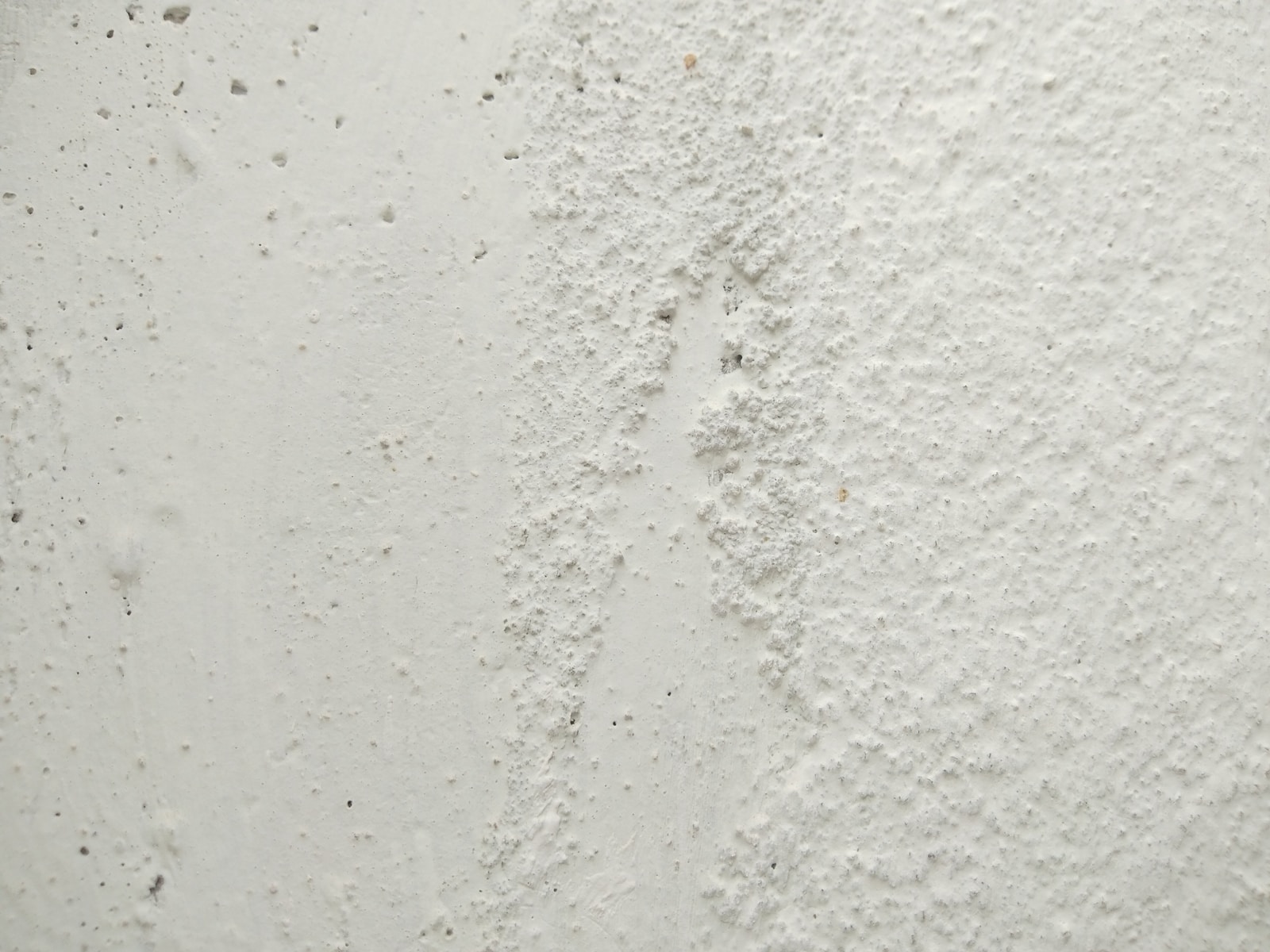
Aluminium Oxide Equipment
Find innovative production technology for making aluminium oxide and connect directly with world-leading specialists
Aluminium oxide or alumina is a naturally occurring compound of aluminium and oxygen made from bauxite, a dull and earthy rock with high aluminium content. Bauxite is the most common ore of aluminium and you can find it in tropical areas Most of the bauxite mined end up producing aluminium with specific aluminium oxide equipment. Statistics have shown that Australia and Guinea have the largest bauxite deposits in the world. Countries like China, Brazil, and India also have a large amount of the rock.
