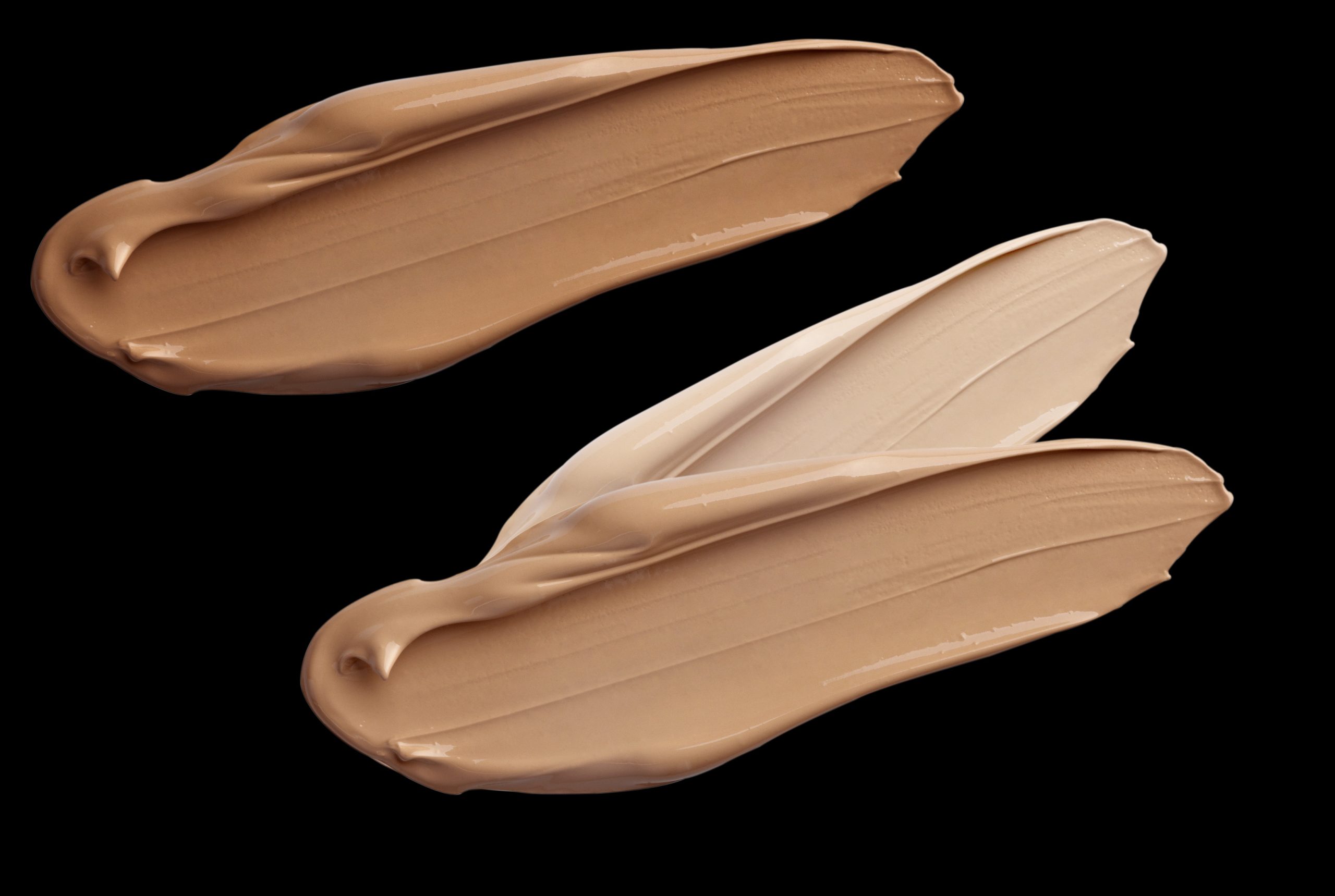
Making Cosmetic Foundation
Find innovative production technology for making cosmetic foundation and connect directly with world-leading specialists
A cosmetic foundation comes in a powder, cream, or liquid form. And did you know that the liquid form came about because women in the 30s and 40s didn't want to wear stockings? So to cover up their legs, they turned to leg makeup, which played an essential role in our liquid foundation formula. The foundation making process involves balancing the oil and water phase interactions during the formulation stage, mixing ingredients, and packaging using a liquid foundation filling machine.
