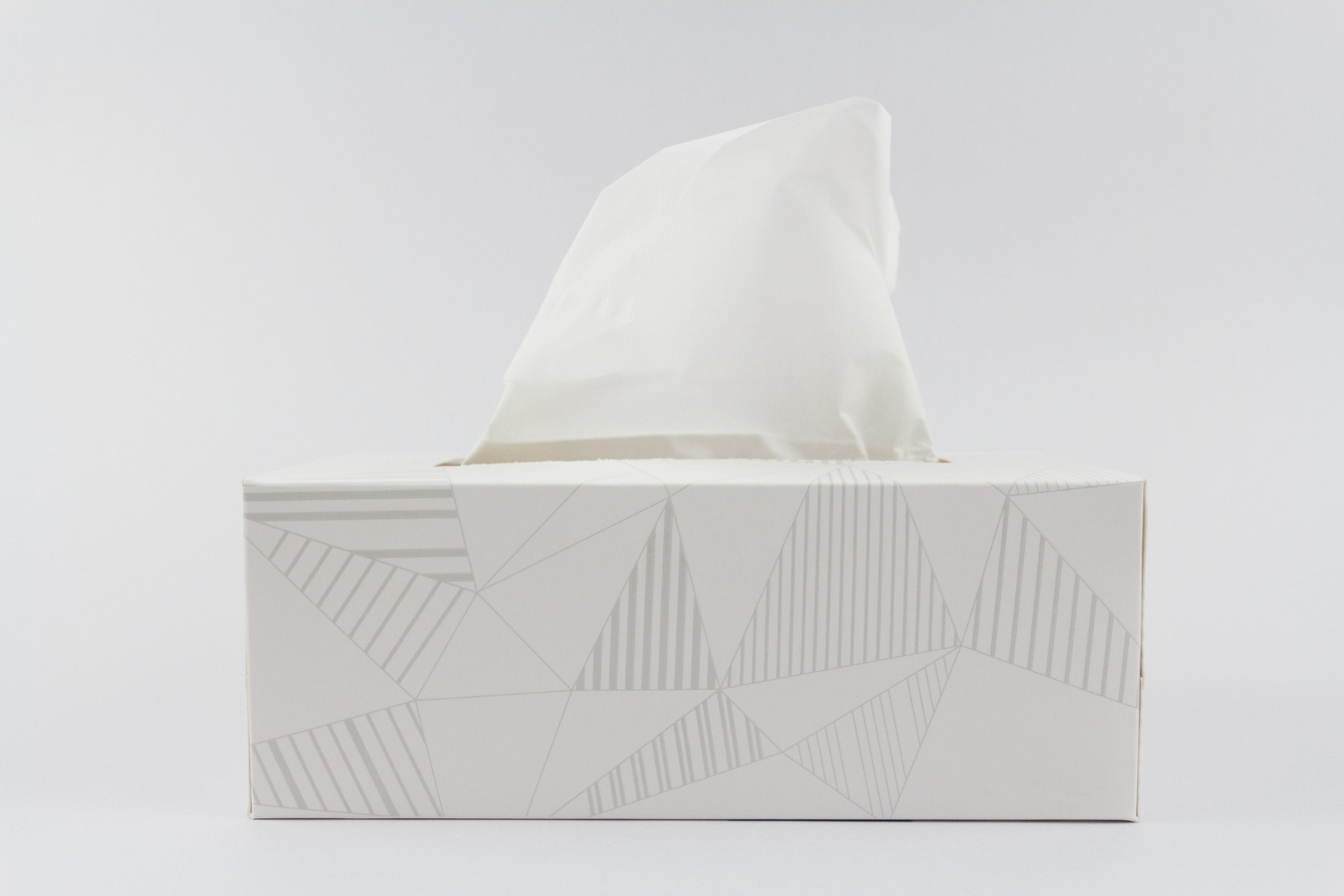
Making Facial Tissues
Find innovative production technology for making facial tissues and connect directly with world-leading specialists
Tissue paper can be traced back to tree fibres. But turning hardwood into soft sheets involves a string of manufacturing processes. Specialized facial tissue making machines adopt industry techniques such as drying and packaging to produce convenient boxes of silky paper.
Tell us about your production challenge
Turn the feedstock into a pulp
The stock material is wood chips or, more frequently, recycled paper. Feed your stock to the pulper, where it will be broken down to its bare elements: the cellulose fibres. Abrasive pulping applies mechanical force, while chemical pulping uses solvents.
The material is then mixed with water to produce the paper pulp. Inject air bubbles to brush the fibers clean of any contaminants.
