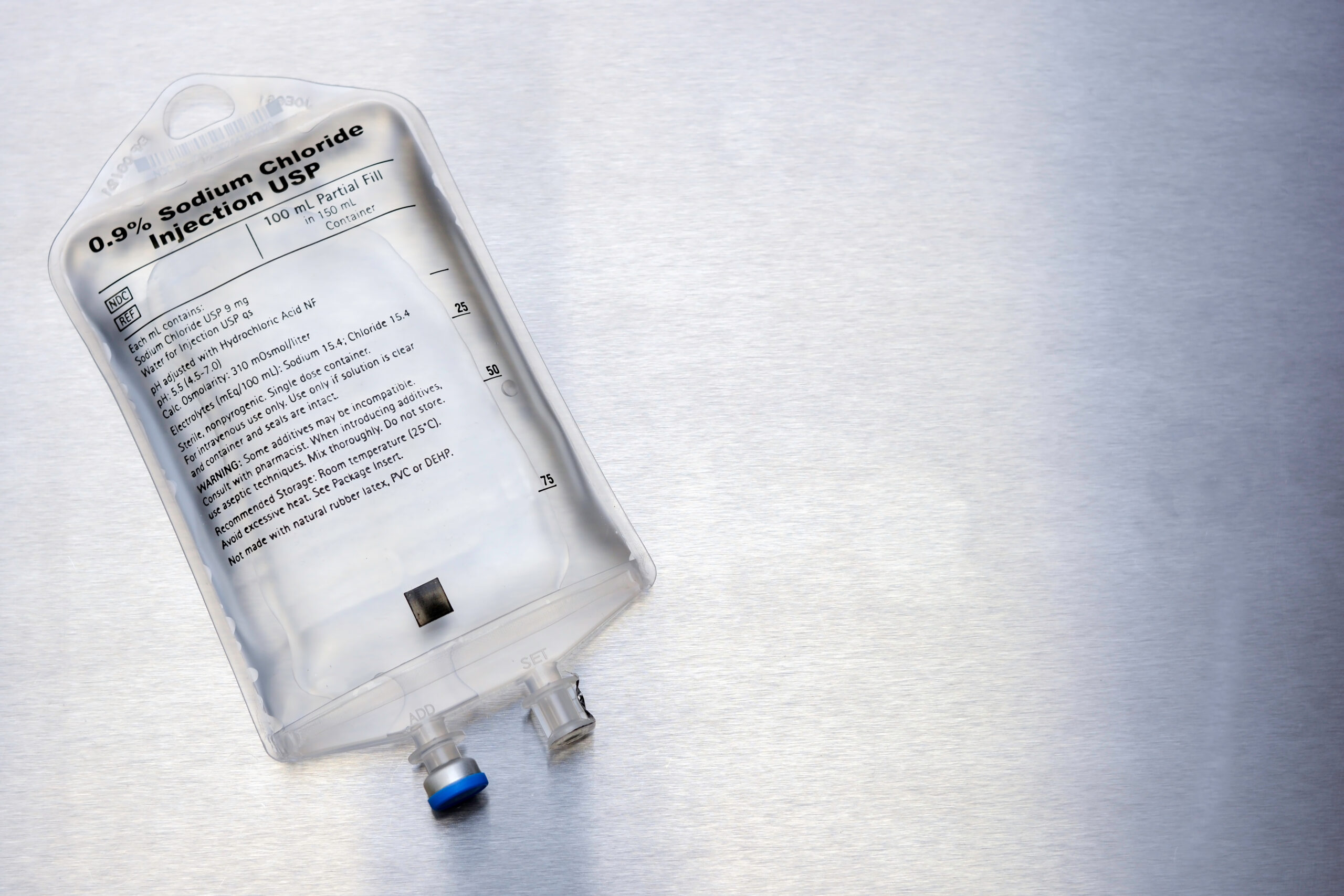
Making Single-Use Bags
Find innovative production technology for making single-use bags and connect directly with world-leading specialists
“How clean does my equipment needs to be?” That's what manufacturers often wonder about in order to meet the high sterilization standards the pharmaceutical industry demands. Lending manufacturers helping hand have been single-use bags, also known as disposable, first introduced in the late 1990s. They immediately gained popularity because they reduce the risk of cross-contamination, minimalize cleaning and sterilization demands, and require a low capital cost.
Select your single-use bags process
Tell us about your production challenge
What is the advantage of working with single-use bags?
Single-use bags play a key role in biopharmaceutical manufacturing by emerging as an alternative to stainless steel technology and can be used for different purposes, such as storage, transportation, or reactors. The main benefit of disposable bags over stainless steel is pretty obvious; the bags are primarily made of plastic components that are welded and sterilized using gamma radiation. This means you are working with something that comes in already clean, thus avoiding weeks of sterilization or cleaning while decreasing the risk of cross-contamination.
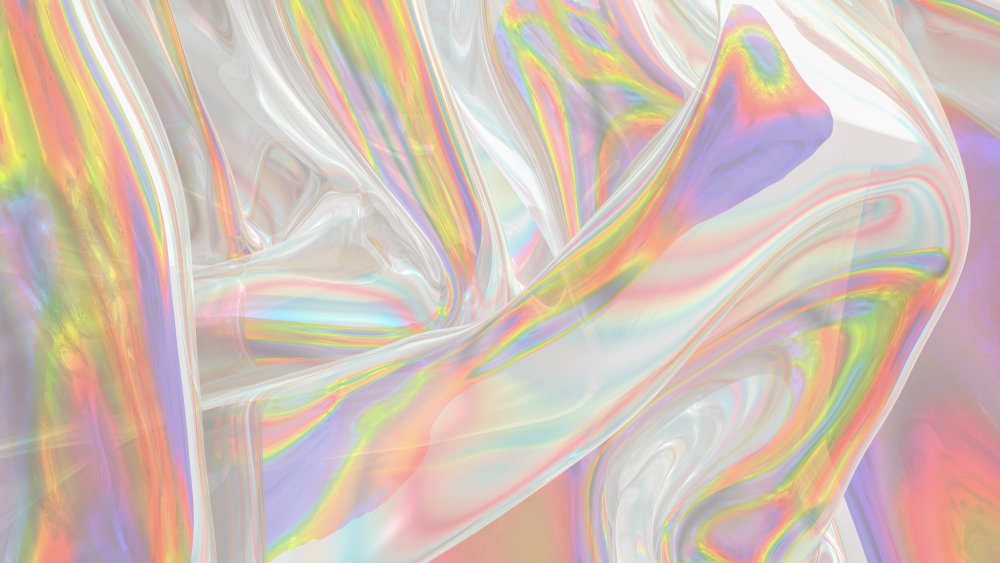
How important is the material when producing single-use bioprocess bags?
