Flexible contained powder discharge into drums
Powdered products are handled every day in the pharmaceutical and bioprocess industries and an efficient means of filling drums while maintaining containment is needed to ensure safe and profitable production processes. Experienced biopharmaceutical manufacturers know that equipment designed for general industry use often falls short and rigid containment and transfer solutions for the biotech industry are often awkward and inefficient. Producers that embrace flexible solutions designed specifically for the challenges of our industry will find an advantage over competitors.
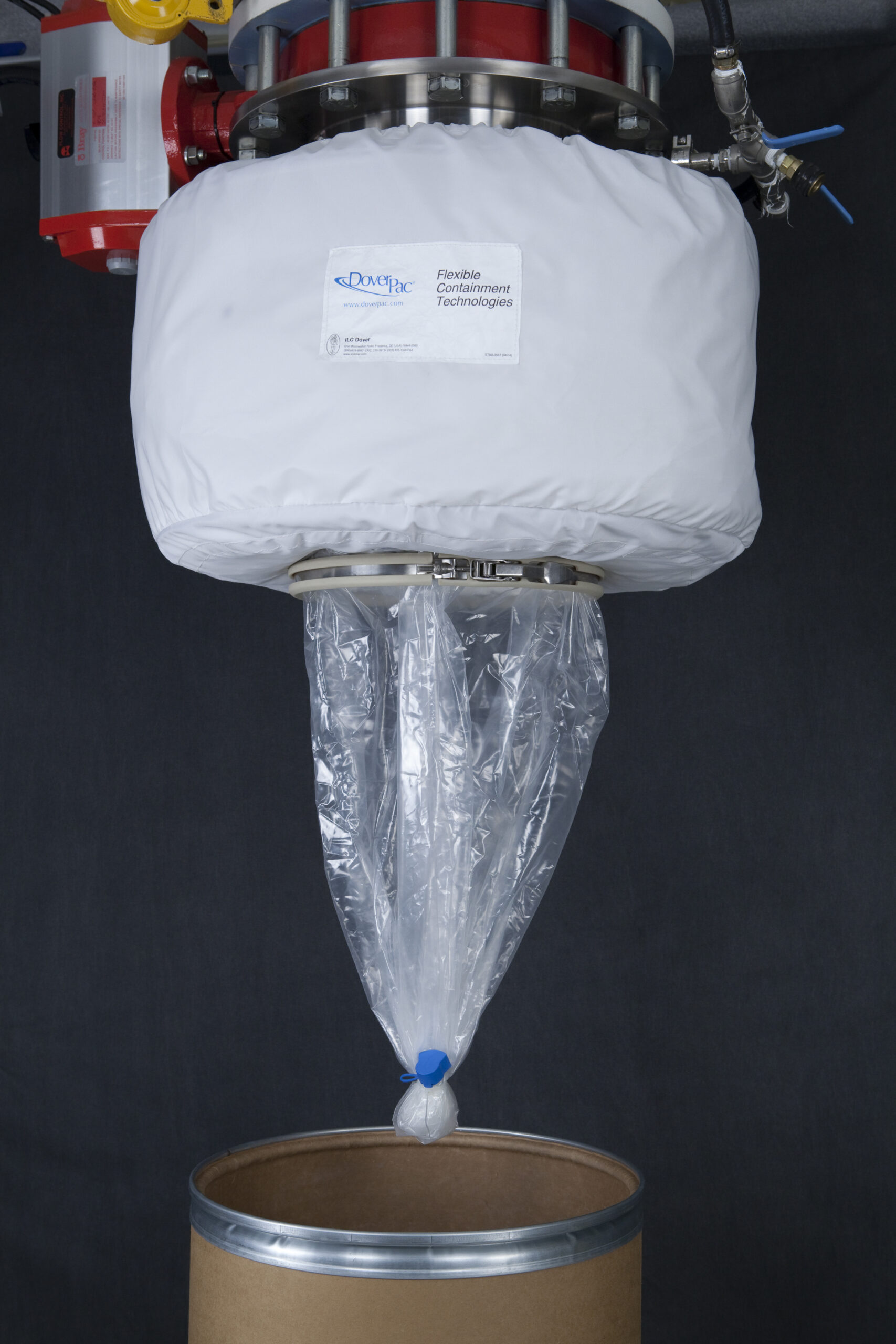
A disposable drum liner for continuous production of powders
ILC Dover is an industry leader in contained material handling solutions for high-tech manufacturers and end users including NASA. For powder discharge into drums, the company has developed the Dover Pac system. The Dover Pac Continuous Liner is typically used to offload powders from vessels into drums for the pharmaceutical and bioprocess industries. The liners interface directly with existing process equipment including down-flow booths and isolators. The liners are continuous which both eliminates cross-contamination of powders, and enhances operation efficiency by eliminating the need for the operator to constantly place new liners over a discharge nozzle as with traditional drum liners. The liners are shipped in pack lengths of 15 M to 45 M with each standard drum using about 1.5 M of liner material. Drums are continuously filled until the liner pack is spent. Spent packs are easily replaced by an operator without breaking the containment of the powder. The continuous liners are available for use with 580mm, 355mm, or 200mm canisters with adapters available for interfaces to smaller canisters if required.
Benefits
- Pre-packaged liners reduce operator error
- Continuous liner design increases containment reducing risk of contamination and employee exposure
- Interfaces directly with a wide array of existing process equipment
- Can also be used with bag in / bag out processes with rigid isolators and flexible enclosures