Top production technologie picks
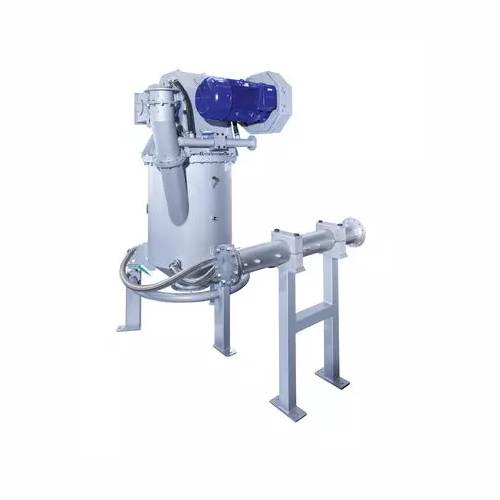
Fluidised bed opposed jet mill for fine particle processing
Achieve precise and consistent particle sizes with high-spee...

Ultra-fine dry grinding mill for glass and ceramics
Achieve ultra-fine particle sizes and energy savings with a dry grind...
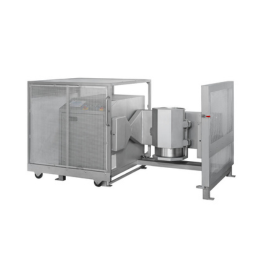
High volume 3D shaker mixer for ceramics
Achieving consistent homogeneity and the logistics of handling and introducing lar...
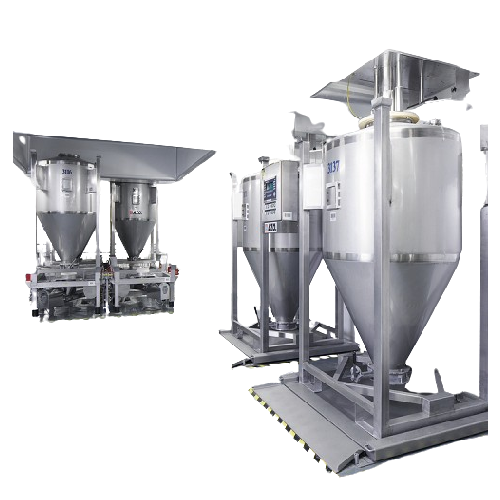
Automated bulk material handling system
Ensure precise batch tracking and efficient handling of challenging bulk materials ...
Tell us about your production challenge
Aluminium oxide equipment, tailored around the unique properties of alumina
The key process in making aluminum oxidee from bauxite is the Bayer process, that dates back to 1888 and crushes and mixes bauxite. The digestion of bauxite involves the use of concentrated sodium hydroxide or caustic soda to make aluminium hydroxide precipitate. To remove water and produce alumina, heat in a kiln at 1000-1200 °C (1832-2192 °F). Aluminum oxide making equipment such as a pneumatic conveying system ensures the passage of the mixture during production. It also makes sure of little or no loss of the mixture powder when passing through the blow-off tanks. It is important to carry out the Bayer process at appropriate conditions to ensure high production yield. Temperature and NaOH concentration, for example, affects the process digestion efficiency.