Single-use bags consist of a multilayer structure of different polymers, having, for example, a contact layer on the inside, typically made of polyethylene, a layer to block the oxygen, and an outer layer that have to provide improved permeation, physical and durability properties. Materials, therefore, are meticulously selected because they must meet the requirements of the biopharmaceutical industry and especially the Code of Federal Regulations, Title 21, Part 211.65. Some of the plastic materials well known to the industry for disposable bags are PVDF (Polyvinylidene Fluoride), PE (Polyethylene), and EVA (Ethylene Vinyl Acetate Copolymers).
Recently, single-layer bags have also been introduced. However, it’s really hard to find materials that have the properties to meet all the criteria required, such as barrier properties or resistance to the sterilization process. Polyvinylidene Fluoride films are the closest solution.
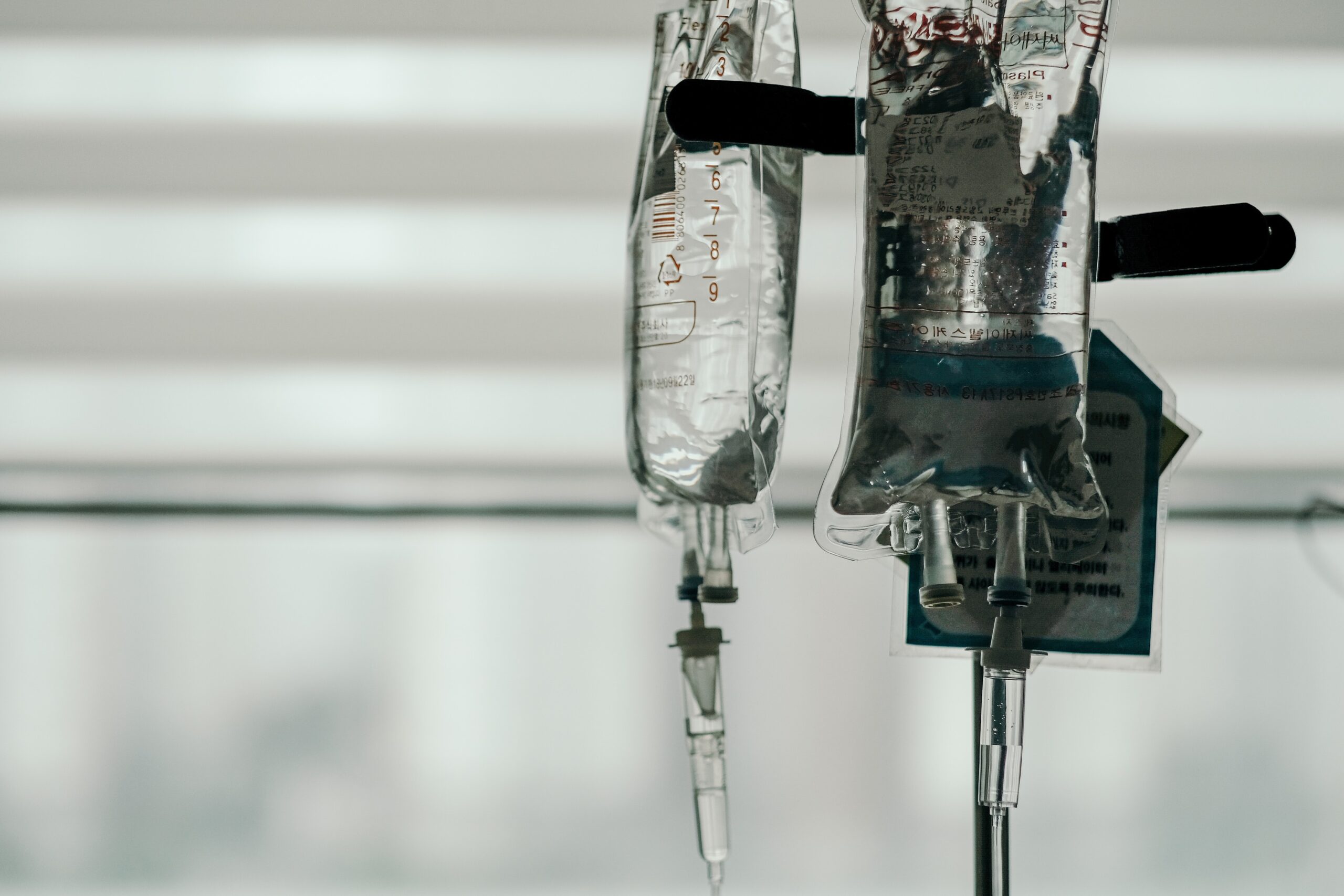
2D or 3D bioprocessing bags. What’s the difference?
One of the significant advances in single-use bioprocess technology was the creation of 2D and 3D bags. A 2D bag or pillow style is usually not placed inside supporting tanks and is used for relatively small volumes, such as from less than 1 to 50 L. This bag is made by simply welding two faces together. On a larger scale, 2D bags become challenging to maintain their integrity; that’s why 3D bags work better (> 50L). They can have a cube, conical, or cylinder shape and are created with multiple films sealed together.
The rise of single-use bioreactors
It has been estimated that the market for single-use systems reached $15.8 bn in 2020, and according to the CAGR (compound annual growth rate) is expected to grow by 16% from 2021 to 2028. This is definitely due to the impressive growing demand for single-use bioreactors that are slowly replacing conventional ones. Single-use or disposable bioreactors are bioreactors that are equipped with a disposable bag instead of a culture vessel made from stainless steel or glass. They are widely used for cell harvesting, purification, and virus inactivation, among others.
Aside from the advantage of avoiding sterilizing equipment and reducing costs, the most common benefit is flexibility. With a stainless steel bioreactor, it can take up from 6 hours to 3 weeks for a product changeover. By using a disposable bioreactor, you can prepare your next batch in 2 hours, drastically reducing the downtime.
The relationship between the environment and single-use bags: is that love?
Would you believe it if I told you that disposable systems in pharma reduce your carbon footprint, energy, and water use, ergo, they are more sustainable than stainless steel equipment?
Yes, I know it seems impossible that something made of plastic and thrown away after use can be called sustainable.
