Powder containment systems for safety and product integrity
Powder containment is a system for safely containing or isolating powder products that are potentially hazardous to the environment, health, or both. Proper containment also avoids cross-contamination between the products and the debris from the open environment, which may compromise the quality of the products. Food and pharmaceutical industries apply powder containment systems for the safety of workers, the environment, and consumers. Not only does it offer safety, but it also helps achieve excellent product quality.
Safety for worker health and the environment – Why powder containment matters?
Powder containment is necessary in the pharmaceutical and chemical industry as various chemicals undergo multiple processes that may change their composition. Depending on the composition of chemicals and their application, some of them may be sensitive to environmental conditions that can cause unstable reactions, and some may also be harmful to workers’ health when exposed. Some risks in handling powders include explosion at high temperatures, allergic reactions or respiratory illnesses if inhaled by operators, and damage to the environment due to the toxicity of chemicals.
Standard regulations are established for pharmaceutical and chemical manufacturers to follow to ensure proper containment of chemicals, such as the U.S FDA’s Current Good Manufacturing Process (cGMPs), Environmental Protection Agency (EPA), Occupational Safety and Health Association, and National Fire Protection Association. FDA requires pharmaceutical and chemical products to be safe for consumption or use.
EPA regulations require manufacturers to properly dispose of chemicals and keep emissions in manufacturing at acceptable levels. OSHA deals with workers’ safety in handling toxic and hazardous waste where operators are required to use proper safety equipment for specific chemicals. NFPA requires manufacturers to follow regulations regarding possible fire risks or explosions.
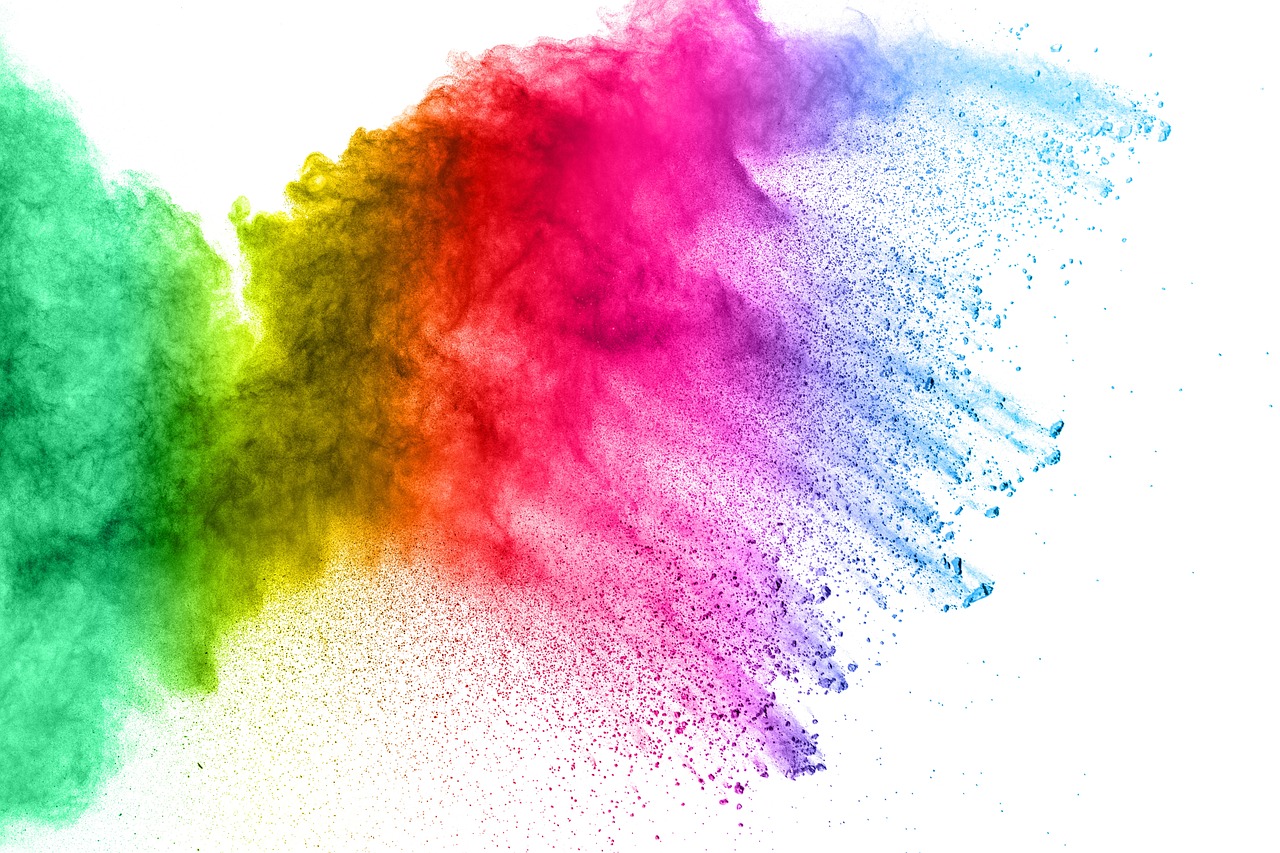
Handling of powders from loading to disposal
As more and more potent substances are developed in the pharmaceutical and chemical industry, requirements for the safe handling of hazardous materials are reaching higher levels. Various powder containment systems are designed to comply with current safety requirements and to prevent cross-contamination. Containment devices have an inlet port on one side where the products enter. Weighing, packing, and inspection of the products are performed by an operator using the supplied gloves and protective clothing. Finished products go to the other side, where an access port for batch containers is placed. A waste chute with a tight sealing system may also be available to remove contaminated materials.
More advanced devices have fans with filtration systems (HEPA filters) in a sealed and controlled environment. Devices, like isolators, can be equipped with a glove panel for the worker to operate without any exposure to highly potent substances.
