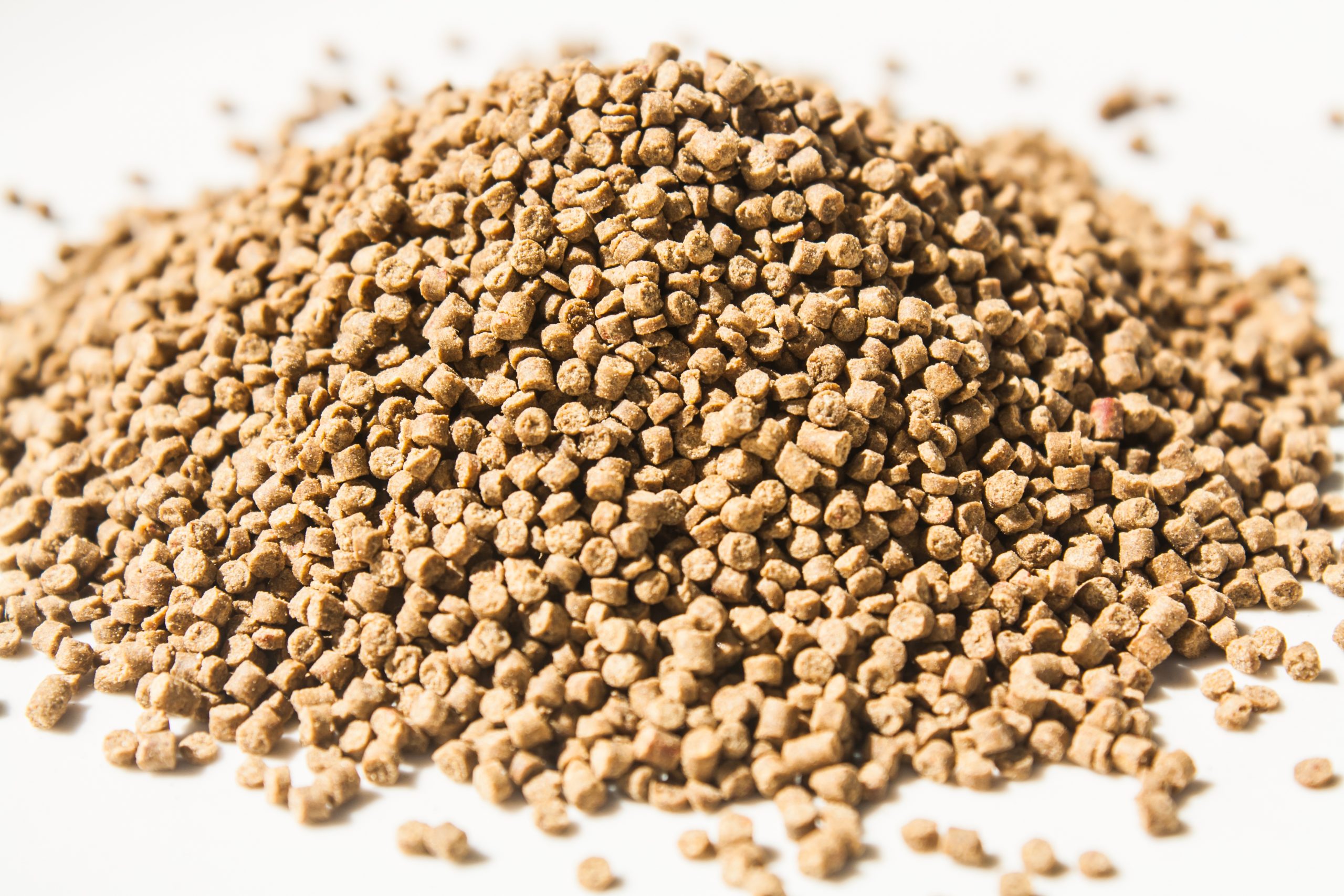
Making Sinking Pellets
Find innovative production technology for making sinking pellets and connect directly with world-leading specialists
In aquafeed, you can find three types of pellets: floating pellets, sinking pellets, and slow-sinking pellets, because not all aquatic species eat at the same height of the water column. In the case of bottom feeders such as shrimp, river crab, sea bass, and some species of catfish, they eat sinking pellets. Contrary to tilapia and carp that feeds from the surface with floating pellets. Sinking pellets production must control water stability to preserve the quality and form of the pellets, avoiding nutrients' dissolution in the water.
Stories about sinking pellets
Select your sinking pellets process
Tell us about your production challenge
Water stability is the most important quality feature in sinking pellets production
Making sinking pellets, needs expertise not only to formulate the right ingredients but to produce the right texture with a fast sinking rate. Water stability is critical in sinking pellets production and must be controlled at all stages of the process because this type of aquafeed has to preserve its physical form and quality, to avoid the loss of nutrients in the water.
When the pellet is stable in the water for hours, you are going to assure a great part of the bottom feeders will eat it, and at the same time, you will avoid water pollution due to the dissolution of ingredients.
