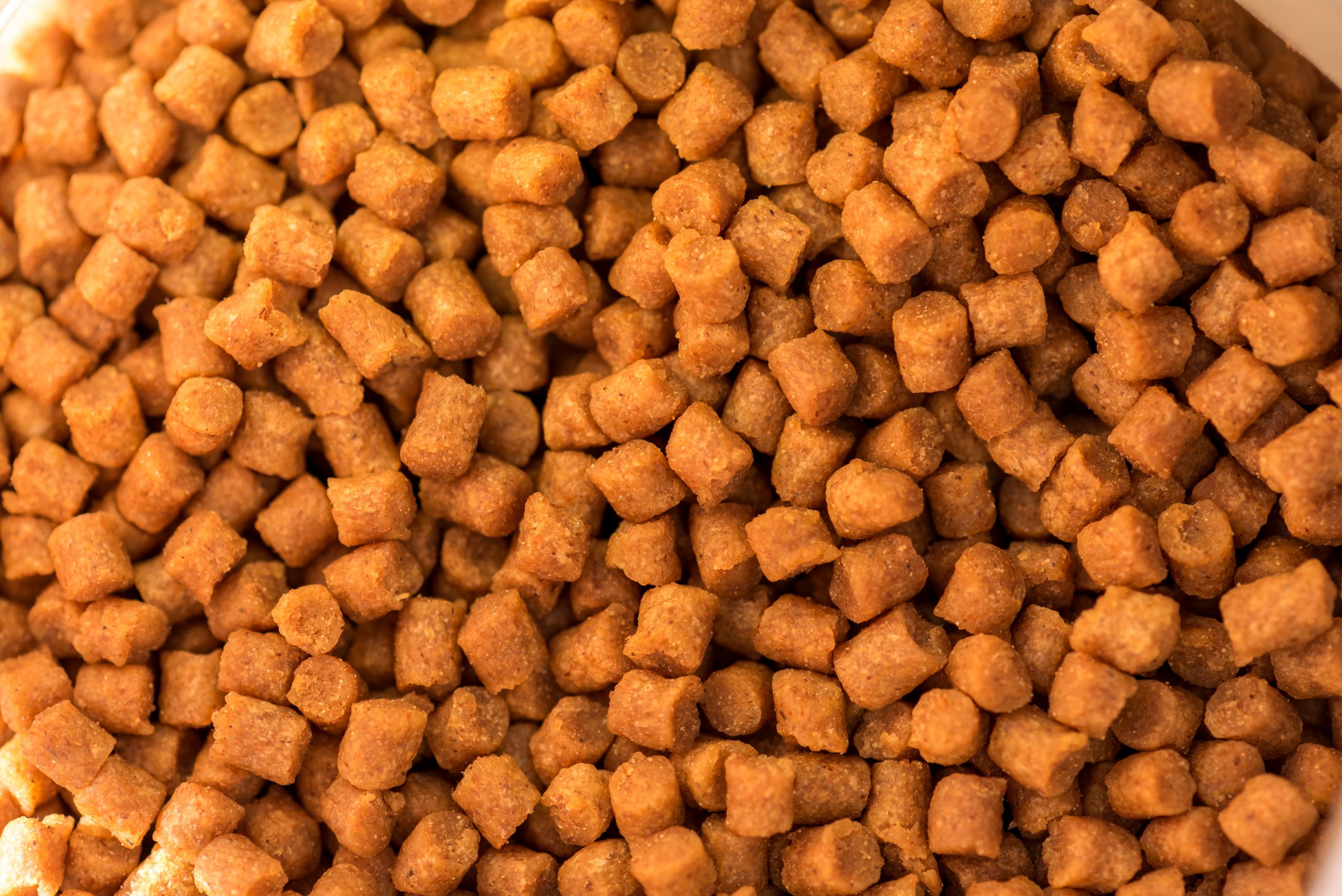
Making Floating Pellets
Find innovative production technology for making floating pellets and connect directly with world-leading specialists
There are two misconceptions about floating pellets. The first one is that they are made with a pellet mill, when the proper floating pellets-making machines are extruders. The second misconception is that floating feed is only used for fish. However, many other species consume feed on the water, such as crocodiles and birds.
Select your floating pellets process
Tell us about your production challenge
Diversify your floating feed formulation with a twin-screw extruder
When it comes to floating pellets making machines, you can choose between a single-screw or a twin-screw extruder. Both give you control of buoyancy to produce a floating, slow sinking, and sinking feeds.
If you choose single-screw, you will have a limited range of functions, which are easy to control. But processing time is longer, and you will need simpler feed formulas. On the other hand, producing floating feed with a twin-screw extruder gives you versatility and efficiency.
Twin-screw extruders allow you to work with a wide range of raw materials, providing flexibility in feed formulas. They have the advantage of micromixing the ingredients and transferring heat more uniformly. This offers better flow properties, low residence time, and better quality. Besides, you can vary the density and size of the “pellet” to produce micro aquafeed.
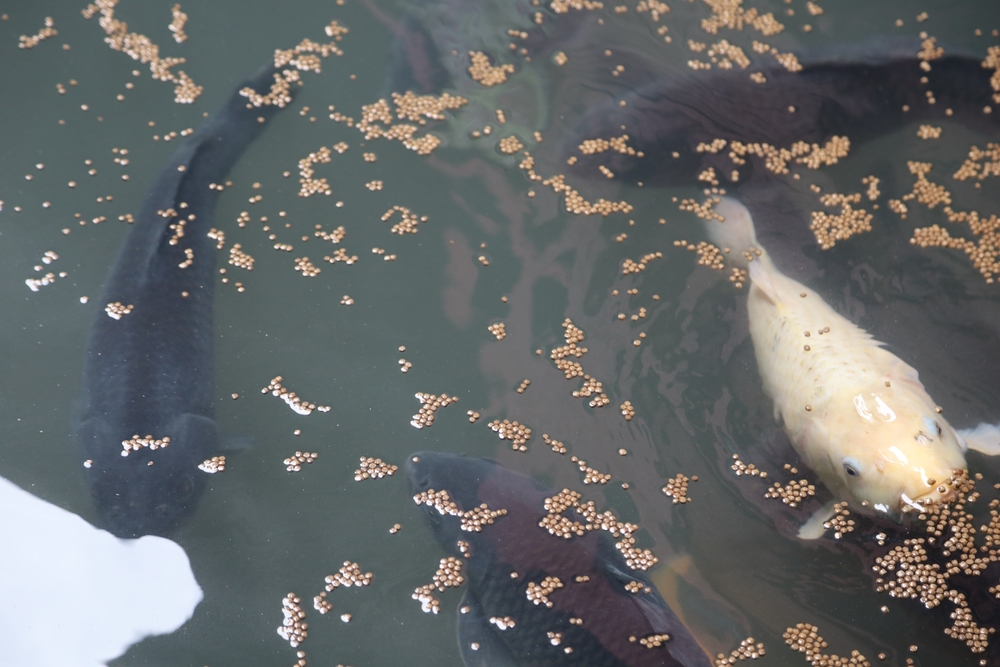
Add a pre-conditioner to raise productivity in floating feed processing
Although an extruder is the main machine required to produce floating pellets, adding a pre-conditioner increases productivity in floating feed manufacturing.
