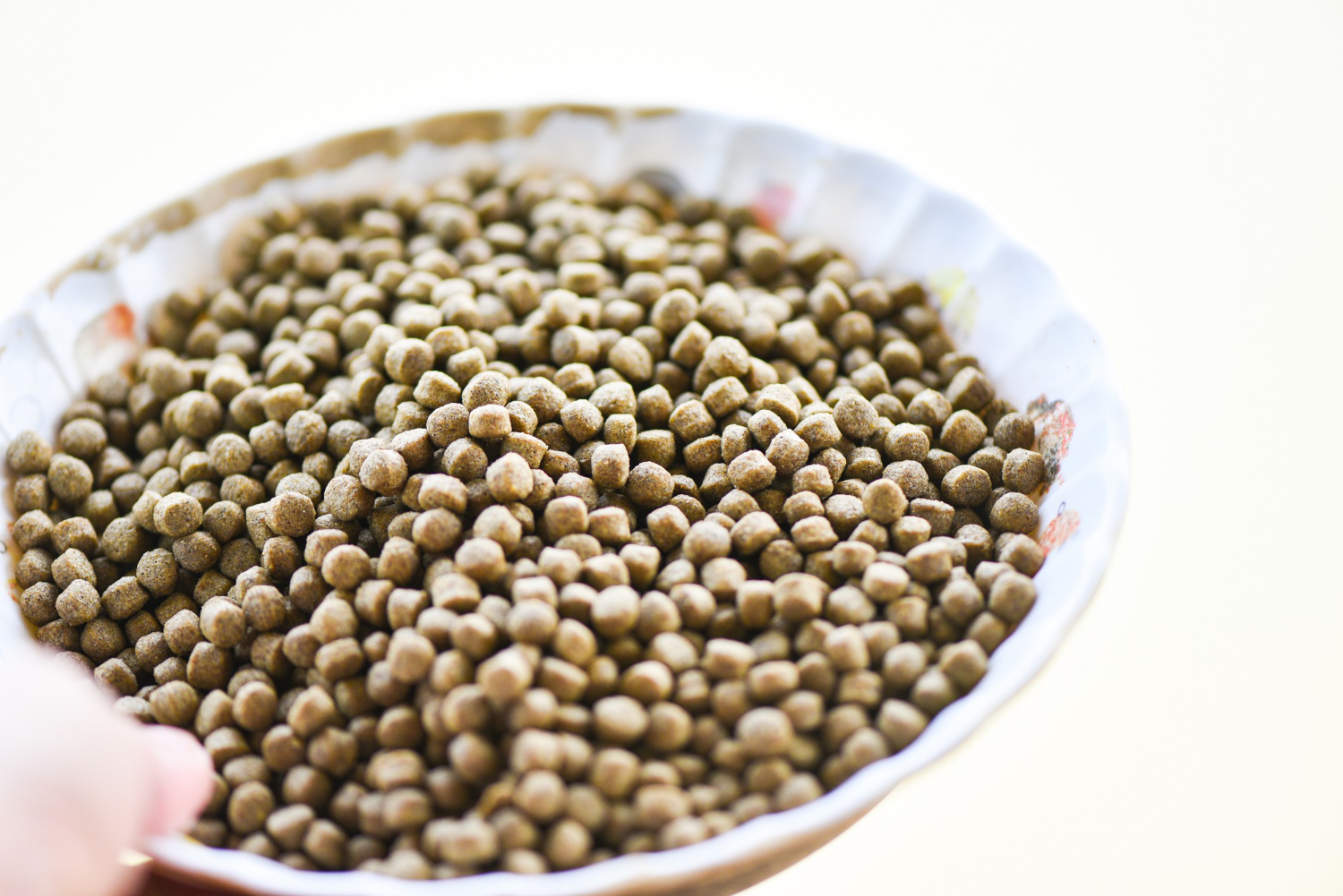
Making Slow Sinking Pellets
Find innovative production technology for making slow sinking pellets and connect directly with world-leading specialists
When it comes to aquafeed, you can find three types of pellets: floating pellets, sinking pellets, and slow-sinking pellets. Not all aquatic species eat at the same height of the water column. For example, tilapia and carp eat at the surface (floating pellets) while shrimp and sea bass eat at the bottom (sinking pellets). Slow-sinking pellets are ideal for species that eat along the water column such as salmon and cod. To get the pellets to sink at the right rate, slow sinking pellets production must control water stability in the products.
Stories about slow sinking pellets
Select your slow sinking pellets process
Tell us about your production challenge
Water stability is the key to successful slow sinking pellets production
Making slow sinking aquafeed, needs expertise and accuracy, to produce the right texture and the sinking rate. Water stability is critical to high-quality slow sinking pellets production and must be controlled at all stages of the process. If the pellets sink too quickly, they will not be visible or accessible along the water column, leaving the fish hungry. Sinking at the proper speed, they preserve their physical form and quality, avoiding water dissolution and the consequent loss of nutrients.