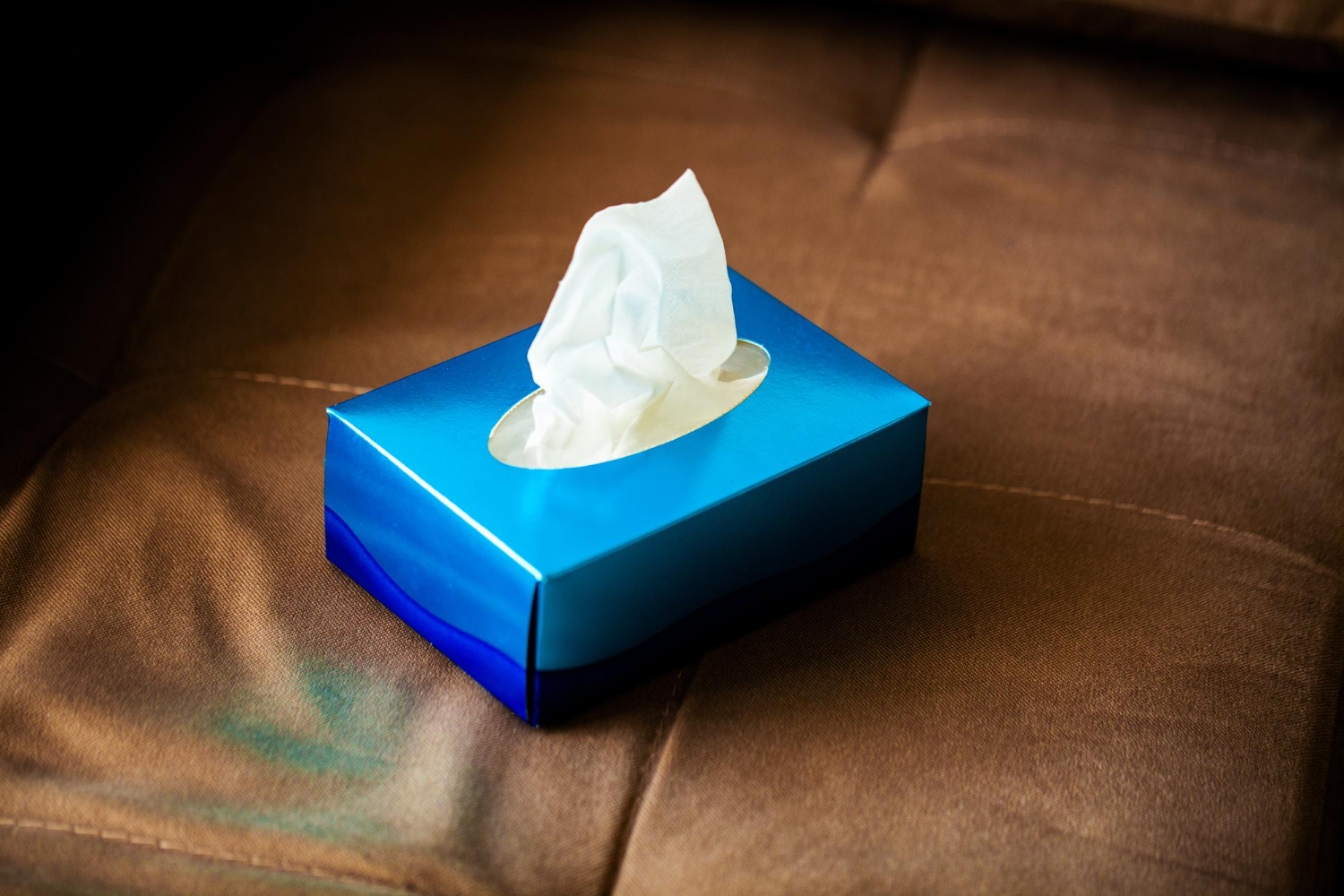
Remove water from the slurry with mechanical force
The water distributes the fibres evenly in the slurry, but once it’s done its job, the pulp must be dewatered. There are two steps to remove the water, first by applying physical pressure and second by drying.
Pump the slurry through a series of rollers to drain out the water. This technique squeezes out enough surface liquid, but the fibres are still wet.
Spread the fibers into a sheet on a screen belt
The water residue after the first dewatering step is vital to distribute the cellulose into a uniform mass. But it still needs to be spread homogeneously. The wet medium finally starts taking shape on a paper machine.
Pump the pulp onto a drying screen belt and pass it through a second line of rollers. This drives out more water and forms the paper mass into a sheet ready for drying.
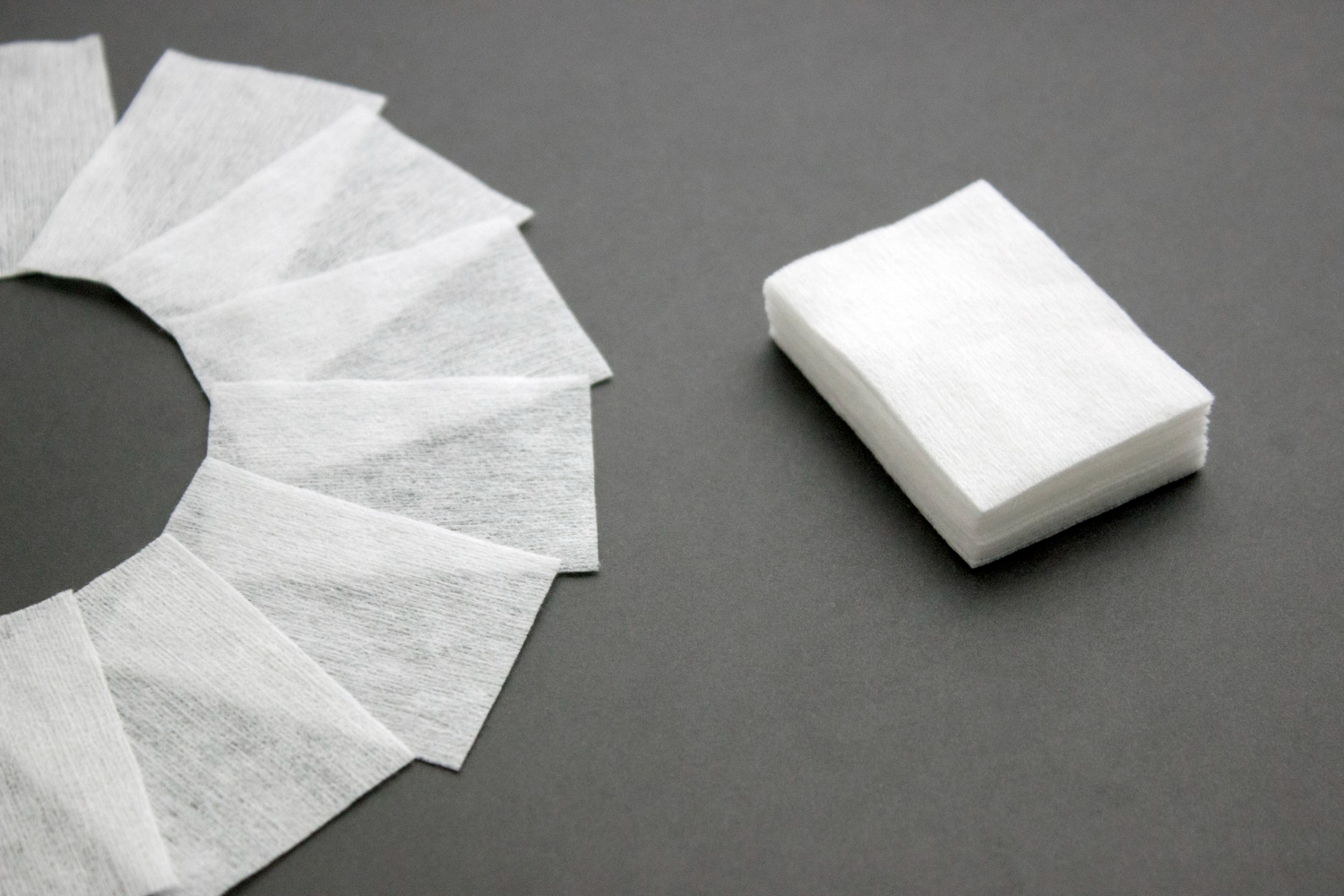
Drying solutions are fundamental facial tissue machine machines
Cellulose fibre is a porous material, trapping water in the mass no matter how hard the rollers press. The drying technique is critical to the quality of the final facial tissue product.
