Dilution system for two or more liquids in one pass
Onsite dilution of liquid process ingredients has historically been associated with several issues that limit its economic benefits. Manufacturers need equipment that can easily dilute liquids with a wide variety of characteristics while avoiding many of the common issues. They need a quick process, a small required equipment foot print, and a resultant mix that is homogeneous and free of air.
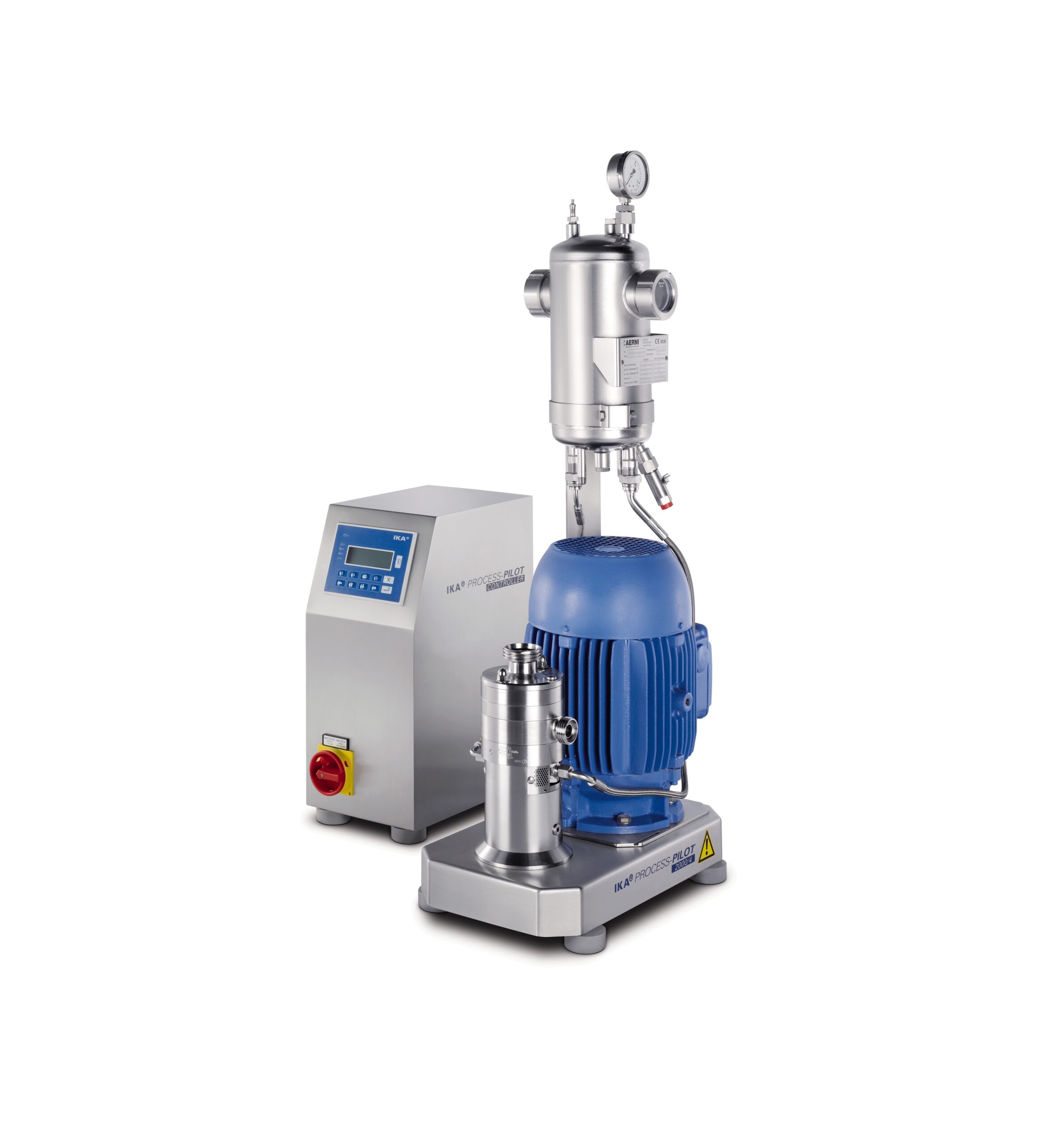
Rapid, accurate closed system dilution
IKA’s DPV Dilution Plant is a completely closed dilution system for combining two or more liquids in a controlled proportion. The closed system eliminates the need for large storage and mixing vessels common to traditional dilution methods and also eliminates the introduction of air and resultant generation of foam. Inputs with a wide range of viscosities and concentrations are easily processed.
The core of the unit is a single stage in-line dispersing unit and metered pumps specially designed for high accuracy delivery. A full array of sensors and feedback is also available and optionally utilized for automation of the system. The components to be mixed are only in contact with each-other immediately before dispersion which avoids any unwanted reactions or lump-formation. Capacities are available from 3.000 to 15.000 liters per hour.
Benefits
- Considerable time saving due to mixture production with one pass
- Homogeneous and truly lump-free results as well as constant dispersion quality
- No foam formation--the fully closed system eliminates air inclusions
- Extremely small footprint compared to conventional mixing and storage vessels
- Readily used with highly variable input material viscosities and concentrations