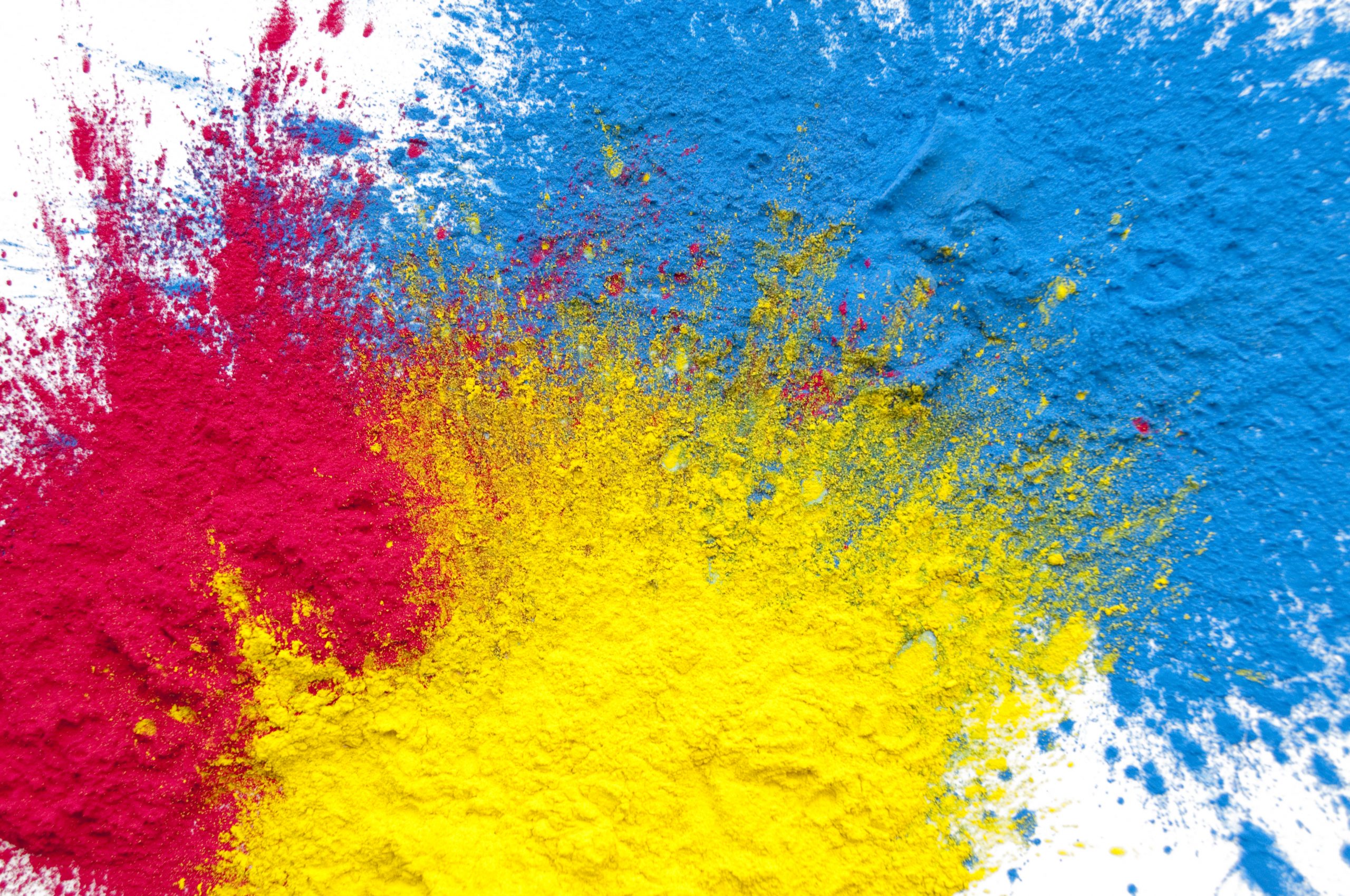
Making Toner
Find innovative production technology for making toner and connect directly with world-leading specialists
A toner is a fine powder located in printer and copier cartridges. One peculiar property the product is their ability to act like liquids. Toner manufacturing equipment sees to it that the particle size is between 5 and 30 micrometers to flow through the cartridge.
Select your toner process
Tell us about your production challenge
Key steps that occur in the toner manufacturing equipment
To manufacture toners, producers need to dispense synthetic resins, colour pigments, and metal oxides into the automated toner powder manufacturing machine. After that, they compound and extrude it on a cooling belt to chill. This stage is vital to produce discrete, free-flowing toners. Once it’s over, they pass the chilled-down sheet into a pre-crusher to break it down and inject the pre-crushed material into the jet mill to further reduce the particle size. It’s important to remove fine toner dust from the jet-milled toner as it can affect the quality of printing or photocopying. Finally, raw toner goes through a high-speed blender for additive coating. When they are ready, manufacturers fill them into tote bins or cartridges.
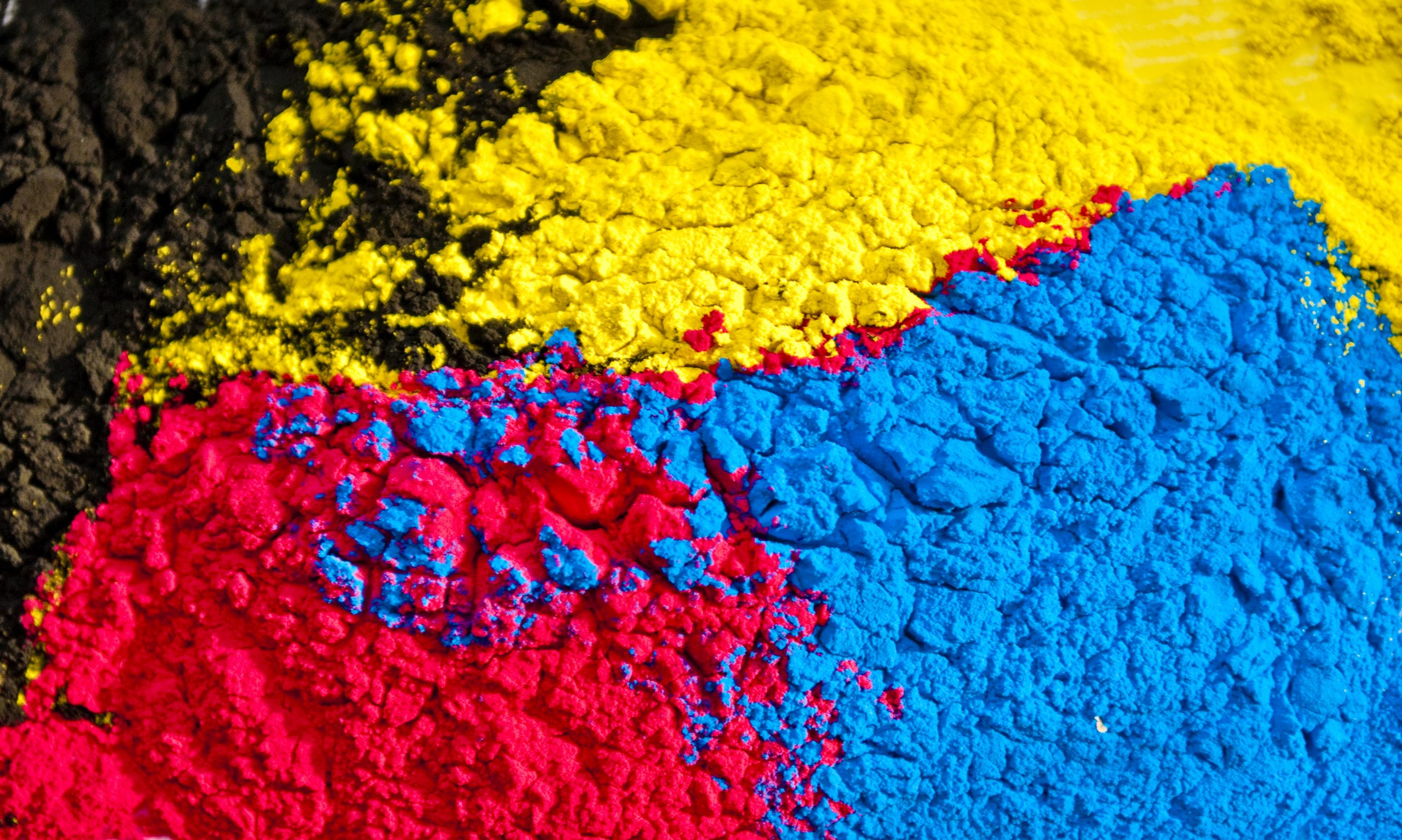
What to choose? Conventional toners versus chemical toners
Chemical toners’ producers claim that their product is more consistent, has a smaller particle size, and produces better image quality. However, conventional toners are still more popular than chemical toners because of the large installed base of machines that use conventional toners. New techniques enable producers of conventional toners to generate smaller and more consistent particles. This allows them to compete against their chemical counterpart.