Direct heating risks burning the stock, whereas indirect systems are relatively slow. An alternative technology is superheated steam drying, applying steam to release bound water molecules and vaporize them instantly.
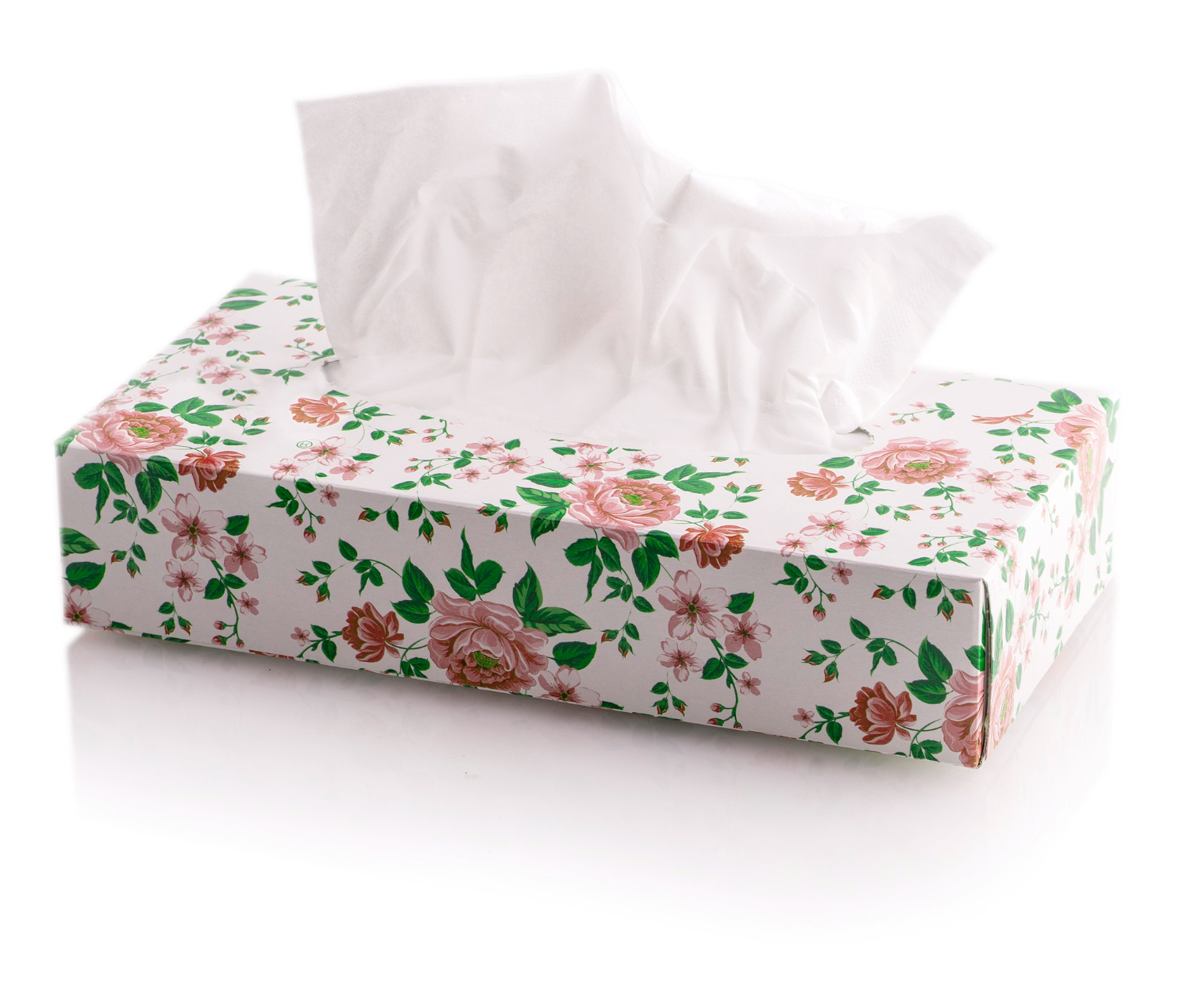
Finish the paper into facial tissue with a converting machine
With the pulp fully dried, the paper is wound into rolls and prepared for finishing. Use a web converting platform to smoothen the paper and remove any creases. A cutting machine shapes the rolls into the final size, so accurate tension control is critical in a converting solution.