Water and steam are added to the dry pre-mixed ingredients in the pre-conditioner. The resulting moisture mix is homogeneous and pre-cooked, facilitating texturizing and extrusion. A pre-conditioner enhances the process and reduces wear of the extruder, with heat efficiency and better mixing. This treatment reduces starch quantity into the formula while improving the final product’s digestibility, uniformity, and water stability.
Include alternative feed sources in your floating pellets
In aquafeed, fishmeal is the primary protein source due to its rich protein and fatty acids content. But as fishmeal production and supply needs sustainable improvements, you can use alternative protein sources to make floating pellets. These alternative sources can be plant-based TVP or insect-based, mixed in the formula, and efficiently processed using a pre-conditioner and a twin-screw extruder.
Processing steps involved in floating pellets making
Which floating pellets technology do you need?
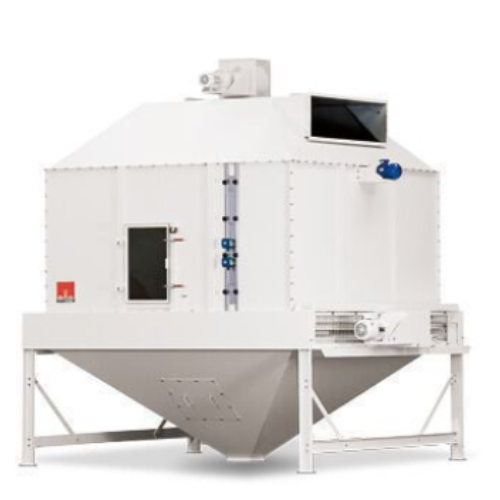
Counterflow dryer for pet food and fish feed
Optimize moisture control and enhance feed quality with efficient drying, cru...
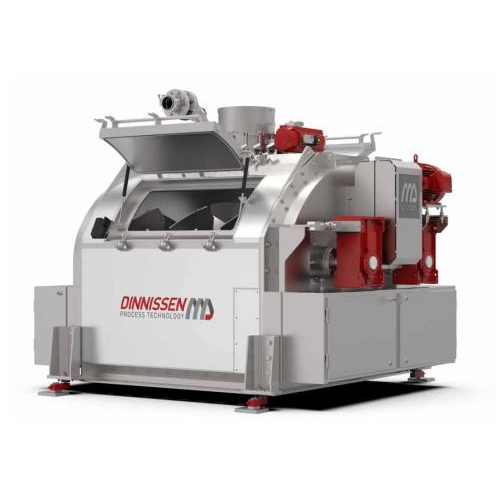
Advanced vacuum coating system for pet food and feed
Achieve uniform saturation in pellets and granules with precise liqu...
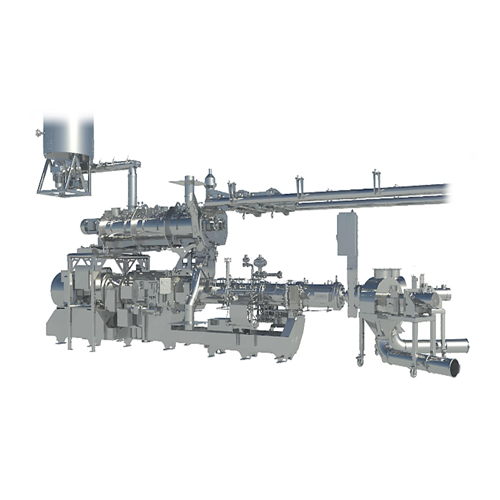
Extruder for aquatic feed production
Efficiently produce a wide range of aquatic and pet feed with precise control over pel...
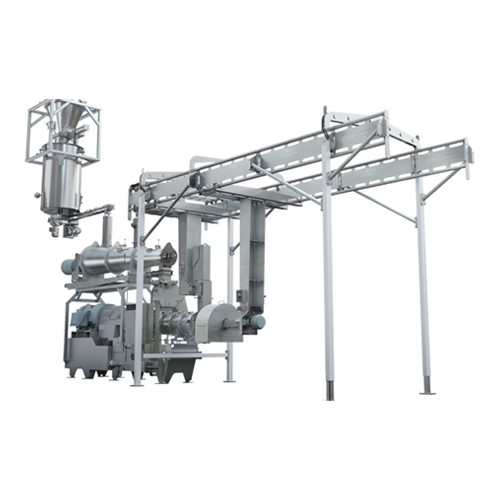
Conical twin screw extruder for pet food and aquatic feed
Precision-engineered for high-speed extrusion and drying proce...
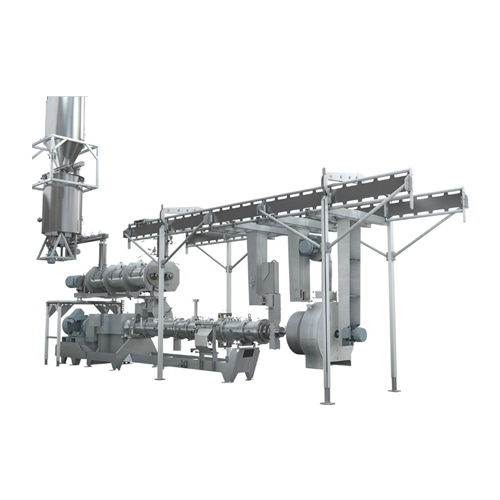
Twin screw extruder for pet and aquatic feed
Achieve exceptional cooking precision with our twin screw extruder, designed ...
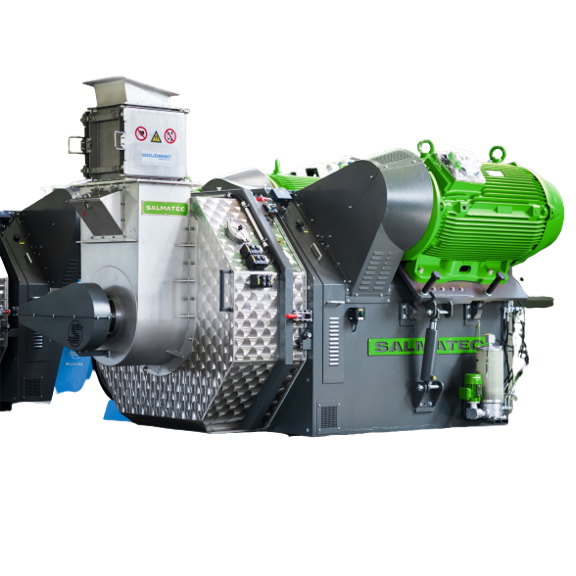
Complete pellet line
Large industries are shifting towards more environment-friendly technology, such as recycling wastes and...