Although the ingredients used for both types are the same, the process of manufacturing chemical toners requires less energy.
The impact of toner machining on health and the environment
Toners are not outrightly toxic, but they can cause genetic mutations. The use of toner manufacturing equipment generates nanoparticles that are capable of altering genetic patterns and metabolic processes. Carbon black, a major constituent of toners, belongs to Group 2B according to the International Agency for Research on Cancer, which means it is possibly carcinogenic. Carbon black effects are a major contributor to climate change as they affect plant health and modify rainfall patterns.
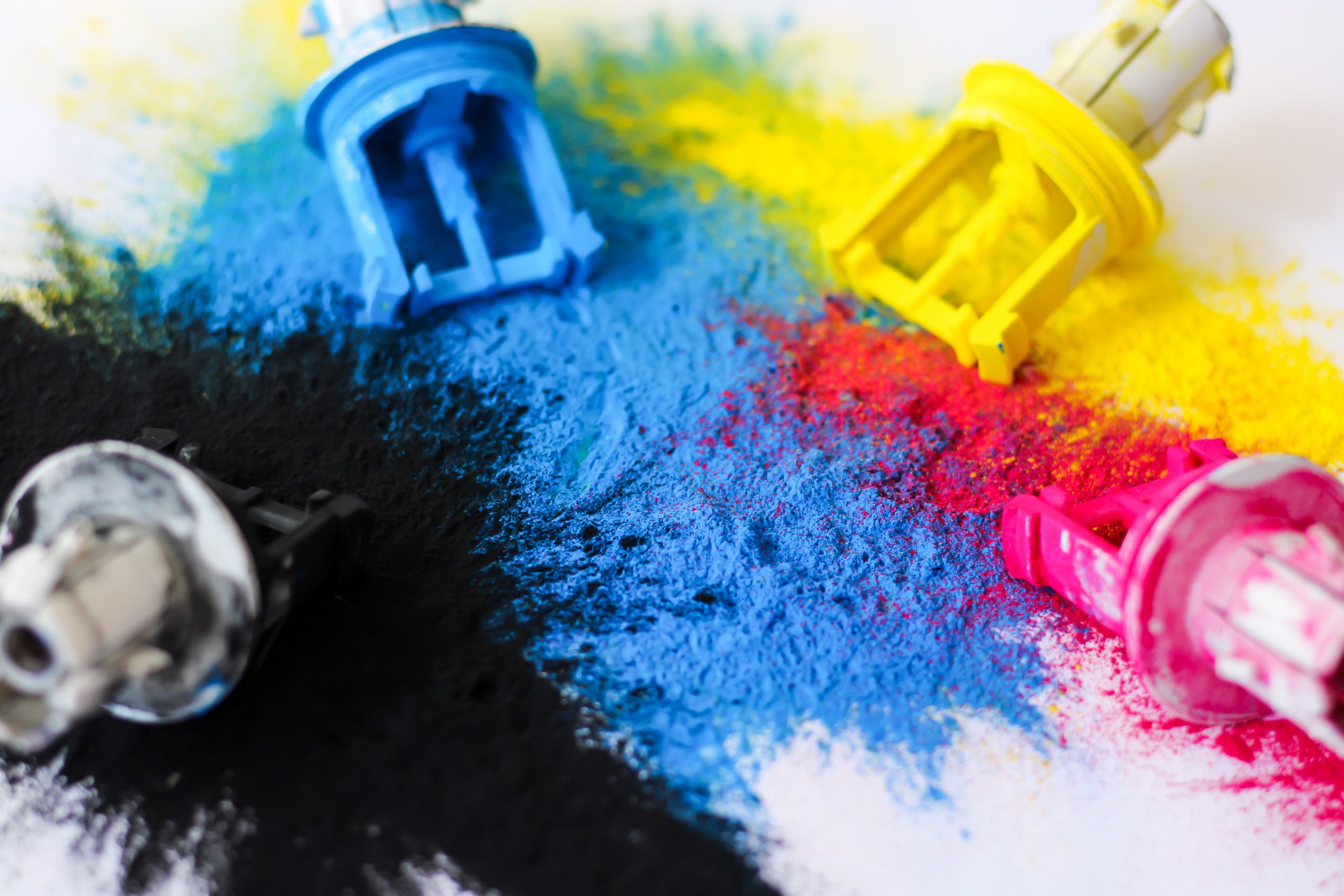
An effective measure against these concerns is to use biotoners. They use plant-based toner powders and, in addition, save up to 3 liters of crude oil. The emissions from their printing process are also safe.
