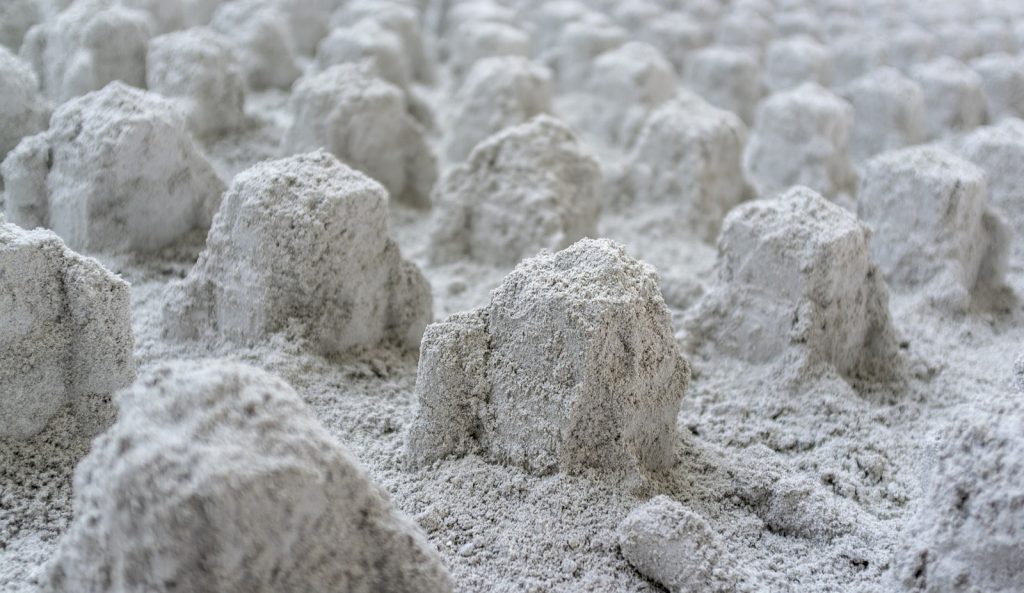
Ceramics Drying Equipment
Find production technology for drying ceramics, and connect directly with leading machine manufacturers worldwide.
The drying of ceramics is a crucial step in the industrial pottery-making process. This process involves removing moisture from the clay body to make it firm and hard. The most common equipment for achieving this is by using either a kiln or a dryer. The choice of equipment you choose will depend on the type of ceramics you would like to produce.
Kilns are typically used for high-temperature firing to create the final ceramic product. The kiln is heated to a specific temperature. Which causes the clay to go through a series of physical and chemical changes. Thus, resulting in a hardened and durable material. Before being placed in the kiln, the clay dries to a point where it is no longer soft or pliable. The clay is usually left to air dry to remove any excess moisture. After the air-drying process, the pottery is fired in a kiln. Where the high temperature causes the water content in the clay to evaporate, resulting in even drying and shrinkage.
Using Industrial Dryers With Ceramics
Another method of drying ceramics is using specialized drying machinery. Dryers are typically used for lower-temperature firing. Furthermore, they are preferred for materials like porcelain, which are susceptible to cracking and breaking. Especially during the drying process. This process involves removing moisture by using evaporation. Ceramics are placed in drying equipment where heated air is circulated. And thus, the moisture is drawn out of the clay. Also, a glaze is usually applied to ceramics after the drying process to add color. But also to protect the ceramics from wear and tear. Another method for protection is using what is called a Grog. This is a mixture of ground-up ceramic material that can also be added to prevent cracking during drying. Producing high-quality ceramics absolutely needs even drying. Humidity and temperature have to be controlled throughout the drying process to prevent cracking and warping.
Which ceramics drying technology do you need?
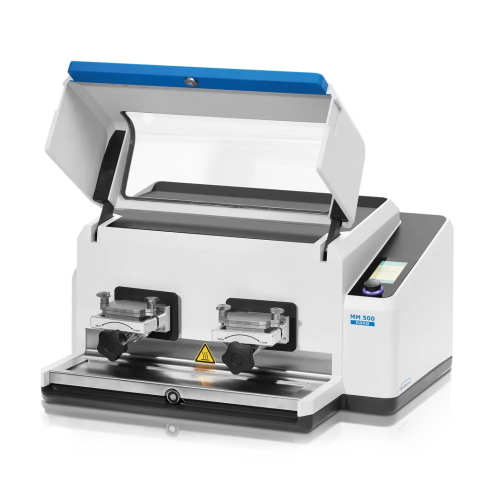
Ultrafine grinding solution for nanoparticles
Achieve ultrafine particle sizes with high-speed precision, ideal for labora...
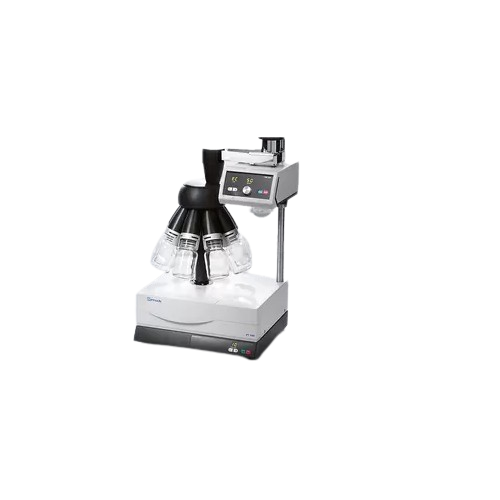
Sample dividing solutions for laboratory applications
Streamline your lab’s precision in sample preparation with so...