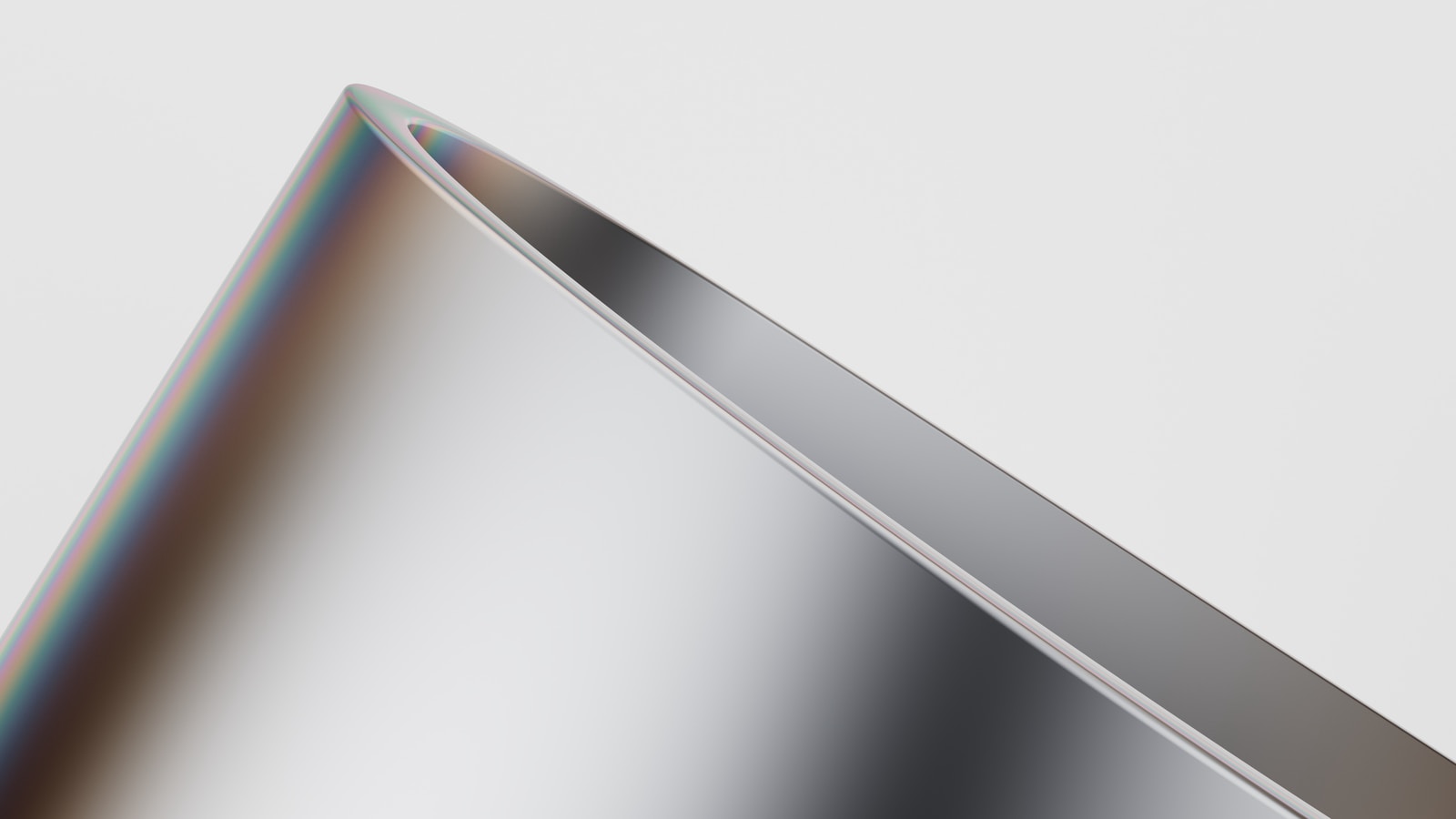
Different applications of aluminium oxide
The downstream process of aluminium oxide may involve further electrolytic reduction into pure aluminium. You may opt to smelt the alumina depending on your project. Despite being the most abundant metal on earth, aluminium does not occur naturally. The key process to making aluminium involves high electric power. This is why it is important to take measures such as using renewable energy sources like hydroelectric power plants to reduce air pollution.
Alumina is versatile and suitable for the chemical and medical industries, protective equipment and other applications. Engineers or manufacturers use aluminium oxide equipment to make alumina for ceramics, refractories, polishes, abrasives, and high temperature appliances like crucibles.
Environmental impact: from bauxite to alumina
The aluminum oxide making, from the extraction process of bauxite to smelting aluminum oxide into pure aluminium, consumes high energy. There is also a high emission of chemicals into the environment during production. Toxic chemicals like carbon and fluorine are released into the atmosphere, land and water, causing acute to severe health issues depending on level of exposure.