Some markets may have their own specificities too. Germany, for instance, implemented the Closed Substance Cycle Waste Management Act (KrWG) of 2012 to foster circular economy and to establish rules for waste generation and management. Toners are included in the act as they need to be sorted and collected separately – so producers or holders of waste need to recover it.
Processing steps involved in toner making
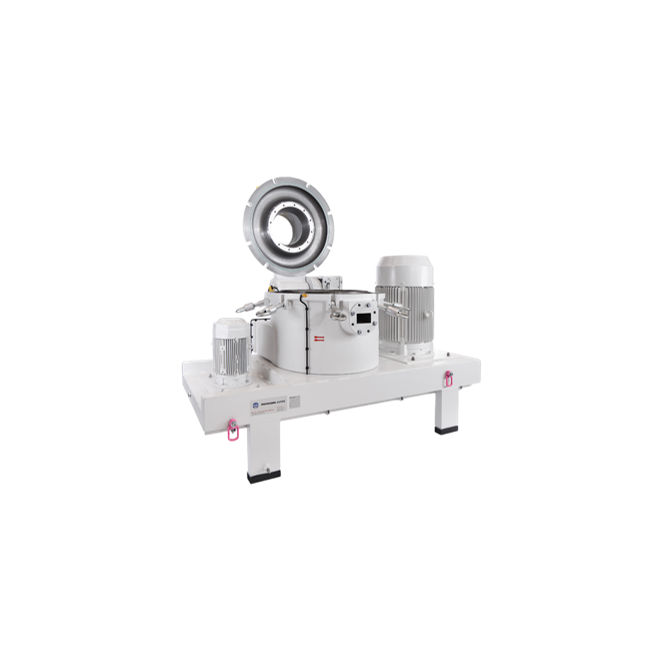
Classifier mills
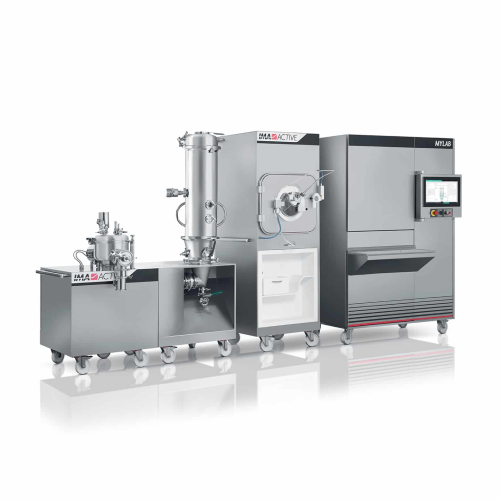
Coating
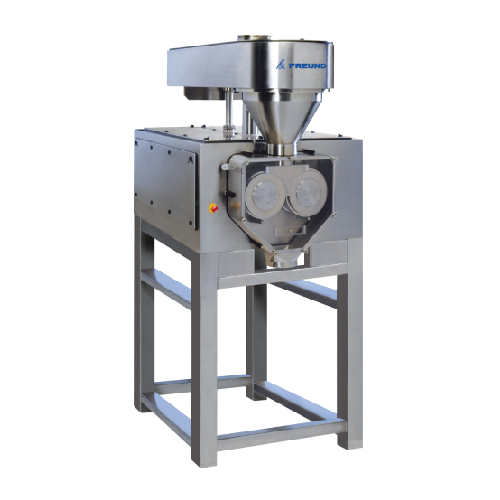
Compaction
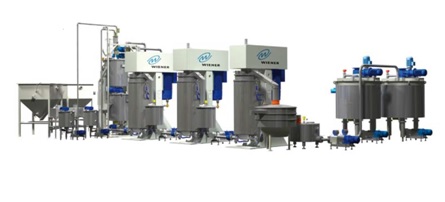
Continuous milling solutions
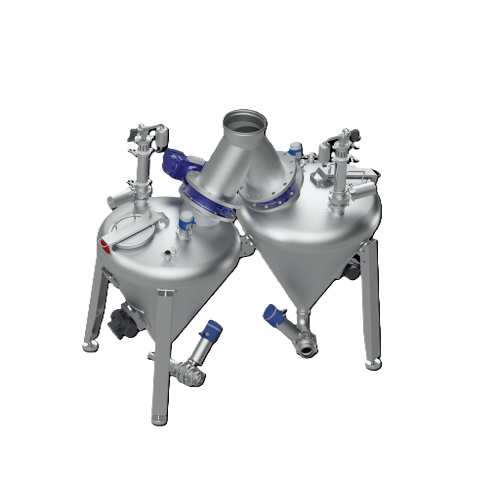
Conveying
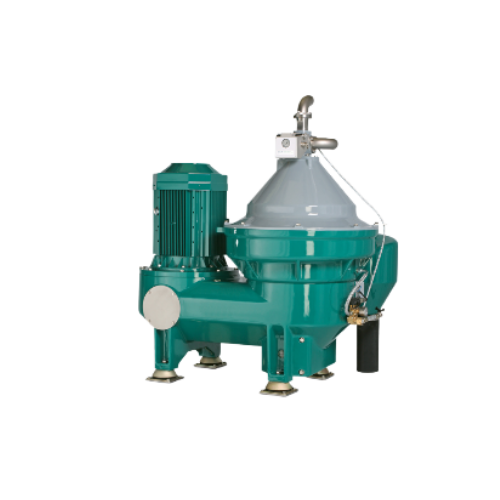
Cooling
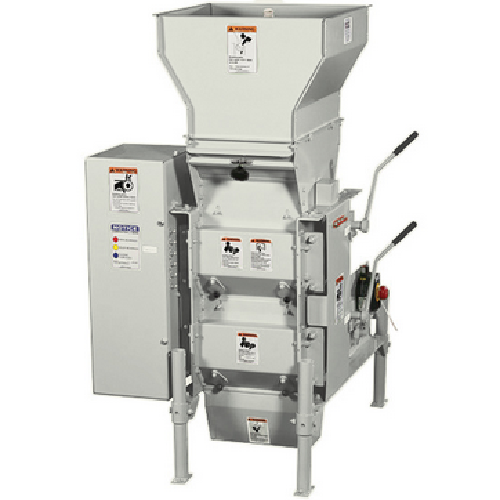
Crushing