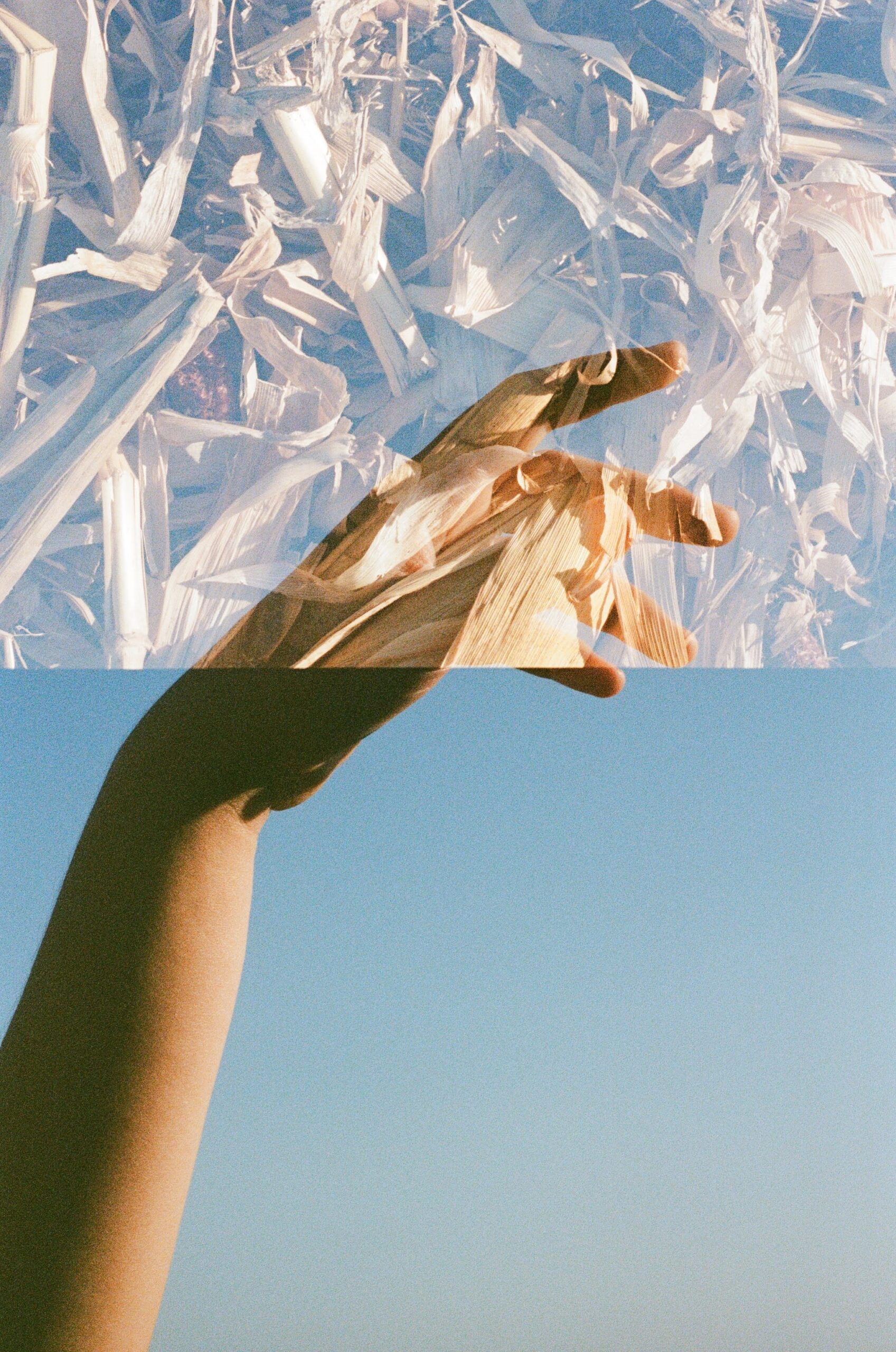
We must understand that the problem with single-use systems is simply the last stage of its life cycle, i.e., how they are disposed of. But if we want to analyze the environmental impact properly, we need to consider the equipment’s entire life cycle. In the pharmaceutical industry, sterilization requirements are very high, so when stainless steel equipment has to be cleaned, vast amounts of water and energy are used. To ensure the equipment is totally sterile, manufacturers use chemicals that will then be released into the wastewater by ending up in the oceans; this has a major impact on our ecosystem.
Processing steps involved in single-use bags making
Which single-use bags technology do you need?
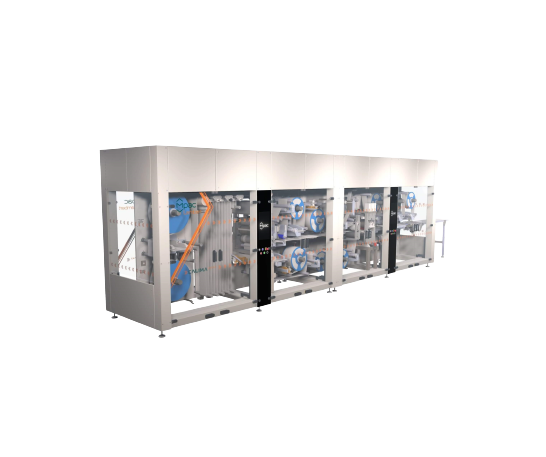
Flexible web converting system for healthcare products
The market for web-based goods moves fast and may outpace the manu...
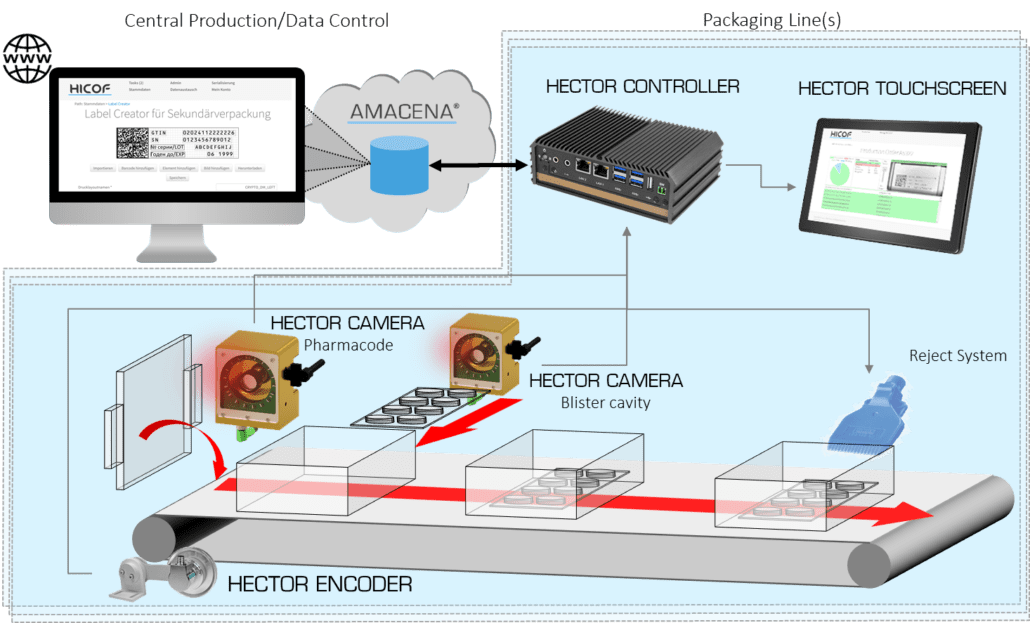
Serialization and aggregation inspection system
Including serialization and aggregation inspection systems to packaging li...