Sinking feed can be pelleted or extruded
To make water-stable sinking feed, you can choose between pellet mills or extruders. Contrary to floating pellets and slow-sinking pellets that can only be extruded. When you use a pellet mill, the previously ground and mixed ingredients are pressed into the pellet die and steamed for better compacting, resulting in a dense feed. This is a more economical process compared to extrusion. Besides the lower costs of processing, there is also a lower risk of losing vitamins in pelleted feed, but it needs to use higher amounts of starch and higher quality raw material.
On the other hand, the extrusion process gives you the versatility to produce granulates of different sizes, including micropellets. Moreover, it can also make floating, slow-sinking, and sinking pellets, with better water stability, and a better feed performance due to a higher digestibility of extruded feeds.
Whether you choose one or the other, it is important to take into account your feed formulations, the type of aquatic animals you are going to feed, the quality of the feed you want to produce, and your production and maintenance costs.
Include alternative feed ingredients in your sinking pellets
In aquafeed, fishmeal is the primary protein source due to its rich protein and fatty acids content. But as fishmeal production and supply, need sustainable improvements, you can use alternative protein ingredients in your formulations such as plant-based TVP or insect-based, to make sinking pellets.
Processing steps involved in sinking pellets making
Which sinking pellets technology do you need?
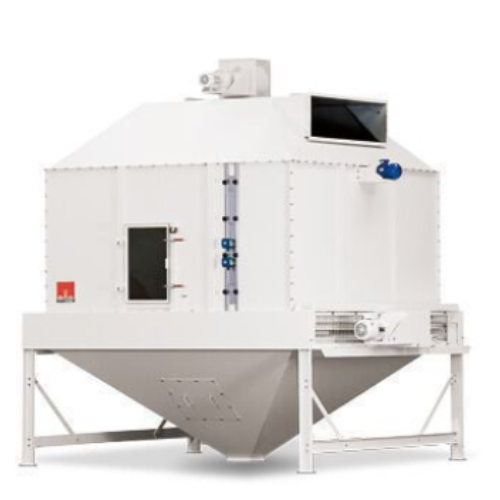
Counterflow dryer for pet food and fish feed
Optimize moisture control and enhance feed quality with efficient drying, cru...
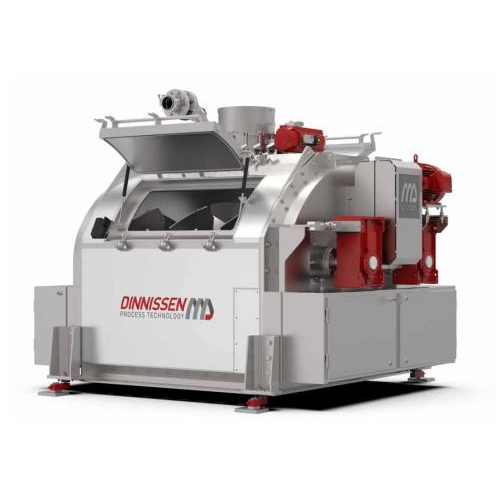
Advanced vacuum coating system for pet food and feed
Achieve uniform saturation in pellets and granules with precise liqu...
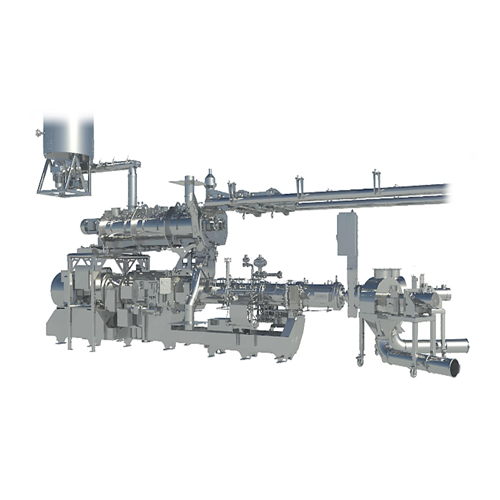
Extruder for aquatic feed production
Efficiently produce a wide range of aquatic and pet feed with precise control over pel...
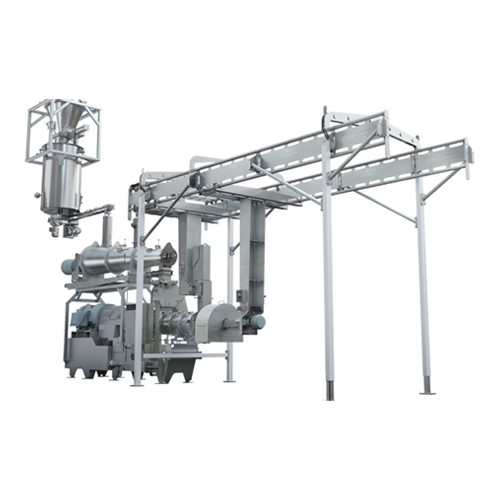
Conical twin screw extruder for pet food and aquatic feed
Precision-engineered for high-speed extrusion and drying proce...
