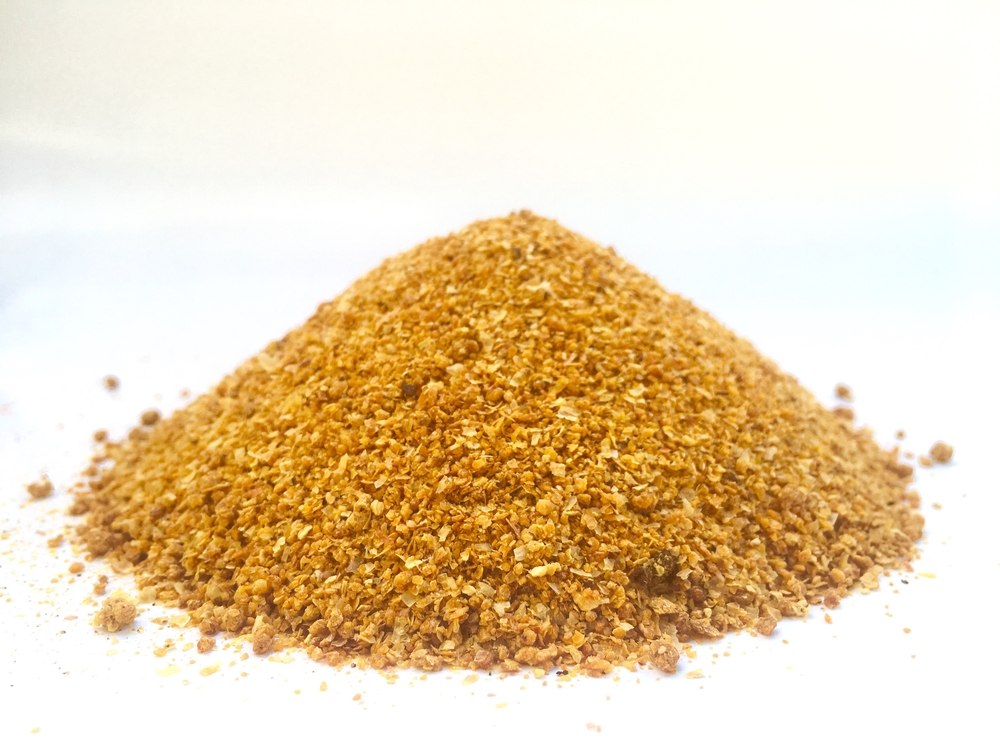
Let's make dried distillers grains (DDGS)
Find innovative production technology for making dried distillers grains (ddgs) and connect directly with world-leading specialists
Although primarily used as food for animals, recent studies have found that dried distillers grains with solubles (DDGS) could reduce heart disease risk in humans. Dried distillers grains are a cereal byproduct of the distillation process - a mix of corn, rice, and other grains dried to 10–12% moisture. DDGS production entails processes from cleaning the grains over cooking to fermentation and drying.
Tell us about your production challenge
DDGS production: the first steps
Dried distillers grains are a coproduct from ethanol production from grains such as corn, rice, soy, wheat, etc. Shortly known as DDGS, the grains are used as protein-rich animal feed for cattle, dairy cows, swine, and some poultry. Grain received in the factory contains foreign materials like dust, straw, and stem residues which must be cleaned before storing in silos and further processing.
The debris is cleaned with the help of equipment such as a pre-cleaner, de-stoner, and magnetic separator. Once the grains are cleaned, they are ground into a powder using a hammer mill or a roller mill. The mixture of ground grains, water, and amylolytic enzymes to hydrolyze starch into glucose is cooked at 40–60°C in the pre-mixing tank. The slurry is passed through a jet cooker where the temperature is maintained at 110 to 120°C, and finally, the process is finished in the liquefaction tank at 90°C. During this process, the long chains of starch are hydrolyzed and broken into smaller chains, increasing the amount of sugars, which lowers viscosity.
The core steps in the production of DDGS
Before starting the fermentation process, the slurry must be cooled down to 32°C. Once the ideal temperature is reached, the DDGS production process is ready for the core step – fermentation. In the fermentation tank, the slurry is mixed with water and activated yeast which consumes the sugars in the grains, producing ethanol and carbon dioxide. Depending on the desired alcohol level, the fermentation process can take around two days.
The resulting mixture, beer, is sent to the distillation column, where the alcohol is separated from the water and other impurities, which produces around 95% ethanol by volume. Stillage, the leftover solids, is processed in a centrifuge where the liquid is separated from the wet cake, as the solid bits are called. The liquid is then transformed into syrup in an evaporation tank and added back to the wet cake, which is then sent to the rotary drum drier, where it must be dried down to around 10% moisture content. Before transportation, it must be cooled in storage.