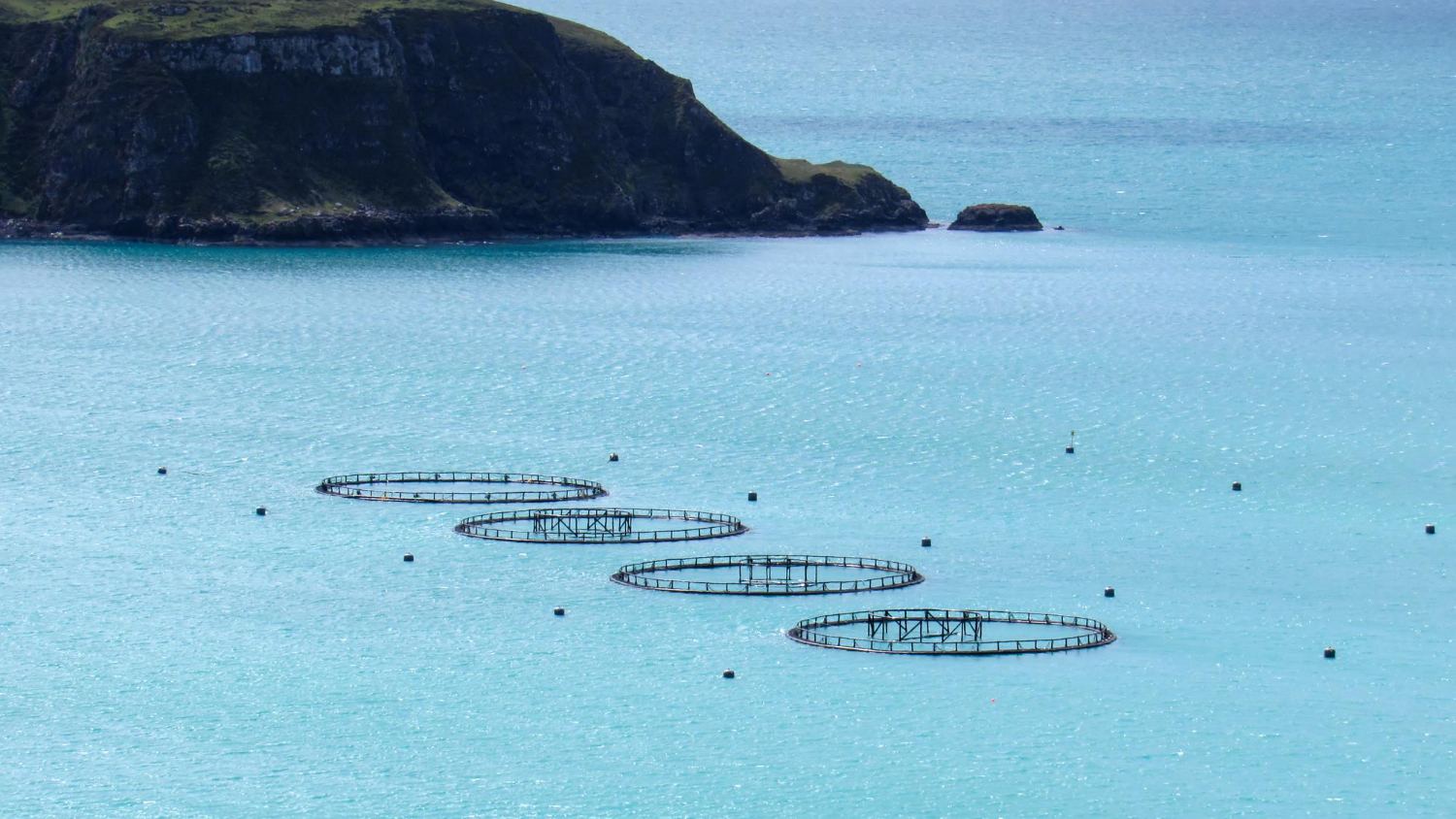
Add pre-conditioners to enhance the digestibility of slow sinking pellets
To make water-stable aquafeed, you will need a single-screw or twin-screw extruder. In the extrusion process, you can control buoyancy and water stability, besides all other required characteristics to make high-quality feed. Every pellet product can be modified with the adequate density and size to cater for the needs of different aquatic species. Choosing between single-screw and twin-screw technology depends on the efficiency and versatility you want to have when managing different types of formulas.
If you add a pre-conditioner to the process, you will improve digestibility, durability, and uniformity and enhance water stability, especially in formulas with a low quantity of starch.