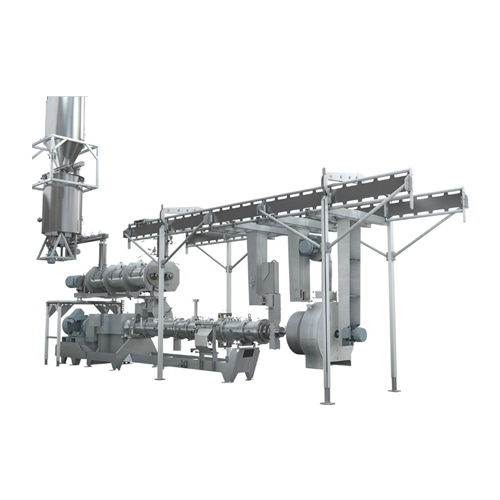
Twin screw extruder for pet and aquatic feed
Achieve exceptional cooking precision with our twin screw extruder, designed ...
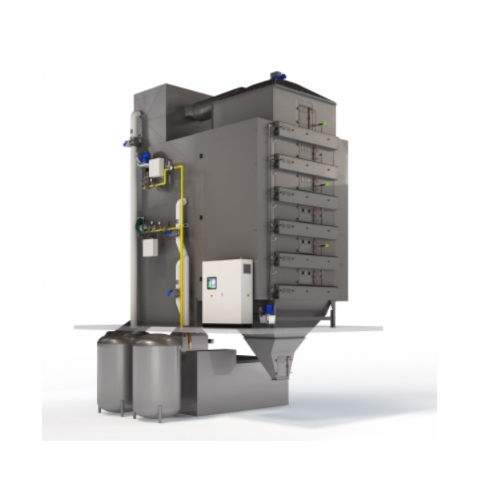
Industrial heat pump dryer
The drying of extruded products is highly energy-demanding in traditional belt dryers that use ga...
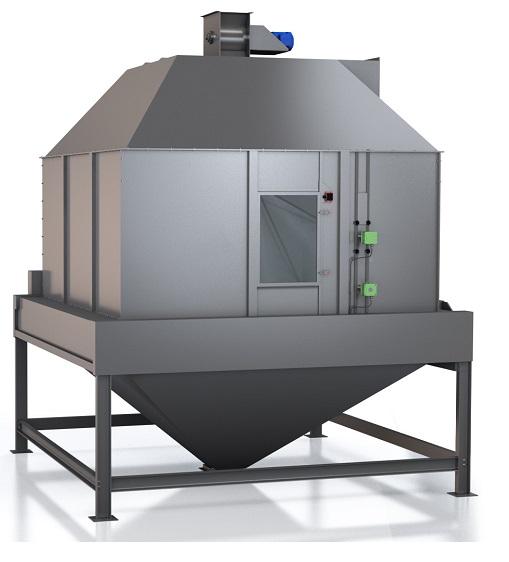
Continuous pellet cooler
Cooling is a very important and critical process for feed hygiene and pellet durability index. Pelle...
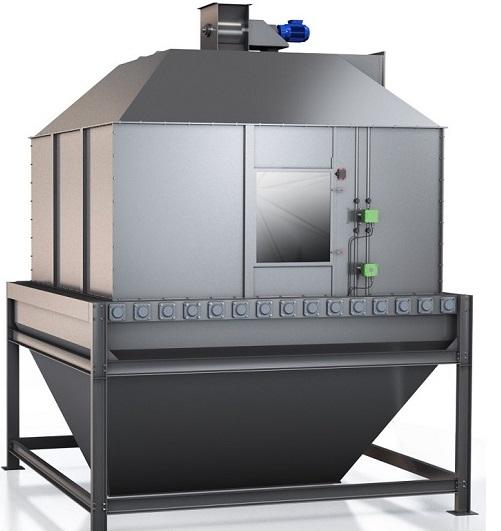
Gravity feed cooler
The food and feed industry has high food safety requirements making frequent cleaning and inspection nece...