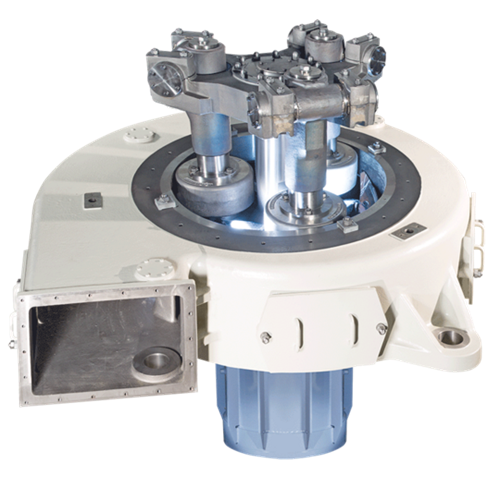
Pendulum mill for fine grinding and drying
Achieve efficient and precise grinding for soft to medium-hard materials while ...
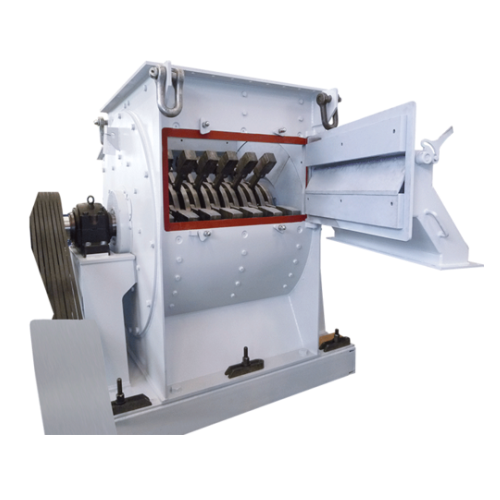
Industrial hammer mill for mineral processing
Optimize your material processing with an advanced hammer mill designed to e...
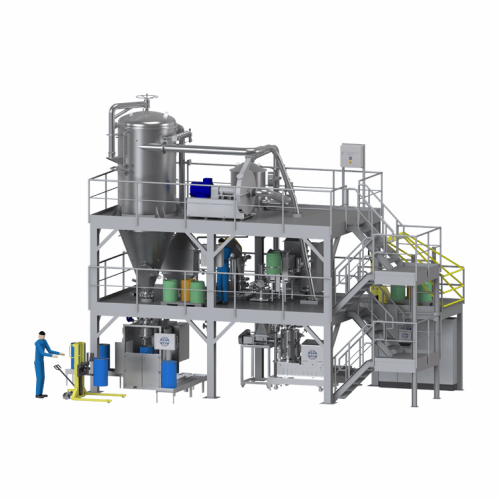
Drying systems for powders and bulk solids
Enhance your production line with precise control of moisture content in powder...
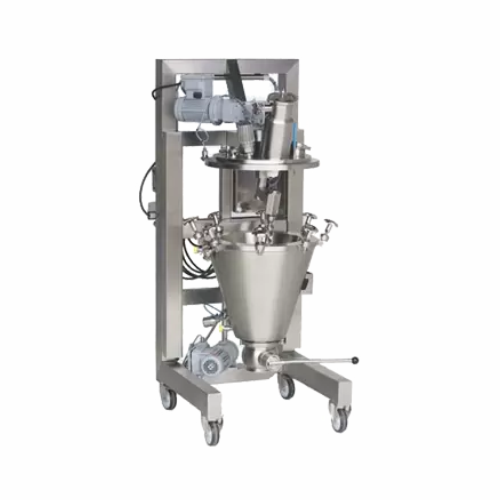
Laboratory vacuum dryer for heat-sensitive materials
Optimize moisture control in heat-sensitive materials with precise a...
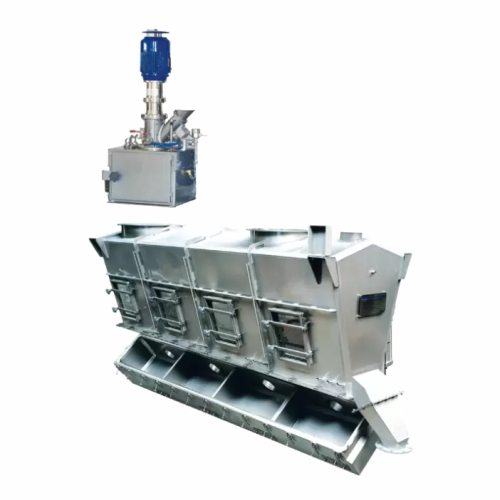
Continuous powder agglomeration system
Enhance product solubility and flowability while minimizing energy consumption with ...
