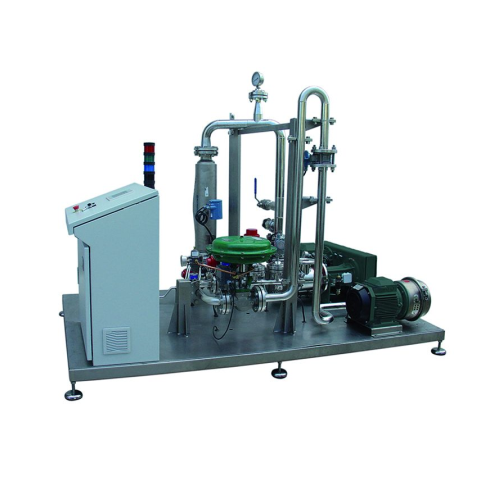
Complete mixing systems for industrial applications
Optimize your production efficiency and product consistency with adva...
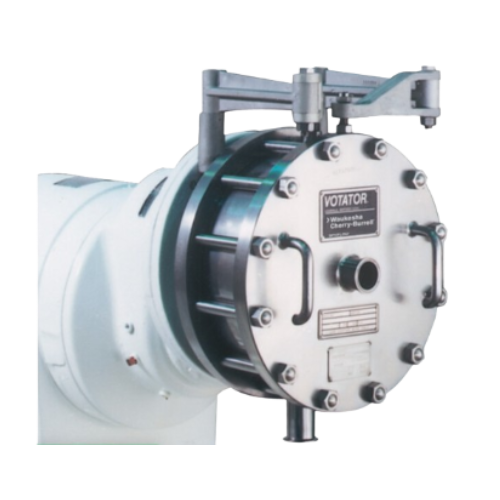
High-shear mixer for emulsions, dispersions, and foams
Achieve precise emulsions and dispersions effortlessly with high-s...
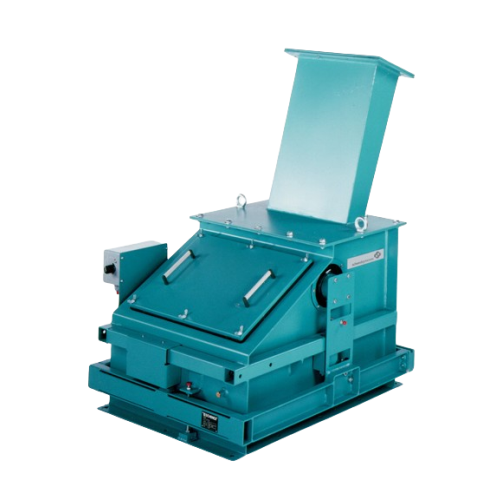
Solids flow meter for bulk solid streams
Ensure precise bulk material measurement with a system designed for accuracy and r...
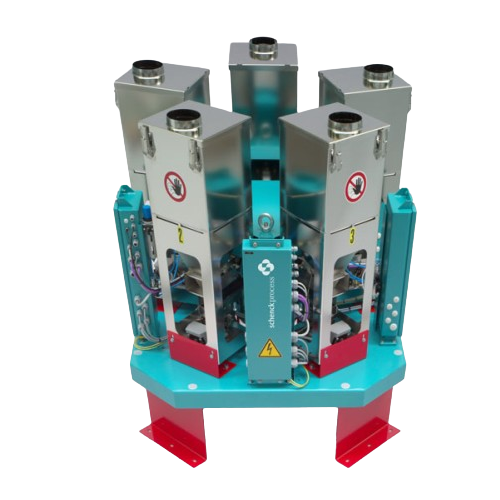
Multipurpose feed station for bulk solids
Optimize your production line with a versatile feeding station designed for simu...