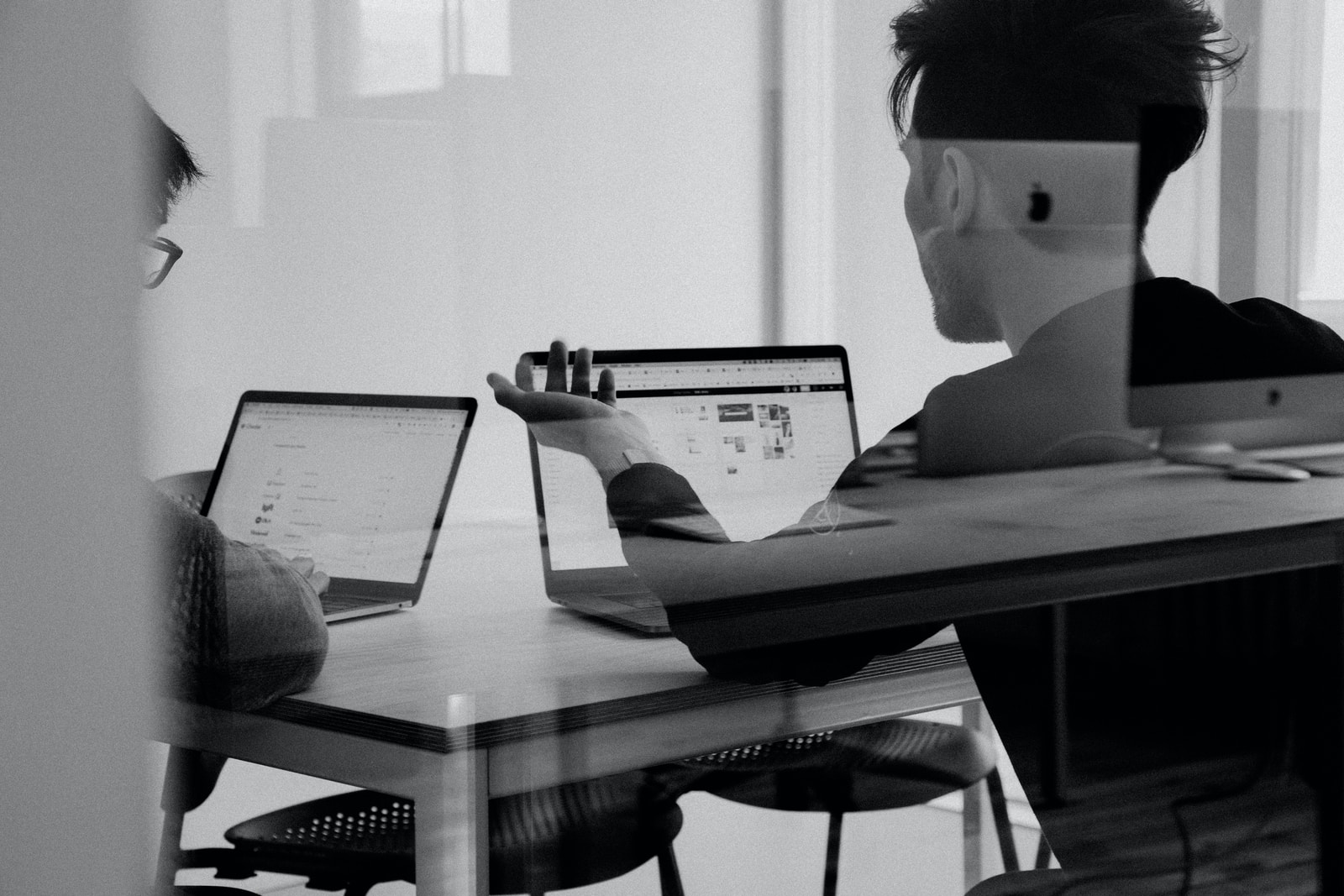
Tell us about your powder containment challenge
Are you looking for technology to set up or improve your powder containment process? And looking for the right production partner to build your line? Tell us about your powder production process and we will connect you quickly with a partner that has experience in making your product.
Containment technology for specific applications
Multiple technologies are available for handling and containing hazardous and sensitive powder products, including transfer systems, isolators, flexible containment bags, safety cabinets, enclosures, and filling and discharging systems. Transfer systems include valves and ports that control the transfer of products from equipment to a container and vice versa while providing a tight seal around the access points to avoid spillage.
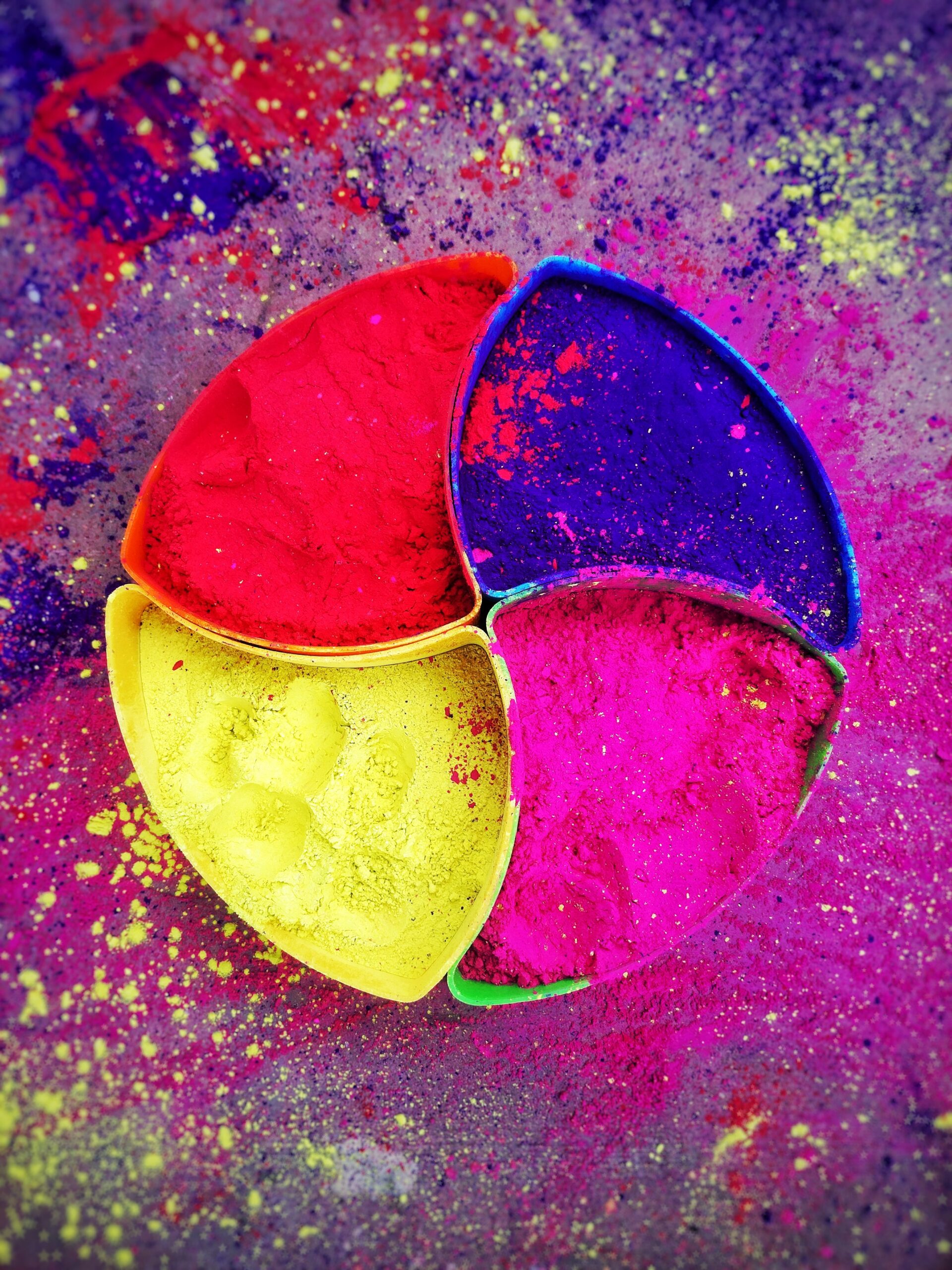
Enclosures are available in the form of flexible covers or solid barriers depending on the required handling specifications to isolate an equipment or process area from another. Isolators are enclosed spaces with a precisely controlled environment that allows the operation or inspection of the product using gloves attached to a glove panel to avoid direct contact or exposure. Gloveboxes are like isolators that utilize an enclosed and environmentally controlled space with gloves attached to a panel. The difference is in the gloveboxes’ materials and construction, where it uses simpler controls for the conditions in the enclosure and uses acrylic panels instead of tempered glass material.