Feed ingredients affect the buoyancy of the pellets, and the buoyancy impacts the nutrient content
Due to multiple factors, such as fluctuation in the price of commodities and protein, supply issues, and sustainability awareness, aquafeed formulas need to be flexible. But changing the formulas to adjust to availability and costs has an impact on the quality of the products. A variation in feed ingredients can affect the buoyancy of the pellets.
If the buoyancy is not adequate, the pellets sink too slowly or quickly while the nutrients risk being washed out by the water, or wasted at the bottom. Thus, the slow sinking pellet process needs to be controlled by an expert to get the right buoyancy for the targeted species every time that the formula changes.
Processing steps involved in slow sinking pellets making
Which slow sinking pellets technology do you need?
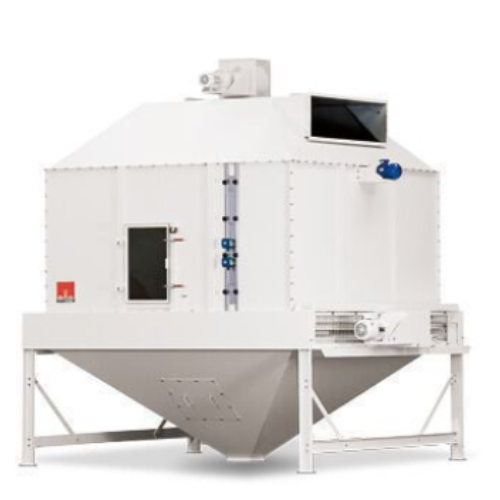
Counterflow dryer for pet food and fish feed
Optimize moisture control and enhance feed quality with efficient drying, cru...
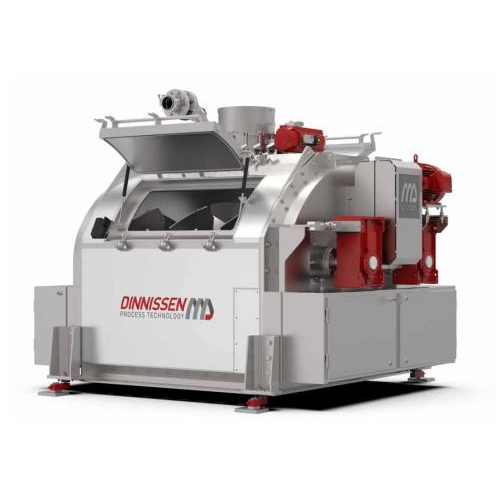
Advanced vacuum coating system for pet food and feed
Achieve uniform saturation in pellets and granules with precise liqu...
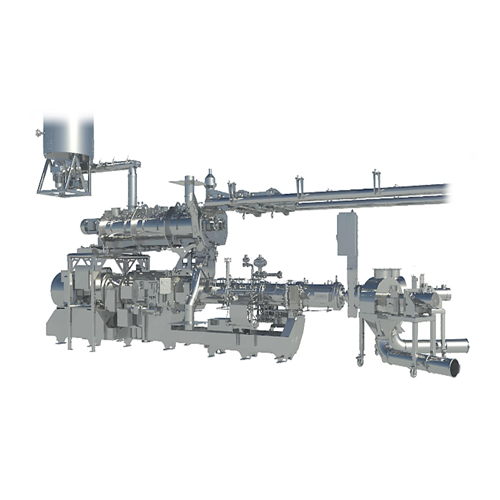
Extruder for aquatic feed production
Efficiently produce a wide range of aquatic and pet feed with precise control over pel...
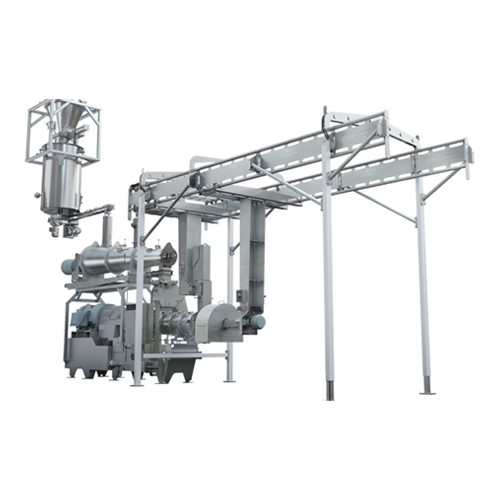
Conical twin screw extruder for pet food and aquatic feed
Precision-engineered for high-speed extrusion and drying proce...