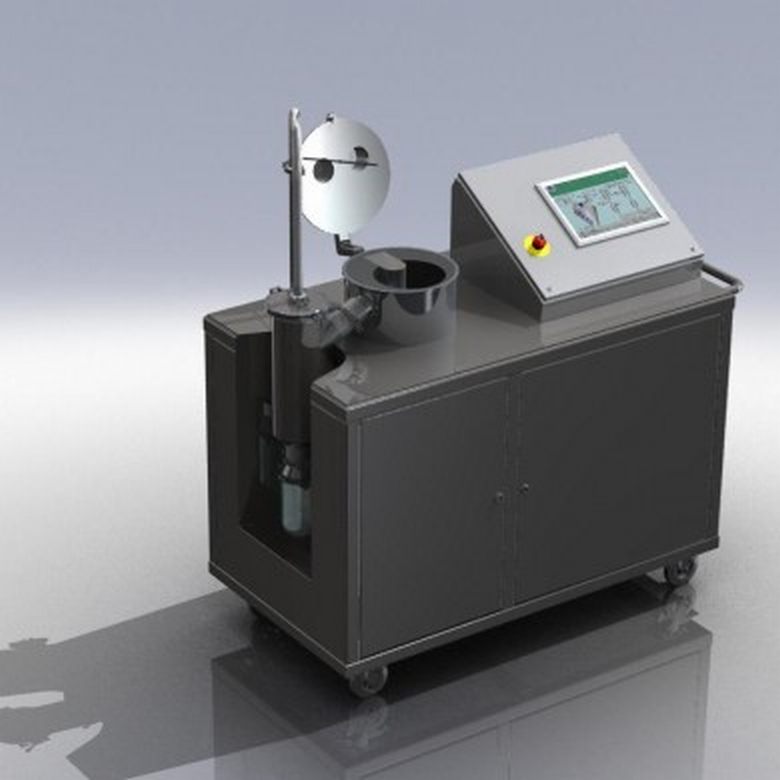
Laboratory scale active freeze dryer
The laboratory-scale active freeze-drying is used for dehydrating high-value products ...
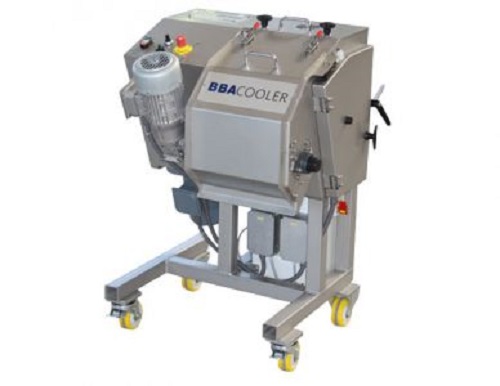
Drum cooler for laboratory hot melt processes
Do you need to cool molten masses to solid, thin film or flakes in an R&...
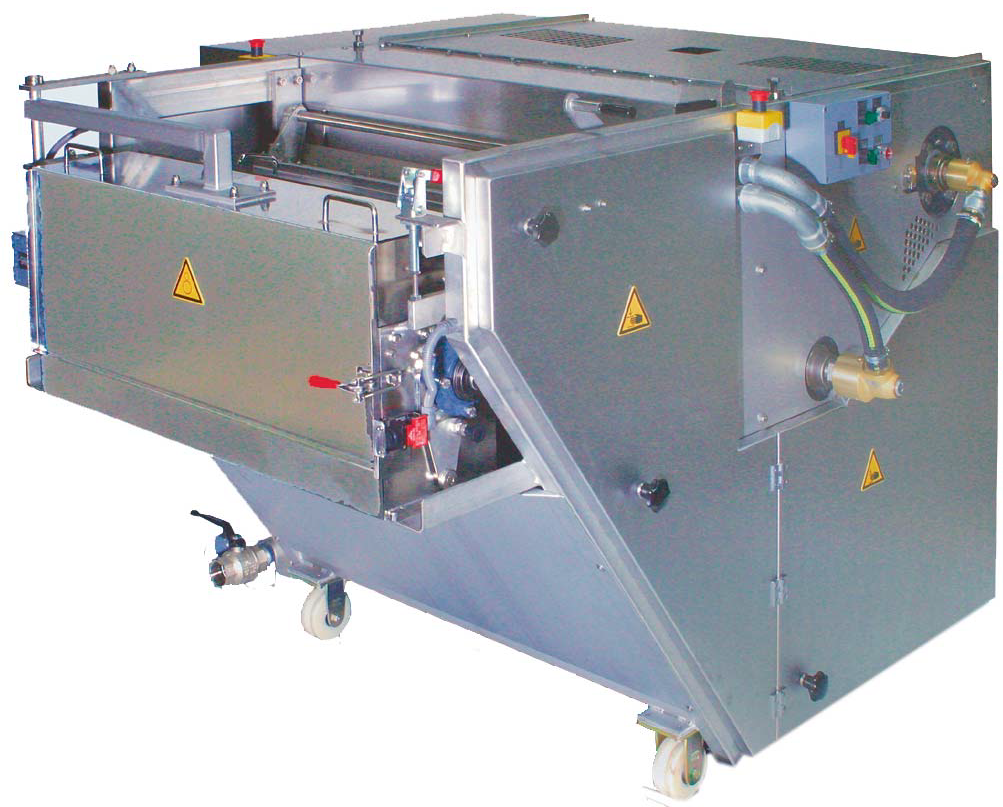
Drum cooler for hot melt processes
Medium-scale production of extruded hot melt masses benefits from reliable, efficient co...