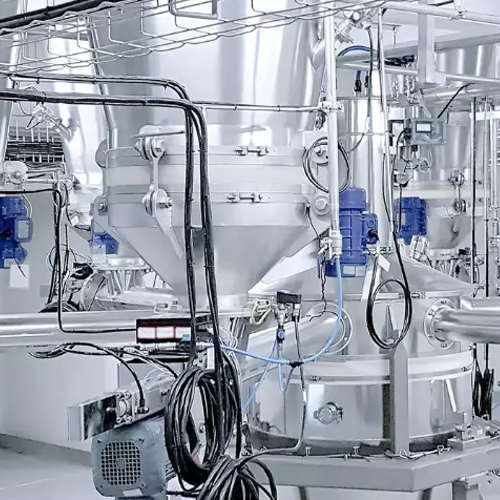
Conical screw mixer for powder blending
Achieve precise and homogeneous blending with the conical screw mixer, ensuring uni...
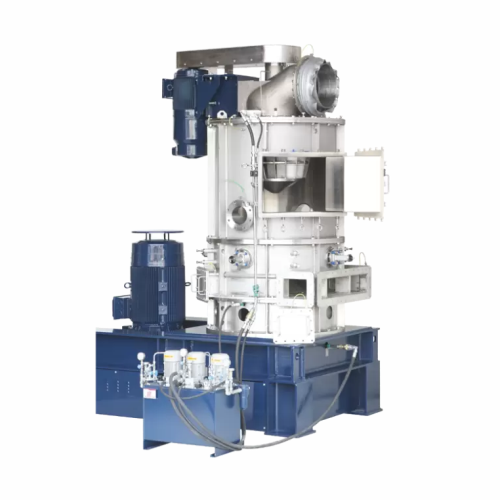
Ultra-fine powder flash drying system
Achieve rapid moisture removal and particle refinement with this integrated system, d...
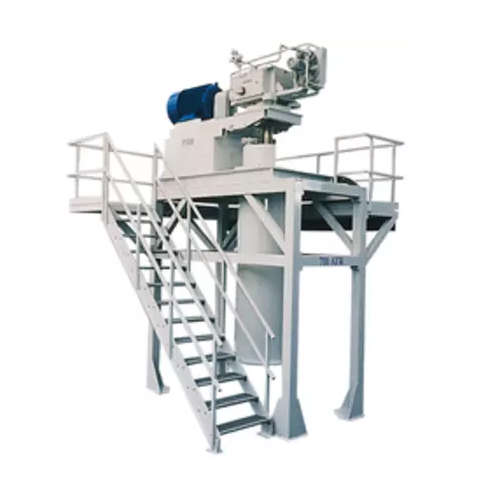
Ultra-fine grinding with ball mills and agitated media mills
Achieve precision in ultra-fine grinding for demanding mate...
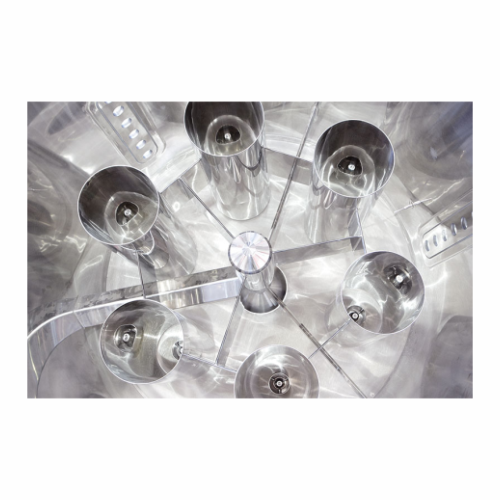
Fluid bed and spouted bed systems for granulation and coating
Optimize your production line with cutting-edge fluid bed ...
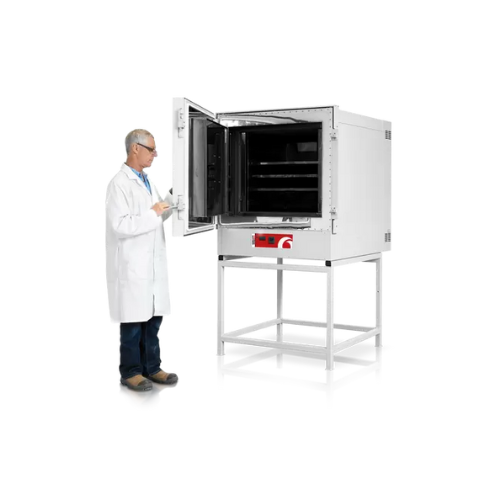
High temperature industrial oven for advanced heating processes
Achieve precise heat treatment for critical components, ...
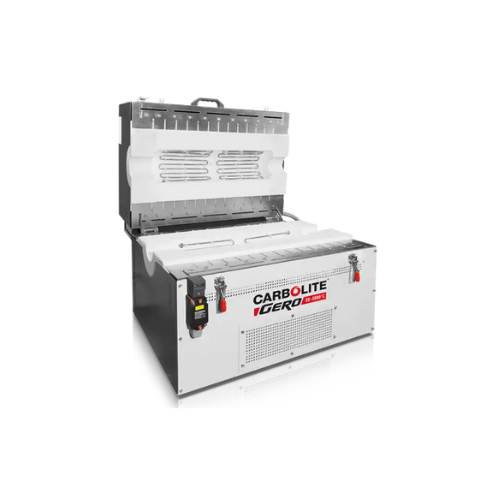
Split tube furnace for high-temperature applications
Enhance your thermal processing operations with a split tube furnace...