This technology is also the key facial tissue making machine if you want to weld multiple plies together, emboss, or coat the paper with lotions or fragrances.
Fold the sheets in a zigzag before loading them in the tissue packing machine
One of the simple conveniences of facial tissue is that there’s always one ready to be picked up from the box. The interleaving technique overlaps the sheets slightly during packaging so that when one is pulled out, it draws the one beneath it.
Pack the interleaved sheets in a plastic sleeve to maintain the compact formation. A tissue cartoning machine then slides the sleeve into the box and seals it closed.
Processing steps involved in facial Tissues making
Which facial tissues technology do you need?
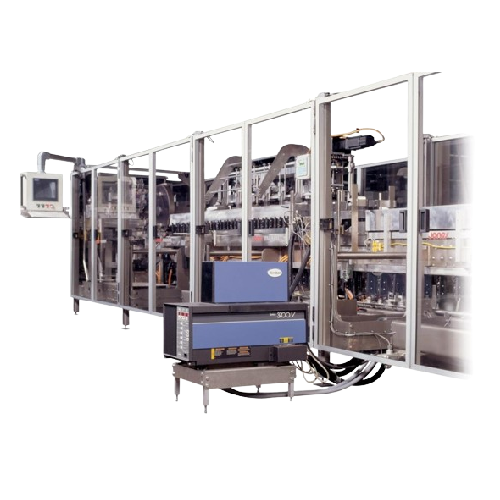
Horizontal end load cartoner for facial tissues
Achieve seamless and efficient cartoning for your tissue products with thi...
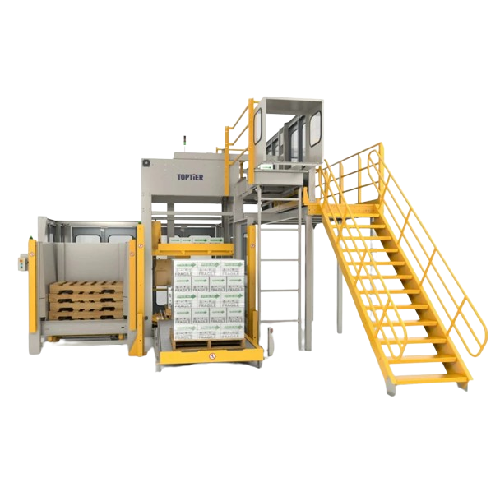
High infeed palletizer for varied product types
Optimize your production line with high infeed palletizers, ensuring seaml...
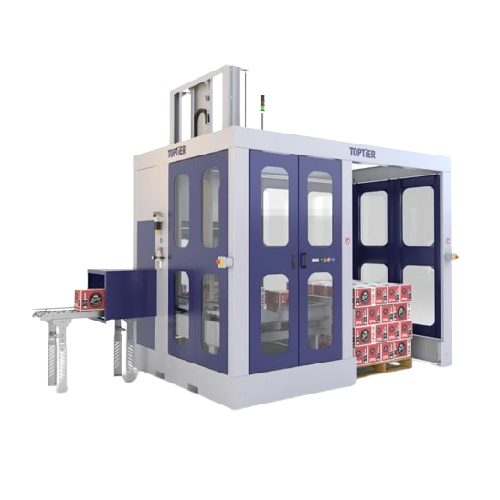
Robotic palletizing solution with smallest footprint
Optimize your production line with a space-efficient robotic palleti...
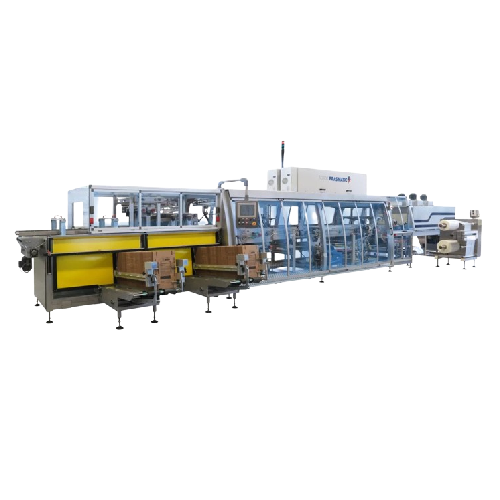
High-speed shrink wrapping for beverage packaging
Optimize end-line packaging with a high-speed solution designed to hand...
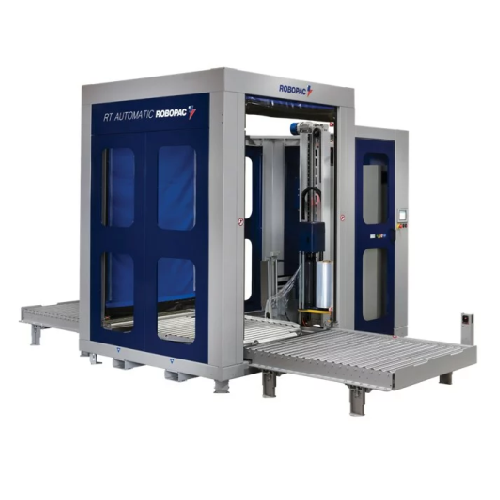
Automatic stretch wrapper for food and beverage industry
Optimize your packaging line with a high-speed stretch wrapper t...