Stories about cosmetic foundation
Tell us about your production challenge
The chemistry of cosmetic foundation
A cosmetic foundation involves a variety of compounds that impart different benefits to it. Coverage pigments like titanium dioxide, zinc oxide, and kaolin are the key ingredients used in a foundation. Filler ingredients like talc, mica, sericite help the primary coverage pigments to spread evenly on the face, making your foundation easier to use.
Colour pigments like red, yellow, and black iron oxides are adjusted in different quantities to create a variety of shades of ivory and beige, to match the color to your skin tone. Binder materials like magnesium stearate or zinc stearate help the foundation stick to your skin.
Instead, light materials like long spreading, wetting lipids, and highlighting or shimmer materials are added to the face powder. In addition to the coverage pigments, filler ingredients, color pigments and binder materials, ingredients like emulsifiers, water, humectant, emollient/silicones, emulsion stabilizers and preservatives are further included in a liquid foundation formula, which may be water in oil/silicone emulsions.
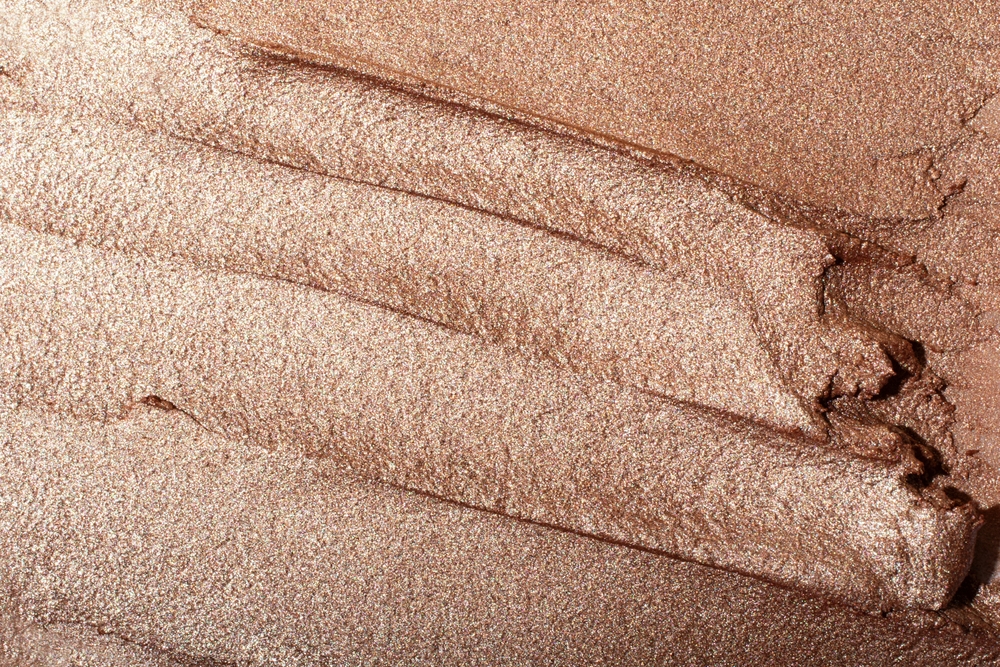
Gentle blending for shimmer materials
Your favorite foundation will generally need some highlighting material to give a variety of shimmer effects like white or bronze pearlescent effects, which add some luster. Shimmer is achieved by mica or other colorants coated, and to retain this shimmer property after mixing, you need to be really gentle on the shimmer powders. If these highlighting powders are put through high shear in the grinding process, the coating will break, and eventually, we will lose all of the pearlescent shimmer and the highlighting effect and luster that we want. So avoid grinding them and only use gentle mixing techniques like dry blending, which ensures homogenous mixing of lipids and shimmer materials by simple stirring.