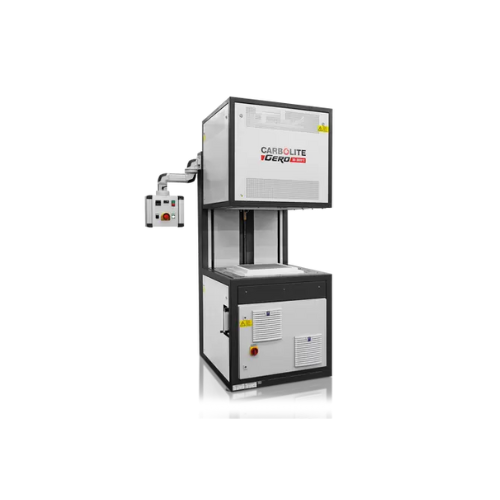
Top hat industrial furnace for high-temperature applications
Achieve precise high-temperature processing with this advan...
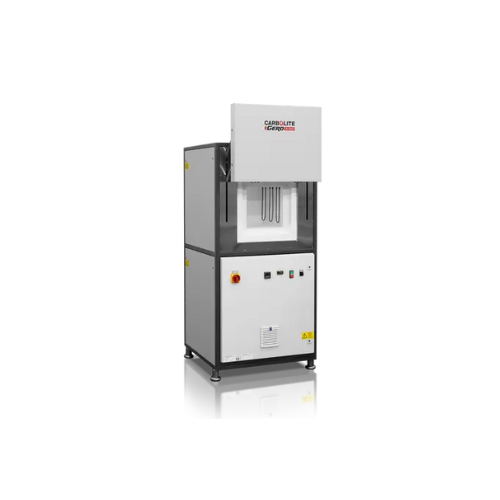
High temperature chamber furnace for sintering ceramics
Achieve precise thermal consistency for high-temperature applicat...
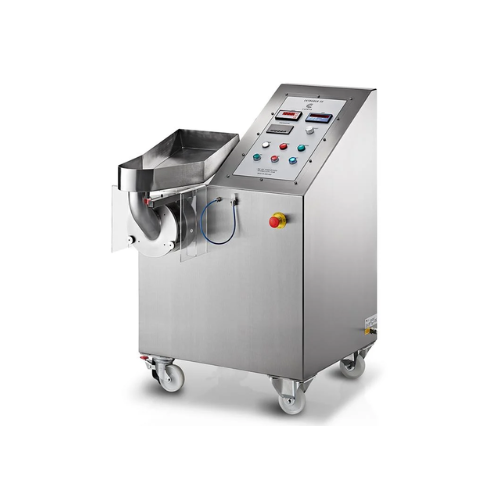
Spheroid extruder spheronizer 50kg per hour
Efficiently handle product development and contract manufacturing with a versa...
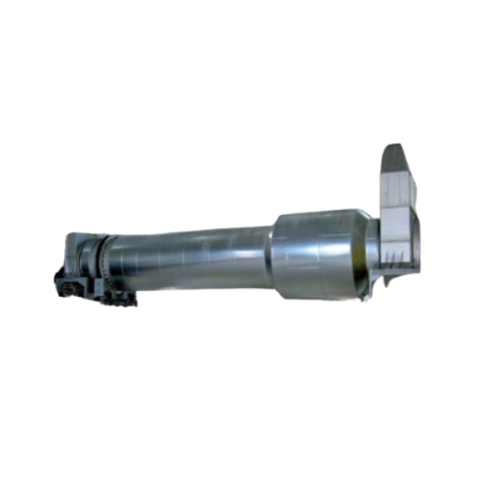
Indirect drying drums for solvent-based products
Optimize energy use and safety with our indirect drying drums, ideal for ...

Industrial drum dryer for bulk solids
Optimize your production line with high-throughput drying for varied particle sizes, ...
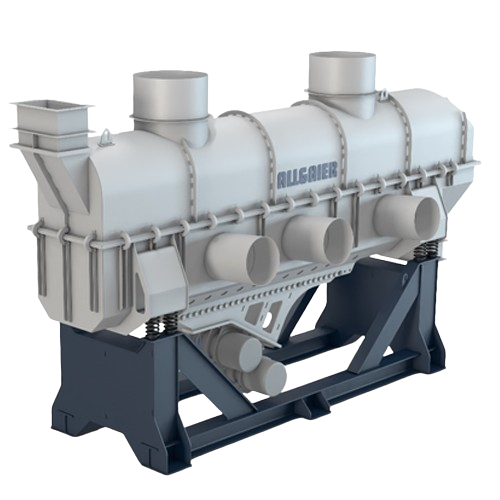
Fluidized bed dryer for industrial materials
Enhance product quality and energy efficiency with fluidized bed dryers, opti...
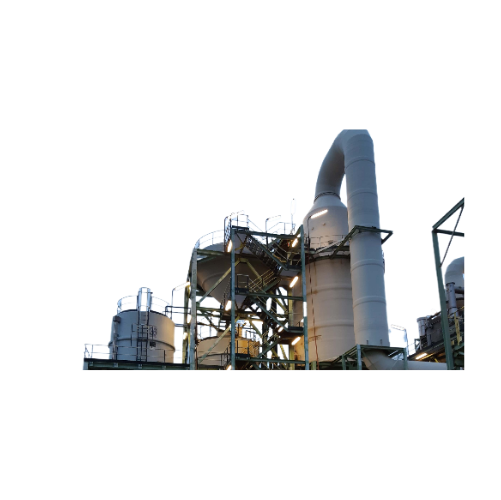
Heavy metal removal system for industrial flue gas
Effectively remove harmful heavy metals from industrial emissions whil...