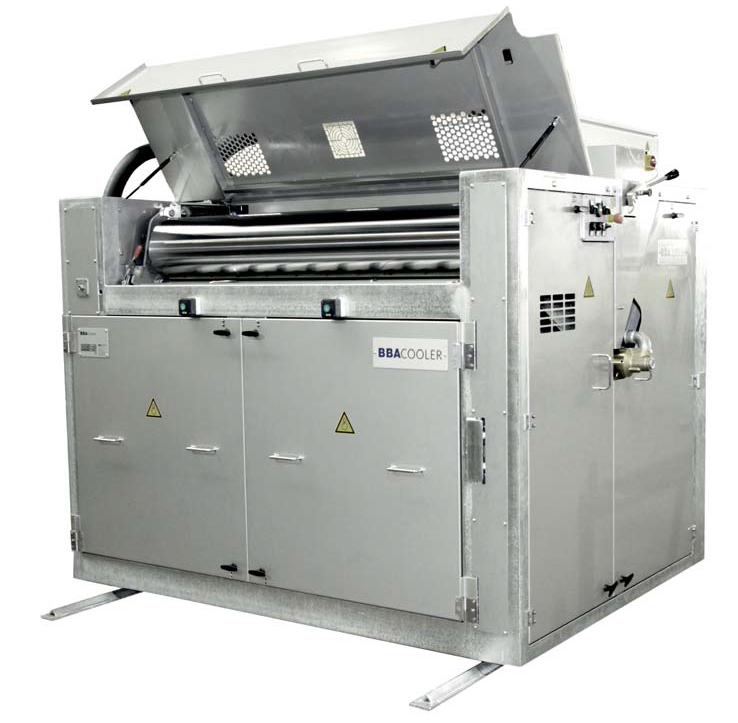
High capacity drum cooler for hot melt extrusion
Large scale cooling and extrusion of hot melt products on a continuous ba...
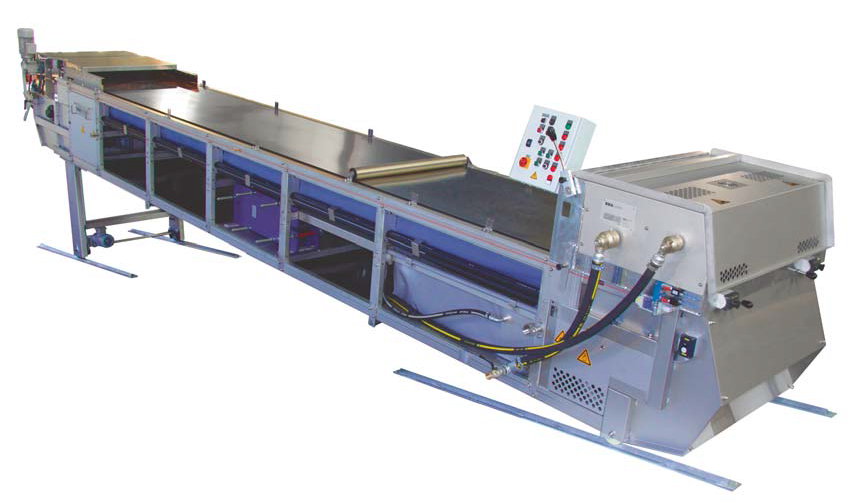
Steel belt cooler for hot melt extrusion
For producing high volumes of extruded hot melt product a flexible, high capacity ...
