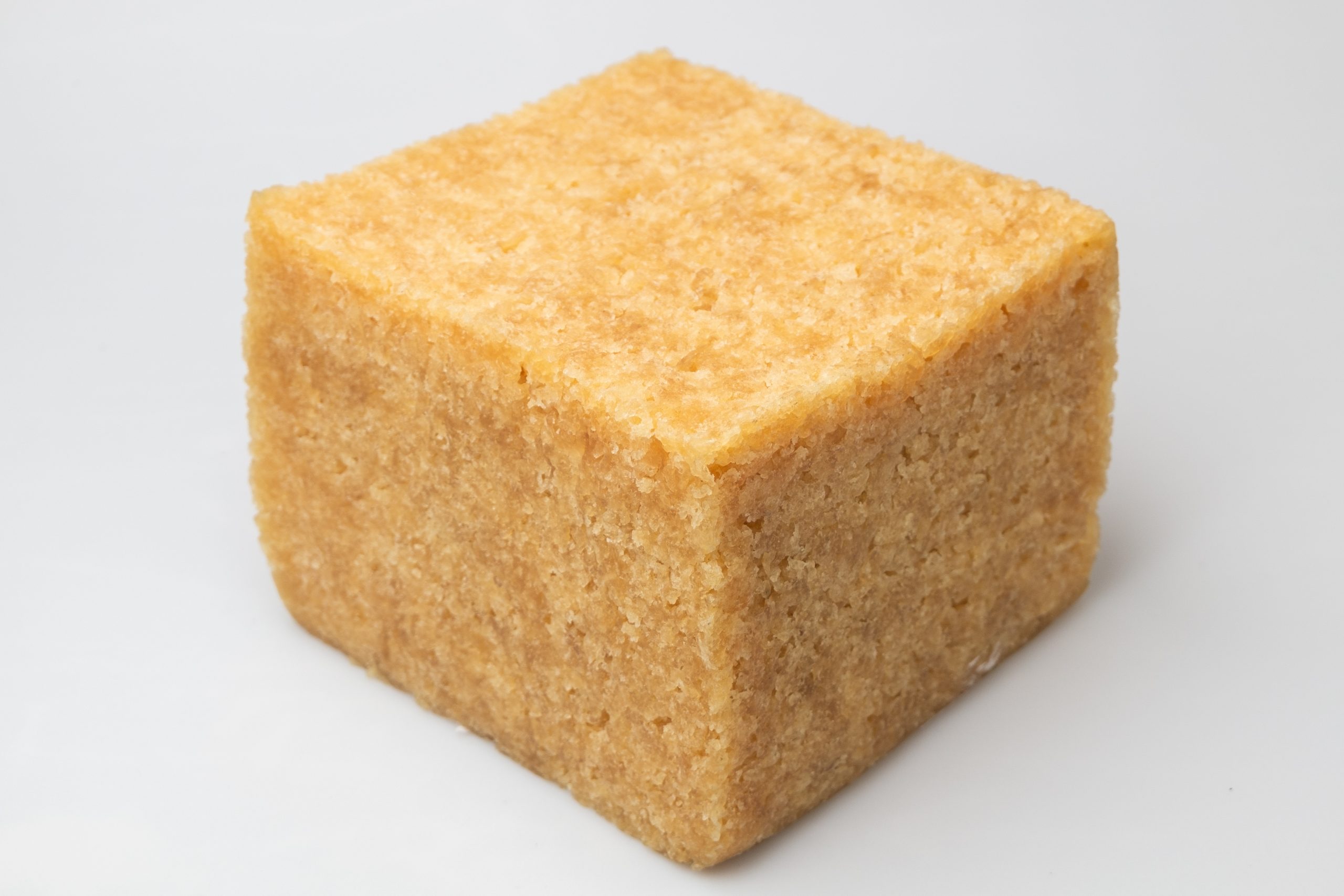
Making Synthetic Rubber
Find innovative production technology for making synthetic rubber and connect directly with world-leading specialists
As traced back to the first half of the 19th century, attempts at synthetic rubber production were simply to reproduce the original material due to the rubber shortage following World War II. Synthetic rubber production processes differentiate between producing the rubber, which can be done via solution polymerization and emulsion polymerization and creating the final product with the help of techniques such as molding and vulcanization.
Tell us about your production challenge

What is synthetic rubber?