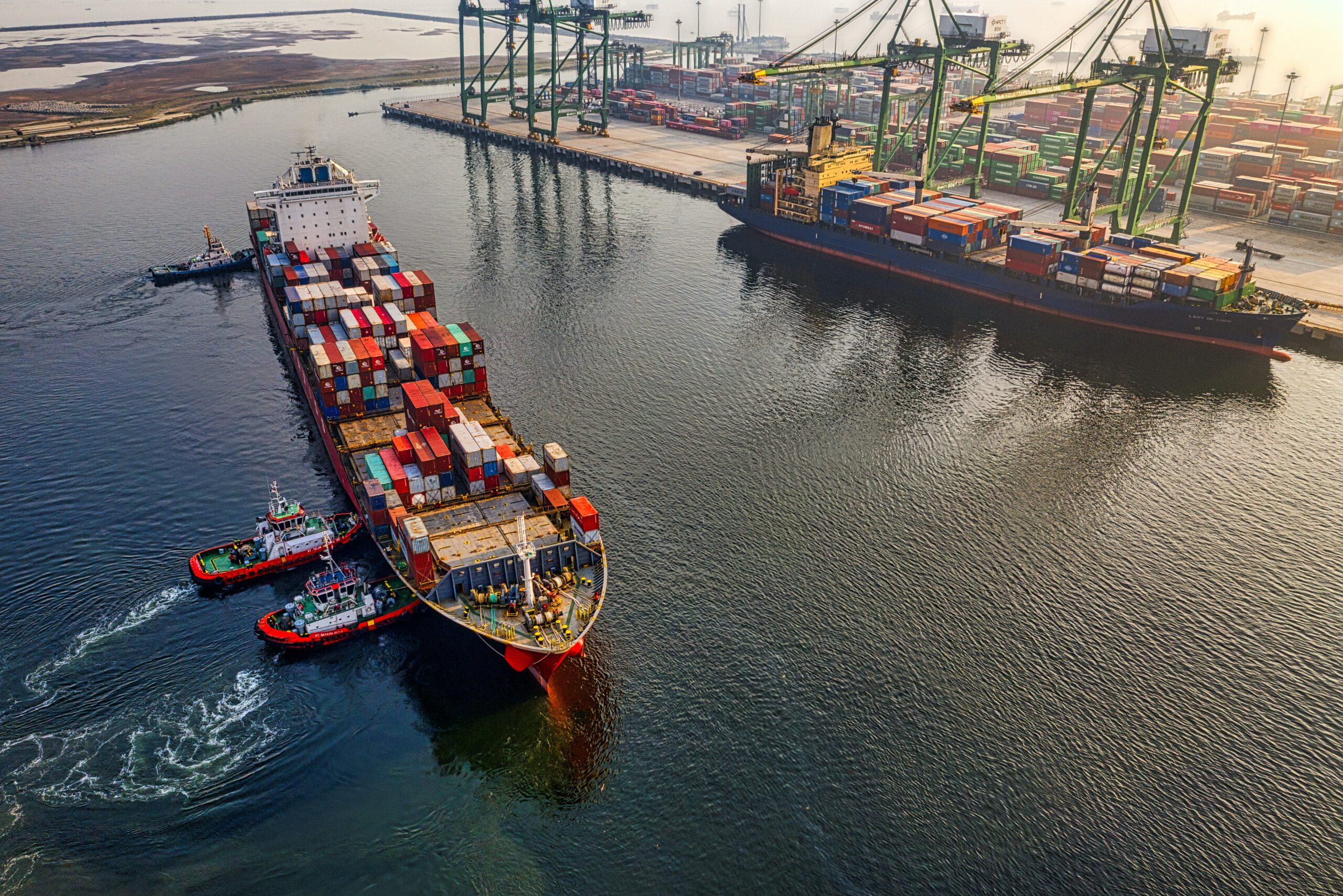
The challenges for DDGS producers
One of the biggest challenges faced by DDGS producers comes after the actual production – in transit. Namely, the potential caking of DDGS in hopper cars or ship cargo due to exposure to various temperature and humidity environments which promotes chemical and physical instability, causes a big logistical problem. One of the solutions to avoid caking is cooling the product after drying to the temperature that will be in the transportation environment. Namely, loading warm products increases the probability of caking. Furthermore, covering the product and therefore limiting moisture exchange with the environment is another possible solution; however, this one requires more scientific research.
The use and production of wet and dried distillers gains
There are two common types of distillers grains: wet and dry. Wet distillers grains, abbreviated as WDG, contain primarily grain residues of the protein, fiber, and fat after the grain’s starch is converted into ethanol, with up to 70% moisture and only 30% of dry matter. WDG has a shelf life of four to five days. Due to the water content and shelf life, WDG is usually used locally. On the other hand, for longer shelf life, almost indefinite, DDGS are dried to about 10% of moisture and may be shipped to any market regardless of its proximity to an ethanol plant.
