Unpacking the world of stick pack cartoning
Its complexity begins with the term itself, which has no clear and precise definition in the industry. As Jan Verweijen and Frank Jeurissen from the Mpac Group explain, the big question is always: is it a sachet or a stick pack?
“What is what” is defined by the way it is sealed, not by its width or length. A stick pack is a product with three seals, one of which is in the middle, lengthwise. Instead, a sachet is a four-sided sealed product with no seal in the middle.
First introduced in Japan in the 70s to pack sugar, these single-use sticks are now used to pack everything you can think of. But what impact does your product have on the cartoning process?
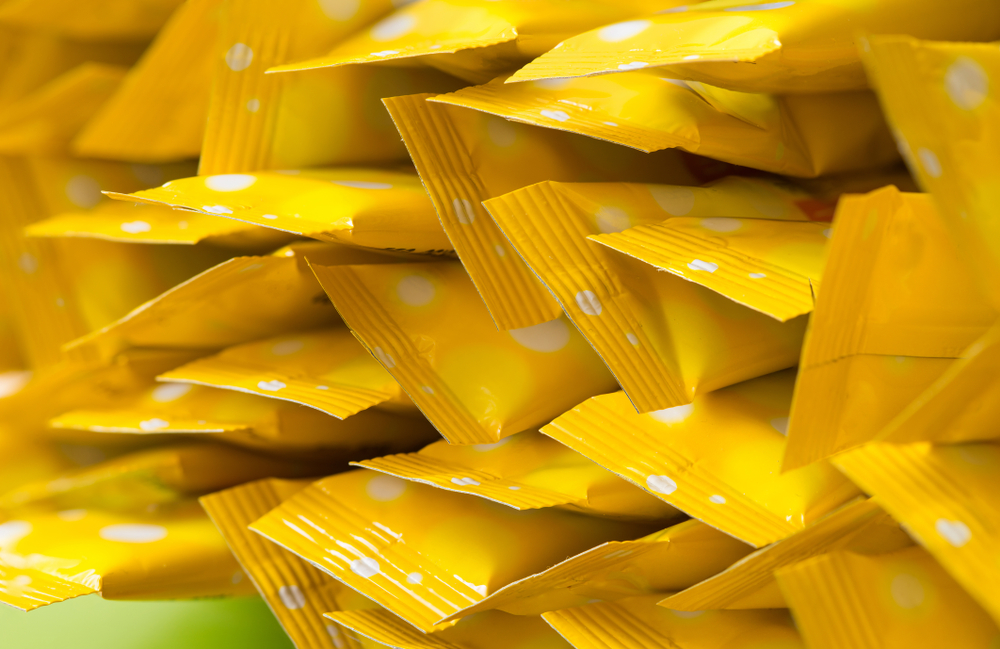
The first step is to find the right balance.
Stick packs are first filled vertically; this means that all the product is on the bottom.
Before entering the stick packs into the cartons, you need to evenly divide the product over the left and the right side of the stick packs. This step is called equalization and it is done by horizontally shaking the product to redistribute the contents inside the sticks.
“If the weight is not evenly distributed, all the stick packs will slide off toward one corner of the box leading to an unstable formation that can damage the sticks.” Frank points out.
For mere mortals, powder is powder, but for the experts, coffee powder, for instance, has a different structure than cocoa powder.
“Liquids do not need equalization as the fluids divide automatically.” Jan explains.
In addition, the sticks must have a minimum size, usually around 80 or 90 millimeters, to be cartoned horizontally and the shorter the sticks, the more difficult to keep them stable.
On edge vs. random orientation – Which side do you stand on?
Premium single-use products, such as coffee or pharmaceuticals, are often packed with the brand name and description always facing the consumer.
“When this is the case, we use a paddle conveyor that brings each stick pack on a single edge so that when pulled out of the box, the branded face is the first thing the consumer sees,” says Jan.
Frank adds: “In 90 percent of cases, manufacturers choose speed over where the stick pack is facing. With random orientation, you can easily speed up to 900 sticks per minute”.
“Our bomb bay system counts each stick individually and puts them together in the quantity the producer requires; then it drops the sticks into the bucket conveyor.” continues Jan.
To prevent damage, the bomb bay system consists of multiple drop levels, and the sticks need to be always dropped at a limited height – no higher than 250 mm.
As every stick has two ends, cartoning single-serve packs may seem easy, but as Jan and Frank explained, the journey from equalization to orientation and bomb bay dropping is not exactly a piece of cake.