Sterile compounding system
Hospitals and compounding centres have traditionally used manual aseptic compounding processes. As well as being labour intensive, these also allow for the introduction of human error, both into dosing and mislabelling, and potential for breaching sterility. A 21st century automatic aseptic compounding system using robotic and RFID technology overcomes these problems at a stroke, increasing productivity, reducing lead times, and guaranteeing dosing accuracy and traceability.
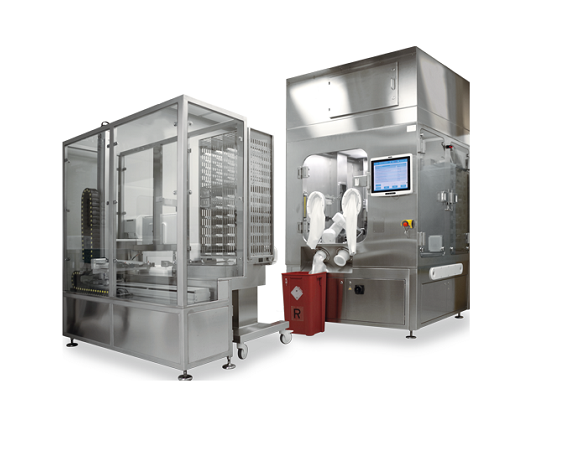
Complete robotic aseptic compounding system
Steriline’s ACS Aseptic Compounding System is a computer-controlled system for compounding intravenous doses into IV or other containers within an ISO 5 environment. It has been designed for use in hospitals and compounding centres, and operates in accordance with all appropriate regulations, including labeling in accordance with industry “best practice” standards.
The ACS can handle both hazardous and non-hazardous medication, and can be used for both patient specific and batch production. Based around tried and tested Isolator technology, ACS includes vaporized hydrogen peroxide (VHP) sterilization as standard. This means it can be installed in an ISO 8 background environment, as per GMP Annex 11.
The ACS uses cutting edge automation and robotics technology to remove the need for human intervention to:
- Sterilize all items with (VHP) prior to compounding;
- Calculate all conversions between weight and volume;
- Reconstitute powder drugs with the appropriate fluid;
- Dilute liquids to required concentrations;
- Remove excess liquid from IV bags and bottles;
- Compound doses into empty containers (including syringes, IV bags, and elastomeric infusors);
- Manage in-process waste.
Safety is paramount, and the Steriline ACS features a raft of features to ensure environmental, operator and patient safety, including ISO5 isolator technology; access restriction systems; zero cross-contamination risk operation; complete identification of all items via combination of vision, RFID and barcode systems; guaranteed traceability.
Benefits
- Fully compliant with all relevant cGMP, GAMP and 21CFR Part11 requirements
- Automation removes human errors from dosing and contamination risks
- An average of 35 doses/hour can be compounded
- Guarantees protection for operators
- Full traceability and item identification using multiple systems