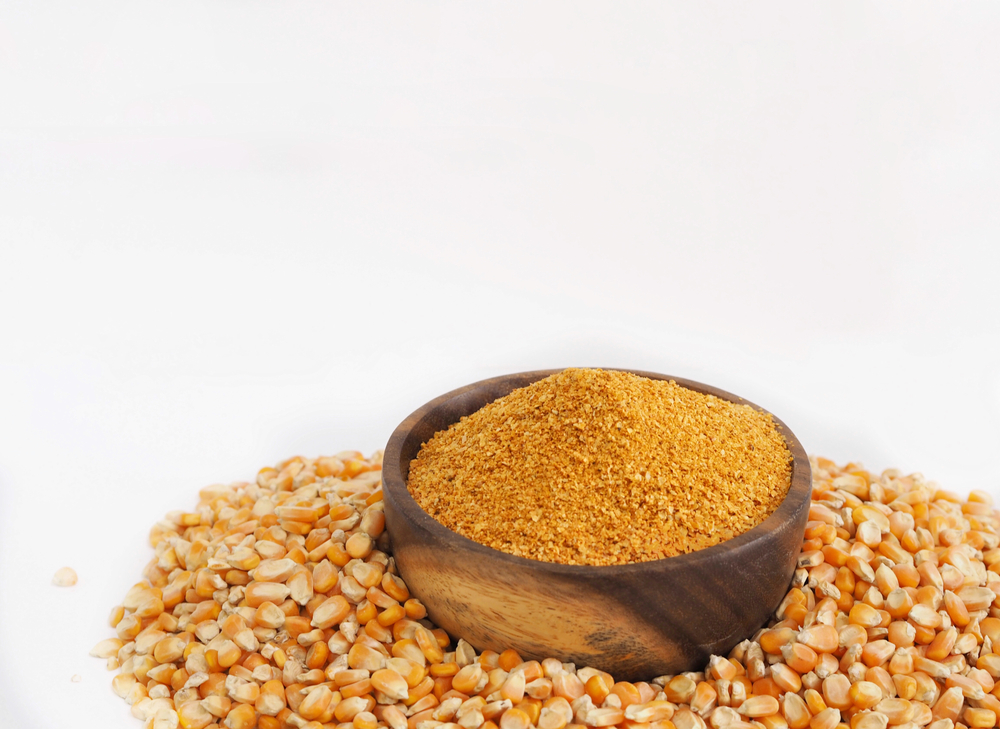
Nutrient enhancement in DDGS
Due to poor essential amino acid profile, corn distillers dried grains with solubles (DDGS) are not nutritionally adequate for nonruminant animals. However, researchers have found a way to enhance its nutritional value by adding ingredients such as coproducts of soybean enzyme-assisted aqueous extraction process, skim (wastewater), and insoluble fiber and enzymes such as pectinase, cellulase, or acid protease. Adding soy into corn DDGS resulted in 10% higher protein, 3% lower fat, and 2% lower fiber. On the other hand, the nutritional value of wheat DDGS, which has a lower nutritional value than corn, can be enhanced by improved fermentation and drying processes and by reducing the impact of NSP with supplementary enzymes or other technologies.
Processing steps involved in dried distillers grains (DDGS) making
Which dried distillers grains (ddgs) technology do you need?
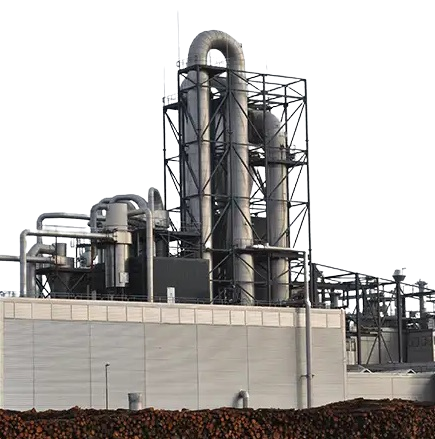
Energy efficient steam dryer for feed products
Traditional drying technologies with low investment cost, such as hot air d...

Macro ingredient dosing system
Traditional dosing systems do not have a very long operational life and are hard and expensiv...
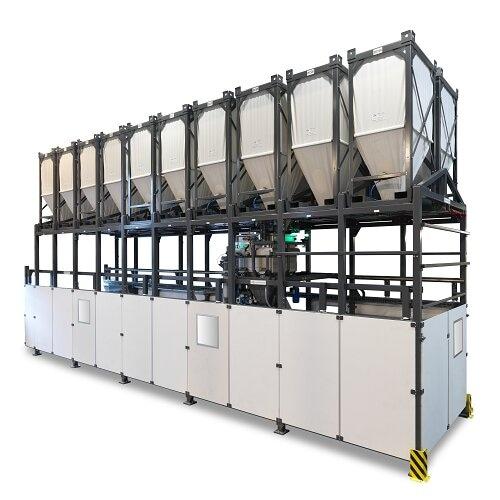
Exchangeable silo dosing system
Rarely used bulk ingredients, like grains, agricultural feed or silage, can get spoilt if th...