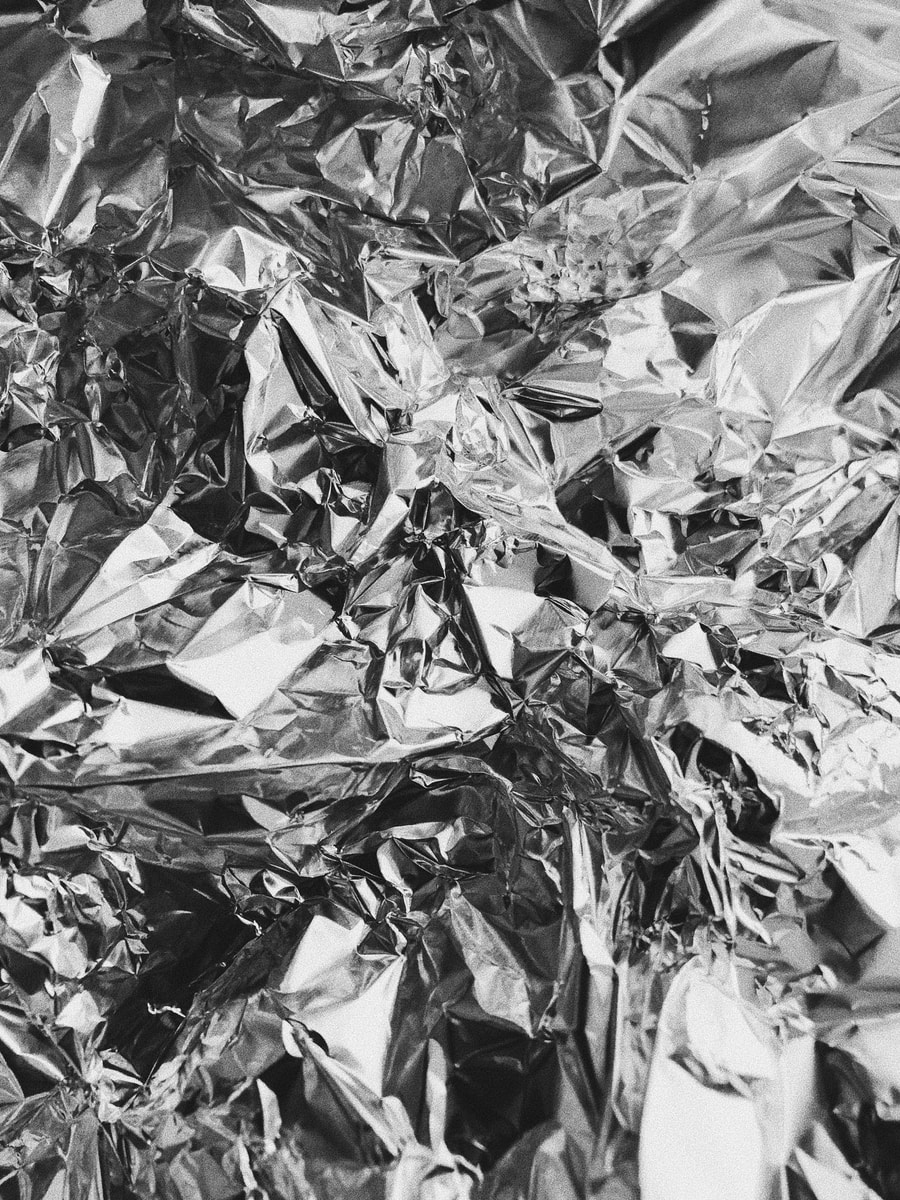
Asides from the adverse effect on humans, environmental pollutants can cause damage to plants, animals and even buildings. Studies have shown that it’s possible to reduce/remove airborne pollutants by condensation and incineration, amongst other methods. To remove pollutants in gases like hydrocarbons, by condensation, convert them to liquid vapour by lowering their temperature and increasing their pressure.
Note that aluminium is considered a “green metal” because of its recyclability. The European Union regulations aim to reduce 55% of greenhouse gases emission by 2030. They intend to achieve this by efficient refining and constant recycling of aluminium. They also encourage aluminium consumption replacement with alternatives such as zirconia instead of aluminium oxide for abrasives.
Which aluminium oxide technology do you need?
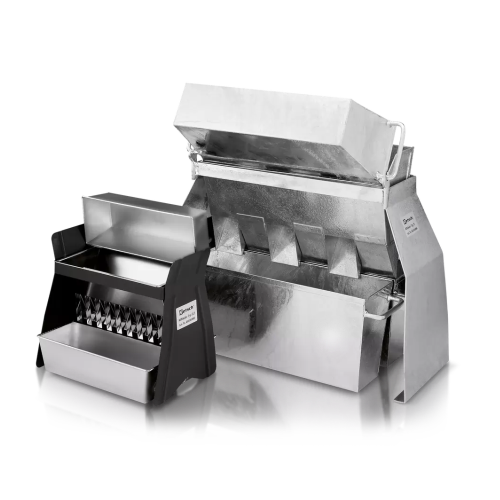
Sample divider for on-site reduction of bulk materials
Ensure consistent sample analysis with precise on-site material di...
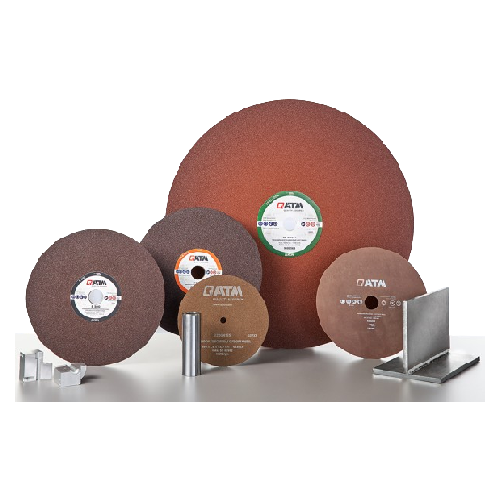
Premium cut-off wheels for metallographic sample preparation
Achieve precise cuts with minimal deformation and temperatu...
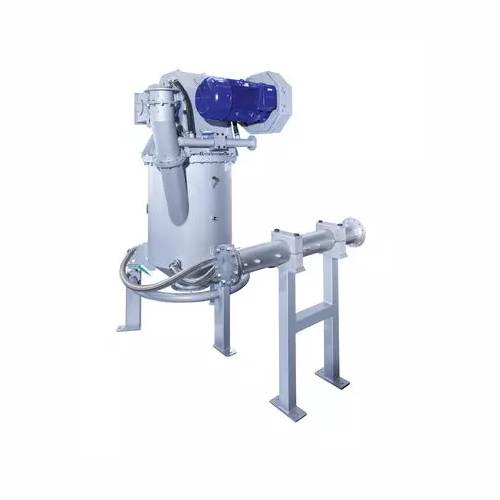
Fluidised bed opposed jet mill for fine particle processing
Achieve precise and consistent particle sizes with high-spee...