What gives you the coverage in a foundation?
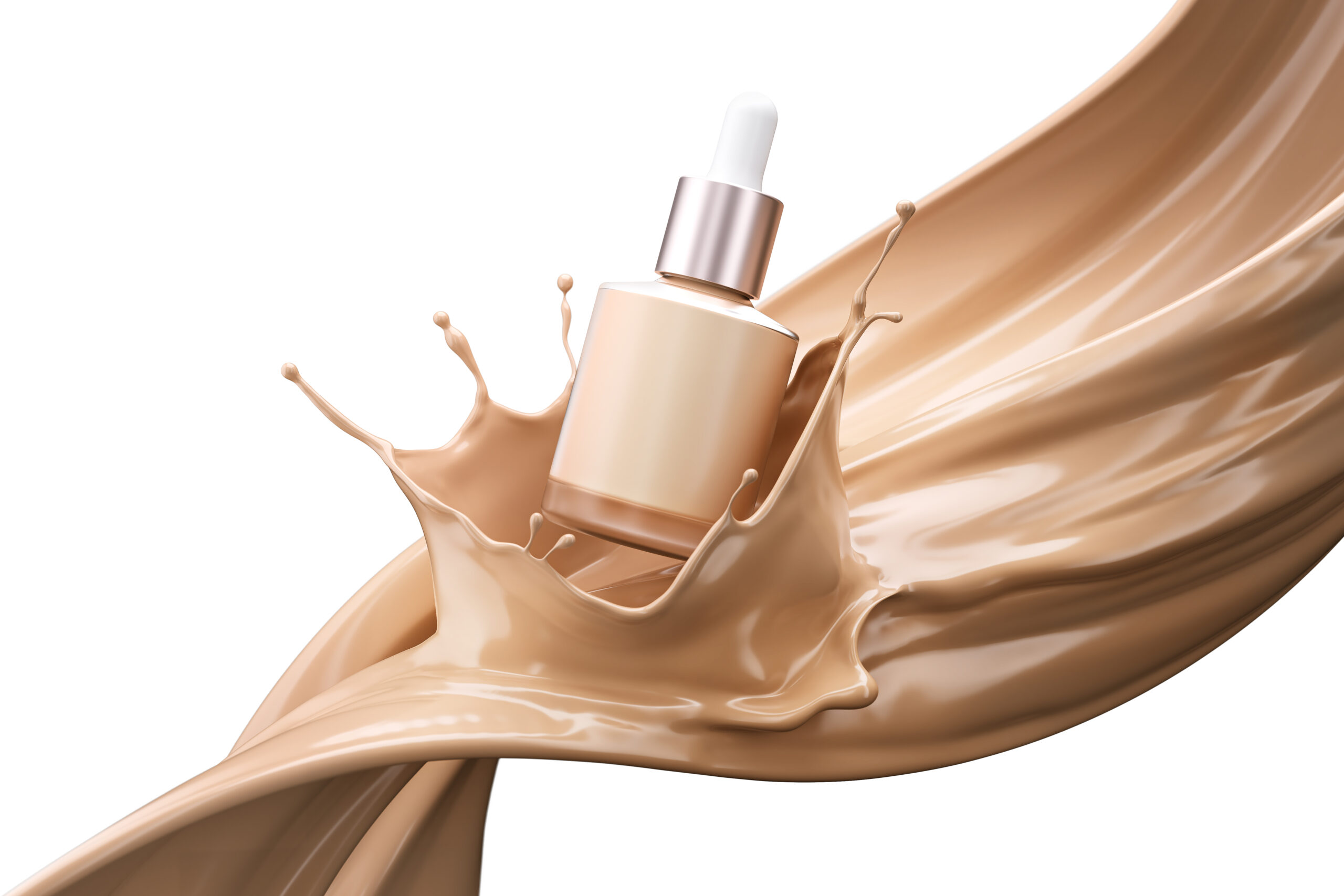
Coverage or opacity in your foundation indicates how much it will conceal on your skin. The opacity is the least in a sheer foundation and the most in a full coverage foundation which arises due to the pigment percentage varying from about 8% up to 35%, respectively. A medium coverage foundation contains about 18–23% pigment. Depending on the opacity or coverage you want in your foundation, the percentage of zinc oxide or titanium dioxide will vary in your formula.
