Wet milling: The revolution in the API production
In the pharmaceutical industry, change often moves at a snail’s pace due to stringent regulations, but it does happen.
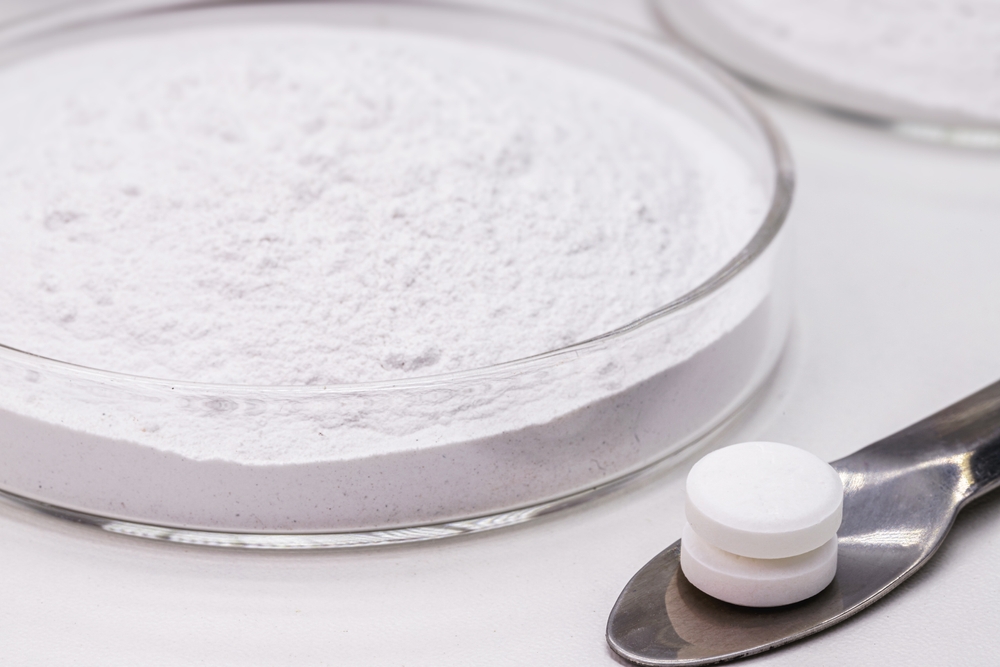
Traditionally, API manufacturers relied on the dry milling process, which begins with crystallization or precipitation within a liquid medium, where crystals form and grow. These crystals are separated using a centrifuge, dried, and finally subjected to dry milling before tableting.
As APIs became more potent, dry handling became problematic due to dust generation, causing cleaning issues and product loss. Furthermore, stricter ATEX regulations for handling hazardous powders have expedited the demand for change.
It’s not as simple as just mixing dry ingredients together, and voila, you have your API. APIs are always, and I mean always, synthesized within a liquid medium to form solid crystals. If liquid is always a part of the equation, why not control the growth of those crystals already in the crystallization step?
And this is where wet milling came into play. This approach allows early particle size control during precipitation, enhancing pharmaceutical manufacturers’ control over the API’s final particle size and distribution.
“The value of an idea lies in the using of it.” – The benefit of early particle size reduction
We had a chance to speak with Werner Kanzinger, IKA Vice President, one of the first to use wet milling for API production. Creating new pharmaceuticals requires starting from scratch and developing principles in the R&D world. To address this need, IKA introduced an innovative three-stage inline dispersing technology called the Magic Lab.
“We knocked on every door in the R&D world and were surprised how the technology was well-received. The industry recognized its potential to simplify production through early-stage particle size reduction,” Werner explains.
According to Werner: “Even at a half-liter batch, APIs are very valuable and pricey. As production scales up to 1000 liters per batch, the cost can be over 1 million, and nobody wants to take any risk.”
To serve the industry across diverse production scales, IKA replicated Magic Lab’s success on a larger scale, ensuring consistent milling outcomes without compromising quality.
No dust, no fuss – Wet milling is here to simplify your life by shortening your production time
In dry milling, solid materials undergo high-speed impact and shearing forces, generating airborne dust particles. This dust settles on equipment, necessitating extensive cleaning to prevent cross-contamination.
“A wet mill is already designed to create a high-turbulence environment, which helps with dust reduction,” Werner continues.
Additionally, wet mills are easier to clean than dry mills due to their smaller and less complex internals, requiring less time and effort. Operating already during the crystallization step, wet milling allows for localized energy application. This reduces energy consumption compared to drum mills.
“IKA three-stage inline technology allows for complete drainage after use. The product flows from the top to the bottom through a three-stage rotor-stator, progressively reducing particle size from coarse to fine. Since it’s vertically installed, no product remains inside, making cleaning straightforward,” Werner concludes.
Just remember, it is better to move forward at a snail’s pace than backward at any pace.