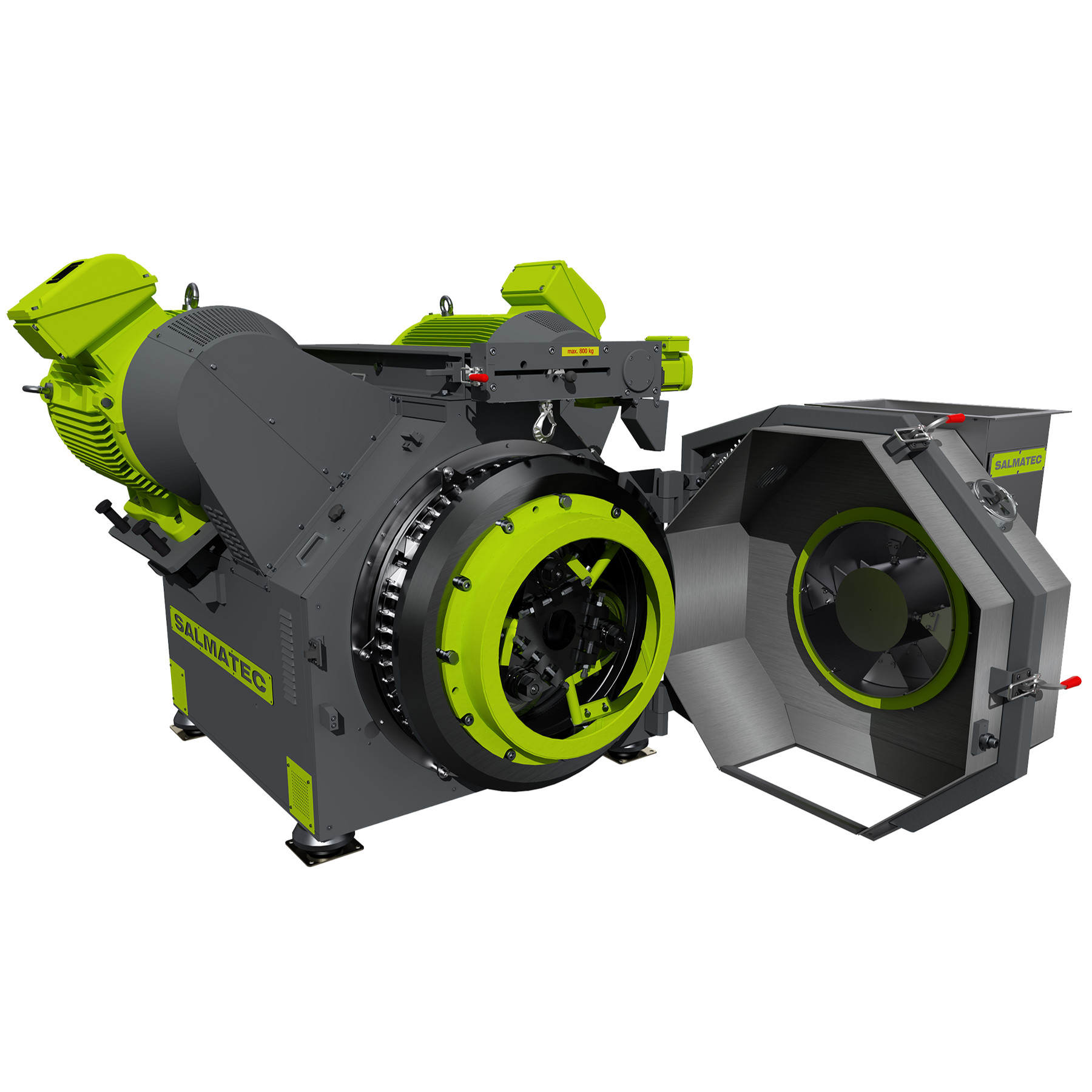
Industrial pellet mill
At the industrial level, the application areas of pellets range widely in fields such as feeds, biomas...
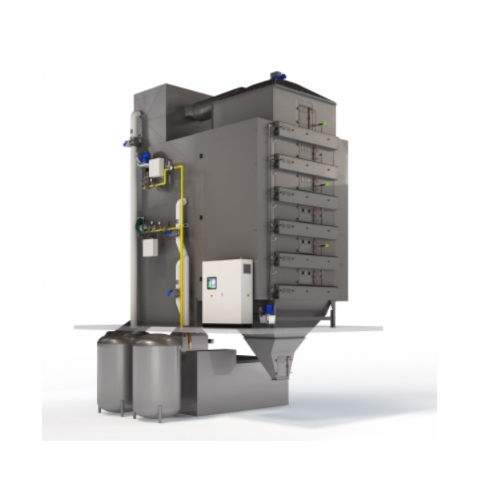
Industrial heat pump dryer
The drying of extruded products is highly energy-demanding in traditional belt dryers that use ga...
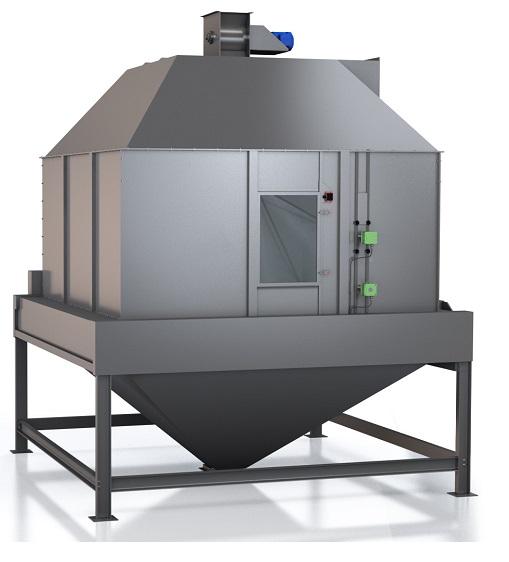
Continuous pellet cooler
Cooling is a very important and critical process for feed hygiene and pellet durability index. Pelle...
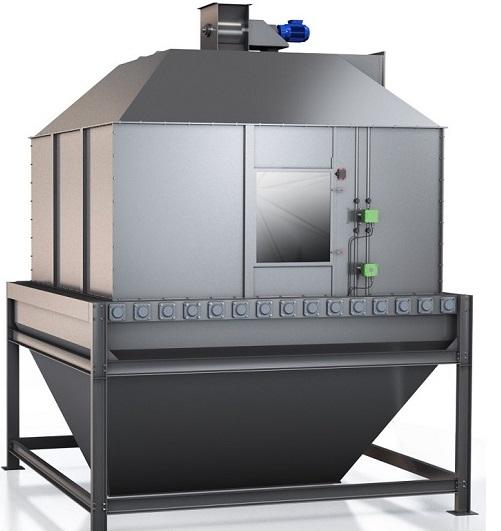
Gravity feed cooler
The food and feed industry has high food safety requirements making frequent cleaning and inspection nece...