Food processing, Chemicals, Pharmaceuticals, and more
Powder containment systems are widely used in different industries for safety purposes and to provide excellent product quality.
Pharmaceutical industry applications for powder containment include mixing and blending active pharmaceutical ingredients (API). Additionally, tablet and capsule manufacturing processes necessitate high-level containment systems to maintain the sterility of materials and ingredients used to produce medications. These stringent containment measures are essential to ensure pharmaceutical products’ safety, efficacy, and quality.
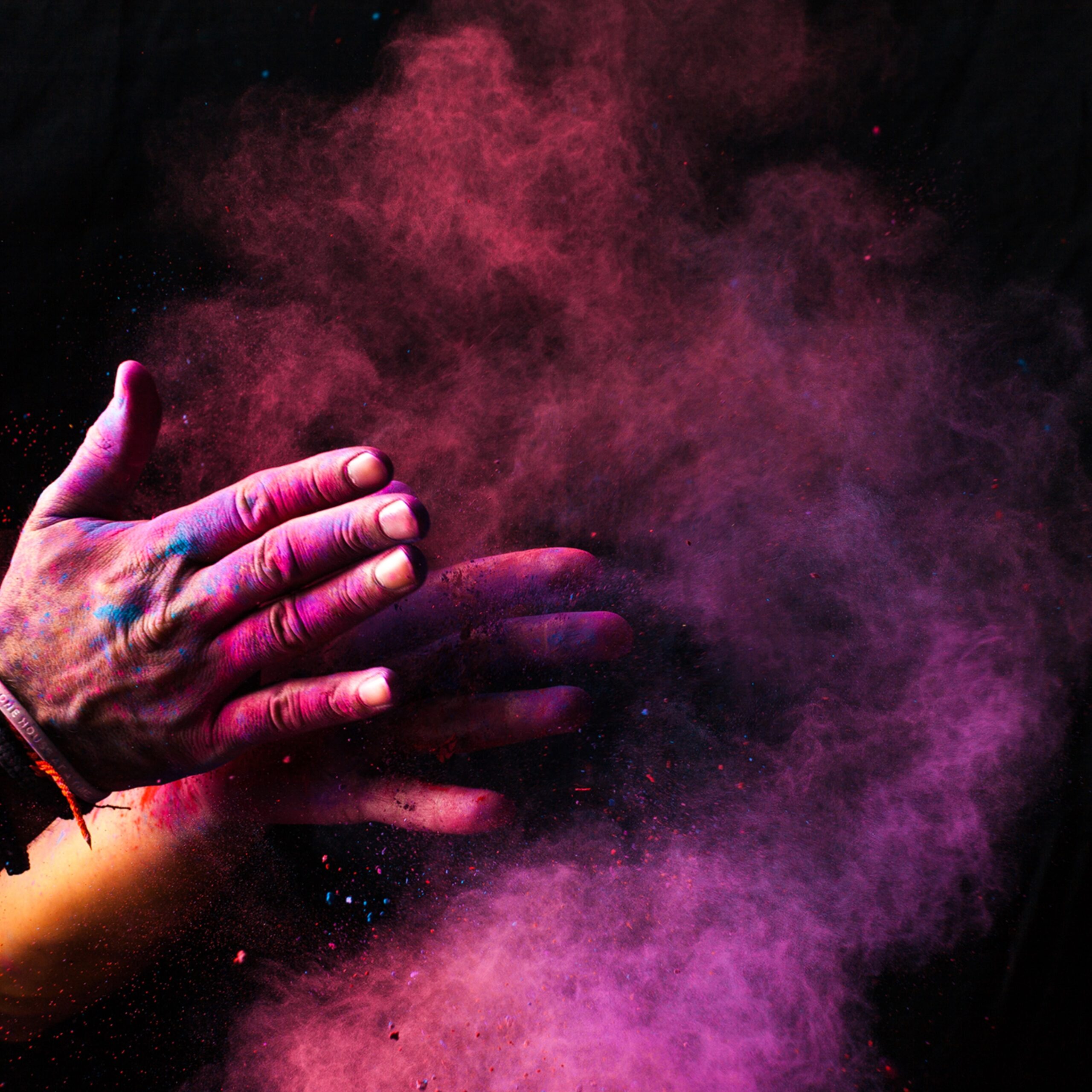
Chemicals manufacturing requires containment systems for most of their processes due to handling hazardous and sensitive substances and to avoid contamination that may alter the composition of their products. Semiconductor industries also have containment systems, as most of their products, such as sensors, are dust-sensitive. Chemical industry applications for powder containment include transferring and mixing potentially hazardous powders from process equipment to flexible bags and vice versa. Isolators and transfer systems ensure these powders’ safe handling and prevent them from being released into the environment.