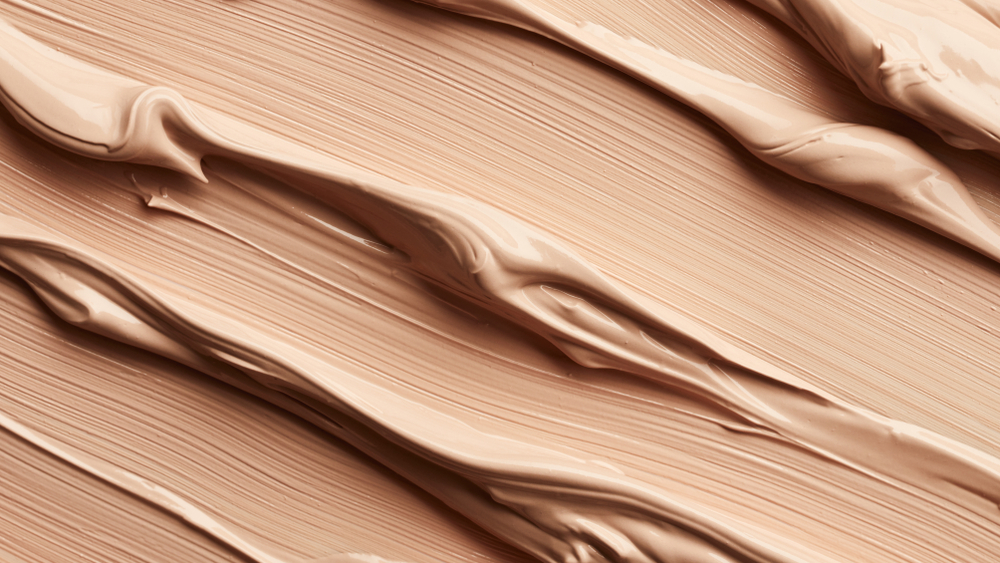
A range of skin tones can be attained with rutile or anatase titanium dioxide, employing the former for more coverage and red, yellow, and black iron oxides. Also, appropriate amounts of the oil phase and humectants are added in high coverage foundations to avoid a dry, cakey appearance. While low coverage formulations commonly necessitate transparent filler ingredients such as talc, silica, nylon, mica or sericite, to prevent the pigment from collecting in pores and creating an uneven appearance.
Bottle it up – What’s the challenge in choosing a liquid foundation filling machine?
The last step of liquid foundation filling is equally challenging as the formulation step, as liquid foundations require emulsion stability while ensuring that the color properly develops and stays uniform throughout the product. Compared to the packaging machines used for powder foundation, the design and selection of packaging equipment and filling lines for a liquid foundation process is more complex due to the challenging factor of the liquid foundation viscosity.
Viscosity is the property that governs the flow behavior of a liquid. It affects the speed with which the liquid travels through the filling lines and is dispensed into the packaging. E.g., a free-flowing product like water with a very low viscosity will flow well through a gravity filler, while products with higher viscosity will need assistance from piston fillers or pump fillers. So the viscosity of the liquid foundation governs the type of product filler used in the liquid foundation filling machine.
Processing steps involved in cosmetic foundation making
Which cosmetic foundation technology do you need?

Automatic tube filling and closing for metal, plastic, and laminate tubes
Enhance your production efficiency with a hi...