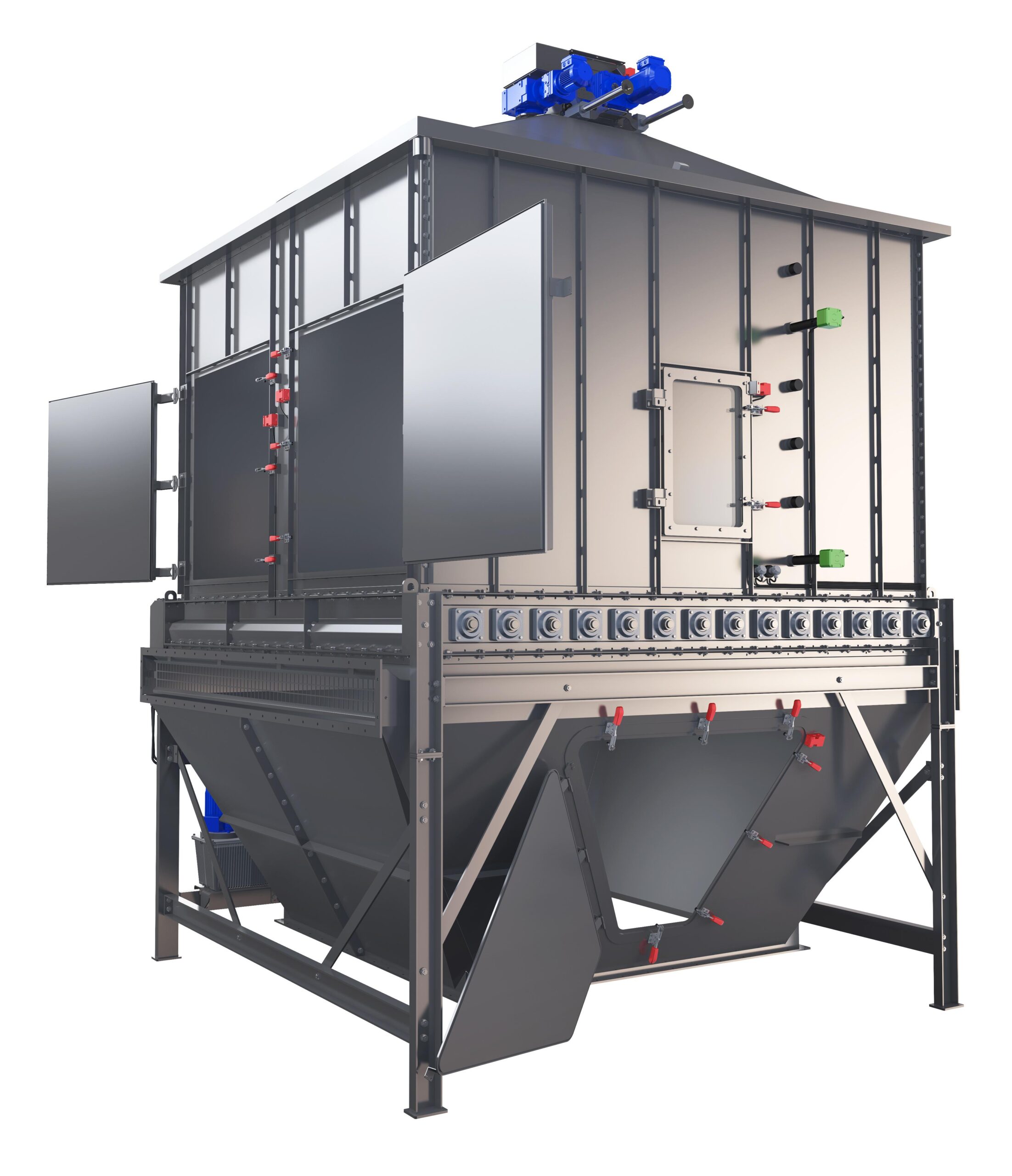
Counterflow pellet cooler
Food and feed industries require the highest standards of hygiene and sanitation. This entails fre...
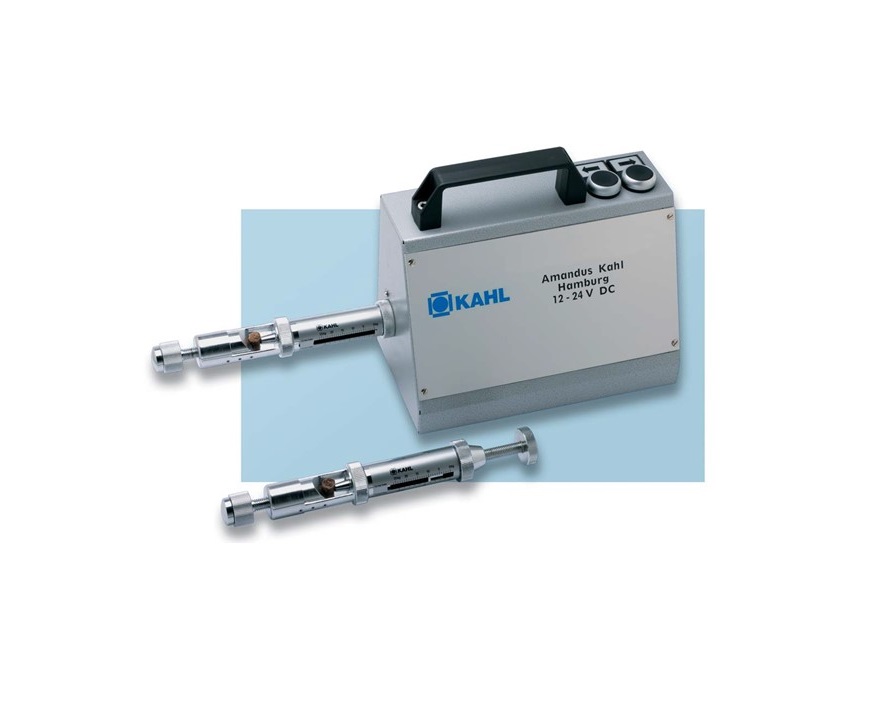
Pellet hardness tester
Control the quality of your pelletizing processes using a pellet hardness tester. Pellet hardness is o...
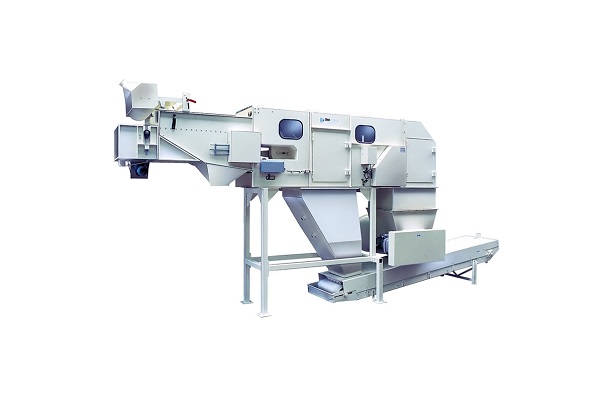
Automatic bag slitter
Unacceptably high dust levels can be generated whilst manual emptying and handling of bags, also produc...
