Closing the containment loop in HPAPI manufacturing
The rise of high-potency ingredients (HPAPI) is taking medication into unchartered territory. Since the turn of the century, the pharmaceutical industry has developed a wave of targeted therapeutics formulated with more potent drugs in smaller doses.
Besides producing a more effective action against their biomedical targets, these innovative medicines are also lighter on excipients and provoke fewer side effects for patients. However, they do cause considerable side effects for manufacturers.
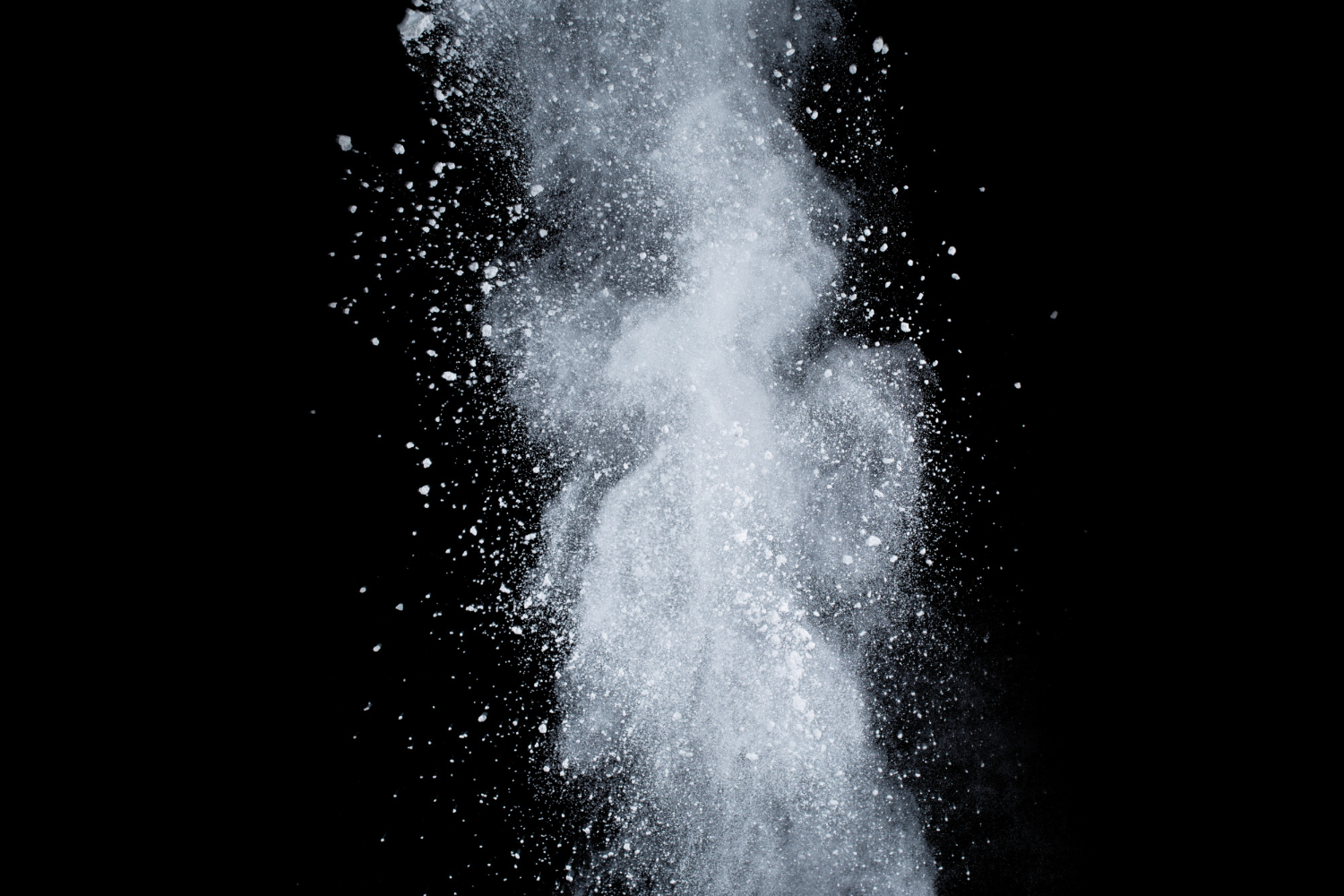
Higher potency can be too much of a good thing
HPAPI materials pose a risk of toxic exposure to operators. Process technology is designed to meet EHS guidelines, protecting handlers from hazardous substances. At the same time, it must also adhere to GMP standards to prevent contamination. However, the real danger lies at the inlets and outlets of the machines, as Andocksysteme Product Manager Duncan Ehrmann points out.
“It is all well and good when a mixer is blending chemicals, or a dryer is reducing moisture,” says Duncan. “But things get tricky while the materials are transferred from the mixer to the dryer.”
There is no such thing as a fully closed system; discharge will always release particles into the air. So, the challenge is to minimize that amount to the greatest extent possible.
The industry answer is the split butterfly valve principle, joining the ‘mouths’ of two systems and opening them synchronously. But engineering the concept into an actual pharma-grade interface is another story.
Big on seals, small on parts
Andocksysteme developed a valve solution that achieves contamination values lower than 1μg/m3. A primary contributor to this degree of containment is the minimalist construction of the interface. Designed with the bare minimum of separate parts, the valves significantly restrict roaming space for flowing powders.
“We designed our technology with large seals to cover the openings,” explains Duncan, “A bigger seal exerts higher pressure, locking the active/passive valves tighter together.”
The state-of-the-art system meets the OEB 5 levels of protection required when handling ingredients with high pharmacological and toxic effects.
HPAPI particles move around a lot during processing. Their manufacturing cycles are long and winding, but high-containment valves hold them safely within that loop.