Generally speaking, synthetic rubber is any artificial elastomer. In technical terms, it is a chain of polymers synthesized from petroleum byproducts. Unlike natural rubber, synthetic rubber can withstand high temperatures, as well as be more durable and resilient. There are about twenty different chemicals used for synthetic rubber production, which yields a large number of synthetic rubber types, for instance, neoprene, EPDM, SBR, butyl rubber, fluoroelastomers, silicone and Buna N rubber.
Solution and emulsion polymerization – the two synthetic rubber production methods
The synthetic rubber production process starts with combining naphtha and natural gas resulting in monomers such as styrene and isoprene that undergo either emulsion polymerization or solution polymerization.
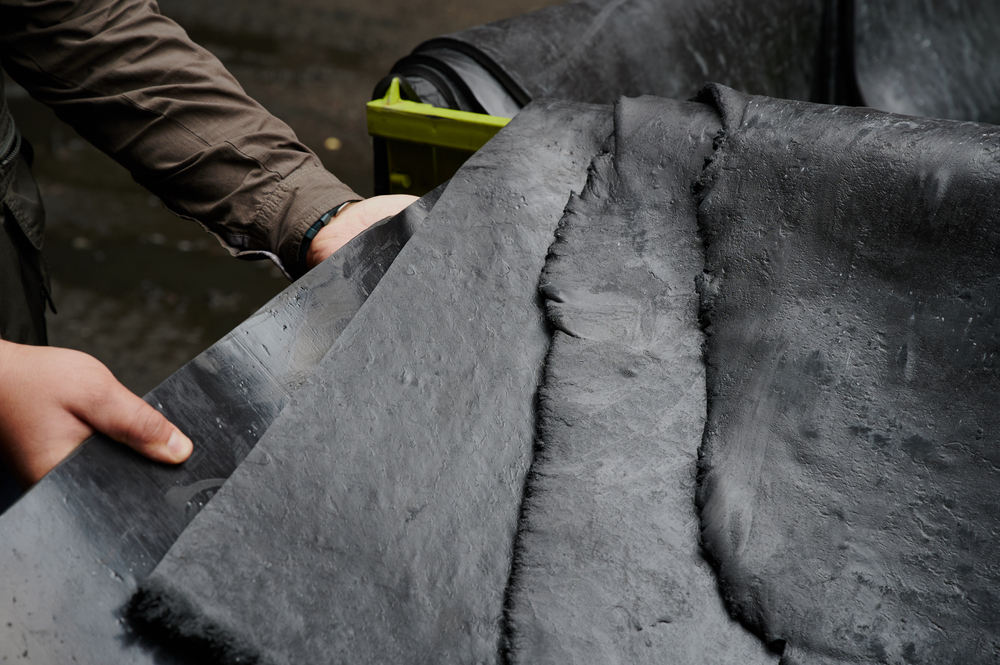
Solution polymerization is a reaction process in which a monomer is dissolved in a solvent, either cyclohexane or hexane, and polymerization is carried out by adding alkyl lithium as an initiator. Polymerization is executed at the temperature of 50-100°C and the period lasts for 60 minutes. The coupling agent used in this process is silicon tetrachloride. Furthermore, the flash desolvation is carried out by adding an anti-aging agent once the temperature reaches 90~100 °C and concentrating the glue at 20%. The flashed concentrated glue liquid is then transferred to the buffer tank and blended. Finally, the remaining solvent in the product is eliminated by using a squeeze-type liquid separator.