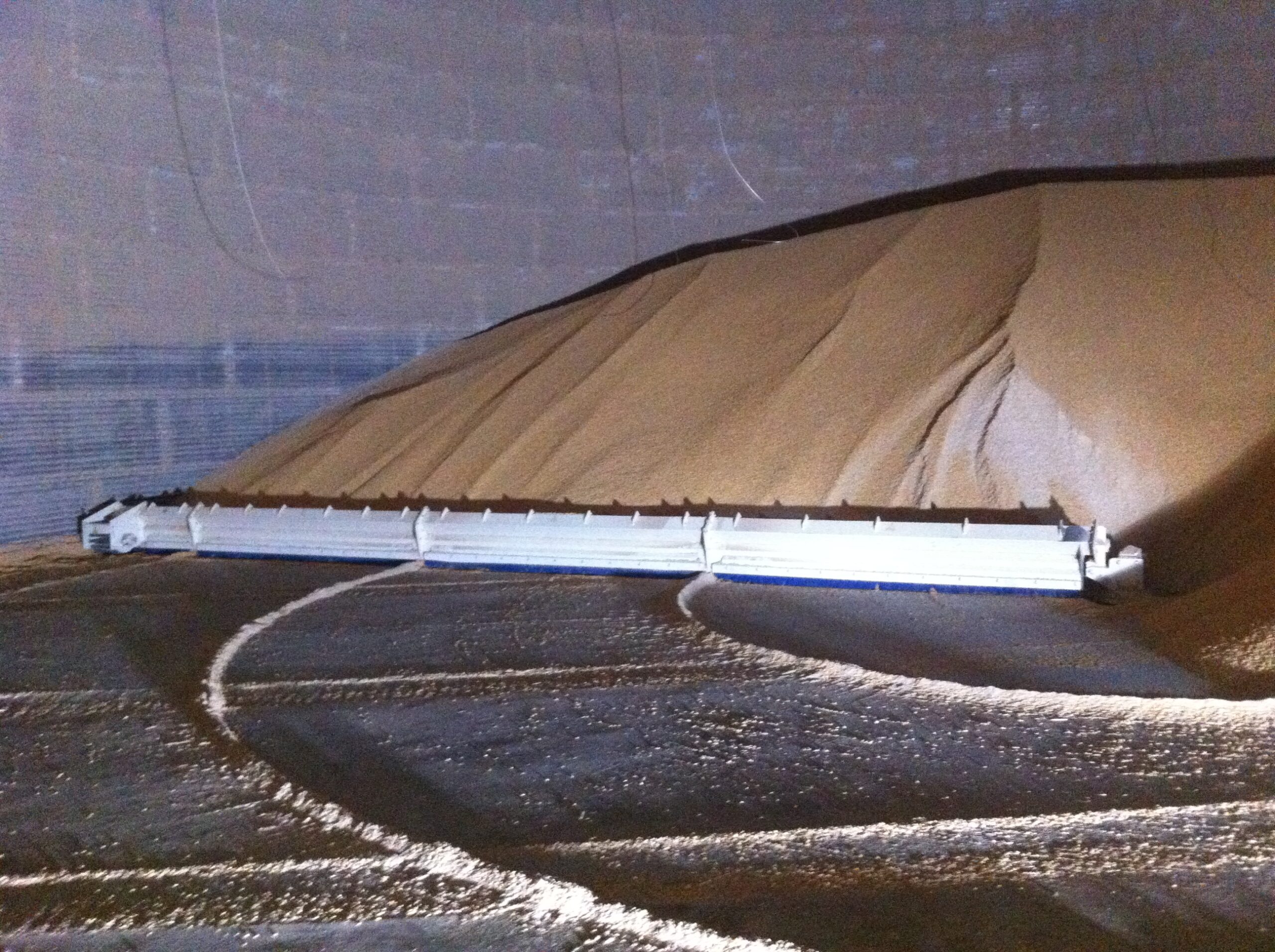
Silo sweep auger
When you store products with good gravity flow (wheat, maize, barley, grains, granules, etc.) in flat bottom ...
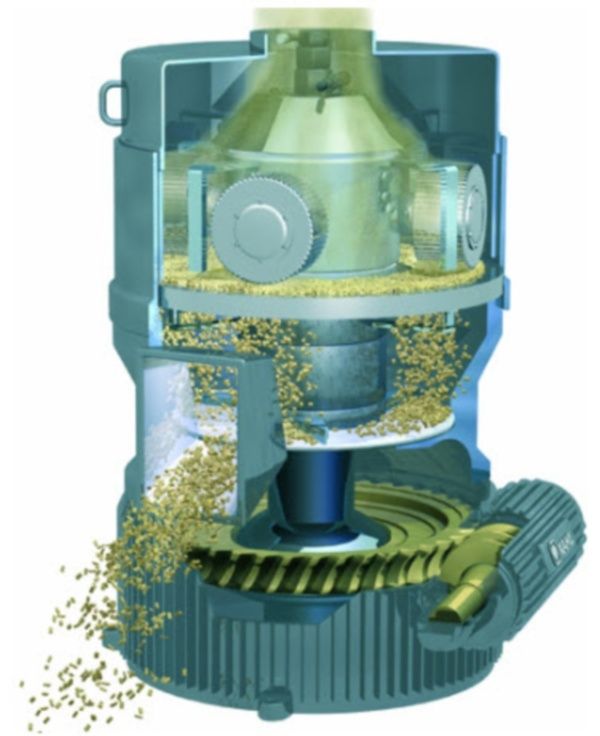
Pelleting press for feed and petfood
The production of agricultural feed and pet food products requires machines and plants...
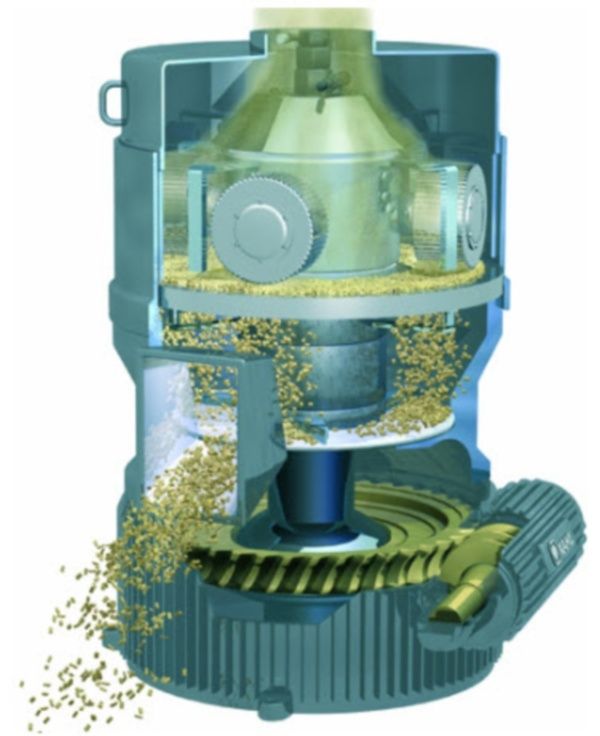
Pelleting press for biomass
Utilization of biomass for energy and other applications requires consistent and reliable compac...