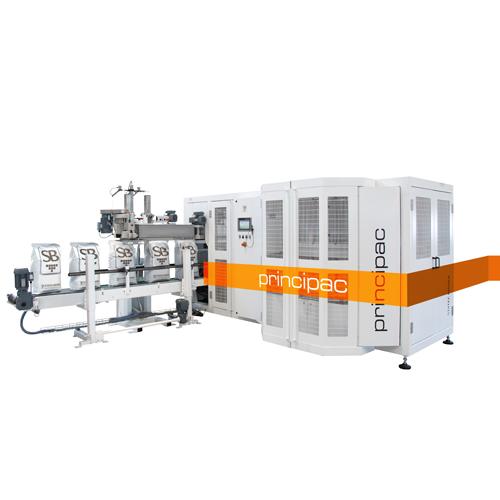
Open mouth bagging machine
If you are a manufacturer of fertilizers, bulk chemicals, sugar, seeds, or any grains it is likel...

Open mouth bag filling machine for powders
The packaging of powdery products such as flour can be challenging as it is cru...
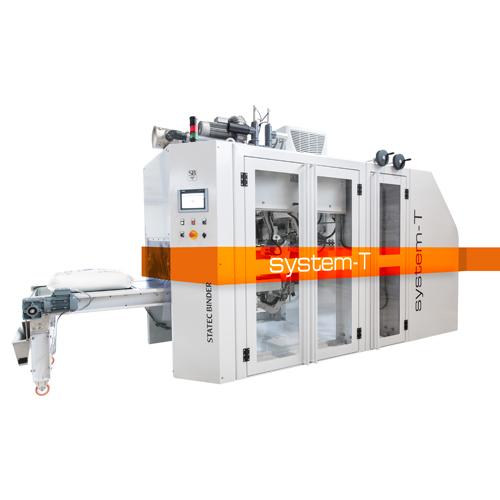
Form fill seal bagging machine
If you are in industries such as petrochemicals, fertilizers, animal feed, food, etc, you mus...
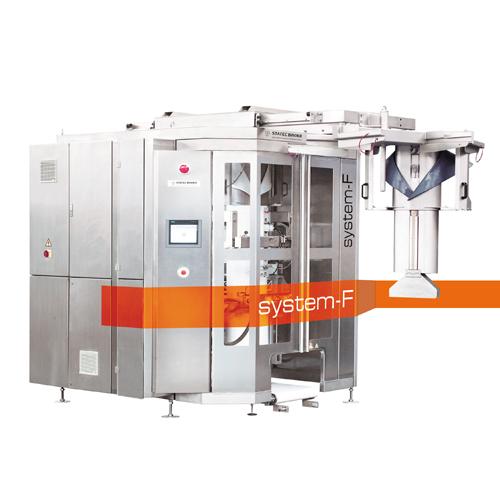
Vertical form fill seal machine
There is an increasing demand for a range of different package sizes of the same product. If...
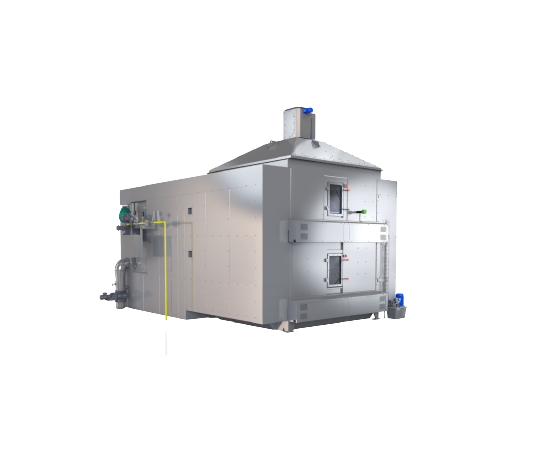
Continuous dryer machine
Traditional drying methods in the pet food, aquafeed, and extruded food industry can be the most ene...
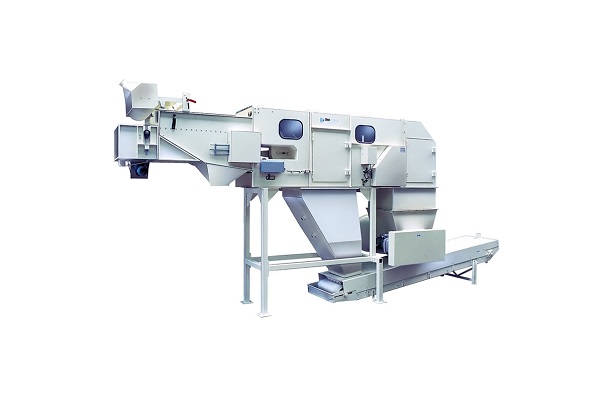
Automatic bag slitter
Unacceptably high dust levels can be generated whilst manual emptying and handling of bags, also produc...