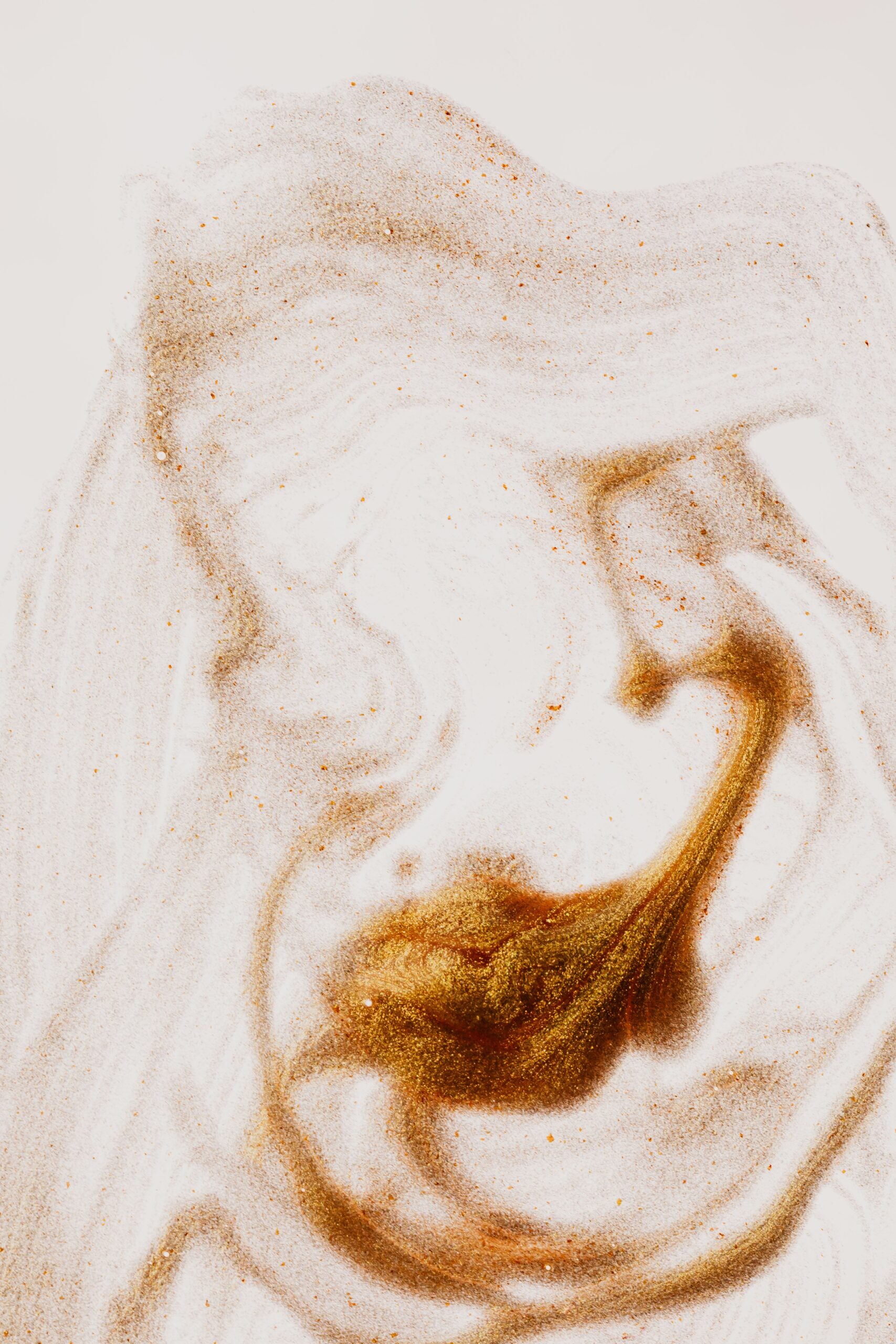
In the food production industry, powder containment systems are critical in safeguarding product integrity and preventing contamination. Quality control and inspection procedures frequently employ isolators across various sectors, including food, chemicals, and pharmaceuticals, to create a barrier between the product and the worker, effectively minimizing direct contact and upholding stringent quality standards. Food processing requires strict containment measures to avoid contamination from insects and other pests.
Clean and safe food processing
Food processing facilities need to comply with food safety regulations set by government agencies like the FDA and USDA to guarantee the consumers that the products are safe for consumption. Other agencies such as OSHA and NFPA also have regulations for the safe operation of food processing facilities. These regulations promote safety practices within the manufacturing area, including proper containment to avoid cross-contamination and health issues such as allergic reactions and respiratory illness due to inhalation of powders.