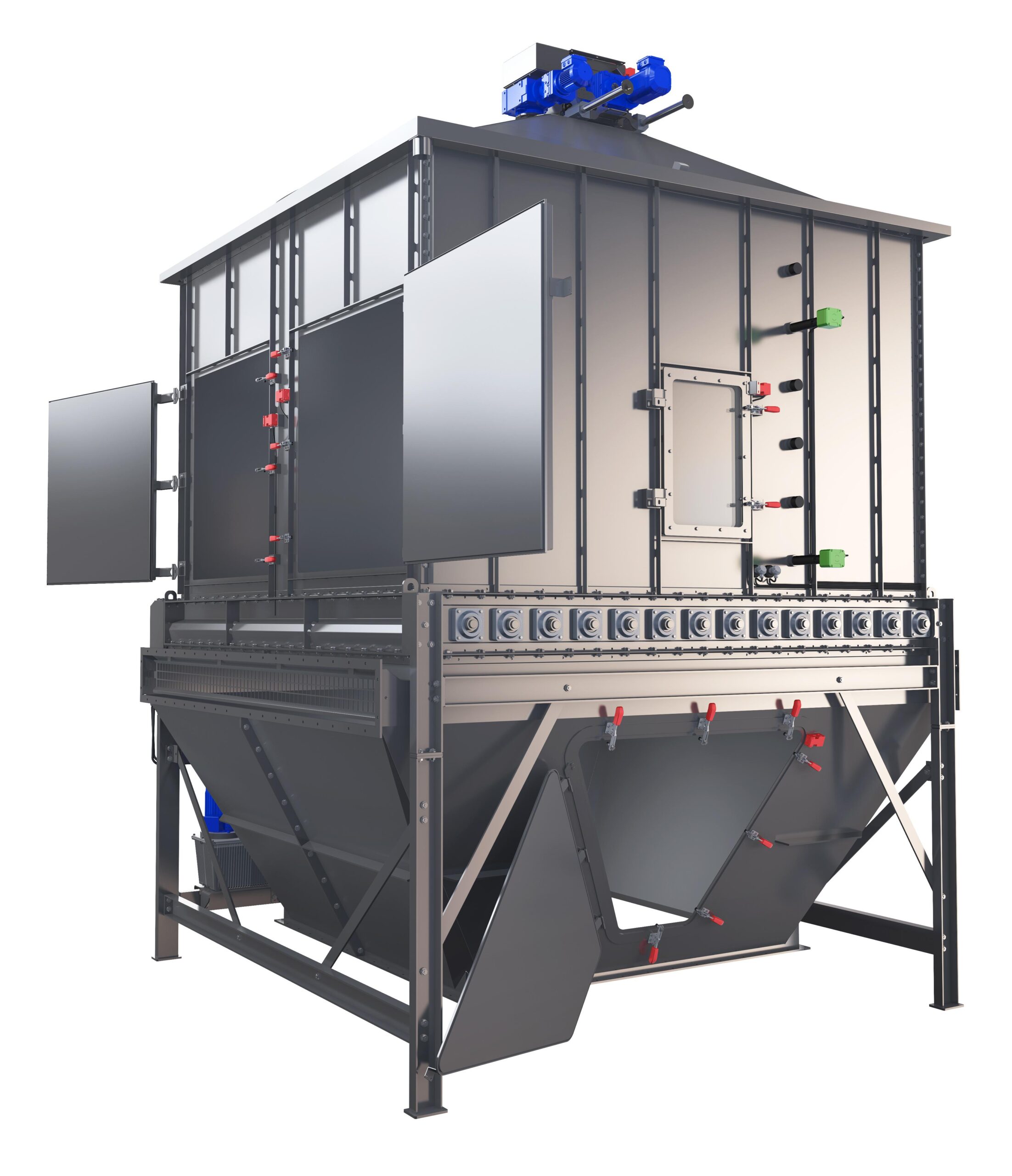
Counterflow pellet cooler
Food and feed industries require the highest standards of hygiene and sanitation. This entails fre...
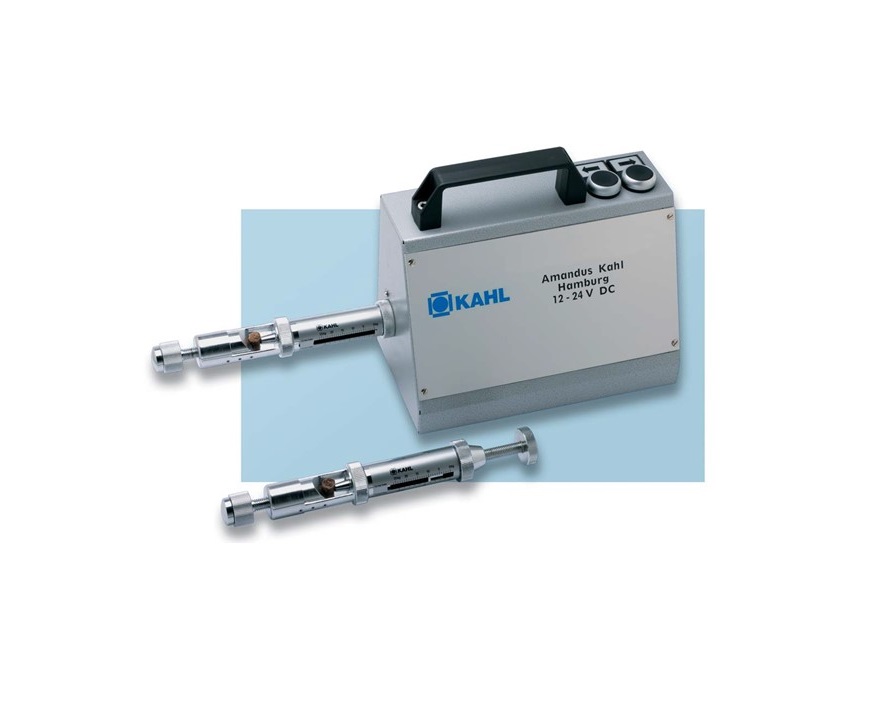
Pellet hardness tester
Control the quality of your pelletizing processes using a pellet hardness tester. Pellet hardness is o...