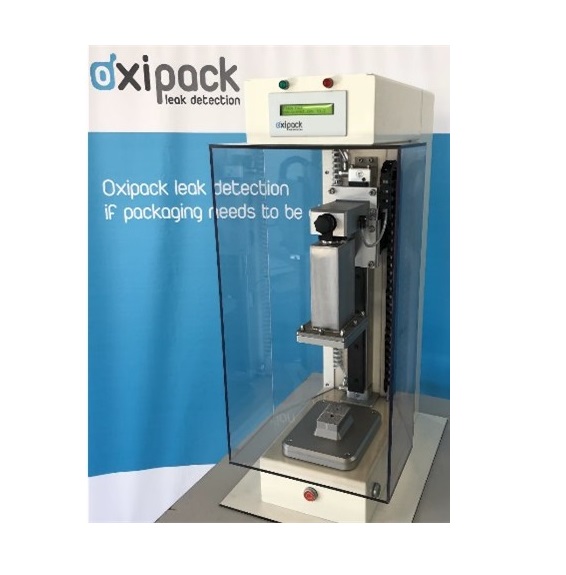
Leak tester for vacuum packaging
Roasted coffee beans, as well as grounded coffee, rapidly diminish in flavor. The oxyge...

Leak tester for pouches and MAP packaging
Nuts are packed with unsaturated fatty acids, which means they are prone to oxid...
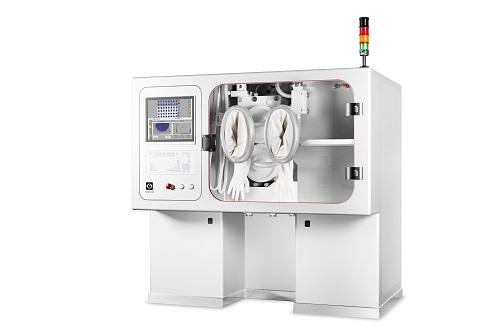
Contained Visual Inspection System
In the medicine industry, it is important to ensure there are no defects in tablets or c...
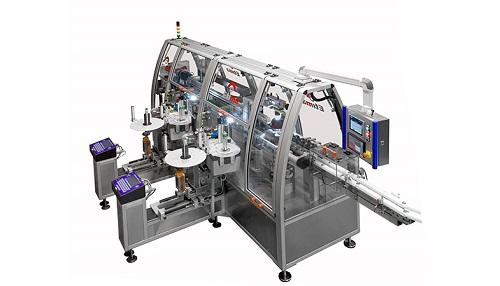
Labeling machine for BFS containers
The pharmaceutical sector is unquestionably one of the major industries that rely on th...
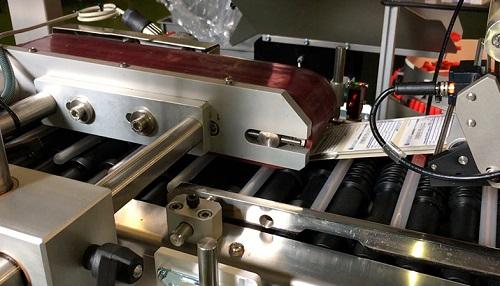
Labeling machine for ampoules
It’s essential for pharmaceutical companies to provide the highest quality ampoules to custome...

Ethylene oxide sterilizer
When medical devices like syringes, catheters, dialysis cartridges, plastic dressings and sutures ...
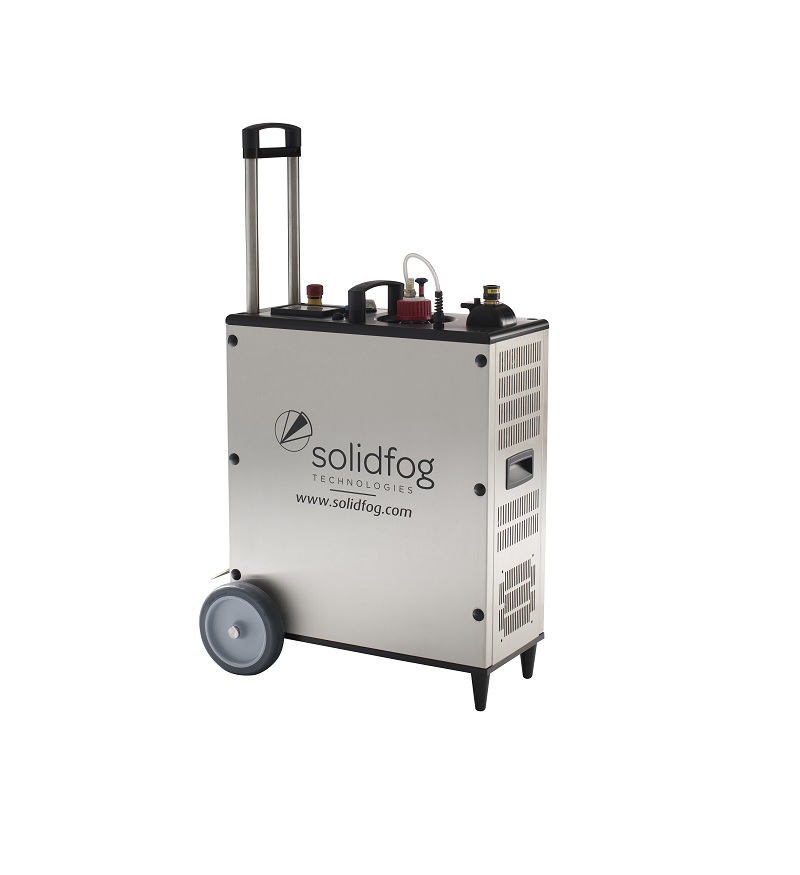
Compact H2O2 disinfection system
Dry fogging provides safe, effective microbiological cleaning of critical areas in biotech,...
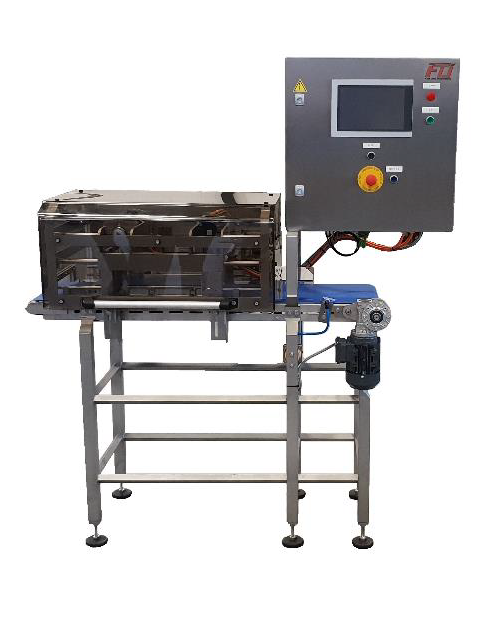
Entry-level high volume package seal tester
Manufactured food products need to be packed in gas-filled pouches to ensure t...