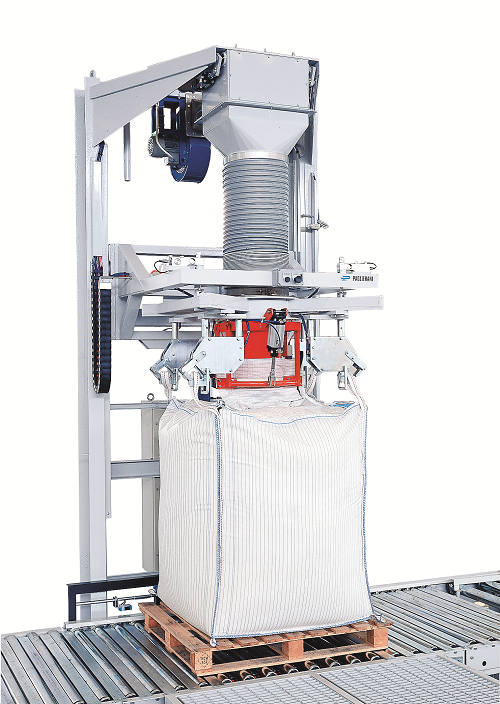
Big bag solutions
Management of big bags requires specialist handling and selection of cost-effective configurations for fill...
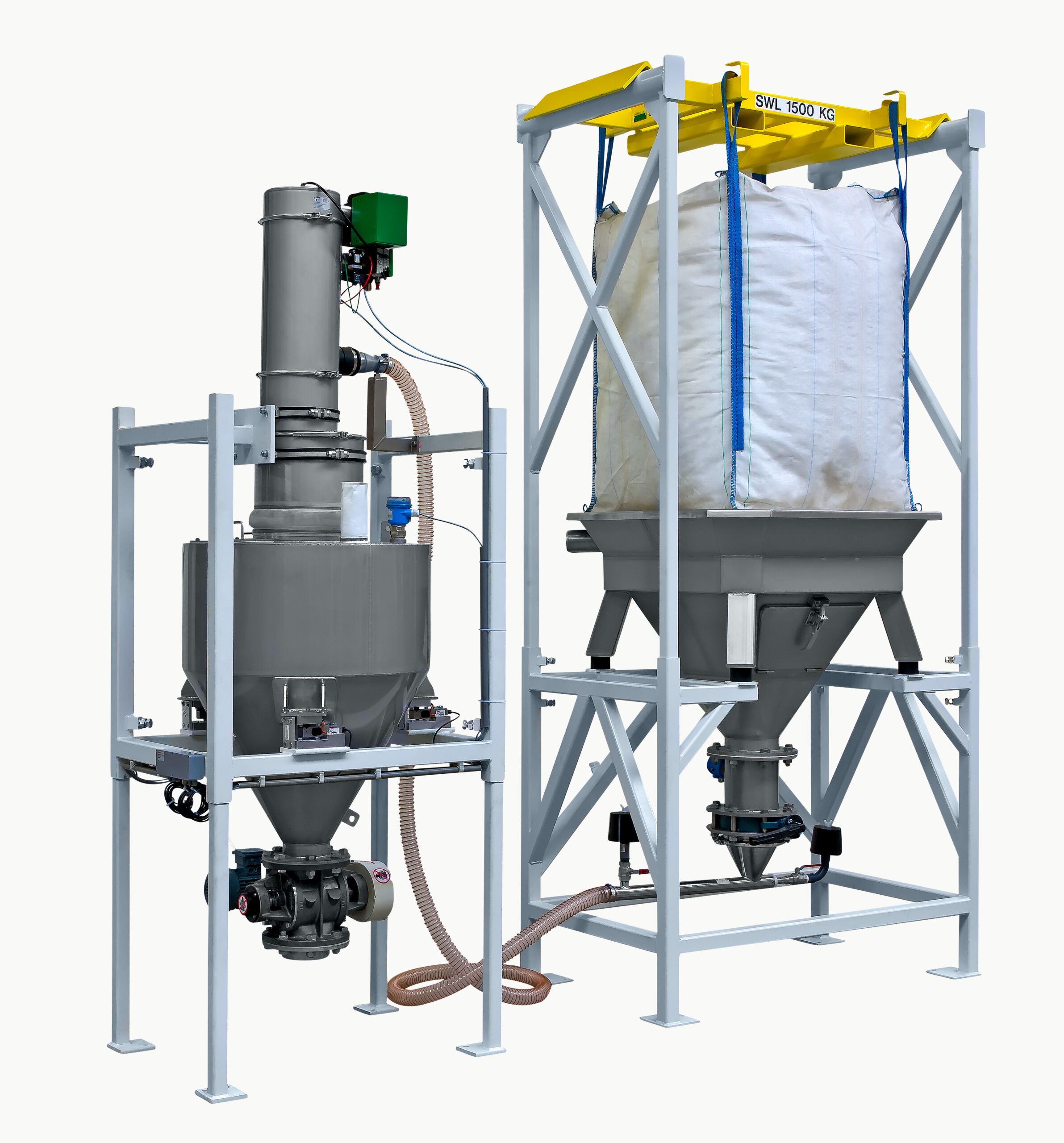
Big bag discharge system
Dust emissions, product loss and product contamination are the main risks when discharging products ...