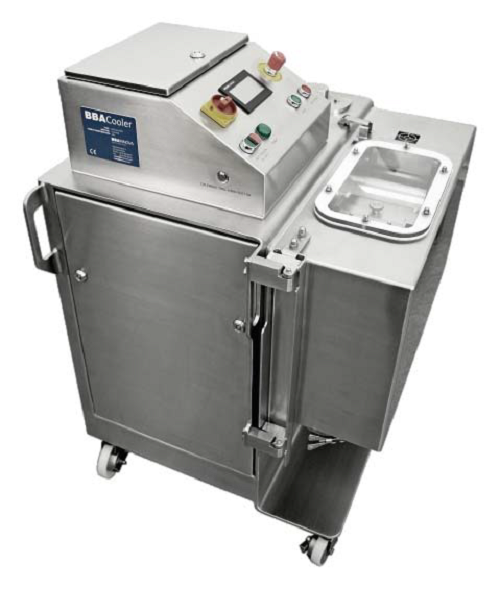
Laboratory GMP cooler for hot melt extrusion
Pharmaceutical R&D and laboratory extrusion of viscous hot melt masses re...
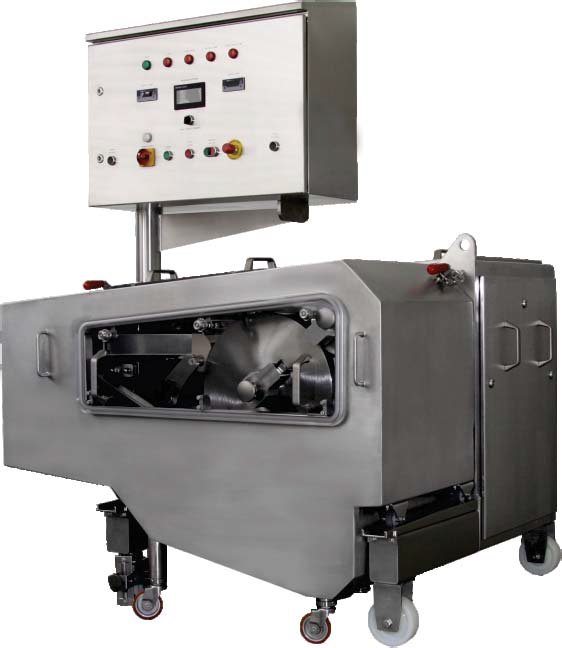
GMP cooler for hot melt extrusion
Pharmaceutical production of extruded hot melt masses requires a GMP designed, FDA approv...
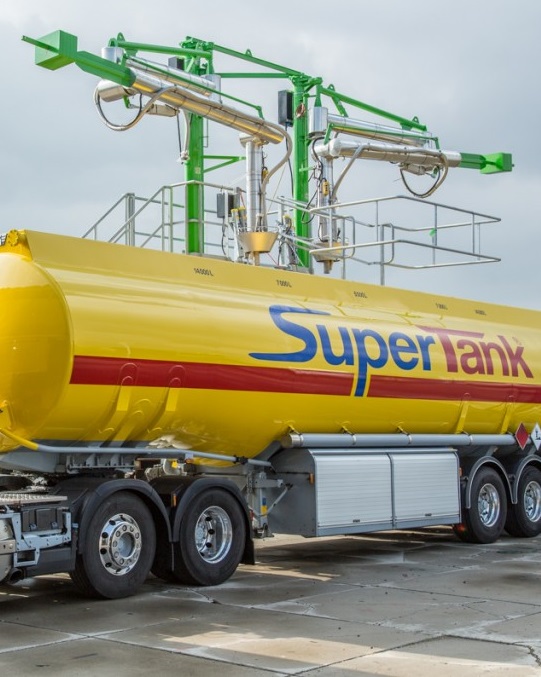
Top loading arm
Load or unload liquids from the top of the tanks safely and securely for trucks, railcars, small or big contai...
