High speed can seamer
Tin plate thickness for cans has gradually reduced over the years, which makes it a hassle to use new cans on old can seamers. This forces operators to keep lower chuck pressure and slow down the machine to avoid chuck slippage.
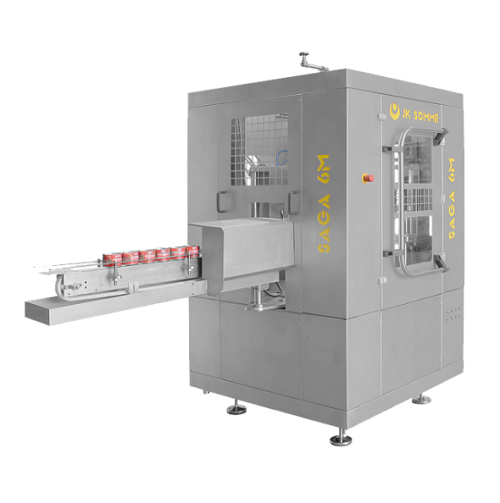
Reducing slippage problems by using gear driven lower lifters
The SAGA M series (consisting of three machines, available with 4, 6 or 8 spindles) by JK Somme has gear driven lower lifters, allowing to seam thinner metal thickness at higher speeds. Gear driven lower lifters result in an increased capacity of seamed cans per minute and it reduces the slipping of the seaming chuck.
The machine will seam cans with pet food, sliced mango, almond paste or a wide range of other canned products. Seaming with this series can be executed atmospheric, with steam vacuum, undercover gassing, liquid nitrogen dosing or clinching. A filled can made of tinplate or aluminum is placed on a belt and lifted up. During a compression stage, force is provided to hold the can that is being sealed against the seamer chuck. The can is then fed to the first roller while the chuck keeps the lid attached to the can while the seamer turntable moves the can upwards towards the chuck. Vacuum sealing machines suck oxygen from the can and put nitrogen gas in before resuming the sealing process. After this, the lid is put on the can and double seamed by the two rollers. The first roller folds the lids curl towards the flange of the can. The second roller tightens the sealing by compressing the hooks of the lid and the flange of the can.
The machine can handle round cans up to a 99 mm diameter, with heights up to 120 mm. Changing to another can shape is quite fast and can be done manually by unscrewing three main bolts and rotating a pinion located on the roof of the machine, which will move the complete seaming turret as well as the lid feeder till it reaches the desired height. Of the three machines, the 4M can seam up to 300 cans per minute, the 6M will do up to 450 can per minute and the 8M will go up to 600 cans per minute.
Benefits
- Versatility in can size
- Increased seam integrity
- Reduction in spring pressure, eliminating mushroom flanges