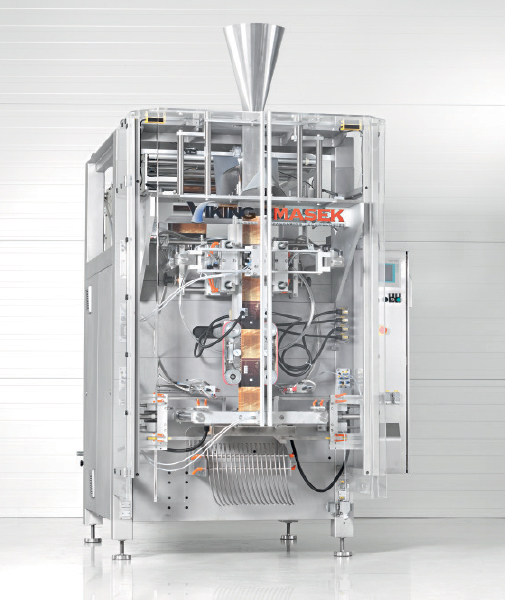
Bagger with servo driven jaw actuation
If you want to accommodate multiple bag designs and dimensions with fast speed and a...
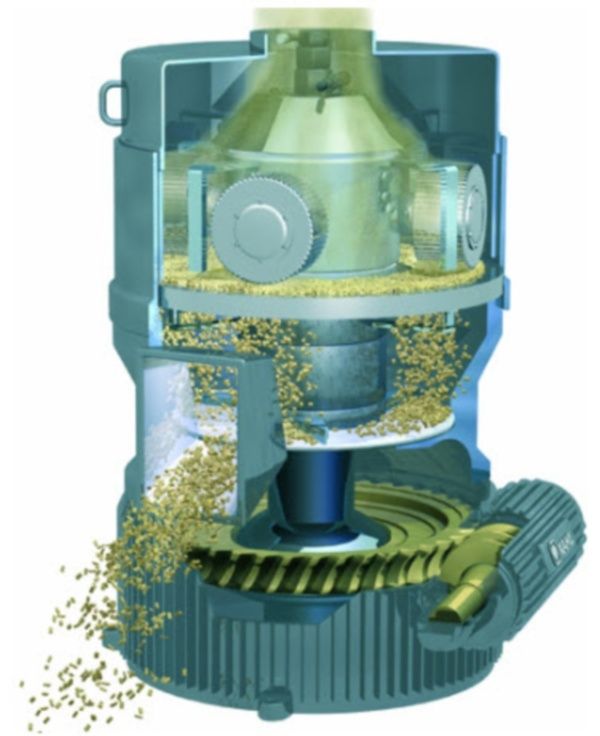
Pelleting press for feed and petfood
The production of agricultural feed and pet food products requires machines and plants...
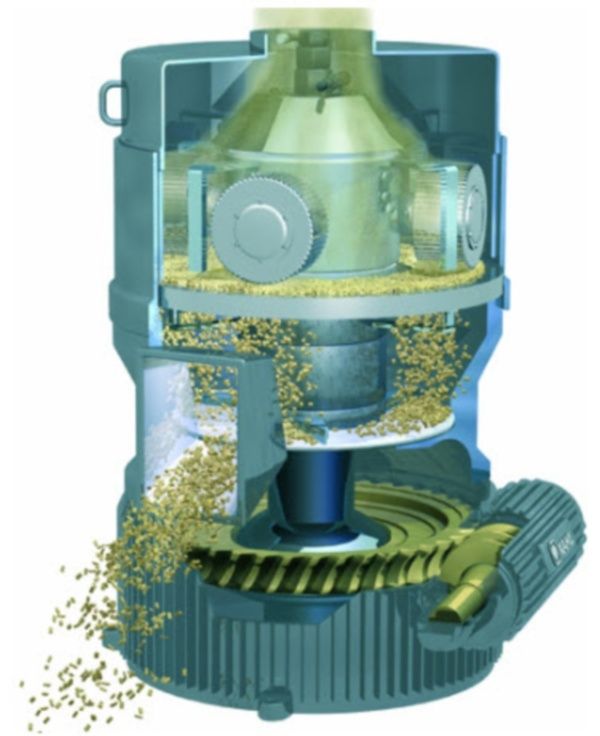
Pelleting press for biomass
Utilization of biomass for energy and other applications requires consistent and reliable compac...