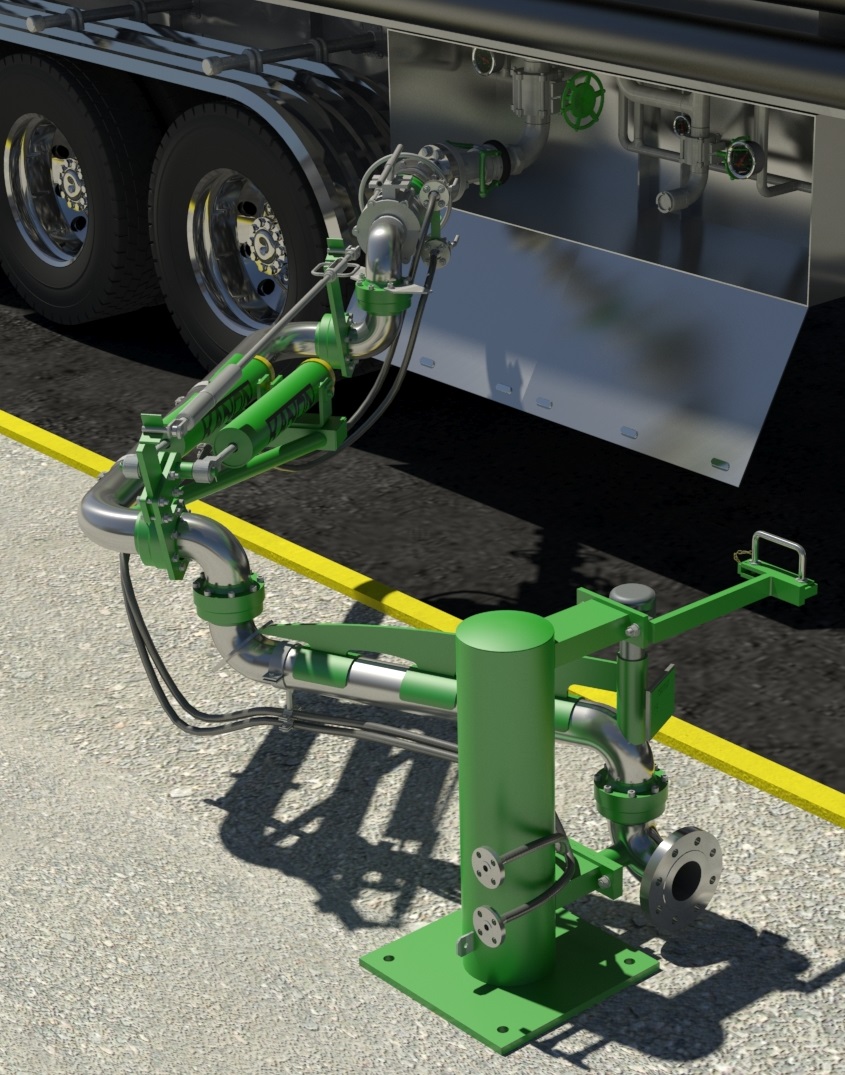
Bottom loading arm
Bottom loading/unloading arms are designed to be connected on the side or on the rear of the tanker and so...
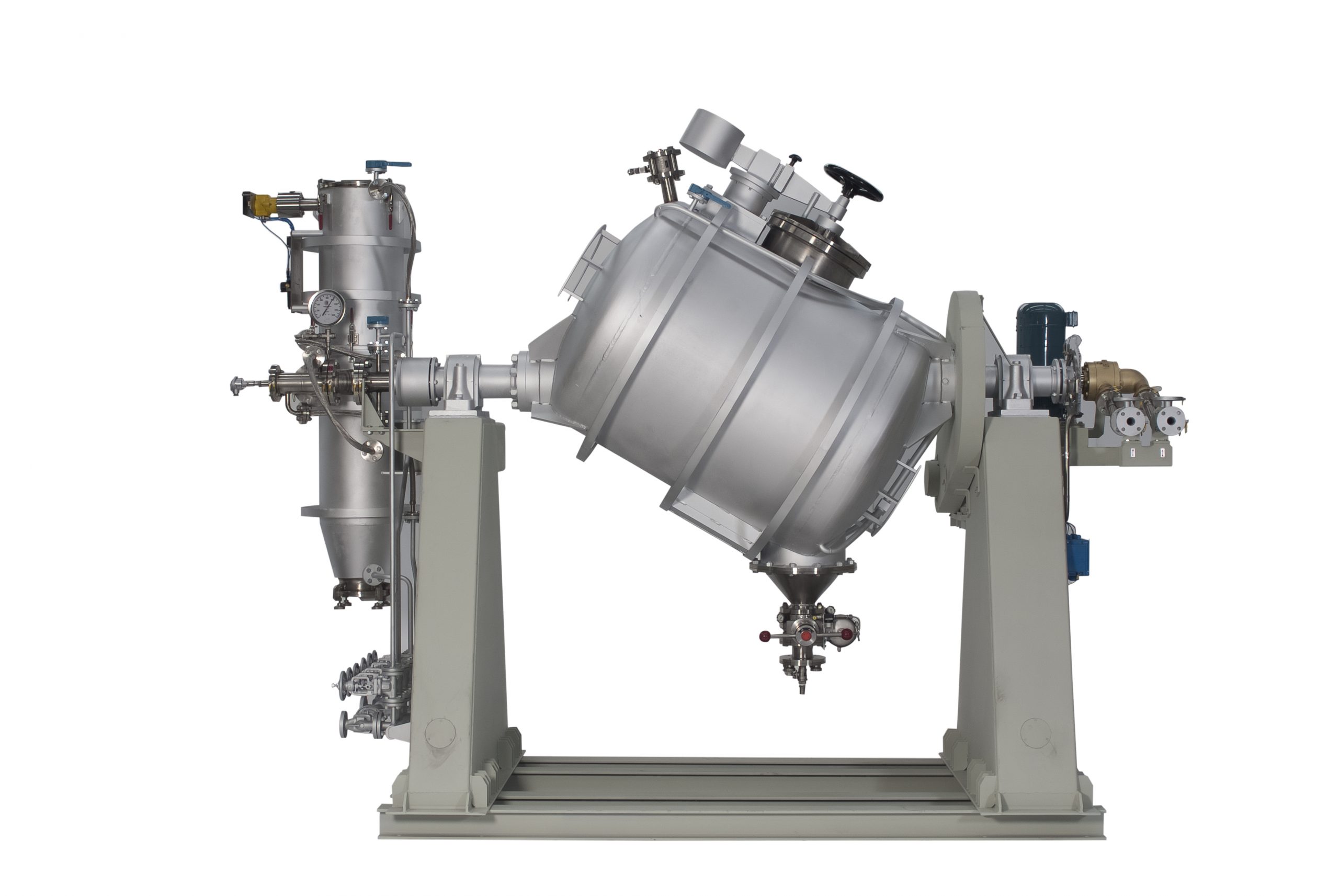
Tumble dryer for granulated plastics
Vacuum drying at high temperatures is important in the production of granulated plasti...