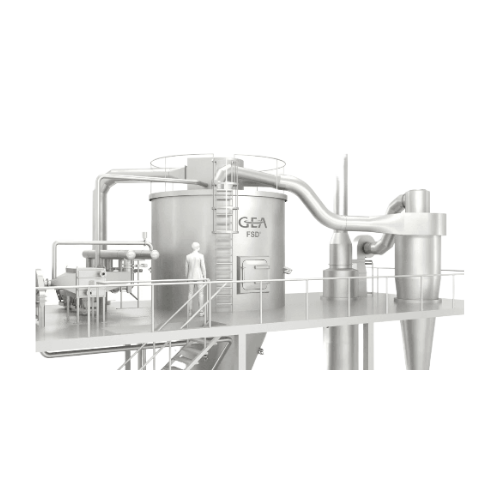
Spray dryers for ceramics and pharma products
Achieve consistent powder quality for heat-sensitive and sticky products wit...
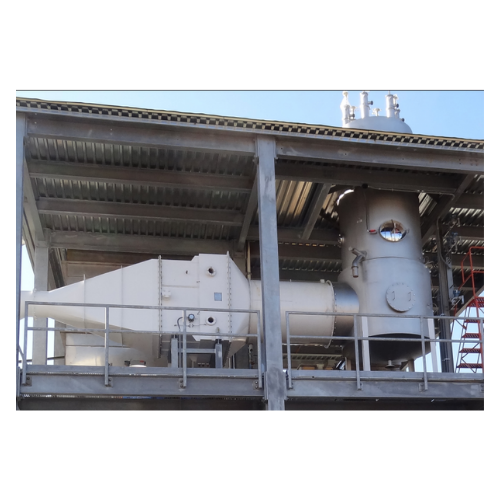
Dust-free granulation system for non-heat sensitive liquid feeds
Transform liquid feeds into dust-free, free-flowing gra...
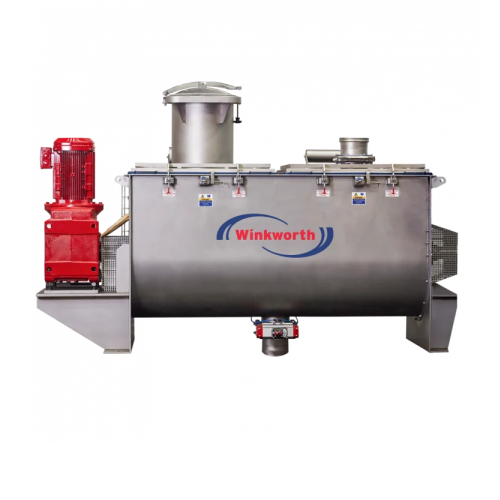
Efficient ribbon mixers for precise powder blending
Achieve consistent and uniform blending with this advanced U-Trough m...
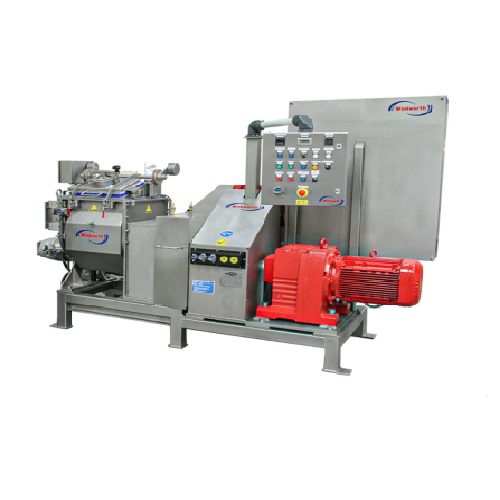
Industrial sigma mixer extruder for homogeneous mixing and extrusion
Achieve precise mixing and seamless extrusion of d...
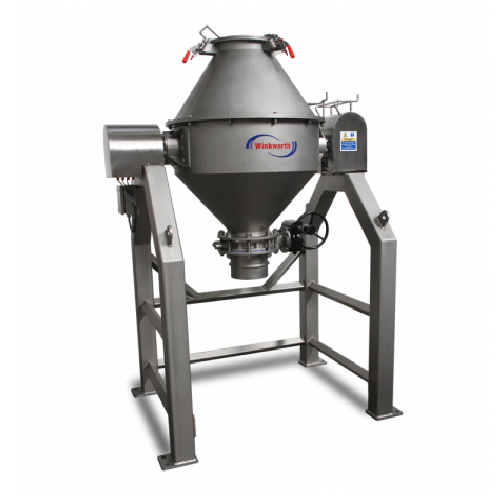
Double cone mixer for free-flowing material blending
Optimize your production with precision blending and gentle drying o...