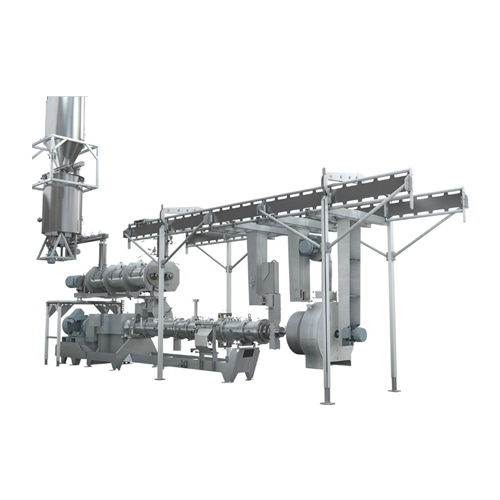
Twin screw extruder for pet and aquatic feed
Achieve exceptional cooking precision with our twin screw extruder, designed ...
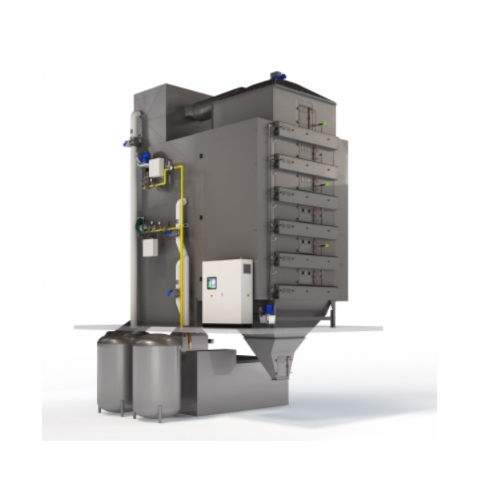
Industrial heat pump dryer
The drying of extruded products is highly energy-demanding in traditional belt dryers that use ga...
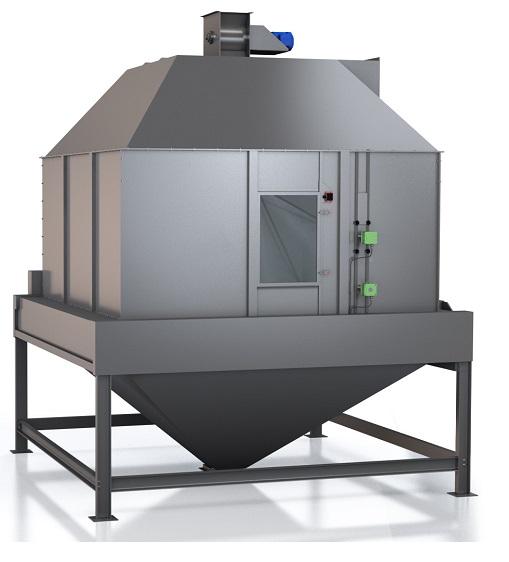
Continuous pellet cooler
Cooling is a very important and critical process for feed hygiene and pellet durability index. Pelle...
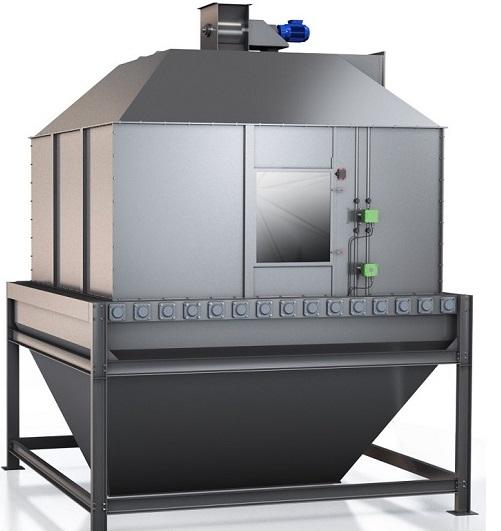
Gravity feed cooler
The food and feed industry has high food safety requirements making frequent cleaning and inspection nece...