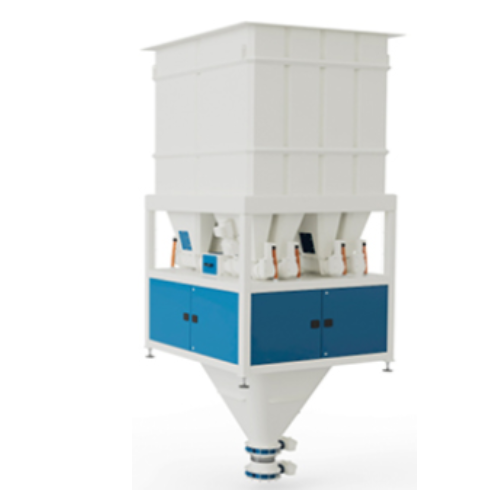
Dosing
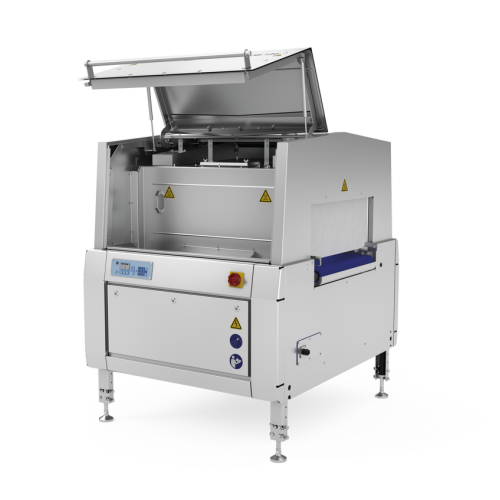
Drying
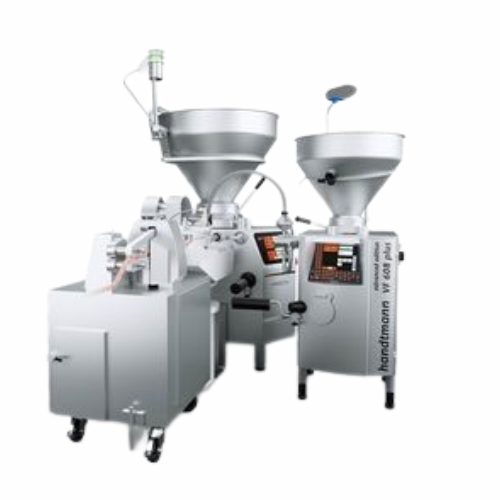
Extrusion
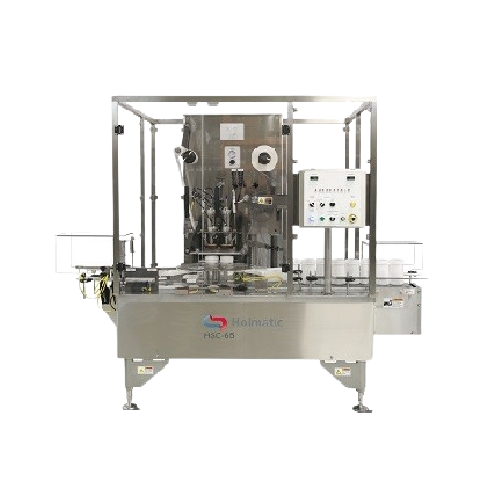
Filling
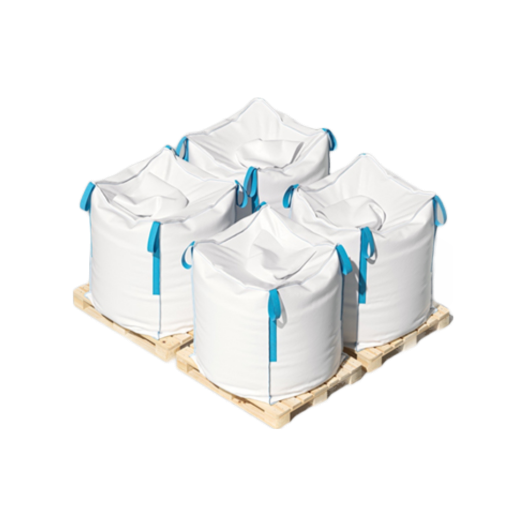
Flexible intermediate bulk containers
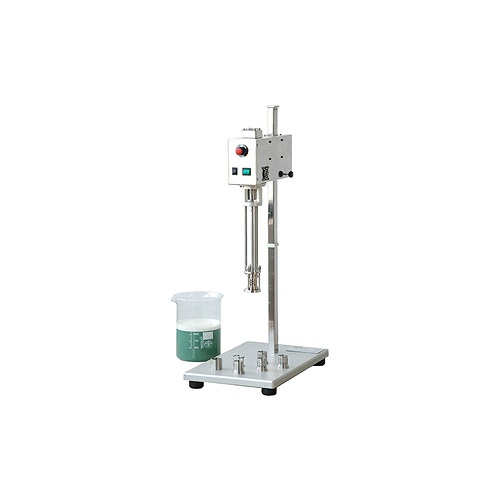
High-shear mixers
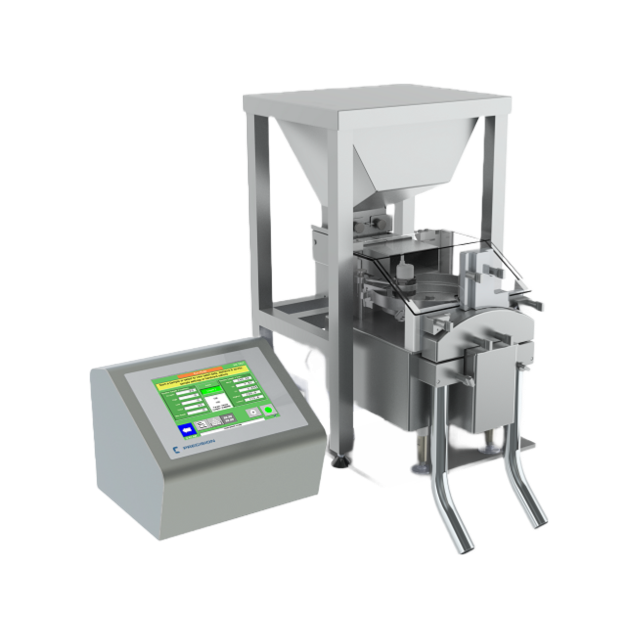
Industrial hoppers
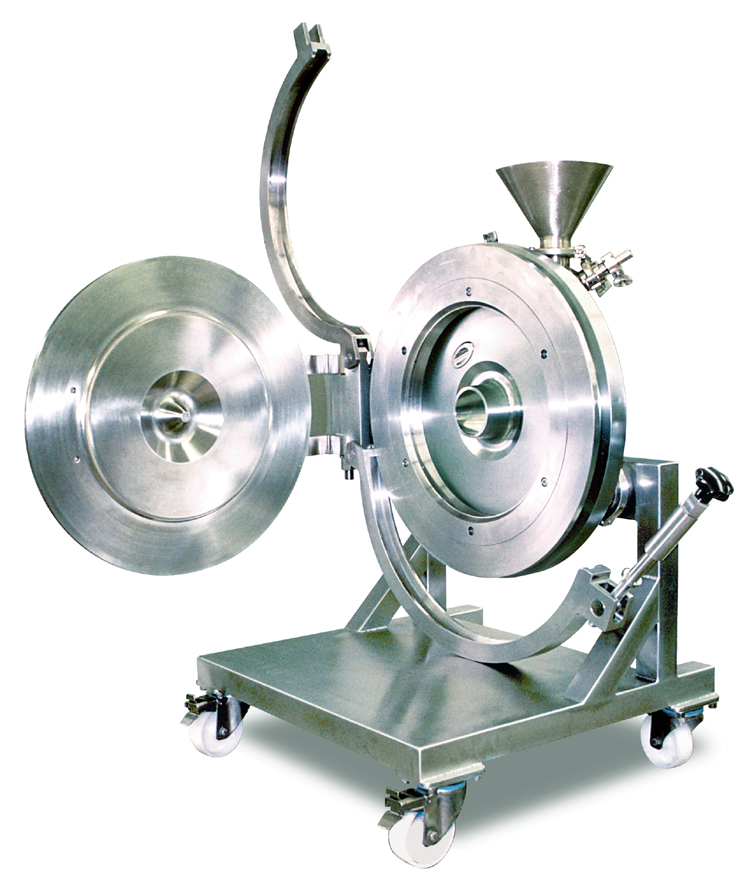
Industrial jet mills
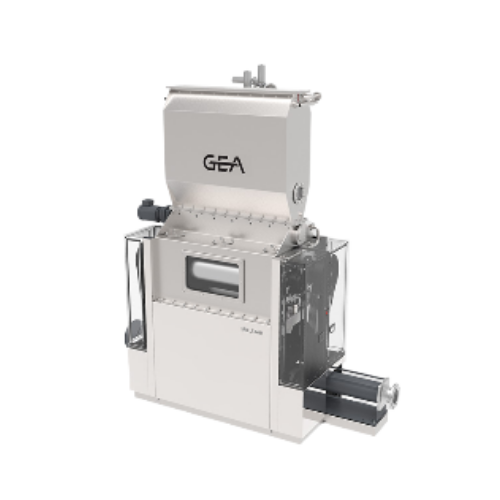
Milling
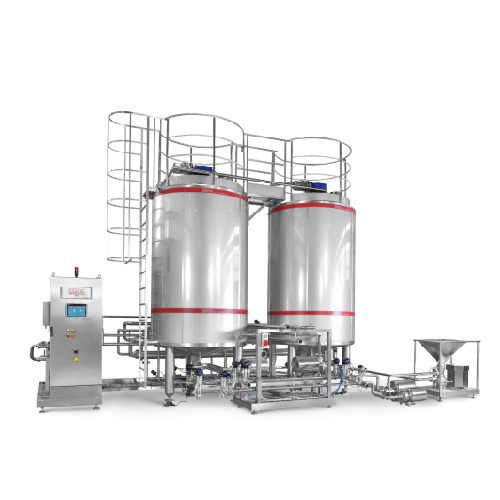
Mixing
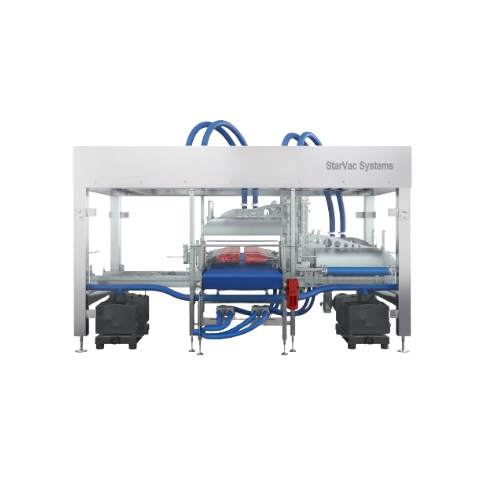
Packing
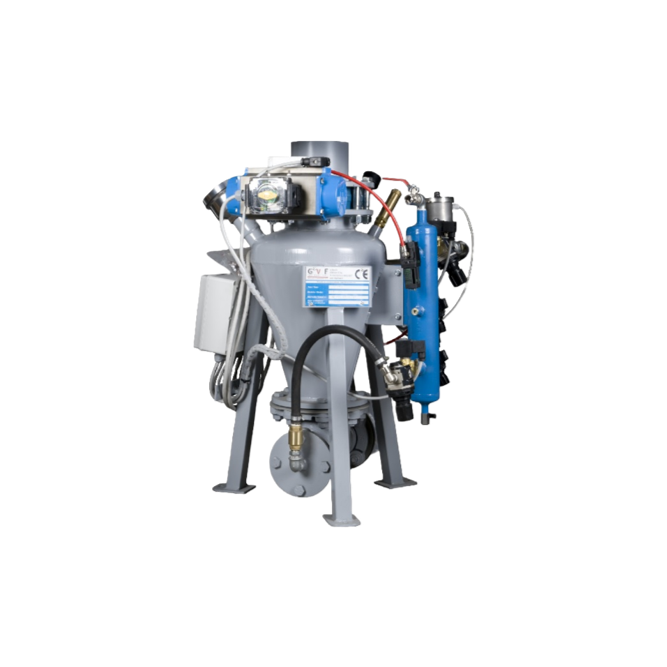
Pneumatic conveyors
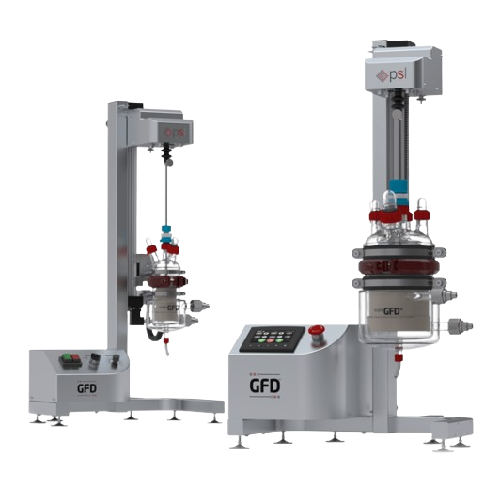
Separation
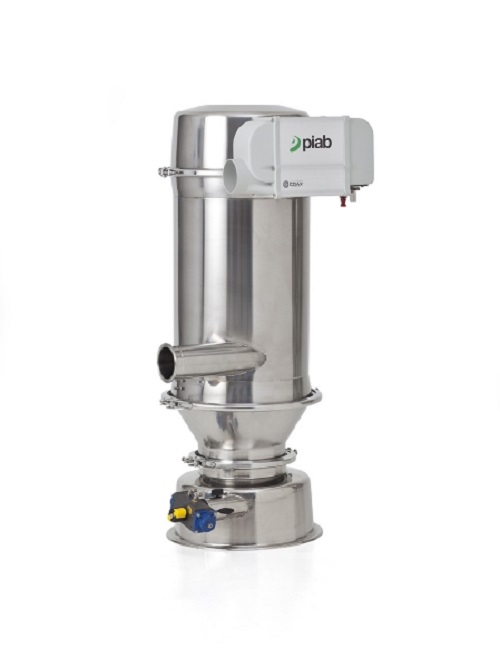
Vacuum conveyors
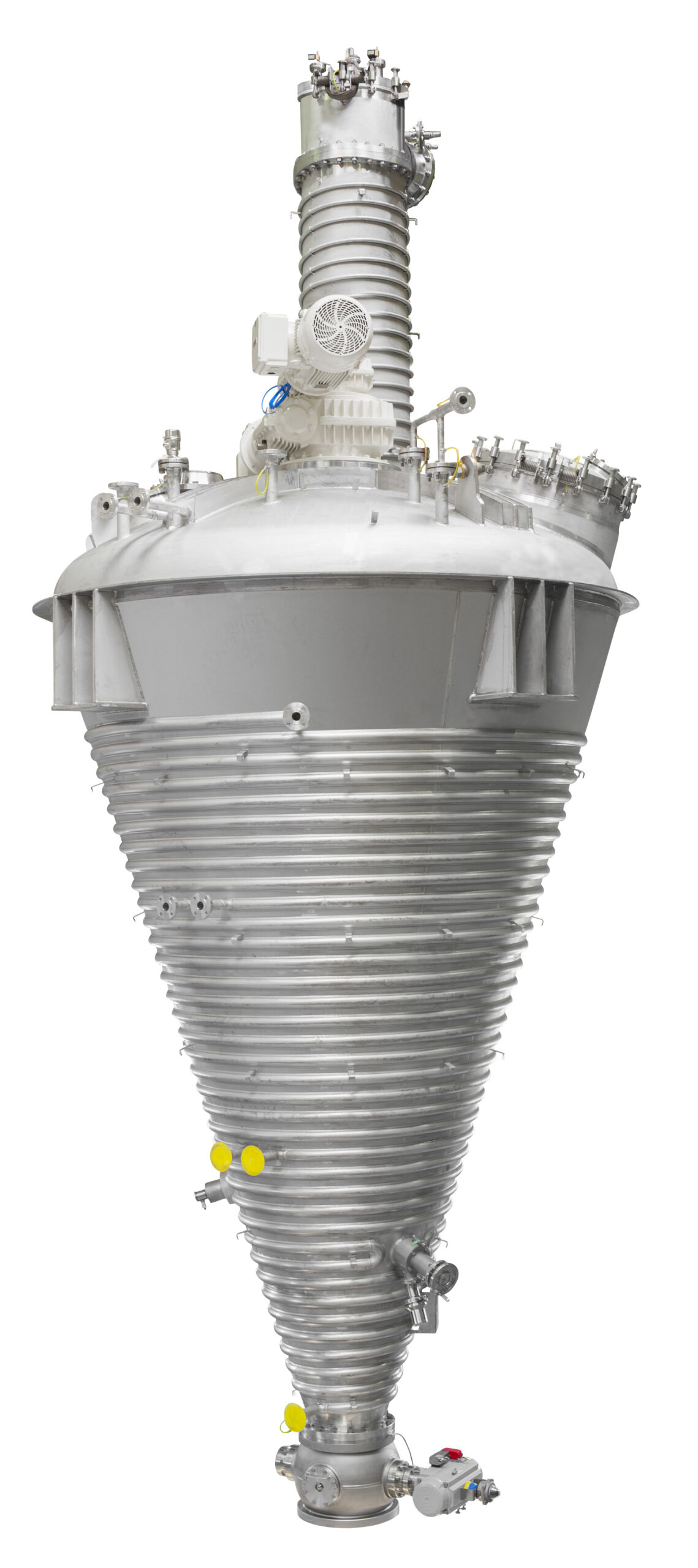
Vacuum dryers
Which toner technology do you need?