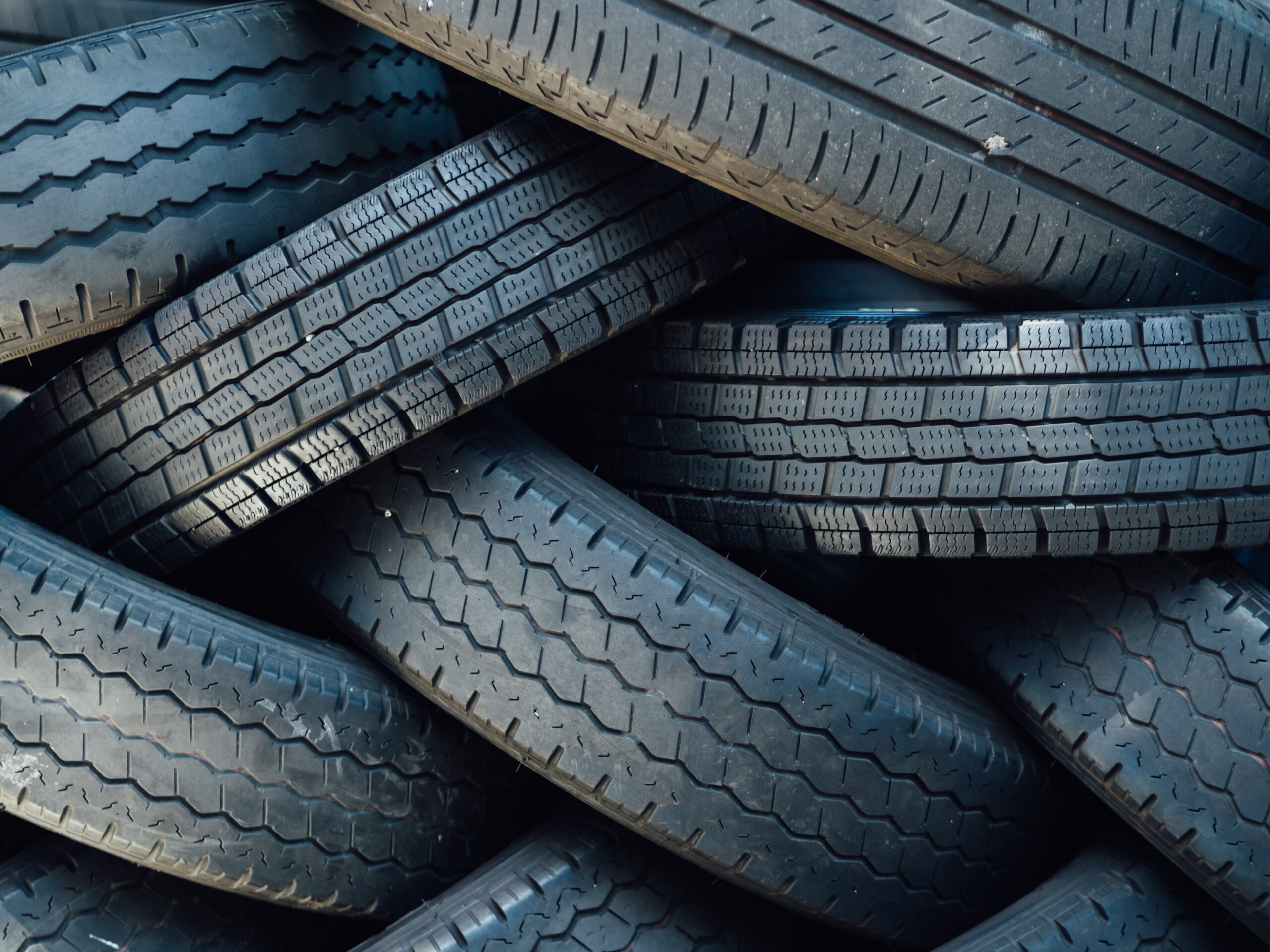
On the other hand, emulsion polymerization is commonly used for copolymer rubbers. The emulsion is created by adding water and an emulsifier prepared from rosin acid and sodium fatty acid soap in a proportionate mixture of monomeric butadiene and styrene. Although, at first, the polymerization temperature is 40-50 °C, in later stages it is controlled at 5-10 °C, which is perfect to start the polymerization reaction which is terminated once it reaches the 60% conversion rate. The post-treatment includes heating and dehydration, similarly to the solution polymerization process.
Manufacturing processes of synthetic rubber: compounding, mixing, shaping and vulcanization
Once synthetic rubber is produced, it comes in the shape of large bales which have to be formed into products ready for everyday use. There are four manufacturing steps: compounding, mixing, shaping and vulcanizing. The compounding phase is used to add chemicals that react during vulcanization to stabilize the rubber polymers and prepare them for their intended use. The mixing step has two stages: mixing the additive into the rubber and adding the chemicals for vulcanization once the rubber is cooled.
The technique used during the shaping stage depends on the desired final product. For instance, for tire production, the preferred method is compression molding, which is one of the three molding methods alongside transfer molding and injection molding. The final process, vulcanization, occurs during the molding stage. Vulcanization manipulates the cross-connections between the polymers. If the desired product is elastic and soft, there should be fewer cross-connections between the rubber polymers.