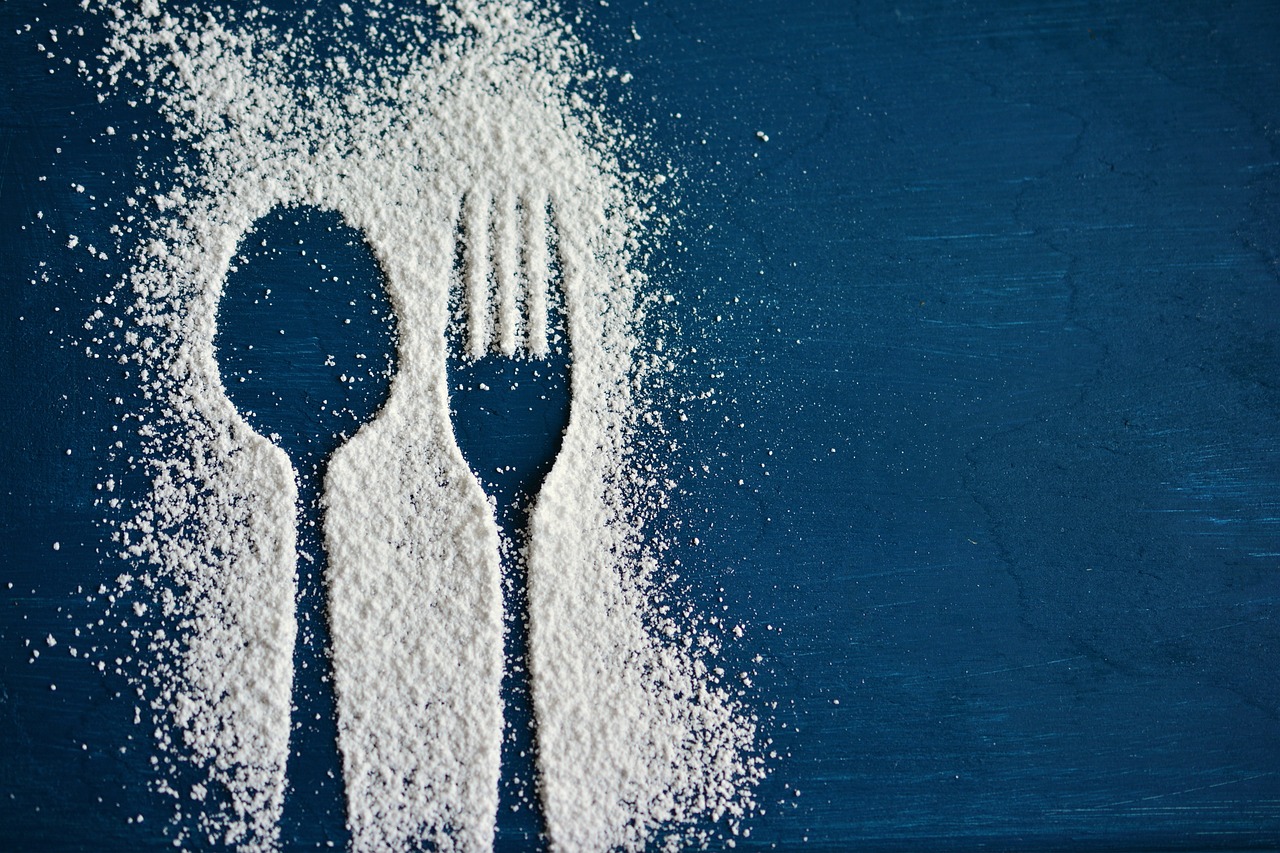
Food manufacturers use various containment technologies for the storage, transportation, and handling of their products. They are commonly used to store powder in large food manufacturing facilities. Possible explosions can occur in silos when loading powder products due to a dust cloud formation that can be a source of ignition when combined with the oxygen inside the silo.
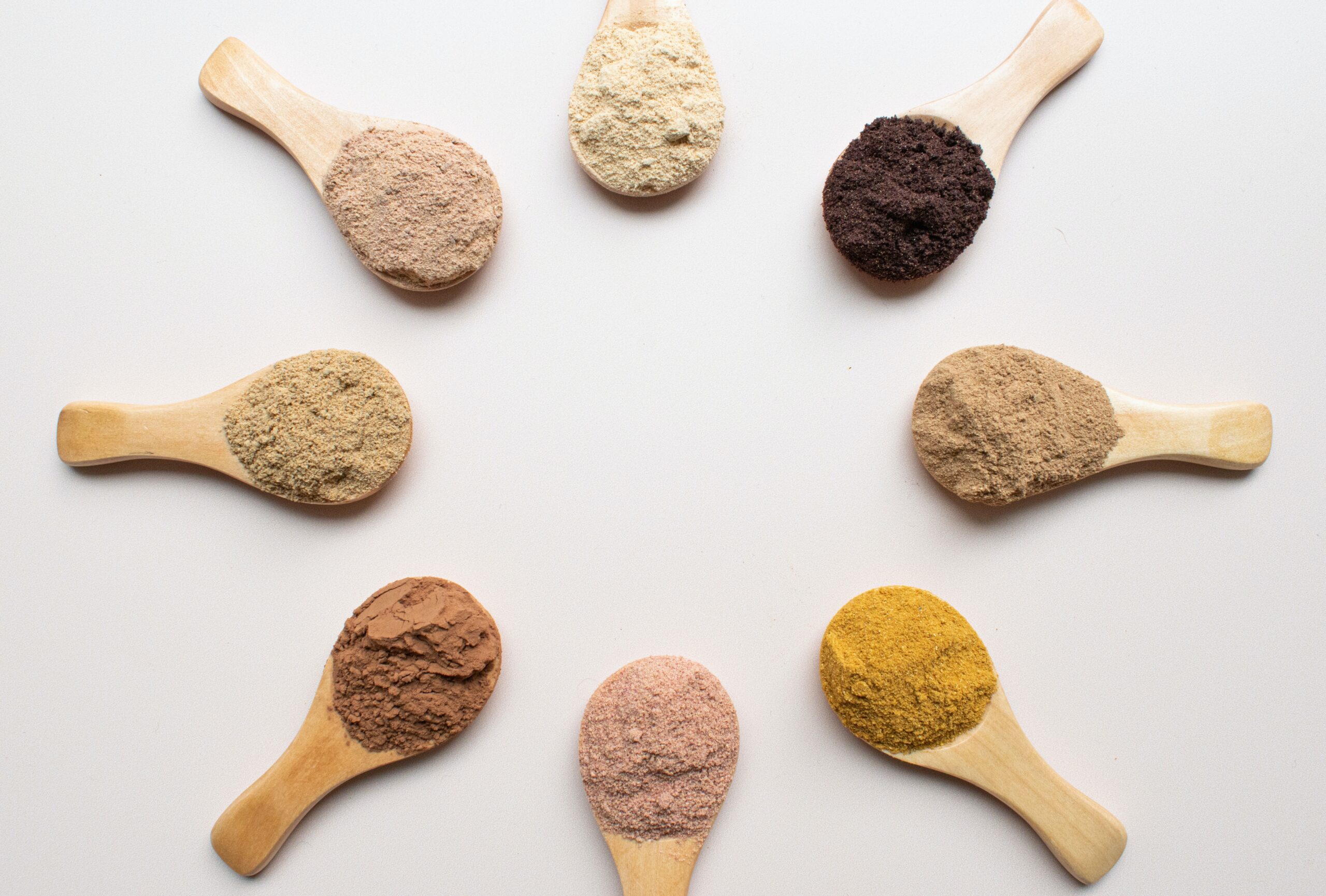
Proper loading and discharge of such powders in silos can be done through flexible intermediate bulk containers (FIBC), which can also be used to store and transport milk powder, chili powder, cocoa powder, and fruit powder effectively. FIBCs are made of thick woven polypropylene material and available in different types such as circular, U-panel, four-panel, and baffle. For hazardous powders, the FIBC must have polypropylene liners to eliminate the sifting of the woven polypropylene. FIBCs allow easy storage and transportation of powders and granules such as feeds, cement, and chemical powders.