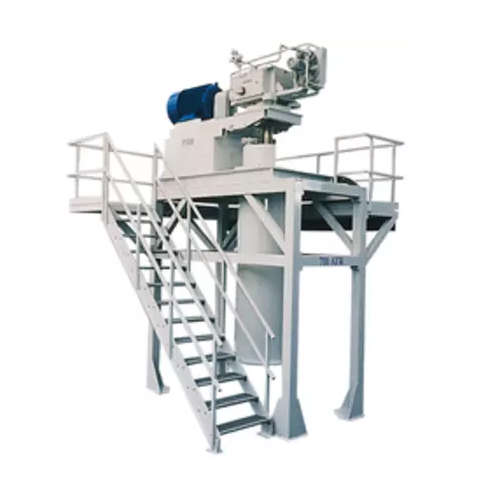
Ultra-fine grinding with ball mills and agitated media mills
Achieve precision in ultra-fine grinding for demanding mate...
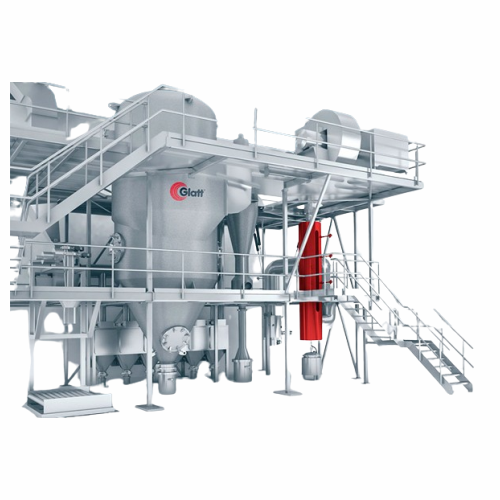
Powder synthesis reactors for nanometer and micrometer particles
Achieve precise particle control and enhance material p...
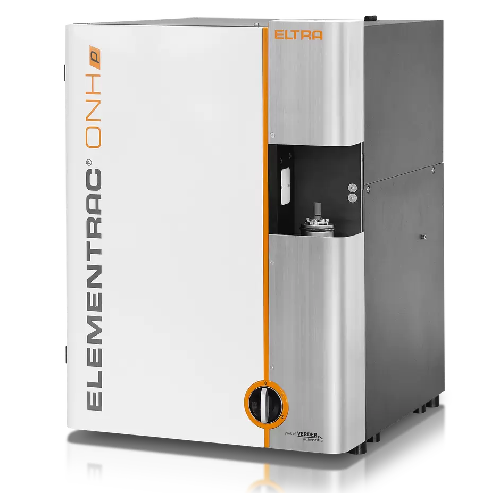
Oxygen / nitrogen / hydrogen analyzers for inorganic samples
Quickly and accurately measure oxygen, nitrogen, and hydrog...
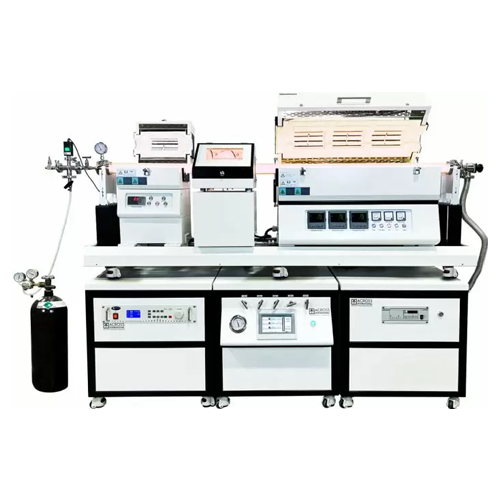
1200°c Pe/cvd furnace for high-temperature material synthesis
Enhance your material processing capabilities with precise...
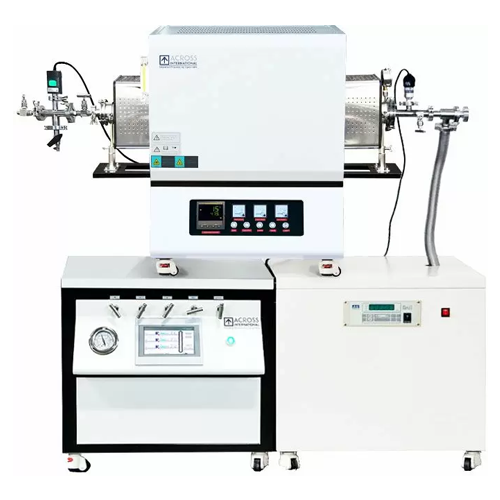
1400°c Cvd tube furnace for advanced material processing
Boost your R&D with a high-temperature 1400°C CVD tube furn...