For the harder rubber, the cross-connections should be increased. This phase includes the addition of chemicals such as sulfur and an “accelerator” to hasten the interlinking reaction, as well as the addition of “activators”, usually zinc oxide and stearic acid, the key to creating sulfur interlinks. Vulcanization is the essential step to achieving the durability and adaptability of rubber.
Styrene-butadiene rubber, the natural rubber alternative
Styrene-butadiene rubber, abbreviated as SBR, is one of the most common types of synthetic rubber, mainly due to its inexpensive production, as well as its resistant properties. By virtue of its comparable characteristics, it can be used as a natural rubber alternative. Therefore, SBR is a predominant material used in tire and other automotive parts manufacturing. Based on its production method, we can differentiate between Emulsion SBR and Solution SBR.
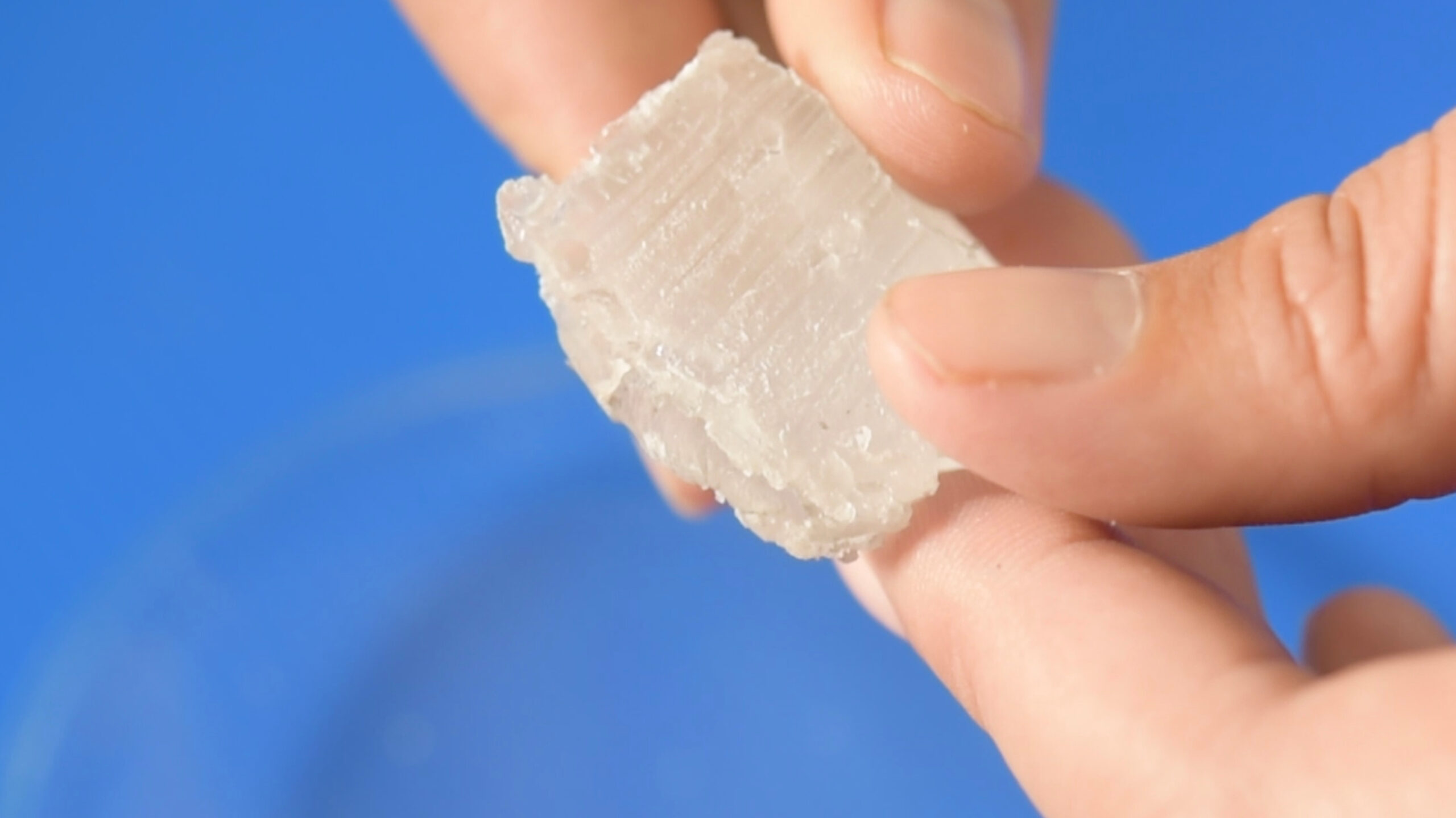
Carried out at 50 to 60°C, the hot emulsion process results in a branched polymer, which reflects characteristics such as low mill shrinkage, good dimensional stability, and good extrusion. On the other hand, about 5° is sufficient for cold emulsion SBR which has superior mechanical properties and better abrasion resistance. Finally, produced by termination-free anionic solution polymerization in a hydrocarbon solvent, solution SBR has tensile strengths and low rolling existence.