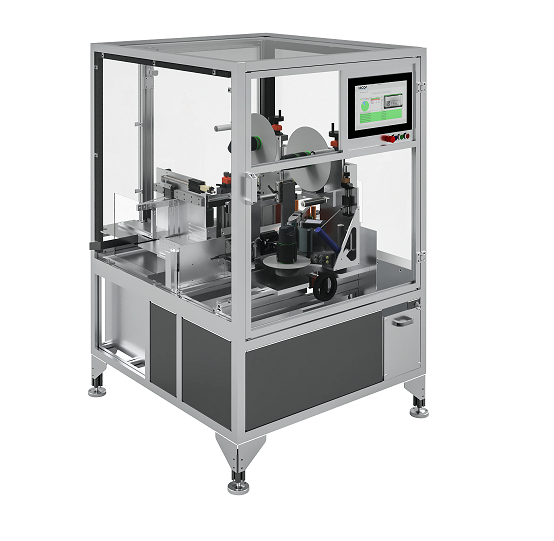
Serialization coding and labeling equipment
In the pharmaceutical industry, product serialization is the cornerstone of al...
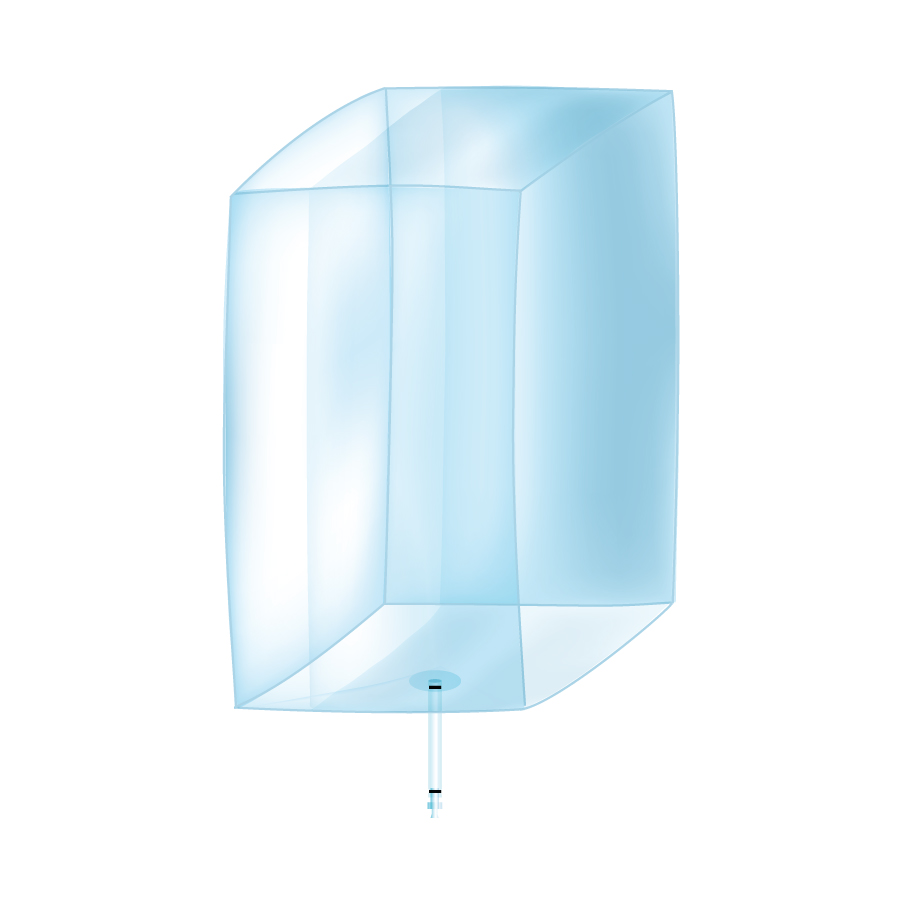
Disposable tank liners
Manufacturers in the bioprocessing industries are increasingly turning to single use solutions for the...

Single-use temperature sensor
Biopharmaceutical manufacturers are increasingly making use of single-use temperature sensors ...
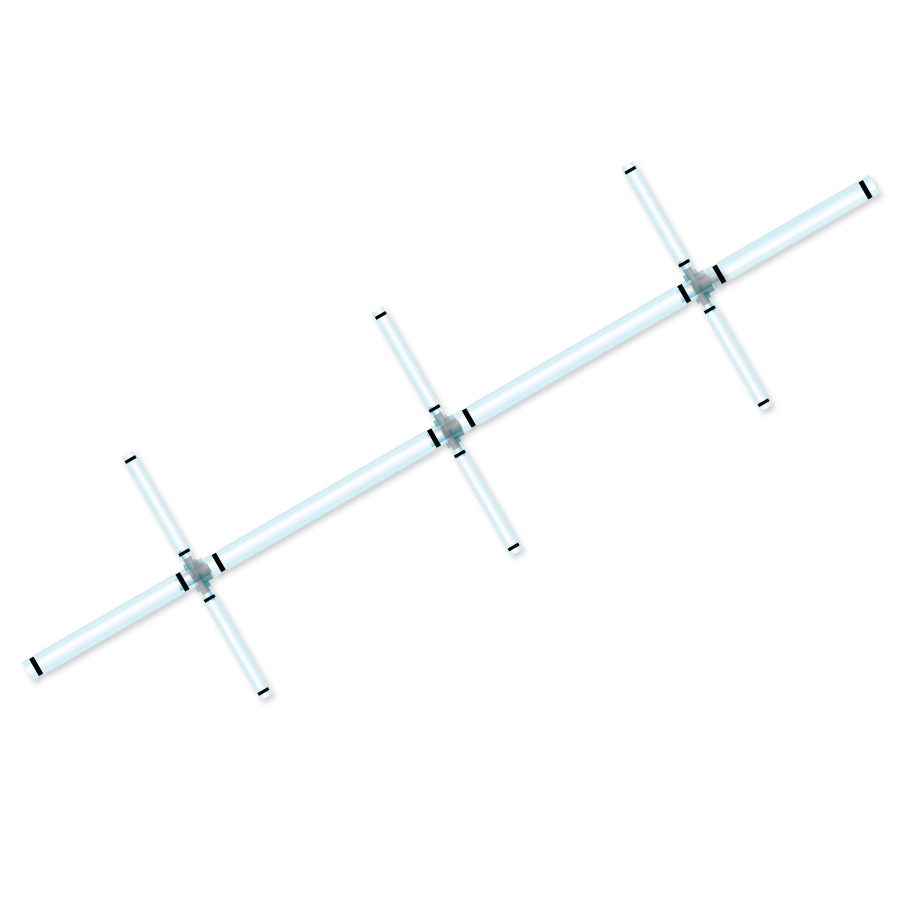
Disposable tubing for manifolds in bioprocesses
Manufacturers in the bioprocessing industries are increasingly turning to ...