Multi-flash evaporators for alumina industry
Experience efficient thermal separation with enhanced heat recovery, ideal fo...
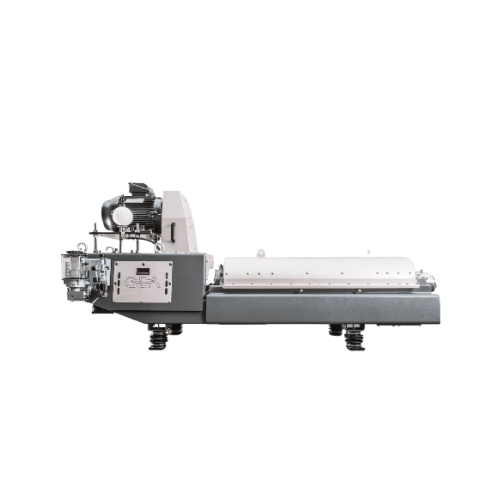
Chemical and mineral processing centrifuge
Optimize your chemical and mineral extraction processes with this high-performa...
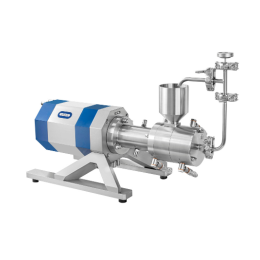
Agitator bead mill for flow chemistry
During the early stages of synthesis, generating only limited product quantities can ...
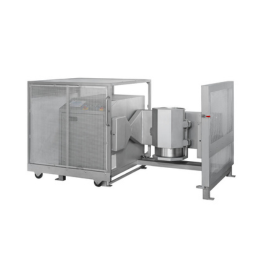
High volume 3D shaker mixer for ceramics
Achieving consistent homogeneity and the logistics of handling and introducing lar...
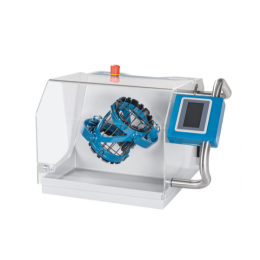
R&D shaker mixer for battery powders and chemicals
Material heterogeneity, agglomeration, and contamination are key param...
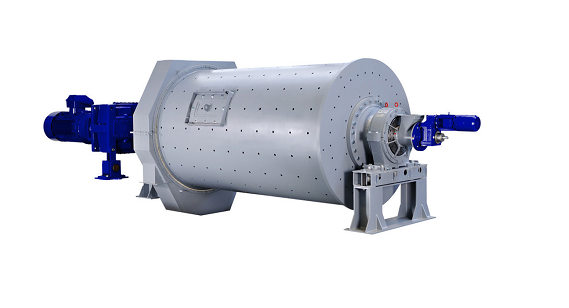
Horizontal rotary ball mill drum
A horizontal rotary ball mill drum can be used for grinding of dry hard materials, such as ...
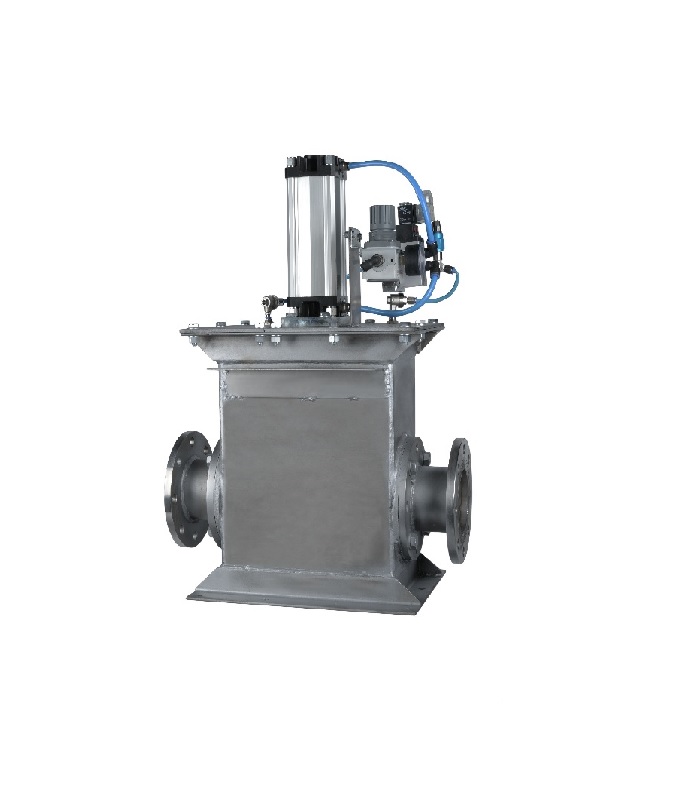
2-way diverter valves for pneumatic conveying
Products conveyed through pneumatic conveyor lines often need to be diverted...