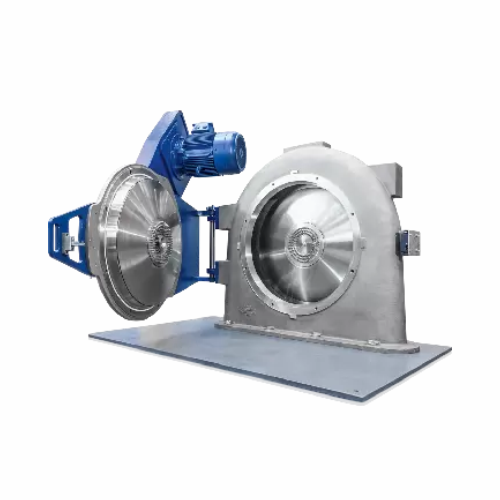
Industrial powder grinder
Achieve precise particle size reduction and classification with advanced equipment designed for co...
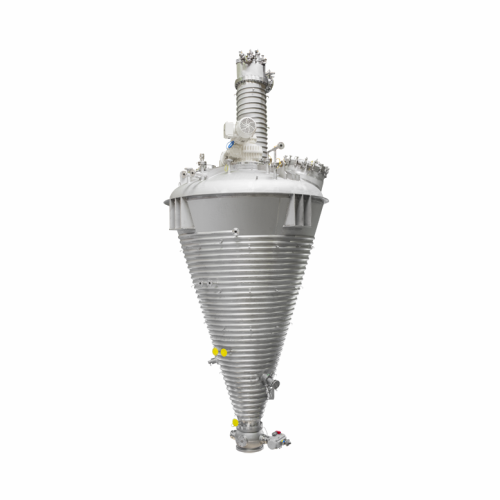
Vacuum dryers for powders and bulk solids
Achieve precise drying and mixing of sensitive materials with advanced vacuum te...
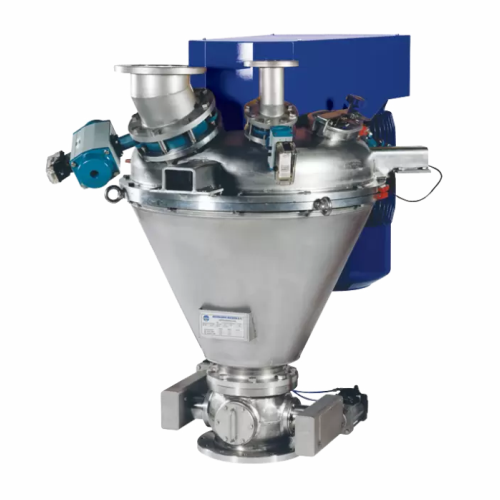
High shear impact mixer for agglomeration and dispersion
Achieve precise homogeneity and efficient agglomeration with a h...
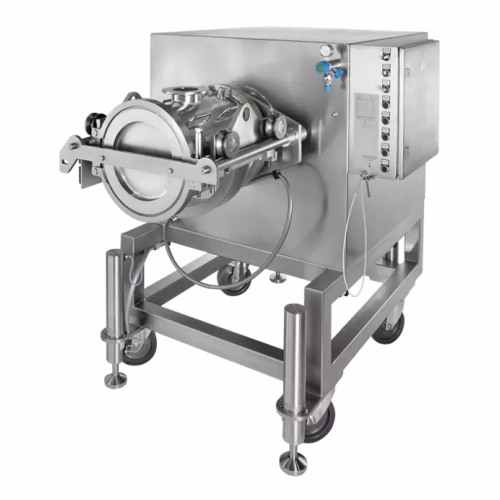
Super high shear mixer for nano to micron powders
Achieve high-precision mixing and surface treatment of nano to micron-s...
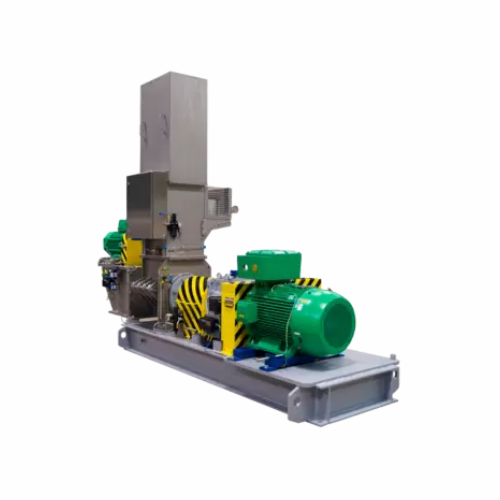
Choppers and disintegrators for industrial size reduction
Enhance your production efficiency by mastering size reduction...
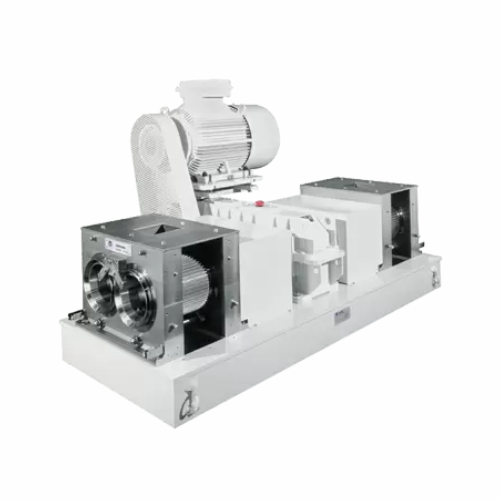
Compactors and granulators for powdery products
Transform loose powders into dense, free-flowing granules that enhance han...
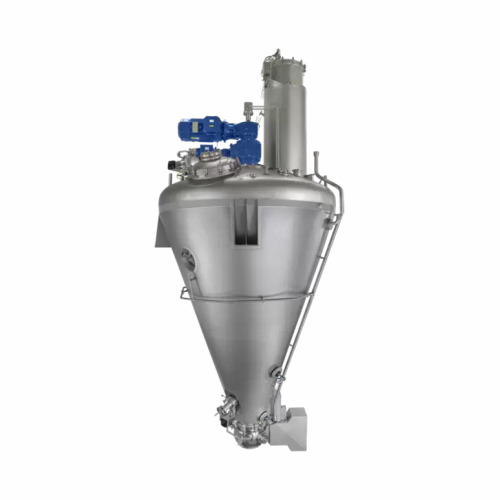
Vacuum dryer for powders and granules
Achieve precise moisture control for sensitive materials with a versatile vacuum dryi...
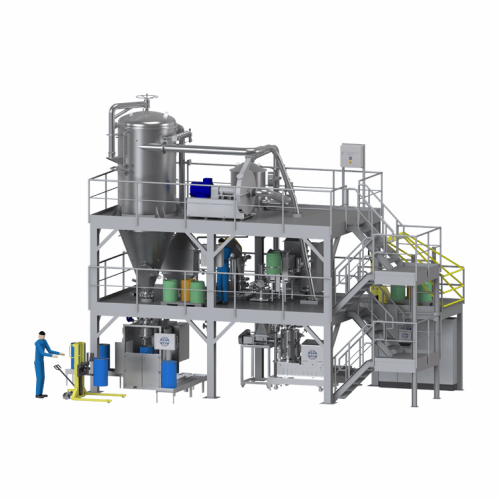
Drying systems for powders and bulk solids
Enhance your production line with precise control of moisture content in powder...