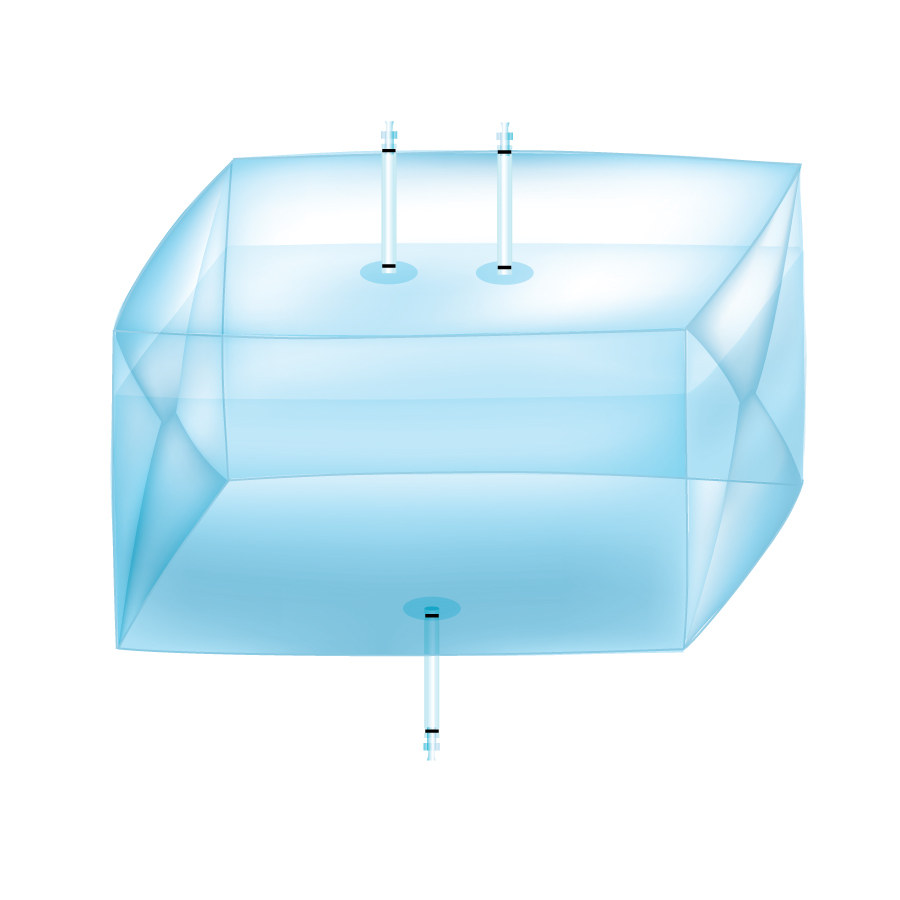
3D disposable bags for bioprocesses
Manufacturers in the bioprocessing industries are increasingly turning to single-use so...
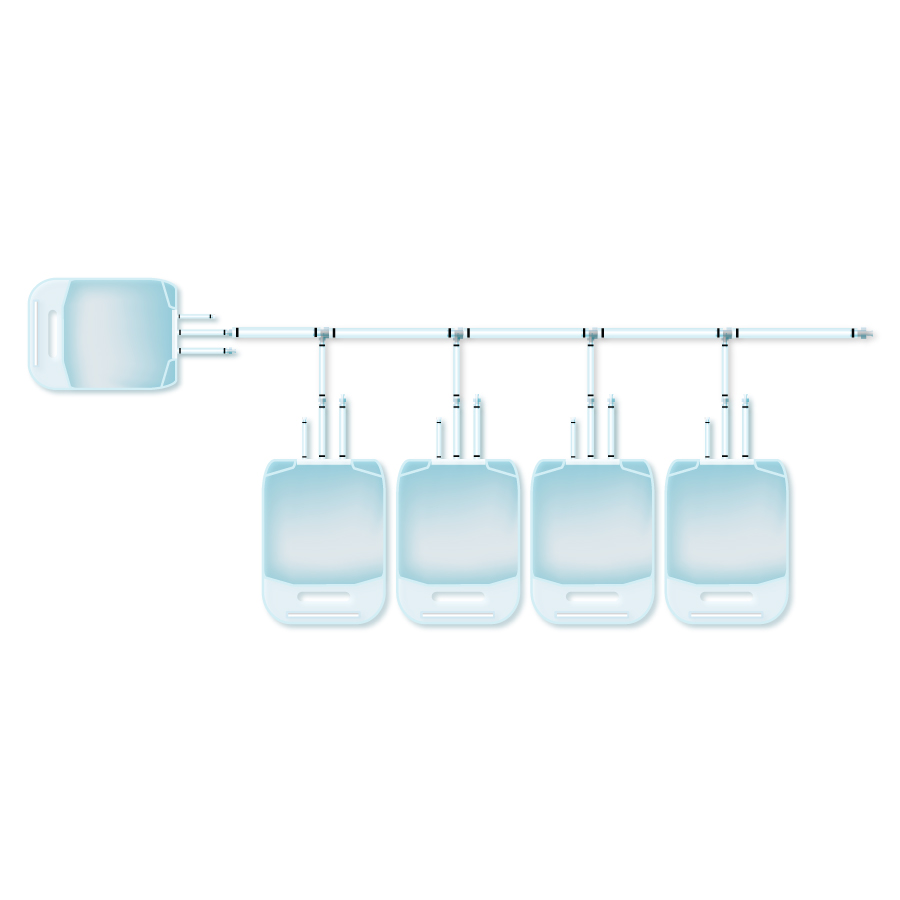
Disposable manifold bags for bioprocesses
Manufacturers in the bioprocessing industries are increasingly turning to dispos...