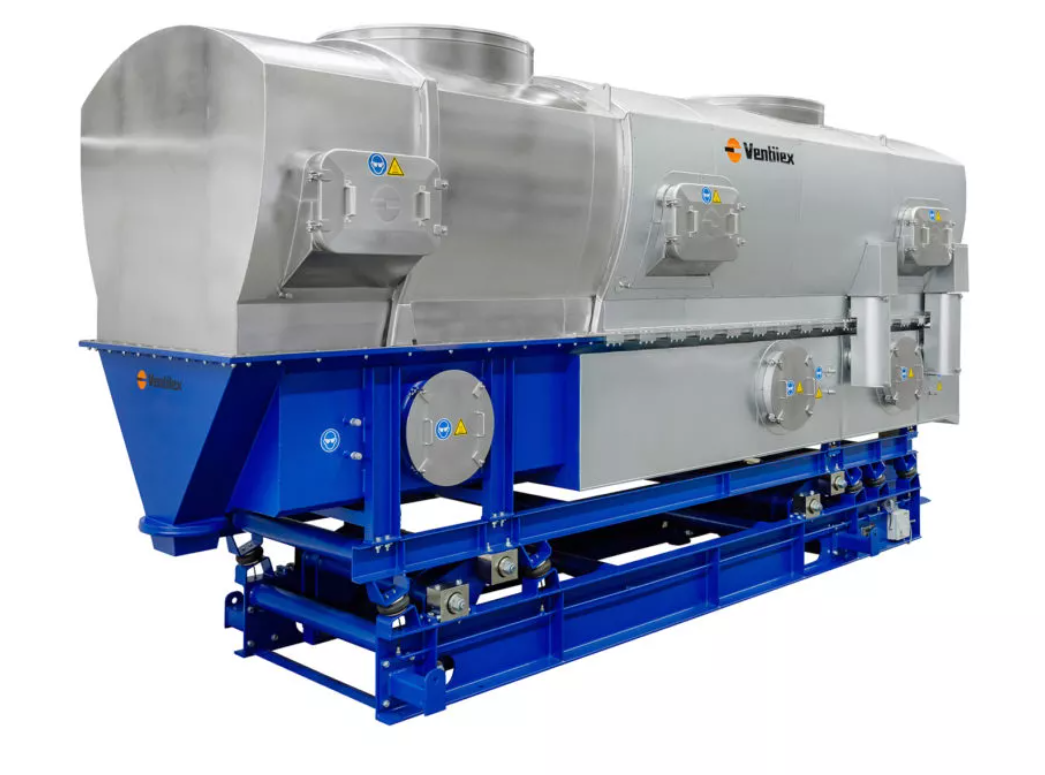
Continuous fluid bed dryer
In a Fluid Bed, a product or solid is made fluid by an upward moving flow of gas. The mechanical ...
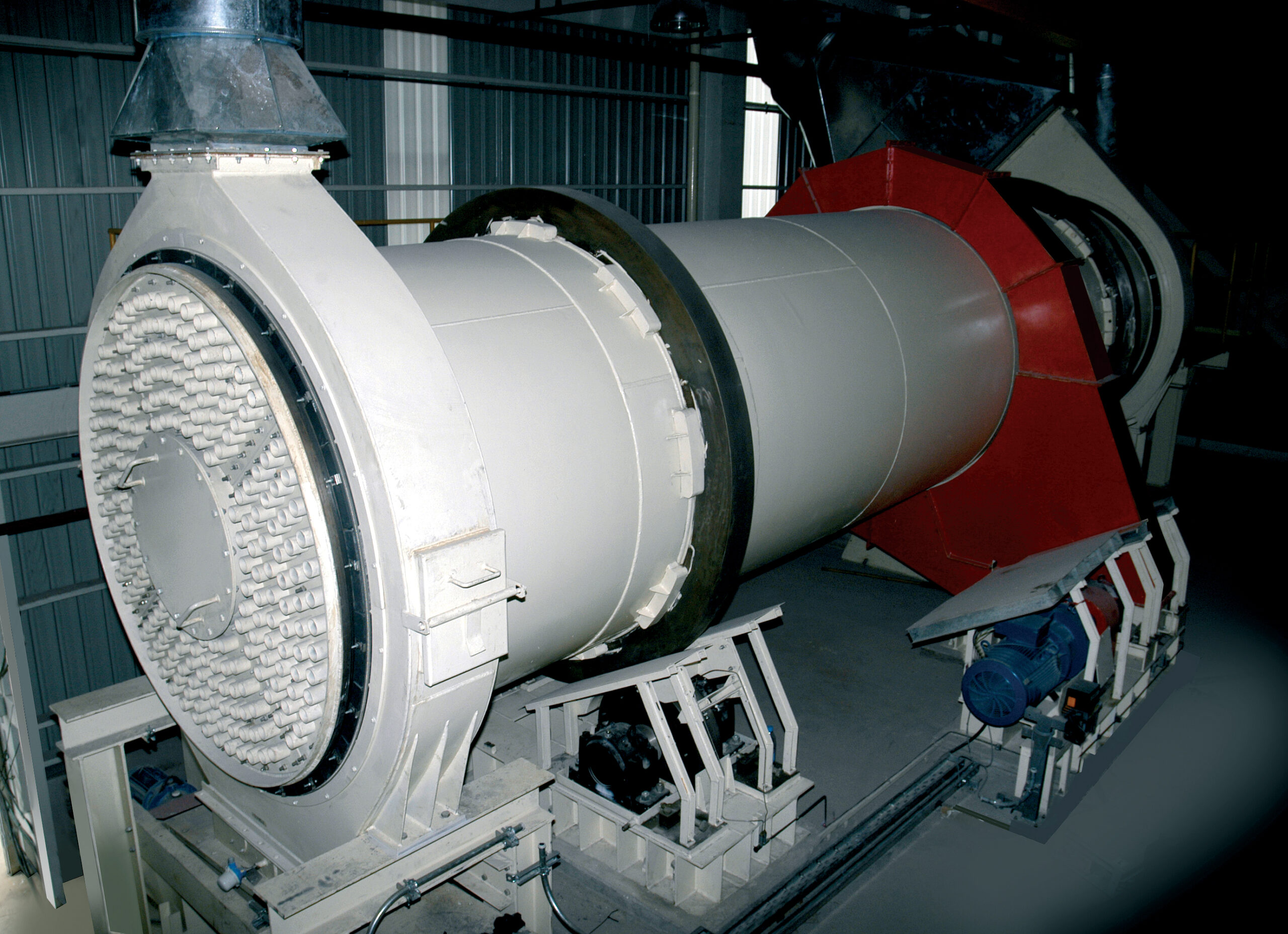
Rotary drum cooler for calcined gypsum products