Containment practices in the pharmaceutical industry
Pharmaceutical companies handle a lot of chemicals that may be harmful to workers when these chemicals are exposed in an open working environment. Other pharmaceutical products may also degrade when exposed to the same working environment due to possible contamination. Either way, pharmaceutical products require stringent containment practices to maintain a safe working environment and to avoid contamination of powder products like pharmaceuticals, protein, collagen, and dry inhaler powders.

Containment systems come in different types depending on the required application. Biosafety cabinets are a workspace that is enclosed and ventilated and is available in a wide range of biosafety levels. Contained transfer systems are designed to contain products as they are transferred from one container to the next, such as drums to processing equipment or discharging products from mixing tanks.
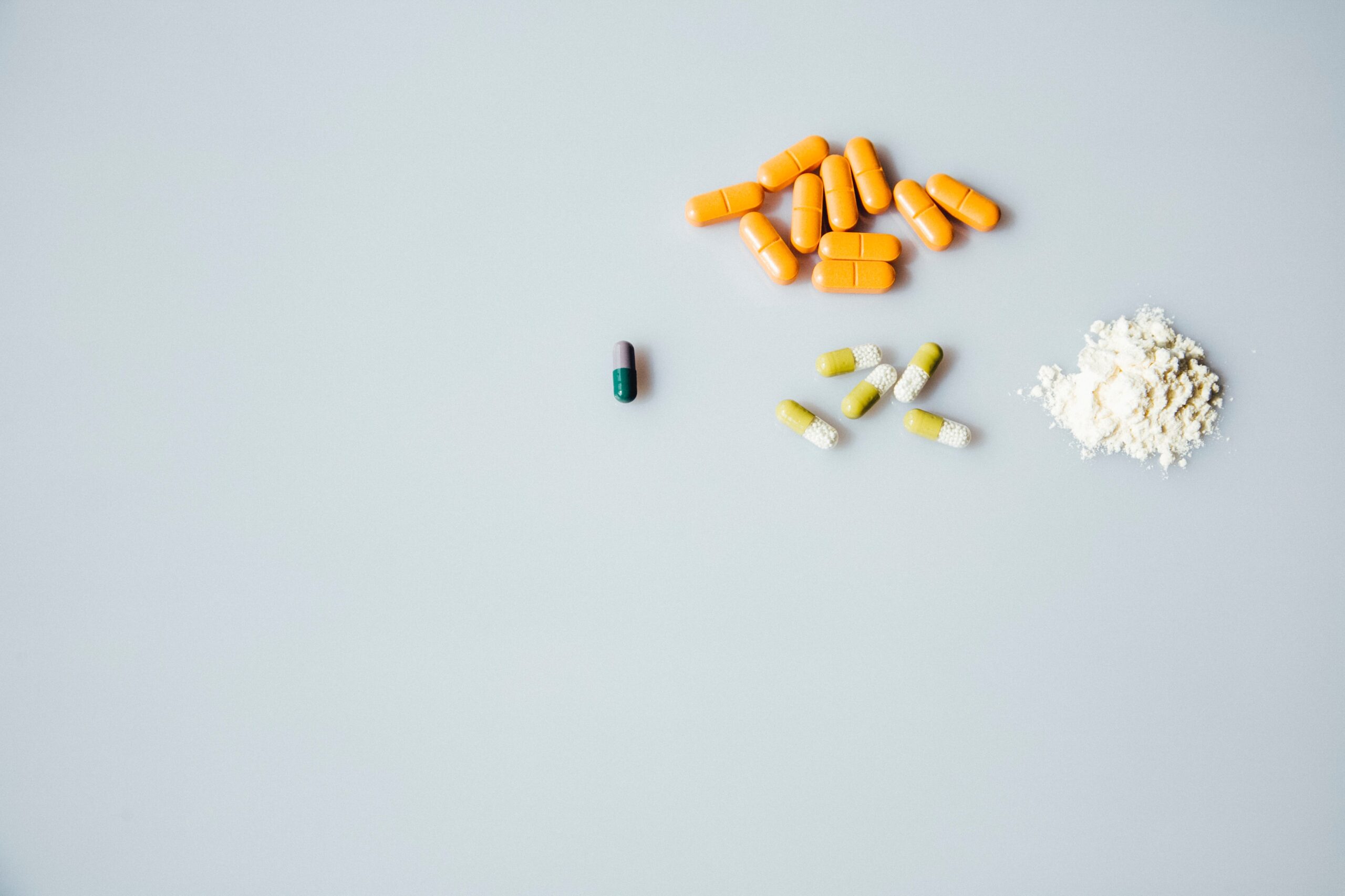
Containment isolators provide a barrier between the operator and the product while allowing access only by using a robotic arm or gloves attached to the glove panel. Downflow booths are commonly used in the pharmaceutical industry for high-level operator protection in powder handling operations and can be integrated with additional processing equipment. Flexible containment systems prevent product loss and exposure of operators to harmful substances during product transfer, such as charging or discharging of powders into bags and flexible containers.