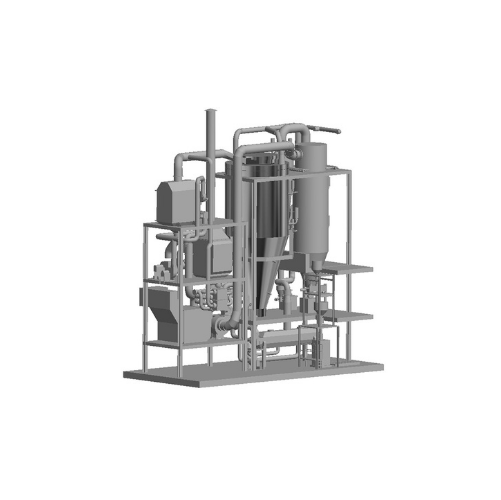
Spray drying system for heat sensitive products
For heat-sensitive products requiring precision drying, this spray drying ...
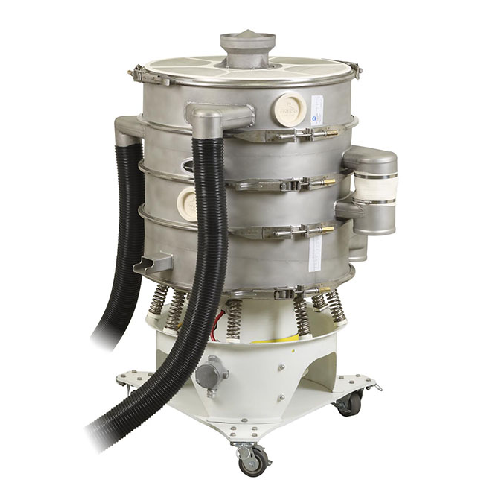
Drying and cooling classifier for plastic pellets
This solution enhances efficiency by combining drying, cooling, and cla...

Continuous drying for cohesive and non-cohesive pastes
Transform high-viscosity liquids and pastes into fine, flowable po...
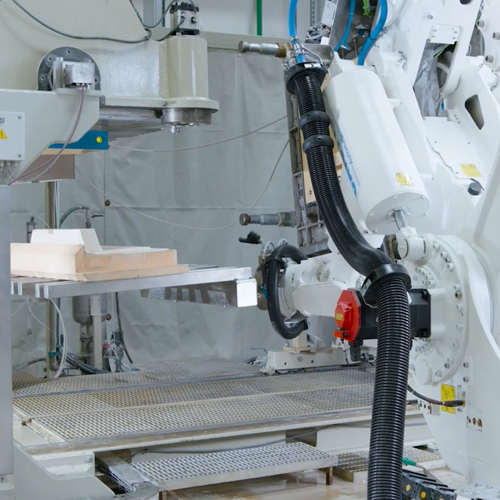
Ceramic sanitaryware casting and drying plants