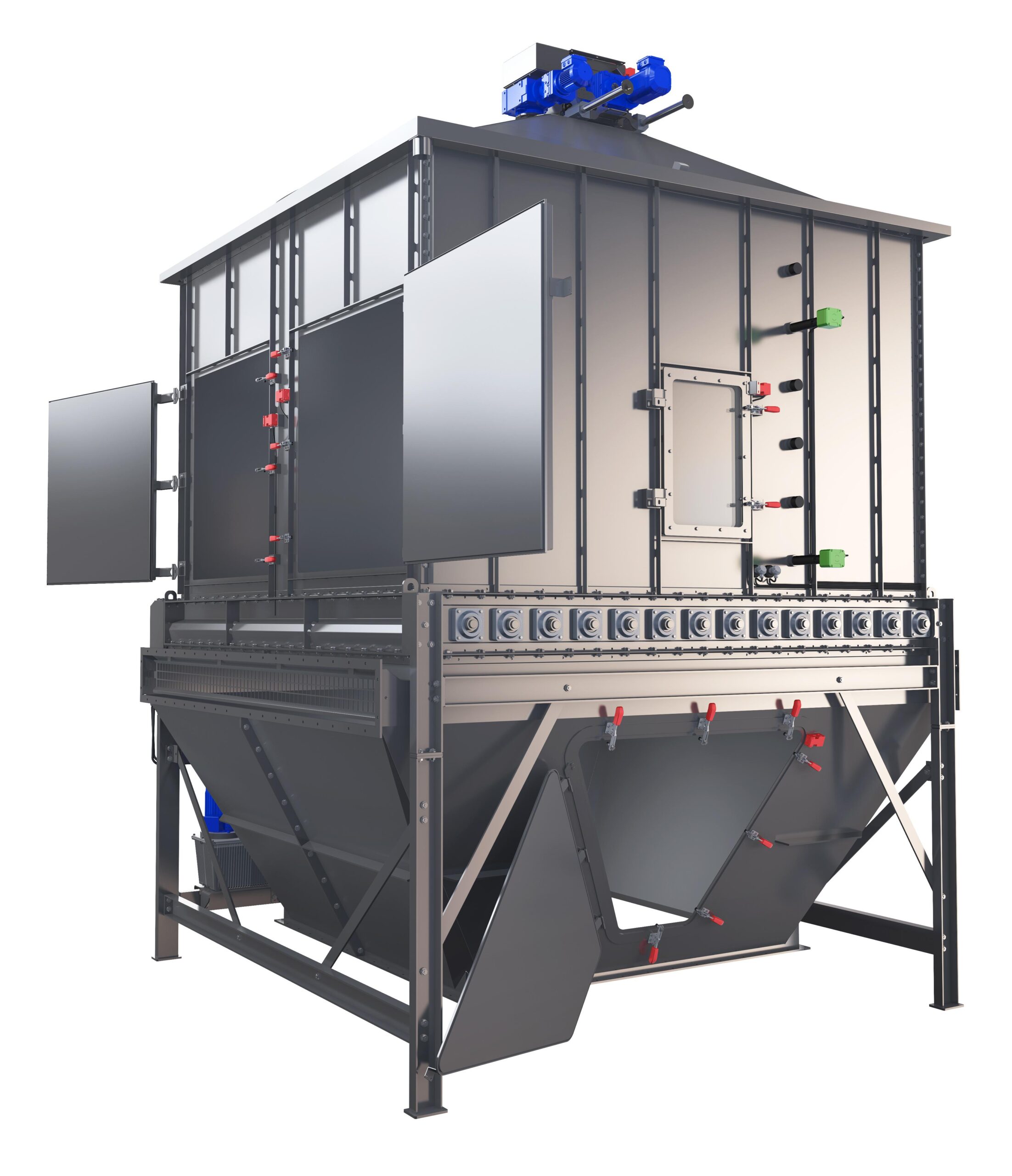
Counterflow pellet cooler
Food and feed industries require the highest standards of hygiene and sanitation. This entails fre...
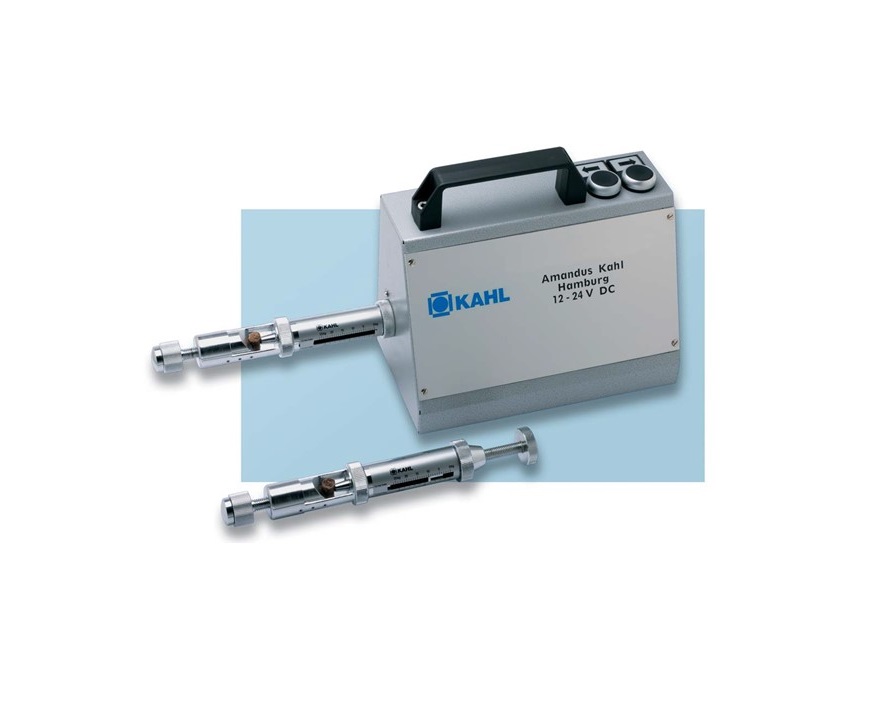
Pellet hardness tester
Control the quality of your pelletizing processes using a pellet hardness tester. Pellet hardness is o...