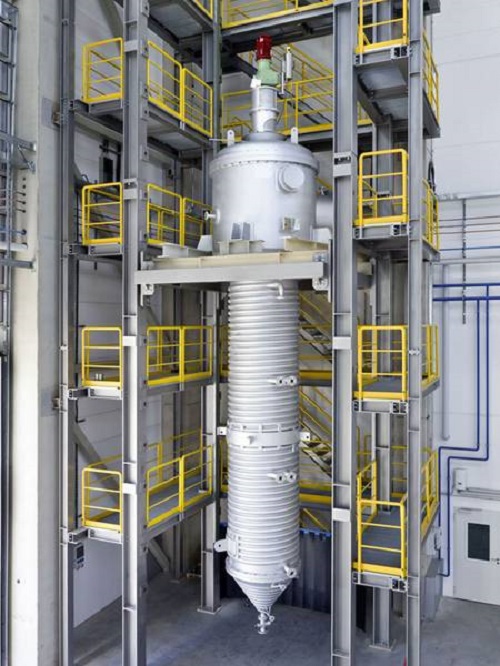
Wiped film evaporator
With wiped film distillation, a substantial decrease of boiling temperature is obtained by reducing the...
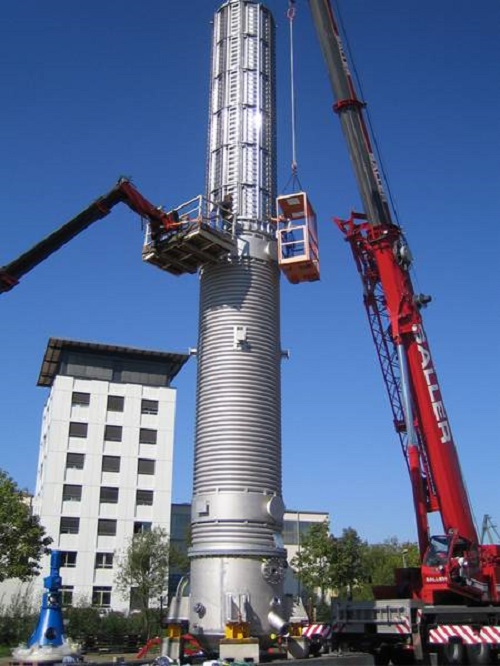
Short path evaporators
With short path distillation, a substantial decrease of boiling temperature is obtained by reducing th...