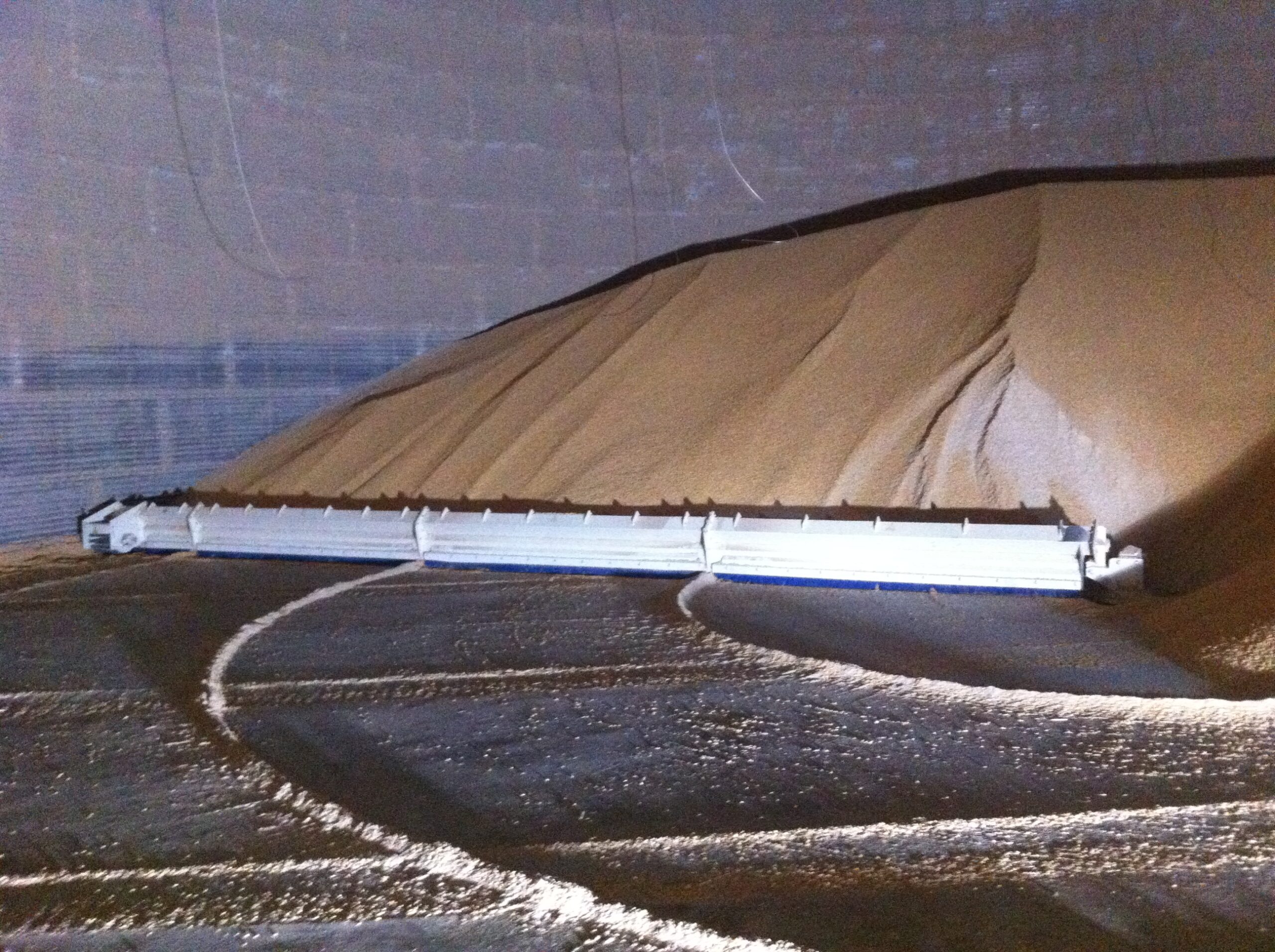
Silo sweep auger
When you store products with good gravity flow (wheat, maize, barley, grains, granules, etc.) in flat bottom ...