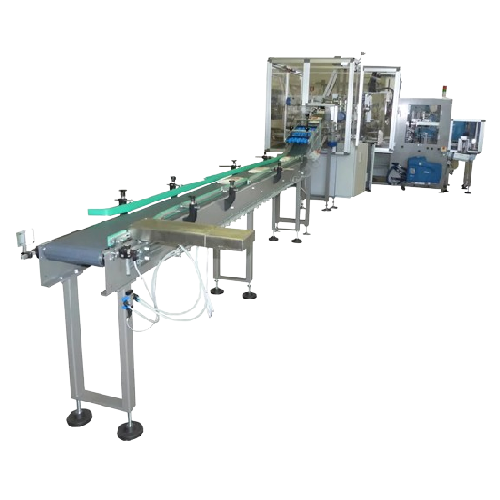
Automatic case packer for soft pillow bags
Streamline your packaging process with a case packer designed to efficiently ha...
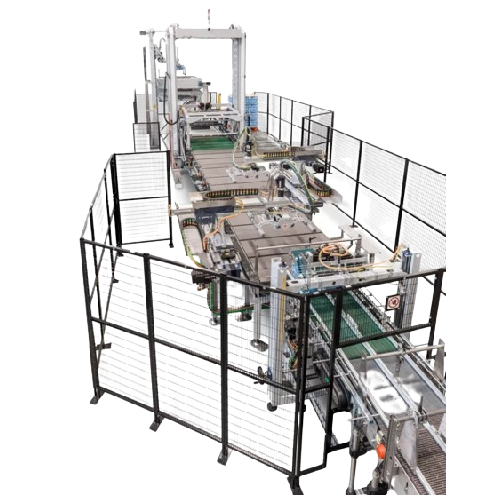
High-speed in-line palletizer for beverage industry
Effortlessly streamline your palletizing processes with a compact, hi...
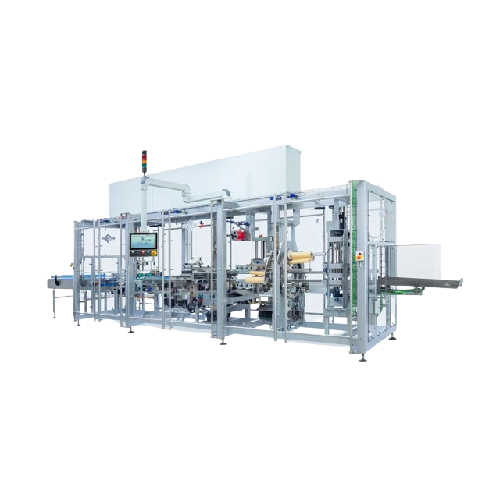
Horizontal stretch-film wrapping system for frozen food
Optimize your packaging line with a high-speed solution that secu...
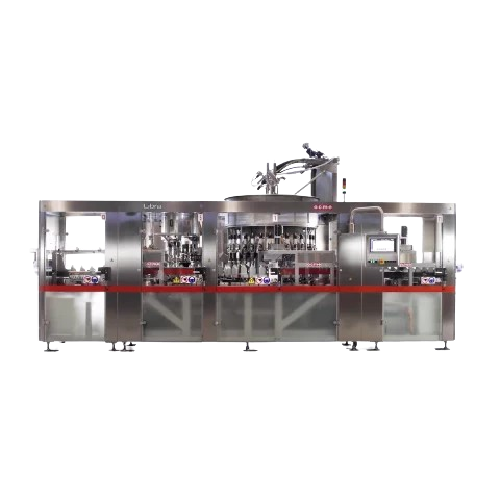
Rotary weight filler for Pet and Hdpe bottles
Enhance your production line with precise weight-based filling, ensuring rap...
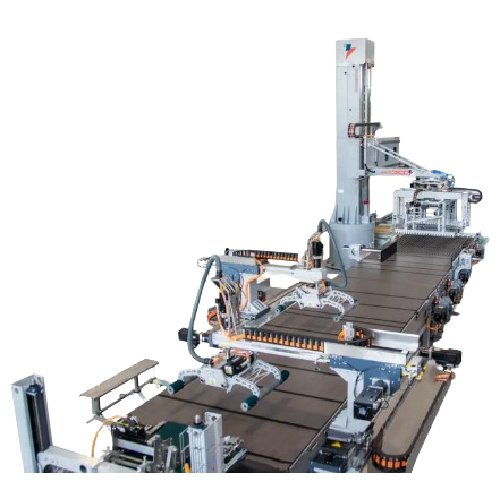
Single-column palletizer for medium to high production
Optimize your production line efficiency with a versatile single-c...
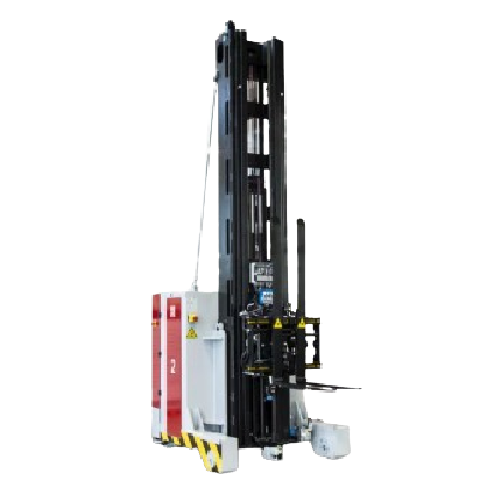
Laser guided vehicle for shuttle management in warehouses
Optimize your warehouse operations with a precision-guided veh...
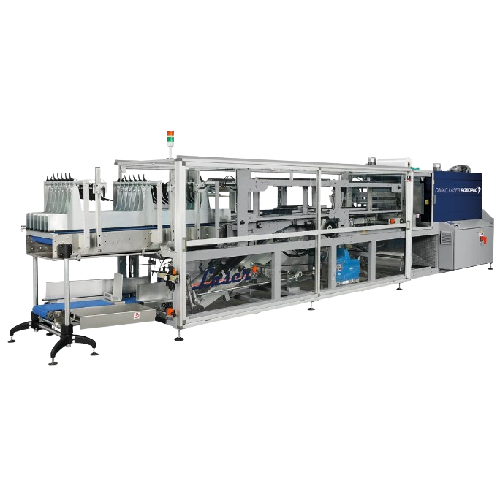
Shrink wrapping solution for low-speed packaging
Achieve seamless low-speed packaging with a shrink wrapping solution desi...