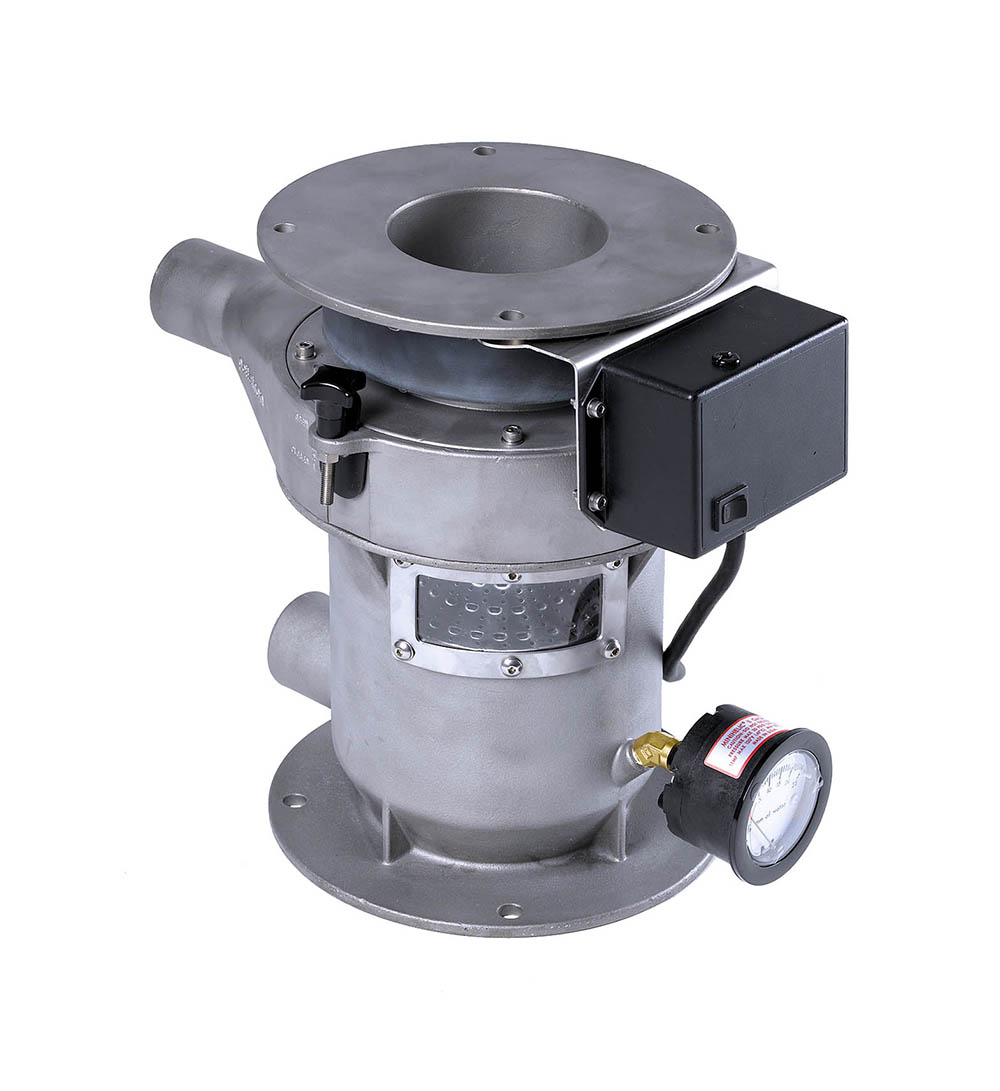
Small scale deduster for plastic granules
Industries that use bulk plastics see better product quality and decreased equip...