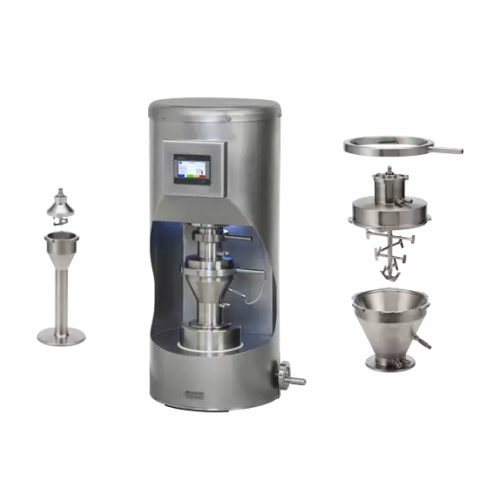
Lab mixer for powder formulations
Achieve precise particle mixing and coating with this stand-alone high-shear lab mixer, d...
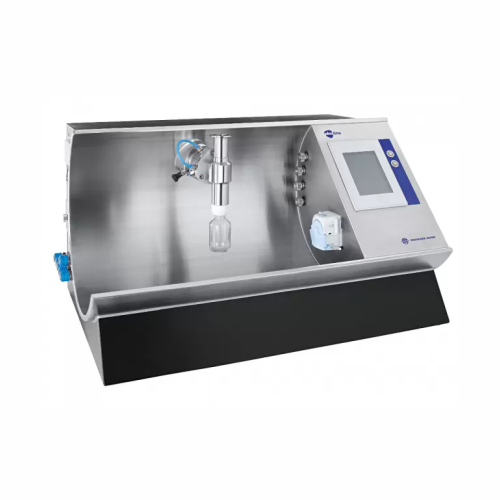
Lab-scale powder processing system
Achieve precise control in ultra-small batch processing with a versatile modular system,...
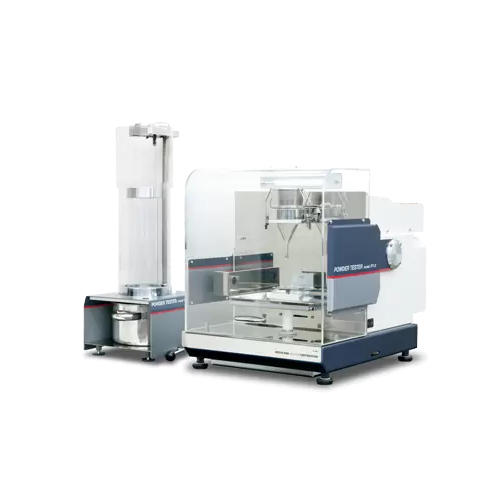
Powder characteristic evaluation
Ensure precise powder analysis and testing in your laboratory to optimize production qualit...
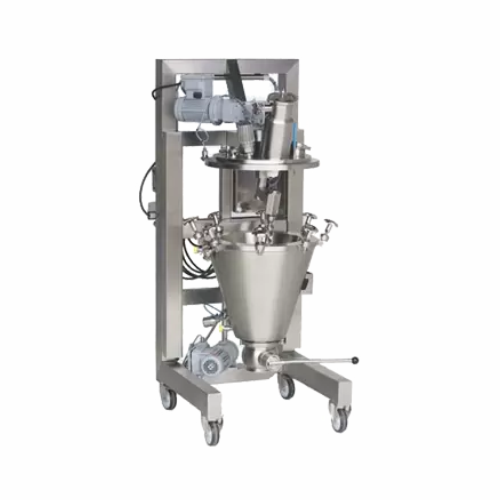
Laboratory vacuum dryer for heat-sensitive materials
Optimize moisture control in heat-sensitive materials with precise a...
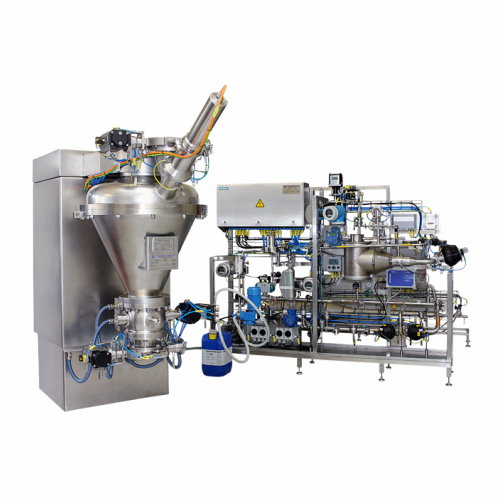
Cip/sip cleaning for solids processing systems
Ensure seamless transitions and maintain hygienic production environments w...
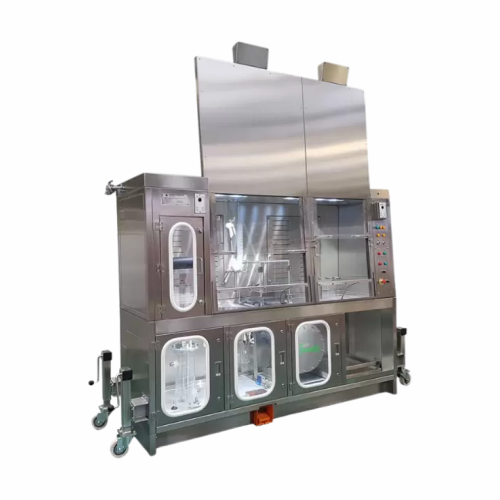
Containment solutions for hazardous material processing
Ensure safe and efficient processing of hazardous materials with ...
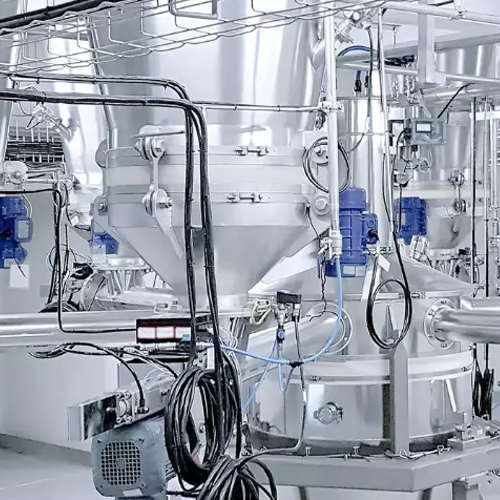
Conical screw mixer for powder blending
Achieve precise and homogeneous blending with the conical screw mixer, ensuring uni...
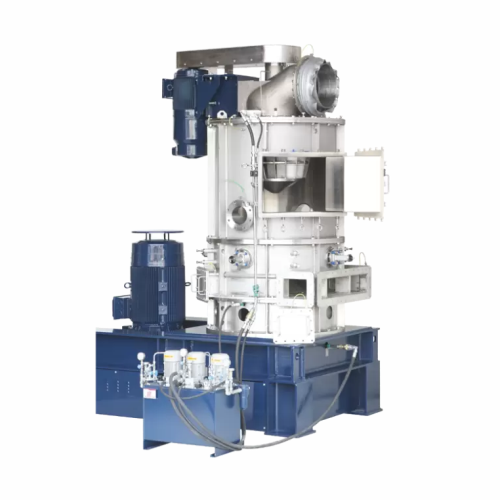
Ultra-fine powder flash drying system
Achieve rapid moisture removal and particle refinement with this integrated system, d...
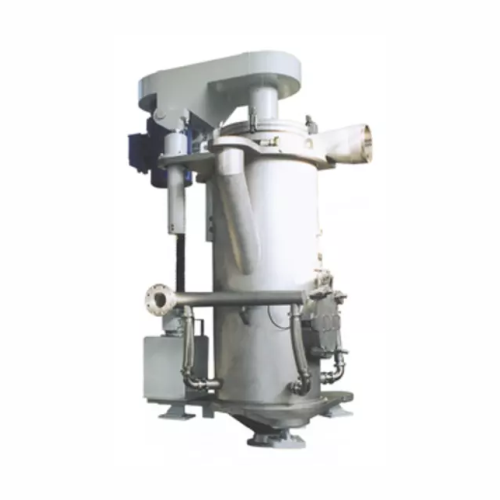
Jet mill for toner and pigment industries
Optimize particle size and distribution for high-demand applications with this h...