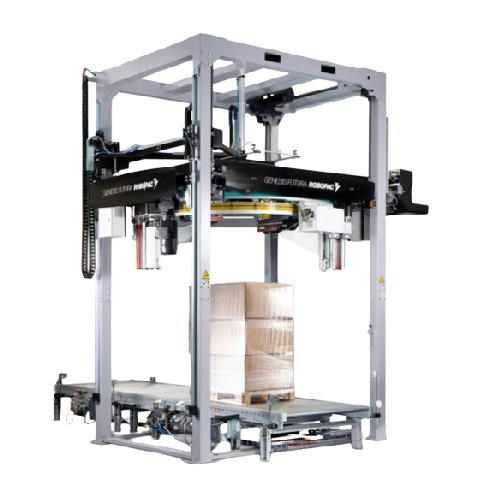
High-speed automatic rotary ring wrapper for stretch wrapping
Optimize your packaging line with a fully automated high-s...
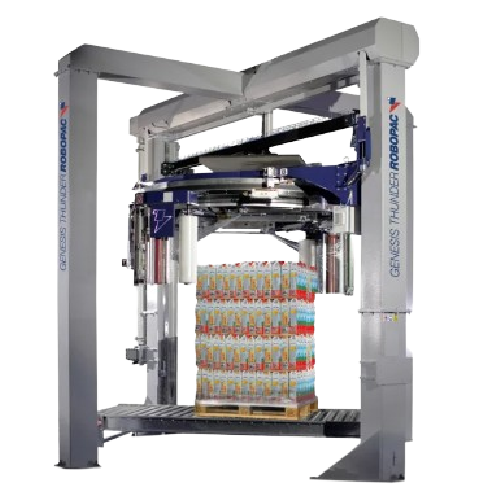
Automatic rotary ring wrapper for high-speed pallet wrapping
Achieve optimal load stability and reduce material usage wi...
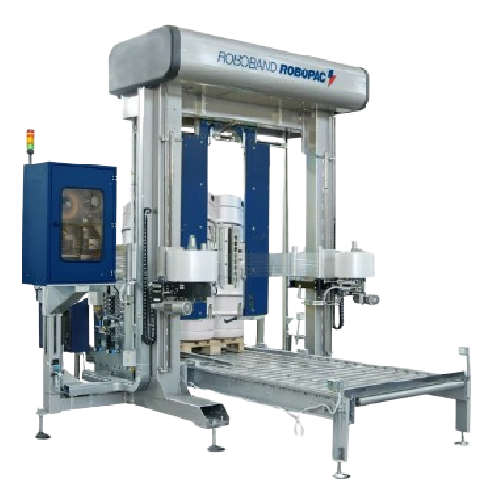
Automatic horizontal banding system for label application
Optimize your end-of-line operations with a high-speed horizon...
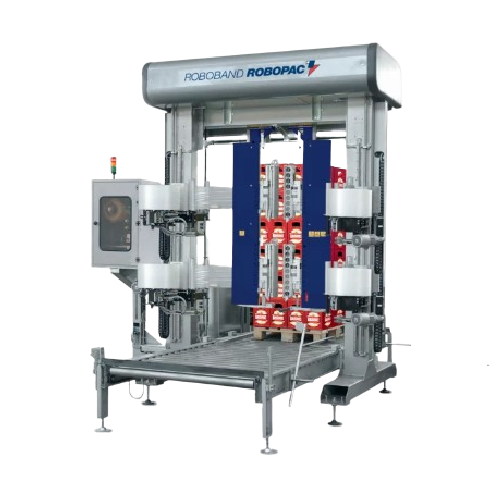
Fully automatic horizontal banding solution for labeling
Optimize your packaging line with a sophisticated banding system...
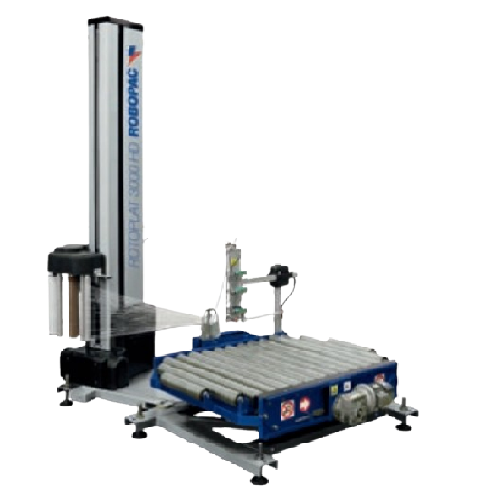
Fully automatic rotating table wrapper for pallet stabilization
Optimize your end-of-line packaging with robust, high-sp...
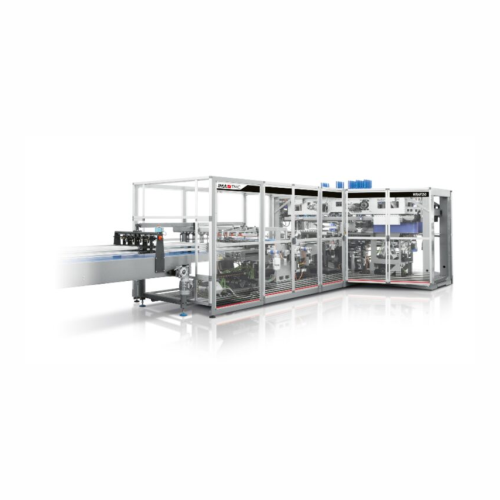
High-speed wrapping solution for tissue rolls
In a dynamic production environment, this high-speed wrapper enhances your o...
