Modified Atmosphere Big Bags
Manufacturers requiring big bag packaging have specific sizes, shapes, and material requirements to ensure their products can be handled safely during transportation and storage. However, the FIBC manufacturing process is only sometimes considered sustainable since these big bags are made of polyethylene, which is difficult to recycle. An ideal solution would be working on preventing waste by producing custom-made big bags of the exact right sizes and shapes required by the manufacturer to save on excess offcuts and material costs and minimize production waste.
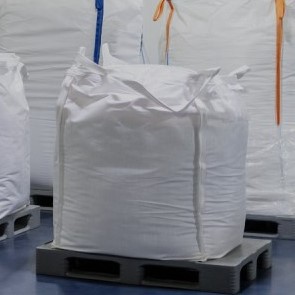
Preventing 10-20% of waste by producing big bags in custom shapes, sizes, and material
Masterpack Group, a leading expert in innovative packaging solutions for bulk materials, designed custom big bag containers used as packaging that provide increased protection, prolong product shelf life, and optimize storage space. FIBCs are available in different shapes, such as circular or U-shape. They can be equipped with specific liner materials like conductive, aluminum, anti-static, dissipative, metalized OPP, or whichever is best for your product. Liners also help protect products from oxygen, moisture, and other possible contaminants while providing safe filling and discharge. The FIBCs are hygienic, and the PE films used as liners are designed and fabricated according to the correct size, not cut to shape from a big tubular PE film. This method minimizes waste in the production of each liner.
Benefits
- Custom size and shape to match the packaging requirements
- Different liner materials available for safe handling
- Less waste in the production of PE liners
- Hygienic and suitable for products in large quantities