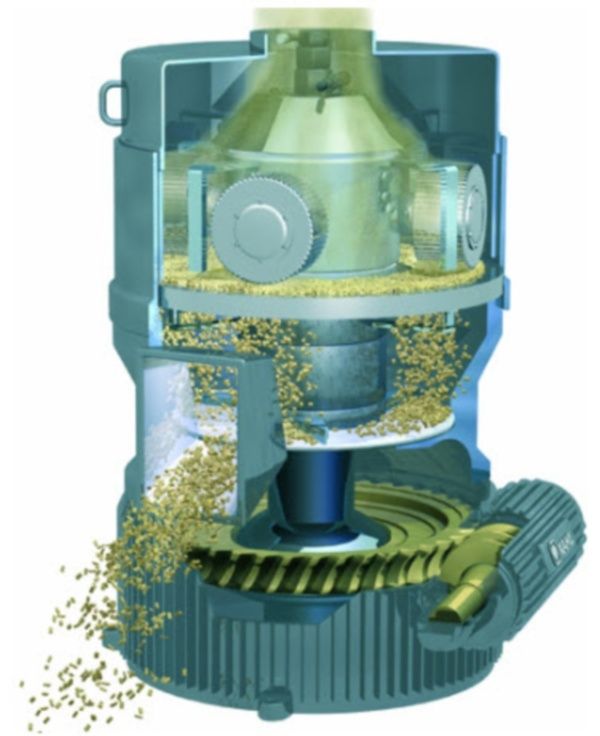
Pelleting press for feed and petfood
The production of agricultural feed and pet food products requires machines and plants...
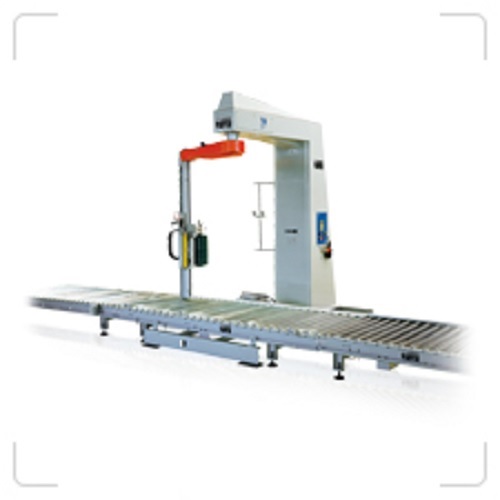
High speed stretch wrapping machine
Where high speed wrapping, without toppling, is required in tightly securing palletised...
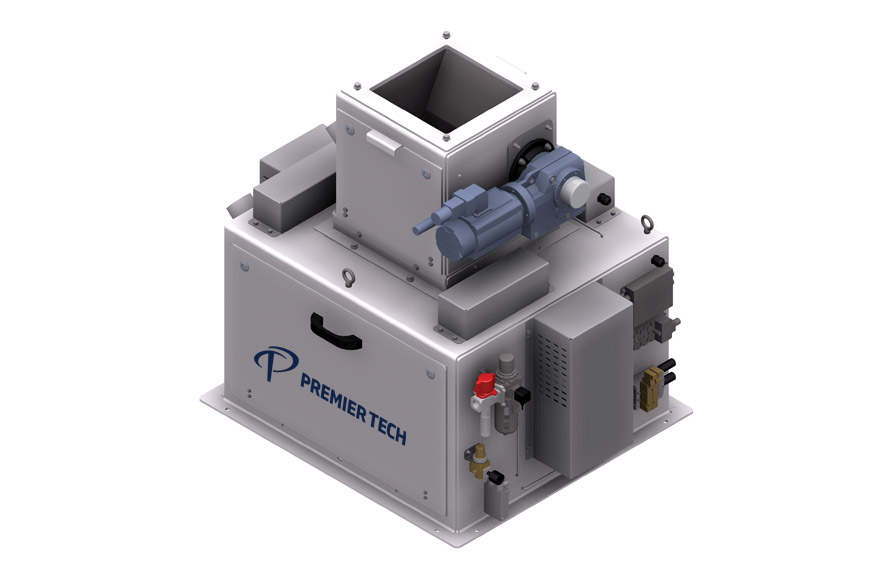
Electronic net weigher for high-capacity baggers
Electronic net weigher raises the industry’s standards to a higher level ...