After the calcining process gypsum products must be cooled from temperatur...
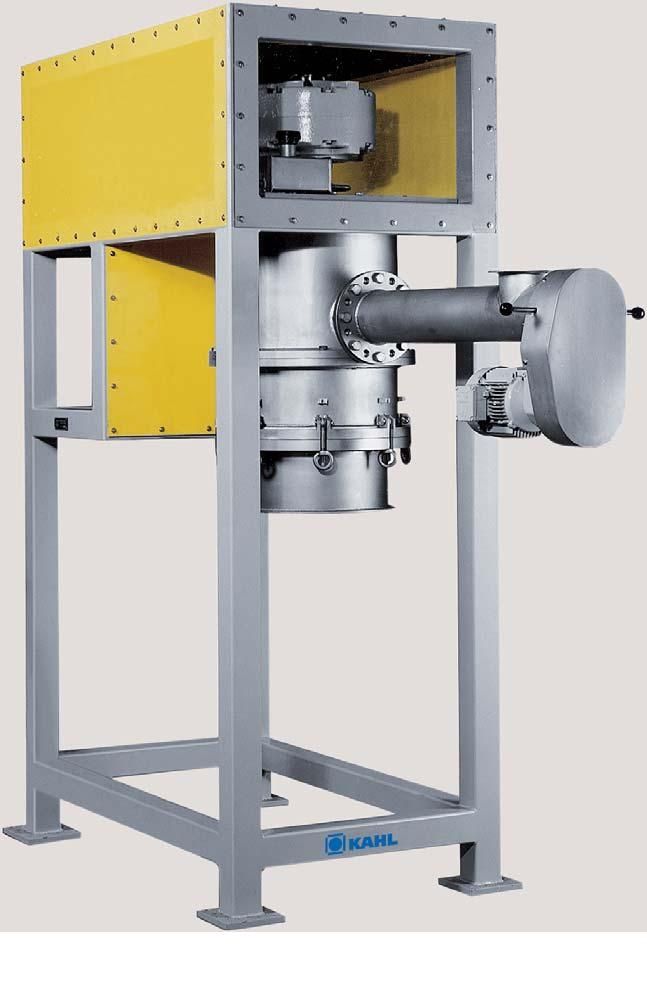
Pelleting press with overhead drive
Production of certain pelletized products requires working with output products of a pa...