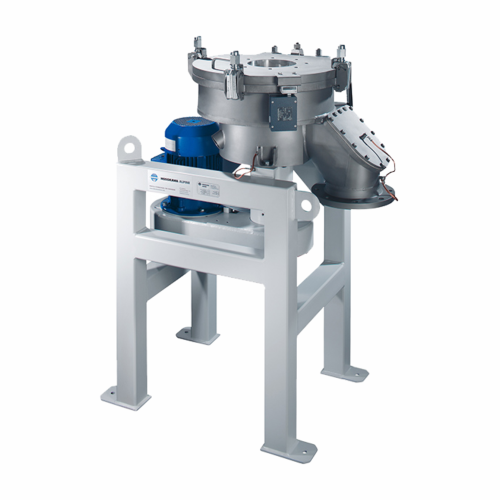
Ultrafine classifier for toner and pigments
Achieve unparalleled precision in classifying fine powders essential for high-...
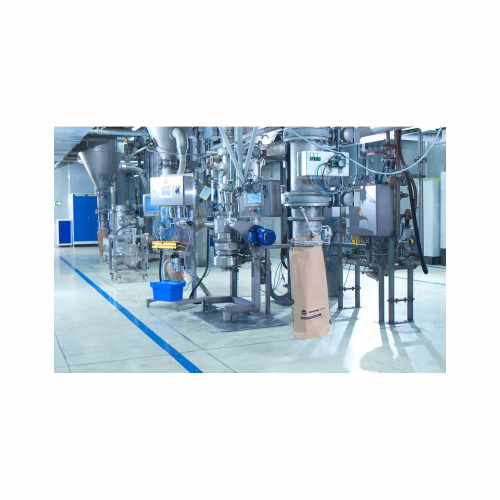
Air classifier for classifying industrial minerals
Achieve precise particle separation with advanced air classifiers, par...

Precision feeders and mixers for plastics processing
Achieve precise blending and feeding for plastics processing with mo...
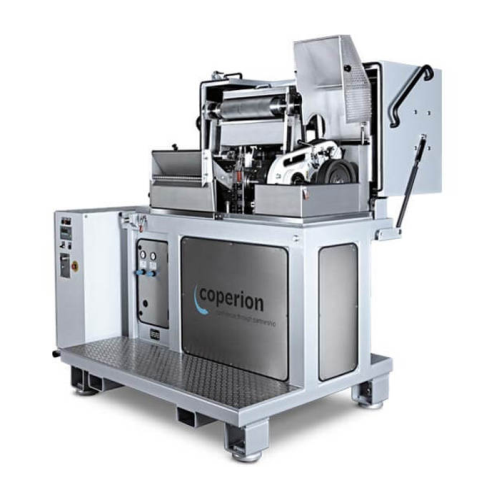
Industrial strand pelletizer for polymer processing
Optimize polymer pellet production with precision engineering, ensuri...
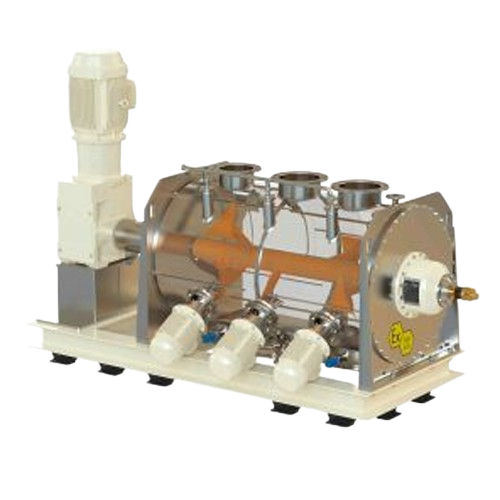
Horizontal ploughshare mixer for solids and powders
Achieve uniform blends of diverse solids and powders with precision a...
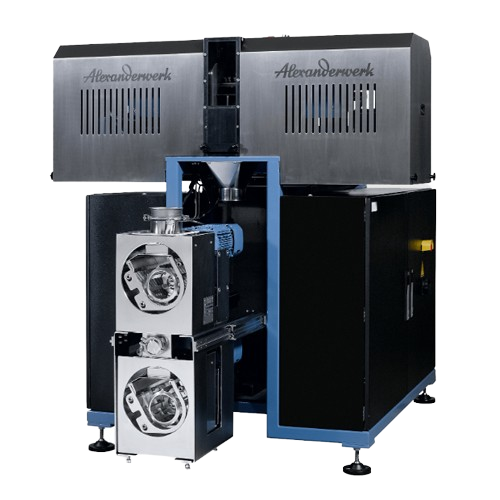
Industrial roller compaction for chemical applications
Enhance material flow and density with advanced roller compaction ...
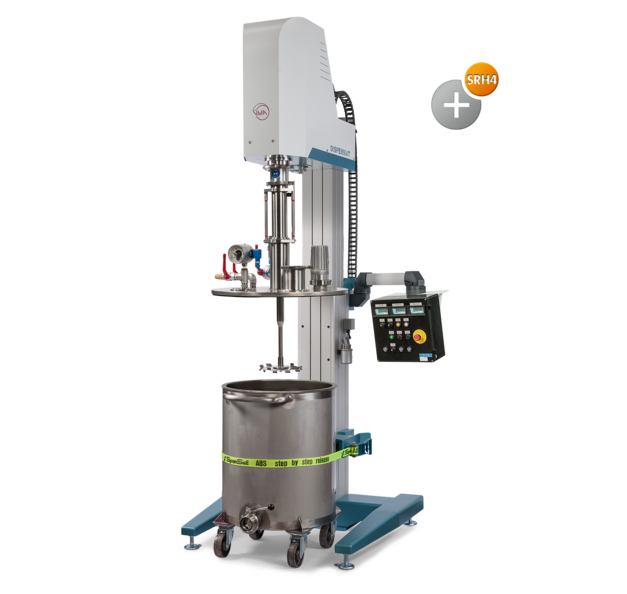
ATEX vacuum dissolver for high viscosity products
Ensure safe and efficient dispersion of high-viscosity materials under...
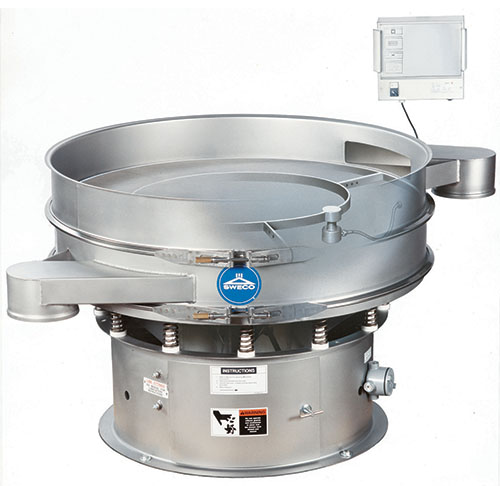
Ultrasonic round vibratory separator for fine powders
Efficiently prevent screen blinding during powder separation proces...
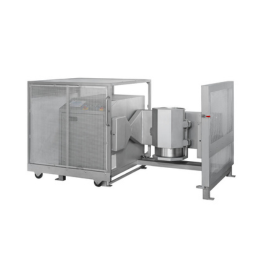
High volume 3D shaker mixer for ceramics
Achieving consistent homogeneity and the logistics of handling and introducing lar...
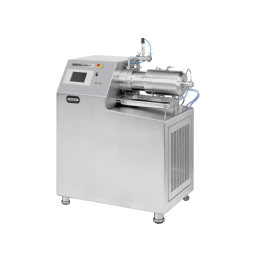
Ultra fine bead mill for nanosuspensions
Ensuring the quality, efficiency, and reproducibility of nanosuspensions throughou...
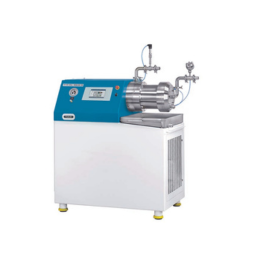
Self-cleaning bead mill for highly viscous materials
To prevent blockages, clogging, and cross-contamination coming from ...