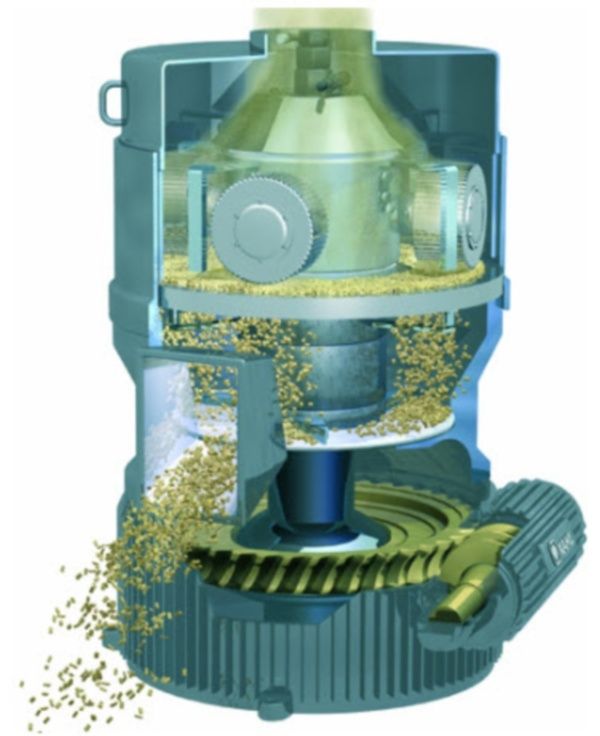
Pelleting press for feed and petfood
The production of agricultural feed and pet food products requires machines and plants...
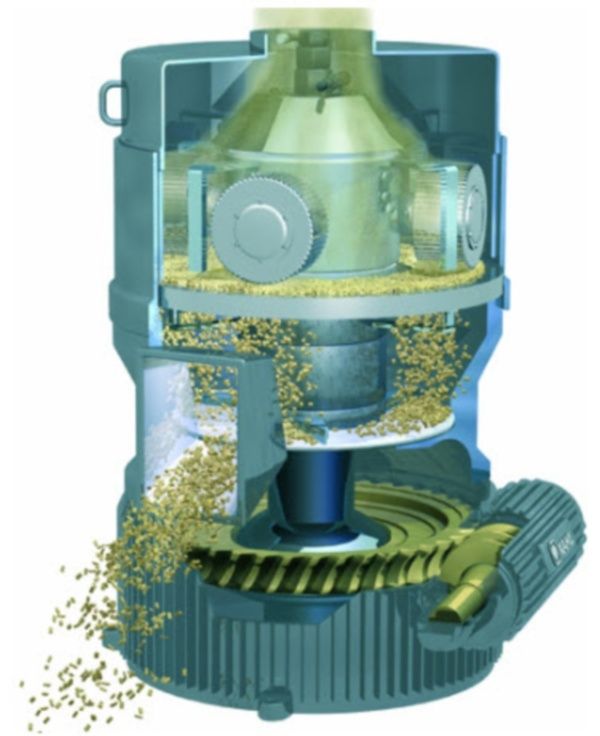
Pelleting press for biomass
Utilization of biomass for energy and other applications requires consistent and reliable compac...
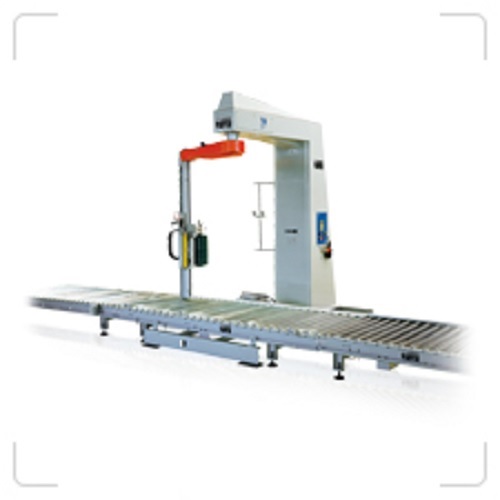
High speed stretch wrapping machine
Where high speed wrapping, without toppling, is required in tightly securing palletised...
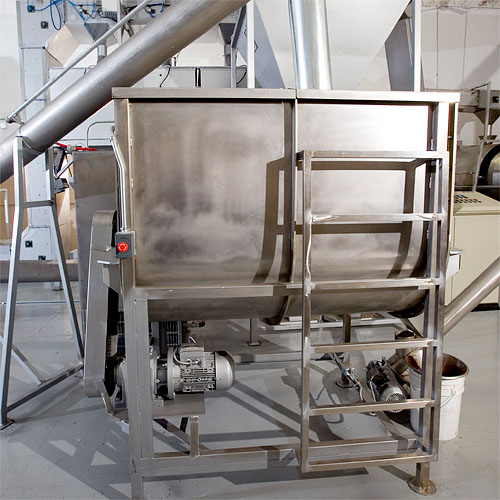
Basic mixer for granular foods
Straightforward blending solution for mixtures of beans, nuts, berries & powdered foods, ...
