Endload cartoning machine
As demand for food production increases, so does that of packaging and sealing the product and making them ready for the end-consumer. With the help of an automated endload cartoning system, the level of output can be consistently increased as per the needs of the manufacturing business without compromising on quality or increasing handling costs.
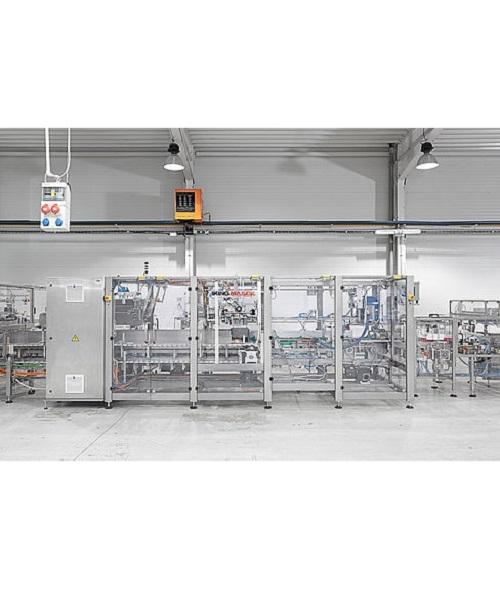
Customizable endload cartoning system for ice-cream, cereal, and frozen food
The CAM systems by Viking Masek are specifically designed for automatic endload cartoning for products ranging from frozen meat to cereal and ice cream to be placed in a pre-folded package and then sealed by the system ready for labelling and distribution.
Viking Masek’s CAM system is available in two versions; continuous and intermittent. The key difference is that one doesn’t stop and continuously operates, and that the other one can operate in batches or on-demand. Because of this, the continuous CAM system can process up to 240 pieces per minute as compared to just 60 for the intermittent variation. Thus, the intermittent can be more suitable for manufacturers who have lower demand, while the continuous would be more suitable for businesses who are looking to maximize their level of output.
Viking Masek endload cartoning solutions are created with the goal to be as flexible as possible to match customer´s applications based on speed and size-range requirements. Furthermore, the CAM cartoner system is completely servo driven, highly flexible, and robust.
The continuous or intermittent motions allow for simple change-overs and a broad range of applications. Featuring easy change-over, various closure systems, and product feeders, the CAM’s customised solutions ensure guaranteed high-quality performance. The systems can handle a range of cartons that vary in size from as little as 225mm x 300mm x 200mm for continuous operations all the way to 400mm x 600mm x 300mm for intermittent processes.
Benefits
- Fully adaptable to a range of product specifications.
- Can easily process between 60 to 240 units per minute depending on product characteristics.
- Optimal folding accuracy.
- Continuous and Intermittent modes of operation are available.