Ensure top-quality ceramic sanitaryware production with comprehensive solut...
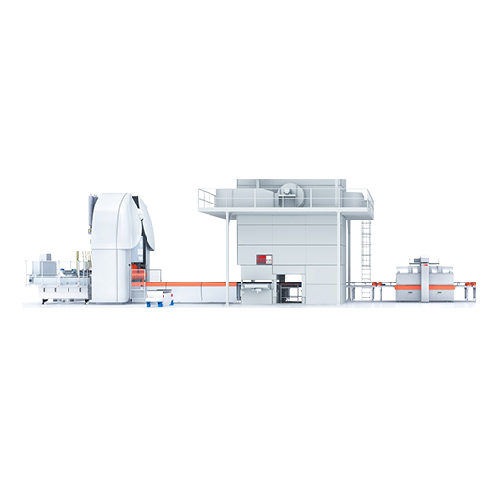
Advanced ceramic tile production line
Elevate your ceramic tile production with an all-encompassing solution that seamlessl...
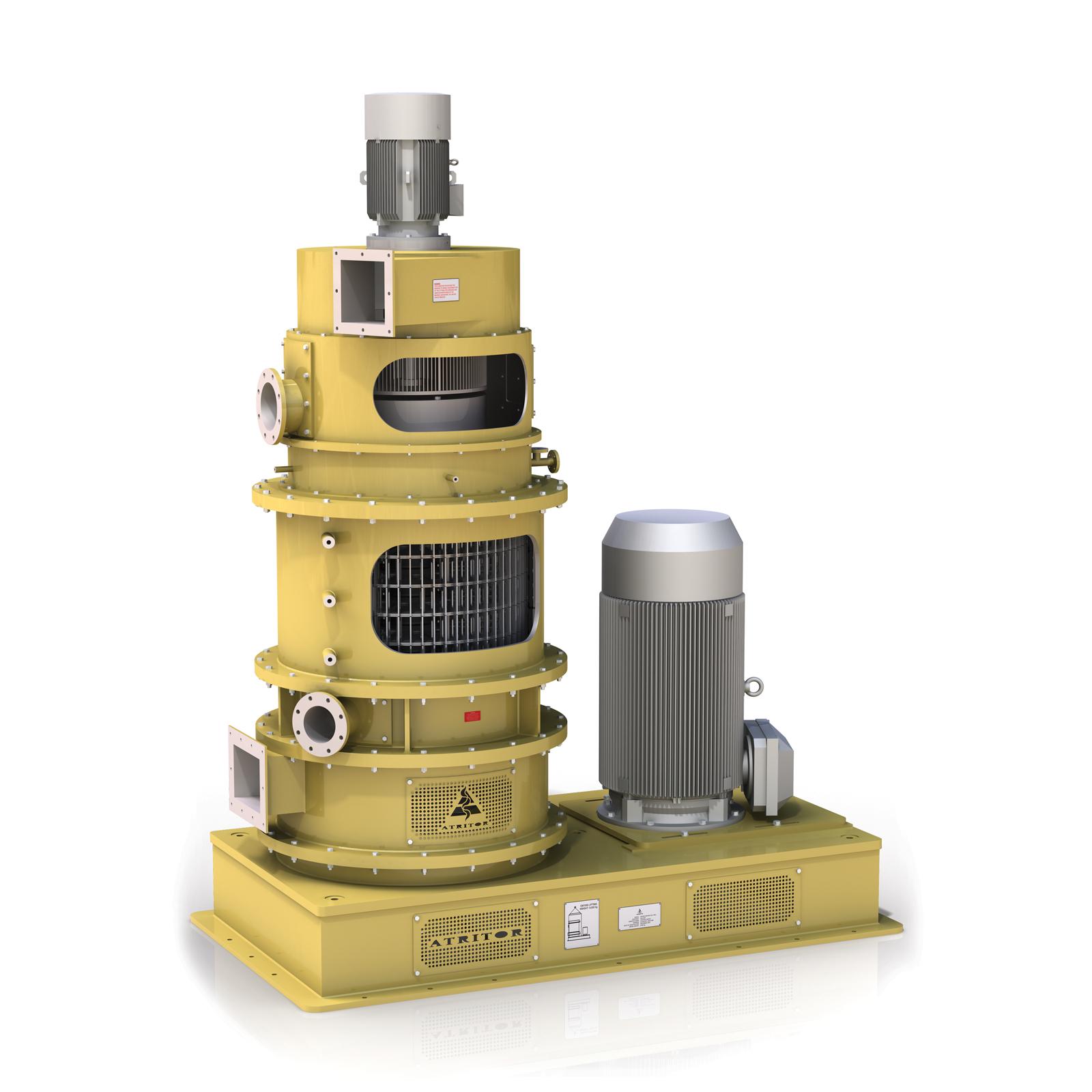
Milling and drying machine for fine powders
When you need to produce ultra-fine powders, the milling and drying process em...
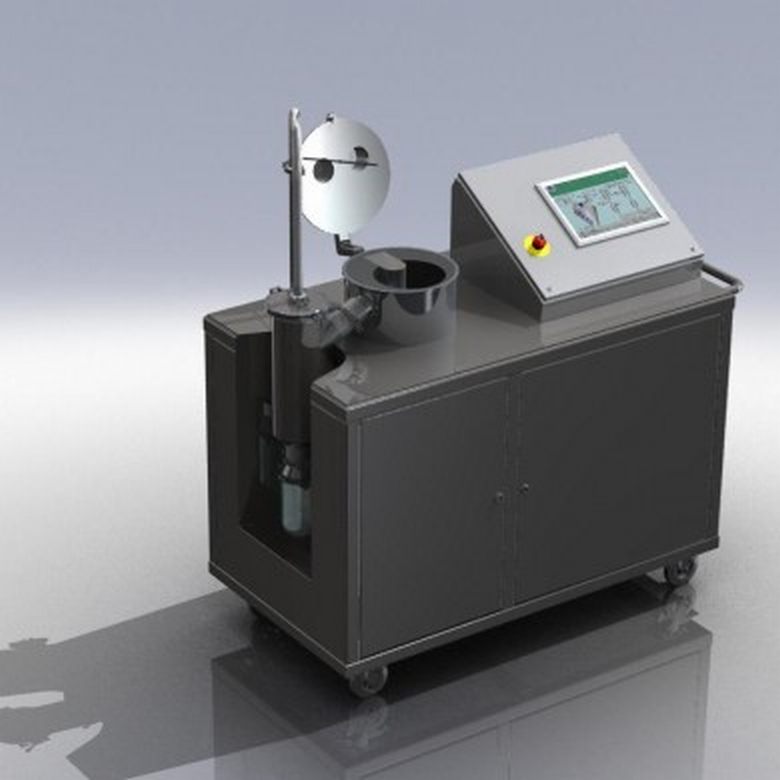
Laboratory scale active freeze dryer
The laboratory-scale active freeze-drying is used for dehydrating high-value products ...