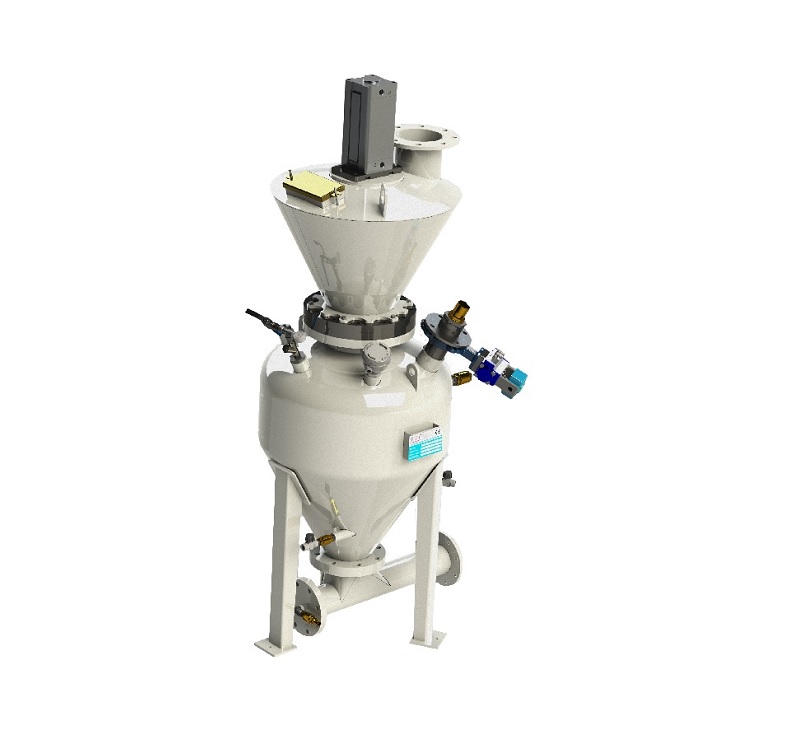
Dense phase conveyor for abrasive materials
Transporting abrasive materials using pneumatic conveyors can cause excessive ...
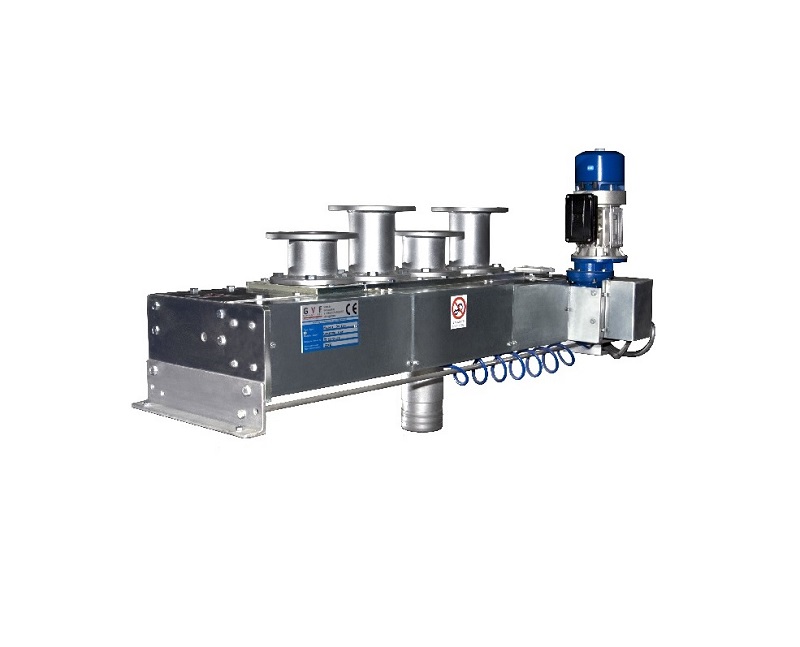
Multi-way diverter valve for pneumatic conveying
Products conveyed through pneumatic conveyor lines often need to be diver...