Processing steps involved in synthetic rubber making
Which synthetic rubber technology do you need?
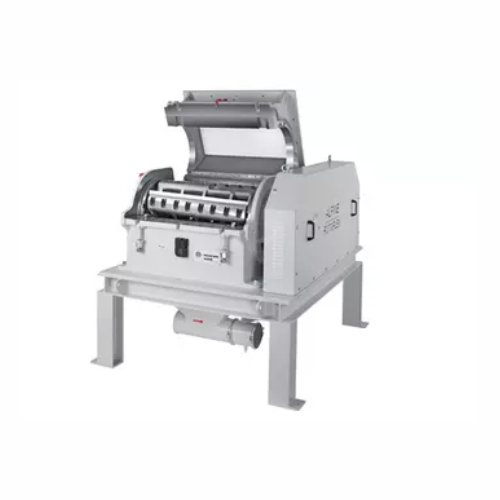
Industrial granulator for high-throughput plastic recycling
Facing challenges in efficiently recycling high-volume plast...
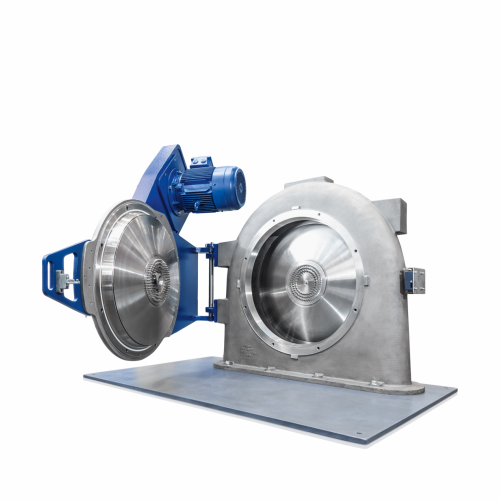
Pin mill for fine grinding of sticky materials
Achieve ultra-fine grinding of challenging materials with high speed and pr...
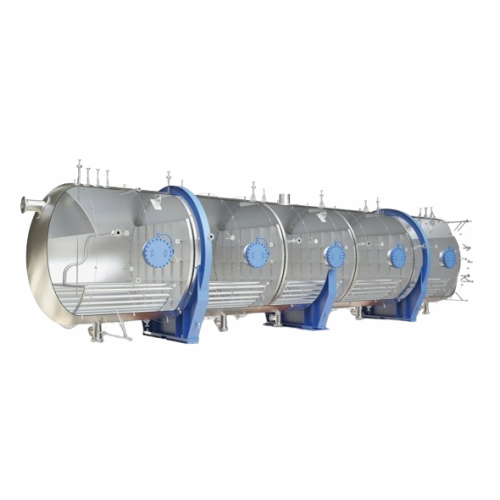
Packed and tray columns for distillation, absorption, and extraction
Enhance your production line with columns designed...
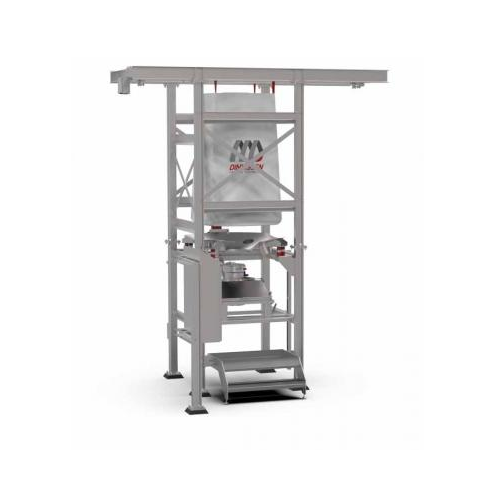
Modular big bag unloading station for various materials
For hassle-free handling of bulk materials, this modular solution...