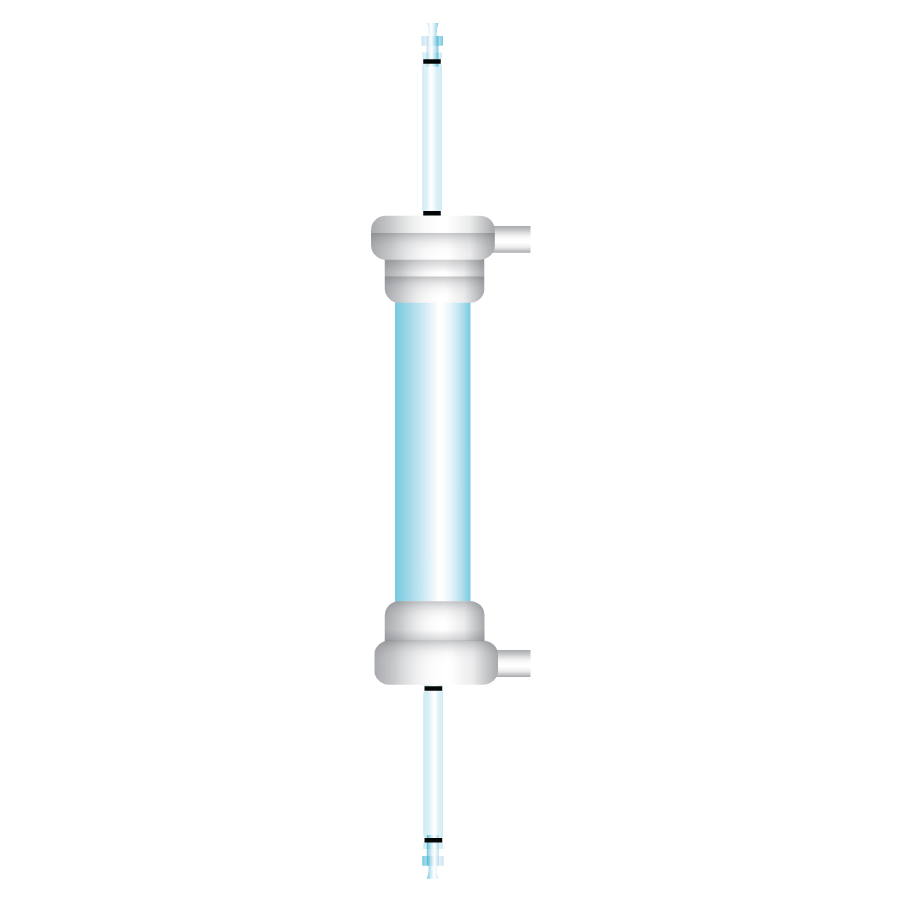
Normal flow filtration sets for bioprocesses
Bio-processors require reliable, high quality, easy to maintain, filtration e...
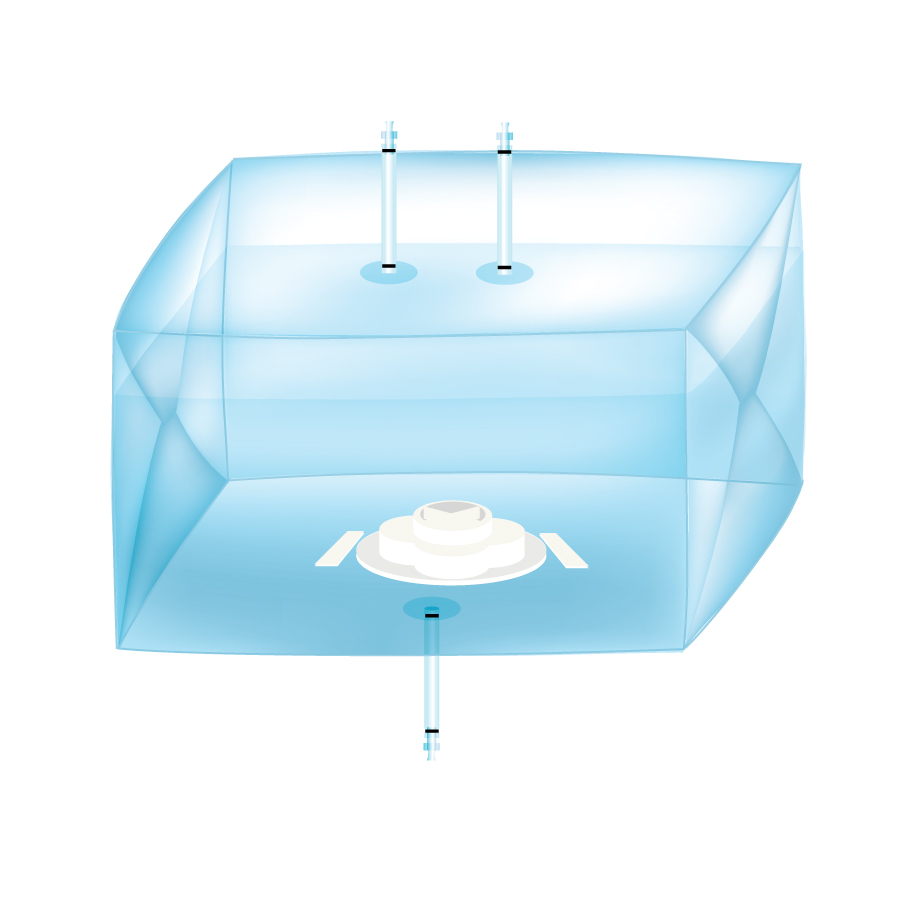
Disposable mixer bags for bioprocesses
Bioprocessors must use ingredients of known high quality and consistency. Inconsist...
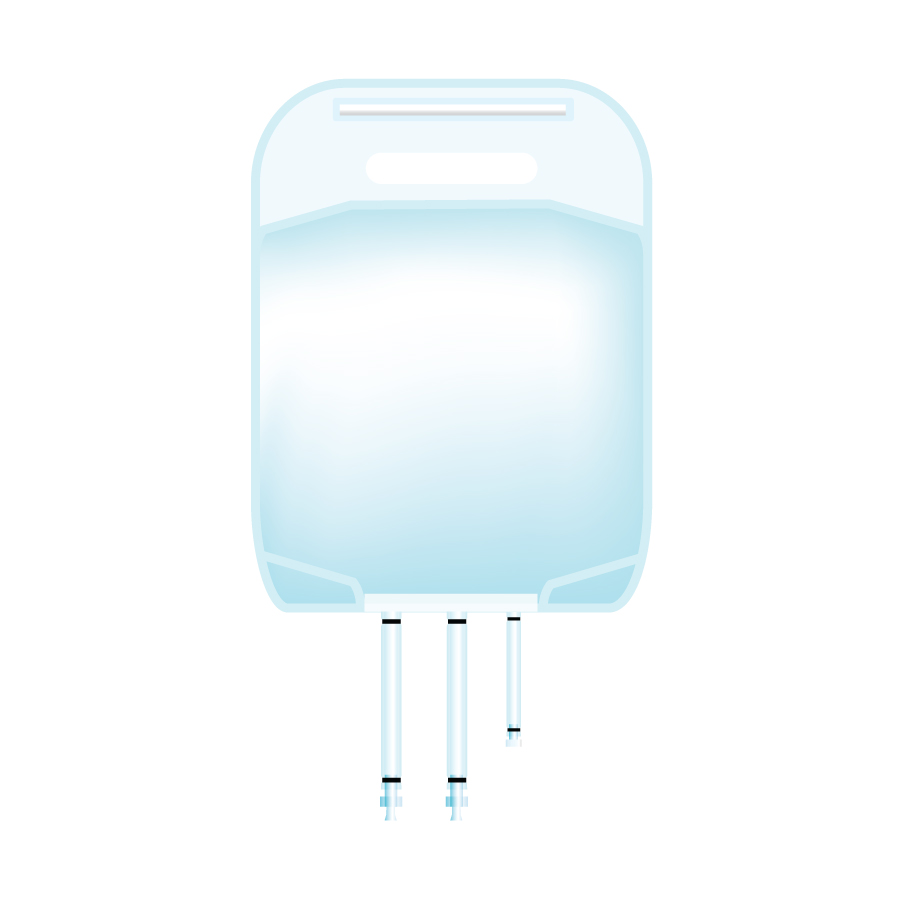
Disposable pillow bags for bioprocesses
Manufacturers in the bioprocessing industries are increasingly turning to single us...