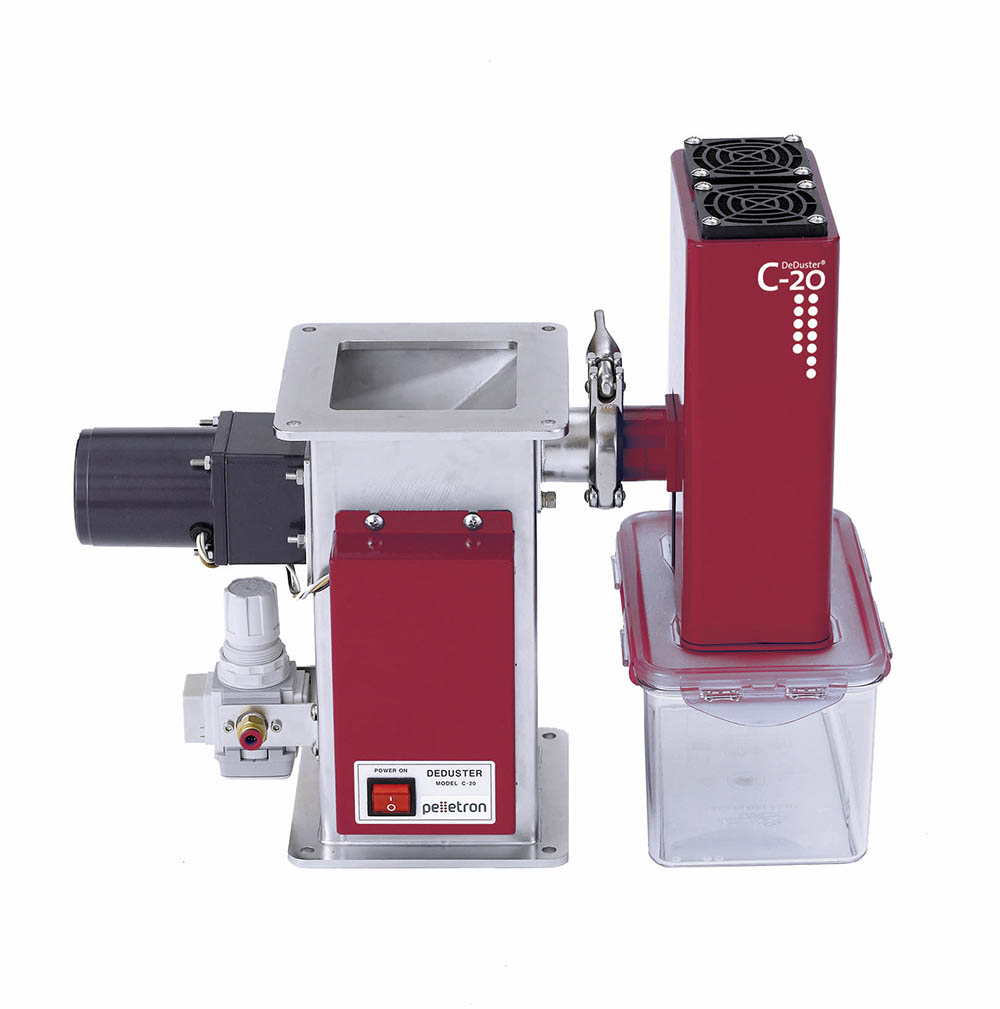
Deduster for injection moulding
High quality injection molded plastic parts require clean bulk resins free of dust and strea...
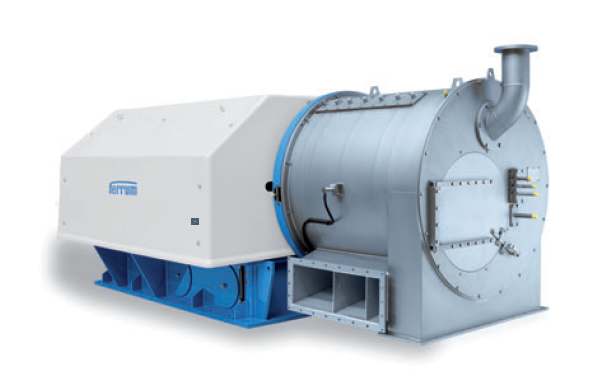
Pusher centrifuge
Pusher centrifuges are continuously operating filter centrifuges and can have several basket stages dependi...