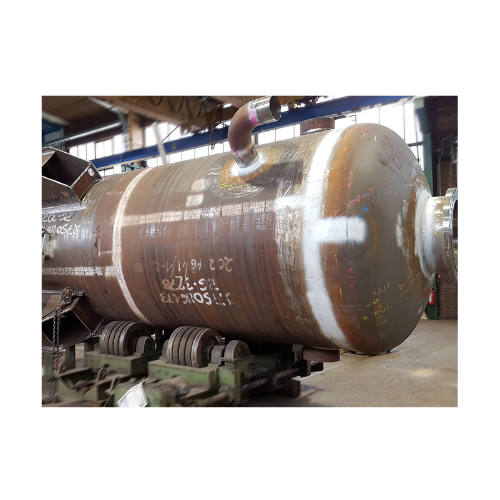
High-pressure preheaters for power plants
Optimize your power plant’s efficiency by efficiently preheating feedwater...
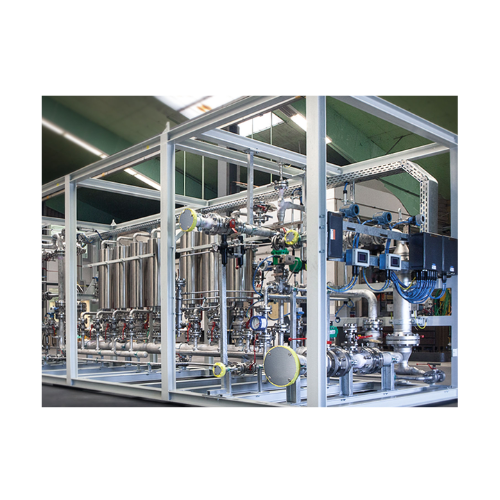
Ethylene recovery unit for ethylene oxide and glycol production
Recover valuable ethylene monomer efficiently from cycle...
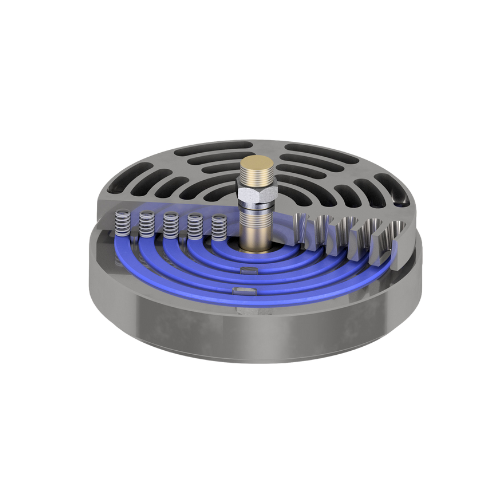
Ring valves for industrial compressor systems
Optimize the efficiency and reliability of your gas compression processes wi...
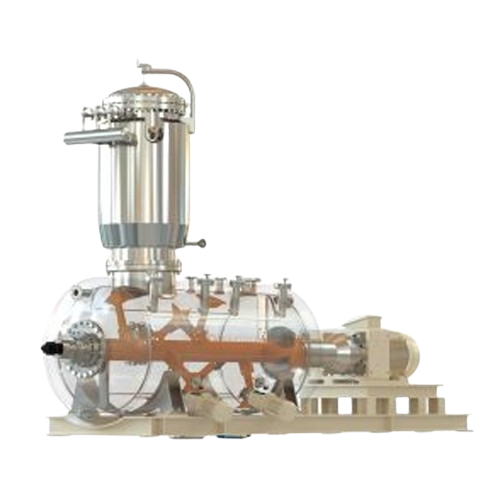
Horizontal vacuum paddle dryer for thermosensitive products
Achieve precise drying and mixing of high-viscosity, thermos...
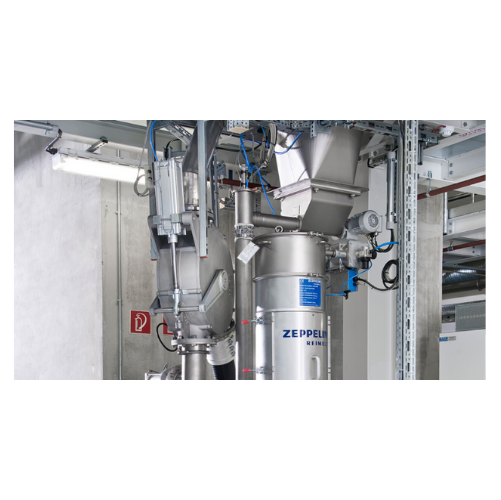
Special chemical plant safety systems
Ensure operational safety and regulatory compliance in chemical processing with advan...
