Confectionery rework tempering solution
Improve confectionery production efficiency by integrating a compact rework tempering solution that minimizes waste and optimizes resource use, ensuring high-quality output with enhanced batch traceability.
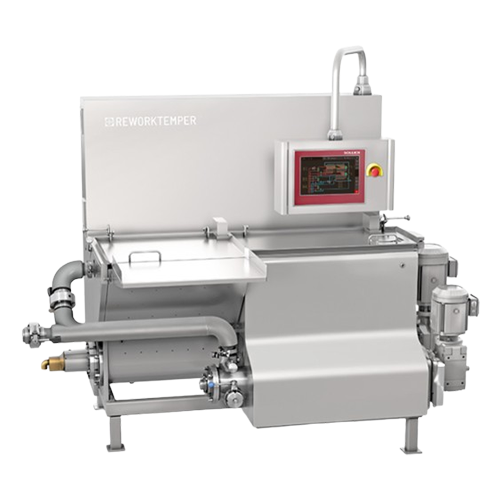
Melts and Tempers Reworked Confectionery Ingredients
The Reworktemper RWT from Sollich is a compact yet powerful machine designed for confectionery manufacturers seeking efficient solutions for reprocessing chocolate and confectionery materials. This integrated melting and tempering unit consolidates two critical processes, enhancing production efficiency and reducing waste. It operates by directly processing rework materials, including those with added ingredients, without the need for intermediate storage, thus streamlining the workflow.
Capable of handling capacities of 125 kg/h, 250 kg/h, and 400 kg/h, the RWT series offers flexible production capabilities for varied operational scales. Its design emphasizes quick process times and improved batch traceability, crucial for maintaining quality standards in confectionery products like milk chocolate bars, pralines, and granola bars.
Automation is at the core of the Reworktemper RWT, equipped with advanced control systems to integrate smoothly into high-speed production lines. It optimizes energy usage and material handling, contributing to sustainable manufacturing practices. Its robust construction ensures durability, with materials designed to withstand the rigorous demands of continuous food processing environments.
The machine’s ease of cleaning and maintenance is supplemented by compatibility with CIP (clean-in-place) systems, minimizing downtime and ensuring hygienic operations. Sollich also provides comprehensive customization and engineering support, allowing you to tailor the unit precisely to your operational needs.
Benefits
- Minimizes production waste by efficiently processing rework materials.
- Enhances batch traceability, aiding in quality control and compliance.
- Seamlessly integrates into existing production lines for optimized workflow.
- Reduces operational labor with automated, continuous processing.
- Supports sustainable practices by optimizing energy and resource utilization.
- Applications
- Biscuits, Dragees, Pralines, Confectionery, Brittles, Fruit bars, Chocolate products, Cereal bars, Sweets, Candy bars, Ice cream, Protein bars
- End products
- Granola bars, Dark chocolate pralines, Nougat candies, Caramelized biscuits, Almond brittles, Vanilla ice cream, Mixed fruit cereal bars, Peanut caramel protein bars, Chocolate nuggets, Cereal pralines, Chocolate-coated dragees, Milk chocolate bars, Chocolate-coated nuts, Peanut brittle bars
- Steps before
- Grinding, Mixing, Melting, Decrystallization
- Steps after
- Packing, Enrobing, Cooling, Decorating
- Input ingredients
- rework materials, confectionery ingredients
- Output ingredients
- tempered chocolate, processed rework, minimized production waste
- Market info
- Sollich is known for manufacturing engineered-to-order equipment for the confectionery industry, particularly chocolate processing and enrobing machines. They have a strong reputation for innovation, quality, and tailored solutions to meet specific customer requirements.
- Capacity
- 125–400 kg/h
- Process Type
- Melting and tempering
- Integration
- Direct rework processing
- Footprint
- Compact design
- Batch traceability
- Improved
- Waste Minimization
- Yes
- Process Efficiency
- Time optimized
- Energy Efficiency
- Sustainable
- Automation
- Automated process
- Handling
- Direct with ingredients
- Automation level
- Manual / PLC / SCADA
- Batch vs. continuous operation
- Batch / Inline Continuous
- CIP/SIP
- CIP 121°C / SIP 135°C
- Cleaning method
- CIP / Manual
- Energy efficiency
- 0.5–2 kWh/kg moisture
- Density/particle size
- 0.5–2.5 g/cm³ / 50–1000 µm
- Compact footprint
- Yes
- Combined melting and tempering unit
- Yes
- Batched Process Integration
- Yes
- Control panel type
- HMI
- Integration possibilities
- Seamless integration with existing production lines
- Compact footprint
- Yes
- Customization of batch size
- 125 kg/h, 250 kg/h, 400 kg/h