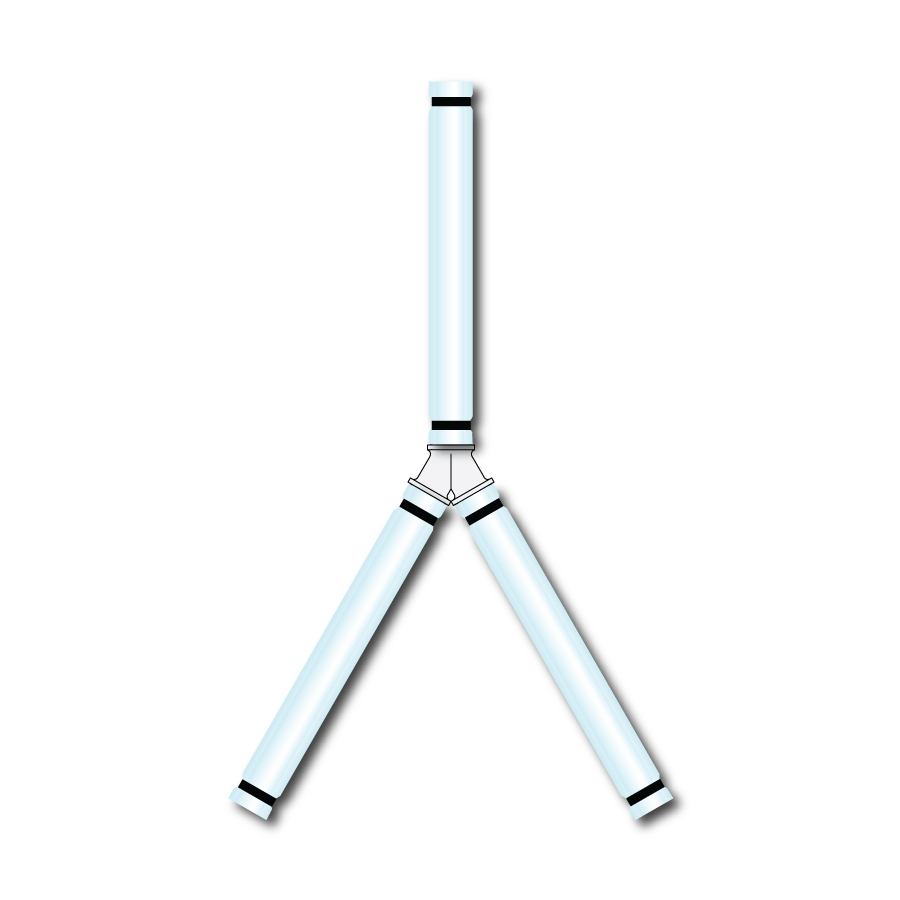
Y sets tubing for bioprocesses
Manufactueres in the bioprocessing industries are increasingly turning to single use solution...
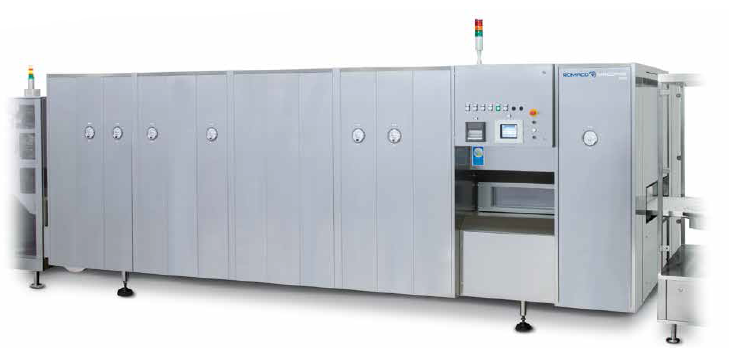
Depyrogenation tunnels for ampoules, vials and bottles
Sterilize and depyrogenize ampoules, vials, bottles and similar gl...
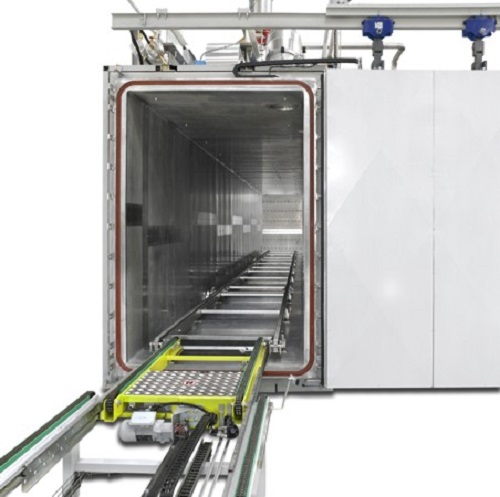
Ethylene oxide sterilization chamber
Designed for the terminal sterilization of temperature sensitive medical-health produc...
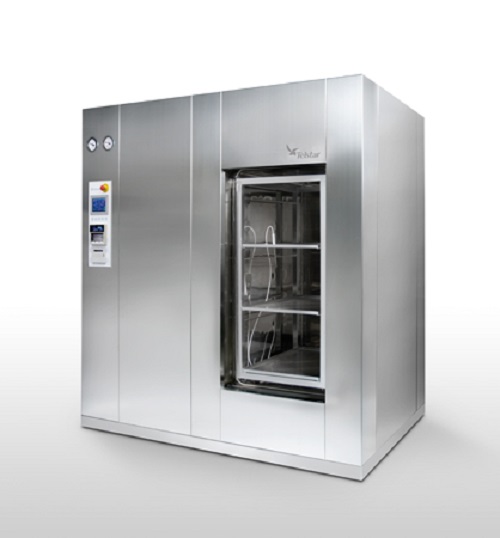
Saturated steam GMP laboratory autoclave
For processing a wide range of products: solid, porous and liquids in a laboratory...