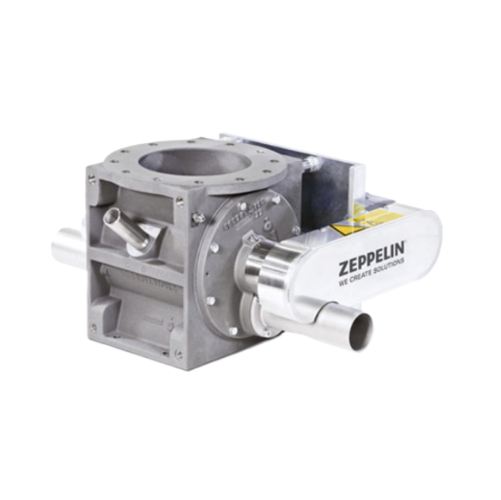
Rotary feeder for powdered bulk materials
Achieve precise control in feeding and discharging powdered materials with a rot...
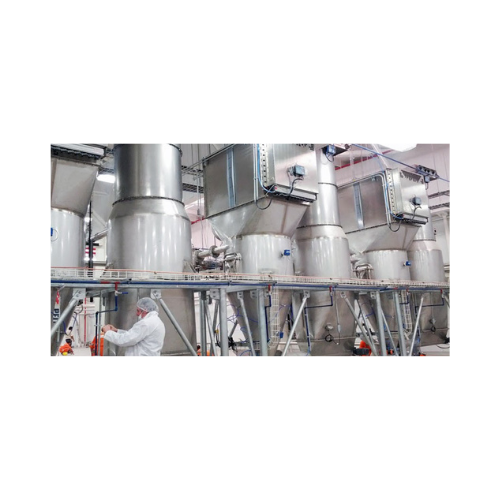
Industrial dust collection system for air filtration
Optimize air quality in your production line with this compact dust ...
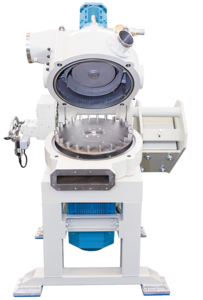
Classifier mill for recovered carbon black
Recovered Carbon Black (rCB) can be recycled back to the tire production chain ...
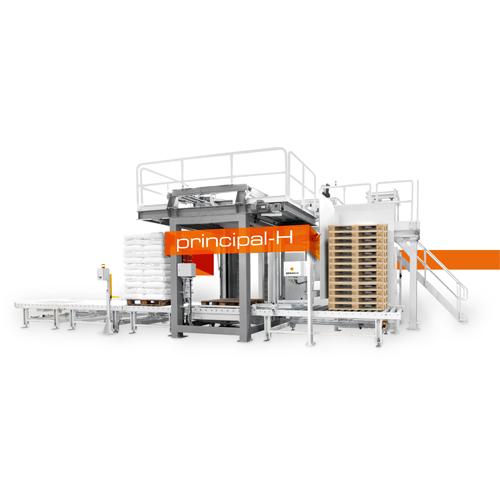
Automatic palletizer machine for bags and boxes
The effective placement and positioning of bags and boxes can be a challen...
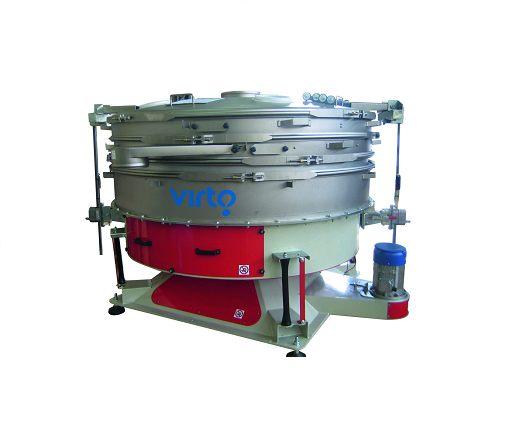
Tumbler sieve for classifying and dedusting granular materials
For the classification of delicate granular material, scr...