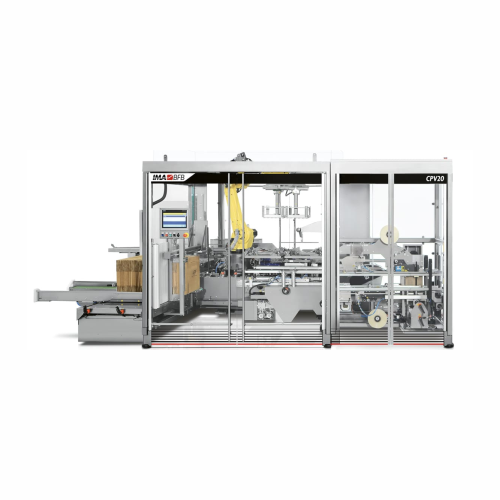
Top-loading case packer for pharmaceutical and cosmetic products
Ensure precision and flexibility in packaging with this...
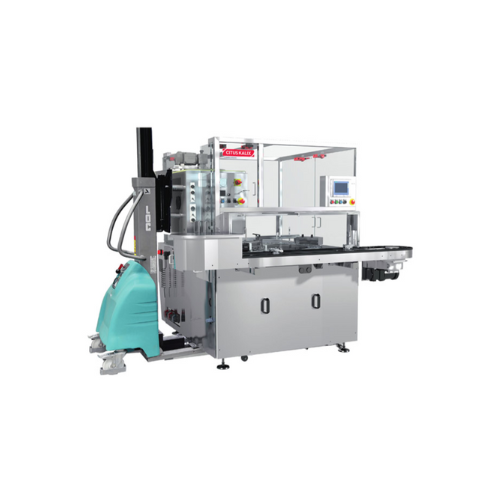
Lipstick moulding solution for cosmetics manufacturing
Streamline lipstick production with high-speed molding and flexibl...

Laboratory and pilot plant horizontal bead mill
Achieve precision milling with minimal product waste, ensuring consistent ...
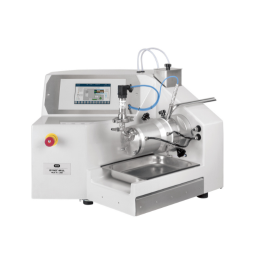
Flexible R&D wet agitator mill for cosmetics