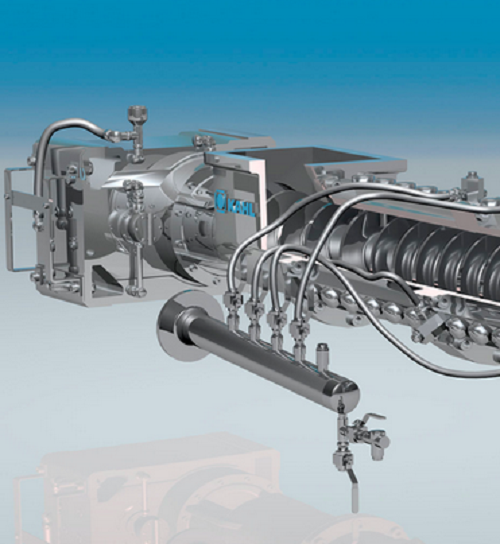
Extruder with annular gap expander
Products can be extruded with various shapes and characteristics by controlling the nozz...
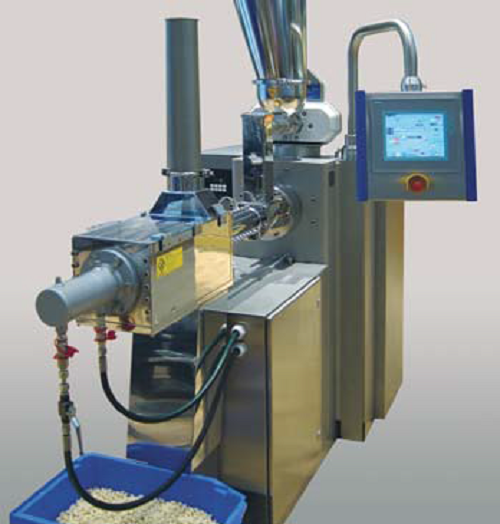
Laboratory extruder
Products can be extruded with a variety of shapes and characteristics by controlling the nozzle geometry ...
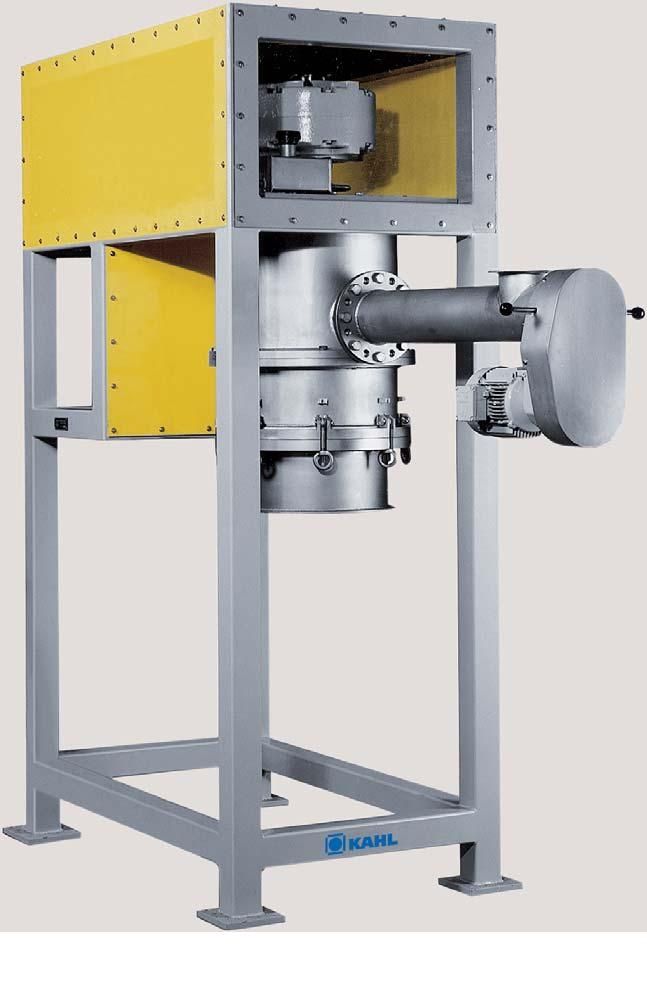
Pelleting press with overhead drive
Production of certain pelletized products requires working with output products of a pa...
