Rotary weigh feeder for high-volume powders
Ensure continuous and accurate high-volume powder dosing in your industrial processes with a compact solution designed for precision and efficiency, even in challenging environments.
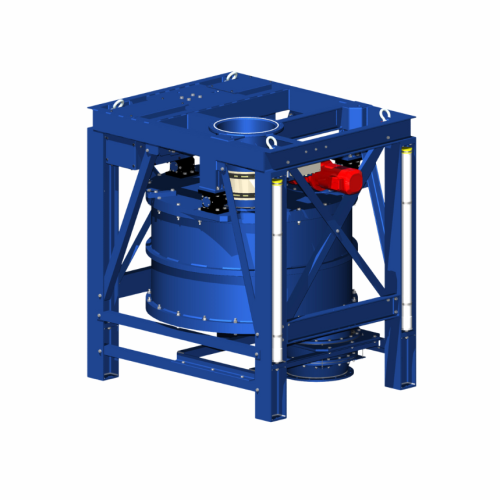
Delivers Consistent Powder Weighing and Dosing
The ROTAWEIGH Rotary Weigh Feeder from HASLER Group is engineered to deliver precision dosing for high-volume powder applications in sectors like cement, fertilizers, and metals processing. Utilizing a multi-cell, rotary design, it ensures continuous operation with vertical material entry and exit, optimizing space and reducing installation footprints. Capable of handling up to 600 m³/h, the ROTAWEIGH maintains accurate feeding within ±0.5% precision, vital for processes like cement kiln feeding and mineral dust handling. Automation is seamlessly managed via the SCMIII control module, allowing real-time monitoring and control. The enclosed design ensures dust-free operation, while modular options offer customization for varied industrial needs. The unit’s robust construction, with a high-temperature variant sustaining up to 130°C, guarantees durability in harsh environments. On-site maintenance is efficient, minimizing downtime and operating costs. Available in several configurations, the ROTAWEIGH also supports applications in technical ceramics, polymers, and water treatment, enhancing process efficiency with its adaptable engineering.
Benefits
- Ensures precise dosing with ±0.5% accuracy, enhancing product quality and consistency.
- Reduces operational costs with easy, on-site maintenance and a low footprint design.
- Increases uptime with durable construction and high-temperature resistance up to 130°C.
- Enhances process flexibility with modular configurations for diverse industrial applications.
- Protects operators with a fully enclosed design, preventing dust release and environmental contamination.
- Applications
- Polymers, Amino acids, Hydrometallurgy, Water treatment, Fertilisers, Metals recycling, Minerals processing, Specialty acids, Technical ceramics, Resins, Flue gas desulphurization, Cement
- End products
- Epoxy resins, Citric acid, Recycled aluminum, Polyethylene compounds, Copper cathodes, Npk fertilizers, Portland cement, Treated wastewater, Glutamic acid, Oxide minerals, Gypsum slurry, Alumina ceramics
- Steps before
- Grinding, Drying, Purification
- Steps after
- Packing, Mixing, Processing
- Input ingredients
- powders, cement, meal, mineral dust, powdery materials
- Output ingredients
- accurate, consistent feed, high flow rate output
- Market info
- HASLER Group is known for manufacturing and supplying industrial engineered-to-order (ETO) equipment, specializing in mixing, filtration, and sealing solutions for various industries, with a reputation for quality and innovation in handling challenging process applications.
- Accuracy
- ±0.5%
- Flow Rate
- up to 600 m³/h
- Temperature Resistance
- up to 130°C
- Operation Mode
- Continuous (24/7)
- Particle Size
- < 1 mm
- Moisture Content
- < 1%
- Design
- Vertical
- Maintenance
- On-site
- Weighing Angle
- 270°
- Working mechanism
- Rotary weigh feeder
- Integrated steps
- Multi-cell weighing
- Flow capacity
- Up to 600 m³/h
- Footprint optimization
- Vertical entry and exit
- Maintenance method
- On-site, quick dismantling
- Continuous operation
- 24/7 availability > 99%
- High-temperature capability
- Up to 130°C
- Dust prevention
- Fully enclosed design
- Sealing capability
- Completely sealed
- Control system
- SCMIII control module
- Abrasion resistance
- Yes
- Corrosive resistance (e.g. acids)
- Yes
- Density/particle size
- 0.5–2.5 g/cm³ / 50–1000 µm
- Cleanability
- Medium
- Heat Resistance
- up to 130°C
- Powdery materials
- Cement, minerals
- Footprint
- Compact, vertical entry and exit on the same axis
- Discharge Method
- Vertical axis discharge
- Machine Size
- Varies—modular, multiple sizes available
- Sealing
- Fully enclosed
- Inspection Access
- Fitted with inspection hatches
- Control panel type
- SCMIII control module