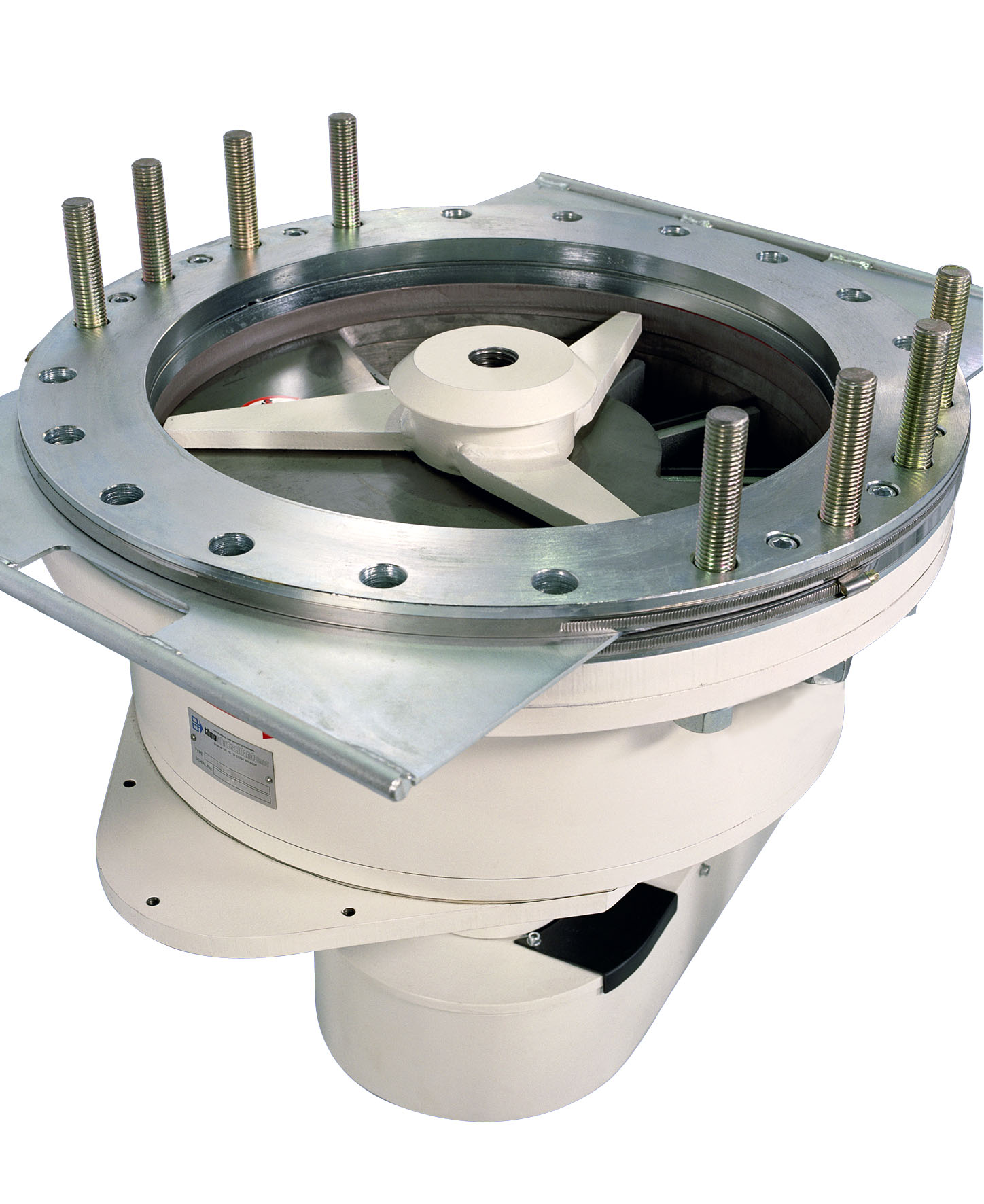
Special duty horizontal metering valve
Occasionally, there is no suitable standard valve available for a particular conveyi...
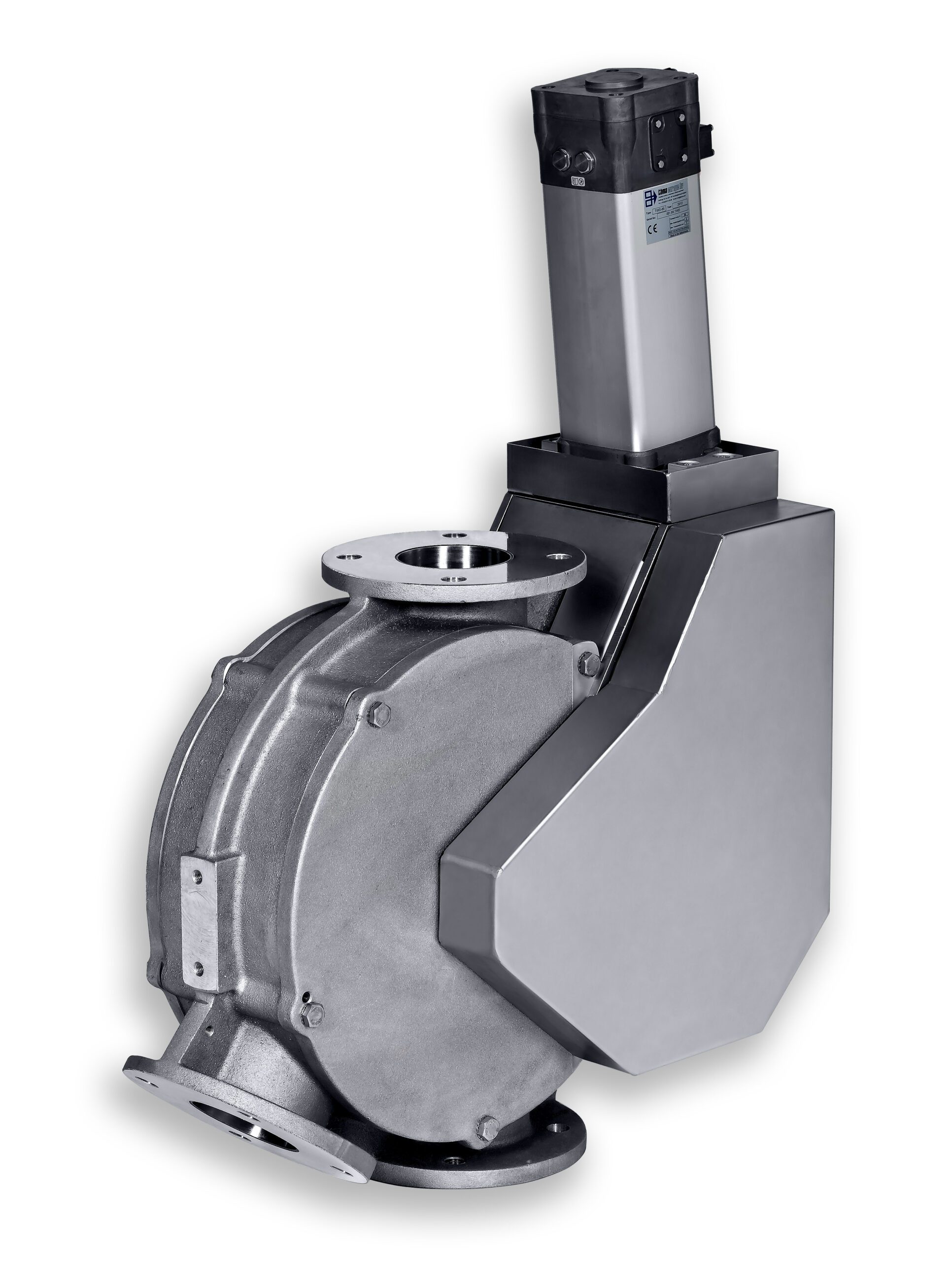
Dual channel plug diverter valve
Short switching times are often required when diverting or combining powder or granular sol...