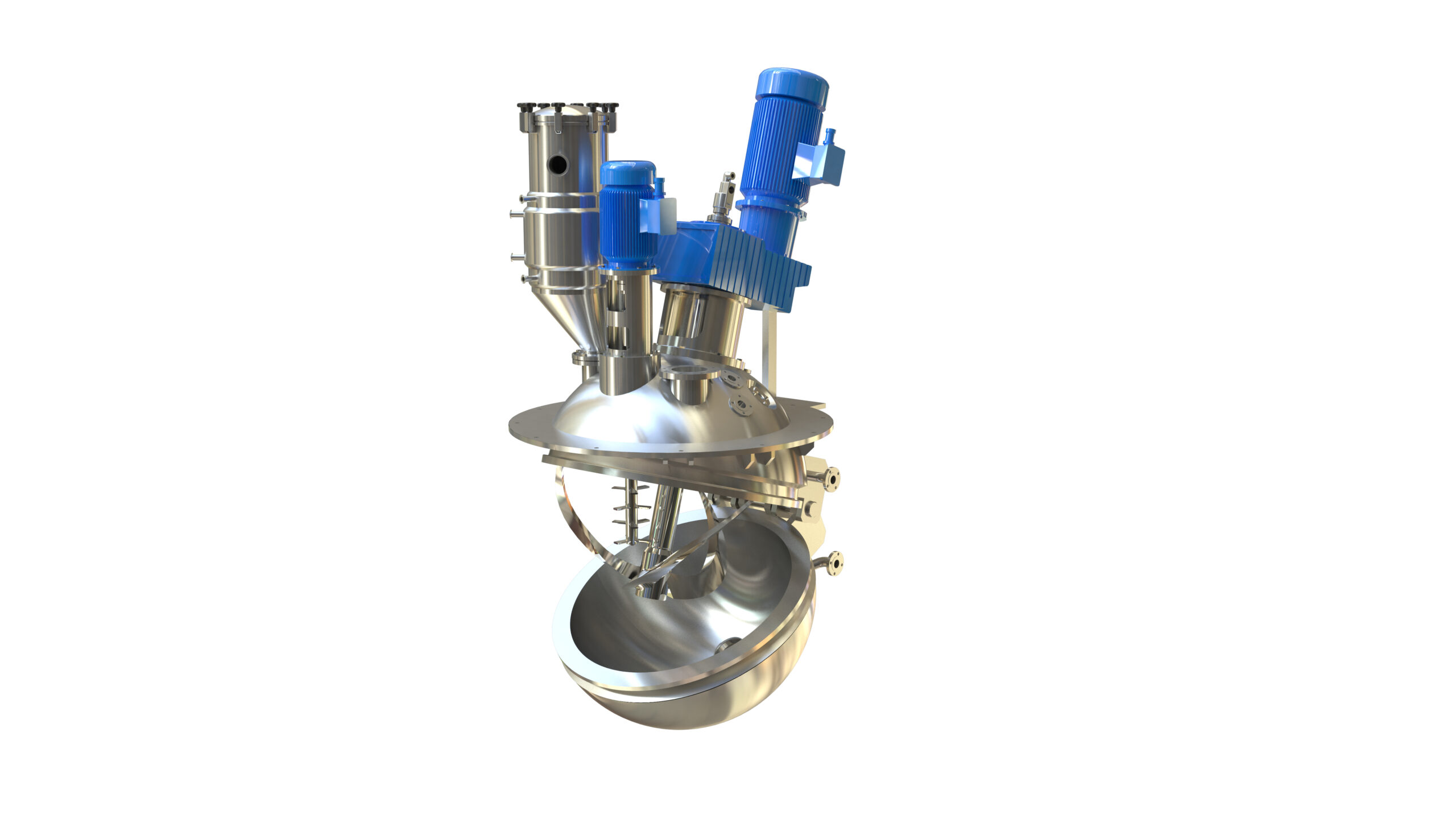
Spherical dryer
Drying vessels that are simple, reliable, and easy to maintain increases product quality and process efficienc...
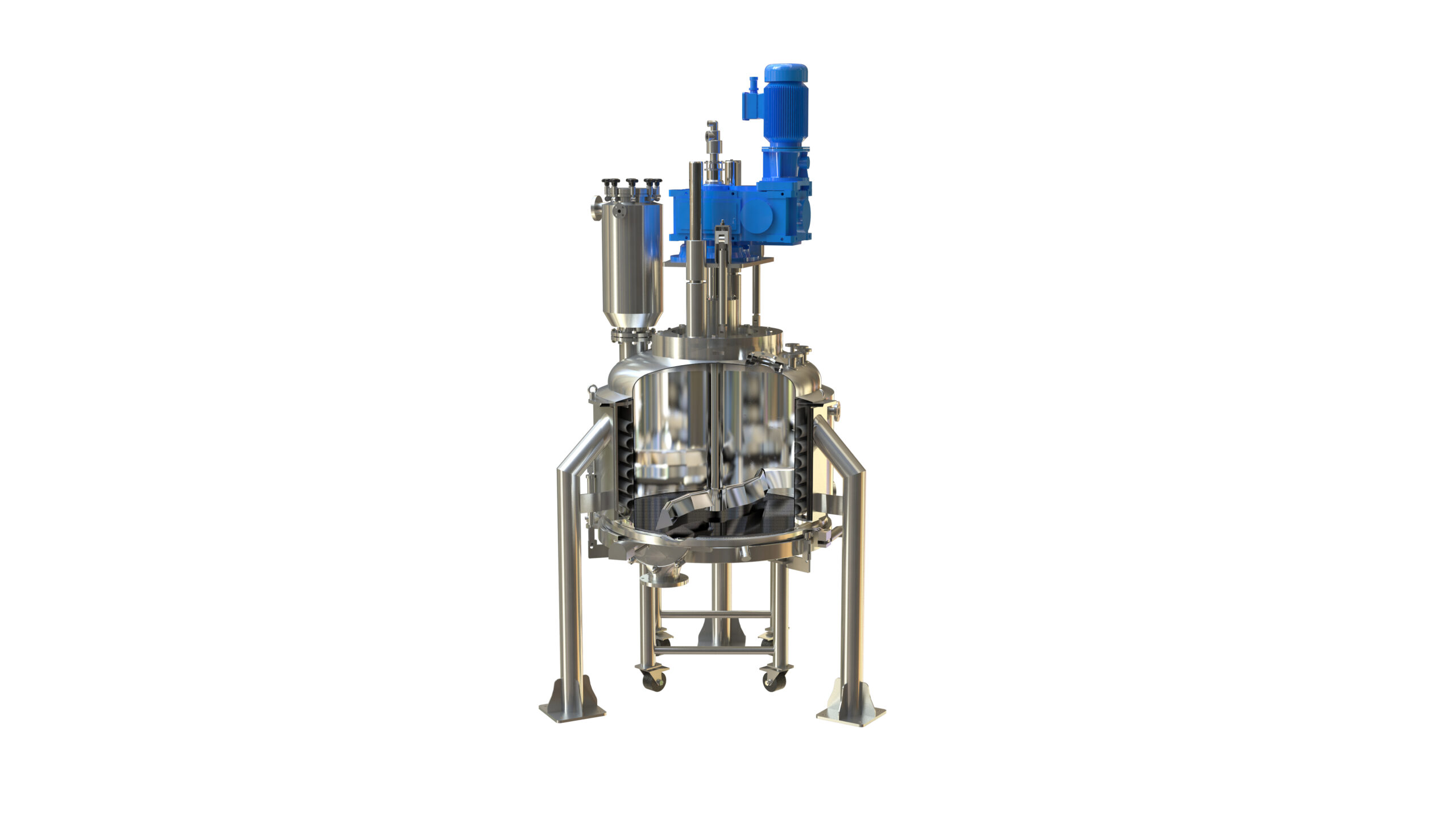
Filter dryer
The pharmaceutical and bioprocess industries need filtration processes of particularly high quality to ensure the...
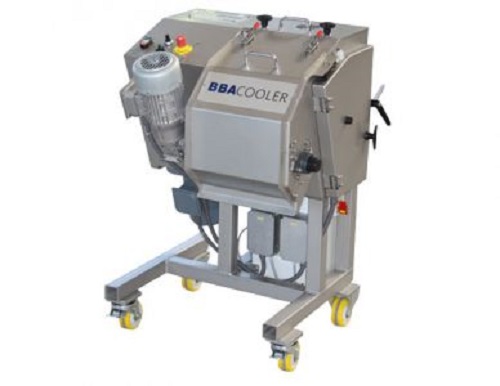
Drum cooler for laboratory hot melt processes
Do you need to cool molten masses to solid, thin film or flakes in an R&...
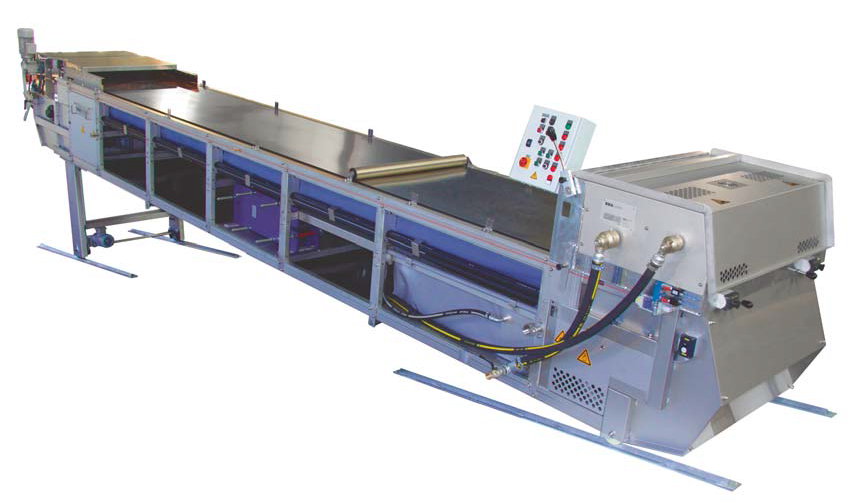
Steel belt cooler for hot melt extrusion
For producing high volumes of extruded hot melt product a flexible, high capacity ...