Using nanoparticles in cosmetics requires precise control over material break...
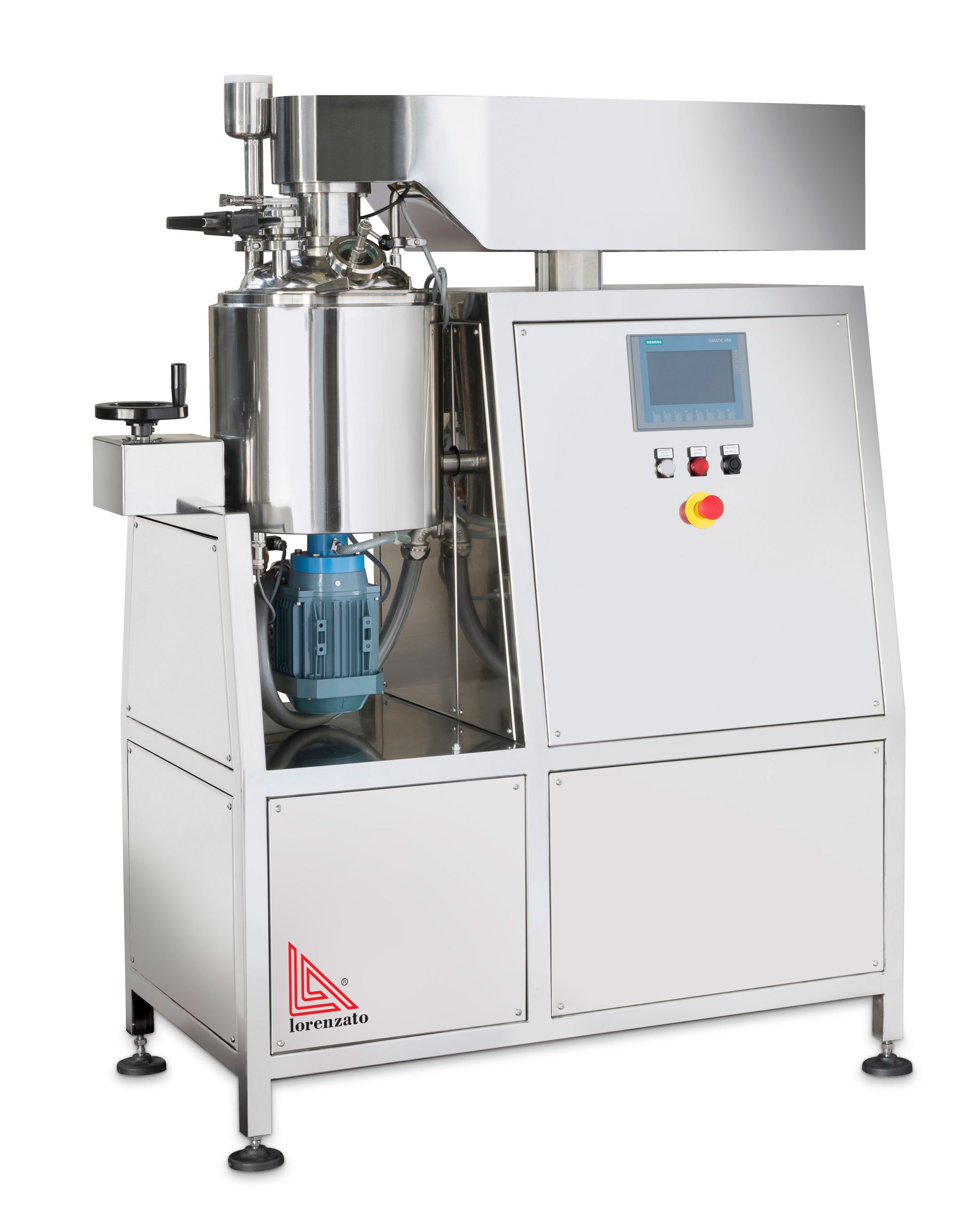
Emulsifier for cosmetic creams
The process of making cream and lotion involves mixing of water phase and oil phase to create...
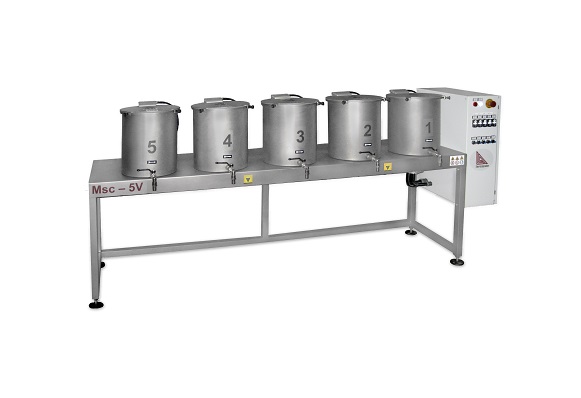
Mixing tanks for liquid cosmetic products
When producing liquid solutions for cosmetics, such as eyeshadow, it’s vital to ...
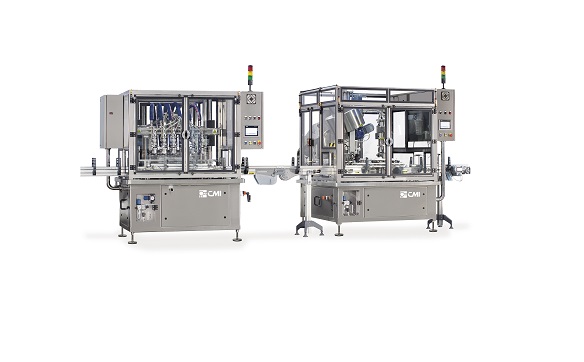
Filling machine for creams
Liquid cosmetics have particular requirements when it comes to filling and capping containers. Mo...