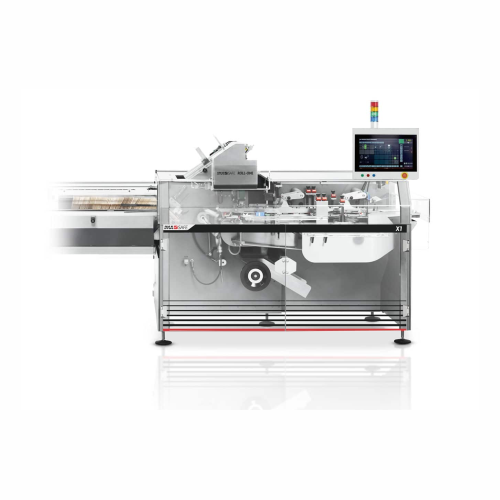
Intermittent motion cartoner for pharma packaging
Streamline your packaging line with versatile cartoning solutions that ...
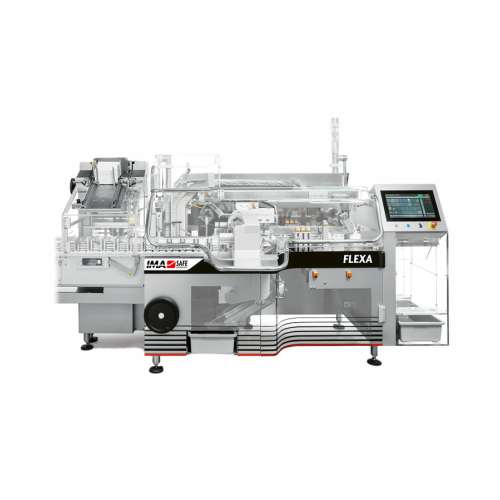
Compact cartoner for pharma packaging needs
Achieve seamless integration in your production line with a cartoning solution...
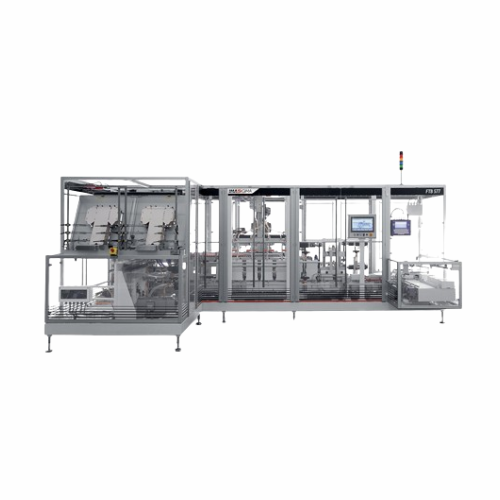
Top loading cartoner for variable box sizes
Achieve precision packaging with a versatile top-loading cartoner that adapts ...
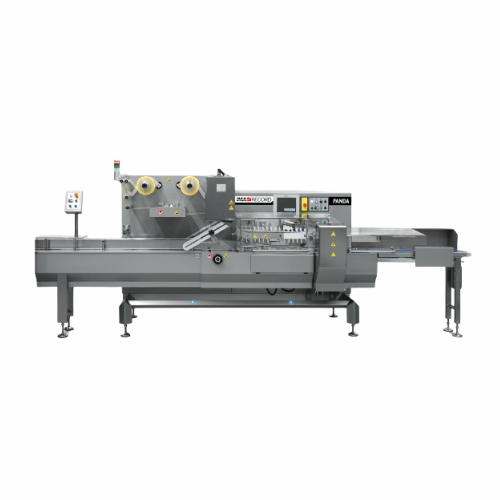
Flexible flow wrapping solution for small and medium products
Enhance your production line with a versatile flow wrappin...

Intermittent motion cartoner for confectionery packaging
For manufacturers needing versatile packaging solutions, this ca...
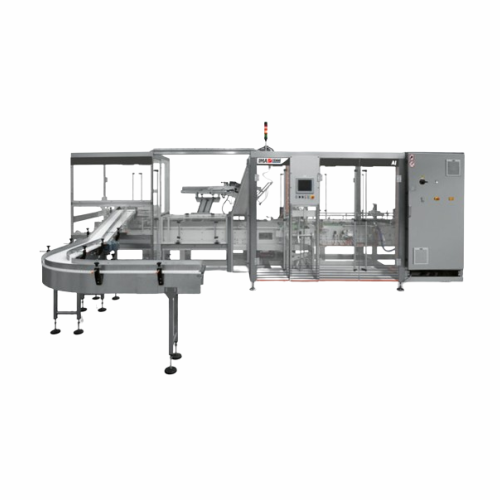
Intermittent cartoner for flexible packaging solutions
Enhance your production line’s efficiency with a versatile c...
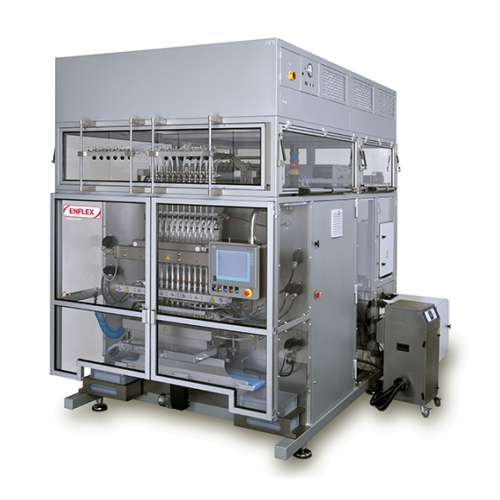
Intermittent stick pack machine for pharma and healthcare
Looking to streamline your packaging operations with high-spee...