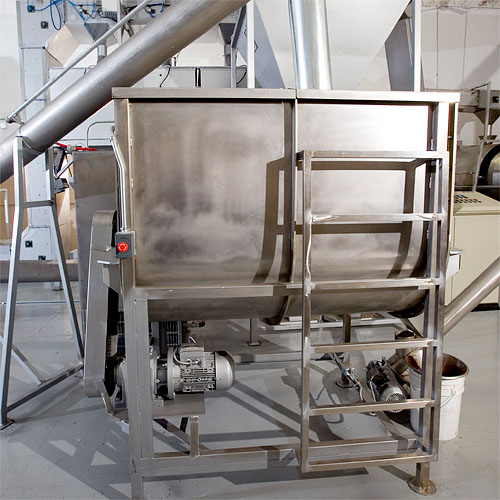
Basic mixer for granular foods
Straightforward blending solution for mixtures of beans, nuts, berries & powdered foods, ...
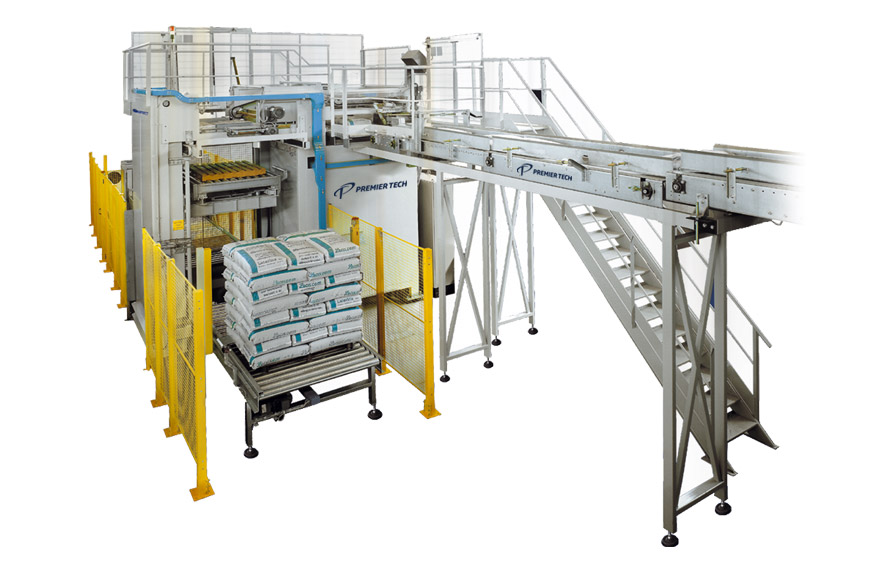
High-level layer palletizer
A palletizer that meets the middle and high-level needs of modern bagging lines. Quite suitable ...
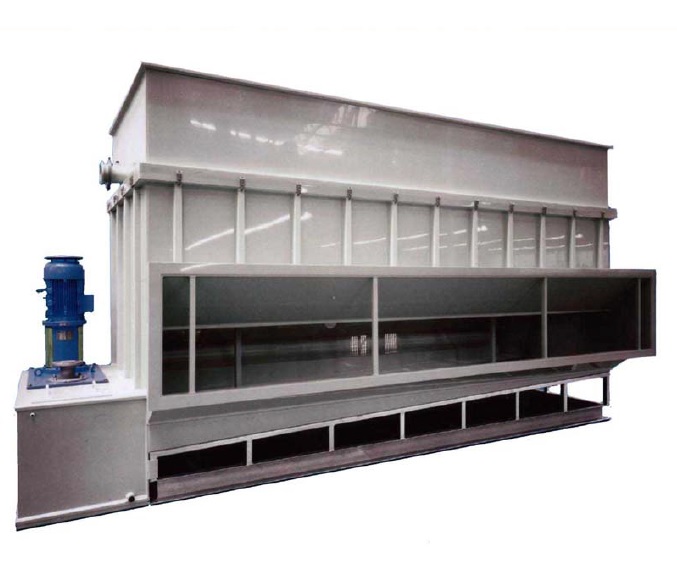
Air dehumidifier for bulk products
When your product or process is sensitive to humidity, using an air dehumidifier may res...