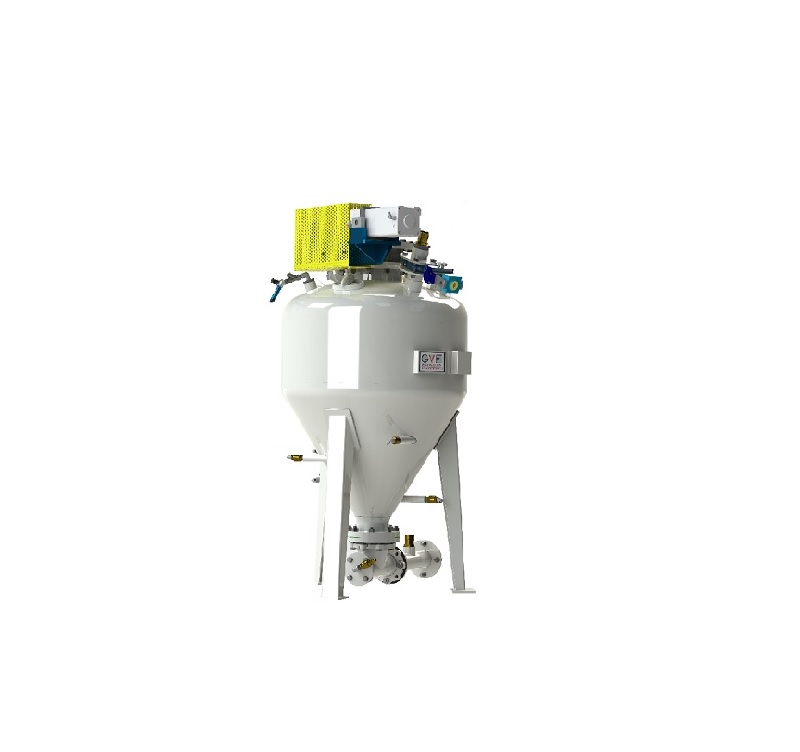
Dense phase conveyor for normal wearing materials
Dense phase pneumatic conveying is used for powders, granules, and grai...
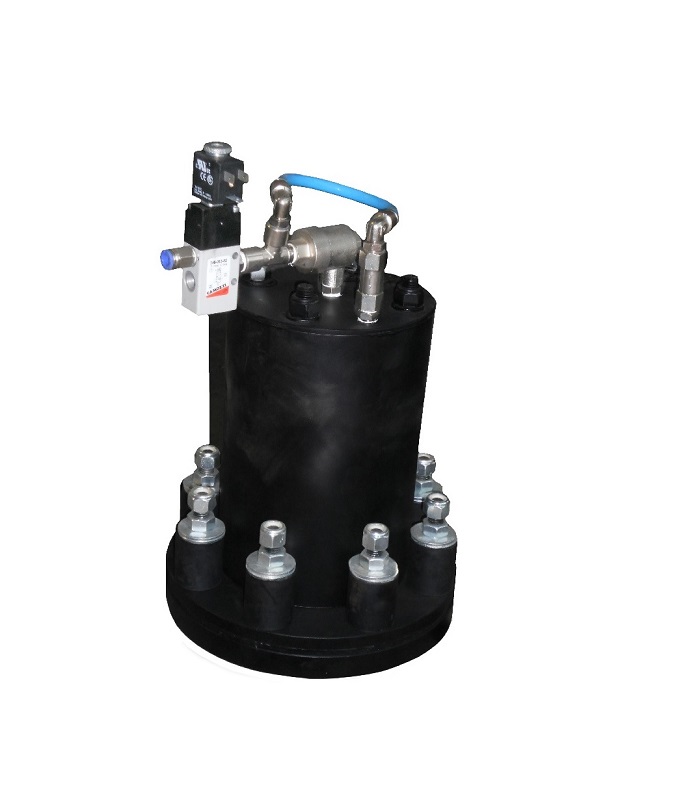
Airshocking hammer
Silos, hoppers, bins, and other containers can build up a layer of powdered product on the internal walls....
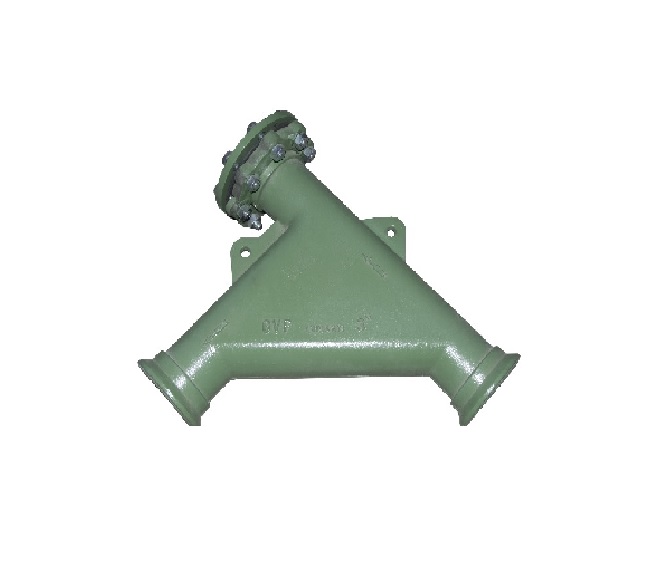
Wear resistant bends for pneumatic conveying
Bends in pneumatic conveyor lines cause load loss leading to lower flow rates...