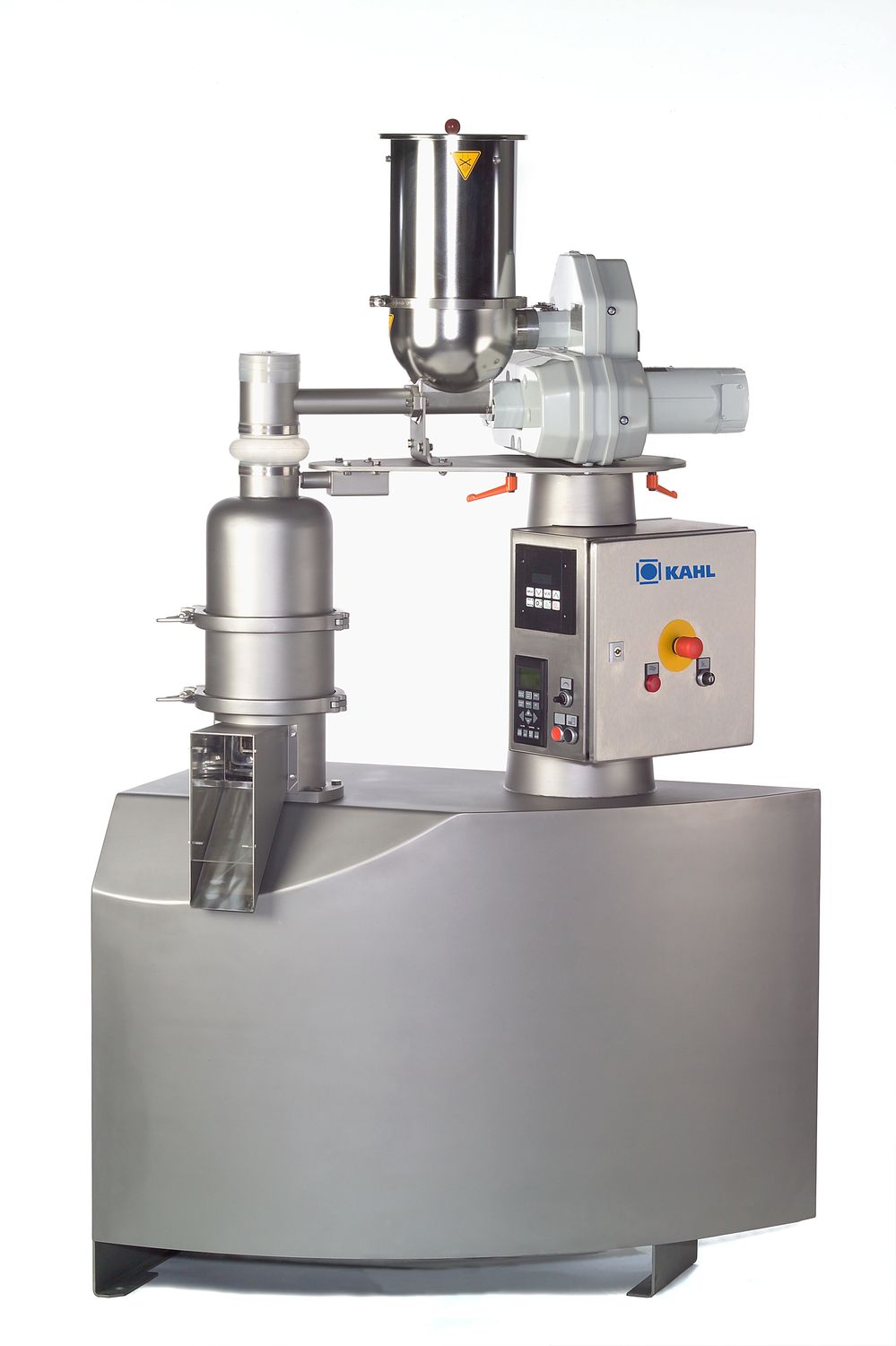
Hygienic pelleting press
The production of pelletized or granularized food products requires hygienic presses designed for hi...

Belt dryer for wood
Processing of wood and biomass into pellets or other volume reduced products requires careful and consist...
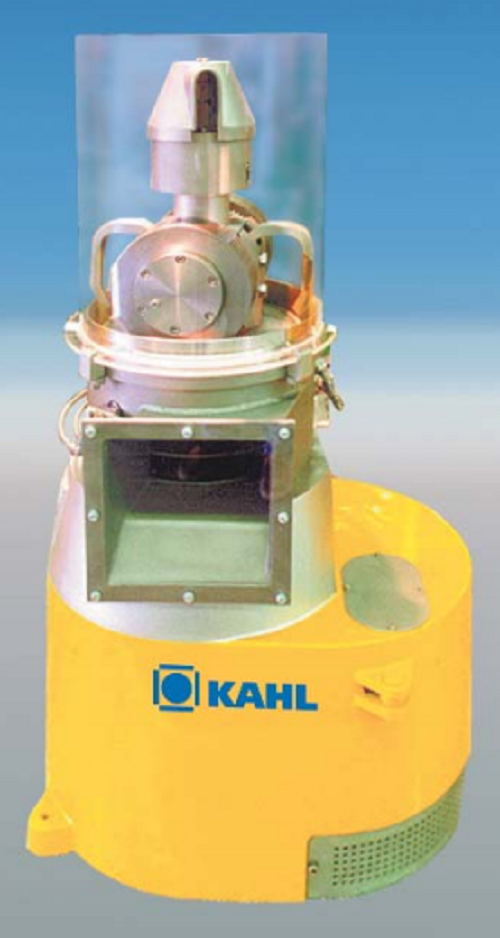
Small scale pelleting press
Many industries require reliable pelletizing equipment with smaller scale production capacities....