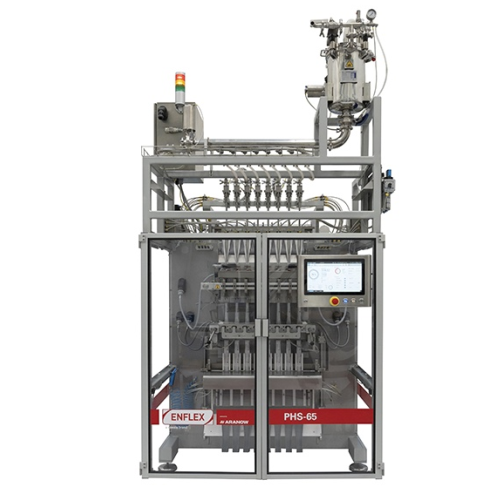
Intermittent stick pack system for pharmaceuticals
Effortlessly streamline your packaging process with a high-speed, mult...
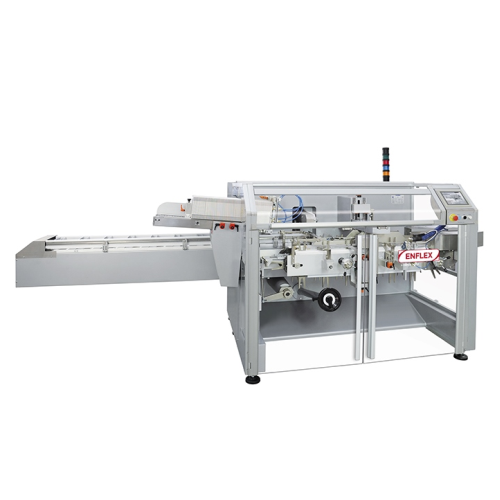
Intermittent side-load cartoner for pouches or stick packs
Optimize your packaging process with an intelligent side-load...
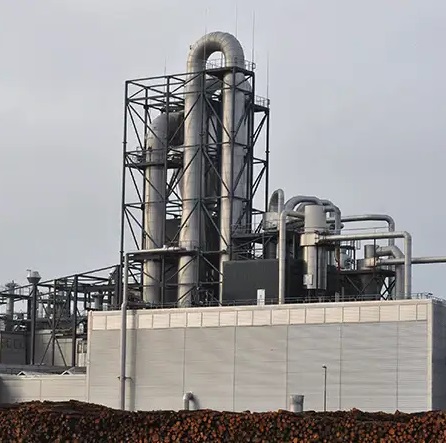
Energy saving vertical steam dryer for paper pulp
Apart from soil and water pollution with cholates, chlorine, and metal ...
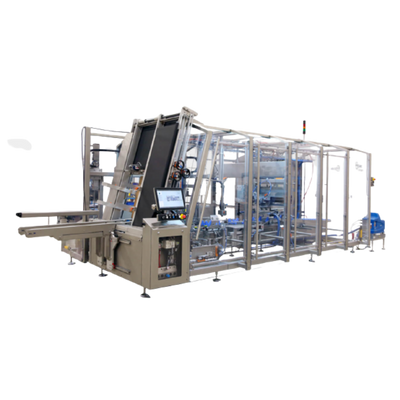
Side Load Case Packer For Facial Tissues
When packing facial tissue boxes into large cases at high speeds, adjustable infee...
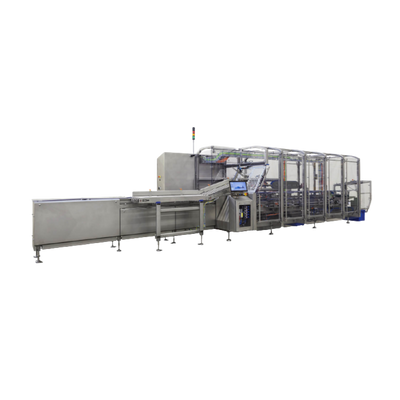
Facial Tissue Box Cartoning Machine
Tissues come in various formats, such as men’s sizes, family boxes, or travel tissue pa...
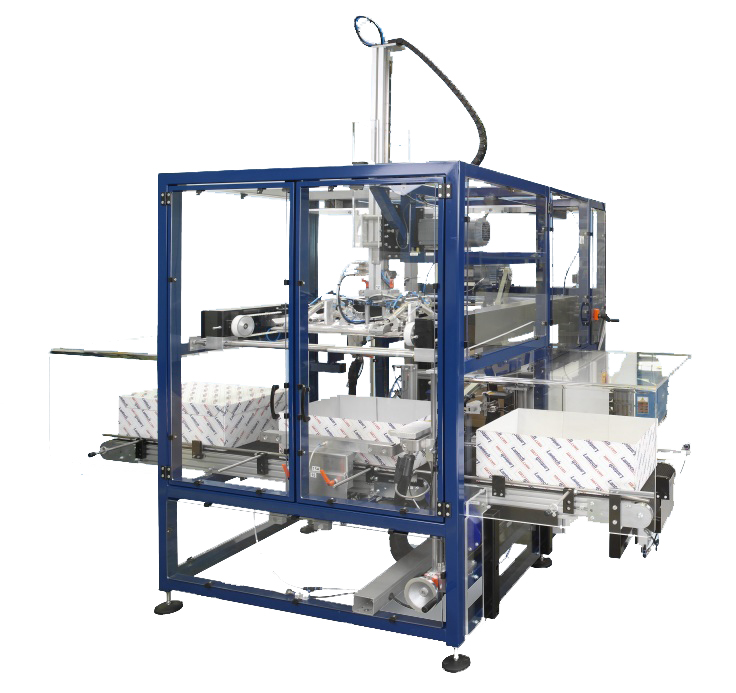
Lid applicator for corrugated cases
For your secondary packaging, you may be considering packing into boxes that require a ...