Centrifuge water saving unit for sustainable cooling
Reduce your cooling water consumption by 99.9% with this efficient solution designed to optimize energy usage and minimize resource waste in continuous high-speed operations.
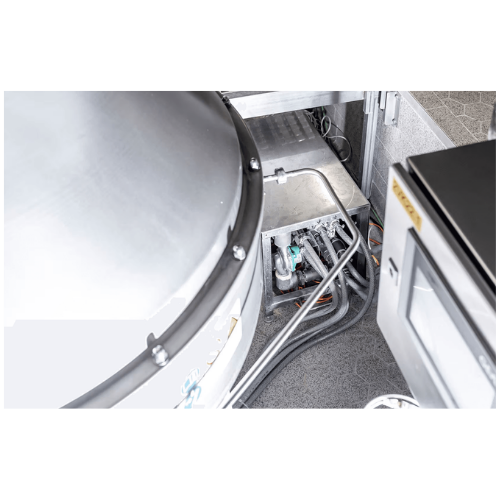
Reduces Cooling Water Usage in Separators
The GEA Centrifuge Water Saving Unit stands out as a leading solution for sustainable industrial processing. It efficiently transfers emitted heat from operating separators to glycol or iced water through recirculating cooling water, drastically reducing cooling water consumption by 99.9%. This system is crucial for applications in dairy, food, beverage, and pharmaceutical processing, resulting in end-products such as milk, cheese, yogurt, and active pharmaceutical ingredients. The unit operates continuously and automatically, with a flow rate of 13 liters per minute, optimizing energy use through separate cooling circuits for the engine and hood/catcher. Compatibility across all GEA separator types allows for seamless integration, whether in new machines or as a retrofit. The system’s CIP optimization reduces energy footprints, while its compact size ensures easy installation and minimal maintenance. Additionally, the Water Saving Unit complies with rigorous environmental standards, supporting your operation’s commitment to sustainability.
Benefits
- Drastically cuts water usage by 99.9%, leading to significant cost savings.
- Lowers energy consumption by optimizing heat transfer processes.
- Minimizes installation and maintenance efforts due to compact design.
- Enables swift integration into existing systems, enhancing flexibility.
- Promotes sustainability and resources conservation in production operations.
- Applications
- Chemical processing, Beverage processing, Environmental applications, Dairy production, Food processing, Pharmaceutical
- End products
- Beverages, Biofuels, Milk, Active pharmaceutical ingredients (apis), Nutraceutical supplements, Cheese, Water treatment, Effluent treatment, Butter, Chemical solvents, Yogurt, Juices
- Steps before
- Separation, Cooling water supply
- Steps after
- Energy recovery, Wastewater reduction
- Input ingredients
- recirculating cooling water, glycol mixture, iced water, continuous minimum supply of iced water or glycol mixture
- Output ingredients
- reduced water consumption, cooled separator components, emitted heat transfer, optimized energy consumption
- Market info
- GEA is known for its expertise in engineering innovative and sustainable equipment and solutions, focusing on sectors such as food, beverages, pharmaceuticals, and energy, with a reputation for quality, efficiency, and advanced technological applications in industrial processing.
- Water Consumption Reduction
- 99.9%
- Cooling Water Throughput
- 3, 600 liters per day
- Flow Rate
- 13 l/min
- Cooling Temperature Range
- 10 °C to 30 °C
- Glycol or Iced Water Supply
- 15 l/min
- Minimum Pressure
- 2 bar
- Size
- 380 (w) x 380 (l) x 485 (h) mm (new version)
- Size
- 380 (w) x 580 (l) x 495 (h) mm (retrofit version)
- Cooling Water Savings
- 1.3 million liters per year per separator
- Working mechanism
- Recirculating cooling water system
- Integrated steps
- Heat transfer via cooling water to glycol or iced water
- CIP/SIP
- CIP optimization
- Changeover time
- Half-day installation
- Batch vs. continuous operation
- Continuous
- Automation level
- PLC / IoT gateway
- Energy efficiency
- Significantly optimized energy consumption
- Cleaning method
- CIP compatible
- Cooling operation
- Separate circuits for engine and hood + catcher
- Corrosive resistance
- Compatible with glycol and iced water
- Cleanability
- Simple cleaning with standard CIP procedures
- Compact footprint
- 380 (w) x 380 (l) x 485 (h) mm
- Retrofit version size
- 380 (w) x 580 (l) x 495 (h) mm
- Compact design
- Fits in small space, size of two water crates
- Control panel type
- Cloud connectivity via IoT gateway
- Integration possibilities
- Connection to GEA UC App and Siemens Mindconnect IoT 2040
- Compatibility
- Compatible with all GEA separator types
- Retrofit availability
- Available for new machines and existing installations
- CIP Optimization
- Included for air-cooled motors
- Possible for water-cooled
- Flow settings
- Customizable temperature between 10 °C and 30 °C