Hazardous chemical powder handling
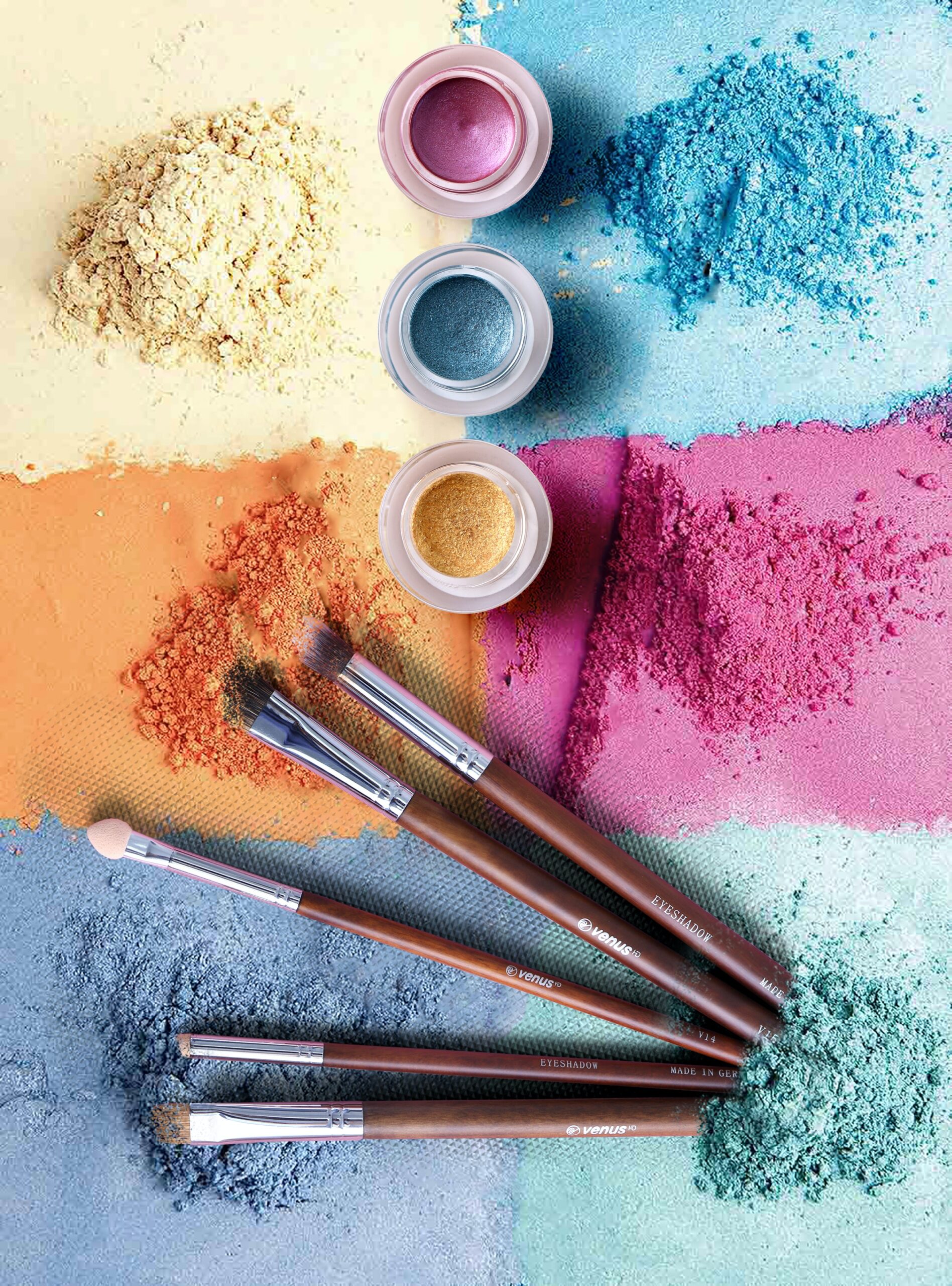
The chemical industry deals with chemicals that can be hazardous to the health of operators and the environment. Processing these chemicals requires containment solutions based on biosafety levels for handling specific chemical products. Containment technology solutions include contained transfer systems such as valves for controlling the charging or discharging of products. Containment isolators and downflow booths are mainly used for high biosafety level containment during processing. Biosafety cabinets provide an enclosed and controlled ventilation workspace, including HEPA filters to remove airborne contaminants. Another containment technology is using flexible containment solutions for safely transferring chemical powder products from equipment into bags and containers and vice versa.