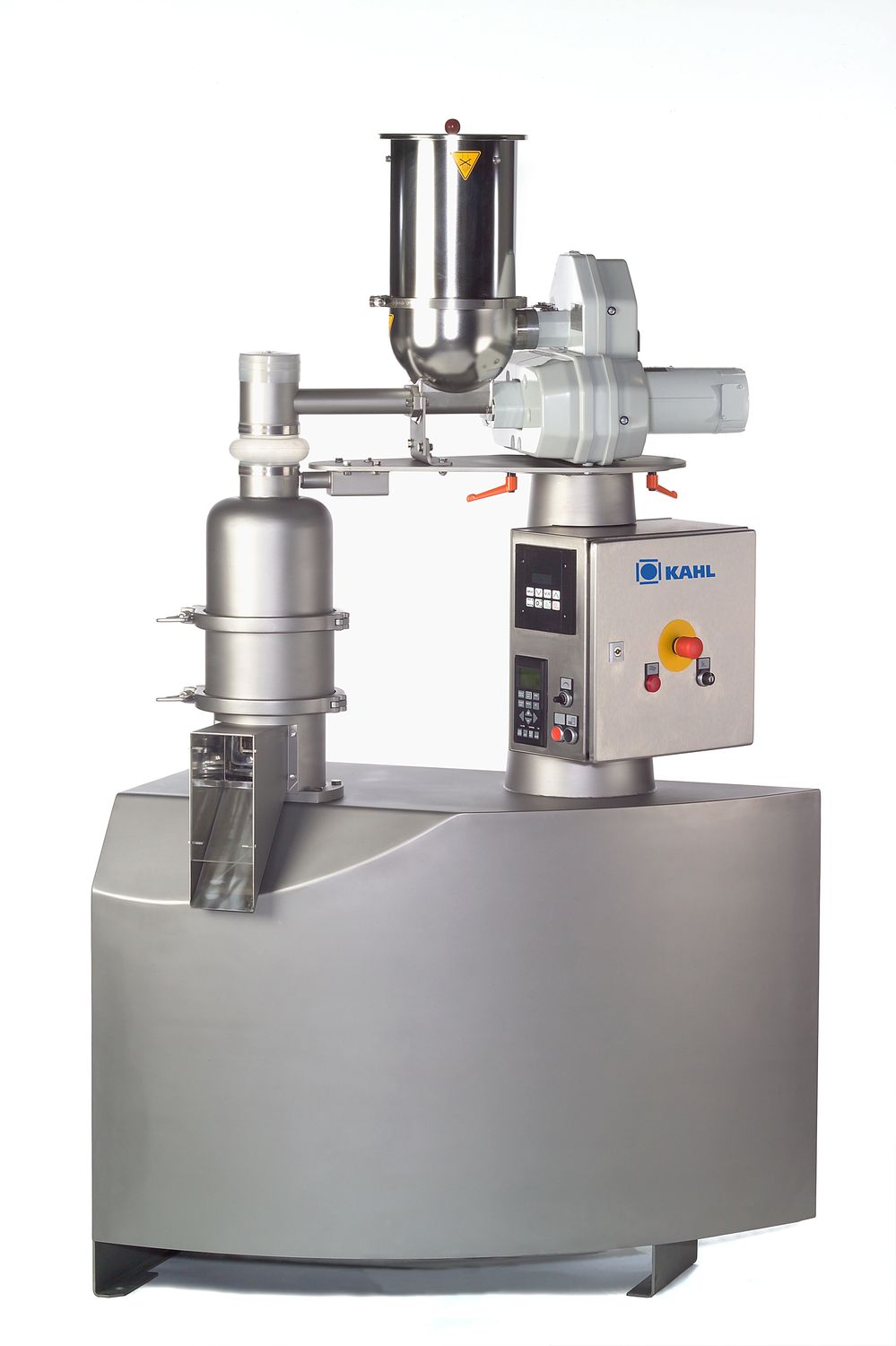
Hygienic pelleting press
The production of pelletized or granularized food products requires hygienic presses designed for hi...
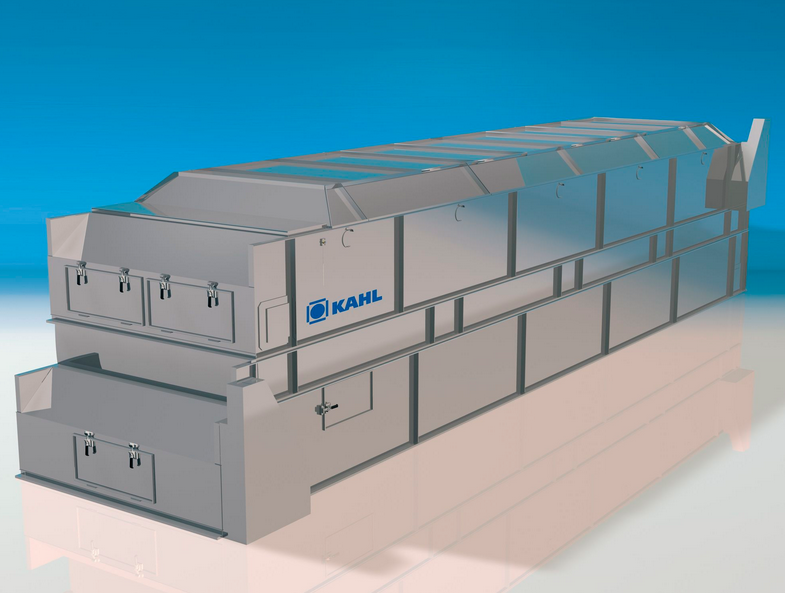
Belt dryer/cooler for pellets and granules
Many industries that process materials in pellet, powder, or crumble form need ...