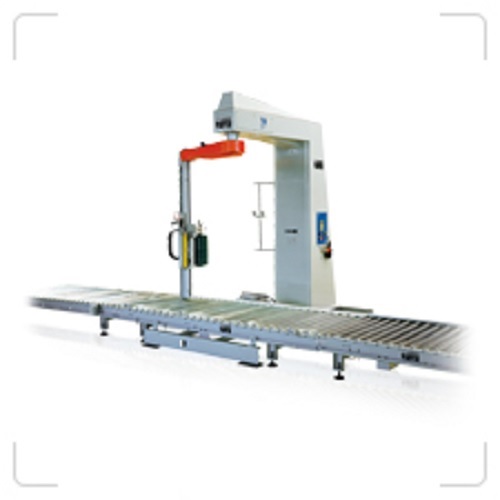
High speed stretch wrapping machine
Where high speed wrapping, without toppling, is required in tightly securing palletised...
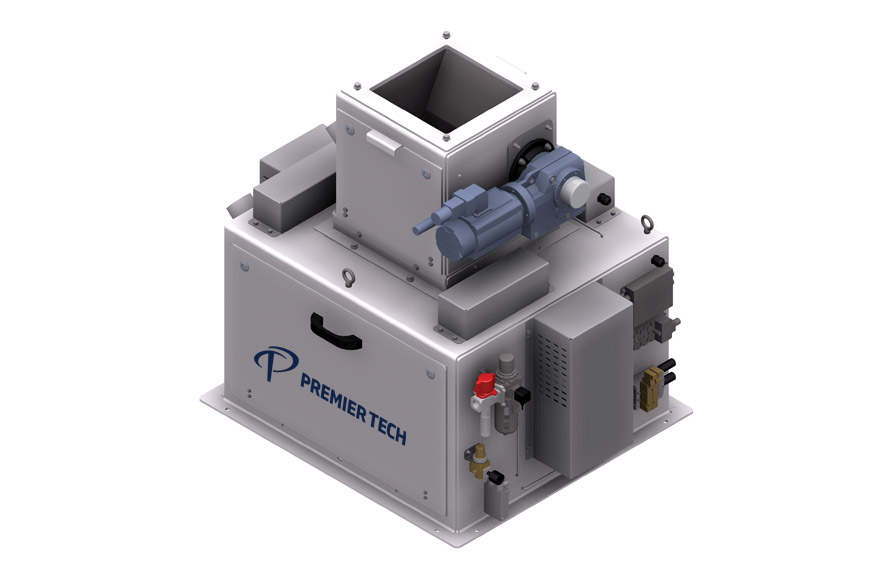
Electronic net weigher for high-capacity baggers
Electronic net weigher raises the industry’s standards to a higher level ...
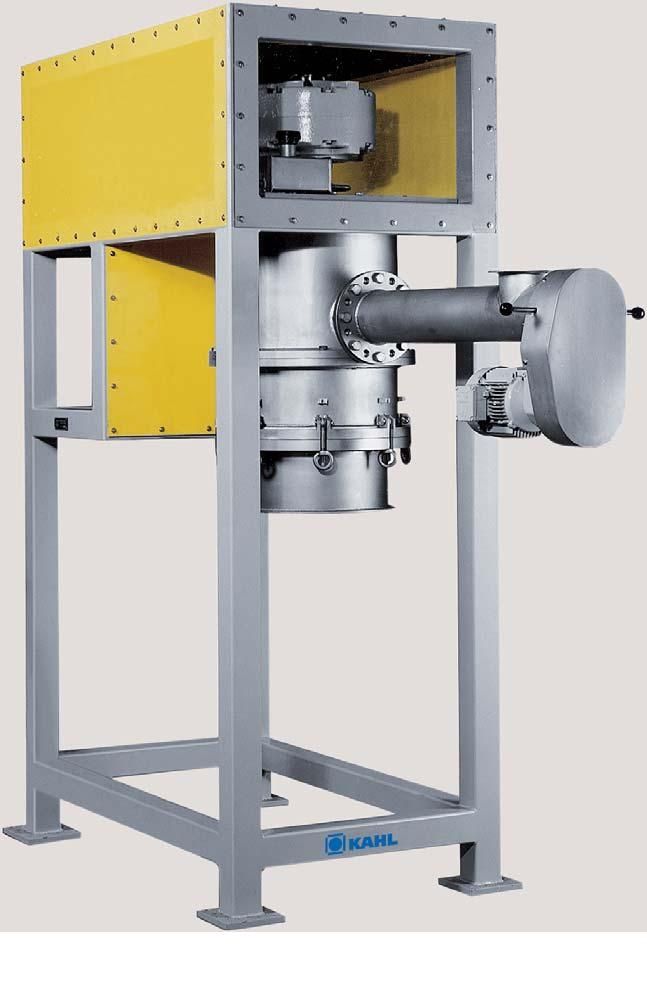
Pelleting press with overhead drive
Production of certain pelletized products requires working with output products of a pa...
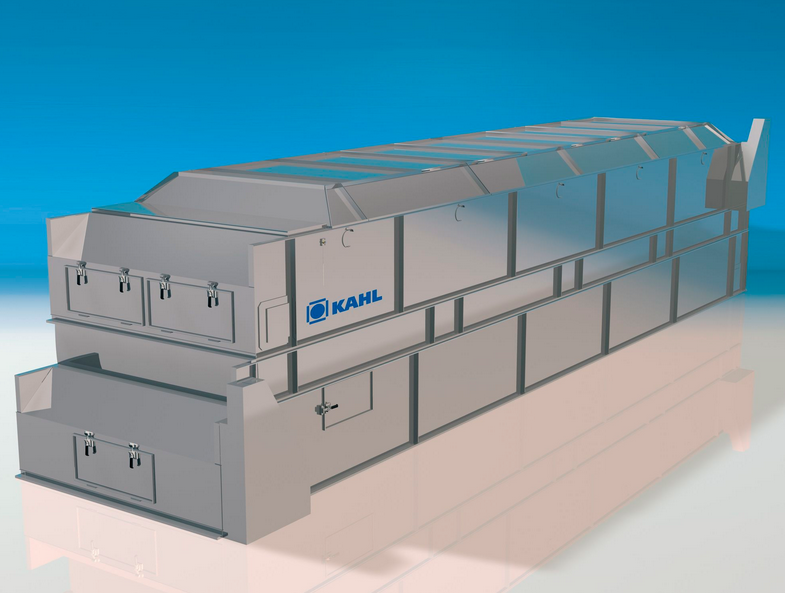
Belt dryer/cooler for pellets and granules
Many industries that process materials in pellet, powder, or crumble form need ...