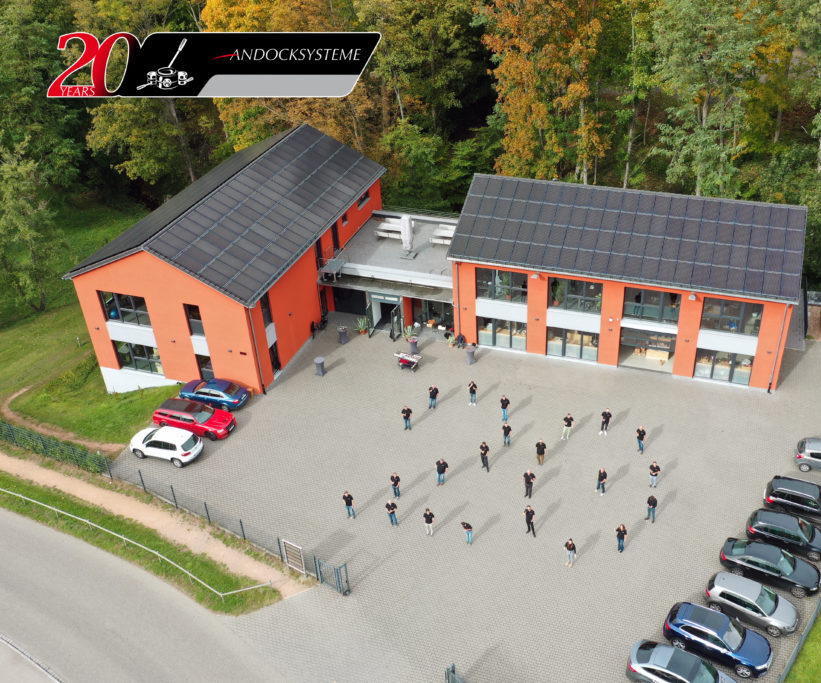
Connect to these experts
Andocksysteme is a specialist in developing high-quality containment docking and solutions for bulk material. They engineer industrial containment solutions for medium and large enterprises and have built a reputation for world-class machinery and equipment. Curious to learn more?
Innovations of containment solutions
As more chemicals are developed, pharmaceutical and chemical industries seek ways to improve aseptic production to keep up with stringent regulations. An example is using single use (SU) technology to improve sterile production and product integrity, as this technology requires the item used in production to be disposed of after a single use. A disposable version of a split butterfly valve (SBV) is one item using SU technology.
The valve is used for the sterile transfer of powders into and out of the equipment. The SBV is made up of 2 components where one component is connected to the equipment and the other attached to a filling container. The component attached to the filling container doesn’t need to be cleaned, as it will be disposed of after filling single-use flexible bags. Manufacturers are also looking into smart technology where the facilities can be monitored in real-time from a mobile device, including the valves used in production lines.
This technology allows manufacturers to identify the containment systems that may require preventive maintenance to help minimize downtime. Eco-friendly solutions include using low-energy consumption motors and frequency inverters to power isolators and other equipment.

Dealing with Powder Containment challenges
Due to more rigorous regulations, as more chemicals are being developed, manufacturers are looking for ways to minimize energy consumption through new technology, such as frequency inverters. Existing containment systems are also retrofitted to keep up with stringent regulations that address health and safety concerns, as well as allowing compatibility with newly developed containment systems. Innovations are also being made in the cleaning systems associated with containment technology. These improvements involve optimizing the placement of spray balls at strategic points to facilitate efficient cleaning of containment systems, minimizing the need for excessive water or cleaning solutions.
Video on powder containment systems
Split Butterfly Valve for safe transfer of hazardous and active (HPAPI) solids
Tablet production
Contained Single Use Transfer Bags for Containment solids handling
Solutions
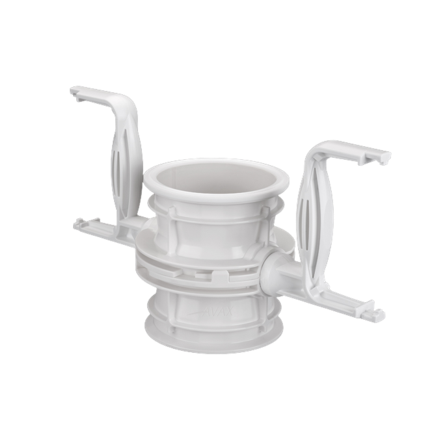
Single-use containment valves
From GMP and HSE perspective material transfer is critical for chemical and pharmaceutical for...
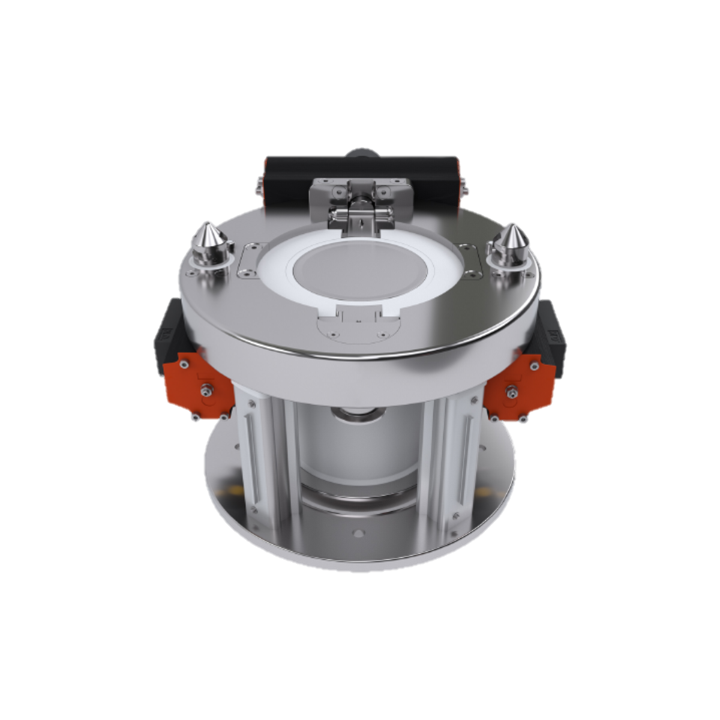
High containment split butterfly valve
Powder containment is the cornerstone of chemical and pharmaceutical manufacturing. ...
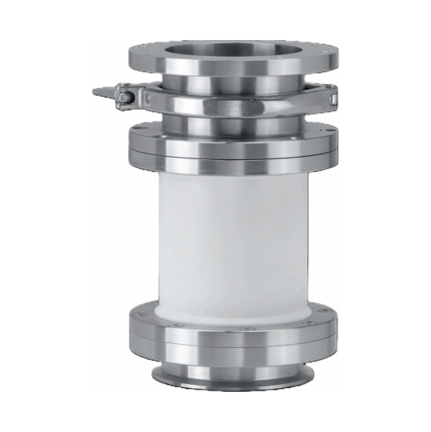
Bellows for pharmaceutical powders
Thermal and mechanical changes can lead to stresses in industrial piping systems. These ...