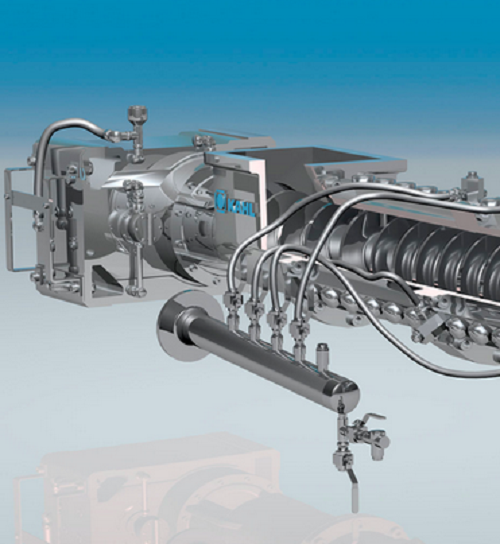
Extruder with annular gap expander
Products can be extruded with various shapes and characteristics by controlling the nozz...
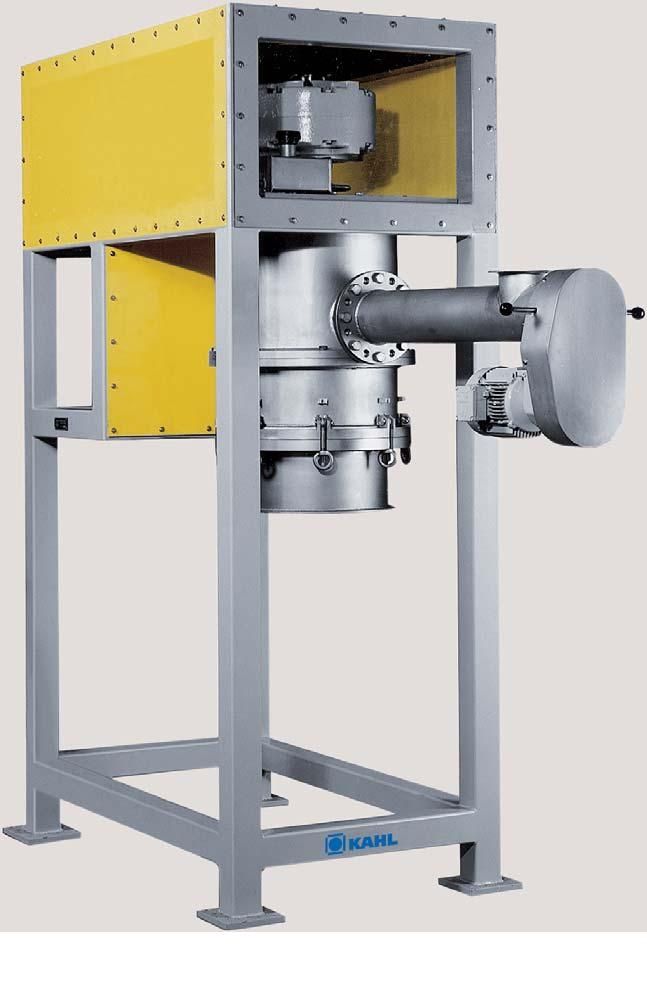
Pelleting press with overhead drive
Production of certain pelletized products requires working with output products of a pa...
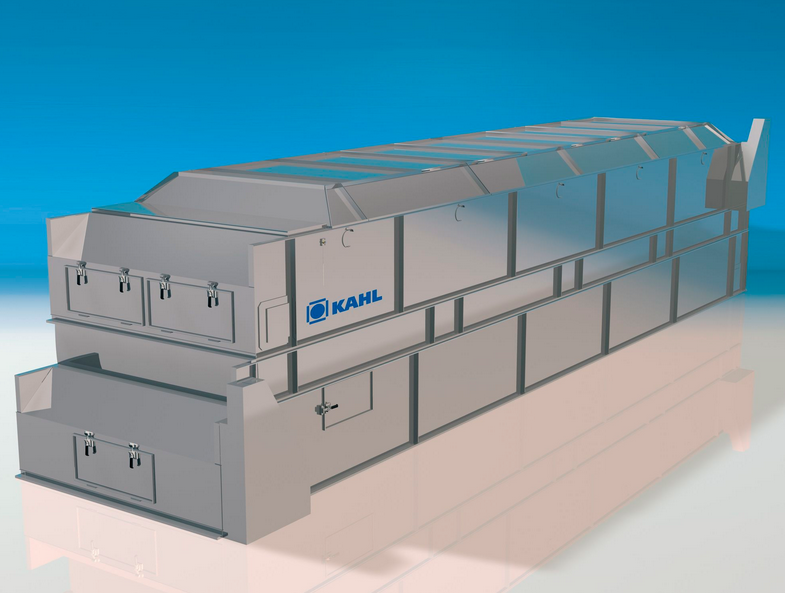
Belt dryer/cooler for pellets and granules
Many industries that process materials in pellet, powder, or crumble form need ...