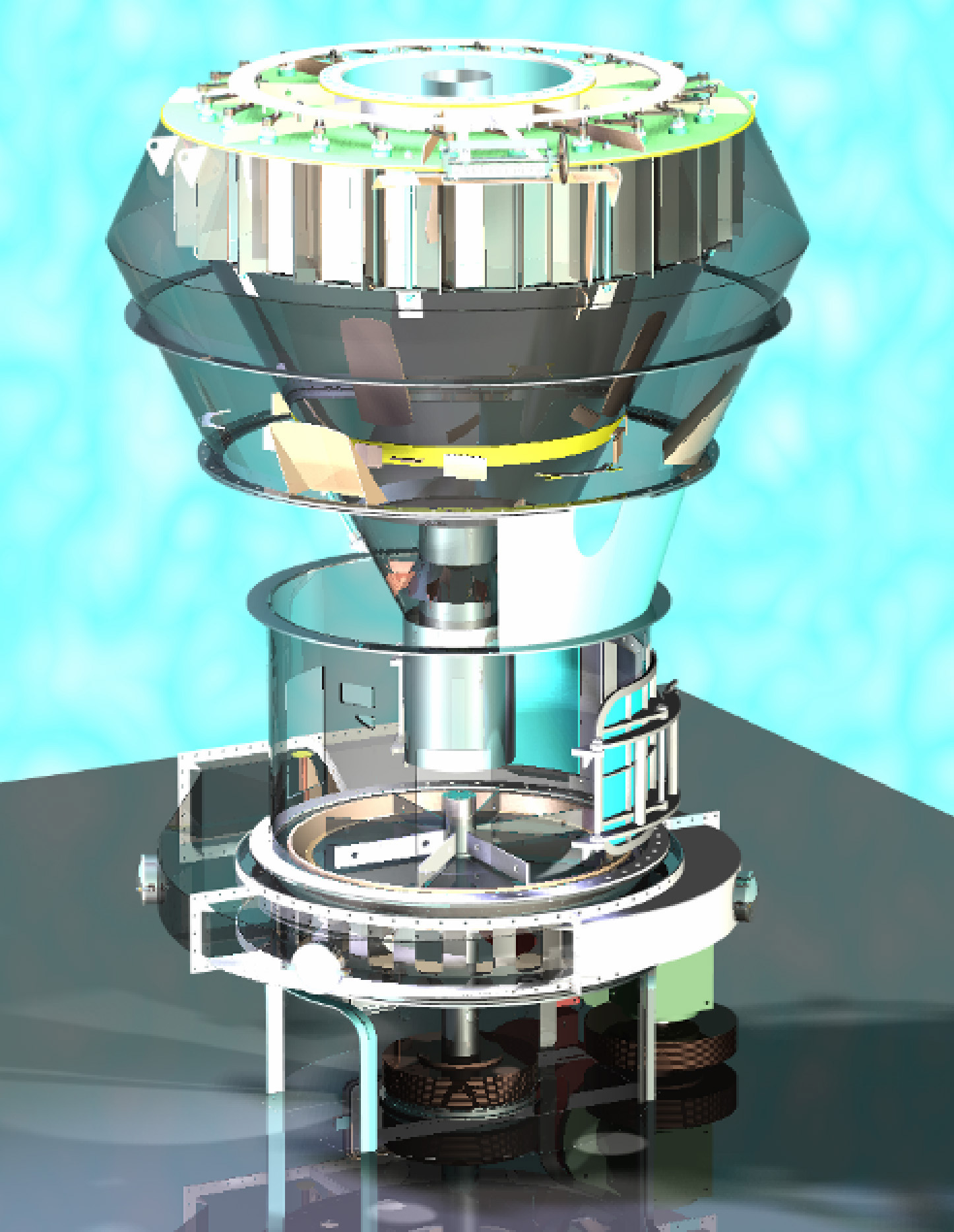
Horizontal impact calciner
Quality of synthetic gypsum and stucco products is highly influenced by the quality of the calcin...
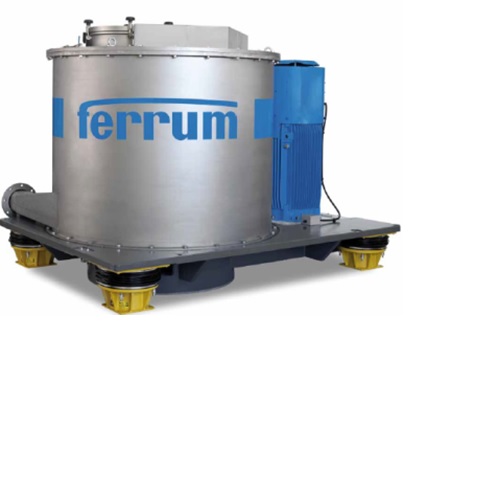
Gypsum centrifuge
Especially designed for flue gas desulphurization, applications in coal fired power plants and waste incine...
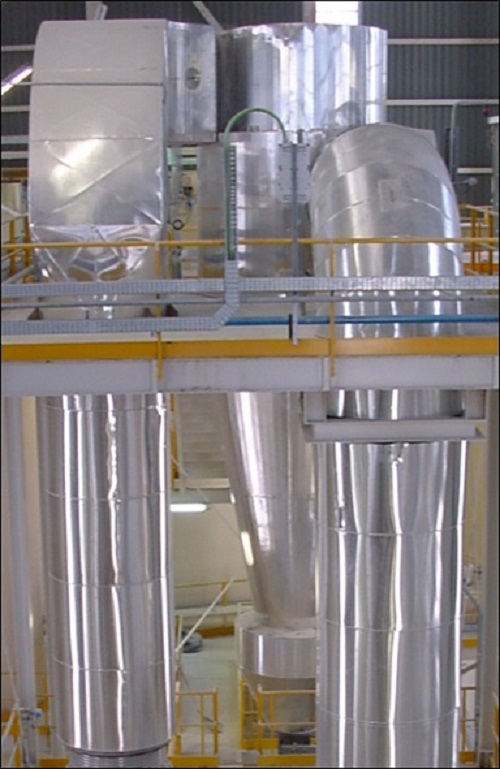
Flash calciner
Quality of gypsum plaster products is highly influenced by the quality of the calcining process employed in pro...